Comprehensive Analysis of Operations Management at IKEA: A Report
VerifiedAdded on 2020/06/06
|17
|4122
|64
Report
AI Summary
This report provides a detailed analysis of IKEA's operations management. It begins with an introduction to the importance of operations management for IKEA, followed by an examination of its various functions, including design, planning, managing, and coordinating. The report then evaluates the process model used in IKEA, emphasizing the significance of efficiency, effectiveness, and excellence. Task 2 delves into the 'Three Es' – efficiency, effectiveness, and excellence – and discusses the tension between cost minimization and quality maximization within organizations. It also explores the importance of five performance objectives: quality, speed, dependability, flexibility, and cost. Task 3 focuses on the application of linear programming, critical path method, and the need for operation planning and control. Finally, Task 4 presents the production outcome for IKEA, a network plan indicating the critical path, and quality management techniques to improve performance. The report concludes with a summary of the key findings and references.
Contribute Materials
Your contribution can guide someone’s learning journey. Share your
documents today.
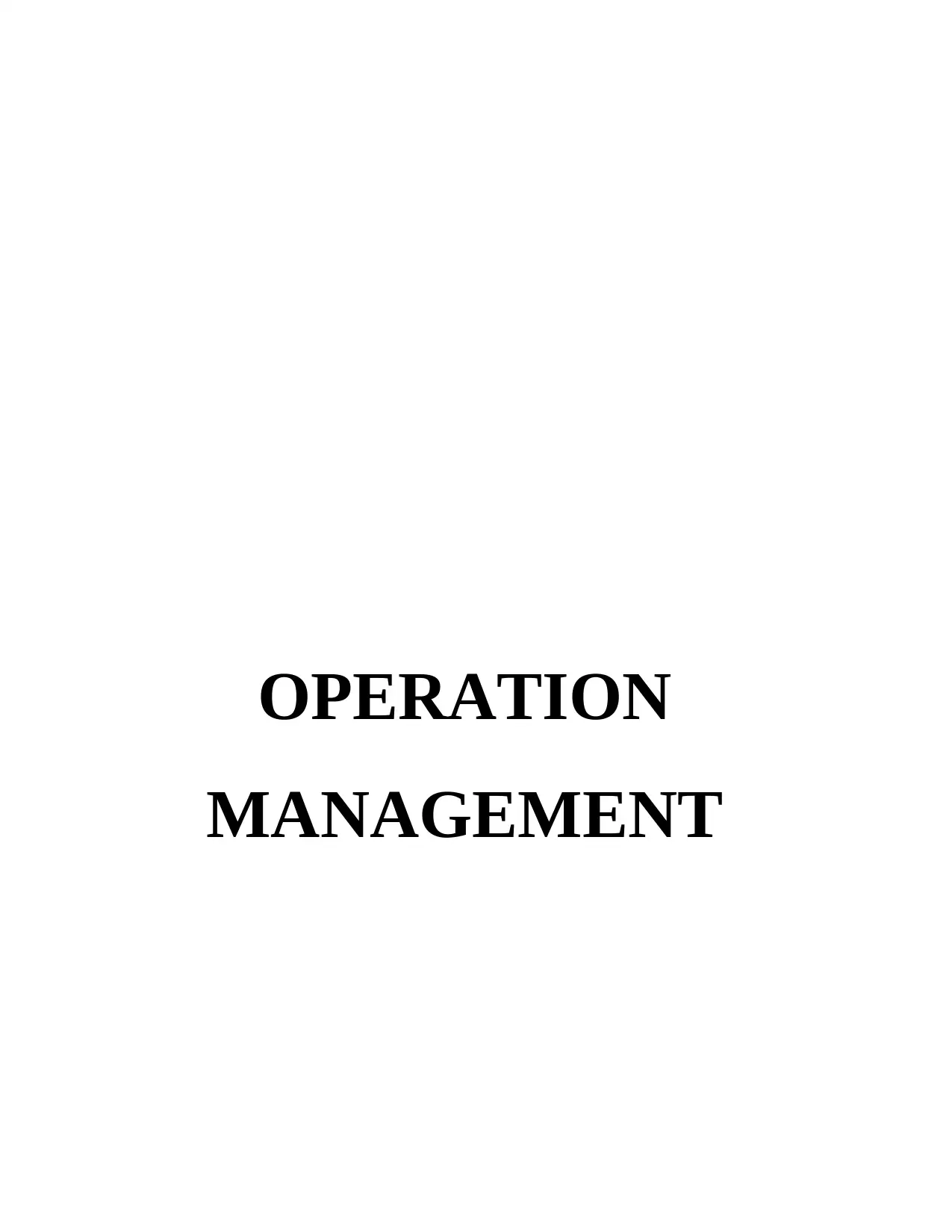
OPERATION
MANAGEMENT
MANAGEMENT
Secure Best Marks with AI Grader
Need help grading? Try our AI Grader for instant feedback on your assignments.
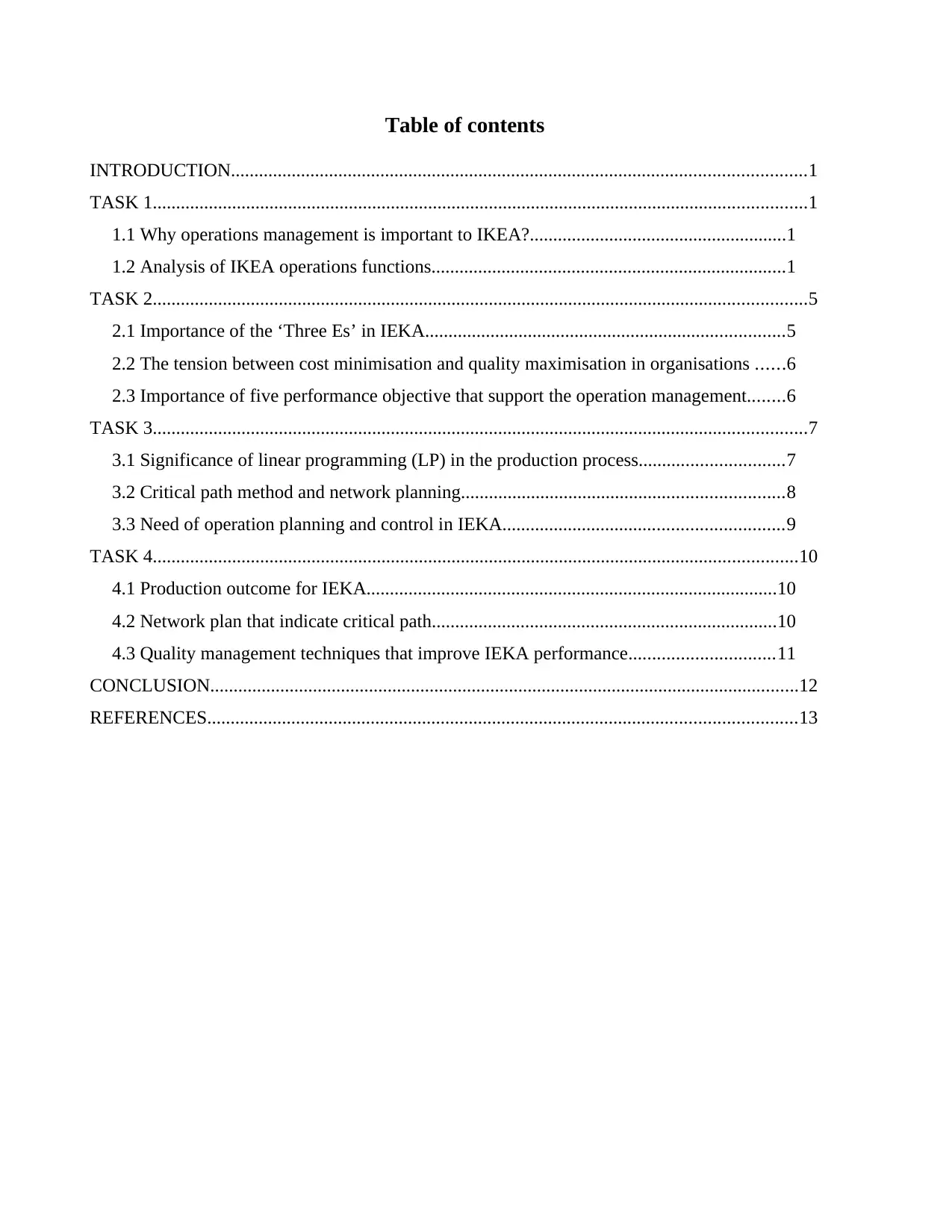
Table of contents
INTRODUCTION...........................................................................................................................1
TASK 1............................................................................................................................................1
1.1 Why operations management is important to IKEA?.......................................................1
1.2 Analysis of IKEA operations functions............................................................................1
TASK 2............................................................................................................................................5
2.1 Importance of the ‘Three Es’ in IEKA.............................................................................5
2.2 The tension between cost minimisation and quality maximisation in organisations ......6
2.3 Importance of five performance objective that support the operation management........6
TASK 3............................................................................................................................................7
3.1 Significance of linear programming (LP) in the production process...............................7
3.2 Critical path method and network planning.....................................................................8
3.3 Need of operation planning and control in IEKA............................................................9
TASK 4..........................................................................................................................................10
4.1 Production outcome for IEKA........................................................................................10
4.2 Network plan that indicate critical path..........................................................................10
4.3 Quality management techniques that improve IEKA performance...............................11
CONCLUSION..............................................................................................................................12
REFERENCES..............................................................................................................................13
INTRODUCTION...........................................................................................................................1
TASK 1............................................................................................................................................1
1.1 Why operations management is important to IKEA?.......................................................1
1.2 Analysis of IKEA operations functions............................................................................1
TASK 2............................................................................................................................................5
2.1 Importance of the ‘Three Es’ in IEKA.............................................................................5
2.2 The tension between cost minimisation and quality maximisation in organisations ......6
2.3 Importance of five performance objective that support the operation management........6
TASK 3............................................................................................................................................7
3.1 Significance of linear programming (LP) in the production process...............................7
3.2 Critical path method and network planning.....................................................................8
3.3 Need of operation planning and control in IEKA............................................................9
TASK 4..........................................................................................................................................10
4.1 Production outcome for IEKA........................................................................................10
4.2 Network plan that indicate critical path..........................................................................10
4.3 Quality management techniques that improve IEKA performance...............................11
CONCLUSION..............................................................................................................................12
