Quality Management for Organisational Excellence: A Case Study Report
VerifiedAdded on 2021/02/21
|12
|3682
|41
Report
AI Summary
This report provides a comprehensive analysis of quality management principles and their practical application within the context of Quality Tooling Company. It begins with an introduction to the importance of quality management in today's business environment, emphasizing the need for organizations to provide high-quality products and services to ensure customer satisfaction and long-term sustainability. The report then delves into the core components of quality management, including quality planning, improvement, control, and assurance, illustrating how these elements can be implemented to enhance the company's operations. It explores various strategies such as Total Quality Management (TQM), Kaizen, Six Sigma, and Lean manufacturing, and their impact on minimizing waste and errors. The report also includes a detailed examination of Quality Assurance, the PDCA cycle, and Quality Control techniques that Quality Tooling Company can adopt to improve product quality and meet customer demands. Finally, the report highlights the significance of a culture of quality within the organization, crucial for sustained success in a competitive global market.
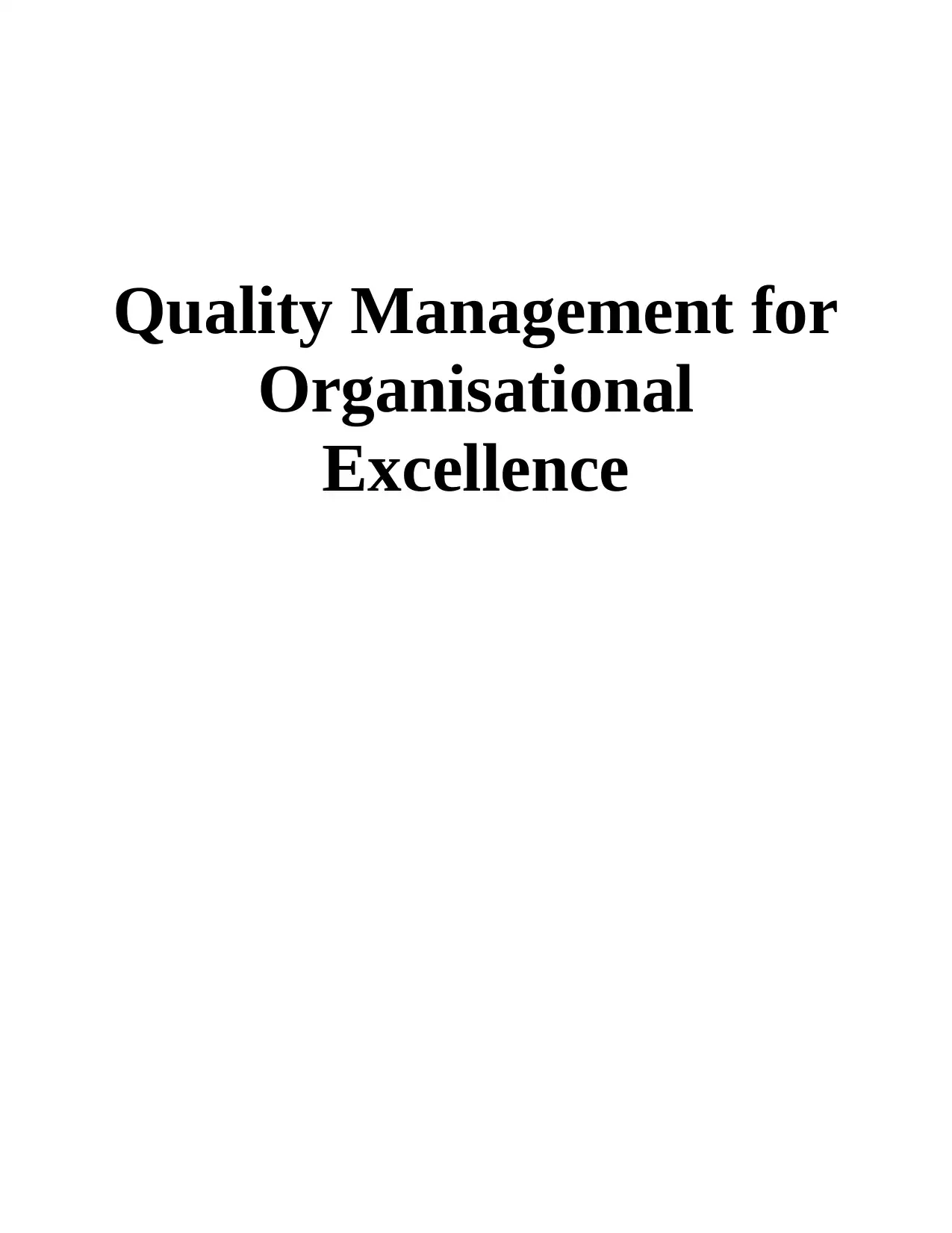
Quality Management for
Organisational
Excellence
Organisational
Excellence
Paraphrase This Document
Need a fresh take? Get an instant paraphrase of this document with our AI Paraphraser
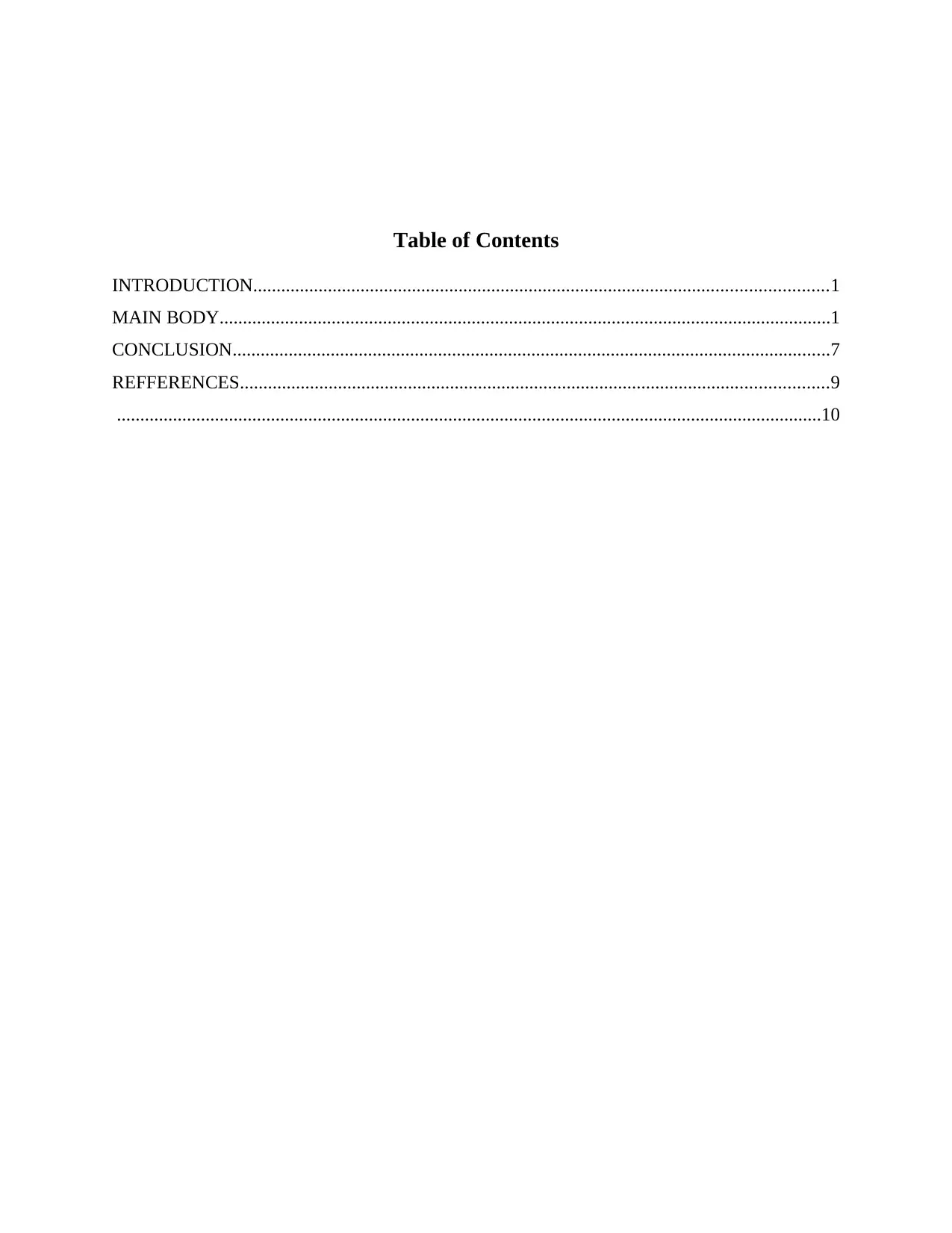
Table of Contents
INTRODUCTION...........................................................................................................................1
MAIN BODY...................................................................................................................................1
CONCLUSION................................................................................................................................7
REFFERENCES..............................................................................................................................9
.......................................................................................................................................................10
INTRODUCTION...........................................................................................................................1
MAIN BODY...................................................................................................................................1
CONCLUSION................................................................................................................................7
REFFERENCES..............................................................................................................................9
.......................................................................................................................................................10
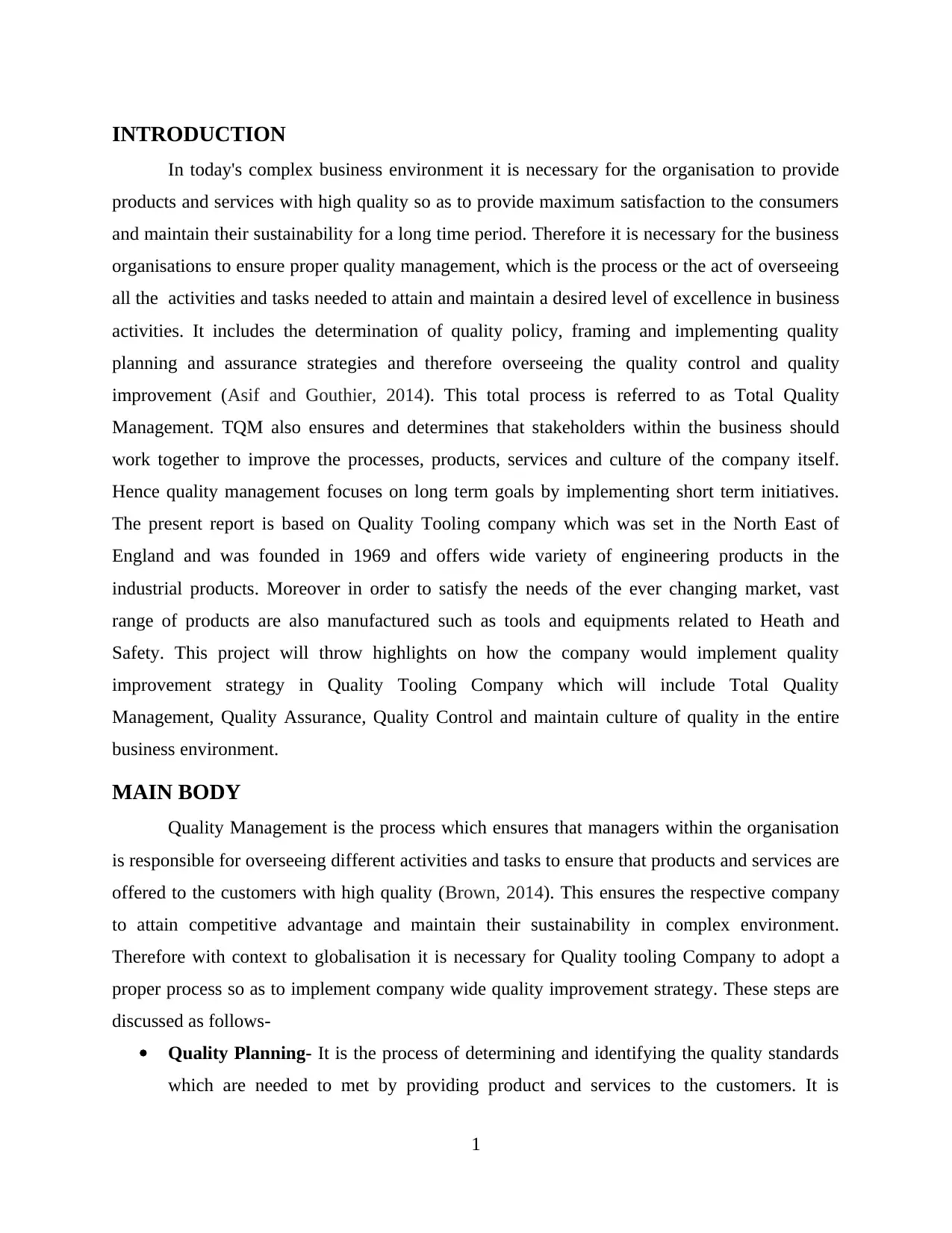
INTRODUCTION
In today's complex business environment it is necessary for the organisation to provide
products and services with high quality so as to provide maximum satisfaction to the consumers
and maintain their sustainability for a long time period. Therefore it is necessary for the business
organisations to ensure proper quality management, which is the process or the act of overseeing
all the activities and tasks needed to attain and maintain a desired level of excellence in business
activities. It includes the determination of quality policy, framing and implementing quality
planning and assurance strategies and therefore overseeing the quality control and quality
improvement (Asif and Gouthier, 2014). This total process is referred to as Total Quality
Management. TQM also ensures and determines that stakeholders within the business should
work together to improve the processes, products, services and culture of the company itself.
Hence quality management focuses on long term goals by implementing short term initiatives.
The present report is based on Quality Tooling company which was set in the North East of
