BSBPMG505A - Assessment 2: Quality Management Plan for WSI Project
VerifiedAdded on 2022/09/08
|11
|2102
|12
Report
AI Summary
This report presents a comprehensive Quality Management Plan (QMP) developed for the WSI Blue Mountains TAFE project (19735 Project 4). The QMP outlines detailed procedures and registers to ensure project outputs comply with specifications and international standards (ISO 9001). It covers project details, team structure, and quality policies, including an audit schedule and quality procedure register. The report further elaborates on various control tools, such as drawing and document control, test plans, and internal procedures. It also includes detailed templates for registers like Client Variation, Cost Control, Site Instruction, Subcontractor Variation, and Non-Conformance, as well as Request for Information and Notification/EOT registers. The plan also incorporates information about the filling system. The QMP aims to ensure efficient project management, quality assurance, and adherence to standards, promoting client satisfaction and project success.
Contribute Materials
Your contribution can guide someone’s learning journey. Share your
documents today.
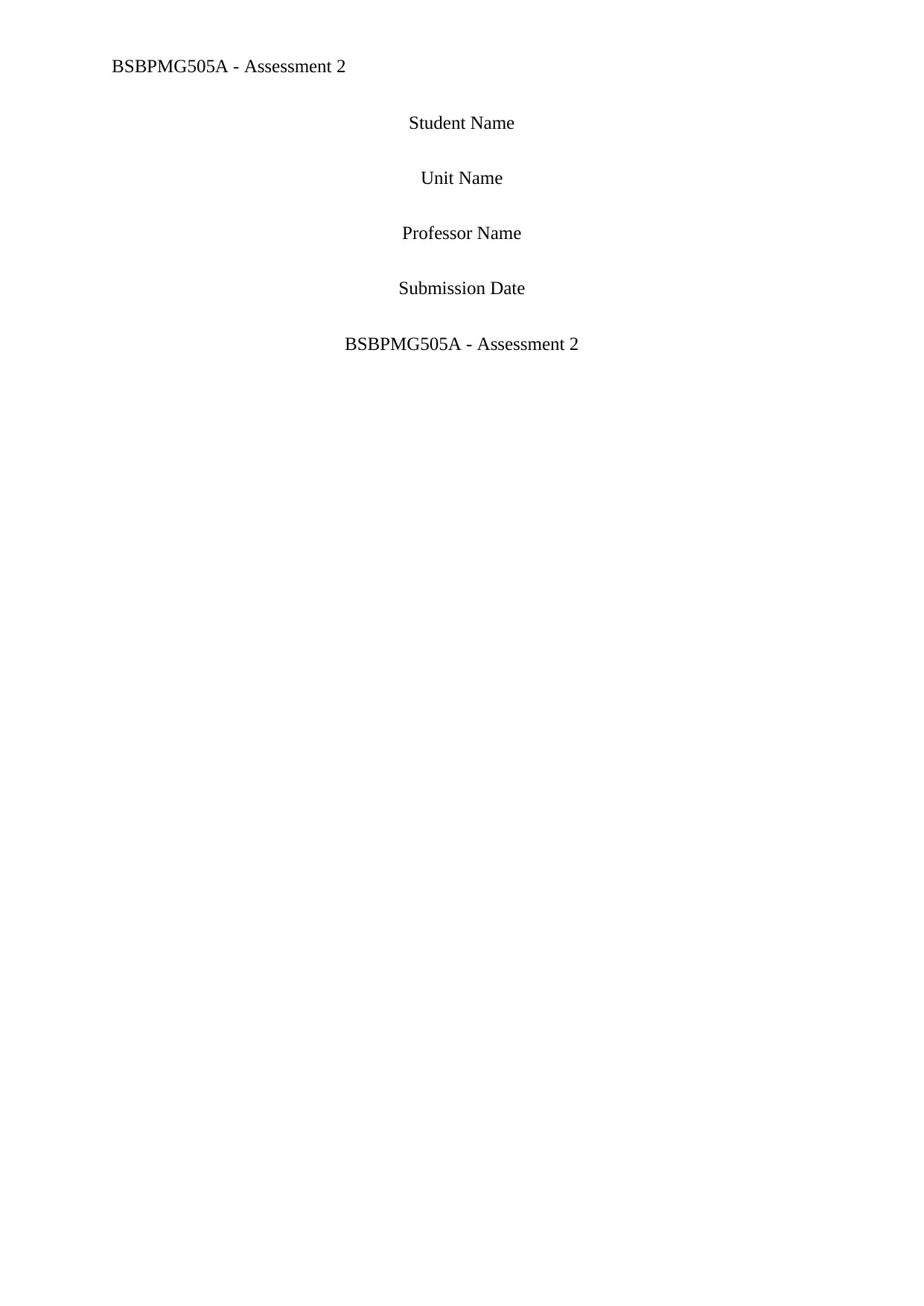
BSBPMG505A - Assessment 2
Student Name
Unit Name
Professor Name
Submission Date
BSBPMG505A - Assessment 2
Student Name
Unit Name
Professor Name
Submission Date
BSBPMG505A - Assessment 2
Secure Best Marks with AI Grader
Need help grading? Try our AI Grader for instant feedback on your assignments.
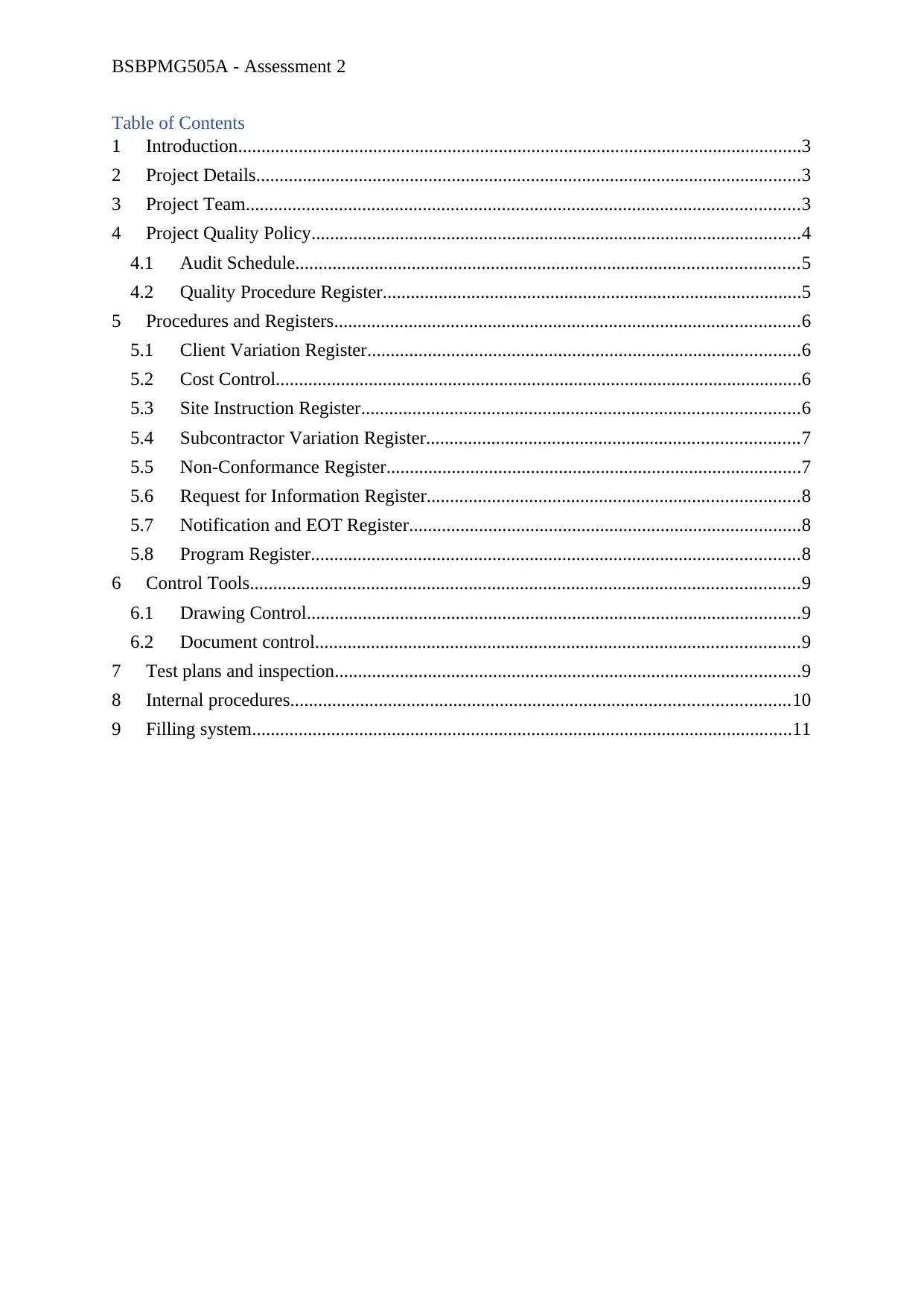
BSBPMG505A - Assessment 2
Table of Contents
1 Introduction.........................................................................................................................3
2 Project Details.....................................................................................................................3
3 Project Team.......................................................................................................................3
4 Project Quality Policy.........................................................................................................4
4.1 Audit Schedule............................................................................................................5
4.2 Quality Procedure Register..........................................................................................5
5 Procedures and Registers....................................................................................................6
5.1 Client Variation Register.............................................................................................6
5.2 Cost Control.................................................................................................................6
5.3 Site Instruction Register..............................................................................................6
5.4 Subcontractor Variation Register................................................................................7
5.5 Non-Conformance Register.........................................................................................7
5.6 Request for Information Register................................................................................8
5.7 Notification and EOT Register....................................................................................8
5.8 Program Register.........................................................................................................8
6 Control Tools......................................................................................................................9
6.1 Drawing Control..........................................................................................................9
6.2 Document control........................................................................................................9
7 Test plans and inspection....................................................................................................9
8 Internal procedures...........................................................................................................10
9 Filling system....................................................................................................................11
Table of Contents
1 Introduction.........................................................................................................................3
2 Project Details.....................................................................................................................3
3 Project Team.......................................................................................................................3
