Dissertation on Optimizing Lubrication for Hot Rolling Machines
VerifiedAdded on 2023/06/03
|42
|9833
|329
Thesis and Dissertation
AI Summary
This dissertation investigates effective lubrication strategies for hot rolling machines, crucial equipment in industries reshaping metals and non-metals. It addresses the lubrication challenges, particularly in vertical rollers, and aims to identify optimal lubricant components. The research analyzes various lubricants, including oil, water emulsions, and nano-particle-based additives, considering their physical properties and the metal surfaces' characteristics at different temperatures and roughness levels. Through primary data collection using external measurement tools to monitor temperature and lubricant effectiveness, the study concludes that a mixture of oil, Al2O2 nano-particles, and water demonstrates the best potential as an effective lubricant, reducing thermal changes, frictional force, and rolling force, thereby enhancing the mechanical efficiency of the rolling machine. The dissertation includes a literature review, research methodology, data presentation, analysis, and a conclusion linking findings with research objectives and future scope.
Contribute Materials
Your contribution can guide someone’s learning journey. Share your
documents today.
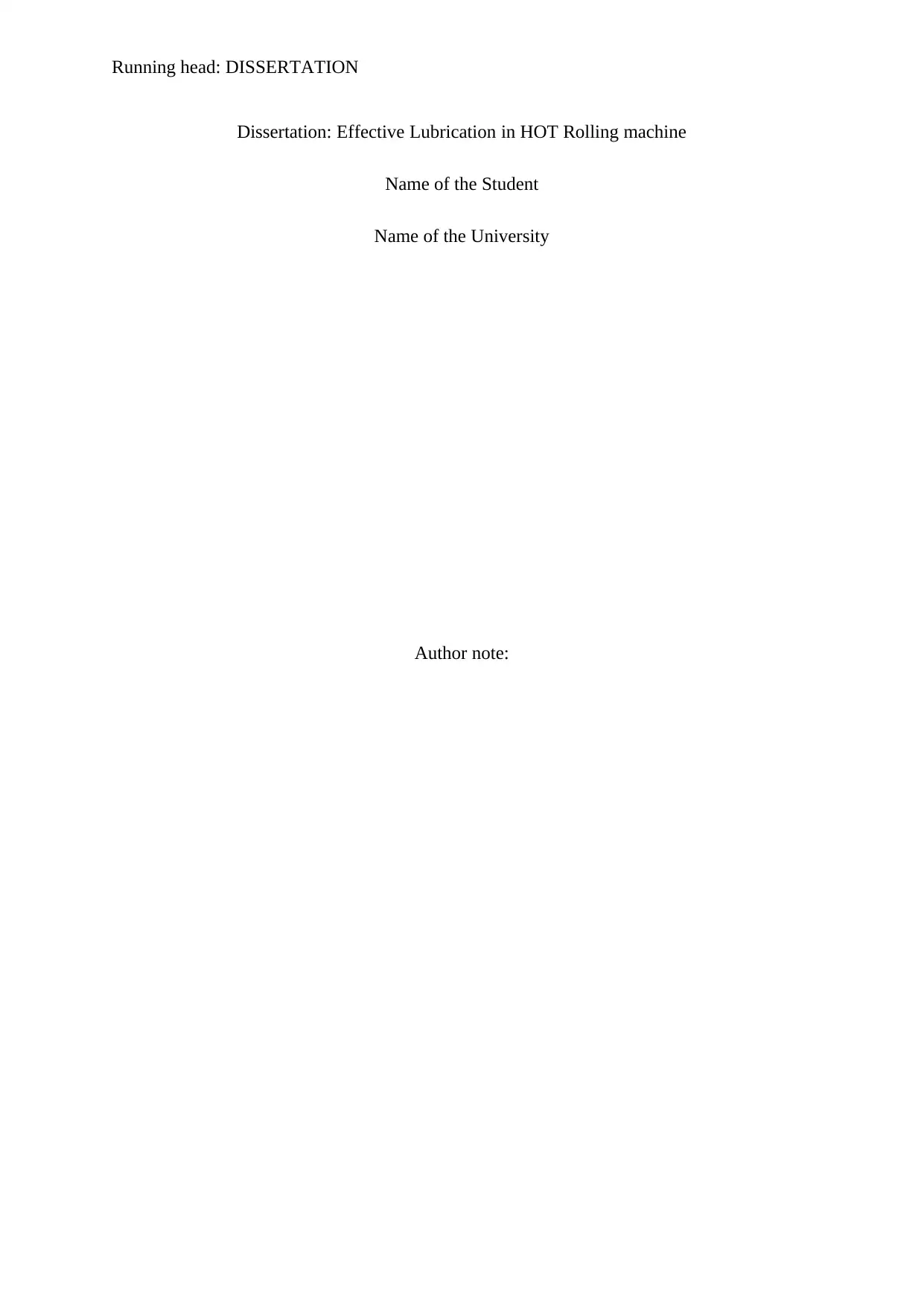
Running head: DISSERTATION
Dissertation: Effective Lubrication in HOT Rolling machine
Name of the Student
Name of the University
Author note:
Dissertation: Effective Lubrication in HOT Rolling machine
Name of the Student
Name of the University
Author note:
Secure Best Marks with AI Grader
Need help grading? Try our AI Grader for instant feedback on your assignments.
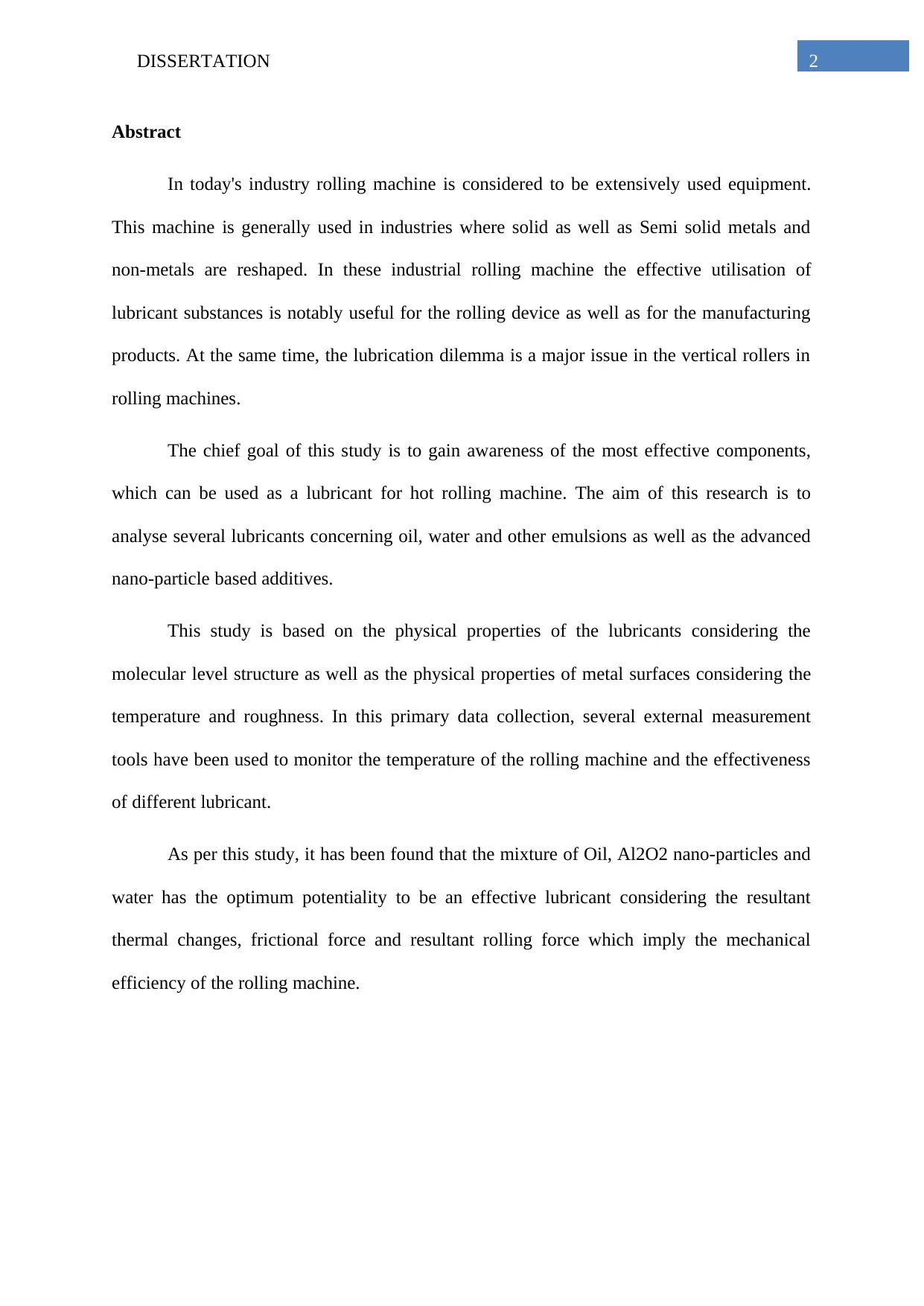
2DISSERTATION
Abstract
In today's industry rolling machine is considered to be extensively used equipment.
This machine is generally used in industries where solid as well as Semi solid metals and
non-metals are reshaped. In these industrial rolling machine the effective utilisation of
lubricant substances is notably useful for the rolling device as well as for the manufacturing
products. At the same time, the lubrication dilemma is a major issue in the vertical rollers in
rolling machines.
The chief goal of this study is to gain awareness of the most effective components,
which can be used as a lubricant for hot rolling machine. The aim of this research is to
analyse several lubricants concerning oil, water and other emulsions as well as the advanced
nano-particle based additives.
This study is based on the physical properties of the lubricants considering the
molecular level structure as well as the physical properties of metal surfaces considering the
temperature and roughness. In this primary data collection, several external measurement
tools have been used to monitor the temperature of the rolling machine and the effectiveness
of different lubricant.
As per this study, it has been found that the mixture of Oil, Al2O2 nano-particles and
water has the optimum potentiality to be an effective lubricant considering the resultant
thermal changes, frictional force and resultant rolling force which imply the mechanical
efficiency of the rolling machine.
Abstract
In today's industry rolling machine is considered to be extensively used equipment.
This machine is generally used in industries where solid as well as Semi solid metals and
non-metals are reshaped. In these industrial rolling machine the effective utilisation of
lubricant substances is notably useful for the rolling device as well as for the manufacturing
products. At the same time, the lubrication dilemma is a major issue in the vertical rollers in
rolling machines.
The chief goal of this study is to gain awareness of the most effective components,
which can be used as a lubricant for hot rolling machine. The aim of this research is to
analyse several lubricants concerning oil, water and other emulsions as well as the advanced
nano-particle based additives.
This study is based on the physical properties of the lubricants considering the
molecular level structure as well as the physical properties of metal surfaces considering the
temperature and roughness. In this primary data collection, several external measurement
tools have been used to monitor the temperature of the rolling machine and the effectiveness
of different lubricant.
As per this study, it has been found that the mixture of Oil, Al2O2 nano-particles and
water has the optimum potentiality to be an effective lubricant considering the resultant
thermal changes, frictional force and resultant rolling force which imply the mechanical
efficiency of the rolling machine.
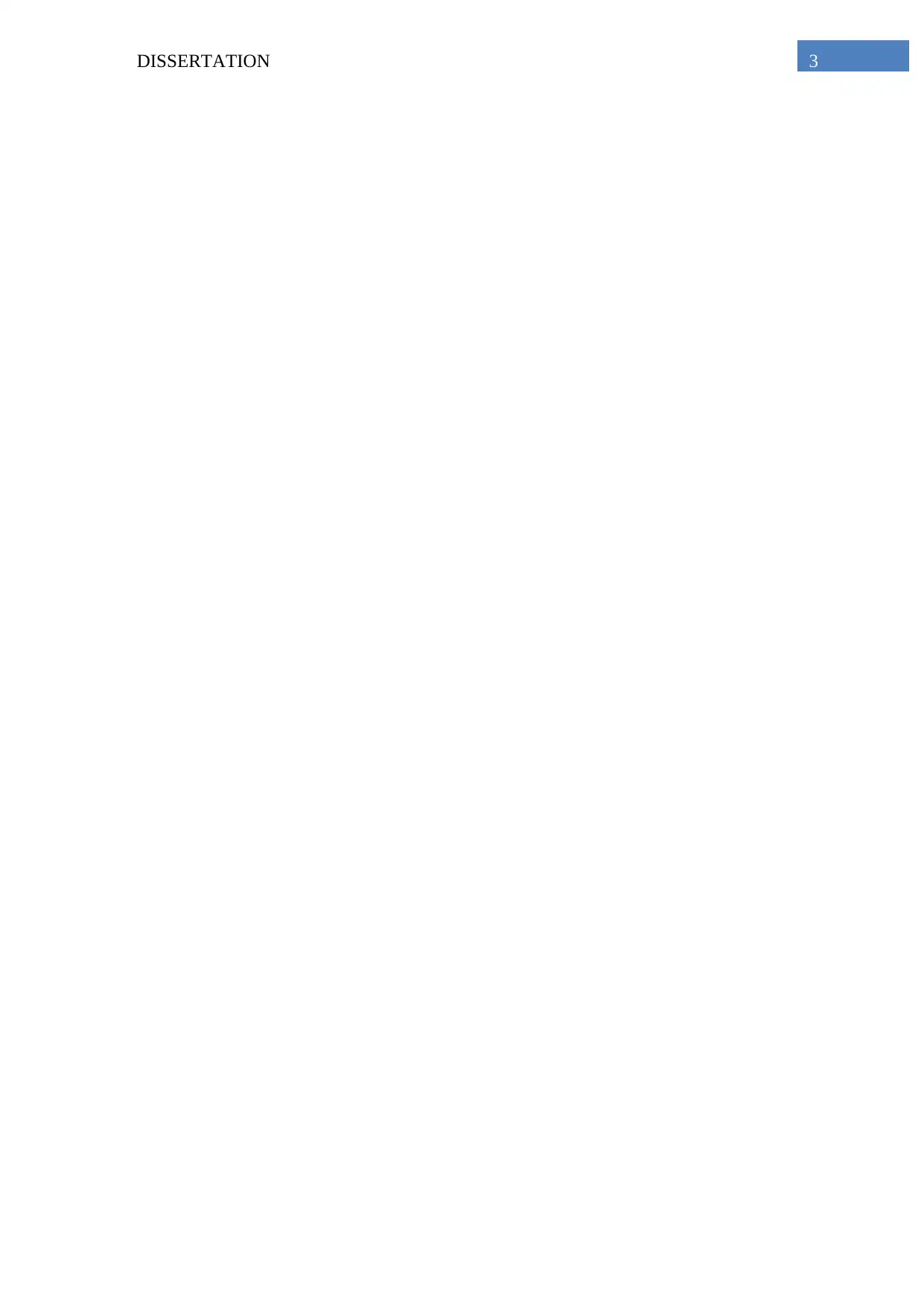
3DISSERTATION
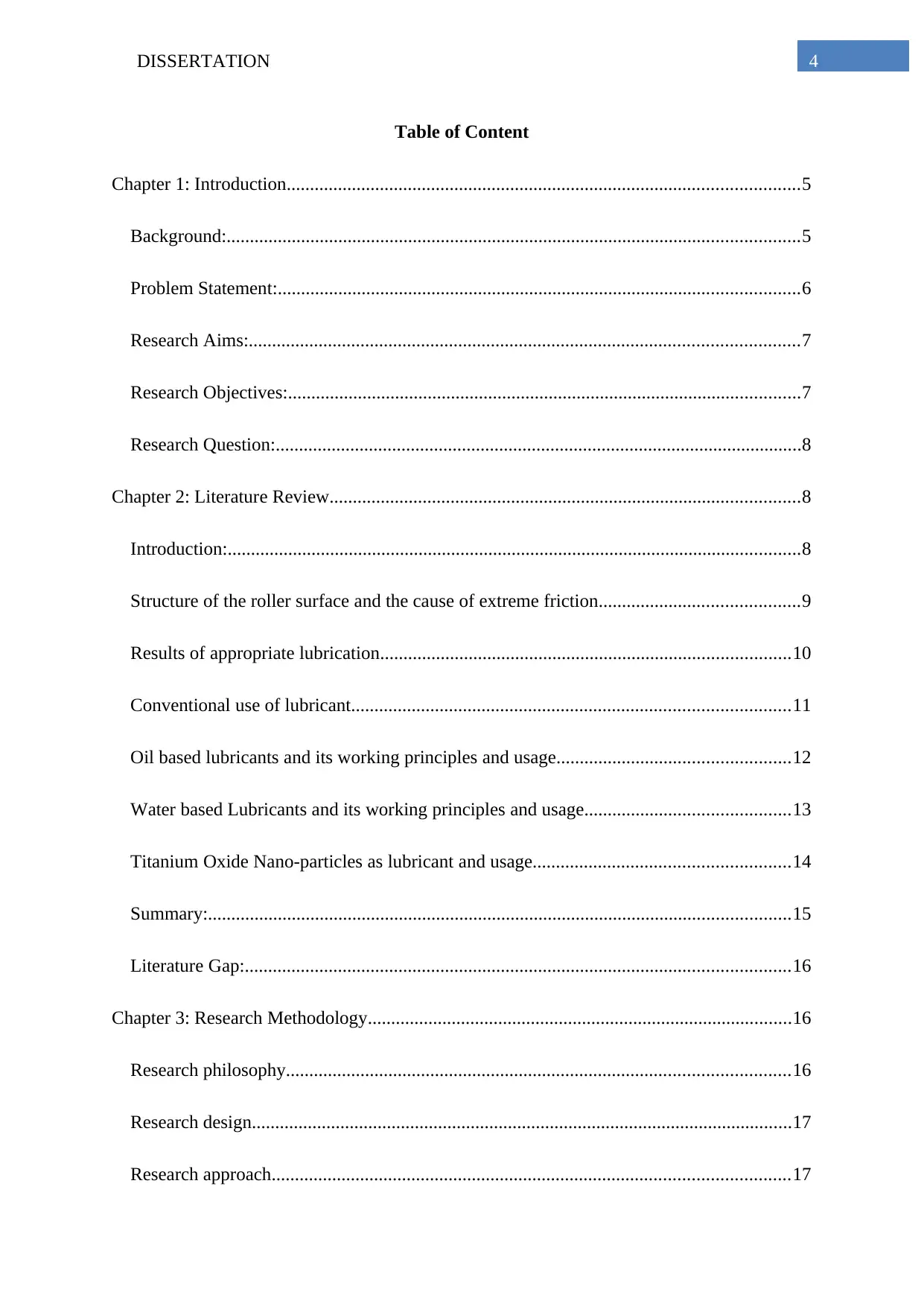
4DISSERTATION
Table of Content
Chapter 1: Introduction..............................................................................................................5
Background:...........................................................................................................................5
Problem Statement:................................................................................................................6
Research Aims:......................................................................................................................7
Research Objectives:..............................................................................................................7
Research Question:.................................................................................................................8
Chapter 2: Literature Review.....................................................................................................8
Introduction:...........................................................................................................................8
Structure of the roller surface and the cause of extreme friction...........................................9
Results of appropriate lubrication........................................................................................10
Conventional use of lubricant..............................................................................................11
Oil based lubricants and its working principles and usage..................................................12
Water based Lubricants and its working principles and usage............................................13
Titanium Oxide Nano-particles as lubricant and usage.......................................................14
Summary:.............................................................................................................................15
Literature Gap:.....................................................................................................................16
Chapter 3: Research Methodology...........................................................................................16
Research philosophy............................................................................................................16
Research design....................................................................................................................17
Research approach...............................................................................................................17
Table of Content
Chapter 1: Introduction..............................................................................................................5
Background:...........................................................................................................................5
Problem Statement:................................................................................................................6
Research Aims:......................................................................................................................7
Research Objectives:..............................................................................................................7
Research Question:.................................................................................................................8
Chapter 2: Literature Review.....................................................................................................8
Introduction:...........................................................................................................................8
Structure of the roller surface and the cause of extreme friction...........................................9
Results of appropriate lubrication........................................................................................10
Conventional use of lubricant..............................................................................................11
Oil based lubricants and its working principles and usage..................................................12
Water based Lubricants and its working principles and usage............................................13
Titanium Oxide Nano-particles as lubricant and usage.......................................................14
Summary:.............................................................................................................................15
Literature Gap:.....................................................................................................................16
Chapter 3: Research Methodology...........................................................................................16
Research philosophy............................................................................................................16
Research design....................................................................................................................17
Research approach...............................................................................................................17
Secure Best Marks with AI Grader
Need help grading? Try our AI Grader for instant feedback on your assignments.
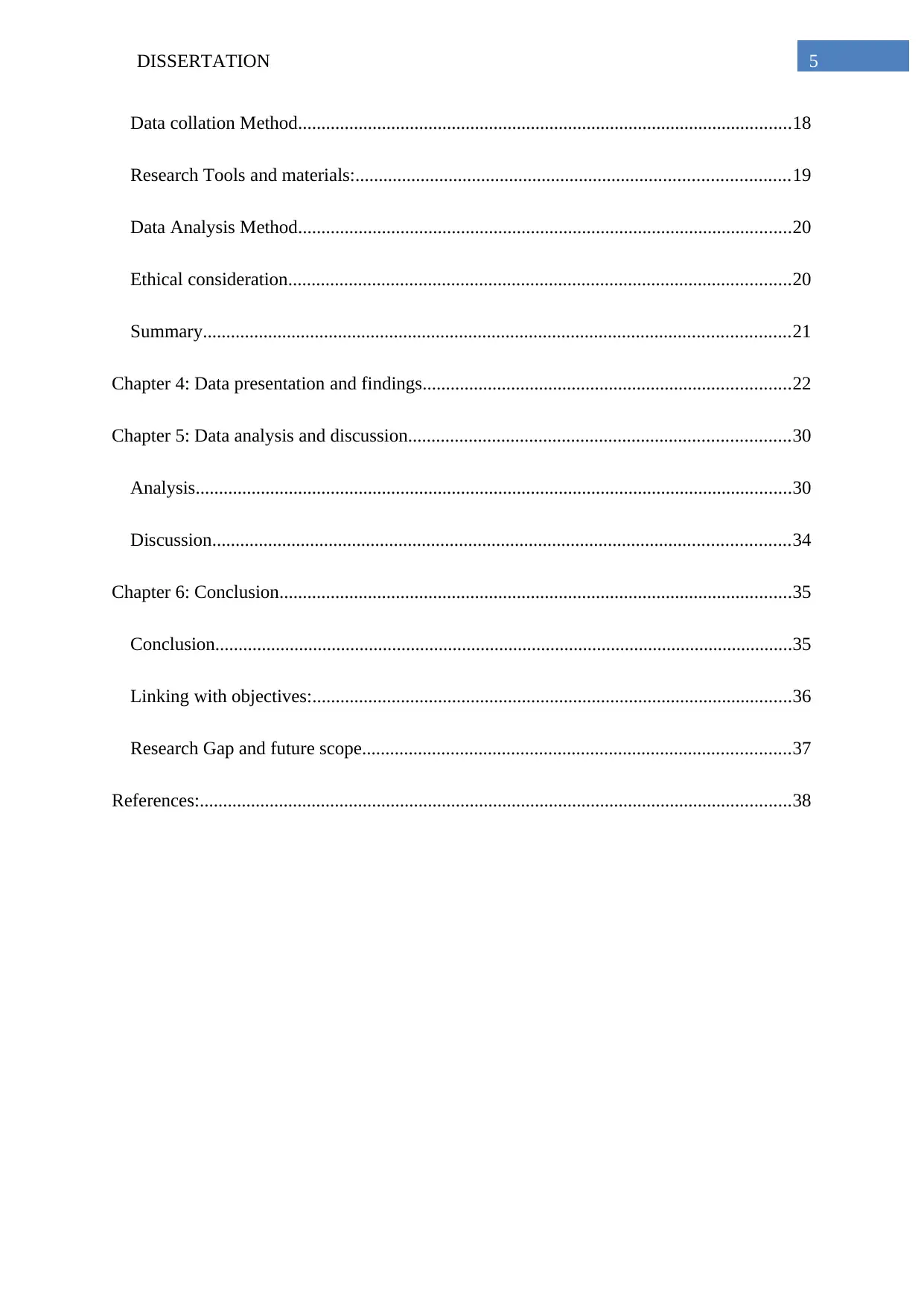
5DISSERTATION
Data collation Method..........................................................................................................18
Research Tools and materials:.............................................................................................19
Data Analysis Method..........................................................................................................20
Ethical consideration............................................................................................................20
Summary..............................................................................................................................21
Chapter 4: Data presentation and findings...............................................................................22
Chapter 5: Data analysis and discussion..................................................................................30
Analysis................................................................................................................................30
Discussion............................................................................................................................34
Chapter 6: Conclusion..............................................................................................................35
Conclusion............................................................................................................................35
Linking with objectives:.......................................................................................................36
Research Gap and future scope............................................................................................37
References:...............................................................................................................................38
Data collation Method..........................................................................................................18
Research Tools and materials:.............................................................................................19
Data Analysis Method..........................................................................................................20
Ethical consideration............................................................................................................20
Summary..............................................................................................................................21
Chapter 4: Data presentation and findings...............................................................................22
Chapter 5: Data analysis and discussion..................................................................................30
Analysis................................................................................................................................30
Discussion............................................................................................................................34
Chapter 6: Conclusion..............................................................................................................35
Conclusion............................................................................................................................35
Linking with objectives:.......................................................................................................36
Research Gap and future scope............................................................................................37
References:...............................................................................................................................38
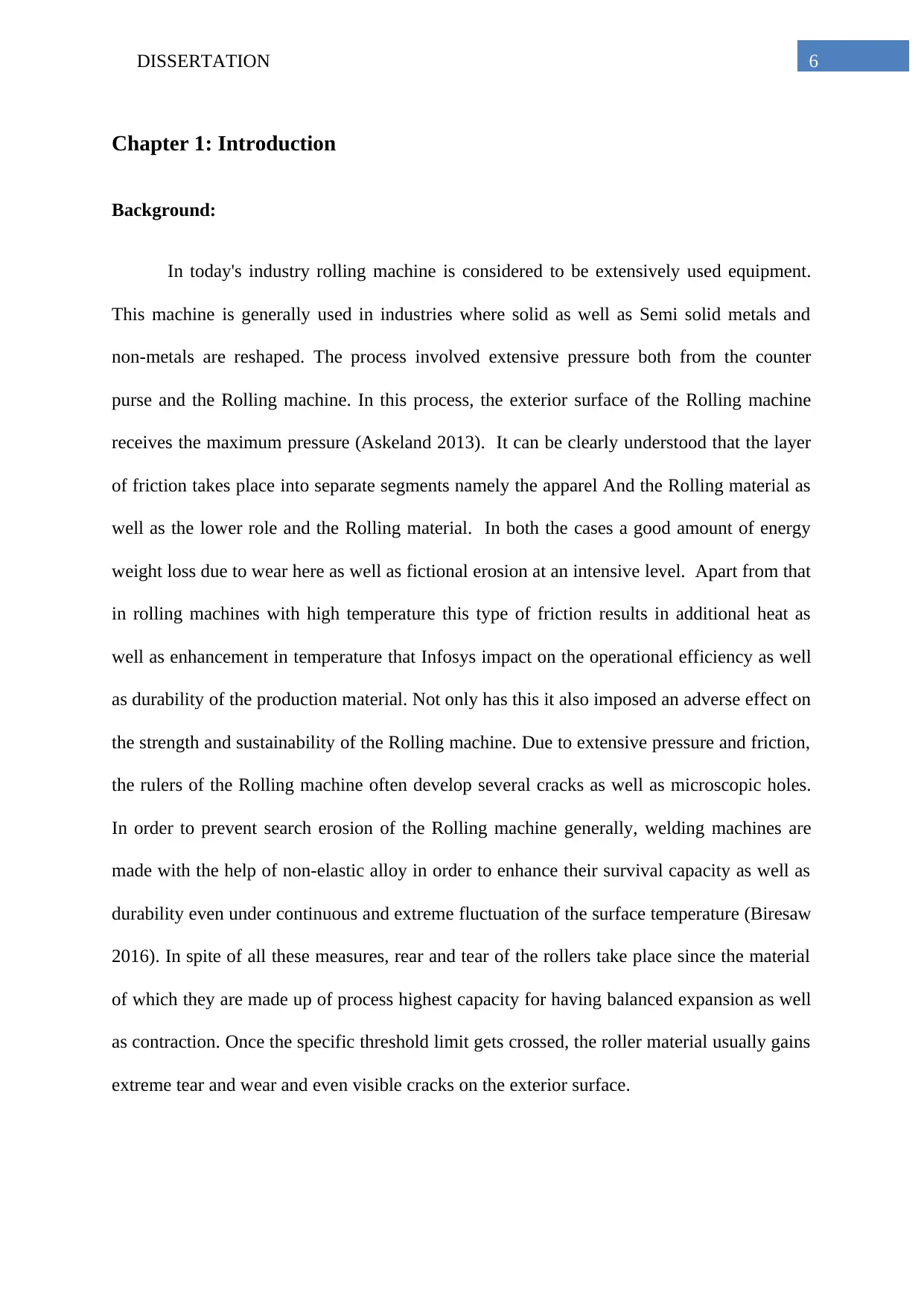
6DISSERTATION
Chapter 1: Introduction
Background:
In today's industry rolling machine is considered to be extensively used equipment.
This machine is generally used in industries where solid as well as Semi solid metals and
non-metals are reshaped. The process involved extensive pressure both from the counter
purse and the Rolling machine. In this process, the exterior surface of the Rolling machine
receives the maximum pressure (Askeland 2013). It can be clearly understood that the layer
of friction takes place into separate segments namely the apparel And the Rolling material as
well as the lower role and the Rolling material. In both the cases a good amount of energy
weight loss due to wear here as well as fictional erosion at an intensive level. Apart from that
in rolling machines with high temperature this type of friction results in additional heat as
well as enhancement in temperature that Infosys impact on the operational efficiency as well
as durability of the production material. Not only has this it also imposed an adverse effect on
the strength and sustainability of the Rolling machine. Due to extensive pressure and friction,
the rulers of the Rolling machine often develop several cracks as well as microscopic holes.
In order to prevent search erosion of the Rolling machine generally, welding machines are
made with the help of non-elastic alloy in order to enhance their survival capacity as well as
durability even under continuous and extreme fluctuation of the surface temperature (Biresaw
2016). In spite of all these measures, rear and tear of the rollers take place since the material
of which they are made up of process highest capacity for having balanced expansion as well
as contraction. Once the specific threshold limit gets crossed, the roller material usually gains
extreme tear and wear and even visible cracks on the exterior surface.
Chapter 1: Introduction
Background:
In today's industry rolling machine is considered to be extensively used equipment.