REFERENCES..............................................................................................................................13
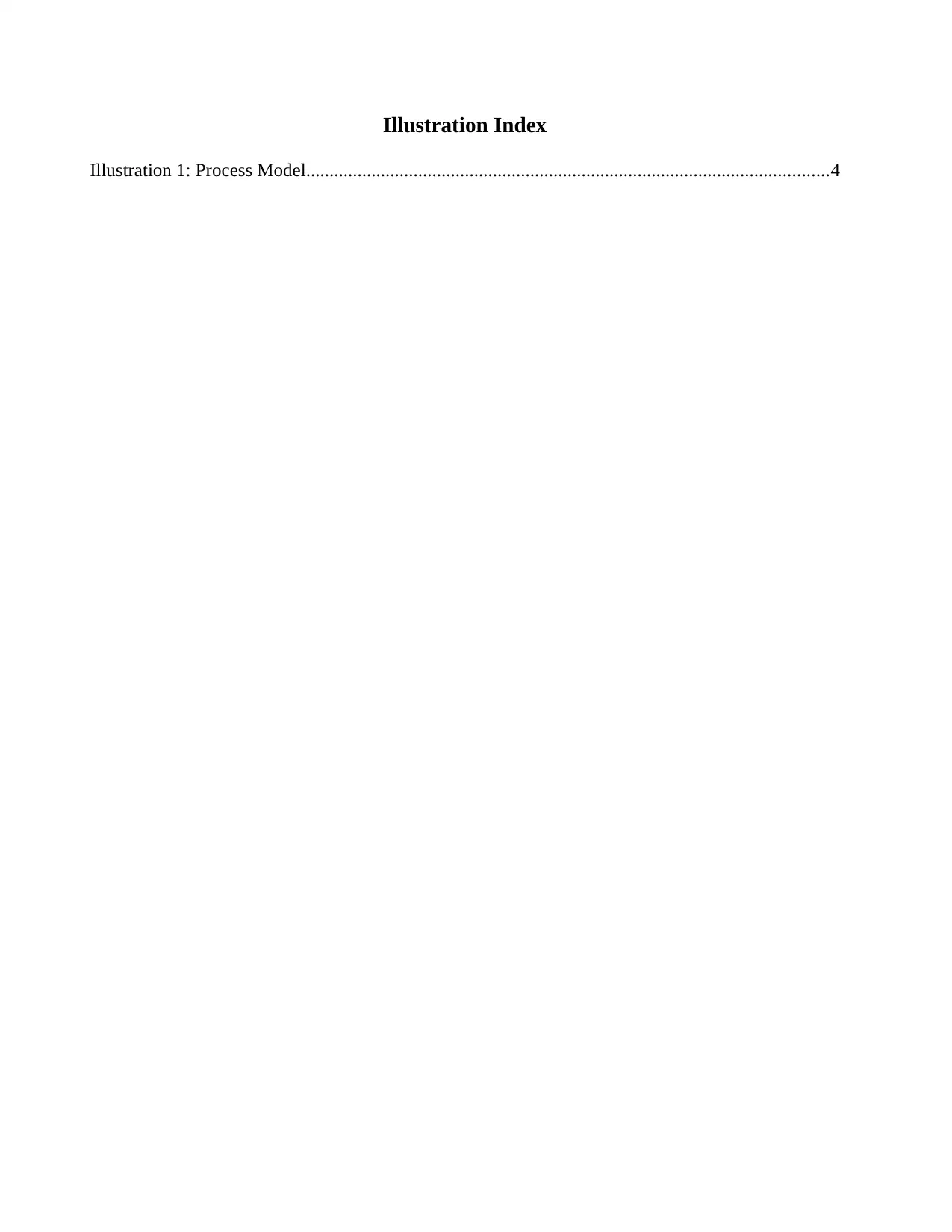
Illustration Index
Illustration 1: Process Model................................................................................................................4
Illustration 1: Process Model................................................................................................................4
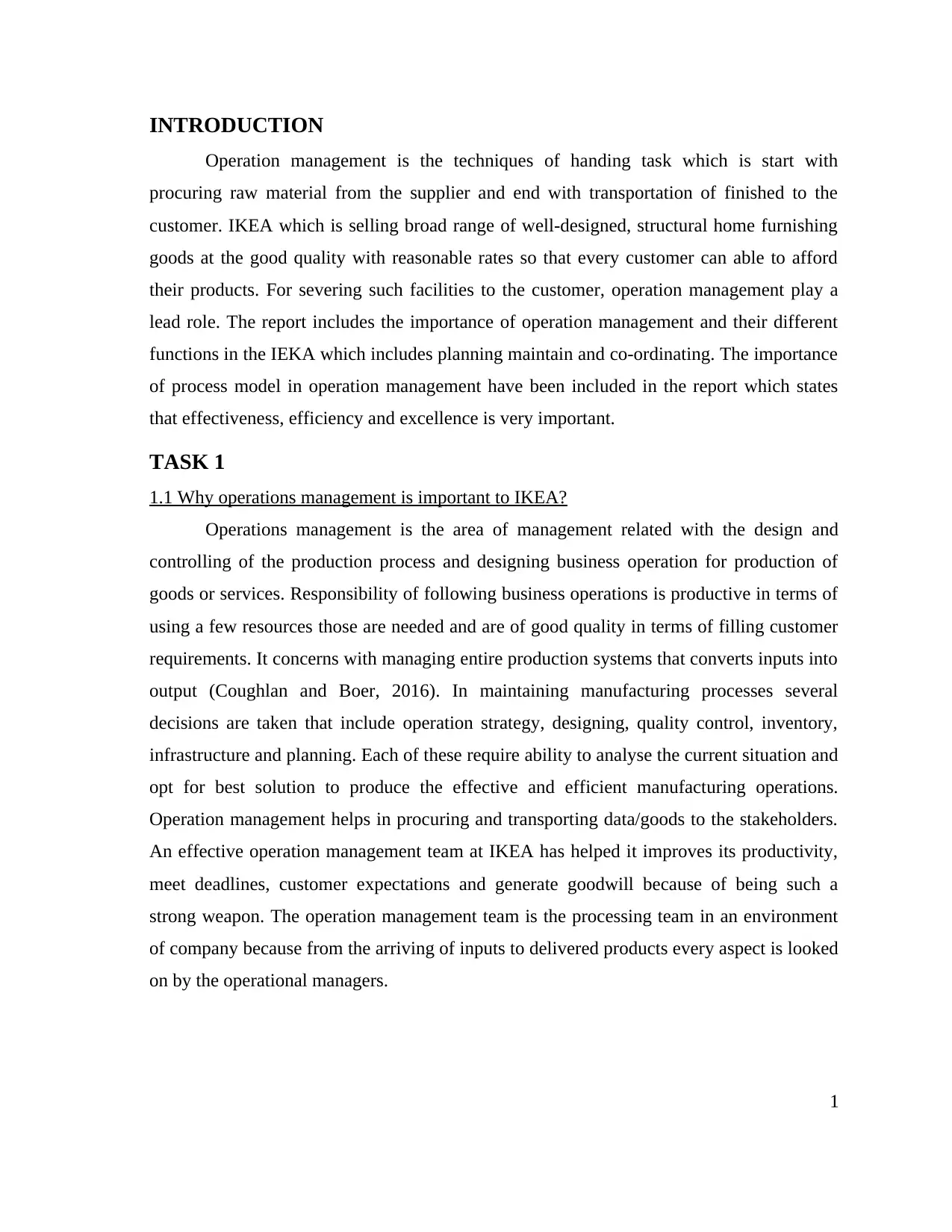
INTRODUCTION
Operation management is the techniques of handing task which is start with
procuring raw material from the supplier and end with transportation of finished to the
customer. IKEA which is selling broad range of well-designed, structural home furnishing
goods at the good quality with reasonable rates so that every customer can able to afford
their products. For severing such facilities to the customer, operation management play a
lead role. The report includes the importance of operation management and their different
functions in the IEKA which includes planning maintain and co-ordinating. The importance
of process model in operation management have been included in the report which states
that effectiveness, efficiency and excellence is very important.
TASK 1
1.1 Why operations management is important to IKEA?
Operations management is the area of management related with the design and
controlling of the production process and designing business operation for production of
goods or services. Responsibility of following business operations is productive in terms of
using a few resources those are needed and are of good quality in terms of filling customer
requirements. It concerns with managing entire production systems that converts inputs into
output (Coughlan and Boer, 2016). In maintaining manufacturing processes several
decisions are taken that include operation strategy, designing, quality control, inventory,
infrastructure and planning. Each of these require ability to analyse the current situation and
opt for best solution to produce the effective and efficient manufacturing operations.
Operation management helps in procuring and transporting data/goods to the stakeholders.
An effective operation management team at IKEA has helped it improves its productivity,
meet deadlines, customer expectations and generate goodwill because of being such a
strong weapon. The operation management team is the processing team in an environment
of company because from the arriving of inputs to delivered products every aspect is looked
on by the operational managers.
1
Operation management is the techniques of handing task which is start with
procuring raw material from the supplier and end with transportation of finished to the
customer. IKEA which is selling broad range of well-designed, structural home furnishing
goods at the good quality with reasonable rates so that every customer can able to afford
their products. For severing such facilities to the customer, operation management play a
lead role. The report includes the importance of operation management and their different
functions in the IEKA which includes planning maintain and co-ordinating. The importance
of process model in operation management have been included in the report which states
that effectiveness, efficiency and excellence is very important.
TASK 1
1.1 Why operations management is important to IKEA?
Operations management is the area of management related with the design and
controlling of the production process and designing business operation for production of
goods or services. Responsibility of following business operations is productive in terms of
using a few resources those are needed and are of good quality in terms of filling customer
requirements. It concerns with managing entire production systems that converts inputs into
output (Coughlan and Boer, 2016). In maintaining manufacturing processes several
decisions are taken that include operation strategy, designing, quality control, inventory,
infrastructure and planning. Each of these require ability to analyse the current situation and
opt for best solution to produce the effective and efficient manufacturing operations.
Operation management helps in procuring and transporting data/goods to the stakeholders.
An effective operation management team at IKEA has helped it improves its productivity,
meet deadlines, customer expectations and generate goodwill because of being such a
strong weapon. The operation management team is the processing team in an environment
of company because from the arriving of inputs to delivered products every aspect is looked
on by the operational managers.
1
Secure Best Marks with AI Grader
Need help grading? Try our AI Grader for instant feedback on your assignments.
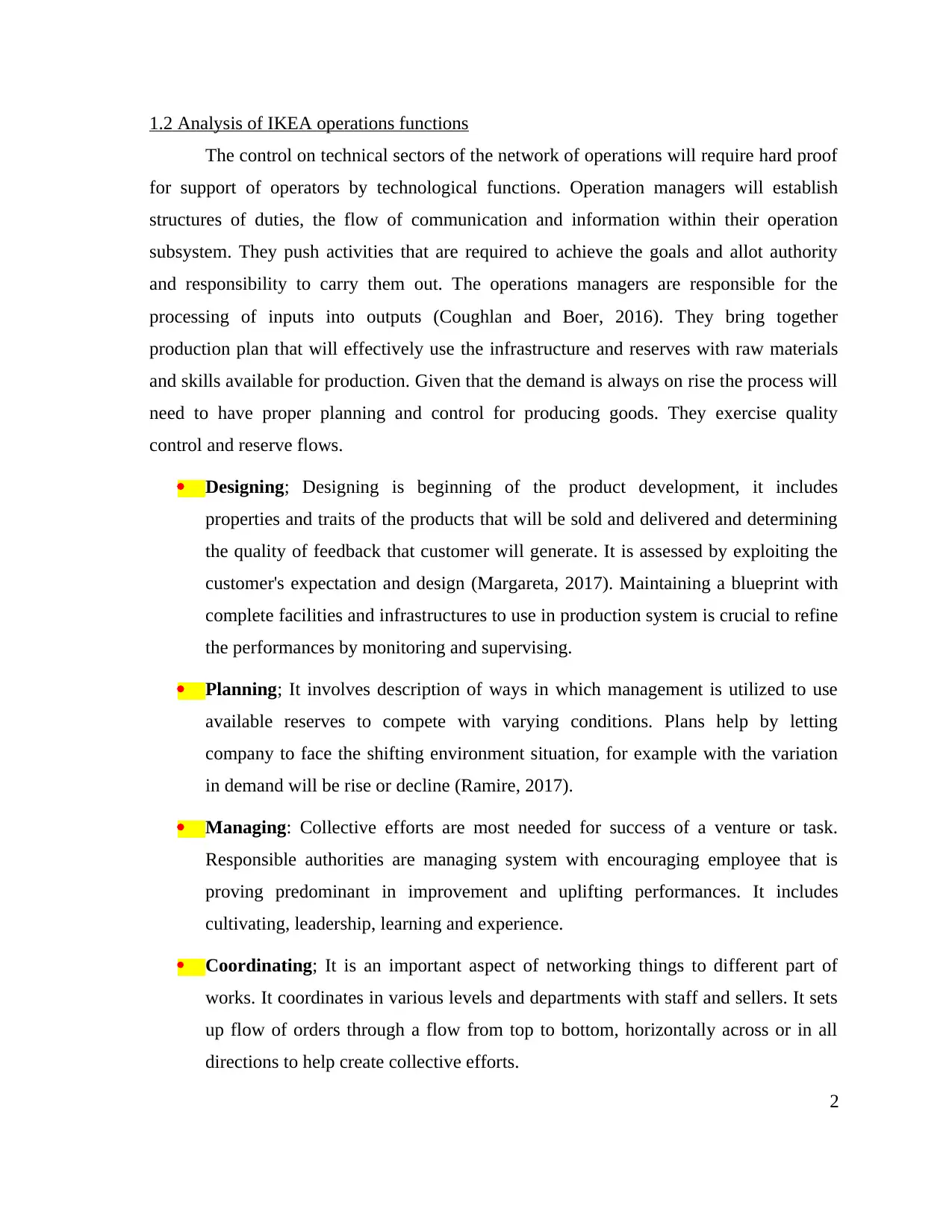
1.2 Analysis of IKEA operations functions
The control on technical sectors of the network of operations will require hard proof
for support of operators by technological functions. Operation managers will establish
structures of duties, the flow of communication and information within their operation
subsystem. They push activities that are required to achieve the goals and allot authority
and responsibility to carry them out. The operations managers are responsible for the
processing of inputs into outputs (Coughlan and Boer, 2016). They bring together
production plan that will effectively use the infrastructure and reserves with raw materials
and skills available for production. Given that the demand is always on rise the process will
need to have proper planning and control for producing goods. They exercise quality
control and reserve flows.