4 Project Quality Policy.........................................................................................................4
4.1 Audit Schedule............................................................................................................5
4.2 Quality Procedure Register..........................................................................................5
5 Procedures and Registers....................................................................................................6
5.1 Client Variation Register.............................................................................................6
5.2 Cost Control.................................................................................................................6
5.3 Site Instruction Register..............................................................................................6
5.4 Subcontractor Variation Register................................................................................7
5.5 Non-Conformance Register.........................................................................................7
5.6 Request for Information Register................................................................................8
5.7 Notification and EOT Register....................................................................................8
5.8 Program Register.........................................................................................................8
6 Control Tools......................................................................................................................9
6.1 Drawing Control..........................................................................................................9
6.2 Document control........................................................................................................9
7 Test plans and inspection....................................................................................................9
8 Internal procedures...........................................................................................................10
9 Filling system....................................................................................................................11
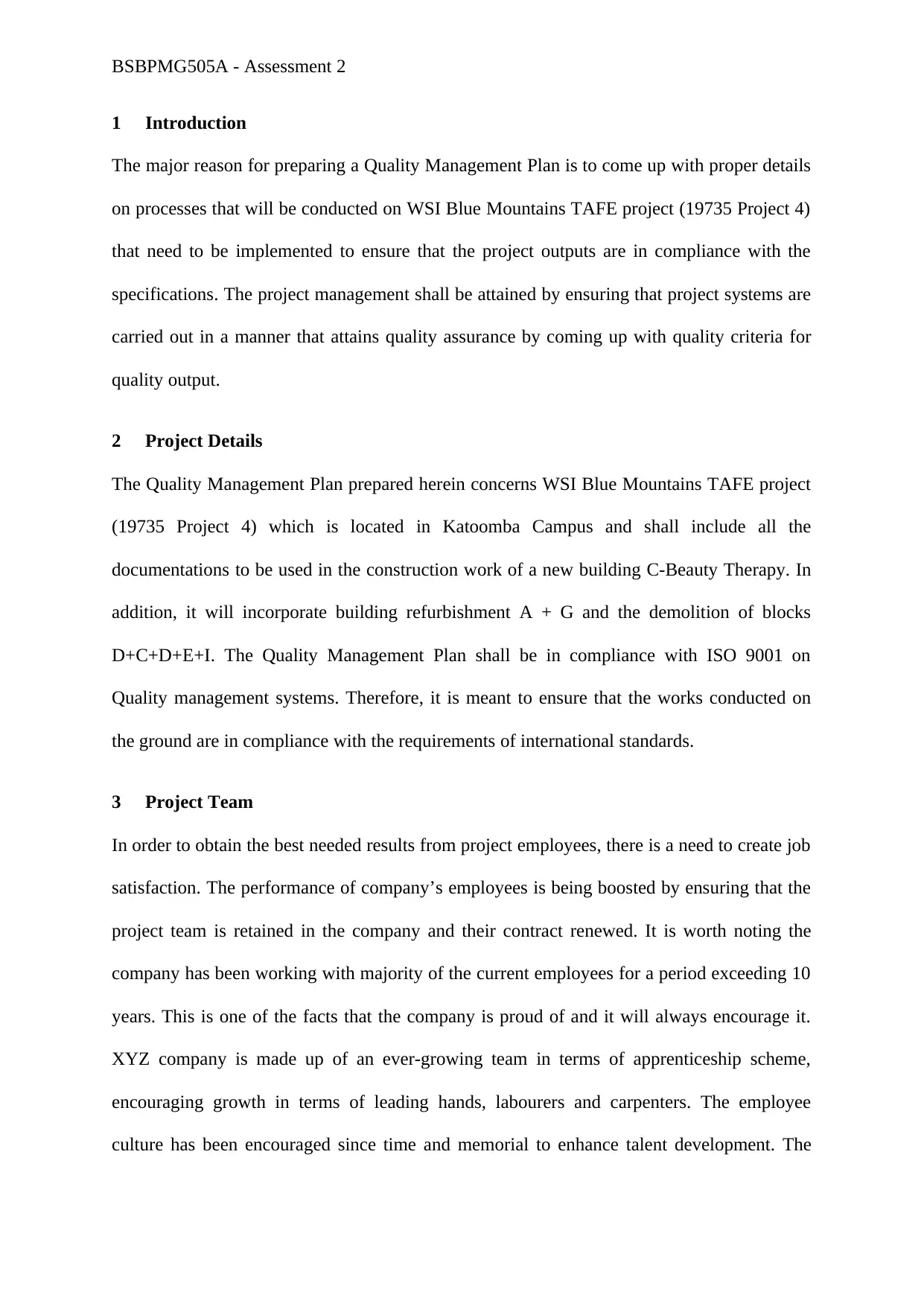
BSBPMG505A - Assessment 2
1 Introduction
The major reason for preparing a Quality Management Plan is to come up with proper details
on processes that will be conducted on WSI Blue Mountains TAFE project (19735 Project 4)
that need to be implemented to ensure that the project outputs are in compliance with the
specifications. The project management shall be attained by ensuring that project systems are
carried out in a manner that attains quality assurance by coming up with quality criteria for
quality output.
2 Project Details
The Quality Management Plan prepared herein concerns WSI Blue Mountains TAFE project
(19735 Project 4) which is located in Katoomba Campus and shall include all the
documentations to be used in the construction work of a new building C-Beauty Therapy. In
addition, it will incorporate building refurbishment A + G and the demolition of blocks
D+C+D+E+I. The Quality Management Plan shall be in compliance with ISO 9001 on
Quality management systems. Therefore, it is meant to ensure that the works conducted on
the ground are in compliance with the requirements of international standards.
3 Project Team
In order to obtain the best needed results from project employees, there is a need to create job
satisfaction. The performance of company’s employees is being boosted by ensuring that the
project team is retained in the company and their contract renewed. It is worth noting the
company has been working with majority of the current employees for a period exceeding 10
years. This is one of the facts that the company is proud of and it will always encourage it.
XYZ company is made up of an ever-growing team in terms of apprenticeship scheme,
encouraging growth in terms of leading hands, labourers and carpenters. The employee
culture has been encouraged since time and memorial to enhance talent development. The
1 Introduction
The major reason for preparing a Quality Management Plan is to come up with proper details
on processes that will be conducted on WSI Blue Mountains TAFE project (19735 Project 4)
that need to be implemented to ensure that the project outputs are in compliance with the
specifications. The project management shall be attained by ensuring that project systems are
carried out in a manner that attains quality assurance by coming up with quality criteria for
quality output.
