Critical Review of Operations Management at Hotpoint: A Report
VerifiedAdded on 2020/11/23
|18
|5660
|263
Report
AI Summary
This report provides a comprehensive analysis of Hotpoint's operations management, focusing on the application and effectiveness of key principles. It begins with an introduction to operations management and its significance, followed by a critical review of operational principles such as Six Sigma, Lean, and Total Quality Management (TQM) within the context of Hotpoint's manufacturing processes. The report then prepares a continuous improvement plan for Hotpoint, leveraging the PDCA cycle to enhance product quality and efficiency. Furthermore, it applies the Product Life Cycle (PLC) concept to a given project, differentiating between large and small-scale projects. Finally, the report reviews the effectiveness of the PLC application, drawing conclusions and providing references to support the analysis. The report aims to evaluate Hotpoint's strategic goals with utmost precision and provide thorough visibility into the operational activities regarding the same.

OPERATIONS AND
PROJECT MANAGEMENT
PROJECT MANAGEMENT
Secure Best Marks with AI Grader
Need help grading? Try our AI Grader for instant feedback on your assignments.
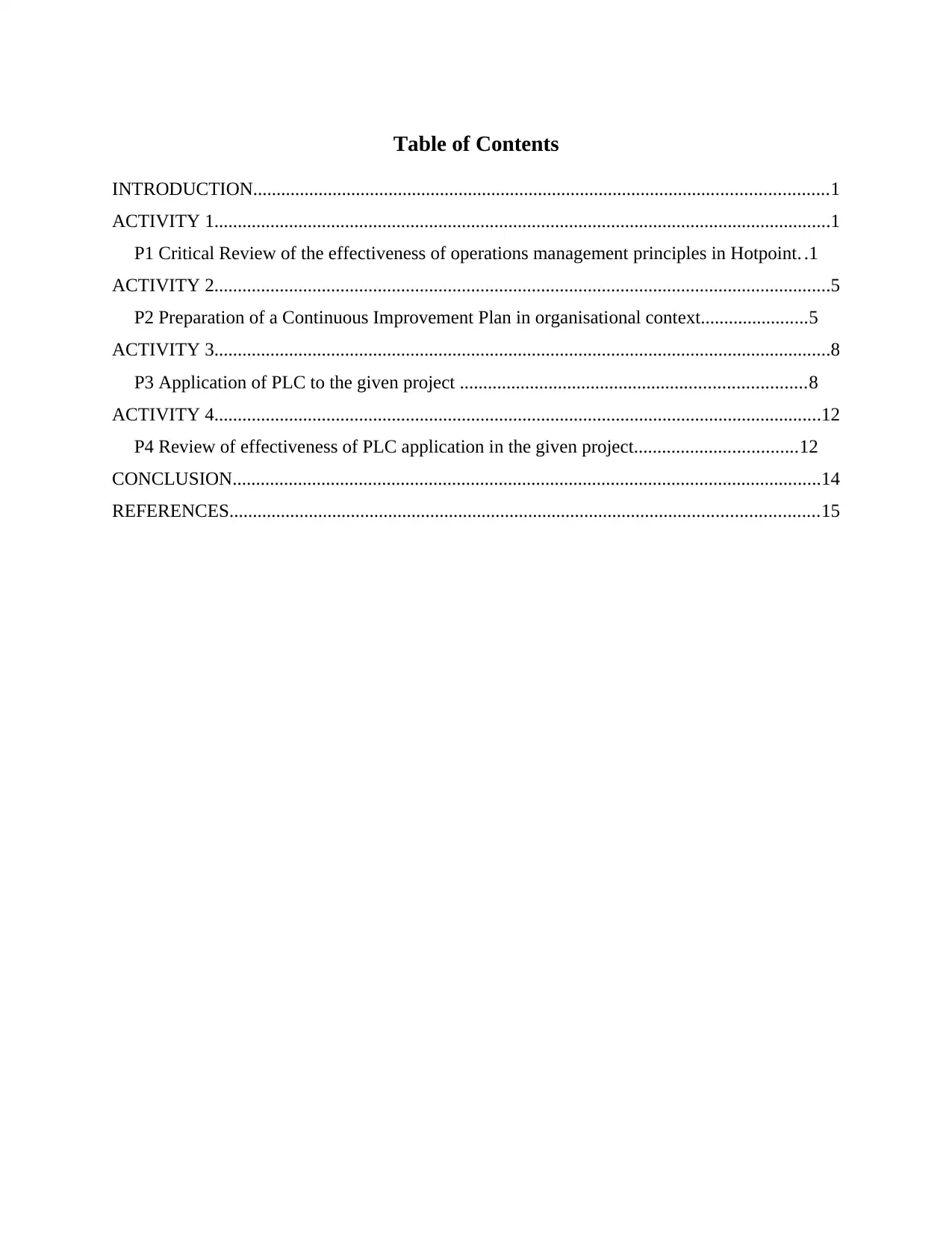
Table of Contents
INTRODUCTION...........................................................................................................................1
ACTIVITY 1....................................................................................................................................1
P1 Critical Review of the effectiveness of operations management principles in Hotpoint. .1
ACTIVITY 2....................................................................................................................................5
P2 Preparation of a Continuous Improvement Plan in organisational context.......................5
ACTIVITY 3....................................................................................................................................8
P3 Application of PLC to the given project ..........................................................................8
ACTIVITY 4..................................................................................................................................12
P4 Review of effectiveness of PLC application in the given project...................................12
CONCLUSION..............................................................................................................................14
REFERENCES..............................................................................................................................15
INTRODUCTION...........................................................................................................................1
ACTIVITY 1....................................................................................................................................1
P1 Critical Review of the effectiveness of operations management principles in Hotpoint. .1
ACTIVITY 2....................................................................................................................................5
P2 Preparation of a Continuous Improvement Plan in organisational context.......................5
ACTIVITY 3....................................................................................................................................8
P3 Application of PLC to the given project ..........................................................................8
ACTIVITY 4..................................................................................................................................12
P4 Review of effectiveness of PLC application in the given project...................................12
CONCLUSION..............................................................................................................................14
REFERENCES..............................................................................................................................15
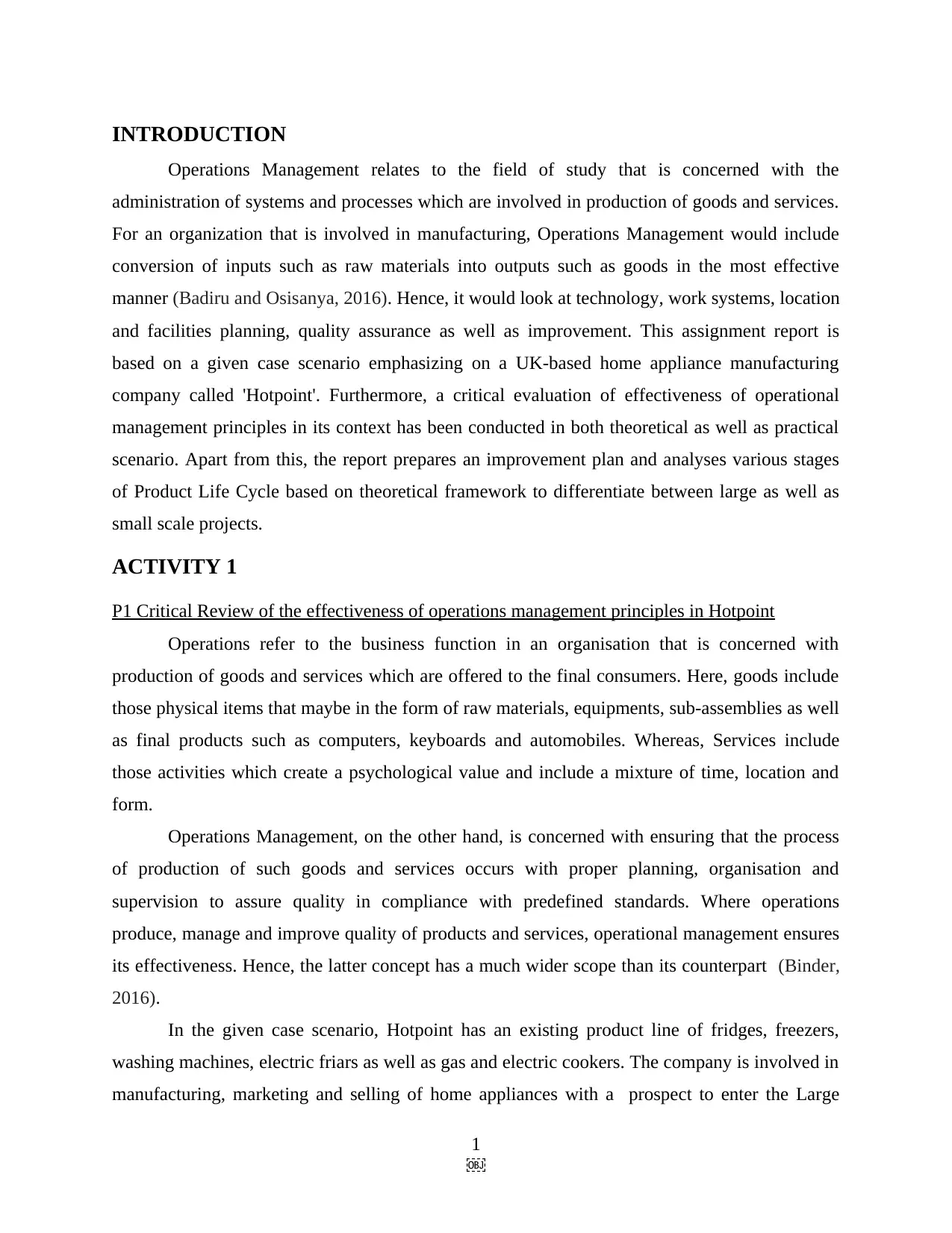
INTRODUCTION
Operations Management relates to the field of study that is concerned with the
administration of systems and processes which are involved in production of goods and services.
For an organization that is involved in manufacturing, Operations Management would include
conversion of inputs such as raw materials into outputs such as goods in the most effective
manner (Badiru and Osisanya, 2016). Hence, it would look at technology, work systems, location
and facilities planning, quality assurance as well as improvement. This assignment report is
based on a given case scenario emphasizing on a UK-based home appliance manufacturing
company called 'Hotpoint'. Furthermore, a critical evaluation of effectiveness of operational
management principles in its context has been conducted in both theoretical as well as practical
scenario. Apart from this, the report prepares an improvement plan and analyses various stages
of Product Life Cycle based on theoretical framework to differentiate between large as well as
small scale projects.
ACTIVITY 1
P1 Critical Review of the effectiveness of operations management principles in Hotpoint
Operations refer to the business function in an organisation that is concerned with
production of goods and services which are offered to the final consumers. Here, goods include
those physical items that maybe in the form of raw materials, equipments, sub-assemblies as well
as final products such as computers, keyboards and automobiles. Whereas, Services include
those activities which create a psychological value and include a mixture of time, location and
form.
Operations Management, on the other hand, is concerned with ensuring that the process
of production of such goods and services occurs with proper planning, organisation and
supervision to assure quality in compliance with predefined standards. Where operations
produce, manage and improve quality of products and services, operational management ensures
its effectiveness. Hence, the latter concept has a much wider scope than its counterpart (Binder,
2016).
In the given case scenario, Hotpoint has an existing product line of fridges, freezers,
washing machines, electric friars as well as gas and electric cookers. The company is involved in
manufacturing, marketing and selling of home appliances with a prospect to enter the Large
1

Operations Management relates to the field of study that is concerned with the
administration of systems and processes which are involved in production of goods and services.
For an organization that is involved in manufacturing, Operations Management would include
conversion of inputs such as raw materials into outputs such as goods in the most effective
manner (Badiru and Osisanya, 2016). Hence, it would look at technology, work systems, location
and facilities planning, quality assurance as well as improvement. This assignment report is
based on a given case scenario emphasizing on a UK-based home appliance manufacturing
company called 'Hotpoint'. Furthermore, a critical evaluation of effectiveness of operational
management principles in its context has been conducted in both theoretical as well as practical
scenario. Apart from this, the report prepares an improvement plan and analyses various stages
of Product Life Cycle based on theoretical framework to differentiate between large as well as
small scale projects.
ACTIVITY 1
P1 Critical Review of the effectiveness of operations management principles in Hotpoint
Operations refer to the business function in an organisation that is concerned with
production of goods and services which are offered to the final consumers. Here, goods include
those physical items that maybe in the form of raw materials, equipments, sub-assemblies as well
as final products such as computers, keyboards and automobiles. Whereas, Services include
those activities which create a psychological value and include a mixture of time, location and
form.
Operations Management, on the other hand, is concerned with ensuring that the process
of production of such goods and services occurs with proper planning, organisation and
supervision to assure quality in compliance with predefined standards. Where operations
produce, manage and improve quality of products and services, operational management ensures
its effectiveness. Hence, the latter concept has a much wider scope than its counterpart (Binder,
2016).
In the given case scenario, Hotpoint has an existing product line of fridges, freezers,
washing machines, electric friars as well as gas and electric cookers. The company is involved in
manufacturing, marketing and selling of home appliances with a prospect to enter the Large
1

