BADM 370: Quality Management Report on A-1 Express Delivery Service
VerifiedAdded on 2022/11/25
|15
|2284
|413
Report
AI Summary
This report provides a comprehensive analysis of quality management principles, theories, tools, and strategies applicable to A-1 Express Delivery Service. It begins with an introduction to quality management, followed by a historical overview and the specific needs for implementing a Quality Management System (QMS) within the company. The report details the Deming Cycle (PDSA) and Six Sigma methodologies, outlining their pros and cons. Furthermore, it explores the roles and responsibilities of senior management in quality improvement programs, along with key metrics for performance monitoring. The report also includes a discussion on general quality strategies and tools, illustrated with a comparative study table. The content is structured to provide a practical understanding of quality management in the context of a transportation and delivery service, offering insights into continuous improvement and customer satisfaction. The report aims to serve as a training manual for the company, providing a foundation for quality management practices.
Contribute Materials
Your contribution can guide someone’s learning journey. Share your
documents today.
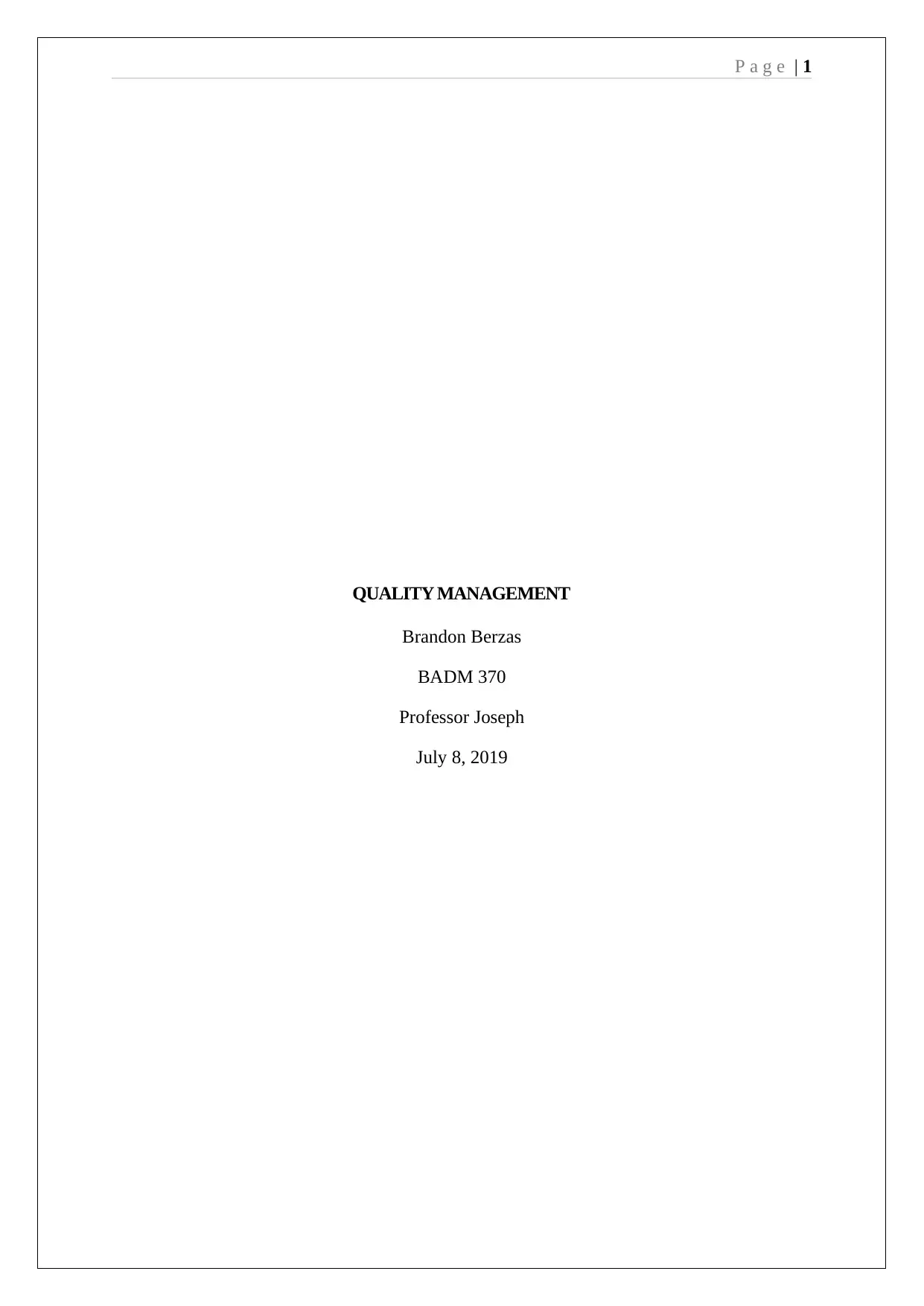
P a g e | 1
QUALITY MANAGEMENT
Brandon Berzas
BADM 370
Professor Joseph
July 8, 2019
QUALITY MANAGEMENT
Brandon Berzas
BADM 370
Professor Joseph
July 8, 2019
Secure Best Marks with AI Grader
Need help grading? Try our AI Grader for instant feedback on your assignments.
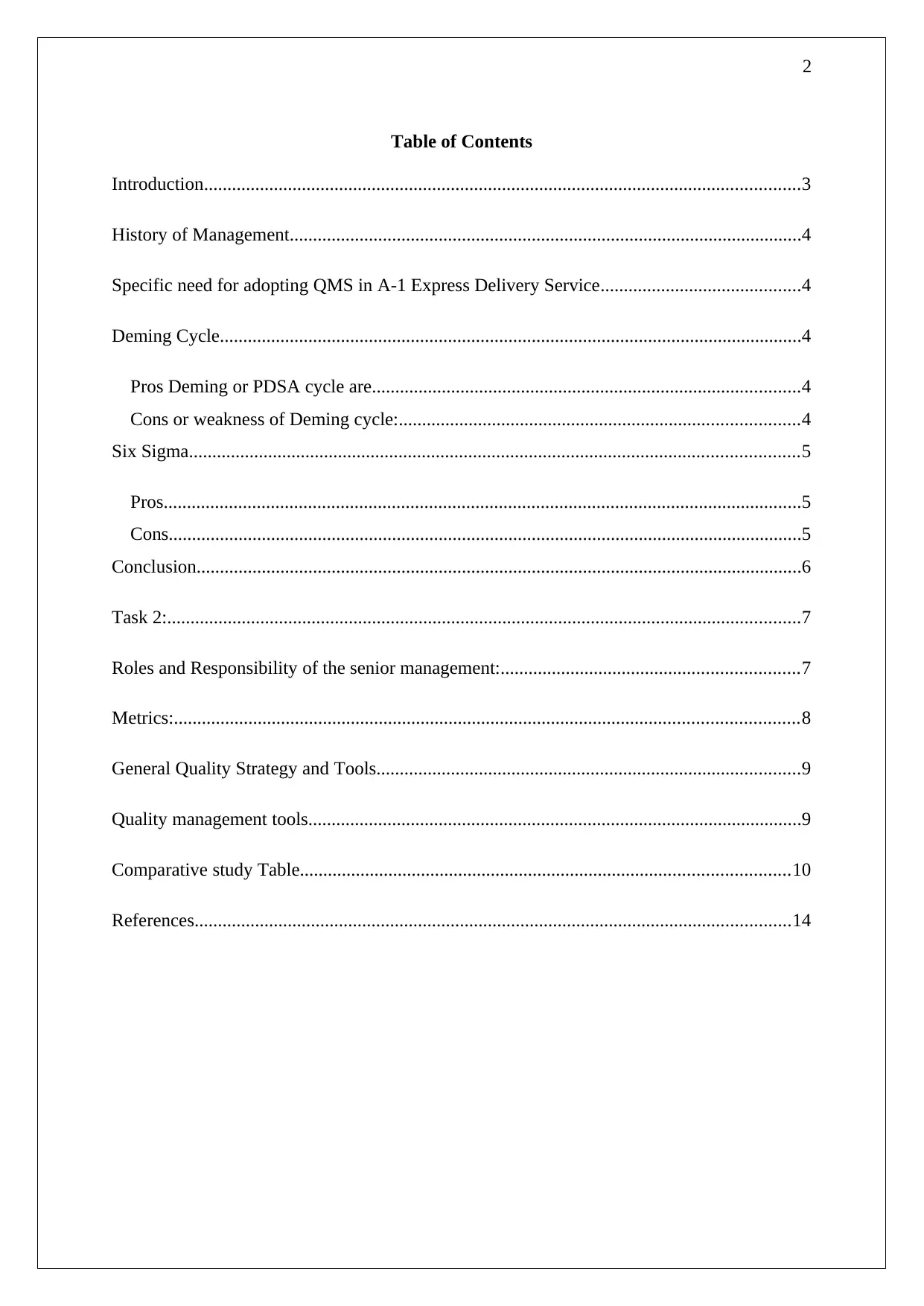
2
Table of Contents
Introduction................................................................................................................................3
History of Management..............................................................................................................4
Specific need for adopting QMS in A-1 Express Delivery Service...........................................4
Deming Cycle.............................................................................................................................4
Pros Deming or PDSA cycle are............................................................................................4
Cons or weakness of Deming cycle:......................................................................................4
Six Sigma...................................................................................................................................5
Pros.........................................................................................................................................5
Cons........................................................................................................................................5
Conclusion..................................................................................................................................6
Task 2:........................................................................................................................................7
Roles and Responsibility of the senior management:................................................................7
Metrics:......................................................................................................................................8
General Quality Strategy and Tools...........................................................................................9
Quality management tools..........................................................................................................9
Comparative study Table.........................................................................................................10
References................................................................................................................................14
Table of Contents
Introduction................................................................................................................................3
History of Management..............................................................................................................4
Specific need for adopting QMS in A-1 Express Delivery Service...........................................4
Deming Cycle.............................................................................................................................4
Pros Deming or PDSA cycle are............................................................................................4
