Project Management Methodologies
VerifiedAdded on 2020/03/16
|11
|3066
|36
Project
AI Summary
The content discusses project management methodologies focusing on continuous improvement at Latino Engineering. It identifies root causes of issues, proposes solutions, and outlines a continuous improvement plan to enhance quality and customer service. The analysis includes various quality control tools and critical success factors necessary for effective project management.
Contribute Materials
Your contribution can guide someone’s learning journey. Share your
documents today.
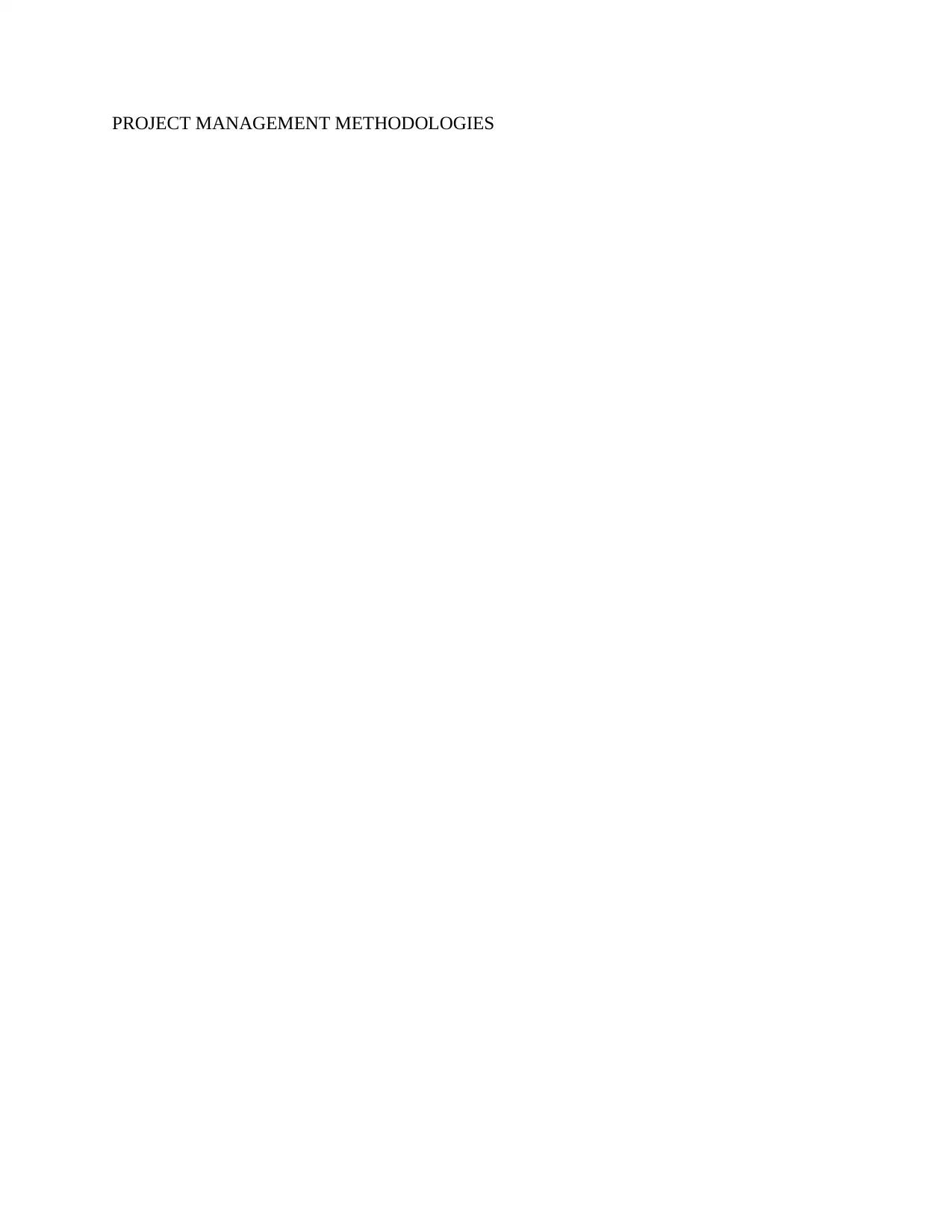
PROJECT MANAGEMENT METHODOLOGIES
Secure Best Marks with AI Grader
Need help grading? Try our AI Grader for instant feedback on your assignments.
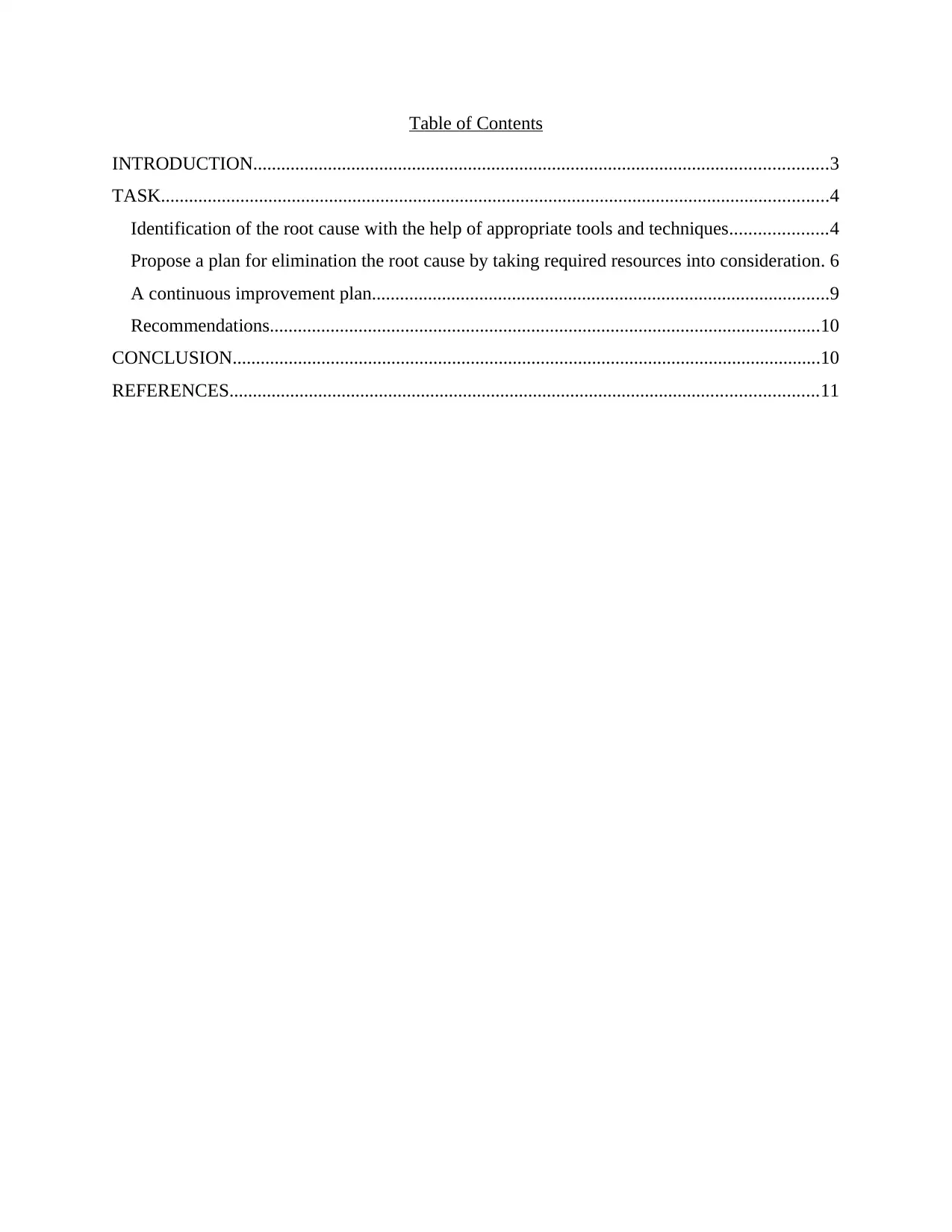
Table of Contents
INTRODUCTION...........................................................................................................................3
TASK...............................................................................................................................................4
Identification of the root cause with the help of appropriate tools and techniques.....................4
Propose a plan for elimination the root cause by taking required resources into consideration. 6
A continuous improvement plan..................................................................................................9
Recommendations......................................................................................................................10
CONCLUSION..............................................................................................................................10
REFERENCES..............................................................................................................................11
INTRODUCTION...........................................................................................................................3
TASK...............................................................................................................................................4
Identification of the root cause with the help of appropriate tools and techniques.....................4
Propose a plan for elimination the root cause by taking required resources into consideration. 6
A continuous improvement plan..................................................................................................9
Recommendations......................................................................................................................10
CONCLUSION..............................................................................................................................10
REFERENCES..............................................................................................................................11
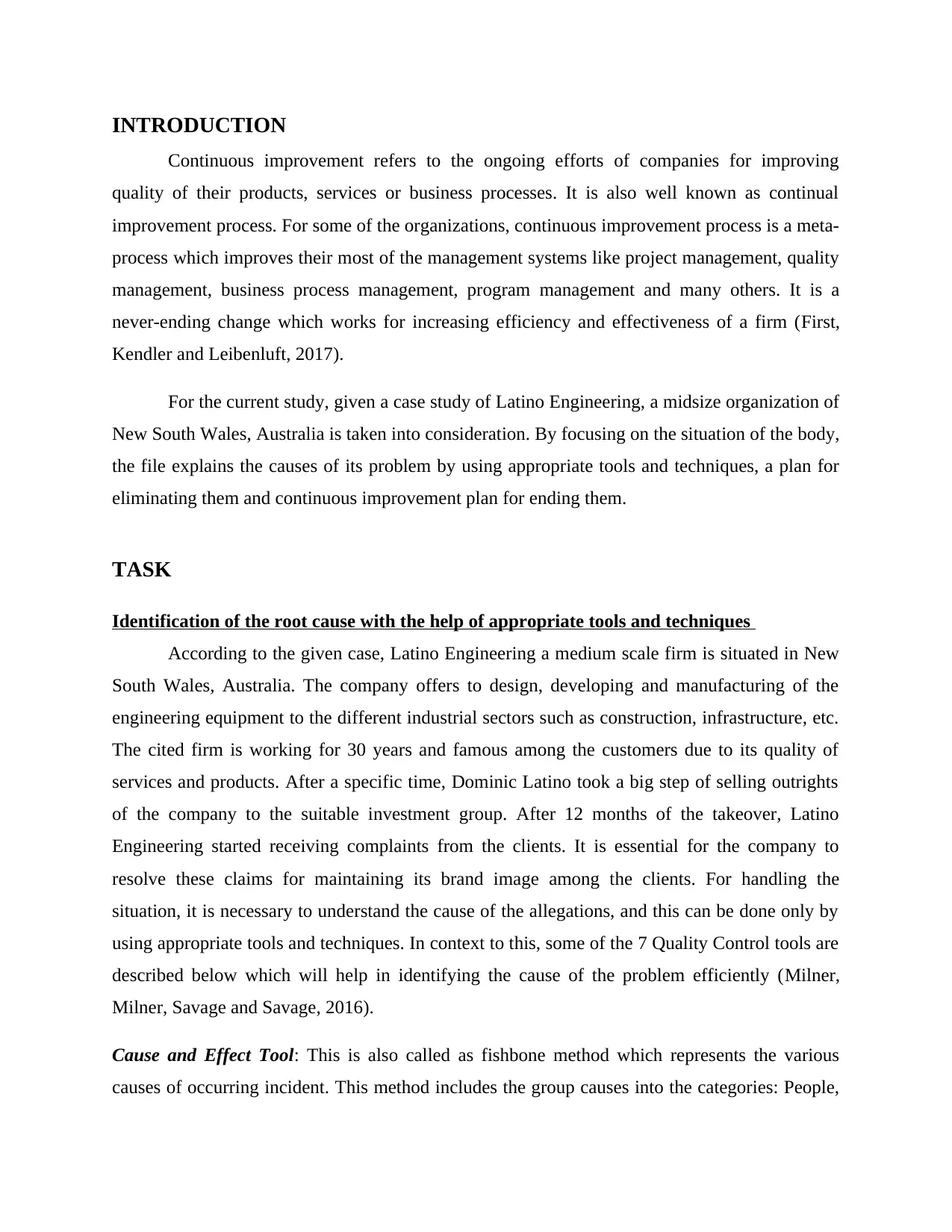
INTRODUCTION
Continuous improvement refers to the ongoing efforts of companies for improving
quality of their products, services or business processes. It is also well known as continual
improvement process. For some of the organizations, continuous improvement process is a meta-
