Quality Management for Organisational Excellence: A Detailed Report
VerifiedAdded on 2022/12/12
|12
|3626
|419
Report
AI Summary
This report examines quality management strategies for organisational excellence, using The Engineering Tooling Company as a case study. It begins with an introduction to quality management and its importance in achieving a competitive advantage. The main body details how a companywide quality improvement strategy, encompassing total quality management, quality assurance, and quality control, can be introduced and implemented within the company. The report explores the implications of these strategies, including customer focus, employee training, and continuous improvement through methods like the Deming cycle. Furthermore, it analyzes how these strategies can sustain a culture of quality, emphasizing the roles of quality inspection, ISO 9000 standards, and the teachings of quality management gurus such as Crosby, Deming, and Juran. The report concludes by summarizing the key findings and recommendations for enhancing quality and organizational performance.
Contribute Materials
Your contribution can guide someone’s learning journey. Share your
documents today.
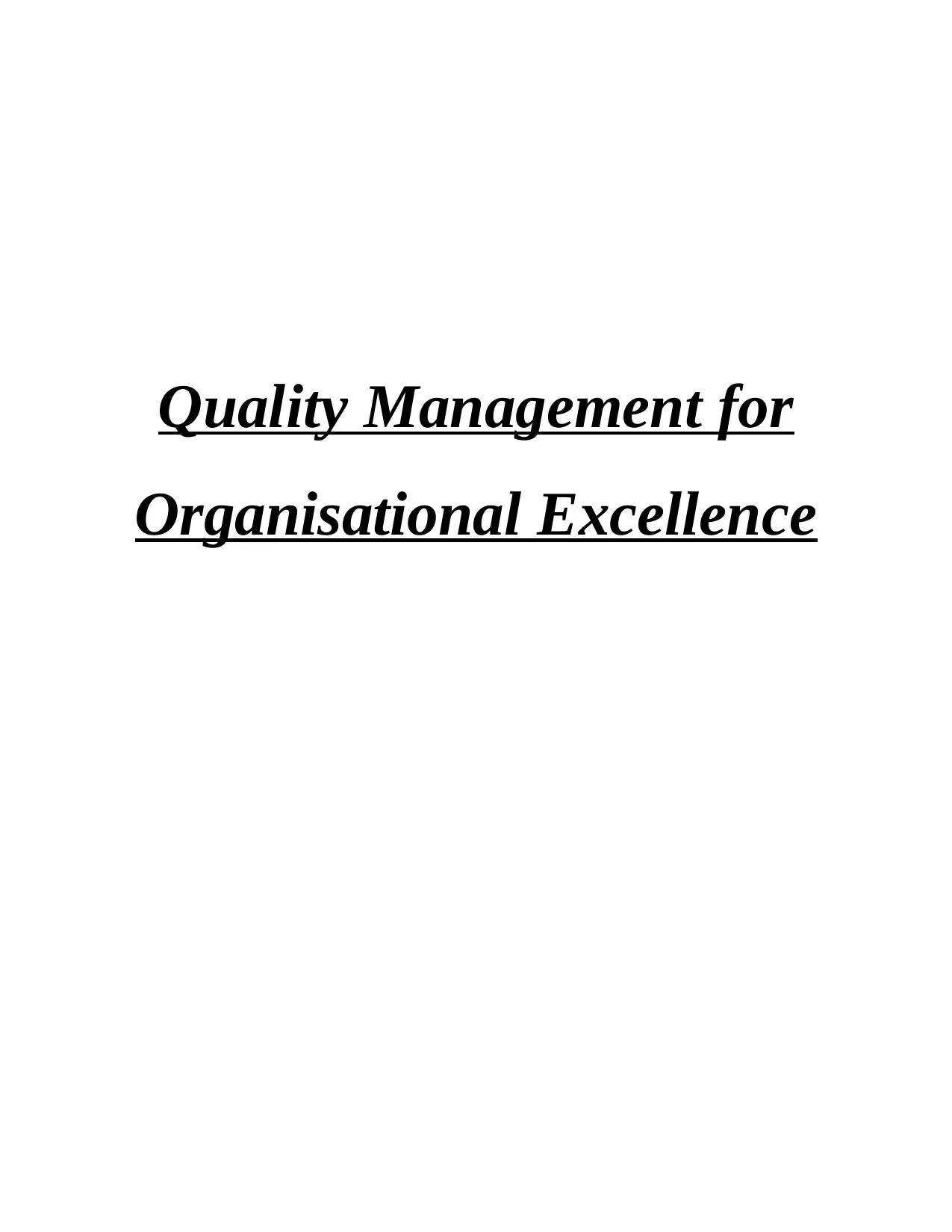
Quality Management for
Organisational Excellence
Organisational Excellence
Secure Best Marks with AI Grader
Need help grading? Try our AI Grader for instant feedback on your assignments.
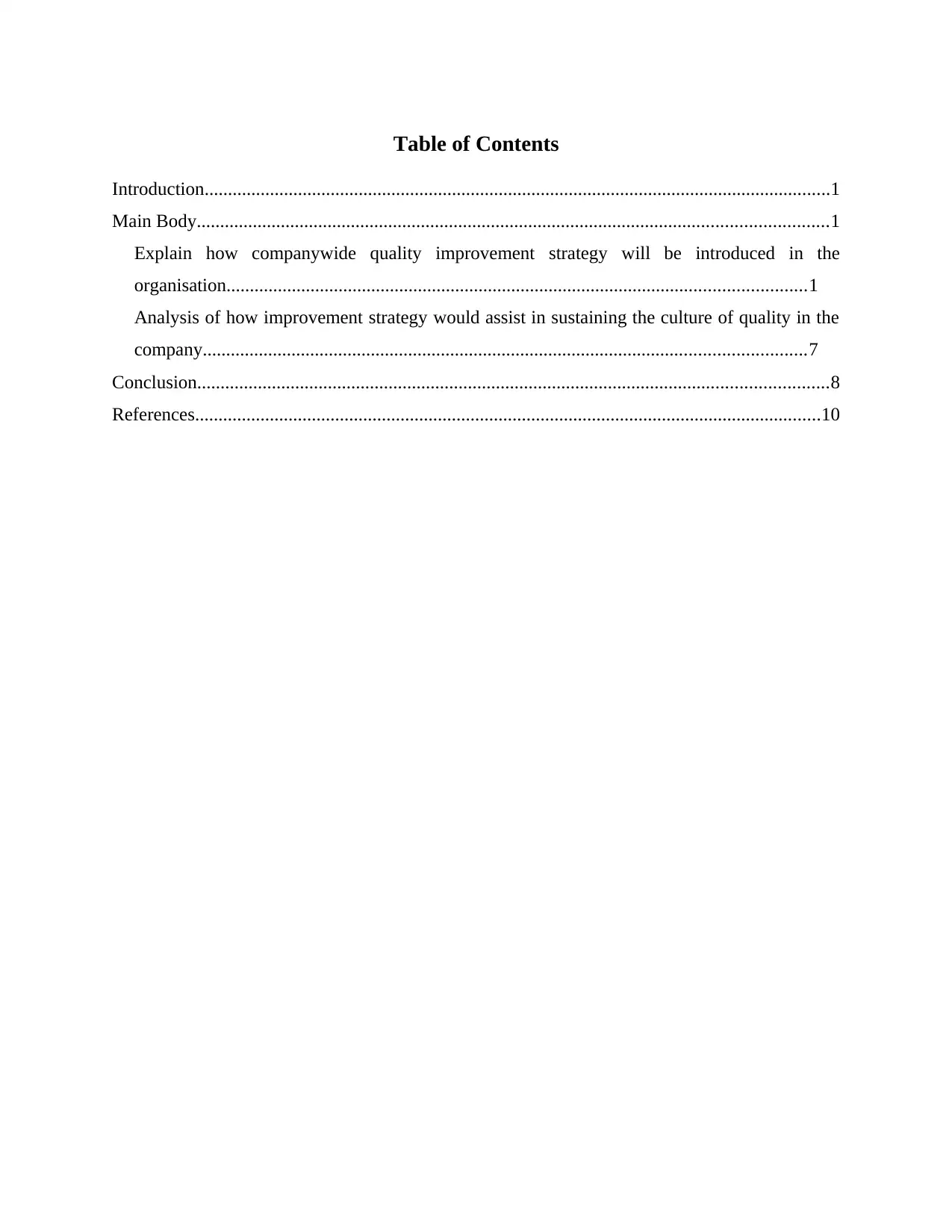
Table of Contents
Introduction......................................................................................................................................1
Main Body.......................................................................................................................................1
Explain how companywide quality improvement strategy will be introduced in the
organisation............................................................................................................................1
Analysis of how improvement strategy would assist in sustaining the culture of quality in the
company.................................................................................................................................7
Conclusion.......................................................................................................................................8
References......................................................................................................................................10
Introduction......................................................................................................................................1
Main Body.......................................................................................................................................1
Explain how companywide quality improvement strategy will be introduced in the
organisation............................................................................................................................1
Analysis of how improvement strategy would assist in sustaining the culture of quality in the
company.................................................................................................................................7
Conclusion.......................................................................................................................................8
References......................................................................................................................................10
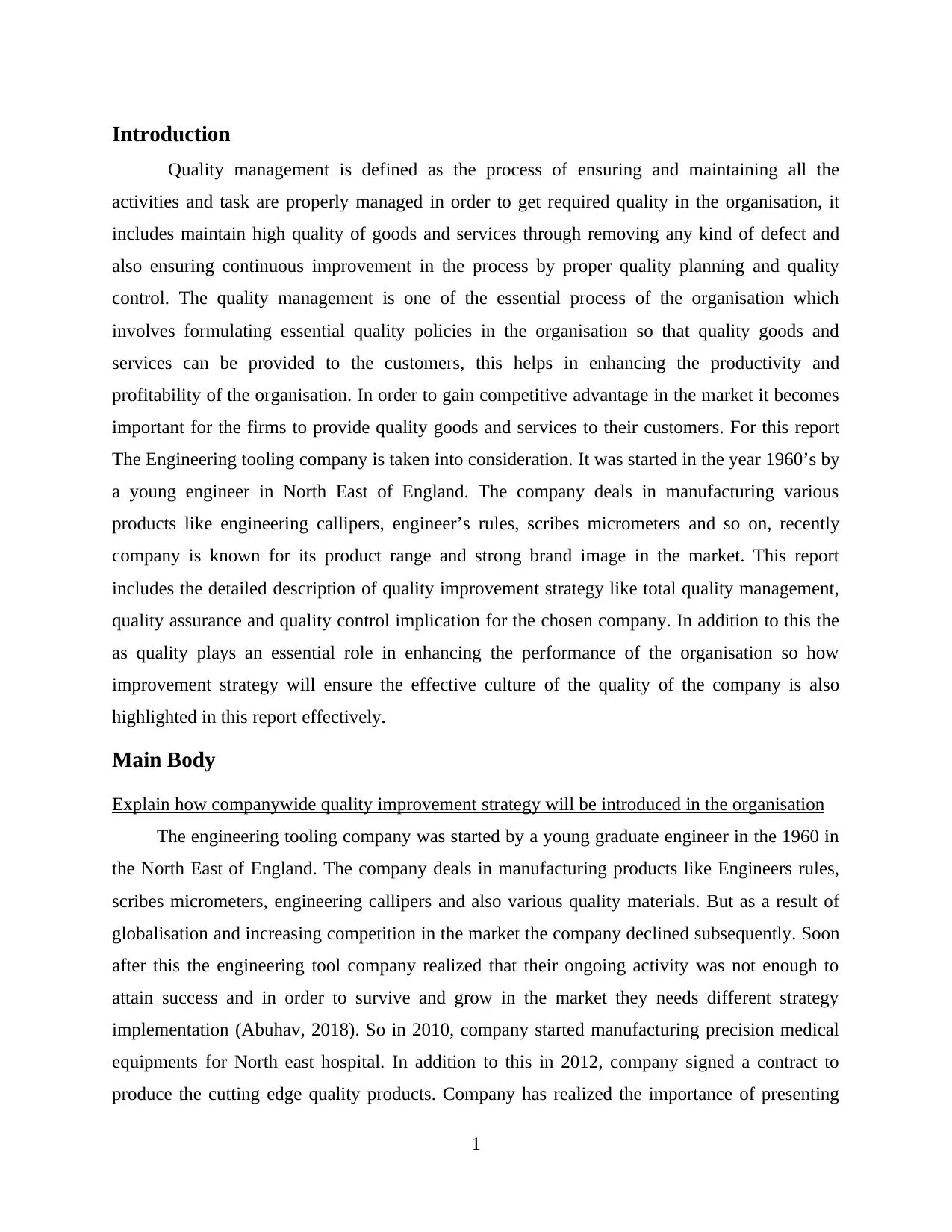
Introduction
Quality management is defined as the process of ensuring and maintaining all the
activities and task are properly managed in order to get required quality in the organisation, it
includes maintain high quality of goods and services through removing any kind of defect and
also ensuring continuous improvement in the process by proper quality planning and quality
control. The quality management is one of the essential process of the organisation which
involves formulating essential quality policies in the organisation so that quality goods and
services can be provided to the customers, this helps in enhancing the productivity and
profitability of the organisation. In order to gain competitive advantage in the market it becomes
important for the firms to provide quality goods and services to their customers. For this report
The Engineering tooling company is taken into consideration. It was started in the year 1960’s by
a young engineer in North East of England. The company deals in manufacturing various
