Improving Panalpina's Supplier Relationships: A Report
VerifiedAdded on 2021/03/03
|17
|6040
|59
Report
AI Summary
This report delves into Panalpina's supplier relationships, a Swiss provider of forwarding and logistics services and a leading supply chain solutions provider. It identifies five key factors influencing these relationships: developing relationship capabilities, mutual benefits and needs, continuous improvement, performance metrics, and building trust. The report then proposes solutions to enhance these relationships, including fostering personal relationships, building trust, improving information sharing and communication, and implementing continuous improvement strategies. Furthermore, it outlines Panalpina's modes of transportation, warehousing services, and performance management systems, including the Balanced Scorecard (BSC). The report emphasizes the importance of the SCOR model and suggests expanding its application to involve subcontractors for aligned goals. It also highlights the role of information sharing, trust-building, and transparent contracts in strengthening supplier relationships, ultimately leading to improved supply chain responsiveness and customer satisfaction.
Contribute Materials
Your contribution can guide someone’s learning journey. Share your
documents today.

1
Table of Contents
1. Executive Summary 2
2. Introduction 2
3. Five factor affect Panalpina's supplier relationships 2-5
4. Solution or suggestion to improve Panalpina's supplier relationships 5-7
5. Five modes of transportations and Five warehousing service 7-10
6. Performance management systems and solution or suggestion on improve its
system 10-12
7. Conclusion 13
8. Reference List 14-20
Table of Contents
1. Executive Summary 2
2. Introduction 2
3. Five factor affect Panalpina's supplier relationships 2-5
4. Solution or suggestion to improve Panalpina's supplier relationships 5-7
5. Five modes of transportations and Five warehousing service 7-10
6. Performance management systems and solution or suggestion on improve its
system 10-12
7. Conclusion 13
8. Reference List 14-20
Secure Best Marks with AI Grader
Need help grading? Try our AI Grader for instant feedback on your assignments.

2
A. Executive Summary
Panalpina Group is a Swiss provider of forwarding and logistics services. The
Panalpina Group is one of the world's leading providers of supply chain solutions.
The factor that affect Panalpina’s supplier relationships which are developing
relationship capabilities,mutual benefits and needs,continuous
improvement,performance metrics and building trust. In additional, the solution or the
suggestion that improve on the Panalpina ‘s supplier relationships are personal
relationship to improve supplier relationship, improving supplier relationship by
building trust, information sharing and sines of communication and improving
supplier relationship through continuous Improvement. Panalpina adopted 5 modes of
transportations and 5 types of warehousing service such as water, air, rail , motor and
pipeline carries. Warehouse management system, order and freight
management,refrigerated warehouse, assembly and reverse logistics those are the
service that Panalpina adopted. Supply Chain Management is a system that uses the
right channel to send the right quantity amount of goods in the right time to customers
(Balakannan et. al., 2016). Panalpina employs a holistic performance management
system which encompasses sustainability, environmental performance, social
responsibility, the health and safety of employees, and solid business management
and processes (Panalpina 2018 Sustainability Report, 2019). Panalpina employs an
integrated management system to ensure the steady advancement of the quality of all
services (Panalpina,2019). Another aspect of performance management that Panalpina
emphasised on is employee safety. In performance evaluation, Panalpina uses a
Balanced Scorecard (BSC) that analyses performance on four aspects: financial,
customer, business process, and R&D (Peters, 2011).
A. Executive Summary
Panalpina Group is a Swiss provider of forwarding and logistics services. The
Panalpina Group is one of the world's leading providers of supply chain solutions.
The factor that affect Panalpina’s supplier relationships which are developing
relationship capabilities,mutual benefits and needs,continuous
improvement,performance metrics and building trust. In additional, the solution or the
suggestion that improve on the Panalpina ‘s supplier relationships are personal
relationship to improve supplier relationship, improving supplier relationship by
building trust, information sharing and sines of communication and improving
supplier relationship through continuous Improvement. Panalpina adopted 5 modes of
transportations and 5 types of warehousing service such as water, air, rail , motor and
pipeline carries. Warehouse management system, order and freight
management,refrigerated warehouse, assembly and reverse logistics those are the
service that Panalpina adopted. Supply Chain Management is a system that uses the
right channel to send the right quantity amount of goods in the right time to customers
(Balakannan et. al., 2016). Panalpina employs a holistic performance management
system which encompasses sustainability, environmental performance, social
responsibility, the health and safety of employees, and solid business management
and processes (Panalpina 2018 Sustainability Report, 2019). Panalpina employs an
integrated management system to ensure the steady advancement of the quality of all
services (Panalpina,2019). Another aspect of performance management that Panalpina
emphasised on is employee safety. In performance evaluation, Panalpina uses a
Balanced Scorecard (BSC) that analyses performance on four aspects: financial,
customer, business process, and R&D (Peters, 2011).

3
B. Introduction of Panalpina Group
Panalpina Group is a Swiss company, is a provider of forwarding and logistics
services (Wikipedia,2019). The Panalpina Group is one of the world's leading
providers of supply chain solutions. The company combines its core products – Air
Freight, Ocean Freight, and Logistics and Manufacturing – to deliver globally
integrated, tailor-made end-to-end solutions for twelve core industries
(Panalpina,2019). Panalpina uses industry-wide technology and custom IT systems to
manage the needs of its customer supply chain, no matter how demanding they may
be. Drawing on in-depth industry know-how and customized IT systems, Panalpina
manages the needs of its customers' supply chains, no matter how demanding they
might be. Project Solutions is a specialized service for the energy and capital projects
sector. he project solution is a professional service for the energy and capital project
department. The Panalpina Group has approximately 500 offices in around 70
countries, and it works with partner companies in another 100 countries. Panalpina
employs approximately 14,500 people worldwide who deliver a comprehensive
service to the highest quality standards – wherever and whenever (Panalpina,2019).
I. Five factor affect Panalpina’s supplier relationships
There are five factors that affected the Panalpina’s supplier relationship. The first
factor is developing relationship capabilities. Panalpina has incorporate with Apollo
for creating long-time relationships company in Perth (Panalpina 2018). The long-
term relationship with Apollo Perth was created because of Panalpina offer the entire
transportation and logistics product portfolio under one roof, as a panalpina unit. This
refers specifically to local. The key qualities that Panalpina seeks in reaching
agreements with Apollo Perth to have long-term supplier relationship are global
networking, financial in strong positon, IT integration and service reliability.
Therefore, the correct capabilities can affect the relationship with suppliers as well as
customers.
Other than that, the factor that can affected Panalpina’s supplier relationship is mutual
benefits and needs. Due to their mutual geographic networks and analogous business
B. Introduction of Panalpina Group
Panalpina Group is a Swiss company, is a provider of forwarding and logistics
services (Wikipedia,2019). The Panalpina Group is one of the world's leading
providers of supply chain solutions. The company combines its core products – Air
Freight, Ocean Freight, and Logistics and Manufacturing – to deliver globally
integrated, tailor-made end-to-end solutions for twelve core industries
(Panalpina,2019). Panalpina uses industry-wide technology and custom IT systems to
manage the needs of its customer supply chain, no matter how demanding they may
be. Drawing on in-depth industry know-how and customized IT systems, Panalpina
manages the needs of its customers' supply chains, no matter how demanding they
might be. Project Solutions is a specialized service for the energy and capital projects
sector. he project solution is a professional service for the energy and capital project
department. The Panalpina Group has approximately 500 offices in around 70
countries, and it works with partner companies in another 100 countries. Panalpina
employs approximately 14,500 people worldwide who deliver a comprehensive
service to the highest quality standards – wherever and whenever (Panalpina,2019).
I. Five factor affect Panalpina’s supplier relationships
There are five factors that affected the Panalpina’s supplier relationship. The first
factor is developing relationship capabilities. Panalpina has incorporate with Apollo
for creating long-time relationships company in Perth (Panalpina 2018). The long-
term relationship with Apollo Perth was created because of Panalpina offer the entire
transportation and logistics product portfolio under one roof, as a panalpina unit. This
refers specifically to local. The key qualities that Panalpina seeks in reaching
agreements with Apollo Perth to have long-term supplier relationship are global
networking, financial in strong positon, IT integration and service reliability.
Therefore, the correct capabilities can affect the relationship with suppliers as well as
customers.
Other than that, the factor that can affected Panalpina’s supplier relationship is mutual
benefits and needs. Due to their mutual geographic networks and analogous business