2 Project Details
The Quality Management Plan prepared herein concerns WSI Blue Mountains TAFE project
(19735 Project 4) which is located in Katoomba Campus and shall include all the
documentations to be used in the construction work of a new building C-Beauty Therapy. In
addition, it will incorporate building refurbishment A + G and the demolition of blocks
D+C+D+E+I. The Quality Management Plan shall be in compliance with ISO 9001 on
Quality management systems. Therefore, it is meant to ensure that the works conducted on
the ground are in compliance with the requirements of international standards.
3 Project Team
In order to obtain the best needed results from project employees, there is a need to create job
satisfaction. The performance of company’s employees is being boosted by ensuring that the
project team is retained in the company and their contract renewed. It is worth noting the
company has been working with majority of the current employees for a period exceeding 10
years. This is one of the facts that the company is proud of and it will always encourage it.
XYZ company is made up of an ever-growing team in terms of apprenticeship scheme,
encouraging growth in terms of leading hands, labourers and carpenters. The employee
culture has been encouraged since time and memorial to enhance talent development. The
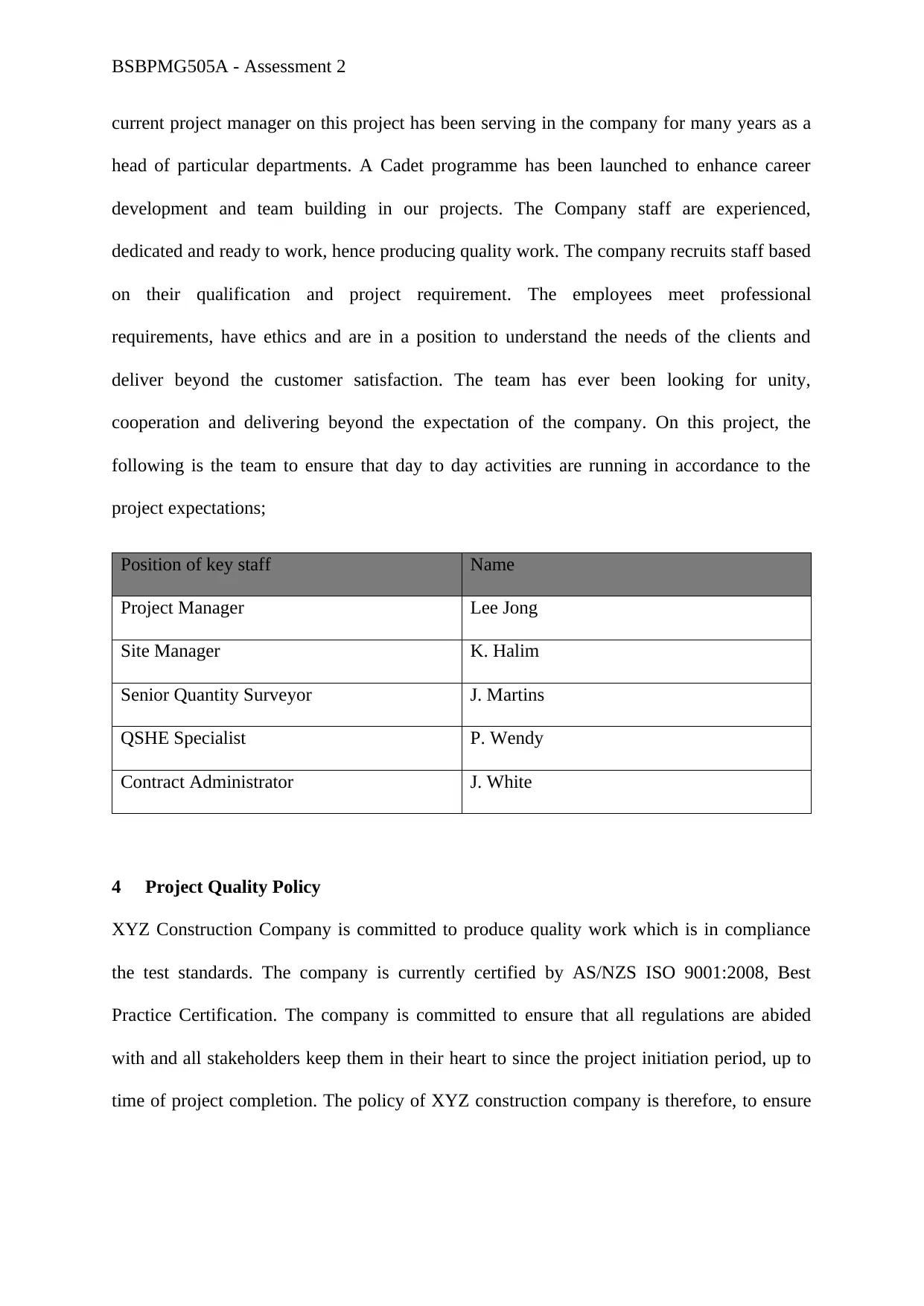
BSBPMG505A - Assessment 2
current project manager on this project has been serving in the company for many years as a
head of particular departments. A Cadet programme has been launched to enhance career
development and team building in our projects. The Company staff are experienced,
dedicated and ready to work, hence producing quality work. The company recruits staff based
on their qualification and project requirement. The employees meet professional
requirements, have ethics and are in a position to understand the needs of the clients and
deliver beyond the customer satisfaction. The team has ever been looking for unity,
cooperation and delivering beyond the expectation of the company. On this project, the
following is the team to ensure that day to day activities are running in accordance to the
project expectations;
Position of key staff Name
Project Manager Lee Jong
Site Manager K. Halim
Senior Quantity Surveyor J. Martins
QSHE Specialist P. Wendy
Contract Administrator J. White
4 Project Quality Policy
XYZ Construction Company is committed to produce quality work which is in compliance
the test standards. The company is currently certified by AS/NZS ISO 9001:2008, Best
Practice Certification. The company is committed to ensure that all regulations are abided
with and all stakeholders keep them in their heart to since the project initiation period, up to
time of project completion. The policy of XYZ construction company is therefore, to ensure
current project manager on this project has been serving in the company for many years as a
head of particular departments. A Cadet programme has been launched to enhance career
development and team building in our projects. The Company staff are experienced,
dedicated and ready to work, hence producing quality work. The company recruits staff based
on their qualification and project requirement. The employees meet professional
requirements, have ethics and are in a position to understand the needs of the clients and
deliver beyond the customer satisfaction. The team has ever been looking for unity,
cooperation and delivering beyond the expectation of the company. On this project, the
following is the team to ensure that day to day activities are running in accordance to the
project expectations;
Position of key staff Name
Project Manager Lee Jong
Site Manager K. Halim
Senior Quantity Surveyor J. Martins
QSHE Specialist P. Wendy
Contract Administrator J. White
4 Project Quality Policy
XYZ Construction Company is committed to produce quality work which is in compliance
the test standards. The company is currently certified by AS/NZS ISO 9001:2008, Best
Practice Certification. The company is committed to ensure that all regulations are abided
with and all stakeholders keep them in their heart to since the project initiation period, up to
time of project completion. The policy of XYZ construction company is therefore, to ensure
Secure Best Marks with AI Grader
Need help grading? Try our AI Grader for instant feedback on your assignments.
