MMGTE202 Operations Management Project: Manufacturing Analysis
VerifiedAdded on 2022/09/02
|7
|3126
|19
Project
AI Summary
This project analyzes operations management within the context of automobile manufacturing. It begins by exploring the influence of operations management on product design and proposes a suitable layout for the manufacturing process. The project then identifies appropriate production process models and key ratios for measuring productivity. It addresses capacity and demand management, potential bottlenecks, and strategies for their mitigation. The project also covers quality inspection processes, the implementation of Total Quality Management (TQM), and the main challenges faced in the industry. Furthermore, it details inventory types, inventory management rules, and creates a Bill of Materials (BOM). Finally, it discusses aggregate planning (MPS) and disaggregating planning (MRP) strategies. The project incorporates various aspects of operations management, offering practical insights and solutions for the automobile manufacturing sector.
Contribute Materials
Your contribution can guide someone’s learning journey. Share your
documents today.
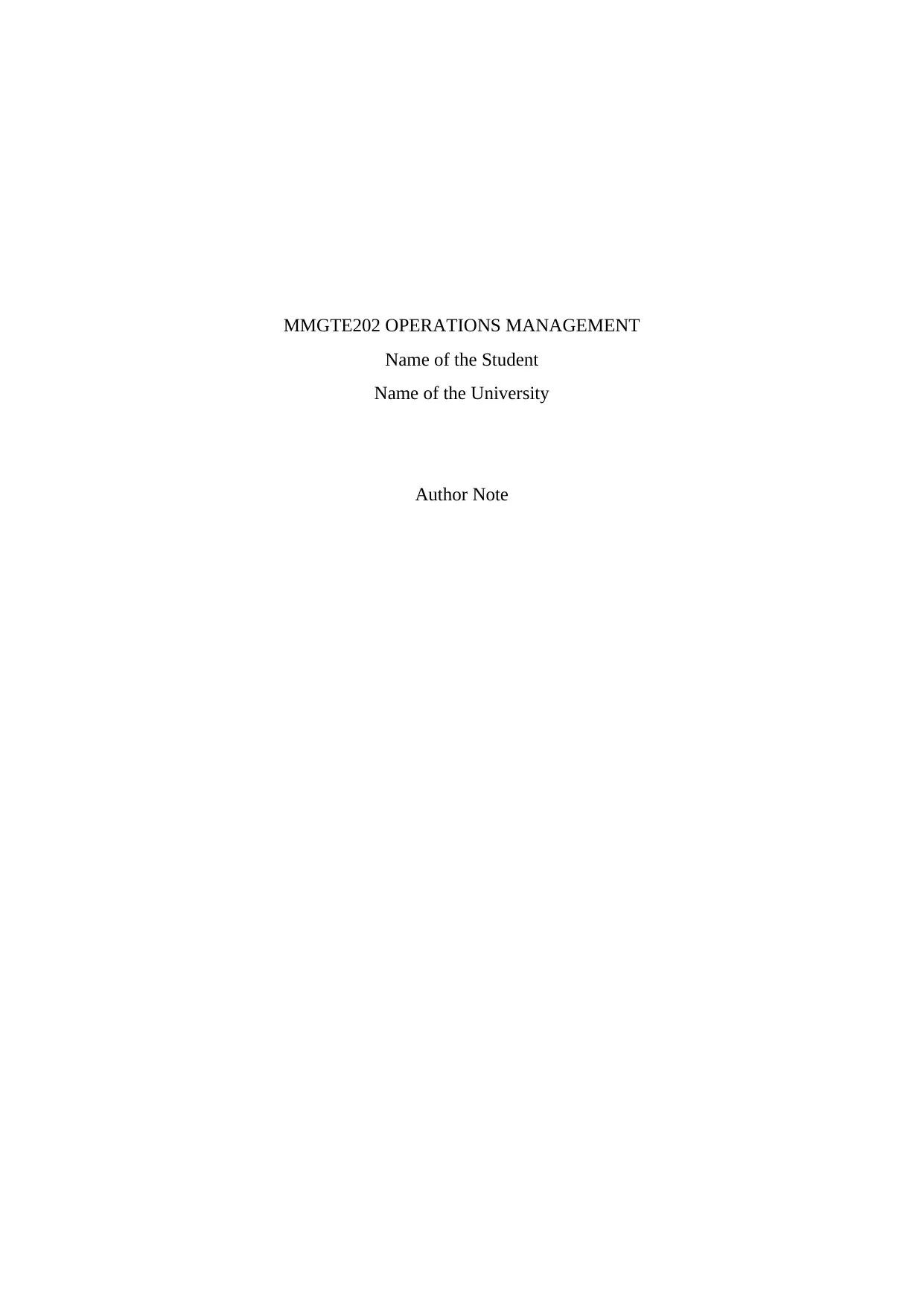
MMGTE202 OPERATIONS MANAGEMENT
Name of the Student
Name of the University
Author Note
Name of the Student
Name of the University
Author Note
Secure Best Marks with AI Grader
Need help grading? Try our AI Grader for instant feedback on your assignments.
