Operations and Service Management Report: Apple Inc. Case Study
VerifiedAdded on 2023/06/09
|10
|2847
|76
Report
AI Summary
This report provides a comprehensive analysis of Apple Inc.'s operations management practices. It identifies key operational practices, focusing on efficiency, particularly in areas such as product quality, inventory control, and governance methods. The report critically examines the impact of these practices on the organization's overall efficiency, highlighting how Apple leverages technology to enhance its operations. Furthermore, it evaluates the integration of technology in various processes, emphasizing how this has improved efficiency, reduced costs, and improved product quality. The report also discusses supporting functions, such as those linked to the First In, First Out (FIFO) inventory system, and their contribution to the company's success. The analysis covers technology acquisition, integration, and verification within Apple's operational framework, showcasing how the company maintains its competitive edge in the global market through the strategic application of information technology.
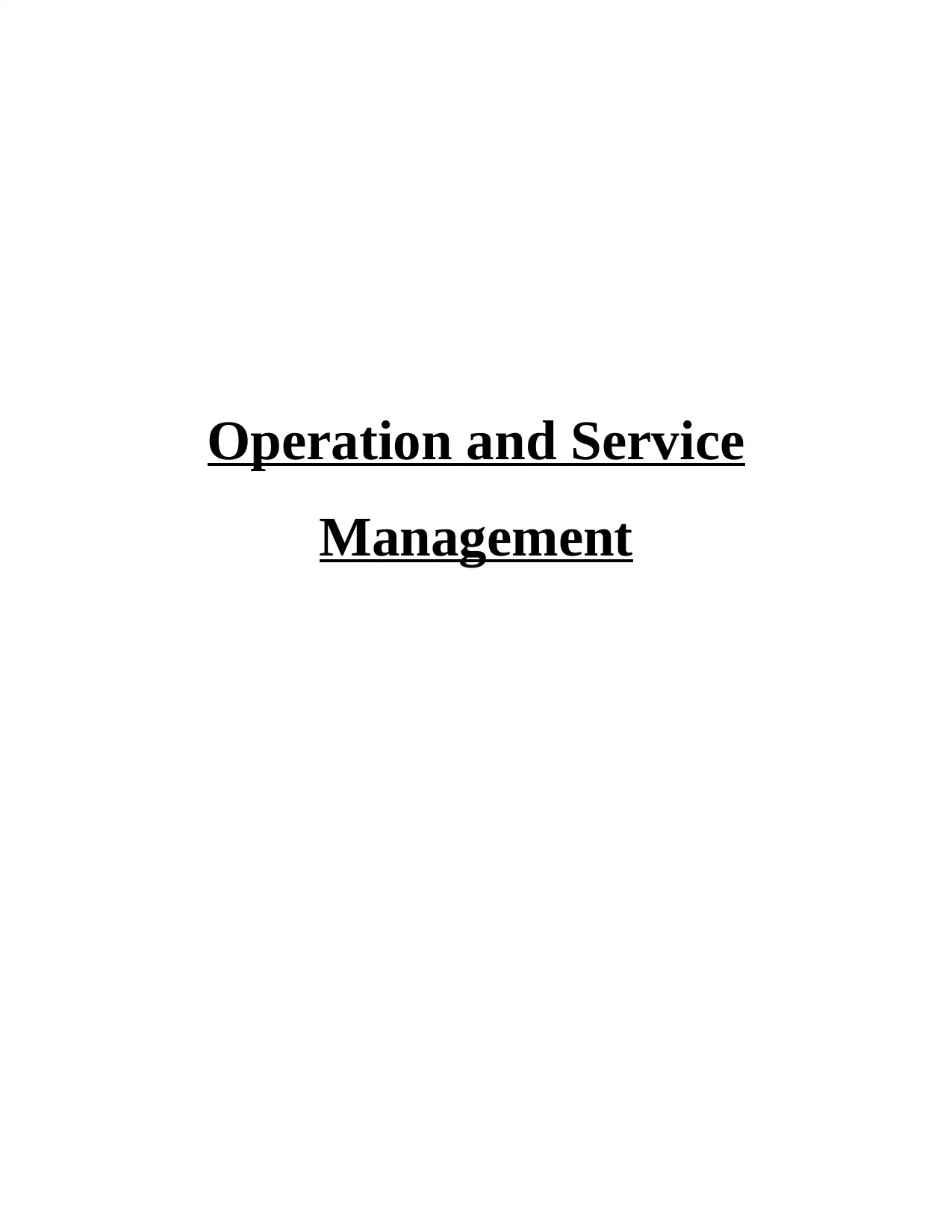
Operation and Service
Management
Management
Paraphrase This Document
Need a fresh take? Get an instant paraphrase of this document with our AI Paraphraser
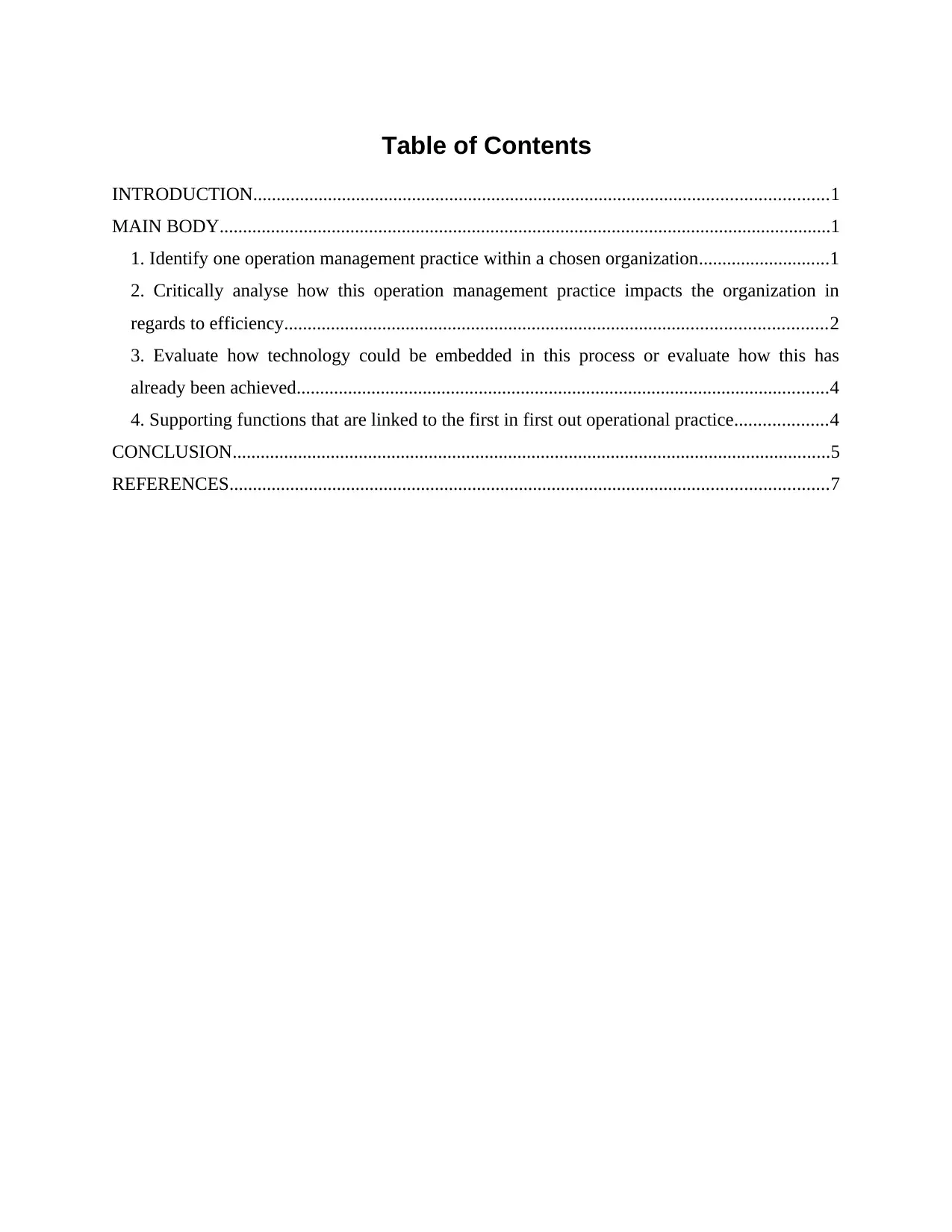
Table of Contents
INTRODUCTION...........................................................................................................................1
MAIN BODY...................................................................................................................................1
1. Identify one operation management practice within a chosen organization............................1
2. Critically analyse how this operation management practice impacts the organization in
regards to efficiency....................................................................................................................2
3. Evaluate how technology could be embedded in this process or evaluate how this has
already been achieved..................................................................................................................4
4. Supporting functions that are linked to the first in first out operational practice....................4
CONCLUSION................................................................................................................................5
REFERENCES................................................................................................................................7
INTRODUCTION...........................................................................................................................1
MAIN BODY...................................................................................................................................1
1. Identify one operation management practice within a chosen organization............................1
2. Critically analyse how this operation management practice impacts the organization in
regards to efficiency....................................................................................................................2
3. Evaluate how technology could be embedded in this process or evaluate how this has
already been achieved..................................................................................................................4
4. Supporting functions that are linked to the first in first out operational practice....................4
CONCLUSION................................................................................................................................5
