UGB262 Quality Management for Organisational Excellence Report
VerifiedAdded on 2023/01/12
|11
|3629
|63
Report
AI Summary
This report provides a comprehensive analysis of quality management principles, tools, and techniques, focusing on their application within a manufacturing company, Quality Tooling Company (QTC). The report explores the importance of quality in meeting customer needs and achieving organizational excellence, discussing key concepts such as Total Quality Management (TQM), Quality Assurance (QA), and Quality Control (QC). It examines seven quality management principles, including customer focus, employee engagement, and continuous improvement. The report delves into the practical implementation of TQM, QA, and QC methods, such as the PDCA cycle, failure testing, statistical process control, and ISO 9000 certification. Furthermore, the report provides recommendations for QTC to sustain a high-quality culture, emphasizing the integration of these tools and strategies to improve product precision, customer satisfaction, and overall business performance. The report concludes by highlighting the significance of quality management in achieving a competitive advantage and sustaining long-term success.
Contribute Materials
Your contribution can guide someone’s learning journey. Share your
documents today.
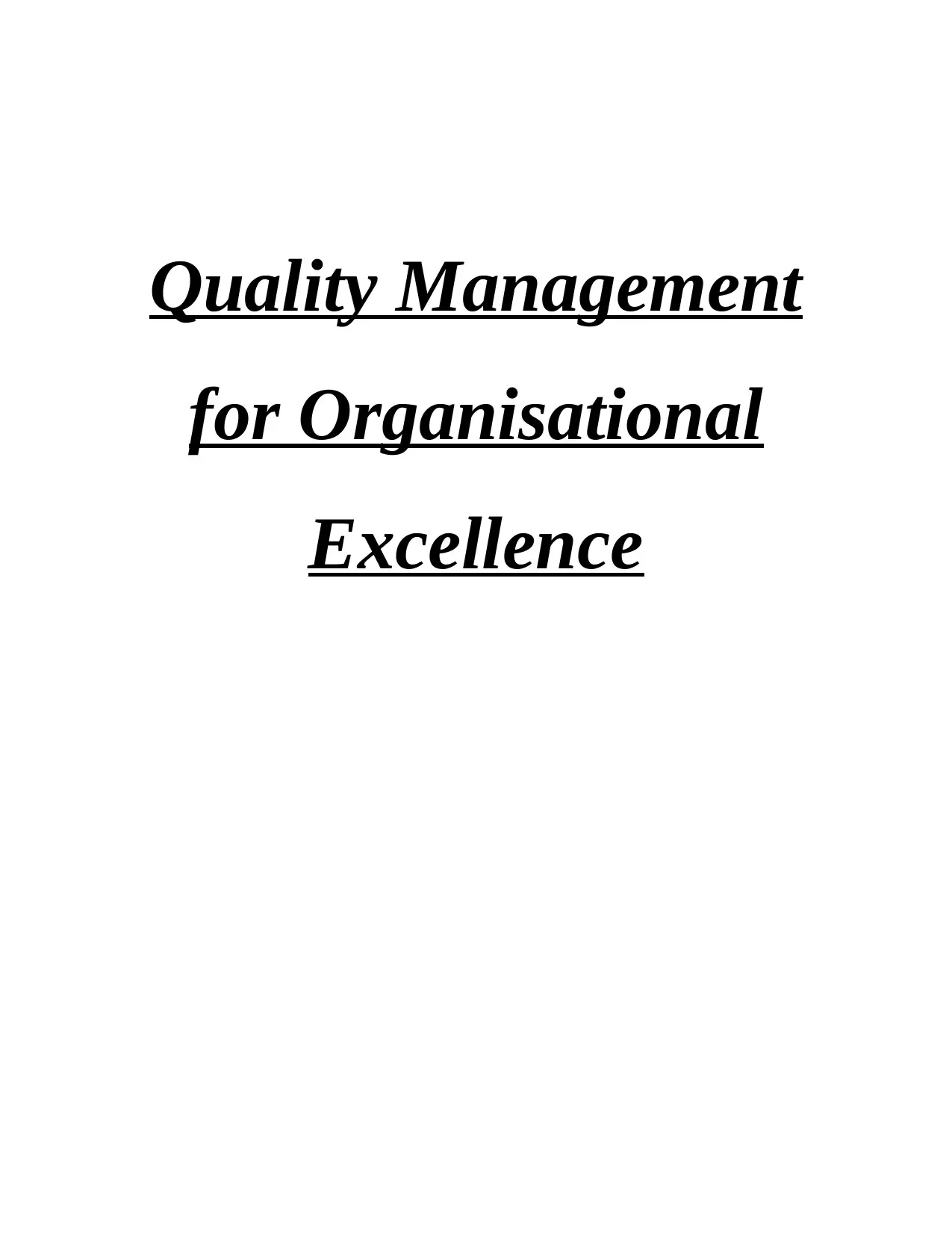
Quality Management
for Organisational
Excellence
for Organisational
Excellence
Secure Best Marks with AI Grader
Need help grading? Try our AI Grader for instant feedback on your assignments.
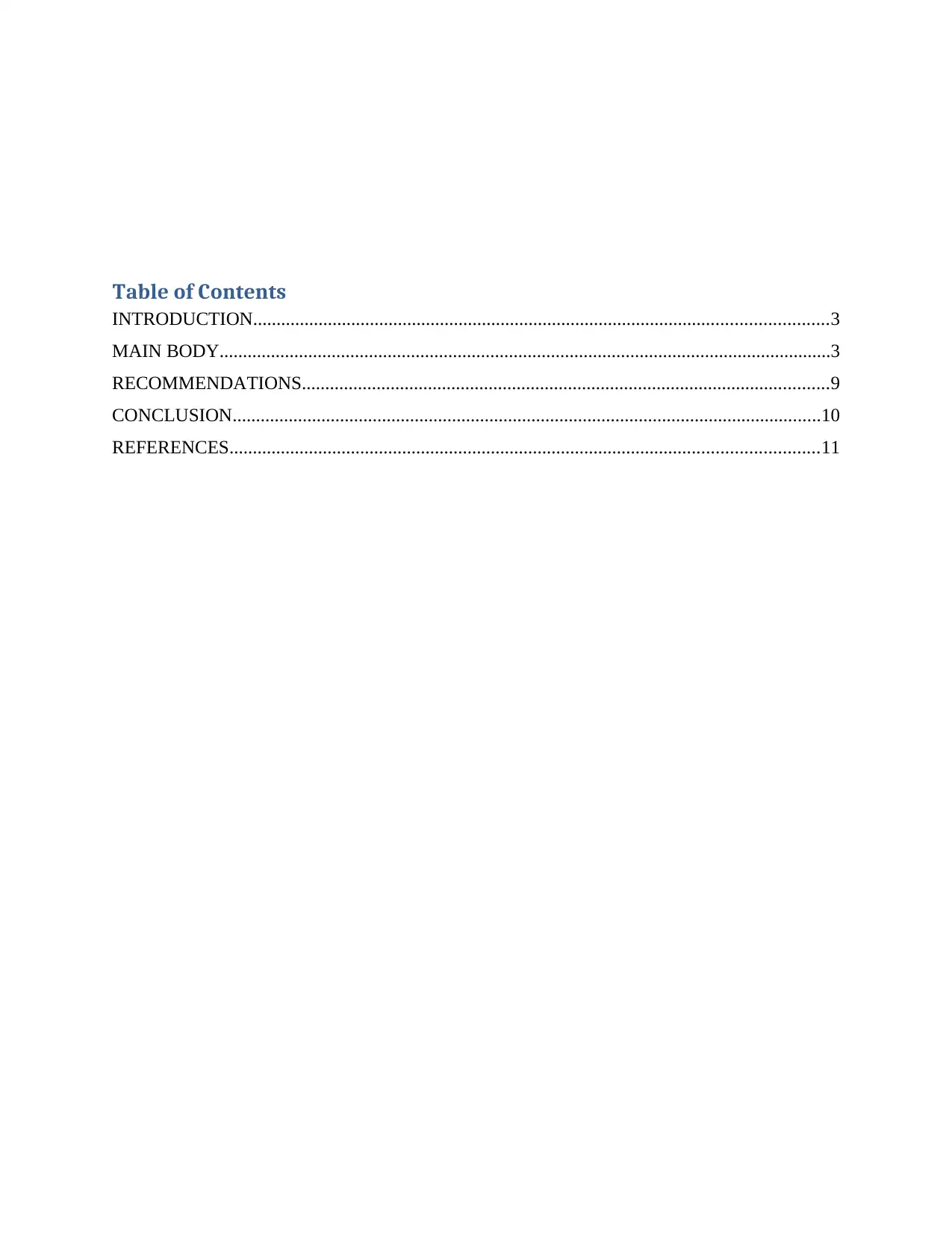
Table of Contents
INTRODUCTION...........................................................................................................................3
MAIN BODY...................................................................................................................................3
RECOMMENDATIONS.................................................................................................................9
CONCLUSION..............................................................................................................................10
REFERENCES..............................................................................................................................11
INTRODUCTION...........................................................................................................................3
MAIN BODY...................................................................................................................................3
RECOMMENDATIONS.................................................................................................................9
CONCLUSION..............................................................................................................................10
REFERENCES..............................................................................................................................11
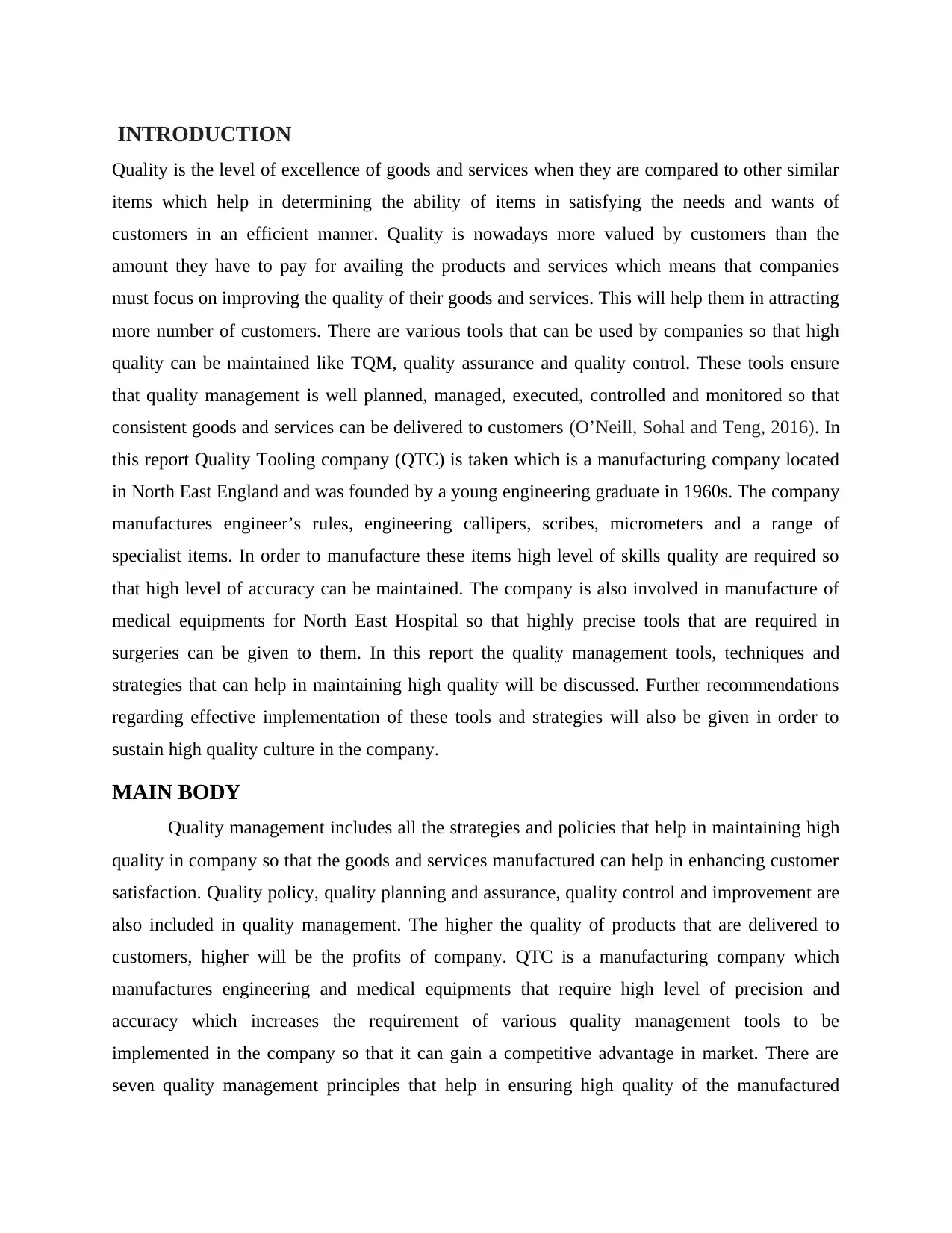
INTRODUCTION
Quality is the level of excellence of goods and services when they are compared to other similar
items which help in determining the ability of items in satisfying the needs and wants of
customers in an efficient manner. Quality is nowadays more valued by customers than the
amount they have to pay for availing the products and services which means that companies
must focus on improving the quality of their goods and services. This will help them in attracting
more number of customers. There are various tools that can be used by companies so that high
quality can be maintained like TQM, quality assurance and quality control. These tools ensure