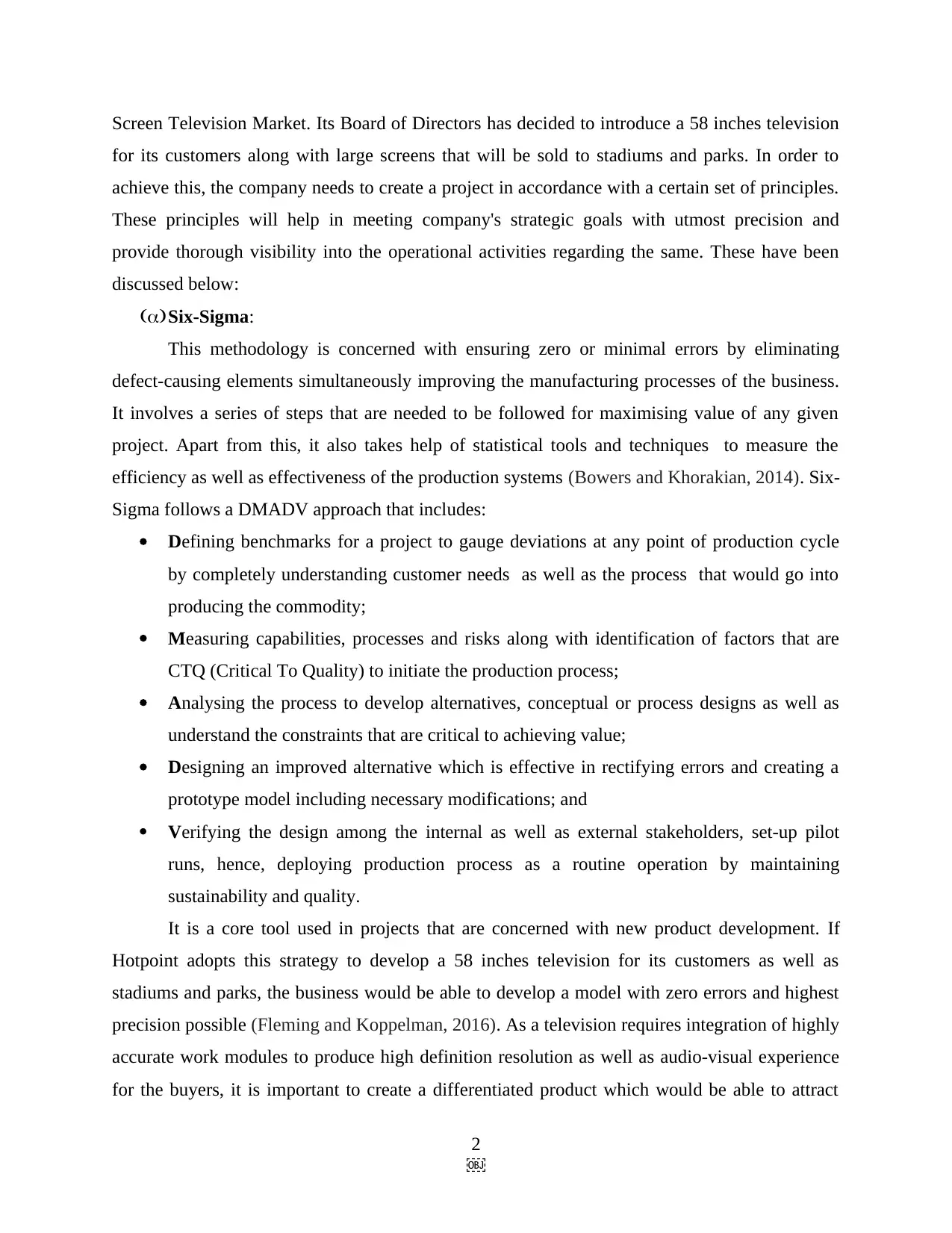
Screen Television Market. Its Board of Directors has decided to introduce a 58 inches television
for its customers along with large screens that will be sold to stadiums and parks. In order to
achieve this, the company needs to create a project in accordance with a certain set of principles.
These principles will help in meeting company's strategic goals with utmost precision and
provide thorough visibility into the operational activities regarding the same. These have been
discussed below:
(a)Six-Sigma:
This methodology is concerned with ensuring zero or minimal errors by eliminating
defect-causing elements simultaneously improving the manufacturing processes of the business.
It involves a series of steps that are needed to be followed for maximising value of any given
project. Apart from this, it also takes help of statistical tools and techniques to measure the
efficiency as well as effectiveness of the production systems (Bowers and Khorakian, 2014). Six-
Sigma follows a DMADV approach that includes:
Defining benchmarks for a project to gauge deviations at any point of production cycle
by completely understanding customer needs as well as the process that would go into
producing the commodity;
Measuring capabilities, processes and risks along with identification of factors that are
CTQ (Critical To Quality) to initiate the production process;
Analysing the process to develop alternatives, conceptual or process designs as well as
understand the constraints that are critical to achieving value;
Designing an improved alternative which is effective in rectifying errors and creating a
prototype model including necessary modifications; and
Verifying the design among the internal as well as external stakeholders, set-up pilot
runs, hence, deploying production process as a routine operation by maintaining
sustainability and quality.
It is a core tool used in projects that are concerned with new product development. If
Hotpoint adopts this strategy to develop a 58 inches television for its customers as well as
stadiums and parks, the business would be able to develop a model with zero errors and highest
precision possible (Fleming and Koppelman, 2016). As a television requires integration of highly
accurate work modules to produce high definition resolution as well as audio-visual experience
for the buyers, it is important to create a differentiated product which would be able to attract
2

for its customers along with large screens that will be sold to stadiums and parks. In order to
achieve this, the company needs to create a project in accordance with a certain set of principles.
These principles will help in meeting company's strategic goals with utmost precision and
provide thorough visibility into the operational activities regarding the same. These have been
discussed below:
(a)Six-Sigma:
This methodology is concerned with ensuring zero or minimal errors by eliminating
defect-causing elements simultaneously improving the manufacturing processes of the business.
It involves a series of steps that are needed to be followed for maximising value of any given
project. Apart from this, it also takes help of statistical tools and techniques to measure the
efficiency as well as effectiveness of the production systems (Bowers and Khorakian, 2014). Six-
Sigma follows a DMADV approach that includes:
Defining benchmarks for a project to gauge deviations at any point of production cycle
by completely understanding customer needs as well as the process that would go into
producing the commodity;
Measuring capabilities, processes and risks along with identification of factors that are
CTQ (Critical To Quality) to initiate the production process;
Analysing the process to develop alternatives, conceptual or process designs as well as
understand the constraints that are critical to achieving value;
Designing an improved alternative which is effective in rectifying errors and creating a
prototype model including necessary modifications; and
Verifying the design among the internal as well as external stakeholders, set-up pilot
runs, hence, deploying production process as a routine operation by maintaining
sustainability and quality.
It is a core tool used in projects that are concerned with new product development. If
Hotpoint adopts this strategy to develop a 58 inches television for its customers as well as
stadiums and parks, the business would be able to develop a model with zero errors and highest
precision possible (Fleming and Koppelman, 2016). As a television requires integration of highly
accurate work modules to produce high definition resolution as well as audio-visual experience
for the buyers, it is important to create a differentiated product which would be able to attract
2

Secure Best Marks with AI Grader
Need help grading? Try our AI Grader for instant feedback on your assignments.
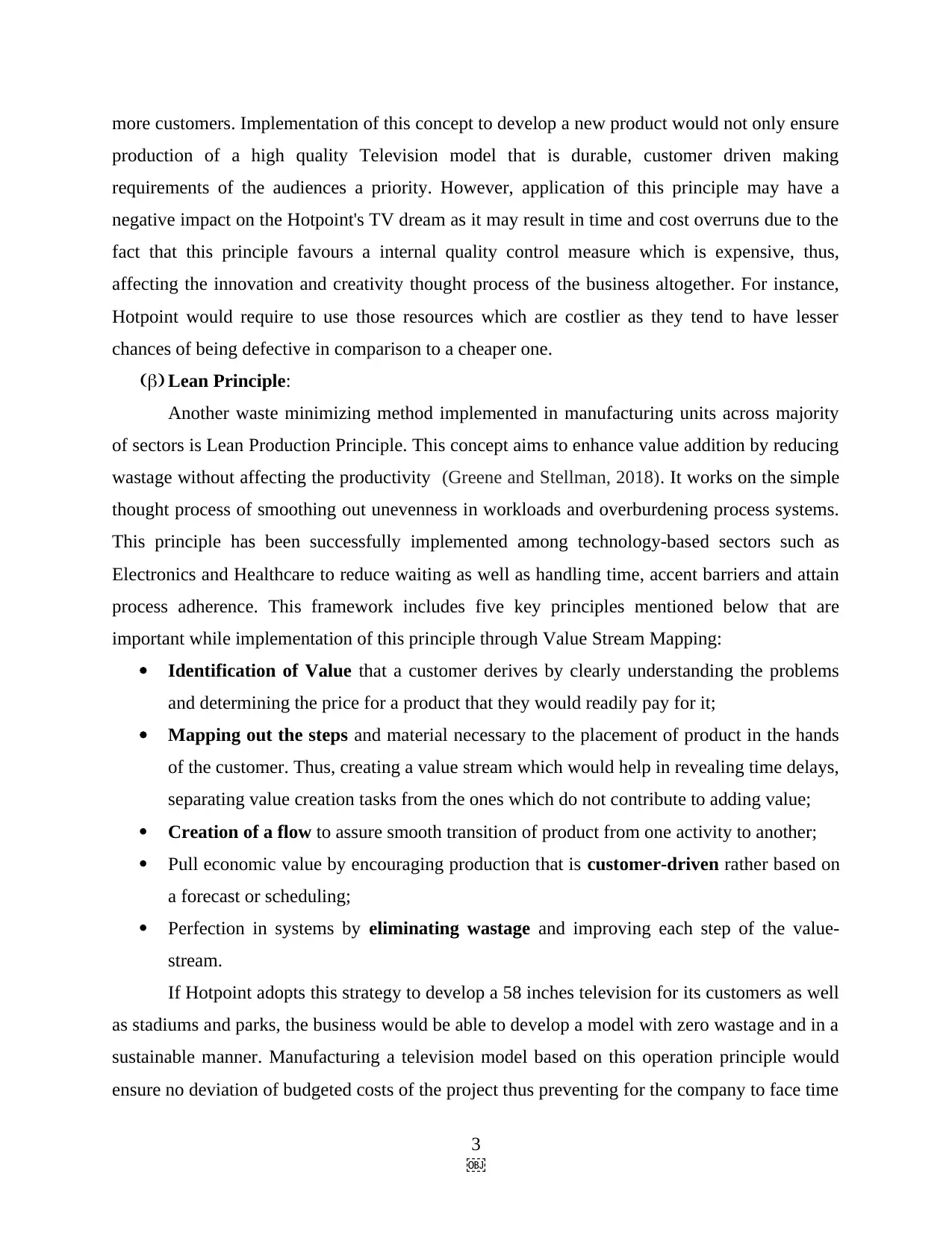
more customers. Implementation of this concept to develop a new product would not only ensure
production of a high quality Television model that is durable, customer driven making
requirements of the audiences a priority. However, application of this principle may have a
negative impact on the Hotpoint's TV dream as it may result in time and cost overruns due to the
fact that this principle favours a internal quality control measure which is expensive, thus,
affecting the innovation and creativity thought process of the business altogether. For instance,
Hotpoint would require to use those resources which are costlier as they tend to have lesser
chances of being defective in comparison to a cheaper one.
(b) Lean Principle:
Another waste minimizing method implemented in manufacturing units across majority
of sectors is Lean Production Principle. This concept aims to enhance value addition by reducing
wastage without affecting the productivity (Greene and Stellman, 2018). It works on the simple
thought process of smoothing out unevenness in workloads and overburdening process systems.
This principle has been successfully implemented among technology-based sectors such as
Electronics and Healthcare to reduce waiting as well as handling time, accent barriers and attain
process adherence. This framework includes five key principles mentioned below that are
important while implementation of this principle through Value Stream Mapping:
Identification of Value that a customer derives by clearly understanding the problems
and determining the price for a product that they would readily pay for it;
Mapping out the steps and material necessary to the placement of product in the hands
of the customer. Thus, creating a value stream which would help in revealing time delays,
separating value creation tasks from the ones which do not contribute to adding value;
Creation of a flow to assure smooth transition of product from one activity to another;
Pull economic value by encouraging production that is customer-driven rather based on
a forecast or scheduling;
Perfection in systems by eliminating wastage and improving each step of the value-
stream.
If Hotpoint adopts this strategy to develop a 58 inches television for its customers as well
as stadiums and parks, the business would be able to develop a model with zero wastage and in a
sustainable manner. Manufacturing a television model based on this operation principle would
ensure no deviation of budgeted costs of the project thus preventing for the company to face time
3

production of a high quality Television model that is durable, customer driven making
requirements of the audiences a priority. However, application of this principle may have a
negative impact on the Hotpoint's TV dream as it may result in time and cost overruns due to the
fact that this principle favours a internal quality control measure which is expensive, thus,
affecting the innovation and creativity thought process of the business altogether. For instance,
Hotpoint would require to use those resources which are costlier as they tend to have lesser
chances of being defective in comparison to a cheaper one.
(b) Lean Principle:
Another waste minimizing method implemented in manufacturing units across majority
of sectors is Lean Production Principle. This concept aims to enhance value addition by reducing
wastage without affecting the productivity (Greene and Stellman, 2018). It works on the simple
thought process of smoothing out unevenness in workloads and overburdening process systems.
This principle has been successfully implemented among technology-based sectors such as
Electronics and Healthcare to reduce waiting as well as handling time, accent barriers and attain
process adherence. This framework includes five key principles mentioned below that are
important while implementation of this principle through Value Stream Mapping:
Identification of Value that a customer derives by clearly understanding the problems
and determining the price for a product that they would readily pay for it;
Mapping out the steps and material necessary to the placement of product in the hands
of the customer. Thus, creating a value stream which would help in revealing time delays,
separating value creation tasks from the ones which do not contribute to adding value;
Creation of a flow to assure smooth transition of product from one activity to another;
Pull economic value by encouraging production that is customer-driven rather based on
a forecast or scheduling;
Perfection in systems by eliminating wastage and improving each step of the value-
stream.
If Hotpoint adopts this strategy to develop a 58 inches television for its customers as well
as stadiums and parks, the business would be able to develop a model with zero wastage and in a
sustainable manner. Manufacturing a television model based on this operation principle would
ensure no deviation of budgeted costs of the project thus preventing for the company to face time
3

