Detailed Report: Operation and Project Management at XYZ Company
VerifiedAdded on 2020/06/04
|17
|5813
|56
Report
AI Summary
This report provides a comprehensive analysis of operation and project management practices within XYZ Company. It begins with an introduction to operation management, emphasizing its role in business efficiency and the conversion of resources into desired outcomes. The report then delves into the effectiveness of operation management, detailing the implementation of various principles and methodologies such as Six Sigma and Lean principles. The study examines the company's approach to new product development, specifically its entry into the large-screen television market, and includes a product life cycle analysis. The report presents a work breakdown structure and Gantt chart for project management. It also provides a rationale for the project methodologies, including the effectiveness of the PLC in application to the project by use of appropriate theories and models, and concludes with a critical evaluation of the product life cycle through a practical and theoretical exploration of its effectiveness. The report highlights areas for improvement and offers recommendations for enhancing efficiency and achieving organizational goals. The assignment showcases how the company can apply different methods of measuring the quality and services of production and operation to bring continuous improvement and success.
Contribute Materials
Your contribution can guide someone’s learning journey. Share your
documents today.
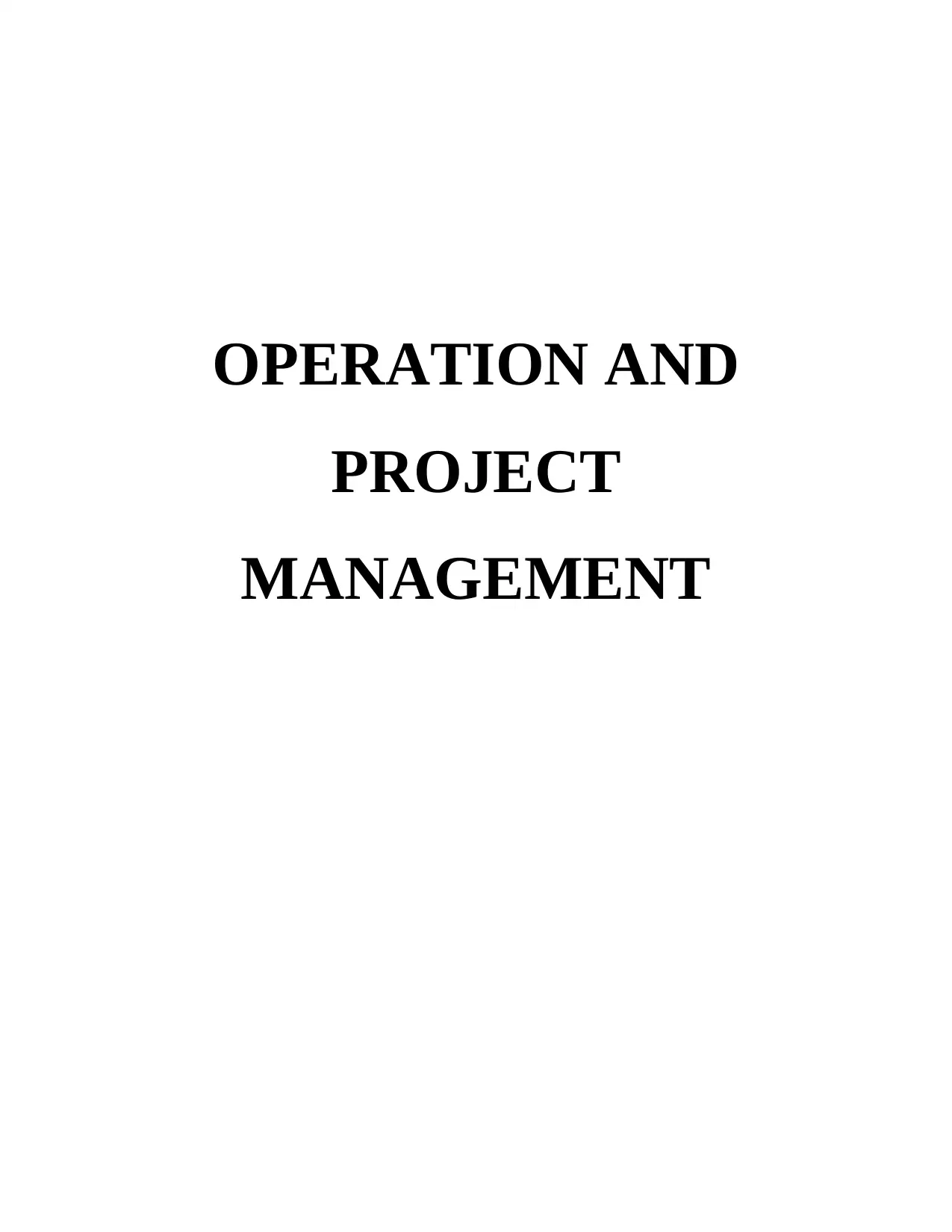
OPERATION AND
PROJECT
MANAGEMENT
PROJECT
MANAGEMENT
Secure Best Marks with AI Grader
Need help grading? Try our AI Grader for instant feedback on your assignments.
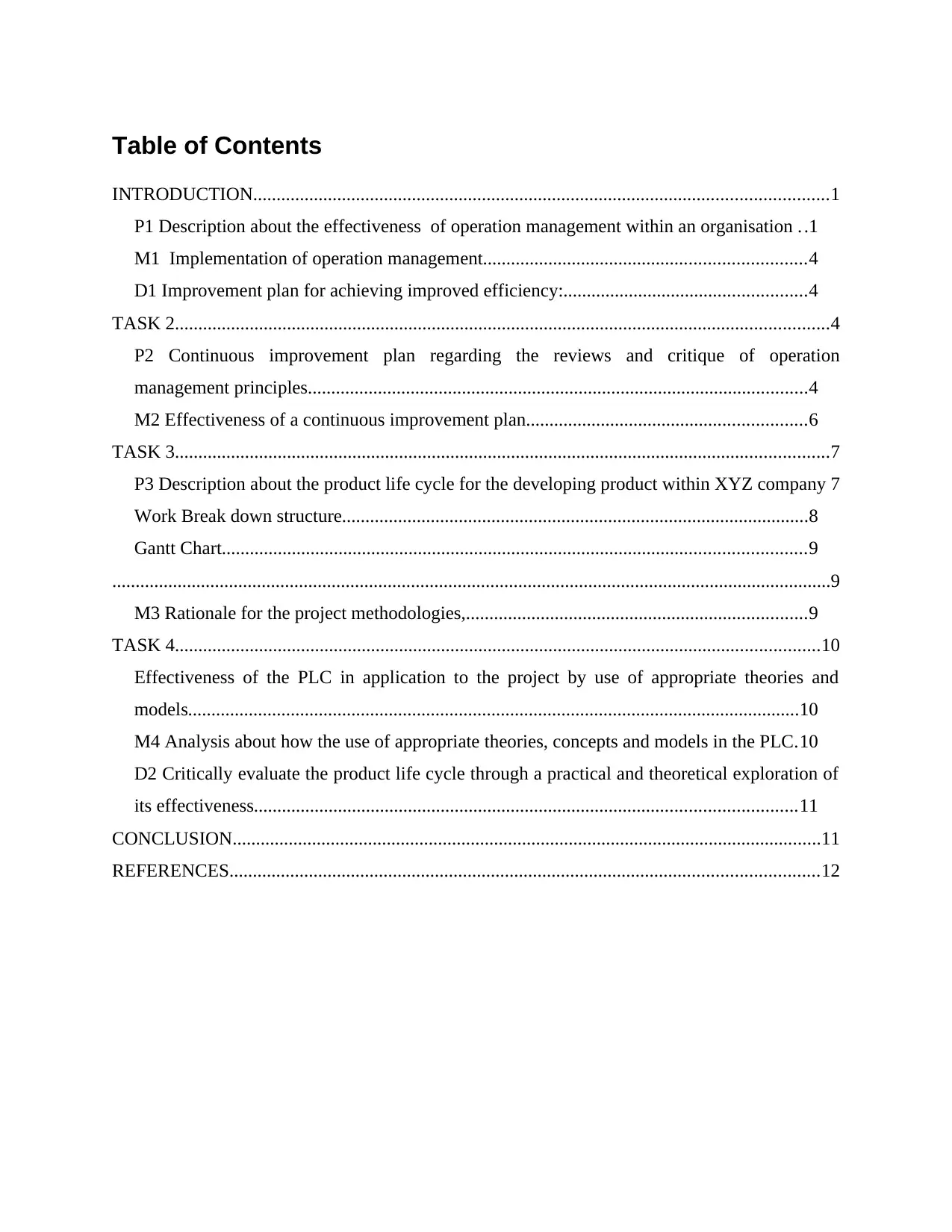
Table of Contents
INTRODUCTION...........................................................................................................................1
P1 Description about the effectiveness of operation management within an organisation ..1
M1 Implementation of operation management.....................................................................4
D1 Improvement plan for achieving improved efficiency:....................................................4
TASK 2............................................................................................................................................4
P2 Continuous improvement plan regarding the reviews and critique of operation
management principles...........................................................................................................4
M2 Effectiveness of a continuous improvement plan............................................................6
TASK 3............................................................................................................................................7
P3 Description about the product life cycle for the developing product within XYZ company 7
Work Break down structure....................................................................................................8
Gantt Chart.............................................................................................................................9
..........................................................................................................................................................9
M3 Rationale for the project methodologies,.........................................................................9
TASK 4..........................................................................................................................................10
Effectiveness of the PLC in application to the project by use of appropriate theories and
models...................................................................................................................................10
M4 Analysis about how the use of appropriate theories, concepts and models in the PLC.10
D2 Critically evaluate the product life cycle through a practical and theoretical exploration of
its effectiveness....................................................................................................................11
CONCLUSION..............................................................................................................................11
REFERENCES..............................................................................................................................12
INTRODUCTION...........................................................................................................................1
P1 Description about the effectiveness of operation management within an organisation ..1
M1 Implementation of operation management.....................................................................4
D1 Improvement plan for achieving improved efficiency:....................................................4
TASK 2............................................................................................................................................4
P2 Continuous improvement plan regarding the reviews and critique of operation
management principles...........................................................................................................4
M2 Effectiveness of a continuous improvement plan............................................................6
TASK 3............................................................................................................................................7
P3 Description about the product life cycle for the developing product within XYZ company 7
Work Break down structure....................................................................................................8
Gantt Chart.............................................................................................................................9
..........................................................................................................................................................9
M3 Rationale for the project methodologies,.........................................................................9
TASK 4..........................................................................................................................................10
Effectiveness of the PLC in application to the project by use of appropriate theories and
models...................................................................................................................................10
M4 Analysis about how the use of appropriate theories, concepts and models in the PLC.10
D2 Critically evaluate the product life cycle through a practical and theoretical exploration of
its effectiveness....................................................................................................................11
CONCLUSION..............................................................................................................................11
REFERENCES..............................................................................................................................12
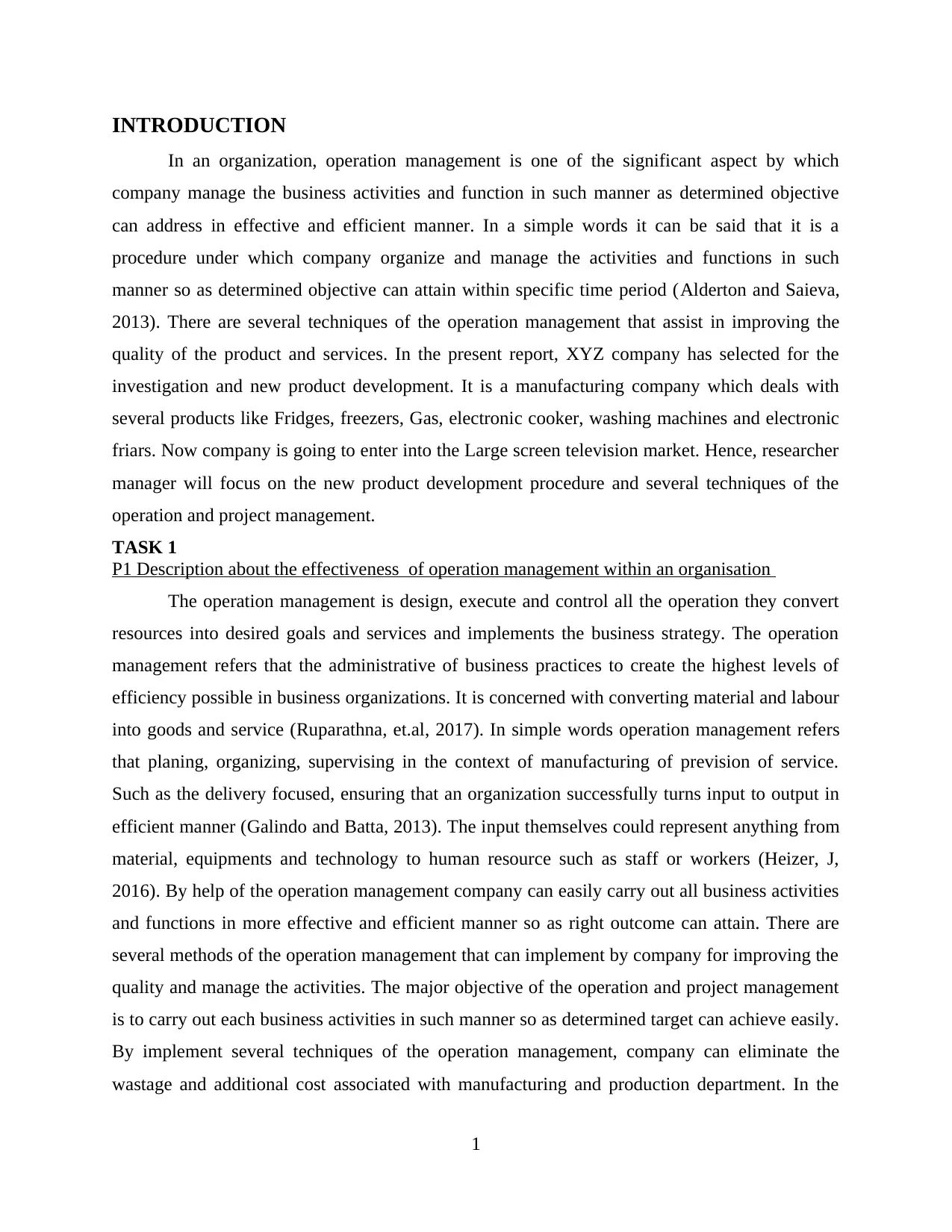
INTRODUCTION
In an organization, operation management is one of the significant aspect by which
company manage the business activities and function in such manner as determined objective
can address in effective and efficient manner. In a simple words it can be said that it is a
procedure under which company organize and manage the activities and functions in such
manner so as determined objective can attain within specific time period (Alderton and Saieva,
2013). There are several techniques of the operation management that assist in improving the
quality of the product and services. In the present report, XYZ company has selected for the
investigation and new product development. It is a manufacturing company which deals with
several products like Fridges, freezers, Gas, electronic cooker, washing machines and electronic
friars. Now company is going to enter into the Large screen television market. Hence, researcher
manager will focus on the new product development procedure and several techniques of the
operation and project management.
