Performance Management Report: Variance Analysis and Strategic Costing
VerifiedAdded on 2022/11/24
|12
|2854
|200
Report
AI Summary
This report delves into the realm of performance management, commencing with a detailed variance calculation for direct materials and labor, analyzing the company's production efficiency, and exploring the application of a Just-in-Time manufacturing system. The report proceeds to evaluate the...
Read More
Contribute Materials
Your contribution can guide someone’s learning journey. Share your
documents today.
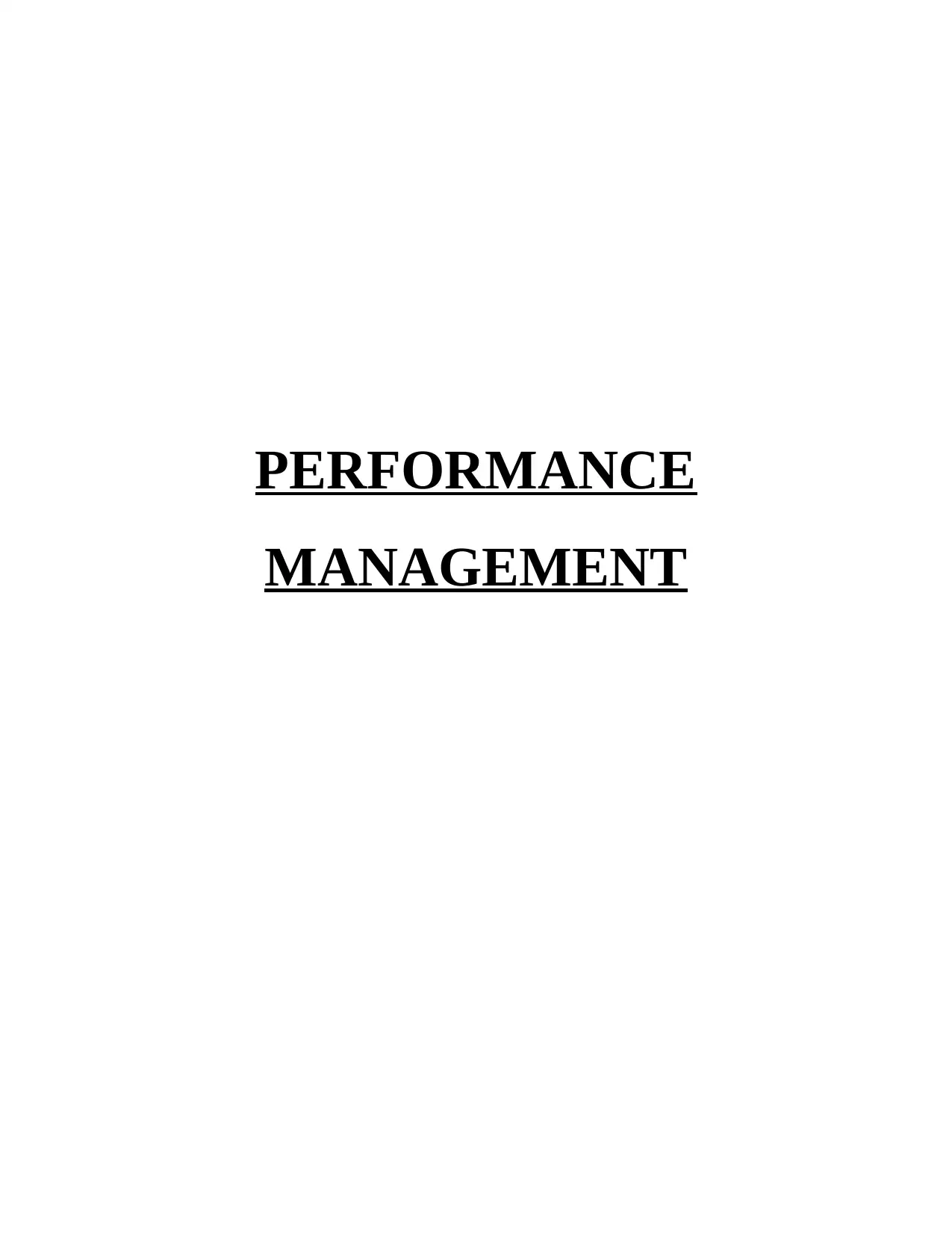
PERFORMANCE
MANAGEMENT
MANAGEMENT
Secure Best Marks with AI Grader
Need help grading? Try our AI Grader for instant feedback on your assignments.
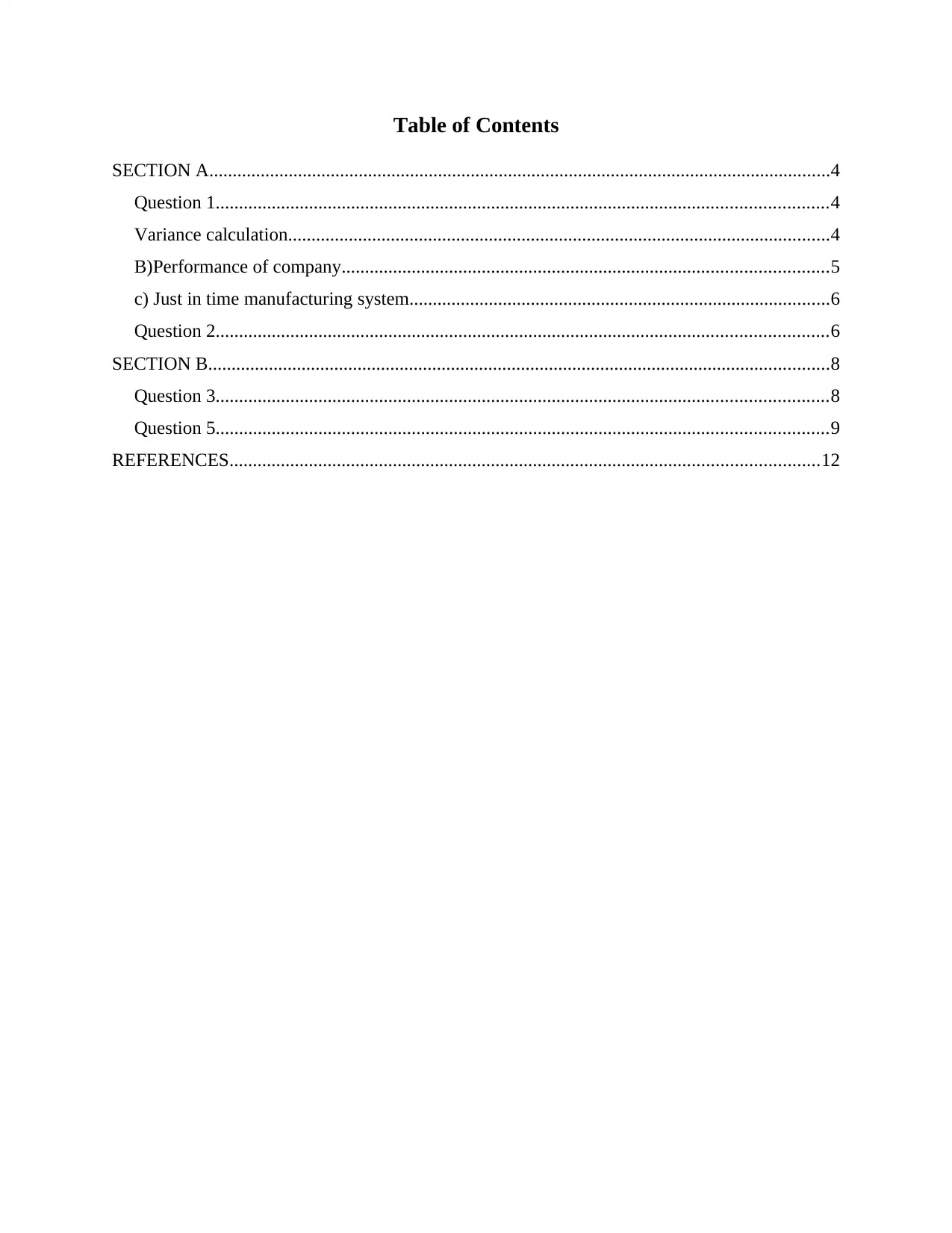
Table of Contents
SECTION A.....................................................................................................................................4
Question 1...................................................................................................................................4
Variance calculation....................................................................................................................4
B)Performance of company........................................................................................................5
c) Just in time manufacturing system..........................................................................................6
Question 2...................................................................................................................................6
SECTION B.....................................................................................................................................8
Question 3...................................................................................................................................8
Question 5...................................................................................................................................9
REFERENCES..............................................................................................................................12
SECTION A.....................................................................................................................................4
Question 1...................................................................................................................................4
Variance calculation....................................................................................................................4
B)Performance of company........................................................................................................5
c) Just in time manufacturing system..........................................................................................6
Question 2...................................................................................................................................6