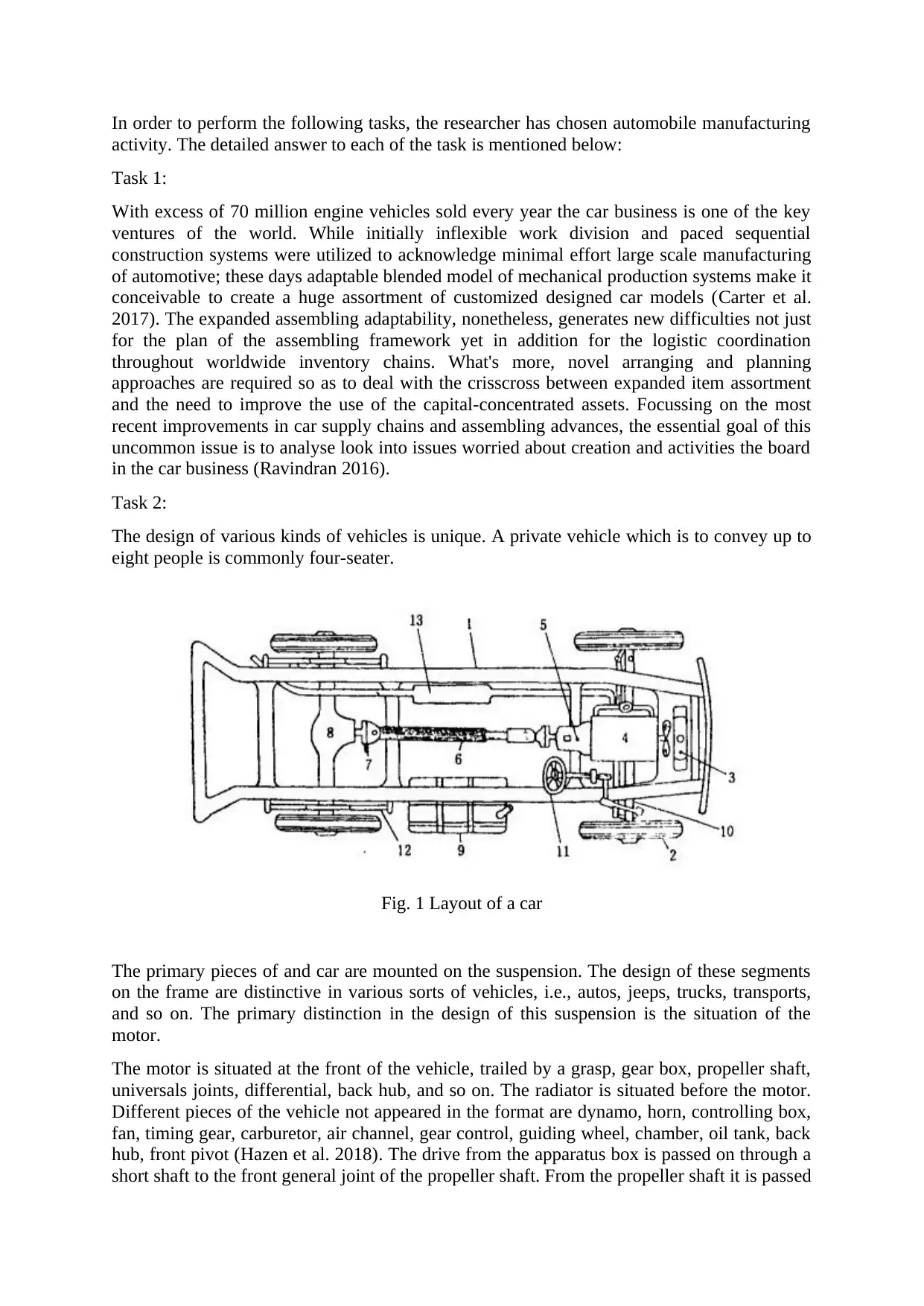
In order to perform the following tasks, the researcher has chosen automobile manufacturing
activity. The detailed answer to each of the task is mentioned below:
Task 1:
With excess of 70 million engine vehicles sold every year the car business is one of the key
ventures of the world. While initially inflexible work division and paced sequential
construction systems were utilized to acknowledge minimal effort large scale manufacturing
of automotive; these days adaptable blended model of mechanical production systems make it
conceivable to create a huge assortment of customized designed car models (Carter et al.
2017). The expanded assembling adaptability, nonetheless, generates new difficulties not just
for the plan of the assembling framework yet in addition for the logistic coordination
throughout worldwide inventory chains. What's more, novel arranging and planning
approaches are required so as to deal with the crisscross between expanded item assortment
and the need to improve the use of the capital-concentrated assets. Focussing on the most
recent improvements in car supply chains and assembling advances, the essential goal of this
uncommon issue is to analyse look into issues worried about creation and activities the board
in the car business (Ravindran 2016).
Task 2:
The design of various kinds of vehicles is unique. A private vehicle which is to convey up to
eight people is commonly four-seater.
Fig. 1 Layout of a car
The primary pieces of and car are mounted on the suspension. The design of these segments
on the frame are distinctive in various sorts of vehicles, i.e., autos, jeeps, trucks, transports,
and so on. The primary distinction in the design of this suspension is the situation of the
motor.
The motor is situated at the front of the vehicle, trailed by a grasp, gear box, propeller shaft,
universals joints, differential, back hub, and so on. The radiator is situated before the motor.
Different pieces of the vehicle not appeared in the format are dynamo, horn, controlling box,
fan, timing gear, carburetor, air channel, gear control, guiding wheel, chamber, oil tank, back
hub, front pivot (Hazen et al. 2018). The drive from the apparatus box is passed on through a
short shaft to the front general joint of the propeller shaft. From the propeller shaft it is passed
activity. The detailed answer to each of the task is mentioned below:
Task 1:
With excess of 70 million engine vehicles sold every year the car business is one of the key
ventures of the world. While initially inflexible work division and paced sequential
construction systems were utilized to acknowledge minimal effort large scale manufacturing
of automotive; these days adaptable blended model of mechanical production systems make it
conceivable to create a huge assortment of customized designed car models (Carter et al.
2017). The expanded assembling adaptability, nonetheless, generates new difficulties not just
for the plan of the assembling framework yet in addition for the logistic coordination
throughout worldwide inventory chains. What's more, novel arranging and planning
approaches are required so as to deal with the crisscross between expanded item assortment
and the need to improve the use of the capital-concentrated assets. Focussing on the most
recent improvements in car supply chains and assembling advances, the essential goal of this
uncommon issue is to analyse look into issues worried about creation and activities the board
in the car business (Ravindran 2016).
Task 2:
The design of various kinds of vehicles is unique. A private vehicle which is to convey up to
eight people is commonly four-seater.
Fig. 1 Layout of a car
The primary pieces of and car are mounted on the suspension. The design of these segments
on the frame are distinctive in various sorts of vehicles, i.e., autos, jeeps, trucks, transports,
and so on. The primary distinction in the design of this suspension is the situation of the
motor.
The motor is situated at the front of the vehicle, trailed by a grasp, gear box, propeller shaft,
universals joints, differential, back hub, and so on. The radiator is situated before the motor.
