Quality Improvement Strategies for Quality Tooling Company Project
VerifiedAdded on 2021/02/21
|12
|3367
|85
Project
AI Summary
This project report examines quality improvement strategies applicable to Quality Tooling Company, a supplier of engineering cutting tools. The report focuses on Total Quality Management (TQM), Quality Assurance, and Quality Control as key strategies. TQM is presented as a method to enhance customer focus, employee involvement, and continuous improvement within the manufacturing process. Quality Assurance is discussed as a preventative measure to avoid defects and ensure products meet quality requirements, emphasizing principles like "fit for purpose" and "right first time." Quality Control is analyzed as a process to evaluate the production process, maintain quality standards, and incorporate customer feedback. The report also highlights the importance of sustaining a culture of quality through employee involvement and clear communication to ensure long-term market sustainability and competitive advantage. The report includes recommendations for implementing these strategies to improve the company's processes, products, and services.
Contribute Materials
Your contribution can guide someone’s learning journey. Share your
documents today.
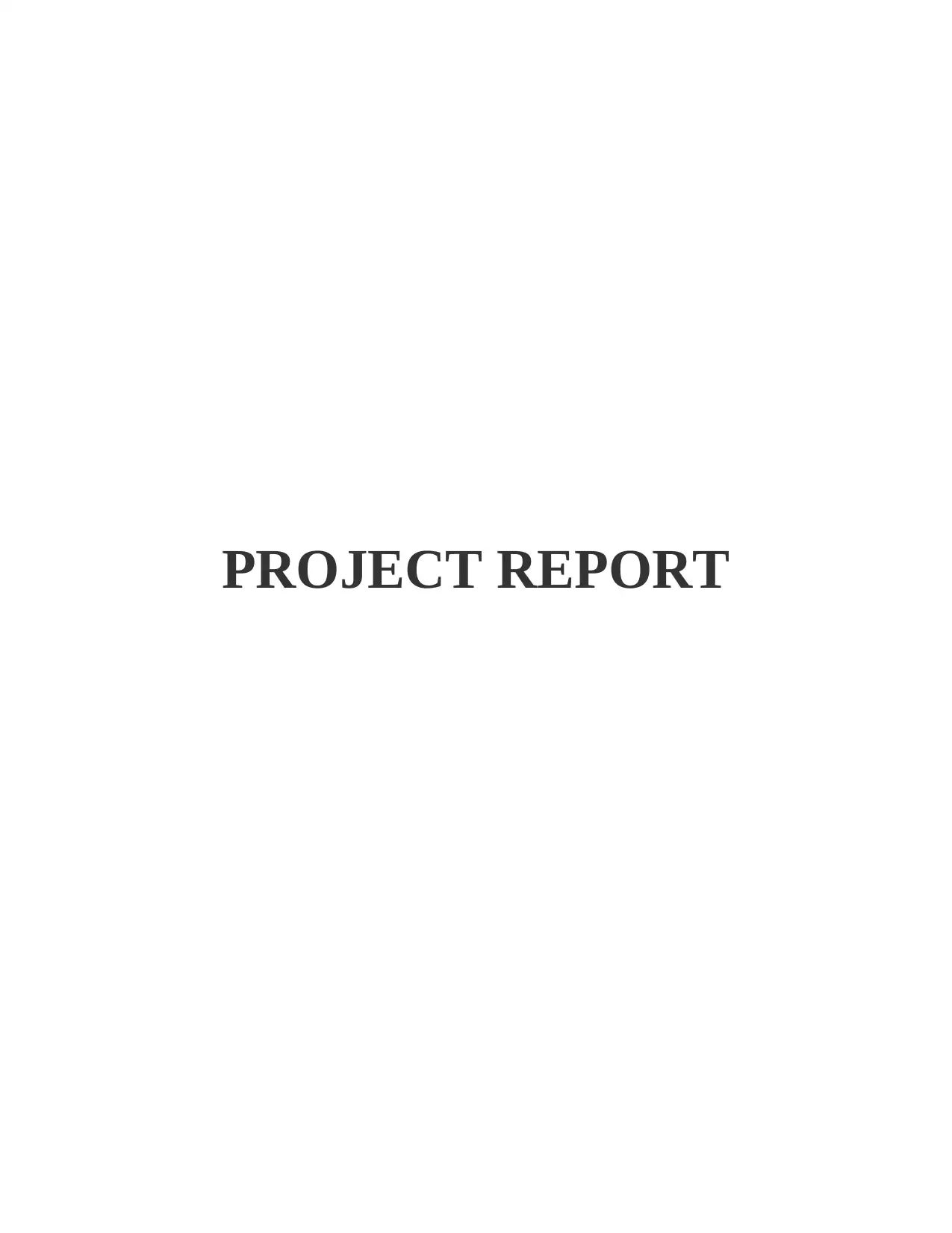
PROJECT REPORT
Secure Best Marks with AI Grader
Need help grading? Try our AI Grader for instant feedback on your assignments.
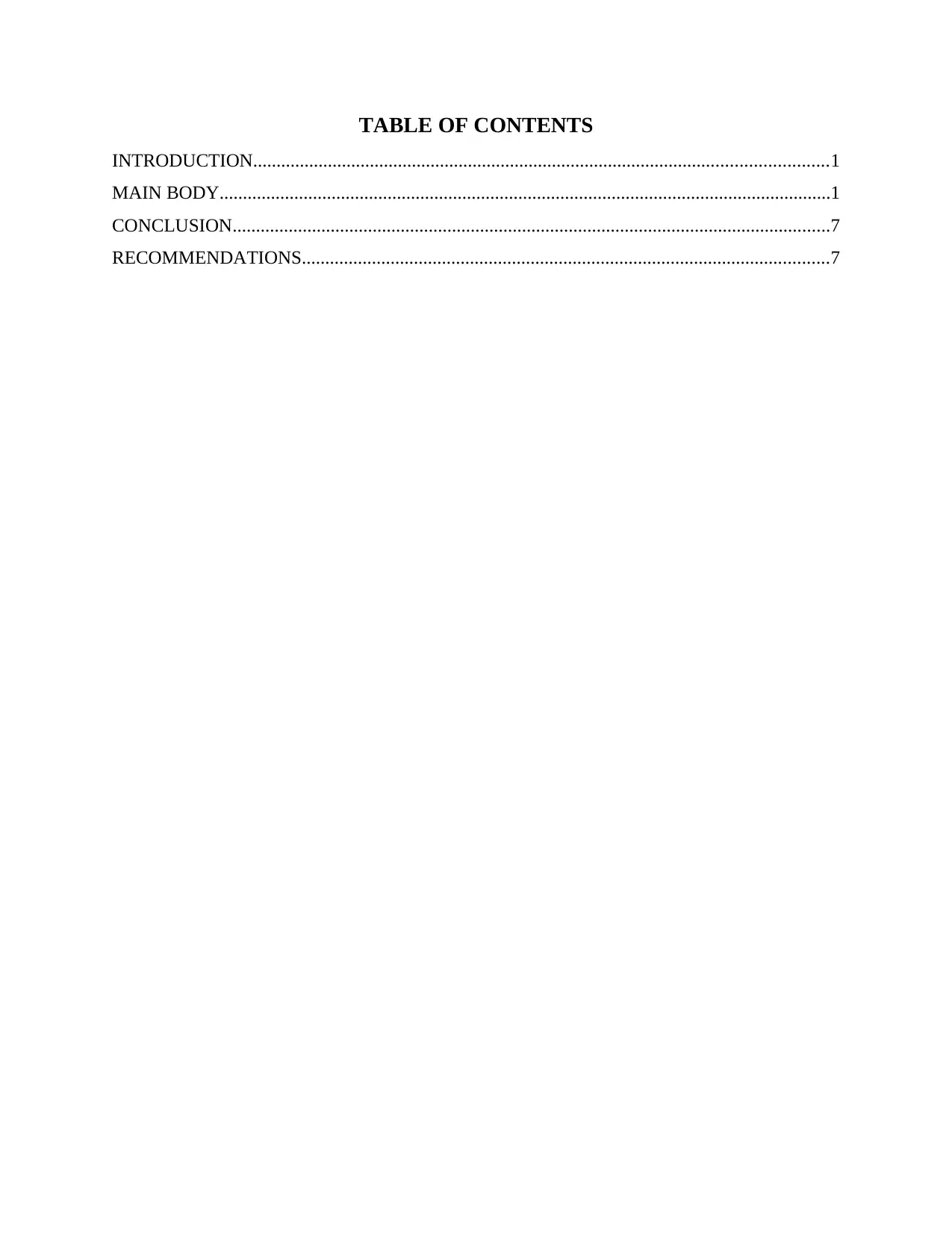
TABLE OF CONTENTS
INTRODUCTION...........................................................................................................................1
MAIN BODY...................................................................................................................................1
CONCLUSION................................................................................................................................7
RECOMMENDATIONS.................................................................................................................7
INTRODUCTION...........................................................................................................................1
MAIN BODY...................................................................................................................................1
CONCLUSION................................................................................................................................7
RECOMMENDATIONS.................................................................................................................7
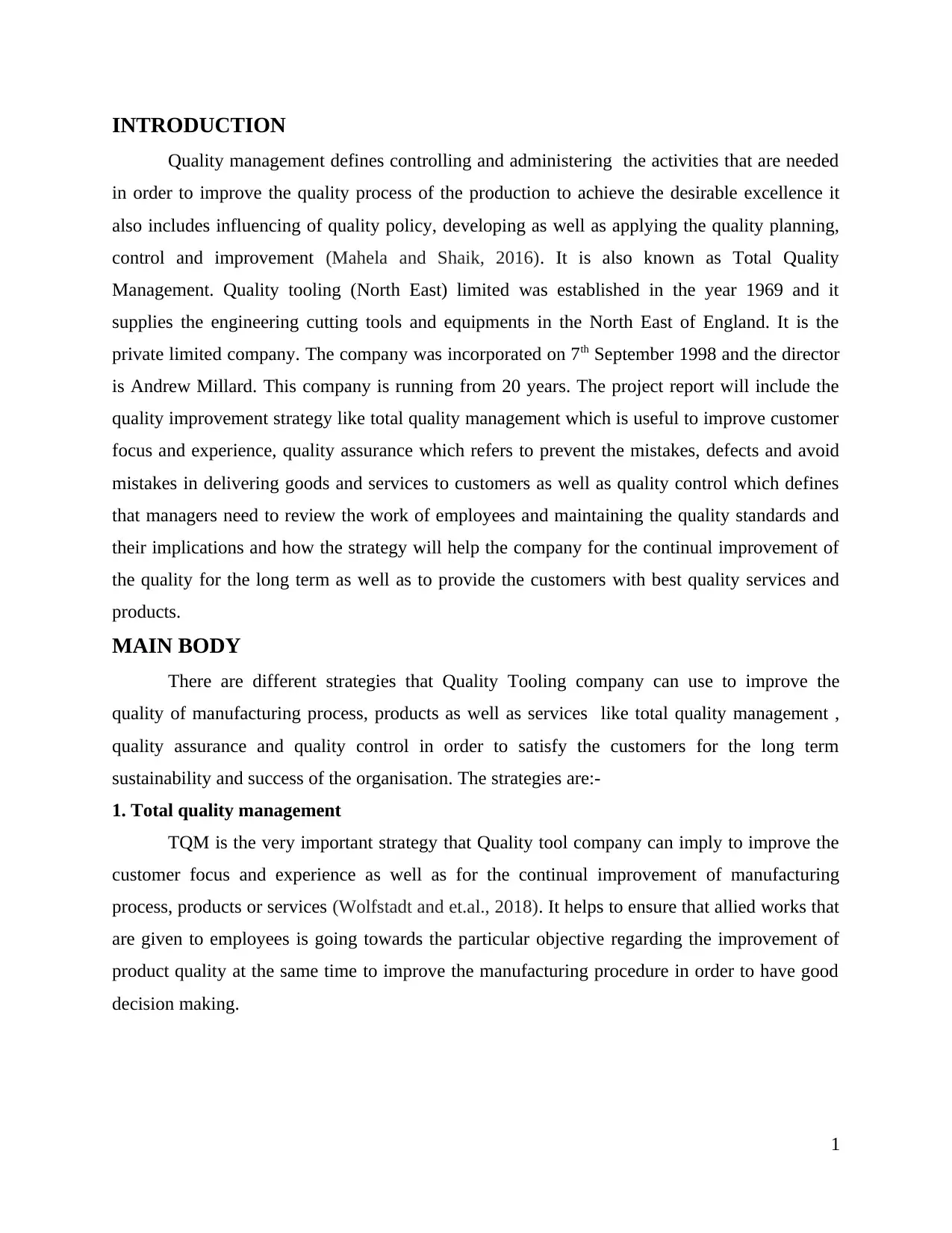
INTRODUCTION
Quality management defines controlling and administering the activities that are needed
in order to improve the quality process of the production to achieve the desirable excellence it
also includes influencing of quality policy, developing as well as applying the quality planning,
control and improvement (Mahela and Shaik, 2016). It is also known as Total Quality
Management. Quality tooling (North East) limited was established in the year 1969 and it
supplies the engineering cutting tools and equipments in the North East of England. It is the
private limited company. The company was incorporated on 7th September 1998 and the director
is Andrew Millard. This company is running from 20 years. The project report will include the
quality improvement strategy like total quality management which is useful to improve customer
focus and experience, quality assurance which refers to prevent the mistakes, defects and avoid
mistakes in delivering goods and services to customers as well as quality control which defines
