Quality Management Strategies for Organisational Excellence Report
VerifiedAdded on 2023/01/12
|11
|3564
|44
Report
AI Summary
This report provides a detailed analysis of quality management strategies, tools, and techniques applicable to Quality Tooling Company (QTC), a manufacturer of precision engineering and medical equipment. It explores the importance of quality in attracting customers and gaining a competitive advantage, focusing on Total Quality Management (TQM) principles such as customer satisfaction, employee commitment, and continuous improvement. The report also examines Quality Assurance (QA) methods, including failure testing, statistical process control, and TQM, as well as the significance of ISO 9000 certification. Furthermore, it discusses Quality Control (QC) tools like checklists, control charts, and histograms. The report offers recommendations for QTC to effectively implement these strategies, fostering a culture of quality to sustain its market position and meet the demands of the medical and engineering sectors. The assignment is a case study report that analyzes the QTC and suggests improvement strategies.
Contribute Materials
Your contribution can guide someone’s learning journey. Share your
documents today.
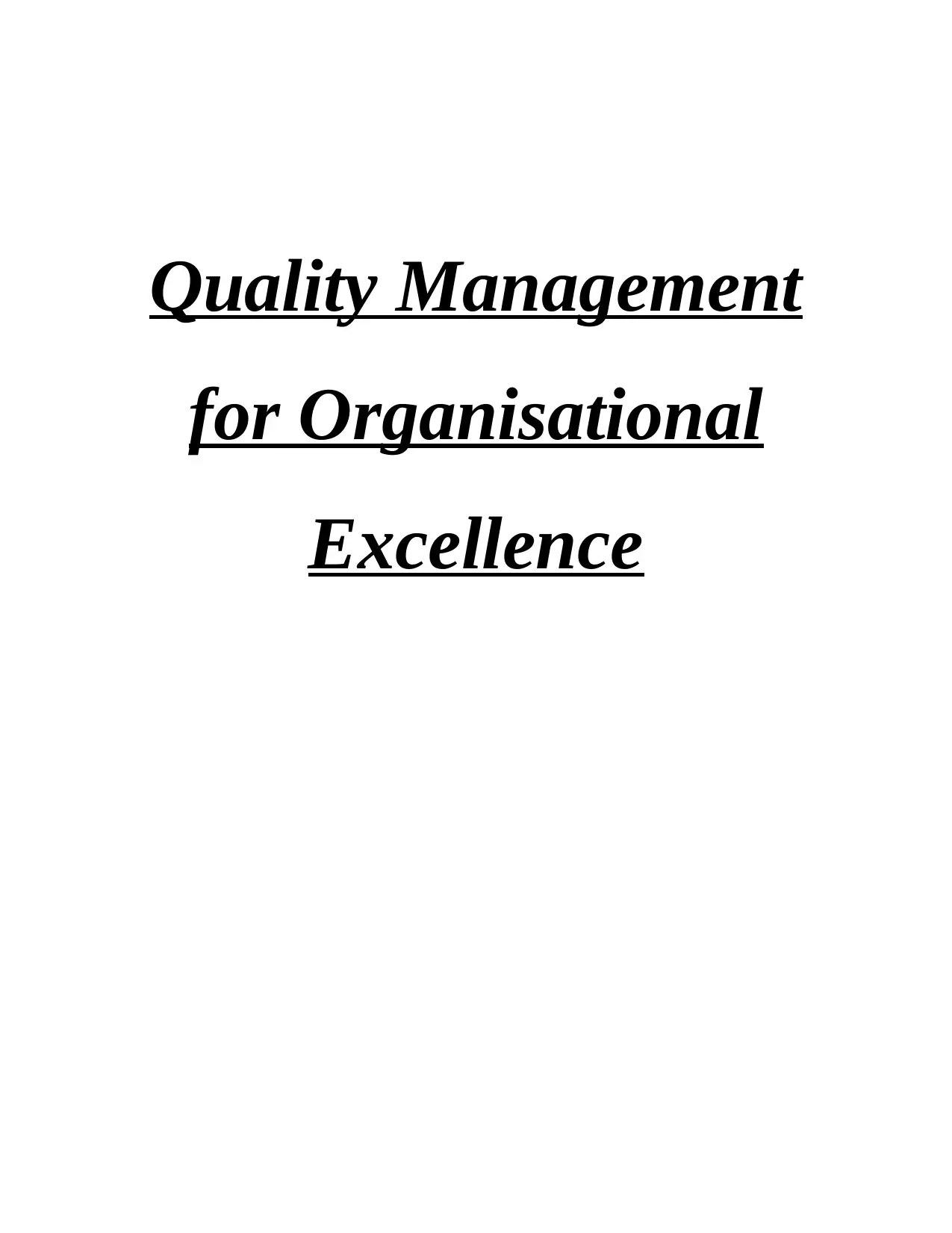
Quality Management
for Organisational
Excellence
for Organisational
Excellence
Secure Best Marks with AI Grader
Need help grading? Try our AI Grader for instant feedback on your assignments.