Designing; Designing is beginning of the product development, it includes
properties and traits of the products that will be sold and delivered and determining
the quality of feedback that customer will generate. It is assessed by exploiting the
customer's expectation and design (Margareta, 2017). Maintaining a blueprint with
complete facilities and infrastructures to use in production system is crucial to refine
the performances by monitoring and supervising.
Planning; It involves description of ways in which management is utilized to use
available reserves to compete with varying conditions. Plans help by letting
company to face the shifting environment situation, for example with the variation
in demand will be rise or decline (Ramire, 2017).
Managing: Collective efforts are most needed for success of a venture or task.
Responsible authorities are managing system with encouraging employee that is
proving predominant in improvement and uplifting performances. It includes
cultivating, leadership, learning and experience.
Coordinating; It is an important aspect of networking things to different part of
works. It coordinates in various levels and departments with staff and sellers. It sets
up flow of orders through a flow from top to bottom, horizontally across or in all
directions to help create collective efforts.
2
The control on technical sectors of the network of operations will require hard proof
for support of operators by technological functions. Operation managers will establish
structures of duties, the flow of communication and information within their operation
subsystem. They push activities that are required to achieve the goals and allot authority
and responsibility to carry them out. The operations managers are responsible for the
processing of inputs into outputs (Coughlan and Boer, 2016). They bring together
production plan that will effectively use the infrastructure and reserves with raw materials
and skills available for production. Given that the demand is always on rise the process will
need to have proper planning and control for producing goods. They exercise quality
control and reserve flows.
Designing; Designing is beginning of the product development, it includes
properties and traits of the products that will be sold and delivered and determining
the quality of feedback that customer will generate. It is assessed by exploiting the
customer's expectation and design (Margareta, 2017). Maintaining a blueprint with
complete facilities and infrastructures to use in production system is crucial to refine
the performances by monitoring and supervising.
Planning; It involves description of ways in which management is utilized to use
available reserves to compete with varying conditions. Plans help by letting
company to face the shifting environment situation, for example with the variation
in demand will be rise or decline (Ramire, 2017).
Managing: Collective efforts are most needed for success of a venture or task.
Responsible authorities are managing system with encouraging employee that is
proving predominant in improvement and uplifting performances. It includes
cultivating, leadership, learning and experience.
Coordinating; It is an important aspect of networking things to different part of
works. It coordinates in various levels and departments with staff and sellers. It sets
up flow of orders through a flow from top to bottom, horizontally across or in all
directions to help create collective efforts.
2
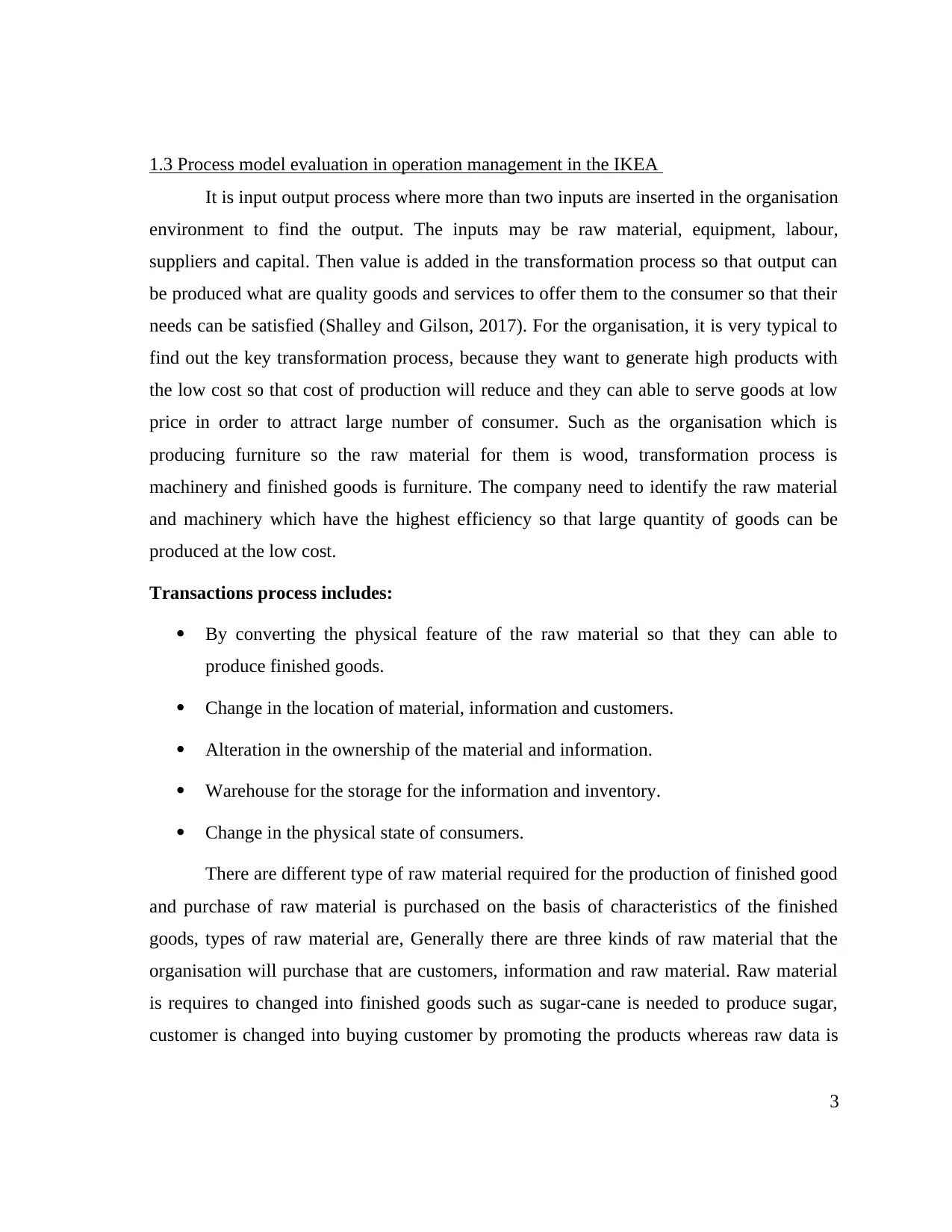
1.3 Process model evaluation in operation management in the IKEA
It is input output process where more than two inputs are inserted in the organisation
environment to find the output. The inputs may be raw material, equipment, labour,
suppliers and capital. Then value is added in the transformation process so that output can
be produced what are quality goods and services to offer them to the consumer so that their
needs can be satisfied (Shalley and Gilson, 2017). For the organisation, it is very typical to
find out the key transformation process, because they want to generate high products with
the low cost so that cost of production will reduce and they can able to serve goods at low
price in order to attract large number of consumer. Such as the organisation which is
producing furniture so the raw material for them is wood, transformation process is
machinery and finished goods is furniture. The company need to identify the raw material
and machinery which have the highest efficiency so that large quantity of goods can be
produced at the low cost.
Transactions process includes:
By converting the physical feature of the raw material so that they can able to
produce finished goods.
Change in the location of material, information and customers.
Alteration in the ownership of the material and information.
Warehouse for the storage for the information and inventory.
Change in the physical state of consumers.
There are different type of raw material required for the production of finished good
and purchase of raw material is purchased on the basis of characteristics of the finished
goods, types of raw material are, Generally there are three kinds of raw material that the
organisation will purchase that are customers, information and raw material. Raw material
is requires to changed into finished goods such as sugar-cane is needed to produce sugar,
customer is changed into buying customer by promoting the products whereas raw data is
3
It is input output process where more than two inputs are inserted in the organisation
environment to find the output. The inputs may be raw material, equipment, labour,
suppliers and capital. Then value is added in the transformation process so that output can
be produced what are quality goods and services to offer them to the consumer so that their
needs can be satisfied (Shalley and Gilson, 2017). For the organisation, it is very typical to
find out the key transformation process, because they want to generate high products with
the low cost so that cost of production will reduce and they can able to serve goods at low
price in order to attract large number of consumer. Such as the organisation which is
producing furniture so the raw material for them is wood, transformation process is
machinery and finished goods is furniture. The company need to identify the raw material
and machinery which have the highest efficiency so that large quantity of goods can be
produced at the low cost.
Transactions process includes:
By converting the physical feature of the raw material so that they can able to
produce finished goods.
Change in the location of material, information and customers.
Alteration in the ownership of the material and information.
Warehouse for the storage for the information and inventory.
Change in the physical state of consumers.
There are different type of raw material required for the production of finished good
and purchase of raw material is purchased on the basis of characteristics of the finished
goods, types of raw material are, Generally there are three kinds of raw material that the
organisation will purchase that are customers, information and raw material. Raw material
is requires to changed into finished goods such as sugar-cane is needed to produce sugar,
customer is changed into buying customer by promoting the products whereas raw data is
3
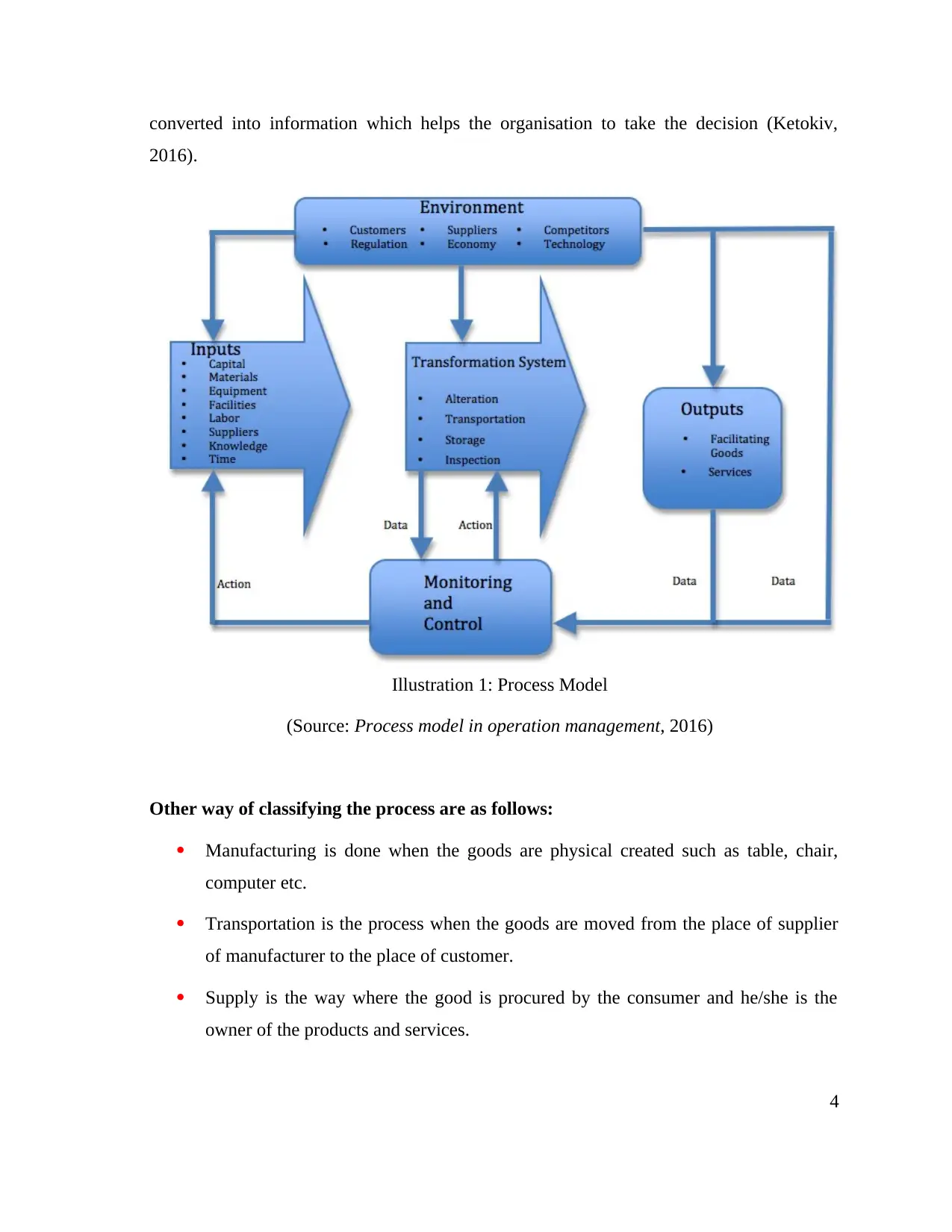
converted into information which helps the organisation to take the decision (Ketokiv,
2016).