that managers need to review the work of employees and maintaining the quality standards and
their implications and how the strategy will help the company for the continual improvement of
the quality for the long term as well as to provide the customers with best quality services and
products.
MAIN BODY
There are different strategies that Quality Tooling company can use to improve the
quality of manufacturing process, products as well as services like total quality management ,
quality assurance and quality control in order to satisfy the customers for the long term
sustainability and success of the organisation. The strategies are:-
1. Total quality management
TQM is the very important strategy that Quality tool company can imply to improve the
customer focus and experience as well as for the continual improvement of manufacturing
process, products or services (Wolfstadt and et.al., 2018). It helps to ensure that allied works that
are given to employees is going towards the particular objective regarding the improvement of
product quality at the same time to improve the manufacturing procedure in order to have good
decision making.
1
Quality management defines controlling and administering the activities that are needed
in order to improve the quality process of the production to achieve the desirable excellence it
also includes influencing of quality policy, developing as well as applying the quality planning,
control and improvement (Mahela and Shaik, 2016). It is also known as Total Quality
Management. Quality tooling (North East) limited was established in the year 1969 and it
supplies the engineering cutting tools and equipments in the North East of England. It is the
private limited company. The company was incorporated on 7th September 1998 and the director
is Andrew Millard. This company is running from 20 years. The project report will include the
quality improvement strategy like total quality management which is useful to improve customer
focus and experience, quality assurance which refers to prevent the mistakes, defects and avoid
mistakes in delivering goods and services to customers as well as quality control which defines
that managers need to review the work of employees and maintaining the quality standards and
their implications and how the strategy will help the company for the continual improvement of
the quality for the long term as well as to provide the customers with best quality services and
products.
MAIN BODY
There are different strategies that Quality Tooling company can use to improve the
quality of manufacturing process, products as well as services like total quality management ,
quality assurance and quality control in order to satisfy the customers for the long term
sustainability and success of the organisation. The strategies are:-
1. Total quality management
TQM is the very important strategy that Quality tool company can imply to improve the
customer focus and experience as well as for the continual improvement of manufacturing
process, products or services (Wolfstadt and et.al., 2018). It helps to ensure that allied works that
are given to employees is going towards the particular objective regarding the improvement of
product quality at the same time to improve the manufacturing procedure in order to have good
decision making.
1
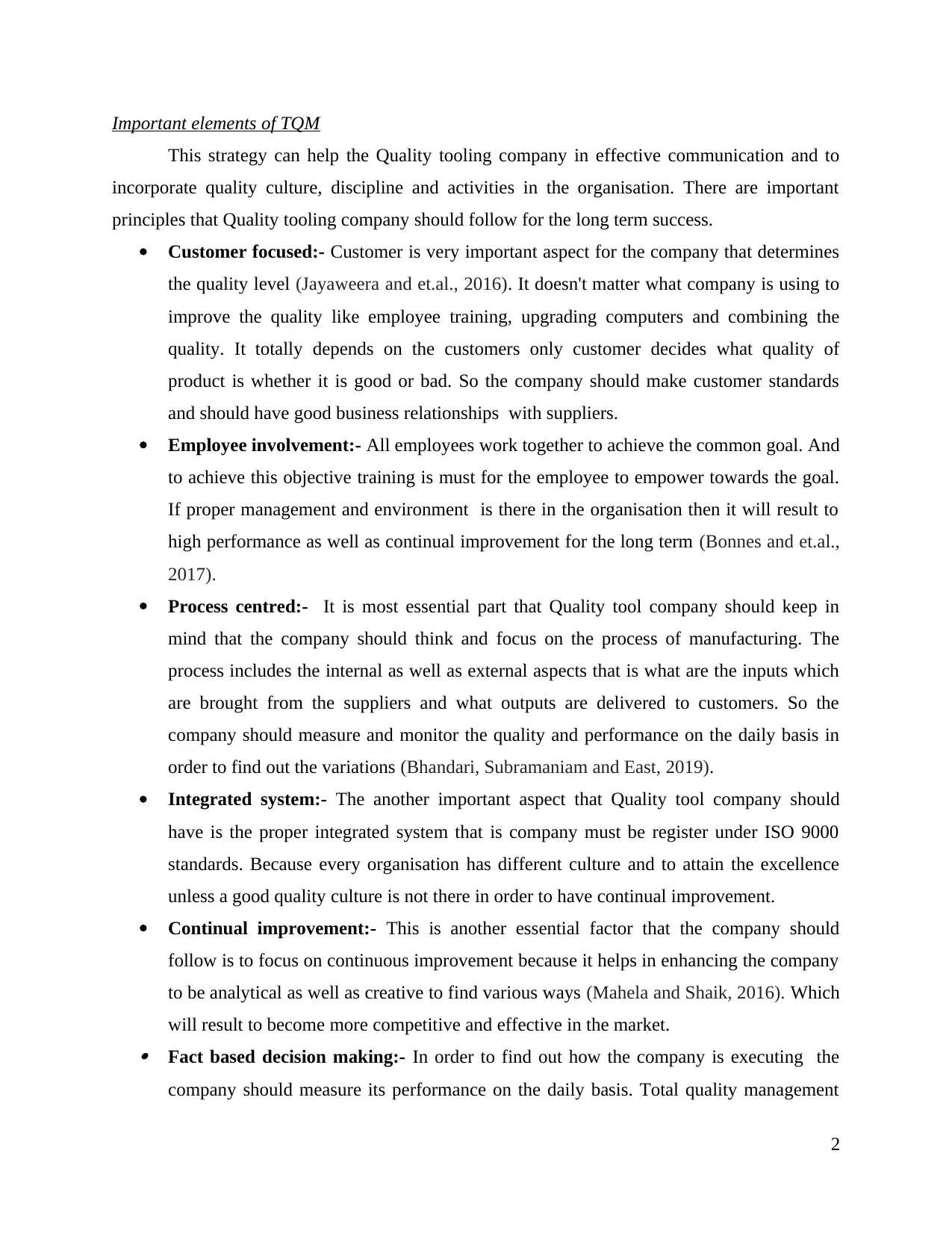
Important elements of TQM
This strategy can help the Quality tooling company in effective communication and to
incorporate quality culture, discipline and activities in the organisation. There are important
principles that Quality tooling company should follow for the long term success.