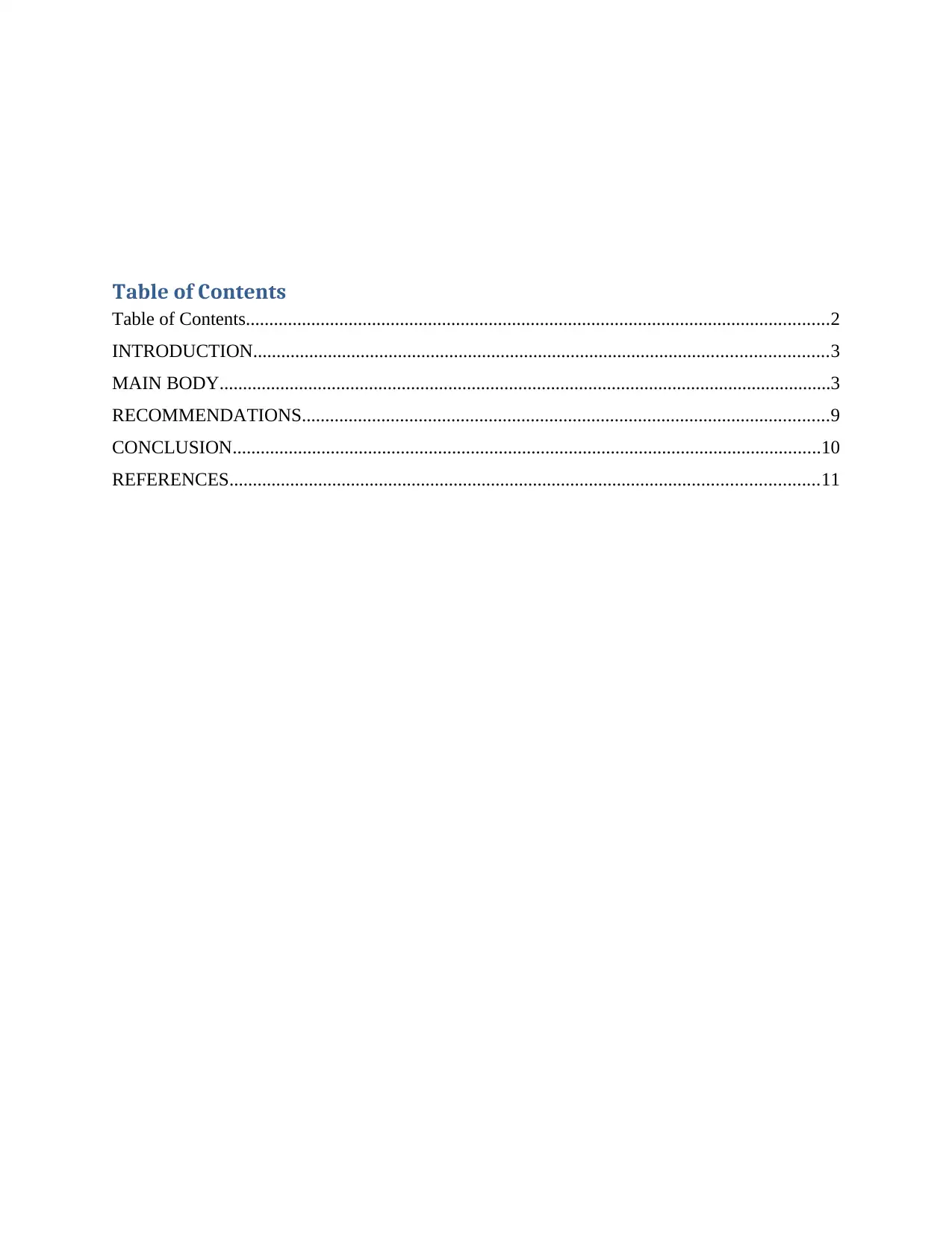
Table of Contents
Table of Contents.............................................................................................................................2
INTRODUCTION...........................................................................................................................3
MAIN BODY...................................................................................................................................3
RECOMMENDATIONS.................................................................................................................9
CONCLUSION..............................................................................................................................10
REFERENCES..............................................................................................................................11
Table of Contents.............................................................................................................................2
INTRODUCTION...........................................................................................................................3
MAIN BODY...................................................................................................................................3
RECOMMENDATIONS.................................................................................................................9
CONCLUSION..............................................................................................................................10
REFERENCES..............................................................................................................................11
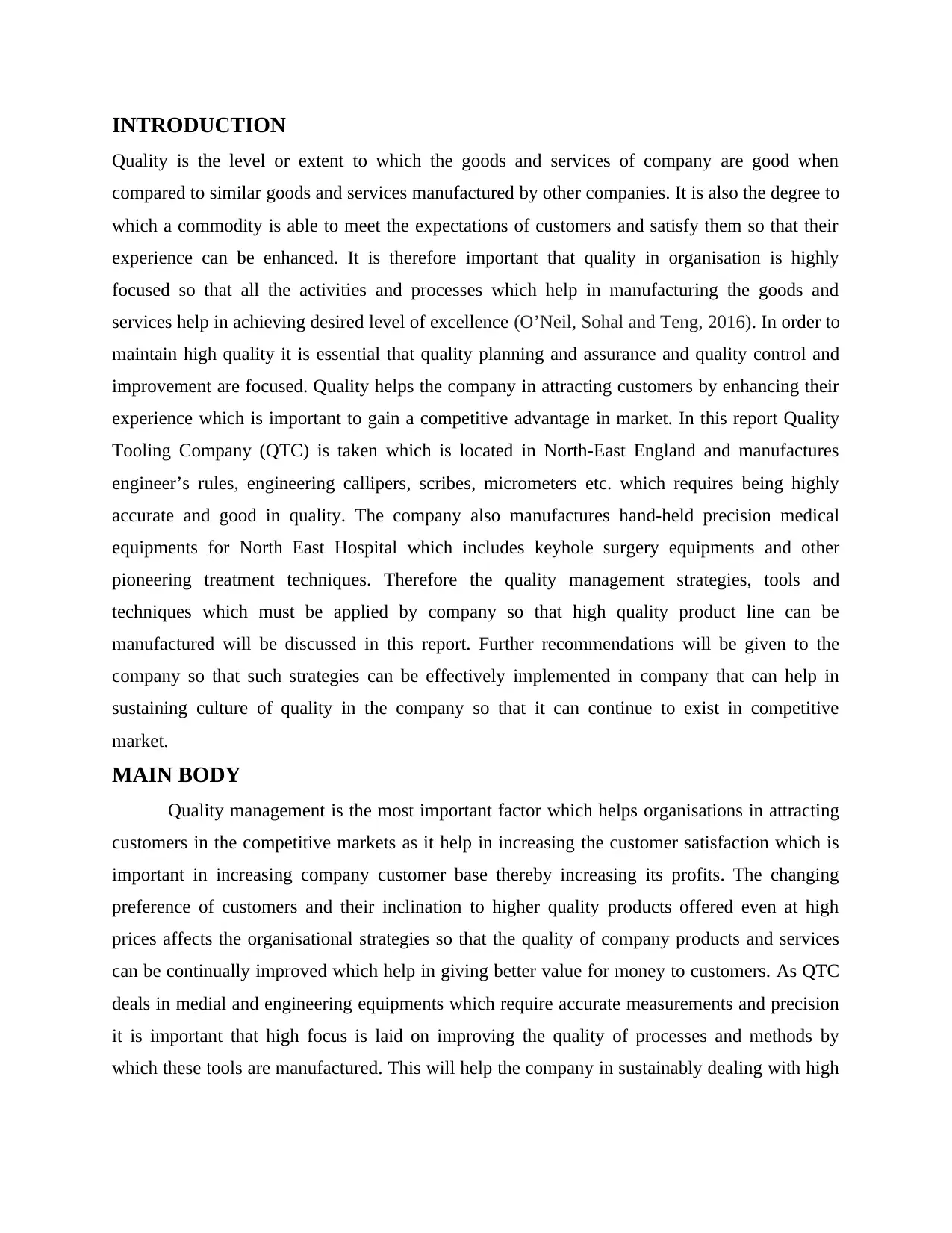
INTRODUCTION
Quality is the level or extent to which the goods and services of company are good when
compared to similar goods and services manufactured by other companies. It is also the degree to