Illustration 1: Process Model
(Source: Process model in operation management, 2016)
Other way of classifying the process are as follows:
Manufacturing is done when the goods are physical created such as table, chair,
computer etc.
Transportation is the process when the goods are moved from the place of supplier
of manufacturer to the place of customer.
Supply is the way where the good is procured by the consumer and he/she is the
owner of the products and services.
4
2016).
Illustration 1: Process Model
(Source: Process model in operation management, 2016)
Other way of classifying the process are as follows:
Manufacturing is done when the goods are physical created such as table, chair,
computer etc.
Transportation is the process when the goods are moved from the place of supplier
of manufacturer to the place of customer.
Supply is the way where the good is procured by the consumer and he/she is the
owner of the products and services.
4
Paraphrase This Document
Need a fresh take? Get an instant paraphrase of this document with our AI Paraphraser
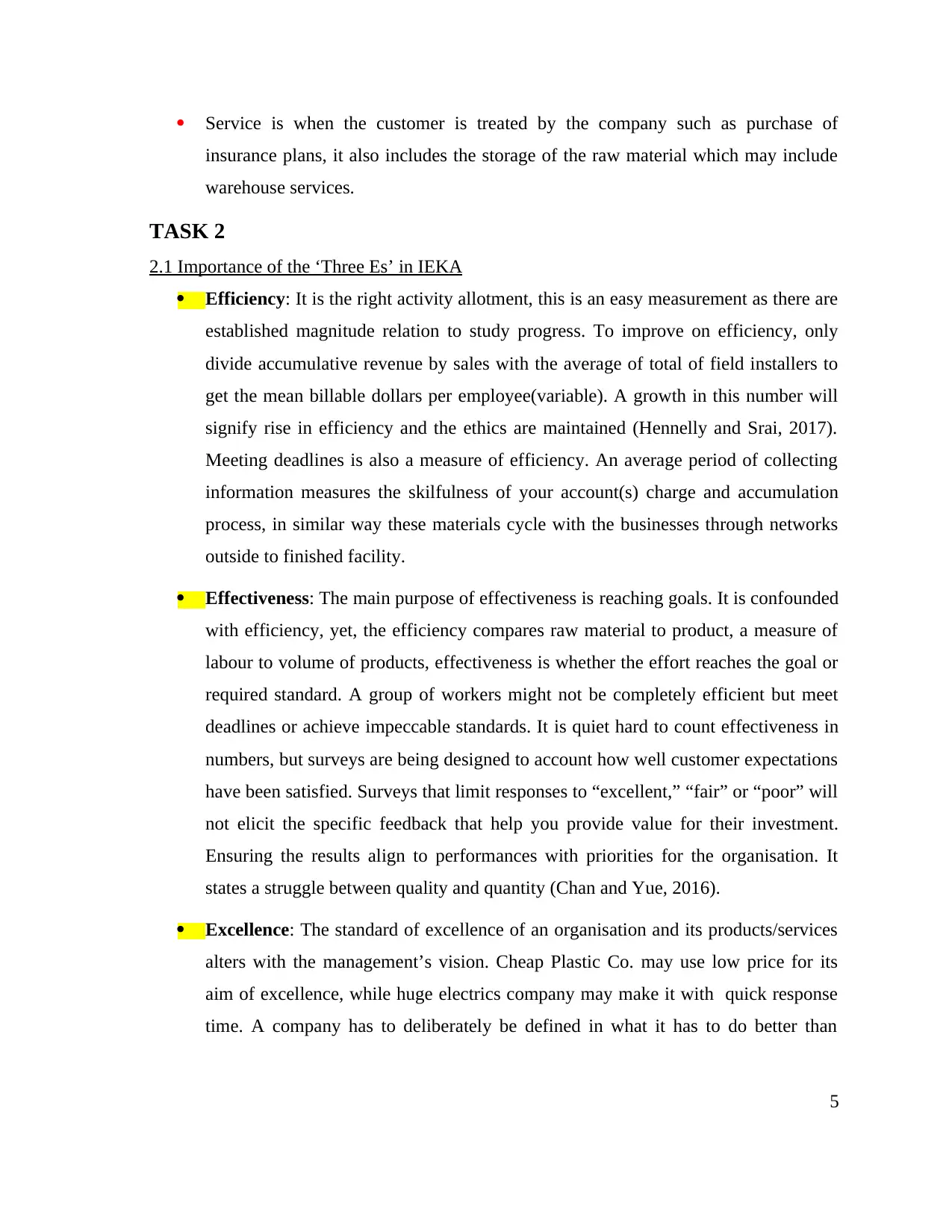
Service is when the customer is treated by the company such as purchase of
insurance plans, it also includes the storage of the raw material which may include
warehouse services.
TASK 2
2.1 Importance of the ‘Three Es’ in IEKA
Efficiency: It is the right activity allotment, this is an easy measurement as there are
established magnitude relation to study progress. To improve on efficiency, only
divide accumulative revenue by sales with the average of total of field installers to
get the mean billable dollars per employee(variable). A growth in this number will
signify rise in efficiency and the ethics are maintained (Hennelly and Srai, 2017).
Meeting deadlines is also a measure of efficiency. An average period of collecting
information measures the skilfulness of your account(s) charge and accumulation
process, in similar way these materials cycle with the businesses through networks
outside to finished facility.
Effectiveness: The main purpose of effectiveness is reaching goals. It is confounded
with efficiency, yet, the efficiency compares raw material to product, a measure of
labour to volume of products, effectiveness is whether the effort reaches the goal or
required standard. A group of workers might not be completely efficient but meet
deadlines or achieve impeccable standards. It is quiet hard to count effectiveness in
numbers, but surveys are being designed to account how well customer expectations
have been satisfied. Surveys that limit responses to “excellent,” “fair” or “poor” will
not elicit the specific feedback that help you provide value for their investment.
Ensuring the results align to performances with priorities for the organisation. It
states a struggle between quality and quantity (Chan and Yue, 2016).
Excellence: The standard of excellence of an organisation and its products/services
alters with the management’s vision. Cheap Plastic Co. may use low price for its
aim of excellence, while huge electrics company may make it with quick response
time. A company has to deliberately be defined in what it has to do better than
5
insurance plans, it also includes the storage of the raw material which may include
warehouse services.
TASK 2
2.1 Importance of the ‘Three Es’ in IEKA
Efficiency: It is the right activity allotment, this is an easy measurement as there are
established magnitude relation to study progress. To improve on efficiency, only
divide accumulative revenue by sales with the average of total of field installers to
get the mean billable dollars per employee(variable). A growth in this number will
signify rise in efficiency and the ethics are maintained (Hennelly and Srai, 2017).
Meeting deadlines is also a measure of efficiency. An average period of collecting
information measures the skilfulness of your account(s) charge and accumulation
process, in similar way these materials cycle with the businesses through networks
outside to finished facility.
Effectiveness: The main purpose of effectiveness is reaching goals. It is confounded
with efficiency, yet, the efficiency compares raw material to product, a measure of
labour to volume of products, effectiveness is whether the effort reaches the goal or
required standard. A group of workers might not be completely efficient but meet
deadlines or achieve impeccable standards. It is quiet hard to count effectiveness in
numbers, but surveys are being designed to account how well customer expectations
have been satisfied. Surveys that limit responses to “excellent,” “fair” or “poor” will
not elicit the specific feedback that help you provide value for their investment.
Ensuring the results align to performances with priorities for the organisation. It
states a struggle between quality and quantity (Chan and Yue, 2016).
Excellence: The standard of excellence of an organisation and its products/services
alters with the management’s vision. Cheap Plastic Co. may use low price for its
aim of excellence, while huge electrics company may make it with quick response
time. A company has to deliberately be defined in what it has to do better than
5
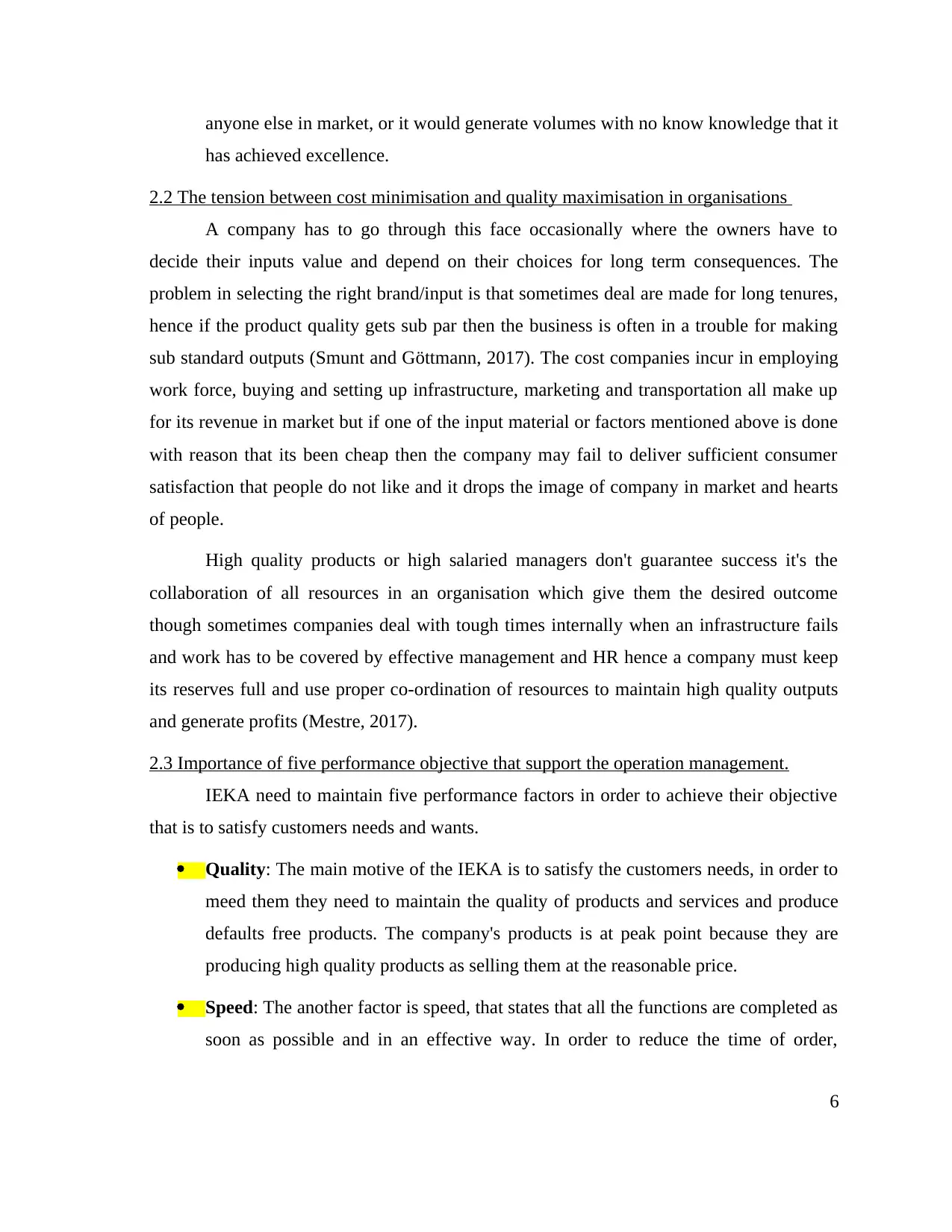
anyone else in market, or it would generate volumes with no know knowledge that it
has achieved excellence.