Customer focused:- Customer is very important aspect for the company that determines
the quality level (Jayaweera and et.al., 2016). It doesn't matter what company is using to
improve the quality like employee training, upgrading computers and combining the
quality. It totally depends on the customers only customer decides what quality of
product is whether it is good or bad. So the company should make customer standards
and should have good business relationships with suppliers.
Employee involvement:- All employees work together to achieve the common goal. And
to achieve this objective training is must for the employee to empower towards the goal.
If proper management and environment is there in the organisation then it will result to
high performance as well as continual improvement for the long term (Bonnes and et.al.,
2017).
Process centred:- It is most essential part that Quality tool company should keep in
mind that the company should think and focus on the process of manufacturing. The
process includes the internal as well as external aspects that is what are the inputs which
are brought from the suppliers and what outputs are delivered to customers. So the
company should measure and monitor the quality and performance on the daily basis in
order to find out the variations (Bhandari, Subramaniam and East, 2019).
Integrated system:- The another important aspect that Quality tool company should
have is the proper integrated system that is company must be register under ISO 9000
standards. Because every organisation has different culture and to attain the excellence
unless a good quality culture is not there in order to have continual improvement.
Continual improvement:- This is another essential factor that the company should
follow is to focus on continuous improvement because it helps in enhancing the company
to be analytical as well as creative to find various ways (Mahela and Shaik, 2016). Which
will result to become more competitive and effective in the market. Fact based decision making:- In order to find out how the company is executing the
company should measure its performance on the daily basis. Total quality management
2
This strategy can help the Quality tooling company in effective communication and to
incorporate quality culture, discipline and activities in the organisation. There are important
principles that Quality tooling company should follow for the long term success.
Customer focused:- Customer is very important aspect for the company that determines
the quality level (Jayaweera and et.al., 2016). It doesn't matter what company is using to
improve the quality like employee training, upgrading computers and combining the
quality. It totally depends on the customers only customer decides what quality of
product is whether it is good or bad. So the company should make customer standards
and should have good business relationships with suppliers.
Employee involvement:- All employees work together to achieve the common goal. And
to achieve this objective training is must for the employee to empower towards the goal.
If proper management and environment is there in the organisation then it will result to
high performance as well as continual improvement for the long term (Bonnes and et.al.,
2017).
Process centred:- It is most essential part that Quality tool company should keep in
mind that the company should think and focus on the process of manufacturing. The
process includes the internal as well as external aspects that is what are the inputs which
are brought from the suppliers and what outputs are delivered to customers. So the
company should measure and monitor the quality and performance on the daily basis in
order to find out the variations (Bhandari, Subramaniam and East, 2019).
Integrated system:- The another important aspect that Quality tool company should
have is the proper integrated system that is company must be register under ISO 9000
standards. Because every organisation has different culture and to attain the excellence
unless a good quality culture is not there in order to have continual improvement.
Continual improvement:- This is another essential factor that the company should
follow is to focus on continuous improvement because it helps in enhancing the company
to be analytical as well as creative to find various ways (Mahela and Shaik, 2016). Which
will result to become more competitive and effective in the market. Fact based decision making:- In order to find out how the company is executing the
company should measure its performance on the daily basis. Total quality management
2
Secure Best Marks with AI Grader
Need help grading? Try our AI Grader for instant feedback on your assignments.
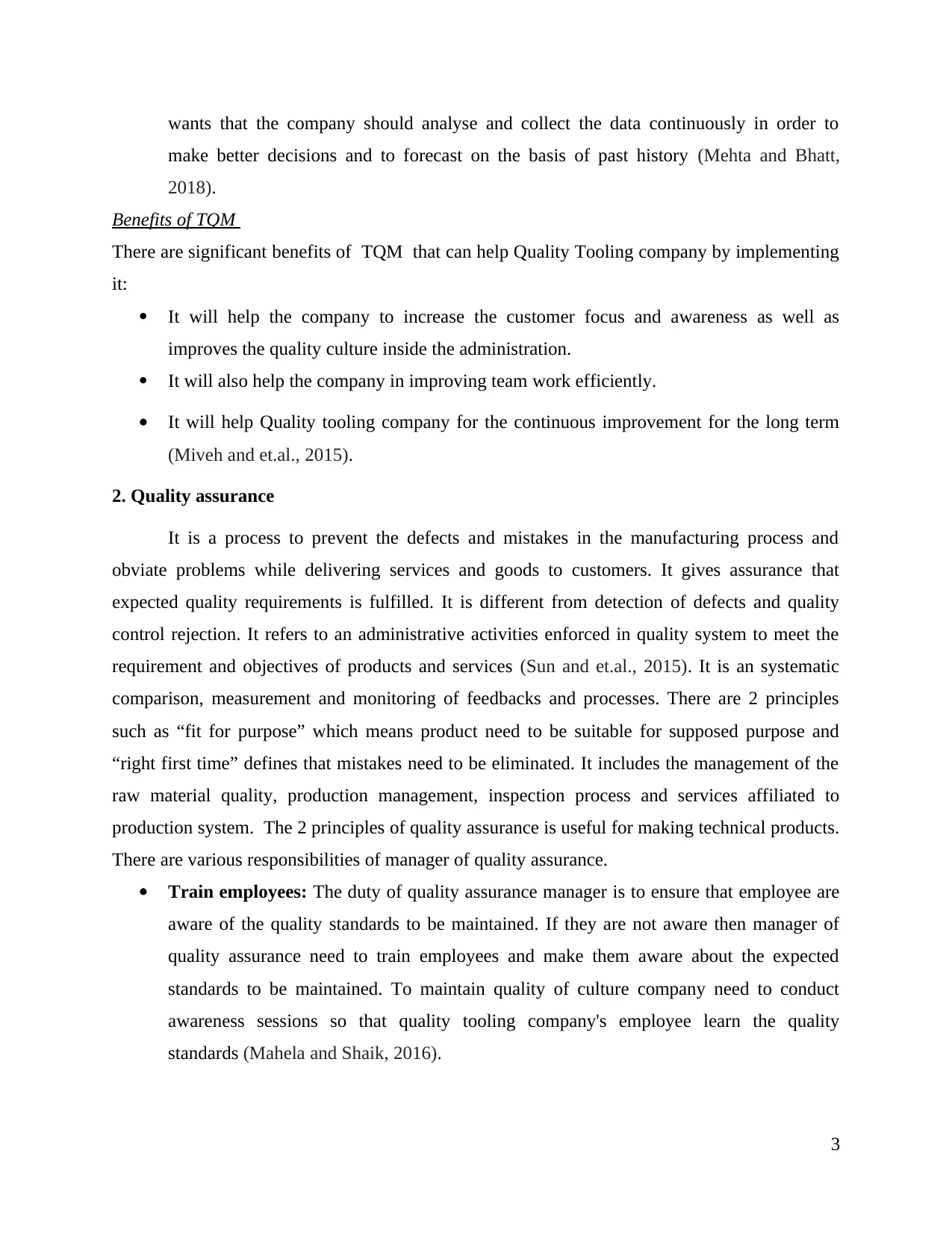
wants that the company should analyse and collect the data continuously in order to
make better decisions and to forecast on the basis of past history (Mehta and Bhatt,
2018).
Benefits of TQM
There are significant benefits of TQM that can help Quality Tooling company by implementing
it:
It will help the company to increase the customer focus and awareness as well as
improves the quality culture inside the administration.
It will also help the company in improving team work efficiently.
It will help Quality tooling company for the continuous improvement for the long term
(Miveh and et.al., 2015).
2. Quality assurance
It is a process to prevent the defects and mistakes in the manufacturing process and
obviate problems while delivering services and goods to customers. It gives assurance that
expected quality requirements is fulfilled. It is different from detection of defects and quality
control rejection. It refers to an administrative activities enforced in quality system to meet the
requirement and objectives of products and services (Sun and et.al., 2015). It is an systematic
comparison, measurement and monitoring of feedbacks and processes. There are 2 principles
such as “fit for purpose” which means product need to be suitable for supposed purpose and
“right first time” defines that mistakes need to be eliminated. It includes the management of the
raw material quality, production management, inspection process and services affiliated to
production system. The 2 principles of quality assurance is useful for making technical products.
There are various responsibilities of manager of quality assurance.
Train employees: The duty of quality assurance manager is to ensure that employee are
aware of the quality standards to be maintained. If they are not aware then manager of
quality assurance need to train employees and make them aware about the expected
standards to be maintained. To maintain quality of culture company need to conduct
awareness sessions so that quality tooling company's employee learn the quality
standards (Mahela and Shaik, 2016).
3
make better decisions and to forecast on the basis of past history (Mehta and Bhatt,
2018).
