Operations & Project Management Report: Warren Equipment Case Study
VerifiedAdded on 2023/06/12
|18
|5143
|148
Report
AI Summary
This report provides a comprehensive analysis of operations and project management principles at Warren Equipment, a company specializing in power generation, construction, and farming implements. It begins by differentiating between operations management and operations, followed by a review and critique of the implementation of operations management principles within the organization, including the reality principle, organizational principle, principle of change, and accountability principle. The report assesses the extent to which the operations management meets the organization's requirements, focusing on minimizing production costs, ensuring quality, and enhancing productivity. It discusses continuous improvement as a philosophy, describing Lean principles such as Six Sigma, and proposes a continuous improvement plan with recommendations for improvement. The report also analyzes project methodologies and tools used by Warren Equipment, evaluates the effectiveness of the project life cycle (PLC), and differentiates between large and small-scale projects in the context of PLC application.
Contribute Materials
Your contribution can guide someone’s learning journey. Share your
documents today.
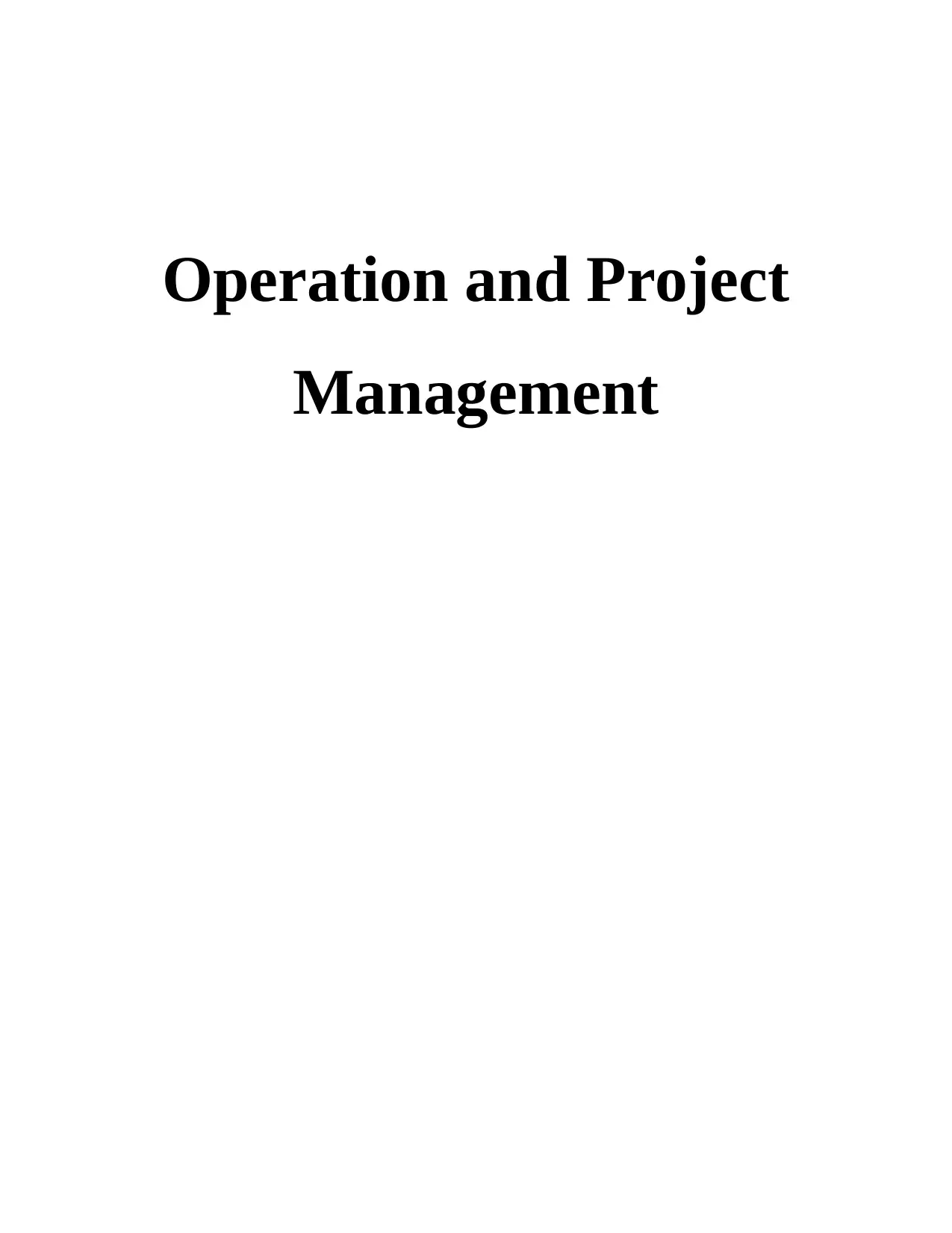
Operation and Project
Management
Management
Secure Best Marks with AI Grader
Need help grading? Try our AI Grader for instant feedback on your assignments.
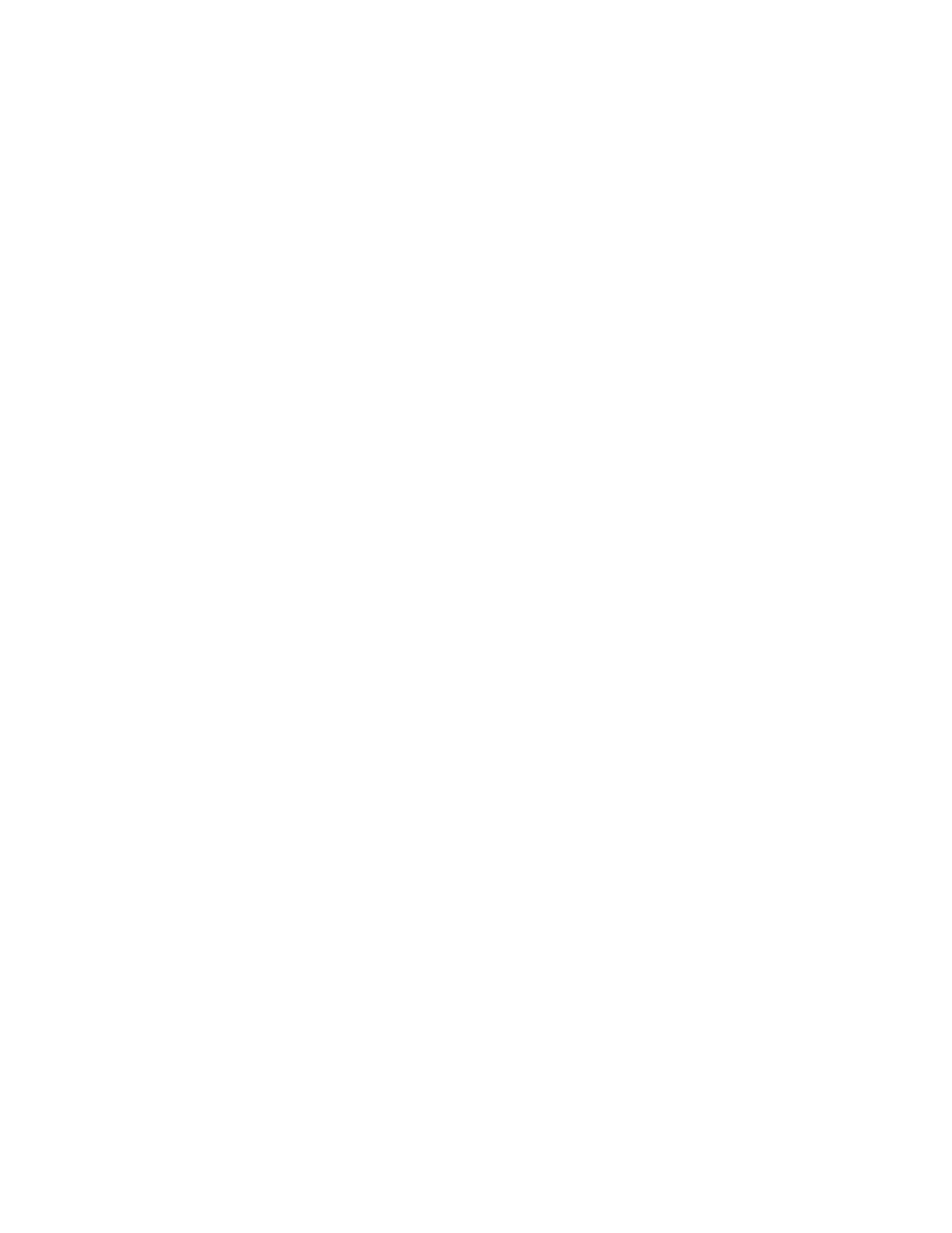
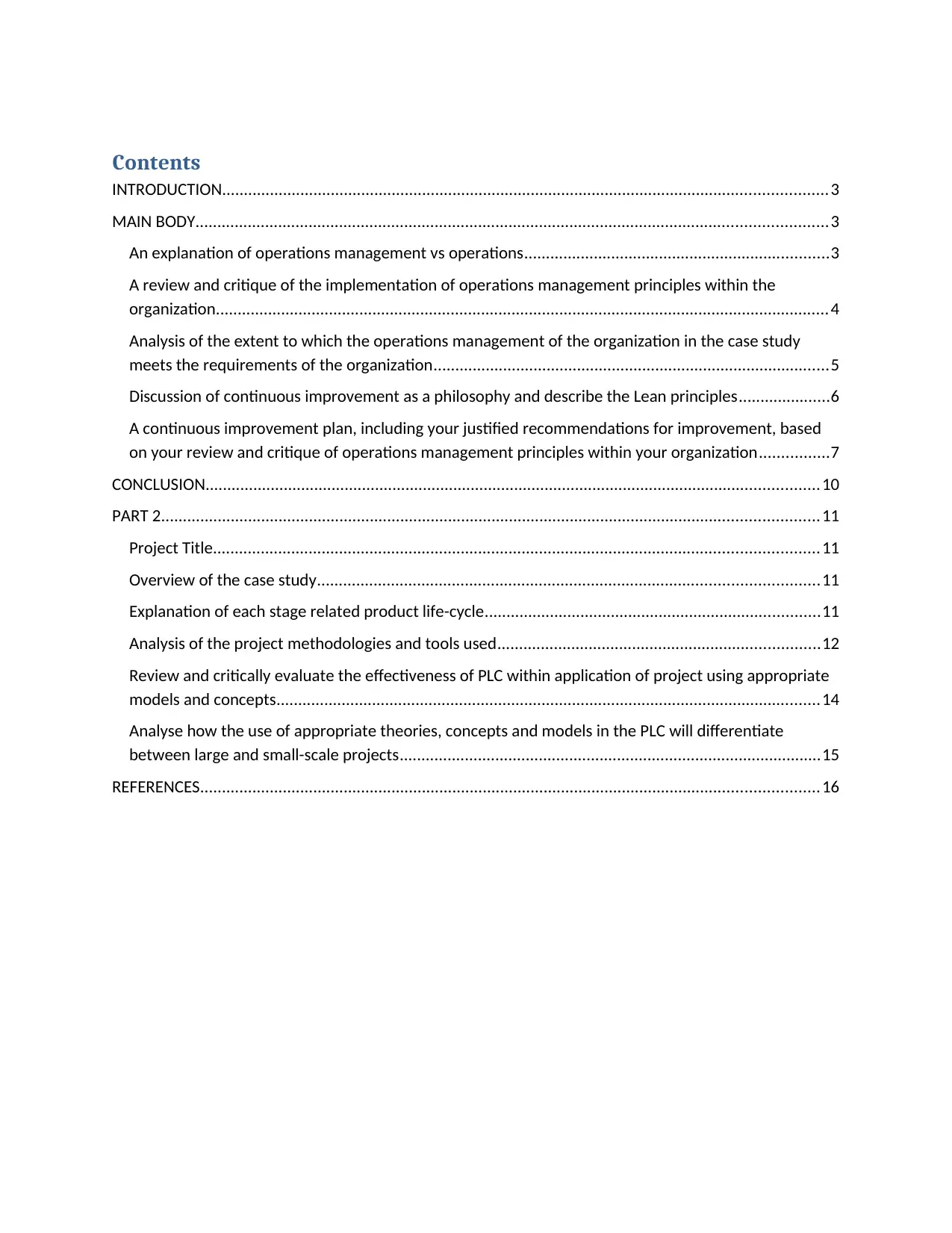
Contents
INTRODUCTION...........................................................................................................................................3
MAIN BODY.................................................................................................................................................3
An explanation of operations management vs operations......................................................................3
A review and critique of the implementation of operations management principles within the
organization.............................................................................................................................................4
Analysis of the extent to which the operations management of the organization in the case study
meets the requirements of the organization...........................................................................................5
Discussion of continuous improvement as a philosophy and describe the Lean principles.....................6
A continuous improvement plan, including your justified recommendations for improvement, based
on your review and critique of operations management principles within your organization................7
CONCLUSION.............................................................................................................................................10
PART 2.......................................................................................................................................................11
Project Title...........................................................................................................................................11
Overview of the case study...................................................................................................................11
Explanation of each stage related product life-cycle.............................................................................11
Analysis of the project methodologies and tools used..........................................................................12
Review and critically evaluate the effectiveness of PLC within application of project using appropriate
models and concepts.............................................................................................................................14
Analyse how the use of appropriate theories, concepts and models in the PLC will differentiate
between large and small-scale projects.................................................................................................15
REFERENCES..............................................................................................................................................16
INTRODUCTION...........................................................................................................................................3
MAIN BODY.................................................................................................................................................3
An explanation of operations management vs operations......................................................................3
A review and critique of the implementation of operations management principles within the
organization.............................................................................................................................................4
Analysis of the extent to which the operations management of the organization in the case study
meets the requirements of the organization...........................................................................................5
Discussion of continuous improvement as a philosophy and describe the Lean principles.....................6
A continuous improvement plan, including your justified recommendations for improvement, based
on your review and critique of operations management principles within your organization................7
CONCLUSION.............................................................................................................................................10
PART 2.......................................................................................................................................................11
Project Title...........................................................................................................................................11
Overview of the case study...................................................................................................................11
Explanation of each stage related product life-cycle.............................................................................11
Analysis of the project methodologies and tools used..........................................................................12
Review and critically evaluate the effectiveness of PLC within application of project using appropriate
models and concepts.............................................................................................................................14
Analyse how the use of appropriate theories, concepts and models in the PLC will differentiate
between large and small-scale projects.................................................................................................15
REFERENCES..............................................................................................................................................16
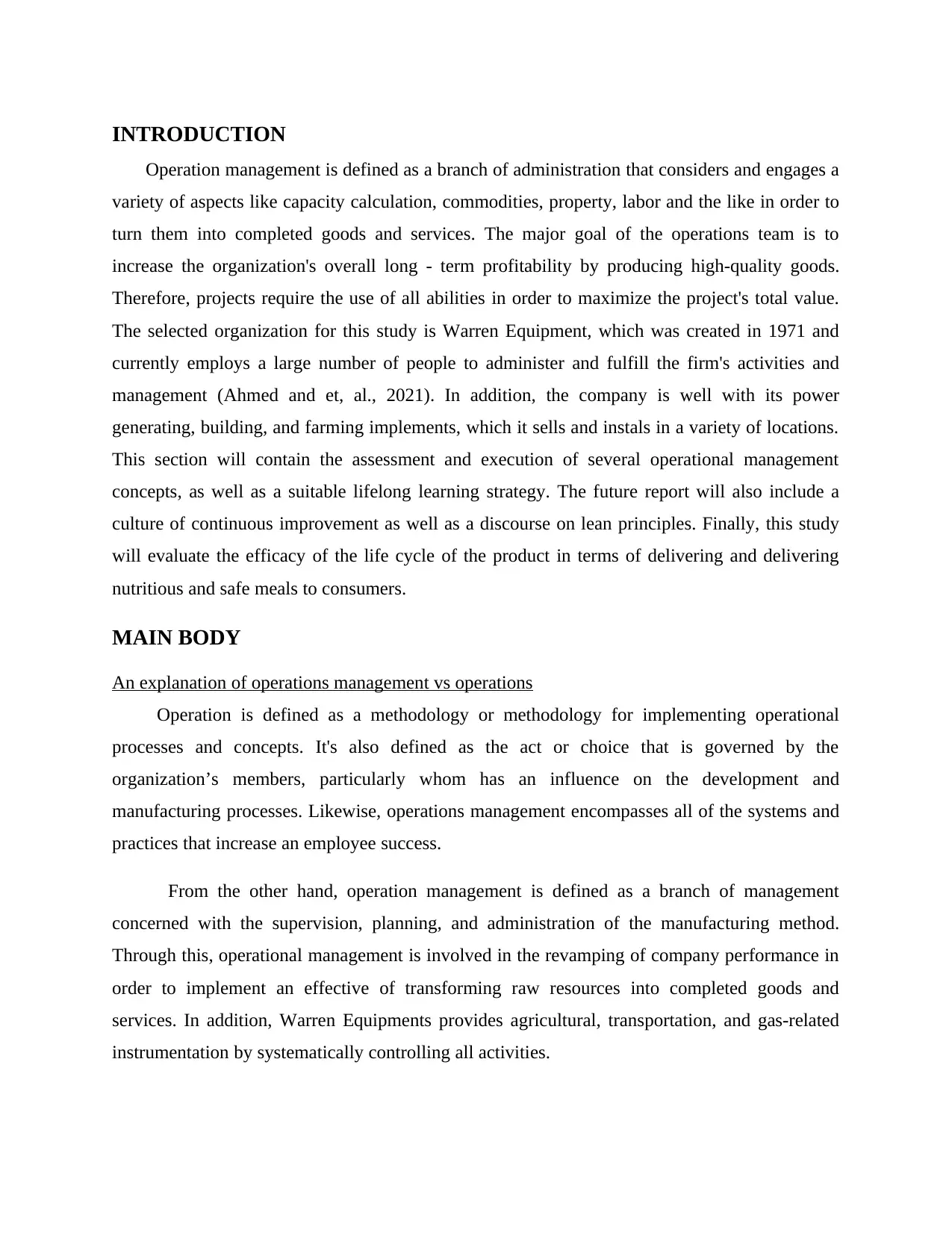
INTRODUCTION
Operation management is defined as a branch of administration that considers and engages a
variety of aspects like capacity calculation, commodities, property, labor and the like in order to
turn them into completed goods and services. The major goal of the operations team is to
increase the organization's overall long - term profitability by producing high-quality goods.
