Project Management Methodologies: Root Cause Analysis
VerifiedAdded on 2020/04/07
|14
|2994
|59
Project
AI Summary
This assignment provides a comprehensive analysis of project management methodologies, emphasizing the identification of root causes for project failures. It begins with an explanation of situational analysis and proposes the use of tools and techniques such as observations, interviews, focus...
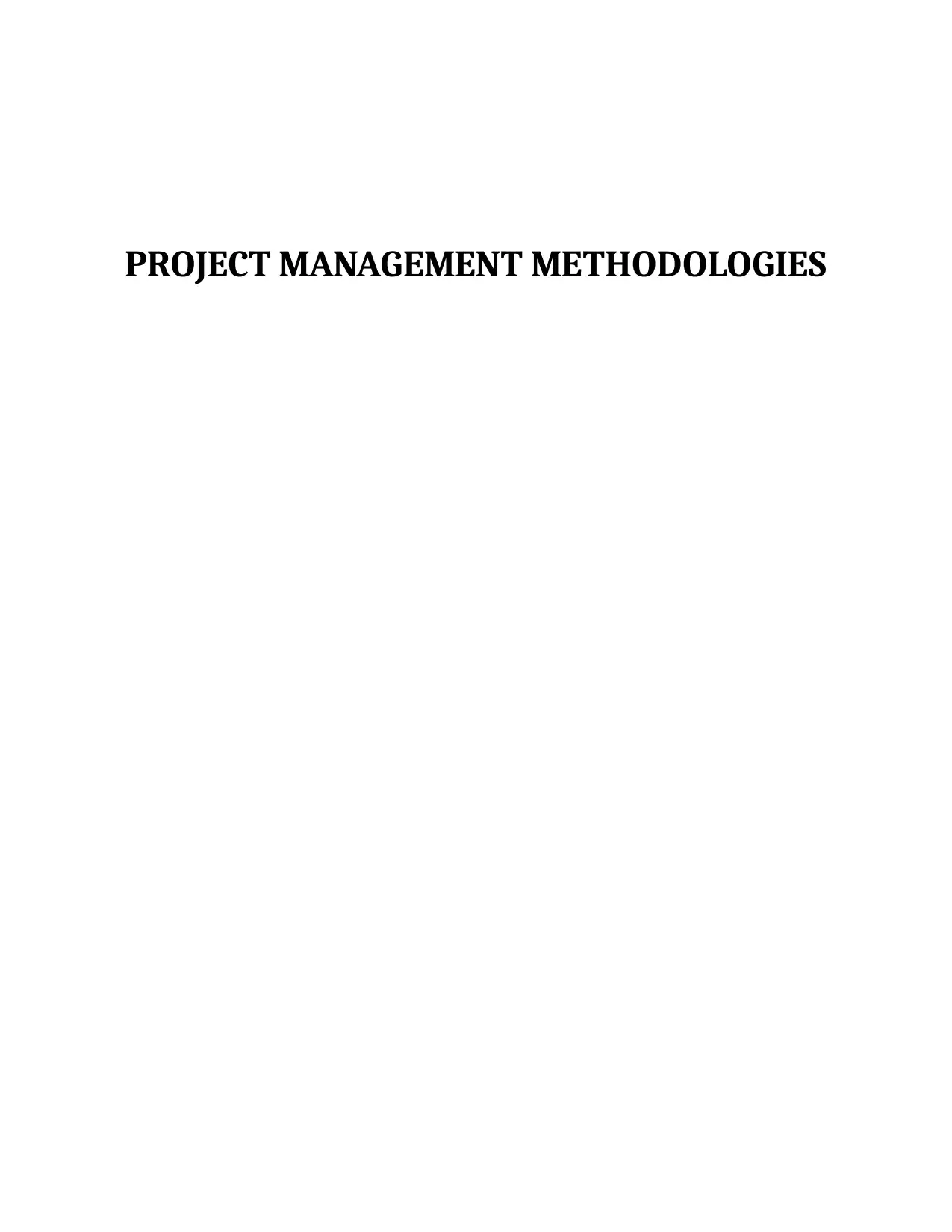
PROJECT MANAGEMENT METHODOLOGIES
Paraphrase This Document
Need a fresh take? Get an instant paraphrase of this document with our AI Paraphraser
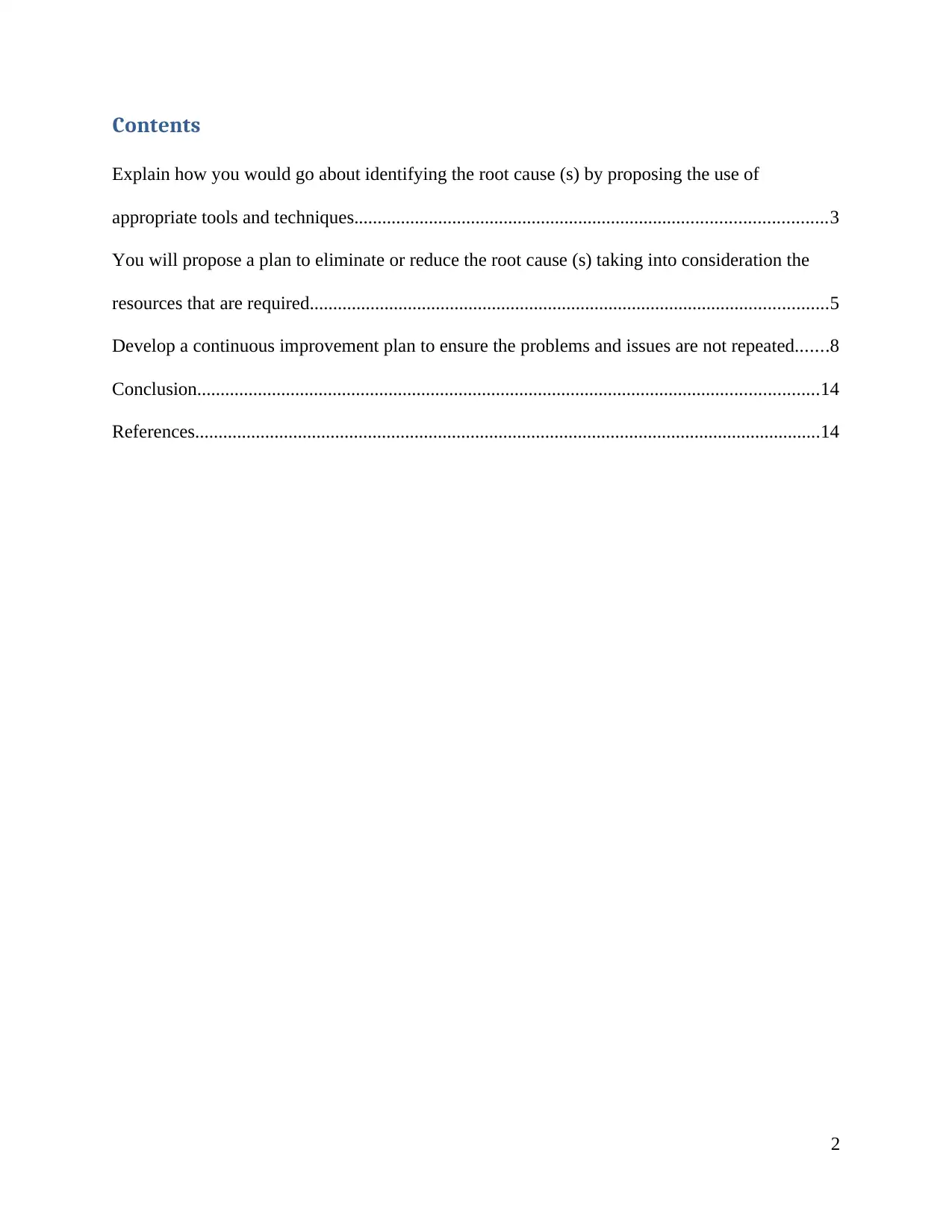
Contents
Explain how you would go about identifying the root cause (s) by proposing the use of
appropriate tools and techniques.....................................................................................................3
You will propose a plan to eliminate or reduce the root cause (s) taking into consideration the
resources that are required...............................................................................................................5
Develop a continuous improvement plan to ensure the problems and issues are not repeated.......8
Conclusion.....................................................................................................................................14
References......................................................................................................................................14
2
Explain how you would go about identifying the root cause (s) by proposing the use of
appropriate tools and techniques.....................................................................................................3
You will propose a plan to eliminate or reduce the root cause (s) taking into consideration the
resources that are required...............................................................................................................5
Develop a continuous improvement plan to ensure the problems and issues are not repeated.......8
Conclusion.....................................................................................................................................14
References......................................................................................................................................14
2
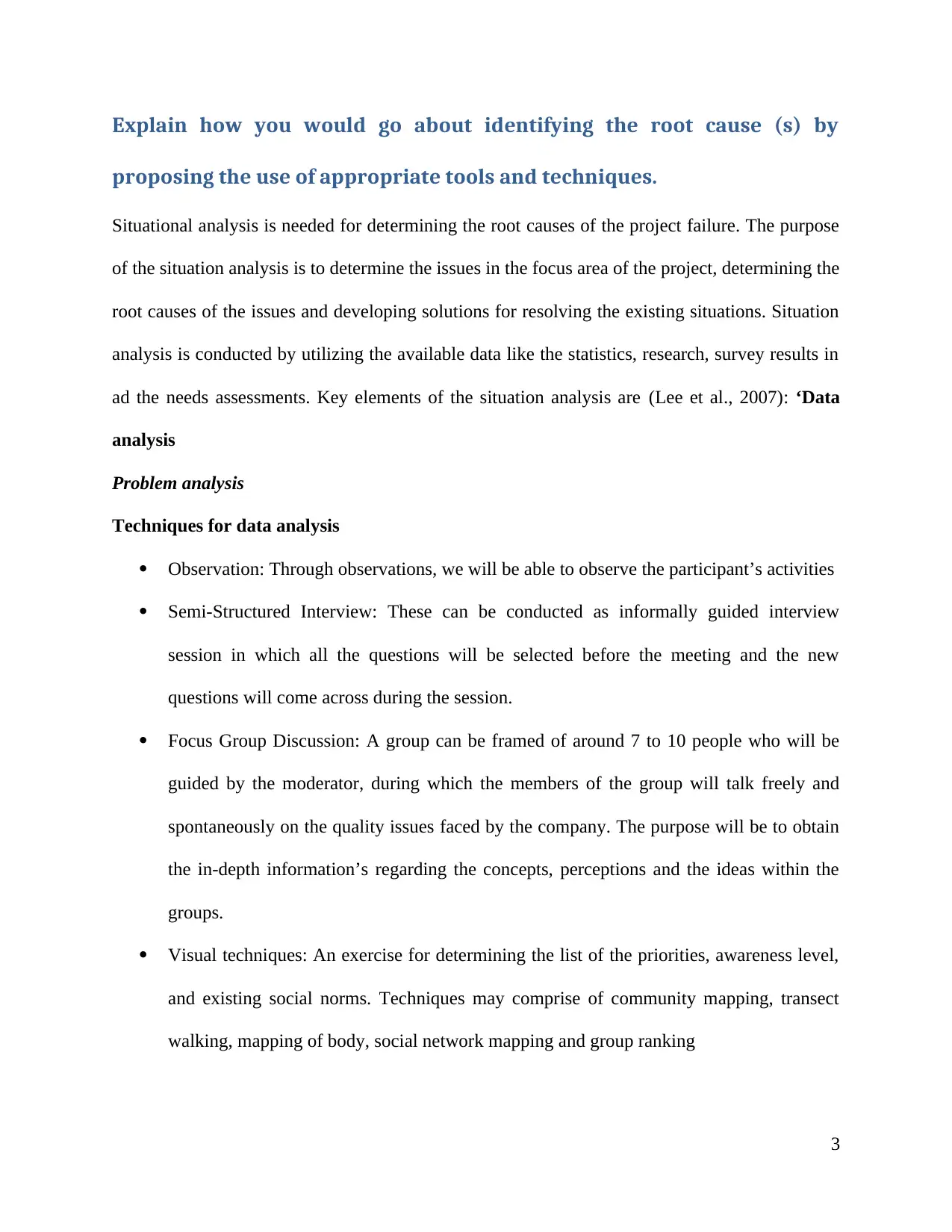
Explain how you would go about identifying the root cause (s) by
proposing the use of appropriate tools and techniques.
Situational analysis is needed for determining the root causes of the project failure. The purpose
of the situation analysis is to determine the issues in the focus area of the project, determining the
root causes of the issues and developing solutions for resolving the existing situations. Situation
analysis is conducted by utilizing the available data like the statistics, research, survey results in