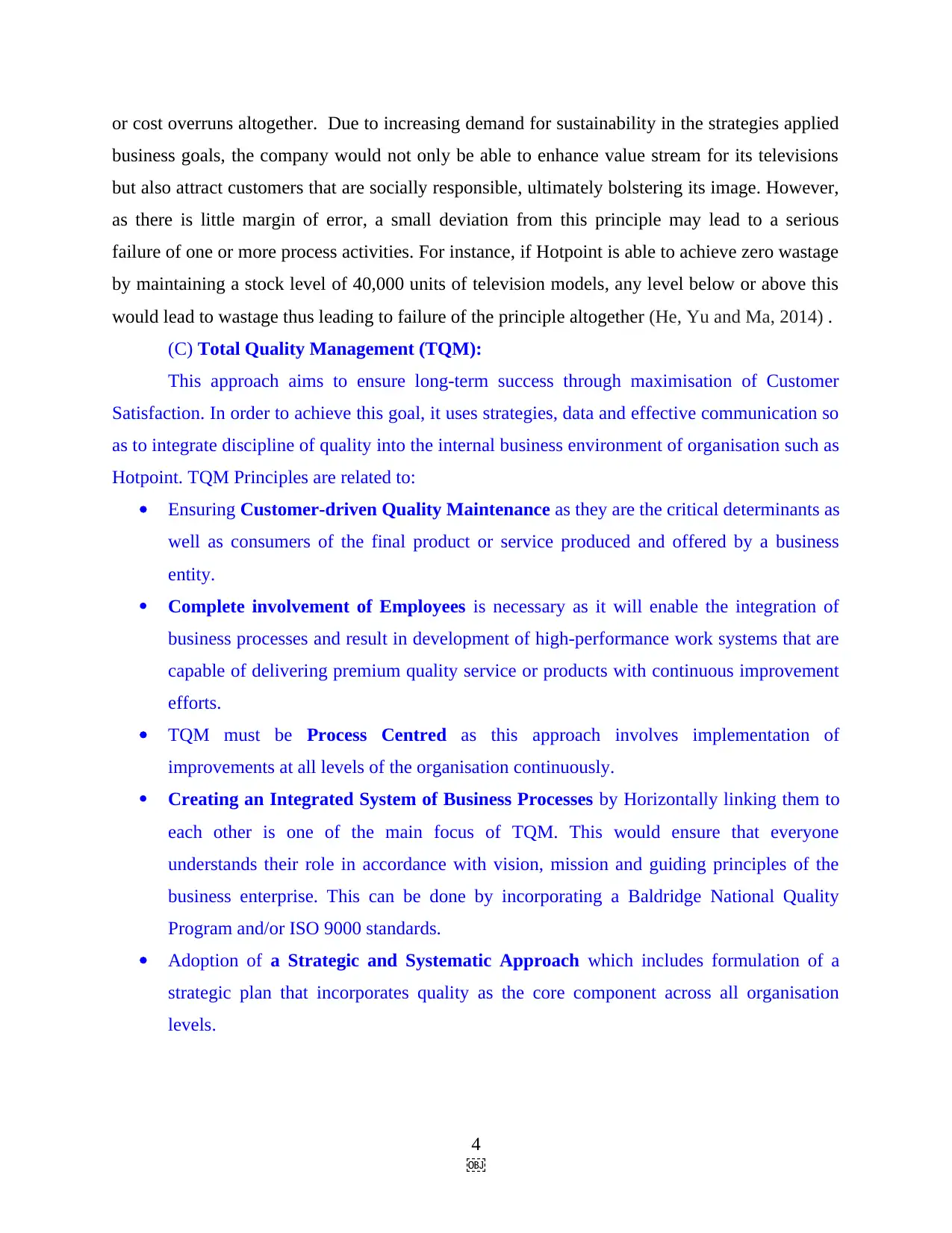
or cost overruns altogether. Due to increasing demand for sustainability in the strategies applied
business goals, the company would not only be able to enhance value stream for its televisions
but also attract customers that are socially responsible, ultimately bolstering its image. However,
as there is little margin of error, a small deviation from this principle may lead to a serious
failure of one or more process activities. For instance, if Hotpoint is able to achieve zero wastage
by maintaining a stock level of 40,000 units of television models, any level below or above this
would lead to wastage thus leading to failure of the principle altogether (He, Yu and Ma, 2014) .
(C) Total Quality Management (TQM):
This approach aims to ensure long-term success through maximisation of Customer
Satisfaction. In order to achieve this goal, it uses strategies, data and effective communication so
as to integrate discipline of quality into the internal business environment of organisation such as
Hotpoint. TQM Principles are related to:
Ensuring Customer-driven Quality Maintenance as they are the critical determinants as
well as consumers of the final product or service produced and offered by a business
entity.
Complete involvement of Employees is necessary as it will enable the integration of
business processes and result in development of high-performance work systems that are
capable of delivering premium quality service or products with continuous improvement
efforts.
TQM must be Process Centred as this approach involves implementation of
improvements at all levels of the organisation continuously.
Creating an Integrated System of Business Processes by Horizontally linking them to
each other is one of the main focus of TQM. This would ensure that everyone
understands their role in accordance with vision, mission and guiding principles of the
business enterprise. This can be done by incorporating a Baldridge National Quality
Program and/or ISO 9000 standards.
Adoption of a Strategic and Systematic Approach which includes formulation of a
strategic plan that incorporates quality as the core component across all organisation
levels.
4

business goals, the company would not only be able to enhance value stream for its televisions
but also attract customers that are socially responsible, ultimately bolstering its image. However,
as there is little margin of error, a small deviation from this principle may lead to a serious
failure of one or more process activities. For instance, if Hotpoint is able to achieve zero wastage
by maintaining a stock level of 40,000 units of television models, any level below or above this
would lead to wastage thus leading to failure of the principle altogether (He, Yu and Ma, 2014) .
(C) Total Quality Management (TQM):
This approach aims to ensure long-term success through maximisation of Customer
Satisfaction. In order to achieve this goal, it uses strategies, data and effective communication so
as to integrate discipline of quality into the internal business environment of organisation such as
Hotpoint. TQM Principles are related to:
Ensuring Customer-driven Quality Maintenance as they are the critical determinants as
well as consumers of the final product or service produced and offered by a business
entity.
Complete involvement of Employees is necessary as it will enable the integration of
business processes and result in development of high-performance work systems that are
capable of delivering premium quality service or products with continuous improvement
efforts.
TQM must be Process Centred as this approach involves implementation of
improvements at all levels of the organisation continuously.
Creating an Integrated System of Business Processes by Horizontally linking them to
each other is one of the main focus of TQM. This would ensure that everyone
understands their role in accordance with vision, mission and guiding principles of the
business enterprise. This can be done by incorporating a Baldridge National Quality
Program and/or ISO 9000 standards.
Adoption of a Strategic and Systematic Approach which includes formulation of a
strategic plan that incorporates quality as the core component across all organisation
levels.
4

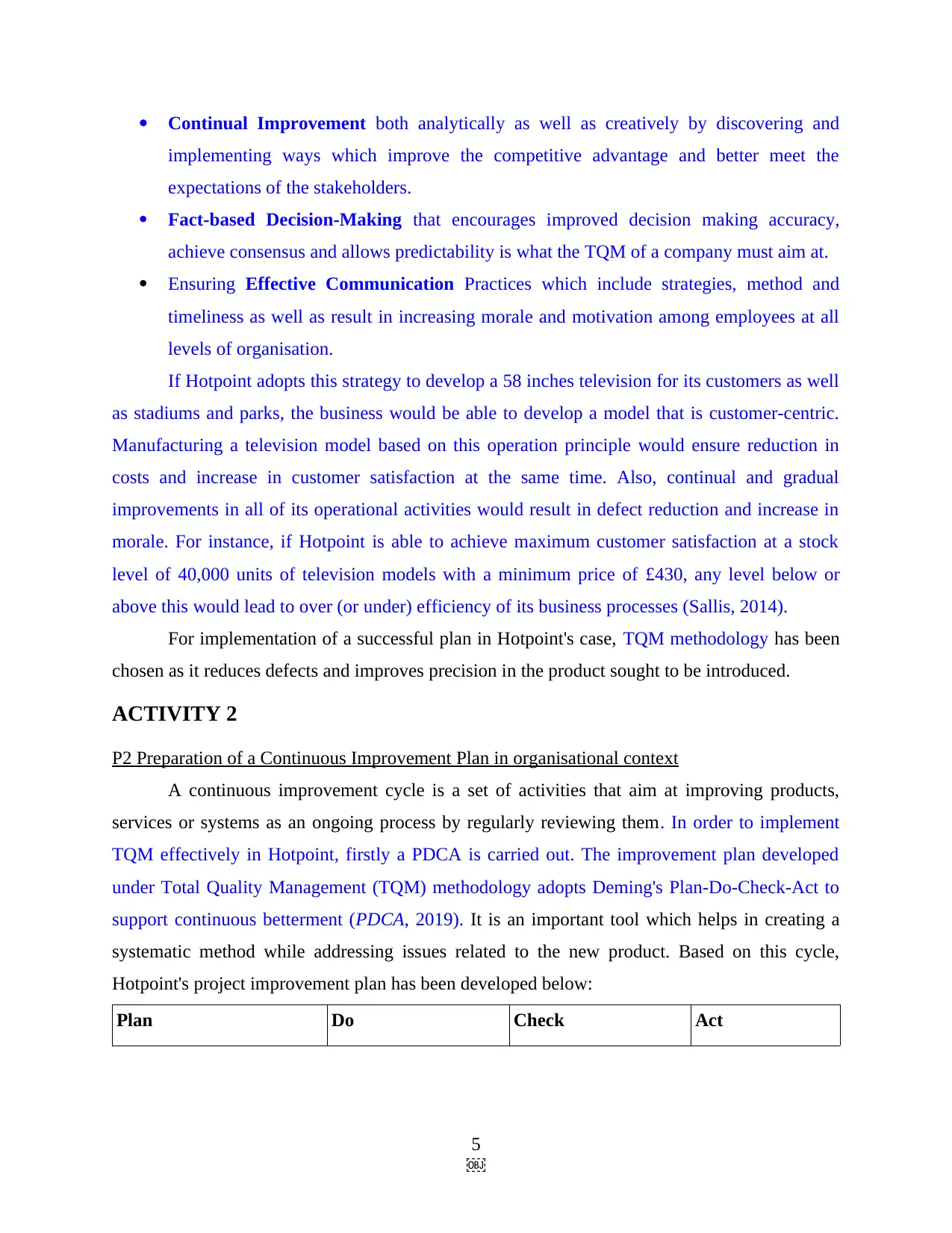
Continual Improvement both analytically as well as creatively by discovering and
implementing ways which improve the competitive advantage and better meet the
expectations of the stakeholders.
Fact-based Decision-Making that encourages improved decision making accuracy,
achieve consensus and allows predictability is what the TQM of a company must aim at.
Ensuring Effective Communication Practices which include strategies, method and
timeliness as well as result in increasing morale and motivation among employees at all
levels of organisation.
If Hotpoint adopts this strategy to develop a 58 inches television for its customers as well
as stadiums and parks, the business would be able to develop a model that is customer-centric.
Manufacturing a television model based on this operation principle would ensure reduction in
costs and increase in customer satisfaction at the same time. Also, continual and gradual
improvements in all of its operational activities would result in defect reduction and increase in
morale. For instance, if Hotpoint is able to achieve maximum customer satisfaction at a stock
level of 40,000 units of television models with a minimum price of £430, any level below or
above this would lead to over (or under) efficiency of its business processes (Sallis, 2014).
For implementation of a successful plan in Hotpoint's case, TQM methodology has been
chosen as it reduces defects and improves precision in the product sought to be introduced.
ACTIVITY 2
P2 Preparation of a Continuous Improvement Plan in organisational context
A continuous improvement cycle is a set of activities that aim at improving products,
services or systems as an ongoing process by regularly reviewing them. In order to implement
TQM effectively in Hotpoint, firstly a PDCA is carried out. The improvement plan developed
under Total Quality Management (TQM) methodology adopts Deming's Plan-Do-Check-Act to
support continuous betterment (PDCA, 2019). It is an important tool which helps in creating a
systematic method while addressing issues related to the new product. Based on this cycle,
Hotpoint's project improvement plan has been developed below:
Plan Do Check Act
5

implementing ways which improve the competitive advantage and better meet the
expectations of the stakeholders.
Fact-based Decision-Making that encourages improved decision making accuracy,
achieve consensus and allows predictability is what the TQM of a company must aim at.
Ensuring Effective Communication Practices which include strategies, method and
timeliness as well as result in increasing morale and motivation among employees at all
levels of organisation.
If Hotpoint adopts this strategy to develop a 58 inches television for its customers as well
as stadiums and parks, the business would be able to develop a model that is customer-centric.
Manufacturing a television model based on this operation principle would ensure reduction in
costs and increase in customer satisfaction at the same time. Also, continual and gradual
improvements in all of its operational activities would result in defect reduction and increase in
morale. For instance, if Hotpoint is able to achieve maximum customer satisfaction at a stock
level of 40,000 units of television models with a minimum price of £430, any level below or
above this would lead to over (or under) efficiency of its business processes (Sallis, 2014).
For implementation of a successful plan in Hotpoint's case, TQM methodology has been
chosen as it reduces defects and improves precision in the product sought to be introduced.
ACTIVITY 2
P2 Preparation of a Continuous Improvement Plan in organisational context
A continuous improvement cycle is a set of activities that aim at improving products,
services or systems as an ongoing process by regularly reviewing them. In order to implement
TQM effectively in Hotpoint, firstly a PDCA is carried out. The improvement plan developed
under Total Quality Management (TQM) methodology adopts Deming's Plan-Do-Check-Act to
support continuous betterment (PDCA, 2019). It is an important tool which helps in creating a
systematic method while addressing issues related to the new product. Based on this cycle,
Hotpoint's project improvement plan has been developed below:
Plan Do Check Act
5

