Management Accounting Report: Variance and Production Analysis
VerifiedAdded on 2023/01/09
|11
|3090
|86
Report
AI Summary
This management accounting report examines the financial performance of XLG, a cleaning product manufacturer, focusing on variance analysis and production decisions. The report begins with an introduction to management accounting and its importance in decision-making, particularly for ...
Read More
Contribute Materials
Your contribution can guide someone’s learning journey. Share your
documents today.
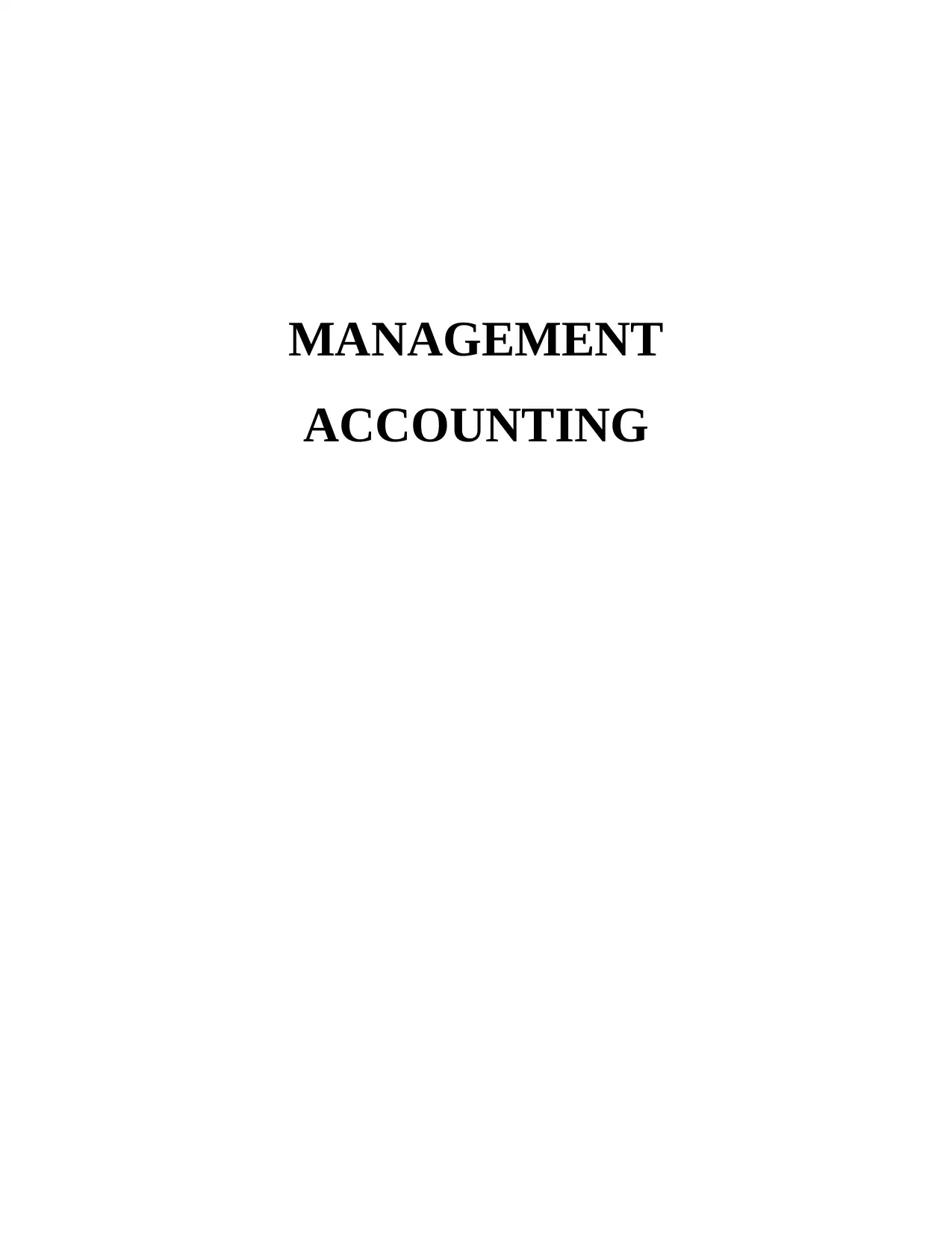
MANAGEMENT
ACCOUNTING
ACCOUNTING
Secure Best Marks with AI Grader
Need help grading? Try our AI Grader for instant feedback on your assignments.
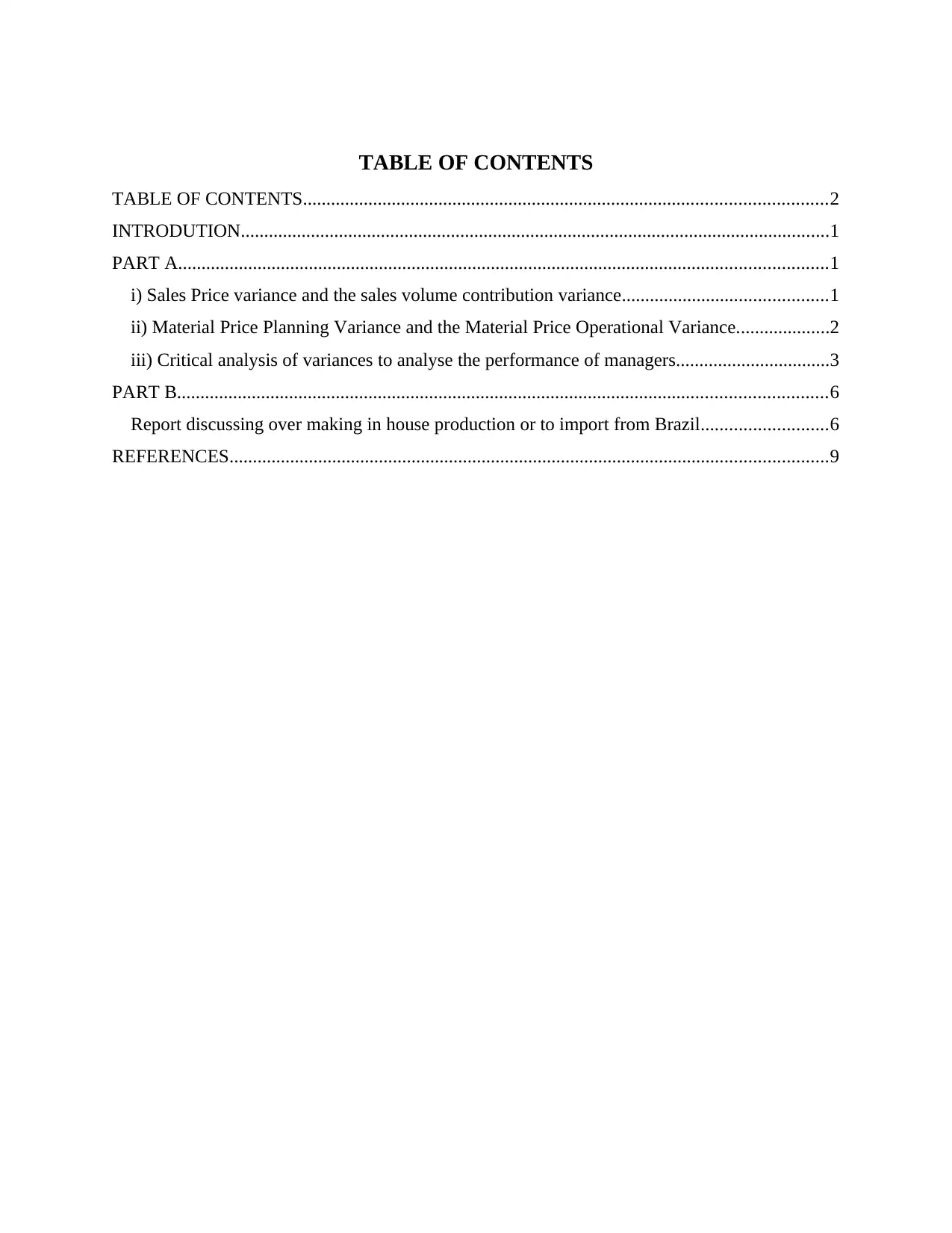
TABLE OF CONTENTS
TABLE OF CONTENTS................................................................................................................2
INTRODUTION..............................................................................................................................1
PART A...........................................................................................................................................1
i) Sales Price variance and the sales volume contribution variance............................................1
ii) Material Price Planning Variance and the Material Price Operational Variance....................2
iii) Critical analysis of variances to analyse the performance of managers.................................3
PART B...........................................................................................................................................6
Report discussing over making in house production or to import from Brazil...........................6
REFERENCES................................................................................................................................9
TABLE OF CONTENTS................................................................................................................2
INTRODUTION..............................................................................................................................1
PART A...........................................................................................................................................1
i) Sales Price variance and the sales volume contribution variance............................................1
ii) Material Price Planning Variance and the Material Price Operational Variance....................2
iii) Critical analysis of variances to analyse the performance of managers.................................3
PART B...........................................................................................................................................6
Report discussing over making in house production or to import from Brazil...........................6
REFERENCES................................................................................................................................9
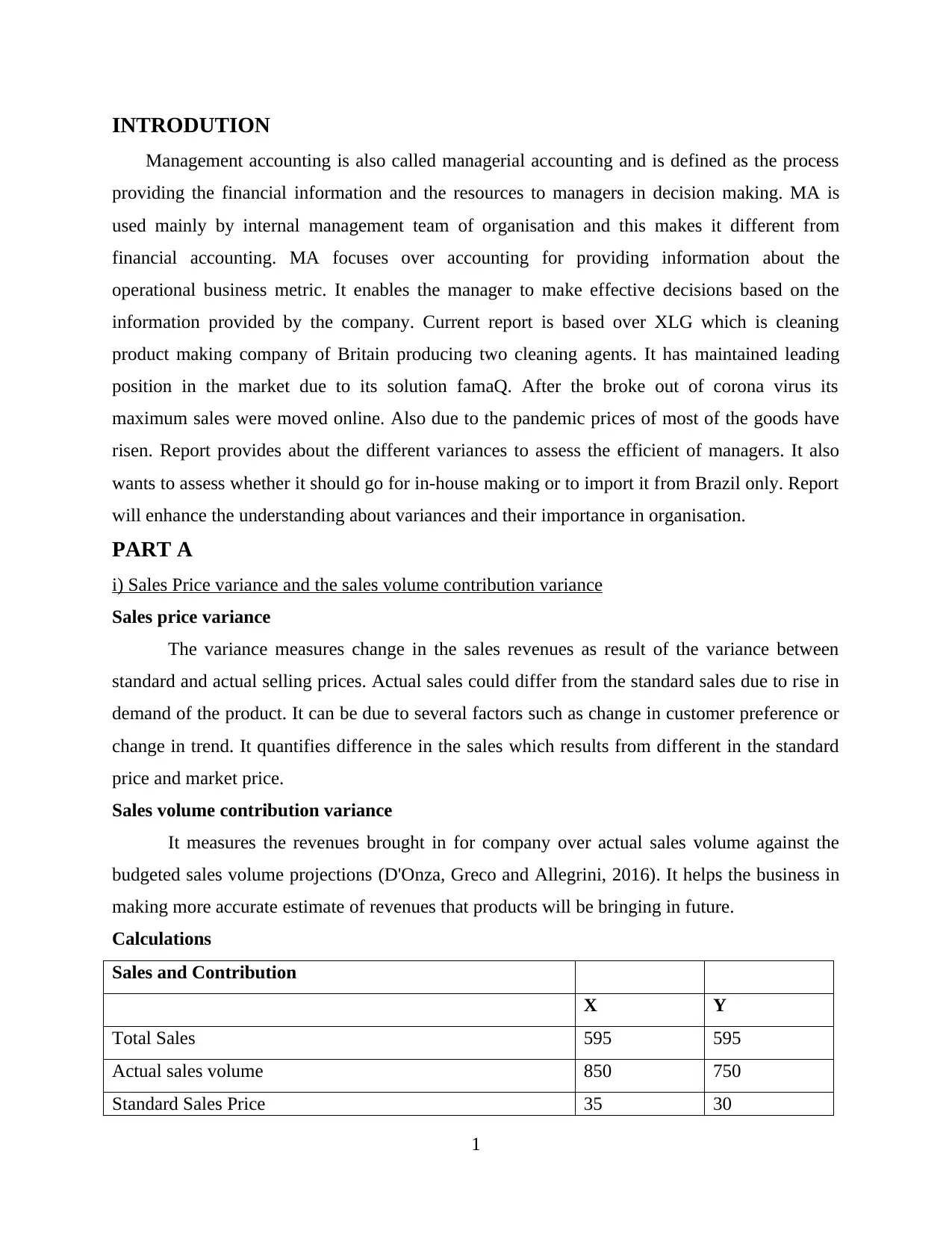
INTRODUTION
Management accounting is also called managerial accounting and is defined as the process
providing the financial information and the resources to managers in decision making. MA is
used mainly by internal management team of organisation and this makes it different from
financial accounting. MA focuses over accounting for providing information about the
operational business metric. It enables the manager to make effective decisions based on the