2.2 The tension between cost minimisation and quality maximisation in organisations
A company has to go through this face occasionally where the owners have to
decide their inputs value and depend on their choices for long term consequences. The
problem in selecting the right brand/input is that sometimes deal are made for long tenures,
hence if the product quality gets sub par then the business is often in a trouble for making
sub standard outputs (Smunt and Göttmann, 2017). The cost companies incur in employing
work force, buying and setting up infrastructure, marketing and transportation all make up
for its revenue in market but if one of the input material or factors mentioned above is done
with reason that its been cheap then the company may fail to deliver sufficient consumer
satisfaction that people do not like and it drops the image of company in market and hearts
of people.
High quality products or high salaried managers don't guarantee success it's the
collaboration of all resources in an organisation which give them the desired outcome
though sometimes companies deal with tough times internally when an infrastructure fails
and work has to be covered by effective management and HR hence a company must keep
its reserves full and use proper co-ordination of resources to maintain high quality outputs
and generate profits (Mestre, 2017).
2.3 Importance of five performance objective that support the operation management.
IEKA need to maintain five performance factors in order to achieve their objective
that is to satisfy customers needs and wants.
Quality: The main motive of the IEKA is to satisfy the customers needs, in order to
meed them they need to maintain the quality of products and services and produce
defaults free products. The company's products is at peak point because they are
producing high quality products as selling them at the reasonable price.
Speed: The another factor is speed, that states that all the functions are completed as
soon as possible and in an effective way. In order to reduce the time of order,
6
has achieved excellence.
2.2 The tension between cost minimisation and quality maximisation in organisations
A company has to go through this face occasionally where the owners have to
decide their inputs value and depend on their choices for long term consequences. The
problem in selecting the right brand/input is that sometimes deal are made for long tenures,
hence if the product quality gets sub par then the business is often in a trouble for making
sub standard outputs (Smunt and Göttmann, 2017). The cost companies incur in employing
work force, buying and setting up infrastructure, marketing and transportation all make up
for its revenue in market but if one of the input material or factors mentioned above is done
with reason that its been cheap then the company may fail to deliver sufficient consumer
satisfaction that people do not like and it drops the image of company in market and hearts
of people.
High quality products or high salaried managers don't guarantee success it's the
collaboration of all resources in an organisation which give them the desired outcome
though sometimes companies deal with tough times internally when an infrastructure fails
and work has to be covered by effective management and HR hence a company must keep
its reserves full and use proper co-ordination of resources to maintain high quality outputs
and generate profits (Mestre, 2017).
2.3 Importance of five performance objective that support the operation management.
IEKA need to maintain five performance factors in order to achieve their objective
that is to satisfy customers needs and wants.
Quality: The main motive of the IEKA is to satisfy the customers needs, in order to
meed them they need to maintain the quality of products and services and produce
defaults free products. The company's products is at peak point because they are
producing high quality products as selling them at the reasonable price.
Speed: The another factor is speed, that states that all the functions are completed as
soon as possible and in an effective way. In order to reduce the time of order,
6
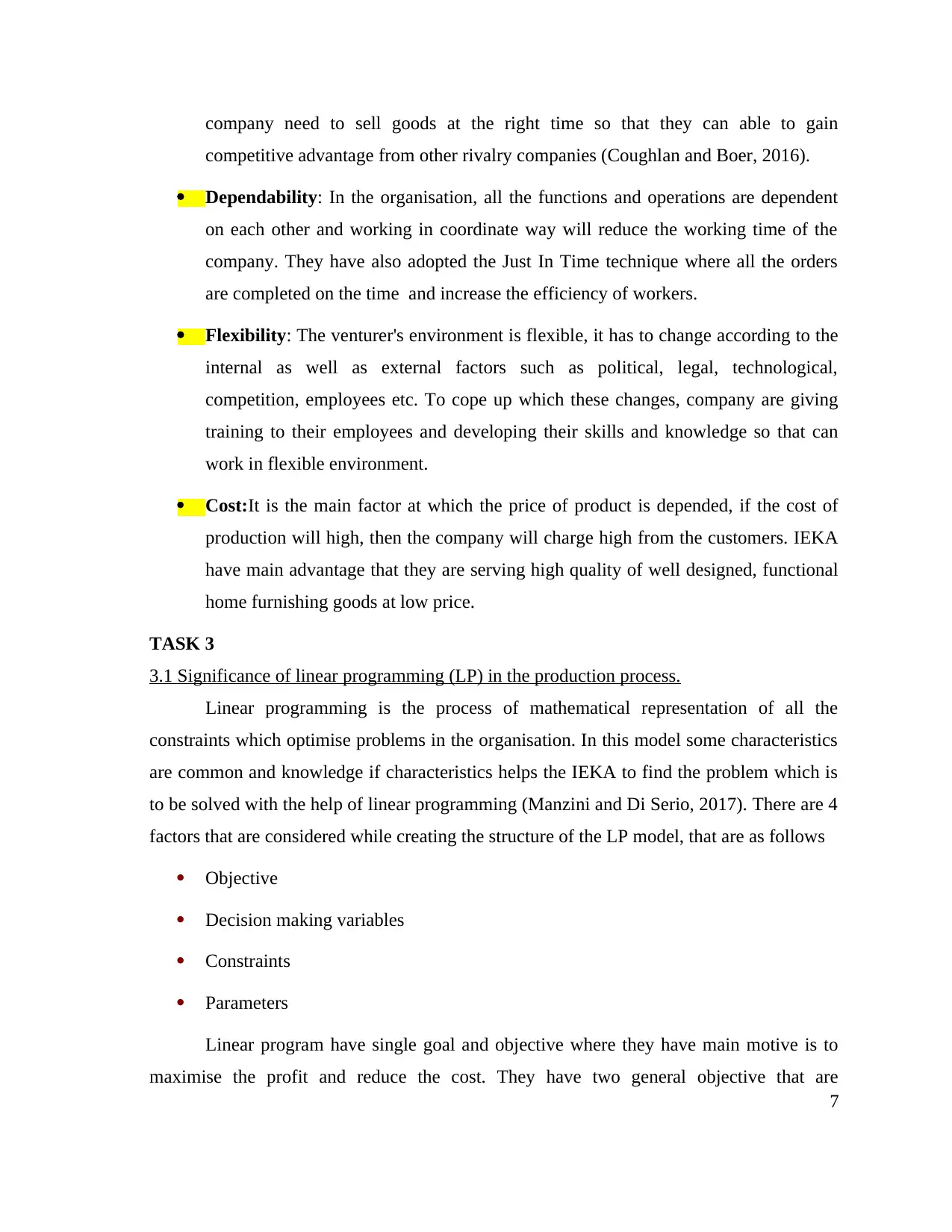
company need to sell goods at the right time so that they can able to gain
competitive advantage from other rivalry companies (Coughlan and Boer, 2016).
Dependability: In the organisation, all the functions and operations are dependent
on each other and working in coordinate way will reduce the working time of the
company. They have also adopted the Just In Time technique where all the orders
are completed on the time and increase the efficiency of workers.
Flexibility: The venturer's environment is flexible, it has to change according to the
internal as well as external factors such as political, legal, technological,
competition, employees etc. To cope up which these changes, company are giving
training to their employees and developing their skills and knowledge so that can
work in flexible environment.
Cost:It is the main factor at which the price of product is depended, if the cost of
production will high, then the company will charge high from the customers. IEKA
have main advantage that they are serving high quality of well designed, functional
home furnishing goods at low price.
TASK 3
3.1 Significance of linear programming (LP) in the production process.
Linear programming is the process of mathematical representation of all the
constraints which optimise problems in the organisation. In this model some characteristics
are common and knowledge if characteristics helps the IEKA to find the problem which is
to be solved with the help of linear programming (Manzini and Di Serio, 2017). There are 4
factors that are considered while creating the structure of the LP model, that are as follows
Objective
Decision making variables
Constraints
Parameters
Linear program have single goal and objective where they have main motive is to
maximise the profit and reduce the cost. They have two general objective that are
7
competitive advantage from other rivalry companies (Coughlan and Boer, 2016).
Dependability: In the organisation, all the functions and operations are dependent
on each other and working in coordinate way will reduce the working time of the
company. They have also adopted the Just In Time technique where all the orders
are completed on the time and increase the efficiency of workers.
Flexibility: The venturer's environment is flexible, it has to change according to the
internal as well as external factors such as political, legal, technological,
competition, employees etc. To cope up which these changes, company are giving
training to their employees and developing their skills and knowledge so that can
work in flexible environment.
Cost:It is the main factor at which the price of product is depended, if the cost of
production will high, then the company will charge high from the customers. IEKA
have main advantage that they are serving high quality of well designed, functional
home furnishing goods at low price.
TASK 3
3.1 Significance of linear programming (LP) in the production process.
Linear programming is the process of mathematical representation of all the
constraints which optimise problems in the organisation. In this model some characteristics
are common and knowledge if characteristics helps the IEKA to find the problem which is
to be solved with the help of linear programming (Manzini and Di Serio, 2017). There are 4
factors that are considered while creating the structure of the LP model, that are as follows
Objective
Decision making variables
Constraints
Parameters
Linear program have single goal and objective where they have main motive is to
maximise the profit and reduce the cost. They have two general objective that are
7
Secure Best Marks with AI Grader
Need help grading? Try our AI Grader for instant feedback on your assignments.