Paraphrase This Document
Need a fresh take? Get an instant paraphrase of this document with our AI Paraphraser
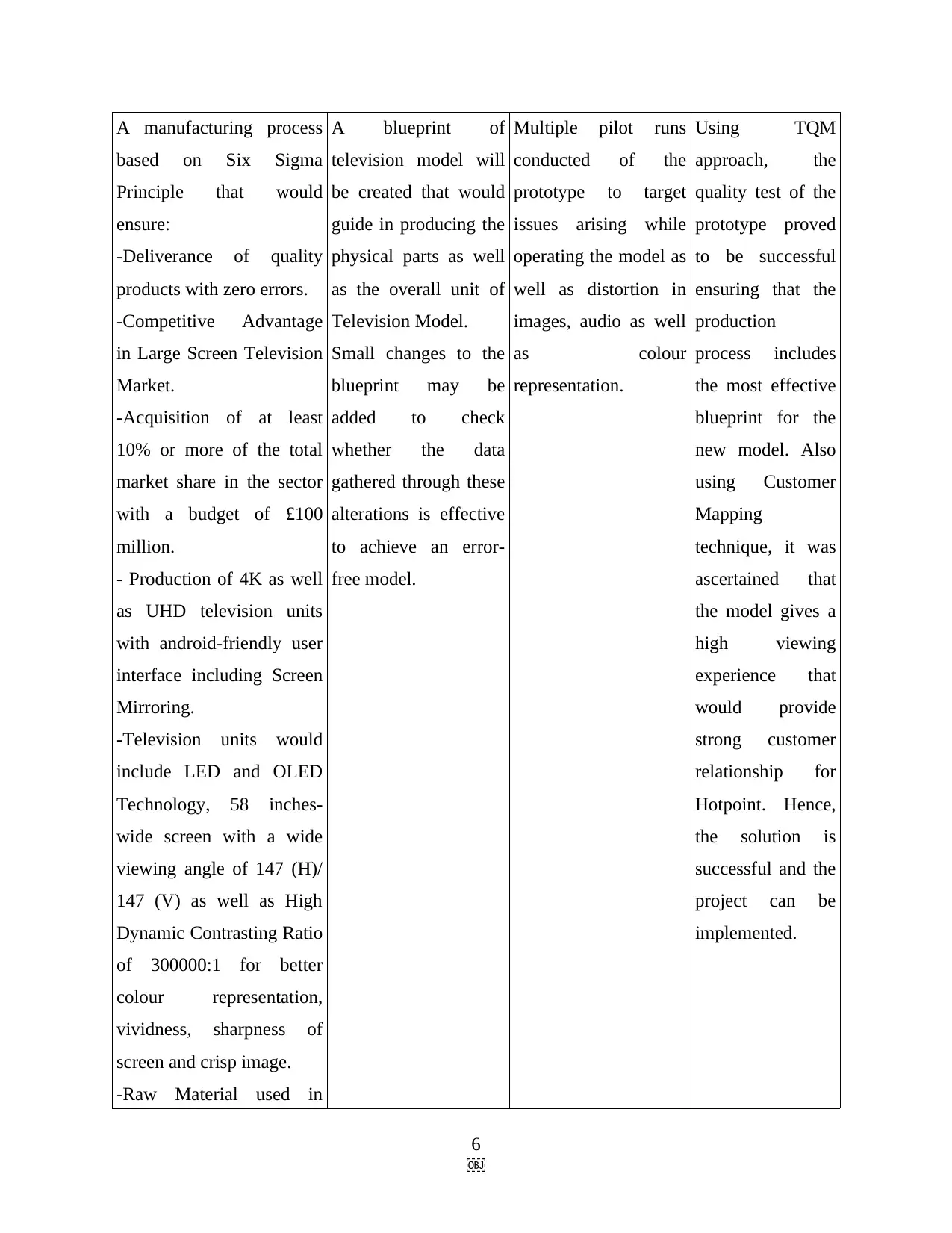
A manufacturing process
based on Six Sigma
Principle that would
ensure:
-Deliverance of quality
products with zero errors.
-Competitive Advantage
in Large Screen Television
Market.
-Acquisition of at least
10% or more of the total
market share in the sector
with a budget of £100
million.
- Production of 4K as well
as UHD television units
with android-friendly user
interface including Screen
Mirroring.
-Television units would
include LED and OLED
Technology, 58 inches-
wide screen with a wide
viewing angle of 147 (H)/
147 (V) as well as High
Dynamic Contrasting Ratio
of 300000:1 for better
colour representation,
vividness, sharpness of
screen and crisp image.
-Raw Material used in
A blueprint of
television model will
be created that would
guide in producing the
physical parts as well
as the overall unit of
Television Model.
Small changes to the
blueprint may be
added to check
whether the data
gathered through these
alterations is effective
to achieve an error-
free model.
Multiple pilot runs
conducted of the
prototype to target
issues arising while
operating the model as
well as distortion in
images, audio as well
as colour
representation.
Using TQM
approach, the
quality test of the
prototype proved
to be successful
ensuring that the
production
process includes
the most effective
blueprint for the
new model. Also
using Customer
Mapping
technique, it was
ascertained that
the model gives a
high viewing
experience that
would provide
strong customer
relationship for
Hotpoint. Hence,
the solution is
successful and the
project can be
implemented.
6

based on Six Sigma
Principle that would
ensure:
-Deliverance of quality
products with zero errors.
-Competitive Advantage
in Large Screen Television
Market.
-Acquisition of at least
10% or more of the total
market share in the sector
with a budget of £100
million.
- Production of 4K as well
as UHD television units
with android-friendly user
interface including Screen
Mirroring.
-Television units would
include LED and OLED
Technology, 58 inches-
wide screen with a wide
viewing angle of 147 (H)/
147 (V) as well as High
Dynamic Contrasting Ratio
of 300000:1 for better
colour representation,
vividness, sharpness of
screen and crisp image.
-Raw Material used in
A blueprint of
television model will
be created that would
guide in producing the
physical parts as well
as the overall unit of
Television Model.
Small changes to the
blueprint may be
added to check
whether the data
gathered through these
alterations is effective
to achieve an error-
free model.
Multiple pilot runs
conducted of the
prototype to target
issues arising while
operating the model as
well as distortion in
images, audio as well
as colour
representation.
Using TQM
approach, the
quality test of the
prototype proved
to be successful
ensuring that the
production
process includes
the most effective
blueprint for the
new model. Also
using Customer
Mapping
technique, it was
ascertained that
the model gives a
high viewing
experience that
would provide
strong customer
relationship for
Hotpoint. Hence,
the solution is
successful and the
project can be
implemented.
6

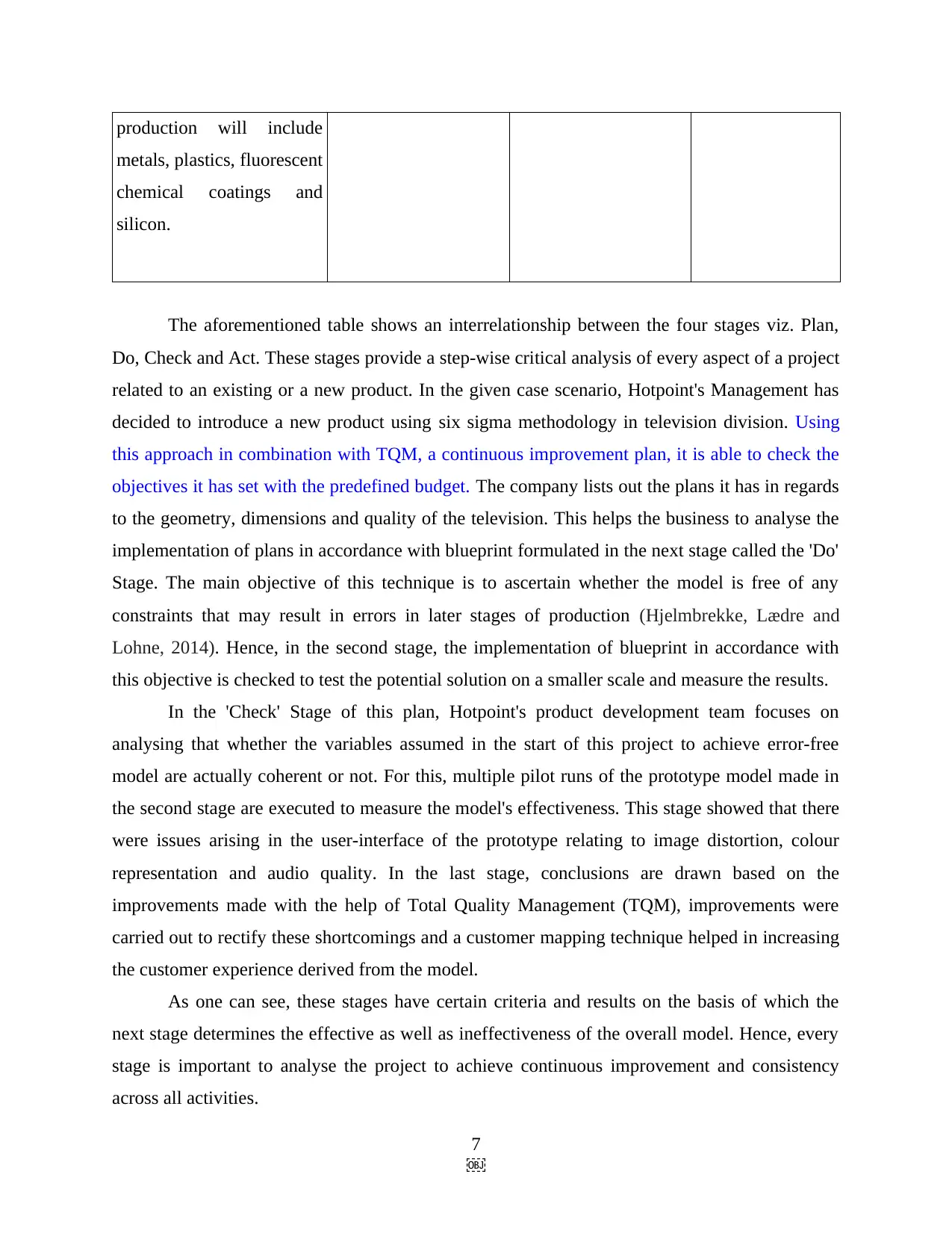
production will include
metals, plastics, fluorescent
chemical coatings and
silicon.
The aforementioned table shows an interrelationship between the four stages viz. Plan,
Do, Check and Act. These stages provide a step-wise critical analysis of every aspect of a project
related to an existing or a new product. In the given case scenario, Hotpoint's Management has
decided to introduce a new product using six sigma methodology in television division. Using
this approach in combination with TQM, a continuous improvement plan, it is able to check the
objectives it has set with the predefined budget. The company lists out the plans it has in regards
to the geometry, dimensions and quality of the television. This helps the business to analyse the
implementation of plans in accordance with blueprint formulated in the next stage called the 'Do'
Stage. The main objective of this technique is to ascertain whether the model is free of any
constraints that may result in errors in later stages of production (Hjelmbrekke, Lædre and
Lohne, 2014). Hence, in the second stage, the implementation of blueprint in accordance with
this objective is checked to test the potential solution on a smaller scale and measure the results.
In the 'Check' Stage of this plan, Hotpoint's product development team focuses on
analysing that whether the variables assumed in the start of this project to achieve error-free
model are actually coherent or not. For this, multiple pilot runs of the prototype model made in
the second stage are executed to measure the model's effectiveness. This stage showed that there
were issues arising in the user-interface of the prototype relating to image distortion, colour
representation and audio quality. In the last stage, conclusions are drawn based on the
improvements made with the help of Total Quality Management (TQM), improvements were
carried out to rectify these shortcomings and a customer mapping technique helped in increasing
the customer experience derived from the model.
As one can see, these stages have certain criteria and results on the basis of which the
next stage determines the effective as well as ineffectiveness of the overall model. Hence, every
stage is important to analyse the project to achieve continuous improvement and consistency
across all activities.
7

metals, plastics, fluorescent
chemical coatings and
silicon.
The aforementioned table shows an interrelationship between the four stages viz. Plan,
Do, Check and Act. These stages provide a step-wise critical analysis of every aspect of a project
related to an existing or a new product. In the given case scenario, Hotpoint's Management has
decided to introduce a new product using six sigma methodology in television division. Using
this approach in combination with TQM, a continuous improvement plan, it is able to check the
objectives it has set with the predefined budget. The company lists out the plans it has in regards
to the geometry, dimensions and quality of the television. This helps the business to analyse the
implementation of plans in accordance with blueprint formulated in the next stage called the 'Do'
Stage. The main objective of this technique is to ascertain whether the model is free of any
constraints that may result in errors in later stages of production (Hjelmbrekke, Lædre and
Lohne, 2014). Hence, in the second stage, the implementation of blueprint in accordance with
this objective is checked to test the potential solution on a smaller scale and measure the results.
In the 'Check' Stage of this plan, Hotpoint's product development team focuses on
analysing that whether the variables assumed in the start of this project to achieve error-free
model are actually coherent or not. For this, multiple pilot runs of the prototype model made in
the second stage are executed to measure the model's effectiveness. This stage showed that there
were issues arising in the user-interface of the prototype relating to image distortion, colour
representation and audio quality. In the last stage, conclusions are drawn based on the
improvements made with the help of Total Quality Management (TQM), improvements were
carried out to rectify these shortcomings and a customer mapping technique helped in increasing
the customer experience derived from the model.
As one can see, these stages have certain criteria and results on the basis of which the
next stage determines the effective as well as ineffectiveness of the overall model. Hence, every
stage is important to analyse the project to achieve continuous improvement and consistency
across all activities.
7

