Operations and Project Management for Tesco: Comprehensive Report
VerifiedAdded on 2023/06/11
|13
|3979
|89
Report
AI Summary
This report provides a comprehensive analysis of operations and project management principles, using Tesco as a case study. Part 1 reviews and critiques Tesco's operations management, including the implementation of Six Sigma and Lean principles, and proposes a continuous improvement plan with recommendations for enhancing operational functions such as adopting a Just-in-Time approach. Part 2 examines the project lifecycle in the context of a Tesco case study focused on reducing staff movement during lunch breaks to promote healthy lifestyles and reduce absenteeism, critically evaluating the effectiveness of the project lifecycle through appropriate theories and models. The report aims to provide a thorough understanding of both operations and project management concepts within a real-world business context, highlighting opportunities for improvement and strategic alignment with organizational goals. Desklib provides access to this and other solved assignments for students.
Contribute Materials
Your contribution can guide someone’s learning journey. Share your
documents today.
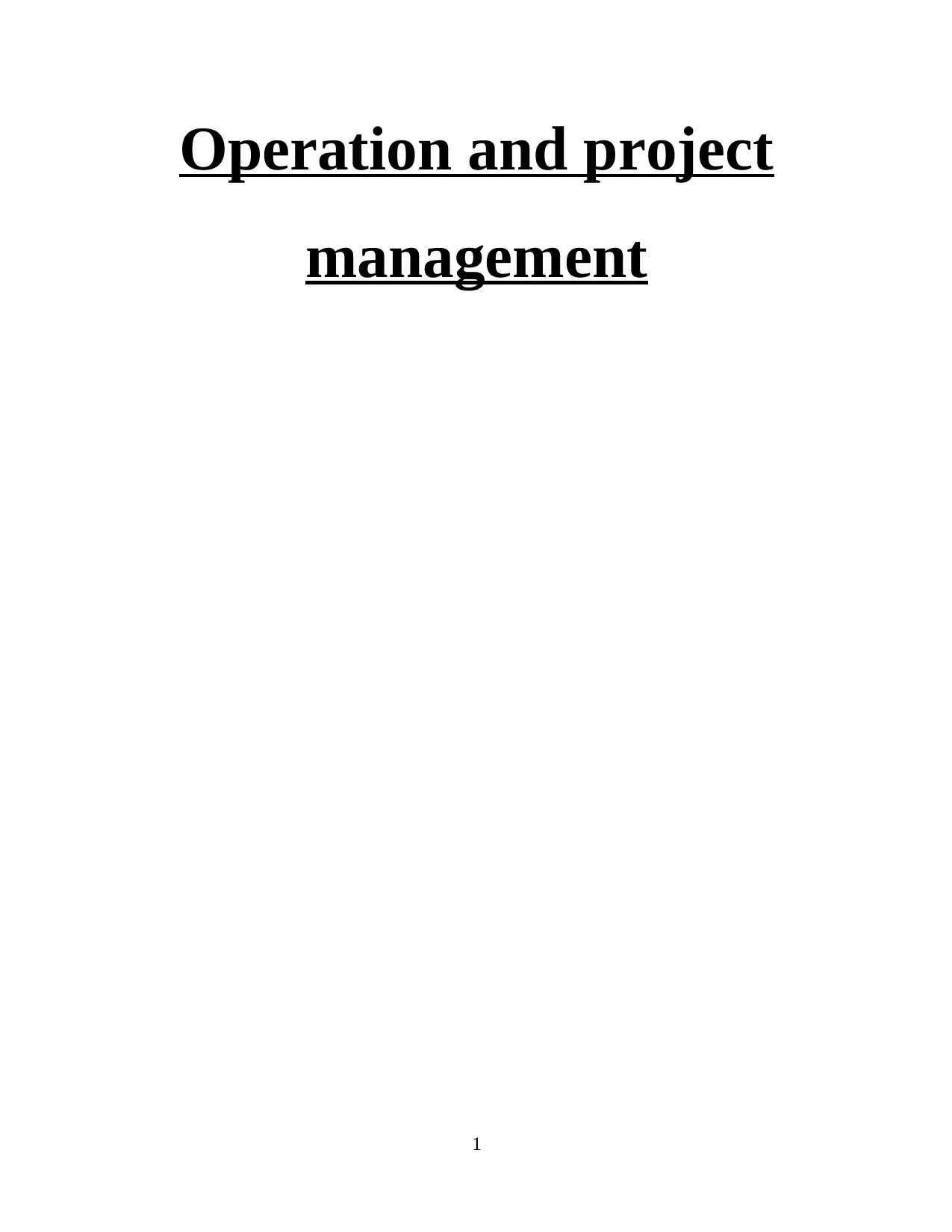
Operation and project
management
1
management
1
Secure Best Marks with AI Grader
Need help grading? Try our AI Grader for instant feedback on your assignments.
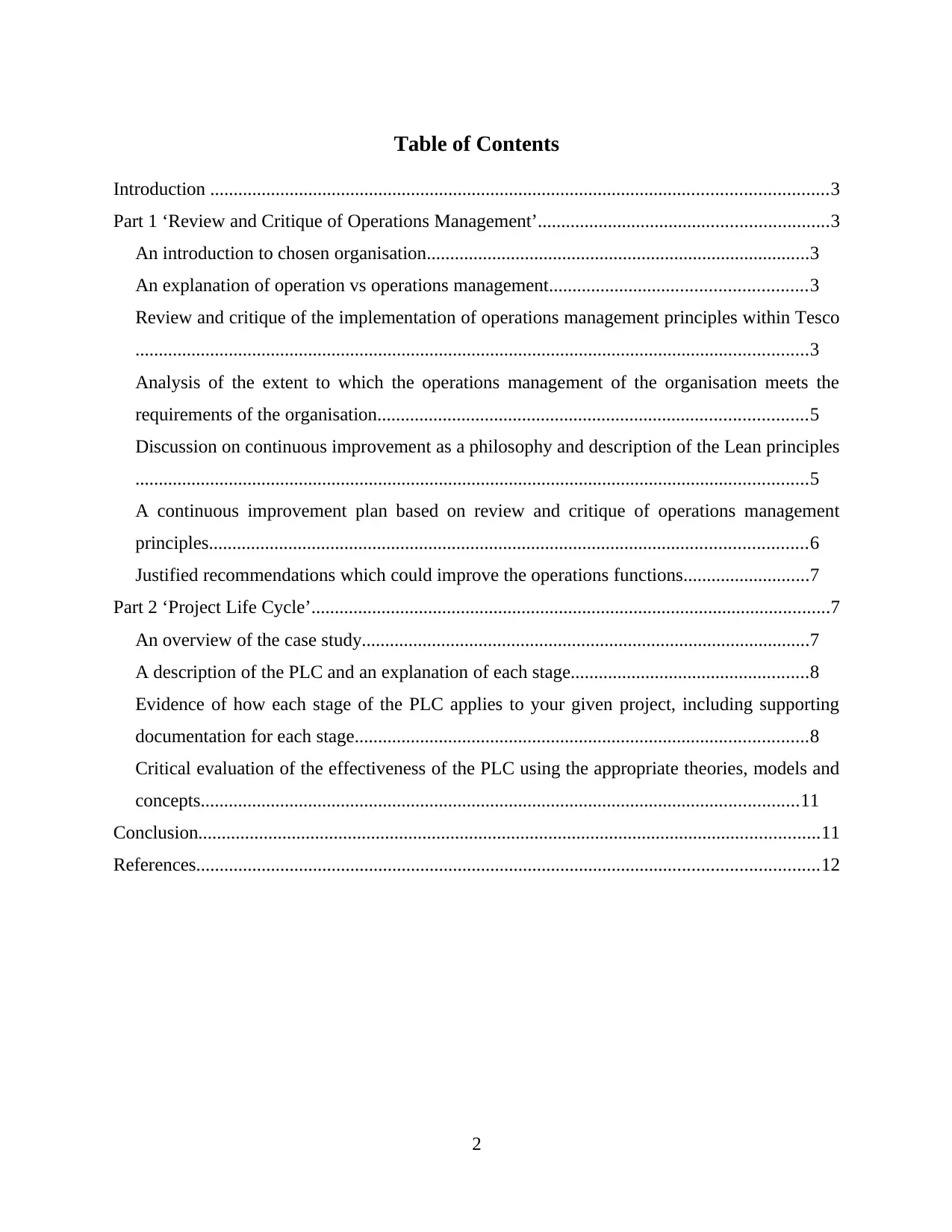
Table of Contents
Introduction ....................................................................................................................................3
Part 1 ‘Review and Critique of Operations Management’..............................................................3
An introduction to chosen organisation..................................................................................3
An explanation of operation vs operations management.......................................................3
Review and critique of the implementation of operations management principles within Tesco
................................................................................................................................................3
Analysis of the extent to which the operations management of the organisation meets the
requirements of the organisation............................................................................................5
Discussion on continuous improvement as a philosophy and description of the Lean principles
................................................................................................................................................5
A continuous improvement plan based on review and critique of operations management
principles................................................................................................................................6
Justified recommendations which could improve the operations functions...........................7
Part 2 ‘Project Life Cycle’...............................................................................................................7
An overview of the case study................................................................................................7
A description of the PLC and an explanation of each stage...................................................8
Evidence of how each stage of the PLC applies to your given project, including supporting
documentation for each stage.................................................................................................8
Critical evaluation of the effectiveness of the PLC using the appropriate theories, models and
concepts................................................................................................................................11
Conclusion.....................................................................................................................................11
References.....................................................................................................................................12
2
Introduction ....................................................................................................................................3
Part 1 ‘Review and Critique of Operations Management’..............................................................3
An introduction to chosen organisation..................................................................................3
An explanation of operation vs operations management.......................................................3
Review and critique of the implementation of operations management principles within Tesco
................................................................................................................................................3
Analysis of the extent to which the operations management of the organisation meets the
requirements of the organisation............................................................................................5
Discussion on continuous improvement as a philosophy and description of the Lean principles
................................................................................................................................................5
A continuous improvement plan based on review and critique of operations management
principles................................................................................................................................6
Justified recommendations which could improve the operations functions...........................7
Part 2 ‘Project Life Cycle’...............................................................................................................7
An overview of the case study................................................................................................7