This machine is generally used in industries where solid as well as Semi solid metals and
non-metals are reshaped. The process involved extensive pressure both from the counter
purse and the Rolling machine. In this process, the exterior surface of the Rolling machine
receives the maximum pressure (Askeland 2013). It can be clearly understood that the layer
of friction takes place into separate segments namely the apparel And the Rolling material as
well as the lower role and the Rolling material. In both the cases a good amount of energy
weight loss due to wear here as well as fictional erosion at an intensive level. Apart from that
in rolling machines with high temperature this type of friction results in additional heat as
well as enhancement in temperature that Infosys impact on the operational efficiency as well
as durability of the production material. Not only has this it also imposed an adverse effect on
the strength and sustainability of the Rolling machine. Due to extensive pressure and friction,
the rulers of the Rolling machine often develop several cracks as well as microscopic holes.
In order to prevent search erosion of the Rolling machine generally, welding machines are
made with the help of non-elastic alloy in order to enhance their survival capacity as well as
durability even under continuous and extreme fluctuation of the surface temperature (Biresaw
2016). In spite of all these measures, rear and tear of the rollers take place since the material
of which they are made up of process highest capacity for having balanced expansion as well
as contraction. Once the specific threshold limit gets crossed, the roller material usually gains
extreme tear and wear and even visible cracks on the exterior surface.
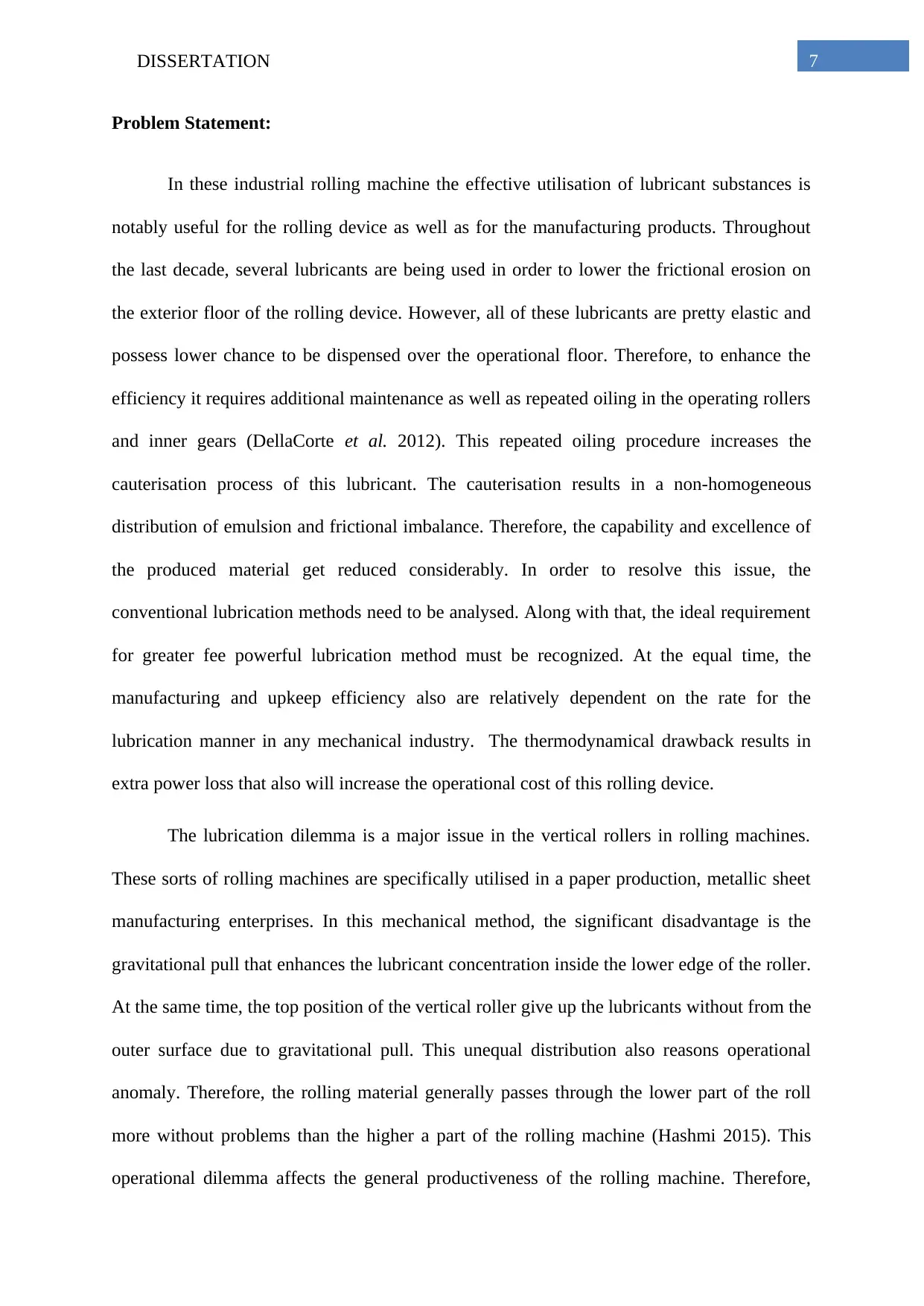
7DISSERTATION
Problem Statement:
In these industrial rolling machine the effective utilisation of lubricant substances is
notably useful for the rolling device as well as for the manufacturing products. Throughout
the last decade, several lubricants are being used in order to lower the frictional erosion on
the exterior floor of the rolling device. However, all of these lubricants are pretty elastic and
possess lower chance to be dispensed over the operational floor. Therefore, to enhance the
efficiency it requires additional maintenance as well as repeated oiling in the operating rollers
and inner gears (DellaCorte et al. 2012). This repeated oiling procedure increases the
cauterisation process of this lubricant. The cauterisation results in a non-homogeneous
distribution of emulsion and frictional imbalance. Therefore, the capability and excellence of
the produced material get reduced considerably. In order to resolve this issue, the
conventional lubrication methods need to be analysed. Along with that, the ideal requirement
for greater fee powerful lubrication method must be recognized. At the equal time, the
manufacturing and upkeep efficiency also are relatively dependent on the rate for the
lubrication manner in any mechanical industry. The thermodynamical drawback results in
extra power loss that also will increase the operational cost of this rolling device.
The lubrication dilemma is a major issue in the vertical rollers in rolling machines.
These sorts of rolling machines are specifically utilised in a paper production, metallic sheet
manufacturing enterprises. In this mechanical method, the significant disadvantage is the
gravitational pull that enhances the lubricant concentration inside the lower edge of the roller.
At the same time, the top position of the vertical roller give up the lubricants without from the
outer surface due to gravitational pull. This unequal distribution also reasons operational
anomaly. Therefore, the rolling material generally passes through the lower part of the roll
more without problems than the higher a part of the rolling machine (Hashmi 2015). This
operational dilemma affects the general productiveness of the rolling machine. Therefore,
Problem Statement:
In these industrial rolling machine the effective utilisation of lubricant substances is
notably useful for the rolling device as well as for the manufacturing products. Throughout
the last decade, several lubricants are being used in order to lower the frictional erosion on
the exterior floor of the rolling device. However, all of these lubricants are pretty elastic and
possess lower chance to be dispensed over the operational floor. Therefore, to enhance the
efficiency it requires additional maintenance as well as repeated oiling in the operating rollers
and inner gears (DellaCorte et al. 2012). This repeated oiling procedure increases the
cauterisation process of this lubricant. The cauterisation results in a non-homogeneous
distribution of emulsion and frictional imbalance. Therefore, the capability and excellence of
the produced material get reduced considerably. In order to resolve this issue, the
conventional lubrication methods need to be analysed. Along with that, the ideal requirement
for greater fee powerful lubrication method must be recognized. At the equal time, the
manufacturing and upkeep efficiency also are relatively dependent on the rate for the
lubrication manner in any mechanical industry. The thermodynamical drawback results in
extra power loss that also will increase the operational cost of this rolling device.
The lubrication dilemma is a major issue in the vertical rollers in rolling machines.
These sorts of rolling machines are specifically utilised in a paper production, metallic sheet
manufacturing enterprises. In this mechanical method, the significant disadvantage is the
gravitational pull that enhances the lubricant concentration inside the lower edge of the roller.
At the same time, the top position of the vertical roller give up the lubricants without from the
outer surface due to gravitational pull. This unequal distribution also reasons operational
anomaly. Therefore, the rolling material generally passes through the lower part of the roll
more without problems than the higher a part of the rolling machine (Hashmi 2015). This
operational dilemma affects the general productiveness of the rolling machine. Therefore,
Paraphrase This Document
Need a fresh take? Get an instant paraphrase of this document with our AI Paraphraser
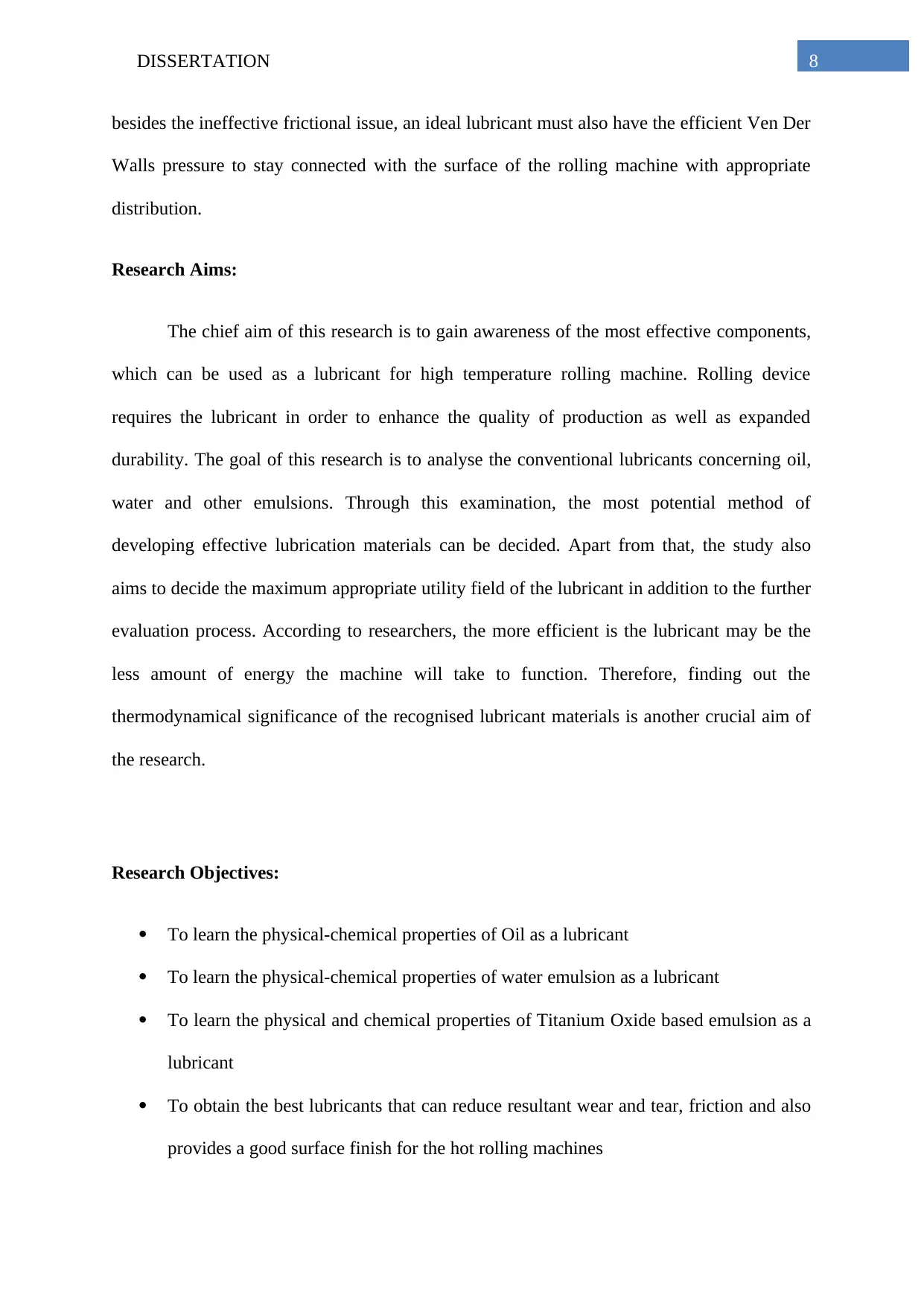
8DISSERTATION
besides the ineffective frictional issue, an ideal lubricant must also have the efficient Ven Der
Walls pressure to stay connected with the surface of the rolling machine with appropriate
distribution.
Research Aims:
The chief aim of this research is to gain awareness of the most effective components,
which can be used as a lubricant for high temperature rolling machine. Rolling device
requires the lubricant in order to enhance the quality of production as well as expanded
durability. The goal of this research is to analyse the conventional lubricants concerning oil,
water and other emulsions. Through this examination, the most potential method of
developing effective lubrication materials can be decided. Apart from that, the study also
aims to decide the maximum appropriate utility field of the lubricant in addition to the further
evaluation process. According to researchers, the more efficient is the lubricant may be the
less amount of energy the machine will take to function. Therefore, finding out the
thermodynamical significance of the recognised lubricant materials is another crucial aim of
the research.
Research Objectives:
To learn the physical-chemical properties of Oil as a lubricant
To learn the physical-chemical properties of water emulsion as a lubricant
To learn the physical and chemical properties of Titanium Oxide based emulsion as a
lubricant
To obtain the best lubricants that can reduce resultant wear and tear, friction and also
provides a good surface finish for the hot rolling machines
besides the ineffective frictional issue, an ideal lubricant must also have the efficient Ven Der
Walls pressure to stay connected with the surface of the rolling machine with appropriate
distribution.
Research Aims:
The chief aim of this research is to gain awareness of the most effective components,
which can be used as a lubricant for high temperature rolling machine. Rolling device
requires the lubricant in order to enhance the quality of production as well as expanded
durability. The goal of this research is to analyse the conventional lubricants concerning oil,
water and other emulsions. Through this examination, the most potential method of
developing effective lubrication materials can be decided. Apart from that, the study also
aims to decide the maximum appropriate utility field of the lubricant in addition to the further
evaluation process. According to researchers, the more efficient is the lubricant may be the
less amount of energy the machine will take to function. Therefore, finding out the
thermodynamical significance of the recognised lubricant materials is another crucial aim of
the research.
Research Objectives:
To learn the physical-chemical properties of Oil as a lubricant
To learn the physical-chemical properties of water emulsion as a lubricant
To learn the physical and chemical properties of Titanium Oxide based emulsion as a
lubricant
To obtain the best lubricants that can reduce resultant wear and tear, friction and also
provides a good surface finish for the hot rolling machines
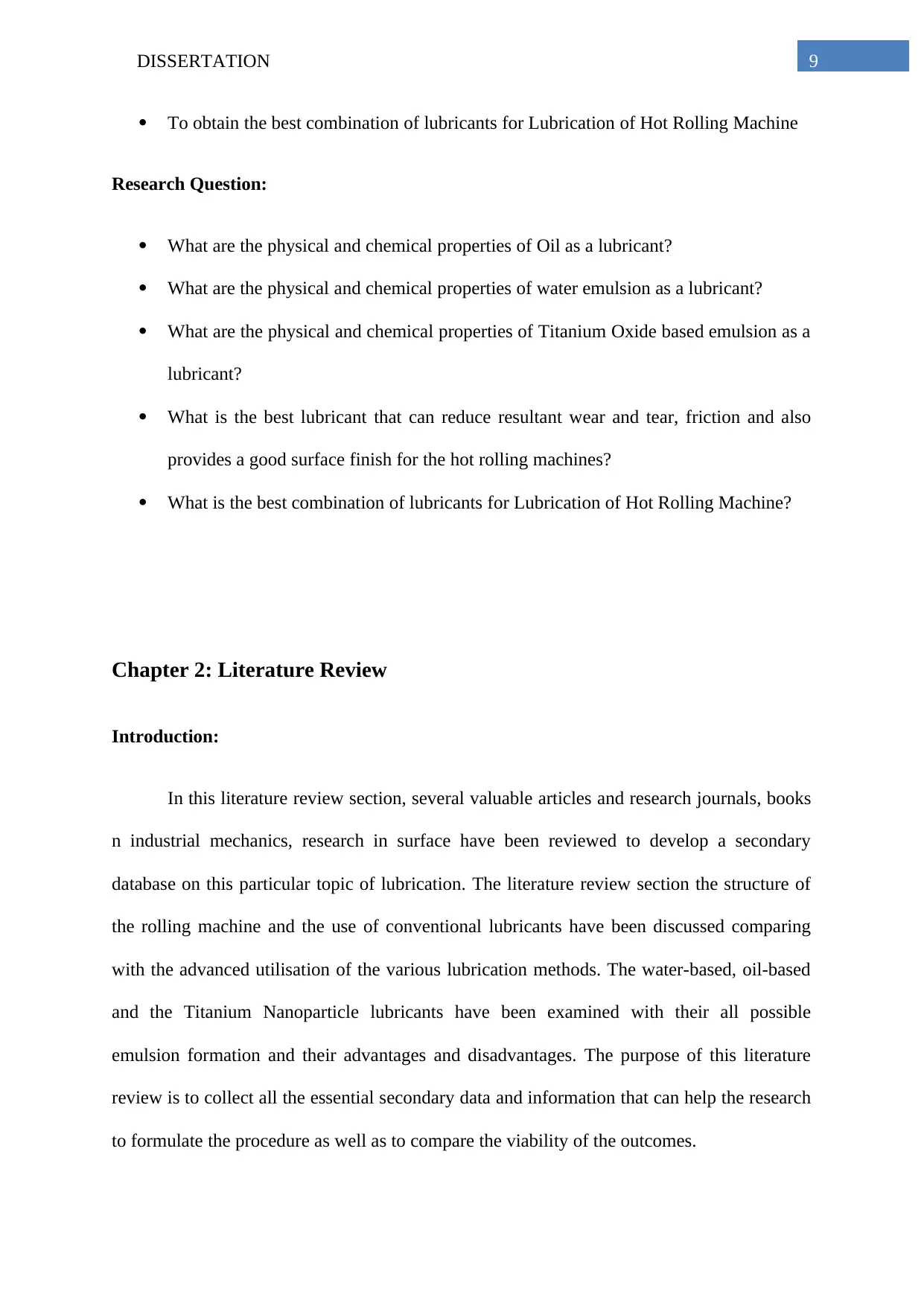
9DISSERTATION
To obtain the best combination of lubricants for Lubrication of Hot Rolling Machine
Research Question:
What are the physical and chemical properties of Oil as a lubricant?
What are the physical and chemical properties of water emulsion as a lubricant?
What are the physical and chemical properties of Titanium Oxide based emulsion as a
lubricant?
What is the best lubricant that can reduce resultant wear and tear, friction and also
provides a good surface finish for the hot rolling machines?
What is the best combination of lubricants for Lubrication of Hot Rolling Machine?
Chapter 2: Literature Review
Introduction:
In this literature review section, several valuable articles and research journals, books
n industrial mechanics, research in surface have been reviewed to develop a secondary
database on this particular topic of lubrication. The literature review section the structure of
the rolling machine and the use of conventional lubricants have been discussed comparing
with the advanced utilisation of the various lubrication methods. The water-based, oil-based
and the Titanium Nanoparticle lubricants have been examined with their all possible
emulsion formation and their advantages and disadvantages. The purpose of this literature
review is to collect all the essential secondary data and information that can help the research
to formulate the procedure as well as to compare the viability of the outcomes.
To obtain the best combination of lubricants for Lubrication of Hot Rolling Machine
Research Question:
What are the physical and chemical properties of Oil as a lubricant?
What are the physical and chemical properties of water emulsion as a lubricant?
What are the physical and chemical properties of Titanium Oxide based emulsion as a
lubricant?
What is the best lubricant that can reduce resultant wear and tear, friction and also
provides a good surface finish for the hot rolling machines?
What is the best combination of lubricants for Lubrication of Hot Rolling Machine?
Chapter 2: Literature Review
Introduction:
In this literature review section, several valuable articles and research journals, books
n industrial mechanics, research in surface have been reviewed to develop a secondary
database on this particular topic of lubrication. The literature review section the structure of
the rolling machine and the use of conventional lubricants have been discussed comparing
with the advanced utilisation of the various lubrication methods. The water-based, oil-based
and the Titanium Nanoparticle lubricants have been examined with their all possible
emulsion formation and their advantages and disadvantages. The purpose of this literature
review is to collect all the essential secondary data and information that can help the research
to formulate the procedure as well as to compare the viability of the outcomes.
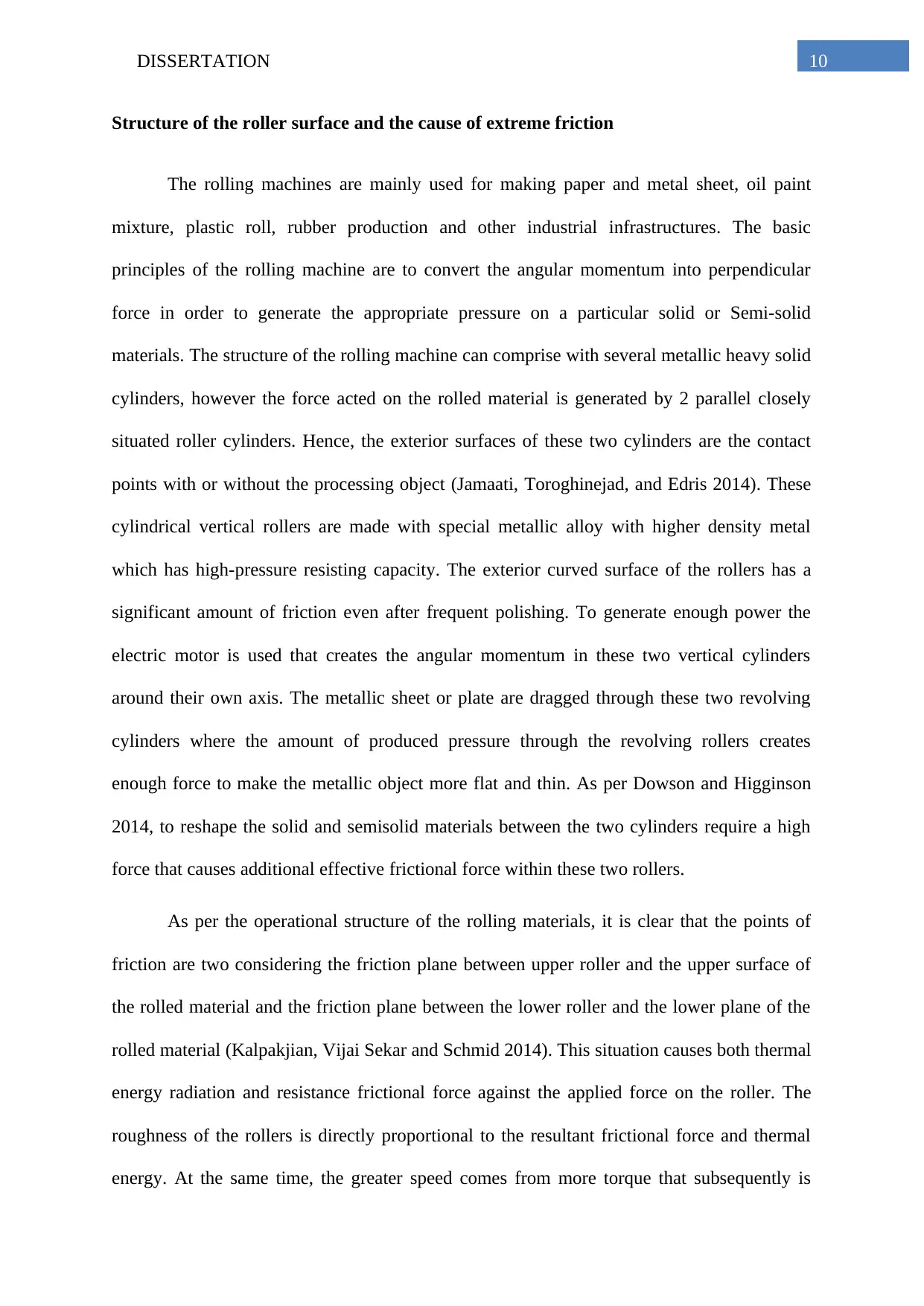
10DISSERTATION
Structure of the roller surface and the cause of extreme friction
The rolling machines are mainly used for making paper and metal sheet, oil paint
mixture, plastic roll, rubber production and other industrial infrastructures. The basic
principles of the rolling machine are to convert the angular momentum into perpendicular
force in order to generate the appropriate pressure on a particular solid or Semi-solid
materials. The structure of the rolling machine can comprise with several metallic heavy solid
cylinders, however the force acted on the rolled material is generated by 2 parallel closely
situated roller cylinders. Hence, the exterior surfaces of these two cylinders are the contact
points with or without the processing object (Jamaati, Toroghinejad, and Edris 2014). These
cylindrical vertical rollers are made with special metallic alloy with higher density metal
which has high-pressure resisting capacity. The exterior curved surface of the rollers has a
significant amount of friction even after frequent polishing. To generate enough power the
electric motor is used that creates the angular momentum in these two vertical cylinders
around their own axis. The metallic sheet or plate are dragged through these two revolving
cylinders where the amount of produced pressure through the revolving rollers creates
enough force to make the metallic object more flat and thin. As per Dowson and Higginson
2014, to reshape the solid and semisolid materials between the two cylinders require a high
force that causes additional effective frictional force within these two rollers.
As per the operational structure of the rolling materials, it is clear that the points of
friction are two considering the friction plane between upper roller and the upper surface of
the rolled material and the friction plane between the lower roller and the lower plane of the
rolled material (Kalpakjian, Vijai Sekar and Schmid 2014). This situation causes both thermal
energy radiation and resistance frictional force against the applied force on the roller. The
roughness of the rollers is directly proportional to the resultant frictional force and thermal
energy. At the same time, the greater speed comes from more torque that subsequently is
Structure of the roller surface and the cause of extreme friction
The rolling machines are mainly used for making paper and metal sheet, oil paint
mixture, plastic roll, rubber production and other industrial infrastructures. The basic
principles of the rolling machine are to convert the angular momentum into perpendicular
force in order to generate the appropriate pressure on a particular solid or Semi-solid
materials. The structure of the rolling machine can comprise with several metallic heavy solid
cylinders, however the force acted on the rolled material is generated by 2 parallel closely
situated roller cylinders. Hence, the exterior surfaces of these two cylinders are the contact
points with or without the processing object (Jamaati, Toroghinejad, and Edris 2014). These
cylindrical vertical rollers are made with special metallic alloy with higher density metal
which has high-pressure resisting capacity. The exterior curved surface of the rollers has a
significant amount of friction even after frequent polishing. To generate enough power the
electric motor is used that creates the angular momentum in these two vertical cylinders
around their own axis. The metallic sheet or plate are dragged through these two revolving
cylinders where the amount of produced pressure through the revolving rollers creates
enough force to make the metallic object more flat and thin. As per Dowson and Higginson
2014, to reshape the solid and semisolid materials between the two cylinders require a high
force that causes additional effective frictional force within these two rollers.
As per the operational structure of the rolling materials, it is clear that the points of
friction are two considering the friction plane between upper roller and the upper surface of
the rolled material and the friction plane between the lower roller and the lower plane of the
rolled material (Kalpakjian, Vijai Sekar and Schmid 2014). This situation causes both thermal
energy radiation and resistance frictional force against the applied force on the roller. The
roughness of the rollers is directly proportional to the resultant frictional force and thermal
energy. At the same time, the greater speed comes from more torque that subsequently is
Secure Best Marks with AI Grader
Need help grading? Try our AI Grader for instant feedback on your assignments.
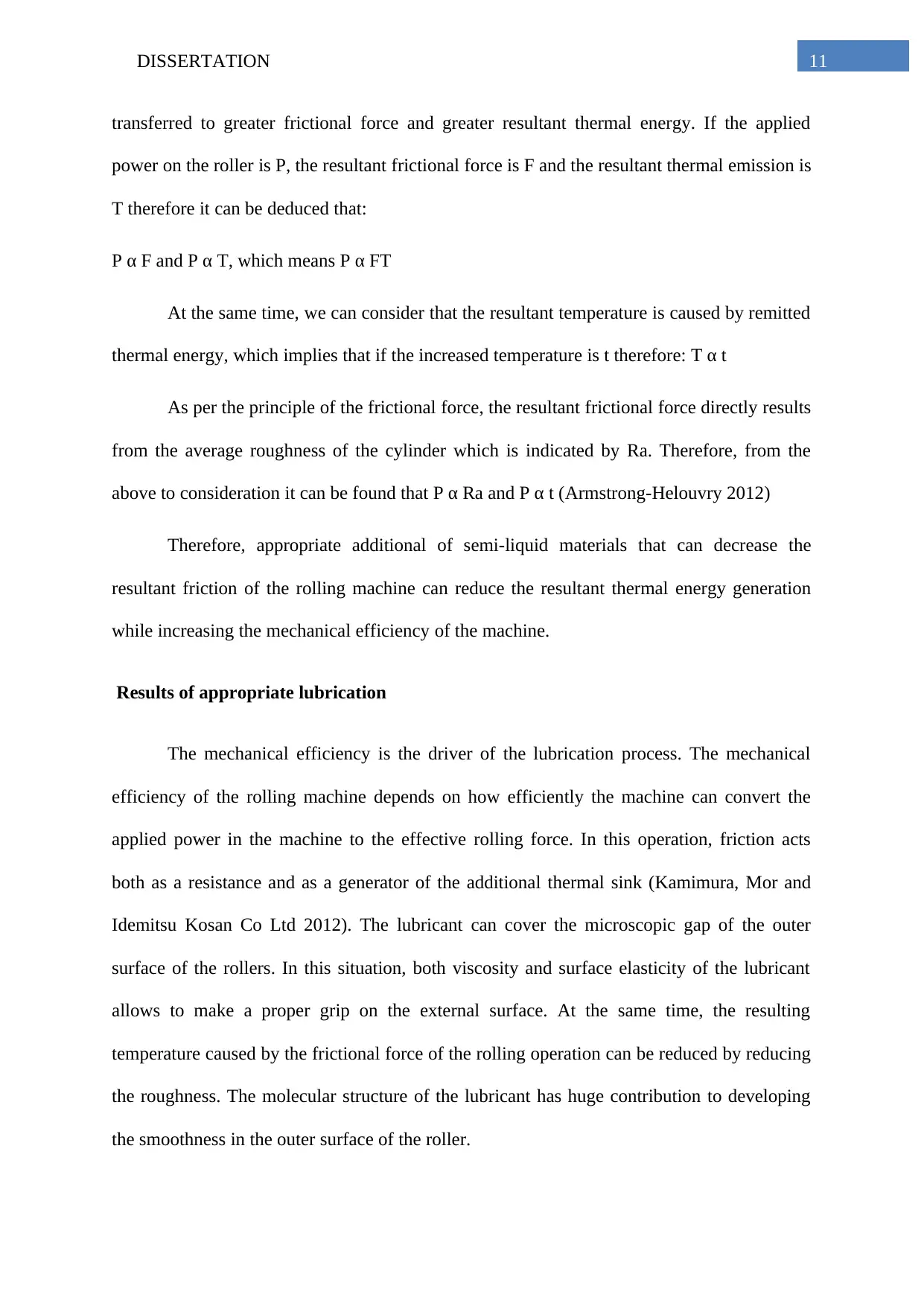
11DISSERTATION
transferred to greater frictional force and greater resultant thermal energy. If the applied
power on the roller is P, the resultant frictional force is F and the resultant thermal emission is
T therefore it can be deduced that:
P α F and P α T, which means P α FT
At the same time, we can consider that the resultant temperature is caused by remitted
thermal energy, which implies that if the increased temperature is t therefore: T α t
As per the principle of the frictional force, the resultant frictional force directly results
from the average roughness of the cylinder which is indicated by Ra. Therefore, from the
above to consideration it can be found that P α Ra and P α t (Armstrong-Helouvry 2012)
Therefore, appropriate additional of semi-liquid materials that can decrease the
resultant friction of the rolling machine can reduce the resultant thermal energy generation
while increasing the mechanical efficiency of the machine.