products like engineering callipers, engineer’s rules, scribes micrometers and so on, recently
company is known for its product range and strong brand image in the market. This report
includes the detailed description of quality improvement strategy like total quality management,
quality assurance and quality control implication for the chosen company. In addition to this the
as quality plays an essential role in enhancing the performance of the organisation so how
improvement strategy will ensure the effective culture of the quality of the company is also
highlighted in this report effectively.
Main Body
Explain how companywide quality improvement strategy will be introduced in the organisation
The engineering tooling company was started by a young graduate engineer in the 1960 in
the North East of England. The company deals in manufacturing products like Engineers rules,
scribes micrometers, engineering callipers and also various quality materials. But as a result of
globalisation and increasing competition in the market the company declined subsequently. Soon
after this the engineering tool company realized that their ongoing activity was not enough to
attain success and in order to survive and grow in the market they needs different strategy
implementation (Abuhav, 2018). So in 2010, company started manufacturing precision medical
equipments for North east hospital. In addition to this in 2012, company signed a contract to
produce the cutting edge quality products. Company has realized the importance of presenting
1
Quality management is defined as the process of ensuring and maintaining all the
activities and task are properly managed in order to get required quality in the organisation, it
includes maintain high quality of goods and services through removing any kind of defect and
also ensuring continuous improvement in the process by proper quality planning and quality
control. The quality management is one of the essential process of the organisation which
involves formulating essential quality policies in the organisation so that quality goods and
services can be provided to the customers, this helps in enhancing the productivity and
profitability of the organisation. In order to gain competitive advantage in the market it becomes
important for the firms to provide quality goods and services to their customers. For this report
The Engineering tooling company is taken into consideration. It was started in the year 1960’s by
a young engineer in North East of England. The company deals in manufacturing various
products like engineering callipers, engineer’s rules, scribes micrometers and so on, recently
company is known for its product range and strong brand image in the market. This report
includes the detailed description of quality improvement strategy like total quality management,
quality assurance and quality control implication for the chosen company. In addition to this the
as quality plays an essential role in enhancing the performance of the organisation so how
improvement strategy will ensure the effective culture of the quality of the company is also
highlighted in this report effectively.
Main Body
Explain how companywide quality improvement strategy will be introduced in the organisation
The engineering tooling company was started by a young graduate engineer in the 1960 in
the North East of England. The company deals in manufacturing products like Engineers rules,
scribes micrometers, engineering callipers and also various quality materials. But as a result of
globalisation and increasing competition in the market the company declined subsequently. Soon
after this the engineering tool company realized that their ongoing activity was not enough to
attain success and in order to survive and grow in the market they needs different strategy
implementation (Abuhav, 2018). So in 2010, company started manufacturing precision medical
equipments for North east hospital. In addition to this in 2012, company signed a contract to
produce the cutting edge quality products. Company has realized the importance of presenting
1
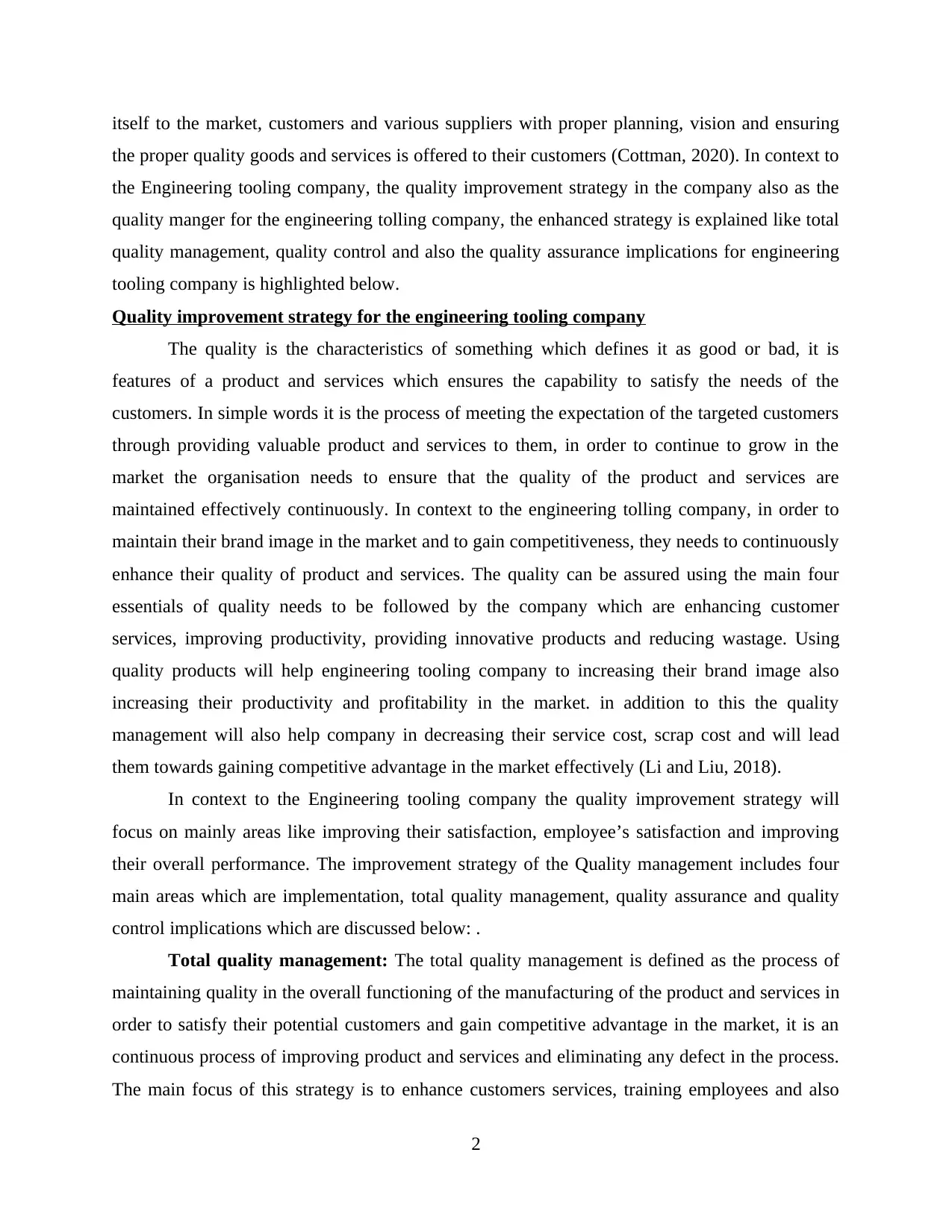
itself to the market, customers and various suppliers with proper planning, vision and ensuring
the proper quality goods and services is offered to their customers (Cottman, 2020). In context to
the Engineering tooling company, the quality improvement strategy in the company also as the
quality manger for the engineering tolling company, the enhanced strategy is explained like total
quality management, quality control and also the quality assurance implications for engineering
tooling company is highlighted below.
