Analysis of Quality Management for Engineering Tooling Company (ETC)
VerifiedAdded on 2022/12/26
|13
|3941
|61
Report
AI Summary
This report provides a detailed analysis of the Engineering Tooling Company (ETC) and its approach to quality management. It begins with an overview of the company, its challenges, and the need for a comprehensive quality improvement strategy. The main body of the report explores the implementation of Total Quality Management (TQM), including key components like customer centricity and employee engagement. It delves into the practical application of TQM, highlighting the 6 C's of effective implementation and the importance of the ISO 9000 standard. The report then examines quality assurance and quality control, emphasizing their roles in ensuring customer satisfaction and identifying/eliminating defects. Process analysis, continuous improvement, and the sustenance of a quality culture are also discussed. The impact of external factors such as Brexit and Covid-19 on the company's CSR and sustainability are assessed. The report concludes with recommendations for ETC to maintain a competitive edge in the industry through effective quality management practices, emphasizing continuous improvement and customer satisfaction.
Contribute Materials
Your contribution can guide someone’s learning journey. Share your
documents today.
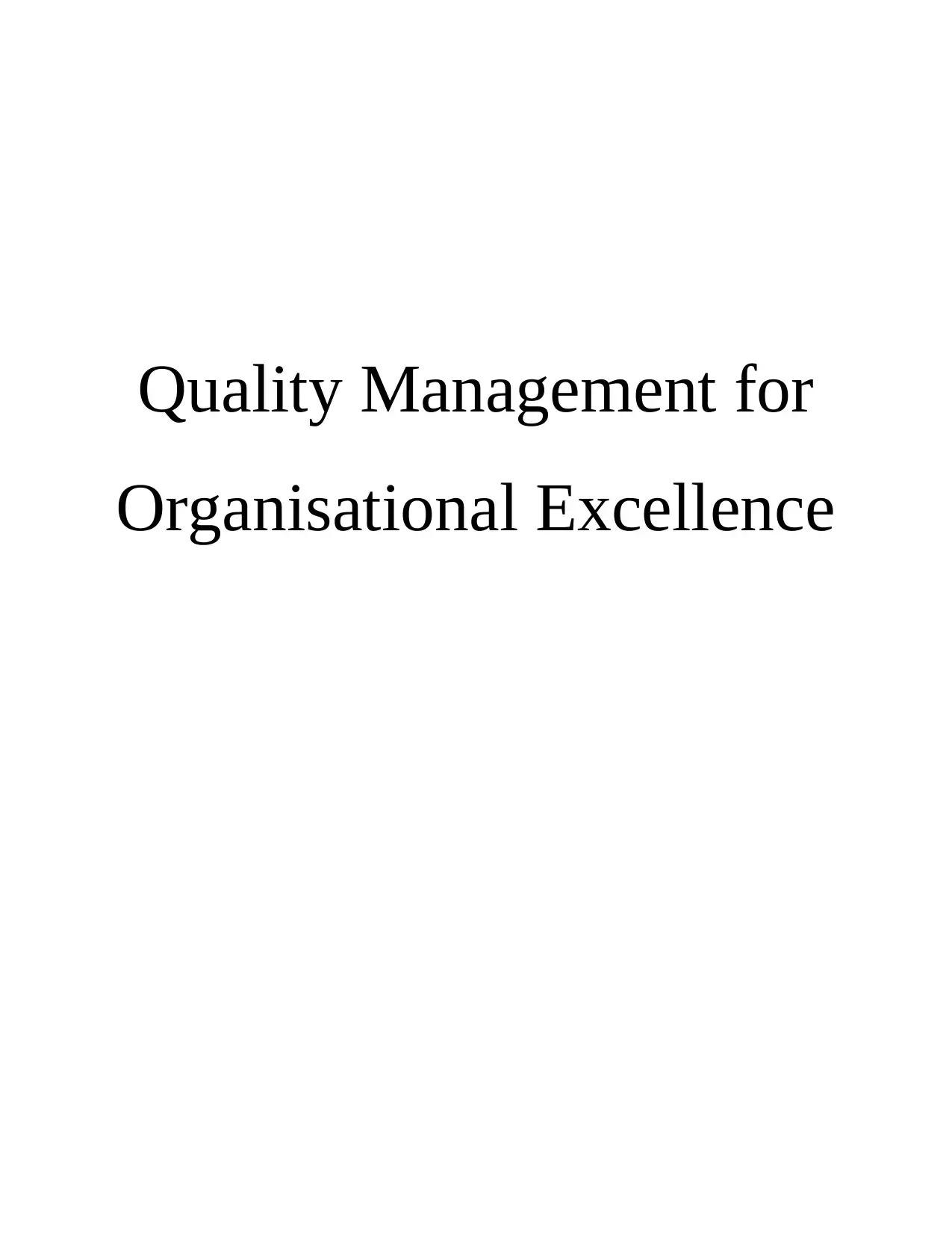
Quality Management for
Organisational Excellence
Organisational Excellence
Secure Best Marks with AI Grader
Need help grading? Try our AI Grader for instant feedback on your assignments.
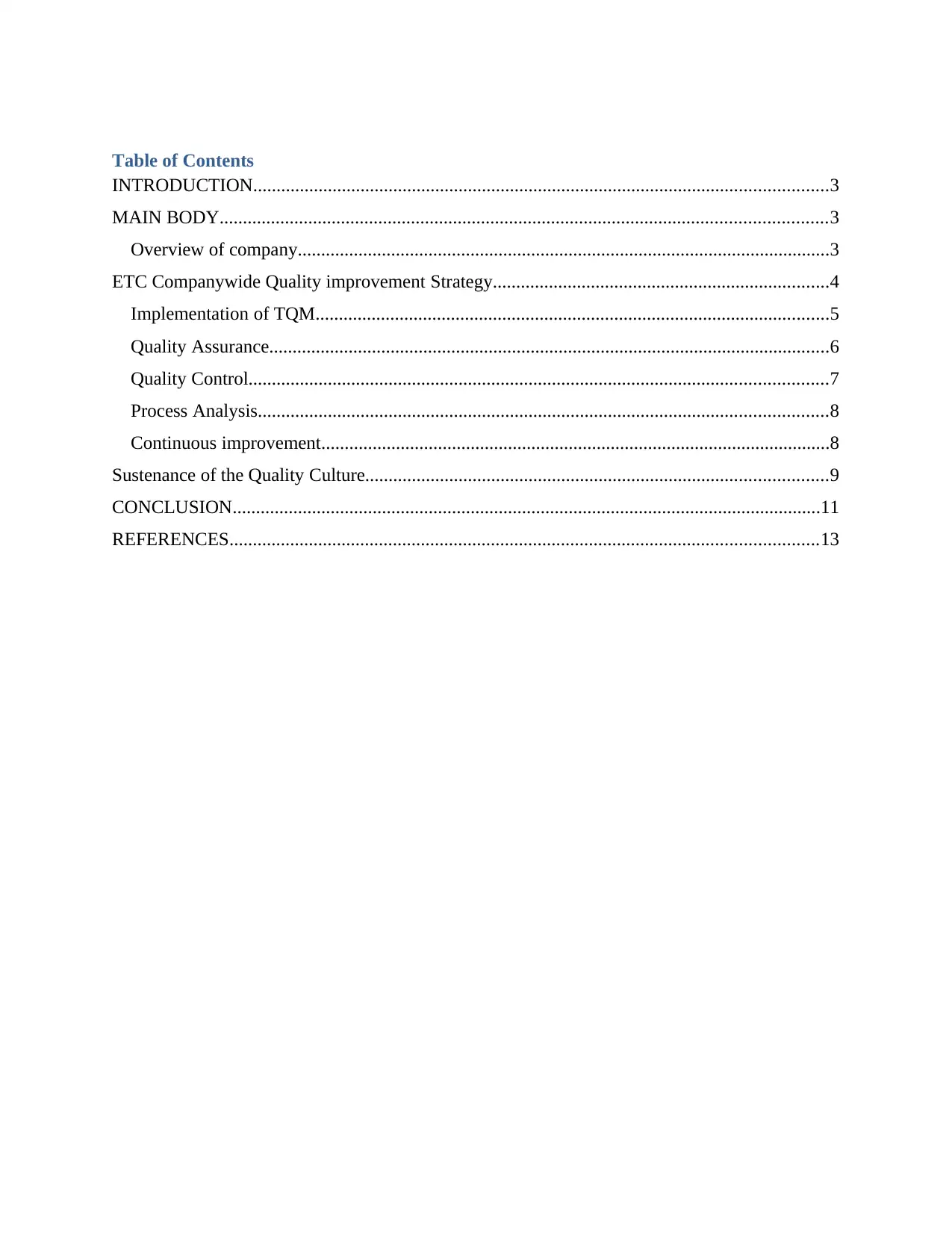
Table of Contents
INTRODUCTION...........................................................................................................................3
MAIN BODY..................................................................................................................................3
Overview of company..................................................................................................................3
ETC Companywide Quality improvement Strategy........................................................................4
Implementation of TQM..............................................................................................................5
Quality Assurance........................................................................................................................6
Quality Control............................................................................................................................7
Process Analysis..........................................................................................................................8
Continuous improvement.............................................................................................................8
Sustenance of the Quality Culture...................................................................................................9
CONCLUSION..............................................................................................................................11
REFERENCES..............................................................................................................................13
INTRODUCTION...........................................................................................................................3
MAIN BODY..................................................................................................................................3
Overview of company..................................................................................................................3
ETC Companywide Quality improvement Strategy........................................................................4
Implementation of TQM..............................................................................................................5
Quality Assurance........................................................................................................................6
Quality Control............................................................................................................................7
Process Analysis..........................................................................................................................8
Continuous improvement.............................................................................................................8
Sustenance of the Quality Culture...................................................................................................9
CONCLUSION..............................................................................................................................11
REFERENCES..............................................................................................................................13
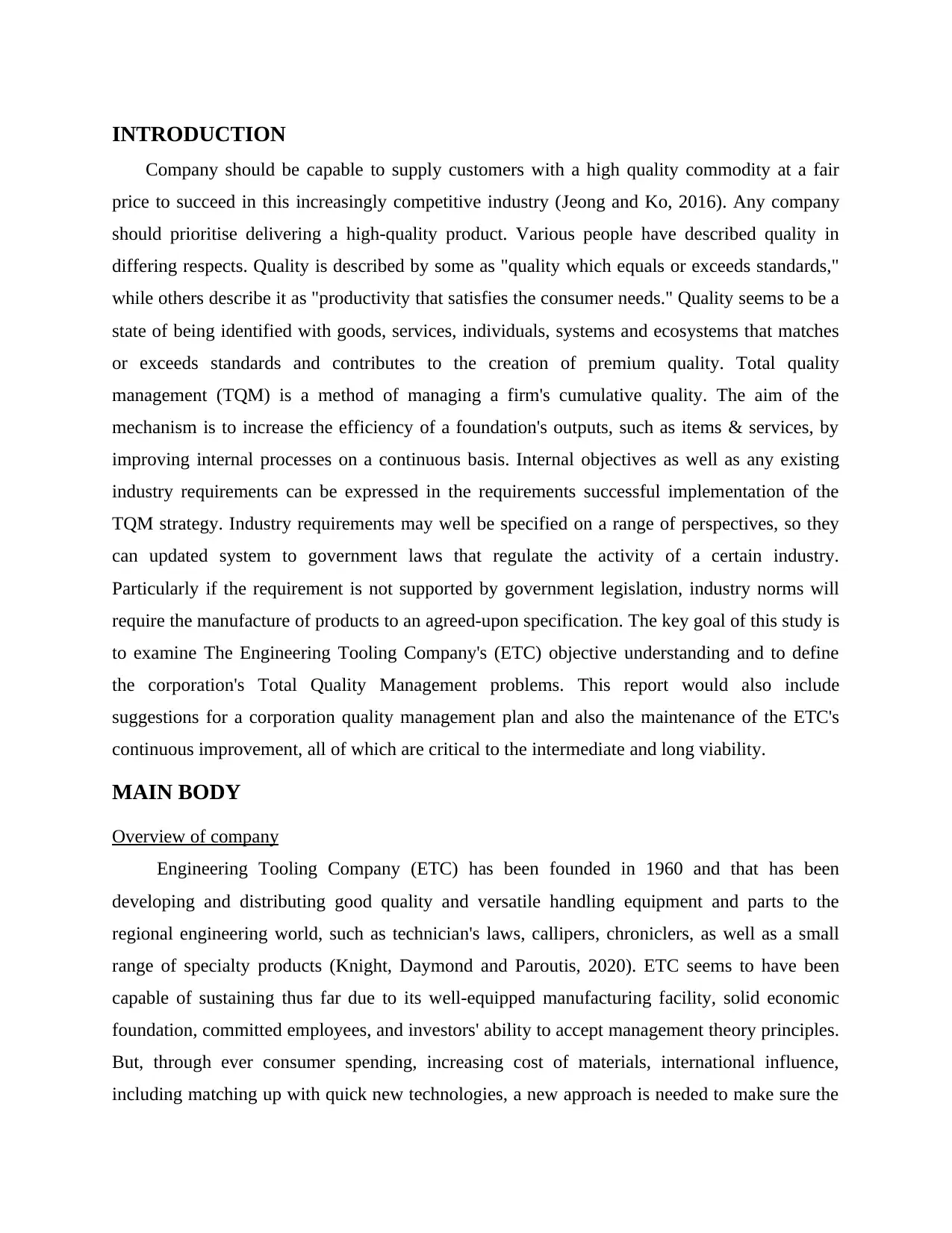
INTRODUCTION
Company should be capable to supply customers with a high quality commodity at a fair
price to succeed in this increasingly competitive industry (Jeong and Ko, 2016). Any company
