Quality Management for Organisational Excellence at TTC: Report
VerifiedAdded on 2020/11/23
|16
|5294
|81
Report
AI Summary
This report, prepared for TTC as part of a quality management strategy, comprehensively addresses the concept of quality, its key elements, and the implementation of Total Quality Management (TQM). As a newly appointed director of quality, the report outlines a company-wide strategy, defining quality and detailing the essential components of TQM, including ethics, integrity, trust, training, leadership, teamwork, communication, and recognition. It further explores the requirements for TQM implementation, such as commitment, culture, continuous improvement, and customer focus. Additionally, it examines the role of ISO 9000 as an entry point into TQM and the use of lean manufacturing. The report aims to establish a robust quality culture within TTC, ensuring organisational excellence through strategic quality management practices.
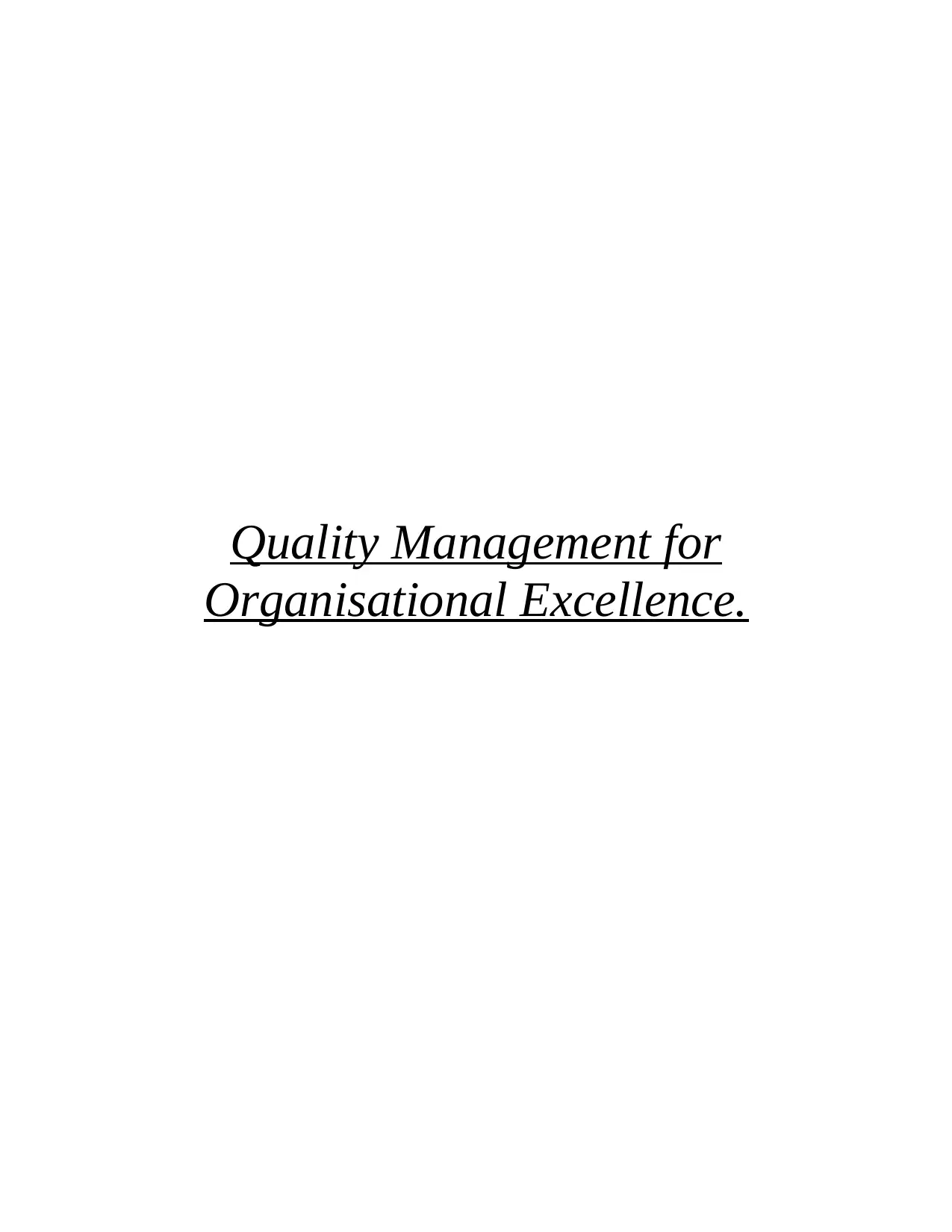
Quality Management for
Organisational Excellence.
Organisational Excellence.
Paraphrase This Document
Need a fresh take? Get an instant paraphrase of this document with our AI Paraphraser
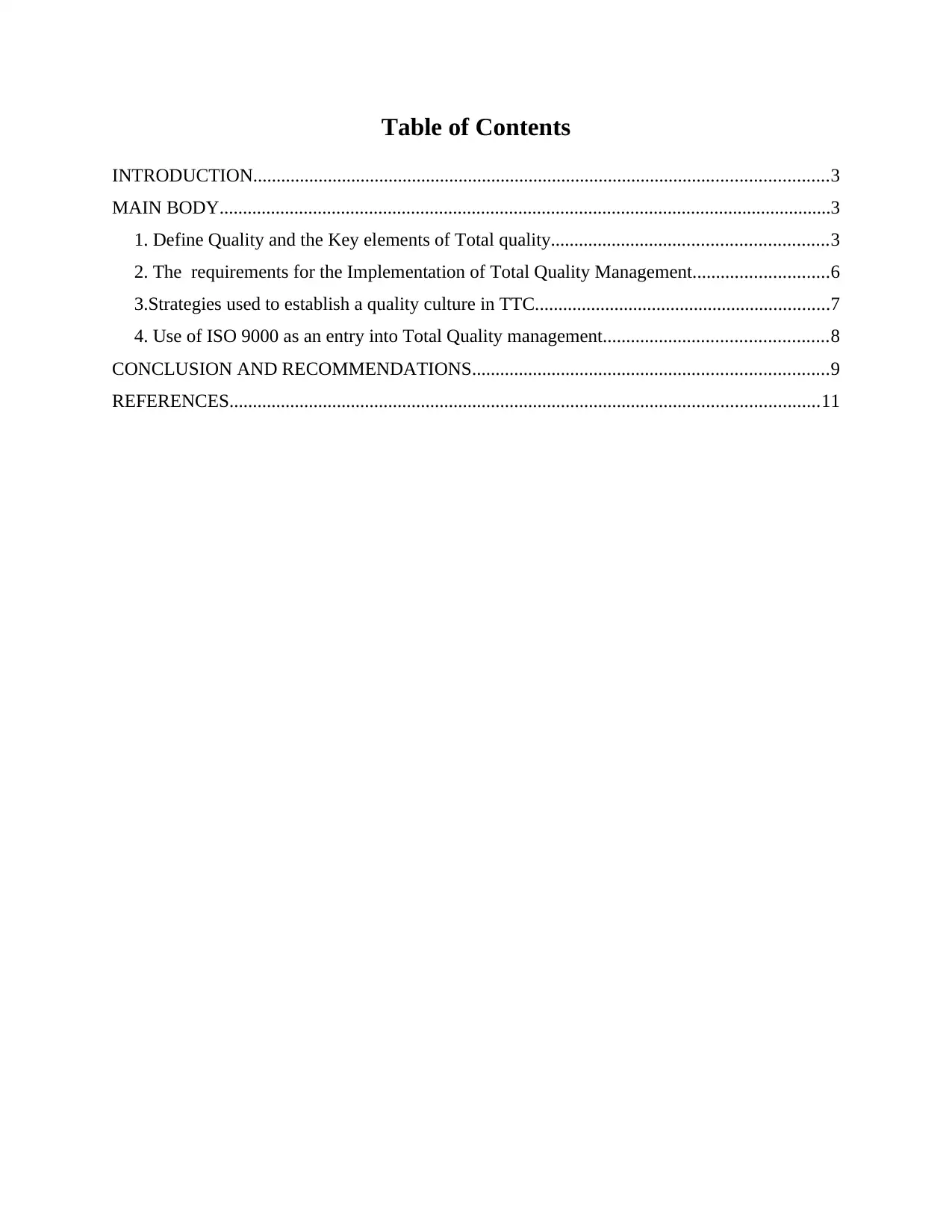
Table of Contents
INTRODUCTION...........................................................................................................................3
MAIN BODY...................................................................................................................................3
1. Define Quality and the Key elements of Total quality...........................................................3
2. The requirements for the Implementation of Total Quality Management.............................6
3.Strategies used to establish a quality culture in TTC...............................................................7
4. Use of ISO 9000 as an entry into Total Quality management................................................8
CONCLUSION AND RECOMMENDATIONS............................................................................9
REFERENCES..............................................................................................................................11
INTRODUCTION...........................................................................................................................3
MAIN BODY...................................................................................................................................3
1. Define Quality and the Key elements of Total quality...........................................................3
2. The requirements for the Implementation of Total Quality Management.............................6
3.Strategies used to establish a quality culture in TTC...............................................................7
4. Use of ISO 9000 as an entry into Total Quality management................................................8
CONCLUSION AND RECOMMENDATIONS............................................................................9
REFERENCES..............................................................................................................................11
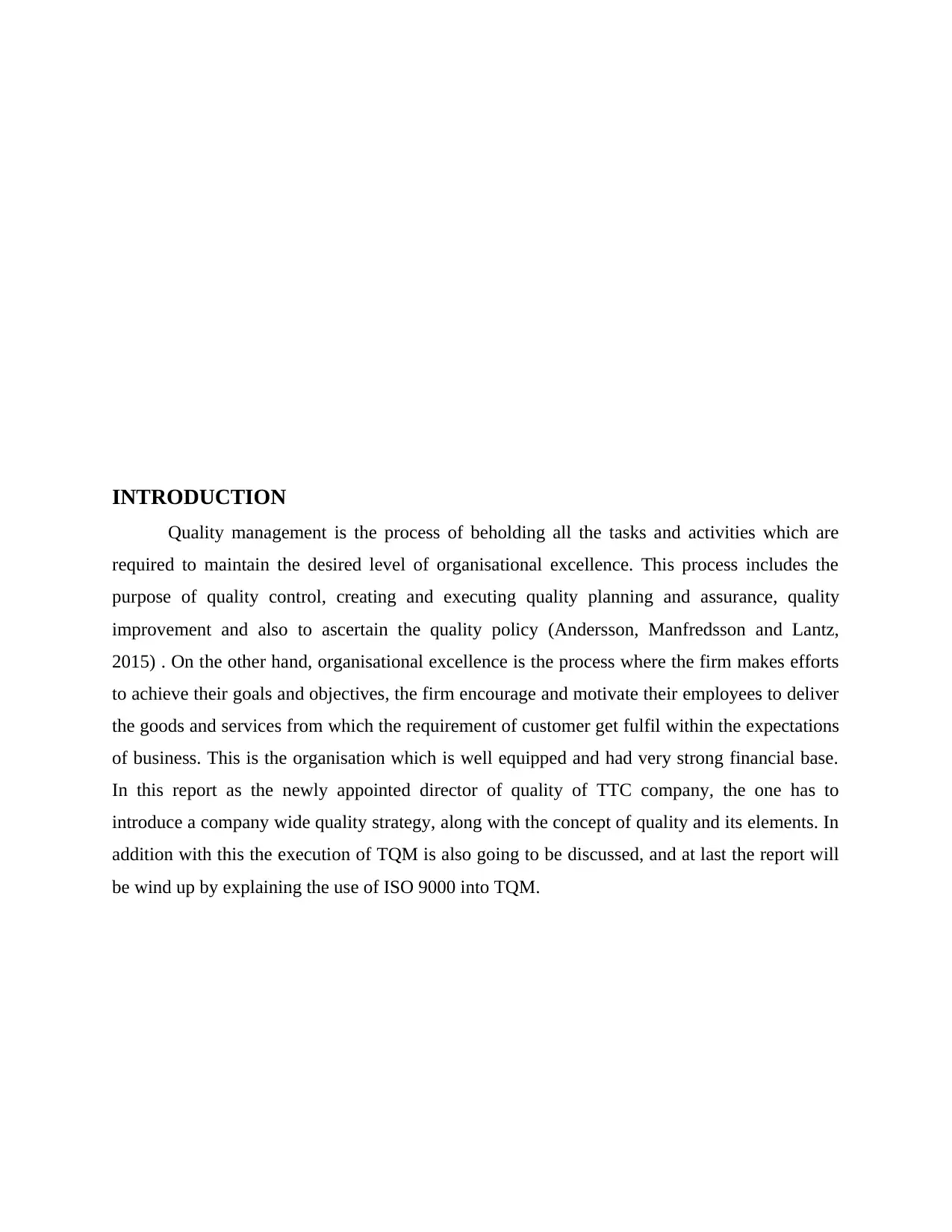
INTRODUCTION
Quality management is the process of beholding all the tasks and activities which are
required to maintain the desired level of organisational excellence. This process includes the
purpose of quality control, creating and executing quality planning and assurance, quality
improvement and also to ascertain the quality policy (Andersson, Manfredsson and Lantz,
2015) . On the other hand, organisational excellence is the process where the firm makes efforts
to achieve their goals and objectives, the firm encourage and motivate their employees to deliver
the goods and services from which the requirement of customer get fulfil within the expectations
of business. This is the organisation which is well equipped and had very strong financial base.
