Operations Management Report: Productivity and Lean Production
VerifiedAdded on 2021/02/20
|8
|2078
|33
Report
AI Summary
This report provides a comprehensive analysis of operations management principles, focusing on productivity, capacity utilization, and lean production. It begins by defining operations management and its core functions, emphasizing the creation and delivery of products and services. The report then delves into the calculation and analysis of productivity, illustrated with a case study of a health club, examining both single and multi-factor productivity. The concept of capacity utilization is also explored, with a detailed assessment of its application within a restaurant setting, including the implications of expansion. Furthermore, the report examines lean production, its components, and the costs associated with holding stock. A case study of Portakabin's production process is presented, evaluating the appropriateness of the 'Just-in-Time' approach and providing recommendations for improvement. The report concludes by summarizing the key findings and emphasizing the importance of integrating quality management methodologies to enhance production processes and achieve economies of scale. The report uses real-world examples to illustrate the concepts and provide practical insights into operations management.
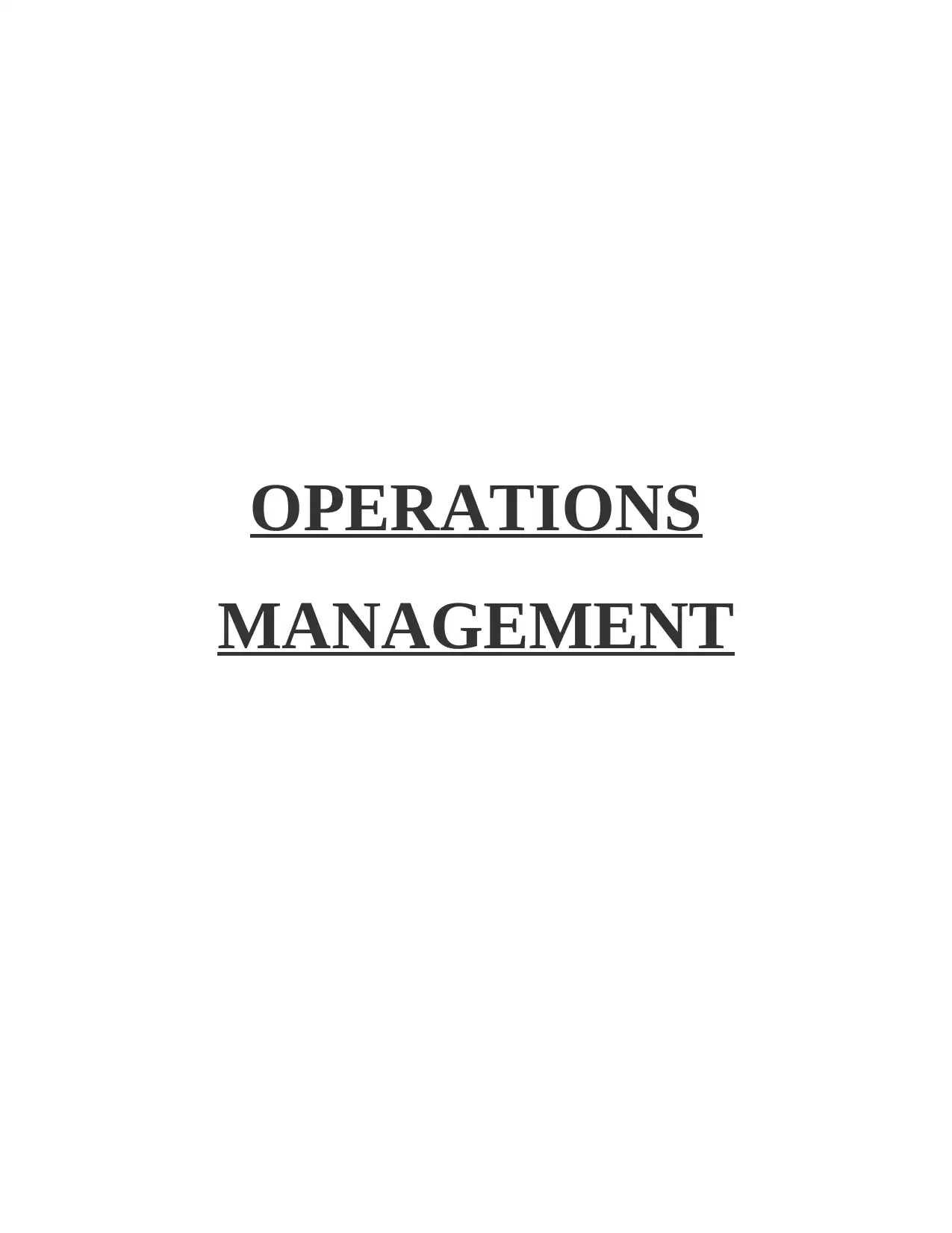
OPERATIONS
MANAGEMENT
MANAGEMENT
Paraphrase This Document
Need a fresh take? Get an instant paraphrase of this document with our AI Paraphraser
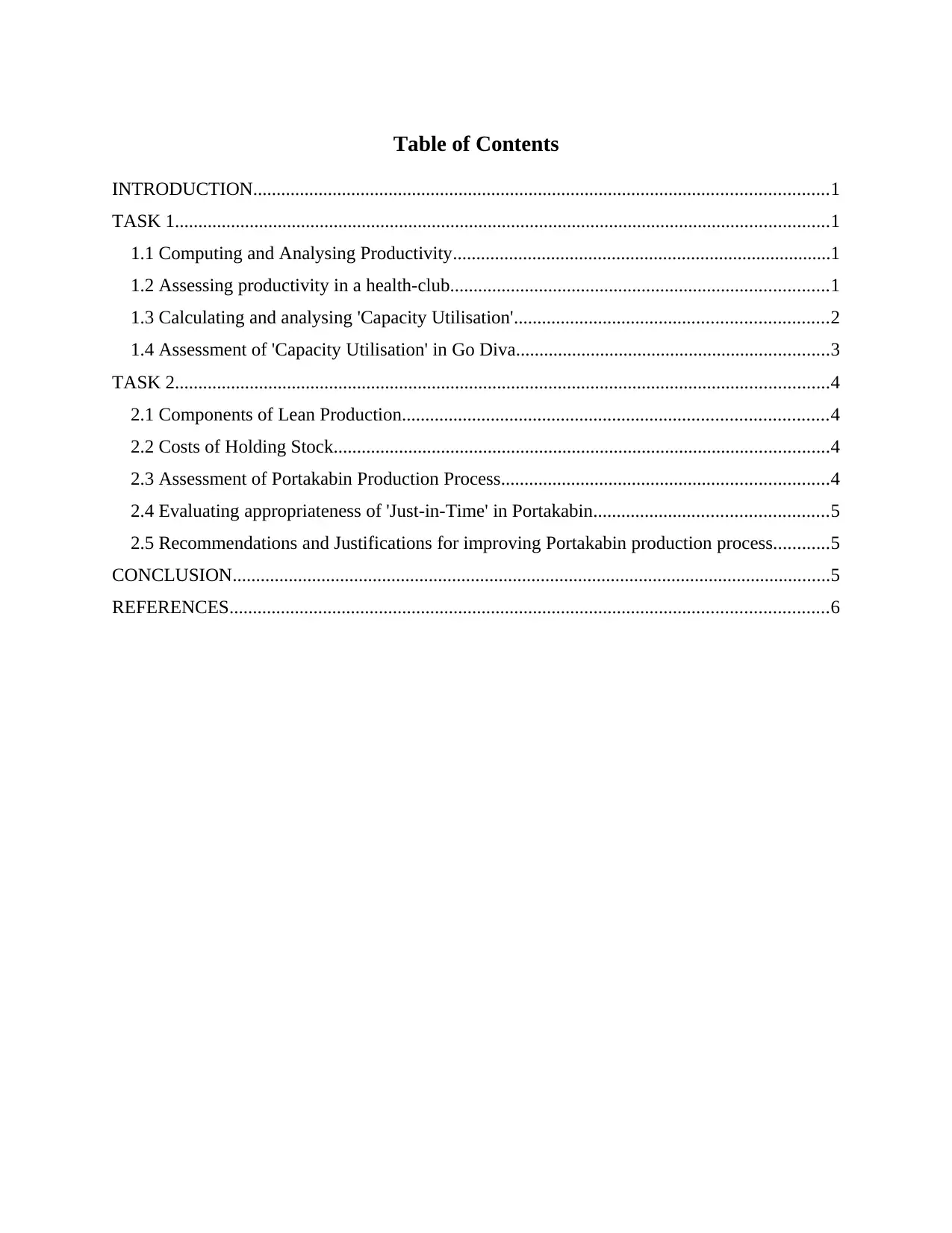
Table of Contents
INTRODUCTION...........................................................................................................................1
TASK 1............................................................................................................................................1
1.1 Computing and Analysing Productivity.................................................................................1
1.2 Assessing productivity in a health-club.................................................................................1
1.3 Calculating and analysing 'Capacity Utilisation'...................................................................2
1.4 Assessment of 'Capacity Utilisation' in Go Diva...................................................................3
TASK 2............................................................................................................................................4
2.1 Components of Lean Production...........................................................................................4
2.2 Costs of Holding Stock..........................................................................................................4
2.3 Assessment of Portakabin Production Process......................................................................4
2.4 Evaluating appropriateness of 'Just-in-Time' in Portakabin..................................................5
