Comprehensive Operation and Project Management Report for XYZ Company
VerifiedAdded on 2020/10/05
|22
|4615
|69
Report
AI Summary
This report provides a comprehensive analysis of project and operation management strategies, focusing on a case study of XYZ Company. It begins with an introduction to project management and operation concepts, followed by a critical evaluation of Six Sigma methodology and lean principles for quality management. The report then prepares and analyzes the effectiveness of a continuous improvement plan, applying operations management principles within XYZ. Furthermore, it critically evaluates each stage of the Project Life Cycle (PLC) and prepares necessary supporting documentation, such as a business case, project plan, and work breakdown structure. The report also explores theories, concepts, and models of PLC, differentiating between large and small-scale projects, culminating in a conclusion that summarizes the key findings and recommendations for improved project management practices within the company. The report emphasizes the importance of continuous improvement, effective planning, and the application of quality management tools to enhance project outcomes.
Contribute Materials
Your contribution can guide someone’s learning journey. Share your
documents today.
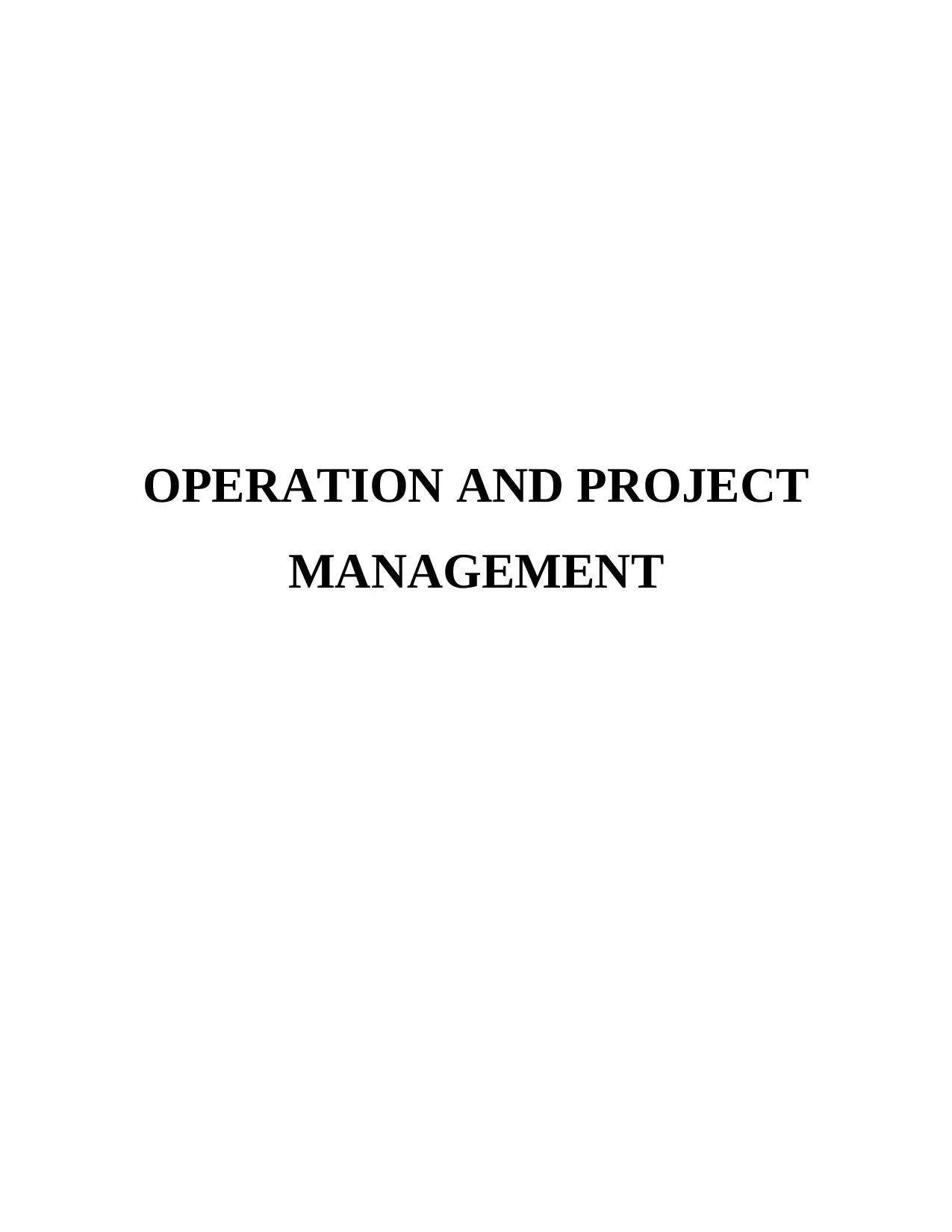
OPERATION AND PROJECT
MANAGEMENT
MANAGEMENT
Secure Best Marks with AI Grader
Need help grading? Try our AI Grader for instant feedback on your assignments.

TABLE OF CONTENTS
INTRODUCTION...........................................................................................................................1
ACTIVITY 1....................................................................................................................................1
Critical evaluation of appropriate theories and concepts (six sigma methodology and lean
principles)...............................................................................................................................1
ACTIVITY 2....................................................................................................................................4
Preparation and analysis of the effectiveness of continuous improvement plan by using
principles of operations management in XYZ........................................................................4
ACTIVITY 3....................................................................................................................................6
Critical evaluation of each stage of Project Life Cycle (PLC) and preparation of necessary
supporting documentation......................................................................................................6
ACTIVITY 4..................................................................................................................................11
Theories, concepts and models of PLC differentiating large and small scale projects........11
CONCLUSION..............................................................................................................................12
REFERENCE.................................................................................................................................14
INTRODUCTION...........................................................................................................................1
ACTIVITY 1....................................................................................................................................1
Critical evaluation of appropriate theories and concepts (six sigma methodology and lean
principles)...............................................................................................................................1
ACTIVITY 2....................................................................................................................................4
Preparation and analysis of the effectiveness of continuous improvement plan by using
principles of operations management in XYZ........................................................................4
ACTIVITY 3....................................................................................................................................6
Critical evaluation of each stage of Project Life Cycle (PLC) and preparation of necessary
supporting documentation......................................................................................................6
ACTIVITY 4..................................................................................................................................11
Theories, concepts and models of PLC differentiating large and small scale projects........11
CONCLUSION..............................................................................................................................12
REFERENCE.................................................................................................................................14
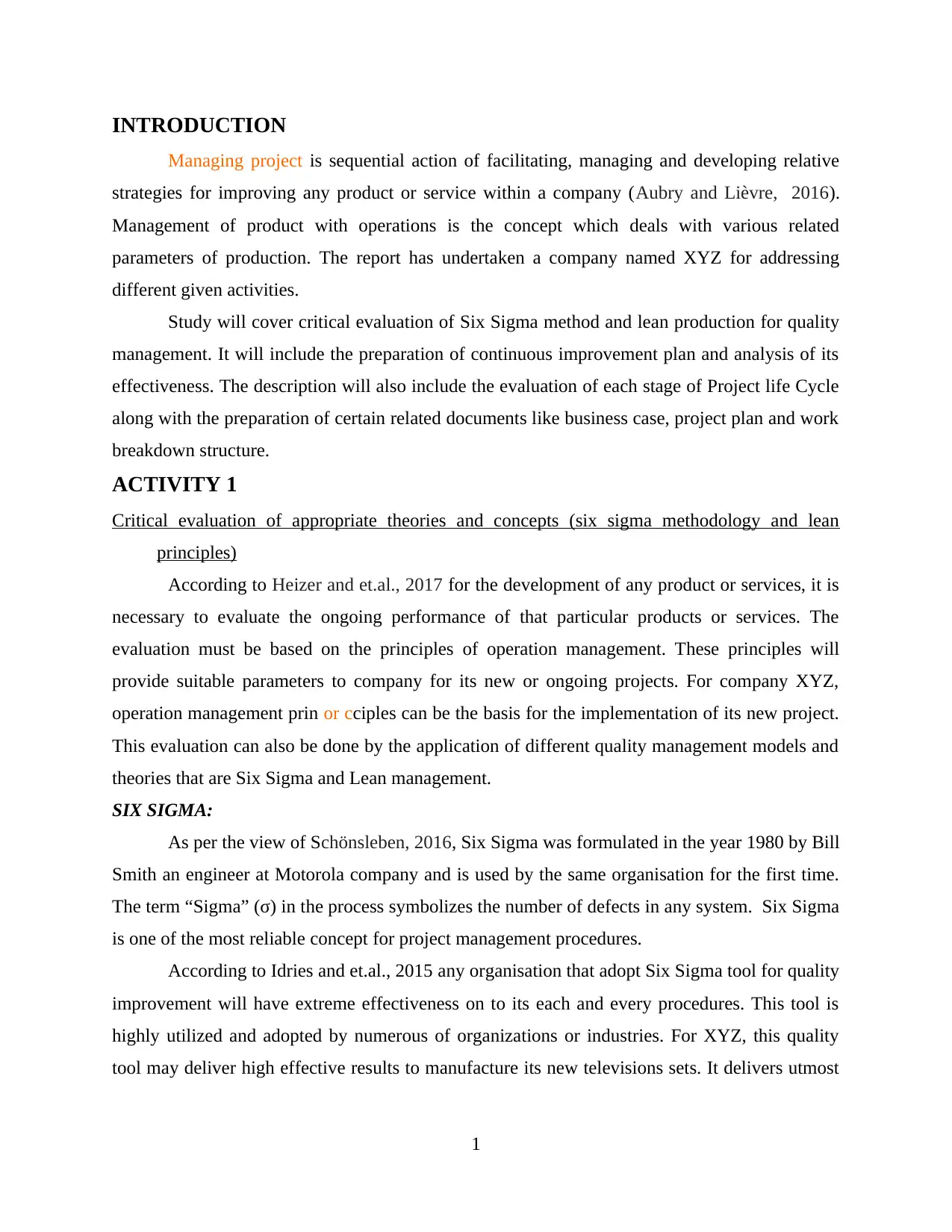
INTRODUCTION
Managing project is sequential action of facilitating, managing and developing relative
strategies for improving any product or service within a company (Aubry and Lièvre, 2016).
Management of product with operations is the concept which deals with various related
parameters of production. The report has undertaken a company named XYZ for addressing
different given activities.
Study will cover critical evaluation of Six Sigma method and lean production for quality
management. It will include the preparation of continuous improvement plan and analysis of its
effectiveness. The description will also include the evaluation of each stage of Project life Cycle
along with the preparation of certain related documents like business case, project plan and work
breakdown structure.
ACTIVITY 1
Critical evaluation of appropriate theories and concepts (six sigma methodology and lean
principles)
According to Heizer and et.al., 2017 for the development of any product or services, it is
necessary to evaluate the ongoing performance of that particular products or services. The
evaluation must be based on the principles of operation management. These principles will
provide suitable parameters to company for its new or ongoing projects. For company XYZ,
operation management prin or cciples can be the basis for the implementation of its new project.
This evaluation can also be done by the application of different quality management models and
theories that are Six Sigma and Lean management.
SIX SIGMA:
As per the view of Schönsleben, 2016, Six Sigma was formulated in the year 1980 by Bill
Smith an engineer at Motorola company and is used by the same organisation for the first time.
The term “Sigma” (σ) in the process symbolizes the number of defects in any system. Six Sigma
is one of the most reliable concept for project management procedures.
According to Idries and et.al., 2015 any organisation that adopt Six Sigma tool for quality
improvement will have extreme effectiveness on to its each and every procedures. This tool is
highly utilized and adopted by numerous of organizations or industries. For XYZ, this quality
tool may deliver high effective results to manufacture its new televisions sets. It delivers utmost
1
Managing project is sequential action of facilitating, managing and developing relative
strategies for improving any product or service within a company (Aubry and Lièvre, 2016).
Management of product with operations is the concept which deals with various related
parameters of production. The report has undertaken a company named XYZ for addressing
different given activities.
Study will cover critical evaluation of Six Sigma method and lean production for quality
management. It will include the preparation of continuous improvement plan and analysis of its
effectiveness. The description will also include the evaluation of each stage of Project life Cycle
along with the preparation of certain related documents like business case, project plan and work
breakdown structure.
ACTIVITY 1
Critical evaluation of appropriate theories and concepts (six sigma methodology and lean
principles)
According to Heizer and et.al., 2017 for the development of any product or services, it is
necessary to evaluate the ongoing performance of that particular products or services. The
evaluation must be based on the principles of operation management. These principles will
provide suitable parameters to company for its new or ongoing projects. For company XYZ,
operation management prin or cciples can be the basis for the implementation of its new project.
This evaluation can also be done by the application of different quality management models and
theories that are Six Sigma and Lean management.
SIX SIGMA:
As per the view of Schönsleben, 2016, Six Sigma was formulated in the year 1980 by Bill
Smith an engineer at Motorola company and is used by the same organisation for the first time.
The term “Sigma” (σ) in the process symbolizes the number of defects in any system. Six Sigma
is one of the most reliable concept for project management procedures.