In this report as the newly appointed director of quality of TTC company, the one has to
introduce a company wide quality strategy, along with the concept of quality and its elements. In
addition with this the execution of TQM is also going to be discussed, and at last the report will
be wind up by explaining the use of ISO 9000 into TQM.
Quality management is the process of beholding all the tasks and activities which are
required to maintain the desired level of organisational excellence. This process includes the
purpose of quality control, creating and executing quality planning and assurance, quality
improvement and also to ascertain the quality policy (Andersson, Manfredsson and Lantz,
2015) . On the other hand, organisational excellence is the process where the firm makes efforts
to achieve their goals and objectives, the firm encourage and motivate their employees to deliver
the goods and services from which the requirement of customer get fulfil within the expectations
of business. This is the organisation which is well equipped and had very strong financial base.
In this report as the newly appointed director of quality of TTC company, the one has to
introduce a company wide quality strategy, along with the concept of quality and its elements. In
addition with this the execution of TQM is also going to be discussed, and at last the report will
be wind up by explaining the use of ISO 9000 into TQM.
You're viewing a preview
Unlock full access by subscribing today!
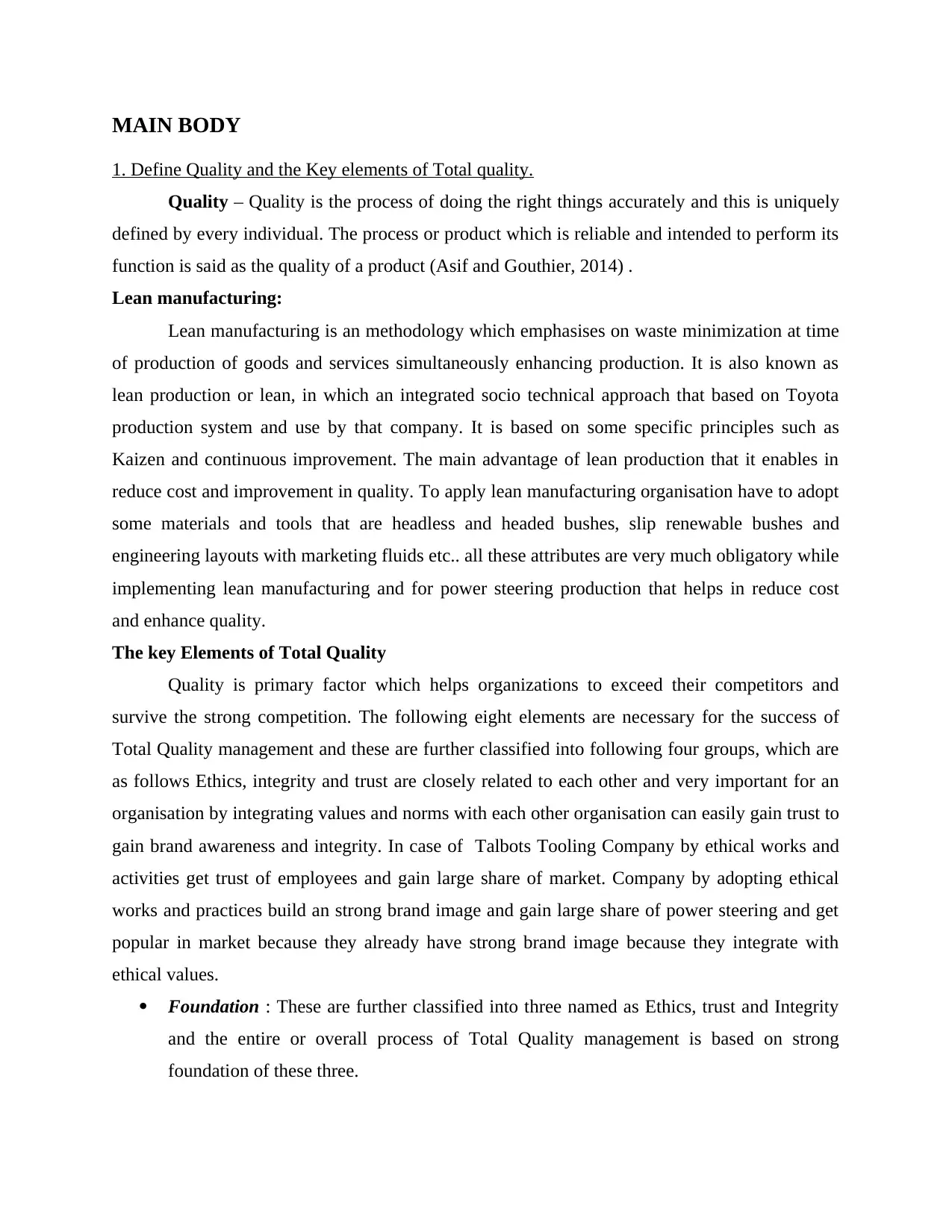
MAIN BODY
1. Define Quality and the Key elements of Total quality.
Quality – Quality is the process of doing the right things accurately and this is uniquely
defined by every individual. The process or product which is reliable and intended to perform its
function is said as the quality of a product (Asif and Gouthier, 2014) .
Lean manufacturing:
Lean manufacturing is an methodology which emphasises on waste minimization at time
of production of goods and services simultaneously enhancing production. It is also known as
lean production or lean, in which an integrated socio technical approach that based on Toyota
production system and use by that company. It is based on some specific principles such as
Kaizen and continuous improvement. The main advantage of lean production that it enables in
reduce cost and improvement in quality. To apply lean manufacturing organisation have to adopt
some materials and tools that are headless and headed bushes, slip renewable bushes and
engineering layouts with marketing fluids etc.. all these attributes are very much obligatory while
implementing lean manufacturing and for power steering production that helps in reduce cost
and enhance quality.
The key Elements of Total Quality
Quality is primary factor which helps organizations to exceed their competitors and
survive the strong competition. The following eight elements are necessary for the success of
Total Quality management and these are further classified into following four groups, which are
as follows Ethics, integrity and trust are closely related to each other and very important for an
organisation by integrating values and norms with each other organisation can easily gain trust to
gain brand awareness and integrity. In case of Talbots Tooling Company by ethical works and
activities get trust of employees and gain large share of market. Company by adopting ethical
works and practices build an strong brand image and gain large share of power steering and get
popular in market because they already have strong brand image because they integrate with
ethical values.
Foundation : These are further classified into three named as Ethics, trust and Integrity
and the entire or overall process of Total Quality management is based on strong
foundation of these three.
1. Define Quality and the Key elements of Total quality.
Quality – Quality is the process of doing the right things accurately and this is uniquely
defined by every individual. The process or product which is reliable and intended to perform its
function is said as the quality of a product (Asif and Gouthier, 2014) .
Lean manufacturing:
Lean manufacturing is an methodology which emphasises on waste minimization at time
of production of goods and services simultaneously enhancing production. It is also known as
lean production or lean, in which an integrated socio technical approach that based on Toyota
production system and use by that company. It is based on some specific principles such as
Kaizen and continuous improvement. The main advantage of lean production that it enables in
reduce cost and improvement in quality. To apply lean manufacturing organisation have to adopt
some materials and tools that are headless and headed bushes, slip renewable bushes and
engineering layouts with marketing fluids etc.. all these attributes are very much obligatory while
implementing lean manufacturing and for power steering production that helps in reduce cost
and enhance quality.
The key Elements of Total Quality
Quality is primary factor which helps organizations to exceed their competitors and
survive the strong competition. The following eight elements are necessary for the success of
Total Quality management and these are further classified into following four groups, which are
as follows Ethics, integrity and trust are closely related to each other and very important for an
organisation by integrating values and norms with each other organisation can easily gain trust to
gain brand awareness and integrity. In case of Talbots Tooling Company by ethical works and
activities get trust of employees and gain large share of market. Company by adopting ethical
works and practices build an strong brand image and gain large share of power steering and get
popular in market because they already have strong brand image because they integrate with
ethical values.
Foundation : These are further classified into three named as Ethics, trust and Integrity
and the entire or overall process of Total Quality management is based on strong
foundation of these three.
Paraphrase This Document
Need a fresh take? Get an instant paraphrase of this document with our AI Paraphraser
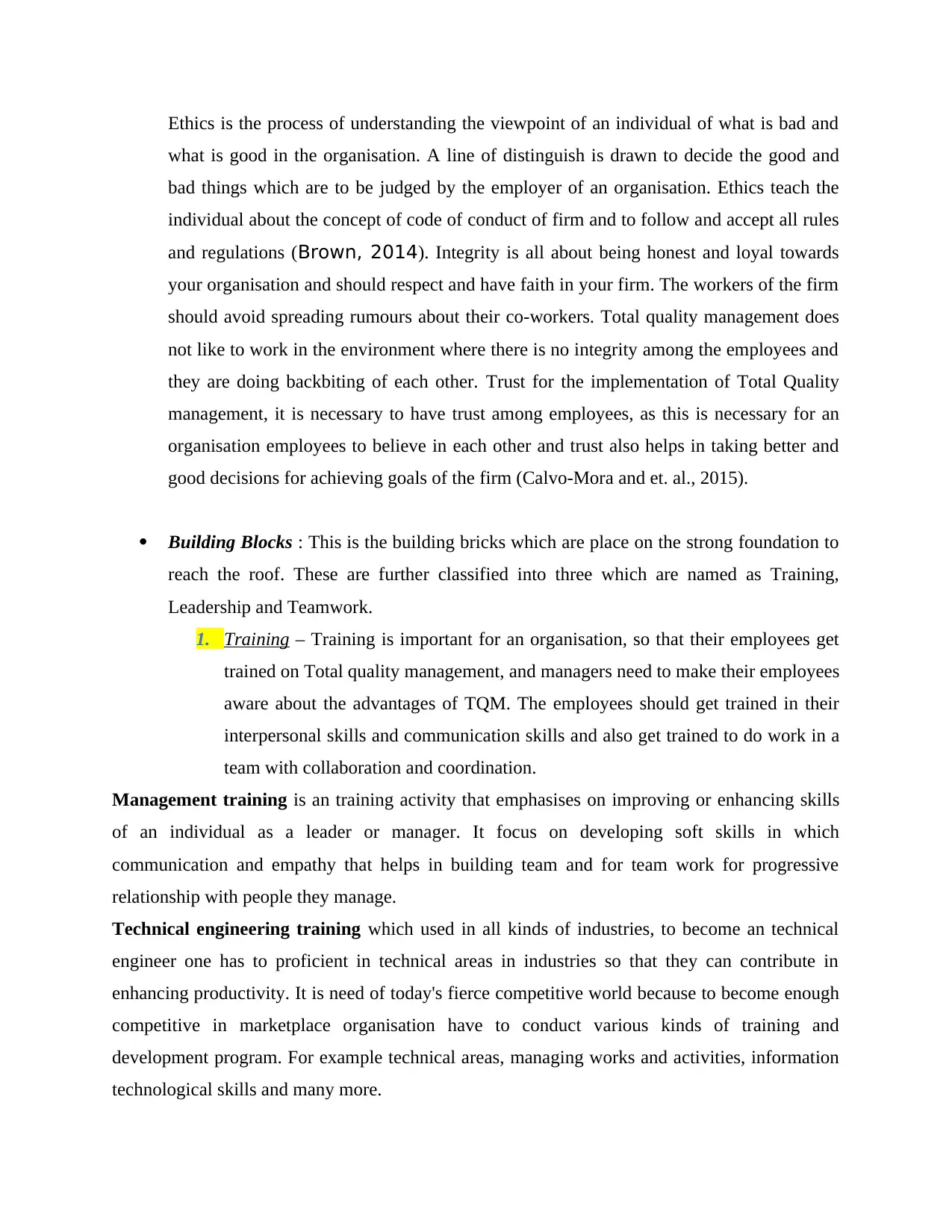
Ethics is the process of understanding the viewpoint of an individual of what is bad and
what is good in the organisation. A line of distinguish is drawn to decide the good and
bad things which are to be judged by the employer of an organisation. Ethics teach the
individual about the concept of code of conduct of firm and to follow and accept all rules
and regulations (Brown, 2014). Integrity is all about being honest and loyal towards
your organisation and should respect and have faith in your firm. The workers of the firm
should avoid spreading rumours about their co-workers. Total quality management does
not like to work in the environment where there is no integrity among the employees and
they are doing backbiting of each other. Trust for the implementation of Total Quality
management, it is necessary to have trust among employees, as this is necessary for an
organisation employees to believe in each other and trust also helps in taking better and
good decisions for achieving goals of the firm (Calvo-Mora and et. al., 2015).
