Operations and Project Management: Whirlpool Case Study and Analysis
VerifiedAdded on 2020/07/23
|16
|4799
|51
Report
AI Summary
This report provides a comprehensive analysis of Whirlpool's operations and project management practices. It begins with a review and critique of the implementation of operational management principles, followed by a continuous improvement plan designed to enhance product development. The report then explores the stages of the Product Life Cycle (PLC) with a business case, project plan, and work breakdown structure, alongside a review and critique of the PLC's effectiveness using relevant theories, concepts, and models. The report focuses on the manufacturing of home appliances and a new product - a 58-inch TV, and applies concepts like Six Sigma and Lean principles to enhance efficiency and quality. The report is structured into tasks that address these key areas, providing detailed insights into Whirlpool's operational strategies.
Contribute Materials
Your contribution can guide someone’s learning journey. Share your
documents today.
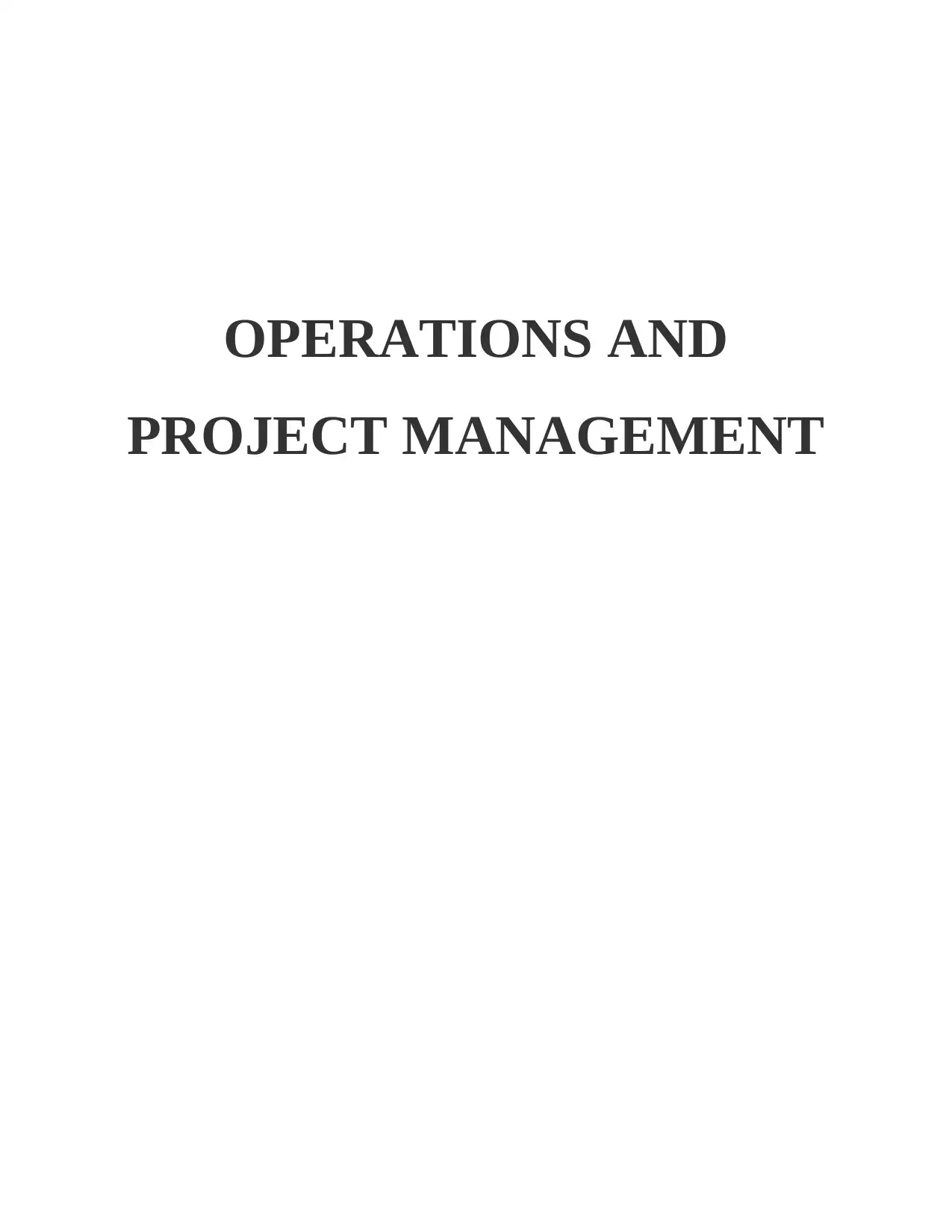
OPERATIONS AND
PROJECT MANAGEMENT
PROJECT MANAGEMENT
Secure Best Marks with AI Grader
Need help grading? Try our AI Grader for instant feedback on your assignments.
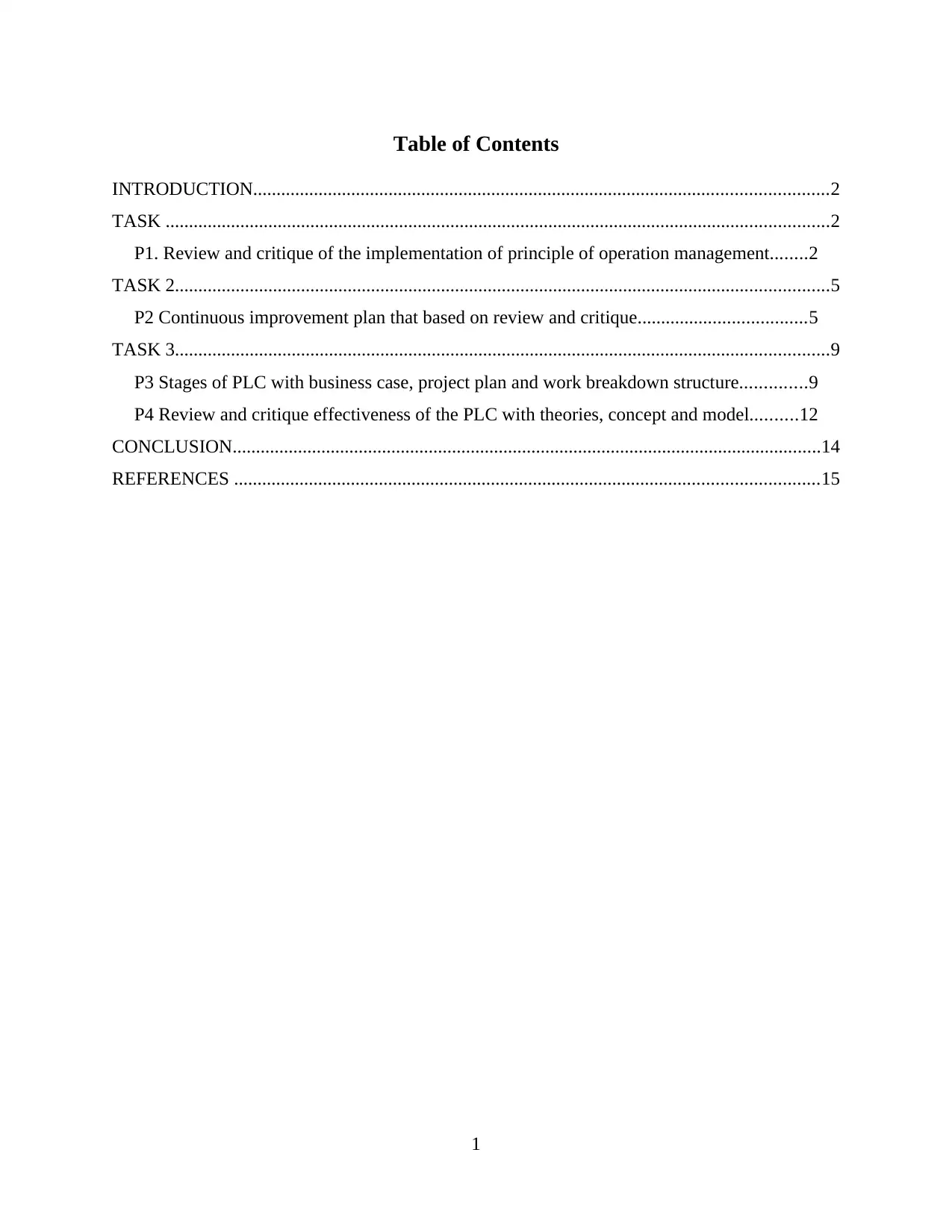
Table of Contents
INTRODUCTION...........................................................................................................................2
TASK ..............................................................................................................................................2
P1. Review and critique of the implementation of principle of operation management........2
TASK 2............................................................................................................................................5
P2 Continuous improvement plan that based on review and critique....................................5
TASK 3............................................................................................................................................9
P3 Stages of PLC with business case, project plan and work breakdown structure..............9
P4 Review and critique effectiveness of the PLC with theories, concept and model..........12
CONCLUSION..............................................................................................................................14
REFERENCES .............................................................................................................................15
1
INTRODUCTION...........................................................................................................................2
TASK ..............................................................................................................................................2
P1. Review and critique of the implementation of principle of operation management........2
TASK 2............................................................................................................................................5
P2 Continuous improvement plan that based on review and critique....................................5
TASK 3............................................................................................................................................9
P3 Stages of PLC with business case, project plan and work breakdown structure..............9
P4 Review and critique effectiveness of the PLC with theories, concept and model..........12
CONCLUSION..............................................................................................................................14
REFERENCES .............................................................................................................................15
1
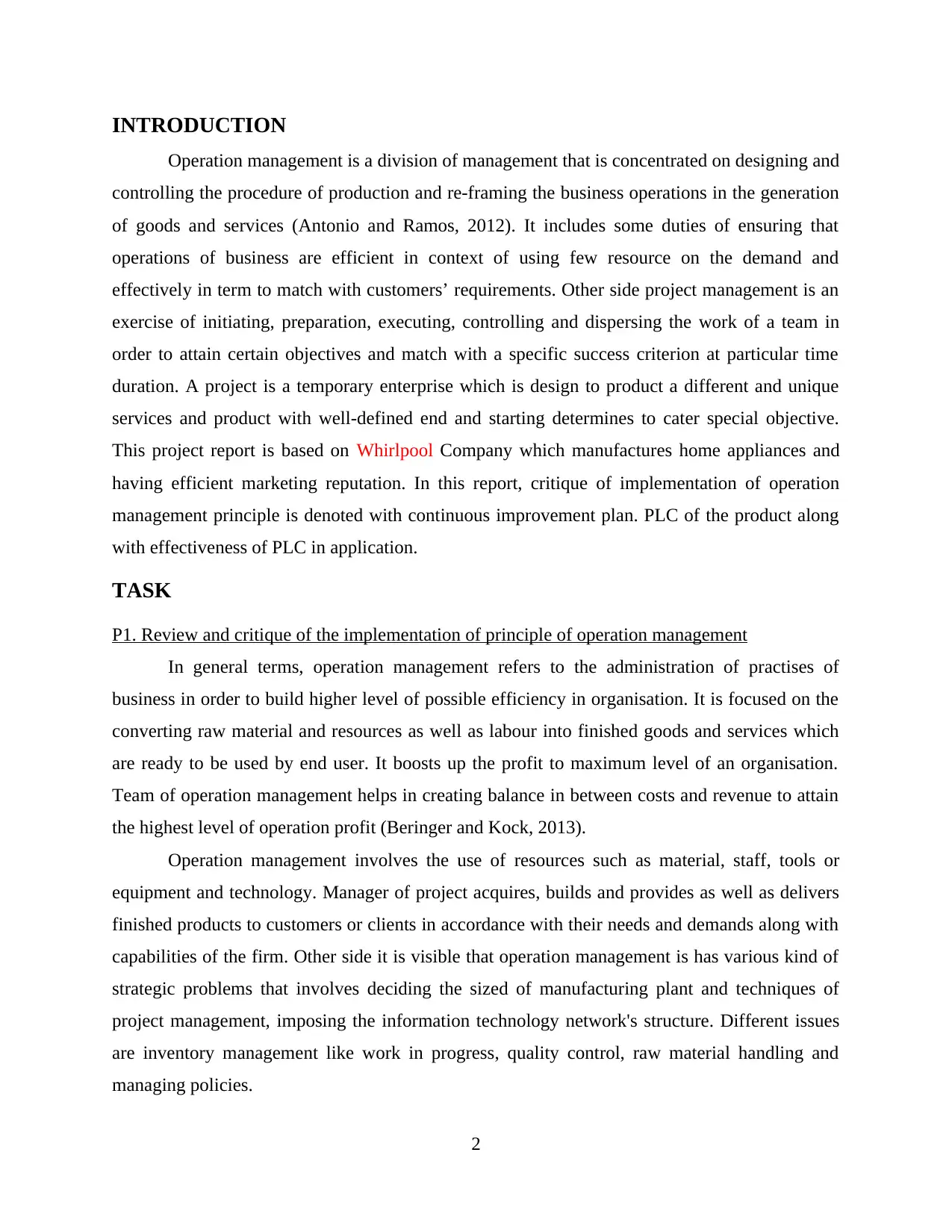
INTRODUCTION
Operation management is a division of management that is concentrated on designing and
controlling the procedure of production and re-framing the business operations in the generation
of goods and services (Antonio and Ramos, 2012). It includes some duties of ensuring that
operations of business are efficient in context of using few resource on the demand and
effectively in term to match with customers’ requirements. Other side project management is an
exercise of initiating, preparation, executing, controlling and dispersing the work of a team in
order to attain certain objectives and match with a specific success criterion at particular time
duration. A project is a temporary enterprise which is design to product a different and unique
services and product with well-defined end and starting determines to cater special objective.
