Project Management Methodologies
VerifiedAdded on 2020/03/23
|13
|3638
|149
Project
AI Summary
The content discusses project management methodologies applied at Latino Engineering to address issues such as product defects and customer dissatisfaction. It emphasizes the importance of Total Quality Management (TQM) and the 5 whys technique in identifying root causes and implementing continuous improvement plans. The project management plan includes training for employees, monitoring progress, and ensuring quality standards are met to enhance overall business performance.
Contribute Materials
Your contribution can guide someone’s learning journey. Share your
documents today.
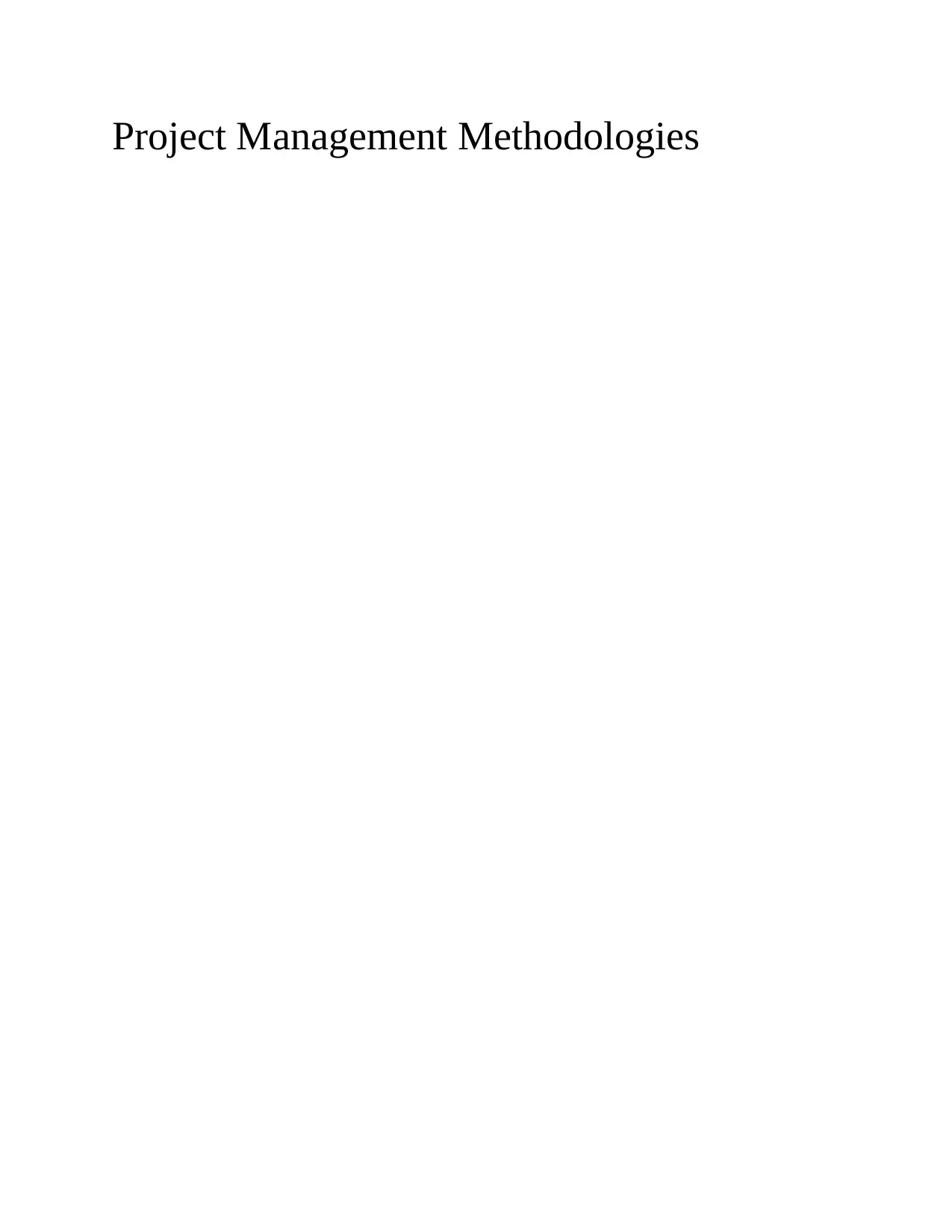
Project Management Methodologies
Secure Best Marks with AI Grader
Need help grading? Try our AI Grader for instant feedback on your assignments.
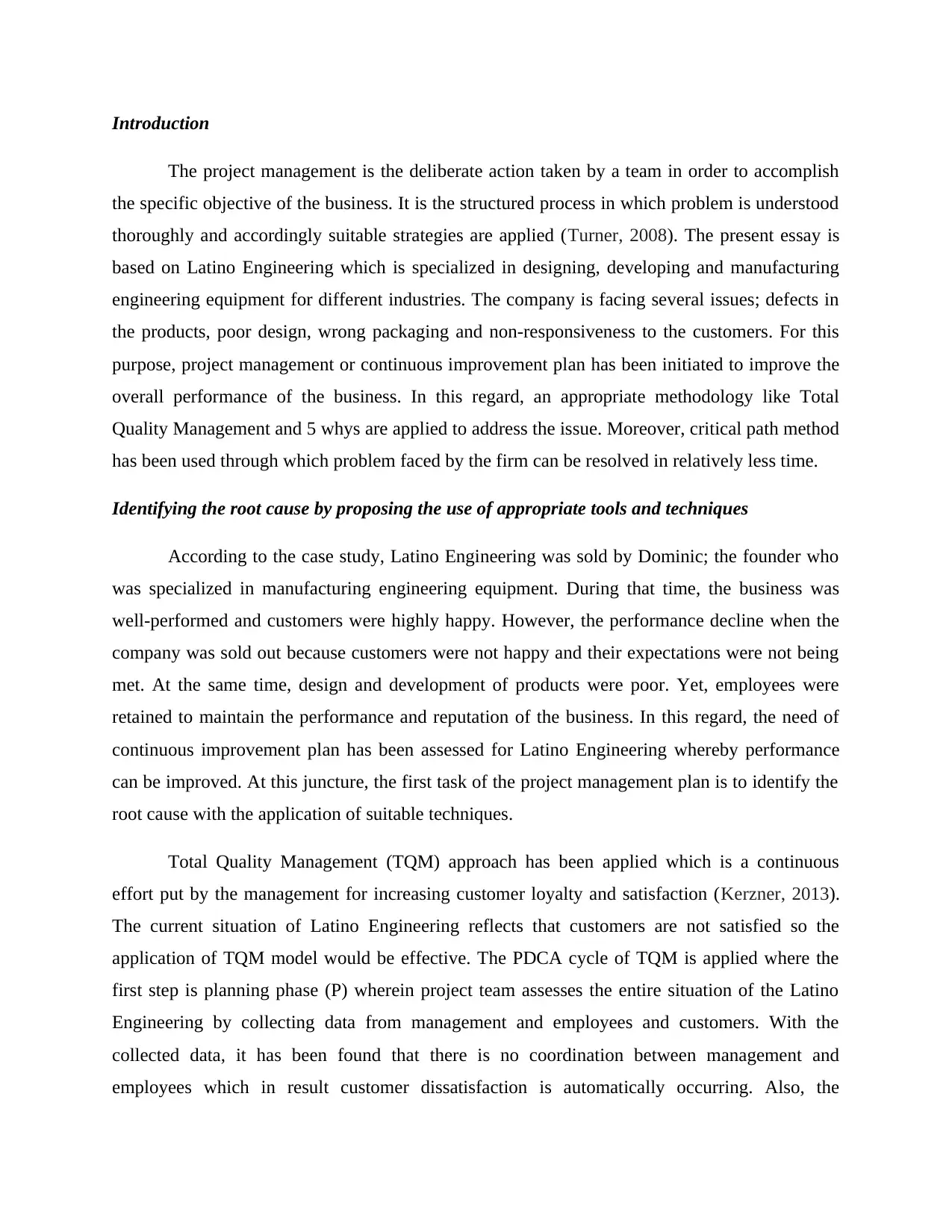
Introduction
The project management is the deliberate action taken by a team in order to accomplish
the specific objective of the business. It is the structured process in which problem is understood
thoroughly and accordingly suitable strategies are applied (Turner, 2008). The present essay is
based on Latino Engineering which is specialized in designing, developing and manufacturing
engineering equipment for different industries. The company is facing several issues; defects in
the products, poor design, wrong packaging and non-responsiveness to the customers. For this
purpose, project management or continuous improvement plan has been initiated to improve the
overall performance of the business. In this regard, an appropriate methodology like Total
Quality Management and 5 whys are applied to address the issue. Moreover, critical path method
has been used through which problem faced by the firm can be resolved in relatively less time.
Identifying the root cause by proposing the use of appropriate tools and techniques
According to the case study, Latino Engineering was sold by Dominic; the founder who
was specialized in manufacturing engineering equipment. During that time, the business was
well-performed and customers were highly happy. However, the performance decline when the
company was sold out because customers were not happy and their expectations were not being
met. At the same time, design and development of products were poor. Yet, employees were
retained to maintain the performance and reputation of the business. In this regard, the need of
continuous improvement plan has been assessed for Latino Engineering whereby performance
can be improved. At this juncture, the first task of the project management plan is to identify the
root cause with the application of suitable techniques.
Total Quality Management (TQM) approach has been applied which is a continuous
effort put by the management for increasing customer loyalty and satisfaction (Kerzner, 2013).
The current situation of Latino Engineering reflects that customers are not satisfied so the
application of TQM model would be effective. The PDCA cycle of TQM is applied where the
first step is planning phase (P) wherein project team assesses the entire situation of the Latino
Engineering by collecting data from management and employees and customers. With the
collected data, it has been found that there is no coordination between management and
employees which in result customer dissatisfaction is automatically occurring. Also, the
The project management is the deliberate action taken by a team in order to accomplish
the specific objective of the business. It is the structured process in which problem is understood
thoroughly and accordingly suitable strategies are applied (Turner, 2008). The present essay is
based on Latino Engineering which is specialized in designing, developing and manufacturing
engineering equipment for different industries. The company is facing several issues; defects in
the products, poor design, wrong packaging and non-responsiveness to the customers. For this
purpose, project management or continuous improvement plan has been initiated to improve the
overall performance of the business. In this regard, an appropriate methodology like Total
Quality Management and 5 whys are applied to address the issue. Moreover, critical path method
has been used through which problem faced by the firm can be resolved in relatively less time.