According to Idries and et.al., 2015 any organisation that adopt Six Sigma tool for quality
improvement will have extreme effectiveness on to its each and every procedures. This tool is
highly utilized and adopted by numerous of organizations or industries. For XYZ, this quality
tool may deliver high effective results to manufacture its new televisions sets. It delivers utmost
1
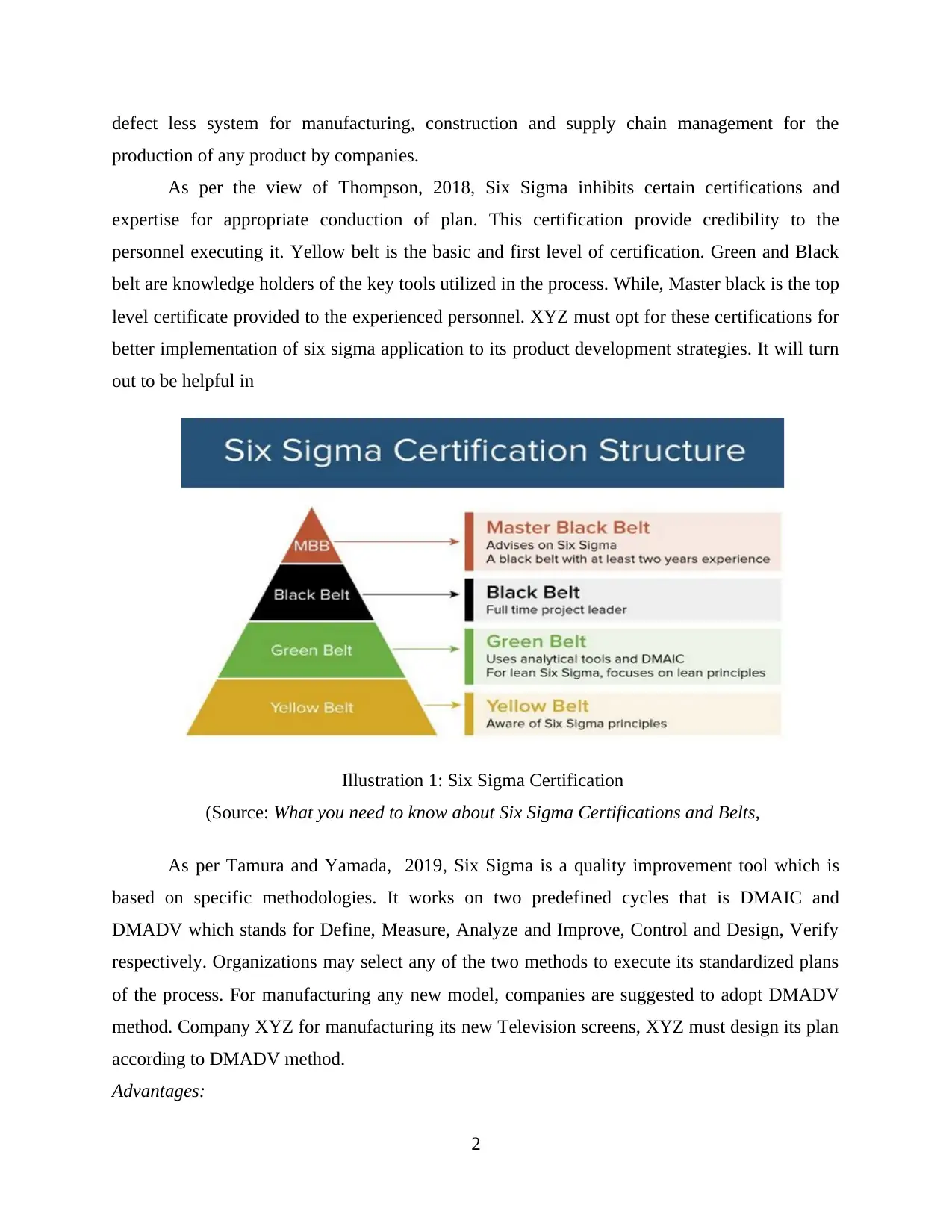
defect less system for manufacturing, construction and supply chain management for the
production of any product by companies.
As per the view of Thompson, 2018, Six Sigma inhibits certain certifications and
expertise for appropriate conduction of plan. This certification provide credibility to the
personnel executing it. Yellow belt is the basic and first level of certification. Green and Black
belt are knowledge holders of the key tools utilized in the process. While, Master black is the top
level certificate provided to the experienced personnel. XYZ must opt for these certifications for
better implementation of six sigma application to its product development strategies. It will turn
out to be helpful in
As per Tamura and Yamada, 2019, Six Sigma is a quality improvement tool which is
based on specific methodologies. It works on two predefined cycles that is DMAIC and
DMADV which stands for Define, Measure, Analyze and Improve, Control and Design, Verify
respectively. Organizations may select any of the two methods to execute its standardized plans
of the process. For manufacturing any new model, companies are suggested to adopt DMADV
method. Company XYZ for manufacturing its new Television screens, XYZ must design its plan
according to DMADV method.
Advantages:
2
Illustration 1: Six Sigma Certification
(Source: What you need to know about Six Sigma Certifications and Belts,
production of any product by companies.
As per the view of Thompson, 2018, Six Sigma inhibits certain certifications and
expertise for appropriate conduction of plan. This certification provide credibility to the
personnel executing it. Yellow belt is the basic and first level of certification. Green and Black
belt are knowledge holders of the key tools utilized in the process. While, Master black is the top
level certificate provided to the experienced personnel. XYZ must opt for these certifications for
better implementation of six sigma application to its product development strategies. It will turn
out to be helpful in
As per Tamura and Yamada, 2019, Six Sigma is a quality improvement tool which is
based on specific methodologies. It works on two predefined cycles that is DMAIC and
DMADV which stands for Define, Measure, Analyze and Improve, Control and Design, Verify
respectively. Organizations may select any of the two methods to execute its standardized plans
of the process. For manufacturing any new model, companies are suggested to adopt DMADV
method. Company XYZ for manufacturing its new Television screens, XYZ must design its plan
according to DMADV method.
Advantages:
2
Illustration 1: Six Sigma Certification
(Source: What you need to know about Six Sigma Certifications and Belts,
Secure Best Marks with AI Grader
Need help grading? Try our AI Grader for instant feedback on your assignments.
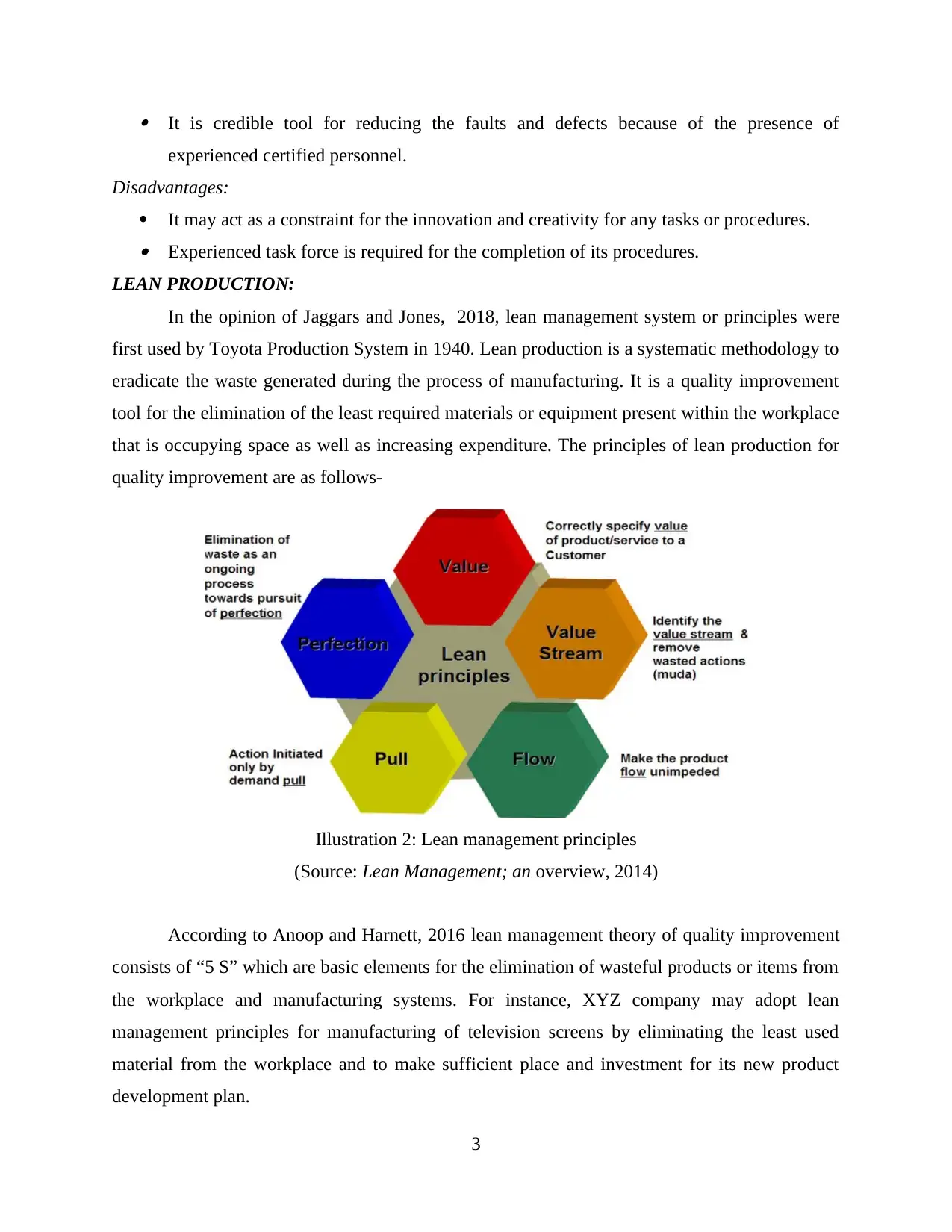
It is credible tool for reducing the faults and defects because of the presence of
experienced certified personnel.
Disadvantages:
It may act as a constraint for the innovation and creativity for any tasks or procedures. Experienced task force is required for the completion of its procedures.
LEAN PRODUCTION:
In the opinion of Jaggars and Jones, 2018, lean management system or principles were
first used by Toyota Production System in 1940. Lean production is a systematic methodology to
eradicate the waste generated during the process of manufacturing. It is a quality improvement
tool for the elimination of the least required materials or equipment present within the workplace
that is occupying space as well as increasing expenditure. The principles of lean production for
quality improvement are as follows-
According to Anoop and Harnett, 2016 lean management theory of quality improvement
consists of “5 S” which are basic elements for the elimination of wasteful products or items from
the workplace and manufacturing systems. For instance, XYZ company may adopt lean
management principles for manufacturing of television screens by eliminating the least used
material from the workplace and to make sufficient place and investment for its new product
development plan.
3
Illustration 2: Lean management principles
(Source: Lean Management; an overview, 2014)
experienced certified personnel.
Disadvantages:
It may act as a constraint for the innovation and creativity for any tasks or procedures. Experienced task force is required for the completion of its procedures.
LEAN PRODUCTION:
In the opinion of Jaggars and Jones, 2018, lean management system or principles were
first used by Toyota Production System in 1940. Lean production is a systematic methodology to
eradicate the waste generated during the process of manufacturing. It is a quality improvement
tool for the elimination of the least required materials or equipment present within the workplace
that is occupying space as well as increasing expenditure. The principles of lean production for
quality improvement are as follows-
According to Anoop and Harnett, 2016 lean management theory of quality improvement
consists of “5 S” which are basic elements for the elimination of wasteful products or items from
the workplace and manufacturing systems. For instance, XYZ company may adopt lean
management principles for manufacturing of television screens by eliminating the least used
material from the workplace and to make sufficient place and investment for its new product
development plan.
3
Illustration 2: Lean management principles
(Source: Lean Management; an overview, 2014)
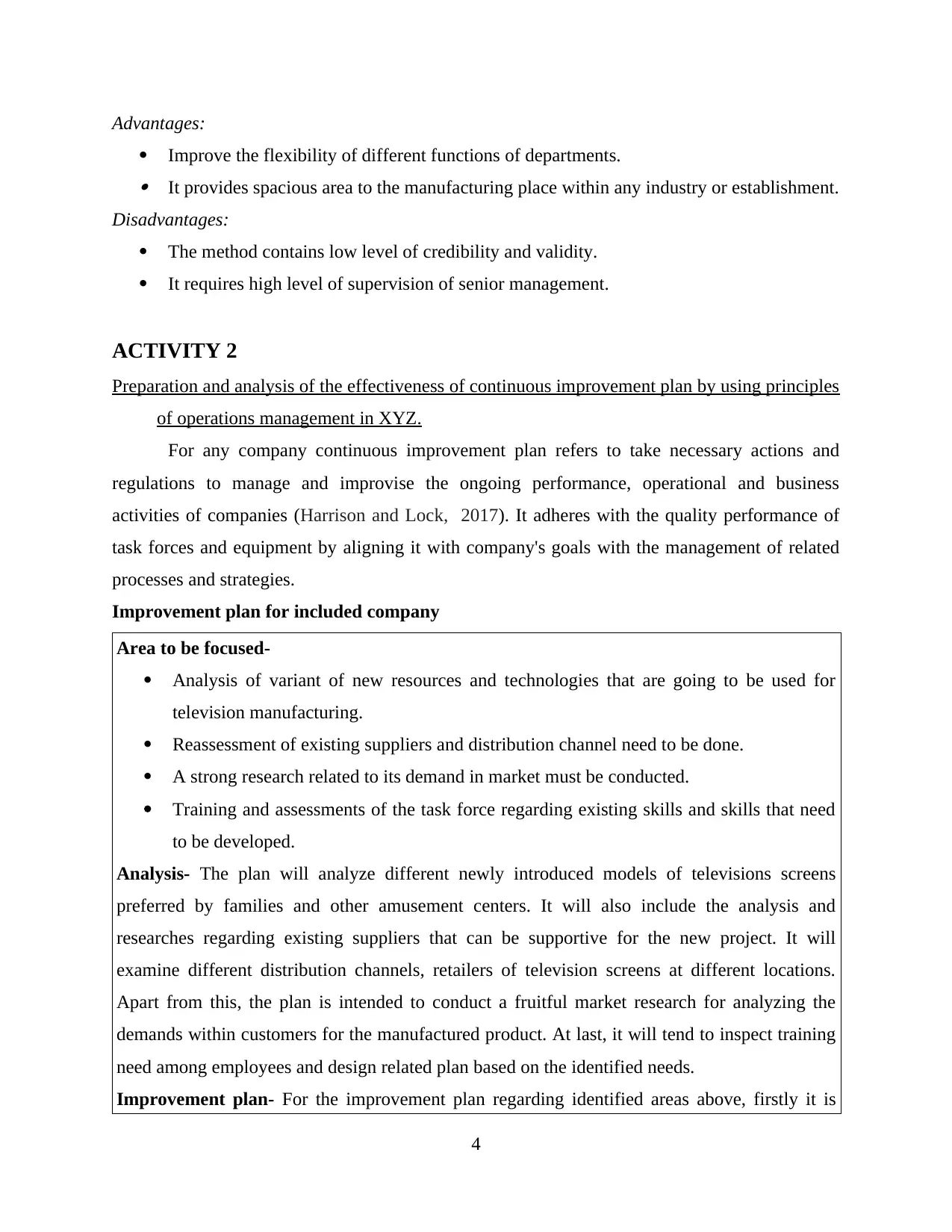
Advantages:
Improve the flexibility of different functions of departments. It provides spacious area to the manufacturing place within any industry or establishment.
Disadvantages:
The method contains low level of credibility and validity.
It requires high level of supervision of senior management.
ACTIVITY 2
Preparation and analysis of the effectiveness of continuous improvement plan by using principles
of operations management in XYZ.
For any company continuous improvement plan refers to take necessary actions and
regulations to manage and improvise the ongoing performance, operational and business
activities of companies (Harrison and Lock, 2017). It adheres with the quality performance of
task forces and equipment by aligning it with company's goals with the management of related
processes and strategies.
Improvement plan for included company
Area to be focused-
Analysis of variant of new resources and technologies that are going to be used for
television manufacturing.
Reassessment of existing suppliers and distribution channel need to be done.
A strong research related to its demand in market must be conducted.
Training and assessments of the task force regarding existing skills and skills that need
to be developed.
Analysis- The plan will analyze different newly introduced models of televisions screens
preferred by families and other amusement centers. It will also include the analysis and
researches regarding existing suppliers that can be supportive for the new project. It will
examine different distribution channels, retailers of television screens at different locations.
