Evaluation of Quality Manuals Application within SMEs: A Report
VerifiedAdded on 2021/04/24
|9
|2763
|44
Report
AI Summary
This report analyzes the role and application of quality management systems and quality manuals within Small and Medium-sized Enterprises (SMEs). It explores how SMEs can design products adhering to quality standards and approved quality management systems (QMS). The essay discusses the importance of QMS in documenting processes and procedures to achieve quality policies and objectives, aligning with organizational goals and strategic directions. It evaluates the application of quality manuals, including ISO 9000, and examines various quality management tools such as Six Sigma, Just-in-Time, Total Quality Management, benchmarking, design methods like Quality Function Deployment (QFD), Poka-Yoke, and world-class manufacturing. The report emphasizes how these methods affect product quality and manufacturing processes, and it highlights the benefits of implementing quality manuals for better service and product quality. The report also acknowledges challenges faced by SMEs in implementing quality programs and offers insights into how SMEs can leverage quality management tools to improve their business processes.
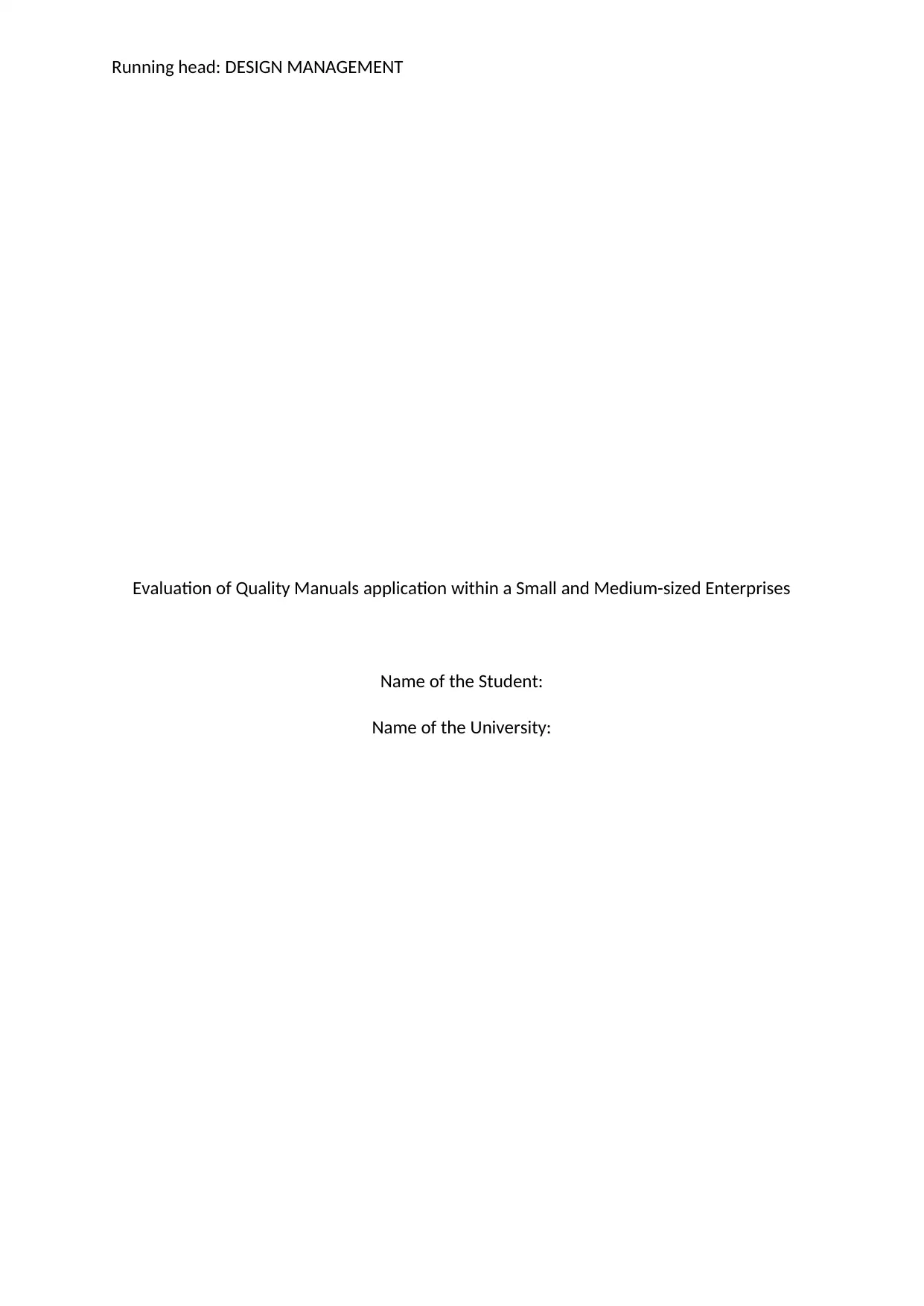
Running head: DESIGN MANAGEMENT
Evaluation of Quality Manuals application within a Small and Medium-sized Enterprises
Name of the Student:
Name of the University:
Evaluation of Quality Manuals application within a Small and Medium-sized Enterprises
Name of the Student:
Name of the University:
Paraphrase This Document
Need a fresh take? Get an instant paraphrase of this document with our AI Paraphraser
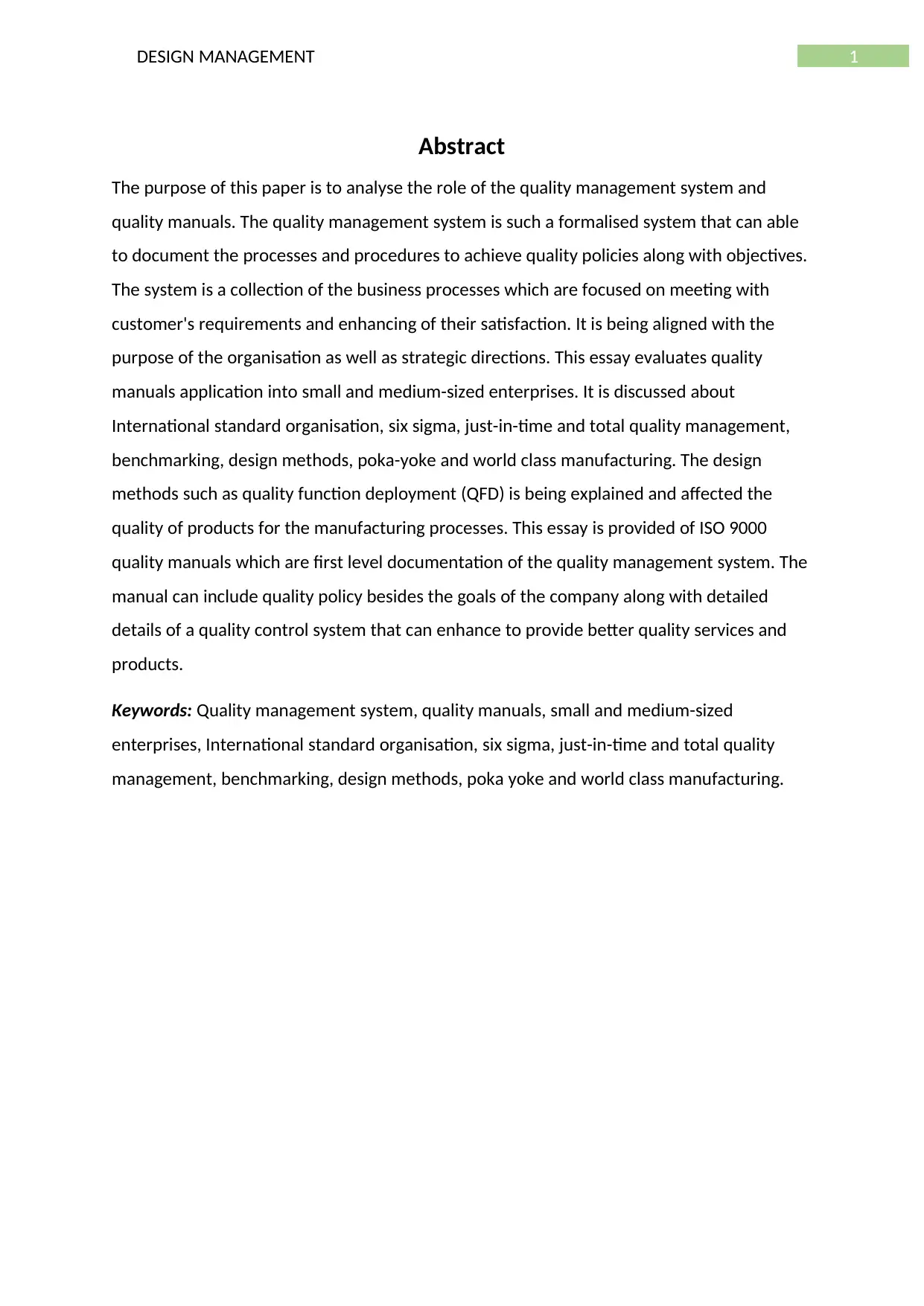
1DESIGN MANAGEMENT
Abstract
The purpose of this paper is to analyse the role of the quality management system and
quality manuals. The quality management system is such a formalised system that can able
to document the processes and procedures to achieve quality policies along with objectives.
