Processes Robust Design and Six Sigma Framework: An Overview
VerifiedAdded on 2022/09/25
|17
|2973
|19
Report
AI Summary
This report provides a comprehensive overview of the Processes Robust Design-Six Sigma Framework, emphasizing its role in enhancing engineering productivity, reducing costs, and improving product quality. The framework, often utilized in conjunction with Six Sigma methodologies, aims to o...
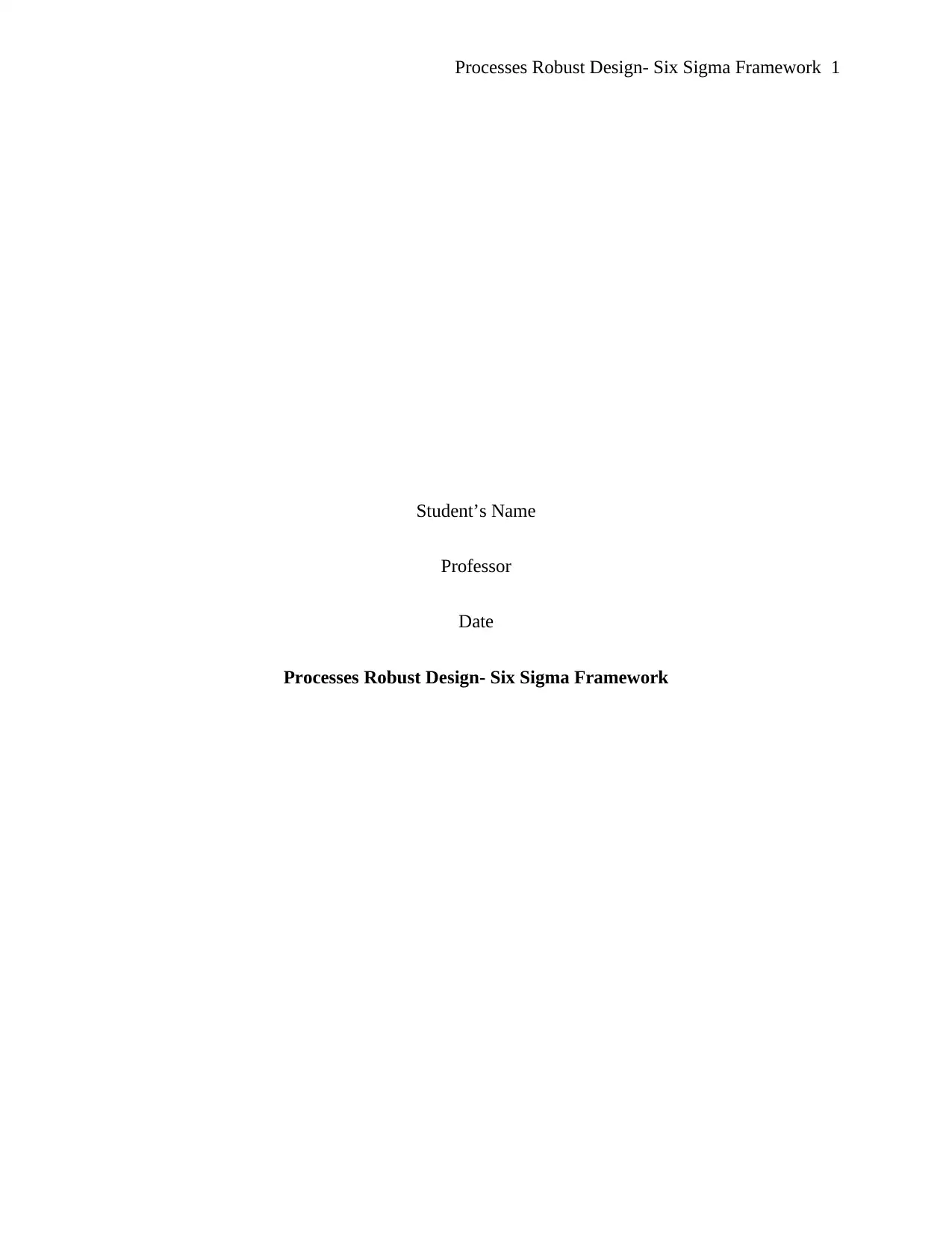
Processes Robust Design- Six Sigma Framework 1
Student’s Name
Professor
Date
Processes Robust Design- Six Sigma Framework
Student’s Name
Professor
Date
Processes Robust Design- Six Sigma Framework
Paraphrase This Document
Need a fresh take? Get an instant paraphrase of this document with our AI Paraphraser
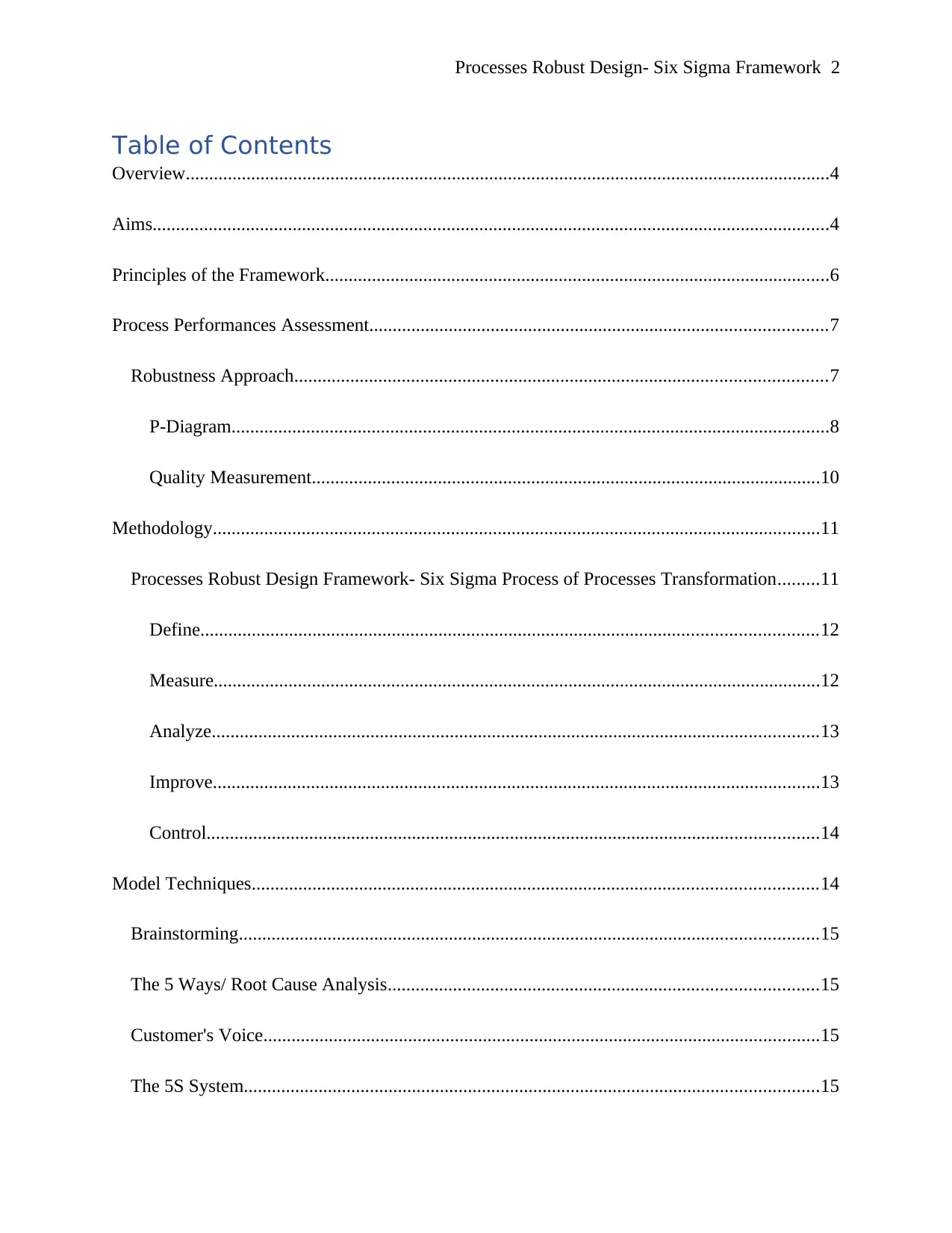
Processes Robust Design- Six Sigma Framework 2
Table of Contents
Overview..........................................................................................................................................4
Aims.................................................................................................................................................4
Principles of the Framework............................................................................................................6
Process Performances Assessment..................................................................................................7
Robustness Approach..................................................................................................................7
P-Diagram................................................................................................................................8
Quality Measurement.............................................................................................................10
Methodology..................................................................................................................................11
Processes Robust Design Framework- Six Sigma Process of Processes Transformation.........11
Define....................................................................................................................................12
Measure..................................................................................................................................12
Analyze..................................................................................................................................13
Improve..................................................................................................................................13
Control...................................................................................................................................14
Model Techniques.........................................................................................................................14
Brainstorming............................................................................................................................15
The 5 Ways/ Root Cause Analysis............................................................................................15
Customer's Voice.......................................................................................................................15
The 5S System...........................................................................................................................15
Table of Contents
Overview..........................................................................................................................................4
Aims.................................................................................................................................................4
Principles of the Framework............................................................................................................6
Process Performances Assessment..................................................................................................7
Robustness Approach..................................................................................................................7
P-Diagram................................................................................................................................8
Quality Measurement.............................................................................................................10
Methodology..................................................................................................................................11
Processes Robust Design Framework- Six Sigma Process of Processes Transformation.........11
Define....................................................................................................................................12
Measure..................................................................................................................................12
Analyze..................................................................................................................................13
Improve..................................................................................................................................13