2.5 Recommendations and Justifications for improving Portakabin production process............5
CONCLUSION................................................................................................................................5
REFERENCES................................................................................................................................6
INTRODUCTION...........................................................................................................................1
TASK 1............................................................................................................................................1
1.1 Computing and Analysing Productivity.................................................................................1
1.2 Assessing productivity in a health-club.................................................................................1
1.3 Calculating and analysing 'Capacity Utilisation'...................................................................2
1.4 Assessment of 'Capacity Utilisation' in Go Diva...................................................................3
TASK 2............................................................................................................................................4
2.1 Components of Lean Production...........................................................................................4
2.2 Costs of Holding Stock..........................................................................................................4
2.3 Assessment of Portakabin Production Process......................................................................4
2.4 Evaluating appropriateness of 'Just-in-Time' in Portakabin..................................................5
2.5 Recommendations and Justifications for improving Portakabin production process............5
CONCLUSION................................................................................................................................5
REFERENCES................................................................................................................................6
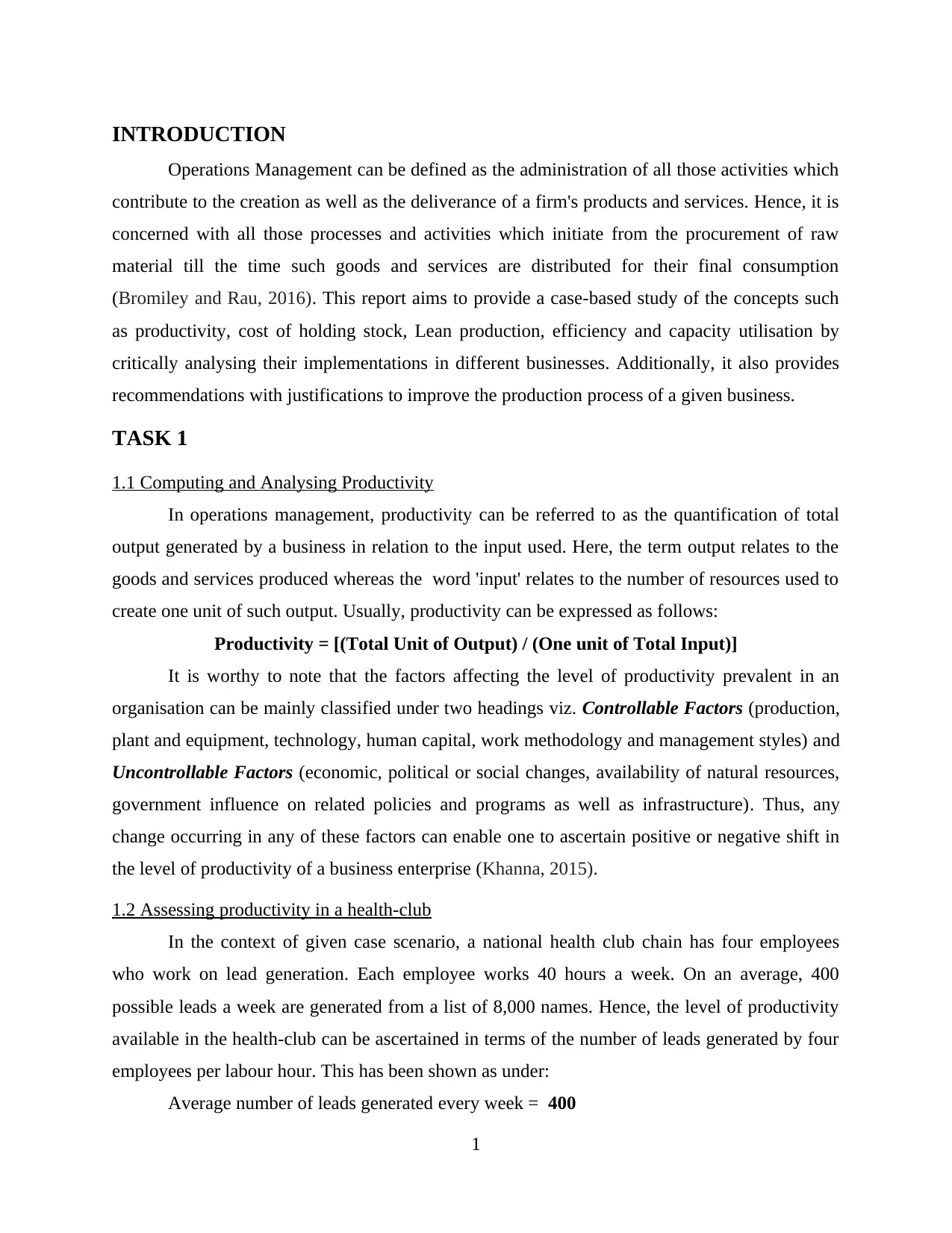
INTRODUCTION
Operations Management can be defined as the administration of all those activities which
contribute to the creation as well as the deliverance of a firm's products and services. Hence, it is
concerned with all those processes and activities which initiate from the procurement of raw
material till the time such goods and services are distributed for their final consumption
(Bromiley and Rau, 2016). This report aims to provide a case-based study of the concepts such
as productivity, cost of holding stock, Lean production, efficiency and capacity utilisation by
critically analysing their implementations in different businesses. Additionally, it also provides
recommendations with justifications to improve the production process of a given business.