information provided by the company. Current report is based over XLG which is cleaning
product making company of Britain producing two cleaning agents. It has maintained leading
position in the market due to its solution famaQ. After the broke out of corona virus its
maximum sales were moved online. Also due to the pandemic prices of most of the goods have
risen. Report provides about the different variances to assess the efficient of managers. It also
wants to assess whether it should go for in-house making or to import it from Brazil only. Report
will enhance the understanding about variances and their importance in organisation.
PART A
i) Sales Price variance and the sales volume contribution variance
Sales price variance
The variance measures change in the sales revenues as result of the variance between
standard and actual selling prices. Actual sales could differ from the standard sales due to rise in
demand of the product. It can be due to several factors such as change in customer preference or
change in trend. It quantifies difference in the sales which results from different in the standard
price and market price.
Sales volume contribution variance
It measures the revenues brought in for company over actual sales volume against the
budgeted sales volume projections (D'Onza, Greco and Allegrini, 2016). It helps the business in
making more accurate estimate of revenues that products will be bringing in future.
Calculations
Sales and Contribution
X Y
Total Sales 595 595
Actual sales volume 850 750
Standard Sales Price 35 30
1
Management accounting is also called managerial accounting and is defined as the process
providing the financial information and the resources to managers in decision making. MA is
used mainly by internal management team of organisation and this makes it different from
financial accounting. MA focuses over accounting for providing information about the
operational business metric. It enables the manager to make effective decisions based on the
information provided by the company. Current report is based over XLG which is cleaning
product making company of Britain producing two cleaning agents. It has maintained leading
position in the market due to its solution famaQ. After the broke out of corona virus its
maximum sales were moved online. Also due to the pandemic prices of most of the goods have
risen. Report provides about the different variances to assess the efficient of managers. It also
wants to assess whether it should go for in-house making or to import it from Brazil only. Report
will enhance the understanding about variances and their importance in organisation.
PART A
i) Sales Price variance and the sales volume contribution variance
Sales price variance
The variance measures change in the sales revenues as result of the variance between
standard and actual selling prices. Actual sales could differ from the standard sales due to rise in
demand of the product. It can be due to several factors such as change in customer preference or
change in trend. It quantifies difference in the sales which results from different in the standard
price and market price.
Sales volume contribution variance
It measures the revenues brought in for company over actual sales volume against the
budgeted sales volume projections (D'Onza, Greco and Allegrini, 2016). It helps the business in
making more accurate estimate of revenues that products will be bringing in future.