Control...................................................................................................................................14
Model Techniques.........................................................................................................................14
Brainstorming............................................................................................................................15
The 5 Ways/ Root Cause Analysis............................................................................................15
Customer's Voice.......................................................................................................................15
The 5S System...........................................................................................................................15
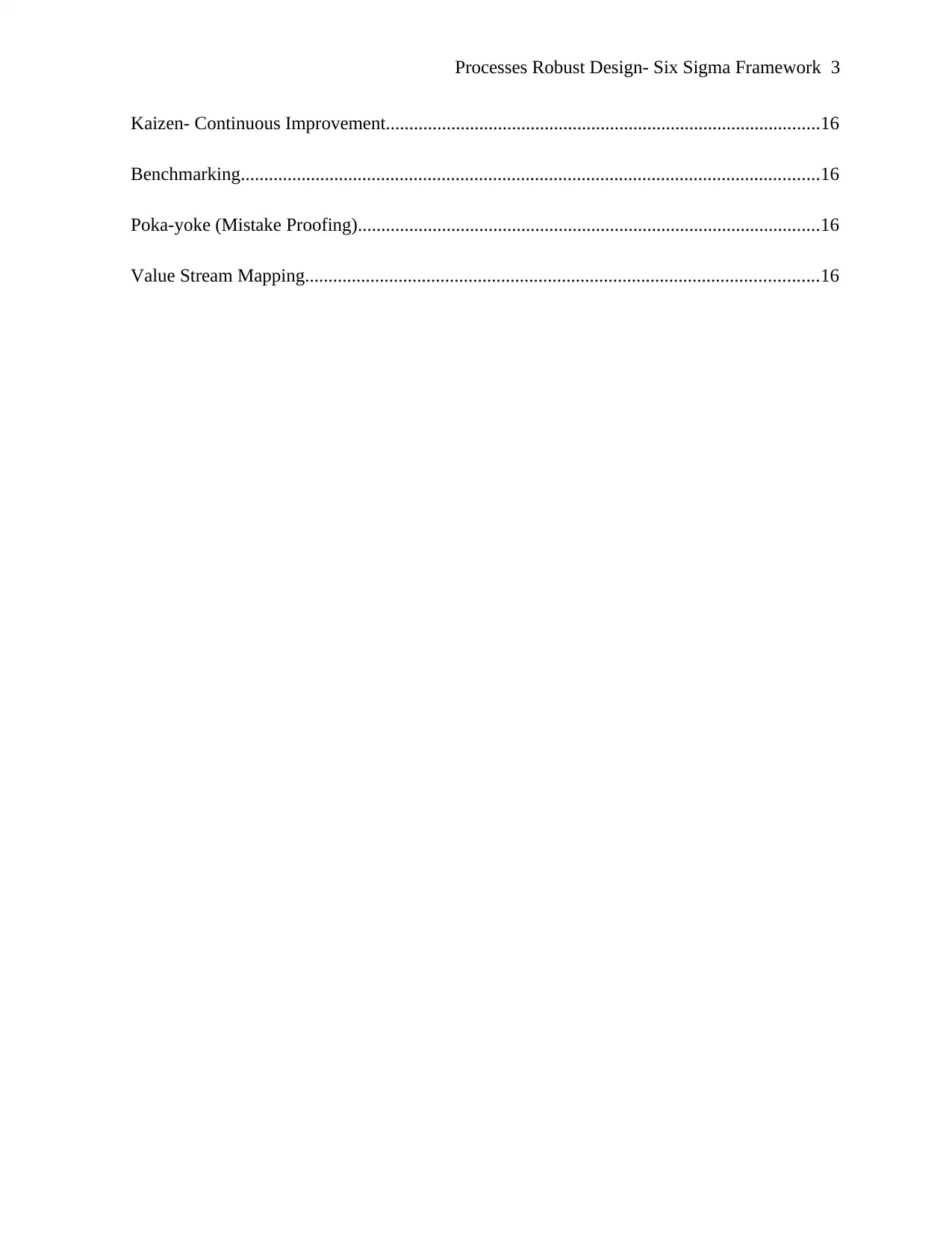
Processes Robust Design- Six Sigma Framework 3
Kaizen- Continuous Improvement.............................................................................................16
Benchmarking............................................................................................................................16
Poka-yoke (Mistake Proofing)...................................................................................................16
Value Stream Mapping..............................................................................................................16
Kaizen- Continuous Improvement.............................................................................................16
Benchmarking............................................................................................................................16
Poka-yoke (Mistake Proofing)...................................................................................................16
Value Stream Mapping..............................................................................................................16
⊘ This is a preview!⊘
Do you want full access?
Subscribe today to unlock all pages.

Trusted by 1+ million students worldwide
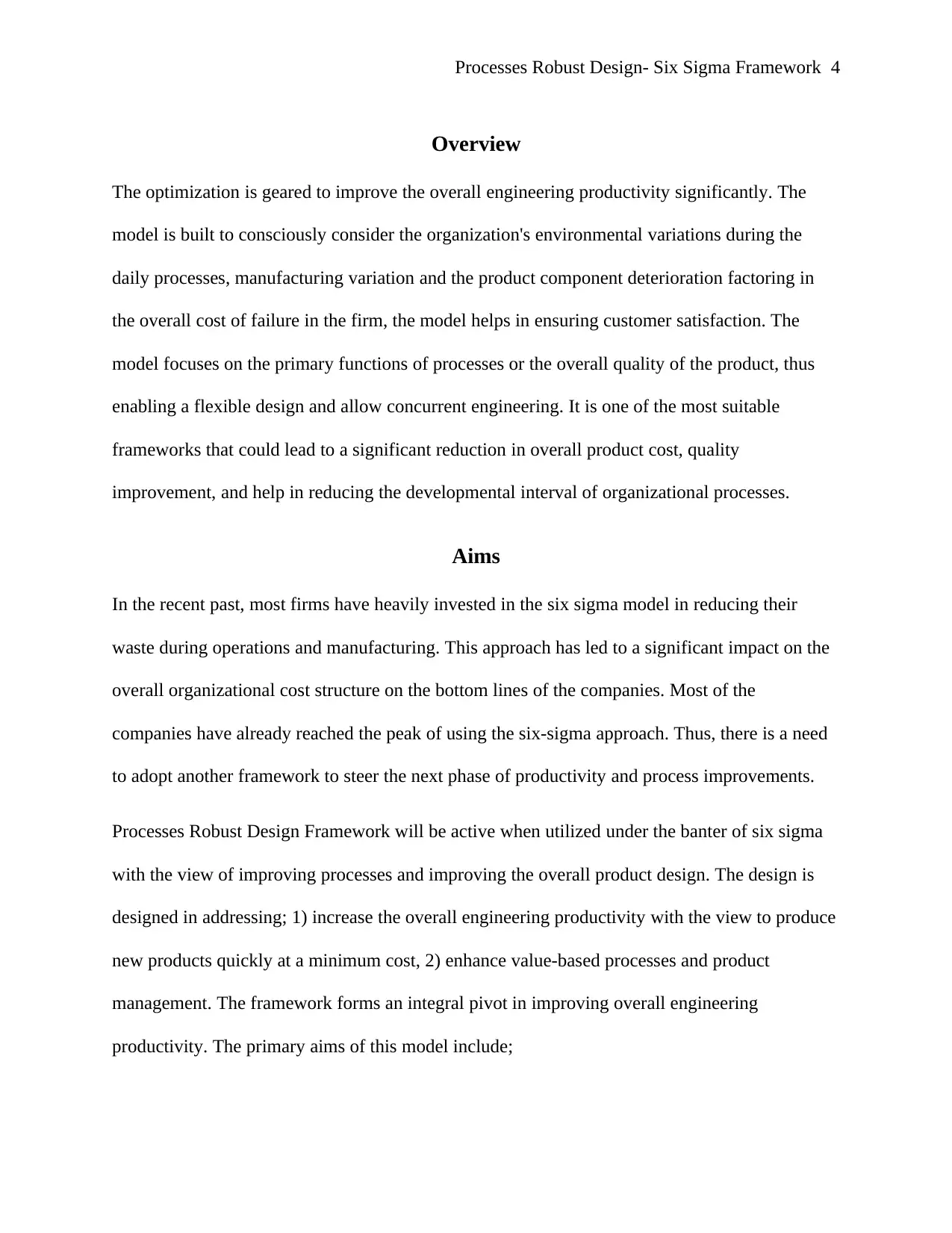
Processes Robust Design- Six Sigma Framework 4
Overview
The optimization is geared to improve the overall engineering productivity significantly. The
model is built to consciously consider the organization's environmental variations during the
daily processes, manufacturing variation and the product component deterioration factoring in
the overall cost of failure in the firm, the model helps in ensuring customer satisfaction. The
model focuses on the primary functions of processes or the overall quality of the product, thus
enabling a flexible design and allow concurrent engineering. It is one of the most suitable
frameworks that could lead to a significant reduction in overall product cost, quality
improvement, and help in reducing the developmental interval of organizational processes.
Aims
In the recent past, most firms have heavily invested in the six sigma model in reducing their
waste during operations and manufacturing. This approach has led to a significant impact on the
overall organizational cost structure on the bottom lines of the companies. Most of the
companies have already reached the peak of using the six-sigma approach. Thus, there is a need
to adopt another framework to steer the next phase of productivity and process improvements.
Processes Robust Design Framework will be active when utilized under the banter of six sigma
with the view of improving processes and improving the overall product design. The design is
designed in addressing; 1) increase the overall engineering productivity with the view to produce
new products quickly at a minimum cost, 2) enhance value-based processes and product
management. The framework forms an integral pivot in improving overall engineering
productivity. The primary aims of this model include;
Overview
The optimization is geared to improve the overall engineering productivity significantly. The
model is built to consciously consider the organization's environmental variations during the
daily processes, manufacturing variation and the product component deterioration factoring in
the overall cost of failure in the firm, the model helps in ensuring customer satisfaction. The
model focuses on the primary functions of processes or the overall quality of the product, thus
enabling a flexible design and allow concurrent engineering. It is one of the most suitable
frameworks that could lead to a significant reduction in overall product cost, quality
improvement, and help in reducing the developmental interval of organizational processes.
Aims
In the recent past, most firms have heavily invested in the six sigma model in reducing their
waste during operations and manufacturing. This approach has led to a significant impact on the
overall organizational cost structure on the bottom lines of the companies. Most of the
companies have already reached the peak of using the six-sigma approach. Thus, there is a need
to adopt another framework to steer the next phase of productivity and process improvements.
