Analysis of Operations Management and Service Excellence at Starbucks
VerifiedAdded on  2023/01/17
|16
|4401
|48
Report
AI Summary
This report provides a comprehensive analysis of Starbucks' operations management and service excellence. Part A covers comparative analyses using the Four Vs framework, performance objectives via polar diagrams, and design analysis of customer service processes and store layouts, comparing Starbucks with Greggs. Part B delves into Starbucks' global operations strategy, the role of quality management, the impact of the macro-business environment, key requirements, capabilities, challenges, and resource management. It evaluates operations performance, addresses challenges, and offers recommendations for improvement, supported by relevant theories and concepts. The report examines various aspects of Starbucks' operations, including volume, variety, variation, and visibility, alongside performance objectives such as cost, speed, quality, flexibility, and dependability. It explores the influence of design on customer service processes and store layouts, linking these elements to Starbucks' overall performance and competitive advantage.
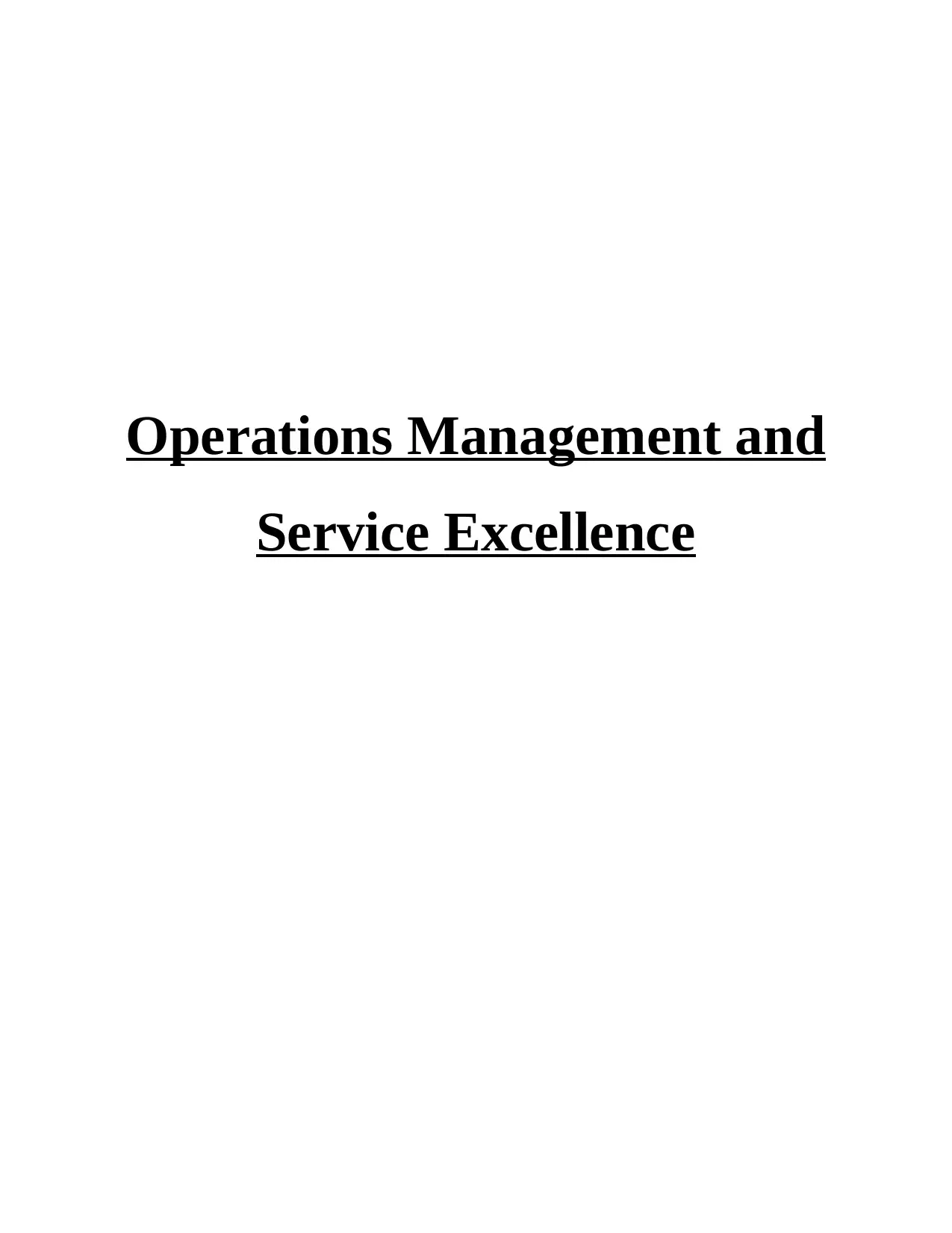
Operations Management and
Service Excellence
Service Excellence
Secure Best Marks with AI Grader
Need help grading? Try our AI Grader for instant feedback on your assignments.
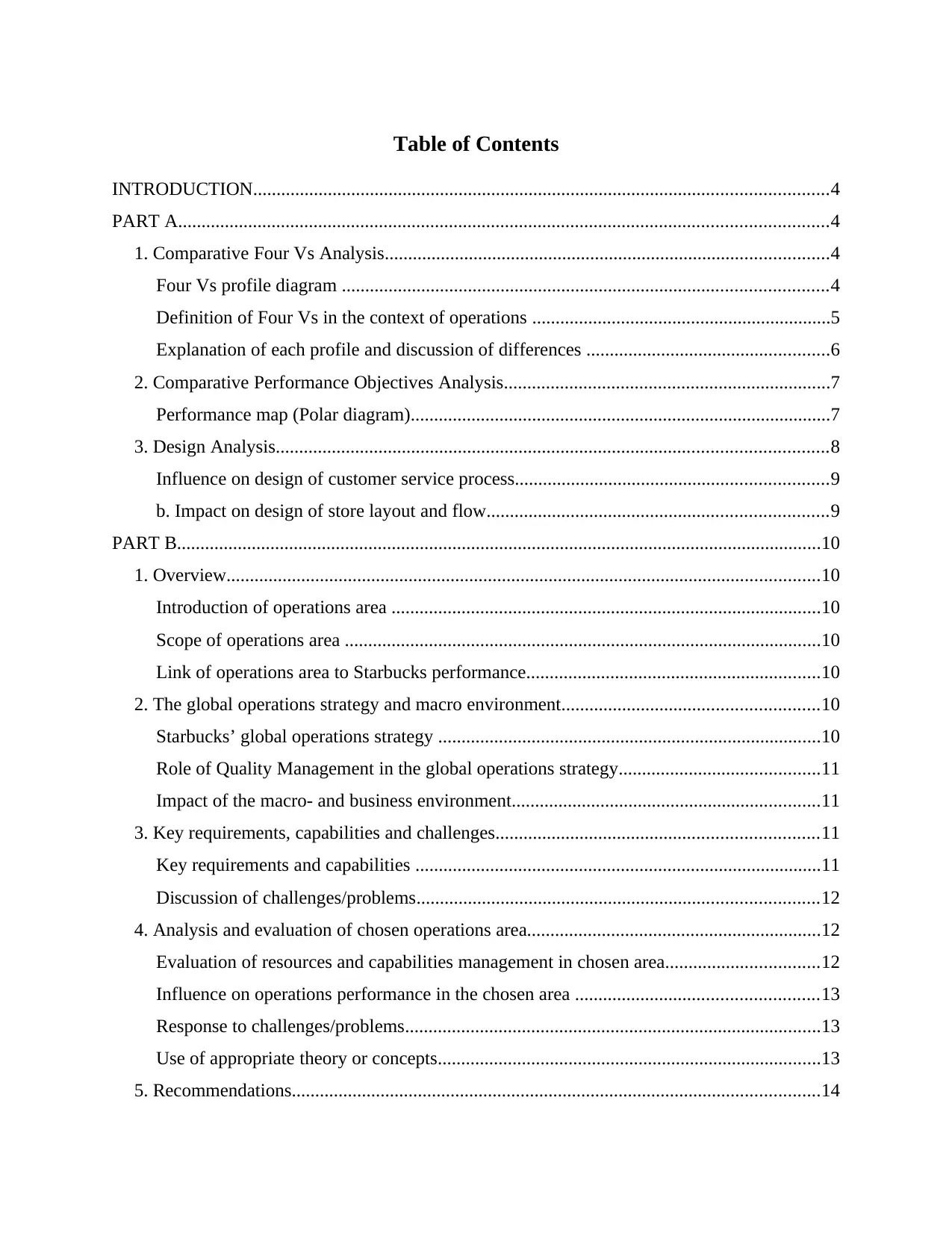
Table of Contents
INTRODUCTION...........................................................................................................................4
PART A...........................................................................................................................................4
1. Comparative Four Vs Analysis...............................................................................................4
Four Vs profile diagram ........................................................................................................4
Definition of Four Vs in the context of operations ................................................................5
Explanation of each profile and discussion of differences ....................................................6
2. Comparative Performance Objectives Analysis......................................................................7
Performance map (Polar diagram)..........................................................................................7
3. Design Analysis......................................................................................................................8
Influence on design of customer service process...................................................................9
b. Impact on design of store layout and flow.........................................................................9
PART B..........................................................................................................................................10
1. Overview...............................................................................................................................10
Introduction of operations area ............................................................................................10
Scope of operations area ......................................................................................................10
Link of operations area to Starbucks performance...............................................................10
2. The global operations strategy and macro environment.......................................................10
Starbucks’ global operations strategy ..................................................................................10
Role of Quality Management in the global operations strategy...........................................11
Impact of the macro- and business environment..................................................................11
3. Key requirements, capabilities and challenges.....................................................................11
Key requirements and capabilities .......................................................................................11
Discussion of challenges/problems......................................................................................12
4. Analysis and evaluation of chosen operations area...............................................................12
Evaluation of resources and capabilities management in chosen area.................................12
Influence on operations performance in the chosen area ....................................................13
Response to challenges/problems.........................................................................................13
Use of appropriate theory or concepts..................................................................................13
5. Recommendations.................................................................................................................14
INTRODUCTION...........................................................................................................................4
PART A...........................................................................................................................................4
1. Comparative Four Vs Analysis...............................................................................................4
Four Vs profile diagram ........................................................................................................4
Definition of Four Vs in the context of operations ................................................................5
Explanation of each profile and discussion of differences ....................................................6
2. Comparative Performance Objectives Analysis......................................................................7
Performance map (Polar diagram)..........................................................................................7
3. Design Analysis......................................................................................................................8
Influence on design of customer service process...................................................................9
b. Impact on design of store layout and flow.........................................................................9
PART B..........................................................................................................................................10
1. Overview...............................................................................................................................10
Introduction of operations area ............................................................................................10
