Graduate Diploma in Purchasing: Operational Management Report
VerifiedAdded on 2023/01/18
|13
|3883
|71
Report
AI Summary
This report, prepared for a Graduate Diploma in Purchasing & Supply Chain Management, analyzes operational management techniques learned at a workshop. It begins with an introduction to operational management, defining its role in designing and controlling production processes. The report then delves into specific techniques, including inventory control, linear programming, network analysis, and decision theory, explaining their applications and benefits. It discusses the reasons for maintaining inventories, objectives of inventory control, and the use of linear programming in optimizing resource allocation. Network analysis is explained as a method for planning and controlling complex projects. Decision theory is covered, including how decision analysis works, the use of decision trees, and expected value calculations. The report provides a real-world example, and concludes by emphasizing the importance of these techniques for operational decision-making and market competitiveness. The report also includes content on inventory management, its objectives, and benefits.
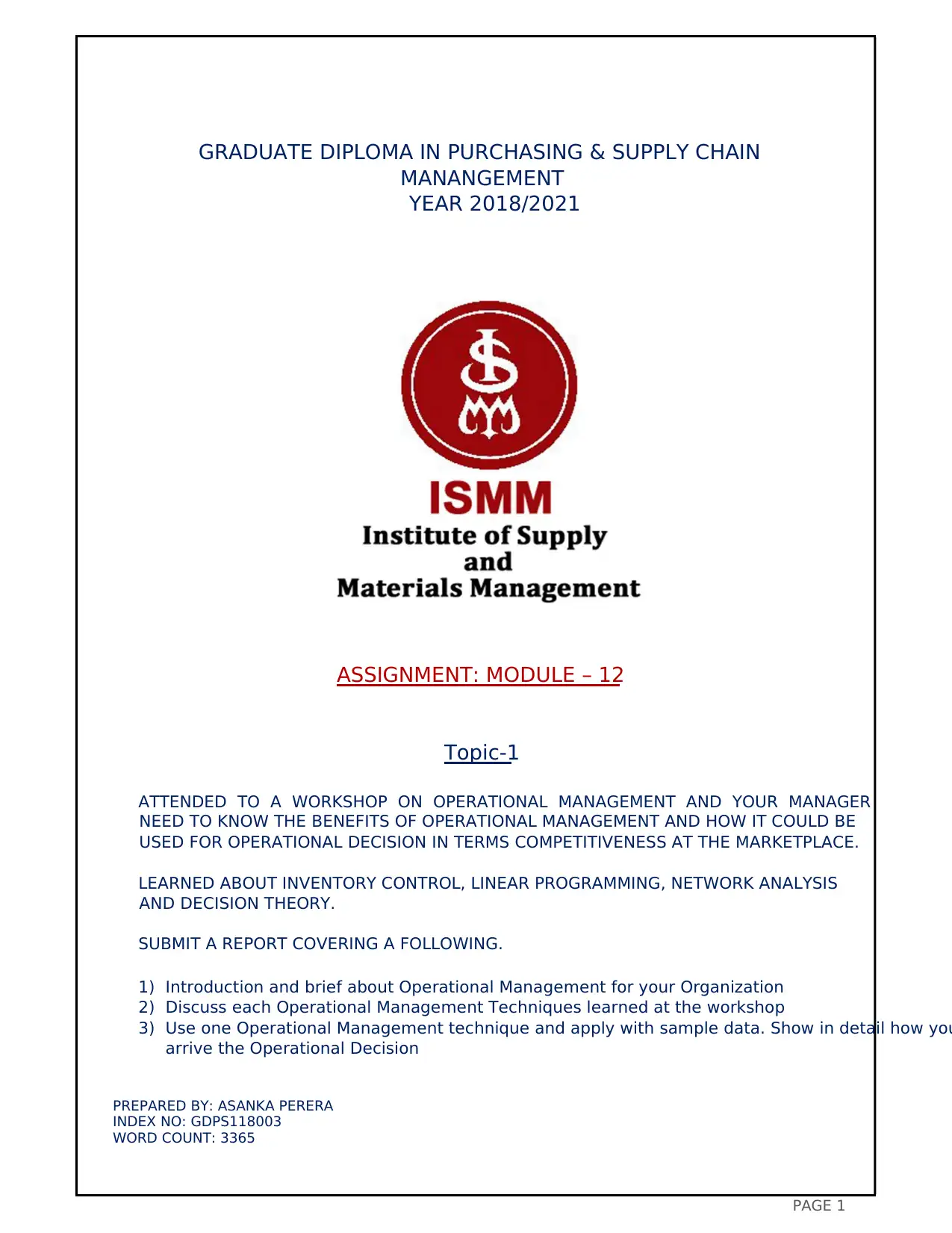
PAGE 1
GRADUATE DIPLOMA IN PURCHASING & SUPPLY CHAIN
MANANGEMENT
YEAR 2018/2021
ASSIGNMENT: MODULE – 12
Topic-1
ATTENDED TO A WORKSHOP ON OPERATIONAL MANAGEMENT AND YOUR MANAGER
NEED TO KNOW THE BENEFITS OF OPERATIONAL MANAGEMENT AND HOW IT COULD BE
USED FOR OPERATIONAL DECISION IN TERMS COMPETITIVENESS AT THE MARKETPLACE.
LEARNED ABOUT INVENTORY CONTROL, LINEAR PROGRAMMING, NETWORK ANALYSIS
AND DECISION THEORY.
SUBMIT A REPORT COVERING A FOLLOWING.
1) Introduction and brief about Operational Management for your Organization
2) Discuss each Operational Management Techniques learned at the workshop
3) Use one Operational Management technique and apply with sample data. Show in detail how you
arrive the Operational Decision
PREPARED BY: ASANKA PERERA
INDEX NO: GDPS118003
WORD COUNT: 3365
GRADUATE DIPLOMA IN PURCHASING & SUPPLY CHAIN
MANANGEMENT
YEAR 2018/2021
ASSIGNMENT: MODULE – 12
Topic-1
ATTENDED TO A WORKSHOP ON OPERATIONAL MANAGEMENT AND YOUR MANAGER
NEED TO KNOW THE BENEFITS OF OPERATIONAL MANAGEMENT AND HOW IT COULD BE
USED FOR OPERATIONAL DECISION IN TERMS COMPETITIVENESS AT THE MARKETPLACE.
LEARNED ABOUT INVENTORY CONTROL, LINEAR PROGRAMMING, NETWORK ANALYSIS
AND DECISION THEORY.
SUBMIT A REPORT COVERING A FOLLOWING.
1) Introduction and brief about Operational Management for your Organization
2) Discuss each Operational Management Techniques learned at the workshop
3) Use one Operational Management technique and apply with sample data. Show in detail how you
arrive the Operational Decision
PREPARED BY: ASANKA PERERA
INDEX NO: GDPS118003
WORD COUNT: 3365
Paraphrase This Document
Need a fresh take? Get an instant paraphrase of this document with our AI Paraphraser
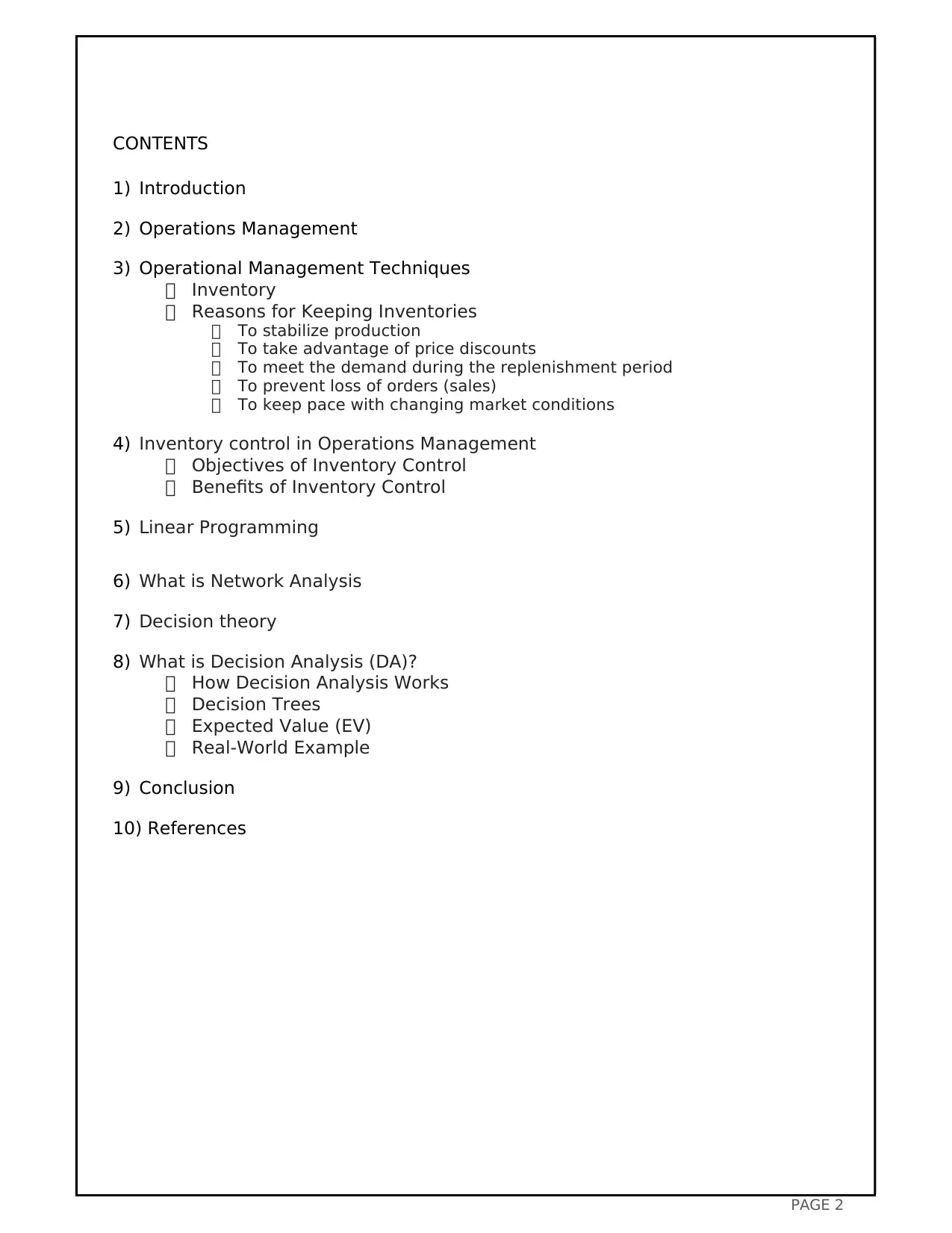
PAGE 2
CONTENTS
1) Introduction
2) Operations Management
3) Operational Management Techniques
Inventory
Reasons for Keeping Inventories
To stabilize production
To take advantage of price discounts
To meet the demand during the replenishment period
To prevent loss of orders (sales)
To keep pace with changing market conditions
4) Inventory control in Operations Management
Objectives of Inventory Control
Benefits of Inventory Control
5) Linear Programming
6) What is Network Analysis
7) Decision theory
8) What is Decision Analysis (DA)?
