Quality Management for Organisational Excellence - Case Study
VerifiedAdded on  2023/01/11
|13
|3897
|61
Report
AI Summary
This report provides a comprehensive analysis of quality management strategies for organisational excellence, using the Quality Tool Company as a case study. It begins with an overview of the company's challenges and the need for improvement, then delves into company-wide quality improvement strategies, emphasizing the importance of real-time data and continuous information. The report explores Total Quality Management (TQM), outlining its benefits and challenges, followed by a detailed discussion of Quality Assurance (QA) and the application of the PDCA cycle. Quality Control (QC) methods and their role in maintaining and improving product quality are also examined. The report concludes by emphasizing the sustainability of a quality-focused culture and offers recommendations for the company to enhance its operations, improve customer satisfaction, and gain a competitive edge in the marketplace. The analysis underscores the importance of implementing effective quality management strategies to ensure long-term success.
Contribute Materials
Your contribution can guide someone’s learning journey. Share your
documents today.
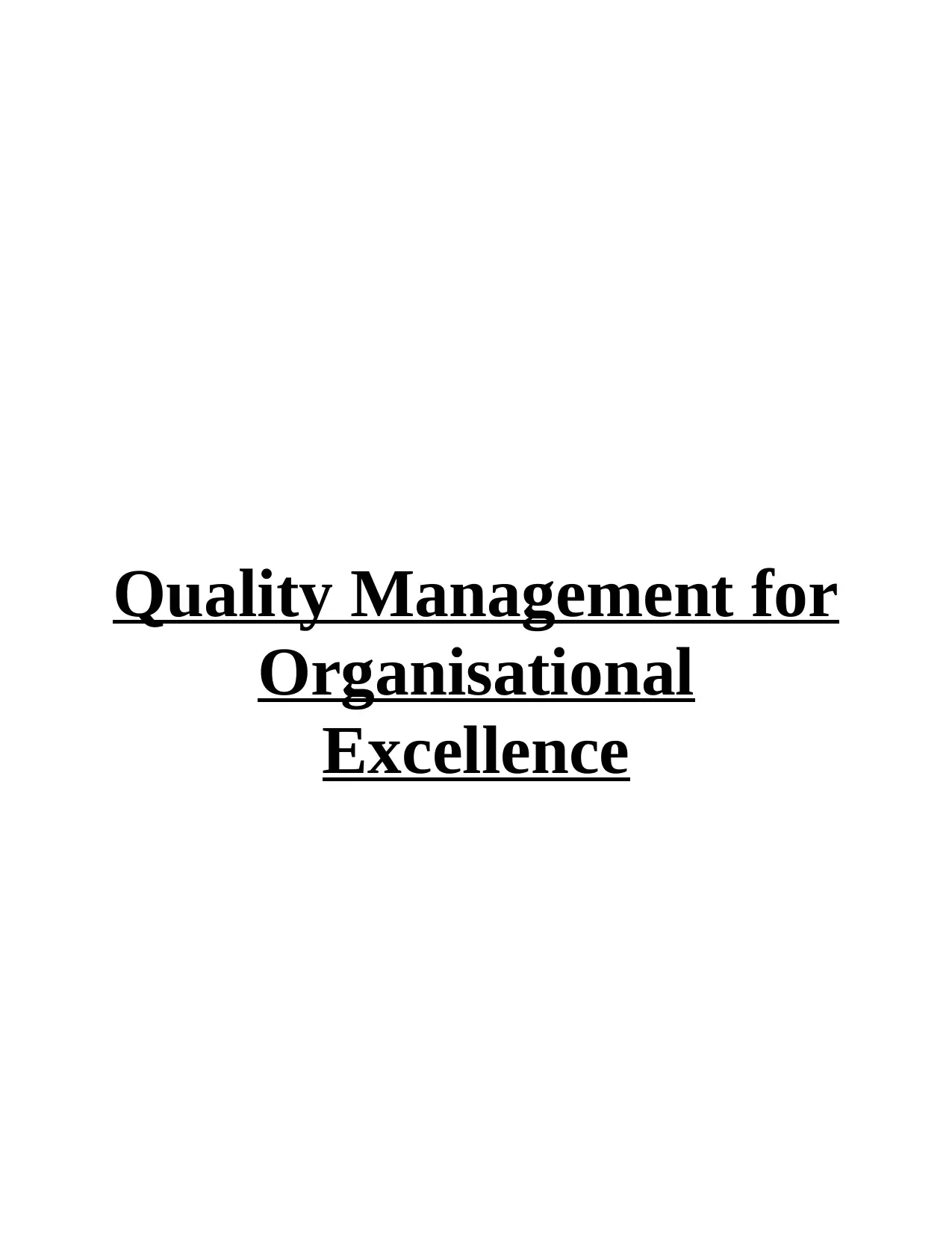
Quality Management for
Organisational
Excellence
Organisational
Excellence
Secure Best Marks with AI Grader
Need help grading? Try our AI Grader for instant feedback on your assignments.

Table of Contents
INTRODUCTION...........................................................................................................................1
MAIN BODY...................................................................................................................................1
Overview of the scenario........................................................................................................1
Company wide quality improvement strategy........................................................................2
Total quality management......................................................................................................3
Quality Assurance..................................................................................................................4
Quality control........................................................................................................................5
Sustainability of the culture of quality...................................................................................6
Recommendations..................................................................................................................6
CONCLUSION................................................................................................................................8
REFERENCES................................................................................................................................9
INTRODUCTION...........................................................................................................................1
MAIN BODY...................................................................................................................................1
Overview of the scenario........................................................................................................1
Company wide quality improvement strategy........................................................................2
Total quality management......................................................................................................3
Quality Assurance..................................................................................................................4
Quality control........................................................................................................................5
Sustainability of the culture of quality...................................................................................6
Recommendations..................................................................................................................6
CONCLUSION................................................................................................................................8
REFERENCES................................................................................................................................9

INTRODUCTION
Business environment involve number of organisations who are performing operations with
an aim to expand their progress. There are number of factors that are changing at high rate in
order to achieve organisational excellence, for this organisation are required to provide superior
value to consumers and make significant increase in performance level as effectively able to
ensure long-term success in business environment (Chen, Lee and Wang, 2020). In simple words
organisational excellence is termed as ongoing efforts undertaken by organisations as an internal
framework of processes and standards in order to motivate employee’s attitude towards offering
qualitative products and services to fulfil needs and demand of consumers. To assure quality
management organisations by taking advantage of quality administration can excellently able to
undertake smooth operation of business processes in time effective manner. Present report has
been conducted on case study of Quality Tool Company, entity operate their services as a
manufacturer of scribbles, engineering calipers, micrometres, limited range of special items,
engineer rules and other initial product range. Quality Tool Company was founded by a graduate
engineer in the year 1960 with having it’s headquartering in North East of England. It has been
identified that entity also started facing decrease in their overall profitability and productivity
ratio because of decline of engineering and significant increase in market place due to
globalisation. In addition to this report also include quality control quality management, quality
assurance and other quality related application as to build efficient quality strategy in order to
enhance organisation operations as to satisfy customers in a best effective manner and further
ensure large base of competitive edge in marketplace.
MAIN BODY
Overview of the scenario
Quality Tool Company, which is the manufacturer of specialist engineering tools,
engineering calipers, scribes, medical equipment, key hole surgery and other pioneer treatment
techniques, engineer rules and so on has already grabbed a good market in north-east England
through contracting with the board for the two years in order to manufacture cutting edge
products on a larger scale (Saffar and Obeidat, 2020). After that, company has started looking
forward to expand its business at international level with the help of its energy, conscience,
vision. In order to do so it will be required by company to develop an effective company white
1
Business environment involve number of organisations who are performing operations with
an aim to expand their progress. There are number of factors that are changing at high rate in
order to achieve organisational excellence, for this organisation are required to provide superior
value to consumers and make significant increase in performance level as effectively able to
ensure long-term success in business environment (Chen, Lee and Wang, 2020). In simple words
organisational excellence is termed as ongoing efforts undertaken by organisations as an internal
framework of processes and standards in order to motivate employee’s attitude towards offering
qualitative products and services to fulfil needs and demand of consumers. To assure quality
management organisations by taking advantage of quality administration can excellently able to
undertake smooth operation of business processes in time effective manner. Present report has
been conducted on case study of Quality Tool Company, entity operate their services as a
manufacturer of scribbles, engineering calipers, micrometres, limited range of special items,
engineer rules and other initial product range. Quality Tool Company was founded by a graduate
engineer in the year 1960 with having it’s headquartering in North East of England. It has been
identified that entity also started facing decrease in their overall profitability and productivity
ratio because of decline of engineering and significant increase in market place due to
globalisation. In addition to this report also include quality control quality management, quality
assurance and other quality related application as to build efficient quality strategy in order to
enhance organisation operations as to satisfy customers in a best effective manner and further
ensure large base of competitive edge in marketplace.