4
models, Panalpina and the NYK subsidiary Yusen Air & Sea Service (YAS) can
preferably bolster each other. The agreement will give both sides with new business
opportunities to increase efficiency while reducing costs. The agency agreement with
Yusen Air and Sea Services will enable Panalpina to integrate all its services,
procurement and domestic activities in Japan. Simultaneously, YAS will access
Panalpina's broad system and market knowledge. Panalpina and YAS will have a
broader customer base and operate efficiently. In addition, they will improve their
competitive edge in Japanese and Asian trading markets. This cooperation has created
global advantages for both sides in their respective markets, including mutually
beneficial co-loading opportunities. Therefore, both sides will strengthen their
respective networks and procurement capabilities to achieve mutual benefit on a
global basis (Panalpina 2018).
Furthermore, the third factor that affecting Panalpina’s supplier relationship is
continuous improvement. Validaide is Panalpina’s supplier, Validaide is an open
platform with a unique community approach (Air Chargo World 2019). All of its
remaining divisions are scheduled to go live on the Validaide platform by the end of
the first quarter of 2018. Focus on air cargo vessels as a tool for qualified suppliers
and assessing the risks of transport routes. The new Panprojects operator service
enables Panalpina to oversee multi-mode heavy lift transport from one end to the
other under a single contract that governs all modes of transport (The Stat Trade Time
2019). In addition, the digital tool they developed is the Validaide system, which
allows Panalpina and its customers to increase the transparency of their carriers and
routes. To further facilitate Panalpina's digital transformation, Validaide has created a
new head of digital innovation position that reports directly to Panalpina.
Moreover, the fourth factor that affects Panalpina’s supplier relationship is
performance metrics. Kosmos is a hacker team and also one of the Panalpina’s
supplier. Kosmos proposed a blockchain method for Panalpina within 42 hours for the
movement of goods in the medical and pharmaceutical supply chains (My news deak
2019). They ensure traceability and authentication of unique goods such as
pharmaceuticals in the pharmaceutical supply chain, and design standards that enable
models, Panalpina and the NYK subsidiary Yusen Air & Sea Service (YAS) can
preferably bolster each other. The agreement will give both sides with new business
opportunities to increase efficiency while reducing costs. The agency agreement with
Yusen Air and Sea Services will enable Panalpina to integrate all its services,
procurement and domestic activities in Japan. Simultaneously, YAS will access
Panalpina's broad system and market knowledge. Panalpina and YAS will have a
broader customer base and operate efficiently. In addition, they will improve their
competitive edge in Japanese and Asian trading markets. This cooperation has created
global advantages for both sides in their respective markets, including mutually
beneficial co-loading opportunities. Therefore, both sides will strengthen their
respective networks and procurement capabilities to achieve mutual benefit on a
global basis (Panalpina 2018).
Furthermore, the third factor that affecting Panalpina’s supplier relationship is
continuous improvement. Validaide is Panalpina’s supplier, Validaide is an open
platform with a unique community approach (Air Chargo World 2019). All of its
remaining divisions are scheduled to go live on the Validaide platform by the end of
the first quarter of 2018. Focus on air cargo vessels as a tool for qualified suppliers
and assessing the risks of transport routes. The new Panprojects operator service
enables Panalpina to oversee multi-mode heavy lift transport from one end to the
other under a single contract that governs all modes of transport (The Stat Trade Time
2019). In addition, the digital tool they developed is the Validaide system, which
allows Panalpina and its customers to increase the transparency of their carriers and
routes. To further facilitate Panalpina's digital transformation, Validaide has created a
new head of digital innovation position that reports directly to Panalpina.
Moreover, the fourth factor that affects Panalpina’s supplier relationship is
performance metrics. Kosmos is a hacker team and also one of the Panalpina’s
supplier. Kosmos proposed a blockchain method for Panalpina within 42 hours for the
movement of goods in the medical and pharmaceutical supply chains (My news deak
2019). They ensure traceability and authentication of unique goods such as
pharmaceuticals in the pharmaceutical supply chain, and design standards that enable
Secure Best Marks with AI Grader
Need help grading? Try our AI Grader for instant feedback on your assignments.

5
different applications to create and partake visible event data within and across the
company. Blockchain technology offers a variety of solutions which are from
standards-compliant manufacturing to tamper-proof packaging and down to
temperature-controlled storage, transportation and delivery. They created a series of
tamper-proof activities by coding in the blockchain. For each new shipping milestone,
they aggregate all events into the detail of a new block and attach it to the blockchain.
Therefore, Kosmos team was participated in 42 hours of planning, hacking,
progressing and refining. It obtained valuable foresights into the new technologies.
Lastly, building trust is one of the factor that affecting Panalpina’s supplier
relationship. Bosch Group is one of the supplier of Panalpina, Bosch Group in South
Germany recognizes Panalpina's achievements in quality service, economy and on-
time delivery during 2001/2002 (HKTDC 2019). Bosch Group gave award to
Panalpina due to trusted services of Panlpina. In the result, it can be seen the
flexibility and reliability of panalpina have led to a partnership based on trust and
mutual respect.
II. Solution or suggestion to improve Panalpina's supplier relationships
Improving Supplier Relationship through Continuous Improvement
Bhuiyan and Baghel (2005) defines continuous improvement as culture of sustained
improvement targeting the elimination of waste in all systems and process in an
organisation. From the definition, we can imply that the changes are incremental with
attention to details that ultimately achieve waste reduction and quality improvement
(Bessant and Caffyn, 1997). In Panalpina, continuous improvement is imperative to
its business. The company uses the SCOR model to provide benchmarking to evaluate
its sea freight forwarding operations (Ramotsedisi, 2011). The SCOR model was
developed by the Supply Chain Council (http://www.supply-chain.org) with the
purpose to address, improve, and communicate supply chain management decisions
within a company and with suppliers and customers of a company. It describes the
business process in the entire supply chain and provides a basis on how to satisfy
customers. The model has helped Panalpina in establishing best practices in its sea
freight segment (Ramotsedisi, 2011). In view of the effectiveness of SCOR, we
different applications to create and partake visible event data within and across the
company. Blockchain technology offers a variety of solutions which are from
standards-compliant manufacturing to tamper-proof packaging and down to
temperature-controlled storage, transportation and delivery. They created a series of
tamper-proof activities by coding in the blockchain. For each new shipping milestone,
they aggregate all events into the detail of a new block and attach it to the blockchain.
Therefore, Kosmos team was participated in 42 hours of planning, hacking,
progressing and refining. It obtained valuable foresights into the new technologies.
Lastly, building trust is one of the factor that affecting Panalpina’s supplier
relationship. Bosch Group is one of the supplier of Panalpina, Bosch Group in South
Germany recognizes Panalpina's achievements in quality service, economy and on-
time delivery during 2001/2002 (HKTDC 2019). Bosch Group gave award to
Panalpina due to trusted services of Panlpina. In the result, it can be seen the
flexibility and reliability of panalpina have led to a partnership based on trust and
mutual respect.
II. Solution or suggestion to improve Panalpina's supplier relationships
Improving Supplier Relationship through Continuous Improvement
Bhuiyan and Baghel (2005) defines continuous improvement as culture of sustained
improvement targeting the elimination of waste in all systems and process in an
organisation. From the definition, we can imply that the changes are incremental with
attention to details that ultimately achieve waste reduction and quality improvement
(Bessant and Caffyn, 1997). In Panalpina, continuous improvement is imperative to
its business. The company uses the SCOR model to provide benchmarking to evaluate
its sea freight forwarding operations (Ramotsedisi, 2011). The SCOR model was
developed by the Supply Chain Council (http://www.supply-chain.org) with the
purpose to address, improve, and communicate supply chain management decisions
within a company and with suppliers and customers of a company. It describes the
business process in the entire supply chain and provides a basis on how to satisfy
customers. The model has helped Panalpina in establishing best practices in its sea
freight segment (Ramotsedisi, 2011). In view of the effectiveness of SCOR, we

