Operations Management Report: Scheduling, Layout, Inventory, Costs
VerifiedAdded on  2023/01/12
|12
|3702
|63
Report
AI Summary
This report provides a comprehensive analysis of operations management, exploring various scheduling techniques such as First Come First Serve, Shortest Processing Time, Earliest Due Date, Slack Time Remaining, and Critical Ratio, along with their applications in organizing work. It delves into layout planning, defining different types of layouts like process, product, hybrid, and fixed position, and assessing their suitability for diverse business environments. The report also examines work system processes, explaining how these systems are designed to optimize productivity. Furthermore, it emphasizes the significance of inventory management policies in controlling production costs, highlighting their role in preparing for demand and supply fluctuations, aiding continuous production, minimizing administrative workloads, reducing material losses, and avoiding over/under ordering. The report uses IKEA as a case study to illustrate these concepts, providing a practical understanding of operations management principles.
Contribute Materials
Your contribution can guide someone’s learning journey. Share your
documents today.

OPERATIONS
MANAGEMENT
MANAGEMENT
Secure Best Marks with AI Grader
Need help grading? Try our AI Grader for instant feedback on your assignments.
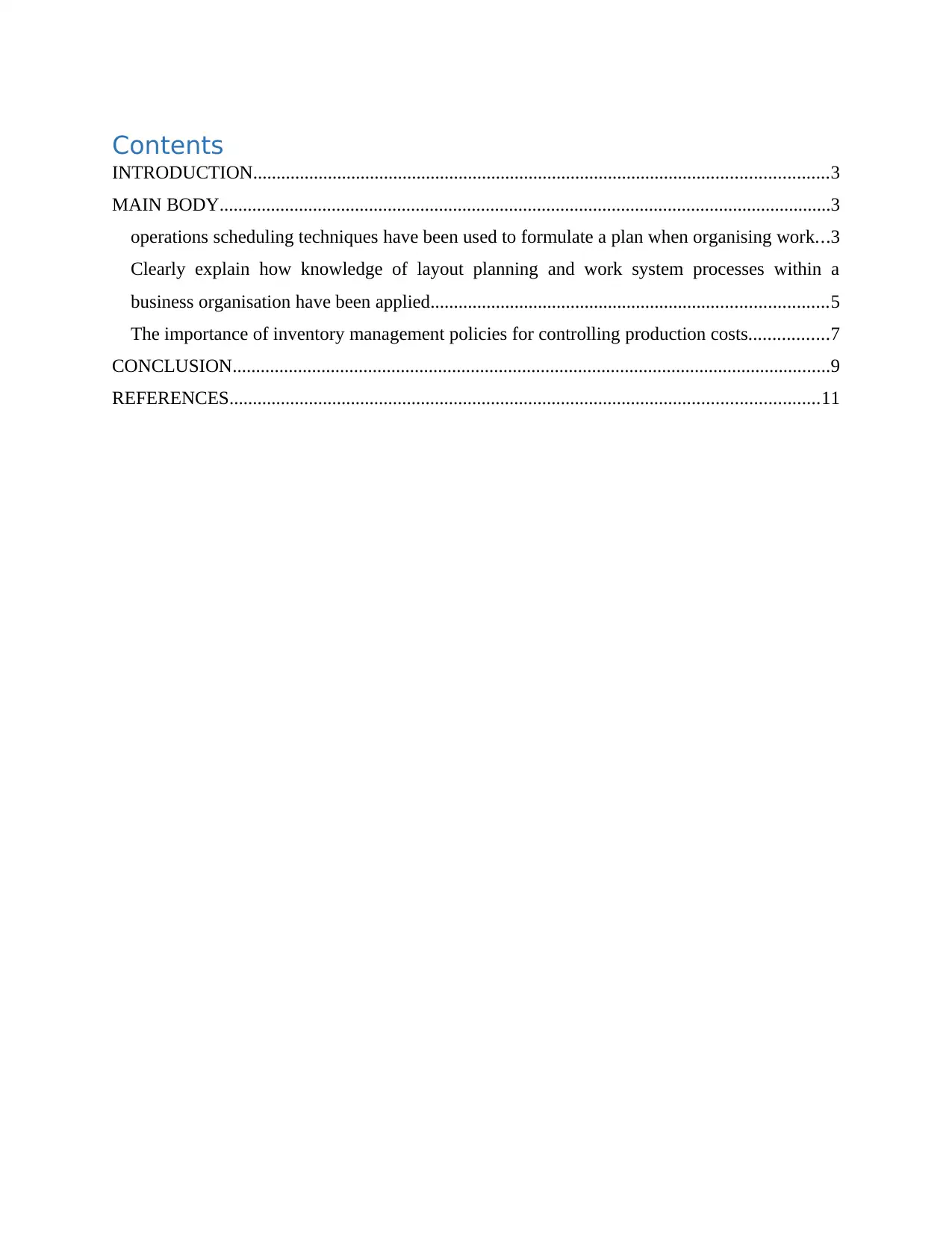
Contents
INTRODUCTION...........................................................................................................................3
MAIN BODY...................................................................................................................................3
operations scheduling techniques have been used to formulate a plan when organising work...3
Clearly explain how knowledge of layout planning and work system processes within a
business organisation have been applied.....................................................................................5
The importance of inventory management policies for controlling production costs.................7
CONCLUSION................................................................................................................................9
REFERENCES..............................................................................................................................11
INTRODUCTION...........................................................................................................................3
MAIN BODY...................................................................................................................................3
operations scheduling techniques have been used to formulate a plan when organising work...3
Clearly explain how knowledge of layout planning and work system processes within a
business organisation have been applied.....................................................................................5
The importance of inventory management policies for controlling production costs.................7
CONCLUSION................................................................................................................................9
REFERENCES..............................................................................................................................11

INTRODUCTION
Operations management is basically defined as that process included in business practices
so that organization can have engaged in achieving highest level of efficiency. It is a process
which assists company in converting raw materials into finished goods and services so that profit
is been maximized easily in company. Work system process can be defined as those phase that
can be described as operations and maintenance. Layout planning is deciding on the best
physical arrangement of all resources that consume space within a facility. This system brings
out changes in implementation process. It assists firm in achieving their ultimate goals and
objectives. Present report will lay emphasis on IKEA. It is the European multination group which
is engaged in selling out furniture, kitchen appliances and home accessories. Company has been
world’s largest furniture retailers since year 2008. Report will lay emphasis on operations layout
planning, work system processes and inventory management policies.
MAIN BODY
Operations scheduling techniques have been used to formulate a plan when organising work
Operations scheduling techniques can be used by organization in order to establish both
the timing and use of resources within an organization. It is basically linked with making proper
utilization of resources and it also includes scheduling of activities related to human resource and
receipt of material.
First come first serve: This approach can be used by organizations when they only have
a single item to produce. This can assist firm in doing proper scheduling of material and
equipment’s. In this scheduling procedure fully rely on what kind of product or service is ordered
by consumer (Parpia and Singh, G., DecisionGPS, 2016). So making use of first come first serve
approach is most suitable in this condition. If company is engaged in producing different
products with different time and deadlines, this process can be less effective and can make
consumer unsatisfied. It can decrease efficiency of organization and they will be unable to
achieve their goals and objectives. This can be managed by making use FIFO queue. This
process is being rarely used in modern operating system as it is really time consuming and
hectic. This scheduling method is non pre-emptive, that is, the process will run until it finishes.
Company when making use of this method can become ineffective and may not be able to
achieve their objectives. It makes firm more unproductive which can also reduce turnover. It can
also increase their cost and expenditure.
Operations management is basically defined as that process included in business practices
so that organization can have engaged in achieving highest level of efficiency. It is a process
which assists company in converting raw materials into finished goods and services so that profit
is been maximized easily in company. Work system process can be defined as those phase that
can be described as operations and maintenance. Layout planning is deciding on the best
physical arrangement of all resources that consume space within a facility. This system brings
out changes in implementation process. It assists firm in achieving their ultimate goals and
objectives. Present report will lay emphasis on IKEA. It is the European multination group which
is engaged in selling out furniture, kitchen appliances and home accessories. Company has been
world’s largest furniture retailers since year 2008. Report will lay emphasis on operations layout
planning, work system processes and inventory management policies.