REFERENCES................................................................................................................................7
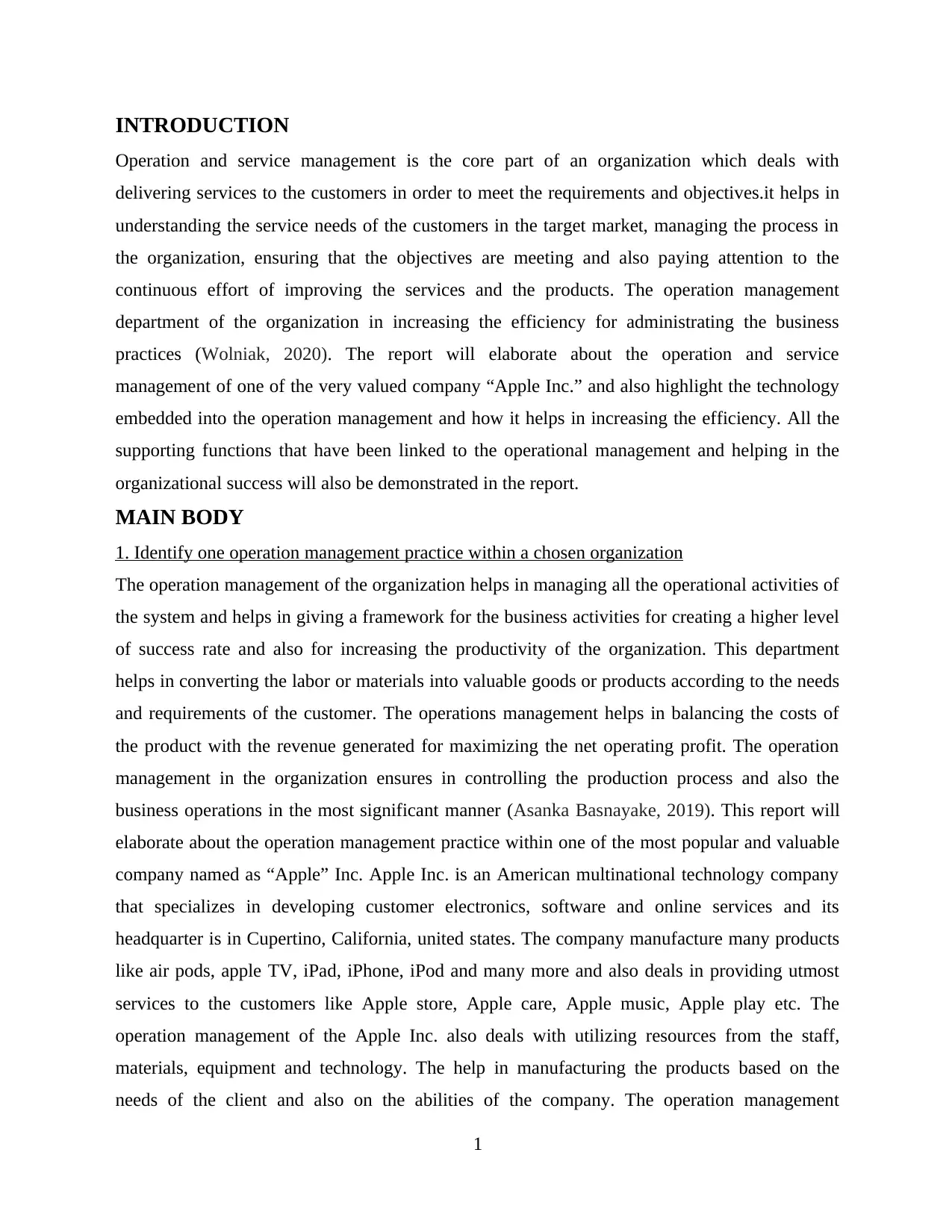
INTRODUCTION
Operation and service management is the core part of an organization which deals with
delivering services to the customers in order to meet the requirements and objectives.it helps in
understanding the service needs of the customers in the target market, managing the process in
the organization, ensuring that the objectives are meeting and also paying attention to the
continuous effort of improving the services and the products. The operation management
department of the organization in increasing the efficiency for administrating the business
practices (Wolniak, 2020). The report will elaborate about the operation and service
management of one of the very valued company “Apple Inc.” and also highlight the technology
embedded into the operation management and how it helps in increasing the efficiency. All the
supporting functions that have been linked to the operational management and helping in the
organizational success will also be demonstrated in the report.
MAIN BODY
1. Identify one operation management practice within a chosen organization
The operation management of the organization helps in managing all the operational activities of
the system and helps in giving a framework for the business activities for creating a higher level
of success rate and also for increasing the productivity of the organization. This department
helps in converting the labor or materials into valuable goods or products according to the needs
and requirements of the customer. The operations management helps in balancing the costs of
the product with the revenue generated for maximizing the net operating profit. The operation
management in the organization ensures in controlling the production process and also the
business operations in the most significant manner (Asanka Basnayake, 2019). This report will
elaborate about the operation management practice within one of the most popular and valuable
company named as “Apple” Inc. Apple Inc. is an American multinational technology company
that specializes in developing customer electronics, software and online services and its
headquarter is in Cupertino, California, united states. The company manufacture many products
like air pods, apple TV, iPad, iPhone, iPod and many more and also deals in providing utmost
services to the customers like Apple store, Apple care, Apple music, Apple play etc. The
operation management of the Apple Inc. also deals with utilizing resources from the staff,
materials, equipment and technology. The help in manufacturing the products based on the
needs of the client and also on the abilities of the company. The operation management
1
Operation and service management is the core part of an organization which deals with
delivering services to the customers in order to meet the requirements and objectives.it helps in
understanding the service needs of the customers in the target market, managing the process in
the organization, ensuring that the objectives are meeting and also paying attention to the
continuous effort of improving the services and the products. The operation management
department of the organization in increasing the efficiency for administrating the business
practices (Wolniak, 2020). The report will elaborate about the operation and service
management of one of the very valued company “Apple Inc.” and also highlight the technology
embedded into the operation management and how it helps in increasing the efficiency. All the
supporting functions that have been linked to the operational management and helping in the
organizational success will also be demonstrated in the report.