Results of appropriate lubrication
The mechanical efficiency is the driver of the lubrication process. The mechanical
efficiency of the rolling machine depends on how efficiently the machine can convert the
applied power in the machine to the effective rolling force. In this operation, friction acts
both as a resistance and as a generator of the additional thermal sink (Kamimura, Mor and
Idemitsu Kosan Co Ltd 2012). The lubricant can cover the microscopic gap of the outer
surface of the rollers. In this situation, both viscosity and surface elasticity of the lubricant
allows to make a proper grip on the external surface. At the same time, the resulting
temperature caused by the frictional force of the rolling operation can be reduced by reducing
the roughness. The molecular structure of the lubricant has huge contribution to developing
the smoothness in the outer surface of the roller.
transferred to greater frictional force and greater resultant thermal energy. If the applied
power on the roller is P, the resultant frictional force is F and the resultant thermal emission is
T therefore it can be deduced that:
P α F and P α T, which means P α FT
At the same time, we can consider that the resultant temperature is caused by remitted
thermal energy, which implies that if the increased temperature is t therefore: T α t
As per the principle of the frictional force, the resultant frictional force directly results
from the average roughness of the cylinder which is indicated by Ra. Therefore, from the
above to consideration it can be found that P α Ra and P α t (Armstrong-Helouvry 2012)
Therefore, appropriate additional of semi-liquid materials that can decrease the
resultant friction of the rolling machine can reduce the resultant thermal energy generation
while increasing the mechanical efficiency of the machine.
Results of appropriate lubrication
The mechanical efficiency is the driver of the lubrication process. The mechanical
efficiency of the rolling machine depends on how efficiently the machine can convert the
applied power in the machine to the effective rolling force. In this operation, friction acts
both as a resistance and as a generator of the additional thermal sink (Kamimura, Mor and
Idemitsu Kosan Co Ltd 2012). The lubricant can cover the microscopic gap of the outer
surface of the rollers. In this situation, both viscosity and surface elasticity of the lubricant
allows to make a proper grip on the external surface. At the same time, the resulting
temperature caused by the frictional force of the rolling operation can be reduced by reducing
the roughness. The molecular structure of the lubricant has huge contribution to developing
the smoothness in the outer surface of the roller.
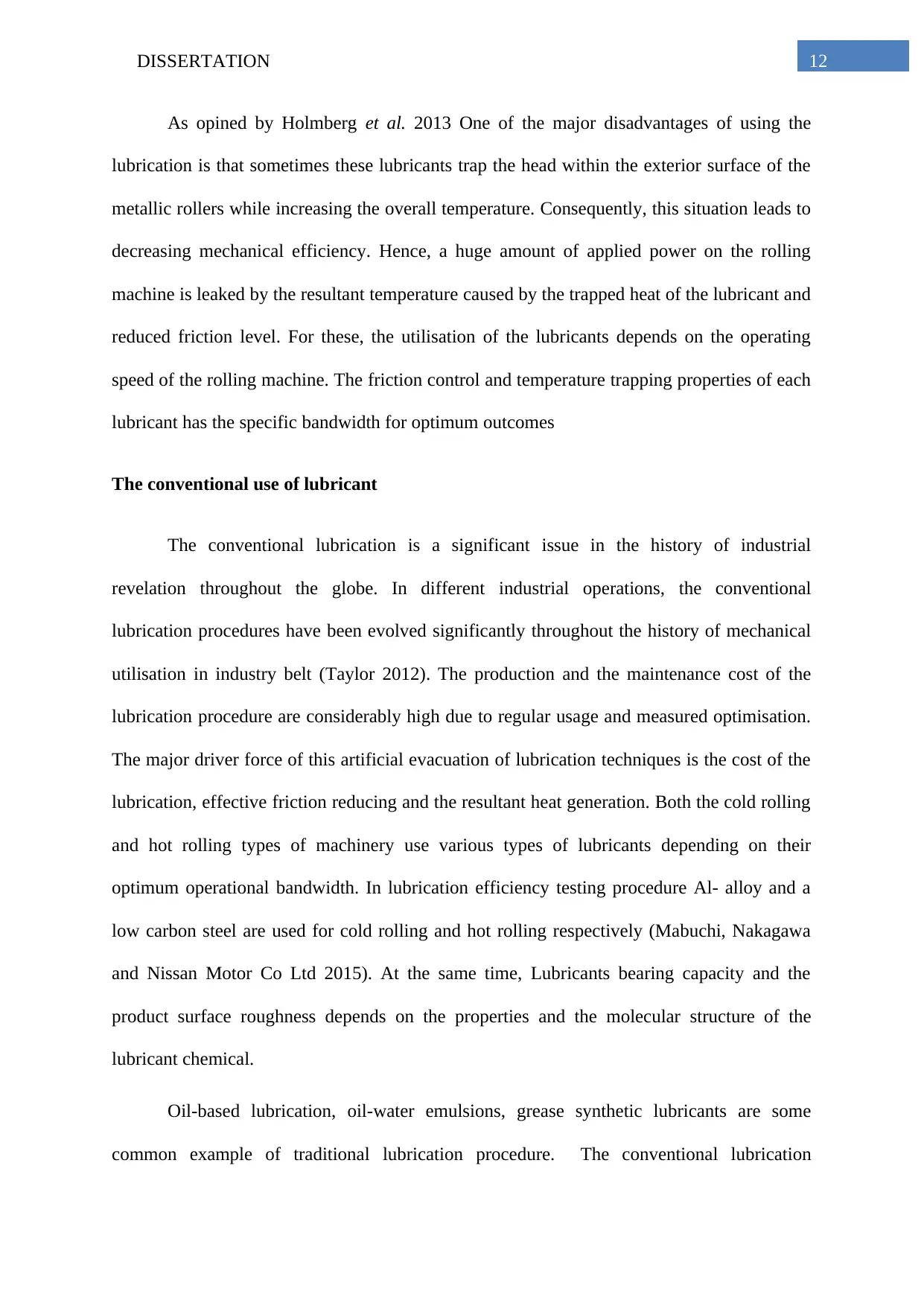
12DISSERTATION
As opined by Holmberg et al. 2013 One of the major disadvantages of using the
lubrication is that sometimes these lubricants trap the head within the exterior surface of the
metallic rollers while increasing the overall temperature. Consequently, this situation leads to
decreasing mechanical efficiency. Hence, a huge amount of applied power on the rolling
machine is leaked by the resultant temperature caused by the trapped heat of the lubricant and
reduced friction level. For these, the utilisation of the lubricants depends on the operating
speed of the rolling machine. The friction control and temperature trapping properties of each
lubricant has the specific bandwidth for optimum outcomes
The conventional use of lubricant
The conventional lubrication is a significant issue in the history of industrial
revelation throughout the globe. In different industrial operations, the conventional
lubrication procedures have been evolved significantly throughout the history of mechanical
utilisation in industry belt (Taylor 2012). The production and the maintenance cost of the
lubrication procedure are considerably high due to regular usage and measured optimisation.
The major driver force of this artificial evacuation of lubrication techniques is the cost of the
lubrication, effective friction reducing and the resultant heat generation. Both the cold rolling
and hot rolling types of machinery use various types of lubricants depending on their
optimum operational bandwidth. In lubrication efficiency testing procedure Al- alloy and a
low carbon steel are used for cold rolling and hot rolling respectively (Mabuchi, Nakagawa
and Nissan Motor Co Ltd 2015). At the same time, Lubricants bearing capacity and the
product surface roughness depends on the properties and the molecular structure of the
lubricant chemical.
Oil-based lubrication, oil-water emulsions, grease synthetic lubricants are some
common example of traditional lubrication procedure. The conventional lubrication
As opined by Holmberg et al. 2013 One of the major disadvantages of using the
lubrication is that sometimes these lubricants trap the head within the exterior surface of the
metallic rollers while increasing the overall temperature. Consequently, this situation leads to
decreasing mechanical efficiency. Hence, a huge amount of applied power on the rolling
machine is leaked by the resultant temperature caused by the trapped heat of the lubricant and
reduced friction level. For these, the utilisation of the lubricants depends on the operating
speed of the rolling machine. The friction control and temperature trapping properties of each
lubricant has the specific bandwidth for optimum outcomes
The conventional use of lubricant
The conventional lubrication is a significant issue in the history of industrial
revelation throughout the globe. In different industrial operations, the conventional
lubrication procedures have been evolved significantly throughout the history of mechanical
utilisation in industry belt (Taylor 2012). The production and the maintenance cost of the
lubrication procedure are considerably high due to regular usage and measured optimisation.
The major driver force of this artificial evacuation of lubrication techniques is the cost of the
lubrication, effective friction reducing and the resultant heat generation. Both the cold rolling
and hot rolling types of machinery use various types of lubricants depending on their
optimum operational bandwidth. In lubrication efficiency testing procedure Al- alloy and a
low carbon steel are used for cold rolling and hot rolling respectively (Mabuchi, Nakagawa
and Nissan Motor Co Ltd 2015). At the same time, Lubricants bearing capacity and the
product surface roughness depends on the properties and the molecular structure of the
lubricant chemical.
Oil-based lubrication, oil-water emulsions, grease synthetic lubricants are some
common example of traditional lubrication procedure. The conventional lubrication
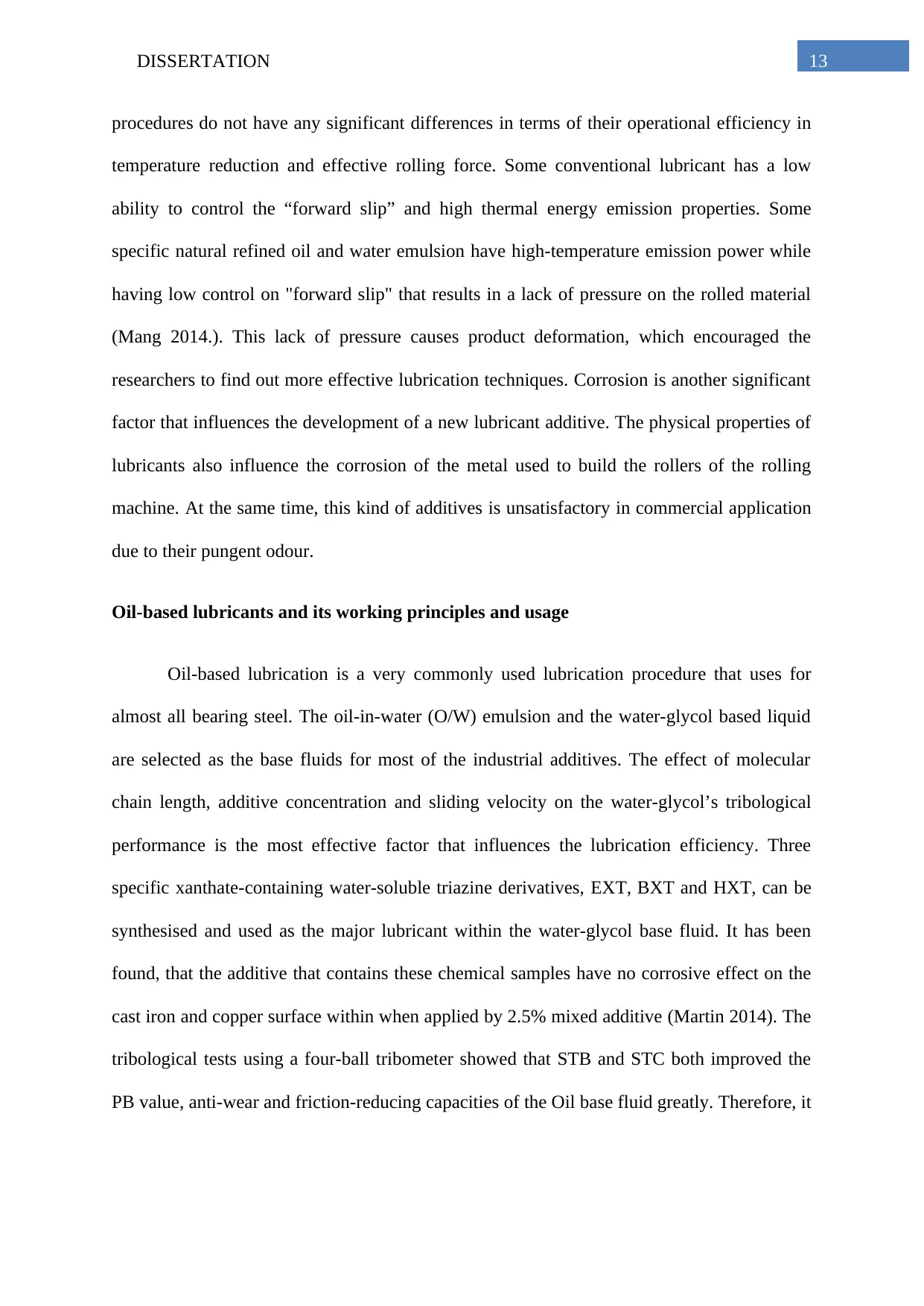
13DISSERTATION
procedures do not have any significant differences in terms of their operational efficiency in
temperature reduction and effective rolling force. Some conventional lubricant has a low
ability to control the “forward slip” and high thermal energy emission properties. Some
specific natural refined oil and water emulsion have high-temperature emission power while
having low control on "forward slip" that results in a lack of pressure on the rolled material
(Mang 2014.). This lack of pressure causes product deformation, which encouraged the
researchers to find out more effective lubrication techniques. Corrosion is another significant
factor that influences the development of a new lubricant additive. The physical properties of
lubricants also influence the corrosion of the metal used to build the rollers of the rolling
machine. At the same time, this kind of additives is unsatisfactory in commercial application
due to their pungent odour.
Oil-based lubricants and its working principles and usage
Oil-based lubrication is a very commonly used lubrication procedure that uses for
almost all bearing steel. The oil-in-water (O/W) emulsion and the water-glycol based liquid
are selected as the base fluids for most of the industrial additives. The effect of molecular
chain length, additive concentration and sliding velocity on the water-glycol’s tribological
performance is the most effective factor that influences the lubrication efficiency. Three
specific xanthate-containing water-soluble triazine derivatives, EXT, BXT and HXT, can be
synthesised and used as the major lubricant within the water-glycol base fluid. It has been
found, that the additive that contains these chemical samples have no corrosive effect on the
cast iron and copper surface within when applied by 2.5% mixed additive (Martin 2014). The
tribological tests using a four-ball tribometer showed that STB and STC both improved the
PB value, anti-wear and friction-reducing capacities of the Oil base fluid greatly. Therefore, it
procedures do not have any significant differences in terms of their operational efficiency in
temperature reduction and effective rolling force. Some conventional lubricant has a low
ability to control the “forward slip” and high thermal energy emission properties. Some
specific natural refined oil and water emulsion have high-temperature emission power while
having low control on "forward slip" that results in a lack of pressure on the rolled material
(Mang 2014.). This lack of pressure causes product deformation, which encouraged the
researchers to find out more effective lubrication techniques. Corrosion is another significant
factor that influences the development of a new lubricant additive. The physical properties of
lubricants also influence the corrosion of the metal used to build the rollers of the rolling
machine. At the same time, this kind of additives is unsatisfactory in commercial application
due to their pungent odour.
Oil-based lubricants and its working principles and usage
Oil-based lubrication is a very commonly used lubrication procedure that uses for
almost all bearing steel. The oil-in-water (O/W) emulsion and the water-glycol based liquid
are selected as the base fluids for most of the industrial additives. The effect of molecular
chain length, additive concentration and sliding velocity on the water-glycol’s tribological
performance is the most effective factor that influences the lubrication efficiency. Three
specific xanthate-containing water-soluble triazine derivatives, EXT, BXT and HXT, can be
synthesised and used as the major lubricant within the water-glycol base fluid. It has been
found, that the additive that contains these chemical samples have no corrosive effect on the
cast iron and copper surface within when applied by 2.5% mixed additive (Martin 2014). The
tribological tests using a four-ball tribometer showed that STB and STC both improved the
PB value, anti-wear and friction-reducing capacities of the Oil base fluid greatly. Therefore, it
Paraphrase This Document
Need a fresh take? Get an instant paraphrase of this document with our AI Paraphraser
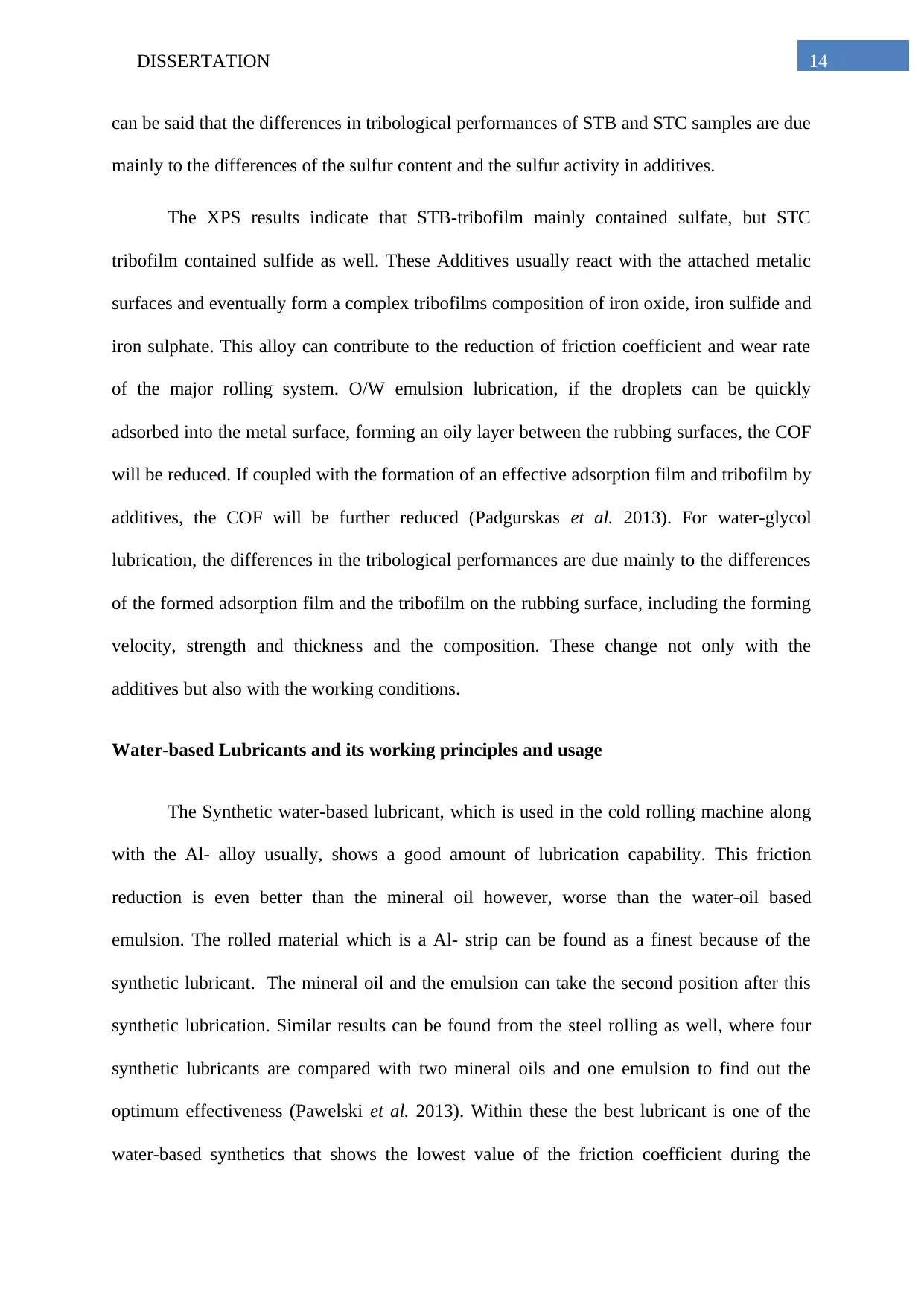
14DISSERTATION
can be said that the differences in tribological performances of STB and STC samples are due
mainly to the differences of the sulfur content and the sulfur activity in additives.
The XPS results indicate that STB-tribofilm mainly contained sulfate, but STC
tribofilm contained sulfide as well. These Additives usually react with the attached metalic
surfaces and eventually form a complex tribofilms composition of iron oxide, iron sulfide and
iron sulphate. This alloy can contribute to the reduction of friction coefficient and wear rate
of the major rolling system. O/W emulsion lubrication, if the droplets can be quickly
adsorbed into the metal surface, forming an oily layer between the rubbing surfaces, the COF
will be reduced. If coupled with the formation of an effective adsorption film and tribofilm by
additives, the COF will be further reduced (Padgurskas et al. 2013). For water-glycol
lubrication, the differences in the tribological performances are due mainly to the differences
of the formed adsorption film and the tribofilm on the rubbing surface, including the forming
velocity, strength and thickness and the composition. These change not only with the
additives but also with the working conditions.
Water-based Lubricants and its working principles and usage
The Synthetic water-based lubricant, which is used in the cold rolling machine along
with the Al- alloy usually, shows a good amount of lubrication capability. This friction
reduction is even better than the mineral oil however, worse than the water-oil based
emulsion. The rolled material which is a Al- strip can be found as a finest because of the
synthetic lubricant. The mineral oil and the emulsion can take the second position after this
synthetic lubrication. Similar results can be found from the steel rolling as well, where four
synthetic lubricants are compared with two mineral oils and one emulsion to find out the
optimum effectiveness (Pawelski et al. 2013). Within these the best lubricant is one of the
water-based synthetics that shows the lowest value of the friction coefficient during the
can be said that the differences in tribological performances of STB and STC samples are due
mainly to the differences of the sulfur content and the sulfur activity in additives.
The XPS results indicate that STB-tribofilm mainly contained sulfate, but STC
tribofilm contained sulfide as well. These Additives usually react with the attached metalic
surfaces and eventually form a complex tribofilms composition of iron oxide, iron sulfide and
iron sulphate. This alloy can contribute to the reduction of friction coefficient and wear rate
of the major rolling system. O/W emulsion lubrication, if the droplets can be quickly
adsorbed into the metal surface, forming an oily layer between the rubbing surfaces, the COF
will be reduced. If coupled with the formation of an effective adsorption film and tribofilm by
additives, the COF will be further reduced (Padgurskas et al. 2013). For water-glycol
lubrication, the differences in the tribological performances are due mainly to the differences
of the formed adsorption film and the tribofilm on the rubbing surface, including the forming
velocity, strength and thickness and the composition. These change not only with the
additives but also with the working conditions.
Water-based Lubricants and its working principles and usage
The Synthetic water-based lubricant, which is used in the cold rolling machine along
with the Al- alloy usually, shows a good amount of lubrication capability. This friction
reduction is even better than the mineral oil however, worse than the water-oil based
emulsion. The rolled material which is a Al- strip can be found as a finest because of the
synthetic lubricant. The mineral oil and the emulsion can take the second position after this
synthetic lubrication. Similar results can be found from the steel rolling as well, where four
synthetic lubricants are compared with two mineral oils and one emulsion to find out the
optimum effectiveness (Pawelski et al. 2013). Within these the best lubricant is one of the
water-based synthetics that shows the lowest value of the friction coefficient during the
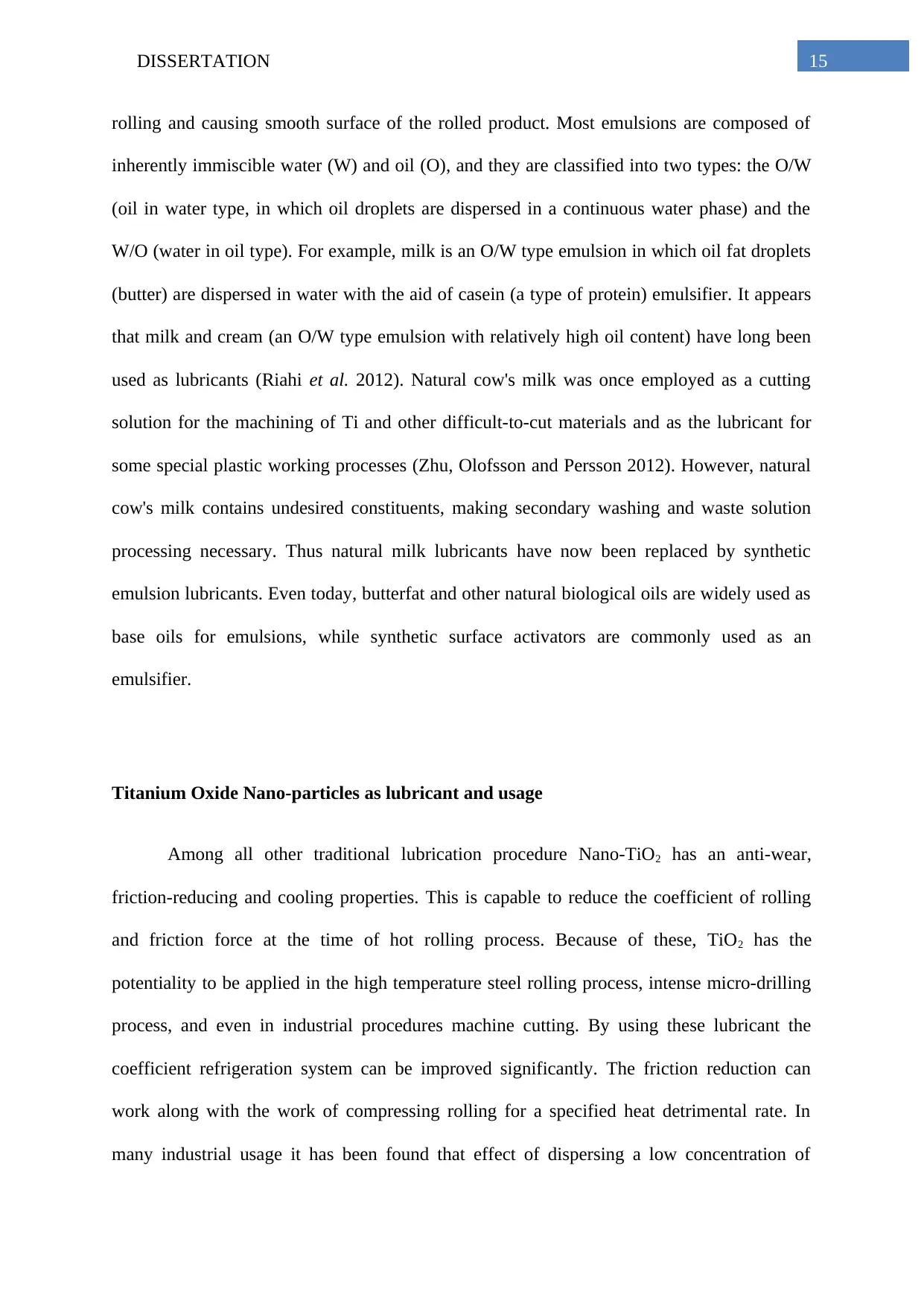
15DISSERTATION
rolling and causing smooth surface of the rolled product. Most emulsions are composed of
inherently immiscible water (W) and oil (O), and they are classified into two types: the O/W
(oil in water type, in which oil droplets are dispersed in a continuous water phase) and the
W/O (water in oil type). For example, milk is an O/W type emulsion in which oil fat droplets
(butter) are dispersed in water with the aid of casein (a type of protein) emulsifier. It appears
that milk and cream (an O/W type emulsion with relatively high oil content) have long been
used as lubricants (Riahi et al. 2012). Natural cow's milk was once employed as a cutting
solution for the machining of Ti and other difficult-to-cut materials and as the lubricant for
some special plastic working processes (Zhu, Olofsson and Persson 2012). However, natural
cow's milk contains undesired constituents, making secondary washing and waste solution
processing necessary. Thus natural milk lubricants have now been replaced by synthetic
emulsion lubricants. Even today, butterfat and other natural biological oils are widely used as
base oils for emulsions, while synthetic surface activators are commonly used as an
emulsifier.
Titanium Oxide Nano-particles as lubricant and usage
Among all other traditional lubrication procedure Nano-TiO2 has an anti-wear,
friction-reducing and cooling properties. This is capable to reduce the coefficient of rolling
and friction force at the time of hot rolling process. Because of these, TiO2 has the
potentiality to be applied in the high temperature steel rolling process, intense micro-drilling
process, and even in industrial procedures machine cutting. By using these lubricant the
coefficient refrigeration system can be improved significantly. The friction reduction can
work along with the work of compressing rolling for a specified heat detrimental rate. In
many industrial usage it has been found that effect of dispersing a low concentration of
rolling and causing smooth surface of the rolled product. Most emulsions are composed of
inherently immiscible water (W) and oil (O), and they are classified into two types: the O/W
(oil in water type, in which oil droplets are dispersed in a continuous water phase) and the
W/O (water in oil type). For example, milk is an O/W type emulsion in which oil fat droplets
(butter) are dispersed in water with the aid of casein (a type of protein) emulsifier. It appears
that milk and cream (an O/W type emulsion with relatively high oil content) have long been
used as lubricants (Riahi et al. 2012). Natural cow's milk was once employed as a cutting
solution for the machining of Ti and other difficult-to-cut materials and as the lubricant for
some special plastic working processes (Zhu, Olofsson and Persson 2012). However, natural
cow's milk contains undesired constituents, making secondary washing and waste solution
processing necessary. Thus natural milk lubricants have now been replaced by synthetic
emulsion lubricants. Even today, butterfat and other natural biological oils are widely used as
base oils for emulsions, while synthetic surface activators are commonly used as an
emulsifier.