ad the needs assessments. Key elements of the situation analysis are (Lee et al., 2007): ‘Data
analysis
Problem analysis
Techniques for data analysis
Observation: Through observations, we will be able to observe the participant’s activities
Semi-Structured Interview: These can be conducted as informally guided interview
session in which all the questions will be selected before the meeting and the new
questions will come across during the session.
Focus Group Discussion: A group can be framed of around 7 to 10 people who will be
guided by the moderator, during which the members of the group will talk freely and
spontaneously on the quality issues faced by the company. The purpose will be to obtain
the in-depth information’s regarding the concepts, perceptions and the ideas within the
groups.
Visual techniques: An exercise for determining the list of the priorities, awareness level,
and existing social norms. Techniques may comprise of community mapping, transect
walking, mapping of body, social network mapping and group ranking
3
proposing the use of appropriate tools and techniques.
Situational analysis is needed for determining the root causes of the project failure. The purpose
of the situation analysis is to determine the issues in the focus area of the project, determining the
root causes of the issues and developing solutions for resolving the existing situations. Situation
analysis is conducted by utilizing the available data like the statistics, research, survey results in
ad the needs assessments. Key elements of the situation analysis are (Lee et al., 2007): ‘Data
analysis
Problem analysis
Techniques for data analysis
Observation: Through observations, we will be able to observe the participant’s activities
Semi-Structured Interview: These can be conducted as informally guided interview
session in which all the questions will be selected before the meeting and the new
questions will come across during the session.
Focus Group Discussion: A group can be framed of around 7 to 10 people who will be
guided by the moderator, during which the members of the group will talk freely and
spontaneously on the quality issues faced by the company. The purpose will be to obtain
the in-depth information’s regarding the concepts, perceptions and the ideas within the
groups.
Visual techniques: An exercise for determining the list of the priorities, awareness level,
and existing social norms. Techniques may comprise of community mapping, transect
walking, mapping of body, social network mapping and group ranking
3
⊘ This is a preview!⊘
Do you want full access?
Subscribe today to unlock all pages.

Trusted by 1+ million students worldwide
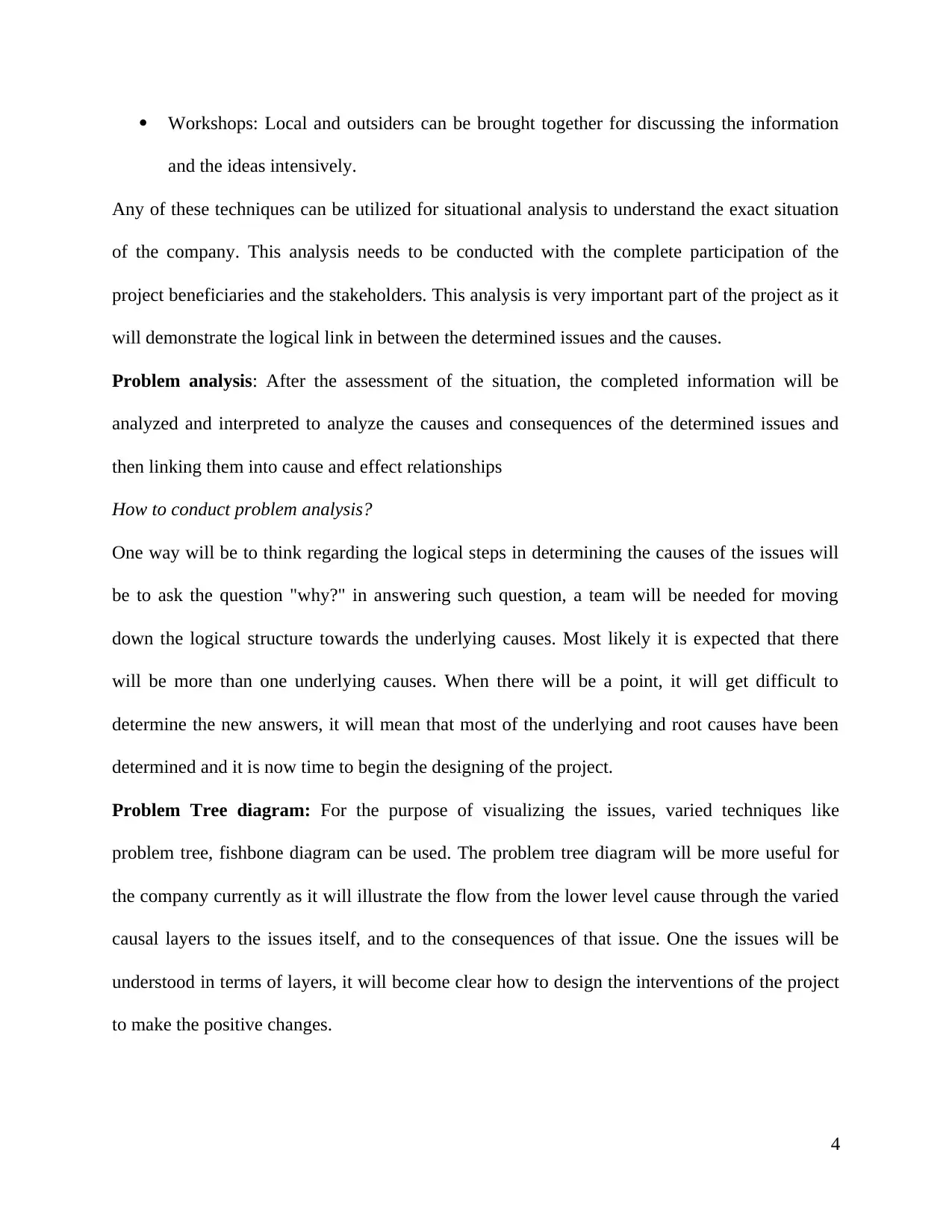
Workshops: Local and outsiders can be brought together for discussing the information
and the ideas intensively.
