Comprehensive Report: Operations and Project Management at XYZ Company
VerifiedAdded on 2020/06/04
|18
|4943
|34
Report
AI Summary
This report provides a comprehensive analysis of operations and project management within XYZ Company, focusing on its expansion into the large-screen television market. It begins by outlining core operations management principles, including inventory, planning, and distribution. The report then delves into the application of Sig Sigma and Lean principles to improve operational efficiency and reduce waste. A significant portion is dedicated to continuous improvement, including the creation of a continuous improvement plan (CIP) and strategies for its effective implementation. The project life cycle for developing a new product, specifically a large-screen television, is examined in detail, including business cases, project plans, work breakdown structures, and Gantt charts. Finally, the report evaluates the effectiveness of the project life cycle, cost-saving techniques, quality assurance methods, and the applicability of different theories to both large and small-scale projects. The report concludes by emphasizing the importance of adapting to market changes and consumer satisfaction.
Contribute Materials
Your contribution can guide someone’s learning journey. Share your
documents today.
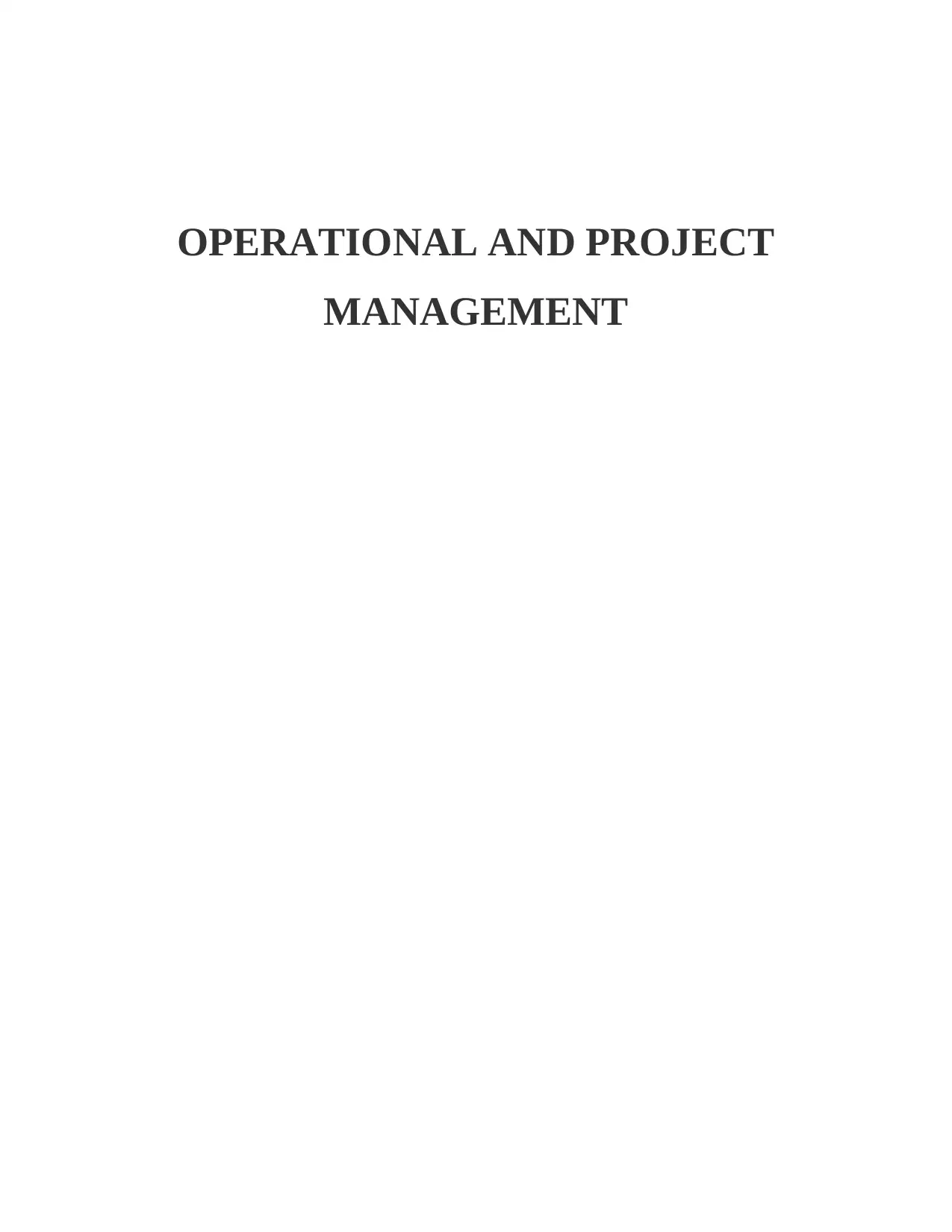
OPERATIONAL AND PROJECT
MANAGEMENT
MANAGEMENT
Secure Best Marks with AI Grader
Need help grading? Try our AI Grader for instant feedback on your assignments.
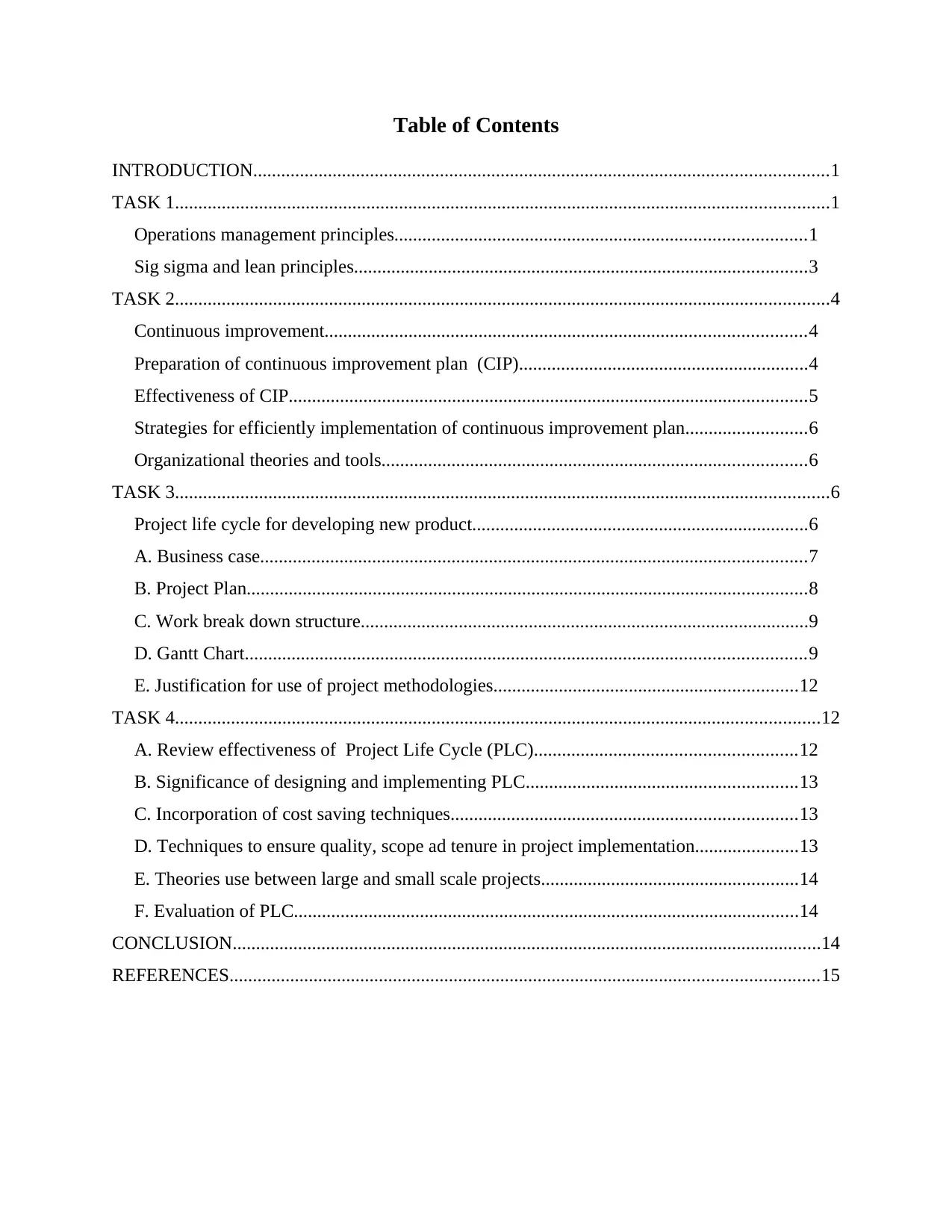
Table of Contents
INTRODUCTION...........................................................................................................................1
TASK 1............................................................................................................................................1
Operations management principles........................................................................................1
Sig sigma and lean principles.................................................................................................3
TASK 2............................................................................................................................................4
Continuous improvement.......................................................................................................4
Preparation of continuous improvement plan (CIP)..............................................................4
Effectiveness of CIP...............................................................................................................5
Strategies for efficiently implementation of continuous improvement plan..........................6
Organizational theories and tools...........................................................................................6
TASK 3............................................................................................................................................6
Project life cycle for developing new product........................................................................6
A. Business case.....................................................................................................................7
B. Project Plan........................................................................................................................8
C. Work break down structure................................................................................................9
D. Gantt Chart........................................................................................................................9
E. Justification for use of project methodologies.................................................................12
TASK 4..........................................................................................................................................12
A. Review effectiveness of Project Life Cycle (PLC)........................................................12
B. Significance of designing and implementing PLC..........................................................13
C. Incorporation of cost saving techniques..........................................................................13
D. Techniques to ensure quality, scope ad tenure in project implementation......................13
E. Theories use between large and small scale projects.......................................................14
F. Evaluation of PLC............................................................................................................14
CONCLUSION..............................................................................................................................14
REFERENCES..............................................................................................................................15
INTRODUCTION...........................................................................................................................1
TASK 1............................................................................................................................................1
Operations management principles........................................................................................1
Sig sigma and lean principles.................................................................................................3
TASK 2............................................................................................................................................4
Continuous improvement.......................................................................................................4
Preparation of continuous improvement plan (CIP)..............................................................4
Effectiveness of CIP...............................................................................................................5
Strategies for efficiently implementation of continuous improvement plan..........................6
Organizational theories and tools...........................................................................................6
TASK 3............................................................................................................................................6
Project life cycle for developing new product........................................................................6
A. Business case.....................................................................................................................7
B. Project Plan........................................................................................................................8
C. Work break down structure................................................................................................9
D. Gantt Chart........................................................................................................................9
E. Justification for use of project methodologies.................................................................12
TASK 4..........................................................................................................................................12
A. Review effectiveness of Project Life Cycle (PLC)........................................................12
B. Significance of designing and implementing PLC..........................................................13
C. Incorporation of cost saving techniques..........................................................................13
D. Techniques to ensure quality, scope ad tenure in project implementation......................13
E. Theories use between large and small scale projects.......................................................14
F. Evaluation of PLC............................................................................................................14
CONCLUSION..............................................................................................................................14
REFERENCES..............................................................................................................................15
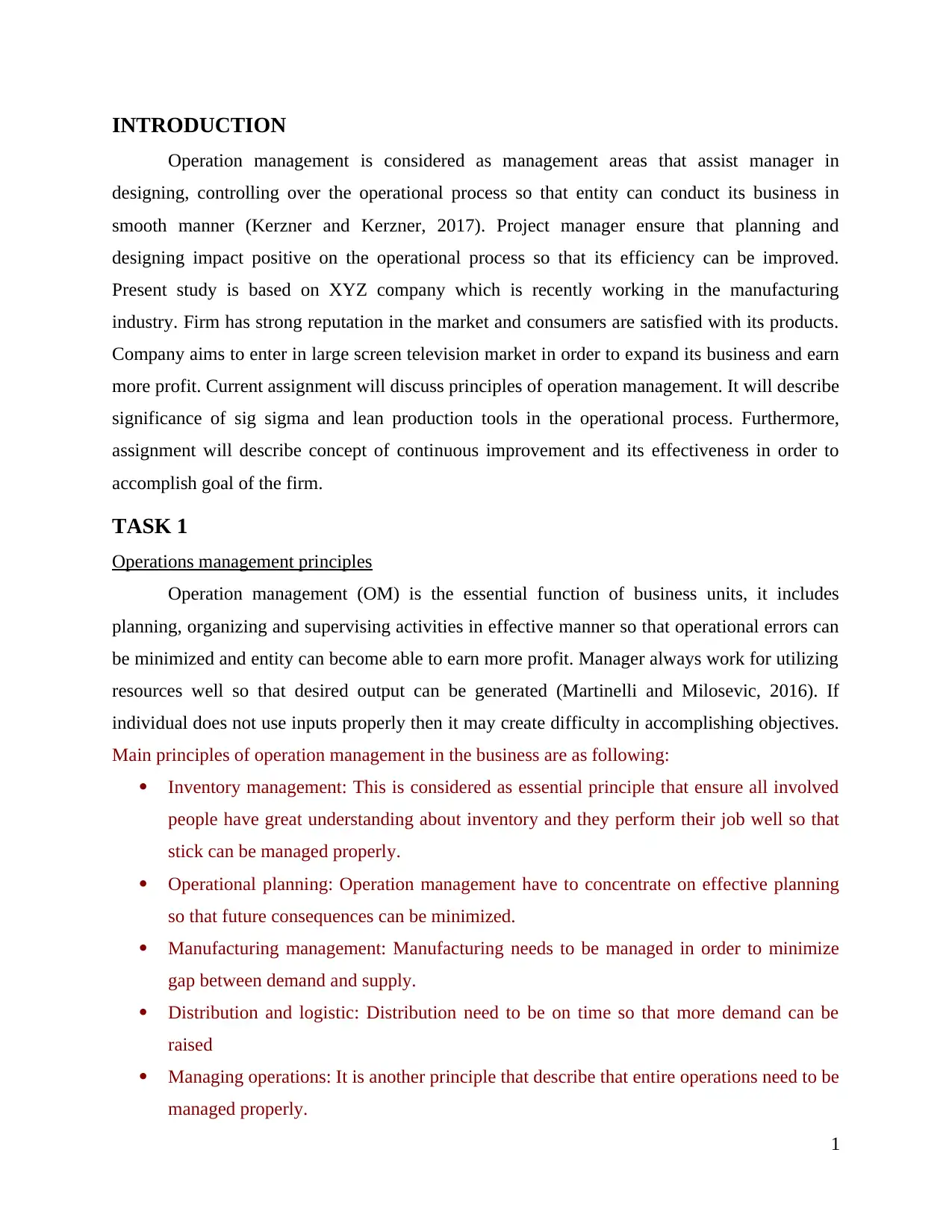
INTRODUCTION
Operation management is considered as management areas that assist manager in
designing, controlling over the operational process so that entity can conduct its business in
smooth manner (Kerzner and Kerzner, 2017). Project manager ensure that planning and
designing impact positive on the operational process so that its efficiency can be improved.