Therefore, projects require the use of all abilities in order to maximize the project's total value.
The selected organization for this study is Warren Equipment, which was created in 1971 and
currently employs a large number of people to administer and fulfill the firm's activities and
management (Ahmed and et, al., 2021). In addition, the company is well with its power
generating, building, and farming implements, which it sells and instals in a variety of locations.
This section will contain the assessment and execution of several operational management
concepts, as well as a suitable lifelong learning strategy. The future report will also include a
culture of continuous improvement as well as a discourse on lean principles. Finally, this study
will evaluate the efficacy of the life cycle of the product in terms of delivering and delivering
nutritious and safe meals to consumers.
MAIN BODY
An explanation of operations management vs operations
Operation is defined as a methodology or methodology for implementing operational
processes and concepts. It's also defined as the act or choice that is governed by the
organization’s members, particularly whom has an influence on the development and
manufacturing processes. Likewise, operations management encompasses all of the systems and
practices that increase an employee success.
From the other hand, operation management is defined as a branch of management
concerned with the supervision, planning, and administration of the manufacturing method.
Through this, operational management is involved in the revamping of company performance in
order to implement an effective of transforming raw resources into completed goods and
services. In addition, Warren Equipments provides agricultural, transportation, and gas-related
instrumentation by systematically controlling all activities.
Operation management is defined as a branch of administration that considers and engages a
variety of aspects like capacity calculation, commodities, property, labor and the like in order to
turn them into completed goods and services. The major goal of the operations team is to
increase the organization's overall long - term profitability by producing high-quality goods.
Therefore, projects require the use of all abilities in order to maximize the project's total value.
The selected organization for this study is Warren Equipment, which was created in 1971 and
currently employs a large number of people to administer and fulfill the firm's activities and
management (Ahmed and et, al., 2021). In addition, the company is well with its power
generating, building, and farming implements, which it sells and instals in a variety of locations.
This section will contain the assessment and execution of several operational management
concepts, as well as a suitable lifelong learning strategy. The future report will also include a
culture of continuous improvement as well as a discourse on lean principles. Finally, this study
will evaluate the efficacy of the life cycle of the product in terms of delivering and delivering
nutritious and safe meals to consumers.
MAIN BODY
An explanation of operations management vs operations
Operation is defined as a methodology or methodology for implementing operational
processes and concepts. It's also defined as the act or choice that is governed by the
organization’s members, particularly whom has an influence on the development and
manufacturing processes. Likewise, operations management encompasses all of the systems and
practices that increase an employee success.
From the other hand, operation management is defined as a branch of management
concerned with the supervision, planning, and administration of the manufacturing method.
Through this, operational management is involved in the revamping of company performance in
order to implement an effective of transforming raw resources into completed goods and
services. In addition, Warren Equipments provides agricultural, transportation, and gas-related
instrumentation by systematically controlling all activities.
Secure Best Marks with AI Grader
Need help grading? Try our AI Grader for instant feedback on your assignments.
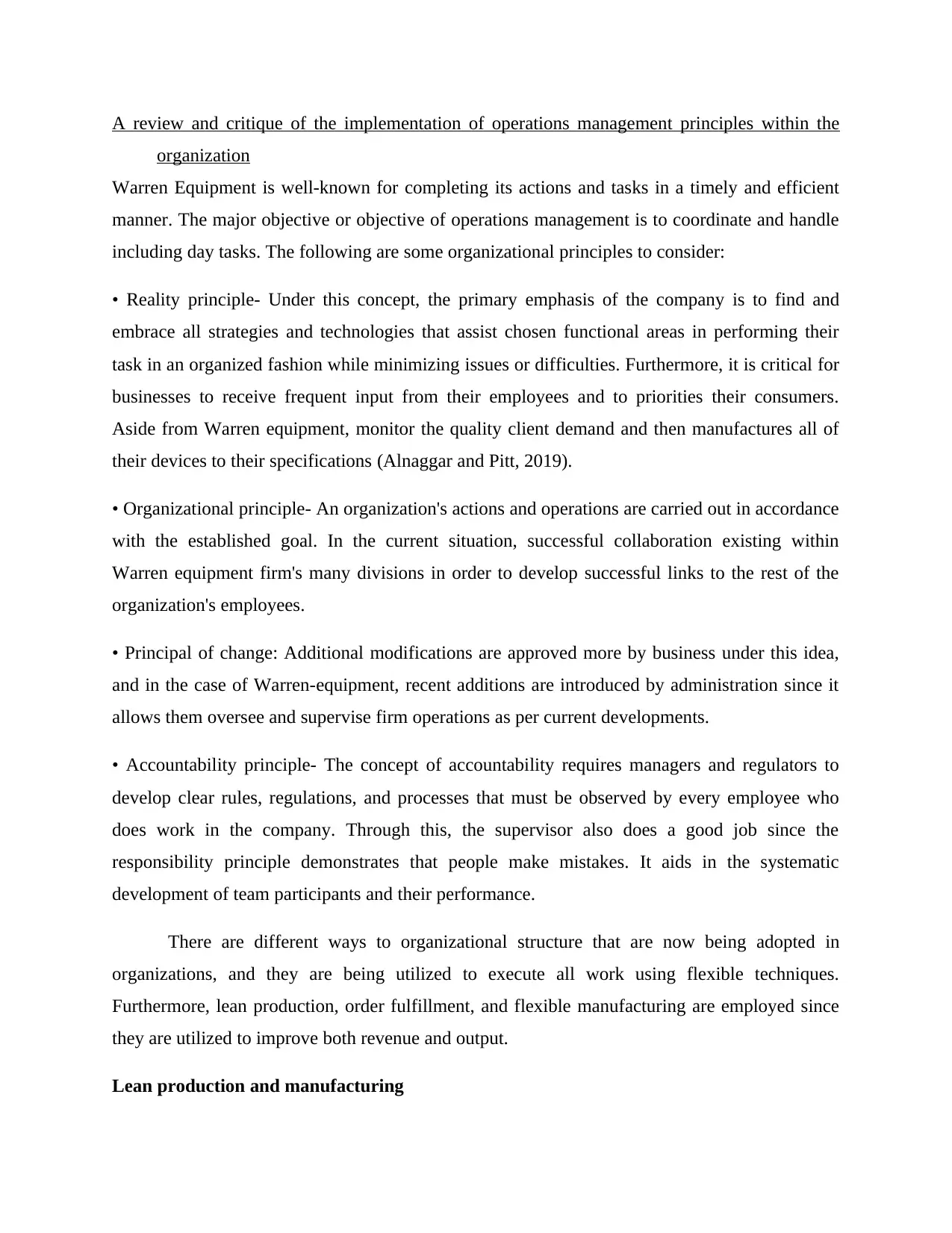
A review and critique of the implementation of operations management principles within the
organization
Warren Equipment is well-known for completing its actions and tasks in a timely and efficient
manner. The major objective or objective of operations management is to coordinate and handle
including day tasks. The following are some organizational principles to consider:
• Reality principle- Under this concept, the primary emphasis of the company is to find and
embrace all strategies and technologies that assist chosen functional areas in performing their
task in an organized fashion while minimizing issues or difficulties. Furthermore, it is critical for
businesses to receive frequent input from their employees and to priorities their consumers.
Aside from Warren equipment, monitor the quality client demand and then manufactures all of
their devices to their specifications (Alnaggar and Pitt, 2019).
• Organizational principle- An organization's actions and operations are carried out in accordance
with the established goal. In the current situation, successful collaboration existing within
Warren equipment firm's many divisions in order to develop successful links to the rest of the
organization's employees.
• Principal of change: Additional modifications are approved more by business under this idea,
and in the case of Warren-equipment, recent additions are introduced by administration since it
allows them oversee and supervise firm operations as per current developments.
• Accountability principle- The concept of accountability requires managers and regulators to
develop clear rules, regulations, and processes that must be observed by every employee who
does work in the company. Through this, the supervisor also does a good job since the
responsibility principle demonstrates that people make mistakes. It aids in the systematic
development of team participants and their performance.
There are different ways to organizational structure that are now being adopted in
organizations, and they are being utilized to execute all work using flexible techniques.
Furthermore, lean production, order fulfillment, and flexible manufacturing are employed since
they are utilized to improve both revenue and output.
Lean production and manufacturing
organization
Warren Equipment is well-known for completing its actions and tasks in a timely and efficient
manner. The major objective or objective of operations management is to coordinate and handle
including day tasks. The following are some organizational principles to consider:
• Reality principle- Under this concept, the primary emphasis of the company is to find and
embrace all strategies and technologies that assist chosen functional areas in performing their
task in an organized fashion while minimizing issues or difficulties. Furthermore, it is critical for
businesses to receive frequent input from their employees and to priorities their consumers.
Aside from Warren equipment, monitor the quality client demand and then manufactures all of
their devices to their specifications (Alnaggar and Pitt, 2019).
• Organizational principle- An organization's actions and operations are carried out in accordance
with the established goal. In the current situation, successful collaboration existing within
Warren equipment firm's many divisions in order to develop successful links to the rest of the
organization's employees.
• Principal of change: Additional modifications are approved more by business under this idea,
and in the case of Warren-equipment, recent additions are introduced by administration since it
allows them oversee and supervise firm operations as per current developments.
• Accountability principle- The concept of accountability requires managers and regulators to
develop clear rules, regulations, and processes that must be observed by every employee who
does work in the company. Through this, the supervisor also does a good job since the
responsibility principle demonstrates that people make mistakes. It aids in the systematic
development of team participants and their performance.
There are different ways to organizational structure that are now being adopted in
organizations, and they are being utilized to execute all work using flexible techniques.
Furthermore, lean production, order fulfillment, and flexible manufacturing are employed since
they are utilized to improve both revenue and output.