process which improves their most of the management systems like project management, quality
management, business process management, program management and many others. It is a
never-ending change which works for increasing efficiency and effectiveness of a firm (First,
Kendler and Leibenluft, 2017).
For the current study, given a case study of Latino Engineering, a midsize organization of
New South Wales, Australia is taken into consideration. By focusing on the situation of the body,
the file explains the causes of its problem by using appropriate tools and techniques, a plan for
eliminating them and continuous improvement plan for ending them.
TASK
Identification of the root cause with the help of appropriate tools and techniques
According to the given case, Latino Engineering a medium scale firm is situated in New
South Wales, Australia. The company offers to design, developing and manufacturing of the
engineering equipment to the different industrial sectors such as construction, infrastructure, etc.
The cited firm is working for 30 years and famous among the customers due to its quality of
services and products. After a specific time, Dominic Latino took a big step of selling outrights
of the company to the suitable investment group. After 12 months of the takeover, Latino
Engineering started receiving complaints from the clients. It is essential for the company to
resolve these claims for maintaining its brand image among the clients. For handling the
situation, it is necessary to understand the cause of the allegations, and this can be done only by
using appropriate tools and techniques. In context to this, some of the 7 Quality Control tools are
described below which will help in identifying the cause of the problem efficiently (Milner,
Milner, Savage and Savage, 2016).
Cause and Effect Tool: This is also called as fishbone method which represents the various
causes of occurring incident. This method includes the group causes into the categories: People,
Continuous improvement refers to the ongoing efforts of companies for improving
quality of their products, services or business processes. It is also well known as continual
improvement process. For some of the organizations, continuous improvement process is a meta-
process which improves their most of the management systems like project management, quality
management, business process management, program management and many others. It is a
never-ending change which works for increasing efficiency and effectiveness of a firm (First,
Kendler and Leibenluft, 2017).
For the current study, given a case study of Latino Engineering, a midsize organization of
New South Wales, Australia is taken into consideration. By focusing on the situation of the body,
the file explains the causes of its problem by using appropriate tools and techniques, a plan for
eliminating them and continuous improvement plan for ending them.
TASK
Identification of the root cause with the help of appropriate tools and techniques
According to the given case, Latino Engineering a medium scale firm is situated in New
South Wales, Australia. The company offers to design, developing and manufacturing of the
engineering equipment to the different industrial sectors such as construction, infrastructure, etc.