MAIN BODY
Operations scheduling techniques have been used to formulate a plan when organising work
Operations scheduling techniques can be used by organization in order to establish both
the timing and use of resources within an organization. It is basically linked with making proper
utilization of resources and it also includes scheduling of activities related to human resource and
receipt of material.
First come first serve: This approach can be used by organizations when they only have
a single item to produce. This can assist firm in doing proper scheduling of material and
equipment’s. In this scheduling procedure fully rely on what kind of product or service is ordered
by consumer (Parpia and Singh, G., DecisionGPS, 2016). So making use of first come first serve
approach is most suitable in this condition. If company is engaged in producing different
products with different time and deadlines, this process can be less effective and can make
consumer unsatisfied. It can decrease efficiency of organization and they will be unable to
achieve their goals and objectives. This can be managed by making use FIFO queue. This
process is being rarely used in modern operating system as it is really time consuming and
hectic. This scheduling method is non pre-emptive, that is, the process will run until it finishes.
Company when making use of this method can become ineffective and may not be able to
achieve their objectives. It makes firm more unproductive which can also reduce turnover. It can
also increase their cost and expenditure.
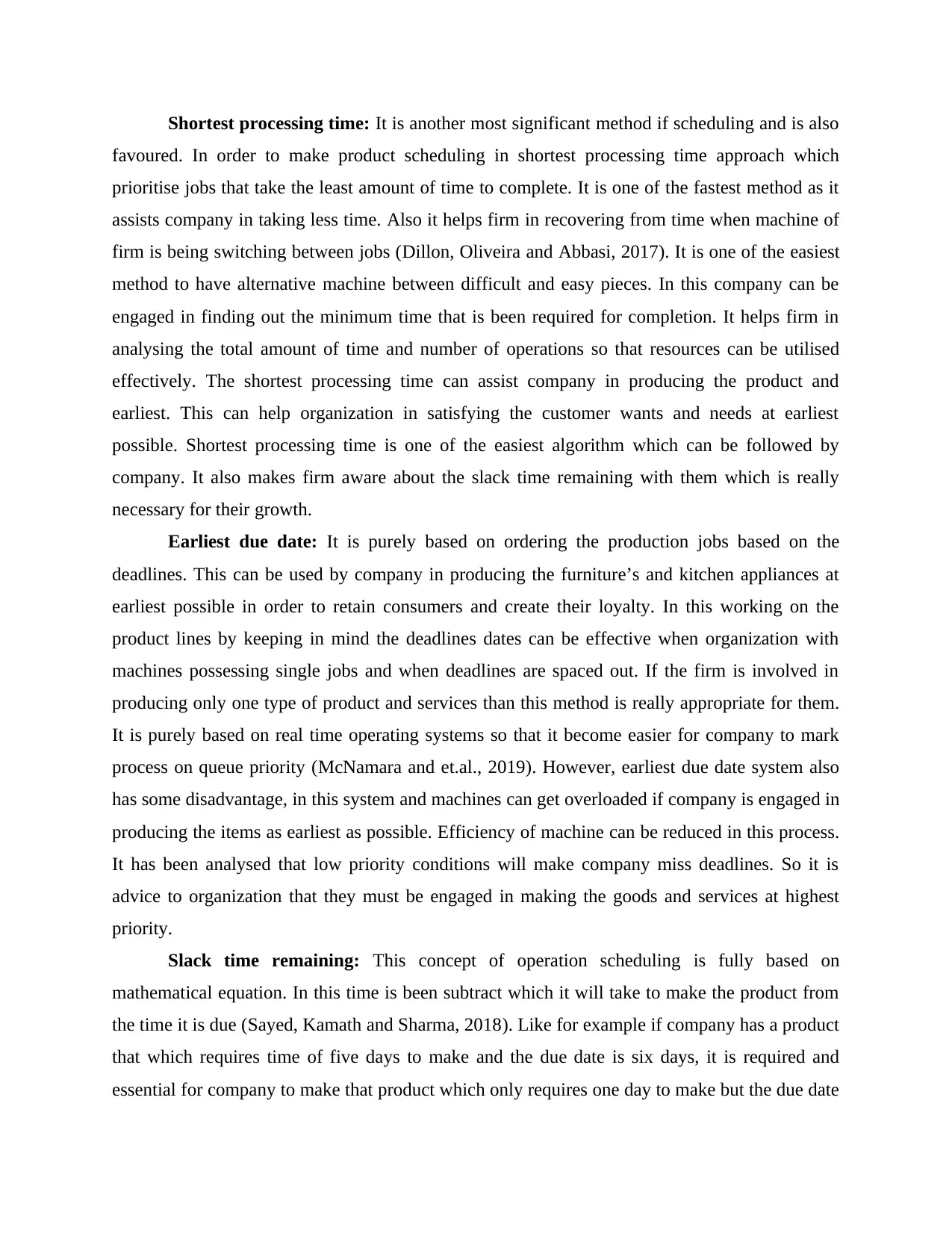
Shortest processing time: It is another most significant method if scheduling and is also
favoured. In order to make product scheduling in shortest processing time approach which
prioritise jobs that take the least amount of time to complete. It is one of the fastest method as it
assists company in taking less time. Also it helps firm in recovering from time when machine of
firm is being switching between jobs (Dillon, Oliveira and Abbasi, 2017). It is one of the easiest
method to have alternative machine between difficult and easy pieces. In this company can be
engaged in finding out the minimum time that is been required for completion. It helps firm in
analysing the total amount of time and number of operations so that resources can be utilised
effectively. The shortest processing time can assist company in producing the product and
earliest. This can help organization in satisfying the customer wants and needs at earliest
possible. Shortest processing time is one of the easiest algorithm which can be followed by
company. It also makes firm aware about the slack time remaining with them which is really
necessary for their growth.
Earliest due date: It is purely based on ordering the production jobs based on the
deadlines. This can be used by company in producing the furniture’s and kitchen appliances at
earliest possible in order to retain consumers and create their loyalty. In this working on the
product lines by keeping in mind the deadlines dates can be effective when organization with
machines possessing single jobs and when deadlines are spaced out. If the firm is involved in
producing only one type of product and services than this method is really appropriate for them.
It is purely based on real time operating systems so that it become easier for company to mark
process on queue priority (McNamara and et.al., 2019). However, earliest due date system also
has some disadvantage, in this system and machines can get overloaded if company is engaged in
producing the items as earliest as possible. Efficiency of machine can be reduced in this process.
It has been analysed that low priority conditions will make company miss deadlines. So it is
advice to organization that they must be engaged in making the goods and services at highest
priority.
Slack time remaining: This concept of operation scheduling is fully based on
mathematical equation. In this time is been subtract which it will take to make the product from
the time it is due (Sayed, Kamath and Sharma, 2018). Like for example if company has a product
that which requires time of five days to make and the due date is six days, it is required and
essential for company to make that product which only requires one day to make but the due date
favoured. In order to make product scheduling in shortest processing time approach which
prioritise jobs that take the least amount of time to complete. It is one of the fastest method as it
assists company in taking less time. Also it helps firm in recovering from time when machine of
firm is being switching between jobs (Dillon, Oliveira and Abbasi, 2017). It is one of the easiest
method to have alternative machine between difficult and easy pieces. In this company can be
engaged in finding out the minimum time that is been required for completion. It helps firm in
analysing the total amount of time and number of operations so that resources can be utilised
effectively. The shortest processing time can assist company in producing the product and
earliest. This can help organization in satisfying the customer wants and needs at earliest
possible. Shortest processing time is one of the easiest algorithm which can be followed by
company. It also makes firm aware about the slack time remaining with them which is really
necessary for their growth.
Earliest due date: It is purely based on ordering the production jobs based on the
deadlines. This can be used by company in producing the furniture’s and kitchen appliances at
earliest possible in order to retain consumers and create their loyalty. In this working on the
product lines by keeping in mind the deadlines dates can be effective when organization with
machines possessing single jobs and when deadlines are spaced out. If the firm is involved in
producing only one type of product and services than this method is really appropriate for them.
It is purely based on real time operating systems so that it become easier for company to mark
process on queue priority (McNamara and et.al., 2019). However, earliest due date system also
has some disadvantage, in this system and machines can get overloaded if company is engaged in
producing the items as earliest as possible. Efficiency of machine can be reduced in this process.
It has been analysed that low priority conditions will make company miss deadlines. So it is
advice to organization that they must be engaged in making the goods and services at highest
priority.