Lean production and manufacturing
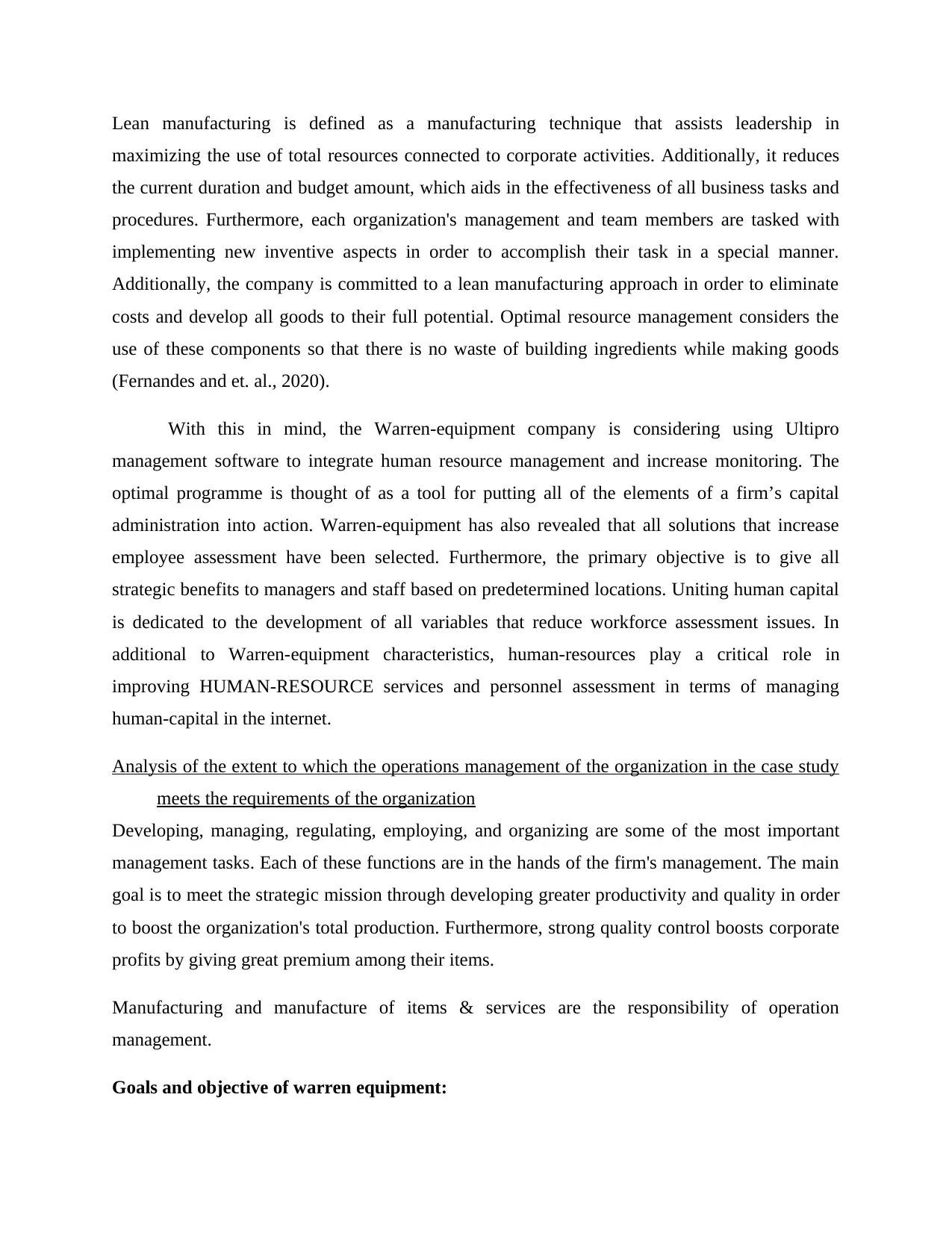
Lean manufacturing is defined as a manufacturing technique that assists leadership in
maximizing the use of total resources connected to corporate activities. Additionally, it reduces
the current duration and budget amount, which aids in the effectiveness of all business tasks and
procedures. Furthermore, each organization's management and team members are tasked with
implementing new inventive aspects in order to accomplish their task in a special manner.
Additionally, the company is committed to a lean manufacturing approach in order to eliminate
costs and develop all goods to their full potential. Optimal resource management considers the
use of these components so that there is no waste of building ingredients while making goods
(Fernandes and et. al., 2020).
With this in mind, the Warren-equipment company is considering using Ultipro
management software to integrate human resource management and increase monitoring. The
optimal programme is thought of as a tool for putting all of the elements of a firm’s capital
administration into action. Warren-equipment has also revealed that all solutions that increase
employee assessment have been selected. Furthermore, the primary objective is to give all
strategic benefits to managers and staff based on predetermined locations. Uniting human capital
is dedicated to the development of all variables that reduce workforce assessment issues. In
additional to Warren-equipment characteristics, human-resources play a critical role in
improving HUMAN-RESOURCE services and personnel assessment in terms of managing
human-capital in the internet.
Analysis of the extent to which the operations management of the organization in the case study
meets the requirements of the organization
Developing, managing, regulating, employing, and organizing are some of the most important
management tasks. Each of these functions are in the hands of the firm's management. The main
goal is to meet the strategic mission through developing greater productivity and quality in order
to boost the organization's total production. Furthermore, strong quality control boosts corporate
profits by giving great premium among their items.
Manufacturing and manufacture of items & services are the responsibility of operation
management.
Goals and objective of warren equipment:
maximizing the use of total resources connected to corporate activities. Additionally, it reduces
the current duration and budget amount, which aids in the effectiveness of all business tasks and
procedures. Furthermore, each organization's management and team members are tasked with
implementing new inventive aspects in order to accomplish their task in a special manner.
Additionally, the company is committed to a lean manufacturing approach in order to eliminate
costs and develop all goods to their full potential. Optimal resource management considers the
use of these components so that there is no waste of building ingredients while making goods
(Fernandes and et. al., 2020).
With this in mind, the Warren-equipment company is considering using Ultipro
management software to integrate human resource management and increase monitoring. The
optimal programme is thought of as a tool for putting all of the elements of a firm’s capital
administration into action. Warren-equipment has also revealed that all solutions that increase
employee assessment have been selected. Furthermore, the primary objective is to give all
strategic benefits to managers and staff based on predetermined locations. Uniting human capital
is dedicated to the development of all variables that reduce workforce assessment issues. In
additional to Warren-equipment characteristics, human-resources play a critical role in
improving HUMAN-RESOURCE services and personnel assessment in terms of managing
human-capital in the internet.
Analysis of the extent to which the operations management of the organization in the case study
meets the requirements of the organization
Developing, managing, regulating, employing, and organizing are some of the most important
management tasks. Each of these functions are in the hands of the firm's management. The main
goal is to meet the strategic mission through developing greater productivity and quality in order
to boost the organization's total production. Furthermore, strong quality control boosts corporate
profits by giving great premium among their items.
Manufacturing and manufacture of items & services are the responsibility of operation
management.
Goals and objective of warren equipment:
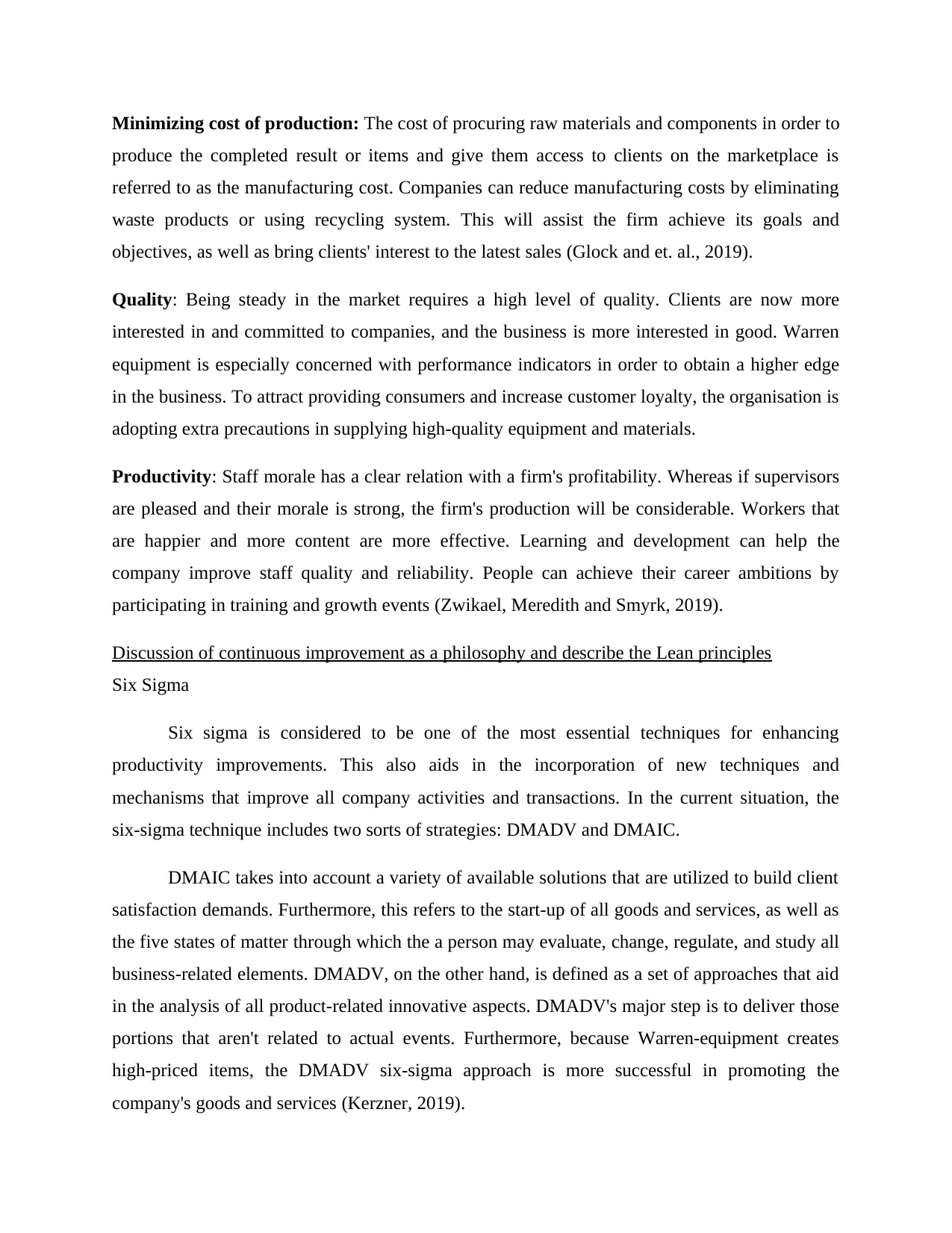
Minimizing cost of production: The cost of procuring raw materials and components in order to
produce the completed result or items and give them access to clients on the marketplace is
referred to as the manufacturing cost. Companies can reduce manufacturing costs by eliminating
waste products or using recycling system. This will assist the firm achieve its goals and
objectives, as well as bring clients' interest to the latest sales (Glock and et. al., 2019).
Quality: Being steady in the market requires a high level of quality. Clients are now more
interested in and committed to companies, and the business is more interested in good. Warren
equipment is especially concerned with performance indicators in order to obtain a higher edge
in the business. To attract providing consumers and increase customer loyalty, the organisation is
adopting extra precautions in supplying high-quality equipment and materials.
Productivity: Staff morale has a clear relation with a firm's profitability. Whereas if supervisors
are pleased and their morale is strong, the firm's production will be considerable. Workers that
are happier and more content are more effective. Learning and development can help the
company improve staff quality and reliability. People can achieve their career ambitions by
participating in training and growth events (Zwikael, Meredith and Smyrk, 2019).
Discussion of continuous improvement as a philosophy and describe the Lean principles
Six Sigma
Six sigma is considered to be one of the most essential techniques for enhancing
productivity improvements. This also aids in the incorporation of new techniques and
mechanisms that improve all company activities and transactions. In the current situation, the
six-sigma technique includes two sorts of strategies: DMADV and DMAIC.
DMAIC takes into account a variety of available solutions that are utilized to build client
satisfaction demands. Furthermore, this refers to the start-up of all goods and services, as well as
the five states of matter through which the a person may evaluate, change, regulate, and study all
business-related elements. DMADV, on the other hand, is defined as a set of approaches that aid
in the analysis of all product-related innovative aspects. DMADV's major step is to deliver those
portions that aren't related to actual events. Furthermore, because Warren-equipment creates
high-priced items, the DMADV six-sigma approach is more successful in promoting the
company's goods and services (Kerzner, 2019).
produce the completed result or items and give them access to clients on the marketplace is
referred to as the manufacturing cost. Companies can reduce manufacturing costs by eliminating
waste products or using recycling system. This will assist the firm achieve its goals and
objectives, as well as bring clients' interest to the latest sales (Glock and et. al., 2019).
Quality: Being steady in the market requires a high level of quality. Clients are now more
interested in and committed to companies, and the business is more interested in good. Warren
equipment is especially concerned with performance indicators in order to obtain a higher edge
in the business. To attract providing consumers and increase customer loyalty, the organisation is
adopting extra precautions in supplying high-quality equipment and materials.
Productivity: Staff morale has a clear relation with a firm's profitability. Whereas if supervisors
are pleased and their morale is strong, the firm's production will be considerable. Workers that
are happier and more content are more effective. Learning and development can help the
company improve staff quality and reliability. People can achieve their career ambitions by
participating in training and growth events (Zwikael, Meredith and Smyrk, 2019).
Discussion of continuous improvement as a philosophy and describe the Lean principles
Six Sigma
Six sigma is considered to be one of the most essential techniques for enhancing
productivity improvements. This also aids in the incorporation of new techniques and
mechanisms that improve all company activities and transactions. In the current situation, the
six-sigma technique includes two sorts of strategies: DMADV and DMAIC.
DMAIC takes into account a variety of available solutions that are utilized to build client
satisfaction demands. Furthermore, this refers to the start-up of all goods and services, as well as
the five states of matter through which the a person may evaluate, change, regulate, and study all
business-related elements. DMADV, on the other hand, is defined as a set of approaches that aid
in the analysis of all product-related innovative aspects. DMADV's major step is to deliver those
portions that aren't related to actual events. Furthermore, because Warren-equipment creates
high-priced items, the DMADV six-sigma approach is more successful in promoting the
company's goods and services (Kerzner, 2019).