The cited firm is working for 30 years and famous among the customers due to its quality of
services and products. After a specific time, Dominic Latino took a big step of selling outrights
of the company to the suitable investment group. After 12 months of the takeover, Latino
Engineering started receiving complaints from the clients. It is essential for the company to
resolve these claims for maintaining its brand image among the clients. For handling the
situation, it is necessary to understand the cause of the allegations, and this can be done only by
using appropriate tools and techniques. In context to this, some of the 7 Quality Control tools are
described below which will help in identifying the cause of the problem efficiently (Milner,
Milner, Savage and Savage, 2016).
Cause and Effect Tool: This is also called as fishbone method which represents the various
causes of occurring incident. This method includes the group causes into the categories: People,
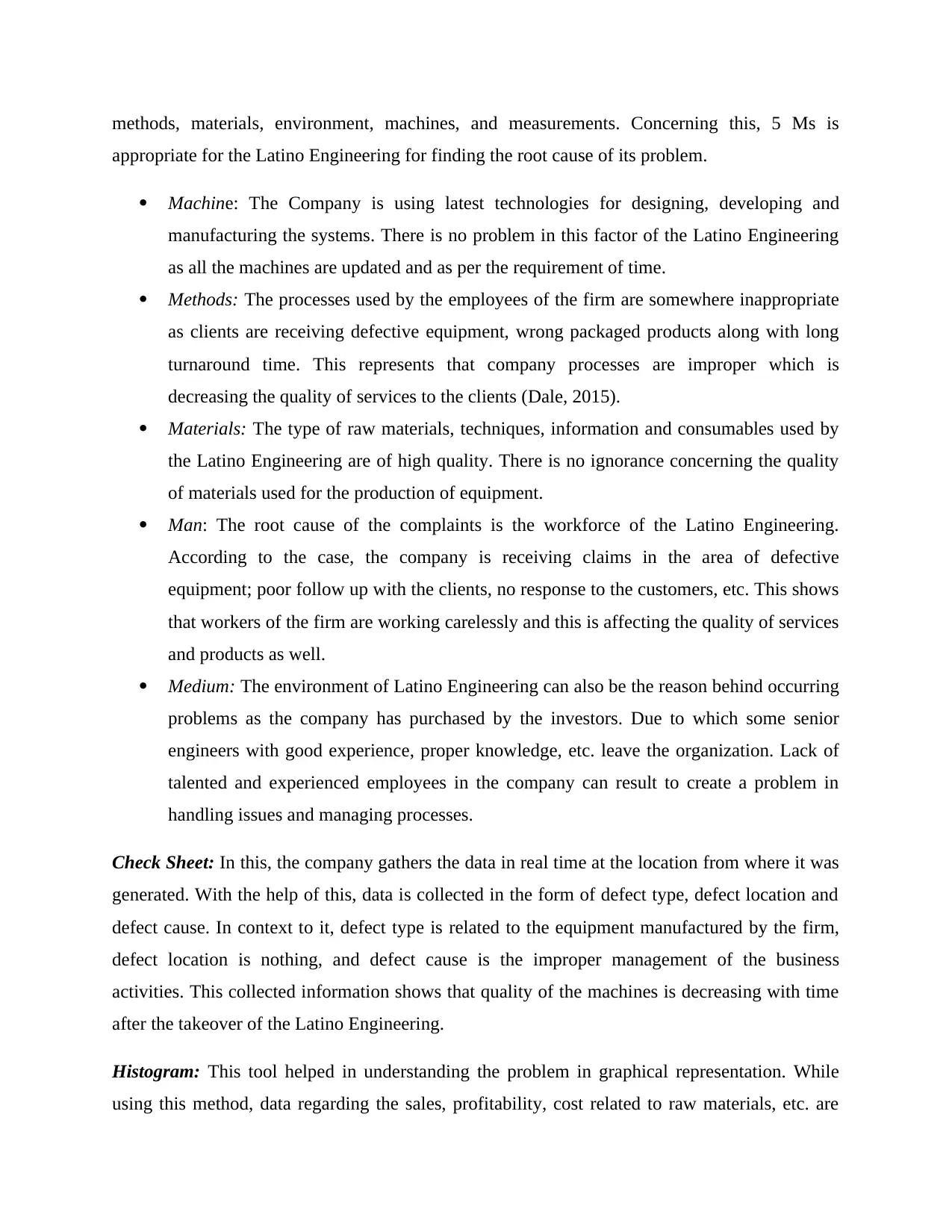
methods, materials, environment, machines, and measurements. Concerning this, 5 Ms is
appropriate for the Latino Engineering for finding the root cause of its problem.
Machine: The Company is using latest technologies for designing, developing and
manufacturing the systems. There is no problem in this factor of the Latino Engineering
as all the machines are updated and as per the requirement of time.
Methods: The processes used by the employees of the firm are somewhere inappropriate
as clients are receiving defective equipment, wrong packaged products along with long
turnaround time. This represents that company processes are improper which is
decreasing the quality of services to the clients (Dale, 2015).
Materials: The type of raw materials, techniques, information and consumables used by
the Latino Engineering are of high quality. There is no ignorance concerning the quality
of materials used for the production of equipment.
Man: The root cause of the complaints is the workforce of the Latino Engineering.
According to the case, the company is receiving claims in the area of defective
equipment; poor follow up with the clients, no response to the customers, etc. This shows
that workers of the firm are working carelessly and this is affecting the quality of services
and products as well.
Medium: The environment of Latino Engineering can also be the reason behind occurring
problems as the company has purchased by the investors. Due to which some senior
engineers with good experience, proper knowledge, etc. leave the organization. Lack of
talented and experienced employees in the company can result to create a problem in
handling issues and managing processes.
Check Sheet: In this, the company gathers the data in real time at the location from where it was
generated. With the help of this, data is collected in the form of defect type, defect location and
defect cause. In context to it, defect type is related to the equipment manufactured by the firm,
defect location is nothing, and defect cause is the improper management of the business
activities. This collected information shows that quality of the machines is decreasing with time
after the takeover of the Latino Engineering.
Histogram: This tool helped in understanding the problem in graphical representation. While
using this method, data regarding the sales, profitability, cost related to raw materials, etc. are
appropriate for the Latino Engineering for finding the root cause of its problem.
Machine: The Company is using latest technologies for designing, developing and
manufacturing the systems. There is no problem in this factor of the Latino Engineering
as all the machines are updated and as per the requirement of time.
Methods: The processes used by the employees of the firm are somewhere inappropriate
as clients are receiving defective equipment, wrong packaged products along with long
turnaround time. This represents that company processes are improper which is
decreasing the quality of services to the clients (Dale, 2015).
Materials: The type of raw materials, techniques, information and consumables used by
the Latino Engineering are of high quality. There is no ignorance concerning the quality
of materials used for the production of equipment.
Man: The root cause of the complaints is the workforce of the Latino Engineering.
According to the case, the company is receiving claims in the area of defective
equipment; poor follow up with the clients, no response to the customers, etc. This shows
that workers of the firm are working carelessly and this is affecting the quality of services
and products as well.
Medium: The environment of Latino Engineering can also be the reason behind occurring
problems as the company has purchased by the investors. Due to which some senior
engineers with good experience, proper knowledge, etc. leave the organization. Lack of
talented and experienced employees in the company can result to create a problem in
handling issues and managing processes.
Check Sheet: In this, the company gathers the data in real time at the location from where it was
generated. With the help of this, data is collected in the form of defect type, defect location and
defect cause. In context to it, defect type is related to the equipment manufactured by the firm,
defect location is nothing, and defect cause is the improper management of the business
activities. This collected information shows that quality of the machines is decreasing with time
after the takeover of the Latino Engineering.
Histogram: This tool helped in understanding the problem in graphical representation. While
using this method, data regarding the sales, profitability, cost related to raw materials, etc. are
Secure Best Marks with AI Grader
Need help grading? Try our AI Grader for instant feedback on your assignments.