SECTION B.....................................................................................................................................8
Question 3...................................................................................................................................8
Question 5...................................................................................................................................9
REFERENCES..............................................................................................................................12
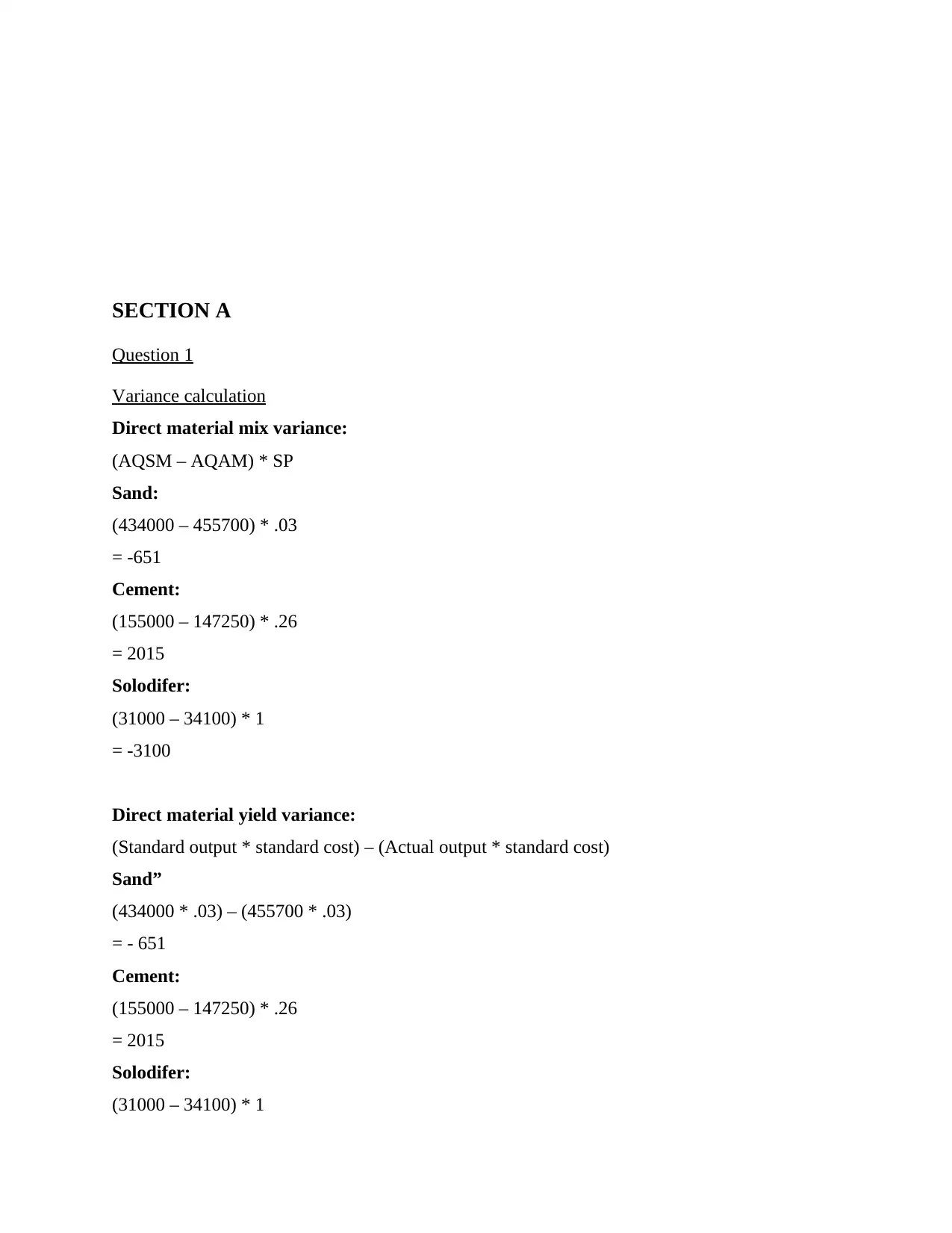
SECTION A
Question 1
Variance calculation
Direct material mix variance:
(AQSM – AQAM) * SP
Sand:
(434000 – 455700) * .03
= -651
Cement:
(155000 – 147250) * .26
= 2015
Solodifer:
(31000 – 34100) * 1
= -3100
Direct material yield variance:
(Standard output * standard cost) – (Actual output * standard cost)
Sand”
(434000 * .03) – (455700 * .03)
= - 651
Cement:
(155000 – 147250) * .26
= 2015
Solodifer:
(31000 – 34100) * 1
Question 1
Variance calculation
Direct material mix variance:
(AQSM – AQAM) * SP
Sand:
(434000 – 455700) * .03
= -651
Cement:
(155000 – 147250) * .26
= 2015
Solodifer:
(31000 – 34100) * 1
= -3100
Direct material yield variance:
(Standard output * standard cost) – (Actual output * standard cost)
Sand”
(434000 * .03) – (455700 * .03)
= - 651
Cement:
(155000 – 147250) * .26
= 2015
Solodifer:
(31000 – 34100) * 1
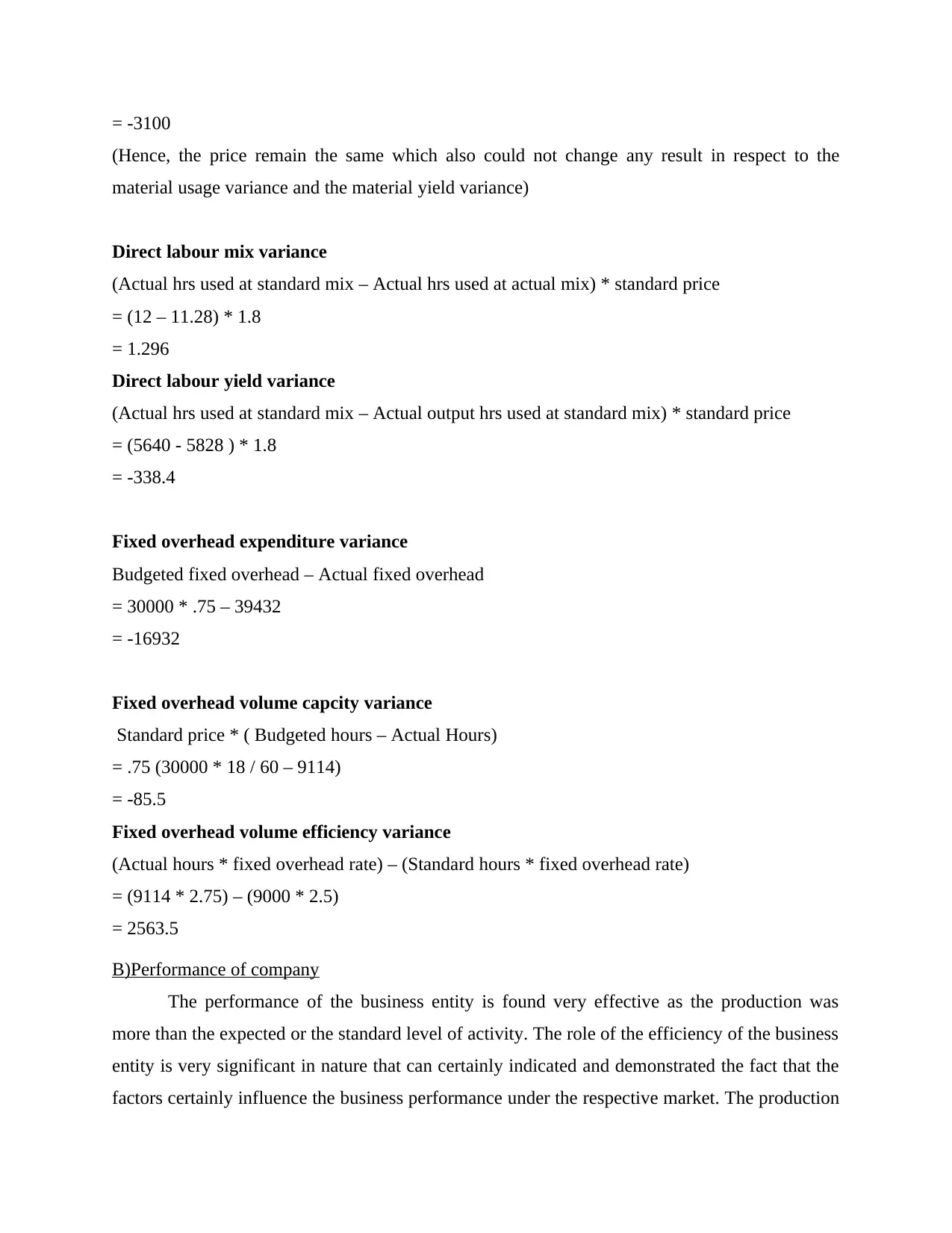
= -3100
(Hence, the price remain the same which also could not change any result in respect to the
material usage variance and the material yield variance)
Direct labour mix variance
(Actual hrs used at standard mix – Actual hrs used at actual mix) * standard price
= (12 – 11.28) * 1.8
= 1.296
Direct labour yield variance
(Actual hrs used at standard mix – Actual output hrs used at standard mix) * standard price
= (5640 - 5828 ) * 1.8
= -338.4
Fixed overhead expenditure variance
Budgeted fixed overhead – Actual fixed overhead
= 30000 * .75 – 39432
= -16932
Fixed overhead volume capcity variance
Standard price * ( Budgeted hours – Actual Hours)
= .75 (30000 * 18 / 60 – 9114)
= -85.5
Fixed overhead volume efficiency variance
(Actual hours * fixed overhead rate) – (Standard hours * fixed overhead rate)
= (9114 * 2.75) – (9000 * 2.5)
= 2563.5
B)Performance of company
The performance of the business entity is found very effective as the production was
more than the expected or the standard level of activity. The role of the efficiency of the business
entity is very significant in nature that can certainly indicated and demonstrated the fact that the
factors certainly influence the business performance under the respective market. The production
(Hence, the price remain the same which also could not change any result in respect to the
material usage variance and the material yield variance)
Direct labour mix variance
(Actual hrs used at standard mix – Actual hrs used at actual mix) * standard price
= (12 – 11.28) * 1.8
= 1.296
Direct labour yield variance
