Quality Management Report: Engineering Tooling Company Analysis
VerifiedAdded on 2023/01/09
|13
|3910
|43
Report
AI Summary
This report analyzes the quality management practices of the Engineering Tooling Company (ETC), focusing on strategies for organizational excellence. It begins with an introduction to quality management and its importance, followed by an exploration of a company-wide quality improvement strategy, emphasizing Total Quality Management (TQM) principles such as customer focus, employee involvement, process orientation, and continuous improvement. The report then delves into quality assurance and quality control methods applicable to ETC, including failure testing and statistical process control. Furthermore, the report discusses how the implemented improvement strategy can help sustain a culture of quality within the company. The analysis highlights the benefits of TQM in enhancing customer satisfaction, streamlining processes, and fostering a culture of continuous improvement within the organization, ultimately contributing to long-term business growth and market competitiveness. The report concludes with a summary of findings and recommendations.
Contribute Materials
Your contribution can guide someone’s learning journey. Share your
documents today.
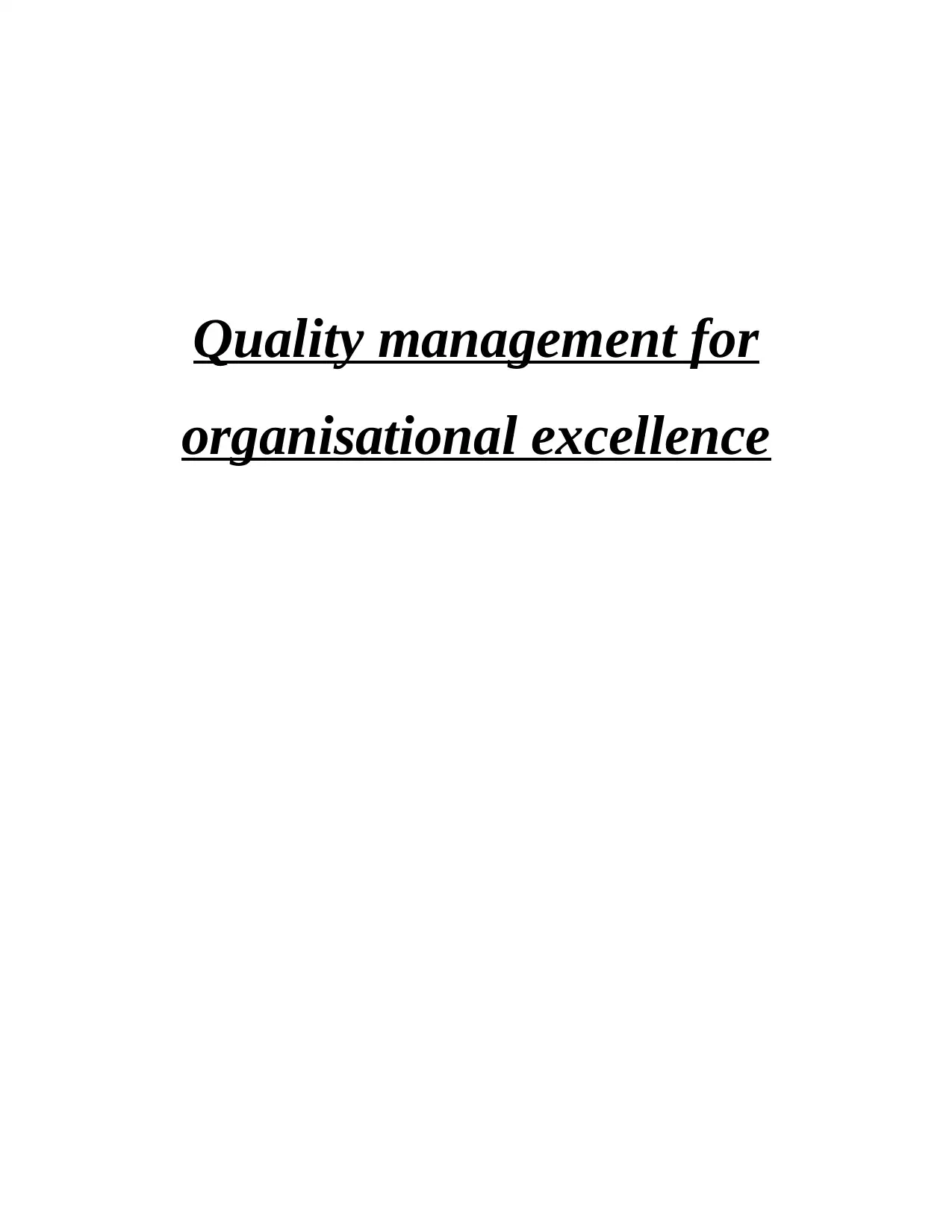
Quality management for
organisational excellence
organisational excellence
Secure Best Marks with AI Grader
Need help grading? Try our AI Grader for instant feedback on your assignments.
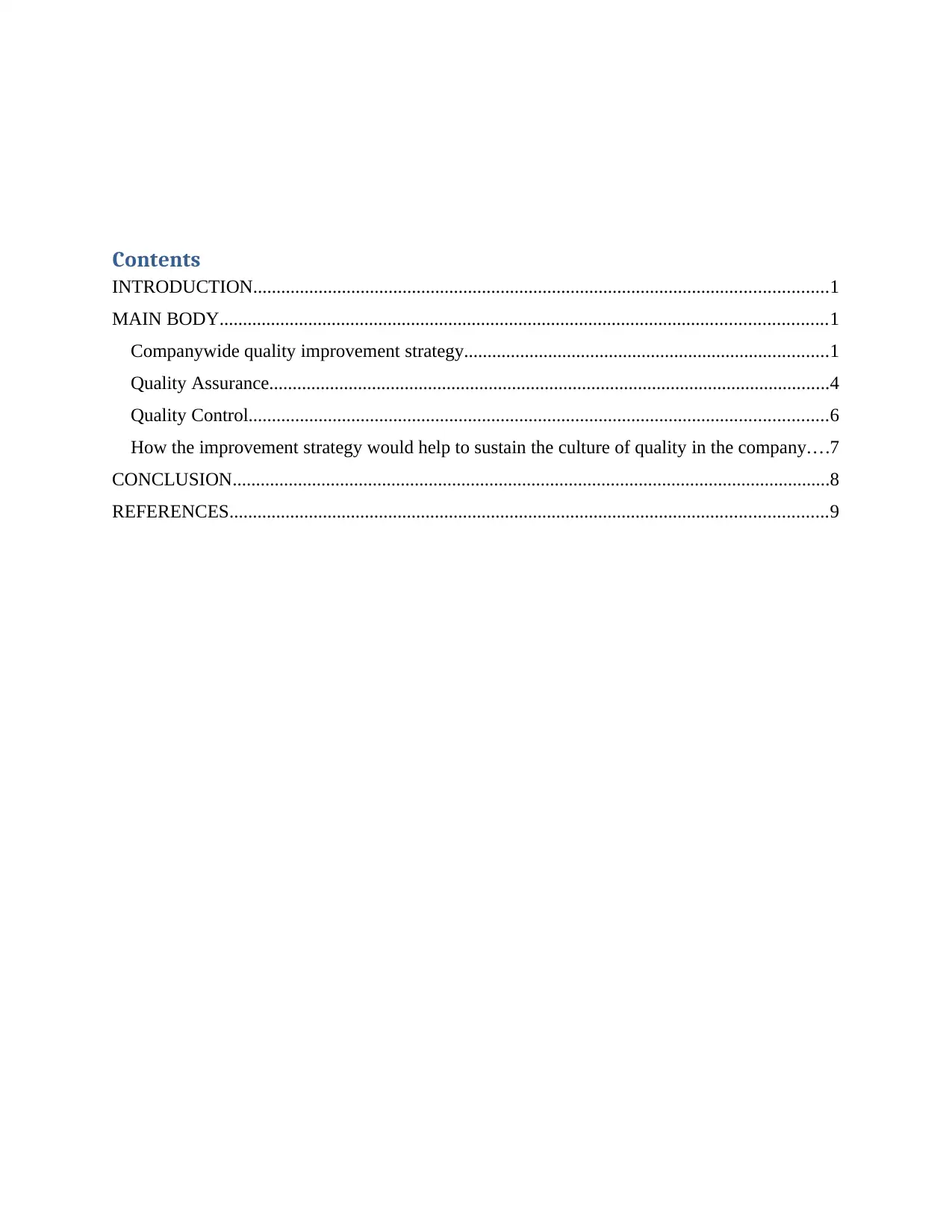
Contents
INTRODUCTION...........................................................................................................................1
MAIN BODY..................................................................................................................................1
Companywide quality improvement strategy..............................................................................1
Quality Assurance........................................................................................................................4
Quality Control............................................................................................................................6
How the improvement strategy would help to sustain the culture of quality in the company....7
CONCLUSION................................................................................................................................8
REFERENCES................................................................................................................................9
INTRODUCTION...........................................................................................................................1
MAIN BODY..................................................................................................................................1
Companywide quality improvement strategy..............................................................................1
Quality Assurance........................................................................................................................4
Quality Control............................................................................................................................6
How the improvement strategy would help to sustain the culture of quality in the company....7
CONCLUSION................................................................................................................................8
REFERENCES................................................................................................................................9
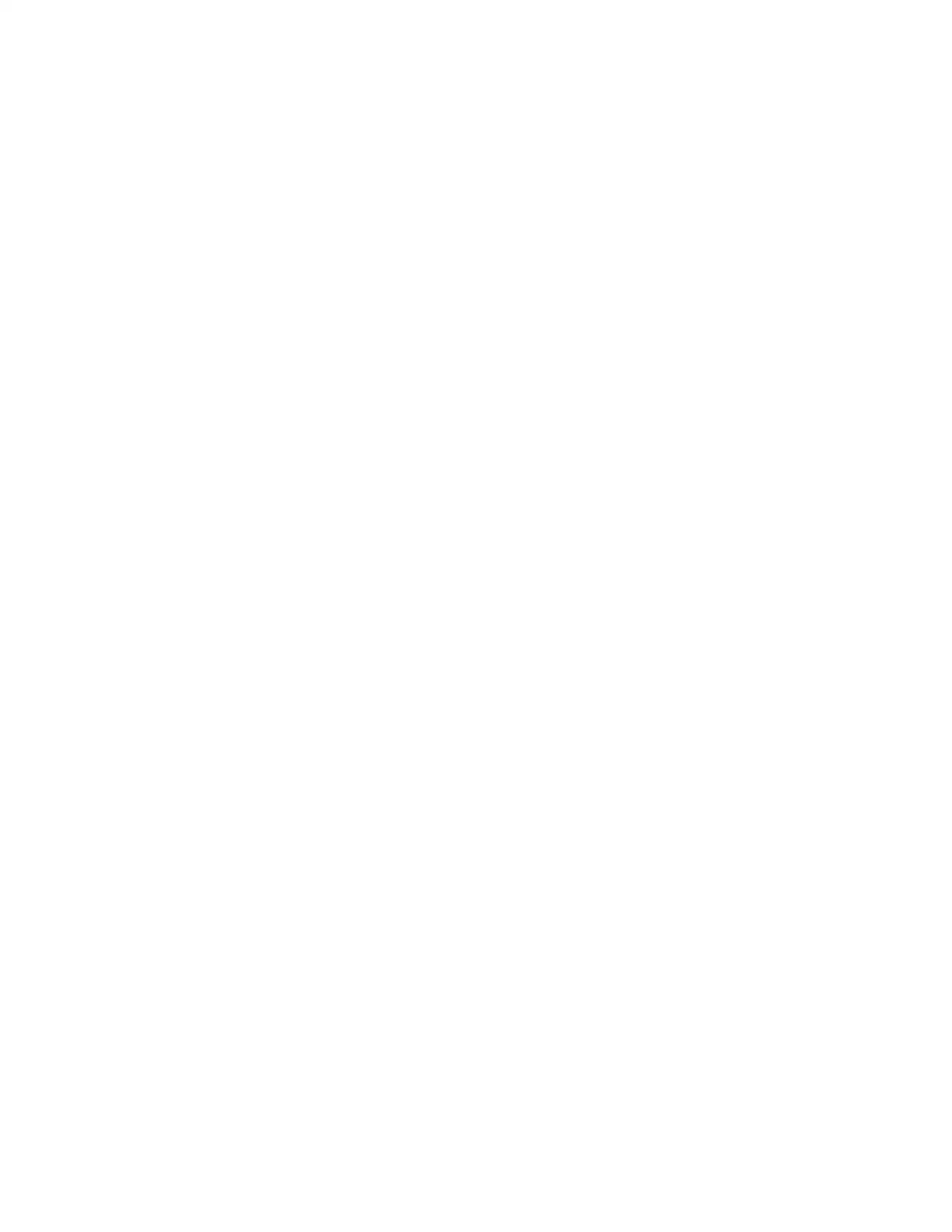
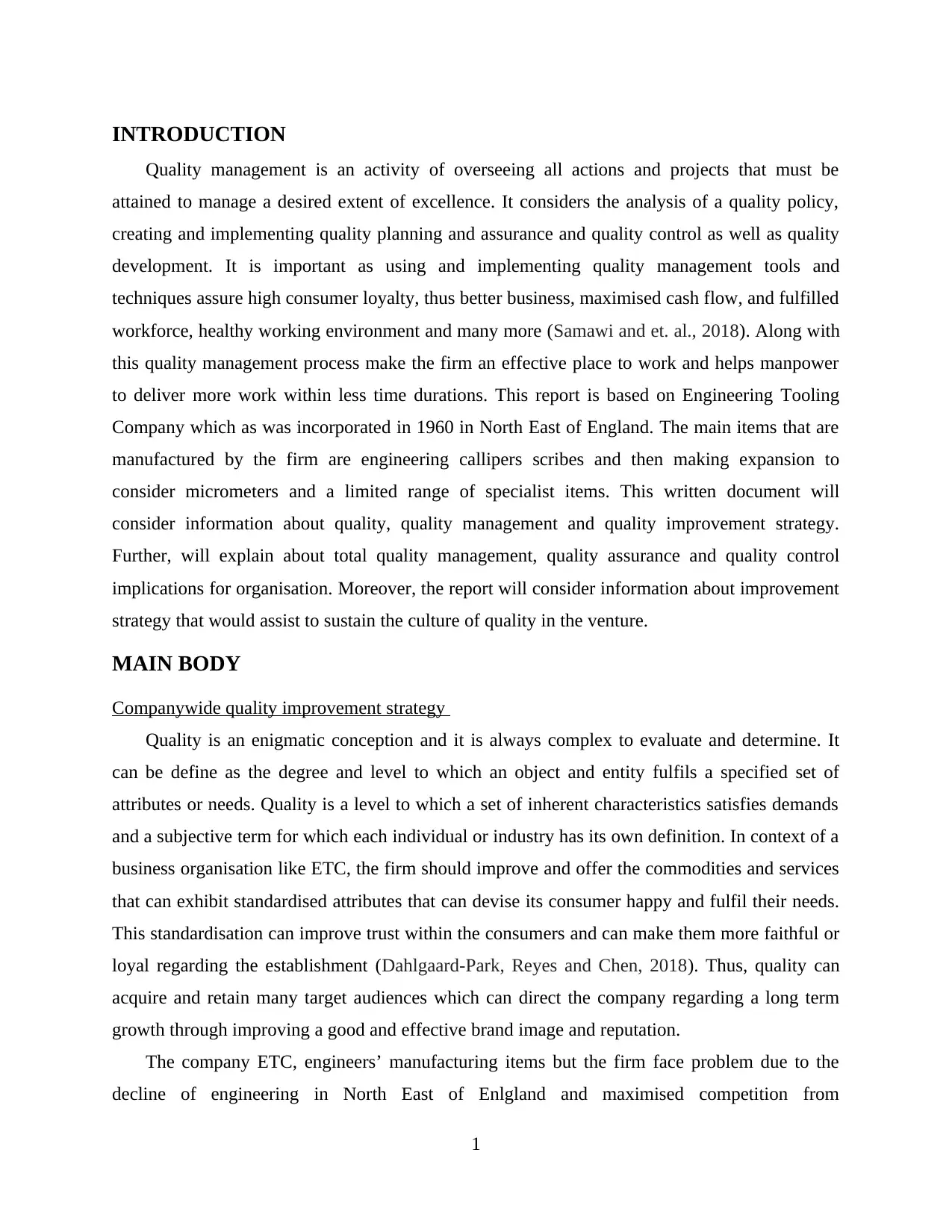
INTRODUCTION
Quality management is an activity of overseeing all actions and projects that must be
attained to manage a desired extent of excellence. It considers the analysis of a quality policy,
creating and implementing quality planning and assurance and quality control as well as quality
development. It is important as using and implementing quality management tools and
techniques assure high consumer loyalty, thus better business, maximised cash flow, and fulfilled
workforce, healthy working environment and many more (Samawi and et. al., 2018). Along with
this quality management process make the firm an effective place to work and helps manpower