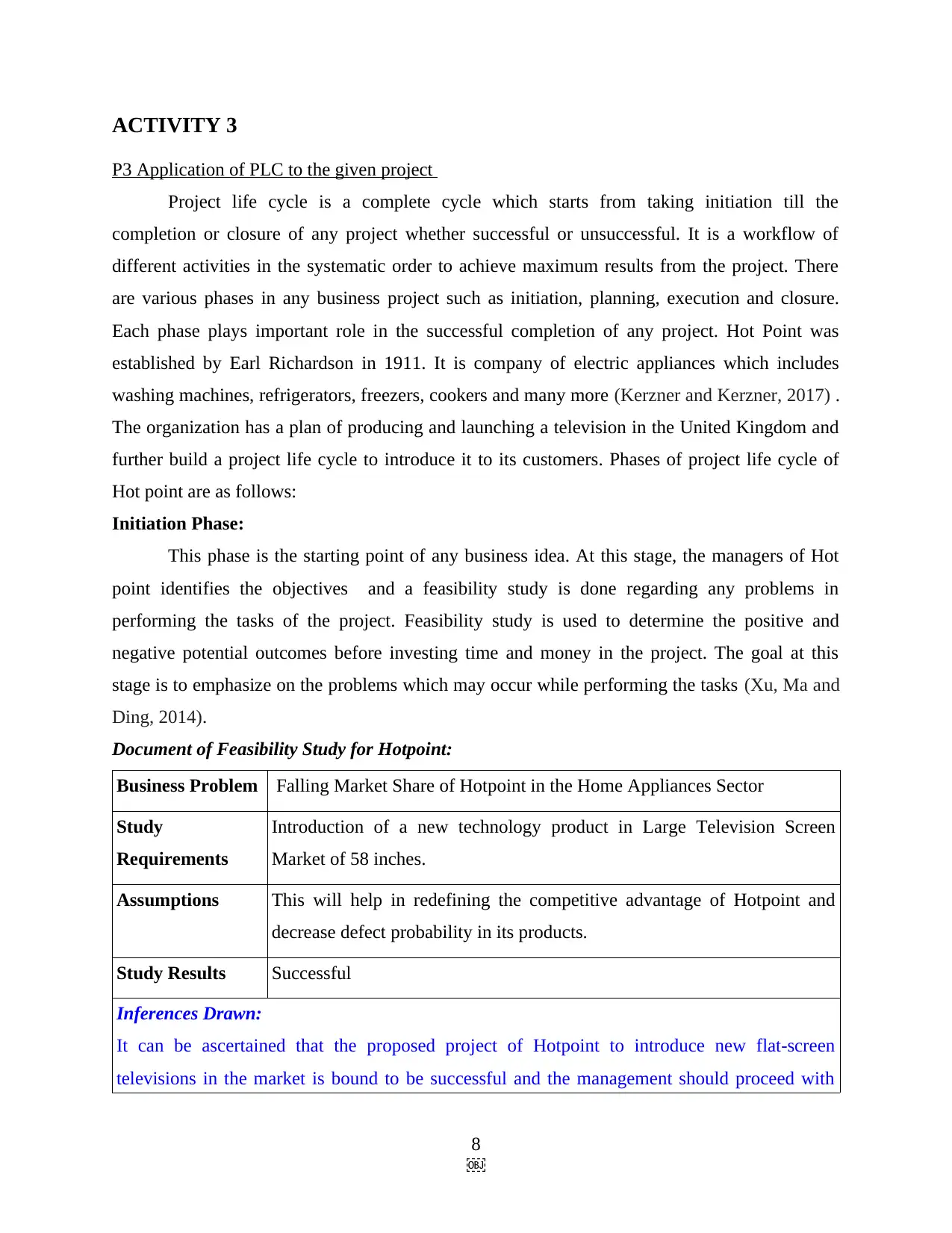
ACTIVITY 3
P3 Application of PLC to the given project
Project life cycle is a complete cycle which starts from taking initiation till the
completion or closure of any project whether successful or unsuccessful. It is a workflow of
different activities in the systematic order to achieve maximum results from the project. There
are various phases in any business project such as initiation, planning, execution and closure.
Each phase plays important role in the successful completion of any project. Hot Point was
established by Earl Richardson in 1911. It is company of electric appliances which includes
washing machines, refrigerators, freezers, cookers and many more (Kerzner and Kerzner, 2017) .
The organization has a plan of producing and launching a television in the United Kingdom and
further build a project life cycle to introduce it to its customers. Phases of project life cycle of
Hot point are as follows:
Initiation Phase:
This phase is the starting point of any business idea. At this stage, the managers of Hot
point identifies the objectives and a feasibility study is done regarding any problems in
performing the tasks of the project. Feasibility study is used to determine the positive and
negative potential outcomes before investing time and money in the project. The goal at this
stage is to emphasize on the problems which may occur while performing the tasks (Xu, Ma and
Ding, 2014).
Document of Feasibility Study for Hotpoint:
Business Problem Falling Market Share of Hotpoint in the Home Appliances Sector
Study
Requirements
Introduction of a new technology product in Large Television Screen
Market of 58 inches.
Assumptions This will help in redefining the competitive advantage of Hotpoint and
decrease defect probability in its products.
Study Results Successful
Inferences Drawn:
It can be ascertained that the proposed project of Hotpoint to introduce new flat-screen
televisions in the market is bound to be successful and the management should proceed with
8

P3 Application of PLC to the given project
Project life cycle is a complete cycle which starts from taking initiation till the
completion or closure of any project whether successful or unsuccessful. It is a workflow of
different activities in the systematic order to achieve maximum results from the project. There
are various phases in any business project such as initiation, planning, execution and closure.
Each phase plays important role in the successful completion of any project. Hot Point was
established by Earl Richardson in 1911. It is company of electric appliances which includes
washing machines, refrigerators, freezers, cookers and many more (Kerzner and Kerzner, 2017) .
The organization has a plan of producing and launching a television in the United Kingdom and
further build a project life cycle to introduce it to its customers. Phases of project life cycle of
Hot point are as follows:
Initiation Phase:
This phase is the starting point of any business idea. At this stage, the managers of Hot
point identifies the objectives and a feasibility study is done regarding any problems in
performing the tasks of the project. Feasibility study is used to determine the positive and
negative potential outcomes before investing time and money in the project. The goal at this
stage is to emphasize on the problems which may occur while performing the tasks (Xu, Ma and
Ding, 2014).
Document of Feasibility Study for Hotpoint:
Business Problem Falling Market Share of Hotpoint in the Home Appliances Sector
Study
Requirements
Introduction of a new technology product in Large Television Screen
Market of 58 inches.
Assumptions This will help in redefining the competitive advantage of Hotpoint and
decrease defect probability in its products.
Study Results Successful
Inferences Drawn:
It can be ascertained that the proposed project of Hotpoint to introduce new flat-screen
televisions in the market is bound to be successful and the management should proceed with
8

Secure Best Marks with AI Grader
Need help grading? Try our AI Grader for instant feedback on your assignments.
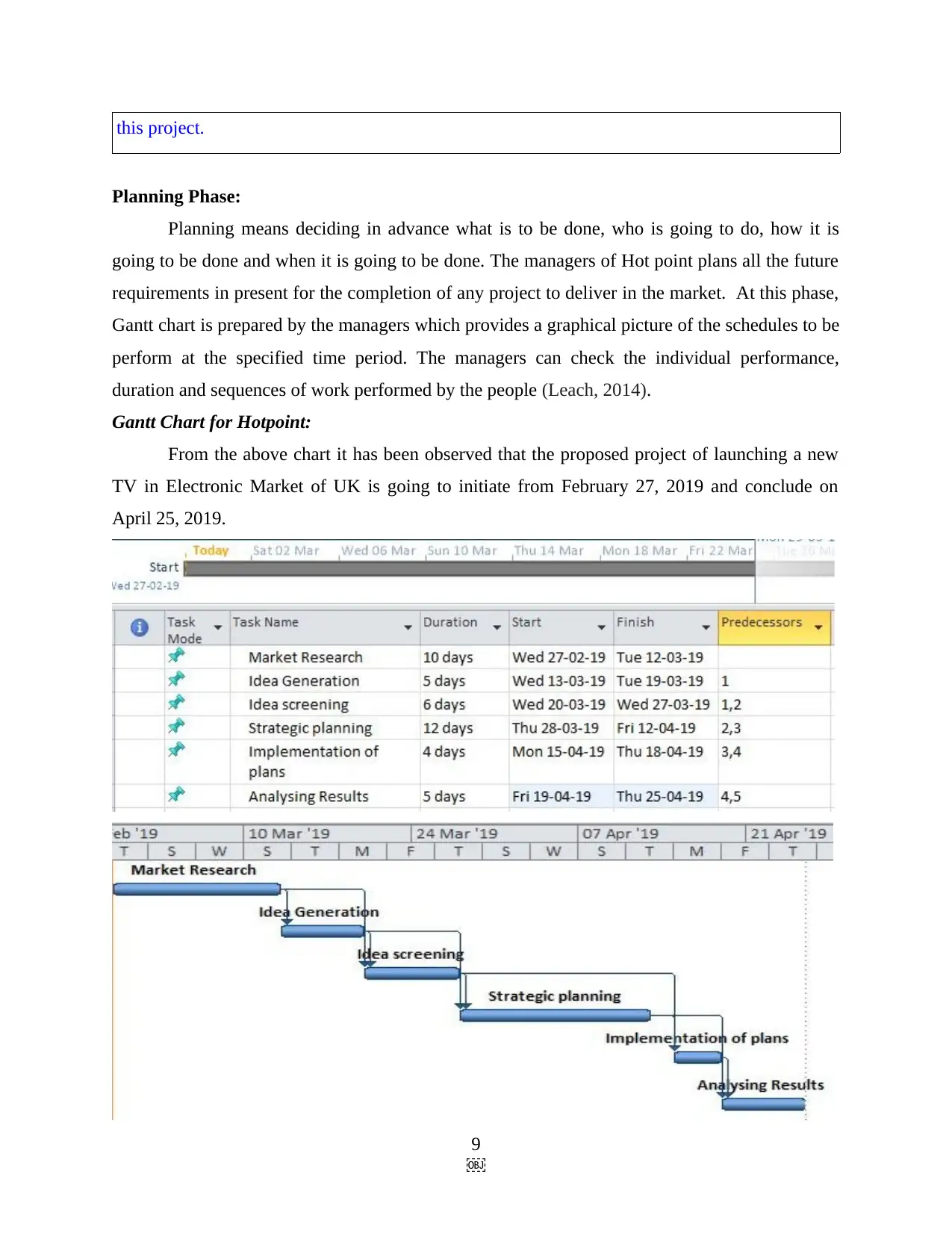
this project.
Planning Phase:
Planning means deciding in advance what is to be done, who is going to do, how it is
going to be done and when it is going to be done. The managers of Hot point plans all the future
requirements in present for the completion of any project to deliver in the market. At this phase,
Gantt chart is prepared by the managers which provides a graphical picture of the schedules to be
perform at the specified time period. The managers can check the individual performance,
duration and sequences of work performed by the people (Leach, 2014).
Gantt Chart for Hotpoint:
From the above chart it has been observed that the proposed project of launching a new
TV in Electronic Market of UK is going to initiate from February 27, 2019 and conclude on
April 25, 2019.
9

Planning Phase:
Planning means deciding in advance what is to be done, who is going to do, how it is
going to be done and when it is going to be done. The managers of Hot point plans all the future
requirements in present for the completion of any project to deliver in the market. At this phase,
Gantt chart is prepared by the managers which provides a graphical picture of the schedules to be
perform at the specified time period. The managers can check the individual performance,
duration and sequences of work performed by the people (Leach, 2014).
Gantt Chart for Hotpoint:
From the above chart it has been observed that the proposed project of launching a new
TV in Electronic Market of UK is going to initiate from February 27, 2019 and conclude on
April 25, 2019.
9