Scope of operations area ......................................................................................................10
Link of operations area to Starbucks performance...............................................................10
2. The global operations strategy and macro environment.......................................................10
Starbucks’ global operations strategy ..................................................................................10
Role of Quality Management in the global operations strategy...........................................11
Impact of the macro- and business environment..................................................................11
3. Key requirements, capabilities and challenges.....................................................................11
Key requirements and capabilities .......................................................................................11
Discussion of challenges/problems......................................................................................12
4. Analysis and evaluation of chosen operations area...............................................................12
Evaluation of resources and capabilities management in chosen area.................................12
Influence on operations performance in the chosen area ....................................................13
Response to challenges/problems.........................................................................................13
Use of appropriate theory or concepts..................................................................................13
5. Recommendations.................................................................................................................14
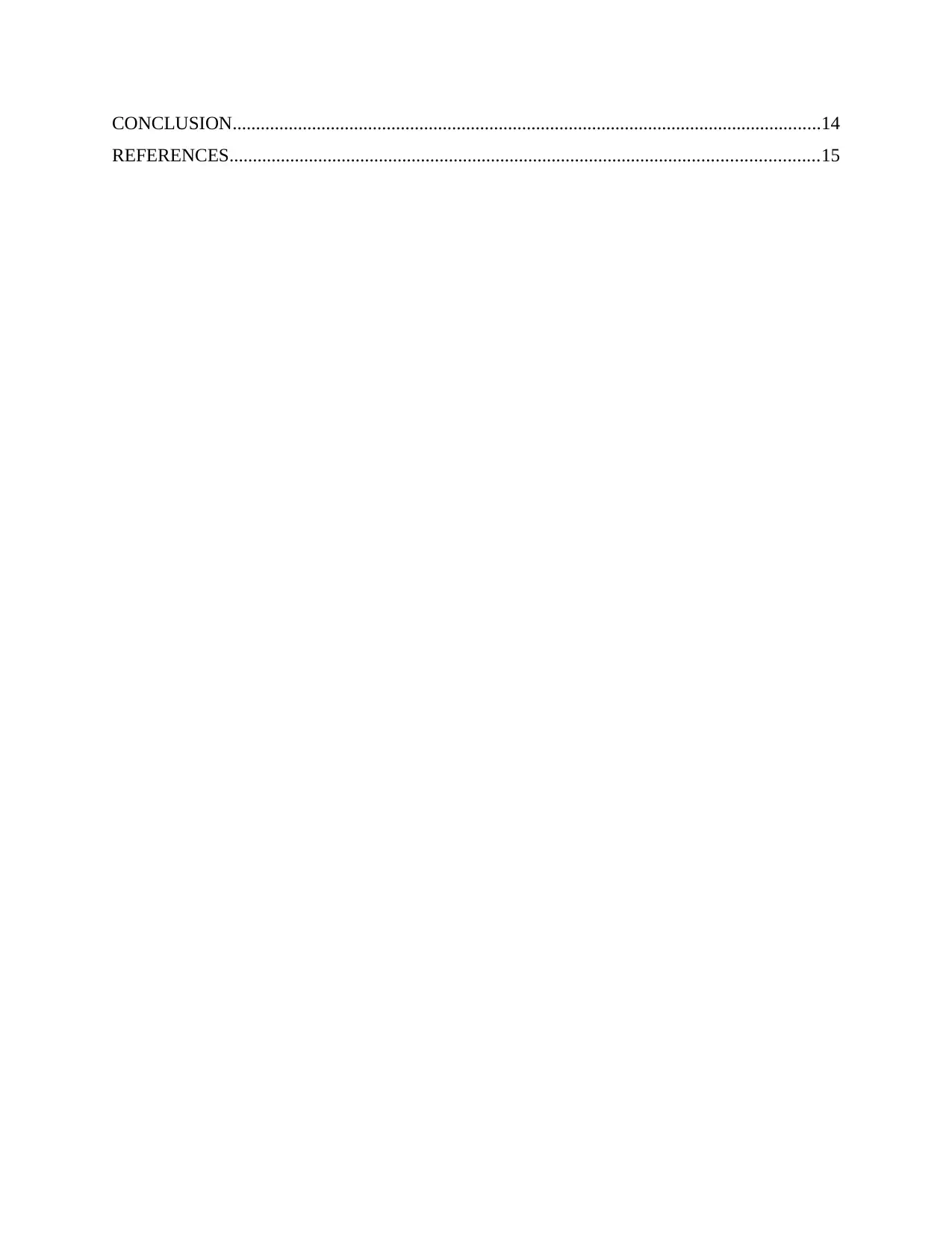
CONCLUSION..............................................................................................................................14
REFERENCES..............................................................................................................................15
REFERENCES..............................................................................................................................15
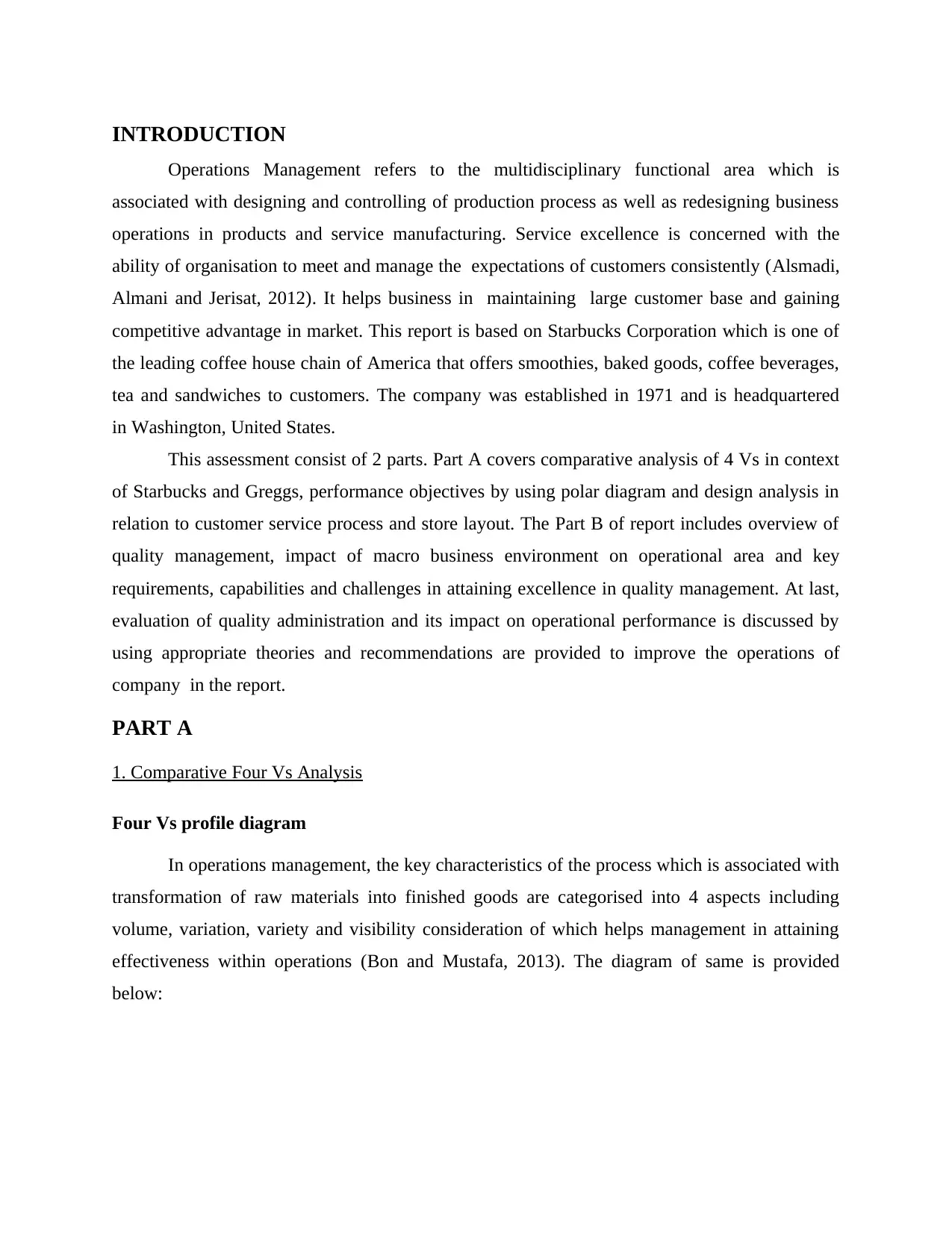
INTRODUCTION
Operations Management refers to the multidisciplinary functional area which is
associated with designing and controlling of production process as well as redesigning business
operations in products and service manufacturing. Service excellence is concerned with the
ability of organisation to meet and manage the expectations of customers consistently (Alsmadi,
Almani and Jerisat, 2012). It helps business in maintaining large customer base and gaining
competitive advantage in market. This report is based on Starbucks Corporation which is one of
the leading coffee house chain of America that offers smoothies, baked goods, coffee beverages,
tea and sandwiches to customers. The company was established in 1971 and is headquartered
in Washington, United States.
This assessment consist of 2 parts. Part A covers comparative analysis of 4 Vs in context
of Starbucks and Greggs, performance objectives by using polar diagram and design analysis in
relation to customer service process and store layout. The Part B of report includes overview of
quality management, impact of macro business environment on operational area and key
requirements, capabilities and challenges in attaining excellence in quality management. At last,
evaluation of quality administration and its impact on operational performance is discussed by
using appropriate theories and recommendations are provided to improve the operations of
company in the report.
PART A
1. Comparative Four Vs Analysis
Four Vs profile diagram
In operations management, the key characteristics of the process which is associated with
transformation of raw materials into finished goods are categorised into 4 aspects including
volume, variation, variety and visibility consideration of which helps management in attaining
effectiveness within operations (Bon and Mustafa, 2013). The diagram of same is provided
below:
Operations Management refers to the multidisciplinary functional area which is
associated with designing and controlling of production process as well as redesigning business
operations in products and service manufacturing. Service excellence is concerned with the
ability of organisation to meet and manage the expectations of customers consistently (Alsmadi,
Almani and Jerisat, 2012). It helps business in maintaining large customer base and gaining
competitive advantage in market. This report is based on Starbucks Corporation which is one of
the leading coffee house chain of America that offers smoothies, baked goods, coffee beverages,
tea and sandwiches to customers. The company was established in 1971 and is headquartered
in Washington, United States.
This assessment consist of 2 parts. Part A covers comparative analysis of 4 Vs in context
of Starbucks and Greggs, performance objectives by using polar diagram and design analysis in
relation to customer service process and store layout. The Part B of report includes overview of
quality management, impact of macro business environment on operational area and key
requirements, capabilities and challenges in attaining excellence in quality management. At last,
evaluation of quality administration and its impact on operational performance is discussed by
using appropriate theories and recommendations are provided to improve the operations of
company in the report.
PART A
1. Comparative Four Vs Analysis
Four Vs profile diagram
In operations management, the key characteristics of the process which is associated with
transformation of raw materials into finished goods are categorised into 4 aspects including
volume, variation, variety and visibility consideration of which helps management in attaining
effectiveness within operations (Bon and Mustafa, 2013). The diagram of same is provided
below:
Secure Best Marks with AI Grader
Need help grading? Try our AI Grader for instant feedback on your assignments.
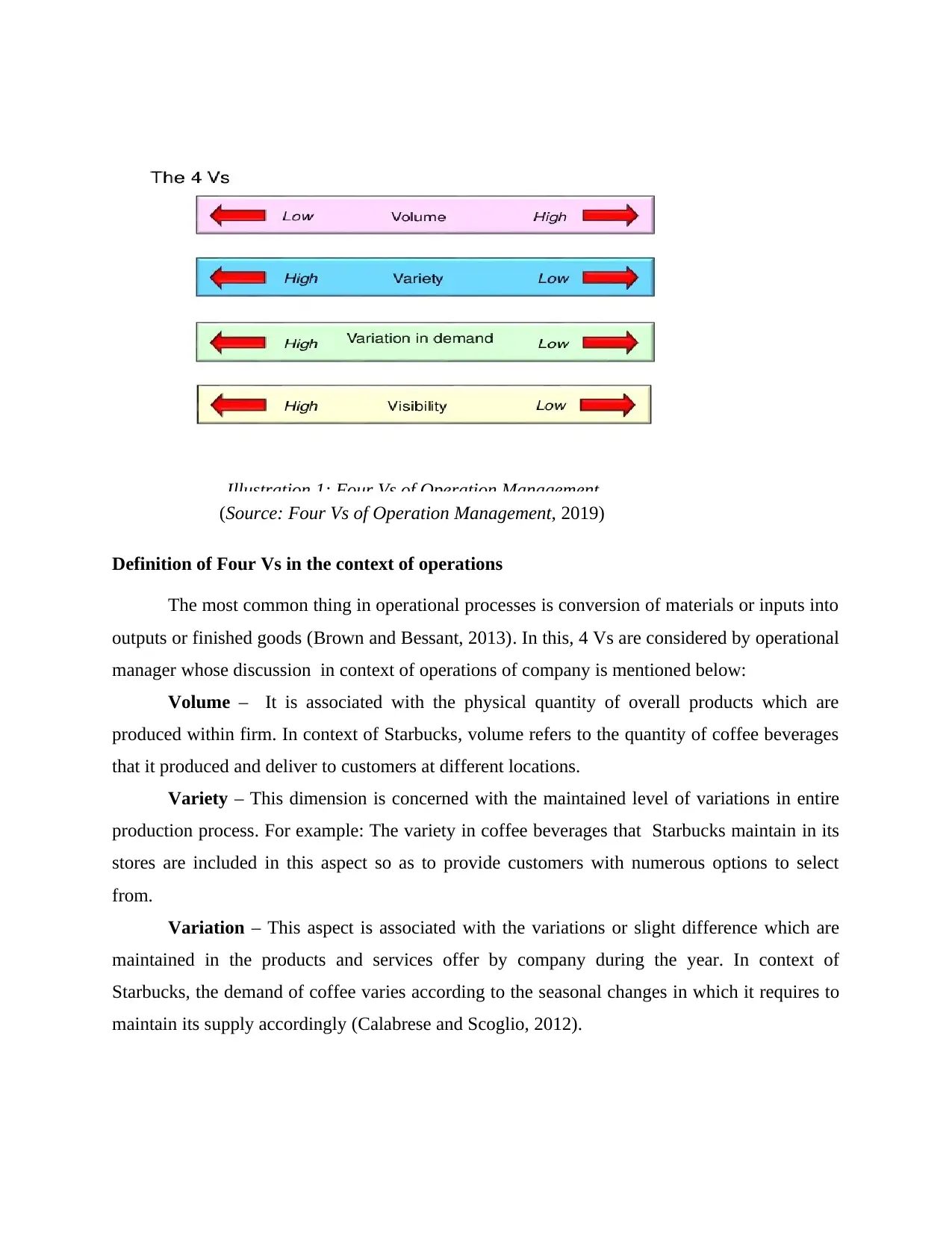
Illustration 1: Four Vs of Operation Management
(Source: Four Vs of Operation Management, 2019)
Definition of Four Vs in the context of operations
The most common thing in operational processes is conversion of materials or inputs into
outputs or finished goods (Brown and Bessant, 2013). In this, 4 Vs are considered by operational
manager whose discussion in context of operations of company is mentioned below:
Volume – It is associated with the physical quantity of overall products which are
produced within firm. In context of Starbucks, volume refers to the quantity of coffee beverages
that it produced and deliver to customers at different locations.