6
suggest that the company expand the model to involve its sub-contractors in other
segments of its businesses. This is because by communicating supply chain
management decisions to suppliers, the directions and goals of both sides can be
aligned. Both the company and suppliers can better manage the expectations towards
each other. This will improve the supply relationship because both sides can enjoy
mutual benefits such as reduced costs and streamlined process (Forker, Ruch &
Hershauer, 1999). In addition, Panalpina can also assist by lending its expertise in
implementing SCOR to its suppliers. The company can benefit from the reciprocal
relationship from the suppliers as a result of improvements in quality. Both sides can
achieve greater financial goals by helping each other and sharing a better relationship.
Information Sharing and Lines of Communication
In supply chain management, the flow of material, information, and financial is the
core concern of supply chain providers (Lee and Whang, 2000). Information such as
inventory, sales, demand forecasting, order status and production schedule are among
the information shared between partners to better coordinate their business operations
(Lee and Whang, 2000). According to study (Lee, So & Tang, 2000), information
sharing in supply chain brings benefits such as costs reduction and inventory
reduction. These mutual benefits will improve the company-suppliers relationship in
the long run because both sides have a shared goal to aim for. While Panalpina put a
lot of emphasis on managing sub-contractors, we suggest the company to improve its
communications with them. It has several modes of communications it can utilize but
modern, electronic communications such as e-mail, EDI, intranet, and e-markets have
become more prevalent (Olhager and Selldin, 2003). The emergence of internet-based
systems has enabled fast and cost-effective information sharing (Lee and Whang,
2000). In addition, we propose the use of an information hub system as demonstrated
in a study (Lee and Whang, 2000) for this purpose. Information on both sides are fed
into an electronic, internet-based system that can be accessed anytime for reference.
Finally, Panalpina can involve suppliers in meetings to allow them the opportunities
to air their grievances and suggestions. This will avoid miscommunications and clear
up misunderstanding and benefits both sides in long term relationships. It can make
the relationship between Panalpina and suppliers becomes more meaningful (Industry
Week, 2009).
suggest that the company expand the model to involve its sub-contractors in other
segments of its businesses. This is because by communicating supply chain
management decisions to suppliers, the directions and goals of both sides can be
aligned. Both the company and suppliers can better manage the expectations towards
each other. This will improve the supply relationship because both sides can enjoy
mutual benefits such as reduced costs and streamlined process (Forker, Ruch &
Hershauer, 1999). In addition, Panalpina can also assist by lending its expertise in
implementing SCOR to its suppliers. The company can benefit from the reciprocal
relationship from the suppliers as a result of improvements in quality. Both sides can
achieve greater financial goals by helping each other and sharing a better relationship.
Information Sharing and Lines of Communication
In supply chain management, the flow of material, information, and financial is the
core concern of supply chain providers (Lee and Whang, 2000). Information such as
inventory, sales, demand forecasting, order status and production schedule are among
the information shared between partners to better coordinate their business operations
(Lee and Whang, 2000). According to study (Lee, So & Tang, 2000), information
sharing in supply chain brings benefits such as costs reduction and inventory
reduction. These mutual benefits will improve the company-suppliers relationship in
the long run because both sides have a shared goal to aim for. While Panalpina put a
lot of emphasis on managing sub-contractors, we suggest the company to improve its
communications with them. It has several modes of communications it can utilize but
modern, electronic communications such as e-mail, EDI, intranet, and e-markets have
become more prevalent (Olhager and Selldin, 2003). The emergence of internet-based
systems has enabled fast and cost-effective information sharing (Lee and Whang,
2000). In addition, we propose the use of an information hub system as demonstrated
in a study (Lee and Whang, 2000) for this purpose. Information on both sides are fed
into an electronic, internet-based system that can be accessed anytime for reference.
Finally, Panalpina can involve suppliers in meetings to allow them the opportunities
to air their grievances and suggestions. This will avoid miscommunications and clear
up misunderstanding and benefits both sides in long term relationships. It can make
the relationship between Panalpina and suppliers becomes more meaningful (Industry
Week, 2009).
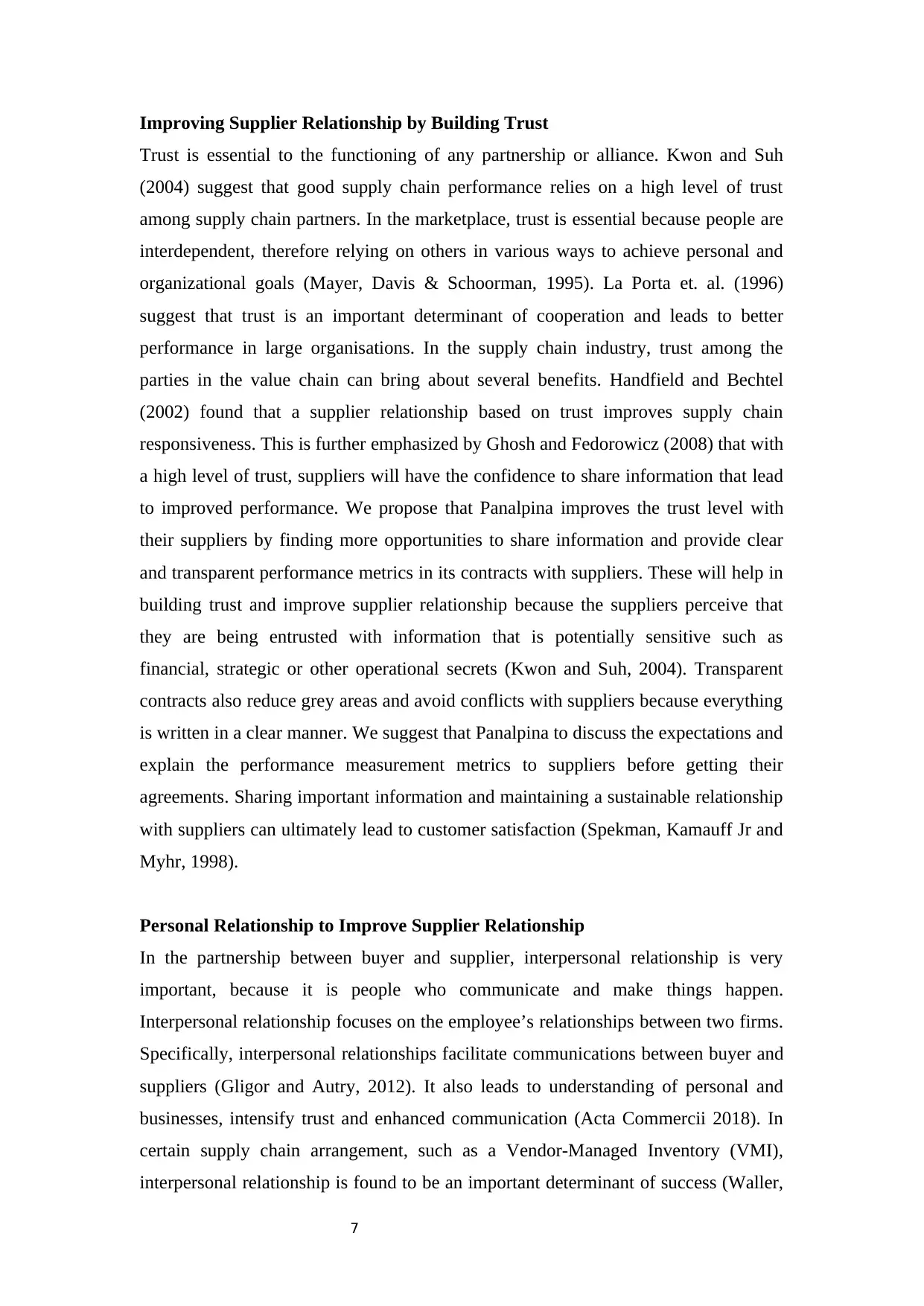
7
Improving Supplier Relationship by Building Trust
Trust is essential to the functioning of any partnership or alliance. Kwon and Suh
(2004) suggest that good supply chain performance relies on a high level of trust
among supply chain partners. In the marketplace, trust is essential because people are
interdependent, therefore relying on others in various ways to achieve personal and
organizational goals (Mayer, Davis & Schoorman, 1995). La Porta et. al. (1996)
suggest that trust is an important determinant of cooperation and leads to better
performance in large organisations. In the supply chain industry, trust among the
parties in the value chain can bring about several benefits. Handfield and Bechtel
(2002) found that a supplier relationship based on trust improves supply chain
responsiveness. This is further emphasized by Ghosh and Fedorowicz (2008) that with
a high level of trust, suppliers will have the confidence to share information that lead
to improved performance. We propose that Panalpina improves the trust level with
their suppliers by finding more opportunities to share information and provide clear
and transparent performance metrics in its contracts with suppliers. These will help in
building trust and improve supplier relationship because the suppliers perceive that
they are being entrusted with information that is potentially sensitive such as
financial, strategic or other operational secrets (Kwon and Suh, 2004). Transparent
contracts also reduce grey areas and avoid conflicts with suppliers because everything
is written in a clear manner. We suggest that Panalpina to discuss the expectations and
explain the performance measurement metrics to suppliers before getting their
agreements. Sharing important information and maintaining a sustainable relationship
with suppliers can ultimately lead to customer satisfaction (Spekman, Kamauff Jr and
Myhr, 1998).
Personal Relationship to Improve Supplier Relationship
In the partnership between buyer and supplier, interpersonal relationship is very
important, because it is people who communicate and make things happen.
Interpersonal relationship focuses on the employee’s relationships between two firms.
Specifically, interpersonal relationships facilitate communications between buyer and
suppliers (Gligor and Autry, 2012). It also leads to understanding of personal and
businesses, intensify trust and enhanced communication (Acta Commercii 2018). In
certain supply chain arrangement, such as a Vendor-Managed Inventory (VMI),
interpersonal relationship is found to be an important determinant of success (Waller,
Improving Supplier Relationship by Building Trust
Trust is essential to the functioning of any partnership or alliance. Kwon and Suh
(2004) suggest that good supply chain performance relies on a high level of trust
among supply chain partners. In the marketplace, trust is essential because people are
interdependent, therefore relying on others in various ways to achieve personal and
organizational goals (Mayer, Davis & Schoorman, 1995). La Porta et. al. (1996)
suggest that trust is an important determinant of cooperation and leads to better
performance in large organisations. In the supply chain industry, trust among the
parties in the value chain can bring about several benefits. Handfield and Bechtel
(2002) found that a supplier relationship based on trust improves supply chain
responsiveness. This is further emphasized by Ghosh and Fedorowicz (2008) that with
a high level of trust, suppliers will have the confidence to share information that lead
to improved performance. We propose that Panalpina improves the trust level with
their suppliers by finding more opportunities to share information and provide clear
and transparent performance metrics in its contracts with suppliers. These will help in
building trust and improve supplier relationship because the suppliers perceive that
they are being entrusted with information that is potentially sensitive such as
financial, strategic or other operational secrets (Kwon and Suh, 2004). Transparent
contracts also reduce grey areas and avoid conflicts with suppliers because everything
is written in a clear manner. We suggest that Panalpina to discuss the expectations and
explain the performance measurement metrics to suppliers before getting their
agreements. Sharing important information and maintaining a sustainable relationship
with suppliers can ultimately lead to customer satisfaction (Spekman, Kamauff Jr and
Myhr, 1998).
Personal Relationship to Improve Supplier Relationship
In the partnership between buyer and supplier, interpersonal relationship is very
important, because it is people who communicate and make things happen.
Interpersonal relationship focuses on the employee’s relationships between two firms.
Specifically, interpersonal relationships facilitate communications between buyer and
suppliers (Gligor and Autry, 2012). It also leads to understanding of personal and
businesses, intensify trust and enhanced communication (Acta Commercii 2018). In
certain supply chain arrangement, such as a Vendor-Managed Inventory (VMI),
interpersonal relationship is found to be an important determinant of success (Waller,
Paraphrase This Document
Need a fresh take? Get an instant paraphrase of this document with our AI Paraphraser