Benefits of TQM
There are significant benefits of TQM that can help Quality Tooling company by implementing
it:
It will help the company to increase the customer focus and awareness as well as
improves the quality culture inside the administration.
It will also help the company in improving team work efficiently.
It will help Quality tooling company for the continuous improvement for the long term
(Miveh and et.al., 2015).
2. Quality assurance
It is a process to prevent the defects and mistakes in the manufacturing process and
obviate problems while delivering services and goods to customers. It gives assurance that
expected quality requirements is fulfilled. It is different from detection of defects and quality
control rejection. It refers to an administrative activities enforced in quality system to meet the
requirement and objectives of products and services (Sun and et.al., 2015). It is an systematic
comparison, measurement and monitoring of feedbacks and processes. There are 2 principles
such as “fit for purpose” which means product need to be suitable for supposed purpose and
“right first time” defines that mistakes need to be eliminated. It includes the management of the
raw material quality, production management, inspection process and services affiliated to
production system. The 2 principles of quality assurance is useful for making technical products.
There are various responsibilities of manager of quality assurance.
Train employees: The duty of quality assurance manager is to ensure that employee are
aware of the quality standards to be maintained. If they are not aware then manager of
quality assurance need to train employees and make them aware about the expected
standards to be maintained. To maintain quality of culture company need to conduct
awareness sessions so that quality tooling company's employee learn the quality
standards (Mahela and Shaik, 2016).
3
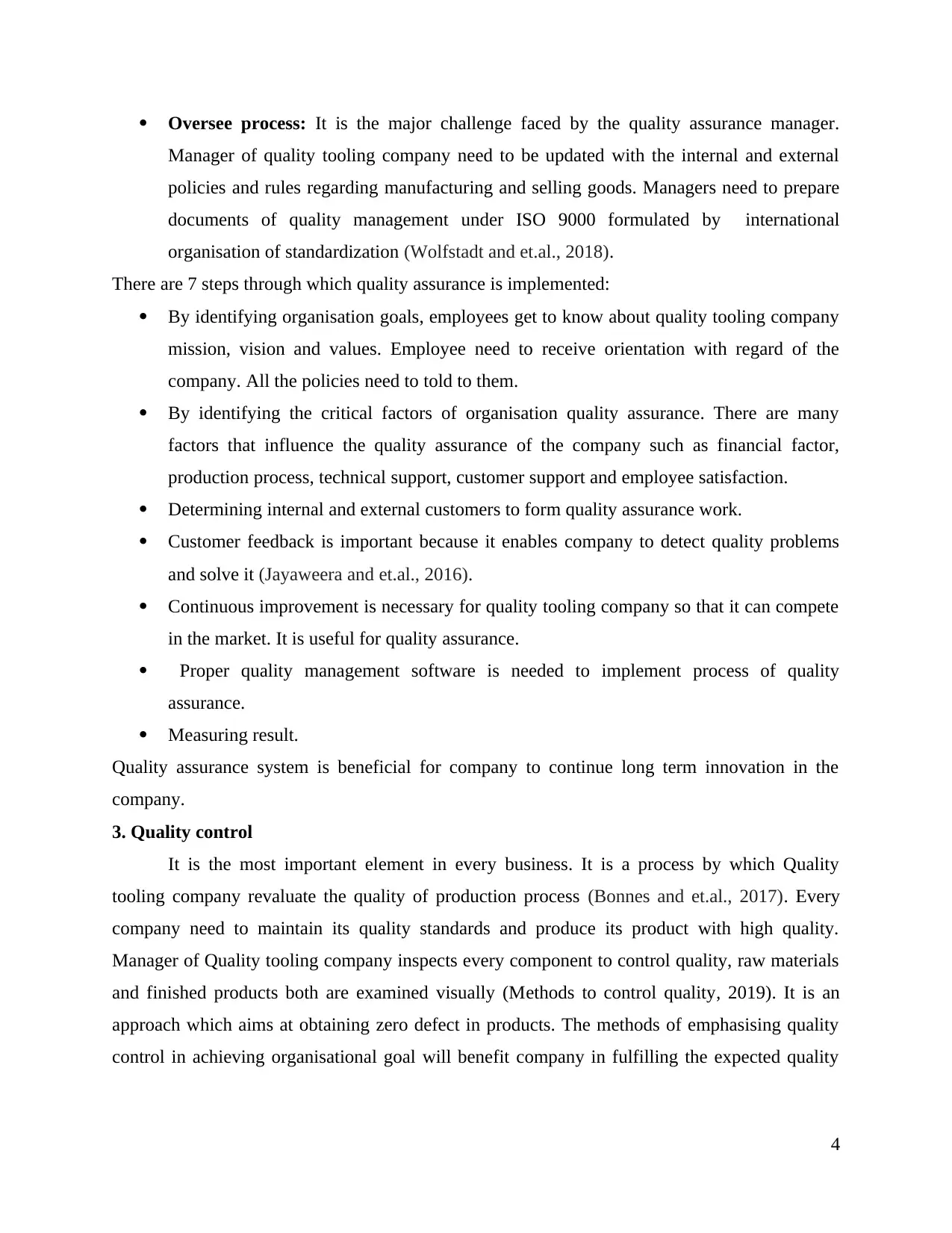
Oversee process: It is the major challenge faced by the quality assurance manager.
Manager of quality tooling company need to be updated with the internal and external
policies and rules regarding manufacturing and selling goods. Managers need to prepare
documents of quality management under ISO 9000 formulated by international
organisation of standardization (Wolfstadt and et.al., 2018).
There are 7 steps through which quality assurance is implemented:
By identifying organisation goals, employees get to know about quality tooling company
mission, vision and values. Employee need to receive orientation with regard of the
company. All the policies need to told to them.
By identifying the critical factors of organisation quality assurance. There are many
factors that influence the quality assurance of the company such as financial factor,
production process, technical support, customer support and employee satisfaction.
Determining internal and external customers to form quality assurance work.
Customer feedback is important because it enables company to detect quality problems
and solve it (Jayaweera and et.al., 2016).
Continuous improvement is necessary for quality tooling company so that it can compete
in the market. It is useful for quality assurance.
Proper quality management software is needed to implement process of quality
assurance.
Measuring result.
Quality assurance system is beneficial for company to continue long term innovation in the
company.
3. Quality control
It is the most important element in every business. It is a process by which Quality
tooling company revaluate the quality of production process (Bonnes and et.al., 2017). Every
company need to maintain its quality standards and produce its product with high quality.
Manager of Quality tooling company inspects every component to control quality, raw materials
and finished products both are examined visually (Methods to control quality, 2019). It is an
approach which aims at obtaining zero defect in products. The methods of emphasising quality
control in achieving organisational goal will benefit company in fulfilling the expected quality
4
Manager of quality tooling company need to be updated with the internal and external
policies and rules regarding manufacturing and selling goods. Managers need to prepare
documents of quality management under ISO 9000 formulated by international
organisation of standardization (Wolfstadt and et.al., 2018).
There are 7 steps through which quality assurance is implemented:
By identifying organisation goals, employees get to know about quality tooling company
mission, vision and values. Employee need to receive orientation with regard of the
company. All the policies need to told to them.
By identifying the critical factors of organisation quality assurance. There are many
factors that influence the quality assurance of the company such as financial factor,
production process, technical support, customer support and employee satisfaction.
Determining internal and external customers to form quality assurance work.
Customer feedback is important because it enables company to detect quality problems
and solve it (Jayaweera and et.al., 2016).
Continuous improvement is necessary for quality tooling company so that it can compete
in the market. It is useful for quality assurance.
Proper quality management software is needed to implement process of quality
assurance.
Measuring result.
Quality assurance system is beneficial for company to continue long term innovation in the
company.
3. Quality control
It is the most important element in every business. It is a process by which Quality
tooling company revaluate the quality of production process (Bonnes and et.al., 2017). Every
company need to maintain its quality standards and produce its product with high quality.