Quality improvement strategy for the engineering tooling company
The quality is the characteristics of something which defines it as good or bad, it is
features of a product and services which ensures the capability to satisfy the needs of the
customers. In simple words it is the process of meeting the expectation of the targeted customers
through providing valuable product and services to them, in order to continue to grow in the
market the organisation needs to ensure that the quality of the product and services are
maintained effectively continuously. In context to the engineering tolling company, in order to
maintain their brand image in the market and to gain competitiveness, they needs to continuously
enhance their quality of product and services. The quality can be assured using the main four
essentials of quality needs to be followed by the company which are enhancing customer
services, improving productivity, providing innovative products and reducing wastage. Using
quality products will help engineering tooling company to increasing their brand image also
increasing their productivity and profitability in the market. in addition to this the quality
management will also help company in decreasing their service cost, scrap cost and will lead
them towards gaining competitive advantage in the market effectively (Li and Liu, 2018).
In context to the Engineering tooling company the quality improvement strategy will
focus on mainly areas like improving their satisfaction, employee’s satisfaction and improving
their overall performance. The improvement strategy of the Quality management includes four
main areas which are implementation, total quality management, quality assurance and quality
control implications which are discussed below: .
Total quality management: The total quality management is defined as the process of
maintaining quality in the overall functioning of the manufacturing of the product and services in
order to satisfy their potential customers and gain competitive advantage in the market, it is an
continuous process of improving product and services and eliminating any defect in the process.
The main focus of this strategy is to enhance customers services, training employees and also
2
the proper quality goods and services is offered to their customers (Cottman, 2020). In context to
the Engineering tooling company, the quality improvement strategy in the company also as the
quality manger for the engineering tolling company, the enhanced strategy is explained like total
quality management, quality control and also the quality assurance implications for engineering
tooling company is highlighted below.
Quality improvement strategy for the engineering tooling company
The quality is the characteristics of something which defines it as good or bad, it is
features of a product and services which ensures the capability to satisfy the needs of the
customers. In simple words it is the process of meeting the expectation of the targeted customers
through providing valuable product and services to them, in order to continue to grow in the
market the organisation needs to ensure that the quality of the product and services are
maintained effectively continuously. In context to the engineering tolling company, in order to
maintain their brand image in the market and to gain competitiveness, they needs to continuously
enhance their quality of product and services. The quality can be assured using the main four
essentials of quality needs to be followed by the company which are enhancing customer
services, improving productivity, providing innovative products and reducing wastage. Using
quality products will help engineering tooling company to increasing their brand image also
increasing their productivity and profitability in the market. in addition to this the quality
management will also help company in decreasing their service cost, scrap cost and will lead
them towards gaining competitive advantage in the market effectively (Li and Liu, 2018).
In context to the Engineering tooling company the quality improvement strategy will
focus on mainly areas like improving their satisfaction, employee’s satisfaction and improving
their overall performance. The improvement strategy of the Quality management includes four
main areas which are implementation, total quality management, quality assurance and quality
control implications which are discussed below: .
Total quality management: The total quality management is defined as the process of
maintaining quality in the overall functioning of the manufacturing of the product and services in
order to satisfy their potential customers and gain competitive advantage in the market, it is an
continuous process of improving product and services and eliminating any defect in the process.
The main focus of this strategy is to enhance customers services, training employees and also
2
Secure Best Marks with AI Grader
Need help grading? Try our AI Grader for instant feedback on your assignments.
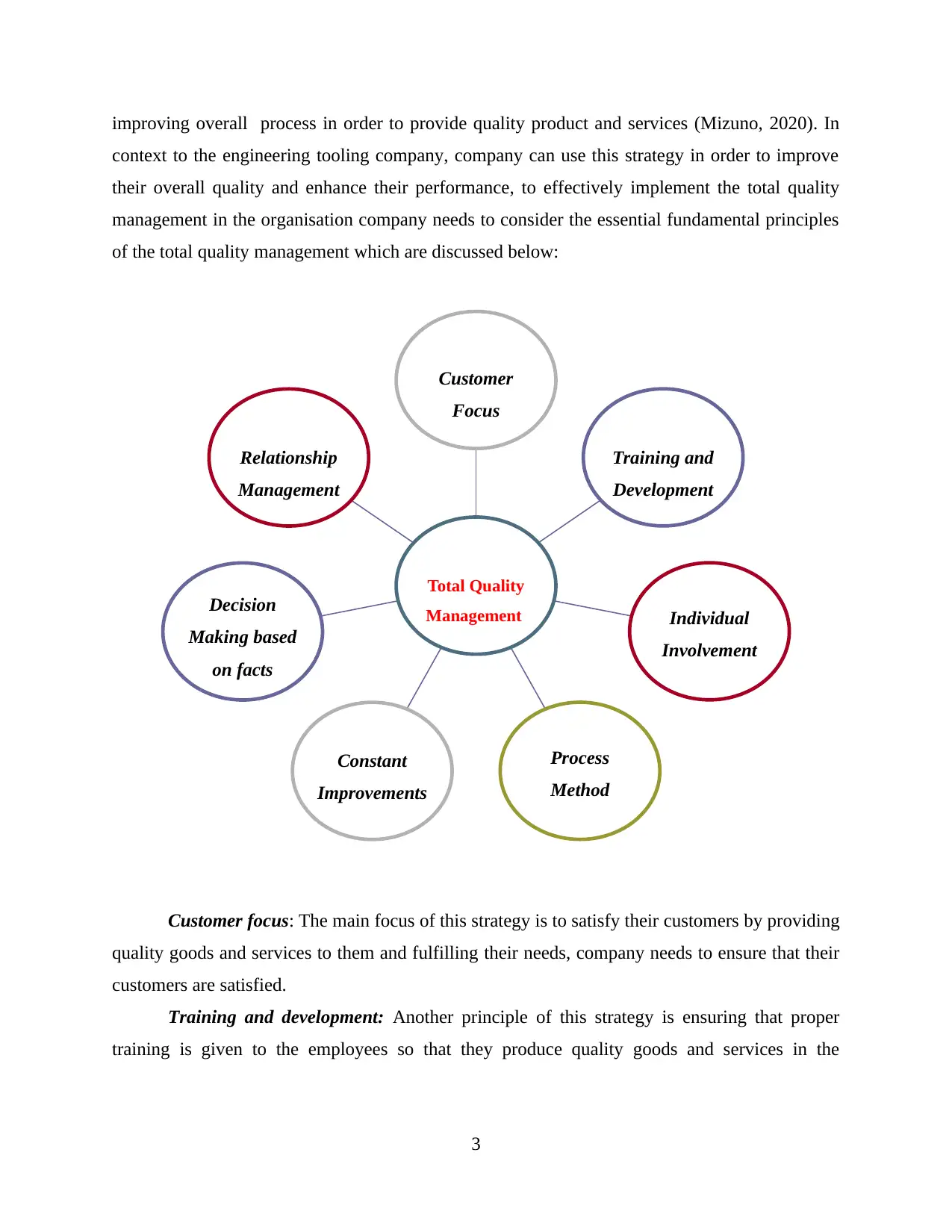
improving overall process in order to provide quality product and services (Mizuno, 2020). In
context to the engineering tooling company, company can use this strategy in order to improve
their overall quality and enhance their performance, to effectively implement the total quality
management in the organisation company needs to consider the essential fundamental principles
of the total quality management which are discussed below:
Customer focus: The main focus of this strategy is to satisfy their customers by providing
quality goods and services to them and fulfilling their needs, company needs to ensure that their
customers are satisfied.