which a commodity is able to meet the expectations of customers and satisfy them so that their
experience can be enhanced. It is therefore important that quality in organisation is highly
focused so that all the activities and processes which help in manufacturing the goods and
services help in achieving desired level of excellence (O’Neil, Sohal and Teng, 2016). In order to
maintain high quality it is essential that quality planning and assurance and quality control and
improvement are focused. Quality helps the company in attracting customers by enhancing their
experience which is important to gain a competitive advantage in market. In this report Quality
Tooling Company (QTC) is taken which is located in North-East England and manufactures
engineer’s rules, engineering callipers, scribes, micrometers etc. which requires being highly
accurate and good in quality. The company also manufactures hand-held precision medical
equipments for North East Hospital which includes keyhole surgery equipments and other
pioneering treatment techniques. Therefore the quality management strategies, tools and
techniques which must be applied by company so that high quality product line can be
manufactured will be discussed in this report. Further recommendations will be given to the
company so that such strategies can be effectively implemented in company that can help in
sustaining culture of quality in the company so that it can continue to exist in competitive
market.
MAIN BODY
Quality management is the most important factor which helps organisations in attracting
customers in the competitive markets as it help in increasing the customer satisfaction which is
important in increasing company customer base thereby increasing its profits. The changing
preference of customers and their inclination to higher quality products offered even at high
prices affects the organisational strategies so that the quality of company products and services
can be continually improved which help in giving better value for money to customers. As QTC