England and was founded in 1969 and offers wide variety of engineering products in the
industrial products. Moreover in order to satisfy the needs of the ever changing market, vast
range of products are also manufactured such as tools and equipments related to Heath and
Safety. This project will throw highlights on how the company would implement quality
improvement strategy in Quality Tooling Company which will include Total Quality
Management, Quality Assurance, Quality Control and maintain culture of quality in the entire
business environment.
MAIN BODY
Quality Management is the process which ensures that managers within the organisation
is responsible for overseeing different activities and tasks to ensure that products and services are
offered to the customers with high quality (Brown, 2014). This ensures the respective company
to attain competitive advantage and maintain their sustainability in complex environment.
Therefore with context to globalisation it is necessary for Quality tooling Company to adopt a
proper process so as to implement company wide quality improvement strategy. These steps are
discussed as follows-
Quality Planning- It is the process of determining and identifying the quality standards
which are needed to met by providing product and services to the customers. It is
1
In today's complex business environment it is necessary for the organisation to provide
products and services with high quality so as to provide maximum satisfaction to the consumers
and maintain their sustainability for a long time period. Therefore it is necessary for the business
organisations to ensure proper quality management, which is the process or the act of overseeing
all the activities and tasks needed to attain and maintain a desired level of excellence in business
activities. It includes the determination of quality policy, framing and implementing quality
planning and assurance strategies and therefore overseeing the quality control and quality
improvement (Asif and Gouthier, 2014). This total process is referred to as Total Quality
Management. TQM also ensures and determines that stakeholders within the business should
work together to improve the processes, products, services and culture of the company itself.
Hence quality management focuses on long term goals by implementing short term initiatives.
The present report is based on Quality Tooling company which was set in the North East of
England and was founded in 1969 and offers wide variety of engineering products in the
industrial products. Moreover in order to satisfy the needs of the ever changing market, vast
range of products are also manufactured such as tools and equipments related to Heath and
Safety. This project will throw highlights on how the company would implement quality
improvement strategy in Quality Tooling Company which will include Total Quality
Management, Quality Assurance, Quality Control and maintain culture of quality in the entire
business environment.
MAIN BODY
Quality Management is the process which ensures that managers within the organisation
is responsible for overseeing different activities and tasks to ensure that products and services are
offered to the customers with high quality (Brown, 2014). This ensures the respective company
to attain competitive advantage and maintain their sustainability in complex environment.
Therefore with context to globalisation it is necessary for Quality tooling Company to adopt a
proper process so as to implement company wide quality improvement strategy. These steps are
discussed as follows-
Quality Planning- It is the process of determining and identifying the quality standards
which are needed to met by providing product and services to the customers. It is
1
⊘ This is a preview!⊘
Do you want full access?
Subscribe today to unlock all pages.

Trusted by 1+ million students worldwide
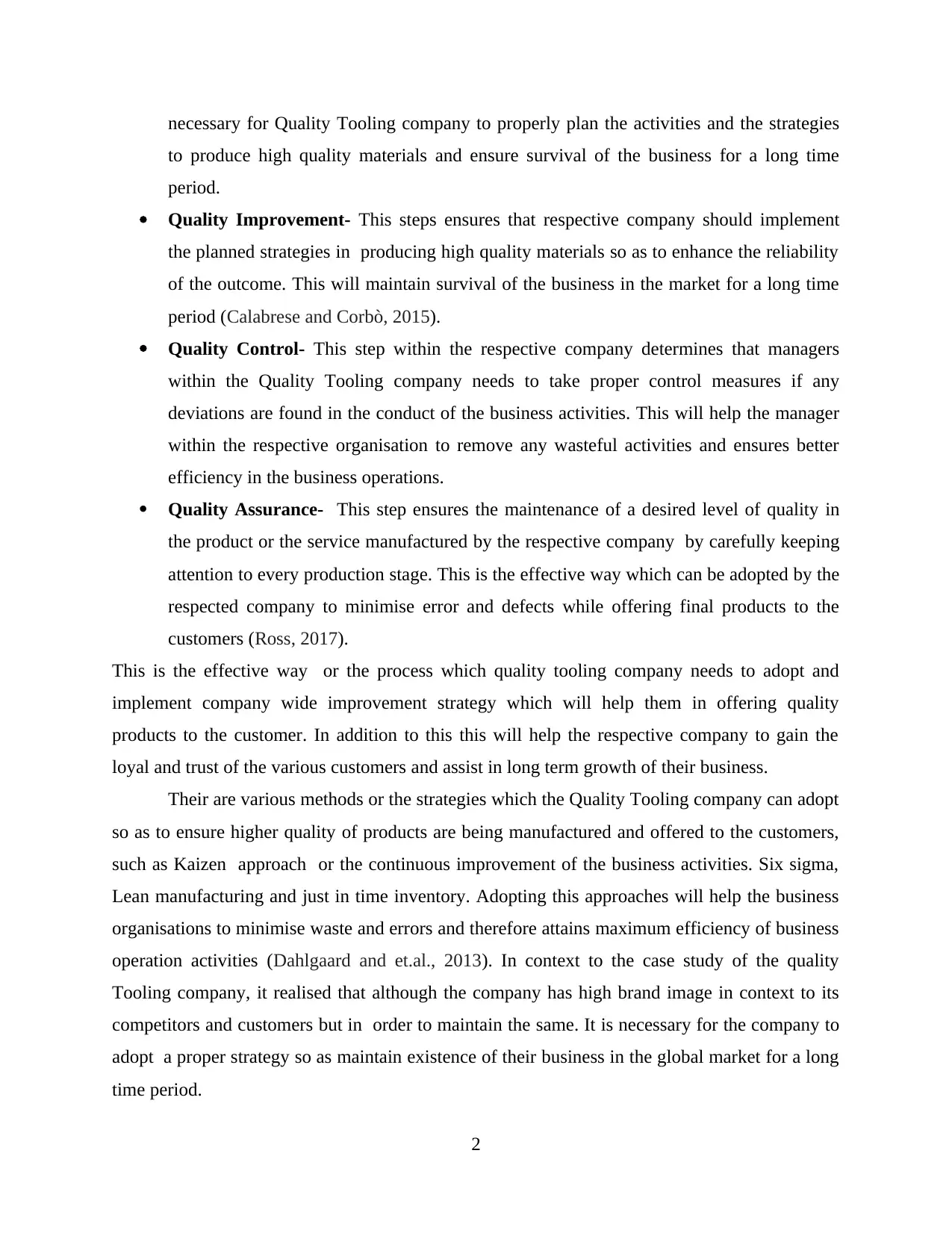
necessary for Quality Tooling company to properly plan the activities and the strategies
to produce high quality materials and ensure survival of the business for a long time
period.