Present study is based on XYZ company which is recently working in the manufacturing
industry. Firm has strong reputation in the market and consumers are satisfied with its products.
Company aims to enter in large screen television market in order to expand its business and earn
more profit. Current assignment will discuss principles of operation management. It will describe
significance of sig sigma and lean production tools in the operational process. Furthermore,
assignment will describe concept of continuous improvement and its effectiveness in order to
accomplish goal of the firm.
TASK 1
Operations management principles
Operation management (OM) is the essential function of business units, it includes
planning, organizing and supervising activities in effective manner so that operational errors can
be minimized and entity can become able to earn more profit. Manager always work for utilizing
resources well so that desired output can be generated (Martinelli and Milosevic, 2016). If
individual does not use inputs properly then it may create difficulty in accomplishing objectives.
Main principles of operation management in the business are as following:
Inventory management: This is considered as essential principle that ensure all involved
people have great understanding about inventory and they perform their job well so that
stick can be managed properly.
Operational planning: Operation management have to concentrate on effective planning
so that future consequences can be minimized.
Manufacturing management: Manufacturing needs to be managed in order to minimize
gap between demand and supply.
Distribution and logistic: Distribution need to be on time so that more demand can be
raised
Managing operations: It is another principle that describe that entire operations need to be
managed properly.
1
Operation management is considered as management areas that assist manager in
designing, controlling over the operational process so that entity can conduct its business in
smooth manner (Kerzner and Kerzner, 2017). Project manager ensure that planning and
designing impact positive on the operational process so that its efficiency can be improved.
Present study is based on XYZ company which is recently working in the manufacturing
industry. Firm has strong reputation in the market and consumers are satisfied with its products.
Company aims to enter in large screen television market in order to expand its business and earn
more profit. Current assignment will discuss principles of operation management. It will describe
significance of sig sigma and lean production tools in the operational process. Furthermore,
assignment will describe concept of continuous improvement and its effectiveness in order to
accomplish goal of the firm.
TASK 1
Operations management principles
Operation management (OM) is the essential function of business units, it includes
planning, organizing and supervising activities in effective manner so that operational errors can
be minimized and entity can become able to earn more profit. Manager always work for utilizing
resources well so that desired output can be generated (Martinelli and Milosevic, 2016). If
individual does not use inputs properly then it may create difficulty in accomplishing objectives.
Main principles of operation management in the business are as following:
Inventory management: This is considered as essential principle that ensure all involved
people have great understanding about inventory and they perform their job well so that
stick can be managed properly.
Operational planning: Operation management have to concentrate on effective planning
so that future consequences can be minimized.
Manufacturing management: Manufacturing needs to be managed in order to minimize
gap between demand and supply.
Distribution and logistic: Distribution need to be on time so that more demand can be
raised
Managing operations: It is another principle that describe that entire operations need to be
managed properly.
1
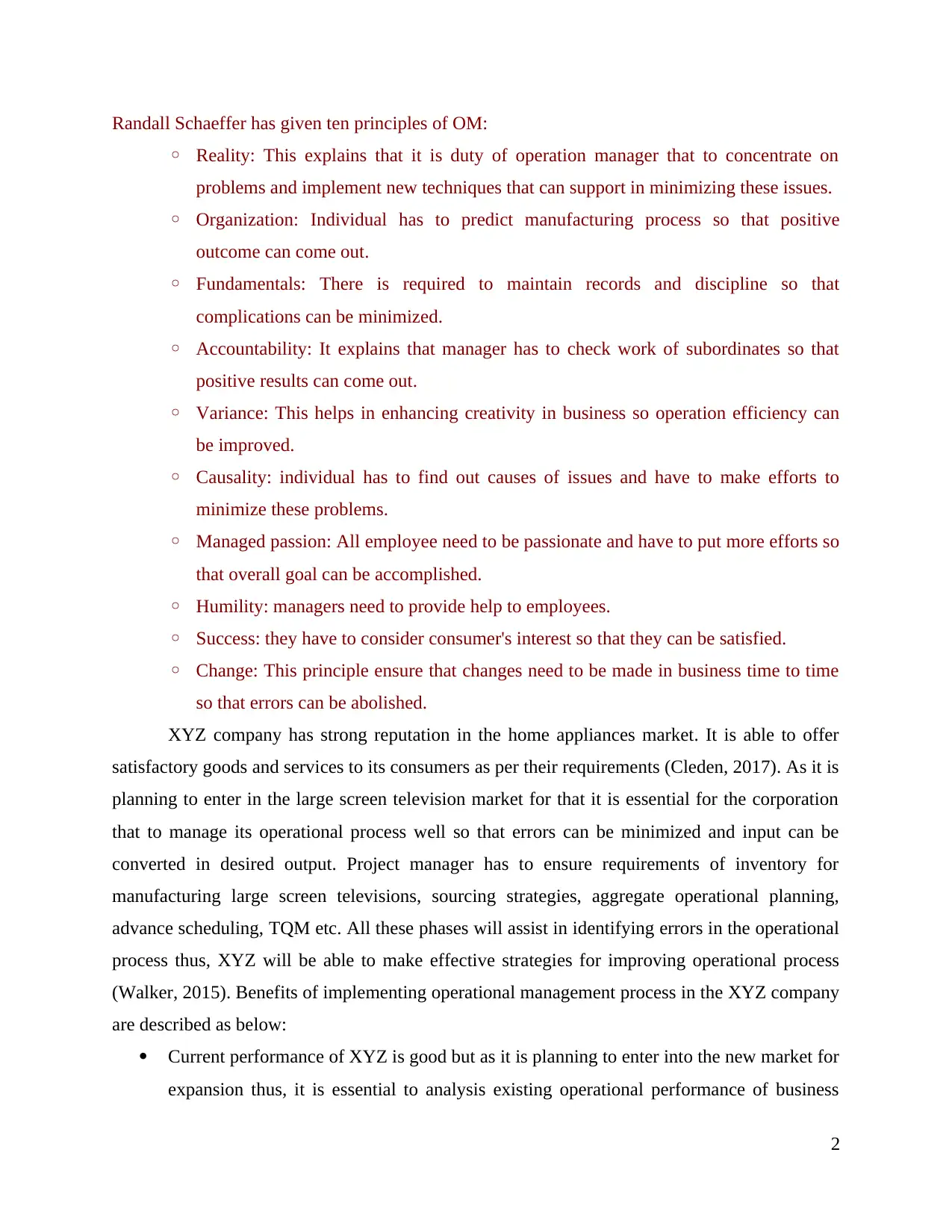
Randall Schaeffer has given ten principles of OM:
◦ Reality: This explains that it is duty of operation manager that to concentrate on
problems and implement new techniques that can support in minimizing these issues.
◦ Organization: Individual has to predict manufacturing process so that positive
outcome can come out.
◦ Fundamentals: There is required to maintain records and discipline so that
complications can be minimized.
◦ Accountability: It explains that manager has to check work of subordinates so that
positive results can come out.
◦ Variance: This helps in enhancing creativity in business so operation efficiency can
be improved.
◦ Causality: individual has to find out causes of issues and have to make efforts to
minimize these problems.
◦ Managed passion: All employee need to be passionate and have to put more efforts so
that overall goal can be accomplished.
◦ Humility: managers need to provide help to employees.
◦ Success: they have to consider consumer's interest so that they can be satisfied.
◦ Change: This principle ensure that changes need to be made in business time to time
so that errors can be abolished.
XYZ company has strong reputation in the home appliances market. It is able to offer
satisfactory goods and services to its consumers as per their requirements (Cleden, 2017). As it is
planning to enter in the large screen television market for that it is essential for the corporation
that to manage its operational process well so that errors can be minimized and input can be
converted in desired output. Project manager has to ensure requirements of inventory for
manufacturing large screen televisions, sourcing strategies, aggregate operational planning,
advance scheduling, TQM etc. All these phases will assist in identifying errors in the operational
process thus, XYZ will be able to make effective strategies for improving operational process
(Walker, 2015). Benefits of implementing operational management process in the XYZ company
are described as below:
Current performance of XYZ is good but as it is planning to enter into the new market for
expansion thus, it is essential to analysis existing operational performance of business
2
◦ Reality: This explains that it is duty of operation manager that to concentrate on
problems and implement new techniques that can support in minimizing these issues.
◦ Organization: Individual has to predict manufacturing process so that positive
outcome can come out.
◦ Fundamentals: There is required to maintain records and discipline so that
complications can be minimized.
◦ Accountability: It explains that manager has to check work of subordinates so that
positive results can come out.
◦ Variance: This helps in enhancing creativity in business so operation efficiency can
be improved.
◦ Causality: individual has to find out causes of issues and have to make efforts to
minimize these problems.
◦ Managed passion: All employee need to be passionate and have to put more efforts so
that overall goal can be accomplished.
◦ Humility: managers need to provide help to employees.
◦ Success: they have to consider consumer's interest so that they can be satisfied.
◦ Change: This principle ensure that changes need to be made in business time to time
so that errors can be abolished.
XYZ company has strong reputation in the home appliances market. It is able to offer
satisfactory goods and services to its consumers as per their requirements (Cleden, 2017). As it is
planning to enter in the large screen television market for that it is essential for the corporation
that to manage its operational process well so that errors can be minimized and input can be
converted in desired output. Project manager has to ensure requirements of inventory for
manufacturing large screen televisions, sourcing strategies, aggregate operational planning,
advance scheduling, TQM etc. All these phases will assist in identifying errors in the operational
process thus, XYZ will be able to make effective strategies for improving operational process
(Walker, 2015). Benefits of implementing operational management process in the XYZ company
are described as below:
Current performance of XYZ is good but as it is planning to enter into the new market for
expansion thus, it is essential to analysis existing operational performance of business
2
Secure Best Marks with AI Grader
Need help grading? Try our AI Grader for instant feedback on your assignments.
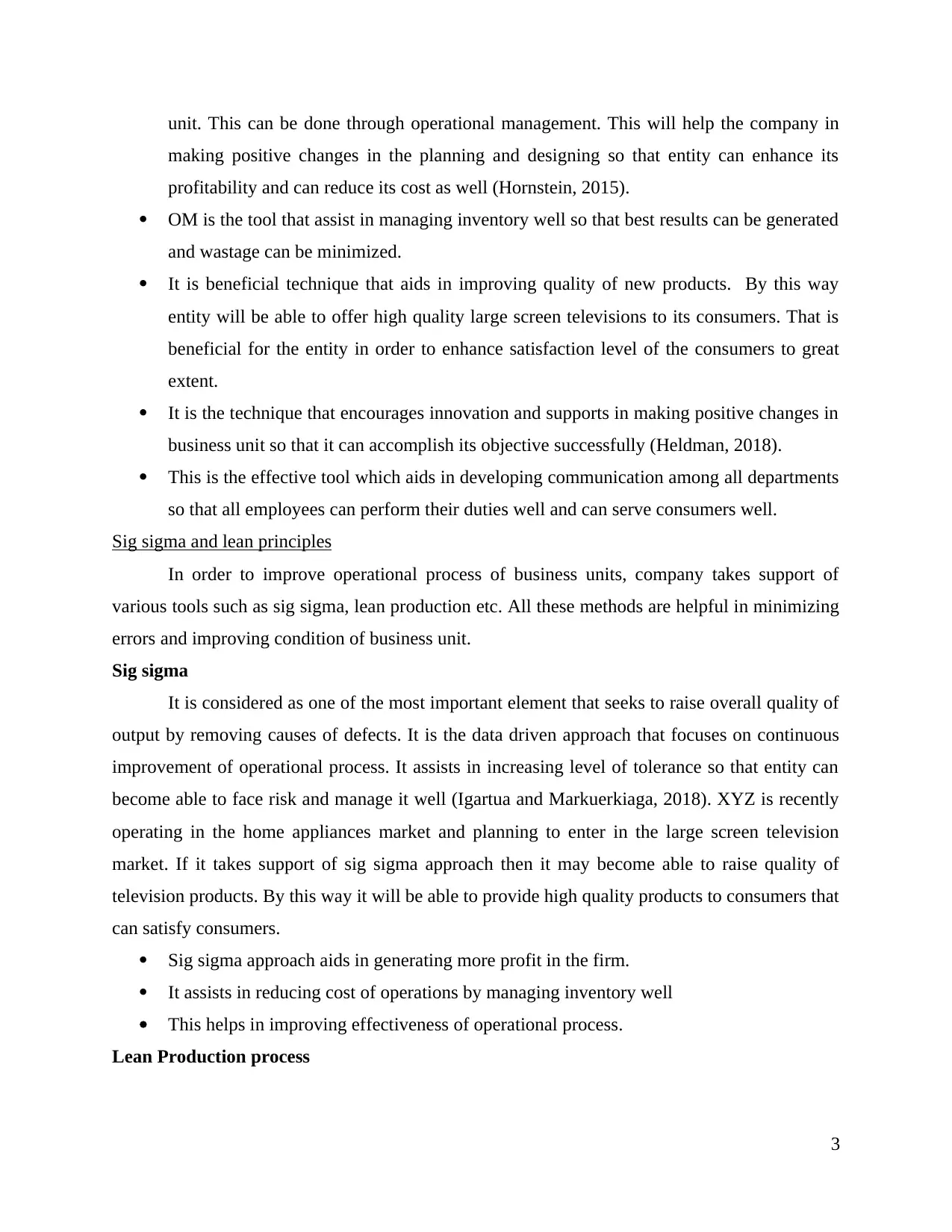
unit. This can be done through operational management. This will help the company in
making positive changes in the planning and designing so that entity can enhance its
profitability and can reduce its cost as well (Hornstein, 2015).