to deliver more work within less time durations. This report is based on Engineering Tooling
Company which as was incorporated in 1960 in North East of England. The main items that are
manufactured by the firm are engineering callipers scribes and then making expansion to
consider micrometers and a limited range of specialist items. This written document will
consider information about quality, quality management and quality improvement strategy.
Further, will explain about total quality management, quality assurance and quality control
implications for organisation. Moreover, the report will consider information about improvement
strategy that would assist to sustain the culture of quality in the venture.
MAIN BODY
Companywide quality improvement strategy
Quality is an enigmatic conception and it is always complex to evaluate and determine. It
can be define as the degree and level to which an object and entity fulfils a specified set of
attributes or needs. Quality is a level to which a set of inherent characteristics satisfies demands
and a subjective term for which each individual or industry has its own definition. In context of a
business organisation like ETC, the firm should improve and offer the commodities and services
that can exhibit standardised attributes that can devise its consumer happy and fulfil their needs.
This standardisation can improve trust within the consumers and can make them more faithful or
loyal regarding the establishment (Dahlgaard-Park, Reyes and Chen, 2018). Thus, quality can
acquire and retain many target audiences which can direct the company regarding a long term
growth through improving a good and effective brand image and reputation.
The company ETC, engineers’ manufacturing items but the firm face problem due to the
decline of engineering in North East of Enlgland and maximised competition from
1
Quality management is an activity of overseeing all actions and projects that must be
attained to manage a desired extent of excellence. It considers the analysis of a quality policy,
creating and implementing quality planning and assurance and quality control as well as quality
development. It is important as using and implementing quality management tools and
techniques assure high consumer loyalty, thus better business, maximised cash flow, and fulfilled
workforce, healthy working environment and many more (Samawi and et. al., 2018). Along with
this quality management process make the firm an effective place to work and helps manpower
to deliver more work within less time durations. This report is based on Engineering Tooling
Company which as was incorporated in 1960 in North East of England. The main items that are
manufactured by the firm are engineering callipers scribes and then making expansion to
consider micrometers and a limited range of specialist items. This written document will
consider information about quality, quality management and quality improvement strategy.
Further, will explain about total quality management, quality assurance and quality control
implications for organisation. Moreover, the report will consider information about improvement
strategy that would assist to sustain the culture of quality in the venture.
MAIN BODY
Companywide quality improvement strategy
Quality is an enigmatic conception and it is always complex to evaluate and determine. It
can be define as the degree and level to which an object and entity fulfils a specified set of
attributes or needs. Quality is a level to which a set of inherent characteristics satisfies demands
and a subjective term for which each individual or industry has its own definition. In context of a
business organisation like ETC, the firm should improve and offer the commodities and services
that can exhibit standardised attributes that can devise its consumer happy and fulfil their needs.
This standardisation can improve trust within the consumers and can make them more faithful or
loyal regarding the establishment (Dahlgaard-Park, Reyes and Chen, 2018). Thus, quality can
acquire and retain many target audiences which can direct the company regarding a long term
growth through improving a good and effective brand image and reputation.
The company ETC, engineers’ manufacturing items but the firm face problem due to the
decline of engineering in North East of Enlgland and maximised competition from
1
Secure Best Marks with AI Grader
Need help grading? Try our AI Grader for instant feedback on your assignments.