Cons or weakness of Deming cycle:......................................................................................4
Six Sigma...................................................................................................................................5
Pros.........................................................................................................................................5
Cons........................................................................................................................................5
Conclusion..................................................................................................................................6
Task 2:........................................................................................................................................7
Roles and Responsibility of the senior management:................................................................7
Metrics:......................................................................................................................................8
General Quality Strategy and Tools...........................................................................................9
Quality management tools..........................................................................................................9
Comparative study Table.........................................................................................................10
References................................................................................................................................14
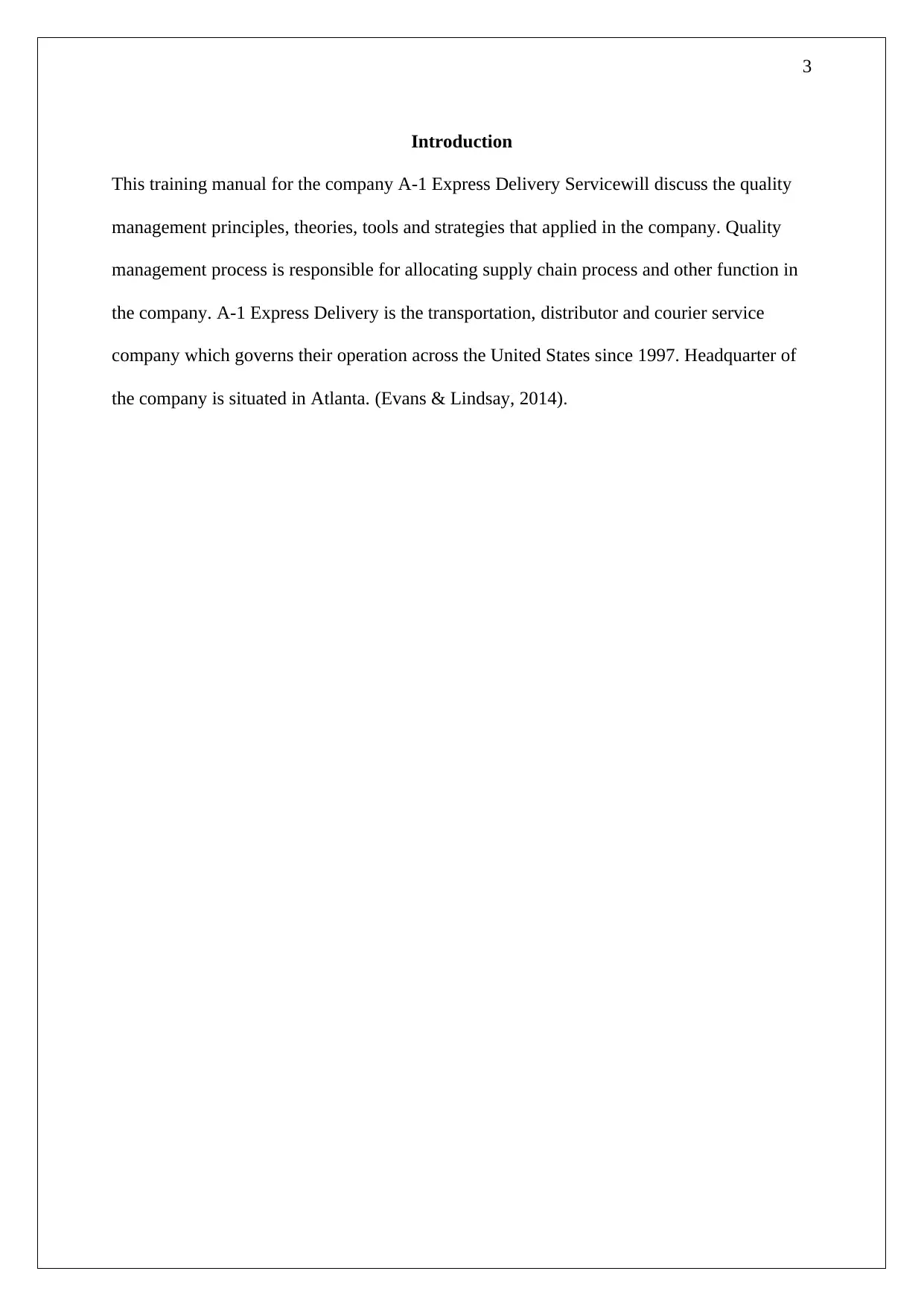
3
Introduction
This training manual for the company A-1 Express Delivery Servicewill discuss the quality
management principles, theories, tools and strategies that applied in the company. Quality
management process is responsible for allocating supply chain process and other function in
the company. A-1 Express Delivery is the transportation, distributor and courier service
company which governs their operation across the United States since 1997. Headquarter of
the company is situated in Atlanta. (Evans & Lindsay, 2014).
Introduction
This training manual for the company A-1 Express Delivery Servicewill discuss the quality
management principles, theories, tools and strategies that applied in the company. Quality
management process is responsible for allocating supply chain process and other function in
the company. A-1 Express Delivery is the transportation, distributor and courier service
company which governs their operation across the United States since 1997. Headquarter of
the company is situated in Atlanta. (Evans & Lindsay, 2014).
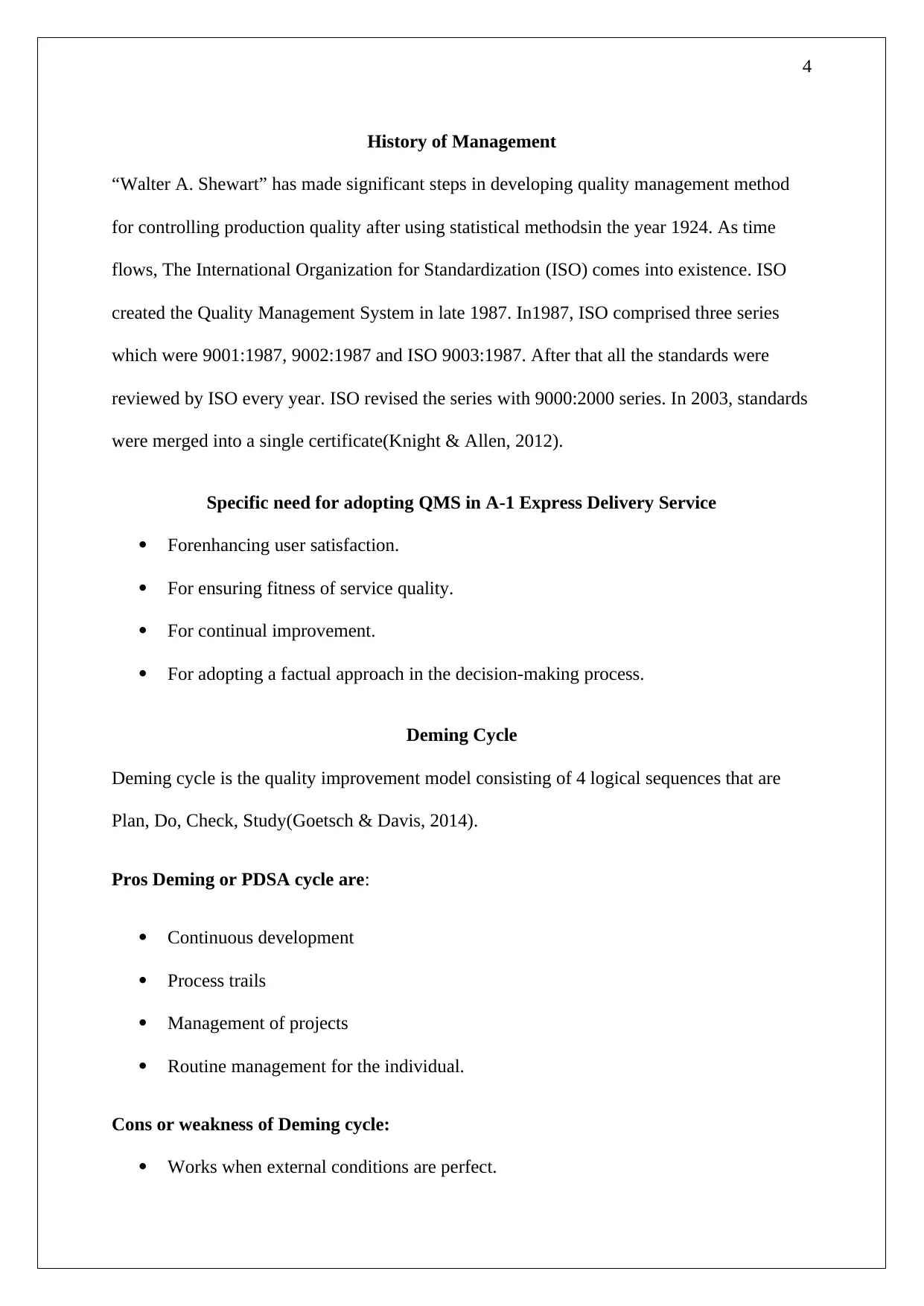
4
History of Management
“Walter A. Shewart” has made significant steps in developing quality management method
for controlling production quality after using statistical methodsin the year 1924. As time
flows, The International Organization for Standardization (ISO) comes into existence. ISO
created the Quality Management System in late 1987. In1987, ISO comprised three series
which were 9001:1987, 9002:1987 and ISO 9003:1987. After that all the standards were
reviewed by ISO every year. ISO revised the series with 9000:2000 series. In 2003, standards
were merged into a single certificate(Knight & Allen, 2012).
Specific need for adopting QMS in A-1 Express Delivery Service
Forenhancing user satisfaction.
For ensuring fitness of service quality.
For continual improvement.
For adopting a factual approach in the decision-making process.
Deming Cycle
Deming cycle is the quality improvement model consisting of 4 logical sequences that are
Plan, Do, Check, Study(Goetsch & Davis, 2014).
Pros Deming or PDSA cycle are:
Continuous development
Process trails
Management of projects
Routine management for the individual.
Cons or weakness of Deming cycle:
Works when external conditions are perfect.
History of Management
“Walter A. Shewart” has made significant steps in developing quality management method
for controlling production quality after using statistical methodsin the year 1924. As time
flows, The International Organization for Standardization (ISO) comes into existence. ISO
created the Quality Management System in late 1987. In1987, ISO comprised three series
which were 9001:1987, 9002:1987 and ISO 9003:1987. After that all the standards were
reviewed by ISO every year. ISO revised the series with 9000:2000 series. In 2003, standards
were merged into a single certificate(Knight & Allen, 2012).