Different pieces of the vehicle not appeared in the format are dynamo, horn, controlling box,
fan, timing gear, carburetor, air channel, gear control, guiding wheel, chamber, oil tank, back
hub, front pivot (Hazen et al. 2018). The drive from the apparatus box is passed on through a
short shaft to the front general joint of the propeller shaft. From the propeller shaft it is passed
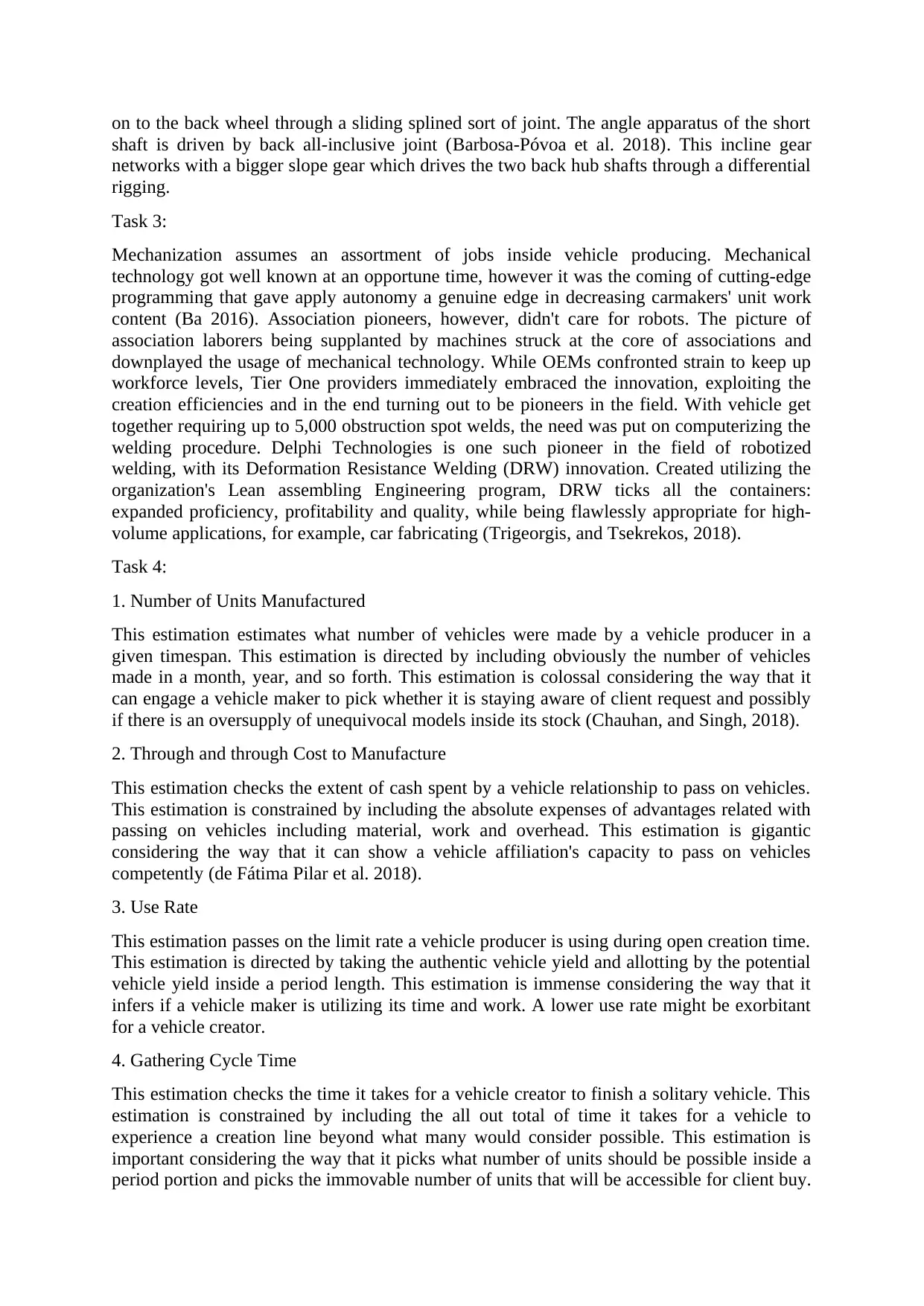
on to the back wheel through a sliding splined sort of joint. The angle apparatus of the short
shaft is driven by back all-inclusive joint (Barbosa-Póvoa et al. 2018). This incline gear
networks with a bigger slope gear which drives the two back hub shafts through a differential
rigging.
Task 3:
Mechanization assumes an assortment of jobs inside vehicle producing. Mechanical
technology got well known at an opportune time, however it was the coming of cutting-edge
programming that gave apply autonomy a genuine edge in decreasing carmakers' unit work
content (Ba 2016). Association pioneers, however, didn't care for robots. The picture of
association laborers being supplanted by machines struck at the core of associations and
downplayed the usage of mechanical technology. While OEMs confronted strain to keep up
workforce levels, Tier One providers immediately embraced the innovation, exploiting the
creation efficiencies and in the end turning out to be pioneers in the field. With vehicle get
together requiring up to 5,000 obstruction spot welds, the need was put on computerizing the
welding procedure. Delphi Technologies is one such pioneer in the field of robotized
welding, with its Deformation Resistance Welding (DRW) innovation. Created utilizing the
organization's Lean assembling Engineering program, DRW ticks all the containers:
expanded proficiency, profitability and quality, while being flawlessly appropriate for high-
volume applications, for example, car fabricating (Trigeorgis, and Tsekrekos, 2018).
Task 4:
1. Number of Units Manufactured
This estimation estimates what number of vehicles were made by a vehicle producer in a
given timespan. This estimation is directed by including obviously the number of vehicles
made in a month, year, and so forth. This estimation is colossal considering the way that it
can engage a vehicle maker to pick whether it is staying aware of client request and possibly
if there is an oversupply of unequivocal models inside its stock (Chauhan, and Singh, 2018).
2. Through and through Cost to Manufacture
This estimation checks the extent of cash spent by a vehicle relationship to pass on vehicles.
This estimation is constrained by including the absolute expenses of advantages related with
passing on vehicles including material, work and overhead. This estimation is gigantic
considering the way that it can show a vehicle affiliation's capacity to pass on vehicles
competently (de Fátima Pilar et al. 2018).
3. Use Rate
This estimation passes on the limit rate a vehicle producer is using during open creation time.
This estimation is directed by taking the authentic vehicle yield and allotting by the potential
vehicle yield inside a period length. This estimation is immense considering the way that it
infers if a vehicle maker is utilizing its time and work. A lower use rate might be exorbitant
for a vehicle creator.
4. Gathering Cycle Time
This estimation checks the time it takes for a vehicle creator to finish a solitary vehicle. This
estimation is constrained by including the all out total of time it takes for a vehicle to
experience a creation line beyond what many would consider possible. This estimation is
important considering the way that it picks what number of units should be possible inside a
period portion and picks the immovable number of units that will be accessible for client buy.
shaft is driven by back all-inclusive joint (Barbosa-Póvoa et al. 2018). This incline gear
networks with a bigger slope gear which drives the two back hub shafts through a differential
rigging.
Task 3:
Mechanization assumes an assortment of jobs inside vehicle producing. Mechanical
technology got well known at an opportune time, however it was the coming of cutting-edge
programming that gave apply autonomy a genuine edge in decreasing carmakers' unit work
content (Ba 2016). Association pioneers, however, didn't care for robots. The picture of
association laborers being supplanted by machines struck at the core of associations and
downplayed the usage of mechanical technology. While OEMs confronted strain to keep up
workforce levels, Tier One providers immediately embraced the innovation, exploiting the
creation efficiencies and in the end turning out to be pioneers in the field. With vehicle get
together requiring up to 5,000 obstruction spot welds, the need was put on computerizing the
welding procedure. Delphi Technologies is one such pioneer in the field of robotized
welding, with its Deformation Resistance Welding (DRW) innovation. Created utilizing the
organization's Lean assembling Engineering program, DRW ticks all the containers:
expanded proficiency, profitability and quality, while being flawlessly appropriate for high-
volume applications, for example, car fabricating (Trigeorgis, and Tsekrekos, 2018).
Task 4:
1. Number of Units Manufactured
This estimation estimates what number of vehicles were made by a vehicle producer in a
given timespan. This estimation is directed by including obviously the number of vehicles
made in a month, year, and so forth. This estimation is colossal considering the way that it
can engage a vehicle maker to pick whether it is staying aware of client request and possibly
if there is an oversupply of unequivocal models inside its stock (Chauhan, and Singh, 2018).
2. Through and through Cost to Manufacture
This estimation checks the extent of cash spent by a vehicle relationship to pass on vehicles.
This estimation is constrained by including the absolute expenses of advantages related with
passing on vehicles including material, work and overhead. This estimation is gigantic
considering the way that it can show a vehicle affiliation's capacity to pass on vehicles
competently (de Fátima Pilar et al. 2018).
3. Use Rate
This estimation passes on the limit rate a vehicle producer is using during open creation time.
This estimation is directed by taking the authentic vehicle yield and allotting by the potential
vehicle yield inside a period length. This estimation is immense considering the way that it
infers if a vehicle maker is utilizing its time and work. A lower use rate might be exorbitant
for a vehicle creator.