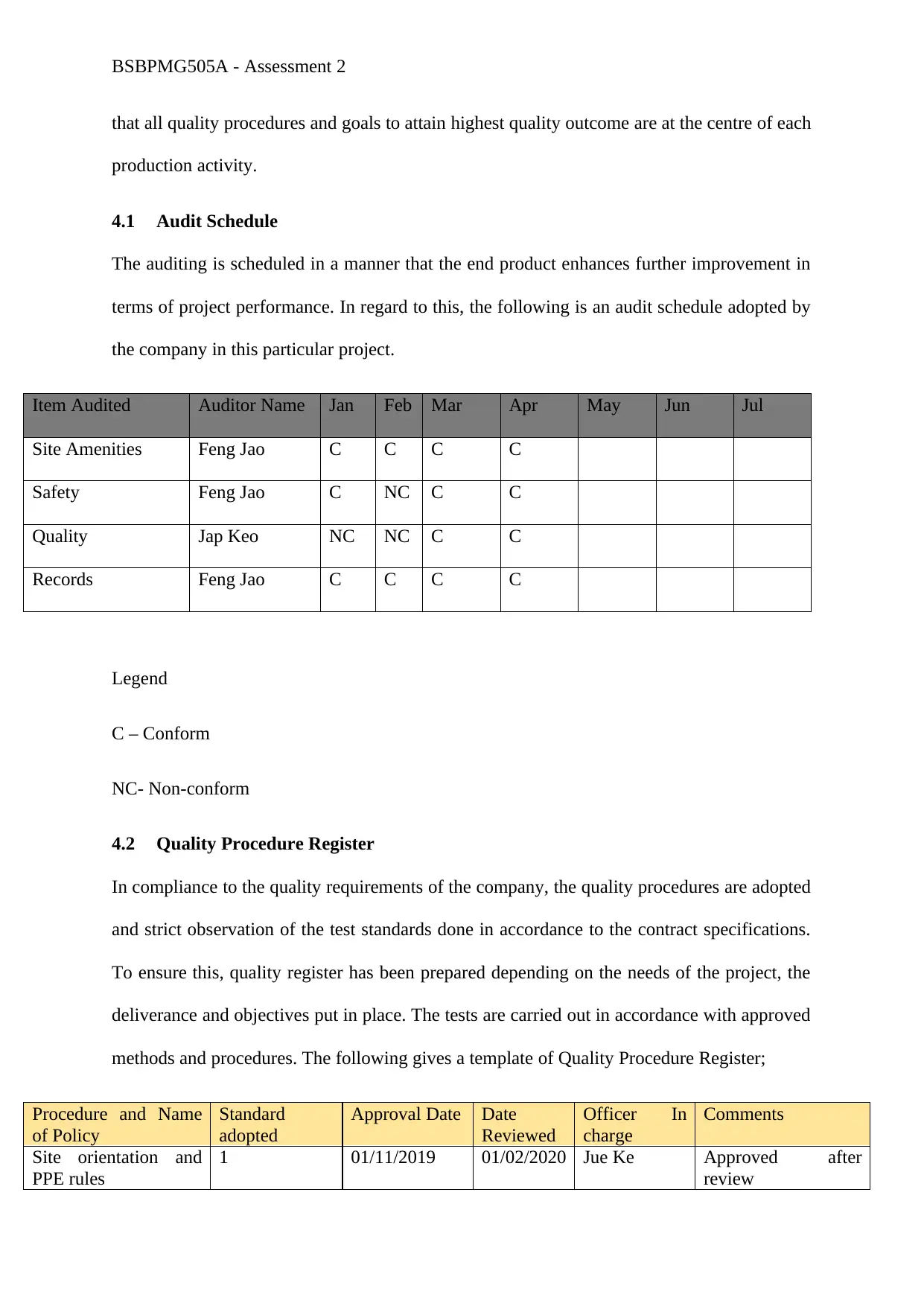
BSBPMG505A - Assessment 2
that all quality procedures and goals to attain highest quality outcome are at the centre of each
production activity.
4.1 Audit Schedule
The auditing is scheduled in a manner that the end product enhances further improvement in
terms of project performance. In regard to this, the following is an audit schedule adopted by
the company in this particular project.
Item Audited Auditor Name Jan Feb Mar Apr May Jun Jul
Site Amenities Feng Jao C C C C
Safety Feng Jao C NC C C
Quality Jap Keo NC NC C C
Records Feng Jao C C C C
Legend
C – Conform
NC- Non-conform
4.2 Quality Procedure Register
In compliance to the quality requirements of the company, the quality procedures are adopted
and strict observation of the test standards done in accordance to the contract specifications.
To ensure this, quality register has been prepared depending on the needs of the project, the
deliverance and objectives put in place. The tests are carried out in accordance with approved
methods and procedures. The following gives a template of Quality Procedure Register;
Procedure and Name
of Policy
Standard
adopted
Approval Date Date
Reviewed
Officer In
charge
Comments
Site orientation and
PPE rules
1 01/11/2019 01/02/2020 Jue Ke Approved after
review
that all quality procedures and goals to attain highest quality outcome are at the centre of each
production activity.
4.1 Audit Schedule
The auditing is scheduled in a manner that the end product enhances further improvement in
terms of project performance. In regard to this, the following is an audit schedule adopted by
the company in this particular project.
Item Audited Auditor Name Jan Feb Mar Apr May Jun Jul
Site Amenities Feng Jao C C C C
Safety Feng Jao C NC C C
Quality Jap Keo NC NC C C
Records Feng Jao C C C C
Legend
C – Conform
NC- Non-conform
4.2 Quality Procedure Register
In compliance to the quality requirements of the company, the quality procedures are adopted
and strict observation of the test standards done in accordance to the contract specifications.
To ensure this, quality register has been prepared depending on the needs of the project, the
deliverance and objectives put in place. The tests are carried out in accordance with approved
methods and procedures. The following gives a template of Quality Procedure Register;
Procedure and Name
of Policy
Standard
adopted
Approval Date Date
Reviewed
Officer In
charge
Comments
Site orientation and
PPE rules
1 01/11/2019 01/02/2020 Jue Ke Approved after
review
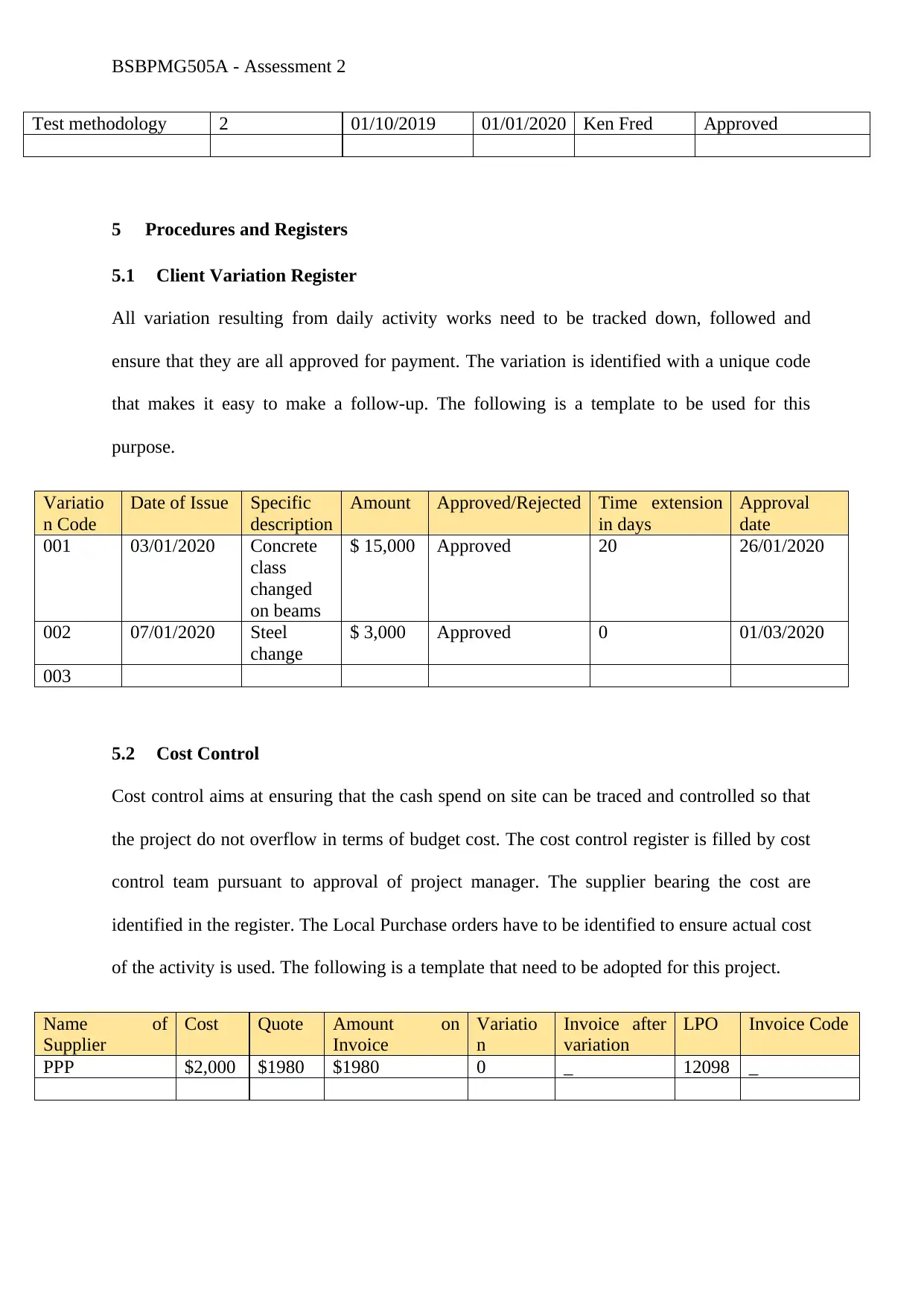
BSBPMG505A - Assessment 2
Test methodology 2 01/10/2019 01/01/2020 Ken Fred Approved
5 Procedures and Registers
5.1 Client Variation Register
All variation resulting from daily activity works need to be tracked down, followed and
ensure that they are all approved for payment. The variation is identified with a unique code
that makes it easy to make a follow-up. The following is a template to be used for this
purpose.