TASK 1
1.1 Computing and Analysing Productivity
In operations management, productivity can be referred to as the quantification of total
output generated by a business in relation to the input used. Here, the term output relates to the
goods and services produced whereas the word 'input' relates to the number of resources used to
create one unit of such output. Usually, productivity can be expressed as follows:
Productivity = [(Total Unit of Output) / (One unit of Total Input)]
It is worthy to note that the factors affecting the level of productivity prevalent in an
organisation can be mainly classified under two headings viz. Controllable Factors (production,
plant and equipment, technology, human capital, work methodology and management styles) and
Uncontrollable Factors (economic, political or social changes, availability of natural resources,
government influence on related policies and programs as well as infrastructure). Thus, any
change occurring in any of these factors can enable one to ascertain positive or negative shift in
the level of productivity of a business enterprise (Khanna, 2015).
1.2 Assessing productivity in a health-club
In the context of given case scenario, a national health club chain has four employees
who work on lead generation. Each employee works 40 hours a week. On an average, 400
possible leads a week are generated from a list of 8,000 names. Hence, the level of productivity
available in the health-club can be ascertained in terms of the number of leads generated by four
employees per labour hour. This has been shown as under:
Average number of leads generated every week = 400
1
Operations Management can be defined as the administration of all those activities which
contribute to the creation as well as the deliverance of a firm's products and services. Hence, it is
concerned with all those processes and activities which initiate from the procurement of raw
material till the time such goods and services are distributed for their final consumption
(Bromiley and Rau, 2016). This report aims to provide a case-based study of the concepts such
as productivity, cost of holding stock, Lean production, efficiency and capacity utilisation by
critically analysing their implementations in different businesses. Additionally, it also provides
recommendations with justifications to improve the production process of a given business.
TASK 1
1.1 Computing and Analysing Productivity
In operations management, productivity can be referred to as the quantification of total
output generated by a business in relation to the input used. Here, the term output relates to the
goods and services produced whereas the word 'input' relates to the number of resources used to
create one unit of such output. Usually, productivity can be expressed as follows:
Productivity = [(Total Unit of Output) / (One unit of Total Input)]
It is worthy to note that the factors affecting the level of productivity prevalent in an
organisation can be mainly classified under two headings viz. Controllable Factors (production,
plant and equipment, technology, human capital, work methodology and management styles) and
Uncontrollable Factors (economic, political or social changes, availability of natural resources,
government influence on related policies and programs as well as infrastructure). Thus, any
change occurring in any of these factors can enable one to ascertain positive or negative shift in
the level of productivity of a business enterprise (Khanna, 2015).
1.2 Assessing productivity in a health-club
In the context of given case scenario, a national health club chain has four employees
who work on lead generation. Each employee works 40 hours a week. On an average, 400
possible leads a week are generated from a list of 8,000 names. Hence, the level of productivity
available in the health-club can be ascertained in terms of the number of leads generated by four
employees per labour hour. This has been shown as under:
Average number of leads generated every week = 400
1
⊘ This is a preview!⊘
Do you want full access?
Subscribe today to unlock all pages.