Building Blocks : This is the building bricks which are place on the strong foundation to
reach the roof. These are further classified into three which are named as Training,
Leadership and Teamwork.
1. Training – Training is important for an organisation, so that their employees get
trained on Total quality management, and managers need to make their employees
aware about the advantages of TQM. The employees should get trained in their
interpersonal skills and communication skills and also get trained to do work in a
team with collaboration and coordination.
Management training is an training activity that emphasises on improving or enhancing skills
of an individual as a leader or manager. It focus on developing soft skills in which
communication and empathy that helps in building team and for team work for progressive
relationship with people they manage.
Technical engineering training which used in all kinds of industries, to become an technical
engineer one has to proficient in technical areas in industries so that they can contribute in
enhancing productivity. It is need of today's fierce competitive world because to become enough
competitive in marketplace organisation have to conduct various kinds of training and
development program. For example technical areas, managing works and activities, information
technological skills and many more.
what is good in the organisation. A line of distinguish is drawn to decide the good and
bad things which are to be judged by the employer of an organisation. Ethics teach the
individual about the concept of code of conduct of firm and to follow and accept all rules
and regulations (Brown, 2014). Integrity is all about being honest and loyal towards
your organisation and should respect and have faith in your firm. The workers of the firm
should avoid spreading rumours about their co-workers. Total quality management does
not like to work in the environment where there is no integrity among the employees and
they are doing backbiting of each other. Trust for the implementation of Total Quality
management, it is necessary to have trust among employees, as this is necessary for an
organisation employees to believe in each other and trust also helps in taking better and
good decisions for achieving goals of the firm (Calvo-Mora and et. al., 2015).
Building Blocks : This is the building bricks which are place on the strong foundation to
reach the roof. These are further classified into three which are named as Training,
Leadership and Teamwork.
1. Training – Training is important for an organisation, so that their employees get
trained on Total quality management, and managers need to make their employees
aware about the advantages of TQM. The employees should get trained in their
interpersonal skills and communication skills and also get trained to do work in a
team with collaboration and coordination.
Management training is an training activity that emphasises on improving or enhancing skills
of an individual as a leader or manager. It focus on developing soft skills in which
communication and empathy that helps in building team and for team work for progressive
relationship with people they manage.
Technical engineering training which used in all kinds of industries, to become an technical
engineer one has to proficient in technical areas in industries so that they can contribute in
enhancing productivity. It is need of today's fierce competitive world because to become enough
competitive in marketplace organisation have to conduct various kinds of training and
development program. For example technical areas, managing works and activities, information
technological skills and many more.
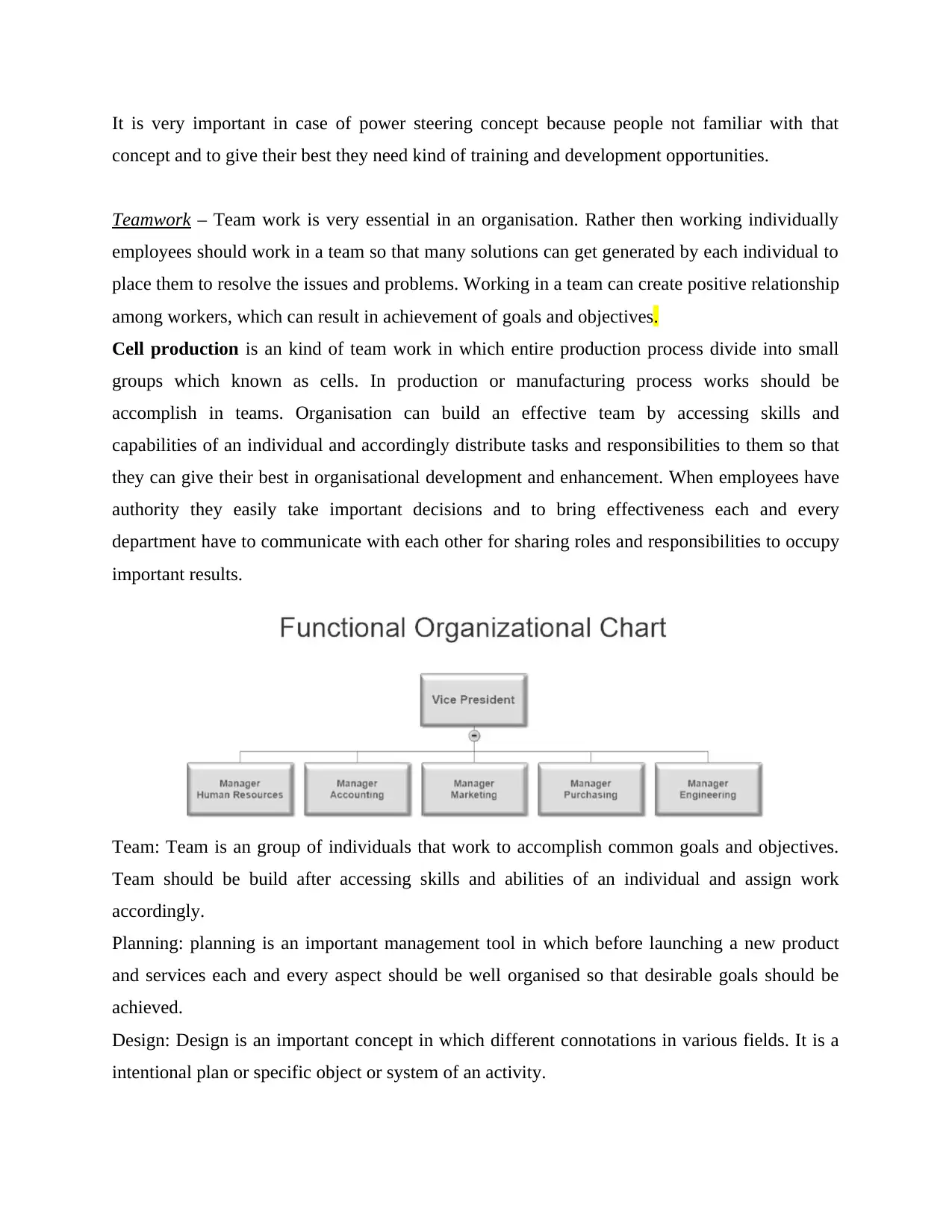
It is very important in case of power steering concept because people not familiar with that
concept and to give their best they need kind of training and development opportunities.
Teamwork – Team work is very essential in an organisation. Rather then working individually
employees should work in a team so that many solutions can get generated by each individual to
place them to resolve the issues and problems. Working in a team can create positive relationship
among workers, which can result in achievement of goals and objectives.
Cell production is an kind of team work in which entire production process divide into small
groups which known as cells. In production or manufacturing process works should be
accomplish in teams. Organisation can build an effective team by accessing skills and
capabilities of an individual and accordingly distribute tasks and responsibilities to them so that
they can give their best in organisational development and enhancement. When employees have
authority they easily take important decisions and to bring effectiveness each and every
department have to communicate with each other for sharing roles and responsibilities to occupy
important results.
Team: Team is an group of individuals that work to accomplish common goals and objectives.
Team should be build after accessing skills and abilities of an individual and assign work
accordingly.
Planning: planning is an important management tool in which before launching a new product
and services each and every aspect should be well organised so that desirable goals should be
achieved.
Design: Design is an important concept in which different connotations in various fields. It is a
intentional plan or specific object or system of an activity.
concept and to give their best they need kind of training and development opportunities.
Teamwork – Team work is very essential in an organisation. Rather then working individually
employees should work in a team so that many solutions can get generated by each individual to
place them to resolve the issues and problems. Working in a team can create positive relationship
among workers, which can result in achievement of goals and objectives.
Cell production is an kind of team work in which entire production process divide into small
groups which known as cells. In production or manufacturing process works should be
accomplish in teams. Organisation can build an effective team by accessing skills and
capabilities of an individual and accordingly distribute tasks and responsibilities to them so that
they can give their best in organisational development and enhancement. When employees have
authority they easily take important decisions and to bring effectiveness each and every
department have to communicate with each other for sharing roles and responsibilities to occupy
important results.
Team: Team is an group of individuals that work to accomplish common goals and objectives.
Team should be build after accessing skills and abilities of an individual and assign work
accordingly.
Planning: planning is an important management tool in which before launching a new product
and services each and every aspect should be well organised so that desirable goals should be
achieved.
Design: Design is an important concept in which different connotations in various fields. It is a
intentional plan or specific object or system of an activity.
You're viewing a preview
Unlock full access by subscribing today!
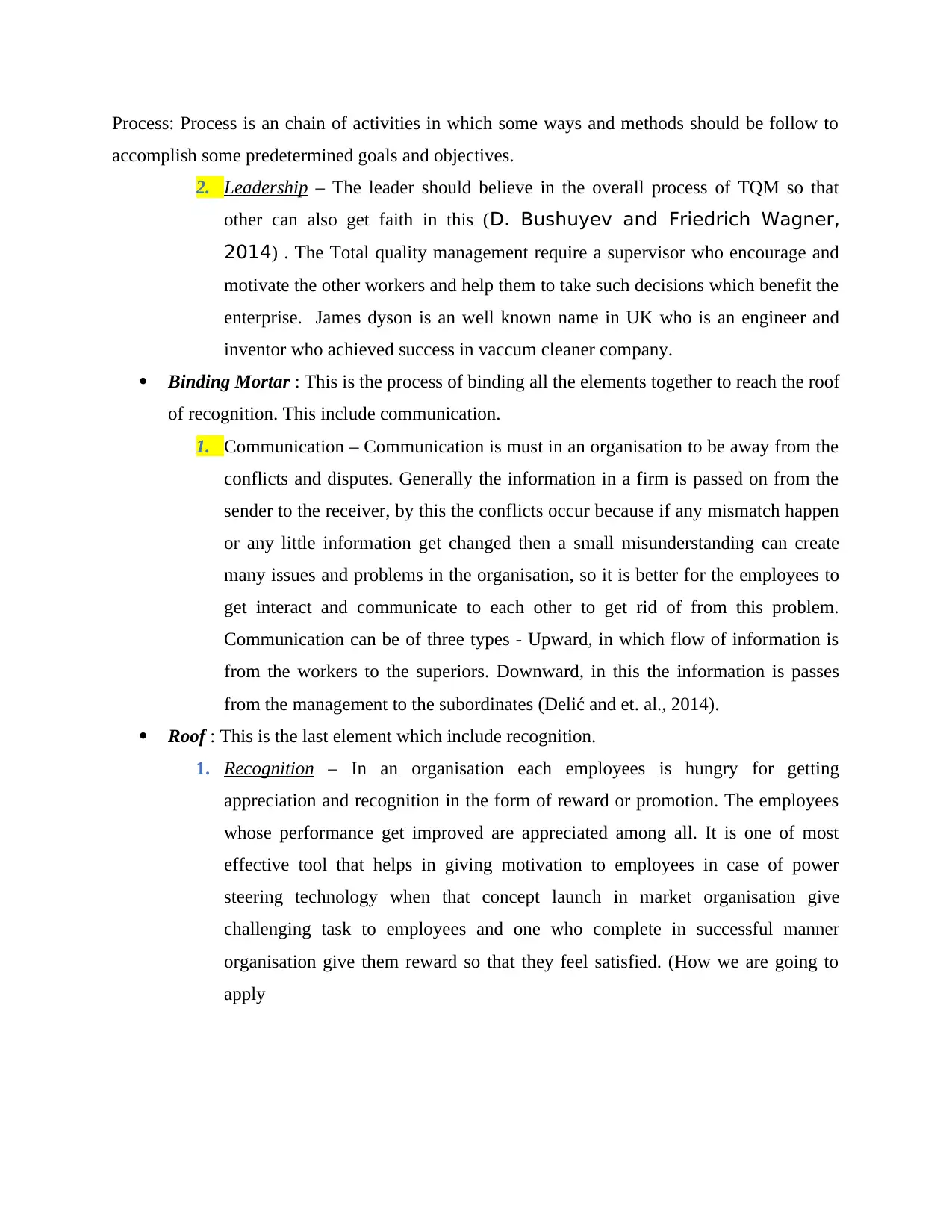
Process: Process is an chain of activities in which some ways and methods should be follow to
accomplish some predetermined goals and objectives.
2. Leadership – The leader should believe in the overall process of TQM so that
other can also get faith in this (D. Bushuyev and Friedrich Wagner,
2014) . The Total quality management require a supervisor who encourage and
motivate the other workers and help them to take such decisions which benefit the
enterprise. James dyson is an well known name in UK who is an engineer and
inventor who achieved success in vaccum cleaner company.
Binding Mortar : This is the process of binding all the elements together to reach the roof
of recognition. This include communication.
1. Communication – Communication is must in an organisation to be away from the
conflicts and disputes. Generally the information in a firm is passed on from the
sender to the receiver, by this the conflicts occur because if any mismatch happen
or any little information get changed then a small misunderstanding can create
many issues and problems in the organisation, so it is better for the employees to
get interact and communicate to each other to get rid of from this problem.
