Six Sigma Project: Frosts Food & Beverage Procurement Analysis
VerifiedAdded on 2023/06/08
|15
|4589
|376
Project
AI Summary
This project analyzes a Lean Six Sigma implementation aimed at improving the procurement process at Frosts Food & Beverage. The assignment begins with a background of the company, its products, and services, followed by a problem statement highlighting delays in the procurement procedure. The project identifies the Voice of Customer (VOC) and Critical to Quality (CTQ) metrics, with the Procurement Request Process Time (PRPT) as the CTQ. The "As-Is" process map is detailed, followed by a Fishbone analysis and brainstorming session to identify root causes, and a Gimba walk to identify wastes. Recommendations are provided for both root causes and wastes. The project also includes countermeasures, a control plan, and a discussion on Lean Six Sigma deployments, including quality improvement processes and challenges. The project concludes with an evaluation and recommendation for adopting Lean Six Sigma, along with references.
Contribute Materials
Your contribution can guide someone’s learning journey. Share your
documents today.
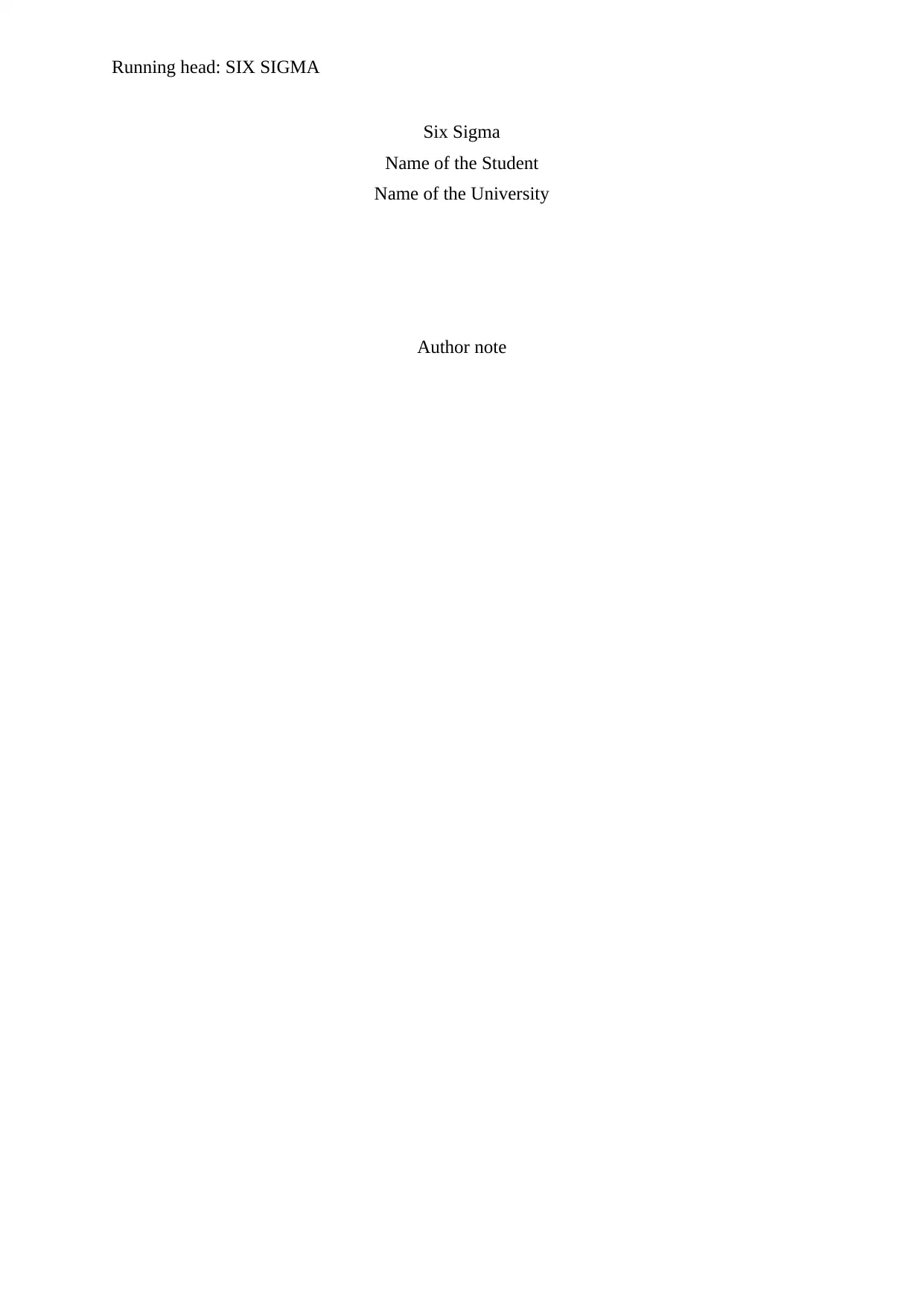
Running head: SIX SIGMA
Six Sigma
Name of the Student
Name of the University
Author note
Six Sigma
Name of the Student
Name of the University
Author note
Secure Best Marks with AI Grader
Need help grading? Try our AI Grader for instant feedback on your assignments.
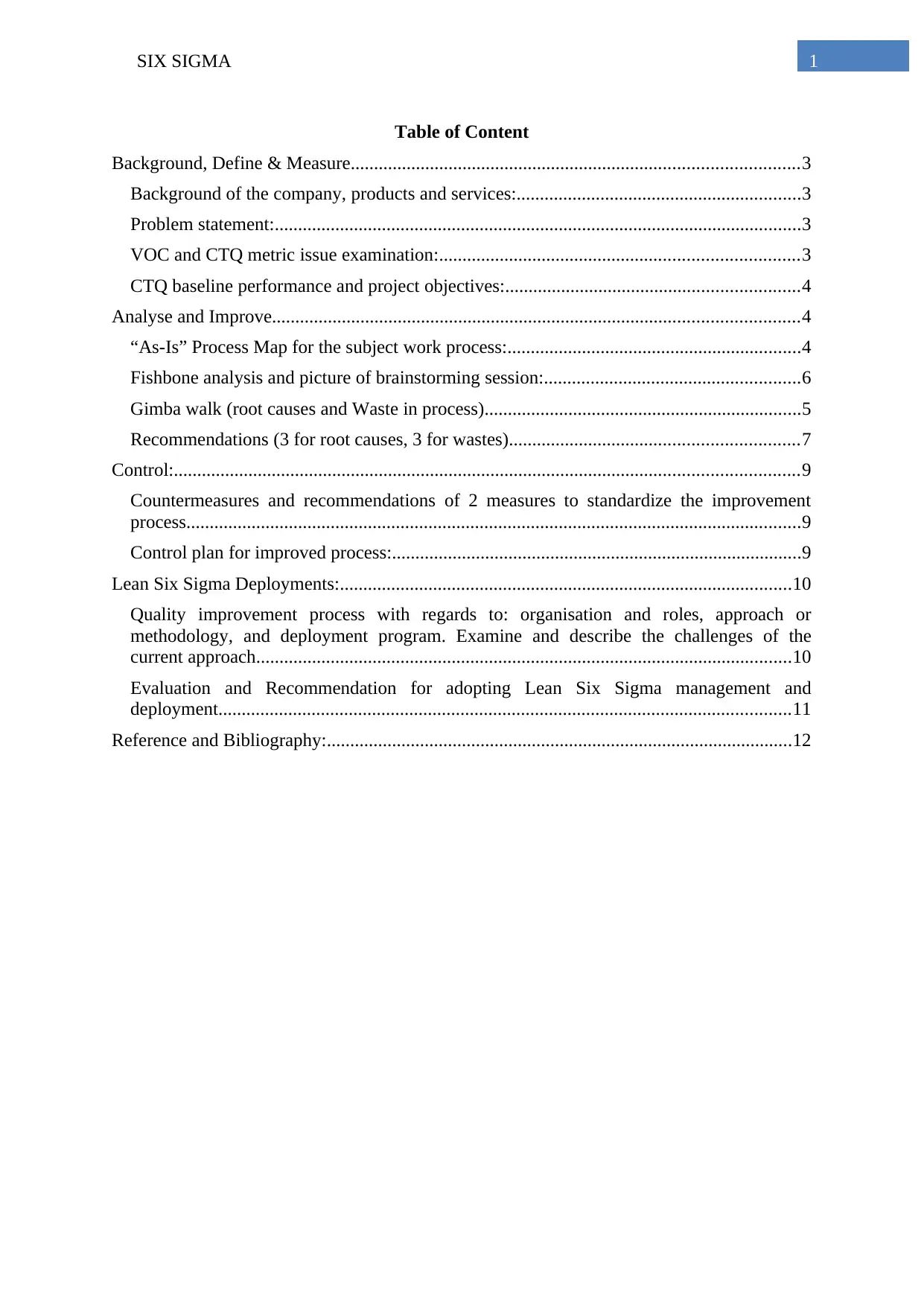
1SIX SIGMA
Table of Content
Background, Define & Measure................................................................................................3
Background of the company, products and services:.............................................................3
Problem statement:.................................................................................................................3
VOC and CTQ metric issue examination:.............................................................................3
CTQ baseline performance and project objectives:...............................................................4
Analyse and Improve.................................................................................................................4
“As-Is” Process Map for the subject work process:...............................................................4
Fishbone analysis and picture of brainstorming session:.......................................................6
Gimba walk (root causes and Waste in process)....................................................................5
Recommendations (3 for root causes, 3 for wastes)..............................................................7
Control:......................................................................................................................................9
Countermeasures and recommendations of 2 measures to standardize the improvement
process....................................................................................................................................9
Control plan for improved process:........................................................................................9
Lean Six Sigma Deployments:.................................................................................................10
Quality improvement process with regards to: organisation and roles, approach or
methodology, and deployment program. Examine and describe the challenges of the
current approach...................................................................................................................10
Evaluation and Recommendation for adopting Lean Six Sigma management and
deployment...........................................................................................................................11
Reference and Bibliography:....................................................................................................12
Table of Content
Background, Define & Measure................................................................................................3
Background of the company, products and services:.............................................................3
Problem statement:.................................................................................................................3
VOC and CTQ metric issue examination:.............................................................................3
CTQ baseline performance and project objectives:...............................................................4
Analyse and Improve.................................................................................................................4
“As-Is” Process Map for the subject work process:...............................................................4
Fishbone analysis and picture of brainstorming session:.......................................................6
Gimba walk (root causes and Waste in process)....................................................................5
Recommendations (3 for root causes, 3 for wastes)..............................................................7
Control:......................................................................................................................................9
Countermeasures and recommendations of 2 measures to standardize the improvement
process....................................................................................................................................9
Control plan for improved process:........................................................................................9
Lean Six Sigma Deployments:.................................................................................................10
Quality improvement process with regards to: organisation and roles, approach or
methodology, and deployment program. Examine and describe the challenges of the
current approach...................................................................................................................10
Evaluation and Recommendation for adopting Lean Six Sigma management and
deployment...........................................................................................................................11
Reference and Bibliography:....................................................................................................12
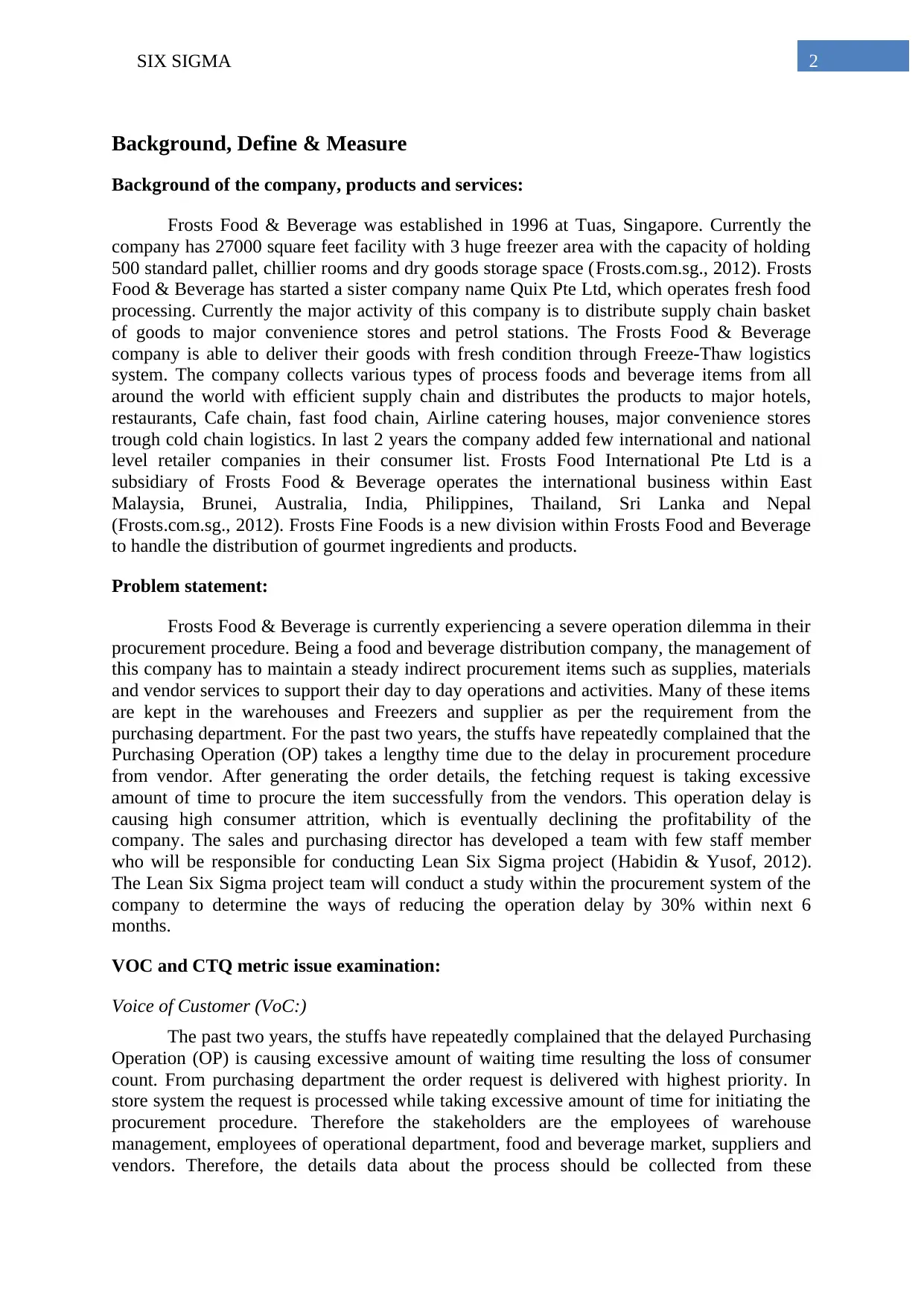
2SIX SIGMA
Background, Define & Measure
Background of the company, products and services:
Frosts Food & Beverage was established in 1996 at Tuas, Singapore. Currently the
company has 27000 square feet facility with 3 huge freezer area with the capacity of holding
500 standard pallet, chillier rooms and dry goods storage space (Frosts.com.sg., 2012). Frosts
Food & Beverage has started a sister company name Quix Pte Ltd, which operates fresh food
processing. Currently the major activity of this company is to distribute supply chain basket
of goods to major convenience stores and petrol stations. The Frosts Food & Beverage
company is able to deliver their goods with fresh condition through Freeze-Thaw logistics
system. The company collects various types of process foods and beverage items from all
around the world with efficient supply chain and distributes the products to major hotels,
restaurants, Cafe chain, fast food chain, Airline catering houses, major convenience stores
trough cold chain logistics. In last 2 years the company added few international and national
level retailer companies in their consumer list. Frosts Food International Pte Ltd is a
subsidiary of Frosts Food & Beverage operates the international business within East
Malaysia, Brunei, Australia, India, Philippines, Thailand, Sri Lanka and Nepal
(Frosts.com.sg., 2012). Frosts Fine Foods is a new division within Frosts Food and Beverage
to handle the distribution of gourmet ingredients and products.