should prioritise delivering a high-quality product. Various people have described quality in
differing respects. Quality is described by some as "quality which equals or exceeds standards,"
while others describe it as "productivity that satisfies the consumer needs." Quality seems to be a
state of being identified with goods, services, individuals, systems and ecosystems that matches
or exceeds standards and contributes to the creation of premium quality. Total quality
management (TQM) is a method of managing a firm's cumulative quality. The aim of the
mechanism is to increase the efficiency of a foundation's outputs, such as items & services, by
improving internal processes on a continuous basis. Internal objectives as well as any existing
industry requirements can be expressed in the requirements successful implementation of the
TQM strategy. Industry requirements may well be specified on a range of perspectives, so they
can updated system to government laws that regulate the activity of a certain industry.
Particularly if the requirement is not supported by government legislation, industry norms will
require the manufacture of products to an agreed-upon specification. The key goal of this study is
to examine The Engineering Tooling Company's (ETC) objective understanding and to define
the corporation's Total Quality Management problems. This report would also include
suggestions for a corporation quality management plan and also the maintenance of the ETC's
continuous improvement, all of which are critical to the intermediate and long viability.
MAIN BODY
Overview of company
Engineering Tooling Company (ETC) has been founded in 1960 and that has been
developing and distributing good quality and versatile handling equipment and parts to the
regional engineering world, such as technician's laws, callipers, chroniclers, as well as a small
range of specialty products (Knight, Daymond and Paroutis, 2020). ETC seems to have been
capable of sustaining thus far due to its well-equipped manufacturing facility, solid economic
foundation, committed employees, and investors' ability to accept management theory principles.
But, through ever consumer spending, increasing cost of materials, international influence,
including matching up with quick new technologies, a new approach is needed to make sure the
Company should be capable to supply customers with a high quality commodity at a fair
price to succeed in this increasingly competitive industry (Jeong and Ko, 2016). Any company
should prioritise delivering a high-quality product. Various people have described quality in
differing respects. Quality is described by some as "quality which equals or exceeds standards,"
while others describe it as "productivity that satisfies the consumer needs." Quality seems to be a
state of being identified with goods, services, individuals, systems and ecosystems that matches
or exceeds standards and contributes to the creation of premium quality. Total quality
management (TQM) is a method of managing a firm's cumulative quality. The aim of the
mechanism is to increase the efficiency of a foundation's outputs, such as items & services, by
improving internal processes on a continuous basis. Internal objectives as well as any existing
industry requirements can be expressed in the requirements successful implementation of the
TQM strategy. Industry requirements may well be specified on a range of perspectives, so they
can updated system to government laws that regulate the activity of a certain industry.
Particularly if the requirement is not supported by government legislation, industry norms will
require the manufacture of products to an agreed-upon specification. The key goal of this study is
to examine The Engineering Tooling Company's (ETC) objective understanding and to define
the corporation's Total Quality Management problems. This report would also include
suggestions for a corporation quality management plan and also the maintenance of the ETC's
continuous improvement, all of which are critical to the intermediate and long viability.
MAIN BODY
Overview of company
Engineering Tooling Company (ETC) has been founded in 1960 and that has been
developing and distributing good quality and versatile handling equipment and parts to the
regional engineering world, such as technician's laws, callipers, chroniclers, as well as a small
range of specialty products (Knight, Daymond and Paroutis, 2020). ETC seems to have been
capable of sustaining thus far due to its well-equipped manufacturing facility, solid economic
foundation, committed employees, and investors' ability to accept management theory principles.
But, through ever consumer spending, increasing cost of materials, international influence,
including matching up with quick new technologies, a new approach is needed to make sure the
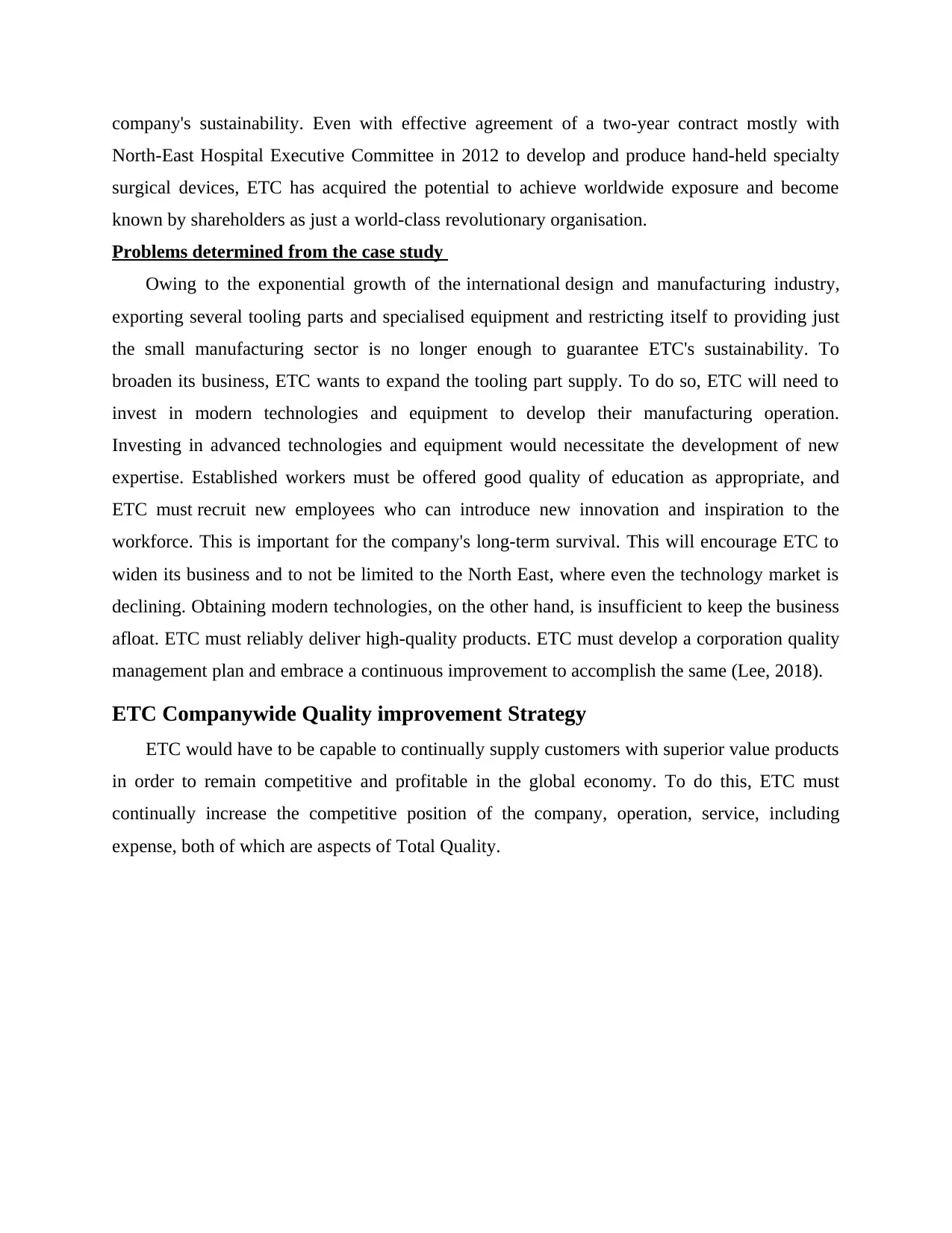
company's sustainability. Even with effective agreement of a two-year contract mostly with
North-East Hospital Executive Committee in 2012 to develop and produce hand-held specialty
surgical devices, ETC has acquired the potential to achieve worldwide exposure and become
known by shareholders as just a world-class revolutionary organisation.