How Decision Analysis Works
Decision Trees
Expected Value (EV)
Real-World Example
9) Conclusion
10) References
CONTENTS
1) Introduction
2) Operations Management
3) Operational Management Techniques
Inventory
Reasons for Keeping Inventories
To stabilize production
To take advantage of price discounts
To meet the demand during the replenishment period
To prevent loss of orders (sales)
To keep pace with changing market conditions
4) Inventory control in Operations Management
Objectives of Inventory Control
Benefits of Inventory Control
5) Linear Programming
6) What is Network Analysis
7) Decision theory
8) What is Decision Analysis (DA)?
How Decision Analysis Works
Decision Trees
Expected Value (EV)
Real-World Example
9) Conclusion
10) References
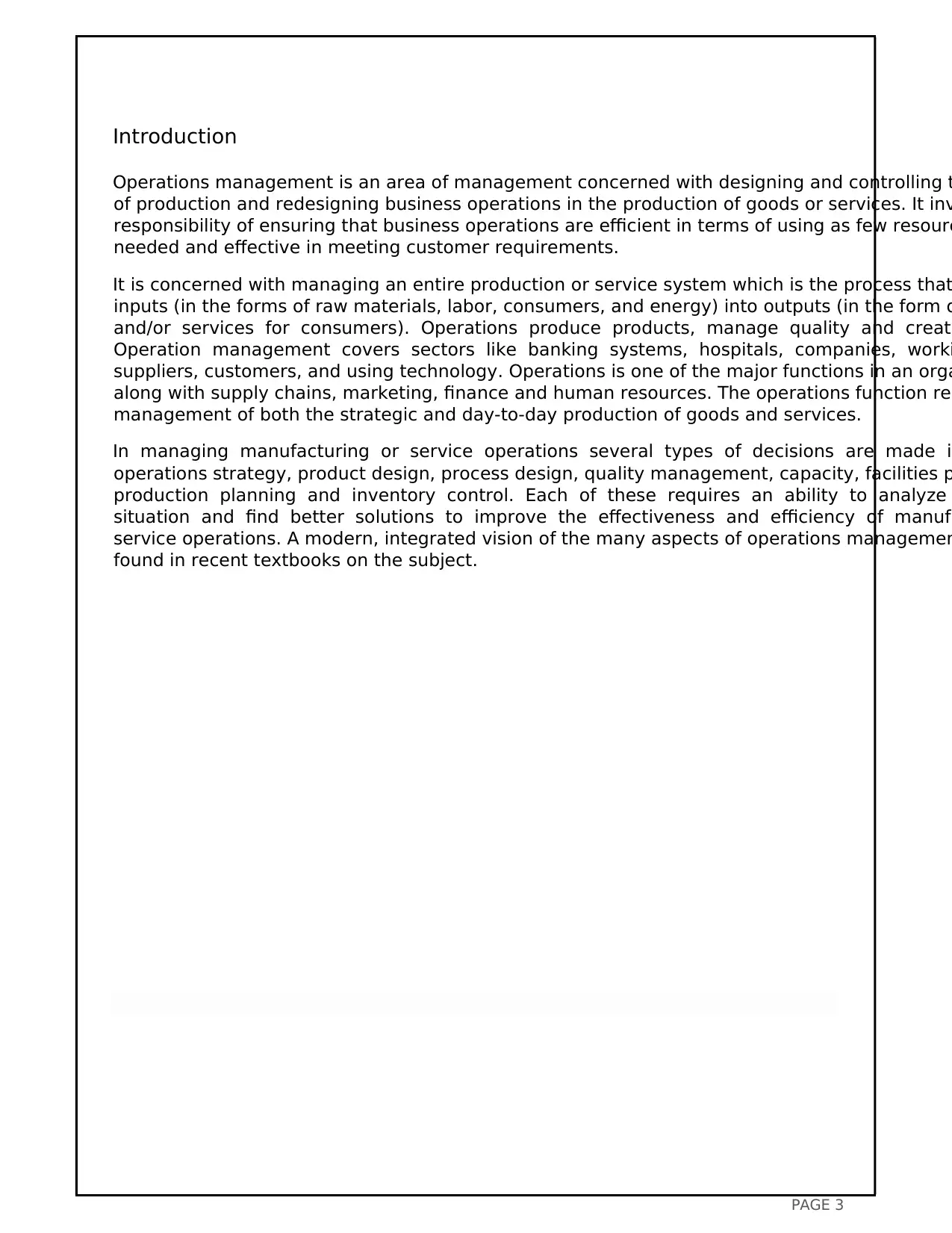
PAGE 3
Introduction
Operations management is an area of management concerned with designing and controlling t
of production and redesigning business operations in the production of goods or services. It inv
responsibility of ensuring that business operations are efficient in terms of using as few resourc
needed and effective in meeting customer requirements.
It is concerned with managing an entire production or service system which is the process that
inputs (in the forms of raw materials, labor, consumers, and energy) into outputs (in the form o
and/or services for consumers). Operations produce products, manage quality and create
Operation management covers sectors like banking systems, hospitals, companies, worki
suppliers, customers, and using technology. Operations is one of the major functions in an orga
along with supply chains, marketing, finance and human resources. The operations function req
management of both the strategic and day-to-day production of goods and services.
In managing manufacturing or service operations several types of decisions are made in
operations strategy, product design, process design, quality management, capacity, facilities p
production planning and inventory control. Each of these requires an ability to analyze
situation and find better solutions to improve the effectiveness and efficiency of manufa
service operations. A modern, integrated vision of the many aspects of operations managemen
found in recent textbooks on the subject.
Introduction
Operations management is an area of management concerned with designing and controlling t
of production and redesigning business operations in the production of goods or services. It inv
responsibility of ensuring that business operations are efficient in terms of using as few resourc
needed and effective in meeting customer requirements.
It is concerned with managing an entire production or service system which is the process that
inputs (in the forms of raw materials, labor, consumers, and energy) into outputs (in the form o
and/or services for consumers). Operations produce products, manage quality and create
Operation management covers sectors like banking systems, hospitals, companies, worki
suppliers, customers, and using technology. Operations is one of the major functions in an orga
along with supply chains, marketing, finance and human resources. The operations function req
management of both the strategic and day-to-day production of goods and services.
In managing manufacturing or service operations several types of decisions are made in
operations strategy, product design, process design, quality management, capacity, facilities p
production planning and inventory control. Each of these requires an ability to analyze
situation and find better solutions to improve the effectiveness and efficiency of manufa
service operations. A modern, integrated vision of the many aspects of operations managemen
found in recent textbooks on the subject.
You're viewing a preview
Unlock full access by subscribing today!
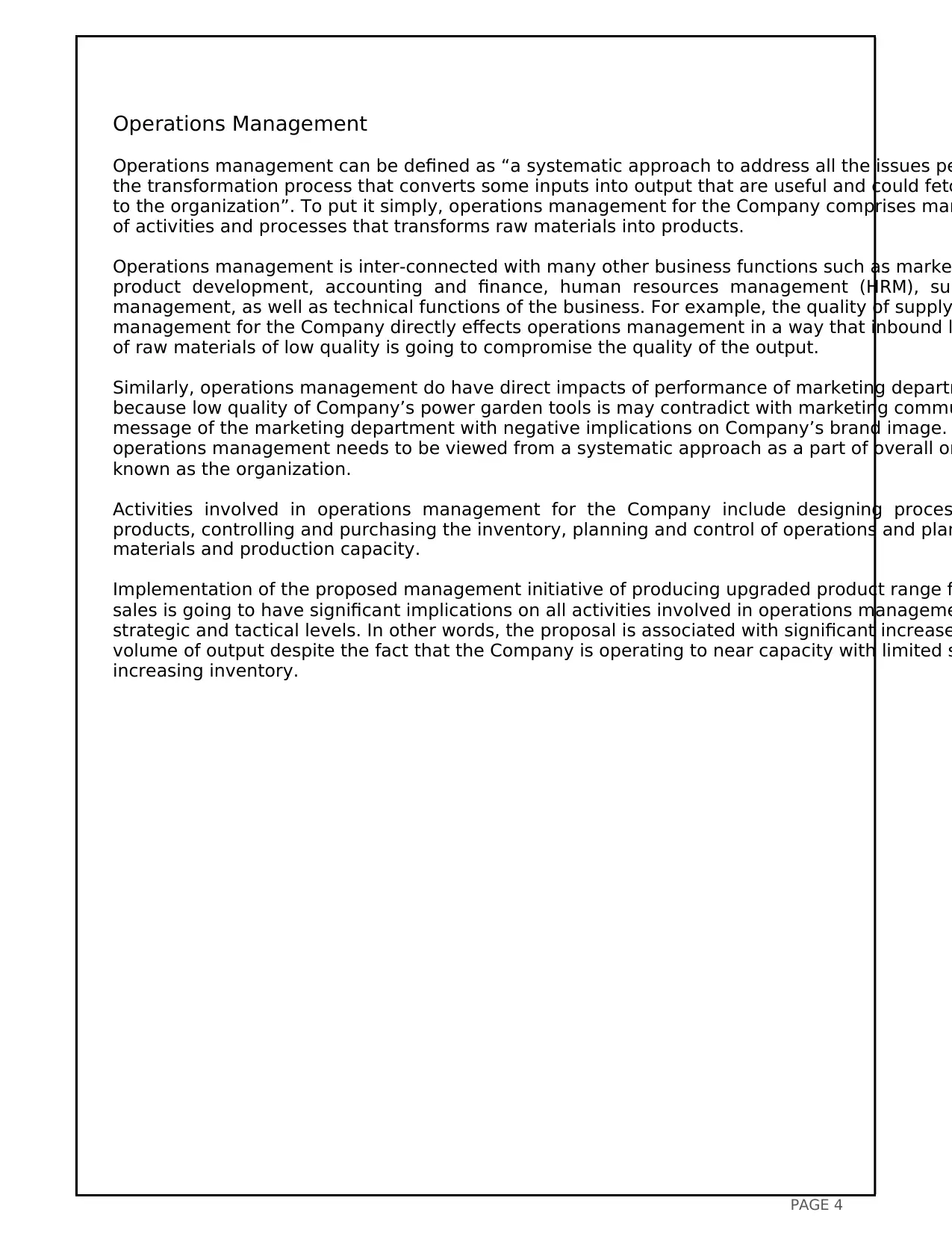
PAGE 4
Operations Management
Operations management can be defined as “a systematic approach to address all the issues pe
the transformation process that converts some inputs into output that are useful and could fetc
to the organization”. To put it simply, operations management for the Company comprises man
of activities and processes that transforms raw materials into products.