Problem statement:
Frosts Food & Beverage is currently experiencing a severe operation dilemma in their
procurement procedure. Being a food and beverage distribution company, the management of
this company has to maintain a steady indirect procurement items such as supplies, materials
and vendor services to support their day to day operations and activities. Many of these items
are kept in the warehouses and Freezers and supplier as per the requirement from the
purchasing department. For the past two years, the stuffs have repeatedly complained that the
Purchasing Operation (OP) takes a lengthy time due to the delay in procurement procedure
from vendor. After generating the order details, the fetching request is taking excessive
amount of time to procure the item successfully from the vendors. This operation delay is
causing high consumer attrition, which is eventually declining the profitability of the
company. The sales and purchasing director has developed a team with few staff member
who will be responsible for conducting Lean Six Sigma project (Habidin & Yusof, 2012).
The Lean Six Sigma project team will conduct a study within the procurement system of the
company to determine the ways of reducing the operation delay by 30% within next 6
months.
VOC and CTQ metric issue examination:
Voice of Customer (VoC:)
The past two years, the stuffs have repeatedly complained that the delayed Purchasing
Operation (OP) is causing excessive amount of waiting time resulting the loss of consumer
count. From purchasing department the order request is delivered with highest priority. In
store system the request is processed while taking excessive amount of time for initiating the
procurement procedure. Therefore the stakeholders are the employees of warehouse
management, employees of operational department, food and beverage market, suppliers and
vendors. Therefore, the details data about the process should be collected from these
Background, Define & Measure
Background of the company, products and services:
Frosts Food & Beverage was established in 1996 at Tuas, Singapore. Currently the
company has 27000 square feet facility with 3 huge freezer area with the capacity of holding
500 standard pallet, chillier rooms and dry goods storage space (Frosts.com.sg., 2012). Frosts
Food & Beverage has started a sister company name Quix Pte Ltd, which operates fresh food
processing. Currently the major activity of this company is to distribute supply chain basket
of goods to major convenience stores and petrol stations. The Frosts Food & Beverage
company is able to deliver their goods with fresh condition through Freeze-Thaw logistics
system. The company collects various types of process foods and beverage items from all
around the world with efficient supply chain and distributes the products to major hotels,
restaurants, Cafe chain, fast food chain, Airline catering houses, major convenience stores
trough cold chain logistics. In last 2 years the company added few international and national
level retailer companies in their consumer list. Frosts Food International Pte Ltd is a
subsidiary of Frosts Food & Beverage operates the international business within East
Malaysia, Brunei, Australia, India, Philippines, Thailand, Sri Lanka and Nepal
(Frosts.com.sg., 2012). Frosts Fine Foods is a new division within Frosts Food and Beverage
to handle the distribution of gourmet ingredients and products.
Problem statement:
Frosts Food & Beverage is currently experiencing a severe operation dilemma in their
procurement procedure. Being a food and beverage distribution company, the management of
this company has to maintain a steady indirect procurement items such as supplies, materials
and vendor services to support their day to day operations and activities. Many of these items
are kept in the warehouses and Freezers and supplier as per the requirement from the
purchasing department. For the past two years, the stuffs have repeatedly complained that the
Purchasing Operation (OP) takes a lengthy time due to the delay in procurement procedure
from vendor. After generating the order details, the fetching request is taking excessive
amount of time to procure the item successfully from the vendors. This operation delay is
causing high consumer attrition, which is eventually declining the profitability of the
company. The sales and purchasing director has developed a team with few staff member
who will be responsible for conducting Lean Six Sigma project (Habidin & Yusof, 2012).
The Lean Six Sigma project team will conduct a study within the procurement system of the
company to determine the ways of reducing the operation delay by 30% within next 6
months.
VOC and CTQ metric issue examination:
Voice of Customer (VoC:)
The past two years, the stuffs have repeatedly complained that the delayed Purchasing
Operation (OP) is causing excessive amount of waiting time resulting the loss of consumer
count. From purchasing department the order request is delivered with highest priority. In
store system the request is processed while taking excessive amount of time for initiating the
procurement procedure. Therefore the stakeholders are the employees of warehouse
management, employees of operational department, food and beverage market, suppliers and
vendors. Therefore, the details data about the process should be collected from these
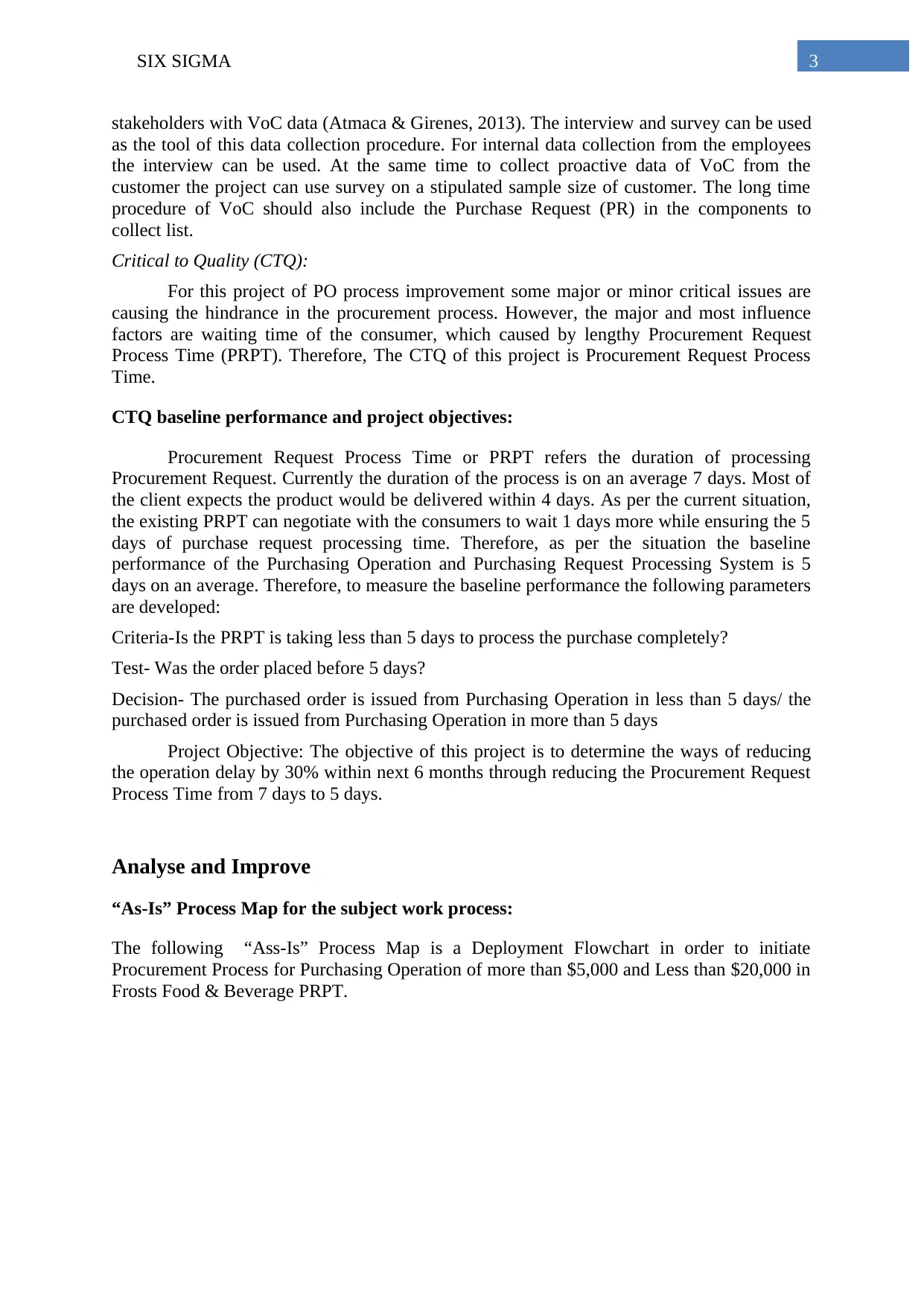
3SIX SIGMA
stakeholders with VoC data (Atmaca & Girenes, 2013). The interview and survey can be used
as the tool of this data collection procedure. For internal data collection from the employees
the interview can be used. At the same time to collect proactive data of VoC from the
customer the project can use survey on a stipulated sample size of customer. The long time
procedure of VoC should also include the Purchase Request (PR) in the components to
collect list.
Critical to Quality (CTQ):
For this project of PO process improvement some major or minor critical issues are
causing the hindrance in the procurement process. However, the major and most influence
factors are waiting time of the consumer, which caused by lengthy Procurement Request
Process Time (PRPT). Therefore, The CTQ of this project is Procurement Request Process
Time.
CTQ baseline performance and project objectives:
Procurement Request Process Time or PRPT refers the duration of processing
Procurement Request. Currently the duration of the process is on an average 7 days. Most of
the client expects the product would be delivered within 4 days. As per the current situation,
the existing PRPT can negotiate with the consumers to wait 1 days more while ensuring the 5
days of purchase request processing time. Therefore, as per the situation the baseline
performance of the Purchasing Operation and Purchasing Request Processing System is 5
days on an average. Therefore, to measure the baseline performance the following parameters
are developed:
Criteria-Is the PRPT is taking less than 5 days to process the purchase completely?
Test- Was the order placed before 5 days?
Decision- The purchased order is issued from Purchasing Operation in less than 5 days/ the
purchased order is issued from Purchasing Operation in more than 5 days
Project Objective: The objective of this project is to determine the ways of reducing
the operation delay by 30% within next 6 months through reducing the Procurement Request
Process Time from 7 days to 5 days.