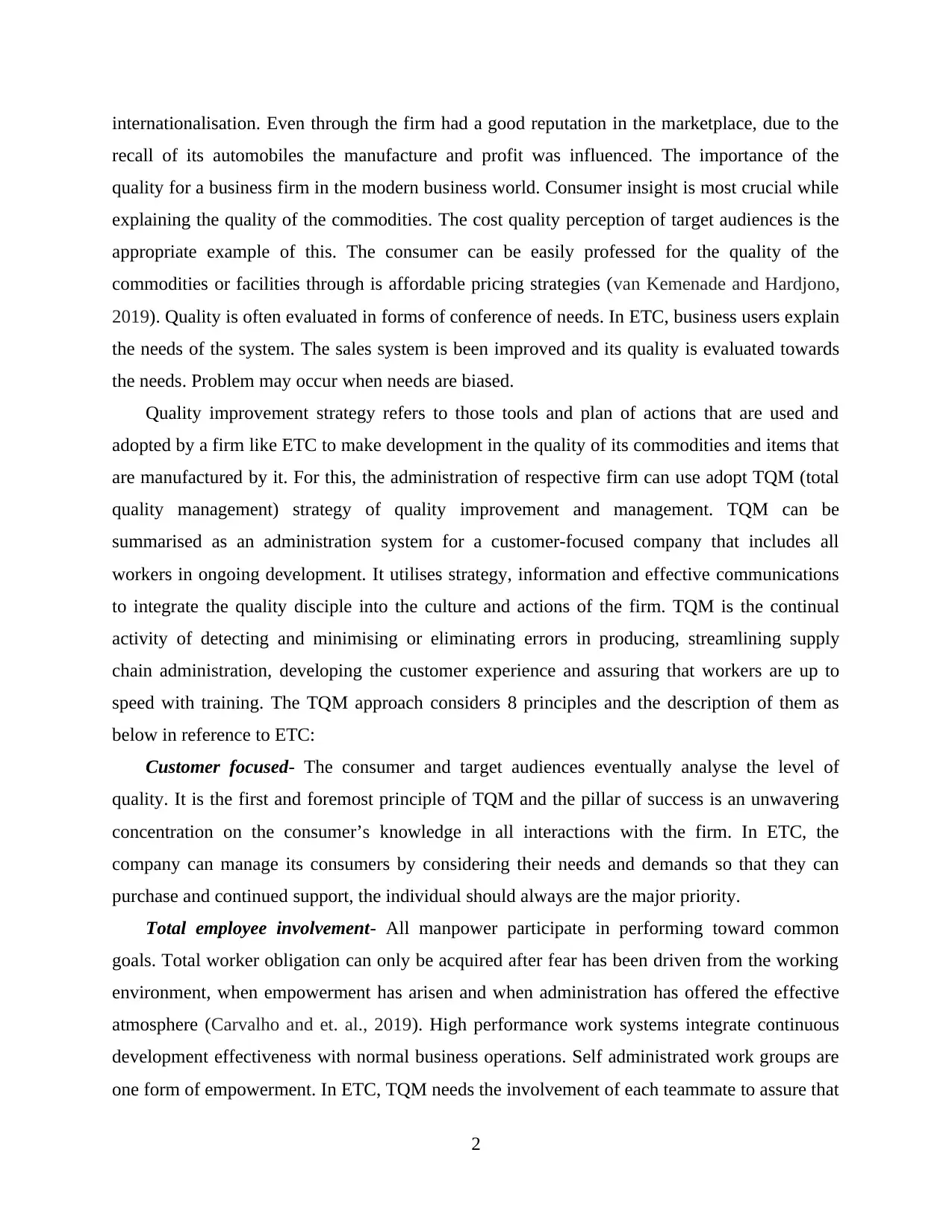
internationalisation. Even through the firm had a good reputation in the marketplace, due to the
recall of its automobiles the manufacture and profit was influenced. The importance of the
quality for a business firm in the modern business world. Consumer insight is most crucial while
explaining the quality of the commodities. The cost quality perception of target audiences is the
appropriate example of this. The consumer can be easily professed for the quality of the
commodities or facilities through is affordable pricing strategies (van Kemenade and Hardjono,
2019). Quality is often evaluated in forms of conference of needs. In ETC, business users explain
the needs of the system. The sales system is been improved and its quality is evaluated towards
the needs. Problem may occur when needs are biased.
Quality improvement strategy refers to those tools and plan of actions that are used and
adopted by a firm like ETC to make development in the quality of its commodities and items that
are manufactured by it. For this, the administration of respective firm can use adopt TQM (total
quality management) strategy of quality improvement and management. TQM can be
summarised as an administration system for a customer-focused company that includes all
workers in ongoing development. It utilises strategy, information and effective communications
to integrate the quality disciple into the culture and actions of the firm. TQM is the continual
activity of detecting and minimising or eliminating errors in producing, streamlining supply
chain administration, developing the customer experience and assuring that workers are up to
speed with training. The TQM approach considers 8 principles and the description of them as
below in reference to ETC:
Customer focused- The consumer and target audiences eventually analyse the level of
quality. It is the first and foremost principle of TQM and the pillar of success is an unwavering
concentration on the consumer’s knowledge in all interactions with the firm. In ETC, the
company can manage its consumers by considering their needs and demands so that they can
purchase and continued support, the individual should always are the major priority.
Total employee involvement- All manpower participate in performing toward common
goals. Total worker obligation can only be acquired after fear has been driven from the working
environment, when empowerment has arisen and when administration has offered the effective
atmosphere (Carvalho and et. al., 2019). High performance work systems integrate continuous
development effectiveness with normal business operations. Self administrated work groups are
one form of empowerment. In ETC, TQM needs the involvement of each teammate to assure that
2
recall of its automobiles the manufacture and profit was influenced. The importance of the
quality for a business firm in the modern business world. Consumer insight is most crucial while
explaining the quality of the commodities. The cost quality perception of target audiences is the
appropriate example of this. The consumer can be easily professed for the quality of the
commodities or facilities through is affordable pricing strategies (van Kemenade and Hardjono,
2019). Quality is often evaluated in forms of conference of needs. In ETC, business users explain
the needs of the system. The sales system is been improved and its quality is evaluated towards
the needs. Problem may occur when needs are biased.
Quality improvement strategy refers to those tools and plan of actions that are used and
adopted by a firm like ETC to make development in the quality of its commodities and items that
are manufactured by it. For this, the administration of respective firm can use adopt TQM (total
quality management) strategy of quality improvement and management. TQM can be
summarised as an administration system for a customer-focused company that includes all
workers in ongoing development. It utilises strategy, information and effective communications
to integrate the quality disciple into the culture and actions of the firm. TQM is the continual
activity of detecting and minimising or eliminating errors in producing, streamlining supply
chain administration, developing the customer experience and assuring that workers are up to
speed with training. The TQM approach considers 8 principles and the description of them as
below in reference to ETC:
Customer focused- The consumer and target audiences eventually analyse the level of
quality. It is the first and foremost principle of TQM and the pillar of success is an unwavering
concentration on the consumer’s knowledge in all interactions with the firm. In ETC, the
company can manage its consumers by considering their needs and demands so that they can
purchase and continued support, the individual should always are the major priority.
Total employee involvement- All manpower participate in performing toward common
goals. Total worker obligation can only be acquired after fear has been driven from the working
environment, when empowerment has arisen and when administration has offered the effective
atmosphere (Carvalho and et. al., 2019). High performance work systems integrate continuous
development effectiveness with normal business operations. Self administrated work groups are
one form of empowerment. In ETC, TQM needs the involvement of each teammate to assure that
2
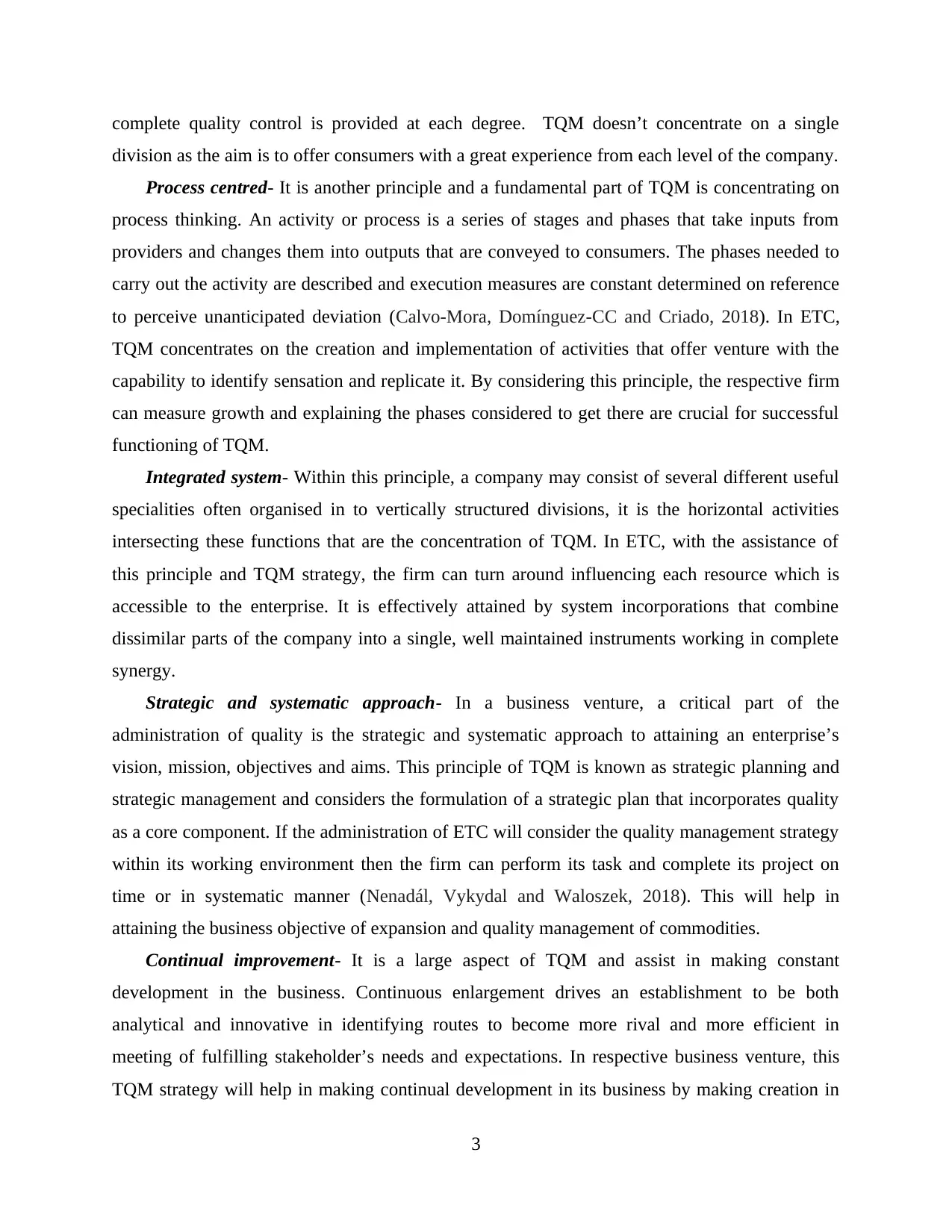
complete quality control is provided at each degree. TQM doesn’t concentrate on a single
division as the aim is to offer consumers with a great experience from each level of the company.
