An Analysis of Operations Management Techniques at Toyota
VerifiedAdded on 2023/01/06
|14
|3986
|1
Report
AI Summary
This report provides a comprehensive analysis of Toyota's operations management, delving into key areas such as operations scheduling techniques, layout planning, and work system processes. It examines the application of both backward and forward scheduling approaches, along with Toyota's implementation of Kanban, Just-in-Time manufacturing, and forecasting techniques. The report further explores layout planning strategies, including process, product, and fixed position layouts, and their relevance to Toyota's manufacturing processes. Additionally, it investigates work system processes, highlighting their role in integrating human participation and machine performance. The integration of layout planning and work system processes is discussed, emphasizing Toyota's commitment to efficiency through techniques like Just-in-Time and Total Quality Management. Finally, the report covers inventory management policies, providing insights into Toyota's strategies for optimizing its supply chain and maintaining its competitive advantage in the global automotive market.
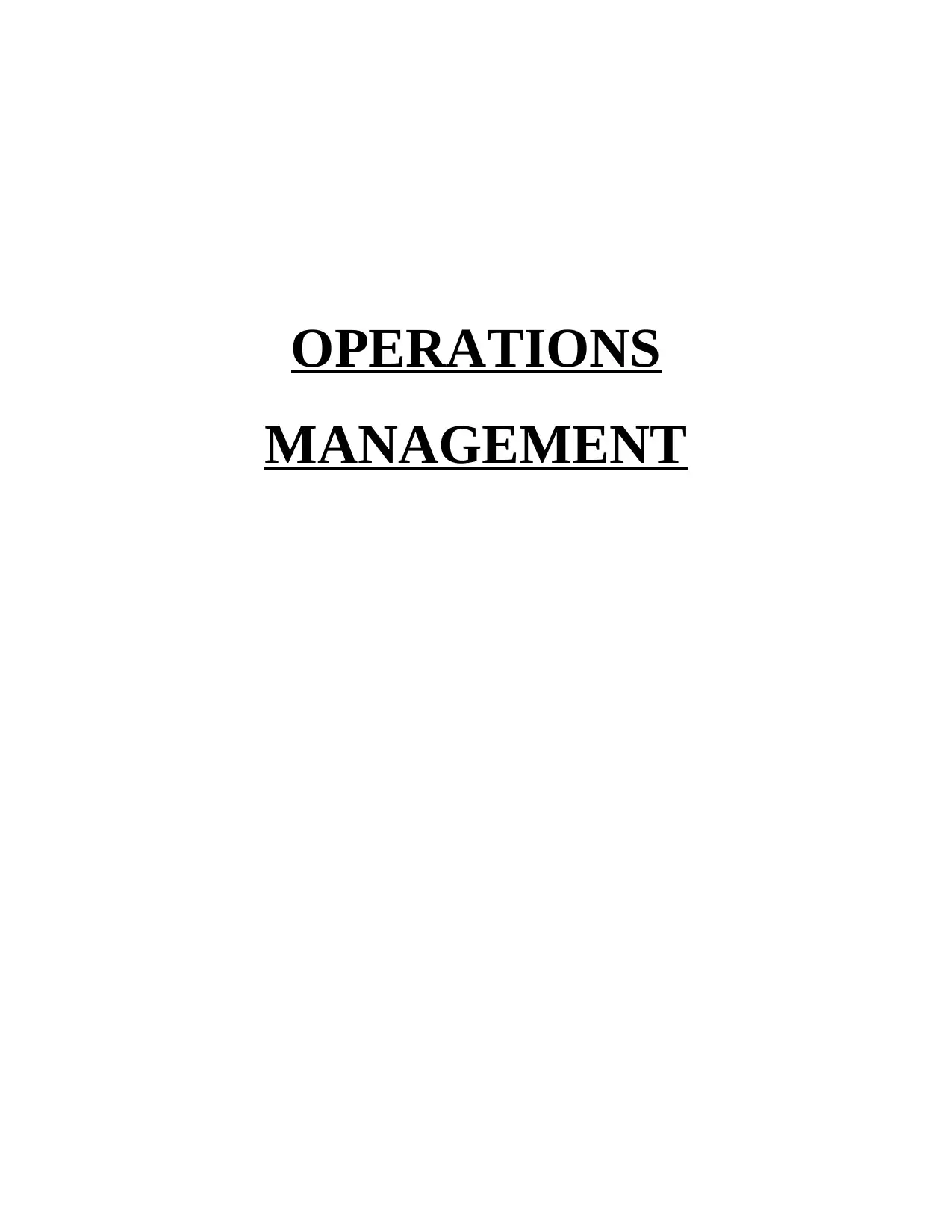
OPERATIONS
MANAGEMENT
MANAGEMENT
Paraphrase This Document
Need a fresh take? Get an instant paraphrase of this document with our AI Paraphraser
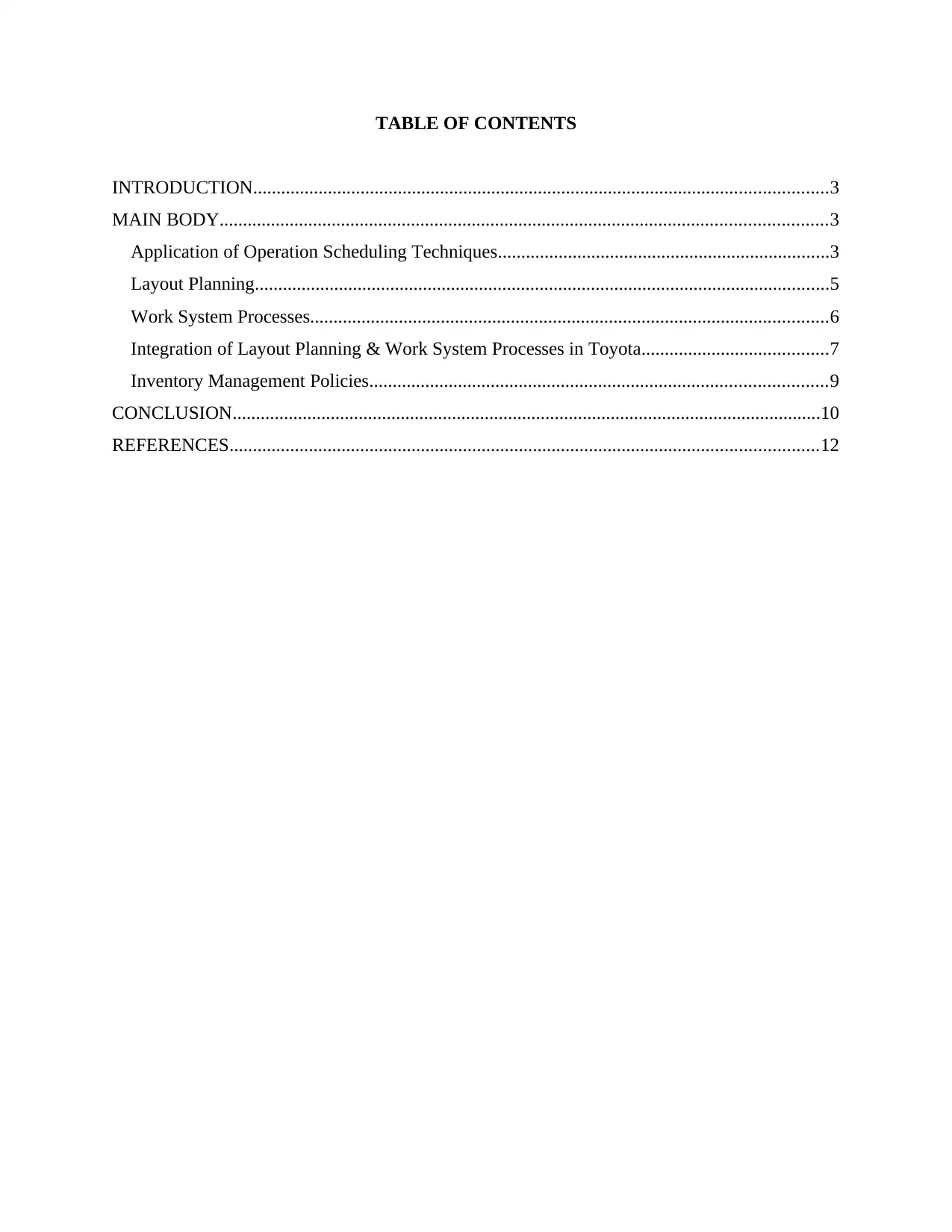
TABLE OF CONTENTS
INTRODUCTION...........................................................................................................................3
MAIN BODY..................................................................................................................................3
Application of Operation Scheduling Techniques.......................................................................3
Layout Planning...........................................................................................................................5
Work System Processes...............................................................................................................6
Integration of Layout Planning & Work System Processes in Toyota........................................7
Inventory Management Policies..................................................................................................9
CONCLUSION..............................................................................................................................10
REFERENCES..............................................................................................................................12
INTRODUCTION...........................................................................................................................3
MAIN BODY..................................................................................................................................3
Application of Operation Scheduling Techniques.......................................................................3
Layout Planning...........................................................................................................................5
Work System Processes...............................................................................................................6
Integration of Layout Planning & Work System Processes in Toyota........................................7
Inventory Management Policies..................................................................................................9
CONCLUSION..............................................................................................................................10
REFERENCES..............................................................................................................................12
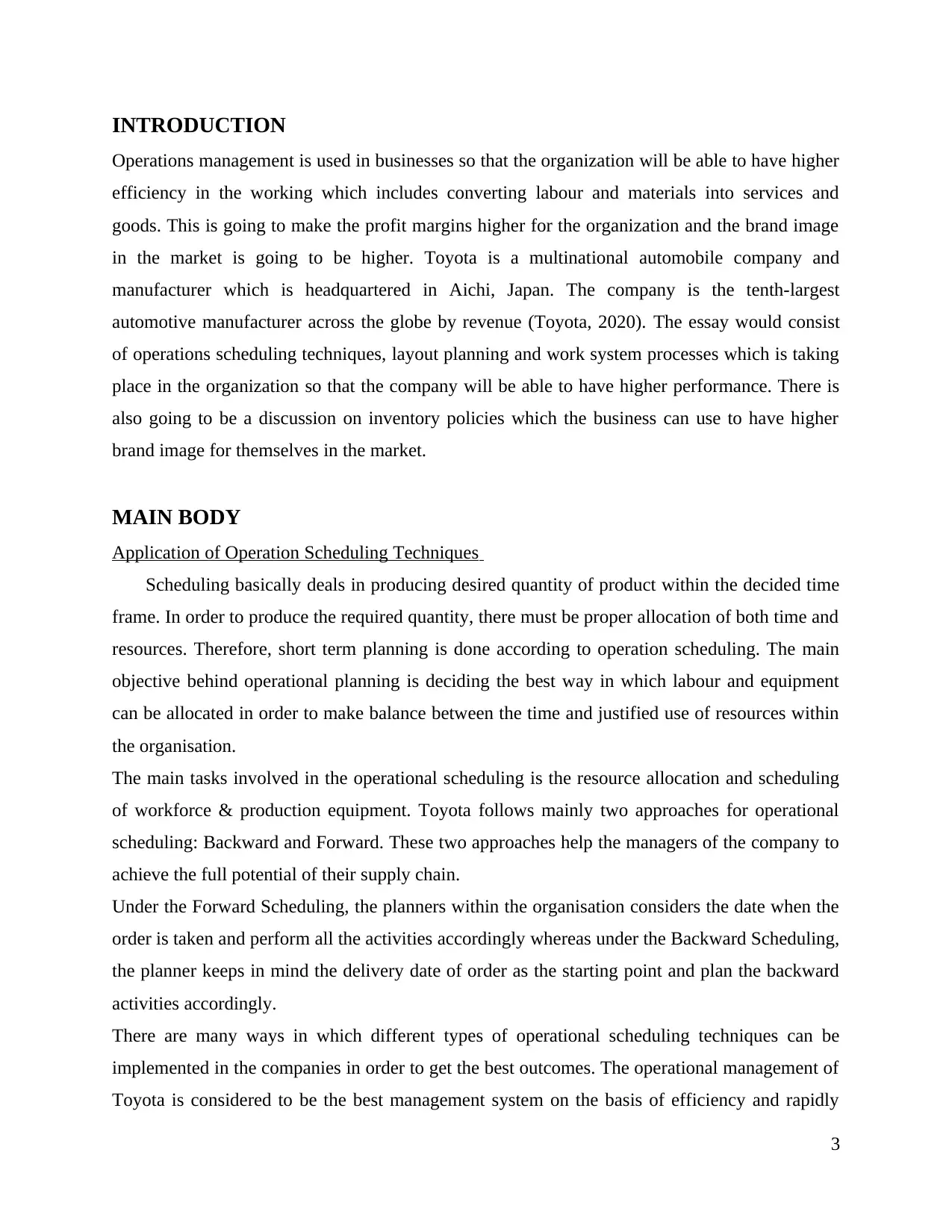
INTRODUCTION
Operations management is used in businesses so that the organization will be able to have higher
efficiency in the working which includes converting labour and materials into services and
goods. This is going to make the profit margins higher for the organization and the brand image
in the market is going to be higher. Toyota is a multinational automobile company and
manufacturer which is headquartered in Aichi, Japan. The company is the tenth-largest
automotive manufacturer across the globe by revenue (Toyota, 2020). The essay would consist