Training and development: Another principle of this strategy is ensuring that proper
training is given to the employees so that they produce quality goods and services in the
3
Relationship
Management
Decision
Making based
on facts
Constant
Improvements
Process
Method
Individual
Involvement
Training and
Development
Customer
Focus
Total Quality
Management
context to the engineering tooling company, company can use this strategy in order to improve
their overall quality and enhance their performance, to effectively implement the total quality
management in the organisation company needs to consider the essential fundamental principles
of the total quality management which are discussed below:
Customer focus: The main focus of this strategy is to satisfy their customers by providing
quality goods and services to them and fulfilling their needs, company needs to ensure that their
customers are satisfied.
Training and development: Another principle of this strategy is ensuring that proper
training is given to the employees so that they produce quality goods and services in the
3
Relationship
Management
Decision
Making based
on facts
Constant
Improvements
Process
Method
Individual
Involvement
Training and
Development
Customer
Focus
Total Quality
Management
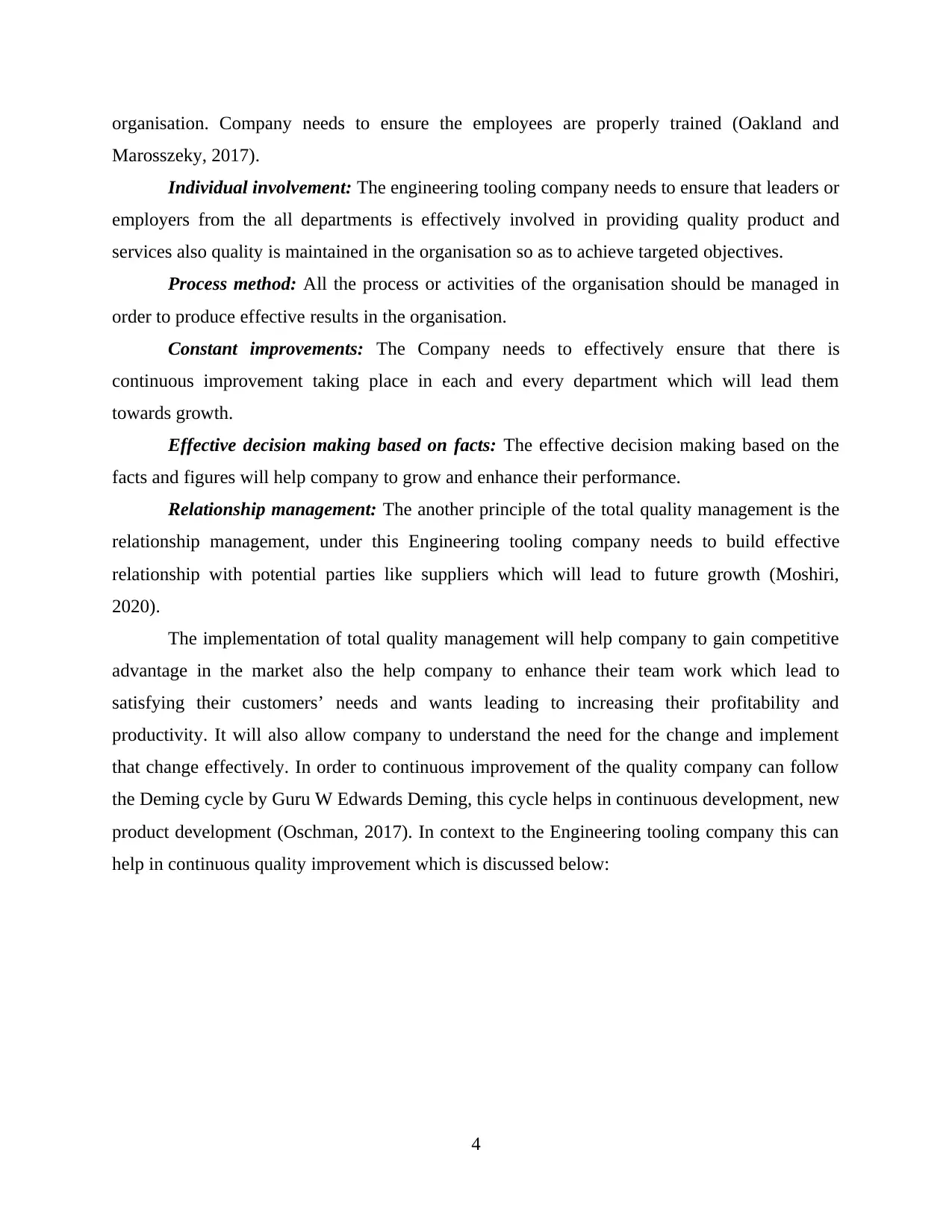
organisation. Company needs to ensure the employees are properly trained (Oakland and
Marosszeky, 2017).
Individual involvement: The engineering tooling company needs to ensure that leaders or
employers from the all departments is effectively involved in providing quality product and
services also quality is maintained in the organisation so as to achieve targeted objectives.
Process method: All the process or activities of the organisation should be managed in
order to produce effective results in the organisation.
Constant improvements: The Company needs to effectively ensure that there is
continuous improvement taking place in each and every department which will lead them
towards growth.
Effective decision making based on facts: The effective decision making based on the
facts and figures will help company to grow and enhance their performance.
Relationship management: The another principle of the total quality management is the
relationship management, under this Engineering tooling company needs to build effective
relationship with potential parties like suppliers which will lead to future growth (Moshiri,
2020).
The implementation of total quality management will help company to gain competitive
advantage in the market also the help company to enhance their team work which lead to
satisfying their customers’ needs and wants leading to increasing their profitability and
productivity. It will also allow company to understand the need for the change and implement
that change effectively. In order to continuous improvement of the quality company can follow
the Deming cycle by Guru W Edwards Deming, this cycle helps in continuous development, new
product development (Oschman, 2017). In context to the Engineering tooling company this can
help in continuous quality improvement which is discussed below:
4
Marosszeky, 2017).
Individual involvement: The engineering tooling company needs to ensure that leaders or
employers from the all departments is effectively involved in providing quality product and
services also quality is maintained in the organisation so as to achieve targeted objectives.
Process method: All the process or activities of the organisation should be managed in
order to produce effective results in the organisation.
Constant improvements: The Company needs to effectively ensure that there is
continuous improvement taking place in each and every department which will lead them
towards growth.
Effective decision making based on facts: The effective decision making based on the
facts and figures will help company to grow and enhance their performance.
Relationship management: The another principle of the total quality management is the
relationship management, under this Engineering tooling company needs to build effective
relationship with potential parties like suppliers which will lead to future growth (Moshiri,
2020).