Identifying the root cause by proposing the use of appropriate tools and techniques
According to the case study, Latino Engineering was sold by Dominic; the founder who
was specialized in manufacturing engineering equipment. During that time, the business was
well-performed and customers were highly happy. However, the performance decline when the
company was sold out because customers were not happy and their expectations were not being
met. At the same time, design and development of products were poor. Yet, employees were
retained to maintain the performance and reputation of the business. In this regard, the need of
continuous improvement plan has been assessed for Latino Engineering whereby performance
can be improved. At this juncture, the first task of the project management plan is to identify the
root cause with the application of suitable techniques.
Total Quality Management (TQM) approach has been applied which is a continuous
effort put by the management for increasing customer loyalty and satisfaction (Kerzner, 2013).
The current situation of Latino Engineering reflects that customers are not satisfied so the
application of TQM model would be effective. The PDCA cycle of TQM is applied where the
first step is planning phase (P) wherein project team assesses the entire situation of the Latino
Engineering by collecting data from management and employees and customers. With the
collected data, it has been found that there is no coordination between management and
employees which in result customer dissatisfaction is automatically occurring. Also, the
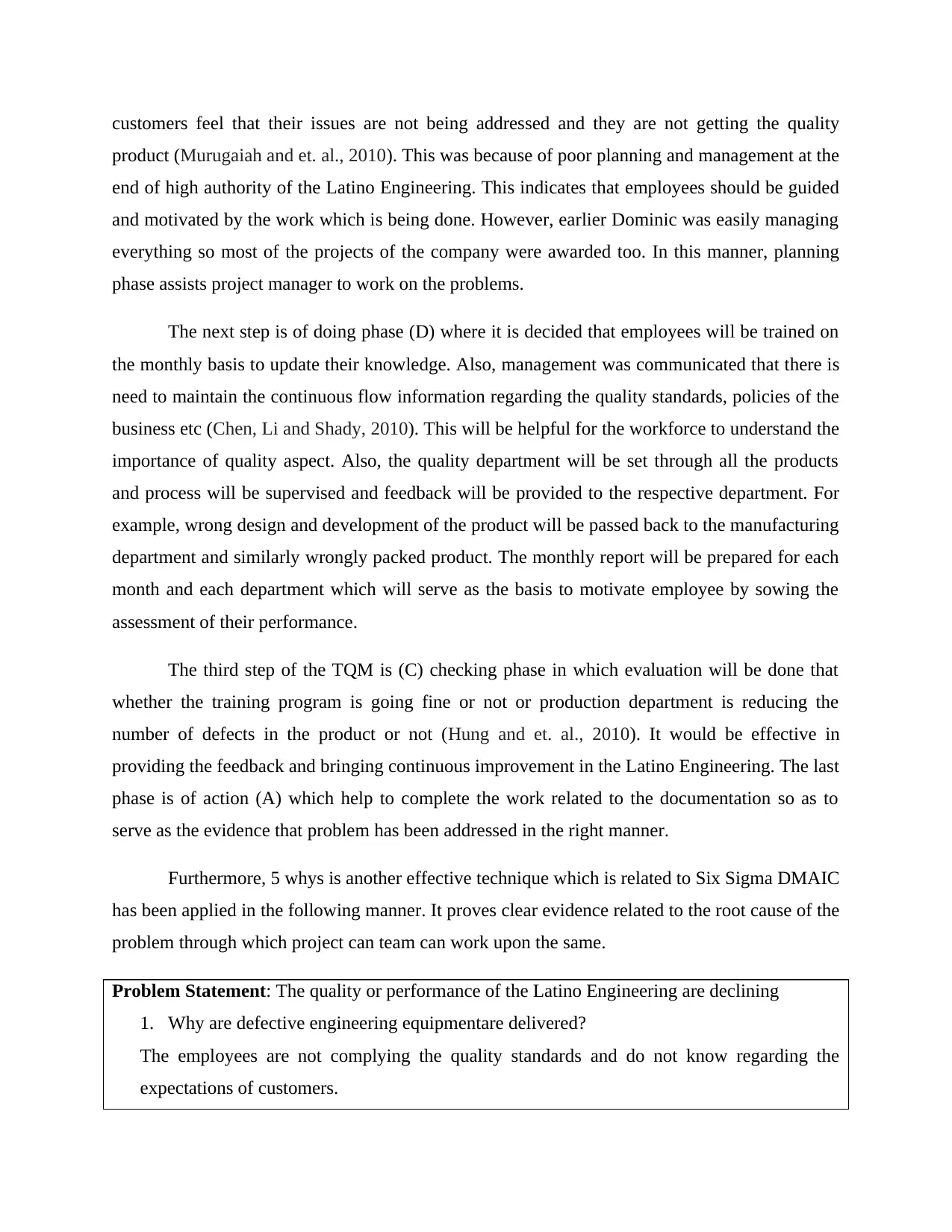
customers feel that their issues are not being addressed and they are not getting the quality
product (Murugaiah and et. al., 2010). This was because of poor planning and management at the
end of high authority of the Latino Engineering. This indicates that employees should be guided
and motivated by the work which is being done. However, earlier Dominic was easily managing
everything so most of the projects of the company were awarded too. In this manner, planning
phase assists project manager to work on the problems.
The next step is of doing phase (D) where it is decided that employees will be trained on
the monthly basis to update their knowledge. Also, management was communicated that there is
need to maintain the continuous flow information regarding the quality standards, policies of the
business etc (Chen, Li and Shady, 2010). This will be helpful for the workforce to understand the
importance of quality aspect. Also, the quality department will be set through all the products
and process will be supervised and feedback will be provided to the respective department. For
example, wrong design and development of the product will be passed back to the manufacturing
department and similarly wrongly packed product. The monthly report will be prepared for each
month and each department which will serve as the basis to motivate employee by sowing the
assessment of their performance.
The third step of the TQM is (C) checking phase in which evaluation will be done that
whether the training program is going fine or not or production department is reducing the
number of defects in the product or not (Hung and et. al., 2010). It would be effective in
providing the feedback and bringing continuous improvement in the Latino Engineering. The last
phase is of action (A) which help to complete the work related to the documentation so as to
serve as the evidence that problem has been addressed in the right manner.
Furthermore, 5 whys is another effective technique which is related to Six Sigma DMAIC
has been applied in the following manner. It proves clear evidence related to the root cause of the
problem through which project can team can work upon the same.
Problem Statement: The quality or performance of the Latino Engineering are declining
1. Why are defective engineering equipmentare delivered?
The employees are not complying the quality standards and do not know regarding the
expectations of customers.
product (Murugaiah and et. al., 2010). This was because of poor planning and management at the
end of high authority of the Latino Engineering. This indicates that employees should be guided
and motivated by the work which is being done. However, earlier Dominic was easily managing
everything so most of the projects of the company were awarded too. In this manner, planning
phase assists project manager to work on the problems.
The next step is of doing phase (D) where it is decided that employees will be trained on
the monthly basis to update their knowledge. Also, management was communicated that there is
need to maintain the continuous flow information regarding the quality standards, policies of the
business etc (Chen, Li and Shady, 2010). This will be helpful for the workforce to understand the
importance of quality aspect. Also, the quality department will be set through all the products
and process will be supervised and feedback will be provided to the respective department. For
example, wrong design and development of the product will be passed back to the manufacturing
department and similarly wrongly packed product. The monthly report will be prepared for each
month and each department which will serve as the basis to motivate employee by sowing the
assessment of their performance.
The third step of the TQM is (C) checking phase in which evaluation will be done that
whether the training program is going fine or not or production department is reducing the
number of defects in the product or not (Hung and et. al., 2010). It would be effective in
providing the feedback and bringing continuous improvement in the Latino Engineering. The last
phase is of action (A) which help to complete the work related to the documentation so as to
serve as the evidence that problem has been addressed in the right manner.
Furthermore, 5 whys is another effective technique which is related to Six Sigma DMAIC
has been applied in the following manner. It proves clear evidence related to the root cause of the
problem through which project can team can work upon the same.
Problem Statement: The quality or performance of the Latino Engineering are declining
1. Why are defective engineering equipmentare delivered?
The employees are not complying the quality standards and do not know regarding the
expectations of customers.