Specific need for adopting QMS in A-1 Express Delivery Service
Forenhancing user satisfaction.
For ensuring fitness of service quality.
For continual improvement.
For adopting a factual approach in the decision-making process.
Deming Cycle
Deming cycle is the quality improvement model consisting of 4 logical sequences that are
Plan, Do, Check, Study(Goetsch & Davis, 2014).
Pros Deming or PDSA cycle are:
Continuous development
Process trails
Management of projects
Routine management for the individual.
Cons or weakness of Deming cycle:
Works when external conditions are perfect.
Secure Best Marks with AI Grader
Need help grading? Try our AI Grader for instant feedback on your assignments.
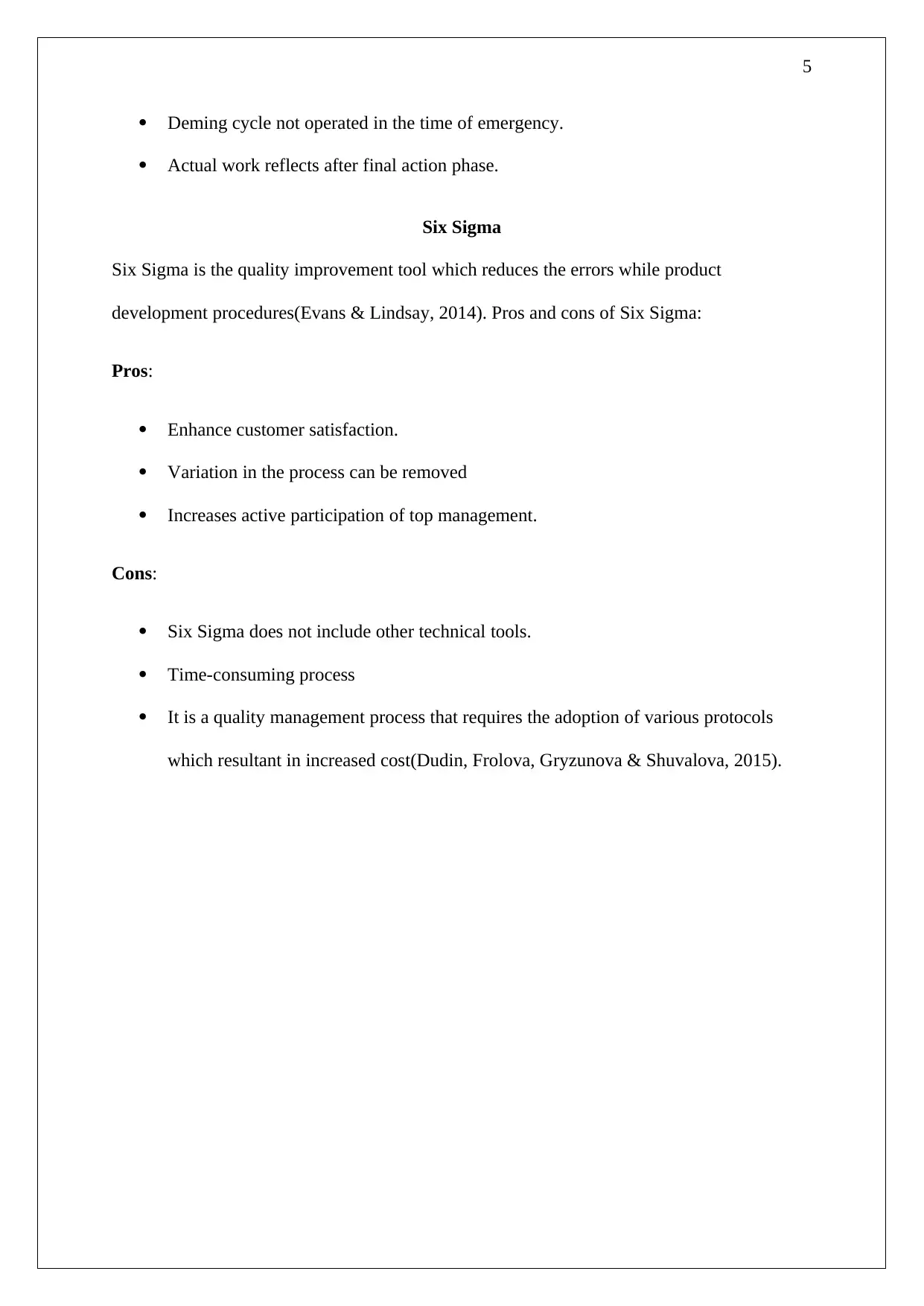
5
Deming cycle not operated in the time of emergency.
Actual work reflects after final action phase.
Six Sigma
Six Sigma is the quality improvement tool which reduces the errors while product
development procedures(Evans & Lindsay, 2014). Pros and cons of Six Sigma:
Pros:
Enhance customer satisfaction.
Variation in the process can be removed
Increases active participation of top management.
Cons:
Six Sigma does not include other technical tools.
Time-consuming process
It is a quality management process that requires the adoption of various protocols
which resultant in increased cost(Dudin, Frolova, Gryzunova & Shuvalova, 2015).
Deming cycle not operated in the time of emergency.
Actual work reflects after final action phase.
Six Sigma
Six Sigma is the quality improvement tool which reduces the errors while product
development procedures(Evans & Lindsay, 2014). Pros and cons of Six Sigma:
Pros:
Enhance customer satisfaction.
Variation in the process can be removed
Increases active participation of top management.
Cons:
Six Sigma does not include other technical tools.
Time-consuming process
It is a quality management process that requires the adoption of various protocols
which resultant in increased cost(Dudin, Frolova, Gryzunova & Shuvalova, 2015).
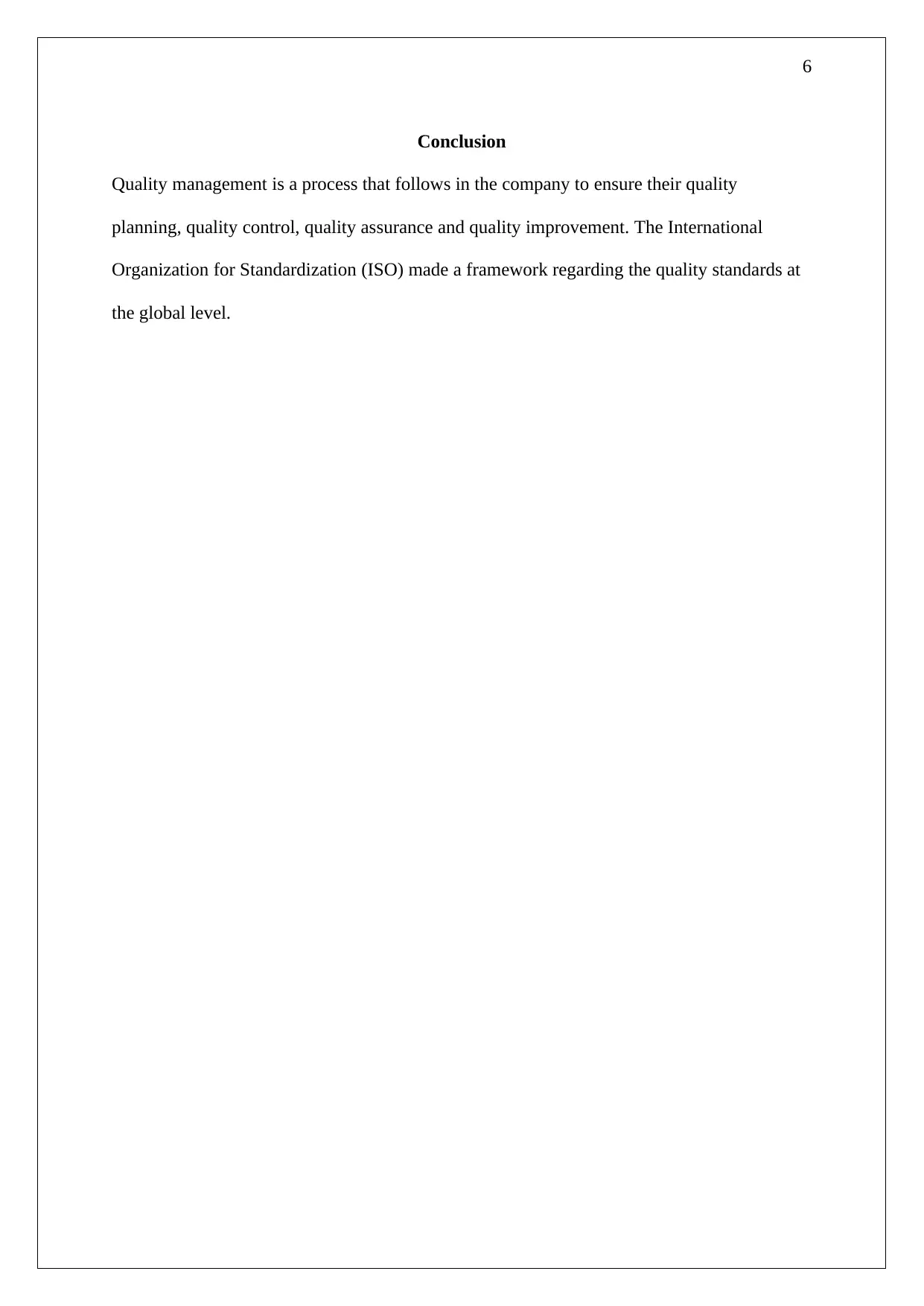
6
Conclusion
Quality management is a process that follows in the company to ensure their quality
planning, quality control, quality assurance and quality improvement. The International
Organization for Standardization (ISO) made a framework regarding the quality standards at
the global level.
Conclusion
Quality management is a process that follows in the company to ensure their quality
planning, quality control, quality assurance and quality improvement. The International
Organization for Standardization (ISO) made a framework regarding the quality standards at
the global level.