Communication can be of three types - Upward, in which flow of information is
from the workers to the superiors. Downward, in this the information is passes
from the management to the subordinates (Delić and et. al., 2014).
Roof : This is the last element which include recognition.
1. Recognition – In an organisation each employees is hungry for getting
appreciation and recognition in the form of reward or promotion. The employees
whose performance get improved are appreciated among all. It is one of most
effective tool that helps in giving motivation to employees in case of power
steering technology when that concept launch in market organisation give
challenging task to employees and one who complete in successful manner
organisation give them reward so that they feel satisfied. (How we are going to
apply
accomplish some predetermined goals and objectives.
2. Leadership – The leader should believe in the overall process of TQM so that
other can also get faith in this (D. Bushuyev and Friedrich Wagner,
2014) . The Total quality management require a supervisor who encourage and
motivate the other workers and help them to take such decisions which benefit the
enterprise. James dyson is an well known name in UK who is an engineer and
inventor who achieved success in vaccum cleaner company.
Binding Mortar : This is the process of binding all the elements together to reach the roof
of recognition. This include communication.
1. Communication – Communication is must in an organisation to be away from the
conflicts and disputes. Generally the information in a firm is passed on from the
sender to the receiver, by this the conflicts occur because if any mismatch happen
or any little information get changed then a small misunderstanding can create
many issues and problems in the organisation, so it is better for the employees to
get interact and communicate to each other to get rid of from this problem.
Communication can be of three types - Upward, in which flow of information is
from the workers to the superiors. Downward, in this the information is passes
from the management to the subordinates (Delić and et. al., 2014).
Roof : This is the last element which include recognition.
1. Recognition – In an organisation each employees is hungry for getting
appreciation and recognition in the form of reward or promotion. The employees
whose performance get improved are appreciated among all. It is one of most
effective tool that helps in giving motivation to employees in case of power
steering technology when that concept launch in market organisation give
challenging task to employees and one who complete in successful manner
organisation give them reward so that they feel satisfied. (How we are going to
apply
Paraphrase This Document
Need a fresh take? Get an instant paraphrase of this document with our AI Paraphraser
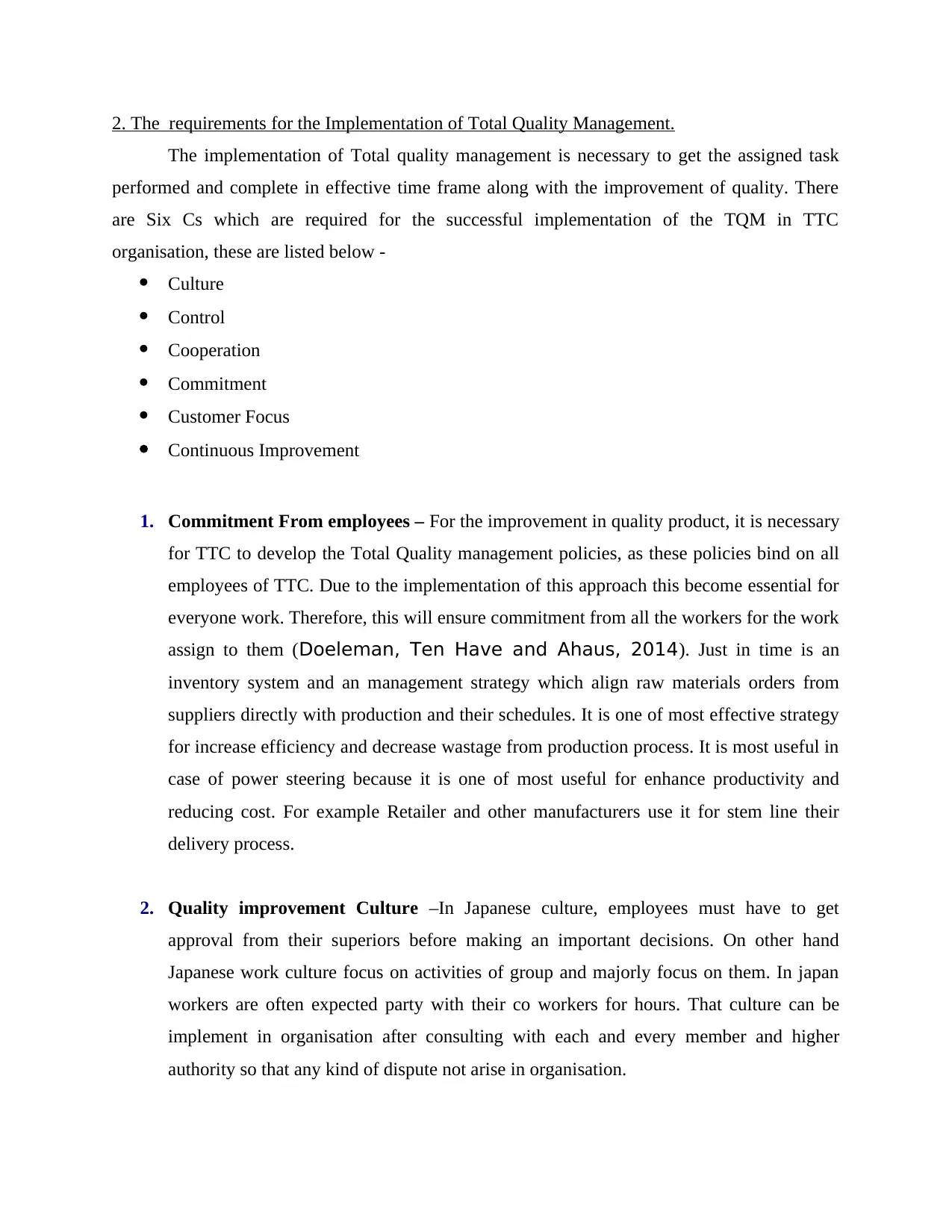
2. The requirements for the Implementation of Total Quality Management.
The implementation of Total quality management is necessary to get the assigned task
performed and complete in effective time frame along with the improvement of quality. There
are Six Cs which are required for the successful implementation of the TQM in TTC
organisation, these are listed below -
Culture
Control
Cooperation
Commitment
Customer Focus
Continuous Improvement
1. Commitment From employees – For the improvement in quality product, it is necessary
for TTC to develop the Total Quality management policies, as these policies bind on all
employees of TTC. Due to the implementation of this approach this become essential for
everyone work. Therefore, this will ensure commitment from all the workers for the work
assign to them (Doeleman, Ten Have and Ahaus, 2014). Just in time is an
inventory system and an management strategy which align raw materials orders from
suppliers directly with production and their schedules. It is one of most effective strategy
for increase efficiency and decrease wastage from production process. It is most useful in
case of power steering because it is one of most useful for enhance productivity and
reducing cost. For example Retailer and other manufacturers use it for stem line their
delivery process.
2. Quality improvement Culture –In Japanese culture, employees must have to get
approval from their superiors before making an important decisions. On other hand
Japanese work culture focus on activities of group and majorly focus on them. In japan
workers are often expected party with their co workers for hours. That culture can be
implement in organisation after consulting with each and every member and higher
authority so that any kind of dispute not arise in organisation.
The implementation of Total quality management is necessary to get the assigned task
performed and complete in effective time frame along with the improvement of quality. There
are Six Cs which are required for the successful implementation of the TQM in TTC
organisation, these are listed below -
Culture
Control
Cooperation
Commitment
Customer Focus
Continuous Improvement
1. Commitment From employees – For the improvement in quality product, it is necessary
for TTC to develop the Total Quality management policies, as these policies bind on all
employees of TTC. Due to the implementation of this approach this become essential for
everyone work. Therefore, this will ensure commitment from all the workers for the work
assign to them (Doeleman, Ten Have and Ahaus, 2014). Just in time is an
inventory system and an management strategy which align raw materials orders from
suppliers directly with production and their schedules. It is one of most effective strategy
for increase efficiency and decrease wastage from production process. It is most useful in
case of power steering because it is one of most useful for enhance productivity and
reducing cost. For example Retailer and other manufacturers use it for stem line their
delivery process.
2. Quality improvement Culture –In Japanese culture, employees must have to get
approval from their superiors before making an important decisions. On other hand
Japanese work culture focus on activities of group and majorly focus on them. In japan
workers are often expected party with their co workers for hours. That culture can be
implement in organisation after consulting with each and every member and higher
authority so that any kind of dispute not arise in organisation.
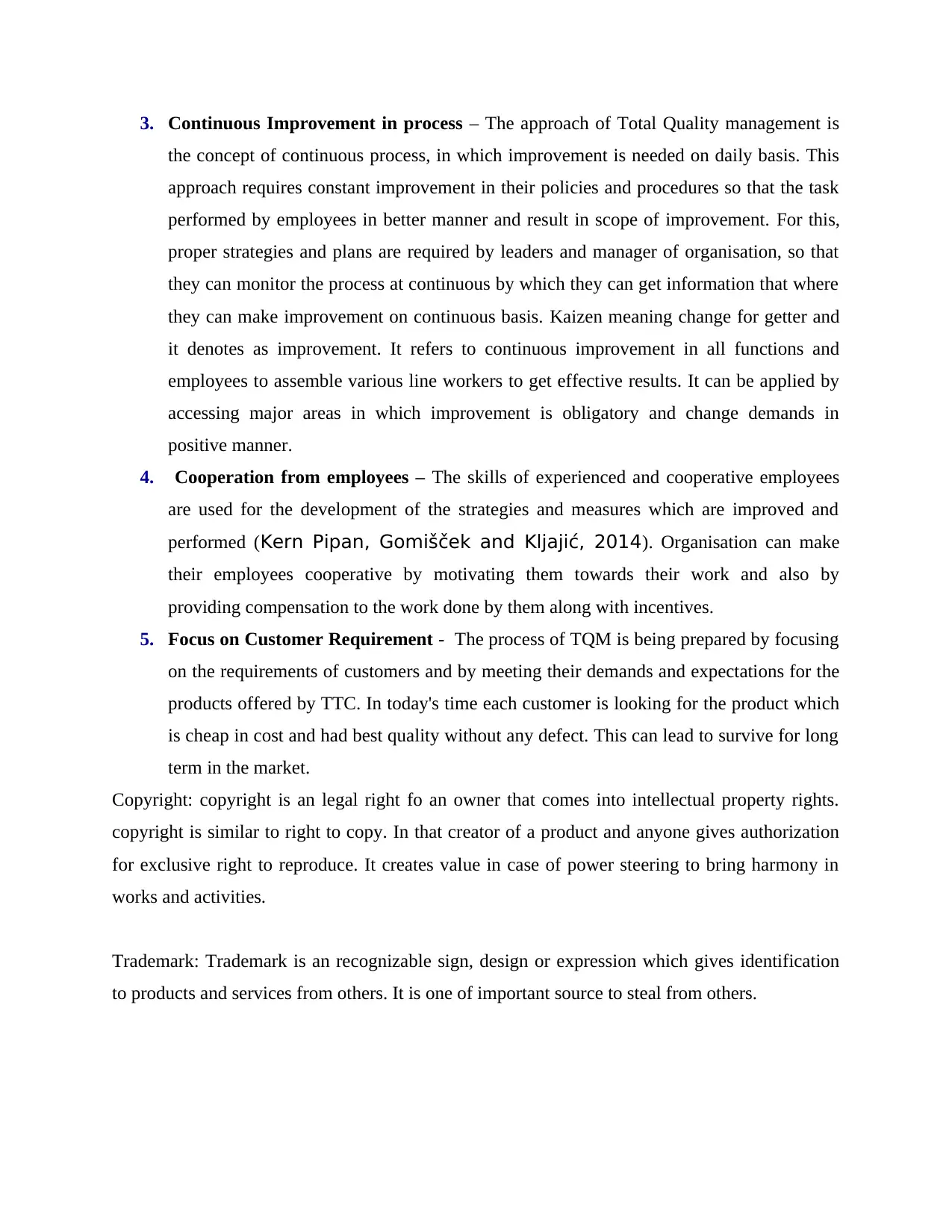
3. Continuous Improvement in process – The approach of Total Quality management is
the concept of continuous process, in which improvement is needed on daily basis. This
approach requires constant improvement in their policies and procedures so that the task
performed by employees in better manner and result in scope of improvement. For this,
proper strategies and plans are required by leaders and manager of organisation, so that
they can monitor the process at continuous by which they can get information that where
they can make improvement on continuous basis. Kaizen meaning change for getter and
it denotes as improvement. It refers to continuous improvement in all functions and
employees to assemble various line workers to get effective results. It can be applied by
accessing major areas in which improvement is obligatory and change demands in
positive manner.
4. Cooperation from employees – The skills of experienced and cooperative employees
are used for the development of the strategies and measures which are improved and
performed (Kern Pipan, Gomišček and Kljajić, 2014). Organisation can make
their employees cooperative by motivating them towards their work and also by
providing compensation to the work done by them along with incentives.