Analyse and Improve
“As-Is” Process Map for the subject work process:
The following “Ass-Is” Process Map is a Deployment Flowchart in order to initiate
Procurement Process for Purchasing Operation of more than $5,000 and Less than $20,000 in
Frosts Food & Beverage PRPT.
stakeholders with VoC data (Atmaca & Girenes, 2013). The interview and survey can be used
as the tool of this data collection procedure. For internal data collection from the employees
the interview can be used. At the same time to collect proactive data of VoC from the
customer the project can use survey on a stipulated sample size of customer. The long time
procedure of VoC should also include the Purchase Request (PR) in the components to
collect list.
Critical to Quality (CTQ):
For this project of PO process improvement some major or minor critical issues are
causing the hindrance in the procurement process. However, the major and most influence
factors are waiting time of the consumer, which caused by lengthy Procurement Request
Process Time (PRPT). Therefore, The CTQ of this project is Procurement Request Process
Time.
CTQ baseline performance and project objectives:
Procurement Request Process Time or PRPT refers the duration of processing
Procurement Request. Currently the duration of the process is on an average 7 days. Most of
the client expects the product would be delivered within 4 days. As per the current situation,
the existing PRPT can negotiate with the consumers to wait 1 days more while ensuring the 5
days of purchase request processing time. Therefore, as per the situation the baseline
performance of the Purchasing Operation and Purchasing Request Processing System is 5
days on an average. Therefore, to measure the baseline performance the following parameters
are developed:
Criteria-Is the PRPT is taking less than 5 days to process the purchase completely?
Test- Was the order placed before 5 days?
Decision- The purchased order is issued from Purchasing Operation in less than 5 days/ the
purchased order is issued from Purchasing Operation in more than 5 days
Project Objective: The objective of this project is to determine the ways of reducing
the operation delay by 30% within next 6 months through reducing the Procurement Request
Process Time from 7 days to 5 days.
Analyse and Improve
“As-Is” Process Map for the subject work process:
The following “Ass-Is” Process Map is a Deployment Flowchart in order to initiate
Procurement Process for Purchasing Operation of more than $5,000 and Less than $20,000 in
Frosts Food & Beverage PRPT.
Secure Best Marks with AI Grader
Need help grading? Try our AI Grader for instant feedback on your assignments.
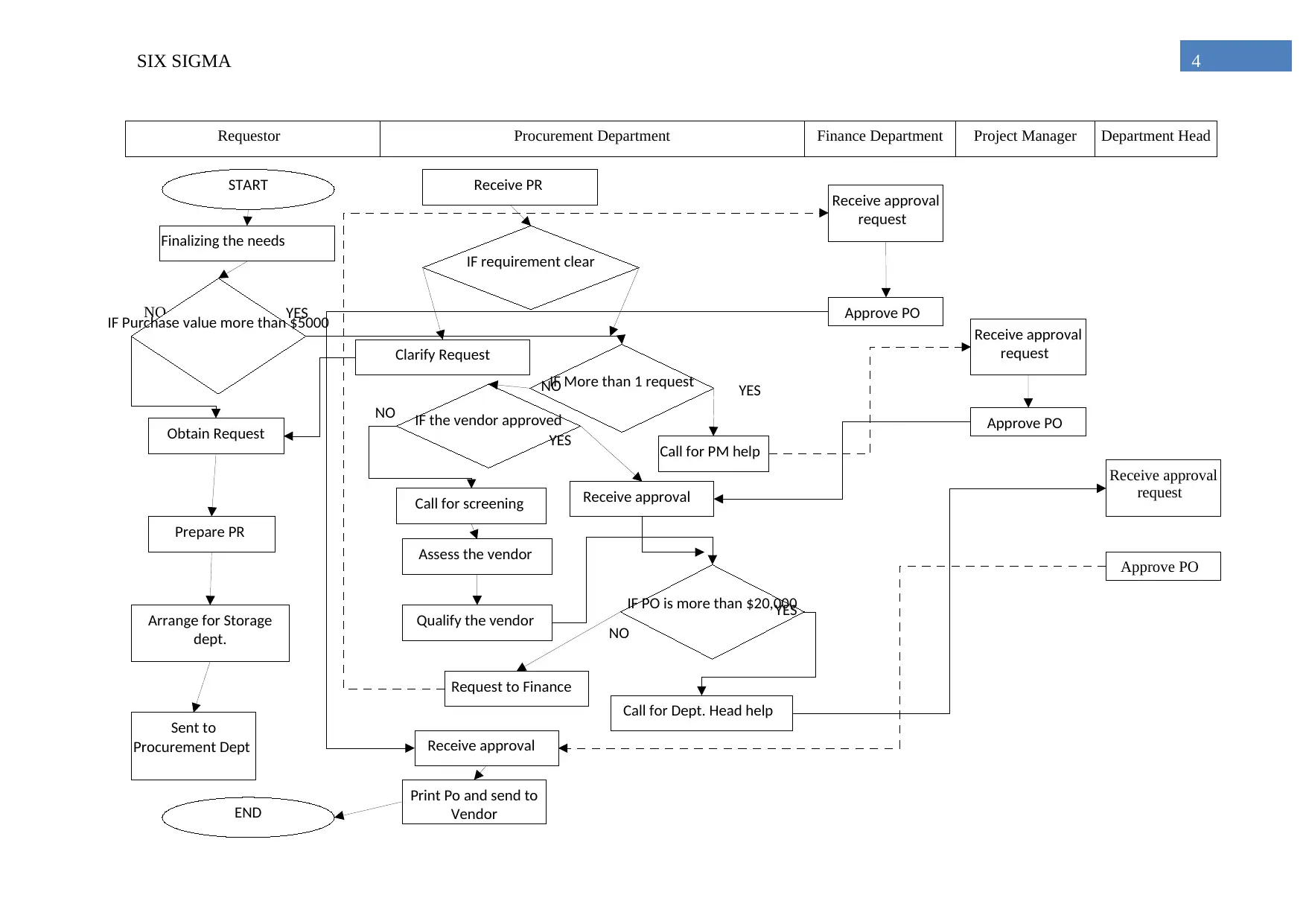
Receive approval
request
Approve PO
NO
START
IF Purchase value more than $5000
Finalizing the needs
Obtain Request
Prepare PR
Arrange for Storage
dept.
Sent to
Procurement Dept
Receive PR
IF requirement clear
Clarify Request
IF More than 1 request
IF the vendor approved
Call for screening
Assess the vendor
Qualify the vendor
IF PO is more than $20,000
Call for Dept. Head help
Request to Finance
Receive approval
Print Po and send to
VendorEND
Receive approval
request
Approve PO
Call for PM help
Receive approval
request
Approve PO
Receive approval
YESNO
YES
NO
YES
NO
YES
Requestor Procurement Department Finance Department Project Manager Department Head
4SIX SIGMA
request
Approve PO
NO
START
IF Purchase value more than $5000
Finalizing the needs
Obtain Request
Prepare PR
Arrange for Storage
dept.
Sent to
Procurement Dept
Receive PR
IF requirement clear
Clarify Request
IF More than 1 request
IF the vendor approved
Call for screening
Assess the vendor
Qualify the vendor
IF PO is more than $20,000
Call for Dept. Head help
Request to Finance
Receive approval
Print Po and send to
VendorEND
Receive approval
request
Approve PO
Call for PM help
Receive approval
request
Approve PO
Receive approval
YESNO
YES
NO
YES
NO
YES
Requestor Procurement Department Finance Department Project Manager Department Head
4SIX SIGMA
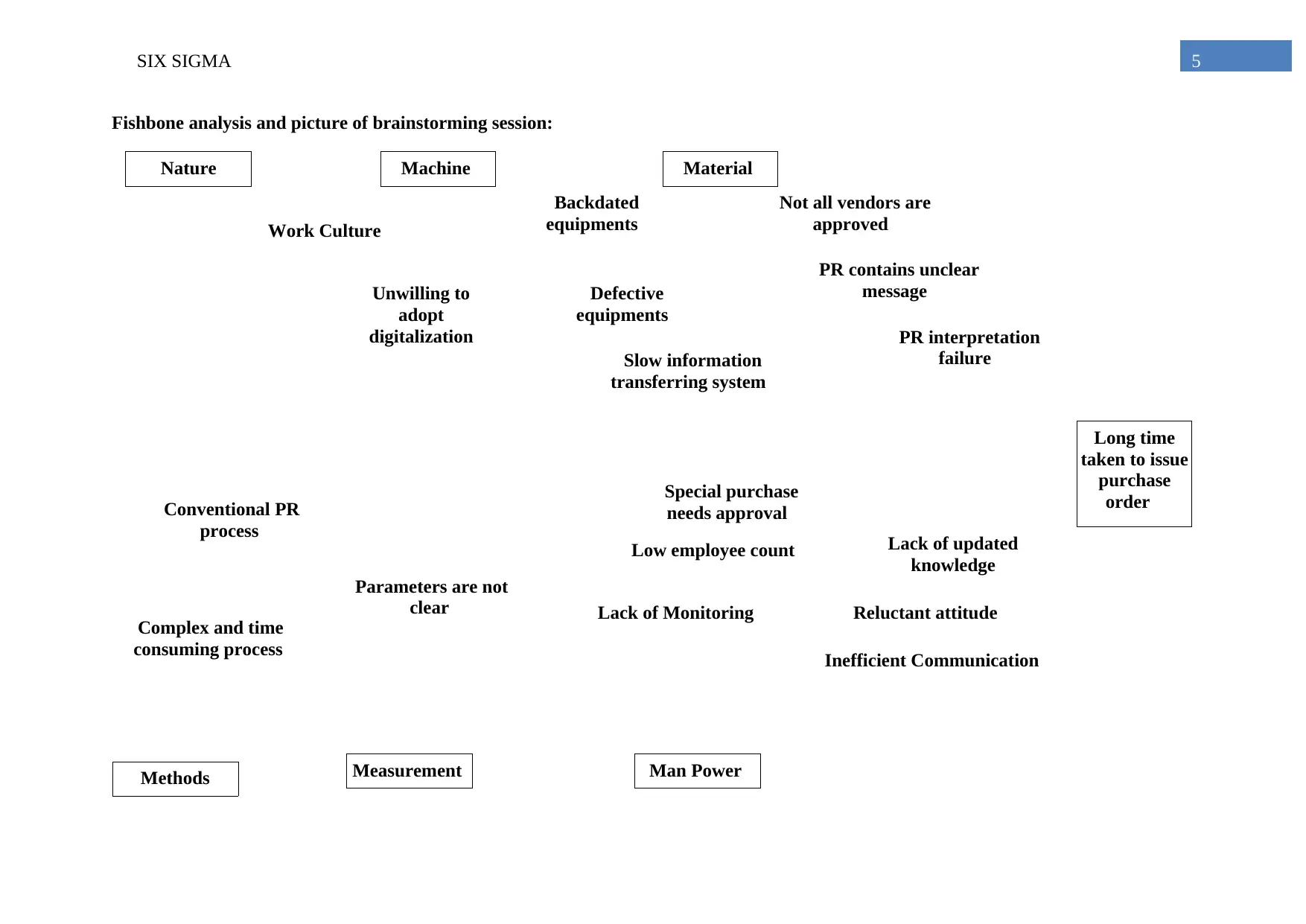
Long time
taken to issue
purchase
order
MaterialMachineNature
Measurement Man Power
Work Culture
Unwilling to
adopt
digitalization
Conventional PR
process
Complex and time
consuming process
Parameters are not
clear
Special purchase
needs approval
Low employee count
Lack of Monitoring
Lack of updated
knowledge
Reluctant attitude
Inefficient Communication
Backdated
equipments
Defective
equipments
Slow information
transferring system
Not all vendors are
approved
PR contains unclear
message
PR interpretation
failure
5SIX SIGMA
Fishbone analysis and picture of brainstorming session:
Methods
taken to issue
purchase
order
MaterialMachineNature
Measurement Man Power
Work Culture
Unwilling to
adopt
digitalization
Conventional PR
process
Complex and time
consuming process
Parameters are not
clear
Special purchase
needs approval
Low employee count
Lack of Monitoring
Lack of updated
knowledge