Manager of Quality tooling company inspects every component to control quality, raw materials
and finished products both are examined visually (Methods to control quality, 2019). It is an
approach which aims at obtaining zero defect in products. The methods of emphasising quality
control in achieving organisational goal will benefit company in fulfilling the expected quality
4
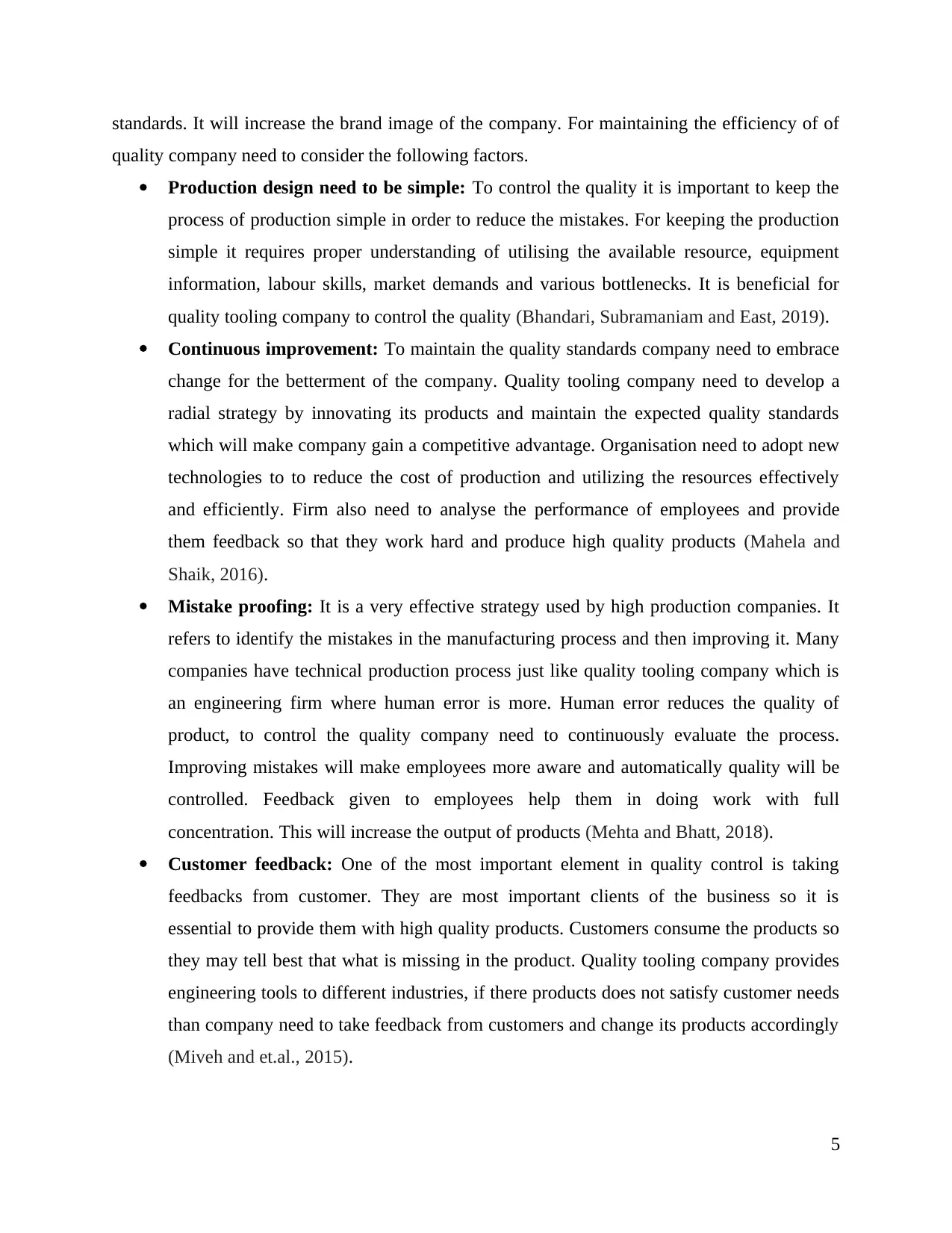
standards. It will increase the brand image of the company. For maintaining the efficiency of of
quality company need to consider the following factors.
Production design need to be simple: To control the quality it is important to keep the
process of production simple in order to reduce the mistakes. For keeping the production
simple it requires proper understanding of utilising the available resource, equipment
information, labour skills, market demands and various bottlenecks. It is beneficial for
quality tooling company to control the quality (Bhandari, Subramaniam and East, 2019).
Continuous improvement: To maintain the quality standards company need to embrace
change for the betterment of the company. Quality tooling company need to develop a
radial strategy by innovating its products and maintain the expected quality standards
which will make company gain a competitive advantage. Organisation need to adopt new
technologies to to reduce the cost of production and utilizing the resources effectively
and efficiently. Firm also need to analyse the performance of employees and provide
them feedback so that they work hard and produce high quality products (Mahela and
Shaik, 2016).
Mistake proofing: It is a very effective strategy used by high production companies. It
refers to identify the mistakes in the manufacturing process and then improving it. Many
companies have technical production process just like quality tooling company which is
an engineering firm where human error is more. Human error reduces the quality of
product, to control the quality company need to continuously evaluate the process.
Improving mistakes will make employees more aware and automatically quality will be
controlled. Feedback given to employees help them in doing work with full
concentration. This will increase the output of products (Mehta and Bhatt, 2018).
Customer feedback: One of the most important element in quality control is taking
feedbacks from customer. They are most important clients of the business so it is
essential to provide them with high quality products. Customers consume the products so
they may tell best that what is missing in the product. Quality tooling company provides
engineering tools to different industries, if there products does not satisfy customer needs
than company need to take feedback from customers and change its products accordingly
(Miveh and et.al., 2015).
5
quality company need to consider the following factors.
Production design need to be simple: To control the quality it is important to keep the
process of production simple in order to reduce the mistakes. For keeping the production
simple it requires proper understanding of utilising the available resource, equipment
information, labour skills, market demands and various bottlenecks. It is beneficial for
quality tooling company to control the quality (Bhandari, Subramaniam and East, 2019).
Continuous improvement: To maintain the quality standards company need to embrace
change for the betterment of the company. Quality tooling company need to develop a
radial strategy by innovating its products and maintain the expected quality standards
which will make company gain a competitive advantage. Organisation need to adopt new
technologies to to reduce the cost of production and utilizing the resources effectively
and efficiently. Firm also need to analyse the performance of employees and provide
them feedback so that they work hard and produce high quality products (Mahela and
Shaik, 2016).
Mistake proofing: It is a very effective strategy used by high production companies. It
refers to identify the mistakes in the manufacturing process and then improving it. Many
companies have technical production process just like quality tooling company which is
an engineering firm where human error is more. Human error reduces the quality of
product, to control the quality company need to continuously evaluate the process.
Improving mistakes will make employees more aware and automatically quality will be
controlled. Feedback given to employees help them in doing work with full
concentration. This will increase the output of products (Mehta and Bhatt, 2018).
Customer feedback: One of the most important element in quality control is taking
feedbacks from customer. They are most important clients of the business so it is
essential to provide them with high quality products. Customers consume the products so
they may tell best that what is missing in the product. Quality tooling company provides
engineering tools to different industries, if there products does not satisfy customer needs
than company need to take feedback from customers and change its products accordingly
(Miveh and et.al., 2015).
5
Paraphrase This Document
Need a fresh take? Get an instant paraphrase of this document with our AI Paraphraser
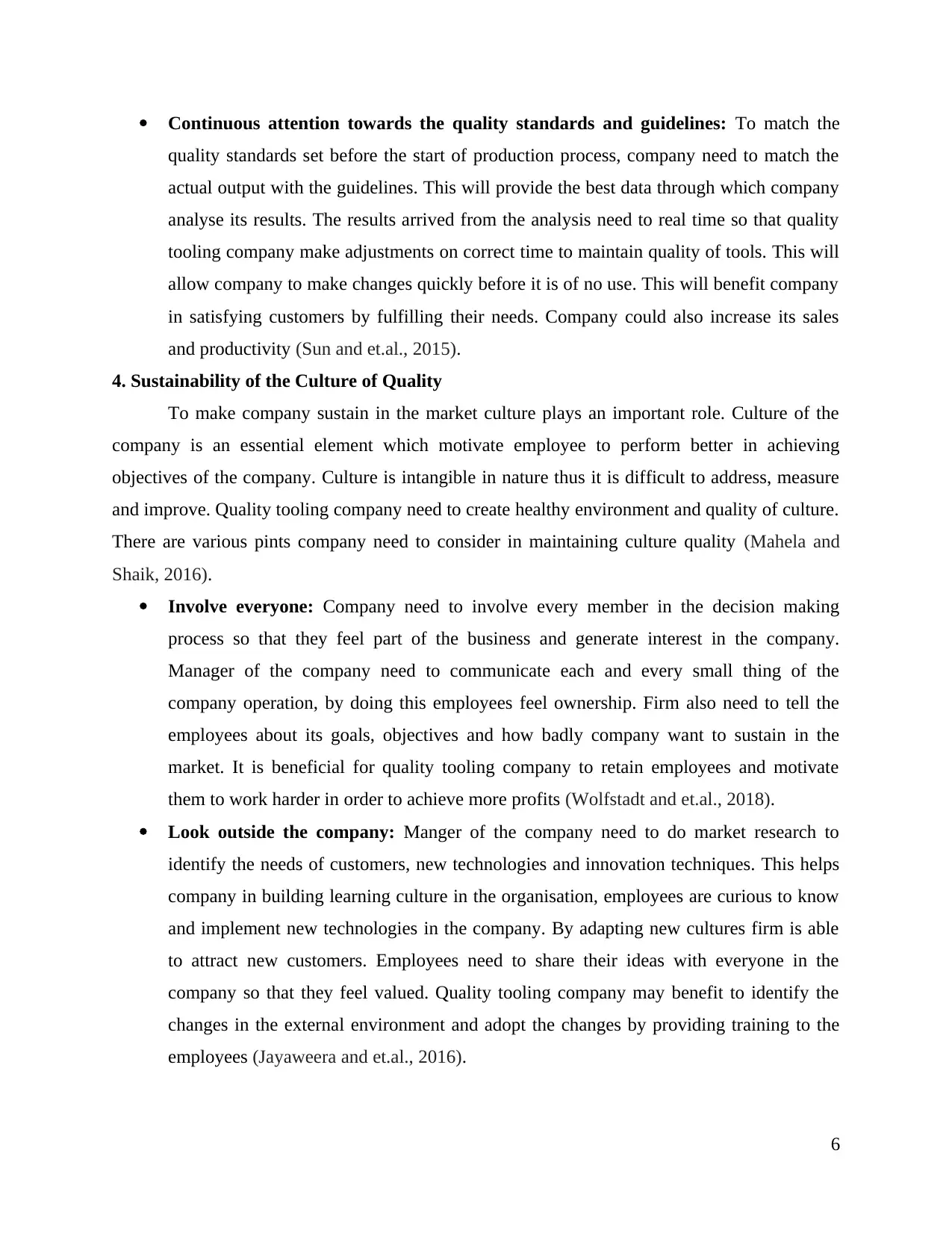
Continuous attention towards the quality standards and guidelines: To match the
quality standards set before the start of production process, company need to match the
actual output with the guidelines. This will provide the best data through which company
analyse its results. The results arrived from the analysis need to real time so that quality
tooling company make adjustments on correct time to maintain quality of tools. This will
allow company to make changes quickly before it is of no use. This will benefit company
in satisfying customers by fulfilling their needs. Company could also increase its sales
and productivity (Sun and et.al., 2015).