MAIN BODY
1. Identify one operation management practice within a chosen organization
The operation management of the organization helps in managing all the operational activities of
the system and helps in giving a framework for the business activities for creating a higher level
of success rate and also for increasing the productivity of the organization. This department
helps in converting the labor or materials into valuable goods or products according to the needs
and requirements of the customer. The operations management helps in balancing the costs of
the product with the revenue generated for maximizing the net operating profit. The operation
management in the organization ensures in controlling the production process and also the
business operations in the most significant manner (Asanka Basnayake, 2019). This report will
elaborate about the operation management practice within one of the most popular and valuable
company named as “Apple” Inc. Apple Inc. is an American multinational technology company
that specializes in developing customer electronics, software and online services and its
headquarter is in Cupertino, California, united states. The company manufacture many products
like air pods, apple TV, iPad, iPhone, iPod and many more and also deals in providing utmost
services to the customers like Apple store, Apple care, Apple music, Apple play etc. The
operation management of the Apple Inc. also deals with utilizing resources from the staff,
materials, equipment and technology. The help in manufacturing the products based on the
needs of the client and also on the abilities of the company. The operation management
1
You're viewing a preview
Unlock full access by subscribing today!
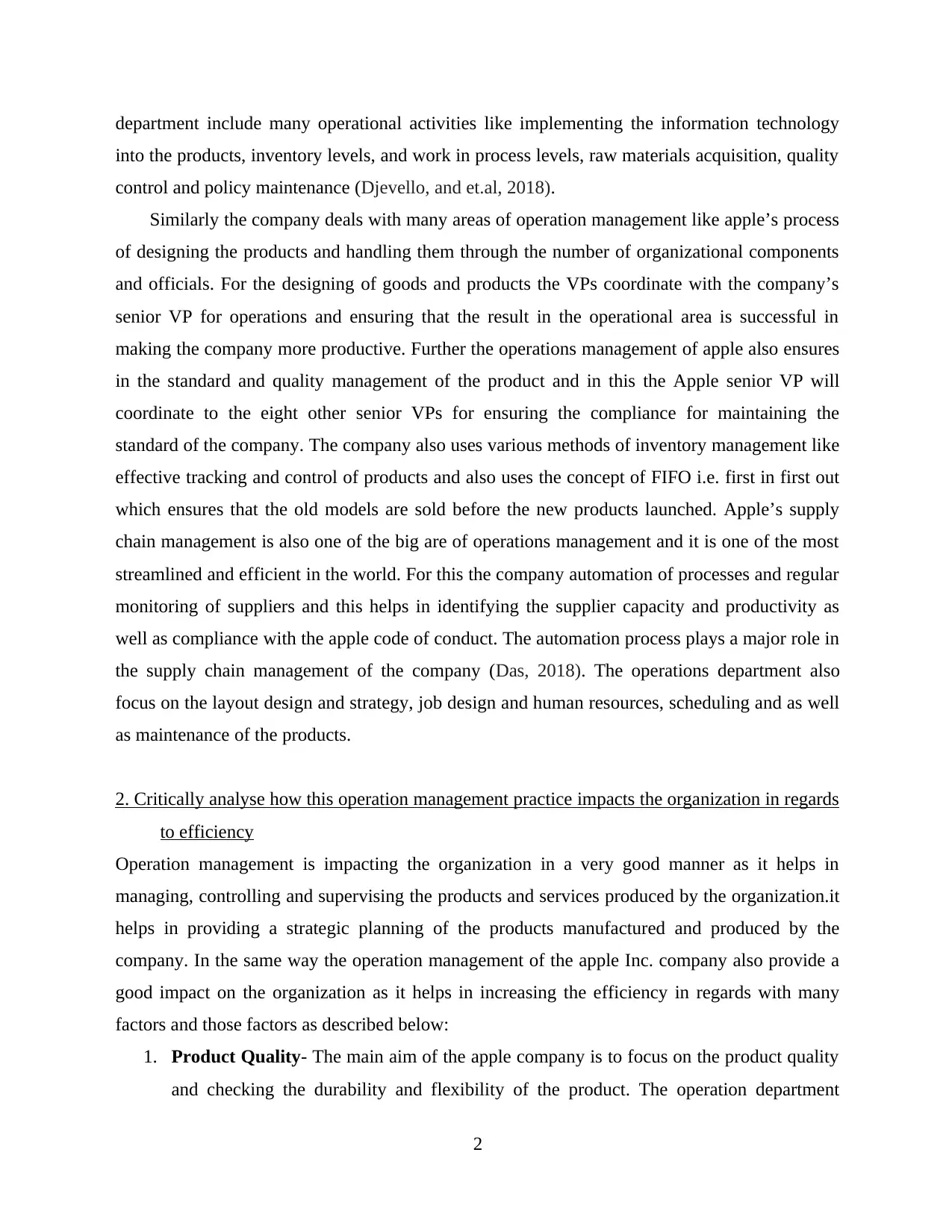
department include many operational activities like implementing the information technology
into the products, inventory levels, and work in process levels, raw materials acquisition, quality
control and policy maintenance (Djevello, and et.al, 2018).
Similarly the company deals with many areas of operation management like apple’s process
of designing the products and handling them through the number of organizational components
and officials. For the designing of goods and products the VPs coordinate with the company’s
senior VP for operations and ensuring that the result in the operational area is successful in
making the company more productive. Further the operations management of apple also ensures
in the standard and quality management of the product and in this the Apple senior VP will
coordinate to the eight other senior VPs for ensuring the compliance for maintaining the
standard of the company. The company also uses various methods of inventory management like
effective tracking and control of products and also uses the concept of FIFO i.e. first in first out
which ensures that the old models are sold before the new products launched. Apple’s supply
chain management is also one of the big are of operations management and it is one of the most
streamlined and efficient in the world. For this the company automation of processes and regular
monitoring of suppliers and this helps in identifying the supplier capacity and productivity as
well as compliance with the apple code of conduct. The automation process plays a major role in
the supply chain management of the company (Das, 2018). The operations department also
focus on the layout design and strategy, job design and human resources, scheduling and as well
as maintenance of the products.
2. Critically analyse how this operation management practice impacts the organization in regards
to efficiency
Operation management is impacting the organization in a very good manner as it helps in
managing, controlling and supervising the products and services produced by the organization.it
helps in providing a strategic planning of the products manufactured and produced by the
company. In the same way the operation management of the apple Inc. company also provide a
good impact on the organization as it helps in increasing the efficiency in regards with many
factors and those factors as described below:
1. Product Quality- The main aim of the apple company is to focus on the product quality
and checking the durability and flexibility of the product. The operation department
2
into the products, inventory levels, and work in process levels, raw materials acquisition, quality
control and policy maintenance (Djevello, and et.al, 2018).
Similarly the company deals with many areas of operation management like apple’s process
of designing the products and handling them through the number of organizational components
and officials. For the designing of goods and products the VPs coordinate with the company’s
senior VP for operations and ensuring that the result in the operational area is successful in
making the company more productive. Further the operations management of apple also ensures
in the standard and quality management of the product and in this the Apple senior VP will
coordinate to the eight other senior VPs for ensuring the compliance for maintaining the
standard of the company. The company also uses various methods of inventory management like
effective tracking and control of products and also uses the concept of FIFO i.e. first in first out
which ensures that the old models are sold before the new products launched. Apple’s supply
chain management is also one of the big are of operations management and it is one of the most
streamlined and efficient in the world. For this the company automation of processes and regular
monitoring of suppliers and this helps in identifying the supplier capacity and productivity as
well as compliance with the apple code of conduct. The automation process plays a major role in
the supply chain management of the company (Das, 2018). The operations department also
focus on the layout design and strategy, job design and human resources, scheduling and as well
as maintenance of the products.