(Actual hrs used at standard mix – Actual output hrs used at standard mix) * standard price
= (5640 - 5828 ) * 1.8
= -338.4
Fixed overhead expenditure variance
Budgeted fixed overhead – Actual fixed overhead
= 30000 * .75 – 39432
= -16932
Fixed overhead volume capcity variance
Standard price * ( Budgeted hours – Actual Hours)
= .75 (30000 * 18 / 60 – 9114)
= -85.5
Fixed overhead volume efficiency variance
(Actual hours * fixed overhead rate) – (Standard hours * fixed overhead rate)
= (9114 * 2.75) – (9000 * 2.5)
= 2563.5
B)Performance of company
The performance of the business entity is found very effective as the production was
more than the expected or the standard level of activity. The role of the efficiency of the business
entity is very significant in nature that can certainly indicated and demonstrated the fact that the
factors certainly influence the business performance under the respective market. The production
Secure Best Marks with AI Grader
Need help grading? Try our AI Grader for instant feedback on your assignments.
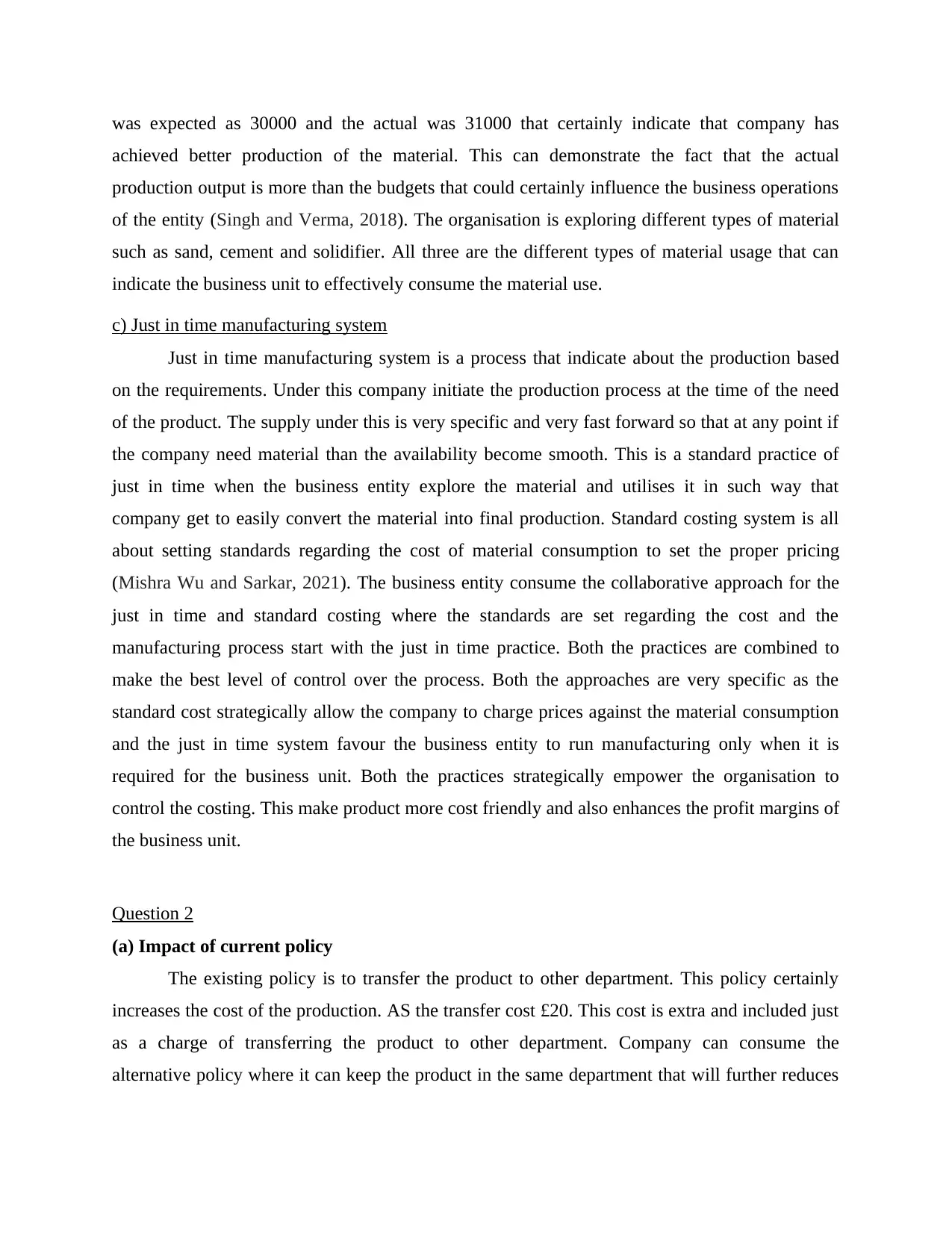
was expected as 30000 and the actual was 31000 that certainly indicate that company has
achieved better production of the material. This can demonstrate the fact that the actual
production output is more than the budgets that could certainly influence the business operations
of the entity (Singh and Verma, 2018). The organisation is exploring different types of material
such as sand, cement and solidifier. All three are the different types of material usage that can
indicate the business unit to effectively consume the material use.
c) Just in time manufacturing system
Just in time manufacturing system is a process that indicate about the production based
on the requirements. Under this company initiate the production process at the time of the need
of the product. The supply under this is very specific and very fast forward so that at any point if
the company need material than the availability become smooth. This is a standard practice of
just in time when the business entity explore the material and utilises it in such way that
company get to easily convert the material into final production. Standard costing system is all
about setting standards regarding the cost of material consumption to set the proper pricing
(Mishra Wu and Sarkar, 2021). The business entity consume the collaborative approach for the
just in time and standard costing where the standards are set regarding the cost and the
manufacturing process start with the just in time practice. Both the practices are combined to
make the best level of control over the process. Both the approaches are very specific as the
standard cost strategically allow the company to charge prices against the material consumption
and the just in time system favour the business entity to run manufacturing only when it is
required for the business unit. Both the practices strategically empower the organisation to
control the costing. This make product more cost friendly and also enhances the profit margins of
the business unit.