deals in medial and engineering equipments which require accurate measurements and precision
it is important that high focus is laid on improving the quality of processes and methods by
which these tools are manufactured. This will help the company in sustainably dealing with high
Quality is the level or extent to which the goods and services of company are good when
compared to similar goods and services manufactured by other companies. It is also the degree to
which a commodity is able to meet the expectations of customers and satisfy them so that their
experience can be enhanced. It is therefore important that quality in organisation is highly
focused so that all the activities and processes which help in manufacturing the goods and
services help in achieving desired level of excellence (O’Neil, Sohal and Teng, 2016). In order to
maintain high quality it is essential that quality planning and assurance and quality control and
improvement are focused. Quality helps the company in attracting customers by enhancing their
experience which is important to gain a competitive advantage in market. In this report Quality
Tooling Company (QTC) is taken which is located in North-East England and manufactures
engineer’s rules, engineering callipers, scribes, micrometers etc. which requires being highly
accurate and good in quality. The company also manufactures hand-held precision medical
equipments for North East Hospital which includes keyhole surgery equipments and other
pioneering treatment techniques. Therefore the quality management strategies, tools and
techniques which must be applied by company so that high quality product line can be
manufactured will be discussed in this report. Further recommendations will be given to the
company so that such strategies can be effectively implemented in company that can help in
sustaining culture of quality in the company so that it can continue to exist in competitive
market.