that quality management is well planned, managed, executed, controlled and monitored so that
consistent goods and services can be delivered to customers (O’Neill, Sohal and Teng, 2016). In
this report Quality Tooling company (QTC) is taken which is a manufacturing company located
in North East England and was founded by a young engineering graduate in 1960s. The company
manufactures engineer’s rules, engineering callipers, scribes, micrometers and a range of
specialist items. In order to manufacture these items high level of skills quality are required so
that high level of accuracy can be maintained. The company is also involved in manufacture of
medical equipments for North East Hospital so that highly precise tools that are required in
surgeries can be given to them. In this report the quality management tools, techniques and
strategies that can help in maintaining high quality will be discussed. Further recommendations
regarding effective implementation of these tools and strategies will also be given in order to
sustain high quality culture in the company.
MAIN BODY
Quality management includes all the strategies and policies that help in maintaining high
quality in company so that the goods and services manufactured can help in enhancing customer
satisfaction. Quality policy, quality planning and assurance, quality control and improvement are
also included in quality management. The higher the quality of products that are delivered to
customers, higher will be the profits of company. QTC is a manufacturing company which
manufactures engineering and medical equipments that require high level of precision and
accuracy which increases the requirement of various quality management tools to be
implemented in the company so that it can gain a competitive advantage in market. There are
seven quality management principles that help in ensuring high quality of the manufactured
Quality is the level of excellence of goods and services when they are compared to other similar
items which help in determining the ability of items in satisfying the needs and wants of
customers in an efficient manner. Quality is nowadays more valued by customers than the
amount they have to pay for availing the products and services which means that companies
must focus on improving the quality of their goods and services. This will help them in attracting
more number of customers. There are various tools that can be used by companies so that high
quality can be maintained like TQM, quality assurance and quality control. These tools ensure
that quality management is well planned, managed, executed, controlled and monitored so that
consistent goods and services can be delivered to customers (O’Neill, Sohal and Teng, 2016). In
this report Quality Tooling company (QTC) is taken which is a manufacturing company located
in North East England and was founded by a young engineering graduate in 1960s. The company
manufactures engineer’s rules, engineering callipers, scribes, micrometers and a range of
specialist items. In order to manufacture these items high level of skills quality are required so
that high level of accuracy can be maintained. The company is also involved in manufacture of
medical equipments for North East Hospital so that highly precise tools that are required in
surgeries can be given to them. In this report the quality management tools, techniques and
strategies that can help in maintaining high quality will be discussed. Further recommendations
regarding effective implementation of these tools and strategies will also be given in order to
sustain high quality culture in the company.