Paraphrase This Document
Need a fresh take? Get an instant paraphrase of this document with our AI Paraphraser
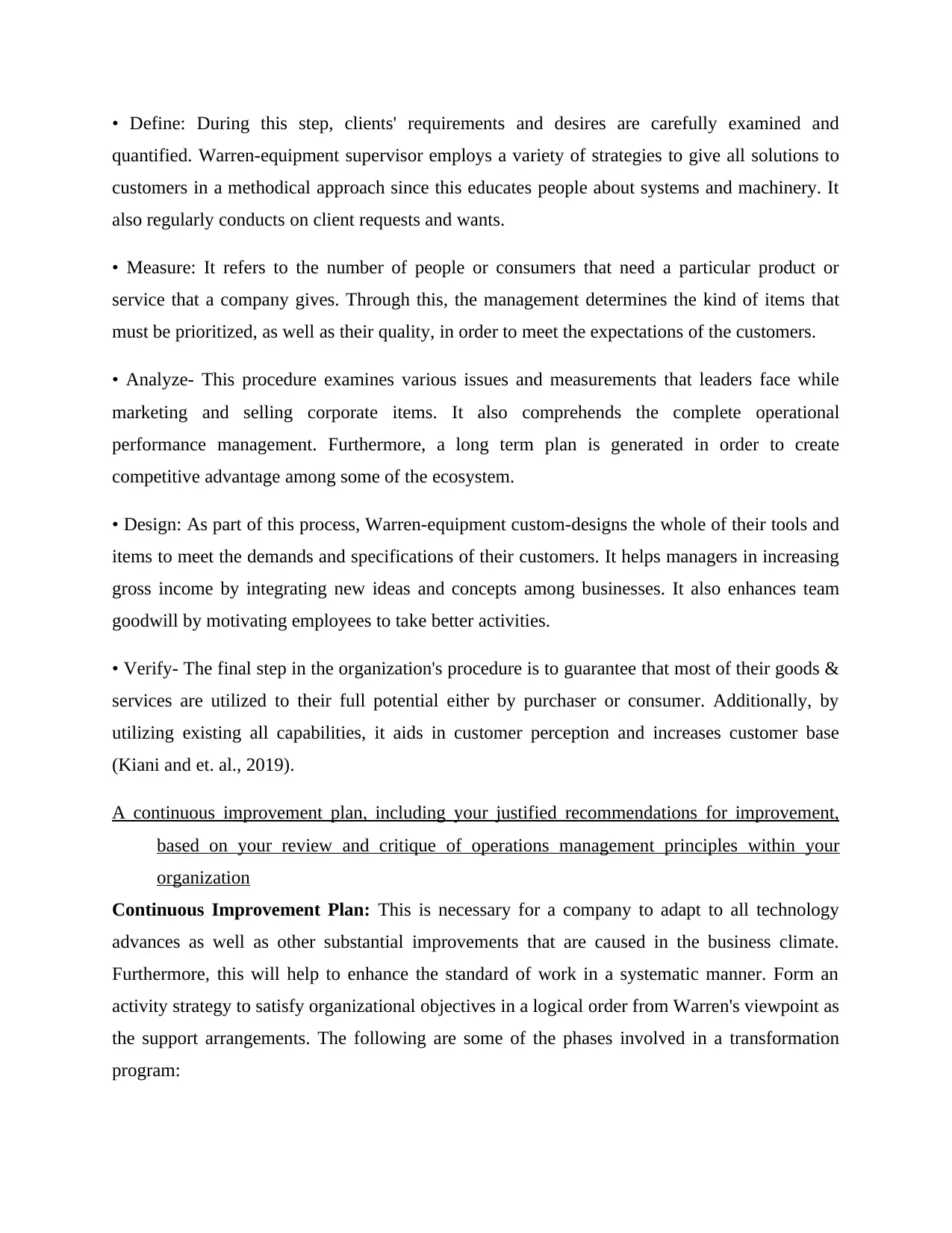
• Define: During this step, clients' requirements and desires are carefully examined and
quantified. Warren-equipment supervisor employs a variety of strategies to give all solutions to
customers in a methodical approach since this educates people about systems and machinery. It
also regularly conducts on client requests and wants.
• Measure: It refers to the number of people or consumers that need a particular product or
service that a company gives. Through this, the management determines the kind of items that
must be prioritized, as well as their quality, in order to meet the expectations of the customers.
• Analyze- This procedure examines various issues and measurements that leaders face while
marketing and selling corporate items. It also comprehends the complete operational
performance management. Furthermore, a long term plan is generated in order to create
competitive advantage among some of the ecosystem.
• Design: As part of this process, Warren-equipment custom-designs the whole of their tools and
items to meet the demands and specifications of their customers. It helps managers in increasing
gross income by integrating new ideas and concepts among businesses. It also enhances team
goodwill by motivating employees to take better activities.
• Verify- The final step in the organization's procedure is to guarantee that most of their goods &
services are utilized to their full potential either by purchaser or consumer. Additionally, by
utilizing existing all capabilities, it aids in customer perception and increases customer base
(Kiani and et. al., 2019).
A continuous improvement plan, including your justified recommendations for improvement,
based on your review and critique of operations management principles within your
organization
Continuous Improvement Plan: This is necessary for a company to adapt to all technology
advances as well as other substantial improvements that are caused in the business climate.
Furthermore, this will help to enhance the standard of work in a systematic manner. Form an
activity strategy to satisfy organizational objectives in a logical order from Warren's viewpoint as
the support arrangements. The following are some of the phases involved in a transformation
program:
quantified. Warren-equipment supervisor employs a variety of strategies to give all solutions to
customers in a methodical approach since this educates people about systems and machinery. It
also regularly conducts on client requests and wants.
• Measure: It refers to the number of people or consumers that need a particular product or
service that a company gives. Through this, the management determines the kind of items that
must be prioritized, as well as their quality, in order to meet the expectations of the customers.
• Analyze- This procedure examines various issues and measurements that leaders face while
marketing and selling corporate items. It also comprehends the complete operational
performance management. Furthermore, a long term plan is generated in order to create
competitive advantage among some of the ecosystem.
• Design: As part of this process, Warren-equipment custom-designs the whole of their tools and
items to meet the demands and specifications of their customers. It helps managers in increasing
gross income by integrating new ideas and concepts among businesses. It also enhances team
goodwill by motivating employees to take better activities.
• Verify- The final step in the organization's procedure is to guarantee that most of their goods &
services are utilized to their full potential either by purchaser or consumer. Additionally, by
utilizing existing all capabilities, it aids in customer perception and increases customer base
(Kiani and et. al., 2019).
A continuous improvement plan, including your justified recommendations for improvement,
based on your review and critique of operations management principles within your
organization
Continuous Improvement Plan: This is necessary for a company to adapt to all technology
advances as well as other substantial improvements that are caused in the business climate.
Furthermore, this will help to enhance the standard of work in a systematic manner. Form an
activity strategy to satisfy organizational objectives in a logical order from Warren's viewpoint as
the support arrangements. The following are some of the phases involved in a transformation
program:
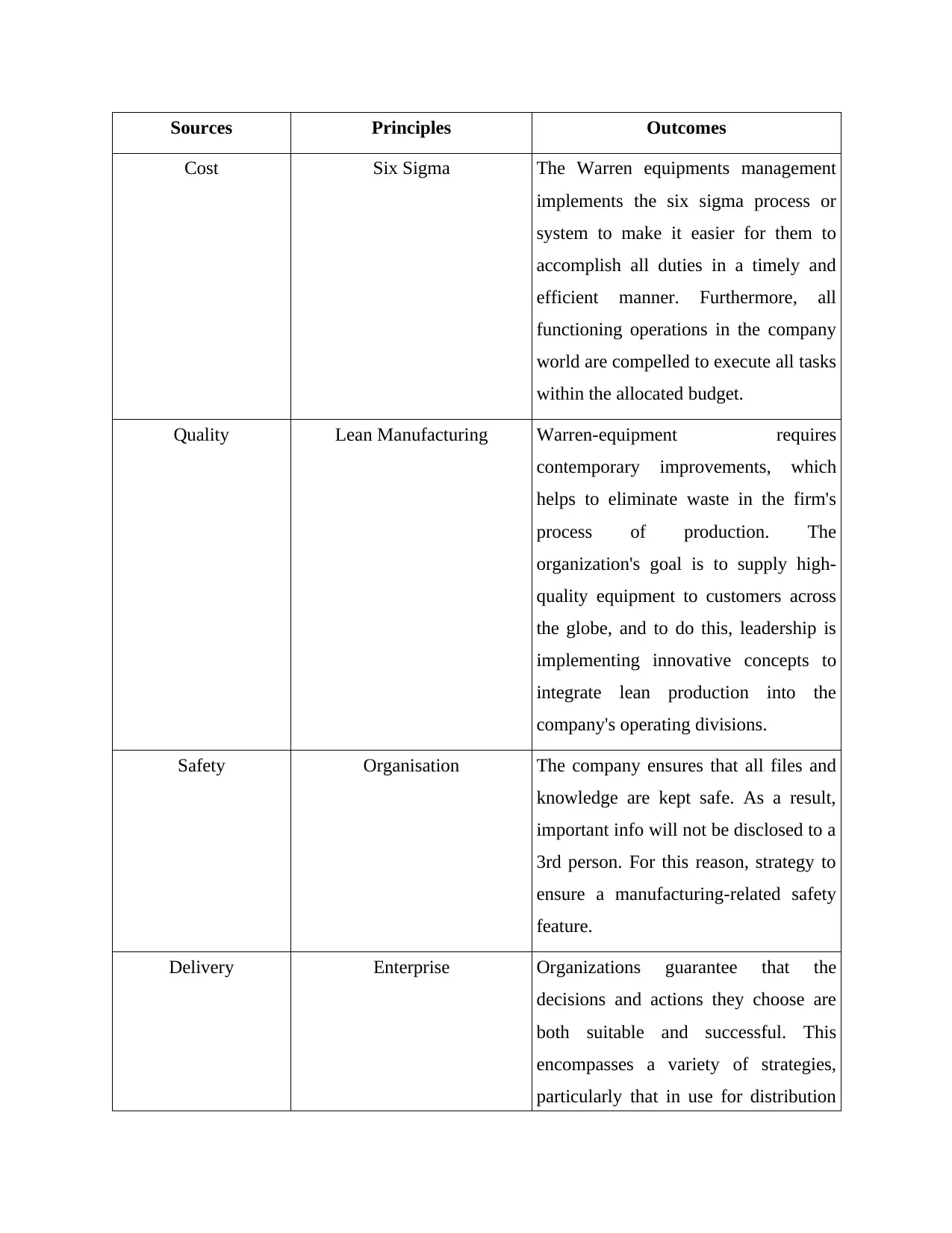
Sources Principles Outcomes
Cost Six Sigma The Warren equipments management
implements the six sigma process or
system to make it easier for them to
accomplish all duties in a timely and
efficient manner. Furthermore, all
functioning operations in the company
world are compelled to execute all tasks
within the allocated budget.
Quality Lean Manufacturing Warren-equipment requires
contemporary improvements, which
helps to eliminate waste in the firm's
process of production. The
organization's goal is to supply high-
quality equipment to customers across
the globe, and to do this, leadership is
implementing innovative concepts to
integrate lean production into the
company's operating divisions.
Safety Organisation The company ensures that all files and
knowledge are kept safe. As a result,
important info will not be disclosed to a
3rd person. For this reason, strategy to
ensure a manufacturing-related safety
feature.
Delivery Enterprise Organizations guarantee that the
decisions and actions they choose are
both suitable and successful. This
encompasses a variety of strategies,
particularly that in use for distribution
Cost Six Sigma The Warren equipments management
implements the six sigma process or
system to make it easier for them to
accomplish all duties in a timely and
efficient manner. Furthermore, all
functioning operations in the company
world are compelled to execute all tasks
within the allocated budget.
Quality Lean Manufacturing Warren-equipment requires
contemporary improvements, which
helps to eliminate waste in the firm's
process of production. The
organization's goal is to supply high-
quality equipment to customers across
the globe, and to do this, leadership is
implementing innovative concepts to
integrate lean production into the
company's operating divisions.
Safety Organisation The company ensures that all files and
knowledge are kept safe. As a result,
important info will not be disclosed to a
3rd person. For this reason, strategy to
ensure a manufacturing-related safety
feature.
Delivery Enterprise Organizations guarantee that the
decisions and actions they choose are
both suitable and successful. This
encompasses a variety of strategies,
particularly that in use for distribution
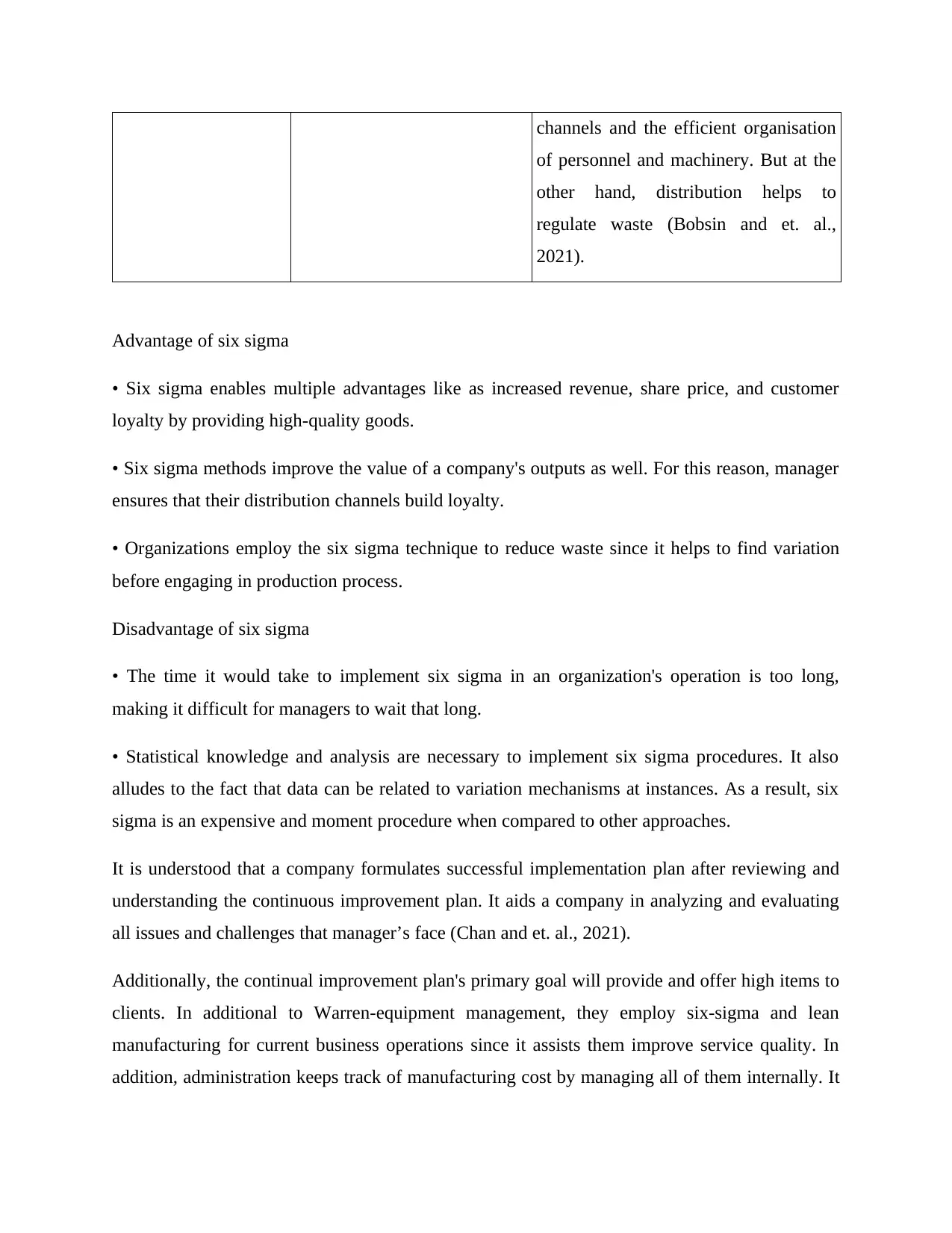
channels and the efficient organisation
of personnel and machinery. But at the
other hand, distribution helps to
regulate waste (Bobsin and et. al.,
2021).