Operations management is inter-connected with many other business functions such as marke
product development, accounting and finance, human resources management (HRM), sup
management, as well as technical functions of the business. For example, the quality of supply
management for the Company directly effects operations management in a way that inbound l
of raw materials of low quality is going to compromise the quality of the output.
Similarly, operations management do have direct impacts of performance of marketing departm
because low quality of Company’s power garden tools is may contradict with marketing commu
message of the marketing department with negative implications on Company’s brand image.
operations management needs to be viewed from a systematic approach as a part of overall or
known as the organization.
Activities involved in operations management for the Company include designing proces
products, controlling and purchasing the inventory, planning and control of operations and plan
materials and production capacity.
Implementation of the proposed management initiative of producing upgraded product range f
sales is going to have significant implications on all activities involved in operations manageme
strategic and tactical levels. In other words, the proposal is associated with significant increase
volume of output despite the fact that the Company is operating to near capacity with limited s
increasing inventory.
Operations Management
Operations management can be defined as “a systematic approach to address all the issues pe
the transformation process that converts some inputs into output that are useful and could fetc
to the organization”. To put it simply, operations management for the Company comprises man
of activities and processes that transforms raw materials into products.
Operations management is inter-connected with many other business functions such as marke
product development, accounting and finance, human resources management (HRM), sup
management, as well as technical functions of the business. For example, the quality of supply
management for the Company directly effects operations management in a way that inbound l
of raw materials of low quality is going to compromise the quality of the output.
Similarly, operations management do have direct impacts of performance of marketing departm
because low quality of Company’s power garden tools is may contradict with marketing commu
message of the marketing department with negative implications on Company’s brand image.
operations management needs to be viewed from a systematic approach as a part of overall or
known as the organization.
Activities involved in operations management for the Company include designing proces
products, controlling and purchasing the inventory, planning and control of operations and plan
materials and production capacity.
Implementation of the proposed management initiative of producing upgraded product range f
sales is going to have significant implications on all activities involved in operations manageme
strategic and tactical levels. In other words, the proposal is associated with significant increase
volume of output despite the fact that the Company is operating to near capacity with limited s
increasing inventory.
Paraphrase This Document
Need a fresh take? Get an instant paraphrase of this document with our AI Paraphraser
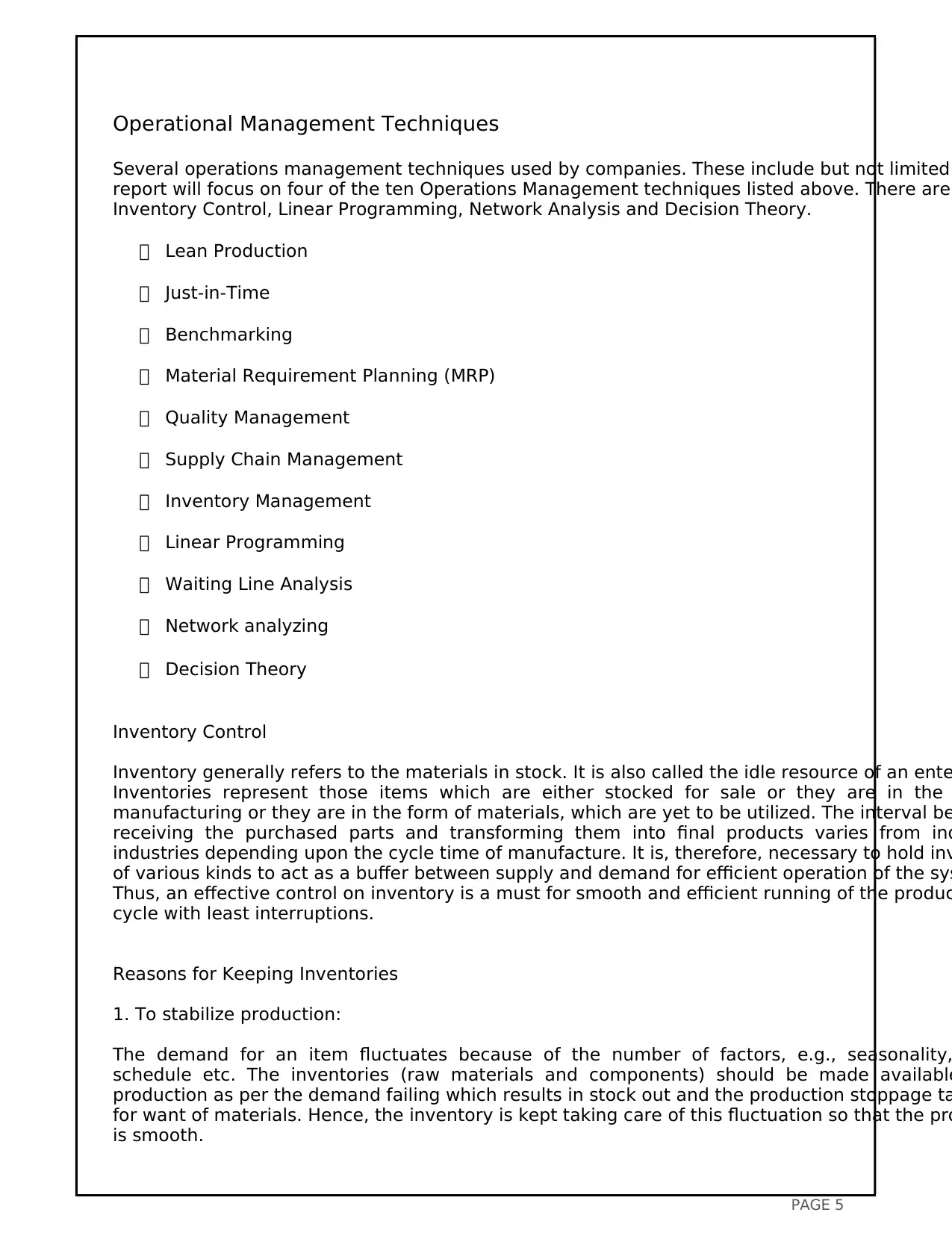
PAGE 5
Operational Management Techniques
Several operations management techniques used by companies. These include but not limited
report will focus on four of the ten Operations Management techniques listed above. There are
Inventory Control, Linear Programming, Network Analysis and Decision Theory.
Lean Production
Just-in-Time
Benchmarking
Material Requirement Planning (MRP)
Quality Management
Supply Chain Management
Inventory Management
Linear Programming
Waiting Line Analysis
Network analyzing
Decision Theory
Inventory Control
Inventory generally refers to the materials in stock. It is also called the idle resource of an ente
Inventories represent those items which are either stocked for sale or they are in the
manufacturing or they are in the form of materials, which are yet to be utilized. The interval be
receiving the purchased parts and transforming them into final products varies from ind
industries depending upon the cycle time of manufacture. It is, therefore, necessary to hold inv
of various kinds to act as a buffer between supply and demand for efficient operation of the sys
Thus, an effective control on inventory is a must for smooth and efficient running of the produc
cycle with least interruptions.
Reasons for Keeping Inventories
1. To stabilize production:
The demand for an item fluctuates because of the number of factors, e.g., seasonality,
schedule etc. The inventories (raw materials and components) should be made available
production as per the demand failing which results in stock out and the production stoppage ta
for want of materials. Hence, the inventory is kept taking care of this fluctuation so that the pro
is smooth.
Operational Management Techniques
Several operations management techniques used by companies. These include but not limited
report will focus on four of the ten Operations Management techniques listed above. There are
Inventory Control, Linear Programming, Network Analysis and Decision Theory.
Lean Production
Just-in-Time
Benchmarking
Material Requirement Planning (MRP)
Quality Management
Supply Chain Management
Inventory Management
Linear Programming
Waiting Line Analysis
Network analyzing
Decision Theory
Inventory Control
Inventory generally refers to the materials in stock. It is also called the idle resource of an ente
Inventories represent those items which are either stocked for sale or they are in the
manufacturing or they are in the form of materials, which are yet to be utilized. The interval be
receiving the purchased parts and transforming them into final products varies from ind
industries depending upon the cycle time of manufacture. It is, therefore, necessary to hold inv
of various kinds to act as a buffer between supply and demand for efficient operation of the sys
Thus, an effective control on inventory is a must for smooth and efficient running of the produc
cycle with least interruptions.
Reasons for Keeping Inventories
1. To stabilize production:
The demand for an item fluctuates because of the number of factors, e.g., seasonality,
schedule etc. The inventories (raw materials and components) should be made available
production as per the demand failing which results in stock out and the production stoppage ta
for want of materials. Hence, the inventory is kept taking care of this fluctuation so that the pro
is smooth.
