Comprehensive Analysis of Process Control Sensors and Systems
VerifiedAdded on 2023/01/13
|3
|1522
|86
Report
AI Summary
This report provides a detailed analysis of sensors and transducers used in process control systems, including their functions and importance. It covers various types of sensors, signal terminology like gain, zero, and span, and the need for standard signal ranges. The report also explores the advantages of automated control systems, controller terminology such as set points, on/off control, and PID controllers, and the impact of distance velocity lag and capacity on system response. The report emphasizes the role of sensors and transducers in enhancing the effectiveness of process control, minimizing the need for secondary safety devices, and improving system performance.
Contribute Materials
Your contribution can guide someone’s learning journey. Share your
documents today.
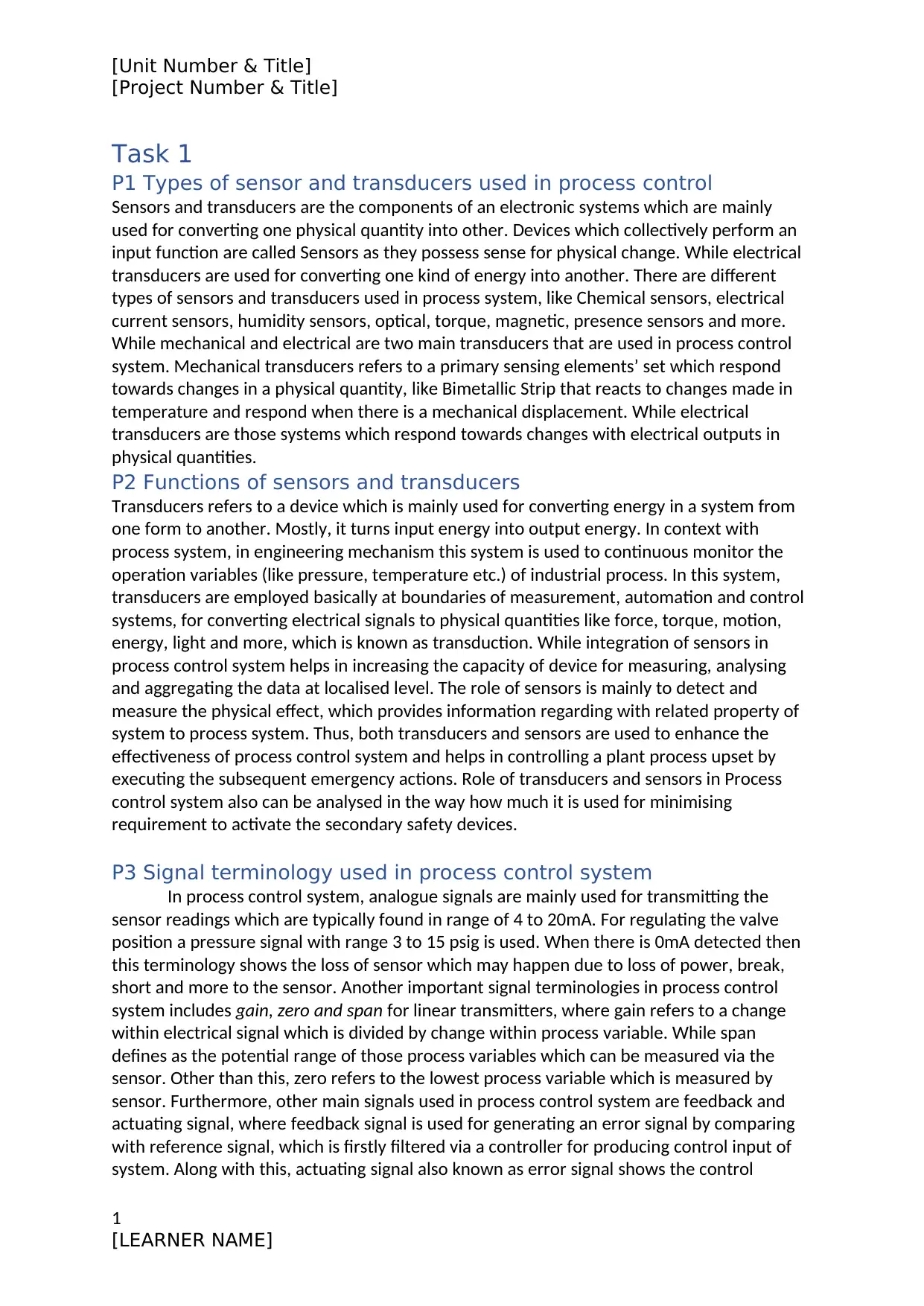
[Unit Number & Title]
[Project Number & Title]
Task 1
P1 Types of sensor and transducers used in process control
Sensors and transducers are the components of an electronic systems which are mainly
used for converting one physical quantity into other. Devices which collectively perform an
input function are called Sensors as they possess sense for physical change. While electrical
transducers are used for converting one kind of energy into another. There are different
types of sensors and transducers used in process system, like Chemical sensors, electrical
current sensors, humidity sensors, optical, torque, magnetic, presence sensors and more.