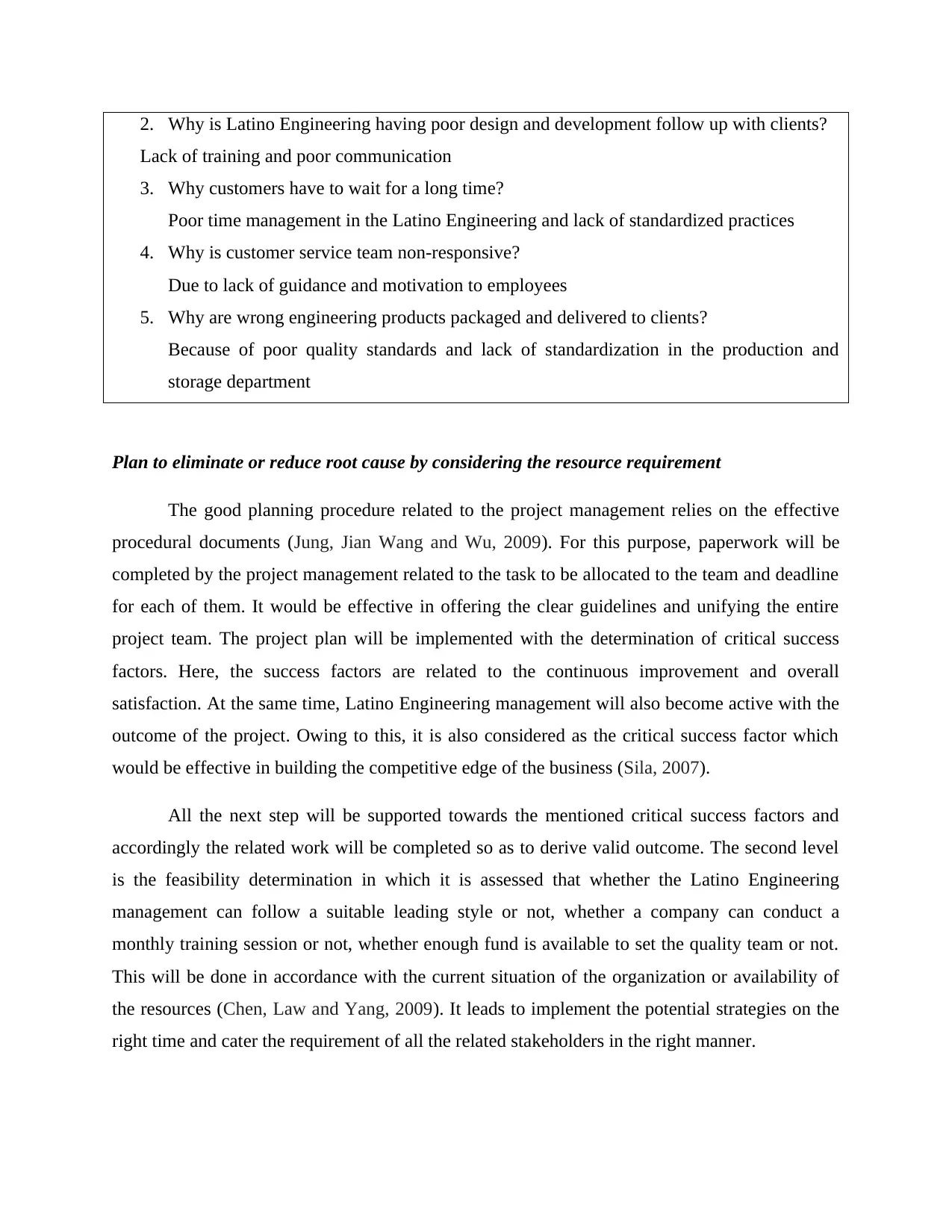
2. Why is Latino Engineering having poor design and development follow up with clients?
Lack of training and poor communication
3. Why customers have to wait for a long time?
Poor time management in the Latino Engineering and lack of standardized practices
4. Why is customer service team non-responsive?
Due to lack of guidance and motivation to employees
5. Why are wrong engineering products packaged and delivered to clients?
Because of poor quality standards and lack of standardization in the production and
storage department
Plan to eliminate or reduce root cause by considering the resource requirement
The good planning procedure related to the project management relies on the effective
procedural documents (Jung, Jian Wang and Wu, 2009). For this purpose, paperwork will be
completed by the project management related to the task to be allocated to the team and deadline
for each of them. It would be effective in offering the clear guidelines and unifying the entire
project team. The project plan will be implemented with the determination of critical success
factors. Here, the success factors are related to the continuous improvement and overall
satisfaction. At the same time, Latino Engineering management will also become active with the
outcome of the project. Owing to this, it is also considered as the critical success factor which
would be effective in building the competitive edge of the business (Sila, 2007).
All the next step will be supported towards the mentioned critical success factors and
accordingly the related work will be completed so as to derive valid outcome. The second level
is the feasibility determination in which it is assessed that whether the Latino Engineering
management can follow a suitable leading style or not, whether a company can conduct a
monthly training session or not, whether enough fund is available to set the quality team or not.
This will be done in accordance with the current situation of the organization or availability of
the resources (Chen, Law and Yang, 2009). It leads to implement the potential strategies on the
right time and cater the requirement of all the related stakeholders in the right manner.
Lack of training and poor communication
3. Why customers have to wait for a long time?
Poor time management in the Latino Engineering and lack of standardized practices
4. Why is customer service team non-responsive?
Due to lack of guidance and motivation to employees
5. Why are wrong engineering products packaged and delivered to clients?
Because of poor quality standards and lack of standardization in the production and
storage department
Plan to eliminate or reduce root cause by considering the resource requirement
The good planning procedure related to the project management relies on the effective
procedural documents (Jung, Jian Wang and Wu, 2009). For this purpose, paperwork will be
completed by the project management related to the task to be allocated to the team and deadline
for each of them. It would be effective in offering the clear guidelines and unifying the entire
project team. The project plan will be implemented with the determination of critical success
factors. Here, the success factors are related to the continuous improvement and overall
satisfaction. At the same time, Latino Engineering management will also become active with the
outcome of the project. Owing to this, it is also considered as the critical success factor which
would be effective in building the competitive edge of the business (Sila, 2007).
All the next step will be supported towards the mentioned critical success factors and
accordingly the related work will be completed so as to derive valid outcome. The second level
is the feasibility determination in which it is assessed that whether the Latino Engineering
management can follow a suitable leading style or not, whether a company can conduct a
monthly training session or not, whether enough fund is available to set the quality team or not.
This will be done in accordance with the current situation of the organization or availability of
the resources (Chen, Law and Yang, 2009). It leads to implement the potential strategies on the
right time and cater the requirement of all the related stakeholders in the right manner.
Secure Best Marks with AI Grader
Need help grading? Try our AI Grader for instant feedback on your assignments.
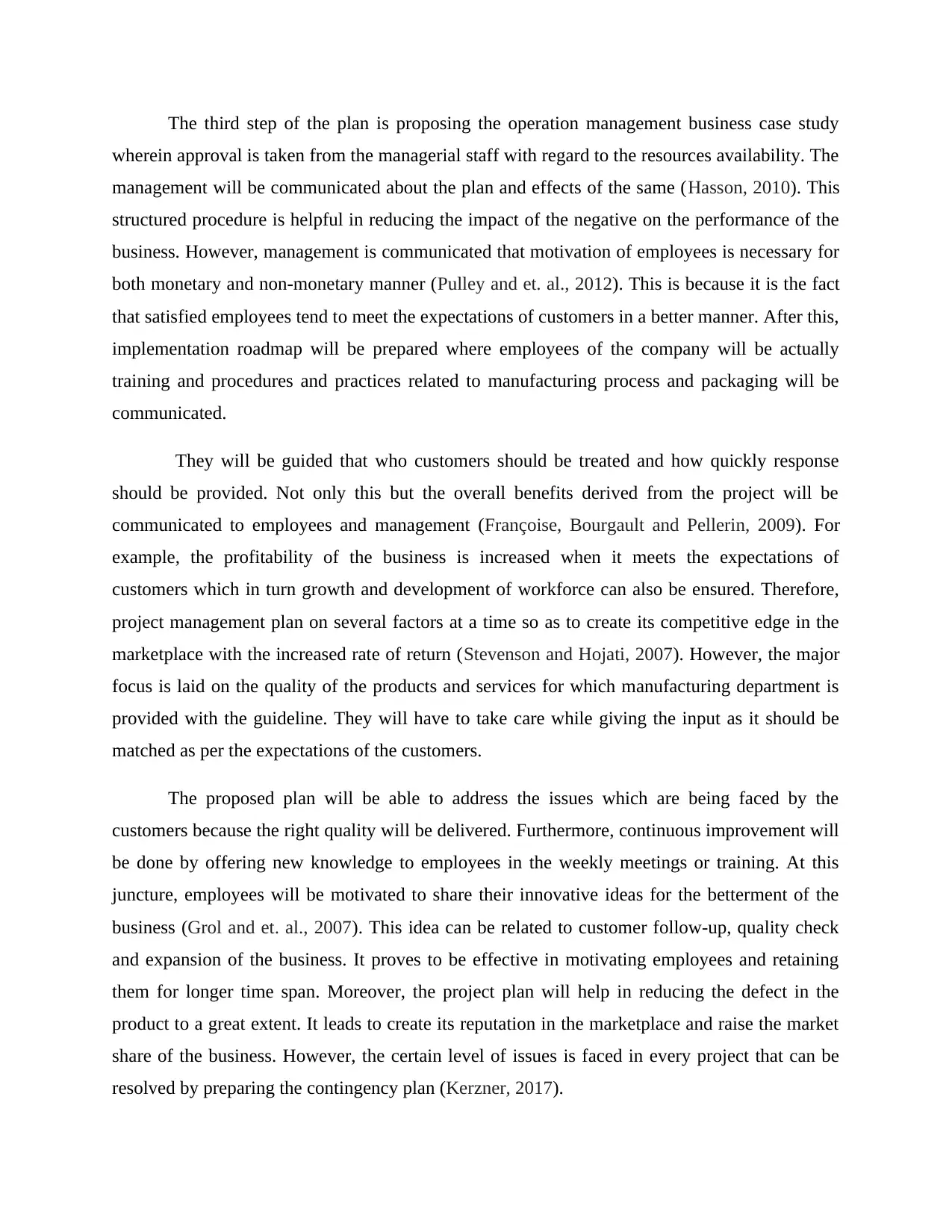
The third step of the plan is proposing the operation management business case study
wherein approval is taken from the managerial staff with regard to the resources availability. The
management will be communicated about the plan and effects of the same (Hasson, 2010). This
structured procedure is helpful in reducing the impact of the negative on the performance of the
business. However, management is communicated that motivation of employees is necessary for
both monetary and non-monetary manner (Pulley and et. al., 2012). This is because it is the fact
that satisfied employees tend to meet the expectations of customers in a better manner. After this,
implementation roadmap will be prepared where employees of the company will be actually
training and procedures and practices related to manufacturing process and packaging will be
communicated.
They will be guided that who customers should be treated and how quickly response
should be provided. Not only this but the overall benefits derived from the project will be
communicated to employees and management (Françoise, Bourgault and Pellerin, 2009). For
example, the profitability of the business is increased when it meets the expectations of
customers which in turn growth and development of workforce can also be ensured. Therefore,
project management plan on several factors at a time so as to create its competitive edge in the
marketplace with the increased rate of return (Stevenson and Hojati, 2007). However, the major
focus is laid on the quality of the products and services for which manufacturing department is
provided with the guideline. They will have to take care while giving the input as it should be
matched as per the expectations of the customers.