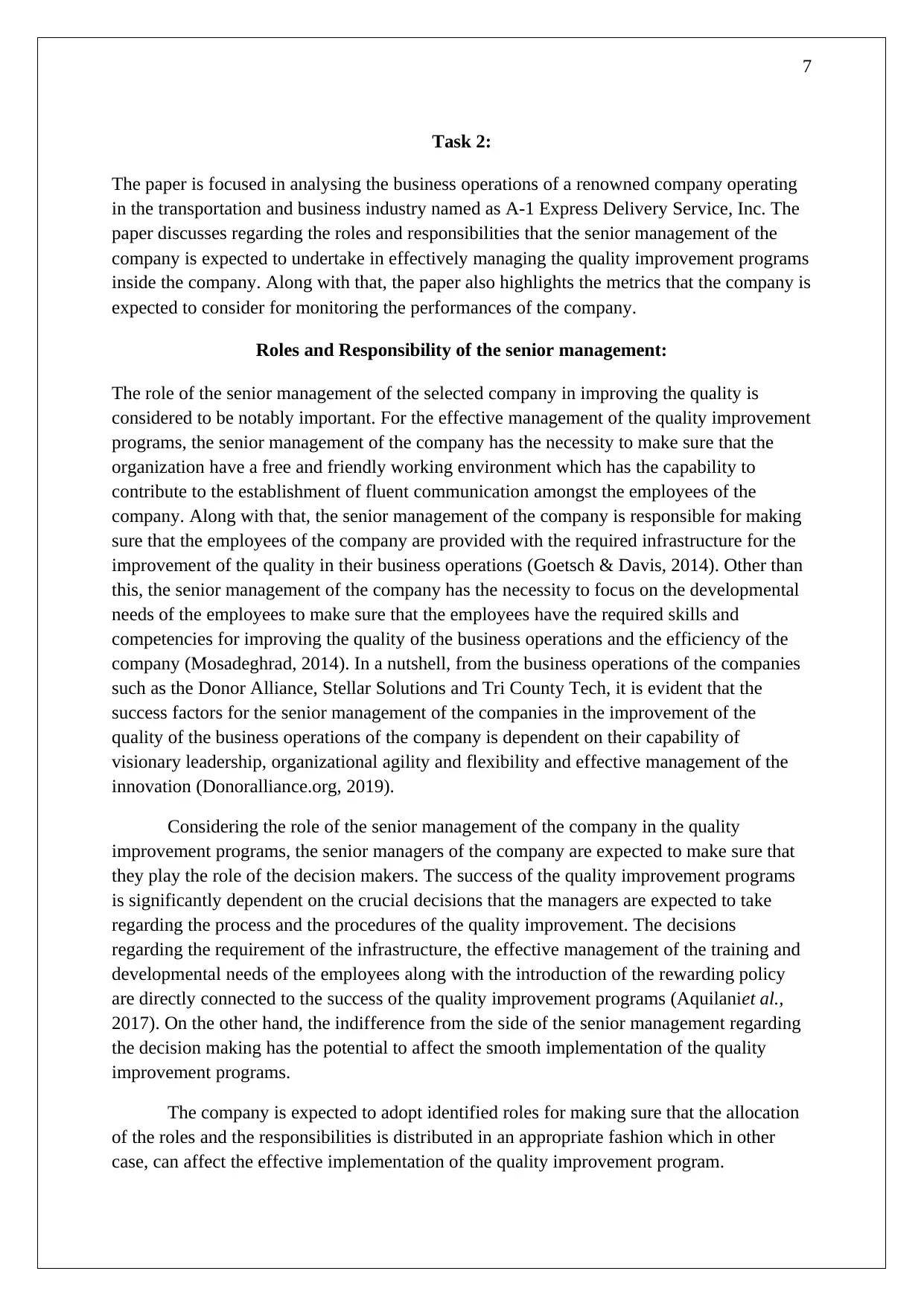
7
Task 2:
The paper is focused in analysing the business operations of a renowned company operating
in the transportation and business industry named as A-1 Express Delivery Service, Inc. The
paper discusses regarding the roles and responsibilities that the senior management of the
company is expected to undertake in effectively managing the quality improvement programs
inside the company. Along with that, the paper also highlights the metrics that the company is
expected to consider for monitoring the performances of the company.
Roles and Responsibility of the senior management:
The role of the senior management of the selected company in improving the quality is
considered to be notably important. For the effective management of the quality improvement
programs, the senior management of the company has the necessity to make sure that the
organization have a free and friendly working environment which has the capability to
contribute to the establishment of fluent communication amongst the employees of the
company. Along with that, the senior management of the company is responsible for making
sure that the employees of the company are provided with the required infrastructure for the
improvement of the quality in their business operations (Goetsch & Davis, 2014). Other than
this, the senior management of the company has the necessity to focus on the developmental
needs of the employees to make sure that the employees have the required skills and
competencies for improving the quality of the business operations and the efficiency of the
company (Mosadeghrad, 2014). In a nutshell, from the business operations of the companies
such as the Donor Alliance, Stellar Solutions and Tri County Tech, it is evident that the
success factors for the senior management of the companies in the improvement of the
quality of the business operations of the company is dependent on their capability of
visionary leadership, organizational agility and flexibility and effective management of the
innovation (Donoralliance.org, 2019).
Considering the role of the senior management of the company in the quality
improvement programs, the senior managers of the company are expected to make sure that
they play the role of the decision makers. The success of the quality improvement programs
is significantly dependent on the crucial decisions that the managers are expected to take
regarding the process and the procedures of the quality improvement. The decisions
regarding the requirement of the infrastructure, the effective management of the training and
developmental needs of the employees along with the introduction of the rewarding policy
are directly connected to the success of the quality improvement programs (Aquilaniet al.,
2017). On the other hand, the indifference from the side of the senior management regarding
the decision making has the potential to affect the smooth implementation of the quality
improvement programs.
The company is expected to adopt identified roles for making sure that the allocation
of the roles and the responsibilities is distributed in an appropriate fashion which in other
case, can affect the effective implementation of the quality improvement program.
Task 2:
The paper is focused in analysing the business operations of a renowned company operating
in the transportation and business industry named as A-1 Express Delivery Service, Inc. The
paper discusses regarding the roles and responsibilities that the senior management of the
company is expected to undertake in effectively managing the quality improvement programs
inside the company. Along with that, the paper also highlights the metrics that the company is
expected to consider for monitoring the performances of the company.
Roles and Responsibility of the senior management:
The role of the senior management of the selected company in improving the quality is
considered to be notably important. For the effective management of the quality improvement
programs, the senior management of the company has the necessity to make sure that the
organization have a free and friendly working environment which has the capability to
contribute to the establishment of fluent communication amongst the employees of the
company. Along with that, the senior management of the company is responsible for making
sure that the employees of the company are provided with the required infrastructure for the
improvement of the quality in their business operations (Goetsch & Davis, 2014). Other than
this, the senior management of the company has the necessity to focus on the developmental
needs of the employees to make sure that the employees have the required skills and
competencies for improving the quality of the business operations and the efficiency of the
company (Mosadeghrad, 2014). In a nutshell, from the business operations of the companies
such as the Donor Alliance, Stellar Solutions and Tri County Tech, it is evident that the
success factors for the senior management of the companies in the improvement of the
quality of the business operations of the company is dependent on their capability of
visionary leadership, organizational agility and flexibility and effective management of the
innovation (Donoralliance.org, 2019).
Considering the role of the senior management of the company in the quality
improvement programs, the senior managers of the company are expected to make sure that
they play the role of the decision makers. The success of the quality improvement programs
is significantly dependent on the crucial decisions that the managers are expected to take
regarding the process and the procedures of the quality improvement. The decisions
regarding the requirement of the infrastructure, the effective management of the training and
developmental needs of the employees along with the introduction of the rewarding policy
are directly connected to the success of the quality improvement programs (Aquilaniet al.,
2017). On the other hand, the indifference from the side of the senior management regarding
the decision making has the potential to affect the smooth implementation of the quality
improvement programs.
The company is expected to adopt identified roles for making sure that the allocation
of the roles and the responsibilities is distributed in an appropriate fashion which in other
case, can affect the effective implementation of the quality improvement program.
Paraphrase This Document
Need a fresh take? Get an instant paraphrase of this document with our AI Paraphraser
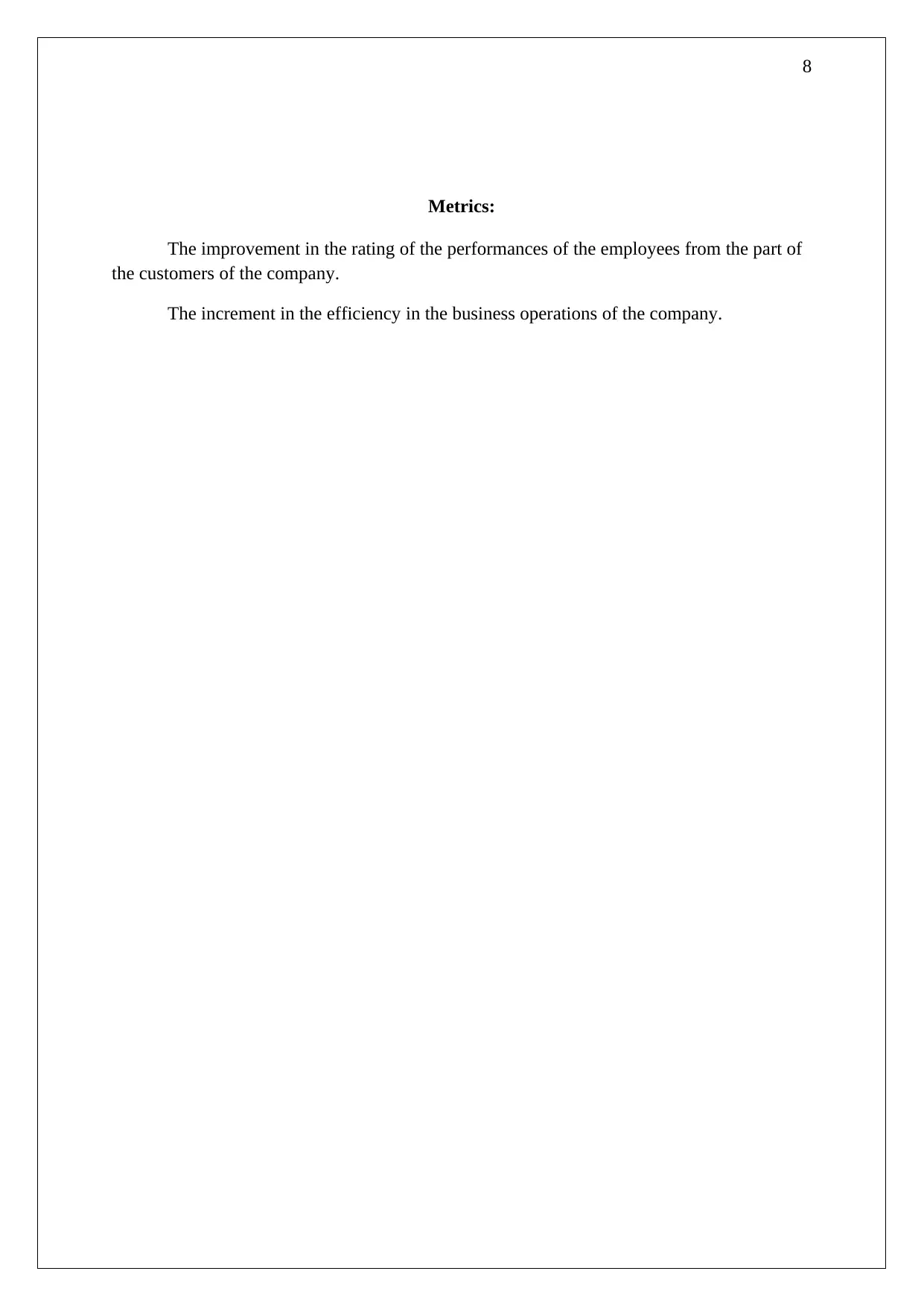
8
Metrics:
The improvement in the rating of the performances of the employees from the part of
the customers of the company.