A description of the PLC and an explanation of each stage...................................................8
Evidence of how each stage of the PLC applies to your given project, including supporting
documentation for each stage.................................................................................................8
Critical evaluation of the effectiveness of the PLC using the appropriate theories, models and
concepts................................................................................................................................11
Conclusion.....................................................................................................................................11
References.....................................................................................................................................12
2
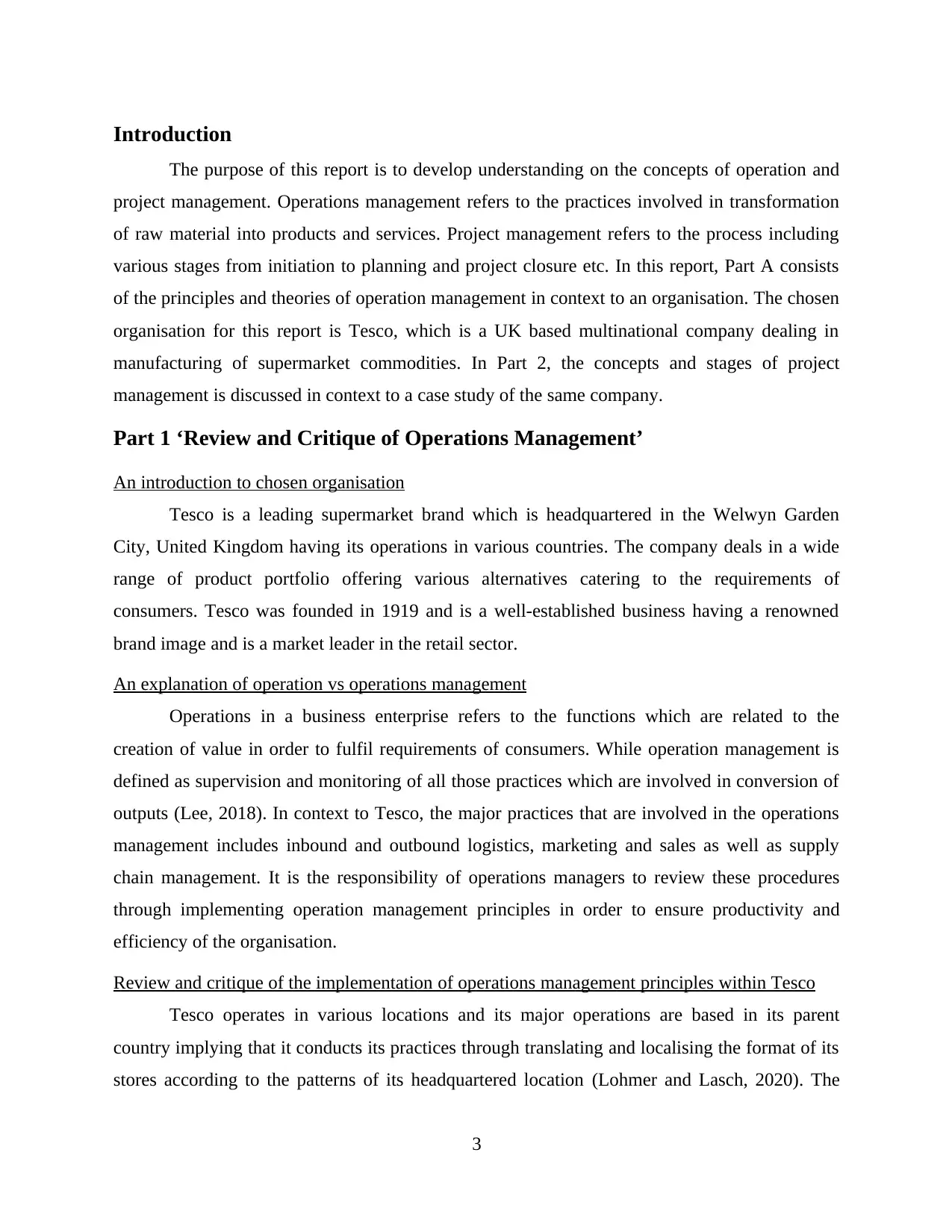
Introduction
The purpose of this report is to develop understanding on the concepts of operation and
project management. Operations management refers to the practices involved in transformation
of raw material into products and services. Project management refers to the process including
various stages from initiation to planning and project closure etc. In this report, Part A consists
of the principles and theories of operation management in context to an organisation. The chosen
organisation for this report is Tesco, which is a UK based multinational company dealing in
manufacturing of supermarket commodities. In Part 2, the concepts and stages of project
management is discussed in context to a case study of the same company.
Part 1 ‘Review and Critique of Operations Management’
An introduction to chosen organisation
Tesco is a leading supermarket brand which is headquartered in the Welwyn Garden
City, United Kingdom having its operations in various countries. The company deals in a wide
range of product portfolio offering various alternatives catering to the requirements of
consumers. Tesco was founded in 1919 and is a well-established business having a renowned
brand image and is a market leader in the retail sector.
An explanation of operation vs operations management
Operations in a business enterprise refers to the functions which are related to the
creation of value in order to fulfil requirements of consumers. While operation management is
defined as supervision and monitoring of all those practices which are involved in conversion of
outputs (Lee, 2018). In context to Tesco, the major practices that are involved in the operations
management includes inbound and outbound logistics, marketing and sales as well as supply
chain management. It is the responsibility of operations managers to review these procedures
through implementing operation management principles in order to ensure productivity and
efficiency of the organisation.
Review and critique of the implementation of operations management principles within Tesco
Tesco operates in various locations and its major operations are based in its parent
country implying that it conducts its practices through translating and localising the format of its
stores according to the patterns of its headquartered location (Lohmer and Lasch, 2020). The
3
The purpose of this report is to develop understanding on the concepts of operation and
project management. Operations management refers to the practices involved in transformation
of raw material into products and services. Project management refers to the process including
various stages from initiation to planning and project closure etc. In this report, Part A consists
of the principles and theories of operation management in context to an organisation. The chosen
organisation for this report is Tesco, which is a UK based multinational company dealing in
manufacturing of supermarket commodities. In Part 2, the concepts and stages of project
management is discussed in context to a case study of the same company.
Part 1 ‘Review and Critique of Operations Management’
An introduction to chosen organisation
Tesco is a leading supermarket brand which is headquartered in the Welwyn Garden
City, United Kingdom having its operations in various countries. The company deals in a wide
range of product portfolio offering various alternatives catering to the requirements of
consumers. Tesco was founded in 1919 and is a well-established business having a renowned
brand image and is a market leader in the retail sector.
An explanation of operation vs operations management
Operations in a business enterprise refers to the functions which are related to the
creation of value in order to fulfil requirements of consumers. While operation management is
defined as supervision and monitoring of all those practices which are involved in conversion of
outputs (Lee, 2018). In context to Tesco, the major practices that are involved in the operations
management includes inbound and outbound logistics, marketing and sales as well as supply
chain management. It is the responsibility of operations managers to review these procedures
through implementing operation management principles in order to ensure productivity and
efficiency of the organisation.
Review and critique of the implementation of operations management principles within Tesco
Tesco operates in various locations and its major operations are based in its parent
country implying that it conducts its practices through translating and localising the format of its
stores according to the patterns of its headquartered location (Lohmer and Lasch, 2020). The
3
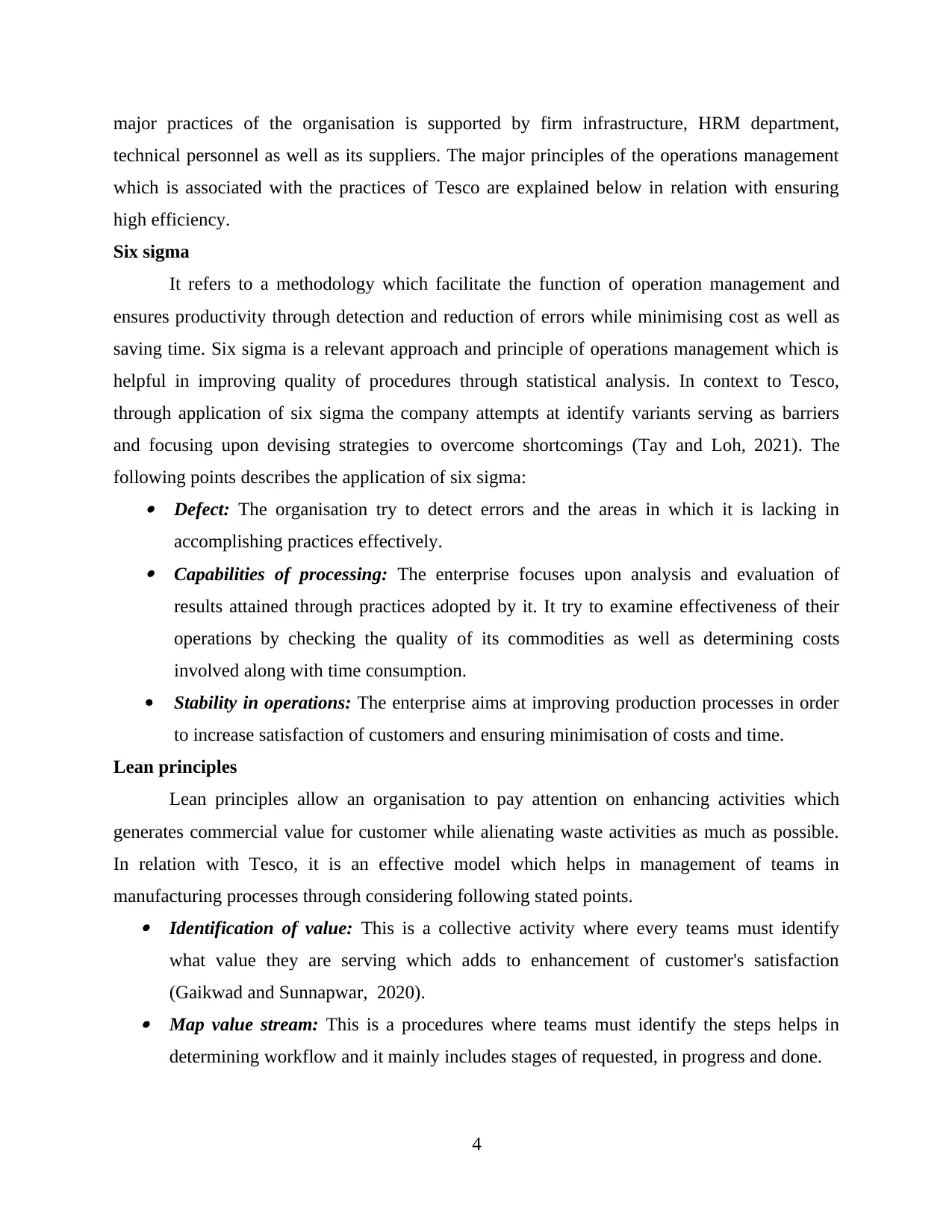
major practices of the organisation is supported by firm infrastructure, HRM department,
technical personnel as well as its suppliers. The major principles of the operations management
which is associated with the practices of Tesco are explained below in relation with ensuring
high efficiency.