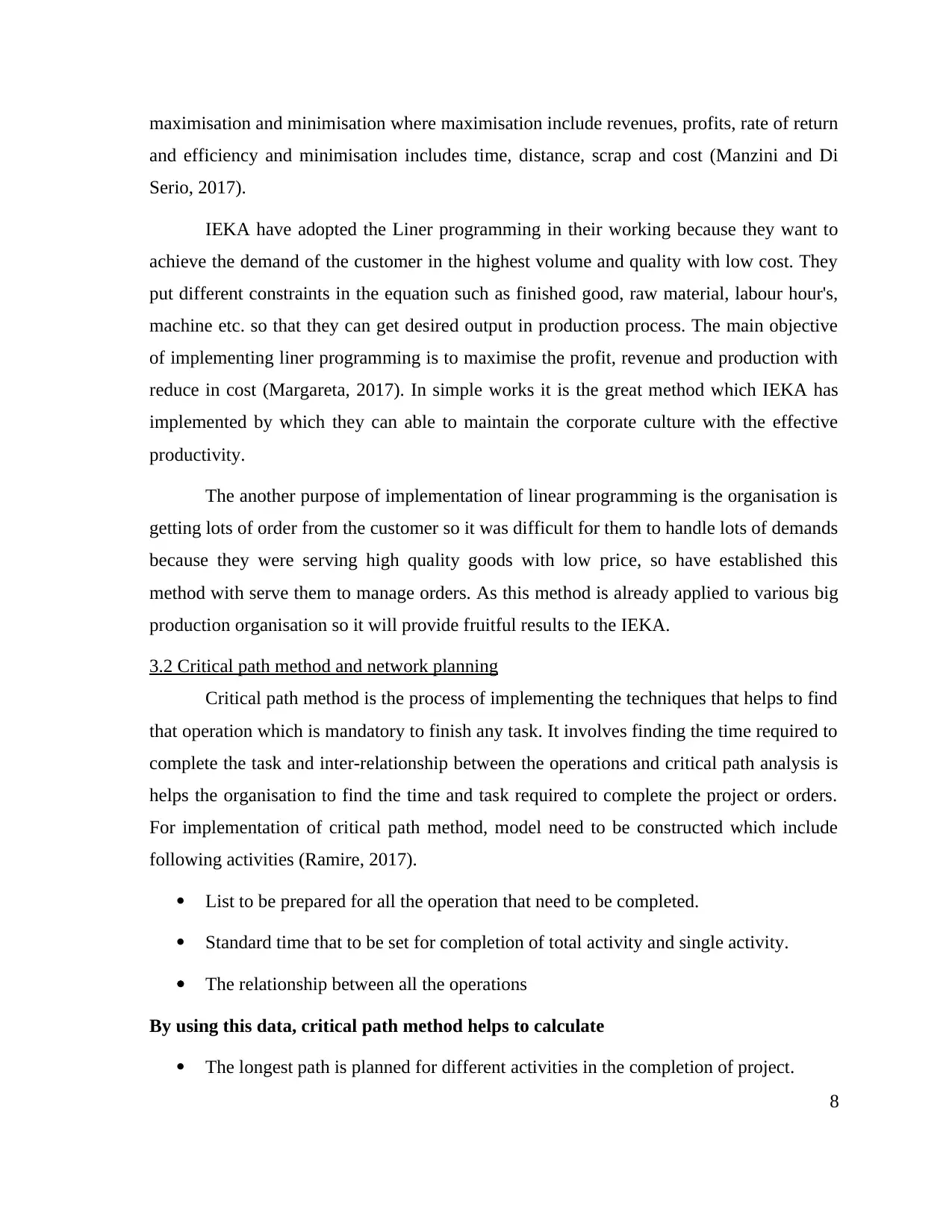
maximisation and minimisation where maximisation include revenues, profits, rate of return
and efficiency and minimisation includes time, distance, scrap and cost (Manzini and Di
Serio, 2017).
IEKA have adopted the Liner programming in their working because they want to
achieve the demand of the customer in the highest volume and quality with low cost. They
put different constraints in the equation such as finished good, raw material, labour hour's,
machine etc. so that they can get desired output in production process. The main objective
of implementing liner programming is to maximise the profit, revenue and production with
reduce in cost (Margareta, 2017). In simple works it is the great method which IEKA has
implemented by which they can able to maintain the corporate culture with the effective
productivity.
The another purpose of implementation of linear programming is the organisation is
getting lots of order from the customer so it was difficult for them to handle lots of demands
because they were serving high quality goods with low price, so have established this
method with serve them to manage orders. As this method is already applied to various big
production organisation so it will provide fruitful results to the IEKA.
3.2 Critical path method and network planning
Critical path method is the process of implementing the techniques that helps to find
that operation which is mandatory to finish any task. It involves finding the time required to
complete the task and inter-relationship between the operations and critical path analysis is
helps the organisation to find the time and task required to complete the project or orders.
For implementation of critical path method, model need to be constructed which include
following activities (Ramire, 2017).
List to be prepared for all the operation that need to be completed.
Standard time that to be set for completion of total activity and single activity.
The relationship between all the operations
By using this data, critical path method helps to calculate
The longest path is planned for different activities in the completion of project.
8
and efficiency and minimisation includes time, distance, scrap and cost (Manzini and Di
Serio, 2017).
IEKA have adopted the Liner programming in their working because they want to
achieve the demand of the customer in the highest volume and quality with low cost. They
put different constraints in the equation such as finished good, raw material, labour hour's,
machine etc. so that they can get desired output in production process. The main objective
of implementing liner programming is to maximise the profit, revenue and production with
reduce in cost (Margareta, 2017). In simple works it is the great method which IEKA has
implemented by which they can able to maintain the corporate culture with the effective
productivity.
The another purpose of implementation of linear programming is the organisation is
getting lots of order from the customer so it was difficult for them to handle lots of demands
because they were serving high quality goods with low price, so have established this
method with serve them to manage orders. As this method is already applied to various big
production organisation so it will provide fruitful results to the IEKA.
3.2 Critical path method and network planning
Critical path method is the process of implementing the techniques that helps to find
that operation which is mandatory to finish any task. It involves finding the time required to
complete the task and inter-relationship between the operations and critical path analysis is
helps the organisation to find the time and task required to complete the project or orders.
For implementation of critical path method, model need to be constructed which include
following activities (Ramire, 2017).
List to be prepared for all the operation that need to be completed.
Standard time that to be set for completion of total activity and single activity.
The relationship between all the operations
By using this data, critical path method helps to calculate
The longest path is planned for different activities in the completion of project.
8
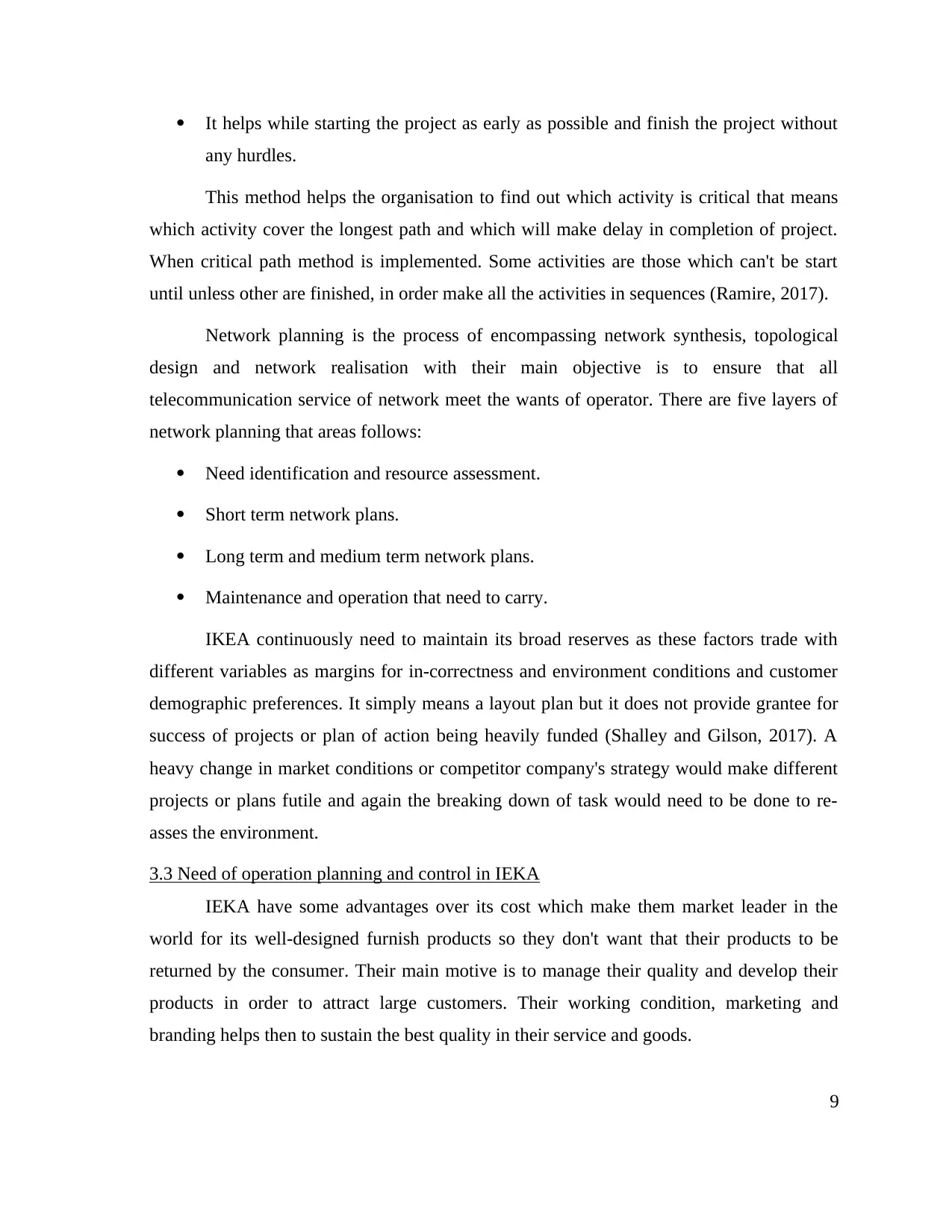
It helps while starting the project as early as possible and finish the project without
any hurdles.
This method helps the organisation to find out which activity is critical that means
which activity cover the longest path and which will make delay in completion of project.
When critical path method is implemented. Some activities are those which can't be start
until unless other are finished, in order make all the activities in sequences (Ramire, 2017).
Network planning is the process of encompassing network synthesis, topological
design and network realisation with their main objective is to ensure that all
telecommunication service of network meet the wants of operator. There are five layers of
network planning that areas follows:
Need identification and resource assessment.
Short term network plans.
Long term and medium term network plans.
Maintenance and operation that need to carry.
IKEA continuously need to maintain its broad reserves as these factors trade with
different variables as margins for in-correctness and environment conditions and customer
demographic preferences. It simply means a layout plan but it does not provide grantee for
success of projects or plan of action being heavily funded (Shalley and Gilson, 2017). A
heavy change in market conditions or competitor company's strategy would make different
projects or plans futile and again the breaking down of task would need to be done to re-
asses the environment.
3.3 Need of operation planning and control in IEKA
IEKA have some advantages over its cost which make them market leader in the
world for its well-designed furnish products so they don't want that their products to be
returned by the consumer. Their main motive is to manage their quality and develop their
products in order to attract large customers. Their working condition, marketing and
branding helps then to sustain the best quality in their service and goods.
9
any hurdles.
This method helps the organisation to find out which activity is critical that means
which activity cover the longest path and which will make delay in completion of project.
When critical path method is implemented. Some activities are those which can't be start
until unless other are finished, in order make all the activities in sequences (Ramire, 2017).
Network planning is the process of encompassing network synthesis, topological
design and network realisation with their main objective is to ensure that all
telecommunication service of network meet the wants of operator. There are five layers of
network planning that areas follows:
Need identification and resource assessment.
Short term network plans.
Long term and medium term network plans.
Maintenance and operation that need to carry.
IKEA continuously need to maintain its broad reserves as these factors trade with
different variables as margins for in-correctness and environment conditions and customer
demographic preferences. It simply means a layout plan but it does not provide grantee for
success of projects or plan of action being heavily funded (Shalley and Gilson, 2017). A
heavy change in market conditions or competitor company's strategy would make different
projects or plans futile and again the breaking down of task would need to be done to re-
asses the environment.
3.3 Need of operation planning and control in IEKA
IEKA have some advantages over its cost which make them market leader in the
world for its well-designed furnish products so they don't want that their products to be
returned by the consumer. Their main motive is to manage their quality and develop their
products in order to attract large customers. Their working condition, marketing and
branding helps then to sustain the best quality in their service and goods.