5. Focus on Customer Requirement - The process of TQM is being prepared by focusing
on the requirements of customers and by meeting their demands and expectations for the
products offered by TTC. In today's time each customer is looking for the product which
is cheap in cost and had best quality without any defect. This can lead to survive for long
term in the market.
Copyright: copyright is an legal right fo an owner that comes into intellectual property rights.
copyright is similar to right to copy. In that creator of a product and anyone gives authorization
for exclusive right to reproduce. It creates value in case of power steering to bring harmony in
works and activities.
Trademark: Trademark is an recognizable sign, design or expression which gives identification
to products and services from others. It is one of important source to steal from others.
the concept of continuous process, in which improvement is needed on daily basis. This
approach requires constant improvement in their policies and procedures so that the task
performed by employees in better manner and result in scope of improvement. For this,
proper strategies and plans are required by leaders and manager of organisation, so that
they can monitor the process at continuous by which they can get information that where
they can make improvement on continuous basis. Kaizen meaning change for getter and
it denotes as improvement. It refers to continuous improvement in all functions and
employees to assemble various line workers to get effective results. It can be applied by
accessing major areas in which improvement is obligatory and change demands in
positive manner.
4. Cooperation from employees – The skills of experienced and cooperative employees
are used for the development of the strategies and measures which are improved and
performed (Kern Pipan, Gomišček and Kljajić, 2014). Organisation can make
their employees cooperative by motivating them towards their work and also by
providing compensation to the work done by them along with incentives.
5. Focus on Customer Requirement - The process of TQM is being prepared by focusing
on the requirements of customers and by meeting their demands and expectations for the
products offered by TTC. In today's time each customer is looking for the product which
is cheap in cost and had best quality without any defect. This can lead to survive for long
term in the market.
Copyright: copyright is an legal right fo an owner that comes into intellectual property rights.
copyright is similar to right to copy. In that creator of a product and anyone gives authorization
for exclusive right to reproduce. It creates value in case of power steering to bring harmony in
works and activities.
Trademark: Trademark is an recognizable sign, design or expression which gives identification
to products and services from others. It is one of important source to steal from others.
You're viewing a preview
Unlock full access by subscribing today!
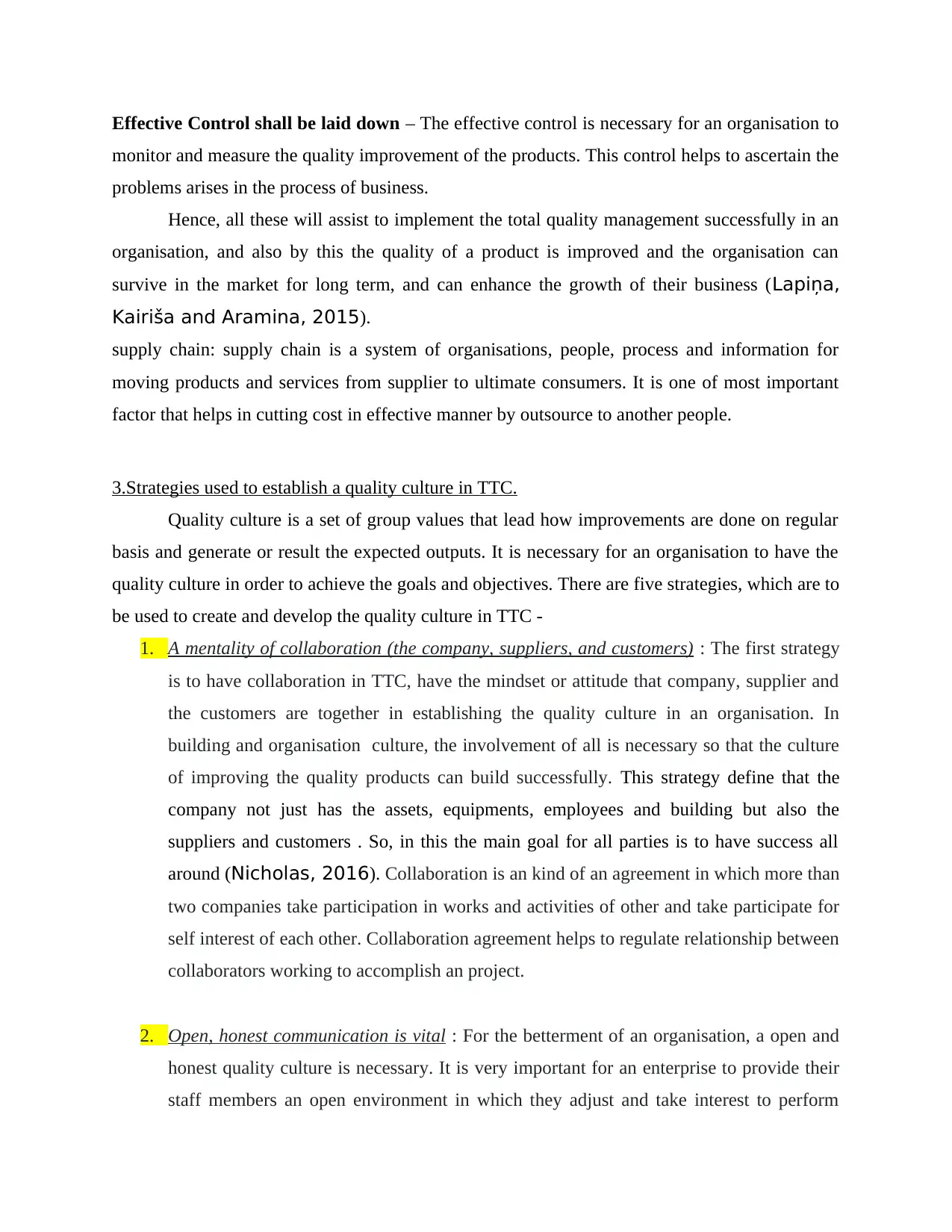
Effective Control shall be laid down – The effective control is necessary for an organisation to
monitor and measure the quality improvement of the products. This control helps to ascertain the
problems arises in the process of business.
Hence, all these will assist to implement the total quality management successfully in an
organisation, and also by this the quality of a product is improved and the organisation can
survive in the market for long term, and can enhance the growth of their business (Lapiņa,
Kairiša and Aramina, 2015).
supply chain: supply chain is a system of organisations, people, process and information for
moving products and services from supplier to ultimate consumers. It is one of most important
factor that helps in cutting cost in effective manner by outsource to another people.
3.Strategies used to establish a quality culture in TTC.
Quality culture is a set of group values that lead how improvements are done on regular
basis and generate or result the expected outputs. It is necessary for an organisation to have the
quality culture in order to achieve the goals and objectives. There are five strategies, which are to
be used to create and develop the quality culture in TTC -
1. A mentality of collaboration (the company, suppliers, and customers) : The first strategy
is to have collaboration in TTC, have the mindset or attitude that company, supplier and
the customers are together in establishing the quality culture in an organisation. In
building and organisation culture, the involvement of all is necessary so that the culture
of improving the quality products can build successfully. This strategy define that the
company not just has the assets, equipments, employees and building but also the
suppliers and customers . So, in this the main goal for all parties is to have success all
around (Nicholas, 2016). Collaboration is an kind of an agreement in which more than
two companies take participation in works and activities of other and take participate for
self interest of each other. Collaboration agreement helps to regulate relationship between
collaborators working to accomplish an project.
2. Open, honest communication is vital : For the betterment of an organisation, a open and
honest quality culture is necessary. It is very important for an enterprise to provide their
staff members an open environment in which they adjust and take interest to perform
monitor and measure the quality improvement of the products. This control helps to ascertain the
problems arises in the process of business.
Hence, all these will assist to implement the total quality management successfully in an
organisation, and also by this the quality of a product is improved and the organisation can
survive in the market for long term, and can enhance the growth of their business (Lapiņa,
Kairiša and Aramina, 2015).
supply chain: supply chain is a system of organisations, people, process and information for
moving products and services from supplier to ultimate consumers. It is one of most important
factor that helps in cutting cost in effective manner by outsource to another people.
3.Strategies used to establish a quality culture in TTC.
Quality culture is a set of group values that lead how improvements are done on regular
basis and generate or result the expected outputs. It is necessary for an organisation to have the
quality culture in order to achieve the goals and objectives. There are five strategies, which are to
be used to create and develop the quality culture in TTC -
1. A mentality of collaboration (the company, suppliers, and customers) : The first strategy
is to have collaboration in TTC, have the mindset or attitude that company, supplier and
the customers are together in establishing the quality culture in an organisation. In
building and organisation culture, the involvement of all is necessary so that the culture
of improving the quality products can build successfully. This strategy define that the
company not just has the assets, equipments, employees and building but also the
suppliers and customers . So, in this the main goal for all parties is to have success all
around (Nicholas, 2016). Collaboration is an kind of an agreement in which more than
two companies take participation in works and activities of other and take participate for
self interest of each other. Collaboration agreement helps to regulate relationship between
collaborators working to accomplish an project.
2. Open, honest communication is vital : For the betterment of an organisation, a open and
honest quality culture is necessary. It is very important for an enterprise to provide their
staff members an open environment in which they adjust and take interest to perform
Paraphrase This Document
Need a fresh take? Get an instant paraphrase of this document with our AI Paraphraser
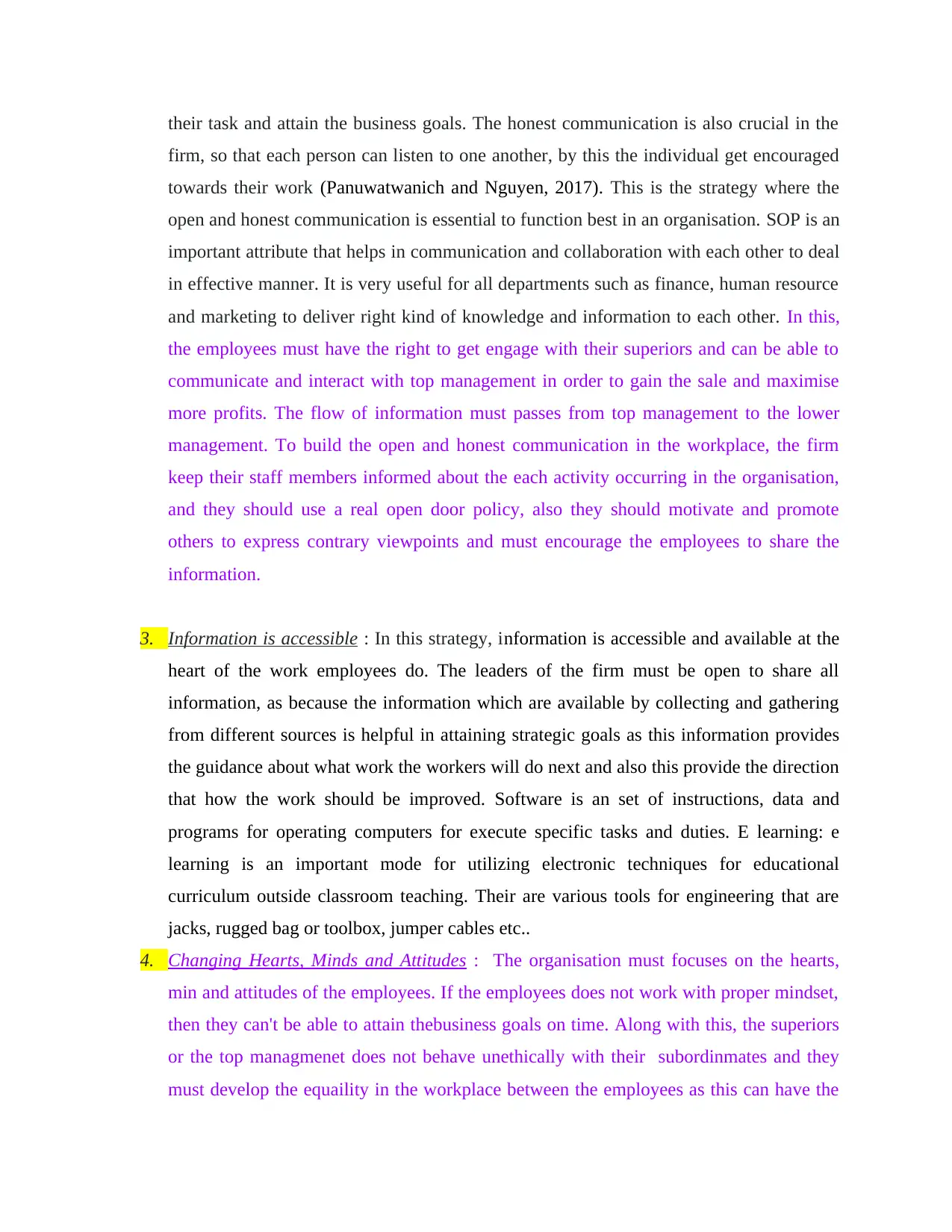
their task and attain the business goals. The honest communication is also crucial in the
firm, so that each person can listen to one another, by this the individual get encouraged
towards their work (Panuwatwanich and Nguyen, 2017). This is the strategy where the
open and honest communication is essential to function best in an organisation. SOP is an
important attribute that helps in communication and collaboration with each other to deal
in effective manner. It is very useful for all departments such as finance, human resource
and marketing to deliver right kind of knowledge and information to each other. In this,
the employees must have the right to get engage with their superiors and can be able to
communicate and interact with top management in order to gain the sale and maximise
more profits. The flow of information must passes from top management to the lower
management. To build the open and honest communication in the workplace, the firm
keep their staff members informed about the each activity occurring in the organisation,
and they should use a real open door policy, also they should motivate and promote
others to express contrary viewpoints and must encourage the employees to share the
information.