MAIN BODY
Overview of the scenario
Quality Tool Company, which is the manufacturer of specialist engineering tools,
engineering calipers, scribes, medical equipment, key hole surgery and other pioneer treatment
techniques, engineer rules and so on has already grabbed a good market in north-east England
through contracting with the board for the two years in order to manufacture cutting edge
products on a larger scale (Saffar and Obeidat, 2020). After that, company has started looking
forward to expand its business at international level with the help of its energy, conscience,
vision. In order to do so it will be required by company to develop an effective company white
1
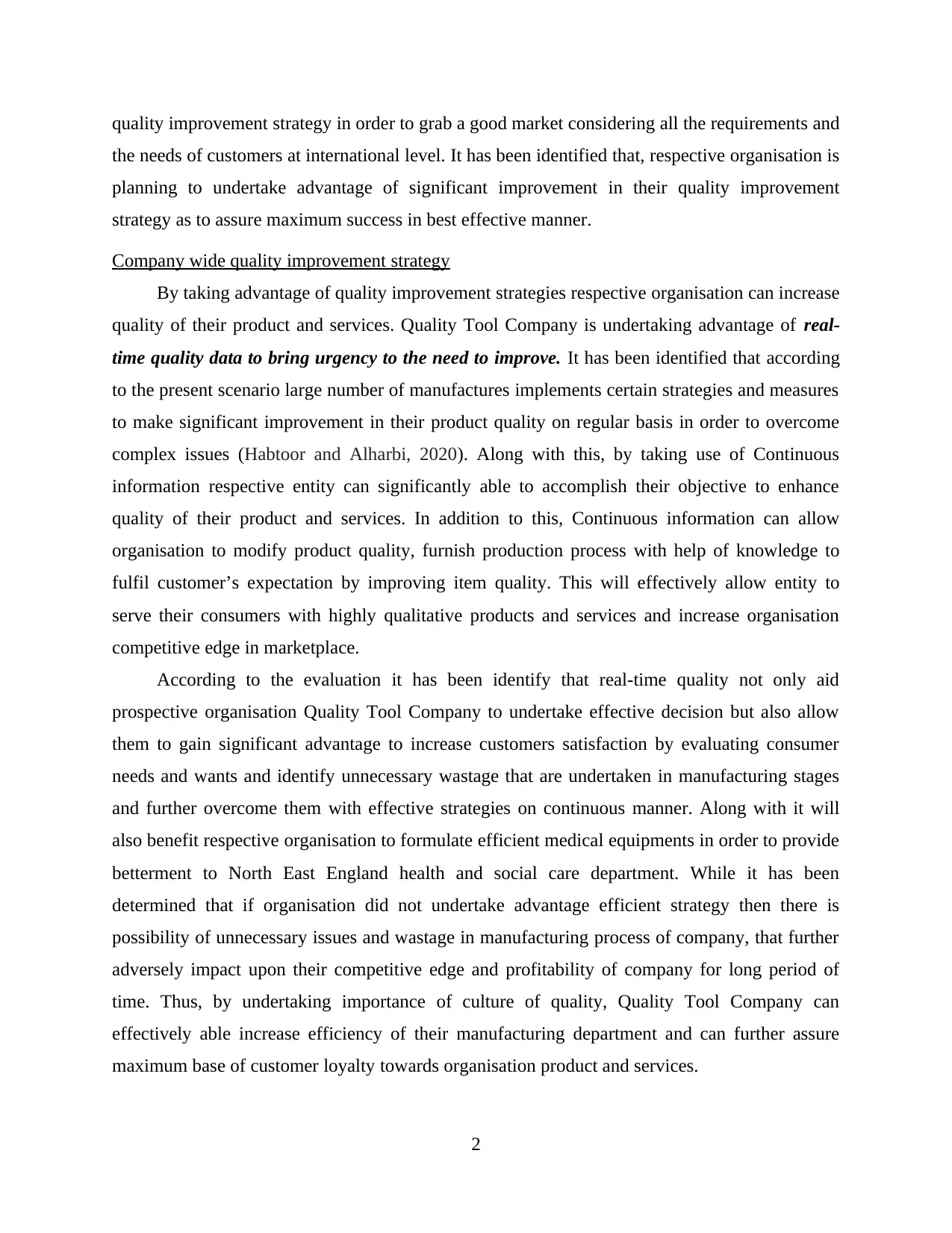
quality improvement strategy in order to grab a good market considering all the requirements and
the needs of customers at international level. It has been identified that, respective organisation is
planning to undertake advantage of significant improvement in their quality improvement
strategy as to assure maximum success in best effective manner.
Company wide quality improvement strategy
By taking advantage of quality improvement strategies respective organisation can increase
quality of their product and services. Quality Tool Company is undertaking advantage of real-
time quality data to bring urgency to the need to improve. It has been identified that according
to the present scenario large number of manufactures implements certain strategies and measures
to make significant improvement in their product quality on regular basis in order to overcome
complex issues (Habtoor and Alharbi, 2020). Along with this, by taking use of Continuous
information respective entity can significantly able to accomplish their objective to enhance
quality of their product and services. In addition to this, Continuous information can allow
organisation to modify product quality, furnish production process with help of knowledge to
fulfil customer’s expectation by improving item quality. This will effectively allow entity to
serve their consumers with highly qualitative products and services and increase organisation
competitive edge in marketplace.
According to the evaluation it has been identify that real-time quality not only aid
prospective organisation Quality Tool Company to undertake effective decision but also allow
them to gain significant advantage to increase customers satisfaction by evaluating consumer
needs and wants and identify unnecessary wastage that are undertaken in manufacturing stages
and further overcome them with effective strategies on continuous manner. Along with it will
also benefit respective organisation to formulate efficient medical equipments in order to provide
betterment to North East England health and social care department. While it has been
determined that if organisation did not undertake advantage efficient strategy then there is
possibility of unnecessary issues and wastage in manufacturing process of company, that further
adversely impact upon their competitive edge and profitability of company for long period of
time. Thus, by undertaking importance of culture of quality, Quality Tool Company can
effectively able increase efficiency of their manufacturing department and can further assure
maximum base of customer loyalty towards organisation product and services.
2
the needs of customers at international level. It has been identified that, respective organisation is
planning to undertake advantage of significant improvement in their quality improvement
strategy as to assure maximum success in best effective manner.
Company wide quality improvement strategy
By taking advantage of quality improvement strategies respective organisation can increase
quality of their product and services. Quality Tool Company is undertaking advantage of real-
time quality data to bring urgency to the need to improve. It has been identified that according
to the present scenario large number of manufactures implements certain strategies and measures
to make significant improvement in their product quality on regular basis in order to overcome
complex issues (Habtoor and Alharbi, 2020). Along with this, by taking use of Continuous
information respective entity can significantly able to accomplish their objective to enhance
quality of their product and services. In addition to this, Continuous information can allow
organisation to modify product quality, furnish production process with help of knowledge to
fulfil customer’s expectation by improving item quality. This will effectively allow entity to
serve their consumers with highly qualitative products and services and increase organisation
competitive edge in marketplace.
According to the evaluation it has been identify that real-time quality not only aid
prospective organisation Quality Tool Company to undertake effective decision but also allow
them to gain significant advantage to increase customers satisfaction by evaluating consumer
needs and wants and identify unnecessary wastage that are undertaken in manufacturing stages
and further overcome them with effective strategies on continuous manner. Along with it will
also benefit respective organisation to formulate efficient medical equipments in order to provide
betterment to North East England health and social care department. While it has been
determined that if organisation did not undertake advantage efficient strategy then there is
possibility of unnecessary issues and wastage in manufacturing process of company, that further
adversely impact upon their competitive edge and profitability of company for long period of
time. Thus, by undertaking importance of culture of quality, Quality Tool Company can
effectively able increase efficiency of their manufacturing department and can further assure
maximum base of customer loyalty towards organisation product and services.
2
Secure Best Marks with AI Grader
Need help grading? Try our AI Grader for instant feedback on your assignments.
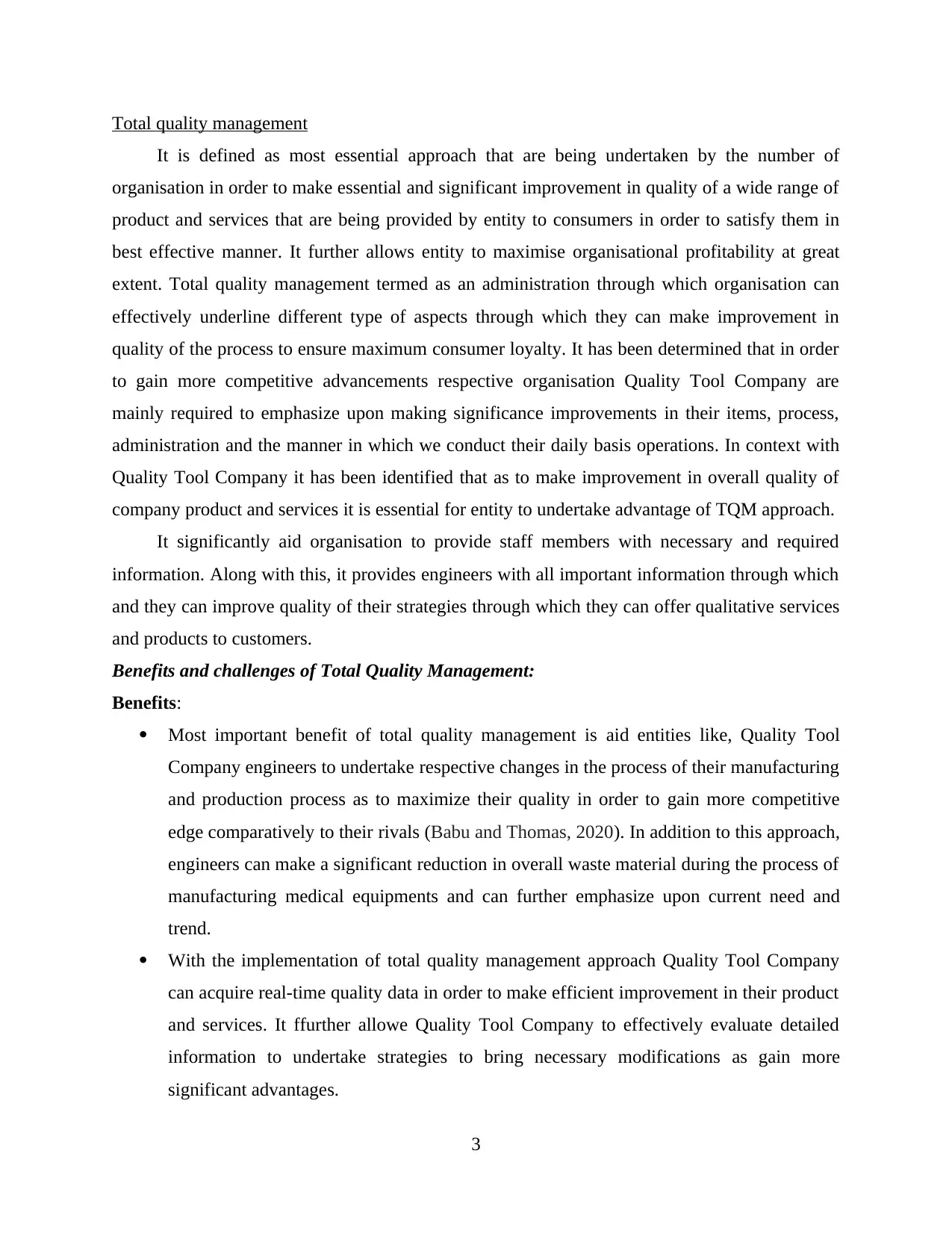
Total quality management
It is defined as most essential approach that are being undertaken by the number of
organisation in order to make essential and significant improvement in quality of a wide range of
product and services that are being provided by entity to consumers in order to satisfy them in
best effective manner. It further allows entity to maximise organisational profitability at great
extent. Total quality management termed as an administration through which organisation can
effectively underline different type of aspects through which they can make improvement in
quality of the process to ensure maximum consumer loyalty. It has been determined that in order
to gain more competitive advancements respective organisation Quality Tool Company are
mainly required to emphasize upon making significance improvements in their items, process,
administration and the manner in which we conduct their daily basis operations. In context with
Quality Tool Company it has been identified that as to make improvement in overall quality of
company product and services it is essential for entity to undertake advantage of TQM approach.