of operations scheduling techniques, layout planning and work system processes which is taking
place in the organization so that the company will be able to have higher performance. There is
also going to be a discussion on inventory policies which the business can use to have higher
brand image for themselves in the market.
MAIN BODY
Application of Operation Scheduling Techniques
Scheduling basically deals in producing desired quantity of product within the decided time
frame. In order to produce the required quantity, there must be proper allocation of both time and
resources. Therefore, short term planning is done according to operation scheduling. The main
objective behind operational planning is deciding the best way in which labour and equipment
can be allocated in order to make balance between the time and justified use of resources within
the organisation.
The main tasks involved in the operational scheduling is the resource allocation and scheduling
of workforce & production equipment. Toyota follows mainly two approaches for operational
scheduling: Backward and Forward. These two approaches help the managers of the company to
achieve the full potential of their supply chain.
Under the Forward Scheduling, the planners within the organisation considers the date when the
order is taken and perform all the activities accordingly whereas under the Backward Scheduling,
the planner keeps in mind the delivery date of order as the starting point and plan the backward
activities accordingly.
There are many ways in which different types of operational scheduling techniques can be
implemented in the companies in order to get the best outcomes. The operational management of
Toyota is considered to be the best management system on the basis of efficiency and rapidly
3
Operations management is used in businesses so that the organization will be able to have higher
efficiency in the working which includes converting labour and materials into services and
goods. This is going to make the profit margins higher for the organization and the brand image
in the market is going to be higher. Toyota is a multinational automobile company and
manufacturer which is headquartered in Aichi, Japan. The company is the tenth-largest
automotive manufacturer across the globe by revenue (Toyota, 2020). The essay would consist
of operations scheduling techniques, layout planning and work system processes which is taking
place in the organization so that the company will be able to have higher performance. There is
also going to be a discussion on inventory policies which the business can use to have higher
brand image for themselves in the market.
MAIN BODY
Application of Operation Scheduling Techniques
Scheduling basically deals in producing desired quantity of product within the decided time
frame. In order to produce the required quantity, there must be proper allocation of both time and
resources. Therefore, short term planning is done according to operation scheduling. The main
objective behind operational planning is deciding the best way in which labour and equipment
can be allocated in order to make balance between the time and justified use of resources within
the organisation.
The main tasks involved in the operational scheduling is the resource allocation and scheduling
of workforce & production equipment. Toyota follows mainly two approaches for operational
scheduling: Backward and Forward. These two approaches help the managers of the company to
achieve the full potential of their supply chain.
Under the Forward Scheduling, the planners within the organisation considers the date when the
order is taken and perform all the activities accordingly whereas under the Backward Scheduling,
the planner keeps in mind the delivery date of order as the starting point and plan the backward
activities accordingly.
There are many ways in which different types of operational scheduling techniques can be
implemented in the companies in order to get the best outcomes. The operational management of
Toyota is considered to be the best management system on the basis of efficiency and rapidly
3
⊘ This is a preview!⊘
Do you want full access?
Subscribe today to unlock all pages.

Trusted by 1+ million students worldwide
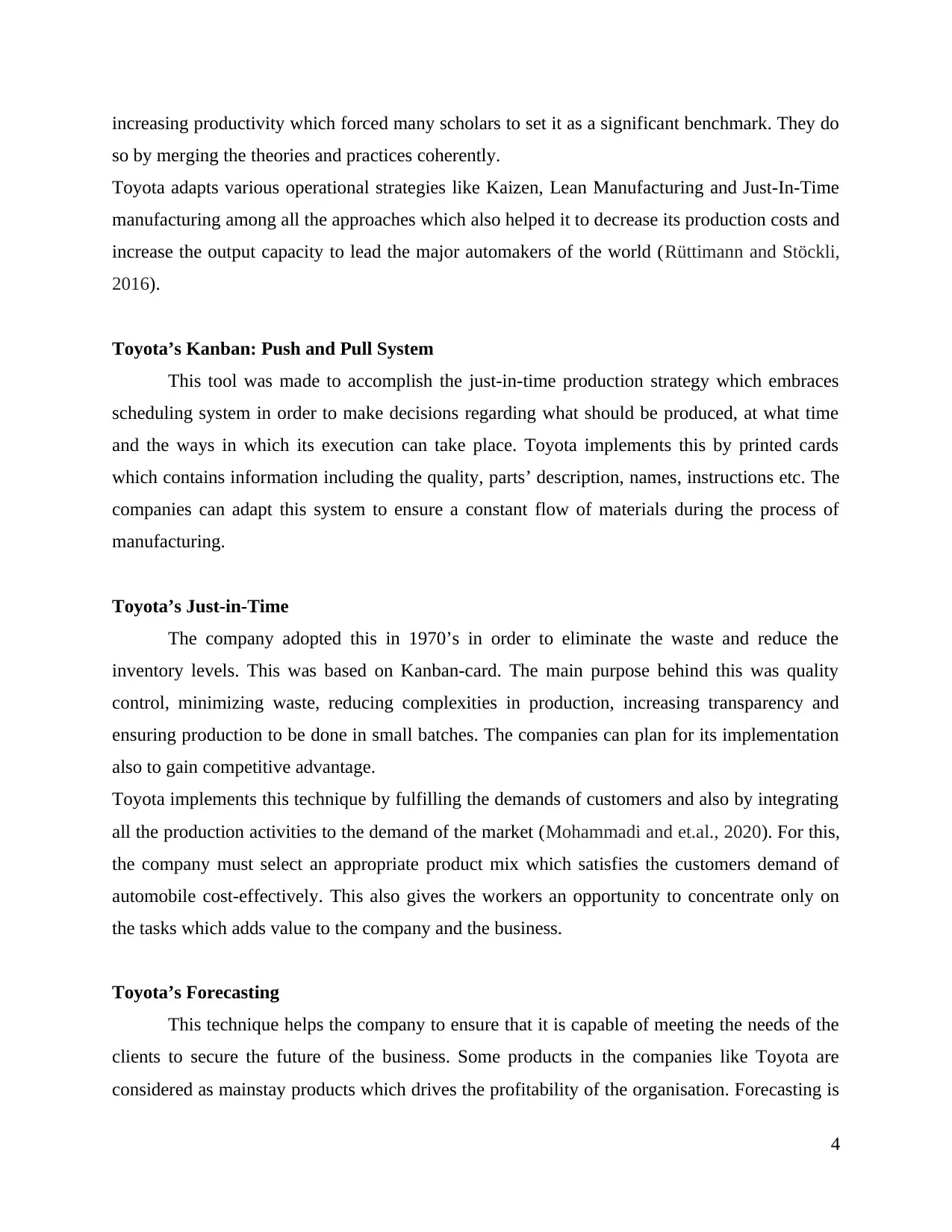
increasing productivity which forced many scholars to set it as a significant benchmark. They do
so by merging the theories and practices coherently.