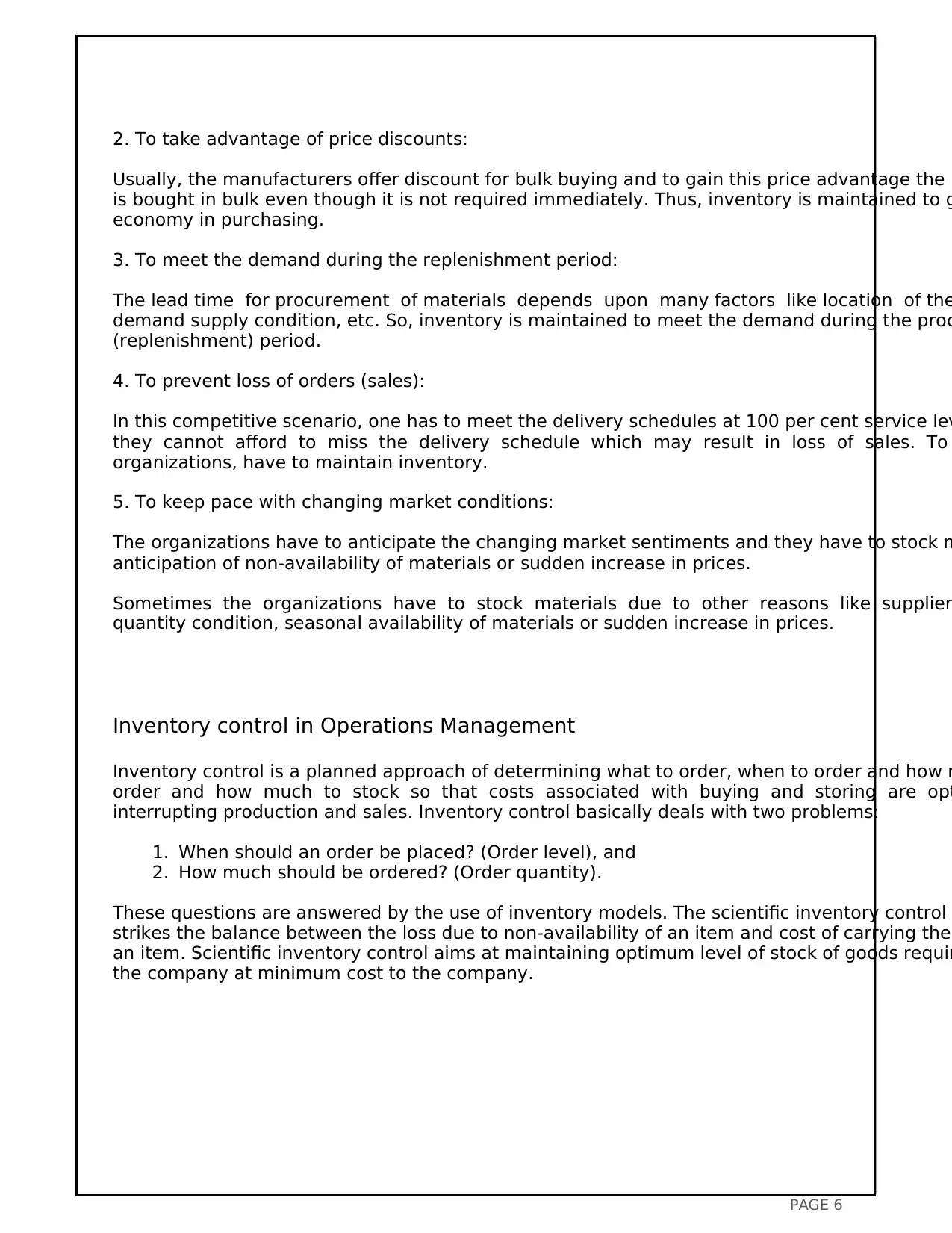
PAGE 6
2. To take advantage of price discounts:
Usually, the manufacturers offer discount for bulk buying and to gain this price advantage the m
is bought in bulk even though it is not required immediately. Thus, inventory is maintained to g
economy in purchasing.
3. To meet the demand during the replenishment period:
The lead time for procurement of materials depends upon many factors like location of the
demand supply condition, etc. So, inventory is maintained to meet the demand during the proc
(replenishment) period.
4. To prevent loss of orders (sales):
In this competitive scenario, one has to meet the delivery schedules at 100 per cent service lev
they cannot afford to miss the delivery schedule which may result in loss of sales. To
organizations, have to maintain inventory.
5. To keep pace with changing market conditions:
The organizations have to anticipate the changing market sentiments and they have to stock m
anticipation of non-availability of materials or sudden increase in prices.
Sometimes the organizations have to stock materials due to other reasons like supplier
quantity condition, seasonal availability of materials or sudden increase in prices.
Inventory control in Operations Management
Inventory control is a planned approach of determining what to order, when to order and how m
order and how much to stock so that costs associated with buying and storing are opt
interrupting production and sales. Inventory control basically deals with two problems:
1. When should an order be placed? (Order level), and
2. How much should be ordered? (Order quantity).
These questions are answered by the use of inventory models. The scientific inventory control s
strikes the balance between the loss due to non-availability of an item and cost of carrying the
an item. Scientific inventory control aims at maintaining optimum level of stock of goods requir
the company at minimum cost to the company.
2. To take advantage of price discounts:
Usually, the manufacturers offer discount for bulk buying and to gain this price advantage the m
is bought in bulk even though it is not required immediately. Thus, inventory is maintained to g
economy in purchasing.
3. To meet the demand during the replenishment period:
The lead time for procurement of materials depends upon many factors like location of the
demand supply condition, etc. So, inventory is maintained to meet the demand during the proc
(replenishment) period.
4. To prevent loss of orders (sales):
In this competitive scenario, one has to meet the delivery schedules at 100 per cent service lev
they cannot afford to miss the delivery schedule which may result in loss of sales. To
organizations, have to maintain inventory.
5. To keep pace with changing market conditions:
The organizations have to anticipate the changing market sentiments and they have to stock m
anticipation of non-availability of materials or sudden increase in prices.
Sometimes the organizations have to stock materials due to other reasons like supplier
quantity condition, seasonal availability of materials or sudden increase in prices.
Inventory control in Operations Management
Inventory control is a planned approach of determining what to order, when to order and how m
order and how much to stock so that costs associated with buying and storing are opt
interrupting production and sales. Inventory control basically deals with two problems:
1. When should an order be placed? (Order level), and
2. How much should be ordered? (Order quantity).
These questions are answered by the use of inventory models. The scientific inventory control s
strikes the balance between the loss due to non-availability of an item and cost of carrying the
an item. Scientific inventory control aims at maintaining optimum level of stock of goods requir
the company at minimum cost to the company.
You're viewing a preview
Unlock full access by subscribing today!
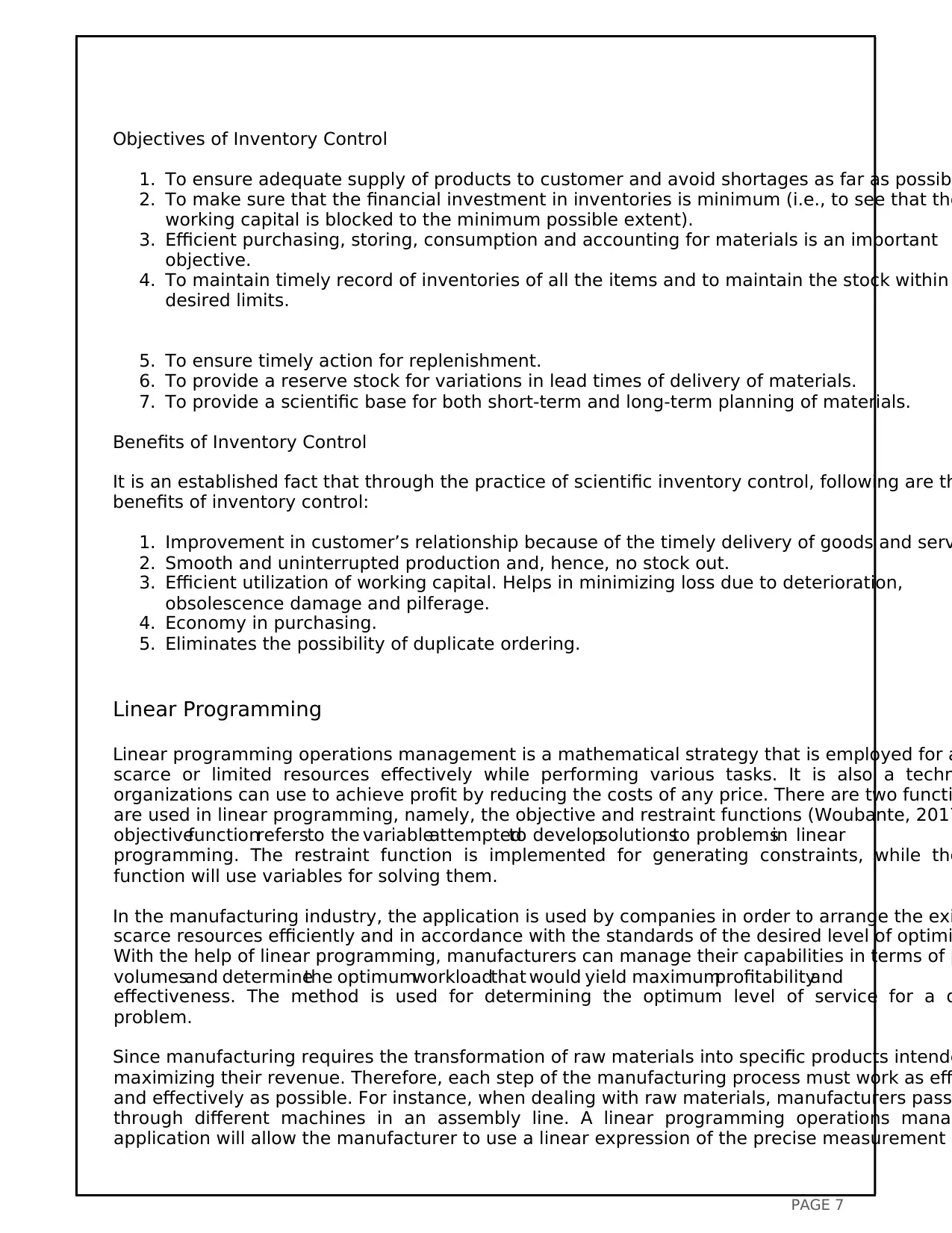
PAGE 7
Objectives of Inventory Control
1. To ensure adequate supply of products to customer and avoid shortages as far as possibl
2. To make sure that the financial investment in inventories is minimum (i.e., to see that the
working capital is blocked to the minimum possible extent).
3. Efficient purchasing, storing, consumption and accounting for materials is an important
objective.
4. To maintain timely record of inventories of all the items and to maintain the stock within
desired limits.
5. To ensure timely action for replenishment.
6. To provide a reserve stock for variations in lead times of delivery of materials.
7. To provide a scientific base for both short-term and long-term planning of materials.
Benefits of Inventory Control
It is an established fact that through the practice of scientific inventory control, following are th
benefits of inventory control:
1. Improvement in customer’s relationship because of the timely delivery of goods and serv
2. Smooth and uninterrupted production and, hence, no stock out.
3. Efficient utilization of working capital. Helps in minimizing loss due to deterioration,
obsolescence damage and pilferage.
4. Economy in purchasing.
5. Eliminates the possibility of duplicate ordering.
Linear Programming
Linear programming operations management is a mathematical strategy that is employed for a
scarce or limited resources effectively while performing various tasks. It is also a techn
organizations can use to achieve profit by reducing the costs of any price. There are two functi
are used in linear programming, namely, the objective and restraint functions (Woubante, 2017
objectivefunctionrefersto the variableattemptedto developsolutionsto problemsin linear
programming. The restraint function is implemented for generating constraints, while the
function will use variables for solving them.