MAIN BODY
Quality management includes all the strategies and policies that help in maintaining high
quality in company so that the goods and services manufactured can help in enhancing customer
satisfaction. Quality policy, quality planning and assurance, quality control and improvement are
also included in quality management. The higher the quality of products that are delivered to
customers, higher will be the profits of company. QTC is a manufacturing company which
manufactures engineering and medical equipments that require high level of precision and
accuracy which increases the requirement of various quality management tools to be
implemented in the company so that it can gain a competitive advantage in market. There are
seven quality management principles that help in ensuring high quality of the manufactured
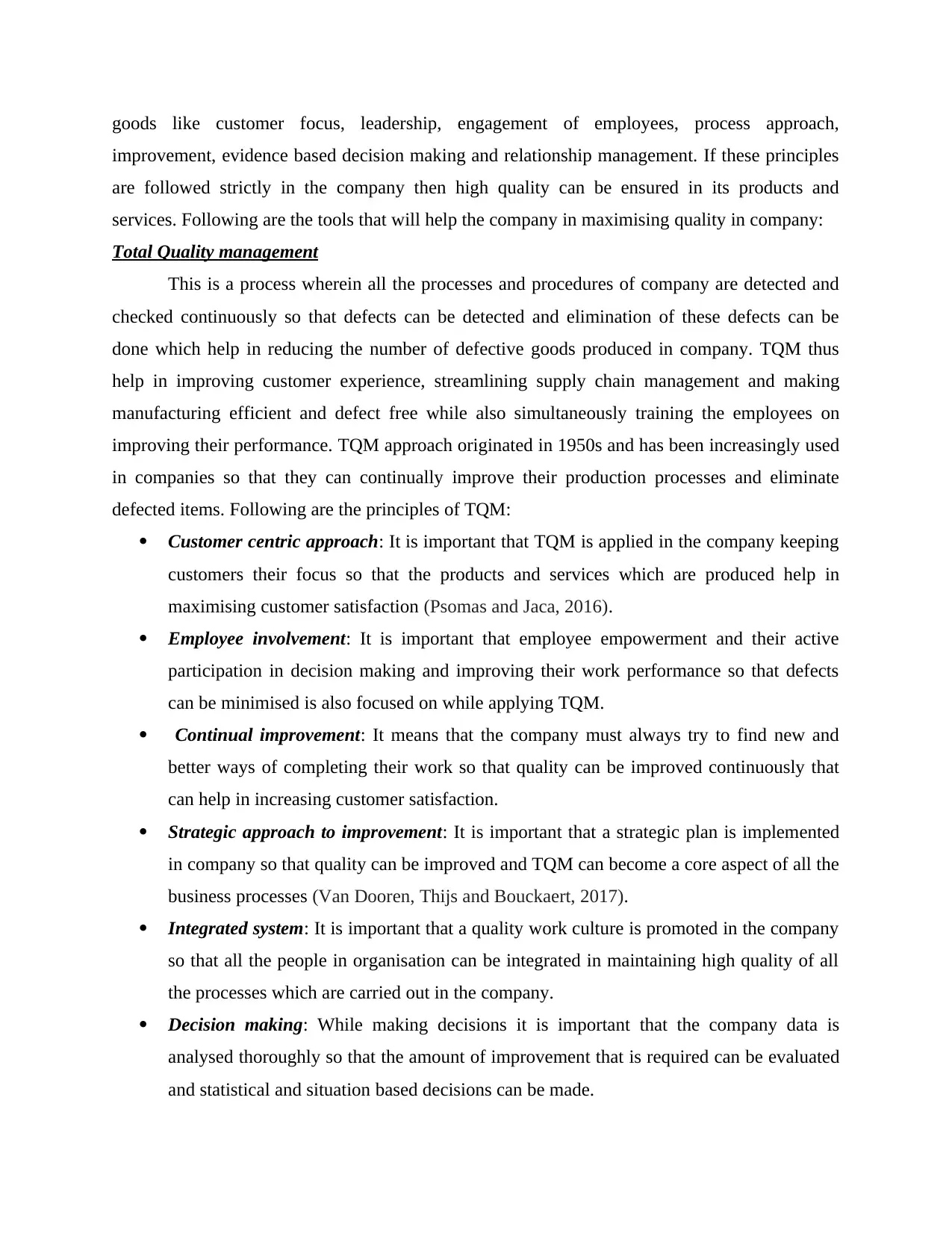
goods like customer focus, leadership, engagement of employees, process approach,
improvement, evidence based decision making and relationship management. If these principles
are followed strictly in the company then high quality can be ensured in its products and
services. Following are the tools that will help the company in maximising quality in company:
Total Quality management
This is a process wherein all the processes and procedures of company are detected and
checked continuously so that defects can be detected and elimination of these defects can be
done which help in reducing the number of defective goods produced in company. TQM thus
help in improving customer experience, streamlining supply chain management and making
manufacturing efficient and defect free while also simultaneously training the employees on
improving their performance. TQM approach originated in 1950s and has been increasingly used
in companies so that they can continually improve their production processes and eliminate
defected items. Following are the principles of TQM:
Customer centric approach: It is important that TQM is applied in the company keeping
customers their focus so that the products and services which are produced help in
maximising customer satisfaction (Psomas and Jaca, 2016).
Employee involvement: It is important that employee empowerment and their active
participation in decision making and improving their work performance so that defects
can be minimised is also focused on while applying TQM.
Continual improvement: It means that the company must always try to find new and
better ways of completing their work so that quality can be improved continuously that
can help in increasing customer satisfaction.
Strategic approach to improvement: It is important that a strategic plan is implemented
in company so that quality can be improved and TQM can become a core aspect of all the
business processes (Van Dooren, Thijs and Bouckaert, 2017).
Integrated system: It is important that a quality work culture is promoted in the company
so that all the people in organisation can be integrated in maintaining high quality of all
the processes which are carried out in the company.
Decision making: While making decisions it is important that the company data is
analysed thoroughly so that the amount of improvement that is required can be evaluated
and statistical and situation based decisions can be made.
improvement, evidence based decision making and relationship management. If these principles
are followed strictly in the company then high quality can be ensured in its products and
services. Following are the tools that will help the company in maximising quality in company:
Total Quality management
This is a process wherein all the processes and procedures of company are detected and
checked continuously so that defects can be detected and elimination of these defects can be
done which help in reducing the number of defective goods produced in company. TQM thus
help in improving customer experience, streamlining supply chain management and making
manufacturing efficient and defect free while also simultaneously training the employees on
improving their performance. TQM approach originated in 1950s and has been increasingly used
in companies so that they can continually improve their production processes and eliminate
defected items. Following are the principles of TQM:
Customer centric approach: It is important that TQM is applied in the company keeping
customers their focus so that the products and services which are produced help in
maximising customer satisfaction (Psomas and Jaca, 2016).
Employee involvement: It is important that employee empowerment and their active
participation in decision making and improving their work performance so that defects
can be minimised is also focused on while applying TQM.
Continual improvement: It means that the company must always try to find new and
better ways of completing their work so that quality can be improved continuously that
can help in increasing customer satisfaction.
Strategic approach to improvement: It is important that a strategic plan is implemented
in company so that quality can be improved and TQM can become a core aspect of all the
business processes (Van Dooren, Thijs and Bouckaert, 2017).
Integrated system: It is important that a quality work culture is promoted in the company
so that all the people in organisation can be integrated in maintaining high quality of all
the processes which are carried out in the company.
Decision making: While making decisions it is important that the company data is
analysed thoroughly so that the amount of improvement that is required can be evaluated
and statistical and situation based decisions can be made.
Secure Best Marks with AI Grader
Need help grading? Try our AI Grader for instant feedback on your assignments.
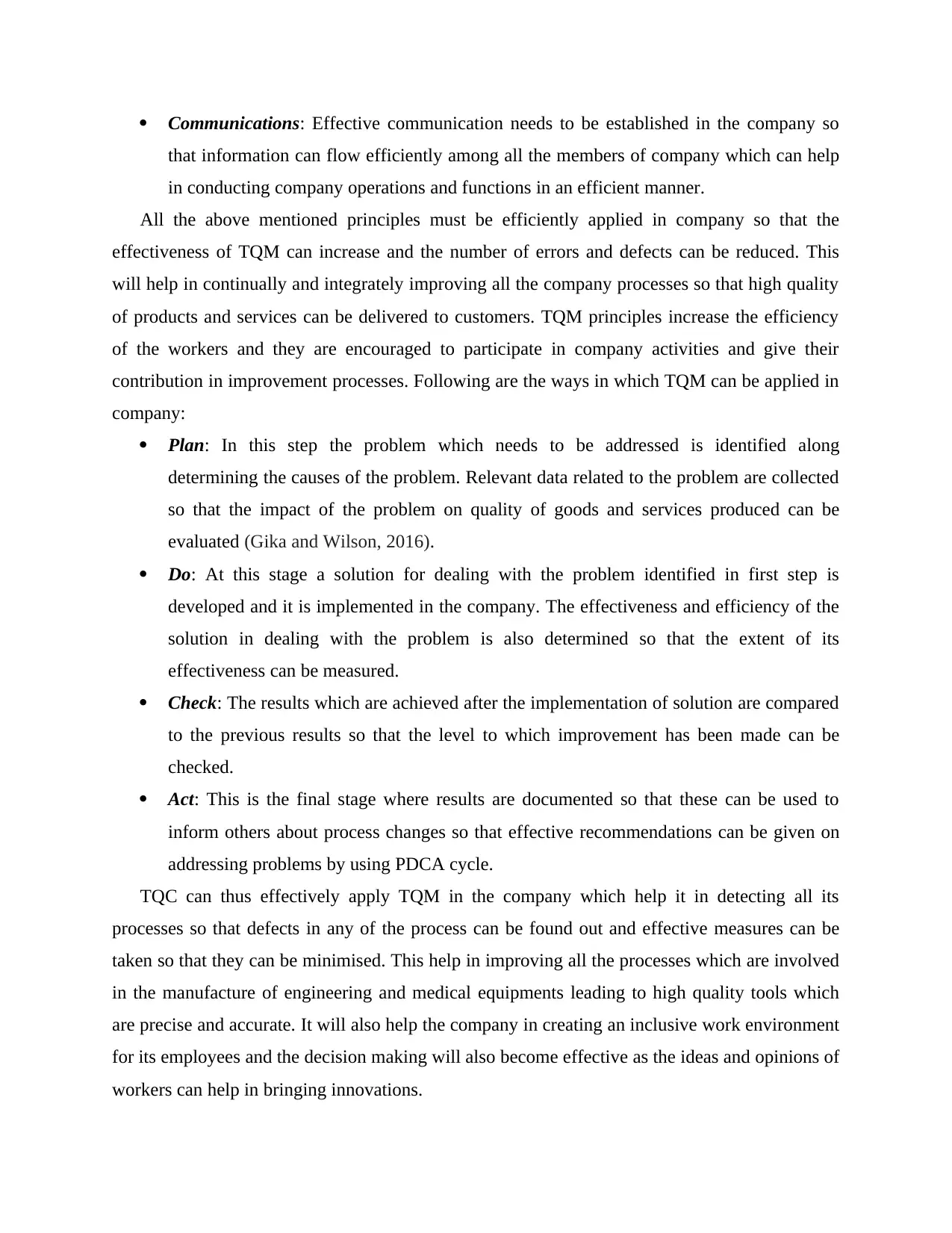
Communications: Effective communication needs to be established in the company so
that information can flow efficiently among all the members of company which can help
in conducting company operations and functions in an efficient manner.