Variatio
n Code
Date of Issue Specific
description
Amount Approved/Rejected Time extension
in days
Approval
date
001 03/01/2020 Concrete
class
changed
on beams
$ 15,000 Approved 20 26/01/2020
002 07/01/2020 Steel
change
$ 3,000 Approved 0 01/03/2020
003
5.2 Cost Control
Cost control aims at ensuring that the cash spend on site can be traced and controlled so that
the project do not overflow in terms of budget cost. The cost control register is filled by cost
control team pursuant to approval of project manager. The supplier bearing the cost are
identified in the register. The Local Purchase orders have to be identified to ensure actual cost
of the activity is used. The following is a template that need to be adopted for this project.
Name of
Supplier
Cost Quote Amount on
Invoice
Variatio
n
Invoice after
variation
LPO Invoice Code
PPP $2,000 $1980 $1980 0 _ 12098 _
Test methodology 2 01/10/2019 01/01/2020 Ken Fred Approved
5 Procedures and Registers
5.1 Client Variation Register
All variation resulting from daily activity works need to be tracked down, followed and
ensure that they are all approved for payment. The variation is identified with a unique code
that makes it easy to make a follow-up. The following is a template to be used for this
purpose.
Variatio
n Code
Date of Issue Specific
description
Amount Approved/Rejected Time extension
in days
Approval
date
001 03/01/2020 Concrete
class
changed
on beams
$ 15,000 Approved 20 26/01/2020
002 07/01/2020 Steel
change
$ 3,000 Approved 0 01/03/2020
003
5.2 Cost Control
Cost control aims at ensuring that the cash spend on site can be traced and controlled so that
the project do not overflow in terms of budget cost. The cost control register is filled by cost
control team pursuant to approval of project manager. The supplier bearing the cost are
identified in the register. The Local Purchase orders have to be identified to ensure actual cost
of the activity is used. The following is a template that need to be adopted for this project.
Name of
Supplier
Cost Quote Amount on
Invoice
Variatio
n
Invoice after
variation
LPO Invoice Code
PPP $2,000 $1980 $1980 0 _ 12098 _
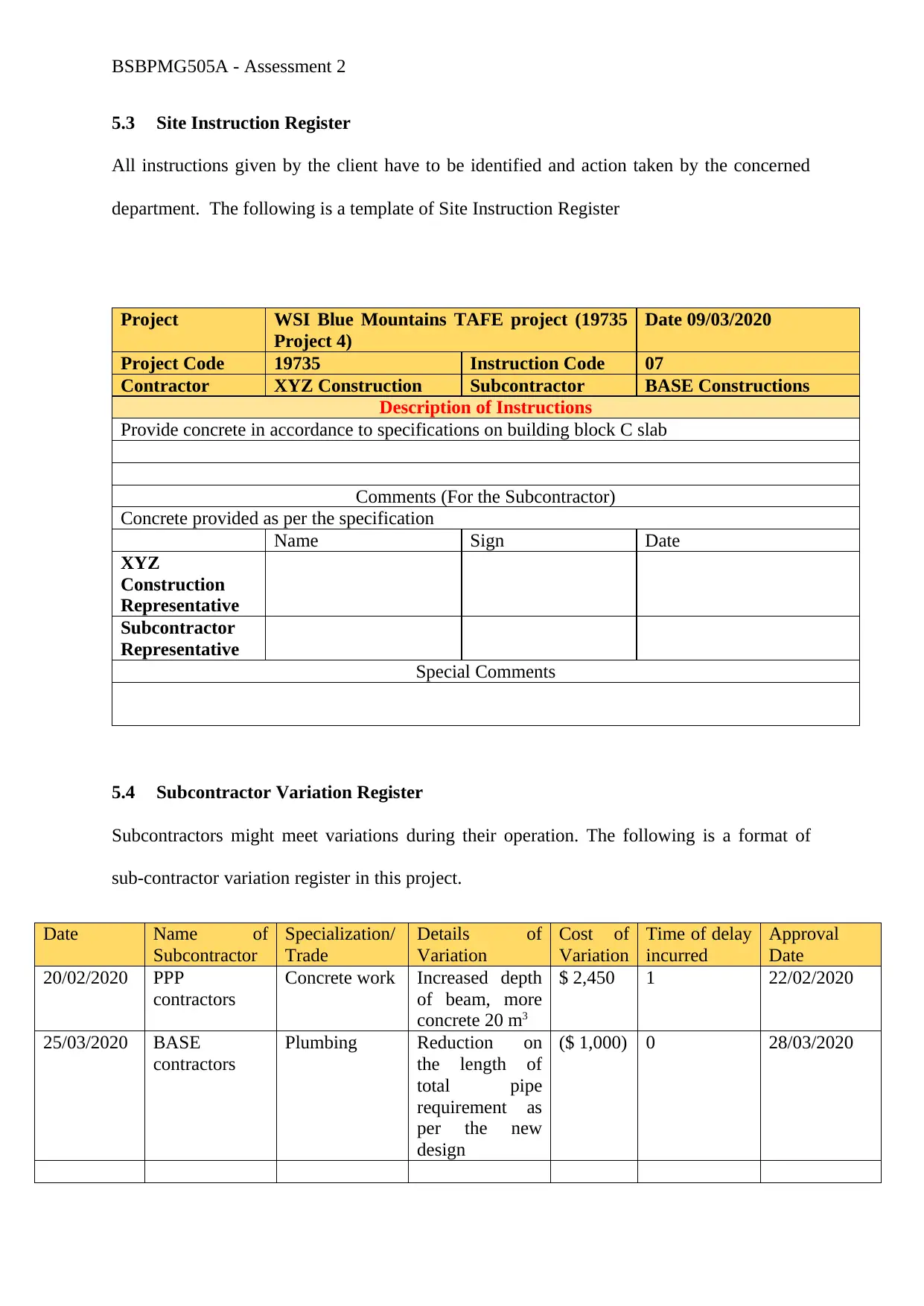
BSBPMG505A - Assessment 2
5.3 Site Instruction Register
All instructions given by the client have to be identified and action taken by the concerned
department. The following is a template of Site Instruction Register
Project WSI Blue Mountains TAFE project (19735
Project 4)
Date 09/03/2020
Project Code 19735 Instruction Code 07
Contractor XYZ Construction Subcontractor BASE Constructions
Description of Instructions
Provide concrete in accordance to specifications on building block C slab
Comments (For the Subcontractor)
Concrete provided as per the specification
Name Sign Date
XYZ
Construction
Representative
Subcontractor
Representative
Special Comments
5.4 Subcontractor Variation Register
Subcontractors might meet variations during their operation. The following is a format of
sub-contractor variation register in this project.
Date Name of
Subcontractor
Specialization/
Trade
Details of
Variation
Cost of
Variation
Time of delay
incurred
Approval
Date
20/02/2020 PPP
contractors
Concrete work Increased depth
of beam, more
concrete 20 m3
$ 2,450 1 22/02/2020
25/03/2020 BASE
contractors
Plumbing Reduction on
the length of
total pipe
requirement as
per the new
design
($ 1,000) 0 28/03/2020
5.3 Site Instruction Register
All instructions given by the client have to be identified and action taken by the concerned
department. The following is a template of Site Instruction Register
Project WSI Blue Mountains TAFE project (19735
Project 4)
Date 09/03/2020
Project Code 19735 Instruction Code 07
Contractor XYZ Construction Subcontractor BASE Constructions
Description of Instructions
Provide concrete in accordance to specifications on building block C slab
Comments (For the Subcontractor)
Concrete provided as per the specification
Name Sign Date
XYZ
Construction
Representative
Subcontractor
Representative
Special Comments
5.4 Subcontractor Variation Register
Subcontractors might meet variations during their operation. The following is a format of
sub-contractor variation register in this project.