OM is the tool that assist in managing inventory well so that best results can be generated
and wastage can be minimized.
It is beneficial technique that aids in improving quality of new products. By this way
entity will be able to offer high quality large screen televisions to its consumers. That is
beneficial for the entity in order to enhance satisfaction level of the consumers to great
extent.
It is the technique that encourages innovation and supports in making positive changes in
business unit so that it can accomplish its objective successfully (Heldman, 2018).
This is the effective tool which aids in developing communication among all departments
so that all employees can perform their duties well and can serve consumers well.
Sig sigma and lean principles
In order to improve operational process of business units, company takes support of
various tools such as sig sigma, lean production etc. All these methods are helpful in minimizing
errors and improving condition of business unit.
Sig sigma
It is considered as one of the most important element that seeks to raise overall quality of
output by removing causes of defects. It is the data driven approach that focuses on continuous
improvement of operational process. It assists in increasing level of tolerance so that entity can
become able to face risk and manage it well (Igartua and Markuerkiaga, 2018). XYZ is recently
operating in the home appliances market and planning to enter in the large screen television
market. If it takes support of sig sigma approach then it may become able to raise quality of
television products. By this way it will be able to provide high quality products to consumers that
can satisfy consumers.
Sig sigma approach aids in generating more profit in the firm.
It assists in reducing cost of operations by managing inventory well
This helps in improving effectiveness of operational process.
Lean Production process
3
making positive changes in the planning and designing so that entity can enhance its
profitability and can reduce its cost as well (Hornstein, 2015).
OM is the tool that assist in managing inventory well so that best results can be generated
and wastage can be minimized.
It is beneficial technique that aids in improving quality of new products. By this way
entity will be able to offer high quality large screen televisions to its consumers. That is
beneficial for the entity in order to enhance satisfaction level of the consumers to great
extent.
It is the technique that encourages innovation and supports in making positive changes in
business unit so that it can accomplish its objective successfully (Heldman, 2018).
This is the effective tool which aids in developing communication among all departments
so that all employees can perform their duties well and can serve consumers well.
Sig sigma and lean principles
In order to improve operational process of business units, company takes support of
various tools such as sig sigma, lean production etc. All these methods are helpful in minimizing
errors and improving condition of business unit.
Sig sigma
It is considered as one of the most important element that seeks to raise overall quality of
output by removing causes of defects. It is the data driven approach that focuses on continuous
improvement of operational process. It assists in increasing level of tolerance so that entity can
become able to face risk and manage it well (Igartua and Markuerkiaga, 2018). XYZ is recently
operating in the home appliances market and planning to enter in the large screen television
market. If it takes support of sig sigma approach then it may become able to raise quality of
television products. By this way it will be able to provide high quality products to consumers that
can satisfy consumers.
Sig sigma approach aids in generating more profit in the firm.
It assists in reducing cost of operations by managing inventory well
This helps in improving effectiveness of operational process.
Lean Production process
3
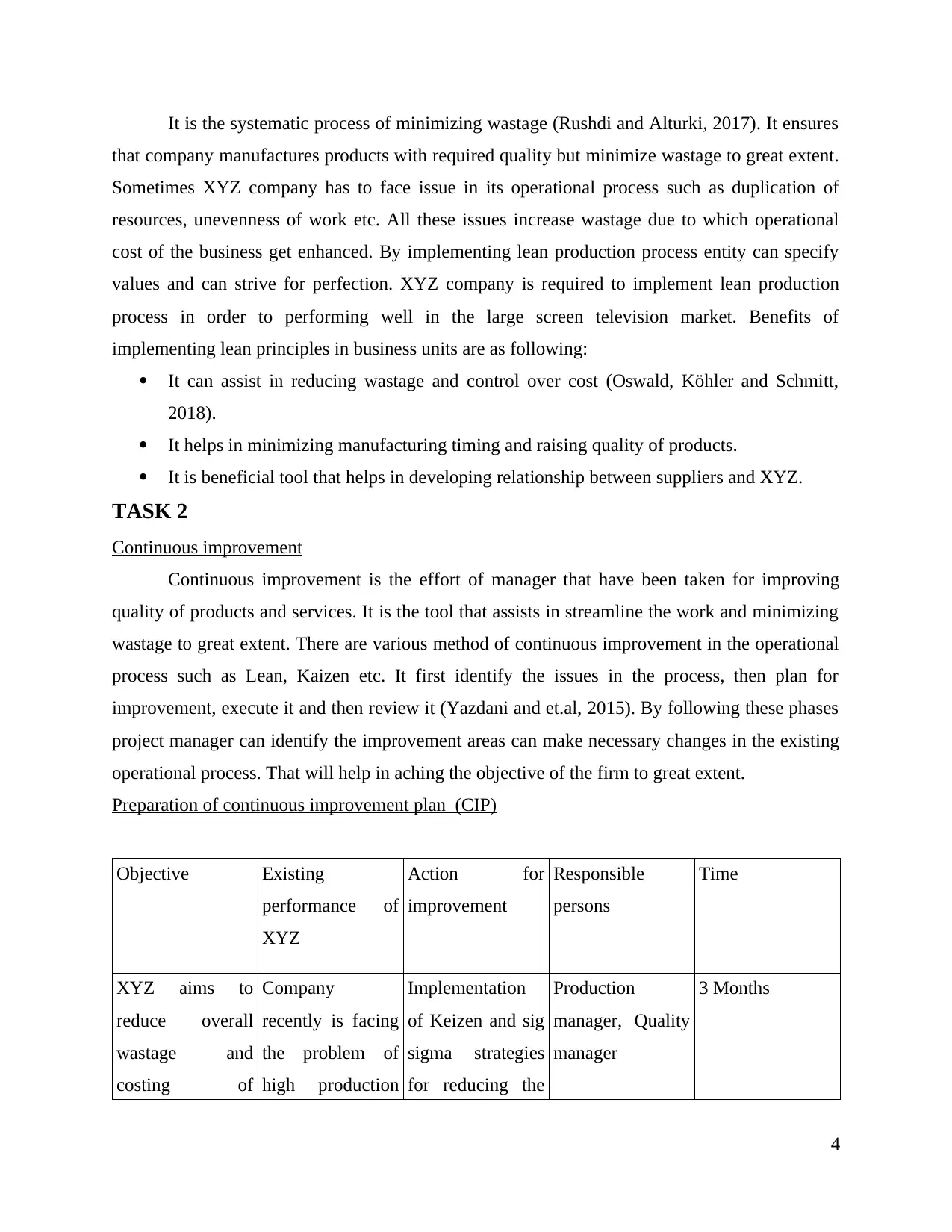
It is the systematic process of minimizing wastage (Rushdi and Alturki, 2017). It ensures
that company manufactures products with required quality but minimize wastage to great extent.
Sometimes XYZ company has to face issue in its operational process such as duplication of
resources, unevenness of work etc. All these issues increase wastage due to which operational
cost of the business get enhanced. By implementing lean production process entity can specify
values and can strive for perfection. XYZ company is required to implement lean production
process in order to performing well in the large screen television market. Benefits of
implementing lean principles in business units are as following:
It can assist in reducing wastage and control over cost (Oswald, Köhler and Schmitt,
2018).
It helps in minimizing manufacturing timing and raising quality of products.
It is beneficial tool that helps in developing relationship between suppliers and XYZ.
TASK 2
Continuous improvement
Continuous improvement is the effort of manager that have been taken for improving
quality of products and services. It is the tool that assists in streamline the work and minimizing
wastage to great extent. There are various method of continuous improvement in the operational
process such as Lean, Kaizen etc. It first identify the issues in the process, then plan for
improvement, execute it and then review it (Yazdani and et.al, 2015). By following these phases
project manager can identify the improvement areas can make necessary changes in the existing
operational process. That will help in aching the objective of the firm to great extent.
Preparation of continuous improvement plan (CIP)
Objective Existing
performance of
XYZ
Action for
improvement
Responsible
persons
Time
XYZ aims to
reduce overall
wastage and
costing of
Company
recently is facing
the problem of
high production
Implementation
of Keizen and sig
sigma strategies
for reducing the
Production
manager, Quality
manager
3 Months
4
that company manufactures products with required quality but minimize wastage to great extent.
Sometimes XYZ company has to face issue in its operational process such as duplication of
resources, unevenness of work etc. All these issues increase wastage due to which operational
cost of the business get enhanced. By implementing lean production process entity can specify
values and can strive for perfection. XYZ company is required to implement lean production
process in order to performing well in the large screen television market. Benefits of
implementing lean principles in business units are as following:
It can assist in reducing wastage and control over cost (Oswald, Köhler and Schmitt,
2018).
It helps in minimizing manufacturing timing and raising quality of products.
It is beneficial tool that helps in developing relationship between suppliers and XYZ.
TASK 2
Continuous improvement
Continuous improvement is the effort of manager that have been taken for improving
quality of products and services. It is the tool that assists in streamline the work and minimizing
wastage to great extent. There are various method of continuous improvement in the operational
process such as Lean, Kaizen etc. It first identify the issues in the process, then plan for
improvement, execute it and then review it (Yazdani and et.al, 2015). By following these phases
project manager can identify the improvement areas can make necessary changes in the existing
operational process. That will help in aching the objective of the firm to great extent.
Preparation of continuous improvement plan (CIP)
Objective Existing
performance of
XYZ
Action for
improvement
Responsible
persons
Time
XYZ aims to
reduce overall
wastage and
costing of
Company
recently is facing
the problem of
high production
Implementation
of Keizen and sig
sigma strategies
for reducing the
Production
manager, Quality
manager
3 Months
4
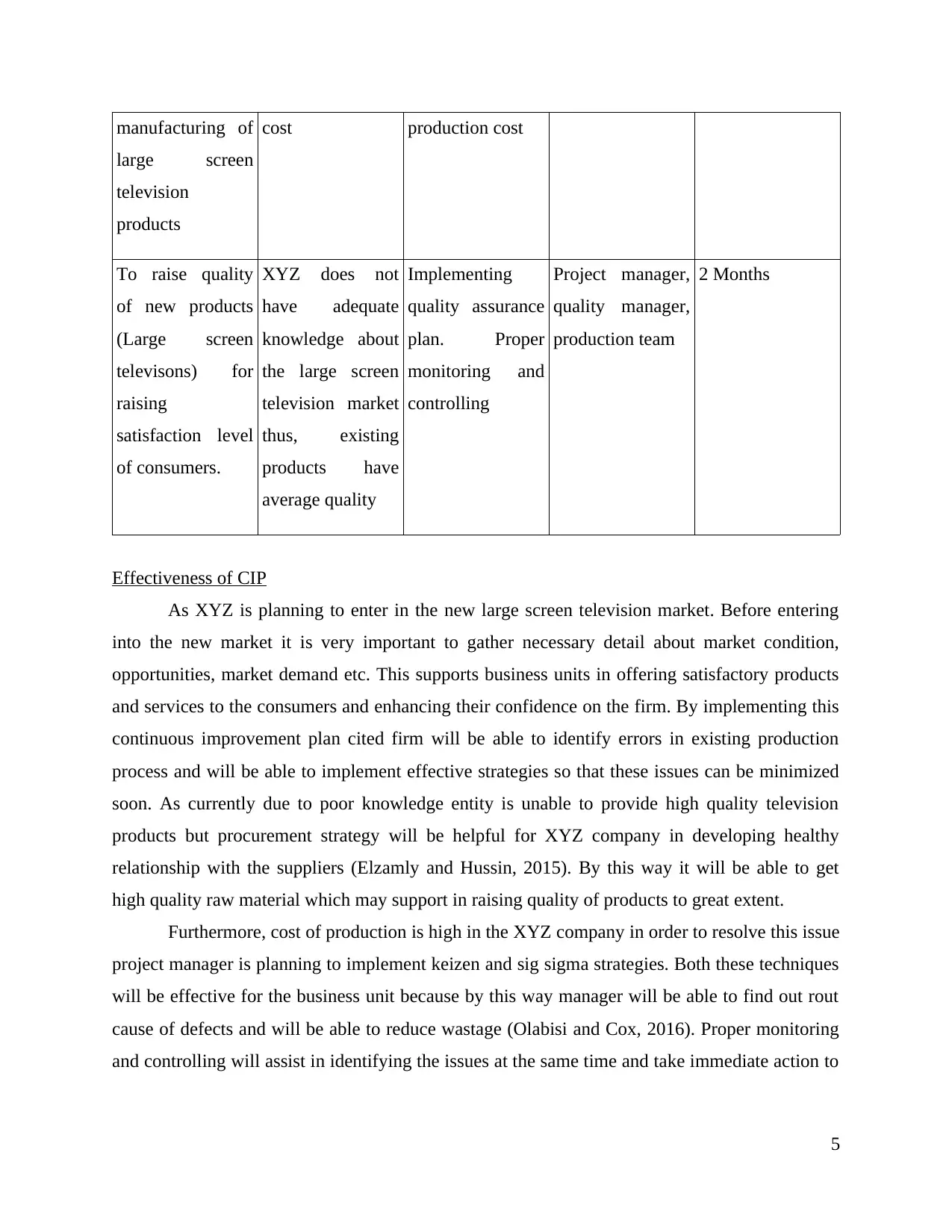
manufacturing of
large screen
television
products
cost production cost
To raise quality
of new products
(Large screen
televisons) for
raising
satisfaction level
of consumers.