Six sigma
It refers to a methodology which facilitate the function of operation management and
ensures productivity through detection and reduction of errors while minimising cost as well as
saving time. Six sigma is a relevant approach and principle of operations management which is
helpful in improving quality of procedures through statistical analysis. In context to Tesco,
through application of six sigma the company attempts at identify variants serving as barriers
and focusing upon devising strategies to overcome shortcomings (Tay and Loh, 2021). The
following points describes the application of six sigma: Defect: The organisation try to detect errors and the areas in which it is lacking in
accomplishing practices effectively. Capabilities of processing: The enterprise focuses upon analysis and evaluation of
results attained through practices adopted by it. It try to examine effectiveness of their
operations by checking the quality of its commodities as well as determining costs
involved along with time consumption.
Stability in operations: The enterprise aims at improving production processes in order
to increase satisfaction of customers and ensuring minimisation of costs and time.
Lean principles
Lean principles allow an organisation to pay attention on enhancing activities which
generates commercial value for customer while alienating waste activities as much as possible.
In relation with Tesco, it is an effective model which helps in management of teams in
manufacturing processes through considering following stated points. Identification of value: This is a collective activity where every teams must identify
what value they are serving which adds to enhancement of customer's satisfaction
(Gaikwad and Sunnapwar, 2020). Map value stream: This is a procedures where teams must identify the steps helps in
determining workflow and it mainly includes stages of requested, in progress and done.
4
technical personnel as well as its suppliers. The major principles of the operations management
which is associated with the practices of Tesco are explained below in relation with ensuring
high efficiency.
Six sigma
It refers to a methodology which facilitate the function of operation management and
ensures productivity through detection and reduction of errors while minimising cost as well as
saving time. Six sigma is a relevant approach and principle of operations management which is
helpful in improving quality of procedures through statistical analysis. In context to Tesco,
through application of six sigma the company attempts at identify variants serving as barriers
and focusing upon devising strategies to overcome shortcomings (Tay and Loh, 2021). The
following points describes the application of six sigma: Defect: The organisation try to detect errors and the areas in which it is lacking in
accomplishing practices effectively. Capabilities of processing: The enterprise focuses upon analysis and evaluation of
results attained through practices adopted by it. It try to examine effectiveness of their
operations by checking the quality of its commodities as well as determining costs
involved along with time consumption.
Stability in operations: The enterprise aims at improving production processes in order
to increase satisfaction of customers and ensuring minimisation of costs and time.
Lean principles
Lean principles allow an organisation to pay attention on enhancing activities which
generates commercial value for customer while alienating waste activities as much as possible.
In relation with Tesco, it is an effective model which helps in management of teams in
manufacturing processes through considering following stated points. Identification of value: This is a collective activity where every teams must identify
what value they are serving which adds to enhancement of customer's satisfaction
(Gaikwad and Sunnapwar, 2020). Map value stream: This is a procedures where teams must identify the steps helps in
determining workflow and it mainly includes stages of requested, in progress and done.
4
Secure Best Marks with AI Grader
Need help grading? Try our AI Grader for instant feedback on your assignments.
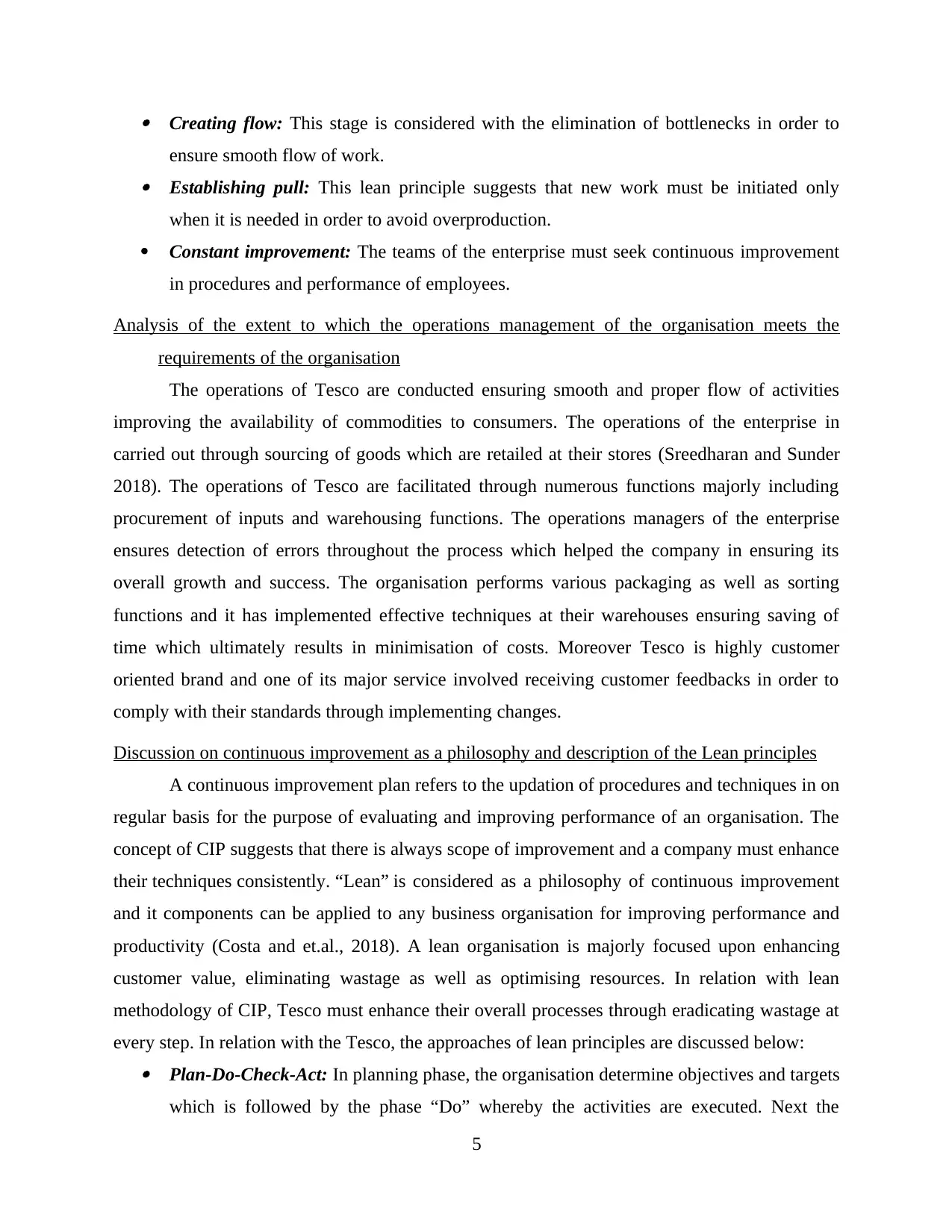
Creating flow: This stage is considered with the elimination of bottlenecks in order to
ensure smooth flow of work. Establishing pull: This lean principle suggests that new work must be initiated only
when it is needed in order to avoid overproduction.
Constant improvement: The teams of the enterprise must seek continuous improvement
in procedures and performance of employees.
Analysis of the extent to which the operations management of the organisation meets the
requirements of the organisation
The operations of Tesco are conducted ensuring smooth and proper flow of activities
improving the availability of commodities to consumers. The operations of the enterprise in
carried out through sourcing of goods which are retailed at their stores (Sreedharan and Sunder
2018). The operations of Tesco are facilitated through numerous functions majorly including
procurement of inputs and warehousing functions. The operations managers of the enterprise
ensures detection of errors throughout the process which helped the company in ensuring its
overall growth and success. The organisation performs various packaging as well as sorting
functions and it has implemented effective techniques at their warehouses ensuring saving of
time which ultimately results in minimisation of costs. Moreover Tesco is highly customer
oriented brand and one of its major service involved receiving customer feedbacks in order to
comply with their standards through implementing changes.
Discussion on continuous improvement as a philosophy and description of the Lean principles
A continuous improvement plan refers to the updation of procedures and techniques in on
regular basis for the purpose of evaluating and improving performance of an organisation. The
concept of CIP suggests that there is always scope of improvement and a company must enhance
their techniques consistently. “Lean” is considered as a philosophy of continuous improvement
and it components can be applied to any business organisation for improving performance and
productivity (Costa and et.al., 2018). A lean organisation is majorly focused upon enhancing
customer value, eliminating wastage as well as optimising resources. In relation with lean
methodology of CIP, Tesco must enhance their overall processes through eradicating wastage at
every step. In relation with the Tesco, the approaches of lean principles are discussed below: Plan-Do-Check-Act: In planning phase, the organisation determine objectives and targets
which is followed by the phase “Do” whereby the activities are executed. Next the
5
ensure smooth flow of work. Establishing pull: This lean principle suggests that new work must be initiated only
when it is needed in order to avoid overproduction.
Constant improvement: The teams of the enterprise must seek continuous improvement
in procedures and performance of employees.