TASK 1
P1 Description about the effectiveness of operation management within an organisation
The operation management is design, execute and control all the operation they convert
resources into desired goals and services and implements the business strategy. The operation
management refers that the administrative of business practices to create the highest levels of
efficiency possible in business organizations. It is concerned with converting material and labour
into goods and service (Ruparathna, et.al, 2017). In simple words operation management refers
that planing, organizing, supervising in the context of manufacturing of prevision of service.
Such as the delivery focused, ensuring that an organization successfully turns input to output in
efficient manner (Galindo and Batta, 2013). The input themselves could represent anything from
material, equipments and technology to human resource such as staff or workers (Heizer, J,
2016). By help of the operation management company can easily carry out all business activities
and functions in more effective and efficient manner so as right outcome can attain. There are
several methods of the operation management that can implement by company for improving the
quality and manage the activities. The major objective of the operation and project management
is to carry out each business activities in such manner so as determined target can achieve easily.
By implement several techniques of the operation management, company can eliminate the
wastage and additional cost associated with manufacturing and production department. In the
1
In an organization, operation management is one of the significant aspect by which
company manage the business activities and function in such manner as determined objective
can address in effective and efficient manner. In a simple words it can be said that it is a
procedure under which company organize and manage the activities and functions in such
manner so as determined objective can attain within specific time period (Alderton and Saieva,
2013). There are several techniques of the operation management that assist in improving the
quality of the product and services. In the present report, XYZ company has selected for the
investigation and new product development. It is a manufacturing company which deals with
several products like Fridges, freezers, Gas, electronic cooker, washing machines and electronic
friars. Now company is going to enter into the Large screen television market. Hence, researcher
manager will focus on the new product development procedure and several techniques of the
operation and project management.
TASK 1
P1 Description about the effectiveness of operation management within an organisation
The operation management is design, execute and control all the operation they convert
resources into desired goals and services and implements the business strategy. The operation
management refers that the administrative of business practices to create the highest levels of
efficiency possible in business organizations. It is concerned with converting material and labour
into goods and service (Ruparathna, et.al, 2017). In simple words operation management refers
that planing, organizing, supervising in the context of manufacturing of prevision of service.
Such as the delivery focused, ensuring that an organization successfully turns input to output in
efficient manner (Galindo and Batta, 2013). The input themselves could represent anything from
material, equipments and technology to human resource such as staff or workers (Heizer, J,
2016). By help of the operation management company can easily carry out all business activities
and functions in more effective and efficient manner so as right outcome can attain. There are
several methods of the operation management that can implement by company for improving the
quality and manage the activities. The major objective of the operation and project management
is to carry out each business activities in such manner so as determined target can achieve easily.
By implement several techniques of the operation management, company can eliminate the
wastage and additional cost associated with manufacturing and production department. In the
1
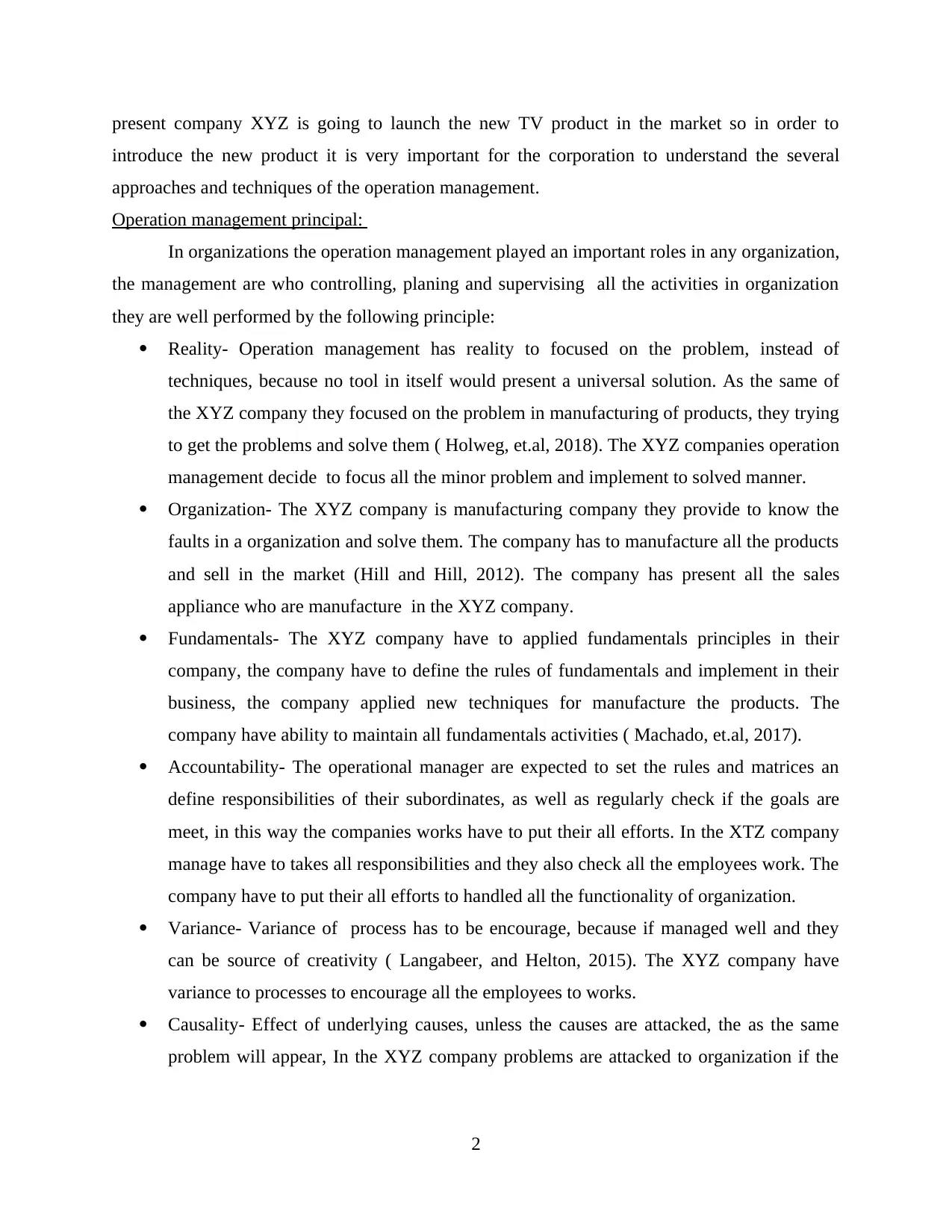
present company XYZ is going to launch the new TV product in the market so in order to
introduce the new product it is very important for the corporation to understand the several
approaches and techniques of the operation management.
Operation management principal:
In organizations the operation management played an important roles in any organization,
the management are who controlling, planing and supervising all the activities in organization
they are well performed by the following principle:
Reality- Operation management has reality to focused on the problem, instead of
techniques, because no tool in itself would present a universal solution. As the same of
the XYZ company they focused on the problem in manufacturing of products, they trying
to get the problems and solve them ( Holweg, et.al, 2018). The XYZ companies operation
management decide to focus all the minor problem and implement to solved manner.
Organization- The XYZ company is manufacturing company they provide to know the
faults in a organization and solve them. The company has to manufacture all the products
and sell in the market (Hill and Hill, 2012). The company has present all the sales
appliance who are manufacture in the XYZ company.
Fundamentals- The XYZ company have to applied fundamentals principles in their
company, the company have to define the rules of fundamentals and implement in their
business, the company applied new techniques for manufacture the products. The
company have ability to maintain all fundamentals activities ( Machado, et.al, 2017).
Accountability- The operational manager are expected to set the rules and matrices an
define responsibilities of their subordinates, as well as regularly check if the goals are
meet, in this way the companies works have to put their all efforts. In the XTZ company
manage have to takes all responsibilities and they also check all the employees work. The
company have to put their all efforts to handled all the functionality of organization.
Variance- Variance of process has to be encourage, because if managed well and they
can be source of creativity ( Langabeer, and Helton, 2015). The XYZ company have
variance to processes to encourage all the employees to works.
Causality- Effect of underlying causes, unless the causes are attacked, the as the same
problem will appear, In the XYZ company problems are attacked to organization if the
2
introduce the new product it is very important for the corporation to understand the several
approaches and techniques of the operation management.
Operation management principal:
In organizations the operation management played an important roles in any organization,
the management are who controlling, planing and supervising all the activities in organization
they are well performed by the following principle:
Reality- Operation management has reality to focused on the problem, instead of
techniques, because no tool in itself would present a universal solution. As the same of
the XYZ company they focused on the problem in manufacturing of products, they trying
to get the problems and solve them ( Holweg, et.al, 2018). The XYZ companies operation
management decide to focus all the minor problem and implement to solved manner.
Organization- The XYZ company is manufacturing company they provide to know the
faults in a organization and solve them. The company has to manufacture all the products
and sell in the market (Hill and Hill, 2012). The company has present all the sales
appliance who are manufacture in the XYZ company.
Fundamentals- The XYZ company have to applied fundamentals principles in their
company, the company have to define the rules of fundamentals and implement in their
business, the company applied new techniques for manufacture the products. The
company have ability to maintain all fundamentals activities ( Machado, et.al, 2017).
Accountability- The operational manager are expected to set the rules and matrices an
define responsibilities of their subordinates, as well as regularly check if the goals are
meet, in this way the companies works have to put their all efforts. In the XTZ company
manage have to takes all responsibilities and they also check all the employees work. The
company have to put their all efforts to handled all the functionality of organization.
Variance- Variance of process has to be encourage, because if managed well and they
can be source of creativity ( Langabeer, and Helton, 2015). The XYZ company have
variance to processes to encourage all the employees to works.
Causality- Effect of underlying causes, unless the causes are attacked, the as the same
problem will appear, In the XYZ company problems are attacked to organization if the
2
Secure Best Marks with AI Grader
Need help grading? Try our AI Grader for instant feedback on your assignments.
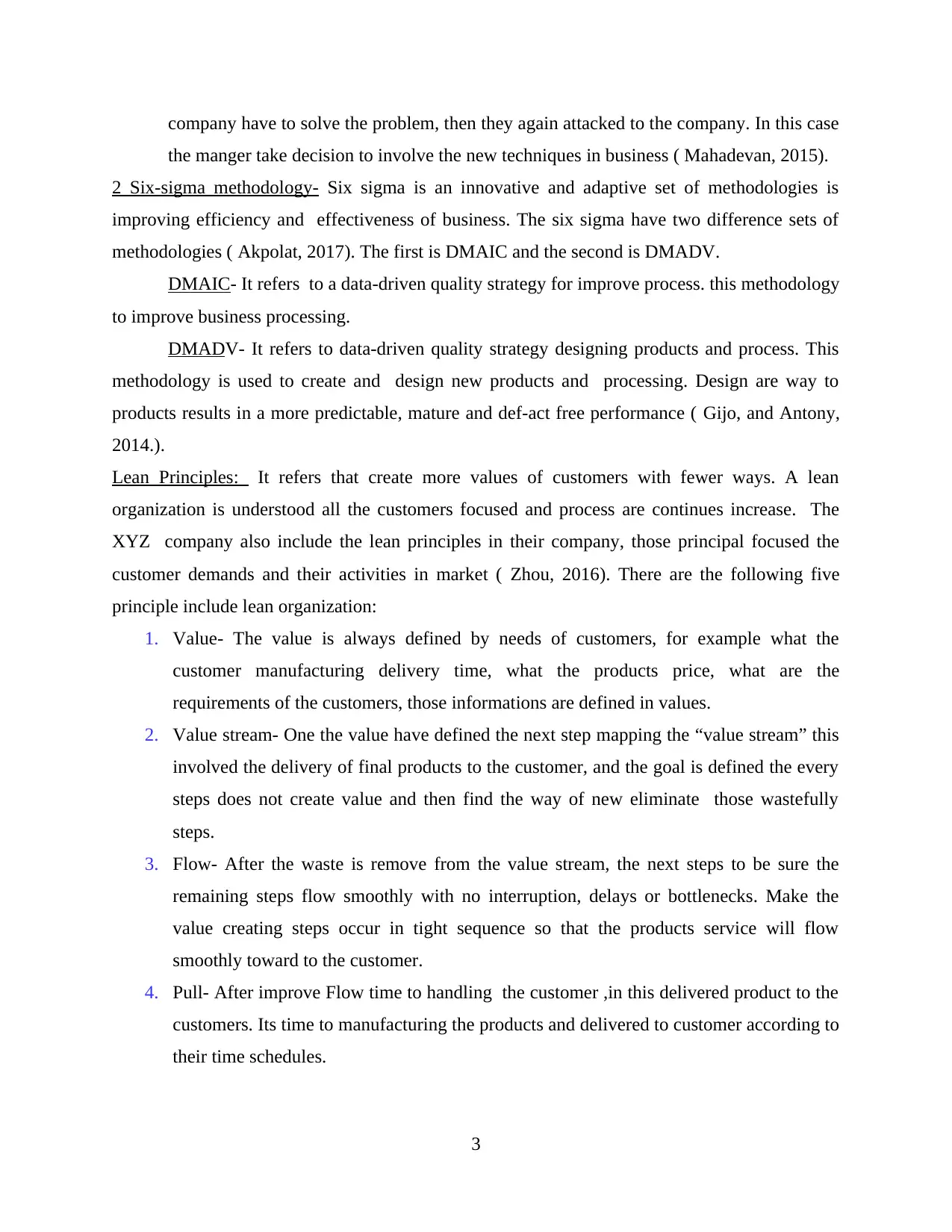
company have to solve the problem, then they again attacked to the company. In this case
the manger take decision to involve the new techniques in business ( Mahadevan, 2015).