It significantly aid organisation to provide staff members with necessary and required
information. Along with this, it provides engineers with all important information through which
and they can improve quality of their strategies through which they can offer qualitative services
and products to customers.
Benefits and challenges of Total Quality Management:
Benefits:
ï‚· Most important benefit of total quality management is aid entities like, Quality Tool
Company engineers to undertake respective changes in the process of their manufacturing
and production process as to maximize their quality in order to gain more competitive
edge comparatively to their rivals (Babu and Thomas, 2020). In addition to this approach,
engineers can make a significant reduction in overall waste material during the process of
manufacturing medical equipments and can further emphasize upon current need and
trend.
ï‚· With the implementation of total quality management approach Quality Tool Company
can acquire real-time quality data in order to make efficient improvement in their product
and services. It ffurther allowe Quality Tool Company to effectively evaluate detailed
information to undertake strategies to bring necessary modifications as gain more
significant advantages.
3
It is defined as most essential approach that are being undertaken by the number of
organisation in order to make essential and significant improvement in quality of a wide range of
product and services that are being provided by entity to consumers in order to satisfy them in
best effective manner. It further allows entity to maximise organisational profitability at great
extent. Total quality management termed as an administration through which organisation can
effectively underline different type of aspects through which they can make improvement in
quality of the process to ensure maximum consumer loyalty. It has been determined that in order
to gain more competitive advancements respective organisation Quality Tool Company are
mainly required to emphasize upon making significance improvements in their items, process,
administration and the manner in which we conduct their daily basis operations. In context with
Quality Tool Company it has been identified that as to make improvement in overall quality of
company product and services it is essential for entity to undertake advantage of TQM approach.
It significantly aid organisation to provide staff members with necessary and required
information. Along with this, it provides engineers with all important information through which
and they can improve quality of their strategies through which they can offer qualitative services
and products to customers.
Benefits and challenges of Total Quality Management:
Benefits:
ï‚· Most important benefit of total quality management is aid entities like, Quality Tool
Company engineers to undertake respective changes in the process of their manufacturing
and production process as to maximize their quality in order to gain more competitive
edge comparatively to their rivals (Babu and Thomas, 2020). In addition to this approach,
engineers can make a significant reduction in overall waste material during the process of
manufacturing medical equipments and can further emphasize upon current need and
trend.
ï‚· With the implementation of total quality management approach Quality Tool Company
can acquire real-time quality data in order to make efficient improvement in their product
and services. It ffurther allowe Quality Tool Company to effectively evaluate detailed
information to undertake strategies to bring necessary modifications as gain more
significant advantages.
3
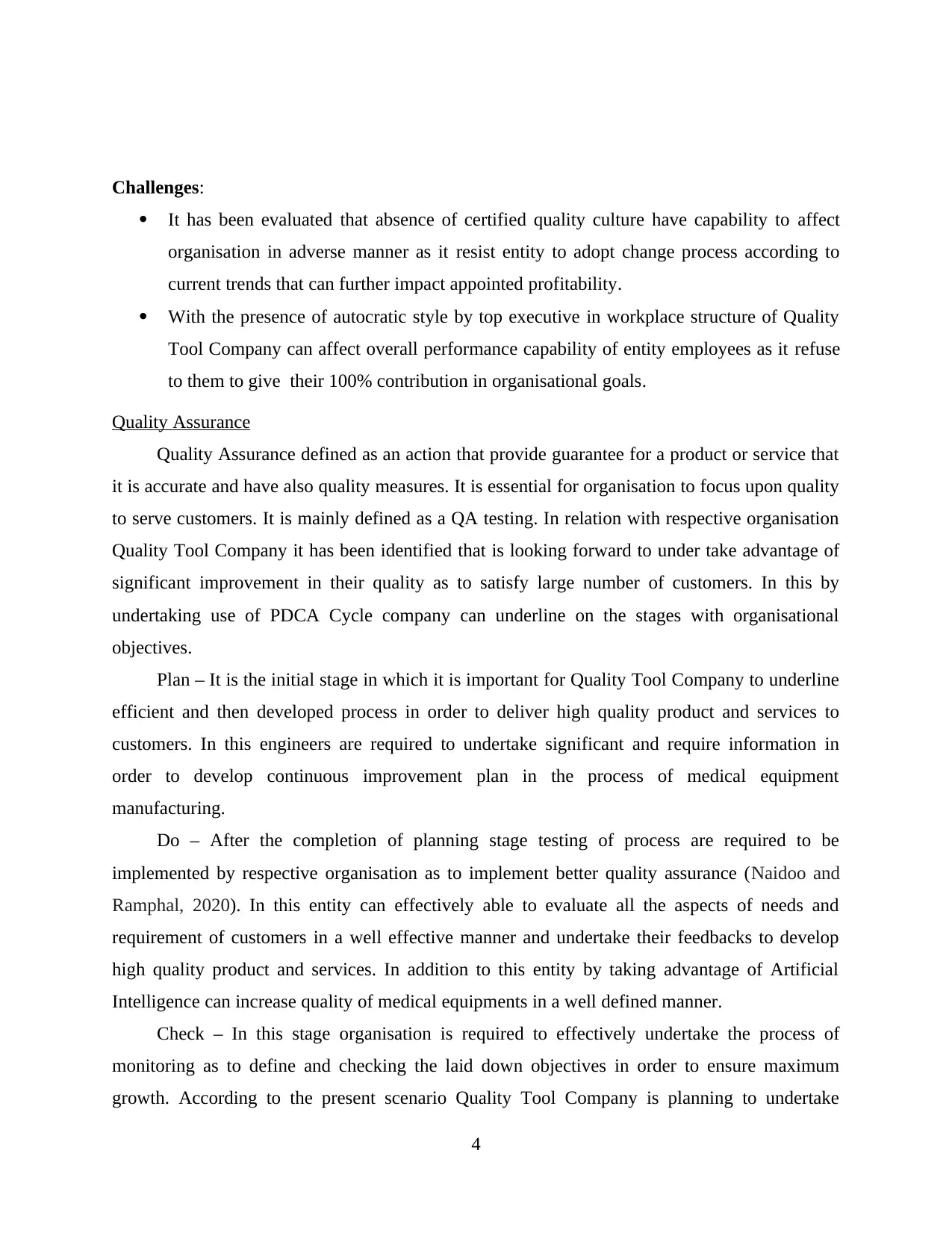
Challenges:
ï‚· It has been evaluated that absence of certified quality culture have capability to affect
organisation in adverse manner as it resist entity to adopt change process according to
current trends that can further impact appointed profitability.
ï‚· With the presence of autocratic style by top executive in workplace structure of Quality
Tool Company can affect overall performance capability of entity employees as it refuse
to them to give their 100% contribution in organisational goals.
Quality Assurance
Quality Assurance defined as an action that provide guarantee for a product or service that
it is accurate and have also quality measures. It is essential for organisation to focus upon quality
to serve customers. It is mainly defined as a QA testing. In relation with respective organisation
Quality Tool Company it has been identified that is looking forward to under take advantage of
significant improvement in their quality as to satisfy large number of customers. In this by
undertaking use of PDCA Cycle company can underline on the stages with organisational
objectives.
Plan – It is the initial stage in which it is important for Quality Tool Company to underline
efficient and then developed process in order to deliver high quality product and services to
customers. In this engineers are required to undertake significant and require information in
order to develop continuous improvement plan in the process of medical equipment
manufacturing.
Do – After the completion of planning stage testing of process are required to be
implemented by respective organisation as to implement better quality assurance (Naidoo and
Ramphal, 2020). In this entity can effectively able to evaluate all the aspects of needs and
requirement of customers in a well effective manner and undertake their feedbacks to develop
high quality product and services. In addition to this entity by taking advantage of Artificial
Intelligence can increase quality of medical equipments in a well defined manner.
Check – In this stage organisation is required to effectively undertake the process of
monitoring as to define and checking the laid down objectives in order to ensure maximum
growth. According to the present scenario Quality Tool Company is planning to undertake
4
ï‚· It has been evaluated that absence of certified quality culture have capability to affect
organisation in adverse manner as it resist entity to adopt change process according to
current trends that can further impact appointed profitability.