Variety – This dimension is concerned with the maintained level of variations in entire
production process. For example: The variety in coffee beverages that Starbucks maintain in its
stores are included in this aspect so as to provide customers with numerous options to select
from.
Variation – This aspect is associated with the variations or slight difference which are
maintained in the products and services offer by company during the year. In context of
Starbucks, the demand of coffee varies according to the seasonal changes in which it requires to
maintain its supply accordingly (Calabrese and Scoglio, 2012).
(Source: Four Vs of Operation Management, 2019)
Definition of Four Vs in the context of operations
The most common thing in operational processes is conversion of materials or inputs into
outputs or finished goods (Brown and Bessant, 2013). In this, 4 Vs are considered by operational
manager whose discussion in context of operations of company is mentioned below:
Volume – It is associated with the physical quantity of overall products which are
produced within firm. In context of Starbucks, volume refers to the quantity of coffee beverages
that it produced and deliver to customers at different locations.
Variety – This dimension is concerned with the maintained level of variations in entire
production process. For example: The variety in coffee beverages that Starbucks maintain in its
stores are included in this aspect so as to provide customers with numerous options to select
from.
Variation – This aspect is associated with the variations or slight difference which are
maintained in the products and services offer by company during the year. In context of
Starbucks, the demand of coffee varies according to the seasonal changes in which it requires to
maintain its supply accordingly (Calabrese and Scoglio, 2012).
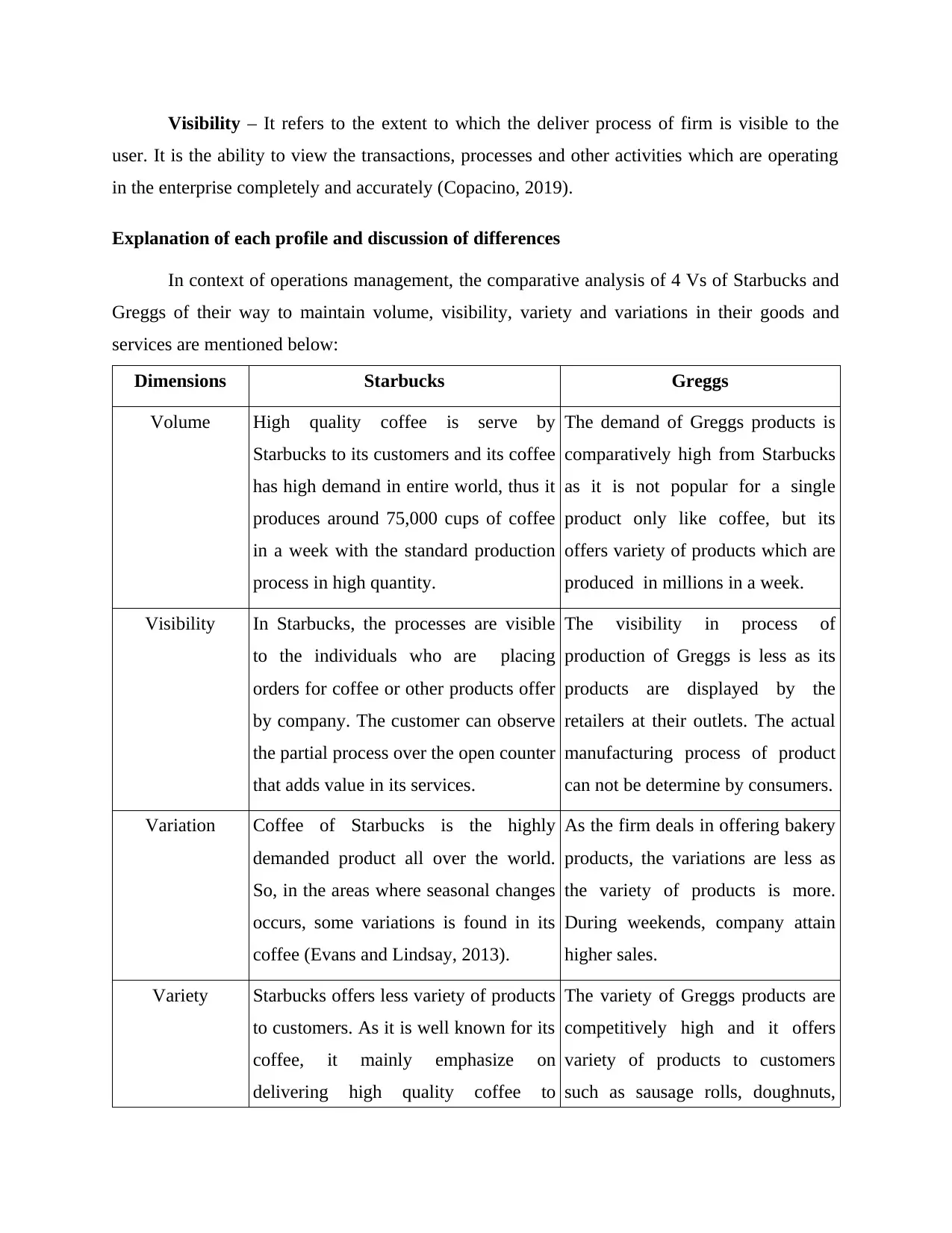
Visibility – It refers to the extent to which the deliver process of firm is visible to the
user. It is the ability to view the transactions, processes and other activities which are operating
in the enterprise completely and accurately (Copacino, 2019).
Explanation of each profile and discussion of differences
In context of operations management, the comparative analysis of 4 Vs of Starbucks and
Greggs of their way to maintain volume, visibility, variety and variations in their goods and
services are mentioned below:
Dimensions Starbucks Greggs
Volume High quality coffee is serve by
Starbucks to its customers and its coffee
has high demand in entire world, thus it
produces around 75,000 cups of coffee
in a week with the standard production
process in high quantity.
The demand of Greggs products is
comparatively high from Starbucks
as it is not popular for a single
product only like coffee, but its
offers variety of products which are
produced in millions in a week.
Visibility In Starbucks, the processes are visible
to the individuals who are placing
orders for coffee or other products offer
by company. The customer can observe
the partial process over the open counter
that adds value in its services.
The visibility in process of
production of Greggs is less as its
products are displayed by the
retailers at their outlets. The actual
manufacturing process of product
can not be determine by consumers.
Variation Coffee of Starbucks is the highly
demanded product all over the world.
So, in the areas where seasonal changes
occurs, some variations is found in its
coffee (Evans and Lindsay, 2013).
As the firm deals in offering bakery
products, the variations are less as
the variety of products is more.
During weekends, company attain
higher sales.
Variety Starbucks offers less variety of products
to customers. As it is well known for its
coffee, it mainly emphasize on
delivering high quality coffee to
The variety of Greggs products are
competitively high and it offers
variety of products to customers
such as sausage rolls, doughnuts,
user. It is the ability to view the transactions, processes and other activities which are operating
in the enterprise completely and accurately (Copacino, 2019).
Explanation of each profile and discussion of differences
In context of operations management, the comparative analysis of 4 Vs of Starbucks and
Greggs of their way to maintain volume, visibility, variety and variations in their goods and
services are mentioned below:
Dimensions Starbucks Greggs
Volume High quality coffee is serve by
Starbucks to its customers and its coffee
has high demand in entire world, thus it
produces around 75,000 cups of coffee
in a week with the standard production
process in high quantity.
The demand of Greggs products is
comparatively high from Starbucks
as it is not popular for a single
product only like coffee, but its
offers variety of products which are
produced in millions in a week.
Visibility In Starbucks, the processes are visible
to the individuals who are placing
orders for coffee or other products offer
by company. The customer can observe
the partial process over the open counter
that adds value in its services.
The visibility in process of
production of Greggs is less as its
products are displayed by the
retailers at their outlets. The actual
manufacturing process of product
can not be determine by consumers.
Variation Coffee of Starbucks is the highly
demanded product all over the world.
So, in the areas where seasonal changes
occurs, some variations is found in its
coffee (Evans and Lindsay, 2013).
As the firm deals in offering bakery
products, the variations are less as
the variety of products is more.
During weekends, company attain
higher sales.
Variety Starbucks offers less variety of products
to customers. As it is well known for its
coffee, it mainly emphasize on
delivering high quality coffee to
The variety of Greggs products are
competitively high and it offers
variety of products to customers
such as sausage rolls, doughnuts,
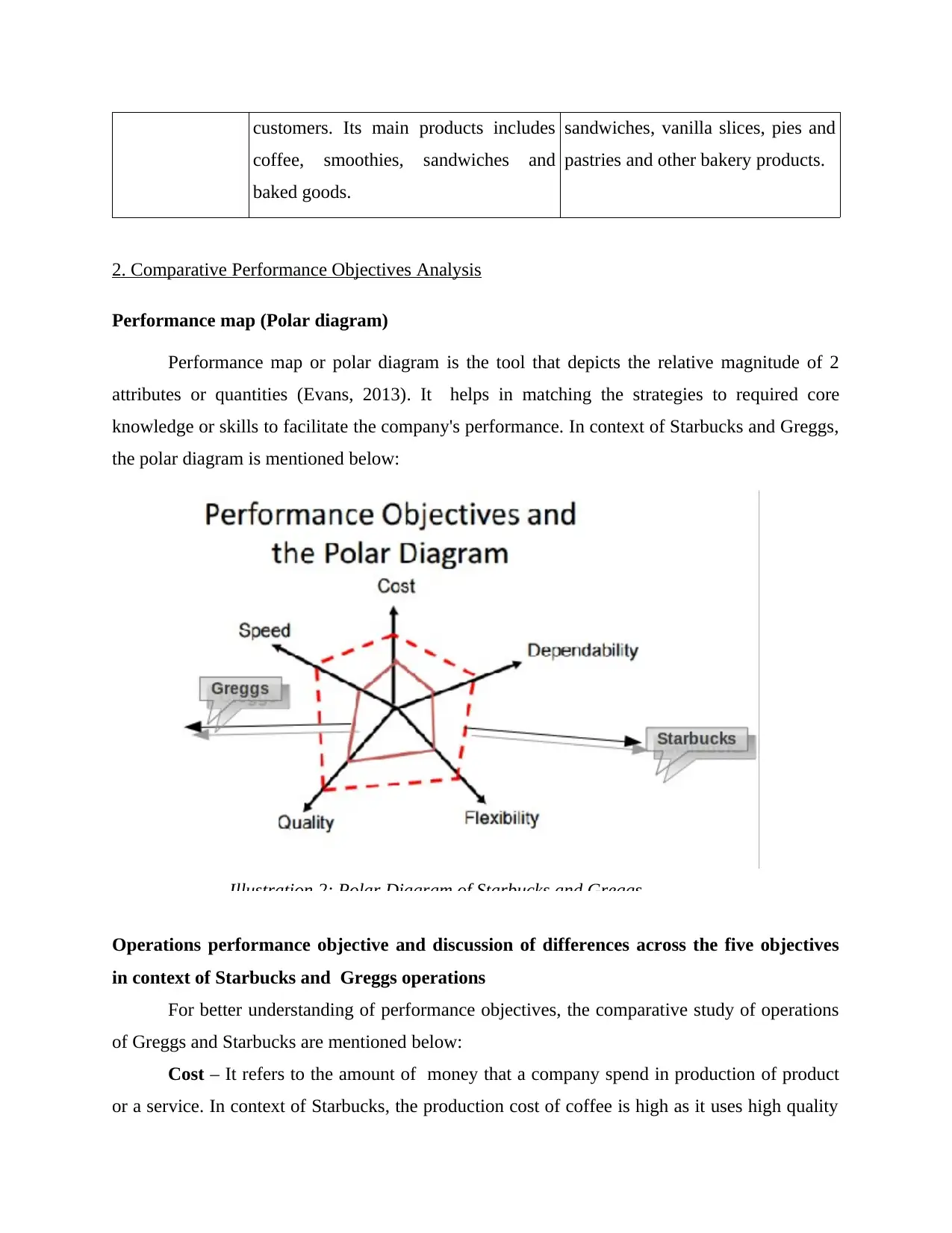
customers. Its main products includes
coffee, smoothies, sandwiches and
baked goods.
sandwiches, vanilla slices, pies and
pastries and other bakery products.