Problems determined from the case study
Owing to the exponential growth of the international design and manufacturing industry,
exporting several tooling parts and specialised equipment and restricting itself to providing just
the small manufacturing sector is no longer enough to guarantee ETC's sustainability. To
broaden its business, ETC wants to expand the tooling part supply. To do so, ETC will need to
invest in modern technologies and equipment to develop their manufacturing operation.
Investing in advanced technologies and equipment would necessitate the development of new
expertise. Established workers must be offered good quality of education as appropriate, and
ETC must recruit new employees who can introduce new innovation and inspiration to the
workforce. This is important for the company's long-term survival. This will encourage ETC to
widen its business and to not be limited to the North East, where even the technology market is
declining. Obtaining modern technologies, on the other hand, is insufficient to keep the business
afloat. ETC must reliably deliver high-quality products. ETC must develop a corporation quality
management plan and embrace a continuous improvement to accomplish the same (Lee, 2018).
ETC Companywide Quality improvement Strategy
ETC would have to be capable to continually supply customers with superior value products
in order to remain competitive and profitable in the global economy. To do this, ETC must
continually increase the competitive position of the company, operation, service, including
expense, both of which are aspects of Total Quality.
North-East Hospital Executive Committee in 2012 to develop and produce hand-held specialty
surgical devices, ETC has acquired the potential to achieve worldwide exposure and become
known by shareholders as just a world-class revolutionary organisation.
Problems determined from the case study
Owing to the exponential growth of the international design and manufacturing industry,
exporting several tooling parts and specialised equipment and restricting itself to providing just
the small manufacturing sector is no longer enough to guarantee ETC's sustainability. To
broaden its business, ETC wants to expand the tooling part supply. To do so, ETC will need to
invest in modern technologies and equipment to develop their manufacturing operation.
Investing in advanced technologies and equipment would necessitate the development of new
expertise. Established workers must be offered good quality of education as appropriate, and
ETC must recruit new employees who can introduce new innovation and inspiration to the
workforce. This is important for the company's long-term survival. This will encourage ETC to
widen its business and to not be limited to the North East, where even the technology market is
declining. Obtaining modern technologies, on the other hand, is insufficient to keep the business
afloat. ETC must reliably deliver high-quality products. ETC must develop a corporation quality
management plan and embrace a continuous improvement to accomplish the same (Lee, 2018).
ETC Companywide Quality improvement Strategy
ETC would have to be capable to continually supply customers with superior value products
in order to remain competitive and profitable in the global economy. To do this, ETC must
continually increase the competitive position of the company, operation, service, including
expense, both of which are aspects of Total Quality.
Secure Best Marks with AI Grader
Need help grading? Try our AI Grader for instant feedback on your assignments.
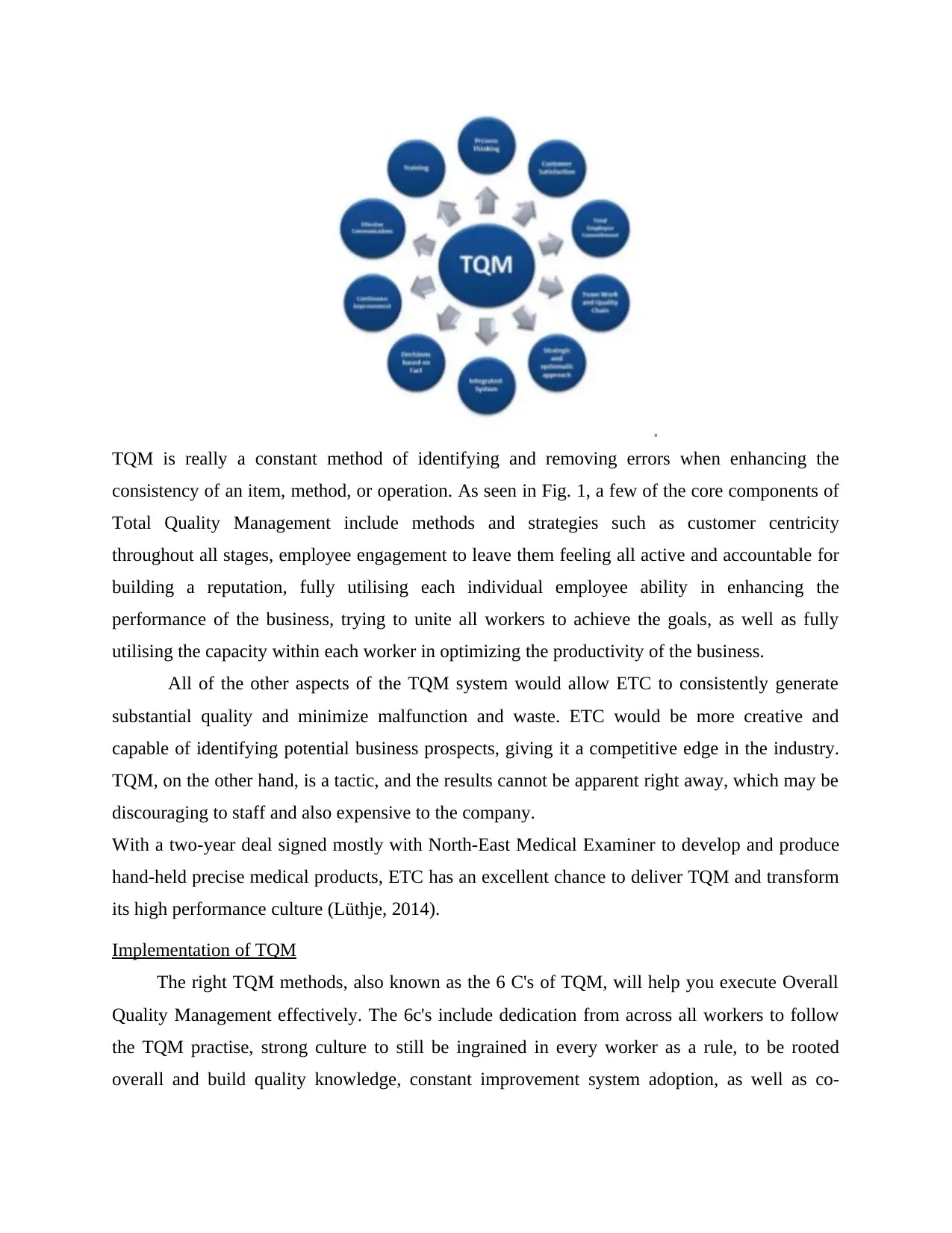
TQM is really a constant method of identifying and removing errors when enhancing the
consistency of an item, method, or operation. As seen in Fig. 1, a few of the core components of
Total Quality Management include methods and strategies such as customer centricity
throughout all stages, employee engagement to leave them feeling all active and accountable for
building a reputation, fully utilising each individual employee ability in enhancing the
performance of the business, trying to unite all workers to achieve the goals, as well as fully
utilising the capacity within each worker in optimizing the productivity of the business.
All of the other aspects of the TQM system would allow ETC to consistently generate
substantial quality and minimize malfunction and waste. ETC would be more creative and
capable of identifying potential business prospects, giving it a competitive edge in the industry.
TQM, on the other hand, is a tactic, and the results cannot be apparent right away, which may be
discouraging to staff and also expensive to the company.
With a two-year deal signed mostly with North-East Medical Examiner to develop and produce
hand-held precise medical products, ETC has an excellent chance to deliver TQM and transform
its high performance culture (Lüthje, 2014).
Implementation of TQM
The right TQM methods, also known as the 6 C's of TQM, will help you execute Overall
Quality Management effectively. The 6c's include dedication from across all workers to follow
the TQM practise, strong culture to still be ingrained in every worker as a rule, to be rooted
overall and build quality knowledge, constant improvement system adoption, as well as co-
consistency of an item, method, or operation. As seen in Fig. 1, a few of the core components of
Total Quality Management include methods and strategies such as customer centricity
throughout all stages, employee engagement to leave them feeling all active and accountable for
building a reputation, fully utilising each individual employee ability in enhancing the
performance of the business, trying to unite all workers to achieve the goals, as well as fully
utilising the capacity within each worker in optimizing the productivity of the business.
All of the other aspects of the TQM system would allow ETC to consistently generate
substantial quality and minimize malfunction and waste. ETC would be more creative and
capable of identifying potential business prospects, giving it a competitive edge in the industry.
TQM, on the other hand, is a tactic, and the results cannot be apparent right away, which may be
discouraging to staff and also expensive to the company.
With a two-year deal signed mostly with North-East Medical Examiner to develop and produce
hand-held precise medical products, ETC has an excellent chance to deliver TQM and transform
its high performance culture (Lüthje, 2014).