XYZ does not
have adequate
knowledge about
the large screen
television market
thus, existing
products have
average quality
Implementing
quality assurance
plan. Proper
monitoring and
controlling
Project manager,
quality manager,
production team
2 Months
Effectiveness of CIP
As XYZ is planning to enter in the new large screen television market. Before entering
into the new market it is very important to gather necessary detail about market condition,
opportunities, market demand etc. This supports business units in offering satisfactory products
and services to the consumers and enhancing their confidence on the firm. By implementing this
continuous improvement plan cited firm will be able to identify errors in existing production
process and will be able to implement effective strategies so that these issues can be minimized
soon. As currently due to poor knowledge entity is unable to provide high quality television
products but procurement strategy will be helpful for XYZ company in developing healthy
relationship with the suppliers (Elzamly and Hussin, 2015). By this way it will be able to get
high quality raw material which may support in raising quality of products to great extent.
Furthermore, cost of production is high in the XYZ company in order to resolve this issue
project manager is planning to implement keizen and sig sigma strategies. Both these techniques
will be effective for the business unit because by this way manager will be able to find out rout
cause of defects and will be able to reduce wastage (Olabisi and Cox, 2016). Proper monitoring
and controlling will assist in identifying the issues at the same time and take immediate action to
5
large screen
television
products
cost production cost
To raise quality
of new products
(Large screen
televisons) for
raising
satisfaction level
of consumers.
XYZ does not
have adequate
knowledge about
the large screen
television market
thus, existing
products have
average quality
Implementing
quality assurance
plan. Proper
monitoring and
controlling
Project manager,
quality manager,
production team
2 Months
Effectiveness of CIP
As XYZ is planning to enter in the new large screen television market. Before entering
into the new market it is very important to gather necessary detail about market condition,
opportunities, market demand etc. This supports business units in offering satisfactory products
and services to the consumers and enhancing their confidence on the firm. By implementing this
continuous improvement plan cited firm will be able to identify errors in existing production
process and will be able to implement effective strategies so that these issues can be minimized
soon. As currently due to poor knowledge entity is unable to provide high quality television
products but procurement strategy will be helpful for XYZ company in developing healthy
relationship with the suppliers (Elzamly and Hussin, 2015). By this way it will be able to get
high quality raw material which may support in raising quality of products to great extent.
Furthermore, cost of production is high in the XYZ company in order to resolve this issue
project manager is planning to implement keizen and sig sigma strategies. Both these techniques
will be effective for the business unit because by this way manager will be able to find out rout
cause of defects and will be able to reduce wastage (Olabisi and Cox, 2016). Proper monitoring
and controlling will assist in identifying the issues at the same time and take immediate action to
5
Paraphrase This Document
Need a fresh take? Get an instant paraphrase of this document with our AI Paraphraser
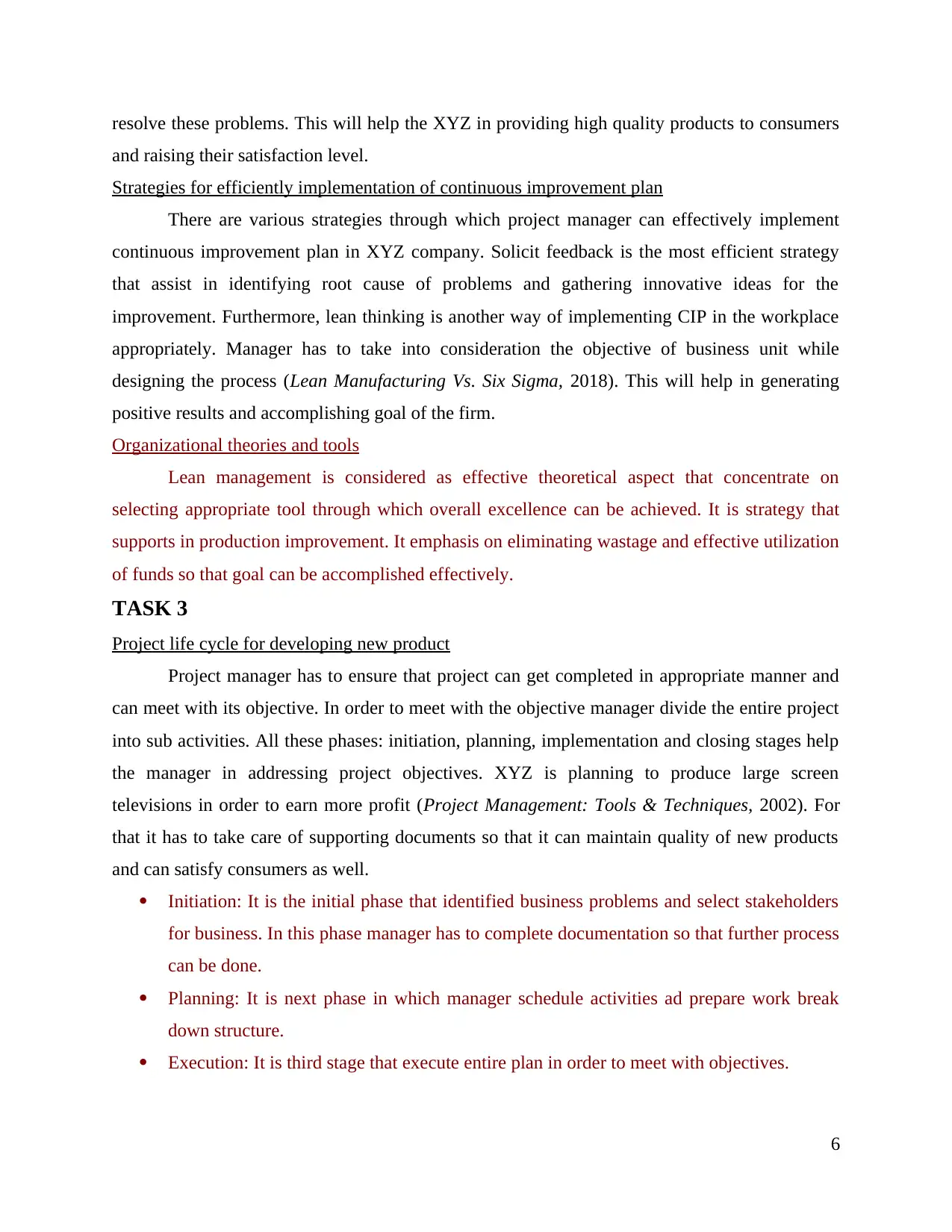
resolve these problems. This will help the XYZ in providing high quality products to consumers
and raising their satisfaction level.
Strategies for efficiently implementation of continuous improvement plan
There are various strategies through which project manager can effectively implement
continuous improvement plan in XYZ company. Solicit feedback is the most efficient strategy
that assist in identifying root cause of problems and gathering innovative ideas for the
improvement. Furthermore, lean thinking is another way of implementing CIP in the workplace
appropriately. Manager has to take into consideration the objective of business unit while
designing the process (Lean Manufacturing Vs. Six Sigma, 2018). This will help in generating
positive results and accomplishing goal of the firm.
Organizational theories and tools
Lean management is considered as effective theoretical aspect that concentrate on
selecting appropriate tool through which overall excellence can be achieved. It is strategy that
supports in production improvement. It emphasis on eliminating wastage and effective utilization
of funds so that goal can be accomplished effectively.
TASK 3
Project life cycle for developing new product
Project manager has to ensure that project can get completed in appropriate manner and
can meet with its objective. In order to meet with the objective manager divide the entire project
into sub activities. All these phases: initiation, planning, implementation and closing stages help
the manager in addressing project objectives. XYZ is planning to produce large screen
televisions in order to earn more profit (Project Management: Tools & Techniques, 2002). For
that it has to take care of supporting documents so that it can maintain quality of new products
and can satisfy consumers as well.
Initiation: It is the initial phase that identified business problems and select stakeholders
for business. In this phase manager has to complete documentation so that further process
can be done.
Planning: It is next phase in which manager schedule activities ad prepare work break
down structure.
Execution: It is third stage that execute entire plan in order to meet with objectives.
6
and raising their satisfaction level.
Strategies for efficiently implementation of continuous improvement plan
There are various strategies through which project manager can effectively implement
continuous improvement plan in XYZ company. Solicit feedback is the most efficient strategy
that assist in identifying root cause of problems and gathering innovative ideas for the
improvement. Furthermore, lean thinking is another way of implementing CIP in the workplace
appropriately. Manager has to take into consideration the objective of business unit while
designing the process (Lean Manufacturing Vs. Six Sigma, 2018). This will help in generating
positive results and accomplishing goal of the firm.
Organizational theories and tools
Lean management is considered as effective theoretical aspect that concentrate on
selecting appropriate tool through which overall excellence can be achieved. It is strategy that
supports in production improvement. It emphasis on eliminating wastage and effective utilization
of funds so that goal can be accomplished effectively.
TASK 3
Project life cycle for developing new product
Project manager has to ensure that project can get completed in appropriate manner and
can meet with its objective. In order to meet with the objective manager divide the entire project
into sub activities. All these phases: initiation, planning, implementation and closing stages help
the manager in addressing project objectives. XYZ is planning to produce large screen
televisions in order to earn more profit (Project Management: Tools & Techniques, 2002). For
that it has to take care of supporting documents so that it can maintain quality of new products
and can satisfy consumers as well.
Initiation: It is the initial phase that identified business problems and select stakeholders
for business. In this phase manager has to complete documentation so that further process
can be done.
Planning: It is next phase in which manager schedule activities ad prepare work break
down structure.
Execution: It is third stage that execute entire plan in order to meet with objectives.
6
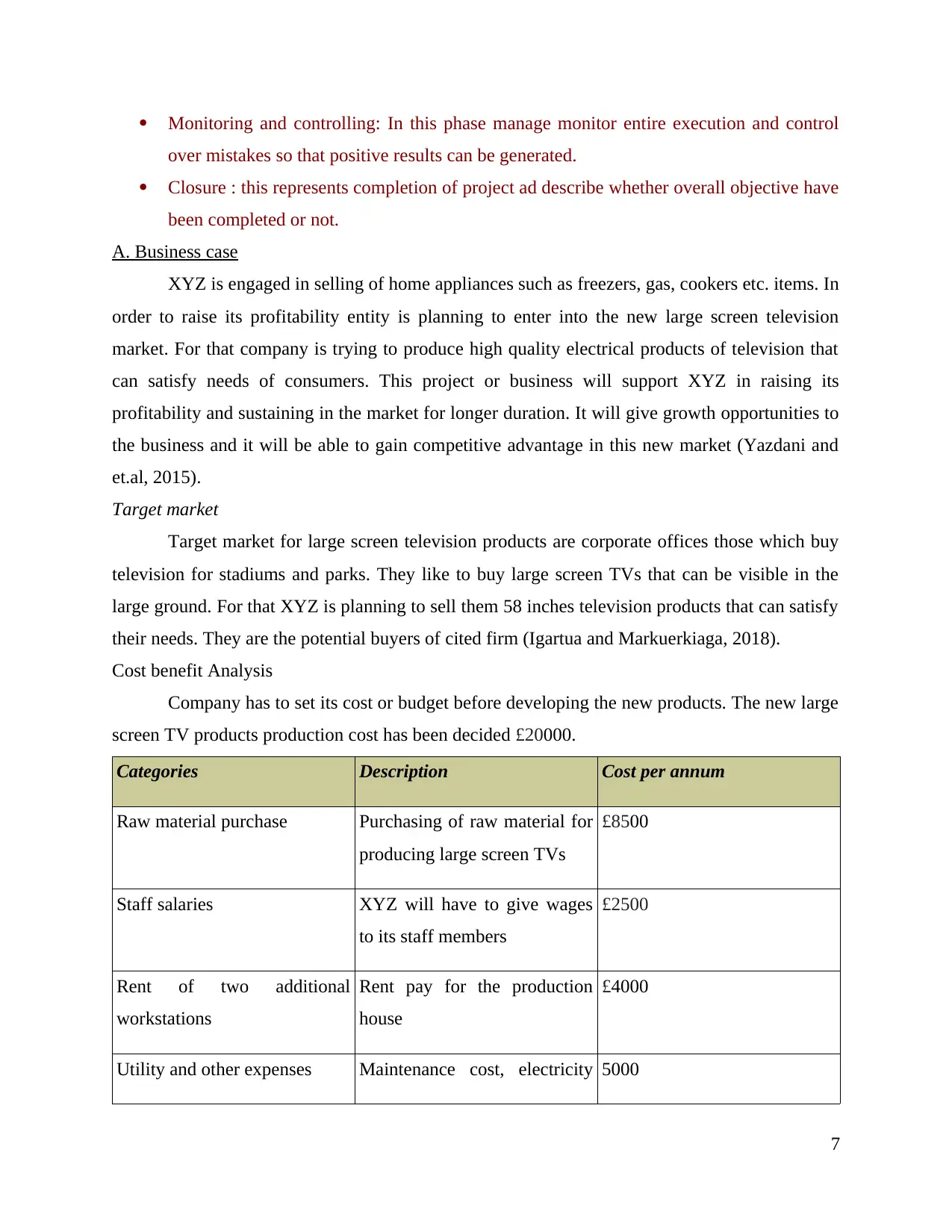
Monitoring and controlling: In this phase manage monitor entire execution and control
over mistakes so that positive results can be generated.
Closure : this represents completion of project ad describe whether overall objective have
been completed or not.
A. Business case
XYZ is engaged in selling of home appliances such as freezers, gas, cookers etc. items. In
order to raise its profitability entity is planning to enter into the new large screen television
market. For that company is trying to produce high quality electrical products of television that
can satisfy needs of consumers. This project or business will support XYZ in raising its
profitability and sustaining in the market for longer duration. It will give growth opportunities to
the business and it will be able to gain competitive advantage in this new market (Yazdani and
et.al, 2015).