2. Comparative Performance Objectives Analysis
Performance map (Polar diagram)
Performance map or polar diagram is the tool that depicts the relative magnitude of 2
attributes or quantities (Evans, 2013). It helps in matching the strategies to required core
knowledge or skills to facilitate the company's performance. In context of Starbucks and Greggs,
the polar diagram is mentioned below:
Illustration 2: Polar Diagram of Starbucks and Greggs
Operations performance objective and discussion of differences across the five objectives
in context of Starbucks and Greggs operations
For better understanding of performance objectives, the comparative study of operations
of Greggs and Starbucks are mentioned below:
Cost – It refers to the amount of money that a company spend in production of product
or a service. In context of Starbucks, the production cost of coffee is high as it uses high quality
coffee, smoothies, sandwiches and
baked goods.
sandwiches, vanilla slices, pies and
pastries and other bakery products.
2. Comparative Performance Objectives Analysis
Performance map (Polar diagram)
Performance map or polar diagram is the tool that depicts the relative magnitude of 2
attributes or quantities (Evans, 2013). It helps in matching the strategies to required core
knowledge or skills to facilitate the company's performance. In context of Starbucks and Greggs,
the polar diagram is mentioned below:
Illustration 2: Polar Diagram of Starbucks and Greggs
Operations performance objective and discussion of differences across the five objectives
in context of Starbucks and Greggs operations
For better understanding of performance objectives, the comparative study of operations
of Greggs and Starbucks are mentioned below:
Cost – It refers to the amount of money that a company spend in production of product
or a service. In context of Starbucks, the production cost of coffee is high as it uses high quality
Paraphrase This Document
Need a fresh take? Get an instant paraphrase of this document with our AI Paraphraser
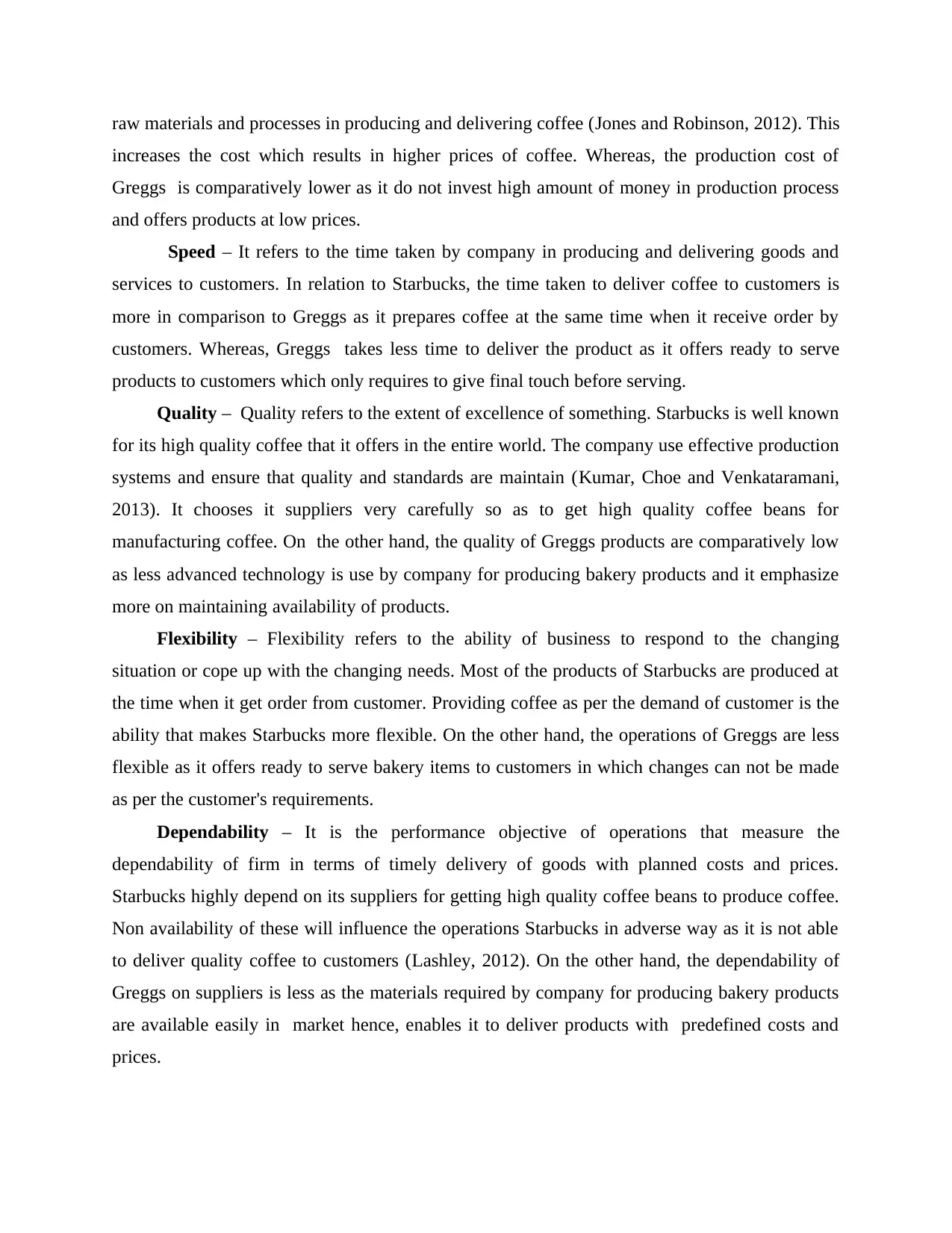
raw materials and processes in producing and delivering coffee (Jones and Robinson, 2012). This
increases the cost which results in higher prices of coffee. Whereas, the production cost of
Greggs is comparatively lower as it do not invest high amount of money in production process
and offers products at low prices.
Speed – It refers to the time taken by company in producing and delivering goods and
services to customers. In relation to Starbucks, the time taken to deliver coffee to customers is
more in comparison to Greggs as it prepares coffee at the same time when it receive order by
customers. Whereas, Greggs takes less time to deliver the product as it offers ready to serve
products to customers which only requires to give final touch before serving.
Quality – Quality refers to the extent of excellence of something. Starbucks is well known
for its high quality coffee that it offers in the entire world. The company use effective production
systems and ensure that quality and standards are maintain (Kumar, Choe and Venkataramani,
2013). It chooses it suppliers very carefully so as to get high quality coffee beans for
manufacturing coffee. On the other hand, the quality of Greggs products are comparatively low
as less advanced technology is use by company for producing bakery products and it emphasize
more on maintaining availability of products.
Flexibility – Flexibility refers to the ability of business to respond to the changing
situation or cope up with the changing needs. Most of the products of Starbucks are produced at
the time when it get order from customer. Providing coffee as per the demand of customer is the
ability that makes Starbucks more flexible. On the other hand, the operations of Greggs are less
flexible as it offers ready to serve bakery items to customers in which changes can not be made
as per the customer's requirements.
Dependability – It is the performance objective of operations that measure the
dependability of firm in terms of timely delivery of goods with planned costs and prices.
Starbucks highly depend on its suppliers for getting high quality coffee beans to produce coffee.
Non availability of these will influence the operations Starbucks in adverse way as it is not able
to deliver quality coffee to customers (Lashley, 2012). On the other hand, the dependability of
Greggs on suppliers is less as the materials required by company for producing bakery products
are available easily in market hence, enables it to deliver products with predefined costs and
prices.
increases the cost which results in higher prices of coffee. Whereas, the production cost of
Greggs is comparatively lower as it do not invest high amount of money in production process
and offers products at low prices.
Speed – It refers to the time taken by company in producing and delivering goods and
services to customers. In relation to Starbucks, the time taken to deliver coffee to customers is
more in comparison to Greggs as it prepares coffee at the same time when it receive order by
customers. Whereas, Greggs takes less time to deliver the product as it offers ready to serve
products to customers which only requires to give final touch before serving.
Quality – Quality refers to the extent of excellence of something. Starbucks is well known
for its high quality coffee that it offers in the entire world. The company use effective production
systems and ensure that quality and standards are maintain (Kumar, Choe and Venkataramani,
2013). It chooses it suppliers very carefully so as to get high quality coffee beans for
manufacturing coffee. On the other hand, the quality of Greggs products are comparatively low
as less advanced technology is use by company for producing bakery products and it emphasize
more on maintaining availability of products.
Flexibility – Flexibility refers to the ability of business to respond to the changing
situation or cope up with the changing needs. Most of the products of Starbucks are produced at
the time when it get order from customer. Providing coffee as per the demand of customer is the
ability that makes Starbucks more flexible. On the other hand, the operations of Greggs are less
flexible as it offers ready to serve bakery items to customers in which changes can not be made
as per the customer's requirements.
Dependability – It is the performance objective of operations that measure the
dependability of firm in terms of timely delivery of goods with planned costs and prices.
Starbucks highly depend on its suppliers for getting high quality coffee beans to produce coffee.
Non availability of these will influence the operations Starbucks in adverse way as it is not able
to deliver quality coffee to customers (Lashley, 2012). On the other hand, the dependability of
Greggs on suppliers is less as the materials required by company for producing bakery products
are available easily in market hence, enables it to deliver products with predefined costs and
prices.
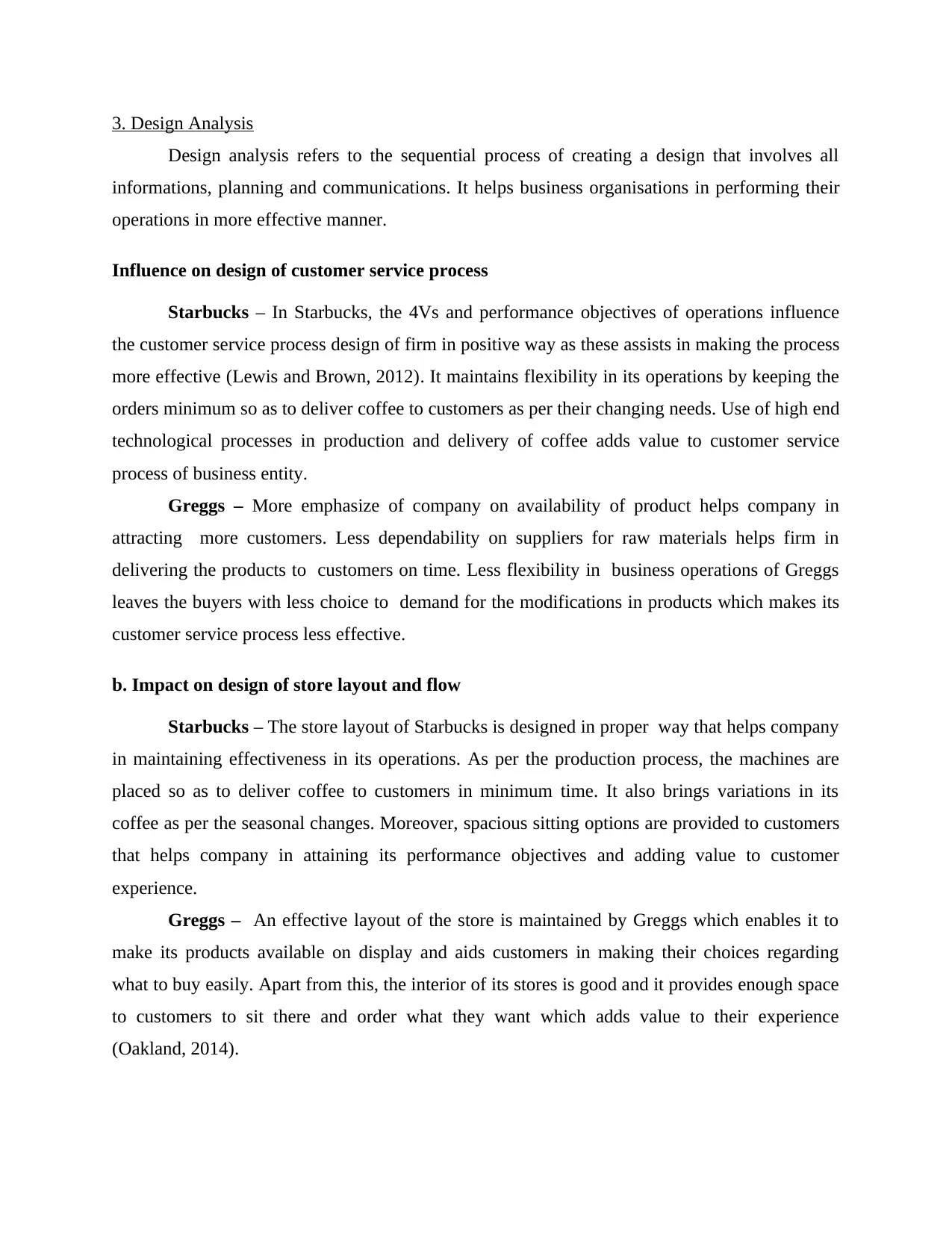
3. Design Analysis
Design analysis refers to the sequential process of creating a design that involves all
informations, planning and communications. It helps business organisations in performing their
operations in more effective manner.