4. Gathering Cycle Time
This estimation checks the time it takes for a vehicle creator to finish a solitary vehicle. This
estimation is constrained by including the all out total of time it takes for a vehicle to
experience a creation line beyond what many would consider possible. This estimation is
important considering the way that it picks what number of units should be possible inside a
period portion and picks the immovable number of units that will be accessible for client buy.
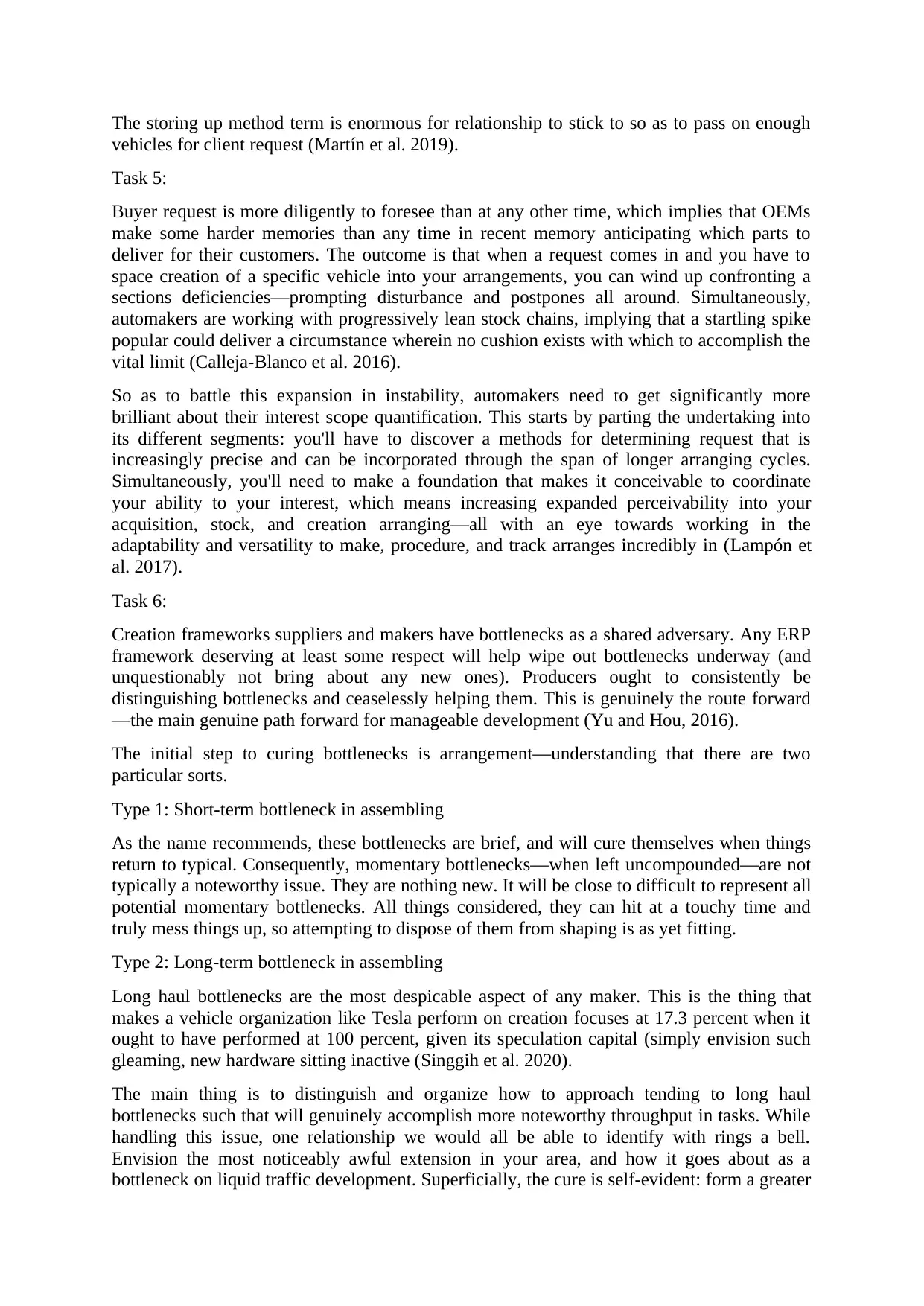
The storing up method term is enormous for relationship to stick to so as to pass on enough
vehicles for client request (Martín et al. 2019).
Task 5:
Buyer request is more diligently to foresee than at any other time, which implies that OEMs
make some harder memories than any time in recent memory anticipating which parts to
deliver for their customers. The outcome is that when a request comes in and you have to
space creation of a specific vehicle into your arrangements, you can wind up confronting a
sections deficiencies—prompting disturbance and postpones all around. Simultaneously,
automakers are working with progressively lean stock chains, implying that a startling spike
popular could deliver a circumstance wherein no cushion exists with which to accomplish the
vital limit (Calleja-Blanco et al. 2016).
So as to battle this expansion in instability, automakers need to get significantly more
brilliant about their interest scope quantification. This starts by parting the undertaking into
its different segments: you'll have to discover a methods for determining request that is
increasingly precise and can be incorporated through the span of longer arranging cycles.
Simultaneously, you'll need to make a foundation that makes it conceivable to coordinate
your ability to your interest, which means increasing expanded perceivability into your
acquisition, stock, and creation arranging—all with an eye towards working in the
adaptability and versatility to make, procedure, and track arranges incredibly in (Lampón et
al. 2017).
Task 6:
Creation frameworks suppliers and makers have bottlenecks as a shared adversary. Any ERP
framework deserving at least some respect will help wipe out bottlenecks underway (and
unquestionably not bring about any new ones). Producers ought to consistently be
distinguishing bottlenecks and ceaselessly helping them. This is genuinely the route forward
—the main genuine path forward for manageable development (Yu and Hou, 2016).
The initial step to curing bottlenecks is arrangement—understanding that there are two
particular sorts.
Type 1: Short-term bottleneck in assembling
As the name recommends, these bottlenecks are brief, and will cure themselves when things
return to typical. Consequently, momentary bottlenecks—when left uncompounded—are not
typically a noteworthy issue. They are nothing new. It will be close to difficult to represent all
potential momentary bottlenecks. All things considered, they can hit at a touchy time and
truly mess things up, so attempting to dispose of them from shaping is as yet fitting.
Type 2: Long-term bottleneck in assembling
Long haul bottlenecks are the most despicable aspect of any maker. This is the thing that
makes a vehicle organization like Tesla perform on creation focuses at 17.3 percent when it
ought to have performed at 100 percent, given its speculation capital (simply envision such
gleaming, new hardware sitting inactive (Singgih et al. 2020).
The main thing is to distinguish and organize how to approach tending to long haul
bottlenecks such that will genuinely accomplish more noteworthy throughput in tasks. While
handling this issue, one relationship we would all be able to identify with rings a bell.
Envision the most noticeably awful extension in your area, and how it goes about as a
bottleneck on liquid traffic development. Superficially, the cure is self-evident: form a greater
vehicles for client request (Martín et al. 2019).