Advantage of six sigma
• Six sigma enables multiple advantages like as increased revenue, share price, and customer
loyalty by providing high-quality goods.
• Six sigma methods improve the value of a company's outputs as well. For this reason, manager
ensures that their distribution channels build loyalty.
• Organizations employ the six sigma technique to reduce waste since it helps to find variation
before engaging in production process.
Disadvantage of six sigma
• The time it would take to implement six sigma in an organization's operation is too long,
making it difficult for managers to wait that long.
• Statistical knowledge and analysis are necessary to implement six sigma procedures. It also
alludes to the fact that data can be related to variation mechanisms at instances. As a result, six
sigma is an expensive and moment procedure when compared to other approaches.
It is understood that a company formulates successful implementation plan after reviewing and
understanding the continuous improvement plan. It aids a company in analyzing and evaluating
all issues and challenges that manager’s face (Chan and et. al., 2021).
Additionally, the continual improvement plan's primary goal will provide and offer high items to
clients. In additional to Warren-equipment management, they employ six-sigma and lean
manufacturing for current business operations since it assists them improve service quality. In
addition, administration keeps track of manufacturing cost by managing all of them internally. It
of personnel and machinery. But at the
other hand, distribution helps to
regulate waste (Bobsin and et. al.,
2021).
Advantage of six sigma
• Six sigma enables multiple advantages like as increased revenue, share price, and customer
loyalty by providing high-quality goods.
• Six sigma methods improve the value of a company's outputs as well. For this reason, manager
ensures that their distribution channels build loyalty.
• Organizations employ the six sigma technique to reduce waste since it helps to find variation
before engaging in production process.
Disadvantage of six sigma
• The time it would take to implement six sigma in an organization's operation is too long,
making it difficult for managers to wait that long.
• Statistical knowledge and analysis are necessary to implement six sigma procedures. It also
alludes to the fact that data can be related to variation mechanisms at instances. As a result, six
sigma is an expensive and moment procedure when compared to other approaches.
It is understood that a company formulates successful implementation plan after reviewing and
understanding the continuous improvement plan. It aids a company in analyzing and evaluating
all issues and challenges that manager’s face (Chan and et. al., 2021).
Additionally, the continual improvement plan's primary goal will provide and offer high items to
clients. In additional to Warren-equipment management, they employ six-sigma and lean
manufacturing for current business operations since it assists them improve service quality. In
addition, administration keeps track of manufacturing cost by managing all of them internally. It
Secure Best Marks with AI Grader
Need help grading? Try our AI Grader for instant feedback on your assignments.
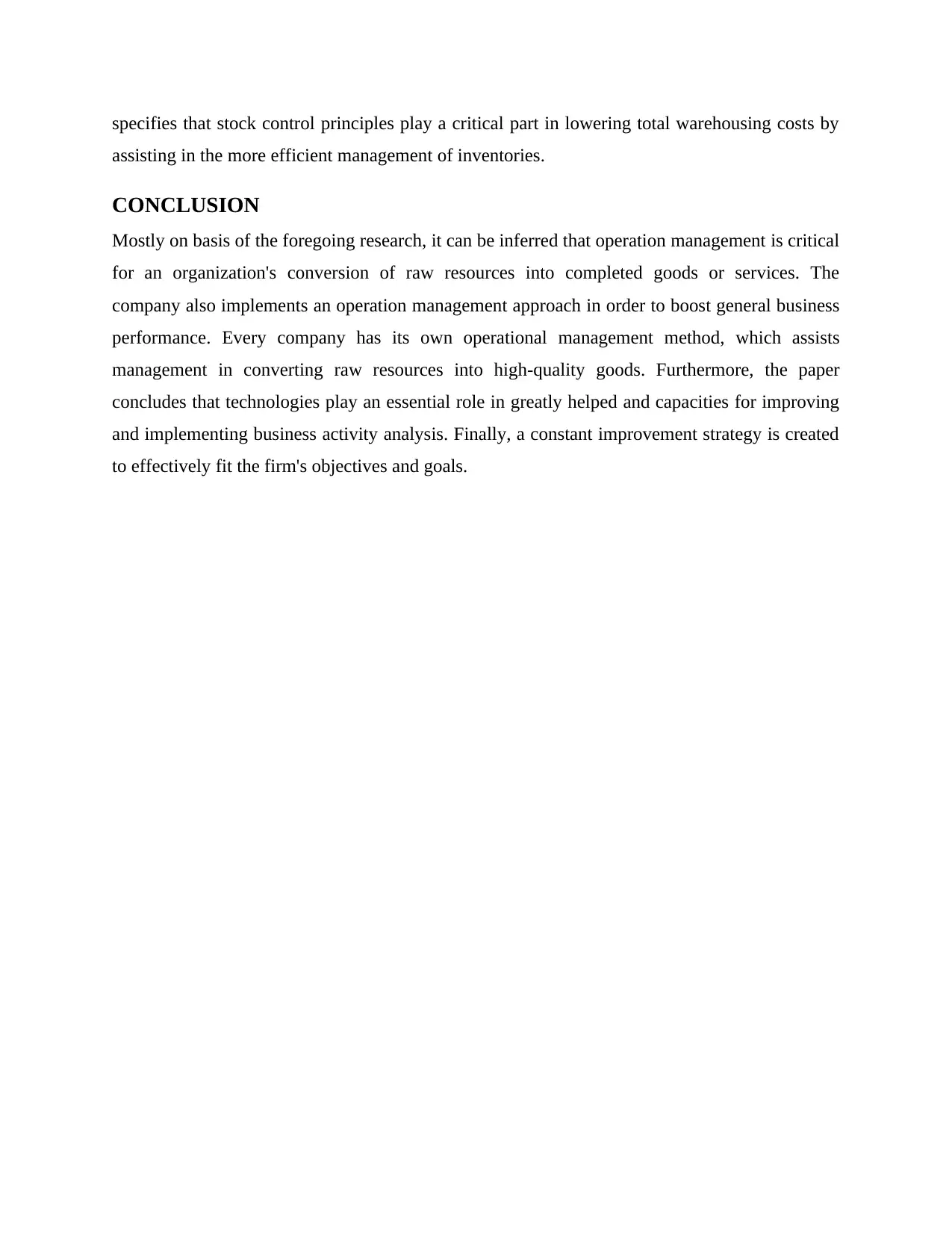
specifies that stock control principles play a critical part in lowering total warehousing costs by
assisting in the more efficient management of inventories.
CONCLUSION
Mostly on basis of the foregoing research, it can be inferred that operation management is critical
for an organization's conversion of raw resources into completed goods or services. The
company also implements an operation management approach in order to boost general business
performance. Every company has its own operational management method, which assists
management in converting raw resources into high-quality goods. Furthermore, the paper
concludes that technologies play an essential role in greatly helped and capacities for improving
and implementing business activity analysis. Finally, a constant improvement strategy is created
to effectively fit the firm's objectives and goals.
assisting in the more efficient management of inventories.
CONCLUSION
Mostly on basis of the foregoing research, it can be inferred that operation management is critical
for an organization's conversion of raw resources into completed goods or services. The
company also implements an operation management approach in order to boost general business
performance. Every company has its own operational management method, which assists
management in converting raw resources into high-quality goods. Furthermore, the paper
concludes that technologies play an essential role in greatly helped and capacities for improving
and implementing business activity analysis. Finally, a constant improvement strategy is created
to effectively fit the firm's objectives and goals.
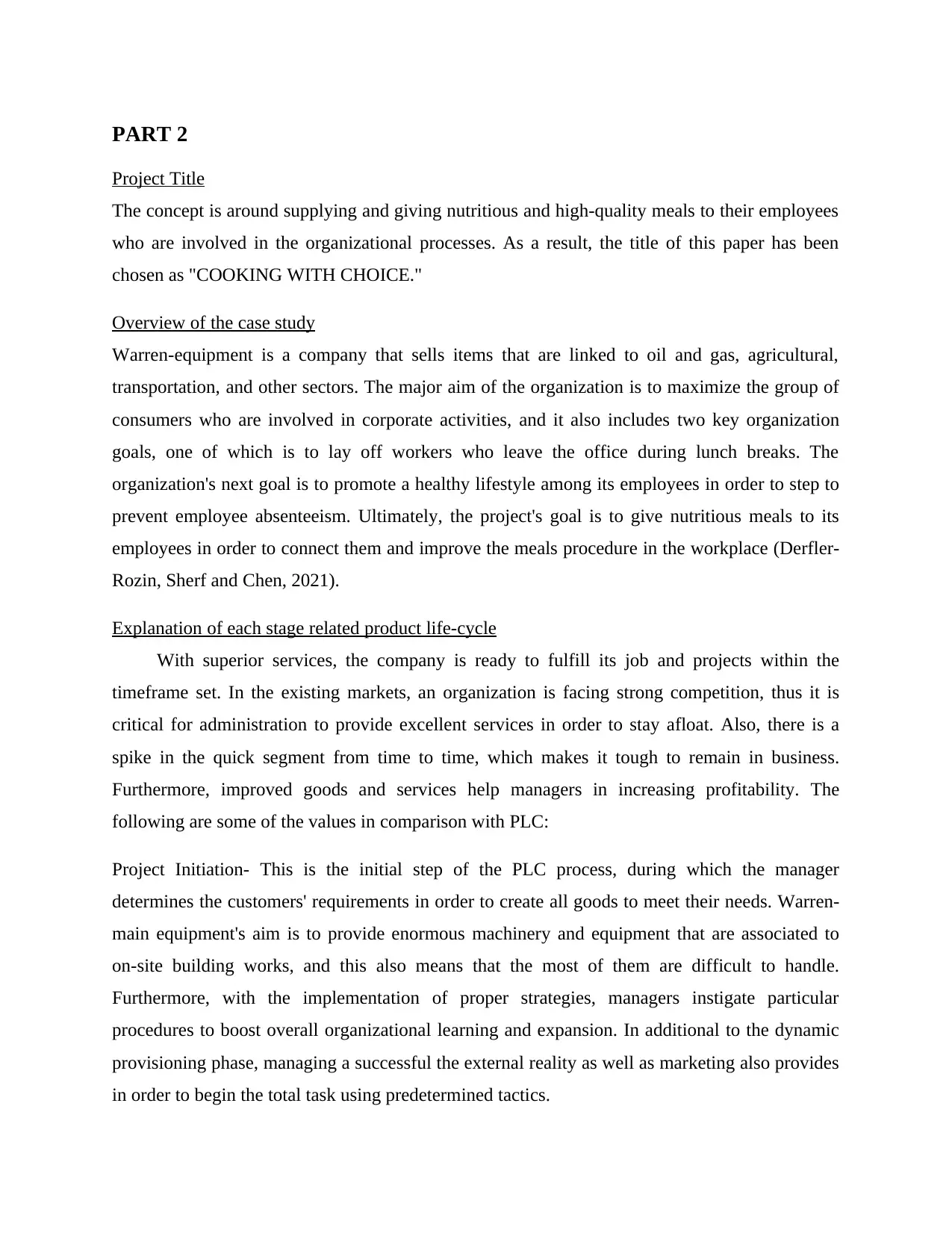
PART 2
Project Title
The concept is around supplying and giving nutritious and high-quality meals to their employees
who are involved in the organizational processes. As a result, the title of this paper has been
chosen as "COOKING WITH CHOICE."
Overview of the case study
Warren-equipment is a company that sells items that are linked to oil and gas, agricultural,
transportation, and other sectors. The major aim of the organization is to maximize the group of
consumers who are involved in corporate activities, and it also includes two key organization
goals, one of which is to lay off workers who leave the office during lunch breaks. The
organization's next goal is to promote a healthy lifestyle among its employees in order to step to
prevent employee absenteeism. Ultimately, the project's goal is to give nutritious meals to its
employees in order to connect them and improve the meals procedure in the workplace (Derfler-
Rozin, Sherf and Chen, 2021).
Explanation of each stage related product life-cycle
With superior services, the company is ready to fulfill its job and projects within the
timeframe set. In the existing markets, an organization is facing strong competition, thus it is
critical for administration to provide excellent services in order to stay afloat. Also, there is a
spike in the quick segment from time to time, which makes it tough to remain in business.