Influence on design of customer service process
Starbucks – In Starbucks, the 4Vs and performance objectives of operations influence
the customer service process design of firm in positive way as these assists in making the process
more effective (Lewis and Brown, 2012). It maintains flexibility in its operations by keeping the
orders minimum so as to deliver coffee to customers as per their changing needs. Use of high end
technological processes in production and delivery of coffee adds value to customer service
process of business entity.
Greggs – More emphasize of company on availability of product helps company in
attracting more customers. Less dependability on suppliers for raw materials helps firm in
delivering the products to customers on time. Less flexibility in business operations of Greggs
leaves the buyers with less choice to demand for the modifications in products which makes its
customer service process less effective.
b. Impact on design of store layout and flow
Starbucks – The store layout of Starbucks is designed in proper way that helps company
in maintaining effectiveness in its operations. As per the production process, the machines are
placed so as to deliver coffee to customers in minimum time. It also brings variations in its
coffee as per the seasonal changes. Moreover, spacious sitting options are provided to customers
that helps company in attaining its performance objectives and adding value to customer
experience.
Greggs – An effective layout of the store is maintained by Greggs which enables it to
make its products available on display and aids customers in making their choices regarding
what to buy easily. Apart from this, the interior of its stores is good and it provides enough space
to customers to sit there and order what they want which adds value to their experience
(Oakland, 2014).
Design analysis refers to the sequential process of creating a design that involves all
informations, planning and communications. It helps business organisations in performing their
operations in more effective manner.
Influence on design of customer service process
Starbucks – In Starbucks, the 4Vs and performance objectives of operations influence
the customer service process design of firm in positive way as these assists in making the process
more effective (Lewis and Brown, 2012). It maintains flexibility in its operations by keeping the
orders minimum so as to deliver coffee to customers as per their changing needs. Use of high end
technological processes in production and delivery of coffee adds value to customer service
process of business entity.
Greggs – More emphasize of company on availability of product helps company in
attracting more customers. Less dependability on suppliers for raw materials helps firm in
delivering the products to customers on time. Less flexibility in business operations of Greggs
leaves the buyers with less choice to demand for the modifications in products which makes its
customer service process less effective.
b. Impact on design of store layout and flow
Starbucks – The store layout of Starbucks is designed in proper way that helps company
in maintaining effectiveness in its operations. As per the production process, the machines are
placed so as to deliver coffee to customers in minimum time. It also brings variations in its
coffee as per the seasonal changes. Moreover, spacious sitting options are provided to customers
that helps company in attaining its performance objectives and adding value to customer
experience.
Greggs – An effective layout of the store is maintained by Greggs which enables it to
make its products available on display and aids customers in making their choices regarding
what to buy easily. Apart from this, the interior of its stores is good and it provides enough space
to customers to sit there and order what they want which adds value to their experience
(Oakland, 2014).
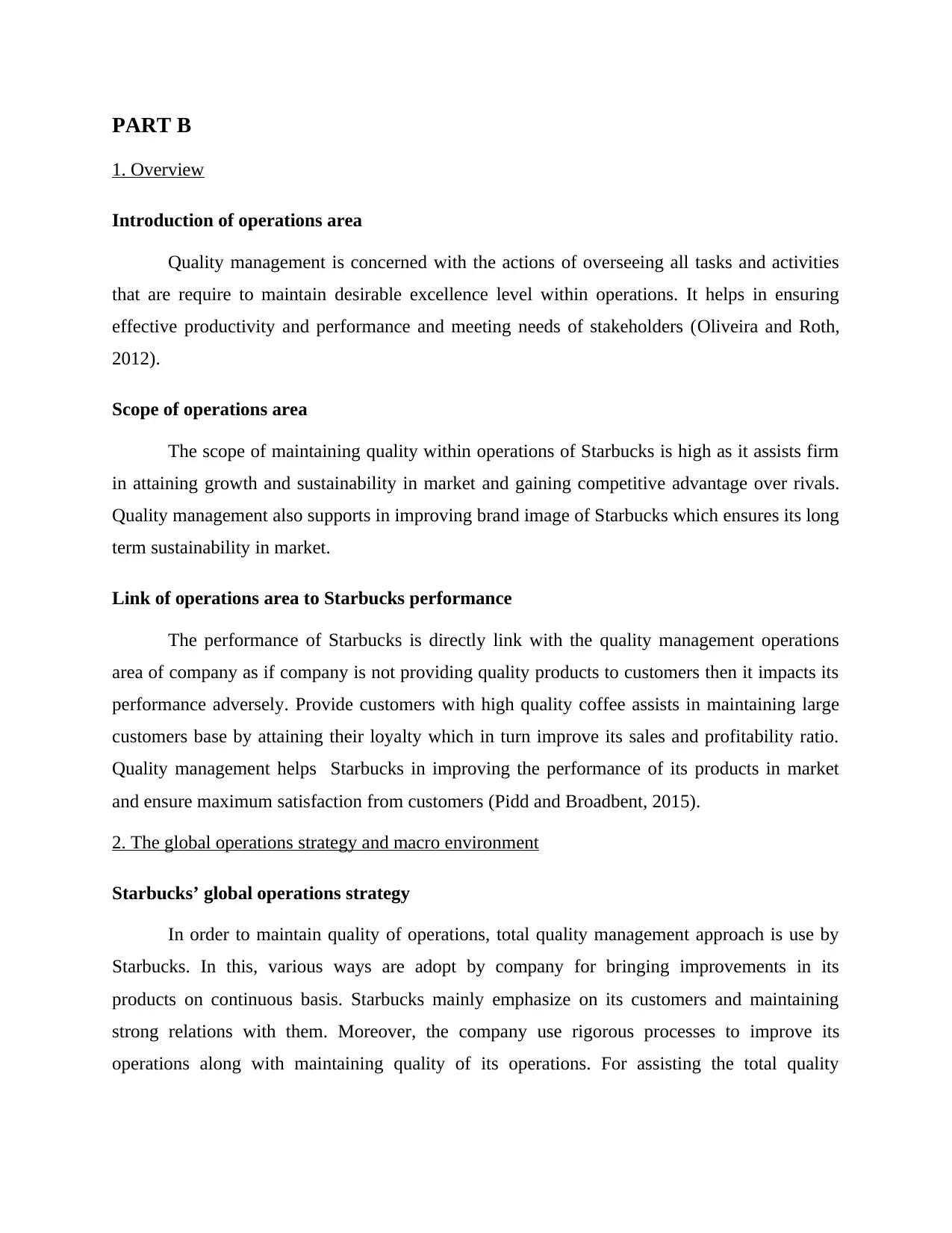
PART B
1. Overview
Introduction of operations area
Quality management is concerned with the actions of overseeing all tasks and activities
that are require to maintain desirable excellence level within operations. It helps in ensuring
effective productivity and performance and meeting needs of stakeholders (Oliveira and Roth,
2012).
Scope of operations area
The scope of maintaining quality within operations of Starbucks is high as it assists firm
in attaining growth and sustainability in market and gaining competitive advantage over rivals.
Quality management also supports in improving brand image of Starbucks which ensures its long
term sustainability in market.
Link of operations area to Starbucks performance
The performance of Starbucks is directly link with the quality management operations
area of company as if company is not providing quality products to customers then it impacts its
performance adversely. Provide customers with high quality coffee assists in maintaining large
customers base by attaining their loyalty which in turn improve its sales and profitability ratio.
Quality management helps Starbucks in improving the performance of its products in market
and ensure maximum satisfaction from customers (Pidd and Broadbent, 2015).
2. The global operations strategy and macro environment
Starbucks’ global operations strategy
In order to maintain quality of operations, total quality management approach is use by
Starbucks. In this, various ways are adopt by company for bringing improvements in its
products on continuous basis. Starbucks mainly emphasize on its customers and maintaining
strong relations with them. Moreover, the company use rigorous processes to improve its
operations along with maintaining quality of its operations. For assisting the total quality
1. Overview
Introduction of operations area
Quality management is concerned with the actions of overseeing all tasks and activities
that are require to maintain desirable excellence level within operations. It helps in ensuring
effective productivity and performance and meeting needs of stakeholders (Oliveira and Roth,
2012).
Scope of operations area
The scope of maintaining quality within operations of Starbucks is high as it assists firm
in attaining growth and sustainability in market and gaining competitive advantage over rivals.
Quality management also supports in improving brand image of Starbucks which ensures its long
term sustainability in market.
Link of operations area to Starbucks performance
The performance of Starbucks is directly link with the quality management operations
area of company as if company is not providing quality products to customers then it impacts its
performance adversely. Provide customers with high quality coffee assists in maintaining large
customers base by attaining their loyalty which in turn improve its sales and profitability ratio.
Quality management helps Starbucks in improving the performance of its products in market
and ensure maximum satisfaction from customers (Pidd and Broadbent, 2015).
2. The global operations strategy and macro environment
Starbucks’ global operations strategy
In order to maintain quality of operations, total quality management approach is use by
Starbucks. In this, various ways are adopt by company for bringing improvements in its
products on continuous basis. Starbucks mainly emphasize on its customers and maintaining
strong relations with them. Moreover, the company use rigorous processes to improve its
operations along with maintaining quality of its operations. For assisting the total quality
Secure Best Marks with AI Grader
Need help grading? Try our AI Grader for instant feedback on your assignments.
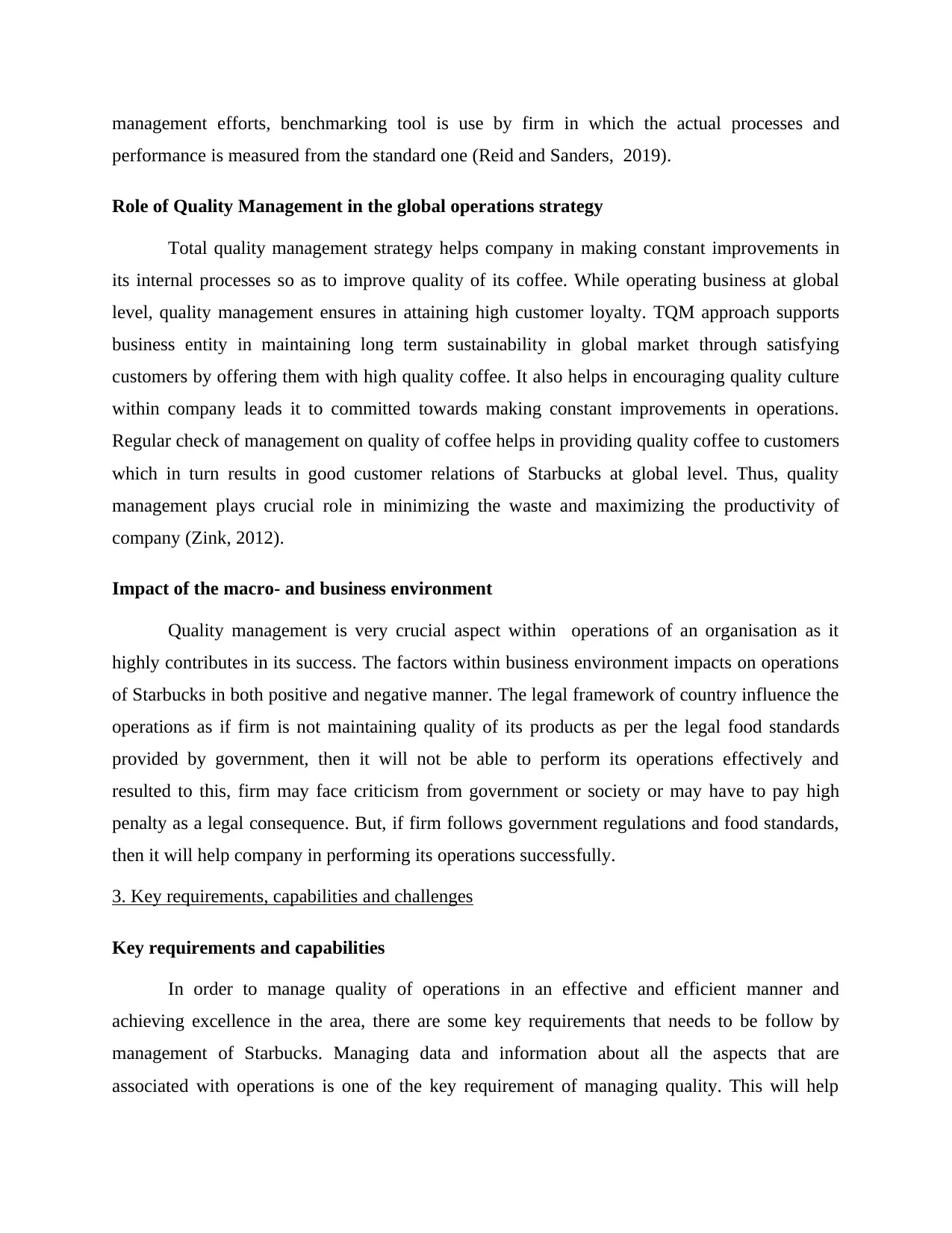
management efforts, benchmarking tool is use by firm in which the actual processes and
performance is measured from the standard one (Reid and Sanders, 2019).