8
Johnson and Davis, 1999). Study by Cai, Jun and Yang (2010) found that
interpersonal relationship affect trust which in turn facilitate information sharing and
collaborative planning. In view of the benefits, we propose that Panalpina to look into
ways to use interpersonal relationships to improve supplier relationship. Findings by
Jiang, Henneberg and Naude (2012) suggest the long-term importance of investing in
human resource assets as well as relationship-specific activities and resources. Top
management in Panalpina should commit resources to train managers and mid-levels
decision-makers to enhance their interpersonal skills. This will give them better
communication skills required to build trust with their counterparts from supplier
firms. The company can also invest in activities that facilitate exchange at
interpersonal level such as anniversary parties or weekend get-together between
managers. This will give them the opportunity to build relationship and communicate
at a personal level.
III. Five modes of transportation
Water Carriers
The first mode of transportation that Panalpina use to ship the cargo is water carriers.
Panalpina is the world’s fourth largest provider of ocean freight services. Panalpina
appreciates organizations with most of the world's greatest sea bearers, contracting
space assignments on an assortment of their courses to oversee limit in accordance
with the interest from its client base. For Panalpina, a worldwide system,
administration dependability, IT joining and budgetary solidness are the significant
characteristics it searches for when protecting concurrences with long haul
accomplices. Panalpina offers three services by using water carriers. The first services
is full container load (FCL), it is the delivery choice that makes up most of
Panalpina's Sea Cargo administration and it includes shipping a full holder as a
solitary unit. For clients this is commonly the quickest and most proficient approach
to move items. The second services is less than container load (LCL), It involves
moving goods that are not full of containers. The goods are used in conjunction with
other goods to maximize the load factor of the container. Customers who ship goods
to the same region or destination can obtain a lower quantity of freight transport,
resulting in economies of scale that are usually limited to complete container
Johnson and Davis, 1999). Study by Cai, Jun and Yang (2010) found that
interpersonal relationship affect trust which in turn facilitate information sharing and
collaborative planning. In view of the benefits, we propose that Panalpina to look into
ways to use interpersonal relationships to improve supplier relationship. Findings by
Jiang, Henneberg and Naude (2012) suggest the long-term importance of investing in
human resource assets as well as relationship-specific activities and resources. Top
management in Panalpina should commit resources to train managers and mid-levels
decision-makers to enhance their interpersonal skills. This will give them better
communication skills required to build trust with their counterparts from supplier
firms. The company can also invest in activities that facilitate exchange at
interpersonal level such as anniversary parties or weekend get-together between
managers. This will give them the opportunity to build relationship and communicate
at a personal level.
III. Five modes of transportation
Water Carriers
The first mode of transportation that Panalpina use to ship the cargo is water carriers.
Panalpina is the world’s fourth largest provider of ocean freight services. Panalpina
appreciates organizations with most of the world's greatest sea bearers, contracting
space assignments on an assortment of their courses to oversee limit in accordance
with the interest from its client base. For Panalpina, a worldwide system,
administration dependability, IT joining and budgetary solidness are the significant
characteristics it searches for when protecting concurrences with long haul
accomplices. Panalpina offers three services by using water carriers. The first services
is full container load (FCL), it is the delivery choice that makes up most of
Panalpina's Sea Cargo administration and it includes shipping a full holder as a
solitary unit. For clients this is commonly the quickest and most proficient approach
to move items. The second services is less than container load (LCL), It involves
moving goods that are not full of containers. The goods are used in conjunction with
other goods to maximize the load factor of the container. Customers who ship goods
to the same region or destination can obtain a lower quantity of freight transport,
resulting in economies of scale that are usually limited to complete container