This project report is based on Whirlpool Company which manufactures home appliances and
having efficient marketing reputation. In this report, critique of implementation of operation
management principle is denoted with continuous improvement plan. PLC of the product along
with effectiveness of PLC in application.
TASK
P1. Review and critique of the implementation of principle of operation management
In general terms, operation management refers to the administration of practises of
business in order to build higher level of possible efficiency in organisation. It is focused on the
converting raw material and resources as well as labour into finished goods and services which
are ready to be used by end user. It boosts up the profit to maximum level of an organisation.
Team of operation management helps in creating balance in between costs and revenue to attain
the highest level of operation profit (Beringer and Kock, 2013).
Operation management involves the use of resources such as material, staff, tools or
equipment and technology. Manager of project acquires, builds and provides as well as delivers
finished products to customers or clients in accordance with their needs and demands along with
capabilities of the firm. Other side it is visible that operation management is has various kind of
strategic problems that involves deciding the sized of manufacturing plant and techniques of
project management, imposing the information technology network's structure. Different issues
are inventory management like work in progress, quality control, raw material handling and
managing policies.
2
Operation management is a division of management that is concentrated on designing and
controlling the procedure of production and re-framing the business operations in the generation
of goods and services (Antonio and Ramos, 2012). It includes some duties of ensuring that
operations of business are efficient in context of using few resource on the demand and
effectively in term to match with customers’ requirements. Other side project management is an
exercise of initiating, preparation, executing, controlling and dispersing the work of a team in
order to attain certain objectives and match with a specific success criterion at particular time
duration. A project is a temporary enterprise which is design to product a different and unique
services and product with well-defined end and starting determines to cater special objective.
This project report is based on Whirlpool Company which manufactures home appliances and
having efficient marketing reputation. In this report, critique of implementation of operation
management principle is denoted with continuous improvement plan. PLC of the product along
with effectiveness of PLC in application.
TASK
P1. Review and critique of the implementation of principle of operation management
In general terms, operation management refers to the administration of practises of
business in order to build higher level of possible efficiency in organisation. It is focused on the
converting raw material and resources as well as labour into finished goods and services which
are ready to be used by end user. It boosts up the profit to maximum level of an organisation.
Team of operation management helps in creating balance in between costs and revenue to attain
the highest level of operation profit (Beringer and Kock, 2013).
Operation management involves the use of resources such as material, staff, tools or
equipment and technology. Manager of project acquires, builds and provides as well as delivers
finished products to customers or clients in accordance with their needs and demands along with
capabilities of the firm. Other side it is visible that operation management is has various kind of
strategic problems that involves deciding the sized of manufacturing plant and techniques of
project management, imposing the information technology network's structure. Different issues
are inventory management like work in progress, quality control, raw material handling and
managing policies.
2
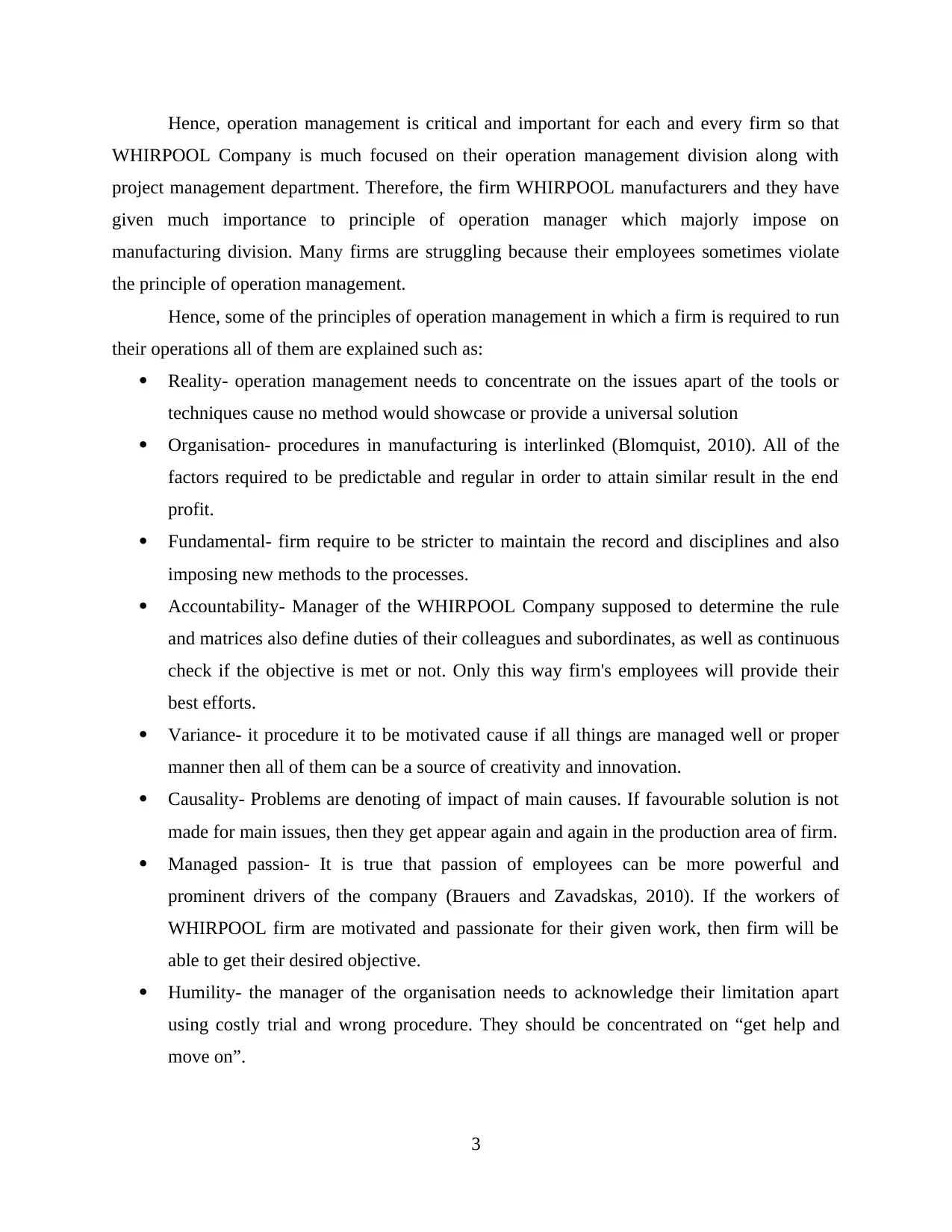
Hence, operation management is critical and important for each and every firm so that
WHIRPOOL Company is much focused on their operation management division along with
project management department. Therefore, the firm WHIRPOOL manufacturers and they have
given much importance to principle of operation manager which majorly impose on
manufacturing division. Many firms are struggling because their employees sometimes violate
the principle of operation management.
Hence, some of the principles of operation management in which a firm is required to run
their operations all of them are explained such as:
Reality- operation management needs to concentrate on the issues apart of the tools or
techniques cause no method would showcase or provide a universal solution
Organisation- procedures in manufacturing is interlinked (Blomquist, 2010). All of the
factors required to be predictable and regular in order to attain similar result in the end
profit.
Fundamental- firm require to be stricter to maintain the record and disciplines and also
imposing new methods to the processes.
Accountability- Manager of the WHIRPOOL Company supposed to determine the rule
and matrices also define duties of their colleagues and subordinates, as well as continuous
check if the objective is met or not. Only this way firm's employees will provide their
best efforts.
Variance- it procedure it to be motivated cause if all things are managed well or proper
manner then all of them can be a source of creativity and innovation.
Causality- Problems are denoting of impact of main causes. If favourable solution is not
made for main issues, then they get appear again and again in the production area of firm.
Managed passion- It is true that passion of employees can be more powerful and
prominent drivers of the company (Brauers and Zavadskas, 2010). If the workers of
WHIRPOOL firm are motivated and passionate for their given work, then firm will be
able to get their desired objective.
Humility- the manager of the organisation needs to acknowledge their limitation apart
using costly trial and wrong procedure. They should be concentrated on “get help and
move on”.
3
WHIRPOOL Company is much focused on their operation management division along with
project management department. Therefore, the firm WHIRPOOL manufacturers and they have
given much importance to principle of operation manager which majorly impose on
manufacturing division. Many firms are struggling because their employees sometimes violate
the principle of operation management.
Hence, some of the principles of operation management in which a firm is required to run
their operations all of them are explained such as:
Reality- operation management needs to concentrate on the issues apart of the tools or
techniques cause no method would showcase or provide a universal solution
Organisation- procedures in manufacturing is interlinked (Blomquist, 2010). All of the
factors required to be predictable and regular in order to attain similar result in the end
profit.
Fundamental- firm require to be stricter to maintain the record and disciplines and also
imposing new methods to the processes.
Accountability- Manager of the WHIRPOOL Company supposed to determine the rule
and matrices also define duties of their colleagues and subordinates, as well as continuous
check if the objective is met or not. Only this way firm's employees will provide their
best efforts.
Variance- it procedure it to be motivated cause if all things are managed well or proper
manner then all of them can be a source of creativity and innovation.
Causality- Problems are denoting of impact of main causes. If favourable solution is not
made for main issues, then they get appear again and again in the production area of firm.
Managed passion- It is true that passion of employees can be more powerful and
prominent drivers of the company (Brauers and Zavadskas, 2010). If the workers of
WHIRPOOL firm are motivated and passionate for their given work, then firm will be
able to get their desired objective.
Humility- the manager of the organisation needs to acknowledge their limitation apart
using costly trial and wrong procedure. They should be concentrated on “get help and
move on”.
3
Secure Best Marks with AI Grader
Need help grading? Try our AI Grader for instant feedback on your assignments.