The system is a collection of the business processes which are focused on meeting with
customer's requirements and enhancing of their satisfaction. It is being aligned with the
purpose of the organisation as well as strategic directions. This essay evaluates quality
manuals application into small and medium-sized enterprises. It is discussed about
International standard organisation, six sigma, just-in-time and total quality management,
benchmarking, design methods, poka-yoke and world class manufacturing. The design
methods such as quality function deployment (QFD) is being explained and affected the
quality of products for the manufacturing processes. This essay is provided of ISO 9000
quality manuals which are first level documentation of the quality management system. The
manual can include quality policy besides the goals of the company along with detailed
details of a quality control system that can enhance to provide better quality services and
products.
Keywords: Quality management system, quality manuals, small and medium-sized
enterprises, International standard organisation, six sigma, just-in-time and total quality
management, benchmarking, design methods, poka yoke and world class manufacturing.
Abstract
The purpose of this paper is to analyse the role of the quality management system and
quality manuals. The quality management system is such a formalised system that can able
to document the processes and procedures to achieve quality policies along with objectives.
The system is a collection of the business processes which are focused on meeting with
customer's requirements and enhancing of their satisfaction. It is being aligned with the
purpose of the organisation as well as strategic directions. This essay evaluates quality
manuals application into small and medium-sized enterprises. It is discussed about
International standard organisation, six sigma, just-in-time and total quality management,
benchmarking, design methods, poka-yoke and world class manufacturing. The design
methods such as quality function deployment (QFD) is being explained and affected the
quality of products for the manufacturing processes. This essay is provided of ISO 9000
quality manuals which are first level documentation of the quality management system. The
manual can include quality policy besides the goals of the company along with detailed
details of a quality control system that can enhance to provide better quality services and
products.
Keywords: Quality management system, quality manuals, small and medium-sized
enterprises, International standard organisation, six sigma, just-in-time and total quality
management, benchmarking, design methods, poka yoke and world class manufacturing.
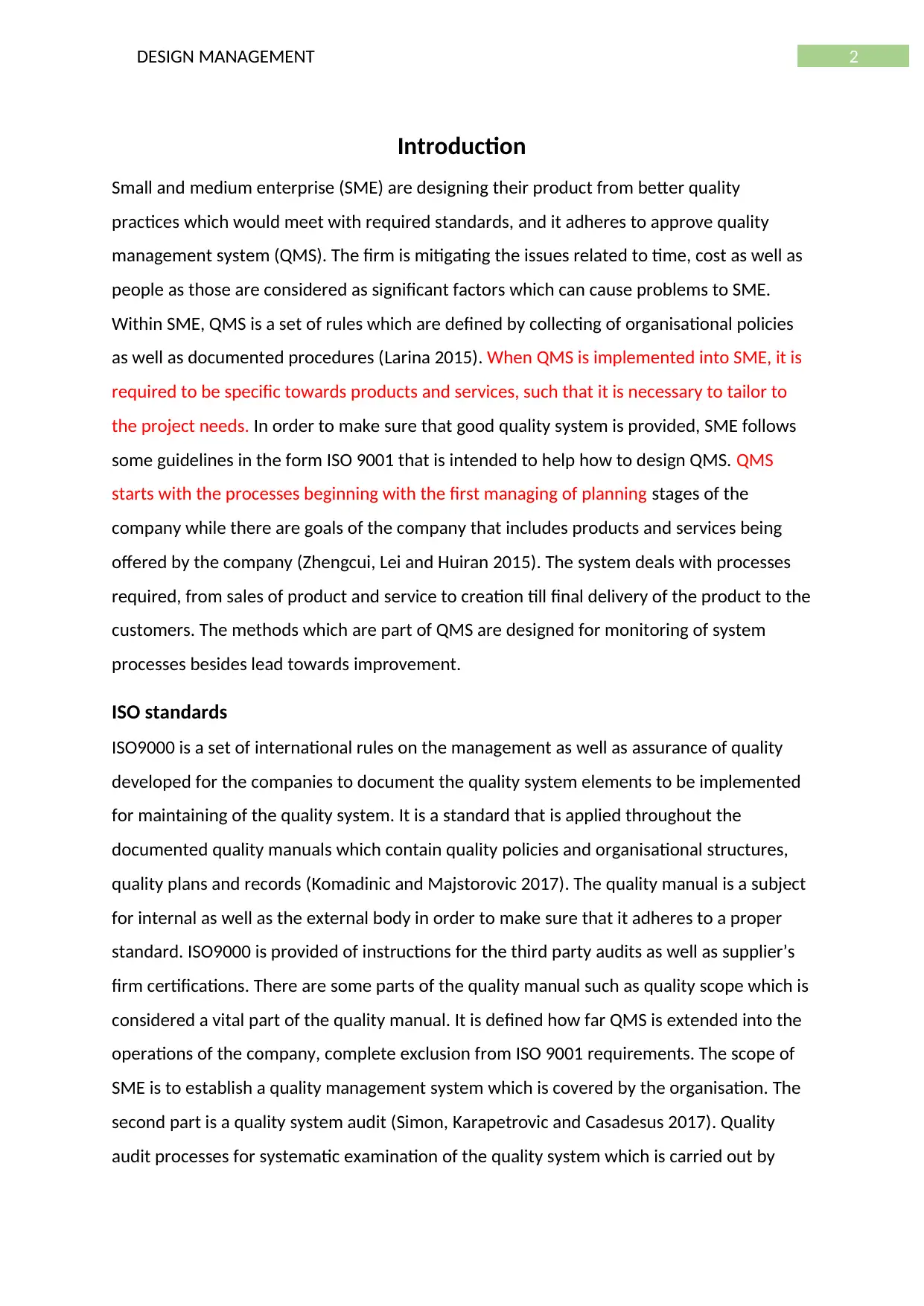
2DESIGN MANAGEMENT
Introduction
Small and medium enterprise (SME) are designing their product from better quality
practices which would meet with required standards, and it adheres to approve quality
management system (QMS). The firm is mitigating the issues related to time, cost as well as
people as those are considered as significant factors which can cause problems to SME.