Task 5:
Buyer request is more diligently to foresee than at any other time, which implies that OEMs
make some harder memories than any time in recent memory anticipating which parts to
deliver for their customers. The outcome is that when a request comes in and you have to
space creation of a specific vehicle into your arrangements, you can wind up confronting a
sections deficiencies—prompting disturbance and postpones all around. Simultaneously,
automakers are working with progressively lean stock chains, implying that a startling spike
popular could deliver a circumstance wherein no cushion exists with which to accomplish the
vital limit (Calleja-Blanco et al. 2016).
So as to battle this expansion in instability, automakers need to get significantly more
brilliant about their interest scope quantification. This starts by parting the undertaking into
its different segments: you'll have to discover a methods for determining request that is
increasingly precise and can be incorporated through the span of longer arranging cycles.
Simultaneously, you'll need to make a foundation that makes it conceivable to coordinate
your ability to your interest, which means increasing expanded perceivability into your
acquisition, stock, and creation arranging—all with an eye towards working in the
adaptability and versatility to make, procedure, and track arranges incredibly in (Lampón et
al. 2017).
Task 6:
Creation frameworks suppliers and makers have bottlenecks as a shared adversary. Any ERP
framework deserving at least some respect will help wipe out bottlenecks underway (and
unquestionably not bring about any new ones). Producers ought to consistently be
distinguishing bottlenecks and ceaselessly helping them. This is genuinely the route forward
—the main genuine path forward for manageable development (Yu and Hou, 2016).
The initial step to curing bottlenecks is arrangement—understanding that there are two
particular sorts.
Type 1: Short-term bottleneck in assembling
As the name recommends, these bottlenecks are brief, and will cure themselves when things
return to typical. Consequently, momentary bottlenecks—when left uncompounded—are not
typically a noteworthy issue. They are nothing new. It will be close to difficult to represent all
potential momentary bottlenecks. All things considered, they can hit at a touchy time and
truly mess things up, so attempting to dispose of them from shaping is as yet fitting.
Type 2: Long-term bottleneck in assembling
Long haul bottlenecks are the most despicable aspect of any maker. This is the thing that
makes a vehicle organization like Tesla perform on creation focuses at 17.3 percent when it
ought to have performed at 100 percent, given its speculation capital (simply envision such
gleaming, new hardware sitting inactive (Singgih et al. 2020).
The main thing is to distinguish and organize how to approach tending to long haul
bottlenecks such that will genuinely accomplish more noteworthy throughput in tasks. While
handling this issue, one relationship we would all be able to identify with rings a bell.
Envision the most noticeably awful extension in your area, and how it goes about as a
bottleneck on liquid traffic development. Superficially, the cure is self-evident: form a greater
Secure Best Marks with AI Grader
Need help grading? Try our AI Grader for instant feedback on your assignments.
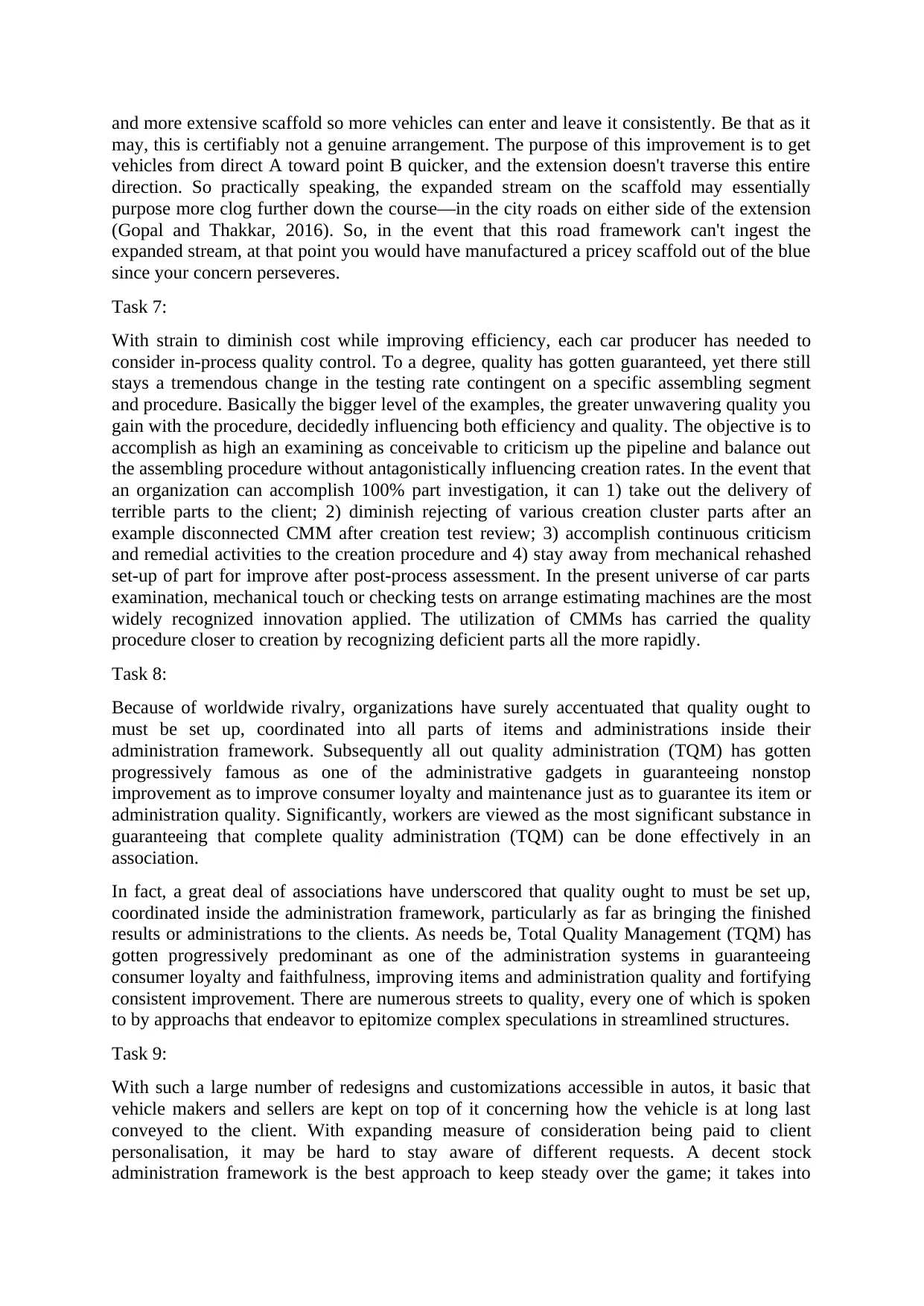
and more extensive scaffold so more vehicles can enter and leave it consistently. Be that as it
may, this is certifiably not a genuine arrangement. The purpose of this improvement is to get
vehicles from direct A toward point B quicker, and the extension doesn't traverse this entire
direction. So practically speaking, the expanded stream on the scaffold may essentially
purpose more clog further down the course—in the city roads on either side of the extension
(Gopal and Thakkar, 2016). So, in the event that this road framework can't ingest the
expanded stream, at that point you would have manufactured a pricey scaffold out of the blue
since your concern perseveres.