Process centred- It is another principle and a fundamental part of TQM is concentrating on
process thinking. An activity or process is a series of stages and phases that take inputs from
providers and changes them into outputs that are conveyed to consumers. The phases needed to
carry out the activity are described and execution measures are constant determined on reference
to perceive unanticipated deviation (Calvo-Mora, Domínguez-CC and Criado, 2018). In ETC,
TQM concentrates on the creation and implementation of activities that offer venture with the
capability to identify sensation and replicate it. By considering this principle, the respective firm
can measure growth and explaining the phases considered to get there are crucial for successful
functioning of TQM.
Integrated system- Within this principle, a company may consist of several different useful
specialities often organised in to vertically structured divisions, it is the horizontal activities
intersecting these functions that are the concentration of TQM. In ETC, with the assistance of
this principle and TQM strategy, the firm can turn around influencing each resource which is
accessible to the enterprise. It is effectively attained by system incorporations that combine
dissimilar parts of the company into a single, well maintained instruments working in complete
synergy.
Strategic and systematic approach- In a business venture, a critical part of the
administration of quality is the strategic and systematic approach to attaining an enterprise’s
vision, mission, objectives and aims. This principle of TQM is known as strategic planning and
strategic management and considers the formulation of a strategic plan that incorporates quality
as a core component. If the administration of ETC will consider the quality management strategy
within its working environment then the firm can perform its task and complete its project on
time or in systematic manner (Nenadál, Vykydal and Waloszek, 2018). This will help in
attaining the business objective of expansion and quality management of commodities.
Continual improvement- It is a large aspect of TQM and assist in making constant
development in the business. Continuous enlargement drives an establishment to be both
analytical and innovative in identifying routes to become more rival and more efficient in
meeting of fulfilling stakeholder’s needs and expectations. In respective business venture, this
TQM strategy will help in making continual development in its business by making creation in
3
division as the aim is to offer consumers with a great experience from each level of the company.
Process centred- It is another principle and a fundamental part of TQM is concentrating on
process thinking. An activity or process is a series of stages and phases that take inputs from
providers and changes them into outputs that are conveyed to consumers. The phases needed to
carry out the activity are described and execution measures are constant determined on reference
to perceive unanticipated deviation (Calvo-Mora, Domínguez-CC and Criado, 2018). In ETC,
TQM concentrates on the creation and implementation of activities that offer venture with the
capability to identify sensation and replicate it. By considering this principle, the respective firm
can measure growth and explaining the phases considered to get there are crucial for successful
functioning of TQM.
Integrated system- Within this principle, a company may consist of several different useful
specialities often organised in to vertically structured divisions, it is the horizontal activities
intersecting these functions that are the concentration of TQM. In ETC, with the assistance of
this principle and TQM strategy, the firm can turn around influencing each resource which is
accessible to the enterprise. It is effectively attained by system incorporations that combine
dissimilar parts of the company into a single, well maintained instruments working in complete
synergy.
Strategic and systematic approach- In a business venture, a critical part of the
administration of quality is the strategic and systematic approach to attaining an enterprise’s
vision, mission, objectives and aims. This principle of TQM is known as strategic planning and
strategic management and considers the formulation of a strategic plan that incorporates quality
as a core component. If the administration of ETC will consider the quality management strategy
within its working environment then the firm can perform its task and complete its project on
time or in systematic manner (Nenadál, Vykydal and Waloszek, 2018). This will help in
attaining the business objective of expansion and quality management of commodities.
Continual improvement- It is a large aspect of TQM and assist in making constant
development in the business. Continuous enlargement drives an establishment to be both
analytical and innovative in identifying routes to become more rival and more efficient in
meeting of fulfilling stakeholder’s needs and expectations. In respective business venture, this
TQM strategy will help in making continual development in its business by making creation in
3
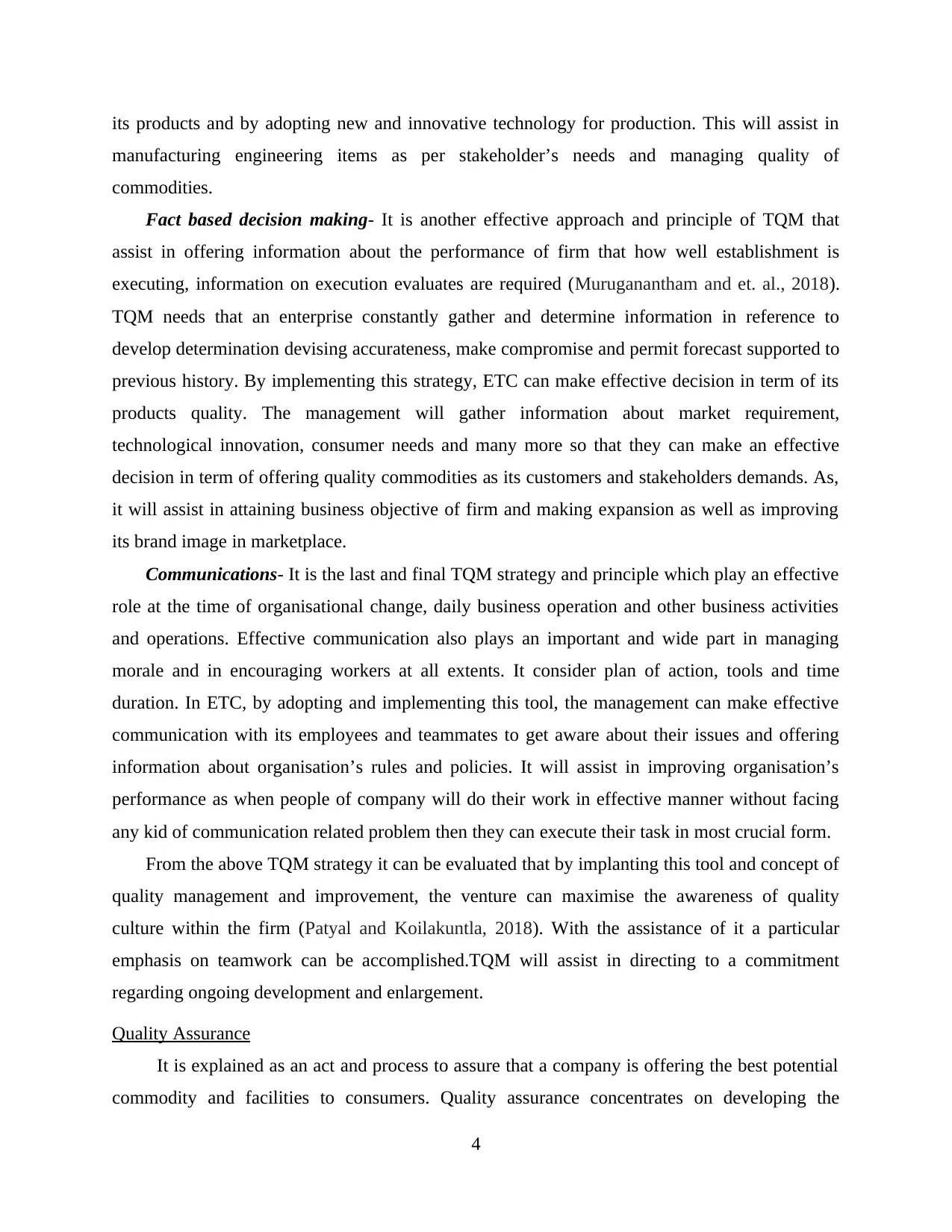
its products and by adopting new and innovative technology for production. This will assist in
manufacturing engineering items as per stakeholder’s needs and managing quality of
commodities.
Fact based decision making- It is another effective approach and principle of TQM that
assist in offering information about the performance of firm that how well establishment is
executing, information on execution evaluates are required (Muruganantham and et. al., 2018).
TQM needs that an enterprise constantly gather and determine information in reference to
develop determination devising accurateness, make compromise and permit forecast supported to
previous history. By implementing this strategy, ETC can make effective decision in term of its
products quality. The management will gather information about market requirement,
technological innovation, consumer needs and many more so that they can make an effective
decision in term of offering quality commodities as its customers and stakeholders demands. As,
it will assist in attaining business objective of firm and making expansion as well as improving
its brand image in marketplace.
Communications- It is the last and final TQM strategy and principle which play an effective
role at the time of organisational change, daily business operation and other business activities
and operations. Effective communication also plays an important and wide part in managing
morale and in encouraging workers at all extents. It consider plan of action, tools and time
duration. In ETC, by adopting and implementing this tool, the management can make effective
communication with its employees and teammates to get aware about their issues and offering
information about organisation’s rules and policies. It will assist in improving organisation’s
performance as when people of company will do their work in effective manner without facing
any kid of communication related problem then they can execute their task in most crucial form.
From the above TQM strategy it can be evaluated that by implanting this tool and concept of
quality management and improvement, the venture can maximise the awareness of quality
culture within the firm (Patyal and Koilakuntla, 2018). With the assistance of it a particular
emphasis on teamwork can be accomplished.TQM will assist in directing to a commitment
regarding ongoing development and enlargement.
Quality Assurance
It is explained as an act and process to assure that a company is offering the best potential
commodity and facilities to consumers. Quality assurance concentrates on developing the
4
manufacturing engineering items as per stakeholder’s needs and managing quality of
commodities.
Fact based decision making- It is another effective approach and principle of TQM that
assist in offering information about the performance of firm that how well establishment is
executing, information on execution evaluates are required (Muruganantham and et. al., 2018).
TQM needs that an enterprise constantly gather and determine information in reference to
develop determination devising accurateness, make compromise and permit forecast supported to
previous history. By implementing this strategy, ETC can make effective decision in term of its
products quality. The management will gather information about market requirement,
technological innovation, consumer needs and many more so that they can make an effective
decision in term of offering quality commodities as its customers and stakeholders demands. As,
it will assist in attaining business objective of firm and making expansion as well as improving
its brand image in marketplace.