Date Name of
Subcontractor
Specialization/
Trade
Details of
Variation
Cost of
Variation
Time of delay
incurred
Approval
Date
20/02/2020 PPP
contractors
Concrete work Increased depth
of beam, more
concrete 20 m3
$ 2,450 1 22/02/2020
25/03/2020 BASE
contractors
Plumbing Reduction on
the length of
total pipe
requirement as
per the new
design
($ 1,000) 0 28/03/2020
Paraphrase This Document
Need a fresh take? Get an instant paraphrase of this document with our AI Paraphraser
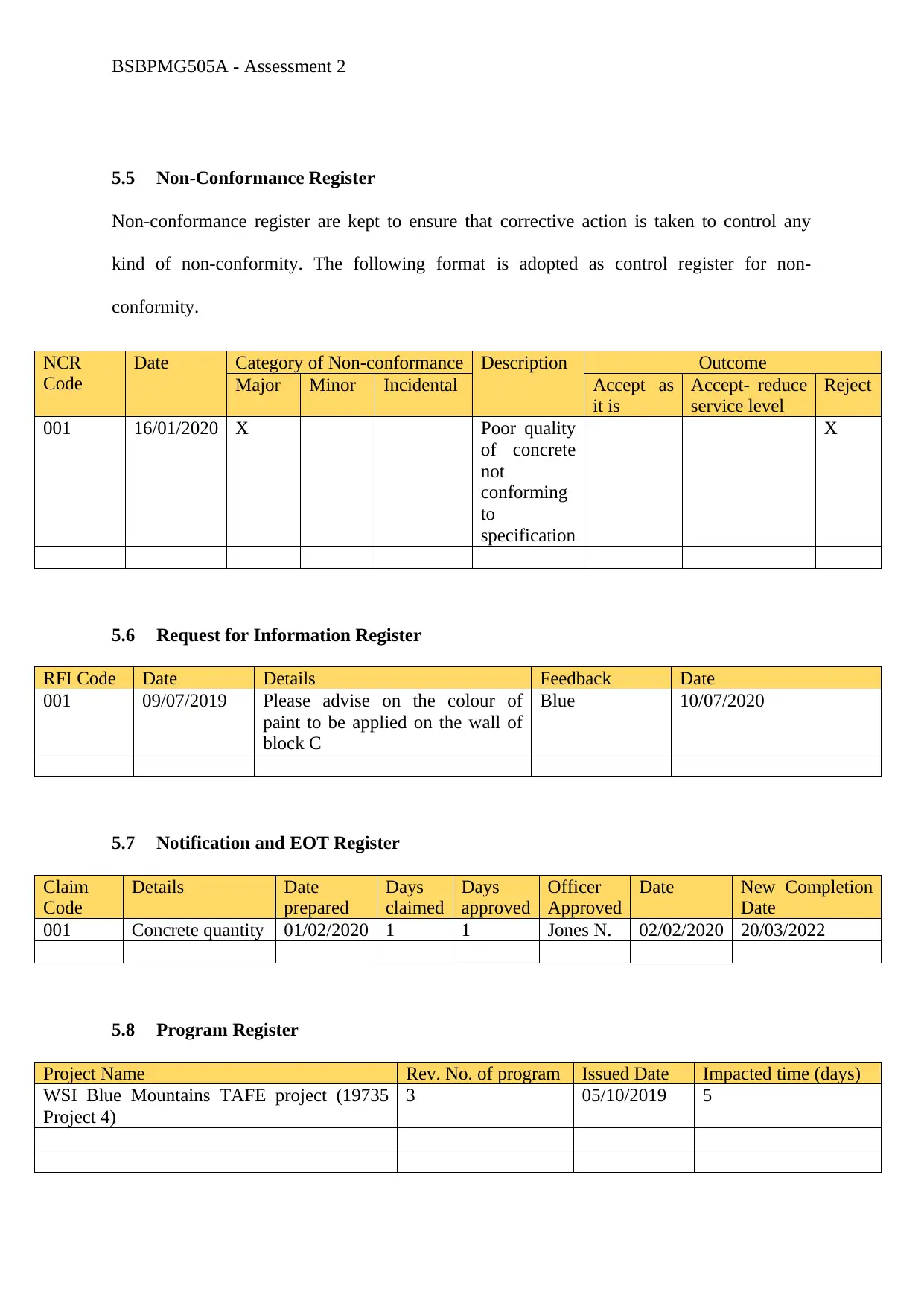
BSBPMG505A - Assessment 2
5.5 Non-Conformance Register
Non-conformance register are kept to ensure that corrective action is taken to control any
kind of non-conformity. The following format is adopted as control register for non-
conformity.
NCR
Code
Date Category of Non-conformance Description Outcome
Major Minor Incidental Accept as
it is
Accept- reduce
service level
Reject
001 16/01/2020 X Poor quality
of concrete
not
conforming
to
specification
X
5.6 Request for Information Register
RFI Code Date Details Feedback Date
001 09/07/2019 Please advise on the colour of
paint to be applied on the wall of
block C
Blue 10/07/2020
5.7 Notification and EOT Register
Claim
Code
Details Date
prepared
Days
claimed
Days
approved
Officer
Approved
Date New Completion
Date
001 Concrete quantity 01/02/2020 1 1 Jones N. 02/02/2020 20/03/2022
5.8 Program Register
Project Name Rev. No. of program Issued Date Impacted time (days)
WSI Blue Mountains TAFE project (19735
Project 4)
3 05/10/2019 5
5.5 Non-Conformance Register
Non-conformance register are kept to ensure that corrective action is taken to control any
kind of non-conformity. The following format is adopted as control register for non-
conformity.
NCR
Code
Date Category of Non-conformance Description Outcome
Major Minor Incidental Accept as
it is
Accept- reduce
service level
Reject
001 16/01/2020 X Poor quality
of concrete
not
conforming
to
specification
X
5.6 Request for Information Register
RFI Code Date Details Feedback Date
001 09/07/2019 Please advise on the colour of
paint to be applied on the wall of
block C
Blue 10/07/2020
5.7 Notification and EOT Register
Claim
Code
Details Date
prepared
Days
claimed
Days
approved
Officer
Approved
Date New Completion
Date
001 Concrete quantity 01/02/2020 1 1 Jones N. 02/02/2020 20/03/2022
5.8 Program Register
Project Name Rev. No. of program Issued Date Impacted time (days)
WSI Blue Mountains TAFE project (19735
Project 4)
3 05/10/2019 5
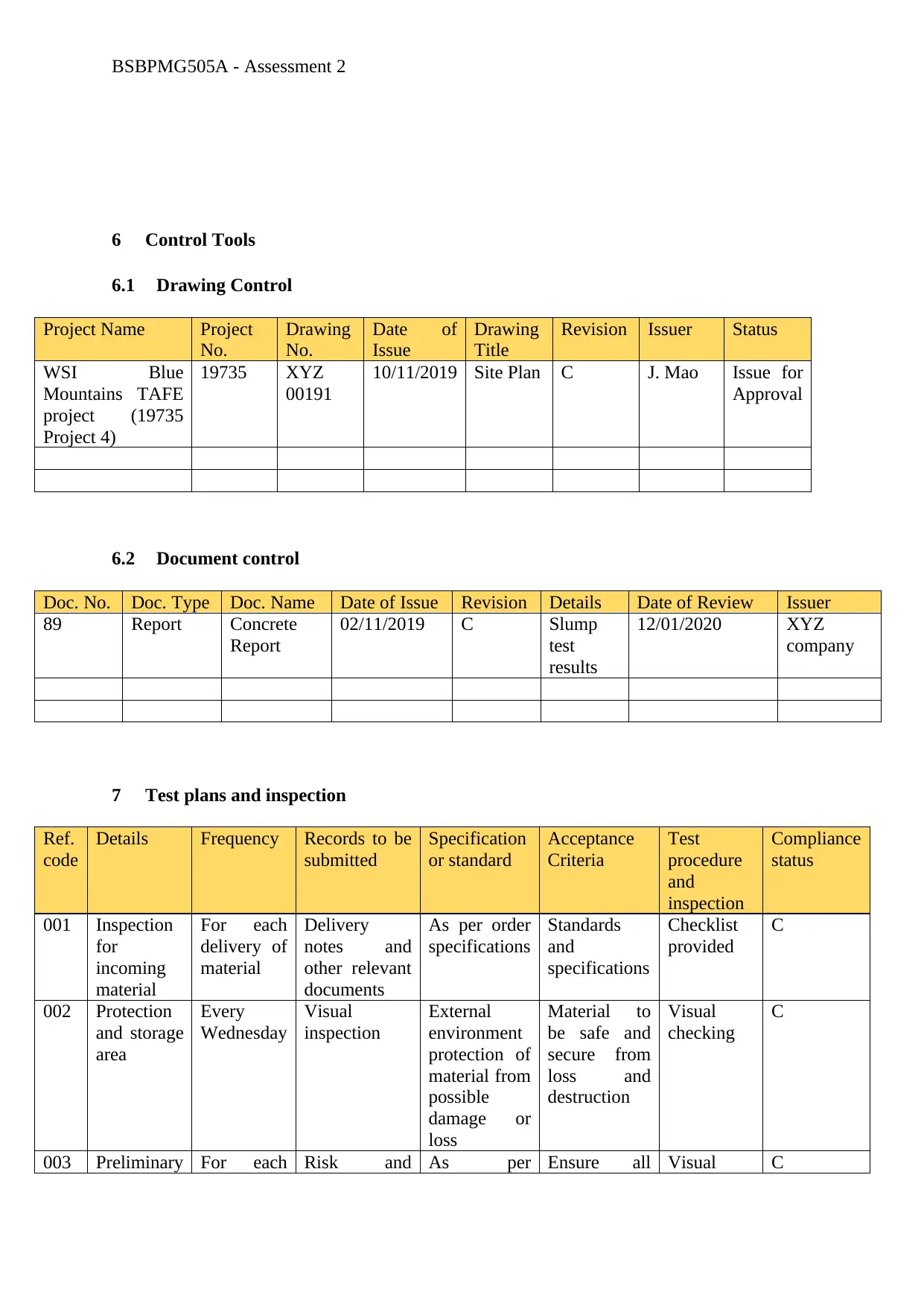
BSBPMG505A - Assessment 2
6 Control Tools
6.1 Drawing Control
Project Name Project
No.