Apart from this, the plan is intended to conduct a fruitful market research for analyzing the
demands within customers for the manufactured product. At last, it will tend to inspect training
need among employees and design related plan based on the identified needs.
Improvement plan- For the improvement plan regarding identified areas above, firstly it is
4
Improve the flexibility of different functions of departments. It provides spacious area to the manufacturing place within any industry or establishment.
Disadvantages:
The method contains low level of credibility and validity.
It requires high level of supervision of senior management.
ACTIVITY 2
Preparation and analysis of the effectiveness of continuous improvement plan by using principles
of operations management in XYZ.
For any company continuous improvement plan refers to take necessary actions and
regulations to manage and improvise the ongoing performance, operational and business
activities of companies (Harrison and Lock, 2017). It adheres with the quality performance of
task forces and equipment by aligning it with company's goals with the management of related
processes and strategies.
Improvement plan for included company
Area to be focused-
Analysis of variant of new resources and technologies that are going to be used for
television manufacturing.
Reassessment of existing suppliers and distribution channel need to be done.
A strong research related to its demand in market must be conducted.
Training and assessments of the task force regarding existing skills and skills that need
to be developed.
Analysis- The plan will analyze different newly introduced models of televisions screens
preferred by families and other amusement centers. It will also include the analysis and
researches regarding existing suppliers that can be supportive for the new project. It will
examine different distribution channels, retailers of television screens at different locations.
Apart from this, the plan is intended to conduct a fruitful market research for analyzing the
demands within customers for the manufactured product. At last, it will tend to inspect training
need among employees and design related plan based on the identified needs.
Improvement plan- For the improvement plan regarding identified areas above, firstly it is
4
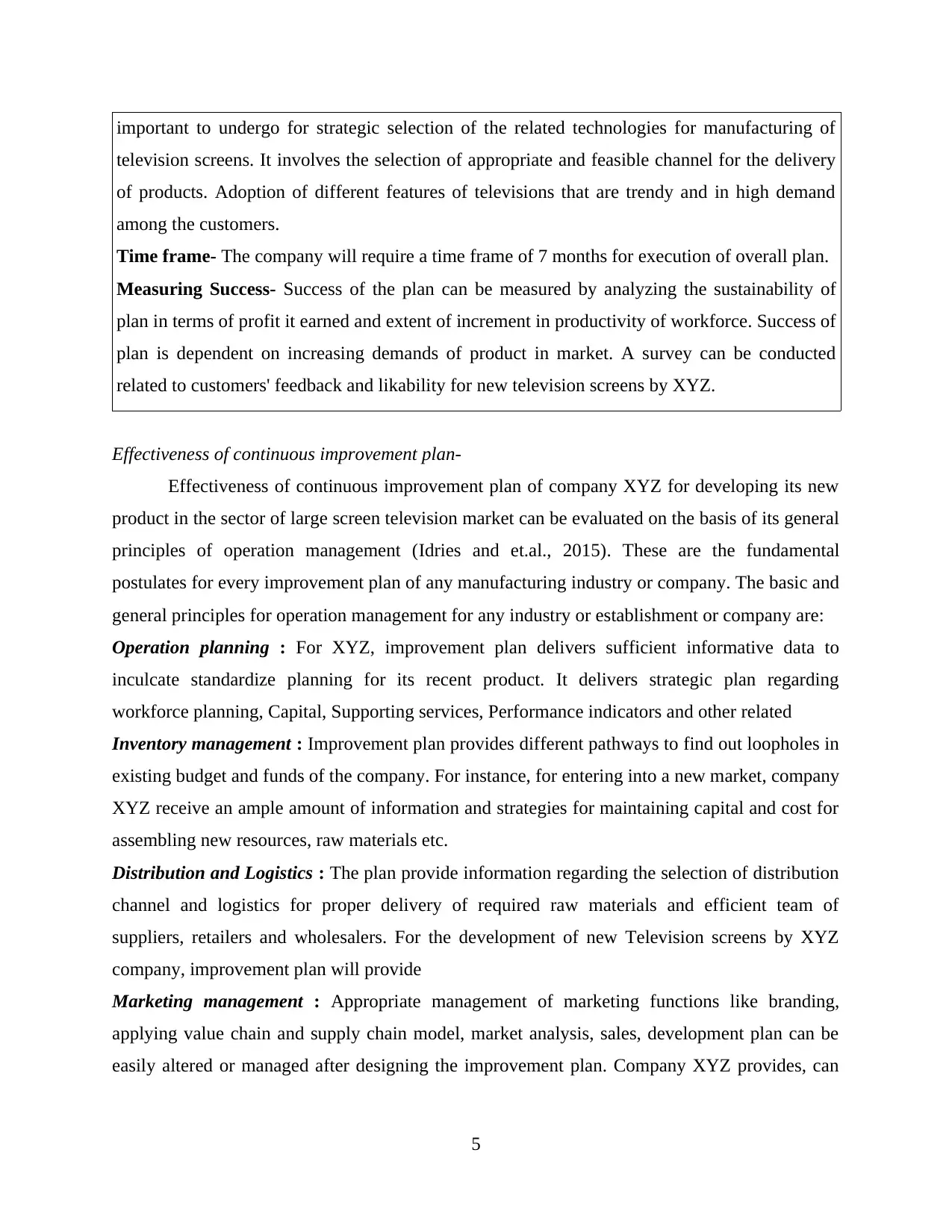
important to undergo for strategic selection of the related technologies for manufacturing of
television screens. It involves the selection of appropriate and feasible channel for the delivery
of products. Adoption of different features of televisions that are trendy and in high demand
among the customers.
Time frame- The company will require a time frame of 7 months for execution of overall plan.
Measuring Success- Success of the plan can be measured by analyzing the sustainability of
plan in terms of profit it earned and extent of increment in productivity of workforce. Success of
plan is dependent on increasing demands of product in market. A survey can be conducted
related to customers' feedback and likability for new television screens by XYZ.
Effectiveness of continuous improvement plan-
Effectiveness of continuous improvement plan of company XYZ for developing its new
product in the sector of large screen television market can be evaluated on the basis of its general
principles of operation management (Idries and et.al., 2015). These are the fundamental
postulates for every improvement plan of any manufacturing industry or company. The basic and
general principles for operation management for any industry or establishment or company are:
Operation planning : For XYZ, improvement plan delivers sufficient informative data to
inculcate standardize planning for its recent product. It delivers strategic plan regarding
workforce planning, Capital, Supporting services, Performance indicators and other related
Inventory management : Improvement plan provides different pathways to find out loopholes in
existing budget and funds of the company. For instance, for entering into a new market, company
XYZ receive an ample amount of information and strategies for maintaining capital and cost for
assembling new resources, raw materials etc.
Distribution and Logistics : The plan provide information regarding the selection of distribution
channel and logistics for proper delivery of required raw materials and efficient team of
suppliers, retailers and wholesalers. For the development of new Television screens by XYZ
company, improvement plan will provide
Marketing management : Appropriate management of marketing functions like branding,
applying value chain and supply chain model, market analysis, sales, development plan can be
easily altered or managed after designing the improvement plan. Company XYZ provides, can
5
television screens. It involves the selection of appropriate and feasible channel for the delivery
of products. Adoption of different features of televisions that are trendy and in high demand
among the customers.
Time frame- The company will require a time frame of 7 months for execution of overall plan.
Measuring Success- Success of the plan can be measured by analyzing the sustainability of
plan in terms of profit it earned and extent of increment in productivity of workforce. Success of
plan is dependent on increasing demands of product in market. A survey can be conducted
related to customers' feedback and likability for new television screens by XYZ.
Effectiveness of continuous improvement plan-
Effectiveness of continuous improvement plan of company XYZ for developing its new
product in the sector of large screen television market can be evaluated on the basis of its general
principles of operation management (Idries and et.al., 2015). These are the fundamental
postulates for every improvement plan of any manufacturing industry or company. The basic and
general principles for operation management for any industry or establishment or company are:
Operation planning : For XYZ, improvement plan delivers sufficient informative data to
inculcate standardize planning for its recent product. It delivers strategic plan regarding
workforce planning, Capital, Supporting services, Performance indicators and other related
Inventory management : Improvement plan provides different pathways to find out loopholes in
existing budget and funds of the company. For instance, for entering into a new market, company
XYZ receive an ample amount of information and strategies for maintaining capital and cost for
assembling new resources, raw materials etc.
Distribution and Logistics : The plan provide information regarding the selection of distribution
channel and logistics for proper delivery of required raw materials and efficient team of
suppliers, retailers and wholesalers. For the development of new Television screens by XYZ
company, improvement plan will provide
Marketing management : Appropriate management of marketing functions like branding,
applying value chain and supply chain model, market analysis, sales, development plan can be
easily altered or managed after designing the improvement plan. Company XYZ provides, can
5
Paraphrase This Document
Need a fresh take? Get an instant paraphrase of this document with our AI Paraphraser
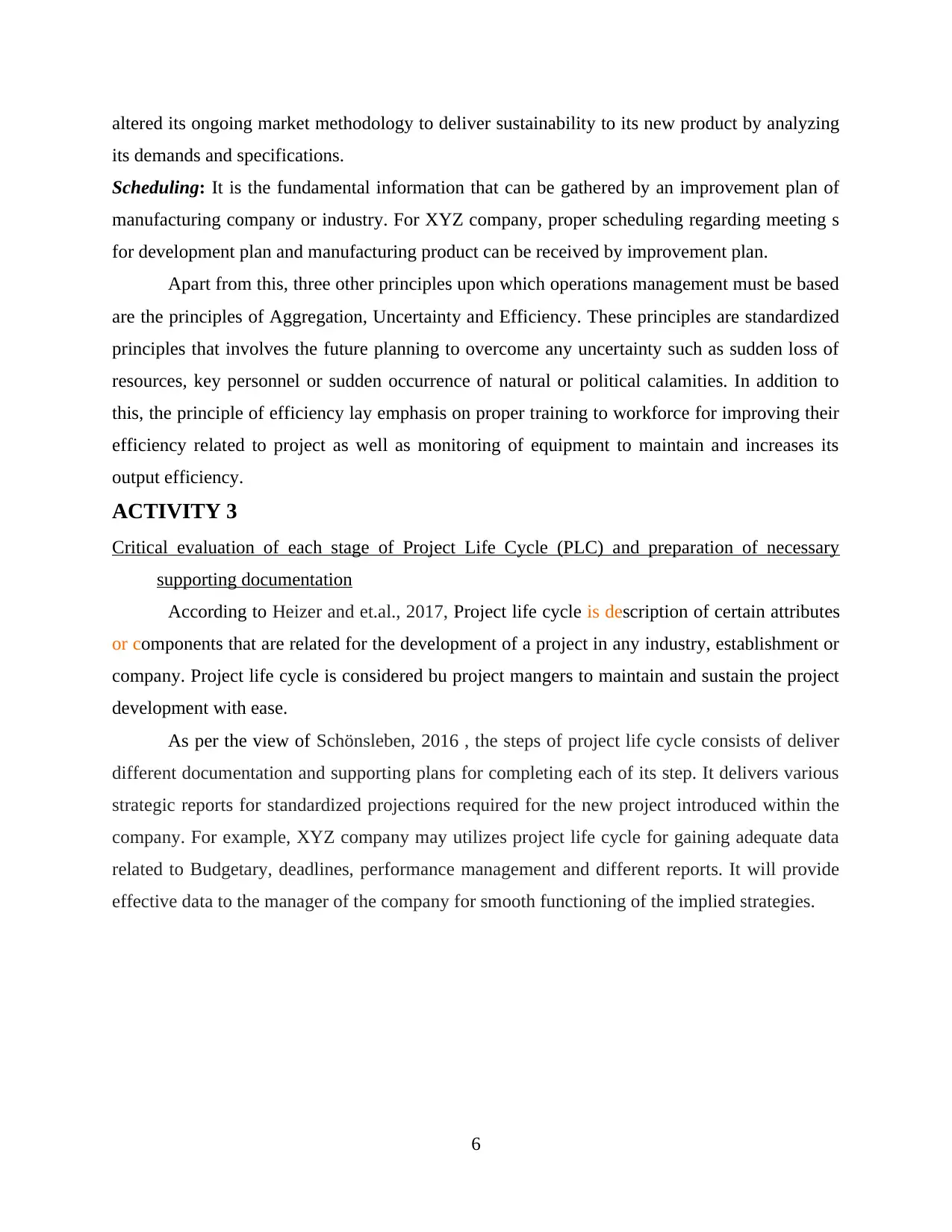
altered its ongoing market methodology to deliver sustainability to its new product by analyzing
its demands and specifications.
Scheduling: It is the fundamental information that can be gathered by an improvement plan of
manufacturing company or industry. For XYZ company, proper scheduling regarding meeting s
for development plan and manufacturing product can be received by improvement plan.
Apart from this, three other principles upon which operations management must be based
are the principles of Aggregation, Uncertainty and Efficiency. These principles are standardized
principles that involves the future planning to overcome any uncertainty such as sudden loss of
resources, key personnel or sudden occurrence of natural or political calamities. In addition to
this, the principle of efficiency lay emphasis on proper training to workforce for improving their
efficiency related to project as well as monitoring of equipment to maintain and increases its
output efficiency.
ACTIVITY 3
Critical evaluation of each stage of Project Life Cycle (PLC) and preparation of necessary
supporting documentation
According to Heizer and et.al., 2017, Project life cycle is description of certain attributes
or components that are related for the development of a project in any industry, establishment or
company. Project life cycle is considered bu project mangers to maintain and sustain the project
development with ease.
As per the view of Schönsleben, 2016 , the steps of project life cycle consists of deliver
different documentation and supporting plans for completing each of its step. It delivers various
strategic reports for standardized projections required for the new project introduced within the
company. For example, XYZ company may utilizes project life cycle for gaining adequate data
related to Budgetary, deadlines, performance management and different reports. It will provide
effective data to the manager of the company for smooth functioning of the implied strategies.
6
its demands and specifications.
Scheduling: It is the fundamental information that can be gathered by an improvement plan of
manufacturing company or industry. For XYZ company, proper scheduling regarding meeting s
for development plan and manufacturing product can be received by improvement plan.
Apart from this, three other principles upon which operations management must be based
are the principles of Aggregation, Uncertainty and Efficiency. These principles are standardized
principles that involves the future planning to overcome any uncertainty such as sudden loss of
resources, key personnel or sudden occurrence of natural or political calamities. In addition to
this, the principle of efficiency lay emphasis on proper training to workforce for improving their
efficiency related to project as well as monitoring of equipment to maintain and increases its
output efficiency.
ACTIVITY 3
Critical evaluation of each stage of Project Life Cycle (PLC) and preparation of necessary
supporting documentation
According to Heizer and et.al., 2017, Project life cycle is description of certain attributes
or components that are related for the development of a project in any industry, establishment or
company. Project life cycle is considered bu project mangers to maintain and sustain the project
development with ease.