Reluctant attitude
Inefficient Communication
Backdated
equipments
Defective
equipments
Slow information
transferring system
Not all vendors are
approved
PR contains unclear
message
PR interpretation
failure
5SIX SIGMA
Fishbone analysis and picture of brainstorming session:
Methods
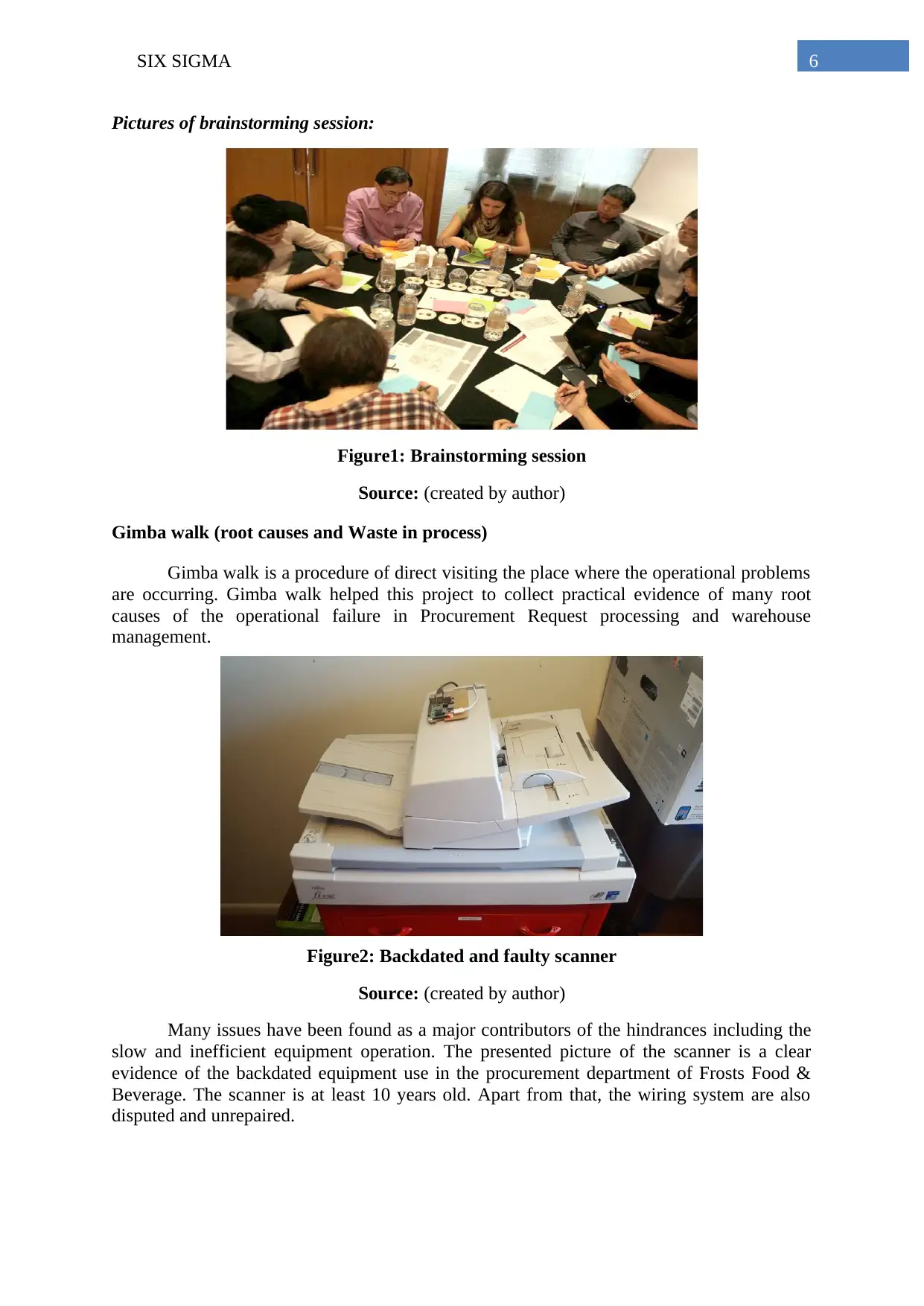
SIX SIGMA 6
Pictures of brainstorming session:
Figure1: Brainstorming session
Source: (created by author)
Gimba walk (root causes and Waste in process)
Gimba walk is a procedure of direct visiting the place where the operational problems
are occurring. Gimba walk helped this project to collect practical evidence of many root
causes of the operational failure in Procurement Request processing and warehouse
management.
Figure2: Backdated and faulty scanner
Source: (created by author)
Many issues have been found as a major contributors of the hindrances including the
slow and inefficient equipment operation. The presented picture of the scanner is a clear
evidence of the backdated equipment use in the procurement department of Frosts Food &
Beverage. The scanner is at least 10 years old. Apart from that, the wiring system are also
disputed and unrepaired.
Pictures of brainstorming session:
Figure1: Brainstorming session
Source: (created by author)
Gimba walk (root causes and Waste in process)
Gimba walk is a procedure of direct visiting the place where the operational problems
are occurring. Gimba walk helped this project to collect practical evidence of many root
causes of the operational failure in Procurement Request processing and warehouse
management.
Figure2: Backdated and faulty scanner
Source: (created by author)
Many issues have been found as a major contributors of the hindrances including the
slow and inefficient equipment operation. The presented picture of the scanner is a clear
evidence of the backdated equipment use in the procurement department of Frosts Food &
Beverage. The scanner is at least 10 years old. Apart from that, the wiring system are also
disputed and unrepaired.
Paraphrase This Document
Need a fresh take? Get an instant paraphrase of this document with our AI Paraphraser
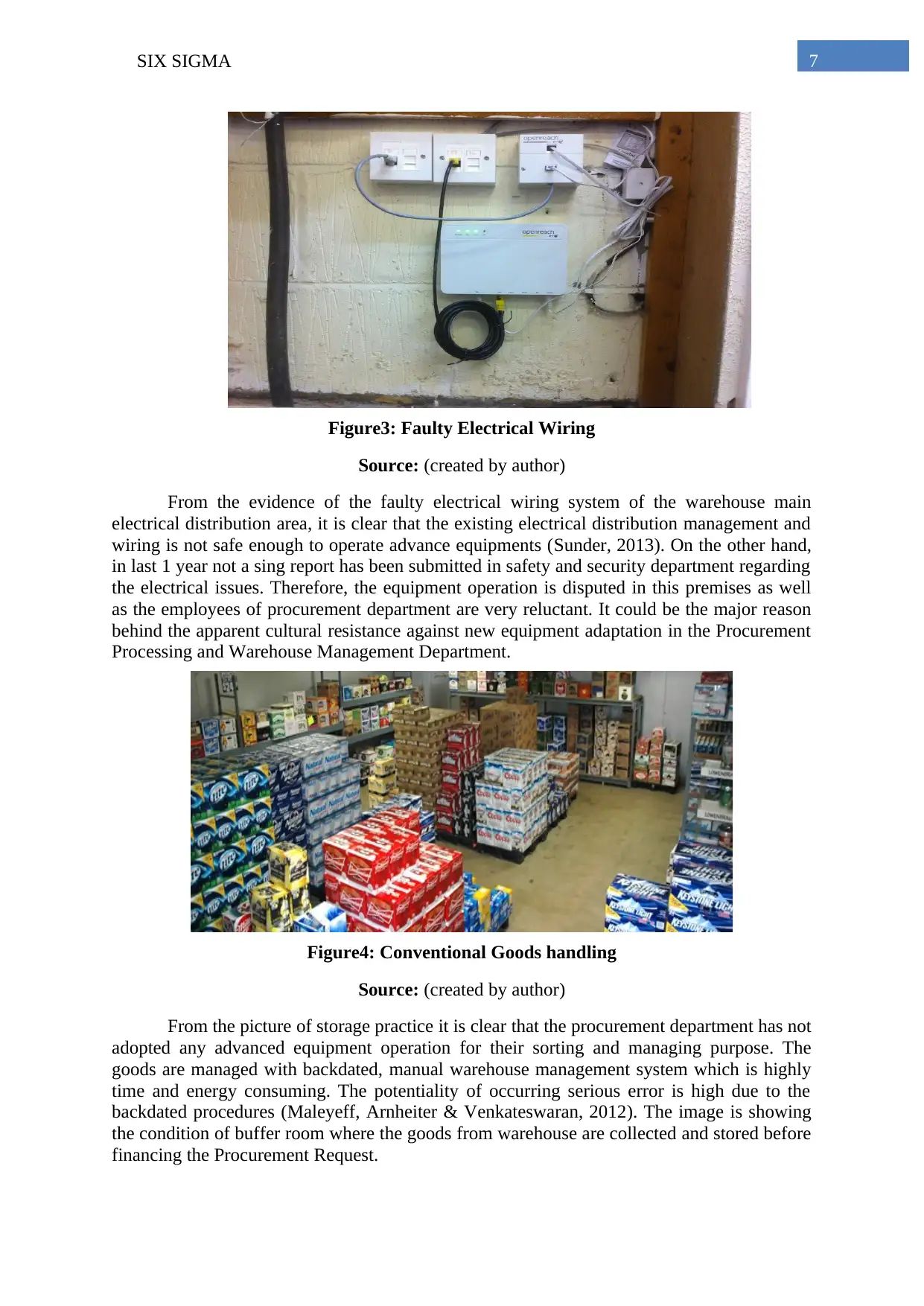
SIX SIGMA 7
Figure3: Faulty Electrical Wiring
Source: (created by author)
From the evidence of the faulty electrical wiring system of the warehouse main
electrical distribution area, it is clear that the existing electrical distribution management and
wiring is not safe enough to operate advance equipments (Sunder, 2013). On the other hand,
in last 1 year not a sing report has been submitted in safety and security department regarding
the electrical issues. Therefore, the equipment operation is disputed in this premises as well
as the employees of procurement department are very reluctant. It could be the major reason
behind the apparent cultural resistance against new equipment adaptation in the Procurement
Processing and Warehouse Management Department.
Figure4: Conventional Goods handling
Source: (created by author)
From the picture of storage practice it is clear that the procurement department has not
adopted any advanced equipment operation for their sorting and managing purpose. The
goods are managed with backdated, manual warehouse management system which is highly
time and energy consuming. The potentiality of occurring serious error is high due to the
backdated procedures (Maleyeff, Arnheiter & Venkateswaran, 2012). The image is showing
the condition of buffer room where the goods from warehouse are collected and stored before
financing the Procurement Request.
Figure3: Faulty Electrical Wiring
Source: (created by author)
From the evidence of the faulty electrical wiring system of the warehouse main
electrical distribution area, it is clear that the existing electrical distribution management and
wiring is not safe enough to operate advance equipments (Sunder, 2013). On the other hand,
in last 1 year not a sing report has been submitted in safety and security department regarding
the electrical issues. Therefore, the equipment operation is disputed in this premises as well
as the employees of procurement department are very reluctant. It could be the major reason
behind the apparent cultural resistance against new equipment adaptation in the Procurement
Processing and Warehouse Management Department.
Figure4: Conventional Goods handling
Source: (created by author)
From the picture of storage practice it is clear that the procurement department has not
adopted any advanced equipment operation for their sorting and managing purpose. The
goods are managed with backdated, manual warehouse management system which is highly
time and energy consuming. The potentiality of occurring serious error is high due to the
backdated procedures (Maleyeff, Arnheiter & Venkateswaran, 2012). The image is showing
the condition of buffer room where the goods from warehouse are collected and stored before
financing the Procurement Request.