Within SME, QMS is a set of rules which are defined by collecting of organisational policies
as well as documented procedures (Larina 2015). When QMS is implemented into SME, it is
required to be specific towards products and services, such that it is necessary to tailor to
the project needs. In order to make sure that good quality system is provided, SME follows
some guidelines in the form ISO 9001 that is intended to help how to design QMS. QMS
starts with the processes beginning with the first managing of planning stages of the
company while there are goals of the company that includes products and services being
offered by the company (Zhengcui, Lei and Huiran 2015). The system deals with processes
required, from sales of product and service to creation till final delivery of the product to the
customers. The methods which are part of QMS are designed for monitoring of system
processes besides lead towards improvement.
ISO standards
ISO9000 is a set of international rules on the management as well as assurance of quality
developed for the companies to document the quality system elements to be implemented
for maintaining of the quality system. It is a standard that is applied throughout the
documented quality manuals which contain quality policies and organisational structures,
quality plans and records (Komadinic and Majstorovic 2017). The quality manual is a subject
for internal as well as the external body in order to make sure that it adheres to a proper
standard. ISO9000 is provided of instructions for the third party audits as well as supplier’s
firm certifications. There are some parts of the quality manual such as quality scope which is
considered a vital part of the quality manual. It is defined how far QMS is extended into the
operations of the company, complete exclusion from ISO 9001 requirements. The scope of
SME is to establish a quality management system which is covered by the organisation. The
second part is a quality system audit (Simon, Karapetrovic and Casadesus 2017). Quality
audit processes for systematic examination of the quality system which is carried out by
Introduction
Small and medium enterprise (SME) are designing their product from better quality
practices which would meet with required standards, and it adheres to approve quality
management system (QMS). The firm is mitigating the issues related to time, cost as well as
people as those are considered as significant factors which can cause problems to SME.
Within SME, QMS is a set of rules which are defined by collecting of organisational policies
as well as documented procedures (Larina 2015). When QMS is implemented into SME, it is
required to be specific towards products and services, such that it is necessary to tailor to
the project needs. In order to make sure that good quality system is provided, SME follows
some guidelines in the form ISO 9001 that is intended to help how to design QMS. QMS
starts with the processes beginning with the first managing of planning stages of the
company while there are goals of the company that includes products and services being
offered by the company (Zhengcui, Lei and Huiran 2015). The system deals with processes
required, from sales of product and service to creation till final delivery of the product to the
customers. The methods which are part of QMS are designed for monitoring of system
processes besides lead towards improvement.
ISO standards
ISO9000 is a set of international rules on the management as well as assurance of quality
developed for the companies to document the quality system elements to be implemented
for maintaining of the quality system. It is a standard that is applied throughout the
documented quality manuals which contain quality policies and organisational structures,
quality plans and records (Komadinic and Majstorovic 2017). The quality manual is a subject
for internal as well as the external body in order to make sure that it adheres to a proper
standard. ISO9000 is provided of instructions for the third party audits as well as supplier’s
firm certifications. There are some parts of the quality manual such as quality scope which is
considered a vital part of the quality manual. It is defined how far QMS is extended into the
operations of the company, complete exclusion from ISO 9001 requirements. The scope of
SME is to establish a quality management system which is covered by the organisation. The
second part is a quality system audit (Simon, Karapetrovic and Casadesus 2017). Quality
audit processes for systematic examination of the quality system which is carried out by
⊘ This is a preview!⊘
Do you want full access?
Subscribe today to unlock all pages.

Trusted by 1+ million students worldwide
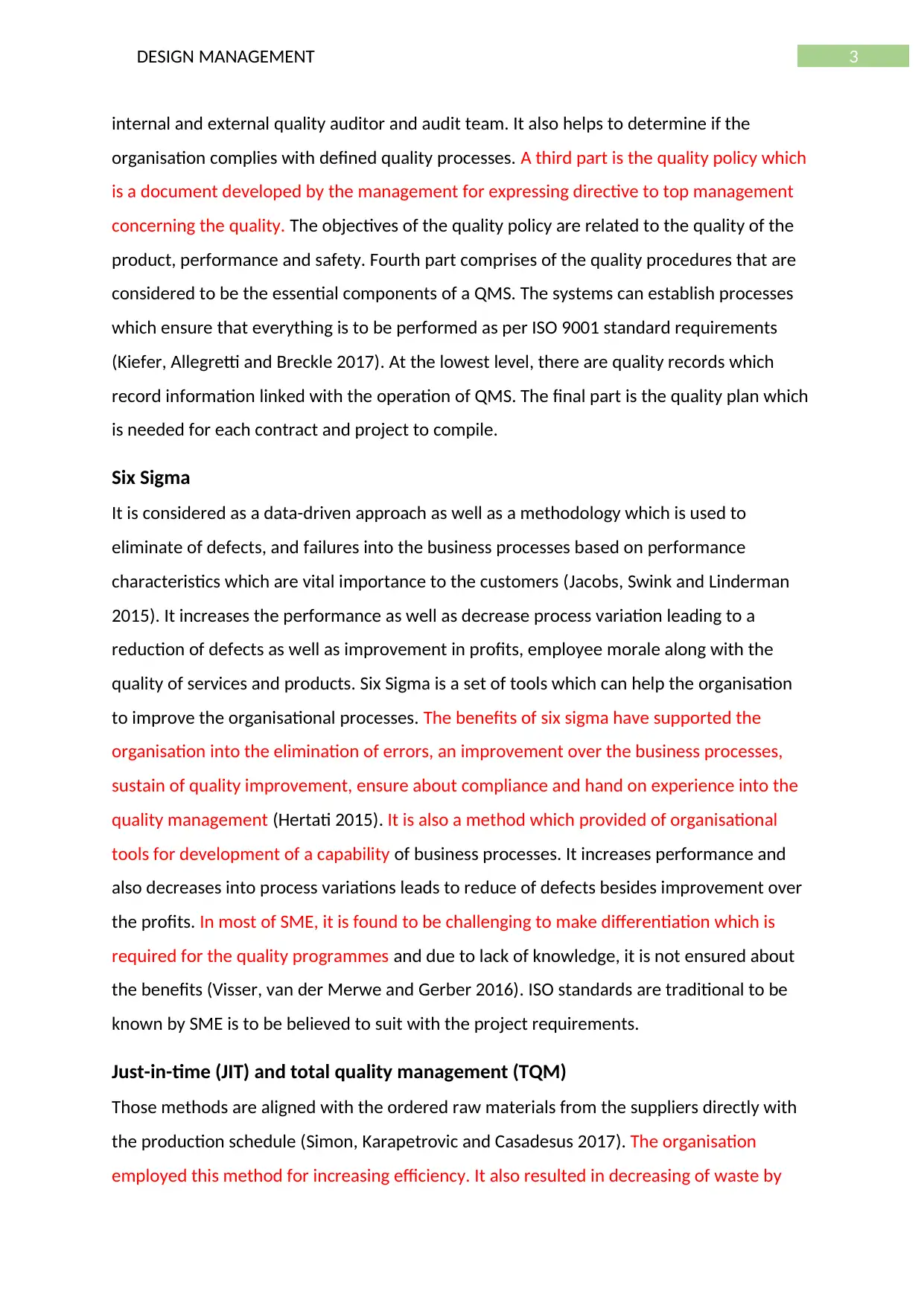
3DESIGN MANAGEMENT
internal and external quality auditor and audit team. It also helps to determine if the
organisation complies with defined quality processes. A third part is the quality policy which
is a document developed by the management for expressing directive to top management
concerning the quality. The objectives of the quality policy are related to the quality of the
product, performance and safety. Fourth part comprises of the quality procedures that are
considered to be the essential components of a QMS. The systems can establish processes
which ensure that everything is to be performed as per ISO 9001 standard requirements
(Kiefer, Allegretti and Breckle 2017). At the lowest level, there are quality records which
record information linked with the operation of QMS. The final part is the quality plan which
is needed for each contract and project to compile.