Analysis of the extent to which the operations management of the organisation meets the
requirements of the organisation
The operations of Tesco are conducted ensuring smooth and proper flow of activities
improving the availability of commodities to consumers. The operations of the enterprise in
carried out through sourcing of goods which are retailed at their stores (Sreedharan and Sunder
2018). The operations of Tesco are facilitated through numerous functions majorly including
procurement of inputs and warehousing functions. The operations managers of the enterprise
ensures detection of errors throughout the process which helped the company in ensuring its
overall growth and success. The organisation performs various packaging as well as sorting
functions and it has implemented effective techniques at their warehouses ensuring saving of
time which ultimately results in minimisation of costs. Moreover Tesco is highly customer
oriented brand and one of its major service involved receiving customer feedbacks in order to
comply with their standards through implementing changes.
Discussion on continuous improvement as a philosophy and description of the Lean principles
A continuous improvement plan refers to the updation of procedures and techniques in on
regular basis for the purpose of evaluating and improving performance of an organisation. The
concept of CIP suggests that there is always scope of improvement and a company must enhance
their techniques consistently. “Lean” is considered as a philosophy of continuous improvement
and it components can be applied to any business organisation for improving performance and
productivity (Costa and et.al., 2018). A lean organisation is majorly focused upon enhancing
customer value, eliminating wastage as well as optimising resources. In relation with lean
methodology of CIP, Tesco must enhance their overall processes through eradicating wastage at
every step. In relation with the Tesco, the approaches of lean principles are discussed below: Plan-Do-Check-Act: In planning phase, the organisation determine objectives and targets
which is followed by the phase “Do” whereby the activities are executed. Next the
5
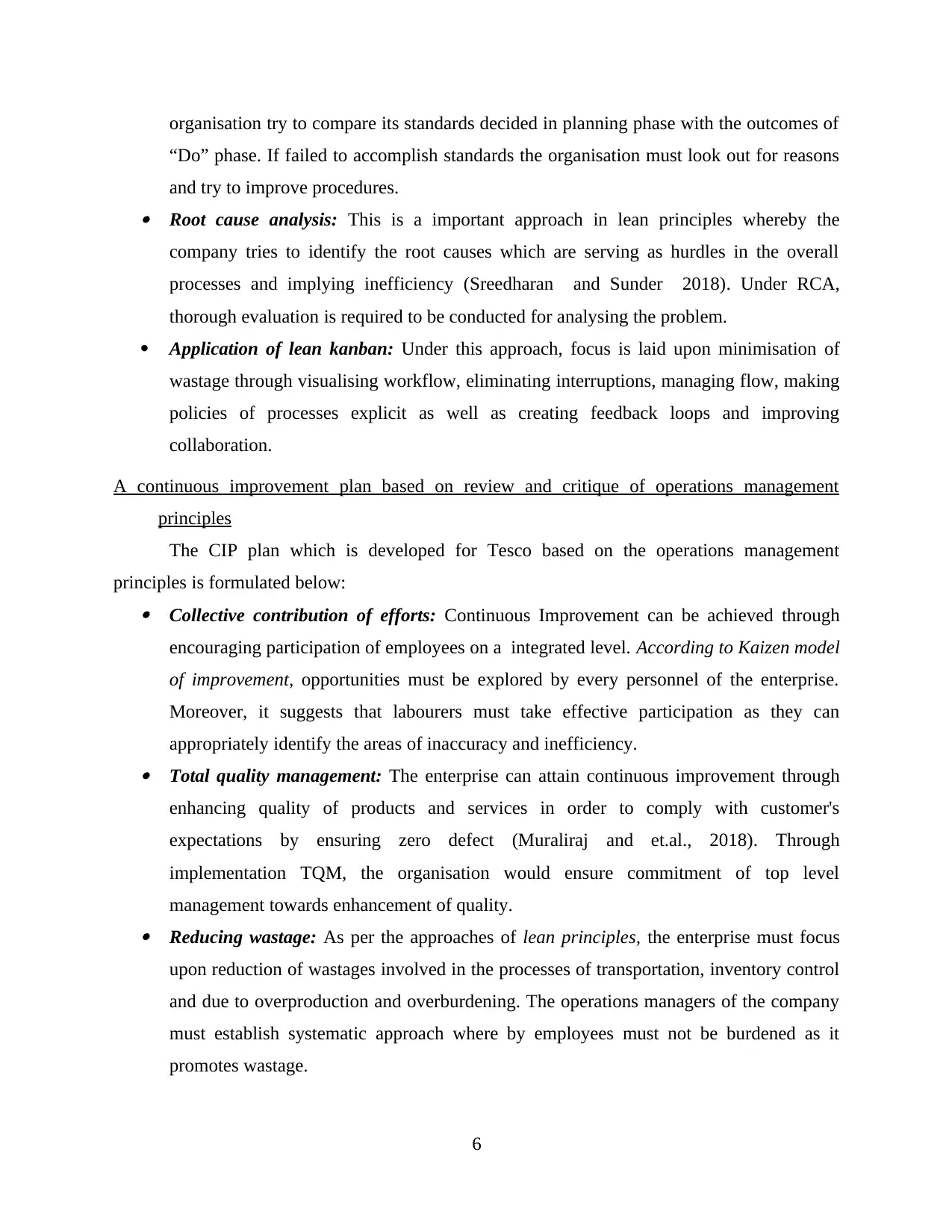
organisation try to compare its standards decided in planning phase with the outcomes of
“Do” phase. If failed to accomplish standards the organisation must look out for reasons
and try to improve procedures. Root cause analysis: This is a important approach in lean principles whereby the
company tries to identify the root causes which are serving as hurdles in the overall
processes and implying inefficiency (Sreedharan and Sunder 2018). Under RCA,
thorough evaluation is required to be conducted for analysing the problem.
Application of lean kanban: Under this approach, focus is laid upon minimisation of
wastage through visualising workflow, eliminating interruptions, managing flow, making
policies of processes explicit as well as creating feedback loops and improving
collaboration.
A continuous improvement plan based on review and critique of operations management
principles
The CIP plan which is developed for Tesco based on the operations management
principles is formulated below: Collective contribution of efforts: Continuous Improvement can be achieved through
encouraging participation of employees on a integrated level. According to Kaizen model
of improvement, opportunities must be explored by every personnel of the enterprise.
Moreover, it suggests that labourers must take effective participation as they can
appropriately identify the areas of inaccuracy and inefficiency. Total quality management: The enterprise can attain continuous improvement through
enhancing quality of products and services in order to comply with customer's
expectations by ensuring zero defect (Muraliraj and et.al., 2018). Through
implementation TQM, the organisation would ensure commitment of top level
management towards enhancement of quality. Reducing wastage: As per the approaches of lean principles, the enterprise must focus
upon reduction of wastages involved in the processes of transportation, inventory control
and due to overproduction and overburdening. The operations managers of the company
must establish systematic approach where by employees must not be burdened as it
promotes wastage.
6
“Do” phase. If failed to accomplish standards the organisation must look out for reasons
and try to improve procedures. Root cause analysis: This is a important approach in lean principles whereby the
company tries to identify the root causes which are serving as hurdles in the overall
processes and implying inefficiency (Sreedharan and Sunder 2018). Under RCA,
thorough evaluation is required to be conducted for analysing the problem.
Application of lean kanban: Under this approach, focus is laid upon minimisation of
wastage through visualising workflow, eliminating interruptions, managing flow, making
policies of processes explicit as well as creating feedback loops and improving
collaboration.
A continuous improvement plan based on review and critique of operations management
principles
The CIP plan which is developed for Tesco based on the operations management
principles is formulated below: Collective contribution of efforts: Continuous Improvement can be achieved through
encouraging participation of employees on a integrated level. According to Kaizen model
of improvement, opportunities must be explored by every personnel of the enterprise.
Moreover, it suggests that labourers must take effective participation as they can
appropriately identify the areas of inaccuracy and inefficiency. Total quality management: The enterprise can attain continuous improvement through
enhancing quality of products and services in order to comply with customer's
expectations by ensuring zero defect (Muraliraj and et.al., 2018). Through
implementation TQM, the organisation would ensure commitment of top level
management towards enhancement of quality. Reducing wastage: As per the approaches of lean principles, the enterprise must focus
upon reduction of wastages involved in the processes of transportation, inventory control
and due to overproduction and overburdening. The operations managers of the company
must establish systematic approach where by employees must not be burdened as it
promotes wastage.