All the above mentioned principles must be efficiently applied in company so that the
effectiveness of TQM can increase and the number of errors and defects can be reduced. This
will help in continually and integrately improving all the company processes so that high quality
of products and services can be delivered to customers. TQM principles increase the efficiency
of the workers and they are encouraged to participate in company activities and give their
contribution in improvement processes. Following are the ways in which TQM can be applied in
company:
Plan: In this step the problem which needs to be addressed is identified along
determining the causes of the problem. Relevant data related to the problem are collected
so that the impact of the problem on quality of goods and services produced can be
evaluated (Gika and Wilson, 2016).
Do: At this stage a solution for dealing with the problem identified in first step is
developed and it is implemented in the company. The effectiveness and efficiency of the
solution in dealing with the problem is also determined so that the extent of its
effectiveness can be measured.
Check: The results which are achieved after the implementation of solution are compared
to the previous results so that the level to which improvement has been made can be
checked.
Act: This is the final stage where results are documented so that these can be used to
inform others about process changes so that effective recommendations can be given on
addressing problems by using PDCA cycle.
TQC can thus effectively apply TQM in the company which help it in detecting all its
processes so that defects in any of the process can be found out and effective measures can be
taken so that they can be minimised. This help in improving all the processes which are involved
in the manufacture of engineering and medical equipments leading to high quality tools which
are precise and accurate. It will also help the company in creating an inclusive work environment
for its employees and the decision making will also become effective as the ideas and opinions of
workers can help in bringing innovations.
that information can flow efficiently among all the members of company which can help
in conducting company operations and functions in an efficient manner.
All the above mentioned principles must be efficiently applied in company so that the
effectiveness of TQM can increase and the number of errors and defects can be reduced. This
will help in continually and integrately improving all the company processes so that high quality
of products and services can be delivered to customers. TQM principles increase the efficiency
of the workers and they are encouraged to participate in company activities and give their
contribution in improvement processes. Following are the ways in which TQM can be applied in
company:
Plan: In this step the problem which needs to be addressed is identified along
determining the causes of the problem. Relevant data related to the problem are collected
so that the impact of the problem on quality of goods and services produced can be
evaluated (Gika and Wilson, 2016).
Do: At this stage a solution for dealing with the problem identified in first step is
developed and it is implemented in the company. The effectiveness and efficiency of the
solution in dealing with the problem is also determined so that the extent of its
effectiveness can be measured.
Check: The results which are achieved after the implementation of solution are compared
to the previous results so that the level to which improvement has been made can be
checked.
Act: This is the final stage where results are documented so that these can be used to
inform others about process changes so that effective recommendations can be given on
addressing problems by using PDCA cycle.
TQC can thus effectively apply TQM in the company which help it in detecting all its
processes so that defects in any of the process can be found out and effective measures can be
taken so that they can be minimised. This help in improving all the processes which are involved
in the manufacture of engineering and medical equipments leading to high quality tools which
are precise and accurate. It will also help the company in creating an inclusive work environment
for its employees and the decision making will also become effective as the ideas and opinions of
workers can help in bringing innovations.
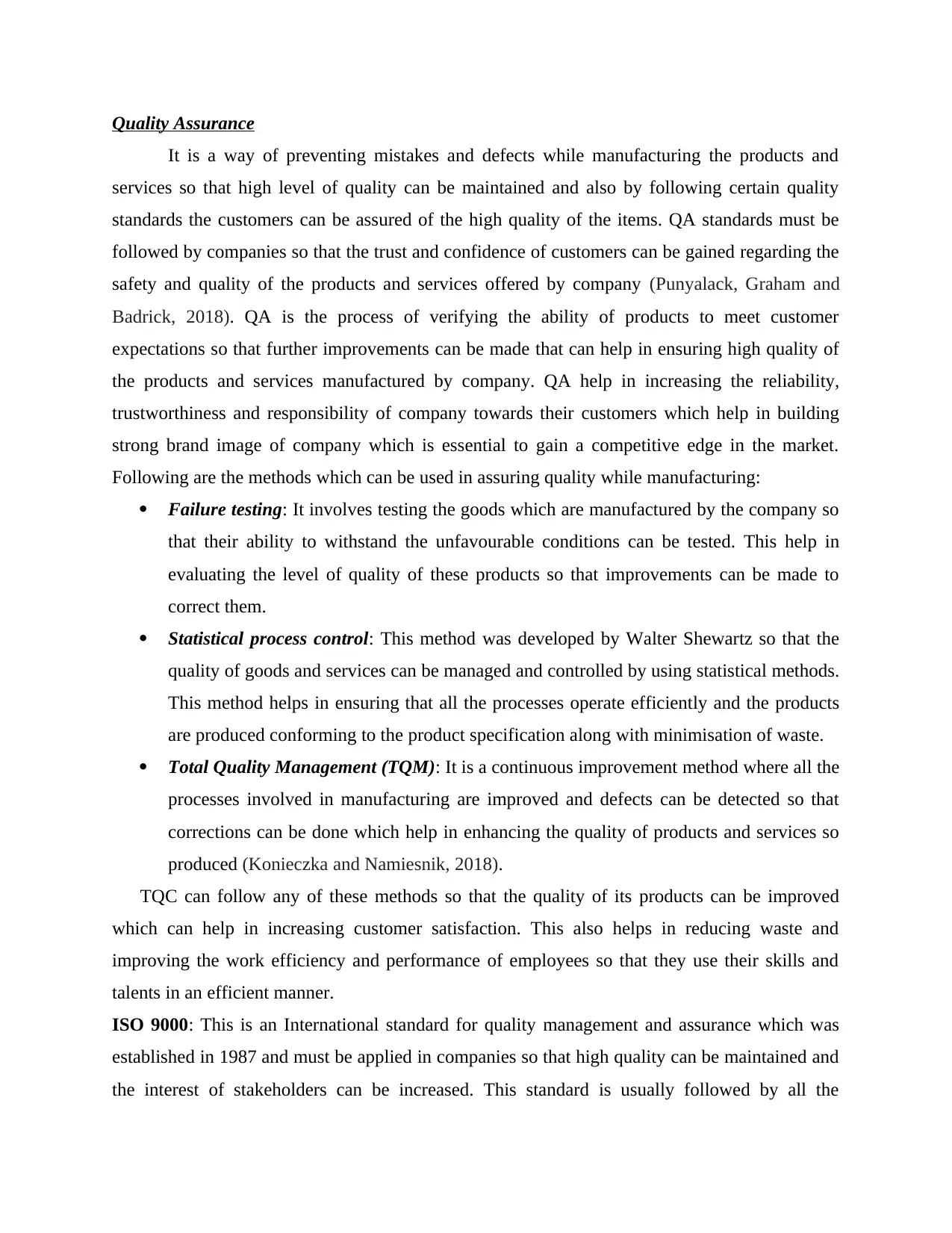
Quality Assurance
It is a way of preventing mistakes and defects while manufacturing the products and
services so that high level of quality can be maintained and also by following certain quality
standards the customers can be assured of the high quality of the items. QA standards must be
followed by companies so that the trust and confidence of customers can be gained regarding the
safety and quality of the products and services offered by company (Punyalack, Graham and
Badrick, 2018). QA is the process of verifying the ability of products to meet customer
expectations so that further improvements can be made that can help in ensuring high quality of
the products and services manufactured by company. QA help in increasing the reliability,
trustworthiness and responsibility of company towards their customers which help in building
strong brand image of company which is essential to gain a competitive edge in the market.
Following are the methods which can be used in assuring quality while manufacturing:
Failure testing: It involves testing the goods which are manufactured by the company so
that their ability to withstand the unfavourable conditions can be tested. This help in
evaluating the level of quality of these products so that improvements can be made to
correct them.
Statistical process control: This method was developed by Walter Shewartz so that the
quality of goods and services can be managed and controlled by using statistical methods.
This method helps in ensuring that all the processes operate efficiently and the products
are produced conforming to the product specification along with minimisation of waste.
Total Quality Management (TQM): It is a continuous improvement method where all the
processes involved in manufacturing are improved and defects can be detected so that
corrections can be done which help in enhancing the quality of products and services so
produced (Konieczka and Namiesnik, 2018).
TQC can follow any of these methods so that the quality of its products can be improved
which can help in increasing customer satisfaction. This also helps in reducing waste and
improving the work efficiency and performance of employees so that they use their skills and
talents in an efficient manner.
ISO 9000: This is an International standard for quality management and assurance which was
established in 1987 and must be applied in companies so that high quality can be maintained and
the interest of stakeholders can be increased. This standard is usually followed by all the
It is a way of preventing mistakes and defects while manufacturing the products and
services so that high level of quality can be maintained and also by following certain quality
standards the customers can be assured of the high quality of the items. QA standards must be
followed by companies so that the trust and confidence of customers can be gained regarding the
safety and quality of the products and services offered by company (Punyalack, Graham and
Badrick, 2018). QA is the process of verifying the ability of products to meet customer
expectations so that further improvements can be made that can help in ensuring high quality of
the products and services manufactured by company. QA help in increasing the reliability,
trustworthiness and responsibility of company towards their customers which help in building
strong brand image of company which is essential to gain a competitive edge in the market.