Processes Robust Design Framework will be active when utilized under the banter of six sigma
with the view of improving processes and improving the overall product design. The design is
designed in addressing; 1) increase the overall engineering productivity with the view to produce
new products quickly at a minimum cost, 2) enhance value-based processes and product
management. The framework forms an integral pivot in improving overall engineering
productivity. The primary aims of this model include;
Paraphrase This Document
Need a fresh take? Get an instant paraphrase of this document with our AI Paraphraser
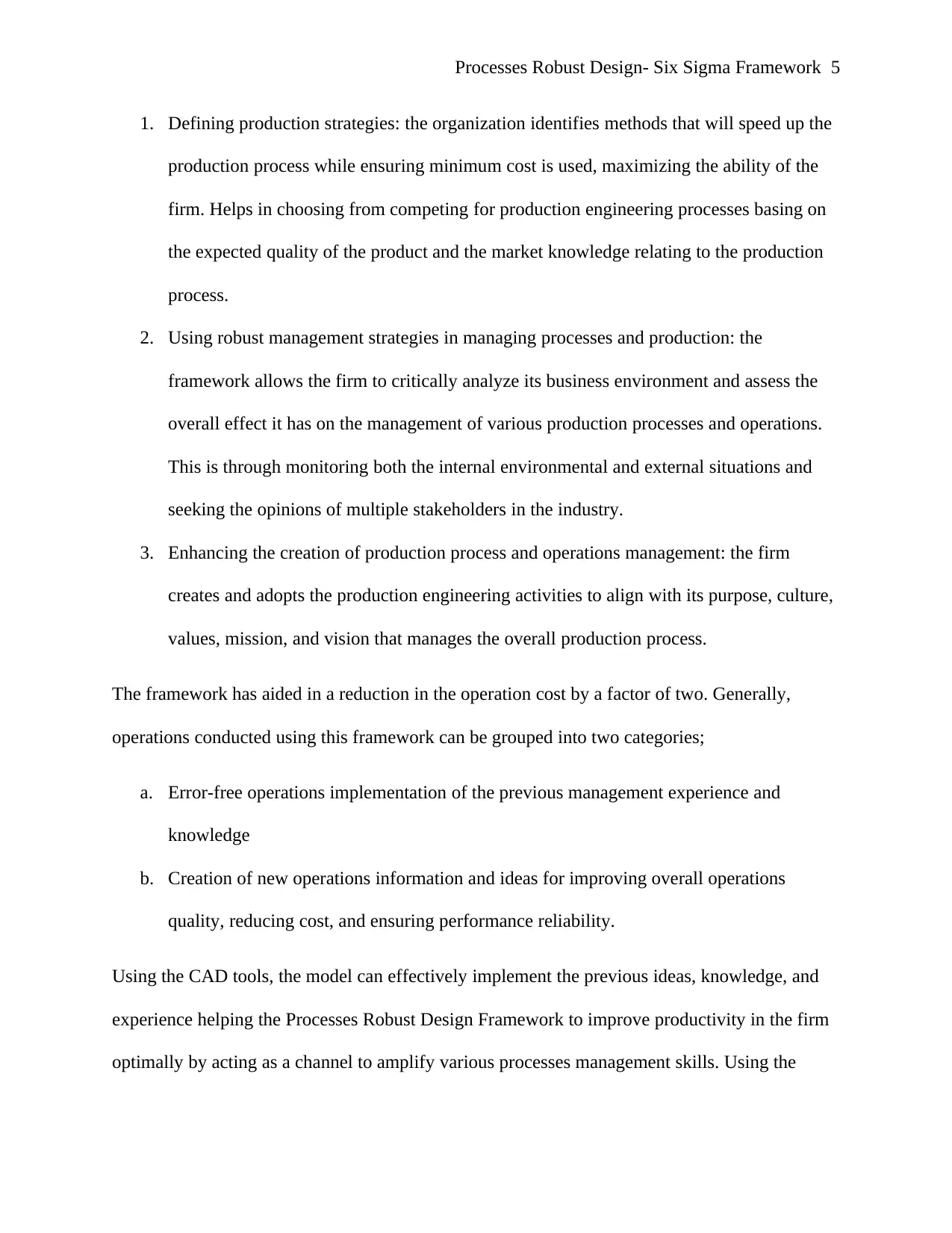
Processes Robust Design- Six Sigma Framework 5
1. Defining production strategies: the organization identifies methods that will speed up the
production process while ensuring minimum cost is used, maximizing the ability of the
firm. Helps in choosing from competing for production engineering processes basing on
the expected quality of the product and the market knowledge relating to the production
process.
2. Using robust management strategies in managing processes and production: the
framework allows the firm to critically analyze its business environment and assess the
overall effect it has on the management of various production processes and operations.
This is through monitoring both the internal environmental and external situations and
seeking the opinions of multiple stakeholders in the industry.
3. Enhancing the creation of production process and operations management: the firm
creates and adopts the production engineering activities to align with its purpose, culture,
values, mission, and vision that manages the overall production process.
The framework has aided in a reduction in the operation cost by a factor of two. Generally,
operations conducted using this framework can be grouped into two categories;
a. Error-free operations implementation of the previous management experience and
knowledge
b. Creation of new operations information and ideas for improving overall operations
quality, reducing cost, and ensuring performance reliability.
Using the CAD tools, the model can effectively implement the previous ideas, knowledge, and
experience helping the Processes Robust Design Framework to improve productivity in the firm
optimally by acting as a channel to amplify various processes management skills. Using the
1. Defining production strategies: the organization identifies methods that will speed up the
production process while ensuring minimum cost is used, maximizing the ability of the
firm. Helps in choosing from competing for production engineering processes basing on
the expected quality of the product and the market knowledge relating to the production
process.
2. Using robust management strategies in managing processes and production: the
framework allows the firm to critically analyze its business environment and assess the
overall effect it has on the management of various production processes and operations.
This is through monitoring both the internal environmental and external situations and
seeking the opinions of multiple stakeholders in the industry.
3. Enhancing the creation of production process and operations management: the firm
creates and adopts the production engineering activities to align with its purpose, culture,
values, mission, and vision that manages the overall production process.
The framework has aided in a reduction in the operation cost by a factor of two. Generally,
operations conducted using this framework can be grouped into two categories;
a. Error-free operations implementation of the previous management experience and
knowledge
b. Creation of new operations information and ideas for improving overall operations
quality, reducing cost, and ensuring performance reliability.
Using the CAD tools, the model can effectively implement the previous ideas, knowledge, and
experience helping the Processes Robust Design Framework to improve productivity in the firm
optimally by acting as a channel to amplify various processes management skills. Using the

Processes Robust Design- Six Sigma Framework 6
Robust model, a firm can effectively attain its technological potential of different ideas leading
to higher profits.
Principles of the Framework
The five fundamental principles that will guide the model are
always focus on the customer: the main aim is to ensure the customers get the maximum
benefits. For this, the model will help pharmacies to fully understand the customers and
create tailored processes that will help meet the customers' requirements. The model will
aid in establishing quality standards according to the needs and demands in the market.
Make your efforts mathematically and scientifically: this principle helps in transforming
inefficient processes that require changes. A robust culture of ensuring efficient and
highly effective methods and establish a flexible, responsive change to eliminate
deviations.
Reduce deviations, waste, and focus on value: once the processes problems have been
identified, they need to be removed. Activities that do not add value to the customer are
removed from the process
ensure processes flow smoothly: all stakeholders are involved in the running of the
operations. A well-structured process is adopted where all teams in the pharmacy
contribute their varied expertise and experience to help in problem-solving.
Understand how all the processes are conducted: the management should have the
required knowledge and expertise in running the process in order to ensure that an
optimal outcome is realized.
Robust model, a firm can effectively attain its technological potential of different ideas leading
to higher profits.
Principles of the Framework
The five fundamental principles that will guide the model are
always focus on the customer: the main aim is to ensure the customers get the maximum
benefits. For this, the model will help pharmacies to fully understand the customers and
create tailored processes that will help meet the customers' requirements. The model will
aid in establishing quality standards according to the needs and demands in the market.
Make your efforts mathematically and scientifically: this principle helps in transforming
inefficient processes that require changes. A robust culture of ensuring efficient and
highly effective methods and establish a flexible, responsive change to eliminate
deviations.
Reduce deviations, waste, and focus on value: once the processes problems have been
identified, they need to be removed. Activities that do not add value to the customer are
removed from the process
ensure processes flow smoothly: all stakeholders are involved in the running of the
operations. A well-structured process is adopted where all teams in the pharmacy
contribute their varied expertise and experience to help in problem-solving.
Understand how all the processes are conducted: the management should have the
required knowledge and expertise in running the process in order to ensure that an
optimal outcome is realized.
⊘ This is a preview!⊘
Do you want full access?
Subscribe today to unlock all pages.

Trusted by 1+ million students worldwide
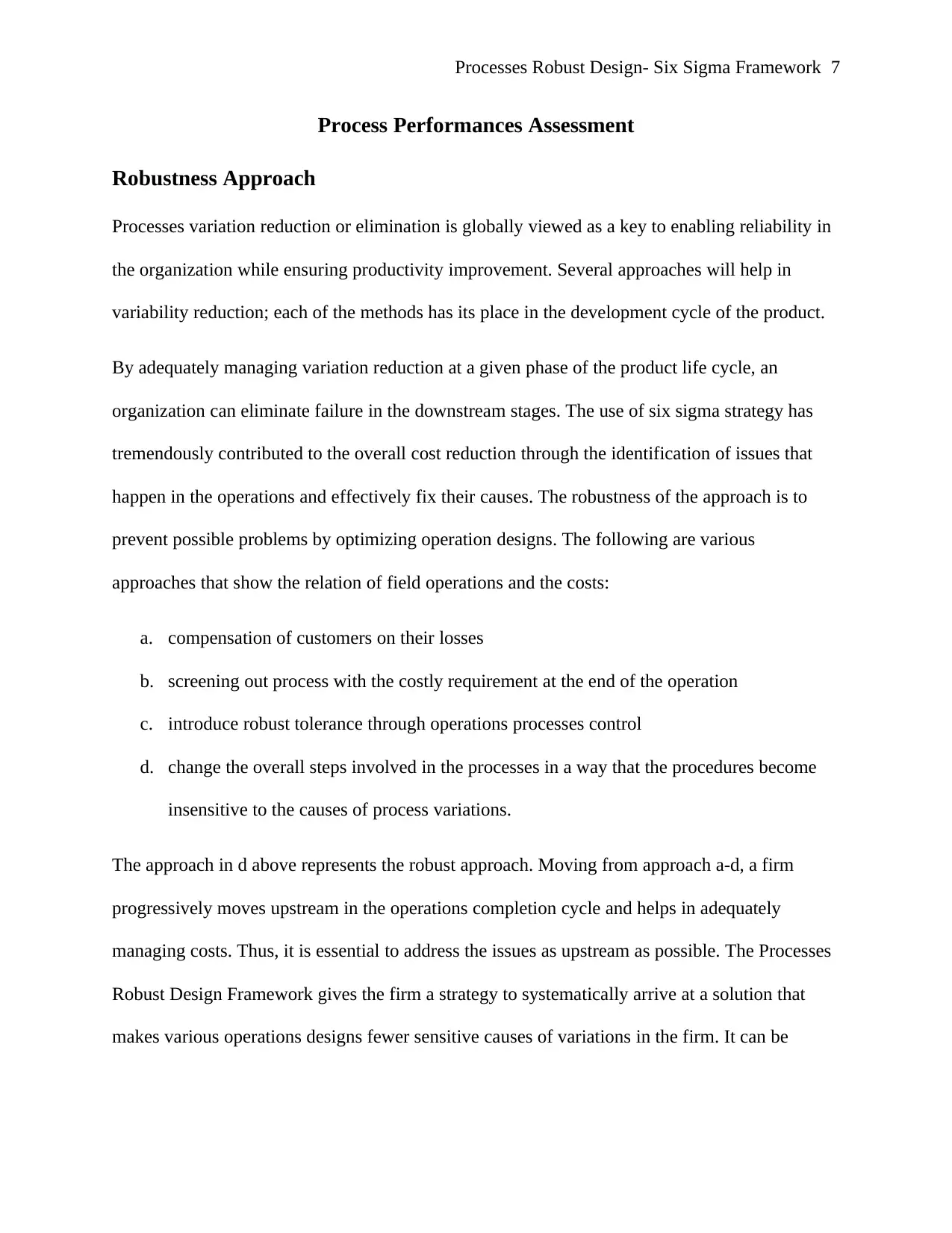
Processes Robust Design- Six Sigma Framework 7
Process Performances Assessment
Robustness Approach
Processes variation reduction or elimination is globally viewed as a key to enabling reliability in
the organization while ensuring productivity improvement. Several approaches will help in
variability reduction; each of the methods has its place in the development cycle of the product.