As per the view of Schönsleben, 2016 , the steps of project life cycle consists of deliver
different documentation and supporting plans for completing each of its step. It delivers various
strategic reports for standardized projections required for the new project introduced within the
company. For example, XYZ company may utilizes project life cycle for gaining adequate data
related to Budgetary, deadlines, performance management and different reports. It will provide
effective data to the manager of the company for smooth functioning of the implied strategies.
6
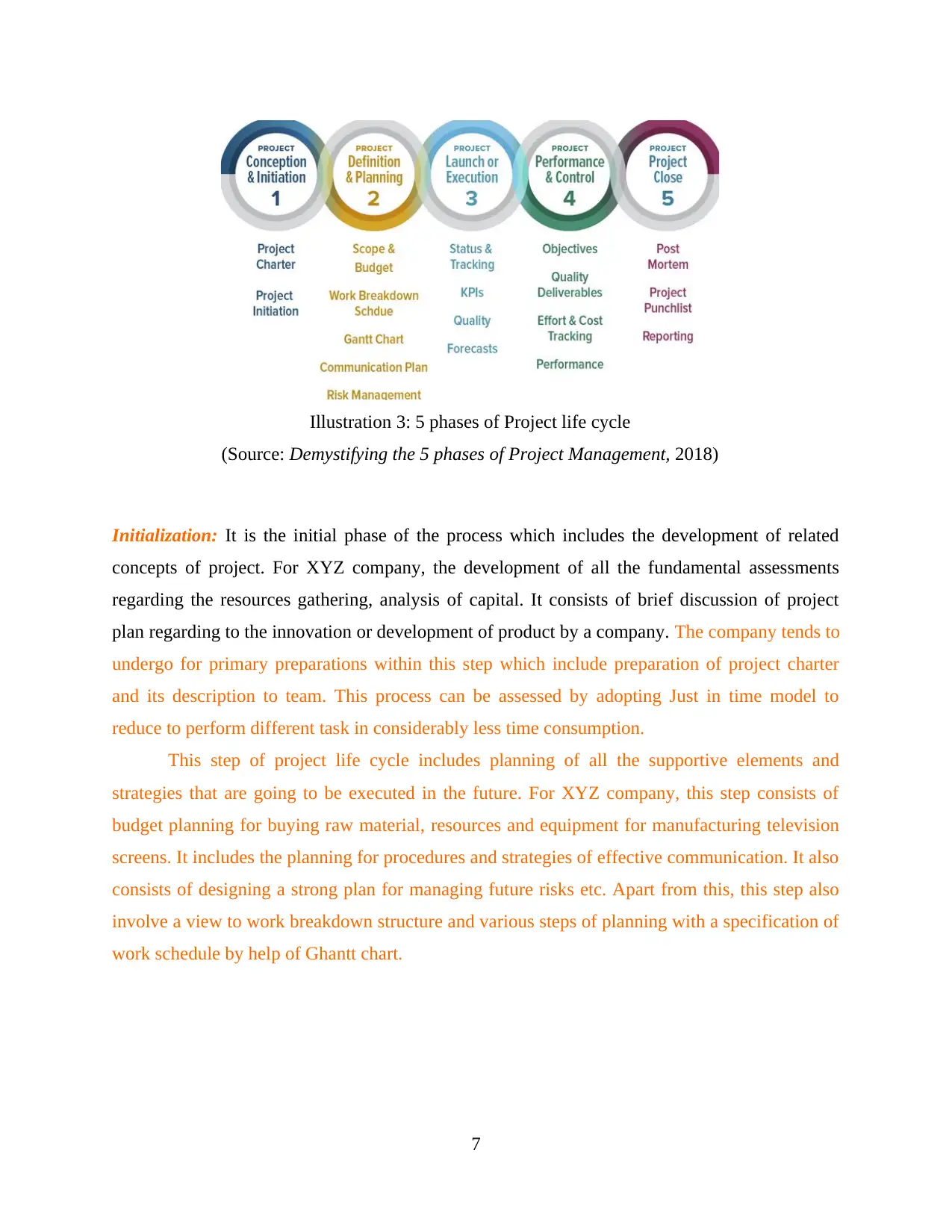
Initialization: It is the initial phase of the process which includes the development of related
concepts of project. For XYZ company, the development of all the fundamental assessments
regarding the resources gathering, analysis of capital. It consists of brief discussion of project
plan regarding to the innovation or development of product by a company. The company tends to
undergo for primary preparations within this step which include preparation of project charter
and its description to team. This process can be assessed by adopting Just in time model to
reduce to perform different task in considerably less time consumption.
This step of project life cycle includes planning of all the supportive elements and
strategies that are going to be executed in the future. For XYZ company, this step consists of
budget planning for buying raw material, resources and equipment for manufacturing television
screens. It includes the planning for procedures and strategies of effective communication. It also
consists of designing a strong plan for managing future risks etc. Apart from this, this step also
involve a view to work breakdown structure and various steps of planning with a specification of
work schedule by help of Ghantt chart.
7
Illustration 3: 5 phases of Project life cycle
(Source: Demystifying the 5 phases of Project Management, 2018)
concepts of project. For XYZ company, the development of all the fundamental assessments
regarding the resources gathering, analysis of capital. It consists of brief discussion of project
plan regarding to the innovation or development of product by a company. The company tends to
undergo for primary preparations within this step which include preparation of project charter
and its description to team. This process can be assessed by adopting Just in time model to
reduce to perform different task in considerably less time consumption.
This step of project life cycle includes planning of all the supportive elements and
strategies that are going to be executed in the future. For XYZ company, this step consists of
budget planning for buying raw material, resources and equipment for manufacturing television
screens. It includes the planning for procedures and strategies of effective communication. It also
consists of designing a strong plan for managing future risks etc. Apart from this, this step also
involve a view to work breakdown structure and various steps of planning with a specification of
work schedule by help of Ghantt chart.
7
Illustration 3: 5 phases of Project life cycle
(Source: Demystifying the 5 phases of Project Management, 2018)
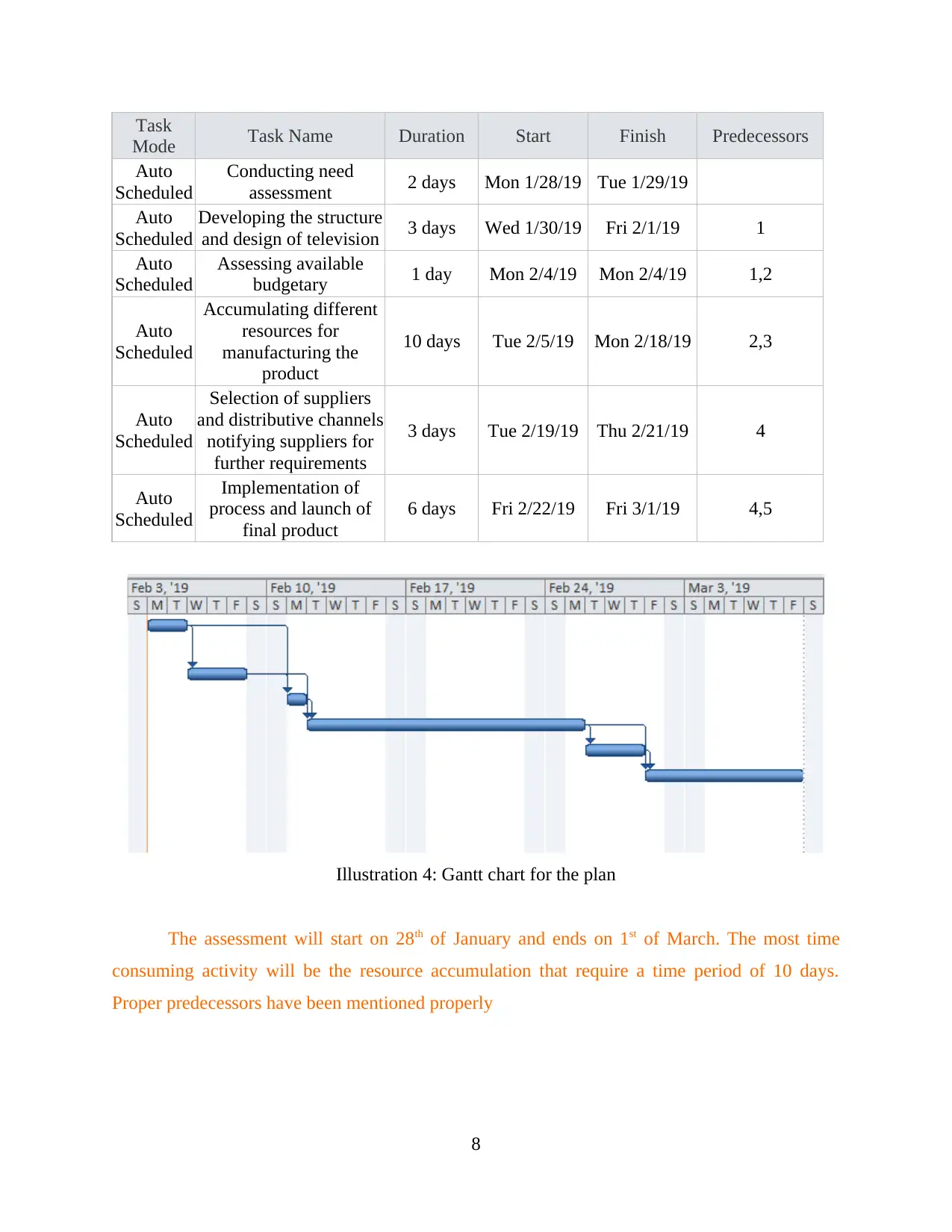
Task
Mode Task Name Duration Start Finish Predecessors
Auto
Scheduled
Conducting need
assessment 2 days Mon 1/28/19 Tue 1/29/19
Auto
Scheduled
Developing the structure
and design of television 3 days Wed 1/30/19 Fri 2/1/19 1
Auto
Scheduled
Assessing available
budgetary 1 day Mon 2/4/19 Mon 2/4/19 1,2
Auto
Scheduled
Accumulating different
resources for
manufacturing the
product
10 days Tue 2/5/19 Mon 2/18/19 2,3
Auto
Scheduled
Selection of suppliers
and distributive channels
notifying suppliers for
further requirements
3 days Tue 2/19/19 Thu 2/21/19 4
Auto
Scheduled
Implementation of
process and launch of
final product
6 days Fri 2/22/19 Fri 3/1/19 4,5
Illustration 4: Gantt chart for the plan
The assessment will start on 28th of January and ends on 1st of March. The most time
consuming activity will be the resource accumulation that require a time period of 10 days.
Proper predecessors have been mentioned properly
8
Mode Task Name Duration Start Finish Predecessors
Auto
Scheduled
Conducting need
assessment 2 days Mon 1/28/19 Tue 1/29/19
Auto
Scheduled
Developing the structure
and design of television 3 days Wed 1/30/19 Fri 2/1/19 1
Auto
Scheduled
Assessing available
budgetary 1 day Mon 2/4/19 Mon 2/4/19 1,2
Auto
Scheduled
Accumulating different
resources for
manufacturing the
product
10 days Tue 2/5/19 Mon 2/18/19 2,3
Auto
Scheduled
Selection of suppliers
and distributive channels
notifying suppliers for
further requirements
3 days Tue 2/19/19 Thu 2/21/19 4
Auto
Scheduled
Implementation of
process and launch of
final product
6 days Fri 2/22/19 Fri 3/1/19 4,5
Illustration 4: Gantt chart for the plan
The assessment will start on 28th of January and ends on 1st of March. The most time
consuming activity will be the resource accumulation that require a time period of 10 days.
Proper predecessors have been mentioned properly
8
Secure Best Marks with AI Grader
Need help grading? Try our AI Grader for instant feedback on your assignments.
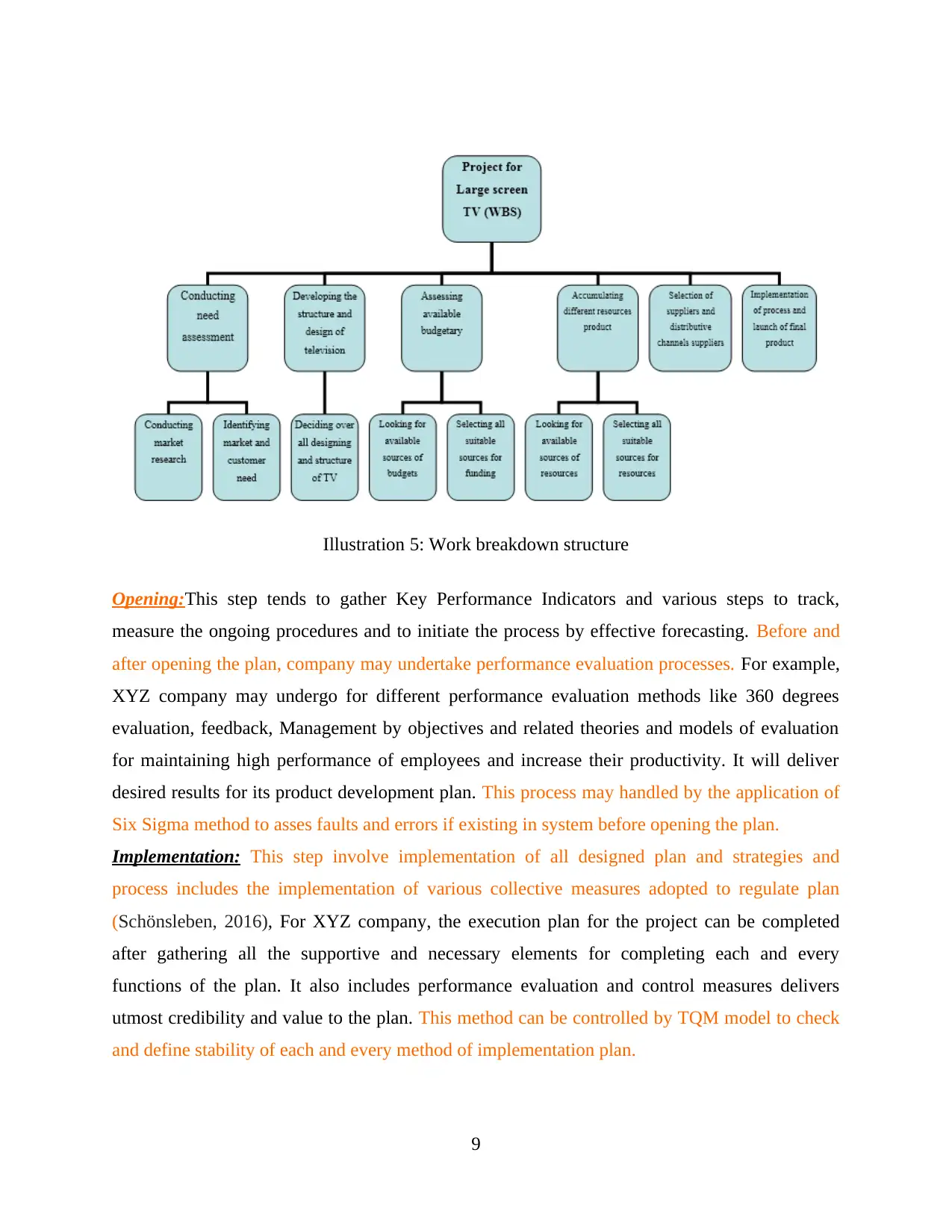
Opening:This step tends to gather Key Performance Indicators and various steps to track,
measure the ongoing procedures and to initiate the process by effective forecasting. Before and
after opening the plan, company may undertake performance evaluation processes. For example,
XYZ company may undergo for different performance evaluation methods like 360 degrees
evaluation, feedback, Management by objectives and related theories and models of evaluation
for maintaining high performance of employees and increase their productivity. It will deliver
desired results for its product development plan. This process may handled by the application of
Six Sigma method to asses faults and errors if existing in system before opening the plan.