ï‚· With the presence of autocratic style by top executive in workplace structure of Quality
Tool Company can affect overall performance capability of entity employees as it refuse
to them to give their 100% contribution in organisational goals.
Quality Assurance
Quality Assurance defined as an action that provide guarantee for a product or service that
it is accurate and have also quality measures. It is essential for organisation to focus upon quality
to serve customers. It is mainly defined as a QA testing. In relation with respective organisation
Quality Tool Company it has been identified that is looking forward to under take advantage of
significant improvement in their quality as to satisfy large number of customers. In this by
undertaking use of PDCA Cycle company can underline on the stages with organisational
objectives.
Plan – It is the initial stage in which it is important for Quality Tool Company to underline
efficient and then developed process in order to deliver high quality product and services to
customers. In this engineers are required to undertake significant and require information in
order to develop continuous improvement plan in the process of medical equipment
manufacturing.
Do – After the completion of planning stage testing of process are required to be
implemented by respective organisation as to implement better quality assurance (Naidoo and
Ramphal, 2020). In this entity can effectively able to evaluate all the aspects of needs and
requirement of customers in a well effective manner and undertake their feedbacks to develop
high quality product and services. In addition to this entity by taking advantage of Artificial
Intelligence can increase quality of medical equipments in a well defined manner.
Check – In this stage organisation is required to effectively undertake the process of
monitoring as to define and checking the laid down objectives in order to ensure maximum
growth. According to the present scenario Quality Tool Company is planning to undertake
4
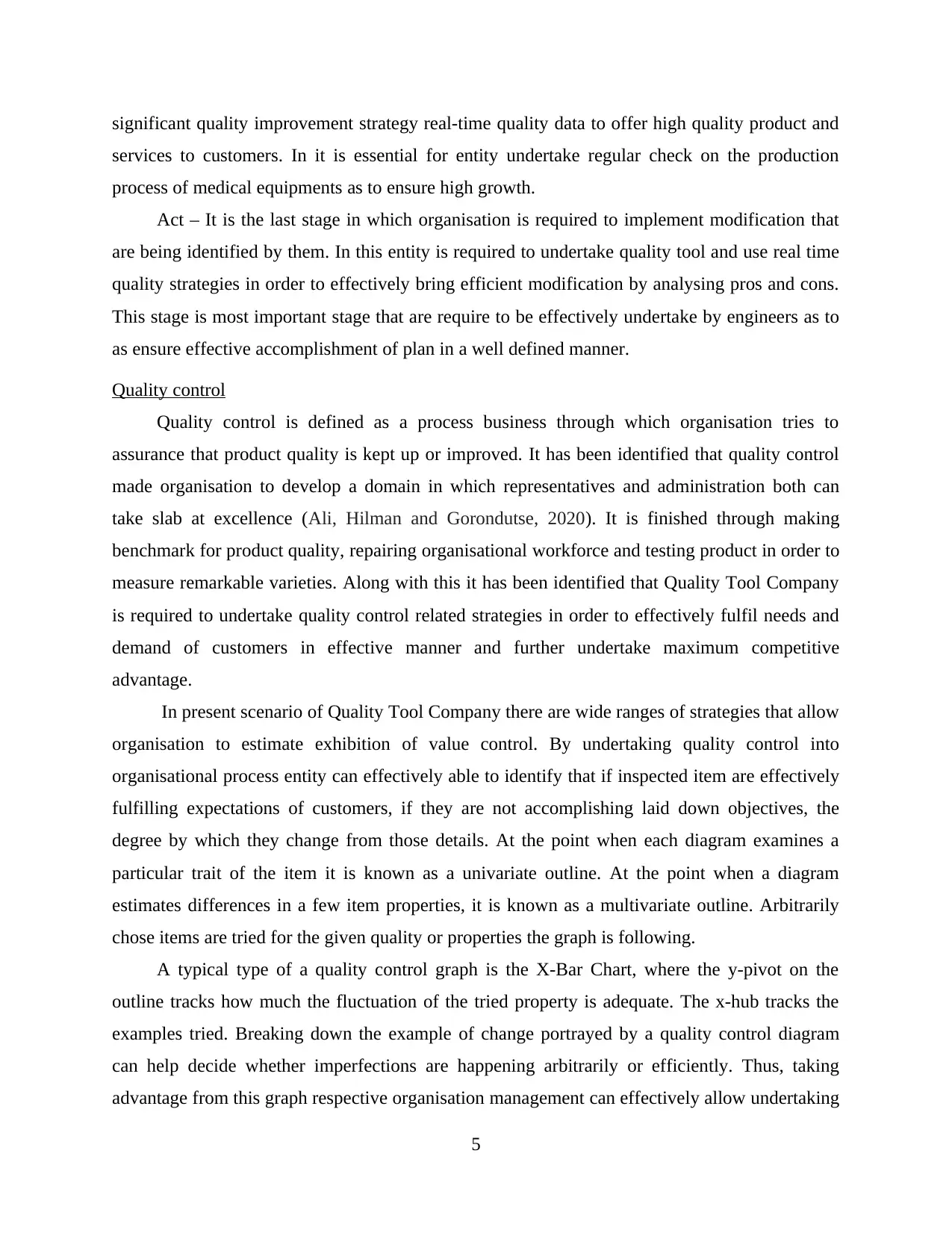
significant quality improvement strategy real-time quality data to offer high quality product and
services to customers. In it is essential for entity undertake regular check on the production
process of medical equipments as to ensure high growth.
Act – It is the last stage in which organisation is required to implement modification that
are being identified by them. In this entity is required to undertake quality tool and use real time
quality strategies in order to effectively bring efficient modification by analysing pros and cons.
This stage is most important stage that are require to be effectively undertake by engineers as to
as ensure effective accomplishment of plan in a well defined manner.
Quality control
Quality control is defined as a process business through which organisation tries to
assurance that product quality is kept up or improved. It has been identified that quality control
made organisation to develop a domain in which representatives and administration both can
take slab at excellence (Ali, Hilman and Gorondutse, 2020). It is finished through making
benchmark for product quality, repairing organisational workforce and testing product in order to
measure remarkable varieties. Along with this it has been identified that Quality Tool Company
is required to undertake quality control related strategies in order to effectively fulfil needs and
demand of customers in effective manner and further undertake maximum competitive
advantage.
In present scenario of Quality Tool Company there are wide ranges of strategies that allow
organisation to estimate exhibition of value control. By undertaking quality control into
organisational process entity can effectively able to identify that if inspected item are effectively
fulfilling expectations of customers, if they are not accomplishing laid down objectives, the
degree by which they change from those details. At the point when each diagram examines a
particular trait of the item it is known as a univariate outline. At the point when a diagram
estimates differences in a few item properties, it is known as a multivariate outline. Arbitrarily
chose items are tried for the given quality or properties the graph is following.
A typical type of a quality control graph is the X-Bar Chart, where the y-pivot on the
outline tracks how much the fluctuation of the tried property is adequate. The x-hub tracks the
examples tried. Breaking down the example of change portrayed by a quality control diagram
can help decide whether imperfections are happening arbitrarily or efficiently. Thus, taking
advantage from this graph respective organisation management can effectively allow undertaking
5
services to customers. In it is essential for entity undertake regular check on the production
process of medical equipments as to ensure high growth.
Act – It is the last stage in which organisation is required to implement modification that
are being identified by them. In this entity is required to undertake quality tool and use real time
quality strategies in order to effectively bring efficient modification by analysing pros and cons.
This stage is most important stage that are require to be effectively undertake by engineers as to
as ensure effective accomplishment of plan in a well defined manner.
Quality control
Quality control is defined as a process business through which organisation tries to
assurance that product quality is kept up or improved. It has been identified that quality control
made organisation to develop a domain in which representatives and administration both can
take slab at excellence (Ali, Hilman and Gorondutse, 2020). It is finished through making
benchmark for product quality, repairing organisational workforce and testing product in order to
measure remarkable varieties. Along with this it has been identified that Quality Tool Company
is required to undertake quality control related strategies in order to effectively fulfil needs and
demand of customers in effective manner and further undertake maximum competitive
advantage.
In present scenario of Quality Tool Company there are wide ranges of strategies that allow
organisation to estimate exhibition of value control. By undertaking quality control into
organisational process entity can effectively able to identify that if inspected item are effectively
fulfilling expectations of customers, if they are not accomplishing laid down objectives, the
degree by which they change from those details. At the point when each diagram examines a
particular trait of the item it is known as a univariate outline. At the point when a diagram
estimates differences in a few item properties, it is known as a multivariate outline. Arbitrarily
chose items are tried for the given quality or properties the graph is following.