3. Information is accessible : In this strategy, information is accessible and available at the
heart of the work employees do. The leaders of the firm must be open to share all
information, as because the information which are available by collecting and gathering
from different sources is helpful in attaining strategic goals as this information provides
the guidance about what work the workers will do next and also this provide the direction
that how the work should be improved. Software is an set of instructions, data and
programs for operating computers for execute specific tasks and duties. E learning: e
learning is an important mode for utilizing electronic techniques for educational
curriculum outside classroom teaching. Their are various tools for engineering that are
jacks, rugged bag or toolbox, jumper cables etc..
4. Changing Hearts, Minds and Attitudes : The organisation must focuses on the hearts,
min and attitudes of the employees. If the employees does not work with proper mindset,
then they can't be able to attain thebusiness goals on time. Along with this, the superiors
or the top managmenet does not behave unethically with their subordinmates and they
must develop the equaility in the workplace between the employees as this can have the
firm, so that each person can listen to one another, by this the individual get encouraged
towards their work (Panuwatwanich and Nguyen, 2017). This is the strategy where the
open and honest communication is essential to function best in an organisation. SOP is an
important attribute that helps in communication and collaboration with each other to deal
in effective manner. It is very useful for all departments such as finance, human resource
and marketing to deliver right kind of knowledge and information to each other. In this,
the employees must have the right to get engage with their superiors and can be able to
communicate and interact with top management in order to gain the sale and maximise
more profits. The flow of information must passes from top management to the lower
management. To build the open and honest communication in the workplace, the firm
keep their staff members informed about the each activity occurring in the organisation,
and they should use a real open door policy, also they should motivate and promote
others to express contrary viewpoints and must encourage the employees to share the
information.
3. Information is accessible : In this strategy, information is accessible and available at the
heart of the work employees do. The leaders of the firm must be open to share all
information, as because the information which are available by collecting and gathering
from different sources is helpful in attaining strategic goals as this information provides
the guidance about what work the workers will do next and also this provide the direction
that how the work should be improved. Software is an set of instructions, data and
programs for operating computers for execute specific tasks and duties. E learning: e
learning is an important mode for utilizing electronic techniques for educational
curriculum outside classroom teaching. Their are various tools for engineering that are
jacks, rugged bag or toolbox, jumper cables etc..
4. Changing Hearts, Minds and Attitudes : The organisation must focuses on the hearts,
min and attitudes of the employees. If the employees does not work with proper mindset,
then they can't be able to attain thebusiness goals on time. Along with this, the superiors
or the top managmenet does not behave unethically with their subordinmates and they
must develop the equaility in the workplace between the employees as this can have the
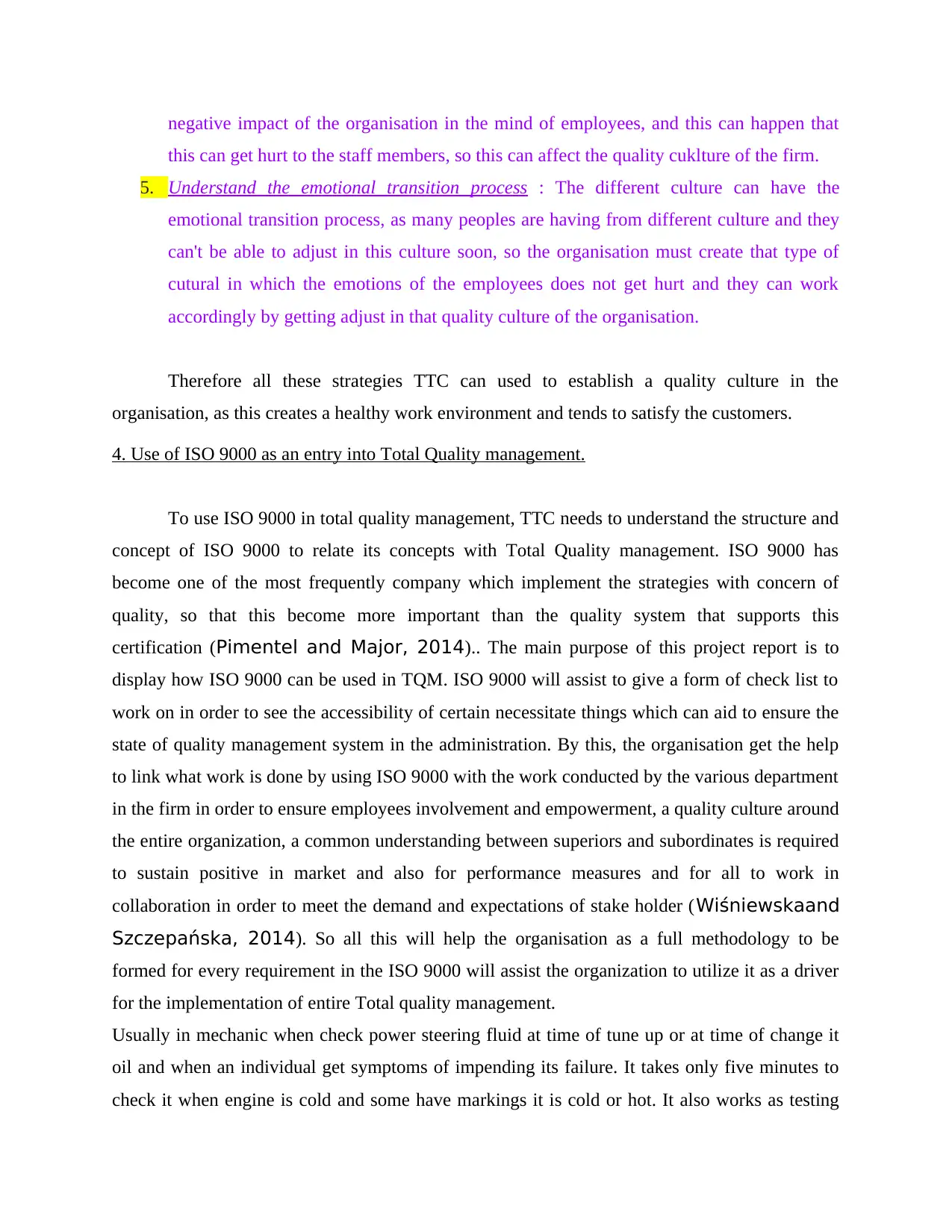
negative impact of the organisation in the mind of employees, and this can happen that
this can get hurt to the staff members, so this can affect the quality cuklture of the firm.
5. Understand the emotional transition process : The different culture can have the
emotional transition process, as many peoples are having from different culture and they
can't be able to adjust in this culture soon, so the organisation must create that type of
cutural in which the emotions of the employees does not get hurt and they can work
accordingly by getting adjust in that quality culture of the organisation.
Therefore all these strategies TTC can used to establish a quality culture in the
organisation, as this creates a healthy work environment and tends to satisfy the customers.
4. Use of ISO 9000 as an entry into Total Quality management.
To use ISO 9000 in total quality management, TTC needs to understand the structure and
concept of ISO 9000 to relate its concepts with Total Quality management. ISO 9000 has
become one of the most frequently company which implement the strategies with concern of
quality, so that this become more important than the quality system that supports this
certification (Pimentel and Major, 2014).. The main purpose of this project report is to
display how ISO 9000 can be used in TQM. ISO 9000 will assist to give a form of check list to
work on in order to see the accessibility of certain necessitate things which can aid to ensure the
state of quality management system in the administration. By this, the organisation get the help
to link what work is done by using ISO 9000 with the work conducted by the various department
in the firm in order to ensure employees involvement and empowerment, a quality culture around
the entire organization, a common understanding between superiors and subordinates is required
to sustain positive in market and also for performance measures and for all to work in
collaboration in order to meet the demand and expectations of stake holder (Wiśniewskaand
Szczepańska, 2014). So all this will help the organisation as a full methodology to be
formed for every requirement in the ISO 9000 will assist the organization to utilize it as a driver
for the implementation of entire Total quality management.
Usually in mechanic when check power steering fluid at time of tune up or at time of change it
oil and when an individual get symptoms of impending its failure. It takes only five minutes to
check it when engine is cold and some have markings it is cold or hot. It also works as testing
this can get hurt to the staff members, so this can affect the quality cuklture of the firm.
5. Understand the emotional transition process : The different culture can have the
emotional transition process, as many peoples are having from different culture and they
can't be able to adjust in this culture soon, so the organisation must create that type of
cutural in which the emotions of the employees does not get hurt and they can work
accordingly by getting adjust in that quality culture of the organisation.
Therefore all these strategies TTC can used to establish a quality culture in the
organisation, as this creates a healthy work environment and tends to satisfy the customers.
4. Use of ISO 9000 as an entry into Total Quality management.
To use ISO 9000 in total quality management, TTC needs to understand the structure and
concept of ISO 9000 to relate its concepts with Total Quality management. ISO 9000 has
become one of the most frequently company which implement the strategies with concern of
quality, so that this become more important than the quality system that supports this
certification (Pimentel and Major, 2014).. The main purpose of this project report is to
display how ISO 9000 can be used in TQM. ISO 9000 will assist to give a form of check list to
work on in order to see the accessibility of certain necessitate things which can aid to ensure the
state of quality management system in the administration. By this, the organisation get the help
to link what work is done by using ISO 9000 with the work conducted by the various department
in the firm in order to ensure employees involvement and empowerment, a quality culture around
the entire organization, a common understanding between superiors and subordinates is required
to sustain positive in market and also for performance measures and for all to work in
collaboration in order to meet the demand and expectations of stake holder (Wiśniewskaand
Szczepańska, 2014). So all this will help the organisation as a full methodology to be
formed for every requirement in the ISO 9000 will assist the organization to utilize it as a driver
for the implementation of entire Total quality management.
Usually in mechanic when check power steering fluid at time of tune up or at time of change it
oil and when an individual get symptoms of impending its failure. It takes only five minutes to
check it when engine is cold and some have markings it is cold or hot. It also works as testing
You're viewing a preview
Unlock full access by subscribing today!
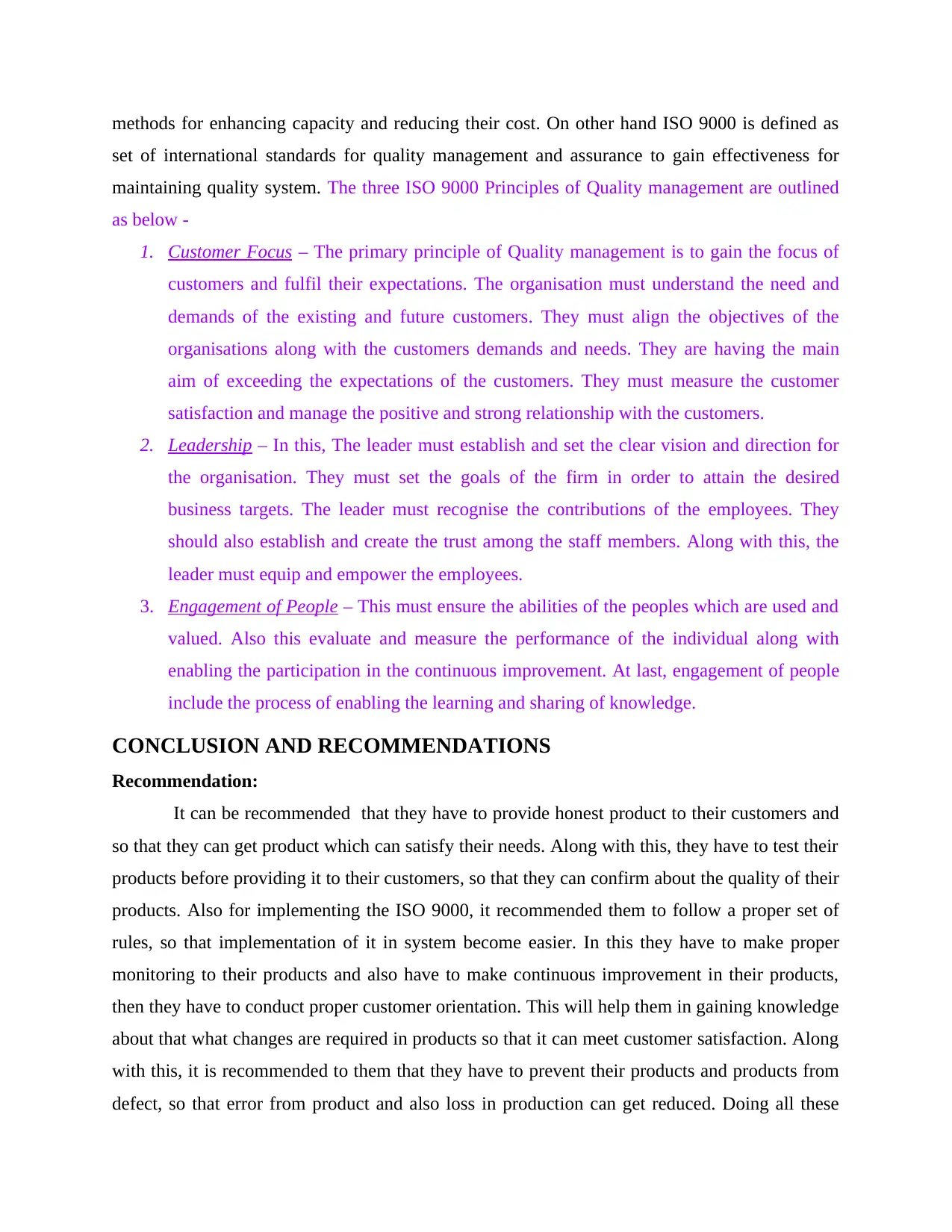
methods for enhancing capacity and reducing their cost. On other hand ISO 9000 is defined as
set of international standards for quality management and assurance to gain effectiveness for
maintaining quality system. The three ISO 9000 Principles of Quality management are outlined
as below -
1. Customer Focus – The primary principle of Quality management is to gain the focus of
customers and fulfil their expectations. The organisation must understand the need and
demands of the existing and future customers. They must align the objectives of the
organisations along with the customers demands and needs. They are having the main
aim of exceeding the expectations of the customers. They must measure the customer
satisfaction and manage the positive and strong relationship with the customers.