Toyota adapts various operational strategies like Kaizen, Lean Manufacturing and Just-In-Time
manufacturing among all the approaches which also helped it to decrease its production costs and
increase the output capacity to lead the major automakers of the world (Rüttimann and Stöckli,
2016).
Toyota’s Kanban: Push and Pull System
This tool was made to accomplish the just-in-time production strategy which embraces
scheduling system in order to make decisions regarding what should be produced, at what time
and the ways in which its execution can take place. Toyota implements this by printed cards
which contains information including the quality, parts’ description, names, instructions etc. The
companies can adapt this system to ensure a constant flow of materials during the process of
manufacturing.
Toyota’s Just-in-Time
The company adopted this in 1970’s in order to eliminate the waste and reduce the
inventory levels. This was based on Kanban-card. The main purpose behind this was quality
control, minimizing waste, reducing complexities in production, increasing transparency and
ensuring production to be done in small batches. The companies can plan for its implementation
also to gain competitive advantage.
Toyota implements this technique by fulfilling the demands of customers and also by integrating
all the production activities to the demand of the market (Mohammadi and et.al., 2020). For this,
the company must select an appropriate product mix which satisfies the customers demand of
automobile cost-effectively. This also gives the workers an opportunity to concentrate only on
the tasks which adds value to the company and the business.
Toyota’s Forecasting
This technique helps the company to ensure that it is capable of meeting the needs of the
clients to secure the future of the business. Some products in the companies like Toyota are
considered as mainstay products which drives the profitability of the organisation. Forecasting is
4
so by merging the theories and practices coherently.
Toyota adapts various operational strategies like Kaizen, Lean Manufacturing and Just-In-Time
manufacturing among all the approaches which also helped it to decrease its production costs and
increase the output capacity to lead the major automakers of the world (Rüttimann and Stöckli,
2016).
Toyota’s Kanban: Push and Pull System
This tool was made to accomplish the just-in-time production strategy which embraces
scheduling system in order to make decisions regarding what should be produced, at what time
and the ways in which its execution can take place. Toyota implements this by printed cards
which contains information including the quality, parts’ description, names, instructions etc. The
companies can adapt this system to ensure a constant flow of materials during the process of
manufacturing.
Toyota’s Just-in-Time
The company adopted this in 1970’s in order to eliminate the waste and reduce the
inventory levels. This was based on Kanban-card. The main purpose behind this was quality
control, minimizing waste, reducing complexities in production, increasing transparency and
ensuring production to be done in small batches. The companies can plan for its implementation
also to gain competitive advantage.
Toyota implements this technique by fulfilling the demands of customers and also by integrating
all the production activities to the demand of the market (Mohammadi and et.al., 2020). For this,
the company must select an appropriate product mix which satisfies the customers demand of
automobile cost-effectively. This also gives the workers an opportunity to concentrate only on
the tasks which adds value to the company and the business.
Toyota’s Forecasting
This technique helps the company to ensure that it is capable of meeting the needs of the
clients to secure the future of the business. Some products in the companies like Toyota are
considered as mainstay products which drives the profitability of the organisation. Forecasting is
4
Paraphrase This Document
Need a fresh take? Get an instant paraphrase of this document with our AI Paraphraser
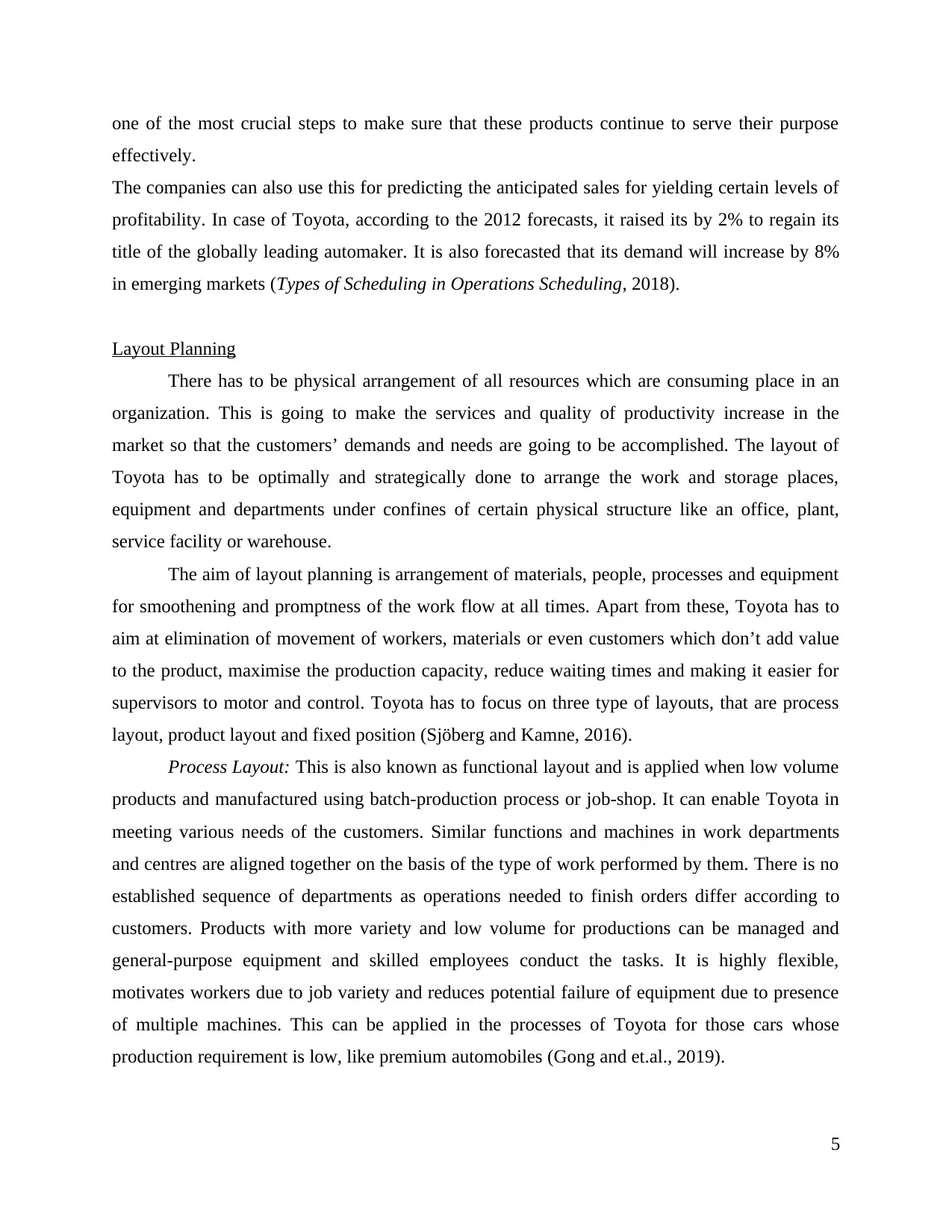
one of the most crucial steps to make sure that these products continue to serve their purpose
effectively.
The companies can also use this for predicting the anticipated sales for yielding certain levels of
profitability. In case of Toyota, according to the 2012 forecasts, it raised its by 2% to regain its
title of the globally leading automaker. It is also forecasted that its demand will increase by 8%
in emerging markets (Types of Scheduling in Operations Scheduling, 2018).
Layout Planning
There has to be physical arrangement of all resources which are consuming place in an
organization. This is going to make the services and quality of productivity increase in the
market so that the customers’ demands and needs are going to be accomplished. The layout of
Toyota has to be optimally and strategically done to arrange the work and storage places,
equipment and departments under confines of certain physical structure like an office, plant,
service facility or warehouse.
The aim of layout planning is arrangement of materials, people, processes and equipment
for smoothening and promptness of the work flow at all times. Apart from these, Toyota has to
aim at elimination of movement of workers, materials or even customers which don’t add value
to the product, maximise the production capacity, reduce waiting times and making it easier for
supervisors to motor and control. Toyota has to focus on three type of layouts, that are process
layout, product layout and fixed position (Sjöberg and Kamne, 2016).
Process Layout: This is also known as functional layout and is applied when low volume
products and manufactured using batch-production process or job-shop. It can enable Toyota in
meeting various needs of the customers. Similar functions and machines in work departments
and centres are aligned together on the basis of the type of work performed by them. There is no
established sequence of departments as operations needed to finish orders differ according to
customers. Products with more variety and low volume for productions can be managed and
general-purpose equipment and skilled employees conduct the tasks. It is highly flexible,
motivates workers due to job variety and reduces potential failure of equipment due to presence
of multiple machines. This can be applied in the processes of Toyota for those cars whose
production requirement is low, like premium automobiles (Gong and et.al., 2019).
5
effectively.
The companies can also use this for predicting the anticipated sales for yielding certain levels of
profitability. In case of Toyota, according to the 2012 forecasts, it raised its by 2% to regain its
title of the globally leading automaker. It is also forecasted that its demand will increase by 8%
in emerging markets (Types of Scheduling in Operations Scheduling, 2018).
Layout Planning
There has to be physical arrangement of all resources which are consuming place in an
organization. This is going to make the services and quality of productivity increase in the
market so that the customers’ demands and needs are going to be accomplished. The layout of
Toyota has to be optimally and strategically done to arrange the work and storage places,
equipment and departments under confines of certain physical structure like an office, plant,
service facility or warehouse.
The aim of layout planning is arrangement of materials, people, processes and equipment
for smoothening and promptness of the work flow at all times. Apart from these, Toyota has to
aim at elimination of movement of workers, materials or even customers which don’t add value
to the product, maximise the production capacity, reduce waiting times and making it easier for
supervisors to motor and control. Toyota has to focus on three type of layouts, that are process
layout, product layout and fixed position (Sjöberg and Kamne, 2016).