Implementation: This step involve implementation of all designed plan and strategies and
process includes the implementation of various collective measures adopted to regulate plan
(Schönsleben, 2016), For XYZ company, the execution plan for the project can be completed
after gathering all the supportive and necessary elements for completing each and every
functions of the plan. It also includes performance evaluation and control measures delivers
utmost credibility and value to the plan. This method can be controlled by TQM model to check
and define stability of each and every method of implementation plan.
9
Illustration 5: Work breakdown structure
measure the ongoing procedures and to initiate the process by effective forecasting. Before and
after opening the plan, company may undertake performance evaluation processes. For example,
XYZ company may undergo for different performance evaluation methods like 360 degrees
evaluation, feedback, Management by objectives and related theories and models of evaluation
for maintaining high performance of employees and increase their productivity. It will deliver
desired results for its product development plan. This process may handled by the application of
Six Sigma method to asses faults and errors if existing in system before opening the plan.
Implementation: This step involve implementation of all designed plan and strategies and
process includes the implementation of various collective measures adopted to regulate plan
(Schönsleben, 2016), For XYZ company, the execution plan for the project can be completed
after gathering all the supportive and necessary elements for completing each and every
functions of the plan. It also includes performance evaluation and control measures delivers
utmost credibility and value to the plan. This method can be controlled by TQM model to check
and define stability of each and every method of implementation plan.
9
Illustration 5: Work breakdown structure
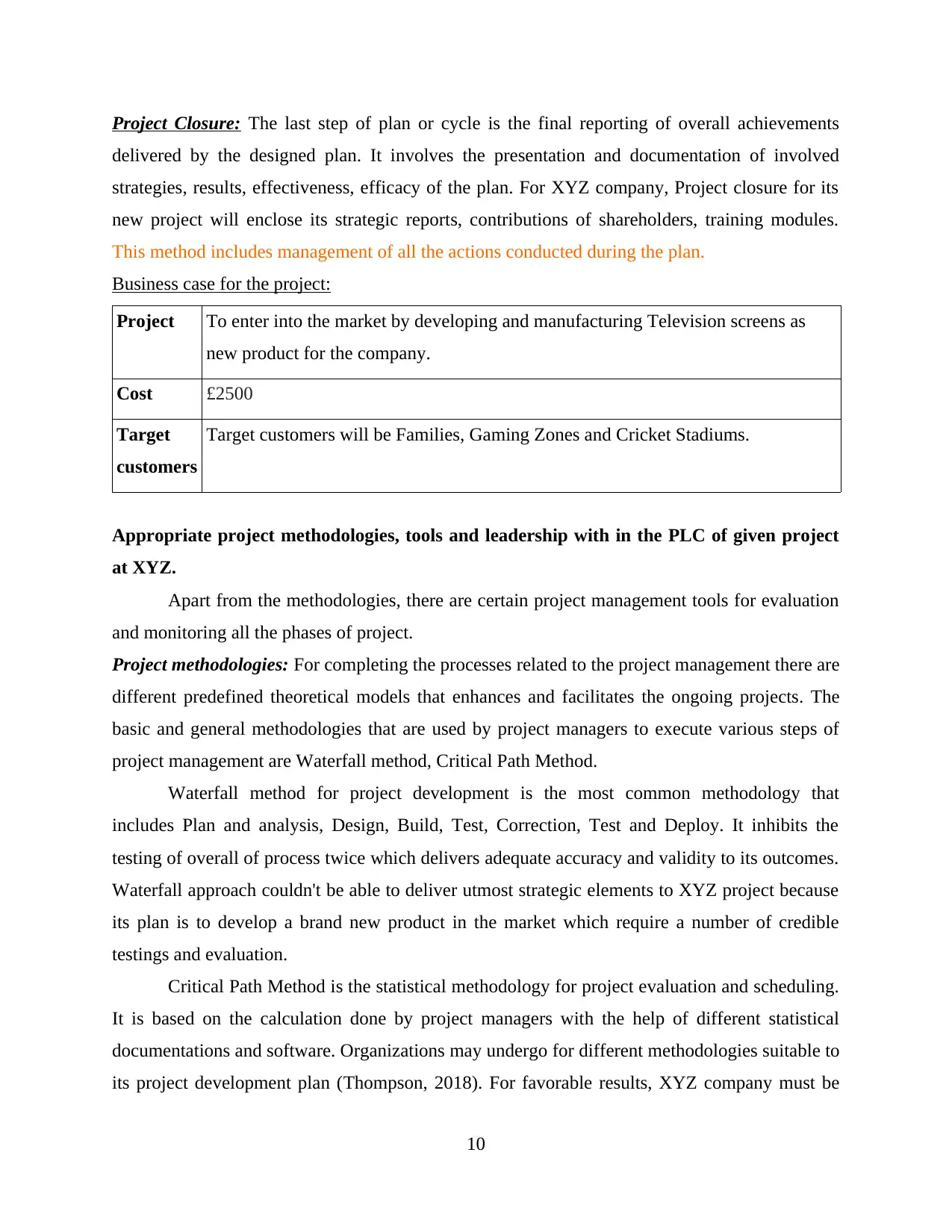
Project Closure: The last step of plan or cycle is the final reporting of overall achievements
delivered by the designed plan. It involves the presentation and documentation of involved
strategies, results, effectiveness, efficacy of the plan. For XYZ company, Project closure for its
new project will enclose its strategic reports, contributions of shareholders, training modules.
This method includes management of all the actions conducted during the plan.
Business case for the project:
Project To enter into the market by developing and manufacturing Television screens as
new product for the company.
Cost £2500
Target
customers
Target customers will be Families, Gaming Zones and Cricket Stadiums.
Appropriate project methodologies, tools and leadership with in the PLC of given project
at XYZ.
Apart from the methodologies, there are certain project management tools for evaluation
and monitoring all the phases of project.
Project methodologies: For completing the processes related to the project management there are
different predefined theoretical models that enhances and facilitates the ongoing projects. The
basic and general methodologies that are used by project managers to execute various steps of
project management are Waterfall method, Critical Path Method.
Waterfall method for project development is the most common methodology that
includes Plan and analysis, Design, Build, Test, Correction, Test and Deploy. It inhibits the
testing of overall of process twice which delivers adequate accuracy and validity to its outcomes.
Waterfall approach couldn't be able to deliver utmost strategic elements to XYZ project because
its plan is to develop a brand new product in the market which require a number of credible
testings and evaluation.
Critical Path Method is the statistical methodology for project evaluation and scheduling.
It is based on the calculation done by project managers with the help of different statistical
documentations and software. Organizations may undergo for different methodologies suitable to
its project development plan (Thompson, 2018). For favorable results, XYZ company must be
10
delivered by the designed plan. It involves the presentation and documentation of involved
strategies, results, effectiveness, efficacy of the plan. For XYZ company, Project closure for its
new project will enclose its strategic reports, contributions of shareholders, training modules.
This method includes management of all the actions conducted during the plan.
Business case for the project:
Project To enter into the market by developing and manufacturing Television screens as
new product for the company.
Cost £2500
Target
customers
Target customers will be Families, Gaming Zones and Cricket Stadiums.
Appropriate project methodologies, tools and leadership with in the PLC of given project
at XYZ.
Apart from the methodologies, there are certain project management tools for evaluation
and monitoring all the phases of project.
Project methodologies: For completing the processes related to the project management there are
different predefined theoretical models that enhances and facilitates the ongoing projects. The
basic and general methodologies that are used by project managers to execute various steps of
project management are Waterfall method, Critical Path Method.
Waterfall method for project development is the most common methodology that
includes Plan and analysis, Design, Build, Test, Correction, Test and Deploy. It inhibits the
testing of overall of process twice which delivers adequate accuracy and validity to its outcomes.
Waterfall approach couldn't be able to deliver utmost strategic elements to XYZ project because
its plan is to develop a brand new product in the market which require a number of credible
testings and evaluation.
Critical Path Method is the statistical methodology for project evaluation and scheduling.
It is based on the calculation done by project managers with the help of different statistical
documentations and software. Organizations may undergo for different methodologies suitable to
its project development plan (Thompson, 2018). For favorable results, XYZ company must be
10
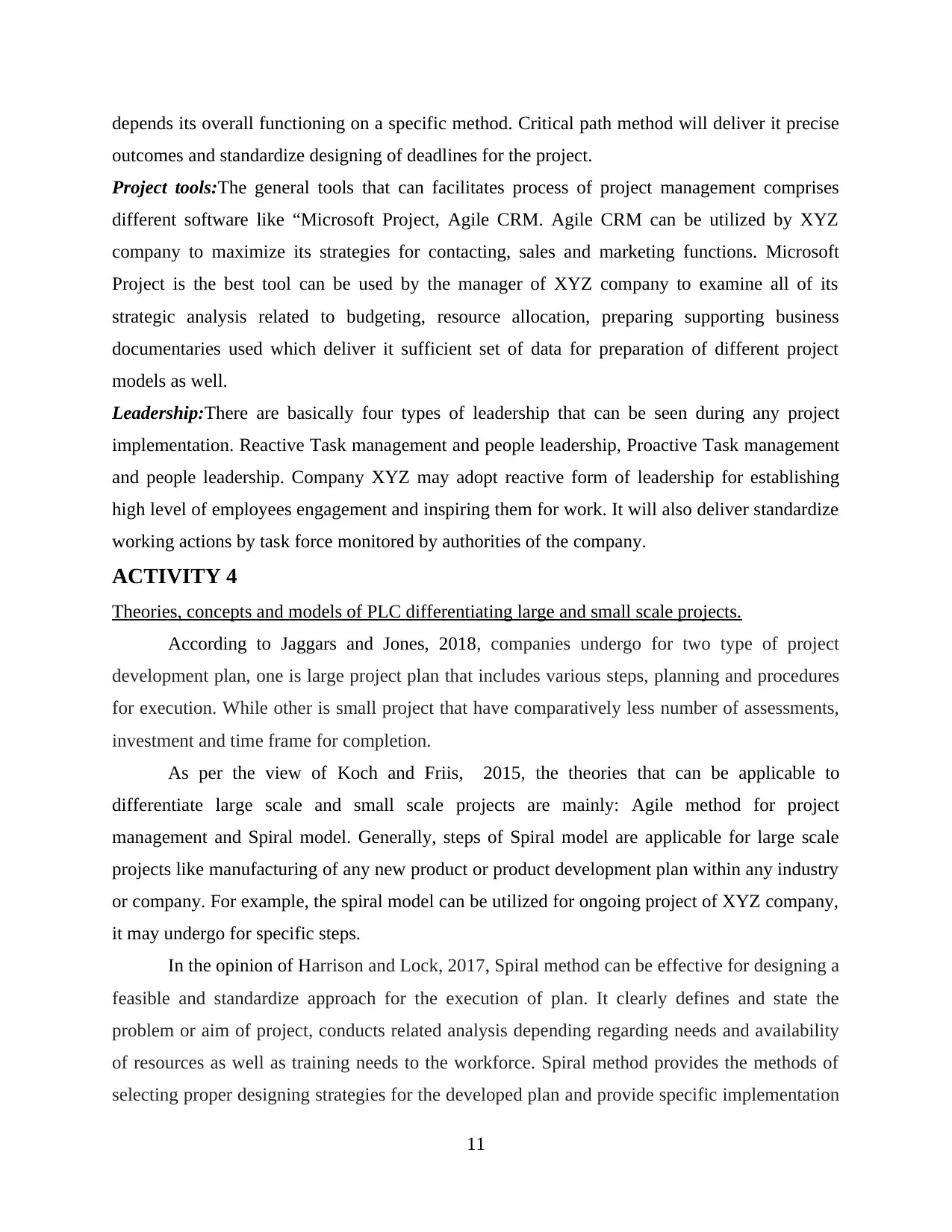
depends its overall functioning on a specific method. Critical path method will deliver it precise
outcomes and standardize designing of deadlines for the project.
Project tools:The general tools that can facilitates process of project management comprises
different software like “Microsoft Project, Agile CRM. Agile CRM can be utilized by XYZ
company to maximize its strategies for contacting, sales and marketing functions. Microsoft
Project is the best tool can be used by the manager of XYZ company to examine all of its
strategic analysis related to budgeting, resource allocation, preparing supporting business
documentaries used which deliver it sufficient set of data for preparation of different project
models as well.
Leadership:There are basically four types of leadership that can be seen during any project
implementation. Reactive Task management and people leadership, Proactive Task management
and people leadership. Company XYZ may adopt reactive form of leadership for establishing
high level of employees engagement and inspiring them for work. It will also deliver standardize
working actions by task force monitored by authorities of the company.
ACTIVITY 4
Theories, concepts and models of PLC differentiating large and small scale projects.
According to Jaggars and Jones, 2018, companies undergo for two type of project
development plan, one is large project plan that includes various steps, planning and procedures
for execution. While other is small project that have comparatively less number of assessments,
investment and time frame for completion.
As per the view of Koch and Friis, 2015, the theories that can be applicable to
differentiate large scale and small scale projects are mainly: Agile method for project
management and Spiral model. Generally, steps of Spiral model are applicable for large scale
projects like manufacturing of any new product or product development plan within any industry
or company. For example, the spiral model can be utilized for ongoing project of XYZ company,
it may undergo for specific steps.
In the opinion of Harrison and Lock, 2017, Spiral method can be effective for designing a
feasible and standardize approach for the execution of plan. It clearly defines and state the
problem or aim of project, conducts related analysis depending regarding needs and availability
of resources as well as training needs to the workforce. Spiral method provides the methods of
selecting proper designing strategies for the developed plan and provide specific implementation
11
outcomes and standardize designing of deadlines for the project.
Project tools:The general tools that can facilitates process of project management comprises
different software like “Microsoft Project, Agile CRM. Agile CRM can be utilized by XYZ
company to maximize its strategies for contacting, sales and marketing functions. Microsoft
Project is the best tool can be used by the manager of XYZ company to examine all of its
strategic analysis related to budgeting, resource allocation, preparing supporting business
documentaries used which deliver it sufficient set of data for preparation of different project
models as well.