Slack time remaining: This concept of operation scheduling is fully based on
mathematical equation. In this time is been subtract which it will take to make the product from
the time it is due (Sayed, Kamath and Sharma, 2018). Like for example if company has a product
that which requires time of five days to make and the due date is six days, it is required and
essential for company to make that product which only requires one day to make but the due date
Secure Best Marks with AI Grader
Need help grading? Try our AI Grader for instant feedback on your assignments.
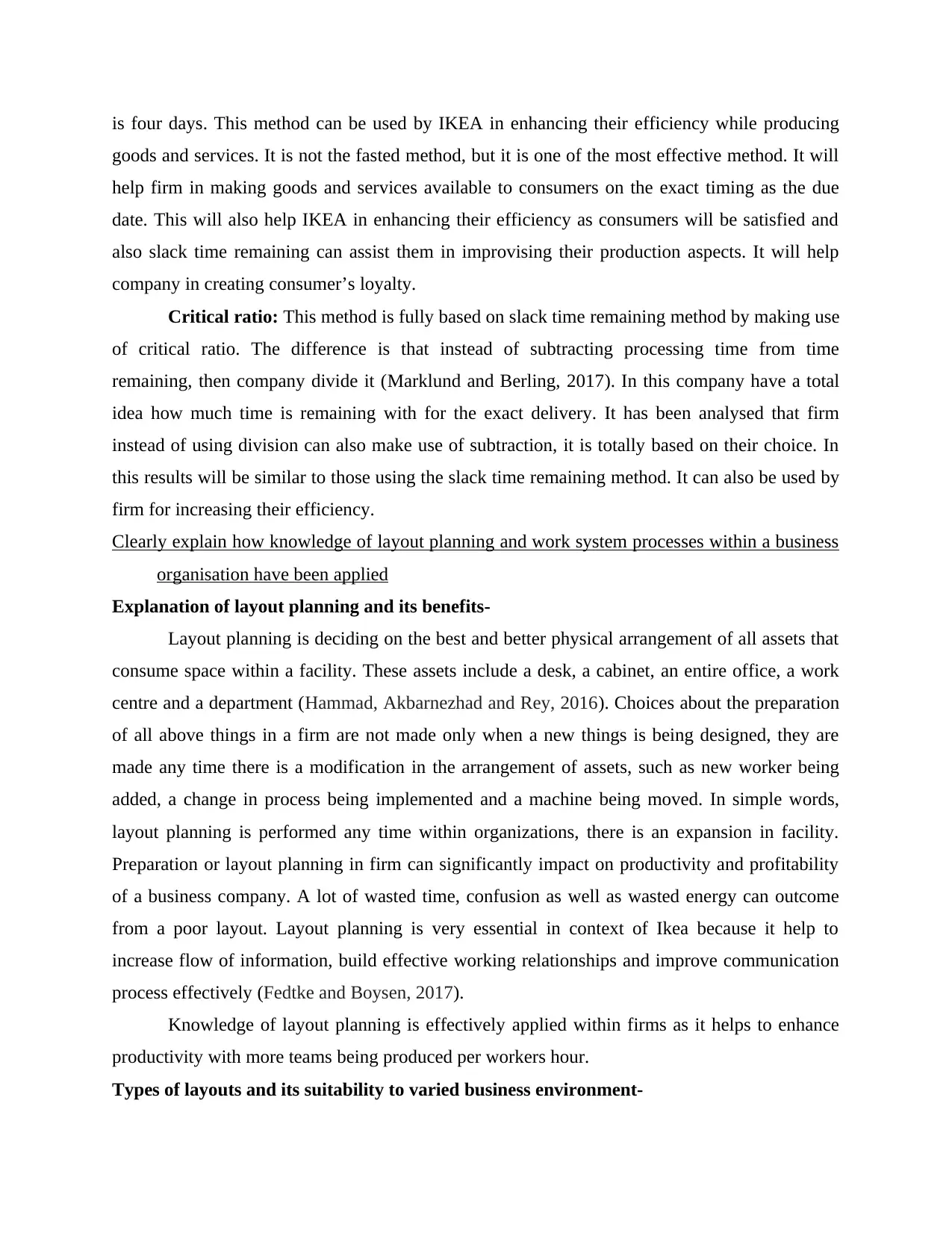
is four days. This method can be used by IKEA in enhancing their efficiency while producing
goods and services. It is not the fasted method, but it is one of the most effective method. It will
help firm in making goods and services available to consumers on the exact timing as the due
date. This will also help IKEA in enhancing their efficiency as consumers will be satisfied and
also slack time remaining can assist them in improvising their production aspects. It will help
company in creating consumer’s loyalty.
Critical ratio: This method is fully based on slack time remaining method by making use
of critical ratio. The difference is that instead of subtracting processing time from time
remaining, then company divide it (Marklund and Berling, 2017). In this company have a total
idea how much time is remaining with for the exact delivery. It has been analysed that firm
instead of using division can also make use of subtraction, it is totally based on their choice. In
this results will be similar to those using the slack time remaining method. It can also be used by
firm for increasing their efficiency.
Clearly explain how knowledge of layout planning and work system processes within a business
organisation have been applied
Explanation of layout planning and its benefits-
Layout planning is deciding on the best and better physical arrangement of all assets that
consume space within a facility. These assets include a desk, a cabinet, an entire office, a work
centre and a department (Hammad, Akbarnezhad and Rey, 2016). Choices about the preparation
of all above things in a firm are not made only when a new things is being designed, they are
made any time there is a modification in the arrangement of assets, such as new worker being
added, a change in process being implemented and a machine being moved. In simple words,
layout planning is performed any time within organizations, there is an expansion in facility.
Preparation or layout planning in firm can significantly impact on productivity and profitability
of a business company. A lot of wasted time, confusion as well as wasted energy can outcome
from a poor layout. Layout planning is very essential in context of Ikea because it help to
increase flow of information, build effective working relationships and improve communication
process effectively (Fedtke and Boysen, 2017).
Knowledge of layout planning is effectively applied within firms as it helps to enhance
productivity with more teams being produced per workers hour.
Types of layouts and its suitability to varied business environment-
goods and services. It is not the fasted method, but it is one of the most effective method. It will
help firm in making goods and services available to consumers on the exact timing as the due
date. This will also help IKEA in enhancing their efficiency as consumers will be satisfied and
also slack time remaining can assist them in improvising their production aspects. It will help
company in creating consumer’s loyalty.
Critical ratio: This method is fully based on slack time remaining method by making use
of critical ratio. The difference is that instead of subtracting processing time from time
remaining, then company divide it (Marklund and Berling, 2017). In this company have a total
idea how much time is remaining with for the exact delivery. It has been analysed that firm
instead of using division can also make use of subtraction, it is totally based on their choice. In
this results will be similar to those using the slack time remaining method. It can also be used by
firm for increasing their efficiency.
Clearly explain how knowledge of layout planning and work system processes within a business
organisation have been applied
Explanation of layout planning and its benefits-
Layout planning is deciding on the best and better physical arrangement of all assets that
consume space within a facility. These assets include a desk, a cabinet, an entire office, a work
centre and a department (Hammad, Akbarnezhad and Rey, 2016). Choices about the preparation
of all above things in a firm are not made only when a new things is being designed, they are
made any time there is a modification in the arrangement of assets, such as new worker being
added, a change in process being implemented and a machine being moved. In simple words,
layout planning is performed any time within organizations, there is an expansion in facility.
Preparation or layout planning in firm can significantly impact on productivity and profitability
of a business company. A lot of wasted time, confusion as well as wasted energy can outcome
from a poor layout. Layout planning is very essential in context of Ikea because it help to
increase flow of information, build effective working relationships and improve communication
process effectively (Fedtke and Boysen, 2017).
Knowledge of layout planning is effectively applied within firms as it helps to enhance
productivity with more teams being produced per workers hour.