6
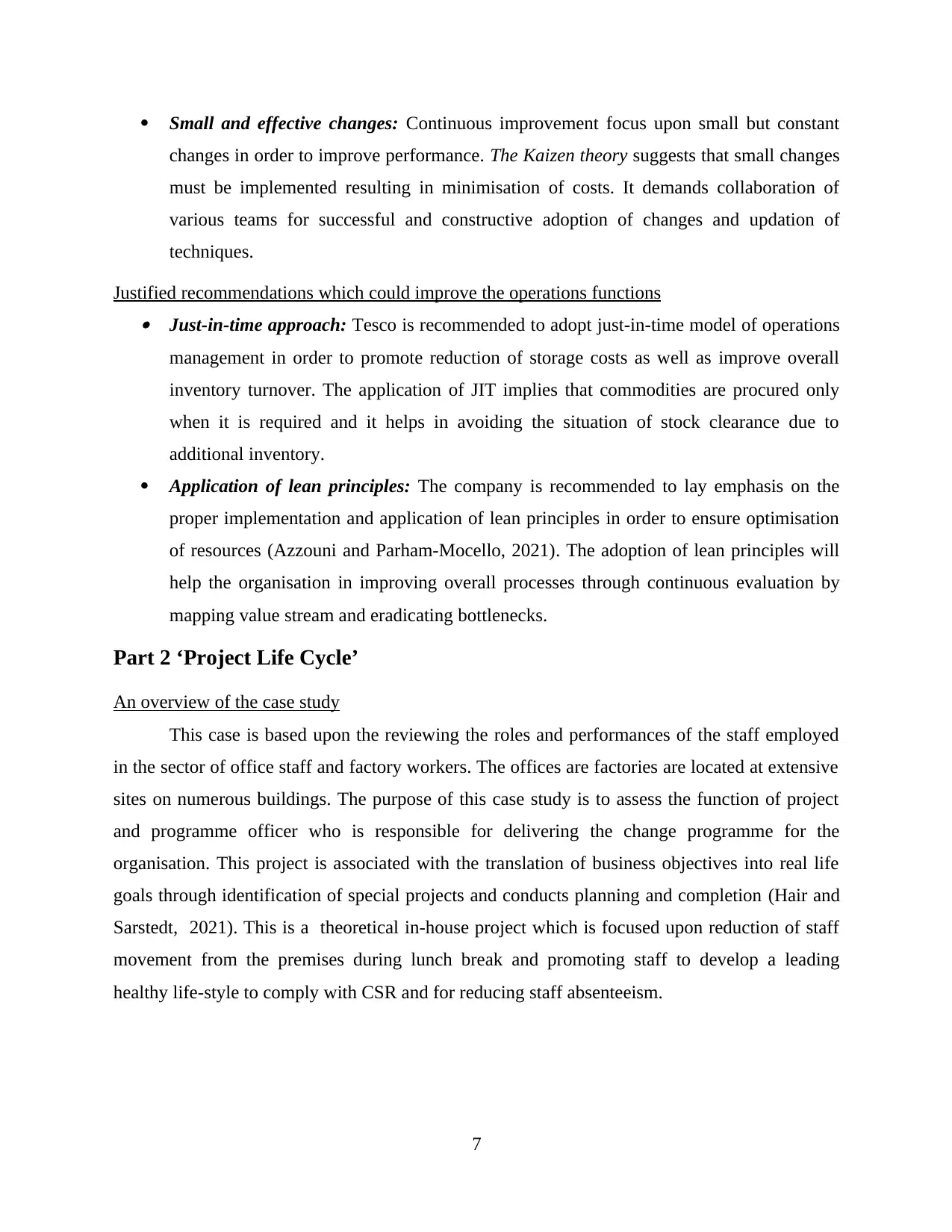
Small and effective changes: Continuous improvement focus upon small but constant
changes in order to improve performance. The Kaizen theory suggests that small changes
must be implemented resulting in minimisation of costs. It demands collaboration of
various teams for successful and constructive adoption of changes and updation of
techniques.
Justified recommendations which could improve the operations functions Just-in-time approach: Tesco is recommended to adopt just-in-time model of operations
management in order to promote reduction of storage costs as well as improve overall
inventory turnover. The application of JIT implies that commodities are procured only
when it is required and it helps in avoiding the situation of stock clearance due to
additional inventory.
Application of lean principles: The company is recommended to lay emphasis on the
proper implementation and application of lean principles in order to ensure optimisation
of resources (Azzouni and Parham-Mocello, 2021). The adoption of lean principles will
help the organisation in improving overall processes through continuous evaluation by
mapping value stream and eradicating bottlenecks.
Part 2 ‘Project Life Cycle’
An overview of the case study
This case is based upon the reviewing the roles and performances of the staff employed
in the sector of office staff and factory workers. The offices are factories are located at extensive
sites on numerous buildings. The purpose of this case study is to assess the function of project
and programme officer who is responsible for delivering the change programme for the
organisation. This project is associated with the translation of business objectives into real life
goals through identification of special projects and conducts planning and completion (Hair and
Sarstedt, 2021). This is a theoretical in-house project which is focused upon reduction of staff
movement from the premises during lunch break and promoting staff to develop a leading
healthy life-style to comply with CSR and for reducing staff absenteeism.
7
changes in order to improve performance. The Kaizen theory suggests that small changes
must be implemented resulting in minimisation of costs. It demands collaboration of
various teams for successful and constructive adoption of changes and updation of
techniques.
Justified recommendations which could improve the operations functions Just-in-time approach: Tesco is recommended to adopt just-in-time model of operations
management in order to promote reduction of storage costs as well as improve overall
inventory turnover. The application of JIT implies that commodities are procured only
when it is required and it helps in avoiding the situation of stock clearance due to
additional inventory.
Application of lean principles: The company is recommended to lay emphasis on the
proper implementation and application of lean principles in order to ensure optimisation
of resources (Azzouni and Parham-Mocello, 2021). The adoption of lean principles will
help the organisation in improving overall processes through continuous evaluation by
mapping value stream and eradicating bottlenecks.
Part 2 ‘Project Life Cycle’
An overview of the case study
This case is based upon the reviewing the roles and performances of the staff employed
in the sector of office staff and factory workers. The offices are factories are located at extensive
sites on numerous buildings. The purpose of this case study is to assess the function of project
and programme officer who is responsible for delivering the change programme for the
organisation. This project is associated with the translation of business objectives into real life
goals through identification of special projects and conducts planning and completion (Hair and
Sarstedt, 2021). This is a theoretical in-house project which is focused upon reduction of staff
movement from the premises during lunch break and promoting staff to develop a leading
healthy life-style to comply with CSR and for reducing staff absenteeism.
7
Paraphrase This Document
Need a fresh take? Get an instant paraphrase of this document with our AI Paraphraser
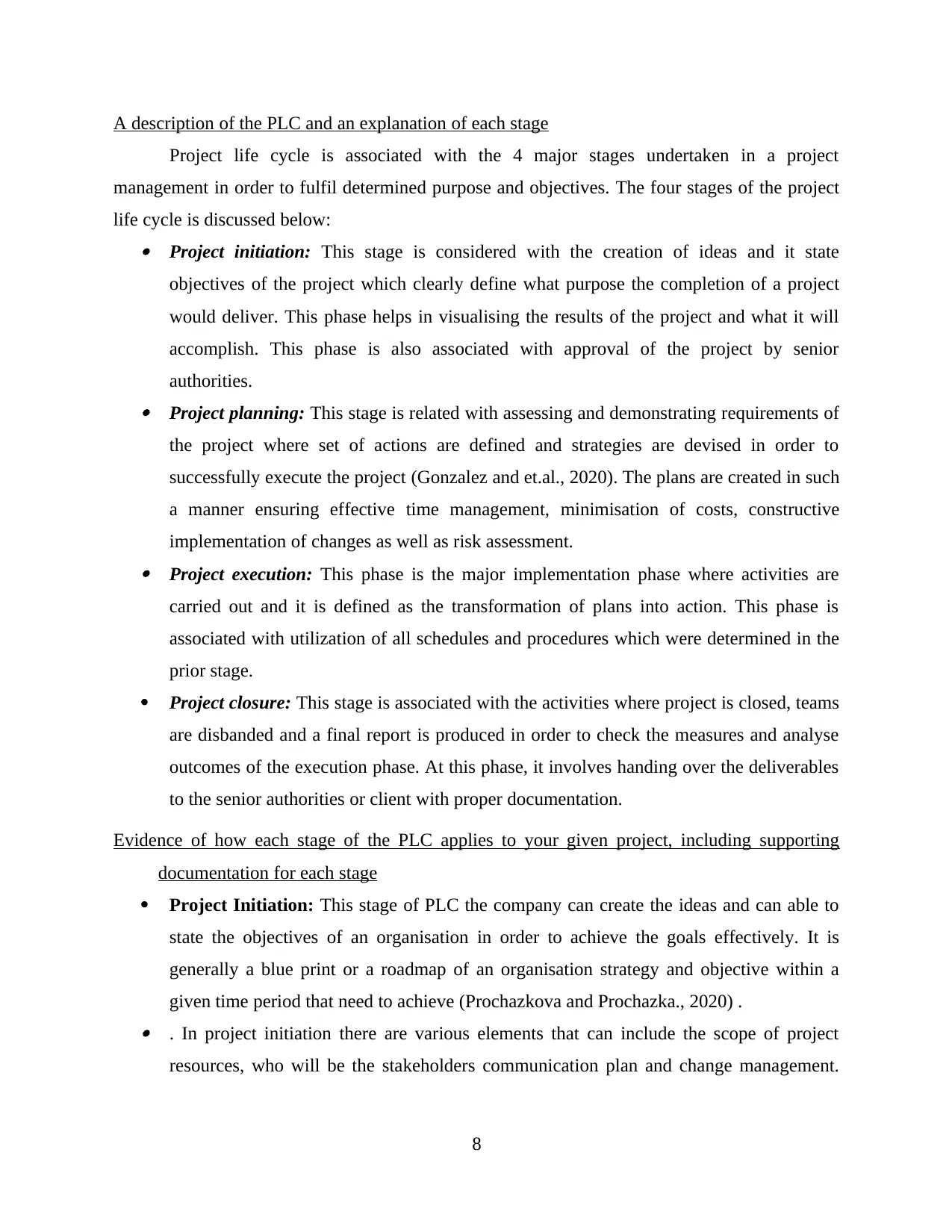
A description of the PLC and an explanation of each stage
Project life cycle is associated with the 4 major stages undertaken in a project
management in order to fulfil determined purpose and objectives. The four stages of the project
life cycle is discussed below: Project initiation: This stage is considered with the creation of ideas and it state
objectives of the project which clearly define what purpose the completion of a project
would deliver. This phase helps in visualising the results of the project and what it will
accomplish. This phase is also associated with approval of the project by senior
authorities. Project planning: This stage is related with assessing and demonstrating requirements of
the project where set of actions are defined and strategies are devised in order to
successfully execute the project (Gonzalez and et.al., 2020). The plans are created in such
a manner ensuring effective time management, minimisation of costs, constructive
implementation of changes as well as risk assessment. Project execution: This phase is the major implementation phase where activities are
carried out and it is defined as the transformation of plans into action. This phase is
associated with utilization of all schedules and procedures which were determined in the
prior stage.
Project closure: This stage is associated with the activities where project is closed, teams
are disbanded and a final report is produced in order to check the measures and analyse
outcomes of the execution phase. At this phase, it involves handing over the deliverables
to the senior authorities or client with proper documentation.
Evidence of how each stage of the PLC applies to your given project, including supporting
documentation for each stage
Project Initiation: This stage of PLC the company can create the ideas and can able to
state the objectives of an organisation in order to achieve the goals effectively. It is
generally a blue print or a roadmap of an organisation strategy and objective within a
given time period that need to achieve (Prochazkova and Prochazka., 2020) . . In project initiation there are various elements that can include the scope of project
resources, who will be the stakeholders communication plan and change management.