Implementation of TQM
The right TQM methods, also known as the 6 C's of TQM, will help you execute Overall
Quality Management effectively. The 6c's include dedication from across all workers to follow
the TQM practise, strong culture to still be ingrained in every worker as a rule, to be rooted
overall and build quality knowledge, constant improvement system adoption, as well as co-
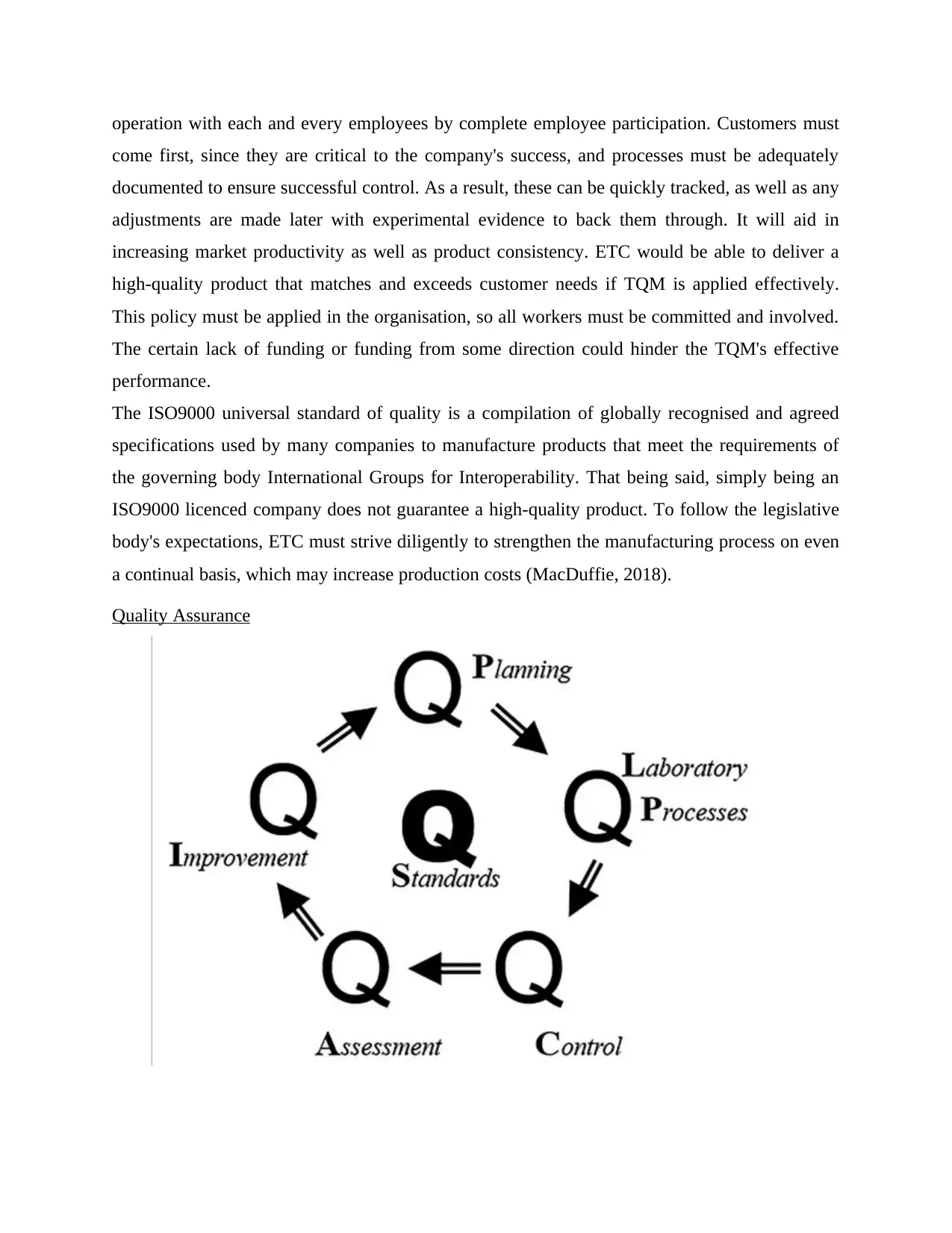
operation with each and every employees by complete employee participation. Customers must
come first, since they are critical to the company's success, and processes must be adequately
documented to ensure successful control. As a result, these can be quickly tracked, as well as any
adjustments are made later with experimental evidence to back them through. It will aid in
increasing market productivity as well as product consistency. ETC would be able to deliver a
high-quality product that matches and exceeds customer needs if TQM is applied effectively.
This policy must be applied in the organisation, so all workers must be committed and involved.
The certain lack of funding or funding from some direction could hinder the TQM's effective
performance.
The ISO9000 universal standard of quality is a compilation of globally recognised and agreed
specifications used by many companies to manufacture products that meet the requirements of
the governing body International Groups for Interoperability. That being said, simply being an
ISO9000 licenced company does not guarantee a high-quality product. To follow the legislative
body's expectations, ETC must strive diligently to strengthen the manufacturing process on even
a continual basis, which may increase production costs (MacDuffie, 2018).
Quality Assurance
come first, since they are critical to the company's success, and processes must be adequately
documented to ensure successful control. As a result, these can be quickly tracked, as well as any
adjustments are made later with experimental evidence to back them through. It will aid in
increasing market productivity as well as product consistency. ETC would be able to deliver a
high-quality product that matches and exceeds customer needs if TQM is applied effectively.
This policy must be applied in the organisation, so all workers must be committed and involved.
The certain lack of funding or funding from some direction could hinder the TQM's effective
performance.
The ISO9000 universal standard of quality is a compilation of globally recognised and agreed
specifications used by many companies to manufacture products that meet the requirements of
the governing body International Groups for Interoperability. That being said, simply being an
ISO9000 licenced company does not guarantee a high-quality product. To follow the legislative
body's expectations, ETC must strive diligently to strengthen the manufacturing process on even
a continual basis, which may increase production costs (MacDuffie, 2018).
Quality Assurance
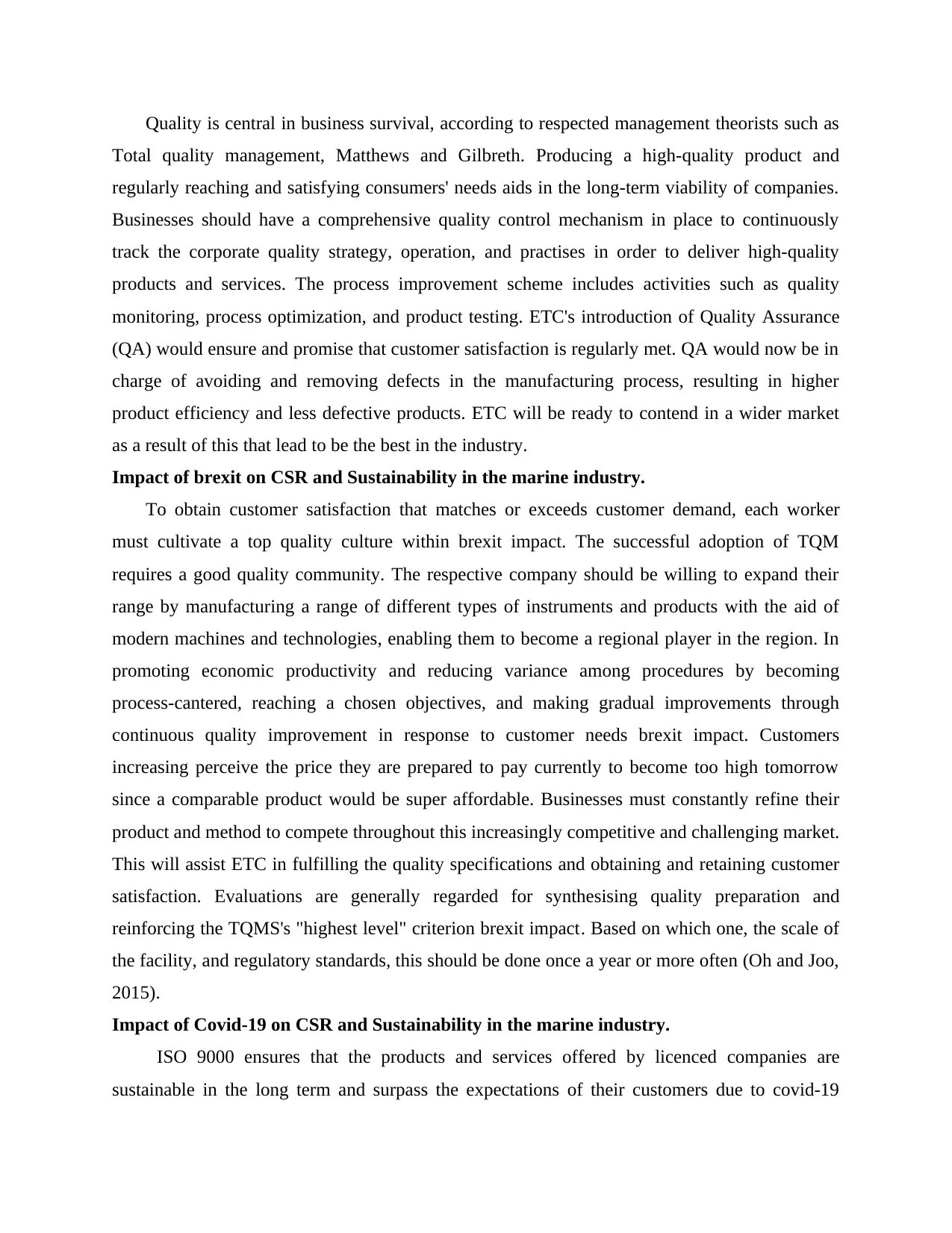
Quality is central in business survival, according to respected management theorists such as
Total quality management, Matthews and Gilbreth. Producing a high-quality product and
regularly reaching and satisfying consumers' needs aids in the long-term viability of companies.
Businesses should have a comprehensive quality control mechanism in place to continuously
track the corporate quality strategy, operation, and practises in order to deliver high-quality
products and services. The process improvement scheme includes activities such as quality
monitoring, process optimization, and product testing. ETC's introduction of Quality Assurance
(QA) would ensure and promise that customer satisfaction is regularly met. QA would now be in
charge of avoiding and removing defects in the manufacturing process, resulting in higher
product efficiency and less defective products. ETC will be ready to contend in a wider market
as a result of this that lead to be the best in the industry.
Impact of brexit on CSR and Sustainability in the marine industry.
To obtain customer satisfaction that matches or exceeds customer demand, each worker
must cultivate a top quality culture within brexit impact. The successful adoption of TQM
requires a good quality community. The respective company should be willing to expand their
range by manufacturing a range of different types of instruments and products with the aid of
modern machines and technologies, enabling them to become a regional player in the region. In
promoting economic productivity and reducing variance among procedures by becoming
process-cantered, reaching a chosen objectives, and making gradual improvements through
continuous quality improvement in response to customer needs brexit impact. Customers
increasing perceive the price they are prepared to pay currently to become too high tomorrow
since a comparable product would be super affordable. Businesses must constantly refine their
product and method to compete throughout this increasingly competitive and challenging market.
This will assist ETC in fulfilling the quality specifications and obtaining and retaining customer
satisfaction. Evaluations are generally regarded for synthesising quality preparation and
reinforcing the TQMS's "highest level" criterion brexit impact. Based on which one, the scale of
the facility, and regulatory standards, this should be done once a year or more often (Oh and Joo,
2015).