In the manufacturing industry, the application is used by companies in order to arrange the exi
scarce resources efficiently and in accordance with the standards of the desired level of optimi
With the help of linear programming, manufacturers can manage their capabilities in terms of p
volumesand determinethe optimumworkloadthat would yield maximumprofitabilityand
effectiveness. The method is used for determining the optimum level of service for a d
problem.
Since manufacturing requires the transformation of raw materials into specific products intende
maximizing their revenue. Therefore, each step of the manufacturing process must work as effi
and effectively as possible. For instance, when dealing with raw materials, manufacturers pass
through different machines in an assembly line. A linear programming operations manag
application will allow the manufacturer to use a linear expression of the precise measurement o
Objectives of Inventory Control
1. To ensure adequate supply of products to customer and avoid shortages as far as possibl
2. To make sure that the financial investment in inventories is minimum (i.e., to see that the
working capital is blocked to the minimum possible extent).
3. Efficient purchasing, storing, consumption and accounting for materials is an important
objective.
4. To maintain timely record of inventories of all the items and to maintain the stock within
desired limits.
5. To ensure timely action for replenishment.
6. To provide a reserve stock for variations in lead times of delivery of materials.
7. To provide a scientific base for both short-term and long-term planning of materials.
Benefits of Inventory Control
It is an established fact that through the practice of scientific inventory control, following are th
benefits of inventory control:
1. Improvement in customer’s relationship because of the timely delivery of goods and serv
2. Smooth and uninterrupted production and, hence, no stock out.
3. Efficient utilization of working capital. Helps in minimizing loss due to deterioration,
obsolescence damage and pilferage.
4. Economy in purchasing.
5. Eliminates the possibility of duplicate ordering.
Linear Programming
Linear programming operations management is a mathematical strategy that is employed for a
scarce or limited resources effectively while performing various tasks. It is also a techn
organizations can use to achieve profit by reducing the costs of any price. There are two functi
are used in linear programming, namely, the objective and restraint functions (Woubante, 2017
objectivefunctionrefersto the variableattemptedto developsolutionsto problemsin linear
programming. The restraint function is implemented for generating constraints, while the
function will use variables for solving them.
In the manufacturing industry, the application is used by companies in order to arrange the exi
scarce resources efficiently and in accordance with the standards of the desired level of optimi
With the help of linear programming, manufacturers can manage their capabilities in terms of p
volumesand determinethe optimumworkloadthat would yield maximumprofitabilityand
effectiveness. The method is used for determining the optimum level of service for a d
problem.
Since manufacturing requires the transformation of raw materials into specific products intende
maximizing their revenue. Therefore, each step of the manufacturing process must work as effi
and effectively as possible. For instance, when dealing with raw materials, manufacturers pass
through different machines in an assembly line. A linear programming operations manag
application will allow the manufacturer to use a linear expression of the precise measurement o
Paraphrase This Document
Need a fresh take? Get an instant paraphrase of this document with our AI Paraphraser
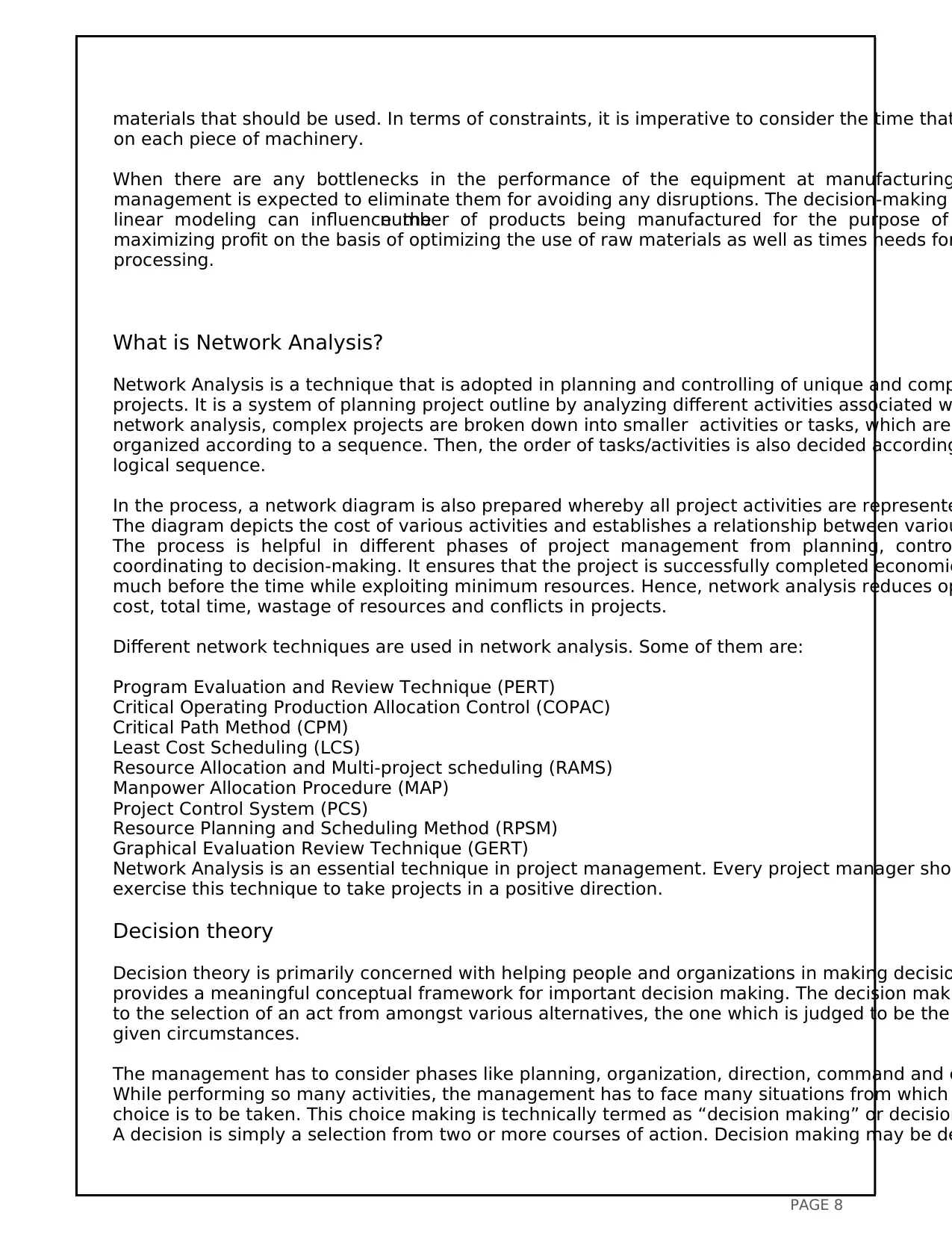
PAGE 8
materials that should be used. In terms of constraints, it is imperative to consider the time that
on each piece of machinery.
When there are any bottlenecks in the performance of the equipment at manufacturing
management is expected to eliminate them for avoiding any disruptions. The decision-making
linear modeling can influence thenumber of products being manufactured for the purpose of
maximizing profit on the basis of optimizing the use of raw materials as well as times needs for
processing.
What is Network Analysis?
Network Analysis is a technique that is adopted in planning and controlling of unique and comp
projects. It is a system of planning project outline by analyzing different activities associated w
network analysis, complex projects are broken down into smaller activities or tasks, which are
organized according to a sequence. Then, the order of tasks/activities is also decided according
logical sequence.
In the process, a network diagram is also prepared whereby all project activities are represente
The diagram depicts the cost of various activities and establishes a relationship between variou
The process is helpful in different phases of project management from planning, contro
coordinating to decision-making. It ensures that the project is successfully completed economic
much before the time while exploiting minimum resources. Hence, network analysis reduces op
cost, total time, wastage of resources and conflicts in projects.
Different network techniques are used in network analysis. Some of them are:
Program Evaluation and Review Technique (PERT)
Critical Operating Production Allocation Control (COPAC)
Critical Path Method (CPM)
Least Cost Scheduling (LCS)
Resource Allocation and Multi-project scheduling (RAMS)
Manpower Allocation Procedure (MAP)
Project Control System (PCS)
Resource Planning and Scheduling Method (RPSM)
Graphical Evaluation Review Technique (GERT)
Network Analysis is an essential technique in project management. Every project manager shou
exercise this technique to take projects in a positive direction.
Decision theory
Decision theory is primarily concerned with helping people and organizations in making decisio
provides a meaningful conceptual framework for important decision making. The decision maki
to the selection of an act from amongst various alternatives, the one which is judged to be the
given circumstances.
The management has to consider phases like planning, organization, direction, command and c
While performing so many activities, the management has to face many situations from which
choice is to be taken. This choice making is technically termed as “decision making” or decision
A decision is simply a selection from two or more courses of action. Decision making may be de
materials that should be used. In terms of constraints, it is imperative to consider the time that
on each piece of machinery.
When there are any bottlenecks in the performance of the equipment at manufacturing
management is expected to eliminate them for avoiding any disruptions. The decision-making
linear modeling can influence thenumber of products being manufactured for the purpose of
maximizing profit on the basis of optimizing the use of raw materials as well as times needs for
processing.
What is Network Analysis?
Network Analysis is a technique that is adopted in planning and controlling of unique and comp
projects. It is a system of planning project outline by analyzing different activities associated w
network analysis, complex projects are broken down into smaller activities or tasks, which are
organized according to a sequence. Then, the order of tasks/activities is also decided according
logical sequence.
In the process, a network diagram is also prepared whereby all project activities are represente
The diagram depicts the cost of various activities and establishes a relationship between variou
The process is helpful in different phases of project management from planning, contro
coordinating to decision-making. It ensures that the project is successfully completed economic
much before the time while exploiting minimum resources. Hence, network analysis reduces op
cost, total time, wastage of resources and conflicts in projects.
Different network techniques are used in network analysis. Some of them are:
Program Evaluation and Review Technique (PERT)
Critical Operating Production Allocation Control (COPAC)
Critical Path Method (CPM)
Least Cost Scheduling (LCS)
Resource Allocation and Multi-project scheduling (RAMS)
Manpower Allocation Procedure (MAP)
Project Control System (PCS)
Resource Planning and Scheduling Method (RPSM)
Graphical Evaluation Review Technique (GERT)
Network Analysis is an essential technique in project management. Every project manager shou
exercise this technique to take projects in a positive direction.