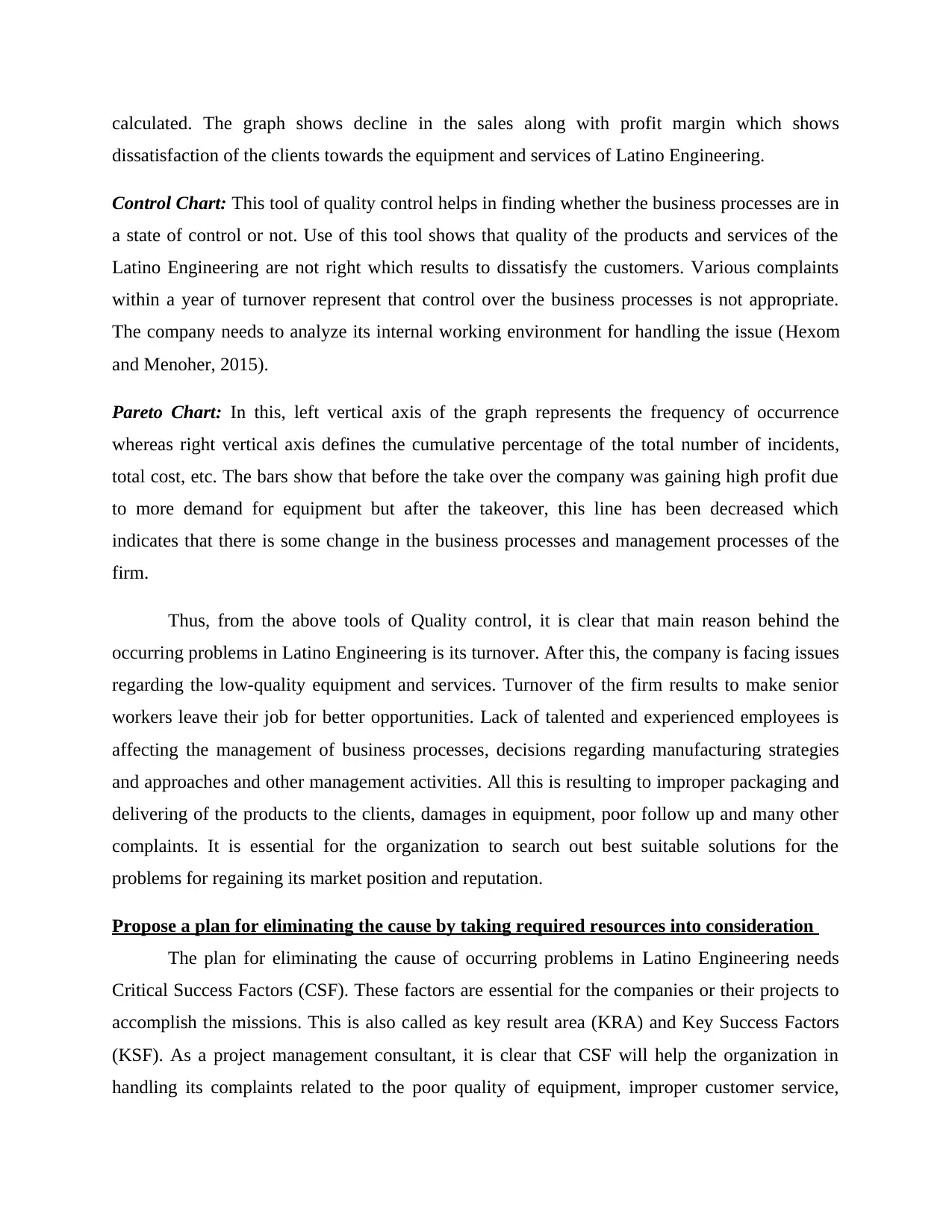
calculated. The graph shows decline in the sales along with profit margin which shows
dissatisfaction of the clients towards the equipment and services of Latino Engineering.
Control Chart: This tool of quality control helps in finding whether the business processes are in
a state of control or not. Use of this tool shows that quality of the products and services of the
Latino Engineering are not right which results to dissatisfy the customers. Various complaints
within a year of turnover represent that control over the business processes is not appropriate.
The company needs to analyze its internal working environment for handling the issue (Hexom
and Menoher, 2015).
Pareto Chart: In this, left vertical axis of the graph represents the frequency of occurrence
whereas right vertical axis defines the cumulative percentage of the total number of incidents,
total cost, etc. The bars show that before the take over the company was gaining high profit due
to more demand for equipment but after the takeover, this line has been decreased which
indicates that there is some change in the business processes and management processes of the
firm.
Thus, from the above tools of Quality control, it is clear that main reason behind the
occurring problems in Latino Engineering is its turnover. After this, the company is facing issues
regarding the low-quality equipment and services. Turnover of the firm results to make senior
workers leave their job for better opportunities. Lack of talented and experienced employees is
affecting the management of business processes, decisions regarding manufacturing strategies
and approaches and other management activities. All this is resulting to improper packaging and
delivering of the products to the clients, damages in equipment, poor follow up and many other
complaints. It is essential for the organization to search out best suitable solutions for the
problems for regaining its market position and reputation.
Propose a plan for eliminating the cause by taking required resources into consideration
The plan for eliminating the cause of occurring problems in Latino Engineering needs
Critical Success Factors (CSF). These factors are essential for the companies or their projects to
accomplish the missions. This is also called as key result area (KRA) and Key Success Factors
(KSF). As a project management consultant, it is clear that CSF will help the organization in
handling its complaints related to the poor quality of equipment, improper customer service,
dissatisfaction of the clients towards the equipment and services of Latino Engineering.
Control Chart: This tool of quality control helps in finding whether the business processes are in
a state of control or not. Use of this tool shows that quality of the products and services of the
Latino Engineering are not right which results to dissatisfy the customers. Various complaints
within a year of turnover represent that control over the business processes is not appropriate.
The company needs to analyze its internal working environment for handling the issue (Hexom
and Menoher, 2015).
Pareto Chart: In this, left vertical axis of the graph represents the frequency of occurrence
whereas right vertical axis defines the cumulative percentage of the total number of incidents,
total cost, etc. The bars show that before the take over the company was gaining high profit due
to more demand for equipment but after the takeover, this line has been decreased which
indicates that there is some change in the business processes and management processes of the
firm.
Thus, from the above tools of Quality control, it is clear that main reason behind the
occurring problems in Latino Engineering is its turnover. After this, the company is facing issues
regarding the low-quality equipment and services. Turnover of the firm results to make senior
workers leave their job for better opportunities. Lack of talented and experienced employees is
affecting the management of business processes, decisions regarding manufacturing strategies
and approaches and other management activities. All this is resulting to improper packaging and
delivering of the products to the clients, damages in equipment, poor follow up and many other
complaints. It is essential for the organization to search out best suitable solutions for the
problems for regaining its market position and reputation.
Propose a plan for eliminating the cause by taking required resources into consideration
The plan for eliminating the cause of occurring problems in Latino Engineering needs
Critical Success Factors (CSF). These factors are essential for the companies or their projects to
accomplish the missions. This is also called as key result area (KRA) and Key Success Factors
(KSF). As a project management consultant, it is clear that CSF will help the organization in
handling its complaints related to the poor quality of equipment, improper customer service,

inappropriate follow-up and many others. For developing an effective continuous improvement
plan, it is necessary to find the right critical success factors which can help the respected firm in
accomplishing its objective of eliminating the root causes of the problems. The CSF which can
help in improving the issues by handling the causes behind them are described as below:
Leadership: According to the given case, employees of the Latino Engineering are unable to
provide desired products and services to the customers who are tending to dissatisfaction. For
handling this issue, it is necessary to have experienced and skilled leader who can guide and
monitor the work of the workers. Under the guidance of the leader, staff members of the cited
firm will able to improve their performance and working capabilities. Along with this, use of
participative leadership style will help workers in taking appropriate decisions regarding the
follow up with clients, handling queries of the customers, delivery, and packaging of the
equipment and many others. Apart from this, leadership will also enhance motivation level and
self-esteem of the employees which will create open and interactive working environment of the
organization (Lewis, 2016).