A typical type of a quality control graph is the X-Bar Chart, where the y-pivot on the
outline tracks how much the fluctuation of the tried property is adequate. The x-hub tracks the
examples tried. Breaking down the example of change portrayed by a quality control diagram
can help decide whether imperfections are happening arbitrarily or efficiently. Thus, taking
advantage from this graph respective organisation management can effectively allow undertaking
5
Paraphrase This Document
Need a fresh take? Get an instant paraphrase of this document with our AI Paraphraser
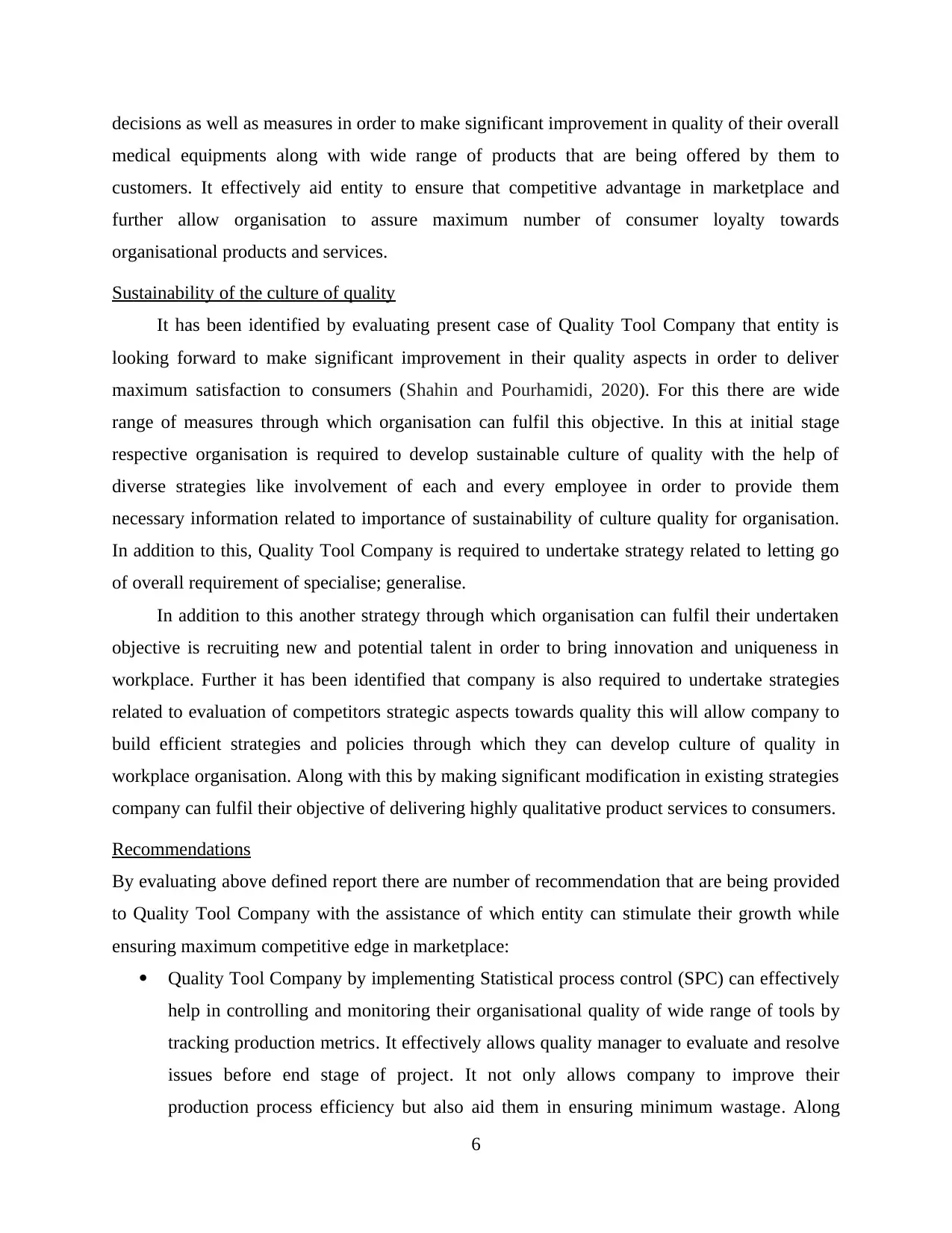
decisions as well as measures in order to make significant improvement in quality of their overall
medical equipments along with wide range of products that are being offered by them to
customers. It effectively aid entity to ensure that competitive advantage in marketplace and
further allow organisation to assure maximum number of consumer loyalty towards
organisational products and services.
Sustainability of the culture of quality
It has been identified by evaluating present case of Quality Tool Company that entity is
looking forward to make significant improvement in their quality aspects in order to deliver
maximum satisfaction to consumers (Shahin and Pourhamidi, 2020). For this there are wide
range of measures through which organisation can fulfil this objective. In this at initial stage
respective organisation is required to develop sustainable culture of quality with the help of
diverse strategies like involvement of each and every employee in order to provide them
necessary information related to importance of sustainability of culture quality for organisation.
In addition to this, Quality Tool Company is required to undertake strategy related to letting go
of overall requirement of specialise; generalise.
In addition to this another strategy through which organisation can fulfil their undertaken
objective is recruiting new and potential talent in order to bring innovation and uniqueness in
workplace. Further it has been identified that company is also required to undertake strategies
related to evaluation of competitors strategic aspects towards quality this will allow company to
build efficient strategies and policies through which they can develop culture of quality in
workplace organisation. Along with this by making significant modification in existing strategies
company can fulfil their objective of delivering highly qualitative product services to consumers.
Recommendations
By evaluating above defined report there are number of recommendation that are being provided
to Quality Tool Company with the assistance of which entity can stimulate their growth while
ensuring maximum competitive edge in marketplace:
ï‚· Quality Tool Company by implementing Statistical process control (SPC) can effectively
help in controlling and monitoring their organisational quality of wide range of tools by
tracking production metrics. It effectively allows quality manager to evaluate and resolve
issues before end stage of project. It not only allows company to improve their
production process efficiency but also aid them in ensuring minimum wastage. Along
6
medical equipments along with wide range of products that are being offered by them to
customers. It effectively aid entity to ensure that competitive advantage in marketplace and
further allow organisation to assure maximum number of consumer loyalty towards
organisational products and services.
Sustainability of the culture of quality
It has been identified by evaluating present case of Quality Tool Company that entity is
looking forward to make significant improvement in their quality aspects in order to deliver
maximum satisfaction to consumers (Shahin and Pourhamidi, 2020). For this there are wide
range of measures through which organisation can fulfil this objective. In this at initial stage
respective organisation is required to develop sustainable culture of quality with the help of
diverse strategies like involvement of each and every employee in order to provide them
necessary information related to importance of sustainability of culture quality for organisation.
In addition to this, Quality Tool Company is required to undertake strategy related to letting go
of overall requirement of specialise; generalise.
In addition to this another strategy through which organisation can fulfil their undertaken
objective is recruiting new and potential talent in order to bring innovation and uniqueness in
workplace. Further it has been identified that company is also required to undertake strategies
related to evaluation of competitors strategic aspects towards quality this will allow company to
build efficient strategies and policies through which they can develop culture of quality in
workplace organisation. Along with this by making significant modification in existing strategies
company can fulfil their objective of delivering highly qualitative product services to consumers.
Recommendations
By evaluating above defined report there are number of recommendation that are being provided
to Quality Tool Company with the assistance of which entity can stimulate their growth while
ensuring maximum competitive edge in marketplace:
ï‚· Quality Tool Company by implementing Statistical process control (SPC) can effectively
help in controlling and monitoring their organisational quality of wide range of tools by
tracking production metrics. It effectively allows quality manager to evaluate and resolve
issues before end stage of project. It not only allows company to improve their
production process efficiency but also aid them in ensuring minimum wastage. Along
6
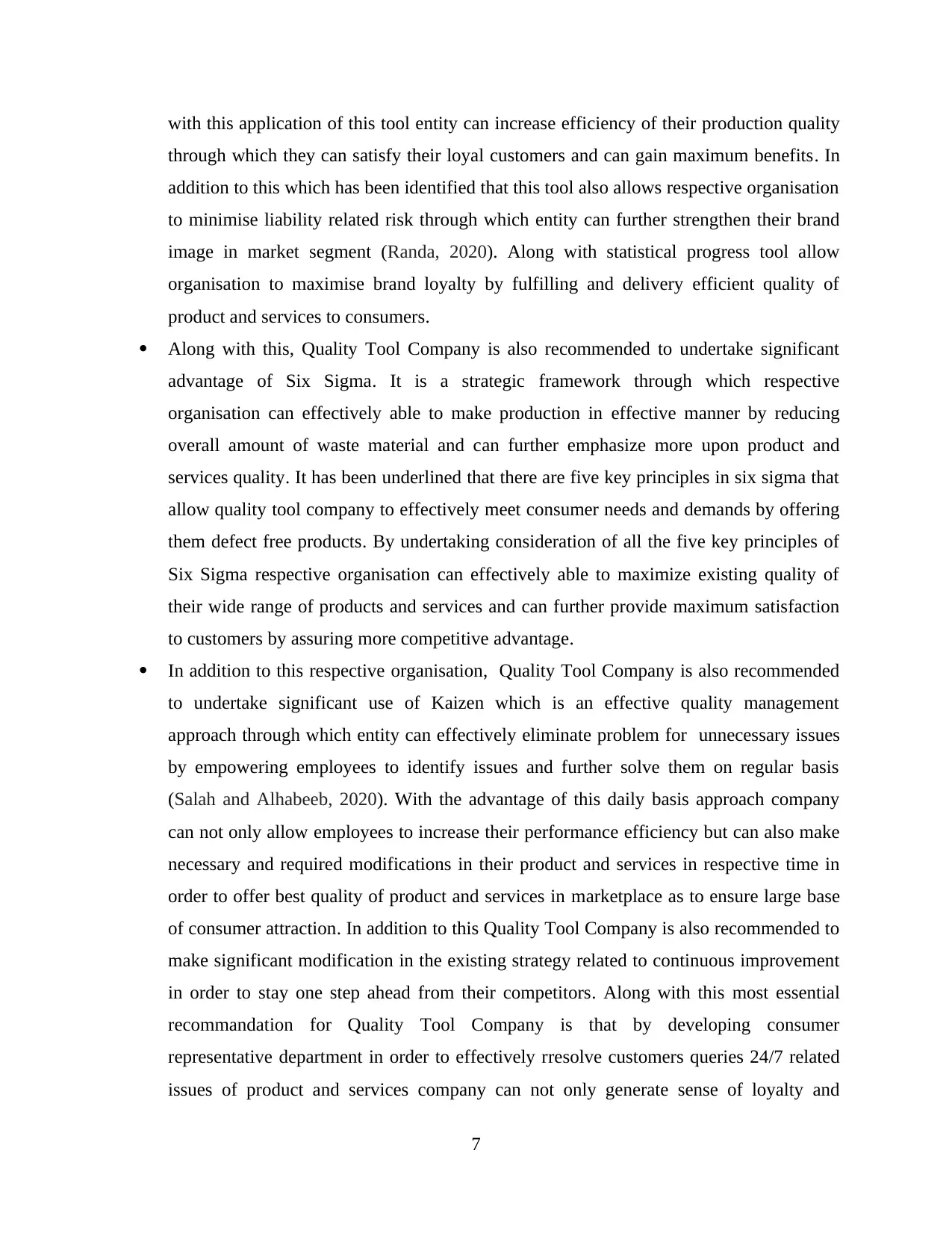
with this application of this tool entity can increase efficiency of their production quality
through which they can satisfy their loyal customers and can gain maximum benefits. In
addition to this which has been identified that this tool also allows respective organisation
to minimise liability related risk through which entity can further strengthen their brand
image in market segment (Randa, 2020). Along with statistical progress tool allow
organisation to maximise brand loyalty by fulfilling and delivery efficient quality of
product and services to consumers.