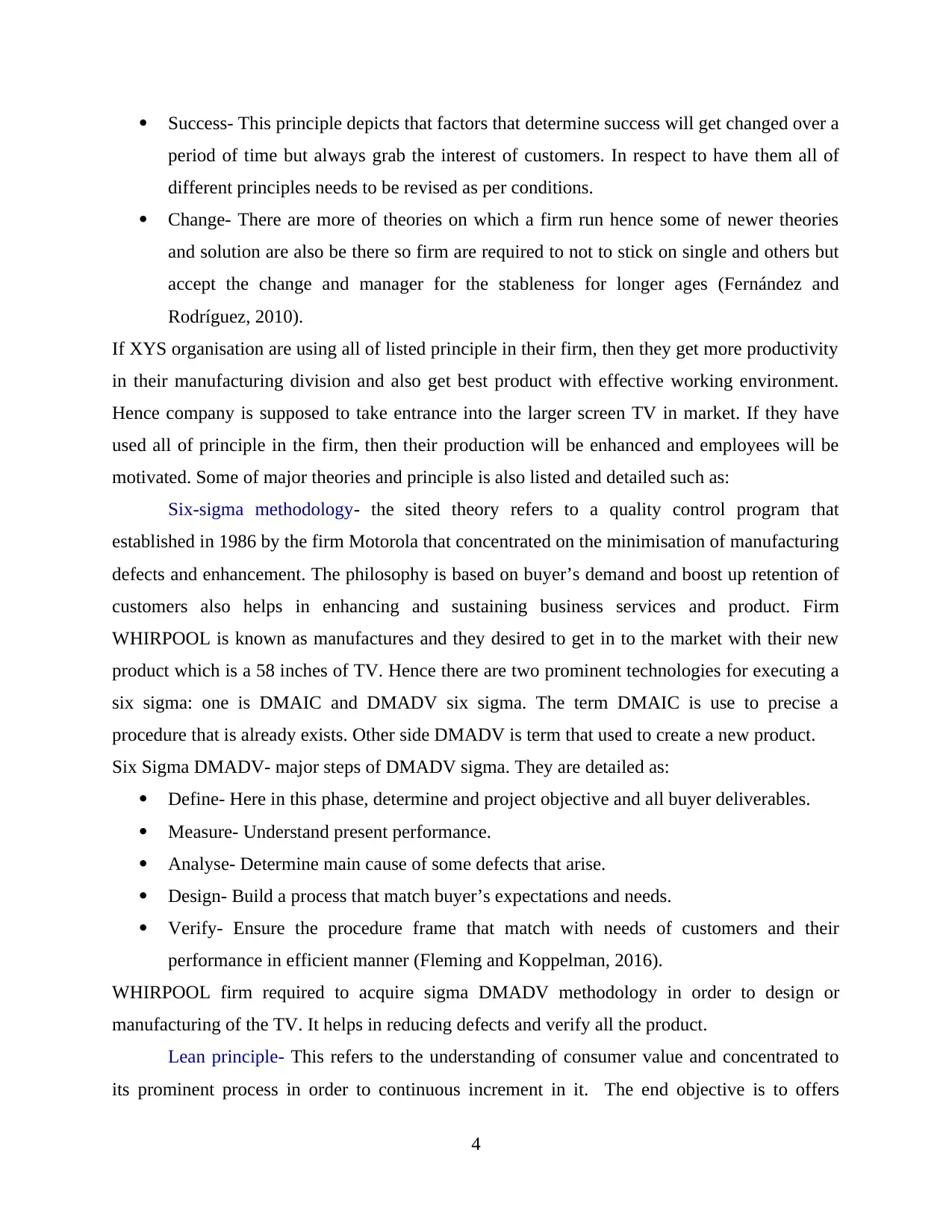
Success- This principle depicts that factors that determine success will get changed over a
period of time but always grab the interest of customers. In respect to have them all of
different principles needs to be revised as per conditions.
Change- There are more of theories on which a firm run hence some of newer theories
and solution are also be there so firm are required to not to stick on single and others but
accept the change and manager for the stableness for longer ages (Fernández and
Rodríguez, 2010).
If XYS organisation are using all of listed principle in their firm, then they get more productivity
in their manufacturing division and also get best product with effective working environment.
Hence company is supposed to take entrance into the larger screen TV in market. If they have
used all of principle in the firm, then their production will be enhanced and employees will be
motivated. Some of major theories and principle is also listed and detailed such as:
Six-sigma methodology- the sited theory refers to a quality control program that
established in 1986 by the firm Motorola that concentrated on the minimisation of manufacturing
defects and enhancement. The philosophy is based on buyer’s demand and boost up retention of
customers also helps in enhancing and sustaining business services and product. Firm
WHIRPOOL is known as manufactures and they desired to get in to the market with their new
product which is a 58 inches of TV. Hence there are two prominent technologies for executing a
six sigma: one is DMAIC and DMADV six sigma. The term DMAIC is use to precise a
procedure that is already exists. Other side DMADV is term that used to create a new product.
Six Sigma DMADV- major steps of DMADV sigma. They are detailed as:
Define- Here in this phase, determine and project objective and all buyer deliverables.
Measure- Understand present performance.
Analyse- Determine main cause of some defects that arise.
Design- Build a process that match buyer’s expectations and needs.
Verify- Ensure the procedure frame that match with needs of customers and their
performance in efficient manner (Fleming and Koppelman, 2016).
WHIRPOOL firm required to acquire sigma DMADV methodology in order to design or
manufacturing of the TV. It helps in reducing defects and verify all the product.
Lean principle- This refers to the understanding of consumer value and concentrated to
its prominent process in order to continuous increment in it. The end objective is to offers
4
period of time but always grab the interest of customers. In respect to have them all of
different principles needs to be revised as per conditions.
Change- There are more of theories on which a firm run hence some of newer theories
and solution are also be there so firm are required to not to stick on single and others but
accept the change and manager for the stableness for longer ages (Fernández and
Rodríguez, 2010).
If XYS organisation are using all of listed principle in their firm, then they get more productivity
in their manufacturing division and also get best product with effective working environment.
Hence company is supposed to take entrance into the larger screen TV in market. If they have
used all of principle in the firm, then their production will be enhanced and employees will be
motivated. Some of major theories and principle is also listed and detailed such as:
Six-sigma methodology- the sited theory refers to a quality control program that
established in 1986 by the firm Motorola that concentrated on the minimisation of manufacturing
defects and enhancement. The philosophy is based on buyer’s demand and boost up retention of
customers also helps in enhancing and sustaining business services and product. Firm
WHIRPOOL is known as manufactures and they desired to get in to the market with their new
product which is a 58 inches of TV. Hence there are two prominent technologies for executing a
six sigma: one is DMAIC and DMADV six sigma. The term DMAIC is use to precise a
procedure that is already exists. Other side DMADV is term that used to create a new product.
Six Sigma DMADV- major steps of DMADV sigma. They are detailed as:
Define- Here in this phase, determine and project objective and all buyer deliverables.
Measure- Understand present performance.
Analyse- Determine main cause of some defects that arise.
Design- Build a process that match buyer’s expectations and needs.
Verify- Ensure the procedure frame that match with needs of customers and their
performance in efficient manner (Fleming and Koppelman, 2016).
WHIRPOOL firm required to acquire sigma DMADV methodology in order to design or
manufacturing of the TV. It helps in reducing defects and verify all the product.
Lean principle- This refers to the understanding of consumer value and concentrated to
its prominent process in order to continuous increment in it. The end objective is to offers
4
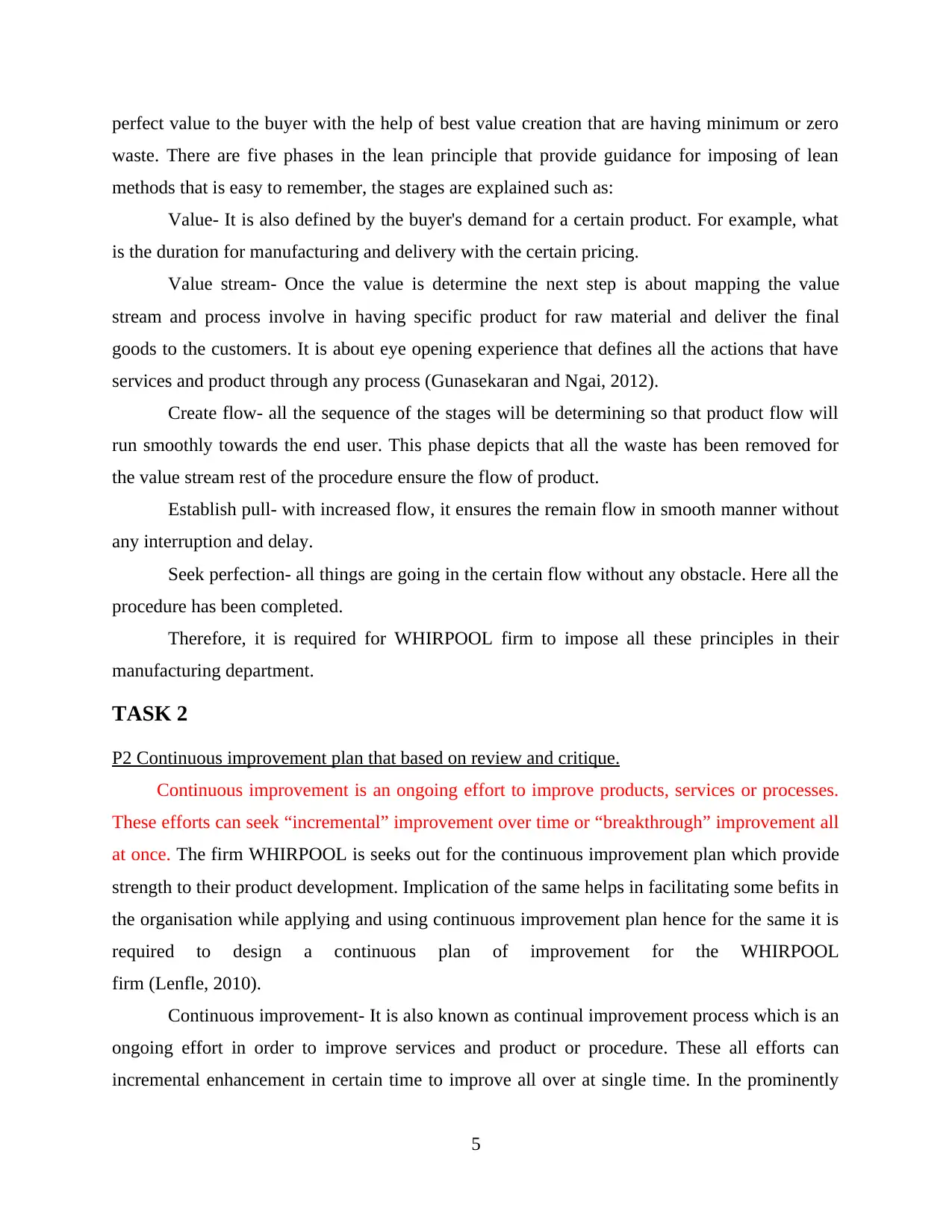
perfect value to the buyer with the help of best value creation that are having minimum or zero
waste. There are five phases in the lean principle that provide guidance for imposing of lean
methods that is easy to remember, the stages are explained such as:
Value- It is also defined by the buyer's demand for a certain product. For example, what
is the duration for manufacturing and delivery with the certain pricing.
Value stream- Once the value is determine the next step is about mapping the value
stream and process involve in having specific product for raw material and deliver the final
goods to the customers. It is about eye opening experience that defines all the actions that have
services and product through any process (Gunasekaran and Ngai, 2012).
Create flow- all the sequence of the stages will be determining so that product flow will
run smoothly towards the end user. This phase depicts that all the waste has been removed for
the value stream rest of the procedure ensure the flow of product.
Establish pull- with increased flow, it ensures the remain flow in smooth manner without
any interruption and delay.
Seek perfection- all things are going in the certain flow without any obstacle. Here all the
procedure has been completed.
Therefore, it is required for WHIRPOOL firm to impose all these principles in their
manufacturing department.
TASK 2
P2 Continuous improvement plan that based on review and critique.
Continuous improvement is an ongoing effort to improve products, services or processes.
These efforts can seek “incremental” improvement over time or “breakthrough” improvement all
at once. The firm WHIRPOOL is seeks out for the continuous improvement plan which provide
strength to their product development. Implication of the same helps in facilitating some befits in
the organisation while applying and using continuous improvement plan hence for the same it is
required to design a continuous plan of improvement for the WHIRPOOL
firm (Lenfle, 2010).
Continuous improvement- It is also known as continual improvement process which is an
ongoing effort in order to improve services and product or procedure. These all efforts can
incremental enhancement in certain time to improve all over at single time. In the prominently
5
waste. There are five phases in the lean principle that provide guidance for imposing of lean
methods that is easy to remember, the stages are explained such as:
Value- It is also defined by the buyer's demand for a certain product. For example, what
is the duration for manufacturing and delivery with the certain pricing.
Value stream- Once the value is determine the next step is about mapping the value
stream and process involve in having specific product for raw material and deliver the final
goods to the customers. It is about eye opening experience that defines all the actions that have
services and product through any process (Gunasekaran and Ngai, 2012).
Create flow- all the sequence of the stages will be determining so that product flow will
run smoothly towards the end user. This phase depicts that all the waste has been removed for
the value stream rest of the procedure ensure the flow of product.
Establish pull- with increased flow, it ensures the remain flow in smooth manner without
any interruption and delay.
Seek perfection- all things are going in the certain flow without any obstacle. Here all the
procedure has been completed.
Therefore, it is required for WHIRPOOL firm to impose all these principles in their
manufacturing department.
TASK 2
P2 Continuous improvement plan that based on review and critique.
Continuous improvement is an ongoing effort to improve products, services or processes.