Any of these techniques can be utilized for situational analysis to understand the exact situation
of the company. This analysis needs to be conducted with the complete participation of the
project beneficiaries and the stakeholders. This analysis is very important part of the project as it
will demonstrate the logical link in between the determined issues and the causes.
Problem analysis: After the assessment of the situation, the completed information will be
analyzed and interpreted to analyze the causes and consequences of the determined issues and
then linking them into cause and effect relationships
How to conduct problem analysis?
One way will be to think regarding the logical steps in determining the causes of the issues will
be to ask the question "why?" in answering such question, a team will be needed for moving
down the logical structure towards the underlying causes. Most likely it is expected that there
will be more than one underlying causes. When there will be a point, it will get difficult to
determine the new answers, it will mean that most of the underlying and root causes have been
determined and it is now time to begin the designing of the project.
Problem Tree diagram: For the purpose of visualizing the issues, varied techniques like
problem tree, fishbone diagram can be used. The problem tree diagram will be more useful for
the company currently as it will illustrate the flow from the lower level cause through the varied
causal layers to the issues itself, and to the consequences of that issue. One the issues will be
understood in terms of layers, it will become clear how to design the interventions of the project
to make the positive changes.
4
and the ideas intensively.
Any of these techniques can be utilized for situational analysis to understand the exact situation
of the company. This analysis needs to be conducted with the complete participation of the
project beneficiaries and the stakeholders. This analysis is very important part of the project as it
will demonstrate the logical link in between the determined issues and the causes.
Problem analysis: After the assessment of the situation, the completed information will be
analyzed and interpreted to analyze the causes and consequences of the determined issues and
then linking them into cause and effect relationships
How to conduct problem analysis?
One way will be to think regarding the logical steps in determining the causes of the issues will
be to ask the question "why?" in answering such question, a team will be needed for moving
down the logical structure towards the underlying causes. Most likely it is expected that there
will be more than one underlying causes. When there will be a point, it will get difficult to
determine the new answers, it will mean that most of the underlying and root causes have been
determined and it is now time to begin the designing of the project.
Problem Tree diagram: For the purpose of visualizing the issues, varied techniques like
problem tree, fishbone diagram can be used. The problem tree diagram will be more useful for
the company currently as it will illustrate the flow from the lower level cause through the varied
causal layers to the issues itself, and to the consequences of that issue. One the issues will be
understood in terms of layers, it will become clear how to design the interventions of the project
to make the positive changes.
4
Paraphrase This Document
Need a fresh take? Get an instant paraphrase of this document with our AI Paraphraser
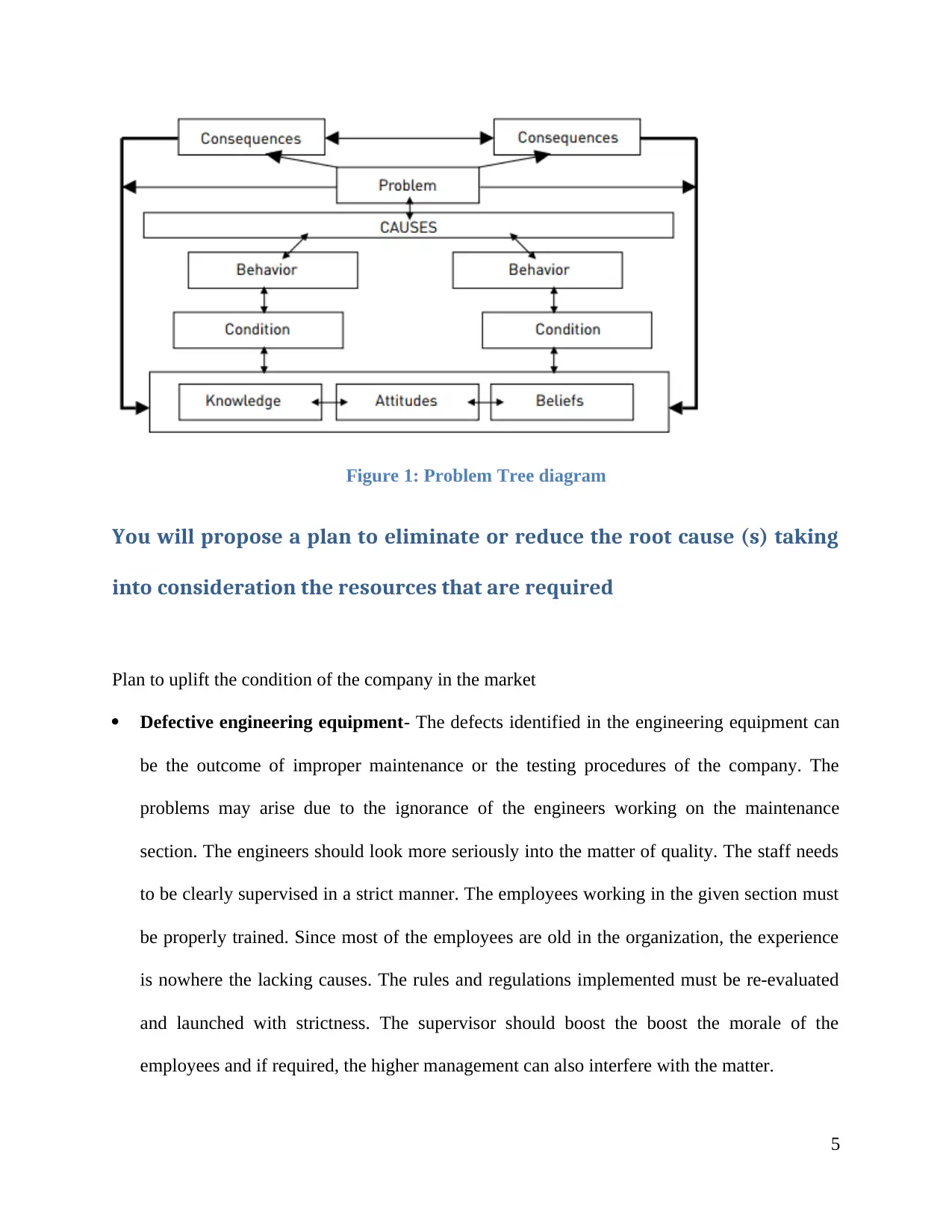
Figure 1: Problem Tree diagram
You will propose a plan to eliminate or reduce the root cause (s) taking
into consideration the resources that are required
Plan to uplift the condition of the company in the market
Defective engineering equipment- The defects identified in the engineering equipment can
be the outcome of improper maintenance or the testing procedures of the company. The
problems may arise due to the ignorance of the engineers working on the maintenance
section. The engineers should look more seriously into the matter of quality. The staff needs
to be clearly supervised in a strict manner. The employees working in the given section must
be properly trained. Since most of the employees are old in the organization, the experience
is nowhere the lacking causes. The rules and regulations implemented must be re-evaluated
and launched with strictness. The supervisor should boost the boost the morale of the
employees and if required, the higher management can also interfere with the matter.
5
You will propose a plan to eliminate or reduce the root cause (s) taking
into consideration the resources that are required
Plan to uplift the condition of the company in the market
Defective engineering equipment- The defects identified in the engineering equipment can
be the outcome of improper maintenance or the testing procedures of the company. The
problems may arise due to the ignorance of the engineers working on the maintenance
section. The engineers should look more seriously into the matter of quality. The staff needs
to be clearly supervised in a strict manner. The employees working in the given section must
be properly trained. Since most of the employees are old in the organization, the experience
is nowhere the lacking causes. The rules and regulations implemented must be re-evaluated
and launched with strictness. The supervisor should boost the boost the morale of the
employees and if required, the higher management can also interfere with the matter.