Quality Improvement- This steps ensures that respective company should implement
the planned strategies in producing high quality materials so as to enhance the reliability
of the outcome. This will maintain survival of the business in the market for a long time
period (Calabrese and Corbò, 2015).
Quality Control- This step within the respective company determines that managers
within the Quality Tooling company needs to take proper control measures if any
deviations are found in the conduct of the business activities. This will help the manager
within the respective organisation to remove any wasteful activities and ensures better
efficiency in the business operations.
Quality Assurance- This step ensures the maintenance of a desired level of quality in
the product or the service manufactured by the respective company by carefully keeping
attention to every production stage. This is the effective way which can be adopted by the
respected company to minimise error and defects while offering final products to the
customers (Ross, 2017).
This is the effective way or the process which quality tooling company needs to adopt and
implement company wide improvement strategy which will help them in offering quality
products to the customer. In addition to this this will help the respective company to gain the
loyal and trust of the various customers and assist in long term growth of their business.
Their are various methods or the strategies which the Quality Tooling company can adopt
so as to ensure higher quality of products are being manufactured and offered to the customers,
such as Kaizen approach or the continuous improvement of the business activities. Six sigma,
Lean manufacturing and just in time inventory. Adopting this approaches will help the business
organisations to minimise waste and errors and therefore attains maximum efficiency of business
operation activities (Dahlgaard and et.al., 2013). In context to the case study of the quality
Tooling company, it realised that although the company has high brand image in context to its
competitors and customers but in order to maintain the same. It is necessary for the company to
adopt a proper strategy so as maintain existence of their business in the global market for a long
time period.
2
to produce high quality materials and ensure survival of the business for a long time
period.
Quality Improvement- This steps ensures that respective company should implement
the planned strategies in producing high quality materials so as to enhance the reliability
of the outcome. This will maintain survival of the business in the market for a long time
period (Calabrese and Corbò, 2015).
Quality Control- This step within the respective company determines that managers
within the Quality Tooling company needs to take proper control measures if any
deviations are found in the conduct of the business activities. This will help the manager
within the respective organisation to remove any wasteful activities and ensures better
efficiency in the business operations.
Quality Assurance- This step ensures the maintenance of a desired level of quality in
the product or the service manufactured by the respective company by carefully keeping
attention to every production stage. This is the effective way which can be adopted by the
respected company to minimise error and defects while offering final products to the
customers (Ross, 2017).
This is the effective way or the process which quality tooling company needs to adopt and
implement company wide improvement strategy which will help them in offering quality
products to the customer. In addition to this this will help the respective company to gain the
loyal and trust of the various customers and assist in long term growth of their business.
Their are various methods or the strategies which the Quality Tooling company can adopt
so as to ensure higher quality of products are being manufactured and offered to the customers,
such as Kaizen approach or the continuous improvement of the business activities. Six sigma,
Lean manufacturing and just in time inventory. Adopting this approaches will help the business
organisations to minimise waste and errors and therefore attains maximum efficiency of business
operation activities (Dahlgaard and et.al., 2013). In context to the case study of the quality
Tooling company, it realised that although the company has high brand image in context to its
competitors and customers but in order to maintain the same. It is necessary for the company to
adopt a proper strategy so as maintain existence of their business in the global market for a long
time period.
2
Paraphrase This Document
Need a fresh take? Get an instant paraphrase of this document with our AI Paraphraser
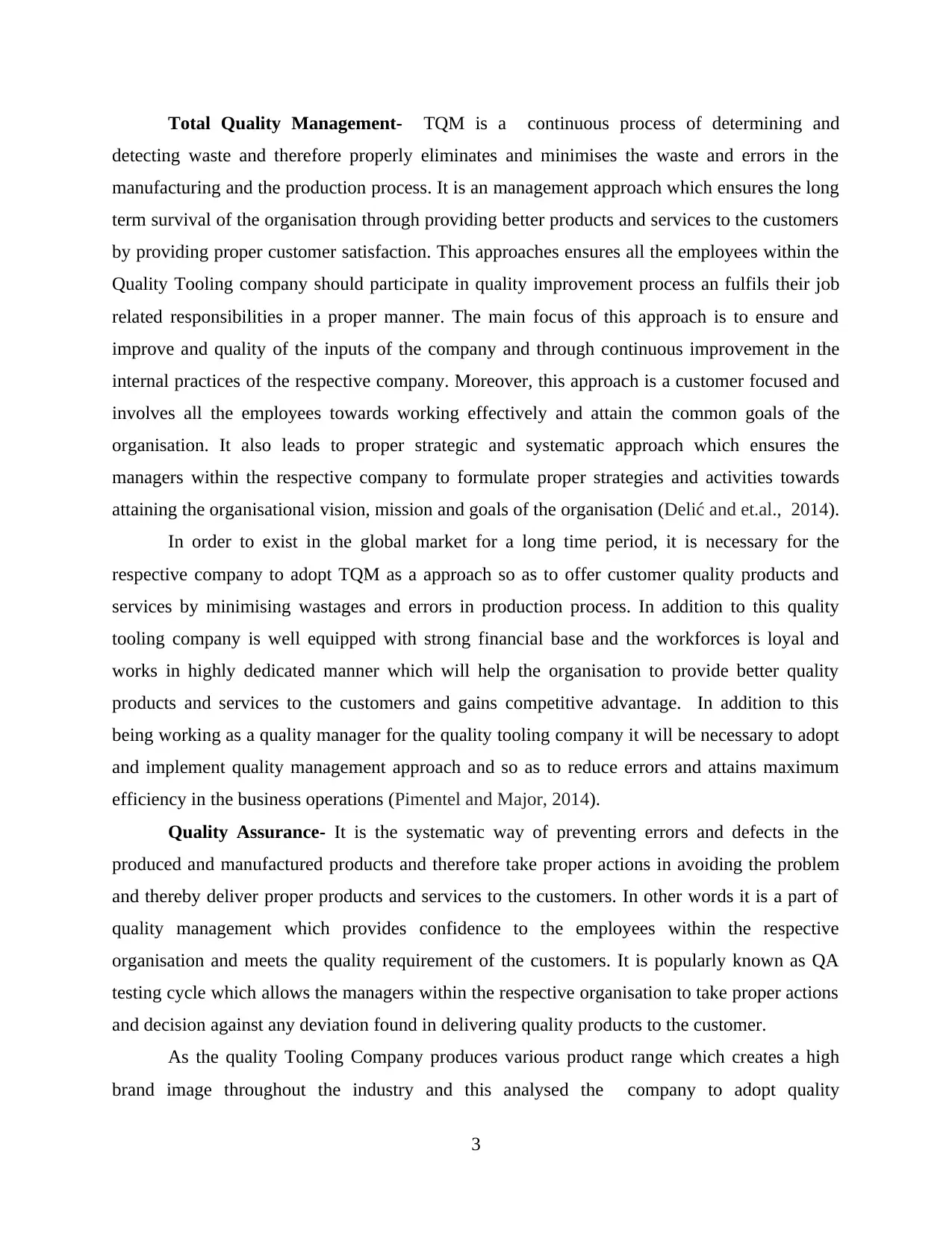
Total Quality Management- TQM is a continuous process of determining and
detecting waste and therefore properly eliminates and minimises the waste and errors in the
manufacturing and the production process. It is an management approach which ensures the long
term survival of the organisation through providing better products and services to the customers
by providing proper customer satisfaction. This approaches ensures all the employees within the
Quality Tooling company should participate in quality improvement process an fulfils their job
related responsibilities in a proper manner. The main focus of this approach is to ensure and
improve and quality of the inputs of the company and through continuous improvement in the
internal practices of the respective company. Moreover, this approach is a customer focused and
involves all the employees towards working effectively and attain the common goals of the
organisation. It also leads to proper strategic and systematic approach which ensures the
managers within the respective company to formulate proper strategies and activities towards
attaining the organisational vision, mission and goals of the organisation (Delić and et.al., 2014).
In order to exist in the global market for a long time period, it is necessary for the
respective company to adopt TQM as a approach so as to offer customer quality products and
services by minimising wastages and errors in production process. In addition to this quality
tooling company is well equipped with strong financial base and the workforces is loyal and
works in highly dedicated manner which will help the organisation to provide better quality
products and services to the customers and gains competitive advantage. In addition to this
being working as a quality manager for the quality tooling company it will be necessary to adopt
and implement quality management approach and so as to reduce errors and attains maximum
efficiency in the business operations (Pimentel and Major, 2014).
Quality Assurance- It is the systematic way of preventing errors and defects in the
produced and manufactured products and therefore take proper actions in avoiding the problem
and thereby deliver proper products and services to the customers. In other words it is a part of
quality management which provides confidence to the employees within the respective
organisation and meets the quality requirement of the customers. It is popularly known as QA
testing cycle which allows the managers within the respective organisation to take proper actions
and decision against any deviation found in delivering quality products to the customer.
As the quality Tooling Company produces various product range which creates a high
brand image throughout the industry and this analysed the company to adopt quality
3
detecting waste and therefore properly eliminates and minimises the waste and errors in the
manufacturing and the production process. It is an management approach which ensures the long
term survival of the organisation through providing better products and services to the customers
by providing proper customer satisfaction. This approaches ensures all the employees within the
Quality Tooling company should participate in quality improvement process an fulfils their job
related responsibilities in a proper manner. The main focus of this approach is to ensure and
improve and quality of the inputs of the company and through continuous improvement in the
internal practices of the respective company. Moreover, this approach is a customer focused and
involves all the employees towards working effectively and attain the common goals of the
organisation. It also leads to proper strategic and systematic approach which ensures the
managers within the respective company to formulate proper strategies and activities towards
attaining the organisational vision, mission and goals of the organisation (Delić and et.al., 2014).