The proposed plan will be able to address the issues which are being faced by the
customers because the right quality will be delivered. Furthermore, continuous improvement will
be done by offering new knowledge to employees in the weekly meetings or training. At this
juncture, employees will be motivated to share their innovative ideas for the betterment of the
business (Grol and et. al., 2007). This idea can be related to customer follow-up, quality check
and expansion of the business. It proves to be effective in motivating employees and retaining
them for longer time span. Moreover, the project plan will help in reducing the defect in the
product to a great extent. It leads to create its reputation in the marketplace and raise the market
share of the business. However, the certain level of issues is faced in every project that can be
resolved by preparing the contingency plan (Kerzner, 2017).
wherein approval is taken from the managerial staff with regard to the resources availability. The
management will be communicated about the plan and effects of the same (Hasson, 2010). This
structured procedure is helpful in reducing the impact of the negative on the performance of the
business. However, management is communicated that motivation of employees is necessary for
both monetary and non-monetary manner (Pulley and et. al., 2012). This is because it is the fact
that satisfied employees tend to meet the expectations of customers in a better manner. After this,
implementation roadmap will be prepared where employees of the company will be actually
training and procedures and practices related to manufacturing process and packaging will be
communicated.
They will be guided that who customers should be treated and how quickly response
should be provided. Not only this but the overall benefits derived from the project will be
communicated to employees and management (Françoise, Bourgault and Pellerin, 2009). For
example, the profitability of the business is increased when it meets the expectations of
customers which in turn growth and development of workforce can also be ensured. Therefore,
project management plan on several factors at a time so as to create its competitive edge in the
marketplace with the increased rate of return (Stevenson and Hojati, 2007). However, the major
focus is laid on the quality of the products and services for which manufacturing department is
provided with the guideline. They will have to take care while giving the input as it should be
matched as per the expectations of the customers.
The proposed plan will be able to address the issues which are being faced by the
customers because the right quality will be delivered. Furthermore, continuous improvement will
be done by offering new knowledge to employees in the weekly meetings or training. At this
juncture, employees will be motivated to share their innovative ideas for the betterment of the
business (Grol and et. al., 2007). This idea can be related to customer follow-up, quality check
and expansion of the business. It proves to be effective in motivating employees and retaining
them for longer time span. Moreover, the project plan will help in reducing the defect in the
product to a great extent. It leads to create its reputation in the marketplace and raise the market
share of the business. However, the certain level of issues is faced in every project that can be
resolved by preparing the contingency plan (Kerzner, 2017).
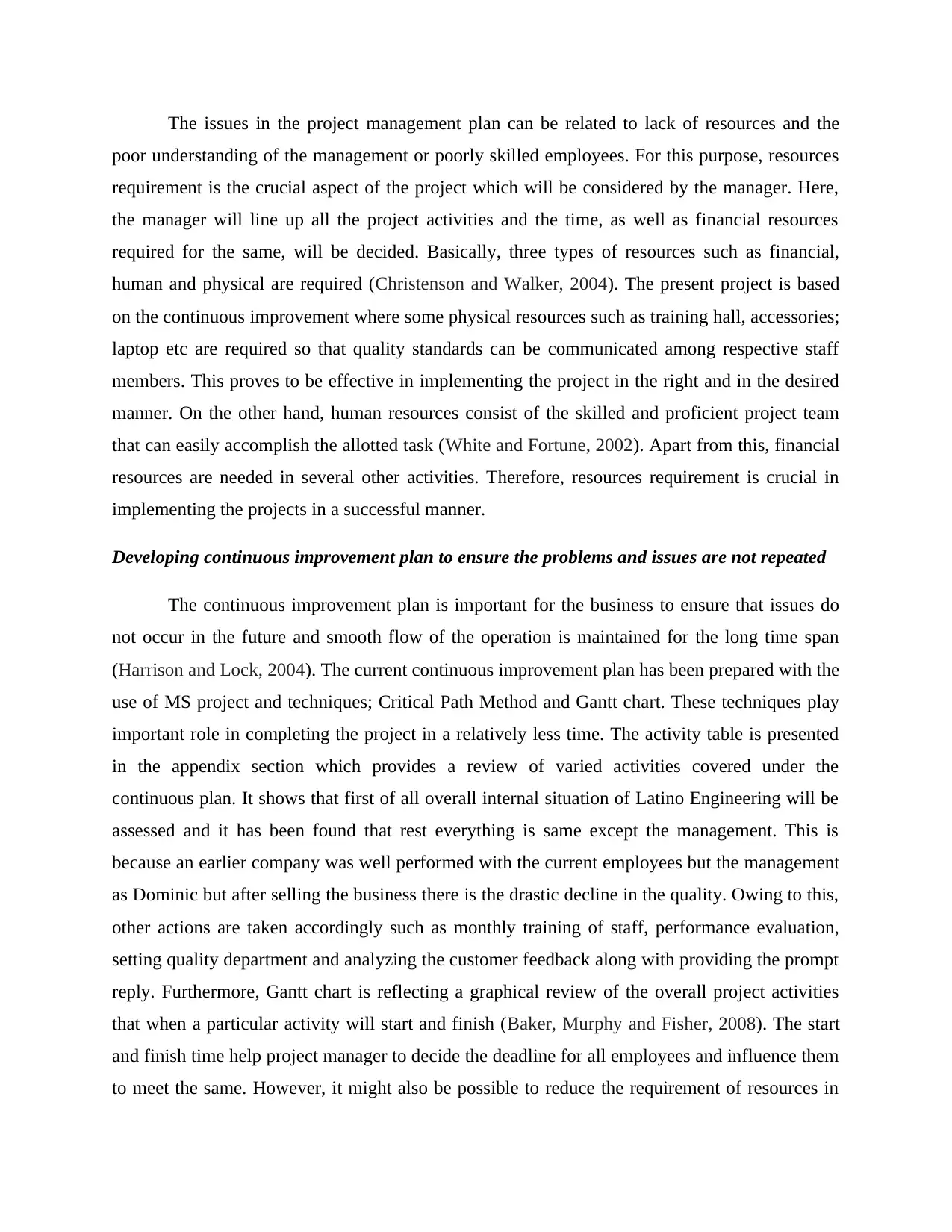
The issues in the project management plan can be related to lack of resources and the
poor understanding of the management or poorly skilled employees. For this purpose, resources
requirement is the crucial aspect of the project which will be considered by the manager. Here,
the manager will line up all the project activities and the time, as well as financial resources
required for the same, will be decided. Basically, three types of resources such as financial,
human and physical are required (Christenson and Walker, 2004). The present project is based
on the continuous improvement where some physical resources such as training hall, accessories;
laptop etc are required so that quality standards can be communicated among respective staff
members. This proves to be effective in implementing the project in the right and in the desired
manner. On the other hand, human resources consist of the skilled and proficient project team
that can easily accomplish the allotted task (White and Fortune, 2002). Apart from this, financial
resources are needed in several other activities. Therefore, resources requirement is crucial in
implementing the projects in a successful manner.
Developing continuous improvement plan to ensure the problems and issues are not repeated
The continuous improvement plan is important for the business to ensure that issues do
not occur in the future and smooth flow of the operation is maintained for the long time span
(Harrison and Lock, 2004). The current continuous improvement plan has been prepared with the
use of MS project and techniques; Critical Path Method and Gantt chart. These techniques play
important role in completing the project in a relatively less time. The activity table is presented
in the appendix section which provides a review of varied activities covered under the
continuous plan. It shows that first of all overall internal situation of Latino Engineering will be
assessed and it has been found that rest everything is same except the management. This is
because an earlier company was well performed with the current employees but the management
as Dominic but after selling the business there is the drastic decline in the quality. Owing to this,
other actions are taken accordingly such as monthly training of staff, performance evaluation,
setting quality department and analyzing the customer feedback along with providing the prompt
reply. Furthermore, Gantt chart is reflecting a graphical review of the overall project activities
that when a particular activity will start and finish (Baker, Murphy and Fisher, 2008). The start
and finish time help project manager to decide the deadline for all employees and influence them
to meet the same. However, it might also be possible to reduce the requirement of resources in
poor understanding of the management or poorly skilled employees. For this purpose, resources
requirement is the crucial aspect of the project which will be considered by the manager. Here,
the manager will line up all the project activities and the time, as well as financial resources
required for the same, will be decided. Basically, three types of resources such as financial,
human and physical are required (Christenson and Walker, 2004). The present project is based
on the continuous improvement where some physical resources such as training hall, accessories;
laptop etc are required so that quality standards can be communicated among respective staff
members. This proves to be effective in implementing the project in the right and in the desired
manner. On the other hand, human resources consist of the skilled and proficient project team
that can easily accomplish the allotted task (White and Fortune, 2002). Apart from this, financial
resources are needed in several other activities. Therefore, resources requirement is crucial in
implementing the projects in a successful manner.