Titanium Oxide Nano-particles as lubricant and usage
Among all other traditional lubrication procedure Nano-TiO2 has an anti-wear,
friction-reducing and cooling properties. This is capable to reduce the coefficient of rolling
and friction force at the time of hot rolling process. Because of these, TiO2 has the
potentiality to be applied in the high temperature steel rolling process, intense micro-drilling
process, and even in industrial procedures machine cutting. By using these lubricant the
coefficient refrigeration system can be improved significantly. The friction reduction can
work along with the work of compressing rolling for a specified heat detrimental rate. In
many industrial usage it has been found that effect of dispersing a low concentration of
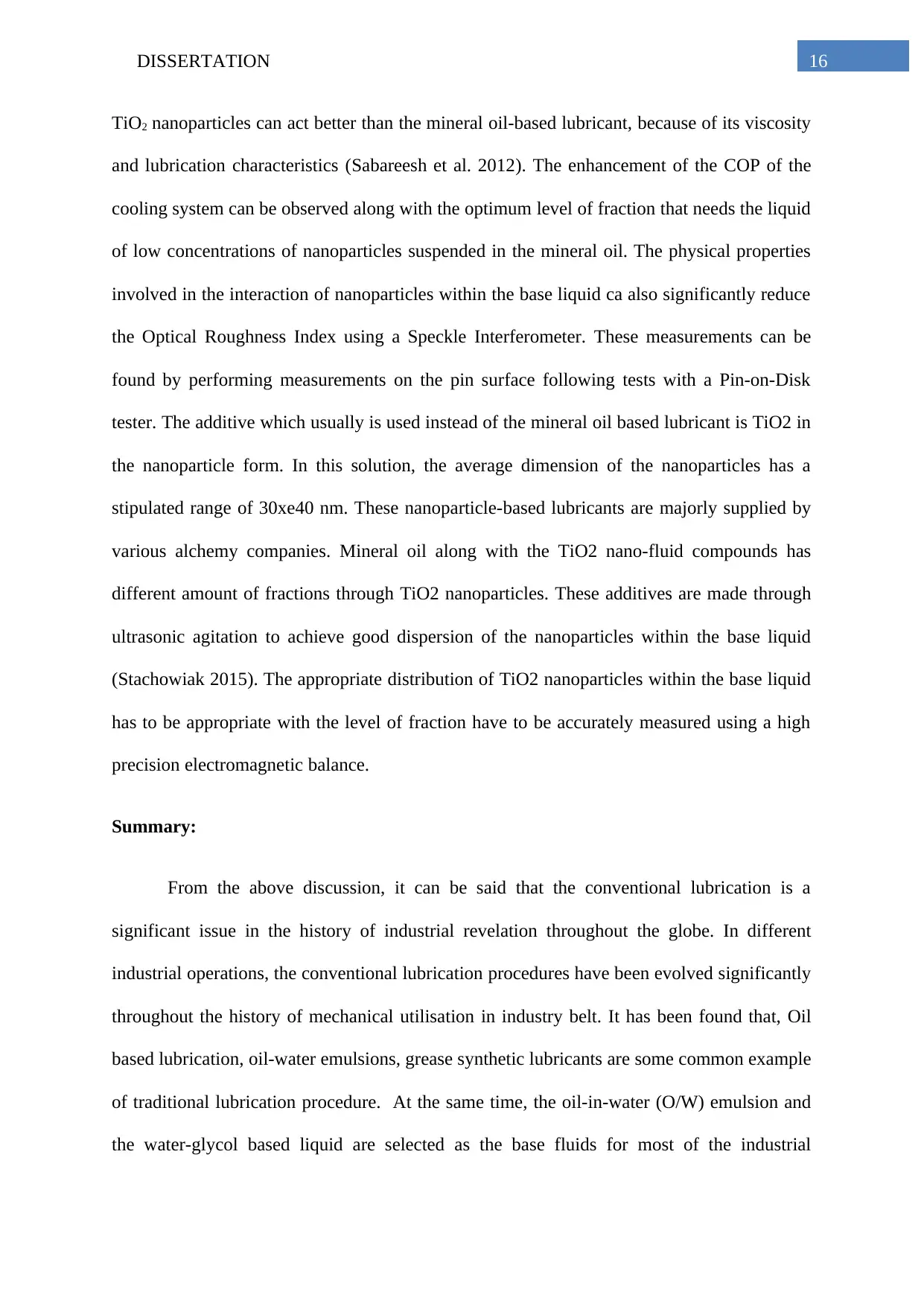
16DISSERTATION
TiO2 nanoparticles can act better than the mineral oil-based lubricant, because of its viscosity
and lubrication characteristics (Sabareesh et al. 2012). The enhancement of the COP of the
cooling system can be observed along with the optimum level of fraction that needs the liquid
of low concentrations of nanoparticles suspended in the mineral oil. The physical properties
involved in the interaction of nanoparticles within the base liquid ca also significantly reduce
the Optical Roughness Index using a Speckle Interferometer. These measurements can be
found by performing measurements on the pin surface following tests with a Pin-on-Disk
tester. The additive which usually is used instead of the mineral oil based lubricant is TiO2 in
the nanoparticle form. In this solution, the average dimension of the nanoparticles has a
stipulated range of 30xe40 nm. These nanoparticle-based lubricants are majorly supplied by
various alchemy companies. Mineral oil along with the TiO2 nano-fluid compounds has
different amount of fractions through TiO2 nanoparticles. These additives are made through
ultrasonic agitation to achieve good dispersion of the nanoparticles within the base liquid
(Stachowiak 2015). The appropriate distribution of TiO2 nanoparticles within the base liquid
has to be appropriate with the level of fraction have to be accurately measured using a high
precision electromagnetic balance.
Summary:
From the above discussion, it can be said that the conventional lubrication is a
significant issue in the history of industrial revelation throughout the globe. In different
industrial operations, the conventional lubrication procedures have been evolved significantly
throughout the history of mechanical utilisation in industry belt. It has been found that, Oil
based lubrication, oil-water emulsions, grease synthetic lubricants are some common example
of traditional lubrication procedure. At the same time, the oil-in-water (O/W) emulsion and
the water-glycol based liquid are selected as the base fluids for most of the industrial
TiO2 nanoparticles can act better than the mineral oil-based lubricant, because of its viscosity
and lubrication characteristics (Sabareesh et al. 2012). The enhancement of the COP of the
cooling system can be observed along with the optimum level of fraction that needs the liquid
of low concentrations of nanoparticles suspended in the mineral oil. The physical properties
involved in the interaction of nanoparticles within the base liquid ca also significantly reduce
the Optical Roughness Index using a Speckle Interferometer. These measurements can be
found by performing measurements on the pin surface following tests with a Pin-on-Disk
tester. The additive which usually is used instead of the mineral oil based lubricant is TiO2 in
the nanoparticle form. In this solution, the average dimension of the nanoparticles has a
stipulated range of 30xe40 nm. These nanoparticle-based lubricants are majorly supplied by
various alchemy companies. Mineral oil along with the TiO2 nano-fluid compounds has
different amount of fractions through TiO2 nanoparticles. These additives are made through
ultrasonic agitation to achieve good dispersion of the nanoparticles within the base liquid
(Stachowiak 2015). The appropriate distribution of TiO2 nanoparticles within the base liquid
has to be appropriate with the level of fraction have to be accurately measured using a high
precision electromagnetic balance.
Summary:
From the above discussion, it can be said that the conventional lubrication is a
significant issue in the history of industrial revelation throughout the globe. In different
industrial operations, the conventional lubrication procedures have been evolved significantly
throughout the history of mechanical utilisation in industry belt. It has been found that, Oil
based lubrication, oil-water emulsions, grease synthetic lubricants are some common example
of traditional lubrication procedure. At the same time, the oil-in-water (O/W) emulsion and
the water-glycol based liquid are selected as the base fluids for most of the industrial
Secure Best Marks with AI Grader
Need help grading? Try our AI Grader for instant feedback on your assignments.
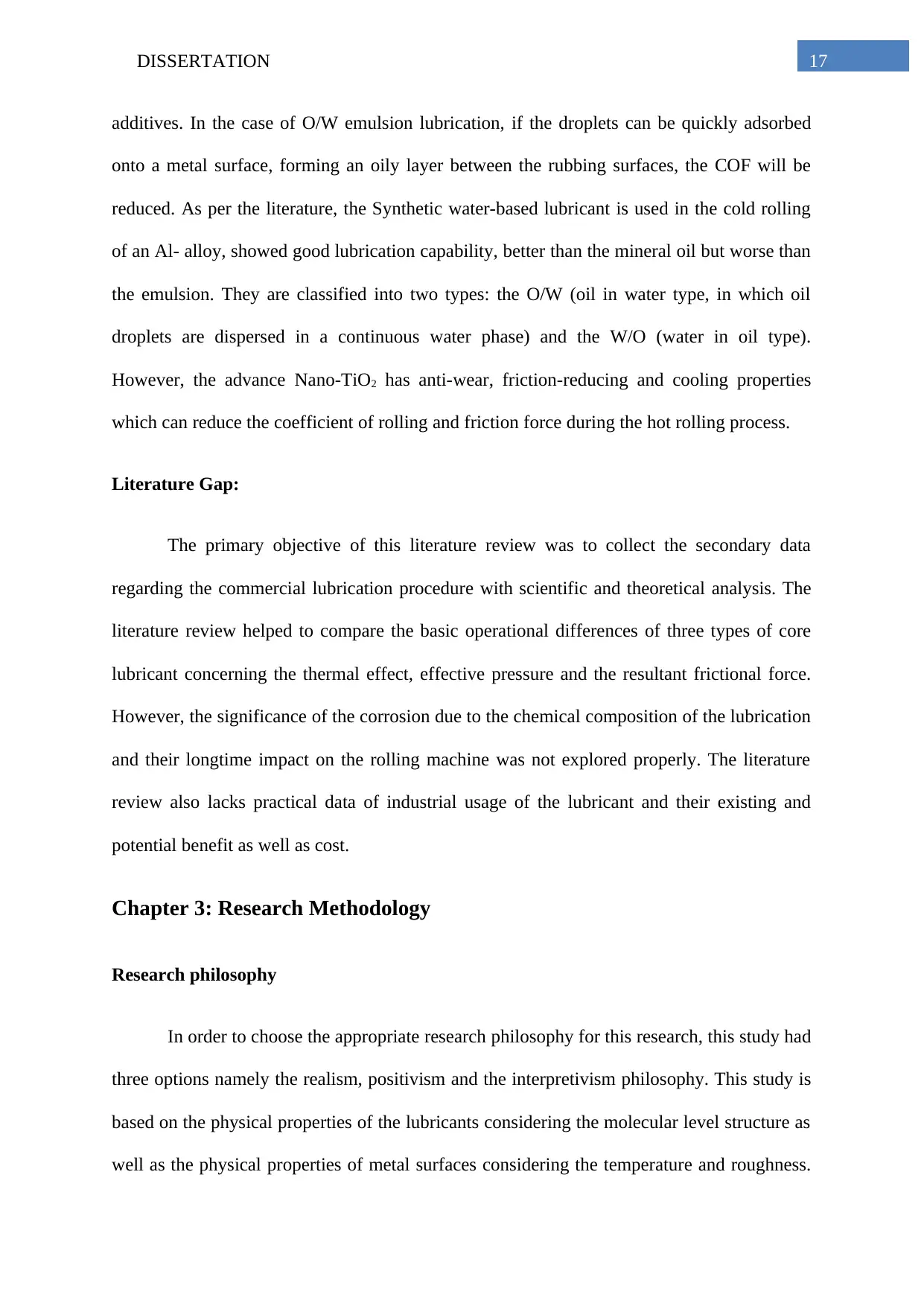
17DISSERTATION
additives. In the case of O/W emulsion lubrication, if the droplets can be quickly adsorbed
onto a metal surface, forming an oily layer between the rubbing surfaces, the COF will be
reduced. As per the literature, the Synthetic water-based lubricant is used in the cold rolling
of an Al- alloy, showed good lubrication capability, better than the mineral oil but worse than
the emulsion. They are classified into two types: the O/W (oil in water type, in which oil
droplets are dispersed in a continuous water phase) and the W/O (water in oil type).
However, the advance Nano-TiO2 has anti-wear, friction-reducing and cooling properties
which can reduce the coefficient of rolling and friction force during the hot rolling process.
Literature Gap:
The primary objective of this literature review was to collect the secondary data
regarding the commercial lubrication procedure with scientific and theoretical analysis. The
literature review helped to compare the basic operational differences of three types of core
lubricant concerning the thermal effect, effective pressure and the resultant frictional force.
However, the significance of the corrosion due to the chemical composition of the lubrication
and their longtime impact on the rolling machine was not explored properly. The literature
review also lacks practical data of industrial usage of the lubricant and their existing and
potential benefit as well as cost.
Chapter 3: Research Methodology
Research philosophy
In order to choose the appropriate research philosophy for this research, this study had
three options namely the realism, positivism and the interpretivism philosophy. This study is
based on the physical properties of the lubricants considering the molecular level structure as
well as the physical properties of metal surfaces considering the temperature and roughness.
additives. In the case of O/W emulsion lubrication, if the droplets can be quickly adsorbed
onto a metal surface, forming an oily layer between the rubbing surfaces, the COF will be
reduced. As per the literature, the Synthetic water-based lubricant is used in the cold rolling
of an Al- alloy, showed good lubrication capability, better than the mineral oil but worse than
the emulsion. They are classified into two types: the O/W (oil in water type, in which oil
droplets are dispersed in a continuous water phase) and the W/O (water in oil type).
However, the advance Nano-TiO2 has anti-wear, friction-reducing and cooling properties
which can reduce the coefficient of rolling and friction force during the hot rolling process.
Literature Gap:
The primary objective of this literature review was to collect the secondary data
regarding the commercial lubrication procedure with scientific and theoretical analysis. The
literature review helped to compare the basic operational differences of three types of core
lubricant concerning the thermal effect, effective pressure and the resultant frictional force.
However, the significance of the corrosion due to the chemical composition of the lubrication
and their longtime impact on the rolling machine was not explored properly. The literature
review also lacks practical data of industrial usage of the lubricant and their existing and
potential benefit as well as cost.
Chapter 3: Research Methodology
Research philosophy
In order to choose the appropriate research philosophy for this research, this study had
three options namely the realism, positivism and the interpretivism philosophy. This study is
based on the physical properties of the lubricants considering the molecular level structure as
well as the physical properties of metal surfaces considering the temperature and roughness.
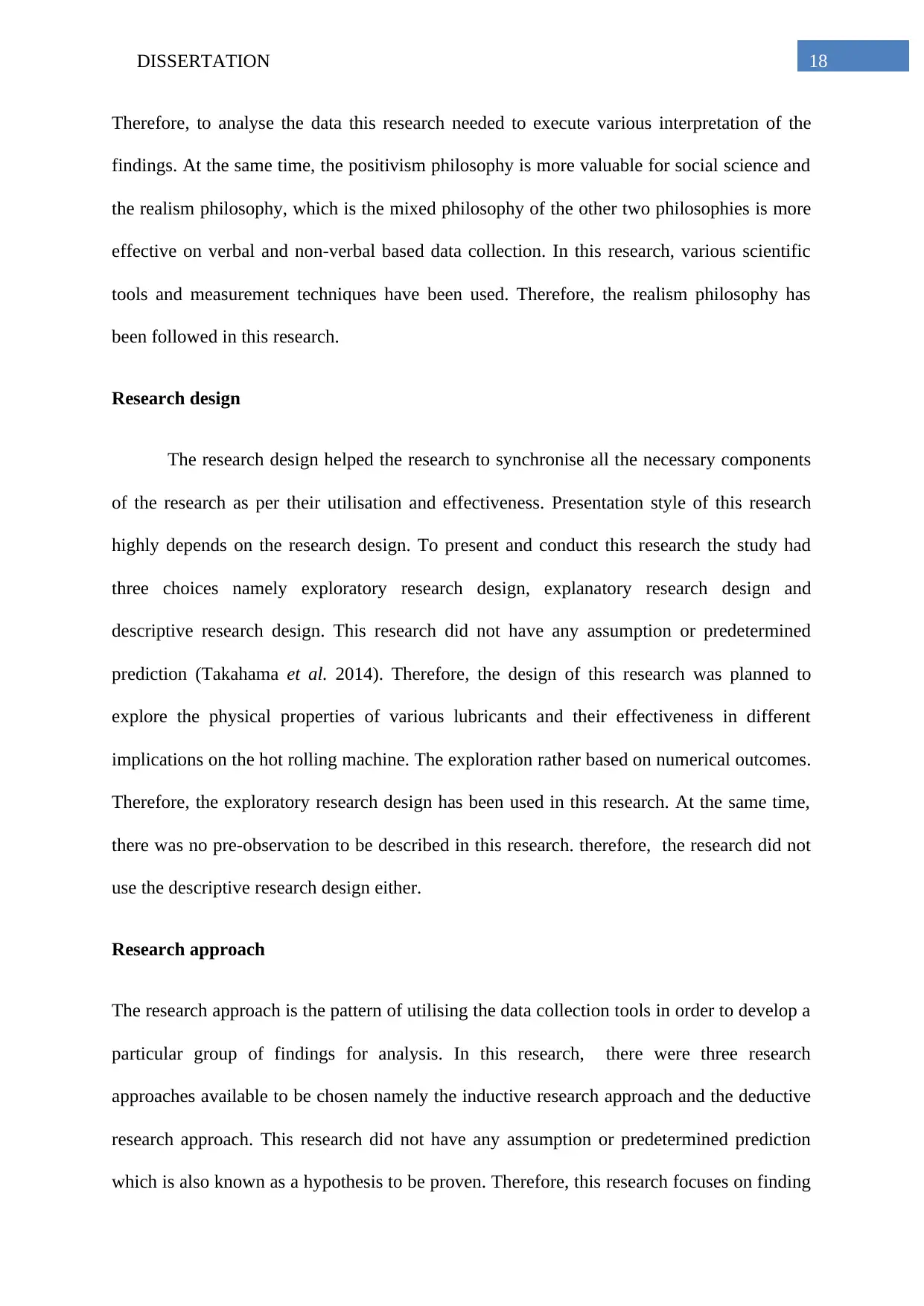
18DISSERTATION
Therefore, to analyse the data this research needed to execute various interpretation of the
findings. At the same time, the positivism philosophy is more valuable for social science and
the realism philosophy, which is the mixed philosophy of the other two philosophies is more
effective on verbal and non-verbal based data collection. In this research, various scientific
tools and measurement techniques have been used. Therefore, the realism philosophy has
been followed in this research.
Research design
The research design helped the research to synchronise all the necessary components
of the research as per their utilisation and effectiveness. Presentation style of this research
highly depends on the research design. To present and conduct this research the study had
three choices namely exploratory research design, explanatory research design and
descriptive research design. This research did not have any assumption or predetermined
prediction (Takahama et al. 2014). Therefore, the design of this research was planned to
explore the physical properties of various lubricants and their effectiveness in different
implications on the hot rolling machine. The exploration rather based on numerical outcomes.
Therefore, the exploratory research design has been used in this research. At the same time,
there was no pre-observation to be described in this research. therefore, the research did not
use the descriptive research design either.
Research approach
The research approach is the pattern of utilising the data collection tools in order to develop a
particular group of findings for analysis. In this research, there were three research
approaches available to be chosen namely the inductive research approach and the deductive
research approach. This research did not have any assumption or predetermined prediction
which is also known as a hypothesis to be proven. Therefore, this research focuses on finding
Therefore, to analyse the data this research needed to execute various interpretation of the
findings. At the same time, the positivism philosophy is more valuable for social science and
the realism philosophy, which is the mixed philosophy of the other two philosophies is more
effective on verbal and non-verbal based data collection. In this research, various scientific
tools and measurement techniques have been used. Therefore, the realism philosophy has
been followed in this research.
Research design
The research design helped the research to synchronise all the necessary components
of the research as per their utilisation and effectiveness. Presentation style of this research
highly depends on the research design. To present and conduct this research the study had
three choices namely exploratory research design, explanatory research design and
descriptive research design. This research did not have any assumption or predetermined
prediction (Takahama et al. 2014). Therefore, the design of this research was planned to
explore the physical properties of various lubricants and their effectiveness in different
implications on the hot rolling machine. The exploration rather based on numerical outcomes.
Therefore, the exploratory research design has been used in this research. At the same time,
there was no pre-observation to be described in this research. therefore, the research did not
use the descriptive research design either.
Research approach
The research approach is the pattern of utilising the data collection tools in order to develop a
particular group of findings for analysis. In this research, there were three research
approaches available to be chosen namely the inductive research approach and the deductive
research approach. This research did not have any assumption or predetermined prediction
which is also known as a hypothesis to be proven. Therefore, this research focuses on finding
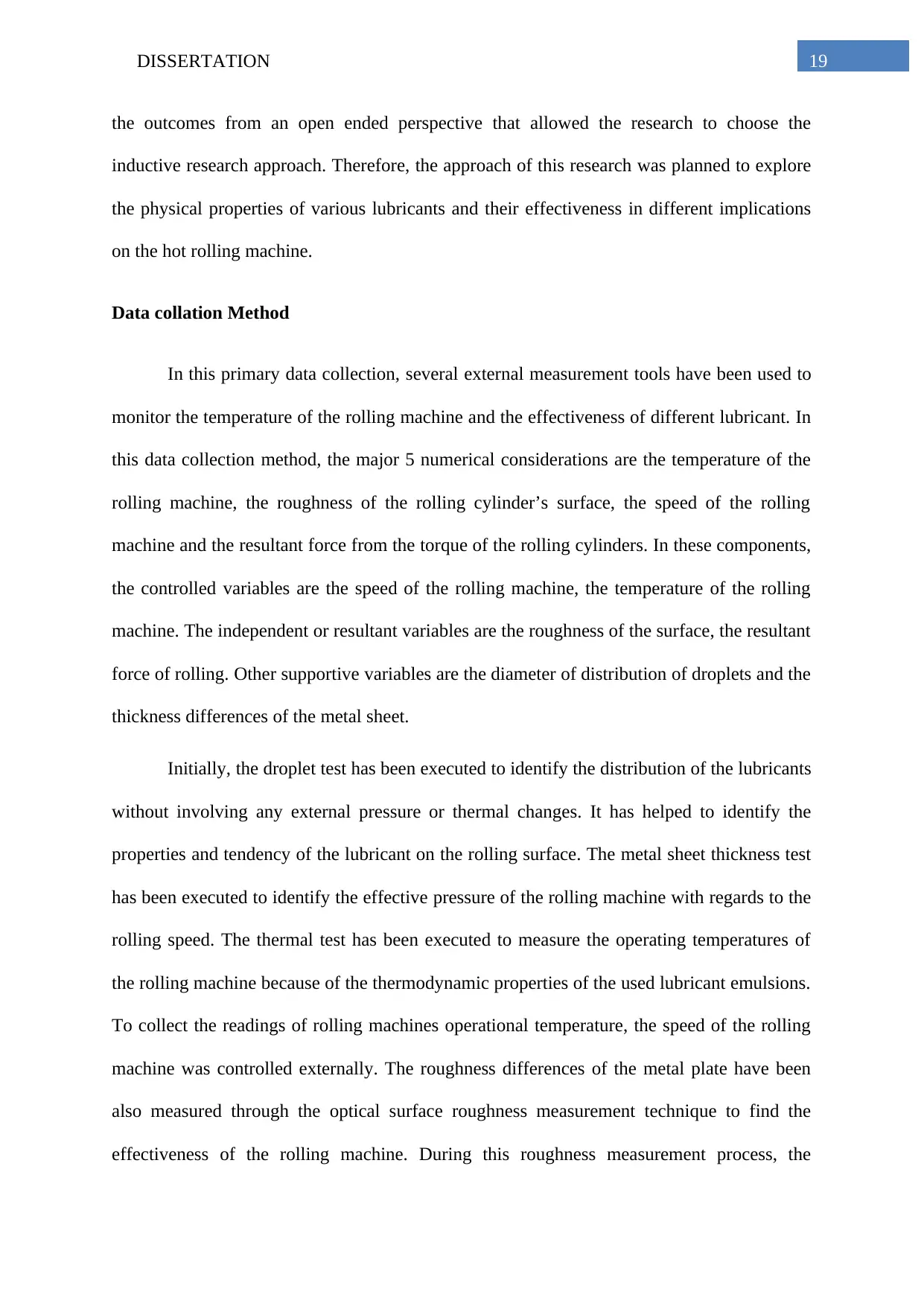
19DISSERTATION
the outcomes from an open ended perspective that allowed the research to choose the
inductive research approach. Therefore, the approach of this research was planned to explore
the physical properties of various lubricants and their effectiveness in different implications
on the hot rolling machine.
Data collation Method
In this primary data collection, several external measurement tools have been used to
monitor the temperature of the rolling machine and the effectiveness of different lubricant. In
this data collection method, the major 5 numerical considerations are the temperature of the
rolling machine, the roughness of the rolling cylinder’s surface, the speed of the rolling
machine and the resultant force from the torque of the rolling cylinders. In these components,
the controlled variables are the speed of the rolling machine, the temperature of the rolling
machine. The independent or resultant variables are the roughness of the surface, the resultant
force of rolling. Other supportive variables are the diameter of distribution of droplets and the
thickness differences of the metal sheet.
Initially, the droplet test has been executed to identify the distribution of the lubricants
without involving any external pressure or thermal changes. It has helped to identify the
properties and tendency of the lubricant on the rolling surface. The metal sheet thickness test
has been executed to identify the effective pressure of the rolling machine with regards to the
rolling speed. The thermal test has been executed to measure the operating temperatures of
the rolling machine because of the thermodynamic properties of the used lubricant emulsions.
To collect the readings of rolling machines operational temperature, the speed of the rolling
machine was controlled externally. The roughness differences of the metal plate have been
also measured through the optical surface roughness measurement technique to find the
effectiveness of the rolling machine. During this roughness measurement process, the
the outcomes from an open ended perspective that allowed the research to choose the
inductive research approach. Therefore, the approach of this research was planned to explore
the physical properties of various lubricants and their effectiveness in different implications
on the hot rolling machine.
Data collation Method
In this primary data collection, several external measurement tools have been used to
monitor the temperature of the rolling machine and the effectiveness of different lubricant. In
this data collection method, the major 5 numerical considerations are the temperature of the
rolling machine, the roughness of the rolling cylinder’s surface, the speed of the rolling
machine and the resultant force from the torque of the rolling cylinders. In these components,
the controlled variables are the speed of the rolling machine, the temperature of the rolling
machine. The independent or resultant variables are the roughness of the surface, the resultant
force of rolling. Other supportive variables are the diameter of distribution of droplets and the
thickness differences of the metal sheet.
Initially, the droplet test has been executed to identify the distribution of the lubricants
without involving any external pressure or thermal changes. It has helped to identify the
properties and tendency of the lubricant on the rolling surface. The metal sheet thickness test
has been executed to identify the effective pressure of the rolling machine with regards to the
rolling speed. The thermal test has been executed to measure the operating temperatures of
the rolling machine because of the thermodynamic properties of the used lubricant emulsions.
To collect the readings of rolling machines operational temperature, the speed of the rolling
machine was controlled externally. The roughness differences of the metal plate have been
also measured through the optical surface roughness measurement technique to find the
effectiveness of the rolling machine. During this roughness measurement process, the
Paraphrase This Document
Need a fresh take? Get an instant paraphrase of this document with our AI Paraphraser
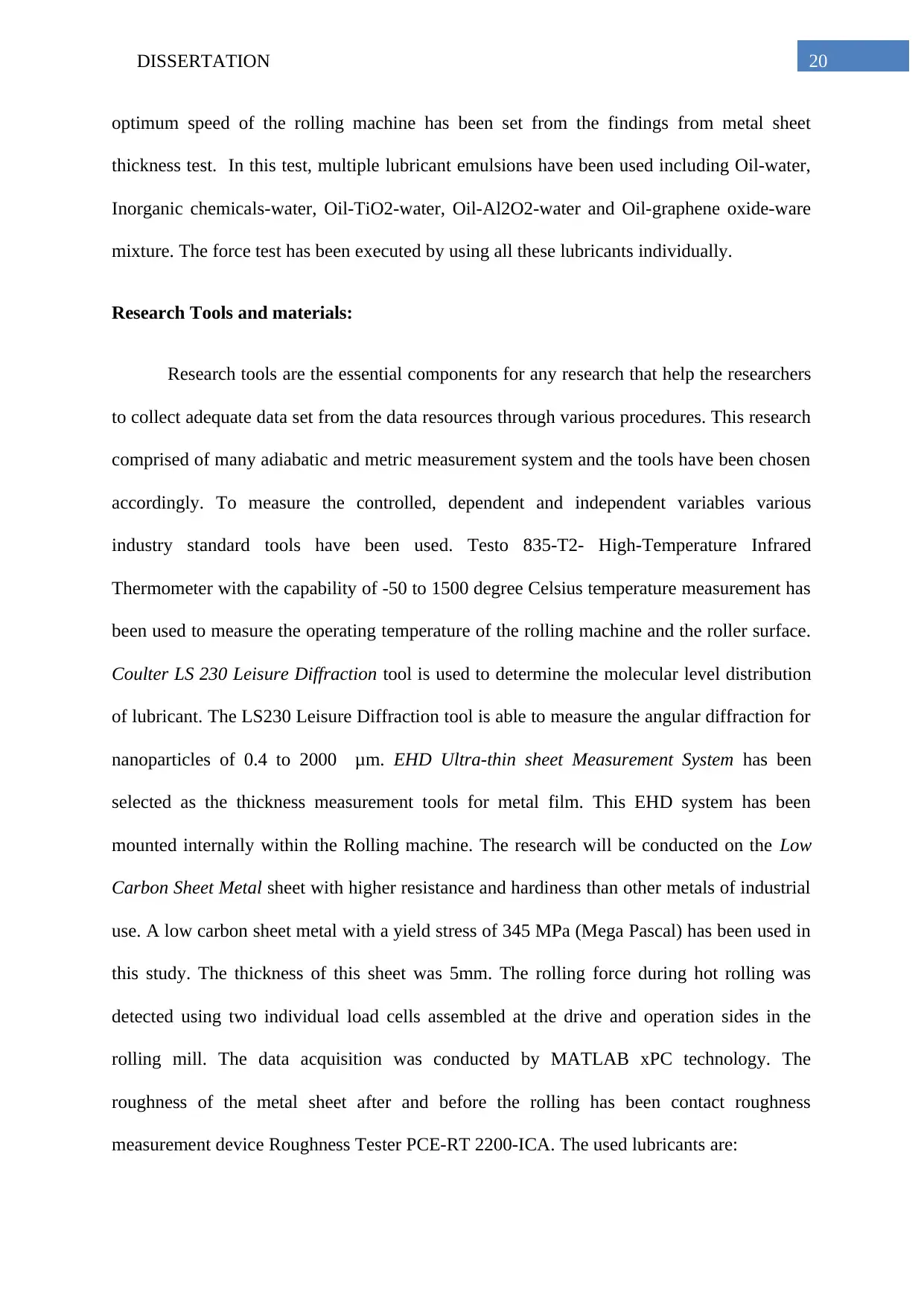
20DISSERTATION
optimum speed of the rolling machine has been set from the findings from metal sheet
thickness test. In this test, multiple lubricant emulsions have been used including Oil-water,
Inorganic chemicals-water, Oil-TiO2-water, Oil-Al2O2-water and Oil-graphene oxide-ware
mixture. The force test has been executed by using all these lubricants individually.
Research Tools and materials:
Research tools are the essential components for any research that help the researchers
to collect adequate data set from the data resources through various procedures. This research
comprised of many adiabatic and metric measurement system and the tools have been chosen
accordingly. To measure the controlled, dependent and independent variables various
industry standard tools have been used. Testo 835-T2- High-Temperature Infrared
Thermometer with the capability of -50 to 1500 degree Celsius temperature measurement has
been used to measure the operating temperature of the rolling machine and the roller surface.