The implementation of total quality management will help company to gain competitive
advantage in the market also the help company to enhance their team work which lead to
satisfying their customers’ needs and wants leading to increasing their profitability and
productivity. It will also allow company to understand the need for the change and implement
that change effectively. In order to continuous improvement of the quality company can follow
the Deming cycle by Guru W Edwards Deming, this cycle helps in continuous development, new
product development (Oschman, 2017). In context to the Engineering tooling company this can
help in continuous quality improvement which is discussed below:
4
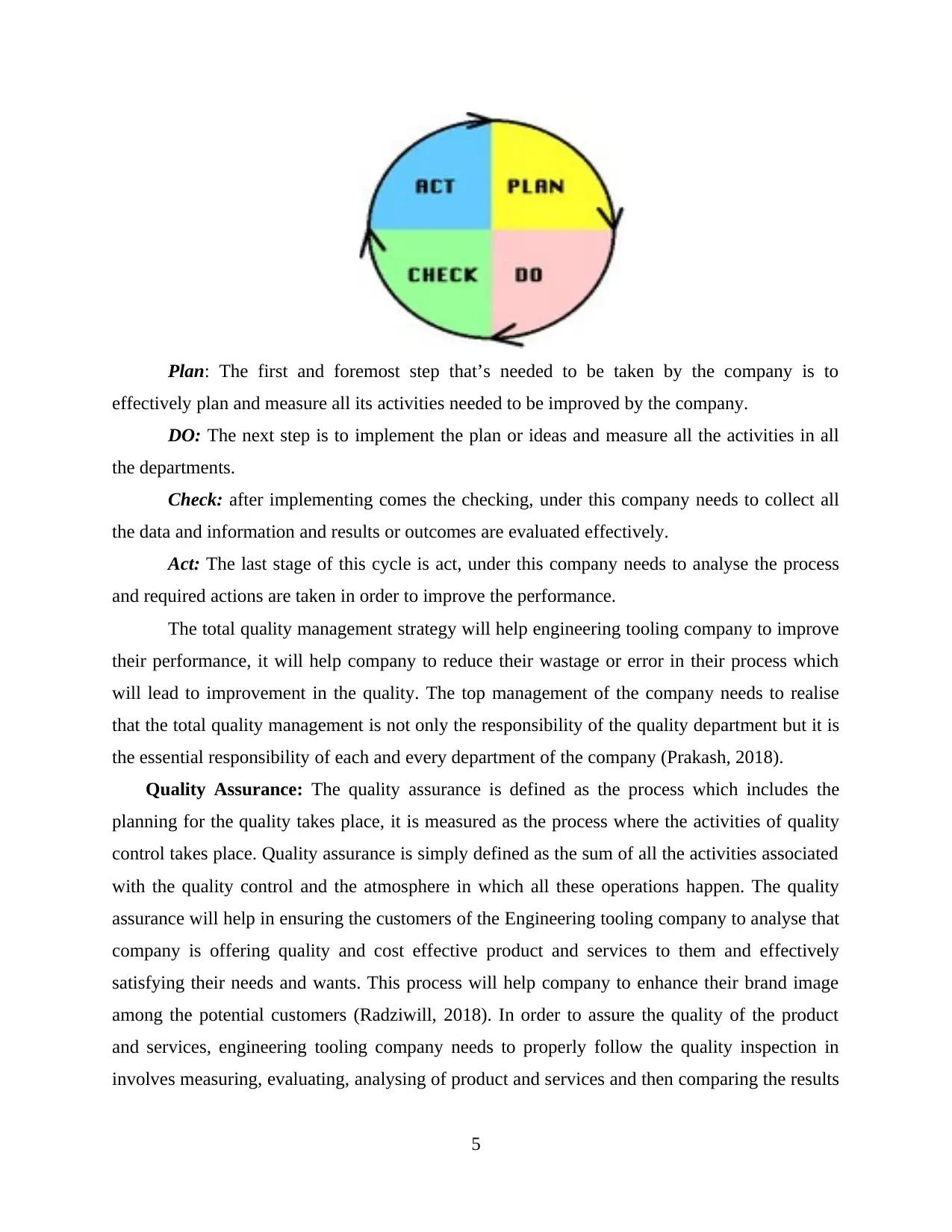
Plan: The first and foremost step that’s needed to be taken by the company is to
effectively plan and measure all its activities needed to be improved by the company.
DO: The next step is to implement the plan or ideas and measure all the activities in all
the departments.
Check: after implementing comes the checking, under this company needs to collect all
the data and information and results or outcomes are evaluated effectively.
Act: The last stage of this cycle is act, under this company needs to analyse the process
and required actions are taken in order to improve the performance.
The total quality management strategy will help engineering tooling company to improve
their performance, it will help company to reduce their wastage or error in their process which
will lead to improvement in the quality. The top management of the company needs to realise
that the total quality management is not only the responsibility of the quality department but it is
the essential responsibility of each and every department of the company (Prakash, 2018).
Quality Assurance: The quality assurance is defined as the process which includes the
planning for the quality takes place, it is measured as the process where the activities of quality
control takes place. Quality assurance is simply defined as the sum of all the activities associated
with the quality control and the atmosphere in which all these operations happen. The quality
assurance will help in ensuring the customers of the Engineering tooling company to analyse that
company is offering quality and cost effective product and services to them and effectively
satisfying their needs and wants. This process will help company to enhance their brand image
among the potential customers (Radziwill, 2018). In order to assure the quality of the product
and services, engineering tooling company needs to properly follow the quality inspection in
involves measuring, evaluating, analysing of product and services and then comparing the results
5
effectively plan and measure all its activities needed to be improved by the company.
DO: The next step is to implement the plan or ideas and measure all the activities in all
the departments.
Check: after implementing comes the checking, under this company needs to collect all
the data and information and results or outcomes are evaluated effectively.
Act: The last stage of this cycle is act, under this company needs to analyse the process
and required actions are taken in order to improve the performance.
The total quality management strategy will help engineering tooling company to improve
their performance, it will help company to reduce their wastage or error in their process which
will lead to improvement in the quality. The top management of the company needs to realise
that the total quality management is not only the responsibility of the quality department but it is
the essential responsibility of each and every department of the company (Prakash, 2018).
Quality Assurance: The quality assurance is defined as the process which includes the
planning for the quality takes place, it is measured as the process where the activities of quality
control takes place. Quality assurance is simply defined as the sum of all the activities associated
with the quality control and the atmosphere in which all these operations happen. The quality
assurance will help in ensuring the customers of the Engineering tooling company to analyse that
company is offering quality and cost effective product and services to them and effectively
satisfying their needs and wants. This process will help company to enhance their brand image
among the potential customers (Radziwill, 2018). In order to assure the quality of the product
and services, engineering tooling company needs to properly follow the quality inspection in
involves measuring, evaluating, analysing of product and services and then comparing the results
5
Paraphrase This Document
Need a fresh take? Get an instant paraphrase of this document with our AI Paraphraser
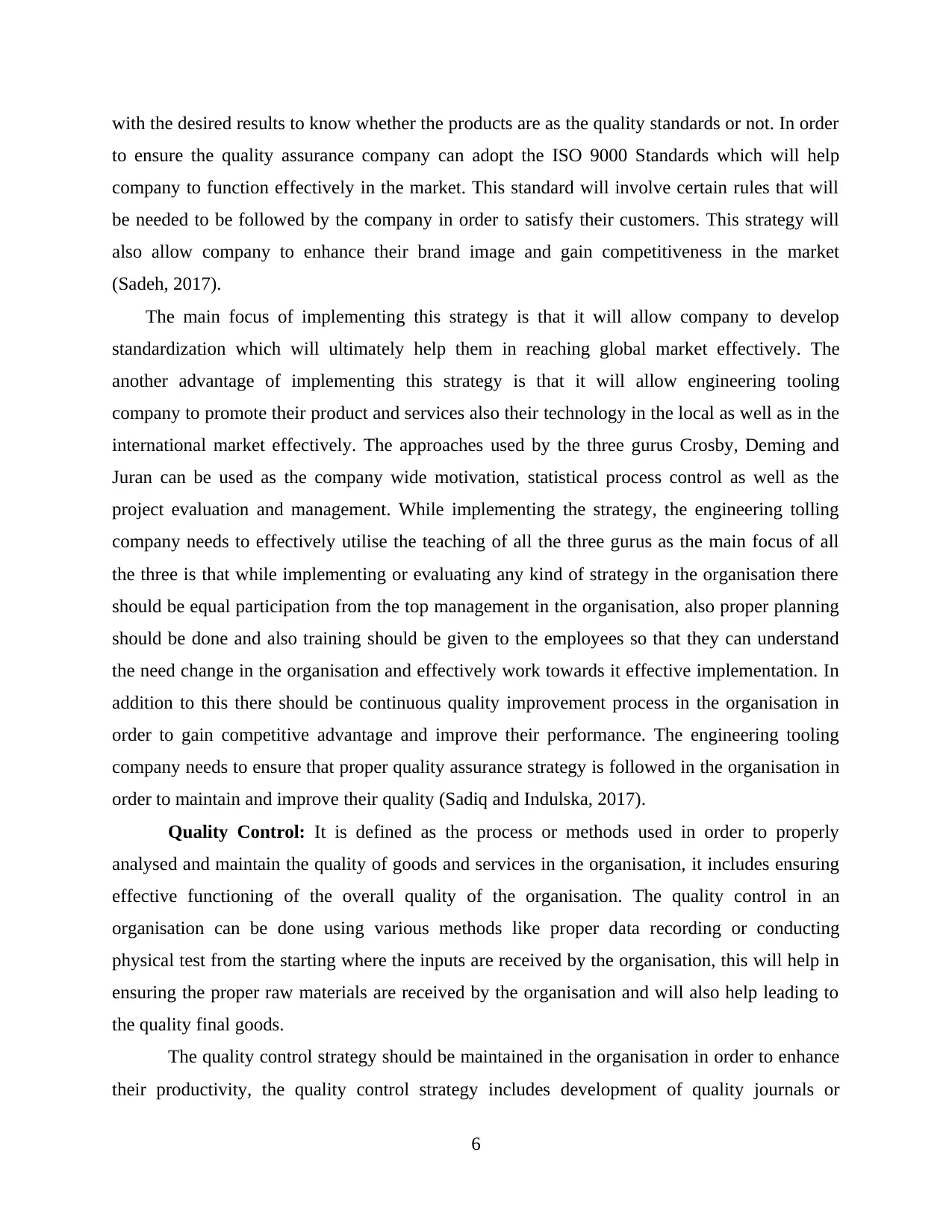
with the desired results to know whether the products are as the quality standards or not. In order
to ensure the quality assurance company can adopt the ISO 9000 Standards which will help
company to function effectively in the market. This standard will involve certain rules that will
be needed to be followed by the company in order to satisfy their customers. This strategy will
also allow company to enhance their brand image and gain competitiveness in the market
(Sadeh, 2017).