Process Layout: This is also known as functional layout and is applied when low volume
products and manufactured using batch-production process or job-shop. It can enable Toyota in
meeting various needs of the customers. Similar functions and machines in work departments
and centres are aligned together on the basis of the type of work performed by them. There is no
established sequence of departments as operations needed to finish orders differ according to
customers. Products with more variety and low volume for productions can be managed and
general-purpose equipment and skilled employees conduct the tasks. It is highly flexible,
motivates workers due to job variety and reduces potential failure of equipment due to presence
of multiple machines. This can be applied in the processes of Toyota for those cars whose
production requirement is low, like premium automobiles (Gong and et.al., 2019).
5
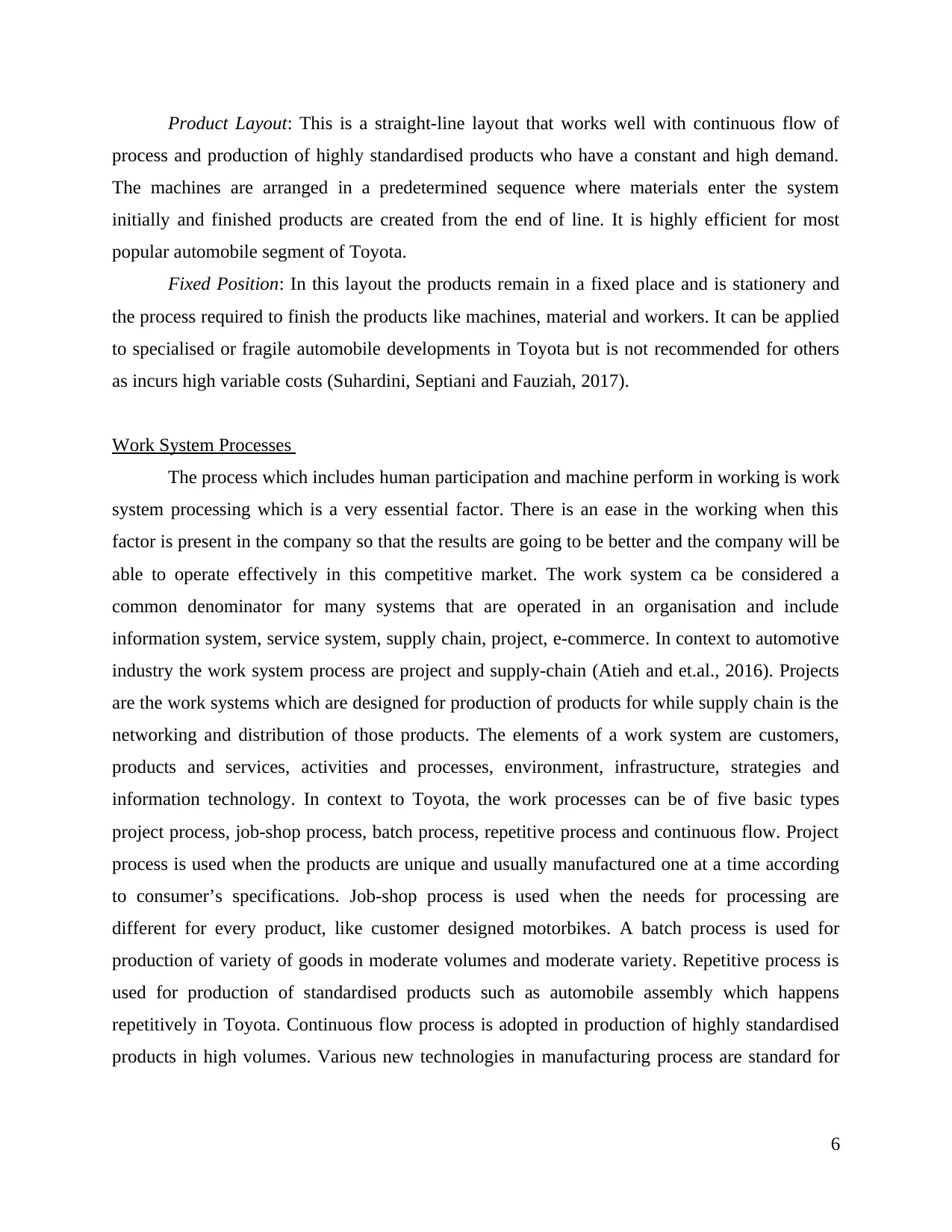
Product Layout: This is a straight-line layout that works well with continuous flow of
process and production of highly standardised products who have a constant and high demand.
The machines are arranged in a predetermined sequence where materials enter the system
initially and finished products are created from the end of line. It is highly efficient for most
popular automobile segment of Toyota.
Fixed Position: In this layout the products remain in a fixed place and is stationery and
the process required to finish the products like machines, material and workers. It can be applied
to specialised or fragile automobile developments in Toyota but is not recommended for others
as incurs high variable costs (Suhardini, Septiani and Fauziah, 2017).
Work System Processes
The process which includes human participation and machine perform in working is work
system processing which is a very essential factor. There is an ease in the working when this
factor is present in the company so that the results are going to be better and the company will be
able to operate effectively in this competitive market. The work system ca be considered a
common denominator for many systems that are operated in an organisation and include
information system, service system, supply chain, project, e-commerce. In context to automotive
industry the work system process are project and supply-chain (Atieh and et.al., 2016). Projects
are the work systems which are designed for production of products for while supply chain is the
networking and distribution of those products. The elements of a work system are customers,
products and services, activities and processes, environment, infrastructure, strategies and
information technology. In context to Toyota, the work processes can be of five basic types
project process, job-shop process, batch process, repetitive process and continuous flow. Project
process is used when the products are unique and usually manufactured one at a time according
to consumer’s specifications. Job-shop process is used when the needs for processing are
different for every product, like customer designed motorbikes. A batch process is used for
production of variety of goods in moderate volumes and moderate variety. Repetitive process is
used for production of standardised products such as automobile assembly which happens
repetitively in Toyota. Continuous flow process is adopted in production of highly standardised
products in high volumes. Various new technologies in manufacturing process are standard for
6
process and production of highly standardised products who have a constant and high demand.
The machines are arranged in a predetermined sequence where materials enter the system
initially and finished products are created from the end of line. It is highly efficient for most
popular automobile segment of Toyota.
Fixed Position: In this layout the products remain in a fixed place and is stationery and
the process required to finish the products like machines, material and workers. It can be applied
to specialised or fragile automobile developments in Toyota but is not recommended for others
as incurs high variable costs (Suhardini, Septiani and Fauziah, 2017).
Work System Processes
The process which includes human participation and machine perform in working is work
system processing which is a very essential factor. There is an ease in the working when this
factor is present in the company so that the results are going to be better and the company will be
able to operate effectively in this competitive market. The work system ca be considered a
common denominator for many systems that are operated in an organisation and include
information system, service system, supply chain, project, e-commerce. In context to automotive
industry the work system process are project and supply-chain (Atieh and et.al., 2016). Projects
are the work systems which are designed for production of products for while supply chain is the
networking and distribution of those products. The elements of a work system are customers,
products and services, activities and processes, environment, infrastructure, strategies and
information technology. In context to Toyota, the work processes can be of five basic types
project process, job-shop process, batch process, repetitive process and continuous flow. Project
process is used when the products are unique and usually manufactured one at a time according
to consumer’s specifications. Job-shop process is used when the needs for processing are
different for every product, like customer designed motorbikes. A batch process is used for
production of variety of goods in moderate volumes and moderate variety. Repetitive process is
used for production of standardised products such as automobile assembly which happens
repetitively in Toyota. Continuous flow process is adopted in production of highly standardised
products in high volumes. Various new technologies in manufacturing process are standard for
6
⊘ This is a preview!⊘
Do you want full access?
Subscribe today to unlock all pages.

Trusted by 1+ million students worldwide
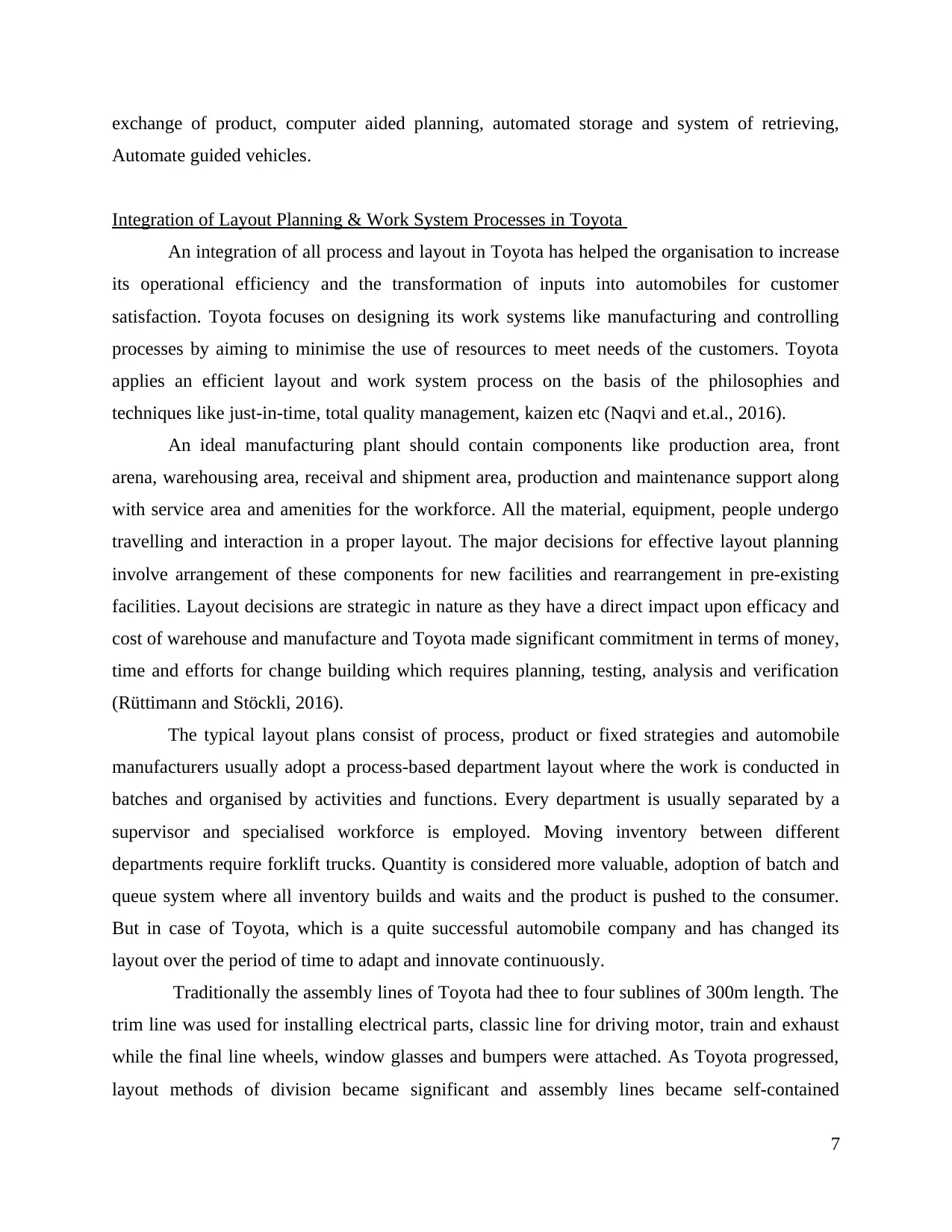
exchange of product, computer aided planning, automated storage and system of retrieving,
Automate guided vehicles.