Following are the methods which can be used in assuring quality while manufacturing:
Failure testing: It involves testing the goods which are manufactured by the company so
that their ability to withstand the unfavourable conditions can be tested. This help in
evaluating the level of quality of these products so that improvements can be made to
correct them.
Statistical process control: This method was developed by Walter Shewartz so that the
quality of goods and services can be managed and controlled by using statistical methods.
This method helps in ensuring that all the processes operate efficiently and the products
are produced conforming to the product specification along with minimisation of waste.
Total Quality Management (TQM): It is a continuous improvement method where all the
processes involved in manufacturing are improved and defects can be detected so that
corrections can be done which help in enhancing the quality of products and services so
produced (Konieczka and Namiesnik, 2018).
TQC can follow any of these methods so that the quality of its products can be improved
which can help in increasing customer satisfaction. This also helps in reducing waste and
improving the work efficiency and performance of employees so that they use their skills and
talents in an efficient manner.
ISO 9000: This is an International standard for quality management and assurance which was
established in 1987 and must be applied in companies so that high quality can be maintained and
the interest of stakeholders can be increased. This standard is usually followed by all the
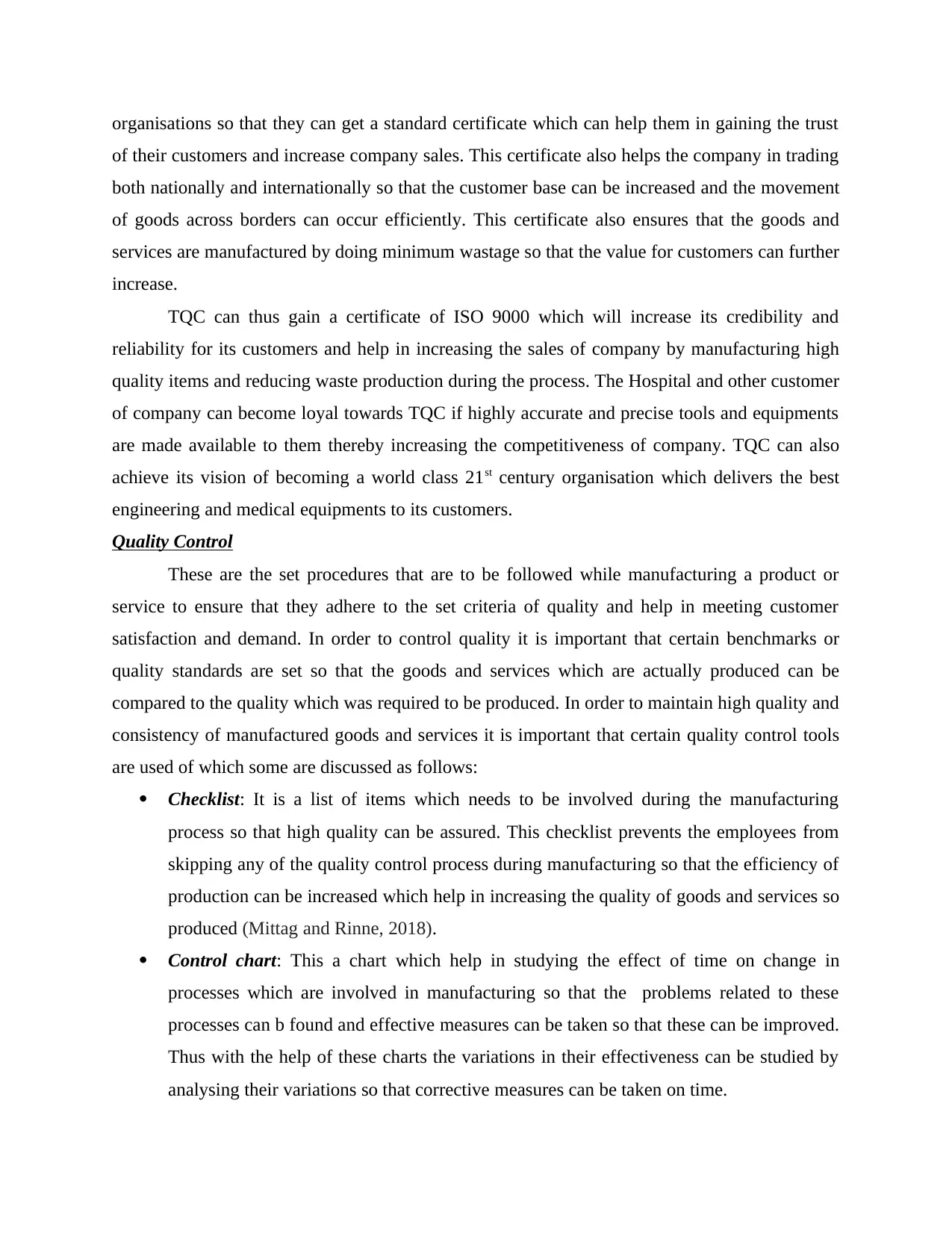
organisations so that they can get a standard certificate which can help them in gaining the trust
of their customers and increase company sales. This certificate also helps the company in trading
both nationally and internationally so that the customer base can be increased and the movement
of goods across borders can occur efficiently. This certificate also ensures that the goods and
services are manufactured by doing minimum wastage so that the value for customers can further
increase.
TQC can thus gain a certificate of ISO 9000 which will increase its credibility and
reliability for its customers and help in increasing the sales of company by manufacturing high
quality items and reducing waste production during the process. The Hospital and other customer
of company can become loyal towards TQC if highly accurate and precise tools and equipments
are made available to them thereby increasing the competitiveness of company. TQC can also
achieve its vision of becoming a world class 21st century organisation which delivers the best
engineering and medical equipments to its customers.
Quality Control
These are the set procedures that are to be followed while manufacturing a product or
service to ensure that they adhere to the set criteria of quality and help in meeting customer
satisfaction and demand. In order to control quality it is important that certain benchmarks or
quality standards are set so that the goods and services which are actually produced can be
compared to the quality which was required to be produced. In order to maintain high quality and
consistency of manufactured goods and services it is important that certain quality control tools
are used of which some are discussed as follows:
Checklist: It is a list of items which needs to be involved during the manufacturing
process so that high quality can be assured. This checklist prevents the employees from
skipping any of the quality control process during manufacturing so that the efficiency of
production can be increased which help in increasing the quality of goods and services so
produced (Mittag and Rinne, 2018).
Control chart: This a chart which help in studying the effect of time on change in
processes which are involved in manufacturing so that the problems related to these
processes can b found and effective measures can be taken so that these can be improved.
Thus with the help of these charts the variations in their effectiveness can be studied by
analysing their variations so that corrective measures can be taken on time.
of their customers and increase company sales. This certificate also helps the company in trading
both nationally and internationally so that the customer base can be increased and the movement
of goods across borders can occur efficiently. This certificate also ensures that the goods and
services are manufactured by doing minimum wastage so that the value for customers can further
increase.
TQC can thus gain a certificate of ISO 9000 which will increase its credibility and
reliability for its customers and help in increasing the sales of company by manufacturing high
quality items and reducing waste production during the process. The Hospital and other customer
of company can become loyal towards TQC if highly accurate and precise tools and equipments
are made available to them thereby increasing the competitiveness of company. TQC can also
achieve its vision of becoming a world class 21st century organisation which delivers the best
engineering and medical equipments to its customers.
Quality Control
These are the set procedures that are to be followed while manufacturing a product or
service to ensure that they adhere to the set criteria of quality and help in meeting customer
satisfaction and demand. In order to control quality it is important that certain benchmarks or
quality standards are set so that the goods and services which are actually produced can be
compared to the quality which was required to be produced. In order to maintain high quality and
consistency of manufactured goods and services it is important that certain quality control tools
are used of which some are discussed as follows:
Checklist: It is a list of items which needs to be involved during the manufacturing
process so that high quality can be assured. This checklist prevents the employees from
skipping any of the quality control process during manufacturing so that the efficiency of
production can be increased which help in increasing the quality of goods and services so
produced (Mittag and Rinne, 2018).
Control chart: This a chart which help in studying the effect of time on change in
processes which are involved in manufacturing so that the problems related to these
processes can b found and effective measures can be taken so that these can be improved.
Thus with the help of these charts the variations in their effectiveness can be studied by
analysing their variations so that corrective measures can be taken on time.