The main focus of implementing this strategy is that it will allow company to develop
standardization which will ultimately help them in reaching global market effectively. The
another advantage of implementing this strategy is that it will allow engineering tooling
company to promote their product and services also their technology in the local as well as in the
international market effectively. The approaches used by the three gurus Crosby, Deming and
Juran can be used as the company wide motivation, statistical process control as well as the
project evaluation and management. While implementing the strategy, the engineering tolling
company needs to effectively utilise the teaching of all the three gurus as the main focus of all
the three is that while implementing or evaluating any kind of strategy in the organisation there
should be equal participation from the top management in the organisation, also proper planning
should be done and also training should be given to the employees so that they can understand
the need change in the organisation and effectively work towards it effective implementation. In
addition to this there should be continuous quality improvement process in the organisation in
order to gain competitive advantage and improve their performance. The engineering tooling
company needs to ensure that proper quality assurance strategy is followed in the organisation in
order to maintain and improve their quality (Sadiq and Indulska, 2017).
Quality Control: It is defined as the process or methods used in order to properly
analysed and maintain the quality of goods and services in the organisation, it includes ensuring
effective functioning of the overall quality of the organisation. The quality control in an
organisation can be done using various methods like proper data recording or conducting
physical test from the starting where the inputs are received by the organisation, this will help in
ensuring the proper raw materials are received by the organisation and will also help leading to
the quality final goods.
The quality control strategy should be maintained in the organisation in order to enhance
their productivity, the quality control strategy includes development of quality journals or
6
to ensure the quality assurance company can adopt the ISO 9000 Standards which will help
company to function effectively in the market. This standard will involve certain rules that will
be needed to be followed by the company in order to satisfy their customers. This strategy will
also allow company to enhance their brand image and gain competitiveness in the market
(Sadeh, 2017).
The main focus of implementing this strategy is that it will allow company to develop
standardization which will ultimately help them in reaching global market effectively. The
another advantage of implementing this strategy is that it will allow engineering tooling
company to promote their product and services also their technology in the local as well as in the
international market effectively. The approaches used by the three gurus Crosby, Deming and
Juran can be used as the company wide motivation, statistical process control as well as the
project evaluation and management. While implementing the strategy, the engineering tolling
company needs to effectively utilise the teaching of all the three gurus as the main focus of all
the three is that while implementing or evaluating any kind of strategy in the organisation there
should be equal participation from the top management in the organisation, also proper planning
should be done and also training should be given to the employees so that they can understand
the need change in the organisation and effectively work towards it effective implementation. In
addition to this there should be continuous quality improvement process in the organisation in
order to gain competitive advantage and improve their performance. The engineering tooling
company needs to ensure that proper quality assurance strategy is followed in the organisation in
order to maintain and improve their quality (Sadiq and Indulska, 2017).
Quality Control: It is defined as the process or methods used in order to properly
analysed and maintain the quality of goods and services in the organisation, it includes ensuring
effective functioning of the overall quality of the organisation. The quality control in an
organisation can be done using various methods like proper data recording or conducting
physical test from the starting where the inputs are received by the organisation, this will help in
ensuring the proper raw materials are received by the organisation and will also help leading to
the quality final goods.
The quality control strategy should be maintained in the organisation in order to enhance
their productivity, the quality control strategy includes development of quality journals or
6
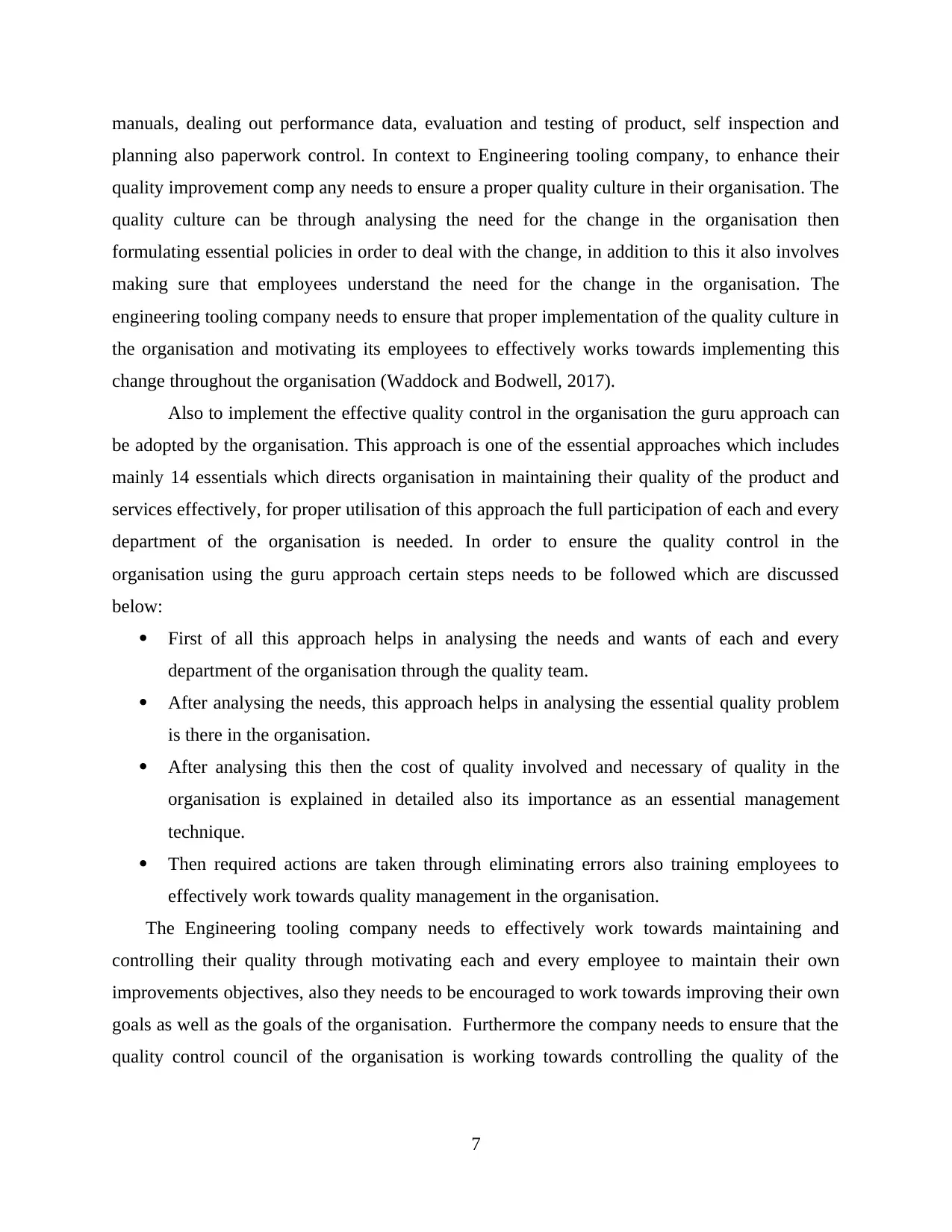
manuals, dealing out performance data, evaluation and testing of product, self inspection and
planning also paperwork control. In context to Engineering tooling company, to enhance their
quality improvement comp any needs to ensure a proper quality culture in their organisation. The
quality culture can be through analysing the need for the change in the organisation then
formulating essential policies in order to deal with the change, in addition to this it also involves
making sure that employees understand the need for the change in the organisation. The
engineering tooling company needs to ensure that proper implementation of the quality culture in
the organisation and motivating its employees to effectively works towards implementing this
change throughout the organisation (Waddock and Bodwell, 2017).
Also to implement the effective quality control in the organisation the guru approach can
be adopted by the organisation. This approach is one of the essential approaches which includes
mainly 14 essentials which directs organisation in maintaining their quality of the product and
services effectively, for proper utilisation of this approach the full participation of each and every
department of the organisation is needed. In order to ensure the quality control in the
organisation using the guru approach certain steps needs to be followed which are discussed
below:
First of all this approach helps in analysing the needs and wants of each and every
department of the organisation through the quality team.
After analysing the needs, this approach helps in analysing the essential quality problem
is there in the organisation.
After analysing this then the cost of quality involved and necessary of quality in the
organisation is explained in detailed also its importance as an essential management
technique.
Then required actions are taken through eliminating errors also training employees to
effectively work towards quality management in the organisation.
The Engineering tooling company needs to effectively work towards maintaining and
controlling their quality through motivating each and every employee to maintain their own
improvements objectives, also they needs to be encouraged to work towards improving their own
goals as well as the goals of the organisation. Furthermore the company needs to ensure that the
quality control council of the organisation is working towards controlling the quality of the
7
planning also paperwork control. In context to Engineering tooling company, to enhance their
quality improvement comp any needs to ensure a proper quality culture in their organisation. The
quality culture can be through analysing the need for the change in the organisation then
formulating essential policies in order to deal with the change, in addition to this it also involves
making sure that employees understand the need for the change in the organisation. The
engineering tooling company needs to ensure that proper implementation of the quality culture in
the organisation and motivating its employees to effectively works towards implementing this
change throughout the organisation (Waddock and Bodwell, 2017).