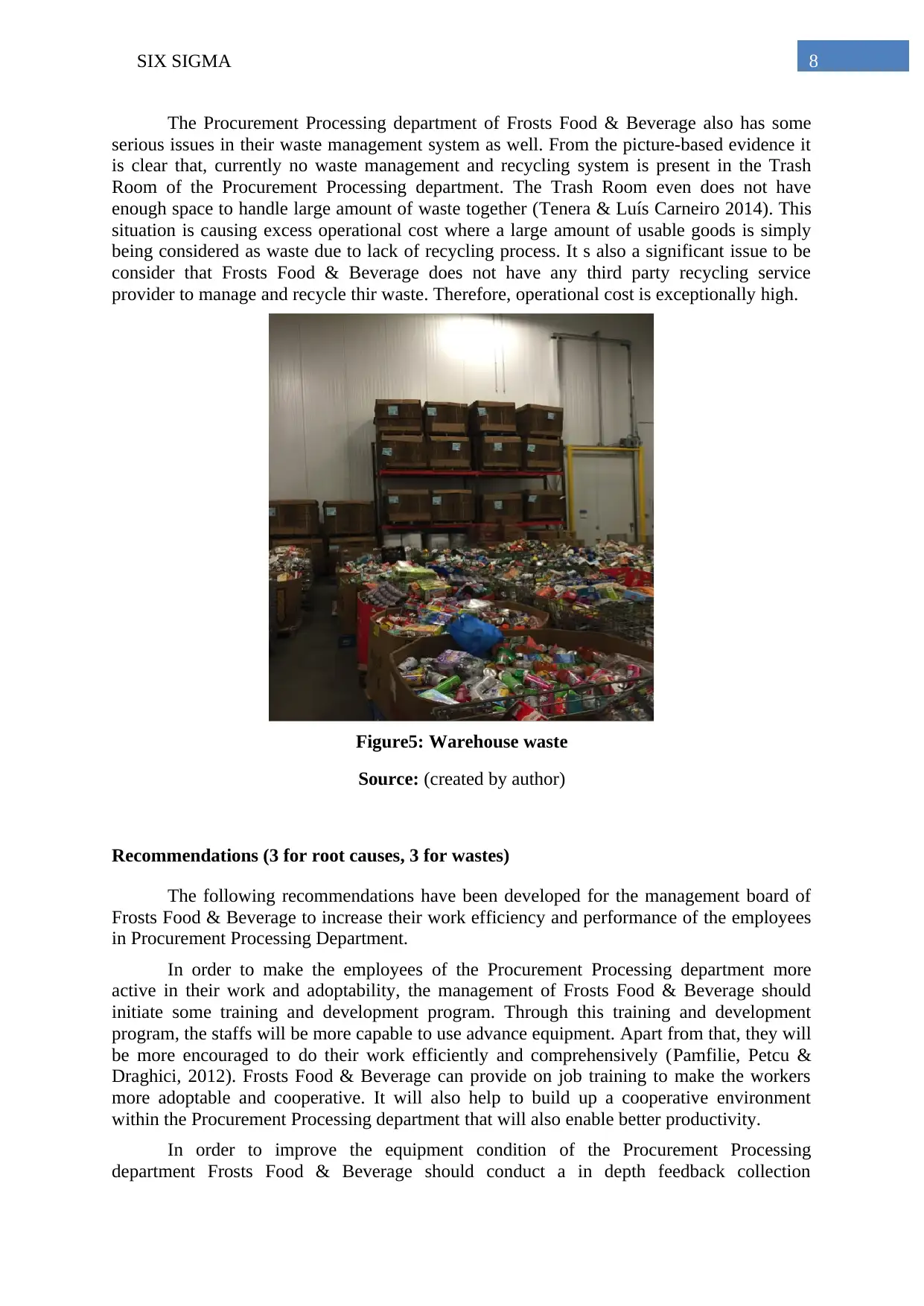
SIX SIGMA 8
The Procurement Processing department of Frosts Food & Beverage also has some
serious issues in their waste management system as well. From the picture-based evidence it
is clear that, currently no waste management and recycling system is present in the Trash
Room of the Procurement Processing department. The Trash Room even does not have
enough space to handle large amount of waste together (Tenera & Luís Carneiro 2014). This
situation is causing excess operational cost where a large amount of usable goods is simply
being considered as waste due to lack of recycling process. It s also a significant issue to be
consider that Frosts Food & Beverage does not have any third party recycling service
provider to manage and recycle thir waste. Therefore, operational cost is exceptionally high.
Figure5: Warehouse waste
Source: (created by author)
Recommendations (3 for root causes, 3 for wastes)
The following recommendations have been developed for the management board of
Frosts Food & Beverage to increase their work efficiency and performance of the employees
in Procurement Processing Department.
In order to make the employees of the Procurement Processing department more
active in their work and adoptability, the management of Frosts Food & Beverage should
initiate some training and development program. Through this training and development
program, the staffs will be more capable to use advance equipment. Apart from that, they will
be more encouraged to do their work efficiently and comprehensively (Pamfilie, Petcu &
Draghici, 2012). Frosts Food & Beverage can provide on job training to make the workers
more adoptable and cooperative. It will also help to build up a cooperative environment
within the Procurement Processing department that will also enable better productivity.
In order to improve the equipment condition of the Procurement Processing
department Frosts Food & Beverage should conduct a in depth feedback collection
The Procurement Processing department of Frosts Food & Beverage also has some
serious issues in their waste management system as well. From the picture-based evidence it
is clear that, currently no waste management and recycling system is present in the Trash
Room of the Procurement Processing department. The Trash Room even does not have
enough space to handle large amount of waste together (Tenera & Luís Carneiro 2014). This
situation is causing excess operational cost where a large amount of usable goods is simply
being considered as waste due to lack of recycling process. It s also a significant issue to be
consider that Frosts Food & Beverage does not have any third party recycling service
provider to manage and recycle thir waste. Therefore, operational cost is exceptionally high.
Figure5: Warehouse waste
Source: (created by author)
Recommendations (3 for root causes, 3 for wastes)
The following recommendations have been developed for the management board of
Frosts Food & Beverage to increase their work efficiency and performance of the employees
in Procurement Processing Department.
In order to make the employees of the Procurement Processing department more
active in their work and adoptability, the management of Frosts Food & Beverage should
initiate some training and development program. Through this training and development
program, the staffs will be more capable to use advance equipment. Apart from that, they will
be more encouraged to do their work efficiently and comprehensively (Pamfilie, Petcu &
Draghici, 2012). Frosts Food & Beverage can provide on job training to make the workers
more adoptable and cooperative. It will also help to build up a cooperative environment
within the Procurement Processing department that will also enable better productivity.
In order to improve the equipment condition of the Procurement Processing
department Frosts Food & Beverage should conduct a in depth feedback collection
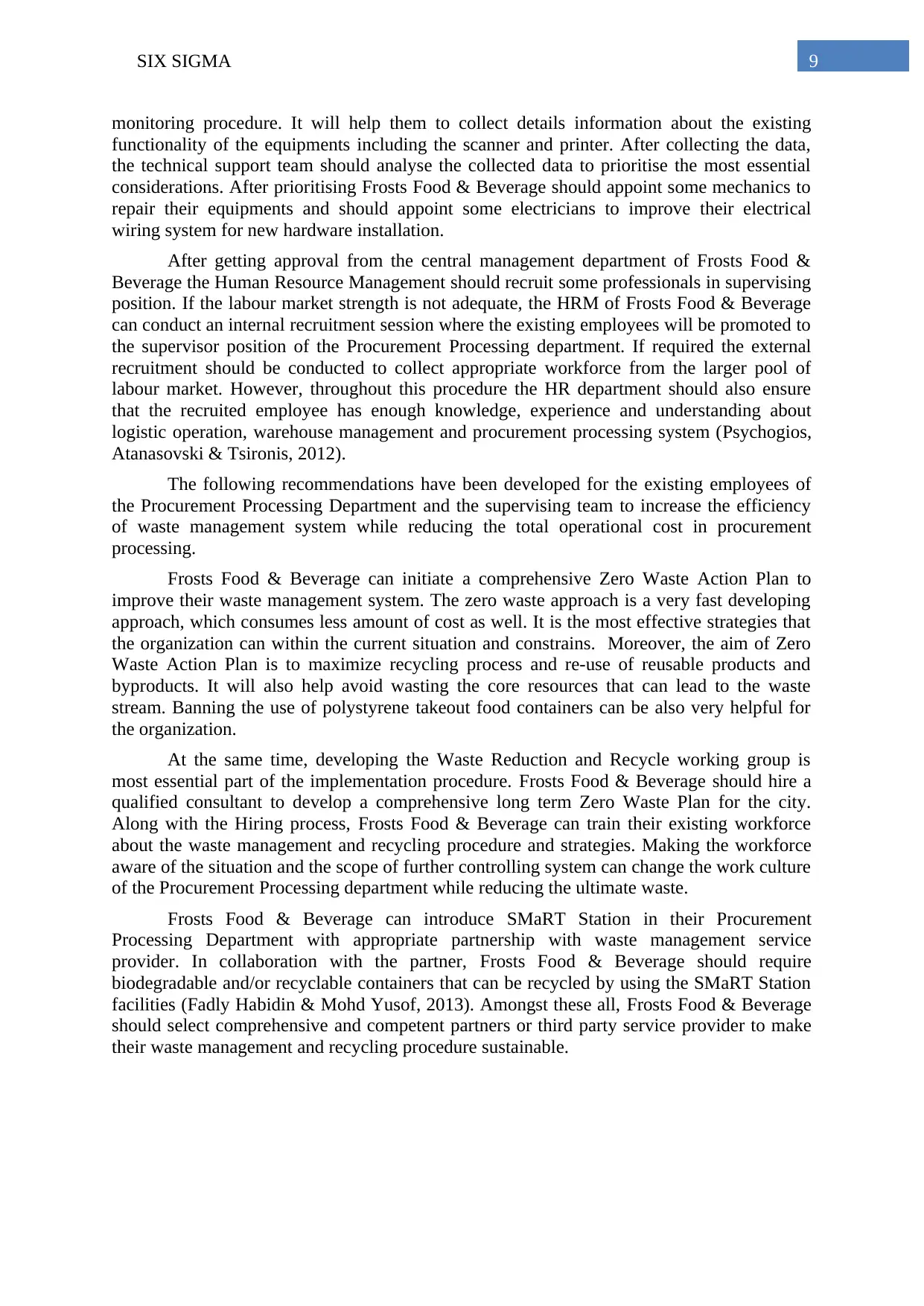
SIX SIGMA 9
monitoring procedure. It will help them to collect details information about the existing
functionality of the equipments including the scanner and printer. After collecting the data,
the technical support team should analyse the collected data to prioritise the most essential
considerations. After prioritising Frosts Food & Beverage should appoint some mechanics to
repair their equipments and should appoint some electricians to improve their electrical
wiring system for new hardware installation.
After getting approval from the central management department of Frosts Food &
Beverage the Human Resource Management should recruit some professionals in supervising
position. If the labour market strength is not adequate, the HRM of Frosts Food & Beverage
can conduct an internal recruitment session where the existing employees will be promoted to
the supervisor position of the Procurement Processing department. If required the external
recruitment should be conducted to collect appropriate workforce from the larger pool of
labour market. However, throughout this procedure the HR department should also ensure
that the recruited employee has enough knowledge, experience and understanding about
logistic operation, warehouse management and procurement processing system (Psychogios,
Atanasovski & Tsironis, 2012).
The following recommendations have been developed for the existing employees of
the Procurement Processing Department and the supervising team to increase the efficiency
of waste management system while reducing the total operational cost in procurement
processing.
Frosts Food & Beverage can initiate a comprehensive Zero Waste Action Plan to
improve their waste management system. The zero waste approach is a very fast developing
approach, which consumes less amount of cost as well. It is the most effective strategies that
the organization can within the current situation and constrains. Moreover, the aim of Zero
Waste Action Plan is to maximize recycling process and re-use of reusable products and
byproducts. It will also help avoid wasting the core resources that can lead to the waste
stream. Banning the use of polystyrene takeout food containers can be also very helpful for
the organization.
At the same time, developing the Waste Reduction and Recycle working group is
most essential part of the implementation procedure. Frosts Food & Beverage should hire a
qualified consultant to develop a comprehensive long term Zero Waste Plan for the city.
Along with the Hiring process, Frosts Food & Beverage can train their existing workforce
about the waste management and recycling procedure and strategies. Making the workforce
aware of the situation and the scope of further controlling system can change the work culture
of the Procurement Processing department while reducing the ultimate waste.
Frosts Food & Beverage can introduce SMaRT Station in their Procurement
Processing Department with appropriate partnership with waste management service
provider. In collaboration with the partner, Frosts Food & Beverage should require
biodegradable and/or recyclable containers that can be recycled by using the SMaRT Station
facilities (Fadly Habidin & Mohd Yusof, 2013). Amongst these all, Frosts Food & Beverage
should select comprehensive and competent partners or third party service provider to make
their waste management and recycling procedure sustainable.
monitoring procedure. It will help them to collect details information about the existing
functionality of the equipments including the scanner and printer. After collecting the data,
the technical support team should analyse the collected data to prioritise the most essential
considerations. After prioritising Frosts Food & Beverage should appoint some mechanics to
repair their equipments and should appoint some electricians to improve their electrical
wiring system for new hardware installation.
After getting approval from the central management department of Frosts Food &
Beverage the Human Resource Management should recruit some professionals in supervising
position. If the labour market strength is not adequate, the HRM of Frosts Food & Beverage
can conduct an internal recruitment session where the existing employees will be promoted to
the supervisor position of the Procurement Processing department. If required the external
recruitment should be conducted to collect appropriate workforce from the larger pool of
labour market. However, throughout this procedure the HR department should also ensure
that the recruited employee has enough knowledge, experience and understanding about
logistic operation, warehouse management and procurement processing system (Psychogios,
Atanasovski & Tsironis, 2012).
The following recommendations have been developed for the existing employees of
the Procurement Processing Department and the supervising team to increase the efficiency
of waste management system while reducing the total operational cost in procurement
processing.
Frosts Food & Beverage can initiate a comprehensive Zero Waste Action Plan to
improve their waste management system. The zero waste approach is a very fast developing
approach, which consumes less amount of cost as well. It is the most effective strategies that
the organization can within the current situation and constrains. Moreover, the aim of Zero
Waste Action Plan is to maximize recycling process and re-use of reusable products and
byproducts. It will also help avoid wasting the core resources that can lead to the waste
stream. Banning the use of polystyrene takeout food containers can be also very helpful for
the organization.