Communications- It is the last and final TQM strategy and principle which play an effective
role at the time of organisational change, daily business operation and other business activities
and operations. Effective communication also plays an important and wide part in managing
morale and in encouraging workers at all extents. It consider plan of action, tools and time
duration. In ETC, by adopting and implementing this tool, the management can make effective
communication with its employees and teammates to get aware about their issues and offering
information about organisation’s rules and policies. It will assist in improving organisation’s
performance as when people of company will do their work in effective manner without facing
any kid of communication related problem then they can execute their task in most crucial form.
From the above TQM strategy it can be evaluated that by implanting this tool and concept of
quality management and improvement, the venture can maximise the awareness of quality
culture within the firm (Patyal and Koilakuntla, 2018). With the assistance of it a particular
emphasis on teamwork can be accomplished.TQM will assist in directing to a commitment
regarding ongoing development and enlargement.
Quality Assurance
It is explained as an act and process to assure that a company is offering the best potential
commodity and facilities to consumers. Quality assurance concentrates on developing the
4
Paraphrase This Document
Need a fresh take? Get an instant paraphrase of this document with our AI Paraphraser
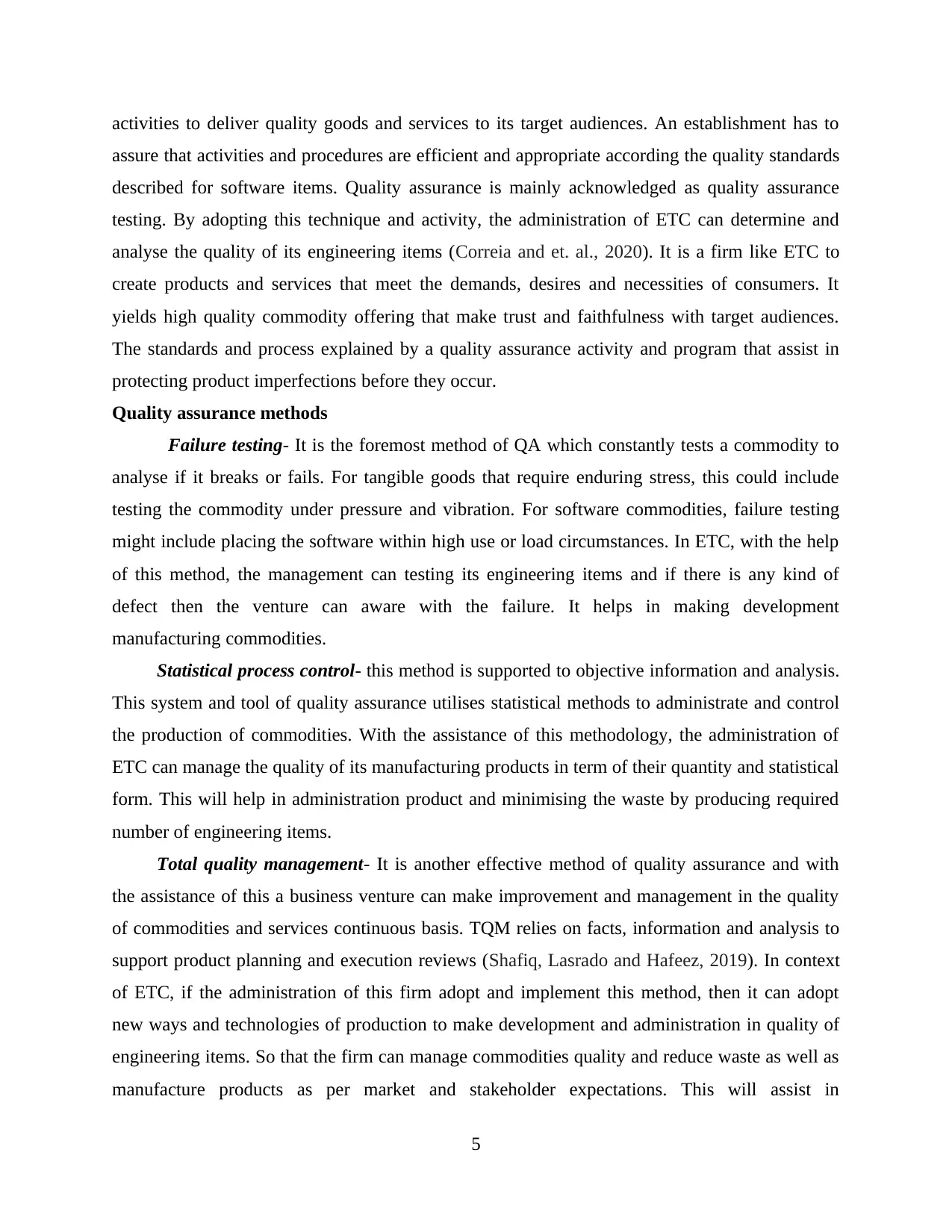
activities to deliver quality goods and services to its target audiences. An establishment has to
assure that activities and procedures are efficient and appropriate according the quality standards
described for software items. Quality assurance is mainly acknowledged as quality assurance
testing. By adopting this technique and activity, the administration of ETC can determine and
analyse the quality of its engineering items (Correia and et. al., 2020). It is a firm like ETC to
create products and services that meet the demands, desires and necessities of consumers. It
yields high quality commodity offering that make trust and faithfulness with target audiences.
The standards and process explained by a quality assurance activity and program that assist in
protecting product imperfections before they occur.
Quality assurance methods
Failure testing- It is the foremost method of QA which constantly tests a commodity to
analyse if it breaks or fails. For tangible goods that require enduring stress, this could include
testing the commodity under pressure and vibration. For software commodities, failure testing
might include placing the software within high use or load circumstances. In ETC, with the help
of this method, the management can testing its engineering items and if there is any kind of
defect then the venture can aware with the failure. It helps in making development
manufacturing commodities.
Statistical process control- this method is supported to objective information and analysis.
This system and tool of quality assurance utilises statistical methods to administrate and control
the production of commodities. With the assistance of this methodology, the administration of
ETC can manage the quality of its manufacturing products in term of their quantity and statistical
form. This will help in administration product and minimising the waste by producing required
number of engineering items.
Total quality management- It is another effective method of quality assurance and with
the assistance of this a business venture can make improvement and management in the quality
of commodities and services continuous basis. TQM relies on facts, information and analysis to
support product planning and execution reviews (Shafiq, Lasrado and Hafeez, 2019). In context
of ETC, if the administration of this firm adopt and implement this method, then it can adopt
new ways and technologies of production to make development and administration in quality of
engineering items. So that the firm can manage commodities quality and reduce waste as well as
manufacture products as per market and stakeholder expectations. This will assist in
5
assure that activities and procedures are efficient and appropriate according the quality standards
described for software items. Quality assurance is mainly acknowledged as quality assurance
testing. By adopting this technique and activity, the administration of ETC can determine and
analyse the quality of its engineering items (Correia and et. al., 2020). It is a firm like ETC to
create products and services that meet the demands, desires and necessities of consumers. It
yields high quality commodity offering that make trust and faithfulness with target audiences.
The standards and process explained by a quality assurance activity and program that assist in
protecting product imperfections before they occur.
Quality assurance methods
Failure testing- It is the foremost method of QA which constantly tests a commodity to
analyse if it breaks or fails. For tangible goods that require enduring stress, this could include
testing the commodity under pressure and vibration. For software commodities, failure testing
might include placing the software within high use or load circumstances. In ETC, with the help
of this method, the management can testing its engineering items and if there is any kind of
defect then the venture can aware with the failure. It helps in making development
manufacturing commodities.
Statistical process control- this method is supported to objective information and analysis.
This system and tool of quality assurance utilises statistical methods to administrate and control
the production of commodities. With the assistance of this methodology, the administration of
ETC can manage the quality of its manufacturing products in term of their quantity and statistical
form. This will help in administration product and minimising the waste by producing required
number of engineering items.
Total quality management- It is another effective method of quality assurance and with
the assistance of this a business venture can make improvement and management in the quality
of commodities and services continuous basis. TQM relies on facts, information and analysis to
support product planning and execution reviews (Shafiq, Lasrado and Hafeez, 2019). In context
of ETC, if the administration of this firm adopt and implement this method, then it can adopt
new ways and technologies of production to make development and administration in quality of
engineering items. So that the firm can manage commodities quality and reduce waste as well as
manufacture products as per market and stakeholder expectations. This will assist in
5
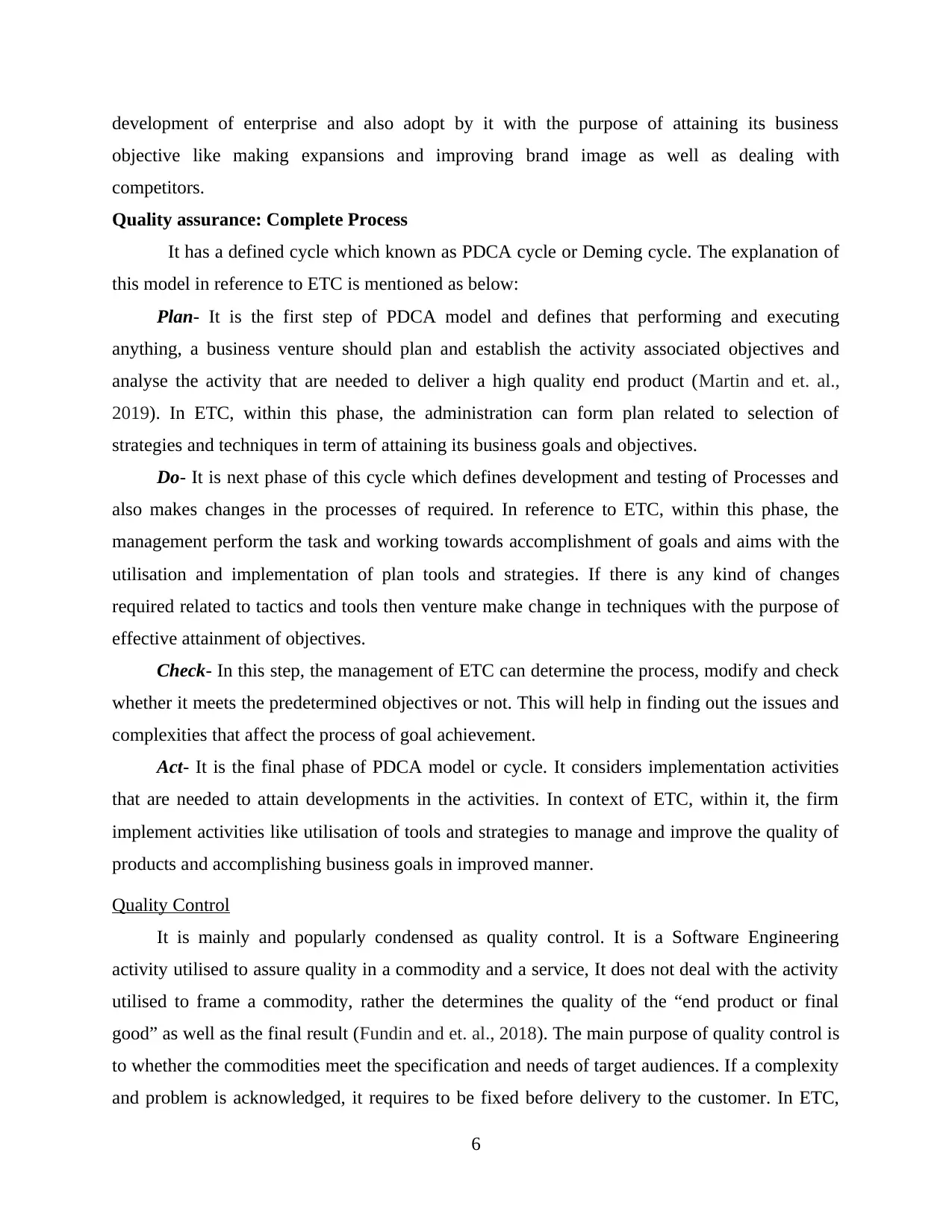
development of enterprise and also adopt by it with the purpose of attaining its business
objective like making expansions and improving brand image as well as dealing with
competitors.
