Lean Production Strategies and Impacts: Portakabin Case Study Analysis
VerifiedAdded on 2020/03/13
|16
|4196
|276
Case Study
AI Summary
This case study examines the implementation of lean production principles at Portakabin, a UK-based construction company specializing in steel buildings. The analysis covers various production methods including flow, cellular, and batch production, highlighting their advantages and disadvantages. The study explores the application of Just-In-Time (JIT) techniques in meeting project targets, particularly for Lilliput Children’s Centres, and details the waste reduction strategies employed by Portakabin, such as modular building and recycling. The case study further evaluates the impacts of lean production on Portakabin, encompassing financial, environmental, and social benefits, and emphasizes the company's commitment to efficiency, quality, and sustainability within the construction industry. The study references various academic sources to support its findings and conclusions.
Contribute Materials
Your contribution can guide someone’s learning journey. Share your
documents today.
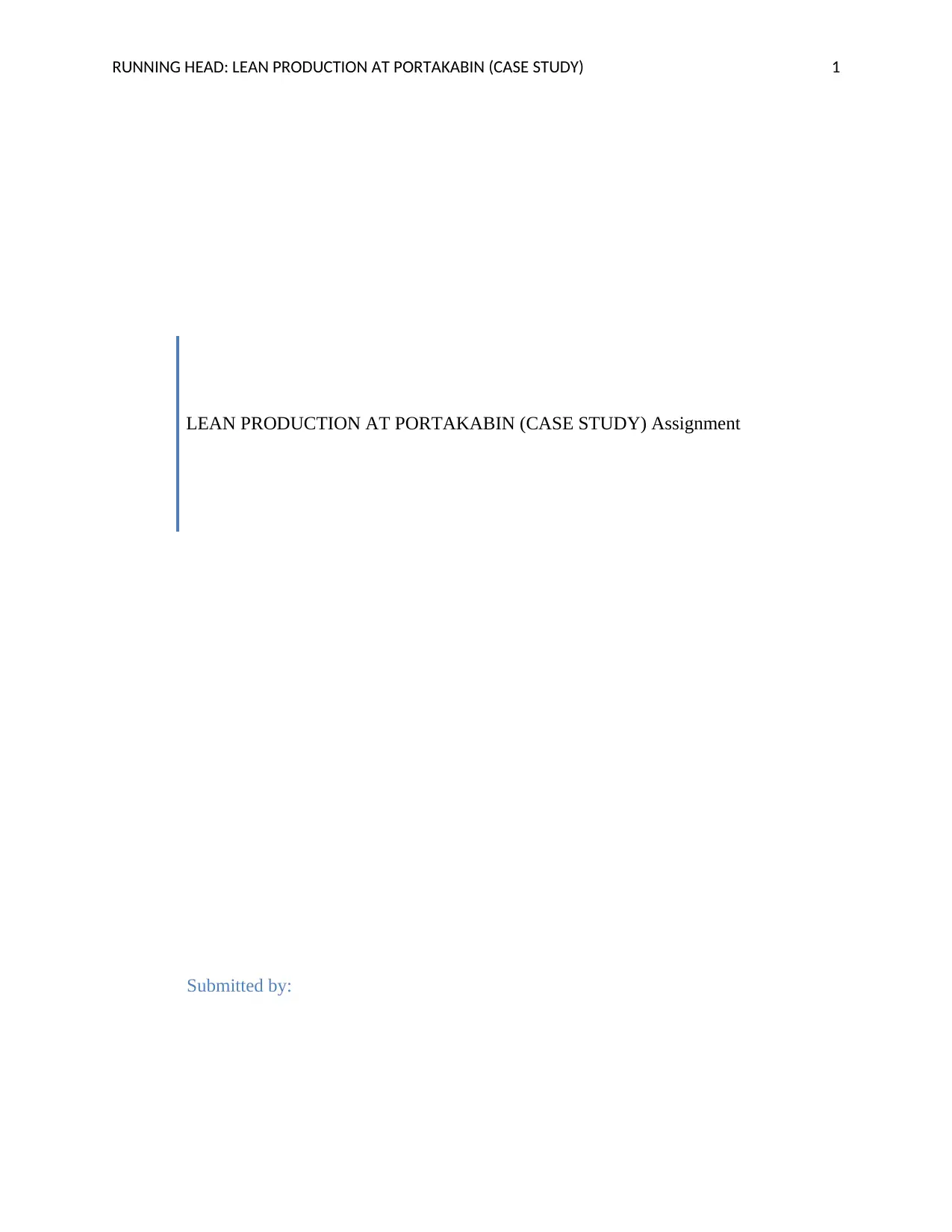
RUNNING HEAD: LEAN PRODUCTION AT PORTAKABIN (CASE STUDY) 1
LEAN PRODUCTION AT PORTAKABIN (CASE STUDY) Assignment
Submitted by:
LEAN PRODUCTION AT PORTAKABIN (CASE STUDY) Assignment
Submitted by:
Secure Best Marks with AI Grader
Need help grading? Try our AI Grader for instant feedback on your assignments.
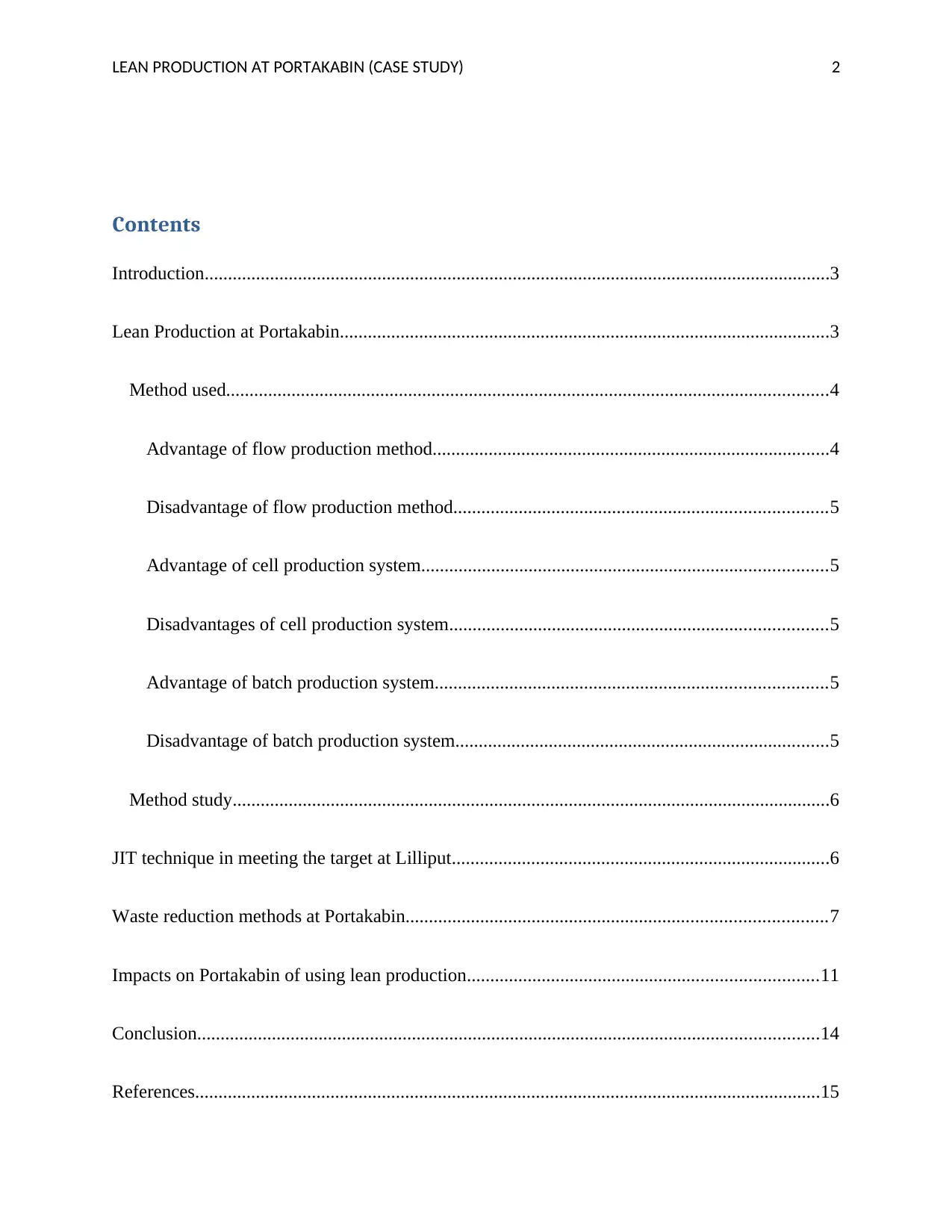
LEAN PRODUCTION AT PORTAKABIN (CASE STUDY) 2
Contents
Introduction......................................................................................................................................3
Lean Production at Portakabin.........................................................................................................3
Method used.................................................................................................................................4
Advantage of flow production method.....................................................................................4
Disadvantage of flow production method................................................................................5
Advantage of cell production system.......................................................................................5
Disadvantages of cell production system.................................................................................5
Advantage of batch production system....................................................................................5
Disadvantage of batch production system................................................................................5
Method study................................................................................................................................6
JIT technique in meeting the target at Lilliput.................................................................................6
Waste reduction methods at Portakabin..........................................................................................7
Impacts on Portakabin of using lean production...........................................................................11
Conclusion.....................................................................................................................................14
References......................................................................................................................................15
Contents
Introduction......................................................................................................................................3
Lean Production at Portakabin.........................................................................................................3
Method used.................................................................................................................................4
Advantage of flow production method.....................................................................................4
Disadvantage of flow production method................................................................................5
Advantage of cell production system.......................................................................................5
Disadvantages of cell production system.................................................................................5
Advantage of batch production system....................................................................................5
Disadvantage of batch production system................................................................................5
Method study................................................................................................................................6
JIT technique in meeting the target at Lilliput.................................................................................6
Waste reduction methods at Portakabin..........................................................................................7
Impacts on Portakabin of using lean production...........................................................................11
Conclusion.....................................................................................................................................14
References......................................................................................................................................15
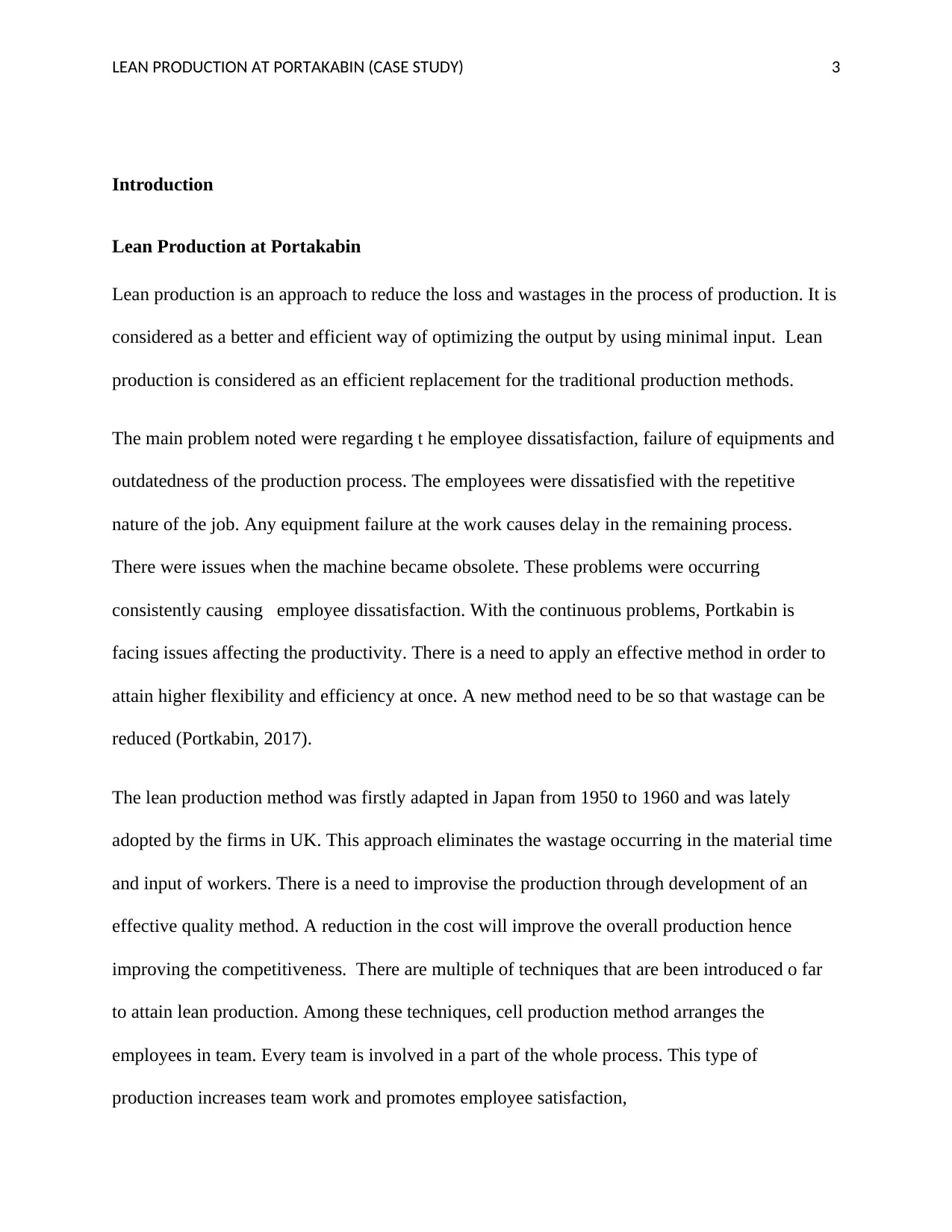
LEAN PRODUCTION AT PORTAKABIN (CASE STUDY) 3
Introduction
Lean Production at Portakabin
Lean production is an approach to reduce the loss and wastages in the process of production. It is
considered as a better and efficient way of optimizing the output by using minimal input. Lean
production is considered as an efficient replacement for the traditional production methods.