In order to exist in the global market for a long time period, it is necessary for the
respective company to adopt TQM as a approach so as to offer customer quality products and
services by minimising wastages and errors in production process. In addition to this quality
tooling company is well equipped with strong financial base and the workforces is loyal and
works in highly dedicated manner which will help the organisation to provide better quality
products and services to the customers and gains competitive advantage. In addition to this
being working as a quality manager for the quality tooling company it will be necessary to adopt
and implement quality management approach and so as to reduce errors and attains maximum
efficiency in the business operations (Pimentel and Major, 2014).
Quality Assurance- It is the systematic way of preventing errors and defects in the
produced and manufactured products and therefore take proper actions in avoiding the problem
and thereby deliver proper products and services to the customers. In other words it is a part of
quality management which provides confidence to the employees within the respective
organisation and meets the quality requirement of the customers. It is popularly known as QA
testing cycle which allows the managers within the respective organisation to take proper actions
and decision against any deviation found in delivering quality products to the customer.
As the quality Tooling Company produces various product range which creates a high
brand image throughout the industry and this analysed the company to adopt quality
3
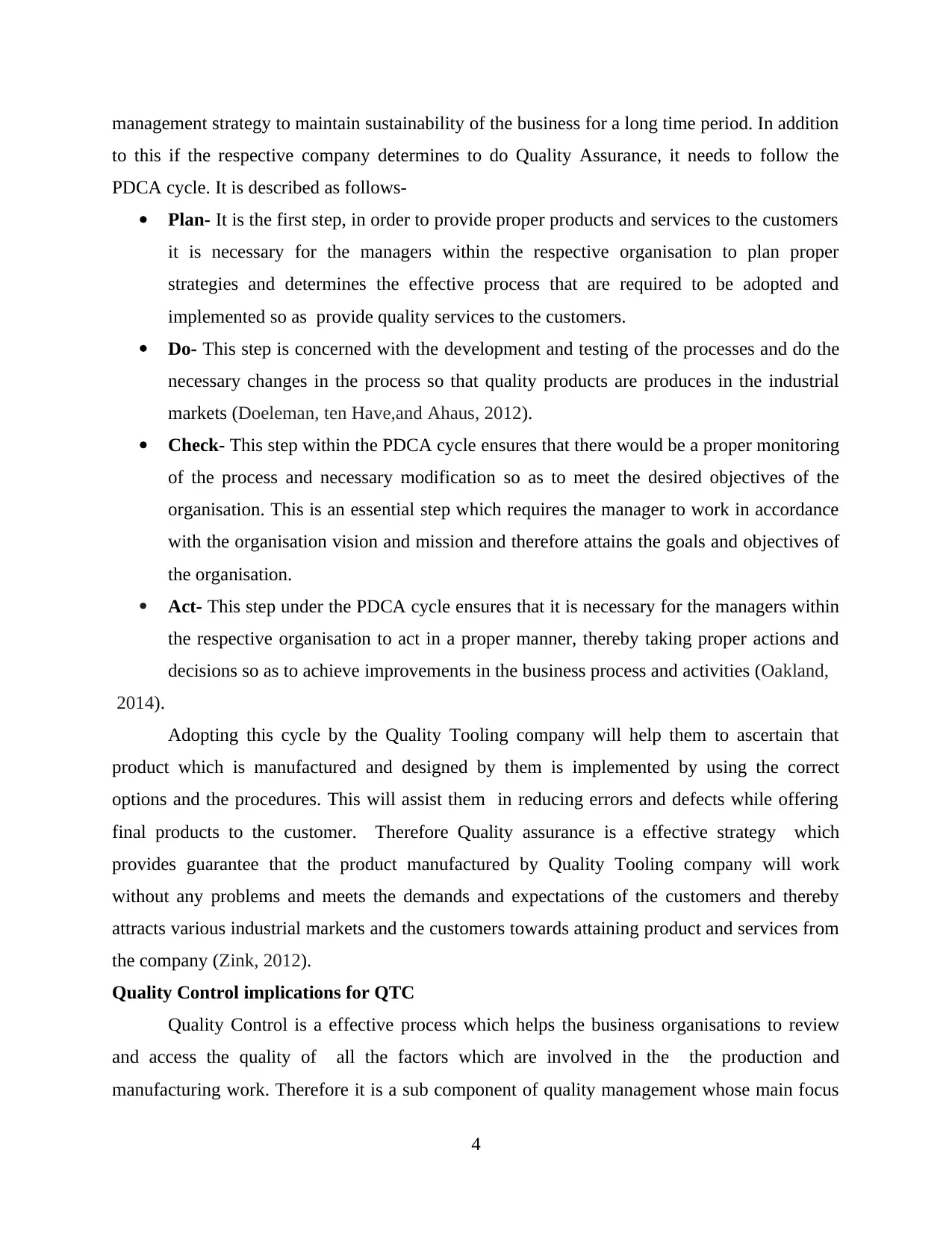
management strategy to maintain sustainability of the business for a long time period. In addition
to this if the respective company determines to do Quality Assurance, it needs to follow the
PDCA cycle. It is described as follows-
Plan- It is the first step, in order to provide proper products and services to the customers
it is necessary for the managers within the respective organisation to plan proper
strategies and determines the effective process that are required to be adopted and
implemented so as provide quality services to the customers.
Do- This step is concerned with the development and testing of the processes and do the
necessary changes in the process so that quality products are produces in the industrial
markets (Doeleman, ten Have,and Ahaus, 2012).
Check- This step within the PDCA cycle ensures that there would be a proper monitoring
of the process and necessary modification so as to meet the desired objectives of the
organisation. This is an essential step which requires the manager to work in accordance
with the organisation vision and mission and therefore attains the goals and objectives of
the organisation.
Act- This step under the PDCA cycle ensures that it is necessary for the managers within
the respective organisation to act in a proper manner, thereby taking proper actions and
decisions so as to achieve improvements in the business process and activities (Oakland,
2014).
Adopting this cycle by the Quality Tooling company will help them to ascertain that
product which is manufactured and designed by them is implemented by using the correct
options and the procedures. This will assist them in reducing errors and defects while offering
final products to the customer. Therefore Quality assurance is a effective strategy which
provides guarantee that the product manufactured by Quality Tooling company will work
without any problems and meets the demands and expectations of the customers and thereby
attracts various industrial markets and the customers towards attaining product and services from
the company (Zink, 2012).
Quality Control implications for QTC
Quality Control is a effective process which helps the business organisations to review
and access the quality of all the factors which are involved in the the production and
manufacturing work. Therefore it is a sub component of quality management whose main focus
4
to this if the respective company determines to do Quality Assurance, it needs to follow the
PDCA cycle. It is described as follows-
Plan- It is the first step, in order to provide proper products and services to the customers
it is necessary for the managers within the respective organisation to plan proper
strategies and determines the effective process that are required to be adopted and
implemented so as provide quality services to the customers.
Do- This step is concerned with the development and testing of the processes and do the
necessary changes in the process so that quality products are produces in the industrial
markets (Doeleman, ten Have,and Ahaus, 2012).
Check- This step within the PDCA cycle ensures that there would be a proper monitoring
of the process and necessary modification so as to meet the desired objectives of the
organisation. This is an essential step which requires the manager to work in accordance
with the organisation vision and mission and therefore attains the goals and objectives of
the organisation.
Act- This step under the PDCA cycle ensures that it is necessary for the managers within
the respective organisation to act in a proper manner, thereby taking proper actions and
decisions so as to achieve improvements in the business process and activities (Oakland,
2014).
Adopting this cycle by the Quality Tooling company will help them to ascertain that
product which is manufactured and designed by them is implemented by using the correct
options and the procedures. This will assist them in reducing errors and defects while offering
final products to the customer. Therefore Quality assurance is a effective strategy which
provides guarantee that the product manufactured by Quality Tooling company will work
without any problems and meets the demands and expectations of the customers and thereby
attracts various industrial markets and the customers towards attaining product and services from
the company (Zink, 2012).
Quality Control implications for QTC
Quality Control is a effective process which helps the business organisations to review
and access the quality of all the factors which are involved in the the production and
manufacturing work. Therefore it is a sub component of quality management whose main focus
4
⊘ This is a preview!⊘
Do you want full access?
Subscribe today to unlock all pages.