Coulter LS 230 Leisure Diffraction tool is used to determine the molecular level distribution
of lubricant. The LS230 Leisure Diffraction tool is able to measure the angular diffraction for
nanoparticles of 0.4 to 2000 μm. EHD Ultra-thin sheet Measurement System has been
selected as the thickness measurement tools for metal film. This EHD system has been
mounted internally within the Rolling machine. The research will be conducted on the Low
Carbon Sheet Metal sheet with higher resistance and hardiness than other metals of industrial
use. A low carbon sheet metal with a yield stress of 345 MPa (Mega Pascal) has been used in
this study. The thickness of this sheet was 5mm. The rolling force during hot rolling was
detected using two individual load cells assembled at the drive and operation sides in the
rolling mill. The data acquisition was conducted by MATLAB xPC technology. The
roughness of the metal sheet after and before the rolling has been contact roughness
measurement device Roughness Tester PCE-RT 2200-ICA. The used lubricants are:
optimum speed of the rolling machine has been set from the findings from metal sheet
thickness test. In this test, multiple lubricant emulsions have been used including Oil-water,
Inorganic chemicals-water, Oil-TiO2-water, Oil-Al2O2-water and Oil-graphene oxide-ware
mixture. The force test has been executed by using all these lubricants individually.
Research Tools and materials:
Research tools are the essential components for any research that help the researchers
to collect adequate data set from the data resources through various procedures. This research
comprised of many adiabatic and metric measurement system and the tools have been chosen
accordingly. To measure the controlled, dependent and independent variables various
industry standard tools have been used. Testo 835-T2- High-Temperature Infrared
Thermometer with the capability of -50 to 1500 degree Celsius temperature measurement has
been used to measure the operating temperature of the rolling machine and the roller surface.
Coulter LS 230 Leisure Diffraction tool is used to determine the molecular level distribution
of lubricant. The LS230 Leisure Diffraction tool is able to measure the angular diffraction for
nanoparticles of 0.4 to 2000 μm. EHD Ultra-thin sheet Measurement System has been
selected as the thickness measurement tools for metal film. This EHD system has been
mounted internally within the Rolling machine. The research will be conducted on the Low
Carbon Sheet Metal sheet with higher resistance and hardiness than other metals of industrial
use. A low carbon sheet metal with a yield stress of 345 MPa (Mega Pascal) has been used in
this study. The thickness of this sheet was 5mm. The rolling force during hot rolling was
detected using two individual load cells assembled at the drive and operation sides in the
rolling mill. The data acquisition was conducted by MATLAB xPC technology. The
roughness of the metal sheet after and before the rolling has been contact roughness
measurement device Roughness Tester PCE-RT 2200-ICA. The used lubricants are:
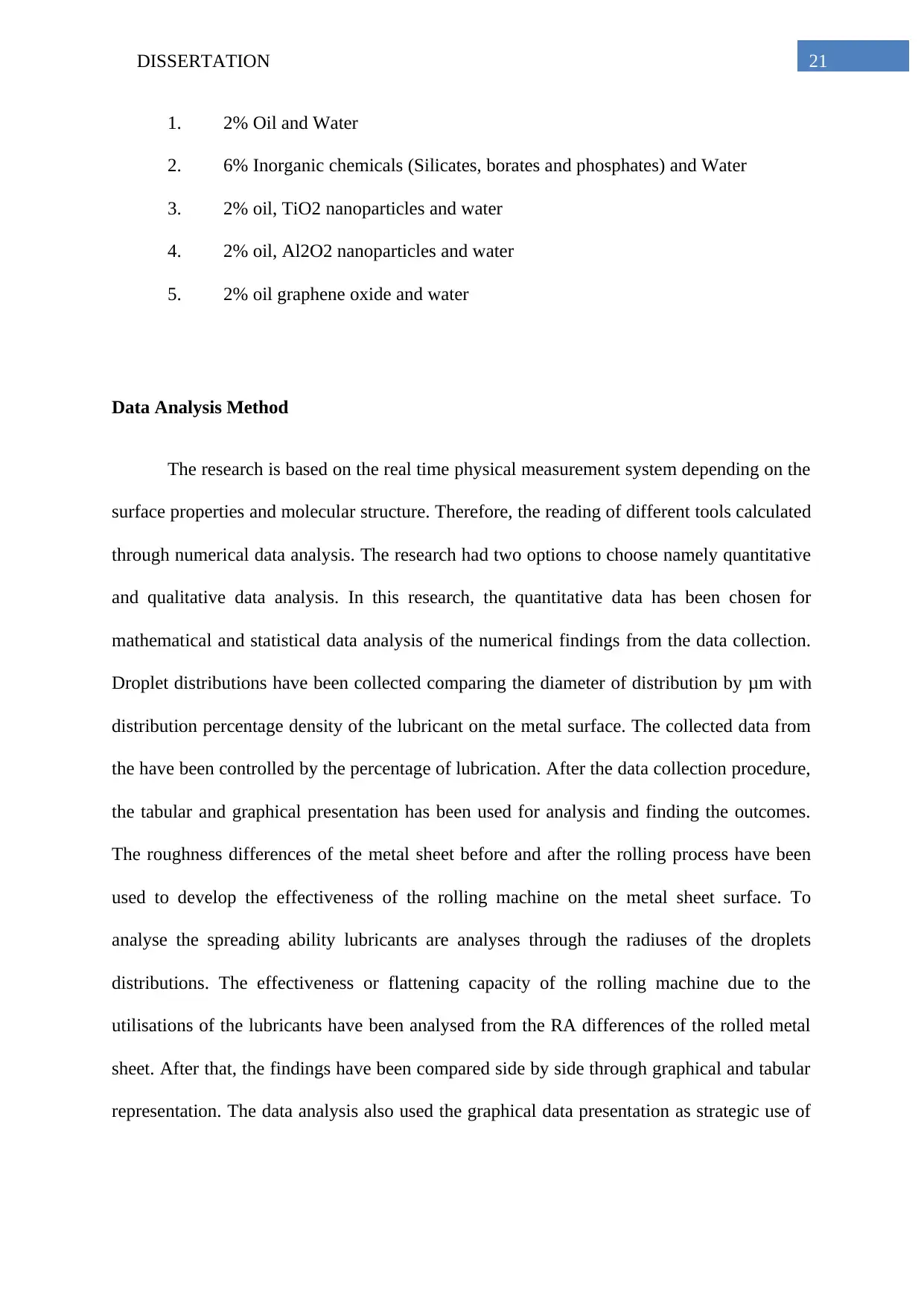
21DISSERTATION
1. 2% Oil and Water
2. 6% Inorganic chemicals (Silicates, borates and phosphates) and Water
3. 2% oil, TiO2 nanoparticles and water
4. 2% oil, Al2O2 nanoparticles and water
5. 2% oil graphene oxide and water
Data Analysis Method
The research is based on the real time physical measurement system depending on the
surface properties and molecular structure. Therefore, the reading of different tools calculated
through numerical data analysis. The research had two options to choose namely quantitative
and qualitative data analysis. In this research, the quantitative data has been chosen for
mathematical and statistical data analysis of the numerical findings from the data collection.
Droplet distributions have been collected comparing the diameter of distribution by μm with
distribution percentage density of the lubricant on the metal surface. The collected data from
the have been controlled by the percentage of lubrication. After the data collection procedure,
the tabular and graphical presentation has been used for analysis and finding the outcomes.
The roughness differences of the metal sheet before and after the rolling process have been
used to develop the effectiveness of the rolling machine on the metal sheet surface. To
analyse the spreading ability lubricants are analyses through the radiuses of the droplets
distributions. The effectiveness or flattening capacity of the rolling machine due to the
utilisations of the lubricants have been analysed from the RA differences of the rolled metal
sheet. After that, the findings have been compared side by side through graphical and tabular
representation. The data analysis also used the graphical data presentation as strategic use of
1. 2% Oil and Water
2. 6% Inorganic chemicals (Silicates, borates and phosphates) and Water
3. 2% oil, TiO2 nanoparticles and water
4. 2% oil, Al2O2 nanoparticles and water
5. 2% oil graphene oxide and water
Data Analysis Method
The research is based on the real time physical measurement system depending on the
surface properties and molecular structure. Therefore, the reading of different tools calculated
through numerical data analysis. The research had two options to choose namely quantitative
and qualitative data analysis. In this research, the quantitative data has been chosen for
mathematical and statistical data analysis of the numerical findings from the data collection.
Droplet distributions have been collected comparing the diameter of distribution by μm with
distribution percentage density of the lubricant on the metal surface. The collected data from
the have been controlled by the percentage of lubrication. After the data collection procedure,
the tabular and graphical presentation has been used for analysis and finding the outcomes.
The roughness differences of the metal sheet before and after the rolling process have been
used to develop the effectiveness of the rolling machine on the metal sheet surface. To
analyse the spreading ability lubricants are analyses through the radiuses of the droplets
distributions. The effectiveness or flattening capacity of the rolling machine due to the
utilisations of the lubricants have been analysed from the RA differences of the rolled metal
sheet. After that, the findings have been compared side by side through graphical and tabular
representation. The data analysis also used the graphical data presentation as strategic use of
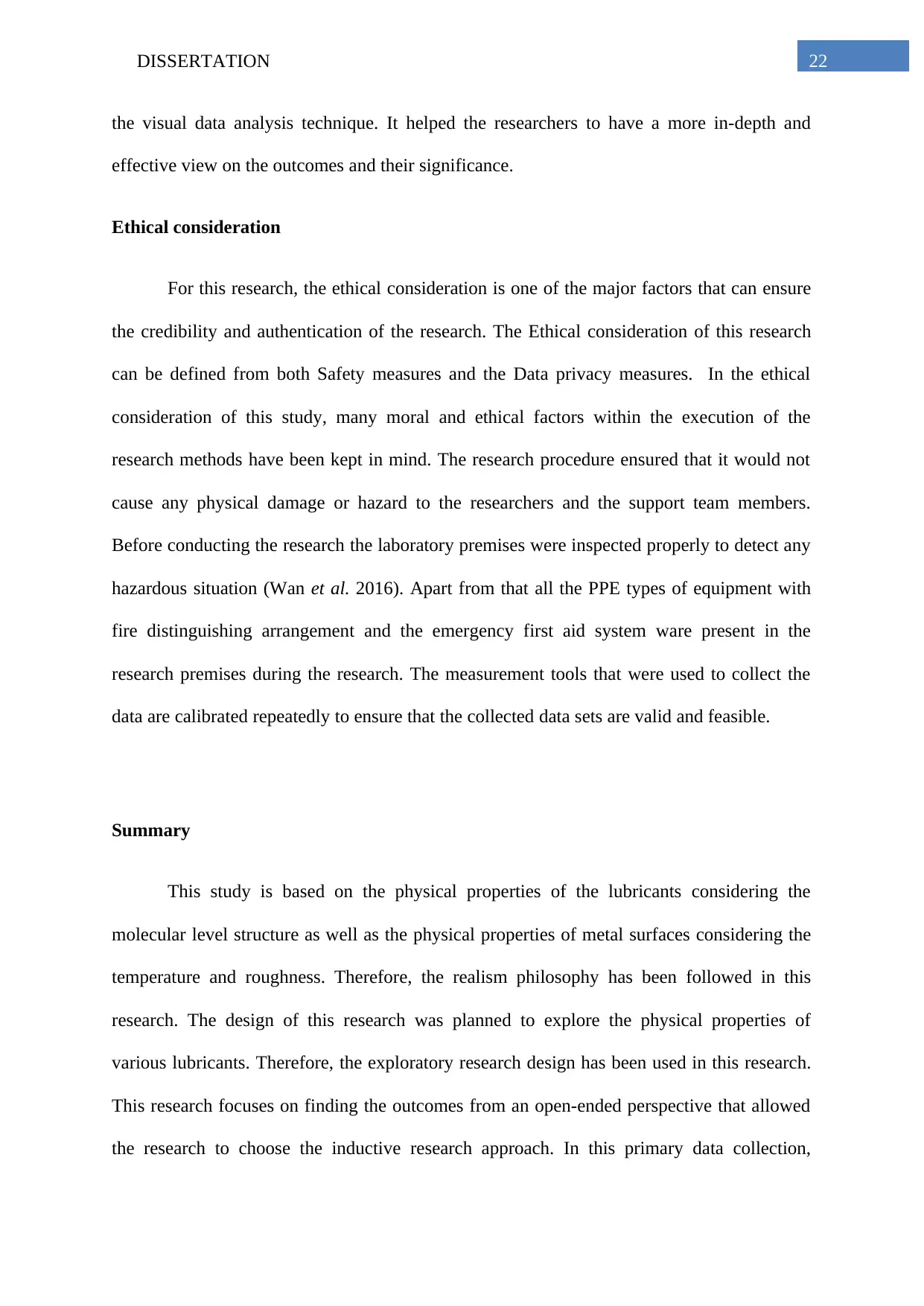
22DISSERTATION
the visual data analysis technique. It helped the researchers to have a more in-depth and
effective view on the outcomes and their significance.
Ethical consideration
For this research, the ethical consideration is one of the major factors that can ensure
the credibility and authentication of the research. The Ethical consideration of this research
can be defined from both Safety measures and the Data privacy measures. In the ethical
consideration of this study, many moral and ethical factors within the execution of the
research methods have been kept in mind. The research procedure ensured that it would not
cause any physical damage or hazard to the researchers and the support team members.
Before conducting the research the laboratory premises were inspected properly to detect any
hazardous situation (Wan et al. 2016). Apart from that all the PPE types of equipment with
fire distinguishing arrangement and the emergency first aid system ware present in the
research premises during the research. The measurement tools that were used to collect the
data are calibrated repeatedly to ensure that the collected data sets are valid and feasible.
Summary
This study is based on the physical properties of the lubricants considering the
molecular level structure as well as the physical properties of metal surfaces considering the
temperature and roughness. Therefore, the realism philosophy has been followed in this
research. The design of this research was planned to explore the physical properties of
various lubricants. Therefore, the exploratory research design has been used in this research.
This research focuses on finding the outcomes from an open-ended perspective that allowed
the research to choose the inductive research approach. In this primary data collection,
the visual data analysis technique. It helped the researchers to have a more in-depth and
effective view on the outcomes and their significance.
Ethical consideration
For this research, the ethical consideration is one of the major factors that can ensure
the credibility and authentication of the research. The Ethical consideration of this research
can be defined from both Safety measures and the Data privacy measures. In the ethical
consideration of this study, many moral and ethical factors within the execution of the
research methods have been kept in mind. The research procedure ensured that it would not
cause any physical damage or hazard to the researchers and the support team members.
Before conducting the research the laboratory premises were inspected properly to detect any
hazardous situation (Wan et al. 2016). Apart from that all the PPE types of equipment with
fire distinguishing arrangement and the emergency first aid system ware present in the
research premises during the research. The measurement tools that were used to collect the
data are calibrated repeatedly to ensure that the collected data sets are valid and feasible.
Summary
This study is based on the physical properties of the lubricants considering the
molecular level structure as well as the physical properties of metal surfaces considering the
temperature and roughness. Therefore, the realism philosophy has been followed in this
research. The design of this research was planned to explore the physical properties of
various lubricants. Therefore, the exploratory research design has been used in this research.
This research focuses on finding the outcomes from an open-ended perspective that allowed
the research to choose the inductive research approach. In this primary data collection,
Secure Best Marks with AI Grader
Need help grading? Try our AI Grader for instant feedback on your assignments.
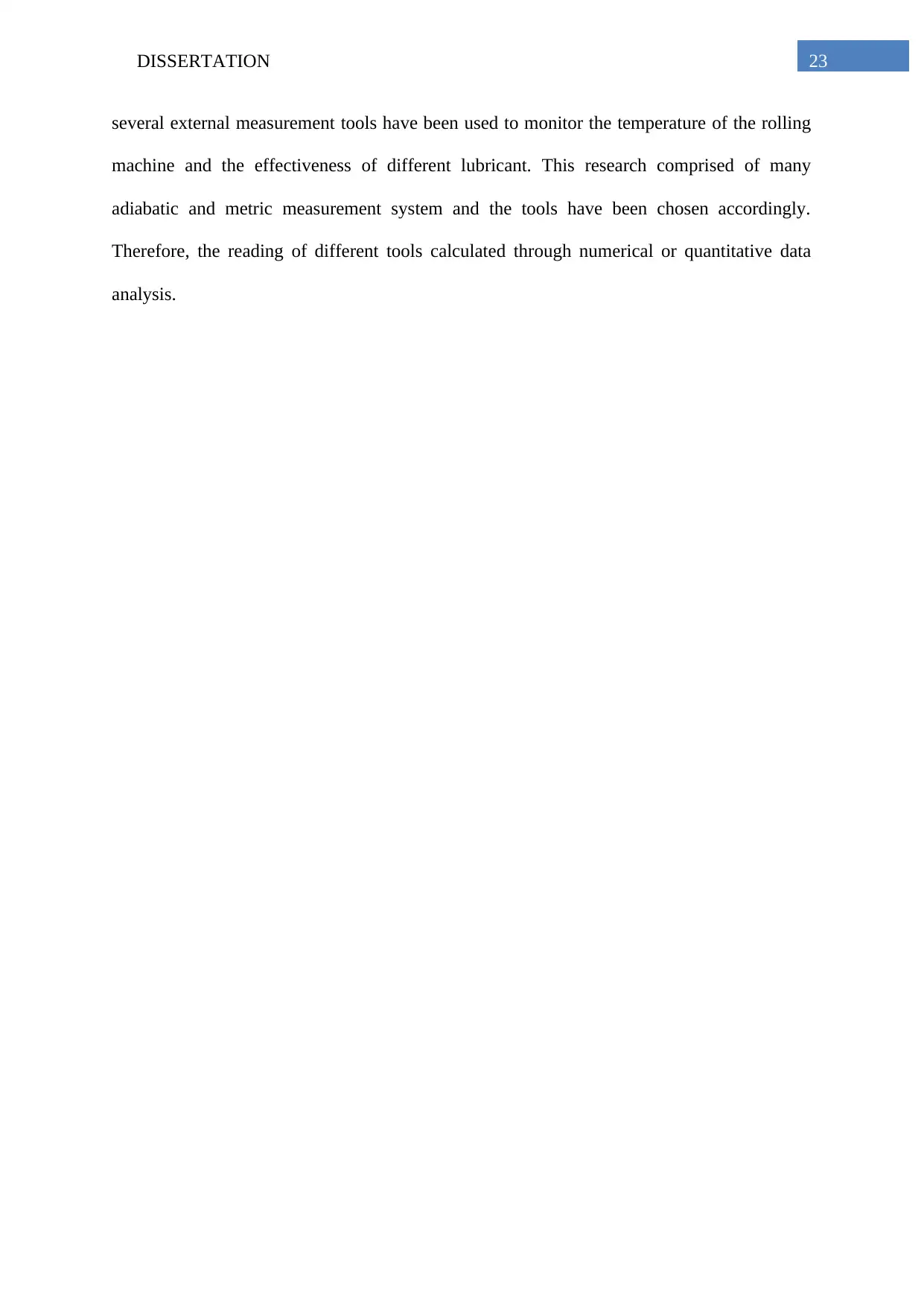
23DISSERTATION
several external measurement tools have been used to monitor the temperature of the rolling