Impact of Covid-19 on CSR and Sustainability in the marine industry.
ISO 9000 ensures that the products and services offered by licenced companies are
sustainable in the long term and surpass the expectations of their customers due to covid-19
Total quality management, Matthews and Gilbreth. Producing a high-quality product and
regularly reaching and satisfying consumers' needs aids in the long-term viability of companies.
Businesses should have a comprehensive quality control mechanism in place to continuously
track the corporate quality strategy, operation, and practises in order to deliver high-quality
products and services. The process improvement scheme includes activities such as quality
monitoring, process optimization, and product testing. ETC's introduction of Quality Assurance
(QA) would ensure and promise that customer satisfaction is regularly met. QA would now be in
charge of avoiding and removing defects in the manufacturing process, resulting in higher
product efficiency and less defective products. ETC will be ready to contend in a wider market
as a result of this that lead to be the best in the industry.
Impact of brexit on CSR and Sustainability in the marine industry.
To obtain customer satisfaction that matches or exceeds customer demand, each worker
must cultivate a top quality culture within brexit impact. The successful adoption of TQM
requires a good quality community. The respective company should be willing to expand their
range by manufacturing a range of different types of instruments and products with the aid of
modern machines and technologies, enabling them to become a regional player in the region. In
promoting economic productivity and reducing variance among procedures by becoming
process-cantered, reaching a chosen objectives, and making gradual improvements through
continuous quality improvement in response to customer needs brexit impact. Customers
increasing perceive the price they are prepared to pay currently to become too high tomorrow
since a comparable product would be super affordable. Businesses must constantly refine their
product and method to compete throughout this increasingly competitive and challenging market.
This will assist ETC in fulfilling the quality specifications and obtaining and retaining customer
satisfaction. Evaluations are generally regarded for synthesising quality preparation and
reinforcing the TQMS's "highest level" criterion brexit impact. Based on which one, the scale of
the facility, and regulatory standards, this should be done once a year or more often (Oh and Joo,
2015).
Impact of Covid-19 on CSR and Sustainability in the marine industry.
ISO 9000 ensures that the products and services offered by licenced companies are
sustainable in the long term and surpass the expectations of their customers due to covid-19
Paraphrase This Document
Need a fresh take? Get an instant paraphrase of this document with our AI Paraphraser

situation. It is completely up to that same companies not whether they wish to be regular
attendees of ISO 9000. ETCs have been capable of manufacturing products with less volatility,
less defects, and less waste as a result of joining ISO 9000, which could increase the company's
competitiveness and performance. Since ISO 9000 is a well-known and recognized range of
quality control guidelines, ETC would be able to achieve more reputation through covid-19.
Quality Assurance would be a mechanism in a manufacturing quality mechanism to ensure and
guarantees that customer requirements quality objectives are achieved. QA is introduced at the
material production period. In such a quality chain, quality assurance (QA) is a protective
measure that eliminates errors in the manufacturing process, thus enhancing customer
satisfaction and increasing market performance. Both firms must adjust their corporate and
performance cultures from respectively in order to satisfy customer demand and effectively in
global marketplace within covid-19. As these ways and continuous improvement, all workers
must support the company's priorities and aspirations (Rakita, Madić and Marković, 2017).
Quality Control
Quality Control (QC) seems to be the component of the performance measurement
mechanism that manages the production line or operations that meet the quality requirements.
QC is in charge of improving and sustaining the customer experience standard. They are in
charge of quality management by detecting faulty goods and withdrawing them from the quality
requirements that must be followed. During the manufacturing level, quality improvement
procedures are introduced as a preventive mechanism to increase the operational efficiency. ETC
would be capable of identifying and eliminate faulty goods by introducing Quality Management
steps. It might assist ETC in meeting the criteria and preventive actions. Inconsistencies in
management or patient outcomes should cause outcome reporting to be halted, disciplinary steps
to be taken, as well as clients to be consulted if needed during the analytical process. New
suspension as well as other issues are reported and checked at frequent intervals to assess and
implement corrective actions (Masschelein, 2018).
Inspection
The quality control scheme includes regular inspections as well. Inspection may take place
during the manufacturer's production stage (in-process) or even at the final step (post-process)
(final). Quality inspection aids in quality management by detecting and eliminating faulty
products before they enter the market. A faulty or low-quality service can jeopardise a reputation
attendees of ISO 9000. ETCs have been capable of manufacturing products with less volatility,
less defects, and less waste as a result of joining ISO 9000, which could increase the company's
competitiveness and performance. Since ISO 9000 is a well-known and recognized range of
quality control guidelines, ETC would be able to achieve more reputation through covid-19.
Quality Assurance would be a mechanism in a manufacturing quality mechanism to ensure and
guarantees that customer requirements quality objectives are achieved. QA is introduced at the
material production period. In such a quality chain, quality assurance (QA) is a protective
measure that eliminates errors in the manufacturing process, thus enhancing customer
satisfaction and increasing market performance. Both firms must adjust their corporate and
performance cultures from respectively in order to satisfy customer demand and effectively in
global marketplace within covid-19. As these ways and continuous improvement, all workers
must support the company's priorities and aspirations (Rakita, Madić and Marković, 2017).
Quality Control
Quality Control (QC) seems to be the component of the performance measurement
mechanism that manages the production line or operations that meet the quality requirements.
QC is in charge of improving and sustaining the customer experience standard. They are in
charge of quality management by detecting faulty goods and withdrawing them from the quality
requirements that must be followed. During the manufacturing level, quality improvement
procedures are introduced as a preventive mechanism to increase the operational efficiency. ETC
would be capable of identifying and eliminate faulty goods by introducing Quality Management
steps. It might assist ETC in meeting the criteria and preventive actions. Inconsistencies in
management or patient outcomes should cause outcome reporting to be halted, disciplinary steps
to be taken, as well as clients to be consulted if needed during the analytical process. New
suspension as well as other issues are reported and checked at frequent intervals to assess and
implement corrective actions (Masschelein, 2018).
Inspection
The quality control scheme includes regular inspections as well. Inspection may take place
during the manufacturer's production stage (in-process) or even at the final step (post-process)
(final). Quality inspection aids in quality management by detecting and eliminating faulty
products before they enter the market. A faulty or low-quality service can jeopardise a reputation
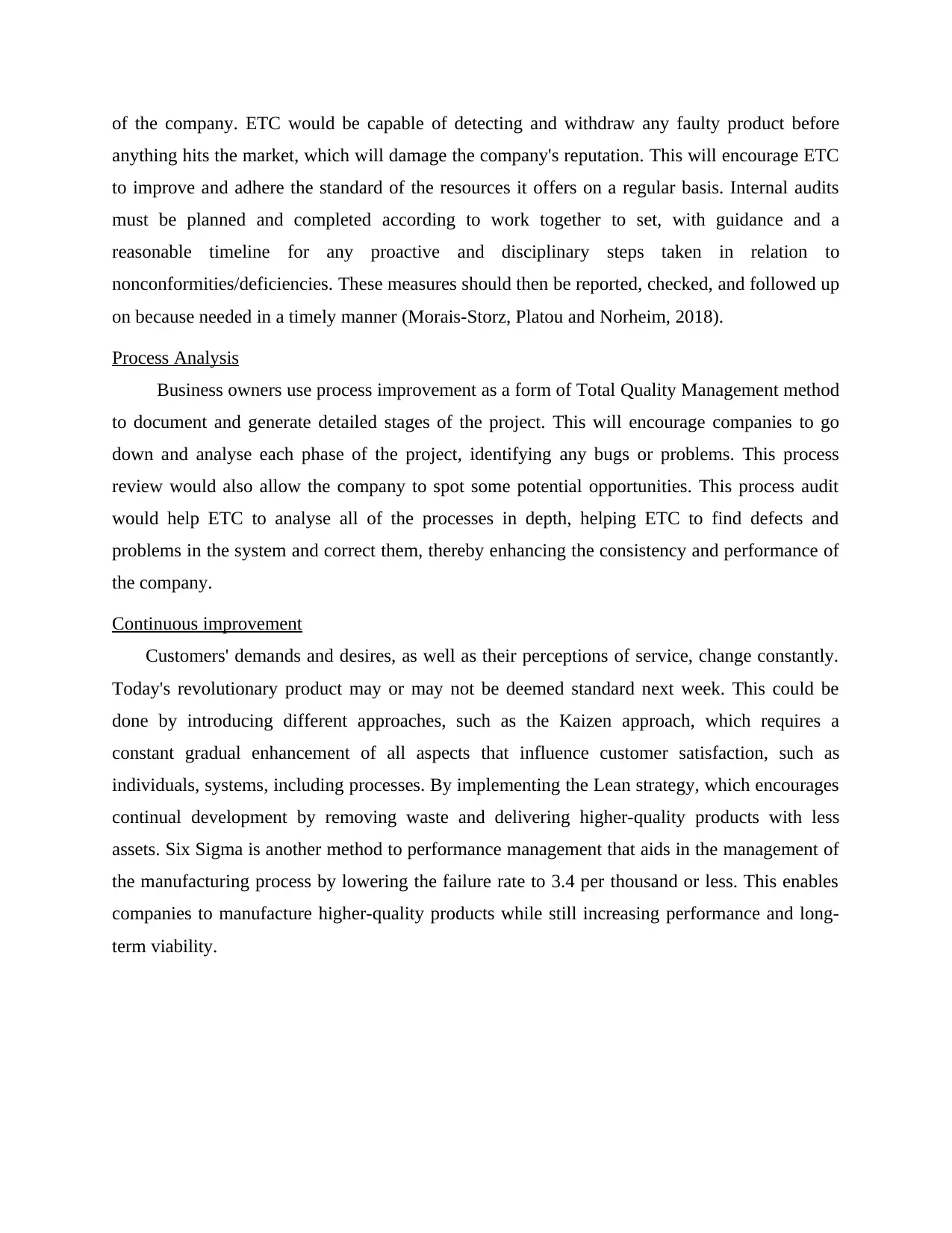
of the company. ETC would be capable of detecting and withdraw any faulty product before
anything hits the market, which will damage the company's reputation. This will encourage ETC
to improve and adhere the standard of the resources it offers on a regular basis. Internal audits
must be planned and completed according to work together to set, with guidance and a
reasonable timeline for any proactive and disciplinary steps taken in relation to
nonconformities/deficiencies. These measures should then be reported, checked, and followed up
on because needed in a timely manner (Morais-Storz, Platou and Norheim, 2018).