Role of Quality Management in the global operations strategy
Total quality management strategy helps company in making constant improvements in
its internal processes so as to improve quality of its coffee. While operating business at global
level, quality management ensures in attaining high customer loyalty. TQM approach supports
business entity in maintaining long term sustainability in global market through satisfying
customers by offering them with high quality coffee. It also helps in encouraging quality culture
within company leads it to committed towards making constant improvements in operations.
Regular check of management on quality of coffee helps in providing quality coffee to customers
which in turn results in good customer relations of Starbucks at global level. Thus, quality
management plays crucial role in minimizing the waste and maximizing the productivity of
company (Zink, 2012).
Impact of the macro- and business environment
Quality management is very crucial aspect within operations of an organisation as it
highly contributes in its success. The factors within business environment impacts on operations
of Starbucks in both positive and negative manner. The legal framework of country influence the
operations as if firm is not maintaining quality of its products as per the legal food standards
provided by government, then it will not be able to perform its operations effectively and
resulted to this, firm may face criticism from government or society or may have to pay high
penalty as a legal consequence. But, if firm follows government regulations and food standards,
then it will help company in performing its operations successfully.
3. Key requirements, capabilities and challenges
Key requirements and capabilities
In order to manage quality of operations in an effective and efficient manner and
achieving excellence in the area, there are some key requirements that needs to be follow by
management of Starbucks. Managing data and information about all the aspects that are
associated with operations is one of the key requirement of managing quality. This will help
performance is measured from the standard one (Reid and Sanders, 2019).
Role of Quality Management in the global operations strategy
Total quality management strategy helps company in making constant improvements in
its internal processes so as to improve quality of its coffee. While operating business at global
level, quality management ensures in attaining high customer loyalty. TQM approach supports
business entity in maintaining long term sustainability in global market through satisfying
customers by offering them with high quality coffee. It also helps in encouraging quality culture
within company leads it to committed towards making constant improvements in operations.
Regular check of management on quality of coffee helps in providing quality coffee to customers
which in turn results in good customer relations of Starbucks at global level. Thus, quality
management plays crucial role in minimizing the waste and maximizing the productivity of
company (Zink, 2012).
Impact of the macro- and business environment
Quality management is very crucial aspect within operations of an organisation as it
highly contributes in its success. The factors within business environment impacts on operations
of Starbucks in both positive and negative manner. The legal framework of country influence the
operations as if firm is not maintaining quality of its products as per the legal food standards
provided by government, then it will not be able to perform its operations effectively and
resulted to this, firm may face criticism from government or society or may have to pay high
penalty as a legal consequence. But, if firm follows government regulations and food standards,
then it will help company in performing its operations successfully.
3. Key requirements, capabilities and challenges
Key requirements and capabilities
In order to manage quality of operations in an effective and efficient manner and
achieving excellence in the area, there are some key requirements that needs to be follow by
management of Starbucks. Managing data and information about all the aspects that are
associated with operations is one of the key requirement of managing quality. This will help
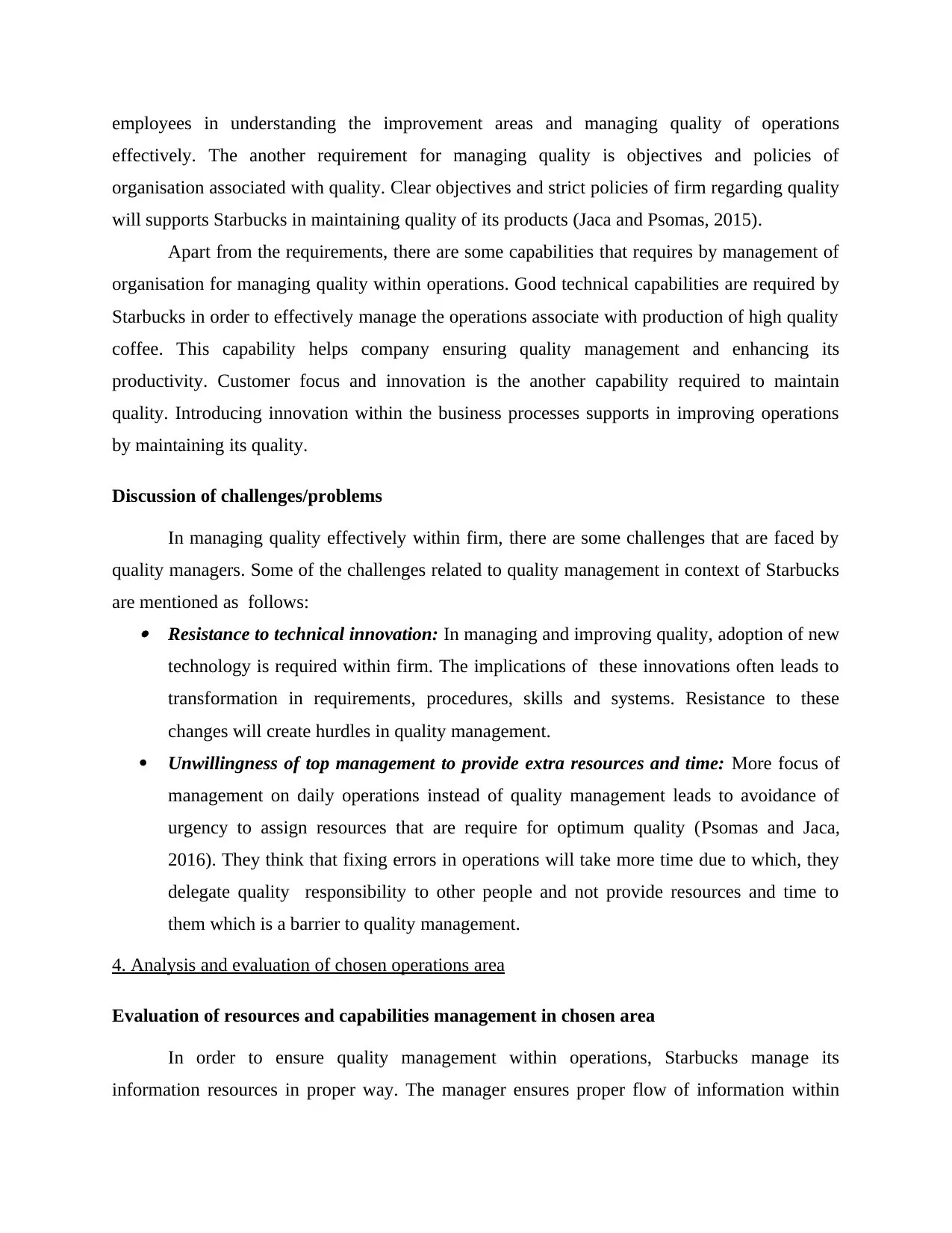
employees in understanding the improvement areas and managing quality of operations
effectively. The another requirement for managing quality is objectives and policies of
organisation associated with quality. Clear objectives and strict policies of firm regarding quality
will supports Starbucks in maintaining quality of its products (Jaca and Psomas, 2015).
Apart from the requirements, there are some capabilities that requires by management of
organisation for managing quality within operations. Good technical capabilities are required by
Starbucks in order to effectively manage the operations associate with production of high quality
coffee. This capability helps company ensuring quality management and enhancing its
productivity. Customer focus and innovation is the another capability required to maintain
quality. Introducing innovation within the business processes supports in improving operations
by maintaining its quality.
Discussion of challenges/problems
In managing quality effectively within firm, there are some challenges that are faced by
quality managers. Some of the challenges related to quality management in context of Starbucks
are mentioned as follows:ï‚· Resistance to technical innovation: In managing and improving quality, adoption of new
technology is required within firm. The implications of these innovations often leads to
transformation in requirements, procedures, skills and systems. Resistance to these
changes will create hurdles in quality management.
ï‚· Unwillingness of top management to provide extra resources and time: More focus of
management on daily operations instead of quality management leads to avoidance of
urgency to assign resources that are require for optimum quality (Psomas and Jaca,
2016). They think that fixing errors in operations will take more time due to which, they
delegate quality responsibility to other people and not provide resources and time to
them which is a barrier to quality management.
4. Analysis and evaluation of chosen operations area
Evaluation of resources and capabilities management in chosen area
In order to ensure quality management within operations, Starbucks manage its
information resources in proper way. The manager ensures proper flow of information within
effectively. The another requirement for managing quality is objectives and policies of
organisation associated with quality. Clear objectives and strict policies of firm regarding quality
will supports Starbucks in maintaining quality of its products (Jaca and Psomas, 2015).
Apart from the requirements, there are some capabilities that requires by management of
organisation for managing quality within operations. Good technical capabilities are required by
Starbucks in order to effectively manage the operations associate with production of high quality
coffee. This capability helps company ensuring quality management and enhancing its
productivity. Customer focus and innovation is the another capability required to maintain
quality. Introducing innovation within the business processes supports in improving operations
by maintaining its quality.
Discussion of challenges/problems
In managing quality effectively within firm, there are some challenges that are faced by
quality managers. Some of the challenges related to quality management in context of Starbucks
are mentioned as follows:ï‚· Resistance to technical innovation: In managing and improving quality, adoption of new
technology is required within firm. The implications of these innovations often leads to
transformation in requirements, procedures, skills and systems. Resistance to these
changes will create hurdles in quality management.
ï‚· Unwillingness of top management to provide extra resources and time: More focus of
management on daily operations instead of quality management leads to avoidance of
urgency to assign resources that are require for optimum quality (Psomas and Jaca,
2016). They think that fixing errors in operations will take more time due to which, they
delegate quality responsibility to other people and not provide resources and time to
them which is a barrier to quality management.