2 Six-sigma methodology- Six sigma is an innovative and adaptive set of methodologies is
improving efficiency and effectiveness of business. The six sigma have two difference sets of
methodologies ( Akpolat, 2017). The first is DMAIC and the second is DMADV.
DMAIC- It refers to a data-driven quality strategy for improve process. this methodology
to improve business processing.
DMADV- It refers to data-driven quality strategy designing products and process. This
methodology is used to create and design new products and processing. Design are way to
products results in a more predictable, mature and def-act free performance ( Gijo, and Antony,
2014.).
Lean Principles: It refers that create more values of customers with fewer ways. A lean
organization is understood all the customers focused and process are continues increase. The
XYZ company also include the lean principles in their company, those principal focused the
customer demands and their activities in market ( Zhou, 2016). There are the following five
principle include lean organization:
1. Value- The value is always defined by needs of customers, for example what the
customer manufacturing delivery time, what the products price, what are the
requirements of the customers, those informations are defined in values.
2. Value stream- One the value have defined the next step mapping the “value stream” this
involved the delivery of final products to the customer, and the goal is defined the every
steps does not create value and then find the way of new eliminate those wastefully
steps.
3. Flow- After the waste is remove from the value stream, the next steps to be sure the
remaining steps flow smoothly with no interruption, delays or bottlenecks. Make the
value creating steps occur in tight sequence so that the products service will flow
smoothly toward to the customer.
4. Pull- After improve Flow time to handling the customer ,in this delivered product to the
customers. Its time to manufacturing the products and delivered to customer according to
their time schedules.
3
the manger take decision to involve the new techniques in business ( Mahadevan, 2015).
2 Six-sigma methodology- Six sigma is an innovative and adaptive set of methodologies is
improving efficiency and effectiveness of business. The six sigma have two difference sets of
methodologies ( Akpolat, 2017). The first is DMAIC and the second is DMADV.
DMAIC- It refers to a data-driven quality strategy for improve process. this methodology
to improve business processing.
DMADV- It refers to data-driven quality strategy designing products and process. This
methodology is used to create and design new products and processing. Design are way to
products results in a more predictable, mature and def-act free performance ( Gijo, and Antony,
2014.).
Lean Principles: It refers that create more values of customers with fewer ways. A lean
organization is understood all the customers focused and process are continues increase. The
XYZ company also include the lean principles in their company, those principal focused the
customer demands and their activities in market ( Zhou, 2016). There are the following five
principle include lean organization:
1. Value- The value is always defined by needs of customers, for example what the
customer manufacturing delivery time, what the products price, what are the
requirements of the customers, those informations are defined in values.
2. Value stream- One the value have defined the next step mapping the “value stream” this
involved the delivery of final products to the customer, and the goal is defined the every
steps does not create value and then find the way of new eliminate those wastefully
steps.
3. Flow- After the waste is remove from the value stream, the next steps to be sure the
remaining steps flow smoothly with no interruption, delays or bottlenecks. Make the
value creating steps occur in tight sequence so that the products service will flow
smoothly toward to the customer.
4. Pull- After improve Flow time to handling the customer ,in this delivered product to the
customers. Its time to manufacturing the products and delivered to customer according to
their time schedules.
3
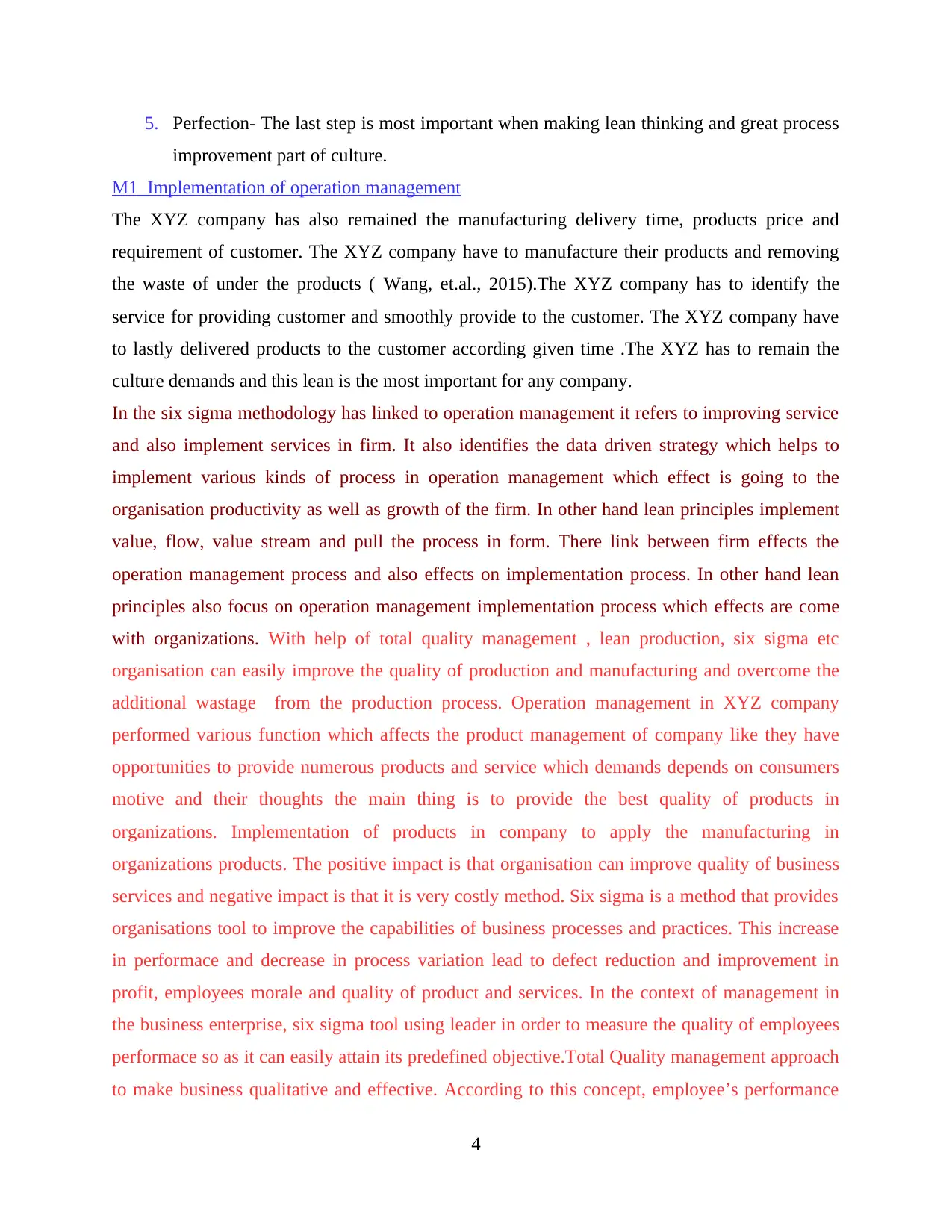
5. Perfection- The last step is most important when making lean thinking and great process
improvement part of culture.
M1 Implementation of operation management
The XYZ company has also remained the manufacturing delivery time, products price and
requirement of customer. The XYZ company have to manufacture their products and removing
the waste of under the products ( Wang, et.al., 2015).The XYZ company has to identify the
service for providing customer and smoothly provide to the customer. The XYZ company have
to lastly delivered products to the customer according given time .The XYZ has to remain the
culture demands and this lean is the most important for any company.
In the six sigma methodology has linked to operation management it refers to improving service
and also implement services in firm. It also identifies the data driven strategy which helps to
implement various kinds of process in operation management which effect is going to the
organisation productivity as well as growth of the firm. In other hand lean principles implement
value, flow, value stream and pull the process in form. There link between firm effects the
operation management process and also effects on implementation process. In other hand lean
principles also focus on operation management implementation process which effects are come
with organizations. With help of total quality management , lean production, six sigma etc
organisation can easily improve the quality of production and manufacturing and overcome the
additional wastage from the production process. Operation management in XYZ company
performed various function which affects the product management of company like they have
opportunities to provide numerous products and service which demands depends on consumers
motive and their thoughts the main thing is to provide the best quality of products in
organizations. Implementation of products in company to apply the manufacturing in
organizations products. The positive impact is that organisation can improve quality of business
services and negative impact is that it is very costly method. Six sigma is a method that provides
organisations tool to improve the capabilities of business processes and practices. This increase
in performace and decrease in process variation lead to defect reduction and improvement in
profit, employees morale and quality of product and services. In the context of management in
the business enterprise, six sigma tool using leader in order to measure the quality of employees
performace so as it can easily attain its predefined objective.Total Quality management approach
to make business qualitative and effective. According to this concept, employee’s performance
4
improvement part of culture.
M1 Implementation of operation management
The XYZ company has also remained the manufacturing delivery time, products price and
requirement of customer. The XYZ company have to manufacture their products and removing
the waste of under the products ( Wang, et.al., 2015).The XYZ company has to identify the
service for providing customer and smoothly provide to the customer. The XYZ company have
to lastly delivered products to the customer according given time .The XYZ has to remain the
culture demands and this lean is the most important for any company.
In the six sigma methodology has linked to operation management it refers to improving service
and also implement services in firm. It also identifies the data driven strategy which helps to
implement various kinds of process in operation management which effect is going to the
organisation productivity as well as growth of the firm. In other hand lean principles implement
value, flow, value stream and pull the process in form. There link between firm effects the
operation management process and also effects on implementation process. In other hand lean
principles also focus on operation management implementation process which effects are come
with organizations. With help of total quality management , lean production, six sigma etc
organisation can easily improve the quality of production and manufacturing and overcome the
additional wastage from the production process. Operation management in XYZ company
performed various function which affects the product management of company like they have
opportunities to provide numerous products and service which demands depends on consumers
motive and their thoughts the main thing is to provide the best quality of products in
organizations. Implementation of products in company to apply the manufacturing in
organizations products. The positive impact is that organisation can improve quality of business
services and negative impact is that it is very costly method. Six sigma is a method that provides
organisations tool to improve the capabilities of business processes and practices. This increase
in performace and decrease in process variation lead to defect reduction and improvement in
profit, employees morale and quality of product and services. In the context of management in
the business enterprise, six sigma tool using leader in order to measure the quality of employees
performace so as it can easily attain its predefined objective.Total Quality management approach
to make business qualitative and effective. According to this concept, employee’s performance
4
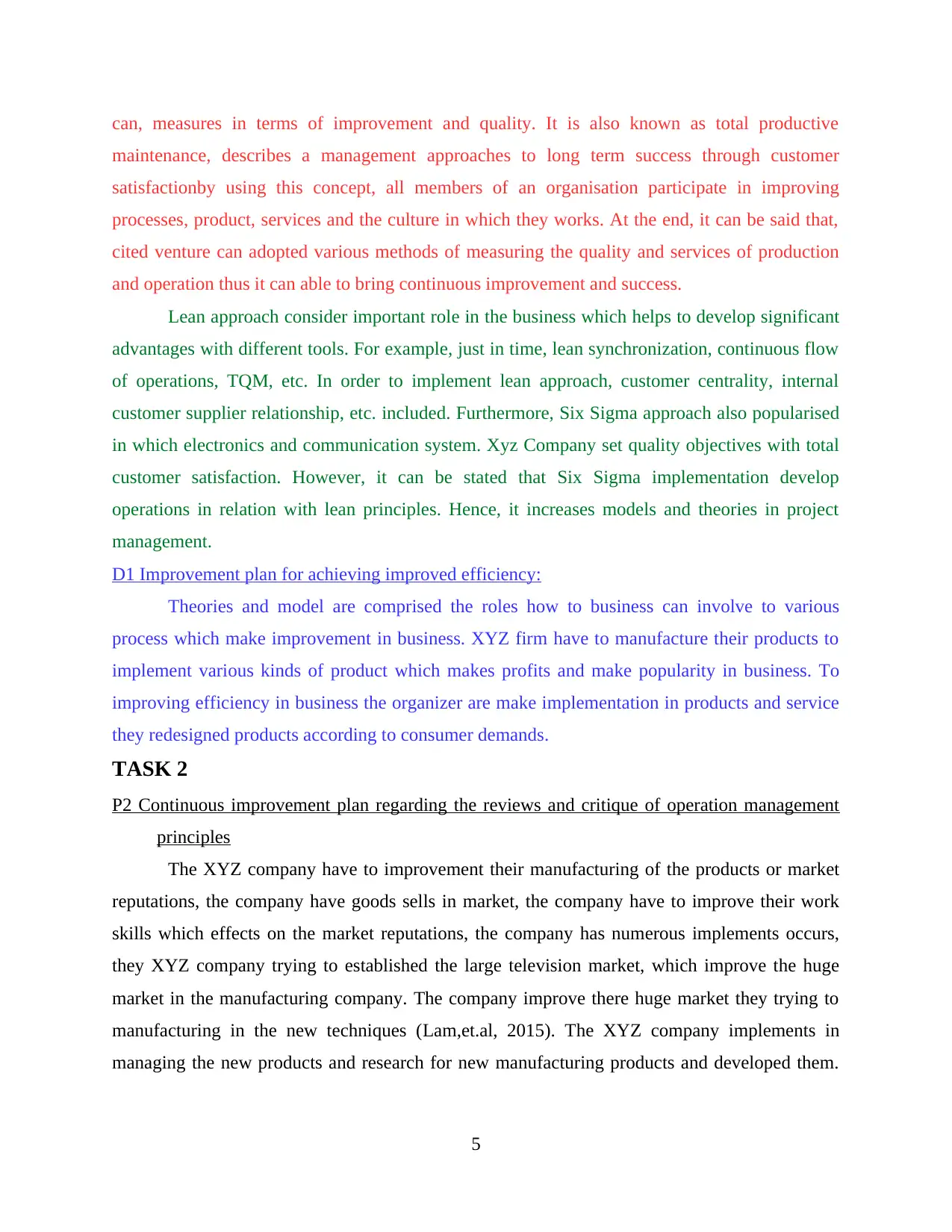
can, measures in terms of improvement and quality. It is also known as total productive
maintenance, describes a management approaches to long term success through customer
satisfactionby using this concept, all members of an organisation participate in improving
processes, product, services and the culture in which they works. At the end, it can be said that,
cited venture can adopted various methods of measuring the quality and services of production
and operation thus it can able to bring continuous improvement and success.