Drawing
No.
Date of
Issue
Drawing
Title
Revision Issuer Status
WSI Blue
Mountains TAFE
project (19735
Project 4)
19735 XYZ
00191
10/11/2019 Site Plan C J. Mao Issue for
Approval
6.2 Document control
Doc. No. Doc. Type Doc. Name Date of Issue Revision Details Date of Review Issuer
89 Report Concrete
Report
02/11/2019 C Slump
test
results
12/01/2020 XYZ
company
7 Test plans and inspection
Ref.
code
Details Frequency Records to be
submitted
Specification
or standard
Acceptance
Criteria
Test
procedure
and
inspection
Compliance
status
001 Inspection
for
incoming
material
For each
delivery of
material
Delivery
notes and
other relevant
documents
As per order
specifications
Standards
and
specifications
Checklist
provided
C
002 Protection
and storage
area
Every
Wednesday
Visual
inspection
External
environment
protection of
material from
possible
damage or
loss
Material to
be safe and
secure from
loss and
destruction
Visual
checking
C
003 Preliminary For each Risk and As per Ensure all Visual C
6 Control Tools
6.1 Drawing Control
Project Name Project
No.
Drawing
No.
Date of
Issue
Drawing
Title
Revision Issuer Status
WSI Blue
Mountains TAFE
project (19735
Project 4)
19735 XYZ
00191
10/11/2019 Site Plan C J. Mao Issue for
Approval
6.2 Document control
Doc. No. Doc. Type Doc. Name Date of Issue Revision Details Date of Review Issuer
89 Report Concrete
Report
02/11/2019 C Slump
test
results
12/01/2020 XYZ
company
7 Test plans and inspection
Ref.
code
Details Frequency Records to be
submitted
Specification
or standard
Acceptance
Criteria
Test
procedure
and
inspection
Compliance
status
001 Inspection
for
incoming
material
For each
delivery of
material
Delivery
notes and
other relevant
documents
As per order
specifications
Standards
and
specifications
Checklist
provided
C
002 Protection
and storage
area
Every
Wednesday
Visual
inspection
External
environment
protection of
material from
possible
damage or
loss
Material to
be safe and
secure from
loss and
destruction
Visual
checking
C
003 Preliminary For each Risk and As per Ensure all Visual C
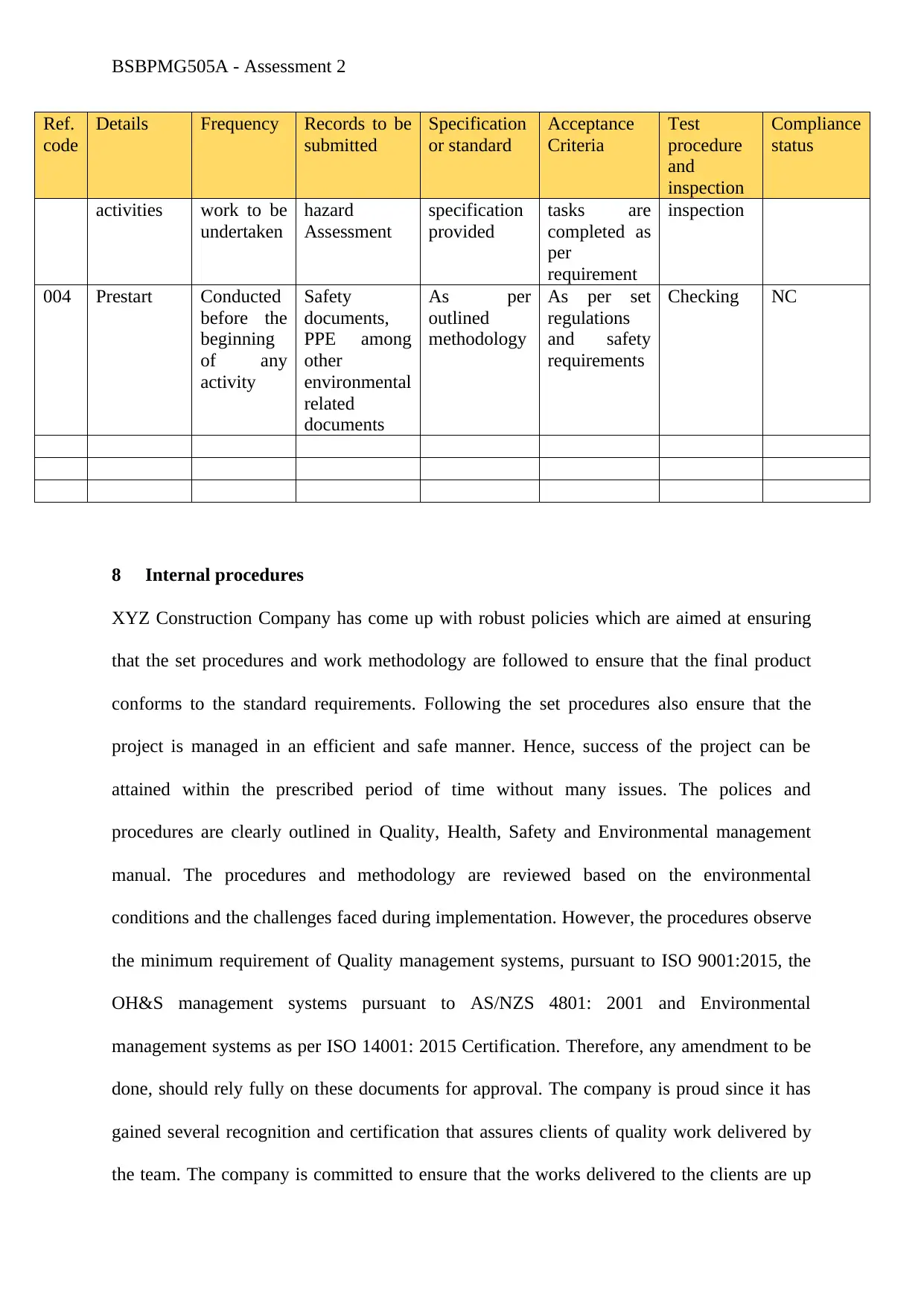
BSBPMG505A - Assessment 2
Ref.