These efforts can seek “incremental” improvement over time or “breakthrough” improvement all
at once. The firm WHIRPOOL is seeks out for the continuous improvement plan which provide
strength to their product development. Implication of the same helps in facilitating some befits in
the organisation while applying and using continuous improvement plan hence for the same it is
required to design a continuous plan of improvement for the WHIRPOOL
firm (Lenfle, 2010).
Continuous improvement- It is also known as continual improvement process which is an
ongoing effort in order to improve services and product or procedure. These all efforts can
incremental enhancement in certain time to improve all over at single time. In the prominently
5
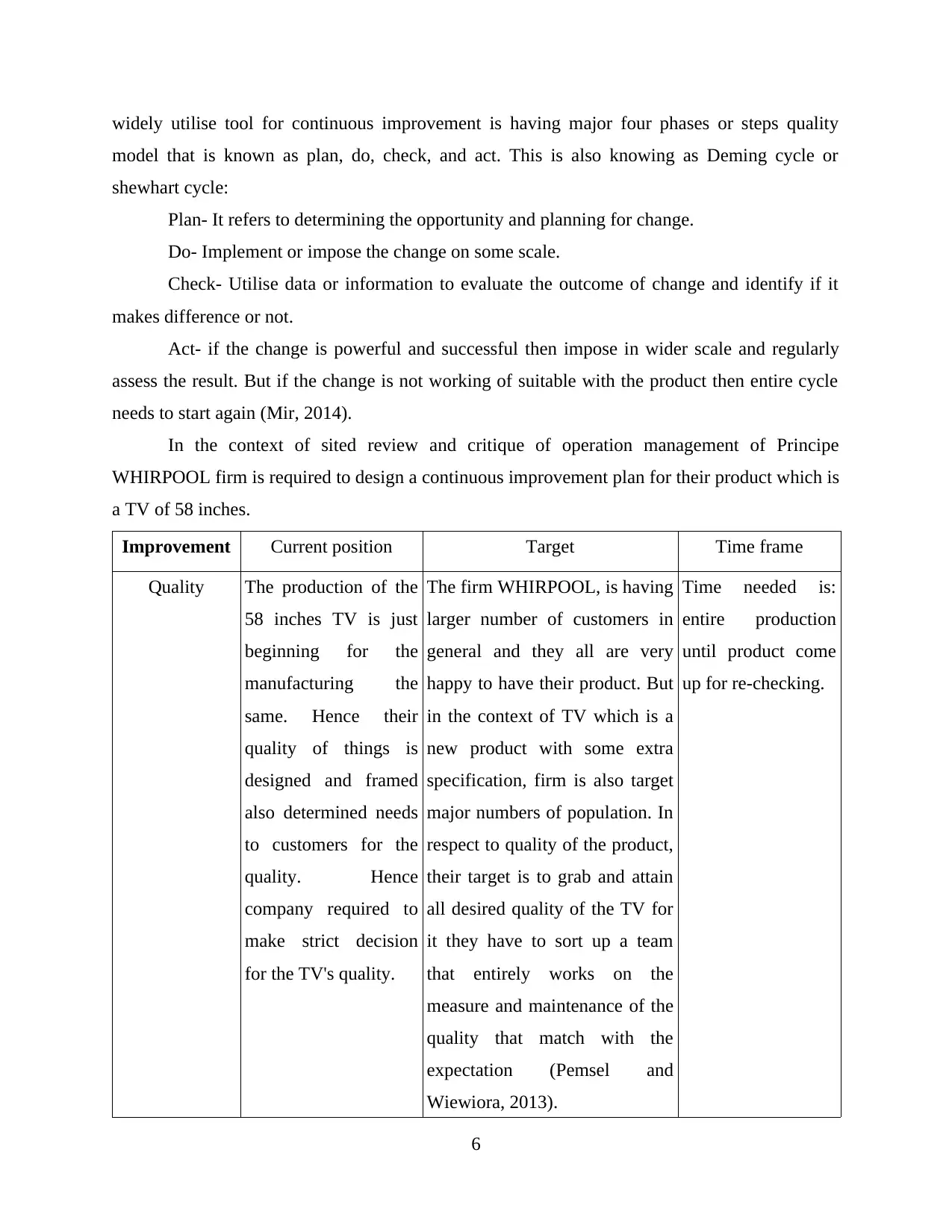
widely utilise tool for continuous improvement is having major four phases or steps quality
model that is known as plan, do, check, and act. This is also knowing as Deming cycle or
shewhart cycle:
Plan- It refers to determining the opportunity and planning for change.
Do- Implement or impose the change on some scale.
Check- Utilise data or information to evaluate the outcome of change and identify if it
makes difference or not.
Act- if the change is powerful and successful then impose in wider scale and regularly
assess the result. But if the change is not working of suitable with the product then entire cycle
needs to start again (Mir, 2014).
In the context of sited review and critique of operation management of Principe
WHIRPOOL firm is required to design a continuous improvement plan for their product which is
a TV of 58 inches.
Improvement Current position Target Time frame
Quality The production of the
58 inches TV is just
beginning for the
manufacturing the
same. Hence their
quality of things is
designed and framed
also determined needs
to customers for the
quality. Hence
company required to
make strict decision
for the TV's quality.
The firm WHIRPOOL, is having
larger number of customers in
general and they all are very
happy to have their product. But
in the context of TV which is a
new product with some extra
specification, firm is also target
major numbers of population. In
respect to quality of the product,
their target is to grab and attain
all desired quality of the TV for
it they have to sort up a team
that entirely works on the
measure and maintenance of the
quality that match with the
expectation (Pemsel and
Wiewiora, 2013).
Time needed is:
entire production
until product come
up for re-checking.
6
model that is known as plan, do, check, and act. This is also knowing as Deming cycle or
shewhart cycle:
Plan- It refers to determining the opportunity and planning for change.
Do- Implement or impose the change on some scale.
Check- Utilise data or information to evaluate the outcome of change and identify if it
makes difference or not.
Act- if the change is powerful and successful then impose in wider scale and regularly
assess the result. But if the change is not working of suitable with the product then entire cycle
needs to start again (Mir, 2014).
In the context of sited review and critique of operation management of Principe
WHIRPOOL firm is required to design a continuous improvement plan for their product which is
a TV of 58 inches.
Improvement Current position Target Time frame
Quality The production of the
58 inches TV is just
beginning for the
manufacturing the
same. Hence their
quality of things is
designed and framed
also determined needs
to customers for the
quality. Hence
company required to
make strict decision
for the TV's quality.
The firm WHIRPOOL, is having
larger number of customers in
general and they all are very
happy to have their product. But
in the context of TV which is a
new product with some extra
specification, firm is also target
major numbers of population. In
respect to quality of the product,
their target is to grab and attain
all desired quality of the TV for
it they have to sort up a team
that entirely works on the
measure and maintenance of the
quality that match with the
expectation (Pemsel and
Wiewiora, 2013).
Time needed is:
entire production
until product come
up for re-checking.
6
Paraphrase This Document
Need a fresh take? Get an instant paraphrase of this document with our AI Paraphraser
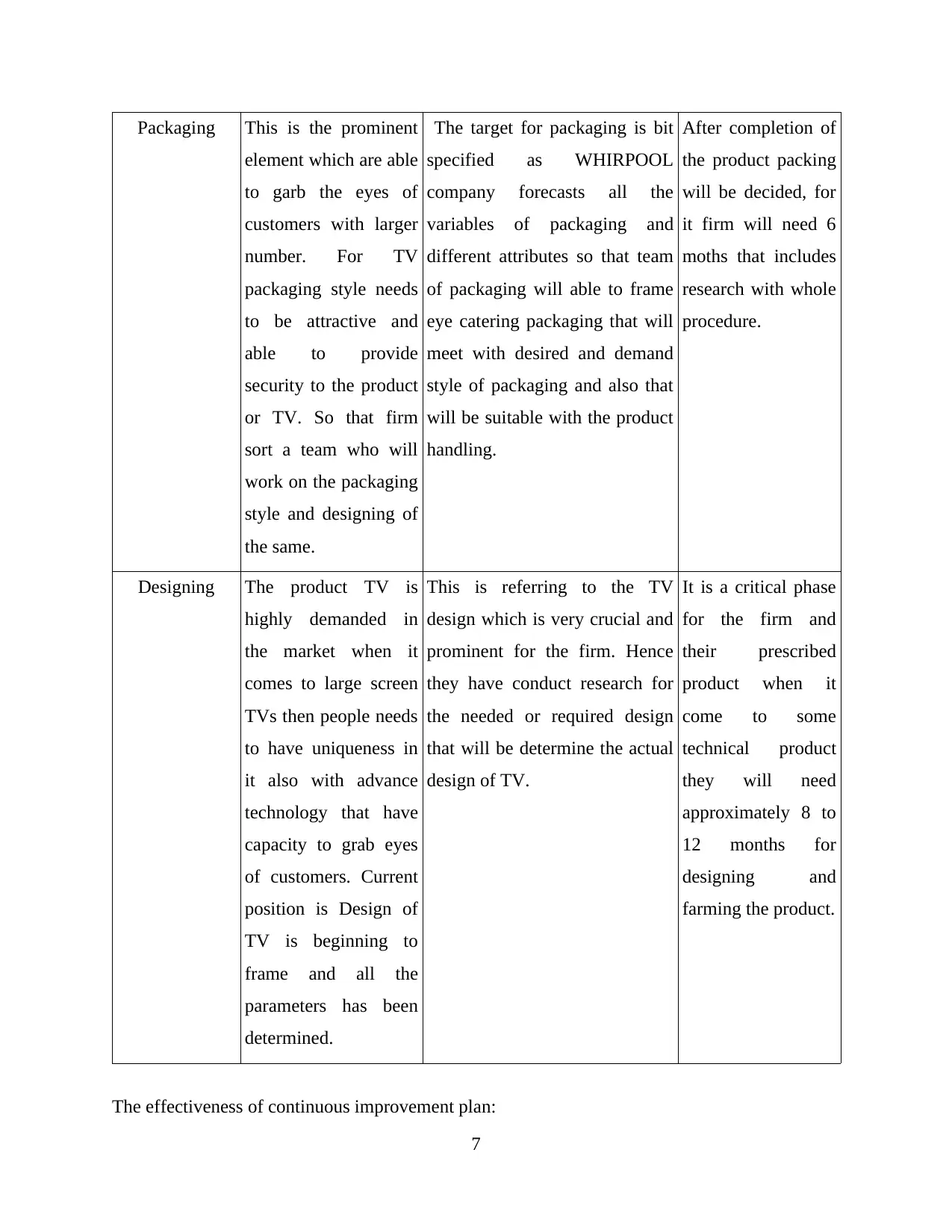
Packaging This is the prominent
element which are able
to garb the eyes of
customers with larger
number. For TV
packaging style needs
to be attractive and
able to provide
security to the product
or TV. So that firm
sort a team who will
work on the packaging
style and designing of
the same.
The target for packaging is bit
specified as WHIRPOOL
company forecasts all the
variables of packaging and
different attributes so that team
of packaging will able to frame
eye catering packaging that will
meet with desired and demand
style of packaging and also that
will be suitable with the product
handling.
After completion of
the product packing
will be decided, for
it firm will need 6
moths that includes
research with whole
procedure.
Designing The product TV is
highly demanded in
the market when it
comes to large screen
TVs then people needs
to have uniqueness in
it also with advance
technology that have
capacity to grab eyes
of customers. Current
position is Design of
TV is beginning to
frame and all the
parameters has been
determined.
This is referring to the TV
design which is very crucial and
prominent for the firm. Hence
they have conduct research for
the needed or required design
that will be determine the actual
design of TV.
It is a critical phase
for the firm and
their prescribed
product when it
come to some
technical product
they will need
approximately 8 to
12 months for
designing and
farming the product.
The effectiveness of continuous improvement plan:
7
element which are able
to garb the eyes of
customers with larger
number. For TV
packaging style needs
to be attractive and
able to provide
security to the product
or TV. So that firm
sort a team who will
work on the packaging
style and designing of
the same.
The target for packaging is bit
specified as WHIRPOOL
company forecasts all the
variables of packaging and
different attributes so that team
of packaging will able to frame
eye catering packaging that will
meet with desired and demand
style of packaging and also that
will be suitable with the product
handling.
After completion of
the product packing
will be decided, for
it firm will need 6
moths that includes
research with whole
procedure.
Designing The product TV is
highly demanded in
the market when it
comes to large screen
TVs then people needs
to have uniqueness in
it also with advance
technology that have
capacity to grab eyes
of customers. Current
position is Design of
TV is beginning to
frame and all the
parameters has been
determined.