Also to implement the effective quality control in the organisation the guru approach can
be adopted by the organisation. This approach is one of the essential approaches which includes
mainly 14 essentials which directs organisation in maintaining their quality of the product and
services effectively, for proper utilisation of this approach the full participation of each and every
department of the organisation is needed. In order to ensure the quality control in the
organisation using the guru approach certain steps needs to be followed which are discussed
below:
First of all this approach helps in analysing the needs and wants of each and every
department of the organisation through the quality team.
After analysing the needs, this approach helps in analysing the essential quality problem
is there in the organisation.
After analysing this then the cost of quality involved and necessary of quality in the
organisation is explained in detailed also its importance as an essential management
technique.
Then required actions are taken through eliminating errors also training employees to
effectively work towards quality management in the organisation.
The Engineering tooling company needs to effectively work towards maintaining and
controlling their quality through motivating each and every employee to maintain their own
improvements objectives, also they needs to be encouraged to work towards improving their own
goals as well as the goals of the organisation. Furthermore the company needs to ensure that the
quality control council of the organisation is working towards controlling the quality of the
7

products and services also enhancing the performance of the employees, there should be
continuous quality control process in the organisation for better results
Analysis of how improvement strategy would assist in sustaining the culture of quality in the
company.
The improvement strategy will help in assisting in sustaining the culture of the quality in
the organisation by continuously improving the overall performance of the employees and the
organisation effectively, it will also help company in clearly defining their values, the various
improvement strategy includes quality control, quality assurance and total quality management
will help in creating and sustaining the culture of the quality in the organisation, these strategies
will allow company to focus on their performance and process also enables company to satisfy
their customers’ needs and wants through quality product and services and will also allow
company to effectively manage their resources and eliminate any kind of defect in the products
and services. The quality culture is essential for any organisation to increase their brand image in
the market and increase their productivity and profitability, in order to gain competitive
advantage in the market it becomes essential for the company to build quality culture in the
organisation (Wilcock and Boys, 2017). The improvement strategy allows organisation to
control, improve and manage their overall quality by removing any kind of defect in the process.
It also helps company to analyse the importance of change and lead to the implementation of the
change. The improvement strategy leads to training employees so that they be motivated towards
maintaining quality culture in the organisation.
Conclusion
From the above report it can be concluded that quality management plays an essential role in
enhancing the brand image of the organisation in the market and can lead an organisation
towards the success or failure. With increasing competition in the market in order to gain
competitive advantage in the market and to satisfy the needs of the customers, providing quality
product and services becomes essential process for an organisation as the main focus of the
quality management is to ensure the satisfaction level of its employees and maintaining their
performance in the market. This report covers the introduction of companywide quality
improvement strategy for the Engineering Tooling Company, various improvement strategies are
highlighted in this report, The strategy includes the Total Quality Management, Quality control
8
continuous quality control process in the organisation for better results
Analysis of how improvement strategy would assist in sustaining the culture of quality in the
company.
The improvement strategy will help in assisting in sustaining the culture of the quality in
the organisation by continuously improving the overall performance of the employees and the
organisation effectively, it will also help company in clearly defining their values, the various
improvement strategy includes quality control, quality assurance and total quality management
will help in creating and sustaining the culture of the quality in the organisation, these strategies
will allow company to focus on their performance and process also enables company to satisfy
their customers’ needs and wants through quality product and services and will also allow
company to effectively manage their resources and eliminate any kind of defect in the products
and services. The quality culture is essential for any organisation to increase their brand image in
the market and increase their productivity and profitability, in order to gain competitive
advantage in the market it becomes essential for the company to build quality culture in the
organisation (Wilcock and Boys, 2017). The improvement strategy allows organisation to
control, improve and manage their overall quality by removing any kind of defect in the process.
It also helps company to analyse the importance of change and lead to the implementation of the
change. The improvement strategy leads to training employees so that they be motivated towards
maintaining quality culture in the organisation.
Conclusion
From the above report it can be concluded that quality management plays an essential role in
enhancing the brand image of the organisation in the market and can lead an organisation
towards the success or failure. With increasing competition in the market in order to gain
competitive advantage in the market and to satisfy the needs of the customers, providing quality
product and services becomes essential process for an organisation as the main focus of the
quality management is to ensure the satisfaction level of its employees and maintaining their
performance in the market. This report covers the introduction of companywide quality
improvement strategy for the Engineering Tooling Company, various improvement strategies are
highlighted in this report, The strategy includes the Total Quality Management, Quality control
8
Secure Best Marks with AI Grader
Need help grading? Try our AI Grader for instant feedback on your assignments.
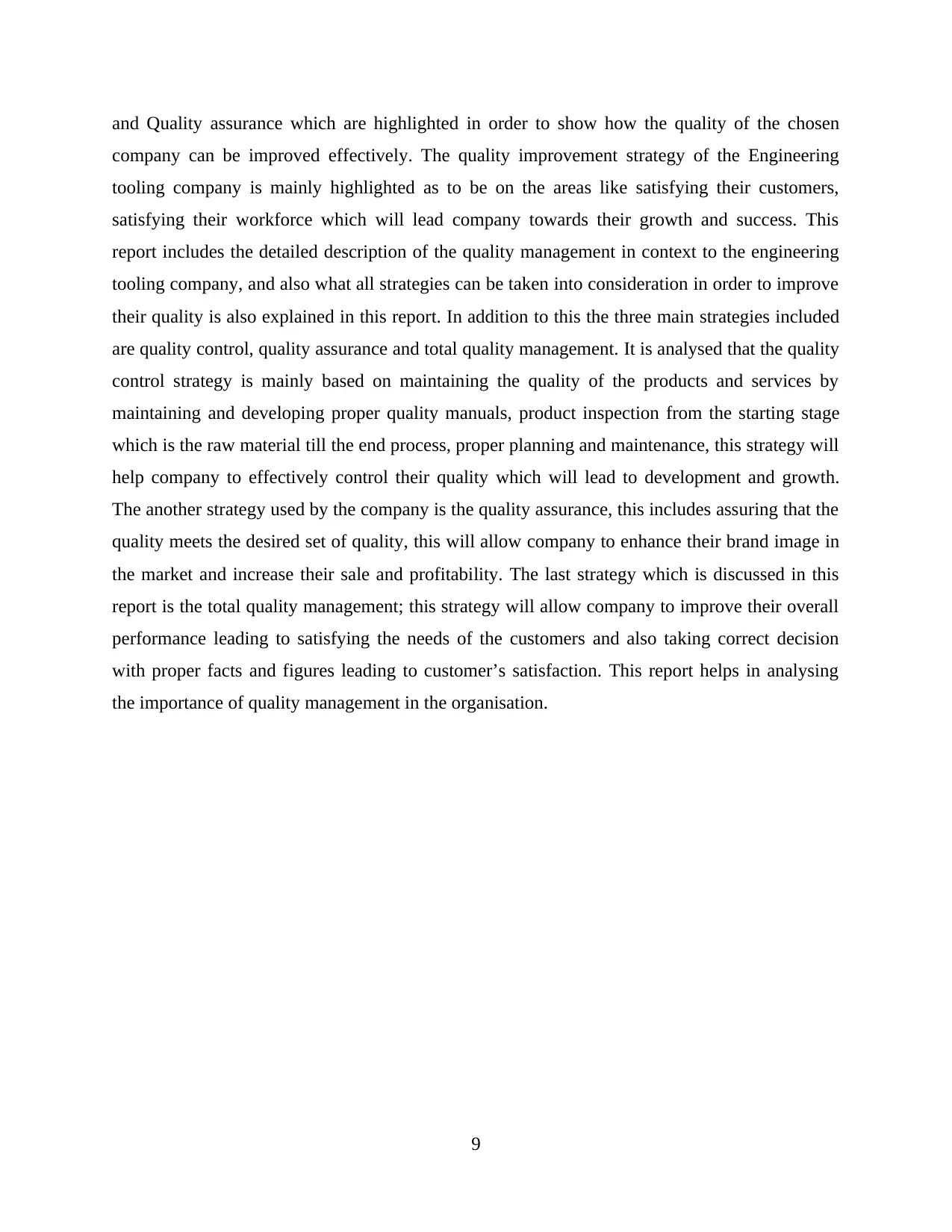
and Quality assurance which are highlighted in order to show how the quality of the chosen
company can be improved effectively. The quality improvement strategy of the Engineering
tooling company is mainly highlighted as to be on the areas like satisfying their customers,
satisfying their workforce which will lead company towards their growth and success. This
report includes the detailed description of the quality management in context to the engineering
tooling company, and also what all strategies can be taken into consideration in order to improve
their quality is also explained in this report. In addition to this the three main strategies included
are quality control, quality assurance and total quality management. It is analysed that the quality
control strategy is mainly based on maintaining the quality of the products and services by
maintaining and developing proper quality manuals, product inspection from the starting stage
which is the raw material till the end process, proper planning and maintenance, this strategy will
help company to effectively control their quality which will lead to development and growth.