Trusted by 1+ million students worldwide
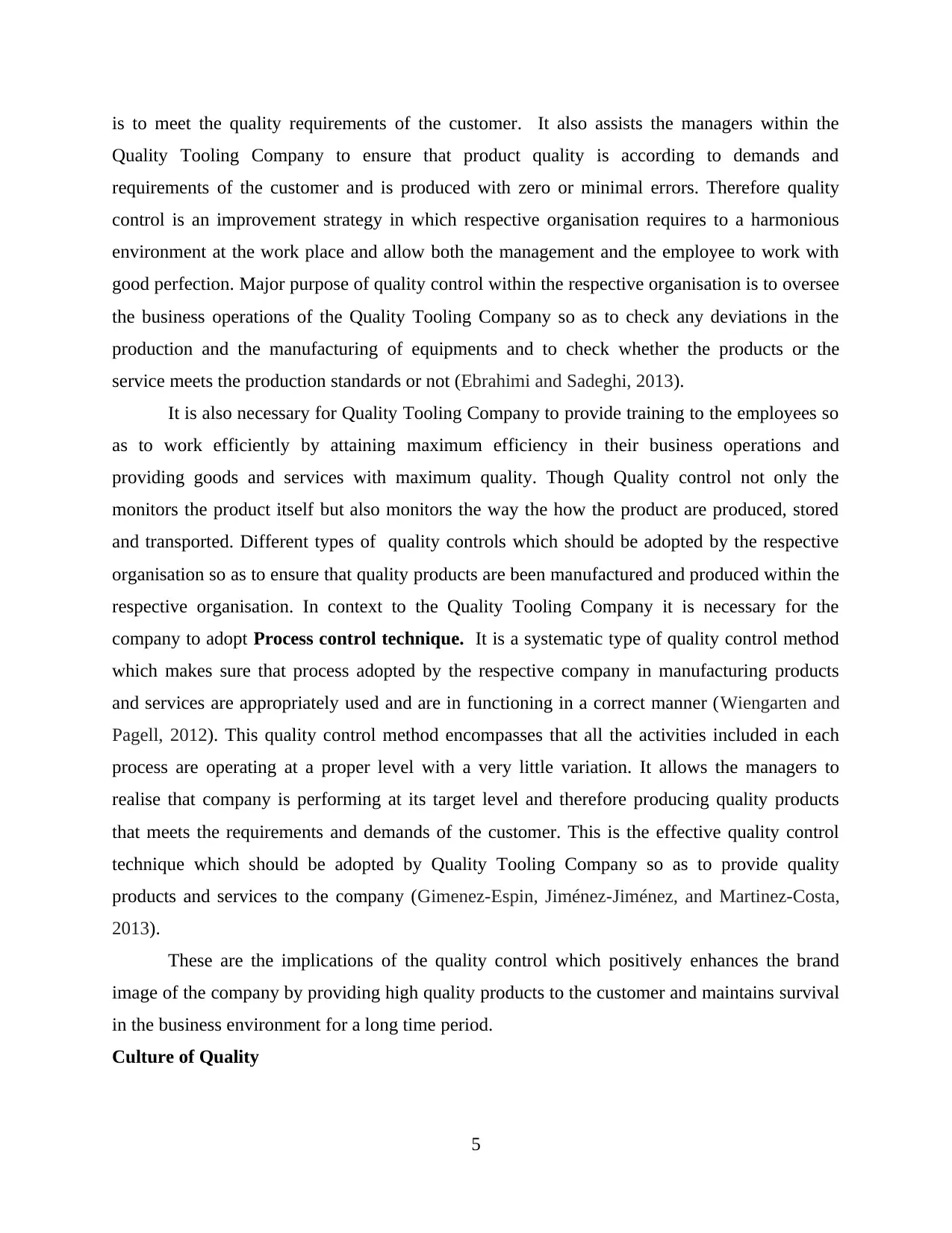
is to meet the quality requirements of the customer. It also assists the managers within the
Quality Tooling Company to ensure that product quality is according to demands and
requirements of the customer and is produced with zero or minimal errors. Therefore quality
control is an improvement strategy in which respective organisation requires to a harmonious
environment at the work place and allow both the management and the employee to work with
good perfection. Major purpose of quality control within the respective organisation is to oversee
the business operations of the Quality Tooling Company so as to check any deviations in the
production and the manufacturing of equipments and to check whether the products or the
service meets the production standards or not (Ebrahimi and Sadeghi, 2013).
It is also necessary for Quality Tooling Company to provide training to the employees so
as to work efficiently by attaining maximum efficiency in their business operations and
providing goods and services with maximum quality. Though Quality control not only the
monitors the product itself but also monitors the way the how the product are produced, stored
and transported. Different types of quality controls which should be adopted by the respective
organisation so as to ensure that quality products are been manufactured and produced within the
respective organisation. In context to the Quality Tooling Company it is necessary for the
company to adopt Process control technique. It is a systematic type of quality control method
which makes sure that process adopted by the respective company in manufacturing products
and services are appropriately used and are in functioning in a correct manner (Wiengarten and
Pagell, 2012). This quality control method encompasses that all the activities included in each
process are operating at a proper level with a very little variation. It allows the managers to
realise that company is performing at its target level and therefore producing quality products
that meets the requirements and demands of the customer. This is the effective quality control
technique which should be adopted by Quality Tooling Company so as to provide quality
products and services to the company (Gimenez-Espin, Jiménez-Jiménez, and Martinez-Costa,
2013).
These are the implications of the quality control which positively enhances the brand
image of the company by providing high quality products to the customer and maintains survival
in the business environment for a long time period.
Culture of Quality
5
Quality Tooling Company to ensure that product quality is according to demands and
requirements of the customer and is produced with zero or minimal errors. Therefore quality
control is an improvement strategy in which respective organisation requires to a harmonious
environment at the work place and allow both the management and the employee to work with
good perfection. Major purpose of quality control within the respective organisation is to oversee
the business operations of the Quality Tooling Company so as to check any deviations in the
production and the manufacturing of equipments and to check whether the products or the
service meets the production standards or not (Ebrahimi and Sadeghi, 2013).
It is also necessary for Quality Tooling Company to provide training to the employees so
as to work efficiently by attaining maximum efficiency in their business operations and
providing goods and services with maximum quality. Though Quality control not only the
monitors the product itself but also monitors the way the how the product are produced, stored
and transported. Different types of quality controls which should be adopted by the respective
organisation so as to ensure that quality products are been manufactured and produced within the
respective organisation. In context to the Quality Tooling Company it is necessary for the
company to adopt Process control technique. It is a systematic type of quality control method
which makes sure that process adopted by the respective company in manufacturing products
and services are appropriately used and are in functioning in a correct manner (Wiengarten and
Pagell, 2012). This quality control method encompasses that all the activities included in each
process are operating at a proper level with a very little variation. It allows the managers to
realise that company is performing at its target level and therefore producing quality products
that meets the requirements and demands of the customer. This is the effective quality control
technique which should be adopted by Quality Tooling Company so as to provide quality
products and services to the company (Gimenez-Espin, Jiménez-Jiménez, and Martinez-Costa,
2013).
These are the implications of the quality control which positively enhances the brand
image of the company by providing high quality products to the customer and maintains survival
in the business environment for a long time period.
Culture of Quality
5
Paraphrase This Document
Need a fresh take? Get an instant paraphrase of this document with our AI Paraphraser
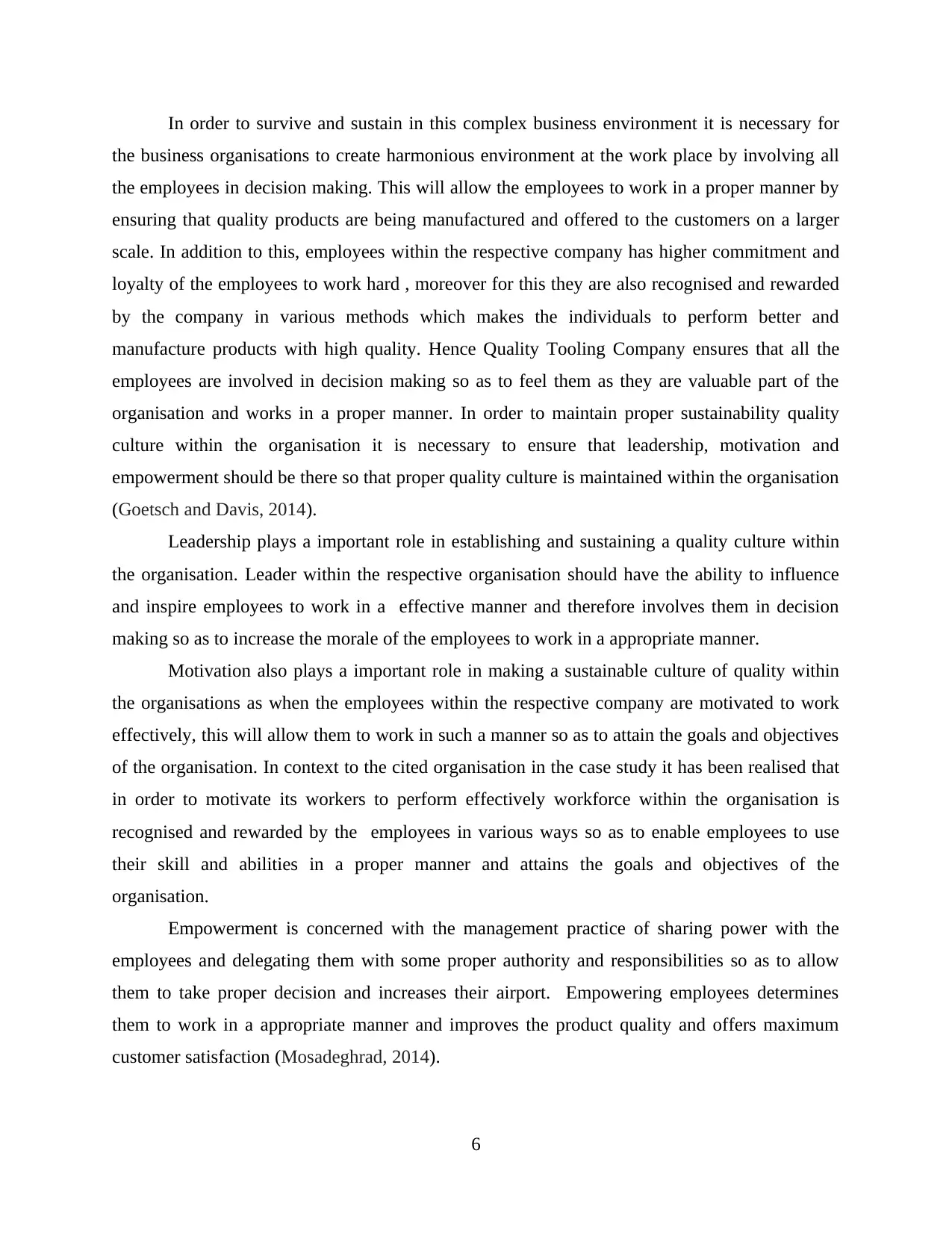
In order to survive and sustain in this complex business environment it is necessary for
the business organisations to create harmonious environment at the work place by involving all
the employees in decision making. This will allow the employees to work in a proper manner by
ensuring that quality products are being manufactured and offered to the customers on a larger
scale. In addition to this, employees within the respective company has higher commitment and
loyalty of the employees to work hard , moreover for this they are also recognised and rewarded
by the company in various methods which makes the individuals to perform better and
manufacture products with high quality. Hence Quality Tooling Company ensures that all the
employees are involved in decision making so as to feel them as they are valuable part of the
organisation and works in a proper manner. In order to maintain proper sustainability quality
culture within the organisation it is necessary to ensure that leadership, motivation and
empowerment should be there so that proper quality culture is maintained within the organisation
(Goetsch and Davis, 2014).