machine and the effectiveness of different lubricant. This research comprised of many
adiabatic and metric measurement system and the tools have been chosen accordingly.
Therefore, the reading of different tools calculated through numerical or quantitative data
analysis.
several external measurement tools have been used to monitor the temperature of the rolling
machine and the effectiveness of different lubricant. This research comprised of many
adiabatic and metric measurement system and the tools have been chosen accordingly.
Therefore, the reading of different tools calculated through numerical or quantitative data
analysis.
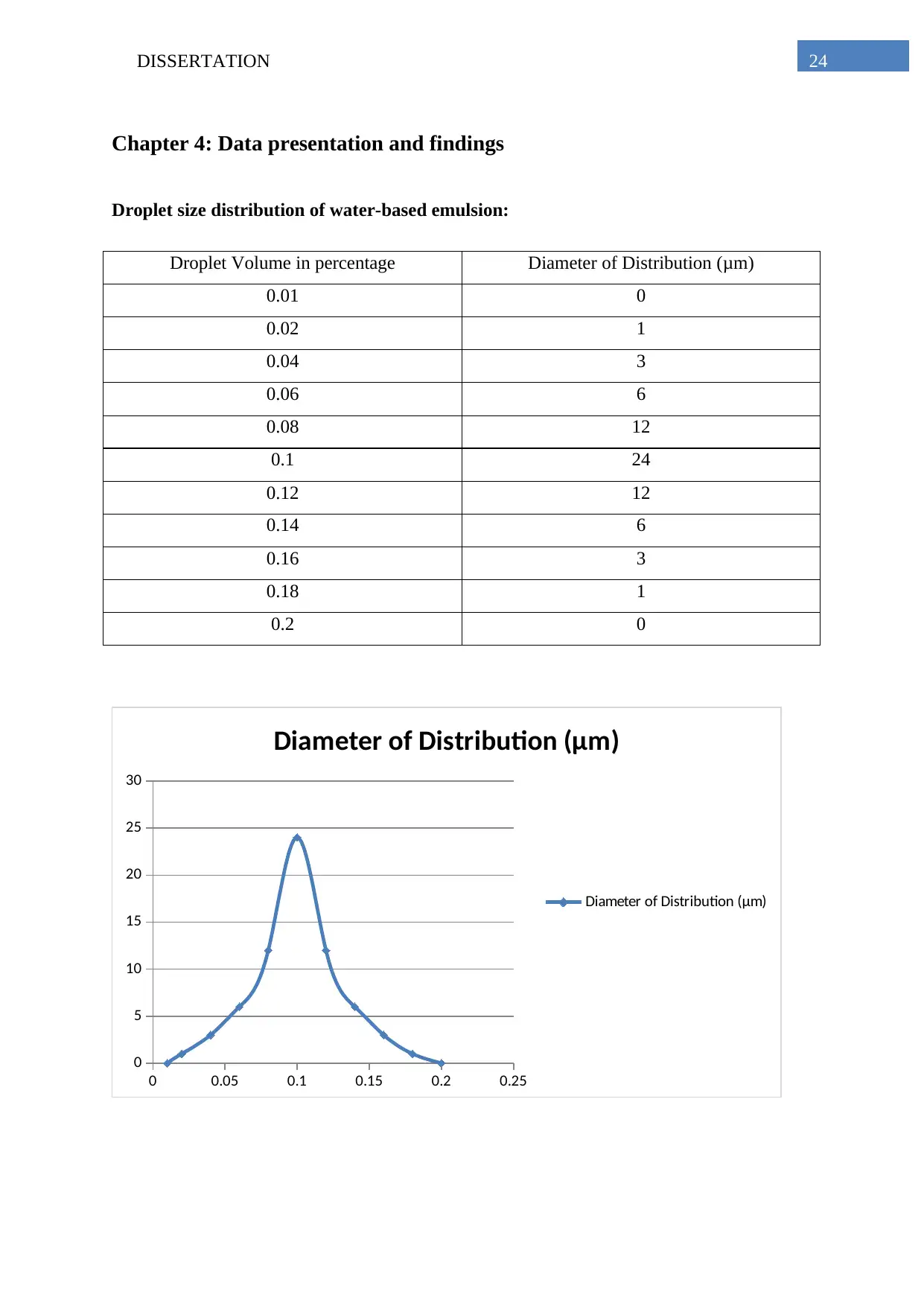
24DISSERTATION
Chapter 4: Data presentation and findings
Droplet size distribution of water-based emulsion:
Droplet Volume in percentage Diameter of Distribution (μm)
0.01 0
0.02 1
0.04 3
0.06 6
0.08 12
0.1 24
0.12 12
0.14 6
0.16 3
0.18 1
0.2 0
0 0.05 0.1 0.15 0.2 0.25
0
5
10
15
20
25
30
Diameter of Distribution (μm)
Diameter of Distribution (μm)
Chapter 4: Data presentation and findings
Droplet size distribution of water-based emulsion:
Droplet Volume in percentage Diameter of Distribution (μm)
0.01 0
0.02 1
0.04 3
0.06 6
0.08 12
0.1 24
0.12 12
0.14 6
0.16 3
0.18 1
0.2 0
0 0.05 0.1 0.15 0.2 0.25
0
5
10
15
20
25
30
Diameter of Distribution (μm)
Diameter of Distribution (μm)
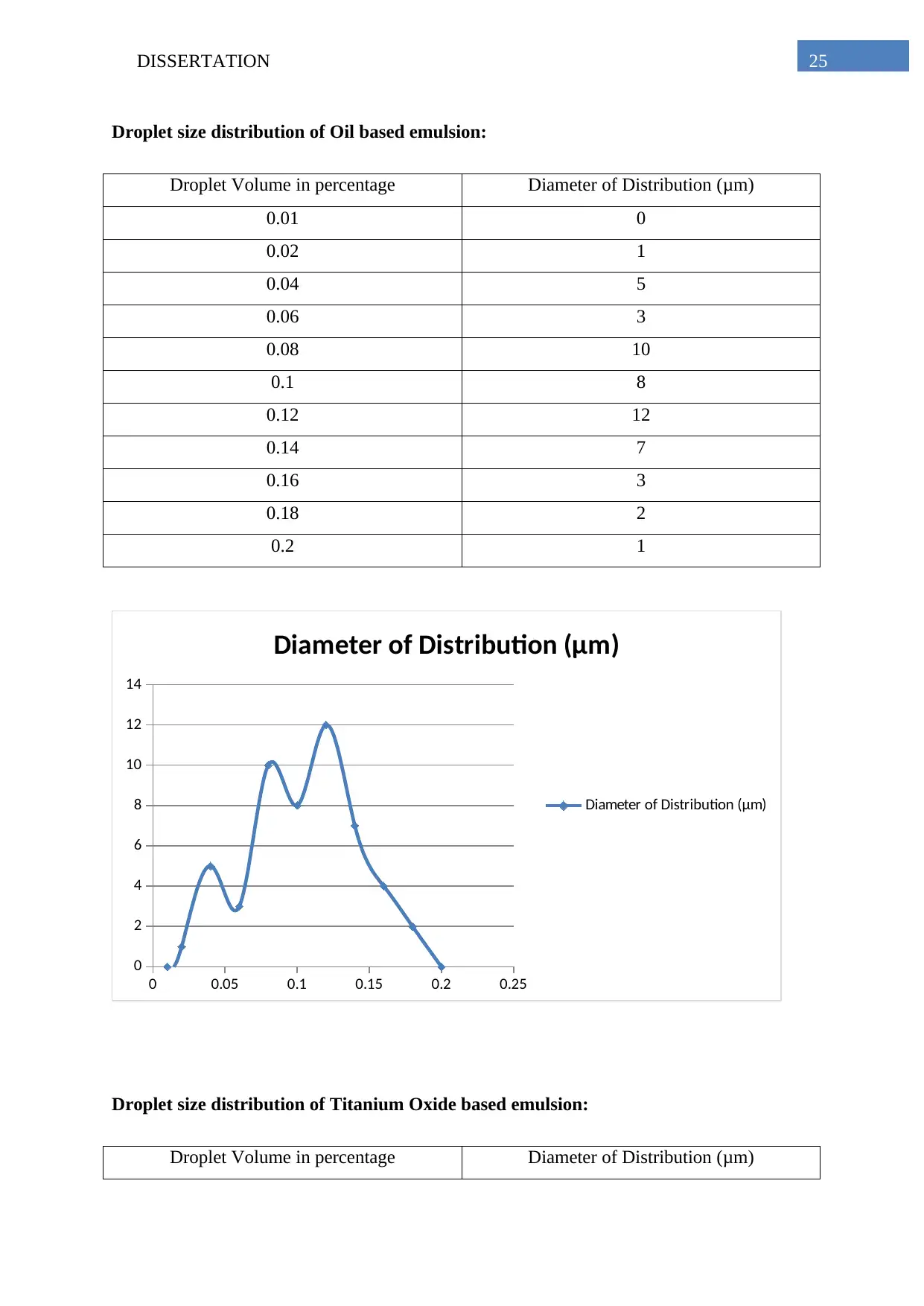
25DISSERTATION
Droplet size distribution of Oil based emulsion:
Droplet Volume in percentage Diameter of Distribution (μm)
0.01 0
0.02 1
0.04 5
0.06 3
0.08 10
0.1 8
0.12 12
0.14 7
0.16 3
0.18 2
0.2 1
0 0.05 0.1 0.15 0.2 0.25
0
2
4
6
8
10
12
14
Diameter of Distribution (μm)
Diameter of Distribution (μm)
Droplet size distribution of Titanium Oxide based emulsion:
Droplet Volume in percentage Diameter of Distribution (μm)
Droplet size distribution of Oil based emulsion:
Droplet Volume in percentage Diameter of Distribution (μm)
0.01 0
0.02 1
0.04 5
0.06 3
0.08 10
0.1 8
0.12 12
0.14 7
0.16 3
0.18 2
0.2 1
0 0.05 0.1 0.15 0.2 0.25
0
2
4
6
8
10
12
14
Diameter of Distribution (μm)
Diameter of Distribution (μm)
Droplet size distribution of Titanium Oxide based emulsion:
Droplet Volume in percentage Diameter of Distribution (μm)
Paraphrase This Document
Need a fresh take? Get an instant paraphrase of this document with our AI Paraphraser
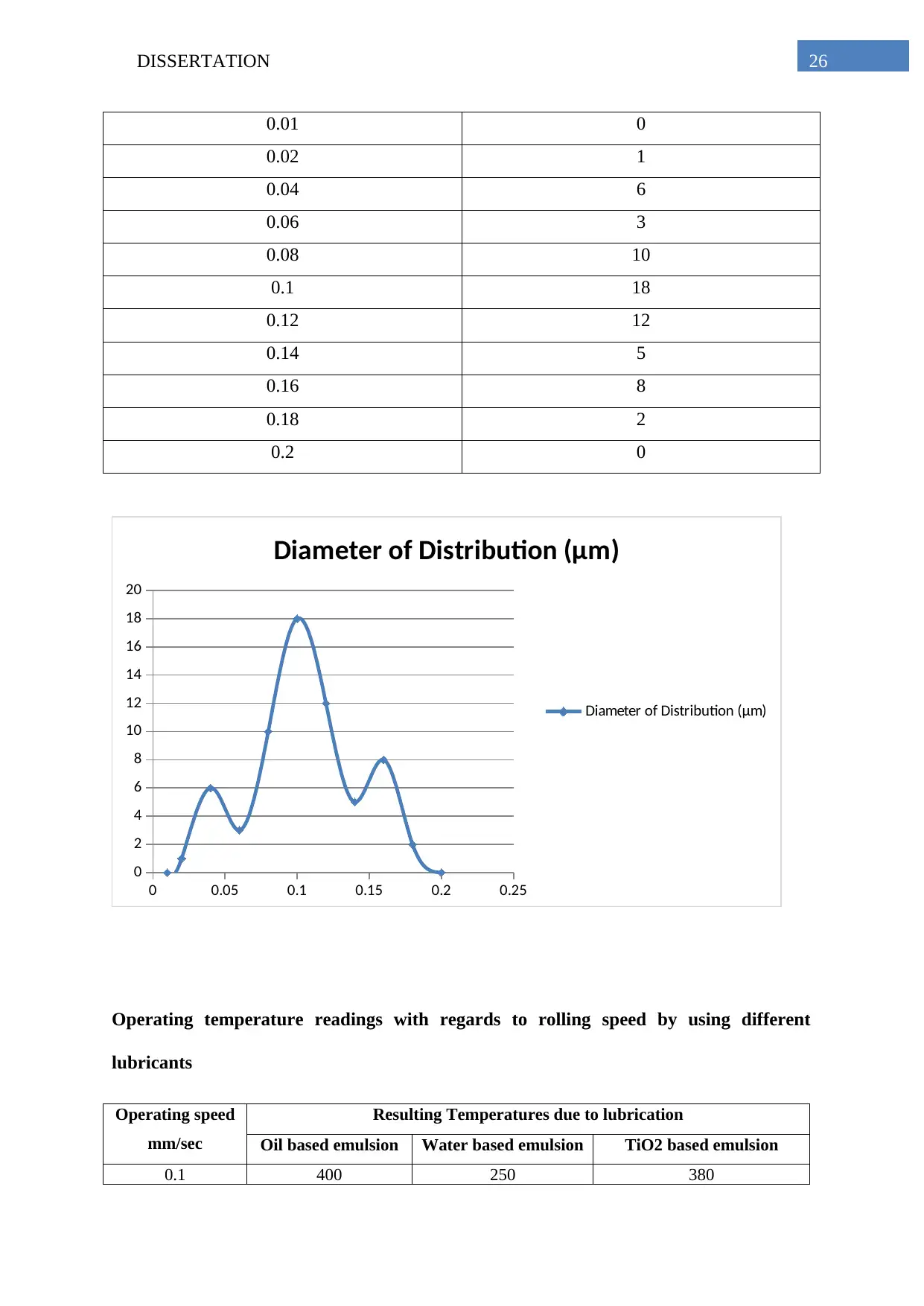
26DISSERTATION
0.01 0
0.02 1
0.04 6
0.06 3
0.08 10
0.1 18
0.12 12
0.14 5
0.16 8
0.18 2
0.2 0
0 0.05 0.1 0.15 0.2 0.25
0
2
4
6
8
10
12
14
16
18
20
Diameter of Distribution (μm)
Diameter of Distribution (μm)
Operating temperature readings with regards to rolling speed by using different
lubricants
Operating speed
mm/sec
Resulting Temperatures due to lubrication
Oil based emulsion Water based emulsion TiO2 based emulsion
0.1 400 250 380
0.01 0
0.02 1
0.04 6
0.06 3
0.08 10
0.1 18
0.12 12
0.14 5
0.16 8
0.18 2
0.2 0
0 0.05 0.1 0.15 0.2 0.25
0
2
4
6
8
10
12
14
16
18
20
Diameter of Distribution (μm)
Diameter of Distribution (μm)
Operating temperature readings with regards to rolling speed by using different
lubricants
Operating speed
mm/sec
Resulting Temperatures due to lubrication
Oil based emulsion Water based emulsion TiO2 based emulsion
0.1 400 250 380
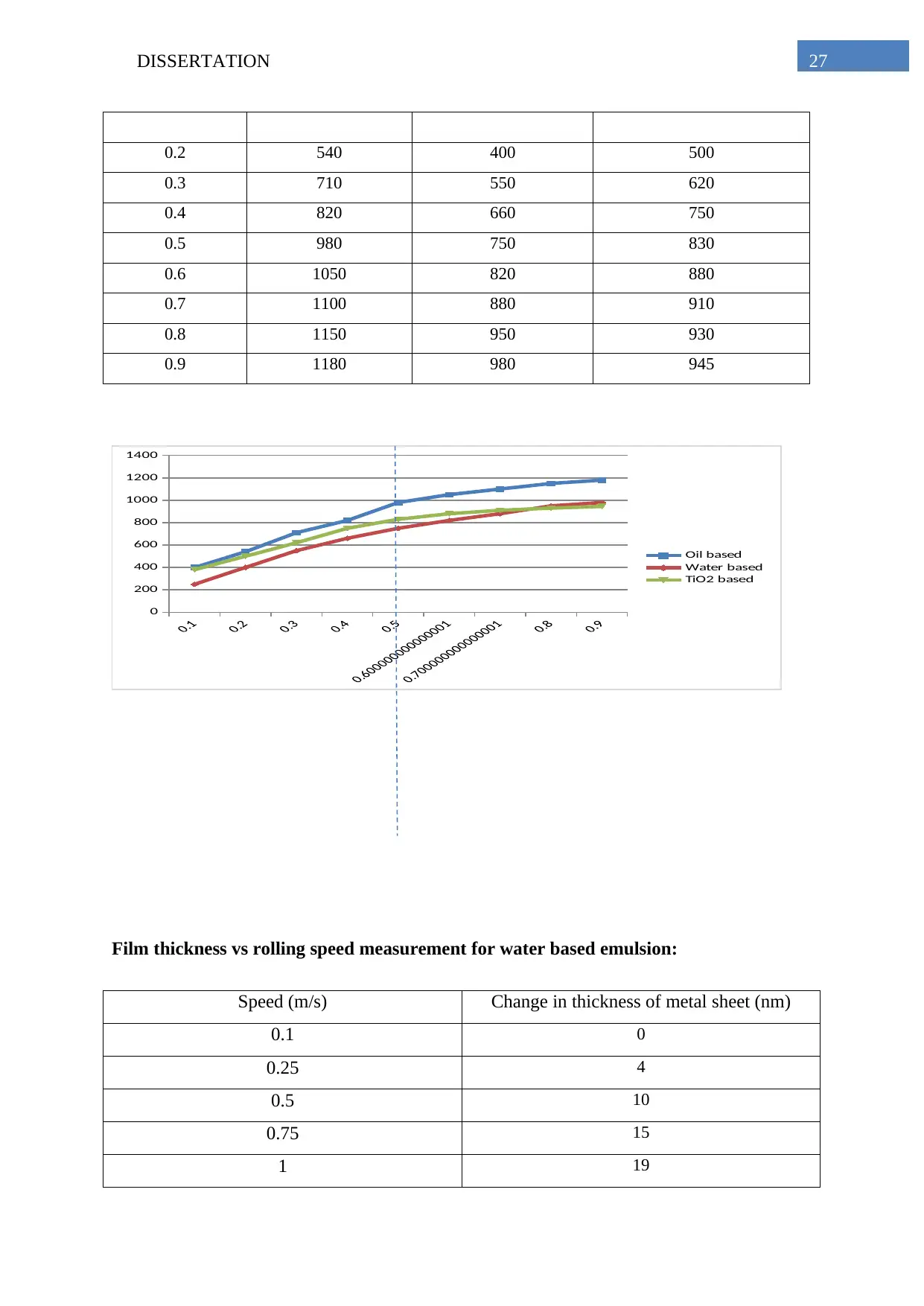
27DISSERTATION
0.2 540 400 500
0.3 710 550 620
0.4 820 660 750
0.5 980 750 830
0.6 1050 820 880
0.7 1100 880 910
0.8 1150 950 930
0.9 1180 980 945
0
200
400
600
800
1000
1200
1400
Oil based
Water based
TiO2 based
Film thickness vs rolling speed measurement for water based emulsion:
Speed (m/s) Change in thickness of metal sheet (nm)
0.1 0
0.25 4
0.5 10
0.75 15
1 19
0.2 540 400 500
0.3 710 550 620
0.4 820 660 750
0.5 980 750 830
0.6 1050 820 880
0.7 1100 880 910
0.8 1150 950 930
0.9 1180 980 945
0
200
400
600
800
1000
1200
1400
Oil based
Water based
TiO2 based
Film thickness vs rolling speed measurement for water based emulsion:
Speed (m/s) Change in thickness of metal sheet (nm)
0.1 0
0.25 4
0.5 10
0.75 15
1 19
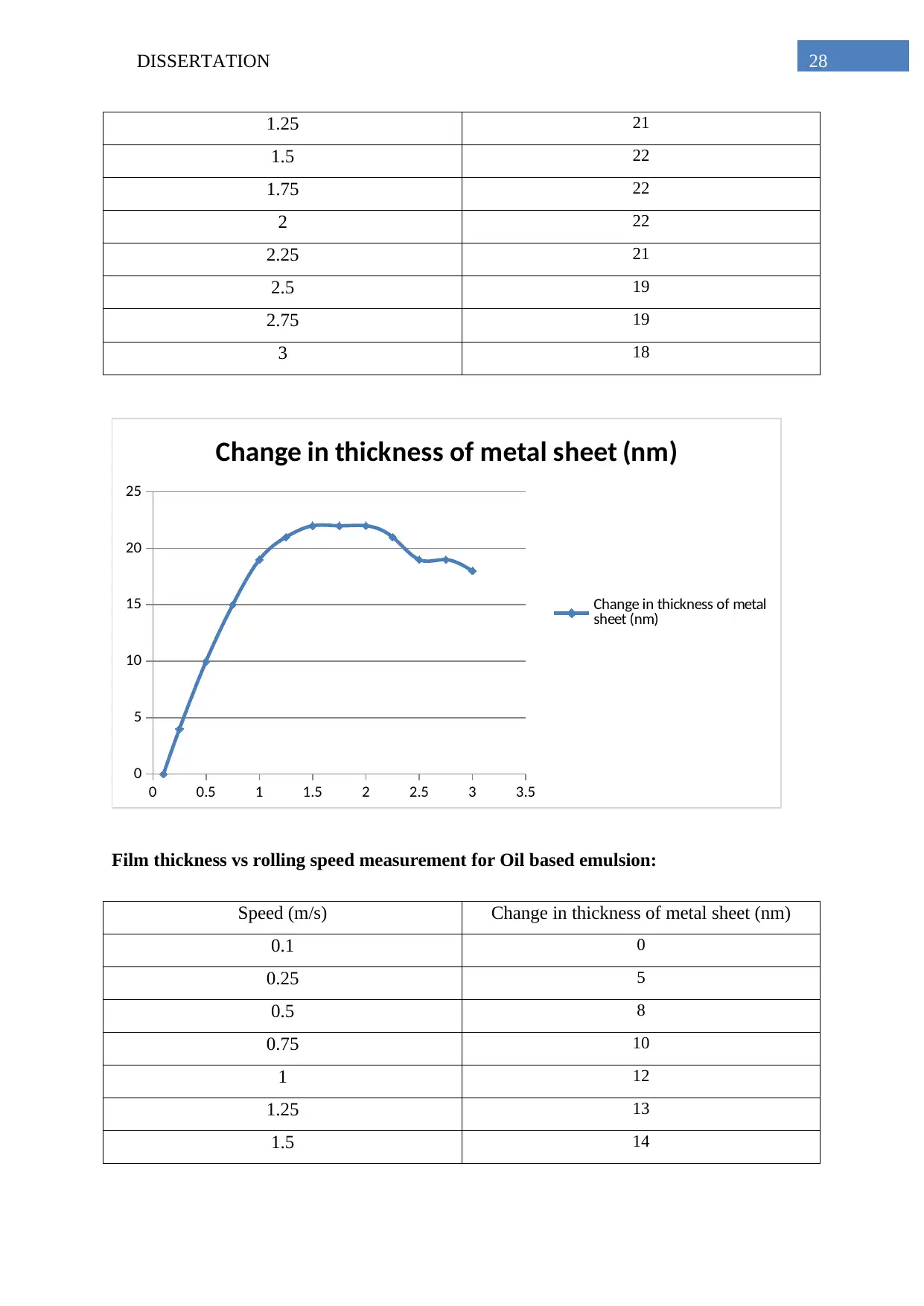
28DISSERTATION
1.25 21
1.5 22
1.75 22
2 22
2.25 21
2.5 19
2.75 19
3 18
0 0.5 1 1.5 2 2.5 3 3.5
0
5
10
15
20
25
Change in thickness of metal sheet (nm)
Change in thickness of metal
sheet (nm)
Film thickness vs rolling speed measurement for Oil based emulsion:
Speed (m/s) Change in thickness of metal sheet (nm)
0.1 0
0.25 5
0.5 8
0.75 10
1 12
1.25 13
1.5 14
1.25 21
1.5 22
1.75 22
2 22
2.25 21
2.5 19
2.75 19
3 18
0 0.5 1 1.5 2 2.5 3 3.5
0
5
10
15
20
25
Change in thickness of metal sheet (nm)
Change in thickness of metal
sheet (nm)
Film thickness vs rolling speed measurement for Oil based emulsion:
Speed (m/s) Change in thickness of metal sheet (nm)
0.1 0
0.25 5
0.5 8
0.75 10
1 12
1.25 13
1.5 14
Secure Best Marks with AI Grader
Need help grading? Try our AI Grader for instant feedback on your assignments.
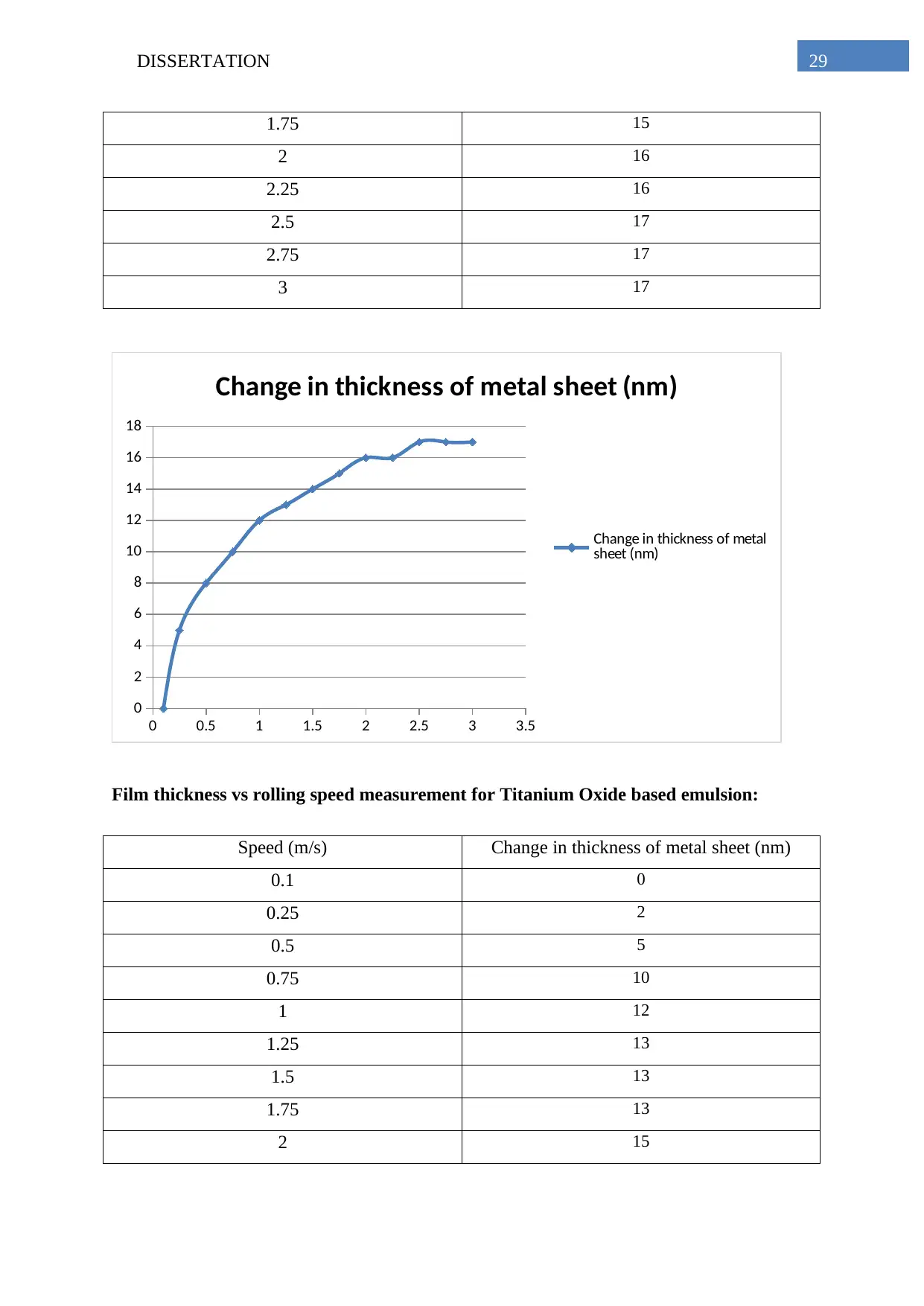
29DISSERTATION
1.75 15
2 16
2.25 16
2.5 17
2.75 17
3 17
0 0.5 1 1.5 2 2.5 3 3.5
0
2
4
6
8
10
12
14
16
18
Change in thickness of metal sheet (nm)
Change in thickness of metal
sheet (nm)
Film thickness vs rolling speed measurement for Titanium Oxide based emulsion:
Speed (m/s) Change in thickness of metal sheet (nm)
0.1 0
0.25 2
0.5 5
0.75 10
1 12
1.25 13
1.5 13
1.75 13
2 15
1.75 15
2 16
2.25 16
2.5 17
2.75 17
3 17
0 0.5 1 1.5 2 2.5 3 3.5
0
2
4
6
8
10
12
14
16
18
Change in thickness of metal sheet (nm)
Change in thickness of metal
sheet (nm)
Film thickness vs rolling speed measurement for Titanium Oxide based emulsion:
Speed (m/s) Change in thickness of metal sheet (nm)
0.1 0
0.25 2
0.5 5
0.75 10
1 12
1.25 13
1.5 13
1.75 13
2 15
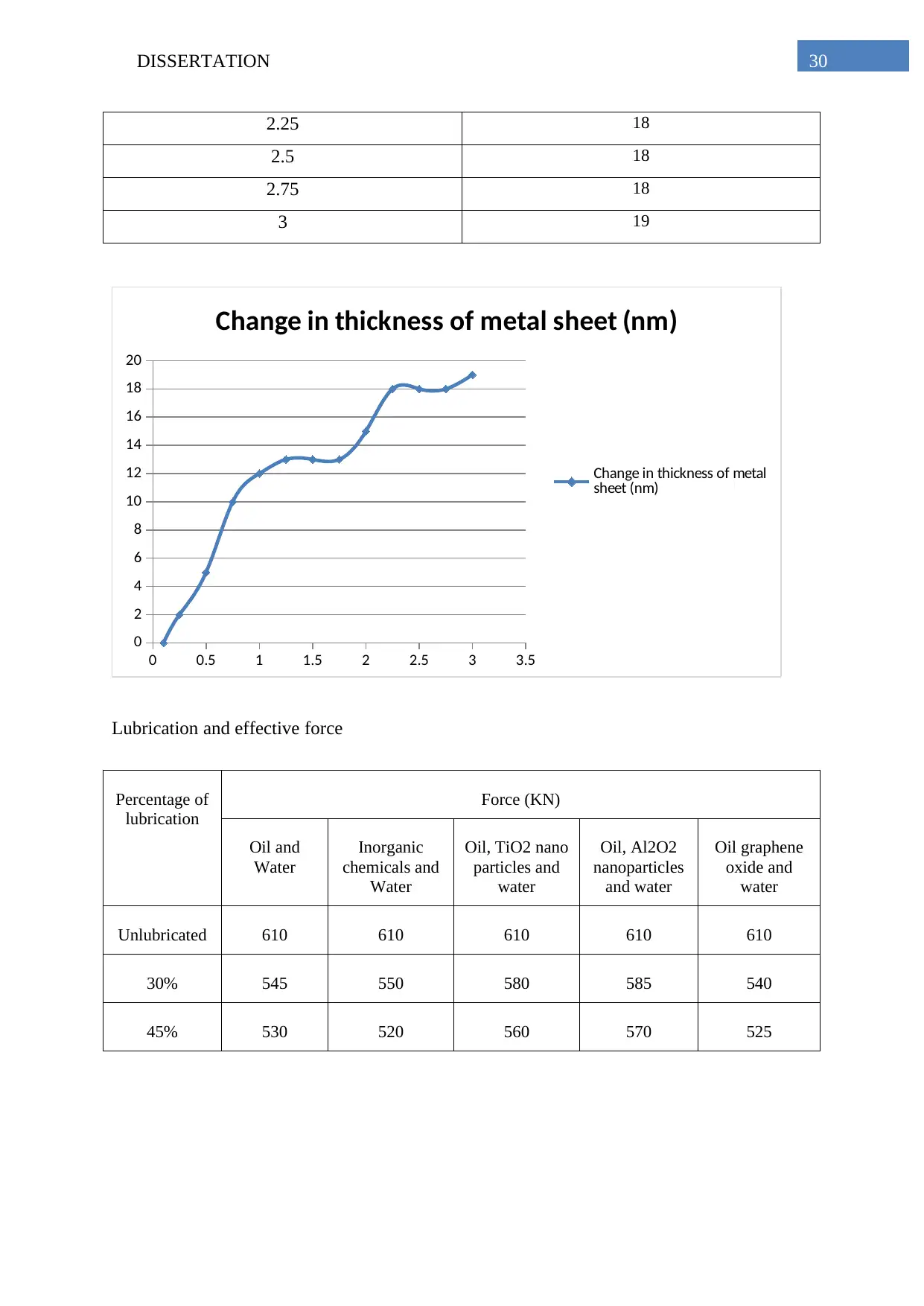
30DISSERTATION
2.25 18
2.5 18
2.75 18
3 19
0 0.5 1 1.5 2 2.5 3 3.5
0
2
4
6
8
10
12
14
16
18
20
Change in thickness of metal sheet (nm)
Change in thickness of metal
sheet (nm)
Lubrication and effective force
Percentage of
lubrication
Force (KN)
Oil and
Water
Inorganic
chemicals and
Water
Oil, TiO2 nano
particles and
water
Oil, Al2O2
nanoparticles
and water
Oil graphene
oxide and
water
Unlubricated 610 610 610 610 610
30% 545 550 580 585 540
45% 530 520 560 570 525
2.25 18
2.5 18
2.75 18
3 19
0 0.5 1 1.5 2 2.5 3 3.5
0
2
4
6
8
10
12
14
16
18
20
Change in thickness of metal sheet (nm)
Change in thickness of metal
sheet (nm)
Lubrication and effective force
Percentage of
lubrication
Force (KN)
Oil and
Water
Inorganic
chemicals and
Water
Oil, TiO2 nano
particles and
water
Oil, Al2O2
nanoparticles
and water
Oil graphene
oxide and
water
Unlubricated 610 610 610 610 610
30% 545 550 580 585 540
45% 530 520 560 570 525
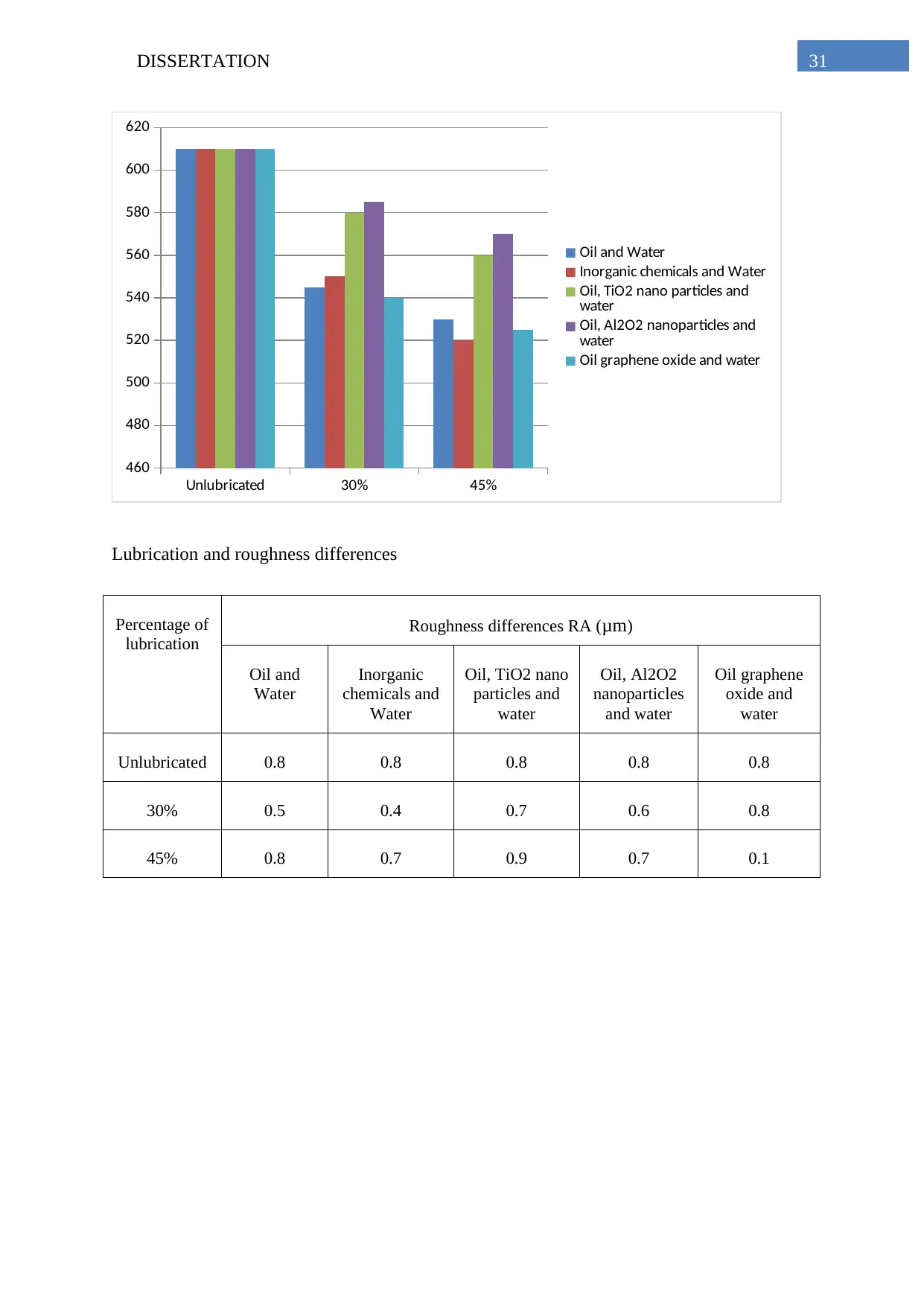
31DISSERTATION
Unlubricated 30% 45%
460
480
500
520
540
560
580
600
620
Oil and Water
Inorganic chemicals and Water
Oil, TiO2 nano particles and
water
Oil, Al2O2 nanoparticles and
water
Oil graphene oxide and water
Lubrication and roughness differences
Percentage of
lubrication
Roughness differences RA (μm)
Oil and
Water
Inorganic
chemicals and
Water
Oil, TiO2 nano
particles and
water
Oil, Al2O2
nanoparticles
and water
Oil graphene
oxide and
water
Unlubricated 0.8 0.8 0.8 0.8 0.8
30% 0.5 0.4 0.7 0.6 0.8
45% 0.8 0.7 0.9 0.7 0.1
Unlubricated 30% 45%
460
480
500
520
540
560
580
600
620
Oil and Water
Inorganic chemicals and Water
Oil, TiO2 nano particles and
water
Oil, Al2O2 nanoparticles and
water
Oil graphene oxide and water
Lubrication and roughness differences
Percentage of
lubrication
Roughness differences RA (μm)
Oil and
Water
Inorganic
chemicals and
Water
Oil, TiO2 nano
particles and
water
Oil, Al2O2
nanoparticles
and water
Oil graphene
oxide and
water
Unlubricated 0.8 0.8 0.8 0.8 0.8
30% 0.5 0.4 0.7 0.6 0.8
45% 0.8 0.7 0.9 0.7 0.1
Paraphrase This Document
Need a fresh take? Get an instant paraphrase of this document with our AI Paraphraser
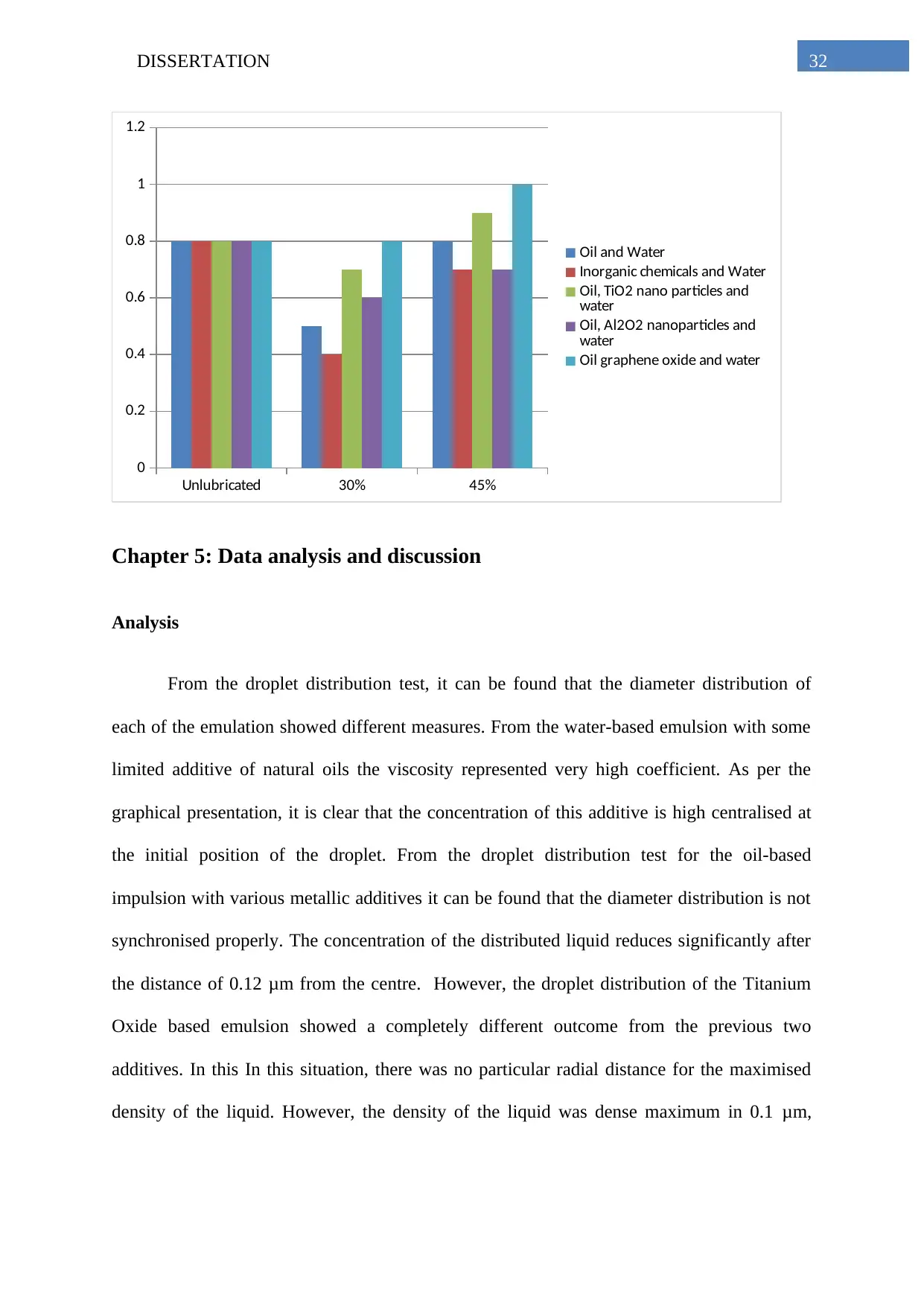
32DISSERTATION
Unlubricated 30% 45%
0
0.2
0.4
0.6
0.8
1
1.2
Oil and Water
Inorganic chemicals and Water
Oil, TiO2 nano particles and
water
Oil, Al2O2 nanoparticles and
water
Oil graphene oxide and water
Chapter 5: Data analysis and discussion
Analysis
From the droplet distribution test, it can be found that the diameter distribution of
each of the emulation showed different measures. From the water-based emulsion with some
limited additive of natural oils the viscosity represented very high coefficient. As per the
graphical presentation, it is clear that the concentration of this additive is high centralised at
the initial position of the droplet. From the droplet distribution test for the oil-based
impulsion with various metallic additives it can be found that the diameter distribution is not
synchronised properly. The concentration of the distributed liquid reduces significantly after
the distance of 0.12 μm from the centre. However, the droplet distribution of the Titanium
Oxide based emulsion showed a completely different outcome from the previous two
additives. In this In this situation, there was no particular radial distance for the maximised
density of the liquid. However, the density of the liquid was dense maximum in 0.1 μm,
Unlubricated 30% 45%
0
0.2
0.4
0.6
0.8
1
1.2
Oil and Water
Inorganic chemicals and Water
Oil, TiO2 nano particles and
water
Oil, Al2O2 nanoparticles and
water
Oil graphene oxide and water
Chapter 5: Data analysis and discussion
Analysis
From the droplet distribution test, it can be found that the diameter distribution of
each of the emulation showed different measures. From the water-based emulsion with some
limited additive of natural oils the viscosity represented very high coefficient. As per the
graphical presentation, it is clear that the concentration of this additive is high centralised at
the initial position of the droplet. From the droplet distribution test for the oil-based
impulsion with various metallic additives it can be found that the diameter distribution is not
synchronised properly. The concentration of the distributed liquid reduces significantly after
the distance of 0.12 μm from the centre. However, the droplet distribution of the Titanium
Oxide based emulsion showed a completely different outcome from the previous two
additives. In this In this situation, there was no particular radial distance for the maximised
density of the liquid. However, the density of the liquid was dense maximum in 0.1 μm,
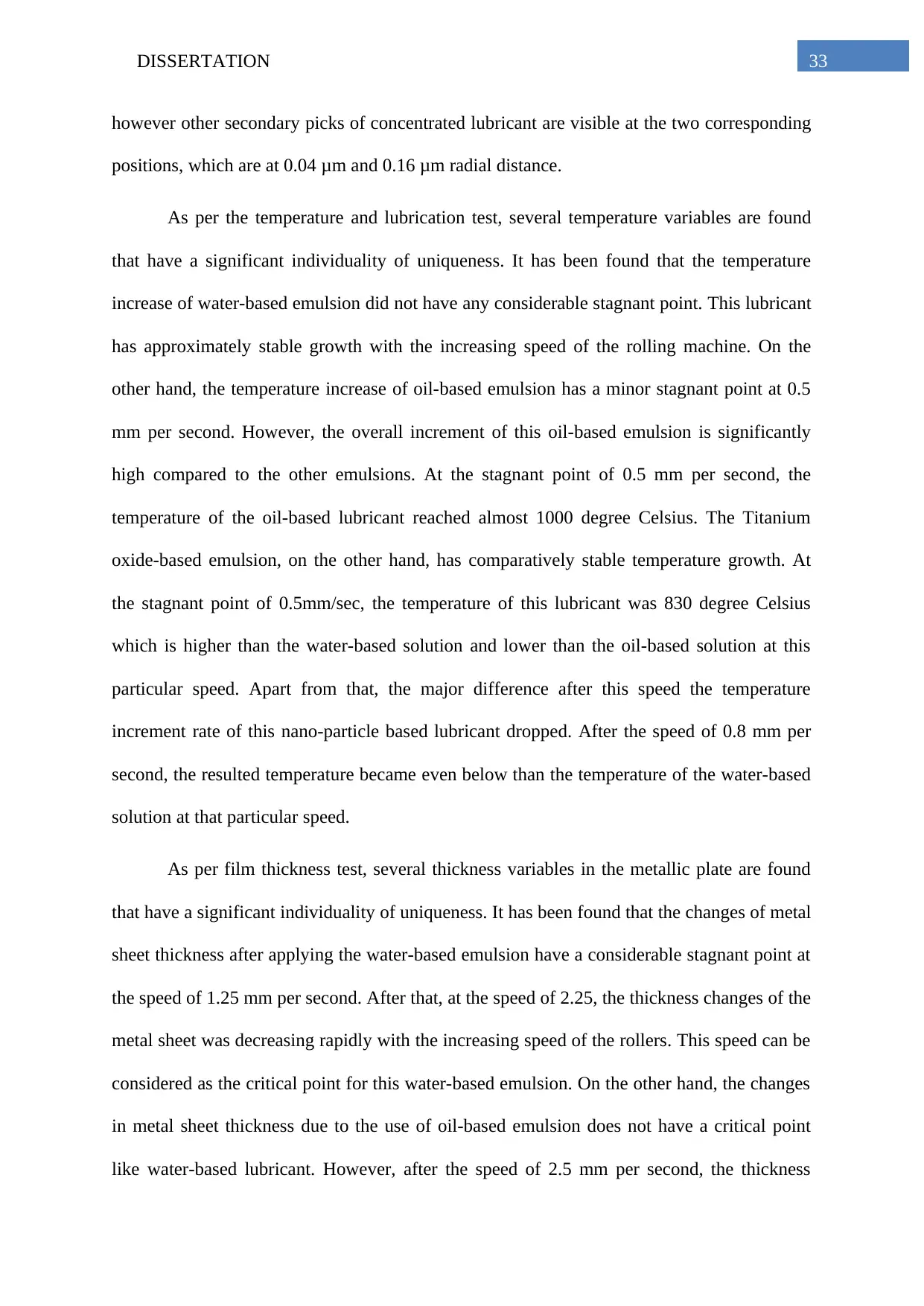
33DISSERTATION
however other secondary picks of concentrated lubricant are visible at the two corresponding
positions, which are at 0.04 μm and 0.16 μm radial distance.