Lean approach consider important role in the business which helps to develop significant
advantages with different tools. For example, just in time, lean synchronization, continuous flow
of operations, TQM, etc. In order to implement lean approach, customer centrality, internal
customer supplier relationship, etc. included. Furthermore, Six Sigma approach also popularised
in which electronics and communication system. Xyz Company set quality objectives with total
customer satisfaction. However, it can be stated that Six Sigma implementation develop
operations in relation with lean principles. Hence, it increases models and theories in project
management.
D1 Improvement plan for achieving improved efficiency:
Theories and model are comprised the roles how to business can involve to various
process which make improvement in business. XYZ firm have to manufacture their products to
implement various kinds of product which makes profits and make popularity in business. To
improving efficiency in business the organizer are make implementation in products and service
they redesigned products according to consumer demands.
TASK 2
P2 Continuous improvement plan regarding the reviews and critique of operation management
principles
The XYZ company have to improvement their manufacturing of the products or market
reputations, the company have goods sells in market, the company have to improve their work
skills which effects on the market reputations, the company has numerous implements occurs,
they XYZ company trying to established the large television market, which improve the huge
market in the manufacturing company. The company improve there huge market they trying to
manufacturing in the new techniques (Lam,et.al, 2015). The XYZ company implements in
managing the new products and research for new manufacturing products and developed them.
5
maintenance, describes a management approaches to long term success through customer
satisfactionby using this concept, all members of an organisation participate in improving
processes, product, services and the culture in which they works. At the end, it can be said that,
cited venture can adopted various methods of measuring the quality and services of production
and operation thus it can able to bring continuous improvement and success.
Lean approach consider important role in the business which helps to develop significant
advantages with different tools. For example, just in time, lean synchronization, continuous flow
of operations, TQM, etc. In order to implement lean approach, customer centrality, internal
customer supplier relationship, etc. included. Furthermore, Six Sigma approach also popularised
in which electronics and communication system. Xyz Company set quality objectives with total
customer satisfaction. However, it can be stated that Six Sigma implementation develop
operations in relation with lean principles. Hence, it increases models and theories in project
management.
D1 Improvement plan for achieving improved efficiency:
Theories and model are comprised the roles how to business can involve to various
process which make improvement in business. XYZ firm have to manufacture their products to
implement various kinds of product which makes profits and make popularity in business. To
improving efficiency in business the organizer are make implementation in products and service
they redesigned products according to consumer demands.
TASK 2
P2 Continuous improvement plan regarding the reviews and critique of operation management
principles
The XYZ company have to improvement their manufacturing of the products or market
reputations, the company have goods sells in market, the company have to improve their work
skills which effects on the market reputations, the company has numerous implements occurs,
they XYZ company trying to established the large television market, which improve the huge
market in the manufacturing company. The company improve there huge market they trying to
manufacturing in the new techniques (Lam,et.al, 2015). The XYZ company implements in
managing the new products and research for new manufacturing products and developed them.
5
Paraphrase This Document
Need a fresh take? Get an instant paraphrase of this document with our AI Paraphraser
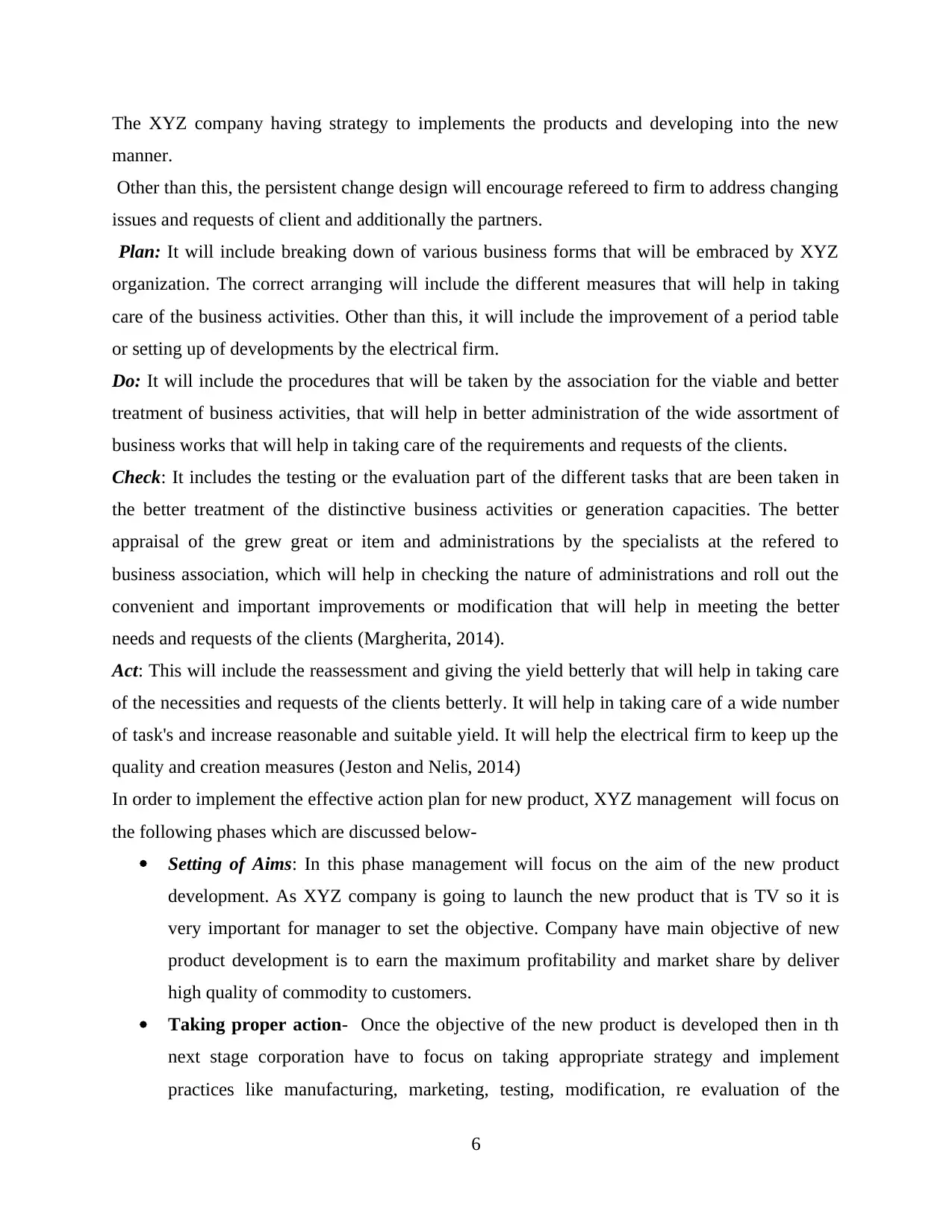
The XYZ company having strategy to implements the products and developing into the new
manner.
Other than this, the persistent change design will encourage refereed to firm to address changing
issues and requests of client and additionally the partners.
Plan: It will include breaking down of various business forms that will be embraced by XYZ
organization. The correct arranging will include the different measures that will help in taking
care of the business activities. Other than this, it will include the improvement of a period table
or setting up of developments by the electrical firm.
Do: It will include the procedures that will be taken by the association for the viable and better
treatment of business activities, that will help in better administration of the wide assortment of
business works that will help in taking care of the requirements and requests of the clients.
Check: It includes the testing or the evaluation part of the different tasks that are been taken in
the better treatment of the distinctive business activities or generation capacities. The better
appraisal of the grew great or item and administrations by the specialists at the refered to
business association, which will help in checking the nature of administrations and roll out the
convenient and important improvements or modification that will help in meeting the better
needs and requests of the clients (Margherita, 2014).
Act: This will include the reassessment and giving the yield betterly that will help in taking care
of the necessities and requests of the clients betterly. It will help in taking care of a wide number
of task's and increase reasonable and suitable yield. It will help the electrical firm to keep up the
quality and creation measures (Jeston and Nelis, 2014)
In order to implement the effective action plan for new product, XYZ management will focus on
the following phases which are discussed below-
Setting of Aims: In this phase management will focus on the aim of the new product
development. As XYZ company is going to launch the new product that is TV so it is
very important for manager to set the objective. Company have main objective of new
product development is to earn the maximum profitability and market share by deliver
high quality of commodity to customers.
Taking proper action- Once the objective of the new product is developed then in th
next stage corporation have to focus on taking appropriate strategy and implement
practices like manufacturing, marketing, testing, modification, re evaluation of the
6
manner.
Other than this, the persistent change design will encourage refereed to firm to address changing
issues and requests of client and additionally the partners.
Plan: It will include breaking down of various business forms that will be embraced by XYZ
organization. The correct arranging will include the different measures that will help in taking
care of the business activities. Other than this, it will include the improvement of a period table
or setting up of developments by the electrical firm.
Do: It will include the procedures that will be taken by the association for the viable and better
treatment of business activities, that will help in better administration of the wide assortment of
business works that will help in taking care of the requirements and requests of the clients.
Check: It includes the testing or the evaluation part of the different tasks that are been taken in
the better treatment of the distinctive business activities or generation capacities. The better
appraisal of the grew great or item and administrations by the specialists at the refered to
business association, which will help in checking the nature of administrations and roll out the
convenient and important improvements or modification that will help in meeting the better
needs and requests of the clients (Margherita, 2014).
Act: This will include the reassessment and giving the yield betterly that will help in taking care
of the necessities and requests of the clients betterly. It will help in taking care of a wide number
of task's and increase reasonable and suitable yield. It will help the electrical firm to keep up the
quality and creation measures (Jeston and Nelis, 2014)
In order to implement the effective action plan for new product, XYZ management will focus on
the following phases which are discussed below-
Setting of Aims: In this phase management will focus on the aim of the new product
development. As XYZ company is going to launch the new product that is TV so it is
very important for manager to set the objective. Company have main objective of new
product development is to earn the maximum profitability and market share by deliver
high quality of commodity to customers.
Taking proper action- Once the objective of the new product is developed then in th
next stage corporation have to focus on taking appropriate strategy and implement
practices like manufacturing, marketing, testing, modification, re evaluation of the
6
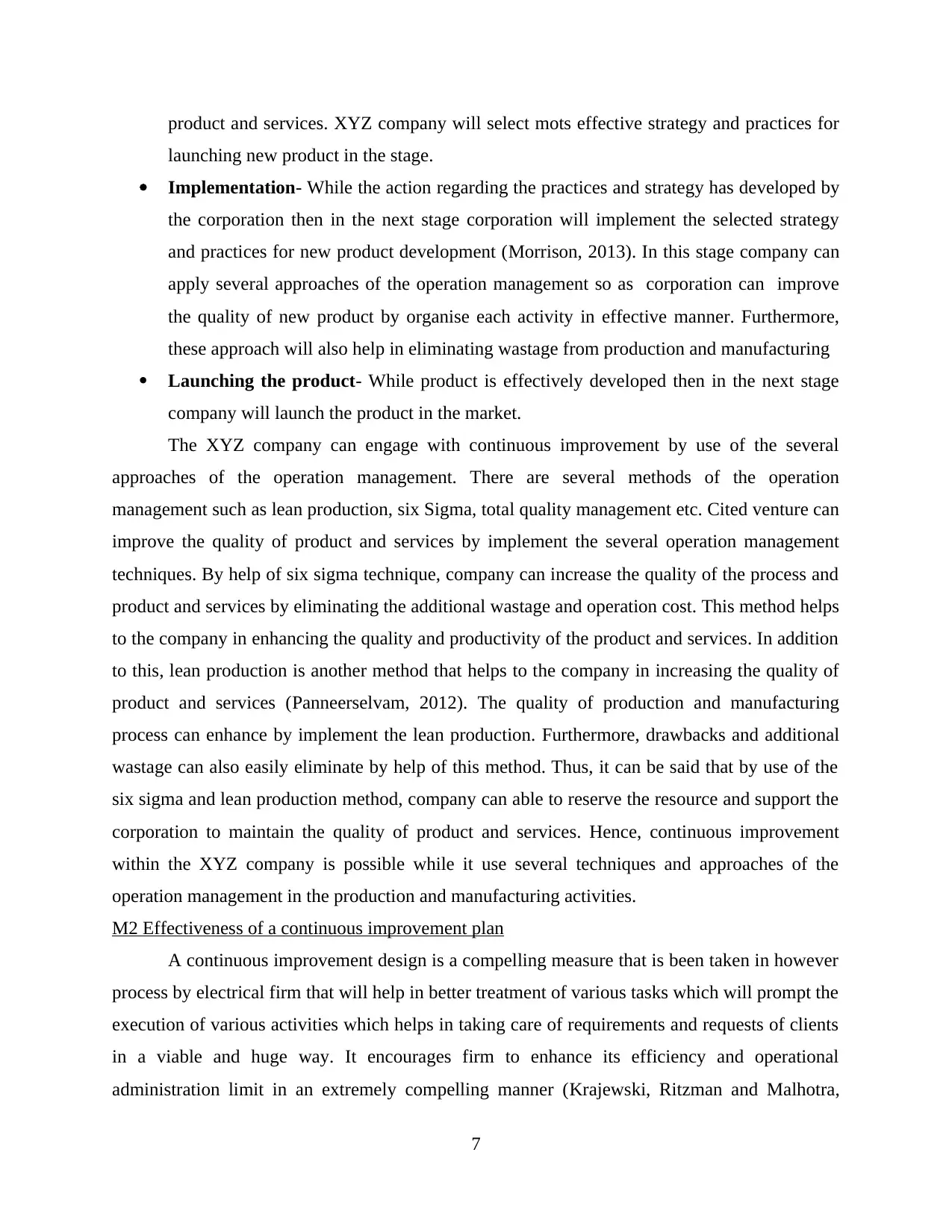
product and services. XYZ company will select mots effective strategy and practices for
launching new product in the stage.