Leadership:There are basically four types of leadership that can be seen during any project
implementation. Reactive Task management and people leadership, Proactive Task management
and people leadership. Company XYZ may adopt reactive form of leadership for establishing
high level of employees engagement and inspiring them for work. It will also deliver standardize
working actions by task force monitored by authorities of the company.
ACTIVITY 4
Theories, concepts and models of PLC differentiating large and small scale projects.
According to Jaggars and Jones, 2018, companies undergo for two type of project
development plan, one is large project plan that includes various steps, planning and procedures
for execution. While other is small project that have comparatively less number of assessments,
investment and time frame for completion.
As per the view of Koch and Friis, 2015, the theories that can be applicable to
differentiate large scale and small scale projects are mainly: Agile method for project
management and Spiral model. Generally, steps of Spiral model are applicable for large scale
projects like manufacturing of any new product or product development plan within any industry
or company. For example, the spiral model can be utilized for ongoing project of XYZ company,
it may undergo for specific steps.
In the opinion of Harrison and Lock, 2017, Spiral method can be effective for designing a
feasible and standardize approach for the execution of plan. It clearly defines and state the
problem or aim of project, conducts related analysis depending regarding needs and availability
of resources as well as training needs to the workforce. Spiral method provides the methods of
selecting proper designing strategies for the developed plan and provide specific implementation
11
Paraphrase This Document
Need a fresh take? Get an instant paraphrase of this document with our AI Paraphraser
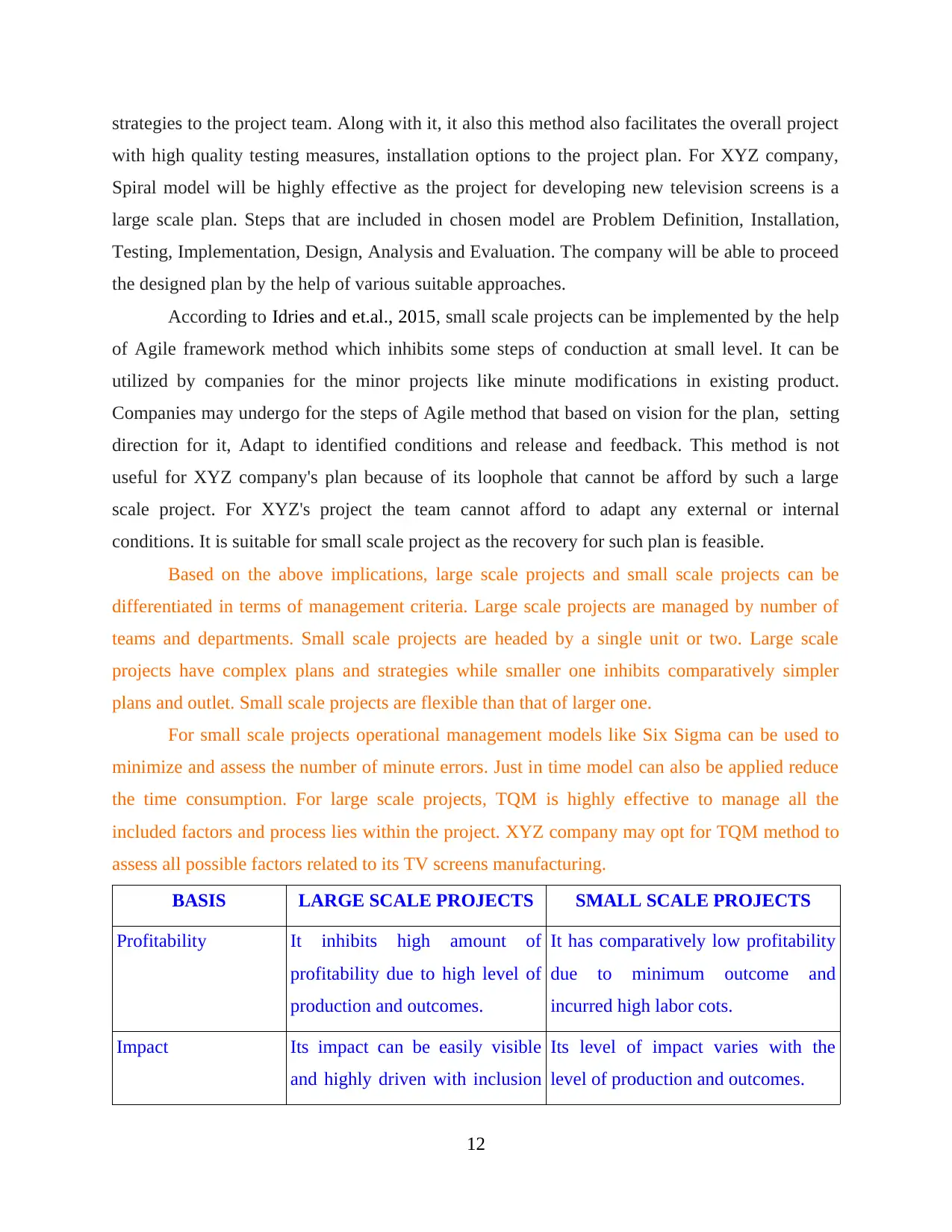
strategies to the project team. Along with it, it also this method also facilitates the overall project
with high quality testing measures, installation options to the project plan. For XYZ company,
Spiral model will be highly effective as the project for developing new television screens is a
large scale plan. Steps that are included in chosen model are Problem Definition, Installation,
Testing, Implementation, Design, Analysis and Evaluation. The company will be able to proceed
the designed plan by the help of various suitable approaches.
According to Idries and et.al., 2015, small scale projects can be implemented by the help
of Agile framework method which inhibits some steps of conduction at small level. It can be
utilized by companies for the minor projects like minute modifications in existing product.
Companies may undergo for the steps of Agile method that based on vision for the plan, setting
direction for it, Adapt to identified conditions and release and feedback. This method is not
useful for XYZ company's plan because of its loophole that cannot be afford by such a large
scale project. For XYZ's project the team cannot afford to adapt any external or internal
conditions. It is suitable for small scale project as the recovery for such plan is feasible.
Based on the above implications, large scale projects and small scale projects can be
differentiated in terms of management criteria. Large scale projects are managed by number of
teams and departments. Small scale projects are headed by a single unit or two. Large scale
projects have complex plans and strategies while smaller one inhibits comparatively simpler
plans and outlet. Small scale projects are flexible than that of larger one.
For small scale projects operational management models like Six Sigma can be used to
minimize and assess the number of minute errors. Just in time model can also be applied reduce
the time consumption. For large scale projects, TQM is highly effective to manage all the
included factors and process lies within the project. XYZ company may opt for TQM method to
assess all possible factors related to its TV screens manufacturing.
BASIS LARGE SCALE PROJECTS SMALL SCALE PROJECTS
Profitability It inhibits high amount of
profitability due to high level of
production and outcomes.
It has comparatively low profitability
due to minimum outcome and
incurred high labor cots.
Impact Its impact can be easily visible
and highly driven with inclusion
Its level of impact varies with the
level of production and outcomes.
12
with high quality testing measures, installation options to the project plan. For XYZ company,
Spiral model will be highly effective as the project for developing new television screens is a
large scale plan. Steps that are included in chosen model are Problem Definition, Installation,
Testing, Implementation, Design, Analysis and Evaluation. The company will be able to proceed
the designed plan by the help of various suitable approaches.
According to Idries and et.al., 2015, small scale projects can be implemented by the help
of Agile framework method which inhibits some steps of conduction at small level. It can be
utilized by companies for the minor projects like minute modifications in existing product.
Companies may undergo for the steps of Agile method that based on vision for the plan, setting
direction for it, Adapt to identified conditions and release and feedback. This method is not
useful for XYZ company's plan because of its loophole that cannot be afford by such a large
scale project. For XYZ's project the team cannot afford to adapt any external or internal
conditions. It is suitable for small scale project as the recovery for such plan is feasible.
Based on the above implications, large scale projects and small scale projects can be
differentiated in terms of management criteria. Large scale projects are managed by number of
teams and departments. Small scale projects are headed by a single unit or two. Large scale
projects have complex plans and strategies while smaller one inhibits comparatively simpler
plans and outlet. Small scale projects are flexible than that of larger one.
For small scale projects operational management models like Six Sigma can be used to
minimize and assess the number of minute errors. Just in time model can also be applied reduce
the time consumption. For large scale projects, TQM is highly effective to manage all the
included factors and process lies within the project. XYZ company may opt for TQM method to
assess all possible factors related to its TV screens manufacturing.
BASIS LARGE SCALE PROJECTS SMALL SCALE PROJECTS
Profitability It inhibits high amount of
profitability due to high level of
production and outcomes.
It has comparatively low profitability
due to minimum outcome and
incurred high labor cots.
Impact Its impact can be easily visible
and highly driven with inclusion
Its level of impact varies with the
level of production and outcomes.
12
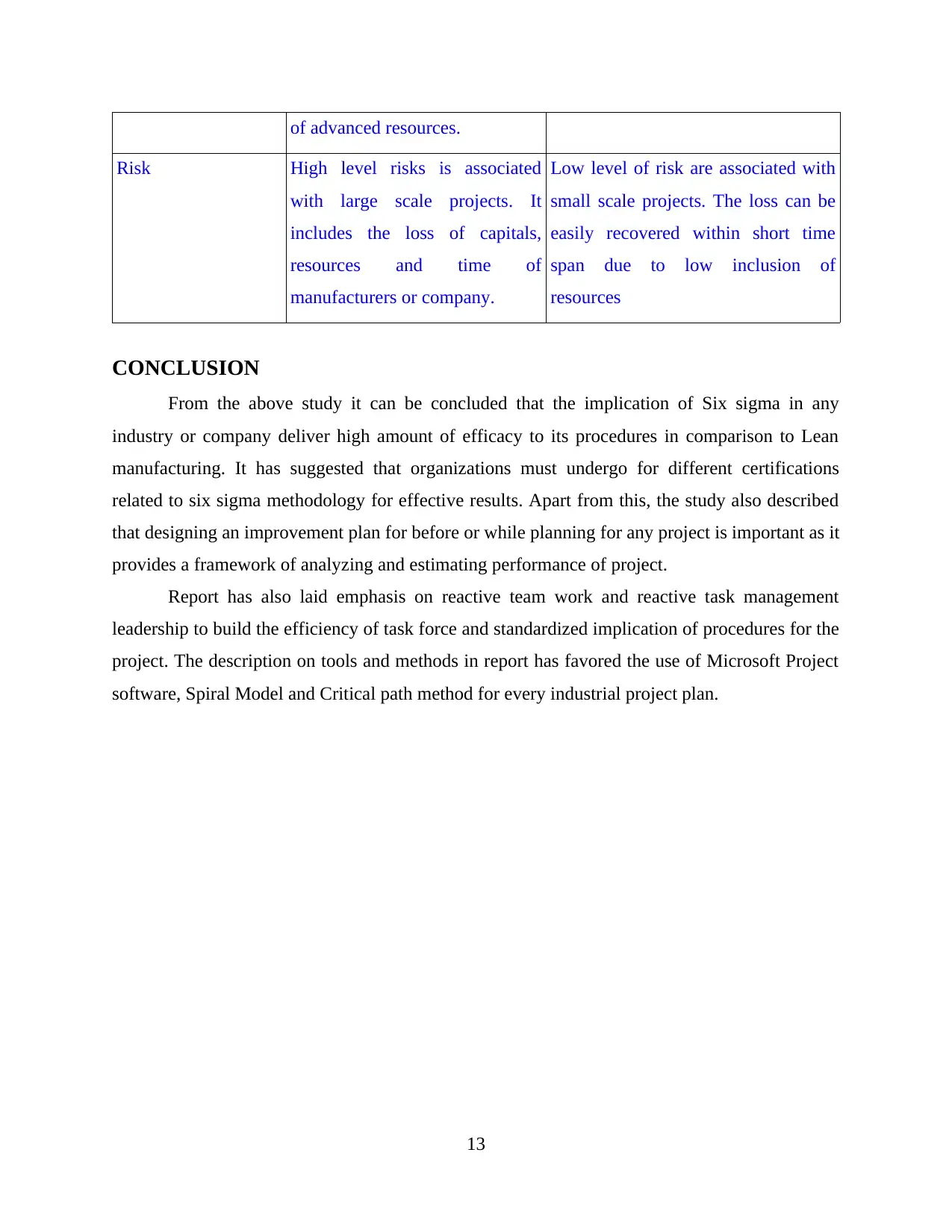
of advanced resources.
Risk High level risks is associated
with large scale projects. It
includes the loss of capitals,
resources and time of
manufacturers or company.
Low level of risk are associated with
small scale projects. The loss can be
easily recovered within short time
span due to low inclusion of
resources
CONCLUSION
From the above study it can be concluded that the implication of Six sigma in any
industry or company deliver high amount of efficacy to its procedures in comparison to Lean
manufacturing. It has suggested that organizations must undergo for different certifications
related to six sigma methodology for effective results. Apart from this, the study also described
that designing an improvement plan for before or while planning for any project is important as it
provides a framework of analyzing and estimating performance of project.
Report has also laid emphasis on reactive team work and reactive task management
leadership to build the efficiency of task force and standardized implication of procedures for the
project. The description on tools and methods in report has favored the use of Microsoft Project
software, Spiral Model and Critical path method for every industrial project plan.
13
Risk High level risks is associated
with large scale projects. It
includes the loss of capitals,
resources and time of
manufacturers or company.
Low level of risk are associated with
small scale projects. The loss can be
easily recovered within short time
span due to low inclusion of
resources
CONCLUSION
From the above study it can be concluded that the implication of Six sigma in any
industry or company deliver high amount of efficacy to its procedures in comparison to Lean
manufacturing. It has suggested that organizations must undergo for different certifications
related to six sigma methodology for effective results. Apart from this, the study also described
that designing an improvement plan for before or while planning for any project is important as it
provides a framework of analyzing and estimating performance of project.
Report has also laid emphasis on reactive team work and reactive task management
leadership to build the efficiency of task force and standardized implication of procedures for the
project. The description on tools and methods in report has favored the use of Microsoft Project
software, Spiral Model and Critical path method for every industrial project plan.