Process Analysis
Business owners use process improvement as a form of Total Quality Management method
to document and generate detailed stages of the project. This will encourage companies to go
down and analyse each phase of the project, identifying any bugs or problems. This process
review would also allow the company to spot some potential opportunities. This process audit
would help ETC to analyse all of the processes in depth, helping ETC to find defects and
problems in the system and correct them, thereby enhancing the consistency and performance of
the company.
Continuous improvement
Customers' demands and desires, as well as their perceptions of service, change constantly.
Today's revolutionary product may or may not be deemed standard next week. This could be
done by introducing different approaches, such as the Kaizen approach, which requires a
constant gradual enhancement of all aspects that influence customer satisfaction, such as
individuals, systems, including processes. By implementing the Lean strategy, which encourages
continual development by removing waste and delivering higher-quality products with less
assets. Six Sigma is another method to performance management that aids in the management of
the manufacturing process by lowering the failure rate to 3.4 per thousand or less. This enables
companies to manufacture higher-quality products while still increasing performance and long-
term viability.
anything hits the market, which will damage the company's reputation. This will encourage ETC
to improve and adhere the standard of the resources it offers on a regular basis. Internal audits
must be planned and completed according to work together to set, with guidance and a
reasonable timeline for any proactive and disciplinary steps taken in relation to
nonconformities/deficiencies. These measures should then be reported, checked, and followed up
on because needed in a timely manner (Morais-Storz, Platou and Norheim, 2018).
Process Analysis
Business owners use process improvement as a form of Total Quality Management method
to document and generate detailed stages of the project. This will encourage companies to go
down and analyse each phase of the project, identifying any bugs or problems. This process
review would also allow the company to spot some potential opportunities. This process audit
would help ETC to analyse all of the processes in depth, helping ETC to find defects and
problems in the system and correct them, thereby enhancing the consistency and performance of
the company.
Continuous improvement
Customers' demands and desires, as well as their perceptions of service, change constantly.
Today's revolutionary product may or may not be deemed standard next week. This could be
done by introducing different approaches, such as the Kaizen approach, which requires a
constant gradual enhancement of all aspects that influence customer satisfaction, such as
individuals, systems, including processes. By implementing the Lean strategy, which encourages
continual development by removing waste and delivering higher-quality products with less
assets. Six Sigma is another method to performance management that aids in the management of
the manufacturing process by lowering the failure rate to 3.4 per thousand or less. This enables
companies to manufacture higher-quality products while still increasing performance and long-
term viability.
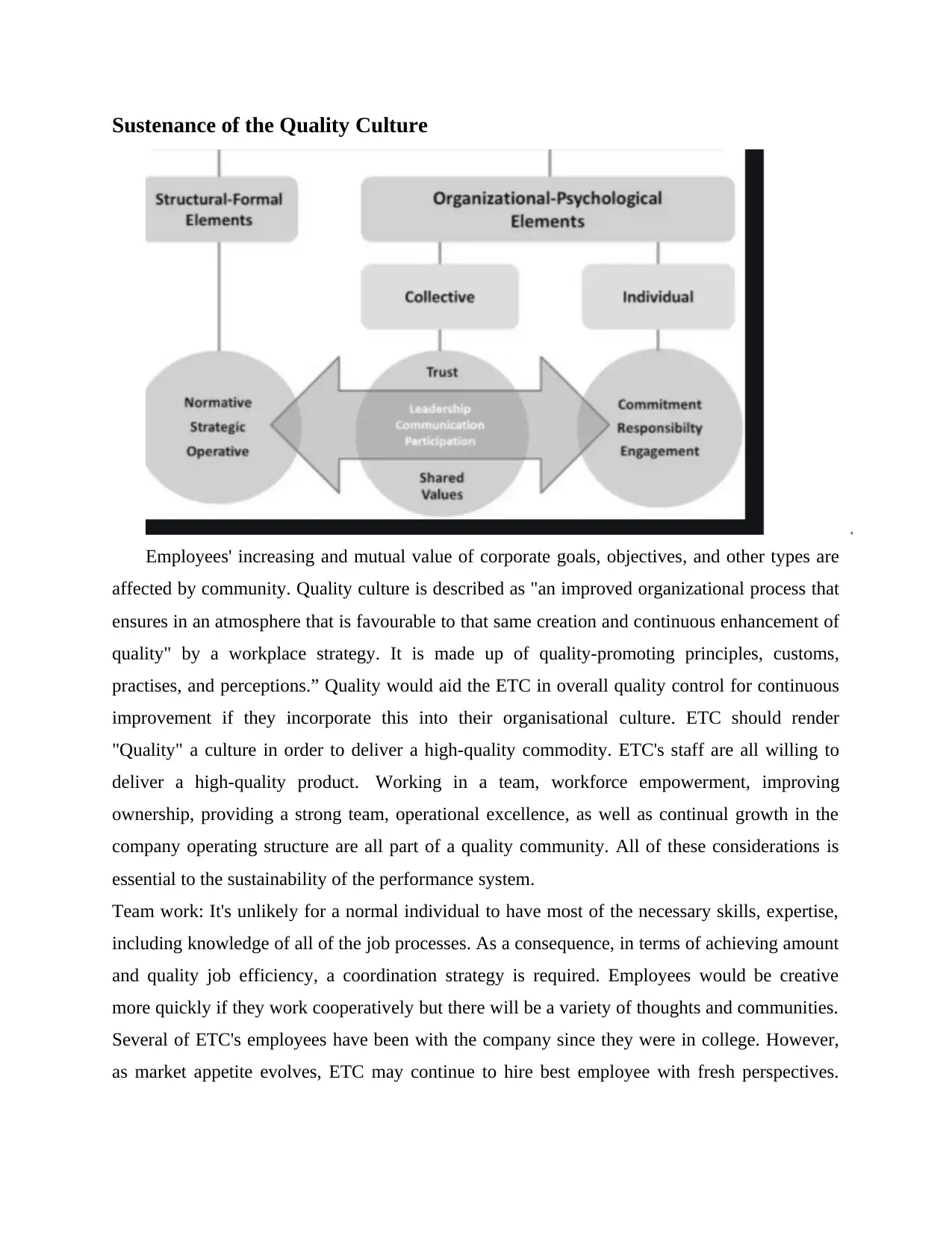
Sustenance of the Quality Culture
Employees' increasing and mutual value of corporate goals, objectives, and other types are
affected by community. Quality culture is described as "an improved organizational process that
ensures in an atmosphere that is favourable to that same creation and continuous enhancement of
quality" by a workplace strategy. It is made up of quality-promoting principles, customs,
practises, and perceptions.” Quality would aid the ETC in overall quality control for continuous
improvement if they incorporate this into their organisational culture. ETC should render
"Quality" a culture in order to deliver a high-quality commodity. ETC's staff are all willing to
deliver a high-quality product. Working in a team, workforce empowerment, improving
ownership, providing a strong team, operational excellence, as well as continual growth in the
company operating structure are all part of a quality community. All of these considerations is
essential to the sustainability of the performance system.
Team work: It's unlikely for a normal individual to have most of the necessary skills, expertise,
including knowledge of all of the job processes. As a consequence, in terms of achieving amount
and quality job efficiency, a coordination strategy is required. Employees would be creative
more quickly if they work cooperatively but there will be a variety of thoughts and communities.
Several of ETC's employees have been with the company since they were in college. However,
as market appetite evolves, ETC may continue to hire best employee with fresh perspectives.
Employees' increasing and mutual value of corporate goals, objectives, and other types are
affected by community. Quality culture is described as "an improved organizational process that
ensures in an atmosphere that is favourable to that same creation and continuous enhancement of
quality" by a workplace strategy. It is made up of quality-promoting principles, customs,
practises, and perceptions.” Quality would aid the ETC in overall quality control for continuous
improvement if they incorporate this into their organisational culture. ETC should render
"Quality" a culture in order to deliver a high-quality commodity. ETC's staff are all willing to
deliver a high-quality product. Working in a team, workforce empowerment, improving
ownership, providing a strong team, operational excellence, as well as continual growth in the
company operating structure are all part of a quality community. All of these considerations is
essential to the sustainability of the performance system.
Team work: It's unlikely for a normal individual to have most of the necessary skills, expertise,
including knowledge of all of the job processes. As a consequence, in terms of achieving amount
and quality job efficiency, a coordination strategy is required. Employees would be creative
more quickly if they work cooperatively but there will be a variety of thoughts and communities.
Several of ETC's employees have been with the company since they were in college. However,
as market appetite evolves, ETC may continue to hire best employee with fresh perspectives.
Secure Best Marks with AI Grader
Need help grading? Try our AI Grader for instant feedback on your assignments.