The another strategy used by the company is the quality assurance, this includes assuring that the
quality meets the desired set of quality, this will allow company to enhance their brand image in
the market and increase their sale and profitability. The last strategy which is discussed in this
report is the total quality management; this strategy will allow company to improve their overall
performance leading to satisfying the needs of the customers and also taking correct decision
with proper facts and figures leading to customer’s satisfaction. This report helps in analysing
the importance of quality management in the organisation.
9
company can be improved effectively. The quality improvement strategy of the Engineering
tooling company is mainly highlighted as to be on the areas like satisfying their customers,
satisfying their workforce which will lead company towards their growth and success. This
report includes the detailed description of the quality management in context to the engineering
tooling company, and also what all strategies can be taken into consideration in order to improve
their quality is also explained in this report. In addition to this the three main strategies included
are quality control, quality assurance and total quality management. It is analysed that the quality
control strategy is mainly based on maintaining the quality of the products and services by
maintaining and developing proper quality manuals, product inspection from the starting stage
which is the raw material till the end process, proper planning and maintenance, this strategy will
help company to effectively control their quality which will lead to development and growth.
The another strategy used by the company is the quality assurance, this includes assuring that the
quality meets the desired set of quality, this will allow company to enhance their brand image in
the market and increase their sale and profitability. The last strategy which is discussed in this
report is the total quality management; this strategy will allow company to improve their overall
performance leading to satisfying the needs of the customers and also taking correct decision
with proper facts and figures leading to customer’s satisfaction. This report helps in analysing
the importance of quality management in the organisation.
9
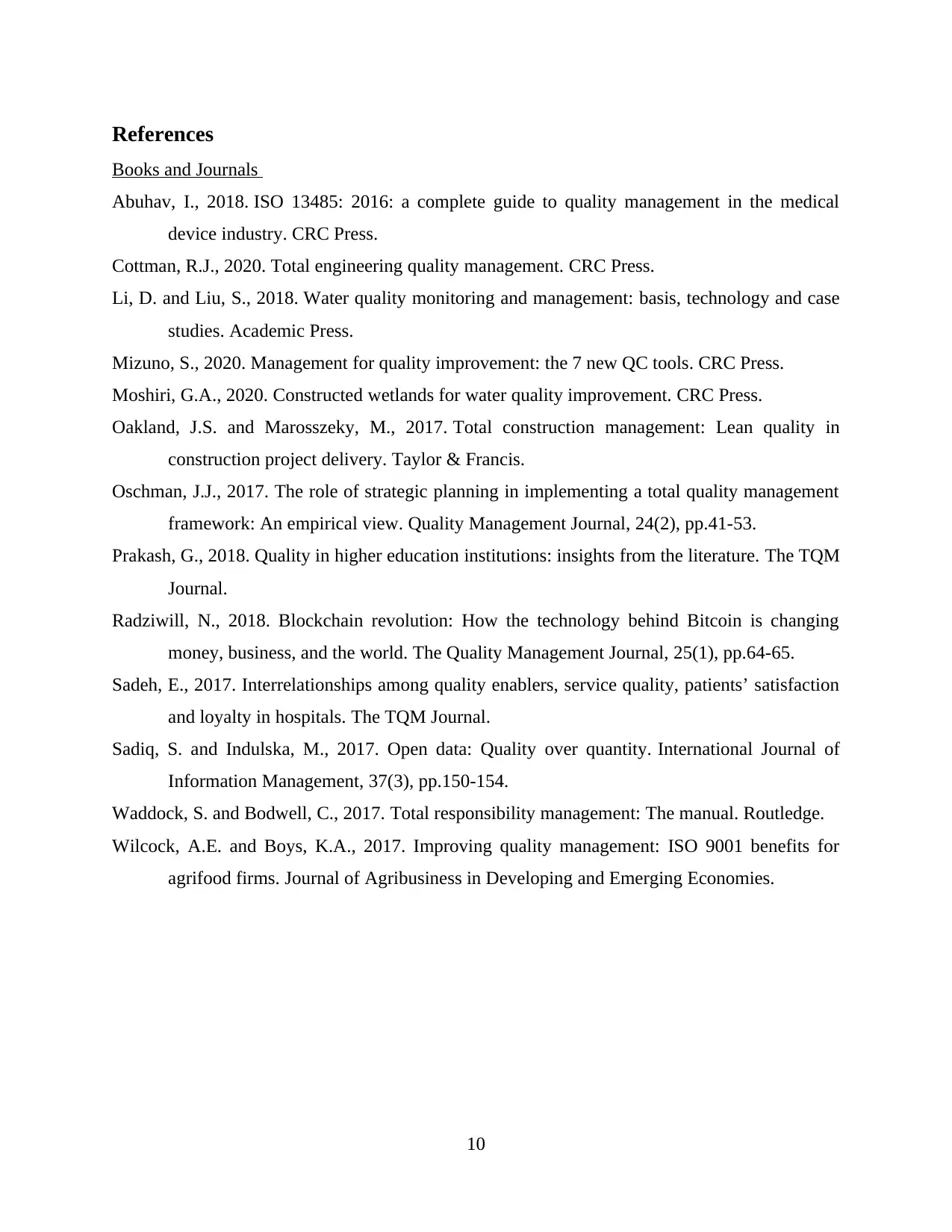
References
Books and Journals
Abuhav, I., 2018. ISO 13485: 2016: a complete guide to quality management in the medical
device industry. CRC Press.
Cottman, R.J., 2020. Total engineering quality management. CRC Press.
Li, D. and Liu, S., 2018. Water quality monitoring and management: basis, technology and case
studies. Academic Press.
Mizuno, S., 2020. Management for quality improvement: the 7 new QC tools. CRC Press.
Moshiri, G.A., 2020. Constructed wetlands for water quality improvement. CRC Press.
Oakland, J.S. and Marosszeky, M., 2017. Total construction management: Lean quality in
construction project delivery. Taylor & Francis.
Oschman, J.J., 2017. The role of strategic planning in implementing a total quality management
framework: An empirical view. Quality Management Journal, 24(2), pp.41-53.
Prakash, G., 2018. Quality in higher education institutions: insights from the literature. The TQM
Journal.
Radziwill, N., 2018. Blockchain revolution: How the technology behind Bitcoin is changing
money, business, and the world. The Quality Management Journal, 25(1), pp.64-65.
Sadeh, E., 2017. Interrelationships among quality enablers, service quality, patients’ satisfaction
and loyalty in hospitals. The TQM Journal.
Sadiq, S. and Indulska, M., 2017. Open data: Quality over quantity. International Journal of
Information Management, 37(3), pp.150-154.
Waddock, S. and Bodwell, C., 2017. Total responsibility management: The manual. Routledge.
Wilcock, A.E. and Boys, K.A., 2017. Improving quality management: ISO 9001 benefits for
agrifood firms. Journal of Agribusiness in Developing and Emerging Economies.
10
Books and Journals
Abuhav, I., 2018. ISO 13485: 2016: a complete guide to quality management in the medical
device industry. CRC Press.
Cottman, R.J., 2020. Total engineering quality management. CRC Press.
Li, D. and Liu, S., 2018. Water quality monitoring and management: basis, technology and case
studies. Academic Press.
Mizuno, S., 2020. Management for quality improvement: the 7 new QC tools. CRC Press.
Moshiri, G.A., 2020. Constructed wetlands for water quality improvement. CRC Press.
Oakland, J.S. and Marosszeky, M., 2017. Total construction management: Lean quality in
construction project delivery. Taylor & Francis.
Oschman, J.J., 2017. The role of strategic planning in implementing a total quality management
framework: An empirical view. Quality Management Journal, 24(2), pp.41-53.
Prakash, G., 2018. Quality in higher education institutions: insights from the literature. The TQM
Journal.
Radziwill, N., 2018. Blockchain revolution: How the technology behind Bitcoin is changing
money, business, and the world. The Quality Management Journal, 25(1), pp.64-65.
Sadeh, E., 2017. Interrelationships among quality enablers, service quality, patients’ satisfaction
and loyalty in hospitals. The TQM Journal.
Sadiq, S. and Indulska, M., 2017. Open data: Quality over quantity. International Journal of
Information Management, 37(3), pp.150-154.
Waddock, S. and Bodwell, C., 2017. Total responsibility management: The manual. Routledge.
Wilcock, A.E. and Boys, K.A., 2017. Improving quality management: ISO 9001 benefits for
agrifood firms. Journal of Agribusiness in Developing and Emerging Economies.
10
1 out of 12
Related Documents

Your All-in-One AI-Powered Toolkit for Academic Success.
+13062052269
info@desklib.com
Available 24*7 on WhatsApp / Email
Unlock your academic potential
© 2024 | Zucol Services PVT LTD | All rights reserved.