2. Critically analyse how this operation management practice impacts the organization in regards
to efficiency
Operation management is impacting the organization in a very good manner as it helps in
managing, controlling and supervising the products and services produced by the organization.it
helps in providing a strategic planning of the products manufactured and produced by the
company. In the same way the operation management of the apple Inc. company also provide a
good impact on the organization as it helps in increasing the efficiency in regards with many
factors and those factors as described below:
1. Product Quality- The main aim of the apple company is to focus on the product quality
and checking the durability and flexibility of the product. The operation department
2
Paraphrase This Document
Need a fresh take? Get an instant paraphrase of this document with our AI Paraphraser
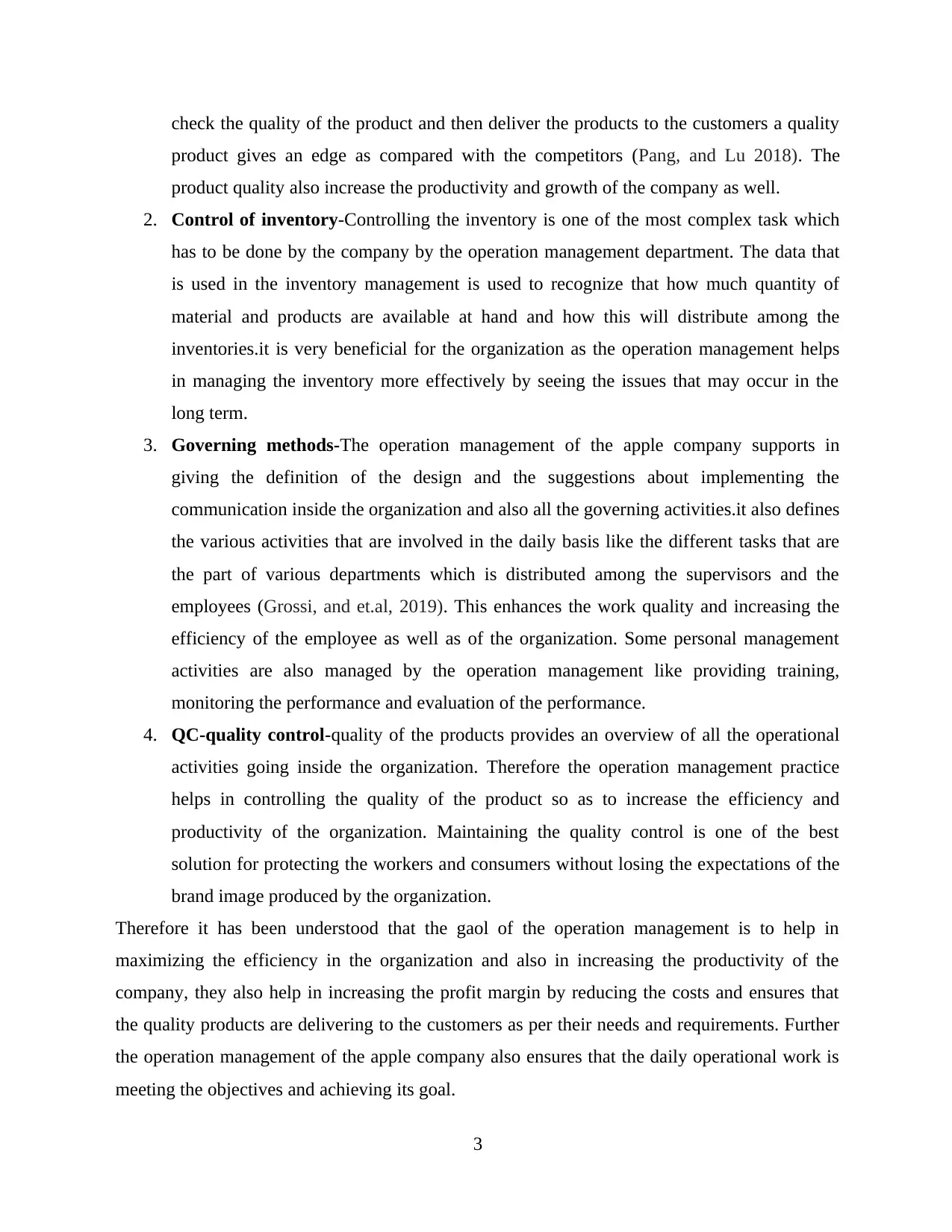
check the quality of the product and then deliver the products to the customers a quality
product gives an edge as compared with the competitors (Pang, and Lu 2018). The
product quality also increase the productivity and growth of the company as well.
2. Control of inventory-Controlling the inventory is one of the most complex task which
has to be done by the company by the operation management department. The data that
is used in the inventory management is used to recognize that how much quantity of
material and products are available at hand and how this will distribute among the
inventories.it is very beneficial for the organization as the operation management helps
in managing the inventory more effectively by seeing the issues that may occur in the
long term.
3. Governing methods-The operation management of the apple company supports in
giving the definition of the design and the suggestions about implementing the
communication inside the organization and also all the governing activities.it also defines
the various activities that are involved in the daily basis like the different tasks that are
the part of various departments which is distributed among the supervisors and the
employees (Grossi, and et.al, 2019). This enhances the work quality and increasing the
efficiency of the employee as well as of the organization. Some personal management
activities are also managed by the operation management like providing training,
monitoring the performance and evaluation of the performance.
4. QC-quality control-quality of the products provides an overview of all the operational
activities going inside the organization. Therefore the operation management practice
helps in controlling the quality of the product so as to increase the efficiency and
productivity of the organization. Maintaining the quality control is one of the best
solution for protecting the workers and consumers without losing the expectations of the
brand image produced by the organization.
Therefore it has been understood that the gaol of the operation management is to help in
maximizing the efficiency in the organization and also in increasing the productivity of the
company, they also help in increasing the profit margin by reducing the costs and ensures that
the quality products are delivering to the customers as per their needs and requirements. Further
the operation management of the apple company also ensures that the daily operational work is
meeting the objectives and achieving its goal.
3
product gives an edge as compared with the competitors (Pang, and Lu 2018). The
product quality also increase the productivity and growth of the company as well.
2. Control of inventory-Controlling the inventory is one of the most complex task which
has to be done by the company by the operation management department. The data that
is used in the inventory management is used to recognize that how much quantity of
material and products are available at hand and how this will distribute among the
inventories.it is very beneficial for the organization as the operation management helps
in managing the inventory more effectively by seeing the issues that may occur in the
long term.
3. Governing methods-The operation management of the apple company supports in
giving the definition of the design and the suggestions about implementing the
communication inside the organization and also all the governing activities.it also defines
the various activities that are involved in the daily basis like the different tasks that are
the part of various departments which is distributed among the supervisors and the
employees (Grossi, and et.al, 2019). This enhances the work quality and increasing the
efficiency of the employee as well as of the organization. Some personal management
activities are also managed by the operation management like providing training,
monitoring the performance and evaluation of the performance.
4. QC-quality control-quality of the products provides an overview of all the operational
activities going inside the organization. Therefore the operation management practice
helps in controlling the quality of the product so as to increase the efficiency and
productivity of the organization. Maintaining the quality control is one of the best
solution for protecting the workers and consumers without losing the expectations of the
brand image produced by the organization.
Therefore it has been understood that the gaol of the operation management is to help in
maximizing the efficiency in the organization and also in increasing the productivity of the
company, they also help in increasing the profit margin by reducing the costs and ensures that
the quality products are delivering to the customers as per their needs and requirements. Further
the operation management of the apple company also ensures that the daily operational work is
meeting the objectives and achieving its goal.