While mechanical and electrical are two main transducers that are used in process control
system. Mechanical transducers refers to a primary sensing elements’ set which respond
towards changes in a physical quantity, like Bimetallic Strip that reacts to changes made in
temperature and respond when there is a mechanical displacement. While electrical
transducers are those systems which respond towards changes with electrical outputs in
physical quantities.
P2 Functions of sensors and transducers
Transducers refers to a device which is mainly used for converting energy in a system from
one form to another. Mostly, it turns input energy into output energy. In context with
process system, in engineering mechanism this system is used to continuous monitor the
operation variables (like pressure, temperature etc.) of industrial process. In this system,
transducers are employed basically at boundaries of measurement, automation and control
systems, for converting electrical signals to physical quantities like force, torque, motion,
energy, light and more, which is known as transduction. While integration of sensors in
process control system helps in increasing the capacity of device for measuring, analysing
and aggregating the data at localised level. The role of sensors is mainly to detect and
measure the physical effect, which provides information regarding with related property of
system to process system. Thus, both transducers and sensors are used to enhance the
effectiveness of process control system and helps in controlling a plant process upset by
executing the subsequent emergency actions. Role of transducers and sensors in Process
control system also can be analysed in the way how much it is used for minimising
requirement to activate the secondary safety devices.
P3 Signal terminology used in process control system
In process control system, analogue signals are mainly used for transmitting the
sensor readings which are typically found in range of 4 to 20mA. For regulating the valve
position a pressure signal with range 3 to 15 psig is used. When there is 0mA detected then
this terminology shows the loss of sensor which may happen due to loss of power, break,
short and more to the sensor. Another important signal terminologies in process control
system includes gain, zero and span for linear transmitters, where gain refers to a change
within electrical signal which is divided by change within process variable. While span
defines as the potential range of those process variables which can be measured via the
sensor. Other than this, zero refers to the lowest process variable which is measured by
sensor. Furthermore, other main signals used in process control system are feedback and
actuating signal, where feedback signal is used for generating an error signal by comparing
with reference signal, which is firstly filtered via a controller for producing control input of
system. Along with this, actuating signal also known as error signal shows the control
1
[LEARNER NAME]
[Project Number & Title]
Task 1
P1 Types of sensor and transducers used in process control
Sensors and transducers are the components of an electronic systems which are mainly
used for converting one physical quantity into other. Devices which collectively perform an
input function are called Sensors as they possess sense for physical change. While electrical
transducers are used for converting one kind of energy into another. There are different
types of sensors and transducers used in process system, like Chemical sensors, electrical
current sensors, humidity sensors, optical, torque, magnetic, presence sensors and more.
While mechanical and electrical are two main transducers that are used in process control
system. Mechanical transducers refers to a primary sensing elements’ set which respond
towards changes in a physical quantity, like Bimetallic Strip that reacts to changes made in
temperature and respond when there is a mechanical displacement. While electrical
transducers are those systems which respond towards changes with electrical outputs in
physical quantities.