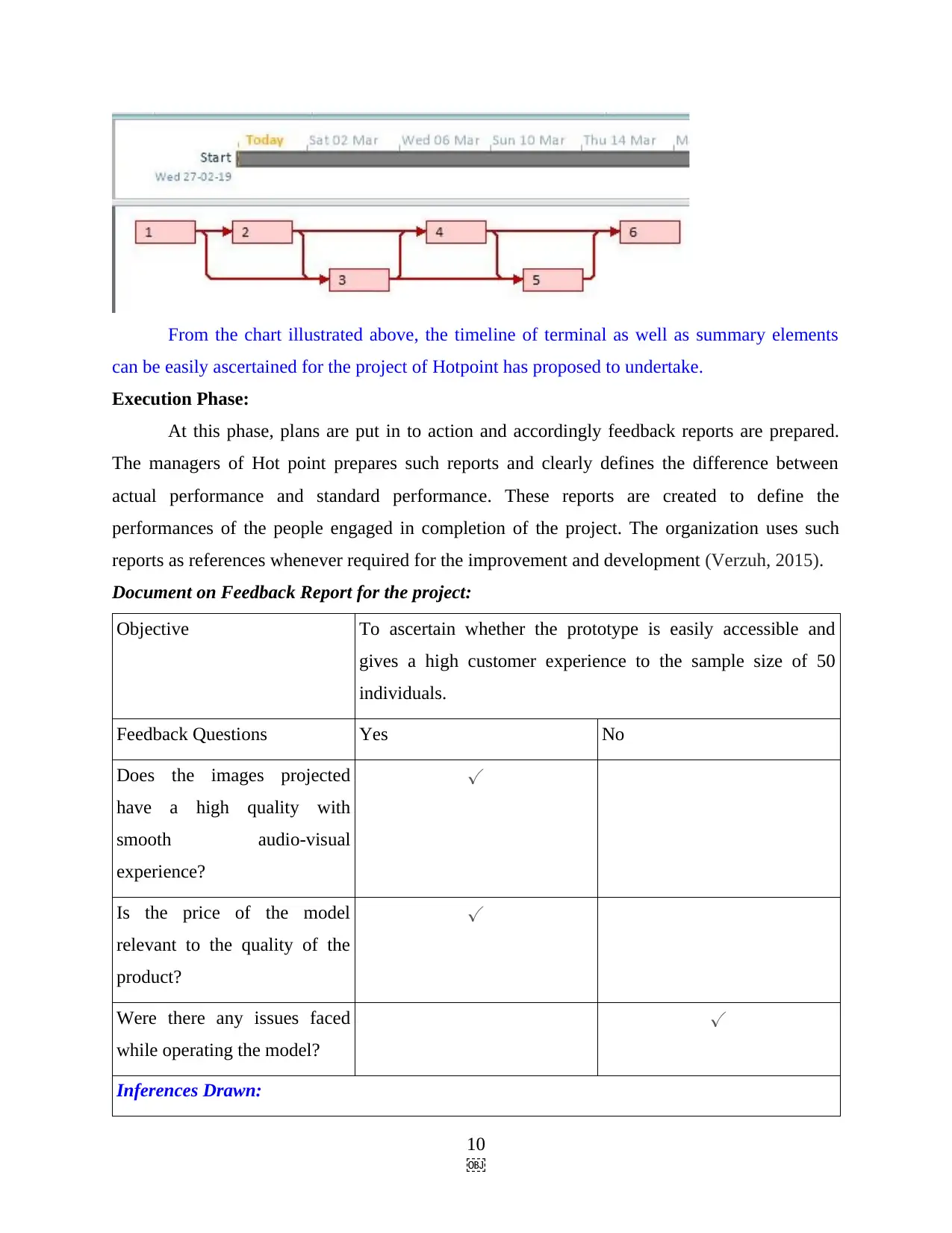
From the chart illustrated above, the timeline of terminal as well as summary elements
can be easily ascertained for the project of Hotpoint has proposed to undertake.
Execution Phase:
At this phase, plans are put in to action and accordingly feedback reports are prepared.
The managers of Hot point prepares such reports and clearly defines the difference between
actual performance and standard performance. These reports are created to define the
performances of the people engaged in completion of the project. The organization uses such
reports as references whenever required for the improvement and development (Verzuh, 2015).
Document on Feedback Report for the project:
Objective To ascertain whether the prototype is easily accessible and
gives a high customer experience to the sample size of 50
individuals.
Feedback Questions Yes No
Does the images projected
have a high quality with
smooth audio-visual
experience?
✓
Is the price of the model
relevant to the quality of the
product?
✓
Were there any issues faced
while operating the model?
✓
Inferences Drawn:
10

can be easily ascertained for the project of Hotpoint has proposed to undertake.
Execution Phase:
At this phase, plans are put in to action and accordingly feedback reports are prepared.
The managers of Hot point prepares such reports and clearly defines the difference between
actual performance and standard performance. These reports are created to define the
performances of the people engaged in completion of the project. The organization uses such
reports as references whenever required for the improvement and development (Verzuh, 2015).
Document on Feedback Report for the project:
Objective To ascertain whether the prototype is easily accessible and
gives a high customer experience to the sample size of 50
individuals.
Feedback Questions Yes No
Does the images projected
have a high quality with
smooth audio-visual
experience?
✓
Is the price of the model
relevant to the quality of the
product?
✓
Were there any issues faced
while operating the model?
✓
Inferences Drawn:
10

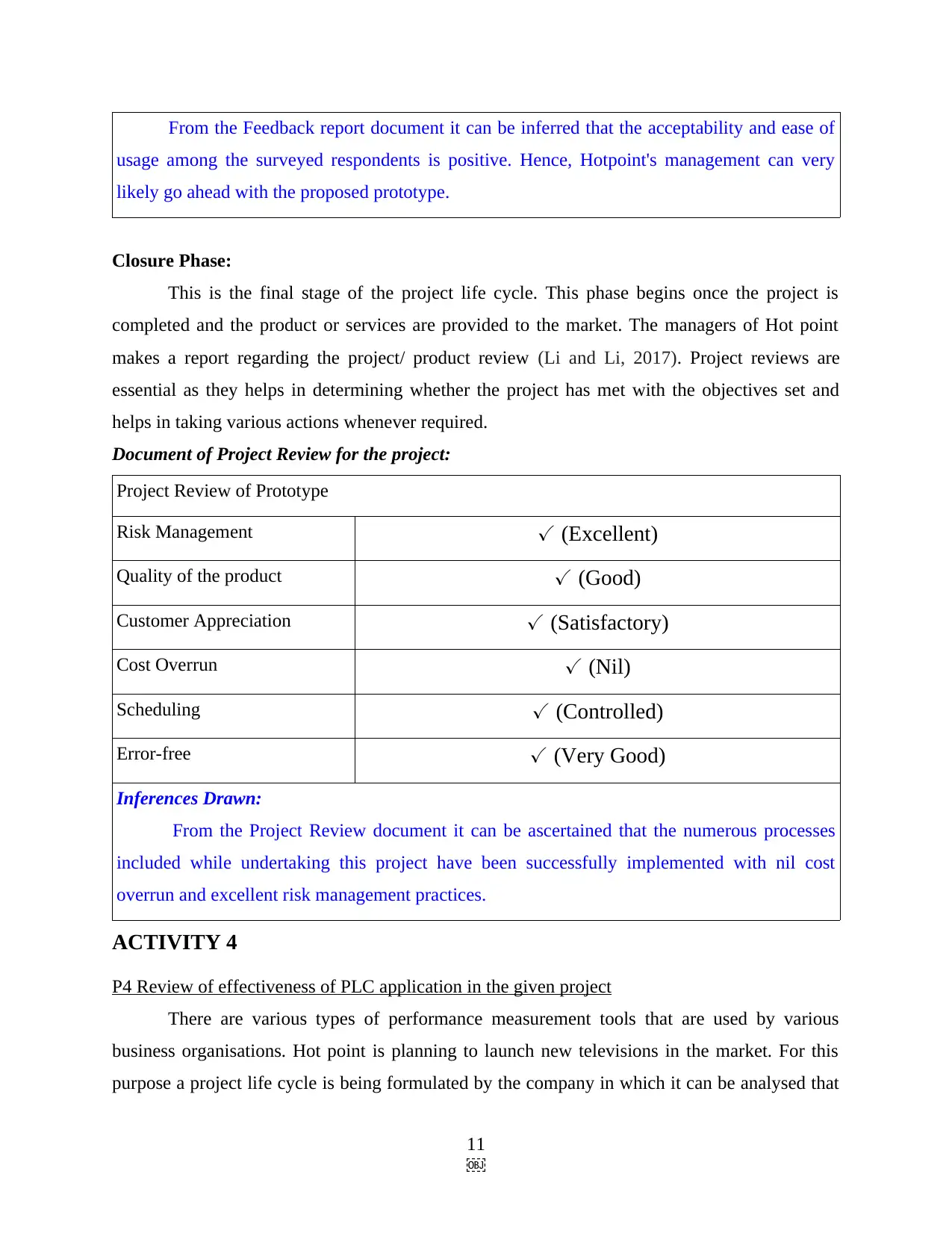
From the Feedback report document it can be inferred that the acceptability and ease of
usage among the surveyed respondents is positive. Hence, Hotpoint's management can very
likely go ahead with the proposed prototype.
Closure Phase:
This is the final stage of the project life cycle. This phase begins once the project is
completed and the product or services are provided to the market. The managers of Hot point
makes a report regarding the project/ product review (Li and Li, 2017). Project reviews are
essential as they helps in determining whether the project has met with the objectives set and
helps in taking various actions whenever required.
Document of Project Review for the project:
Project Review of Prototype
Risk Management ✓ (Excellent)
Quality of the product ✓ (Good)
Customer Appreciation ✓ (Satisfactory)
Cost Overrun ✓ (Nil)
Scheduling ✓ (Controlled)
Error-free ✓ (Very Good)
Inferences Drawn:
From the Project Review document it can be ascertained that the numerous processes
included while undertaking this project have been successfully implemented with nil cost
overrun and excellent risk management practices.
ACTIVITY 4
P4 Review of effectiveness of PLC application in the given project
There are various types of performance measurement tools that are used by various
business organisations. Hot point is planning to launch new televisions in the market. For this
purpose a project life cycle is being formulated by the company in which it can be analysed that
11

usage among the surveyed respondents is positive. Hence, Hotpoint's management can very
likely go ahead with the proposed prototype.
Closure Phase:
This is the final stage of the project life cycle. This phase begins once the project is
completed and the product or services are provided to the market. The managers of Hot point
makes a report regarding the project/ product review (Li and Li, 2017). Project reviews are
essential as they helps in determining whether the project has met with the objectives set and
helps in taking various actions whenever required.
Document of Project Review for the project:
Project Review of Prototype
Risk Management ✓ (Excellent)
Quality of the product ✓ (Good)
Customer Appreciation ✓ (Satisfactory)
Cost Overrun ✓ (Nil)
Scheduling ✓ (Controlled)
Error-free ✓ (Very Good)
Inferences Drawn:
From the Project Review document it can be ascertained that the numerous processes
included while undertaking this project have been successfully implemented with nil cost
overrun and excellent risk management practices.
ACTIVITY 4
P4 Review of effectiveness of PLC application in the given project
There are various types of performance measurement tools that are used by various
business organisations. Hot point is planning to launch new televisions in the market. For this
purpose a project life cycle is being formulated by the company in which it can be analysed that
11

Paraphrase This Document
Need a fresh take? Get an instant paraphrase of this document with our AI Paraphraser
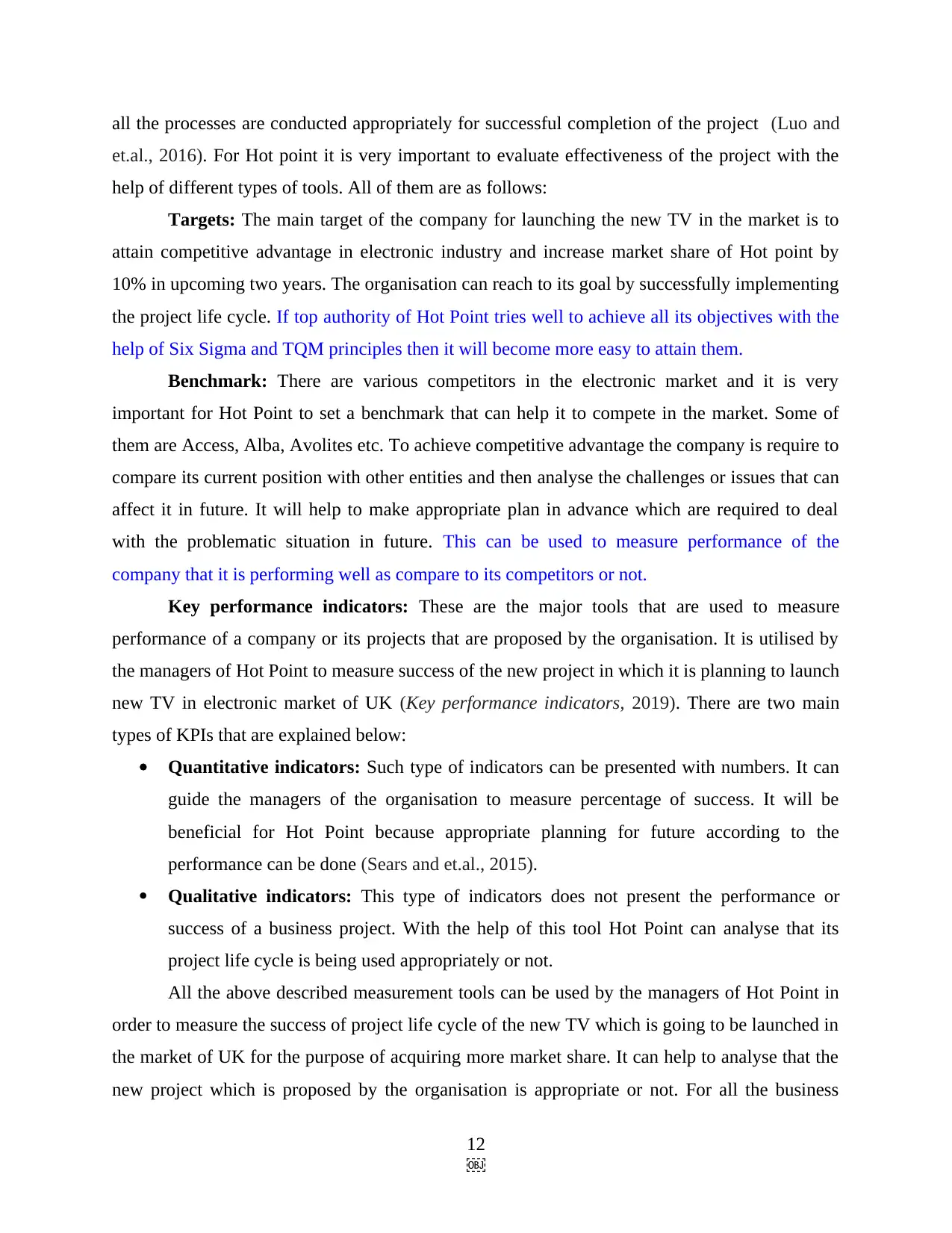
all the processes are conducted appropriately for successful completion of the project (Luo and
et.al., 2016). For Hot point it is very important to evaluate effectiveness of the project with the
help of different types of tools. All of them are as follows:
Targets: The main target of the company for launching the new TV in the market is to
attain competitive advantage in electronic industry and increase market share of Hot point by
10% in upcoming two years. The organisation can reach to its goal by successfully implementing
the project life cycle. If top authority of Hot Point tries well to achieve all its objectives with the
help of Six Sigma and TQM principles then it will become more easy to attain them.
Benchmark: There are various competitors in the electronic market and it is very
important for Hot Point to set a benchmark that can help it to compete in the market. Some of
them are Access, Alba, Avolites etc. To achieve competitive advantage the company is require to
compare its current position with other entities and then analyse the challenges or issues that can
affect it in future. It will help to make appropriate plan in advance which are required to deal
with the problematic situation in future. This can be used to measure performance of the
company that it is performing well as compare to its competitors or not.
Key performance indicators: These are the major tools that are used to measure
performance of a company or its projects that are proposed by the organisation. It is utilised by
the managers of Hot Point to measure success of the new project in which it is planning to launch
new TV in electronic market of UK (Key performance indicators, 2019). There are two main
types of KPIs that are explained below:
Quantitative indicators: Such type of indicators can be presented with numbers. It can
guide the managers of the organisation to measure percentage of success. It will be
beneficial for Hot Point because appropriate planning for future according to the
performance can be done (Sears and et.al., 2015).
Qualitative indicators: This type of indicators does not present the performance or
success of a business project. With the help of this tool Hot Point can analyse that its
project life cycle is being used appropriately or not.
All the above described measurement tools can be used by the managers of Hot Point in
order to measure the success of project life cycle of the new TV which is going to be launched in
the market of UK for the purpose of acquiring more market share. It can help to analyse that the
new project which is proposed by the organisation is appropriate or not. For all the business
12