13
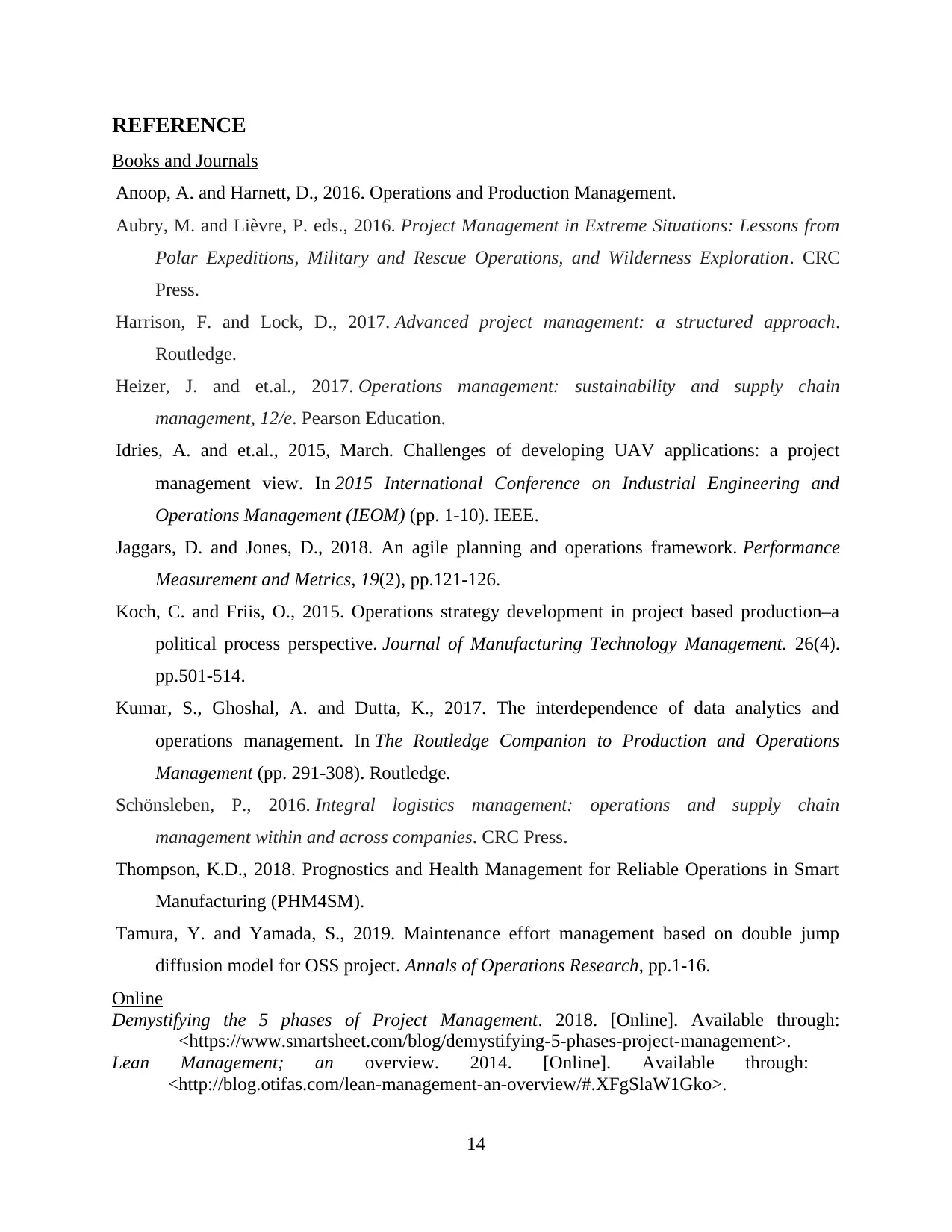
REFERENCE
Books and Journals
Anoop, A. and Harnett, D., 2016. Operations and Production Management.
Aubry, M. and Lièvre, P. eds., 2016. Project Management in Extreme Situations: Lessons from
Polar Expeditions, Military and Rescue Operations, and Wilderness Exploration. CRC
Press.
Harrison, F. and Lock, D., 2017. Advanced project management: a structured approach.
Routledge.
Heizer, J. and et.al., 2017. Operations management: sustainability and supply chain
management, 12/e. Pearson Education.
Idries, A. and et.al., 2015, March. Challenges of developing UAV applications: a project
management view. In 2015 International Conference on Industrial Engineering and
Operations Management (IEOM) (pp. 1-10). IEEE.
Jaggars, D. and Jones, D., 2018. An agile planning and operations framework. Performance
Measurement and Metrics, 19(2), pp.121-126.
Koch, C. and Friis, O., 2015. Operations strategy development in project based production–a
political process perspective. Journal of Manufacturing Technology Management. 26(4).
pp.501-514.
Kumar, S., Ghoshal, A. and Dutta, K., 2017. The interdependence of data analytics and
operations management. In The Routledge Companion to Production and Operations
Management (pp. 291-308). Routledge.
Schönsleben, P., 2016. Integral logistics management: operations and supply chain
management within and across companies. CRC Press.
Thompson, K.D., 2018. Prognostics and Health Management for Reliable Operations in Smart
Manufacturing (PHM4SM).
Tamura, Y. and Yamada, S., 2019. Maintenance effort management based on double jump
diffusion model for OSS project. Annals of Operations Research, pp.1-16.
Online 5 Phases of Project Management
Demystifying the 5 phases of Project Management. 2018. [Online]. Available through:
<https://www.smartsheet.com/blog/demystifying-5-phases-project-management>.
Lean Management; an overview. 2014. [Online]. Available through:
<http://blog.otifas.com/lean-management-an-overview/#.XFgSlaW1Gko>.
14
Books and Journals
Anoop, A. and Harnett, D., 2016. Operations and Production Management.
Aubry, M. and Lièvre, P. eds., 2016. Project Management in Extreme Situations: Lessons from
Polar Expeditions, Military and Rescue Operations, and Wilderness Exploration. CRC
Press.
Harrison, F. and Lock, D., 2017. Advanced project management: a structured approach.
Routledge.
Heizer, J. and et.al., 2017. Operations management: sustainability and supply chain
management, 12/e. Pearson Education.
Idries, A. and et.al., 2015, March. Challenges of developing UAV applications: a project
management view. In 2015 International Conference on Industrial Engineering and
Operations Management (IEOM) (pp. 1-10). IEEE.
Jaggars, D. and Jones, D., 2018. An agile planning and operations framework. Performance
Measurement and Metrics, 19(2), pp.121-126.
Koch, C. and Friis, O., 2015. Operations strategy development in project based production–a
political process perspective. Journal of Manufacturing Technology Management. 26(4).
pp.501-514.
Kumar, S., Ghoshal, A. and Dutta, K., 2017. The interdependence of data analytics and
operations management. In The Routledge Companion to Production and Operations
Management (pp. 291-308). Routledge.
Schönsleben, P., 2016. Integral logistics management: operations and supply chain
management within and across companies. CRC Press.
Thompson, K.D., 2018. Prognostics and Health Management for Reliable Operations in Smart
Manufacturing (PHM4SM).
Tamura, Y. and Yamada, S., 2019. Maintenance effort management based on double jump
diffusion model for OSS project. Annals of Operations Research, pp.1-16.
Online 5 Phases of Project Management
Demystifying the 5 phases of Project Management. 2018. [Online]. Available through:
<https://www.smartsheet.com/blog/demystifying-5-phases-project-management>.
Lean Management; an overview. 2014. [Online]. Available through:
<http://blog.otifas.com/lean-management-an-overview/#.XFgSlaW1Gko>.
14
Secure Best Marks with AI Grader
Need help grading? Try our AI Grader for instant feedback on your assignments.
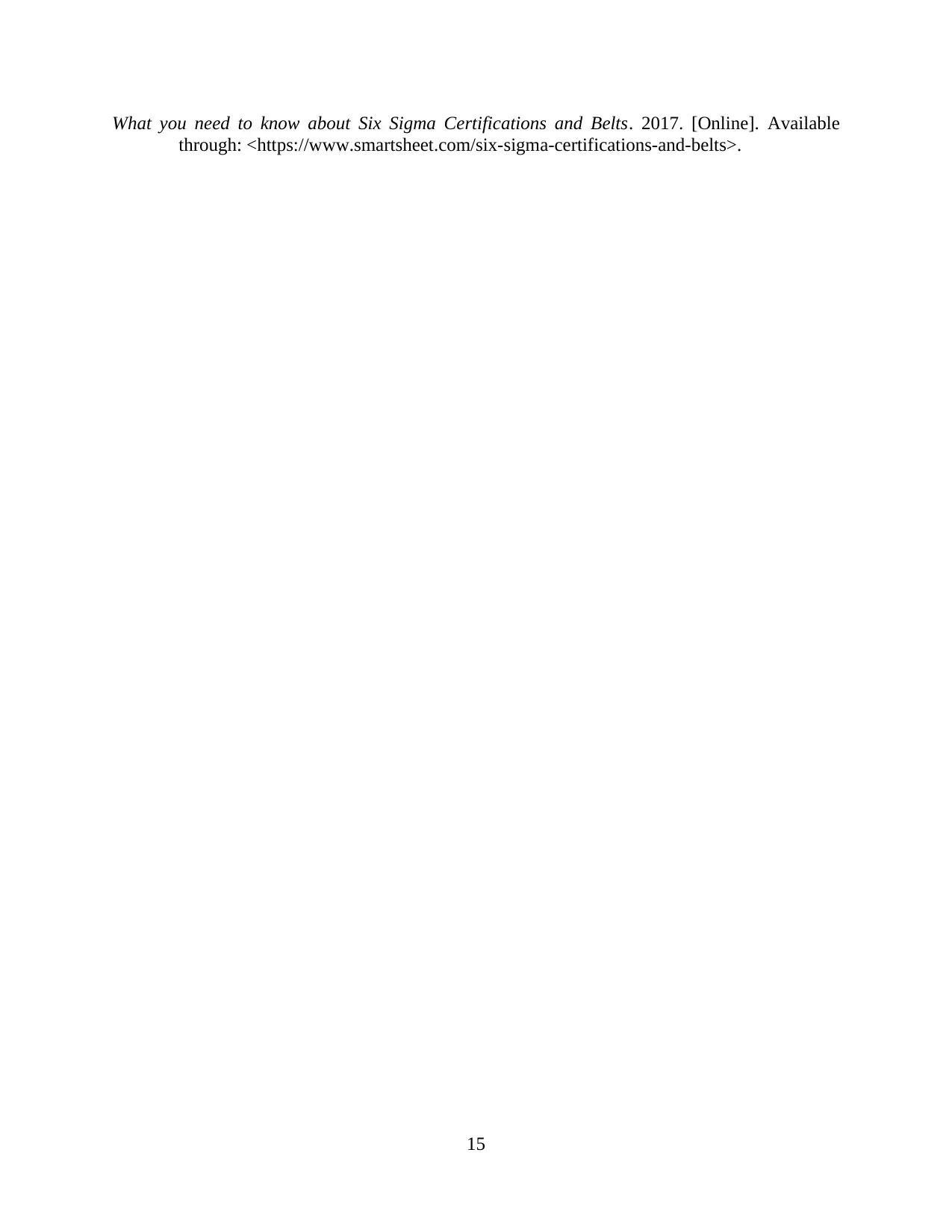
What you need to know about Six Sigma Certifications and Belts. 2017. [Online]. Available
through: <https://www.smartsheet.com/six-sigma-certifications-and-belts>.
15
through: <https://www.smartsheet.com/six-sigma-certifications-and-belts>.