The increment in the efficiency in the business operations of the company.
Metrics:
The improvement in the rating of the performances of the employees from the part of
the customers of the company.
The increment in the efficiency in the business operations of the company.
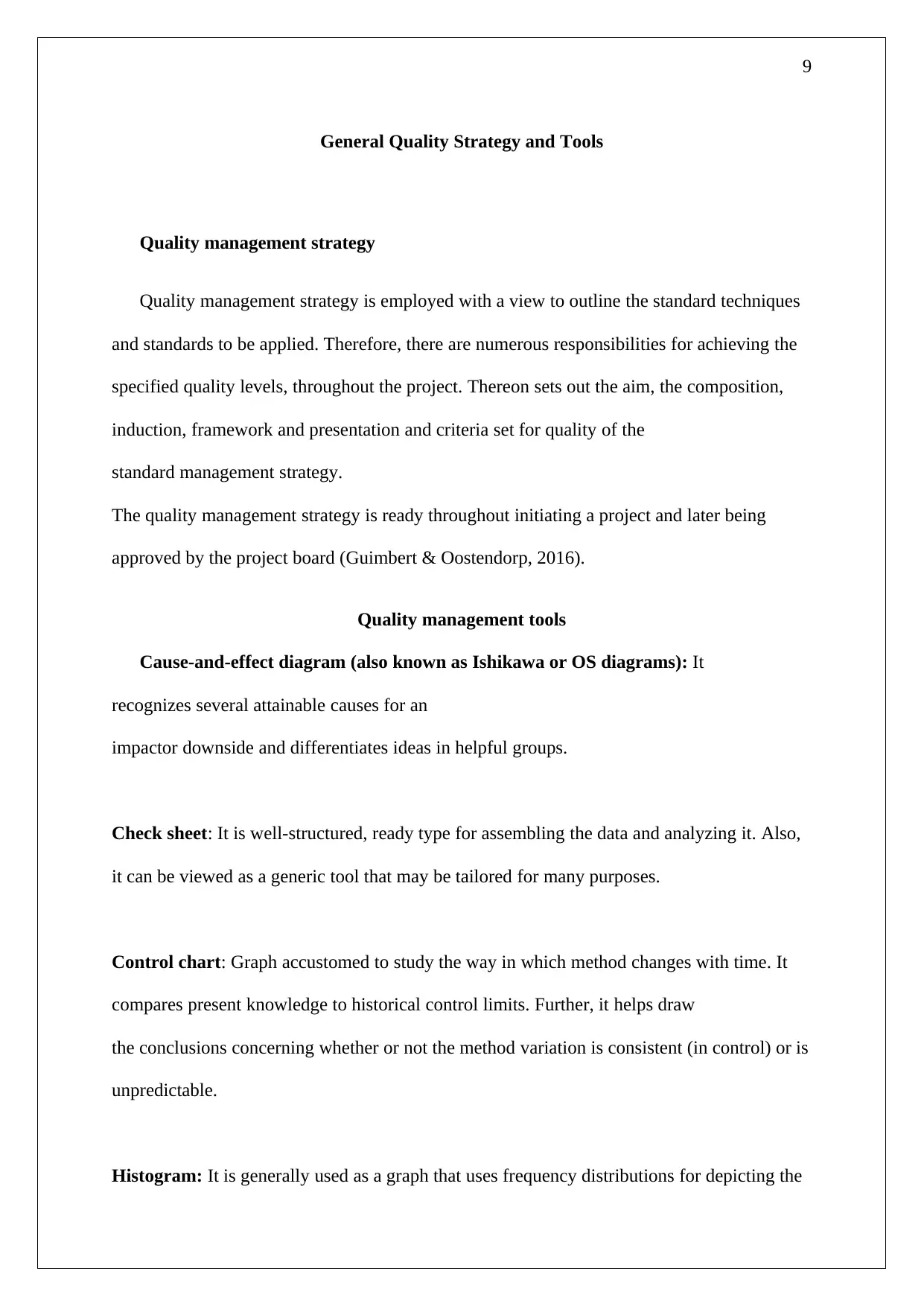
9
General Quality Strategy and Tools
Quality management strategy
Quality management strategy is employed with a view to outline the standard techniques
and standards to be applied. Therefore, there are numerous responsibilities for achieving the
specified quality levels, throughout the project. Thereon sets out the aim, the composition,
induction, framework and presentation and criteria set for quality of the
standard management strategy.
The quality management strategy is ready throughout initiating a project and later being
approved by the project board (Guimbert & Oostendorp, 2016).
Quality management tools
Cause-and-effect diagram (also known as Ishikawa or OS diagrams): It
recognizes several attainable causes for an
impactor downside and differentiates ideas in helpful groups.
Check sheet: It is well-structured, ready type for assembling the data and analyzing it. Also,
it can be viewed as a generic tool that may be tailored for many purposes.
Control chart: Graph accustomed to study the way in which method changes with time. It
compares present knowledge to historical control limits. Further, it helps draw
the conclusions concerning whether or not the method variation is consistent (in control) or is
unpredictable.
Histogram: It is generally used as a graph that uses frequency distributions for depicting the
General Quality Strategy and Tools
Quality management strategy
Quality management strategy is employed with a view to outline the standard techniques
and standards to be applied. Therefore, there are numerous responsibilities for achieving the
specified quality levels, throughout the project. Thereon sets out the aim, the composition,
induction, framework and presentation and criteria set for quality of the
standard management strategy.
The quality management strategy is ready throughout initiating a project and later being
approved by the project board (Guimbert & Oostendorp, 2016).
Quality management tools
Cause-and-effect diagram (also known as Ishikawa or OS diagrams): It
recognizes several attainable causes for an
impactor downside and differentiates ideas in helpful groups.
Check sheet: It is well-structured, ready type for assembling the data and analyzing it. Also,
it can be viewed as a generic tool that may be tailored for many purposes.
Control chart: Graph accustomed to study the way in which method changes with time. It
compares present knowledge to historical control limits. Further, it helps draw
the conclusions concerning whether or not the method variation is consistent (in control) or is
unpredictable.
Histogram: It is generally used as a graph that uses frequency distributions for depicting the
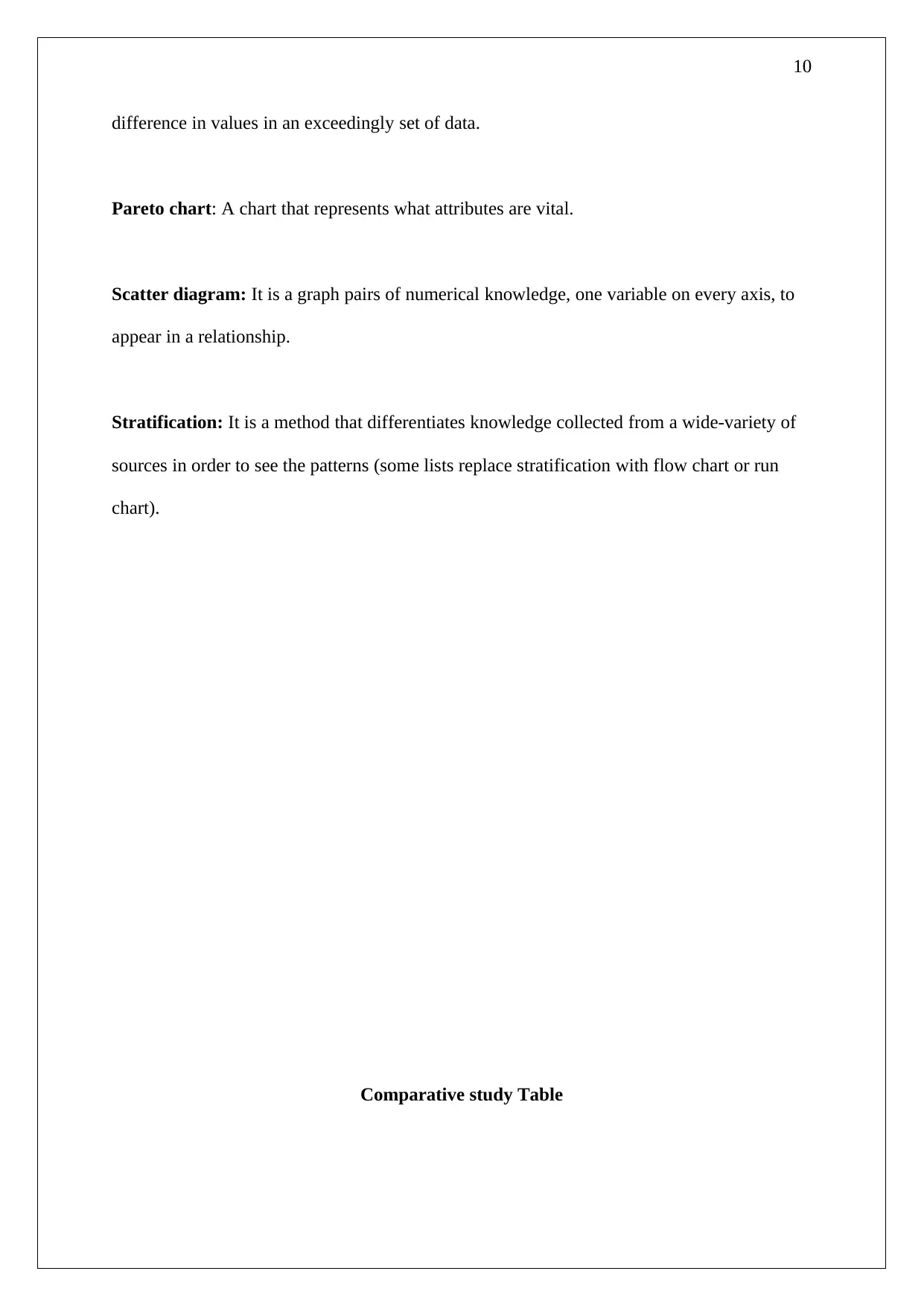
10
difference in values in an exceedingly set of data.