Quality assurance: Complete Process
It has a defined cycle which known as PDCA cycle or Deming cycle. The explanation of
this model in reference to ETC is mentioned as below:
Plan- It is the first step of PDCA model and defines that performing and executing
anything, a business venture should plan and establish the activity associated objectives and
analyse the activity that are needed to deliver a high quality end product (Martin and et. al.,
2019). In ETC, within this phase, the administration can form plan related to selection of
strategies and techniques in term of attaining its business goals and objectives.
Do- It is next phase of this cycle which defines development and testing of Processes and
also makes changes in the processes of required. In reference to ETC, within this phase, the
management perform the task and working towards accomplishment of goals and aims with the
utilisation and implementation of plan tools and strategies. If there is any kind of changes
required related to tactics and tools then venture make change in techniques with the purpose of
effective attainment of objectives.
Check- In this step, the management of ETC can determine the process, modify and check
whether it meets the predetermined objectives or not. This will help in finding out the issues and
complexities that affect the process of goal achievement.
Act- It is the final phase of PDCA model or cycle. It considers implementation activities
that are needed to attain developments in the activities. In context of ETC, within it, the firm
implement activities like utilisation of tools and strategies to manage and improve the quality of
products and accomplishing business goals in improved manner.
Quality Control
It is mainly and popularly condensed as quality control. It is a Software Engineering
activity utilised to assure quality in a commodity and a service, It does not deal with the activity
utilised to frame a commodity, rather the determines the quality of the “end product or final
good” as well as the final result (Fundin and et. al., 2018). The main purpose of quality control is
to whether the commodities meet the specification and needs of target audiences. If a complexity
and problem is acknowledged, it requires to be fixed before delivery to the customer. In ETC,
6
objective like making expansions and improving brand image as well as dealing with
competitors.
Quality assurance: Complete Process
It has a defined cycle which known as PDCA cycle or Deming cycle. The explanation of
this model in reference to ETC is mentioned as below:
Plan- It is the first step of PDCA model and defines that performing and executing
anything, a business venture should plan and establish the activity associated objectives and
analyse the activity that are needed to deliver a high quality end product (Martin and et. al.,
2019). In ETC, within this phase, the administration can form plan related to selection of
strategies and techniques in term of attaining its business goals and objectives.
Do- It is next phase of this cycle which defines development and testing of Processes and
also makes changes in the processes of required. In reference to ETC, within this phase, the
management perform the task and working towards accomplishment of goals and aims with the
utilisation and implementation of plan tools and strategies. If there is any kind of changes
required related to tactics and tools then venture make change in techniques with the purpose of
effective attainment of objectives.
Check- In this step, the management of ETC can determine the process, modify and check
whether it meets the predetermined objectives or not. This will help in finding out the issues and
complexities that affect the process of goal achievement.
Act- It is the final phase of PDCA model or cycle. It considers implementation activities
that are needed to attain developments in the activities. In context of ETC, within it, the firm
implement activities like utilisation of tools and strategies to manage and improve the quality of
products and accomplishing business goals in improved manner.
Quality Control
It is mainly and popularly condensed as quality control. It is a Software Engineering
activity utilised to assure quality in a commodity and a service, It does not deal with the activity
utilised to frame a commodity, rather the determines the quality of the “end product or final
good” as well as the final result (Fundin and et. al., 2018). The main purpose of quality control is
to whether the commodities meet the specification and needs of target audiences. If a complexity
and problem is acknowledged, it requires to be fixed before delivery to the customer. In ETC,
6
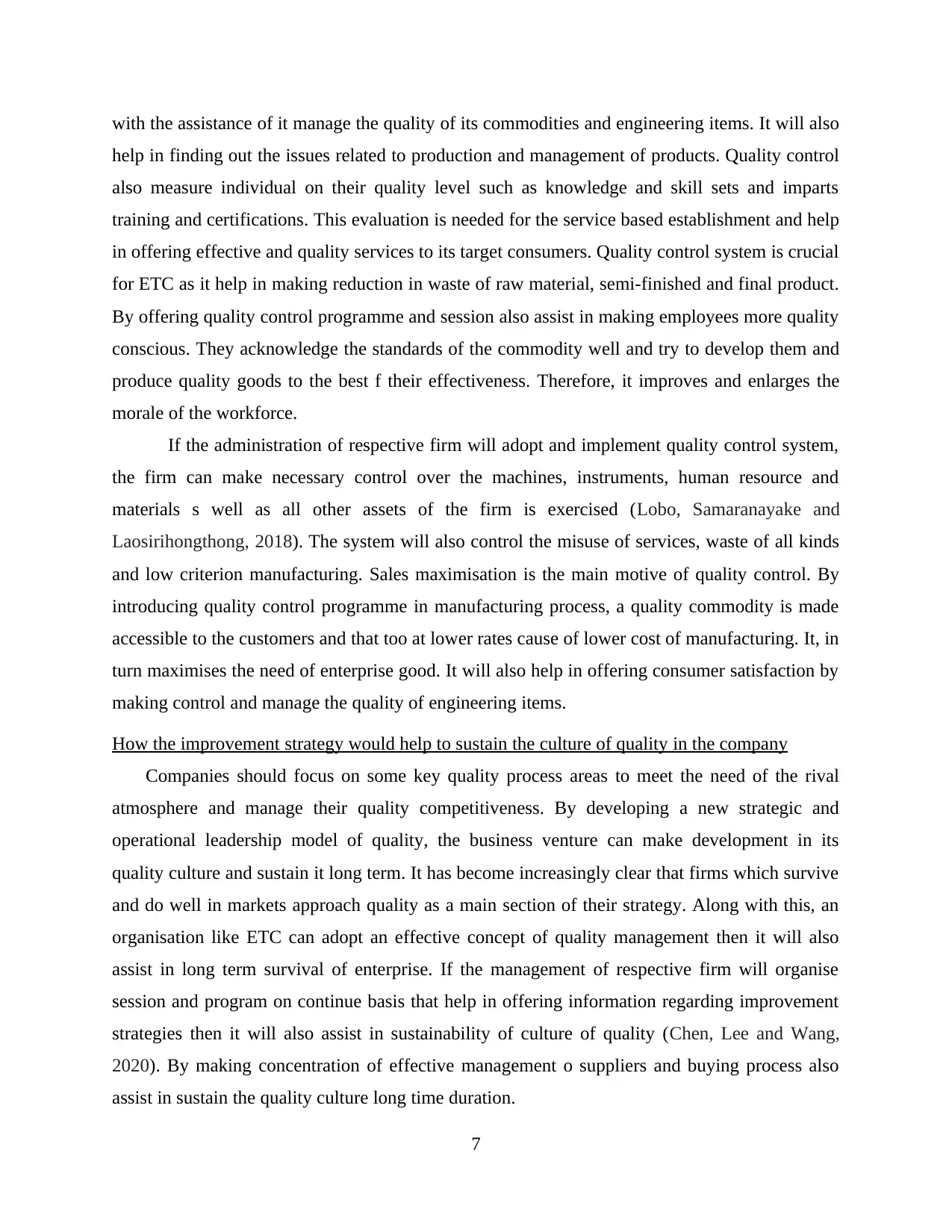
with the assistance of it manage the quality of its commodities and engineering items. It will also
help in finding out the issues related to production and management of products. Quality control
also measure individual on their quality level such as knowledge and skill sets and imparts
training and certifications. This evaluation is needed for the service based establishment and help
in offering effective and quality services to its target consumers. Quality control system is crucial
for ETC as it help in making reduction in waste of raw material, semi-finished and final product.
By offering quality control programme and session also assist in making employees more quality
conscious. They acknowledge the standards of the commodity well and try to develop them and
produce quality goods to the best f their effectiveness. Therefore, it improves and enlarges the
morale of the workforce.
If the administration of respective firm will adopt and implement quality control system,
the firm can make necessary control over the machines, instruments, human resource and
materials s well as all other assets of the firm is exercised (Lobo, Samaranayake and
Laosirihongthong, 2018). The system will also control the misuse of services, waste of all kinds
and low criterion manufacturing. Sales maximisation is the main motive of quality control. By
introducing quality control programme in manufacturing process, a quality commodity is made
accessible to the customers and that too at lower rates cause of lower cost of manufacturing. It, in
turn maximises the need of enterprise good. It will also help in offering consumer satisfaction by
making control and manage the quality of engineering items.
How the improvement strategy would help to sustain the culture of quality in the company
Companies should focus on some key quality process areas to meet the need of the rival
atmosphere and manage their quality competitiveness. By developing a new strategic and
operational leadership model of quality, the business venture can make development in its
quality culture and sustain it long term. It has become increasingly clear that firms which survive
and do well in markets approach quality as a main section of their strategy. Along with this, an
organisation like ETC can adopt an effective concept of quality management then it will also
assist in long term survival of enterprise. If the management of respective firm will organise
session and program on continue basis that help in offering information regarding improvement
strategies then it will also assist in sustainability of culture of quality (Chen, Lee and Wang,
2020). By making concentration of effective management o suppliers and buying process also
assist in sustain the quality culture long time duration.