3
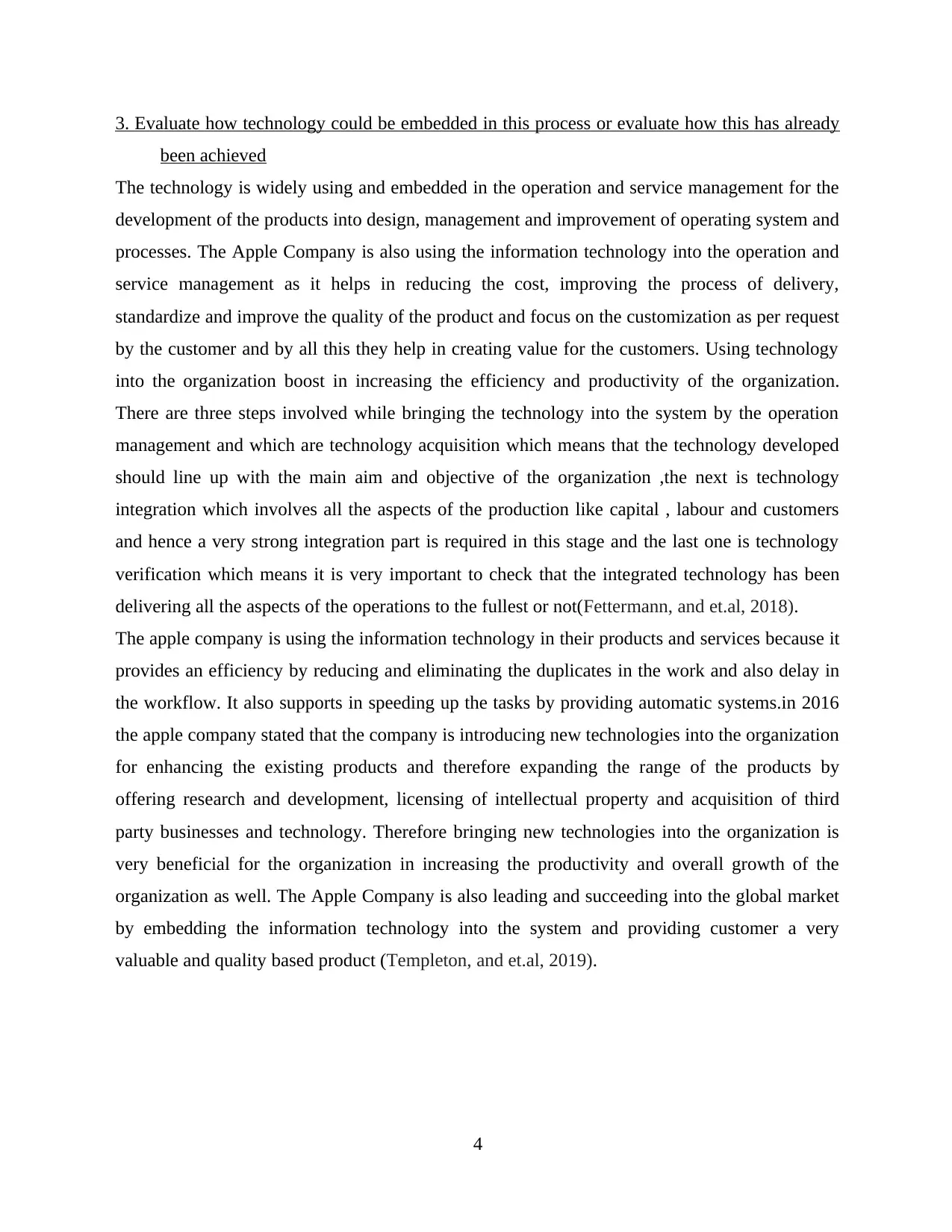
3. Evaluate how technology could be embedded in this process or evaluate how this has already
been achieved
The technology is widely using and embedded in the operation and service management for the
development of the products into design, management and improvement of operating system and
processes. The Apple Company is also using the information technology into the operation and
service management as it helps in reducing the cost, improving the process of delivery,
standardize and improve the quality of the product and focus on the customization as per request
by the customer and by all this they help in creating value for the customers. Using technology
into the organization boost in increasing the efficiency and productivity of the organization.
There are three steps involved while bringing the technology into the system by the operation
management and which are technology acquisition which means that the technology developed
should line up with the main aim and objective of the organization ,the next is technology
integration which involves all the aspects of the production like capital , labour and customers
and hence a very strong integration part is required in this stage and the last one is technology
verification which means it is very important to check that the integrated technology has been
delivering all the aspects of the operations to the fullest or not(Fettermann, and et.al, 2018).
The apple company is using the information technology in their products and services because it
provides an efficiency by reducing and eliminating the duplicates in the work and also delay in
the workflow. It also supports in speeding up the tasks by providing automatic systems.in 2016
the apple company stated that the company is introducing new technologies into the organization
for enhancing the existing products and therefore expanding the range of the products by
offering research and development, licensing of intellectual property and acquisition of third
party businesses and technology. Therefore bringing new technologies into the organization is
very beneficial for the organization in increasing the productivity and overall growth of the
organization as well. The Apple Company is also leading and succeeding into the global market
by embedding the information technology into the system and providing customer a very
valuable and quality based product (Templeton, and et.al, 2019).
4
been achieved
The technology is widely using and embedded in the operation and service management for the
development of the products into design, management and improvement of operating system and
processes. The Apple Company is also using the information technology into the operation and
service management as it helps in reducing the cost, improving the process of delivery,
standardize and improve the quality of the product and focus on the customization as per request
by the customer and by all this they help in creating value for the customers. Using technology
into the organization boost in increasing the efficiency and productivity of the organization.
There are three steps involved while bringing the technology into the system by the operation
management and which are technology acquisition which means that the technology developed
should line up with the main aim and objective of the organization ,the next is technology
integration which involves all the aspects of the production like capital , labour and customers
and hence a very strong integration part is required in this stage and the last one is technology
verification which means it is very important to check that the integrated technology has been
delivering all the aspects of the operations to the fullest or not(Fettermann, and et.al, 2018).
The apple company is using the information technology in their products and services because it
provides an efficiency by reducing and eliminating the duplicates in the work and also delay in
the workflow. It also supports in speeding up the tasks by providing automatic systems.in 2016
the apple company stated that the company is introducing new technologies into the organization
for enhancing the existing products and therefore expanding the range of the products by
offering research and development, licensing of intellectual property and acquisition of third
party businesses and technology. Therefore bringing new technologies into the organization is
very beneficial for the organization in increasing the productivity and overall growth of the
organization as well. The Apple Company is also leading and succeeding into the global market
by embedding the information technology into the system and providing customer a very
valuable and quality based product (Templeton, and et.al, 2019).
4
You're viewing a preview
Unlock full access by subscribing today!