By adequately managing variation reduction at a given phase of the product life cycle, an
organization can eliminate failure in the downstream stages. The use of six sigma strategy has
tremendously contributed to the overall cost reduction through the identification of issues that
happen in the operations and effectively fix their causes. The robustness of the approach is to
prevent possible problems by optimizing operation designs. The following are various
approaches that show the relation of field operations and the costs:
a. compensation of customers on their losses
b. screening out process with the costly requirement at the end of the operation
c. introduce robust tolerance through operations processes control
d. change the overall steps involved in the processes in a way that the procedures become
insensitive to the causes of process variations.
The approach in d above represents the robust approach. Moving from approach a-d, a firm
progressively moves upstream in the operations completion cycle and helps in adequately
managing costs. Thus, it is essential to address the issues as upstream as possible. The Processes
Robust Design Framework gives the firm a strategy to systematically arrive at a solution that
makes various operations designs fewer sensitive causes of variations in the firm. It can be
Process Performances Assessment
Robustness Approach
Processes variation reduction or elimination is globally viewed as a key to enabling reliability in
the organization while ensuring productivity improvement. Several approaches will help in
variability reduction; each of the methods has its place in the development cycle of the product.
By adequately managing variation reduction at a given phase of the product life cycle, an
organization can eliminate failure in the downstream stages. The use of six sigma strategy has
tremendously contributed to the overall cost reduction through the identification of issues that
happen in the operations and effectively fix their causes. The robustness of the approach is to
prevent possible problems by optimizing operation designs. The following are various
approaches that show the relation of field operations and the costs:
a. compensation of customers on their losses
b. screening out process with the costly requirement at the end of the operation
c. introduce robust tolerance through operations processes control
d. change the overall steps involved in the processes in a way that the procedures become
insensitive to the causes of process variations.
The approach in d above represents the robust approach. Moving from approach a-d, a firm
progressively moves upstream in the operations completion cycle and helps in adequately
managing costs. Thus, it is essential to address the issues as upstream as possible. The Processes
Robust Design Framework gives the firm a strategy to systematically arrive at a solution that
makes various operations designs fewer sensitive causes of variations in the firm. It can be
Paraphrase This Document
Need a fresh take? Get an instant paraphrase of this document with our AI Paraphraser
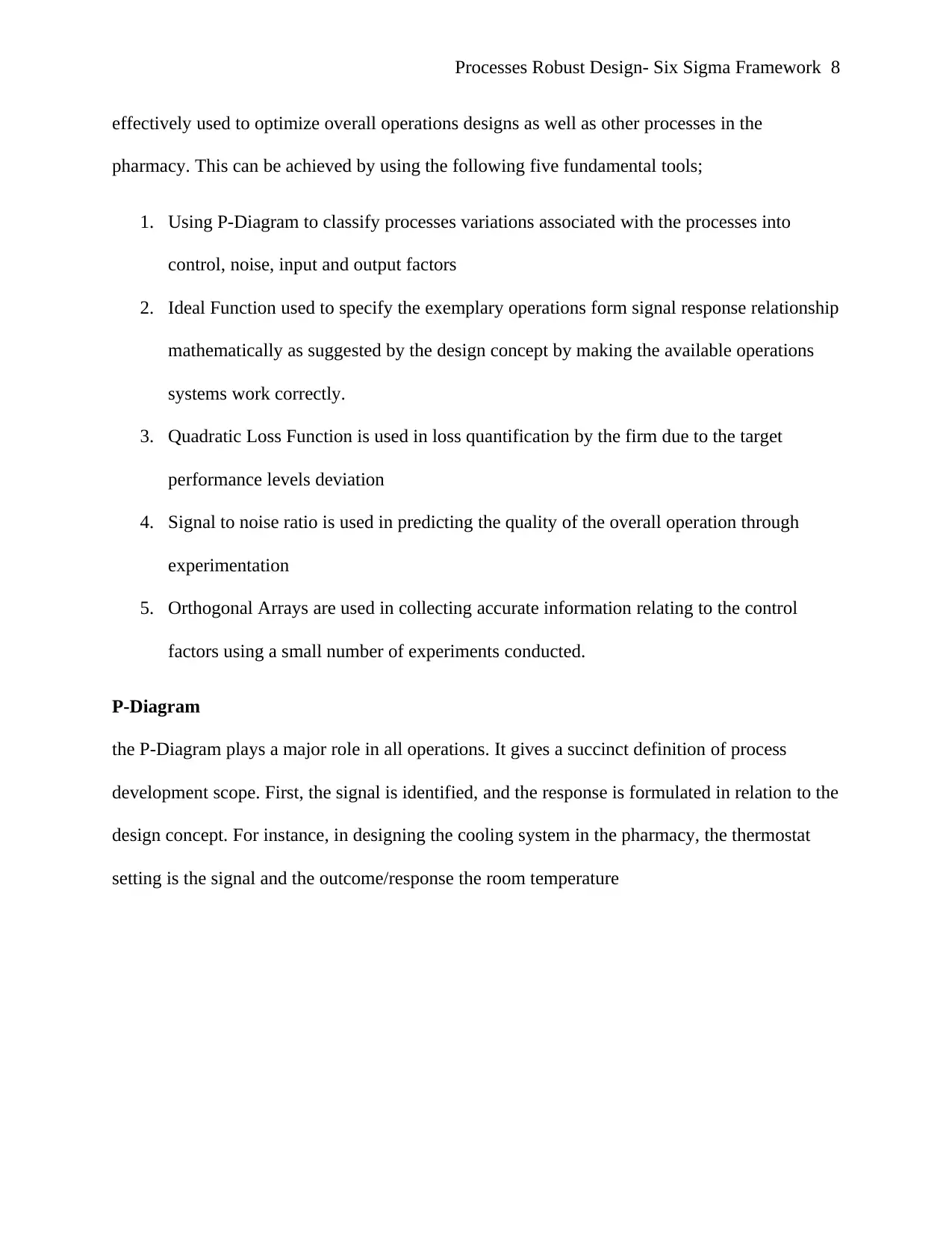
Processes Robust Design- Six Sigma Framework 8
effectively used to optimize overall operations designs as well as other processes in the
pharmacy. This can be achieved by using the following five fundamental tools;
1. Using P-Diagram to classify processes variations associated with the processes into
control, noise, input and output factors
2. Ideal Function used to specify the exemplary operations form signal response relationship
mathematically as suggested by the design concept by making the available operations
systems work correctly.
3. Quadratic Loss Function is used in loss quantification by the firm due to the target
performance levels deviation
4. Signal to noise ratio is used in predicting the quality of the overall operation through
experimentation
5. Orthogonal Arrays are used in collecting accurate information relating to the control
factors using a small number of experiments conducted.
P-Diagram
the P-Diagram plays a major role in all operations. It gives a succinct definition of process
development scope. First, the signal is identified, and the response is formulated in relation to the
design concept. For instance, in designing the cooling system in the pharmacy, the thermostat
setting is the signal and the outcome/response the room temperature
effectively used to optimize overall operations designs as well as other processes in the
pharmacy. This can be achieved by using the following five fundamental tools;
1. Using P-Diagram to classify processes variations associated with the processes into
control, noise, input and output factors
2. Ideal Function used to specify the exemplary operations form signal response relationship
mathematically as suggested by the design concept by making the available operations
systems work correctly.
3. Quadratic Loss Function is used in loss quantification by the firm due to the target
performance levels deviation
4. Signal to noise ratio is used in predicting the quality of the overall operation through
experimentation
5. Orthogonal Arrays are used in collecting accurate information relating to the control
factors using a small number of experiments conducted.
P-Diagram
the P-Diagram plays a major role in all operations. It gives a succinct definition of process
development scope. First, the signal is identified, and the response is formulated in relation to the
design concept. For instance, in designing the cooling system in the pharmacy, the thermostat
setting is the signal and the outcome/response the room temperature
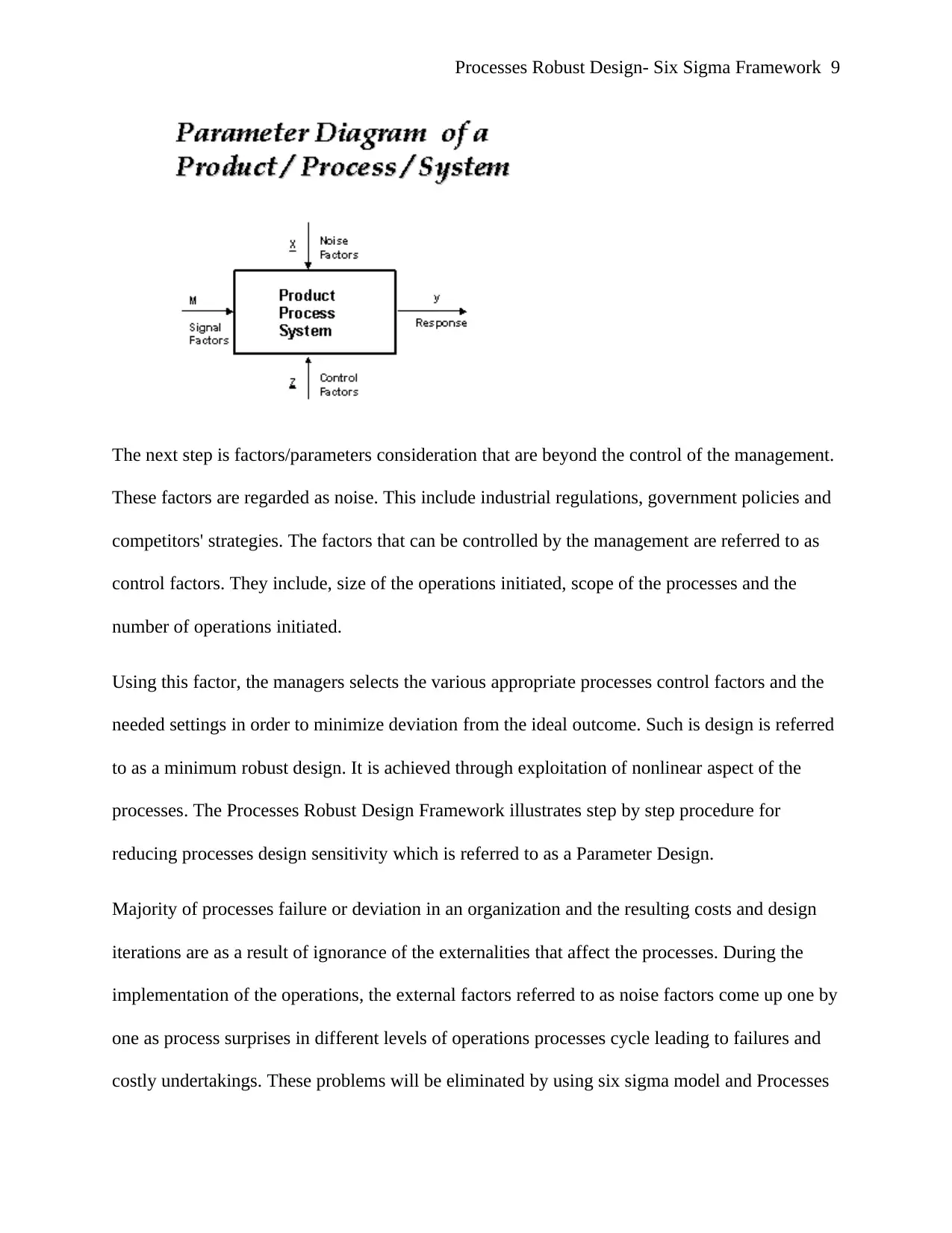
Processes Robust Design- Six Sigma Framework 9
The next step is factors/parameters consideration that are beyond the control of the management.