9
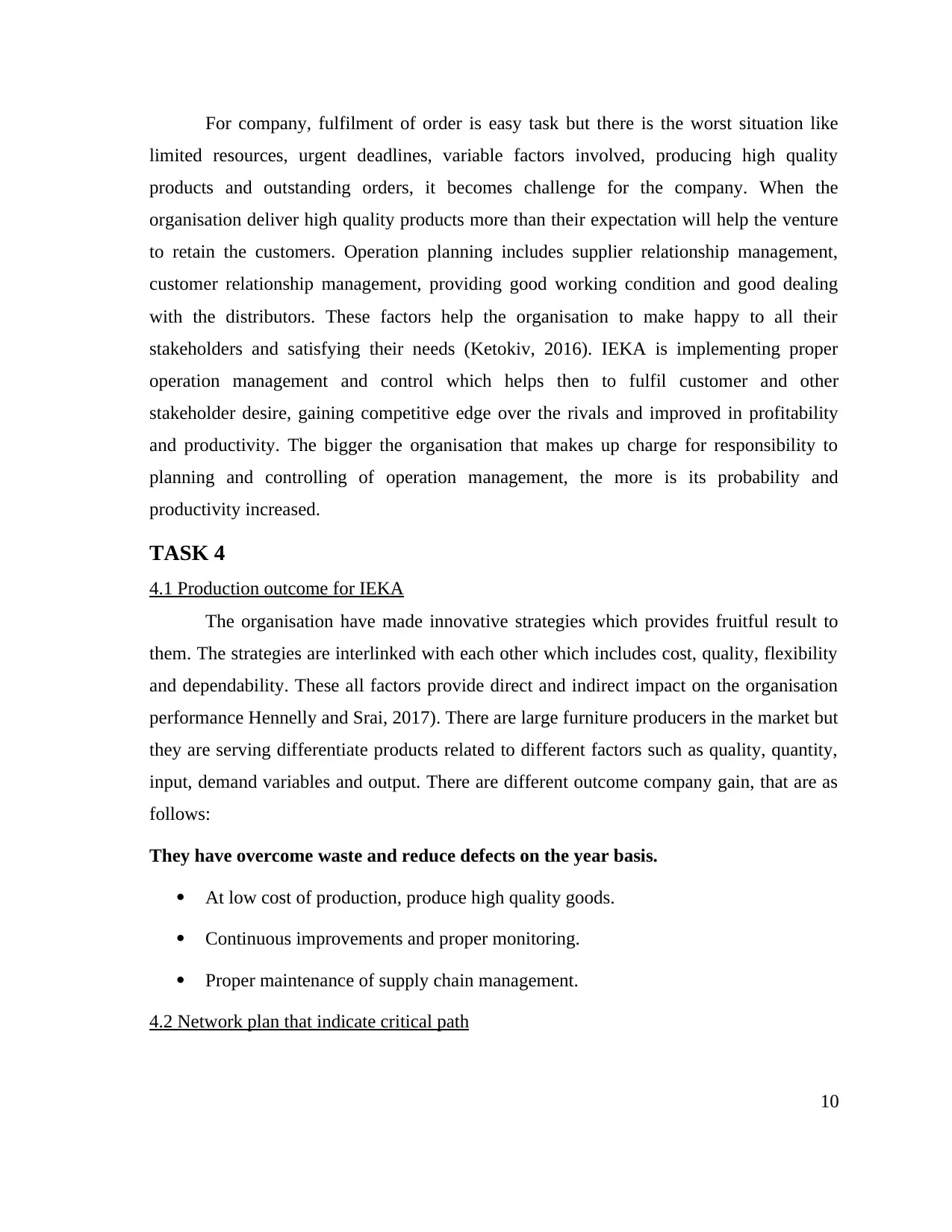
For company, fulfilment of order is easy task but there is the worst situation like
limited resources, urgent deadlines, variable factors involved, producing high quality
products and outstanding orders, it becomes challenge for the company. When the
organisation deliver high quality products more than their expectation will help the venture
to retain the customers. Operation planning includes supplier relationship management,
customer relationship management, providing good working condition and good dealing
with the distributors. These factors help the organisation to make happy to all their
stakeholders and satisfying their needs (Ketokiv, 2016). IEKA is implementing proper
operation management and control which helps then to fulfil customer and other
stakeholder desire, gaining competitive edge over the rivals and improved in profitability
and productivity. The bigger the organisation that makes up charge for responsibility to
planning and controlling of operation management, the more is its probability and
productivity increased.
TASK 4
4.1 Production outcome for IEKA
The organisation have made innovative strategies which provides fruitful result to
them. The strategies are interlinked with each other which includes cost, quality, flexibility
and dependability. These all factors provide direct and indirect impact on the organisation
performance Hennelly and Srai, 2017). There are large furniture producers in the market but
they are serving differentiate products related to different factors such as quality, quantity,
input, demand variables and output. There are different outcome company gain, that are as
follows:
They have overcome waste and reduce defects on the year basis.
At low cost of production, produce high quality goods.
Continuous improvements and proper monitoring.
Proper maintenance of supply chain management.
4.2 Network plan that indicate critical path
10
limited resources, urgent deadlines, variable factors involved, producing high quality
products and outstanding orders, it becomes challenge for the company. When the
organisation deliver high quality products more than their expectation will help the venture
to retain the customers. Operation planning includes supplier relationship management,
customer relationship management, providing good working condition and good dealing
with the distributors. These factors help the organisation to make happy to all their
stakeholders and satisfying their needs (Ketokiv, 2016). IEKA is implementing proper
operation management and control which helps then to fulfil customer and other
stakeholder desire, gaining competitive edge over the rivals and improved in profitability
and productivity. The bigger the organisation that makes up charge for responsibility to
planning and controlling of operation management, the more is its probability and
productivity increased.
TASK 4
4.1 Production outcome for IEKA
The organisation have made innovative strategies which provides fruitful result to
them. The strategies are interlinked with each other which includes cost, quality, flexibility
and dependability. These all factors provide direct and indirect impact on the organisation
performance Hennelly and Srai, 2017). There are large furniture producers in the market but
they are serving differentiate products related to different factors such as quality, quantity,
input, demand variables and output. There are different outcome company gain, that are as
follows:
They have overcome waste and reduce defects on the year basis.
At low cost of production, produce high quality goods.
Continuous improvements and proper monitoring.
Proper maintenance of supply chain management.
4.2 Network plan that indicate critical path
10
Paraphrase This Document
Need a fresh take? Get an instant paraphrase of this document with our AI Paraphraser
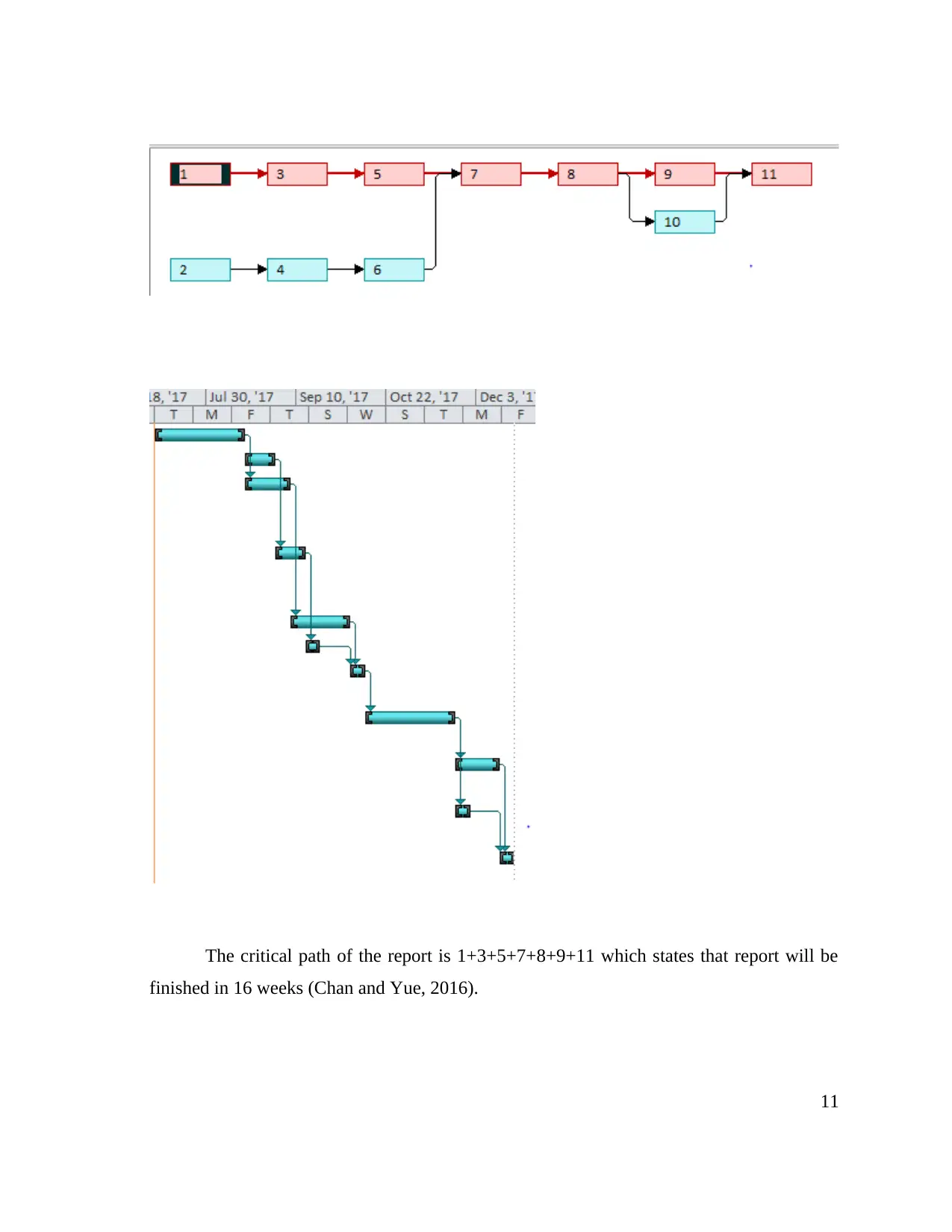
The critical path of the report is 1+3+5+7+8+9+11 which states that report will be
finished in 16 weeks (Chan and Yue, 2016).
11
finished in 16 weeks (Chan and Yue, 2016).
11
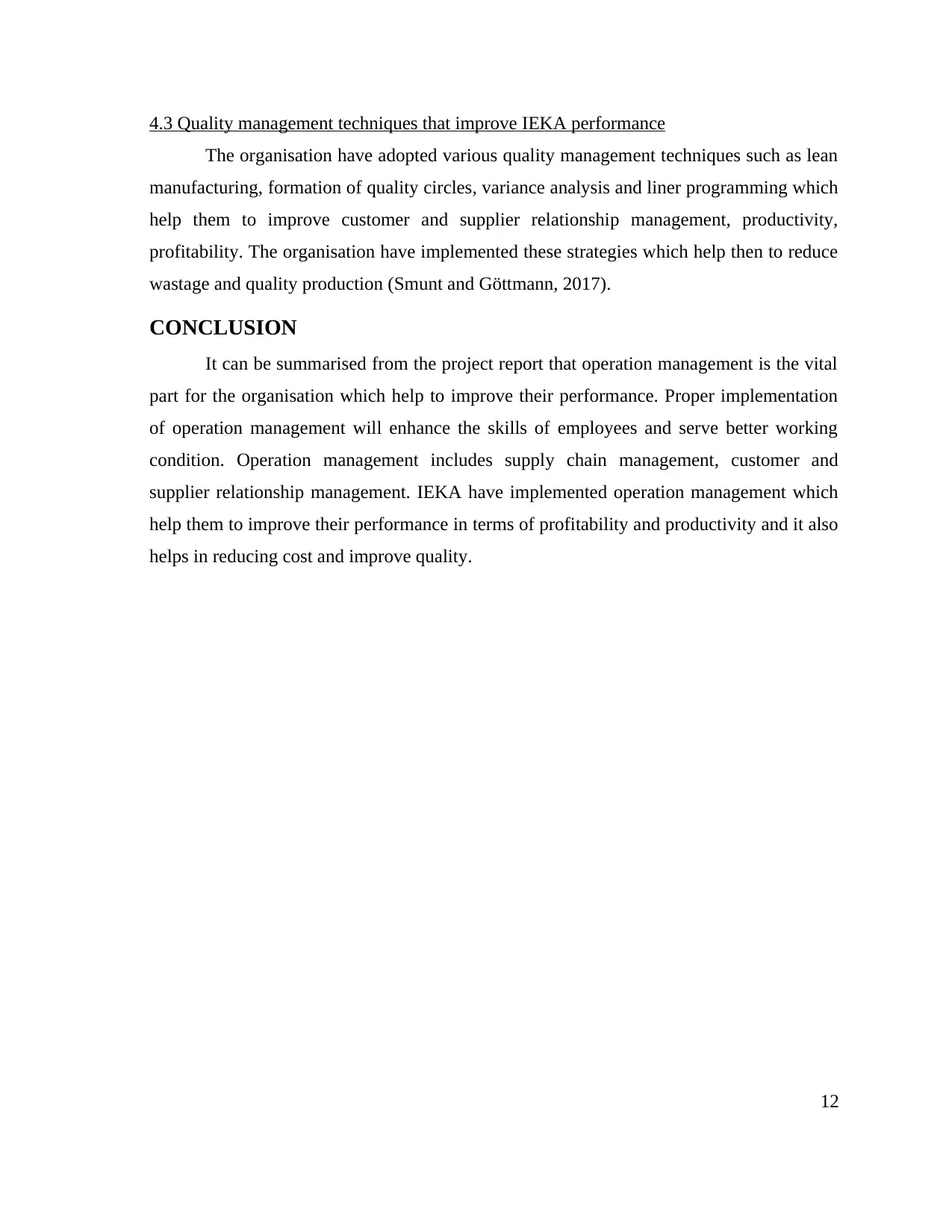
4.3 Quality management techniques that improve IEKA performance
The organisation have adopted various quality management techniques such as lean
manufacturing, formation of quality circles, variance analysis and liner programming which
help them to improve customer and supplier relationship management, productivity,
profitability. The organisation have implemented these strategies which help then to reduce
wastage and quality production (Smunt and Göttmann, 2017).