At the same time, developing the Waste Reduction and Recycle working group is
most essential part of the implementation procedure. Frosts Food & Beverage should hire a
qualified consultant to develop a comprehensive long term Zero Waste Plan for the city.
Along with the Hiring process, Frosts Food & Beverage can train their existing workforce
about the waste management and recycling procedure and strategies. Making the workforce
aware of the situation and the scope of further controlling system can change the work culture
of the Procurement Processing department while reducing the ultimate waste.
Frosts Food & Beverage can introduce SMaRT Station in their Procurement
Processing Department with appropriate partnership with waste management service
provider. In collaboration with the partner, Frosts Food & Beverage should require
biodegradable and/or recyclable containers that can be recycled by using the SMaRT Station
facilities (Fadly Habidin & Mohd Yusof, 2013). Amongst these all, Frosts Food & Beverage
should select comprehensive and competent partners or third party service provider to make
their waste management and recycling procedure sustainable.
Secure Best Marks with AI Grader
Need help grading? Try our AI Grader for instant feedback on your assignments.
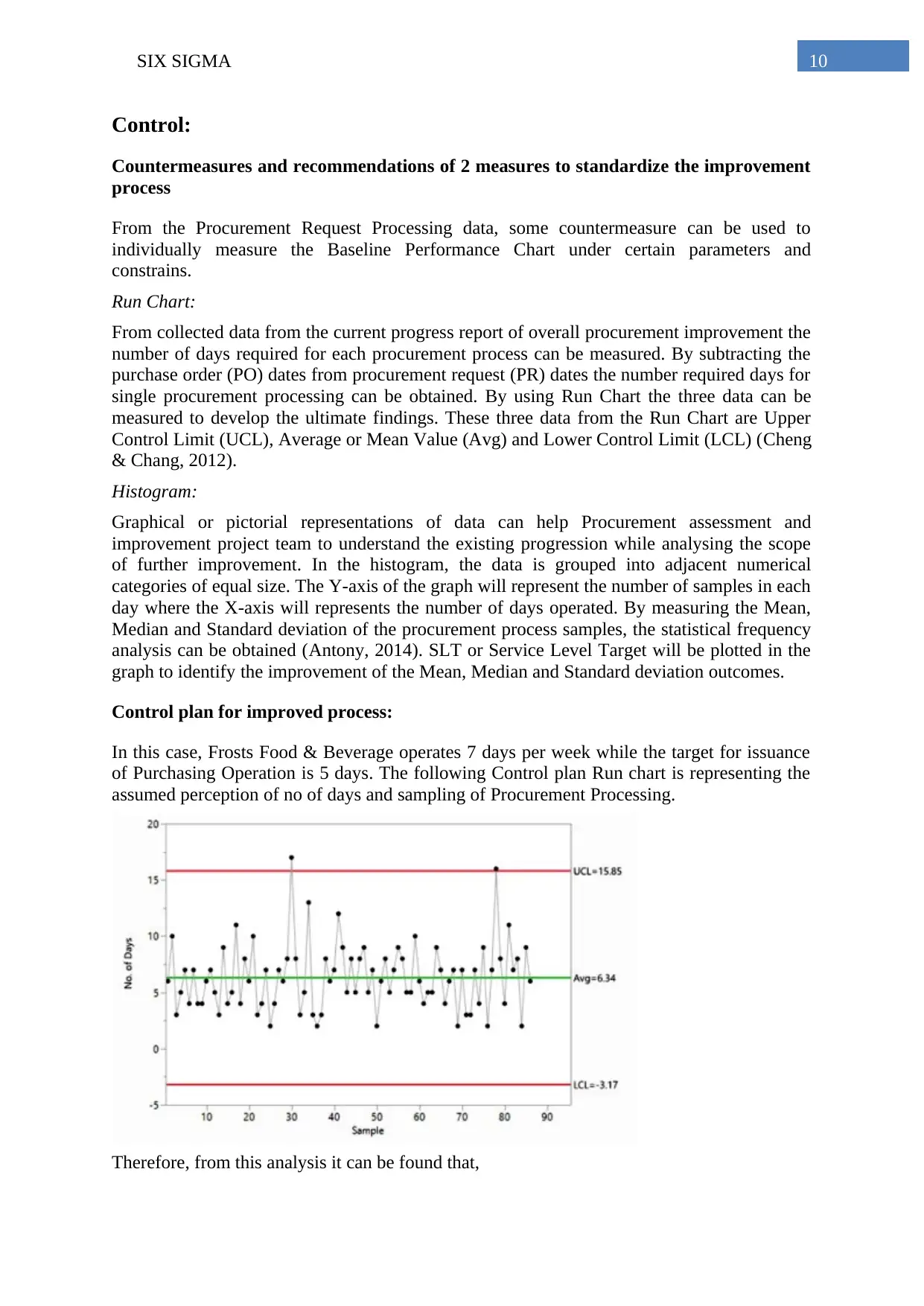
SIX SIGMA 10
Control:
Countermeasures and recommendations of 2 measures to standardize the improvement
process
From the Procurement Request Processing data, some countermeasure can be used to
individually measure the Baseline Performance Chart under certain parameters and
constrains.
Run Chart:
From collected data from the current progress report of overall procurement improvement the
number of days required for each procurement process can be measured. By subtracting the
purchase order (PO) dates from procurement request (PR) dates the number required days for
single procurement processing can be obtained. By using Run Chart the three data can be
measured to develop the ultimate findings. These three data from the Run Chart are Upper
Control Limit (UCL), Average or Mean Value (Avg) and Lower Control Limit (LCL) (Cheng
& Chang, 2012).
Histogram:
Graphical or pictorial representations of data can help Procurement assessment and
improvement project team to understand the existing progression while analysing the scope
of further improvement. In the histogram, the data is grouped into adjacent numerical
categories of equal size. The Y-axis of the graph will represent the number of samples in each
day where the X-axis will represents the number of days operated. By measuring the Mean,
Median and Standard deviation of the procurement process samples, the statistical frequency
analysis can be obtained (Antony, 2014). SLT or Service Level Target will be plotted in the
graph to identify the improvement of the Mean, Median and Standard deviation outcomes.
Control plan for improved process:
In this case, Frosts Food & Beverage operates 7 days per week while the target for issuance
of Purchasing Operation is 5 days. The following Control plan Run chart is representing the
assumed perception of no of days and sampling of Procurement Processing.
Therefore, from this analysis it can be found that,
Control:
Countermeasures and recommendations of 2 measures to standardize the improvement
process
From the Procurement Request Processing data, some countermeasure can be used to
individually measure the Baseline Performance Chart under certain parameters and
constrains.
Run Chart:
From collected data from the current progress report of overall procurement improvement the
number of days required for each procurement process can be measured. By subtracting the
purchase order (PO) dates from procurement request (PR) dates the number required days for
single procurement processing can be obtained. By using Run Chart the three data can be
measured to develop the ultimate findings. These three data from the Run Chart are Upper
Control Limit (UCL), Average or Mean Value (Avg) and Lower Control Limit (LCL) (Cheng
& Chang, 2012).
Histogram:
Graphical or pictorial representations of data can help Procurement assessment and
improvement project team to understand the existing progression while analysing the scope
of further improvement. In the histogram, the data is grouped into adjacent numerical
categories of equal size. The Y-axis of the graph will represent the number of samples in each
day where the X-axis will represents the number of days operated. By measuring the Mean,
Median and Standard deviation of the procurement process samples, the statistical frequency
analysis can be obtained (Antony, 2014). SLT or Service Level Target will be plotted in the
graph to identify the improvement of the Mean, Median and Standard deviation outcomes.
Control plan for improved process:
In this case, Frosts Food & Beverage operates 7 days per week while the target for issuance
of Purchasing Operation is 5 days. The following Control plan Run chart is representing the
assumed perception of no of days and sampling of Procurement Processing.
Therefore, from this analysis it can be found that,
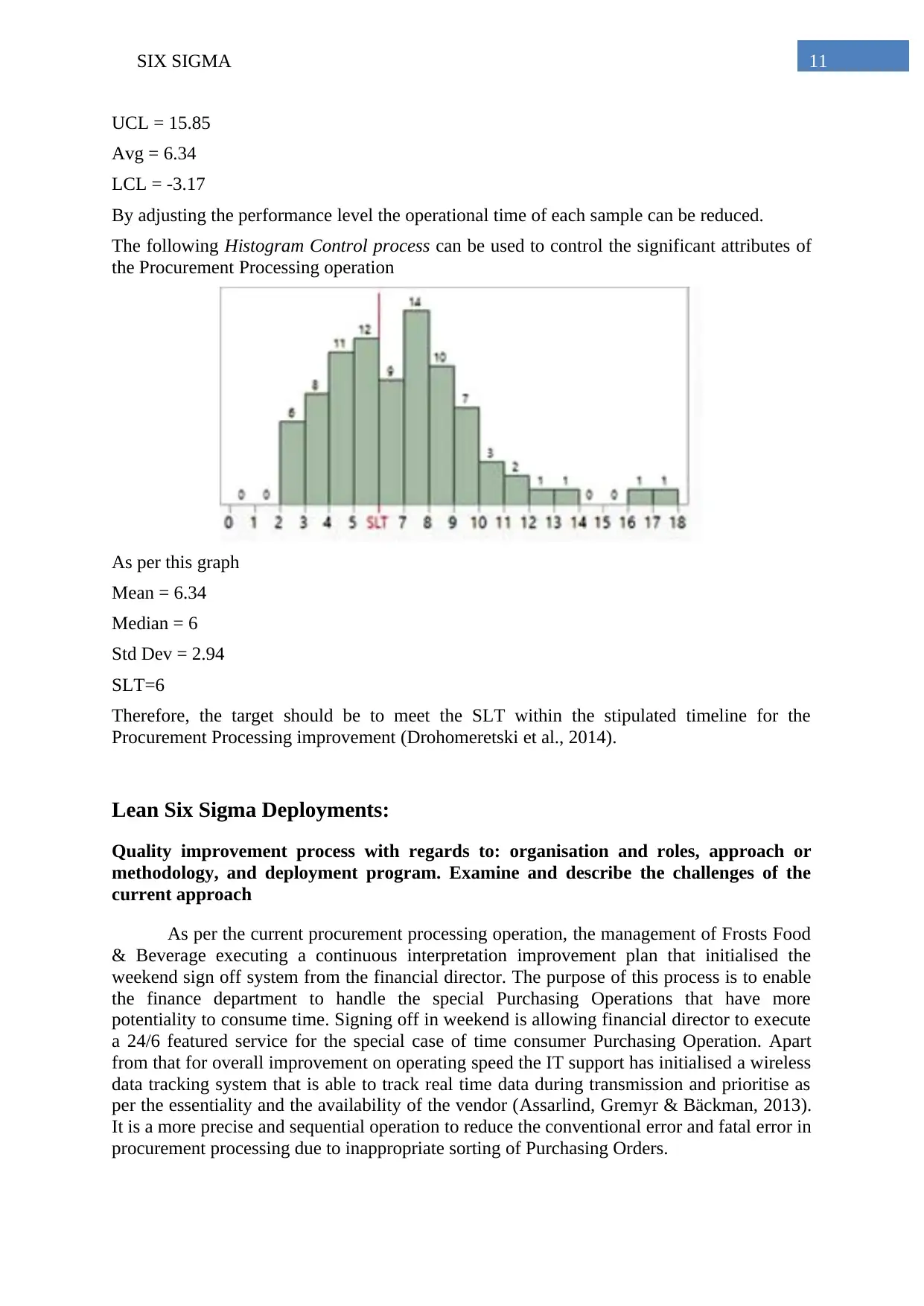
SIX SIGMA 11
UCL = 15.85
Avg = 6.34
LCL = -3.17
By adjusting the performance level the operational time of each sample can be reduced.
The following Histogram Control process can be used to control the significant attributes of
the Procurement Processing operation
As per this graph
Mean = 6.34
Median = 6
Std Dev = 2.94
SLT=6
Therefore, the target should be to meet the SLT within the stipulated timeline for the
Procurement Processing improvement (Drohomeretski et al., 2014).
Lean Six Sigma Deployments:
Quality improvement process with regards to: organisation and roles, approach or
methodology, and deployment program. Examine and describe the challenges of the
current approach
As per the current procurement processing operation, the management of Frosts Food
& Beverage executing a continuous interpretation improvement plan that initialised the
weekend sign off system from the financial director. The purpose of this process is to enable
the finance department to handle the special Purchasing Operations that have more
potentiality to consume time. Signing off in weekend is allowing financial director to execute
a 24/6 featured service for the special case of time consumer Purchasing Operation. Apart
from that for overall improvement on operating speed the IT support has initialised a wireless
data tracking system that is able to track real time data during transmission and prioritise as
per the essentiality and the availability of the vendor (Assarlind, Gremyr & Bäckman, 2013).