9
transport. The third services is non-containerized load, NCL services cover goods that
require special handling and are not included in standard containers or oversized
goods are not suitable for standard containers. In addition to moving the goods
through ships, Panalpina arranges road or other transport assistance for the final
destination. Panalpina provide wide range of service option, including door-to-door,
port-to-port, door-to-port and port-to-door. Whether it is standard shipment or
complex projects, Panalpina always provides customers with the right solutions to
meet their transportation needs. Panalpina's shipping experts operate in 500 locations
in more than 80 countries and are ready to use their experience, expertise and
creativity to find appropriate solutions for customers anytime, anywhere.
Air Carriers
The second mode of transportation that adopted by Panalpina is air planes services.
There are four Air Freight service lines which is General, Special, Express, and
intermodal. General air freight service means for the goods that do not require special
handling and there are two service levels in general air freight service which is
PanPremium and PanBasic. PanPremium means a flexible and regular transport
option with priority access to capacity and short transit times at a fair price and
PanBasic means a low-cost air freight option that is focuses on price more than
flexibility. Moreover, special air freight means for the products that require special
handling, transportation and storage. Panalpina offers variety services that fall under
special air freight is that PanCool for temperature-sensitive goods, PanProtect for
high-value goods, PanFresh for perishables, PanOversized for out-of-gauge food and
PanCare for dangerous goods. Express Air Freight It is the fastest way to transport
goods in the world. Because it ensures the capacity of the aircraft and accelerates
processing and transportation on the ground, it runs like a clockwork. Intermodal
Freight means Panalpina's multimodal transport service series combines the time-
saving advantages of air transportation with the cost-saving advantages of shipping.
Multimodal transport makes full use of the sky and oceans to provide your goods in
the most efficient and cost-effective manner. There are two levels of multimodal
transport services available-both of which reduce transport time by 50% compared
with pure shipping which is PanSeaAir and PanAirSea. PanSeaAir means the service
transport. The third services is non-containerized load, NCL services cover goods that
require special handling and are not included in standard containers or oversized
goods are not suitable for standard containers. In addition to moving the goods
through ships, Panalpina arranges road or other transport assistance for the final
destination. Panalpina provide wide range of service option, including door-to-door,
port-to-port, door-to-port and port-to-door. Whether it is standard shipment or
complex projects, Panalpina always provides customers with the right solutions to
meet their transportation needs. Panalpina's shipping experts operate in 500 locations
in more than 80 countries and are ready to use their experience, expertise and
creativity to find appropriate solutions for customers anytime, anywhere.
Air Carriers
The second mode of transportation that adopted by Panalpina is air planes services.
There are four Air Freight service lines which is General, Special, Express, and
intermodal. General air freight service means for the goods that do not require special
handling and there are two service levels in general air freight service which is
PanPremium and PanBasic. PanPremium means a flexible and regular transport
option with priority access to capacity and short transit times at a fair price and
PanBasic means a low-cost air freight option that is focuses on price more than
flexibility. Moreover, special air freight means for the products that require special
handling, transportation and storage. Panalpina offers variety services that fall under
special air freight is that PanCool for temperature-sensitive goods, PanProtect for
high-value goods, PanFresh for perishables, PanOversized for out-of-gauge food and
PanCare for dangerous goods. Express Air Freight It is the fastest way to transport
goods in the world. Because it ensures the capacity of the aircraft and accelerates
processing and transportation on the ground, it runs like a clockwork. Intermodal
Freight means Panalpina's multimodal transport service series combines the time-
saving advantages of air transportation with the cost-saving advantages of shipping.
Multimodal transport makes full use of the sky and oceans to provide your goods in
the most efficient and cost-effective manner. There are two levels of multimodal
transport services available-both of which reduce transport time by 50% compared
with pure shipping which is PanSeaAir and PanAirSea. PanSeaAir means the service

10
starts the sea journey and is completed by air and PanAirSea is the service began to
sail and was completed by sea. It is an ideal choice to reach remote coastal areas.
Motor Carriers
The third mode of transportation that adopted by Panalpina is trucking. Panalpina
offers its customers reliable and time-definite door-to-door transport. Panalpina had
practical experience in creating and working client explicit trucking administrations
for conveyance or inbound coordinations. Execution control through control tower
structures and characterized key execution markers, upheld by our IT arrangements,
guarantee an ideal material stream inside your inventory network. By associating our
areas, we can offer you customized answers for full truck or not exactly full truck
freight loads. Full Truck Load (FTL) speaks to the quickest way to-entryway
administration with the briefest travel, both for standard administrations just as
uncommon vehicles, similar to overwhelming or curiously large products. Moreover,
Less than Truck Load (LTL) and consolidation means cost-effective option in contrast
to exclusively bundled shipments with most extreme adaptability and unwavering
quality. You'll profit by a complete offering of associated transport arrangements.
Rail Services
The fourth mode of transportation that adopted by Panalpina is rail mode. It is a
railway networks which directly with the railway operator and partnering with the
providers that has trusted services and experienced. This can solve customer’s
individual door-to-door solution. Panalpina can provide direct rail access and require
pre- or post-carriage in the same time with other services such as warehousing,
distribution, cargo handling and more services. However, Panalpina’s rail solutions
offer coverage in Europe and all CIS countries only. Well, China Trans-Siberian or
Central Asian routes is depending on customers’ specific requirement. For businesses,
Panalpina provide Less than Container Load (LCL) rail services that is more fast,
economical and reliable. LCL will ensure that the transport departure once a week. So
that, the rail services is more fast and economical compare with air freight and ocean
freight. This LCL is more suitable to the shipments that united from China to Europe.
Customers did not worry that the cargo are unsafe in long transport because Panalpina
has best controls and manages all operations. When the cargo pick-up from any place
starts the sea journey and is completed by air and PanAirSea is the service began to
sail and was completed by sea. It is an ideal choice to reach remote coastal areas.
Motor Carriers
The third mode of transportation that adopted by Panalpina is trucking. Panalpina
offers its customers reliable and time-definite door-to-door transport. Panalpina had
practical experience in creating and working client explicit trucking administrations
for conveyance or inbound coordinations. Execution control through control tower
structures and characterized key execution markers, upheld by our IT arrangements,
guarantee an ideal material stream inside your inventory network. By associating our
areas, we can offer you customized answers for full truck or not exactly full truck
freight loads. Full Truck Load (FTL) speaks to the quickest way to-entryway
administration with the briefest travel, both for standard administrations just as
uncommon vehicles, similar to overwhelming or curiously large products. Moreover,
Less than Truck Load (LTL) and consolidation means cost-effective option in contrast
to exclusively bundled shipments with most extreme adaptability and unwavering
quality. You'll profit by a complete offering of associated transport arrangements.
Rail Services
The fourth mode of transportation that adopted by Panalpina is rail mode. It is a
railway networks which directly with the railway operator and partnering with the
providers that has trusted services and experienced. This can solve customer’s
individual door-to-door solution. Panalpina can provide direct rail access and require
pre- or post-carriage in the same time with other services such as warehousing,
distribution, cargo handling and more services. However, Panalpina’s rail solutions
offer coverage in Europe and all CIS countries only. Well, China Trans-Siberian or
Central Asian routes is depending on customers’ specific requirement. For businesses,
Panalpina provide Less than Container Load (LCL) rail services that is more fast,
economical and reliable. LCL will ensure that the transport departure once a week. So
that, the rail services is more fast and economical compare with air freight and ocean
freight. This LCL is more suitable to the shipments that united from China to Europe.
Customers did not worry that the cargo are unsafe in long transport because Panalpina
has best controls and manages all operations. When the cargo pick-up from any place
Secure Best Marks with AI Grader
Need help grading? Try our AI Grader for instant feedback on your assignments.