As per the temperature and lubrication test, several temperature variables are found
that have a significant individuality of uniqueness. It has been found that the temperature
increase of water-based emulsion did not have any considerable stagnant point. This lubricant
has approximately stable growth with the increasing speed of the rolling machine. On the
other hand, the temperature increase of oil-based emulsion has a minor stagnant point at 0.5
mm per second. However, the overall increment of this oil-based emulsion is significantly
high compared to the other emulsions. At the stagnant point of 0.5 mm per second, the
temperature of the oil-based lubricant reached almost 1000 degree Celsius. The Titanium
oxide-based emulsion, on the other hand, has comparatively stable temperature growth. At
the stagnant point of 0.5mm/sec, the temperature of this lubricant was 830 degree Celsius
which is higher than the water-based solution and lower than the oil-based solution at this
particular speed. Apart from that, the major difference after this speed the temperature
increment rate of this nano-particle based lubricant dropped. After the speed of 0.8 mm per
second, the resulted temperature became even below than the temperature of the water-based
solution at that particular speed.
As per film thickness test, several thickness variables in the metallic plate are found
that have a significant individuality of uniqueness. It has been found that the changes of metal
sheet thickness after applying the water-based emulsion have a considerable stagnant point at
the speed of 1.25 mm per second. After that, at the speed of 2.25, the thickness changes of the
metal sheet was decreasing rapidly with the increasing speed of the rollers. This speed can be
considered as the critical point for this water-based emulsion. On the other hand, the changes
in metal sheet thickness due to the use of oil-based emulsion does not have a critical point
like water-based lubricant. However, after the speed of 2.5 mm per second, the thickness
however other secondary picks of concentrated lubricant are visible at the two corresponding
positions, which are at 0.04 μm and 0.16 μm radial distance.
As per the temperature and lubrication test, several temperature variables are found
that have a significant individuality of uniqueness. It has been found that the temperature
increase of water-based emulsion did not have any considerable stagnant point. This lubricant
has approximately stable growth with the increasing speed of the rolling machine. On the
other hand, the temperature increase of oil-based emulsion has a minor stagnant point at 0.5
mm per second. However, the overall increment of this oil-based emulsion is significantly
high compared to the other emulsions. At the stagnant point of 0.5 mm per second, the
temperature of the oil-based lubricant reached almost 1000 degree Celsius. The Titanium
oxide-based emulsion, on the other hand, has comparatively stable temperature growth. At
the stagnant point of 0.5mm/sec, the temperature of this lubricant was 830 degree Celsius
which is higher than the water-based solution and lower than the oil-based solution at this
particular speed. Apart from that, the major difference after this speed the temperature
increment rate of this nano-particle based lubricant dropped. After the speed of 0.8 mm per
second, the resulted temperature became even below than the temperature of the water-based
solution at that particular speed.
As per film thickness test, several thickness variables in the metallic plate are found
that have a significant individuality of uniqueness. It has been found that the changes of metal
sheet thickness after applying the water-based emulsion have a considerable stagnant point at
the speed of 1.25 mm per second. After that, at the speed of 2.25, the thickness changes of the
metal sheet was decreasing rapidly with the increasing speed of the rollers. This speed can be
considered as the critical point for this water-based emulsion. On the other hand, the changes
in metal sheet thickness due to the use of oil-based emulsion does not have a critical point
like water-based lubricant. However, after the speed of 2.5 mm per second, the thickness

34DISSERTATION
changes of the metal sheet became apparently constant. The Titanium oxide-based emulsion,
on the other hand, has comparatively unstable changes of the metal sheet thickness. For this
nano-particle based lubricant, there were multiple stagnant points where the thickness
changes showed a constant value temporarily. However, there was no permanent stagnant
point as per the graphical expression. The major difference for this lubricant is, in this case,
the resultant changes of metal sheet thickness is continuously increasing even at the speed of
3mm per second.
As per rolling force test and the roughness difference test, several variables of the
resultant pressure measurement and the metallic plate roughness were found that have a
significant individuality of uniqueness. In this situation, the research should prioritise both
the roughness of the output metal sheet and the resultant force. In order to do the following
comparison table and graphical presentation has been made for more in-depth analysis an
comparison.
Lubrication comparison table
UNLUBRICATED 30% LUBRICATION 45% LUBRICATION
SAMPLES Rolling
Force
(KN)
Roughness
Difference
s (μm)
Rolling
Force
(KN)
Roughness
Difference
s (μm)
Rolling
Force
(KN)
Roughness
Differences
(μm)
Oil and
Water
610 0.8 545 0.5 530 0.8
Inorganic
chemicals
and Water
610 0.8 550 0.4 520 0.7
Oil, TiO2
nano
particles and
water
610 0.8 580 0.7 560 0.9
Oil, Al2O2
nanoparticles
and water
610 0.8 585 0.6 570 0.7
changes of the metal sheet became apparently constant. The Titanium oxide-based emulsion,
on the other hand, has comparatively unstable changes of the metal sheet thickness. For this
nano-particle based lubricant, there were multiple stagnant points where the thickness
changes showed a constant value temporarily. However, there was no permanent stagnant
point as per the graphical expression. The major difference for this lubricant is, in this case,
the resultant changes of metal sheet thickness is continuously increasing even at the speed of
3mm per second.
As per rolling force test and the roughness difference test, several variables of the
resultant pressure measurement and the metallic plate roughness were found that have a
significant individuality of uniqueness. In this situation, the research should prioritise both
the roughness of the output metal sheet and the resultant force. In order to do the following
comparison table and graphical presentation has been made for more in-depth analysis an
comparison.
Lubrication comparison table
UNLUBRICATED 30% LUBRICATION 45% LUBRICATION
SAMPLES Rolling
Force
(KN)
Roughness
Difference
s (μm)
Rolling
Force
(KN)
Roughness
Difference
s (μm)
Rolling
Force
(KN)
Roughness
Differences
(μm)
Oil and
Water
610 0.8 545 0.5 530 0.8
Inorganic
chemicals
and Water
610 0.8 550 0.4 520 0.7
Oil, TiO2
nano
particles and
water
610 0.8 580 0.7 560 0.9
Oil, Al2O2
nanoparticles
and water
610 0.8 585 0.6 570 0.7
Secure Best Marks with AI Grader
Need help grading? Try our AI Grader for instant feedback on your assignments.
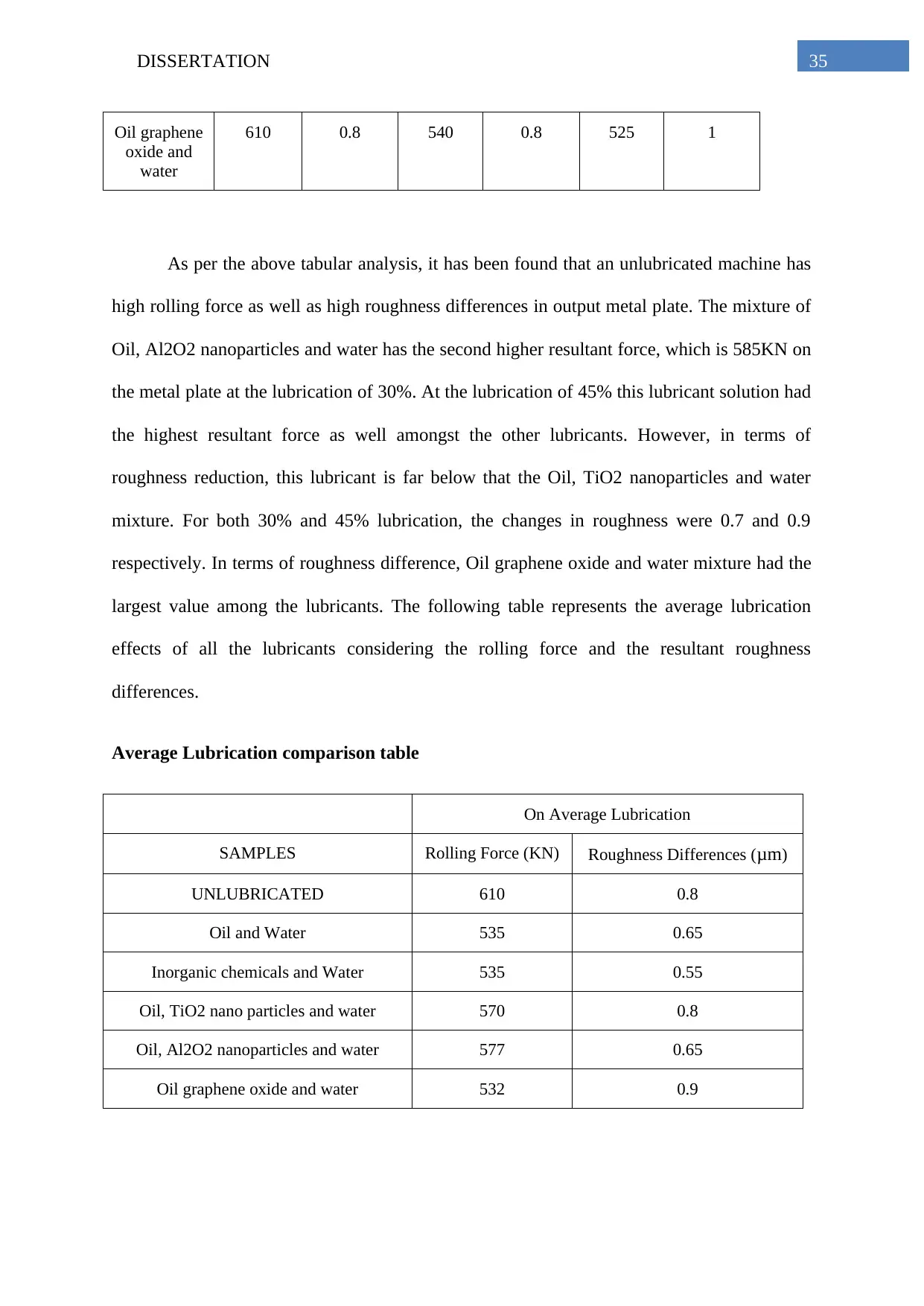
35DISSERTATION
Oil graphene
oxide and
water
610 0.8 540 0.8 525 1
As per the above tabular analysis, it has been found that an unlubricated machine has
high rolling force as well as high roughness differences in output metal plate. The mixture of
Oil, Al2O2 nanoparticles and water has the second higher resultant force, which is 585KN on
the metal plate at the lubrication of 30%. At the lubrication of 45% this lubricant solution had
the highest resultant force as well amongst the other lubricants. However, in terms of
roughness reduction, this lubricant is far below that the Oil, TiO2 nanoparticles and water
mixture. For both 30% and 45% lubrication, the changes in roughness were 0.7 and 0.9
respectively. In terms of roughness difference, Oil graphene oxide and water mixture had the
largest value among the lubricants. The following table represents the average lubrication
effects of all the lubricants considering the rolling force and the resultant roughness
differences.
Average Lubrication comparison table
On Average Lubrication
SAMPLES Rolling Force (KN) Roughness Differences (μm)
UNLUBRICATED 610 0.8
Oil and Water 535 0.65
Inorganic chemicals and Water 535 0.55
Oil, TiO2 nano particles and water 570 0.8
Oil, Al2O2 nanoparticles and water 577 0.65
Oil graphene oxide and water 532 0.9
Oil graphene
oxide and
water
610 0.8 540 0.8 525 1
As per the above tabular analysis, it has been found that an unlubricated machine has
high rolling force as well as high roughness differences in output metal plate. The mixture of
Oil, Al2O2 nanoparticles and water has the second higher resultant force, which is 585KN on
the metal plate at the lubrication of 30%. At the lubrication of 45% this lubricant solution had
the highest resultant force as well amongst the other lubricants. However, in terms of
roughness reduction, this lubricant is far below that the Oil, TiO2 nanoparticles and water
mixture. For both 30% and 45% lubrication, the changes in roughness were 0.7 and 0.9
respectively. In terms of roughness difference, Oil graphene oxide and water mixture had the
largest value among the lubricants. The following table represents the average lubrication
effects of all the lubricants considering the rolling force and the resultant roughness
differences.
Average Lubrication comparison table
On Average Lubrication
SAMPLES Rolling Force (KN) Roughness Differences (μm)
UNLUBRICATED 610 0.8
Oil and Water 535 0.65
Inorganic chemicals and Water 535 0.55
Oil, TiO2 nano particles and water 570 0.8
Oil, Al2O2 nanoparticles and water 577 0.65
Oil graphene oxide and water 532 0.9
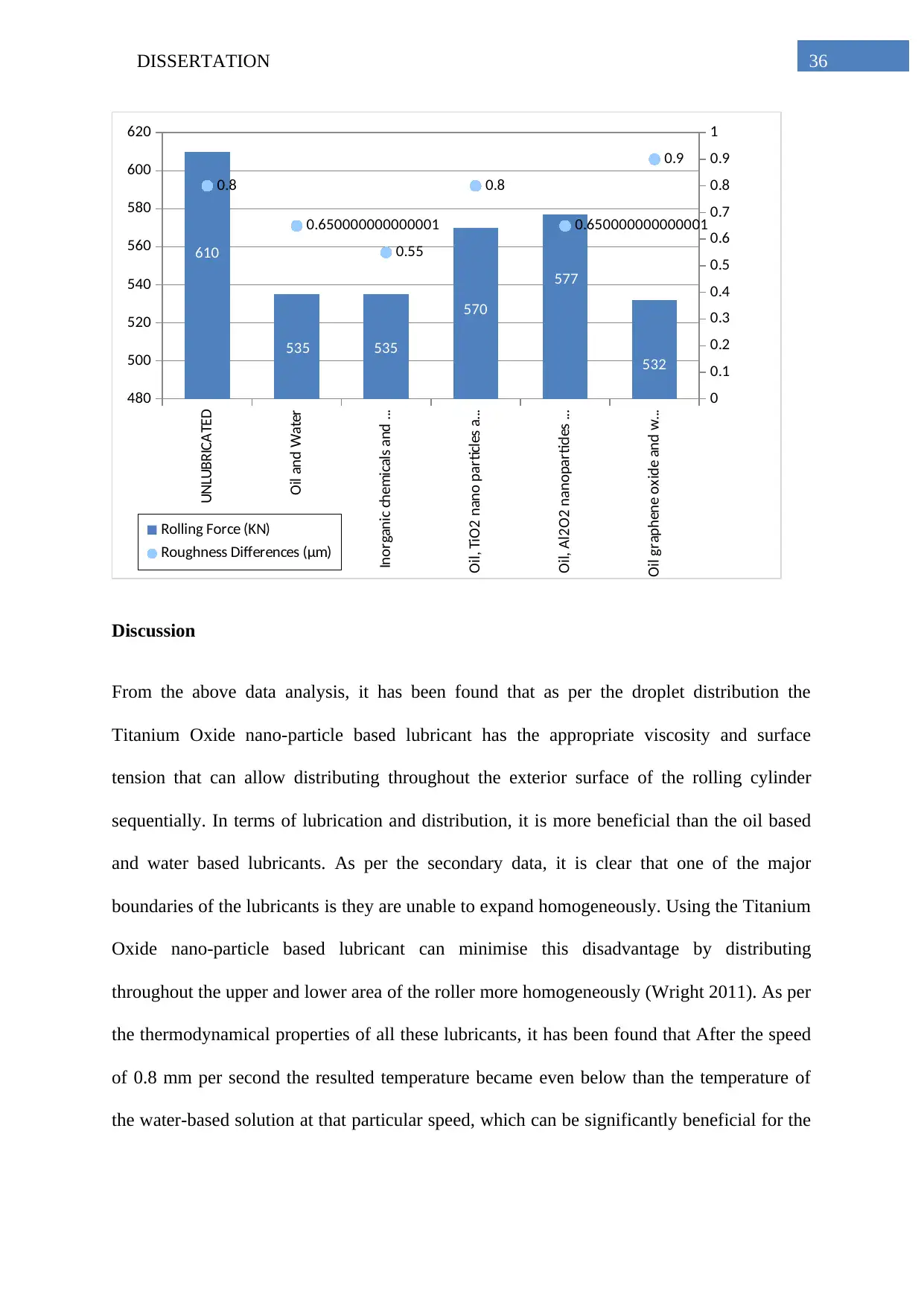
36DISSERTATION
UNLUBRICATED
Oil and Water
Inorganic chemicals and ...
Oil, TiO2 nano particles a...
Oil, Al2O2 nanoparticles ...
Oil graphene oxide and w...480
500
520
540
560
580
600
620
0
0.1
0.2
0.3
0.4
0.5
0.6
0.7
0.8
0.9
1
610
535 535
570
577
532
0.8
0.650000000000001
0.55
0.8
0.650000000000001
0.9
Rolling Force (KN)
Roughness Differences (μm)
Discussion
From the above data analysis, it has been found that as per the droplet distribution the
Titanium Oxide nano-particle based lubricant has the appropriate viscosity and surface
tension that can allow distributing throughout the exterior surface of the rolling cylinder
sequentially. In terms of lubrication and distribution, it is more beneficial than the oil based
and water based lubricants. As per the secondary data, it is clear that one of the major
boundaries of the lubricants is they are unable to expand homogeneously. Using the Titanium
Oxide nano-particle based lubricant can minimise this disadvantage by distributing
throughout the upper and lower area of the roller more homogeneously (Wright 2011). As per
the thermodynamical properties of all these lubricants, it has been found that After the speed
of 0.8 mm per second the resulted temperature became even below than the temperature of
the water-based solution at that particular speed, which can be significantly beneficial for the
UNLUBRICATED
Oil and Water
Inorganic chemicals and ...
Oil, TiO2 nano particles a...
Oil, Al2O2 nanoparticles ...
Oil graphene oxide and w...480
500
520
540
560
580
600
620
0
0.1
0.2
0.3
0.4
0.5
0.6
0.7
0.8
0.9
1
610
535 535
570
577
532
0.8
0.650000000000001
0.55
0.8
0.650000000000001
0.9
Rolling Force (KN)
Roughness Differences (μm)
Discussion
From the above data analysis, it has been found that as per the droplet distribution the
Titanium Oxide nano-particle based lubricant has the appropriate viscosity and surface
tension that can allow distributing throughout the exterior surface of the rolling cylinder
sequentially. In terms of lubrication and distribution, it is more beneficial than the oil based
and water based lubricants. As per the secondary data, it is clear that one of the major
boundaries of the lubricants is they are unable to expand homogeneously. Using the Titanium
Oxide nano-particle based lubricant can minimise this disadvantage by distributing
throughout the upper and lower area of the roller more homogeneously (Wright 2011). As per
the thermodynamical properties of all these lubricants, it has been found that After the speed
of 0.8 mm per second the resulted temperature became even below than the temperature of
the water-based solution at that particular speed, which can be significantly beneficial for the
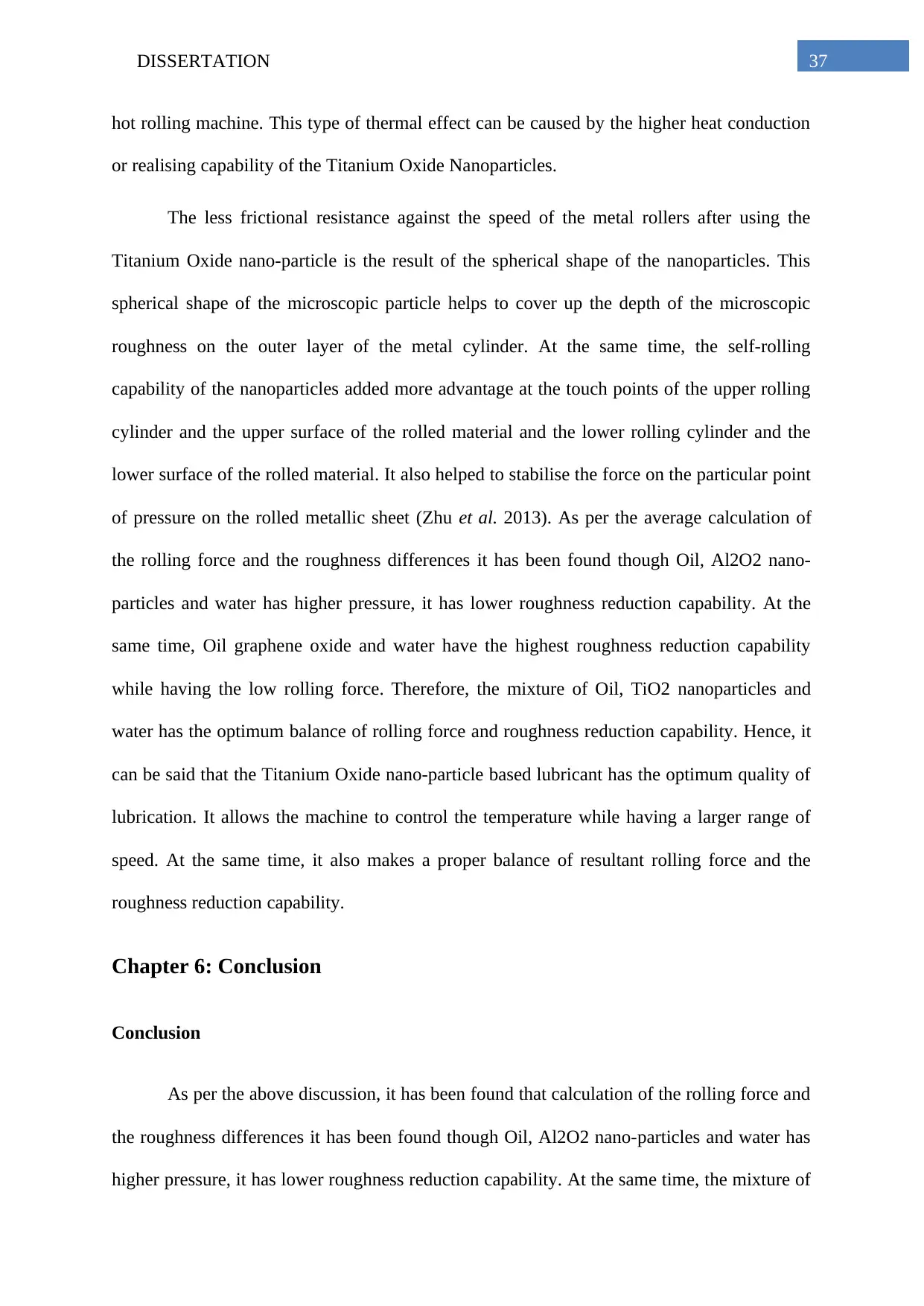
37DISSERTATION
hot rolling machine. This type of thermal effect can be caused by the higher heat conduction
or realising capability of the Titanium Oxide Nanoparticles.
The less frictional resistance against the speed of the metal rollers after using the
Titanium Oxide nano-particle is the result of the spherical shape of the nanoparticles. This
spherical shape of the microscopic particle helps to cover up the depth of the microscopic
roughness on the outer layer of the metal cylinder. At the same time, the self-rolling
capability of the nanoparticles added more advantage at the touch points of the upper rolling
cylinder and the upper surface of the rolled material and the lower rolling cylinder and the
lower surface of the rolled material. It also helped to stabilise the force on the particular point
of pressure on the rolled metallic sheet (Zhu et al. 2013). As per the average calculation of
the rolling force and the roughness differences it has been found though Oil, Al2O2 nano-
particles and water has higher pressure, it has lower roughness reduction capability. At the
same time, Oil graphene oxide and water have the highest roughness reduction capability
while having the low rolling force. Therefore, the mixture of Oil, TiO2 nanoparticles and
water has the optimum balance of rolling force and roughness reduction capability. Hence, it
can be said that the Titanium Oxide nano-particle based lubricant has the optimum quality of
lubrication. It allows the machine to control the temperature while having a larger range of
speed. At the same time, it also makes a proper balance of resultant rolling force and the
roughness reduction capability.
Chapter 6: Conclusion
Conclusion
As per the above discussion, it has been found that calculation of the rolling force and
the roughness differences it has been found though Oil, Al2O2 nano-particles and water has
higher pressure, it has lower roughness reduction capability. At the same time, the mixture of
hot rolling machine. This type of thermal effect can be caused by the higher heat conduction
or realising capability of the Titanium Oxide Nanoparticles.