Developing continuous improvement plan to ensure the problems and issues are not repeated
The continuous improvement plan is important for the business to ensure that issues do
not occur in the future and smooth flow of the operation is maintained for the long time span
(Harrison and Lock, 2004). The current continuous improvement plan has been prepared with the
use of MS project and techniques; Critical Path Method and Gantt chart. These techniques play
important role in completing the project in a relatively less time. The activity table is presented
in the appendix section which provides a review of varied activities covered under the
continuous plan. It shows that first of all overall internal situation of Latino Engineering will be
assessed and it has been found that rest everything is same except the management. This is
because an earlier company was well performed with the current employees but the management
as Dominic but after selling the business there is the drastic decline in the quality. Owing to this,
other actions are taken accordingly such as monthly training of staff, performance evaluation,
setting quality department and analyzing the customer feedback along with providing the prompt
reply. Furthermore, Gantt chart is reflecting a graphical review of the overall project activities
that when a particular activity will start and finish (Baker, Murphy and Fisher, 2008). The start
and finish time help project manager to decide the deadline for all employees and influence them
to meet the same. However, it might also be possible to reduce the requirement of resources in
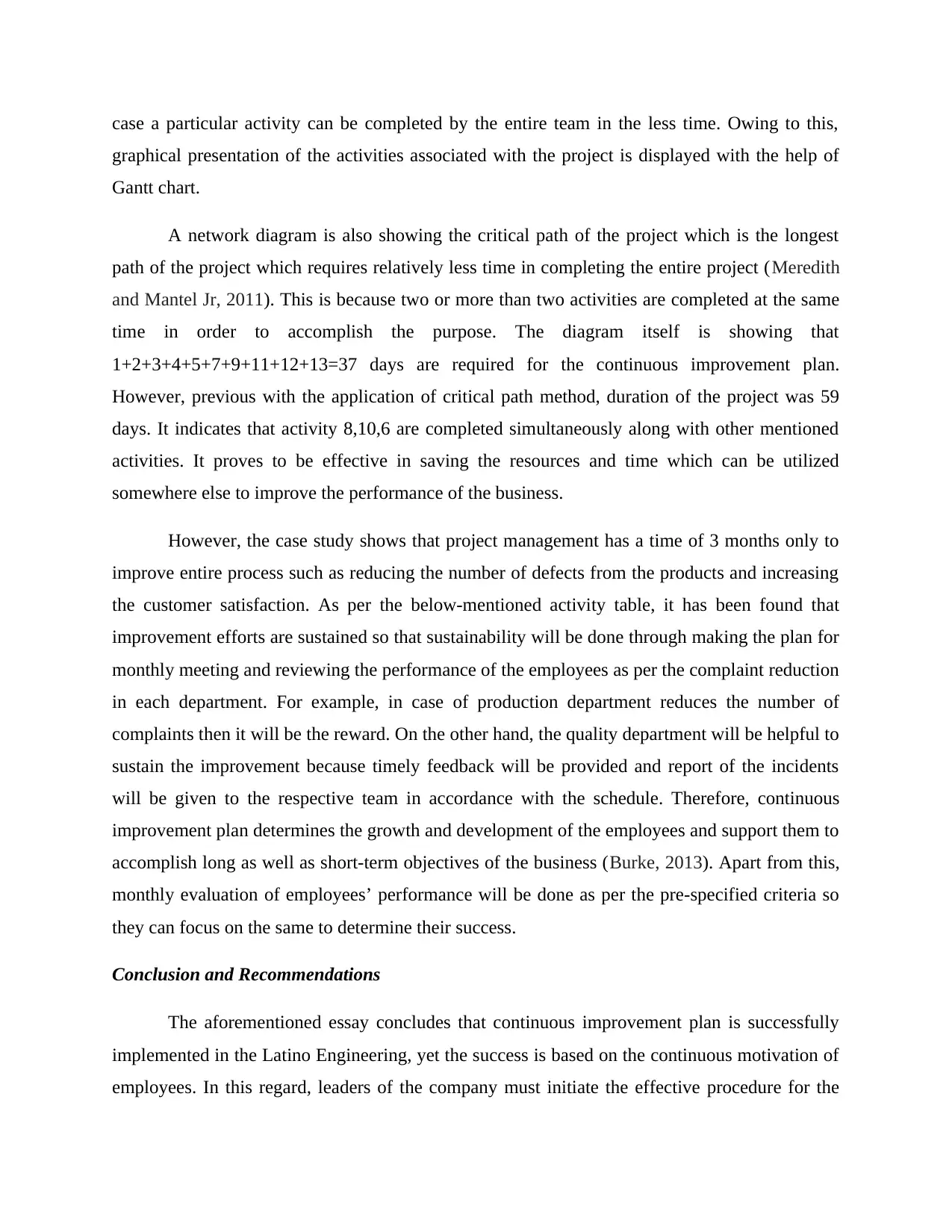
case a particular activity can be completed by the entire team in the less time. Owing to this,
graphical presentation of the activities associated with the project is displayed with the help of
Gantt chart.
A network diagram is also showing the critical path of the project which is the longest
path of the project which requires relatively less time in completing the entire project (Meredith
and Mantel Jr, 2011). This is because two or more than two activities are completed at the same
time in order to accomplish the purpose. The diagram itself is showing that
1+2+3+4+5+7+9+11+12+13=37 days are required for the continuous improvement plan.
However, previous with the application of critical path method, duration of the project was 59
days. It indicates that activity 8,10,6 are completed simultaneously along with other mentioned
activities. It proves to be effective in saving the resources and time which can be utilized
somewhere else to improve the performance of the business.
However, the case study shows that project management has a time of 3 months only to
improve entire process such as reducing the number of defects from the products and increasing
the customer satisfaction. As per the below-mentioned activity table, it has been found that
improvement efforts are sustained so that sustainability will be done through making the plan for
monthly meeting and reviewing the performance of the employees as per the complaint reduction
in each department. For example, in case of production department reduces the number of
complaints then it will be the reward. On the other hand, the quality department will be helpful to
sustain the improvement because timely feedback will be provided and report of the incidents
will be given to the respective team in accordance with the schedule. Therefore, continuous
improvement plan determines the growth and development of the employees and support them to
accomplish long as well as short-term objectives of the business (Burke, 2013). Apart from this,
monthly evaluation of employees’ performance will be done as per the pre-specified criteria so
they can focus on the same to determine their success.
Conclusion and Recommendations
The aforementioned essay concludes that continuous improvement plan is successfully
implemented in the Latino Engineering, yet the success is based on the continuous motivation of
employees. In this regard, leaders of the company must initiate the effective procedure for the
graphical presentation of the activities associated with the project is displayed with the help of
Gantt chart.
A network diagram is also showing the critical path of the project which is the longest
path of the project which requires relatively less time in completing the entire project (Meredith
and Mantel Jr, 2011). This is because two or more than two activities are completed at the same
time in order to accomplish the purpose. The diagram itself is showing that
1+2+3+4+5+7+9+11+12+13=37 days are required for the continuous improvement plan.
However, previous with the application of critical path method, duration of the project was 59
days. It indicates that activity 8,10,6 are completed simultaneously along with other mentioned
activities. It proves to be effective in saving the resources and time which can be utilized
somewhere else to improve the performance of the business.
However, the case study shows that project management has a time of 3 months only to
improve entire process such as reducing the number of defects from the products and increasing
the customer satisfaction. As per the below-mentioned activity table, it has been found that
improvement efforts are sustained so that sustainability will be done through making the plan for
monthly meeting and reviewing the performance of the employees as per the complaint reduction
in each department. For example, in case of production department reduces the number of
complaints then it will be the reward. On the other hand, the quality department will be helpful to
sustain the improvement because timely feedback will be provided and report of the incidents
will be given to the respective team in accordance with the schedule. Therefore, continuous
improvement plan determines the growth and development of the employees and support them to
accomplish long as well as short-term objectives of the business (Burke, 2013). Apart from this,
monthly evaluation of employees’ performance will be done as per the pre-specified criteria so
they can focus on the same to determine their success.
Conclusion and Recommendations
The aforementioned essay concludes that continuous improvement plan is successfully
implemented in the Latino Engineering, yet the success is based on the continuous motivation of
employees. In this regard, leaders of the company must initiate the effective procedure for the
Paraphrase This Document
Need a fresh take? Get an instant paraphrase of this document with our AI Paraphraser
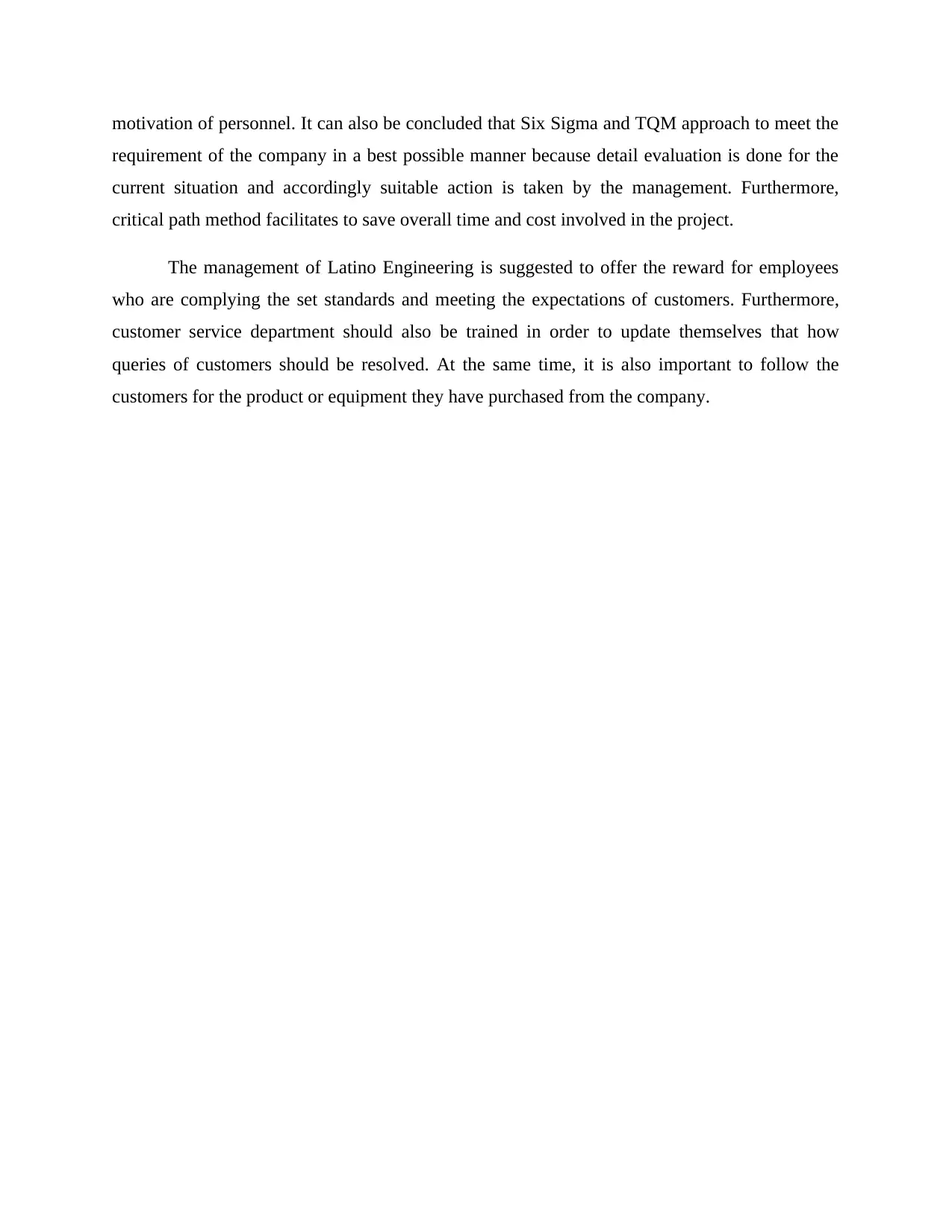
motivation of personnel. It can also be concluded that Six Sigma and TQM approach to meet the
requirement of the company in a best possible manner because detail evaluation is done for the
current situation and accordingly suitable action is taken by the management. Furthermore,
critical path method facilitates to save overall time and cost involved in the project.