Integration of Layout Planning & Work System Processes in Toyota
An integration of all process and layout in Toyota has helped the organisation to increase
its operational efficiency and the transformation of inputs into automobiles for customer
satisfaction. Toyota focuses on designing its work systems like manufacturing and controlling
processes by aiming to minimise the use of resources to meet needs of the customers. Toyota
applies an efficient layout and work system process on the basis of the philosophies and
techniques like just-in-time, total quality management, kaizen etc (Naqvi and et.al., 2016).
An ideal manufacturing plant should contain components like production area, front
arena, warehousing area, receival and shipment area, production and maintenance support along
with service area and amenities for the workforce. All the material, equipment, people undergo
travelling and interaction in a proper layout. The major decisions for effective layout planning
involve arrangement of these components for new facilities and rearrangement in pre-existing
facilities. Layout decisions are strategic in nature as they have a direct impact upon efficacy and
cost of warehouse and manufacture and Toyota made significant commitment in terms of money,
time and efforts for change building which requires planning, testing, analysis and verification
(Rüttimann and Stöckli, 2016).
The typical layout plans consist of process, product or fixed strategies and automobile
manufacturers usually adopt a process-based department layout where the work is conducted in
batches and organised by activities and functions. Every department is usually separated by a
supervisor and specialised workforce is employed. Moving inventory between different
departments require forklift trucks. Quantity is considered more valuable, adoption of batch and
queue system where all inventory builds and waits and the product is pushed to the consumer.
But in case of Toyota, which is a quite successful automobile company and has changed its
layout over the period of time to adapt and innovate continuously.
Traditionally the assembly lines of Toyota had thee to four sublines of 300m length. The
trim line was used for installing electrical parts, classic line for driving motor, train and exhaust
while the final line wheels, window glasses and bumpers were attached. As Toyota progressed,
layout methods of division became significant and assembly lines became self-contained
7
Automate guided vehicles.
Integration of Layout Planning & Work System Processes in Toyota
An integration of all process and layout in Toyota has helped the organisation to increase
its operational efficiency and the transformation of inputs into automobiles for customer
satisfaction. Toyota focuses on designing its work systems like manufacturing and controlling
processes by aiming to minimise the use of resources to meet needs of the customers. Toyota
applies an efficient layout and work system process on the basis of the philosophies and
techniques like just-in-time, total quality management, kaizen etc (Naqvi and et.al., 2016).
An ideal manufacturing plant should contain components like production area, front
arena, warehousing area, receival and shipment area, production and maintenance support along
with service area and amenities for the workforce. All the material, equipment, people undergo
travelling and interaction in a proper layout. The major decisions for effective layout planning
involve arrangement of these components for new facilities and rearrangement in pre-existing
facilities. Layout decisions are strategic in nature as they have a direct impact upon efficacy and
cost of warehouse and manufacture and Toyota made significant commitment in terms of money,
time and efforts for change building which requires planning, testing, analysis and verification
(Rüttimann and Stöckli, 2016).
The typical layout plans consist of process, product or fixed strategies and automobile
manufacturers usually adopt a process-based department layout where the work is conducted in
batches and organised by activities and functions. Every department is usually separated by a
supervisor and specialised workforce is employed. Moving inventory between different
departments require forklift trucks. Quantity is considered more valuable, adoption of batch and
queue system where all inventory builds and waits and the product is pushed to the consumer.
But in case of Toyota, which is a quite successful automobile company and has changed its
layout over the period of time to adapt and innovate continuously.
Traditionally the assembly lines of Toyota had thee to four sublines of 300m length. The
trim line was used for installing electrical parts, classic line for driving motor, train and exhaust
while the final line wheels, window glasses and bumpers were attached. As Toyota progressed,
layout methods of division became significant and assembly lines became self-contained
7
Paraphrase This Document
Need a fresh take? Get an instant paraphrase of this document with our AI Paraphraser
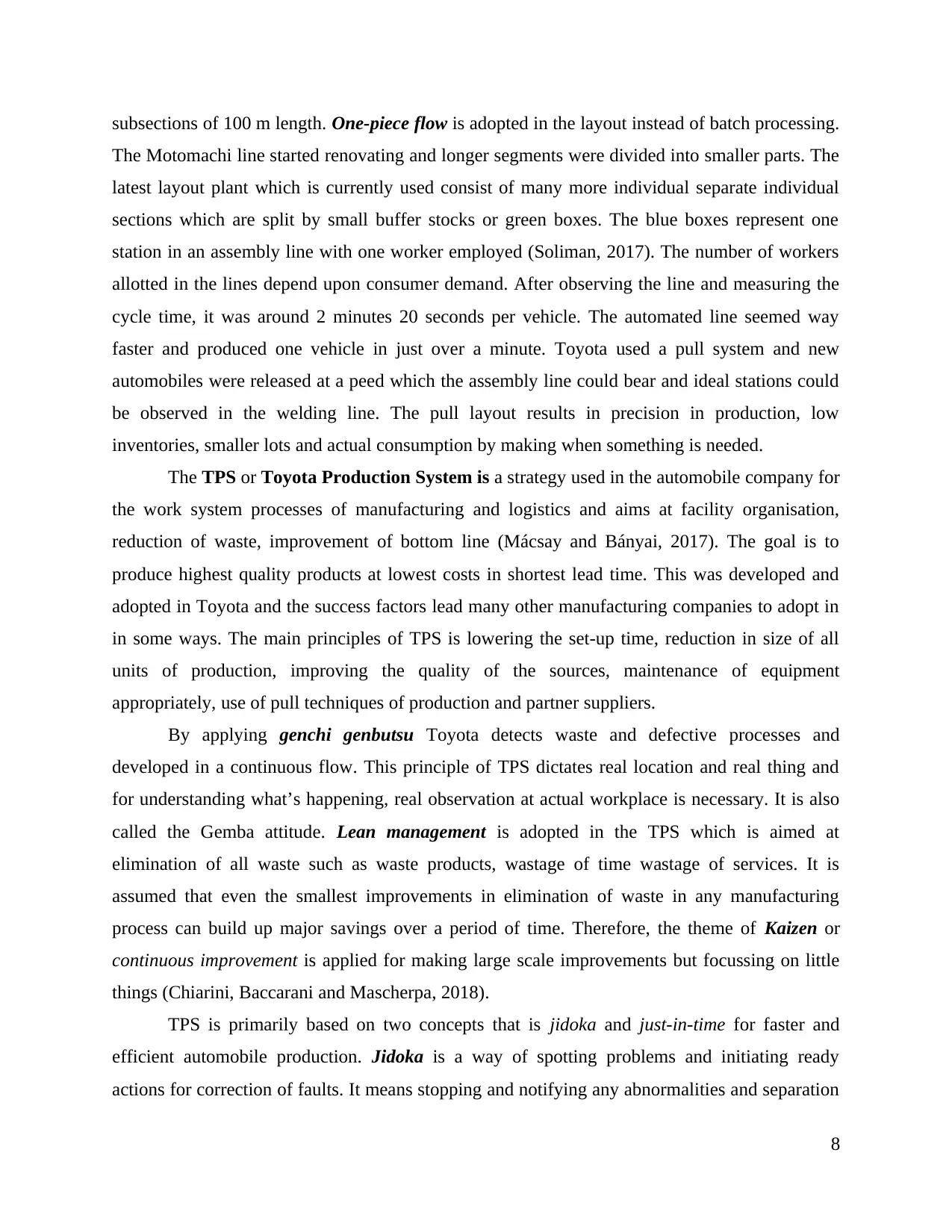
subsections of 100 m length. One-piece flow is adopted in the layout instead of batch processing.
The Motomachi line started renovating and longer segments were divided into smaller parts. The
latest layout plant which is currently used consist of many more individual separate individual
sections which are split by small buffer stocks or green boxes. The blue boxes represent one
station in an assembly line with one worker employed (Soliman, 2017). The number of workers
allotted in the lines depend upon consumer demand. After observing the line and measuring the
cycle time, it was around 2 minutes 20 seconds per vehicle. The automated line seemed way
faster and produced one vehicle in just over a minute. Toyota used a pull system and new
automobiles were released at a peed which the assembly line could bear and ideal stations could
be observed in the welding line. The pull layout results in precision in production, low
inventories, smaller lots and actual consumption by making when something is needed.