Pareto chart: A chart that represents what attributes are vital.
Scatter diagram: It is a graph pairs of numerical knowledge, one variable on every axis, to
appear in a relationship.
Stratification: It is a method that differentiates knowledge collected from a wide-variety of
sources in order to see the patterns (some lists replace stratification with flow chart or run
chart).
Comparative study Table
difference in values in an exceedingly set of data.
Pareto chart: A chart that represents what attributes are vital.
Scatter diagram: It is a graph pairs of numerical knowledge, one variable on every axis, to
appear in a relationship.
Stratification: It is a method that differentiates knowledge collected from a wide-variety of
sources in order to see the patterns (some lists replace stratification with flow chart or run
chart).
Comparative study Table
Secure Best Marks with AI Grader
Need help grading? Try our AI Grader for instant feedback on your assignments.
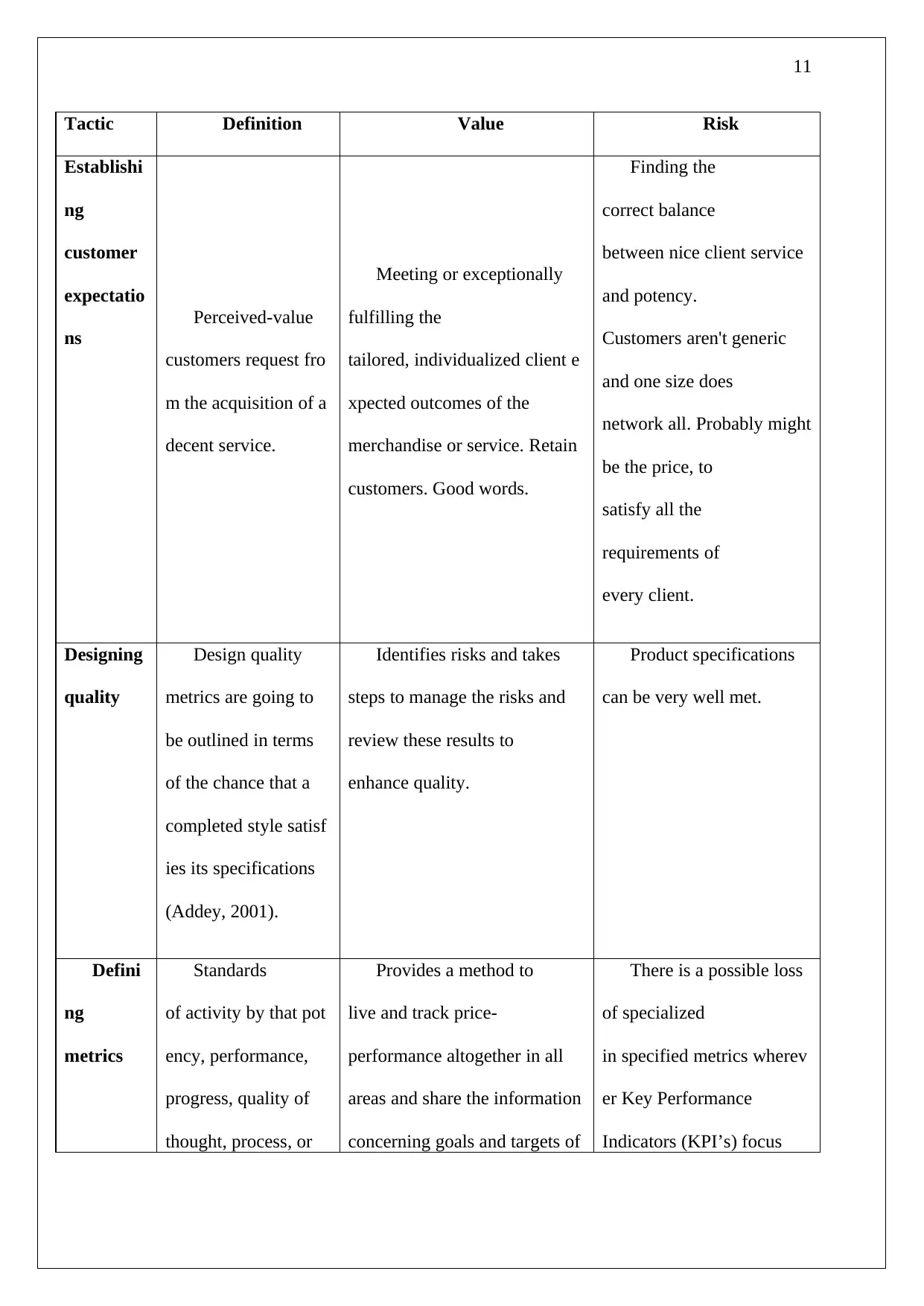
11
Tactic Definition Value Risk
Establishi
ng
customer
expectatio
ns
Perceived-value
customers request fro
m the acquisition of a
decent service.
Meeting or exceptionally
fulfilling the
tailored, individualized client e
xpected outcomes of the
merchandise or service. Retain
customers. Good words.
Finding the
correct balance
between nice client service
and potency.
Customers aren't generic
and one size does
network all. Probably might
be the price, to
satisfy all the
requirements of
every client.
Designing
quality
Design quality
metrics are going to
be outlined in terms
of the chance that a
completed style satisf
ies its specifications
(Addey, 2001).
Identifies risks and takes
steps to manage the risks and
review these results to
enhance quality.
Product specifications
can be very well met.
Defini
ng
metrics
Standards
of activity by that pot
ency, performance,
progress, quality of
thought, process, or
Provides a method to
live and track price-
performance altogether in all
areas and share the information
concerning goals and targets of
There is a possible loss
of specialized
in specified metrics wherev
er Key Performance
Indicators (KPI’s) focus
Tactic Definition Value Risk
Establishi
ng
customer
expectatio
ns
Perceived-value
customers request fro
m the acquisition of a
decent service.
Meeting or exceptionally
fulfilling the
tailored, individualized client e
xpected outcomes of the
merchandise or service. Retain
customers. Good words.
Finding the
correct balance
between nice client service
and potency.
Customers aren't generic
and one size does
network all. Probably might
be the price, to
satisfy all the
requirements of
every client.
Designing
quality
Design quality
metrics are going to
be outlined in terms
of the chance that a
completed style satisf
ies its specifications
(Addey, 2001).
Identifies risks and takes
steps to manage the risks and
review these results to
enhance quality.
Product specifications
can be very well met.
Defini
ng
metrics
Standards
of activity by that pot
ency, performance,
progress, quality of
thought, process, or
Provides a method to
live and track price-
performance altogether in all
areas and share the information
concerning goals and targets of
There is a possible loss
of specialized
in specified metrics wherev
er Key Performance
Indicators (KPI’s) focus
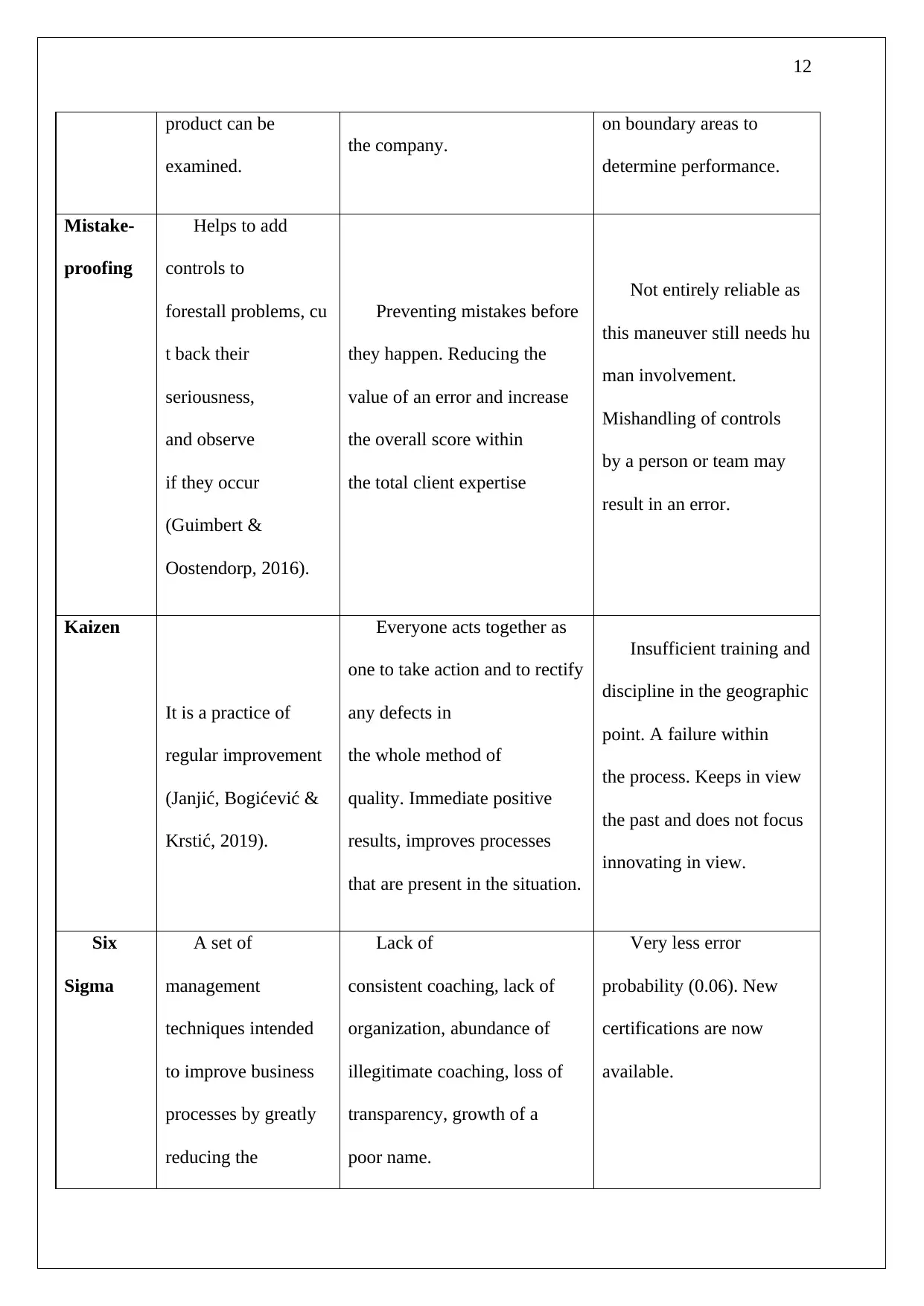
12
product can be
examined.