The main problem noted were regarding t he employee dissatisfaction, failure of equipments and
outdatedness of the production process. The employees were dissatisfied with the repetitive
nature of the job. Any equipment failure at the work causes delay in the remaining process.
There were issues when the machine became obsolete. These problems were occurring
consistently causing employee dissatisfaction. With the continuous problems, Portkabin is
facing issues affecting the productivity. There is a need to apply an effective method in order to
attain higher flexibility and efficiency at once. A new method need to be so that wastage can be
reduced (Portkabin, 2017).
The lean production method was firstly adapted in Japan from 1950 to 1960 and was lately
adopted by the firms in UK. This approach eliminates the wastage occurring in the material time
and input of workers. There is a need to improvise the production through development of an
effective quality method. A reduction in the cost will improve the overall production hence
improving the competitiveness. There are multiple of techniques that are been introduced o far
to attain lean production. Among these techniques, cell production method arranges the
employees in team. Every team is involved in a part of the whole process. This type of
production increases team work and promotes employee satisfaction,
Introduction
Lean Production at Portakabin
Lean production is an approach to reduce the loss and wastages in the process of production. It is
considered as a better and efficient way of optimizing the output by using minimal input. Lean
production is considered as an efficient replacement for the traditional production methods.
The main problem noted were regarding t he employee dissatisfaction, failure of equipments and
outdatedness of the production process. The employees were dissatisfied with the repetitive
nature of the job. Any equipment failure at the work causes delay in the remaining process.
There were issues when the machine became obsolete. These problems were occurring
consistently causing employee dissatisfaction. With the continuous problems, Portkabin is
facing issues affecting the productivity. There is a need to apply an effective method in order to
attain higher flexibility and efficiency at once. A new method need to be so that wastage can be
reduced (Portkabin, 2017).
The lean production method was firstly adapted in Japan from 1950 to 1960 and was lately
adopted by the firms in UK. This approach eliminates the wastage occurring in the material time
and input of workers. There is a need to improvise the production through development of an
effective quality method. A reduction in the cost will improve the overall production hence
improving the competitiveness. There are multiple of techniques that are been introduced o far
to attain lean production. Among these techniques, cell production method arranges the
employees in team. Every team is involved in a part of the whole process. This type of
production increases team work and promotes employee satisfaction,
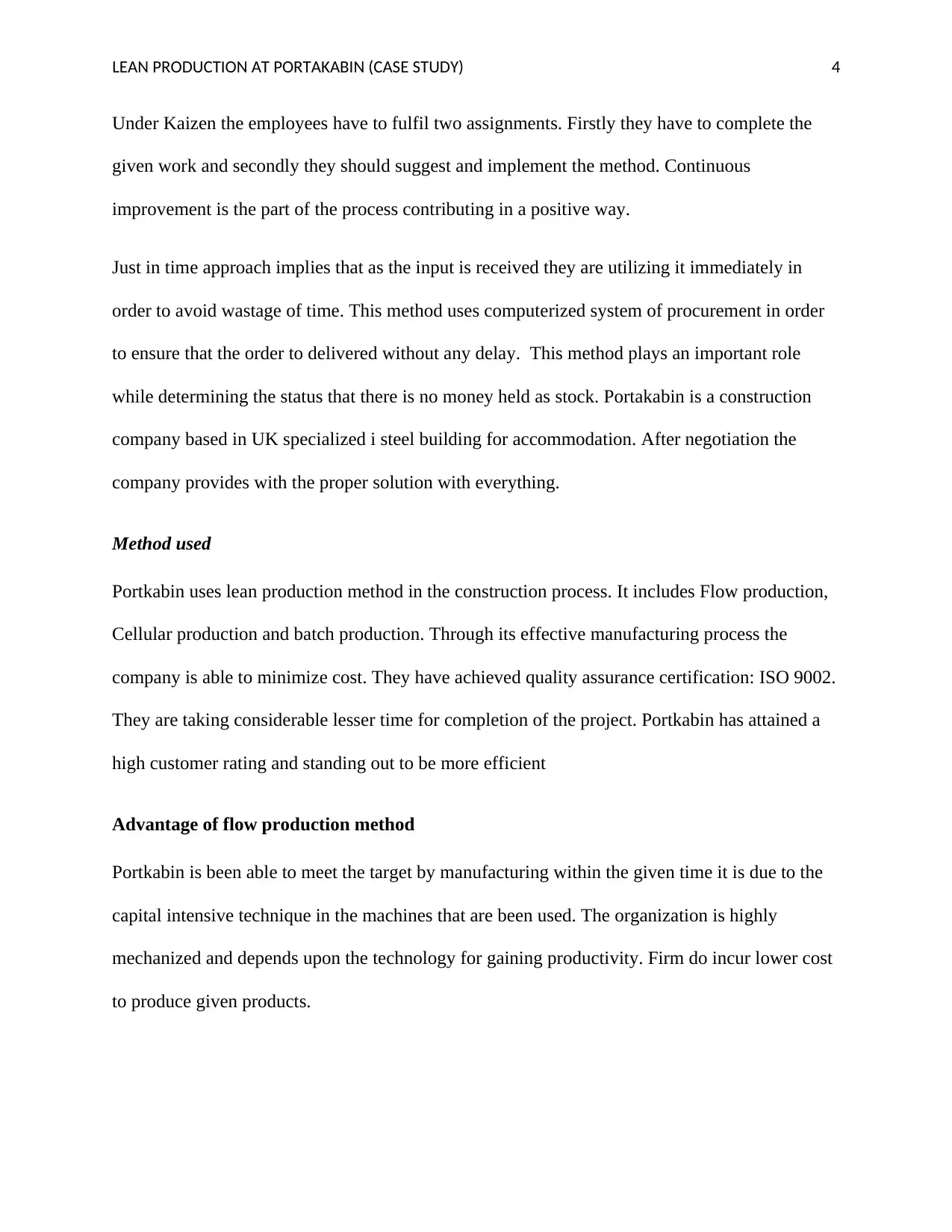
LEAN PRODUCTION AT PORTAKABIN (CASE STUDY) 4
Under Kaizen the employees have to fulfil two assignments. Firstly they have to complete the
given work and secondly they should suggest and implement the method. Continuous
improvement is the part of the process contributing in a positive way.
Just in time approach implies that as the input is received they are utilizing it immediately in
order to avoid wastage of time. This method uses computerized system of procurement in order
to ensure that the order to delivered without any delay. This method plays an important role
while determining the status that there is no money held as stock. Portakabin is a construction
company based in UK specialized i steel building for accommodation. After negotiation the
company provides with the proper solution with everything.
Method used
Portkabin uses lean production method in the construction process. It includes Flow production,
Cellular production and batch production. Through its effective manufacturing process the
company is able to minimize cost. They have achieved quality assurance certification: ISO 9002.
They are taking considerable lesser time for completion of the project. Portkabin has attained a
high customer rating and standing out to be more efficient
Advantage of flow production method
Portkabin is been able to meet the target by manufacturing within the given time it is due to the
capital intensive technique in the machines that are been used. The organization is highly
mechanized and depends upon the technology for gaining productivity. Firm do incur lower cost
to produce given products.
Under Kaizen the employees have to fulfil two assignments. Firstly they have to complete the
given work and secondly they should suggest and implement the method. Continuous
improvement is the part of the process contributing in a positive way.
Just in time approach implies that as the input is received they are utilizing it immediately in
order to avoid wastage of time. This method uses computerized system of procurement in order
to ensure that the order to delivered without any delay. This method plays an important role
while determining the status that there is no money held as stock. Portakabin is a construction
company based in UK specialized i steel building for accommodation. After negotiation the
company provides with the proper solution with everything.
Method used
Portkabin uses lean production method in the construction process. It includes Flow production,
Cellular production and batch production. Through its effective manufacturing process the
company is able to minimize cost. They have achieved quality assurance certification: ISO 9002.
They are taking considerable lesser time for completion of the project. Portkabin has attained a
high customer rating and standing out to be more efficient
Advantage of flow production method
Portkabin is been able to meet the target by manufacturing within the given time it is due to the
capital intensive technique in the machines that are been used. The organization is highly
mechanized and depends upon the technology for gaining productivity. Firm do incur lower cost
to produce given products.
Secure Best Marks with AI Grader
Need help grading? Try our AI Grader for instant feedback on your assignments.
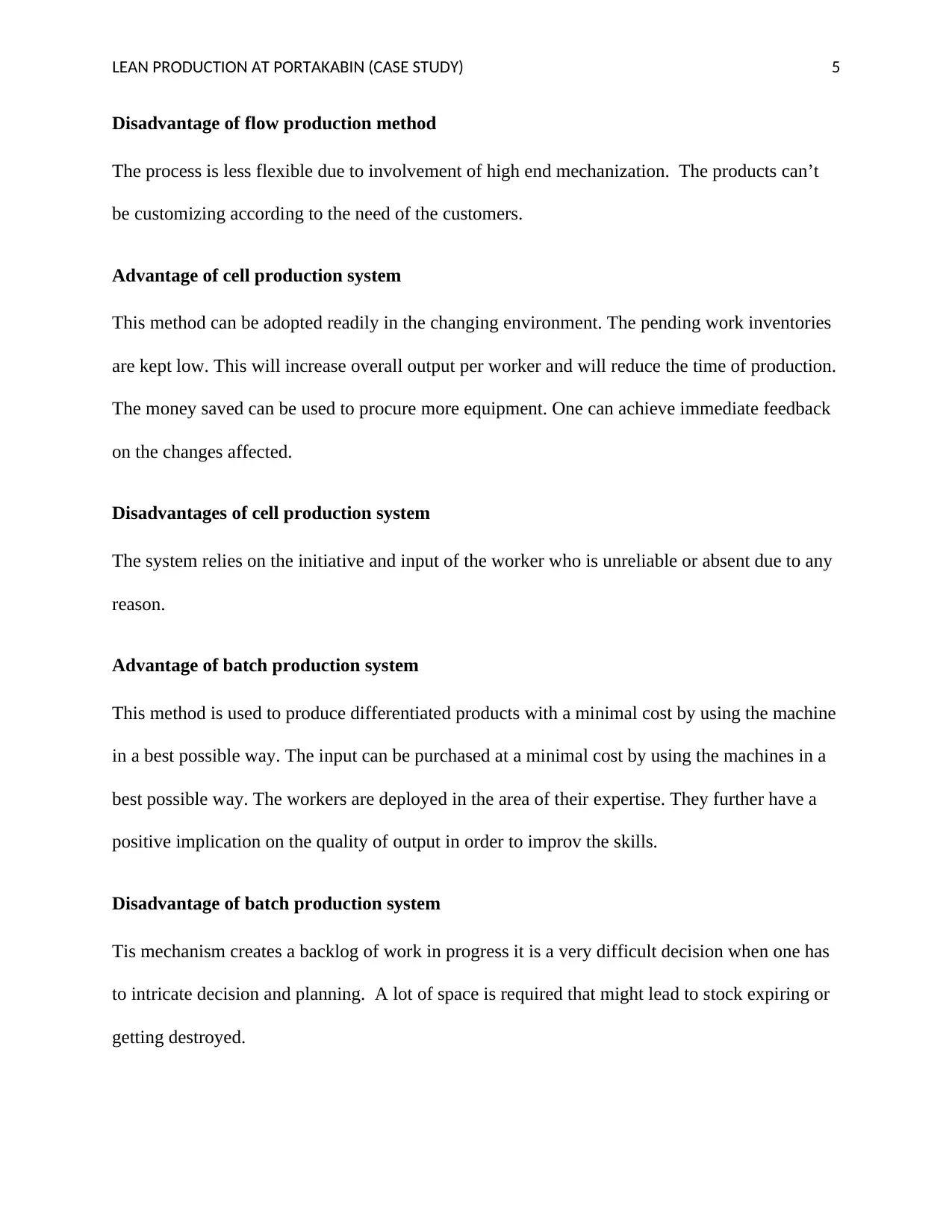
LEAN PRODUCTION AT PORTAKABIN (CASE STUDY) 5
Disadvantage of flow production method
The process is less flexible due to involvement of high end mechanization. The products can’t
be customizing according to the need of the customers.