It is a more precise and sequential operation to reduce the conventional error and fatal error in
procurement processing due to inappropriate sorting of Purchasing Orders.
UCL = 15.85
Avg = 6.34
LCL = -3.17
By adjusting the performance level the operational time of each sample can be reduced.
The following Histogram Control process can be used to control the significant attributes of
the Procurement Processing operation
As per this graph
Mean = 6.34
Median = 6
Std Dev = 2.94
SLT=6
Therefore, the target should be to meet the SLT within the stipulated timeline for the
Procurement Processing improvement (Drohomeretski et al., 2014).
Lean Six Sigma Deployments:
Quality improvement process with regards to: organisation and roles, approach or
methodology, and deployment program. Examine and describe the challenges of the
current approach
As per the current procurement processing operation, the management of Frosts Food
& Beverage executing a continuous interpretation improvement plan that initialised the
weekend sign off system from the financial director. The purpose of this process is to enable
the finance department to handle the special Purchasing Operations that have more
potentiality to consume time. Signing off in weekend is allowing financial director to execute
a 24/6 featured service for the special case of time consumer Purchasing Operation. Apart
from that for overall improvement on operating speed the IT support has initialised a wireless
data tracking system that is able to track real time data during transmission and prioritise as
per the essentiality and the availability of the vendor (Assarlind, Gremyr & Bäckman, 2013).
It is a more precise and sequential operation to reduce the conventional error and fatal error in
procurement processing due to inappropriate sorting of Purchasing Orders.
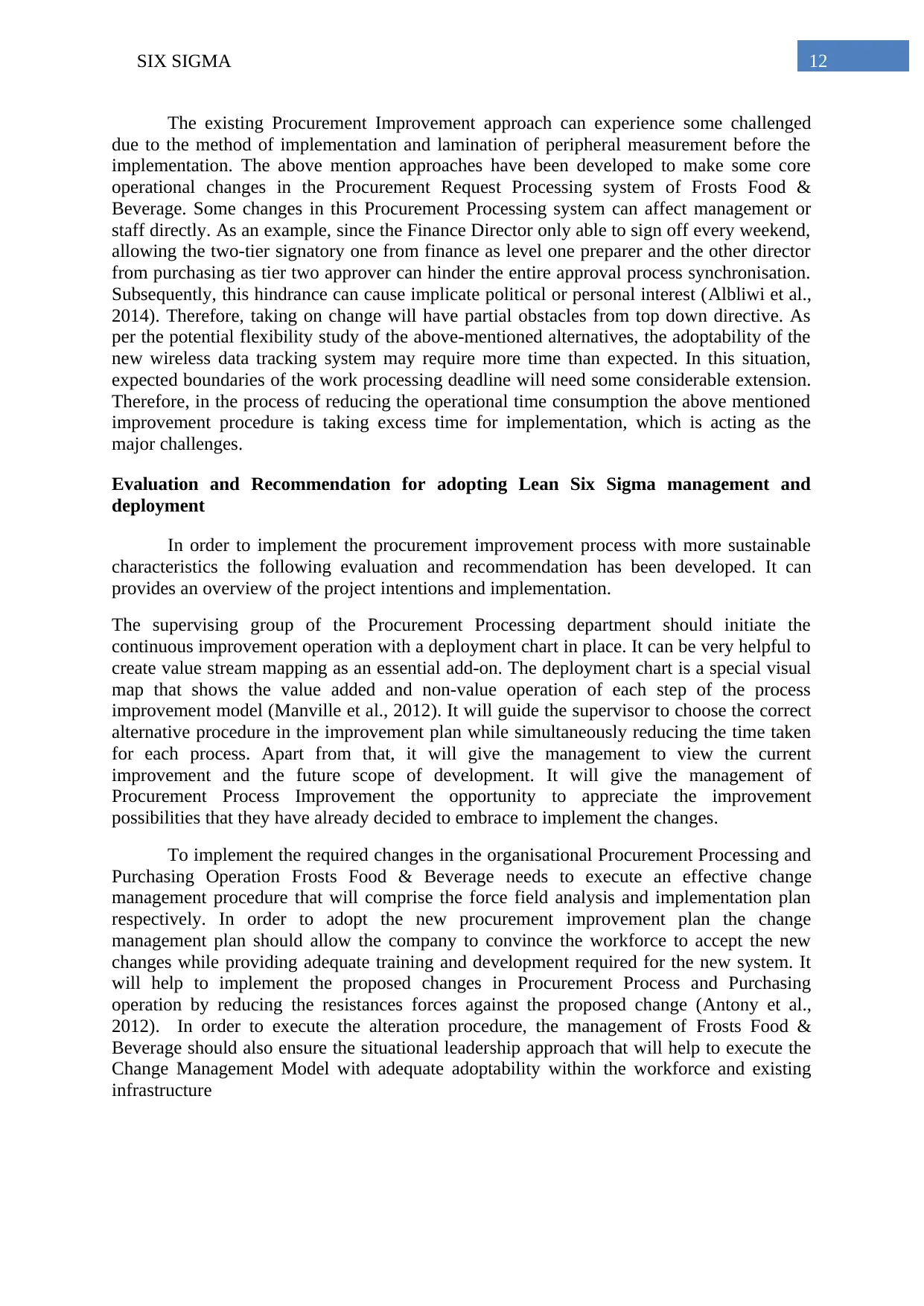
SIX SIGMA 12
The existing Procurement Improvement approach can experience some challenged
due to the method of implementation and lamination of peripheral measurement before the
implementation. The above mention approaches have been developed to make some core
operational changes in the Procurement Request Processing system of Frosts Food &
Beverage. Some changes in this Procurement Processing system can affect management or
staff directly. As an example, since the Finance Director only able to sign off every weekend,
allowing the two-tier signatory one from finance as level one preparer and the other director
from purchasing as tier two approver can hinder the entire approval process synchronisation.
Subsequently, this hindrance can cause implicate political or personal interest (Albliwi et al.,
2014). Therefore, taking on change will have partial obstacles from top down directive. As
per the potential flexibility study of the above-mentioned alternatives, the adoptability of the
new wireless data tracking system may require more time than expected. In this situation,
expected boundaries of the work processing deadline will need some considerable extension.
Therefore, in the process of reducing the operational time consumption the above mentioned
improvement procedure is taking excess time for implementation, which is acting as the
major challenges.
Evaluation and Recommendation for adopting Lean Six Sigma management and
deployment
In order to implement the procurement improvement process with more sustainable
characteristics the following evaluation and recommendation has been developed. It can
provides an overview of the project intentions and implementation.
The supervising group of the Procurement Processing department should initiate the
continuous improvement operation with a deployment chart in place. It can be very helpful to
create value stream mapping as an essential add-on. The deployment chart is a special visual
map that shows the value added and non-value operation of each step of the process
improvement model (Manville et al., 2012). It will guide the supervisor to choose the correct
alternative procedure in the improvement plan while simultaneously reducing the time taken
for each process. Apart from that, it will give the management to view the current
improvement and the future scope of development. It will give the management of
Procurement Process Improvement the opportunity to appreciate the improvement
possibilities that they have already decided to embrace to implement the changes.
To implement the required changes in the organisational Procurement Processing and
Purchasing Operation Frosts Food & Beverage needs to execute an effective change
management procedure that will comprise the force field analysis and implementation plan
respectively. In order to adopt the new procurement improvement plan the change
management plan should allow the company to convince the workforce to accept the new
changes while providing adequate training and development required for the new system. It
will help to implement the proposed changes in Procurement Process and Purchasing
operation by reducing the resistances forces against the proposed change (Antony et al.,
2012). In order to execute the alteration procedure, the management of Frosts Food &
Beverage should also ensure the situational leadership approach that will help to execute the
Change Management Model with adequate adoptability within the workforce and existing
infrastructure
The existing Procurement Improvement approach can experience some challenged
due to the method of implementation and lamination of peripheral measurement before the
implementation. The above mention approaches have been developed to make some core
operational changes in the Procurement Request Processing system of Frosts Food &
Beverage. Some changes in this Procurement Processing system can affect management or
staff directly. As an example, since the Finance Director only able to sign off every weekend,
allowing the two-tier signatory one from finance as level one preparer and the other director
from purchasing as tier two approver can hinder the entire approval process synchronisation.
Subsequently, this hindrance can cause implicate political or personal interest (Albliwi et al.,
2014). Therefore, taking on change will have partial obstacles from top down directive. As
per the potential flexibility study of the above-mentioned alternatives, the adoptability of the
new wireless data tracking system may require more time than expected. In this situation,
expected boundaries of the work processing deadline will need some considerable extension.
Therefore, in the process of reducing the operational time consumption the above mentioned
improvement procedure is taking excess time for implementation, which is acting as the
major challenges.
Evaluation and Recommendation for adopting Lean Six Sigma management and
deployment
In order to implement the procurement improvement process with more sustainable
characteristics the following evaluation and recommendation has been developed. It can
provides an overview of the project intentions and implementation.
The supervising group of the Procurement Processing department should initiate the
continuous improvement operation with a deployment chart in place. It can be very helpful to
create value stream mapping as an essential add-on. The deployment chart is a special visual
map that shows the value added and non-value operation of each step of the process
improvement model (Manville et al., 2012). It will guide the supervisor to choose the correct
alternative procedure in the improvement plan while simultaneously reducing the time taken
for each process. Apart from that, it will give the management to view the current
improvement and the future scope of development. It will give the management of
Procurement Process Improvement the opportunity to appreciate the improvement
possibilities that they have already decided to embrace to implement the changes.
To implement the required changes in the organisational Procurement Processing and
Purchasing Operation Frosts Food & Beverage needs to execute an effective change
management procedure that will comprise the force field analysis and implementation plan
respectively. In order to adopt the new procurement improvement plan the change
management plan should allow the company to convince the workforce to accept the new
changes while providing adequate training and development required for the new system. It
will help to implement the proposed changes in Procurement Process and Purchasing
operation by reducing the resistances forces against the proposed change (Antony et al.,
2012). In order to execute the alteration procedure, the management of Frosts Food &
Beverage should also ensure the situational leadership approach that will help to execute the
Change Management Model with adequate adoptability within the workforce and existing
infrastructure
Paraphrase This Document
Need a fresh take? Get an instant paraphrase of this document with our AI Paraphraser
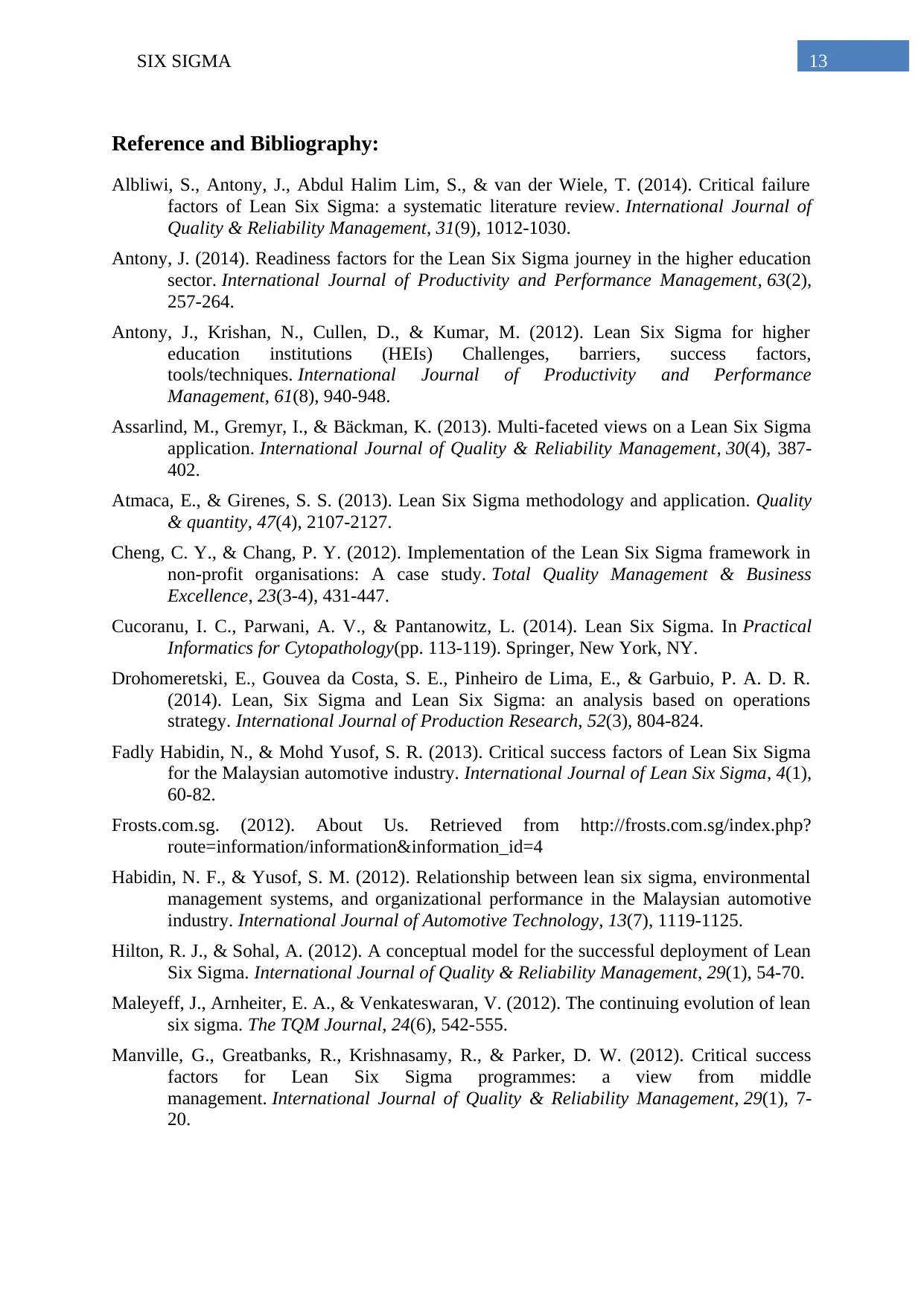
SIX SIGMA 13
Reference and Bibliography:
Albliwi, S., Antony, J., Abdul Halim Lim, S., & van der Wiele, T. (2014). Critical failure
factors of Lean Six Sigma: a systematic literature review. International Journal of
Quality & Reliability Management, 31(9), 1012-1030.