Furthermore, improved goods and services help managers in increasing profitability. The
following are some of the values in comparison with PLC:
Project Initiation- This is the initial step of the PLC process, during which the manager
determines the customers' requirements in order to create all goods to meet their needs. Warren-
main equipment's aim is to provide enormous machinery and equipment that are associated to
on-site building works, and this also means that the most of them are difficult to handle.
Furthermore, with the implementation of proper strategies, managers instigate particular
procedures to boost overall organizational learning and expansion. In additional to the dynamic
provisioning phase, managing a successful the external reality as well as marketing also provides
in order to begin the total task using predetermined tactics.
Project Title
The concept is around supplying and giving nutritious and high-quality meals to their employees
who are involved in the organizational processes. As a result, the title of this paper has been
chosen as "COOKING WITH CHOICE."
Overview of the case study
Warren-equipment is a company that sells items that are linked to oil and gas, agricultural,
transportation, and other sectors. The major aim of the organization is to maximize the group of
consumers who are involved in corporate activities, and it also includes two key organization
goals, one of which is to lay off workers who leave the office during lunch breaks. The
organization's next goal is to promote a healthy lifestyle among its employees in order to step to
prevent employee absenteeism. Ultimately, the project's goal is to give nutritious meals to its
employees in order to connect them and improve the meals procedure in the workplace (Derfler-
Rozin, Sherf and Chen, 2021).
Explanation of each stage related product life-cycle
With superior services, the company is ready to fulfill its job and projects within the
timeframe set. In the existing markets, an organization is facing strong competition, thus it is
critical for administration to provide excellent services in order to stay afloat. Also, there is a
spike in the quick segment from time to time, which makes it tough to remain in business.
Furthermore, improved goods and services help managers in increasing profitability. The
following are some of the values in comparison with PLC:
Project Initiation- This is the initial step of the PLC process, during which the manager
determines the customers' requirements in order to create all goods to meet their needs. Warren-
main equipment's aim is to provide enormous machinery and equipment that are associated to
on-site building works, and this also means that the most of them are difficult to handle.
Furthermore, with the implementation of proper strategies, managers instigate particular
procedures to boost overall organizational learning and expansion. In additional to the dynamic
provisioning phase, managing a successful the external reality as well as marketing also provides
in order to begin the total task using predetermined tactics.
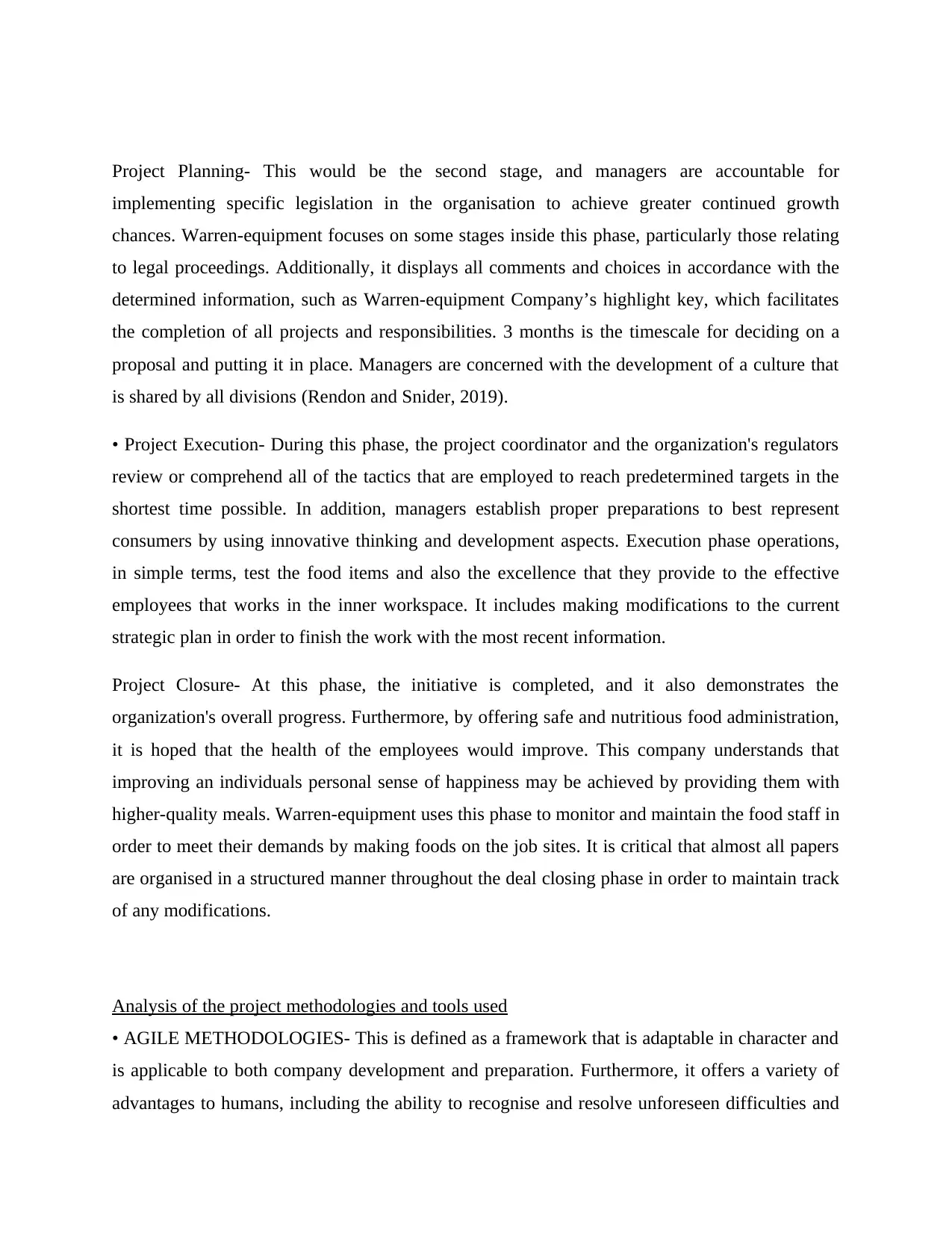
Project Planning- This would be the second stage, and managers are accountable for
implementing specific legislation in the organisation to achieve greater continued growth
chances. Warren-equipment focuses on some stages inside this phase, particularly those relating
to legal proceedings. Additionally, it displays all comments and choices in accordance with the
determined information, such as Warren-equipment Company’s highlight key, which facilitates
the completion of all projects and responsibilities. 3 months is the timescale for deciding on a
proposal and putting it in place. Managers are concerned with the development of a culture that
is shared by all divisions (Rendon and Snider, 2019).
• Project Execution- During this phase, the project coordinator and the organization's regulators
review or comprehend all of the tactics that are employed to reach predetermined targets in the
shortest time possible. In addition, managers establish proper preparations to best represent
consumers by using innovative thinking and development aspects. Execution phase operations,
in simple terms, test the food items and also the excellence that they provide to the effective
employees that works in the inner workspace. It includes making modifications to the current
strategic plan in order to finish the work with the most recent information.
Project Closure- At this phase, the initiative is completed, and it also demonstrates the
organization's overall progress. Furthermore, by offering safe and nutritious food administration,
it is hoped that the health of the employees would improve. This company understands that
improving an individuals personal sense of happiness may be achieved by providing them with
higher-quality meals. Warren-equipment uses this phase to monitor and maintain the food staff in
order to meet their demands by making foods on the job sites. It is critical that almost all papers
are organised in a structured manner throughout the deal closing phase in order to maintain track
of any modifications.
Analysis of the project methodologies and tools used
• AGILE METHODOLOGIES- This is defined as a framework that is adaptable in character and
is applicable to both company development and preparation. Furthermore, it offers a variety of
advantages to humans, including the ability to recognise and resolve unforeseen difficulties and
implementing specific legislation in the organisation to achieve greater continued growth
chances. Warren-equipment focuses on some stages inside this phase, particularly those relating
to legal proceedings. Additionally, it displays all comments and choices in accordance with the
determined information, such as Warren-equipment Company’s highlight key, which facilitates
the completion of all projects and responsibilities. 3 months is the timescale for deciding on a
proposal and putting it in place. Managers are concerned with the development of a culture that
is shared by all divisions (Rendon and Snider, 2019).
• Project Execution- During this phase, the project coordinator and the organization's regulators
review or comprehend all of the tactics that are employed to reach predetermined targets in the
shortest time possible. In addition, managers establish proper preparations to best represent
consumers by using innovative thinking and development aspects. Execution phase operations,
in simple terms, test the food items and also the excellence that they provide to the effective
employees that works in the inner workspace. It includes making modifications to the current
strategic plan in order to finish the work with the most recent information.
Project Closure- At this phase, the initiative is completed, and it also demonstrates the
organization's overall progress. Furthermore, by offering safe and nutritious food administration,
it is hoped that the health of the employees would improve. This company understands that
improving an individuals personal sense of happiness may be achieved by providing them with
higher-quality meals. Warren-equipment uses this phase to monitor and maintain the food staff in
order to meet their demands by making foods on the job sites. It is critical that almost all papers
are organised in a structured manner throughout the deal closing phase in order to maintain track
of any modifications.
Analysis of the project methodologies and tools used
• AGILE METHODOLOGIES- This is defined as a framework that is adaptable in character and
is applicable to both company development and preparation. Furthermore, it offers a variety of
advantages to humans, including the ability to recognise and resolve unforeseen difficulties and
Paraphrase This Document
Need a fresh take? Get an instant paraphrase of this document with our AI Paraphraser
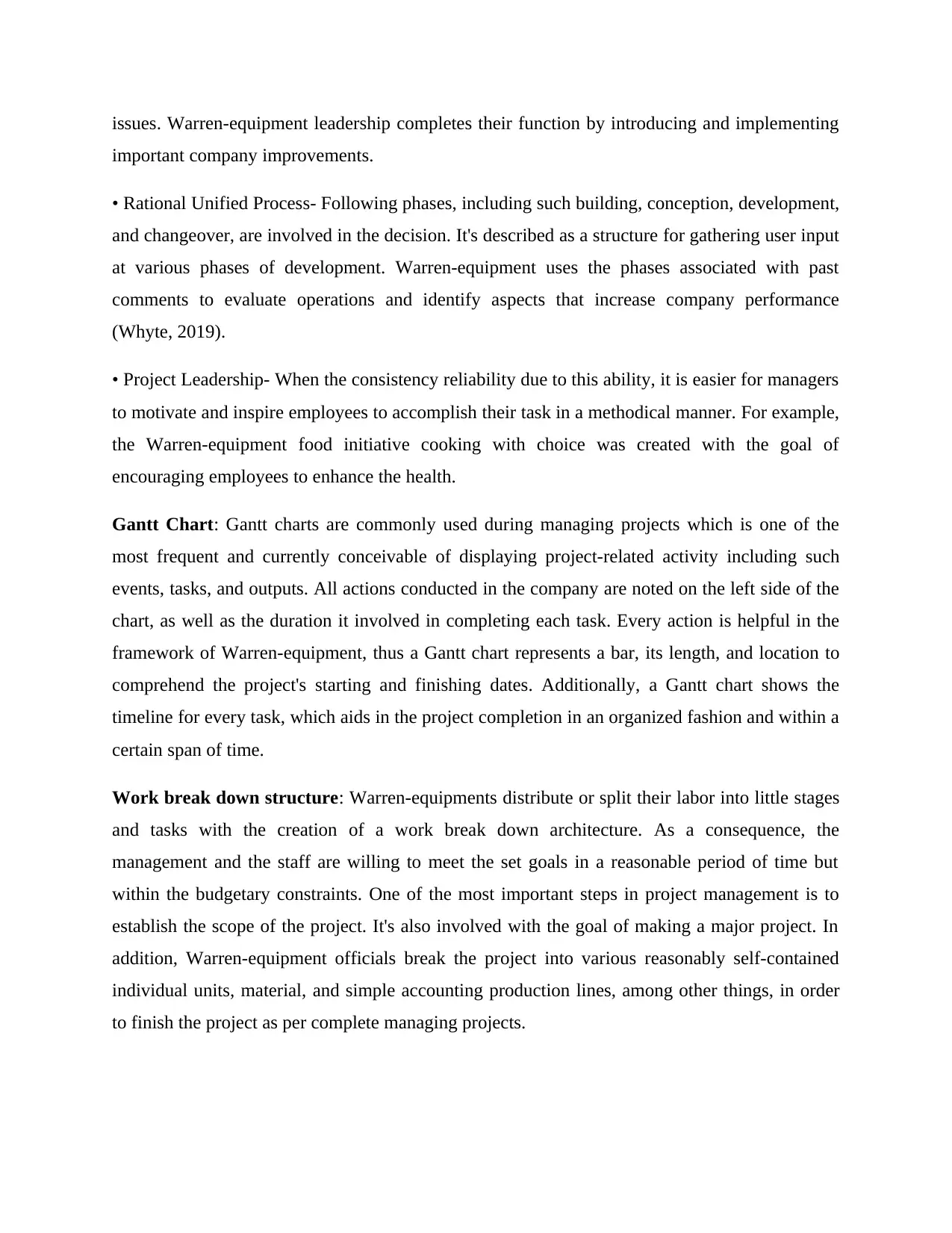
issues. Warren-equipment leadership completes their function by introducing and implementing
important company improvements.
• Rational Unified Process- Following phases, including such building, conception, development,
and changeover, are involved in the decision. It's described as a structure for gathering user input
at various phases of development. Warren-equipment uses the phases associated with past
comments to evaluate operations and identify aspects that increase company performance
(Whyte, 2019).
• Project Leadership- When the consistency reliability due to this ability, it is easier for managers
to motivate and inspire employees to accomplish their task in a methodical manner. For example,
the Warren-equipment food initiative cooking with choice was created with the goal of
encouraging employees to enhance the health.
Gantt Chart: Gantt charts are commonly used during managing projects which is one of the
most frequent and currently conceivable of displaying project-related activity including such
events, tasks, and outputs. All actions conducted in the company are noted on the left side of the
chart, as well as the duration it involved in completing each task. Every action is helpful in the
framework of Warren-equipment, thus a Gantt chart represents a bar, its length, and location to
comprehend the project's starting and finishing dates. Additionally, a Gantt chart shows the
timeline for every task, which aids in the project completion in an organized fashion and within a
certain span of time.