Six Sigma
It is considered as a data-driven approach as well as a methodology which is used to
eliminate of defects, and failures into the business processes based on performance
characteristics which are vital importance to the customers (Jacobs, Swink and Linderman
2015). It increases the performance as well as decrease process variation leading to a
reduction of defects as well as improvement in profits, employee morale along with the
quality of services and products. Six Sigma is a set of tools which can help the organisation
to improve the organisational processes. The benefits of six sigma have supported the
organisation into the elimination of errors, an improvement over the business processes,
sustain of quality improvement, ensure about compliance and hand on experience into the
quality management (Hertati 2015). It is also a method which provided of organisational
tools for development of a capability of business processes. It increases performance and
also decreases into process variations leads to reduce of defects besides improvement over
the profits. In most of SME, it is found to be challenging to make differentiation which is
required for the quality programmes and due to lack of knowledge, it is not ensured about
the benefits (Visser, van der Merwe and Gerber 2016). ISO standards are traditional to be
known by SME is to be believed to suit with the project requirements.
Just-in-time (JIT) and total quality management (TQM)
Those methods are aligned with the ordered raw materials from the suppliers directly with
the production schedule (Simon, Karapetrovic and Casadesus 2017). The organisation
employed this method for increasing efficiency. It also resulted in decreasing of waste by
internal and external quality auditor and audit team. It also helps to determine if the
organisation complies with defined quality processes. A third part is the quality policy which
is a document developed by the management for expressing directive to top management
concerning the quality. The objectives of the quality policy are related to the quality of the
product, performance and safety. Fourth part comprises of the quality procedures that are
considered to be the essential components of a QMS. The systems can establish processes
which ensure that everything is to be performed as per ISO 9001 standard requirements
(Kiefer, Allegretti and Breckle 2017). At the lowest level, there are quality records which
record information linked with the operation of QMS. The final part is the quality plan which
is needed for each contract and project to compile.
Six Sigma
It is considered as a data-driven approach as well as a methodology which is used to
eliminate of defects, and failures into the business processes based on performance
characteristics which are vital importance to the customers (Jacobs, Swink and Linderman
2015). It increases the performance as well as decrease process variation leading to a
reduction of defects as well as improvement in profits, employee morale along with the
quality of services and products. Six Sigma is a set of tools which can help the organisation
to improve the organisational processes. The benefits of six sigma have supported the
organisation into the elimination of errors, an improvement over the business processes,
sustain of quality improvement, ensure about compliance and hand on experience into the
quality management (Hertati 2015). It is also a method which provided of organisational
tools for development of a capability of business processes. It increases performance and
also decreases into process variations leads to reduce of defects besides improvement over
the profits. In most of SME, it is found to be challenging to make differentiation which is
required for the quality programmes and due to lack of knowledge, it is not ensured about
the benefits (Visser, van der Merwe and Gerber 2016). ISO standards are traditional to be
known by SME is to be believed to suit with the project requirements.
Just-in-time (JIT) and total quality management (TQM)
Those methods are aligned with the ordered raw materials from the suppliers directly with
the production schedule (Simon, Karapetrovic and Casadesus 2017). The organisation
employed this method for increasing efficiency. It also resulted in decreasing of waste by
Paraphrase This Document
Need a fresh take? Get an instant paraphrase of this document with our AI Paraphraser
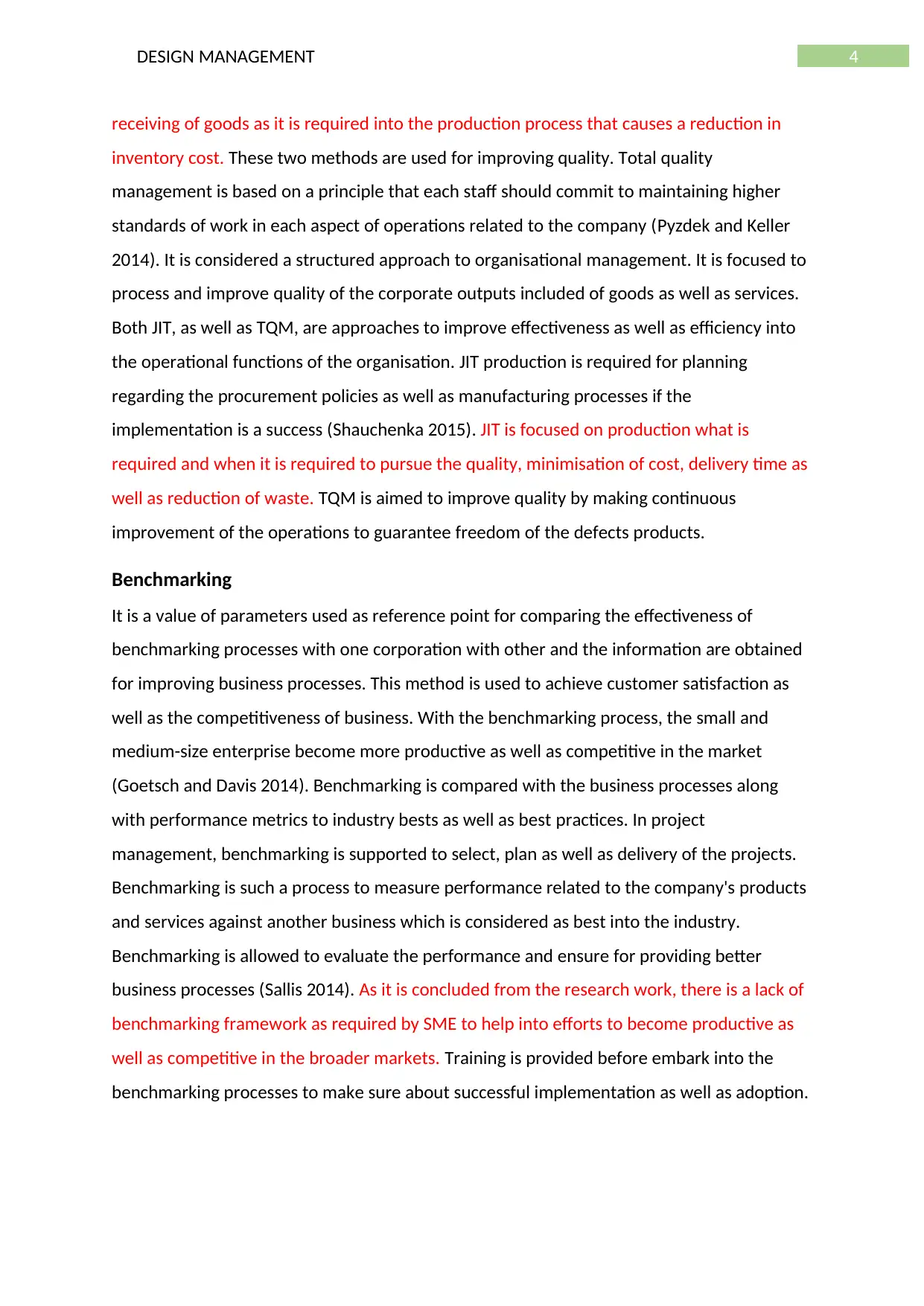
4DESIGN MANAGEMENT
receiving of goods as it is required into the production process that causes a reduction in
inventory cost. These two methods are used for improving quality. Total quality
management is based on a principle that each staff should commit to maintaining higher
standards of work in each aspect of operations related to the company (Pyzdek and Keller
2014). It is considered a structured approach to organisational management. It is focused to
process and improve quality of the corporate outputs included of goods as well as services.