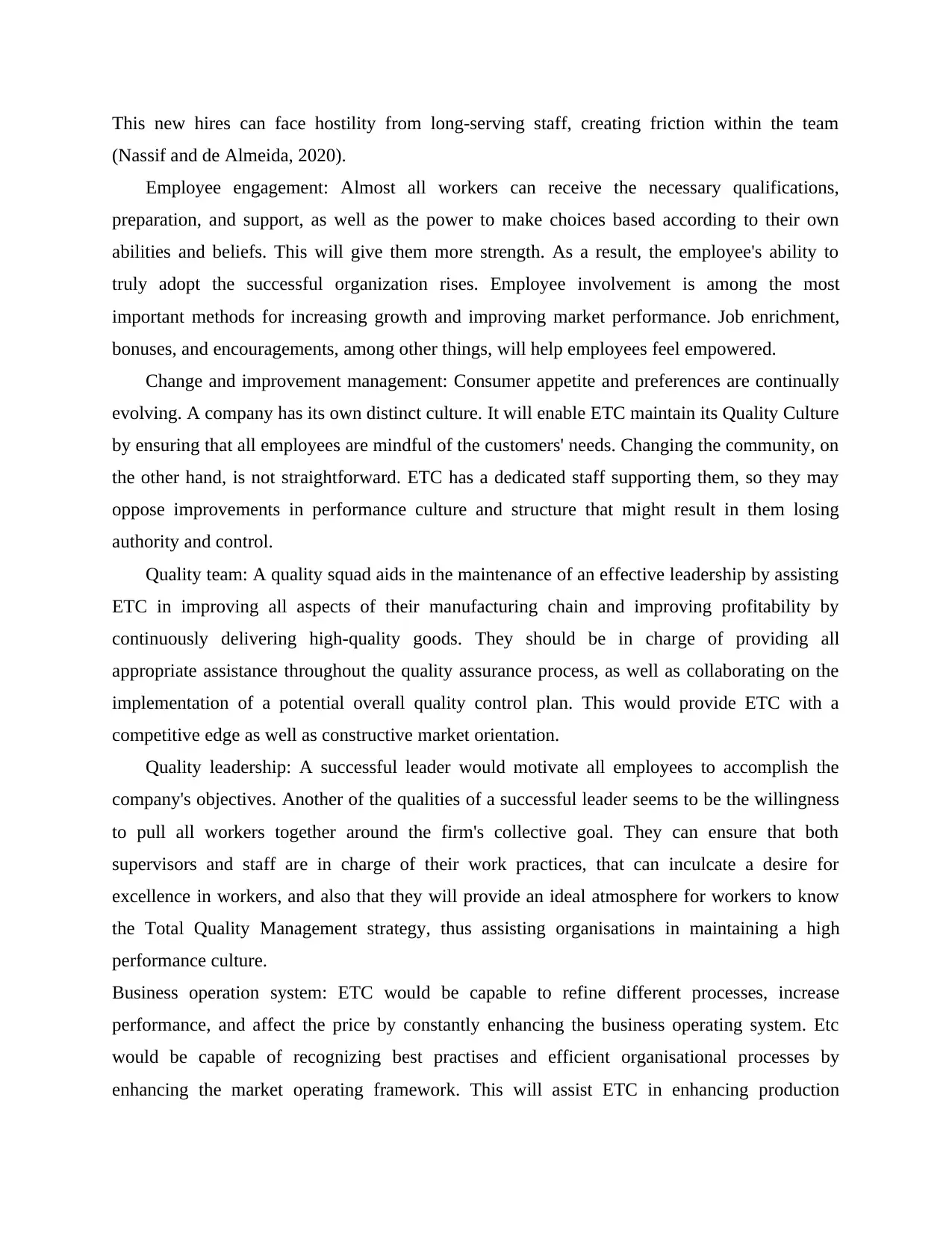
This new hires can face hostility from long-serving staff, creating friction within the team
(Nassif and de Almeida, 2020).
Employee engagement: Almost all workers can receive the necessary qualifications,
preparation, and support, as well as the power to make choices based according to their own
abilities and beliefs. This will give them more strength. As a result, the employee's ability to
truly adopt the successful organization rises. Employee involvement is among the most
important methods for increasing growth and improving market performance. Job enrichment,
bonuses, and encouragements, among other things, will help employees feel empowered.
Change and improvement management: Consumer appetite and preferences are continually
evolving. A company has its own distinct culture. It will enable ETC maintain its Quality Culture
by ensuring that all employees are mindful of the customers' needs. Changing the community, on
the other hand, is not straightforward. ETC has a dedicated staff supporting them, so they may
oppose improvements in performance culture and structure that might result in them losing
authority and control.
Quality team: A quality squad aids in the maintenance of an effective leadership by assisting
ETC in improving all aspects of their manufacturing chain and improving profitability by
continuously delivering high-quality goods. They should be in charge of providing all
appropriate assistance throughout the quality assurance process, as well as collaborating on the
implementation of a potential overall quality control plan. This would provide ETC with a
competitive edge as well as constructive market orientation.
Quality leadership: A successful leader would motivate all employees to accomplish the
company's objectives. Another of the qualities of a successful leader seems to be the willingness
to pull all workers together around the firm's collective goal. They can ensure that both
supervisors and staff are in charge of their work practices, that can inculcate a desire for
excellence in workers, and also that they will provide an ideal atmosphere for workers to know
the Total Quality Management strategy, thus assisting organisations in maintaining a high
performance culture.
Business operation system: ETC would be capable to refine different processes, increase
performance, and affect the price by constantly enhancing the business operating system. Etc
would be capable of recognizing best practises and efficient organisational processes by
enhancing the market operating framework. This will assist ETC in enhancing production
(Nassif and de Almeida, 2020).
Employee engagement: Almost all workers can receive the necessary qualifications,
preparation, and support, as well as the power to make choices based according to their own
abilities and beliefs. This will give them more strength. As a result, the employee's ability to
truly adopt the successful organization rises. Employee involvement is among the most
important methods for increasing growth and improving market performance. Job enrichment,
bonuses, and encouragements, among other things, will help employees feel empowered.
Change and improvement management: Consumer appetite and preferences are continually
evolving. A company has its own distinct culture. It will enable ETC maintain its Quality Culture
by ensuring that all employees are mindful of the customers' needs. Changing the community, on
the other hand, is not straightforward. ETC has a dedicated staff supporting them, so they may
oppose improvements in performance culture and structure that might result in them losing
authority and control.
Quality team: A quality squad aids in the maintenance of an effective leadership by assisting
ETC in improving all aspects of their manufacturing chain and improving profitability by
continuously delivering high-quality goods. They should be in charge of providing all
appropriate assistance throughout the quality assurance process, as well as collaborating on the
implementation of a potential overall quality control plan. This would provide ETC with a
competitive edge as well as constructive market orientation.
Quality leadership: A successful leader would motivate all employees to accomplish the
company's objectives. Another of the qualities of a successful leader seems to be the willingness
to pull all workers together around the firm's collective goal. They can ensure that both
supervisors and staff are in charge of their work practices, that can inculcate a desire for
excellence in workers, and also that they will provide an ideal atmosphere for workers to know
the Total Quality Management strategy, thus assisting organisations in maintaining a high
performance culture.
Business operation system: ETC would be capable to refine different processes, increase
performance, and affect the price by constantly enhancing the business operating system. Etc
would be capable of recognizing best practises and efficient organisational processes by
enhancing the market operating framework. This will assist ETC in enhancing production
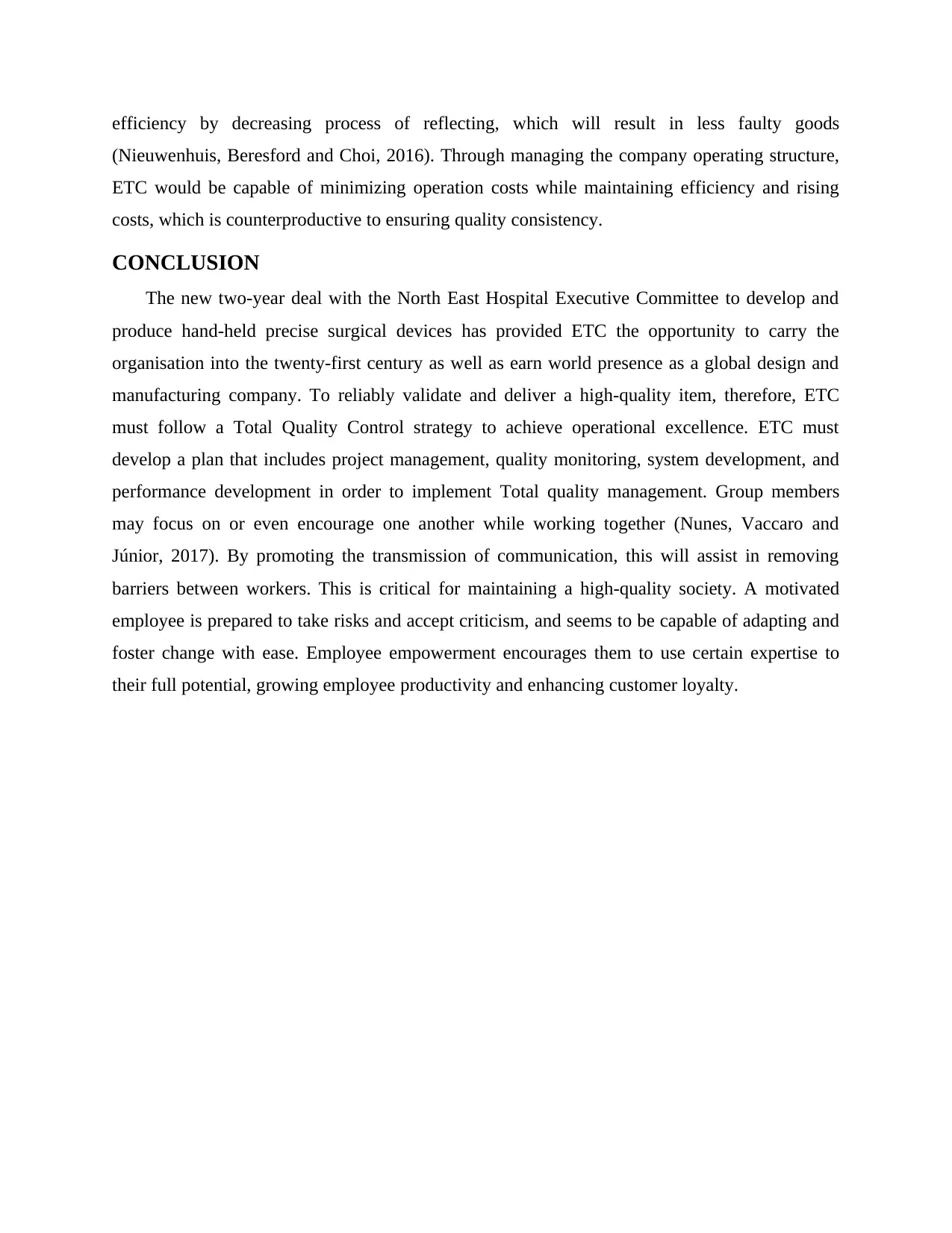
efficiency by decreasing process of reflecting, which will result in less faulty goods
(Nieuwenhuis, Beresford and Choi, 2016). Through managing the company operating structure,
ETC would be capable of minimizing operation costs while maintaining efficiency and rising
costs, which is counterproductive to ensuring quality consistency.