Advantage of cell production system
This method can be adopted readily in the changing environment. The pending work inventories
are kept low. This will increase overall output per worker and will reduce the time of production.
The money saved can be used to procure more equipment. One can achieve immediate feedback
on the changes affected.
Disadvantages of cell production system
The system relies on the initiative and input of the worker who is unreliable or absent due to any
reason.
Advantage of batch production system
This method is used to produce differentiated products with a minimal cost by using the machine
in a best possible way. The input can be purchased at a minimal cost by using the machines in a
best possible way. The workers are deployed in the area of their expertise. They further have a
positive implication on the quality of output in order to improv the skills.
Disadvantage of batch production system
Tis mechanism creates a backlog of work in progress it is a very difficult decision when one has
to intricate decision and planning. A lot of space is required that might lead to stock expiring or
getting destroyed.
Disadvantage of flow production method
The process is less flexible due to involvement of high end mechanization. The products can’t
be customizing according to the need of the customers.
Advantage of cell production system
This method can be adopted readily in the changing environment. The pending work inventories
are kept low. This will increase overall output per worker and will reduce the time of production.
The money saved can be used to procure more equipment. One can achieve immediate feedback
on the changes affected.
Disadvantages of cell production system
The system relies on the initiative and input of the worker who is unreliable or absent due to any
reason.
Advantage of batch production system
This method is used to produce differentiated products with a minimal cost by using the machine
in a best possible way. The input can be purchased at a minimal cost by using the machines in a
best possible way. The workers are deployed in the area of their expertise. They further have a
positive implication on the quality of output in order to improv the skills.
Disadvantage of batch production system
Tis mechanism creates a backlog of work in progress it is a very difficult decision when one has
to intricate decision and planning. A lot of space is required that might lead to stock expiring or
getting destroyed.
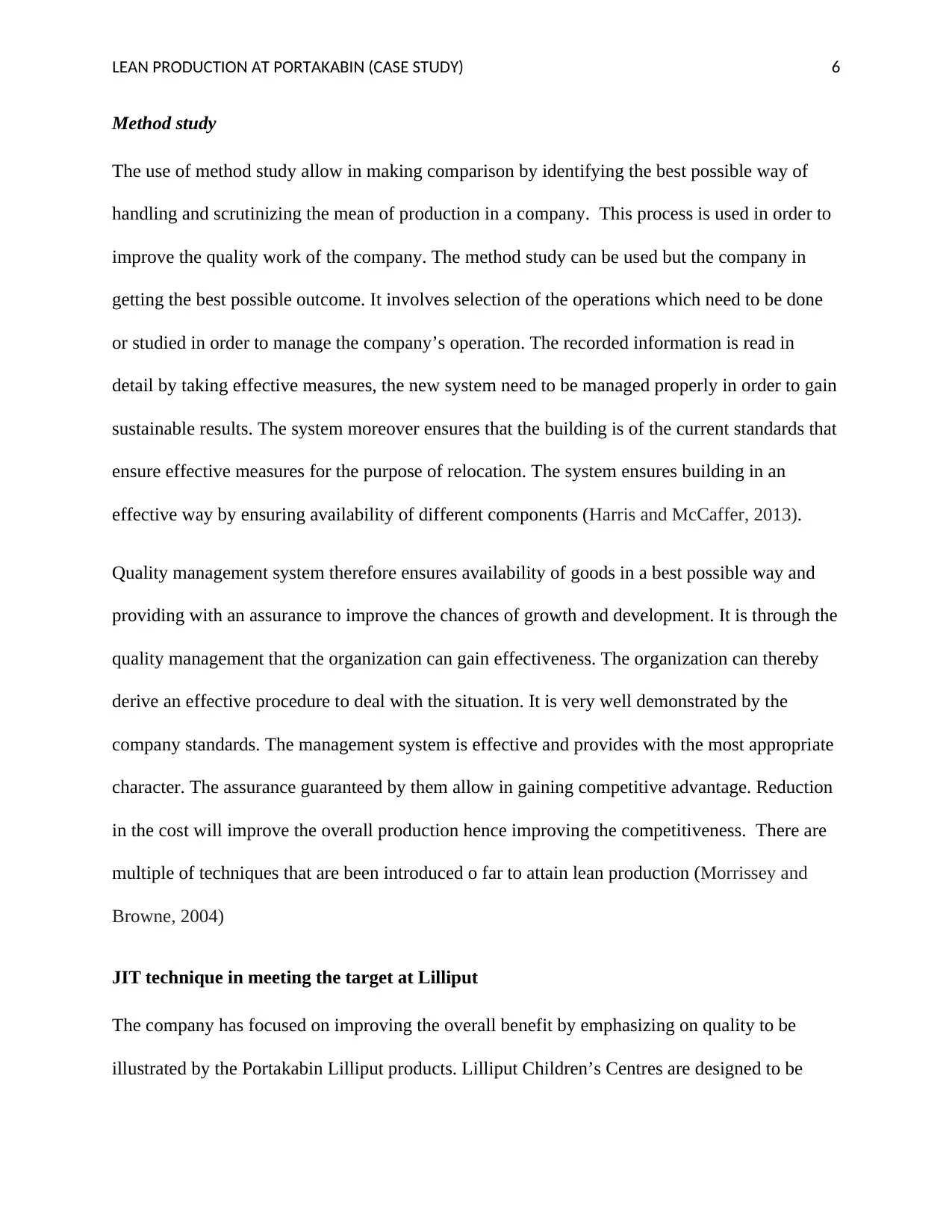
LEAN PRODUCTION AT PORTAKABIN (CASE STUDY) 6
Method study
The use of method study allow in making comparison by identifying the best possible way of
handling and scrutinizing the mean of production in a company. This process is used in order to
improve the quality work of the company. The method study can be used but the company in
getting the best possible outcome. It involves selection of the operations which need to be done
or studied in order to manage the company’s operation. The recorded information is read in
detail by taking effective measures, the new system need to be managed properly in order to gain
sustainable results. The system moreover ensures that the building is of the current standards that
ensure effective measures for the purpose of relocation. The system ensures building in an
effective way by ensuring availability of different components (Harris and McCaffer, 2013).
Quality management system therefore ensures availability of goods in a best possible way and
providing with an assurance to improve the chances of growth and development. It is through the
quality management that the organization can gain effectiveness. The organization can thereby
derive an effective procedure to deal with the situation. It is very well demonstrated by the
company standards. The management system is effective and provides with the most appropriate
character. The assurance guaranteed by them allow in gaining competitive advantage. Reduction
in the cost will improve the overall production hence improving the competitiveness. There are
multiple of techniques that are been introduced o far to attain lean production (Morrissey and
Browne, 2004)
JIT technique in meeting the target at Lilliput
The company has focused on improving the overall benefit by emphasizing on quality to be
illustrated by the Portakabin Lilliput products. Lilliput Children’s Centres are designed to be
Method study
The use of method study allow in making comparison by identifying the best possible way of
handling and scrutinizing the mean of production in a company. This process is used in order to
improve the quality work of the company. The method study can be used but the company in
getting the best possible outcome. It involves selection of the operations which need to be done
or studied in order to manage the company’s operation. The recorded information is read in
detail by taking effective measures, the new system need to be managed properly in order to gain
sustainable results. The system moreover ensures that the building is of the current standards that
ensure effective measures for the purpose of relocation. The system ensures building in an
effective way by ensuring availability of different components (Harris and McCaffer, 2013).
Quality management system therefore ensures availability of goods in a best possible way and
providing with an assurance to improve the chances of growth and development. It is through the
quality management that the organization can gain effectiveness. The organization can thereby
derive an effective procedure to deal with the situation. It is very well demonstrated by the
company standards. The management system is effective and provides with the most appropriate
character. The assurance guaranteed by them allow in gaining competitive advantage. Reduction
in the cost will improve the overall production hence improving the competitiveness. There are
multiple of techniques that are been introduced o far to attain lean production (Morrissey and
Browne, 2004)
JIT technique in meeting the target at Lilliput
The company has focused on improving the overall benefit by emphasizing on quality to be
illustrated by the Portakabin Lilliput products. Lilliput Children’s Centres are designed to be
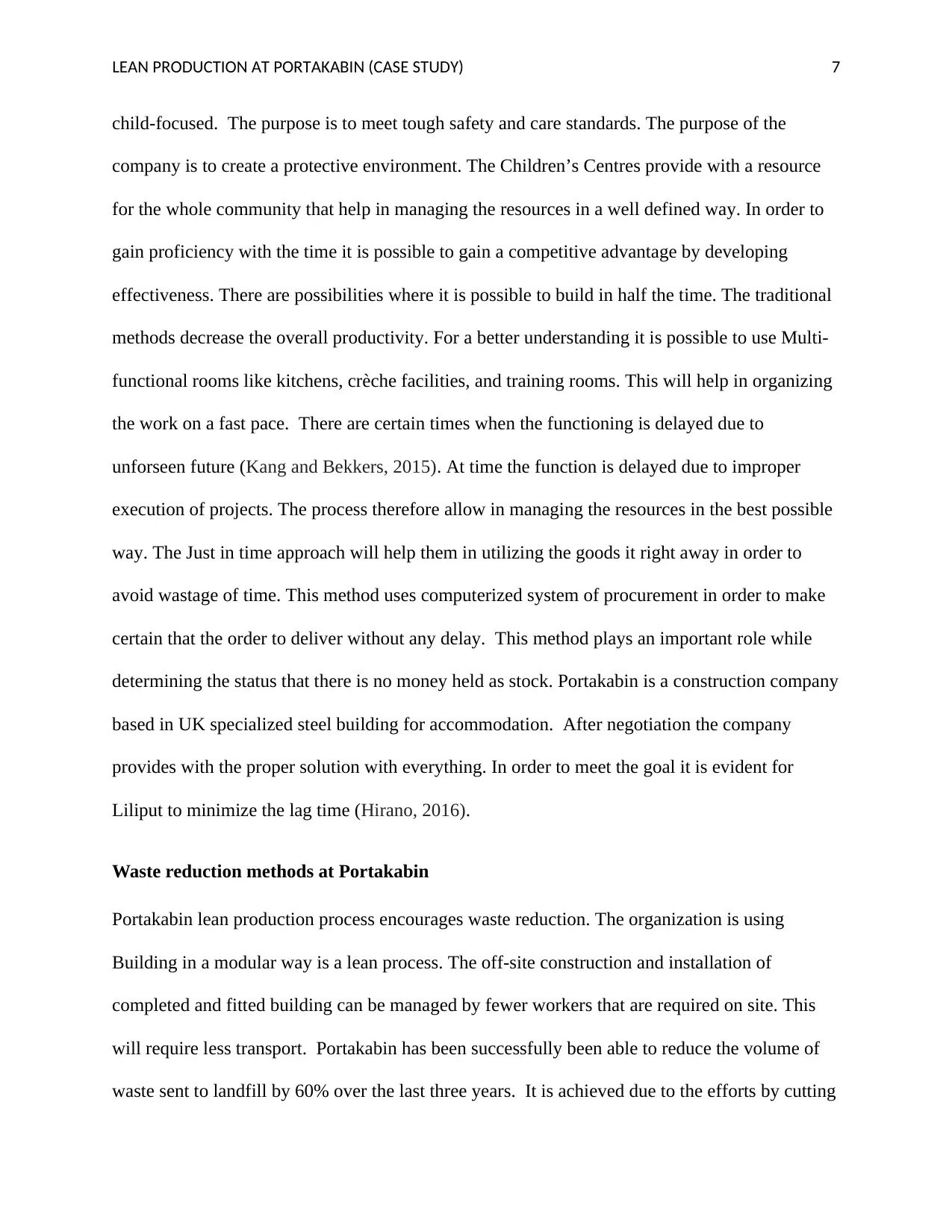
LEAN PRODUCTION AT PORTAKABIN (CASE STUDY) 7
child-focused. The purpose is to meet tough safety and care standards. The purpose of the
company is to create a protective environment. The Children’s Centres provide with a resource
for the whole community that help in managing the resources in a well defined way. In order to
gain proficiency with the time it is possible to gain a competitive advantage by developing
effectiveness. There are possibilities where it is possible to build in half the time. The traditional
methods decrease the overall productivity. For a better understanding it is possible to use Multi-
functional rooms like kitchens, crèche facilities, and training rooms. This will help in organizing
the work on a fast pace. There are certain times when the functioning is delayed due to
unforseen future (Kang and Bekkers, 2015). At time the function is delayed due to improper
execution of projects. The process therefore allow in managing the resources in the best possible
way. The Just in time approach will help them in utilizing the goods it right away in order to
avoid wastage of time. This method uses computerized system of procurement in order to make
certain that the order to deliver without any delay. This method plays an important role while
determining the status that there is no money held as stock. Portakabin is a construction company
based in UK specialized steel building for accommodation. After negotiation the company
provides with the proper solution with everything. In order to meet the goal it is evident for
Liliput to minimize the lag time (Hirano, 2016).