Both JIT, as well as TQM, are approaches to improve effectiveness as well as efficiency into
the operational functions of the organisation. JIT production is required for planning
regarding the procurement policies as well as manufacturing processes if the
implementation is a success (Shauchenka 2015). JIT is focused on production what is
required and when it is required to pursue the quality, minimisation of cost, delivery time as
well as reduction of waste. TQM is aimed to improve quality by making continuous
improvement of the operations to guarantee freedom of the defects products.
Benchmarking
It is a value of parameters used as reference point for comparing the effectiveness of
benchmarking processes with one corporation with other and the information are obtained
for improving business processes. This method is used to achieve customer satisfaction as
well as the competitiveness of business. With the benchmarking process, the small and
medium-size enterprise become more productive as well as competitive in the market
(Goetsch and Davis 2014). Benchmarking is compared with the business processes along
with performance metrics to industry bests as well as best practices. In project
management, benchmarking is supported to select, plan as well as delivery of the projects.
Benchmarking is such a process to measure performance related to the company's products
and services against another business which is considered as best into the industry.
Benchmarking is allowed to evaluate the performance and ensure for providing better
business processes (Sallis 2014). As it is concluded from the research work, there is a lack of
benchmarking framework as required by SME to help into efforts to become productive as
well as competitive in the broader markets. Training is provided before embark into the
benchmarking processes to make sure about successful implementation as well as adoption.
receiving of goods as it is required into the production process that causes a reduction in
inventory cost. These two methods are used for improving quality. Total quality
management is based on a principle that each staff should commit to maintaining higher
standards of work in each aspect of operations related to the company (Pyzdek and Keller
2014). It is considered a structured approach to organisational management. It is focused to
process and improve quality of the corporate outputs included of goods as well as services.
Both JIT, as well as TQM, are approaches to improve effectiveness as well as efficiency into
the operational functions of the organisation. JIT production is required for planning
regarding the procurement policies as well as manufacturing processes if the
implementation is a success (Shauchenka 2015). JIT is focused on production what is
required and when it is required to pursue the quality, minimisation of cost, delivery time as
well as reduction of waste. TQM is aimed to improve quality by making continuous
improvement of the operations to guarantee freedom of the defects products.
Benchmarking
It is a value of parameters used as reference point for comparing the effectiveness of
benchmarking processes with one corporation with other and the information are obtained
for improving business processes. This method is used to achieve customer satisfaction as
well as the competitiveness of business. With the benchmarking process, the small and
medium-size enterprise become more productive as well as competitive in the market
(Goetsch and Davis 2014). Benchmarking is compared with the business processes along
with performance metrics to industry bests as well as best practices. In project
management, benchmarking is supported to select, plan as well as delivery of the projects.
Benchmarking is such a process to measure performance related to the company's products
and services against another business which is considered as best into the industry.
Benchmarking is allowed to evaluate the performance and ensure for providing better
business processes (Sallis 2014). As it is concluded from the research work, there is a lack of
benchmarking framework as required by SME to help into efforts to become productive as
well as competitive in the broader markets. Training is provided before embark into the
benchmarking processes to make sure about successful implementation as well as adoption.
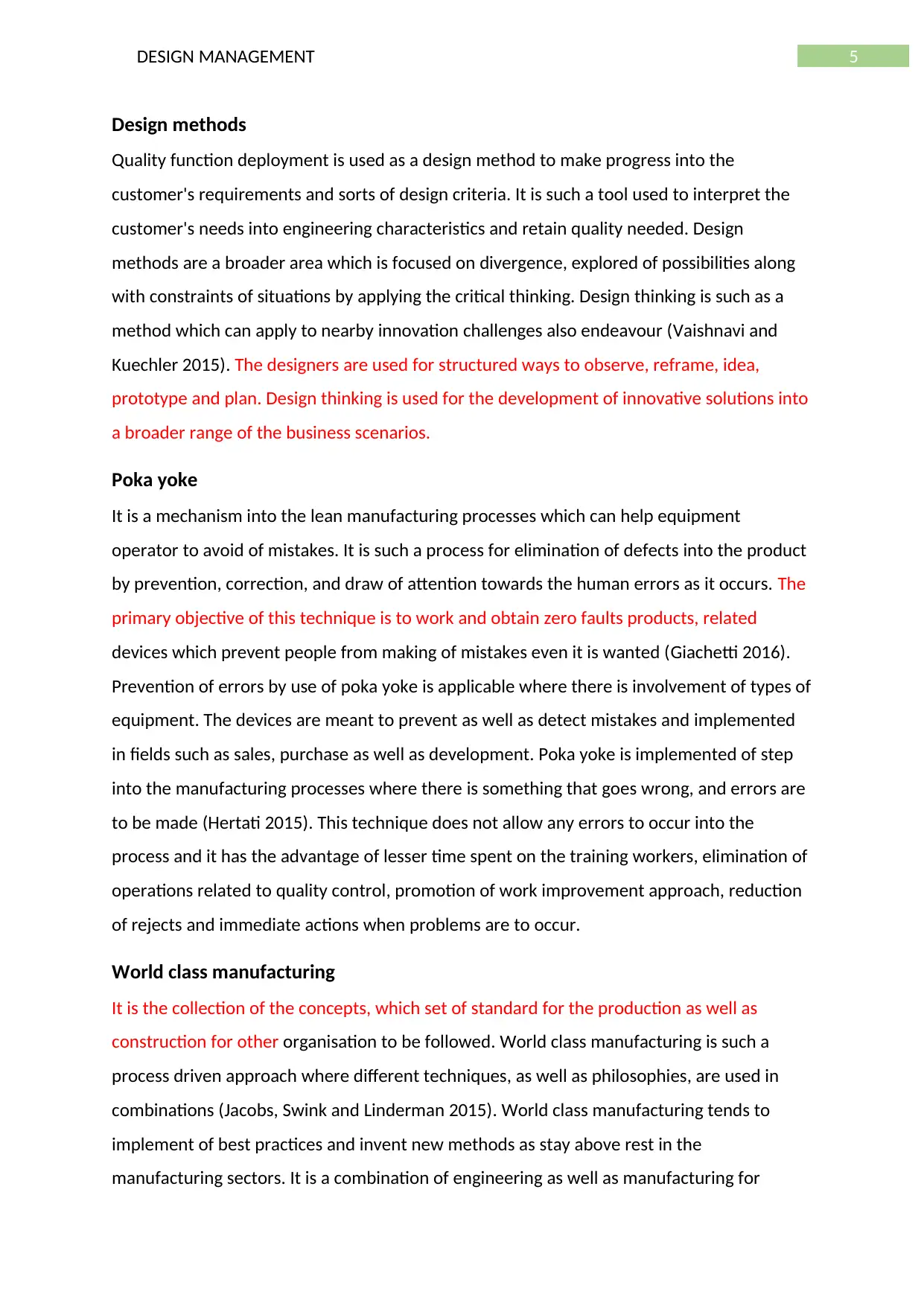
5DESIGN MANAGEMENT
Design methods
Quality function deployment is used as a design method to make progress into the
customer's requirements and sorts of design criteria. It is such a tool used to interpret the
customer's needs into engineering characteristics and retain quality needed. Design
methods are a broader area which is focused on divergence, explored of possibilities along
with constraints of situations by applying the critical thinking. Design thinking is such as a
method which can apply to nearby innovation challenges also endeavour (Vaishnavi and
Kuechler 2015). The designers are used for structured ways to observe, reframe, idea,
prototype and plan. Design thinking is used for the development of innovative solutions into
a broader range of the business scenarios.