These factors are regarded as noise. This include industrial regulations, government policies and
competitors' strategies. The factors that can be controlled by the management are referred to as
control factors. They include, size of the operations initiated, scope of the processes and the
number of operations initiated.
Using this factor, the managers selects the various appropriate processes control factors and the
needed settings in order to minimize deviation from the ideal outcome. Such is design is referred
to as a minimum robust design. It is achieved through exploitation of nonlinear aspect of the
processes. The Processes Robust Design Framework illustrates step by step procedure for
reducing processes design sensitivity which is referred to as a Parameter Design.
Majority of processes failure or deviation in an organization and the resulting costs and design
iterations are as a result of ignorance of the externalities that affect the processes. During the
implementation of the operations, the external factors referred to as noise factors come up one by
one as process surprises in different levels of operations processes cycle leading to failures and
costly undertakings. These problems will be eliminated by using six sigma model and Processes
The next step is factors/parameters consideration that are beyond the control of the management.
These factors are regarded as noise. This include industrial regulations, government policies and
competitors' strategies. The factors that can be controlled by the management are referred to as
control factors. They include, size of the operations initiated, scope of the processes and the
number of operations initiated.
Using this factor, the managers selects the various appropriate processes control factors and the
needed settings in order to minimize deviation from the ideal outcome. Such is design is referred
to as a minimum robust design. It is achieved through exploitation of nonlinear aspect of the
processes. The Processes Robust Design Framework illustrates step by step procedure for
reducing processes design sensitivity which is referred to as a Parameter Design.
Majority of processes failure or deviation in an organization and the resulting costs and design
iterations are as a result of ignorance of the externalities that affect the processes. During the
implementation of the operations, the external factors referred to as noise factors come up one by
one as process surprises in different levels of operations processes cycle leading to failures and
costly undertakings. These problems will be eliminated by using six sigma model and Processes
⊘ This is a preview!⊘
Do you want full access?
Subscribe today to unlock all pages.

Trusted by 1+ million students worldwide
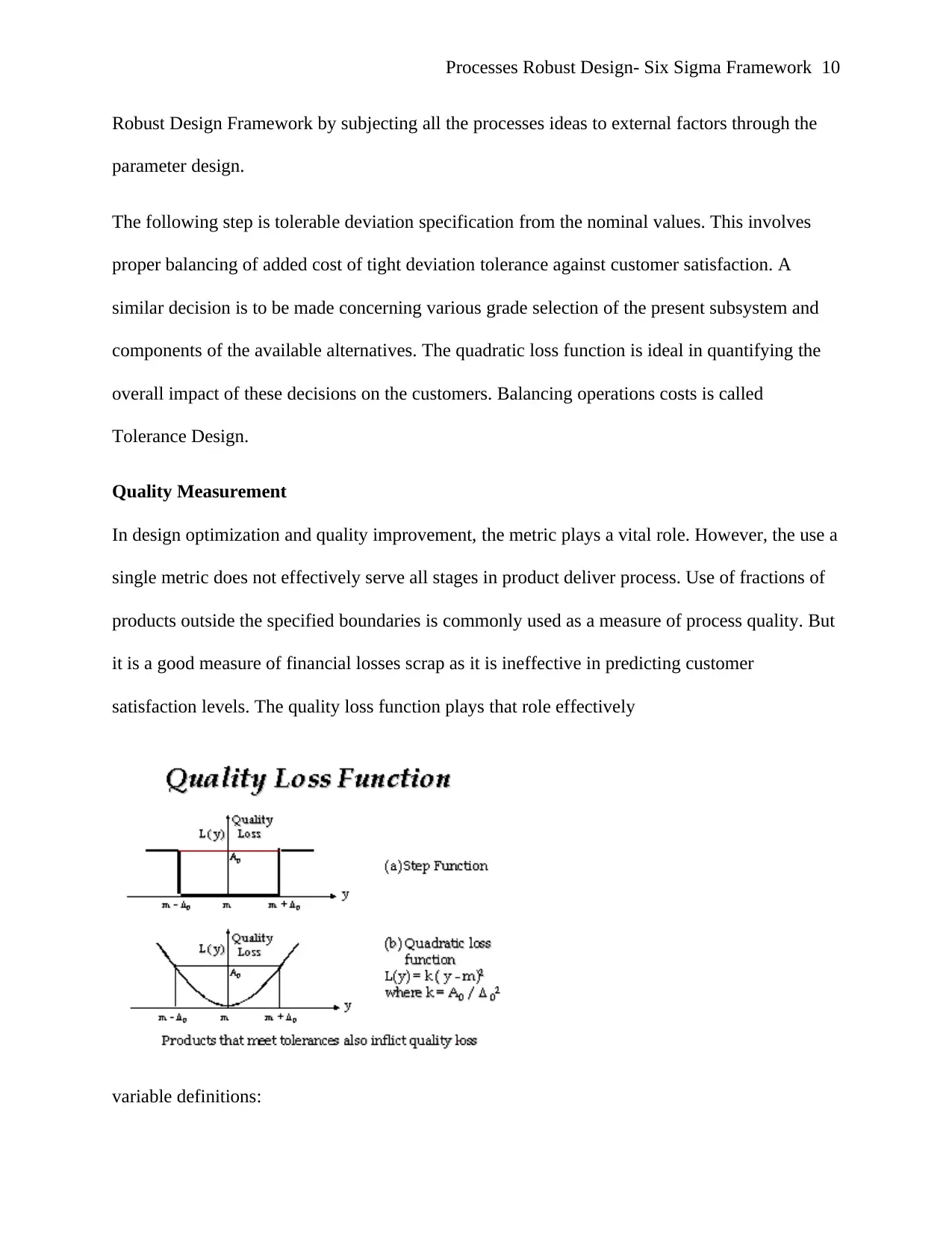
Processes Robust Design- Six Sigma Framework 10
Robust Design Framework by subjecting all the processes ideas to external factors through the
parameter design.
The following step is tolerable deviation specification from the nominal values. This involves
proper balancing of added cost of tight deviation tolerance against customer satisfaction. A
similar decision is to be made concerning various grade selection of the present subsystem and
components of the available alternatives. The quadratic loss function is ideal in quantifying the
overall impact of these decisions on the customers. Balancing operations costs is called
Tolerance Design.
Quality Measurement
In design optimization and quality improvement, the metric plays a vital role. However, the use a
single metric does not effectively serve all stages in product deliver process. Use of fractions of
products outside the specified boundaries is commonly used as a measure of process quality. But
it is a good measure of financial losses scrap as it is ineffective in predicting customer
satisfaction levels. The quality loss function plays that role effectively
variable definitions:
Robust Design Framework by subjecting all the processes ideas to external factors through the
parameter design.
The following step is tolerable deviation specification from the nominal values. This involves
proper balancing of added cost of tight deviation tolerance against customer satisfaction. A
similar decision is to be made concerning various grade selection of the present subsystem and
components of the available alternatives. The quadratic loss function is ideal in quantifying the
overall impact of these decisions on the customers. Balancing operations costs is called
Tolerance Design.