The TPS or Toyota Production System is a strategy used in the automobile company for
the work system processes of manufacturing and logistics and aims at facility organisation,
reduction of waste, improvement of bottom line (Mácsay and Bányai, 2017). The goal is to
produce highest quality products at lowest costs in shortest lead time. This was developed and
adopted in Toyota and the success factors lead many other manufacturing companies to adopt in
in some ways. The main principles of TPS is lowering the set-up time, reduction in size of all
units of production, improving the quality of the sources, maintenance of equipment
appropriately, use of pull techniques of production and partner suppliers.
By applying genchi genbutsu Toyota detects waste and defective processes and
developed in a continuous flow. This principle of TPS dictates real location and real thing and
for understanding what’s happening, real observation at actual workplace is necessary. It is also
called the Gemba attitude. Lean management is adopted in the TPS which is aimed at
elimination of all waste such as waste products, wastage of time wastage of services. It is
assumed that even the smallest improvements in elimination of waste in any manufacturing
process can build up major savings over a period of time. Therefore, the theme of Kaizen or
continuous improvement is applied for making large scale improvements but focussing on little
things (Chiarini, Baccarani and Mascherpa, 2018).
TPS is primarily based on two concepts that is jidoka and just-in-time for faster and
efficient automobile production. Jidoka is a way of spotting problems and initiating ready
actions for correction of faults. It means stopping and notifying any abnormalities and separation
8
The Motomachi line started renovating and longer segments were divided into smaller parts. The
latest layout plant which is currently used consist of many more individual separate individual
sections which are split by small buffer stocks or green boxes. The blue boxes represent one
station in an assembly line with one worker employed (Soliman, 2017). The number of workers
allotted in the lines depend upon consumer demand. After observing the line and measuring the
cycle time, it was around 2 minutes 20 seconds per vehicle. The automated line seemed way
faster and produced one vehicle in just over a minute. Toyota used a pull system and new
automobiles were released at a peed which the assembly line could bear and ideal stations could
be observed in the welding line. The pull layout results in precision in production, low
inventories, smaller lots and actual consumption by making when something is needed.
The TPS or Toyota Production System is a strategy used in the automobile company for
the work system processes of manufacturing and logistics and aims at facility organisation,
reduction of waste, improvement of bottom line (Mácsay and Bányai, 2017). The goal is to
produce highest quality products at lowest costs in shortest lead time. This was developed and
adopted in Toyota and the success factors lead many other manufacturing companies to adopt in
in some ways. The main principles of TPS is lowering the set-up time, reduction in size of all
units of production, improving the quality of the sources, maintenance of equipment
appropriately, use of pull techniques of production and partner suppliers.
By applying genchi genbutsu Toyota detects waste and defective processes and
developed in a continuous flow. This principle of TPS dictates real location and real thing and
for understanding what’s happening, real observation at actual workplace is necessary. It is also
called the Gemba attitude. Lean management is adopted in the TPS which is aimed at
elimination of all waste such as waste products, wastage of time wastage of services. It is
assumed that even the smallest improvements in elimination of waste in any manufacturing
process can build up major savings over a period of time. Therefore, the theme of Kaizen or
continuous improvement is applied for making large scale improvements but focussing on little
things (Chiarini, Baccarani and Mascherpa, 2018).
TPS is primarily based on two concepts that is jidoka and just-in-time for faster and
efficient automobile production. Jidoka is a way of spotting problems and initiating ready
actions for correction of faults. It means stopping and notifying any abnormalities and separation
8
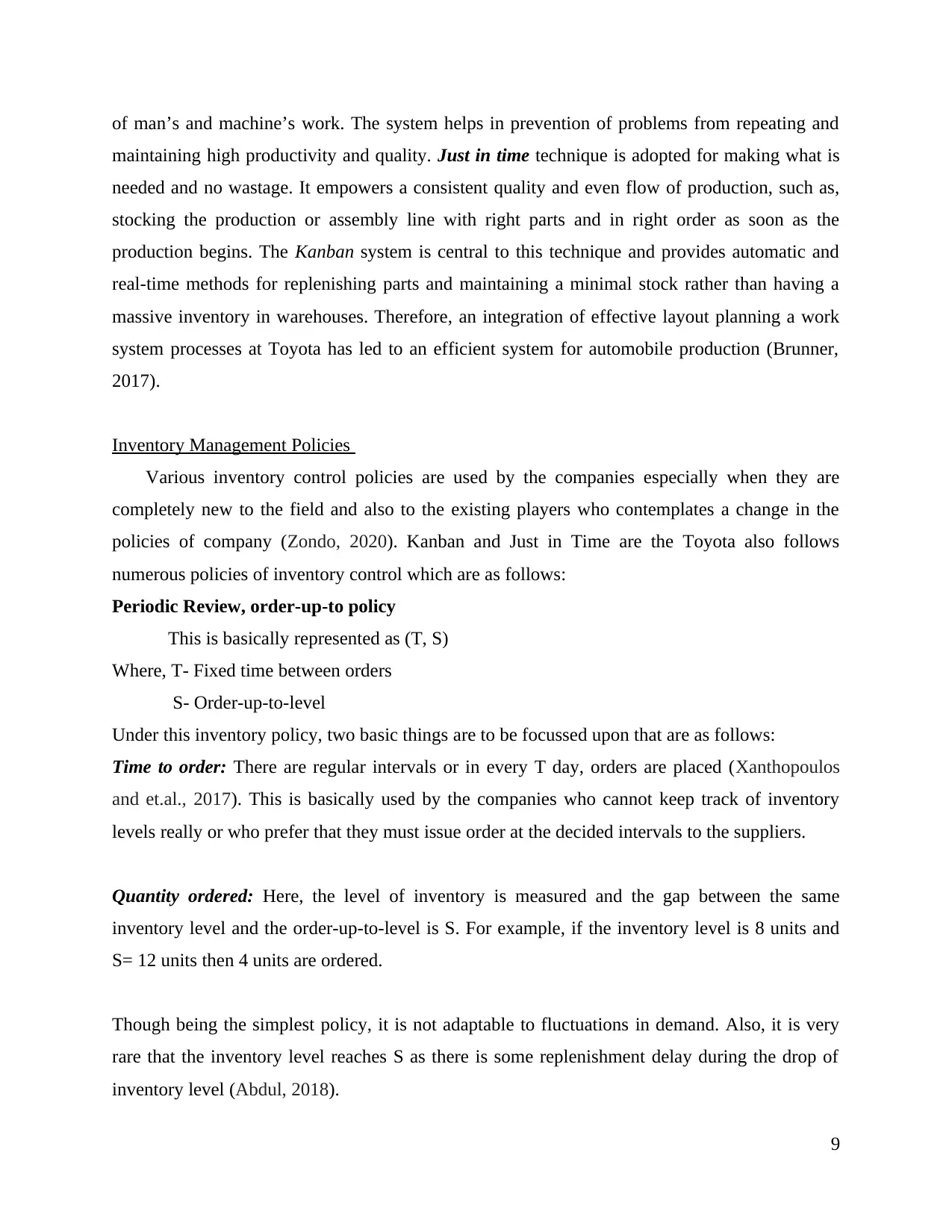
of man’s and machine’s work. The system helps in prevention of problems from repeating and
maintaining high productivity and quality. Just in time technique is adopted for making what is
needed and no wastage. It empowers a consistent quality and even flow of production, such as,
stocking the production or assembly line with right parts and in right order as soon as the
production begins. The Kanban system is central to this technique and provides automatic and
real-time methods for replenishing parts and maintaining a minimal stock rather than having a
massive inventory in warehouses. Therefore, an integration of effective layout planning a work
system processes at Toyota has led to an efficient system for automobile production (Brunner,
2017).
Inventory Management Policies
Various inventory control policies are used by the companies especially when they are
completely new to the field and also to the existing players who contemplates a change in the
policies of company (Zondo, 2020). Kanban and Just in Time are the Toyota also follows
numerous policies of inventory control which are as follows:
Periodic Review, order-up-to policy
This is basically represented as (T, S)
Where, T- Fixed time between orders
S- Order-up-to-level
Under this inventory policy, two basic things are to be focussed upon that are as follows:
Time to order: There are regular intervals or in every T day, orders are placed (Xanthopoulos
and et.al., 2017). This is basically used by the companies who cannot keep track of inventory
levels really or who prefer that they must issue order at the decided intervals to the suppliers.
Quantity ordered: Here, the level of inventory is measured and the gap between the same
inventory level and the order-up-to-level is S. For example, if the inventory level is 8 units and
S= 12 units then 4 units are ordered.
Though being the simplest policy, it is not adaptable to fluctuations in demand. Also, it is very
rare that the inventory level reaches S as there is some replenishment delay during the drop of
inventory level (Abdul, 2018).
9
maintaining high productivity and quality. Just in time technique is adopted for making what is
needed and no wastage. It empowers a consistent quality and even flow of production, such as,
stocking the production or assembly line with right parts and in right order as soon as the
production begins. The Kanban system is central to this technique and provides automatic and
real-time methods for replenishing parts and maintaining a minimal stock rather than having a
massive inventory in warehouses. Therefore, an integration of effective layout planning a work
system processes at Toyota has led to an efficient system for automobile production (Brunner,
2017).
Inventory Management Policies
Various inventory control policies are used by the companies especially when they are
completely new to the field and also to the existing players who contemplates a change in the
policies of company (Zondo, 2020). Kanban and Just in Time are the Toyota also follows
numerous policies of inventory control which are as follows:
Periodic Review, order-up-to policy
This is basically represented as (T, S)
Where, T- Fixed time between orders
S- Order-up-to-level
Under this inventory policy, two basic things are to be focussed upon that are as follows:
Time to order: There are regular intervals or in every T day, orders are placed (Xanthopoulos
and et.al., 2017). This is basically used by the companies who cannot keep track of inventory
levels really or who prefer that they must issue order at the decided intervals to the suppliers.