code
Details Frequency Records to be
submitted
Specification
or standard
Acceptance
Criteria
Test
procedure
and
inspection
Compliance
status
activities work to be
undertaken
hazard
Assessment
specification
provided
tasks are
completed as
per
requirement
inspection
004 Prestart Conducted
before the
beginning
of any
activity
Safety
documents,
PPE among
other
environmental
related
documents
As per
outlined
methodology
As per set
regulations
and safety
requirements
Checking NC
8 Internal procedures
XYZ Construction Company has come up with robust policies which are aimed at ensuring
that the set procedures and work methodology are followed to ensure that the final product
conforms to the standard requirements. Following the set procedures also ensure that the
project is managed in an efficient and safe manner. Hence, success of the project can be
attained within the prescribed period of time without many issues. The polices and
procedures are clearly outlined in Quality, Health, Safety and Environmental management
manual. The procedures and methodology are reviewed based on the environmental
conditions and the challenges faced during implementation. However, the procedures observe
the minimum requirement of Quality management systems, pursuant to ISO 9001:2015, the
OH&S management systems pursuant to AS/NZS 4801: 2001 and Environmental
management systems as per ISO 14001: 2015 Certification. Therefore, any amendment to be
done, should rely fully on these documents for approval. The company is proud since it has
gained several recognition and certification that assures clients of quality work delivered by
the team. The company is committed to ensure that the works delivered to the clients are up
Ref.
code
Details Frequency Records to be
submitted
Specification
or standard
Acceptance
Criteria
Test
procedure
and
inspection
Compliance
status
activities work to be
undertaken
hazard
Assessment
specification
provided
tasks are
completed as
per
requirement
inspection
004 Prestart Conducted
before the
beginning
of any
activity
Safety
documents,
PPE among
other
environmental
related
documents
As per
outlined
methodology
As per set
regulations
and safety
requirements
Checking NC
8 Internal procedures
XYZ Construction Company has come up with robust policies which are aimed at ensuring
that the set procedures and work methodology are followed to ensure that the final product
conforms to the standard requirements. Following the set procedures also ensure that the
project is managed in an efficient and safe manner. Hence, success of the project can be
attained within the prescribed period of time without many issues. The polices and
procedures are clearly outlined in Quality, Health, Safety and Environmental management
manual. The procedures and methodology are reviewed based on the environmental
conditions and the challenges faced during implementation. However, the procedures observe
the minimum requirement of Quality management systems, pursuant to ISO 9001:2015, the
OH&S management systems pursuant to AS/NZS 4801: 2001 and Environmental
management systems as per ISO 14001: 2015 Certification. Therefore, any amendment to be
done, should rely fully on these documents for approval. The company is proud since it has
gained several recognition and certification that assures clients of quality work delivered by
the team. The company is committed to ensure that the works delivered to the clients are up
Secure Best Marks with AI Grader
Need help grading? Try our AI Grader for instant feedback on your assignments.
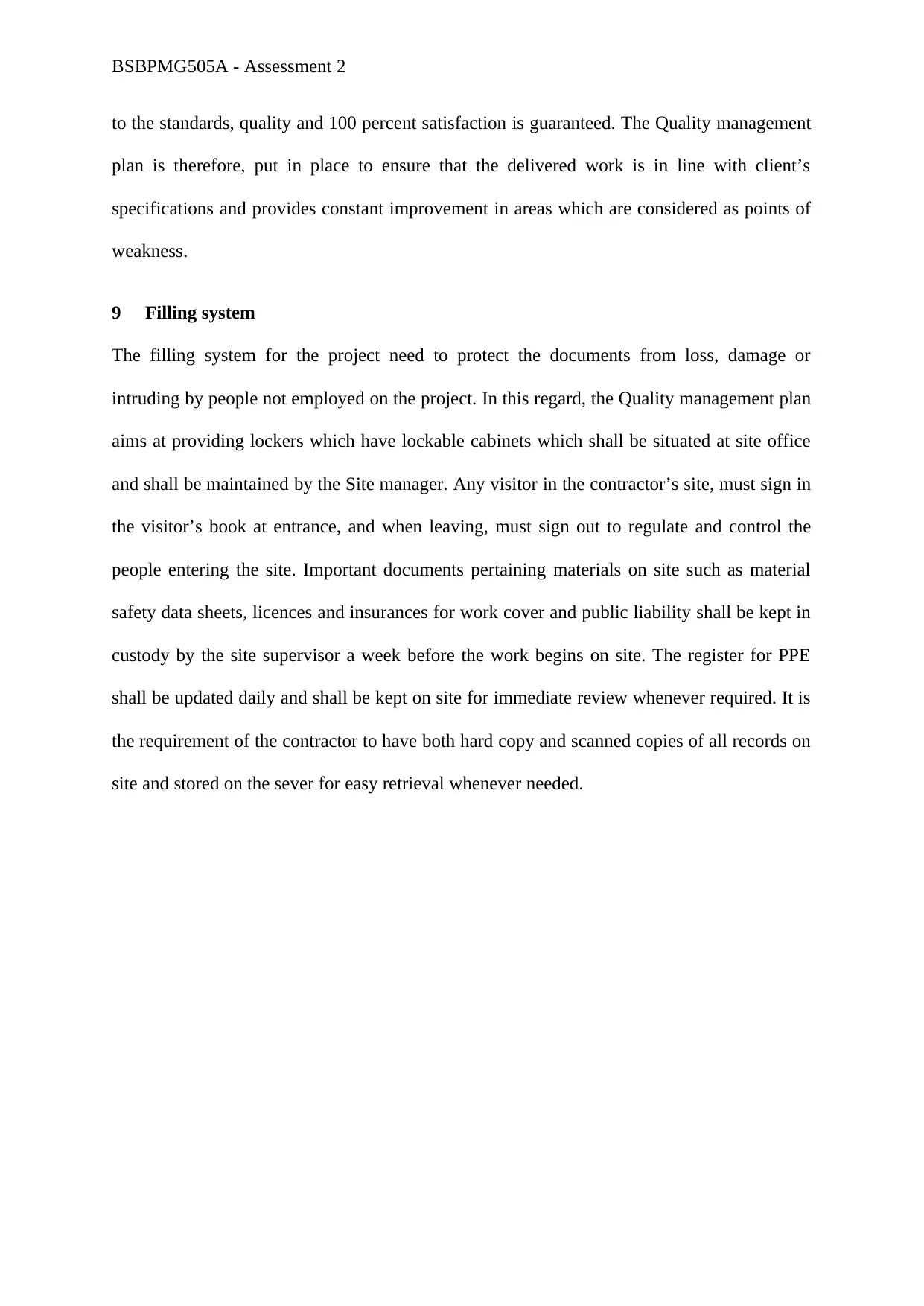
BSBPMG505A - Assessment 2
to the standards, quality and 100 percent satisfaction is guaranteed. The Quality management
plan is therefore, put in place to ensure that the delivered work is in line with client’s
specifications and provides constant improvement in areas which are considered as points of
weakness.
9 Filling system
The filling system for the project need to protect the documents from loss, damage or
intruding by people not employed on the project. In this regard, the Quality management plan
aims at providing lockers which have lockable cabinets which shall be situated at site office
and shall be maintained by the Site manager. Any visitor in the contractor’s site, must sign in
the visitor’s book at entrance, and when leaving, must sign out to regulate and control the
people entering the site. Important documents pertaining materials on site such as material
safety data sheets, licences and insurances for work cover and public liability shall be kept in
custody by the site supervisor a week before the work begins on site. The register for PPE
shall be updated daily and shall be kept on site for immediate review whenever required. It is
the requirement of the contractor to have both hard copy and scanned copies of all records on
site and stored on the sever for easy retrieval whenever needed.
to the standards, quality and 100 percent satisfaction is guaranteed. The Quality management
plan is therefore, put in place to ensure that the delivered work is in line with client’s
specifications and provides constant improvement in areas which are considered as points of
weakness.
9 Filling system
The filling system for the project need to protect the documents from loss, damage or
intruding by people not employed on the project. In this regard, the Quality management plan
aims at providing lockers which have lockable cabinets which shall be situated at site office
and shall be maintained by the Site manager. Any visitor in the contractor’s site, must sign in
the visitor’s book at entrance, and when leaving, must sign out to regulate and control the
people entering the site. Important documents pertaining materials on site such as material
safety data sheets, licences and insurances for work cover and public liability shall be kept in
custody by the site supervisor a week before the work begins on site. The register for PPE
shall be updated daily and shall be kept on site for immediate review whenever required. It is
the requirement of the contractor to have both hard copy and scanned copies of all records on
site and stored on the sever for easy retrieval whenever needed.
1 out of 11
Related Documents

Your All-in-One AI-Powered Toolkit for Academic Success.
+13062052269
info@desklib.com
Available 24*7 on WhatsApp / Email
Unlock your academic potential
© 2024 | Zucol Services PVT LTD | All rights reserved.