15
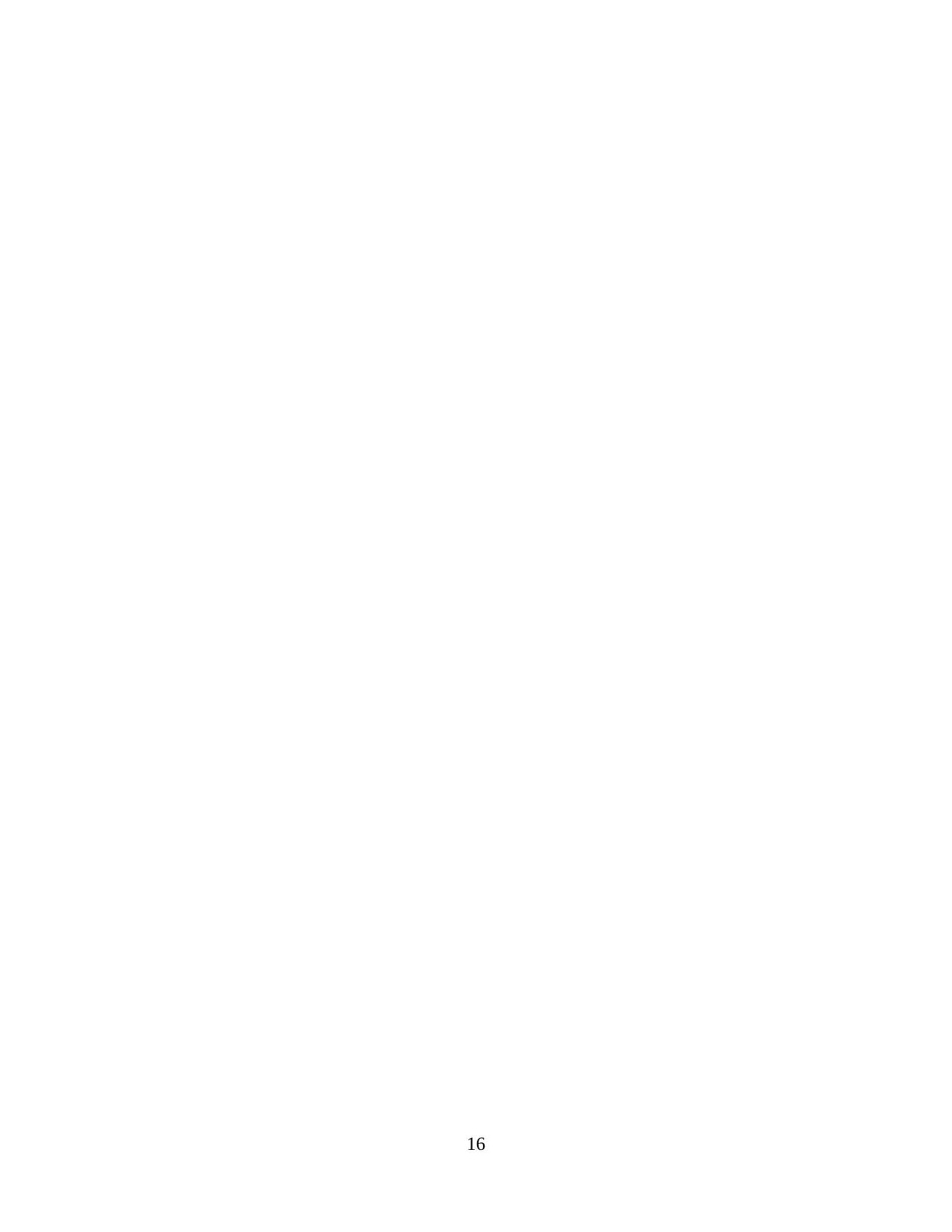
16
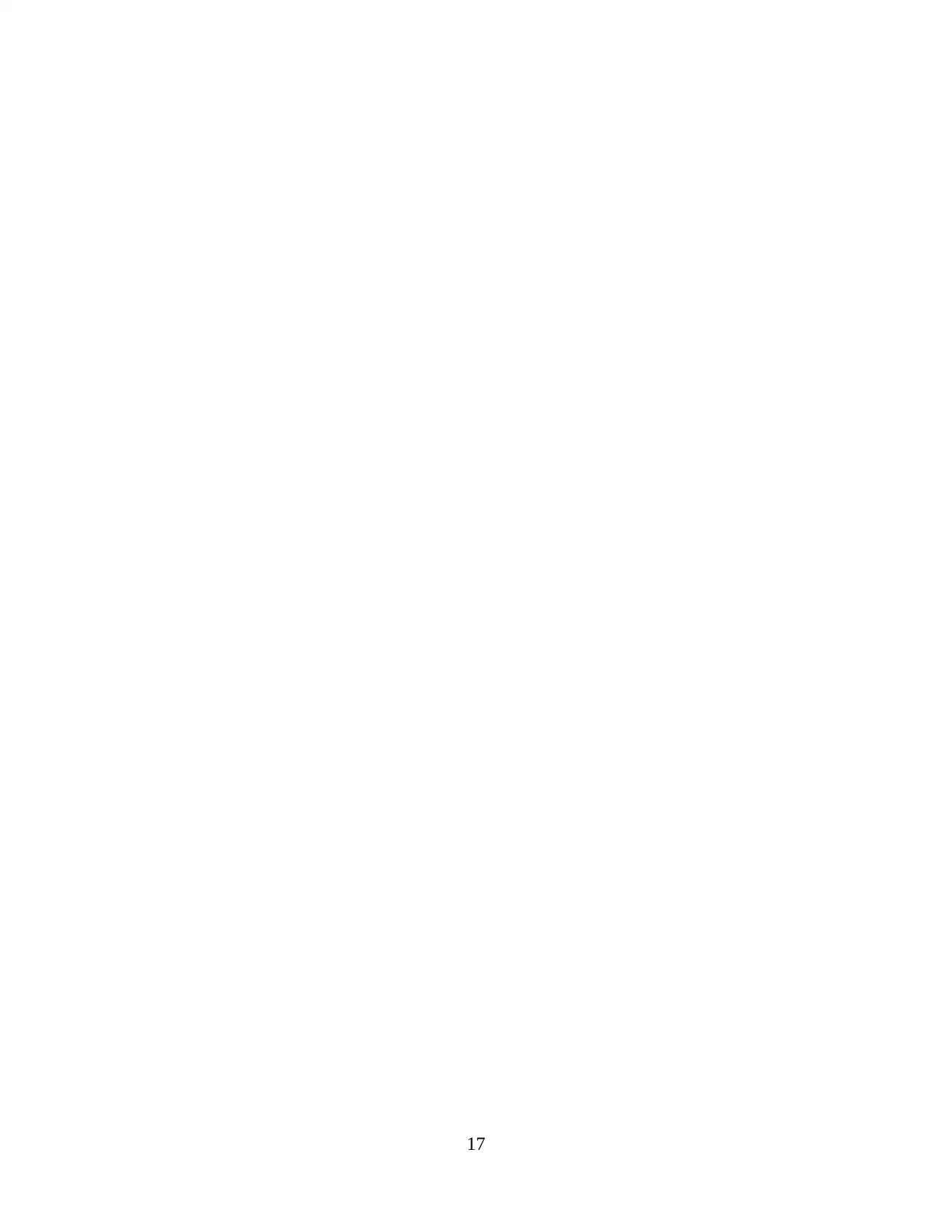
17
Paraphrase This Document
Need a fresh take? Get an instant paraphrase of this document with our AI Paraphraser
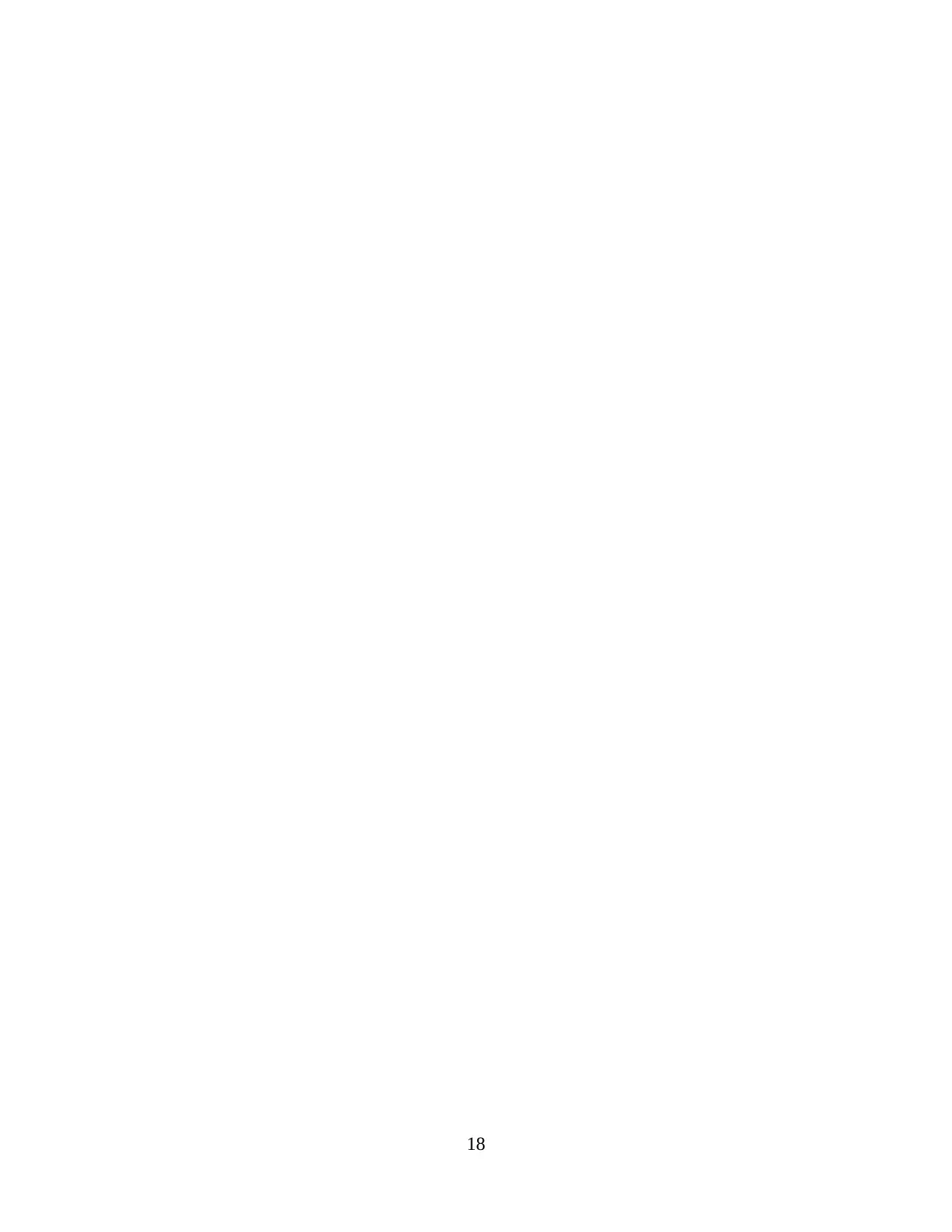
18
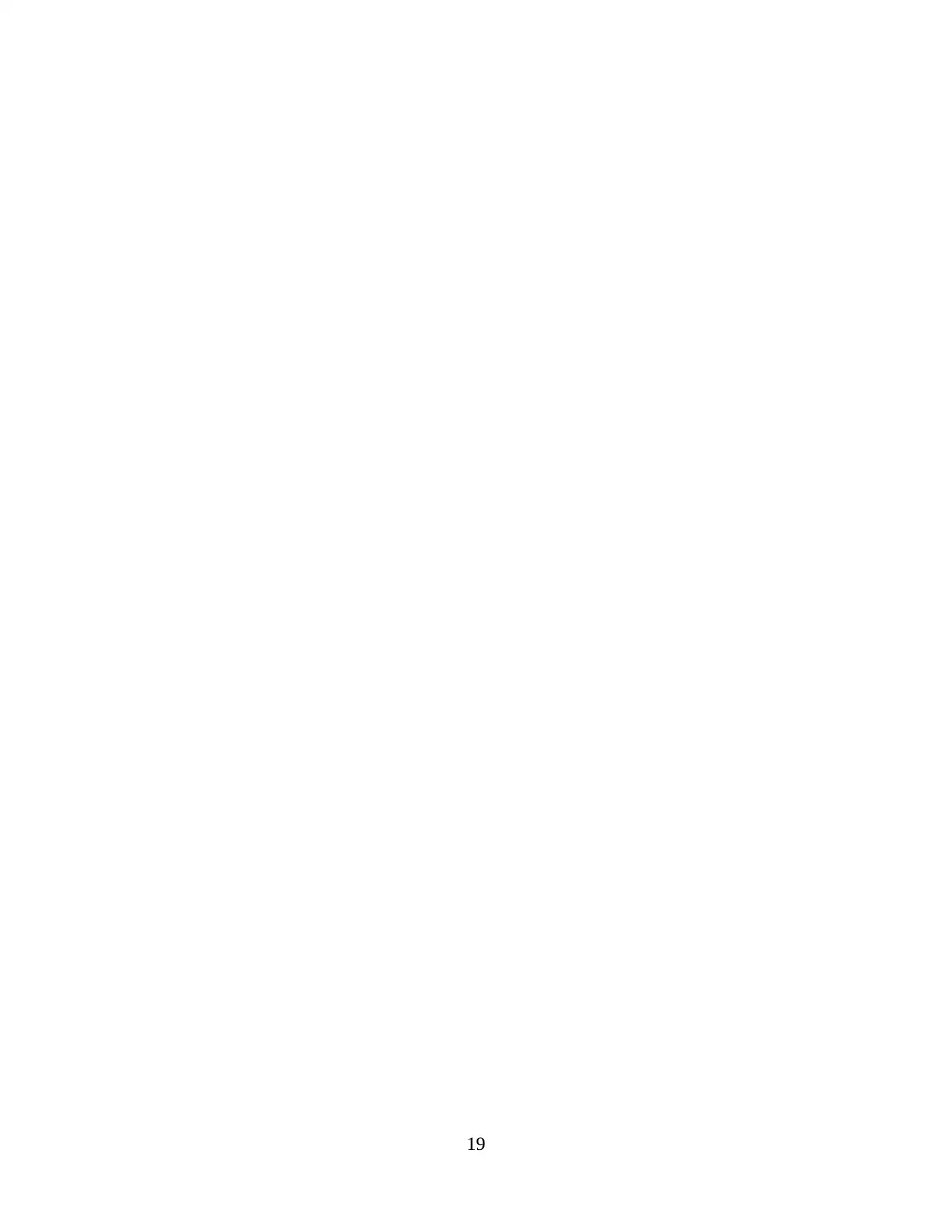
19
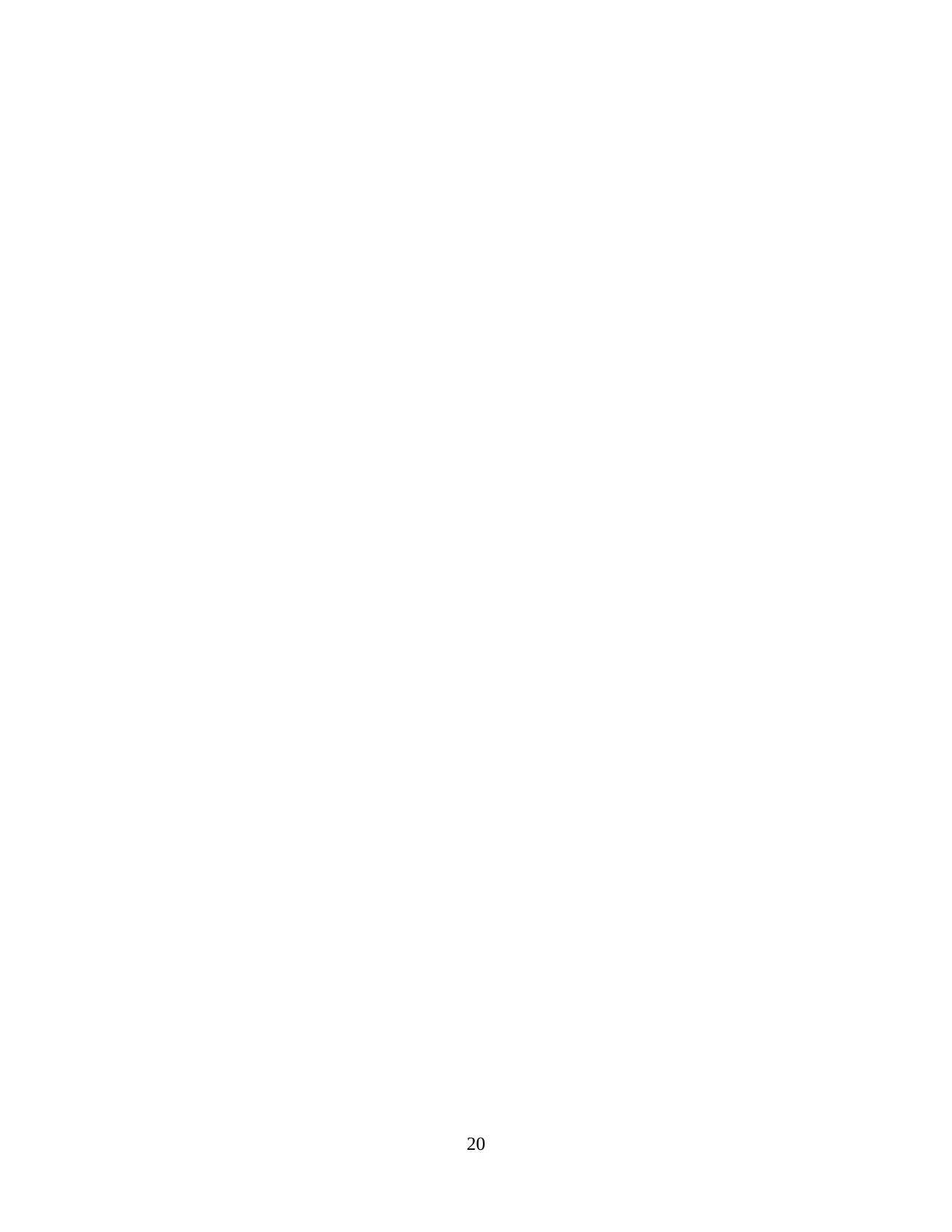
20
1 out of 22
Related Documents

Your All-in-One AI-Powered Toolkit for Academic Success.
+13062052269
info@desklib.com
Available 24*7 on WhatsApp / Email
Unlock your academic potential
© 2024 | Zucol Services PVT LTD | All rights reserved.