Leadership plays a important role in establishing and sustaining a quality culture within
the organisation. Leader within the respective organisation should have the ability to influence
and inspire employees to work in a effective manner and therefore involves them in decision
making so as to increase the morale of the employees to work in a appropriate manner.
Motivation also plays a important role in making a sustainable culture of quality within
the organisations as when the employees within the respective company are motivated to work
effectively, this will allow them to work in such a manner so as to attain the goals and objectives
of the organisation. In context to the cited organisation in the case study it has been realised that
in order to motivate its workers to perform effectively workforce within the organisation is
recognised and rewarded by the employees in various ways so as to enable employees to use
their skill and abilities in a proper manner and attains the goals and objectives of the
organisation.
Empowerment is concerned with the management practice of sharing power with the
employees and delegating them with some proper authority and responsibilities so as to allow
them to take proper decision and increases their airport. Empowering employees determines
them to work in a appropriate manner and improves the product quality and offers maximum
customer satisfaction (Mosadeghrad, 2014).
6
the business organisations to create harmonious environment at the work place by involving all
the employees in decision making. This will allow the employees to work in a proper manner by
ensuring that quality products are being manufactured and offered to the customers on a larger
scale. In addition to this, employees within the respective company has higher commitment and
loyalty of the employees to work hard , moreover for this they are also recognised and rewarded
by the company in various methods which makes the individuals to perform better and
manufacture products with high quality. Hence Quality Tooling Company ensures that all the
employees are involved in decision making so as to feel them as they are valuable part of the
organisation and works in a proper manner. In order to maintain proper sustainability quality
culture within the organisation it is necessary to ensure that leadership, motivation and
empowerment should be there so that proper quality culture is maintained within the organisation
(Goetsch and Davis, 2014).
Leadership plays a important role in establishing and sustaining a quality culture within
the organisation. Leader within the respective organisation should have the ability to influence
and inspire employees to work in a effective manner and therefore involves them in decision
making so as to increase the morale of the employees to work in a appropriate manner.
Motivation also plays a important role in making a sustainable culture of quality within
the organisations as when the employees within the respective company are motivated to work
effectively, this will allow them to work in such a manner so as to attain the goals and objectives
of the organisation. In context to the cited organisation in the case study it has been realised that
in order to motivate its workers to perform effectively workforce within the organisation is
recognised and rewarded by the employees in various ways so as to enable employees to use
their skill and abilities in a proper manner and attains the goals and objectives of the
organisation.
Empowerment is concerned with the management practice of sharing power with the
employees and delegating them with some proper authority and responsibilities so as to allow
them to take proper decision and increases their airport. Empowering employees determines
them to work in a appropriate manner and improves the product quality and offers maximum
customer satisfaction (Mosadeghrad, 2014).
6
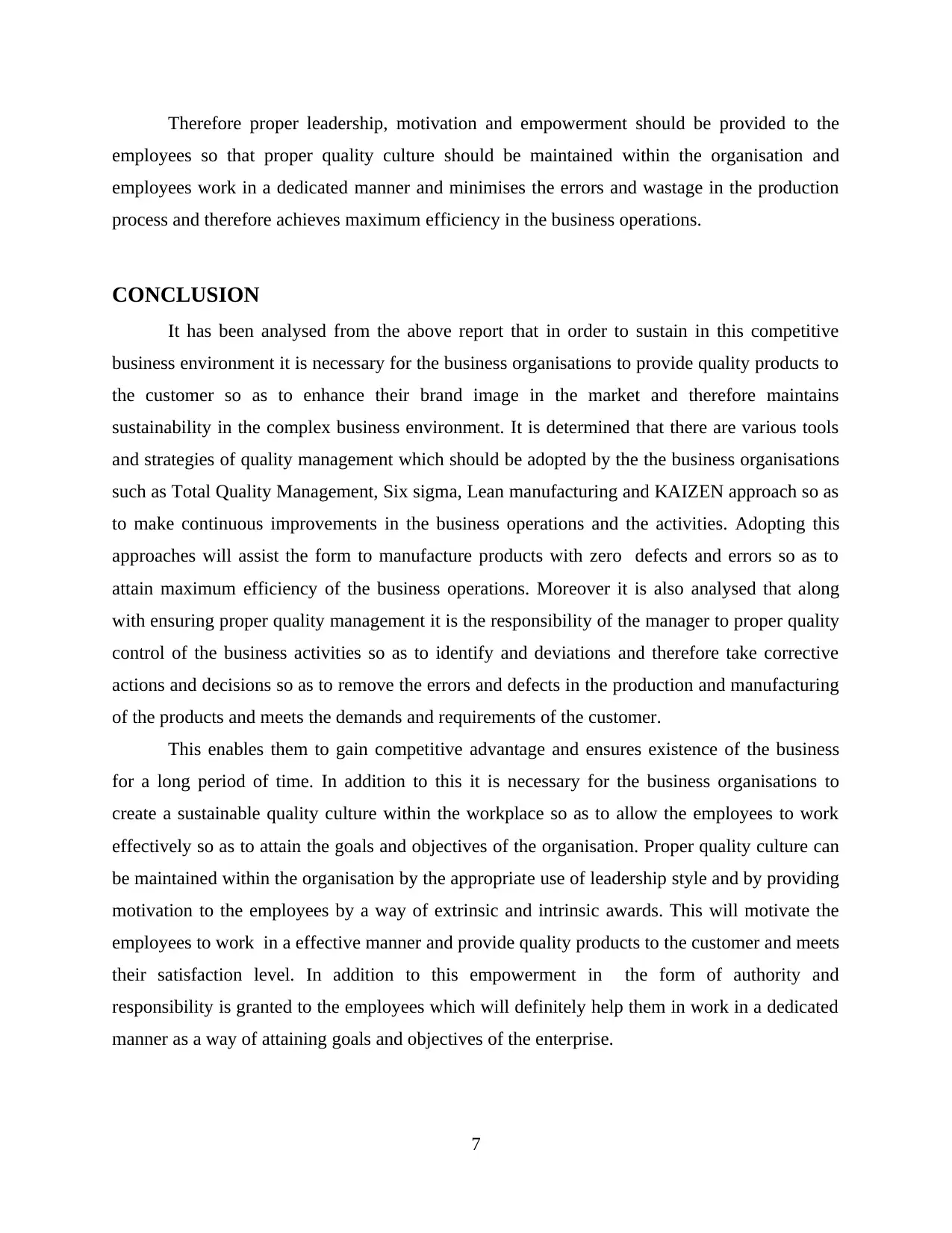
Therefore proper leadership, motivation and empowerment should be provided to the
employees so that proper quality culture should be maintained within the organisation and
employees work in a dedicated manner and minimises the errors and wastage in the production
process and therefore achieves maximum efficiency in the business operations.
CONCLUSION
It has been analysed from the above report that in order to sustain in this competitive
business environment it is necessary for the business organisations to provide quality products to
the customer so as to enhance their brand image in the market and therefore maintains
sustainability in the complex business environment. It is determined that there are various tools
and strategies of quality management which should be adopted by the the business organisations
such as Total Quality Management, Six sigma, Lean manufacturing and KAIZEN approach so as
to make continuous improvements in the business operations and the activities. Adopting this
approaches will assist the form to manufacture products with zero defects and errors so as to
attain maximum efficiency of the business operations. Moreover it is also analysed that along
with ensuring proper quality management it is the responsibility of the manager to proper quality
control of the business activities so as to identify and deviations and therefore take corrective
actions and decisions so as to remove the errors and defects in the production and manufacturing
of the products and meets the demands and requirements of the customer.
This enables them to gain competitive advantage and ensures existence of the business
for a long period of time. In addition to this it is necessary for the business organisations to
create a sustainable quality culture within the workplace so as to allow the employees to work
effectively so as to attain the goals and objectives of the organisation. Proper quality culture can
be maintained within the organisation by the appropriate use of leadership style and by providing
motivation to the employees by a way of extrinsic and intrinsic awards. This will motivate the
employees to work in a effective manner and provide quality products to the customer and meets
their satisfaction level. In addition to this empowerment in the form of authority and
responsibility is granted to the employees which will definitely help them in work in a dedicated
manner as a way of attaining goals and objectives of the enterprise.
7
employees so that proper quality culture should be maintained within the organisation and
employees work in a dedicated manner and minimises the errors and wastage in the production
process and therefore achieves maximum efficiency in the business operations.
CONCLUSION
It has been analysed from the above report that in order to sustain in this competitive
business environment it is necessary for the business organisations to provide quality products to
the customer so as to enhance their brand image in the market and therefore maintains
sustainability in the complex business environment. It is determined that there are various tools
and strategies of quality management which should be adopted by the the business organisations
such as Total Quality Management, Six sigma, Lean manufacturing and KAIZEN approach so as
to make continuous improvements in the business operations and the activities. Adopting this
approaches will assist the form to manufacture products with zero defects and errors so as to
attain maximum efficiency of the business operations. Moreover it is also analysed that along
with ensuring proper quality management it is the responsibility of the manager to proper quality
control of the business activities so as to identify and deviations and therefore take corrective
actions and decisions so as to remove the errors and defects in the production and manufacturing
of the products and meets the demands and requirements of the customer.