8
Project life cycle is associated with the 4 major stages undertaken in a project
management in order to fulfil determined purpose and objectives. The four stages of the project
life cycle is discussed below: Project initiation: This stage is considered with the creation of ideas and it state
objectives of the project which clearly define what purpose the completion of a project
would deliver. This phase helps in visualising the results of the project and what it will
accomplish. This phase is also associated with approval of the project by senior
authorities. Project planning: This stage is related with assessing and demonstrating requirements of
the project where set of actions are defined and strategies are devised in order to
successfully execute the project (Gonzalez and et.al., 2020). The plans are created in such
a manner ensuring effective time management, minimisation of costs, constructive
implementation of changes as well as risk assessment. Project execution: This phase is the major implementation phase where activities are
carried out and it is defined as the transformation of plans into action. This phase is
associated with utilization of all schedules and procedures which were determined in the
prior stage.
Project closure: This stage is associated with the activities where project is closed, teams
are disbanded and a final report is produced in order to check the measures and analyse
outcomes of the execution phase. At this phase, it involves handing over the deliverables
to the senior authorities or client with proper documentation.
Evidence of how each stage of the PLC applies to your given project, including supporting
documentation for each stage
Project Initiation: This stage of PLC the company can create the ideas and can able to
state the objectives of an organisation in order to achieve the goals effectively. It is
generally a blue print or a roadmap of an organisation strategy and objective within a
given time period that need to achieve (Prochazkova and Prochazka., 2020) . . In project initiation there are various elements that can include the scope of project
resources, who will be the stakeholders communication plan and change management.
8
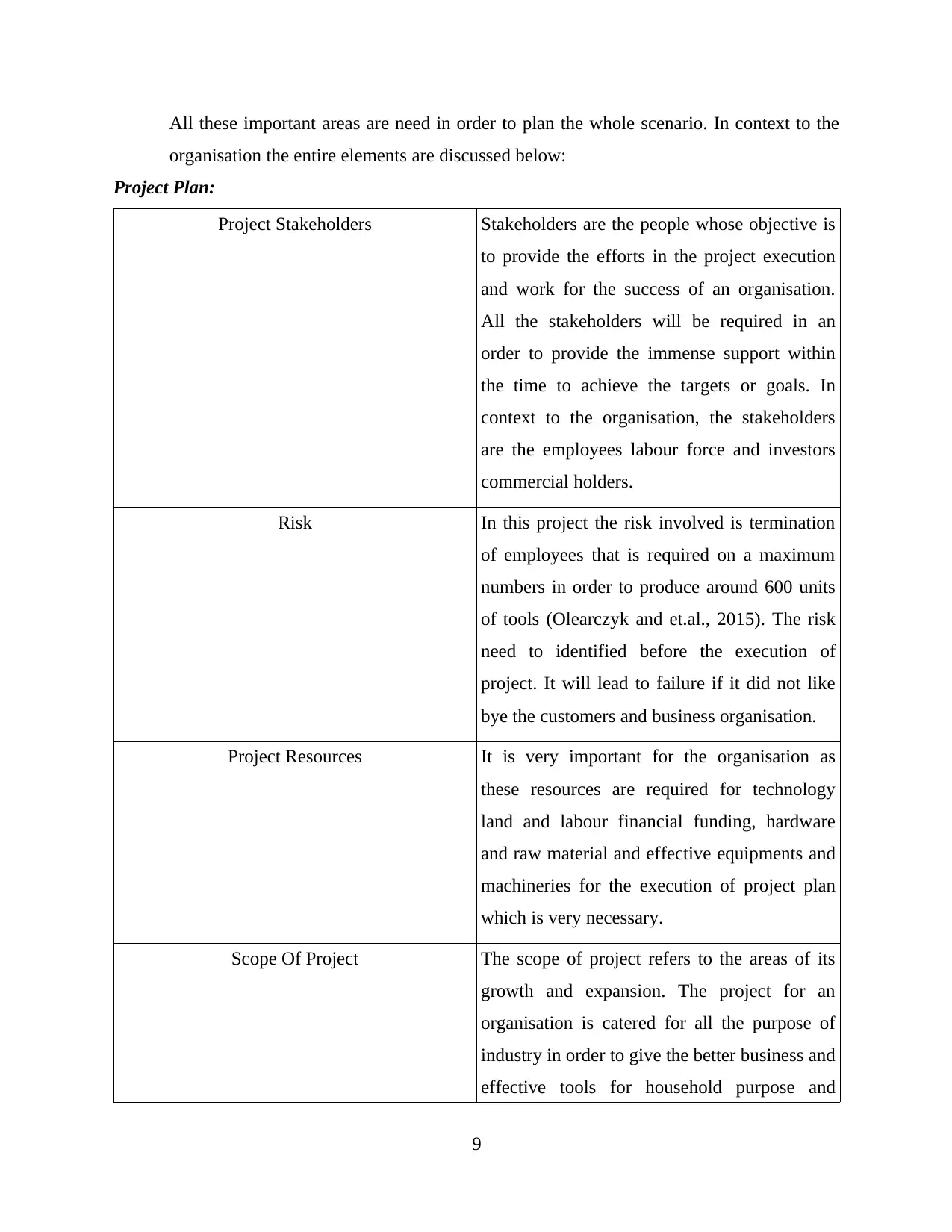
All these important areas are need in order to plan the whole scenario. In context to the
organisation the entire elements are discussed below:
Project Plan:
Project Stakeholders Stakeholders are the people whose objective is
to provide the efforts in the project execution
and work for the success of an organisation.
All the stakeholders will be required in an
order to provide the immense support within
the time to achieve the targets or goals. In
context to the organisation, the stakeholders
are the employees labour force and investors
commercial holders.
Risk In this project the risk involved is termination
of employees that is required on a maximum
numbers in order to produce around 600 units
of tools (Olearczyk and et.al., 2015). The risk
need to identified before the execution of
project. It will lead to failure if it did not like
bye the customers and business organisation.
Project Resources It is very important for the organisation as
these resources are required for technology
land and labour financial funding, hardware
and raw material and effective equipments and
machineries for the execution of project plan
which is very necessary.
Scope Of Project The scope of project refers to the areas of its
growth and expansion. The project for an
organisation is catered for all the purpose of
industry in order to give the better business and
effective tools for household purpose and
9
organisation the entire elements are discussed below:
Project Plan:
Project Stakeholders Stakeholders are the people whose objective is
to provide the efforts in the project execution
and work for the success of an organisation.
All the stakeholders will be required in an
order to provide the immense support within
the time to achieve the targets or goals. In
context to the organisation, the stakeholders
are the employees labour force and investors
commercial holders.
Risk In this project the risk involved is termination
of employees that is required on a maximum
numbers in order to produce around 600 units
of tools (Olearczyk and et.al., 2015). The risk
need to identified before the execution of
project. It will lead to failure if it did not like
bye the customers and business organisation.
Project Resources It is very important for the organisation as
these resources are required for technology
land and labour financial funding, hardware
and raw material and effective equipments and
machineries for the execution of project plan
which is very necessary.
Scope Of Project The scope of project refers to the areas of its
growth and expansion. The project for an
organisation is catered for all the purpose of
industry in order to give the better business and
effective tools for household purpose and
9
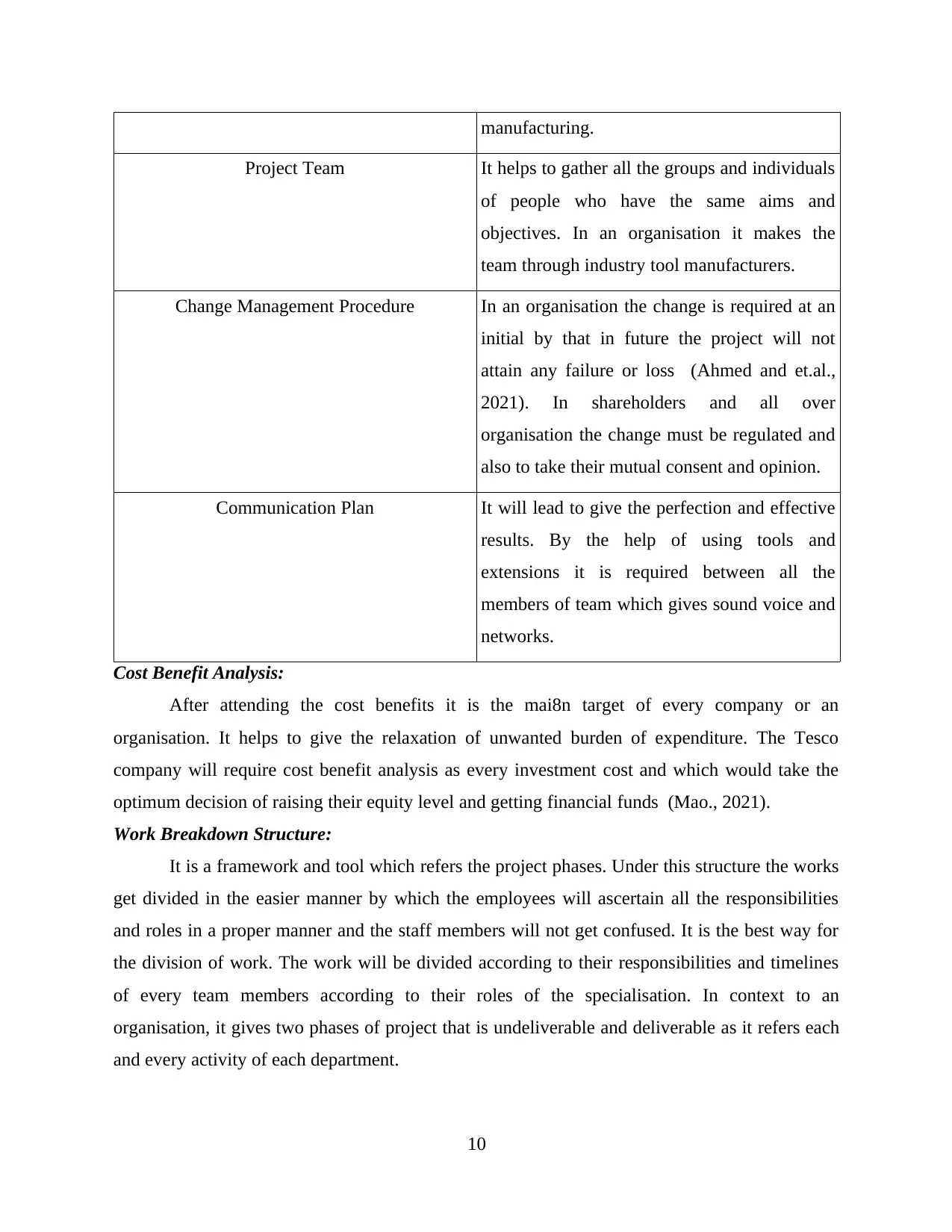
manufacturing.