This is referring to the TV
design which is very crucial and
prominent for the firm. Hence
they have conduct research for
the needed or required design
that will be determine the actual
design of TV.
It is a critical phase
for the firm and
their prescribed
product when it
come to some
technical product
they will need
approximately 8 to
12 months for
designing and
farming the product.
The effectiveness of continuous improvement plan:
7
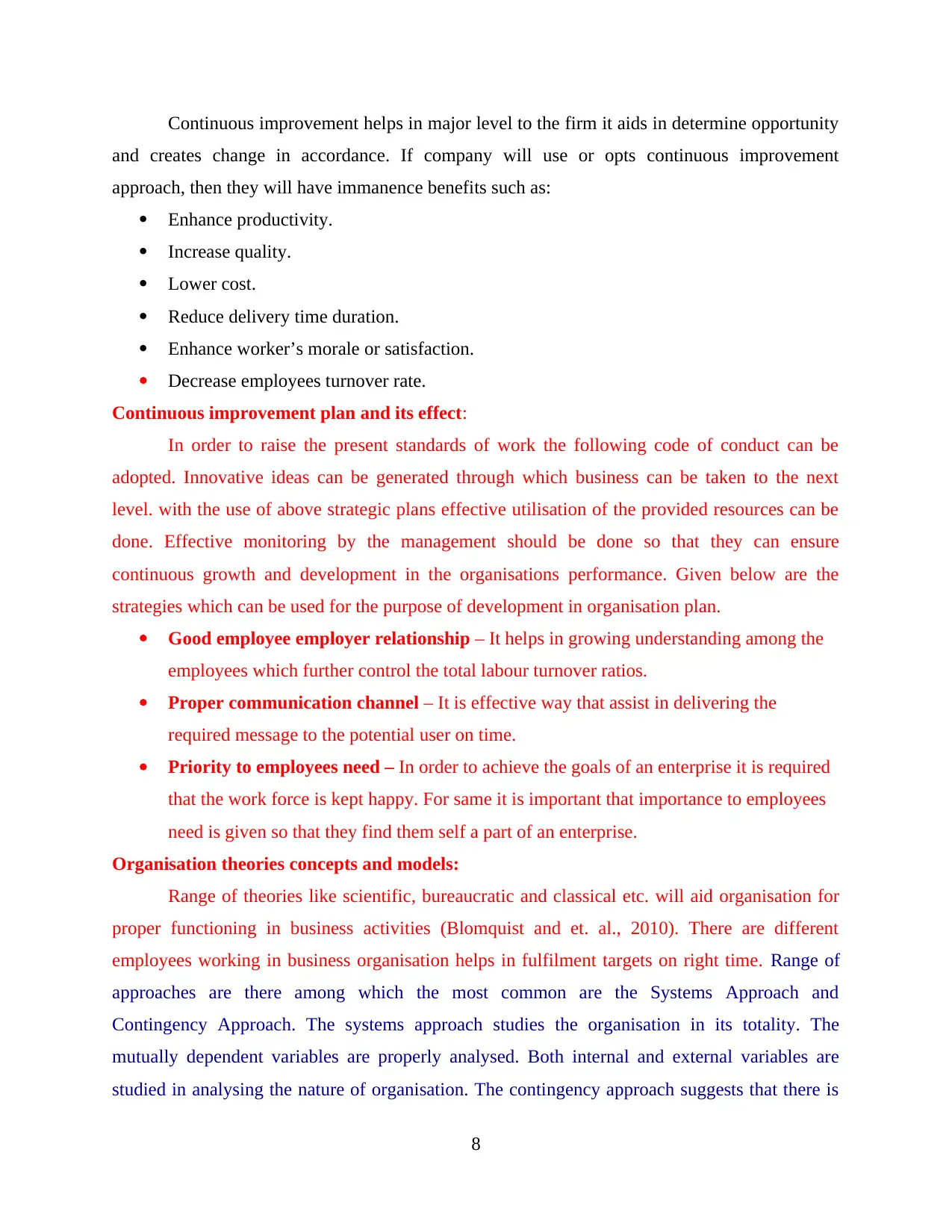
Continuous improvement helps in major level to the firm it aids in determine opportunity
and creates change in accordance. If company will use or opts continuous improvement
approach, then they will have immanence benefits such as:
Enhance productivity.
Increase quality.
Lower cost.
Reduce delivery time duration.
Enhance worker’s morale or satisfaction.
Decrease employees turnover rate.
Continuous improvement plan and its effect:
In order to raise the present standards of work the following code of conduct can be
adopted. Innovative ideas can be generated through which business can be taken to the next
level. with the use of above strategic plans effective utilisation of the provided resources can be
done. Effective monitoring by the management should be done so that they can ensure
continuous growth and development in the organisations performance. Given below are the
strategies which can be used for the purpose of development in organisation plan.
Good employee employer relationship – It helps in growing understanding among the
employees which further control the total labour turnover ratios.
Proper communication channel – It is effective way that assist in delivering the
required message to the potential user on time.
Priority to employees need – In order to achieve the goals of an enterprise it is required
that the work force is kept happy. For same it is important that importance to employees
need is given so that they find them self a part of an enterprise.
Organisation theories concepts and models:
Range of theories like scientific, bureaucratic and classical etc. will aid organisation for
proper functioning in business activities (Blomquist and et. al., 2010). There are different
employees working in business organisation helps in fulfilment targets on right time. Range of
approaches are there among which the most common are the Systems Approach and
Contingency Approach. The systems approach studies the organisation in its totality. The
mutually dependent variables are properly analysed. Both internal and external variables are
studied in analysing the nature of organisation. The contingency approach suggests that there is
8
and creates change in accordance. If company will use or opts continuous improvement
approach, then they will have immanence benefits such as:
Enhance productivity.
Increase quality.
Lower cost.
Reduce delivery time duration.
Enhance worker’s morale or satisfaction.
Decrease employees turnover rate.
Continuous improvement plan and its effect:
In order to raise the present standards of work the following code of conduct can be
adopted. Innovative ideas can be generated through which business can be taken to the next
level. with the use of above strategic plans effective utilisation of the provided resources can be
done. Effective monitoring by the management should be done so that they can ensure
continuous growth and development in the organisations performance. Given below are the
strategies which can be used for the purpose of development in organisation plan.
Good employee employer relationship – It helps in growing understanding among the
employees which further control the total labour turnover ratios.
Proper communication channel – It is effective way that assist in delivering the
required message to the potential user on time.
Priority to employees need – In order to achieve the goals of an enterprise it is required
that the work force is kept happy. For same it is important that importance to employees
need is given so that they find them self a part of an enterprise.
Organisation theories concepts and models:
Range of theories like scientific, bureaucratic and classical etc. will aid organisation for
proper functioning in business activities (Blomquist and et. al., 2010). There are different
employees working in business organisation helps in fulfilment targets on right time. Range of
approaches are there among which the most common are the Systems Approach and
Contingency Approach. The systems approach studies the organisation in its totality. The
mutually dependent variables are properly analysed. Both internal and external variables are
studied in analysing the nature of organisation. The contingency approach suggests that there is
8
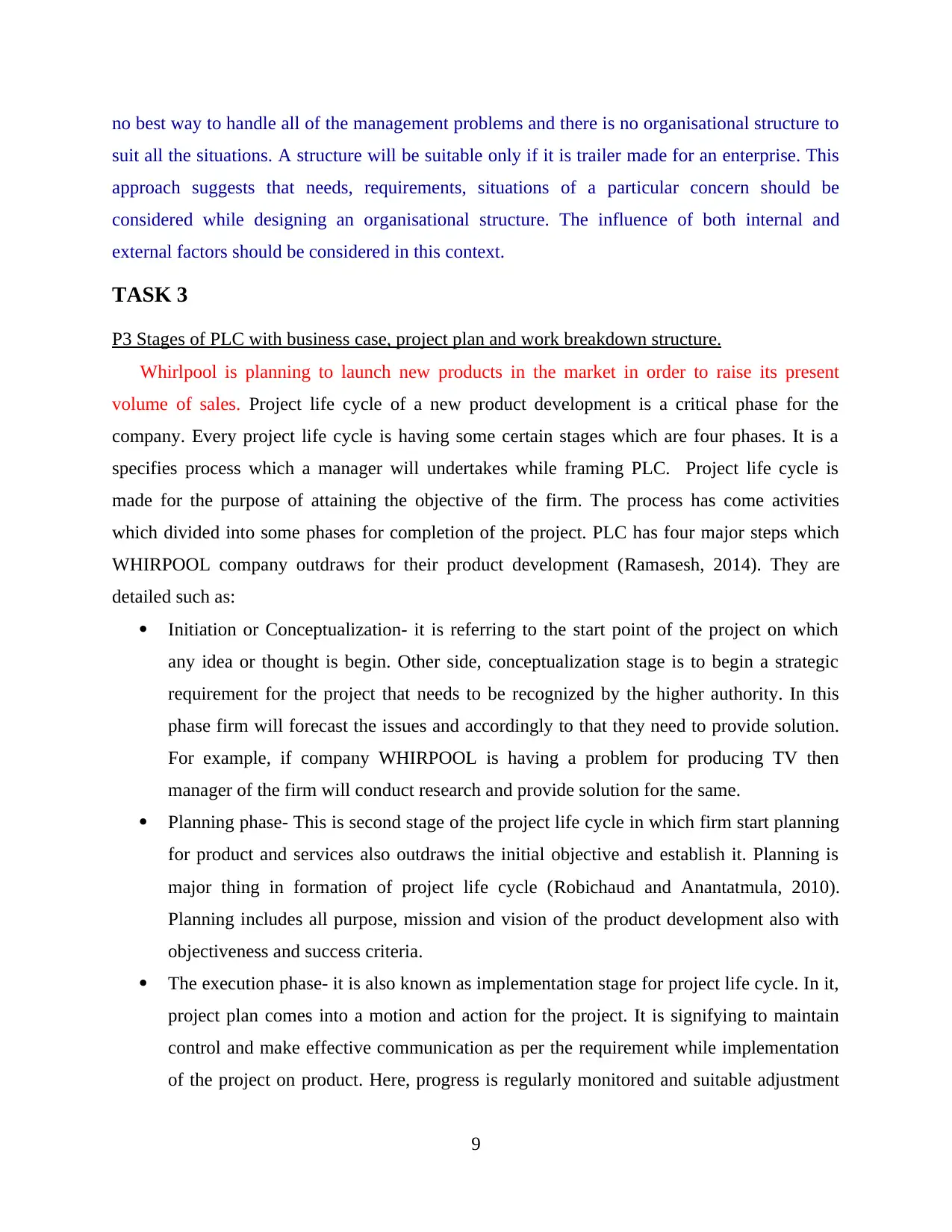
no best way to handle all of the management problems and there is no organisational structure to
suit all the situations. A structure will be suitable only if it is trailer made for an enterprise. This
approach suggests that needs, requirements, situations of a particular concern should be
considered while designing an organisational structure. The influence of both internal and
external factors should be considered in this context.
TASK 3
P3 Stages of PLC with business case, project plan and work breakdown structure.
Whirlpool is planning to launch new products in the market in order to raise its present
volume of sales. Project life cycle of a new product development is a critical phase for the
company. Every project life cycle is having some certain stages which are four phases. It is a
specifies process which a manager will undertakes while framing PLC. Project life cycle is
made for the purpose of attaining the objective of the firm. The process has come activities
which divided into some phases for completion of the project. PLC has four major steps which
WHIRPOOL company outdraws for their product development (Ramasesh, 2014). They are
detailed such as:
Initiation or Conceptualization- it is referring to the start point of the project on which
any idea or thought is begin. Other side, conceptualization stage is to begin a strategic
requirement for the project that needs to be recognized by the higher authority. In this
phase firm will forecast the issues and accordingly to that they need to provide solution.
For example, if company WHIRPOOL is having a problem for producing TV then
manager of the firm will conduct research and provide solution for the same.
Planning phase- This is second stage of the project life cycle in which firm start planning
for product and services also outdraws the initial objective and establish it. Planning is
major thing in formation of project life cycle (Robichaud and Anantatmula, 2010).
Planning includes all purpose, mission and vision of the product development also with
objectiveness and success criteria.
The execution phase- it is also known as implementation stage for project life cycle. In it,
project plan comes into a motion and action for the project. It is signifying to maintain
control and make effective communication as per the requirement while implementation
of the project on product. Here, progress is regularly monitored and suitable adjustment
9
suit all the situations. A structure will be suitable only if it is trailer made for an enterprise. This
approach suggests that needs, requirements, situations of a particular concern should be
considered while designing an organisational structure. The influence of both internal and
external factors should be considered in this context.