Trusted by 1+ million students worldwide
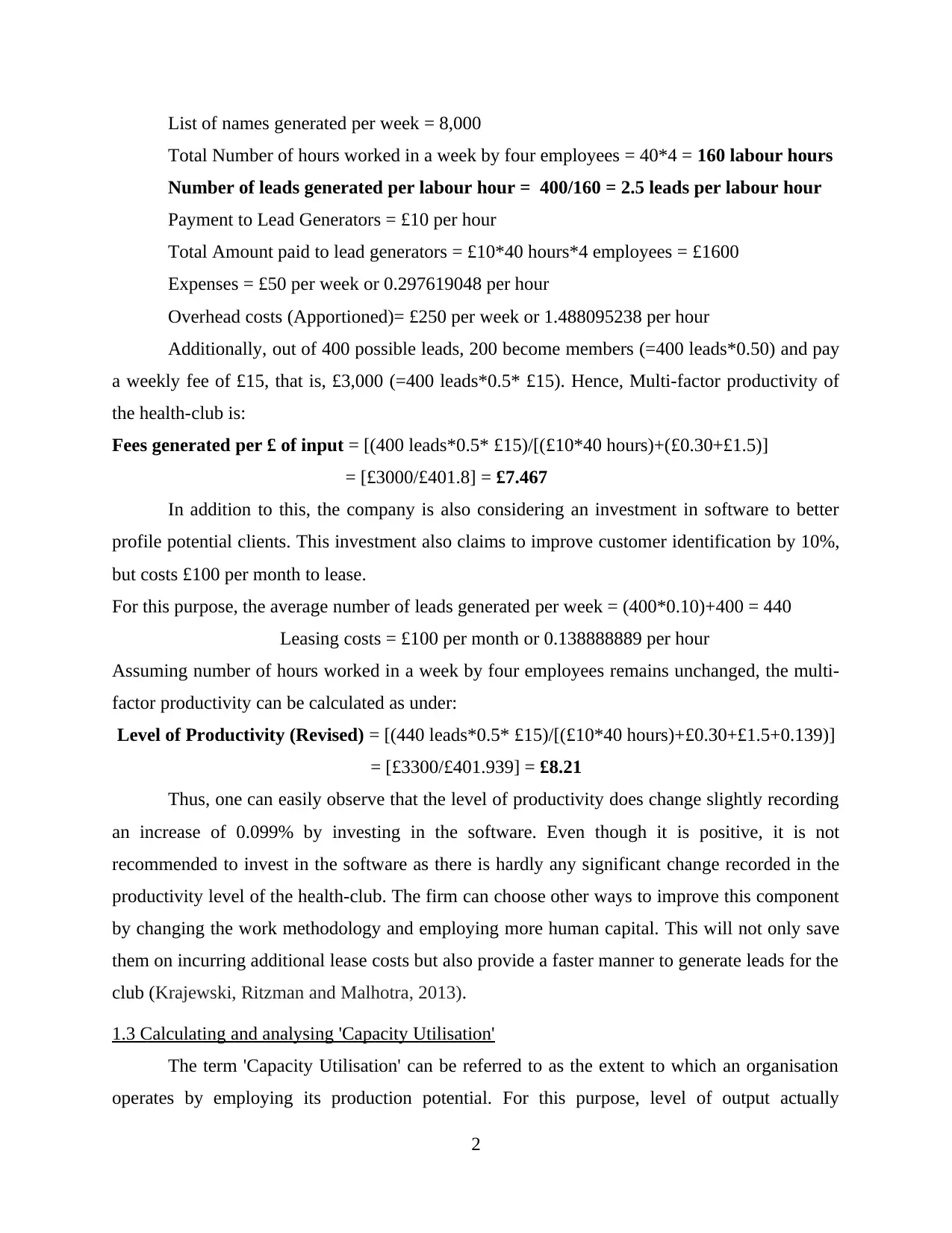
List of names generated per week = 8,000
Total Number of hours worked in a week by four employees = 40*4 = 160 labour hours
Number of leads generated per labour hour = 400/160 = 2.5 leads per labour hour
Payment to Lead Generators = £10 per hour
Total Amount paid to lead generators = £10*40 hours*4 employees = £1600
Expenses = £50 per week or 0.297619048 per hour
Overhead costs (Apportioned)= £250 per week or 1.488095238 per hour
Additionally, out of 400 possible leads, 200 become members (=400 leads*0.50) and pay
a weekly fee of £15, that is, £3,000 (=400 leads*0.5* £15). Hence, Multi-factor productivity of
the health-club is:
Fees generated per £ of input = [(400 leads*0.5* £15)/[(£10*40 hours)+(£0.30+£1.5)]
= [£3000/£401.8] = £7.467
In addition to this, the company is also considering an investment in software to better
profile potential clients. This investment also claims to improve customer identification by 10%,
but costs £100 per month to lease.
For this purpose, the average number of leads generated per week = (400*0.10)+400 = 440
Leasing costs = £100 per month or 0.138888889 per hour
Assuming number of hours worked in a week by four employees remains unchanged, the multi-
factor productivity can be calculated as under:
Level of Productivity (Revised) = [(440 leads*0.5* £15)/[(£10*40 hours)+£0.30+£1.5+0.139)]
= [£3300/£401.939] = £8.21
Thus, one can easily observe that the level of productivity does change slightly recording
an increase of 0.099% by investing in the software. Even though it is positive, it is not
recommended to invest in the software as there is hardly any significant change recorded in the
productivity level of the health-club. The firm can choose other ways to improve this component
by changing the work methodology and employing more human capital. This will not only save
them on incurring additional lease costs but also provide a faster manner to generate leads for the
club (Krajewski, Ritzman and Malhotra, 2013).
1.3 Calculating and analysing 'Capacity Utilisation'
The term 'Capacity Utilisation' can be referred to as the extent to which an organisation
operates by employing its production potential. For this purpose, level of output actually
2
Total Number of hours worked in a week by four employees = 40*4 = 160 labour hours
Number of leads generated per labour hour = 400/160 = 2.5 leads per labour hour
Payment to Lead Generators = £10 per hour
Total Amount paid to lead generators = £10*40 hours*4 employees = £1600
Expenses = £50 per week or 0.297619048 per hour
Overhead costs (Apportioned)= £250 per week or 1.488095238 per hour
Additionally, out of 400 possible leads, 200 become members (=400 leads*0.50) and pay
a weekly fee of £15, that is, £3,000 (=400 leads*0.5* £15). Hence, Multi-factor productivity of
the health-club is:
Fees generated per £ of input = [(400 leads*0.5* £15)/[(£10*40 hours)+(£0.30+£1.5)]
= [£3000/£401.8] = £7.467
In addition to this, the company is also considering an investment in software to better
profile potential clients. This investment also claims to improve customer identification by 10%,
but costs £100 per month to lease.
For this purpose, the average number of leads generated per week = (400*0.10)+400 = 440
Leasing costs = £100 per month or 0.138888889 per hour
Assuming number of hours worked in a week by four employees remains unchanged, the multi-
factor productivity can be calculated as under:
Level of Productivity (Revised) = [(440 leads*0.5* £15)/[(£10*40 hours)+£0.30+£1.5+0.139)]
= [£3300/£401.939] = £8.21
Thus, one can easily observe that the level of productivity does change slightly recording
an increase of 0.099% by investing in the software. Even though it is positive, it is not
recommended to invest in the software as there is hardly any significant change recorded in the
productivity level of the health-club. The firm can choose other ways to improve this component
by changing the work methodology and employing more human capital. This will not only save
them on incurring additional lease costs but also provide a faster manner to generate leads for the
club (Krajewski, Ritzman and Malhotra, 2013).