4. Sustainability of the Culture of Quality
To make company sustain in the market culture plays an important role. Culture of the
company is an essential element which motivate employee to perform better in achieving
objectives of the company. Culture is intangible in nature thus it is difficult to address, measure
and improve. Quality tooling company need to create healthy environment and quality of culture.
There are various pints company need to consider in maintaining culture quality (Mahela and
Shaik, 2016).
Involve everyone: Company need to involve every member in the decision making
process so that they feel part of the business and generate interest in the company.
Manager of the company need to communicate each and every small thing of the
company operation, by doing this employees feel ownership. Firm also need to tell the
employees about its goals, objectives and how badly company want to sustain in the
market. It is beneficial for quality tooling company to retain employees and motivate
them to work harder in order to achieve more profits (Wolfstadt and et.al., 2018).
Look outside the company: Manger of the company need to do market research to
identify the needs of customers, new technologies and innovation techniques. This helps
company in building learning culture in the organisation, employees are curious to know
and implement new technologies in the company. By adapting new cultures firm is able
to attract new customers. Employees need to share their ideas with everyone in the
company so that they feel valued. Quality tooling company may benefit to identify the
changes in the external environment and adopt the changes by providing training to the
employees (Jayaweera and et.al., 2016).
6
quality standards set before the start of production process, company need to match the
actual output with the guidelines. This will provide the best data through which company
analyse its results. The results arrived from the analysis need to real time so that quality
tooling company make adjustments on correct time to maintain quality of tools. This will
allow company to make changes quickly before it is of no use. This will benefit company
in satisfying customers by fulfilling their needs. Company could also increase its sales
and productivity (Sun and et.al., 2015).
4. Sustainability of the Culture of Quality
To make company sustain in the market culture plays an important role. Culture of the
company is an essential element which motivate employee to perform better in achieving
objectives of the company. Culture is intangible in nature thus it is difficult to address, measure
and improve. Quality tooling company need to create healthy environment and quality of culture.
There are various pints company need to consider in maintaining culture quality (Mahela and
Shaik, 2016).
Involve everyone: Company need to involve every member in the decision making
process so that they feel part of the business and generate interest in the company.
Manager of the company need to communicate each and every small thing of the
company operation, by doing this employees feel ownership. Firm also need to tell the
employees about its goals, objectives and how badly company want to sustain in the
market. It is beneficial for quality tooling company to retain employees and motivate
them to work harder in order to achieve more profits (Wolfstadt and et.al., 2018).
Look outside the company: Manger of the company need to do market research to
identify the needs of customers, new technologies and innovation techniques. This helps
company in building learning culture in the organisation, employees are curious to know
and implement new technologies in the company. By adapting new cultures firm is able
to attract new customers. Employees need to share their ideas with everyone in the
company so that they feel valued. Quality tooling company may benefit to identify the
changes in the external environment and adopt the changes by providing training to the
employees (Jayaweera and et.al., 2016).
6
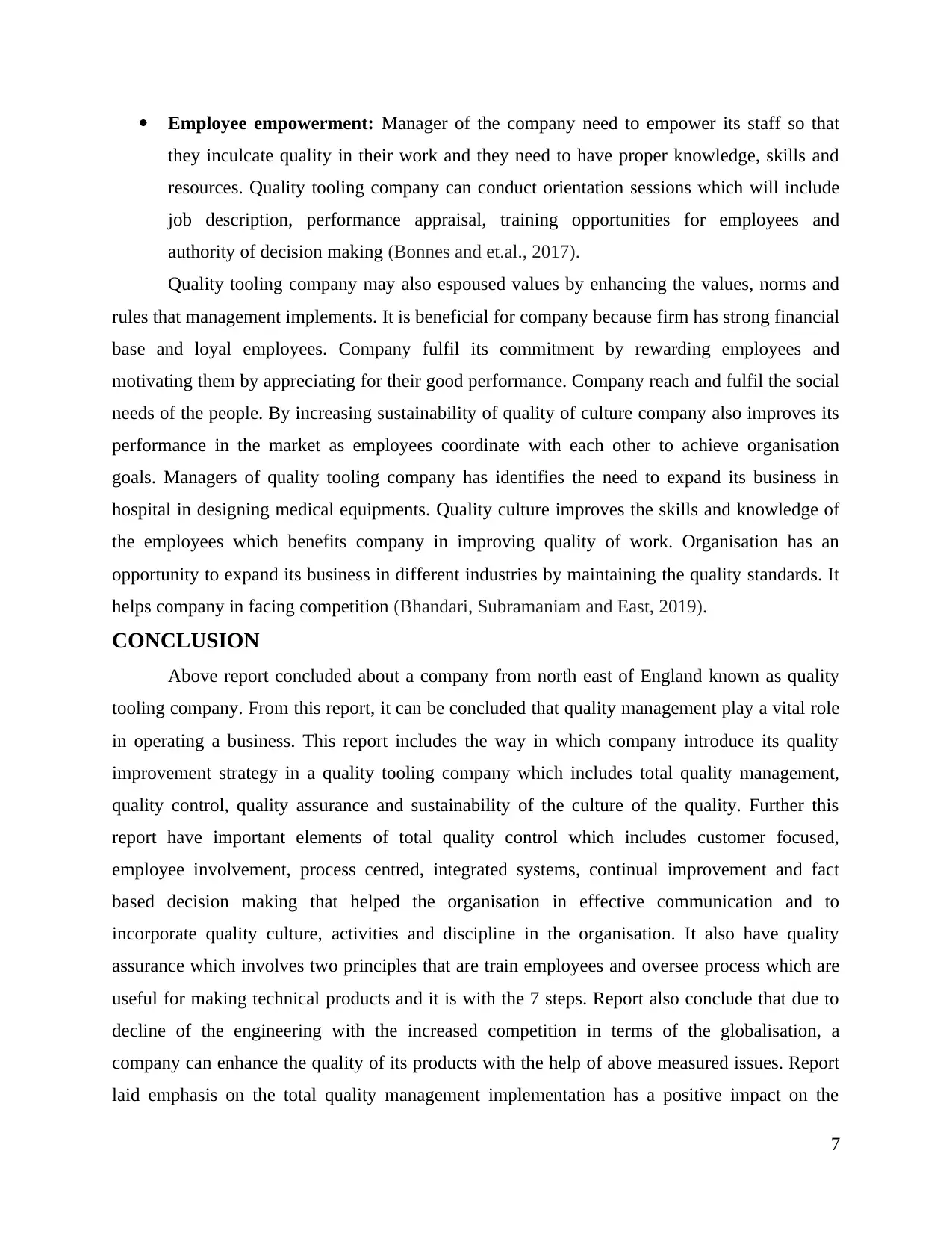
Employee empowerment: Manager of the company need to empower its staff so that
they inculcate quality in their work and they need to have proper knowledge, skills and
resources. Quality tooling company can conduct orientation sessions which will include
job description, performance appraisal, training opportunities for employees and
authority of decision making (Bonnes and et.al., 2017).
Quality tooling company may also espoused values by enhancing the values, norms and
rules that management implements. It is beneficial for company because firm has strong financial
base and loyal employees. Company fulfil its commitment by rewarding employees and
motivating them by appreciating for their good performance. Company reach and fulfil the social
needs of the people. By increasing sustainability of quality of culture company also improves its
performance in the market as employees coordinate with each other to achieve organisation
goals. Managers of quality tooling company has identifies the need to expand its business in
hospital in designing medical equipments. Quality culture improves the skills and knowledge of
the employees which benefits company in improving quality of work. Organisation has an
opportunity to expand its business in different industries by maintaining the quality standards. It
helps company in facing competition (Bhandari, Subramaniam and East, 2019).
CONCLUSION
Above report concluded about a company from north east of England known as quality
tooling company. From this report, it can be concluded that quality management play a vital role
in operating a business. This report includes the way in which company introduce its quality
improvement strategy in a quality tooling company which includes total quality management,
quality control, quality assurance and sustainability of the culture of the quality. Further this
report have important elements of total quality control which includes customer focused,
employee involvement, process centred, integrated systems, continual improvement and fact
based decision making that helped the organisation in effective communication and to
incorporate quality culture, activities and discipline in the organisation. It also have quality
assurance which involves two principles that are train employees and oversee process which are
useful for making technical products and it is with the 7 steps. Report also conclude that due to
decline of the engineering with the increased competition in terms of the globalisation, a
company can enhance the quality of its products with the help of above measured issues. Report
laid emphasis on the total quality management implementation has a positive impact on the
7
they inculcate quality in their work and they need to have proper knowledge, skills and
resources. Quality tooling company can conduct orientation sessions which will include
job description, performance appraisal, training opportunities for employees and
authority of decision making (Bonnes and et.al., 2017).