11
in China and European cities, the cargo is deconsolidated across Europe by truck and
delivered to final destinations. So that, cargo is safety and fast when reach on
customers’ hands.
Pipeline Carriers
At the present time, Some of Panalpina customers that related with gas and oil is
drilling Khazzan-Makarem gas field program in Oman. This project needs 15-year to
complete. Based on Baosteels’ customer list, China’s biggest steel manufacturers
support 62 kilometers of oil pipeline in this project. The project is to lesser welding on
site just because fast-track development is meat that customer need longer time than
usual pipes. During the project of three weeks, 3600 pipes that shipped by three ships
from Shanghai was unload at the port of Duqm in Oman. In Oman, there has
Panalpina supervisor to customizing the pipe on the management transportation
engineering for last 400km to extension.
Five types of warehousing service
Reverse logistics
The first warehousing service that provided by Panalpina is reverse logistics.
Panalpina believes that reverse logistics is a strategic area for growth. In order to
supplement its reverse logistics offering in the technology field, Panalpina has entered
into a strategic coalition with Hong Kong-based company Spread Logistics. The two
companies work closely together to retrieve defective consumer electronics at origin,
perform failure analysis, and return them to the original manufacturer which is in
mainland China when necessary. Customers can understand the visibility of all
returned materials in the supply chain and make decisions about reuse, repair, disposal
and even redesign of the products based on data. Panalpina is also able to restock,
redistribute and recycle the products, components and raw materials more efficiently
and effectively. (Panalpina 2018)
Assembly
in China and European cities, the cargo is deconsolidated across Europe by truck and
delivered to final destinations. So that, cargo is safety and fast when reach on
customers’ hands.
Pipeline Carriers
At the present time, Some of Panalpina customers that related with gas and oil is
drilling Khazzan-Makarem gas field program in Oman. This project needs 15-year to
complete. Based on Baosteels’ customer list, China’s biggest steel manufacturers
support 62 kilometers of oil pipeline in this project. The project is to lesser welding on
site just because fast-track development is meat that customer need longer time than
usual pipes. During the project of three weeks, 3600 pipes that shipped by three ships
from Shanghai was unload at the port of Duqm in Oman. In Oman, there has
Panalpina supervisor to customizing the pipe on the management transportation
engineering for last 400km to extension.
Five types of warehousing service
Reverse logistics
The first warehousing service that provided by Panalpina is reverse logistics.
Panalpina believes that reverse logistics is a strategic area for growth. In order to
supplement its reverse logistics offering in the technology field, Panalpina has entered
into a strategic coalition with Hong Kong-based company Spread Logistics. The two
companies work closely together to retrieve defective consumer electronics at origin,
perform failure analysis, and return them to the original manufacturer which is in
mainland China when necessary. Customers can understand the visibility of all
returned materials in the supply chain and make decisions about reuse, repair, disposal
and even redesign of the products based on data. Panalpina is also able to restock,
redistribute and recycle the products, components and raw materials more efficiently
and effectively. (Panalpina 2018)
Assembly

12
Panalpina also provides assembly service. Panalpina is managing the assembly of
semi-knocked down units for base stations of mobile networks now. Panalpina not
only performs the final assembly, but also completely own the entire process - from
planning to quality control. In addition, there are five sections of customer’s supply
chain which are terminals, spare parts for terminals, semi-knocked down (SKD)
assembly, end products and spare parts for end products. SKD consists of five
different assembly lines. In the final assembly and test line, Panalpina employees
assembled the base station boards and cabinets as well as ran software updates and
tests. The finished products are then packaged, labelled and sent to the warehouse
next door for delivery. (Panalpina 2018)
Refrigerated warehouse
Refrigerated warehouse is also one of the warehousing service that adopted by
Panalpina. Panalpina holds a refrigerated warehouse in Carolina. The refrigerators are
mainly used by pharmaceutical companies to assure the quality of unfinished
materials and consumer products. Furthermore, the ‘Smart point’ technology can
allow customers to remotely monitor the cargo temperature and humidity control 24
hours a day, ranging from 2 degrees Celsius to 25 degrees Celsius and confirm their
goods from products pick-up to delivery. The customers will be able to reduce
transportation and storage costs and rely on Panalpina to receive their products on
time and in good condition. (News is My Business 2018)
Order and freight management
The fourth warehousing service that adopted by Panalpina is order and freight
management. In the order management product of Panalpina, customers will benefit
from enhanced order processing functions, make better visibility, automate exception
management and alerts for offering a more panoramic and granular view of the
business environment. For example, Panalpina handles the procedure from the
issuance of the purchase order to the final destination delivery so it can shorten the
delivery times. Besides that, Panalpina also administers the milestone activities and
Panalpina also provides assembly service. Panalpina is managing the assembly of
semi-knocked down units for base stations of mobile networks now. Panalpina not
only performs the final assembly, but also completely own the entire process - from
planning to quality control. In addition, there are five sections of customer’s supply
chain which are terminals, spare parts for terminals, semi-knocked down (SKD)
assembly, end products and spare parts for end products. SKD consists of five
different assembly lines. In the final assembly and test line, Panalpina employees
assembled the base station boards and cabinets as well as ran software updates and
tests. The finished products are then packaged, labelled and sent to the warehouse
next door for delivery. (Panalpina 2018)
Refrigerated warehouse
Refrigerated warehouse is also one of the warehousing service that adopted by
Panalpina. Panalpina holds a refrigerated warehouse in Carolina. The refrigerators are
mainly used by pharmaceutical companies to assure the quality of unfinished
materials and consumer products. Furthermore, the ‘Smart point’ technology can
allow customers to remotely monitor the cargo temperature and humidity control 24
hours a day, ranging from 2 degrees Celsius to 25 degrees Celsius and confirm their
goods from products pick-up to delivery. The customers will be able to reduce
transportation and storage costs and rely on Panalpina to receive their products on
time and in good condition. (News is My Business 2018)
Order and freight management
The fourth warehousing service that adopted by Panalpina is order and freight
management. In the order management product of Panalpina, customers will benefit
from enhanced order processing functions, make better visibility, automate exception
management and alerts for offering a more panoramic and granular view of the
business environment. For example, Panalpina handles the procedure from the
issuance of the purchase order to the final destination delivery so it can shorten the
delivery times. Besides that, Panalpina also administers the milestone activities and