Waste reduction methods at Portakabin
Portakabin lean production process encourages waste reduction. The organization is using
Building in a modular way is a lean process. The off-site construction and installation of
completed and fitted building can be managed by fewer workers that are required on site. This
will require less transport. Portakabin has been successfully been able to reduce the volume of
waste sent to landfill by 60% over the last three years. It is achieved due to the efforts by cutting
child-focused. The purpose is to meet tough safety and care standards. The purpose of the
company is to create a protective environment. The Children’s Centres provide with a resource
for the whole community that help in managing the resources in a well defined way. In order to
gain proficiency with the time it is possible to gain a competitive advantage by developing
effectiveness. There are possibilities where it is possible to build in half the time. The traditional
methods decrease the overall productivity. For a better understanding it is possible to use Multi-
functional rooms like kitchens, crèche facilities, and training rooms. This will help in organizing
the work on a fast pace. There are certain times when the functioning is delayed due to
unforseen future (Kang and Bekkers, 2015). At time the function is delayed due to improper
execution of projects. The process therefore allow in managing the resources in the best possible
way. The Just in time approach will help them in utilizing the goods it right away in order to
avoid wastage of time. This method uses computerized system of procurement in order to make
certain that the order to deliver without any delay. This method plays an important role while
determining the status that there is no money held as stock. Portakabin is a construction company
based in UK specialized steel building for accommodation. After negotiation the company
provides with the proper solution with everything. In order to meet the goal it is evident for
Liliput to minimize the lag time (Hirano, 2016).
Waste reduction methods at Portakabin
Portakabin lean production process encourages waste reduction. The organization is using
Building in a modular way is a lean process. The off-site construction and installation of
completed and fitted building can be managed by fewer workers that are required on site. This
will require less transport. Portakabin has been successfully been able to reduce the volume of
waste sent to landfill by 60% over the last three years. It is achieved due to the efforts by cutting
Paraphrase This Document
Need a fresh take? Get an instant paraphrase of this document with our AI Paraphraser
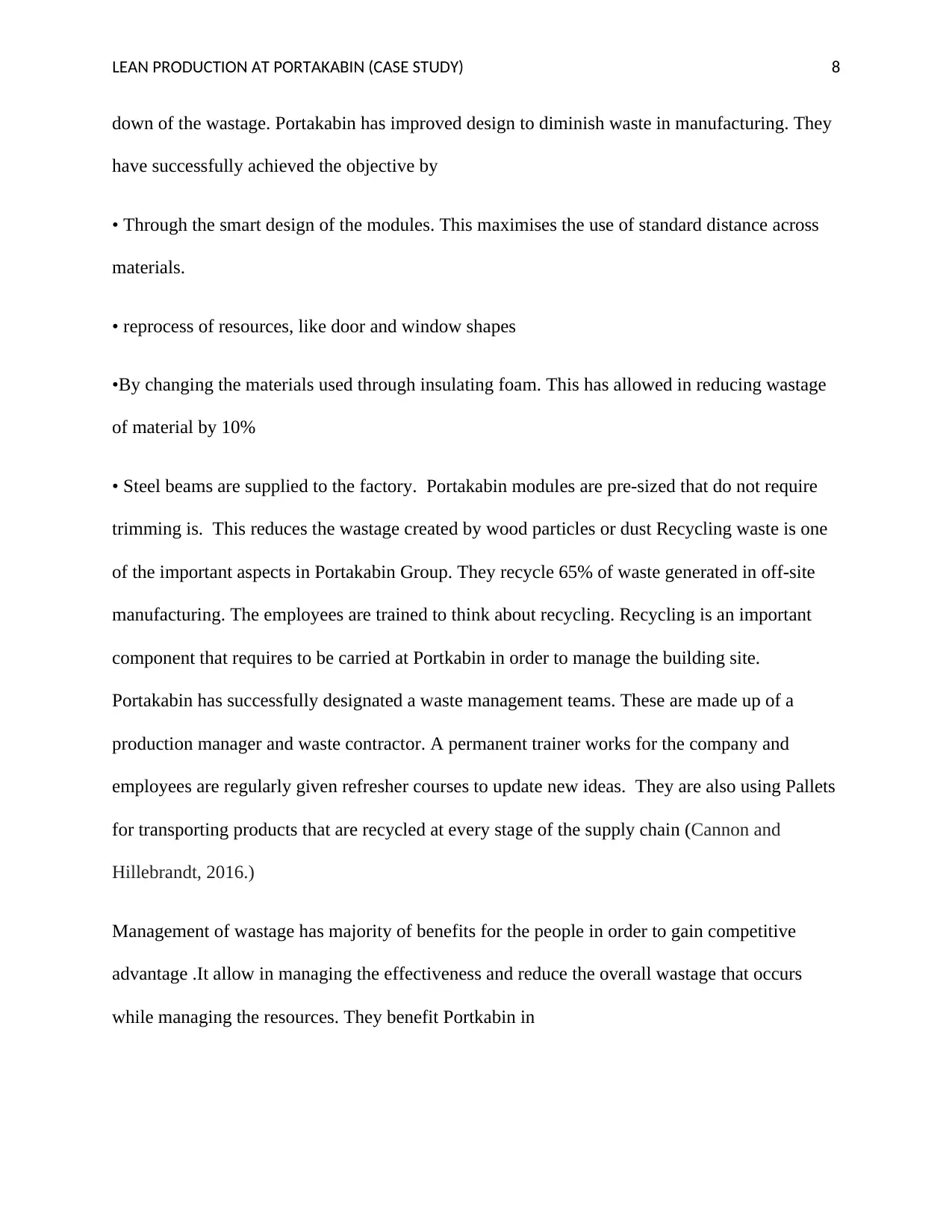
LEAN PRODUCTION AT PORTAKABIN (CASE STUDY) 8
down of the wastage. Portakabin has improved design to diminish waste in manufacturing. They
have successfully achieved the objective by
• Through the smart design of the modules. This maximises the use of standard distance across
materials.
• reprocess of resources, like door and window shapes
•By changing the materials used through insulating foam. This has allowed in reducing wastage
of material by 10%
• Steel beams are supplied to the factory. Portakabin modules are pre-sized that do not require
trimming is. This reduces the wastage created by wood particles or dust Recycling waste is one
of the important aspects in Portakabin Group. They recycle 65% of waste generated in off-site
manufacturing. The employees are trained to think about recycling. Recycling is an important
component that requires to be carried at Portkabin in order to manage the building site.
Portakabin has successfully designated a waste management teams. These are made up of a
production manager and waste contractor. A permanent trainer works for the company and
employees are regularly given refresher courses to update new ideas. They are also using Pallets
for transporting products that are recycled at every stage of the supply chain (Cannon and
Hillebrandt, 2016.)
Management of wastage has majority of benefits for the people in order to gain competitive
advantage .It allow in managing the effectiveness and reduce the overall wastage that occurs
while managing the resources. They benefit Portkabin in
down of the wastage. Portakabin has improved design to diminish waste in manufacturing. They
have successfully achieved the objective by
• Through the smart design of the modules. This maximises the use of standard distance across
materials.
• reprocess of resources, like door and window shapes
•By changing the materials used through insulating foam. This has allowed in reducing wastage
of material by 10%
• Steel beams are supplied to the factory. Portakabin modules are pre-sized that do not require
trimming is. This reduces the wastage created by wood particles or dust Recycling waste is one
of the important aspects in Portakabin Group. They recycle 65% of waste generated in off-site
manufacturing. The employees are trained to think about recycling. Recycling is an important
component that requires to be carried at Portkabin in order to manage the building site.
Portakabin has successfully designated a waste management teams. These are made up of a
production manager and waste contractor. A permanent trainer works for the company and
employees are regularly given refresher courses to update new ideas. They are also using Pallets
for transporting products that are recycled at every stage of the supply chain (Cannon and
Hillebrandt, 2016.)