Types of layouts and its suitability to varied business environment-
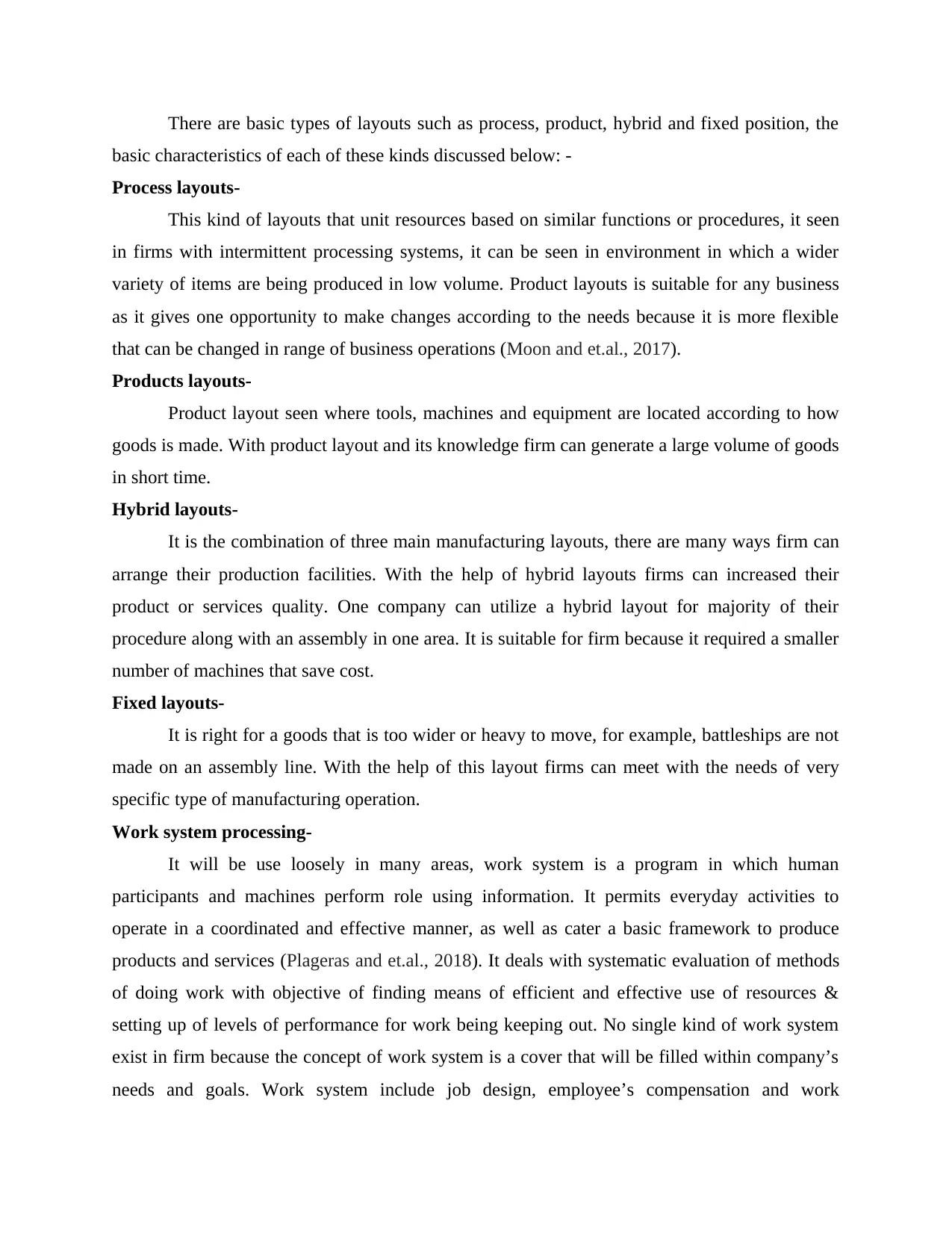
There are basic types of layouts such as process, product, hybrid and fixed position, the
basic characteristics of each of these kinds discussed below: -
Process layouts-
This kind of layouts that unit resources based on similar functions or procedures, it seen
in firms with intermittent processing systems, it can be seen in environment in which a wider
variety of items are being produced in low volume. Product layouts is suitable for any business
as it gives one opportunity to make changes according to the needs because it is more flexible
that can be changed in range of business operations (Moon and et.al., 2017).
Products layouts-
Product layout seen where tools, machines and equipment are located according to how
goods is made. With product layout and its knowledge firm can generate a large volume of goods
in short time.
Hybrid layouts-
It is the combination of three main manufacturing layouts, there are many ways firm can
arrange their production facilities. With the help of hybrid layouts firms can increased their
product or services quality. One company can utilize a hybrid layout for majority of their
procedure along with an assembly in one area. It is suitable for firm because it required a smaller
number of machines that save cost.
Fixed layouts-
It is right for a goods that is too wider or heavy to move, for example, battleships are not
made on an assembly line. With the help of this layout firms can meet with the needs of very
specific type of manufacturing operation.
Work system processing-
It will be use loosely in many areas, work system is a program in which human
participants and machines perform role using information. It permits everyday activities to
operate in a coordinated and effective manner, as well as cater a basic framework to produce
products and services (Plageras and et.al., 2018). It deals with systematic evaluation of methods
of doing work with objective of finding means of efficient and effective use of resources &
setting up of levels of performance for work being keeping out. No single kind of work system
exist in firm because the concept of work system is a cover that will be filled within company’s
needs and goals. Work system include job design, employee’s compensation and work
basic characteristics of each of these kinds discussed below: -
Process layouts-
This kind of layouts that unit resources based on similar functions or procedures, it seen
in firms with intermittent processing systems, it can be seen in environment in which a wider
variety of items are being produced in low volume. Product layouts is suitable for any business
as it gives one opportunity to make changes according to the needs because it is more flexible
that can be changed in range of business operations (Moon and et.al., 2017).
Products layouts-
Product layout seen where tools, machines and equipment are located according to how
goods is made. With product layout and its knowledge firm can generate a large volume of goods
in short time.
Hybrid layouts-
It is the combination of three main manufacturing layouts, there are many ways firm can
arrange their production facilities. With the help of hybrid layouts firms can increased their
product or services quality. One company can utilize a hybrid layout for majority of their
procedure along with an assembly in one area. It is suitable for firm because it required a smaller
number of machines that save cost.
Fixed layouts-
It is right for a goods that is too wider or heavy to move, for example, battleships are not
made on an assembly line. With the help of this layout firms can meet with the needs of very
specific type of manufacturing operation.