Implementation- While the action regarding the practices and strategy has developed by
the corporation then in the next stage corporation will implement the selected strategy
and practices for new product development (Morrison, 2013). In this stage company can
apply several approaches of the operation management so as corporation can improve
the quality of new product by organise each activity in effective manner. Furthermore,
these approach will also help in eliminating wastage from production and manufacturing
Launching the product- While product is effectively developed then in the next stage
company will launch the product in the market.
The XYZ company can engage with continuous improvement by use of the several
approaches of the operation management. There are several methods of the operation
management such as lean production, six Sigma, total quality management etc. Cited venture can
improve the quality of product and services by implement the several operation management
techniques. By help of six sigma technique, company can increase the quality of the process and
product and services by eliminating the additional wastage and operation cost. This method helps
to the company in enhancing the quality and productivity of the product and services. In addition
to this, lean production is another method that helps to the company in increasing the quality of
product and services (Panneerselvam, 2012). The quality of production and manufacturing
process can enhance by implement the lean production. Furthermore, drawbacks and additional
wastage can also easily eliminate by help of this method. Thus, it can be said that by use of the
six sigma and lean production method, company can able to reserve the resource and support the
corporation to maintain the quality of product and services. Hence, continuous improvement
within the XYZ company is possible while it use several techniques and approaches of the
operation management in the production and manufacturing activities.
M2 Effectiveness of a continuous improvement plan
A continuous improvement design is a compelling measure that is been taken in however
process by electrical firm that will help in better treatment of various tasks which will prompt the
execution of various activities which helps in taking care of requirements and requests of clients
in a viable and huge way. It encourages firm to enhance its efficiency and operational
administration limit in an extremely compelling manner (Krajewski, Ritzman and Malhotra,
7
launching new product in the stage.
Implementation- While the action regarding the practices and strategy has developed by
the corporation then in the next stage corporation will implement the selected strategy
and practices for new product development (Morrison, 2013). In this stage company can
apply several approaches of the operation management so as corporation can improve
the quality of new product by organise each activity in effective manner. Furthermore,
these approach will also help in eliminating wastage from production and manufacturing
Launching the product- While product is effectively developed then in the next stage
company will launch the product in the market.
The XYZ company can engage with continuous improvement by use of the several
approaches of the operation management. There are several methods of the operation
management such as lean production, six Sigma, total quality management etc. Cited venture can
improve the quality of product and services by implement the several operation management
techniques. By help of six sigma technique, company can increase the quality of the process and
product and services by eliminating the additional wastage and operation cost. This method helps
to the company in enhancing the quality and productivity of the product and services. In addition
to this, lean production is another method that helps to the company in increasing the quality of
product and services (Panneerselvam, 2012). The quality of production and manufacturing
process can enhance by implement the lean production. Furthermore, drawbacks and additional
wastage can also easily eliminate by help of this method. Thus, it can be said that by use of the
six sigma and lean production method, company can able to reserve the resource and support the
corporation to maintain the quality of product and services. Hence, continuous improvement
within the XYZ company is possible while it use several techniques and approaches of the
operation management in the production and manufacturing activities.
M2 Effectiveness of a continuous improvement plan
A continuous improvement design is a compelling measure that is been taken in however
process by electrical firm that will help in better treatment of various tasks which will prompt the
execution of various activities which helps in taking care of requirements and requests of clients
in a viable and huge way. It encourages firm to enhance its efficiency and operational
administration limit in an extremely compelling manner (Krajewski, Ritzman and Malhotra,
7
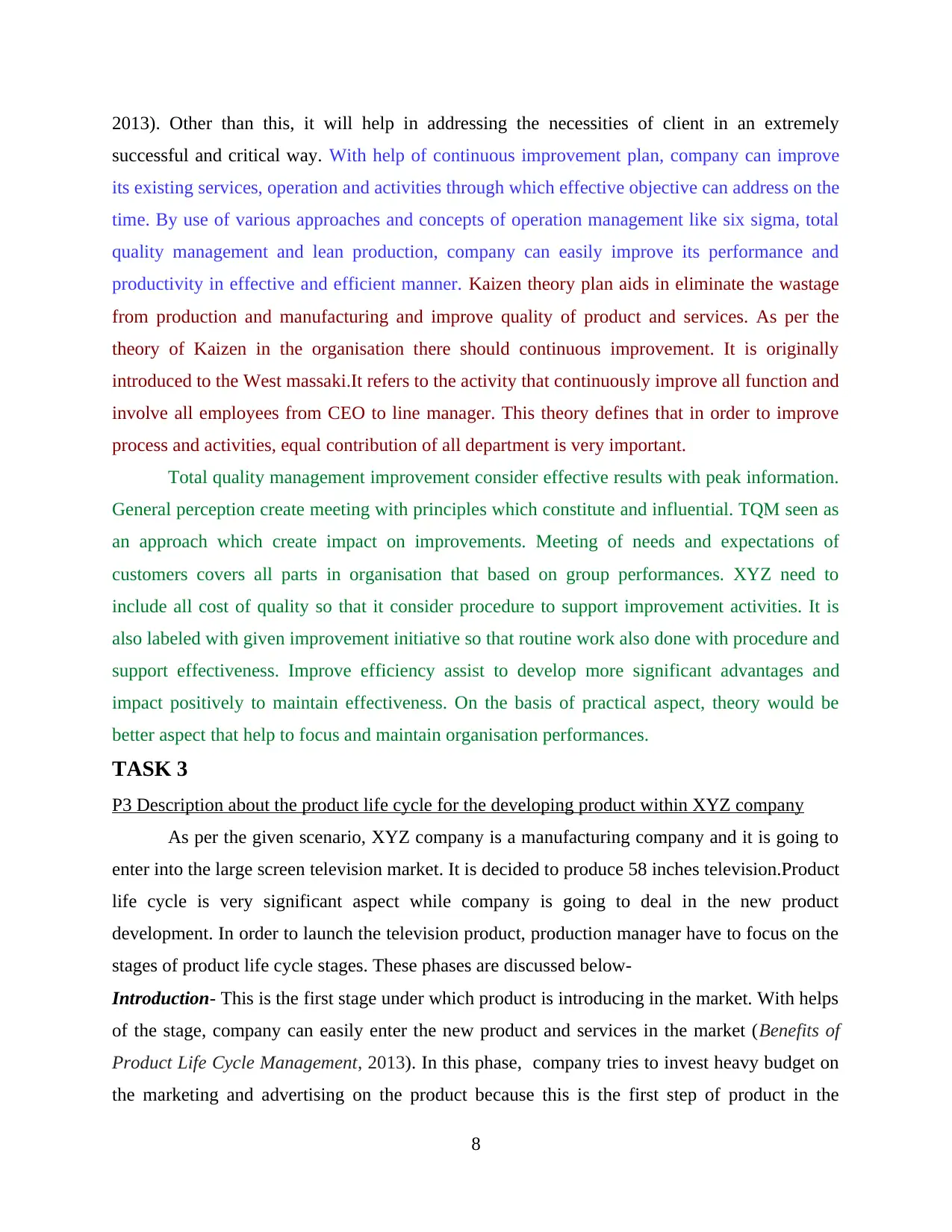
2013). Other than this, it will help in addressing the necessities of client in an extremely
successful and critical way. With help of continuous improvement plan, company can improve
its existing services, operation and activities through which effective objective can address on the
time. By use of various approaches and concepts of operation management like six sigma, total
quality management and lean production, company can easily improve its performance and
productivity in effective and efficient manner. Kaizen theory plan aids in eliminate the wastage
from production and manufacturing and improve quality of product and services. As per the
theory of Kaizen in the organisation there should continuous improvement. It is originally
introduced to the West massaki.It refers to the activity that continuously improve all function and
involve all employees from CEO to line manager. This theory defines that in order to improve
process and activities, equal contribution of all department is very important.
Total quality management improvement consider effective results with peak information.
General perception create meeting with principles which constitute and influential. TQM seen as
an approach which create impact on improvements. Meeting of needs and expectations of
customers covers all parts in organisation that based on group performances. XYZ need to
include all cost of quality so that it consider procedure to support improvement activities. It is
also labeled with given improvement initiative so that routine work also done with procedure and
support effectiveness. Improve efficiency assist to develop more significant advantages and
impact positively to maintain effectiveness. On the basis of practical aspect, theory would be
better aspect that help to focus and maintain organisation performances.
TASK 3
P3 Description about the product life cycle for the developing product within XYZ company
As per the given scenario, XYZ company is a manufacturing company and it is going to
enter into the large screen television market. It is decided to produce 58 inches television.Product
life cycle is very significant aspect while company is going to deal in the new product
development. In order to launch the television product, production manager have to focus on the
stages of product life cycle stages. These phases are discussed below-
Introduction- This is the first stage under which product is introducing in the market. With helps
of the stage, company can easily enter the new product and services in the market (Benefits of
Product Life Cycle Management, 2013). In this phase, company tries to invest heavy budget on
the marketing and advertising on the product because this is the first step of product in the
8
successful and critical way. With help of continuous improvement plan, company can improve
its existing services, operation and activities through which effective objective can address on the
time. By use of various approaches and concepts of operation management like six sigma, total
quality management and lean production, company can easily improve its performance and
productivity in effective and efficient manner. Kaizen theory plan aids in eliminate the wastage
from production and manufacturing and improve quality of product and services. As per the
theory of Kaizen in the organisation there should continuous improvement. It is originally
introduced to the West massaki.It refers to the activity that continuously improve all function and
involve all employees from CEO to line manager. This theory defines that in order to improve
process and activities, equal contribution of all department is very important.
Total quality management improvement consider effective results with peak information.
General perception create meeting with principles which constitute and influential. TQM seen as
an approach which create impact on improvements. Meeting of needs and expectations of
customers covers all parts in organisation that based on group performances. XYZ need to
include all cost of quality so that it consider procedure to support improvement activities. It is
also labeled with given improvement initiative so that routine work also done with procedure and
support effectiveness. Improve efficiency assist to develop more significant advantages and
impact positively to maintain effectiveness. On the basis of practical aspect, theory would be
better aspect that help to focus and maintain organisation performances.
TASK 3
P3 Description about the product life cycle for the developing product within XYZ company
As per the given scenario, XYZ company is a manufacturing company and it is going to
enter into the large screen television market. It is decided to produce 58 inches television.Product
life cycle is very significant aspect while company is going to deal in the new product
development. In order to launch the television product, production manager have to focus on the
stages of product life cycle stages. These phases are discussed below-
Introduction- This is the first stage under which product is introducing in the market. With helps
of the stage, company can easily enter the new product and services in the market (Benefits of
Product Life Cycle Management, 2013). In this phase, company tries to invest heavy budget on
the marketing and advertising on the product because this is the first step of product in the
8
Secure Best Marks with AI Grader
Need help grading? Try our AI Grader for instant feedback on your assignments.
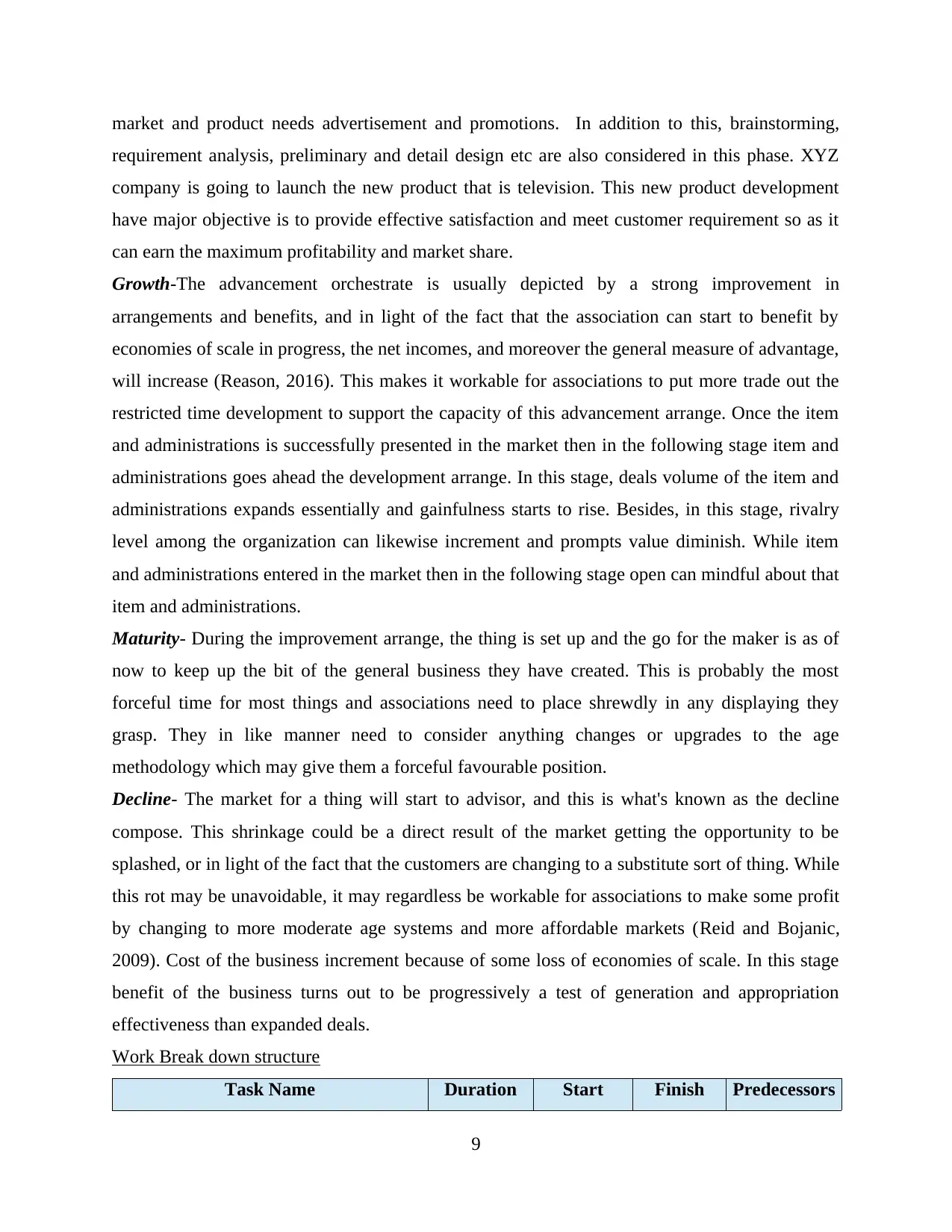
market and product needs advertisement and promotions. In addition to this, brainstorming,
requirement analysis, preliminary and detail design etc are also considered in this phase. XYZ
company is going to launch the new product that is television. This new product development
have major objective is to provide effective satisfaction and meet customer requirement so as it
can earn the maximum profitability and market share.