Management of wastage has majority of benefits for the people in order to gain competitive
advantage .It allow in managing the effectiveness and reduce the overall wastage that occurs
while managing the resources. They benefit Portkabin in
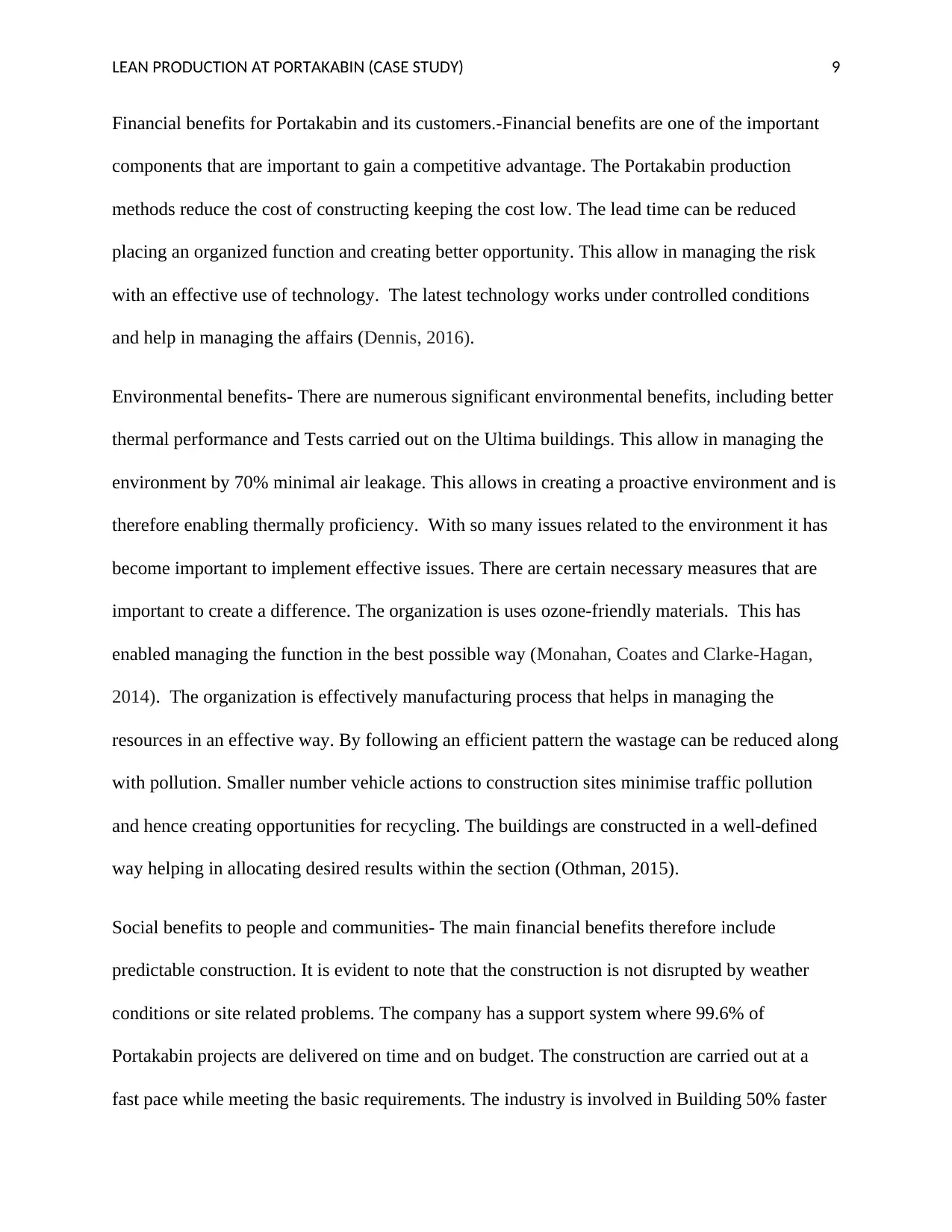
LEAN PRODUCTION AT PORTAKABIN (CASE STUDY) 9
Financial benefits for Portakabin and its customers.-Financial benefits are one of the important
components that are important to gain a competitive advantage. The Portakabin production
methods reduce the cost of constructing keeping the cost low. The lead time can be reduced
placing an organized function and creating better opportunity. This allow in managing the risk
with an effective use of technology. The latest technology works under controlled conditions
and help in managing the affairs (Dennis, 2016).
Environmental benefits- There are numerous significant environmental benefits, including better
thermal performance and Tests carried out on the Ultima buildings. This allow in managing the
environment by 70% minimal air leakage. This allows in creating a proactive environment and is
therefore enabling thermally proficiency. With so many issues related to the environment it has
become important to implement effective issues. There are certain necessary measures that are
important to create a difference. The organization is uses ozone-friendly materials. This has
enabled managing the function in the best possible way (Monahan, Coates and Clarke-Hagan,
2014). The organization is effectively manufacturing process that helps in managing the
resources in an effective way. By following an efficient pattern the wastage can be reduced along
with pollution. Smaller number vehicle actions to construction sites minimise traffic pollution
and hence creating opportunities for recycling. The buildings are constructed in a well-defined
way helping in allocating desired results within the section (Othman, 2015).
Social benefits to people and communities- The main financial benefits therefore include
predictable construction. It is evident to note that the construction is not disrupted by weather
conditions or site related problems. The company has a support system where 99.6% of
Portakabin projects are delivered on time and on budget. The construction are carried out at a
fast pace while meeting the basic requirements. The industry is involved in Building 50% faster
Financial benefits for Portakabin and its customers.-Financial benefits are one of the important
components that are important to gain a competitive advantage. The Portakabin production
methods reduce the cost of constructing keeping the cost low. The lead time can be reduced
placing an organized function and creating better opportunity. This allow in managing the risk
with an effective use of technology. The latest technology works under controlled conditions
and help in managing the affairs (Dennis, 2016).
Environmental benefits- There are numerous significant environmental benefits, including better
thermal performance and Tests carried out on the Ultima buildings. This allow in managing the
environment by 70% minimal air leakage. This allows in creating a proactive environment and is
therefore enabling thermally proficiency. With so many issues related to the environment it has
become important to implement effective issues. There are certain necessary measures that are
important to create a difference. The organization is uses ozone-friendly materials. This has
enabled managing the function in the best possible way (Monahan, Coates and Clarke-Hagan,
2014). The organization is effectively manufacturing process that helps in managing the
resources in an effective way. By following an efficient pattern the wastage can be reduced along
with pollution. Smaller number vehicle actions to construction sites minimise traffic pollution
and hence creating opportunities for recycling. The buildings are constructed in a well-defined
way helping in allocating desired results within the section (Othman, 2015).
Social benefits to people and communities- The main financial benefits therefore include
predictable construction. It is evident to note that the construction is not disrupted by weather
conditions or site related problems. The company has a support system where 99.6% of
Portakabin projects are delivered on time and on budget. The construction are carried out at a
fast pace while meeting the basic requirements. The industry is involved in Building 50% faster
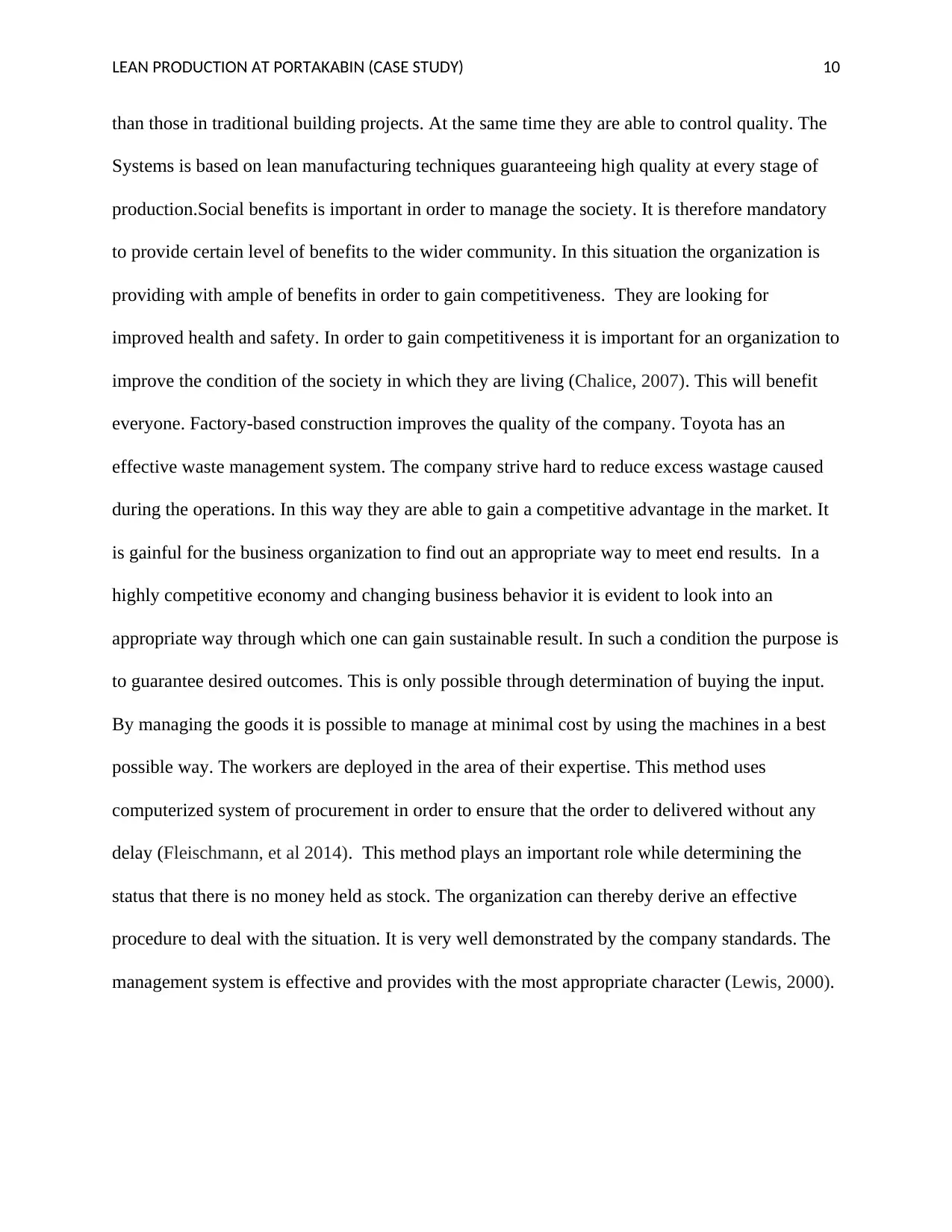
LEAN PRODUCTION AT PORTAKABIN (CASE STUDY) 10
than those in traditional building projects. At the same time they are able to control quality. The
Systems is based on lean manufacturing techniques guaranteeing high quality at every stage of
production.Social benefits is important in order to manage the society. It is therefore mandatory
to provide certain level of benefits to the wider community. In this situation the organization is
providing with ample of benefits in order to gain competitiveness. They are looking for
improved health and safety. In order to gain competitiveness it is important for an organization to
improve the condition of the society in which they are living (Chalice, 2007). This will benefit
everyone. Factory-based construction improves the quality of the company. Toyota has an
effective waste management system. The company strive hard to reduce excess wastage caused
during the operations. In this way they are able to gain a competitive advantage in the market. It
is gainful for the business organization to find out an appropriate way to meet end results. In a
highly competitive economy and changing business behavior it is evident to look into an
appropriate way through which one can gain sustainable result. In such a condition the purpose is
to guarantee desired outcomes. This is only possible through determination of buying the input.
By managing the goods it is possible to manage at minimal cost by using the machines in a best
possible way. The workers are deployed in the area of their expertise. This method uses
computerized system of procurement in order to ensure that the order to delivered without any
delay (Fleischmann, et al 2014). This method plays an important role while determining the
status that there is no money held as stock. The organization can thereby derive an effective
procedure to deal with the situation. It is very well demonstrated by the company standards. The
management system is effective and provides with the most appropriate character (Lewis, 2000).
than those in traditional building projects. At the same time they are able to control quality. The
Systems is based on lean manufacturing techniques guaranteeing high quality at every stage of
production.Social benefits is important in order to manage the society. It is therefore mandatory
to provide certain level of benefits to the wider community. In this situation the organization is
providing with ample of benefits in order to gain competitiveness. They are looking for
improved health and safety. In order to gain competitiveness it is important for an organization to
improve the condition of the society in which they are living (Chalice, 2007). This will benefit
everyone. Factory-based construction improves the quality of the company. Toyota has an
effective waste management system. The company strive hard to reduce excess wastage caused
during the operations. In this way they are able to gain a competitive advantage in the market. It
is gainful for the business organization to find out an appropriate way to meet end results. In a
highly competitive economy and changing business behavior it is evident to look into an
appropriate way through which one can gain sustainable result. In such a condition the purpose is
to guarantee desired outcomes. This is only possible through determination of buying the input.
By managing the goods it is possible to manage at minimal cost by using the machines in a best
possible way. The workers are deployed in the area of their expertise. This method uses
computerized system of procurement in order to ensure that the order to delivered without any
delay (Fleischmann, et al 2014). This method plays an important role while determining the
status that there is no money held as stock. The organization can thereby derive an effective
procedure to deal with the situation. It is very well demonstrated by the company standards. The
management system is effective and provides with the most appropriate character (Lewis, 2000).
Secure Best Marks with AI Grader
Need help grading? Try our AI Grader for instant feedback on your assignments.