Work break down structure: Warren-equipments distribute or split their labor into little stages
and tasks with the creation of a work break down architecture. As a consequence, the
management and the staff are willing to meet the set goals in a reasonable period of time but
within the budgetary constraints. One of the most important steps in project management is to
establish the scope of the project. It's also involved with the goal of making a major project. In
addition, Warren-equipment officials break the project into various reasonably self-contained
individual units, material, and simple accounting production lines, among other things, in order
to finish the project as per complete managing projects.
important company improvements.
• Rational Unified Process- Following phases, including such building, conception, development,
and changeover, are involved in the decision. It's described as a structure for gathering user input
at various phases of development. Warren-equipment uses the phases associated with past
comments to evaluate operations and identify aspects that increase company performance
(Whyte, 2019).
• Project Leadership- When the consistency reliability due to this ability, it is easier for managers
to motivate and inspire employees to accomplish their task in a methodical manner. For example,
the Warren-equipment food initiative cooking with choice was created with the goal of
encouraging employees to enhance the health.
Gantt Chart: Gantt charts are commonly used during managing projects which is one of the
most frequent and currently conceivable of displaying project-related activity including such
events, tasks, and outputs. All actions conducted in the company are noted on the left side of the
chart, as well as the duration it involved in completing each task. Every action is helpful in the
framework of Warren-equipment, thus a Gantt chart represents a bar, its length, and location to
comprehend the project's starting and finishing dates. Additionally, a Gantt chart shows the
timeline for every task, which aids in the project completion in an organized fashion and within a
certain span of time.
Work break down structure: Warren-equipments distribute or split their labor into little stages
and tasks with the creation of a work break down architecture. As a consequence, the
management and the staff are willing to meet the set goals in a reasonable period of time but
within the budgetary constraints. One of the most important steps in project management is to
establish the scope of the project. It's also involved with the goal of making a major project. In
addition, Warren-equipment officials break the project into various reasonably self-contained
individual units, material, and simple accounting production lines, among other things, in order
to finish the project as per complete managing projects.
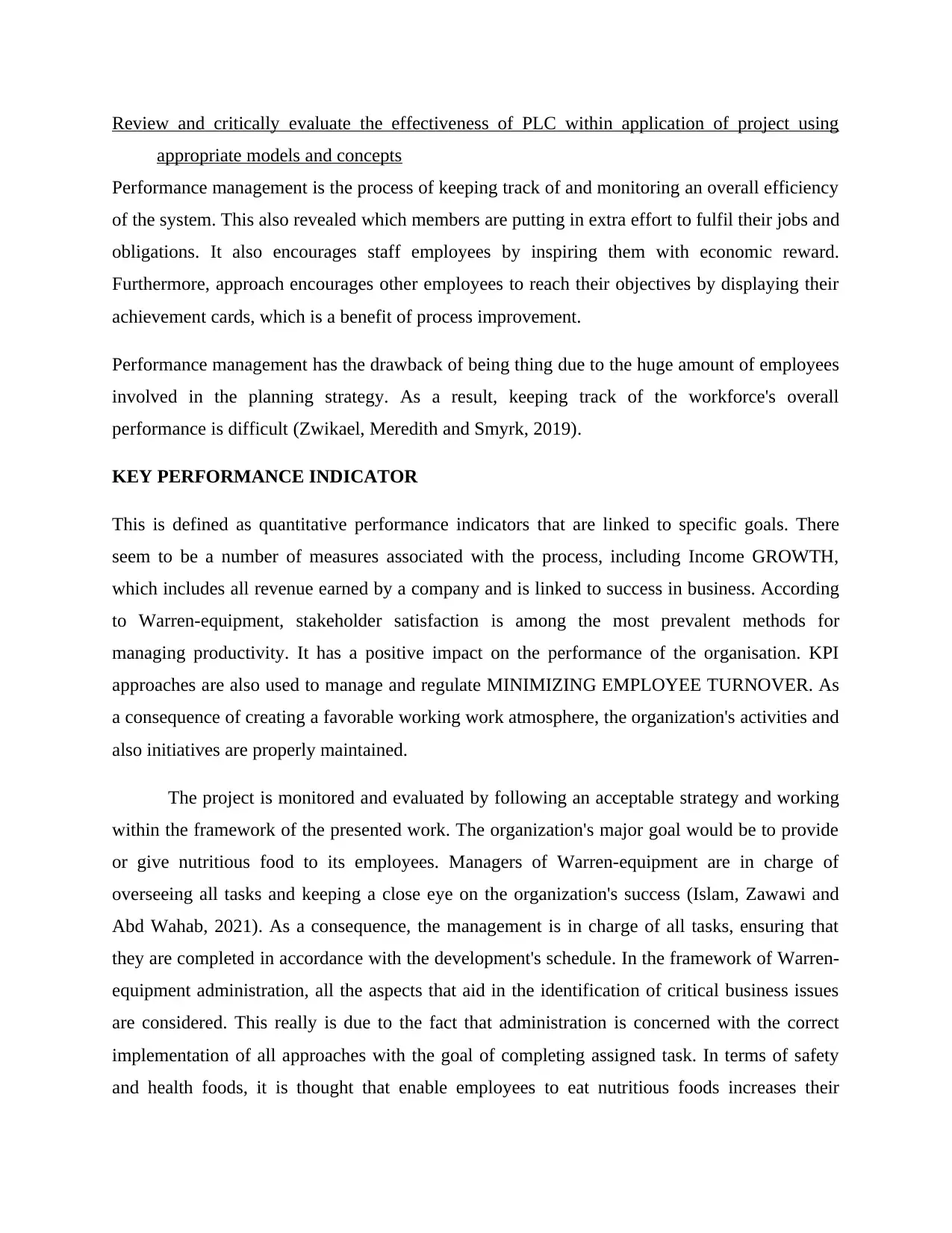
Review and critically evaluate the effectiveness of PLC within application of project using
appropriate models and concepts
Performance management is the process of keeping track of and monitoring an overall efficiency
of the system. This also revealed which members are putting in extra effort to fulfil their jobs and
obligations. It also encourages staff employees by inspiring them with economic reward.
Furthermore, approach encourages other employees to reach their objectives by displaying their
achievement cards, which is a benefit of process improvement.
Performance management has the drawback of being thing due to the huge amount of employees
involved in the planning strategy. As a result, keeping track of the workforce's overall
performance is difficult (Zwikael, Meredith and Smyrk, 2019).
KEY PERFORMANCE INDICATOR
This is defined as quantitative performance indicators that are linked to specific goals. There
seem to be a number of measures associated with the process, including Income GROWTH,
which includes all revenue earned by a company and is linked to success in business. According
to Warren-equipment, stakeholder satisfaction is among the most prevalent methods for
managing productivity. It has a positive impact on the performance of the organisation. KPI
approaches are also used to manage and regulate MINIMIZING EMPLOYEE TURNOVER. As
a consequence of creating a favorable working work atmosphere, the organization's activities and
also initiatives are properly maintained.
The project is monitored and evaluated by following an acceptable strategy and working
within the framework of the presented work. The organization's major goal would be to provide
or give nutritious food to its employees. Managers of Warren-equipment are in charge of
overseeing all tasks and keeping a close eye on the organization's success (Islam, Zawawi and
Abd Wahab, 2021). As a consequence, the management is in charge of all tasks, ensuring that
they are completed in accordance with the development's schedule. In the framework of Warren-
equipment administration, all the aspects that aid in the identification of critical business issues
are considered. This really is due to the fact that administration is concerned with the correct
implementation of all approaches with the goal of completing assigned task. In terms of safety
and health foods, it is thought that enable employees to eat nutritious foods increases their
appropriate models and concepts
Performance management is the process of keeping track of and monitoring an overall efficiency
of the system. This also revealed which members are putting in extra effort to fulfil their jobs and
obligations. It also encourages staff employees by inspiring them with economic reward.
Furthermore, approach encourages other employees to reach their objectives by displaying their
achievement cards, which is a benefit of process improvement.
Performance management has the drawback of being thing due to the huge amount of employees
involved in the planning strategy. As a result, keeping track of the workforce's overall
performance is difficult (Zwikael, Meredith and Smyrk, 2019).
KEY PERFORMANCE INDICATOR
This is defined as quantitative performance indicators that are linked to specific goals. There
seem to be a number of measures associated with the process, including Income GROWTH,
which includes all revenue earned by a company and is linked to success in business. According
to Warren-equipment, stakeholder satisfaction is among the most prevalent methods for
managing productivity. It has a positive impact on the performance of the organisation. KPI
approaches are also used to manage and regulate MINIMIZING EMPLOYEE TURNOVER. As
a consequence of creating a favorable working work atmosphere, the organization's activities and
also initiatives are properly maintained.
The project is monitored and evaluated by following an acceptable strategy and working
within the framework of the presented work. The organization's major goal would be to provide
or give nutritious food to its employees. Managers of Warren-equipment are in charge of
overseeing all tasks and keeping a close eye on the organization's success (Islam, Zawawi and
Abd Wahab, 2021). As a consequence, the management is in charge of all tasks, ensuring that
they are completed in accordance with the development's schedule. In the framework of Warren-
equipment administration, all the aspects that aid in the identification of critical business issues
are considered. This really is due to the fact that administration is concerned with the correct
implementation of all approaches with the goal of completing assigned task. In terms of safety
and health foods, it is thought that enable employees to eat nutritious foods increases their
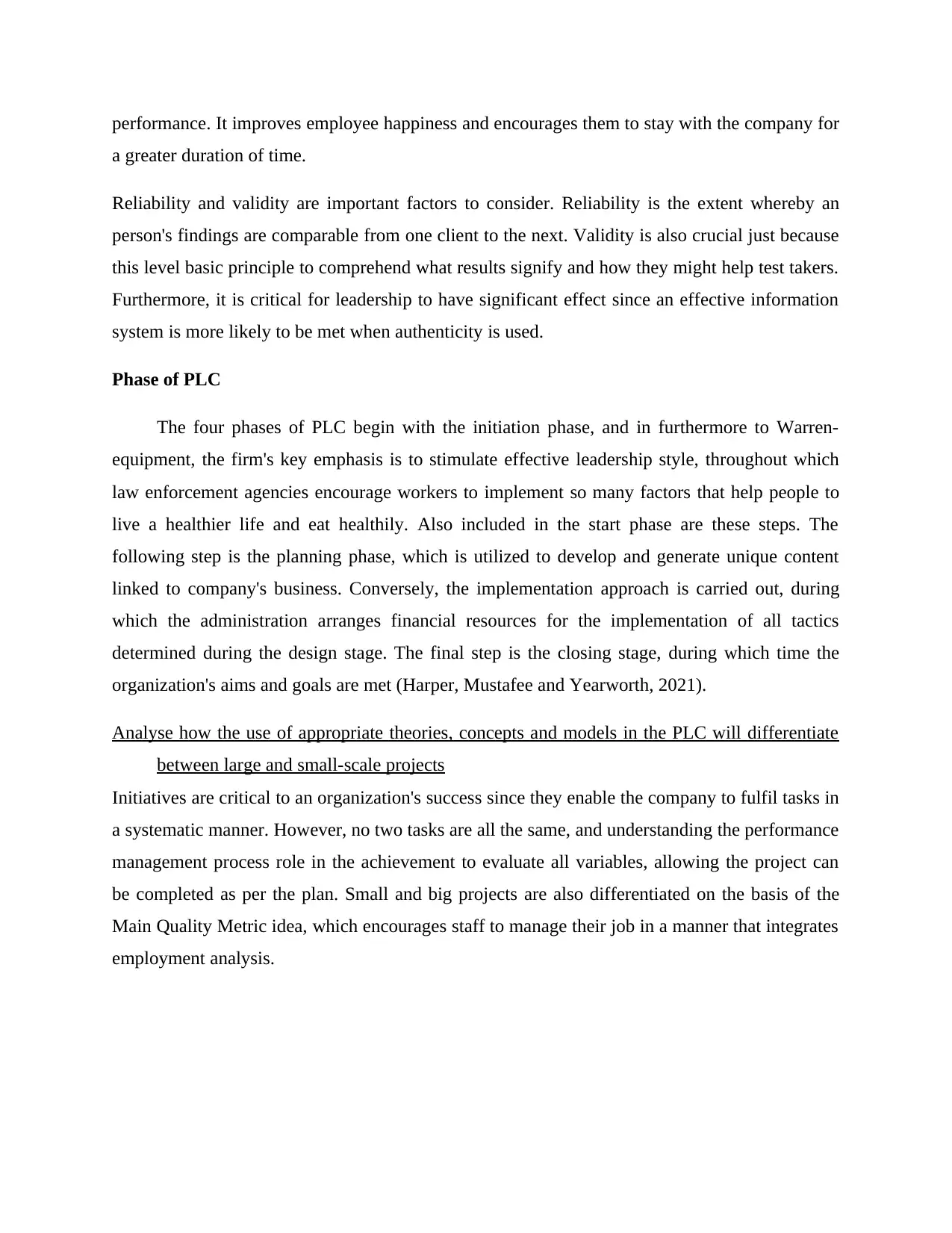
performance. It improves employee happiness and encourages them to stay with the company for
a greater duration of time.
Reliability and validity are important factors to consider. Reliability is the extent whereby an
person's findings are comparable from one client to the next. Validity is also crucial just because
this level basic principle to comprehend what results signify and how they might help test takers.
Furthermore, it is critical for leadership to have significant effect since an effective information
system is more likely to be met when authenticity is used.
Phase of PLC
The four phases of PLC begin with the initiation phase, and in furthermore to Warren-
equipment, the firm's key emphasis is to stimulate effective leadership style, throughout which
law enforcement agencies encourage workers to implement so many factors that help people to
live a healthier life and eat healthily. Also included in the start phase are these steps. The
following step is the planning phase, which is utilized to develop and generate unique content
linked to company's business. Conversely, the implementation approach is carried out, during
which the administration arranges financial resources for the implementation of all tactics
determined during the design stage. The final step is the closing stage, during which time the
organization's aims and goals are met (Harper, Mustafee and Yearworth, 2021).