5
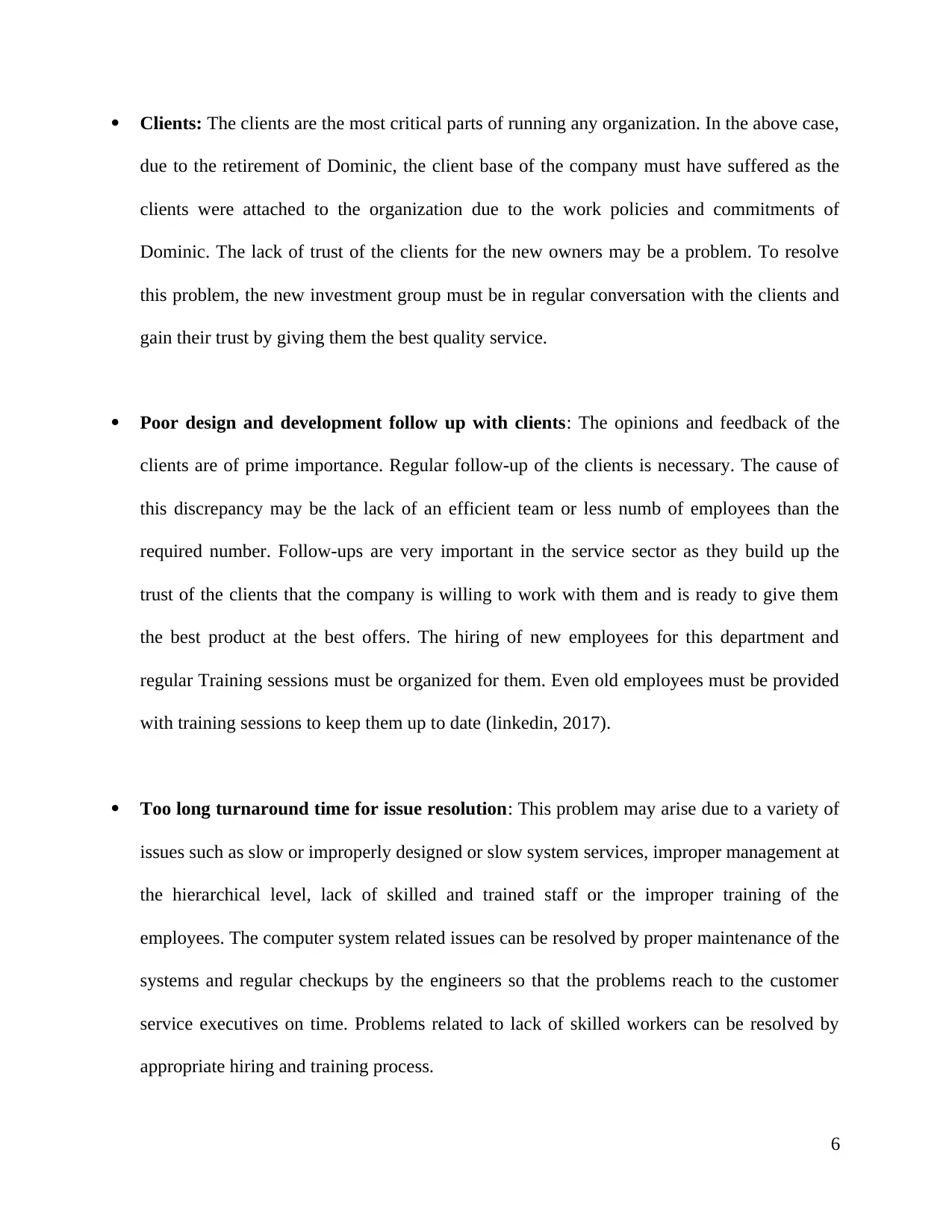
Clients: The clients are the most critical parts of running any organization. In the above case,
due to the retirement of Dominic, the client base of the company must have suffered as the
clients were attached to the organization due to the work policies and commitments of
Dominic. The lack of trust of the clients for the new owners may be a problem. To resolve
this problem, the new investment group must be in regular conversation with the clients and
gain their trust by giving them the best quality service.
Poor design and development follow up with clients: The opinions and feedback of the
clients are of prime importance. Regular follow-up of the clients is necessary. The cause of
this discrepancy may be the lack of an efficient team or less numb of employees than the
required number. Follow-ups are very important in the service sector as they build up the
trust of the clients that the company is willing to work with them and is ready to give them
the best product at the best offers. The hiring of new employees for this department and
regular Training sessions must be organized for them. Even old employees must be provided
with training sessions to keep them up to date (linkedin, 2017).
Too long turnaround time for issue resolution: This problem may arise due to a variety of
issues such as slow or improperly designed or slow system services, improper management at
the hierarchical level, lack of skilled and trained staff or the improper training of the
employees. The computer system related issues can be resolved by proper maintenance of the
systems and regular checkups by the engineers so that the problems reach to the customer
service executives on time. Problems related to lack of skilled workers can be resolved by
appropriate hiring and training process.
6
due to the retirement of Dominic, the client base of the company must have suffered as the
clients were attached to the organization due to the work policies and commitments of
Dominic. The lack of trust of the clients for the new owners may be a problem. To resolve
this problem, the new investment group must be in regular conversation with the clients and
gain their trust by giving them the best quality service.
Poor design and development follow up with clients: The opinions and feedback of the
clients are of prime importance. Regular follow-up of the clients is necessary. The cause of
this discrepancy may be the lack of an efficient team or less numb of employees than the
required number. Follow-ups are very important in the service sector as they build up the
trust of the clients that the company is willing to work with them and is ready to give them
the best product at the best offers. The hiring of new employees for this department and
regular Training sessions must be organized for them. Even old employees must be provided
with training sessions to keep them up to date (linkedin, 2017).
Too long turnaround time for issue resolution: This problem may arise due to a variety of
issues such as slow or improperly designed or slow system services, improper management at
the hierarchical level, lack of skilled and trained staff or the improper training of the
employees. The computer system related issues can be resolved by proper maintenance of the
systems and regular checkups by the engineers so that the problems reach to the customer
service executives on time. Problems related to lack of skilled workers can be resolved by
appropriate hiring and training process.
6
⊘ This is a preview!⊘
Do you want full access?
Subscribe today to unlock all pages.

Trusted by 1+ million students worldwide
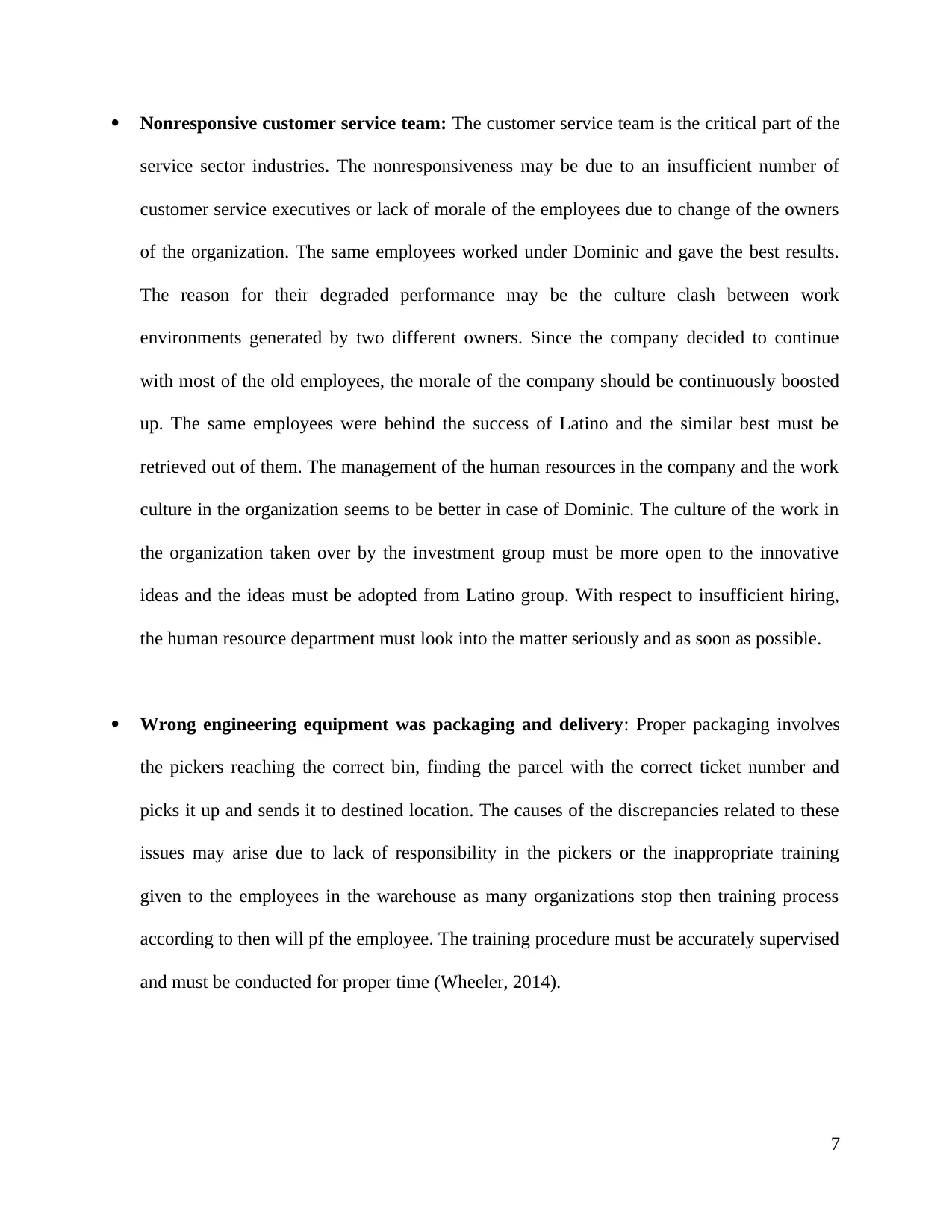
Nonresponsive customer service team: The customer service team is the critical part of the
service sector industries. The nonresponsiveness may be due to an insufficient number of
customer service executives or lack of morale of the employees due to change of the owners
of the organization. The same employees worked under Dominic and gave the best results.