1.3 Calculating and analysing 'Capacity Utilisation'
The term 'Capacity Utilisation' can be referred to as the extent to which an organisation
operates by employing its production potential. For this purpose, level of output actually
2
Paraphrase This Document
Need a fresh take? Get an instant paraphrase of this document with our AI Paraphraser
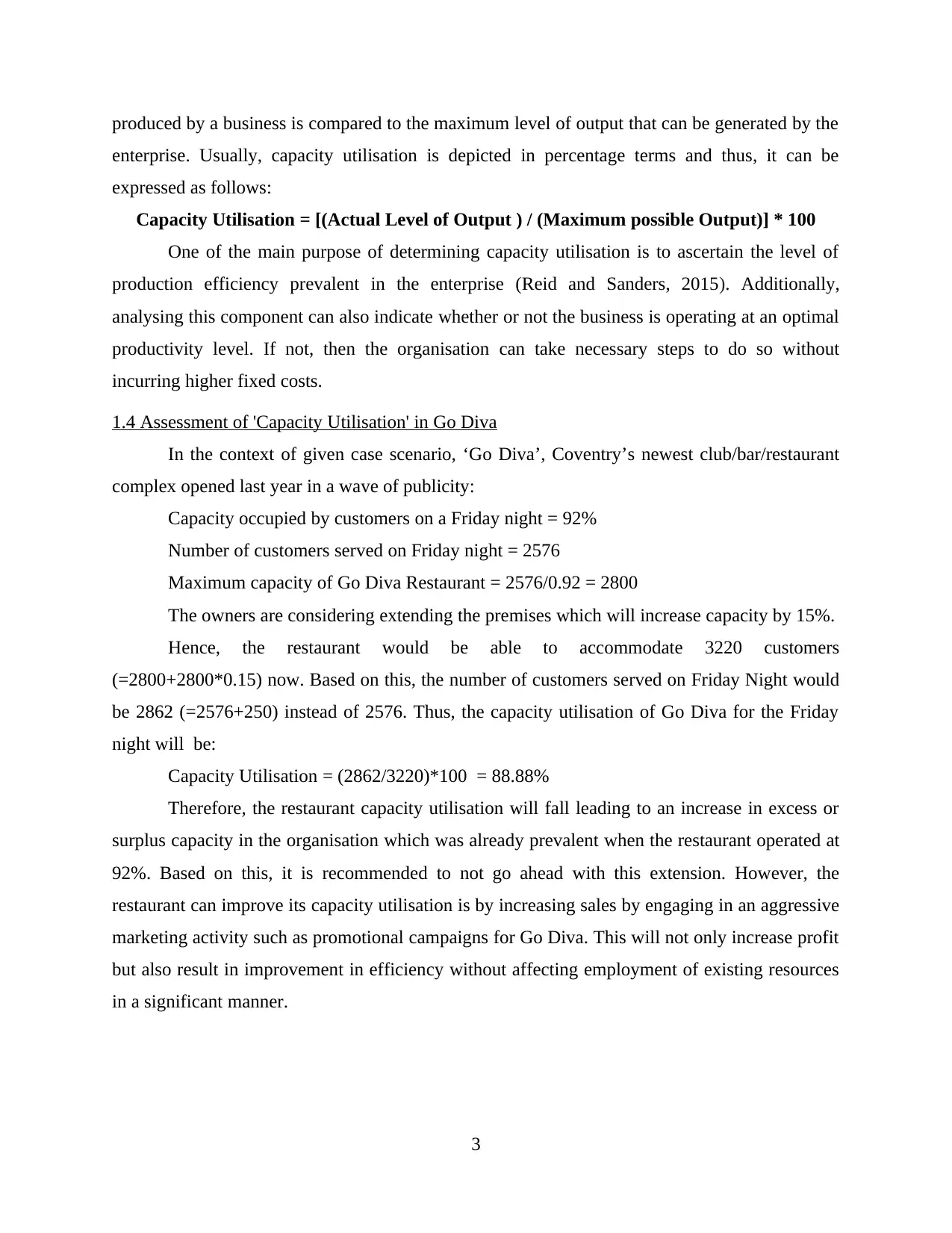
produced by a business is compared to the maximum level of output that can be generated by the
enterprise. Usually, capacity utilisation is depicted in percentage terms and thus, it can be
expressed as follows:
Capacity Utilisation = [(Actual Level of Output ) / (Maximum possible Output)] * 100
One of the main purpose of determining capacity utilisation is to ascertain the level of
production efficiency prevalent in the enterprise (Reid and Sanders, 2015). Additionally,
analysing this component can also indicate whether or not the business is operating at an optimal
productivity level. If not, then the organisation can take necessary steps to do so without
incurring higher fixed costs.
1.4 Assessment of 'Capacity Utilisation' in Go Diva
In the context of given case scenario, ‘Go Diva’, Coventry’s newest club/bar/restaurant
complex opened last year in a wave of publicity:
Capacity occupied by customers on a Friday night = 92%
Number of customers served on Friday night = 2576
Maximum capacity of Go Diva Restaurant = 2576/0.92 = 2800
The owners are considering extending the premises which will increase capacity by 15%.
Hence, the restaurant would be able to accommodate 3220 customers
(=2800+2800*0.15) now. Based on this, the number of customers served on Friday Night would
be 2862 (=2576+250) instead of 2576. Thus, the capacity utilisation of Go Diva for the Friday
night will be:
Capacity Utilisation = (2862/3220)*100 = 88.88%
Therefore, the restaurant capacity utilisation will fall leading to an increase in excess or
surplus capacity in the organisation which was already prevalent when the restaurant operated at
92%. Based on this, it is recommended to not go ahead with this extension. However, the
restaurant can improve its capacity utilisation is by increasing sales by engaging in an aggressive
marketing activity such as promotional campaigns for Go Diva. This will not only increase profit
but also result in improvement in efficiency without affecting employment of existing resources
in a significant manner.
3
enterprise. Usually, capacity utilisation is depicted in percentage terms and thus, it can be
expressed as follows:
Capacity Utilisation = [(Actual Level of Output ) / (Maximum possible Output)] * 100
One of the main purpose of determining capacity utilisation is to ascertain the level of
production efficiency prevalent in the enterprise (Reid and Sanders, 2015). Additionally,
analysing this component can also indicate whether or not the business is operating at an optimal
productivity level. If not, then the organisation can take necessary steps to do so without
incurring higher fixed costs.
1.4 Assessment of 'Capacity Utilisation' in Go Diva
In the context of given case scenario, ‘Go Diva’, Coventry’s newest club/bar/restaurant
complex opened last year in a wave of publicity:
Capacity occupied by customers on a Friday night = 92%
Number of customers served on Friday night = 2576
Maximum capacity of Go Diva Restaurant = 2576/0.92 = 2800
The owners are considering extending the premises which will increase capacity by 15%.
Hence, the restaurant would be able to accommodate 3220 customers
(=2800+2800*0.15) now. Based on this, the number of customers served on Friday Night would
be 2862 (=2576+250) instead of 2576. Thus, the capacity utilisation of Go Diva for the Friday
night will be:
Capacity Utilisation = (2862/3220)*100 = 88.88%
Therefore, the restaurant capacity utilisation will fall leading to an increase in excess or
surplus capacity in the organisation which was already prevalent when the restaurant operated at
92%. Based on this, it is recommended to not go ahead with this extension. However, the
restaurant can improve its capacity utilisation is by increasing sales by engaging in an aggressive
marketing activity such as promotional campaigns for Go Diva. This will not only increase profit
but also result in improvement in efficiency without affecting employment of existing resources
in a significant manner.