Decision theory
Decision theory is primarily concerned with helping people and organizations in making decisio
provides a meaningful conceptual framework for important decision making. The decision maki
to the selection of an act from amongst various alternatives, the one which is judged to be the
given circumstances.
The management has to consider phases like planning, organization, direction, command and c
While performing so many activities, the management has to face many situations from which
choice is to be taken. This choice making is technically termed as “decision making” or decision
A decision is simply a selection from two or more courses of action. Decision making may be de
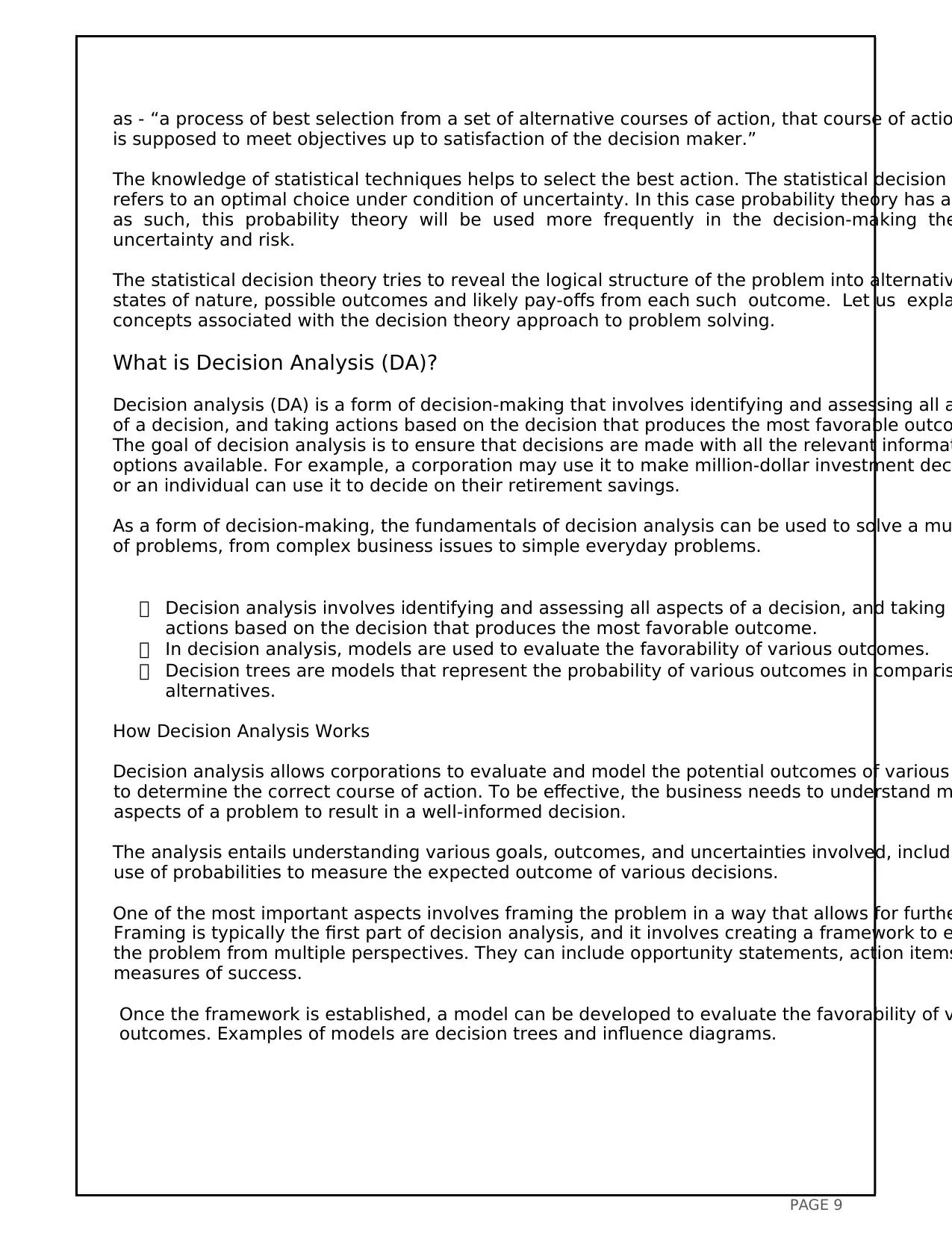
PAGE 9
as - “a process of best selection from a set of alternative courses of action, that course of actio
is supposed to meet objectives up to satisfaction of the decision maker.”
The knowledge of statistical techniques helps to select the best action. The statistical decision
refers to an optimal choice under condition of uncertainty. In this case probability theory has a
as such, this probability theory will be used more frequently in the decision-making the
uncertainty and risk.
The statistical decision theory tries to reveal the logical structure of the problem into alternativ
states of nature, possible outcomes and likely pay-offs from each such outcome. Let us expla
concepts associated with the decision theory approach to problem solving.
What is Decision Analysis (DA)?
Decision analysis (DA) is a form of decision-making that involves identifying and assessing all a
of a decision, and taking actions based on the decision that produces the most favorable outco
The goal of decision analysis is to ensure that decisions are made with all the relevant informat
options available. For example, a corporation may use it to make million-dollar investment deci
or an individual can use it to decide on their retirement savings.
As a form of decision-making, the fundamentals of decision analysis can be used to solve a mu
of problems, from complex business issues to simple everyday problems.
Decision analysis involves identifying and assessing all aspects of a decision, and taking
actions based on the decision that produces the most favorable outcome.
In decision analysis, models are used to evaluate the favorability of various outcomes.
Decision trees are models that represent the probability of various outcomes in comparis
alternatives.
How Decision Analysis Works
Decision analysis allows corporations to evaluate and model the potential outcomes of various
to determine the correct course of action. To be effective, the business needs to understand m
aspects of a problem to result in a well-informed decision.
The analysis entails understanding various goals, outcomes, and uncertainties involved, includi
use of probabilities to measure the expected outcome of various decisions.
One of the most important aspects involves framing the problem in a way that allows for furthe
Framing is typically the first part of decision analysis, and it involves creating a framework to e
the problem from multiple perspectives. They can include opportunity statements, action items
measures of success.
Once the framework is established, a model can be developed to evaluate the favorability of v
outcomes. Examples of models are decision trees and influence diagrams.
as - “a process of best selection from a set of alternative courses of action, that course of actio
is supposed to meet objectives up to satisfaction of the decision maker.”
The knowledge of statistical techniques helps to select the best action. The statistical decision
refers to an optimal choice under condition of uncertainty. In this case probability theory has a
as such, this probability theory will be used more frequently in the decision-making the
uncertainty and risk.
The statistical decision theory tries to reveal the logical structure of the problem into alternativ
states of nature, possible outcomes and likely pay-offs from each such outcome. Let us expla
concepts associated with the decision theory approach to problem solving.
What is Decision Analysis (DA)?
Decision analysis (DA) is a form of decision-making that involves identifying and assessing all a
of a decision, and taking actions based on the decision that produces the most favorable outco
The goal of decision analysis is to ensure that decisions are made with all the relevant informat
options available. For example, a corporation may use it to make million-dollar investment deci
or an individual can use it to decide on their retirement savings.
As a form of decision-making, the fundamentals of decision analysis can be used to solve a mu
of problems, from complex business issues to simple everyday problems.
Decision analysis involves identifying and assessing all aspects of a decision, and taking
actions based on the decision that produces the most favorable outcome.
In decision analysis, models are used to evaluate the favorability of various outcomes.
Decision trees are models that represent the probability of various outcomes in comparis
alternatives.
How Decision Analysis Works
Decision analysis allows corporations to evaluate and model the potential outcomes of various
to determine the correct course of action. To be effective, the business needs to understand m
aspects of a problem to result in a well-informed decision.
The analysis entails understanding various goals, outcomes, and uncertainties involved, includi
use of probabilities to measure the expected outcome of various decisions.
One of the most important aspects involves framing the problem in a way that allows for furthe
Framing is typically the first part of decision analysis, and it involves creating a framework to e
the problem from multiple perspectives. They can include opportunity statements, action items
measures of success.
Once the framework is established, a model can be developed to evaluate the favorability of v
outcomes. Examples of models are decision trees and influence diagrams.
You're viewing a preview
Unlock full access by subscribing today!
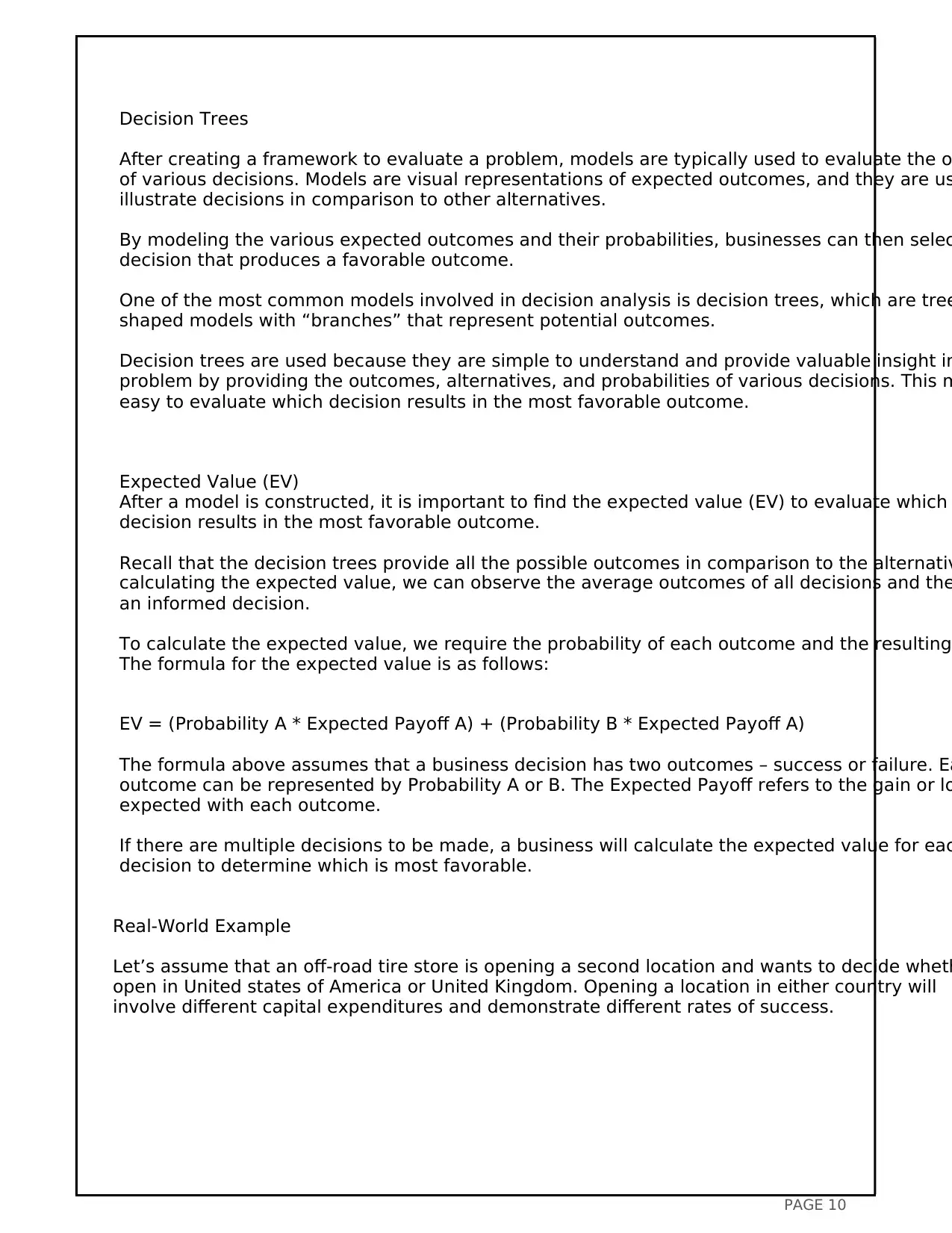
PAGE 10
Decision Trees
After creating a framework to evaluate a problem, models are typically used to evaluate the o
of various decisions. Models are visual representations of expected outcomes, and they are us
illustrate decisions in comparison to other alternatives.