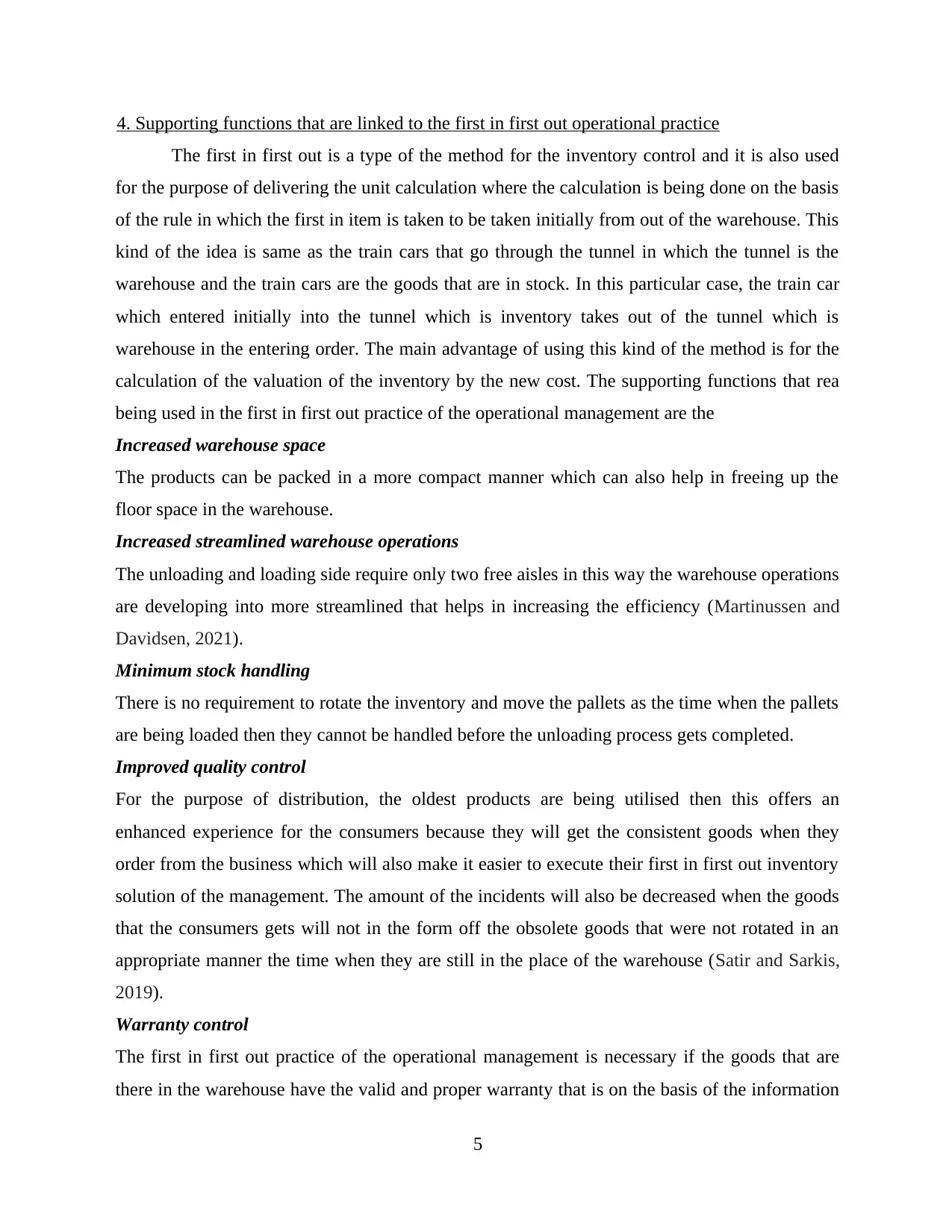
4. Supporting functions that are linked to the first in first out operational practice
The first in first out is a type of the method for the inventory control and it is also used
for the purpose of delivering the unit calculation where the calculation is being done on the basis
of the rule in which the first in item is taken to be taken initially from out of the warehouse. This
kind of the idea is same as the train cars that go through the tunnel in which the tunnel is the
warehouse and the train cars are the goods that are in stock. In this particular case, the train car
which entered initially into the tunnel which is inventory takes out of the tunnel which is
warehouse in the entering order. The main advantage of using this kind of the method is for the
calculation of the valuation of the inventory by the new cost. The supporting functions that rea
being used in the first in first out practice of the operational management are the
Increased warehouse space
The products can be packed in a more compact manner which can also help in freeing up the
floor space in the warehouse.
Increased streamlined warehouse operations
The unloading and loading side require only two free aisles in this way the warehouse operations
are developing into more streamlined that helps in increasing the efficiency (Martinussen and
Davidsen, 2021).
Minimum stock handling
There is no requirement to rotate the inventory and move the pallets as the time when the pallets
are being loaded then they cannot be handled before the unloading process gets completed.
Improved quality control
For the purpose of distribution, the oldest products are being utilised then this offers an
enhanced experience for the consumers because they will get the consistent goods when they
order from the business which will also make it easier to execute their first in first out inventory
solution of the management. The amount of the incidents will also be decreased when the goods
that the consumers gets will not in the form off the obsolete goods that were not rotated in an
appropriate manner the time when they are still in the place of the warehouse (Satir and Sarkis,
2019).
Warranty control
The first in first out practice of the operational management is necessary if the goods that are
there in the warehouse have the valid and proper warranty that is on the basis of the information
5
The first in first out is a type of the method for the inventory control and it is also used
for the purpose of delivering the unit calculation where the calculation is being done on the basis
of the rule in which the first in item is taken to be taken initially from out of the warehouse. This
kind of the idea is same as the train cars that go through the tunnel in which the tunnel is the
warehouse and the train cars are the goods that are in stock. In this particular case, the train car
which entered initially into the tunnel which is inventory takes out of the tunnel which is
warehouse in the entering order. The main advantage of using this kind of the method is for the
calculation of the valuation of the inventory by the new cost. The supporting functions that rea
being used in the first in first out practice of the operational management are the
Increased warehouse space
The products can be packed in a more compact manner which can also help in freeing up the
floor space in the warehouse.
Increased streamlined warehouse operations
The unloading and loading side require only two free aisles in this way the warehouse operations
are developing into more streamlined that helps in increasing the efficiency (Martinussen and
Davidsen, 2021).
Minimum stock handling
There is no requirement to rotate the inventory and move the pallets as the time when the pallets
are being loaded then they cannot be handled before the unloading process gets completed.
Improved quality control
For the purpose of distribution, the oldest products are being utilised then this offers an
enhanced experience for the consumers because they will get the consistent goods when they
order from the business which will also make it easier to execute their first in first out inventory
solution of the management. The amount of the incidents will also be decreased when the goods
that the consumers gets will not in the form off the obsolete goods that were not rotated in an
appropriate manner the time when they are still in the place of the warehouse (Satir and Sarkis,
2019).