Training and education: Latino engineering needs to provide appropriate training to its
employees for developing their management, communication, decision making, etc. skills along
with knowledge regarding the production, packaging, and delivery of the produced equipment.
This critical success factor will help in fulfilling the absence of senior engineers for handling the
business processes effectively and efficiently. Training will also enhance the quality of
production which will improve the complaints of the clients regarding this. Along with this,
training needs to be conducted under the guidance of experts which will lead to answering the
queries of the employees regarding the poor services. Training is required in order to provide
customer service team of the Latino Engineering for enhancing their problem solving,
communication, time management, and relationship management skills. This will eliminate the
complaint of customers regarding the non-responsive customer service team.
Customer Focus: Another critical success factor for eliminating the cause is to pay attention to
the demands and needs of the clients. By focusing on the customer requirements, employees of
the company will able to handle the issues regarding the wrong engineering equipment
packaging and delivery, defective engineering equipment and too long turnaround time for the
issue resolution. It is the prime responsibility of the organizations to fulfill wants, desires, and
plan, it is necessary to find the right critical success factors which can help the respected firm in
accomplishing its objective of eliminating the root causes of the problems. The CSF which can
help in improving the issues by handling the causes behind them are described as below:
Leadership: According to the given case, employees of the Latino Engineering are unable to
provide desired products and services to the customers who are tending to dissatisfaction. For
handling this issue, it is necessary to have experienced and skilled leader who can guide and
monitor the work of the workers. Under the guidance of the leader, staff members of the cited
firm will able to improve their performance and working capabilities. Along with this, use of
participative leadership style will help workers in taking appropriate decisions regarding the
follow up with clients, handling queries of the customers, delivery, and packaging of the
equipment and many others. Apart from this, leadership will also enhance motivation level and
self-esteem of the employees which will create open and interactive working environment of the
organization (Lewis, 2016).
Training and education: Latino engineering needs to provide appropriate training to its
employees for developing their management, communication, decision making, etc. skills along
with knowledge regarding the production, packaging, and delivery of the produced equipment.
This critical success factor will help in fulfilling the absence of senior engineers for handling the
business processes effectively and efficiently. Training will also enhance the quality of
production which will improve the complaints of the clients regarding this. Along with this,
training needs to be conducted under the guidance of experts which will lead to answering the
queries of the employees regarding the poor services. Training is required in order to provide
customer service team of the Latino Engineering for enhancing their problem solving,
communication, time management, and relationship management skills. This will eliminate the
complaint of customers regarding the non-responsive customer service team.
Customer Focus: Another critical success factor for eliminating the cause is to pay attention to
the demands and needs of the clients. By focusing on the customer requirements, employees of
the company will able to handle the issues regarding the wrong engineering equipment
packaging and delivery, defective engineering equipment and too long turnaround time for the
issue resolution. It is the prime responsibility of the organizations to fulfill wants, desires, and
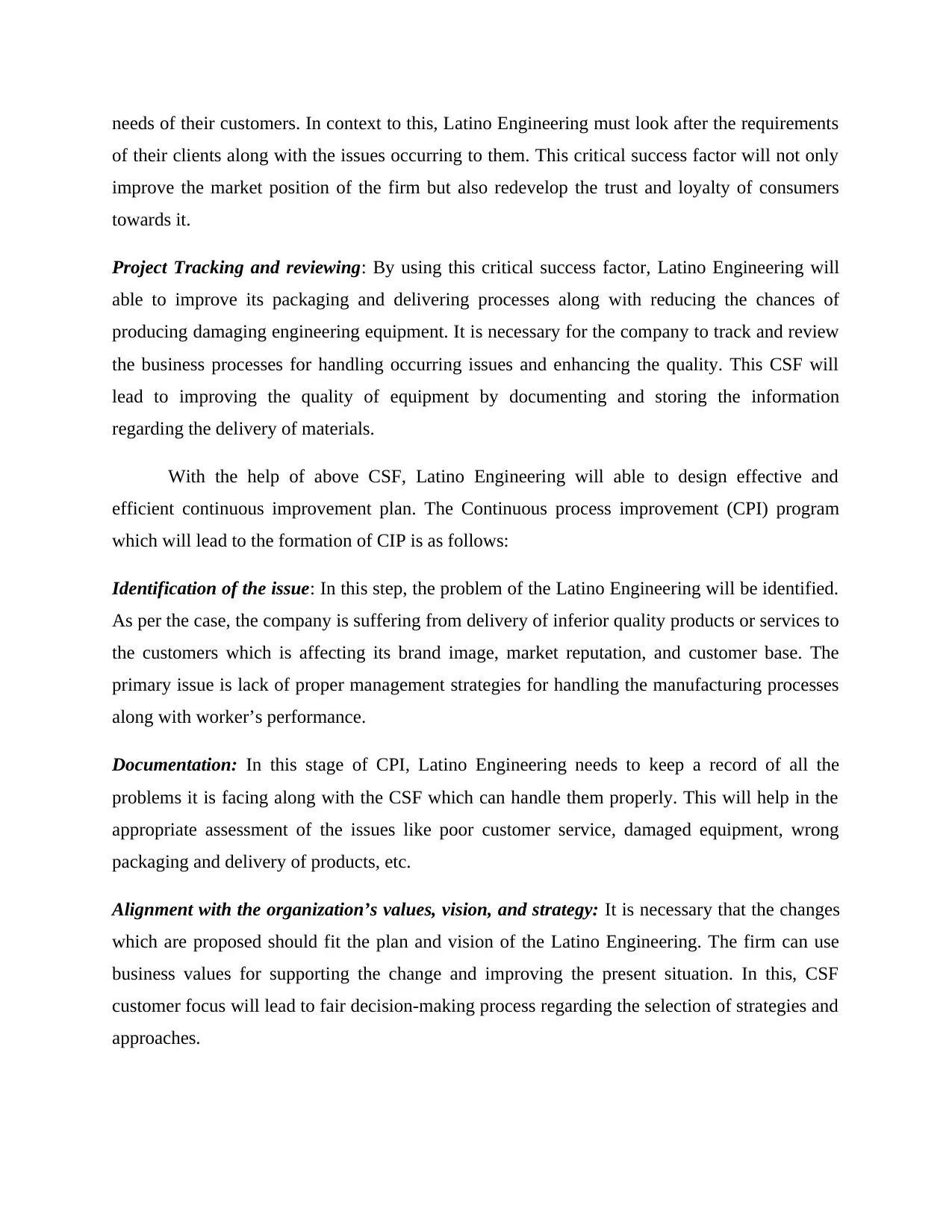
needs of their customers. In context to this, Latino Engineering must look after the requirements
of their clients along with the issues occurring to them. This critical success factor will not only
improve the market position of the firm but also redevelop the trust and loyalty of consumers
towards it.
Project Tracking and reviewing: By using this critical success factor, Latino Engineering will
able to improve its packaging and delivering processes along with reducing the chances of
producing damaging engineering equipment. It is necessary for the company to track and review
the business processes for handling occurring issues and enhancing the quality. This CSF will
lead to improving the quality of equipment by documenting and storing the information
regarding the delivery of materials.