13
disruptions and it can reduce the overall logistics expenses. Next, Panalpina enhance
the actual stages of international supply chain to lessen the net working capital.
(Panalpina 2018)
Warehouse management system
The last warehousing service that adopted by Panalpina is warehouse management
system. Panalpina declares its intention to dispose a single warehouse management
system (WMS) in all of its global logistics facilities. The launch of WMS is based on
Panalpina's logistics strategy and is the first 3PL to enhance inventory management
by assisting customers raise asset flow rates, moving products faster and reducing
warehouse inventory. JDA WMS provides a variety of scanning and verification
checkpoints throughout the warehousing procedure, enabling Panalpina to provide its
customers highly customizable solutions. Panalpina also uses this system to track and
contrast the performance of its global four-wall operations and then use it for
benchmarking, for example in terms of very high inventory accuracy. Panalpina
exploited its own rapid deployment model for JDA WMS to provide customers a
standardized methods and consistent implementation procedure worldwide. This
unique model is especially useful for international customers with short lifecycles
products because system deployment can be done quickly and cost-effectively.
(Panalpina 2018)
IV.Performance management system and solution or suggestion to improve its system
Supply Chain Management is a system that uses the right channel to send the right
quantity amount of goods in the right time to customers (Balakannan et. al., 2016). In
an increasingly globalised environment today, supply chain has become a crucial
component as companies source their materials and components from around the
world. Therefore, the performance of logistics companies is very important to ensure
the fulfilment of company’s as well as customers’ goals. A performance management
system is a set of methods used to gather information and utilisation of the
information gathered to set goals, allocate resources and help managers in decision-
making (Amaratunga and Baldry, 2002).
disruptions and it can reduce the overall logistics expenses. Next, Panalpina enhance
the actual stages of international supply chain to lessen the net working capital.
(Panalpina 2018)
Warehouse management system
The last warehousing service that adopted by Panalpina is warehouse management
system. Panalpina declares its intention to dispose a single warehouse management
system (WMS) in all of its global logistics facilities. The launch of WMS is based on
Panalpina's logistics strategy and is the first 3PL to enhance inventory management
by assisting customers raise asset flow rates, moving products faster and reducing
warehouse inventory. JDA WMS provides a variety of scanning and verification
checkpoints throughout the warehousing procedure, enabling Panalpina to provide its
customers highly customizable solutions. Panalpina also uses this system to track and
contrast the performance of its global four-wall operations and then use it for
benchmarking, for example in terms of very high inventory accuracy. Panalpina
exploited its own rapid deployment model for JDA WMS to provide customers a
standardized methods and consistent implementation procedure worldwide. This
unique model is especially useful for international customers with short lifecycles
products because system deployment can be done quickly and cost-effectively.
(Panalpina 2018)
IV.Performance management system and solution or suggestion to improve its system
Supply Chain Management is a system that uses the right channel to send the right
quantity amount of goods in the right time to customers (Balakannan et. al., 2016). In
an increasingly globalised environment today, supply chain has become a crucial
component as companies source their materials and components from around the
world. Therefore, the performance of logistics companies is very important to ensure
the fulfilment of company’s as well as customers’ goals. A performance management
system is a set of methods used to gather information and utilisation of the
information gathered to set goals, allocate resources and help managers in decision-
making (Amaratunga and Baldry, 2002).
Paraphrase This Document
Need a fresh take? Get an instant paraphrase of this document with our AI Paraphraser

14
Panalpina employs a holistic performance management system which encompasses
sustainability, environmental performance, social responsibility, the health and safety
of employees, and solid business management and processes (Panalpina 2018
Sustainability Report, 2019). The holistic approach ensures that the entire value chain
is evaluated from time to time to eliminate errors as mistakes in any part of it can
have a negative impact on performance. For example, if they charter an air freight
service that is always not on time, this will lower customer satisfactions and impact
company performance. This holistic approach gives Panalpina’s managers a complete
picture of the supply chain and ability to pinpoint problems that arose and take quick
corrective measures.
Panalpina employs an integrated management system to ensure the steady
advancement of the quality of all services (Panalpina,2019). Panalpina’s internal
auditing team continuously screens the overall impact of its standards and ensures
compliance on each site level. Their worldwide quality management organization
supervises local quality improvement programs to enhance operational excellence in
all countries. This is crucial to their performance management system because the
auditors feed it with data from time to time for analysis. The results are then used as
reference across the supply chain to improve compliance and reduce errors. Apart
from intra-organisational efforts, the performance management also involves their
customers. The data collected are analysed and the performance results are measured
against KPIs contained in every contract. This allows the performance of the supply
chain to be evaluated in an objective manner and enable them to manage customer
expectations in a systematic way with less disputes. This translates to an increase in
customer satisfactions and improve the company’s standing in the market.
Another aspect of performance management that Panalpina emphasised on is
employee safety. Panalpina is committed to an incident-free workplace, every day,
everywhere. This is important because the performance of the company depends on
continuous quality improvement and protecting their employees by giving them a safe
workplace is one way to achieve that. It provides safety training, risks assessment, and
consultation and development to minimize the risks at their workplaces (QHSE
Policy, 2019). As a result, the company reported a 72% reduction in injuries to staffs
since 2013 (Panalpina 2018 Sustainability Report, 2019). Study (Ajala, 2012) has
Panalpina employs a holistic performance management system which encompasses
sustainability, environmental performance, social responsibility, the health and safety
of employees, and solid business management and processes (Panalpina 2018
Sustainability Report, 2019). The holistic approach ensures that the entire value chain
is evaluated from time to time to eliminate errors as mistakes in any part of it can
have a negative impact on performance. For example, if they charter an air freight
service that is always not on time, this will lower customer satisfactions and impact
company performance. This holistic approach gives Panalpina’s managers a complete
picture of the supply chain and ability to pinpoint problems that arose and take quick
corrective measures.
Panalpina employs an integrated management system to ensure the steady
advancement of the quality of all services (Panalpina,2019). Panalpina’s internal
auditing team continuously screens the overall impact of its standards and ensures
compliance on each site level. Their worldwide quality management organization
supervises local quality improvement programs to enhance operational excellence in
all countries. This is crucial to their performance management system because the
auditors feed it with data from time to time for analysis. The results are then used as
reference across the supply chain to improve compliance and reduce errors. Apart
from intra-organisational efforts, the performance management also involves their
customers. The data collected are analysed and the performance results are measured
against KPIs contained in every contract. This allows the performance of the supply
chain to be evaluated in an objective manner and enable them to manage customer
expectations in a systematic way with less disputes. This translates to an increase in
customer satisfactions and improve the company’s standing in the market.
Another aspect of performance management that Panalpina emphasised on is
employee safety. Panalpina is committed to an incident-free workplace, every day,
everywhere. This is important because the performance of the company depends on
continuous quality improvement and protecting their employees by giving them a safe
workplace is one way to achieve that. It provides safety training, risks assessment, and
consultation and development to minimize the risks at their workplaces (QHSE
Policy, 2019). As a result, the company reported a 72% reduction in injuries to staffs
since 2013 (Panalpina 2018 Sustainability Report, 2019). Study (Ajala, 2012) has