The management of Latino Engineering is suggested to offer the reward for employees
who are complying the set standards and meeting the expectations of customers. Furthermore,
customer service department should also be trained in order to update themselves that how
queries of customers should be resolved. At the same time, it is also important to follow the
customers for the product or equipment they have purchased from the company.
requirement of the company in a best possible manner because detail evaluation is done for the
current situation and accordingly suitable action is taken by the management. Furthermore,
critical path method facilitates to save overall time and cost involved in the project.
The management of Latino Engineering is suggested to offer the reward for employees
who are complying the set standards and meeting the expectations of customers. Furthermore,
customer service department should also be trained in order to update themselves that how
queries of customers should be resolved. At the same time, it is also important to follow the
customers for the product or equipment they have purchased from the company.
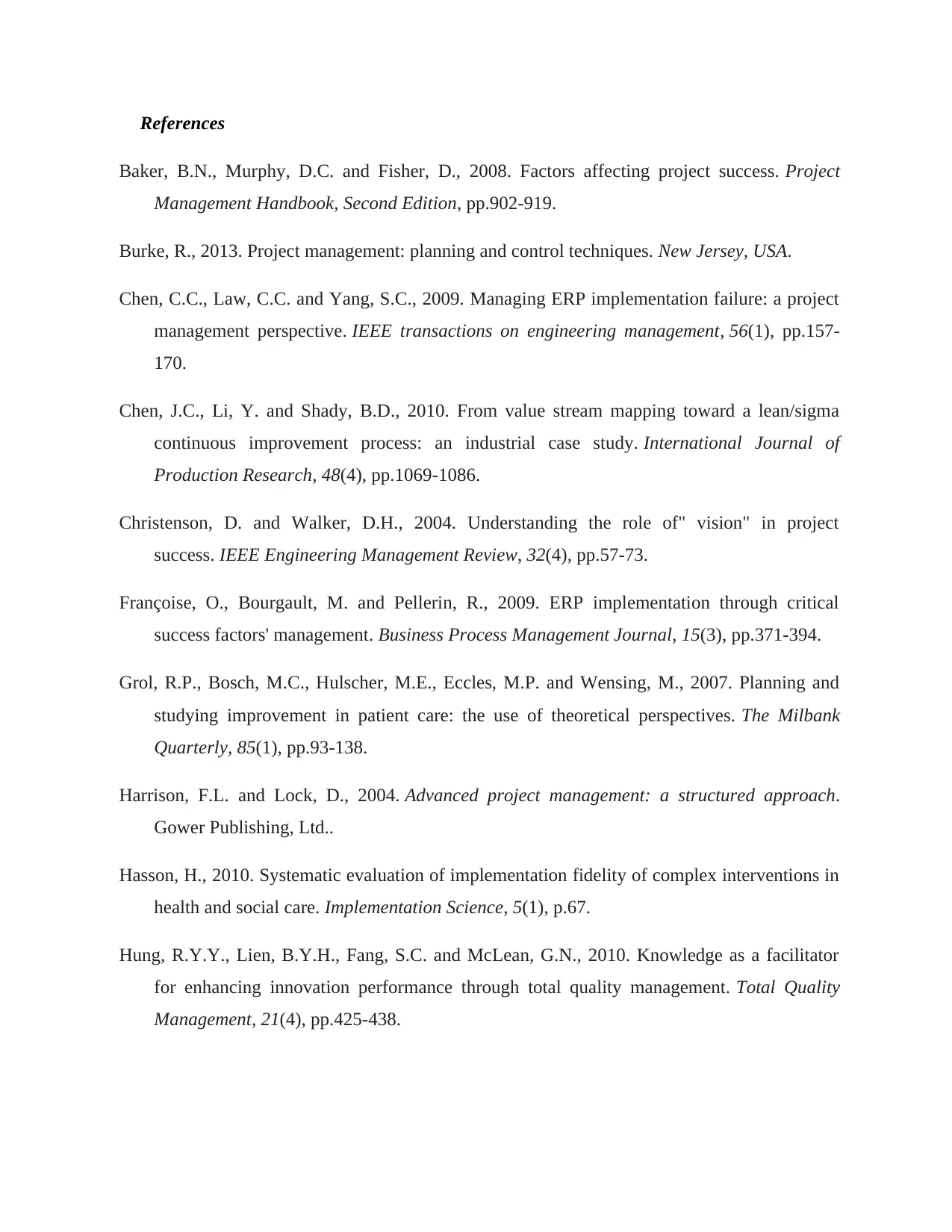
References
Baker, B.N., Murphy, D.C. and Fisher, D., 2008. Factors affecting project success. Project
Management Handbook, Second Edition, pp.902-919.
Burke, R., 2013. Project management: planning and control techniques. New Jersey, USA.
Chen, C.C., Law, C.C. and Yang, S.C., 2009. Managing ERP implementation failure: a project
management perspective. IEEE transactions on engineering management, 56(1), pp.157-
170.
Chen, J.C., Li, Y. and Shady, B.D., 2010. From value stream mapping toward a lean/sigma
continuous improvement process: an industrial case study. International Journal of
Production Research, 48(4), pp.1069-1086.
Christenson, D. and Walker, D.H., 2004. Understanding the role of" vision" in project
success. IEEE Engineering Management Review, 32(4), pp.57-73.
Françoise, O., Bourgault, M. and Pellerin, R., 2009. ERP implementation through critical
success factors' management. Business Process Management Journal, 15(3), pp.371-394.
Grol, R.P., Bosch, M.C., Hulscher, M.E., Eccles, M.P. and Wensing, M., 2007. Planning and
studying improvement in patient care: the use of theoretical perspectives. The Milbank
Quarterly, 85(1), pp.93-138.
Harrison, F.L. and Lock, D., 2004. Advanced project management: a structured approach.
Gower Publishing, Ltd..
Hasson, H., 2010. Systematic evaluation of implementation fidelity of complex interventions in
health and social care. Implementation Science, 5(1), p.67.
Hung, R.Y.Y., Lien, B.Y.H., Fang, S.C. and McLean, G.N., 2010. Knowledge as a facilitator
for enhancing innovation performance through total quality management. Total Quality
Management, 21(4), pp.425-438.
Baker, B.N., Murphy, D.C. and Fisher, D., 2008. Factors affecting project success. Project
Management Handbook, Second Edition, pp.902-919.
Burke, R., 2013. Project management: planning and control techniques. New Jersey, USA.
Chen, C.C., Law, C.C. and Yang, S.C., 2009. Managing ERP implementation failure: a project
management perspective. IEEE transactions on engineering management, 56(1), pp.157-
170.
Chen, J.C., Li, Y. and Shady, B.D., 2010. From value stream mapping toward a lean/sigma
continuous improvement process: an industrial case study. International Journal of
Production Research, 48(4), pp.1069-1086.
Christenson, D. and Walker, D.H., 2004. Understanding the role of" vision" in project
success. IEEE Engineering Management Review, 32(4), pp.57-73.
Françoise, O., Bourgault, M. and Pellerin, R., 2009. ERP implementation through critical
success factors' management. Business Process Management Journal, 15(3), pp.371-394.
Grol, R.P., Bosch, M.C., Hulscher, M.E., Eccles, M.P. and Wensing, M., 2007. Planning and
studying improvement in patient care: the use of theoretical perspectives. The Milbank
Quarterly, 85(1), pp.93-138.
Harrison, F.L. and Lock, D., 2004. Advanced project management: a structured approach.
Gower Publishing, Ltd..
Hasson, H., 2010. Systematic evaluation of implementation fidelity of complex interventions in
health and social care. Implementation Science, 5(1), p.67.
Hung, R.Y.Y., Lien, B.Y.H., Fang, S.C. and McLean, G.N., 2010. Knowledge as a facilitator
for enhancing innovation performance through total quality management. Total Quality
Management, 21(4), pp.425-438.