Calculations
Sales and Contribution
X Y
Total Sales 595 595
Actual sales volume 850 750
Standard Sales Price 35 30
1
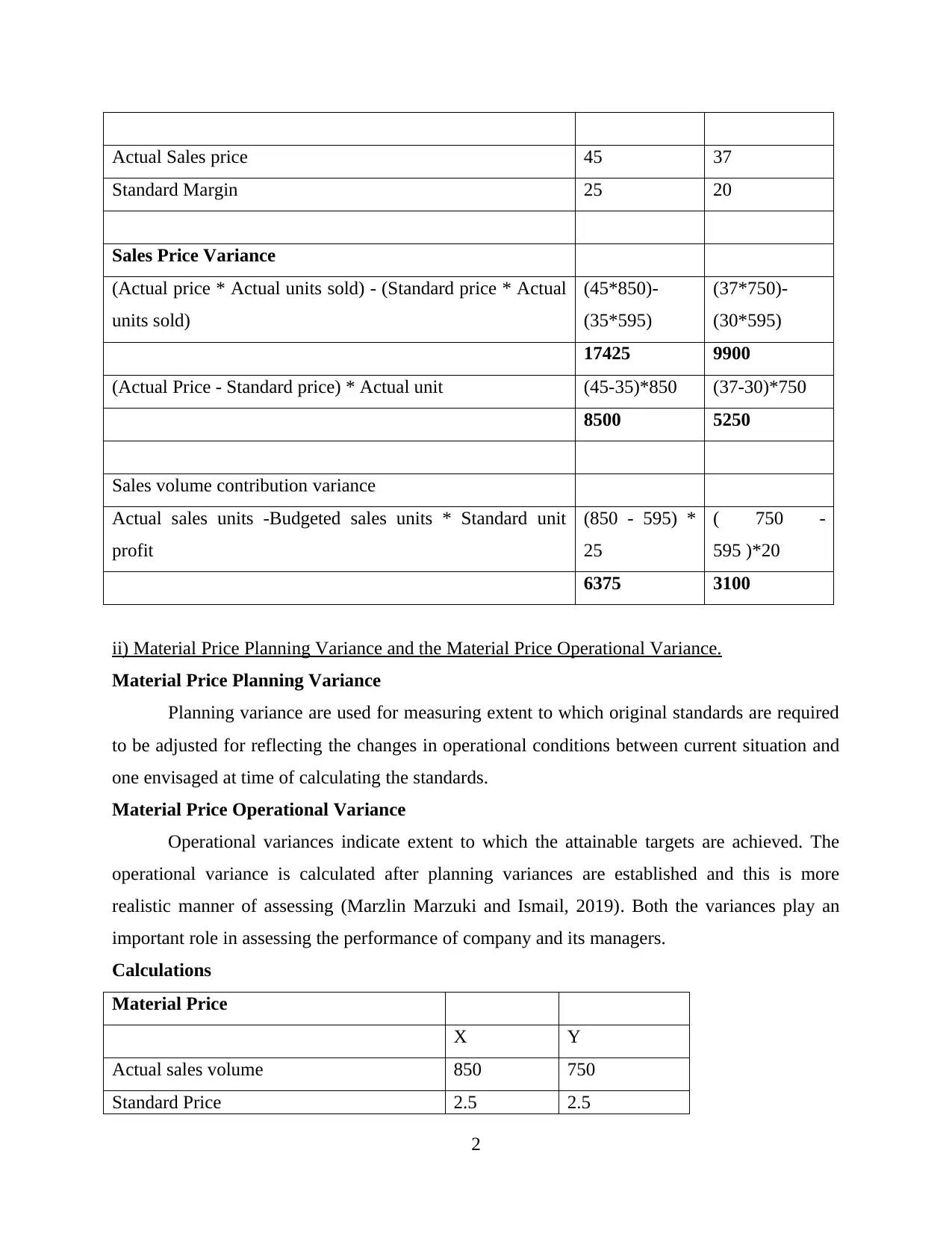
Actual Sales price 45 37
Standard Margin 25 20
Sales Price Variance
(Actual price * Actual units sold) - (Standard price * Actual
units sold)
(45*850)-
(35*595)
(37*750)-
(30*595)
17425 9900
(Actual Price - Standard price) * Actual unit (45-35)*850 (37-30)*750
8500 5250
Sales volume contribution variance
Actual sales units -Budgeted sales units * Standard unit
profit
(850 - 595) *
25
( 750 -
595 )*20
6375 3100
ii) Material Price Planning Variance and the Material Price Operational Variance.
Material Price Planning Variance
Planning variance are used for measuring extent to which original standards are required
to be adjusted for reflecting the changes in operational conditions between current situation and
one envisaged at time of calculating the standards.
Material Price Operational Variance
Operational variances indicate extent to which the attainable targets are achieved. The
operational variance is calculated after planning variances are established and this is more
realistic manner of assessing (Marzlin Marzuki and Ismail, 2019). Both the variances play an
important role in assessing the performance of company and its managers.
Calculations
Material Price
X Y
Actual sales volume 850 750
Standard Price 2.5 2.5
2
Standard Margin 25 20
Sales Price Variance
(Actual price * Actual units sold) - (Standard price * Actual
units sold)
(45*850)-
(35*595)
(37*750)-
(30*595)
17425 9900
(Actual Price - Standard price) * Actual unit (45-35)*850 (37-30)*750
8500 5250
Sales volume contribution variance
Actual sales units -Budgeted sales units * Standard unit
profit
(850 - 595) *
25
( 750 -
595 )*20
6375 3100
ii) Material Price Planning Variance and the Material Price Operational Variance.
Material Price Planning Variance
Planning variance are used for measuring extent to which original standards are required
to be adjusted for reflecting the changes in operational conditions between current situation and
one envisaged at time of calculating the standards.
Material Price Operational Variance
Operational variances indicate extent to which the attainable targets are achieved. The
operational variance is calculated after planning variances are established and this is more
realistic manner of assessing (Marzlin Marzuki and Ismail, 2019). Both the variances play an
important role in assessing the performance of company and its managers.
Calculations
Material Price
X Y
Actual sales volume 850 750
Standard Price 2.5 2.5
2
Secure Best Marks with AI Grader
Need help grading? Try our AI Grader for instant feedback on your assignments.
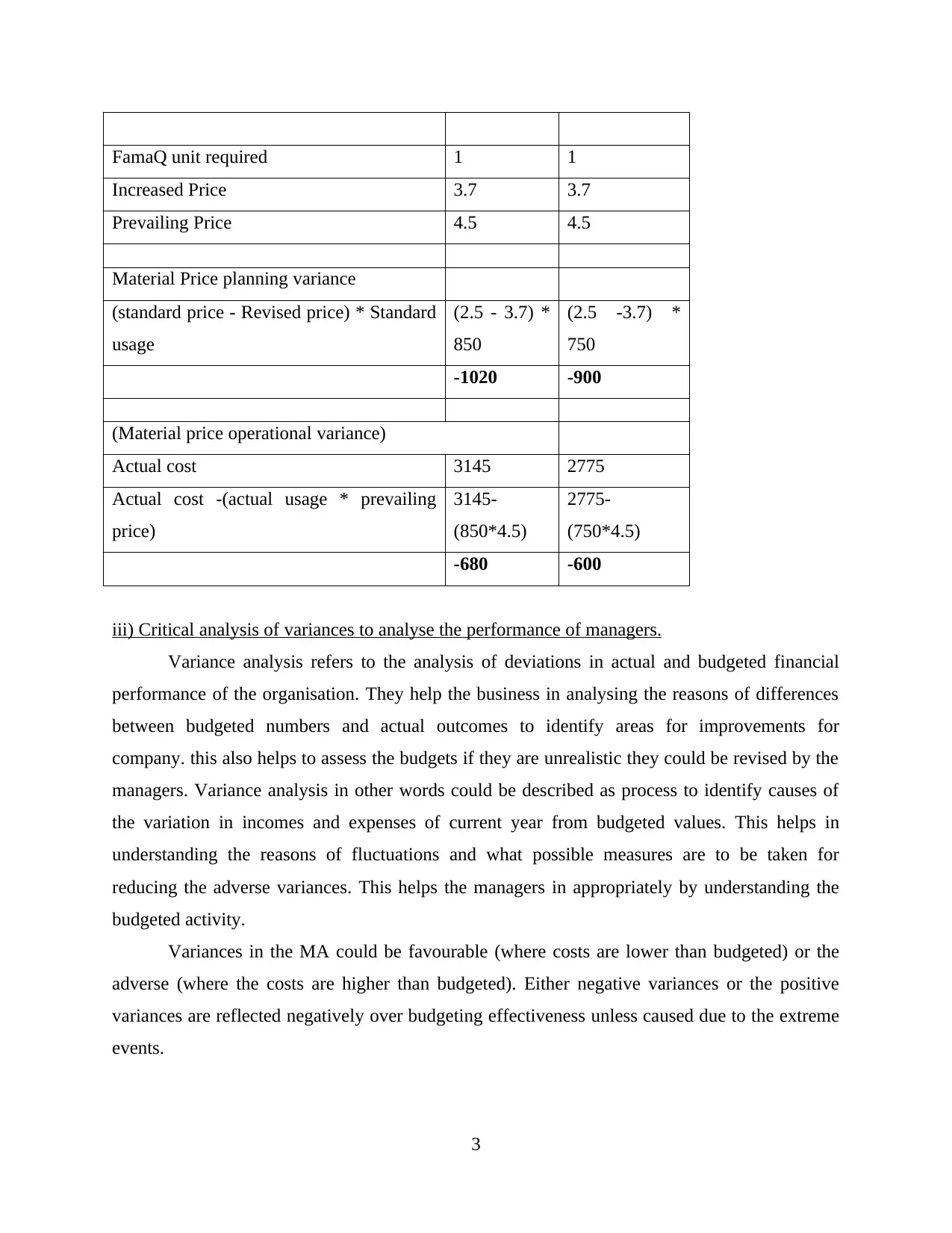
FamaQ unit required 1 1
Increased Price 3.7 3.7
Prevailing Price 4.5 4.5
Material Price planning variance
(standard price - Revised price) * Standard
usage
(2.5 - 3.7) *
850
(2.5 -3.7) *
750
-1020 -900
(Material price operational variance)
Actual cost 3145 2775
Actual cost -(actual usage * prevailing
price)
3145-
(850*4.5)
2775-
(750*4.5)
-680 -600
iii) Critical analysis of variances to analyse the performance of managers.