Task 7:
With strain to diminish cost while improving efficiency, each car producer has needed to
consider in-process quality control. To a degree, quality has gotten guaranteed, yet there still
stays a tremendous change in the testing rate contingent on a specific assembling segment
and procedure. Basically the bigger level of the examples, the greater unwavering quality you
gain with the procedure, decidedly influencing both efficiency and quality. The objective is to
accomplish as high an examining as conceivable to criticism up the pipeline and balance out
the assembling procedure without antagonistically influencing creation rates. In the event that
an organization can accomplish 100% part investigation, it can 1) take out the delivery of
terrible parts to the client; 2) diminish rejecting of various creation cluster parts after an
example disconnected CMM after creation test review; 3) accomplish continuous criticism
and remedial activities to the creation procedure and 4) stay away from mechanical rehashed
set-up of part for improve after post-process assessment. In the present universe of car parts
examination, mechanical touch or checking tests on arrange estimating machines are the most
widely recognized innovation applied. The utilization of CMMs has carried the quality
procedure closer to creation by recognizing deficient parts all the more rapidly.
Task 8:
Because of worldwide rivalry, organizations have surely accentuated that quality ought to
must be set up, coordinated into all parts of items and administrations inside their
administration framework. Subsequently all out quality administration (TQM) has gotten
progressively famous as one of the administrative gadgets in guaranteeing nonstop
improvement as to improve consumer loyalty and maintenance just as to guarantee its item or
administration quality. Significantly, workers are viewed as the most significant substance in
guaranteeing that complete quality administration (TQM) can be done effectively in an
association.
In fact, a great deal of associations have underscored that quality ought to must be set up,
coordinated inside the administration framework, particularly as far as bringing the finished
results or administrations to the clients. As needs be, Total Quality Management (TQM) has
gotten progressively predominant as one of the administration systems in guaranteeing
consumer loyalty and faithfulness, improving items and administration quality and fortifying
consistent improvement. There are numerous streets to quality, every one of which is spoken
to by approachs that endeavor to epitomize complex speculations in streamlined structures.
Task 9:
With such a large number of redesigns and customizations accessible in autos, it basic that
vehicle makers and sellers are kept on top of it concerning how the vehicle is at long last
conveyed to the client. With expanding measure of consideration being paid to client
personalisation, it may be hard to stay aware of different requests. A decent stock
administration framework is the best approach to keep steady over the game; it takes into
may, this is certifiably not a genuine arrangement. The purpose of this improvement is to get
vehicles from direct A toward point B quicker, and the extension doesn't traverse this entire
direction. So practically speaking, the expanded stream on the scaffold may essentially
purpose more clog further down the course—in the city roads on either side of the extension
(Gopal and Thakkar, 2016). So, in the event that this road framework can't ingest the
expanded stream, at that point you would have manufactured a pricey scaffold out of the blue
since your concern perseveres.
Task 7:
With strain to diminish cost while improving efficiency, each car producer has needed to
consider in-process quality control. To a degree, quality has gotten guaranteed, yet there still
stays a tremendous change in the testing rate contingent on a specific assembling segment
and procedure. Basically the bigger level of the examples, the greater unwavering quality you
gain with the procedure, decidedly influencing both efficiency and quality. The objective is to
accomplish as high an examining as conceivable to criticism up the pipeline and balance out
the assembling procedure without antagonistically influencing creation rates. In the event that
an organization can accomplish 100% part investigation, it can 1) take out the delivery of
terrible parts to the client; 2) diminish rejecting of various creation cluster parts after an
example disconnected CMM after creation test review; 3) accomplish continuous criticism
and remedial activities to the creation procedure and 4) stay away from mechanical rehashed
set-up of part for improve after post-process assessment. In the present universe of car parts
examination, mechanical touch or checking tests on arrange estimating machines are the most
widely recognized innovation applied. The utilization of CMMs has carried the quality
procedure closer to creation by recognizing deficient parts all the more rapidly.
Task 8:
Because of worldwide rivalry, organizations have surely accentuated that quality ought to
must be set up, coordinated into all parts of items and administrations inside their
administration framework. Subsequently all out quality administration (TQM) has gotten
progressively famous as one of the administrative gadgets in guaranteeing nonstop
improvement as to improve consumer loyalty and maintenance just as to guarantee its item or
administration quality. Significantly, workers are viewed as the most significant substance in