15
shown that a good work environment can lead to increase in employee well-being,
morale, efficiency and productivity. The employee will then be able to focus more on
their jobs. This helps towards achieving the objective of constantly improving the
quality of the supply chain.
In performance evaluation, Panalpina uses a Balanced Scorecard (BSC) that analyses
performance on four aspects: financial, customer, business process, and R&D (Peters,
2011). BSC captures and measures the performance of the company using numerical
figures such as On-time delivery percentage (%) and percentage of customer
complaints (%). It has the advantage of simplicity and objectivity and managers can
use the results as a guide to improve on areas that are found unsatisfactory. For
example, if the On-time delivery percentage is low, the managers must identify the
root of the problem (human error or faulty transports) and take corrective steps
immediately or risks losing their customers. In view of this, BSC can be a
performance driver for Panalpina as it is linked to the strategy of the company
(Kaplan and Norton, 1996). The measures are formulated by studying the company’s
vision, mission, and every aspect of the company’s operations. A BSC model is built
using the information obtained from the study to be used as a performance
management for Panalpina’s managers.
While it has become a popular tool in performance management, BSC has its
limitations which could impact the performance management process (Salem, Hasnan
and Osman, 2012). Norreklit (2003) noted that BSC does not incorporate suppliers,
which are important to supply chain providers like Panalpina. Suppliers or
subcontractors is a major part of the company’s business process (Panalpina
Subcontractor Management, 2019). We suggest that measurements regarding
subcontractors to be added into the BSC of Panalpina. Measurements such as
“number of accidents involving subcontractors” or “number of complaints filed
against subcontractors” can be added to the business process matrix.
Another problem with BSC is the lack of time dimension (Norreklit, 2003). BSC
measures performance in a static manner and does not consider the effect of time on
the company. However, Panalpina’s quality improvement is a continuous process that
happens over time. A corrective action taken must wait for the passing of time to see
shown that a good work environment can lead to increase in employee well-being,
morale, efficiency and productivity. The employee will then be able to focus more on
their jobs. This helps towards achieving the objective of constantly improving the
quality of the supply chain.
In performance evaluation, Panalpina uses a Balanced Scorecard (BSC) that analyses
performance on four aspects: financial, customer, business process, and R&D (Peters,
2011). BSC captures and measures the performance of the company using numerical
figures such as On-time delivery percentage (%) and percentage of customer
complaints (%). It has the advantage of simplicity and objectivity and managers can
use the results as a guide to improve on areas that are found unsatisfactory. For
example, if the On-time delivery percentage is low, the managers must identify the
root of the problem (human error or faulty transports) and take corrective steps
immediately or risks losing their customers. In view of this, BSC can be a
performance driver for Panalpina as it is linked to the strategy of the company
(Kaplan and Norton, 1996). The measures are formulated by studying the company’s
vision, mission, and every aspect of the company’s operations. A BSC model is built
using the information obtained from the study to be used as a performance
management for Panalpina’s managers.
While it has become a popular tool in performance management, BSC has its
limitations which could impact the performance management process (Salem, Hasnan
and Osman, 2012). Norreklit (2003) noted that BSC does not incorporate suppliers,
which are important to supply chain providers like Panalpina. Suppliers or
subcontractors is a major part of the company’s business process (Panalpina
Subcontractor Management, 2019). We suggest that measurements regarding
subcontractors to be added into the BSC of Panalpina. Measurements such as
“number of accidents involving subcontractors” or “number of complaints filed
against subcontractors” can be added to the business process matrix.
Another problem with BSC is the lack of time dimension (Norreklit, 2003). BSC
measures performance in a static manner and does not consider the effect of time on
the company. However, Panalpina’s quality improvement is a continuous process that
happens over time. A corrective action taken must wait for the passing of time to see

16
its effects. For example, safety training given to employees that lasts 2 months can
only see a decrease in workplace accidents after a while (more than 2 months).
Measuring the results every month would produce an accurate picture as the effects
have yet to set in. We propose integrating time element into the BSC model. Using
the example above, the management in Panalpina can set ‘decrease of workplace
accidents by 20% from the third month after the completion of the safety training’ as
objective. In between, they can use ‘temporary objective’ (Norreklit, 2003) such as a
5% reduction of accidents in the first month of training as a KPI to measure. By
incorporating the time element, the measurement of performance can be done more
accurately and in line with Panalpina’s continuous quality improvement approach.
While Panalpina takes workplace very seriously, we suggest them to take it a step
further by inculcating safety culture. The Confederation of British Industry (CBI,
1991) defined safety culture as ‘the ideas and beliefs that all members of the
organisation share about risk, accidents and ill health”. Safety culture should be the
dominating culture in high risk industries and not just sub-component of corporate
culture (Cooper, 2000). In recent years, it is noted that many supply chain firms are
beginning to adopt the term ‘sustainability’ which include the element of health and
safety (Carter and Rogers, 2008). From here, it is prevalent that safety culture is
becoming more important in the workplace. We suggest that the top management of
Panalpina gives more concern on the well-being of their employees by giving support
both financially and morally towards improving workplace safety. In addition,
employees should be given authority to participate in safety-related activities and
implement safety practices. This will lead to employees’ commitment towards
achieving better results for the company (Hajmohammad and Vachon, 2014). This is
because the employees feel that their safety and well-being is given attention by top
management. As a result, they reciprocate it by achieving a better firm performance.
Conclusion
Panalpina is a giant in the logistics industry. Its multi-faceted operations offer a
complete range of logistic services ranging from air freight, ocean freight, truck, to
its effects. For example, safety training given to employees that lasts 2 months can
only see a decrease in workplace accidents after a while (more than 2 months).
Measuring the results every month would produce an accurate picture as the effects
have yet to set in. We propose integrating time element into the BSC model. Using
the example above, the management in Panalpina can set ‘decrease of workplace
accidents by 20% from the third month after the completion of the safety training’ as
objective. In between, they can use ‘temporary objective’ (Norreklit, 2003) such as a
5% reduction of accidents in the first month of training as a KPI to measure. By
incorporating the time element, the measurement of performance can be done more
accurately and in line with Panalpina’s continuous quality improvement approach.
While Panalpina takes workplace very seriously, we suggest them to take it a step
further by inculcating safety culture. The Confederation of British Industry (CBI,
1991) defined safety culture as ‘the ideas and beliefs that all members of the
organisation share about risk, accidents and ill health”. Safety culture should be the
dominating culture in high risk industries and not just sub-component of corporate
culture (Cooper, 2000). In recent years, it is noted that many supply chain firms are
beginning to adopt the term ‘sustainability’ which include the element of health and
safety (Carter and Rogers, 2008). From here, it is prevalent that safety culture is
becoming more important in the workplace. We suggest that the top management of
Panalpina gives more concern on the well-being of their employees by giving support
both financially and morally towards improving workplace safety. In addition,
employees should be given authority to participate in safety-related activities and
implement safety practices. This will lead to employees’ commitment towards
achieving better results for the company (Hajmohammad and Vachon, 2014). This is
because the employees feel that their safety and well-being is given attention by top
management. As a result, they reciprocate it by achieving a better firm performance.
Conclusion
Panalpina is a giant in the logistics industry. Its multi-faceted operations offer a
complete range of logistic services ranging from air freight, ocean freight, truck, to
Secure Best Marks with AI Grader
Need help grading? Try our AI Grader for instant feedback on your assignments.

17
warehousing and turnkey pipeline projects. From the businesses the company
conducts, it is clear that the logistic industry is a complex and challenging one. A
supply chain involves multiple parties at various stages, and everyone must play his
part in order to create value for customers. Any weakness in any part can lead to a
drop in quality or worst still, unfulfilled customer orders. Many factors are at play in
the logistics business affecting various aspects of the company at various levels. It is
also affected by the environment it operates in such as the government as well as laws
and regulations. As students of SCM, studying Panalpina is a has allow us some
insights into the world of supply chain albeit from an academic perspective.
warehousing and turnkey pipeline projects. From the businesses the company
conducts, it is clear that the logistic industry is a complex and challenging one. A
supply chain involves multiple parties at various stages, and everyone must play his
part in order to create value for customers. Any weakness in any part can lead to a
drop in quality or worst still, unfulfilled customer orders. Many factors are at play in
the logistics business affecting various aspects of the company at various levels. It is
also affected by the environment it operates in such as the government as well as laws
and regulations. As students of SCM, studying Panalpina is a has allow us some
insights into the world of supply chain albeit from an academic perspective.
1 out of 17
Related Documents

Your All-in-One AI-Powered Toolkit for Academic Success.
+13062052269
info@desklib.com
Available 24*7 on WhatsApp / Email
Unlock your academic potential
© 2024 | Zucol Services PVT LTD | All rights reserved.