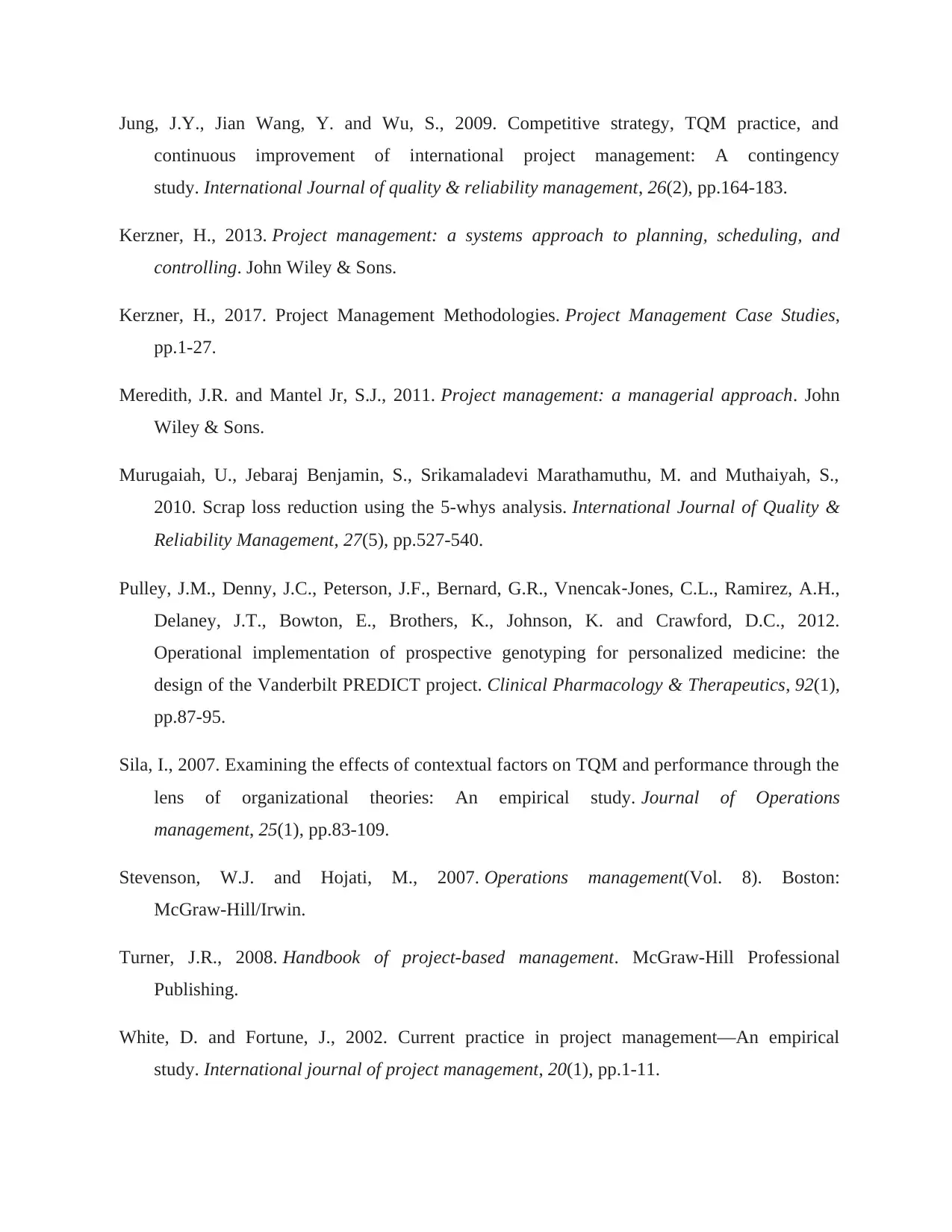
Jung, J.Y., Jian Wang, Y. and Wu, S., 2009. Competitive strategy, TQM practice, and
continuous improvement of international project management: A contingency
study. International Journal of quality & reliability management, 26(2), pp.164-183.
Kerzner, H., 2013. Project management: a systems approach to planning, scheduling, and
controlling. John Wiley & Sons.
Kerzner, H., 2017. Project Management Methodologies. Project Management Case Studies,
pp.1-27.
Meredith, J.R. and Mantel Jr, S.J., 2011. Project management: a managerial approach. John
Wiley & Sons.
Murugaiah, U., Jebaraj Benjamin, S., Srikamaladevi Marathamuthu, M. and Muthaiyah, S.,
2010. Scrap loss reduction using the 5-whys analysis. International Journal of Quality &
Reliability Management, 27(5), pp.527-540.
Pulley, J.M., Denny, J.C., Peterson, J.F., Bernard, G.R., Vnencak‐Jones, C.L., Ramirez, A.H.,
Delaney, J.T., Bowton, E., Brothers, K., Johnson, K. and Crawford, D.C., 2012.
Operational implementation of prospective genotyping for personalized medicine: the
design of the Vanderbilt PREDICT project. Clinical Pharmacology & Therapeutics, 92(1),
pp.87-95.
Sila, I., 2007. Examining the effects of contextual factors on TQM and performance through the
lens of organizational theories: An empirical study. Journal of Operations
management, 25(1), pp.83-109.
Stevenson, W.J. and Hojati, M., 2007. Operations management(Vol. 8). Boston:
McGraw-Hill/Irwin.
Turner, J.R., 2008. Handbook of project-based management. McGraw-Hill Professional
Publishing.
White, D. and Fortune, J., 2002. Current practice in project management—An empirical
study. International journal of project management, 20(1), pp.1-11.
continuous improvement of international project management: A contingency
study. International Journal of quality & reliability management, 26(2), pp.164-183.
Kerzner, H., 2013. Project management: a systems approach to planning, scheduling, and
controlling. John Wiley & Sons.
Kerzner, H., 2017. Project Management Methodologies. Project Management Case Studies,
pp.1-27.
Meredith, J.R. and Mantel Jr, S.J., 2011. Project management: a managerial approach. John
Wiley & Sons.
Murugaiah, U., Jebaraj Benjamin, S., Srikamaladevi Marathamuthu, M. and Muthaiyah, S.,
2010. Scrap loss reduction using the 5-whys analysis. International Journal of Quality &
Reliability Management, 27(5), pp.527-540.
Pulley, J.M., Denny, J.C., Peterson, J.F., Bernard, G.R., Vnencak‐Jones, C.L., Ramirez, A.H.,
Delaney, J.T., Bowton, E., Brothers, K., Johnson, K. and Crawford, D.C., 2012.
Operational implementation of prospective genotyping for personalized medicine: the
design of the Vanderbilt PREDICT project. Clinical Pharmacology & Therapeutics, 92(1),
pp.87-95.
Sila, I., 2007. Examining the effects of contextual factors on TQM and performance through the
lens of organizational theories: An empirical study. Journal of Operations