Warranty control
The first in first out practice of the operational management is necessary if the goods that are
there in the warehouse have the valid and proper warranty that is on the basis of the information
5
Paraphrase This Document
Need a fresh take? Get an instant paraphrase of this document with our AI Paraphraser
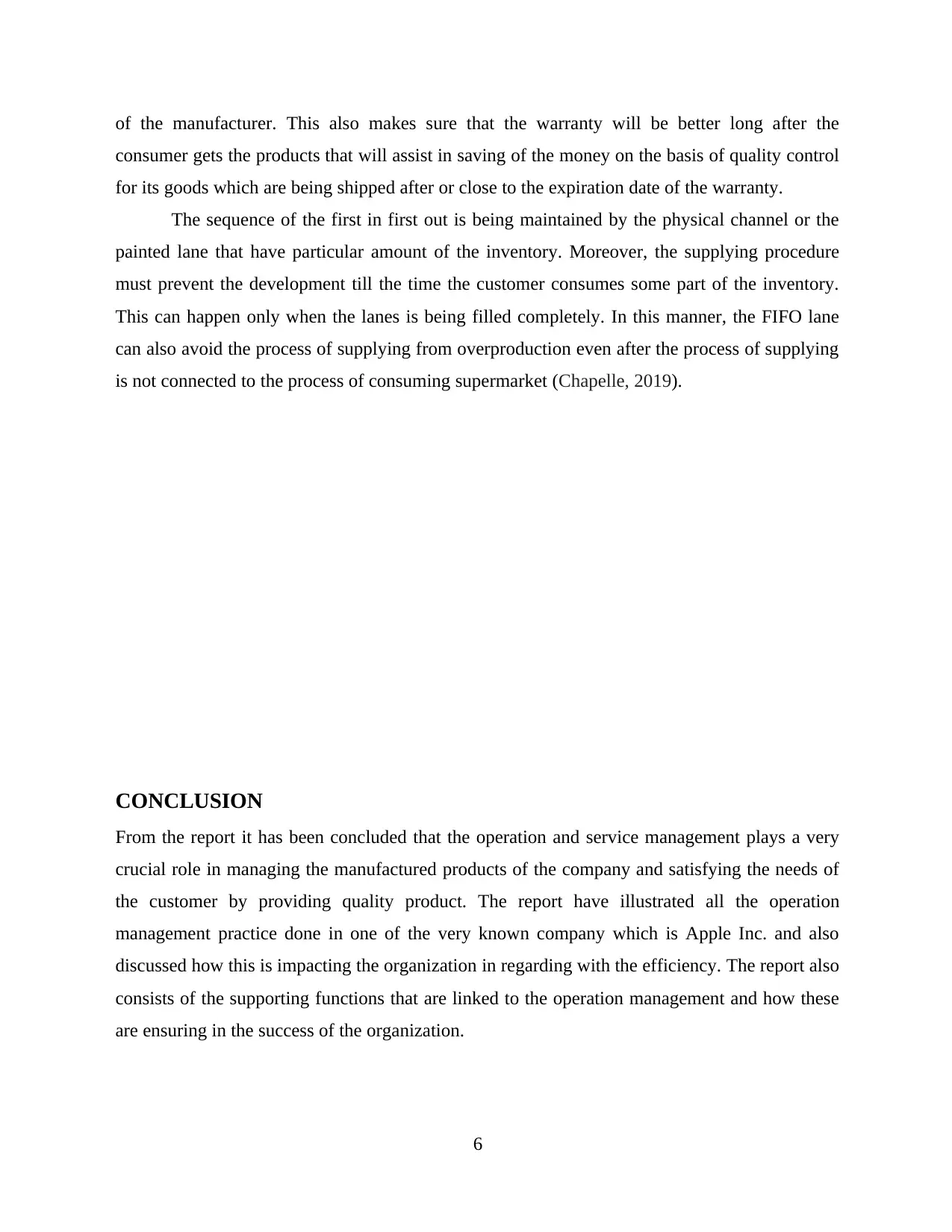
of the manufacturer. This also makes sure that the warranty will be better long after the
consumer gets the products that will assist in saving of the money on the basis of quality control
for its goods which are being shipped after or close to the expiration date of the warranty.
The sequence of the first in first out is being maintained by the physical channel or the
painted lane that have particular amount of the inventory. Moreover, the supplying procedure
must prevent the development till the time the customer consumes some part of the inventory.
This can happen only when the lanes is being filled completely. In this manner, the FIFO lane
can also avoid the process of supplying from overproduction even after the process of supplying
is not connected to the process of consuming supermarket (Chapelle, 2019).
CONCLUSION
From the report it has been concluded that the operation and service management plays a very
crucial role in managing the manufactured products of the company and satisfying the needs of
the customer by providing quality product. The report have illustrated all the operation
management practice done in one of the very known company which is Apple Inc. and also
discussed how this is impacting the organization in regarding with the efficiency. The report also
consists of the supporting functions that are linked to the operation management and how these
are ensuring in the success of the organization.
6
consumer gets the products that will assist in saving of the money on the basis of quality control
for its goods which are being shipped after or close to the expiration date of the warranty.
The sequence of the first in first out is being maintained by the physical channel or the
painted lane that have particular amount of the inventory. Moreover, the supplying procedure
must prevent the development till the time the customer consumes some part of the inventory.
This can happen only when the lanes is being filled completely. In this manner, the FIFO lane
can also avoid the process of supplying from overproduction even after the process of supplying
is not connected to the process of consuming supermarket (Chapelle, 2019).
CONCLUSION
From the report it has been concluded that the operation and service management plays a very
crucial role in managing the manufactured products of the company and satisfying the needs of
the customer by providing quality product. The report have illustrated all the operation
management practice done in one of the very known company which is Apple Inc. and also
discussed how this is impacting the organization in regarding with the efficiency. The report also
consists of the supporting functions that are linked to the operation management and how these
are ensuring in the success of the organization.
6
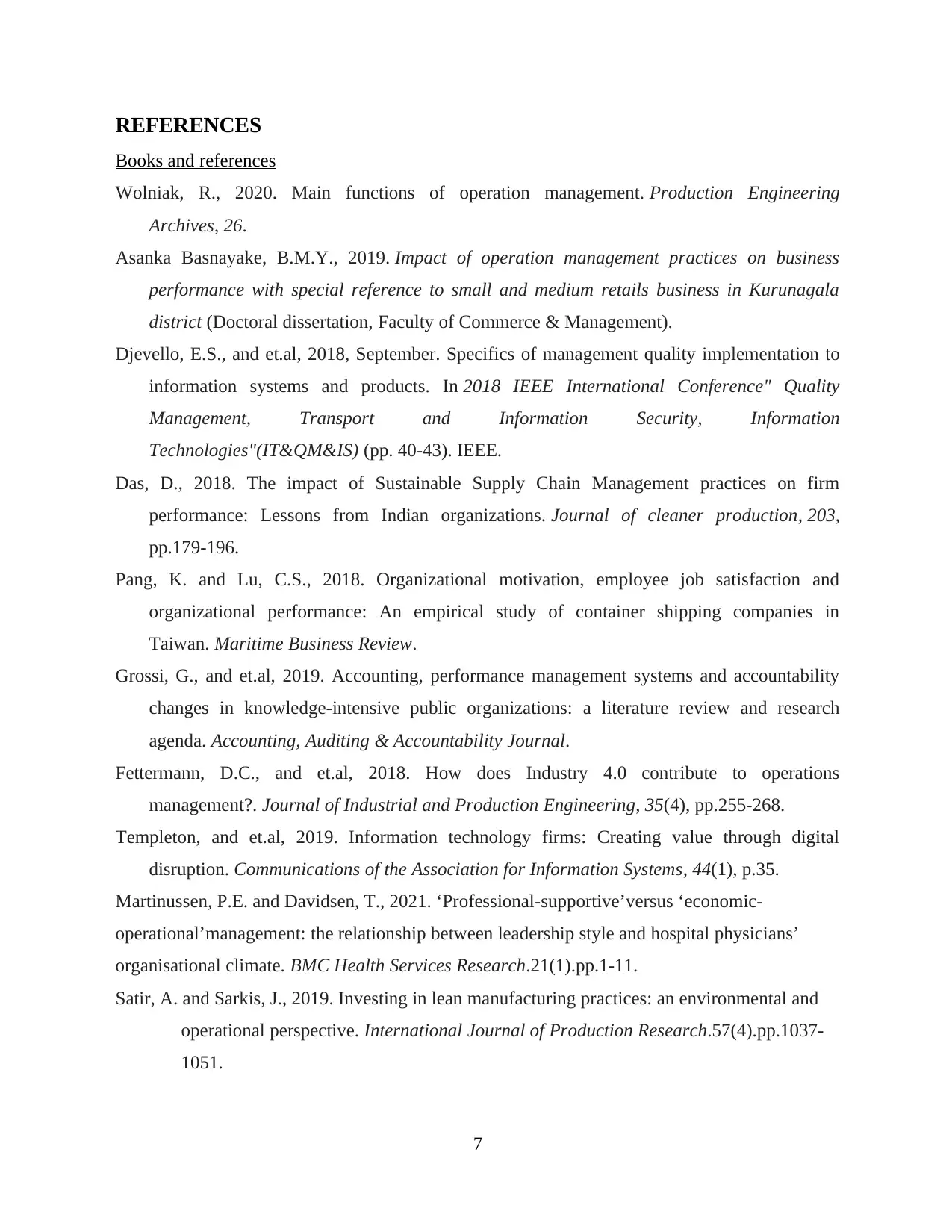
REFERENCES
Books and references
Wolniak, R., 2020. Main functions of operation management. Production Engineering
Archives, 26.