Growth-The advancement orchestrate is usually depicted by a strong improvement in
arrangements and benefits, and in light of the fact that the association can start to benefit by
economies of scale in progress, the net incomes, and moreover the general measure of advantage,
will increase (Reason, 2016). This makes it workable for associations to put more trade out the
restricted time development to support the capacity of this advancement arrange. Once the item
and administrations is successfully presented in the market then in the following stage item and
administrations goes ahead the development arrange. In this stage, deals volume of the item and
administrations expands essentially and gainfulness starts to rise. Besides, in this stage, rivalry
level among the organization can likewise increment and prompts value diminish. While item
and administrations entered in the market then in the following stage open can mindful about that
item and administrations.
Maturity- During the improvement arrange, the thing is set up and the go for the maker is as of
now to keep up the bit of the general business they have created. This is probably the most
forceful time for most things and associations need to place shrewdly in any displaying they
grasp. They in like manner need to consider anything changes or upgrades to the age
methodology which may give them a forceful favourable position.
Decline- The market for a thing will start to advisor, and this is what's known as the decline
compose. This shrinkage could be a direct result of the market getting the opportunity to be
splashed, or in light of the fact that the customers are changing to a substitute sort of thing. While
this rot may be unavoidable, it may regardless be workable for associations to make some profit
by changing to more moderate age systems and more affordable markets (Reid and Bojanic,
2009). Cost of the business increment because of some loss of economies of scale. In this stage
benefit of the business turns out to be progressively a test of generation and appropriation
effectiveness than expanded deals.
Work Break down structure
Task Name Duration Start Finish Predecessors
9
requirement analysis, preliminary and detail design etc are also considered in this phase. XYZ
company is going to launch the new product that is television. This new product development
have major objective is to provide effective satisfaction and meet customer requirement so as it
can earn the maximum profitability and market share.
Growth-The advancement orchestrate is usually depicted by a strong improvement in
arrangements and benefits, and in light of the fact that the association can start to benefit by
economies of scale in progress, the net incomes, and moreover the general measure of advantage,
will increase (Reason, 2016). This makes it workable for associations to put more trade out the
restricted time development to support the capacity of this advancement arrange. Once the item
and administrations is successfully presented in the market then in the following stage item and
administrations goes ahead the development arrange. In this stage, deals volume of the item and
administrations expands essentially and gainfulness starts to rise. Besides, in this stage, rivalry
level among the organization can likewise increment and prompts value diminish. While item
and administrations entered in the market then in the following stage open can mindful about that
item and administrations.
Maturity- During the improvement arrange, the thing is set up and the go for the maker is as of
now to keep up the bit of the general business they have created. This is probably the most
forceful time for most things and associations need to place shrewdly in any displaying they
grasp. They in like manner need to consider anything changes or upgrades to the age
methodology which may give them a forceful favourable position.
Decline- The market for a thing will start to advisor, and this is what's known as the decline
compose. This shrinkage could be a direct result of the market getting the opportunity to be
splashed, or in light of the fact that the customers are changing to a substitute sort of thing. While
this rot may be unavoidable, it may regardless be workable for associations to make some profit
by changing to more moderate age systems and more affordable markets (Reid and Bojanic,
2009). Cost of the business increment because of some loss of economies of scale. In this stage
benefit of the business turns out to be progressively a test of generation and appropriation
effectiveness than expanded deals.
Work Break down structure
Task Name Duration Start Finish Predecessors
9
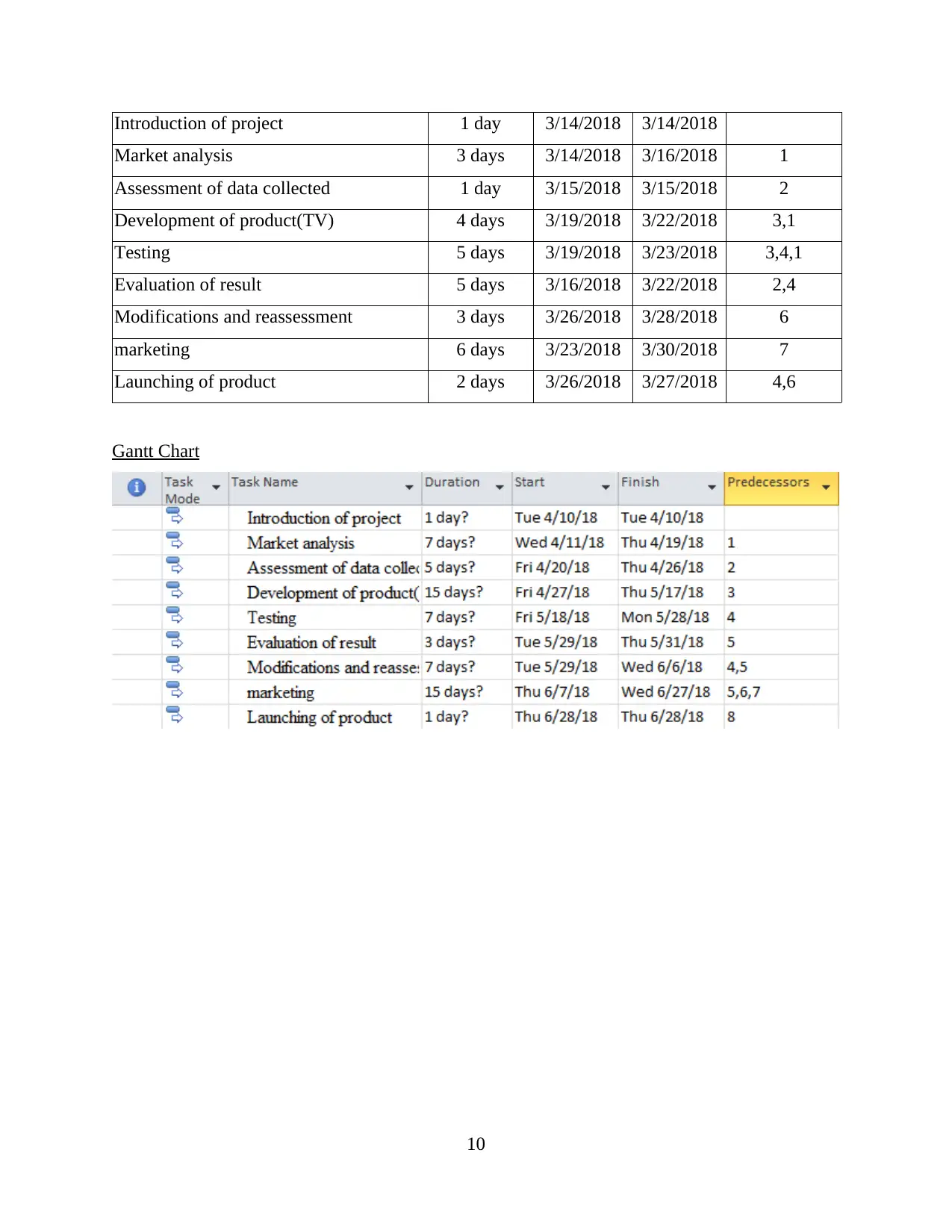
Introduction of project 1 day 3/14/2018 3/14/2018
Market analysis 3 days 3/14/2018 3/16/2018 1
Assessment of data collected 1 day 3/15/2018 3/15/2018 2
Development of product(TV) 4 days 3/19/2018 3/22/2018 3,1
Testing 5 days 3/19/2018 3/23/2018 3,4,1
Evaluation of result 5 days 3/16/2018 3/22/2018 2,4
Modifications and reassessment 3 days 3/26/2018 3/28/2018 6
marketing 6 days 3/23/2018 3/30/2018 7
Launching of product 2 days 3/26/2018 3/27/2018 4,6
Gantt Chart
10
Market analysis 3 days 3/14/2018 3/16/2018 1
Assessment of data collected 1 day 3/15/2018 3/15/2018 2
Development of product(TV) 4 days 3/19/2018 3/22/2018 3,1
Testing 5 days 3/19/2018 3/23/2018 3,4,1
Evaluation of result 5 days 3/16/2018 3/22/2018 2,4
Modifications and reassessment 3 days 3/26/2018 3/28/2018 6
marketing 6 days 3/23/2018 3/30/2018 7
Launching of product 2 days 3/26/2018 3/27/2018 4,6
Gantt Chart
10
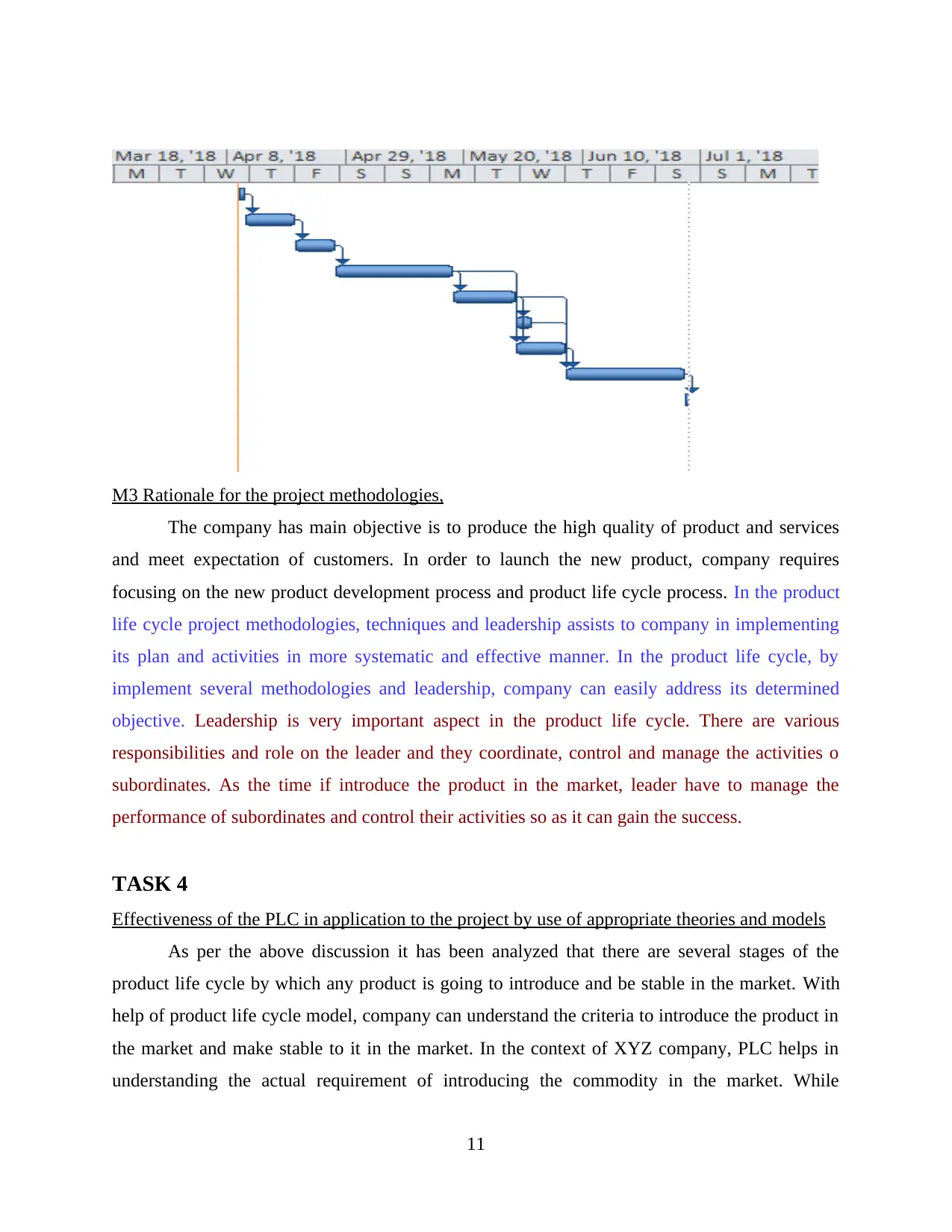
M3 Rationale for the project methodologies,
The company has main objective is to produce the high quality of product and services
and meet expectation of customers. In order to launch the new product, company requires
focusing on the new product development process and product life cycle process. In the product
life cycle project methodologies, techniques and leadership assists to company in implementing
its plan and activities in more systematic and effective manner. In the product life cycle, by
implement several methodologies and leadership, company can easily address its determined
objective. Leadership is very important aspect in the product life cycle. There are various
responsibilities and role on the leader and they coordinate, control and manage the activities o
subordinates. As the time if introduce the product in the market, leader have to manage the
performance of subordinates and control their activities so as it can gain the success.