Project Team It helps to gather all the groups and individuals
of people who have the same aims and
objectives. In an organisation it makes the
team through industry tool manufacturers.
Change Management Procedure In an organisation the change is required at an
initial by that in future the project will not
attain any failure or loss (Ahmed and et.al.,
2021). In shareholders and all over
organisation the change must be regulated and
also to take their mutual consent and opinion.
Communication Plan It will lead to give the perfection and effective
results. By the help of using tools and
extensions it is required between all the
members of team which gives sound voice and
networks.
Cost Benefit Analysis:
After attending the cost benefits it is the mai8n target of every company or an
organisation. It helps to give the relaxation of unwanted burden of expenditure. The Tesco
company will require cost benefit analysis as every investment cost and which would take the
optimum decision of raising their equity level and getting financial funds (Mao., 2021).
Work Breakdown Structure:
It is a framework and tool which refers the project phases. Under this structure the works
get divided in the easier manner by which the employees will ascertain all the responsibilities
and roles in a proper manner and the staff members will not get confused. It is the best way for
the division of work. The work will be divided according to their responsibilities and timelines
of every team members according to their roles of the specialisation. In context to an
organisation, it gives two phases of project that is undeliverable and deliverable as it refers each
and every activity of each department.
10
Project Team It helps to gather all the groups and individuals
of people who have the same aims and
objectives. In an organisation it makes the
team through industry tool manufacturers.
Change Management Procedure In an organisation the change is required at an
initial by that in future the project will not
attain any failure or loss (Ahmed and et.al.,
2021). In shareholders and all over
organisation the change must be regulated and
also to take their mutual consent and opinion.
Communication Plan It will lead to give the perfection and effective
results. By the help of using tools and
extensions it is required between all the
members of team which gives sound voice and
networks.
Cost Benefit Analysis:
After attending the cost benefits it is the mai8n target of every company or an
organisation. It helps to give the relaxation of unwanted burden of expenditure. The Tesco
company will require cost benefit analysis as every investment cost and which would take the
optimum decision of raising their equity level and getting financial funds (Mao., 2021).
Work Breakdown Structure:
It is a framework and tool which refers the project phases. Under this structure the works
get divided in the easier manner by which the employees will ascertain all the responsibilities
and roles in a proper manner and the staff members will not get confused. It is the best way for
the division of work. The work will be divided according to their responsibilities and timelines
of every team members according to their roles of the specialisation. In context to an
organisation, it gives two phases of project that is undeliverable and deliverable as it refers each
and every activity of each department.
10
Secure Best Marks with AI Grader
Need help grading? Try our AI Grader for instant feedback on your assignments.
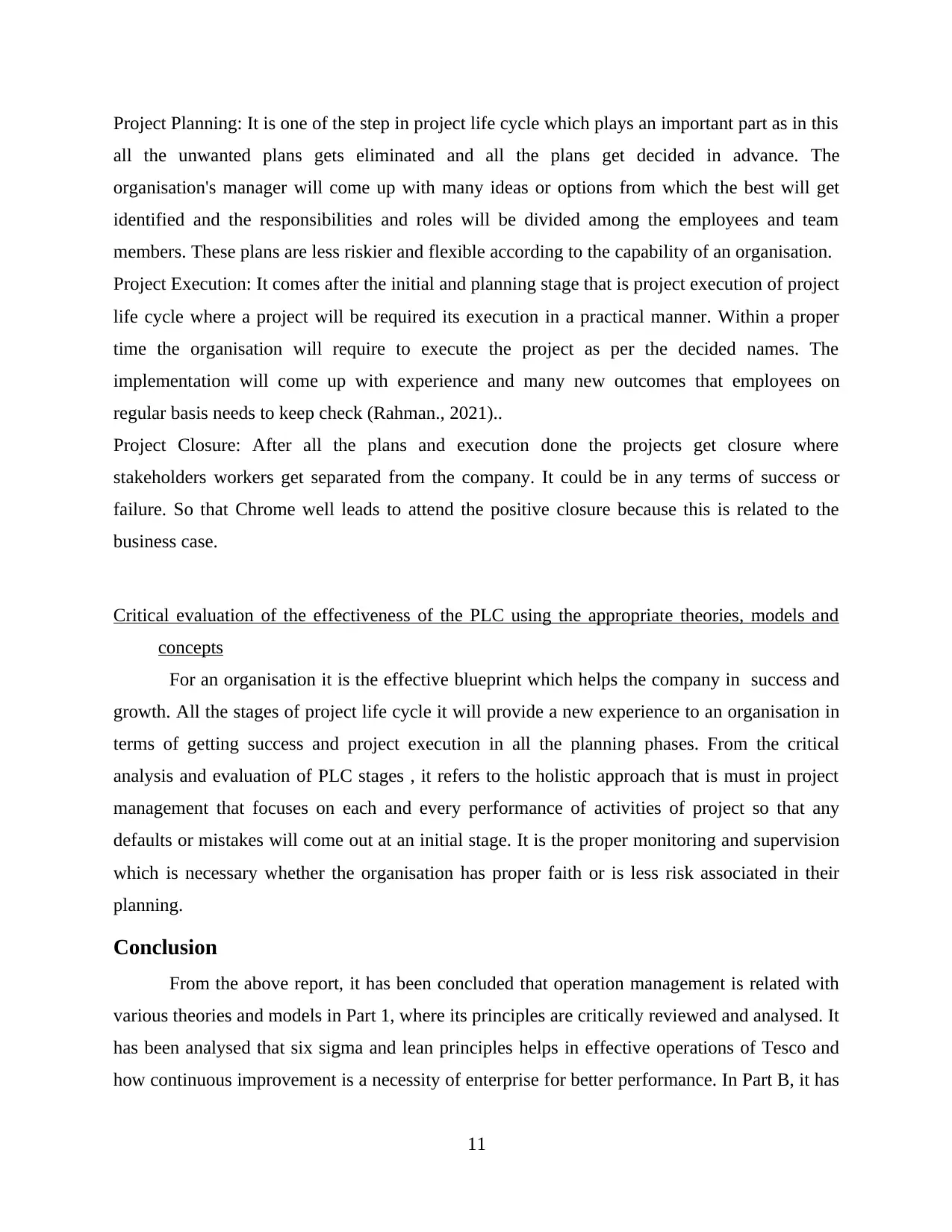
Project Planning: It is one of the step in project life cycle which plays an important part as in this
all the unwanted plans gets eliminated and all the plans get decided in advance. The
organisation's manager will come up with many ideas or options from which the best will get
identified and the responsibilities and roles will be divided among the employees and team
members. These plans are less riskier and flexible according to the capability of an organisation.
Project Execution: It comes after the initial and planning stage that is project execution of project
life cycle where a project will be required its execution in a practical manner. Within a proper
time the organisation will require to execute the project as per the decided names. The
implementation will come up with experience and many new outcomes that employees on
regular basis needs to keep check (Rahman., 2021)..
Project Closure: After all the plans and execution done the projects get closure where
stakeholders workers get separated from the company. It could be in any terms of success or
failure. So that Chrome well leads to attend the positive closure because this is related to the
business case.
Critical evaluation of the effectiveness of the PLC using the appropriate theories, models and
concepts
For an organisation it is the effective blueprint which helps the company in success and
growth. All the stages of project life cycle it will provide a new experience to an organisation in
terms of getting success and project execution in all the planning phases. From the critical
analysis and evaluation of PLC stages , it refers to the holistic approach that is must in project
management that focuses on each and every performance of activities of project so that any
defaults or mistakes will come out at an initial stage. It is the proper monitoring and supervision
which is necessary whether the organisation has proper faith or is less risk associated in their
planning.
Conclusion
From the above report, it has been concluded that operation management is related with
various theories and models in Part 1, where its principles are critically reviewed and analysed. It
has been analysed that six sigma and lean principles helps in effective operations of Tesco and
how continuous improvement is a necessity of enterprise for better performance. In Part B, it has
11
all the unwanted plans gets eliminated and all the plans get decided in advance. The
organisation's manager will come up with many ideas or options from which the best will get
identified and the responsibilities and roles will be divided among the employees and team
members. These plans are less riskier and flexible according to the capability of an organisation.
Project Execution: It comes after the initial and planning stage that is project execution of project
life cycle where a project will be required its execution in a practical manner. Within a proper
time the organisation will require to execute the project as per the decided names. The
implementation will come up with experience and many new outcomes that employees on
regular basis needs to keep check (Rahman., 2021)..
Project Closure: After all the plans and execution done the projects get closure where
stakeholders workers get separated from the company. It could be in any terms of success or
failure. So that Chrome well leads to attend the positive closure because this is related to the
business case.
Critical evaluation of the effectiveness of the PLC using the appropriate theories, models and
concepts
For an organisation it is the effective blueprint which helps the company in success and
growth. All the stages of project life cycle it will provide a new experience to an organisation in
terms of getting success and project execution in all the planning phases. From the critical
analysis and evaluation of PLC stages , it refers to the holistic approach that is must in project
management that focuses on each and every performance of activities of project so that any
defaults or mistakes will come out at an initial stage. It is the proper monitoring and supervision
which is necessary whether the organisation has proper faith or is less risk associated in their
planning.