Variance analysis refers to the analysis of deviations in actual and budgeted financial
performance of the organisation. They help the business in analysing the reasons of differences
between budgeted numbers and actual outcomes to identify areas for improvements for
company. this also helps to assess the budgets if they are unrealistic they could be revised by the
managers. Variance analysis in other words could be described as process to identify causes of
the variation in incomes and expenses of current year from budgeted values. This helps in
understanding the reasons of fluctuations and what possible measures are to be taken for
reducing the adverse variances. This helps the managers in appropriately by understanding the
budgeted activity.
Variances in the MA could be favourable (where costs are lower than budgeted) or the
adverse (where the costs are higher than budgeted). Either negative variances or the positive
variances are reflected negatively over budgeting effectiveness unless caused due to the extreme
events.
3
Increased Price 3.7 3.7
Prevailing Price 4.5 4.5
Material Price planning variance
(standard price - Revised price) * Standard
usage
(2.5 - 3.7) *
850
(2.5 -3.7) *
750
-1020 -900
(Material price operational variance)
Actual cost 3145 2775
Actual cost -(actual usage * prevailing
price)
3145-
(850*4.5)
2775-
(750*4.5)
-680 -600
iii) Critical analysis of variances to analyse the performance of managers.
Variance analysis refers to the analysis of deviations in actual and budgeted financial
performance of the organisation. They help the business in analysing the reasons of differences
between budgeted numbers and actual outcomes to identify areas for improvements for
company. this also helps to assess the budgets if they are unrealistic they could be revised by the
managers. Variance analysis in other words could be described as process to identify causes of
the variation in incomes and expenses of current year from budgeted values. This helps in
understanding the reasons of fluctuations and what possible measures are to be taken for
reducing the adverse variances. This helps the managers in appropriately by understanding the
budgeted activity.
Variances in the MA could be favourable (where costs are lower than budgeted) or the
adverse (where the costs are higher than budgeted). Either negative variances or the positive
variances are reflected negatively over budgeting effectiveness unless caused due to the extreme
events.
3
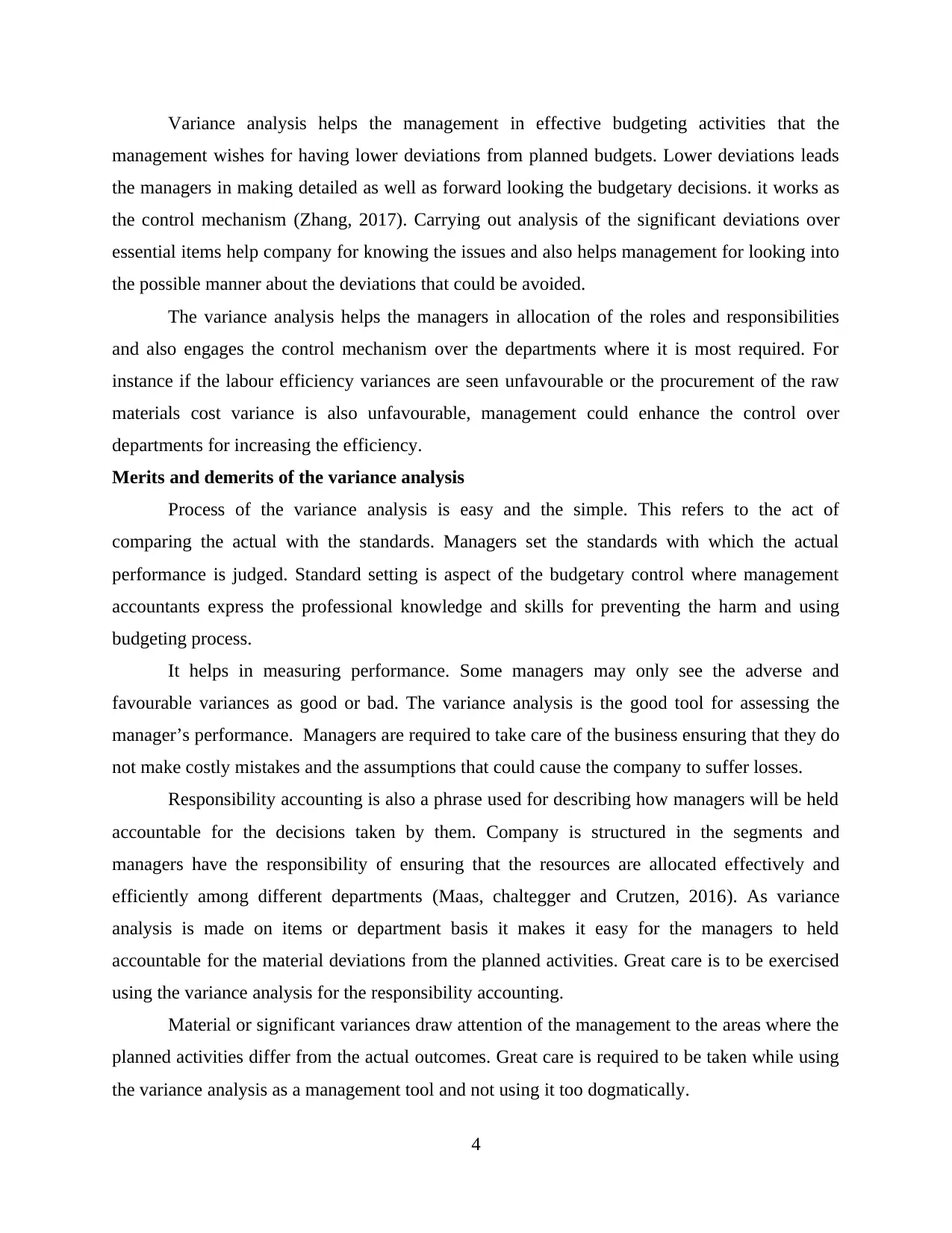
Variance analysis helps the management in effective budgeting activities that the
management wishes for having lower deviations from planned budgets. Lower deviations leads
the managers in making detailed as well as forward looking the budgetary decisions. it works as
the control mechanism (Zhang, 2017). Carrying out analysis of the significant deviations over
essential items help company for knowing the issues and also helps management for looking into
the possible manner about the deviations that could be avoided.
The variance analysis helps the managers in allocation of the roles and responsibilities
and also engages the control mechanism over the departments where it is most required. For
instance if the labour efficiency variances are seen unfavourable or the procurement of the raw
materials cost variance is also unfavourable, management could enhance the control over
departments for increasing the efficiency.
Merits and demerits of the variance analysis
Process of the variance analysis is easy and the simple. This refers to the act of
comparing the actual with the standards. Managers set the standards with which the actual
performance is judged. Standard setting is aspect of the budgetary control where management
accountants express the professional knowledge and skills for preventing the harm and using
budgeting process.
It helps in measuring performance. Some managers may only see the adverse and
favourable variances as good or bad. The variance analysis is the good tool for assessing the
manager’s performance. Managers are required to take care of the business ensuring that they do
not make costly mistakes and the assumptions that could cause the company to suffer losses.
Responsibility accounting is also a phrase used for describing how managers will be held
accountable for the decisions taken by them. Company is structured in the segments and
managers have the responsibility of ensuring that the resources are allocated effectively and
efficiently among different departments (Maas, chaltegger and Crutzen, 2016). As variance
analysis is made on items or department basis it makes it easy for the managers to held
accountable for the material deviations from the planned activities. Great care is to be exercised
using the variance analysis for the responsibility accounting.
Material or significant variances draw attention of the management to the areas where the
planned activities differ from the actual outcomes. Great care is required to be taken while using
the variance analysis as a management tool and not using it too dogmatically.
4
management wishes for having lower deviations from planned budgets. Lower deviations leads
the managers in making detailed as well as forward looking the budgetary decisions. it works as
the control mechanism (Zhang, 2017). Carrying out analysis of the significant deviations over
essential items help company for knowing the issues and also helps management for looking into
the possible manner about the deviations that could be avoided.
The variance analysis helps the managers in allocation of the roles and responsibilities
and also engages the control mechanism over the departments where it is most required. For
instance if the labour efficiency variances are seen unfavourable or the procurement of the raw
materials cost variance is also unfavourable, management could enhance the control over
departments for increasing the efficiency.
Merits and demerits of the variance analysis
Process of the variance analysis is easy and the simple. This refers to the act of
comparing the actual with the standards. Managers set the standards with which the actual
performance is judged. Standard setting is aspect of the budgetary control where management
accountants express the professional knowledge and skills for preventing the harm and using
budgeting process.