Quantity ordered: Here, the level of inventory is measured and the gap between the same
inventory level and the order-up-to-level is S. For example, if the inventory level is 8 units and
S= 12 units then 4 units are ordered.
Though being the simplest policy, it is not adaptable to fluctuations in demand. Also, it is very
rare that the inventory level reaches S as there is some replenishment delay during the drop of
inventory level (Abdul, 2018).
9
⊘ This is a preview!⊘
Do you want full access?
Subscribe today to unlock all pages.

Trusted by 1+ million students worldwide
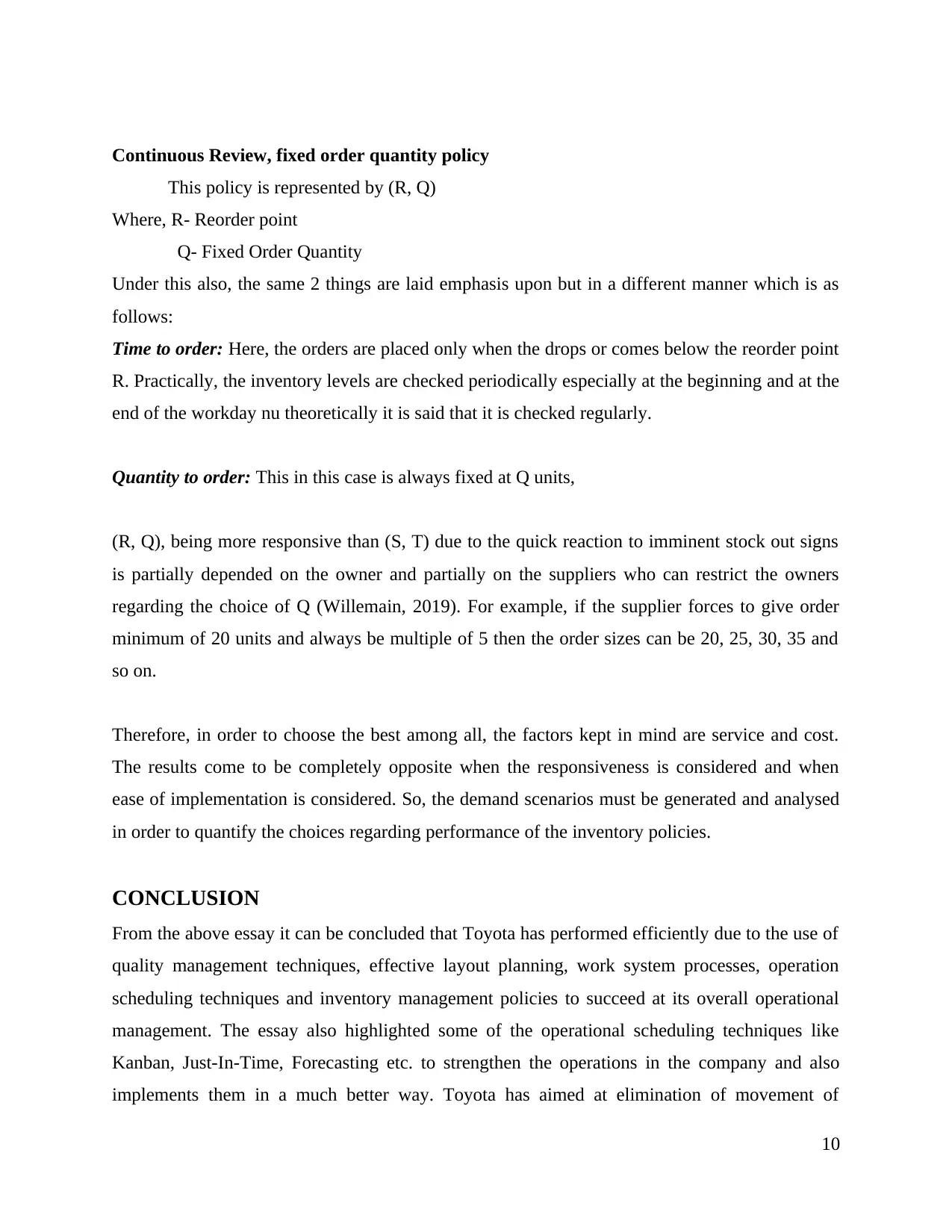
Continuous Review, fixed order quantity policy
This policy is represented by (R, Q)
Where, R- Reorder point
Q- Fixed Order Quantity
Under this also, the same 2 things are laid emphasis upon but in a different manner which is as
follows:
Time to order: Here, the orders are placed only when the drops or comes below the reorder point
R. Practically, the inventory levels are checked periodically especially at the beginning and at the
end of the workday nu theoretically it is said that it is checked regularly.
Quantity to order: This in this case is always fixed at Q units,
(R, Q), being more responsive than (S, T) due to the quick reaction to imminent stock out signs
is partially depended on the owner and partially on the suppliers who can restrict the owners
regarding the choice of Q (Willemain, 2019). For example, if the supplier forces to give order
minimum of 20 units and always be multiple of 5 then the order sizes can be 20, 25, 30, 35 and
so on.
Therefore, in order to choose the best among all, the factors kept in mind are service and cost.
The results come to be completely opposite when the responsiveness is considered and when
ease of implementation is considered. So, the demand scenarios must be generated and analysed
in order to quantify the choices regarding performance of the inventory policies.
CONCLUSION
From the above essay it can be concluded that Toyota has performed efficiently due to the use of
quality management techniques, effective layout planning, work system processes, operation
scheduling techniques and inventory management policies to succeed at its overall operational
management. The essay also highlighted some of the operational scheduling techniques like
Kanban, Just-In-Time, Forecasting etc. to strengthen the operations in the company and also
implements them in a much better way. Toyota has aimed at elimination of movement of
10
This policy is represented by (R, Q)
Where, R- Reorder point
Q- Fixed Order Quantity
Under this also, the same 2 things are laid emphasis upon but in a different manner which is as
follows:
Time to order: Here, the orders are placed only when the drops or comes below the reorder point
R. Practically, the inventory levels are checked periodically especially at the beginning and at the
end of the workday nu theoretically it is said that it is checked regularly.
Quantity to order: This in this case is always fixed at Q units,
(R, Q), being more responsive than (S, T) due to the quick reaction to imminent stock out signs
is partially depended on the owner and partially on the suppliers who can restrict the owners
regarding the choice of Q (Willemain, 2019). For example, if the supplier forces to give order
minimum of 20 units and always be multiple of 5 then the order sizes can be 20, 25, 30, 35 and
so on.
Therefore, in order to choose the best among all, the factors kept in mind are service and cost.
The results come to be completely opposite when the responsiveness is considered and when
ease of implementation is considered. So, the demand scenarios must be generated and analysed
in order to quantify the choices regarding performance of the inventory policies.
CONCLUSION
From the above essay it can be concluded that Toyota has performed efficiently due to the use of
quality management techniques, effective layout planning, work system processes, operation
scheduling techniques and inventory management policies to succeed at its overall operational
management. The essay also highlighted some of the operational scheduling techniques like
Kanban, Just-In-Time, Forecasting etc. to strengthen the operations in the company and also
implements them in a much better way. Toyota has aimed at elimination of movement of
10
Paraphrase This Document
Need a fresh take? Get an instant paraphrase of this document with our AI Paraphraser
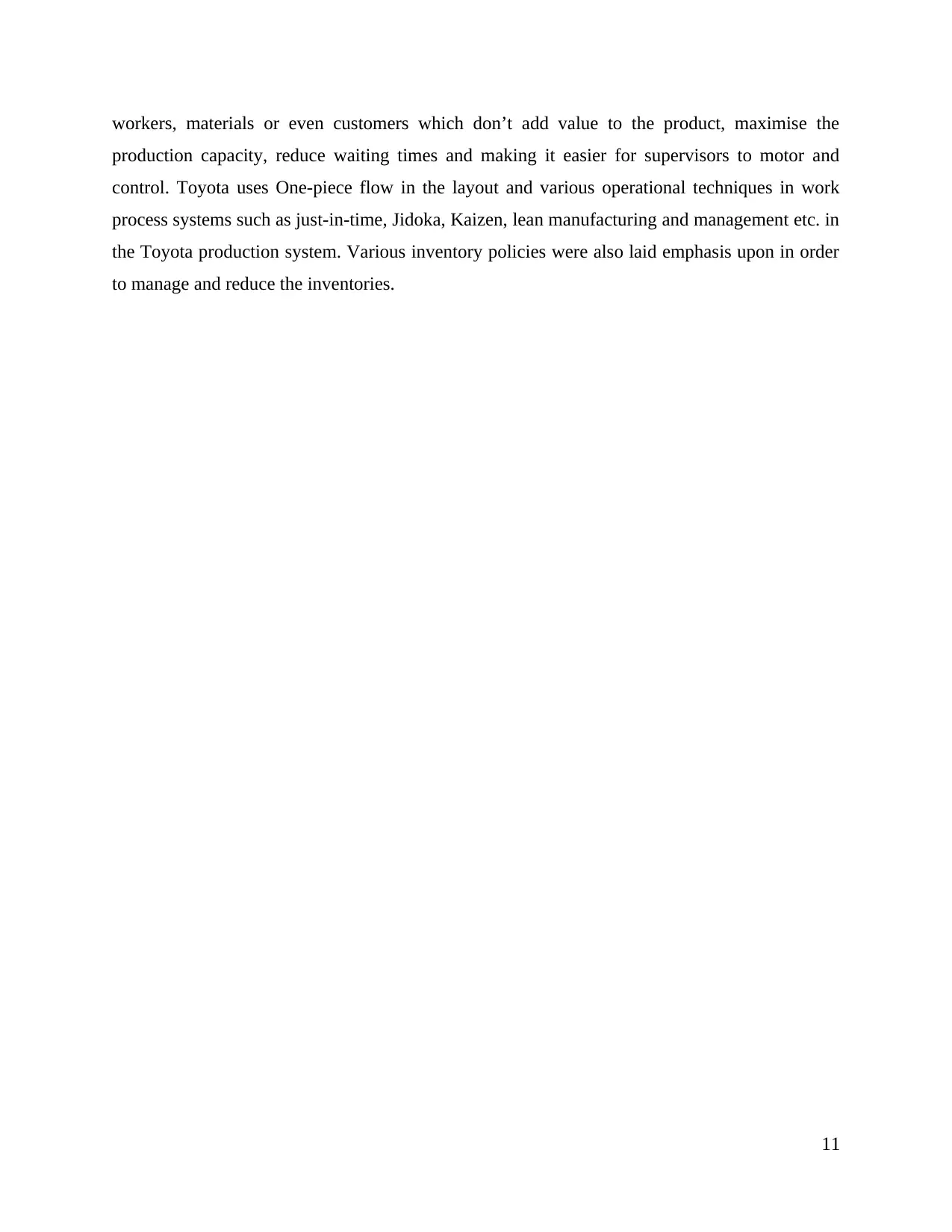
workers, materials or even customers which don’t add value to the product, maximise the
production capacity, reduce waiting times and making it easier for supervisors to motor and
control. Toyota uses One-piece flow in the layout and various operational techniques in work
process systems such as just-in-time, Jidoka, Kaizen, lean manufacturing and management etc. in
the Toyota production system. Various inventory policies were also laid emphasis upon in order
to manage and reduce the inventories.