Question 2
(a) Impact of current policy
The existing policy is to transfer the product to other department. This policy certainly
increases the cost of the production. AS the transfer cost £20. This cost is extra and included just
as a charge of transferring the product to other department. Company can consume the
alternative policy where it can keep the product in the same department that will further reduces
achieved better production of the material. This can demonstrate the fact that the actual
production output is more than the budgets that could certainly influence the business operations
of the entity (Singh and Verma, 2018). The organisation is exploring different types of material
such as sand, cement and solidifier. All three are the different types of material usage that can
indicate the business unit to effectively consume the material use.
c) Just in time manufacturing system
Just in time manufacturing system is a process that indicate about the production based
on the requirements. Under this company initiate the production process at the time of the need
of the product. The supply under this is very specific and very fast forward so that at any point if
the company need material than the availability become smooth. This is a standard practice of
just in time when the business entity explore the material and utilises it in such way that
company get to easily convert the material into final production. Standard costing system is all
about setting standards regarding the cost of material consumption to set the proper pricing
(Mishra Wu and Sarkar, 2021). The business entity consume the collaborative approach for the
just in time and standard costing where the standards are set regarding the cost and the
manufacturing process start with the just in time practice. Both the practices are combined to
make the best level of control over the process. Both the approaches are very specific as the
standard cost strategically allow the company to charge prices against the material consumption
and the just in time system favour the business entity to run manufacturing only when it is
required for the business unit. Both the practices strategically empower the organisation to
control the costing. This make product more cost friendly and also enhances the profit margins of
the business unit.
Question 2
(a) Impact of current policy
The existing policy is to transfer the product to other department. This policy certainly
increases the cost of the production. AS the transfer cost £20. This cost is extra and included just
as a charge of transferring the product to other department. Company can consume the
alternative policy where it can keep the product in the same department that will further reduces
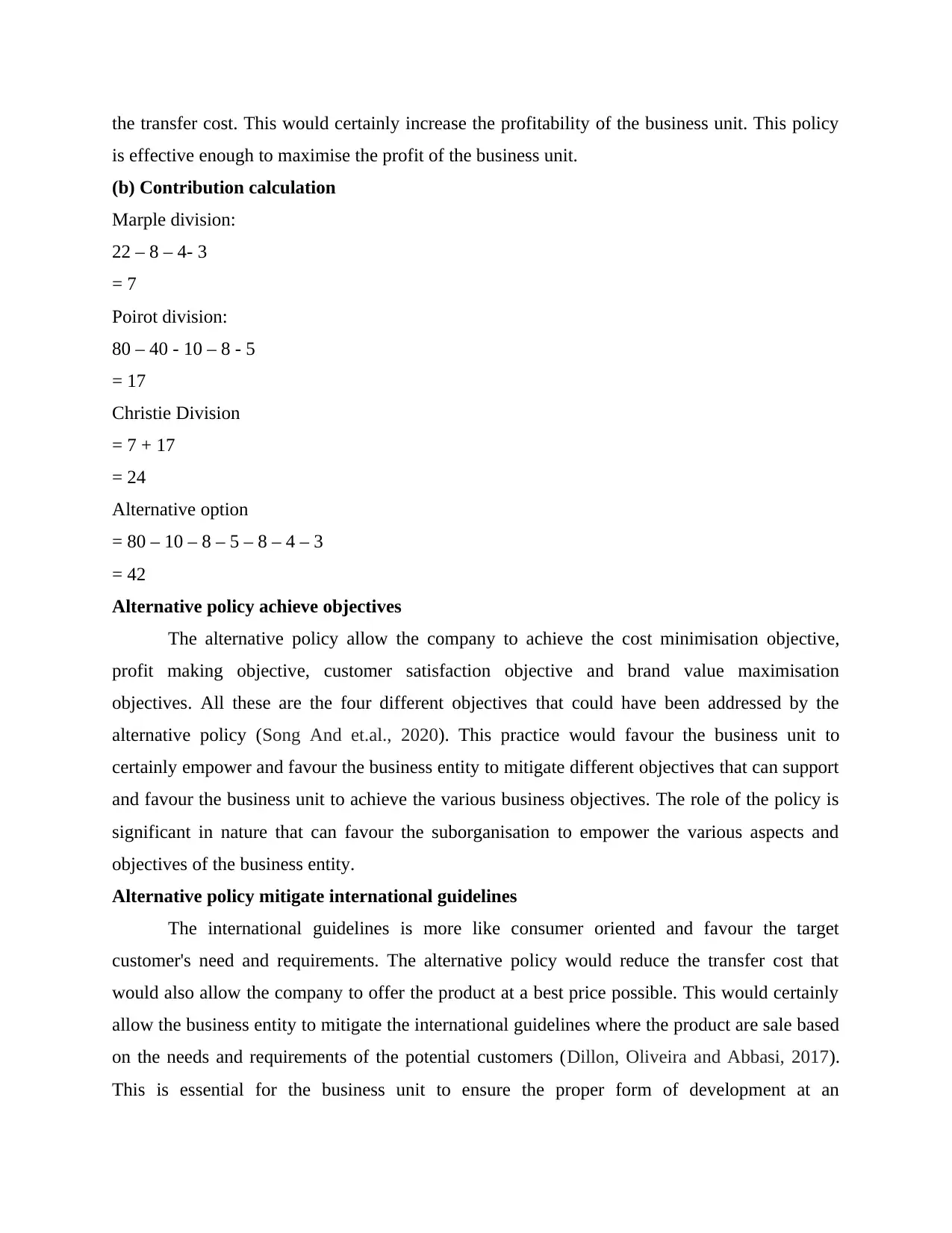
the transfer cost. This would certainly increase the profitability of the business unit. This policy
is effective enough to maximise the profit of the business unit.
(b) Contribution calculation
Marple division:
22 – 8 – 4- 3
= 7
Poirot division:
80 – 40 - 10 – 8 - 5
= 17
Christie Division
= 7 + 17
= 24
Alternative option
= 80 – 10 – 8 – 5 – 8 – 4 – 3
= 42
Alternative policy achieve objectives
The alternative policy allow the company to achieve the cost minimisation objective,
profit making objective, customer satisfaction objective and brand value maximisation
objectives. All these are the four different objectives that could have been addressed by the
alternative policy (Song And et.al., 2020). This practice would favour the business unit to
certainly empower and favour the business entity to mitigate different objectives that can support
and favour the business unit to achieve the various business objectives. The role of the policy is
significant in nature that can favour the suborganisation to empower the various aspects and
objectives of the business entity.
Alternative policy mitigate international guidelines
The international guidelines is more like consumer oriented and favour the target
customer's need and requirements. The alternative policy would reduce the transfer cost that
would also allow the company to offer the product at a best price possible. This would certainly
allow the business entity to mitigate the international guidelines where the product are sale based
on the needs and requirements of the potential customers (Dillon, Oliveira and Abbasi, 2017).
This is essential for the business unit to ensure the proper form of development at an
is effective enough to maximise the profit of the business unit.
(b) Contribution calculation
Marple division:
22 – 8 – 4- 3
= 7
Poirot division:
80 – 40 - 10 – 8 - 5
= 17
Christie Division
= 7 + 17
= 24
Alternative option
= 80 – 10 – 8 – 5 – 8 – 4 – 3
= 42
Alternative policy achieve objectives
The alternative policy allow the company to achieve the cost minimisation objective,
profit making objective, customer satisfaction objective and brand value maximisation
objectives. All these are the four different objectives that could have been addressed by the
alternative policy (Song And et.al., 2020). This practice would favour the business unit to
certainly empower and favour the business entity to mitigate different objectives that can support
and favour the business unit to achieve the various business objectives. The role of the policy is
significant in nature that can favour the suborganisation to empower the various aspects and
objectives of the business entity.
Alternative policy mitigate international guidelines
The international guidelines is more like consumer oriented and favour the target
customer's need and requirements. The alternative policy would reduce the transfer cost that
would also allow the company to offer the product at a best price possible. This would certainly
allow the business entity to mitigate the international guidelines where the product are sale based
on the needs and requirements of the potential customers (Dillon, Oliveira and Abbasi, 2017).