3
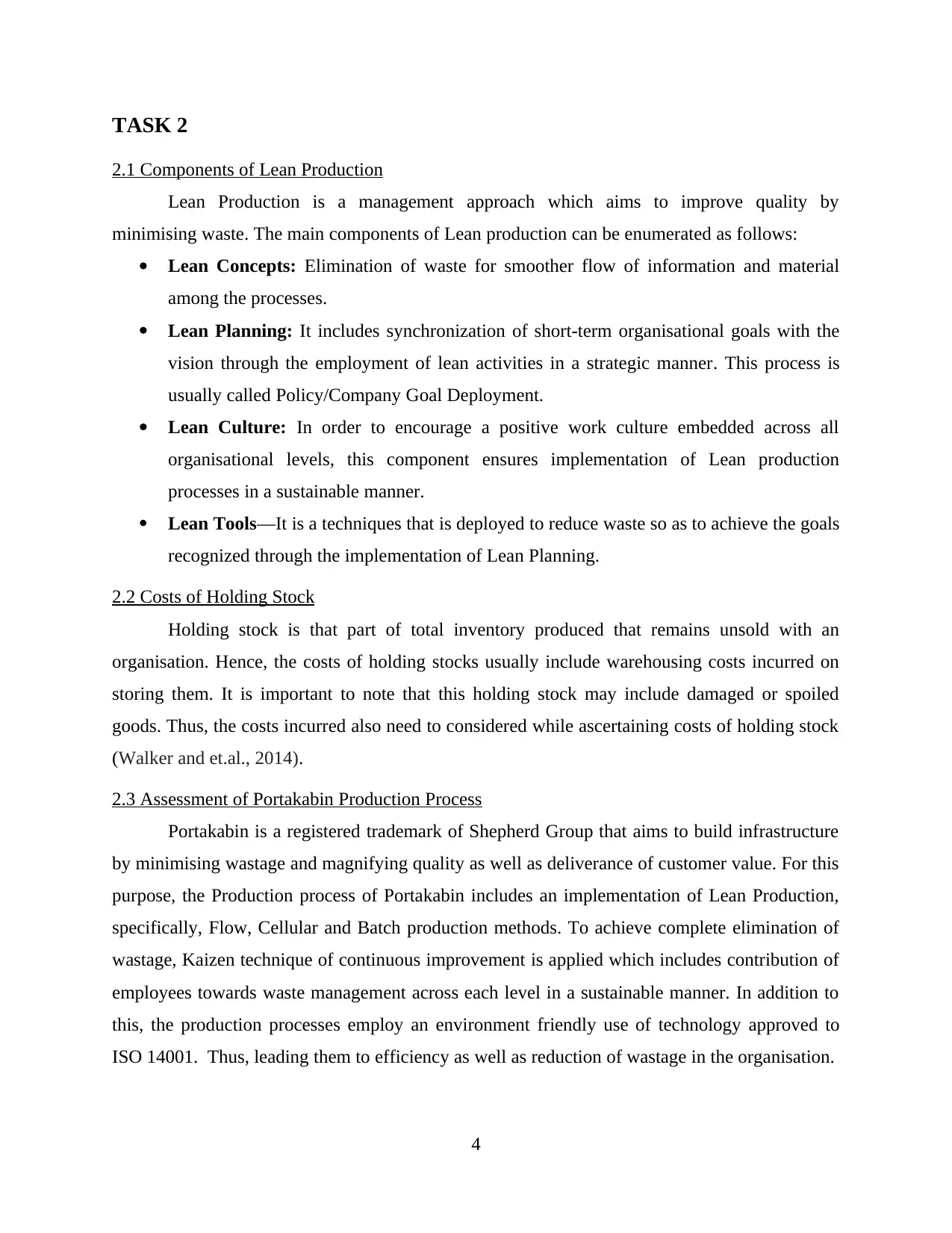
TASK 2
2.1 Components of Lean Production
Lean Production is a management approach which aims to improve quality by
minimising waste. The main components of Lean production can be enumerated as follows:
Lean Concepts: Elimination of waste for smoother flow of information and material
among the processes.
Lean Planning: It includes synchronization of short-term organisational goals with the
vision through the employment of lean activities in a strategic manner. This process is
usually called Policy/Company Goal Deployment.
Lean Culture: In order to encourage a positive work culture embedded across all
organisational levels, this component ensures implementation of Lean production
processes in a sustainable manner.
Lean Tools—It is a techniques that is deployed to reduce waste so as to achieve the goals
recognized through the implementation of Lean Planning.
2.2 Costs of Holding Stock
Holding stock is that part of total inventory produced that remains unsold with an
organisation. Hence, the costs of holding stocks usually include warehousing costs incurred on
storing them. It is important to note that this holding stock may include damaged or spoiled
goods. Thus, the costs incurred also need to considered while ascertaining costs of holding stock
(Walker and et.al., 2014).
2.3 Assessment of Portakabin Production Process
Portakabin is a registered trademark of Shepherd Group that aims to build infrastructure
by minimising wastage and magnifying quality as well as deliverance of customer value. For this
purpose, the Production process of Portakabin includes an implementation of Lean Production,
specifically, Flow, Cellular and Batch production methods. To achieve complete elimination of
wastage, Kaizen technique of continuous improvement is applied which includes contribution of
employees towards waste management across each level in a sustainable manner. In addition to
this, the production processes employ an environment friendly use of technology approved to
ISO 14001. Thus, leading them to efficiency as well as reduction of wastage in the organisation.
4
2.1 Components of Lean Production
Lean Production is a management approach which aims to improve quality by
minimising waste. The main components of Lean production can be enumerated as follows:
Lean Concepts: Elimination of waste for smoother flow of information and material
among the processes.
Lean Planning: It includes synchronization of short-term organisational goals with the
vision through the employment of lean activities in a strategic manner. This process is
usually called Policy/Company Goal Deployment.
Lean Culture: In order to encourage a positive work culture embedded across all
organisational levels, this component ensures implementation of Lean production
processes in a sustainable manner.
Lean Tools—It is a techniques that is deployed to reduce waste so as to achieve the goals
recognized through the implementation of Lean Planning.