ï‚· Along with this, Quality Tool Company is also recommended to undertake significant
advantage of Six Sigma. It is a strategic framework through which respective
organisation can effectively able to make production in effective manner by reducing
overall amount of waste material and can further emphasize more upon product and
services quality. It has been underlined that there are five key principles in six sigma that
allow quality tool company to effectively meet consumer needs and demands by offering
them defect free products. By undertaking consideration of all the five key principles of
Six Sigma respective organisation can effectively able to maximize existing quality of
their wide range of products and services and can further provide maximum satisfaction
to customers by assuring more competitive advantage.
ï‚· In addition to this respective organisation, Quality Tool Company is also recommended
to undertake significant use of Kaizen which is an effective quality management
approach through which entity can effectively eliminate problem for unnecessary issues
by empowering employees to identify issues and further solve them on regular basis
(Salah and Alhabeeb, 2020). With the advantage of this daily basis approach company
can not only allow employees to increase their performance efficiency but can also make
necessary and required modifications in their product and services in respective time in
order to offer best quality of product and services in marketplace as to ensure large base
of consumer attraction. In addition to this Quality Tool Company is also recommended to
make significant modification in the existing strategy related to continuous improvement
in order to stay one step ahead from their competitors. Along with this most essential
recommandation for Quality Tool Company is that by developing consumer
representative department in order to effectively rresolve customers queries 24/7 related
issues of product and services company can not only generate sense of loyalty and
7
through which they can satisfy their loyal customers and can gain maximum benefits. In
addition to this which has been identified that this tool also allows respective organisation
to minimise liability related risk through which entity can further strengthen their brand
image in market segment (Randa, 2020). Along with statistical progress tool allow
organisation to maximise brand loyalty by fulfilling and delivery efficient quality of
product and services to consumers.
ï‚· Along with this, Quality Tool Company is also recommended to undertake significant
advantage of Six Sigma. It is a strategic framework through which respective
organisation can effectively able to make production in effective manner by reducing
overall amount of waste material and can further emphasize more upon product and
services quality. It has been underlined that there are five key principles in six sigma that
allow quality tool company to effectively meet consumer needs and demands by offering
them defect free products. By undertaking consideration of all the five key principles of
Six Sigma respective organisation can effectively able to maximize existing quality of
their wide range of products and services and can further provide maximum satisfaction
to customers by assuring more competitive advantage.
ï‚· In addition to this respective organisation, Quality Tool Company is also recommended
to undertake significant use of Kaizen which is an effective quality management
approach through which entity can effectively eliminate problem for unnecessary issues
by empowering employees to identify issues and further solve them on regular basis
(Salah and Alhabeeb, 2020). With the advantage of this daily basis approach company
can not only allow employees to increase their performance efficiency but can also make
necessary and required modifications in their product and services in respective time in
order to offer best quality of product and services in marketplace as to ensure large base
of consumer attraction. In addition to this Quality Tool Company is also recommended to
make significant modification in the existing strategy related to continuous improvement
in order to stay one step ahead from their competitors. Along with this most essential
recommandation for Quality Tool Company is that by developing consumer
representative department in order to effectively rresolve customers queries 24/7 related
issues of product and services company can not only generate sense of loyalty and
7
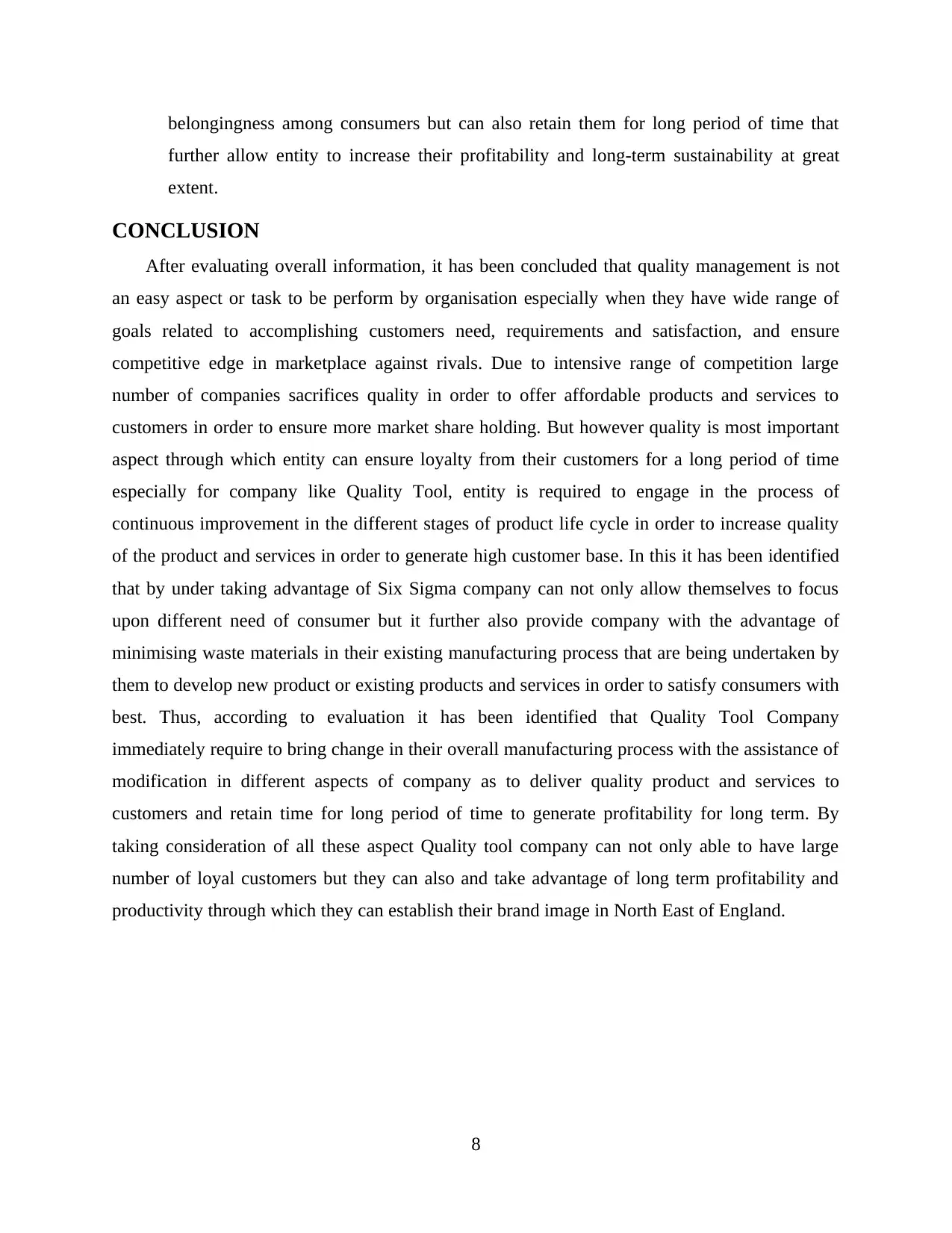
belongingness among consumers but can also retain them for long period of time that
further allow entity to increase their profitability and long-term sustainability at great
extent.
CONCLUSION
After evaluating overall information, it has been concluded that quality management is not
an easy aspect or task to be perform by organisation especially when they have wide range of
goals related to accomplishing customers need, requirements and satisfaction, and ensure
competitive edge in marketplace against rivals. Due to intensive range of competition large
number of companies sacrifices quality in order to offer affordable products and services to
customers in order to ensure more market share holding. But however quality is most important
aspect through which entity can ensure loyalty from their customers for a long period of time
especially for company like Quality Tool, entity is required to engage in the process of
continuous improvement in the different stages of product life cycle in order to increase quality
of the product and services in order to generate high customer base. In this it has been identified
that by under taking advantage of Six Sigma company can not only allow themselves to focus
upon different need of consumer but it further also provide company with the advantage of
minimising waste materials in their existing manufacturing process that are being undertaken by
them to develop new product or existing products and services in order to satisfy consumers with
best. Thus, according to evaluation it has been identified that Quality Tool Company
immediately require to bring change in their overall manufacturing process with the assistance of
modification in different aspects of company as to deliver quality product and services to
customers and retain time for long period of time to generate profitability for long term. By
taking consideration of all these aspect Quality tool company can not only able to have large
number of loyal customers but they can also and take advantage of long term profitability and
productivity through which they can establish their brand image in North East of England.
8
further allow entity to increase their profitability and long-term sustainability at great
extent.