This is essential for the business unit to ensure the proper form of development at an
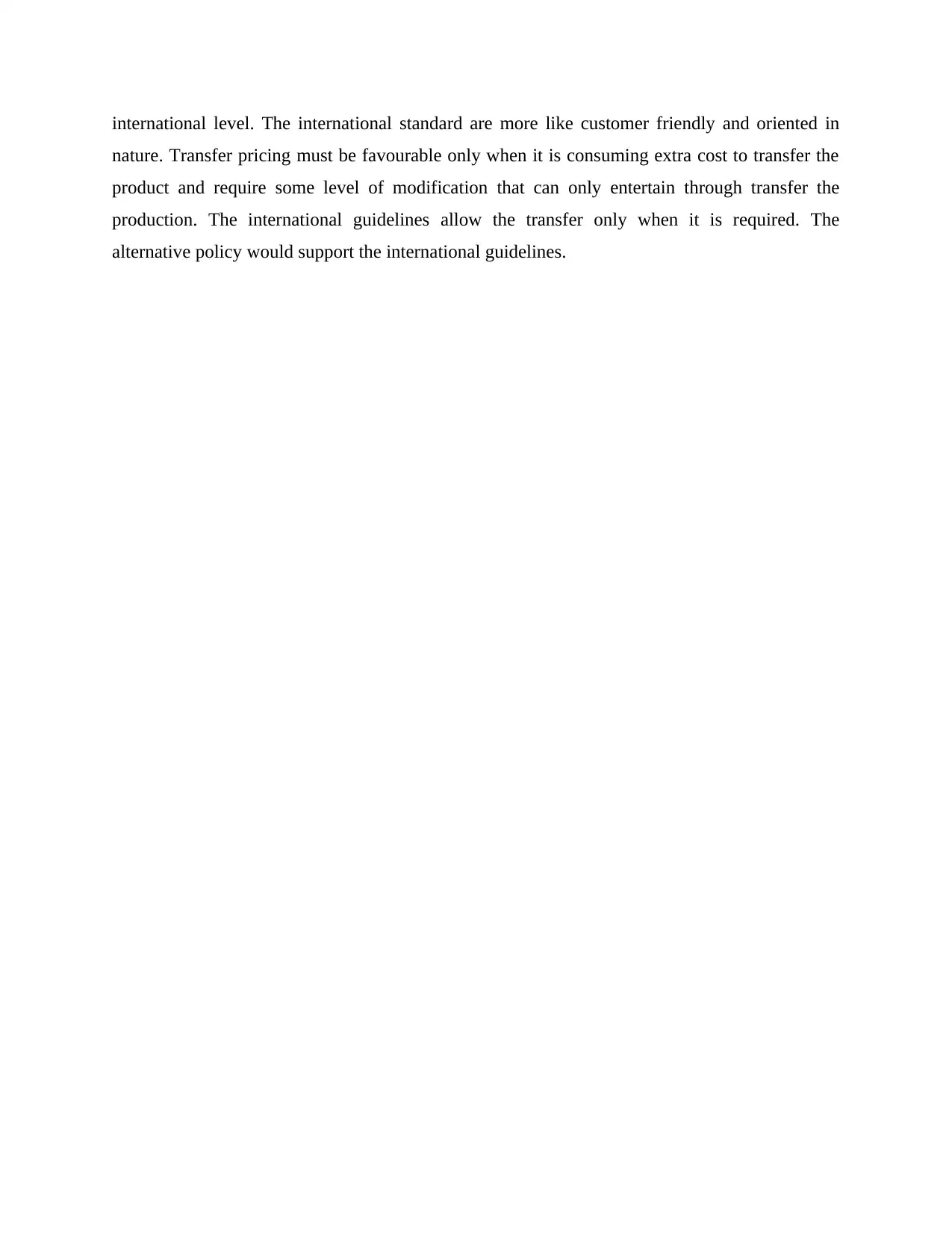
international level. The international standard are more like customer friendly and oriented in
nature. Transfer pricing must be favourable only when it is consuming extra cost to transfer the
product and require some level of modification that can only entertain through transfer the
production. The international guidelines allow the transfer only when it is required. The
alternative policy would support the international guidelines.
nature. Transfer pricing must be favourable only when it is consuming extra cost to transfer the
product and require some level of modification that can only entertain through transfer the
production. The international guidelines allow the transfer only when it is required. The
alternative policy would support the international guidelines.
Paraphrase This Document
Need a fresh take? Get an instant paraphrase of this document with our AI Paraphraser
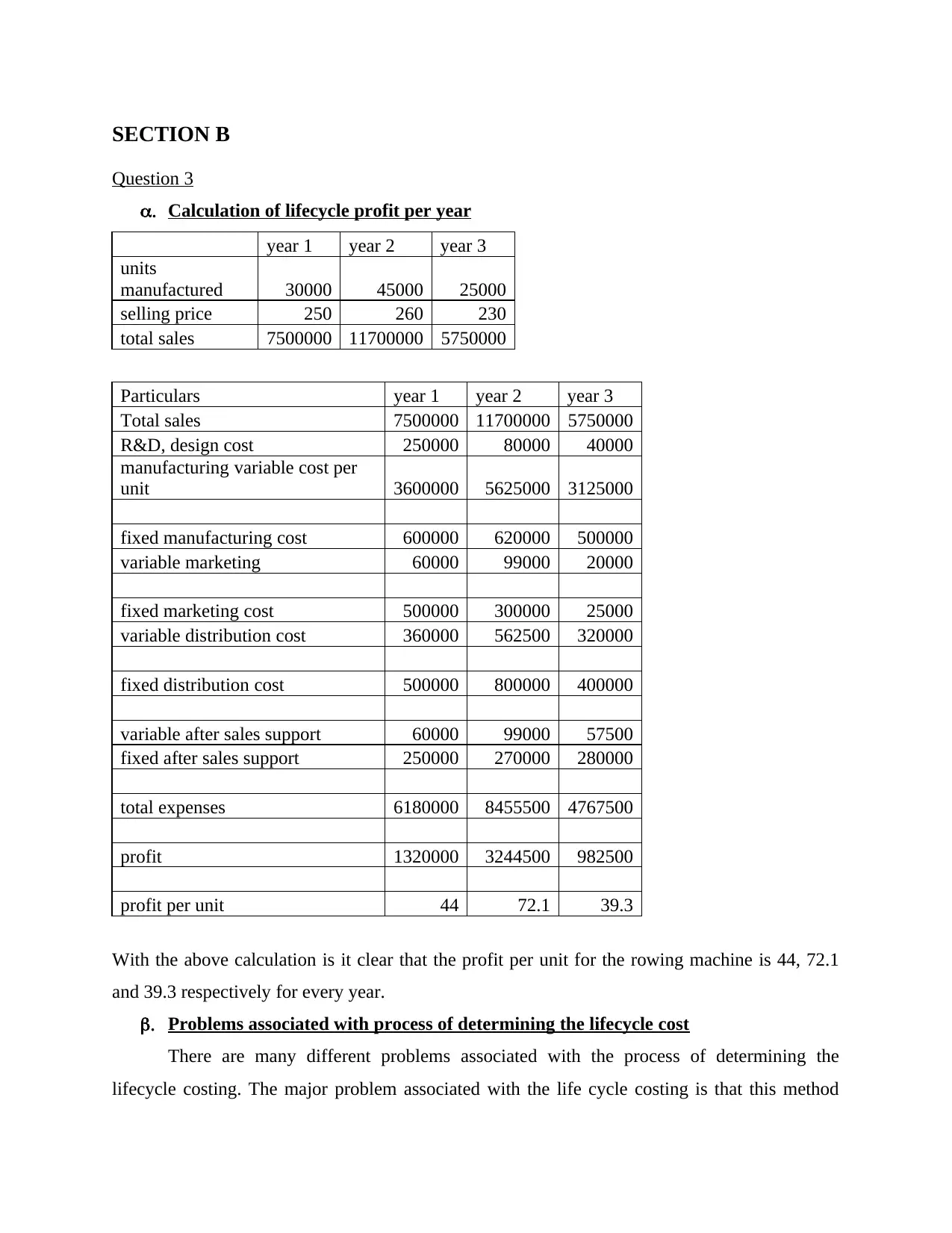
SECTION B
Question 3
a. Calculation of lifecycle profit per year
year 1 year 2 year 3
units
manufactured 30000 45000 25000
selling price 250 260 230
total sales 7500000 11700000 5750000
Particulars year 1 year 2 year 3
Total sales 7500000 11700000 5750000
R&D, design cost 250000 80000 40000
manufacturing variable cost per
unit 3600000 5625000 3125000
fixed manufacturing cost 600000 620000 500000
variable marketing 60000 99000 20000
fixed marketing cost 500000 300000 25000
variable distribution cost 360000 562500 320000
fixed distribution cost 500000 800000 400000
variable after sales support 60000 99000 57500
fixed after sales support 250000 270000 280000
total expenses 6180000 8455500 4767500
profit 1320000 3244500 982500
profit per unit 44 72.1 39.3
With the above calculation is it clear that the profit per unit for the rowing machine is 44, 72.1
and 39.3 respectively for every year.