The reason for their degraded performance may be the culture clash between work
environments generated by two different owners. Since the company decided to continue
with most of the old employees, the morale of the company should be continuously boosted
up. The same employees were behind the success of Latino and the similar best must be
retrieved out of them. The management of the human resources in the company and the work
culture in the organization seems to be better in case of Dominic. The culture of the work in
the organization taken over by the investment group must be more open to the innovative
ideas and the ideas must be adopted from Latino group. With respect to insufficient hiring,
the human resource department must look into the matter seriously and as soon as possible.
Wrong engineering equipment was packaging and delivery: Proper packaging involves
the pickers reaching the correct bin, finding the parcel with the correct ticket number and
picks it up and sends it to destined location. The causes of the discrepancies related to these
issues may arise due to lack of responsibility in the pickers or the inappropriate training
given to the employees in the warehouse as many organizations stop then training process
according to then will pf the employee. The training procedure must be accurately supervised
and must be conducted for proper time (Wheeler, 2014).
7
service sector industries. The nonresponsiveness may be due to an insufficient number of
customer service executives or lack of morale of the employees due to change of the owners
of the organization. The same employees worked under Dominic and gave the best results.
The reason for their degraded performance may be the culture clash between work
environments generated by two different owners. Since the company decided to continue
with most of the old employees, the morale of the company should be continuously boosted
up. The same employees were behind the success of Latino and the similar best must be
retrieved out of them. The management of the human resources in the company and the work
culture in the organization seems to be better in case of Dominic. The culture of the work in
the organization taken over by the investment group must be more open to the innovative
ideas and the ideas must be adopted from Latino group. With respect to insufficient hiring,
the human resource department must look into the matter seriously and as soon as possible.
Wrong engineering equipment was packaging and delivery: Proper packaging involves
the pickers reaching the correct bin, finding the parcel with the correct ticket number and
picks it up and sends it to destined location. The causes of the discrepancies related to these
issues may arise due to lack of responsibility in the pickers or the inappropriate training
given to the employees in the warehouse as many organizations stop then training process
according to then will pf the employee. The training procedure must be accurately supervised
and must be conducted for proper time (Wheeler, 2014).
7
Paraphrase This Document
Need a fresh take? Get an instant paraphrase of this document with our AI Paraphraser
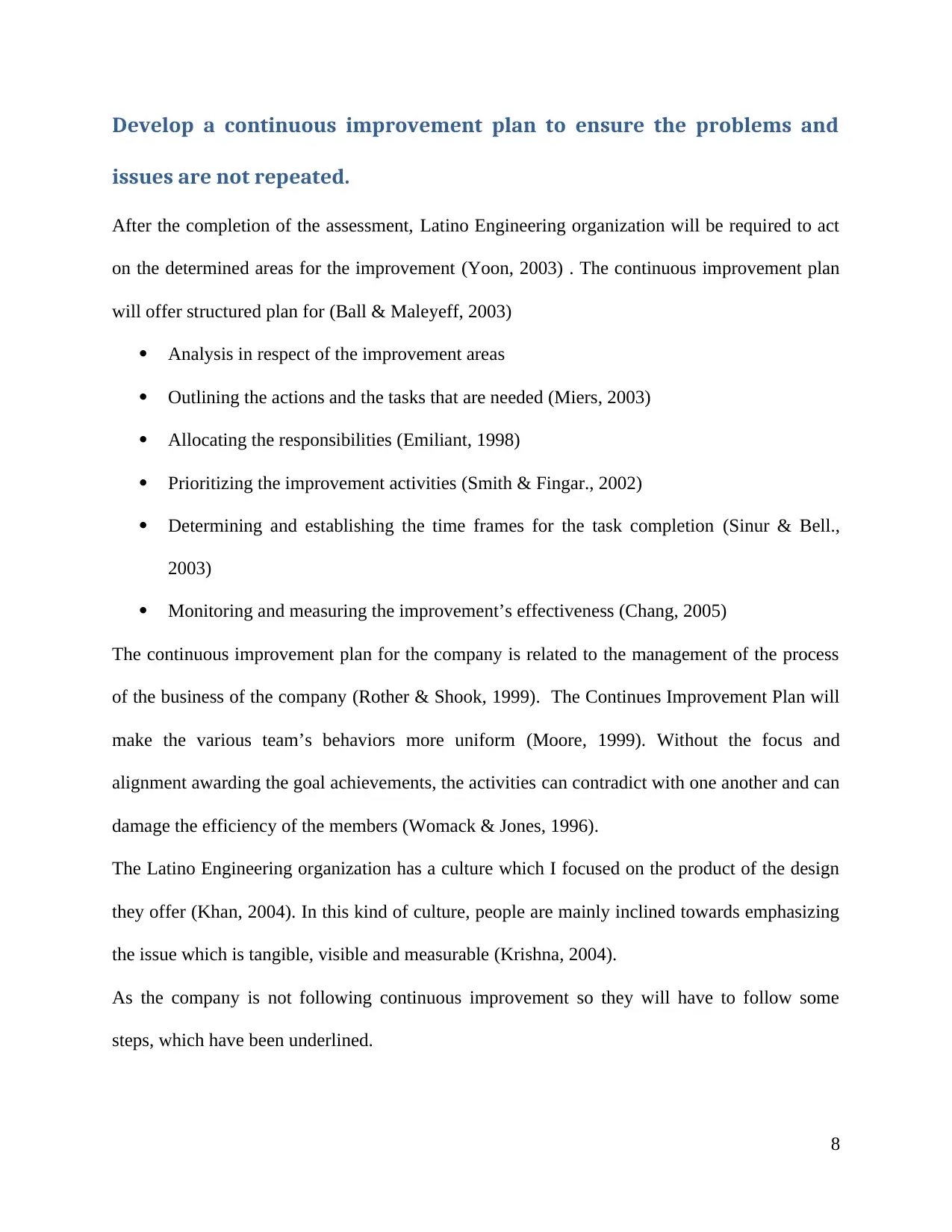
Develop a continuous improvement plan to ensure the problems and
issues are not repeated.
After the completion of the assessment, Latino Engineering organization will be required to act
on the determined areas for the improvement (Yoon, 2003) . The continuous improvement plan
will offer structured plan for (Ball & Maleyeff, 2003)
Analysis in respect of the improvement areas
Outlining the actions and the tasks that are needed (Miers, 2003)
Allocating the responsibilities (Emiliant, 1998)
Prioritizing the improvement activities (Smith & Fingar., 2002)
Determining and establishing the time frames for the task completion (Sinur & Bell.,
2003)
Monitoring and measuring the improvement’s effectiveness (Chang, 2005)
The continuous improvement plan for the company is related to the management of the process
of the business of the company (Rother & Shook, 1999). The Continues Improvement Plan will
make the various team’s behaviors more uniform (Moore, 1999). Without the focus and
alignment awarding the goal achievements, the activities can contradict with one another and can
damage the efficiency of the members (Womack & Jones, 1996).
The Latino Engineering organization has a culture which I focused on the product of the design
they offer (Khan, 2004). In this kind of culture, people are mainly inclined towards emphasizing
the issue which is tangible, visible and measurable (Krishna, 2004).
As the company is not following continuous improvement so they will have to follow some
steps, which have been underlined.
8
issues are not repeated.
After the completion of the assessment, Latino Engineering organization will be required to act
on the determined areas for the improvement (Yoon, 2003) . The continuous improvement plan
will offer structured plan for (Ball & Maleyeff, 2003)
Analysis in respect of the improvement areas
Outlining the actions and the tasks that are needed (Miers, 2003)
Allocating the responsibilities (Emiliant, 1998)
Prioritizing the improvement activities (Smith & Fingar., 2002)
Determining and establishing the time frames for the task completion (Sinur & Bell.,
2003)
Monitoring and measuring the improvement’s effectiveness (Chang, 2005)
The continuous improvement plan for the company is related to the management of the process
of the business of the company (Rother & Shook, 1999). The Continues Improvement Plan will
make the various team’s behaviors more uniform (Moore, 1999). Without the focus and
alignment awarding the goal achievements, the activities can contradict with one another and can
damage the efficiency of the members (Womack & Jones, 1996).
The Latino Engineering organization has a culture which I focused on the product of the design
they offer (Khan, 2004). In this kind of culture, people are mainly inclined towards emphasizing
the issue which is tangible, visible and measurable (Krishna, 2004).
As the company is not following continuous improvement so they will have to follow some
steps, which have been underlined.
8

Goal: there is need for entering the SMART components and the value the developments
(Harmon, 2003)
Strategy: The Company needs to offer the stronger leadership for guiding the projects
through the continuous improvement plan.