With the help of above CSF, Latino Engineering will able to design effective and
efficient continuous improvement plan. The Continuous process improvement (CPI) program
which will lead to the formation of CIP is as follows:
Identification of the issue: In this step, the problem of the Latino Engineering will be identified.
As per the case, the company is suffering from delivery of inferior quality products or services to
the customers which is affecting its brand image, market reputation, and customer base. The
primary issue is lack of proper management strategies for handling the manufacturing processes
along with worker’s performance.
Documentation: In this stage of CPI, Latino Engineering needs to keep a record of all the
problems it is facing along with the CSF which can handle them properly. This will help in the
appropriate assessment of the issues like poor customer service, damaged equipment, wrong
packaging and delivery of products, etc.
Alignment with the organization’s values, vision, and strategy: It is necessary that the changes
which are proposed should fit the plan and vision of the Latino Engineering. The firm can use
business values for supporting the change and improving the present situation. In this, CSF
customer focus will lead to fair decision-making process regarding the selection of strategies and
approaches.
of their clients along with the issues occurring to them. This critical success factor will not only
improve the market position of the firm but also redevelop the trust and loyalty of consumers
towards it.
Project Tracking and reviewing: By using this critical success factor, Latino Engineering will
able to improve its packaging and delivering processes along with reducing the chances of
producing damaging engineering equipment. It is necessary for the company to track and review
the business processes for handling occurring issues and enhancing the quality. This CSF will
lead to improving the quality of equipment by documenting and storing the information
regarding the delivery of materials.
With the help of above CSF, Latino Engineering will able to design effective and
efficient continuous improvement plan. The Continuous process improvement (CPI) program
which will lead to the formation of CIP is as follows:
Identification of the issue: In this step, the problem of the Latino Engineering will be identified.
As per the case, the company is suffering from delivery of inferior quality products or services to
the customers which is affecting its brand image, market reputation, and customer base. The
primary issue is lack of proper management strategies for handling the manufacturing processes
along with worker’s performance.
Documentation: In this stage of CPI, Latino Engineering needs to keep a record of all the
problems it is facing along with the CSF which can handle them properly. This will help in the
appropriate assessment of the issues like poor customer service, damaged equipment, wrong
packaging and delivery of products, etc.
Alignment with the organization’s values, vision, and strategy: It is necessary that the changes
which are proposed should fit the plan and vision of the Latino Engineering. The firm can use
business values for supporting the change and improving the present situation. In this, CSF
customer focus will lead to fair decision-making process regarding the selection of strategies and
approaches.
Paraphrase This Document
Need a fresh take? Get an instant paraphrase of this document with our AI Paraphraser

What is needed? In this, Latino Engineering will segregate the processes which need to stop,
improve and replace. This division of operations will handle them as per the requirement and
lead to taking decisions related to implementing changes (10 Steps to Continuous Improvement.
2017).
Delegation: Latino engineering will make sure that all the workers along with their leaders will
support the change. This will lead to the commission of work and responsibilities as per the
talent and expertise of the employees. Nomination of the most desirable candidate will help in
driving change regarding the improvement in customer services, change in strategies for
packaging and delivery of products, etc.
Communication: By communicating the needed changes along with regular updates regarding
the implementation will lead to better results. Sharing the information with the employees will
increase their contribution and interest in making appropriate adjustments for handling the
issues. CSF like training, leadership, etc. will help in applying this step of CPI effectively.
Starting small: By breaking the changes into the small goals, Latino Engineering will able to
resolve each complaint one by one. This will also implement the changes more easily and
effectively. One by one resolution of the problem will improve and enhance the quality of
equipment and services.
Feedback: In this step, top management level of the company will have to take feedbacks from
the both customers and employees. These reviews about the implemented change will aware
about the results and level of improvement occurred in the problems. An open discussion will
inform about the actual image of implemented solutions for handling the complaints discussed in
the case.
Monitoring: It is important to monitor every step of collecting information regarding the impact
of change on the overall performance and quality of the business processes and workers. Regular
monitoring will also help in handling the issues causes during the process of implementation of
change into the working environment of Latino Engineering. Project tracking and reviewing CSF
will assist in monitoring the impact of applied solutions for improving the quality of services.
improve and replace. This division of operations will handle them as per the requirement and
lead to taking decisions related to implementing changes (10 Steps to Continuous Improvement.
2017).
Delegation: Latino engineering will make sure that all the workers along with their leaders will
support the change. This will lead to the commission of work and responsibilities as per the
talent and expertise of the employees. Nomination of the most desirable candidate will help in
driving change regarding the improvement in customer services, change in strategies for
packaging and delivery of products, etc.
Communication: By communicating the needed changes along with regular updates regarding
the implementation will lead to better results. Sharing the information with the employees will
increase their contribution and interest in making appropriate adjustments for handling the
issues. CSF like training, leadership, etc. will help in applying this step of CPI effectively.
Starting small: By breaking the changes into the small goals, Latino Engineering will able to
resolve each complaint one by one. This will also implement the changes more easily and
effectively. One by one resolution of the problem will improve and enhance the quality of
equipment and services.
Feedback: In this step, top management level of the company will have to take feedbacks from
the both customers and employees. These reviews about the implemented change will aware
about the results and level of improvement occurred in the problems. An open discussion will
inform about the actual image of implemented solutions for handling the complaints discussed in
the case.
Monitoring: It is important to monitor every step of collecting information regarding the impact
of change on the overall performance and quality of the business processes and workers. Regular
monitoring will also help in handling the issues causes during the process of implementation of
change into the working environment of Latino Engineering. Project tracking and reviewing CSF
will assist in monitoring the impact of applied solutions for improving the quality of services.
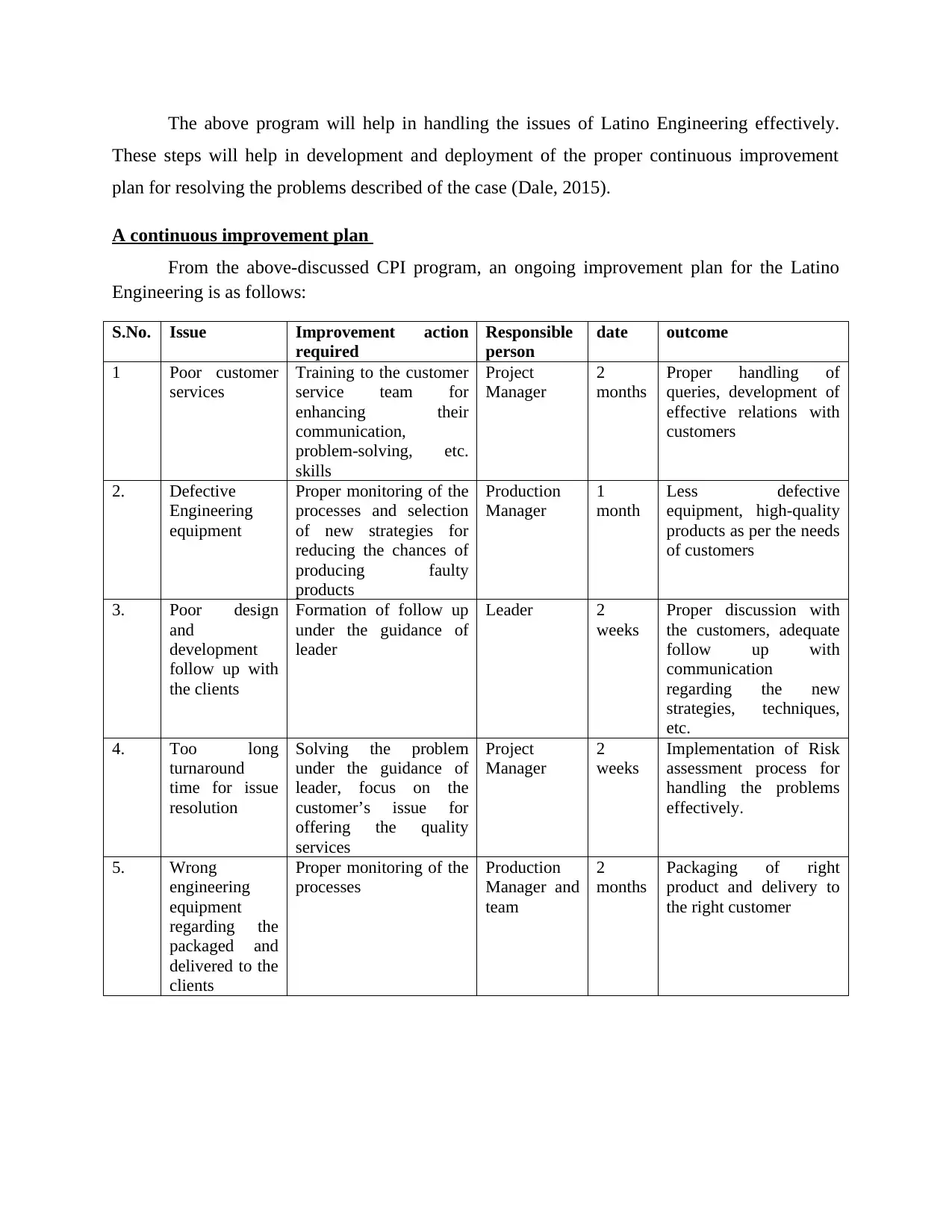
The above program will help in handling the issues of Latino Engineering effectively.