Conclusion
From the above report, it has been concluded that operation management is related with
various theories and models in Part 1, where its principles are critically reviewed and analysed. It
has been analysed that six sigma and lean principles helps in effective operations of Tesco and
how continuous improvement is a necessity of enterprise for better performance. In Part B, it has
11
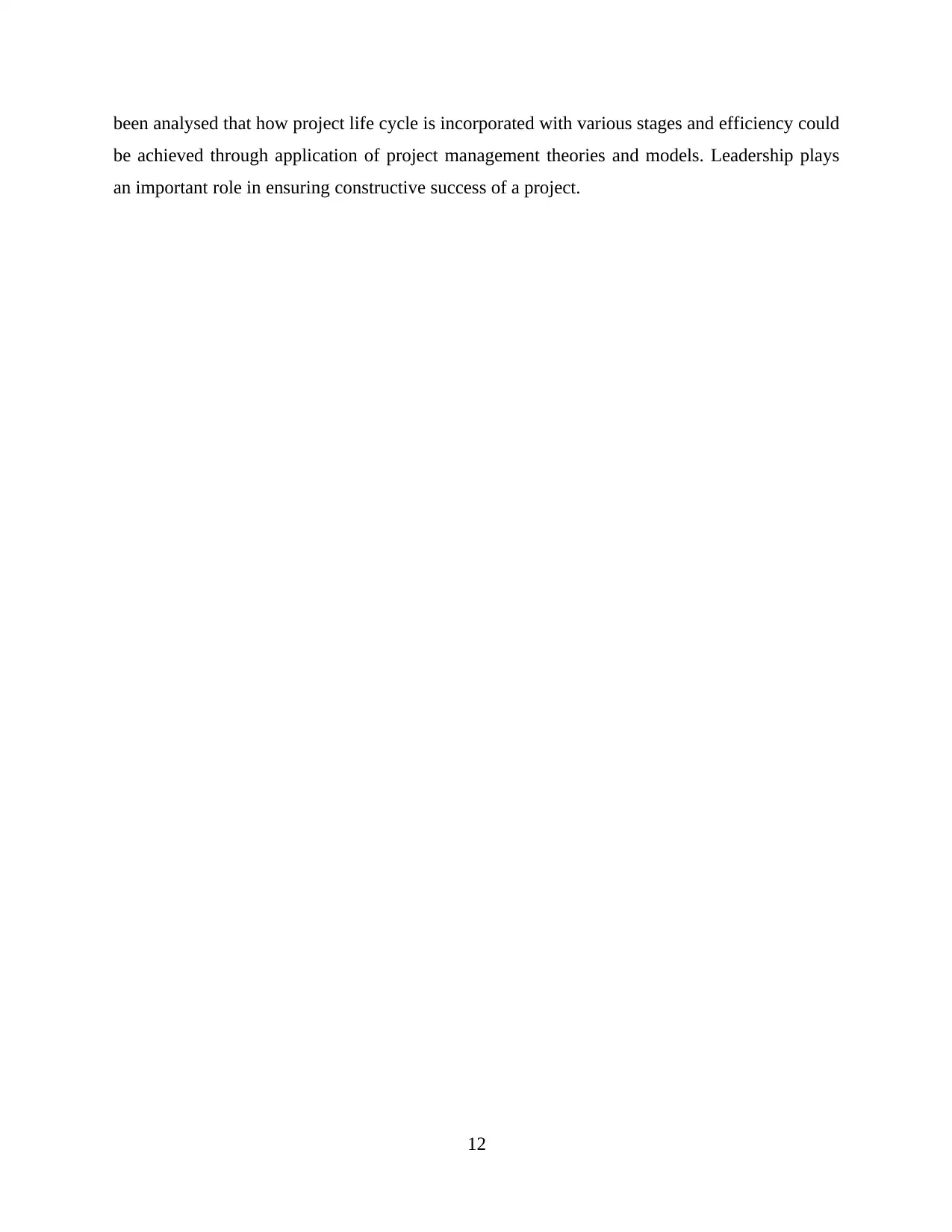
been analysed that how project life cycle is incorporated with various stages and efficiency could
be achieved through application of project management theories and models. Leadership plays
an important role in ensuring constructive success of a project.
12
be achieved through application of project management theories and models. Leadership plays
an important role in ensuring constructive success of a project.
12

References
Ahmed and et.al., 2021. Reducing completion time and optimizing resource use of resource-
constrained construction operation by means of simulation modeling. International
Journal of Construction Management, 21(4), pp.404-415.
Azzouni, A. and Parham-Mocello, J., 2021, October. A Method for Evaluating a Computing
Program's Continuous Improvement Plan. In 2021 IEEE Frontiers in Education
Conference (FIE) (pp. 1-4). IEEE.
Costa, L.B.M. and et.al., 2018. Lean, six sigma and lean six sigma in the food industry: A
systematic literature review. Trends in Food Science & Technology, 82, pp.122-133.
Gaikwad, L. and Sunnapwar, V., 2020. An integrated Lean, Green and Six Sigma strategies: A
systematic literature review and directions for future research. The TQM Journal.
Gonzalez, A.G. and et.al., 2020. CSP Quasi-Dynamic Performance Model Development for All
Project Life Cycle Stages and Considering Operation Modes. Validation Using One Year
Data. Energies, 14(1), pp.1-22.
Hair, J.F. and Sarstedt, M., 2021. Explanation plus prediction—The logical focus of project
management research. Project Management Journal, 52(4), pp.319-322.
Lee, C.K.H., 2018. A review of applications of genetic algorithms in operations
management. Engineering Applications of Artificial Intelligence, 76, pp.1-12.
Lohmer, J. and Lasch, R., 2020. Blockchain in operations management and manufacturing:
Potential and barriers. Computers & Industrial Engineering, 149, p.106789.
Mao, Q., 2021. Risk management of project information system operation and maintenance
based on Cloud Computing. International Journal of System Assurance Engineering and
Management, pp.1-12.
Muraliraj, J. and et.al., 2018. Annotated methodological review of lean six sigma. International
Journal of Lean Six Sigma.
Olearczyk and et.al., 2015. Intelligent crane management algorithm for construction operation
(iCrane). In ISARC. Proceedings of the International Symposium on Automation and
Robotics in Construction (Vol. 32, p. 1). IAARC Publications.
Prochazkova, D. and Prochazka, J., 2020. Tools for Risk Management of Technical Facilities
Operation. European Journal of Engineering and Technology Research, 5(4), pp.494-
500.
Rahman, H.Z., Operation Maintenance Contract Scheme in Railway Infrastructure Project.
Sreedharan V, R. and Sunder M, V., 2018. A novel approach to lean six sigma project
management: a conceptual framework and empirical application. Production Planning &
Control, 29(11), pp.895-907.
Sreedharan V, R. and Sunder M, V., 2018. Critical success factors of TQM, Six Sigma, Lean
and Lean Six Sigma: A literature review and key findings. Benchmarking: An
International Journal, 25(9), pp.3479-3504.
Tay, H.L. and Loh, H.S., 2021. Digital transformations and supply chain management: a Lean
Six Sigma perspective. Journal of Asia Business Studies.
13
Ahmed and et.al., 2021. Reducing completion time and optimizing resource use of resource-
constrained construction operation by means of simulation modeling. International
Journal of Construction Management, 21(4), pp.404-415.
Azzouni, A. and Parham-Mocello, J., 2021, October. A Method for Evaluating a Computing
Program's Continuous Improvement Plan. In 2021 IEEE Frontiers in Education
Conference (FIE) (pp. 1-4). IEEE.
Costa, L.B.M. and et.al., 2018. Lean, six sigma and lean six sigma in the food industry: A
systematic literature review. Trends in Food Science & Technology, 82, pp.122-133.
Gaikwad, L. and Sunnapwar, V., 2020. An integrated Lean, Green and Six Sigma strategies: A
systematic literature review and directions for future research. The TQM Journal.
Gonzalez, A.G. and et.al., 2020. CSP Quasi-Dynamic Performance Model Development for All
Project Life Cycle Stages and Considering Operation Modes. Validation Using One Year
Data. Energies, 14(1), pp.1-22.
Hair, J.F. and Sarstedt, M., 2021. Explanation plus prediction—The logical focus of project
management research. Project Management Journal, 52(4), pp.319-322.
Lee, C.K.H., 2018. A review of applications of genetic algorithms in operations
management. Engineering Applications of Artificial Intelligence, 76, pp.1-12.
Lohmer, J. and Lasch, R., 2020. Blockchain in operations management and manufacturing:
Potential and barriers. Computers & Industrial Engineering, 149, p.106789.
Mao, Q., 2021. Risk management of project information system operation and maintenance
based on Cloud Computing. International Journal of System Assurance Engineering and
Management, pp.1-12.
Muraliraj, J. and et.al., 2018. Annotated methodological review of lean six sigma. International
Journal of Lean Six Sigma.
Olearczyk and et.al., 2015. Intelligent crane management algorithm for construction operation
(iCrane). In ISARC. Proceedings of the International Symposium on Automation and
Robotics in Construction (Vol. 32, p. 1). IAARC Publications.
Prochazkova, D. and Prochazka, J., 2020. Tools for Risk Management of Technical Facilities
Operation. European Journal of Engineering and Technology Research, 5(4), pp.494-
500.
Rahman, H.Z., Operation Maintenance Contract Scheme in Railway Infrastructure Project.
Sreedharan V, R. and Sunder M, V., 2018. A novel approach to lean six sigma project
management: a conceptual framework and empirical application. Production Planning &
Control, 29(11), pp.895-907.
Sreedharan V, R. and Sunder M, V., 2018. Critical success factors of TQM, Six Sigma, Lean
and Lean Six Sigma: A literature review and key findings. Benchmarking: An
International Journal, 25(9), pp.3479-3504.
Tay, H.L. and Loh, H.S., 2021. Digital transformations and supply chain management: a Lean
Six Sigma perspective. Journal of Asia Business Studies.
13
1 out of 13
Related Documents

Your All-in-One AI-Powered Toolkit for Academic Success.
+13062052269
info@desklib.com
Available 24*7 on WhatsApp / Email
Unlock your academic potential
© 2024 | Zucol Services PVT LTD | All rights reserved.