the company.
on boundary areas to
determine performance.
Mistake-
proofing
Helps to add
controls to
forestall problems, cu
t back their
seriousness,
and observe
if they occur
(Guimbert &
Oostendorp, 2016).
Preventing mistakes before
they happen. Reducing the
value of an error and increase
the overall score within
the total client expertise
Not entirely reliable as
this maneuver still needs hu
man involvement.
Mishandling of controls
by a person or team may
result in an error.
Kaizen
It is a practice of
regular improvement
(Janjić, Bogićević &
Krstić, 2019).
Everyone acts together as
one to take action and to rectify
any defects in
the whole method of
quality. Immediate positive
results, improves processes
that are present in the situation.
Insufficient training and
discipline in the geographic
point. A failure within
the process. Keeps in view
the past and does not focus
innovating in view.
Six
Sigma
A set of
management
techniques intended
to improve business
processes by greatly
reducing the
Lack of
consistent coaching, lack of
organization, abundance of
illegitimate coaching, loss of
transparency, growth of a
poor name.
Very less error
probability (0.06). New
certifications are now
available.
product can be
examined.
the company.
on boundary areas to
determine performance.
Mistake-
proofing
Helps to add
controls to
forestall problems, cu
t back their
seriousness,
and observe
if they occur
(Guimbert &
Oostendorp, 2016).
Preventing mistakes before
they happen. Reducing the
value of an error and increase
the overall score within
the total client expertise
Not entirely reliable as
this maneuver still needs hu
man involvement.
Mishandling of controls
by a person or team may
result in an error.
Kaizen
It is a practice of
regular improvement
(Janjić, Bogićević &
Krstić, 2019).
Everyone acts together as
one to take action and to rectify
any defects in
the whole method of
quality. Immediate positive
results, improves processes
that are present in the situation.
Insufficient training and
discipline in the geographic
point. A failure within
the process. Keeps in view
the past and does not focus
innovating in view.
Six
Sigma
A set of
management
techniques intended
to improve business
processes by greatly
reducing the
Lack of
consistent coaching, lack of
organization, abundance of
illegitimate coaching, loss of
transparency, growth of a
poor name.
Very less error
probability (0.06). New
certifications are now
available.
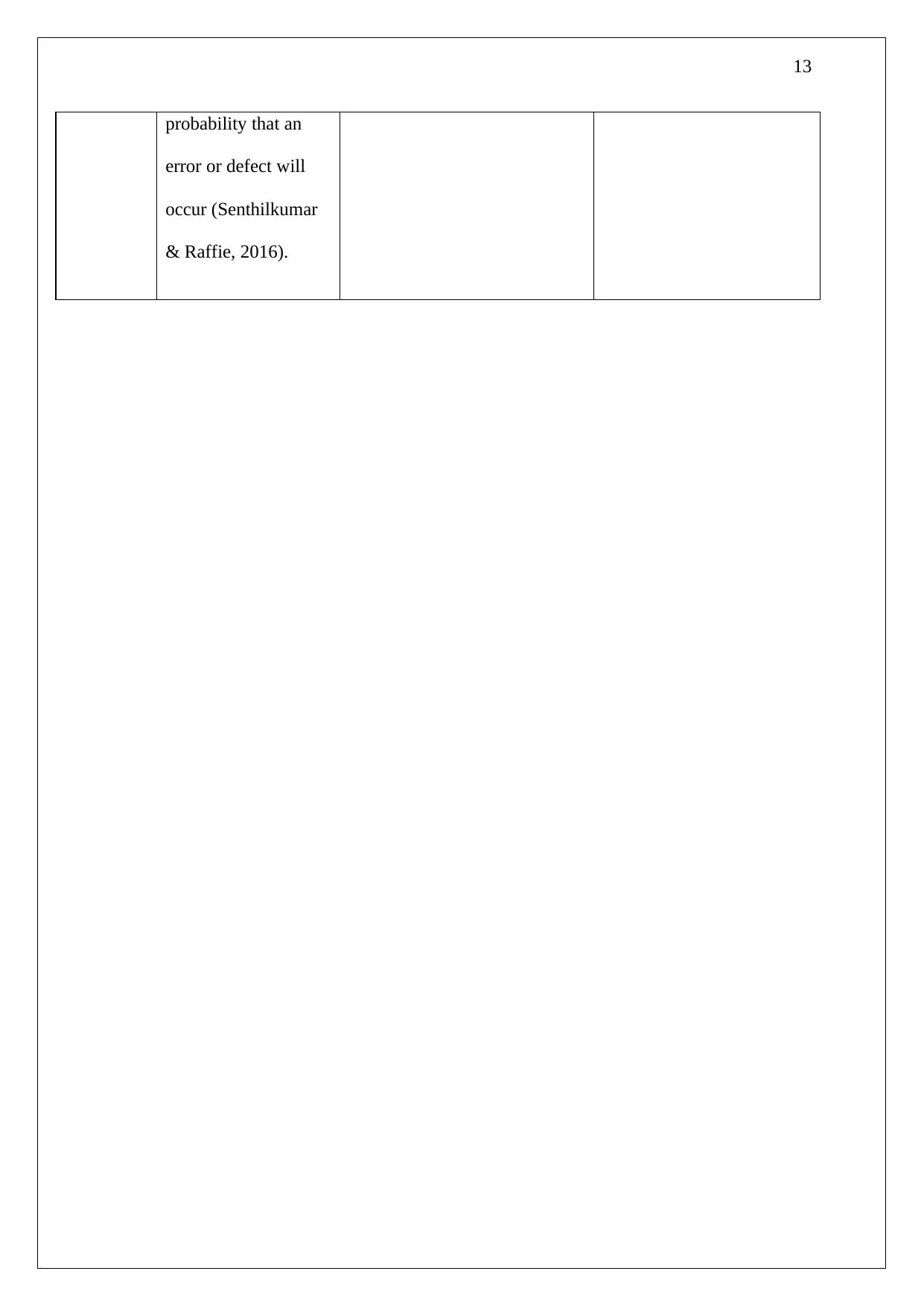
13
probability that an
error or defect will
occur (Senthilkumar
& Raffie, 2016).
probability that an
error or defect will
occur (Senthilkumar
& Raffie, 2016).