Work system processing-
It will be use loosely in many areas, work system is a program in which human
participants and machines perform role using information. It permits everyday activities to
operate in a coordinated and effective manner, as well as cater a basic framework to produce
products and services (Plageras and et.al., 2018). It deals with systematic evaluation of methods
of doing work with objective of finding means of efficient and effective use of resources &
setting up of levels of performance for work being keeping out. No single kind of work system
exist in firm because the concept of work system is a cover that will be filled within company’s
needs and goals. Work system include job design, employee’s compensation and work
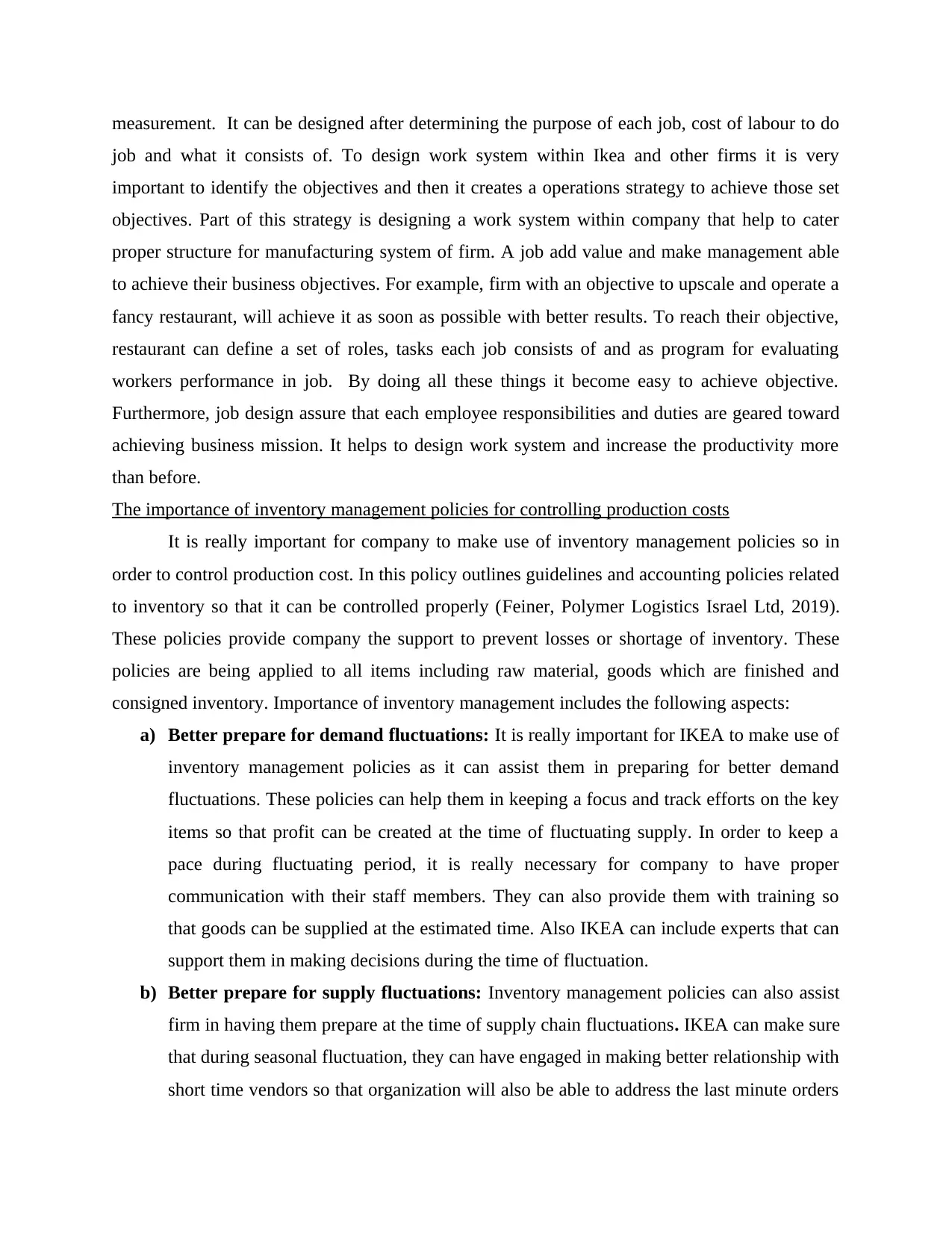
measurement. It can be designed after determining the purpose of each job, cost of labour to do
job and what it consists of. To design work system within Ikea and other firms it is very
important to identify the objectives and then it creates a operations strategy to achieve those set
objectives. Part of this strategy is designing a work system within company that help to cater
proper structure for manufacturing system of firm. A job add value and make management able
to achieve their business objectives. For example, firm with an objective to upscale and operate a
fancy restaurant, will achieve it as soon as possible with better results. To reach their objective,
restaurant can define a set of roles, tasks each job consists of and as program for evaluating
workers performance in job. By doing all these things it become easy to achieve objective.
Furthermore, job design assure that each employee responsibilities and duties are geared toward
achieving business mission. It helps to design work system and increase the productivity more
than before.
The importance of inventory management policies for controlling production costs
It is really important for company to make use of inventory management policies so in
order to control production cost. In this policy outlines guidelines and accounting policies related
to inventory so that it can be controlled properly (Feiner, Polymer Logistics Israel Ltd, 2019).
These policies provide company the support to prevent losses or shortage of inventory. These
policies are being applied to all items including raw material, goods which are finished and
consigned inventory. Importance of inventory management includes the following aspects:
a) Better prepare for demand fluctuations: It is really important for IKEA to make use of
inventory management policies as it can assist them in preparing for better demand
fluctuations. These policies can help them in keeping a focus and track efforts on the key
items so that profit can be created at the time of fluctuating supply. In order to keep a
pace during fluctuating period, it is really necessary for company to have proper
communication with their staff members. They can also provide them with training so
that goods can be supplied at the estimated time. Also IKEA can include experts that can
support them in making decisions during the time of fluctuation.
b) Better prepare for supply fluctuations: Inventory management policies can also assist
firm in having them prepare at the time of supply chain fluctuations. IKEA can make sure
that during seasonal fluctuation, they can have engaged in making better relationship with
short time vendors so that organization will also be able to address the last minute orders
job and what it consists of. To design work system within Ikea and other firms it is very
important to identify the objectives and then it creates a operations strategy to achieve those set
objectives. Part of this strategy is designing a work system within company that help to cater
proper structure for manufacturing system of firm. A job add value and make management able
to achieve their business objectives. For example, firm with an objective to upscale and operate a
fancy restaurant, will achieve it as soon as possible with better results. To reach their objective,
restaurant can define a set of roles, tasks each job consists of and as program for evaluating
workers performance in job. By doing all these things it become easy to achieve objective.
Furthermore, job design assure that each employee responsibilities and duties are geared toward
achieving business mission. It helps to design work system and increase the productivity more
than before.
The importance of inventory management policies for controlling production costs
It is really important for company to make use of inventory management policies so in
order to control production cost. In this policy outlines guidelines and accounting policies related
to inventory so that it can be controlled properly (Feiner, Polymer Logistics Israel Ltd, 2019).
These policies provide company the support to prevent losses or shortage of inventory. These
policies are being applied to all items including raw material, goods which are finished and
consigned inventory. Importance of inventory management includes the following aspects:
a) Better prepare for demand fluctuations: It is really important for IKEA to make use of
inventory management policies as it can assist them in preparing for better demand
fluctuations. These policies can help them in keeping a focus and track efforts on the key
items so that profit can be created at the time of fluctuating supply. In order to keep a
pace during fluctuating period, it is really necessary for company to have proper
communication with their staff members. They can also provide them with training so
that goods can be supplied at the estimated time. Also IKEA can include experts that can
support them in making decisions during the time of fluctuation.
b) Better prepare for supply fluctuations: Inventory management policies can also assist
firm in having them prepare at the time of supply chain fluctuations. IKEA can make sure
that during seasonal fluctuation, they can have engaged in making better relationship with
short time vendors so that organization will also be able to address the last minute orders
Paraphrase This Document
Need a fresh take? Get an instant paraphrase of this document with our AI Paraphraser
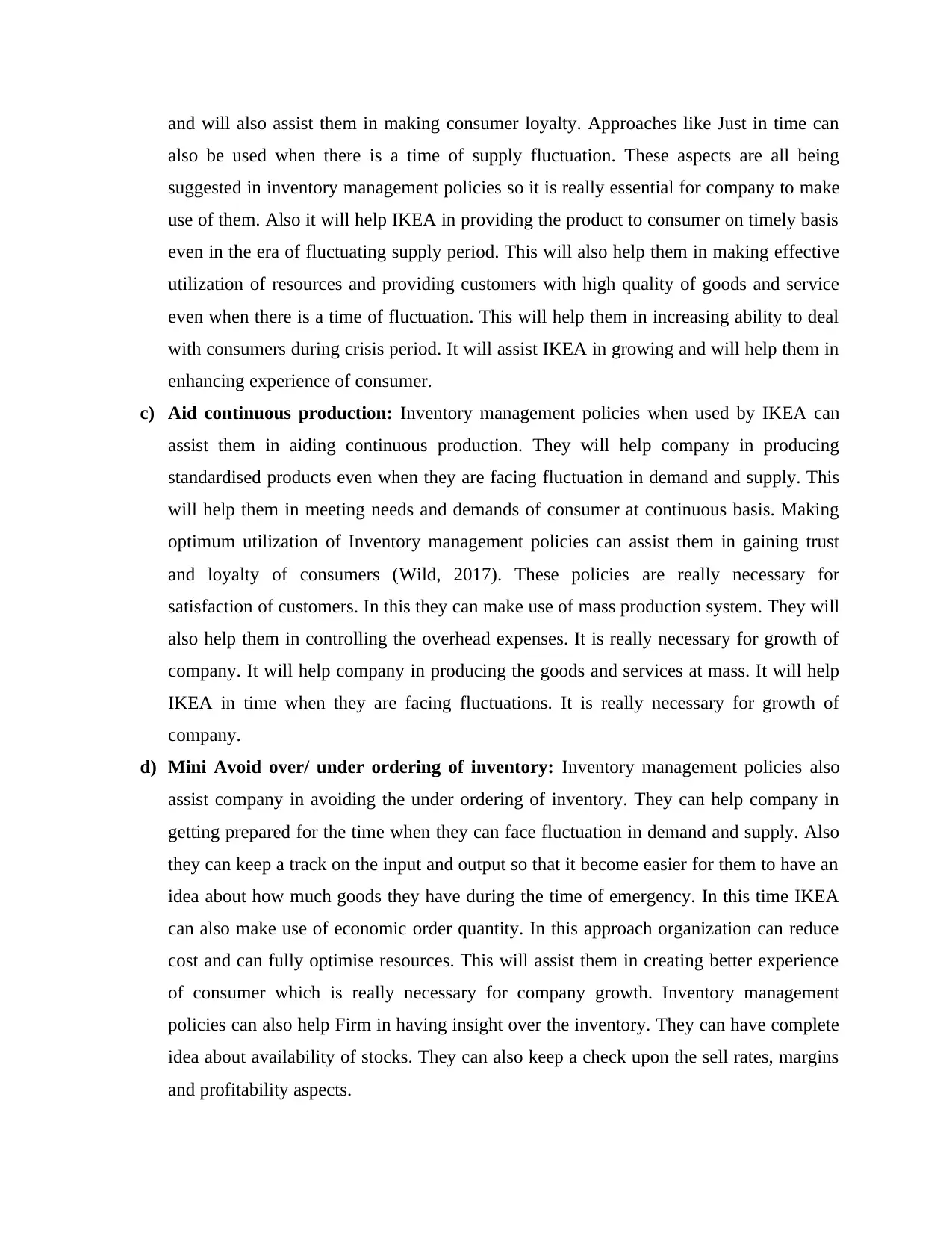
and will also assist them in making consumer loyalty. Approaches like Just in time can
also be used when there is a time of supply fluctuation. These aspects are all being
suggested in inventory management policies so it is really essential for company to make
use of them. Also it will help IKEA in providing the product to consumer on timely basis
even in the era of fluctuating supply period. This will also help them in making effective
utilization of resources and providing customers with high quality of goods and service
even when there is a time of fluctuation. This will help them in increasing ability to deal
with consumers during crisis period. It will assist IKEA in growing and will help them in
enhancing experience of consumer.