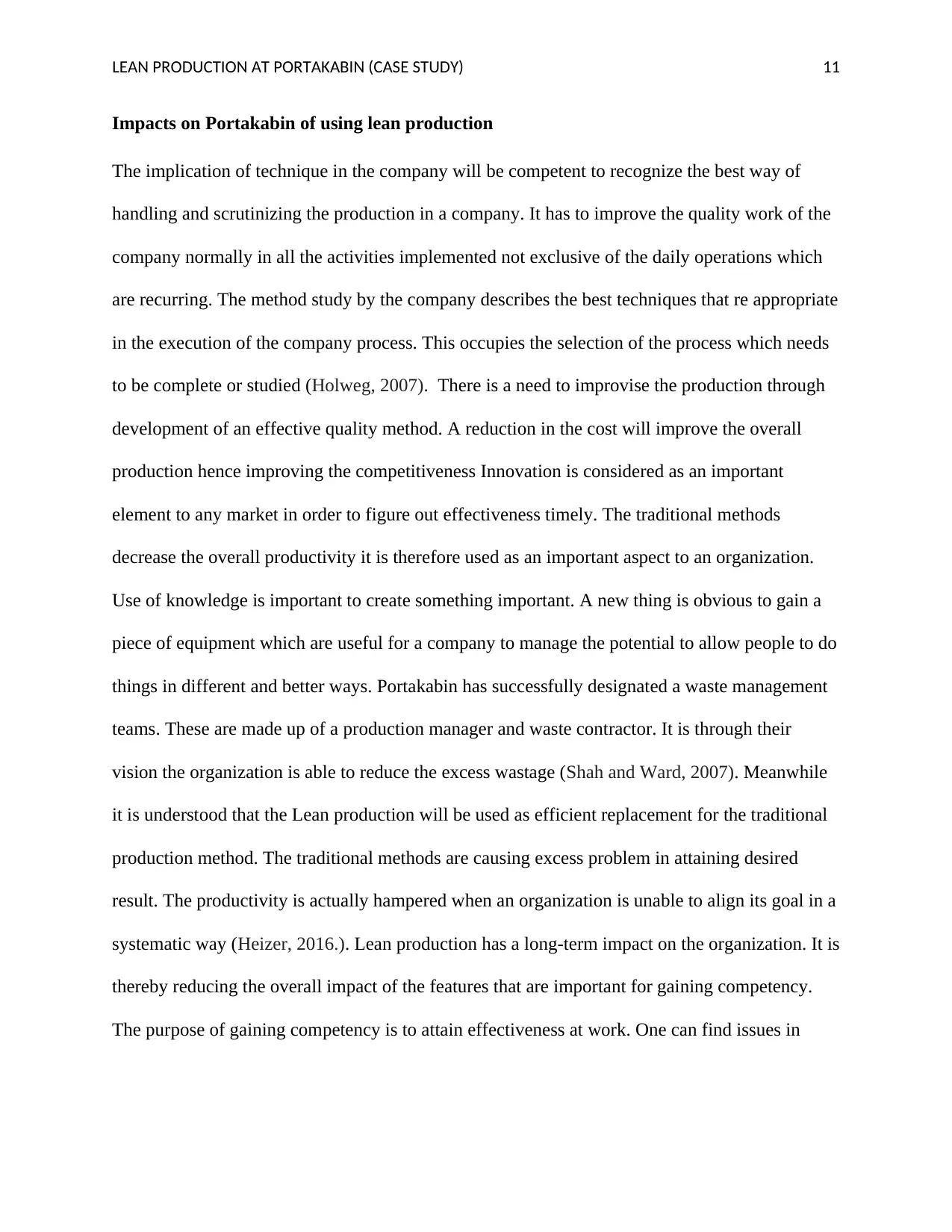
LEAN PRODUCTION AT PORTAKABIN (CASE STUDY) 11
Impacts on Portakabin of using lean production
The implication of technique in the company will be competent to recognize the best way of
handling and scrutinizing the production in a company. It has to improve the quality work of the
company normally in all the activities implemented not exclusive of the daily operations which
are recurring. The method study by the company describes the best techniques that re appropriate
in the execution of the company process. This occupies the selection of the process which needs
to be complete or studied (Holweg, 2007). There is a need to improvise the production through
development of an effective quality method. A reduction in the cost will improve the overall
production hence improving the competitiveness Innovation is considered as an important
element to any market in order to figure out effectiveness timely. The traditional methods
decrease the overall productivity it is therefore used as an important aspect to an organization.
Use of knowledge is important to create something important. A new thing is obvious to gain a
piece of equipment which are useful for a company to manage the potential to allow people to do
things in different and better ways. Portakabin has successfully designated a waste management
teams. These are made up of a production manager and waste contractor. It is through their
vision the organization is able to reduce the excess wastage (Shah and Ward, 2007). Meanwhile
it is understood that the Lean production will be used as efficient replacement for the traditional
production method. The traditional methods are causing excess problem in attaining desired
result. The productivity is actually hampered when an organization is unable to align its goal in a
systematic way (Heizer, 2016.). Lean production has a long-term impact on the organization. It is
thereby reducing the overall impact of the features that are important for gaining competency.
The purpose of gaining competency is to attain effectiveness at work. One can find issues in
Impacts on Portakabin of using lean production
The implication of technique in the company will be competent to recognize the best way of
handling and scrutinizing the production in a company. It has to improve the quality work of the
company normally in all the activities implemented not exclusive of the daily operations which
are recurring. The method study by the company describes the best techniques that re appropriate
in the execution of the company process. This occupies the selection of the process which needs
to be complete or studied (Holweg, 2007). There is a need to improvise the production through
development of an effective quality method. A reduction in the cost will improve the overall
production hence improving the competitiveness Innovation is considered as an important
element to any market in order to figure out effectiveness timely. The traditional methods
decrease the overall productivity it is therefore used as an important aspect to an organization.
Use of knowledge is important to create something important. A new thing is obvious to gain a
piece of equipment which are useful for a company to manage the potential to allow people to do
things in different and better ways. Portakabin has successfully designated a waste management
teams. These are made up of a production manager and waste contractor. It is through their
vision the organization is able to reduce the excess wastage (Shah and Ward, 2007). Meanwhile
it is understood that the Lean production will be used as efficient replacement for the traditional
production method. The traditional methods are causing excess problem in attaining desired
result. The productivity is actually hampered when an organization is unable to align its goal in a
systematic way (Heizer, 2016.). Lean production has a long-term impact on the organization. It is
thereby reducing the overall impact of the features that are important for gaining competency.
The purpose of gaining competency is to attain effectiveness at work. One can find issues in
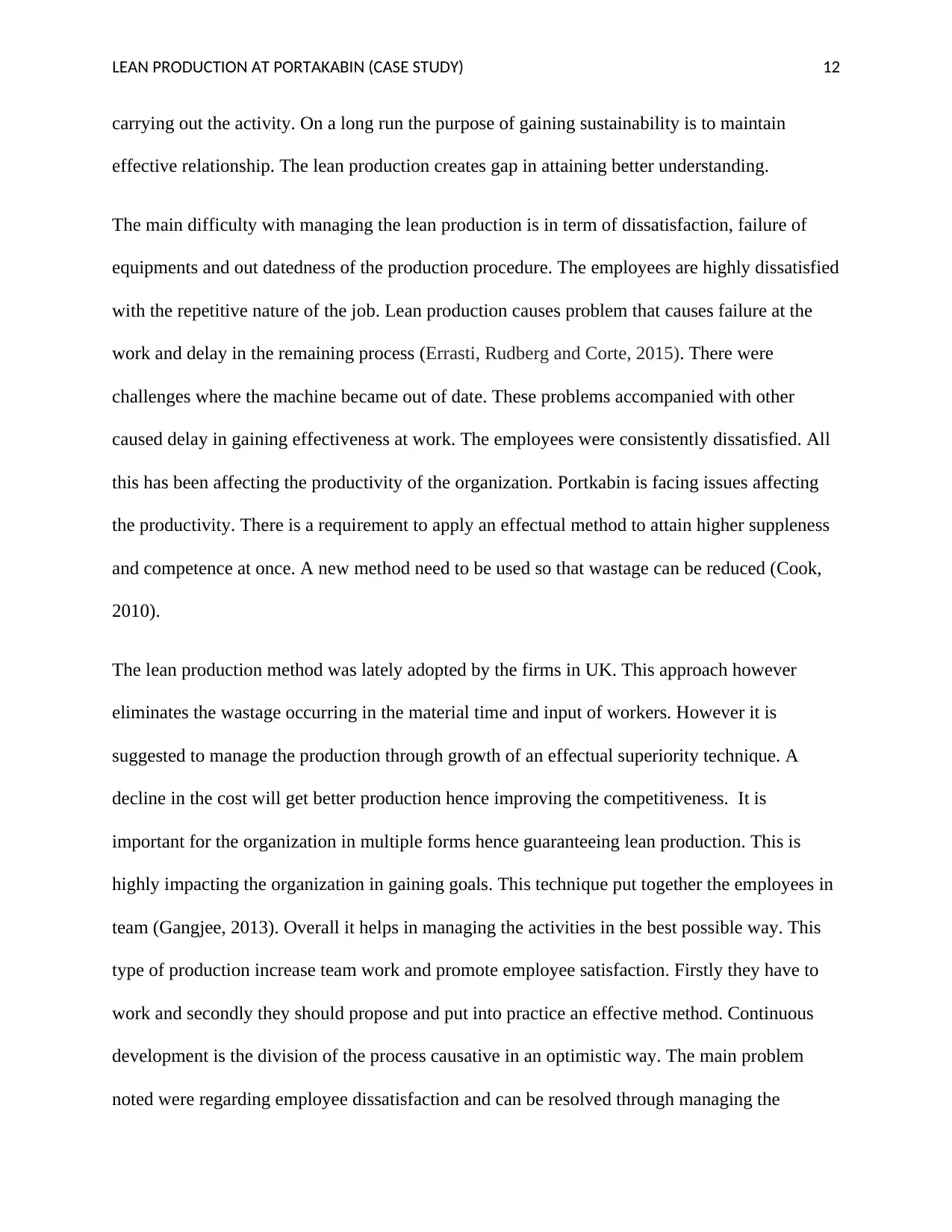
LEAN PRODUCTION AT PORTAKABIN (CASE STUDY) 12
carrying out the activity. On a long run the purpose of gaining sustainability is to maintain
effective relationship. The lean production creates gap in attaining better understanding.
The main difficulty with managing the lean production is in term of dissatisfaction, failure of
equipments and out datedness of the production procedure. The employees are highly dissatisfied
with the repetitive nature of the job. Lean production causes problem that causes failure at the
work and delay in the remaining process (Errasti, Rudberg and Corte, 2015). There were
challenges where the machine became out of date. These problems accompanied with other
caused delay in gaining effectiveness at work. The employees were consistently dissatisfied. All
this has been affecting the productivity of the organization. Portkabin is facing issues affecting
the productivity. There is a requirement to apply an effectual method to attain higher suppleness
and competence at once. A new method need to be used so that wastage can be reduced (Cook,
2010).
The lean production method was lately adopted by the firms in UK. This approach however
eliminates the wastage occurring in the material time and input of workers. However it is
suggested to manage the production through growth of an effectual superiority technique. A
decline in the cost will get better production hence improving the competitiveness. It is
important for the organization in multiple forms hence guaranteeing lean production. This is
highly impacting the organization in gaining goals. This technique put together the employees in
team (Gangjee, 2013). Overall it helps in managing the activities in the best possible way. This
type of production increase team work and promote employee satisfaction. Firstly they have to
work and secondly they should propose and put into practice an effective method. Continuous
development is the division of the process causative in an optimistic way. The main problem
noted were regarding employee dissatisfaction and can be resolved through managing the
carrying out the activity. On a long run the purpose of gaining sustainability is to maintain
effective relationship. The lean production creates gap in attaining better understanding.
The main difficulty with managing the lean production is in term of dissatisfaction, failure of
equipments and out datedness of the production procedure. The employees are highly dissatisfied
with the repetitive nature of the job. Lean production causes problem that causes failure at the
work and delay in the remaining process (Errasti, Rudberg and Corte, 2015). There were
challenges where the machine became out of date. These problems accompanied with other
caused delay in gaining effectiveness at work. The employees were consistently dissatisfied. All
this has been affecting the productivity of the organization. Portkabin is facing issues affecting
the productivity. There is a requirement to apply an effectual method to attain higher suppleness
and competence at once. A new method need to be used so that wastage can be reduced (Cook,
2010).