P2 Functions of sensors and transducers
Transducers refers to a device which is mainly used for converting energy in a system from
one form to another. Mostly, it turns input energy into output energy. In context with
process system, in engineering mechanism this system is used to continuous monitor the
operation variables (like pressure, temperature etc.) of industrial process. In this system,
transducers are employed basically at boundaries of measurement, automation and control
systems, for converting electrical signals to physical quantities like force, torque, motion,
energy, light and more, which is known as transduction. While integration of sensors in
process control system helps in increasing the capacity of device for measuring, analysing
and aggregating the data at localised level. The role of sensors is mainly to detect and
measure the physical effect, which provides information regarding with related property of
system to process system. Thus, both transducers and sensors are used to enhance the
effectiveness of process control system and helps in controlling a plant process upset by
executing the subsequent emergency actions. Role of transducers and sensors in Process
control system also can be analysed in the way how much it is used for minimising
requirement to activate the secondary safety devices.
P3 Signal terminology used in process control system
In process control system, analogue signals are mainly used for transmitting the
sensor readings which are typically found in range of 4 to 20mA. For regulating the valve
position a pressure signal with range 3 to 15 psig is used. When there is 0mA detected then
this terminology shows the loss of sensor which may happen due to loss of power, break,
short and more to the sensor. Another important signal terminologies in process control
system includes gain, zero and span for linear transmitters, where gain refers to a change
within electrical signal which is divided by change within process variable. While span
defines as the potential range of those process variables which can be measured via the
sensor. Other than this, zero refers to the lowest process variable which is measured by
sensor. Furthermore, other main signals used in process control system are feedback and
actuating signal, where feedback signal is used for generating an error signal by comparing
with reference signal, which is firstly filtered via a controller for producing control input of
system. Along with this, actuating signal also known as error signal shows the control
1
[LEARNER NAME]
Secure Best Marks with AI Grader
Need help grading? Try our AI Grader for instant feedback on your assignments.
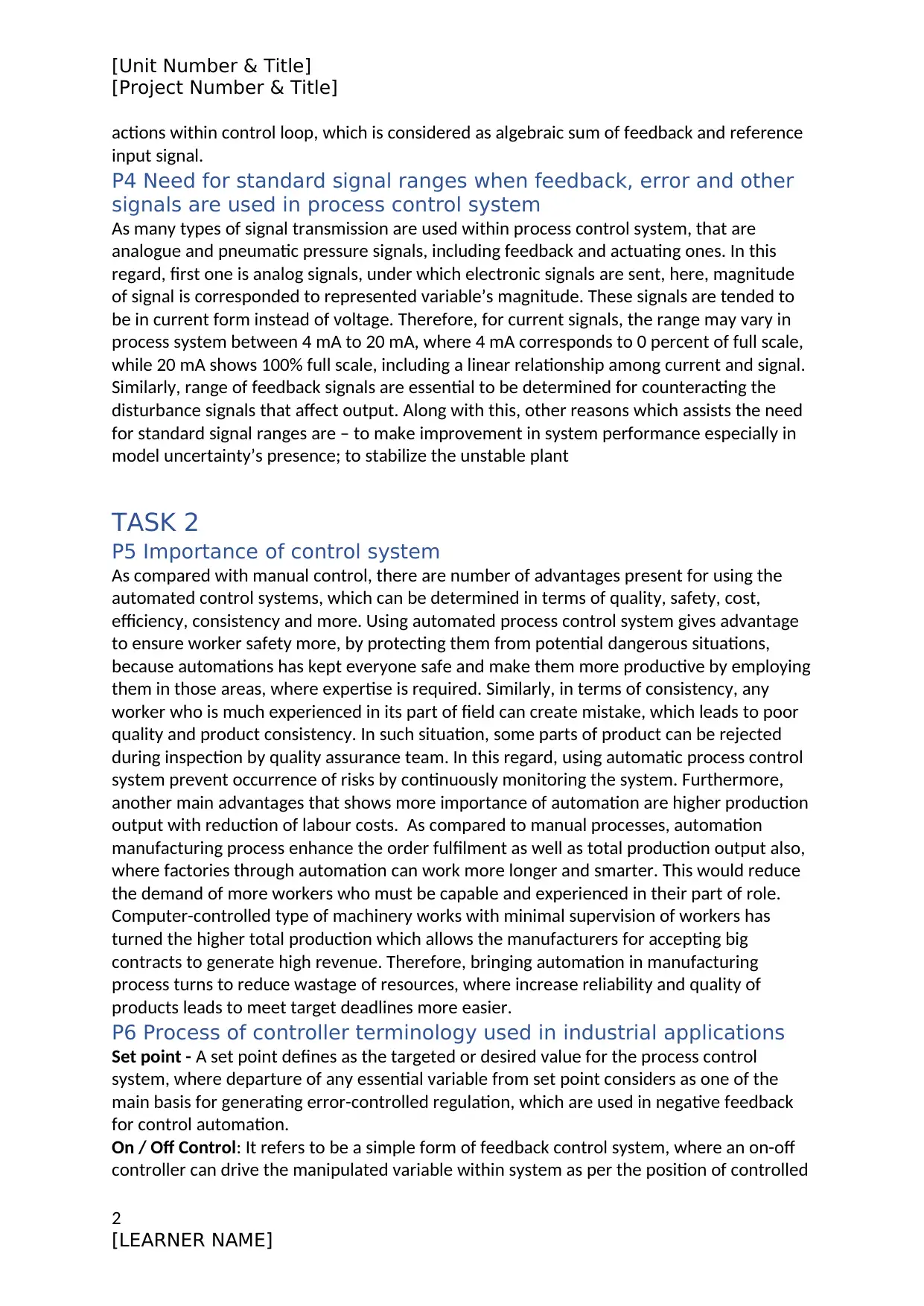
[Unit Number & Title]
[Project Number & Title]
actions within control loop, which is considered as algebraic sum of feedback and reference
input signal.