Target market
Target market for large screen television products are corporate offices those which buy
television for stadiums and parks. They like to buy large screen TVs that can be visible in the
large ground. For that XYZ is planning to sell them 58 inches television products that can satisfy
their needs. They are the potential buyers of cited firm (Igartua and Markuerkiaga, 2018).
Cost benefit Analysis
Company has to set its cost or budget before developing the new products. The new large
screen TV products production cost has been decided £20000.
Categories Description Cost per annum
Raw material purchase Purchasing of raw material for
producing large screen TVs
£8500
Staff salaries XYZ will have to give wages
to its staff members
£2500
Rent of two additional
workstations
Rent pay for the production
house
£4000
Utility and other expenses Maintenance cost, electricity 5000
7
over mistakes so that positive results can be generated.
Closure : this represents completion of project ad describe whether overall objective have
been completed or not.
A. Business case
XYZ is engaged in selling of home appliances such as freezers, gas, cookers etc. items. In
order to raise its profitability entity is planning to enter into the new large screen television
market. For that company is trying to produce high quality electrical products of television that
can satisfy needs of consumers. This project or business will support XYZ in raising its
profitability and sustaining in the market for longer duration. It will give growth opportunities to
the business and it will be able to gain competitive advantage in this new market (Yazdani and
et.al, 2015).
Target market
Target market for large screen television products are corporate offices those which buy
television for stadiums and parks. They like to buy large screen TVs that can be visible in the
large ground. For that XYZ is planning to sell them 58 inches television products that can satisfy
their needs. They are the potential buyers of cited firm (Igartua and Markuerkiaga, 2018).
Cost benefit Analysis
Company has to set its cost or budget before developing the new products. The new large
screen TV products production cost has been decided £20000.
Categories Description Cost per annum
Raw material purchase Purchasing of raw material for
producing large screen TVs
£8500
Staff salaries XYZ will have to give wages
to its staff members
£2500
Rent of two additional
workstations
Rent pay for the production
house
£4000
Utility and other expenses Maintenance cost, electricity 5000
7
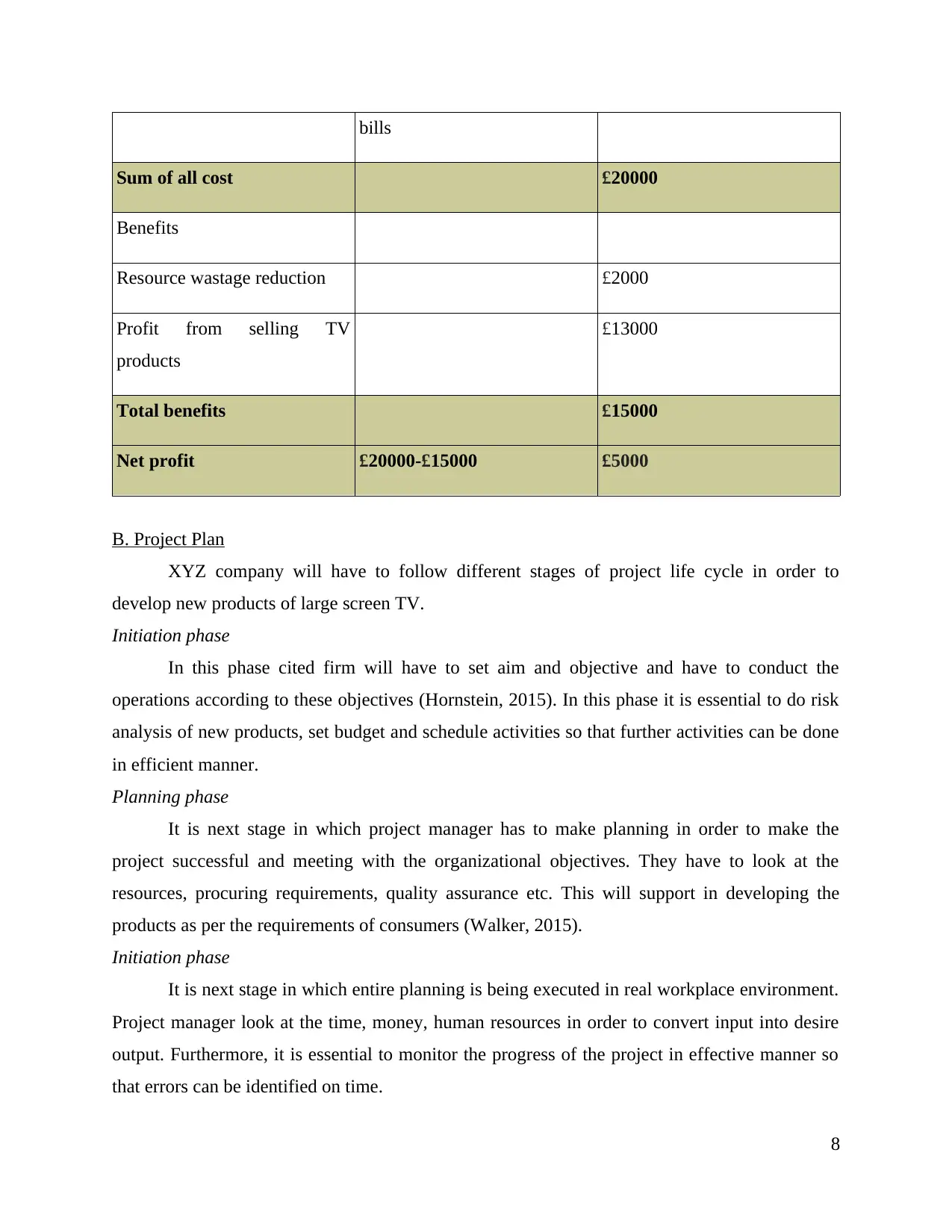
bills
Sum of all cost £20000
Benefits
Resource wastage reduction £2000
Profit from selling TV
products
£13000
Total benefits £15000
Net profit £20000-£15000 £5000
B. Project Plan
XYZ company will have to follow different stages of project life cycle in order to
develop new products of large screen TV.
Initiation phase
In this phase cited firm will have to set aim and objective and have to conduct the
operations according to these objectives (Hornstein, 2015). In this phase it is essential to do risk
analysis of new products, set budget and schedule activities so that further activities can be done
in efficient manner.
Planning phase
It is next stage in which project manager has to make planning in order to make the
project successful and meeting with the organizational objectives. They have to look at the
resources, procuring requirements, quality assurance etc. This will support in developing the
products as per the requirements of consumers (Walker, 2015).
Initiation phase
It is next stage in which entire planning is being executed in real workplace environment.
Project manager look at the time, money, human resources in order to convert input into desire
output. Furthermore, it is essential to monitor the progress of the project in effective manner so
that errors can be identified on time.
8
Sum of all cost £20000
Benefits
Resource wastage reduction £2000
Profit from selling TV
products
£13000
Total benefits £15000
Net profit £20000-£15000 £5000
B. Project Plan
XYZ company will have to follow different stages of project life cycle in order to
develop new products of large screen TV.
Initiation phase
In this phase cited firm will have to set aim and objective and have to conduct the
operations according to these objectives (Hornstein, 2015). In this phase it is essential to do risk
analysis of new products, set budget and schedule activities so that further activities can be done
in efficient manner.
Planning phase
It is next stage in which project manager has to make planning in order to make the
project successful and meeting with the organizational objectives. They have to look at the
resources, procuring requirements, quality assurance etc. This will support in developing the
products as per the requirements of consumers (Walker, 2015).
Initiation phase
It is next stage in which entire planning is being executed in real workplace environment.
Project manager look at the time, money, human resources in order to convert input into desire
output. Furthermore, it is essential to monitor the progress of the project in effective manner so
that errors can be identified on time.
8
Secure Best Marks with AI Grader
Need help grading? Try our AI Grader for instant feedback on your assignments.
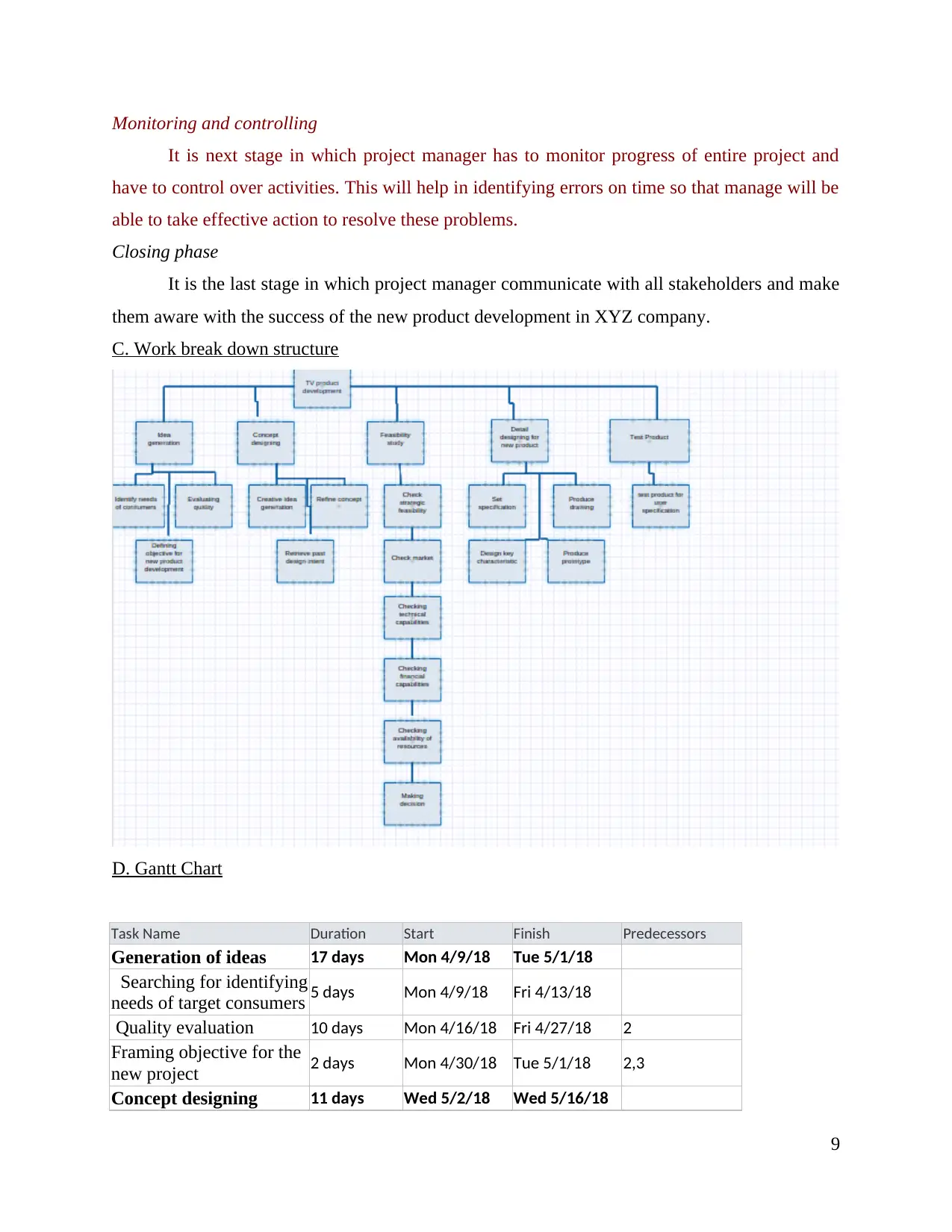
Monitoring and controlling
It is next stage in which project manager has to monitor progress of entire project and
have to control over activities. This will help in identifying errors on time so that manage will be
able to take effective action to resolve these problems.
Closing phase
It is the last stage in which project manager communicate with all stakeholders and make
them aware with the success of the new product development in XYZ company.
C. Work break down structure
D. Gantt Chart
Task Name Duration Start Finish Predecessors
Generation of ideas 17 days Mon 4/9/18 Tue 5/1/18
Searching for identifying
needs of target consumers 5 days Mon 4/9/18 Fri 4/13/18
Quality evaluation 10 days Mon 4/16/18 Fri 4/27/18 2
Framing objective for the
new project 2 days Mon 4/30/18 Tue 5/1/18 2,3
Concept designing 11 days Wed 5/2/18 Wed 5/16/18
9
It is next stage in which project manager has to monitor progress of entire project and
have to control over activities. This will help in identifying errors on time so that manage will be
able to take effective action to resolve these problems.
Closing phase
It is the last stage in which project manager communicate with all stakeholders and make
them aware with the success of the new product development in XYZ company.