CONCLUSION
The new two-year deal with the North East Hospital Executive Committee to develop and
produce hand-held precise surgical devices has provided ETC the opportunity to carry the
organisation into the twenty-first century as well as earn world presence as a global design and
manufacturing company. To reliably validate and deliver a high-quality item, therefore, ETC
must follow a Total Quality Control strategy to achieve operational excellence. ETC must
develop a plan that includes project management, quality monitoring, system development, and
performance development in order to implement Total quality management. Group members
may focus on or even encourage one another while working together (Nunes, Vaccaro and
Júnior, 2017). By promoting the transmission of communication, this will assist in removing
barriers between workers. This is critical for maintaining a high-quality society. A motivated
employee is prepared to take risks and accept criticism, and seems to be capable of adapting and
foster change with ease. Employee empowerment encourages them to use certain expertise to
their full potential, growing employee productivity and enhancing customer loyalty.
(Nieuwenhuis, Beresford and Choi, 2016). Through managing the company operating structure,
ETC would be capable of minimizing operation costs while maintaining efficiency and rising
costs, which is counterproductive to ensuring quality consistency.
CONCLUSION
The new two-year deal with the North East Hospital Executive Committee to develop and
produce hand-held precise surgical devices has provided ETC the opportunity to carry the
organisation into the twenty-first century as well as earn world presence as a global design and
manufacturing company. To reliably validate and deliver a high-quality item, therefore, ETC
must follow a Total Quality Control strategy to achieve operational excellence. ETC must
develop a plan that includes project management, quality monitoring, system development, and
performance development in order to implement Total quality management. Group members
may focus on or even encourage one another while working together (Nunes, Vaccaro and
Júnior, 2017). By promoting the transmission of communication, this will assist in removing
barriers between workers. This is critical for maintaining a high-quality society. A motivated
employee is prepared to take risks and accept criticism, and seems to be capable of adapting and
foster change with ease. Employee empowerment encourages them to use certain expertise to
their full potential, growing employee productivity and enhancing customer loyalty.
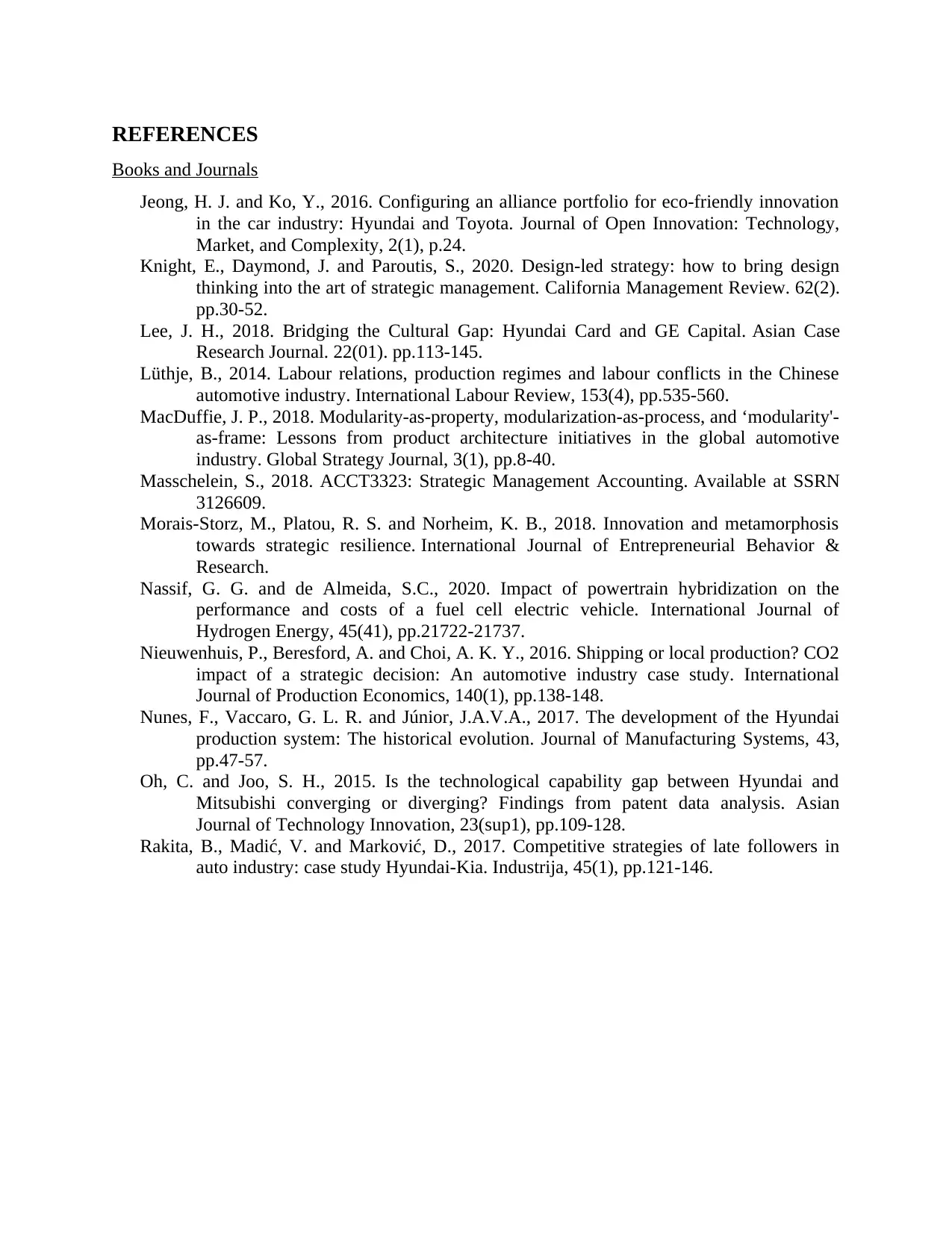
REFERENCES
Books and Journals
Jeong, H. J. and Ko, Y., 2016. Configuring an alliance portfolio for eco-friendly innovation
in the car industry: Hyundai and Toyota. Journal of Open Innovation: Technology,
Market, and Complexity, 2(1), p.24.
Knight, E., Daymond, J. and Paroutis, S., 2020. Design-led strategy: how to bring design
thinking into the art of strategic management. California Management Review. 62(2).
pp.30-52.
Lee, J. H., 2018. Bridging the Cultural Gap: Hyundai Card and GE Capital. Asian Case
Research Journal. 22(01). pp.113-145.
Lüthje, B., 2014. Labour relations, production regimes and labour conflicts in the Chinese
automotive industry. International Labour Review, 153(4), pp.535-560.
MacDuffie, J. P., 2018. Modularity‐as‐property, modularization‐as‐process, and ‘modularity'‐
as‐frame: Lessons from product architecture initiatives in the global automotive
industry. Global Strategy Journal, 3(1), pp.8-40.
Masschelein, S., 2018. ACCT3323: Strategic Management Accounting. Available at SSRN
3126609.
Morais-Storz, M., Platou, R. S. and Norheim, K. B., 2018. Innovation and metamorphosis
towards strategic resilience. International Journal of Entrepreneurial Behavior &
Research.
Nassif, G. G. and de Almeida, S.C., 2020. Impact of powertrain hybridization on the
performance and costs of a fuel cell electric vehicle. International Journal of
Hydrogen Energy, 45(41), pp.21722-21737.
Nieuwenhuis, P., Beresford, A. and Choi, A. K. Y., 2016. Shipping or local production? CO2
impact of a strategic decision: An automotive industry case study. International
Journal of Production Economics, 140(1), pp.138-148.
Nunes, F., Vaccaro, G. L. R. and Júnior, J.A.V.A., 2017. The development of the Hyundai
production system: The historical evolution. Journal of Manufacturing Systems, 43,
pp.47-57.
Oh, C. and Joo, S. H., 2015. Is the technological capability gap between Hyundai and
Mitsubishi converging or diverging? Findings from patent data analysis. Asian
Journal of Technology Innovation, 23(sup1), pp.109-128.
Rakita, B., Madić, V. and Marković, D., 2017. Competitive strategies of late followers in
auto industry: case study Hyundai-Kia. Industrija, 45(1), pp.121-146.
Books and Journals
Jeong, H. J. and Ko, Y., 2016. Configuring an alliance portfolio for eco-friendly innovation
in the car industry: Hyundai and Toyota. Journal of Open Innovation: Technology,
Market, and Complexity, 2(1), p.24.
Knight, E., Daymond, J. and Paroutis, S., 2020. Design-led strategy: how to bring design
thinking into the art of strategic management. California Management Review. 62(2).
pp.30-52.
Lee, J. H., 2018. Bridging the Cultural Gap: Hyundai Card and GE Capital. Asian Case
Research Journal. 22(01). pp.113-145.
Lüthje, B., 2014. Labour relations, production regimes and labour conflicts in the Chinese
automotive industry. International Labour Review, 153(4), pp.535-560.
MacDuffie, J. P., 2018. Modularity‐as‐property, modularization‐as‐process, and ‘modularity'‐
as‐frame: Lessons from product architecture initiatives in the global automotive
industry. Global Strategy Journal, 3(1), pp.8-40.
Masschelein, S., 2018. ACCT3323: Strategic Management Accounting. Available at SSRN
3126609.
Morais-Storz, M., Platou, R. S. and Norheim, K. B., 2018. Innovation and metamorphosis
towards strategic resilience. International Journal of Entrepreneurial Behavior &
Research.
Nassif, G. G. and de Almeida, S.C., 2020. Impact of powertrain hybridization on the
performance and costs of a fuel cell electric vehicle. International Journal of
Hydrogen Energy, 45(41), pp.21722-21737.
Nieuwenhuis, P., Beresford, A. and Choi, A. K. Y., 2016. Shipping or local production? CO2
impact of a strategic decision: An automotive industry case study. International
Journal of Production Economics, 140(1), pp.138-148.
Nunes, F., Vaccaro, G. L. R. and Júnior, J.A.V.A., 2017. The development of the Hyundai
production system: The historical evolution. Journal of Manufacturing Systems, 43,
pp.47-57.
Oh, C. and Joo, S. H., 2015. Is the technological capability gap between Hyundai and
Mitsubishi converging or diverging? Findings from patent data analysis. Asian
Journal of Technology Innovation, 23(sup1), pp.109-128.
Rakita, B., Madić, V. and Marković, D., 2017. Competitive strategies of late followers in
auto industry: case study Hyundai-Kia. Industrija, 45(1), pp.121-146.
1 out of 13
Related Documents

Your All-in-One AI-Powered Toolkit for Academic Success.
+13062052269
info@desklib.com
Available 24*7 on WhatsApp / Email
Unlock your academic potential
© 2024 | Zucol Services PVT LTD | All rights reserved.