The lean production method was lately adopted by the firms in UK. This approach however
eliminates the wastage occurring in the material time and input of workers. However it is
suggested to manage the production through growth of an effectual superiority technique. A
decline in the cost will get better production hence improving the competitiveness. It is
important for the organization in multiple forms hence guaranteeing lean production. This is
highly impacting the organization in gaining goals. This technique put together the employees in
team (Gangjee, 2013). Overall it helps in managing the activities in the best possible way. This
type of production increase team work and promote employee satisfaction. Firstly they have to
work and secondly they should propose and put into practice an effective method. Continuous
development is the division of the process causative in an optimistic way. The main problem
noted were regarding employee dissatisfaction and can be resolved through managing the
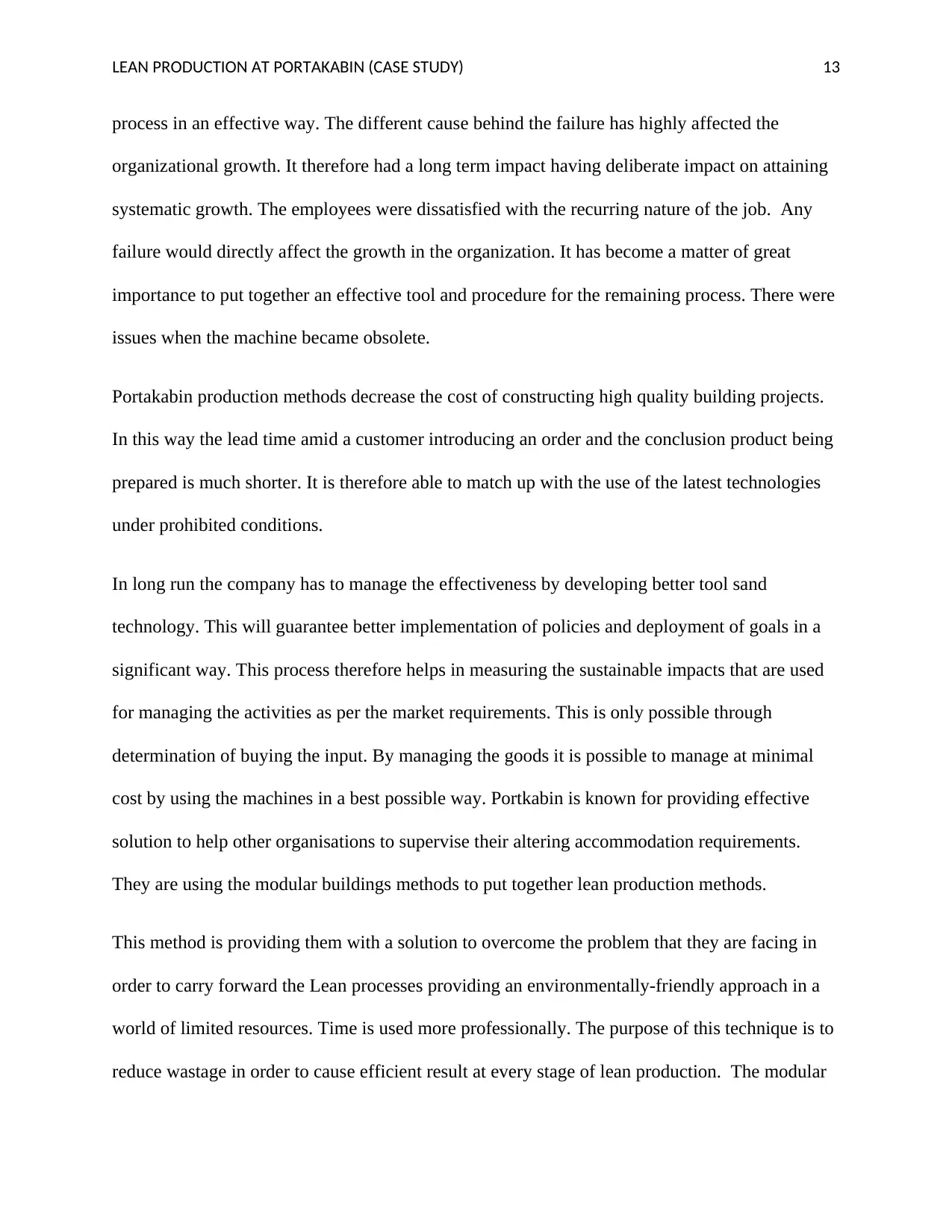
LEAN PRODUCTION AT PORTAKABIN (CASE STUDY) 13
process in an effective way. The different cause behind the failure has highly affected the
organizational growth. It therefore had a long term impact having deliberate impact on attaining
systematic growth. The employees were dissatisfied with the recurring nature of the job. Any
failure would directly affect the growth in the organization. It has become a matter of great
importance to put together an effective tool and procedure for the remaining process. There were
issues when the machine became obsolete.
Portakabin production methods decrease the cost of constructing high quality building projects.
In this way the lead time amid a customer introducing an order and the conclusion product being
prepared is much shorter. It is therefore able to match up with the use of the latest technologies
under prohibited conditions.
In long run the company has to manage the effectiveness by developing better tool sand
technology. This will guarantee better implementation of policies and deployment of goals in a
significant way. This process therefore helps in measuring the sustainable impacts that are used
for managing the activities as per the market requirements. This is only possible through
determination of buying the input. By managing the goods it is possible to manage at minimal
cost by using the machines in a best possible way. Portkabin is known for providing effective
solution to help other organisations to supervise their altering accommodation requirements.
They are using the modular buildings methods to put together lean production methods.
This method is providing them with a solution to overcome the problem that they are facing in
order to carry forward the Lean processes providing an environmentally-friendly approach in a
world of limited resources. Time is used more professionally. The purpose of this technique is to
reduce wastage in order to cause efficient result at every stage of lean production. The modular
process in an effective way. The different cause behind the failure has highly affected the
organizational growth. It therefore had a long term impact having deliberate impact on attaining
systematic growth. The employees were dissatisfied with the recurring nature of the job. Any
failure would directly affect the growth in the organization. It has become a matter of great
importance to put together an effective tool and procedure for the remaining process. There were
issues when the machine became obsolete.
Portakabin production methods decrease the cost of constructing high quality building projects.
In this way the lead time amid a customer introducing an order and the conclusion product being
prepared is much shorter. It is therefore able to match up with the use of the latest technologies
under prohibited conditions.
In long run the company has to manage the effectiveness by developing better tool sand
technology. This will guarantee better implementation of policies and deployment of goals in a
significant way. This process therefore helps in measuring the sustainable impacts that are used
for managing the activities as per the market requirements. This is only possible through
determination of buying the input. By managing the goods it is possible to manage at minimal
cost by using the machines in a best possible way. Portkabin is known for providing effective
solution to help other organisations to supervise their altering accommodation requirements.
They are using the modular buildings methods to put together lean production methods.
This method is providing them with a solution to overcome the problem that they are facing in
order to carry forward the Lean processes providing an environmentally-friendly approach in a
world of limited resources. Time is used more professionally. The purpose of this technique is to
reduce wastage in order to cause efficient result at every stage of lean production. The modular
Paraphrase This Document
Need a fresh take? Get an instant paraphrase of this document with our AI Paraphraser
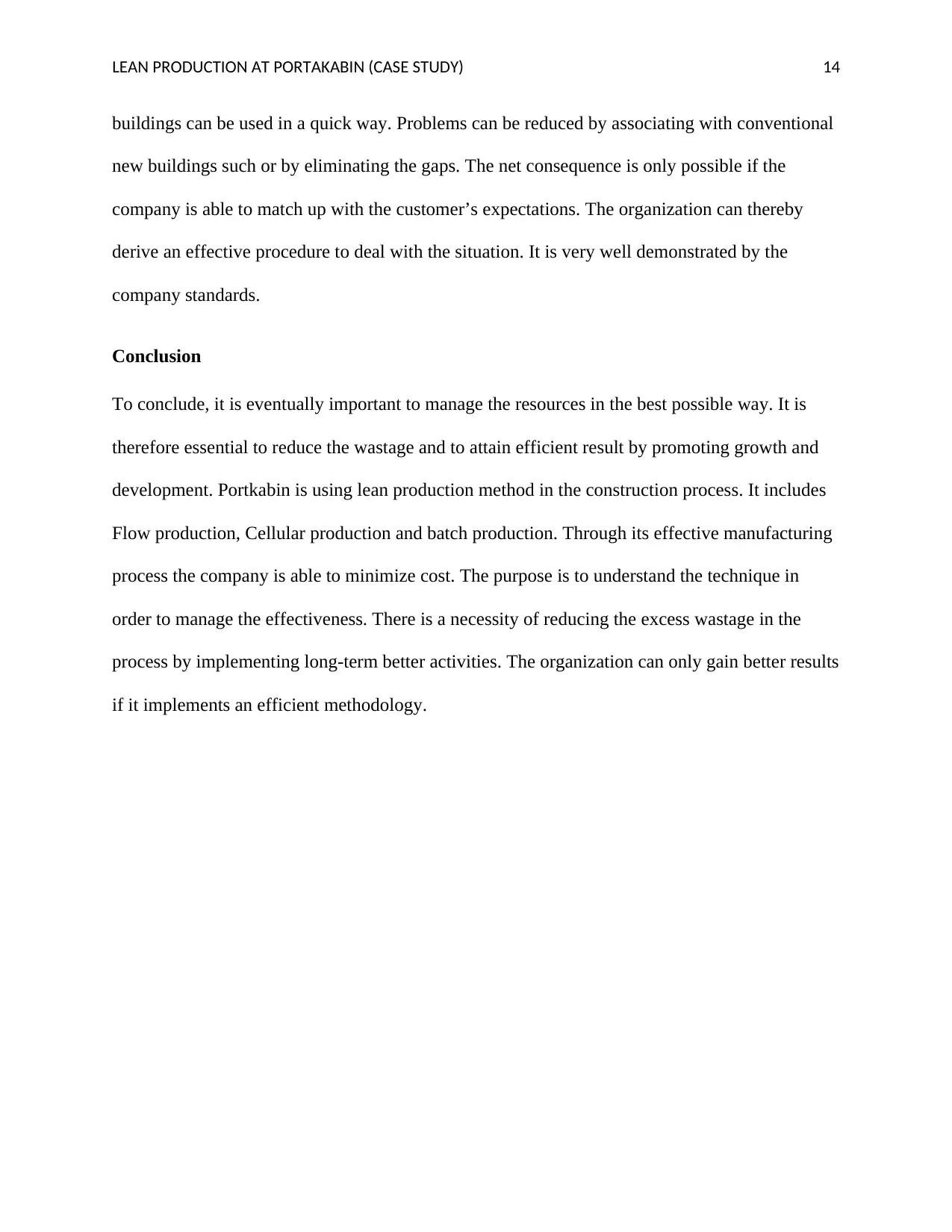
LEAN PRODUCTION AT PORTAKABIN (CASE STUDY) 14
buildings can be used in a quick way. Problems can be reduced by associating with conventional
new buildings such or by eliminating the gaps. The net consequence is only possible if the
company is able to match up with the customer’s expectations. The organization can thereby
derive an effective procedure to deal with the situation. It is very well demonstrated by the
company standards.
Conclusion
To conclude, it is eventually important to manage the resources in the best possible way. It is
therefore essential to reduce the wastage and to attain efficient result by promoting growth and
development. Portkabin is using lean production method in the construction process. It includes
Flow production, Cellular production and batch production. Through its effective manufacturing
process the company is able to minimize cost. The purpose is to understand the technique in
order to manage the effectiveness. There is a necessity of reducing the excess wastage in the
process by implementing long-term better activities. The organization can only gain better results
if it implements an efficient methodology.
buildings can be used in a quick way. Problems can be reduced by associating with conventional
new buildings such or by eliminating the gaps. The net consequence is only possible if the
company is able to match up with the customer’s expectations. The organization can thereby
derive an effective procedure to deal with the situation. It is very well demonstrated by the
company standards.
Conclusion
To conclude, it is eventually important to manage the resources in the best possible way. It is
therefore essential to reduce the wastage and to attain efficient result by promoting growth and
development. Portkabin is using lean production method in the construction process. It includes
Flow production, Cellular production and batch production. Through its effective manufacturing
process the company is able to minimize cost. The purpose is to understand the technique in
order to manage the effectiveness. There is a necessity of reducing the excess wastage in the
process by implementing long-term better activities. The organization can only gain better results
if it implements an efficient methodology.