Antony, J. (2014). Readiness factors for the Lean Six Sigma journey in the higher education
sector. International Journal of Productivity and Performance Management, 63(2),
257-264.
Antony, J., Krishan, N., Cullen, D., & Kumar, M. (2012). Lean Six Sigma for higher
education institutions (HEIs) Challenges, barriers, success factors,
tools/techniques. International Journal of Productivity and Performance
Management, 61(8), 940-948.
Assarlind, M., Gremyr, I., & Bäckman, K. (2013). Multi-faceted views on a Lean Six Sigma
application. International Journal of Quality & Reliability Management, 30(4), 387-
402.
Atmaca, E., & Girenes, S. S. (2013). Lean Six Sigma methodology and application. Quality
& quantity, 47(4), 2107-2127.
Cheng, C. Y., & Chang, P. Y. (2012). Implementation of the Lean Six Sigma framework in
non-profit organisations: A case study. Total Quality Management & Business
Excellence, 23(3-4), 431-447.
Cucoranu, I. C., Parwani, A. V., & Pantanowitz, L. (2014). Lean Six Sigma. In Practical
Informatics for Cytopathology(pp. 113-119). Springer, New York, NY.
Drohomeretski, E., Gouvea da Costa, S. E., Pinheiro de Lima, E., & Garbuio, P. A. D. R.
(2014). Lean, Six Sigma and Lean Six Sigma: an analysis based on operations
strategy. International Journal of Production Research, 52(3), 804-824.
Fadly Habidin, N., & Mohd Yusof, S. R. (2013). Critical success factors of Lean Six Sigma
for the Malaysian automotive industry. International Journal of Lean Six Sigma, 4(1),
60-82.
Frosts.com.sg. (2012). About Us. Retrieved from http://frosts.com.sg/index.php?
route=information/information&information_id=4
Habidin, N. F., & Yusof, S. M. (2012). Relationship between lean six sigma, environmental
management systems, and organizational performance in the Malaysian automotive
industry. International Journal of Automotive Technology, 13(7), 1119-1125.
Hilton, R. J., & Sohal, A. (2012). A conceptual model for the successful deployment of Lean
Six Sigma. International Journal of Quality & Reliability Management, 29(1), 54-70.
Maleyeff, J., Arnheiter, E. A., & Venkateswaran, V. (2012). The continuing evolution of lean
six sigma. The TQM Journal, 24(6), 542-555.
Manville, G., Greatbanks, R., Krishnasamy, R., & Parker, D. W. (2012). Critical success
factors for Lean Six Sigma programmes: a view from middle
management. International Journal of Quality & Reliability Management, 29(1), 7-
20.
Reference and Bibliography:
Albliwi, S., Antony, J., Abdul Halim Lim, S., & van der Wiele, T. (2014). Critical failure
factors of Lean Six Sigma: a systematic literature review. International Journal of
Quality & Reliability Management, 31(9), 1012-1030.
Antony, J. (2014). Readiness factors for the Lean Six Sigma journey in the higher education
sector. International Journal of Productivity and Performance Management, 63(2),
257-264.
Antony, J., Krishan, N., Cullen, D., & Kumar, M. (2012). Lean Six Sigma for higher
education institutions (HEIs) Challenges, barriers, success factors,
tools/techniques. International Journal of Productivity and Performance
Management, 61(8), 940-948.
Assarlind, M., Gremyr, I., & Bäckman, K. (2013). Multi-faceted views on a Lean Six Sigma
application. International Journal of Quality & Reliability Management, 30(4), 387-
402.
Atmaca, E., & Girenes, S. S. (2013). Lean Six Sigma methodology and application. Quality
& quantity, 47(4), 2107-2127.
Cheng, C. Y., & Chang, P. Y. (2012). Implementation of the Lean Six Sigma framework in
non-profit organisations: A case study. Total Quality Management & Business
Excellence, 23(3-4), 431-447.
Cucoranu, I. C., Parwani, A. V., & Pantanowitz, L. (2014). Lean Six Sigma. In Practical
Informatics for Cytopathology(pp. 113-119). Springer, New York, NY.
Drohomeretski, E., Gouvea da Costa, S. E., Pinheiro de Lima, E., & Garbuio, P. A. D. R.
(2014). Lean, Six Sigma and Lean Six Sigma: an analysis based on operations
strategy. International Journal of Production Research, 52(3), 804-824.
Fadly Habidin, N., & Mohd Yusof, S. R. (2013). Critical success factors of Lean Six Sigma
for the Malaysian automotive industry. International Journal of Lean Six Sigma, 4(1),
60-82.
Frosts.com.sg. (2012). About Us. Retrieved from http://frosts.com.sg/index.php?
route=information/information&information_id=4
Habidin, N. F., & Yusof, S. M. (2012). Relationship between lean six sigma, environmental
management systems, and organizational performance in the Malaysian automotive
industry. International Journal of Automotive Technology, 13(7), 1119-1125.
Hilton, R. J., & Sohal, A. (2012). A conceptual model for the successful deployment of Lean
Six Sigma. International Journal of Quality & Reliability Management, 29(1), 54-70.
Maleyeff, J., Arnheiter, E. A., & Venkateswaran, V. (2012). The continuing evolution of lean
six sigma. The TQM Journal, 24(6), 542-555.
Manville, G., Greatbanks, R., Krishnasamy, R., & Parker, D. W. (2012). Critical success
factors for Lean Six Sigma programmes: a view from middle
management. International Journal of Quality & Reliability Management, 29(1), 7-
20.
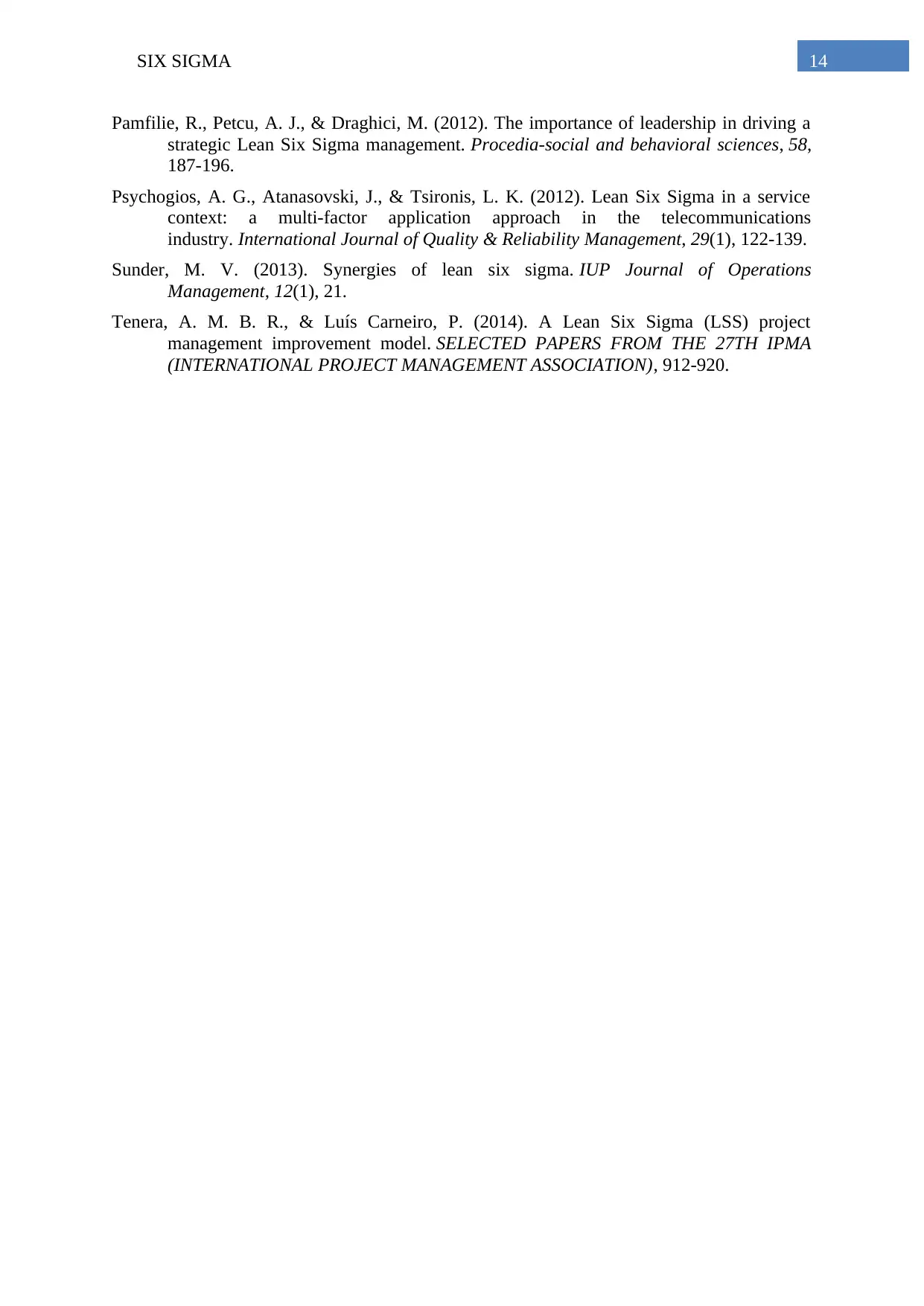
SIX SIGMA 14
Pamfilie, R., Petcu, A. J., & Draghici, M. (2012). The importance of leadership in driving a
strategic Lean Six Sigma management. Procedia-social and behavioral sciences, 58,
187-196.
Psychogios, A. G., Atanasovski, J., & Tsironis, L. K. (2012). Lean Six Sigma in a service
context: a multi-factor application approach in the telecommunications
industry. International Journal of Quality & Reliability Management, 29(1), 122-139.
Sunder, M. V. (2013). Synergies of lean six sigma. IUP Journal of Operations
Management, 12(1), 21.
Tenera, A. M. B. R., & Luís Carneiro, P. (2014). A Lean Six Sigma (LSS) project
management improvement model. SELECTED PAPERS FROM THE 27TH IPMA
(INTERNATIONAL PROJECT MANAGEMENT ASSOCIATION), 912-920.
Pamfilie, R., Petcu, A. J., & Draghici, M. (2012). The importance of leadership in driving a
strategic Lean Six Sigma management. Procedia-social and behavioral sciences, 58,
187-196.
Psychogios, A. G., Atanasovski, J., & Tsironis, L. K. (2012). Lean Six Sigma in a service
context: a multi-factor application approach in the telecommunications
industry. International Journal of Quality & Reliability Management, 29(1), 122-139.
Sunder, M. V. (2013). Synergies of lean six sigma. IUP Journal of Operations
Management, 12(1), 21.
Tenera, A. M. B. R., & Luís Carneiro, P. (2014). A Lean Six Sigma (LSS) project
management improvement model. SELECTED PAPERS FROM THE 27TH IPMA
(INTERNATIONAL PROJECT MANAGEMENT ASSOCIATION), 912-920.
1 out of 15
Related Documents

Your All-in-One AI-Powered Toolkit for Academic Success.
+13062052269
info@desklib.com
Available 24*7 on WhatsApp / Email
Unlock your academic potential
© 2024 | Zucol Services PVT LTD | All rights reserved.