This enables them to gain competitive advantage and ensures existence of the business
for a long period of time. In addition to this it is necessary for the business organisations to
create a sustainable quality culture within the workplace so as to allow the employees to work
effectively so as to attain the goals and objectives of the organisation. Proper quality culture can
be maintained within the organisation by the appropriate use of leadership style and by providing
motivation to the employees by a way of extrinsic and intrinsic awards. This will motivate the
employees to work in a effective manner and provide quality products to the customer and meets
their satisfaction level. In addition to this empowerment in the form of authority and
responsibility is granted to the employees which will definitely help them in work in a dedicated
manner as a way of attaining goals and objectives of the enterprise.
7
⊘ This is a preview!⊘
Do you want full access?
Subscribe today to unlock all pages.

Trusted by 1+ million students worldwide
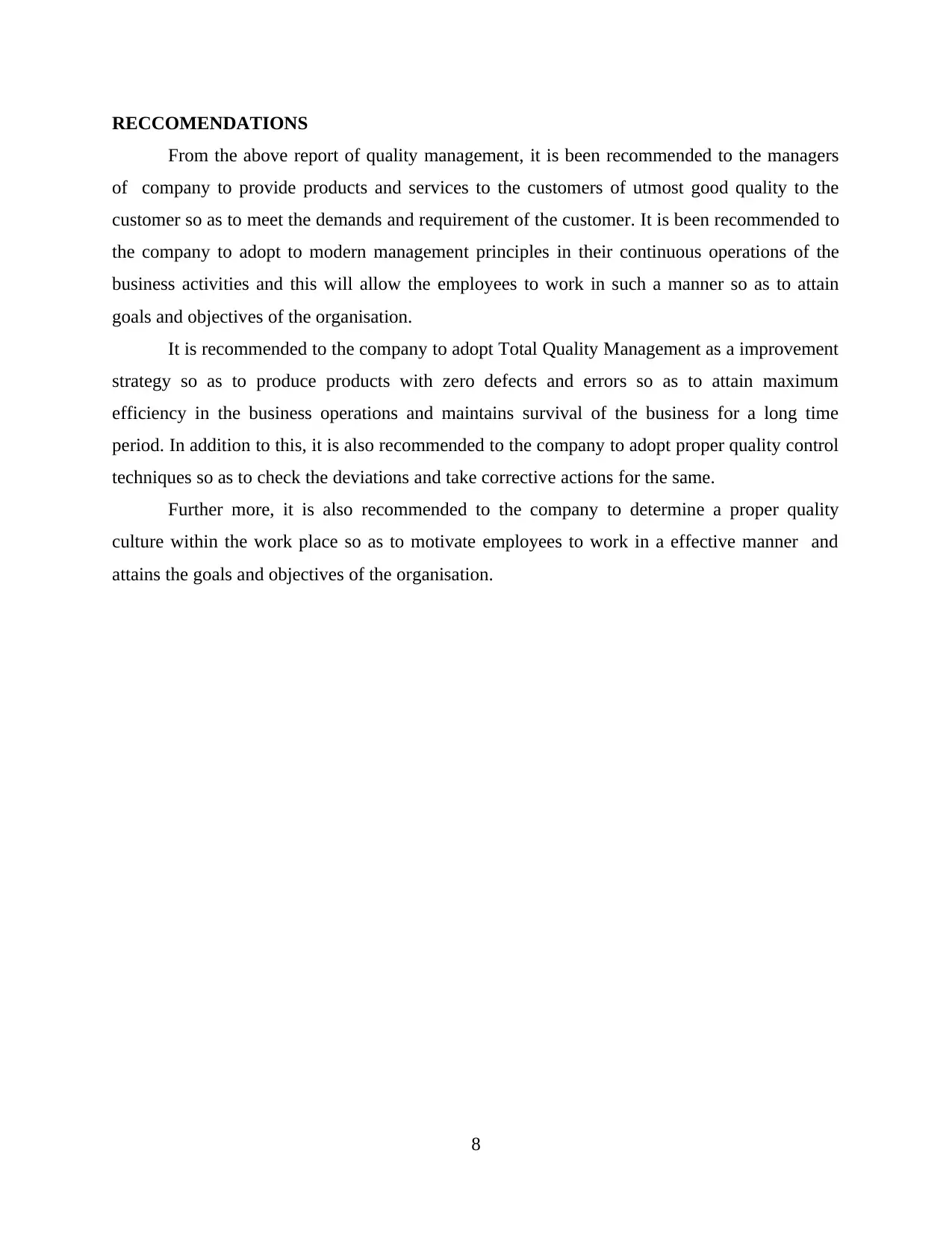
RECCOMENDATIONS
From the above report of quality management, it is been recommended to the managers
of company to provide products and services to the customers of utmost good quality to the
customer so as to meet the demands and requirement of the customer. It is been recommended to
the company to adopt to modern management principles in their continuous operations of the
business activities and this will allow the employees to work in such a manner so as to attain
goals and objectives of the organisation.
It is recommended to the company to adopt Total Quality Management as a improvement
strategy so as to produce products with zero defects and errors so as to attain maximum
efficiency in the business operations and maintains survival of the business for a long time
period. In addition to this, it is also recommended to the company to adopt proper quality control
techniques so as to check the deviations and take corrective actions for the same.
Further more, it is also recommended to the company to determine a proper quality
culture within the work place so as to motivate employees to work in a effective manner and
attains the goals and objectives of the organisation.
8
From the above report of quality management, it is been recommended to the managers
of company to provide products and services to the customers of utmost good quality to the
customer so as to meet the demands and requirement of the customer. It is been recommended to
the company to adopt to modern management principles in their continuous operations of the
business activities and this will allow the employees to work in such a manner so as to attain
goals and objectives of the organisation.
It is recommended to the company to adopt Total Quality Management as a improvement
strategy so as to produce products with zero defects and errors so as to attain maximum
efficiency in the business operations and maintains survival of the business for a long time
period. In addition to this, it is also recommended to the company to adopt proper quality control
techniques so as to check the deviations and take corrective actions for the same.
Further more, it is also recommended to the company to determine a proper quality
culture within the work place so as to motivate employees to work in a effective manner and
attains the goals and objectives of the organisation.
8
Paraphrase This Document
Need a fresh take? Get an instant paraphrase of this document with our AI Paraphraser
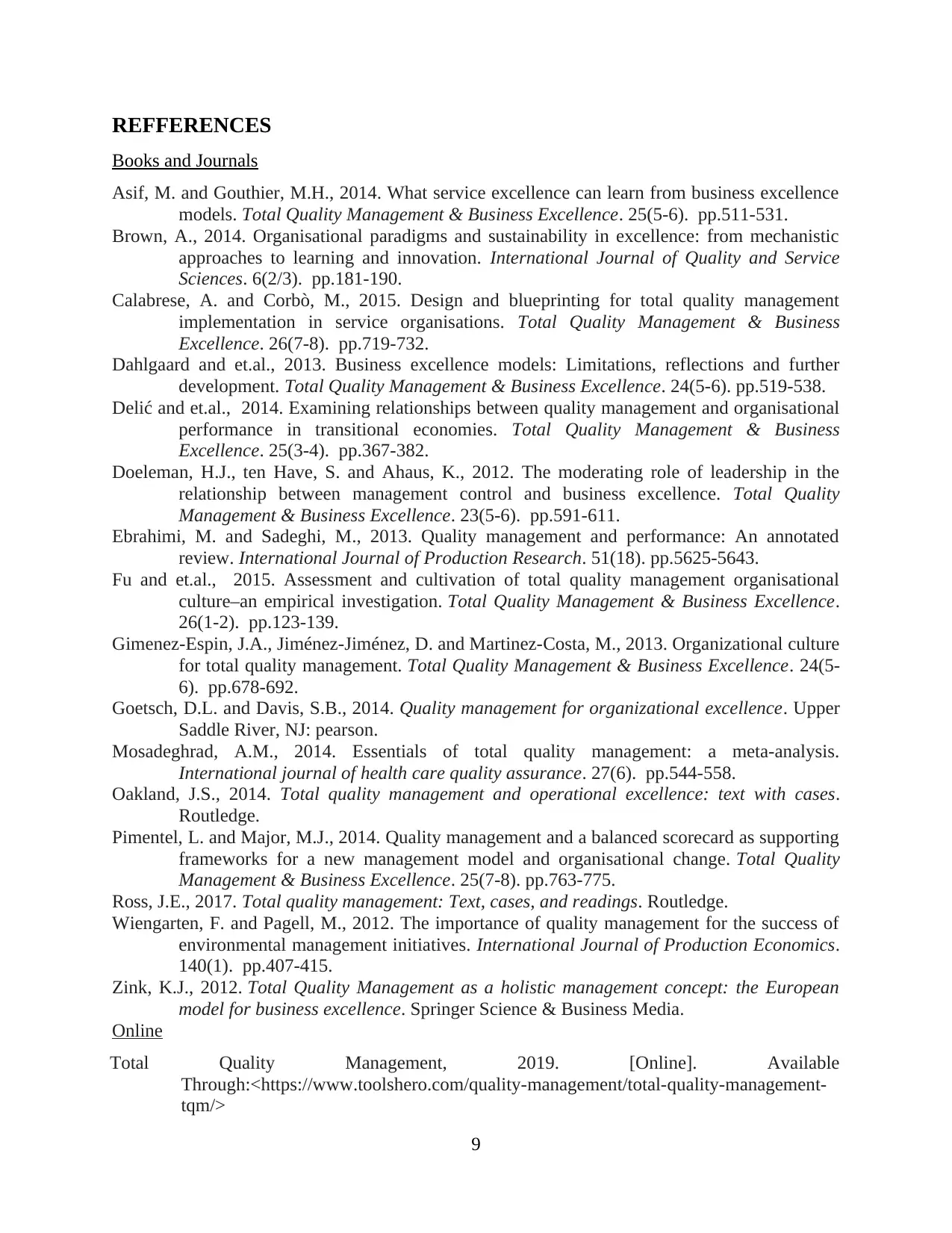
REFFERENCES
Books and Journals
Asif, M. and Gouthier, M.H., 2014. What service excellence can learn from business excellence
models. Total Quality Management & Business Excellence. 25(5-6). pp.511-531.