4. Analysis and evaluation of chosen operations area
Evaluation of resources and capabilities management in chosen area
In order to ensure quality management within operations, Starbucks manage its
information resources in proper way. The manager ensures proper flow of information within
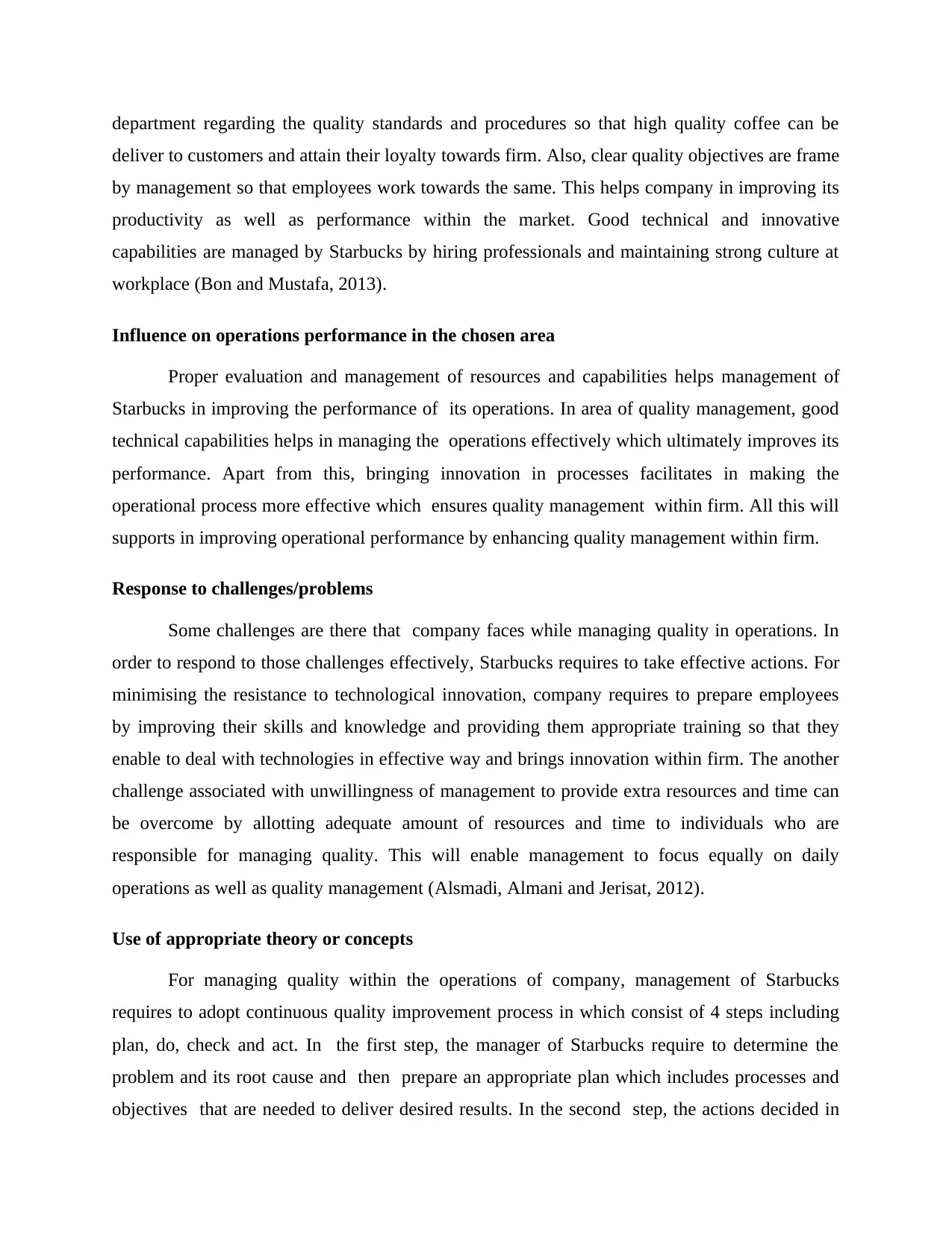
department regarding the quality standards and procedures so that high quality coffee can be
deliver to customers and attain their loyalty towards firm. Also, clear quality objectives are frame
by management so that employees work towards the same. This helps company in improving its
productivity as well as performance within the market. Good technical and innovative
capabilities are managed by Starbucks by hiring professionals and maintaining strong culture at
workplace (Bon and Mustafa, 2013).
Influence on operations performance in the chosen area
Proper evaluation and management of resources and capabilities helps management of
Starbucks in improving the performance of its operations. In area of quality management, good
technical capabilities helps in managing the operations effectively which ultimately improves its
performance. Apart from this, bringing innovation in processes facilitates in making the
operational process more effective which ensures quality management within firm. All this will
supports in improving operational performance by enhancing quality management within firm.
Response to challenges/problems
Some challenges are there that company faces while managing quality in operations. In
order to respond to those challenges effectively, Starbucks requires to take effective actions. For
minimising the resistance to technological innovation, company requires to prepare employees
by improving their skills and knowledge and providing them appropriate training so that they
enable to deal with technologies in effective way and brings innovation within firm. The another
challenge associated with unwillingness of management to provide extra resources and time can
be overcome by allotting adequate amount of resources and time to individuals who are
responsible for managing quality. This will enable management to focus equally on daily
operations as well as quality management (Alsmadi, Almani and Jerisat, 2012).
Use of appropriate theory or concepts
For managing quality within the operations of company, management of Starbucks
requires to adopt continuous quality improvement process in which consist of 4 steps including
plan, do, check and act. In the first step, the manager of Starbucks require to determine the
problem and its root cause and then prepare an appropriate plan which includes processes and
objectives that are needed to deliver desired results. In the second step, the actions decided in
deliver to customers and attain their loyalty towards firm. Also, clear quality objectives are frame
by management so that employees work towards the same. This helps company in improving its
productivity as well as performance within the market. Good technical and innovative
capabilities are managed by Starbucks by hiring professionals and maintaining strong culture at
workplace (Bon and Mustafa, 2013).
Influence on operations performance in the chosen area
Proper evaluation and management of resources and capabilities helps management of
Starbucks in improving the performance of its operations. In area of quality management, good
technical capabilities helps in managing the operations effectively which ultimately improves its
performance. Apart from this, bringing innovation in processes facilitates in making the
operational process more effective which ensures quality management within firm. All this will
supports in improving operational performance by enhancing quality management within firm.
Response to challenges/problems
Some challenges are there that company faces while managing quality in operations. In
order to respond to those challenges effectively, Starbucks requires to take effective actions. For
minimising the resistance to technological innovation, company requires to prepare employees
by improving their skills and knowledge and providing them appropriate training so that they
enable to deal with technologies in effective way and brings innovation within firm. The another
challenge associated with unwillingness of management to provide extra resources and time can
be overcome by allotting adequate amount of resources and time to individuals who are
responsible for managing quality. This will enable management to focus equally on daily
operations as well as quality management (Alsmadi, Almani and Jerisat, 2012).
Use of appropriate theory or concepts
For managing quality within the operations of company, management of Starbucks
requires to adopt continuous quality improvement process in which consist of 4 steps including
plan, do, check and act. In the first step, the manager of Starbucks require to determine the
problem and its root cause and then prepare an appropriate plan which includes processes and
objectives that are needed to deliver desired results. In the second step, the actions decided in
Paraphrase This Document
Need a fresh take? Get an instant paraphrase of this document with our AI Paraphraser
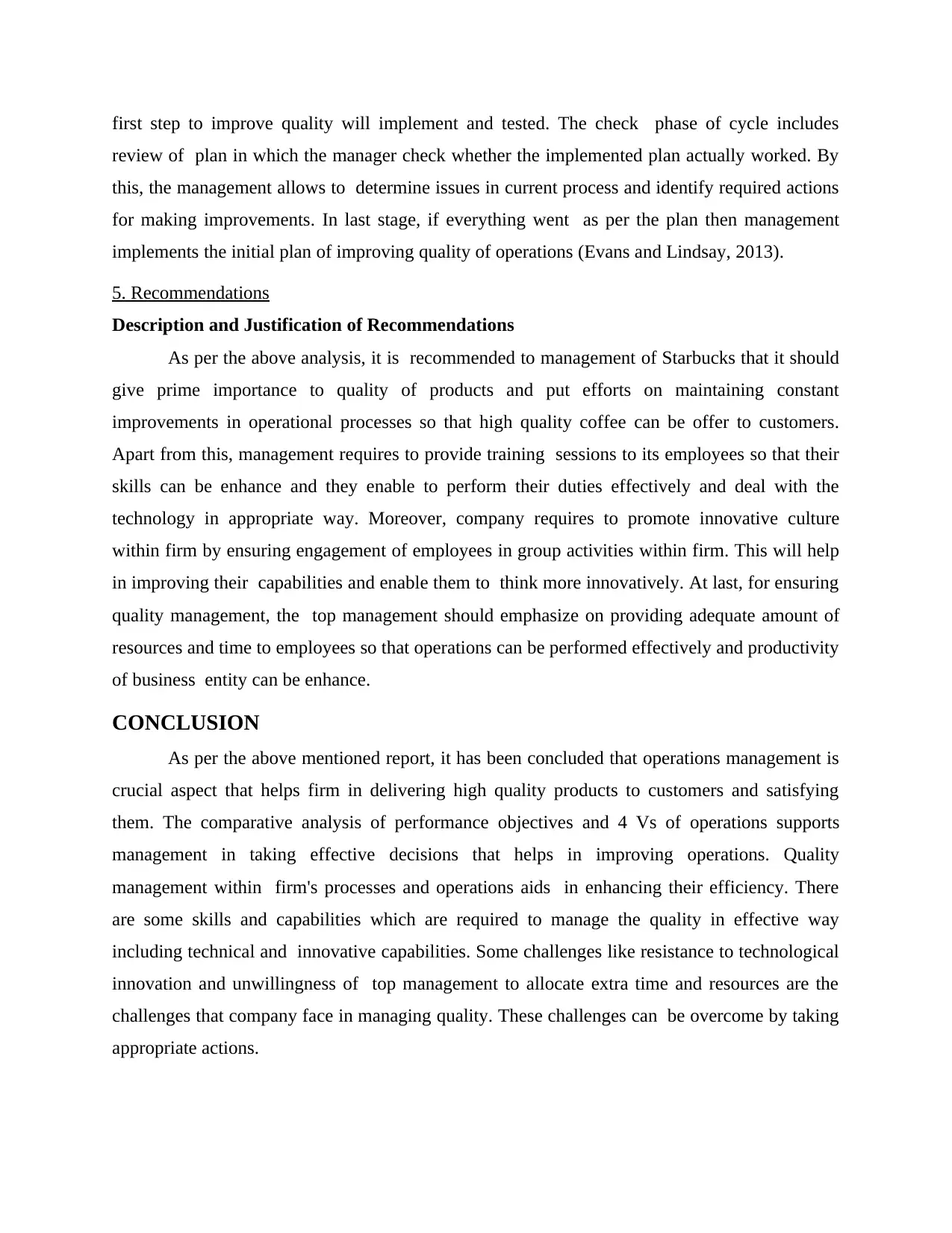
first step to improve quality will implement and tested. The check phase of cycle includes
review of plan in which the manager check whether the implemented plan actually worked. By
this, the management allows to determine issues in current process and identify required actions
for making improvements. In last stage, if everything went as per the plan then management
implements the initial plan of improving quality of operations (Evans and Lindsay, 2013).
5. Recommendations
Description and Justification of Recommendations
As per the above analysis, it is recommended to management of Starbucks that it should
give prime importance to quality of products and put efforts on maintaining constant
improvements in operational processes so that high quality coffee can be offer to customers.
Apart from this, management requires to provide training sessions to its employees so that their
skills can be enhance and they enable to perform their duties effectively and deal with the
technology in appropriate way. Moreover, company requires to promote innovative culture
within firm by ensuring engagement of employees in group activities within firm. This will help
in improving their capabilities and enable them to think more innovatively. At last, for ensuring
quality management, the top management should emphasize on providing adequate amount of
resources and time to employees so that operations can be performed effectively and productivity
of business entity can be enhance.
CONCLUSION
As per the above mentioned report, it has been concluded that operations management is
crucial aspect that helps firm in delivering high quality products to customers and satisfying
them. The comparative analysis of performance objectives and 4 Vs of operations supports
management in taking effective decisions that helps in improving operations. Quality
management within firm's processes and operations aids in enhancing their efficiency. There
are some skills and capabilities which are required to manage the quality in effective way
including technical and innovative capabilities. Some challenges like resistance to technological
innovation and unwillingness of top management to allocate extra time and resources are the
challenges that company face in managing quality. These challenges can be overcome by taking
appropriate actions.
review of plan in which the manager check whether the implemented plan actually worked. By
this, the management allows to determine issues in current process and identify required actions
for making improvements. In last stage, if everything went as per the plan then management
implements the initial plan of improving quality of operations (Evans and Lindsay, 2013).
5. Recommendations
Description and Justification of Recommendations
As per the above analysis, it is recommended to management of Starbucks that it should
give prime importance to quality of products and put efforts on maintaining constant
improvements in operational processes so that high quality coffee can be offer to customers.
Apart from this, management requires to provide training sessions to its employees so that their
skills can be enhance and they enable to perform their duties effectively and deal with the
technology in appropriate way. Moreover, company requires to promote innovative culture
within firm by ensuring engagement of employees in group activities within firm. This will help
in improving their capabilities and enable them to think more innovatively. At last, for ensuring
quality management, the top management should emphasize on providing adequate amount of
resources and time to employees so that operations can be performed effectively and productivity
of business entity can be enhance.
CONCLUSION
As per the above mentioned report, it has been concluded that operations management is
crucial aspect that helps firm in delivering high quality products to customers and satisfying
them. The comparative analysis of performance objectives and 4 Vs of operations supports
management in taking effective decisions that helps in improving operations. Quality
management within firm's processes and operations aids in enhancing their efficiency. There
are some skills and capabilities which are required to manage the quality in effective way
including technical and innovative capabilities. Some challenges like resistance to technological
innovation and unwillingness of top management to allocate extra time and resources are the
challenges that company face in managing quality. These challenges can be overcome by taking
appropriate actions.