2.2 Costs of Holding Stock
Holding stock is that part of total inventory produced that remains unsold with an
organisation. Hence, the costs of holding stocks usually include warehousing costs incurred on
storing them. It is important to note that this holding stock may include damaged or spoiled
goods. Thus, the costs incurred also need to considered while ascertaining costs of holding stock
(Walker and et.al., 2014).
2.3 Assessment of Portakabin Production Process
Portakabin is a registered trademark of Shepherd Group that aims to build infrastructure
by minimising wastage and magnifying quality as well as deliverance of customer value. For this
purpose, the Production process of Portakabin includes an implementation of Lean Production,
specifically, Flow, Cellular and Batch production methods. To achieve complete elimination of
wastage, Kaizen technique of continuous improvement is applied which includes contribution of
employees towards waste management across each level in a sustainable manner. In addition to
this, the production processes employ an environment friendly use of technology approved to
ISO 14001. Thus, leading them to efficiency as well as reduction of wastage in the organisation.
4
⊘ This is a preview!⊘
Do you want full access?
Subscribe today to unlock all pages.

Trusted by 1+ million students worldwide
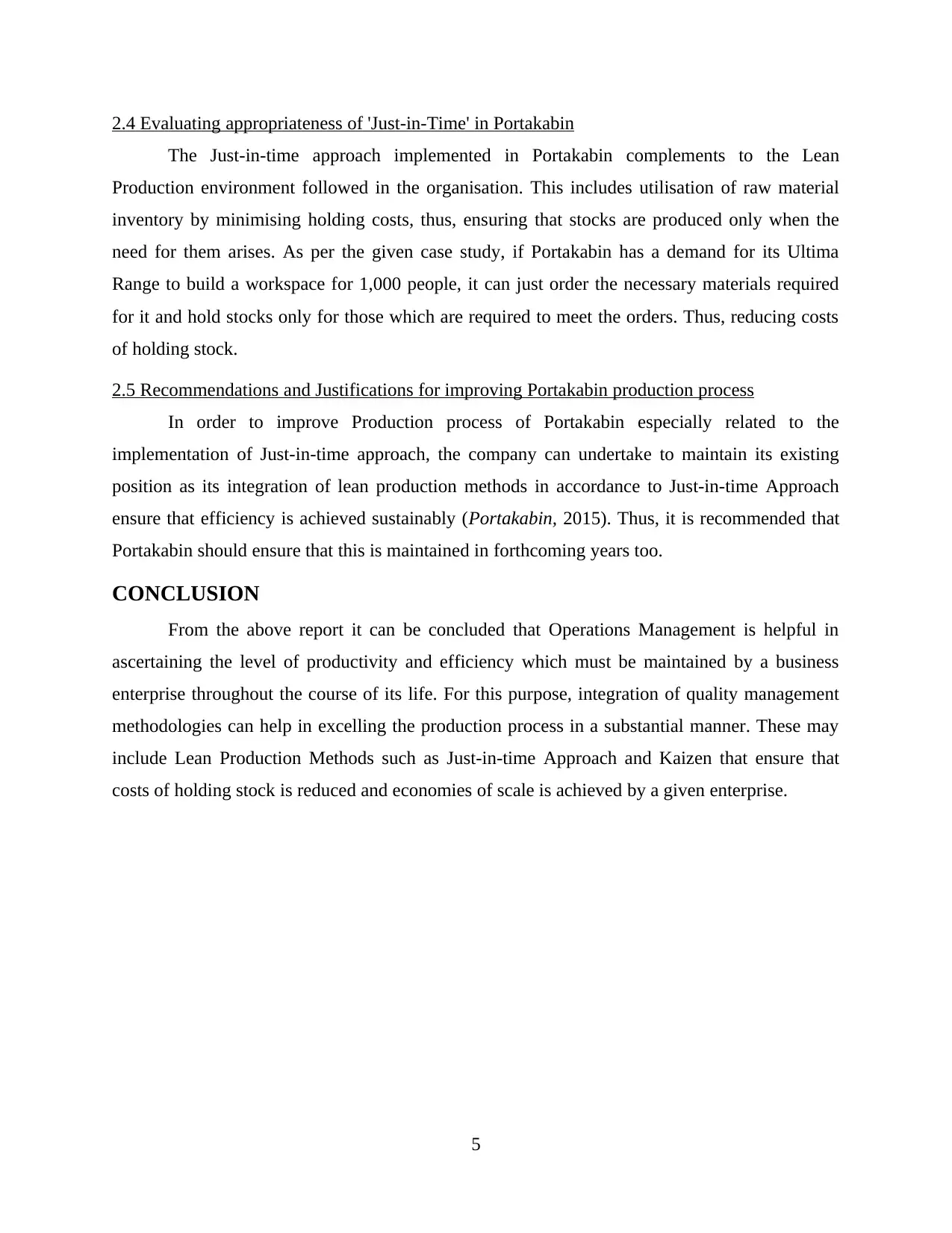
2.4 Evaluating appropriateness of 'Just-in-Time' in Portakabin
The Just-in-time approach implemented in Portakabin complements to the Lean
Production environment followed in the organisation. This includes utilisation of raw material
inventory by minimising holding costs, thus, ensuring that stocks are produced only when the
need for them arises. As per the given case study, if Portakabin has a demand for its Ultima
Range to build a workspace for 1,000 people, it can just order the necessary materials required
for it and hold stocks only for those which are required to meet the orders. Thus, reducing costs
of holding stock.
2.5 Recommendations and Justifications for improving Portakabin production process
In order to improve Production process of Portakabin especially related to the
implementation of Just-in-time approach, the company can undertake to maintain its existing
position as its integration of lean production methods in accordance to Just-in-time Approach
ensure that efficiency is achieved sustainably (Portakabin, 2015). Thus, it is recommended that
Portakabin should ensure that this is maintained in forthcoming years too.
CONCLUSION
From the above report it can be concluded that Operations Management is helpful in
ascertaining the level of productivity and efficiency which must be maintained by a business
enterprise throughout the course of its life. For this purpose, integration of quality management
methodologies can help in excelling the production process in a substantial manner. These may
include Lean Production Methods such as Just-in-time Approach and Kaizen that ensure that
costs of holding stock is reduced and economies of scale is achieved by a given enterprise.
5
The Just-in-time approach implemented in Portakabin complements to the Lean
Production environment followed in the organisation. This includes utilisation of raw material
inventory by minimising holding costs, thus, ensuring that stocks are produced only when the
need for them arises. As per the given case study, if Portakabin has a demand for its Ultima
Range to build a workspace for 1,000 people, it can just order the necessary materials required
for it and hold stocks only for those which are required to meet the orders. Thus, reducing costs
of holding stock.