Paraphrase This Document
Need a fresh take? Get an instant paraphrase of this document with our AI Paraphraser
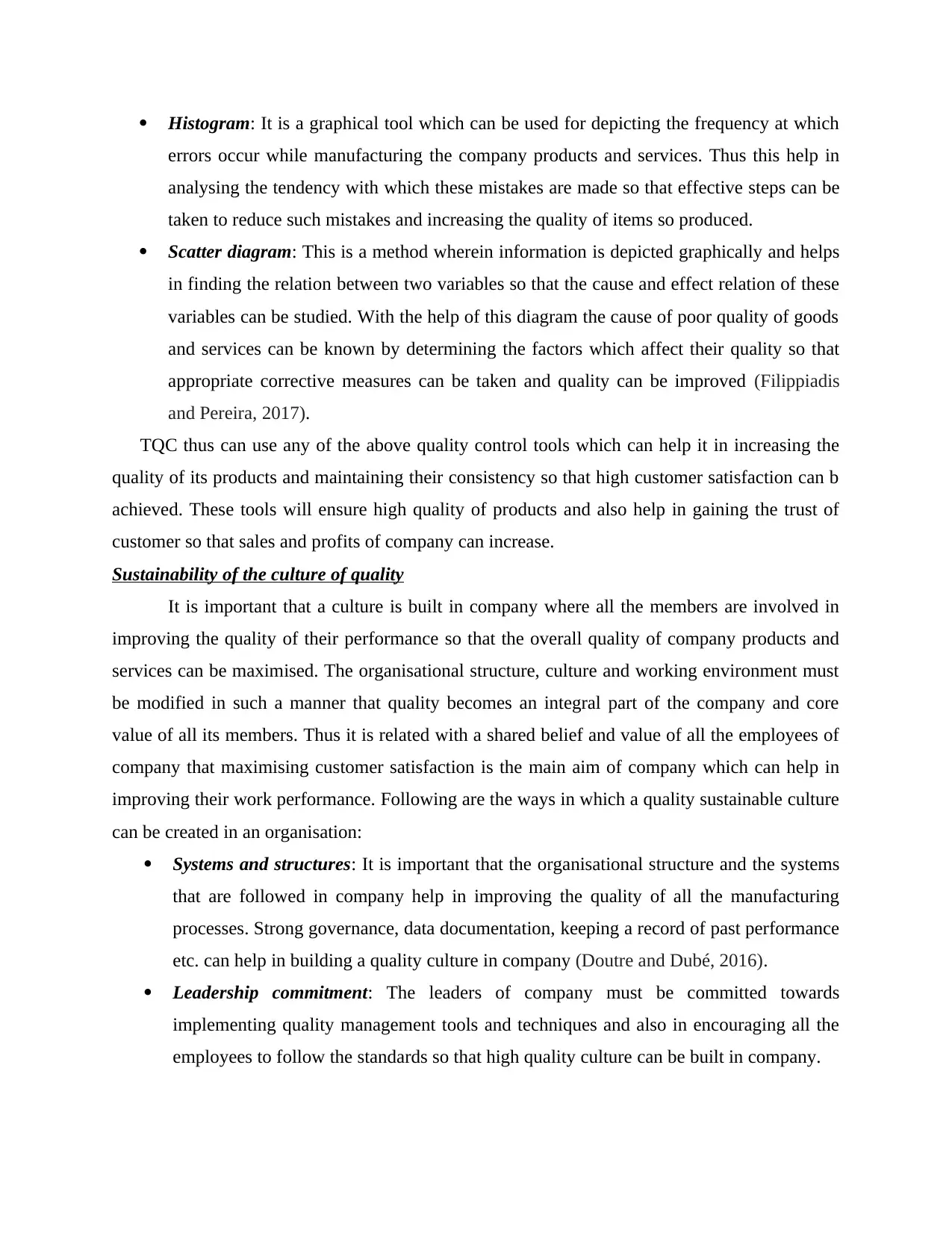
Histogram: It is a graphical tool which can be used for depicting the frequency at which
errors occur while manufacturing the company products and services. Thus this help in
analysing the tendency with which these mistakes are made so that effective steps can be
taken to reduce such mistakes and increasing the quality of items so produced.
Scatter diagram: This is a method wherein information is depicted graphically and helps
in finding the relation between two variables so that the cause and effect relation of these
variables can be studied. With the help of this diagram the cause of poor quality of goods
and services can be known by determining the factors which affect their quality so that
appropriate corrective measures can be taken and quality can be improved (Filippiadis
and Pereira, 2017).
TQC thus can use any of the above quality control tools which can help it in increasing the
quality of its products and maintaining their consistency so that high customer satisfaction can b
achieved. These tools will ensure high quality of products and also help in gaining the trust of
customer so that sales and profits of company can increase.
Sustainability of the culture of quality
It is important that a culture is built in company where all the members are involved in
improving the quality of their performance so that the overall quality of company products and
services can be maximised. The organisational structure, culture and working environment must
be modified in such a manner that quality becomes an integral part of the company and core
value of all its members. Thus it is related with a shared belief and value of all the employees of
company that maximising customer satisfaction is the main aim of company which can help in
improving their work performance. Following are the ways in which a quality sustainable culture
can be created in an organisation:
Systems and structures: It is important that the organisational structure and the systems
that are followed in company help in improving the quality of all the manufacturing
processes. Strong governance, data documentation, keeping a record of past performance
etc. can help in building a quality culture in company (Doutre and Dubé, 2016).
Leadership commitment: The leaders of company must be committed towards
implementing quality management tools and techniques and also in encouraging all the
employees to follow the standards so that high quality culture can be built in company.
errors occur while manufacturing the company products and services. Thus this help in
analysing the tendency with which these mistakes are made so that effective steps can be
taken to reduce such mistakes and increasing the quality of items so produced.
Scatter diagram: This is a method wherein information is depicted graphically and helps
in finding the relation between two variables so that the cause and effect relation of these
variables can be studied. With the help of this diagram the cause of poor quality of goods
and services can be known by determining the factors which affect their quality so that
appropriate corrective measures can be taken and quality can be improved (Filippiadis
and Pereira, 2017).
TQC thus can use any of the above quality control tools which can help it in increasing the
quality of its products and maintaining their consistency so that high customer satisfaction can b
achieved. These tools will ensure high quality of products and also help in gaining the trust of
customer so that sales and profits of company can increase.
Sustainability of the culture of quality
It is important that a culture is built in company where all the members are involved in
improving the quality of their performance so that the overall quality of company products and
services can be maximised. The organisational structure, culture and working environment must
be modified in such a manner that quality becomes an integral part of the company and core
value of all its members. Thus it is related with a shared belief and value of all the employees of
company that maximising customer satisfaction is the main aim of company which can help in
improving their work performance. Following are the ways in which a quality sustainable culture
can be created in an organisation:
Systems and structures: It is important that the organisational structure and the systems
that are followed in company help in improving the quality of all the manufacturing
processes. Strong governance, data documentation, keeping a record of past performance
etc. can help in building a quality culture in company (Doutre and Dubé, 2016).
Leadership commitment: The leaders of company must be committed towards
implementing quality management tools and techniques and also in encouraging all the
employees to follow the standards so that high quality culture can be built in company.
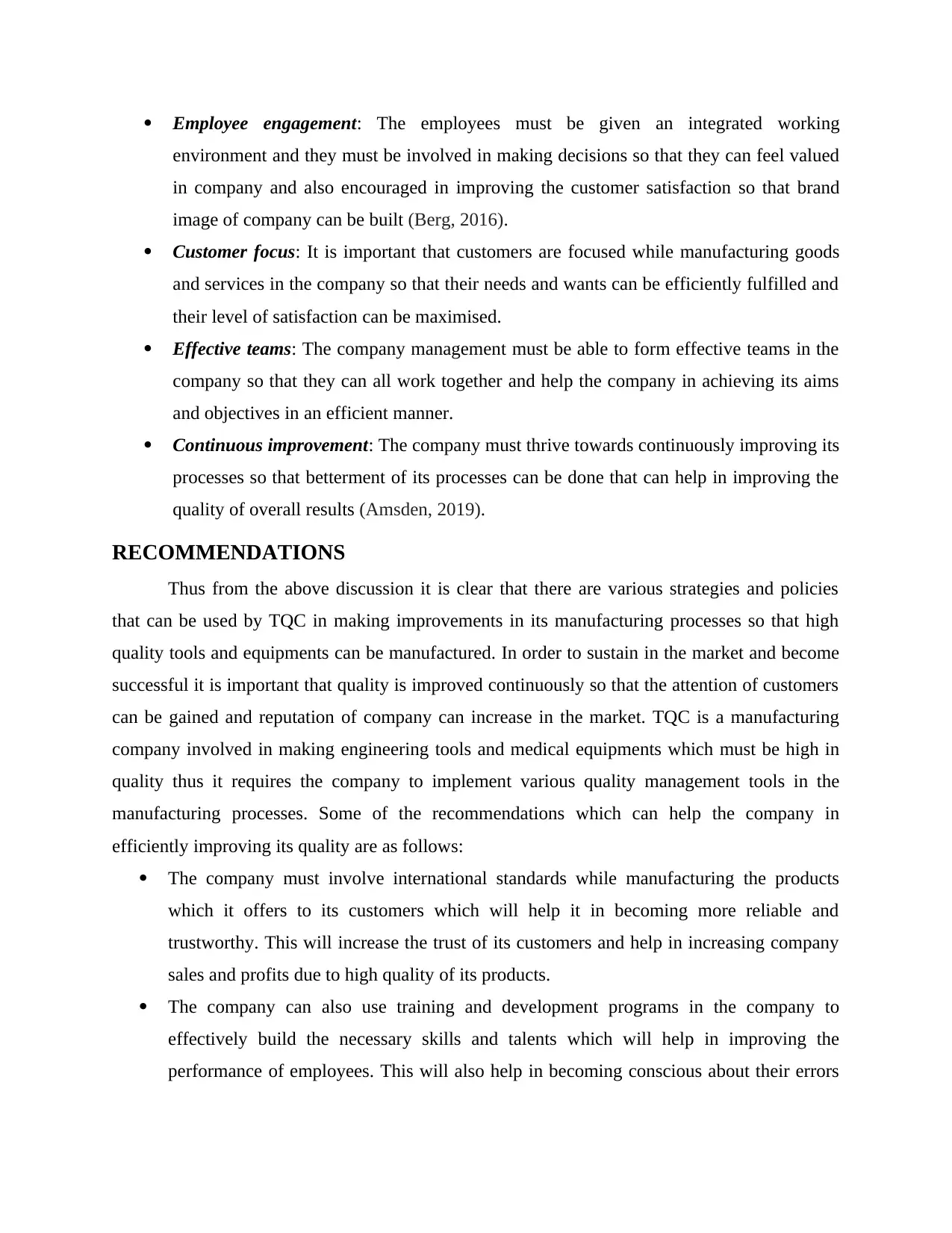
Employee engagement: The employees must be given an integrated working
environment and they must be involved in making decisions so that they can feel valued
in company and also encouraged in improving the customer satisfaction so that brand
image of company can be built (Berg, 2016).