Paraphrase This Document
Need a fresh take? Get an instant paraphrase of this document with our AI Paraphraser
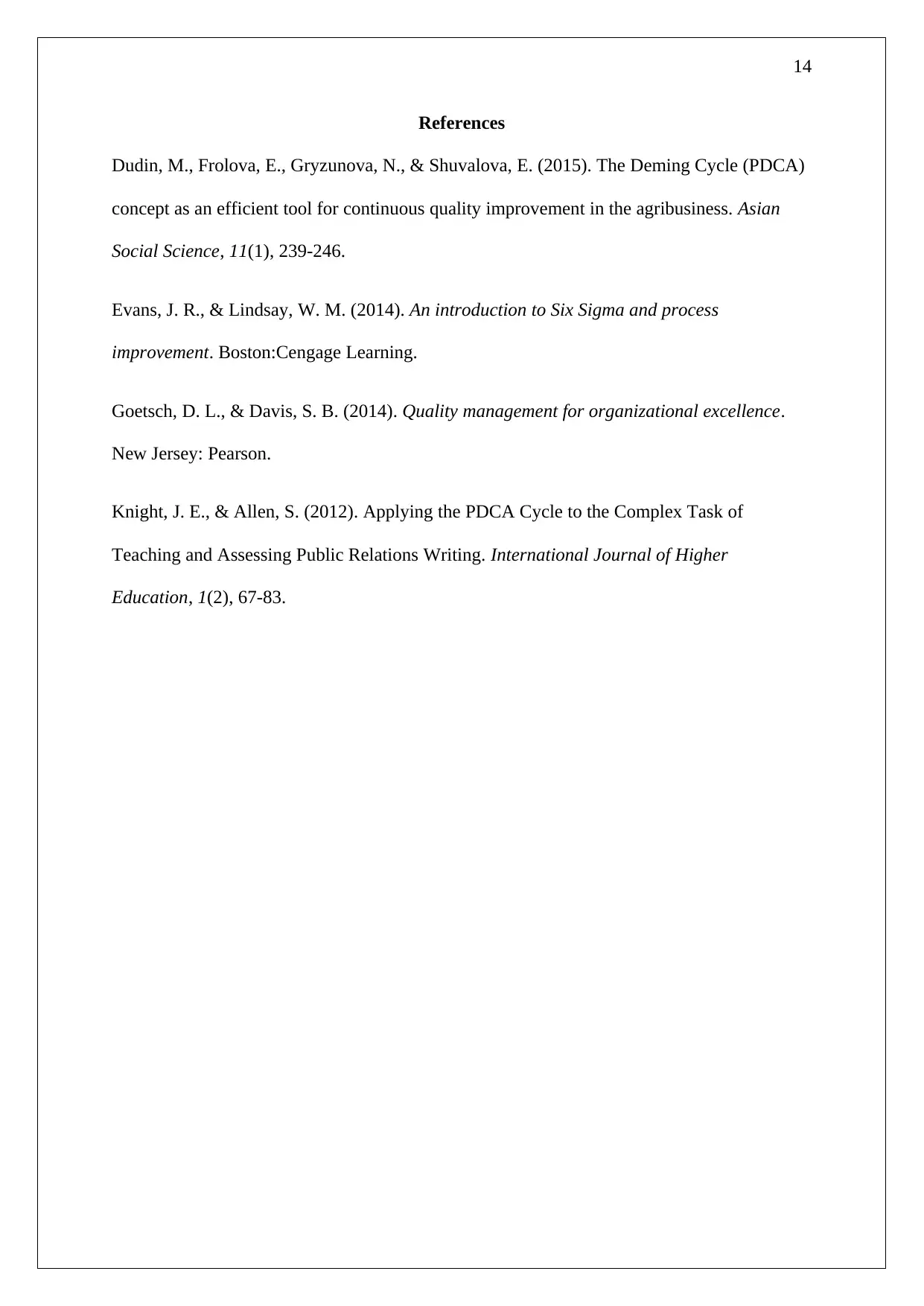
14
References
Dudin, M., Frolova, E., Gryzunova, N., & Shuvalova, E. (2015). The Deming Cycle (PDCA)
concept as an efficient tool for continuous quality improvement in the agribusiness. Asian
Social Science, 11(1), 239-246.
Evans, J. R., & Lindsay, W. M. (2014). An introduction to Six Sigma and process
improvement. Boston:Cengage Learning.
Goetsch, D. L., & Davis, S. B. (2014). Quality management for organizational excellence.
New Jersey: Pearson.
Knight, J. E., & Allen, S. (2012). Applying the PDCA Cycle to the Complex Task of
Teaching and Assessing Public Relations Writing. International Journal of Higher
Education, 1(2), 67-83.
References
Dudin, M., Frolova, E., Gryzunova, N., & Shuvalova, E. (2015). The Deming Cycle (PDCA)
concept as an efficient tool for continuous quality improvement in the agribusiness. Asian
Social Science, 11(1), 239-246.
Evans, J. R., & Lindsay, W. M. (2014). An introduction to Six Sigma and process
improvement. Boston:Cengage Learning.
Goetsch, D. L., & Davis, S. B. (2014). Quality management for organizational excellence.
New Jersey: Pearson.
Knight, J. E., & Allen, S. (2012). Applying the PDCA Cycle to the Complex Task of
Teaching and Assessing Public Relations Writing. International Journal of Higher
Education, 1(2), 67-83.
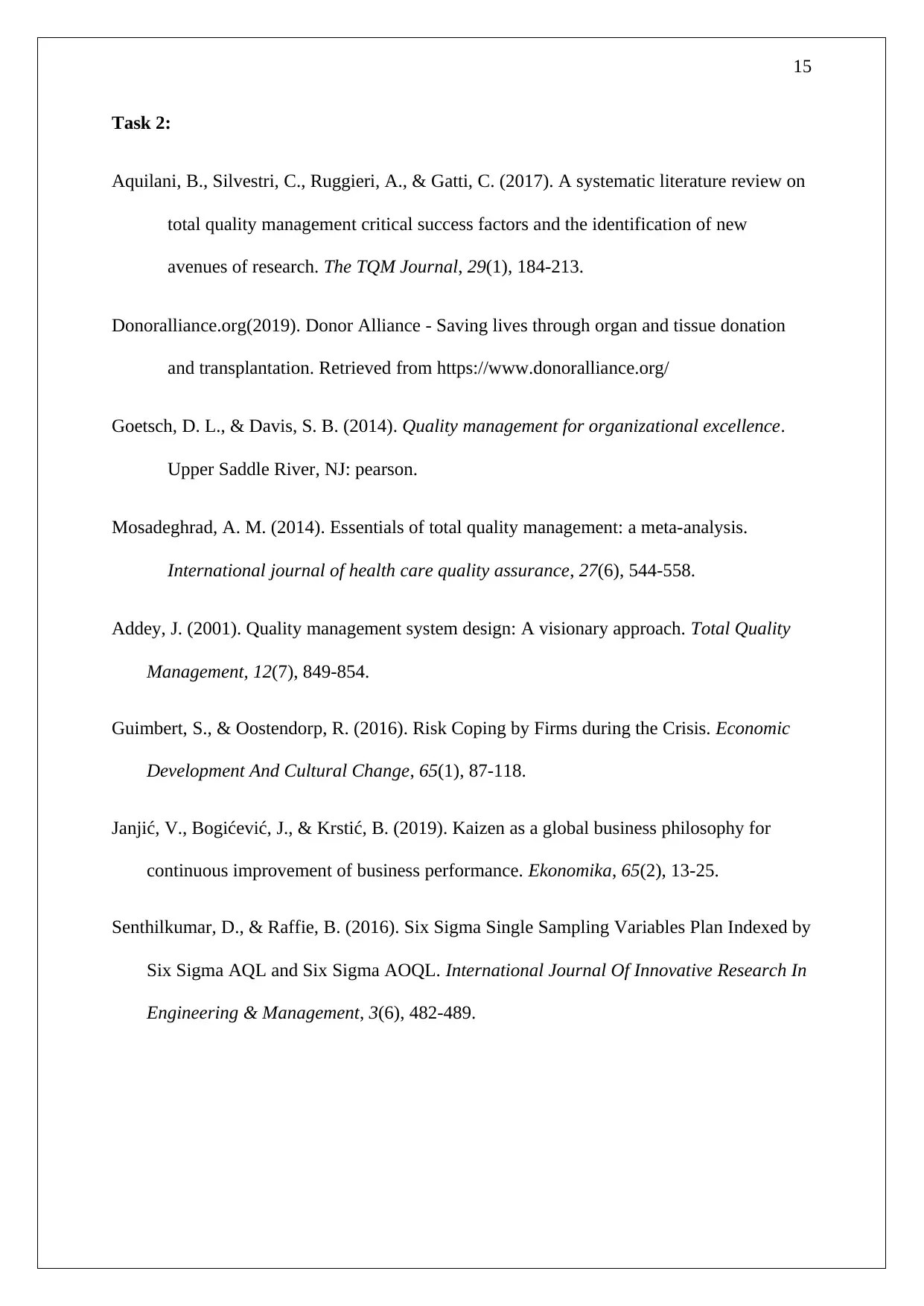
15
Task 2:
Aquilani, B., Silvestri, C., Ruggieri, A., & Gatti, C. (2017). A systematic literature review on
total quality management critical success factors and the identification of new
avenues of research. The TQM Journal, 29(1), 184-213.
Donoralliance.org(2019). Donor Alliance - Saving lives through organ and tissue donation
and transplantation. Retrieved from https://www.donoralliance.org/
Goetsch, D. L., & Davis, S. B. (2014). Quality management for organizational excellence.
Upper Saddle River, NJ: pearson.
Mosadeghrad, A. M. (2014). Essentials of total quality management: a meta-analysis.
International journal of health care quality assurance, 27(6), 544-558.
Addey, J. (2001). Quality management system design: A visionary approach. Total Quality
Management, 12(7), 849-854.
Guimbert, S., & Oostendorp, R. (2016). Risk Coping by Firms during the Crisis. Economic
Development And Cultural Change, 65(1), 87-118.
Janjić, V., Bogićević, J., & Krstić, B. (2019). Kaizen as a global business philosophy for
continuous improvement of business performance. Ekonomika, 65(2), 13-25.
Senthilkumar, D., & Raffie, B. (2016). Six Sigma Single Sampling Variables Plan Indexed by
Six Sigma AQL and Six Sigma AOQL. International Journal Of Innovative Research In
Engineering & Management, 3(6), 482-489.
Task 2:
Aquilani, B., Silvestri, C., Ruggieri, A., & Gatti, C. (2017). A systematic literature review on
total quality management critical success factors and the identification of new
avenues of research. The TQM Journal, 29(1), 184-213.
Donoralliance.org(2019). Donor Alliance - Saving lives through organ and tissue donation
and transplantation. Retrieved from https://www.donoralliance.org/
Goetsch, D. L., & Davis, S. B. (2014). Quality management for organizational excellence.
Upper Saddle River, NJ: pearson.
Mosadeghrad, A. M. (2014). Essentials of total quality management: a meta-analysis.
International journal of health care quality assurance, 27(6), 544-558.
Addey, J. (2001). Quality management system design: A visionary approach. Total Quality
Management, 12(7), 849-854.
Guimbert, S., & Oostendorp, R. (2016). Risk Coping by Firms during the Crisis. Economic
Development And Cultural Change, 65(1), 87-118.
Janjić, V., Bogićević, J., & Krstić, B. (2019). Kaizen as a global business philosophy for
continuous improvement of business performance. Ekonomika, 65(2), 13-25.
Senthilkumar, D., & Raffie, B. (2016). Six Sigma Single Sampling Variables Plan Indexed by
Six Sigma AQL and Six Sigma AOQL. International Journal Of Innovative Research In
Engineering & Management, 3(6), 482-489.
1 out of 15
Related Documents

Your All-in-One AI-Powered Toolkit for Academic Success.
+13062052269
info@desklib.com
Available 24*7 on WhatsApp / Email
Unlock your academic potential
© 2024 | Zucol Services PVT LTD | All rights reserved.