The less frictional resistance against the speed of the metal rollers after using the
Titanium Oxide nano-particle is the result of the spherical shape of the nanoparticles. This
spherical shape of the microscopic particle helps to cover up the depth of the microscopic
roughness on the outer layer of the metal cylinder. At the same time, the self-rolling
capability of the nanoparticles added more advantage at the touch points of the upper rolling
cylinder and the upper surface of the rolled material and the lower rolling cylinder and the
lower surface of the rolled material. It also helped to stabilise the force on the particular point
of pressure on the rolled metallic sheet (Zhu et al. 2013). As per the average calculation of
the rolling force and the roughness differences it has been found though Oil, Al2O2 nano-
particles and water has higher pressure, it has lower roughness reduction capability. At the
same time, Oil graphene oxide and water have the highest roughness reduction capability
while having the low rolling force. Therefore, the mixture of Oil, TiO2 nanoparticles and
water has the optimum balance of rolling force and roughness reduction capability. Hence, it
can be said that the Titanium Oxide nano-particle based lubricant has the optimum quality of
lubrication. It allows the machine to control the temperature while having a larger range of
speed. At the same time, it also makes a proper balance of resultant rolling force and the
roughness reduction capability.
Chapter 6: Conclusion
Conclusion
As per the above discussion, it has been found that calculation of the rolling force and
the roughness differences it has been found though Oil, Al2O2 nano-particles and water has
higher pressure, it has lower roughness reduction capability. At the same time, the mixture of
Paraphrase This Document
Need a fresh take? Get an instant paraphrase of this document with our AI Paraphraser
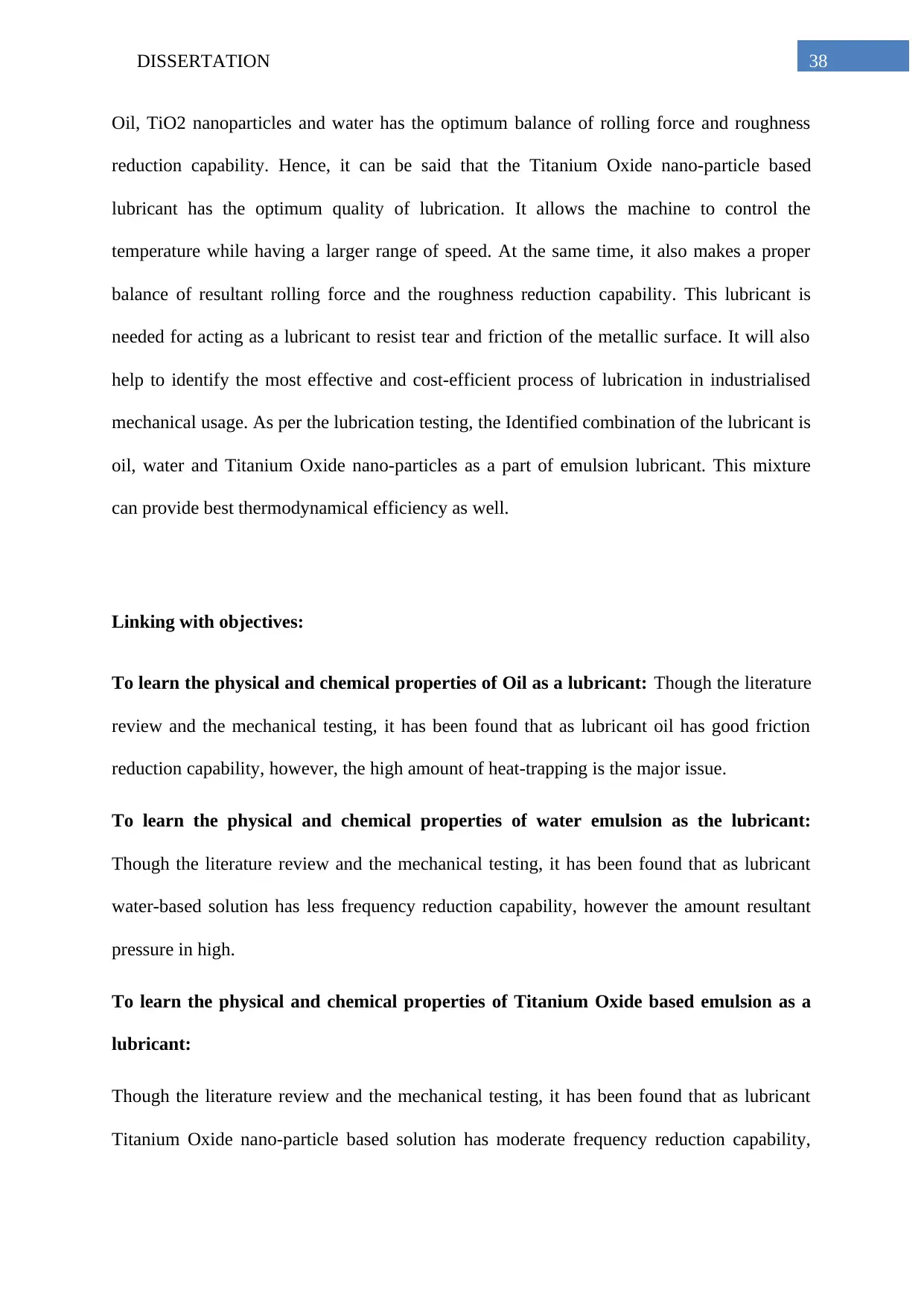
38DISSERTATION
Oil, TiO2 nanoparticles and water has the optimum balance of rolling force and roughness
reduction capability. Hence, it can be said that the Titanium Oxide nano-particle based
lubricant has the optimum quality of lubrication. It allows the machine to control the
temperature while having a larger range of speed. At the same time, it also makes a proper
balance of resultant rolling force and the roughness reduction capability. This lubricant is
needed for acting as a lubricant to resist tear and friction of the metallic surface. It will also
help to identify the most effective and cost-efficient process of lubrication in industrialised
mechanical usage. As per the lubrication testing, the Identified combination of the lubricant is
oil, water and Titanium Oxide nano-particles as a part of emulsion lubricant. This mixture
can provide best thermodynamical efficiency as well.
Linking with objectives:
To learn the physical and chemical properties of Oil as a lubricant: Though the literature
review and the mechanical testing, it has been found that as lubricant oil has good friction
reduction capability, however, the high amount of heat-trapping is the major issue.
To learn the physical and chemical properties of water emulsion as the lubricant:
Though the literature review and the mechanical testing, it has been found that as lubricant
water-based solution has less frequency reduction capability, however the amount resultant
pressure in high.
To learn the physical and chemical properties of Titanium Oxide based emulsion as a
lubricant:
Though the literature review and the mechanical testing, it has been found that as lubricant
Titanium Oxide nano-particle based solution has moderate frequency reduction capability,
Oil, TiO2 nanoparticles and water has the optimum balance of rolling force and roughness
reduction capability. Hence, it can be said that the Titanium Oxide nano-particle based
lubricant has the optimum quality of lubrication. It allows the machine to control the
temperature while having a larger range of speed. At the same time, it also makes a proper
balance of resultant rolling force and the roughness reduction capability. This lubricant is
needed for acting as a lubricant to resist tear and friction of the metallic surface. It will also
help to identify the most effective and cost-efficient process of lubrication in industrialised
mechanical usage. As per the lubrication testing, the Identified combination of the lubricant is
oil, water and Titanium Oxide nano-particles as a part of emulsion lubricant. This mixture
can provide best thermodynamical efficiency as well.
Linking with objectives:
To learn the physical and chemical properties of Oil as a lubricant: Though the literature
review and the mechanical testing, it has been found that as lubricant oil has good friction
reduction capability, however, the high amount of heat-trapping is the major issue.
To learn the physical and chemical properties of water emulsion as the lubricant:
Though the literature review and the mechanical testing, it has been found that as lubricant
water-based solution has less frequency reduction capability, however the amount resultant
pressure in high.
To learn the physical and chemical properties of Titanium Oxide based emulsion as a
lubricant:
Though the literature review and the mechanical testing, it has been found that as lubricant
Titanium Oxide nano-particle based solution has moderate frequency reduction capability,
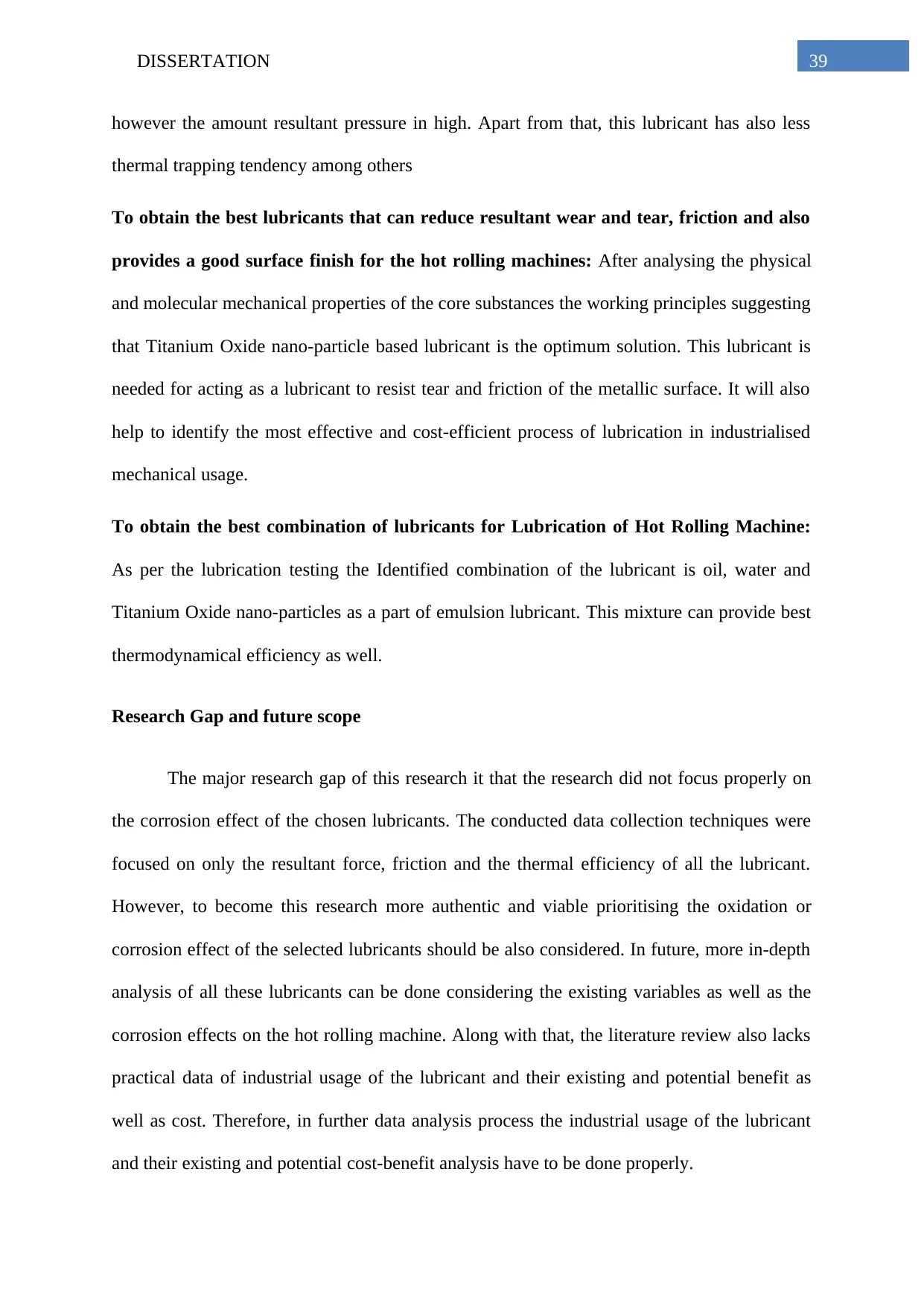
39DISSERTATION
however the amount resultant pressure in high. Apart from that, this lubricant has also less
thermal trapping tendency among others
To obtain the best lubricants that can reduce resultant wear and tear, friction and also
provides a good surface finish for the hot rolling machines: After analysing the physical
and molecular mechanical properties of the core substances the working principles suggesting
that Titanium Oxide nano-particle based lubricant is the optimum solution. This lubricant is
needed for acting as a lubricant to resist tear and friction of the metallic surface. It will also
help to identify the most effective and cost-efficient process of lubrication in industrialised
mechanical usage.
To obtain the best combination of lubricants for Lubrication of Hot Rolling Machine:
As per the lubrication testing the Identified combination of the lubricant is oil, water and
Titanium Oxide nano-particles as a part of emulsion lubricant. This mixture can provide best
thermodynamical efficiency as well.
Research Gap and future scope
The major research gap of this research it that the research did not focus properly on
the corrosion effect of the chosen lubricants. The conducted data collection techniques were
focused on only the resultant force, friction and the thermal efficiency of all the lubricant.
However, to become this research more authentic and viable prioritising the oxidation or
corrosion effect of the selected lubricants should be also considered. In future, more in-depth
analysis of all these lubricants can be done considering the existing variables as well as the
corrosion effects on the hot rolling machine. Along with that, the literature review also lacks
practical data of industrial usage of the lubricant and their existing and potential benefit as
well as cost. Therefore, in further data analysis process the industrial usage of the lubricant
and their existing and potential cost-benefit analysis have to be done properly.
however the amount resultant pressure in high. Apart from that, this lubricant has also less
thermal trapping tendency among others
To obtain the best lubricants that can reduce resultant wear and tear, friction and also
provides a good surface finish for the hot rolling machines: After analysing the physical
and molecular mechanical properties of the core substances the working principles suggesting
that Titanium Oxide nano-particle based lubricant is the optimum solution. This lubricant is
needed for acting as a lubricant to resist tear and friction of the metallic surface. It will also
help to identify the most effective and cost-efficient process of lubrication in industrialised
mechanical usage.
To obtain the best combination of lubricants for Lubrication of Hot Rolling Machine:
As per the lubrication testing the Identified combination of the lubricant is oil, water and
Titanium Oxide nano-particles as a part of emulsion lubricant. This mixture can provide best
thermodynamical efficiency as well.
Research Gap and future scope
The major research gap of this research it that the research did not focus properly on
the corrosion effect of the chosen lubricants. The conducted data collection techniques were
focused on only the resultant force, friction and the thermal efficiency of all the lubricant.
However, to become this research more authentic and viable prioritising the oxidation or
corrosion effect of the selected lubricants should be also considered. In future, more in-depth
analysis of all these lubricants can be done considering the existing variables as well as the
corrosion effects on the hot rolling machine. Along with that, the literature review also lacks
practical data of industrial usage of the lubricant and their existing and potential benefit as
well as cost. Therefore, in further data analysis process the industrial usage of the lubricant
and their existing and potential cost-benefit analysis have to be done properly.
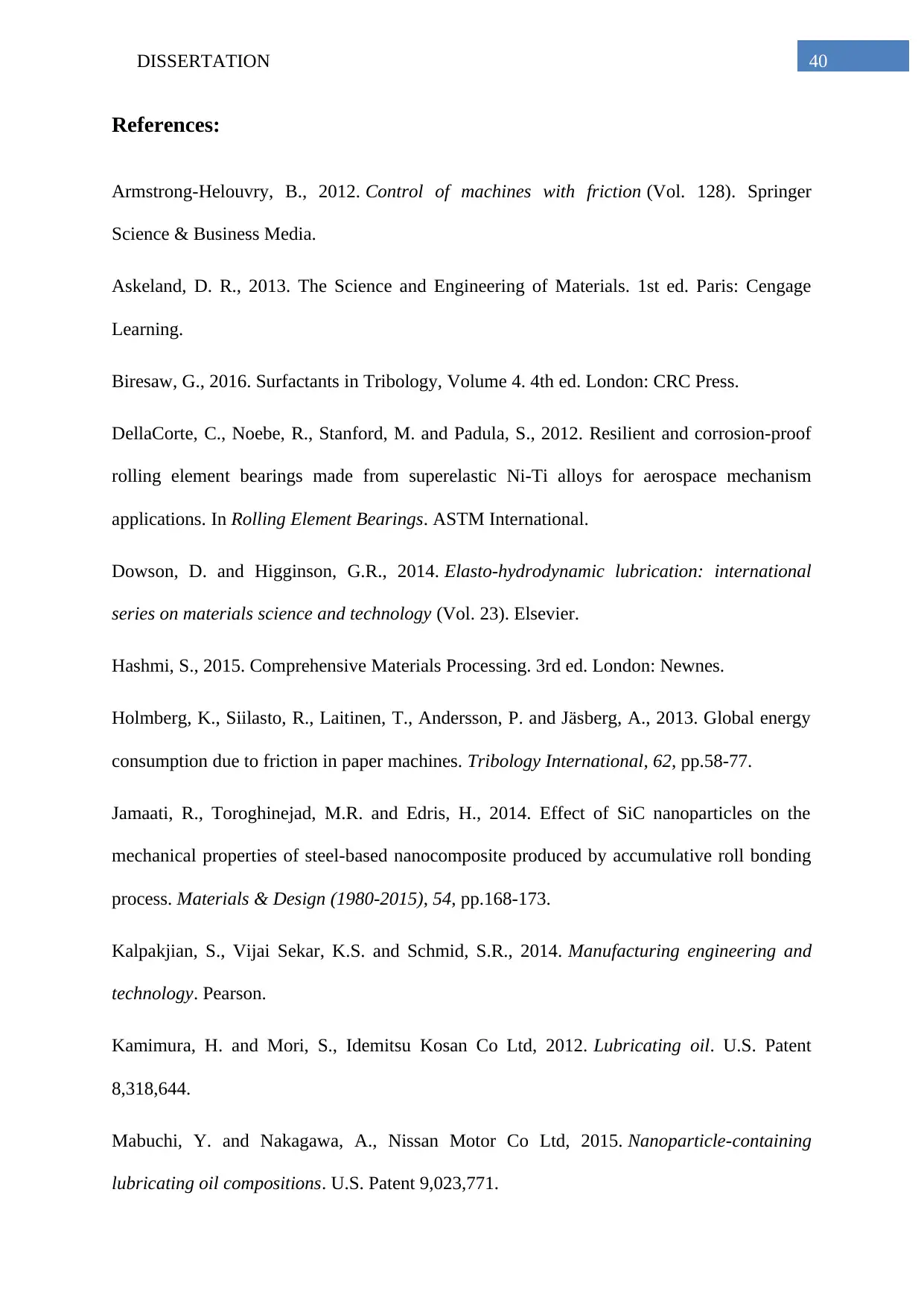
40DISSERTATION
References:
Armstrong-Helouvry, B., 2012. Control of machines with friction (Vol. 128). Springer
Science & Business Media.
Askeland, D. R., 2013. The Science and Engineering of Materials. 1st ed. Paris: Cengage
Learning.
Biresaw, G., 2016. Surfactants in Tribology, Volume 4. 4th ed. London: CRC Press.
DellaCorte, C., Noebe, R., Stanford, M. and Padula, S., 2012. Resilient and corrosion-proof
rolling element bearings made from superelastic Ni-Ti alloys for aerospace mechanism
applications. In Rolling Element Bearings. ASTM International.
Dowson, D. and Higginson, G.R., 2014. Elasto-hydrodynamic lubrication: international
series on materials science and technology (Vol. 23). Elsevier.
Hashmi, S., 2015. Comprehensive Materials Processing. 3rd ed. London: Newnes.
Holmberg, K., Siilasto, R., Laitinen, T., Andersson, P. and Jäsberg, A., 2013. Global energy
consumption due to friction in paper machines. Tribology International, 62, pp.58-77.
Jamaati, R., Toroghinejad, M.R. and Edris, H., 2014. Effect of SiC nanoparticles on the
mechanical properties of steel-based nanocomposite produced by accumulative roll bonding
process. Materials & Design (1980-2015), 54, pp.168-173.
Kalpakjian, S., Vijai Sekar, K.S. and Schmid, S.R., 2014. Manufacturing engineering and
technology. Pearson.
Kamimura, H. and Mori, S., Idemitsu Kosan Co Ltd, 2012. Lubricating oil. U.S. Patent
8,318,644.
Mabuchi, Y. and Nakagawa, A., Nissan Motor Co Ltd, 2015. Nanoparticle-containing
lubricating oil compositions. U.S. Patent 9,023,771.
References:
Armstrong-Helouvry, B., 2012. Control of machines with friction (Vol. 128). Springer
Science & Business Media.
Askeland, D. R., 2013. The Science and Engineering of Materials. 1st ed. Paris: Cengage
Learning.
Biresaw, G., 2016. Surfactants in Tribology, Volume 4. 4th ed. London: CRC Press.
DellaCorte, C., Noebe, R., Stanford, M. and Padula, S., 2012. Resilient and corrosion-proof
rolling element bearings made from superelastic Ni-Ti alloys for aerospace mechanism
applications. In Rolling Element Bearings. ASTM International.
Dowson, D. and Higginson, G.R., 2014. Elasto-hydrodynamic lubrication: international
series on materials science and technology (Vol. 23). Elsevier.
Hashmi, S., 2015. Comprehensive Materials Processing. 3rd ed. London: Newnes.
Holmberg, K., Siilasto, R., Laitinen, T., Andersson, P. and Jäsberg, A., 2013. Global energy
consumption due to friction in paper machines. Tribology International, 62, pp.58-77.
Jamaati, R., Toroghinejad, M.R. and Edris, H., 2014. Effect of SiC nanoparticles on the
mechanical properties of steel-based nanocomposite produced by accumulative roll bonding
process. Materials & Design (1980-2015), 54, pp.168-173.
Kalpakjian, S., Vijai Sekar, K.S. and Schmid, S.R., 2014. Manufacturing engineering and
technology. Pearson.
Kamimura, H. and Mori, S., Idemitsu Kosan Co Ltd, 2012. Lubricating oil. U.S. Patent
8,318,644.
Mabuchi, Y. and Nakagawa, A., Nissan Motor Co Ltd, 2015. Nanoparticle-containing
lubricating oil compositions. U.S. Patent 9,023,771.
Secure Best Marks with AI Grader
Need help grading? Try our AI Grader for instant feedback on your assignments.

41DISSERTATION
Mang, T., 2014. Encyclopedia of Lubricants and Lubrication. Springer Berlin Heidelberg.
Martin, J. M., 2014. Nanolubricants. 2nd ed. Chicago: John Wiley & Sons,
Padgurskas, J., Rukuiza, R., Prosyčevas, I. and Kreivaitis, R., 2013. Tribological properties of
lubricant additives of Fe, Cu and Co nanoparticles. Tribology International, 60, pp.224-232.
Pawelski, H., Richter, H.P. and Seidel, J., SMS Group GmbH, 2016. Method and device for
lubricating rollers and a rolled strip of a rolling stand. U.S. Patent 9,254,513.
Riahi, A.R., Gali, O.A., Januszkiewicz, K.R. and Pattemore, D., 2012. Experimental study of
the disturbed layer generation during hot rolling contact of aluminum with steel. Tribology
International, 54, pp.42-50.
Sabareesh, R.K., Gobinath, N., Sajith, V., Das, S. and Sobhan, C.B., 2012. Application of
TiO2 nanoparticles as a lubricant-additive for vapor compression refrigeration systems–An
experimental investigation. international journal of refrigeration, 35(7), pp.1989-1996.
Stachowiak, G., 2015. Experimental Methods in Tribology. 4th ed. Berlin: Elsevier.
Takahama, Y., Shiraishi, T., Ogawa, S., Vanel, L., Hauret, G., Laugier, M. and Masson, P.,
ArcelorMittal France SA, Nippon Steel and Sumitomo Metal Corp, 2014. Method of
supplying lubrication oil in cold rolling. U.S. Patent 8,720,244.
Taylor, R.I., 2012. Tribology and energy efficiency: from molecules to lubricated contacts to
complete machines. Faraday discussions, 156(1), pp.361-382.
Wan, S., Tieu, A.K., Xia, Y., Zhu, H., Tran, B.H. and Cui, S., 2016. An overview of
inorganic polymer as potential lubricant additive for high temperature tribology. Tribology
International, 102, pp.620-635.
Wright, W. J., 2011. Chemical Abstracts, 4th ed. Texas: American Chemical Society.
Mang, T., 2014. Encyclopedia of Lubricants and Lubrication. Springer Berlin Heidelberg.
Martin, J. M., 2014. Nanolubricants. 2nd ed. Chicago: John Wiley & Sons,
Padgurskas, J., Rukuiza, R., Prosyčevas, I. and Kreivaitis, R., 2013. Tribological properties of
lubricant additives of Fe, Cu and Co nanoparticles. Tribology International, 60, pp.224-232.
Pawelski, H., Richter, H.P. and Seidel, J., SMS Group GmbH, 2016. Method and device for
lubricating rollers and a rolled strip of a rolling stand. U.S. Patent 9,254,513.
Riahi, A.R., Gali, O.A., Januszkiewicz, K.R. and Pattemore, D., 2012. Experimental study of
the disturbed layer generation during hot rolling contact of aluminum with steel. Tribology
International, 54, pp.42-50.
Sabareesh, R.K., Gobinath, N., Sajith, V., Das, S. and Sobhan, C.B., 2012. Application of
TiO2 nanoparticles as a lubricant-additive for vapor compression refrigeration systems–An
experimental investigation. international journal of refrigeration, 35(7), pp.1989-1996.
Stachowiak, G., 2015. Experimental Methods in Tribology. 4th ed. Berlin: Elsevier.
Takahama, Y., Shiraishi, T., Ogawa, S., Vanel, L., Hauret, G., Laugier, M. and Masson, P.,
ArcelorMittal France SA, Nippon Steel and Sumitomo Metal Corp, 2014. Method of
supplying lubrication oil in cold rolling. U.S. Patent 8,720,244.
Taylor, R.I., 2012. Tribology and energy efficiency: from molecules to lubricated contacts to
complete machines. Faraday discussions, 156(1), pp.361-382.
Wan, S., Tieu, A.K., Xia, Y., Zhu, H., Tran, B.H. and Cui, S., 2016. An overview of
inorganic polymer as potential lubricant additive for high temperature tribology. Tribology
International, 102, pp.620-635.
Wright, W. J., 2011. Chemical Abstracts, 4th ed. Texas: American Chemical Society.
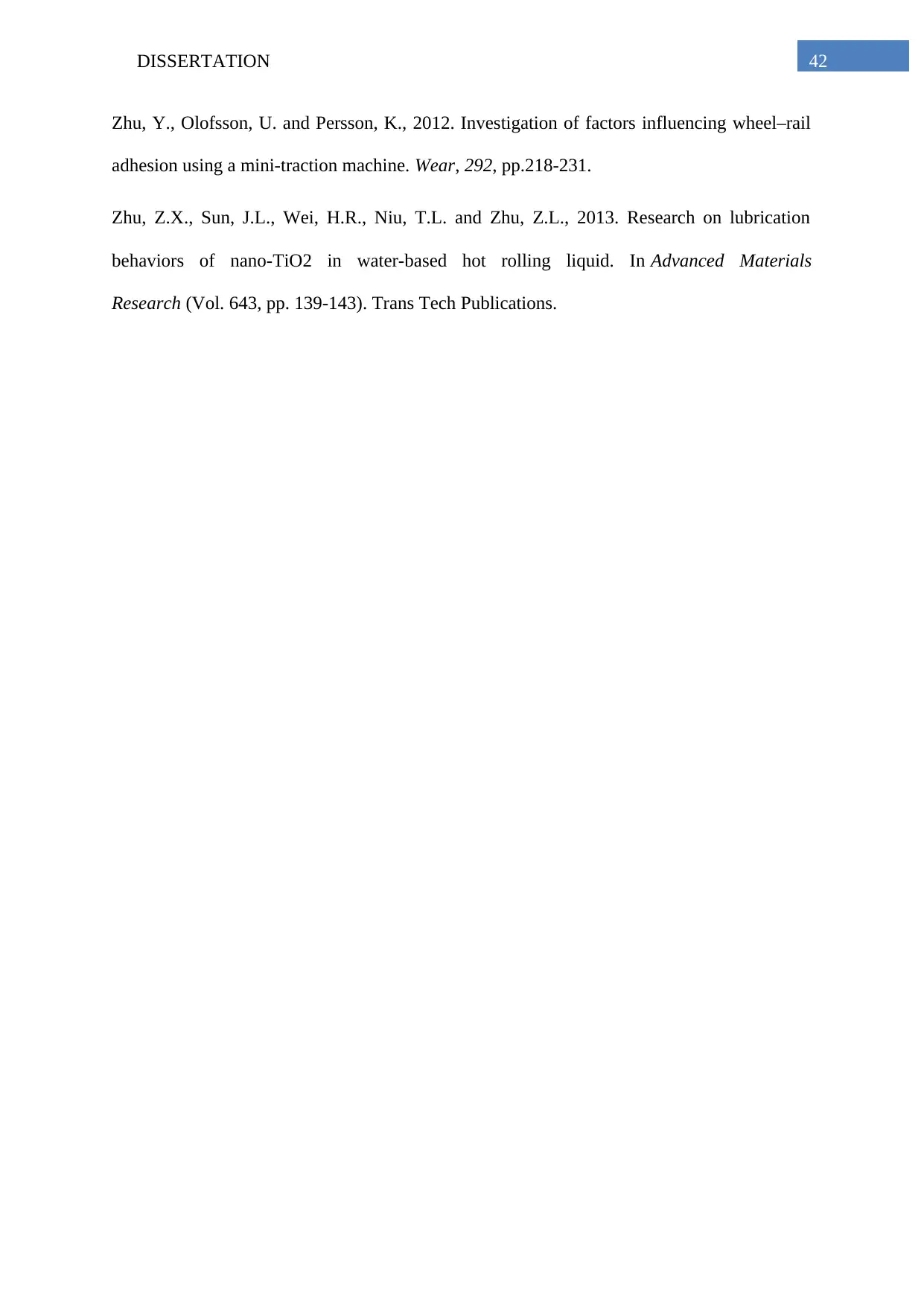
42DISSERTATION
Zhu, Y., Olofsson, U. and Persson, K., 2012. Investigation of factors influencing wheel–rail
adhesion using a mini-traction machine. Wear, 292, pp.218-231.
Zhu, Z.X., Sun, J.L., Wei, H.R., Niu, T.L. and Zhu, Z.L., 2013. Research on lubrication
behaviors of nano-TiO2 in water-based hot rolling liquid. In Advanced Materials
Research (Vol. 643, pp. 139-143). Trans Tech Publications.
Zhu, Y., Olofsson, U. and Persson, K., 2012. Investigation of factors influencing wheel–rail
adhesion using a mini-traction machine. Wear, 292, pp.218-231.
Zhu, Z.X., Sun, J.L., Wei, H.R., Niu, T.L. and Zhu, Z.L., 2013. Research on lubrication
behaviors of nano-TiO2 in water-based hot rolling liquid. In Advanced Materials
Research (Vol. 643, pp. 139-143). Trans Tech Publications.
1 out of 42

Your All-in-One AI-Powered Toolkit for Academic Success.
+13062052269
info@desklib.com
Available 24*7 on WhatsApp / Email
Unlock your academic potential
© 2024 | Zucol Services PVT LTD | All rights reserved.