TASK 3
P3 Stages of PLC with business case, project plan and work breakdown structure.
Whirlpool is planning to launch new products in the market in order to raise its present
volume of sales. Project life cycle of a new product development is a critical phase for the
company. Every project life cycle is having some certain stages which are four phases. It is a
specifies process which a manager will undertakes while framing PLC. Project life cycle is
made for the purpose of attaining the objective of the firm. The process has come activities
which divided into some phases for completion of the project. PLC has four major steps which
WHIRPOOL company outdraws for their product development (Ramasesh, 2014). They are
detailed such as:
Initiation or Conceptualization- it is referring to the start point of the project on which
any idea or thought is begin. Other side, conceptualization stage is to begin a strategic
requirement for the project that needs to be recognized by the higher authority. In this
phase firm will forecast the issues and accordingly to that they need to provide solution.
For example, if company WHIRPOOL is having a problem for producing TV then
manager of the firm will conduct research and provide solution for the same.
Planning phase- This is second stage of the project life cycle in which firm start planning
for product and services also outdraws the initial objective and establish it. Planning is
major thing in formation of project life cycle (Robichaud and Anantatmula, 2010).
Planning includes all purpose, mission and vision of the product development also with
objectiveness and success criteria.
The execution phase- it is also known as implementation stage for project life cycle. In it,
project plan comes into a motion and action for the project. It is signifying to maintain
control and make effective communication as per the requirement while implementation
of the project on product. Here, progress is regularly monitored and suitable adjustment
9
Secure Best Marks with AI Grader
Need help grading? Try our AI Grader for instant feedback on your assignments.
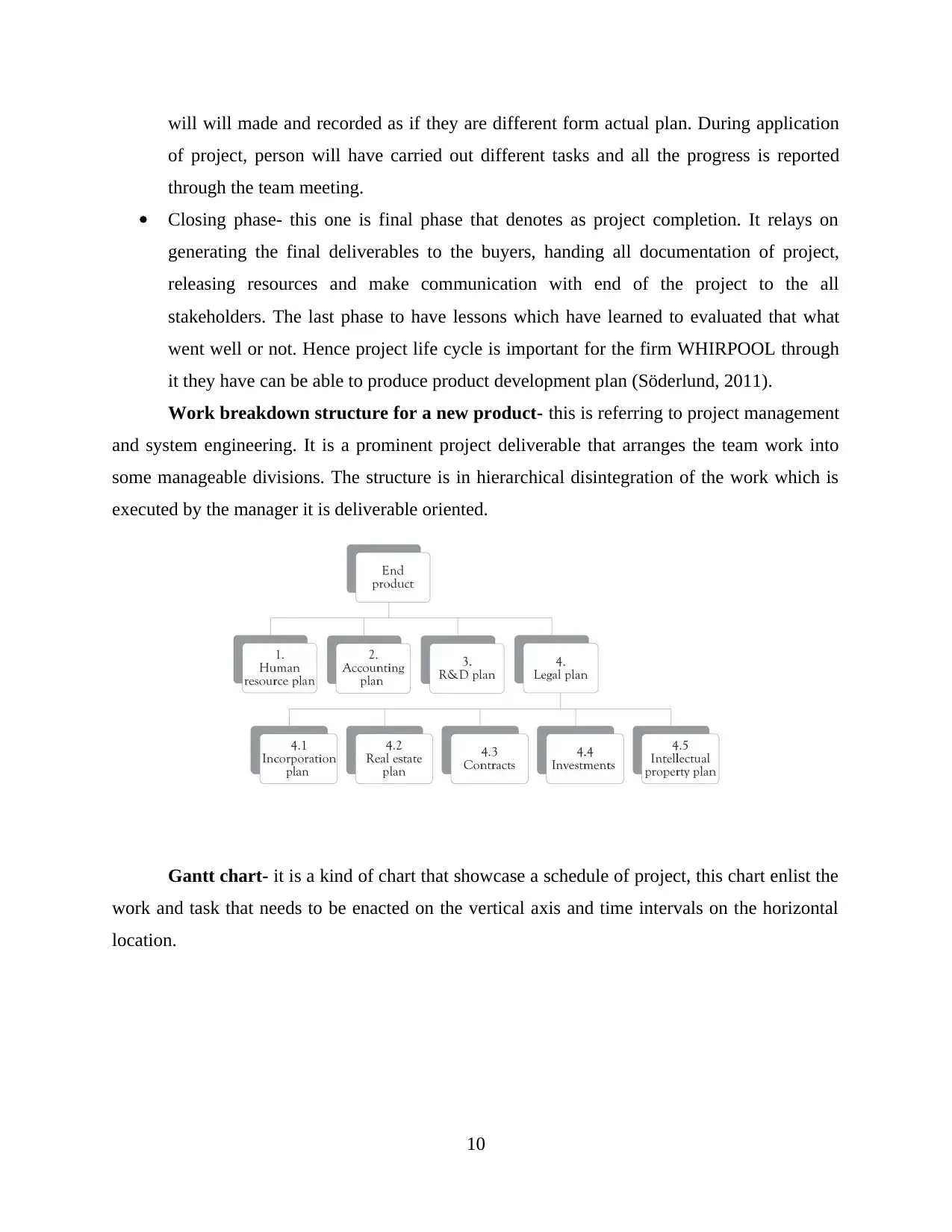
will will made and recorded as if they are different form actual plan. During application
of project, person will have carried out different tasks and all the progress is reported
through the team meeting.
Closing phase- this one is final phase that denotes as project completion. It relays on
generating the final deliverables to the buyers, handing all documentation of project,
releasing resources and make communication with end of the project to the all
stakeholders. The last phase to have lessons which have learned to evaluated that what
went well or not. Hence project life cycle is important for the firm WHIRPOOL through
it they have can be able to produce product development plan (Söderlund, 2011).
Work breakdown structure for a new product- this is referring to project management
and system engineering. It is a prominent project deliverable that arranges the team work into
some manageable divisions. The structure is in hierarchical disintegration of the work which is
executed by the manager it is deliverable oriented.
Gantt chart- it is a kind of chart that showcase a schedule of project, this chart enlist the
work and task that needs to be enacted on the vertical axis and time intervals on the horizontal
location.
10
of project, person will have carried out different tasks and all the progress is reported
through the team meeting.
Closing phase- this one is final phase that denotes as project completion. It relays on
generating the final deliverables to the buyers, handing all documentation of project,
releasing resources and make communication with end of the project to the all
stakeholders. The last phase to have lessons which have learned to evaluated that what
went well or not. Hence project life cycle is important for the firm WHIRPOOL through
it they have can be able to produce product development plan (Söderlund, 2011).
Work breakdown structure for a new product- this is referring to project management
and system engineering. It is a prominent project deliverable that arranges the team work into
some manageable divisions. The structure is in hierarchical disintegration of the work which is
executed by the manager it is deliverable oriented.
Gantt chart- it is a kind of chart that showcase a schedule of project, this chart enlist the
work and task that needs to be enacted on the vertical axis and time intervals on the horizontal
location.
10
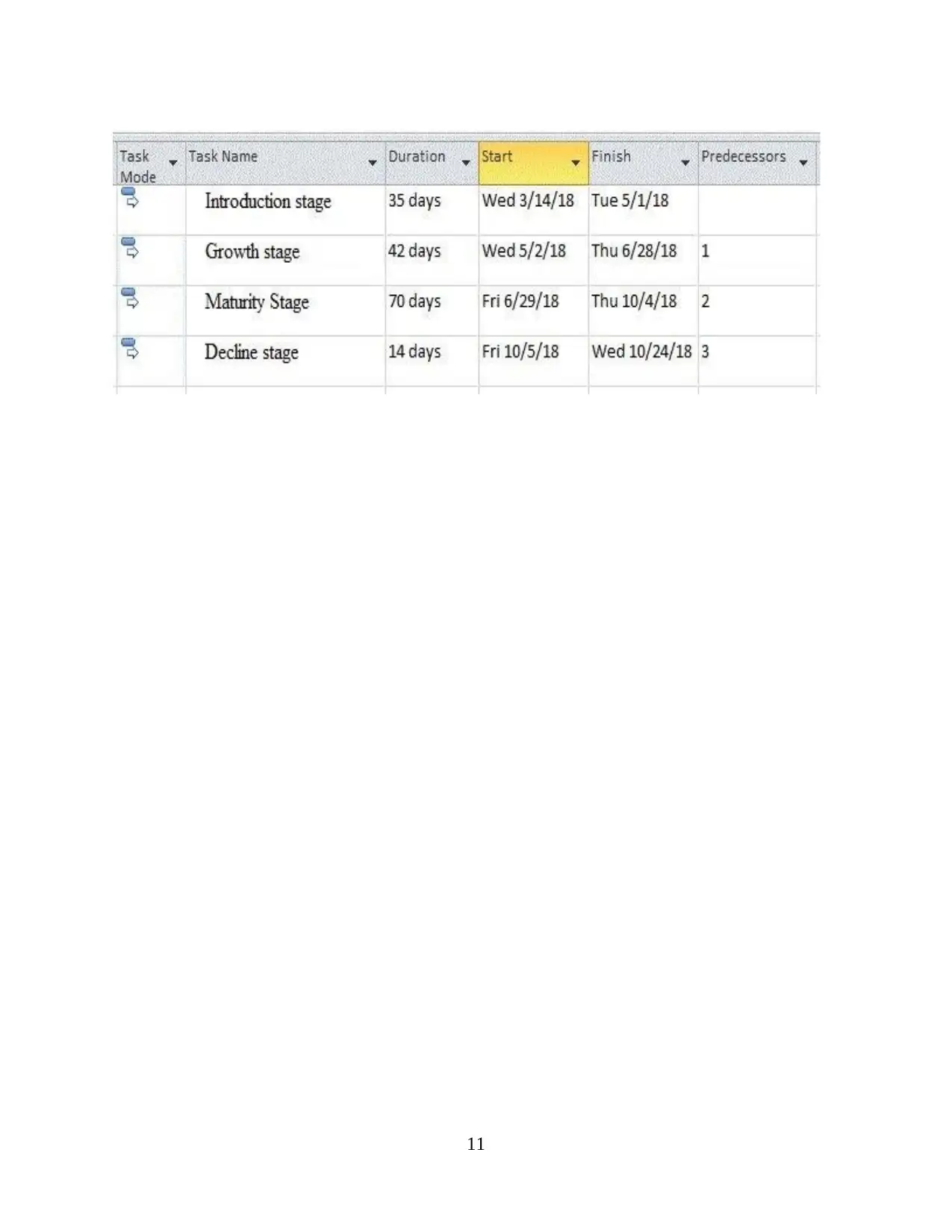
11
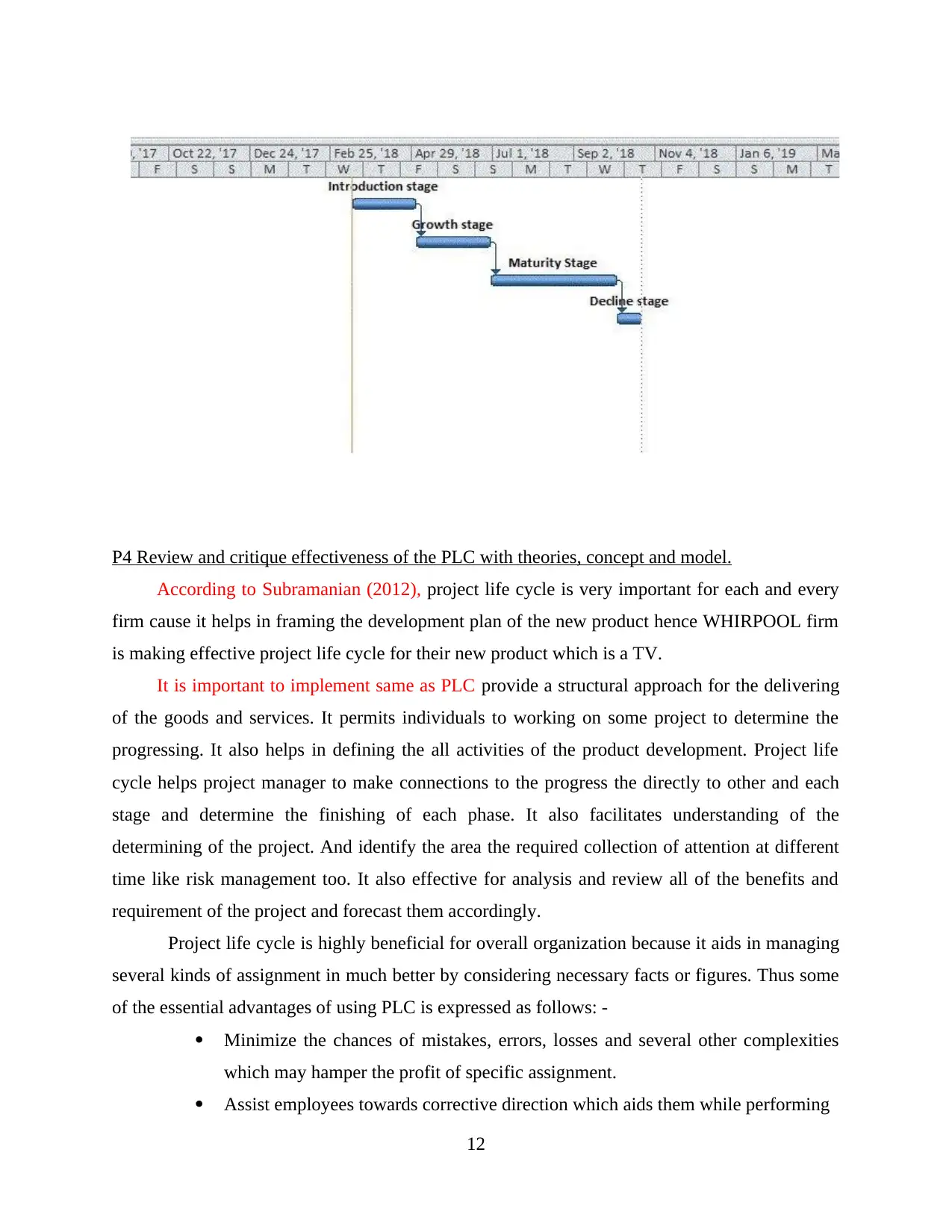
P4 Review and critique effectiveness of the PLC with theories, concept and model.