2. Leadership – In this, The leader must establish and set the clear vision and direction for
the organisation. They must set the goals of the firm in order to attain the desired
business targets. The leader must recognise the contributions of the employees. They
should also establish and create the trust among the staff members. Along with this, the
leader must equip and empower the employees.
3. Engagement of People – This must ensure the abilities of the peoples which are used and
valued. Also this evaluate and measure the performance of the individual along with
enabling the participation in the continuous improvement. At last, engagement of people
include the process of enabling the learning and sharing of knowledge.
CONCLUSION AND RECOMMENDATIONS
Recommendation:
It can be recommended that they have to provide honest product to their customers and
so that they can get product which can satisfy their needs. Along with this, they have to test their
products before providing it to their customers, so that they can confirm about the quality of their
products. Also for implementing the ISO 9000, it recommended them to follow a proper set of
rules, so that implementation of it in system become easier. In this they have to make proper
monitoring to their products and also have to make continuous improvement in their products,
then they have to conduct proper customer orientation. This will help them in gaining knowledge
about that what changes are required in products so that it can meet customer satisfaction. Along
with this, it is recommended to them that they have to prevent their products and products from
defect, so that error from product and also loss in production can get reduced. Doing all these
set of international standards for quality management and assurance to gain effectiveness for
maintaining quality system. The three ISO 9000 Principles of Quality management are outlined
as below -
1. Customer Focus – The primary principle of Quality management is to gain the focus of
customers and fulfil their expectations. The organisation must understand the need and
demands of the existing and future customers. They must align the objectives of the
organisations along with the customers demands and needs. They are having the main
aim of exceeding the expectations of the customers. They must measure the customer
satisfaction and manage the positive and strong relationship with the customers.
2. Leadership – In this, The leader must establish and set the clear vision and direction for
the organisation. They must set the goals of the firm in order to attain the desired
business targets. The leader must recognise the contributions of the employees. They
should also establish and create the trust among the staff members. Along with this, the
leader must equip and empower the employees.
3. Engagement of People – This must ensure the abilities of the peoples which are used and
valued. Also this evaluate and measure the performance of the individual along with
enabling the participation in the continuous improvement. At last, engagement of people
include the process of enabling the learning and sharing of knowledge.
CONCLUSION AND RECOMMENDATIONS
Recommendation:
It can be recommended that they have to provide honest product to their customers and
so that they can get product which can satisfy their needs. Along with this, they have to test their
products before providing it to their customers, so that they can confirm about the quality of their
products. Also for implementing the ISO 9000, it recommended them to follow a proper set of
rules, so that implementation of it in system become easier. In this they have to make proper
monitoring to their products and also have to make continuous improvement in their products,
then they have to conduct proper customer orientation. This will help them in gaining knowledge
about that what changes are required in products so that it can meet customer satisfaction. Along
with this, it is recommended to them that they have to prevent their products and products from
defect, so that error from product and also loss in production can get reduced. Doing all these
Paraphrase This Document
Need a fresh take? Get an instant paraphrase of this document with our AI Paraphraser
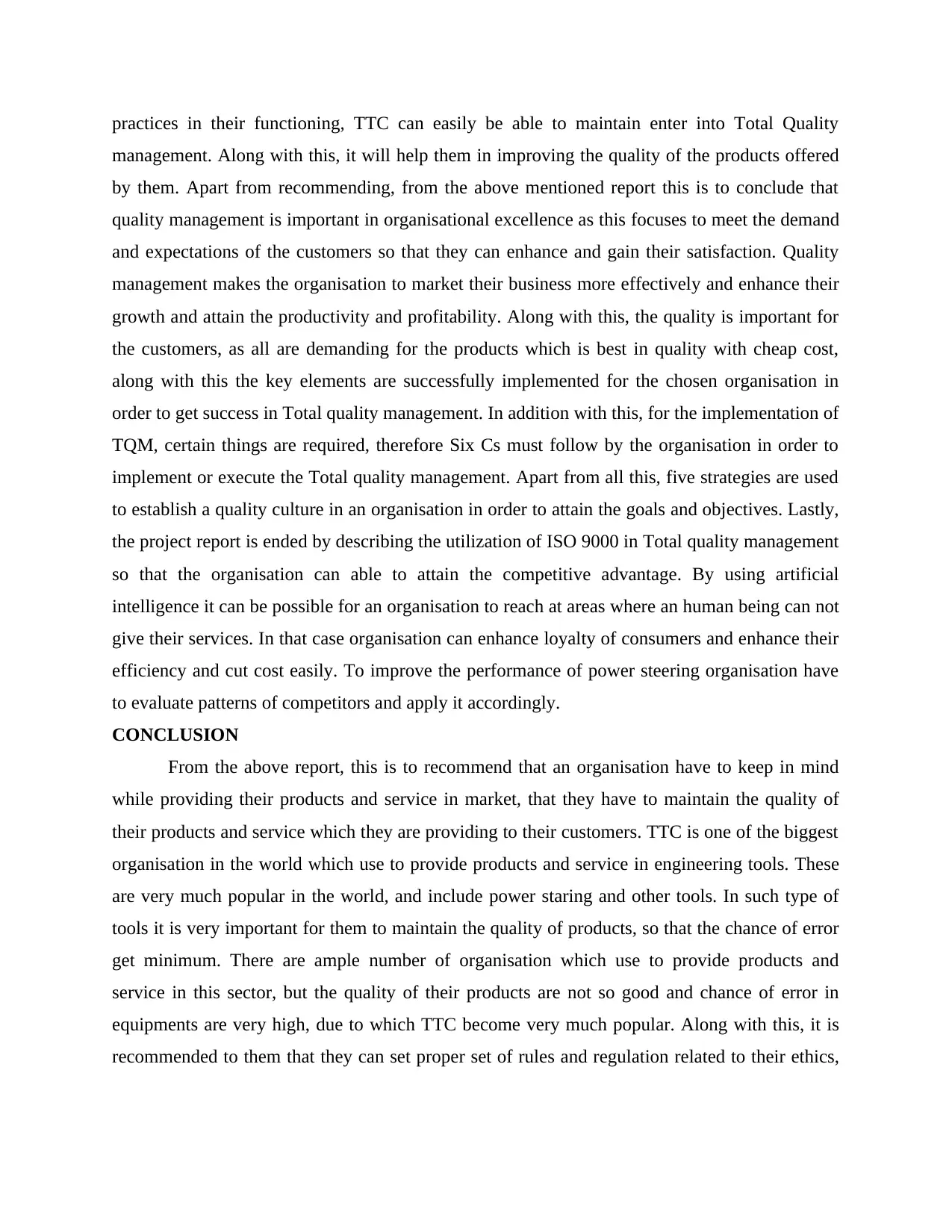
practices in their functioning, TTC can easily be able to maintain enter into Total Quality
management. Along with this, it will help them in improving the quality of the products offered
by them. Apart from recommending, from the above mentioned report this is to conclude that
quality management is important in organisational excellence as this focuses to meet the demand
and expectations of the customers so that they can enhance and gain their satisfaction. Quality
management makes the organisation to market their business more effectively and enhance their
growth and attain the productivity and profitability. Along with this, the quality is important for
the customers, as all are demanding for the products which is best in quality with cheap cost,
along with this the key elements are successfully implemented for the chosen organisation in
order to get success in Total quality management. In addition with this, for the implementation of
TQM, certain things are required, therefore Six Cs must follow by the organisation in order to
implement or execute the Total quality management. Apart from all this, five strategies are used
to establish a quality culture in an organisation in order to attain the goals and objectives. Lastly,
the project report is ended by describing the utilization of ISO 9000 in Total quality management
so that the organisation can able to attain the competitive advantage. By using artificial
intelligence it can be possible for an organisation to reach at areas where an human being can not
give their services. In that case organisation can enhance loyalty of consumers and enhance their
efficiency and cut cost easily. To improve the performance of power steering organisation have
to evaluate patterns of competitors and apply it accordingly.
CONCLUSION
From the above report, this is to recommend that an organisation have to keep in mind
while providing their products and service in market, that they have to maintain the quality of
their products and service which they are providing to their customers. TTC is one of the biggest
organisation in the world which use to provide products and service in engineering tools. These
are very much popular in the world, and include power staring and other tools. In such type of
tools it is very important for them to maintain the quality of products, so that the chance of error
get minimum. There are ample number of organisation which use to provide products and
service in this sector, but the quality of their products are not so good and chance of error in
equipments are very high, due to which TTC become very much popular. Along with this, it is
recommended to them that they can set proper set of rules and regulation related to their ethics,
management. Along with this, it will help them in improving the quality of the products offered
by them. Apart from recommending, from the above mentioned report this is to conclude that
quality management is important in organisational excellence as this focuses to meet the demand
and expectations of the customers so that they can enhance and gain their satisfaction. Quality
management makes the organisation to market their business more effectively and enhance their
growth and attain the productivity and profitability. Along with this, the quality is important for
the customers, as all are demanding for the products which is best in quality with cheap cost,
along with this the key elements are successfully implemented for the chosen organisation in
order to get success in Total quality management. In addition with this, for the implementation of
TQM, certain things are required, therefore Six Cs must follow by the organisation in order to
implement or execute the Total quality management. Apart from all this, five strategies are used
to establish a quality culture in an organisation in order to attain the goals and objectives. Lastly,
the project report is ended by describing the utilization of ISO 9000 in Total quality management
so that the organisation can able to attain the competitive advantage. By using artificial
intelligence it can be possible for an organisation to reach at areas where an human being can not
give their services. In that case organisation can enhance loyalty of consumers and enhance their
efficiency and cut cost easily. To improve the performance of power steering organisation have
to evaluate patterns of competitors and apply it accordingly.