Action Steps: The stakeholders need to ensure the equitable and supportive environment
(Verma, 2009)
Implementation of the Continuous Improvement plan
The company is mainly needed to implement the concept of the lean management for the
business process of company. For the improvement, the company is mainly required for
implementing the process management of business. The procedure will mainly help in
increasing the services and products with the help of structured approach towards the
performance improvement (Jeston & Nelis, 2010). Though the value stream mapping is an
effective methodology for the description of the rules and process of the business, there is
requirement for the adaptation of the new tool of business process management for the decrease
in the waste and increment in the values (Snabe et al., 2008).
Specification of the value
The company’s procedure is mainly to design the tools that comprises of the budget
establishment. The main value of the complete process is mainly to decrease the waste in the
budgets and accomplishments of the goals of the increasing money value.
Determining the process flow
The value stream needs to be used as a main tool and technique which will encompass the varied
acts, relations and the structure of the project as a base for the illustration of the future flows. The
procedure will be involving the design receipts and the budget estimation for the budget.
9
(Harmon, 2003)
Strategy: The Company needs to offer the stronger leadership for guiding the projects
through the continuous improvement plan.
Action Steps: The stakeholders need to ensure the equitable and supportive environment
(Verma, 2009)
Implementation of the Continuous Improvement plan
The company is mainly needed to implement the concept of the lean management for the
business process of company. For the improvement, the company is mainly required for
implementing the process management of business. The procedure will mainly help in
increasing the services and products with the help of structured approach towards the
performance improvement (Jeston & Nelis, 2010). Though the value stream mapping is an
effective methodology for the description of the rules and process of the business, there is
requirement for the adaptation of the new tool of business process management for the decrease
in the waste and increment in the values (Snabe et al., 2008).
Specification of the value
The company’s procedure is mainly to design the tools that comprises of the budget
establishment. The main value of the complete process is mainly to decrease the waste in the
budgets and accomplishments of the goals of the increasing money value.
Determining the process flow
The value stream needs to be used as a main tool and technique which will encompass the varied
acts, relations and the structure of the project as a base for the illustration of the future flows. The
procedure will be involving the design receipts and the budget estimation for the budget.
9
⊘ This is a preview!⊘
Do you want full access?
Subscribe today to unlock all pages.

Trusted by 1+ million students worldwide
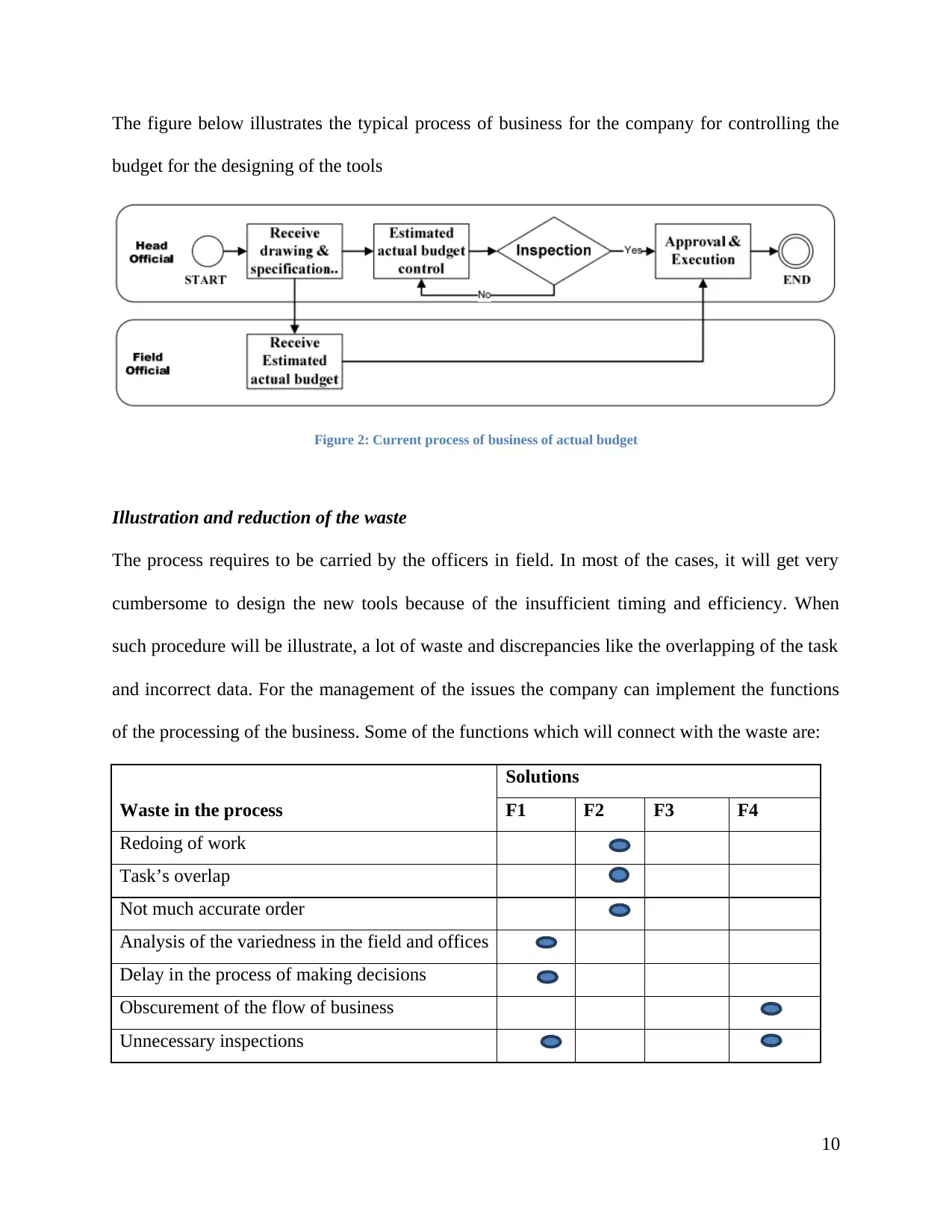
The figure below illustrates the typical process of business for the company for controlling the
budget for the designing of the tools
Figure 2: Current process of business of actual budget
Illustration and reduction of the waste
The process requires to be carried by the officers in field. In most of the cases, it will get very
cumbersome to design the new tools because of the insufficient timing and efficiency. When
such procedure will be illustrate, a lot of waste and discrepancies like the overlapping of the task
and incorrect data. For the management of the issues the company can implement the functions
of the processing of the business. Some of the functions which will connect with the waste are:
Waste in the process
Solutions
F1 F2 F3 F4
Redoing of work
Task’s overlap
Not much accurate order
Analysis of the variedness in the field and offices
Delay in the process of making decisions
Obscurement of the flow of business
Unnecessary inspections
10
budget for the designing of the tools
Figure 2: Current process of business of actual budget
Illustration and reduction of the waste
The process requires to be carried by the officers in field. In most of the cases, it will get very
cumbersome to design the new tools because of the insufficient timing and efficiency. When
such procedure will be illustrate, a lot of waste and discrepancies like the overlapping of the task
and incorrect data. For the management of the issues the company can implement the functions
of the processing of the business. Some of the functions which will connect with the waste are:
Waste in the process
Solutions
F1 F2 F3 F4
Redoing of work
Task’s overlap
Not much accurate order
Analysis of the variedness in the field and offices
Delay in the process of making decisions
Obscurement of the flow of business
Unnecessary inspections
10
Paraphrase This Document
Need a fresh take? Get an instant paraphrase of this document with our AI Paraphraser

F1: Management of Performance
F2: Process Automation
F3: Management of Knowledge
F4: Process Management
Value development with the business processing
After the reduction in the waste, the managers of the designing department will have to manage
the waste which might occur in the future. The process of the management of the business will
be able to provide the support to the participants of the process through information, machines
and people. The figure below reveals the systematized creation of value from the improvement
plan.
Activity
Date of
Receivin
g
Date of
Start
ing
Key Indicator
of
Performance
Schedu
led day
end
day
Progre
ss state
Com
plete
In
charge
person
Departm
ent
Receiving and
determining the
specifications
5/10/201
7
5/10/201
7 4 months - - Not yet -
Project
Inc.
charge
Project
managem
ent
Filling the estimated
actual budget
5/10/201
7
5/10/201
7
5 months - - Not yet - Project
Inc.
Project
managem
11
F2: Process Automation
F3: Management of Knowledge
F4: Process Management
Value development with the business processing
After the reduction in the waste, the managers of the designing department will have to manage
the waste which might occur in the future. The process of the management of the business will
be able to provide the support to the participants of the process through information, machines
and people. The figure below reveals the systematized creation of value from the improvement
plan.
Activity
Date of
Receivin
g
Date of
Start
ing
Key Indicator
of
Performance
Schedu
led day
end
day
Progre
ss state
Com
plete
In
charge
person
Departm
ent
Receiving and
determining the
specifications
5/10/201
7
5/10/201
7 4 months - - Not yet -
Project
Inc.
charge
Project
managem
ent
Filling the estimated
actual budget
5/10/201
7
5/10/201
7
5 months - - Not yet - Project
Inc.