By modeling the various expected outcomes and their probabilities, businesses can then selec
decision that produces a favorable outcome.
One of the most common models involved in decision analysis is decision trees, which are tree
shaped models with “branches” that represent potential outcomes.
Decision trees are used because they are simple to understand and provide valuable insight in
problem by providing the outcomes, alternatives, and probabilities of various decisions. This m
easy to evaluate which decision results in the most favorable outcome.
Expected Value (EV)
After a model is constructed, it is important to find the expected value (EV) to evaluate which
decision results in the most favorable outcome.
Recall that the decision trees provide all the possible outcomes in comparison to the alternativ
calculating the expected value, we can observe the average outcomes of all decisions and the
an informed decision.
To calculate the expected value, we require the probability of each outcome and the resulting
The formula for the expected value is as follows:
EV = (Probability A * Expected Payoff A) + (Probability B * Expected Payoff A)
The formula above assumes that a business decision has two outcomes – success or failure. Ea
outcome can be represented by Probability A or B. The Expected Payoff refers to the gain or lo
expected with each outcome.
If there are multiple decisions to be made, a business will calculate the expected value for eac
decision to determine which is most favorable.
Real-World Example
Let’s assume that an off-road tire store is opening a second location and wants to decide wheth
open in United states of America or United Kingdom. Opening a location in either country will
involve different capital expenditures and demonstrate different rates of success.
Decision Trees
After creating a framework to evaluate a problem, models are typically used to evaluate the o
of various decisions. Models are visual representations of expected outcomes, and they are us
illustrate decisions in comparison to other alternatives.
By modeling the various expected outcomes and their probabilities, businesses can then selec
decision that produces a favorable outcome.
One of the most common models involved in decision analysis is decision trees, which are tree
shaped models with “branches” that represent potential outcomes.
Decision trees are used because they are simple to understand and provide valuable insight in
problem by providing the outcomes, alternatives, and probabilities of various decisions. This m
easy to evaluate which decision results in the most favorable outcome.
Expected Value (EV)
After a model is constructed, it is important to find the expected value (EV) to evaluate which
decision results in the most favorable outcome.
Recall that the decision trees provide all the possible outcomes in comparison to the alternativ
calculating the expected value, we can observe the average outcomes of all decisions and the
an informed decision.
To calculate the expected value, we require the probability of each outcome and the resulting
The formula for the expected value is as follows:
EV = (Probability A * Expected Payoff A) + (Probability B * Expected Payoff A)
The formula above assumes that a business decision has two outcomes – success or failure. Ea
outcome can be represented by Probability A or B. The Expected Payoff refers to the gain or lo
expected with each outcome.
If there are multiple decisions to be made, a business will calculate the expected value for eac
decision to determine which is most favorable.
Real-World Example
Let’s assume that an off-road tire store is opening a second location and wants to decide wheth
open in United states of America or United Kingdom. Opening a location in either country will
involve different capital expenditures and demonstrate different rates of success.
Paraphrase This Document
Need a fresh take? Get an instant paraphrase of this document with our AI Paraphraser
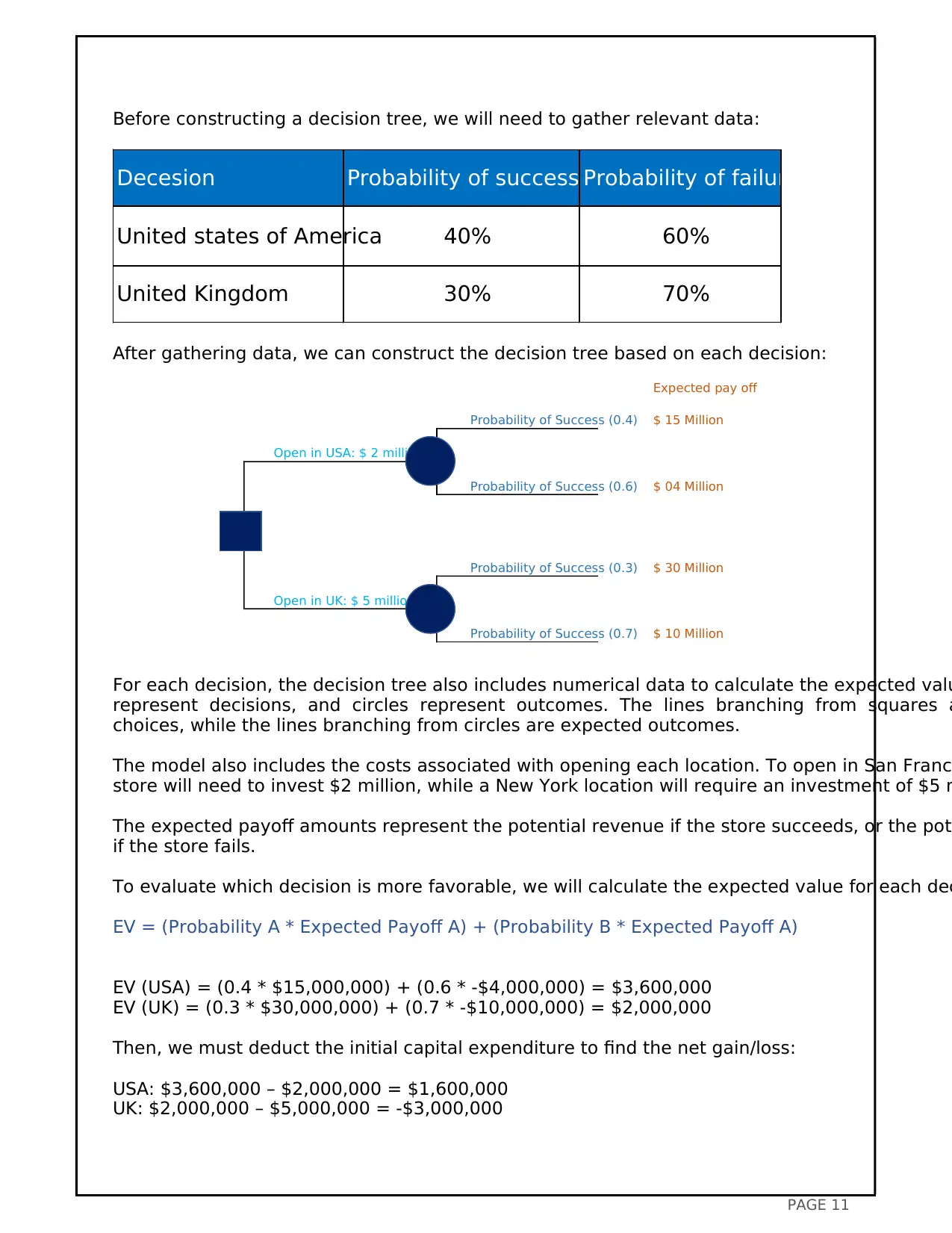
PAGE 11
Before constructing a decision tree, we will need to gather relevant data:
After gathering data, we can construct the decision tree based on each decision:
For each decision, the decision tree also includes numerical data to calculate the expected valu
represent decisions, and circles represent outcomes. The lines branching from squares a
choices, while the lines branching from circles are expected outcomes.
The model also includes the costs associated with opening each location. To open in San Franci
store will need to invest $2 million, while a New York location will require an investment of $5 m
The expected payoff amounts represent the potential revenue if the store succeeds, or the pote
if the store fails.
To evaluate which decision is more favorable, we will calculate the expected value for each dec
EV = (Probability A * Expected Payoff A) + (Probability B * Expected Payoff A)
EV (USA) = (0.4 * $15,000,000) + (0.6 * -$4,000,000) = $3,600,000
EV (UK) = (0.3 * $30,000,000) + (0.7 * -$10,000,000) = $2,000,000
Then, we must deduct the initial capital expenditure to find the net gain/loss:
USA: $3,600,000 – $2,000,000 = $1,600,000
UK: $2,000,000 – $5,000,000 = -$3,000,000
Decesion Probability of success Probability of failure
United states of America 40% 60%
United Kingdom 30% 70%
Expected pay off
Probability of Success (0.4) $ 15 Million
Open in USA: $ 2 million
Probability of Success (0.6) $ 04 Million
Probability of Success (0.3) $ 30 Million
Open in UK: $ 5 million
Probability of Success (0.7) $ 10 Million
Before constructing a decision tree, we will need to gather relevant data:
After gathering data, we can construct the decision tree based on each decision:
For each decision, the decision tree also includes numerical data to calculate the expected valu
represent decisions, and circles represent outcomes. The lines branching from squares a
choices, while the lines branching from circles are expected outcomes.
The model also includes the costs associated with opening each location. To open in San Franci
store will need to invest $2 million, while a New York location will require an investment of $5 m
The expected payoff amounts represent the potential revenue if the store succeeds, or the pote
if the store fails.