Poka yoke
It is a mechanism into the lean manufacturing processes which can help equipment
operator to avoid of mistakes. It is such a process for elimination of defects into the product
by prevention, correction, and draw of attention towards the human errors as it occurs. The
primary objective of this technique is to work and obtain zero faults products, related
devices which prevent people from making of mistakes even it is wanted (Giachetti 2016).
Prevention of errors by use of poka yoke is applicable where there is involvement of types of
equipment. The devices are meant to prevent as well as detect mistakes and implemented
in fields such as sales, purchase as well as development. Poka yoke is implemented of step
into the manufacturing processes where there is something that goes wrong, and errors are
to be made (Hertati 2015). This technique does not allow any errors to occur into the
process and it has the advantage of lesser time spent on the training workers, elimination of
operations related to quality control, promotion of work improvement approach, reduction
of rejects and immediate actions when problems are to occur.
World class manufacturing
It is the collection of the concepts, which set of standard for the production as well as
construction for other organisation to be followed. World class manufacturing is such a
process driven approach where different techniques, as well as philosophies, are used in
combinations (Jacobs, Swink and Linderman 2015). World class manufacturing tends to
implement of best practices and invent new methods as stay above rest in the
manufacturing sectors. It is a combination of engineering as well as manufacturing for
Design methods
Quality function deployment is used as a design method to make progress into the
customer's requirements and sorts of design criteria. It is such a tool used to interpret the
customer's needs into engineering characteristics and retain quality needed. Design
methods are a broader area which is focused on divergence, explored of possibilities along
with constraints of situations by applying the critical thinking. Design thinking is such as a
method which can apply to nearby innovation challenges also endeavour (Vaishnavi and
Kuechler 2015). The designers are used for structured ways to observe, reframe, idea,
prototype and plan. Design thinking is used for the development of innovative solutions into
a broader range of the business scenarios.
Poka yoke
It is a mechanism into the lean manufacturing processes which can help equipment
operator to avoid of mistakes. It is such a process for elimination of defects into the product
by prevention, correction, and draw of attention towards the human errors as it occurs. The
primary objective of this technique is to work and obtain zero faults products, related
devices which prevent people from making of mistakes even it is wanted (Giachetti 2016).
Prevention of errors by use of poka yoke is applicable where there is involvement of types of
equipment. The devices are meant to prevent as well as detect mistakes and implemented
in fields such as sales, purchase as well as development. Poka yoke is implemented of step
into the manufacturing processes where there is something that goes wrong, and errors are
to be made (Hertati 2015). This technique does not allow any errors to occur into the
process and it has the advantage of lesser time spent on the training workers, elimination of
operations related to quality control, promotion of work improvement approach, reduction
of rejects and immediate actions when problems are to occur.
World class manufacturing
It is the collection of the concepts, which set of standard for the production as well as
construction for other organisation to be followed. World class manufacturing is such a
process driven approach where different techniques, as well as philosophies, are used in
combinations (Jacobs, Swink and Linderman 2015). World class manufacturing tends to
implement of best practices and invent new methods as stay above rest in the
manufacturing sectors. It is a combination of engineering as well as manufacturing for
⊘ This is a preview!⊘
Do you want full access?
Subscribe today to unlock all pages.

Trusted by 1+ million students worldwide
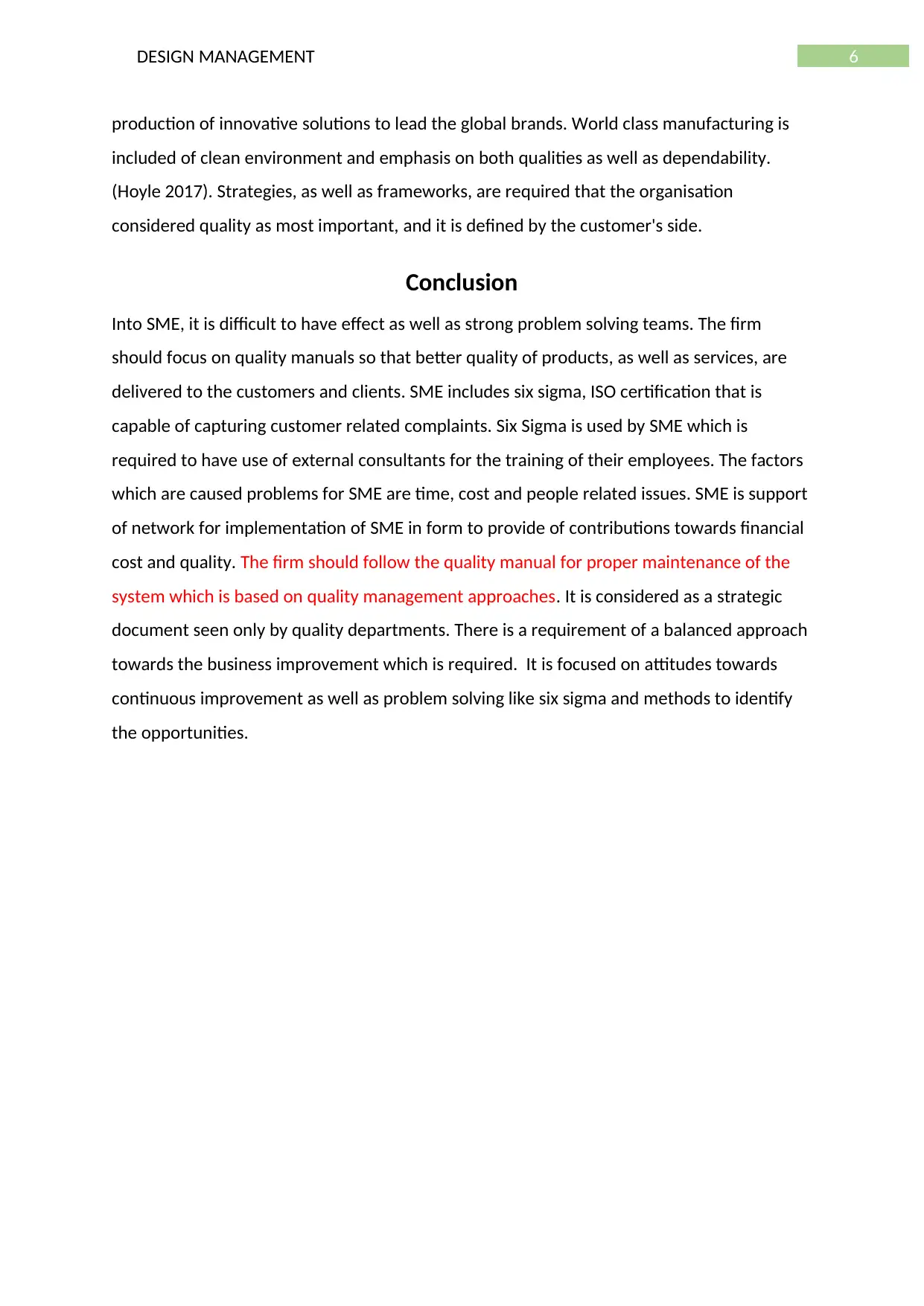
6DESIGN MANAGEMENT
production of innovative solutions to lead the global brands. World class manufacturing is
included of clean environment and emphasis on both qualities as well as dependability.
(Hoyle 2017). Strategies, as well as frameworks, are required that the organisation
considered quality as most important, and it is defined by the customer's side.