management, 25(1), pp.83-109.
Stevenson, W.J. and Hojati, M., 2007. Operations management(Vol. 8). Boston:
McGraw-Hill/Irwin.
Turner, J.R., 2008. Handbook of project-based management. McGraw-Hill Professional
Publishing.
White, D. and Fortune, J., 2002. Current practice in project management—An empirical
study. International journal of project management, 20(1), pp.1-11.
Secure Best Marks with AI Grader
Need help grading? Try our AI Grader for instant feedback on your assignments.
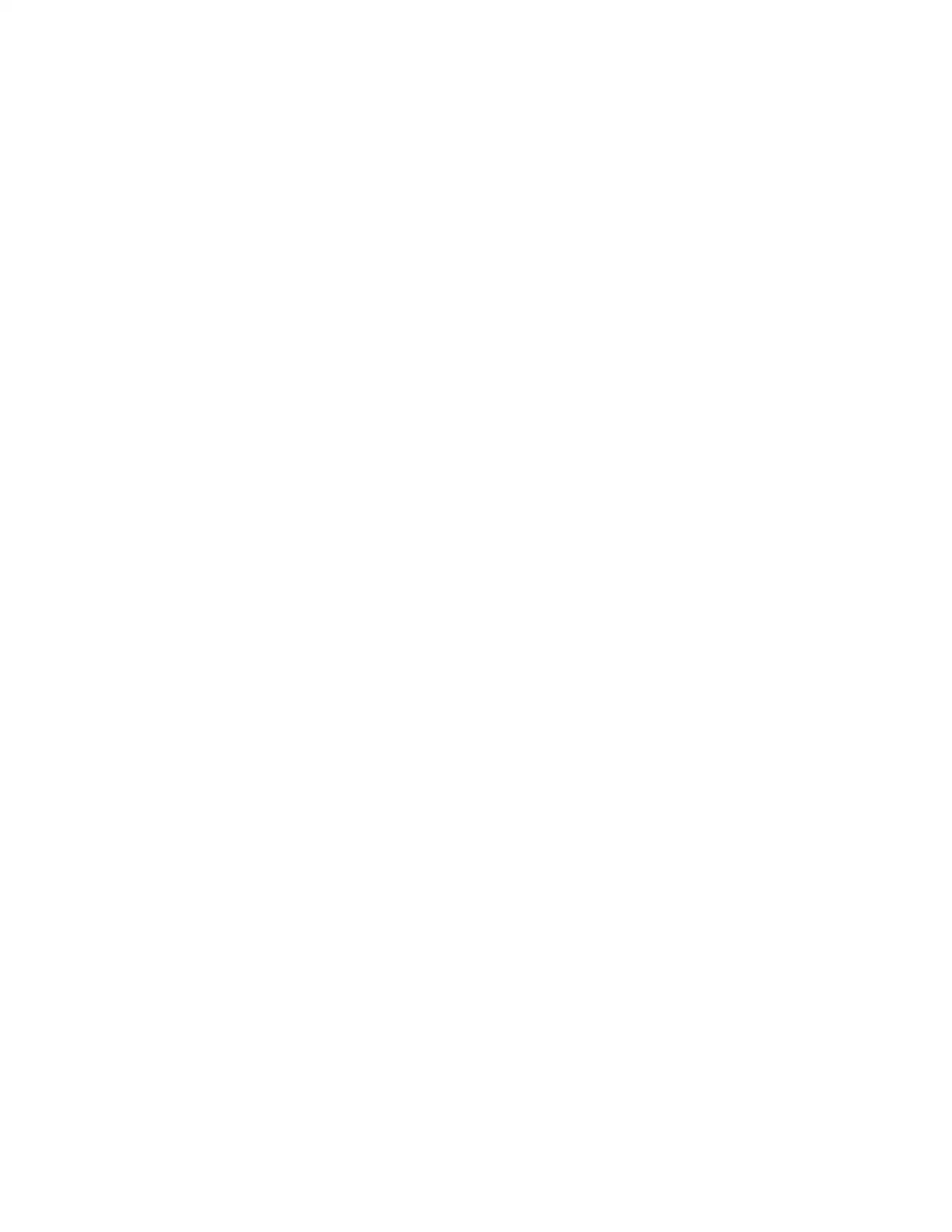
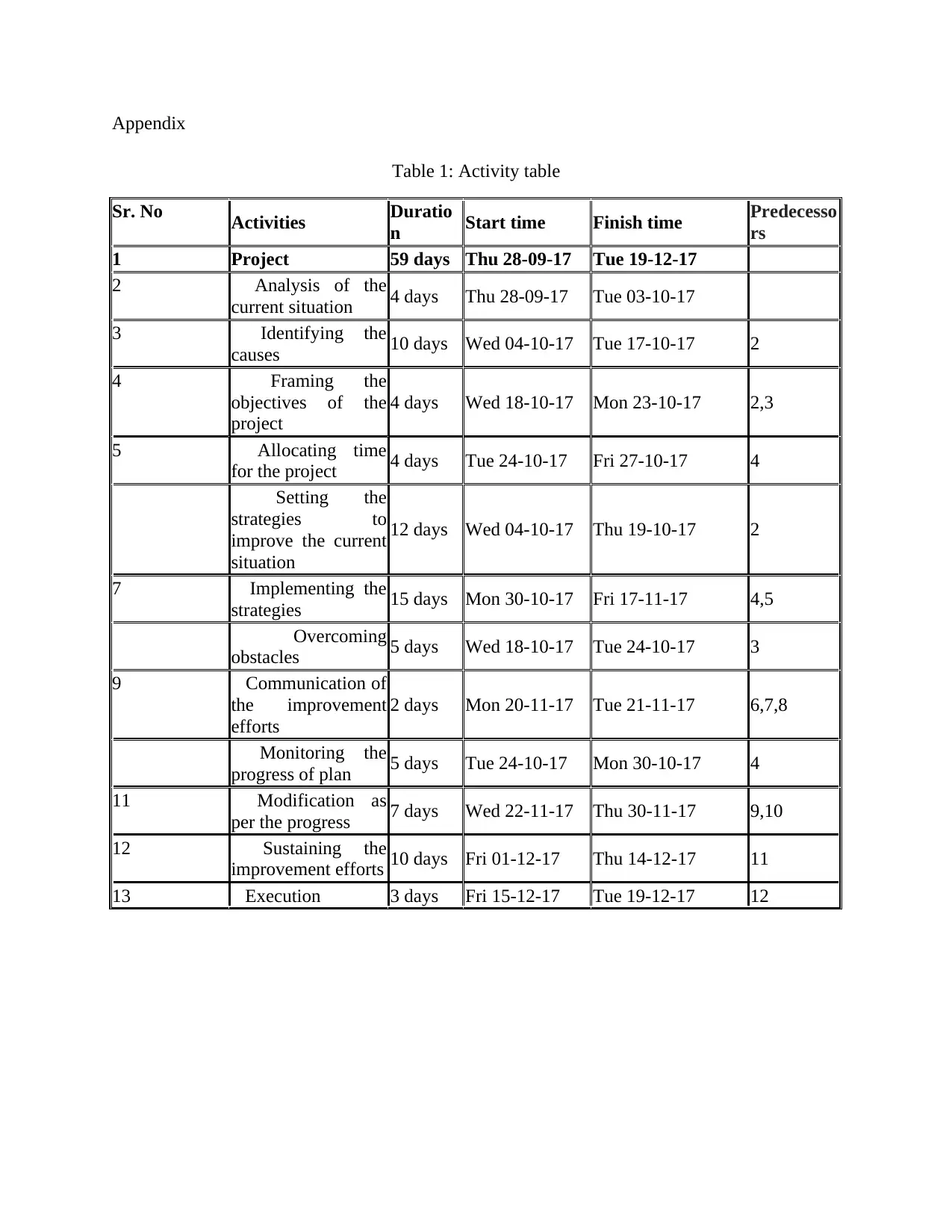
Appendix
Table 1: Activity table
Sr. No Activities Duratio
n Start time Finish time Predecesso
rs
1 Project 59 days Thu 28-09-17 Tue 19-12-17
2 Analysis of the
current situation 4 days Thu 28-09-17 Tue 03-10-17
3 Identifying the
causes 10 days Wed 04-10-17 Tue 17-10-17 2
4 Framing the
objectives of the
project
4 days Wed 18-10-17 Mon 23-10-17 2,3
5 Allocating time
for the project 4 days Tue 24-10-17 Fri 27-10-17 4
Setting the
strategies to
improve the current
situation
12 days Wed 04-10-17 Thu 19-10-17 2
7 Implementing the
strategies 15 days Mon 30-10-17 Fri 17-11-17 4,5
Overcoming
obstacles 5 days Wed 18-10-17 Tue 24-10-17 3
9 Communication of
the improvement
efforts
2 days Mon 20-11-17 Tue 21-11-17 6,7,8
Monitoring the
progress of plan 5 days Tue 24-10-17 Mon 30-10-17 4
11 Modification as
per the progress 7 days Wed 22-11-17 Thu 30-11-17 9,10
12 Sustaining the
improvement efforts 10 days Fri 01-12-17 Thu 14-12-17 11
13 Execution 3 days Fri 15-12-17 Tue 19-12-17 12
Table 1: Activity table
Sr. No Activities Duratio
n Start time Finish time Predecesso
rs
1 Project 59 days Thu 28-09-17 Tue 19-12-17
2 Analysis of the
current situation 4 days Thu 28-09-17 Tue 03-10-17
3 Identifying the
causes 10 days Wed 04-10-17 Tue 17-10-17 2
4 Framing the
objectives of the
project
4 days Wed 18-10-17 Mon 23-10-17 2,3
5 Allocating time
for the project 4 days Tue 24-10-17 Fri 27-10-17 4
Setting the
strategies to
improve the current
situation
12 days Wed 04-10-17 Thu 19-10-17 2
7 Implementing the
strategies 15 days Mon 30-10-17 Fri 17-11-17 4,5
Overcoming
obstacles 5 days Wed 18-10-17 Tue 24-10-17 3
9 Communication of
the improvement
efforts
2 days Mon 20-11-17 Tue 21-11-17 6,7,8
Monitoring the
progress of plan 5 days Tue 24-10-17 Mon 30-10-17 4
11 Modification as
per the progress 7 days Wed 22-11-17 Thu 30-11-17 9,10
12 Sustaining the
improvement efforts 10 days Fri 01-12-17 Thu 14-12-17 11
13 Execution 3 days Fri 15-12-17 Tue 19-12-17 12
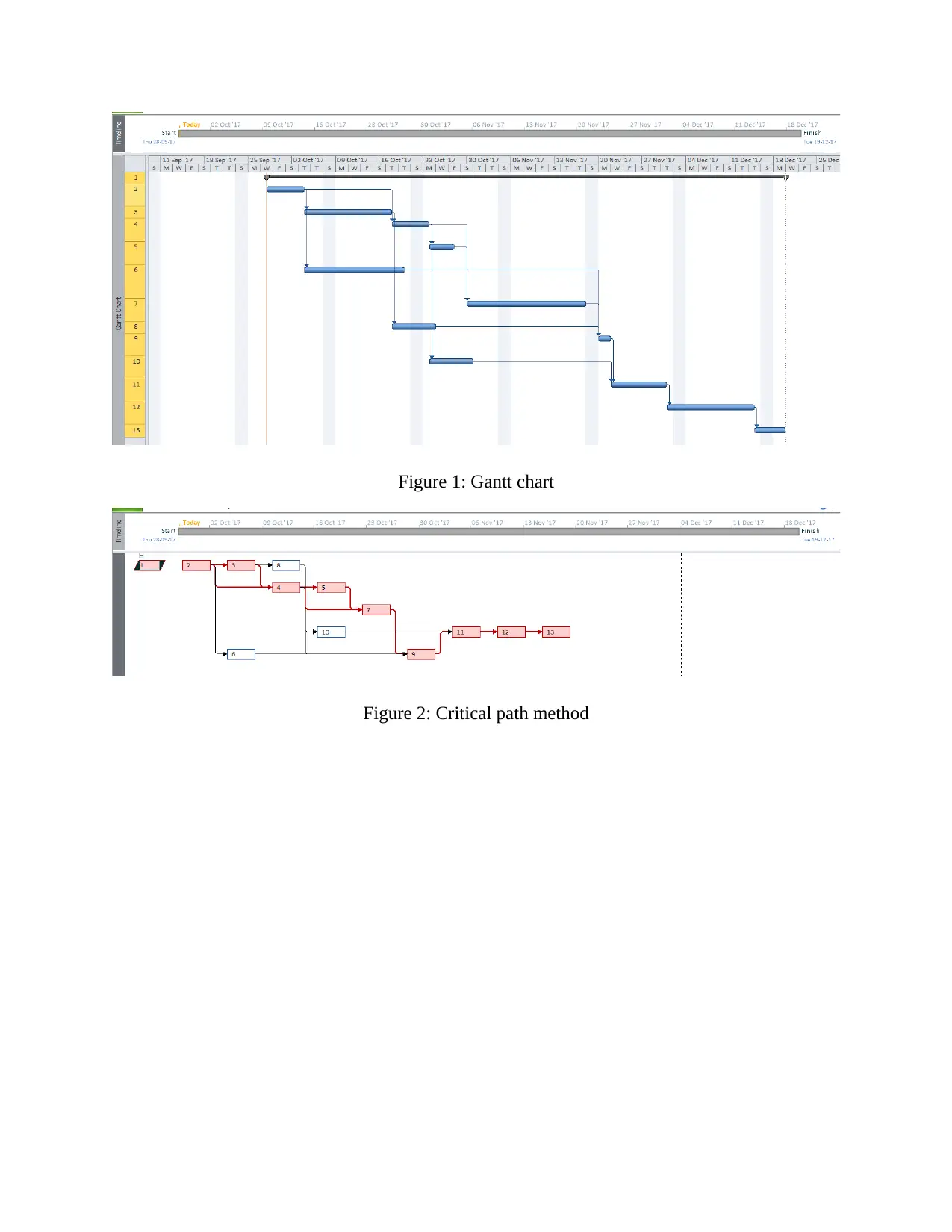
Figure 1: Gantt chart
Figure 2: Critical path method
Figure 2: Critical path method
1 out of 13
Related Documents

Your All-in-One AI-Powered Toolkit for Academic Success.
+13062052269
info@desklib.com
Available 24*7 on WhatsApp / Email
Unlock your academic potential
© 2024 | Zucol Services PVT LTD | All rights reserved.