According to Subramanian (2012), project life cycle is very important for each and every
firm cause it helps in framing the development plan of the new product hence WHIRPOOL firm
is making effective project life cycle for their new product which is a TV.
It is important to implement same as PLC provide a structural approach for the delivering
of the goods and services. It permits individuals to working on some project to determine the
progressing. It also helps in defining the all activities of the product development. Project life
cycle helps project manager to make connections to the progress the directly to other and each
stage and determine the finishing of each phase. It also facilitates understanding of the
determining of the project. And identify the area the required collection of attention at different
time like risk management too. It also effective for analysis and review all of the benefits and
requirement of the project and forecast them accordingly.
Project life cycle is highly beneficial for overall organization because it aids in managing
several kinds of assignment in much better by considering necessary facts or figures. Thus some
of the essential advantages of using PLC is expressed as follows: -
Minimize the chances of mistakes, errors, losses and several other complexities
which may hamper the profit of specific assignment.
Assist employees towards corrective direction which aids them while performing
12
According to Subramanian (2012), project life cycle is very important for each and every
firm cause it helps in framing the development plan of the new product hence WHIRPOOL firm
is making effective project life cycle for their new product which is a TV.
It is important to implement same as PLC provide a structural approach for the delivering
of the goods and services. It permits individuals to working on some project to determine the
progressing. It also helps in defining the all activities of the product development. Project life
cycle helps project manager to make connections to the progress the directly to other and each
stage and determine the finishing of each phase. It also facilitates understanding of the
determining of the project. And identify the area the required collection of attention at different
time like risk management too. It also effective for analysis and review all of the benefits and
requirement of the project and forecast them accordingly.
Project life cycle is highly beneficial for overall organization because it aids in managing
several kinds of assignment in much better by considering necessary facts or figures. Thus some
of the essential advantages of using PLC is expressed as follows: -
Minimize the chances of mistakes, errors, losses and several other complexities
which may hamper the profit of specific assignment.
Assist employees towards corrective direction which aids them while performing
12
Paraphrase This Document
Need a fresh take? Get an instant paraphrase of this document with our AI Paraphraser
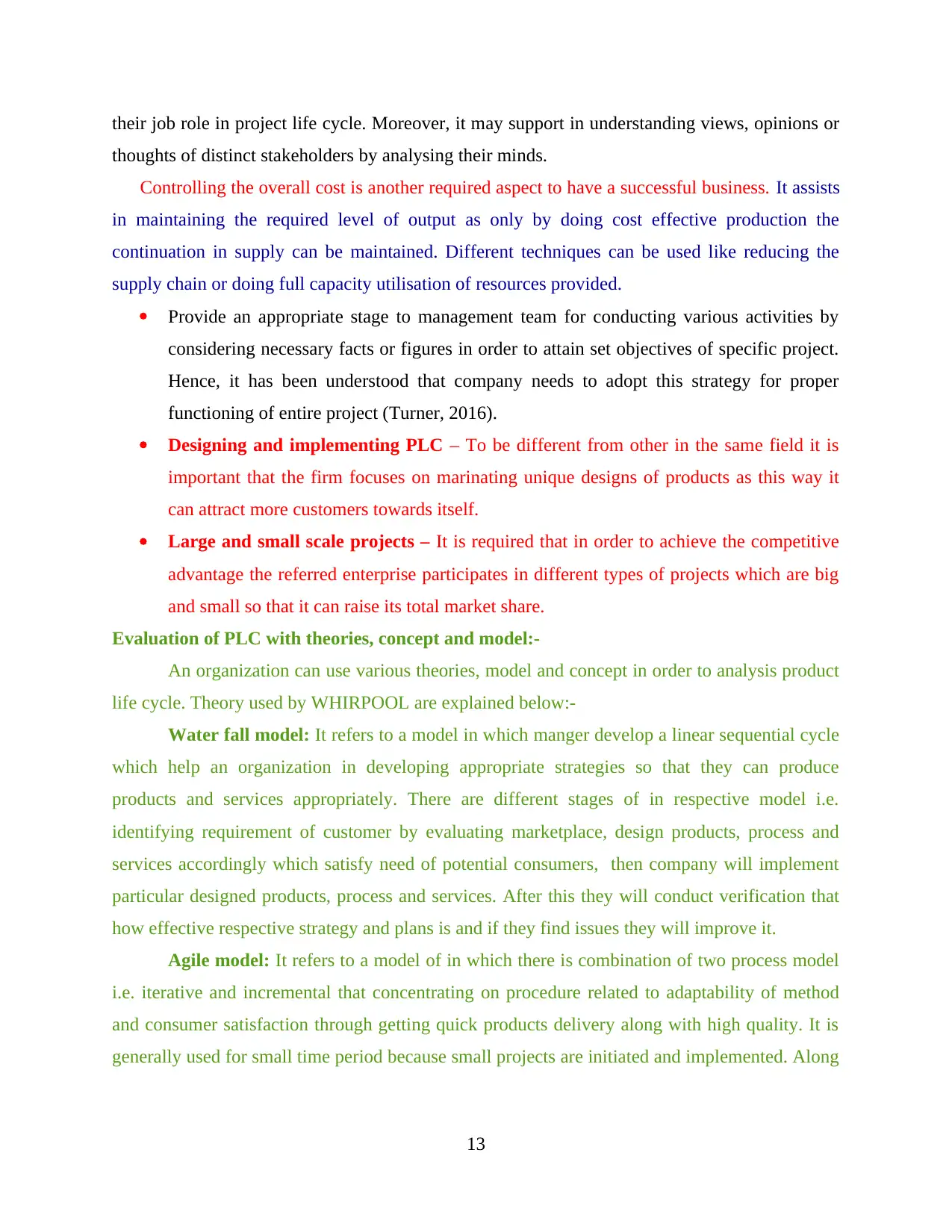
their job role in project life cycle. Moreover, it may support in understanding views, opinions or
thoughts of distinct stakeholders by analysing their minds.
Controlling the overall cost is another required aspect to have a successful business. It assists
in maintaining the required level of output as only by doing cost effective production the
continuation in supply can be maintained. Different techniques can be used like reducing the
supply chain or doing full capacity utilisation of resources provided.
Provide an appropriate stage to management team for conducting various activities by
considering necessary facts or figures in order to attain set objectives of specific project.
Hence, it has been understood that company needs to adopt this strategy for proper
functioning of entire project (Turner, 2016).
Designing and implementing PLC – To be different from other in the same field it is
important that the firm focuses on marinating unique designs of products as this way it
can attract more customers towards itself.
Large and small scale projects – It is required that in order to achieve the competitive
advantage the referred enterprise participates in different types of projects which are big
and small so that it can raise its total market share.
Evaluation of PLC with theories, concept and model:-
An organization can use various theories, model and concept in order to analysis product
life cycle. Theory used by WHIRPOOL are explained below:-
Water fall model: It refers to a model in which manger develop a linear sequential cycle
which help an organization in developing appropriate strategies so that they can produce
products and services appropriately. There are different stages of in respective model i.e.
identifying requirement of customer by evaluating marketplace, design products, process and
services accordingly which satisfy need of potential consumers, then company will implement
particular designed products, process and services. After this they will conduct verification that
how effective respective strategy and plans is and if they find issues they will improve it.
Agile model: It refers to a model of in which there is combination of two process model
i.e. iterative and incremental that concentrating on procedure related to adaptability of method
and consumer satisfaction through getting quick products delivery along with high quality. It is
generally used for small time period because small projects are initiated and implemented. Along
13
thoughts of distinct stakeholders by analysing their minds.
Controlling the overall cost is another required aspect to have a successful business. It assists
in maintaining the required level of output as only by doing cost effective production the
continuation in supply can be maintained. Different techniques can be used like reducing the
supply chain or doing full capacity utilisation of resources provided.
Provide an appropriate stage to management team for conducting various activities by
considering necessary facts or figures in order to attain set objectives of specific project.
Hence, it has been understood that company needs to adopt this strategy for proper
functioning of entire project (Turner, 2016).
Designing and implementing PLC – To be different from other in the same field it is
important that the firm focuses on marinating unique designs of products as this way it
can attract more customers towards itself.
Large and small scale projects – It is required that in order to achieve the competitive
advantage the referred enterprise participates in different types of projects which are big
and small so that it can raise its total market share.
Evaluation of PLC with theories, concept and model:-
An organization can use various theories, model and concept in order to analysis product
life cycle. Theory used by WHIRPOOL are explained below:-
Water fall model: It refers to a model in which manger develop a linear sequential cycle
which help an organization in developing appropriate strategies so that they can produce
products and services appropriately. There are different stages of in respective model i.e.
identifying requirement of customer by evaluating marketplace, design products, process and
services accordingly which satisfy need of potential consumers, then company will implement
particular designed products, process and services. After this they will conduct verification that
how effective respective strategy and plans is and if they find issues they will improve it.