Conclusion
Into SME, it is difficult to have effect as well as strong problem solving teams. The firm
should focus on quality manuals so that better quality of products, as well as services, are
delivered to the customers and clients. SME includes six sigma, ISO certification that is
capable of capturing customer related complaints. Six Sigma is used by SME which is
required to have use of external consultants for the training of their employees. The factors
which are caused problems for SME are time, cost and people related issues. SME is support
of network for implementation of SME in form to provide of contributions towards financial
cost and quality. The firm should follow the quality manual for proper maintenance of the
system which is based on quality management approaches. It is considered as a strategic
document seen only by quality departments. There is a requirement of a balanced approach
towards the business improvement which is required. It is focused on attitudes towards
continuous improvement as well as problem solving like six sigma and methods to identify
the opportunities.
production of innovative solutions to lead the global brands. World class manufacturing is
included of clean environment and emphasis on both qualities as well as dependability.
(Hoyle 2017). Strategies, as well as frameworks, are required that the organisation
considered quality as most important, and it is defined by the customer's side.
Conclusion
Into SME, it is difficult to have effect as well as strong problem solving teams. The firm
should focus on quality manuals so that better quality of products, as well as services, are
delivered to the customers and clients. SME includes six sigma, ISO certification that is
capable of capturing customer related complaints. Six Sigma is used by SME which is
required to have use of external consultants for the training of their employees. The factors
which are caused problems for SME are time, cost and people related issues. SME is support
of network for implementation of SME in form to provide of contributions towards financial
cost and quality. The firm should follow the quality manual for proper maintenance of the
system which is based on quality management approaches. It is considered as a strategic
document seen only by quality departments. There is a requirement of a balanced approach
towards the business improvement which is required. It is focused on attitudes towards
continuous improvement as well as problem solving like six sigma and methods to identify
the opportunities.
Paraphrase This Document
Need a fresh take? Get an instant paraphrase of this document with our AI Paraphraser
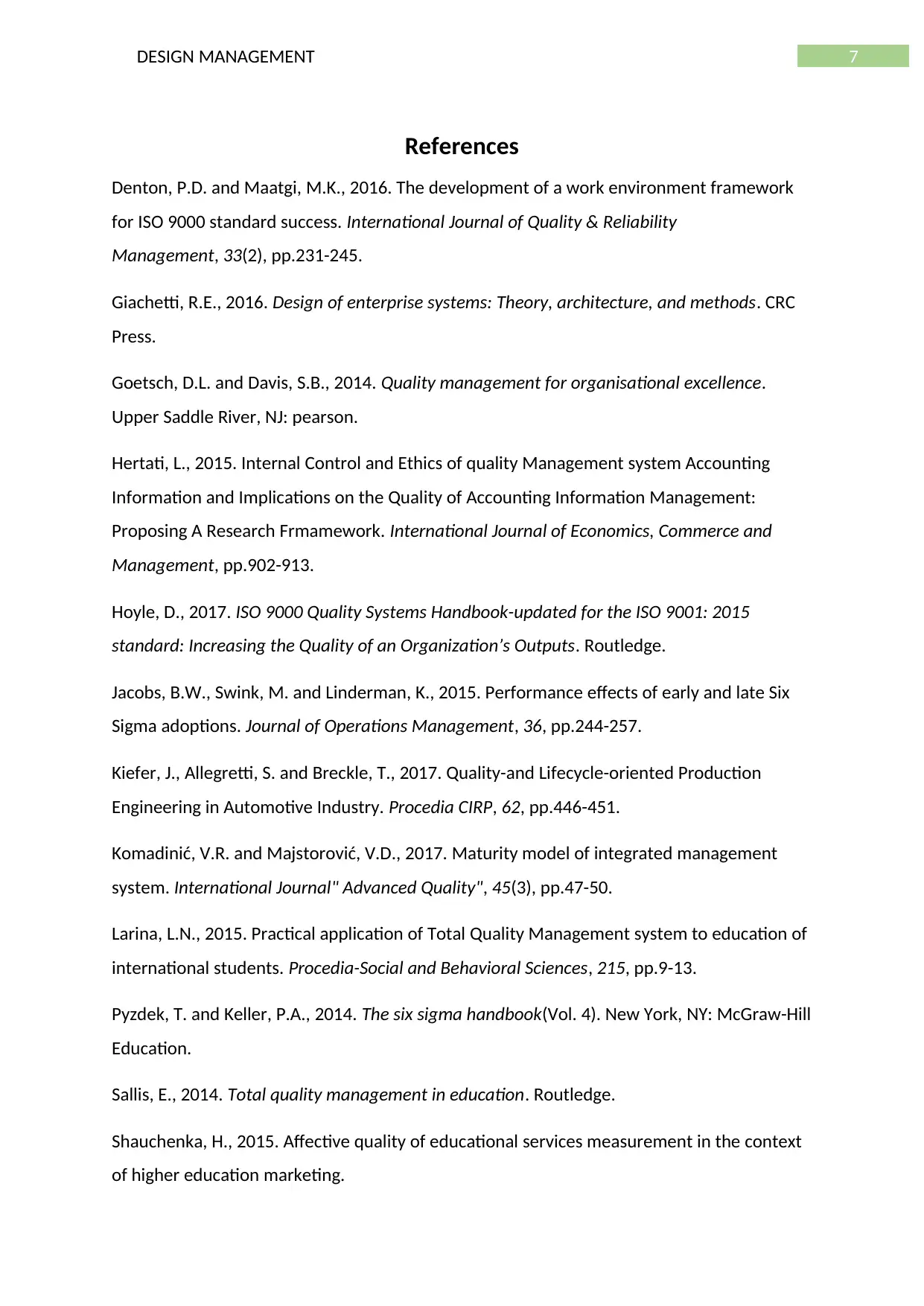
7DESIGN MANAGEMENT
References
Denton, P.D. and Maatgi, M.K., 2016. The development of a work environment framework
for ISO 9000 standard success. International Journal of Quality & Reliability
Management, 33(2), pp.231-245.
Giachetti, R.E., 2016. Design of enterprise systems: Theory, architecture, and methods. CRC
Press.
Goetsch, D.L. and Davis, S.B., 2014. Quality management for organisational excellence.
Upper Saddle River, NJ: pearson.
Hertati, L., 2015. Internal Control and Ethics of quality Management system Accounting
Information and Implications on the Quality of Accounting Information Management:
Proposing A Research Frmamework. International Journal of Economics, Commerce and
Management, pp.902-913.
Hoyle, D., 2017. ISO 9000 Quality Systems Handbook-updated for the ISO 9001: 2015
standard: Increasing the Quality of an Organization’s Outputs. Routledge.
Jacobs, B.W., Swink, M. and Linderman, K., 2015. Performance effects of early and late Six
Sigma adoptions. Journal of Operations Management, 36, pp.244-257.
Kiefer, J., Allegretti, S. and Breckle, T., 2017. Quality-and Lifecycle-oriented Production
Engineering in Automotive Industry. Procedia CIRP, 62, pp.446-451.
Komadinić, V.R. and Majstorović, V.D., 2017. Maturity model of integrated management
system. International Journal" Advanced Quality", 45(3), pp.47-50.
Larina, L.N., 2015. Practical application of Total Quality Management system to education of
international students. Procedia-Social and Behavioral Sciences, 215, pp.9-13.
Pyzdek, T. and Keller, P.A., 2014. The six sigma handbook(Vol. 4). New York, NY: McGraw-Hill
Education.
Sallis, E., 2014. Total quality management in education. Routledge.
Shauchenka, H., 2015. Affective quality of educational services measurement in the context
of higher education marketing.