Project
managem
11
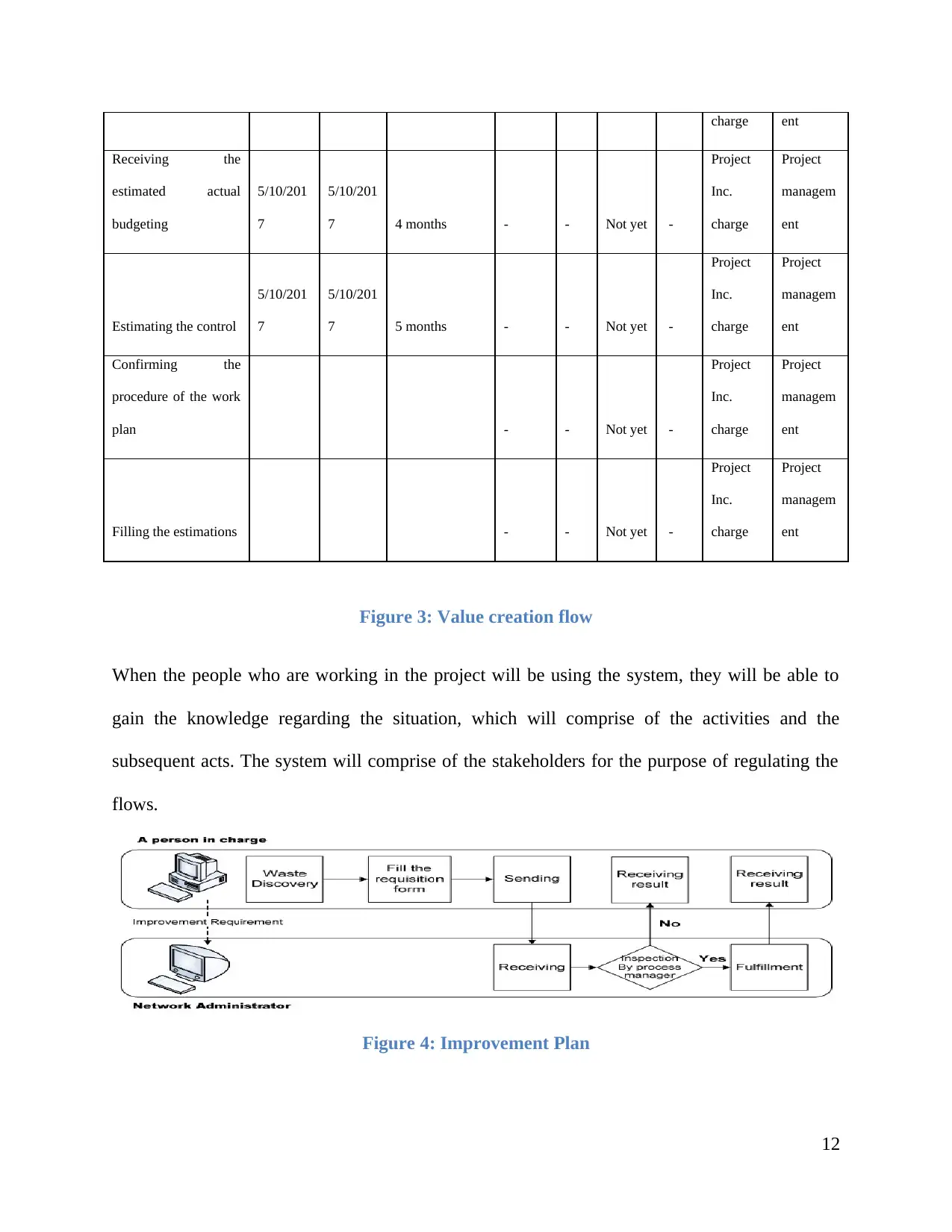
charge ent
Receiving the
estimated actual
budgeting
5/10/201
7
5/10/201
7 4 months - - Not yet -
Project
Inc.
charge
Project
managem
ent
Estimating the control
5/10/201
7
5/10/201
7 5 months - - Not yet -
Project
Inc.
charge
Project
managem
ent
Confirming the
procedure of the work
plan - - Not yet -
Project
Inc.
charge
Project
managem
ent
Filling the estimations - - Not yet -
Project
Inc.
charge
Project
managem
ent
Figure 3: Value creation flow
When the people who are working in the project will be using the system, they will be able to
gain the knowledge regarding the situation, which will comprise of the activities and the
subsequent acts. The system will comprise of the stakeholders for the purpose of regulating the
flows.
Figure 4: Improvement Plan
12
Receiving the
estimated actual
budgeting
5/10/201
7
5/10/201
7 4 months - - Not yet -
Project
Inc.
charge
Project
managem
ent
Estimating the control
5/10/201
7
5/10/201
7 5 months - - Not yet -
Project
Inc.
charge
Project
managem
ent
Confirming the
procedure of the work
plan - - Not yet -
Project
Inc.
charge
Project
managem
ent
Filling the estimations - - Not yet -
Project
Inc.
charge
Project
managem
ent
Figure 3: Value creation flow
When the people who are working in the project will be using the system, they will be able to
gain the knowledge regarding the situation, which will comprise of the activities and the
subsequent acts. The system will comprise of the stakeholders for the purpose of regulating the
flows.
Figure 4: Improvement Plan
12
⊘ This is a preview!⊘
Do you want full access?
Subscribe today to unlock all pages.

Trusted by 1+ million students worldwide
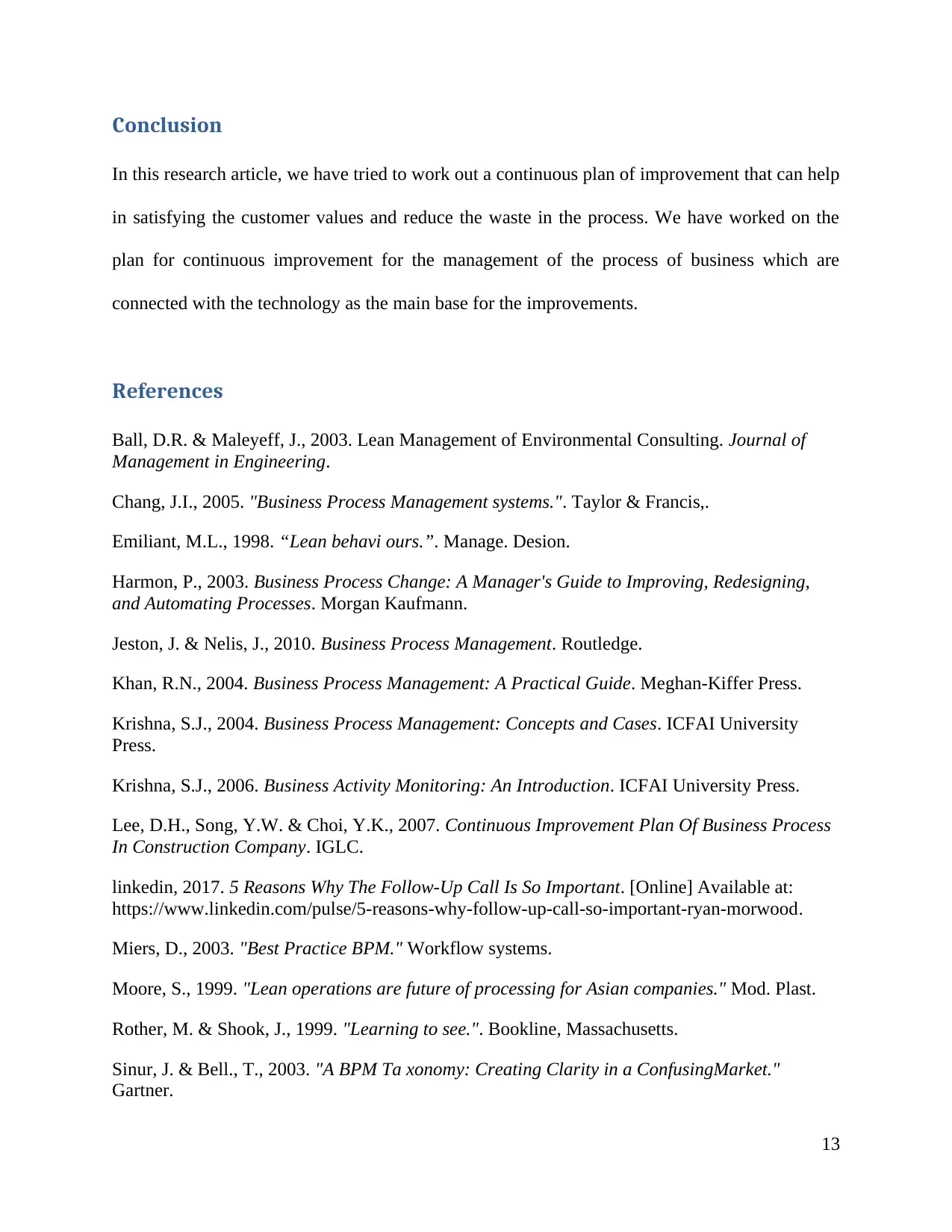
Conclusion
In this research article, we have tried to work out a continuous plan of improvement that can help
in satisfying the customer values and reduce the waste in the process. We have worked on the
plan for continuous improvement for the management of the process of business which are
connected with the technology as the main base for the improvements.