Quality Measurement
In design optimization and quality improvement, the metric plays a vital role. However, the use a
single metric does not effectively serve all stages in product deliver process. Use of fractions of
products outside the specified boundaries is commonly used as a measure of process quality. But
it is a good measure of financial losses scrap as it is ineffective in predicting customer
satisfaction levels. The quality loss function plays that role effectively
variable definitions:
Paraphrase This Document
Need a fresh take? Get an instant paraphrase of this document with our AI Paraphraser
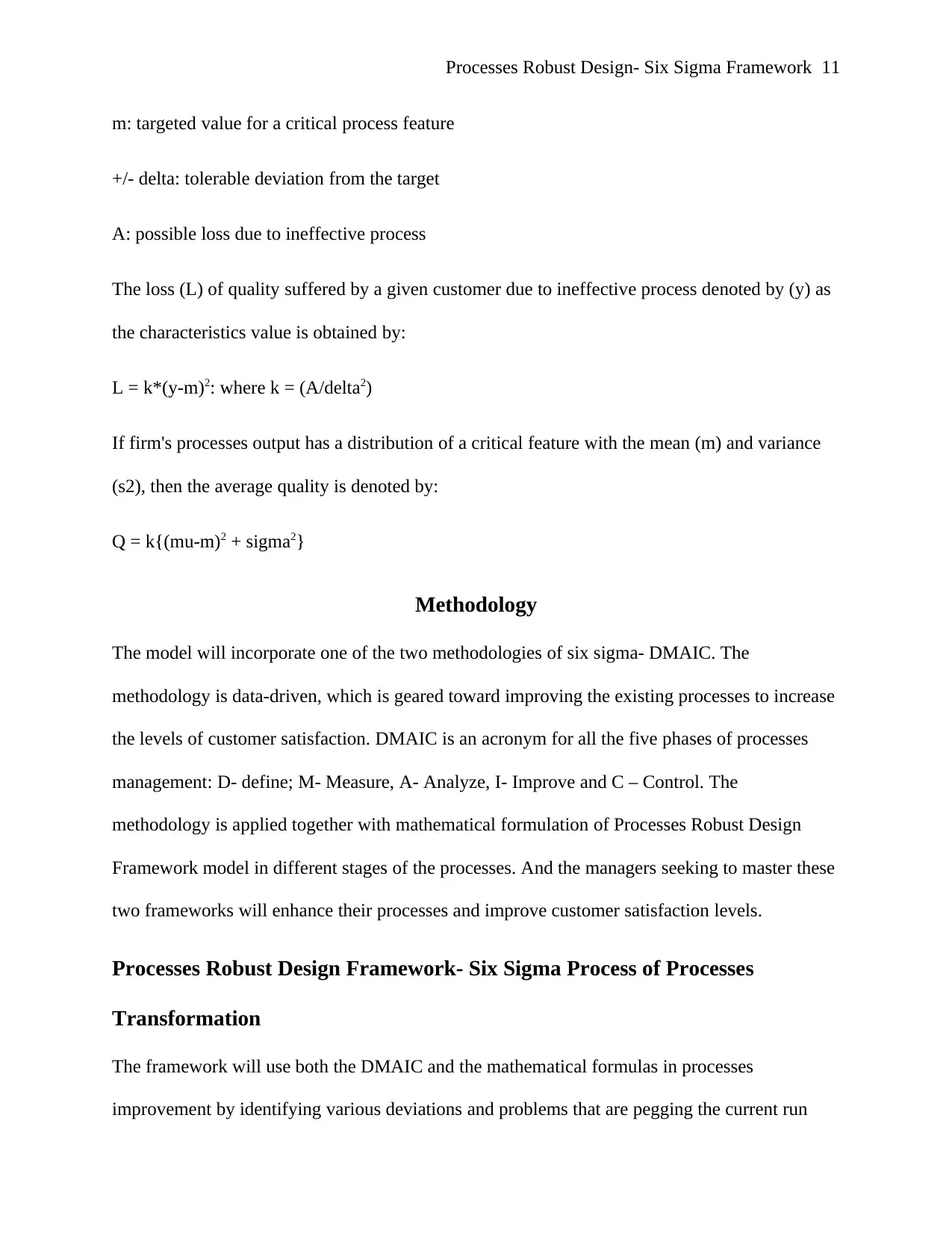
Processes Robust Design- Six Sigma Framework 11
m: targeted value for a critical process feature
+/- delta: tolerable deviation from the target
A: possible loss due to ineffective process
The loss (L) of quality suffered by a given customer due to ineffective process denoted by (y) as
the characteristics value is obtained by:
L = k*(y-m)2: where k = (A/delta2)
If firm's processes output has a distribution of a critical feature with the mean (m) and variance
(s2), then the average quality is denoted by:
Q = k{(mu-m)2 + sigma2}
Methodology
The model will incorporate one of the two methodologies of six sigma- DMAIC. The
methodology is data-driven, which is geared toward improving the existing processes to increase
the levels of customer satisfaction. DMAIC is an acronym for all the five phases of processes
management: D- define; M- Measure, A- Analyze, I- Improve and C – Control. The
methodology is applied together with mathematical formulation of Processes Robust Design
Framework model in different stages of the processes. And the managers seeking to master these
two frameworks will enhance their processes and improve customer satisfaction levels.
Processes Robust Design Framework- Six Sigma Process of Processes
Transformation
The framework will use both the DMAIC and the mathematical formulas in processes
improvement by identifying various deviations and problems that are pegging the current run
m: targeted value for a critical process feature
+/- delta: tolerable deviation from the target
A: possible loss due to ineffective process
The loss (L) of quality suffered by a given customer due to ineffective process denoted by (y) as
the characteristics value is obtained by:
L = k*(y-m)2: where k = (A/delta2)
If firm's processes output has a distribution of a critical feature with the mean (m) and variance
(s2), then the average quality is denoted by:
Q = k{(mu-m)2 + sigma2}
Methodology
The model will incorporate one of the two methodologies of six sigma- DMAIC. The
methodology is data-driven, which is geared toward improving the existing processes to increase
the levels of customer satisfaction. DMAIC is an acronym for all the five phases of processes
management: D- define; M- Measure, A- Analyze, I- Improve and C – Control. The
methodology is applied together with mathematical formulation of Processes Robust Design
Framework model in different stages of the processes. And the managers seeking to master these
two frameworks will enhance their processes and improve customer satisfaction levels.
Processes Robust Design Framework- Six Sigma Process of Processes
Transformation
The framework will use both the DMAIC and the mathematical formulas in processes
improvement by identifying various deviations and problems that are pegging the current run

Processes Robust Design- Six Sigma Framework 12
processes. The data-driven approach used by the System is useful in optimizing and improving
the business processes. The major framework is the strong customer focus and aggressive use of
data and statistics to offer conclusive efficient processes.
Model Phases
in each of the above steps, are numerous other steps
Define
the model will start by fully focusing on the customer needs:
Step 1: Processes problems are identified from the perspective of the customer
Step 2: Objectives are set. What the model is to achieve is defined, and the available resources
that will be used in achieving the goals are identified.
Step 3: process mapping. verification if the firm is on the right track with the help of other
stakeholders
Measure
The next stage of the process focuses on the project metrics and the tools that are used in
measuring the processes. How can the processes be improved? How can the improvement be
quantified?
processes. The data-driven approach used by the System is useful in optimizing and improving
the business processes. The major framework is the strong customer focus and aggressive use of
data and statistics to offer conclusive efficient processes.
Model Phases
in each of the above steps, are numerous other steps
Define
the model will start by fully focusing on the customer needs:
Step 1: Processes problems are identified from the perspective of the customer
Step 2: Objectives are set. What the model is to achieve is defined, and the available resources
that will be used in achieving the goals are identified.
Step 3: process mapping. verification if the firm is on the right track with the help of other
stakeholders
Measure
The next stage of the process focuses on the project metrics and the tools that are used in
measuring the processes. How can the processes be improved? How can the improvement be
quantified?
⊘ This is a preview!⊘
Do you want full access?
Subscribe today to unlock all pages.

Trusted by 1+ million students worldwide
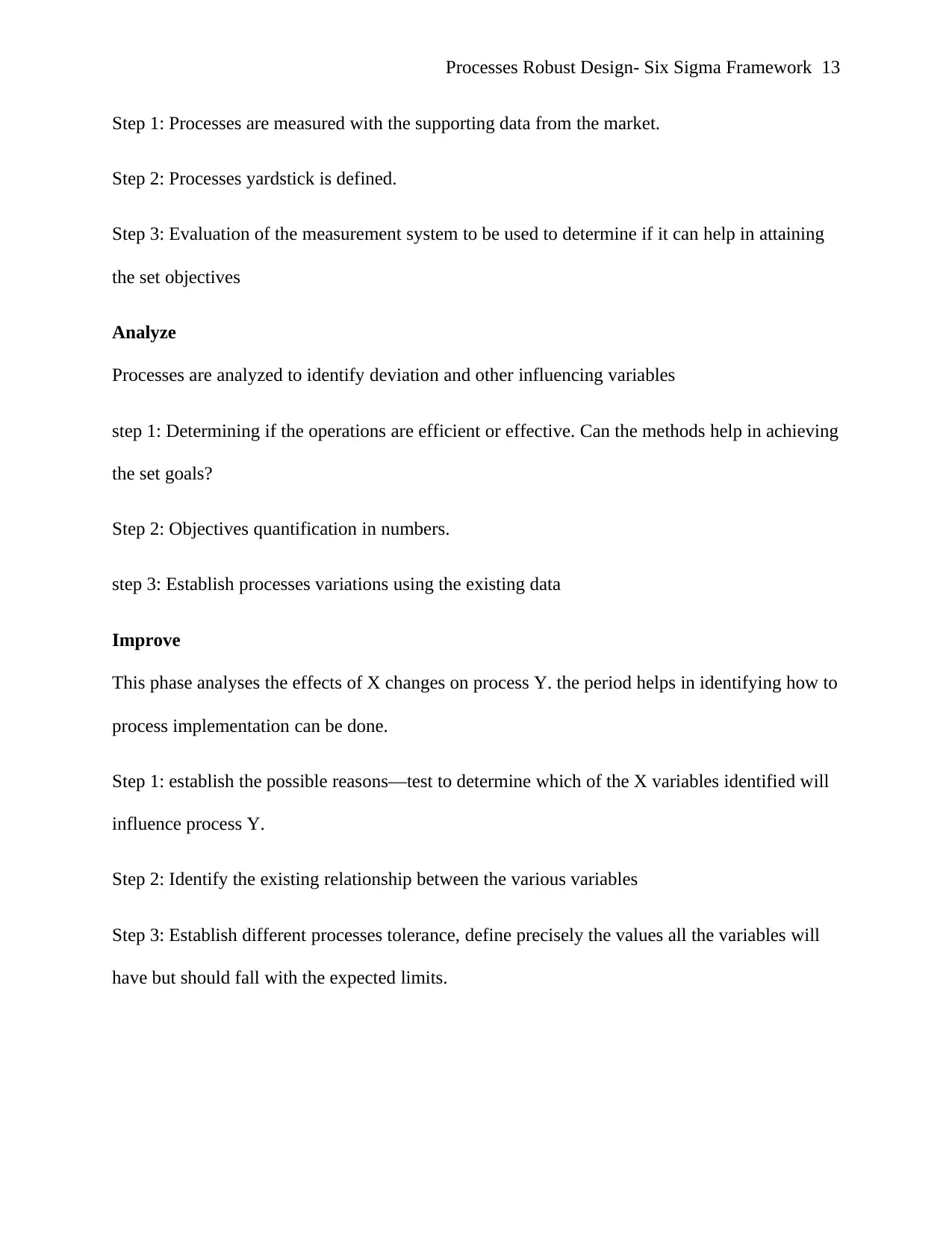
Processes Robust Design- Six Sigma Framework 13
Step 1: Processes are measured with the supporting data from the market.
Step 2: Processes yardstick is defined.
Step 3: Evaluation of the measurement system to be used to determine if it can help in attaining
the set objectives
Analyze
Processes are analyzed to identify deviation and other influencing variables
step 1: Determining if the operations are efficient or effective. Can the methods help in achieving
the set goals?
Step 2: Objectives quantification in numbers.
step 3: Establish processes variations using the existing data
Improve
This phase analyses the effects of X changes on process Y. the period helps in identifying how to
process implementation can be done.
Step 1: establish the possible reasons—test to determine which of the X variables identified will
influence process Y.
Step 2: Identify the existing relationship between the various variables
Step 3: Establish different processes tolerance, define precisely the values all the variables will
have but should fall with the expected limits.
Step 1: Processes are measured with the supporting data from the market.
Step 2: Processes yardstick is defined.
Step 3: Evaluation of the measurement system to be used to determine if it can help in attaining
the set objectives
Analyze
Processes are analyzed to identify deviation and other influencing variables
step 1: Determining if the operations are efficient or effective. Can the methods help in achieving
the set goals?
Step 2: Objectives quantification in numbers.
step 3: Establish processes variations using the existing data
Improve
This phase analyses the effects of X changes on process Y. the period helps in identifying how to
process implementation can be done.
Step 1: establish the possible reasons—test to determine which of the X variables identified will
influence process Y.