TASK 4
Effectiveness of the PLC in application to the project by use of appropriate theories and models
As per the above discussion it has been analyzed that there are several stages of the
product life cycle by which any product is going to introduce and be stable in the market. With
help of product life cycle model, company can understand the criteria to introduce the product in
the market and make stable to it in the market. In the context of XYZ company, PLC helps in
understanding the actual requirement of introducing the commodity in the market. While
11
The company has main objective is to produce the high quality of product and services
and meet expectation of customers. In order to launch the new product, company requires
focusing on the new product development process and product life cycle process. In the product
life cycle project methodologies, techniques and leadership assists to company in implementing
its plan and activities in more systematic and effective manner. In the product life cycle, by
implement several methodologies and leadership, company can easily address its determined
objective. Leadership is very important aspect in the product life cycle. There are various
responsibilities and role on the leader and they coordinate, control and manage the activities o
subordinates. As the time if introduce the product in the market, leader have to manage the
performance of subordinates and control their activities so as it can gain the success.
TASK 4
Effectiveness of the PLC in application to the project by use of appropriate theories and models
As per the above discussion it has been analyzed that there are several stages of the
product life cycle by which any product is going to introduce and be stable in the market. With
help of product life cycle model, company can understand the criteria to introduce the product in
the market and make stable to it in the market. In the context of XYZ company, PLC helps in
understanding the actual requirement of introducing the commodity in the market. While
11
Paraphrase This Document
Need a fresh take? Get an instant paraphrase of this document with our AI Paraphraser
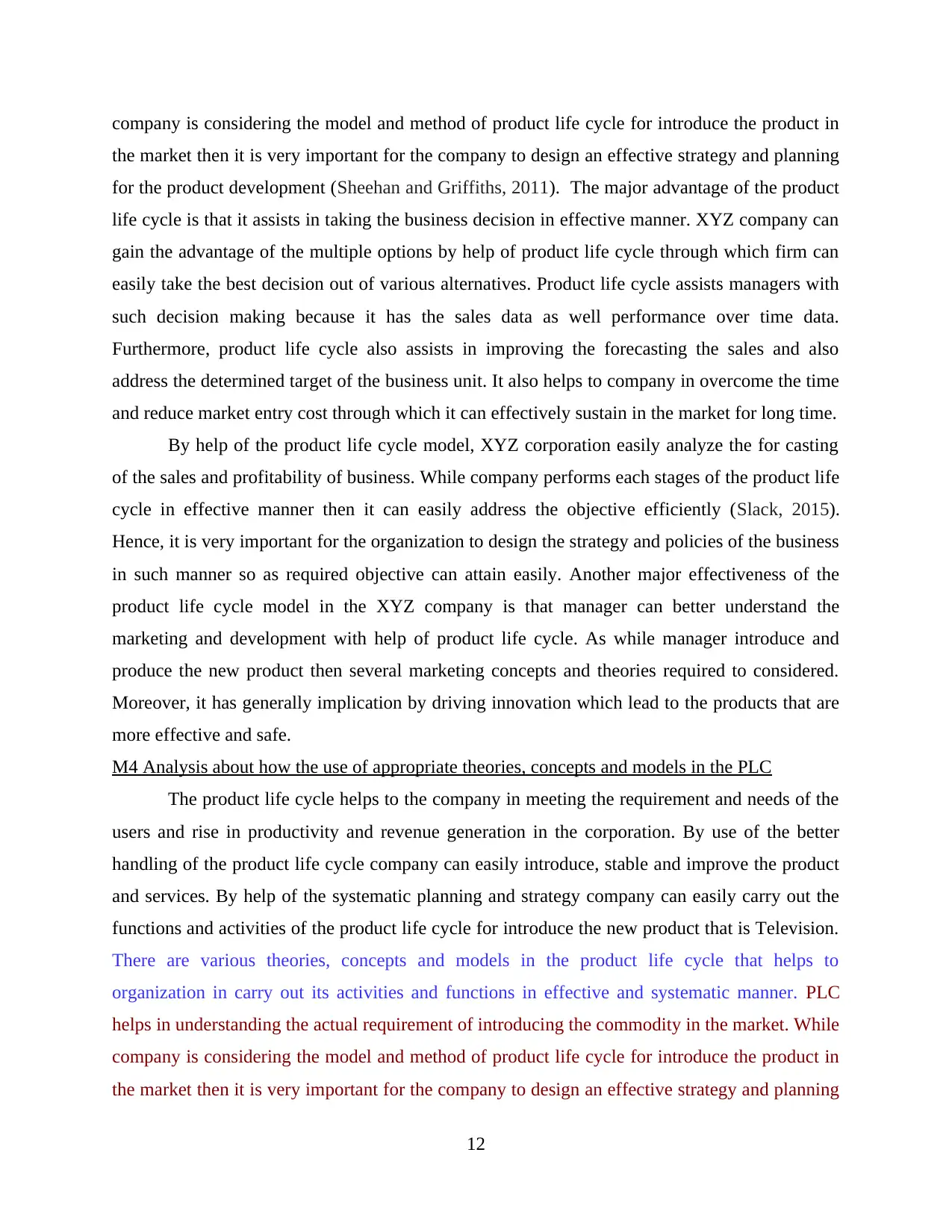
company is considering the model and method of product life cycle for introduce the product in
the market then it is very important for the company to design an effective strategy and planning
for the product development (Sheehan and Griffiths, 2011). The major advantage of the product
life cycle is that it assists in taking the business decision in effective manner. XYZ company can
gain the advantage of the multiple options by help of product life cycle through which firm can
easily take the best decision out of various alternatives. Product life cycle assists managers with
such decision making because it has the sales data as well performance over time data.
Furthermore, product life cycle also assists in improving the forecasting the sales and also
address the determined target of the business unit. It also helps to company in overcome the time
and reduce market entry cost through which it can effectively sustain in the market for long time.
By help of the product life cycle model, XYZ corporation easily analyze the for casting
of the sales and profitability of business. While company performs each stages of the product life
cycle in effective manner then it can easily address the objective efficiently (Slack, 2015).
Hence, it is very important for the organization to design the strategy and policies of the business
in such manner so as required objective can attain easily. Another major effectiveness of the
product life cycle model in the XYZ company is that manager can better understand the
marketing and development with help of product life cycle. As while manager introduce and
produce the new product then several marketing concepts and theories required to considered.
Moreover, it has generally implication by driving innovation which lead to the products that are
more effective and safe.
M4 Analysis about how the use of appropriate theories, concepts and models in the PLC
The product life cycle helps to the company in meeting the requirement and needs of the
users and rise in productivity and revenue generation in the corporation. By use of the better
handling of the product life cycle company can easily introduce, stable and improve the product
and services. By help of the systematic planning and strategy company can easily carry out the
functions and activities of the product life cycle for introduce the new product that is Television.
There are various theories, concepts and models in the product life cycle that helps to
organization in carry out its activities and functions in effective and systematic manner. PLC
helps in understanding the actual requirement of introducing the commodity in the market. While
company is considering the model and method of product life cycle for introduce the product in
the market then it is very important for the company to design an effective strategy and planning
12
the market then it is very important for the company to design an effective strategy and planning
for the product development (Sheehan and Griffiths, 2011). The major advantage of the product
life cycle is that it assists in taking the business decision in effective manner. XYZ company can
gain the advantage of the multiple options by help of product life cycle through which firm can
easily take the best decision out of various alternatives. Product life cycle assists managers with
such decision making because it has the sales data as well performance over time data.
Furthermore, product life cycle also assists in improving the forecasting the sales and also
address the determined target of the business unit. It also helps to company in overcome the time
and reduce market entry cost through which it can effectively sustain in the market for long time.
By help of the product life cycle model, XYZ corporation easily analyze the for casting
of the sales and profitability of business. While company performs each stages of the product life
cycle in effective manner then it can easily address the objective efficiently (Slack, 2015).
Hence, it is very important for the organization to design the strategy and policies of the business
in such manner so as required objective can attain easily. Another major effectiveness of the
product life cycle model in the XYZ company is that manager can better understand the
marketing and development with help of product life cycle. As while manager introduce and
produce the new product then several marketing concepts and theories required to considered.
Moreover, it has generally implication by driving innovation which lead to the products that are
more effective and safe.
M4 Analysis about how the use of appropriate theories, concepts and models in the PLC
The product life cycle helps to the company in meeting the requirement and needs of the
users and rise in productivity and revenue generation in the corporation. By use of the better
handling of the product life cycle company can easily introduce, stable and improve the product
and services. By help of the systematic planning and strategy company can easily carry out the
functions and activities of the product life cycle for introduce the new product that is Television.
There are various theories, concepts and models in the product life cycle that helps to
organization in carry out its activities and functions in effective and systematic manner. PLC
helps in understanding the actual requirement of introducing the commodity in the market. While
company is considering the model and method of product life cycle for introduce the product in
the market then it is very important for the company to design an effective strategy and planning
12
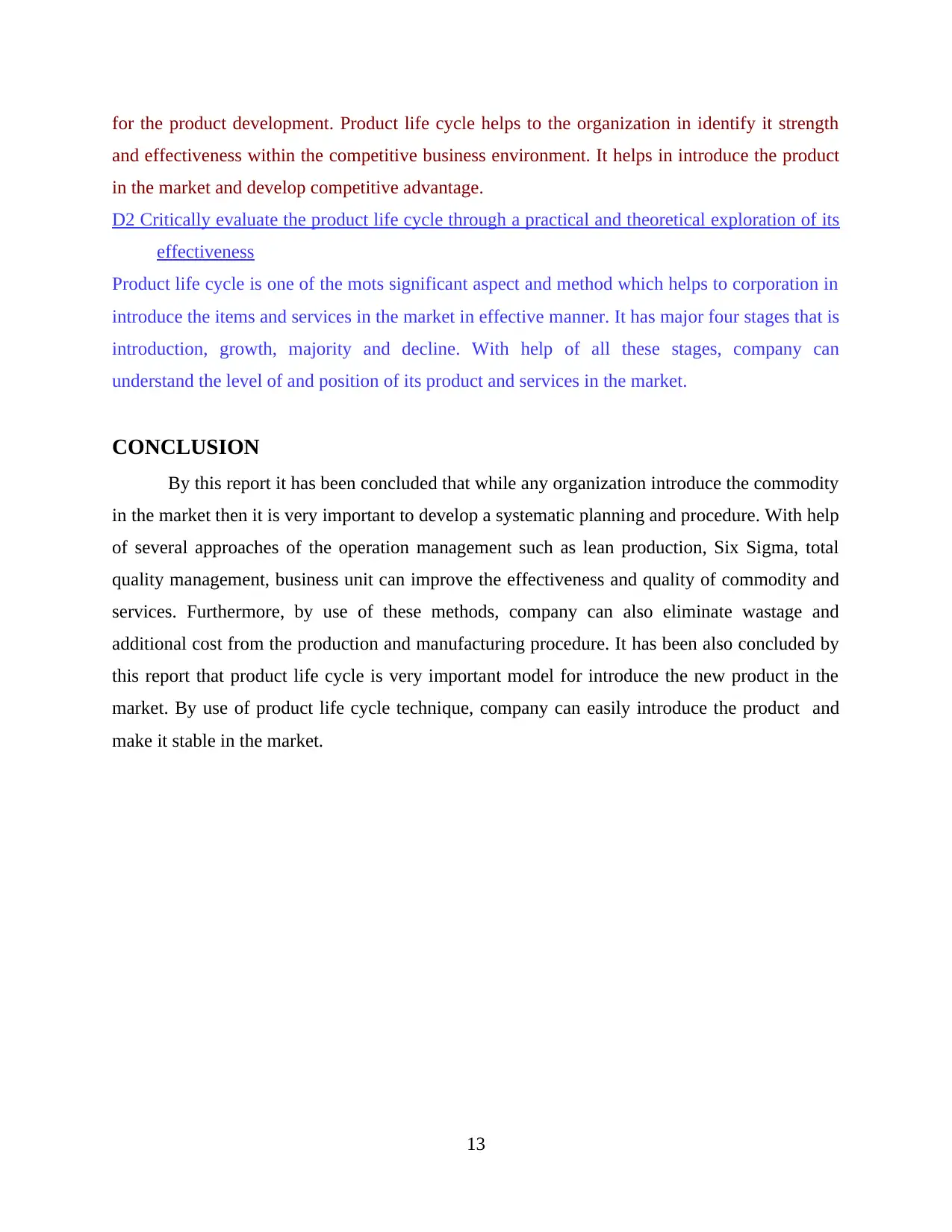
for the product development. Product life cycle helps to the organization in identify it strength
and effectiveness within the competitive business environment. It helps in introduce the product
in the market and develop competitive advantage.
D2 Critically evaluate the product life cycle through a practical and theoretical exploration of its
effectiveness
Product life cycle is one of the mots significant aspect and method which helps to corporation in
introduce the items and services in the market in effective manner. It has major four stages that is
introduction, growth, majority and decline. With help of all these stages, company can
understand the level of and position of its product and services in the market.
CONCLUSION
By this report it has been concluded that while any organization introduce the commodity
in the market then it is very important to develop a systematic planning and procedure. With help
of several approaches of the operation management such as lean production, Six Sigma, total
quality management, business unit can improve the effectiveness and quality of commodity and
services. Furthermore, by use of these methods, company can also eliminate wastage and
additional cost from the production and manufacturing procedure. It has been also concluded by
this report that product life cycle is very important model for introduce the new product in the
market. By use of product life cycle technique, company can easily introduce the product and
make it stable in the market.
13
and effectiveness within the competitive business environment. It helps in introduce the product
in the market and develop competitive advantage.
D2 Critically evaluate the product life cycle through a practical and theoretical exploration of its
effectiveness
Product life cycle is one of the mots significant aspect and method which helps to corporation in
introduce the items and services in the market in effective manner. It has major four stages that is
introduction, growth, majority and decline. With help of all these stages, company can
understand the level of and position of its product and services in the market.
CONCLUSION
By this report it has been concluded that while any organization introduce the commodity
in the market then it is very important to develop a systematic planning and procedure. With help
of several approaches of the operation management such as lean production, Six Sigma, total
quality management, business unit can improve the effectiveness and quality of commodity and
services. Furthermore, by use of these methods, company can also eliminate wastage and
additional cost from the production and manufacturing procedure. It has been also concluded by
this report that product life cycle is very important model for introduce the new product in the
market. By use of product life cycle technique, company can easily introduce the product and
make it stable in the market.