CONCLUSION
From the above report, this is to recommend that an organisation have to keep in mind
while providing their products and service in market, that they have to maintain the quality of
their products and service which they are providing to their customers. TTC is one of the biggest
organisation in the world which use to provide products and service in engineering tools. These
are very much popular in the world, and include power staring and other tools. In such type of
tools it is very important for them to maintain the quality of products, so that the chance of error
get minimum. There are ample number of organisation which use to provide products and
service in this sector, but the quality of their products are not so good and chance of error in
equipments are very high, due to which TTC become very much popular. Along with this, it is
recommended to them that they can set proper set of rules and regulation related to their ethics,
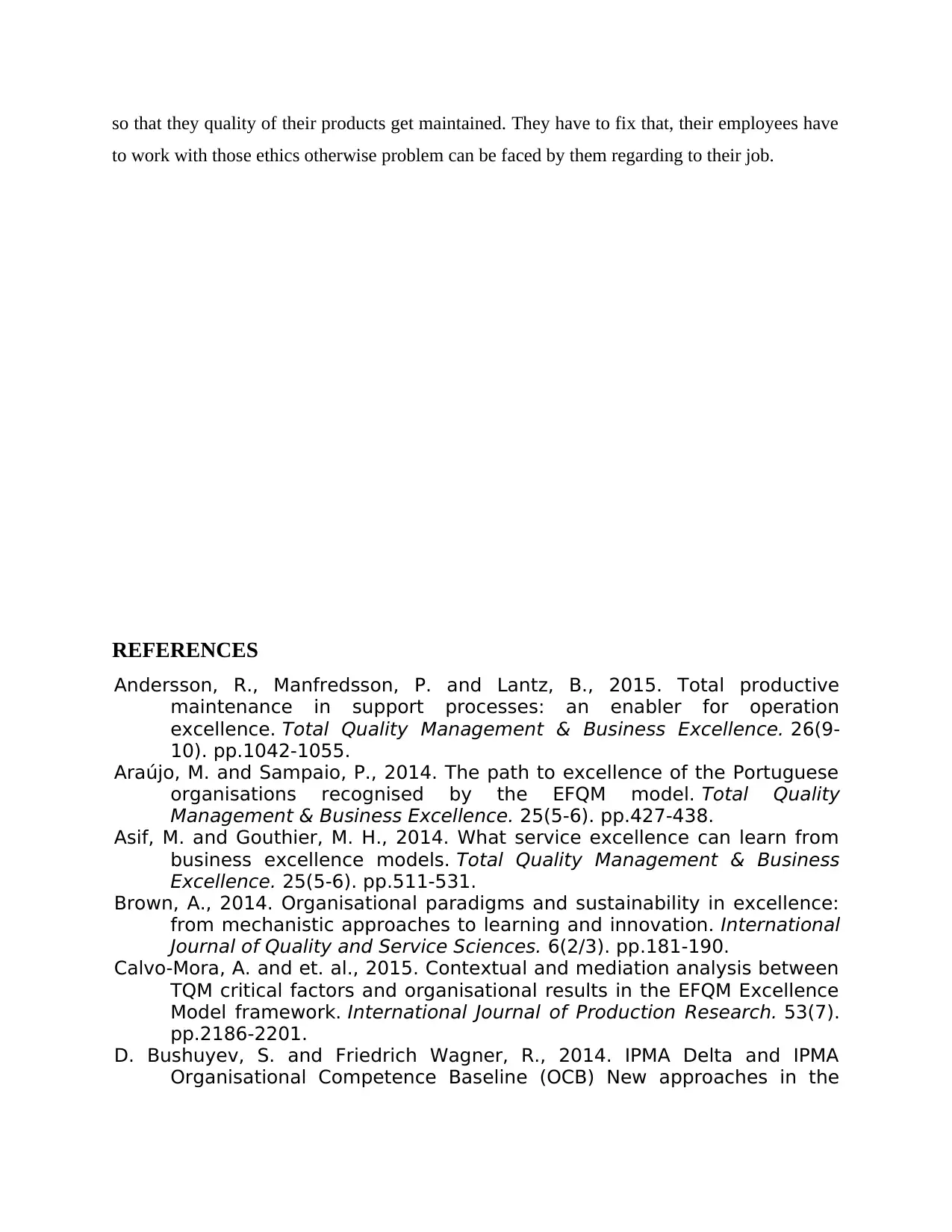
so that they quality of their products get maintained. They have to fix that, their employees have
to work with those ethics otherwise problem can be faced by them regarding to their job.
REFERENCES
Andersson, R., Manfredsson, P. and Lantz, B., 2015. Total productive
maintenance in support processes: an enabler for operation
excellence. Total Quality Management & Business Excellence. 26(9-
10). pp.1042-1055.
Araújo, M. and Sampaio, P., 2014. The path to excellence of the Portuguese
organisations recognised by the EFQM model. Total Quality
Management & Business Excellence. 25(5-6). pp.427-438.
Asif, M. and Gouthier, M. H., 2014. What service excellence can learn from
business excellence models. Total Quality Management & Business
Excellence. 25(5-6). pp.511-531.
Brown, A., 2014. Organisational paradigms and sustainability in excellence:
from mechanistic approaches to learning and innovation. International
Journal of Quality and Service Sciences. 6(2/3). pp.181-190.
Calvo-Mora, A. and et. al., 2015. Contextual and mediation analysis between
TQM critical factors and organisational results in the EFQM Excellence
Model framework. International Journal of Production Research. 53(7).
pp.2186-2201.
D. Bushuyev, S. and Friedrich Wagner, R., 2014. IPMA Delta and IPMA
Organisational Competence Baseline (OCB) New approaches in the
to work with those ethics otherwise problem can be faced by them regarding to their job.
REFERENCES
Andersson, R., Manfredsson, P. and Lantz, B., 2015. Total productive
maintenance in support processes: an enabler for operation
excellence. Total Quality Management & Business Excellence. 26(9-
10). pp.1042-1055.
Araújo, M. and Sampaio, P., 2014. The path to excellence of the Portuguese
organisations recognised by the EFQM model. Total Quality
Management & Business Excellence. 25(5-6). pp.427-438.
Asif, M. and Gouthier, M. H., 2014. What service excellence can learn from
business excellence models. Total Quality Management & Business
Excellence. 25(5-6). pp.511-531.
Brown, A., 2014. Organisational paradigms and sustainability in excellence:
from mechanistic approaches to learning and innovation. International
Journal of Quality and Service Sciences. 6(2/3). pp.181-190.
Calvo-Mora, A. and et. al., 2015. Contextual and mediation analysis between
TQM critical factors and organisational results in the EFQM Excellence
Model framework. International Journal of Production Research. 53(7).
pp.2186-2201.
D. Bushuyev, S. and Friedrich Wagner, R., 2014. IPMA Delta and IPMA
Organisational Competence Baseline (OCB) New approaches in the
You're viewing a preview
Unlock full access by subscribing today!
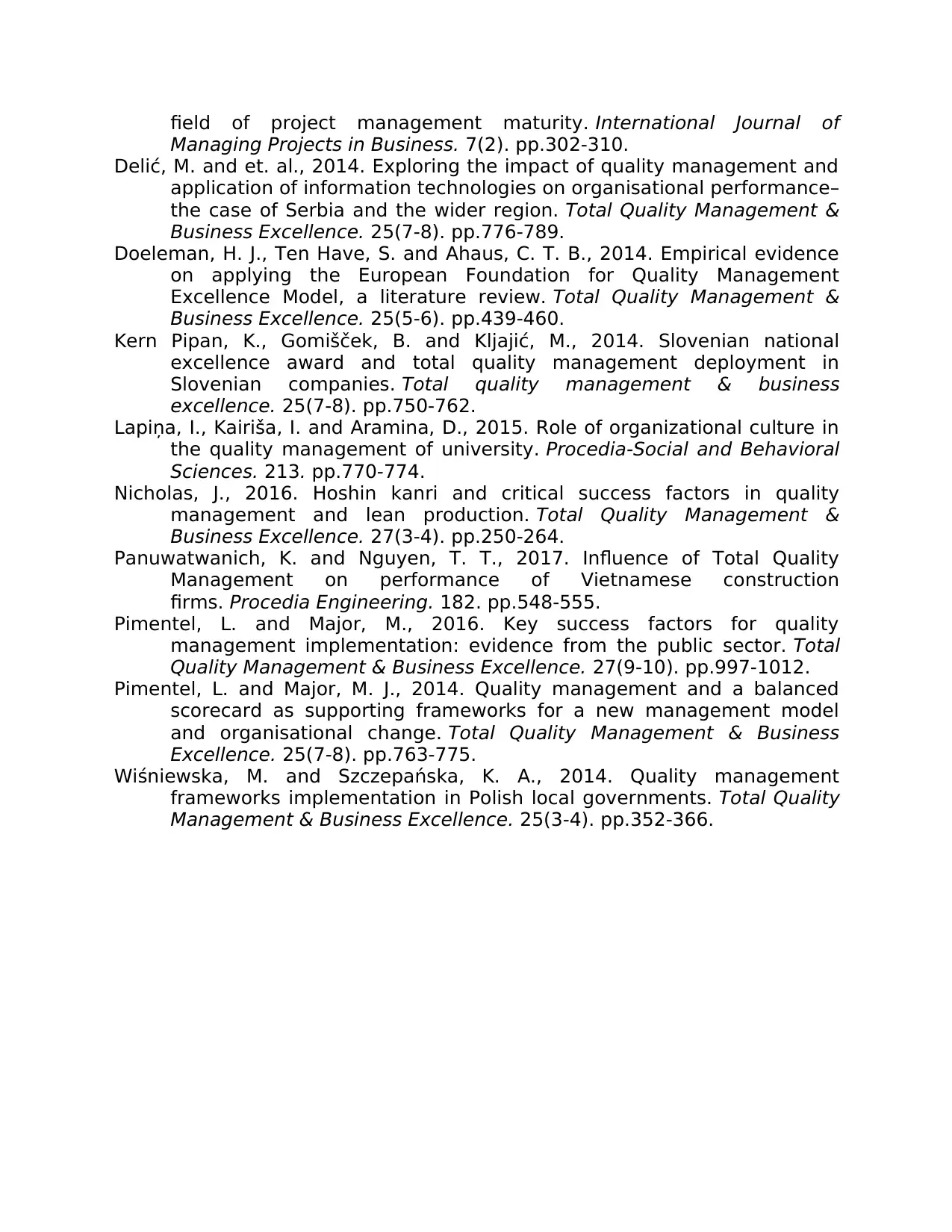
field of project management maturity. International Journal of
Managing Projects in Business. 7(2). pp.302-310.
Delić, M. and et. al., 2014. Exploring the impact of quality management and
application of information technologies on organisational performance–
the case of Serbia and the wider region. Total Quality Management &
Business Excellence. 25(7-8). pp.776-789.
Doeleman, H. J., Ten Have, S. and Ahaus, C. T. B., 2014. Empirical evidence
on applying the European Foundation for Quality Management
Excellence Model, a literature review. Total Quality Management &
Business Excellence. 25(5-6). pp.439-460.
Kern Pipan, K., Gomišček, B. and Kljajić, M., 2014. Slovenian national
excellence award and total quality management deployment in
Slovenian companies. Total quality management & business
excellence. 25(7-8). pp.750-762.
Lapiņa, I., Kairiša, I. and Aramina, D., 2015. Role of organizational culture in
the quality management of university. Procedia-Social and Behavioral
Sciences. 213. pp.770-774.
Nicholas, J., 2016. Hoshin kanri and critical success factors in quality
management and lean production. Total Quality Management &
Business Excellence. 27(3-4). pp.250-264.
Panuwatwanich, K. and Nguyen, T. T., 2017. Influence of Total Quality
Management on performance of Vietnamese construction
firms. Procedia Engineering. 182. pp.548-555.
Pimentel, L. and Major, M., 2016. Key success factors for quality
management implementation: evidence from the public sector. Total
Quality Management & Business Excellence. 27(9-10). pp.997-1012.
Pimentel, L. and Major, M. J., 2014. Quality management and a balanced
scorecard as supporting frameworks for a new management model
and organisational change. Total Quality Management & Business
Excellence. 25(7-8). pp.763-775.
Wiśniewska, M. and Szczepańska, K. A., 2014. Quality management
frameworks implementation in Polish local governments. Total Quality
Management & Business Excellence. 25(3-4). pp.352-366.
Managing Projects in Business. 7(2). pp.302-310.
Delić, M. and et. al., 2014. Exploring the impact of quality management and
application of information technologies on organisational performance–
the case of Serbia and the wider region. Total Quality Management &
Business Excellence. 25(7-8). pp.776-789.
Doeleman, H. J., Ten Have, S. and Ahaus, C. T. B., 2014. Empirical evidence
on applying the European Foundation for Quality Management
Excellence Model, a literature review. Total Quality Management &
Business Excellence. 25(5-6). pp.439-460.
Kern Pipan, K., Gomišček, B. and Kljajić, M., 2014. Slovenian national
excellence award and total quality management deployment in
Slovenian companies. Total quality management & business
excellence. 25(7-8). pp.750-762.
Lapiņa, I., Kairiša, I. and Aramina, D., 2015. Role of organizational culture in
the quality management of university. Procedia-Social and Behavioral
Sciences. 213. pp.770-774.
Nicholas, J., 2016. Hoshin kanri and critical success factors in quality
management and lean production. Total Quality Management &
Business Excellence. 27(3-4). pp.250-264.
Panuwatwanich, K. and Nguyen, T. T., 2017. Influence of Total Quality
Management on performance of Vietnamese construction
firms. Procedia Engineering. 182. pp.548-555.
Pimentel, L. and Major, M., 2016. Key success factors for quality
management implementation: evidence from the public sector. Total
Quality Management & Business Excellence. 27(9-10). pp.997-1012.
Pimentel, L. and Major, M. J., 2014. Quality management and a balanced
scorecard as supporting frameworks for a new management model
and organisational change. Total Quality Management & Business
Excellence. 25(7-8). pp.763-775.
Wiśniewska, M. and Szczepańska, K. A., 2014. Quality management
frameworks implementation in Polish local governments. Total Quality
Management & Business Excellence. 25(3-4). pp.352-366.
1 out of 16
Related Documents

Your All-in-One AI-Powered Toolkit for Academic Success.
+13062052269
info@desklib.com
Available 24*7 on WhatsApp / Email
Unlock your academic potential
© 2024 | Zucol Services PVT LTD | All rights reserved.