P4 Need for standard signal ranges when feedback, error and other
signals are used in process control system
As many types of signal transmission are used within process control system, that are
analogue and pneumatic pressure signals, including feedback and actuating ones. In this
regard, first one is analog signals, under which electronic signals are sent, here, magnitude
of signal is corresponded to represented variable’s magnitude. These signals are tended to
be in current form instead of voltage. Therefore, for current signals, the range may vary in
process system between 4 mA to 20 mA, where 4 mA corresponds to 0 percent of full scale,
while 20 mA shows 100% full scale, including a linear relationship among current and signal.
Similarly, range of feedback signals are essential to be determined for counteracting the
disturbance signals that affect output. Along with this, other reasons which assists the need
for standard signal ranges are – to make improvement in system performance especially in
model uncertainty’s presence; to stabilize the unstable plant
TASK 2
P5 Importance of control system
As compared with manual control, there are number of advantages present for using the
automated control systems, which can be determined in terms of quality, safety, cost,
efficiency, consistency and more. Using automated process control system gives advantage
to ensure worker safety more, by protecting them from potential dangerous situations,
because automations has kept everyone safe and make them more productive by employing
them in those areas, where expertise is required. Similarly, in terms of consistency, any
worker who is much experienced in its part of field can create mistake, which leads to poor
quality and product consistency. In such situation, some parts of product can be rejected
during inspection by quality assurance team. In this regard, using automatic process control
system prevent occurrence of risks by continuously monitoring the system. Furthermore,
another main advantages that shows more importance of automation are higher production
output with reduction of labour costs. As compared to manual processes, automation
manufacturing process enhance the order fulfilment as well as total production output also,
where factories through automation can work more longer and smarter. This would reduce
the demand of more workers who must be capable and experienced in their part of role.
Computer-controlled type of machinery works with minimal supervision of workers has
turned the higher total production which allows the manufacturers for accepting big
contracts to generate high revenue. Therefore, bringing automation in manufacturing
process turns to reduce wastage of resources, where increase reliability and quality of
products leads to meet target deadlines more easier.
P6 Process of controller terminology used in industrial applications
Set point - A set point defines as the targeted or desired value for the process control
system, where departure of any essential variable from set point considers as one of the
main basis for generating error-controlled regulation, which are used in negative feedback
for control automation.
On / Off Control: It refers to be a simple form of feedback control system, where an on-off
controller can drive the manipulated variable within system as per the position of controlled
2
[LEARNER NAME]
[Project Number & Title]
actions within control loop, which is considered as algebraic sum of feedback and reference
input signal.
P4 Need for standard signal ranges when feedback, error and other
signals are used in process control system
As many types of signal transmission are used within process control system, that are
analogue and pneumatic pressure signals, including feedback and actuating ones. In this
regard, first one is analog signals, under which electronic signals are sent, here, magnitude
of signal is corresponded to represented variable’s magnitude. These signals are tended to
be in current form instead of voltage. Therefore, for current signals, the range may vary in
process system between 4 mA to 20 mA, where 4 mA corresponds to 0 percent of full scale,
while 20 mA shows 100% full scale, including a linear relationship among current and signal.