These steps will help in development and deployment of the proper continuous improvement
plan for resolving the problems described of the case (Dale, 2015).
A continuous improvement plan
From the above-discussed CPI program, an ongoing improvement plan for the Latino
Engineering is as follows:
S.No. Issue Improvement action
required
Responsible
person
date outcome
1 Poor customer
services
Training to the customer
service team for
enhancing their
communication,
problem-solving, etc.
skills
Project
Manager
2
months
Proper handling of
queries, development of
effective relations with
customers
2. Defective
Engineering
equipment
Proper monitoring of the
processes and selection
of new strategies for
reducing the chances of
producing faulty
products
Production
Manager
1
month
Less defective
equipment, high-quality
products as per the needs
of customers
3. Poor design
and
development
follow up with
the clients
Formation of follow up
under the guidance of
leader
Leader 2
weeks
Proper discussion with
the customers, adequate
follow up with
communication
regarding the new
strategies, techniques,
etc.
4. Too long
turnaround
time for issue
resolution
Solving the problem
under the guidance of
leader, focus on the
customer’s issue for
offering the quality
services
Project
Manager
2
weeks
Implementation of Risk
assessment process for
handling the problems
effectively.
5. Wrong
engineering
equipment
regarding the
packaged and
delivered to the
clients
Proper monitoring of the
processes
Production
Manager and
team
2
months
Packaging of right
product and delivery to
the right customer
These steps will help in development and deployment of the proper continuous improvement
plan for resolving the problems described of the case (Dale, 2015).
A continuous improvement plan
From the above-discussed CPI program, an ongoing improvement plan for the Latino
Engineering is as follows:
S.No. Issue Improvement action
required
Responsible
person
date outcome
1 Poor customer
services
Training to the customer
service team for
enhancing their
communication,
problem-solving, etc.
skills
Project
Manager
2
months
Proper handling of
queries, development of
effective relations with
customers
2. Defective
Engineering
equipment
Proper monitoring of the
processes and selection
of new strategies for
reducing the chances of
producing faulty
products
Production
Manager
1
month
Less defective
equipment, high-quality
products as per the needs
of customers
3. Poor design
and
development
follow up with
the clients
Formation of follow up
under the guidance of
leader
Leader 2
weeks
Proper discussion with
the customers, adequate
follow up with
communication
regarding the new
strategies, techniques,
etc.
4. Too long
turnaround
time for issue
resolution
Solving the problem
under the guidance of
leader, focus on the
customer’s issue for
offering the quality
services
Project
Manager
2
weeks
Implementation of Risk
assessment process for
handling the problems
effectively.
5. Wrong
engineering
equipment
regarding the
packaged and
delivered to the
clients
Proper monitoring of the
processes
Production
Manager and
team
2
months
Packaging of right
product and delivery to
the right customer
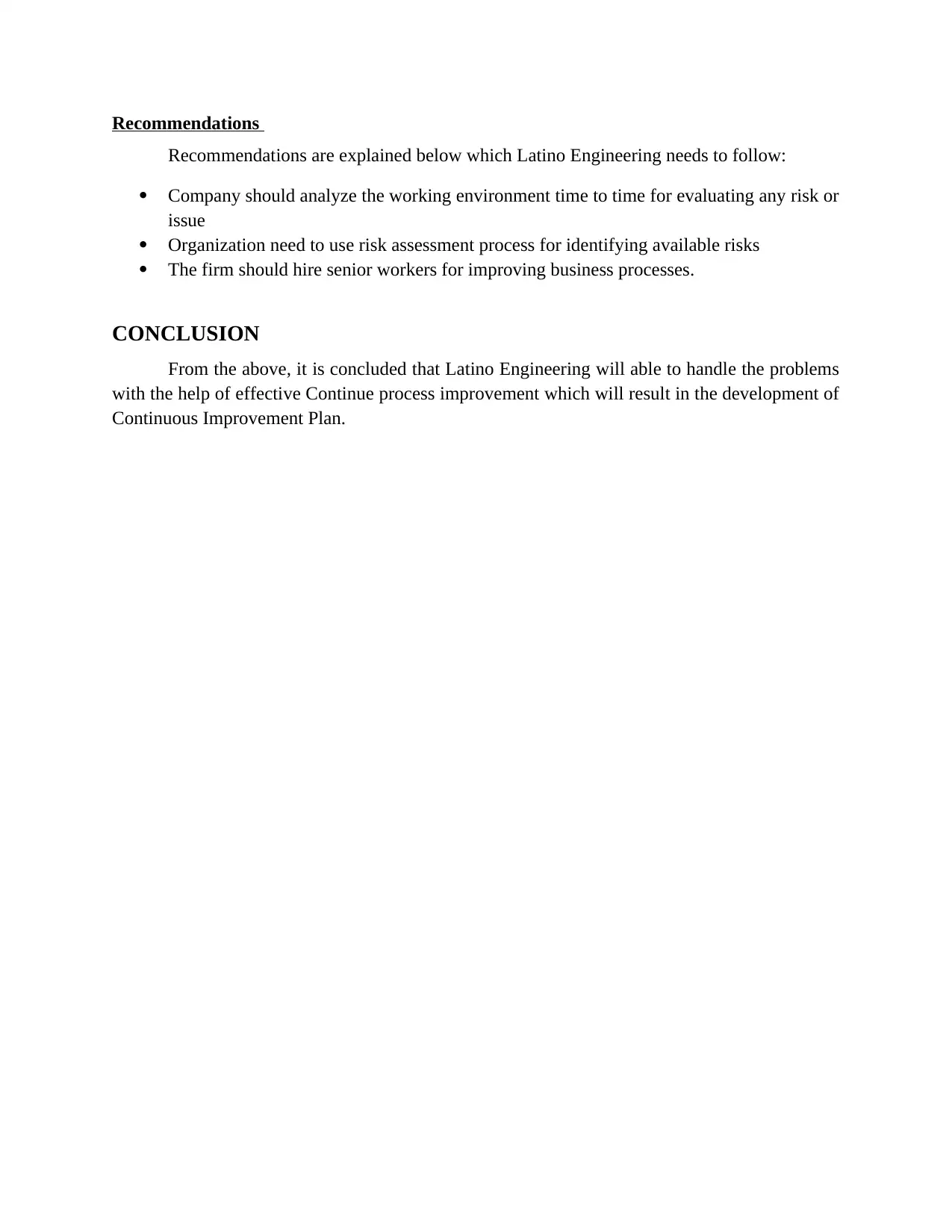
Recommendations
Recommendations are explained below which Latino Engineering needs to follow:
Company should analyze the working environment time to time for evaluating any risk or
issue
Organization need to use risk assessment process for identifying available risks
The firm should hire senior workers for improving business processes.