References
Denton, P.D. and Maatgi, M.K., 2016. The development of a work environment framework
for ISO 9000 standard success. International Journal of Quality & Reliability
Management, 33(2), pp.231-245.
Giachetti, R.E., 2016. Design of enterprise systems: Theory, architecture, and methods. CRC
Press.
Goetsch, D.L. and Davis, S.B., 2014. Quality management for organisational excellence.
Upper Saddle River, NJ: pearson.
Hertati, L., 2015. Internal Control and Ethics of quality Management system Accounting
Information and Implications on the Quality of Accounting Information Management:
Proposing A Research Frmamework. International Journal of Economics, Commerce and
Management, pp.902-913.
Hoyle, D., 2017. ISO 9000 Quality Systems Handbook-updated for the ISO 9001: 2015
standard: Increasing the Quality of an Organization’s Outputs. Routledge.
Jacobs, B.W., Swink, M. and Linderman, K., 2015. Performance effects of early and late Six
Sigma adoptions. Journal of Operations Management, 36, pp.244-257.
Kiefer, J., Allegretti, S. and Breckle, T., 2017. Quality-and Lifecycle-oriented Production
Engineering in Automotive Industry. Procedia CIRP, 62, pp.446-451.
Komadinić, V.R. and Majstorović, V.D., 2017. Maturity model of integrated management
system. International Journal" Advanced Quality", 45(3), pp.47-50.
Larina, L.N., 2015. Practical application of Total Quality Management system to education of
international students. Procedia-Social and Behavioral Sciences, 215, pp.9-13.
Pyzdek, T. and Keller, P.A., 2014. The six sigma handbook(Vol. 4). New York, NY: McGraw-Hill
Education.
Sallis, E., 2014. Total quality management in education. Routledge.
Shauchenka, H., 2015. Affective quality of educational services measurement in the context
of higher education marketing.
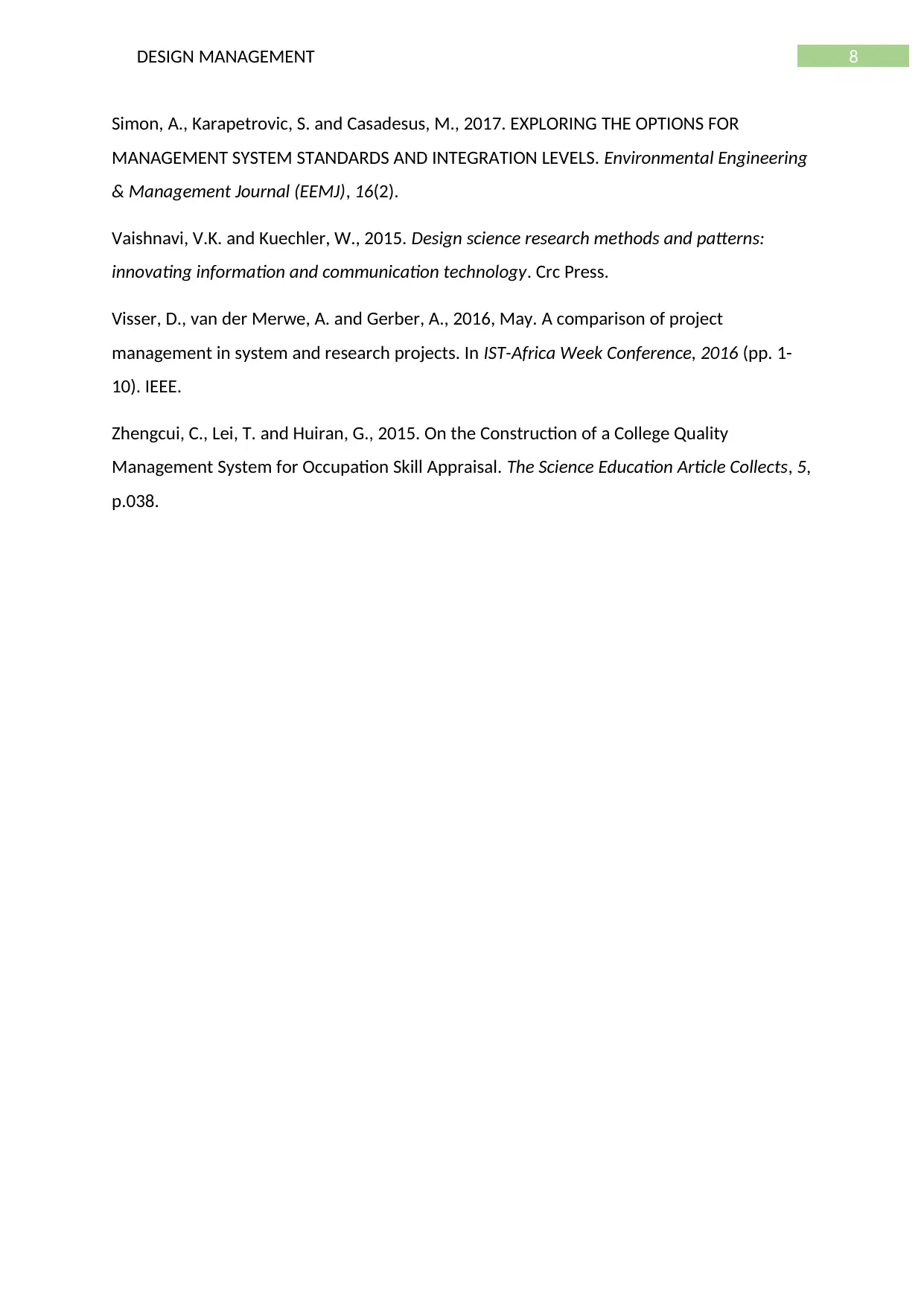
8DESIGN MANAGEMENT
Simon, A., Karapetrovic, S. and Casadesus, M., 2017. EXPLORING THE OPTIONS FOR
MANAGEMENT SYSTEM STANDARDS AND INTEGRATION LEVELS. Environmental Engineering
& Management Journal (EEMJ), 16(2).
Vaishnavi, V.K. and Kuechler, W., 2015. Design science research methods and patterns:
innovating information and communication technology. Crc Press.
Visser, D., van der Merwe, A. and Gerber, A., 2016, May. A comparison of project
management in system and research projects. In IST-Africa Week Conference, 2016 (pp. 1-
10). IEEE.
Zhengcui, C., Lei, T. and Huiran, G., 2015. On the Construction of a College Quality
Management System for Occupation Skill Appraisal. The Science Education Article Collects, 5,
p.038.
Simon, A., Karapetrovic, S. and Casadesus, M., 2017. EXPLORING THE OPTIONS FOR
MANAGEMENT SYSTEM STANDARDS AND INTEGRATION LEVELS. Environmental Engineering
& Management Journal (EEMJ), 16(2).
Vaishnavi, V.K. and Kuechler, W., 2015. Design science research methods and patterns:
innovating information and communication technology. Crc Press.
Visser, D., van der Merwe, A. and Gerber, A., 2016, May. A comparison of project
management in system and research projects. In IST-Africa Week Conference, 2016 (pp. 1-
10). IEEE.
Zhengcui, C., Lei, T. and Huiran, G., 2015. On the Construction of a College Quality
Management System for Occupation Skill Appraisal. The Science Education Article Collects, 5,
p.038.
⊘ This is a preview!⊘
Do you want full access?
Subscribe today to unlock all pages.

Trusted by 1+ million students worldwide
1 out of 9
Related Documents

Your All-in-One AI-Powered Toolkit for Academic Success.
+13062052269
info@desklib.com
Available 24*7 on WhatsApp / Email
Unlock your academic potential
© 2024 | Zucol Services PVT LTD | All rights reserved.