Customer focus: It is important that customers are focused while manufacturing goods
and services in the company so that their needs and wants can be efficiently fulfilled and
their level of satisfaction can be maximised.
Effective teams: The company management must be able to form effective teams in the
company so that they can all work together and help the company in achieving its aims
and objectives in an efficient manner.
Continuous improvement: The company must thrive towards continuously improving its
processes so that betterment of its processes can be done that can help in improving the
quality of overall results (Amsden, 2019).
RECOMMENDATIONS
Thus from the above discussion it is clear that there are various strategies and policies
that can be used by TQC in making improvements in its manufacturing processes so that high
quality tools and equipments can be manufactured. In order to sustain in the market and become
successful it is important that quality is improved continuously so that the attention of customers
can be gained and reputation of company can increase in the market. TQC is a manufacturing
company involved in making engineering tools and medical equipments which must be high in
quality thus it requires the company to implement various quality management tools in the
manufacturing processes. Some of the recommendations which can help the company in
efficiently improving its quality are as follows:
The company must involve international standards while manufacturing the products
which it offers to its customers which will help it in becoming more reliable and
trustworthy. This will increase the trust of its customers and help in increasing company
sales and profits due to high quality of its products.
The company can also use training and development programs in the company to
effectively build the necessary skills and talents which will help in improving the
performance of employees. This will also help in becoming conscious about their errors
environment and they must be involved in making decisions so that they can feel valued
in company and also encouraged in improving the customer satisfaction so that brand
image of company can be built (Berg, 2016).
Customer focus: It is important that customers are focused while manufacturing goods
and services in the company so that their needs and wants can be efficiently fulfilled and
their level of satisfaction can be maximised.
Effective teams: The company management must be able to form effective teams in the
company so that they can all work together and help the company in achieving its aims
and objectives in an efficient manner.
Continuous improvement: The company must thrive towards continuously improving its
processes so that betterment of its processes can be done that can help in improving the
quality of overall results (Amsden, 2019).
RECOMMENDATIONS
Thus from the above discussion it is clear that there are various strategies and policies
that can be used by TQC in making improvements in its manufacturing processes so that high
quality tools and equipments can be manufactured. In order to sustain in the market and become
successful it is important that quality is improved continuously so that the attention of customers
can be gained and reputation of company can increase in the market. TQC is a manufacturing
company involved in making engineering tools and medical equipments which must be high in
quality thus it requires the company to implement various quality management tools in the
manufacturing processes. Some of the recommendations which can help the company in
efficiently improving its quality are as follows:
The company must involve international standards while manufacturing the products
which it offers to its customers which will help it in becoming more reliable and
trustworthy. This will increase the trust of its customers and help in increasing company
sales and profits due to high quality of its products.
The company can also use training and development programs in the company to
effectively build the necessary skills and talents which will help in improving the
performance of employees. This will also help in becoming conscious about their errors
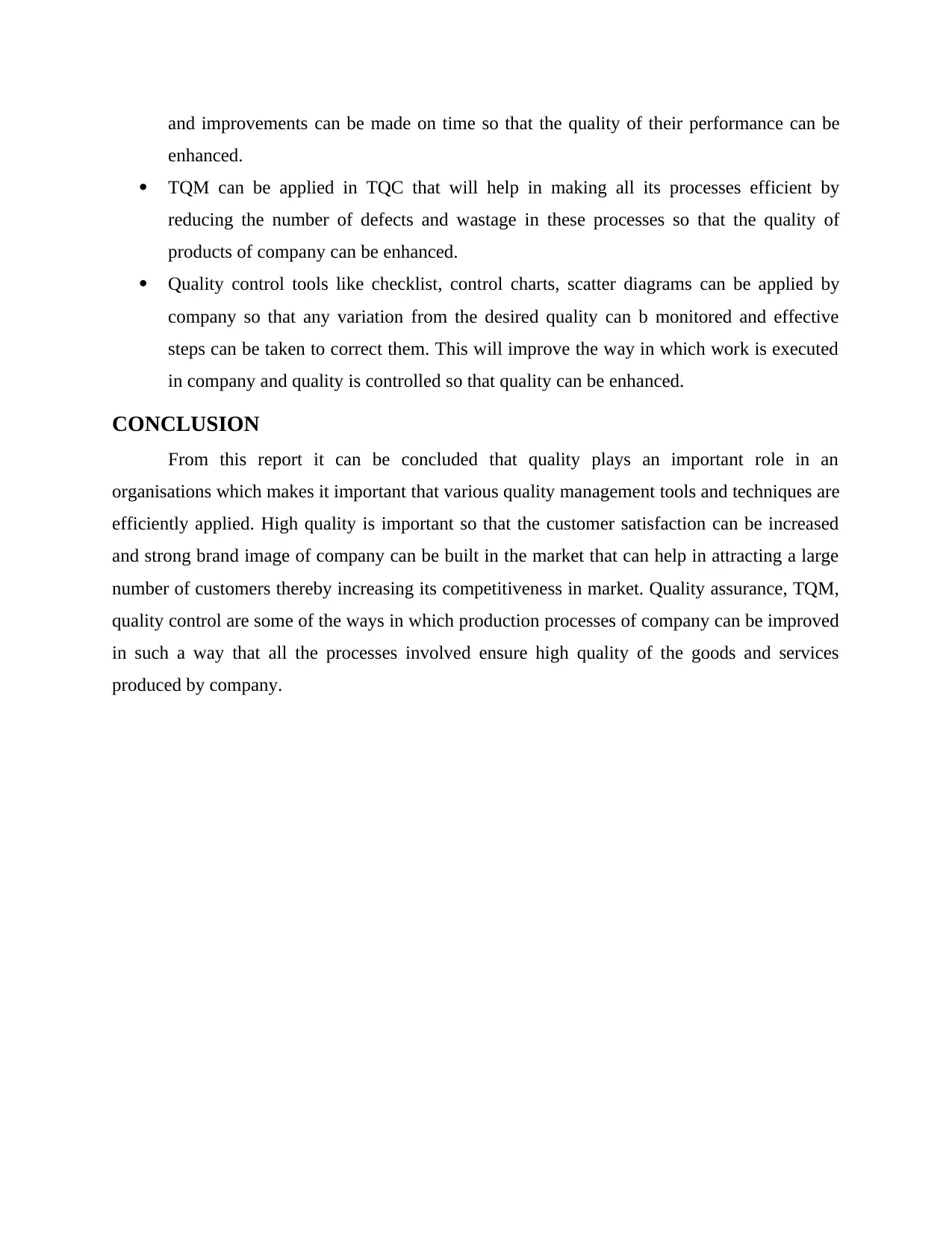
and improvements can be made on time so that the quality of their performance can be
enhanced.
TQM can be applied in TQC that will help in making all its processes efficient by
reducing the number of defects and wastage in these processes so that the quality of
products of company can be enhanced.
Quality control tools like checklist, control charts, scatter diagrams can be applied by
company so that any variation from the desired quality can b monitored and effective
steps can be taken to correct them. This will improve the way in which work is executed
in company and quality is controlled so that quality can be enhanced.
CONCLUSION
From this report it can be concluded that quality plays an important role in an
organisations which makes it important that various quality management tools and techniques are
efficiently applied. High quality is important so that the customer satisfaction can be increased
and strong brand image of company can be built in the market that can help in attracting a large
number of customers thereby increasing its competitiveness in market. Quality assurance, TQM,
quality control are some of the ways in which production processes of company can be improved
in such a way that all the processes involved ensure high quality of the goods and services
produced by company.
enhanced.