C. Work break down structure
D. Gantt Chart
Task Name Duration Start Finish Predecessors
Generation of ideas 17 days Mon 4/9/18 Tue 5/1/18
Searching for identifying
needs of target consumers 5 days Mon 4/9/18 Fri 4/13/18
Quality evaluation 10 days Mon 4/16/18 Fri 4/27/18 2
Framing objective for the
new project 2 days Mon 4/30/18 Tue 5/1/18 2,3
Concept designing 11 days Wed 5/2/18 Wed 5/16/18
9
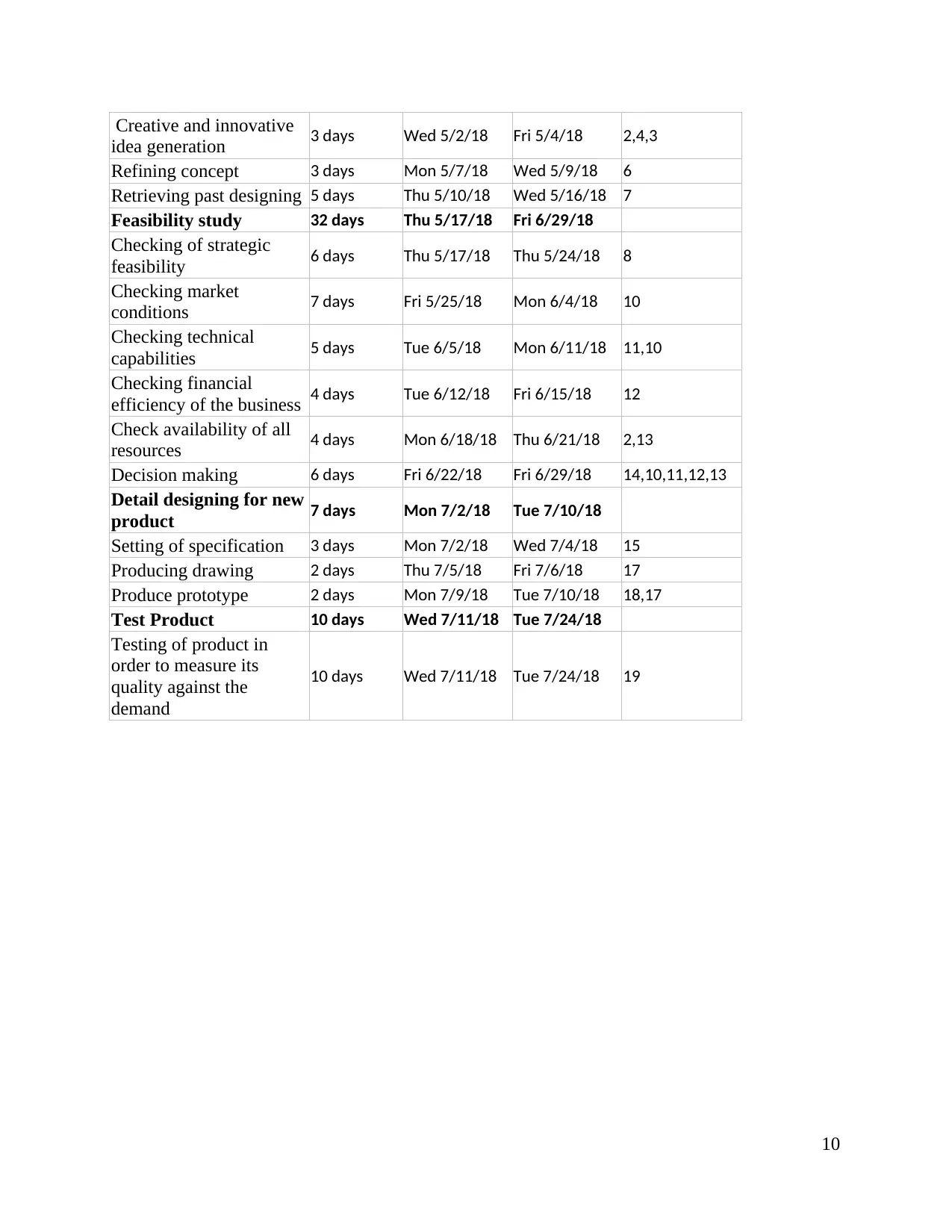
Creative and innovative
idea generation 3 days Wed 5/2/18 Fri 5/4/18 2,4,3
Refining concept 3 days Mon 5/7/18 Wed 5/9/18 6
Retrieving past designing 5 days Thu 5/10/18 Wed 5/16/18 7
Feasibility study 32 days Thu 5/17/18 Fri 6/29/18
Checking of strategic
feasibility 6 days Thu 5/17/18 Thu 5/24/18 8
Checking market
conditions 7 days Fri 5/25/18 Mon 6/4/18 10
Checking technical
capabilities 5 days Tue 6/5/18 Mon 6/11/18 11,10
Checking financial
efficiency of the business 4 days Tue 6/12/18 Fri 6/15/18 12
Check availability of all
resources 4 days Mon 6/18/18 Thu 6/21/18 2,13
Decision making 6 days Fri 6/22/18 Fri 6/29/18 14,10,11,12,13
Detail designing for new
product 7 days Mon 7/2/18 Tue 7/10/18
Setting of specification 3 days Mon 7/2/18 Wed 7/4/18 15
Producing drawing 2 days Thu 7/5/18 Fri 7/6/18 17
Produce prototype 2 days Mon 7/9/18 Tue 7/10/18 18,17
Test Product 10 days Wed 7/11/18 Tue 7/24/18
Testing of product in
order to measure its
quality against the
demand
10 days Wed 7/11/18 Tue 7/24/18 19
10
idea generation 3 days Wed 5/2/18 Fri 5/4/18 2,4,3
Refining concept 3 days Mon 5/7/18 Wed 5/9/18 6
Retrieving past designing 5 days Thu 5/10/18 Wed 5/16/18 7
Feasibility study 32 days Thu 5/17/18 Fri 6/29/18
Checking of strategic
feasibility 6 days Thu 5/17/18 Thu 5/24/18 8
Checking market
conditions 7 days Fri 5/25/18 Mon 6/4/18 10
Checking technical
capabilities 5 days Tue 6/5/18 Mon 6/11/18 11,10
Checking financial
efficiency of the business 4 days Tue 6/12/18 Fri 6/15/18 12
Check availability of all
resources 4 days Mon 6/18/18 Thu 6/21/18 2,13
Decision making 6 days Fri 6/22/18 Fri 6/29/18 14,10,11,12,13
Detail designing for new
product 7 days Mon 7/2/18 Tue 7/10/18
Setting of specification 3 days Mon 7/2/18 Wed 7/4/18 15
Producing drawing 2 days Thu 7/5/18 Fri 7/6/18 17
Produce prototype 2 days Mon 7/9/18 Tue 7/10/18 18,17
Test Product 10 days Wed 7/11/18 Tue 7/24/18
Testing of product in
order to measure its
quality against the
demand
10 days Wed 7/11/18 Tue 7/24/18 19
10
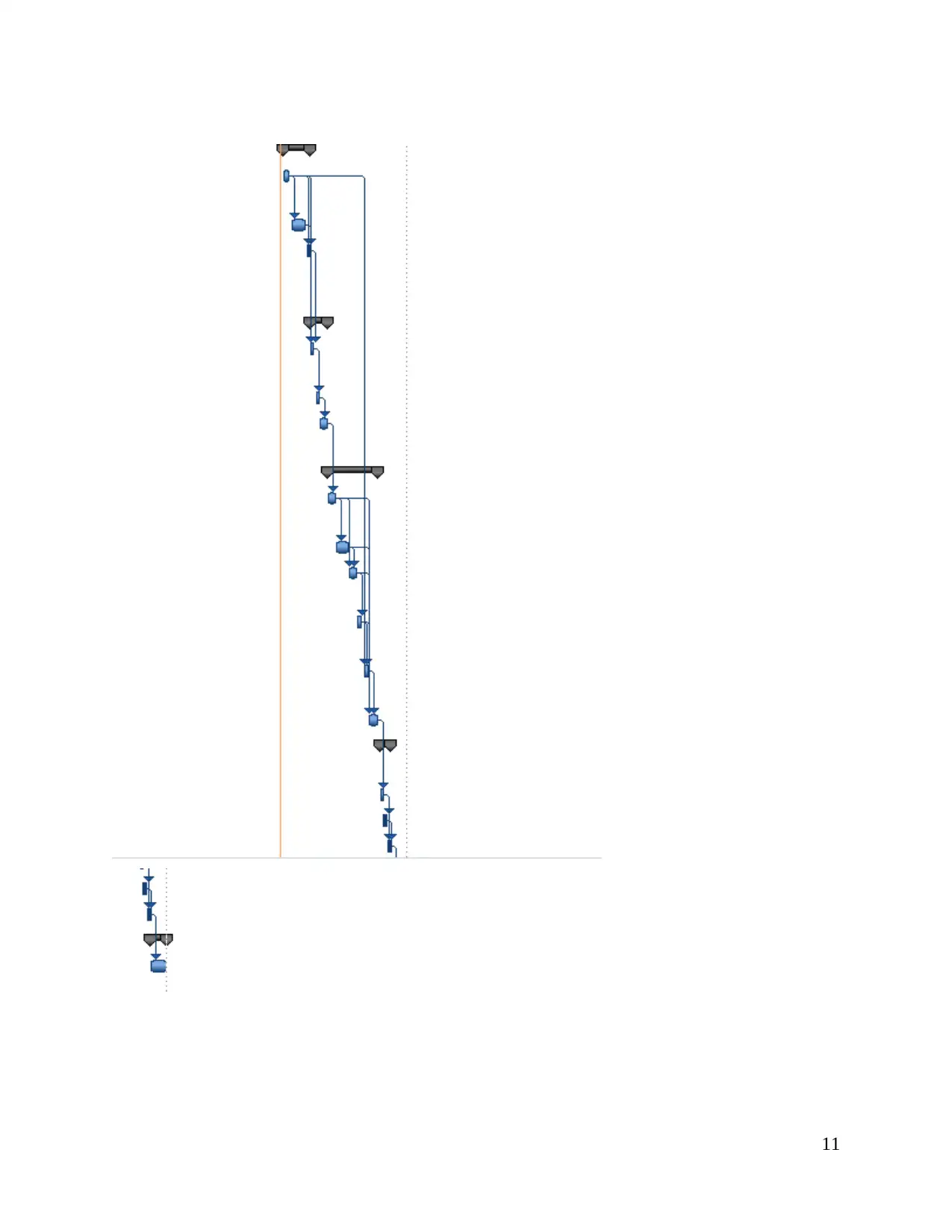
11
Paraphrase This Document
Need a fresh take? Get an instant paraphrase of this document with our AI Paraphraser
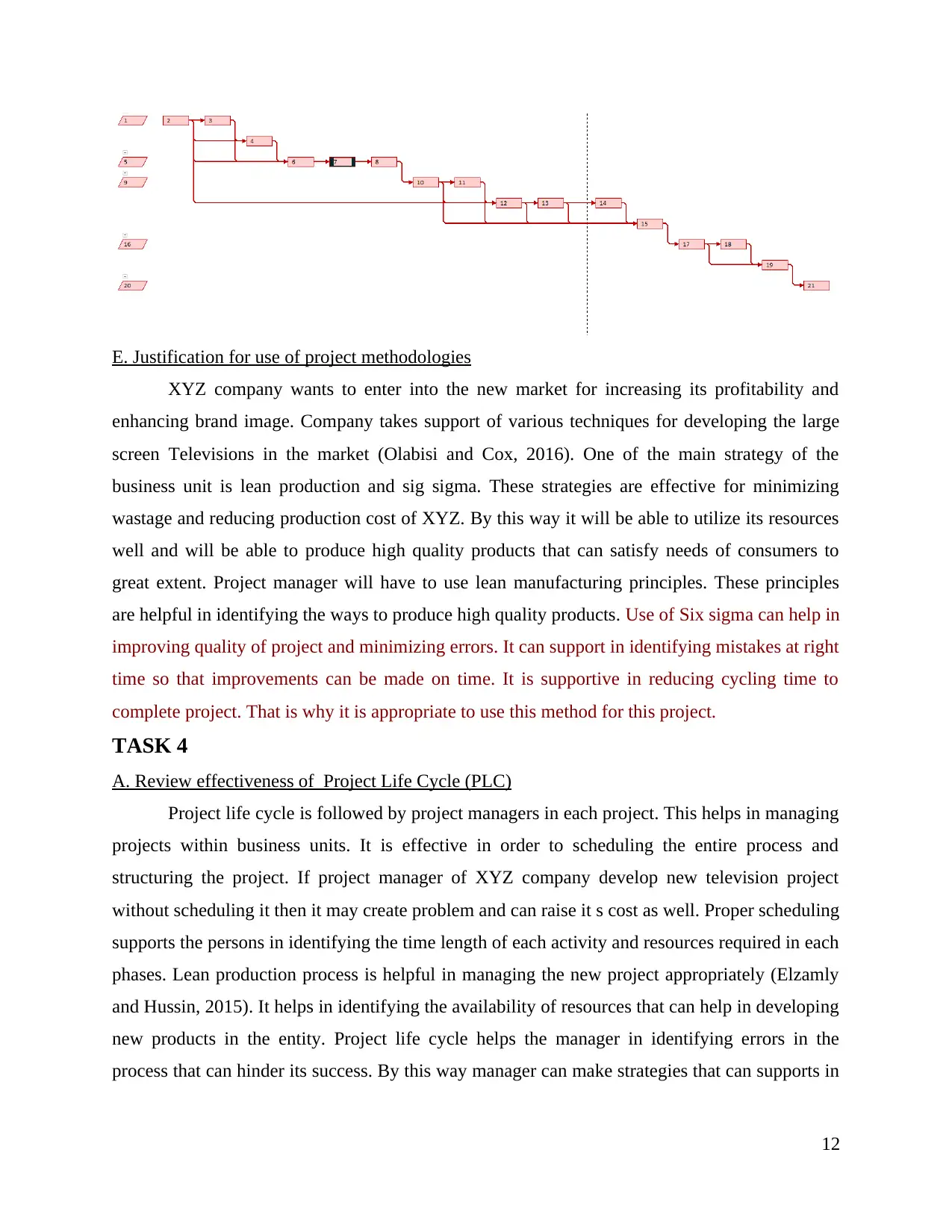
E. Justification for use of project methodologies
XYZ company wants to enter into the new market for increasing its profitability and
enhancing brand image. Company takes support of various techniques for developing the large
screen Televisions in the market (Olabisi and Cox, 2016). One of the main strategy of the
business unit is lean production and sig sigma. These strategies are effective for minimizing
wastage and reducing production cost of XYZ. By this way it will be able to utilize its resources
well and will be able to produce high quality products that can satisfy needs of consumers to
great extent. Project manager will have to use lean manufacturing principles. These principles
are helpful in identifying the ways to produce high quality products. Use of Six sigma can help in
improving quality of project and minimizing errors. It can support in identifying mistakes at right
time so that improvements can be made on time. It is supportive in reducing cycling time to
complete project. That is why it is appropriate to use this method for this project.