2.5 Recommendations and Justifications for improving Portakabin production process
In order to improve Production process of Portakabin especially related to the
implementation of Just-in-time approach, the company can undertake to maintain its existing
position as its integration of lean production methods in accordance to Just-in-time Approach
ensure that efficiency is achieved sustainably (Portakabin, 2015). Thus, it is recommended that
Portakabin should ensure that this is maintained in forthcoming years too.
CONCLUSION
From the above report it can be concluded that Operations Management is helpful in
ascertaining the level of productivity and efficiency which must be maintained by a business
enterprise throughout the course of its life. For this purpose, integration of quality management
methodologies can help in excelling the production process in a substantial manner. These may
include Lean Production Methods such as Just-in-time Approach and Kaizen that ensure that
costs of holding stock is reduced and economies of scale is achieved by a given enterprise.
5
Paraphrase This Document
Need a fresh take? Get an instant paraphrase of this document with our AI Paraphraser
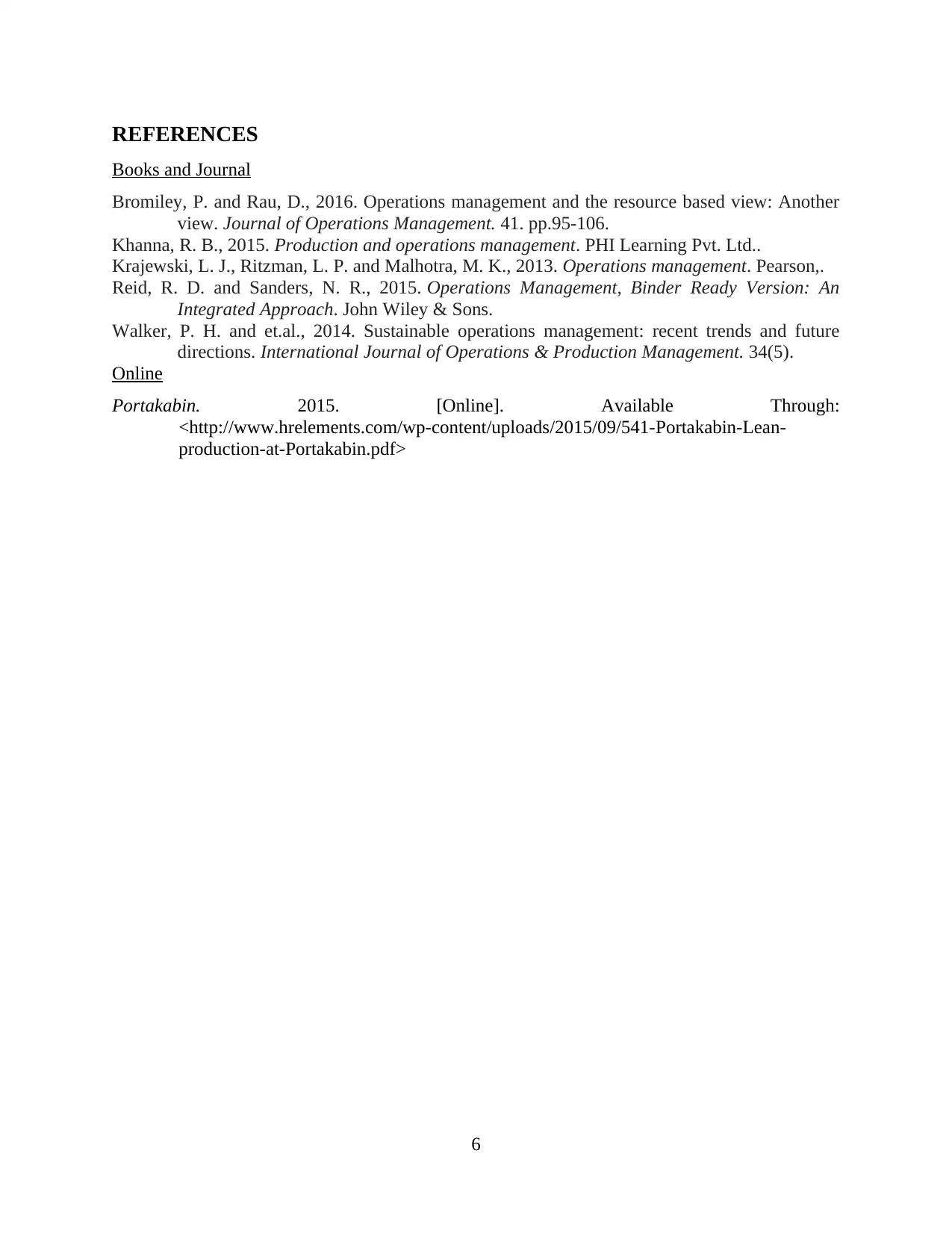
REFERENCES
Books and Journal
Bromiley, P. and Rau, D., 2016. Operations management and the resource based view: Another
view. Journal of Operations Management. 41. pp.95-106.
Khanna, R. B., 2015. Production and operations management. PHI Learning Pvt. Ltd..
Krajewski, L. J., Ritzman, L. P. and Malhotra, M. K., 2013. Operations management. Pearson,.
Reid, R. D. and Sanders, N. R., 2015. Operations Management, Binder Ready Version: An
Integrated Approach. John Wiley & Sons.
Walker, P. H. and et.al., 2014. Sustainable operations management: recent trends and future
directions. International Journal of Operations & Production Management. 34(5).
Online
Portakabin. 2015. [Online]. Available Through:
<http://www.hrelements.com/wp-content/uploads/2015/09/541-Portakabin-Lean-
production-at-Portakabin.pdf>
6
Books and Journal
Bromiley, P. and Rau, D., 2016. Operations management and the resource based view: Another
view. Journal of Operations Management. 41. pp.95-106.
Khanna, R. B., 2015. Production and operations management. PHI Learning Pvt. Ltd..
Krajewski, L. J., Ritzman, L. P. and Malhotra, M. K., 2013. Operations management. Pearson,.
Reid, R. D. and Sanders, N. R., 2015. Operations Management, Binder Ready Version: An
Integrated Approach. John Wiley & Sons.
Walker, P. H. and et.al., 2014. Sustainable operations management: recent trends and future
directions. International Journal of Operations & Production Management. 34(5).
Online
Portakabin. 2015. [Online]. Available Through:
<http://www.hrelements.com/wp-content/uploads/2015/09/541-Portakabin-Lean-
production-at-Portakabin.pdf>
6
1 out of 8