It helps in measuring performance. Some managers may only see the adverse and
favourable variances as good or bad. The variance analysis is the good tool for assessing the
manager’s performance. Managers are required to take care of the business ensuring that they do
not make costly mistakes and the assumptions that could cause the company to suffer losses.
Responsibility accounting is also a phrase used for describing how managers will be held
accountable for the decisions taken by them. Company is structured in the segments and
managers have the responsibility of ensuring that the resources are allocated effectively and
efficiently among different departments (Maas, chaltegger and Crutzen, 2016). As variance
analysis is made on items or department basis it makes it easy for the managers to held
accountable for the material deviations from the planned activities. Great care is to be exercised
using the variance analysis for the responsibility accounting.
Material or significant variances draw attention of the management to the areas where the
planned activities differ from the actual outcomes. Great care is required to be taken while using
the variance analysis as a management tool and not using it too dogmatically.
4
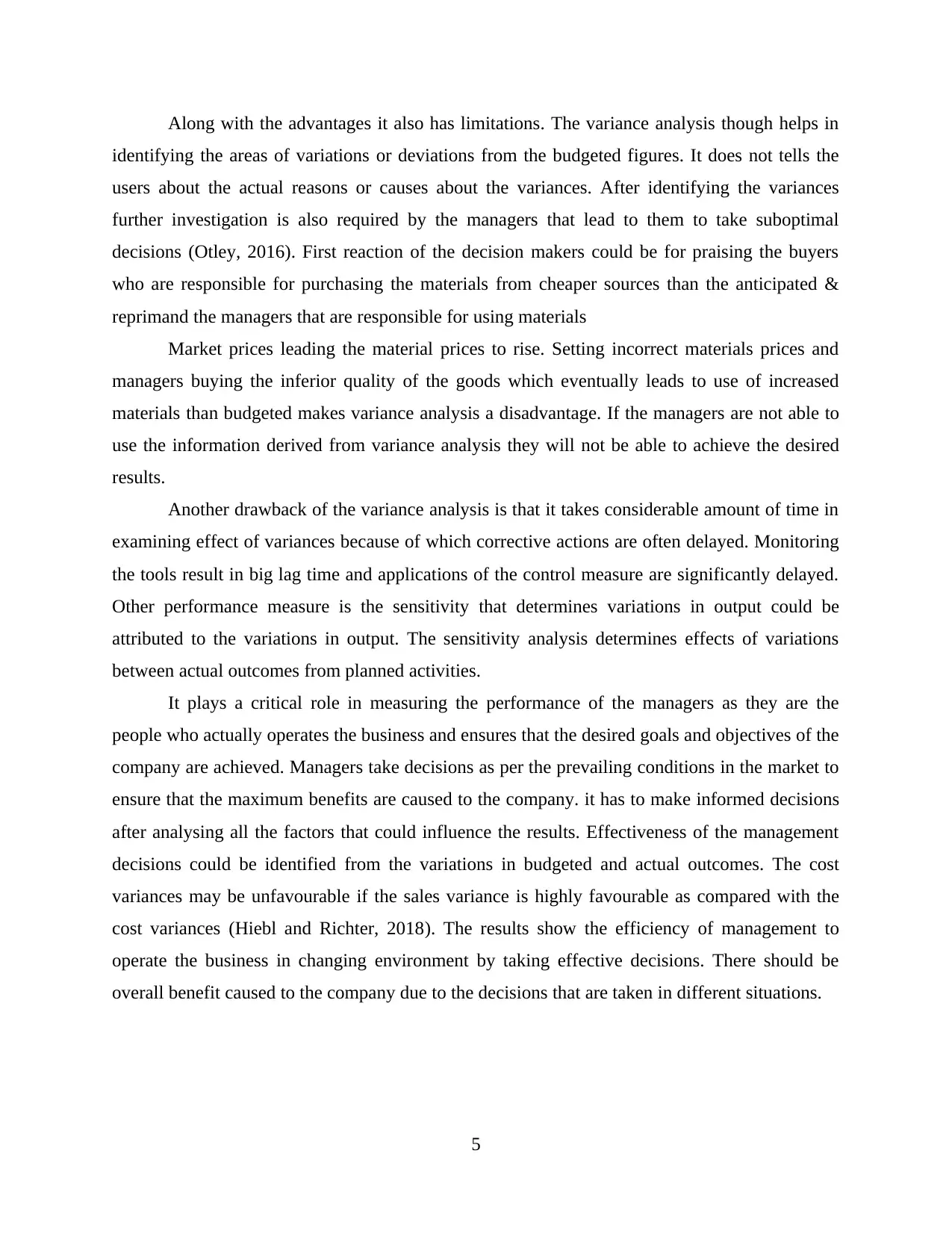
Along with the advantages it also has limitations. The variance analysis though helps in
identifying the areas of variations or deviations from the budgeted figures. It does not tells the
users about the actual reasons or causes about the variances. After identifying the variances
further investigation is also required by the managers that lead to them to take suboptimal
decisions (Otley, 2016). First reaction of the decision makers could be for praising the buyers
who are responsible for purchasing the materials from cheaper sources than the anticipated &
reprimand the managers that are responsible for using materials
Market prices leading the material prices to rise. Setting incorrect materials prices and
managers buying the inferior quality of the goods which eventually leads to use of increased
materials than budgeted makes variance analysis a disadvantage. If the managers are not able to
use the information derived from variance analysis they will not be able to achieve the desired
results.
Another drawback of the variance analysis is that it takes considerable amount of time in
examining effect of variances because of which corrective actions are often delayed. Monitoring
the tools result in big lag time and applications of the control measure are significantly delayed.
Other performance measure is the sensitivity that determines variations in output could be
attributed to the variations in output. The sensitivity analysis determines effects of variations
between actual outcomes from planned activities.
It plays a critical role in measuring the performance of the managers as they are the
people who actually operates the business and ensures that the desired goals and objectives of the
company are achieved. Managers take decisions as per the prevailing conditions in the market to
ensure that the maximum benefits are caused to the company. it has to make informed decisions
after analysing all the factors that could influence the results. Effectiveness of the management
decisions could be identified from the variations in budgeted and actual outcomes. The cost
variances may be unfavourable if the sales variance is highly favourable as compared with the
cost variances (Hiebl and Richter, 2018). The results show the efficiency of management to
operate the business in changing environment by taking effective decisions. There should be
overall benefit caused to the company due to the decisions that are taken in different situations.
5
identifying the areas of variations or deviations from the budgeted figures. It does not tells the
users about the actual reasons or causes about the variances. After identifying the variances
further investigation is also required by the managers that lead to them to take suboptimal
decisions (Otley, 2016). First reaction of the decision makers could be for praising the buyers
who are responsible for purchasing the materials from cheaper sources than the anticipated &
reprimand the managers that are responsible for using materials
Market prices leading the material prices to rise. Setting incorrect materials prices and
managers buying the inferior quality of the goods which eventually leads to use of increased
materials than budgeted makes variance analysis a disadvantage. If the managers are not able to
use the information derived from variance analysis they will not be able to achieve the desired
results.
Another drawback of the variance analysis is that it takes considerable amount of time in
examining effect of variances because of which corrective actions are often delayed. Monitoring
the tools result in big lag time and applications of the control measure are significantly delayed.
Other performance measure is the sensitivity that determines variations in output could be
attributed to the variations in output. The sensitivity analysis determines effects of variations
between actual outcomes from planned activities.
It plays a critical role in measuring the performance of the managers as they are the
people who actually operates the business and ensures that the desired goals and objectives of the
company are achieved. Managers take decisions as per the prevailing conditions in the market to
ensure that the maximum benefits are caused to the company. it has to make informed decisions
after analysing all the factors that could influence the results. Effectiveness of the management
decisions could be identified from the variations in budgeted and actual outcomes. The cost
variances may be unfavourable if the sales variance is highly favourable as compared with the
cost variances (Hiebl and Richter, 2018). The results show the efficiency of management to
operate the business in changing environment by taking effective decisions. There should be
overall benefit caused to the company due to the decisions that are taken in different situations.