TASK 4
A. Review effectiveness of Project Life Cycle (PLC)
Project life cycle is followed by project managers in each project. This helps in managing
projects within business units. It is effective in order to scheduling the entire process and
structuring the project. If project manager of XYZ company develop new television project
without scheduling it then it may create problem and can raise it s cost as well. Proper scheduling
supports the persons in identifying the time length of each activity and resources required in each
phases. Lean production process is helpful in managing the new project appropriately (Elzamly
and Hussin, 2015). It helps in identifying the availability of resources that can help in developing
new products in the entity. Project life cycle helps the manager in identifying errors in the
process that can hinder its success. By this way manager can make strategies that can supports in
12
XYZ company wants to enter into the new market for increasing its profitability and
enhancing brand image. Company takes support of various techniques for developing the large
screen Televisions in the market (Olabisi and Cox, 2016). One of the main strategy of the
business unit is lean production and sig sigma. These strategies are effective for minimizing
wastage and reducing production cost of XYZ. By this way it will be able to utilize its resources
well and will be able to produce high quality products that can satisfy needs of consumers to
great extent. Project manager will have to use lean manufacturing principles. These principles
are helpful in identifying the ways to produce high quality products. Use of Six sigma can help in
improving quality of project and minimizing errors. It can support in identifying mistakes at right
time so that improvements can be made on time. It is supportive in reducing cycling time to
complete project. That is why it is appropriate to use this method for this project.
TASK 4
A. Review effectiveness of Project Life Cycle (PLC)
Project life cycle is followed by project managers in each project. This helps in managing
projects within business units. It is effective in order to scheduling the entire process and
structuring the project. If project manager of XYZ company develop new television project
without scheduling it then it may create problem and can raise it s cost as well. Proper scheduling
supports the persons in identifying the time length of each activity and resources required in each
phases. Lean production process is helpful in managing the new project appropriately (Elzamly
and Hussin, 2015). It helps in identifying the availability of resources that can help in developing
new products in the entity. Project life cycle helps the manager in identifying errors in the
process that can hinder its success. By this way manager can make strategies that can supports in
12
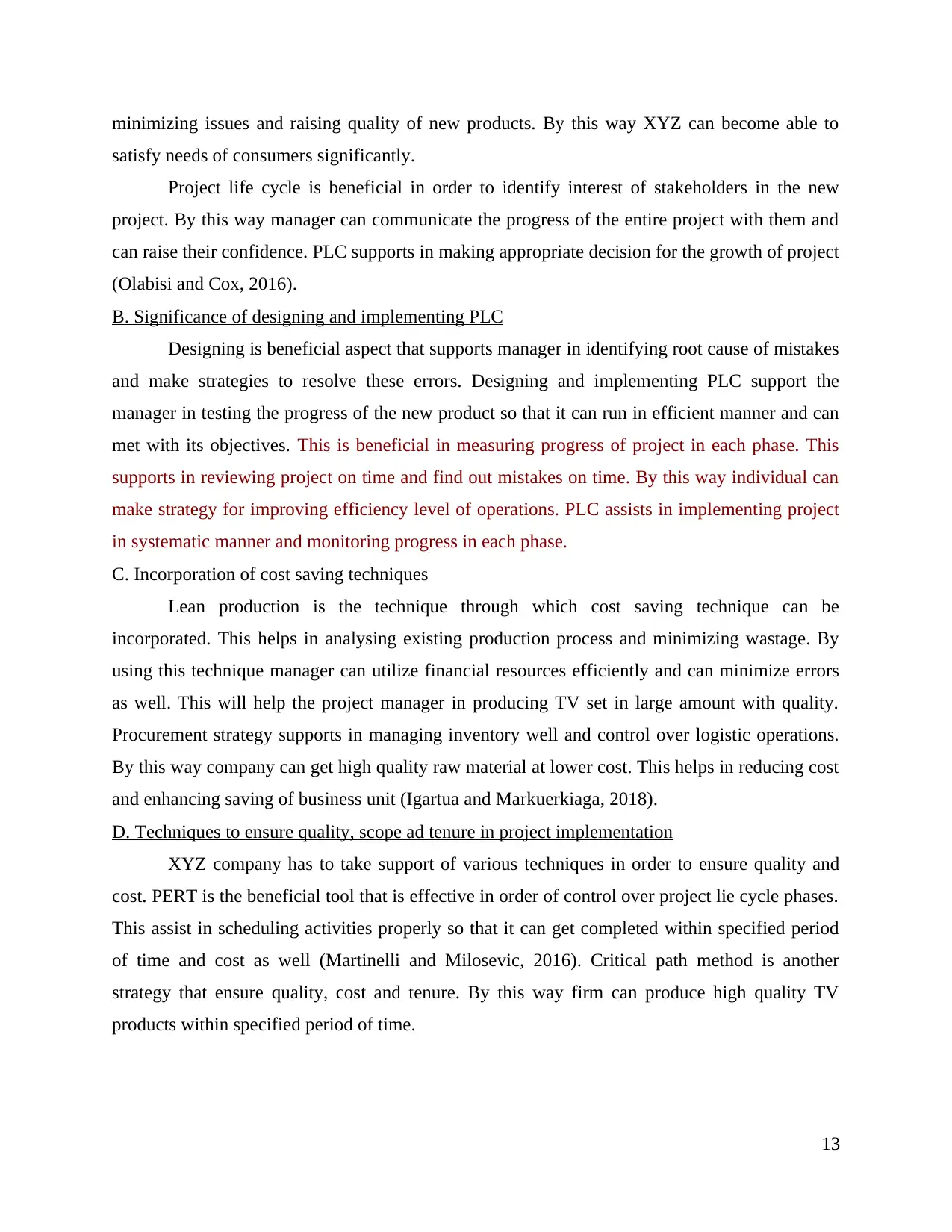
minimizing issues and raising quality of new products. By this way XYZ can become able to
satisfy needs of consumers significantly.
Project life cycle is beneficial in order to identify interest of stakeholders in the new
project. By this way manager can communicate the progress of the entire project with them and
can raise their confidence. PLC supports in making appropriate decision for the growth of project
(Olabisi and Cox, 2016).
B. Significance of designing and implementing PLC
Designing is beneficial aspect that supports manager in identifying root cause of mistakes
and make strategies to resolve these errors. Designing and implementing PLC support the
manager in testing the progress of the new product so that it can run in efficient manner and can
met with its objectives. This is beneficial in measuring progress of project in each phase. This
supports in reviewing project on time and find out mistakes on time. By this way individual can
make strategy for improving efficiency level of operations. PLC assists in implementing project
in systematic manner and monitoring progress in each phase.
C. Incorporation of cost saving techniques
Lean production is the technique through which cost saving technique can be
incorporated. This helps in analysing existing production process and minimizing wastage. By
using this technique manager can utilize financial resources efficiently and can minimize errors
as well. This will help the project manager in producing TV set in large amount with quality.
Procurement strategy supports in managing inventory well and control over logistic operations.
By this way company can get high quality raw material at lower cost. This helps in reducing cost
and enhancing saving of business unit (Igartua and Markuerkiaga, 2018).
D. Techniques to ensure quality, scope ad tenure in project implementation
XYZ company has to take support of various techniques in order to ensure quality and
cost. PERT is the beneficial tool that is effective in order of control over project lie cycle phases.
This assist in scheduling activities properly so that it can get completed within specified period
of time and cost as well (Martinelli and Milosevic, 2016). Critical path method is another
strategy that ensure quality, cost and tenure. By this way firm can produce high quality TV
products within specified period of time.
13
satisfy needs of consumers significantly.
Project life cycle is beneficial in order to identify interest of stakeholders in the new
project. By this way manager can communicate the progress of the entire project with them and
can raise their confidence. PLC supports in making appropriate decision for the growth of project
(Olabisi and Cox, 2016).
B. Significance of designing and implementing PLC
Designing is beneficial aspect that supports manager in identifying root cause of mistakes
and make strategies to resolve these errors. Designing and implementing PLC support the
manager in testing the progress of the new product so that it can run in efficient manner and can
met with its objectives. This is beneficial in measuring progress of project in each phase. This
supports in reviewing project on time and find out mistakes on time. By this way individual can
make strategy for improving efficiency level of operations. PLC assists in implementing project
in systematic manner and monitoring progress in each phase.
C. Incorporation of cost saving techniques
Lean production is the technique through which cost saving technique can be
incorporated. This helps in analysing existing production process and minimizing wastage. By
using this technique manager can utilize financial resources efficiently and can minimize errors
as well. This will help the project manager in producing TV set in large amount with quality.
Procurement strategy supports in managing inventory well and control over logistic operations.
By this way company can get high quality raw material at lower cost. This helps in reducing cost
and enhancing saving of business unit (Igartua and Markuerkiaga, 2018).
D. Techniques to ensure quality, scope ad tenure in project implementation
XYZ company has to take support of various techniques in order to ensure quality and
cost. PERT is the beneficial tool that is effective in order of control over project lie cycle phases.
This assist in scheduling activities properly so that it can get completed within specified period
of time and cost as well (Martinelli and Milosevic, 2016). Critical path method is another
strategy that ensure quality, cost and tenure. By this way firm can produce high quality TV
products within specified period of time.
13
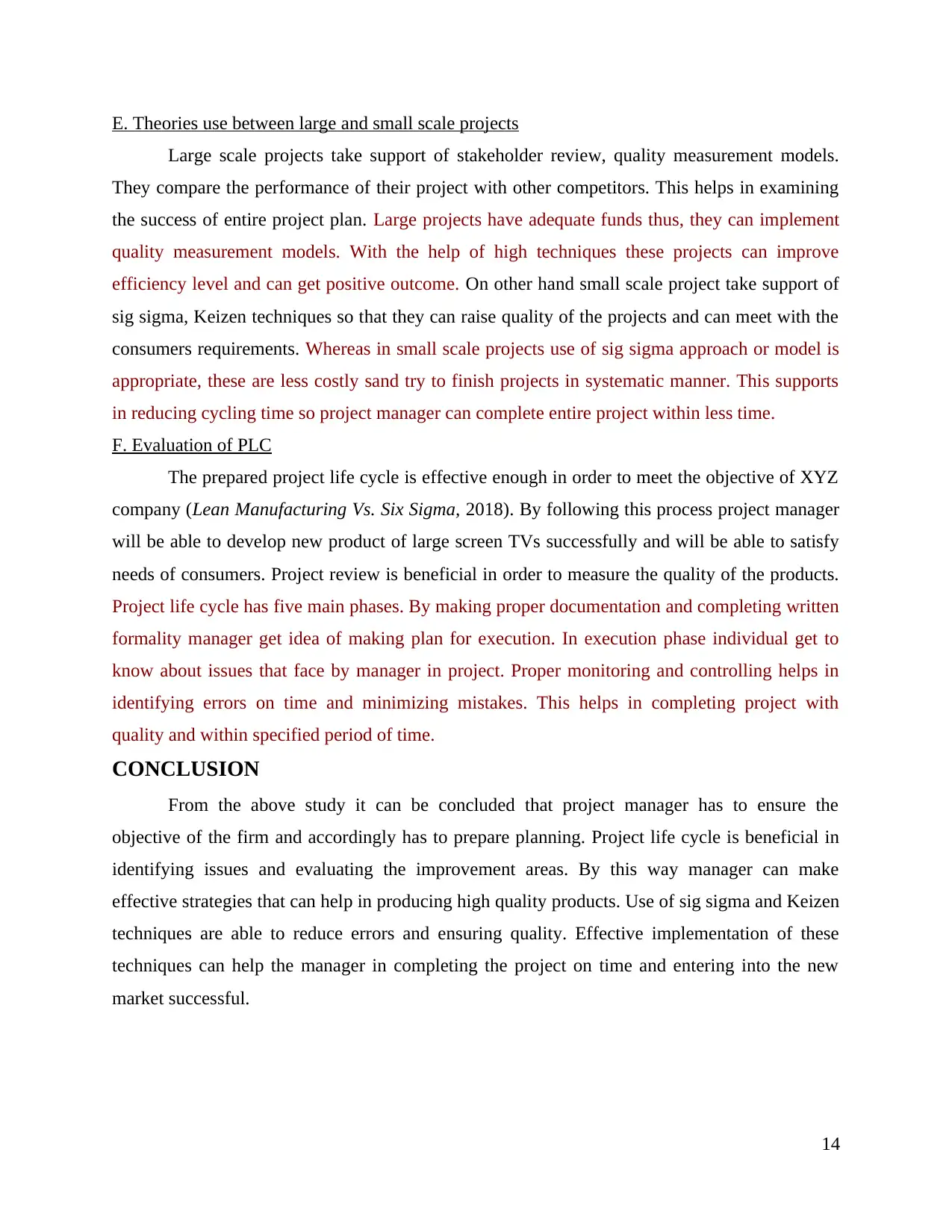
E. Theories use between large and small scale projects
Large scale projects take support of stakeholder review, quality measurement models.
They compare the performance of their project with other competitors. This helps in examining
the success of entire project plan. Large projects have adequate funds thus, they can implement
quality measurement models. With the help of high techniques these projects can improve
efficiency level and can get positive outcome. On other hand small scale project take support of
sig sigma, Keizen techniques so that they can raise quality of the projects and can meet with the
consumers requirements. Whereas in small scale projects use of sig sigma approach or model is
appropriate, these are less costly sand try to finish projects in systematic manner. This supports
in reducing cycling time so project manager can complete entire project within less time.
F. Evaluation of PLC
The prepared project life cycle is effective enough in order to meet the objective of XYZ
company (Lean Manufacturing Vs. Six Sigma, 2018). By following this process project manager
will be able to develop new product of large screen TVs successfully and will be able to satisfy
needs of consumers. Project review is beneficial in order to measure the quality of the products.
Project life cycle has five main phases. By making proper documentation and completing written
formality manager get idea of making plan for execution. In execution phase individual get to
know about issues that face by manager in project. Proper monitoring and controlling helps in
identifying errors on time and minimizing mistakes. This helps in completing project with
quality and within specified period of time.