Agile model: It refers to a model of in which there is combination of two process model
i.e. iterative and incremental that concentrating on procedure related to adaptability of method
and consumer satisfaction through getting quick products delivery along with high quality. It is
generally used for small time period because small projects are initiated and implemented. Along
13
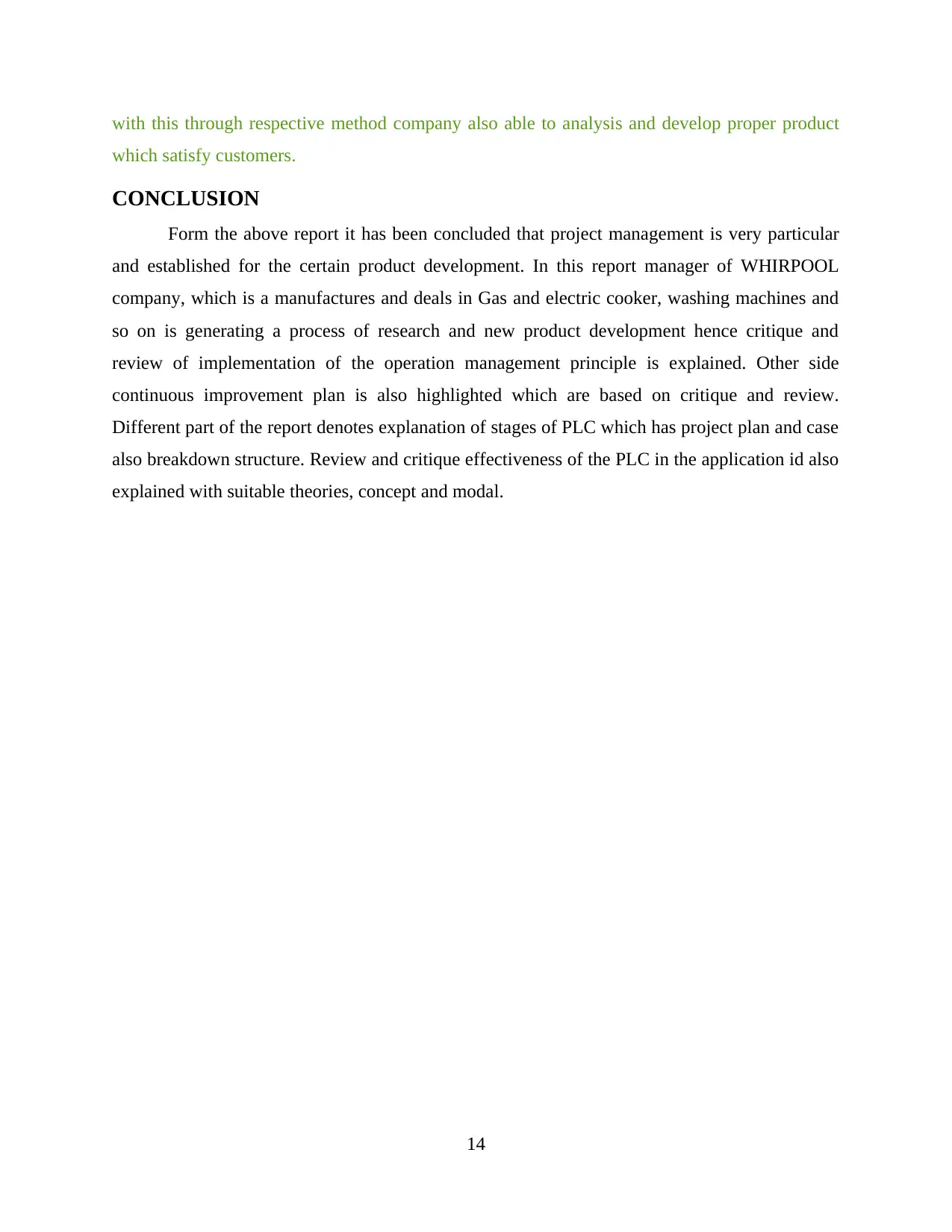
with this through respective method company also able to analysis and develop proper product
which satisfy customers.
CONCLUSION
Form the above report it has been concluded that project management is very particular
and established for the certain product development. In this report manager of WHIRPOOL
company, which is a manufactures and deals in Gas and electric cooker, washing machines and
so on is generating a process of research and new product development hence critique and
review of implementation of the operation management principle is explained. Other side
continuous improvement plan is also highlighted which are based on critique and review.
Different part of the report denotes explanation of stages of PLC which has project plan and case
also breakdown structure. Review and critique effectiveness of the PLC in the application id also
explained with suitable theories, concept and modal.
14
which satisfy customers.
CONCLUSION
Form the above report it has been concluded that project management is very particular
and established for the certain product development. In this report manager of WHIRPOOL
company, which is a manufactures and deals in Gas and electric cooker, washing machines and
so on is generating a process of research and new product development hence critique and
review of implementation of the operation management principle is explained. Other side
continuous improvement plan is also highlighted which are based on critique and review.
Different part of the report denotes explanation of stages of PLC which has project plan and case
also breakdown structure. Review and critique effectiveness of the PLC in the application id also
explained with suitable theories, concept and modal.
14
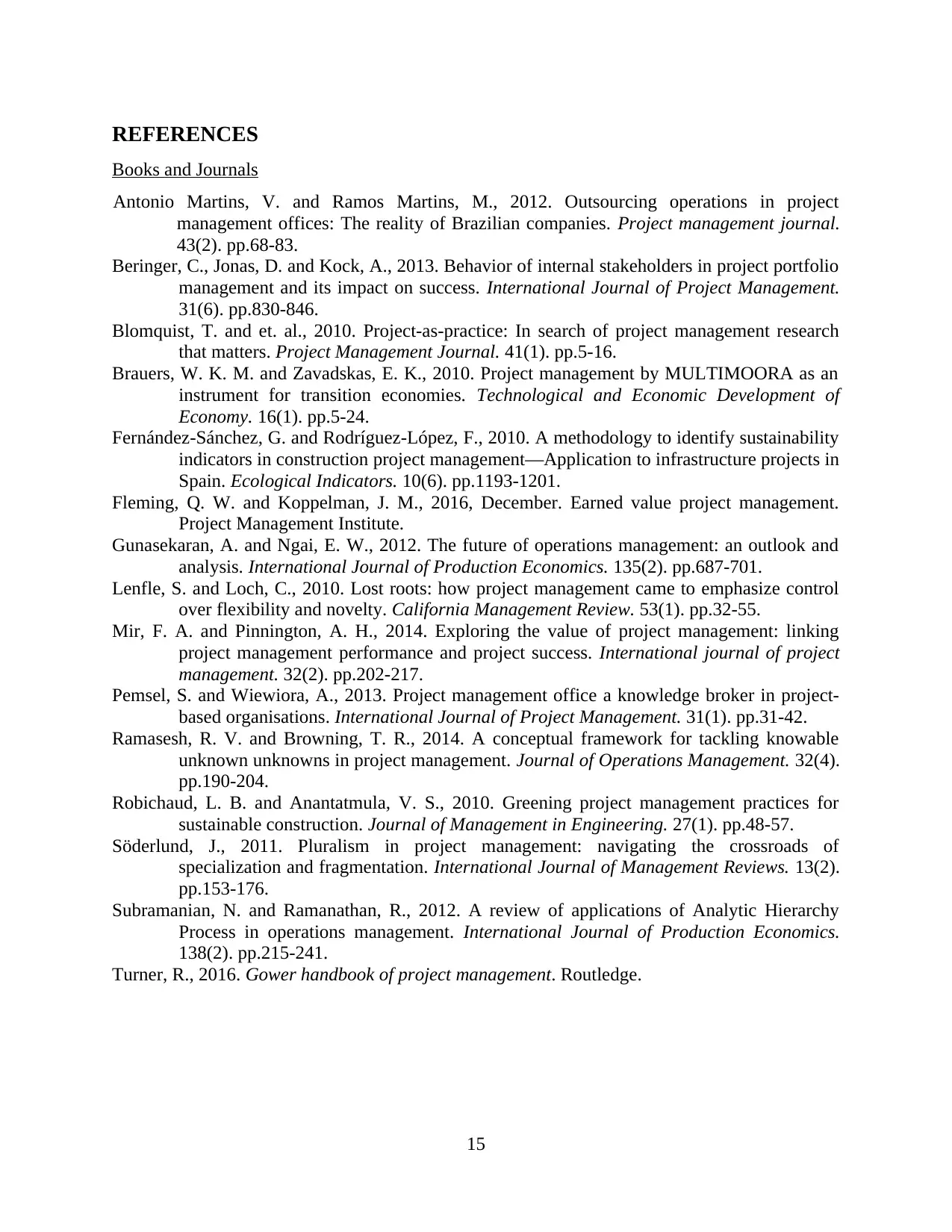
REFERENCES
Books and Journals
Antonio Martins, V. and Ramos Martins, M., 2012. Outsourcing operations in project
management offices: The reality of Brazilian companies. Project management journal.
43(2). pp.68-83.
Beringer, C., Jonas, D. and Kock, A., 2013. Behavior of internal stakeholders in project portfolio
management and its impact on success. International Journal of Project Management.
31(6). pp.830-846.
Blomquist, T. and et. al., 2010. Project‐as‐practice: In search of project management research
that matters. Project Management Journal. 41(1). pp.5-16.
Brauers, W. K. M. and Zavadskas, E. K., 2010. Project management by MULTIMOORA as an
instrument for transition economies. Technological and Economic Development of
Economy. 16(1). pp.5-24.
Fernández-Sánchez, G. and Rodríguez-López, F., 2010. A methodology to identify sustainability
indicators in construction project management—Application to infrastructure projects in
Spain. Ecological Indicators. 10(6). pp.1193-1201.
Fleming, Q. W. and Koppelman, J. M., 2016, December. Earned value project management.
Project Management Institute.
Gunasekaran, A. and Ngai, E. W., 2012. The future of operations management: an outlook and
analysis. International Journal of Production Economics. 135(2). pp.687-701.
Lenfle, S. and Loch, C., 2010. Lost roots: how project management came to emphasize control
over flexibility and novelty. California Management Review. 53(1). pp.32-55.
Mir, F. A. and Pinnington, A. H., 2014. Exploring the value of project management: linking
project management performance and project success. International journal of project
management. 32(2). pp.202-217.
Pemsel, S. and Wiewiora, A., 2013. Project management office a knowledge broker in project-
based organisations. International Journal of Project Management. 31(1). pp.31-42.
Ramasesh, R. V. and Browning, T. R., 2014. A conceptual framework for tackling knowable
unknown unknowns in project management. Journal of Operations Management. 32(4).
pp.190-204.
Robichaud, L. B. and Anantatmula, V. S., 2010. Greening project management practices for
sustainable construction. Journal of Management in Engineering. 27(1). pp.48-57.
Söderlund, J., 2011. Pluralism in project management: navigating the crossroads of
specialization and fragmentation. International Journal of Management Reviews. 13(2).
pp.153-176.
Subramanian, N. and Ramanathan, R., 2012. A review of applications of Analytic Hierarchy
Process in operations management. International Journal of Production Economics.
138(2). pp.215-241.
Turner, R., 2016. Gower handbook of project management. Routledge.
15
Books and Journals
Antonio Martins, V. and Ramos Martins, M., 2012. Outsourcing operations in project
management offices: The reality of Brazilian companies. Project management journal.
43(2). pp.68-83.
Beringer, C., Jonas, D. and Kock, A., 2013. Behavior of internal stakeholders in project portfolio
management and its impact on success. International Journal of Project Management.
31(6). pp.830-846.
Blomquist, T. and et. al., 2010. Project‐as‐practice: In search of project management research
that matters. Project Management Journal. 41(1). pp.5-16.
Brauers, W. K. M. and Zavadskas, E. K., 2010. Project management by MULTIMOORA as an
instrument for transition economies. Technological and Economic Development of
Economy. 16(1). pp.5-24.
Fernández-Sánchez, G. and Rodríguez-López, F., 2010. A methodology to identify sustainability
indicators in construction project management—Application to infrastructure projects in
Spain. Ecological Indicators. 10(6). pp.1193-1201.
Fleming, Q. W. and Koppelman, J. M., 2016, December. Earned value project management.
Project Management Institute.
Gunasekaran, A. and Ngai, E. W., 2012. The future of operations management: an outlook and
analysis. International Journal of Production Economics. 135(2). pp.687-701.
Lenfle, S. and Loch, C., 2010. Lost roots: how project management came to emphasize control
over flexibility and novelty. California Management Review. 53(1). pp.32-55.
Mir, F. A. and Pinnington, A. H., 2014. Exploring the value of project management: linking
project management performance and project success. International journal of project
management. 32(2). pp.202-217.
Pemsel, S. and Wiewiora, A., 2013. Project management office a knowledge broker in project-
based organisations. International Journal of Project Management. 31(1). pp.31-42.
Ramasesh, R. V. and Browning, T. R., 2014. A conceptual framework for tackling knowable
unknown unknowns in project management. Journal of Operations Management. 32(4).
pp.190-204.
Robichaud, L. B. and Anantatmula, V. S., 2010. Greening project management practices for
sustainable construction. Journal of Management in Engineering. 27(1). pp.48-57.
Söderlund, J., 2011. Pluralism in project management: navigating the crossroads of
specialization and fragmentation. International Journal of Management Reviews. 13(2).
pp.153-176.
Subramanian, N. and Ramanathan, R., 2012. A review of applications of Analytic Hierarchy
Process in operations management. International Journal of Production Economics.
138(2). pp.215-241.
Turner, R., 2016. Gower handbook of project management. Routledge.
15
1 out of 16
Related Documents

Your All-in-One AI-Powered Toolkit for Academic Success.
+13062052269
info@desklib.com
Available 24*7 on WhatsApp / Email
Unlock your academic potential
© 2024 | Zucol Services PVT LTD | All rights reserved.