c) Aid continuous production: Inventory management policies when used by IKEA can
assist them in aiding continuous production. They will help company in producing
standardised products even when they are facing fluctuation in demand and supply. This
will help them in meeting needs and demands of consumer at continuous basis. Making
optimum utilization of Inventory management policies can assist them in gaining trust
and loyalty of consumers (Wild, 2017). These policies are really necessary for
satisfaction of customers. In this they can make use of mass production system. They will
also help them in controlling the overhead expenses. It is really necessary for growth of
company. It will help company in producing the goods and services at mass. It will help
IKEA in time when they are facing fluctuations. It is really necessary for growth of
company.
d) Mini Avoid over/ under ordering of inventory: Inventory management policies also
assist company in avoiding the under ordering of inventory. They can help company in
getting prepared for the time when they can face fluctuation in demand and supply. Also
they can keep a track on the input and output so that it become easier for them to have an
idea about how much goods they have during the time of emergency. In this time IKEA
can also make use of economic order quantity. In this approach organization can reduce
cost and can fully optimise resources. This will assist them in creating better experience
of consumer which is really necessary for company growth. Inventory management
policies can also help Firm in having insight over the inventory. They can have complete
idea about availability of stocks. They can also keep a check upon the sell rates, margins
and profitability aspects.
also be used when there is a time of supply fluctuation. These aspects are all being
suggested in inventory management policies so it is really essential for company to make
use of them. Also it will help IKEA in providing the product to consumer on timely basis
even in the era of fluctuating supply period. This will also help them in making effective
utilization of resources and providing customers with high quality of goods and service
even when there is a time of fluctuation. This will help them in increasing ability to deal
with consumers during crisis period. It will assist IKEA in growing and will help them in
enhancing experience of consumer.
c) Aid continuous production: Inventory management policies when used by IKEA can
assist them in aiding continuous production. They will help company in producing
standardised products even when they are facing fluctuation in demand and supply. This
will help them in meeting needs and demands of consumer at continuous basis. Making
optimum utilization of Inventory management policies can assist them in gaining trust
and loyalty of consumers (Wild, 2017). These policies are really necessary for
satisfaction of customers. In this they can make use of mass production system. They will
also help them in controlling the overhead expenses. It is really necessary for growth of
company. It will help company in producing the goods and services at mass. It will help
IKEA in time when they are facing fluctuations. It is really necessary for growth of
company.
d) Mini Avoid over/ under ordering of inventory: Inventory management policies also
assist company in avoiding the under ordering of inventory. They can help company in
getting prepared for the time when they can face fluctuation in demand and supply. Also
they can keep a track on the input and output so that it become easier for them to have an
idea about how much goods they have during the time of emergency. In this time IKEA
can also make use of economic order quantity. In this approach organization can reduce
cost and can fully optimise resources. This will assist them in creating better experience
of consumer which is really necessary for company growth. Inventory management
policies can also help Firm in having insight over the inventory. They can have complete
idea about availability of stocks. They can also keep a check upon the sell rates, margins
and profitability aspects.
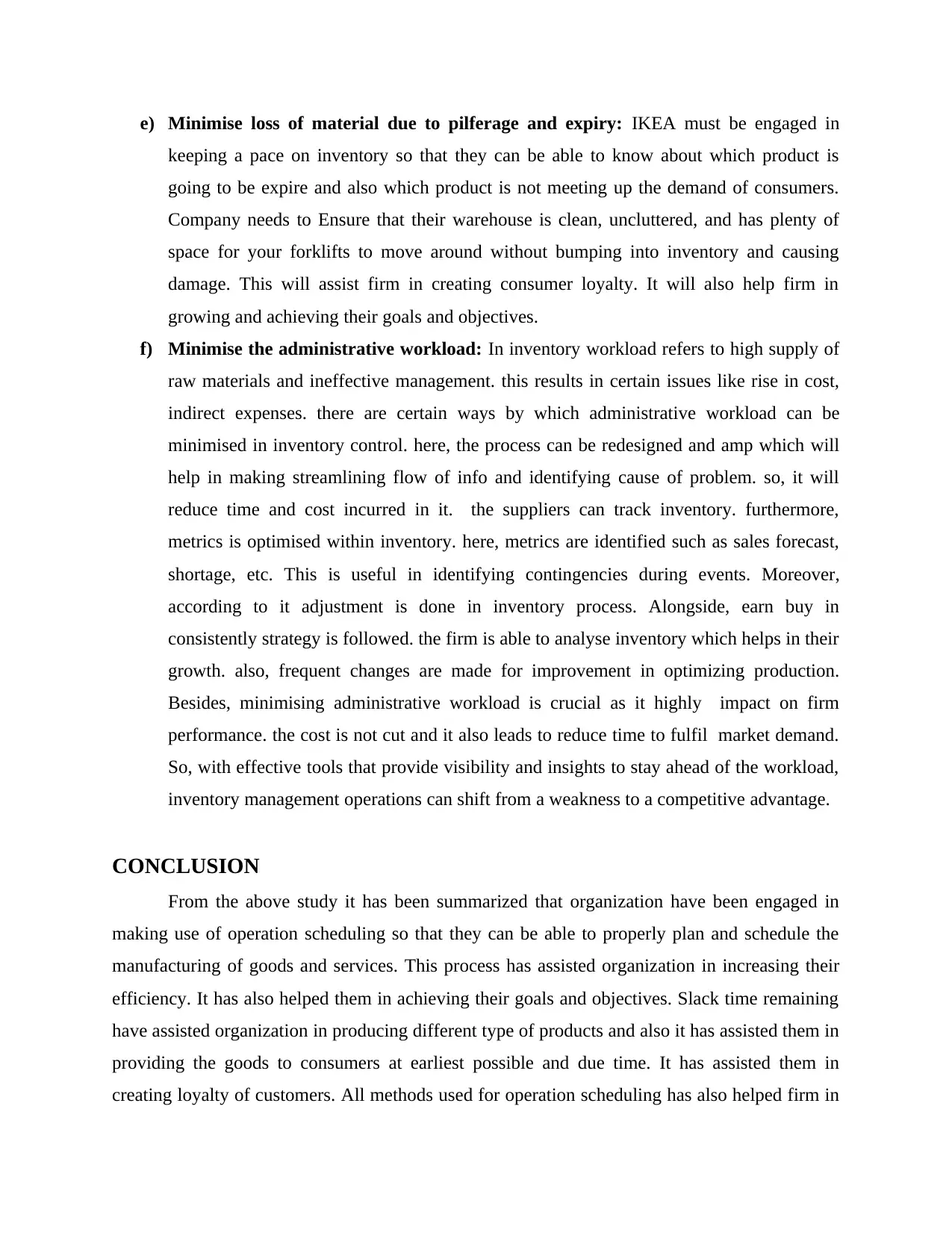
e) Minimise loss of material due to pilferage and expiry: IKEA must be engaged in
keeping a pace on inventory so that they can be able to know about which product is
going to be expire and also which product is not meeting up the demand of consumers.