7
help in finding out the issues related to production and management of products. Quality control
also measure individual on their quality level such as knowledge and skill sets and imparts
training and certifications. This evaluation is needed for the service based establishment and help
in offering effective and quality services to its target consumers. Quality control system is crucial
for ETC as it help in making reduction in waste of raw material, semi-finished and final product.
By offering quality control programme and session also assist in making employees more quality
conscious. They acknowledge the standards of the commodity well and try to develop them and
produce quality goods to the best f their effectiveness. Therefore, it improves and enlarges the
morale of the workforce.
If the administration of respective firm will adopt and implement quality control system,
the firm can make necessary control over the machines, instruments, human resource and
materials s well as all other assets of the firm is exercised (Lobo, Samaranayake and
Laosirihongthong, 2018). The system will also control the misuse of services, waste of all kinds
and low criterion manufacturing. Sales maximisation is the main motive of quality control. By
introducing quality control programme in manufacturing process, a quality commodity is made
accessible to the customers and that too at lower rates cause of lower cost of manufacturing. It, in
turn maximises the need of enterprise good. It will also help in offering consumer satisfaction by
making control and manage the quality of engineering items.
How the improvement strategy would help to sustain the culture of quality in the company
Companies should focus on some key quality process areas to meet the need of the rival
atmosphere and manage their quality competitiveness. By developing a new strategic and
operational leadership model of quality, the business venture can make development in its
quality culture and sustain it long term. It has become increasingly clear that firms which survive
and do well in markets approach quality as a main section of their strategy. Along with this, an
organisation like ETC can adopt an effective concept of quality management then it will also
assist in long term survival of enterprise. If the management of respective firm will organise
session and program on continue basis that help in offering information regarding improvement
strategies then it will also assist in sustainability of culture of quality (Chen, Lee and Wang,
2020). By making concentration of effective management o suppliers and buying process also
assist in sustain the quality culture long time duration.
7
Secure Best Marks with AI Grader
Need help grading? Try our AI Grader for instant feedback on your assignments.
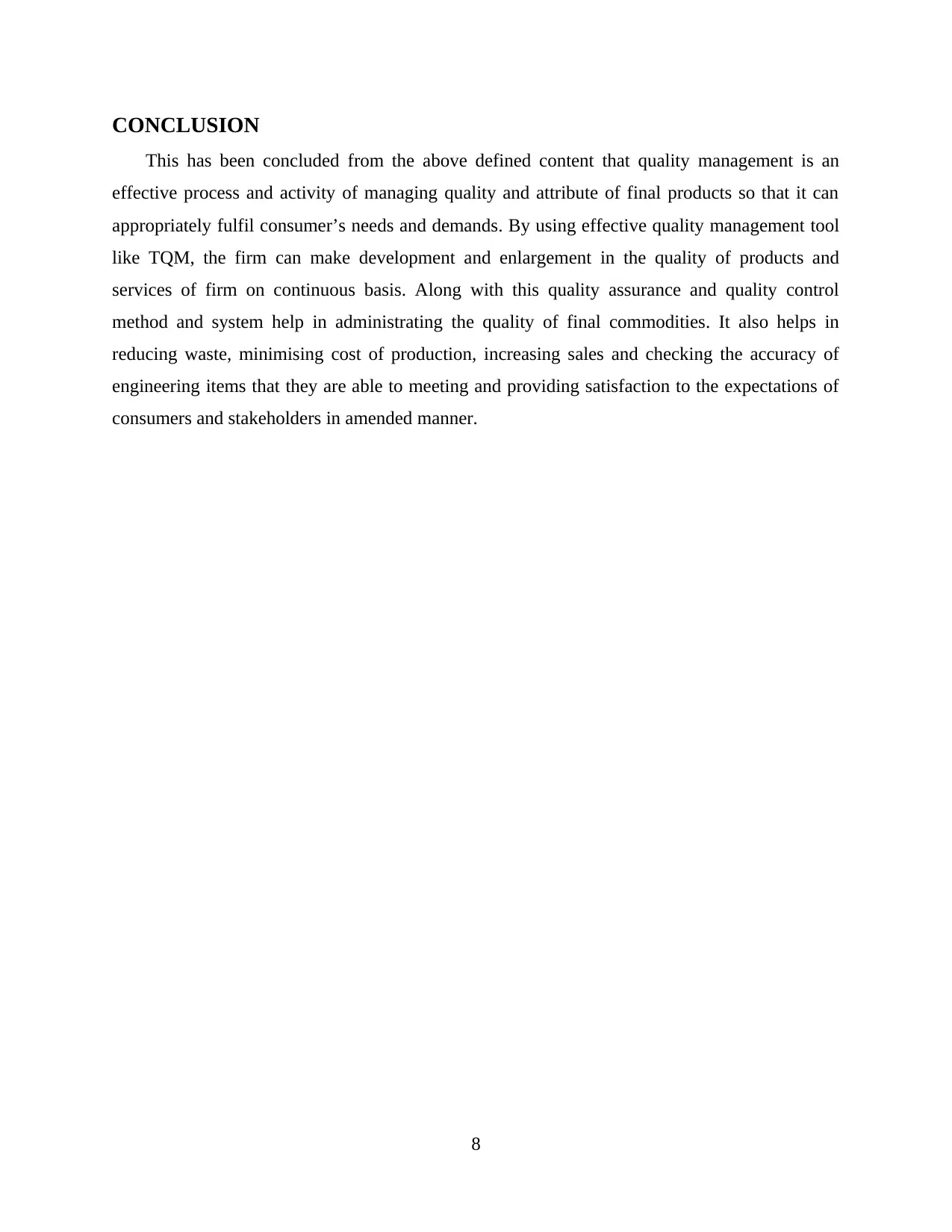
CONCLUSION
This has been concluded from the above defined content that quality management is an
effective process and activity of managing quality and attribute of final products so that it can
appropriately fulfil consumer’s needs and demands. By using effective quality management tool
like TQM, the firm can make development and enlargement in the quality of products and
services of firm on continuous basis. Along with this quality assurance and quality control
method and system help in administrating the quality of final commodities. It also helps in
reducing waste, minimising cost of production, increasing sales and checking the accuracy of
engineering items that they are able to meeting and providing satisfaction to the expectations of
consumers and stakeholders in amended manner.
8
This has been concluded from the above defined content that quality management is an
effective process and activity of managing quality and attribute of final products so that it can
appropriately fulfil consumer’s needs and demands. By using effective quality management tool
like TQM, the firm can make development and enlargement in the quality of products and
services of firm on continuous basis. Along with this quality assurance and quality control
method and system help in administrating the quality of final commodities. It also helps in
reducing waste, minimising cost of production, increasing sales and checking the accuracy of
engineering items that they are able to meeting and providing satisfaction to the expectations of
consumers and stakeholders in amended manner.
8
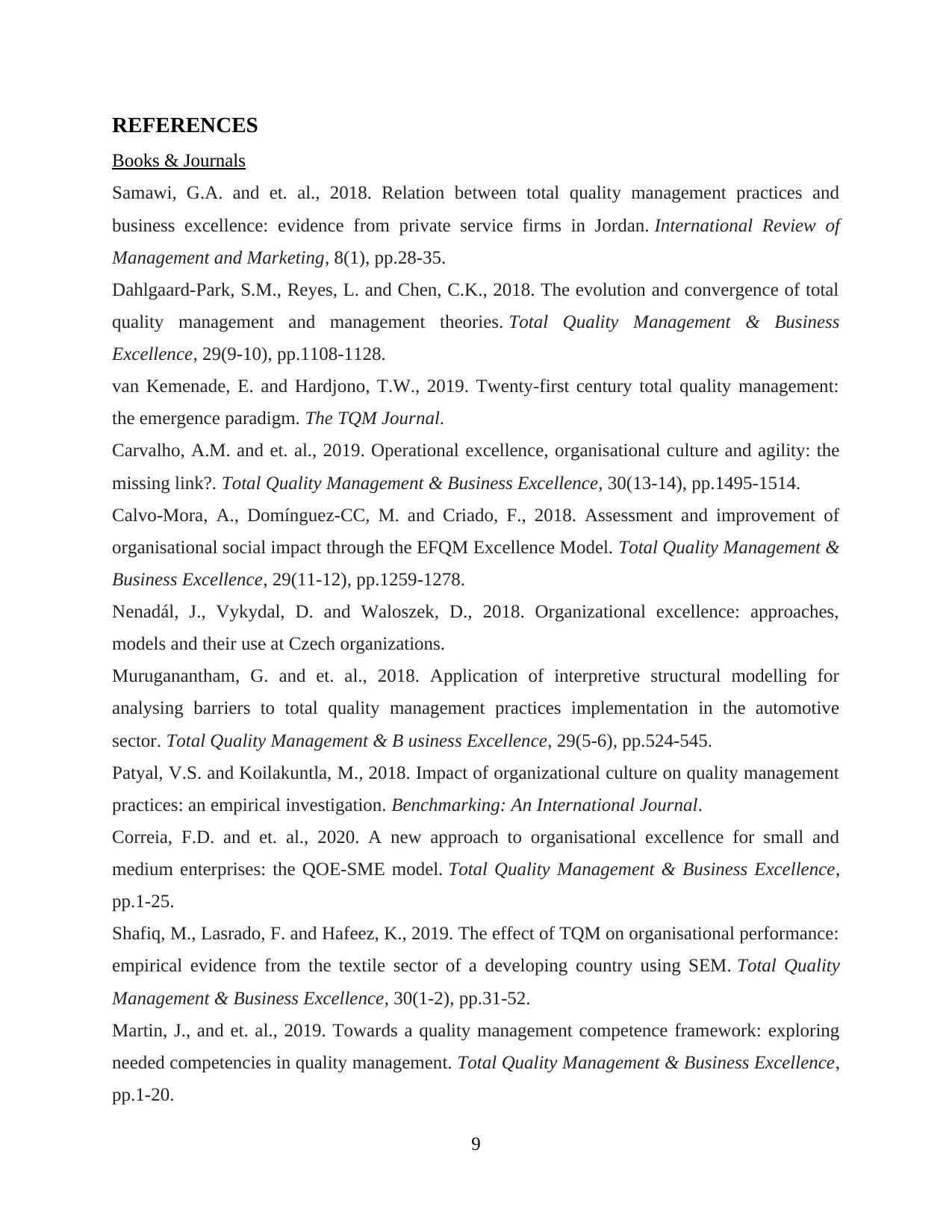
REFERENCES
Books & Journals
Samawi, G.A. and et. al., 2018. Relation between total quality management practices and
business excellence: evidence from private service firms in Jordan. International Review of
Management and Marketing, 8(1), pp.28-35.