b. Problems associated with process of determining the lifecycle cost
There are many different problems associated with the process of determining the
lifecycle costing. The major problem associated with the life cycle costing is that this method
Question 3
a. Calculation of lifecycle profit per year
year 1 year 2 year 3
units
manufactured 30000 45000 25000
selling price 250 260 230
total sales 7500000 11700000 5750000
Particulars year 1 year 2 year 3
Total sales 7500000 11700000 5750000
R&D, design cost 250000 80000 40000
manufacturing variable cost per
unit 3600000 5625000 3125000
fixed manufacturing cost 600000 620000 500000
variable marketing 60000 99000 20000
fixed marketing cost 500000 300000 25000
variable distribution cost 360000 562500 320000
fixed distribution cost 500000 800000 400000
variable after sales support 60000 99000 57500
fixed after sales support 250000 270000 280000
total expenses 6180000 8455500 4767500
profit 1320000 3244500 982500
profit per unit 44 72.1 39.3
With the above calculation is it clear that the profit per unit for the rowing machine is 44, 72.1
and 39.3 respectively for every year.
b. Problems associated with process of determining the lifecycle cost
There are many different problems associated with the process of determining the
lifecycle costing. The major problem associated with the life cycle costing is that this method
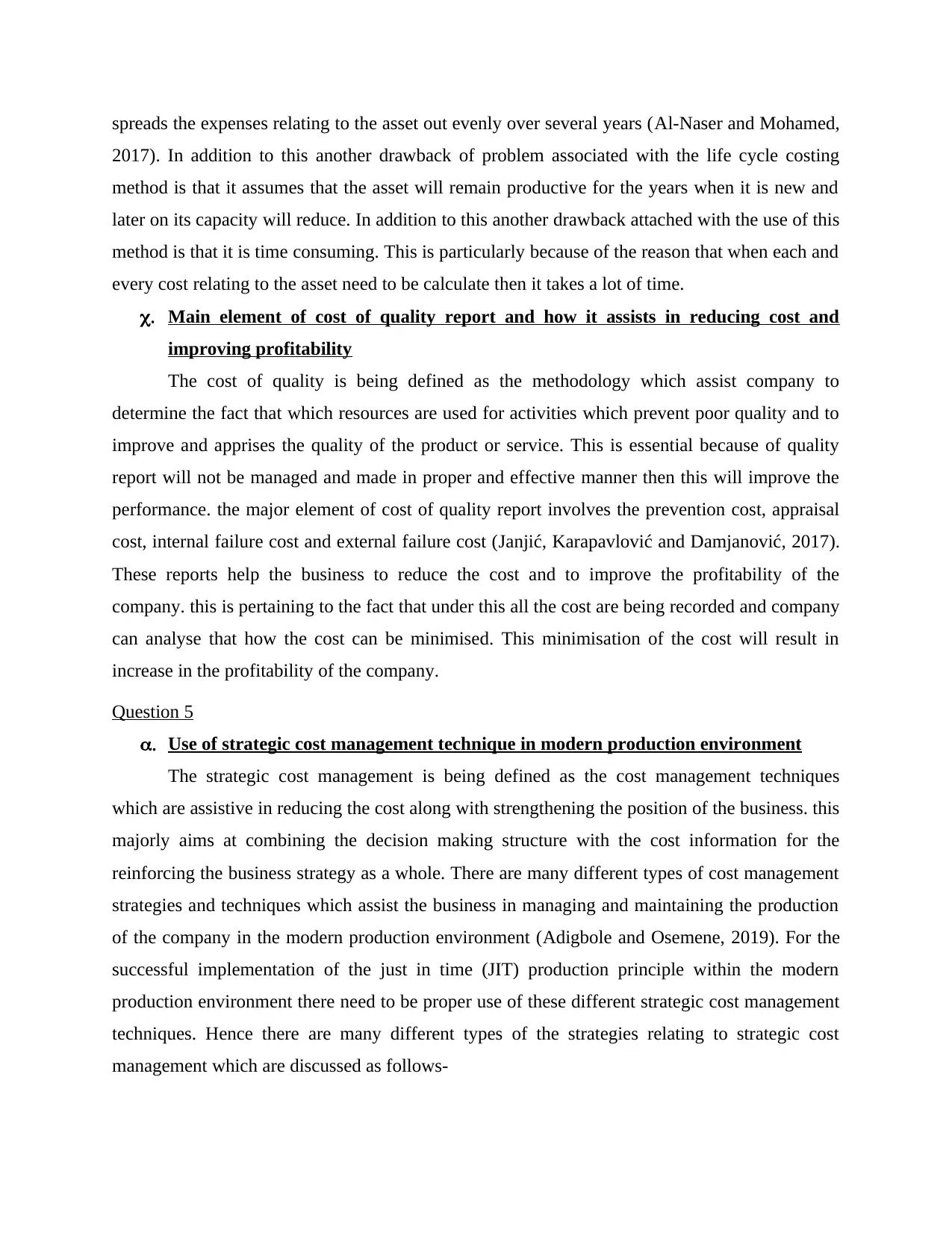
spreads the expenses relating to the asset out evenly over several years (Al-Naser and Mohamed,
2017). In addition to this another drawback of problem associated with the life cycle costing
method is that it assumes that the asset will remain productive for the years when it is new and
later on its capacity will reduce. In addition to this another drawback attached with the use of this
method is that it is time consuming. This is particularly because of the reason that when each and
every cost relating to the asset need to be calculate then it takes a lot of time.
c. Main element of cost of quality report and how it assists in reducing cost and
improving profitability
The cost of quality is being defined as the methodology which assist company to
determine the fact that which resources are used for activities which prevent poor quality and to
improve and apprises the quality of the product or service. This is essential because of quality
report will not be managed and made in proper and effective manner then this will improve the
performance. the major element of cost of quality report involves the prevention cost, appraisal
cost, internal failure cost and external failure cost (Janjić, Karapavlović and Damjanović, 2017).
These reports help the business to reduce the cost and to improve the profitability of the
company. this is pertaining to the fact that under this all the cost are being recorded and company
can analyse that how the cost can be minimised. This minimisation of the cost will result in
increase in the profitability of the company.
Question 5
a. Use of strategic cost management technique in modern production environment
The strategic cost management is being defined as the cost management techniques
which are assistive in reducing the cost along with strengthening the position of the business. this
majorly aims at combining the decision making structure with the cost information for the
reinforcing the business strategy as a whole. There are many different types of cost management
strategies and techniques which assist the business in managing and maintaining the production
of the company in the modern production environment (Adigbole and Osemene, 2019). For the
successful implementation of the just in time (JIT) production principle within the modern
production environment there need to be proper use of these different strategic cost management
techniques. Hence there are many different types of the strategies relating to strategic cost
management which are discussed as follows-
2017). In addition to this another drawback of problem associated with the life cycle costing
method is that it assumes that the asset will remain productive for the years when it is new and
later on its capacity will reduce. In addition to this another drawback attached with the use of this
method is that it is time consuming. This is particularly because of the reason that when each and
every cost relating to the asset need to be calculate then it takes a lot of time.
c. Main element of cost of quality report and how it assists in reducing cost and
improving profitability
The cost of quality is being defined as the methodology which assist company to
determine the fact that which resources are used for activities which prevent poor quality and to
improve and apprises the quality of the product or service. This is essential because of quality
report will not be managed and made in proper and effective manner then this will improve the
performance. the major element of cost of quality report involves the prevention cost, appraisal
cost, internal failure cost and external failure cost (Janjić, Karapavlović and Damjanović, 2017).
These reports help the business to reduce the cost and to improve the profitability of the
company. this is pertaining to the fact that under this all the cost are being recorded and company
can analyse that how the cost can be minimised. This minimisation of the cost will result in
increase in the profitability of the company.