guaranteeing that complete quality administration (TQM) can be done effectively in an
association.
In fact, a great deal of associations have underscored that quality ought to must be set up,
coordinated inside the administration framework, particularly as far as bringing the finished
results or administrations to the clients. As needs be, Total Quality Management (TQM) has
gotten progressively predominant as one of the administration systems in guaranteeing
consumer loyalty and faithfulness, improving items and administration quality and fortifying
consistent improvement. There are numerous streets to quality, every one of which is spoken
to by approachs that endeavor to epitomize complex speculations in streamlined structures.
Task 9:
With such a large number of redesigns and customizations accessible in autos, it basic that
vehicle makers and sellers are kept on top of it concerning how the vehicle is at long last
conveyed to the client. With expanding measure of consideration being paid to client
personalisation, it may be hard to stay aware of different requests. A decent stock
administration framework is the best approach to keep steady over the game; it takes into
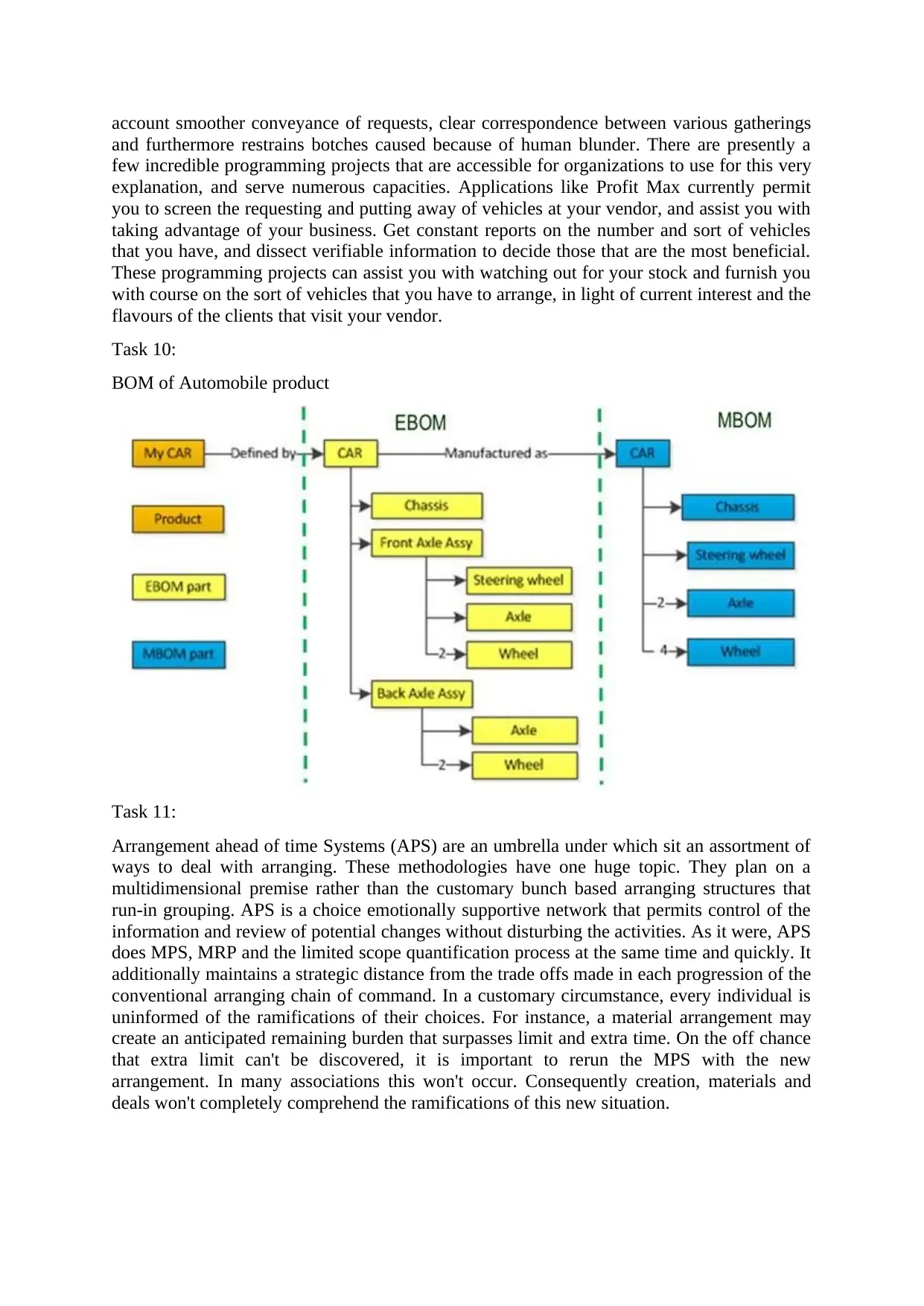
account smoother conveyance of requests, clear correspondence between various gatherings
and furthermore restrains botches caused because of human blunder. There are presently a
few incredible programming projects that are accessible for organizations to use for this very
explanation, and serve numerous capacities. Applications like Profit Max currently permit
you to screen the requesting and putting away of vehicles at your vendor, and assist you with
taking advantage of your business. Get constant reports on the number and sort of vehicles
that you have, and dissect verifiable information to decide those that are the most beneficial.
These programming projects can assist you with watching out for your stock and furnish you
with course on the sort of vehicles that you have to arrange, in light of current interest and the
flavours of the clients that visit your vendor.
Task 10:
BOM of Automobile product
Task 11:
Arrangement ahead of time Systems (APS) are an umbrella under which sit an assortment of
ways to deal with arranging. These methodologies have one huge topic. They plan on a
multidimensional premise rather than the customary bunch based arranging structures that
run-in grouping. APS is a choice emotionally supportive network that permits control of the
information and review of potential changes without disturbing the activities. As it were, APS
does MPS, MRP and the limited scope quantification process at the same time and quickly. It
additionally maintains a strategic distance from the trade offs made in each progression of the
conventional arranging chain of command. In a customary circumstance, every individual is
uninformed of the ramifications of their choices. For instance, a material arrangement may
create an anticipated remaining burden that surpasses limit and extra time. On the off chance
that extra limit can't be discovered, it is important to rerun the MPS with the new
arrangement. In many associations this won't occur. Consequently creation, materials and
deals won't completely comprehend the ramifications of this new situation.
and furthermore restrains botches caused because of human blunder. There are presently a
few incredible programming projects that are accessible for organizations to use for this very
explanation, and serve numerous capacities. Applications like Profit Max currently permit
you to screen the requesting and putting away of vehicles at your vendor, and assist you with
taking advantage of your business. Get constant reports on the number and sort of vehicles
that you have, and dissect verifiable information to decide those that are the most beneficial.
These programming projects can assist you with watching out for your stock and furnish you
with course on the sort of vehicles that you have to arrange, in light of current interest and the
flavours of the clients that visit your vendor.
Task 10:
BOM of Automobile product
Task 11:
Arrangement ahead of time Systems (APS) are an umbrella under which sit an assortment of
ways to deal with arranging. These methodologies have one huge topic. They plan on a
multidimensional premise rather than the customary bunch based arranging structures that
run-in grouping. APS is a choice emotionally supportive network that permits control of the
information and review of potential changes without disturbing the activities. As it were, APS
does MPS, MRP and the limited scope quantification process at the same time and quickly. It
additionally maintains a strategic distance from the trade offs made in each progression of the
conventional arranging chain of command. In a customary circumstance, every individual is
uninformed of the ramifications of their choices. For instance, a material arrangement may
create an anticipated remaining burden that surpasses limit and extra time. On the off chance
that extra limit can't be discovered, it is important to rerun the MPS with the new
arrangement. In many associations this won't occur. Consequently creation, materials and
deals won't completely comprehend the ramifications of this new situation.
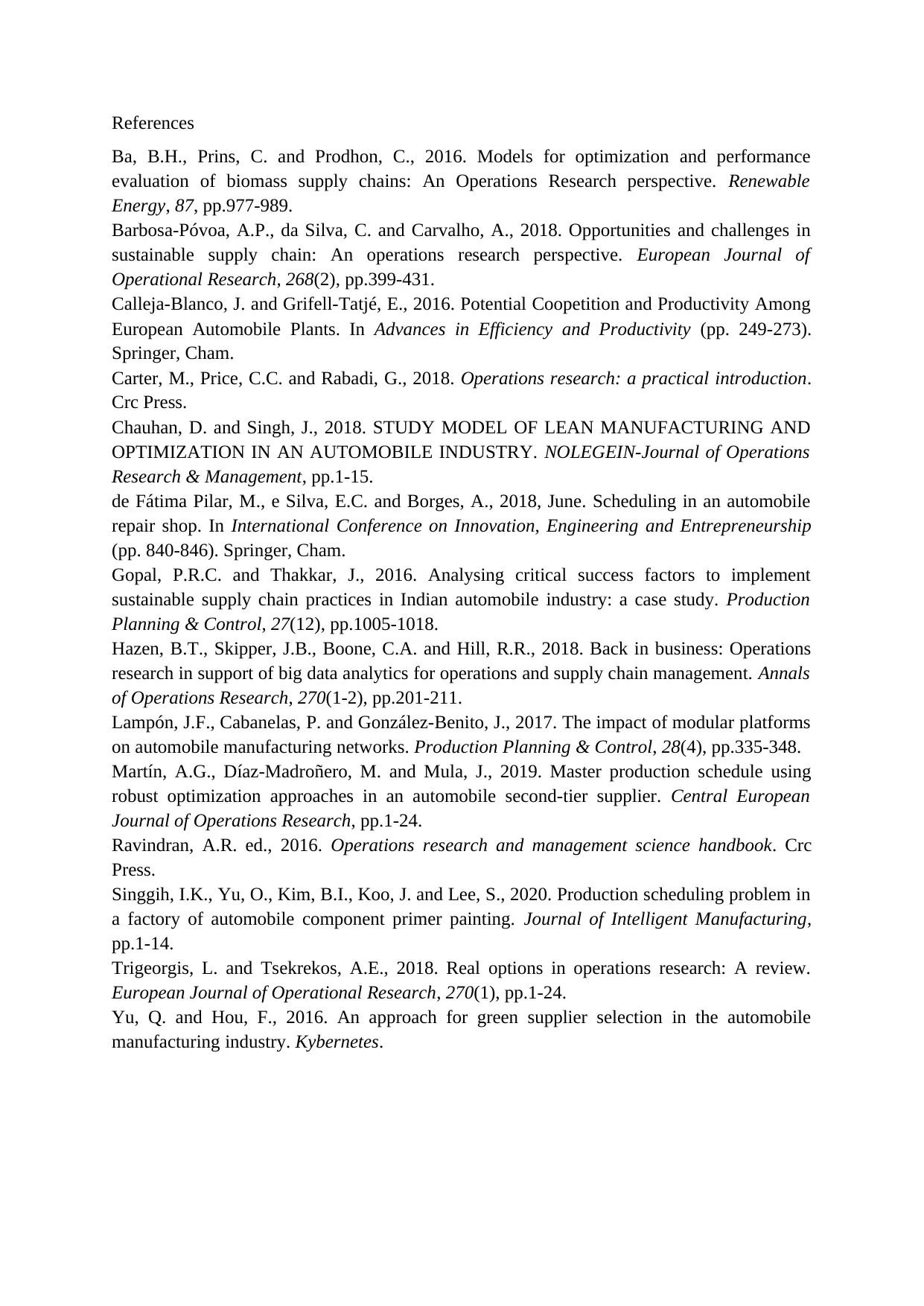
References
Ba, B.H., Prins, C. and Prodhon, C., 2016. Models for optimization and performance
evaluation of biomass supply chains: An Operations Research perspective. Renewable
Energy, 87, pp.977-989.