Quality tooling company may also espoused values by enhancing the values, norms and
rules that management implements. It is beneficial for company because firm has strong financial
base and loyal employees. Company fulfil its commitment by rewarding employees and
motivating them by appreciating for their good performance. Company reach and fulfil the social
needs of the people. By increasing sustainability of quality of culture company also improves its
performance in the market as employees coordinate with each other to achieve organisation
goals. Managers of quality tooling company has identifies the need to expand its business in
hospital in designing medical equipments. Quality culture improves the skills and knowledge of
the employees which benefits company in improving quality of work. Organisation has an
opportunity to expand its business in different industries by maintaining the quality standards. It
helps company in facing competition (Bhandari, Subramaniam and East, 2019).
CONCLUSION
Above report concluded about a company from north east of England known as quality
tooling company. From this report, it can be concluded that quality management play a vital role
in operating a business. This report includes the way in which company introduce its quality
improvement strategy in a quality tooling company which includes total quality management,
quality control, quality assurance and sustainability of the culture of the quality. Further this
report have important elements of total quality control which includes customer focused,
employee involvement, process centred, integrated systems, continual improvement and fact
based decision making that helped the organisation in effective communication and to
incorporate quality culture, activities and discipline in the organisation. It also have quality
assurance which involves two principles that are train employees and oversee process which are
useful for making technical products and it is with the 7 steps. Report also conclude that due to
decline of the engineering with the increased competition in terms of the globalisation, a
company can enhance the quality of its products with the help of above measured issues. Report
laid emphasis on the total quality management implementation has a positive impact on the
7
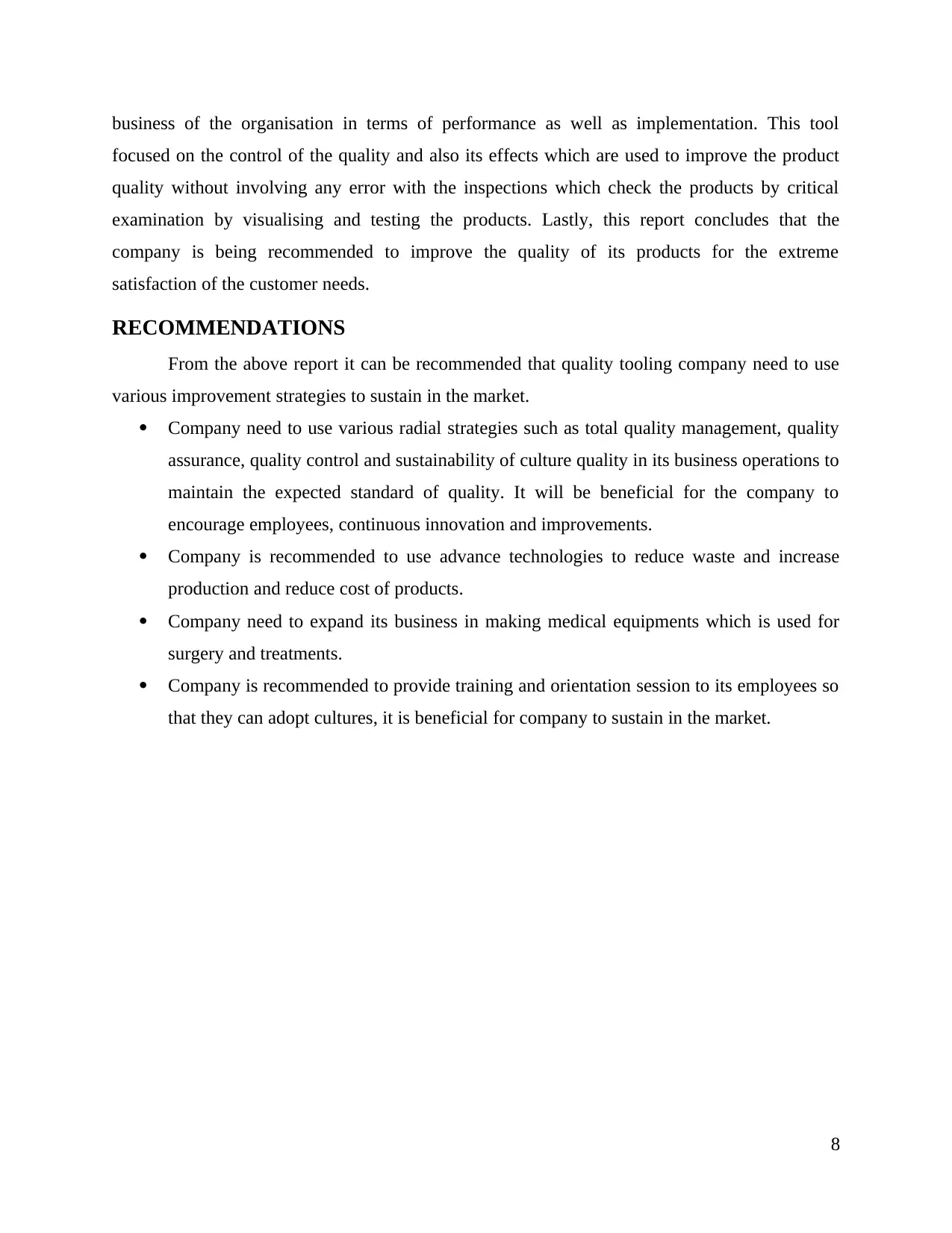
business of the organisation in terms of performance as well as implementation. This tool
focused on the control of the quality and also its effects which are used to improve the product
quality without involving any error with the inspections which check the products by critical
examination by visualising and testing the products. Lastly, this report concludes that the
company is being recommended to improve the quality of its products for the extreme
satisfaction of the customer needs.
RECOMMENDATIONS
From the above report it can be recommended that quality tooling company need to use
various improvement strategies to sustain in the market.
Company need to use various radial strategies such as total quality management, quality
assurance, quality control and sustainability of culture quality in its business operations to
maintain the expected standard of quality. It will be beneficial for the company to
encourage employees, continuous innovation and improvements.
Company is recommended to use advance technologies to reduce waste and increase
production and reduce cost of products.
Company need to expand its business in making medical equipments which is used for
surgery and treatments.
Company is recommended to provide training and orientation session to its employees so
that they can adopt cultures, it is beneficial for company to sustain in the market.
8
focused on the control of the quality and also its effects which are used to improve the product
quality without involving any error with the inspections which check the products by critical
examination by visualising and testing the products. Lastly, this report concludes that the
company is being recommended to improve the quality of its products for the extreme
satisfaction of the customer needs.
RECOMMENDATIONS
From the above report it can be recommended that quality tooling company need to use
various improvement strategies to sustain in the market.
Company need to use various radial strategies such as total quality management, quality
assurance, quality control and sustainability of culture quality in its business operations to
maintain the expected standard of quality. It will be beneficial for the company to
encourage employees, continuous innovation and improvements.
Company is recommended to use advance technologies to reduce waste and increase
production and reduce cost of products.
Company need to expand its business in making medical equipments which is used for
surgery and treatments.
Company is recommended to provide training and orientation session to its employees so
that they can adopt cultures, it is beneficial for company to sustain in the market.
8
Secure Best Marks with AI Grader
Need help grading? Try our AI Grader for instant feedback on your assignments.
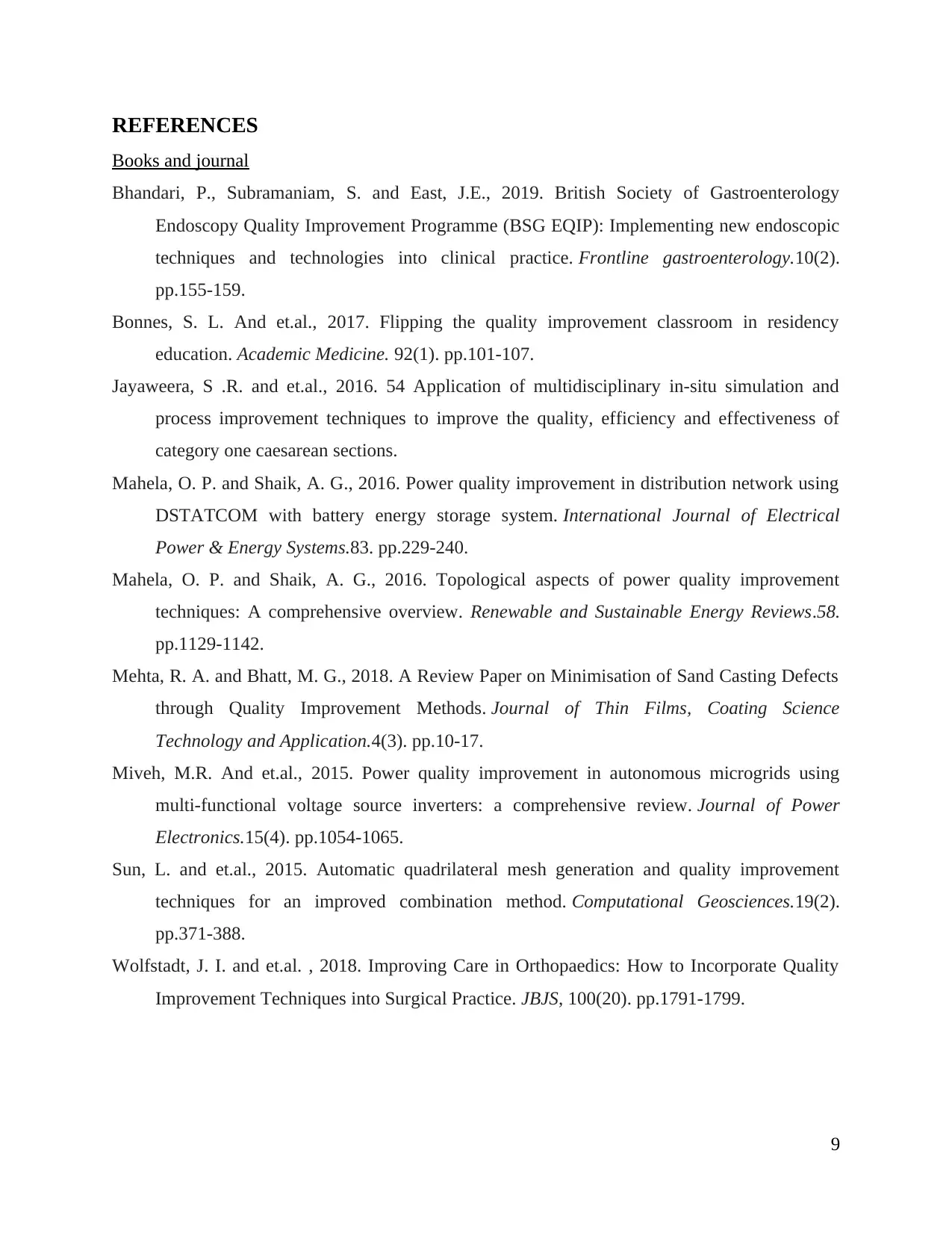
REFERENCES
Books and journal
Bhandari, P., Subramaniam, S. and East, J.E., 2019. British Society of Gastroenterology
Endoscopy Quality Improvement Programme (BSG EQIP): Implementing new endoscopic
techniques and technologies into clinical practice. Frontline gastroenterology.10(2).