Analyse how the use of appropriate theories, concepts and models in the PLC will differentiate
between large and small-scale projects
Initiatives are critical to an organization's success since they enable the company to fulfil tasks in
a systematic manner. However, no two tasks are all the same, and understanding the performance
management process role in the achievement to evaluate all variables, allowing the project can
be completed as per the plan. Small and big projects are also differentiated on the basis of the
Main Quality Metric idea, which encourages staff to manage their job in a manner that integrates
employment analysis.
a greater duration of time.
Reliability and validity are important factors to consider. Reliability is the extent whereby an
person's findings are comparable from one client to the next. Validity is also crucial just because
this level basic principle to comprehend what results signify and how they might help test takers.
Furthermore, it is critical for leadership to have significant effect since an effective information
system is more likely to be met when authenticity is used.
Phase of PLC
The four phases of PLC begin with the initiation phase, and in furthermore to Warren-
equipment, the firm's key emphasis is to stimulate effective leadership style, throughout which
law enforcement agencies encourage workers to implement so many factors that help people to
live a healthier life and eat healthily. Also included in the start phase are these steps. The
following step is the planning phase, which is utilized to develop and generate unique content
linked to company's business. Conversely, the implementation approach is carried out, during
which the administration arranges financial resources for the implementation of all tactics
determined during the design stage. The final step is the closing stage, during which time the
organization's aims and goals are met (Harper, Mustafee and Yearworth, 2021).
Analyse how the use of appropriate theories, concepts and models in the PLC will differentiate
between large and small-scale projects
Initiatives are critical to an organization's success since they enable the company to fulfil tasks in
a systematic manner. However, no two tasks are all the same, and understanding the performance
management process role in the achievement to evaluate all variables, allowing the project can
be completed as per the plan. Small and big projects are also differentiated on the basis of the
Main Quality Metric idea, which encourages staff to manage their job in a manner that integrates
employment analysis.
Secure Best Marks with AI Grader
Need help grading? Try our AI Grader for instant feedback on your assignments.
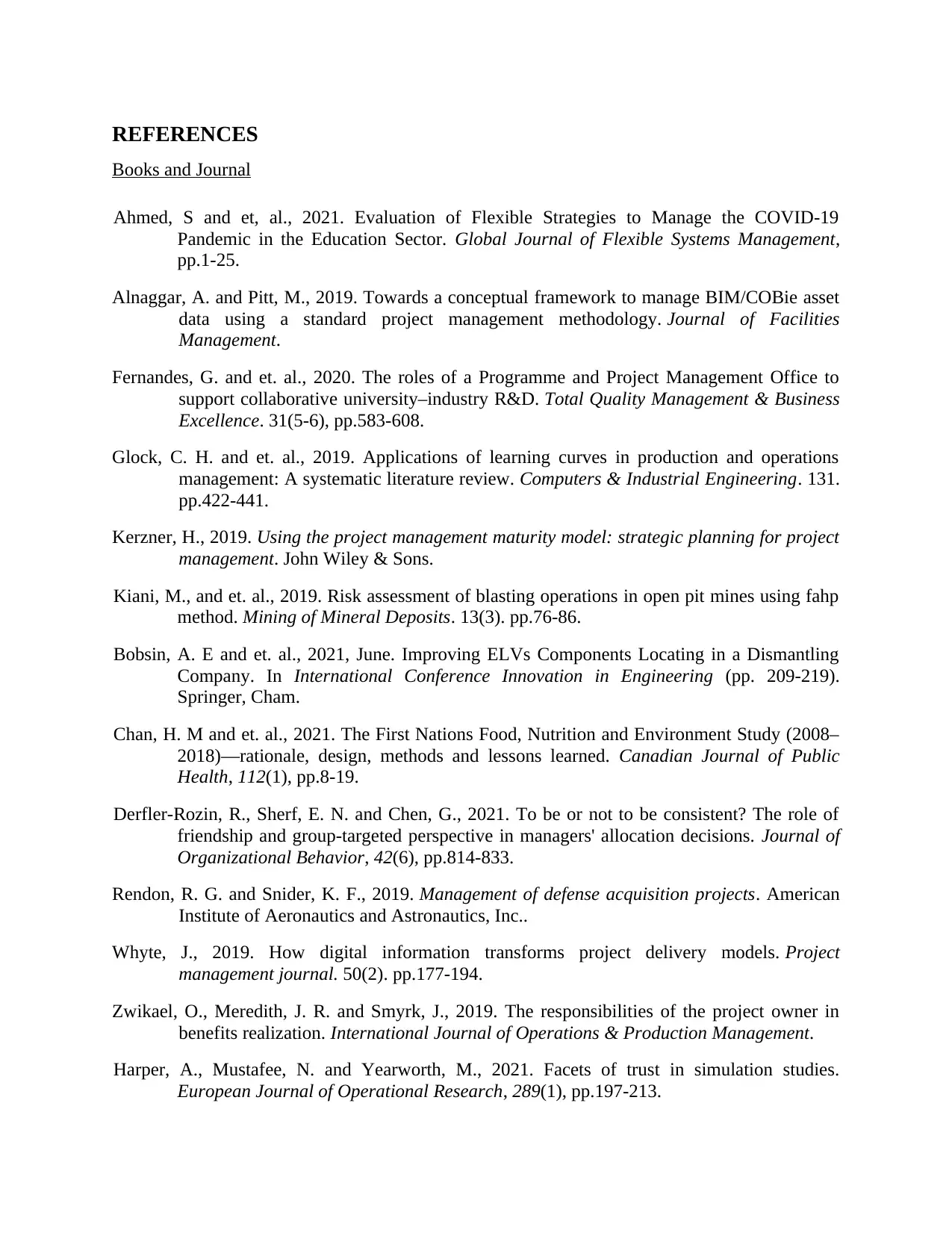
REFERENCES
Books and Journal
Ahmed, S and et, al., 2021. Evaluation of Flexible Strategies to Manage the COVID-19
Pandemic in the Education Sector. Global Journal of Flexible Systems Management,
pp.1-25.
Alnaggar, A. and Pitt, M., 2019. Towards a conceptual framework to manage BIM/COBie asset
data using a standard project management methodology. Journal of Facilities
Management.
Fernandes, G. and et. al., 2020. The roles of a Programme and Project Management Office to
support collaborative university–industry R&D. Total Quality Management & Business
Excellence. 31(5-6), pp.583-608.
Glock, C. H. and et. al., 2019. Applications of learning curves in production and operations
management: A systematic literature review. Computers & Industrial Engineering. 131.
pp.422-441.
Kerzner, H., 2019. Using the project management maturity model: strategic planning for project
management. John Wiley & Sons.
Kiani, M., and et. al., 2019. Risk assessment of blasting operations in open pit mines using fahp
method. Mining of Mineral Deposits. 13(3). pp.76-86.
Bobsin, A. E and et. al., 2021, June. Improving ELVs Components Locating in a Dismantling
Company. In International Conference Innovation in Engineering (pp. 209-219).
Springer, Cham.
Chan, H. M and et. al., 2021. The First Nations Food, Nutrition and Environment Study (2008–
2018)—rationale, design, methods and lessons learned. Canadian Journal of Public
Health, 112(1), pp.8-19.
Derfler-Rozin, R., Sherf, E. N. and Chen, G., 2021. To be or not to be consistent? The role of
friendship and group-targeted perspective in managers' allocation decisions. Journal of
Organizational Behavior, 42(6), pp.814-833.
Rendon, R. G. and Snider, K. F., 2019. Management of defense acquisition projects. American
Institute of Aeronautics and Astronautics, Inc..
Whyte, J., 2019. How digital information transforms project delivery models. Project
management journal. 50(2). pp.177-194.
Zwikael, O., Meredith, J. R. and Smyrk, J., 2019. The responsibilities of the project owner in
benefits realization. International Journal of Operations & Production Management.
Harper, A., Mustafee, N. and Yearworth, M., 2021. Facets of trust in simulation studies.
European Journal of Operational Research, 289(1), pp.197-213.
Books and Journal
Ahmed, S and et, al., 2021. Evaluation of Flexible Strategies to Manage the COVID-19
Pandemic in the Education Sector. Global Journal of Flexible Systems Management,
pp.1-25.
Alnaggar, A. and Pitt, M., 2019. Towards a conceptual framework to manage BIM/COBie asset
data using a standard project management methodology. Journal of Facilities
Management.
Fernandes, G. and et. al., 2020. The roles of a Programme and Project Management Office to
support collaborative university–industry R&D. Total Quality Management & Business
Excellence. 31(5-6), pp.583-608.
Glock, C. H. and et. al., 2019. Applications of learning curves in production and operations
management: A systematic literature review. Computers & Industrial Engineering. 131.
pp.422-441.
Kerzner, H., 2019. Using the project management maturity model: strategic planning for project
management. John Wiley & Sons.
Kiani, M., and et. al., 2019. Risk assessment of blasting operations in open pit mines using fahp
method. Mining of Mineral Deposits. 13(3). pp.76-86.
Bobsin, A. E and et. al., 2021, June. Improving ELVs Components Locating in a Dismantling
Company. In International Conference Innovation in Engineering (pp. 209-219).
Springer, Cham.
Chan, H. M and et. al., 2021. The First Nations Food, Nutrition and Environment Study (2008–
2018)—rationale, design, methods and lessons learned. Canadian Journal of Public
Health, 112(1), pp.8-19.
Derfler-Rozin, R., Sherf, E. N. and Chen, G., 2021. To be or not to be consistent? The role of
friendship and group-targeted perspective in managers' allocation decisions. Journal of
Organizational Behavior, 42(6), pp.814-833.
Rendon, R. G. and Snider, K. F., 2019. Management of defense acquisition projects. American
Institute of Aeronautics and Astronautics, Inc..
Whyte, J., 2019. How digital information transforms project delivery models. Project
management journal. 50(2). pp.177-194.
Zwikael, O., Meredith, J. R. and Smyrk, J., 2019. The responsibilities of the project owner in
benefits realization. International Journal of Operations & Production Management.
Harper, A., Mustafee, N. and Yearworth, M., 2021. Facets of trust in simulation studies.
European Journal of Operational Research, 289(1), pp.197-213.
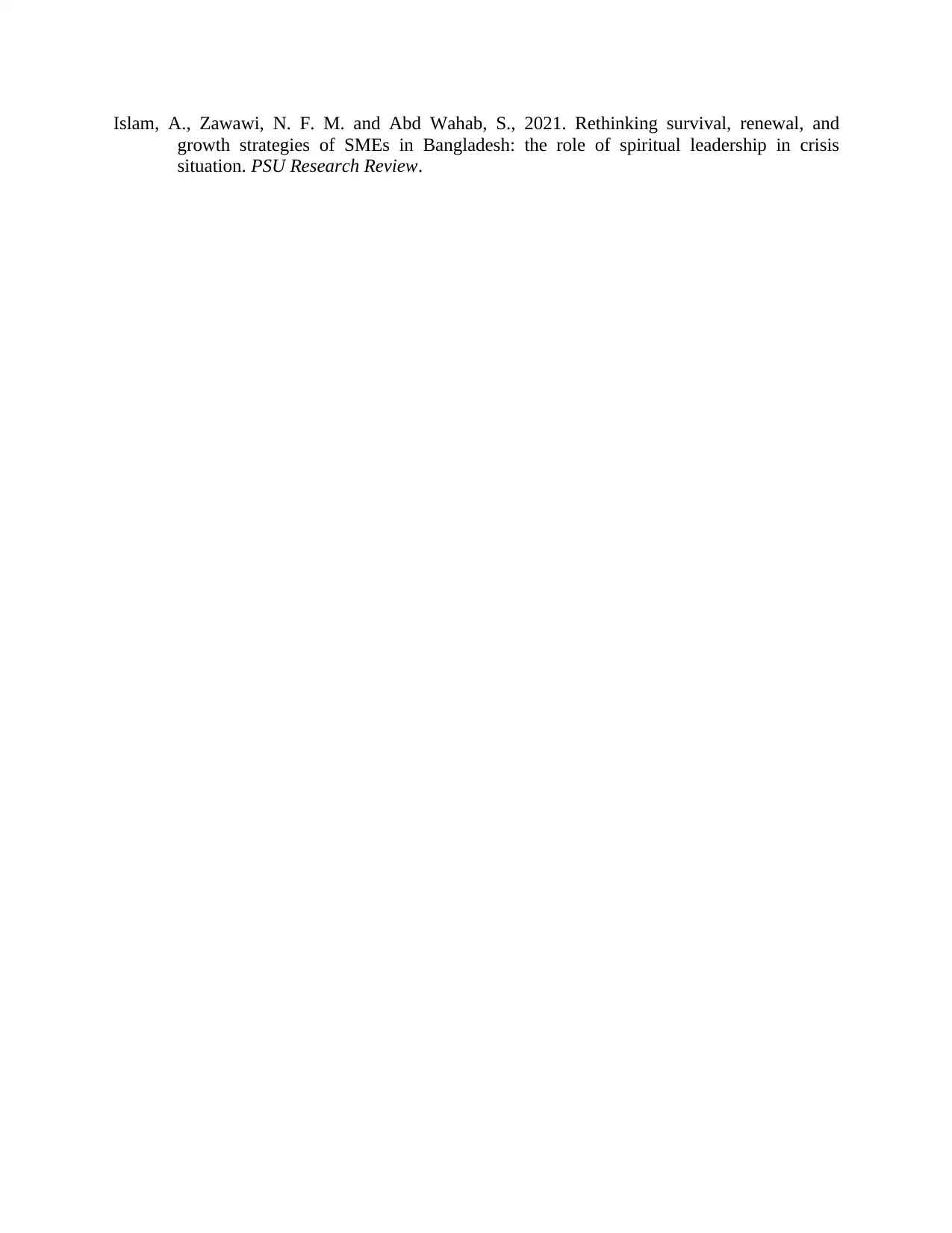
Islam, A., Zawawi, N. F. M. and Abd Wahab, S., 2021. Rethinking survival, renewal, and
growth strategies of SMEs in Bangladesh: the role of spiritual leadership in crisis
situation. PSU Research Review.
growth strategies of SMEs in Bangladesh: the role of spiritual leadership in crisis
situation. PSU Research Review.
1 out of 18
Related Documents

Your All-in-One AI-Powered Toolkit for Academic Success.
+13062052269
info@desklib.com
Available 24*7 on WhatsApp / Email
Unlock your academic potential
© 2024 | Zucol Services PVT LTD | All rights reserved.