Barbosa-Póvoa, A.P., da Silva, C. and Carvalho, A., 2018. Opportunities and challenges in
sustainable supply chain: An operations research perspective. European Journal of
Operational Research, 268(2), pp.399-431.
Calleja-Blanco, J. and Grifell-Tatjé, E., 2016. Potential Coopetition and Productivity Among
European Automobile Plants. In Advances in Efficiency and Productivity (pp. 249-273).
Springer, Cham.
Carter, M., Price, C.C. and Rabadi, G., 2018. Operations research: a practical introduction.
Crc Press.
Chauhan, D. and Singh, J., 2018. STUDY MODEL OF LEAN MANUFACTURING AND
OPTIMIZATION IN AN AUTOMOBILE INDUSTRY. NOLEGEIN-Journal of Operations
Research & Management, pp.1-15.
de Fátima Pilar, M., e Silva, E.C. and Borges, A., 2018, June. Scheduling in an automobile
repair shop. In International Conference on Innovation, Engineering and Entrepreneurship
(pp. 840-846). Springer, Cham.
Gopal, P.R.C. and Thakkar, J., 2016. Analysing critical success factors to implement
sustainable supply chain practices in Indian automobile industry: a case study. Production
Planning & Control, 27(12), pp.1005-1018.
Hazen, B.T., Skipper, J.B., Boone, C.A. and Hill, R.R., 2018. Back in business: Operations
research in support of big data analytics for operations and supply chain management. Annals
of Operations Research, 270(1-2), pp.201-211.
Lampón, J.F., Cabanelas, P. and González-Benito, J., 2017. The impact of modular platforms
on automobile manufacturing networks. Production Planning & Control, 28(4), pp.335-348.
Martín, A.G., Díaz-Madroñero, M. and Mula, J., 2019. Master production schedule using
robust optimization approaches in an automobile second-tier supplier. Central European
Journal of Operations Research, pp.1-24.
Ravindran, A.R. ed., 2016. Operations research and management science handbook. Crc
Press.
Singgih, I.K., Yu, O., Kim, B.I., Koo, J. and Lee, S., 2020. Production scheduling problem in
a factory of automobile component primer painting. Journal of Intelligent Manufacturing,
pp.1-14.
Trigeorgis, L. and Tsekrekos, A.E., 2018. Real options in operations research: A review.
European Journal of Operational Research, 270(1), pp.1-24.
Yu, Q. and Hou, F., 2016. An approach for green supplier selection in the automobile
manufacturing industry. Kybernetes.
Ba, B.H., Prins, C. and Prodhon, C., 2016. Models for optimization and performance
evaluation of biomass supply chains: An Operations Research perspective. Renewable
Energy, 87, pp.977-989.
Barbosa-Póvoa, A.P., da Silva, C. and Carvalho, A., 2018. Opportunities and challenges in
sustainable supply chain: An operations research perspective. European Journal of
Operational Research, 268(2), pp.399-431.
Calleja-Blanco, J. and Grifell-Tatjé, E., 2016. Potential Coopetition and Productivity Among
European Automobile Plants. In Advances in Efficiency and Productivity (pp. 249-273).
Springer, Cham.
Carter, M., Price, C.C. and Rabadi, G., 2018. Operations research: a practical introduction.
Crc Press.
Chauhan, D. and Singh, J., 2018. STUDY MODEL OF LEAN MANUFACTURING AND
OPTIMIZATION IN AN AUTOMOBILE INDUSTRY. NOLEGEIN-Journal of Operations
Research & Management, pp.1-15.
de Fátima Pilar, M., e Silva, E.C. and Borges, A., 2018, June. Scheduling in an automobile
repair shop. In International Conference on Innovation, Engineering and Entrepreneurship
(pp. 840-846). Springer, Cham.
Gopal, P.R.C. and Thakkar, J., 2016. Analysing critical success factors to implement
sustainable supply chain practices in Indian automobile industry: a case study. Production
Planning & Control, 27(12), pp.1005-1018.
Hazen, B.T., Skipper, J.B., Boone, C.A. and Hill, R.R., 2018. Back in business: Operations
research in support of big data analytics for operations and supply chain management. Annals
of Operations Research, 270(1-2), pp.201-211.
Lampón, J.F., Cabanelas, P. and González-Benito, J., 2017. The impact of modular platforms
on automobile manufacturing networks. Production Planning & Control, 28(4), pp.335-348.
Martín, A.G., Díaz-Madroñero, M. and Mula, J., 2019. Master production schedule using
robust optimization approaches in an automobile second-tier supplier. Central European
Journal of Operations Research, pp.1-24.
Ravindran, A.R. ed., 2016. Operations research and management science handbook. Crc
Press.
Singgih, I.K., Yu, O., Kim, B.I., Koo, J. and Lee, S., 2020. Production scheduling problem in
a factory of automobile component primer painting. Journal of Intelligent Manufacturing,
pp.1-14.
Trigeorgis, L. and Tsekrekos, A.E., 2018. Real options in operations research: A review.
European Journal of Operational Research, 270(1), pp.1-24.
Yu, Q. and Hou, F., 2016. An approach for green supplier selection in the automobile
manufacturing industry. Kybernetes.
1 out of 7

Your All-in-One AI-Powered Toolkit for Academic Success.
+13062052269
info@desklib.com
Available 24*7 on WhatsApp / Email
Unlock your academic potential
© 2024 | Zucol Services PVT LTD | All rights reserved.