Similarly, range of feedback signals are essential to be determined for counteracting the
disturbance signals that affect output. Along with this, other reasons which assists the need
for standard signal ranges are – to make improvement in system performance especially in
model uncertainty’s presence; to stabilize the unstable plant
TASK 2
P5 Importance of control system
As compared with manual control, there are number of advantages present for using the
automated control systems, which can be determined in terms of quality, safety, cost,
efficiency, consistency and more. Using automated process control system gives advantage
to ensure worker safety more, by protecting them from potential dangerous situations,
because automations has kept everyone safe and make them more productive by employing
them in those areas, where expertise is required. Similarly, in terms of consistency, any
worker who is much experienced in its part of field can create mistake, which leads to poor
quality and product consistency. In such situation, some parts of product can be rejected
during inspection by quality assurance team. In this regard, using automatic process control
system prevent occurrence of risks by continuously monitoring the system. Furthermore,
another main advantages that shows more importance of automation are higher production
output with reduction of labour costs. As compared to manual processes, automation
manufacturing process enhance the order fulfilment as well as total production output also,
where factories through automation can work more longer and smarter. This would reduce
the demand of more workers who must be capable and experienced in their part of role.
Computer-controlled type of machinery works with minimal supervision of workers has
turned the higher total production which allows the manufacturers for accepting big
contracts to generate high revenue. Therefore, bringing automation in manufacturing
process turns to reduce wastage of resources, where increase reliability and quality of
products leads to meet target deadlines more easier.
P6 Process of controller terminology used in industrial applications
Set point - A set point defines as the targeted or desired value for the process control
system, where departure of any essential variable from set point considers as one of the
main basis for generating error-controlled regulation, which are used in negative feedback
for control automation.
On / Off Control: It refers to be a simple form of feedback control system, where an on-off
controller can drive the manipulated variable within system as per the position of controlled
2
[LEARNER NAME]
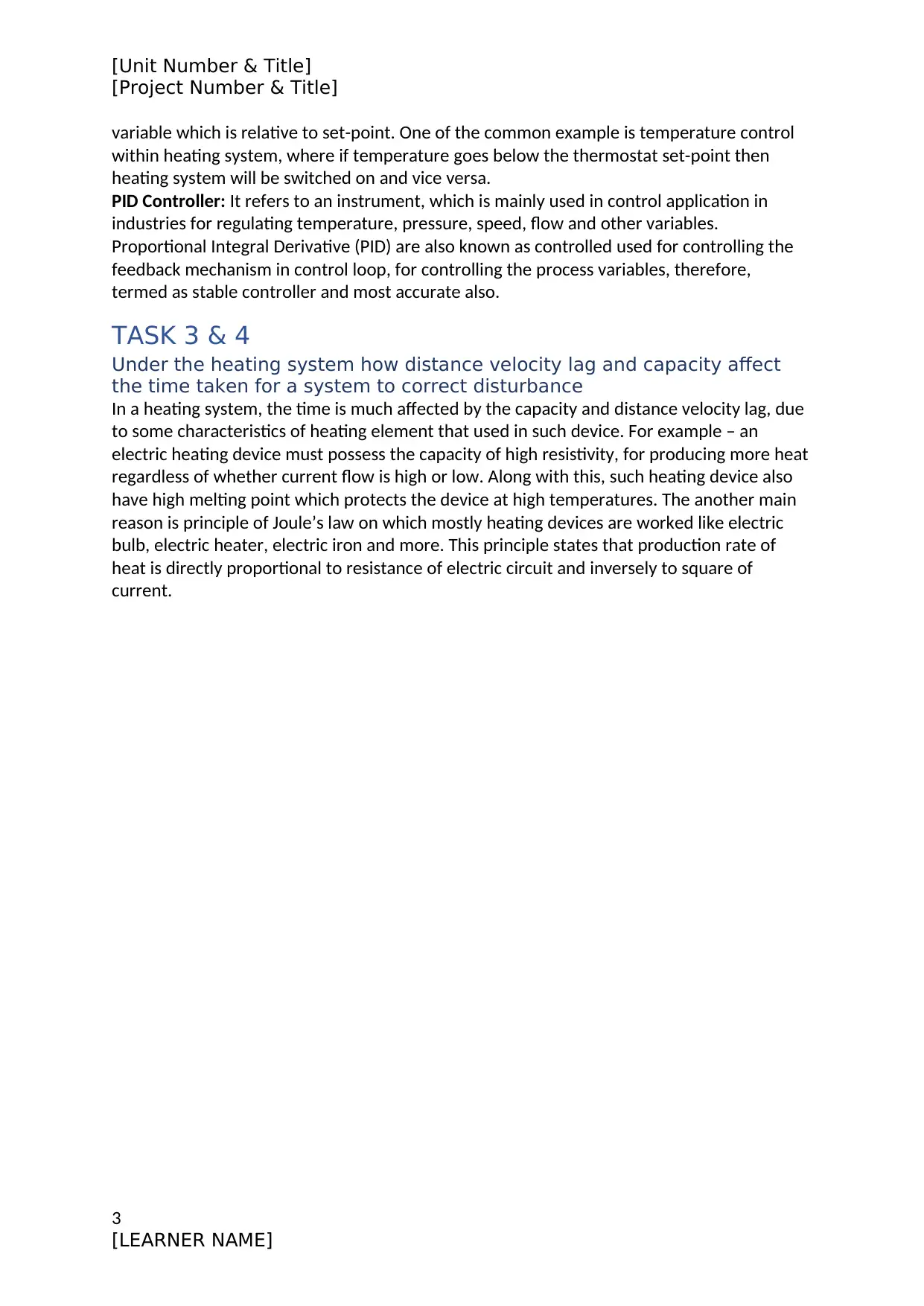
[Unit Number & Title]
[Project Number & Title]
variable which is relative to set-point. One of the common example is temperature control
within heating system, where if temperature goes below the thermostat set-point then
heating system will be switched on and vice versa.
PID Controller: It refers to an instrument, which is mainly used in control application in