Company needs to Ensure that their warehouse is clean, uncluttered, and has plenty of
space for your forklifts to move around without bumping into inventory and causing
damage. This will assist firm in creating consumer loyalty. It will also help firm in
growing and achieving their goals and objectives.
f) Minimise the administrative workload: In inventory workload refers to high supply of
raw materials and ineffective management. this results in certain issues like rise in cost,
indirect expenses. there are certain ways by which administrative workload can be
minimised in inventory control. here, the process can be redesigned and amp which will
help in making streamlining flow of info and identifying cause of problem. so, it will
reduce time and cost incurred in it. the suppliers can track inventory. furthermore,
metrics is optimised within inventory. here, metrics are identified such as sales forecast,
shortage, etc. This is useful in identifying contingencies during events. Moreover,
according to it adjustment is done in inventory process. Alongside, earn buy in
consistently strategy is followed. the firm is able to analyse inventory which helps in their
growth. also, frequent changes are made for improvement in optimizing production.
Besides, minimising administrative workload is crucial as it highly impact on firm
performance. the cost is not cut and it also leads to reduce time to fulfil market demand.
So, with effective tools that provide visibility and insights to stay ahead of the workload,
inventory management operations can shift from a weakness to a competitive advantage.
CONCLUSION
From the above study it has been summarized that organization have been engaged in
making use of operation scheduling so that they can be able to properly plan and schedule the
manufacturing of goods and services. This process has assisted organization in increasing their
efficiency. It has also helped them in achieving their goals and objectives. Slack time remaining
have assisted organization in producing different type of products and also it has assisted them in
providing the goods to consumers at earliest possible and due time. It has assisted them in
creating loyalty of customers. All methods used for operation scheduling has also helped firm in
keeping a pace on inventory so that they can be able to know about which product is
going to be expire and also which product is not meeting up the demand of consumers.
Company needs to Ensure that their warehouse is clean, uncluttered, and has plenty of
space for your forklifts to move around without bumping into inventory and causing
damage. This will assist firm in creating consumer loyalty. It will also help firm in
growing and achieving their goals and objectives.
f) Minimise the administrative workload: In inventory workload refers to high supply of
raw materials and ineffective management. this results in certain issues like rise in cost,
indirect expenses. there are certain ways by which administrative workload can be
minimised in inventory control. here, the process can be redesigned and amp which will
help in making streamlining flow of info and identifying cause of problem. so, it will
reduce time and cost incurred in it. the suppliers can track inventory. furthermore,
metrics is optimised within inventory. here, metrics are identified such as sales forecast,
shortage, etc. This is useful in identifying contingencies during events. Moreover,
according to it adjustment is done in inventory process. Alongside, earn buy in
consistently strategy is followed. the firm is able to analyse inventory which helps in their
growth. also, frequent changes are made for improvement in optimizing production.
Besides, minimising administrative workload is crucial as it highly impact on firm
performance. the cost is not cut and it also leads to reduce time to fulfil market demand.
So, with effective tools that provide visibility and insights to stay ahead of the workload,
inventory management operations can shift from a weakness to a competitive advantage.
CONCLUSION
From the above study it has been summarized that organization have been engaged in
making use of operation scheduling so that they can be able to properly plan and schedule the
manufacturing of goods and services. This process has assisted organization in increasing their
efficiency. It has also helped them in achieving their goals and objectives. Slack time remaining
have assisted organization in producing different type of products and also it has assisted them in
providing the goods to consumers at earliest possible and due time. It has assisted them in
creating loyalty of customers. All methods used for operation scheduling has also helped firm in
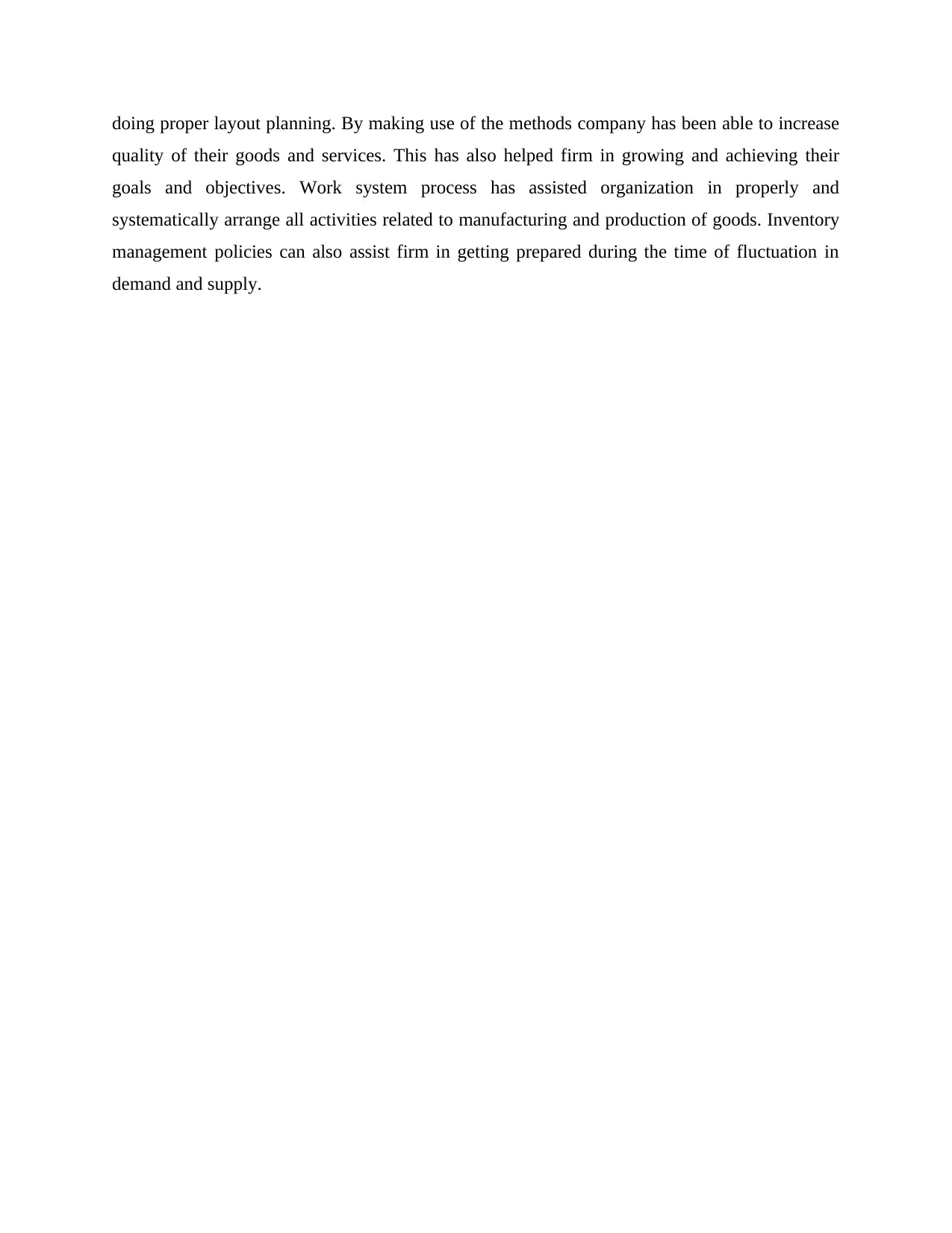
doing proper layout planning. By making use of the methods company has been able to increase
quality of their goods and services. This has also helped firm in growing and achieving their
goals and objectives. Work system process has assisted organization in properly and
systematically arrange all activities related to manufacturing and production of goods. Inventory
management policies can also assist firm in getting prepared during the time of fluctuation in
demand and supply.
quality of their goods and services. This has also helped firm in growing and achieving their
goals and objectives. Work system process has assisted organization in properly and
systematically arrange all activities related to manufacturing and production of goods. Inventory
management policies can also assist firm in getting prepared during the time of fluctuation in
demand and supply.