5
Paraphrase This Document
Need a fresh take? Get an instant paraphrase of this document with our AI Paraphraser
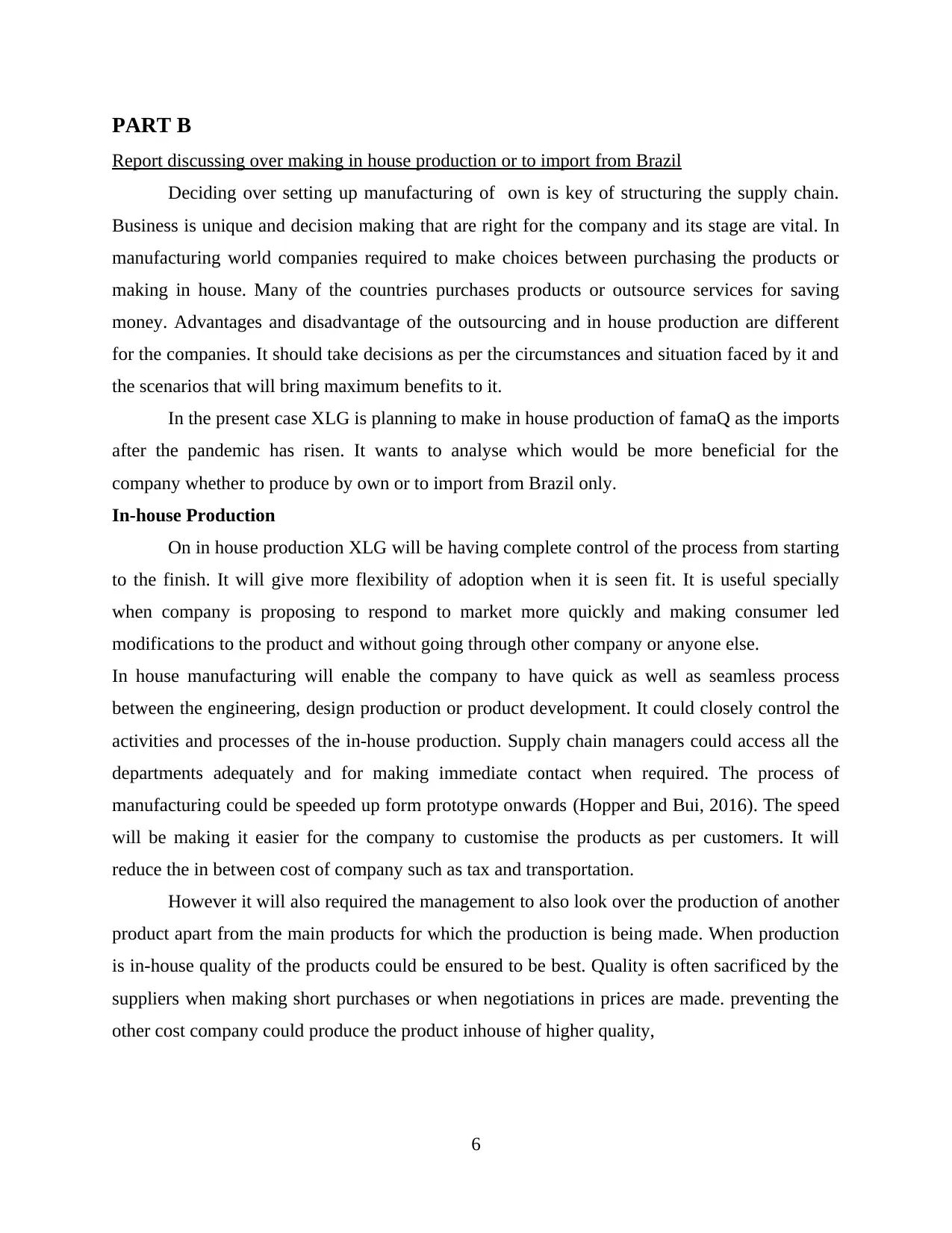
PART B
Report discussing over making in house production or to import from Brazil
Deciding over setting up manufacturing of own is key of structuring the supply chain.
Business is unique and decision making that are right for the company and its stage are vital. In
manufacturing world companies required to make choices between purchasing the products or
making in house. Many of the countries purchases products or outsource services for saving
money. Advantages and disadvantage of the outsourcing and in house production are different
for the companies. It should take decisions as per the circumstances and situation faced by it and
the scenarios that will bring maximum benefits to it.
In the present case XLG is planning to make in house production of famaQ as the imports
after the pandemic has risen. It wants to analyse which would be more beneficial for the
company whether to produce by own or to import from Brazil only.
In-house Production
On in house production XLG will be having complete control of the process from starting
to the finish. It will give more flexibility of adoption when it is seen fit. It is useful specially
when company is proposing to respond to market more quickly and making consumer led
modifications to the product and without going through other company or anyone else.
In house manufacturing will enable the company to have quick as well as seamless process
between the engineering, design production or product development. It could closely control the
activities and processes of the in-house production. Supply chain managers could access all the
departments adequately and for making immediate contact when required. The process of
manufacturing could be speeded up form prototype onwards (Hopper and Bui, 2016). The speed
will be making it easier for the company to customise the products as per customers. It will
reduce the in between cost of company such as tax and transportation.
However it will also required the management to also look over the production of another
product apart from the main products for which the production is being made. When production
is in-house quality of the products could be ensured to be best. Quality is often sacrificed by the
suppliers when making short purchases or when negotiations in prices are made. preventing the
other cost company could produce the product inhouse of higher quality,
6
Report discussing over making in house production or to import from Brazil
Deciding over setting up manufacturing of own is key of structuring the supply chain.
Business is unique and decision making that are right for the company and its stage are vital. In
manufacturing world companies required to make choices between purchasing the products or
making in house. Many of the countries purchases products or outsource services for saving
money. Advantages and disadvantage of the outsourcing and in house production are different
for the companies. It should take decisions as per the circumstances and situation faced by it and
the scenarios that will bring maximum benefits to it.
In the present case XLG is planning to make in house production of famaQ as the imports
after the pandemic has risen. It wants to analyse which would be more beneficial for the
company whether to produce by own or to import from Brazil only.
In-house Production
On in house production XLG will be having complete control of the process from starting
to the finish. It will give more flexibility of adoption when it is seen fit. It is useful specially
when company is proposing to respond to market more quickly and making consumer led
modifications to the product and without going through other company or anyone else.
In house manufacturing will enable the company to have quick as well as seamless process
between the engineering, design production or product development. It could closely control the
activities and processes of the in-house production. Supply chain managers could access all the
departments adequately and for making immediate contact when required. The process of
manufacturing could be speeded up form prototype onwards (Hopper and Bui, 2016). The speed
will be making it easier for the company to customise the products as per customers. It will
reduce the in between cost of company such as tax and transportation.
However it will also required the management to also look over the production of another
product apart from the main products for which the production is being made. When production
is in-house quality of the products could be ensured to be best. Quality is often sacrificed by the
suppliers when making short purchases or when negotiations in prices are made. preventing the
other cost company could produce the product inhouse of higher quality,
6
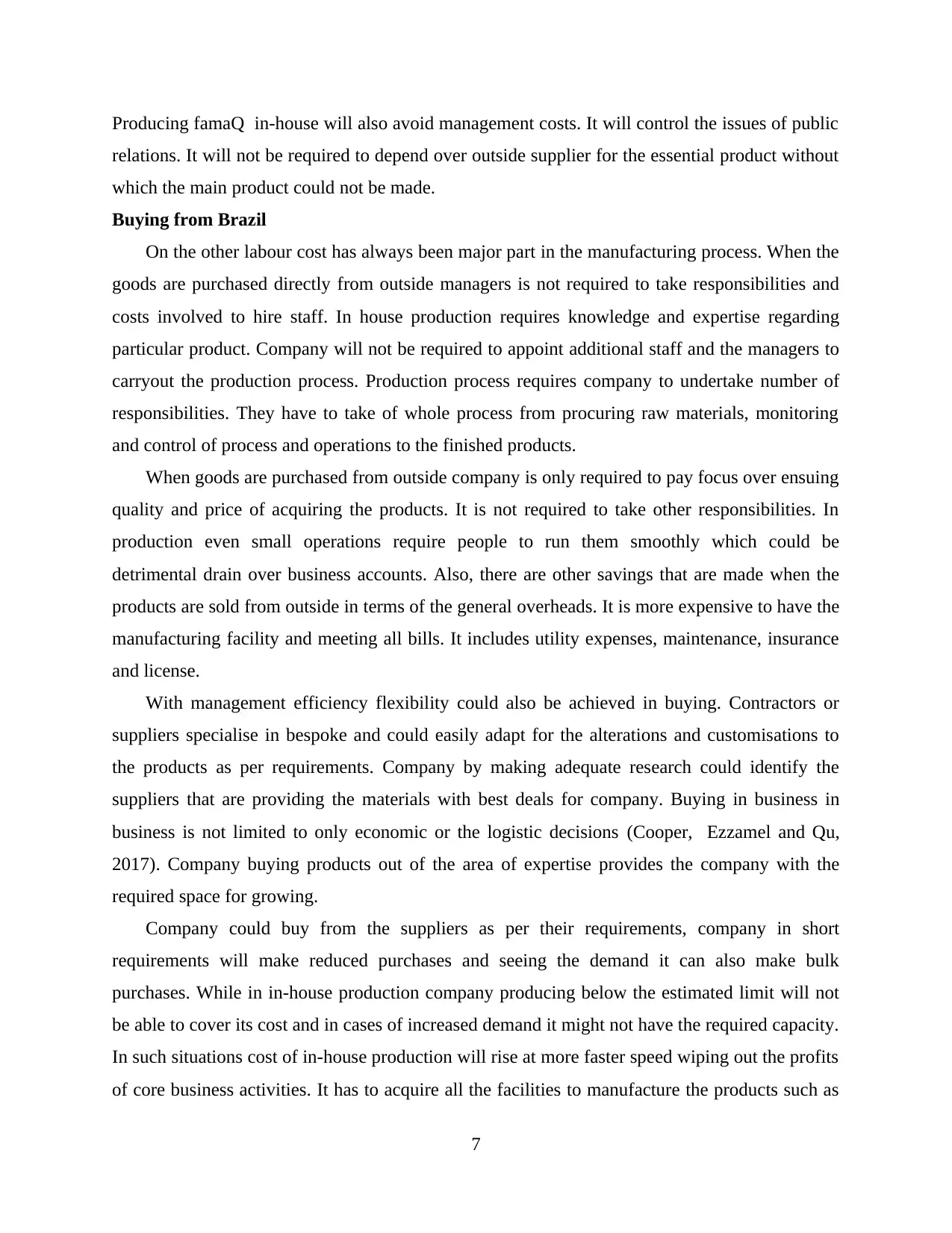
Producing famaQ in-house will also avoid management costs. It will control the issues of public
relations. It will not be required to depend over outside supplier for the essential product without
which the main product could not be made.