References
Ball, D.R. & Maleyeff, J., 2003. Lean Management of Environmental Consulting. Journal of
Management in Engineering.
Chang, J.I., 2005. "Business Process Management systems.". Taylor & Francis,.
Emiliant, M.L., 1998. “Lean behavi ours.”. Manage. Desion.
Harmon, P., 2003. Business Process Change: A Manager's Guide to Improving, Redesigning,
and Automating Processes. Morgan Kaufmann.
Jeston, J. & Nelis, J., 2010. Business Process Management. Routledge.
Khan, R.N., 2004. Business Process Management: A Practical Guide. Meghan-Kiffer Press.
Krishna, S.J., 2004. Business Process Management: Concepts and Cases. ICFAI University
Press.
Krishna, S.J., 2006. Business Activity Monitoring: An Introduction. ICFAI University Press.
Lee, D.H., Song, Y.W. & Choi, Y.K., 2007. Continuous Improvement Plan Of Business Process
In Construction Company. IGLC.
linkedin, 2017. 5 Reasons Why The Follow-Up Call Is So Important. [Online] Available at:
https://www.linkedin.com/pulse/5-reasons-why-follow-up-call-so-important-ryan-morwood.
Miers, D., 2003. "Best Practice BPM." Workflow systems.
Moore, S., 1999. "Lean operations are future of processing for Asian companies." Mod. Plast.
Rother, M. & Shook, J., 1999. "Learning to see.". Bookline, Massachusetts.
Sinur, J. & Bell., T., 2003. "A BPM Ta xonomy: Creating Clarity in a ConfusingMarket."
Gartner.
13
In this research article, we have tried to work out a continuous plan of improvement that can help
in satisfying the customer values and reduce the waste in the process. We have worked on the
plan for continuous improvement for the management of the process of business which are
connected with the technology as the main base for the improvements.
References
Ball, D.R. & Maleyeff, J., 2003. Lean Management of Environmental Consulting. Journal of
Management in Engineering.
Chang, J.I., 2005. "Business Process Management systems.". Taylor & Francis,.
Emiliant, M.L., 1998. “Lean behavi ours.”. Manage. Desion.
Harmon, P., 2003. Business Process Change: A Manager's Guide to Improving, Redesigning,
and Automating Processes. Morgan Kaufmann.
Jeston, J. & Nelis, J., 2010. Business Process Management. Routledge.
Khan, R.N., 2004. Business Process Management: A Practical Guide. Meghan-Kiffer Press.
Krishna, S.J., 2004. Business Process Management: Concepts and Cases. ICFAI University
Press.
Krishna, S.J., 2006. Business Activity Monitoring: An Introduction. ICFAI University Press.
Lee, D.H., Song, Y.W. & Choi, Y.K., 2007. Continuous Improvement Plan Of Business Process
In Construction Company. IGLC.
linkedin, 2017. 5 Reasons Why The Follow-Up Call Is So Important. [Online] Available at:
https://www.linkedin.com/pulse/5-reasons-why-follow-up-call-so-important-ryan-morwood.
Miers, D., 2003. "Best Practice BPM." Workflow systems.
Moore, S., 1999. "Lean operations are future of processing for Asian companies." Mod. Plast.
Rother, M. & Shook, J., 1999. "Learning to see.". Bookline, Massachusetts.
Sinur, J. & Bell., T., 2003. "A BPM Ta xonomy: Creating Clarity in a ConfusingMarket."
Gartner.
13
Paraphrase This Document
Need a fresh take? Get an instant paraphrase of this document with our AI Paraphraser
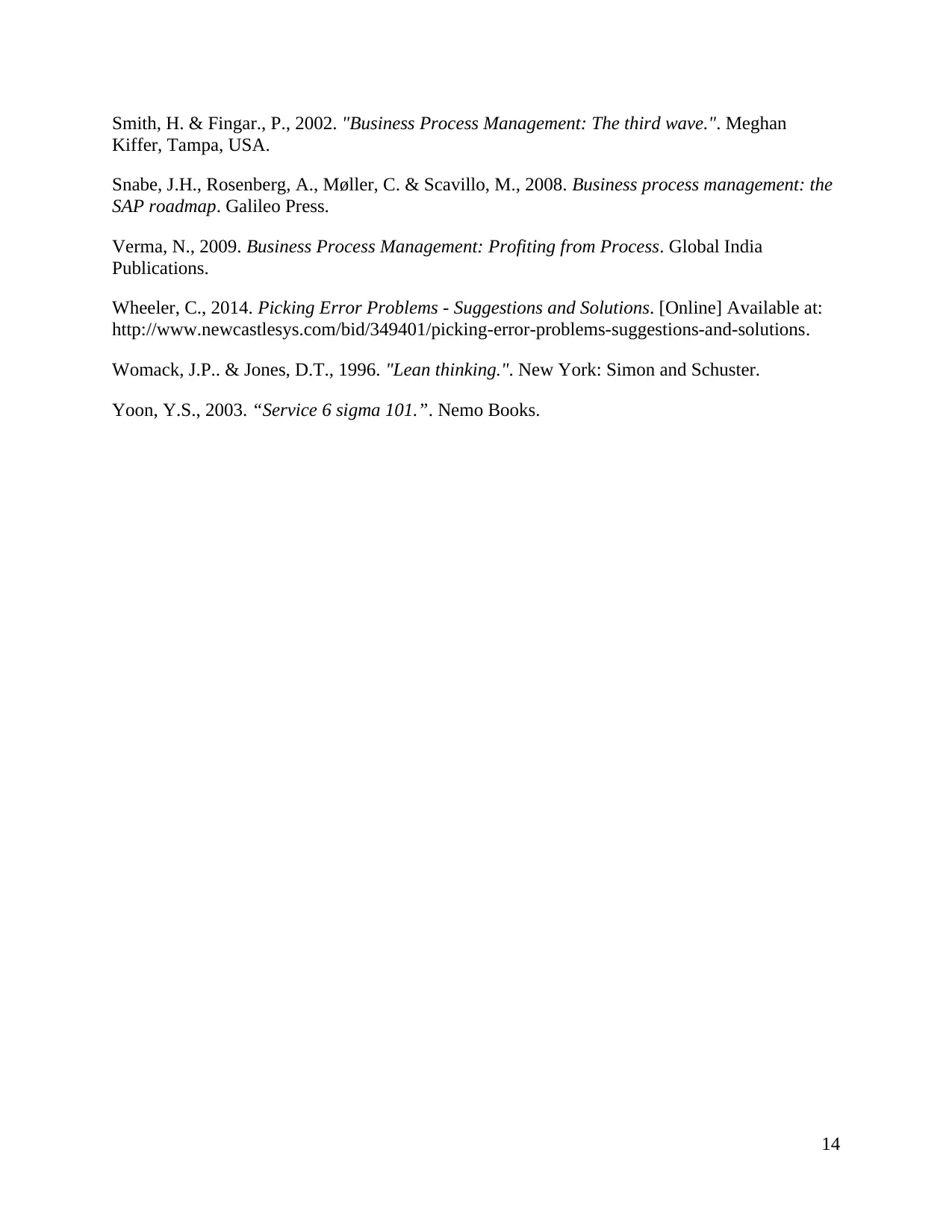
Smith, H. & Fingar., P., 2002. "Business Process Management: The third wave.". Meghan
Kiffer, Tampa, USA.
Snabe, J.H., Rosenberg, A., Møller, C. & Scavillo, M., 2008. Business process management: the
SAP roadmap. Galileo Press.
Verma, N., 2009. Business Process Management: Profiting from Process. Global India
Publications.
Wheeler, C., 2014. Picking Error Problems - Suggestions and Solutions. [Online] Available at:
http://www.newcastlesys.com/bid/349401/picking-error-problems-suggestions-and-solutions.
Womack, J.P.. & Jones, D.T., 1996. "Lean thinking.". New York: Simon and Schuster.
Yoon, Y.S., 2003. “Service 6 sigma 101.”. Nemo Books.
14
Kiffer, Tampa, USA.
Snabe, J.H., Rosenberg, A., Møller, C. & Scavillo, M., 2008. Business process management: the
SAP roadmap. Galileo Press.
Verma, N., 2009. Business Process Management: Profiting from Process. Global India
Publications.
Wheeler, C., 2014. Picking Error Problems - Suggestions and Solutions. [Online] Available at:
http://www.newcastlesys.com/bid/349401/picking-error-problems-suggestions-and-solutions.
Womack, J.P.. & Jones, D.T., 1996. "Lean thinking.". New York: Simon and Schuster.
Yoon, Y.S., 2003. “Service 6 sigma 101.”. Nemo Books.
14
1 out of 14
Related Documents

Your All-in-One AI-Powered Toolkit for Academic Success.
+13062052269
info@desklib.com
Available 24*7 on WhatsApp / Email
Unlock your academic potential
© 2024 | Zucol Services PVT LTD | All rights reserved.