Brown, A., 2014. Organisational paradigms and sustainability in excellence: from mechanistic
approaches to learning and innovation. International Journal of Quality and Service
Sciences. 6(2/3). pp.181-190.
Calabrese, A. and Corbò, M., 2015. Design and blueprinting for total quality management
implementation in service organisations. Total Quality Management & Business
Excellence. 26(7-8). pp.719-732.
Dahlgaard and et.al., 2013. Business excellence models: Limitations, reflections and further
development. Total Quality Management & Business Excellence. 24(5-6). pp.519-538.
Delić and et.al., 2014. Examining relationships between quality management and organisational
performance in transitional economies. Total Quality Management & Business
Excellence. 25(3-4). pp.367-382.
Doeleman, H.J., ten Have, S. and Ahaus, K., 2012. The moderating role of leadership in the
relationship between management control and business excellence. Total Quality
Management & Business Excellence. 23(5-6). pp.591-611.
Ebrahimi, M. and Sadeghi, M., 2013. Quality management and performance: An annotated
review. International Journal of Production Research. 51(18). pp.5625-5643.
Fu and et.al., 2015. Assessment and cultivation of total quality management organisational
culture–an empirical investigation. Total Quality Management & Business Excellence.
26(1-2). pp.123-139.
Gimenez-Espin, J.A., Jiménez-Jiménez, D. and Martinez-Costa, M., 2013. Organizational culture
for total quality management. Total Quality Management & Business Excellence. 24(5-
6). pp.678-692.
Goetsch, D.L. and Davis, S.B., 2014. Quality management for organizational excellence. Upper
Saddle River, NJ: pearson.
Mosadeghrad, A.M., 2014. Essentials of total quality management: a meta-analysis.
International journal of health care quality assurance. 27(6). pp.544-558.
Oakland, J.S., 2014. Total quality management and operational excellence: text with cases.
Routledge.
Pimentel, L. and Major, M.J., 2014. Quality management and a balanced scorecard as supporting
frameworks for a new management model and organisational change. Total Quality
Management & Business Excellence. 25(7-8). pp.763-775.
Ross, J.E., 2017. Total quality management: Text, cases, and readings. Routledge.
Wiengarten, F. and Pagell, M., 2012. The importance of quality management for the success of
environmental management initiatives. International Journal of Production Economics.
140(1). pp.407-415.
Zink, K.J., 2012. Total Quality Management as a holistic management concept: the European
model for business excellence. Springer Science & Business Media.
Online
Total Quality Management, 2019. [Online]. Available
Through:<https://www.toolshero.com/quality-management/total-quality-management-
tqm/>
9
Books and Journals
Asif, M. and Gouthier, M.H., 2014. What service excellence can learn from business excellence
models. Total Quality Management & Business Excellence. 25(5-6). pp.511-531.
Brown, A., 2014. Organisational paradigms and sustainability in excellence: from mechanistic
approaches to learning and innovation. International Journal of Quality and Service
Sciences. 6(2/3). pp.181-190.
Calabrese, A. and Corbò, M., 2015. Design and blueprinting for total quality management
implementation in service organisations. Total Quality Management & Business
Excellence. 26(7-8). pp.719-732.
Dahlgaard and et.al., 2013. Business excellence models: Limitations, reflections and further
development. Total Quality Management & Business Excellence. 24(5-6). pp.519-538.
Delić and et.al., 2014. Examining relationships between quality management and organisational
performance in transitional economies. Total Quality Management & Business
Excellence. 25(3-4). pp.367-382.
Doeleman, H.J., ten Have, S. and Ahaus, K., 2012. The moderating role of leadership in the
relationship between management control and business excellence. Total Quality
Management & Business Excellence. 23(5-6). pp.591-611.
Ebrahimi, M. and Sadeghi, M., 2013. Quality management and performance: An annotated
review. International Journal of Production Research. 51(18). pp.5625-5643.
Fu and et.al., 2015. Assessment and cultivation of total quality management organisational
culture–an empirical investigation. Total Quality Management & Business Excellence.
26(1-2). pp.123-139.
Gimenez-Espin, J.A., Jiménez-Jiménez, D. and Martinez-Costa, M., 2013. Organizational culture
for total quality management. Total Quality Management & Business Excellence. 24(5-
6). pp.678-692.
Goetsch, D.L. and Davis, S.B., 2014. Quality management for organizational excellence. Upper
Saddle River, NJ: pearson.
Mosadeghrad, A.M., 2014. Essentials of total quality management: a meta-analysis.
International journal of health care quality assurance. 27(6). pp.544-558.
Oakland, J.S., 2014. Total quality management and operational excellence: text with cases.
Routledge.
Pimentel, L. and Major, M.J., 2014. Quality management and a balanced scorecard as supporting
frameworks for a new management model and organisational change. Total Quality
Management & Business Excellence. 25(7-8). pp.763-775.
Ross, J.E., 2017. Total quality management: Text, cases, and readings. Routledge.
Wiengarten, F. and Pagell, M., 2012. The importance of quality management for the success of
environmental management initiatives. International Journal of Production Economics.
140(1). pp.407-415.
Zink, K.J., 2012. Total Quality Management as a holistic management concept: the European
model for business excellence. Springer Science & Business Media.
Online
Total Quality Management, 2019. [Online]. Available
Through:<https://www.toolshero.com/quality-management/total-quality-management-
tqm/>
9
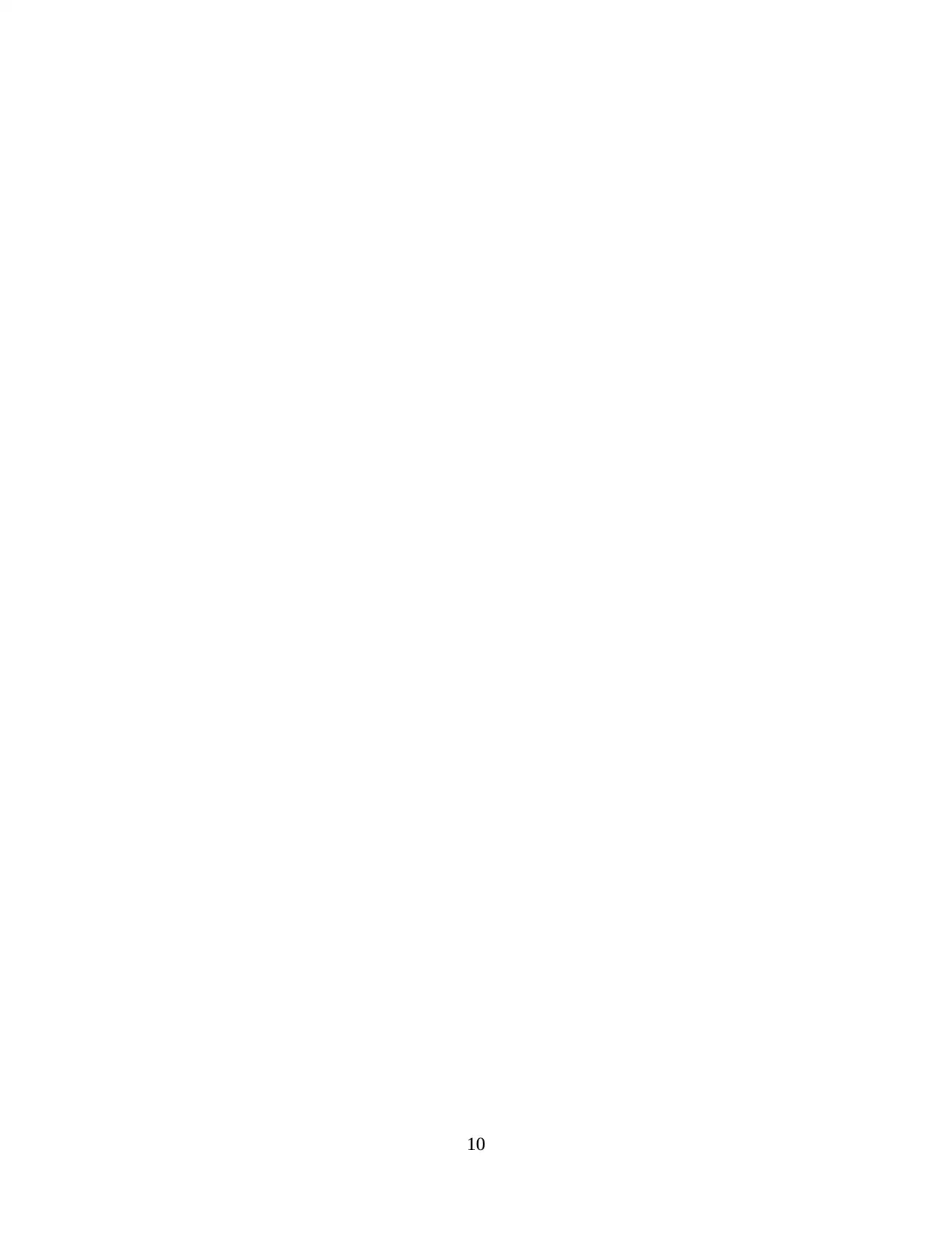
10
⊘ This is a preview!⊘
Do you want full access?
Subscribe today to unlock all pages.

Trusted by 1+ million students worldwide
1 out of 12
Related Documents

Your All-in-One AI-Powered Toolkit for Academic Success.
+13062052269
info@desklib.com
Available 24*7 on WhatsApp / Email
Unlock your academic potential
Copyright © 2020–2025 A2Z Services. All Rights Reserved. Developed and managed by ZUCOL.