Secure Best Marks with AI Grader
Need help grading? Try our AI Grader for instant feedback on your assignments.

REFERENCES
Books and Journals
Dillon, M., Oliveira, F. and Abbasi, B., 2017. A two-stage stochastic programming model for
inventory management in the blood supply chain. International Journal of Production
Economics, 187, pp.27-41.
Fedtke, S. and Boysen, N., 2017. Layout planning of sortation conveyors in parcel distribution
centers. Transportation Science. 51(1). pp.3-18.
Feiner, G., Polymer Logistics Israel Ltd, 2019. Inventory management system. U.S. Patent
10,364,052.
Hammad, A.W.A., Akbarnezhad, A. and Rey, D., 2016. A multi-objective mixed integer
nonlinear programming model for construction site layout planning to minimise noise
pollution and transport costs. Automation in construction. 61. pp.73-85.
Mamani, H., Nassiri, S. and Wagner, M.R., 2017. Closed-form solutions for robust inventory
management. Management Science. 63(5). pp.1625-1643.
Marklund, J. and Berling, P., 2017. Green inventory management. In Sustainable supply
chains (pp. 189-218). Springer, Cham.
McKirdy, S., 2016. Barcode generation and implementation method and system for processing
information. U.S. Patent 9.367.860.
McNamara, A.M. and et.al., 2019. Dynamic inventory management user interface. U.S. Patent
10,303,187.
Moon, D.H and et.al., 2017. EFFECT OF PART TRANSFER POLICIES IN TWO TYPES OF
LAYOUTS IN AUTOMOTIVE BODY SHOPS. International Journal of Industrial
Engineering. 24(2).
Parpia, I.H. and Singh, G., DecisionGPS, LLC, 2016. Automated inventory management. U.S.
Patent 9,280,757.
Plageras, A.P and et.al., 2018. Efficient IoT-based sensor BIG Data collection–processing and
analysis in smart buildings. Future Generation Computer Systems. 82. pp.349-357.
Sayed, S., Kamath, A. and Sharma, A., 2018. System for inventory management. U.S. Patent
Application 15/359,854.
Wild, T., 2017. Best practice in inventory management. Routledge.
Books and Journals
Dillon, M., Oliveira, F. and Abbasi, B., 2017. A two-stage stochastic programming model for
inventory management in the blood supply chain. International Journal of Production
Economics, 187, pp.27-41.
Fedtke, S. and Boysen, N., 2017. Layout planning of sortation conveyors in parcel distribution
centers. Transportation Science. 51(1). pp.3-18.
Feiner, G., Polymer Logistics Israel Ltd, 2019. Inventory management system. U.S. Patent
10,364,052.
Hammad, A.W.A., Akbarnezhad, A. and Rey, D., 2016. A multi-objective mixed integer
nonlinear programming model for construction site layout planning to minimise noise
pollution and transport costs. Automation in construction. 61. pp.73-85.
Mamani, H., Nassiri, S. and Wagner, M.R., 2017. Closed-form solutions for robust inventory
management. Management Science. 63(5). pp.1625-1643.
Marklund, J. and Berling, P., 2017. Green inventory management. In Sustainable supply
chains (pp. 189-218). Springer, Cham.
McKirdy, S., 2016. Barcode generation and implementation method and system for processing
information. U.S. Patent 9.367.860.
McNamara, A.M. and et.al., 2019. Dynamic inventory management user interface. U.S. Patent
10,303,187.
Moon, D.H and et.al., 2017. EFFECT OF PART TRANSFER POLICIES IN TWO TYPES OF
LAYOUTS IN AUTOMOTIVE BODY SHOPS. International Journal of Industrial
Engineering. 24(2).
Parpia, I.H. and Singh, G., DecisionGPS, LLC, 2016. Automated inventory management. U.S.
Patent 9,280,757.
Plageras, A.P and et.al., 2018. Efficient IoT-based sensor BIG Data collection–processing and
analysis in smart buildings. Future Generation Computer Systems. 82. pp.349-357.
Sayed, S., Kamath, A. and Sharma, A., 2018. System for inventory management. U.S. Patent
Application 15/359,854.
Wild, T., 2017. Best practice in inventory management. Routledge.
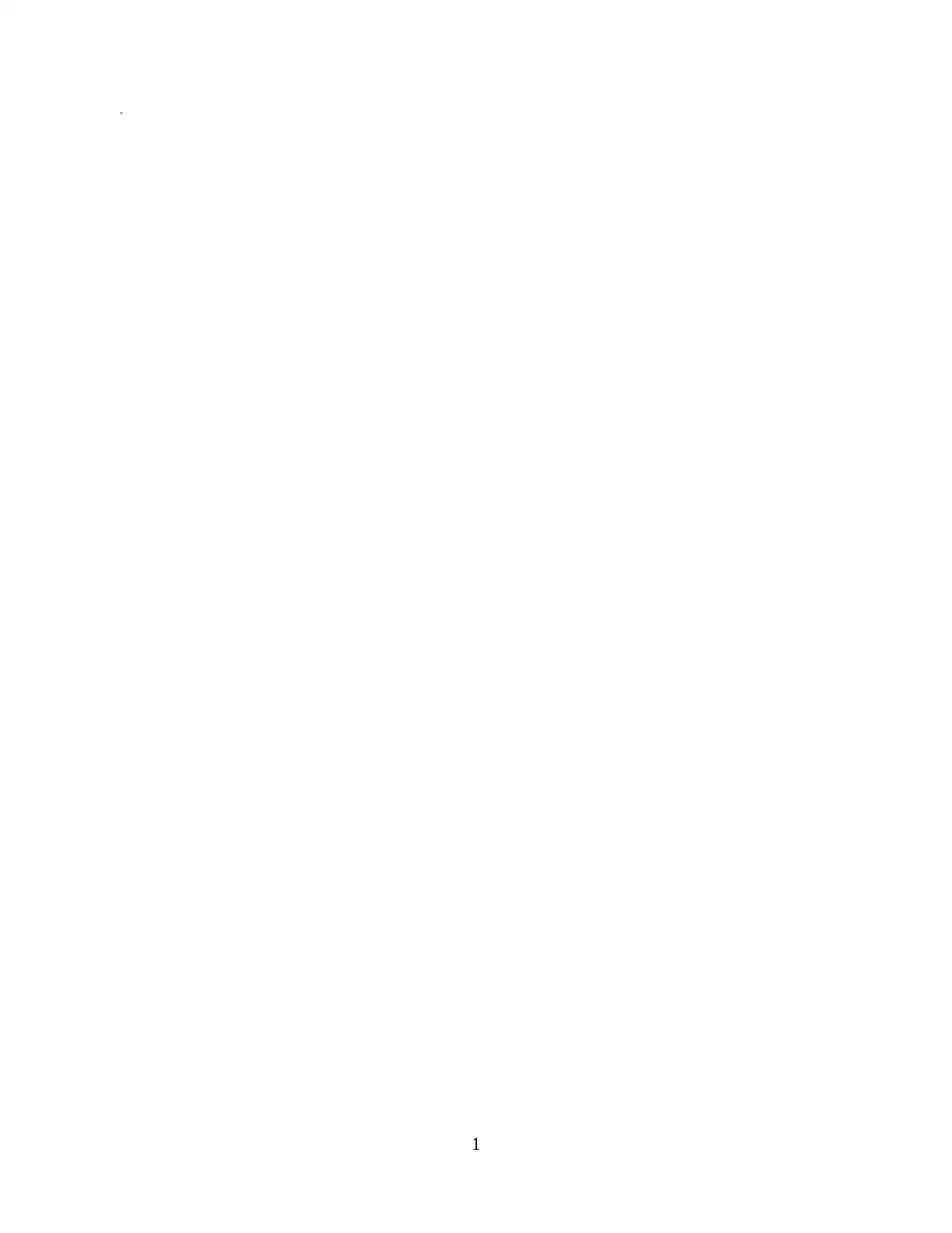
1
1 out of 12
Related Documents

Your All-in-One AI-Powered Toolkit for Academic Success.
 +13062052269
info@desklib.com
Available 24*7 on WhatsApp / Email
Unlock your academic potential
© 2024  |  Zucol Services PVT LTD  |  All rights reserved.