Asanka Basnayake, B.M.Y., 2019. Impact of operation management practices on business
performance with special reference to small and medium retails business in Kurunagala
district (Doctoral dissertation, Faculty of Commerce & Management).
Djevello, E.S., and et.al, 2018, September. Specifics of management quality implementation to
information systems and products. In 2018 IEEE International Conference" Quality
Management, Transport and Information Security, Information
Technologies"(IT&QM&IS) (pp. 40-43). IEEE.
Das, D., 2018. The impact of Sustainable Supply Chain Management practices on firm
performance: Lessons from Indian organizations. Journal of cleaner production, 203,
pp.179-196.
Pang, K. and Lu, C.S., 2018. Organizational motivation, employee job satisfaction and
organizational performance: An empirical study of container shipping companies in
Taiwan. Maritime Business Review.
Grossi, G., and et.al, 2019. Accounting, performance management systems and accountability
changes in knowledge-intensive public organizations: a literature review and research
agenda. Accounting, Auditing & Accountability Journal.
Fettermann, D.C., and et.al, 2018. How does Industry 4.0 contribute to operations
management?. Journal of Industrial and Production Engineering, 35(4), pp.255-268.
Templeton, and et.al, 2019. Information technology firms: Creating value through digital
disruption. Communications of the Association for Information Systems, 44(1), p.35.
Martinussen, P.E. and Davidsen, T., 2021. ‘Professional-supportive’versus ‘economic-
operational’management: the relationship between leadership style and hospital physicians’
organisational climate. BMC Health Services Research.21(1).pp.1-11.
Satir, A. and Sarkis, J., 2019. Investing in lean manufacturing practices: an environmental and
operational perspective. International Journal of Production Research.57(4).pp.1037-
1051.
7
Books and references
Wolniak, R., 2020. Main functions of operation management. Production Engineering
Archives, 26.
Asanka Basnayake, B.M.Y., 2019. Impact of operation management practices on business
performance with special reference to small and medium retails business in Kurunagala
district (Doctoral dissertation, Faculty of Commerce & Management).
Djevello, E.S., and et.al, 2018, September. Specifics of management quality implementation to
information systems and products. In 2018 IEEE International Conference" Quality
Management, Transport and Information Security, Information
Technologies"(IT&QM&IS) (pp. 40-43). IEEE.
Das, D., 2018. The impact of Sustainable Supply Chain Management practices on firm
performance: Lessons from Indian organizations. Journal of cleaner production, 203,
pp.179-196.
Pang, K. and Lu, C.S., 2018. Organizational motivation, employee job satisfaction and
organizational performance: An empirical study of container shipping companies in
Taiwan. Maritime Business Review.
Grossi, G., and et.al, 2019. Accounting, performance management systems and accountability
changes in knowledge-intensive public organizations: a literature review and research
agenda. Accounting, Auditing & Accountability Journal.
Fettermann, D.C., and et.al, 2018. How does Industry 4.0 contribute to operations
management?. Journal of Industrial and Production Engineering, 35(4), pp.255-268.
Templeton, and et.al, 2019. Information technology firms: Creating value through digital
disruption. Communications of the Association for Information Systems, 44(1), p.35.
Martinussen, P.E. and Davidsen, T., 2021. ‘Professional-supportive’versus ‘economic-
operational’management: the relationship between leadership style and hospital physicians’
organisational climate. BMC Health Services Research.21(1).pp.1-11.
Satir, A. and Sarkis, J., 2019. Investing in lean manufacturing practices: an environmental and
operational perspective. International Journal of Production Research.57(4).pp.1037-
1051.
7
You're viewing a preview
Unlock full access by subscribing today!
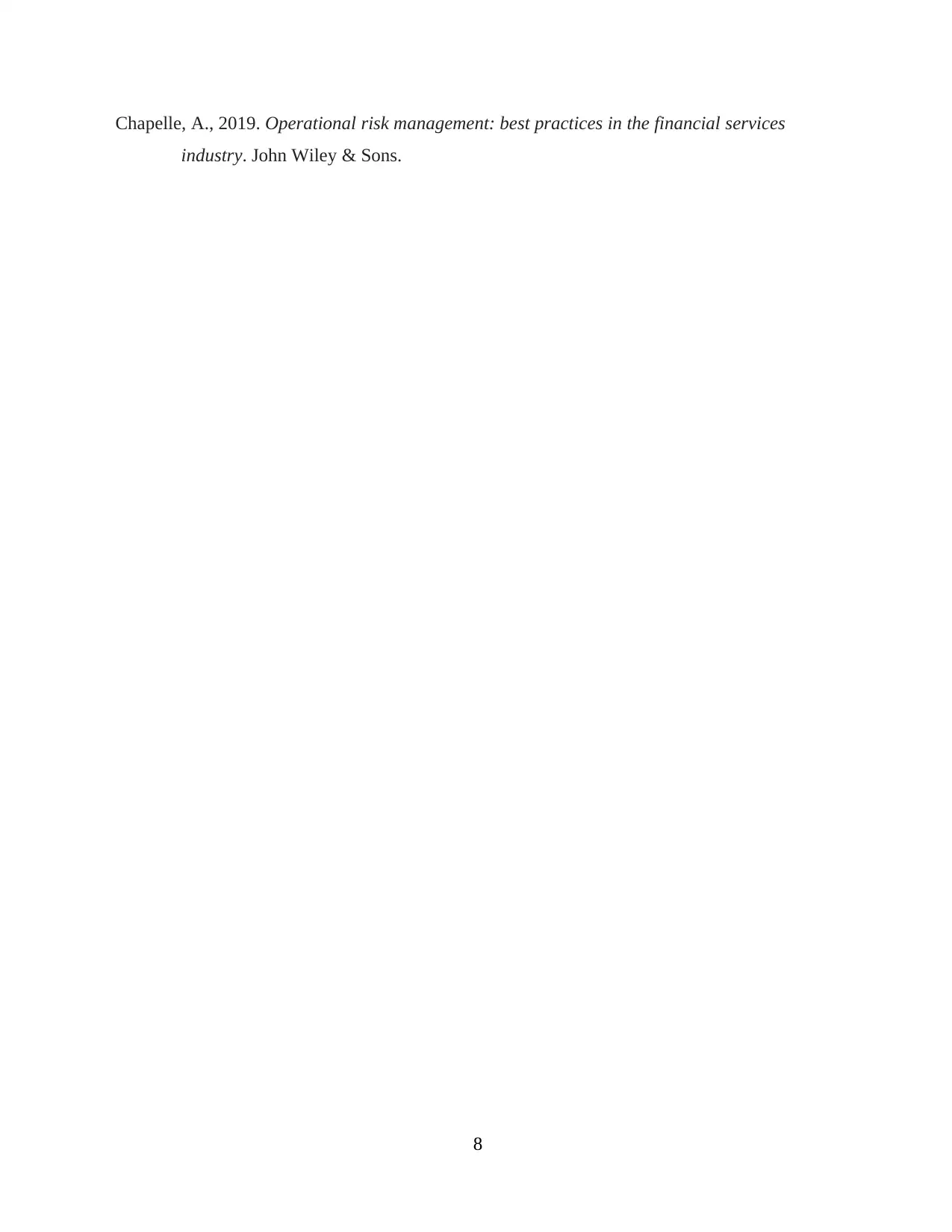
Chapelle, A., 2019. Operational risk management: best practices in the financial services
industry. John Wiley & Sons.
8
industry. John Wiley & Sons.
8
1 out of 10
Related Documents

Your All-in-One AI-Powered Toolkit for Academic Success.
+13062052269
info@desklib.com
Available 24*7 on WhatsApp / Email
Unlock your academic potential
© 2024 | Zucol Services PVT LTD | All rights reserved.