Question 5
a. Use of strategic cost management technique in modern production environment
The strategic cost management is being defined as the cost management techniques
which are assistive in reducing the cost along with strengthening the position of the business. this
majorly aims at combining the decision making structure with the cost information for the
reinforcing the business strategy as a whole. There are many different types of cost management
strategies and techniques which assist the business in managing and maintaining the production
of the company in the modern production environment (Adigbole and Osemene, 2019). For the
successful implementation of the just in time (JIT) production principle within the modern
production environment there need to be proper use of these different strategic cost management
techniques. Hence there are many different types of the strategies relating to strategic cost
management which are discussed as follows-
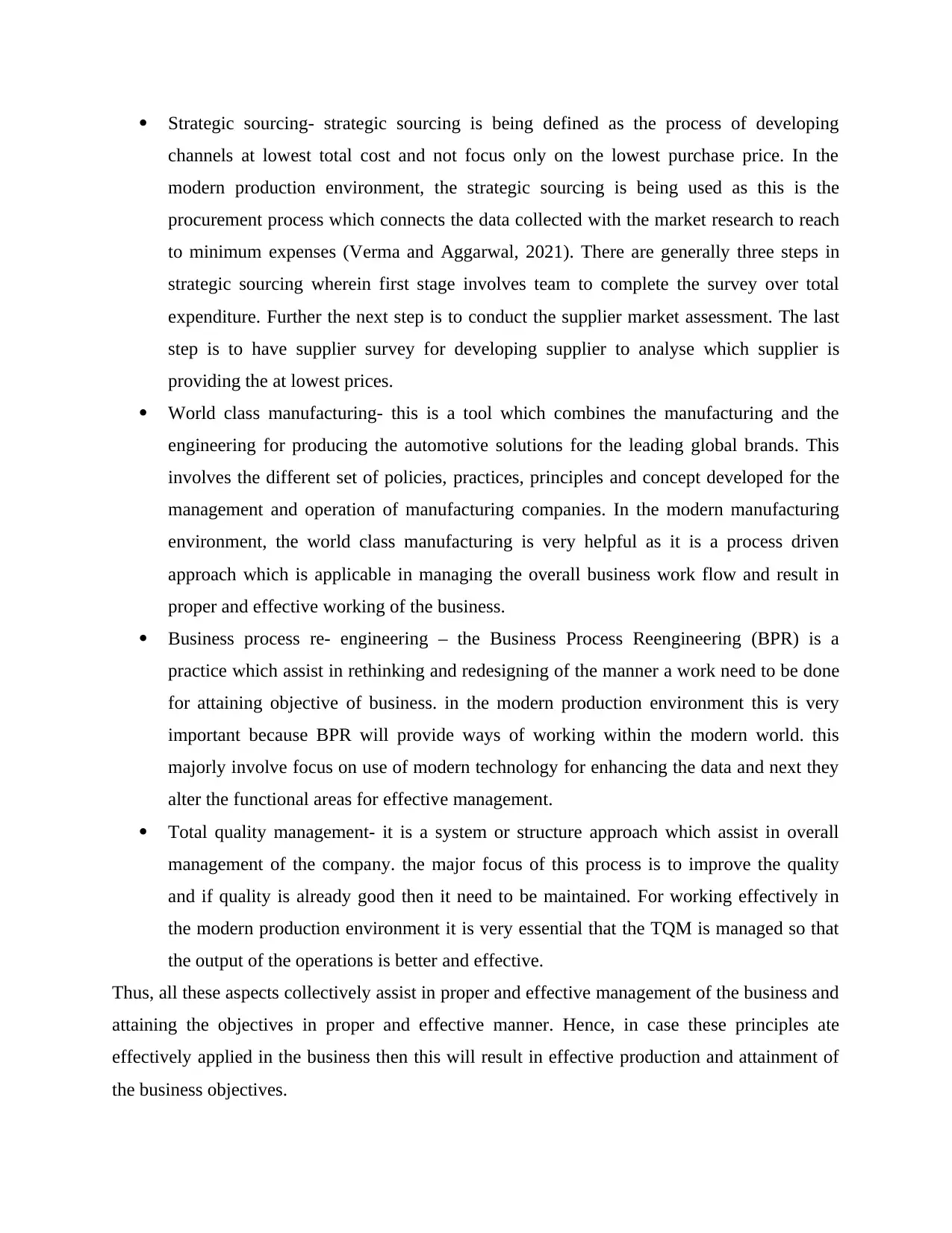
Strategic sourcing- strategic sourcing is being defined as the process of developing
channels at lowest total cost and not focus only on the lowest purchase price. In the
modern production environment, the strategic sourcing is being used as this is the
procurement process which connects the data collected with the market research to reach
to minimum expenses (Verma and Aggarwal, 2021). There are generally three steps in
strategic sourcing wherein first stage involves team to complete the survey over total
expenditure. Further the next step is to conduct the supplier market assessment. The last
step is to have supplier survey for developing supplier to analyse which supplier is
providing the at lowest prices.
World class manufacturing- this is a tool which combines the manufacturing and the
engineering for producing the automotive solutions for the leading global brands. This
involves the different set of policies, practices, principles and concept developed for the
management and operation of manufacturing companies. In the modern manufacturing
environment, the world class manufacturing is very helpful as it is a process driven
approach which is applicable in managing the overall business work flow and result in
proper and effective working of the business.
Business process re- engineering – the Business Process Reengineering (BPR) is a
practice which assist in rethinking and redesigning of the manner a work need to be done
for attaining objective of business. in the modern production environment this is very
important because BPR will provide ways of working within the modern world. this
majorly involve focus on use of modern technology for enhancing the data and next they
alter the functional areas for effective management.
Total quality management- it is a system or structure approach which assist in overall
management of the company. the major focus of this process is to improve the quality
and if quality is already good then it need to be maintained. For working effectively in
the modern production environment it is very essential that the TQM is managed so that
the output of the operations is better and effective.
Thus, all these aspects collectively assist in proper and effective management of the business and
attaining the objectives in proper and effective manner. Hence, in case these principles ate
effectively applied in the business then this will result in effective production and attainment of
the business objectives.
channels at lowest total cost and not focus only on the lowest purchase price. In the
modern production environment, the strategic sourcing is being used as this is the
procurement process which connects the data collected with the market research to reach
to minimum expenses (Verma and Aggarwal, 2021). There are generally three steps in
strategic sourcing wherein first stage involves team to complete the survey over total
expenditure. Further the next step is to conduct the supplier market assessment. The last
step is to have supplier survey for developing supplier to analyse which supplier is
providing the at lowest prices.
World class manufacturing- this is a tool which combines the manufacturing and the
engineering for producing the automotive solutions for the leading global brands. This
involves the different set of policies, practices, principles and concept developed for the
management and operation of manufacturing companies. In the modern manufacturing
environment, the world class manufacturing is very helpful as it is a process driven
approach which is applicable in managing the overall business work flow and result in
proper and effective working of the business.
Business process re- engineering – the Business Process Reengineering (BPR) is a
practice which assist in rethinking and redesigning of the manner a work need to be done
for attaining objective of business. in the modern production environment this is very
important because BPR will provide ways of working within the modern world. this
majorly involve focus on use of modern technology for enhancing the data and next they
alter the functional areas for effective management.
Total quality management- it is a system or structure approach which assist in overall
management of the company. the major focus of this process is to improve the quality
and if quality is already good then it need to be maintained. For working effectively in
the modern production environment it is very essential that the TQM is managed so that
the output of the operations is better and effective.
Thus, all these aspects collectively assist in proper and effective management of the business and
attaining the objectives in proper and effective manner. Hence, in case these principles ate
effectively applied in the business then this will result in effective production and attainment of
the business objectives.
Secure Best Marks with AI Grader
Need help grading? Try our AI Grader for instant feedback on your assignments.

b. Impact firms factor for the successful implementation of JIT production principles
There are many different factors which creates an impact over the successful
implementation of the JIT production principles. Hence, it is essential for the company that they
must effectively take into consideration all these factors.
Close geographical proximity of supplier and customer- at time of implementing the JIT
principles there need to be a close proximity of geographical proximity of supplier and
customers. This is because of the reason that when the supplier and consumer will be
placed nearby then this will result in effective implementation of the principles of JIT
(Shehadeh, 2017).
Highly competitive market- this also assist in effective implementation of the JIT
principles. This is particularly because of the reason that when the market will be highly
competitive then this will result in the effective management of operations and company
will be competent in facing the intense competition.
Flexible manufacturing technology- the flexible manufacturing system (FMS) is being
designed in order to be readily adapted to changes within the quantity of goods being
produced. This will also assist in proper management of the overall production and
reduction of the labour and other cost as well.
Low degree of vertical integration- for having successful implementation of the JIT
production principles it is essential to consider the degree of vertical integration as well.
this is particularly because of the reason that if there is option of vertical integration then
this will improve the working efficiency of the company.
There are many different factors which creates an impact over the successful
implementation of the JIT production principles. Hence, it is essential for the company that they
must effectively take into consideration all these factors.
Close geographical proximity of supplier and customer- at time of implementing the JIT
principles there need to be a close proximity of geographical proximity of supplier and
customers. This is because of the reason that when the supplier and consumer will be
placed nearby then this will result in effective implementation of the principles of JIT
(Shehadeh, 2017).