CONCLUSION
After evaluating overall information, it has been concluded that quality management is not
an easy aspect or task to be perform by organisation especially when they have wide range of
goals related to accomplishing customers need, requirements and satisfaction, and ensure
competitive edge in marketplace against rivals. Due to intensive range of competition large
number of companies sacrifices quality in order to offer affordable products and services to
customers in order to ensure more market share holding. But however quality is most important
aspect through which entity can ensure loyalty from their customers for a long period of time
especially for company like Quality Tool, entity is required to engage in the process of
continuous improvement in the different stages of product life cycle in order to increase quality
of the product and services in order to generate high customer base. In this it has been identified
that by under taking advantage of Six Sigma company can not only allow themselves to focus
upon different need of consumer but it further also provide company with the advantage of
minimising waste materials in their existing manufacturing process that are being undertaken by
them to develop new product or existing products and services in order to satisfy consumers with
best. Thus, according to evaluation it has been identified that Quality Tool Company
immediately require to bring change in their overall manufacturing process with the assistance of
modification in different aspects of company as to deliver quality product and services to
customers and retain time for long period of time to generate profitability for long term. By
taking consideration of all these aspect Quality tool company can not only able to have large
number of loyal customers but they can also and take advantage of long term profitability and
productivity through which they can establish their brand image in North East of England.
8
Secure Best Marks with AI Grader
Need help grading? Try our AI Grader for instant feedback on your assignments.
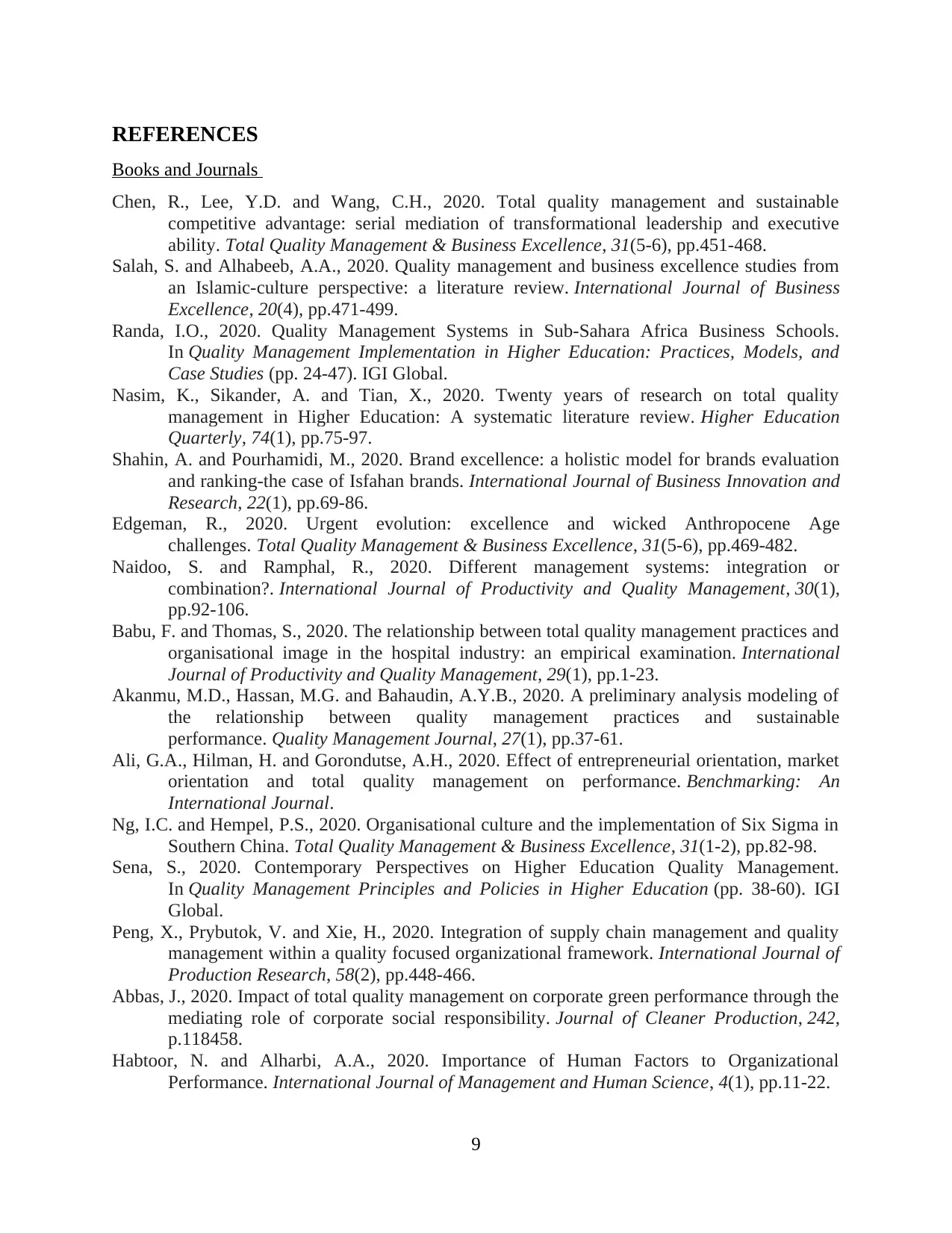
REFERENCES
Books and Journals
Chen, R., Lee, Y.D. and Wang, C.H., 2020. Total quality management and sustainable
competitive advantage: serial mediation of transformational leadership and executive
ability. Total Quality Management & Business Excellence, 31(5-6), pp.451-468.
Salah, S. and Alhabeeb, A.A., 2020. Quality management and business excellence studies from
an Islamic-culture perspective: a literature review. International Journal of Business
Excellence, 20(4), pp.471-499.
Randa, I.O., 2020. Quality Management Systems in Sub-Sahara Africa Business Schools.
In Quality Management Implementation in Higher Education: Practices, Models, and
Case Studies (pp. 24-47). IGI Global.
Nasim, K., Sikander, A. and Tian, X., 2020. Twenty years of research on total quality
management in Higher Education: A systematic literature review. Higher Education
Quarterly, 74(1), pp.75-97.
Shahin, A. and Pourhamidi, M., 2020. Brand excellence: a holistic model for brands evaluation
and ranking-the case of Isfahan brands. International Journal of Business Innovation and
Research, 22(1), pp.69-86.
Edgeman, R., 2020. Urgent evolution: excellence and wicked Anthropocene Age
challenges. Total Quality Management & Business Excellence, 31(5-6), pp.469-482.
Naidoo, S. and Ramphal, R., 2020. Different management systems: integration or
combination?. International Journal of Productivity and Quality Management, 30(1),
pp.92-106.
Babu, F. and Thomas, S., 2020. The relationship between total quality management practices and
organisational image in the hospital industry: an empirical examination. International
Journal of Productivity and Quality Management, 29(1), pp.1-23.
Akanmu, M.D., Hassan, M.G. and Bahaudin, A.Y.B., 2020. A preliminary analysis modeling of
the relationship between quality management practices and sustainable
performance. Quality Management Journal, 27(1), pp.37-61.
Ali, G.A., Hilman, H. and Gorondutse, A.H., 2020. Effect of entrepreneurial orientation, market
orientation and total quality management on performance. Benchmarking: An
International Journal.
Ng, I.C. and Hempel, P.S., 2020. Organisational culture and the implementation of Six Sigma in
Southern China. Total Quality Management & Business Excellence, 31(1-2), pp.82-98.
Sena, S., 2020. Contemporary Perspectives on Higher Education Quality Management.
In Quality Management Principles and Policies in Higher Education (pp. 38-60). IGI
Global.
Peng, X., Prybutok, V. and Xie, H., 2020. Integration of supply chain management and quality
management within a quality focused organizational framework. International Journal of
Production Research, 58(2), pp.448-466.
Abbas, J., 2020. Impact of total quality management on corporate green performance through the
mediating role of corporate social responsibility. Journal of Cleaner Production, 242,
p.118458.
Habtoor, N. and Alharbi, A.A., 2020. Importance of Human Factors to Organizational
Performance. International Journal of Management and Human Science, 4(1), pp.11-22.
9
Books and Journals
Chen, R., Lee, Y.D. and Wang, C.H., 2020. Total quality management and sustainable
competitive advantage: serial mediation of transformational leadership and executive
ability. Total Quality Management & Business Excellence, 31(5-6), pp.451-468.
Salah, S. and Alhabeeb, A.A., 2020. Quality management and business excellence studies from
an Islamic-culture perspective: a literature review. International Journal of Business
Excellence, 20(4), pp.471-499.
Randa, I.O., 2020. Quality Management Systems in Sub-Sahara Africa Business Schools.
In Quality Management Implementation in Higher Education: Practices, Models, and
Case Studies (pp. 24-47). IGI Global.
Nasim, K., Sikander, A. and Tian, X., 2020. Twenty years of research on total quality
management in Higher Education: A systematic literature review. Higher Education
Quarterly, 74(1), pp.75-97.
Shahin, A. and Pourhamidi, M., 2020. Brand excellence: a holistic model for brands evaluation
and ranking-the case of Isfahan brands. International Journal of Business Innovation and
Research, 22(1), pp.69-86.
Edgeman, R., 2020. Urgent evolution: excellence and wicked Anthropocene Age
challenges. Total Quality Management & Business Excellence, 31(5-6), pp.469-482.
Naidoo, S. and Ramphal, R., 2020. Different management systems: integration or
combination?. International Journal of Productivity and Quality Management, 30(1),
pp.92-106.
Babu, F. and Thomas, S., 2020. The relationship between total quality management practices and
organisational image in the hospital industry: an empirical examination. International
Journal of Productivity and Quality Management, 29(1), pp.1-23.
Akanmu, M.D., Hassan, M.G. and Bahaudin, A.Y.B., 2020. A preliminary analysis modeling of
the relationship between quality management practices and sustainable
performance. Quality Management Journal, 27(1), pp.37-61.