et.al., 2016). For Hot point it is very important to evaluate effectiveness of the project with the
help of different types of tools. All of them are as follows:
Targets: The main target of the company for launching the new TV in the market is to
attain competitive advantage in electronic industry and increase market share of Hot point by
10% in upcoming two years. The organisation can reach to its goal by successfully implementing
the project life cycle. If top authority of Hot Point tries well to achieve all its objectives with the
help of Six Sigma and TQM principles then it will become more easy to attain them.
Benchmark: There are various competitors in the electronic market and it is very
important for Hot Point to set a benchmark that can help it to compete in the market. Some of
them are Access, Alba, Avolites etc. To achieve competitive advantage the company is require to
compare its current position with other entities and then analyse the challenges or issues that can
affect it in future. It will help to make appropriate plan in advance which are required to deal
with the problematic situation in future. This can be used to measure performance of the
company that it is performing well as compare to its competitors or not.
Key performance indicators: These are the major tools that are used to measure
performance of a company or its projects that are proposed by the organisation. It is utilised by
the managers of Hot Point to measure success of the new project in which it is planning to launch
new TV in electronic market of UK (Key performance indicators, 2019). There are two main
types of KPIs that are explained below:
Quantitative indicators: Such type of indicators can be presented with numbers. It can
guide the managers of the organisation to measure percentage of success. It will be
beneficial for Hot Point because appropriate planning for future according to the
performance can be done (Sears and et.al., 2015).
Qualitative indicators: This type of indicators does not present the performance or
success of a business project. With the help of this tool Hot Point can analyse that its
project life cycle is being used appropriately or not.
All the above described measurement tools can be used by the managers of Hot Point in
order to measure the success of project life cycle of the new TV which is going to be launched in
the market of UK for the purpose of acquiring more market share. It can help to analyse that the
new project which is proposed by the organisation is appropriate or not. For all the business
12

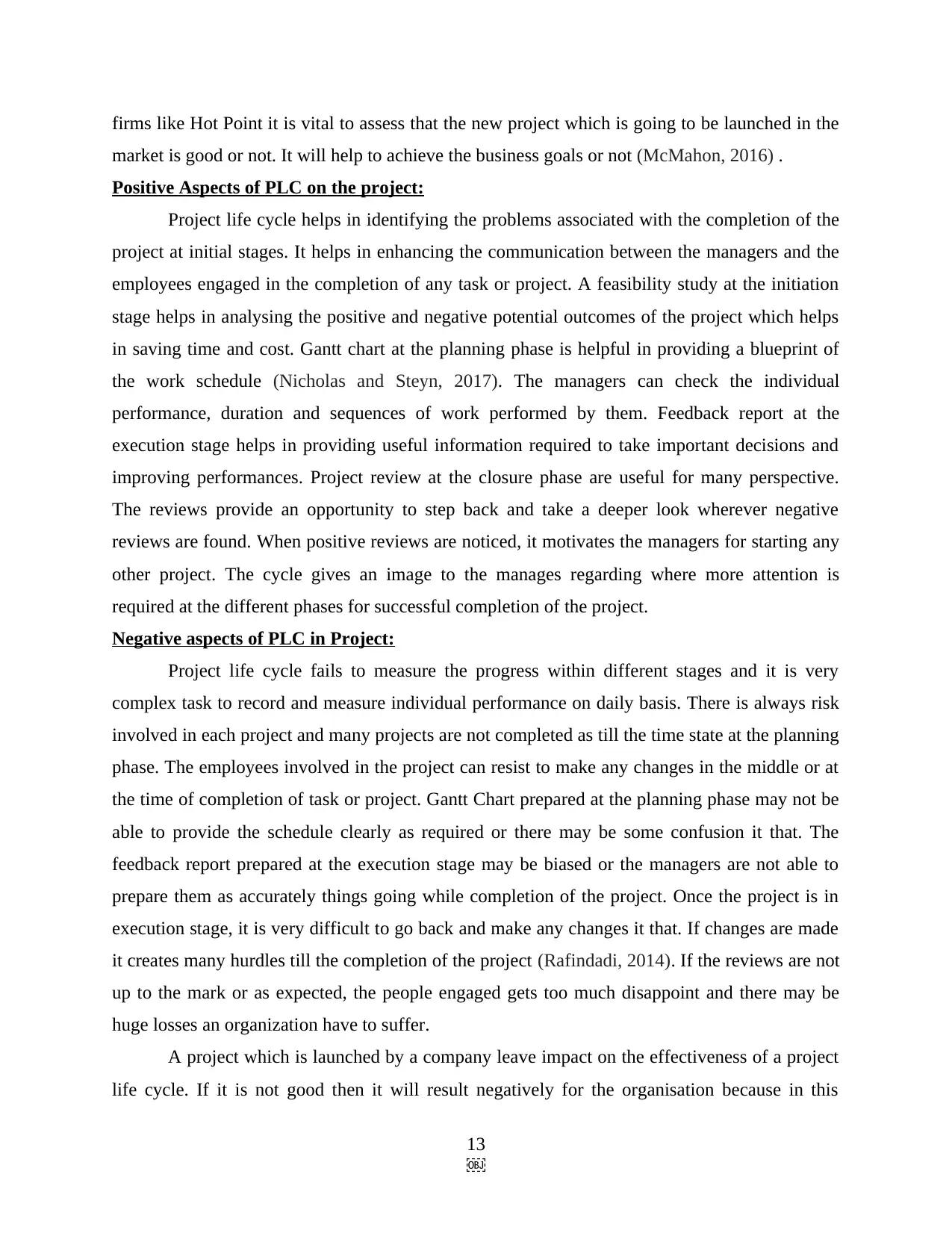
firms like Hot Point it is vital to assess that the new project which is going to be launched in the
market is good or not. It will help to achieve the business goals or not (McMahon, 2016) .
Positive Aspects of PLC on the project:
Project life cycle helps in identifying the problems associated with the completion of the
project at initial stages. It helps in enhancing the communication between the managers and the
employees engaged in the completion of any task or project. A feasibility study at the initiation
stage helps in analysing the positive and negative potential outcomes of the project which helps
in saving time and cost. Gantt chart at the planning phase is helpful in providing a blueprint of
the work schedule (Nicholas and Steyn, 2017). The managers can check the individual
performance, duration and sequences of work performed by them. Feedback report at the
execution stage helps in providing useful information required to take important decisions and
improving performances. Project review at the closure phase are useful for many perspective.
The reviews provide an opportunity to step back and take a deeper look wherever negative
reviews are found. When positive reviews are noticed, it motivates the managers for starting any
other project. The cycle gives an image to the manages regarding where more attention is
required at the different phases for successful completion of the project.
Negative aspects of PLC in Project:
Project life cycle fails to measure the progress within different stages and it is very
complex task to record and measure individual performance on daily basis. There is always risk
involved in each project and many projects are not completed as till the time state at the planning
phase. The employees involved in the project can resist to make any changes in the middle or at
the time of completion of task or project. Gantt Chart prepared at the planning phase may not be
able to provide the schedule clearly as required or there may be some confusion it that. The
feedback report prepared at the execution stage may be biased or the managers are not able to
prepare them as accurately things going while completion of the project. Once the project is in
execution stage, it is very difficult to go back and make any changes it that. If changes are made
it creates many hurdles till the completion of the project (Rafindadi, 2014). If the reviews are not
up to the mark or as expected, the people engaged gets too much disappoint and there may be
huge losses an organization have to suffer.
A project which is launched by a company leave impact on the effectiveness of a project
life cycle. If it is not good then it will result negatively for the organisation because in this
13

market is good or not. It will help to achieve the business goals or not (McMahon, 2016) .
Positive Aspects of PLC on the project:
Project life cycle helps in identifying the problems associated with the completion of the
project at initial stages. It helps in enhancing the communication between the managers and the
employees engaged in the completion of any task or project. A feasibility study at the initiation
stage helps in analysing the positive and negative potential outcomes of the project which helps
in saving time and cost. Gantt chart at the planning phase is helpful in providing a blueprint of
the work schedule (Nicholas and Steyn, 2017). The managers can check the individual
performance, duration and sequences of work performed by them. Feedback report at the
execution stage helps in providing useful information required to take important decisions and
improving performances. Project review at the closure phase are useful for many perspective.
The reviews provide an opportunity to step back and take a deeper look wherever negative
reviews are found. When positive reviews are noticed, it motivates the managers for starting any
other project. The cycle gives an image to the manages regarding where more attention is
required at the different phases for successful completion of the project.
Negative aspects of PLC in Project:
Project life cycle fails to measure the progress within different stages and it is very
complex task to record and measure individual performance on daily basis. There is always risk
involved in each project and many projects are not completed as till the time state at the planning
phase. The employees involved in the project can resist to make any changes in the middle or at
the time of completion of task or project. Gantt Chart prepared at the planning phase may not be
able to provide the schedule clearly as required or there may be some confusion it that. The
feedback report prepared at the execution stage may be biased or the managers are not able to
prepare them as accurately things going while completion of the project. Once the project is in
execution stage, it is very difficult to go back and make any changes it that. If changes are made
it creates many hurdles till the completion of the project (Rafindadi, 2014). If the reviews are not
up to the mark or as expected, the people engaged gets too much disappoint and there may be
huge losses an organization have to suffer.
A project which is launched by a company leave impact on the effectiveness of a project
life cycle. If it is not good then it will result negatively for the organisation because in this
13


situation it will not be able to achieve all its long term objectives that are proposed while
planning for a new launch. As Hot Point is going to launch a new TV in UK and to achieve
success it is very important to measure its effectiveness. If it is not monitored then it will become
difficult to reach business goals.
If a business is using appropriate theories, concepts and models in the PLC then it will
differentiate between large and small business projects because in little projects organisation
does not require to form a PLC because all the plans are made on lower level. In the case of huge
projects PLC if made to make sure that the new product which is going to be launched in the
market will help to achieve all the business goals (Rokooei, 2015).
For all the business entities it is very important to implement appropriate theories and
models while formulating a project life cycle because it can help to assess that it will result
positively for the organisation or not.
CONCLUSION
From the above report it can be concluded that operations management is an ongoing
process that helps in planning, measuring, identifying, checking and controlling production
process of a business' products and services. This report focuses on new product development for
a new market through application of six sigma methodology and attempts to analyse its project
life cycle to ensure whether the organisation is able to achieve its set goals in terms of quality
and customer satisfaction along with related documents such as Feasibility Study, Feedback
Report, Gantt Chart and Project Review.
14

planning for a new launch. As Hot Point is going to launch a new TV in UK and to achieve
success it is very important to measure its effectiveness. If it is not monitored then it will become
difficult to reach business goals.
If a business is using appropriate theories, concepts and models in the PLC then it will
differentiate between large and small business projects because in little projects organisation
does not require to form a PLC because all the plans are made on lower level. In the case of huge
projects PLC if made to make sure that the new product which is going to be launched in the
market will help to achieve all the business goals (Rokooei, 2015).
For all the business entities it is very important to implement appropriate theories and
models while formulating a project life cycle because it can help to assess that it will result
positively for the organisation or not.
CONCLUSION
From the above report it can be concluded that operations management is an ongoing
process that helps in planning, measuring, identifying, checking and controlling production
process of a business' products and services. This report focuses on new product development for
a new market through application of six sigma methodology and attempts to analyse its project
life cycle to ensure whether the organisation is able to achieve its set goals in terms of quality
and customer satisfaction along with related documents such as Feasibility Study, Feedback
Report, Gantt Chart and Project Review.
14