industries for regulating temperature, pressure, speed, flow and other variables.
Proportional Integral Derivative (PID) are also known as controlled used for controlling the
feedback mechanism in control loop, for controlling the process variables, therefore,
termed as stable controller and most accurate also.
TASK 3 & 4
Under the heating system how distance velocity lag and capacity affect
the time taken for a system to correct disturbance
In a heating system, the time is much affected by the capacity and distance velocity lag, due
to some characteristics of heating element that used in such device. For example – an
electric heating device must possess the capacity of high resistivity, for producing more heat
regardless of whether current flow is high or low. Along with this, such heating device also
have high melting point which protects the device at high temperatures. The another main
reason is principle of Joule’s law on which mostly heating devices are worked like electric
bulb, electric heater, electric iron and more. This principle states that production rate of
heat is directly proportional to resistance of electric circuit and inversely to square of
current.
3
[LEARNER NAME]
[Project Number & Title]
variable which is relative to set-point. One of the common example is temperature control
within heating system, where if temperature goes below the thermostat set-point then
heating system will be switched on and vice versa.
PID Controller: It refers to an instrument, which is mainly used in control application in
industries for regulating temperature, pressure, speed, flow and other variables.
Proportional Integral Derivative (PID) are also known as controlled used for controlling the
feedback mechanism in control loop, for controlling the process variables, therefore,
termed as stable controller and most accurate also.
TASK 3 & 4
Under the heating system how distance velocity lag and capacity affect
the time taken for a system to correct disturbance
In a heating system, the time is much affected by the capacity and distance velocity lag, due
to some characteristics of heating element that used in such device. For example – an
electric heating device must possess the capacity of high resistivity, for producing more heat
regardless of whether current flow is high or low. Along with this, such heating device also
have high melting point which protects the device at high temperatures. The another main
reason is principle of Joule’s law on which mostly heating devices are worked like electric
bulb, electric heater, electric iron and more. This principle states that production rate of
heat is directly proportional to resistance of electric circuit and inversely to square of
current.
3
[LEARNER NAME]
1 out of 3
Related Documents

Your All-in-One AI-Powered Toolkit for Academic Success.
+13062052269
info@desklib.com
Available 24*7 on WhatsApp / Email
Unlock your academic potential
© 2024 | Zucol Services PVT LTD | All rights reserved.