pp.155-159.
Bonnes, S. L. And et.al., 2017. Flipping the quality improvement classroom in residency
education. Academic Medicine. 92(1). pp.101-107.
Jayaweera, S .R. and et.al., 2016. 54 Application of multidisciplinary in-situ simulation and
process improvement techniques to improve the quality, efficiency and effectiveness of
category one caesarean sections.
Mahela, O. P. and Shaik, A. G., 2016. Power quality improvement in distribution network using
DSTATCOM with battery energy storage system. International Journal of Electrical
Power & Energy Systems.83. pp.229-240.
Mahela, O. P. and Shaik, A. G., 2016. Topological aspects of power quality improvement
techniques: A comprehensive overview. Renewable and Sustainable Energy Reviews.58.
pp.1129-1142.
Mehta, R. A. and Bhatt, M. G., 2018. A Review Paper on Minimisation of Sand Casting Defects
through Quality Improvement Methods. Journal of Thin Films, Coating Science
Technology and Application.4(3). pp.10-17.
Miveh, M.R. And et.al., 2015. Power quality improvement in autonomous microgrids using
multi-functional voltage source inverters: a comprehensive review. Journal of Power
Electronics.15(4). pp.1054-1065.
Sun, L. and et.al., 2015. Automatic quadrilateral mesh generation and quality improvement
techniques for an improved combination method. Computational Geosciences.19(2).
pp.371-388.
Wolfstadt, J. I. and et.al. , 2018. Improving Care in Orthopaedics: How to Incorporate Quality
Improvement Techniques into Surgical Practice. JBJS, 100(20). pp.1791-1799.
9
Books and journal
Bhandari, P., Subramaniam, S. and East, J.E., 2019. British Society of Gastroenterology
Endoscopy Quality Improvement Programme (BSG EQIP): Implementing new endoscopic
techniques and technologies into clinical practice. Frontline gastroenterology.10(2).
pp.155-159.
Bonnes, S. L. And et.al., 2017. Flipping the quality improvement classroom in residency
education. Academic Medicine. 92(1). pp.101-107.
Jayaweera, S .R. and et.al., 2016. 54 Application of multidisciplinary in-situ simulation and
process improvement techniques to improve the quality, efficiency and effectiveness of
category one caesarean sections.
Mahela, O. P. and Shaik, A. G., 2016. Power quality improvement in distribution network using
DSTATCOM with battery energy storage system. International Journal of Electrical
Power & Energy Systems.83. pp.229-240.
Mahela, O. P. and Shaik, A. G., 2016. Topological aspects of power quality improvement
techniques: A comprehensive overview. Renewable and Sustainable Energy Reviews.58.
pp.1129-1142.
Mehta, R. A. and Bhatt, M. G., 2018. A Review Paper on Minimisation of Sand Casting Defects
through Quality Improvement Methods. Journal of Thin Films, Coating Science
Technology and Application.4(3). pp.10-17.
Miveh, M.R. And et.al., 2015. Power quality improvement in autonomous microgrids using
multi-functional voltage source inverters: a comprehensive review. Journal of Power
Electronics.15(4). pp.1054-1065.
Sun, L. and et.al., 2015. Automatic quadrilateral mesh generation and quality improvement
techniques for an improved combination method. Computational Geosciences.19(2).
pp.371-388.
Wolfstadt, J. I. and et.al. , 2018. Improving Care in Orthopaedics: How to Incorporate Quality
Improvement Techniques into Surgical Practice. JBJS, 100(20). pp.1791-1799.
9
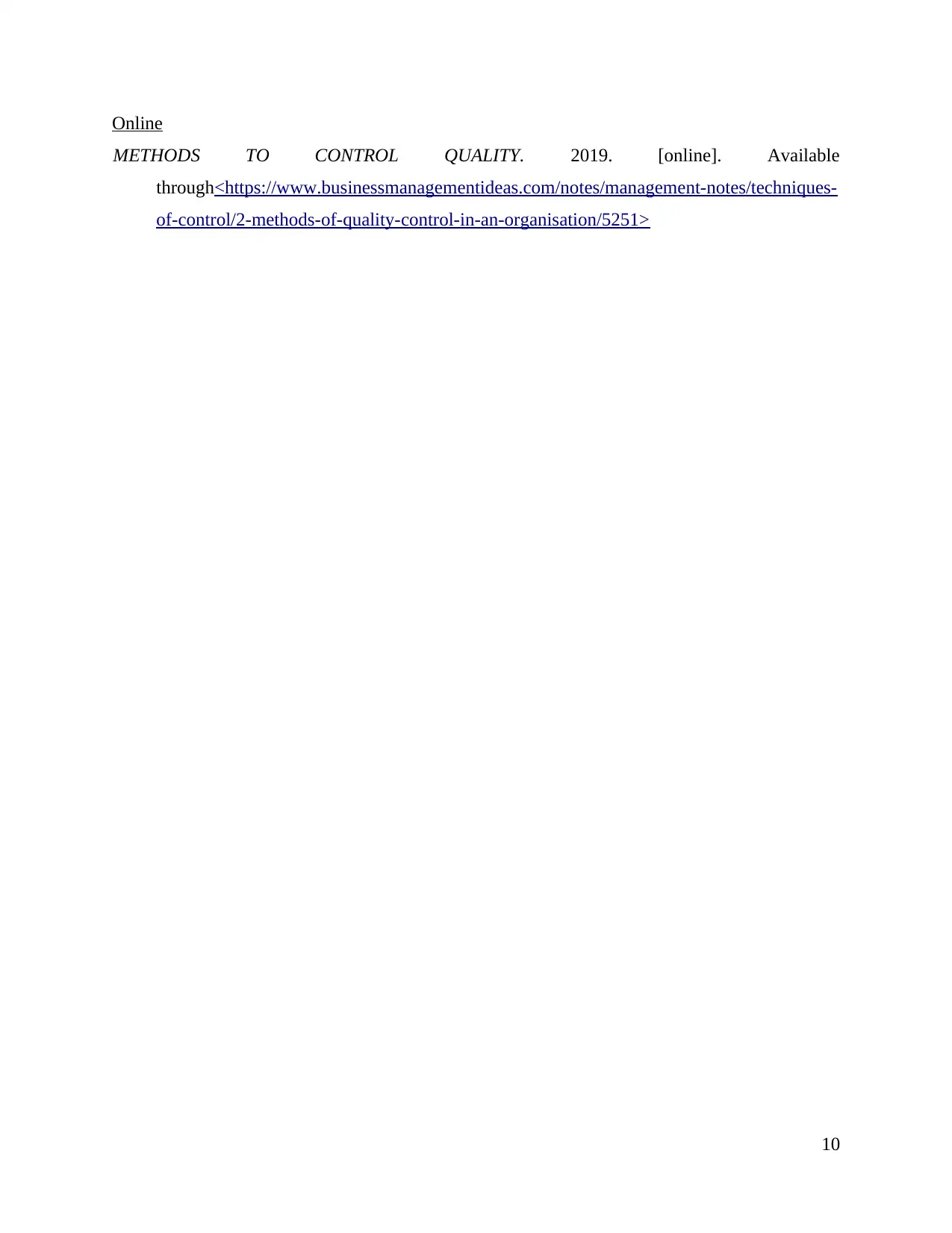
Online
METHODS TO CONTROL QUALITY. 2019. [online]. Available
through<https://www.businessmanagementideas.com/notes/management-notes/techniques-
of-control/2-methods-of-quality-control-in-an-organisation/5251>
10
METHODS TO CONTROL QUALITY. 2019. [online]. Available
through<https://www.businessmanagementideas.com/notes/management-notes/techniques-
of-control/2-methods-of-quality-control-in-an-organisation/5251>
10
1 out of 12
Related Documents

Your All-in-One AI-Powered Toolkit for Academic Success.
+13062052269
info@desklib.com
Available 24*7 on WhatsApp / Email
Unlock your academic potential
© 2024 | Zucol Services PVT LTD | All rights reserved.