CONCLUSION
From the above study it can be concluded that project manager has to ensure the
objective of the firm and accordingly has to prepare planning. Project life cycle is beneficial in
identifying issues and evaluating the improvement areas. By this way manager can make
effective strategies that can help in producing high quality products. Use of sig sigma and Keizen
techniques are able to reduce errors and ensuring quality. Effective implementation of these
techniques can help the manager in completing the project on time and entering into the new
market successful.
14
Large scale projects take support of stakeholder review, quality measurement models.
They compare the performance of their project with other competitors. This helps in examining
the success of entire project plan. Large projects have adequate funds thus, they can implement
quality measurement models. With the help of high techniques these projects can improve
efficiency level and can get positive outcome. On other hand small scale project take support of
sig sigma, Keizen techniques so that they can raise quality of the projects and can meet with the
consumers requirements. Whereas in small scale projects use of sig sigma approach or model is
appropriate, these are less costly sand try to finish projects in systematic manner. This supports
in reducing cycling time so project manager can complete entire project within less time.
F. Evaluation of PLC
The prepared project life cycle is effective enough in order to meet the objective of XYZ
company (Lean Manufacturing Vs. Six Sigma, 2018). By following this process project manager
will be able to develop new product of large screen TVs successfully and will be able to satisfy
needs of consumers. Project review is beneficial in order to measure the quality of the products.
Project life cycle has five main phases. By making proper documentation and completing written
formality manager get idea of making plan for execution. In execution phase individual get to
know about issues that face by manager in project. Proper monitoring and controlling helps in
identifying errors on time and minimizing mistakes. This helps in completing project with
quality and within specified period of time.
CONCLUSION
From the above study it can be concluded that project manager has to ensure the
objective of the firm and accordingly has to prepare planning. Project life cycle is beneficial in
identifying issues and evaluating the improvement areas. By this way manager can make
effective strategies that can help in producing high quality products. Use of sig sigma and Keizen
techniques are able to reduce errors and ensuring quality. Effective implementation of these
techniques can help the manager in completing the project on time and entering into the new
market successful.
14
Secure Best Marks with AI Grader
Need help grading? Try our AI Grader for instant feedback on your assignments.
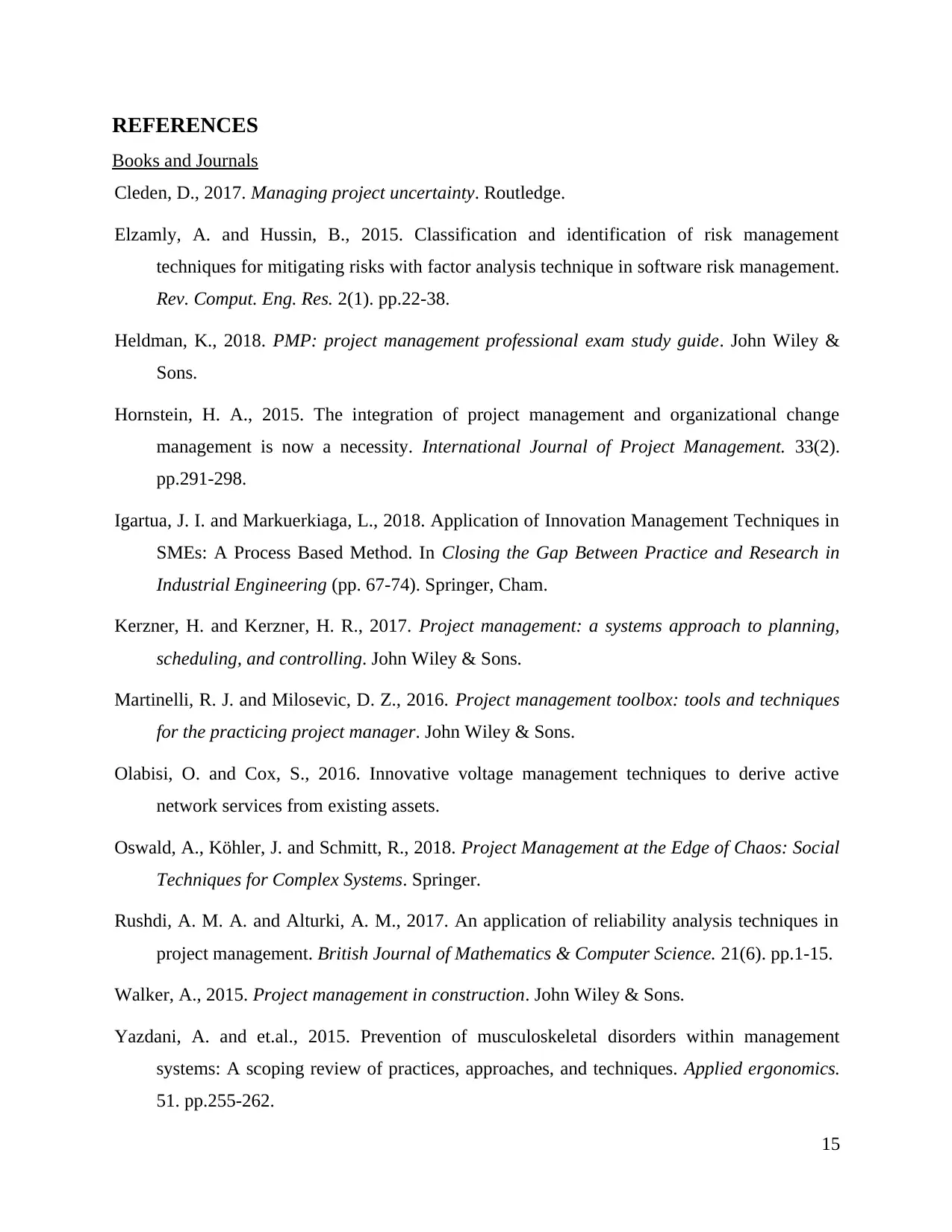
REFERENCES
Books and Journals
Cleden, D., 2017. Managing project uncertainty. Routledge.
Elzamly, A. and Hussin, B., 2015. Classification and identification of risk management
techniques for mitigating risks with factor analysis technique in software risk management.
Rev. Comput. Eng. Res. 2(1). pp.22-38.
Heldman, K., 2018. PMP: project management professional exam study guide. John Wiley &
Sons.
Hornstein, H. A., 2015. The integration of project management and organizational change
management is now a necessity. International Journal of Project Management. 33(2).
pp.291-298.
Igartua, J. I. and Markuerkiaga, L., 2018. Application of Innovation Management Techniques in
SMEs: A Process Based Method. In Closing the Gap Between Practice and Research in
Industrial Engineering (pp. 67-74). Springer, Cham.
Kerzner, H. and Kerzner, H. R., 2017. Project management: a systems approach to planning,
scheduling, and controlling. John Wiley & Sons.
Martinelli, R. J. and Milosevic, D. Z., 2016. Project management toolbox: tools and techniques
for the practicing project manager. John Wiley & Sons.
Olabisi, O. and Cox, S., 2016. Innovative voltage management techniques to derive active
network services from existing assets.
Oswald, A., Köhler, J. and Schmitt, R., 2018. Project Management at the Edge of Chaos: Social
Techniques for Complex Systems. Springer.
Rushdi, A. M. A. and Alturki, A. M., 2017. An application of reliability analysis techniques in
project management. British Journal of Mathematics & Computer Science. 21(6). pp.1-15.
Walker, A., 2015. Project management in construction. John Wiley & Sons.
Yazdani, A. and et.al., 2015. Prevention of musculoskeletal disorders within management
systems: A scoping review of practices, approaches, and techniques. Applied ergonomics.
51. pp.255-262.
15
Books and Journals
Cleden, D., 2017. Managing project uncertainty. Routledge.
Elzamly, A. and Hussin, B., 2015. Classification and identification of risk management
techniques for mitigating risks with factor analysis technique in software risk management.
Rev. Comput. Eng. Res. 2(1). pp.22-38.
Heldman, K., 2018. PMP: project management professional exam study guide. John Wiley &
Sons.
Hornstein, H. A., 2015. The integration of project management and organizational change
management is now a necessity. International Journal of Project Management. 33(2).
pp.291-298.
Igartua, J. I. and Markuerkiaga, L., 2018. Application of Innovation Management Techniques in
SMEs: A Process Based Method. In Closing the Gap Between Practice and Research in
Industrial Engineering (pp. 67-74). Springer, Cham.
Kerzner, H. and Kerzner, H. R., 2017. Project management: a systems approach to planning,
scheduling, and controlling. John Wiley & Sons.
Martinelli, R. J. and Milosevic, D. Z., 2016. Project management toolbox: tools and techniques
for the practicing project manager. John Wiley & Sons.
Olabisi, O. and Cox, S., 2016. Innovative voltage management techniques to derive active
network services from existing assets.
Oswald, A., Köhler, J. and Schmitt, R., 2018. Project Management at the Edge of Chaos: Social
Techniques for Complex Systems. Springer.
Rushdi, A. M. A. and Alturki, A. M., 2017. An application of reliability analysis techniques in
project management. British Journal of Mathematics & Computer Science. 21(6). pp.1-15.
Walker, A., 2015. Project management in construction. John Wiley & Sons.
Yazdani, A. and et.al., 2015. Prevention of musculoskeletal disorders within management
systems: A scoping review of practices, approaches, and techniques. Applied ergonomics.
51. pp.255-262.
15
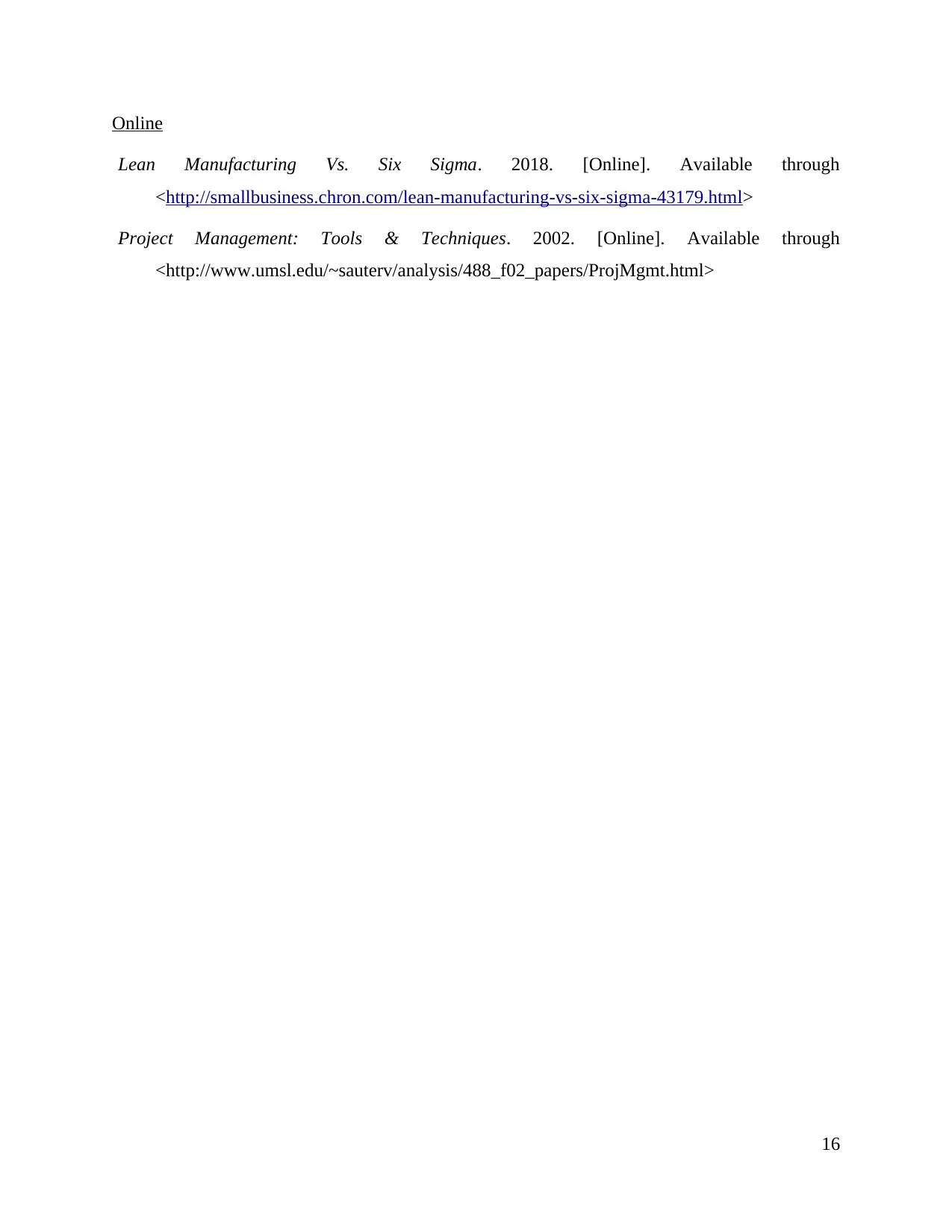
Online
Lean Manufacturing Vs. Six Sigma. 2018. [Online]. Available through
<http://smallbusiness.chron.com/lean-manufacturing-vs-six-sigma-43179.html>
Project Management: Tools & Techniques. 2002. [Online]. Available through
<http://www.umsl.edu/~sauterv/analysis/488_f02_papers/ProjMgmt.html>
16
Lean Manufacturing Vs. Six Sigma. 2018. [Online]. Available through
<http://smallbusiness.chron.com/lean-manufacturing-vs-six-sigma-43179.html>
Project Management: Tools & Techniques. 2002. [Online]. Available through
<http://www.umsl.edu/~sauterv/analysis/488_f02_papers/ProjMgmt.html>
16
1 out of 18
Related Documents

Your All-in-One AI-Powered Toolkit for Academic Success.
+13062052269
info@desklib.com
Available 24*7 on WhatsApp / Email
Unlock your academic potential
© 2024 | Zucol Services PVT LTD | All rights reserved.