Buying from Brazil
On the other labour cost has always been major part in the manufacturing process. When the
goods are purchased directly from outside managers is not required to take responsibilities and
costs involved to hire staff. In house production requires knowledge and expertise regarding
particular product. Company will not be required to appoint additional staff and the managers to
carryout the production process. Production process requires company to undertake number of
responsibilities. They have to take of whole process from procuring raw materials, monitoring
and control of process and operations to the finished products.
When goods are purchased from outside company is only required to pay focus over ensuing
quality and price of acquiring the products. It is not required to take other responsibilities. In
production even small operations require people to run them smoothly which could be
detrimental drain over business accounts. Also, there are other savings that are made when the
products are sold from outside in terms of the general overheads. It is more expensive to have the
manufacturing facility and meeting all bills. It includes utility expenses, maintenance, insurance
and license.
With management efficiency flexibility could also be achieved in buying. Contractors or
suppliers specialise in bespoke and could easily adapt for the alterations and customisations to
the products as per requirements. Company by making adequate research could identify the
suppliers that are providing the materials with best deals for company. Buying in business in
business is not limited to only economic or the logistic decisions (Cooper, Ezzamel and Qu,
2017). Company buying products out of the area of expertise provides the company with the
required space for growing.
Company could buy from the suppliers as per their requirements, company in short
requirements will make reduced purchases and seeing the demand it can also make bulk
purchases. While in in-house production company producing below the estimated limit will not
be able to cover its cost and in cases of increased demand it might not have the required capacity.
In such situations cost of in-house production will rise at more faster speed wiping out the profits
of core business activities. It has to acquire all the facilities to manufacture the products such as
7
relations. It will not be required to depend over outside supplier for the essential product without
which the main product could not be made.
Buying from Brazil
On the other labour cost has always been major part in the manufacturing process. When the
goods are purchased directly from outside managers is not required to take responsibilities and
costs involved to hire staff. In house production requires knowledge and expertise regarding
particular product. Company will not be required to appoint additional staff and the managers to
carryout the production process. Production process requires company to undertake number of
responsibilities. They have to take of whole process from procuring raw materials, monitoring
and control of process and operations to the finished products.
When goods are purchased from outside company is only required to pay focus over ensuing
quality and price of acquiring the products. It is not required to take other responsibilities. In
production even small operations require people to run them smoothly which could be
detrimental drain over business accounts. Also, there are other savings that are made when the
products are sold from outside in terms of the general overheads. It is more expensive to have the
manufacturing facility and meeting all bills. It includes utility expenses, maintenance, insurance
and license.
With management efficiency flexibility could also be achieved in buying. Contractors or
suppliers specialise in bespoke and could easily adapt for the alterations and customisations to
the products as per requirements. Company by making adequate research could identify the
suppliers that are providing the materials with best deals for company. Buying in business in
business is not limited to only economic or the logistic decisions (Cooper, Ezzamel and Qu,
2017). Company buying products out of the area of expertise provides the company with the
required space for growing.
Company could buy from the suppliers as per their requirements, company in short
requirements will make reduced purchases and seeing the demand it can also make bulk
purchases. While in in-house production company producing below the estimated limit will not
be able to cover its cost and in cases of increased demand it might not have the required capacity.
In such situations cost of in-house production will rise at more faster speed wiping out the profits
of core business activities. It has to acquire all the facilities to manufacture the products such as
7
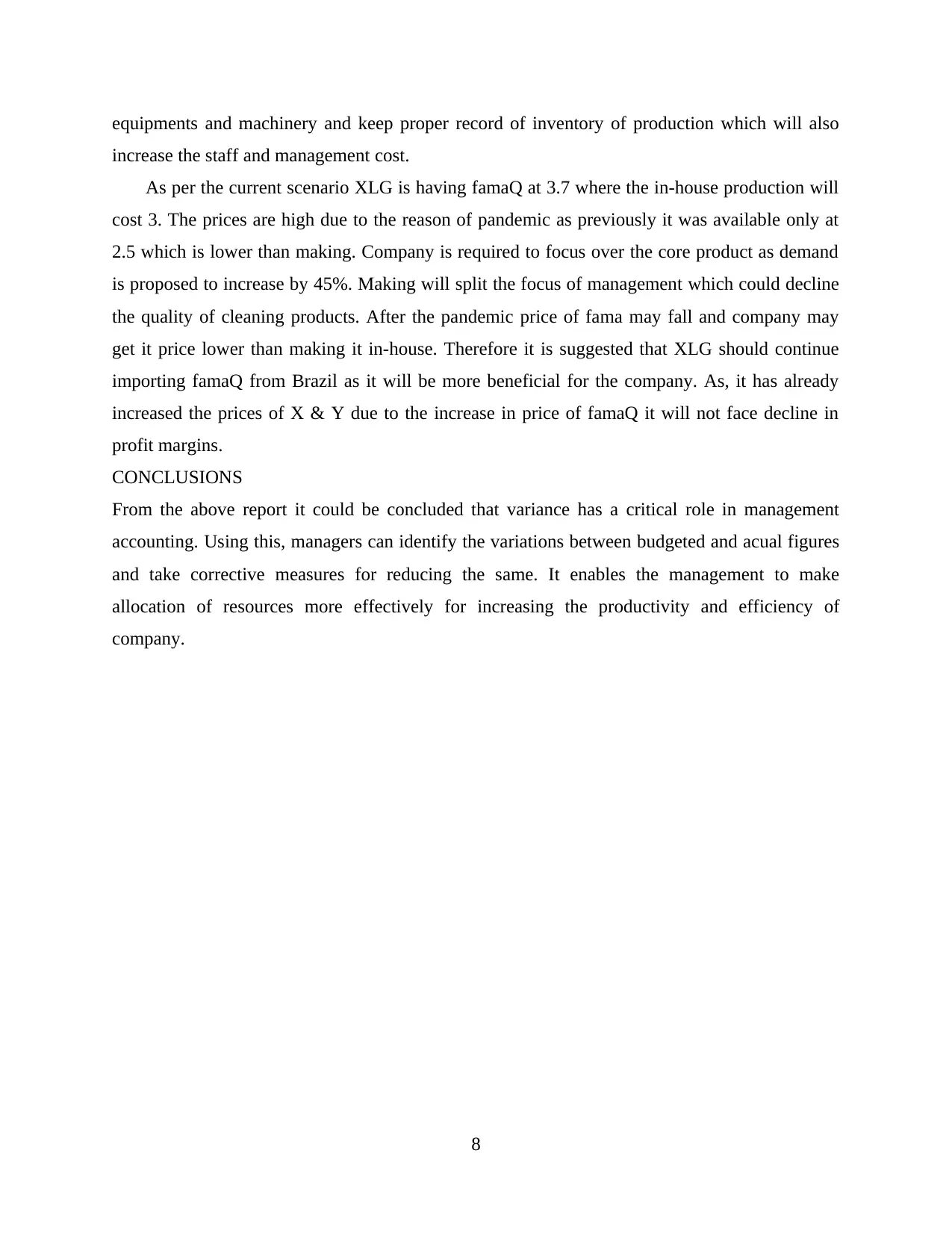
equipments and machinery and keep proper record of inventory of production which will also
increase the staff and management cost.