To evaluate which decision is more favorable, we will calculate the expected value for each dec
EV = (Probability A * Expected Payoff A) + (Probability B * Expected Payoff A)
EV (USA) = (0.4 * $15,000,000) + (0.6 * -$4,000,000) = $3,600,000
EV (UK) = (0.3 * $30,000,000) + (0.7 * -$10,000,000) = $2,000,000
Then, we must deduct the initial capital expenditure to find the net gain/loss:
USA: $3,600,000 – $2,000,000 = $1,600,000
UK: $2,000,000 – $5,000,000 = -$3,000,000
Decesion Probability of success Probability of failure
United states of America 40% 60%
United Kingdom 30% 70%
Expected pay off
Probability of Success (0.4) $ 15 Million
Open in USA: $ 2 million
Probability of Success (0.6) $ 04 Million
Probability of Success (0.3) $ 30 Million
Open in UK: $ 5 million
Probability of Success (0.7) $ 10 Million
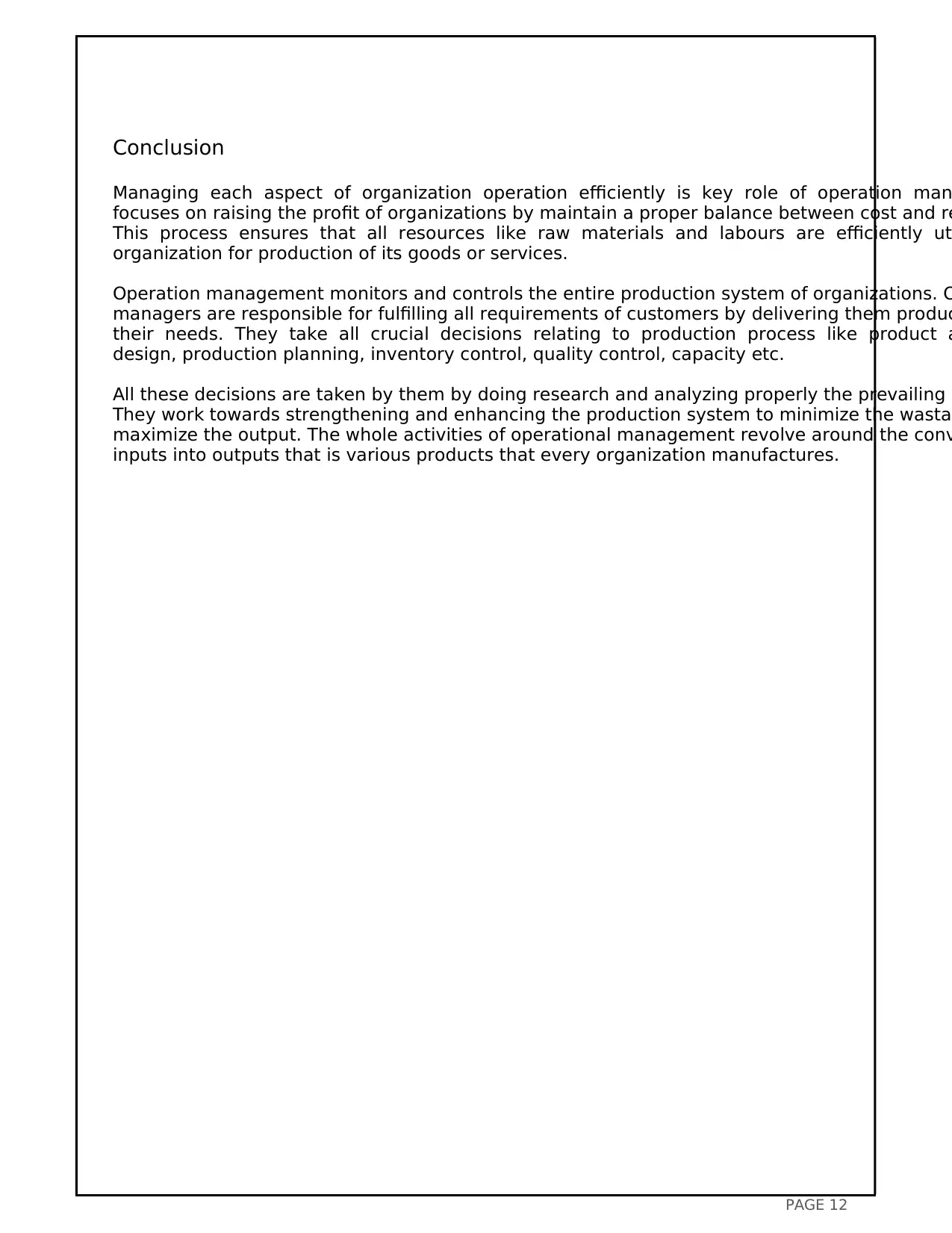
PAGE 12
Conclusion
Managing each aspect of organization operation efficiently is key role of operation man
focuses on raising the profit of organizations by maintain a proper balance between cost and re
This process ensures that all resources like raw materials and labours are efficiently uti
organization for production of its goods or services.
Operation management monitors and controls the entire production system of organizations. O
managers are responsible for fulfilling all requirements of customers by delivering them produc
their needs. They take all crucial decisions relating to production process like product a
design, production planning, inventory control, quality control, capacity etc.
All these decisions are taken by them by doing research and analyzing properly the prevailing s
They work towards strengthening and enhancing the production system to minimize the wastag
maximize the output. The whole activities of operational management revolve around the conv
inputs into outputs that is various products that every organization manufactures.
Conclusion
Managing each aspect of organization operation efficiently is key role of operation man
focuses on raising the profit of organizations by maintain a proper balance between cost and re
This process ensures that all resources like raw materials and labours are efficiently uti
organization for production of its goods or services.
Operation management monitors and controls the entire production system of organizations. O
managers are responsible for fulfilling all requirements of customers by delivering them produc
their needs. They take all crucial decisions relating to production process like product a
design, production planning, inventory control, quality control, capacity etc.
All these decisions are taken by them by doing research and analyzing properly the prevailing s
They work towards strengthening and enhancing the production system to minimize the wastag
maximize the output. The whole activities of operational management revolve around the conv
inputs into outputs that is various products that every organization manufactures.
You're viewing a preview
Unlock full access by subscribing today!
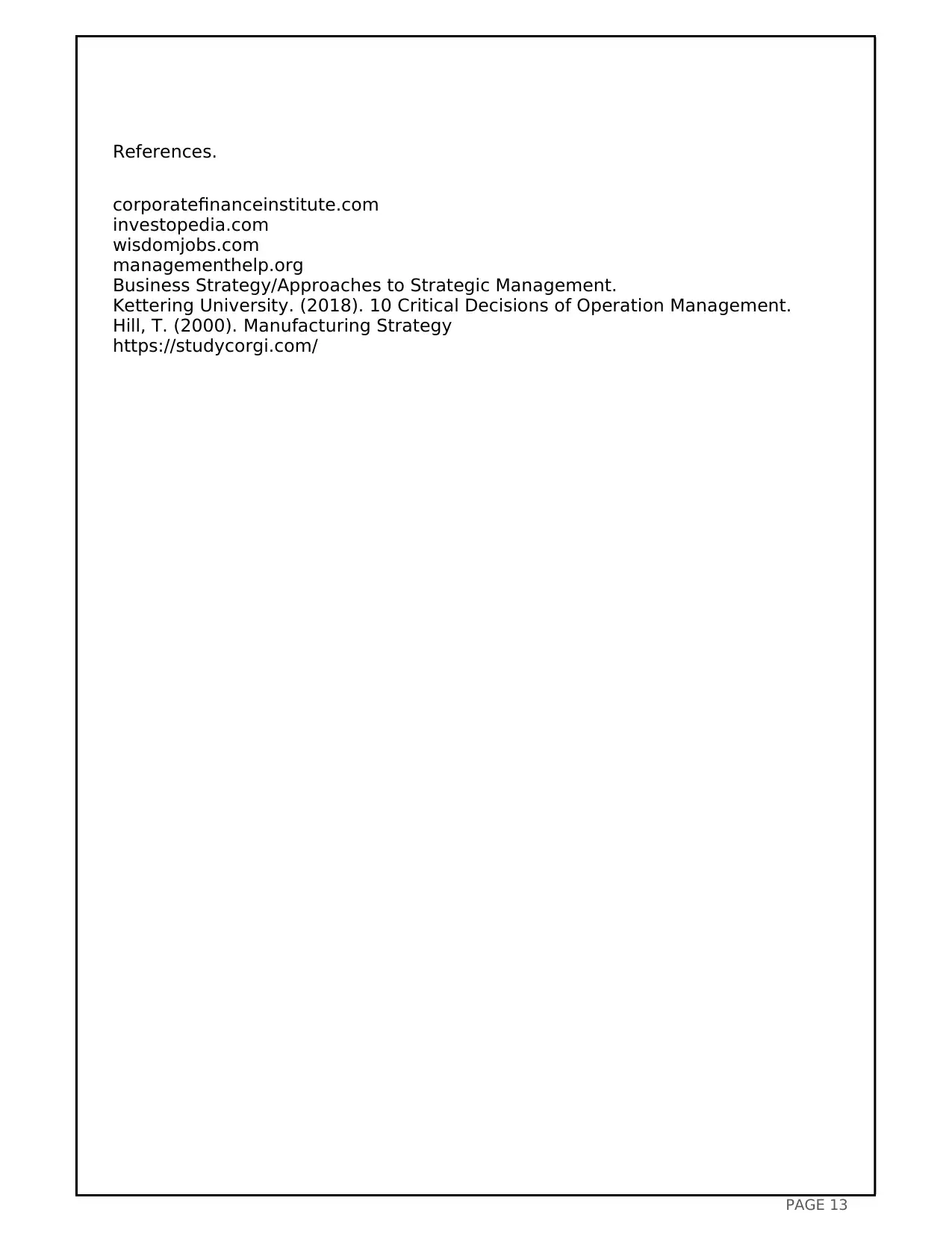
PAGE 13
References.
corporatefinanceinstitute.com
investopedia.com
wisdomjobs.com
managementhelp.org
Business Strategy/Approaches to Strategic Management.
Kettering University. (2018). 10 Critical Decisions of Operation Management.
Hill, T. (2000). Manufacturing Strategy
https://studycorgi.com/
References.
corporatefinanceinstitute.com
investopedia.com
wisdomjobs.com
managementhelp.org
Business Strategy/Approaches to Strategic Management.
Kettering University. (2018). 10 Critical Decisions of Operation Management.
Hill, T. (2000). Manufacturing Strategy
https://studycorgi.com/
1 out of 13
Related Documents

Your All-in-One AI-Powered Toolkit for Academic Success.
+13062052269
info@desklib.com
Available 24*7 on WhatsApp / Email
Unlock your academic potential
© 2024 | Zucol Services PVT LTD | All rights reserved.