Dahlgaard-Park, S.M., Reyes, L. and Chen, C.K., 2018. The evolution and convergence of total
quality management and management theories. Total Quality Management & Business
Excellence, 29(9-10), pp.1108-1128.
van Kemenade, E. and Hardjono, T.W., 2019. Twenty-first century total quality management:
the emergence paradigm. The TQM Journal.
Carvalho, A.M. and et. al., 2019. Operational excellence, organisational culture and agility: the
missing link?. Total Quality Management & Business Excellence, 30(13-14), pp.1495-1514.
Calvo-Mora, A., Domínguez-CC, M. and Criado, F., 2018. Assessment and improvement of
organisational social impact through the EFQM Excellence Model. Total Quality Management &
Business Excellence, 29(11-12), pp.1259-1278.
Nenadál, J., Vykydal, D. and Waloszek, D., 2018. Organizational excellence: approaches,
models and their use at Czech organizations.
Muruganantham, G. and et. al., 2018. Application of interpretive structural modelling for
analysing barriers to total quality management practices implementation in the automotive
sector. Total Quality Management & B usiness Excellence, 29(5-6), pp.524-545.
Patyal, V.S. and Koilakuntla, M., 2018. Impact of organizational culture on quality management
practices: an empirical investigation. Benchmarking: An International Journal.
Correia, F.D. and et. al., 2020. A new approach to organisational excellence for small and
medium enterprises: the QOE-SME model. Total Quality Management & Business Excellence,
pp.1-25.
Shafiq, M., Lasrado, F. and Hafeez, K., 2019. The effect of TQM on organisational performance:
empirical evidence from the textile sector of a developing country using SEM. Total Quality
Management & Business Excellence, 30(1-2), pp.31-52.
Martin, J., and et. al., 2019. Towards a quality management competence framework: exploring
needed competencies in quality management. Total Quality Management & Business Excellence,
pp.1-20.
9
Books & Journals
Samawi, G.A. and et. al., 2018. Relation between total quality management practices and
business excellence: evidence from private service firms in Jordan. International Review of
Management and Marketing, 8(1), pp.28-35.
Dahlgaard-Park, S.M., Reyes, L. and Chen, C.K., 2018. The evolution and convergence of total
quality management and management theories. Total Quality Management & Business
Excellence, 29(9-10), pp.1108-1128.
van Kemenade, E. and Hardjono, T.W., 2019. Twenty-first century total quality management:
the emergence paradigm. The TQM Journal.
Carvalho, A.M. and et. al., 2019. Operational excellence, organisational culture and agility: the
missing link?. Total Quality Management & Business Excellence, 30(13-14), pp.1495-1514.
Calvo-Mora, A., Domínguez-CC, M. and Criado, F., 2018. Assessment and improvement of
organisational social impact through the EFQM Excellence Model. Total Quality Management &
Business Excellence, 29(11-12), pp.1259-1278.
Nenadál, J., Vykydal, D. and Waloszek, D., 2018. Organizational excellence: approaches,
models and their use at Czech organizations.
Muruganantham, G. and et. al., 2018. Application of interpretive structural modelling for
analysing barriers to total quality management practices implementation in the automotive
sector. Total Quality Management & B usiness Excellence, 29(5-6), pp.524-545.
Patyal, V.S. and Koilakuntla, M., 2018. Impact of organizational culture on quality management
practices: an empirical investigation. Benchmarking: An International Journal.
Correia, F.D. and et. al., 2020. A new approach to organisational excellence for small and
medium enterprises: the QOE-SME model. Total Quality Management & Business Excellence,
pp.1-25.
Shafiq, M., Lasrado, F. and Hafeez, K., 2019. The effect of TQM on organisational performance:
empirical evidence from the textile sector of a developing country using SEM. Total Quality
Management & Business Excellence, 30(1-2), pp.31-52.
Martin, J., and et. al., 2019. Towards a quality management competence framework: exploring
needed competencies in quality management. Total Quality Management & Business Excellence,
pp.1-20.
9
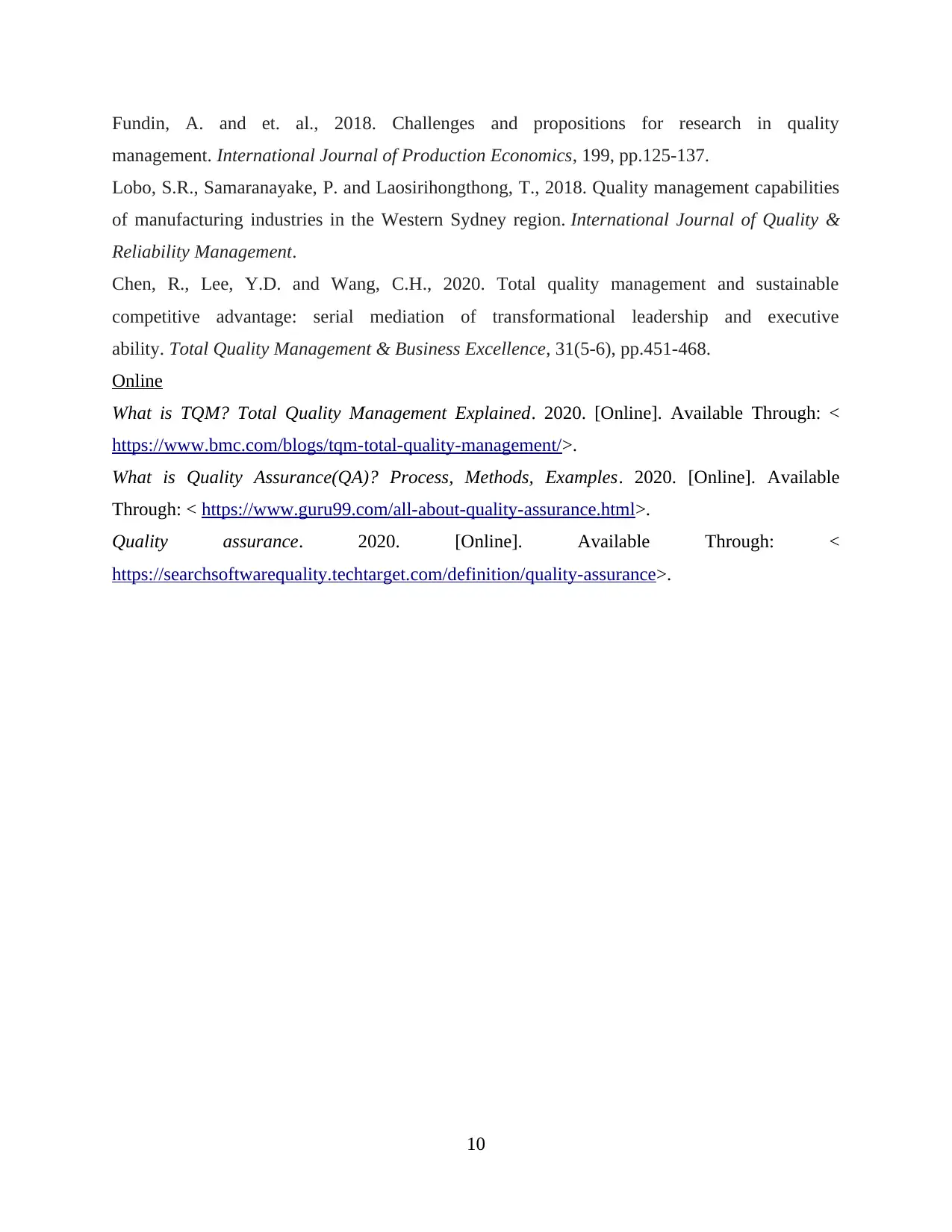
Fundin, A. and et. al., 2018. Challenges and propositions for research in quality
management. International Journal of Production Economics, 199, pp.125-137.
Lobo, S.R., Samaranayake, P. and Laosirihongthong, T., 2018. Quality management capabilities
of manufacturing industries in the Western Sydney region. International Journal of Quality &
Reliability Management.
Chen, R., Lee, Y.D. and Wang, C.H., 2020. Total quality management and sustainable
competitive advantage: serial mediation of transformational leadership and executive
ability. Total Quality Management & Business Excellence, 31(5-6), pp.451-468.
Online
What is TQM? Total Quality Management Explained. 2020. [Online]. Available Through: <
https://www.bmc.com/blogs/tqm-total-quality-management/>.
What is Quality Assurance(QA)? Process, Methods, Examples. 2020. [Online]. Available
Through: < https://www.guru99.com/all-about-quality-assurance.html>.
Quality assurance. 2020. [Online]. Available Through: <
https://searchsoftwarequality.techtarget.com/definition/quality-assurance>.
10
management. International Journal of Production Economics, 199, pp.125-137.
Lobo, S.R., Samaranayake, P. and Laosirihongthong, T., 2018. Quality management capabilities
of manufacturing industries in the Western Sydney region. International Journal of Quality &
Reliability Management.
Chen, R., Lee, Y.D. and Wang, C.H., 2020. Total quality management and sustainable
competitive advantage: serial mediation of transformational leadership and executive
ability. Total Quality Management & Business Excellence, 31(5-6), pp.451-468.
Online
What is TQM? Total Quality Management Explained. 2020. [Online]. Available Through: <
https://www.bmc.com/blogs/tqm-total-quality-management/>.
What is Quality Assurance(QA)? Process, Methods, Examples. 2020. [Online]. Available
Through: < https://www.guru99.com/all-about-quality-assurance.html>.
Quality assurance. 2020. [Online]. Available Through: <
https://searchsoftwarequality.techtarget.com/definition/quality-assurance>.
10
1 out of 13
Related Documents

Your All-in-One AI-Powered Toolkit for Academic Success.
+13062052269
info@desklib.com
Available 24*7 on WhatsApp / Email
Unlock your academic potential
© 2024 | Zucol Services PVT LTD | All rights reserved.