CONCLUSION
From the above, it is concluded that Latino Engineering will able to handle the problems
with the help of effective Continue process improvement which will result in the development of
Continuous Improvement Plan.
Recommendations are explained below which Latino Engineering needs to follow:
Company should analyze the working environment time to time for evaluating any risk or
issue
Organization need to use risk assessment process for identifying available risks
The firm should hire senior workers for improving business processes.
CONCLUSION
From the above, it is concluded that Latino Engineering will able to handle the problems
with the help of effective Continue process improvement which will result in the development of
Continuous Improvement Plan.
Secure Best Marks with AI Grader
Need help grading? Try our AI Grader for instant feedback on your assignments.
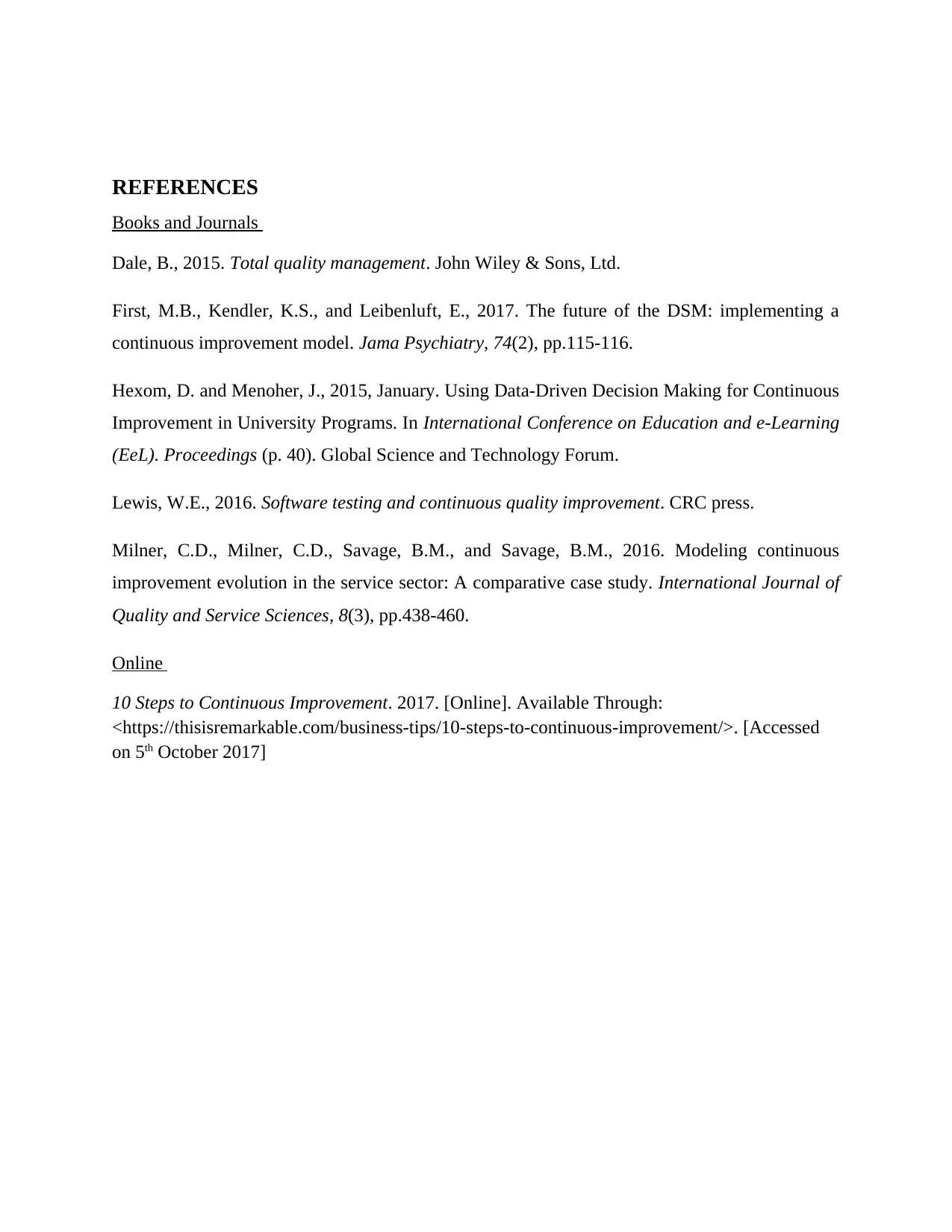
REFERENCES
Books and Journals
Dale, B., 2015. Total quality management. John Wiley & Sons, Ltd.
First, M.B., Kendler, K.S., and Leibenluft, E., 2017. The future of the DSM: implementing a
continuous improvement model. Jama Psychiatry, 74(2), pp.115-116.
Hexom, D. and Menoher, J., 2015, January. Using Data-Driven Decision Making for Continuous
Improvement in University Programs. In International Conference on Education and e-Learning
(EeL). Proceedings (p. 40). Global Science and Technology Forum.
Lewis, W.E., 2016. Software testing and continuous quality improvement. CRC press.
Milner, C.D., Milner, C.D., Savage, B.M., and Savage, B.M., 2016. Modeling continuous
improvement evolution in the service sector: A comparative case study. International Journal of
Quality and Service Sciences, 8(3), pp.438-460.
Online
10 Steps to Continuous Improvement. 2017. [Online]. Available Through:
<https://thisisremarkable.com/business-tips/10-steps-to-continuous-improvement/>. [Accessed
on 5th October 2017]
Books and Journals
Dale, B., 2015. Total quality management. John Wiley & Sons, Ltd.
First, M.B., Kendler, K.S., and Leibenluft, E., 2017. The future of the DSM: implementing a
continuous improvement model. Jama Psychiatry, 74(2), pp.115-116.
Hexom, D. and Menoher, J., 2015, January. Using Data-Driven Decision Making for Continuous
Improvement in University Programs. In International Conference on Education and e-Learning
(EeL). Proceedings (p. 40). Global Science and Technology Forum.
Lewis, W.E., 2016. Software testing and continuous quality improvement. CRC press.
Milner, C.D., Milner, C.D., Savage, B.M., and Savage, B.M., 2016. Modeling continuous
improvement evolution in the service sector: A comparative case study. International Journal of
Quality and Service Sciences, 8(3), pp.438-460.
Online
10 Steps to Continuous Improvement. 2017. [Online]. Available Through:
<https://thisisremarkable.com/business-tips/10-steps-to-continuous-improvement/>. [Accessed
on 5th October 2017]
1 out of 11
Related Documents

Your All-in-One AI-Powered Toolkit for Academic Success.
+13062052269
info@desklib.com
Available 24*7 on WhatsApp / Email
Unlock your academic potential
© 2024 | Zucol Services PVT LTD | All rights reserved.