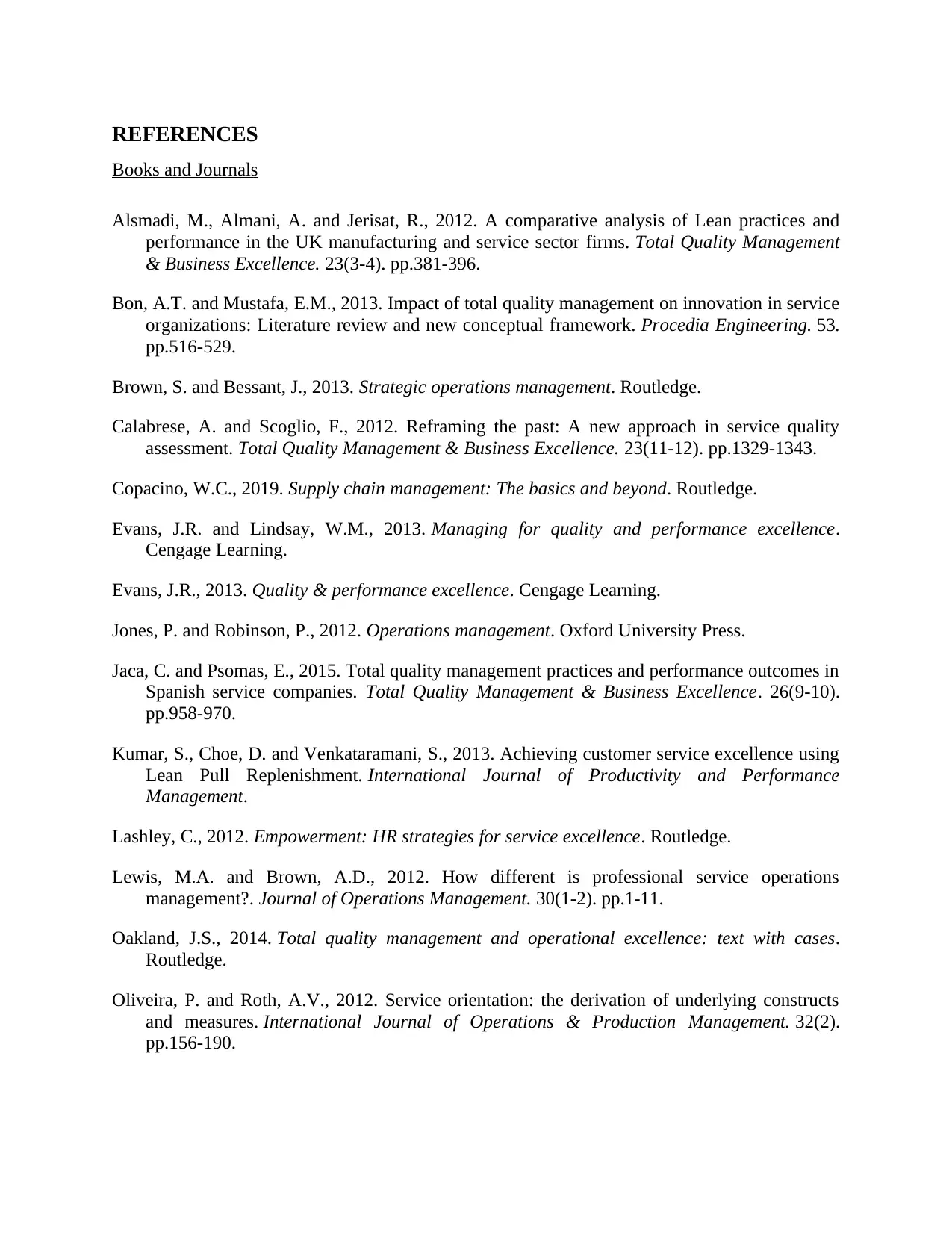
REFERENCES
Books and Journals
Alsmadi, M., Almani, A. and Jerisat, R., 2012. A comparative analysis of Lean practices and
performance in the UK manufacturing and service sector firms. Total Quality Management
& Business Excellence. 23(3-4). pp.381-396.
Bon, A.T. and Mustafa, E.M., 2013. Impact of total quality management on innovation in service
organizations: Literature review and new conceptual framework. Procedia Engineering. 53.
pp.516-529.
Brown, S. and Bessant, J., 2013. Strategic operations management. Routledge.
Calabrese, A. and Scoglio, F., 2012. Reframing the past: A new approach in service quality
assessment. Total Quality Management & Business Excellence. 23(11-12). pp.1329-1343.
Copacino, W.C., 2019. Supply chain management: The basics and beyond. Routledge.
Evans, J.R. and Lindsay, W.M., 2013. Managing for quality and performance excellence.
Cengage Learning.
Evans, J.R., 2013. Quality & performance excellence. Cengage Learning.
Jones, P. and Robinson, P., 2012. Operations management. Oxford University Press.
Jaca, C. and Psomas, E., 2015. Total quality management practices and performance outcomes in
Spanish service companies. Total Quality Management & Business Excellence. 26(9-10).
pp.958-970.
Kumar, S., Choe, D. and Venkataramani, S., 2013. Achieving customer service excellence using
Lean Pull Replenishment. International Journal of Productivity and Performance
Management.
Lashley, C., 2012. Empowerment: HR strategies for service excellence. Routledge.
Lewis, M.A. and Brown, A.D., 2012. How different is professional service operations
management?. Journal of Operations Management. 30(1-2). pp.1-11.
Oakland, J.S., 2014. Total quality management and operational excellence: text with cases.
Routledge.
Oliveira, P. and Roth, A.V., 2012. Service orientation: the derivation of underlying constructs
and measures. International Journal of Operations & Production Management. 32(2).
pp.156-190.
Books and Journals
Alsmadi, M., Almani, A. and Jerisat, R., 2012. A comparative analysis of Lean practices and
performance in the UK manufacturing and service sector firms. Total Quality Management
& Business Excellence. 23(3-4). pp.381-396.
Bon, A.T. and Mustafa, E.M., 2013. Impact of total quality management on innovation in service
organizations: Literature review and new conceptual framework. Procedia Engineering. 53.
pp.516-529.
Brown, S. and Bessant, J., 2013. Strategic operations management. Routledge.
Calabrese, A. and Scoglio, F., 2012. Reframing the past: A new approach in service quality
assessment. Total Quality Management & Business Excellence. 23(11-12). pp.1329-1343.
Copacino, W.C., 2019. Supply chain management: The basics and beyond. Routledge.
Evans, J.R. and Lindsay, W.M., 2013. Managing for quality and performance excellence.
Cengage Learning.
Evans, J.R., 2013. Quality & performance excellence. Cengage Learning.
Jones, P. and Robinson, P., 2012. Operations management. Oxford University Press.
Jaca, C. and Psomas, E., 2015. Total quality management practices and performance outcomes in
Spanish service companies. Total Quality Management & Business Excellence. 26(9-10).
pp.958-970.
Kumar, S., Choe, D. and Venkataramani, S., 2013. Achieving customer service excellence using
Lean Pull Replenishment. International Journal of Productivity and Performance
Management.
Lashley, C., 2012. Empowerment: HR strategies for service excellence. Routledge.
Lewis, M.A. and Brown, A.D., 2012. How different is professional service operations
management?. Journal of Operations Management. 30(1-2). pp.1-11.
Oakland, J.S., 2014. Total quality management and operational excellence: text with cases.
Routledge.
Oliveira, P. and Roth, A.V., 2012. Service orientation: the derivation of underlying constructs
and measures. International Journal of Operations & Production Management. 32(2).
pp.156-190.
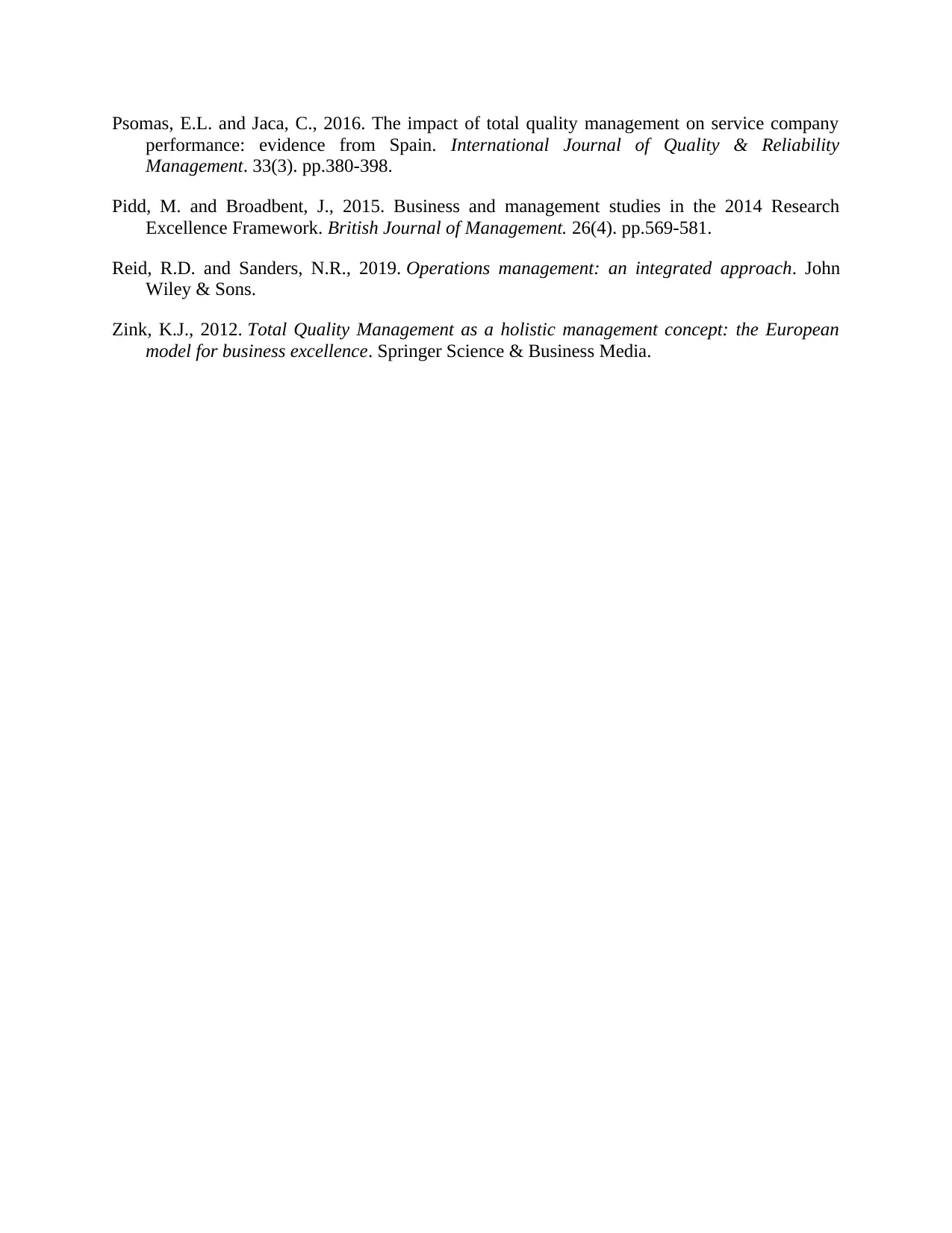
Psomas, E.L. and Jaca, C., 2016. The impact of total quality management on service company
performance: evidence from Spain. International Journal of Quality & Reliability
Management. 33(3). pp.380-398.
Pidd, M. and Broadbent, J., 2015. Business and management studies in the 2014 Research
Excellence Framework. British Journal of Management. 26(4). pp.569-581.
Reid, R.D. and Sanders, N.R., 2019. Operations management: an integrated approach. John
Wiley & Sons.
Zink, K.J., 2012. Total Quality Management as a holistic management concept: the European
model for business excellence. Springer Science & Business Media.
performance: evidence from Spain. International Journal of Quality & Reliability
Management. 33(3). pp.380-398.
Pidd, M. and Broadbent, J., 2015. Business and management studies in the 2014 Research
Excellence Framework. British Journal of Management. 26(4). pp.569-581.
Reid, R.D. and Sanders, N.R., 2019. Operations management: an integrated approach. John
Wiley & Sons.
Zink, K.J., 2012. Total Quality Management as a holistic management concept: the European
model for business excellence. Springer Science & Business Media.
1 out of 16
Related Documents

Your All-in-One AI-Powered Toolkit for Academic Success.
 +13062052269
info@desklib.com
Available 24*7 on WhatsApp / Email
Unlock your academic potential
© 2024  |  Zucol Services PVT LTD  |  All rights reserved.