Highly competitive market- this also assist in effective implementation of the JIT
principles. This is particularly because of the reason that when the market will be highly
competitive then this will result in the effective management of operations and company
will be competent in facing the intense competition.
Flexible manufacturing technology- the flexible manufacturing system (FMS) is being
designed in order to be readily adapted to changes within the quantity of goods being
produced. This will also assist in proper management of the overall production and
reduction of the labour and other cost as well.
Low degree of vertical integration- for having successful implementation of the JIT
production principles it is essential to consider the degree of vertical integration as well.
this is particularly because of the reason that if there is option of vertical integration then
this will improve the working efficiency of the company.
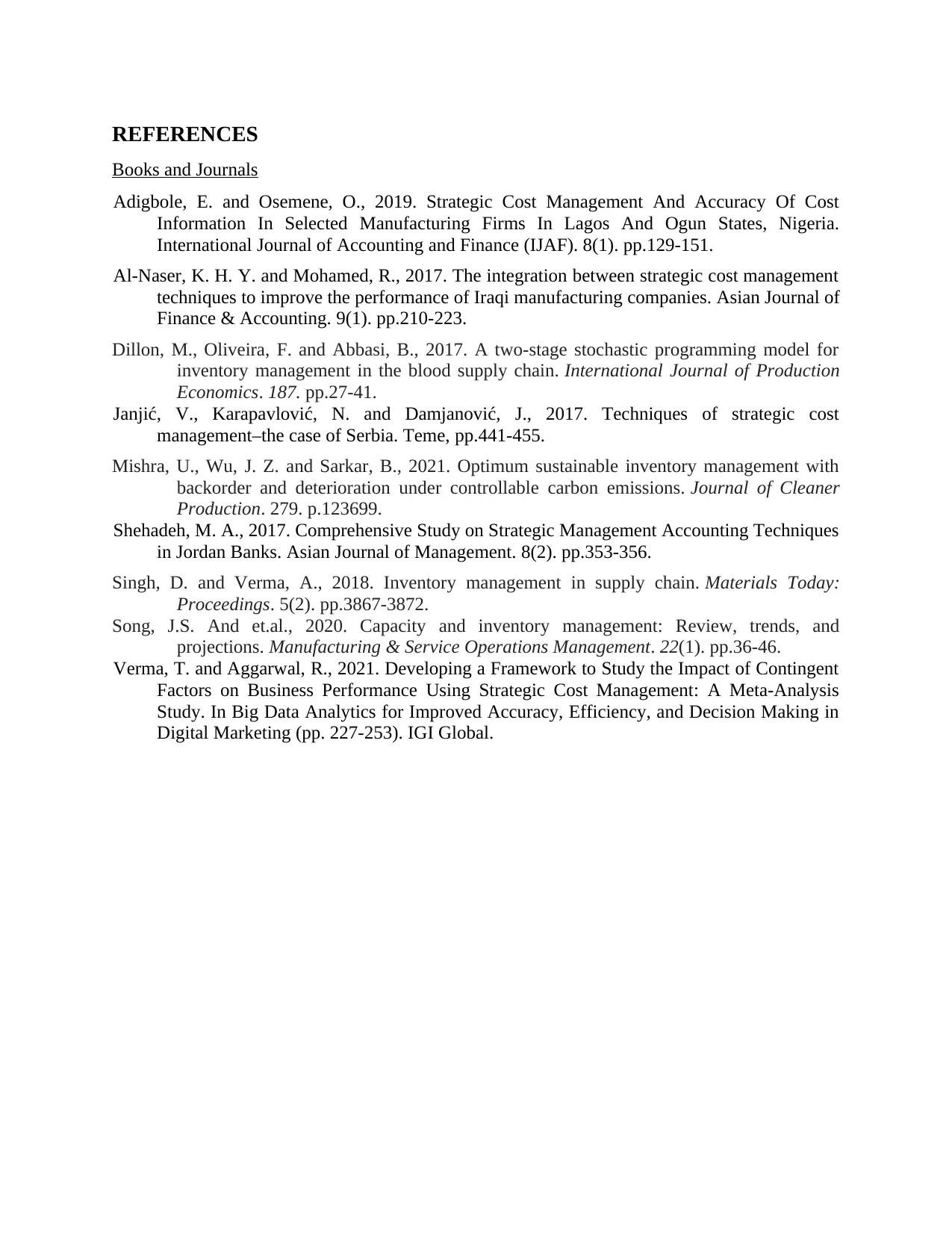
REFERENCES
Books and Journals
Adigbole, E. and Osemene, O., 2019. Strategic Cost Management And Accuracy Of Cost
Information In Selected Manufacturing Firms In Lagos And Ogun States, Nigeria.
International Journal of Accounting and Finance (IJAF). 8(1). pp.129-151.
Al-Naser, K. H. Y. and Mohamed, R., 2017. The integration between strategic cost management
techniques to improve the performance of Iraqi manufacturing companies. Asian Journal of
Finance & Accounting. 9(1). pp.210-223.
Dillon, M., Oliveira, F. and Abbasi, B., 2017. A two-stage stochastic programming model for
inventory management in the blood supply chain. International Journal of Production
Economics. 187. pp.27-41.
Janjić, V., Karapavlović, N. and Damjanović, J., 2017. Techniques of strategic cost
management–the case of Serbia. Teme, pp.441-455.
Mishra, U., Wu, J. Z. and Sarkar, B., 2021. Optimum sustainable inventory management with
backorder and deterioration under controllable carbon emissions. Journal of Cleaner
Production. 279. p.123699.
Shehadeh, M. A., 2017. Comprehensive Study on Strategic Management Accounting Techniques
in Jordan Banks. Asian Journal of Management. 8(2). pp.353-356.
Singh, D. and Verma, A., 2018. Inventory management in supply chain. Materials Today:
Proceedings. 5(2). pp.3867-3872.
Song, J.S. And et.al., 2020. Capacity and inventory management: Review, trends, and
projections. Manufacturing & Service Operations Management. 22(1). pp.36-46.
Verma, T. and Aggarwal, R., 2021. Developing a Framework to Study the Impact of Contingent
Factors on Business Performance Using Strategic Cost Management: A Meta-Analysis
Study. In Big Data Analytics for Improved Accuracy, Efficiency, and Decision Making in
Digital Marketing (pp. 227-253). IGI Global.
Books and Journals
Adigbole, E. and Osemene, O., 2019. Strategic Cost Management And Accuracy Of Cost
Information In Selected Manufacturing Firms In Lagos And Ogun States, Nigeria.
International Journal of Accounting and Finance (IJAF). 8(1). pp.129-151.
Al-Naser, K. H. Y. and Mohamed, R., 2017. The integration between strategic cost management
techniques to improve the performance of Iraqi manufacturing companies. Asian Journal of
Finance & Accounting. 9(1). pp.210-223.
Dillon, M., Oliveira, F. and Abbasi, B., 2017. A two-stage stochastic programming model for
inventory management in the blood supply chain. International Journal of Production
Economics. 187. pp.27-41.
Janjić, V., Karapavlović, N. and Damjanović, J., 2017. Techniques of strategic cost
management–the case of Serbia. Teme, pp.441-455.
Mishra, U., Wu, J. Z. and Sarkar, B., 2021. Optimum sustainable inventory management with
backorder and deterioration under controllable carbon emissions. Journal of Cleaner
Production. 279. p.123699.
Shehadeh, M. A., 2017. Comprehensive Study on Strategic Management Accounting Techniques
in Jordan Banks. Asian Journal of Management. 8(2). pp.353-356.
Singh, D. and Verma, A., 2018. Inventory management in supply chain. Materials Today:
Proceedings. 5(2). pp.3867-3872.
Song, J.S. And et.al., 2020. Capacity and inventory management: Review, trends, and
projections. Manufacturing & Service Operations Management. 22(1). pp.36-46.
Verma, T. and Aggarwal, R., 2021. Developing a Framework to Study the Impact of Contingent
Factors on Business Performance Using Strategic Cost Management: A Meta-Analysis
Study. In Big Data Analytics for Improved Accuracy, Efficiency, and Decision Making in
Digital Marketing (pp. 227-253). IGI Global.
1 out of 12

Your All-in-One AI-Powered Toolkit for Academic Success.
+13062052269
info@desklib.com
Available 24*7 on WhatsApp / Email
Unlock your academic potential
© 2024 | Zucol Services PVT LTD | All rights reserved.