Step 2: Identify the existing relationship between the various variables
Step 3: Establish different processes tolerance, define precisely the values all the variables will
have but should fall with the expected limits.
Paraphrase This Document
Need a fresh take? Get an instant paraphrase of this document with our AI Paraphraser
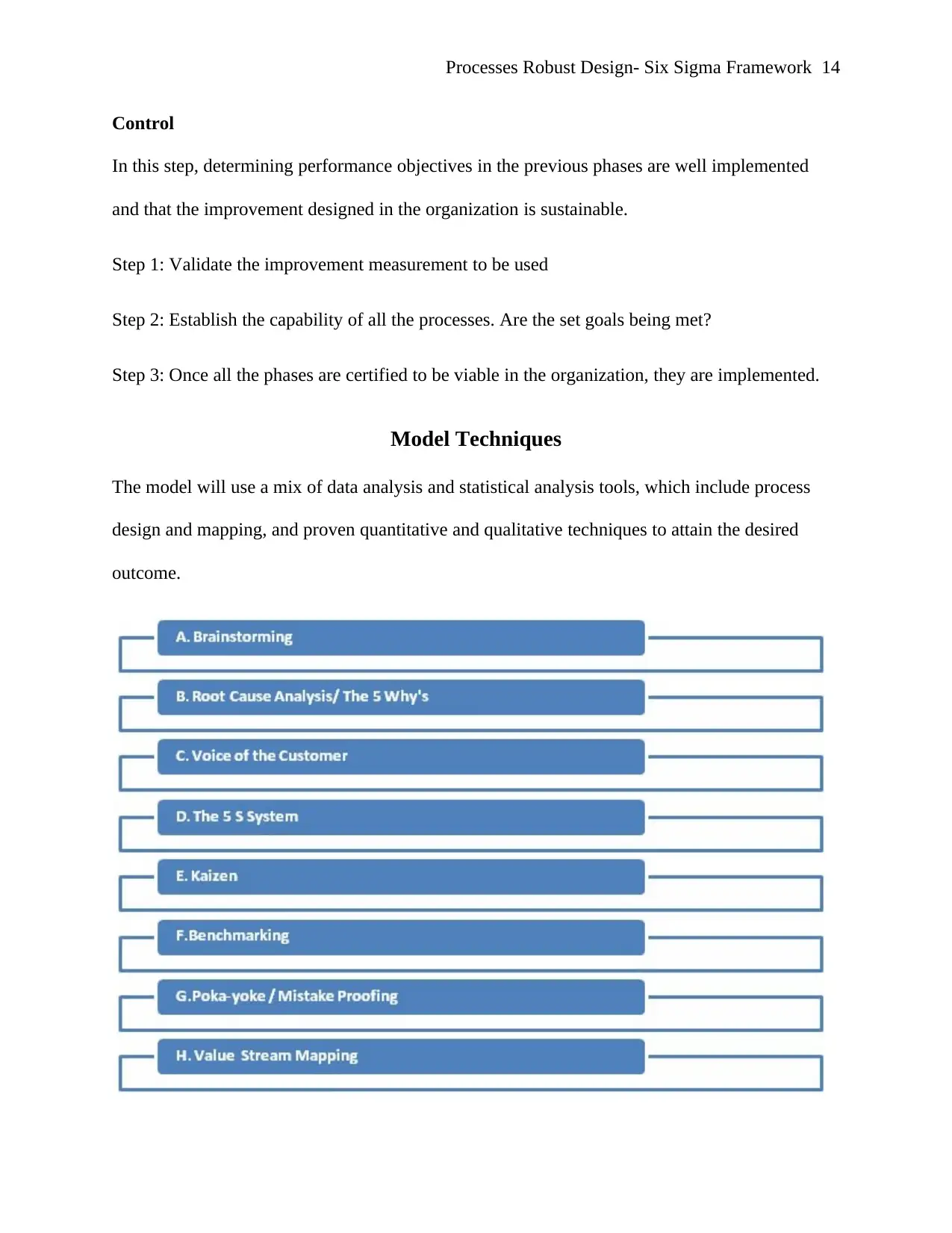
Processes Robust Design- Six Sigma Framework 14
Control
In this step, determining performance objectives in the previous phases are well implemented
and that the improvement designed in the organization is sustainable.
Step 1: Validate the improvement measurement to be used
Step 2: Establish the capability of all the processes. Are the set goals being met?
Step 3: Once all the phases are certified to be viable in the organization, they are implemented.
Model Techniques
The model will use a mix of data analysis and statistical analysis tools, which include process
design and mapping, and proven quantitative and qualitative techniques to attain the desired
outcome.
Control
In this step, determining performance objectives in the previous phases are well implemented
and that the improvement designed in the organization is sustainable.
Step 1: Validate the improvement measurement to be used
Step 2: Establish the capability of all the processes. Are the set goals being met?
Step 3: Once all the phases are certified to be viable in the organization, they are implemented.
Model Techniques
The model will use a mix of data analysis and statistical analysis tools, which include process
design and mapping, and proven quantitative and qualitative techniques to attain the desired
outcome.
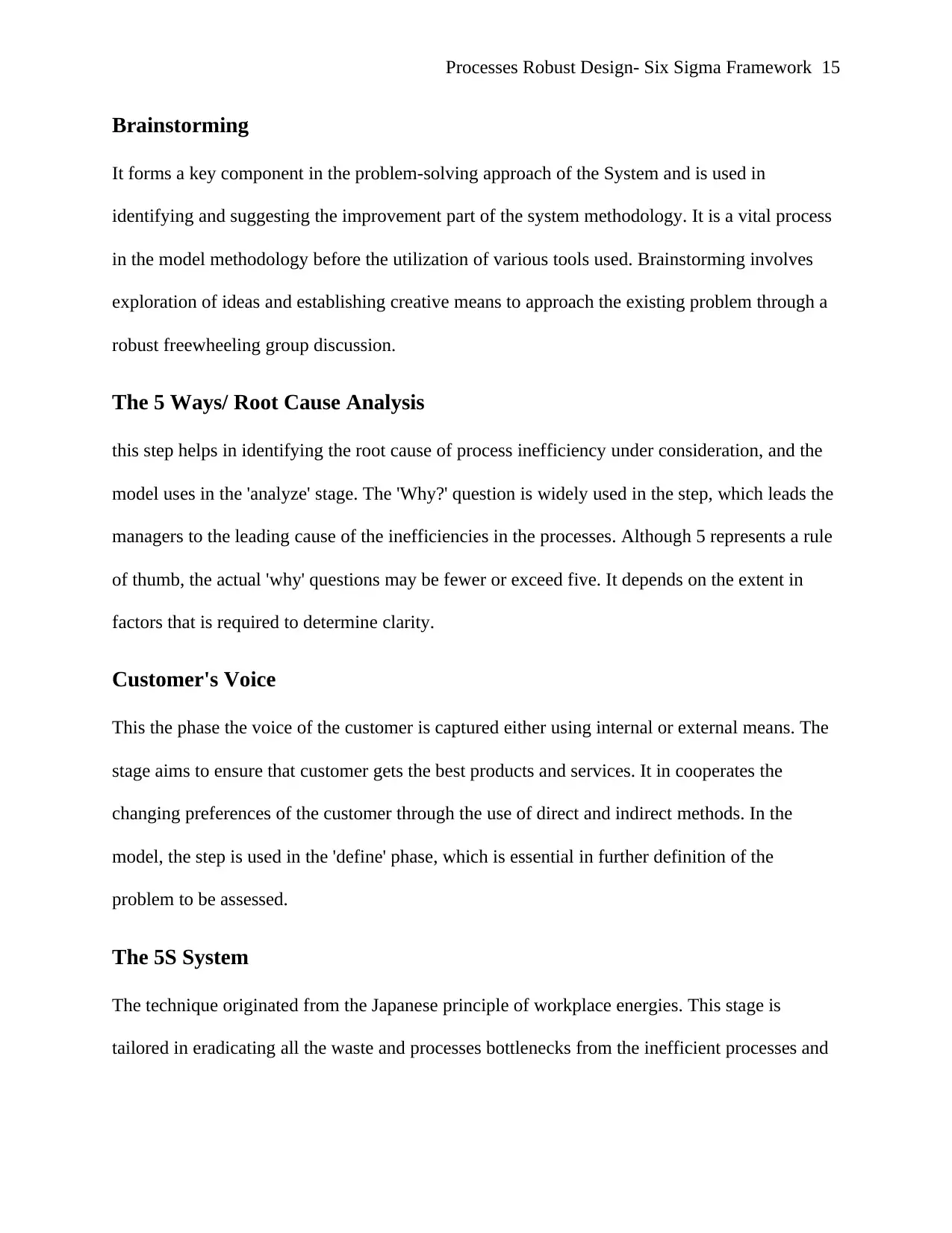
Processes Robust Design- Six Sigma Framework 15
Brainstorming
It forms a key component in the problem-solving approach of the System and is used in
identifying and suggesting the improvement part of the system methodology. It is a vital process
in the model methodology before the utilization of various tools used. Brainstorming involves
exploration of ideas and establishing creative means to approach the existing problem through a
robust freewheeling group discussion.
The 5 Ways/ Root Cause Analysis
this step helps in identifying the root cause of process inefficiency under consideration, and the
model uses in the 'analyze' stage. The 'Why?' question is widely used in the step, which leads the
managers to the leading cause of the inefficiencies in the processes. Although 5 represents a rule
of thumb, the actual 'why' questions may be fewer or exceed five. It depends on the extent in
factors that is required to determine clarity.
Customer's Voice
This the phase the voice of the customer is captured either using internal or external means. The
stage aims to ensure that customer gets the best products and services. It in cooperates the
changing preferences of the customer through the use of direct and indirect methods. In the
model, the step is used in the 'define' phase, which is essential in further definition of the
problem to be assessed.
The 5S System
The technique originated from the Japanese principle of workplace energies. This stage is
tailored in eradicating all the waste and processes bottlenecks from the inefficient processes and
Brainstorming
It forms a key component in the problem-solving approach of the System and is used in
identifying and suggesting the improvement part of the system methodology. It is a vital process
in the model methodology before the utilization of various tools used. Brainstorming involves
exploration of ideas and establishing creative means to approach the existing problem through a
robust freewheeling group discussion.
The 5 Ways/ Root Cause Analysis
this step helps in identifying the root cause of process inefficiency under consideration, and the
model uses in the 'analyze' stage. The 'Why?' question is widely used in the step, which leads the
managers to the leading cause of the inefficiencies in the processes. Although 5 represents a rule
of thumb, the actual 'why' questions may be fewer or exceed five. It depends on the extent in
factors that is required to determine clarity.
Customer's Voice
This the phase the voice of the customer is captured either using internal or external means. The
stage aims to ensure that customer gets the best products and services. It in cooperates the
changing preferences of the customer through the use of direct and indirect methods. In the
model, the step is used in the 'define' phase, which is essential in further definition of the
problem to be assessed.