CONCLUSION
It can be summarised from the project report that operation management is the vital
part for the organisation which help to improve their performance. Proper implementation
of operation management will enhance the skills of employees and serve better working
condition. Operation management includes supply chain management, customer and
supplier relationship management. IEKA have implemented operation management which
help them to improve their performance in terms of profitability and productivity and it also
helps in reducing cost and improve quality.
12
The organisation have adopted various quality management techniques such as lean
manufacturing, formation of quality circles, variance analysis and liner programming which
help them to improve customer and supplier relationship management, productivity,
profitability. The organisation have implemented these strategies which help then to reduce
wastage and quality production (Smunt and Göttmann, 2017).
CONCLUSION
It can be summarised from the project report that operation management is the vital
part for the organisation which help to improve their performance. Proper implementation
of operation management will enhance the skills of employees and serve better working
condition. Operation management includes supply chain management, customer and
supplier relationship management. IEKA have implemented operation management which
help them to improve their performance in terms of profitability and productivity and it also
helps in reducing cost and improve quality.
12

REFERENCES
Books and Journal
Mestre, M. J. O., 2017. Teamwork dynamics analysis as a teaching resource in operations
management courses. WPOM-Working Papers on Operations Management. 8. pp.76-80.
Choi, T. M. and Zhao, X., 2016. Multi‐Methodological Research in Operations
Management. Production and Operations Management. 25(3). pp.379-389.
Lee, H. and Zhang, H., 2017. Special Issue of Production and Operations Management:
Innovations and Sustainability. Production and Operations Management. 26(4). pp.757-
757.
Smunt, T. L. and Göttmann, S., 2017. Applications of learning curves in production and
operations management: A systematic literature review (No. 87150). Darmstadt Technical
University, Department of Business Administration, Economics and Law, Institute for
Business Studies (BWL).
Chan, H. K. and Yue, X., 2016. Guest editorial big data analytics: Risk and operations
management for industrial applications. IEEE Transactions on Industrial Informatics.
12(3). pp.1214-1218.
Coughlan, P. and Boer, H., 2016. Operations and supply chain management: The role of
academics and practitioners in the development of research and practice. International
Journal of Operations & Production Management. 36(12). pp.1673-1695.
Manzini, R. B. and Di Serio, L. C., 2017. Current thinking on cluster theory and its
translation in economic geography and strategic and operations management: is a
reconciliation possible?. Competitiveness Review: An International Business Journal, (just-
accepted), pp.00-00.
Margareta, C., 2017. Increase of value added through the improvement of Operations
Management”(on the basis of materials from the clothing industry from the Republic of
Moldova). Development.
13
Books and Journal
Mestre, M. J. O., 2017. Teamwork dynamics analysis as a teaching resource in operations
management courses. WPOM-Working Papers on Operations Management. 8. pp.76-80.
Choi, T. M. and Zhao, X., 2016. Multi‐Methodological Research in Operations
Management. Production and Operations Management. 25(3). pp.379-389.
Lee, H. and Zhang, H., 2017. Special Issue of Production and Operations Management:
Innovations and Sustainability. Production and Operations Management. 26(4). pp.757-
757.
Smunt, T. L. and Göttmann, S., 2017. Applications of learning curves in production and
operations management: A systematic literature review (No. 87150). Darmstadt Technical
University, Department of Business Administration, Economics and Law, Institute for
Business Studies (BWL).
Chan, H. K. and Yue, X., 2016. Guest editorial big data analytics: Risk and operations
management for industrial applications. IEEE Transactions on Industrial Informatics.
12(3). pp.1214-1218.
Coughlan, P. and Boer, H., 2016. Operations and supply chain management: The role of
academics and practitioners in the development of research and practice. International
Journal of Operations & Production Management. 36(12). pp.1673-1695.
Manzini, R. B. and Di Serio, L. C., 2017. Current thinking on cluster theory and its
translation in economic geography and strategic and operations management: is a
reconciliation possible?. Competitiveness Review: An International Business Journal, (just-
accepted), pp.00-00.
Margareta, C., 2017. Increase of value added through the improvement of Operations
Management”(on the basis of materials from the clothing industry from the Republic of
Moldova). Development.
13
Secure Best Marks with AI Grader
Need help grading? Try our AI Grader for instant feedback on your assignments.
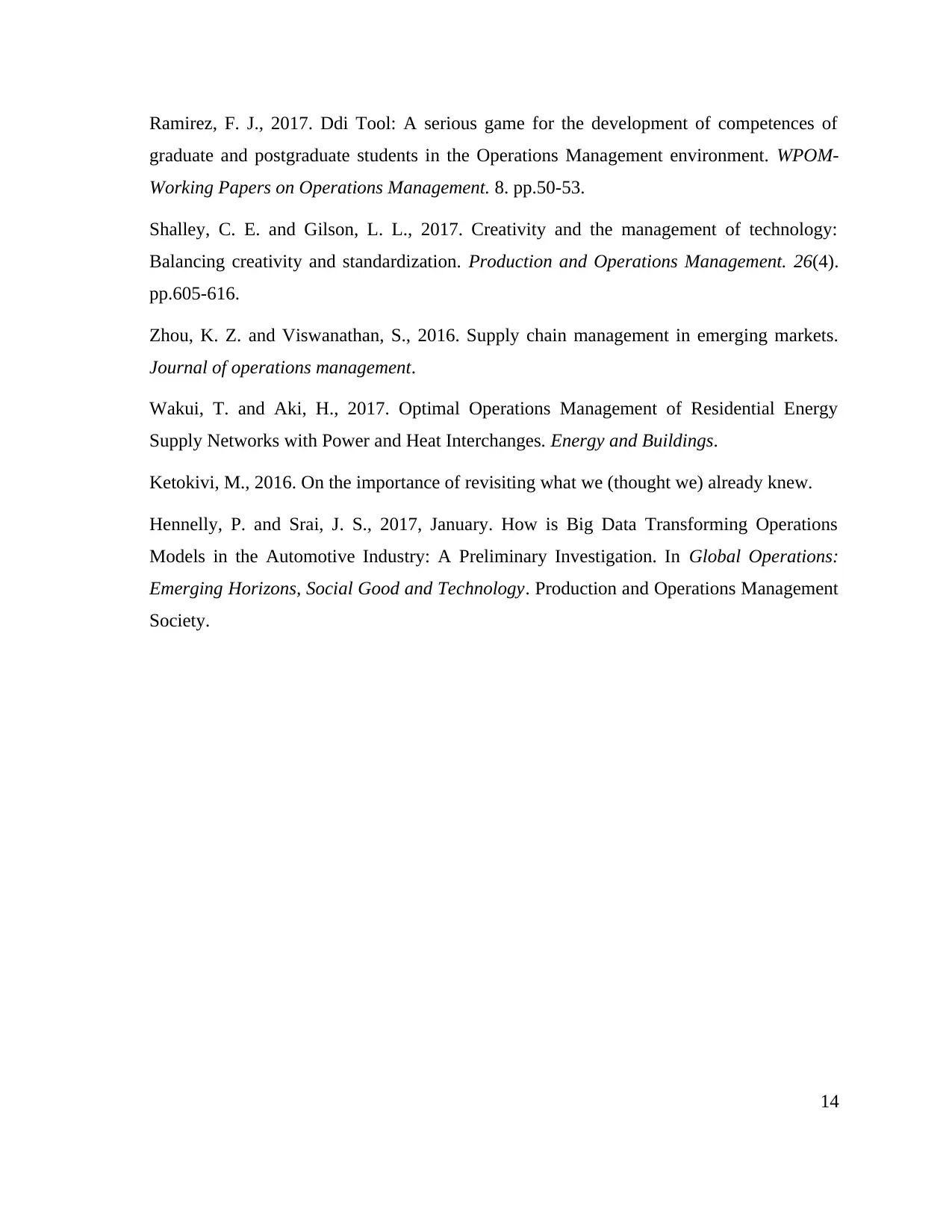
Ramirez, F. J., 2017. Ddi Tool: A serious game for the development of competences of
graduate and postgraduate students in the Operations Management environment. WPOM-
Working Papers on Operations Management. 8. pp.50-53.
Shalley, C. E. and Gilson, L. L., 2017. Creativity and the management of technology:
Balancing creativity and standardization. Production and Operations Management. 26(4).
pp.605-616.
Zhou, K. Z. and Viswanathan, S., 2016. Supply chain management in emerging markets.
Journal of operations management.
Wakui, T. and Aki, H., 2017. Optimal Operations Management of Residential Energy
Supply Networks with Power and Heat Interchanges. Energy and Buildings.
Ketokivi, M., 2016. On the importance of revisiting what we (thought we) already knew.
Hennelly, P. and Srai, J. S., 2017, January. How is Big Data Transforming Operations
Models in the Automotive Industry: A Preliminary Investigation. In Global Operations:
Emerging Horizons, Social Good and Technology. Production and Operations Management
Society.
14
graduate and postgraduate students in the Operations Management environment. WPOM-
Working Papers on Operations Management. 8. pp.50-53.
Shalley, C. E. and Gilson, L. L., 2017. Creativity and the management of technology:
Balancing creativity and standardization. Production and Operations Management. 26(4).
pp.605-616.
Zhou, K. Z. and Viswanathan, S., 2016. Supply chain management in emerging markets.
Journal of operations management.
Wakui, T. and Aki, H., 2017. Optimal Operations Management of Residential Energy
Supply Networks with Power and Heat Interchanges. Energy and Buildings.
Ketokivi, M., 2016. On the importance of revisiting what we (thought we) already knew.
Hennelly, P. and Srai, J. S., 2017, January. How is Big Data Transforming Operations
Models in the Automotive Industry: A Preliminary Investigation. In Global Operations:
Emerging Horizons, Social Good and Technology. Production and Operations Management
Society.
14
1 out of 17
Related Documents

Your All-in-One AI-Powered Toolkit for Academic Success.
+13062052269
info@desklib.com
Available 24*7 on WhatsApp / Email
Unlock your academic potential
© 2024 | Zucol Services PVT LTD | All rights reserved.