11
production capacity, reduce waiting times and making it easier for supervisors to motor and
control. Toyota uses One-piece flow in the layout and various operational techniques in work
process systems such as just-in-time, Jidoka, Kaizen, lean manufacturing and management etc. in
the Toyota production system. Various inventory policies were also laid emphasis upon in order
to manage and reduce the inventories.
11
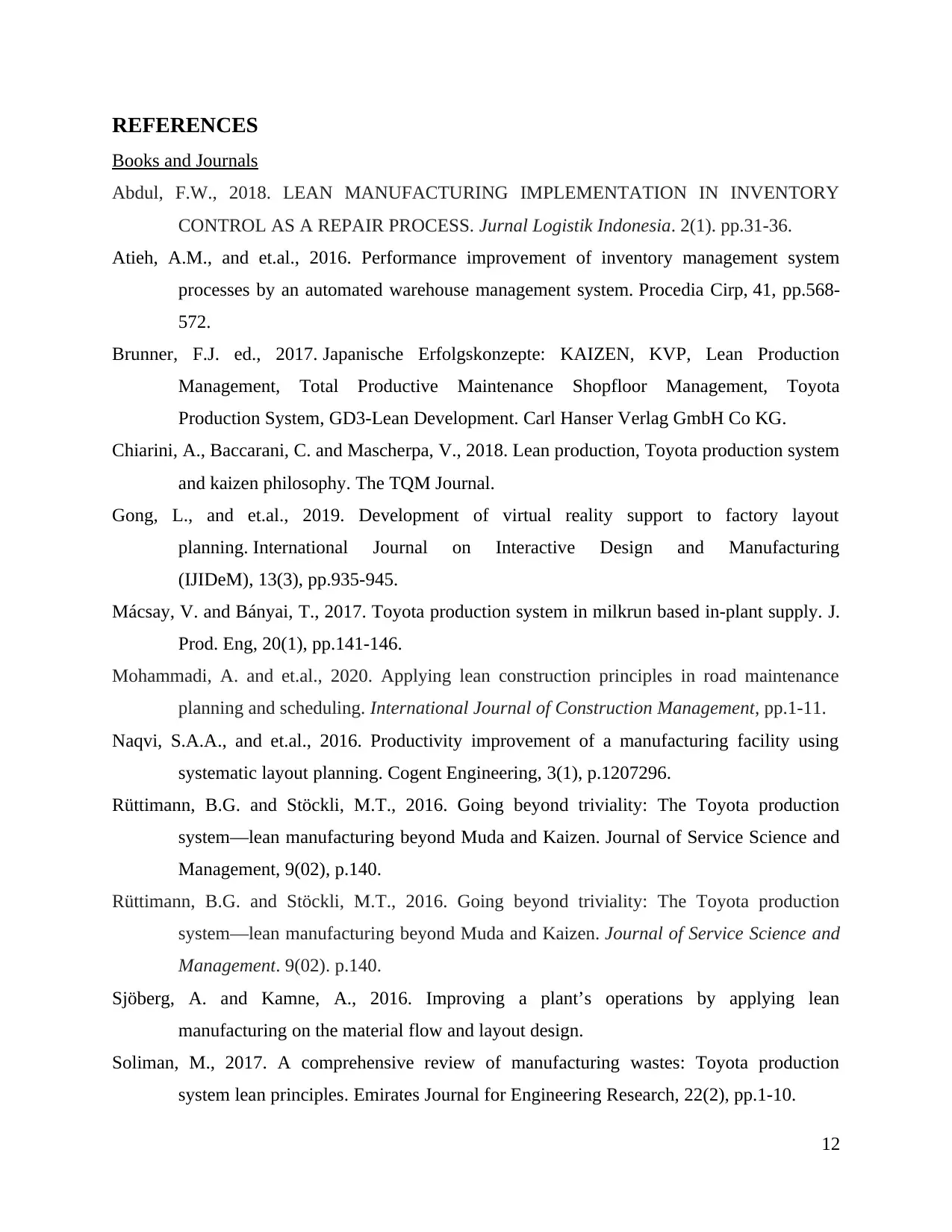
REFERENCES
Books and Journals
Abdul, F.W., 2018. LEAN MANUFACTURING IMPLEMENTATION IN INVENTORY
CONTROL AS A REPAIR PROCESS. Jurnal Logistik Indonesia. 2(1). pp.31-36.
Atieh, A.M., and et.al., 2016. Performance improvement of inventory management system
processes by an automated warehouse management system. Procedia Cirp, 41, pp.568-
572.
Brunner, F.J. ed., 2017. Japanische Erfolgskonzepte: KAIZEN, KVP, Lean Production
Management, Total Productive Maintenance Shopfloor Management, Toyota
Production System, GD3-Lean Development. Carl Hanser Verlag GmbH Co KG.
Chiarini, A., Baccarani, C. and Mascherpa, V., 2018. Lean production, Toyota production system
and kaizen philosophy. The TQM Journal.
Gong, L., and et.al., 2019. Development of virtual reality support to factory layout
planning. International Journal on Interactive Design and Manufacturing
(IJIDeM), 13(3), pp.935-945.
Mácsay, V. and Bányai, T., 2017. Toyota production system in milkrun based in-plant supply. J.
Prod. Eng, 20(1), pp.141-146.
Mohammadi, A. and et.al., 2020. Applying lean construction principles in road maintenance
planning and scheduling. International Journal of Construction Management, pp.1-11.
Naqvi, S.A.A., and et.al., 2016. Productivity improvement of a manufacturing facility using
systematic layout planning. Cogent Engineering, 3(1), p.1207296.
Rüttimann, B.G. and Stöckli, M.T., 2016. Going beyond triviality: The Toyota production
system—lean manufacturing beyond Muda and Kaizen. Journal of Service Science and
Management, 9(02), p.140.
Rüttimann, B.G. and Stöckli, M.T., 2016. Going beyond triviality: The Toyota production
system—lean manufacturing beyond Muda and Kaizen. Journal of Service Science and
Management. 9(02). p.140.
Sjöberg, A. and Kamne, A., 2016. Improving a plant’s operations by applying lean
manufacturing on the material flow and layout design.
Soliman, M., 2017. A comprehensive review of manufacturing wastes: Toyota production
system lean principles. Emirates Journal for Engineering Research, 22(2), pp.1-10.
12
Books and Journals
Abdul, F.W., 2018. LEAN MANUFACTURING IMPLEMENTATION IN INVENTORY
CONTROL AS A REPAIR PROCESS. Jurnal Logistik Indonesia. 2(1). pp.31-36.
Atieh, A.M., and et.al., 2016. Performance improvement of inventory management system
processes by an automated warehouse management system. Procedia Cirp, 41, pp.568-
572.
Brunner, F.J. ed., 2017. Japanische Erfolgskonzepte: KAIZEN, KVP, Lean Production
Management, Total Productive Maintenance Shopfloor Management, Toyota
Production System, GD3-Lean Development. Carl Hanser Verlag GmbH Co KG.
Chiarini, A., Baccarani, C. and Mascherpa, V., 2018. Lean production, Toyota production system
and kaizen philosophy. The TQM Journal.
Gong, L., and et.al., 2019. Development of virtual reality support to factory layout
planning. International Journal on Interactive Design and Manufacturing
(IJIDeM), 13(3), pp.935-945.
Mácsay, V. and Bányai, T., 2017. Toyota production system in milkrun based in-plant supply. J.
Prod. Eng, 20(1), pp.141-146.
Mohammadi, A. and et.al., 2020. Applying lean construction principles in road maintenance
planning and scheduling. International Journal of Construction Management, pp.1-11.
Naqvi, S.A.A., and et.al., 2016. Productivity improvement of a manufacturing facility using
systematic layout planning. Cogent Engineering, 3(1), p.1207296.
Rüttimann, B.G. and Stöckli, M.T., 2016. Going beyond triviality: The Toyota production
system—lean manufacturing beyond Muda and Kaizen. Journal of Service Science and
Management, 9(02), p.140.
Rüttimann, B.G. and Stöckli, M.T., 2016. Going beyond triviality: The Toyota production
system—lean manufacturing beyond Muda and Kaizen. Journal of Service Science and
Management. 9(02). p.140.
Sjöberg, A. and Kamne, A., 2016. Improving a plant’s operations by applying lean
manufacturing on the material flow and layout design.
Soliman, M., 2017. A comprehensive review of manufacturing wastes: Toyota production
system lean principles. Emirates Journal for Engineering Research, 22(2), pp.1-10.
12
⊘ This is a preview!⊘
Do you want full access?
Subscribe today to unlock all pages.

Trusted by 1+ million students worldwide
1 out of 14