The 5S System
The technique originated from the Japanese principle of workplace energies. This stage is
tailored in eradicating all the waste and processes bottlenecks from the inefficient processes and
⊘ This is a preview!⊘
Do you want full access?
Subscribe today to unlock all pages.

Trusted by 1+ million students worldwide
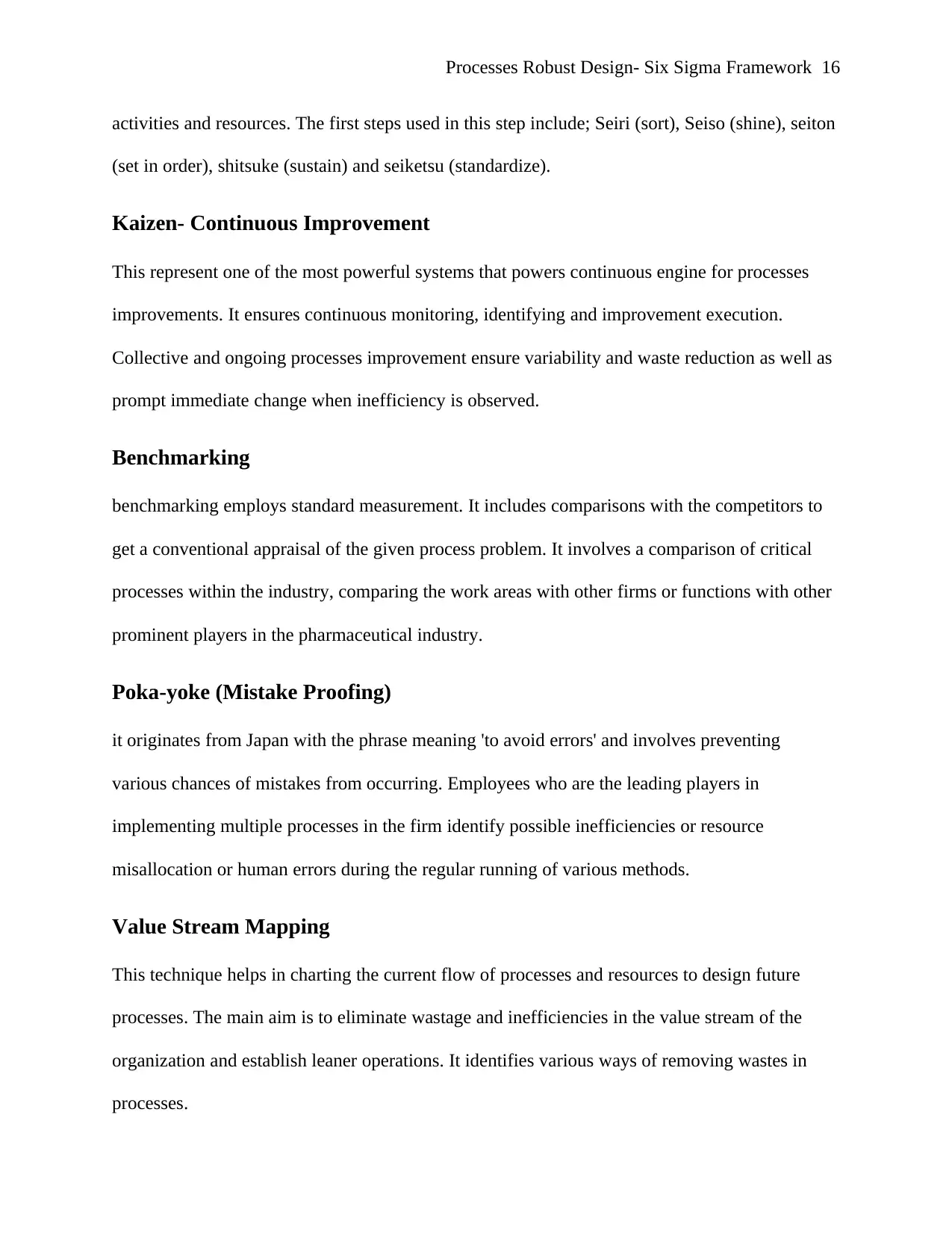
Processes Robust Design- Six Sigma Framework 16
activities and resources. The first steps used in this step include; Seiri (sort), Seiso (shine), seiton
(set in order), shitsuke (sustain) and seiketsu (standardize).
Kaizen- Continuous Improvement
This represent one of the most powerful systems that powers continuous engine for processes
improvements. It ensures continuous monitoring, identifying and improvement execution.
Collective and ongoing processes improvement ensure variability and waste reduction as well as
prompt immediate change when inefficiency is observed.
Benchmarking
benchmarking employs standard measurement. It includes comparisons with the competitors to
get a conventional appraisal of the given process problem. It involves a comparison of critical
processes within the industry, comparing the work areas with other firms or functions with other
prominent players in the pharmaceutical industry.
Poka-yoke (Mistake Proofing)
it originates from Japan with the phrase meaning 'to avoid errors' and involves preventing
various chances of mistakes from occurring. Employees who are the leading players in
implementing multiple processes in the firm identify possible inefficiencies or resource
misallocation or human errors during the regular running of various methods.
Value Stream Mapping
This technique helps in charting the current flow of processes and resources to design future
processes. The main aim is to eliminate wastage and inefficiencies in the value stream of the
organization and establish leaner operations. It identifies various ways of removing wastes in
processes.
activities and resources. The first steps used in this step include; Seiri (sort), Seiso (shine), seiton
(set in order), shitsuke (sustain) and seiketsu (standardize).
Kaizen- Continuous Improvement
This represent one of the most powerful systems that powers continuous engine for processes
improvements. It ensures continuous monitoring, identifying and improvement execution.
Collective and ongoing processes improvement ensure variability and waste reduction as well as
prompt immediate change when inefficiency is observed.
Benchmarking
benchmarking employs standard measurement. It includes comparisons with the competitors to
get a conventional appraisal of the given process problem. It involves a comparison of critical
processes within the industry, comparing the work areas with other firms or functions with other
prominent players in the pharmaceutical industry.
Poka-yoke (Mistake Proofing)
it originates from Japan with the phrase meaning 'to avoid errors' and involves preventing
various chances of mistakes from occurring. Employees who are the leading players in
implementing multiple processes in the firm identify possible inefficiencies or resource
misallocation or human errors during the regular running of various methods.
Value Stream Mapping
This technique helps in charting the current flow of processes and resources to design future
processes. The main aim is to eliminate wastage and inefficiencies in the value stream of the
organization and establish leaner operations. It identifies various ways of removing wastes in
processes.
Paraphrase This Document
Need a fresh take? Get an instant paraphrase of this document with our AI Paraphraser
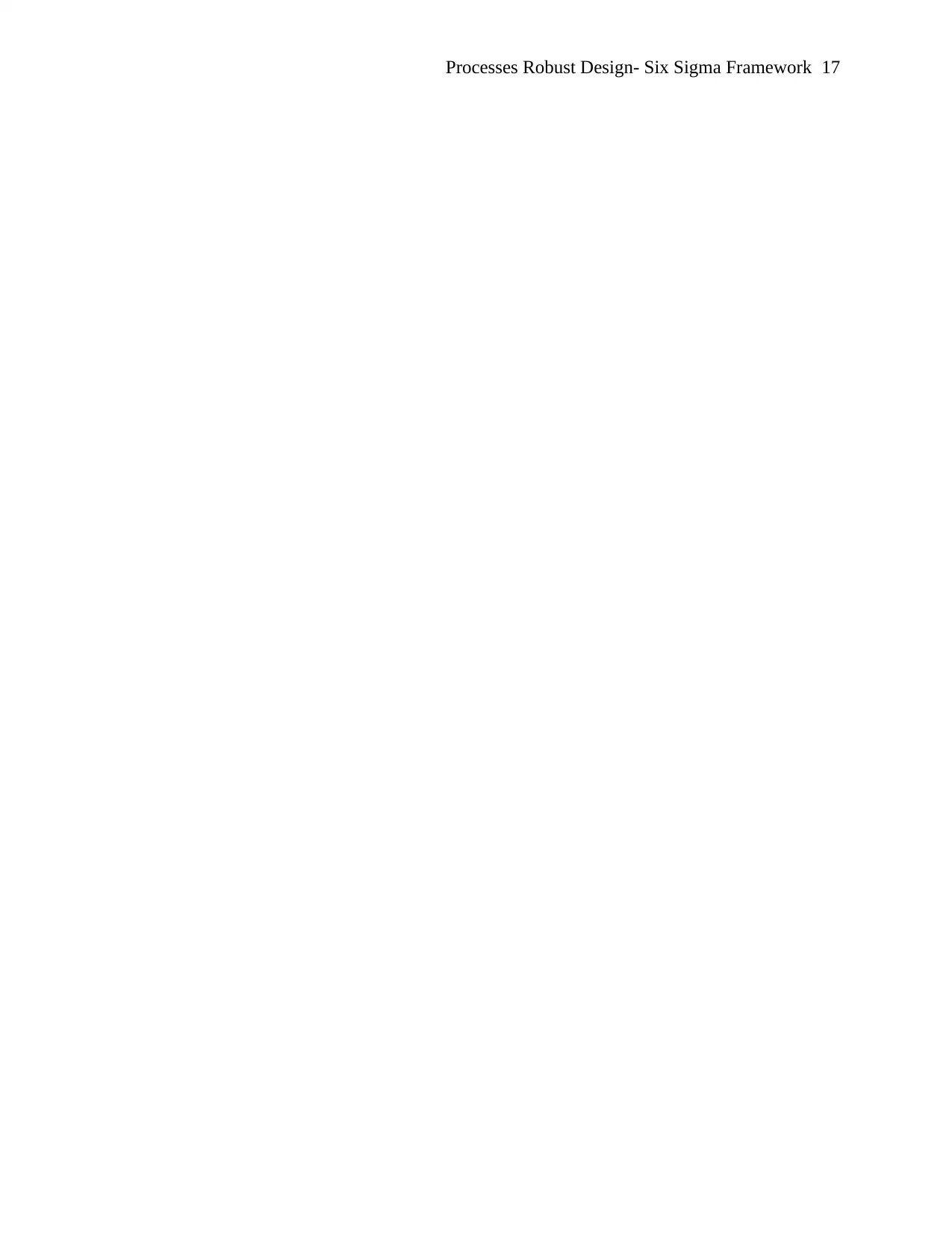
Processes Robust Design- Six Sigma Framework 17
1 out of 17
Related Documents

Your All-in-One AI-Powered Toolkit for Academic Success.
+13062052269
info@desklib.com
Available 24*7 on WhatsApp / Email
Unlock your academic potential
© 2024 | Zucol Services PVT LTD | All rights reserved.