Secure Best Marks with AI Grader
Need help grading? Try our AI Grader for instant feedback on your assignments.
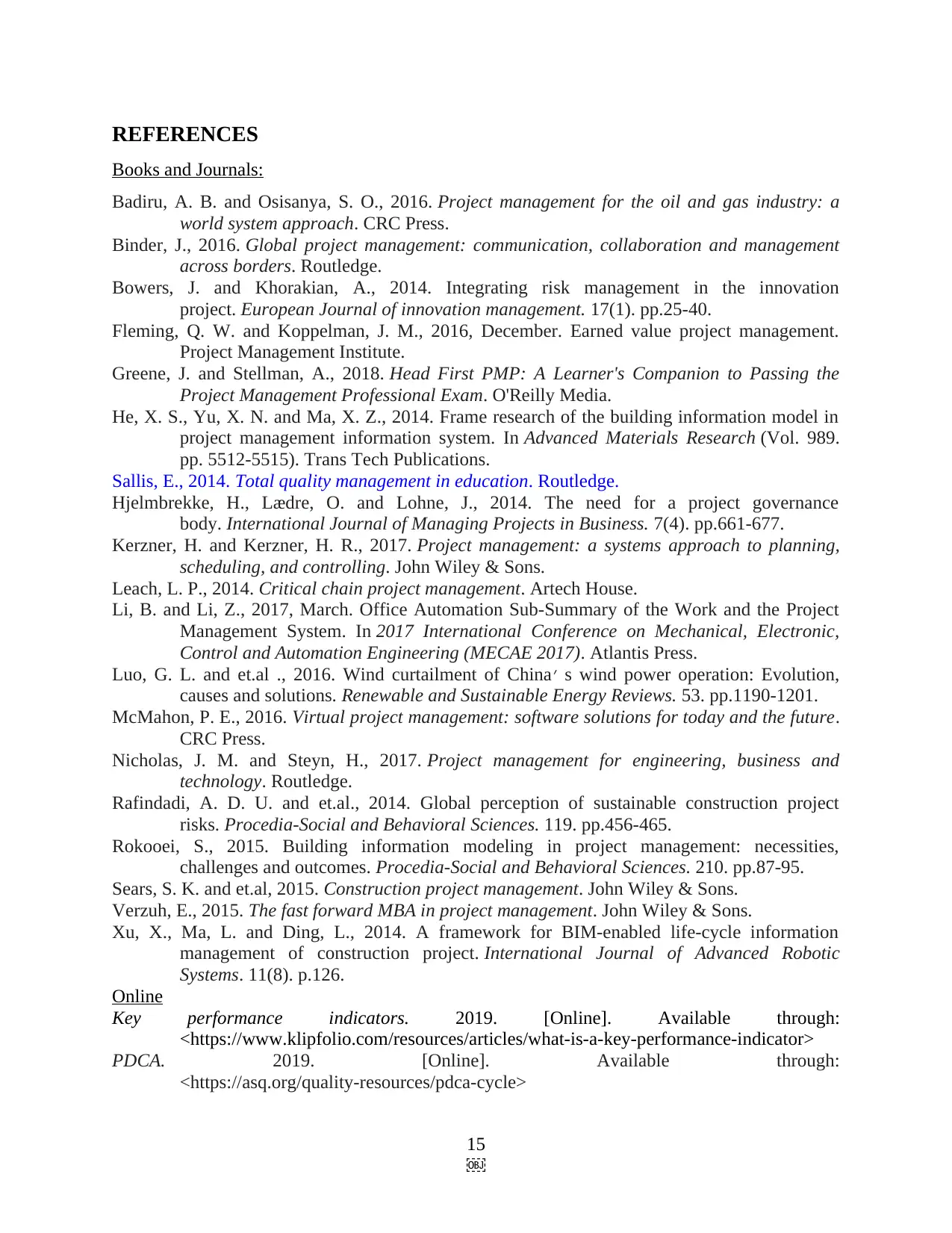
REFERENCES
Books and Journals:
Badiru, A. B. and Osisanya, S. O., 2016. Project management for the oil and gas industry: a
world system approach. CRC Press.
Binder, J., 2016. Global project management: communication, collaboration and management
across borders. Routledge.
Bowers, J. and Khorakian, A., 2014. Integrating risk management in the innovation
project. European Journal of innovation management. 17(1). pp.25-40.
Fleming, Q. W. and Koppelman, J. M., 2016, December. Earned value project management.
Project Management Institute.
Greene, J. and Stellman, A., 2018. Head First PMP: A Learner's Companion to Passing the
Project Management Professional Exam. O'Reilly Media.
He, X. S., Yu, X. N. and Ma, X. Z., 2014. Frame research of the building information model in
project management information system. In Advanced Materials Research (Vol. 989.
pp. 5512-5515). Trans Tech Publications.
Sallis, E., 2014. Total quality management in education. Routledge.
Hjelmbrekke, H., Lædre, O. and Lohne, J., 2014. The need for a project governance
body. International Journal of Managing Projects in Business. 7(4). pp.661-677.
Kerzner, H. and Kerzner, H. R., 2017. Project management: a systems approach to planning,
scheduling, and controlling. John Wiley & Sons.
Leach, L. P., 2014. Critical chain project management. Artech House.
Li, B. and Li, Z., 2017, March. Office Automation Sub-Summary of the Work and the Project
Management System. In 2017 International Conference on Mechanical, Electronic,
Control and Automation Engineering (MECAE 2017). Atlantis Press.
Luo, G. L. and et.al ., 2016. Wind curtailment of China׳ s wind power operation: Evolution,
causes and solutions. Renewable and Sustainable Energy Reviews. 53. pp.1190-1201.
McMahon, P. E., 2016. Virtual project management: software solutions for today and the future.
CRC Press.
Nicholas, J. M. and Steyn, H., 2017. Project management for engineering, business and
technology. Routledge.
Rafindadi, A. D. U. and et.al., 2014. Global perception of sustainable construction project
risks. Procedia-Social and Behavioral Sciences. 119. pp.456-465.
Rokooei, S., 2015. Building information modeling in project management: necessities,
challenges and outcomes. Procedia-Social and Behavioral Sciences. 210. pp.87-95.
Sears, S. K. and et.al, 2015. Construction project management. John Wiley & Sons.
Verzuh, E., 2015. The fast forward MBA in project management. John Wiley & Sons.
Xu, X., Ma, L. and Ding, L., 2014. A framework for BIM-enabled life-cycle information
management of construction project. International Journal of Advanced Robotic
Systems. 11(8). p.126.
Online
Key performance indicators. 2019. [Online]. Available through:
<https://www.klipfolio.com/resources/articles/what-is-a-key-performance-indicator>
PDCA. 2019. [Online]. Available through:
<https://asq.org/quality-resources/pdca-cycle>
15

Books and Journals:
Badiru, A. B. and Osisanya, S. O., 2016. Project management for the oil and gas industry: a
world system approach. CRC Press.
Binder, J., 2016. Global project management: communication, collaboration and management
across borders. Routledge.
Bowers, J. and Khorakian, A., 2014. Integrating risk management in the innovation
project. European Journal of innovation management. 17(1). pp.25-40.
Fleming, Q. W. and Koppelman, J. M., 2016, December. Earned value project management.
Project Management Institute.
Greene, J. and Stellman, A., 2018. Head First PMP: A Learner's Companion to Passing the
Project Management Professional Exam. O'Reilly Media.
He, X. S., Yu, X. N. and Ma, X. Z., 2014. Frame research of the building information model in
project management information system. In Advanced Materials Research (Vol. 989.
pp. 5512-5515). Trans Tech Publications.
Sallis, E., 2014. Total quality management in education. Routledge.
Hjelmbrekke, H., Lædre, O. and Lohne, J., 2014. The need for a project governance
body. International Journal of Managing Projects in Business. 7(4). pp.661-677.
Kerzner, H. and Kerzner, H. R., 2017. Project management: a systems approach to planning,
scheduling, and controlling. John Wiley & Sons.
Leach, L. P., 2014. Critical chain project management. Artech House.
Li, B. and Li, Z., 2017, March. Office Automation Sub-Summary of the Work and the Project
Management System. In 2017 International Conference on Mechanical, Electronic,
Control and Automation Engineering (MECAE 2017). Atlantis Press.
Luo, G. L. and et.al ., 2016. Wind curtailment of China׳ s wind power operation: Evolution,
causes and solutions. Renewable and Sustainable Energy Reviews. 53. pp.1190-1201.
McMahon, P. E., 2016. Virtual project management: software solutions for today and the future.
CRC Press.
Nicholas, J. M. and Steyn, H., 2017. Project management for engineering, business and
technology. Routledge.
Rafindadi, A. D. U. and et.al., 2014. Global perception of sustainable construction project
risks. Procedia-Social and Behavioral Sciences. 119. pp.456-465.
Rokooei, S., 2015. Building information modeling in project management: necessities,
challenges and outcomes. Procedia-Social and Behavioral Sciences. 210. pp.87-95.
Sears, S. K. and et.al, 2015. Construction project management. John Wiley & Sons.
Verzuh, E., 2015. The fast forward MBA in project management. John Wiley & Sons.
Xu, X., Ma, L. and Ding, L., 2014. A framework for BIM-enabled life-cycle information
management of construction project. International Journal of Advanced Robotic
Systems. 11(8). p.126.
Online
Key performance indicators. 2019. [Online]. Available through:
<https://www.klipfolio.com/resources/articles/what-is-a-key-performance-indicator>
PDCA. 2019. [Online]. Available through:
<https://asq.org/quality-resources/pdca-cycle>
15

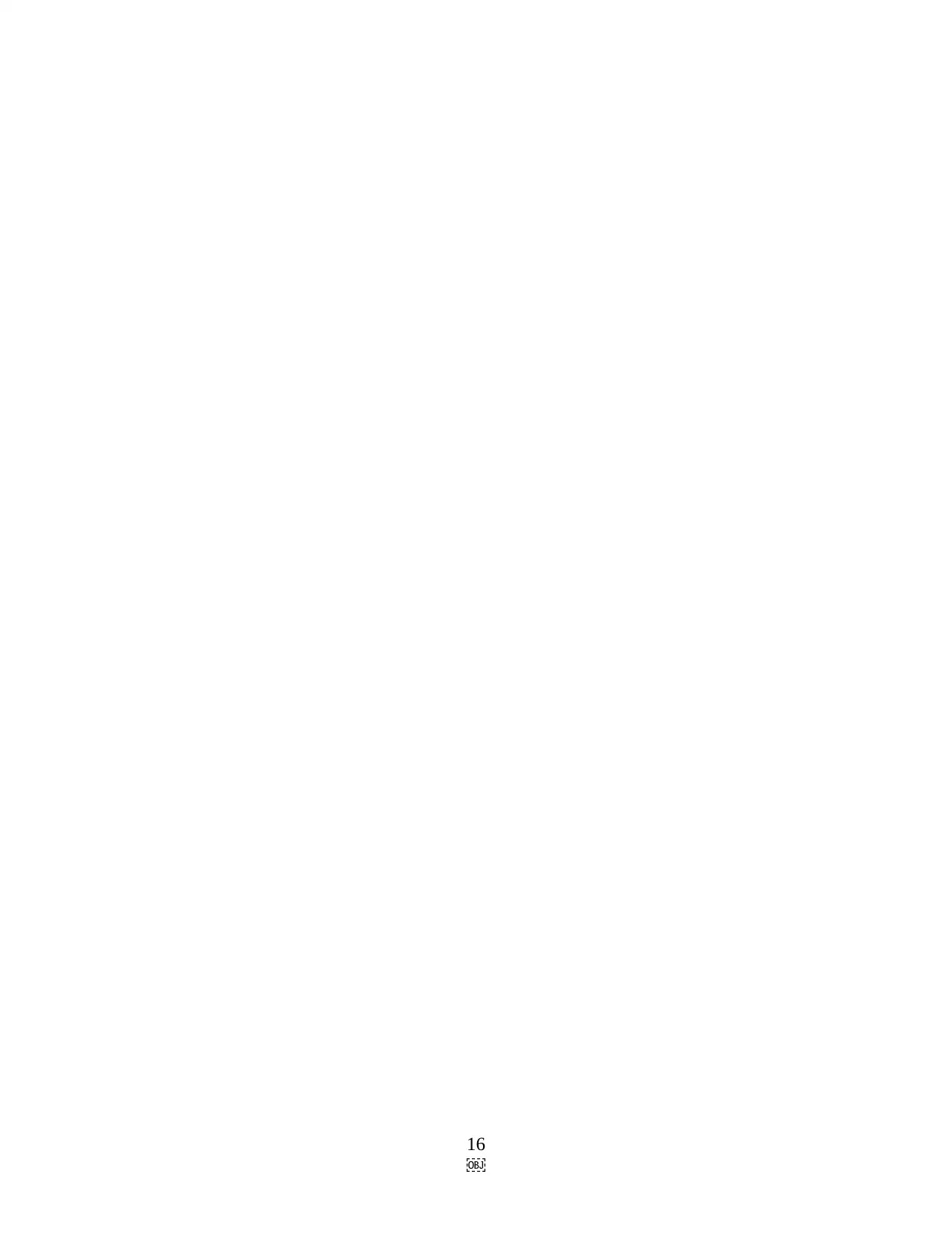
16


1 out of 18
Related Documents

Your All-in-One AI-Powered Toolkit for Academic Success.
+13062052269
info@desklib.com
Available 24*7 on WhatsApp / Email
Unlock your academic potential
© 2024 | Zucol Services PVT LTD | All rights reserved.