As per the current scenario XLG is having famaQ at 3.7 where the in-house production will
cost 3. The prices are high due to the reason of pandemic as previously it was available only at
2.5 which is lower than making. Company is required to focus over the core product as demand
is proposed to increase by 45%. Making will split the focus of management which could decline
the quality of cleaning products. After the pandemic price of fama may fall and company may
get it price lower than making it in-house. Therefore it is suggested that XLG should continue
importing famaQ from Brazil as it will be more beneficial for the company. As, it has already
increased the prices of X & Y due to the increase in price of famaQ it will not face decline in
profit margins.
CONCLUSIONS
From the above report it could be concluded that variance has a critical role in management
accounting. Using this, managers can identify the variations between budgeted and acual figures
and take corrective measures for reducing the same. It enables the management to make
allocation of resources more effectively for increasing the productivity and efficiency of
company.
8
increase the staff and management cost.
As per the current scenario XLG is having famaQ at 3.7 where the in-house production will
cost 3. The prices are high due to the reason of pandemic as previously it was available only at
2.5 which is lower than making. Company is required to focus over the core product as demand
is proposed to increase by 45%. Making will split the focus of management which could decline
the quality of cleaning products. After the pandemic price of fama may fall and company may
get it price lower than making it in-house. Therefore it is suggested that XLG should continue
importing famaQ from Brazil as it will be more beneficial for the company. As, it has already
increased the prices of X & Y due to the increase in price of famaQ it will not face decline in
profit margins.
CONCLUSIONS
From the above report it could be concluded that variance has a critical role in management
accounting. Using this, managers can identify the variations between budgeted and acual figures
and take corrective measures for reducing the same. It enables the management to make
allocation of resources more effectively for increasing the productivity and efficiency of
company.
8
Secure Best Marks with AI Grader
Need help grading? Try our AI Grader for instant feedback on your assignments.
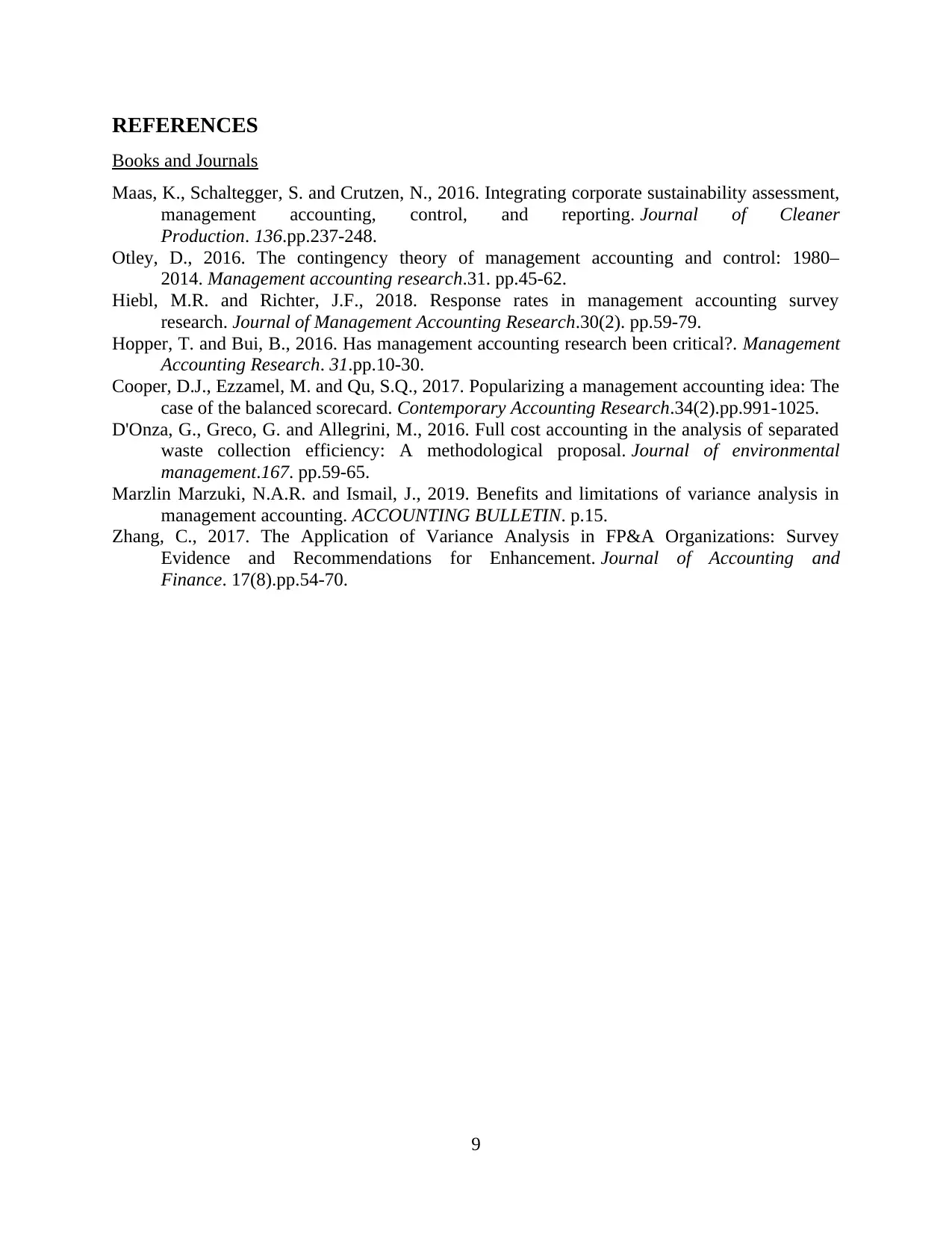
REFERENCES
Books and Journals
Maas, K., Schaltegger, S. and Crutzen, N., 2016. Integrating corporate sustainability assessment,
management accounting, control, and reporting. Journal of Cleaner
Production. 136.pp.237-248.
Otley, D., 2016. The contingency theory of management accounting and control: 1980–
2014. Management accounting research.31. pp.45-62.
Hiebl, M.R. and Richter, J.F., 2018. Response rates in management accounting survey
research. Journal of Management Accounting Research.30(2). pp.59-79.
Hopper, T. and Bui, B., 2016. Has management accounting research been critical?. Management
Accounting Research. 31.pp.10-30.
Cooper, D.J., Ezzamel, M. and Qu, S.Q., 2017. Popularizing a management accounting idea: The
case of the balanced scorecard. Contemporary Accounting Research.34(2).pp.991-1025.
D'Onza, G., Greco, G. and Allegrini, M., 2016. Full cost accounting in the analysis of separated
waste collection efficiency: A methodological proposal. Journal of environmental
management.167. pp.59-65.
Marzlin Marzuki, N.A.R. and Ismail, J., 2019. Benefits and limitations of variance analysis in
management accounting. ACCOUNTING BULLETIN. p.15.
Zhang, C., 2017. The Application of Variance Analysis in FP&A Organizations: Survey
Evidence and Recommendations for Enhancement. Journal of Accounting and
Finance. 17(8).pp.54-70.
9
Books and Journals
Maas, K., Schaltegger, S. and Crutzen, N., 2016. Integrating corporate sustainability assessment,
management accounting, control, and reporting. Journal of Cleaner
Production. 136.pp.237-248.
Otley, D., 2016. The contingency theory of management accounting and control: 1980–
2014. Management accounting research.31. pp.45-62.
Hiebl, M.R. and Richter, J.F., 2018. Response rates in management accounting survey
research. Journal of Management Accounting Research.30(2). pp.59-79.
Hopper, T. and Bui, B., 2016. Has management accounting research been critical?. Management
Accounting Research. 31.pp.10-30.
Cooper, D.J., Ezzamel, M. and Qu, S.Q., 2017. Popularizing a management accounting idea: The
case of the balanced scorecard. Contemporary Accounting Research.34(2).pp.991-1025.
D'Onza, G., Greco, G. and Allegrini, M., 2016. Full cost accounting in the analysis of separated
waste collection efficiency: A methodological proposal. Journal of environmental
management.167. pp.59-65.
Marzlin Marzuki, N.A.R. and Ismail, J., 2019. Benefits and limitations of variance analysis in
management accounting. ACCOUNTING BULLETIN. p.15.
Zhang, C., 2017. The Application of Variance Analysis in FP&A Organizations: Survey
Evidence and Recommendations for Enhancement. Journal of Accounting and
Finance. 17(8).pp.54-70.
9
1 out of 11
Related Documents

Your All-in-One AI-Powered Toolkit for Academic Success.
+13062052269
info@desklib.com
Available 24*7 on WhatsApp / Email
Unlock your academic potential
© 2024 | Zucol Services PVT LTD | All rights reserved.