Ali, G.A., Hilman, H. and Gorondutse, A.H., 2020. Effect of entrepreneurial orientation, market
orientation and total quality management on performance. Benchmarking: An
International Journal.
Ng, I.C. and Hempel, P.S., 2020. Organisational culture and the implementation of Six Sigma in
Southern China. Total Quality Management & Business Excellence, 31(1-2), pp.82-98.
Sena, S., 2020. Contemporary Perspectives on Higher Education Quality Management.
In Quality Management Principles and Policies in Higher Education (pp. 38-60). IGI
Global.
Peng, X., Prybutok, V. and Xie, H., 2020. Integration of supply chain management and quality
management within a quality focused organizational framework. International Journal of
Production Research, 58(2), pp.448-466.
Abbas, J., 2020. Impact of total quality management on corporate green performance through the
mediating role of corporate social responsibility. Journal of Cleaner Production, 242,
p.118458.
Habtoor, N. and Alharbi, A.A., 2020. Importance of Human Factors to Organizational
Performance. International Journal of Management and Human Science, 4(1), pp.11-22.
9
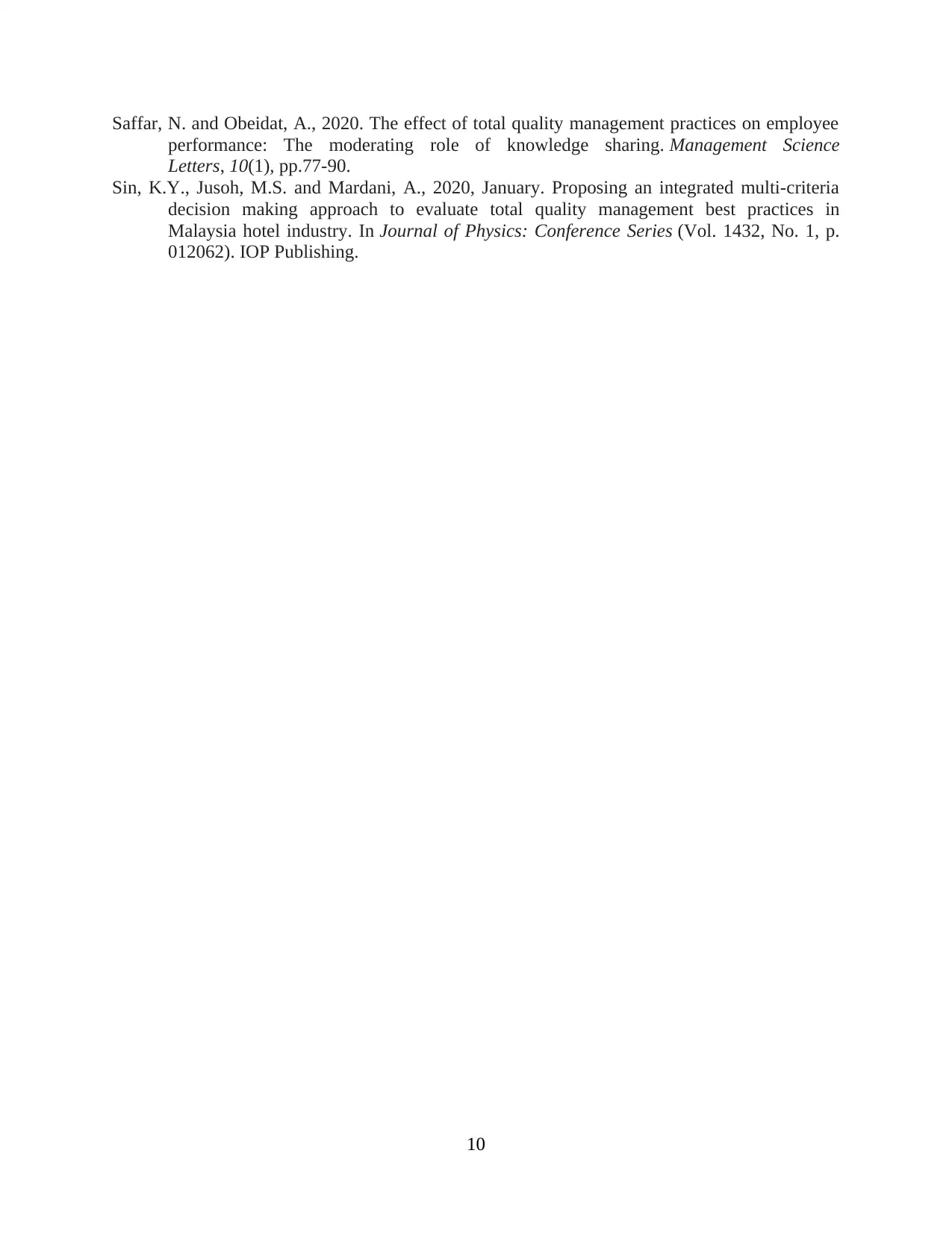
Saffar, N. and Obeidat, A., 2020. The effect of total quality management practices on employee
performance: The moderating role of knowledge sharing. Management Science
Letters, 10(1), pp.77-90.
Sin, K.Y., Jusoh, M.S. and Mardani, A., 2020, January. Proposing an integrated multi-criteria
decision making approach to evaluate total quality management best practices in
Malaysia hotel industry. In Journal of Physics: Conference Series (Vol. 1432, No. 1, p.
012062). IOP Publishing.
10
performance: The moderating role of knowledge sharing. Management Science
Letters, 10(1), pp.77-90.
Sin, K.Y., Jusoh, M.S. and Mardani, A., 2020, January. Proposing an integrated multi-criteria
decision making approach to evaluate total quality management best practices in
Malaysia hotel industry. In Journal of Physics: Conference Series (Vol. 1432, No. 1, p.
012062). IOP Publishing.
10
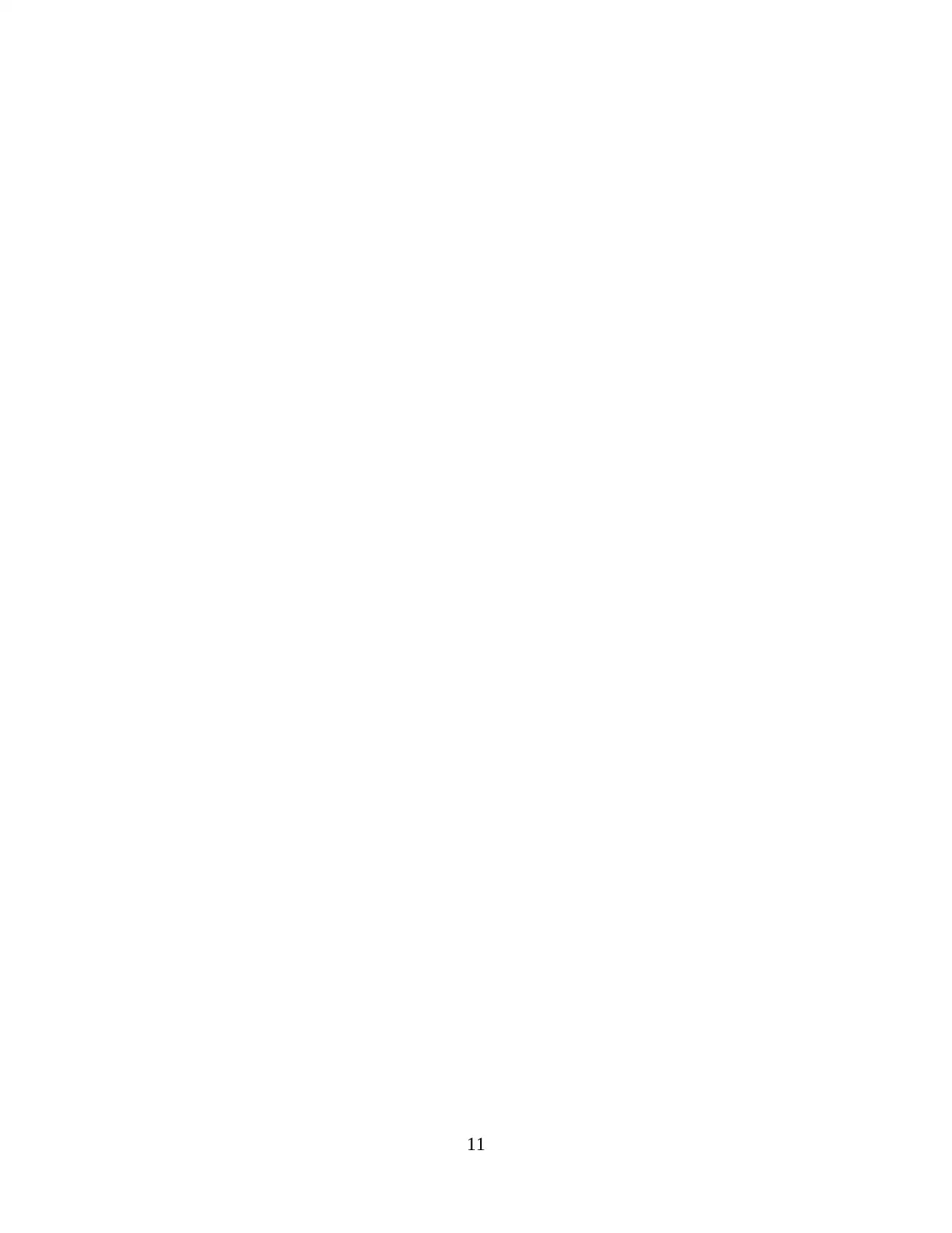
11
1 out of 13
Related Documents

Your All-in-One AI-Powered Toolkit for Academic Success.
 +13062052269
info@desklib.com
Available 24*7 on WhatsApp / Email
Unlock your academic potential
© 2024  |  Zucol Services PVT LTD  |  All rights reserved.