13
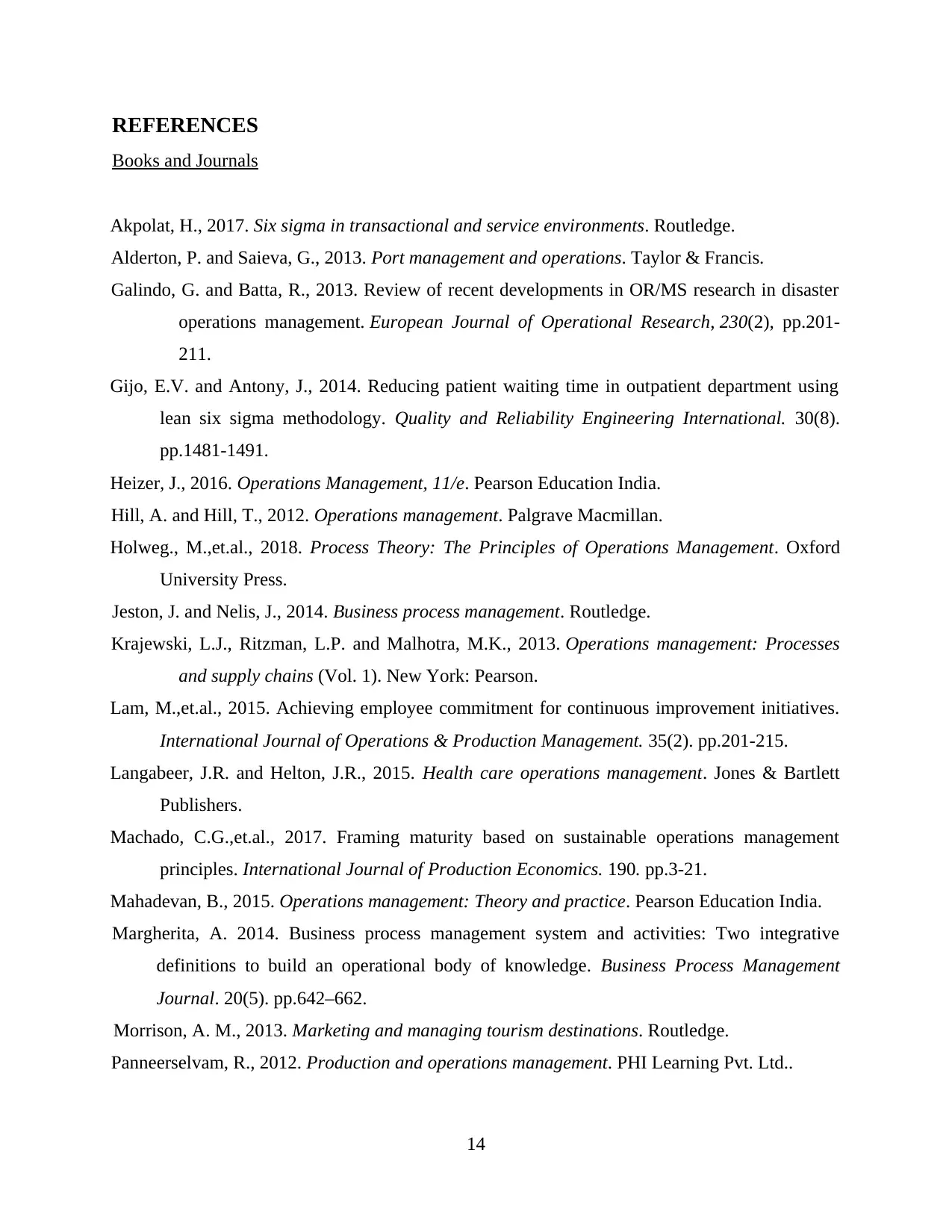
REFERENCES
Books and Journals
Akpolat, H., 2017. Six sigma in transactional and service environments. Routledge.
Alderton, P. and Saieva, G., 2013. Port management and operations. Taylor & Francis.
Galindo, G. and Batta, R., 2013. Review of recent developments in OR/MS research in disaster
operations management. European Journal of Operational Research, 230(2), pp.201-
211.
Gijo, E.V. and Antony, J., 2014. Reducing patient waiting time in outpatient department using
lean six sigma methodology. Quality and Reliability Engineering International. 30(8).
pp.1481-1491.
Heizer, J., 2016. Operations Management, 11/e. Pearson Education India.
Hill, A. and Hill, T., 2012. Operations management. Palgrave Macmillan.
Holweg., M.,et.al., 2018. Process Theory: The Principles of Operations Management. Oxford
University Press.
Jeston, J. and Nelis, J., 2014. Business process management. Routledge.
Krajewski, L.J., Ritzman, L.P. and Malhotra, M.K., 2013. Operations management: Processes
and supply chains (Vol. 1). New York: Pearson.
Lam, M.,et.al., 2015. Achieving employee commitment for continuous improvement initiatives.
International Journal of Operations & Production Management. 35(2). pp.201-215.
Langabeer, J.R. and Helton, J.R., 2015. Health care operations management. Jones & Bartlett
Publishers.
Machado, C.G.,et.al., 2017. Framing maturity based on sustainable operations management
principles. International Journal of Production Economics. 190. pp.3-21.
Mahadevan, B., 2015. Operations management: Theory and practice. Pearson Education India.
Margherita, A. 2014. Business process management system and activities: Two integrative
definitions to build an operational body of knowledge. Business Process Management
Journal. 20(5). pp.642–662.
Morrison, A. M., 2013. Marketing and managing tourism destinations. Routledge.
Panneerselvam, R., 2012. Production and operations management. PHI Learning Pvt. Ltd..
14
Books and Journals
Akpolat, H., 2017. Six sigma in transactional and service environments. Routledge.
Alderton, P. and Saieva, G., 2013. Port management and operations. Taylor & Francis.
Galindo, G. and Batta, R., 2013. Review of recent developments in OR/MS research in disaster
operations management. European Journal of Operational Research, 230(2), pp.201-
211.
Gijo, E.V. and Antony, J., 2014. Reducing patient waiting time in outpatient department using
lean six sigma methodology. Quality and Reliability Engineering International. 30(8).
pp.1481-1491.
Heizer, J., 2016. Operations Management, 11/e. Pearson Education India.
Hill, A. and Hill, T., 2012. Operations management. Palgrave Macmillan.
Holweg., M.,et.al., 2018. Process Theory: The Principles of Operations Management. Oxford
University Press.
Jeston, J. and Nelis, J., 2014. Business process management. Routledge.
Krajewski, L.J., Ritzman, L.P. and Malhotra, M.K., 2013. Operations management: Processes
and supply chains (Vol. 1). New York: Pearson.
Lam, M.,et.al., 2015. Achieving employee commitment for continuous improvement initiatives.
International Journal of Operations & Production Management. 35(2). pp.201-215.
Langabeer, J.R. and Helton, J.R., 2015. Health care operations management. Jones & Bartlett
Publishers.
Machado, C.G.,et.al., 2017. Framing maturity based on sustainable operations management
principles. International Journal of Production Economics. 190. pp.3-21.
Mahadevan, B., 2015. Operations management: Theory and practice. Pearson Education India.
Margherita, A. 2014. Business process management system and activities: Two integrative
definitions to build an operational body of knowledge. Business Process Management
Journal. 20(5). pp.642–662.
Morrison, A. M., 2013. Marketing and managing tourism destinations. Routledge.
Panneerselvam, R., 2012. Production and operations management. PHI Learning Pvt. Ltd..
14
Secure Best Marks with AI Grader
Need help grading? Try our AI Grader for instant feedback on your assignments.
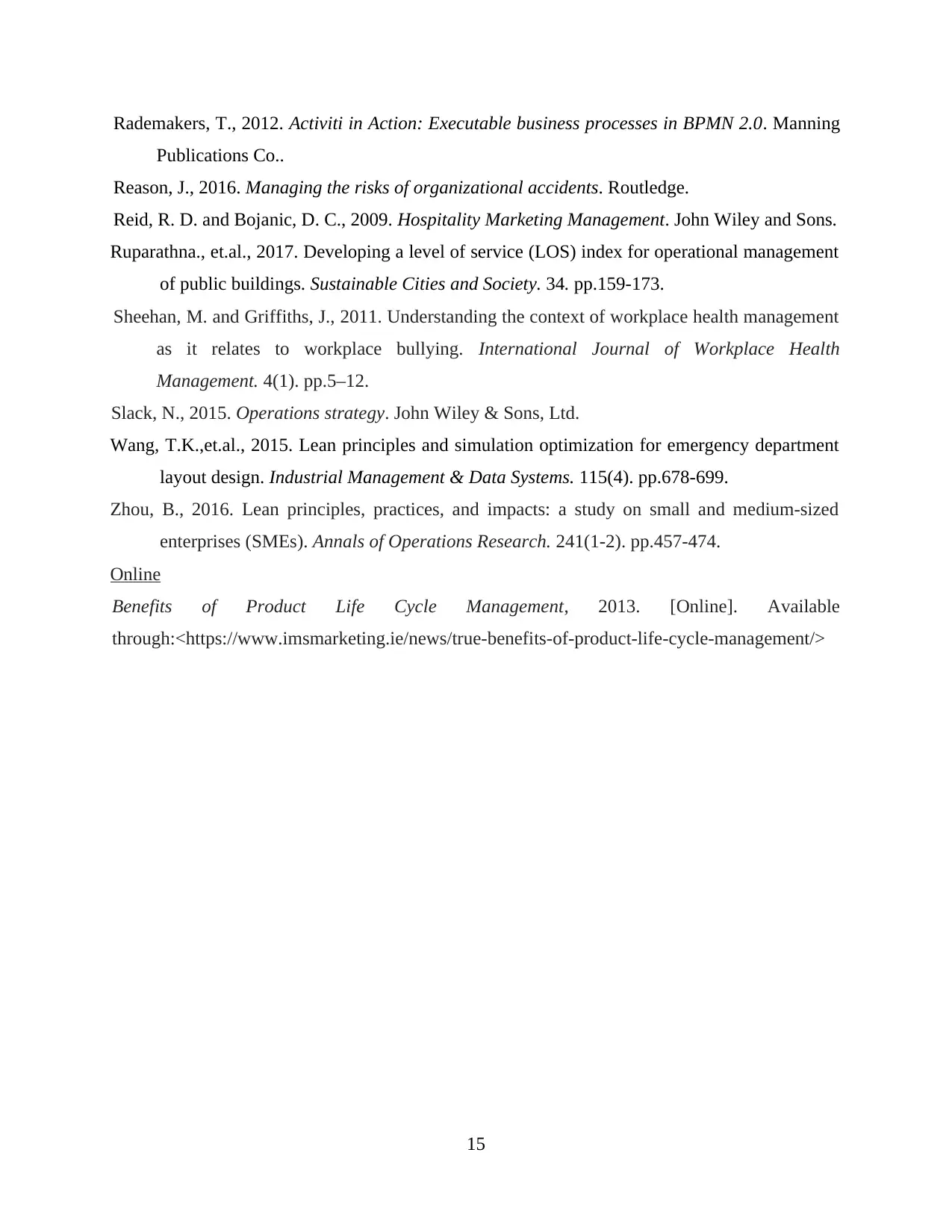
Rademakers, T., 2012. Activiti in Action: Executable business processes in BPMN 2.0. Manning
Publications Co..
Reason, J., 2016. Managing the risks of organizational accidents. Routledge.
Reid, R. D. and Bojanic, D. C., 2009. Hospitality Marketing Management. John Wiley and Sons.
Ruparathna., et.al., 2017. Developing a level of service (LOS) index for operational management
of public buildings. Sustainable Cities and Society. 34. pp.159-173.
Sheehan, M. and Griffiths, J., 2011. Understanding the context of workplace health management
as it relates to workplace bullying. International Journal of Workplace Health
Management. 4(1). pp.5–12.
Slack, N., 2015. Operations strategy. John Wiley & Sons, Ltd.
Wang, T.K.,et.al., 2015. Lean principles and simulation optimization for emergency department
layout design. Industrial Management & Data Systems. 115(4). pp.678-699.
Zhou, B., 2016. Lean principles, practices, and impacts: a study on small and medium-sized
enterprises (SMEs). Annals of Operations Research. 241(1-2). pp.457-474.
Online
Benefits of Product Life Cycle Management, 2013. [Online]. Available
through:<https://www.imsmarketing.ie/news/true-benefits-of-product-life-cycle-management/>
15
Publications Co..
Reason, J., 2016. Managing the risks of organizational accidents. Routledge.
Reid, R. D. and Bojanic, D. C., 2009. Hospitality Marketing Management. John Wiley and Sons.
Ruparathna., et.al., 2017. Developing a level of service (LOS) index for operational management
of public buildings. Sustainable Cities and Society. 34. pp.159-173.
Sheehan, M. and Griffiths, J., 2011. Understanding the context of workplace health management
as it relates to workplace bullying. International Journal of Workplace Health
Management. 4(1). pp.5–12.
Slack, N., 2015. Operations strategy. John Wiley & Sons, Ltd.
Wang, T.K.,et.al., 2015. Lean principles and simulation optimization for emergency department
layout design. Industrial Management & Data Systems. 115(4). pp.678-699.
Zhou, B., 2016. Lean principles, practices, and impacts: a study on small and medium-sized
enterprises (SMEs). Annals of Operations Research. 241(1-2). pp.457-474.
Online
Benefits of Product Life Cycle Management, 2013. [Online]. Available
through:<https://www.imsmarketing.ie/news/true-benefits-of-product-life-cycle-management/>
15
1 out of 17
Related Documents

Your All-in-One AI-Powered Toolkit for Academic Success.
+13062052269
info@desklib.com
Available 24*7 on WhatsApp / Email
Unlock your academic potential
© 2024 | Zucol Services PVT LTD | All rights reserved.