TQM can be applied in TQC that will help in making all its processes efficient by
reducing the number of defects and wastage in these processes so that the quality of
products of company can be enhanced.
Quality control tools like checklist, control charts, scatter diagrams can be applied by
company so that any variation from the desired quality can b monitored and effective
steps can be taken to correct them. This will improve the way in which work is executed
in company and quality is controlled so that quality can be enhanced.
CONCLUSION
From this report it can be concluded that quality plays an important role in an
organisations which makes it important that various quality management tools and techniques are
efficiently applied. High quality is important so that the customer satisfaction can be increased
and strong brand image of company can be built in the market that can help in attracting a large
number of customers thereby increasing its competitiveness in market. Quality assurance, TQM,
quality control are some of the ways in which production processes of company can be improved
in such a way that all the processes involved ensure high quality of the goods and services
produced by company.
Secure Best Marks with AI Grader
Need help grading? Try our AI Grader for instant feedback on your assignments.
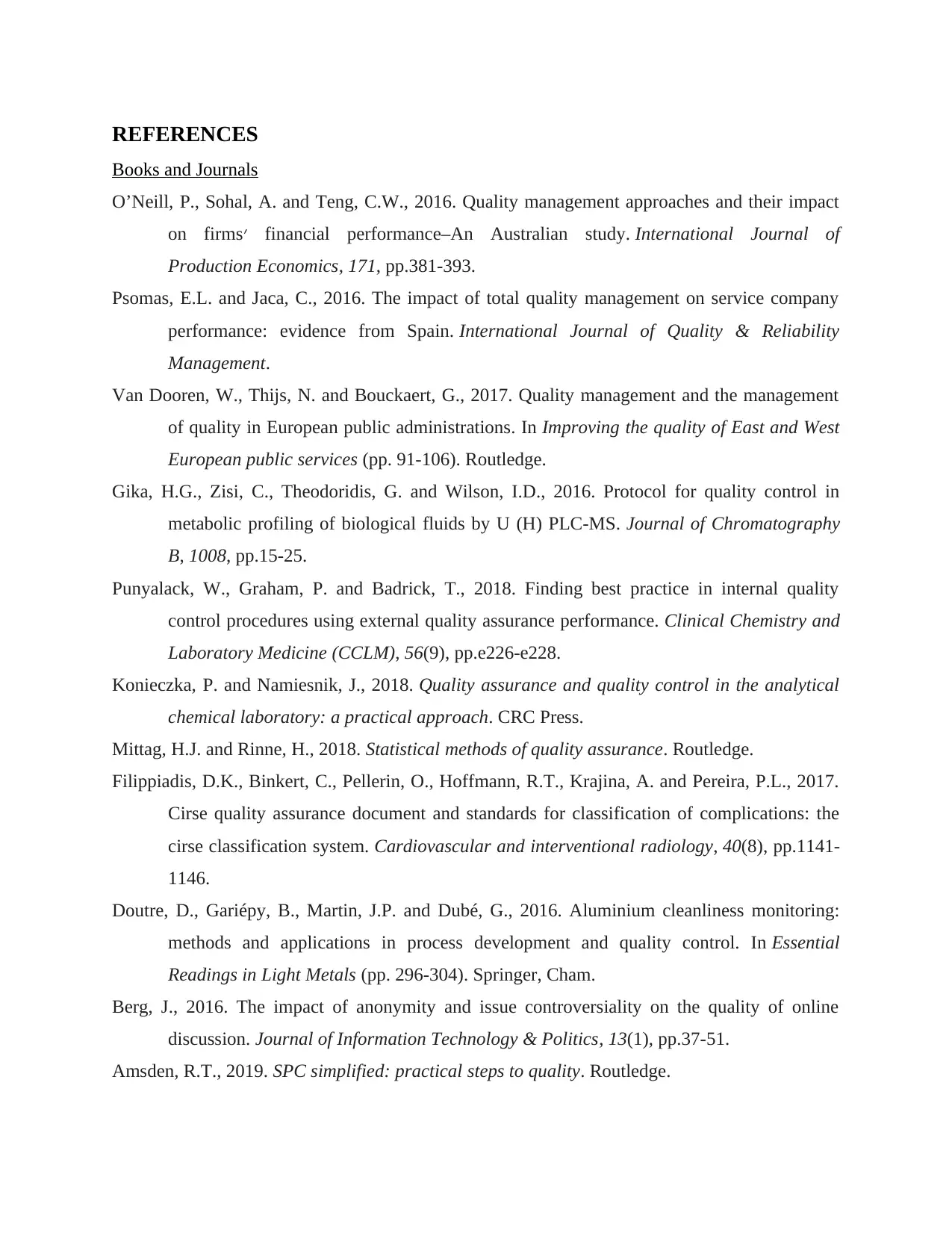
REFERENCES
Books and Journals
O’Neill, P., Sohal, A. and Teng, C.W., 2016. Quality management approaches and their impact
on firms׳ financial performance–An Australian study. International Journal of
Production Economics, 171, pp.381-393.
Psomas, E.L. and Jaca, C., 2016. The impact of total quality management on service company
performance: evidence from Spain. International Journal of Quality & Reliability
Management.
Van Dooren, W., Thijs, N. and Bouckaert, G., 2017. Quality management and the management
of quality in European public administrations. In Improving the quality of East and West
European public services (pp. 91-106). Routledge.
Gika, H.G., Zisi, C., Theodoridis, G. and Wilson, I.D., 2016. Protocol for quality control in
metabolic profiling of biological fluids by U (H) PLC-MS. Journal of Chromatography
B, 1008, pp.15-25.
Punyalack, W., Graham, P. and Badrick, T., 2018. Finding best practice in internal quality
control procedures using external quality assurance performance. Clinical Chemistry and
Laboratory Medicine (CCLM), 56(9), pp.e226-e228.
Konieczka, P. and Namiesnik, J., 2018. Quality assurance and quality control in the analytical
chemical laboratory: a practical approach. CRC Press.
Mittag, H.J. and Rinne, H., 2018. Statistical methods of quality assurance. Routledge.
Filippiadis, D.K., Binkert, C., Pellerin, O., Hoffmann, R.T., Krajina, A. and Pereira, P.L., 2017.
Cirse quality assurance document and standards for classification of complications: the
cirse classification system. Cardiovascular and interventional radiology, 40(8), pp.1141-
1146.
Doutre, D., Gariépy, B., Martin, J.P. and Dubé, G., 2016. Aluminium cleanliness monitoring:
methods and applications in process development and quality control. In Essential
Readings in Light Metals (pp. 296-304). Springer, Cham.
Berg, J., 2016. The impact of anonymity and issue controversiality on the quality of online
discussion. Journal of Information Technology & Politics, 13(1), pp.37-51.
Amsden, R.T., 2019. SPC simplified: practical steps to quality. Routledge.
Books and Journals
O’Neill, P., Sohal, A. and Teng, C.W., 2016. Quality management approaches and their impact
on firms׳ financial performance–An Australian study. International Journal of
Production Economics, 171, pp.381-393.
Psomas, E.L. and Jaca, C., 2016. The impact of total quality management on service company
performance: evidence from Spain. International Journal of Quality & Reliability
Management.
Van Dooren, W., Thijs, N. and Bouckaert, G., 2017. Quality management and the management
of quality in European public administrations. In Improving the quality of East and West
European public services (pp. 91-106). Routledge.
Gika, H.G., Zisi, C., Theodoridis, G. and Wilson, I.D., 2016. Protocol for quality control in
metabolic profiling of biological fluids by U (H) PLC-MS. Journal of Chromatography
B, 1008, pp.15-25.
Punyalack, W., Graham, P. and Badrick, T., 2018. Finding best practice in internal quality
control procedures using external quality assurance performance. Clinical Chemistry and
Laboratory Medicine (CCLM), 56(9), pp.e226-e228.
Konieczka, P. and Namiesnik, J., 2018. Quality assurance and quality control in the analytical
chemical laboratory: a practical approach. CRC Press.
Mittag, H.J. and Rinne, H., 2018. Statistical methods of quality assurance. Routledge.
Filippiadis, D.K., Binkert, C., Pellerin, O., Hoffmann, R.T., Krajina, A. and Pereira, P.L., 2017.
Cirse quality assurance document and standards for classification of complications: the
cirse classification system. Cardiovascular and interventional radiology, 40(8), pp.1141-
1146.
Doutre, D., Gariépy, B., Martin, J.P. and Dubé, G., 2016. Aluminium cleanliness monitoring:
methods and applications in process development and quality control. In Essential
Readings in Light Metals (pp. 296-304). Springer, Cham.
Berg, J., 2016. The impact of anonymity and issue controversiality on the quality of online
discussion. Journal of Information Technology & Politics, 13(1), pp.37-51.
Amsden, R.T., 2019. SPC simplified: practical steps to quality. Routledge.
1 out of 11
Related Documents

Your All-in-One AI-Powered Toolkit for Academic Success.
+13062052269
info@desklib.com
Available 24*7 on WhatsApp / Email
Unlock your academic potential
© 2024 | Zucol Services PVT LTD | All rights reserved.