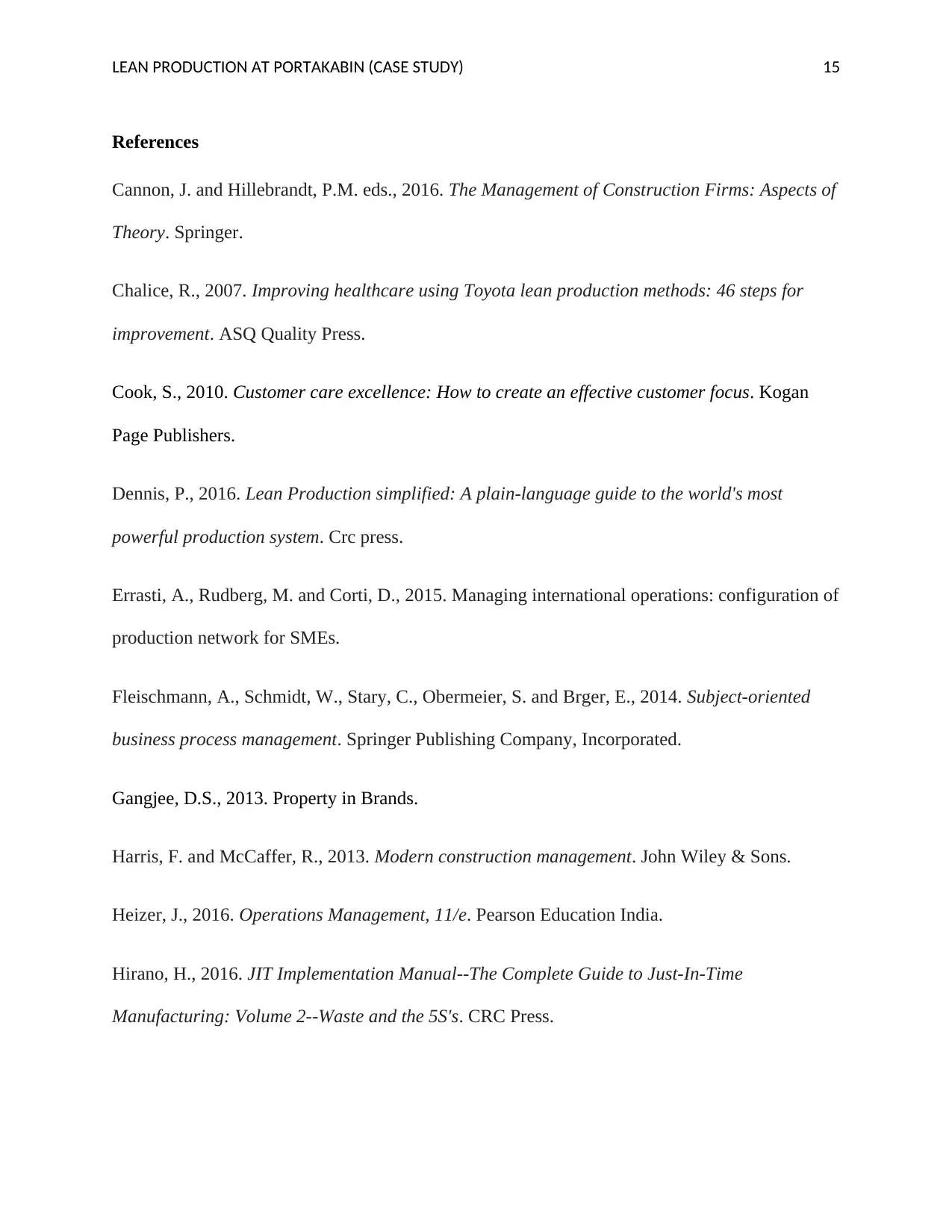
LEAN PRODUCTION AT PORTAKABIN (CASE STUDY) 15
References
Cannon, J. and Hillebrandt, P.M. eds., 2016. The Management of Construction Firms: Aspects of
Theory. Springer.
Chalice, R., 2007. Improving healthcare using Toyota lean production methods: 46 steps for
improvement. ASQ Quality Press.
Cook, S., 2010. Customer care excellence: How to create an effective customer focus. Kogan
Page Publishers.
Dennis, P., 2016. Lean Production simplified: A plain-language guide to the world's most
powerful production system. Crc press.
Errasti, A., Rudberg, M. and Corti, D., 2015. Managing international operations: configuration of
production network for SMEs.
Fleischmann, A., Schmidt, W., Stary, C., Obermeier, S. and Brger, E., 2014. Subject-oriented
business process management. Springer Publishing Company, Incorporated.
Gangjee, D.S., 2013. Property in Brands.
Harris, F. and McCaffer, R., 2013. Modern construction management. John Wiley & Sons.
Heizer, J., 2016. Operations Management, 11/e. Pearson Education India.
Hirano, H., 2016. JIT Implementation Manual--The Complete Guide to Just-In-Time
Manufacturing: Volume 2--Waste and the 5S's. CRC Press.
References
Cannon, J. and Hillebrandt, P.M. eds., 2016. The Management of Construction Firms: Aspects of
Theory. Springer.
Chalice, R., 2007. Improving healthcare using Toyota lean production methods: 46 steps for
improvement. ASQ Quality Press.
Cook, S., 2010. Customer care excellence: How to create an effective customer focus. Kogan
Page Publishers.
Dennis, P., 2016. Lean Production simplified: A plain-language guide to the world's most
powerful production system. Crc press.
Errasti, A., Rudberg, M. and Corti, D., 2015. Managing international operations: configuration of
production network for SMEs.
Fleischmann, A., Schmidt, W., Stary, C., Obermeier, S. and Brger, E., 2014. Subject-oriented
business process management. Springer Publishing Company, Incorporated.
Gangjee, D.S., 2013. Property in Brands.
Harris, F. and McCaffer, R., 2013. Modern construction management. John Wiley & Sons.
Heizer, J., 2016. Operations Management, 11/e. Pearson Education India.
Hirano, H., 2016. JIT Implementation Manual--The Complete Guide to Just-In-Time
Manufacturing: Volume 2--Waste and the 5S's. CRC Press.
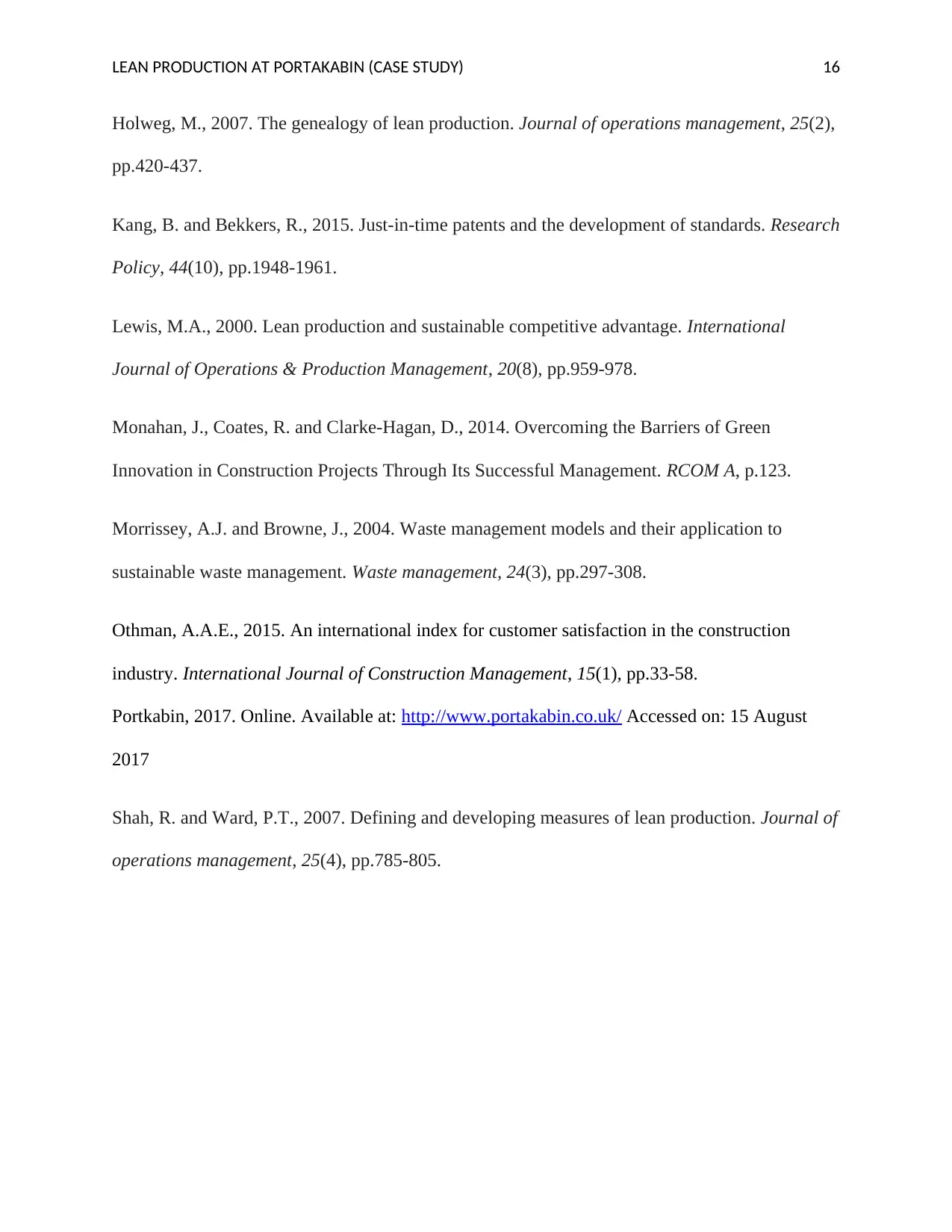
LEAN PRODUCTION AT PORTAKABIN (CASE STUDY) 16
Holweg, M., 2007. The genealogy of lean production. Journal of operations management, 25(2),
pp.420-437.
Kang, B. and Bekkers, R., 2015. Just-in-time patents and the development of standards. Research
Policy, 44(10), pp.1948-1961.
Lewis, M.A., 2000. Lean production and sustainable competitive advantage. International
Journal of Operations & Production Management, 20(8), pp.959-978.
Monahan, J., Coates, R. and Clarke-Hagan, D., 2014. Overcoming the Barriers of Green
Innovation in Construction Projects Through Its Successful Management. RCOM A, p.123.
Morrissey, A.J. and Browne, J., 2004. Waste management models and their application to
sustainable waste management. Waste management, 24(3), pp.297-308.
Othman, A.A.E., 2015. An international index for customer satisfaction in the construction
industry. International Journal of Construction Management, 15(1), pp.33-58.
Portkabin, 2017. Online. Available at: http://www.portakabin.co.uk/ Accessed on: 15 August
2017
Shah, R. and Ward, P.T., 2007. Defining and developing measures of lean production. Journal of
operations management, 25(4), pp.785-805.
Holweg, M., 2007. The genealogy of lean production. Journal of operations management, 25(2),
pp.420-437.
Kang, B. and Bekkers, R., 2015. Just-in-time patents and the development of standards. Research
Policy, 44(10), pp.1948-1961.
Lewis, M.A., 2000. Lean production and sustainable competitive advantage. International
Journal of Operations & Production Management, 20(8), pp.959-978.
Monahan, J., Coates, R. and Clarke-Hagan, D., 2014. Overcoming the Barriers of Green
Innovation in Construction Projects Through Its Successful Management. RCOM A, p.123.
Morrissey, A.J. and Browne, J., 2004. Waste management models and their application to
sustainable waste management. Waste management, 24(3), pp.297-308.
Othman, A.A.E., 2015. An international index for customer satisfaction in the construction
industry. International Journal of Construction Management, 15(1), pp.33-58.
Portkabin, 2017. Online. Available at: http://www.portakabin.co.uk/ Accessed on: 15 August
2017
Shah, R. and Ward, P.T., 2007. Defining and developing measures of lean production. Journal of
operations management, 25(4), pp.785-805.
1 out of 16
Related Documents

Your All-in-One AI-Powered Toolkit for Academic Success.
+13062052269
info@desklib.com
Available 24*7 on WhatsApp / Email
Unlock your academic potential
© 2024 | Zucol Services PVT LTD | All rights reserved.