MAIN BODY
Quality management is the most important factor which helps organisations in attracting
customers in the competitive markets as it help in increasing the customer satisfaction which is
important in increasing company customer base thereby increasing its profits. The changing
preference of customers and their inclination to higher quality products offered even at high
prices affects the organisational strategies so that the quality of company products and services
can be continually improved which help in giving better value for money to customers. As QTC
deals in medial and engineering equipments which require accurate measurements and precision
it is important that high focus is laid on improving the quality of processes and methods by
which these tools are manufactured. This will help the company in sustainably dealing with high
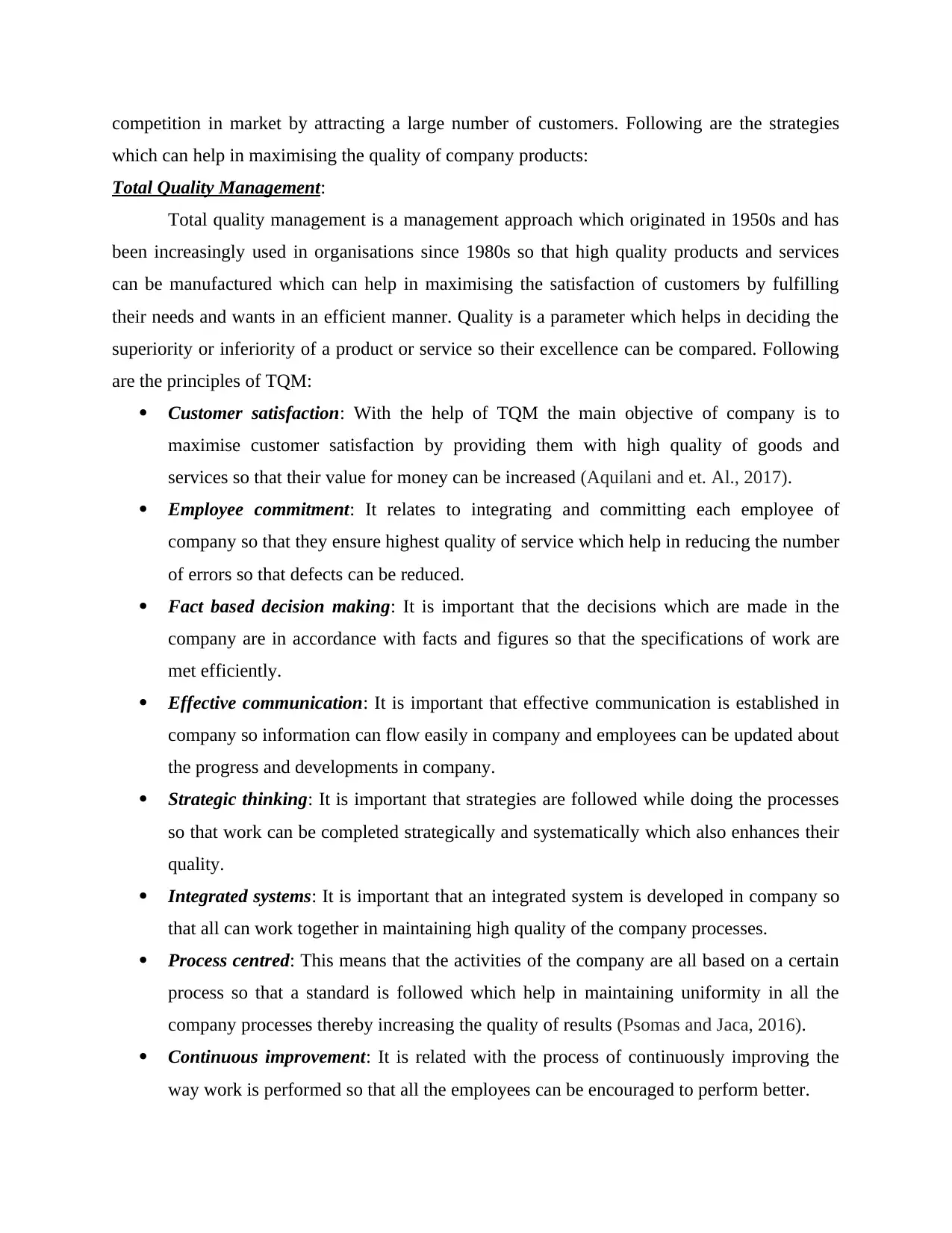
competition in market by attracting a large number of customers. Following are the strategies
which can help in maximising the quality of company products:
Total Quality Management:
Total quality management is a management approach which originated in 1950s and has
been increasingly used in organisations since 1980s so that high quality products and services
can be manufactured which can help in maximising the satisfaction of customers by fulfilling
their needs and wants in an efficient manner. Quality is a parameter which helps in deciding the
superiority or inferiority of a product or service so their excellence can be compared. Following
are the principles of TQM:
Customer satisfaction: With the help of TQM the main objective of company is to
maximise customer satisfaction by providing them with high quality of goods and
services so that their value for money can be increased (Aquilani and et. Al., 2017).
Employee commitment: It relates to integrating and committing each employee of
company so that they ensure highest quality of service which help in reducing the number
of errors so that defects can be reduced.
Fact based decision making: It is important that the decisions which are made in the
company are in accordance with facts and figures so that the specifications of work are
met efficiently.
Effective communication: It is important that effective communication is established in
company so information can flow easily in company and employees can be updated about
the progress and developments in company.
Strategic thinking: It is important that strategies are followed while doing the processes
so that work can be completed strategically and systematically which also enhances their
quality.
Integrated systems: It is important that an integrated system is developed in company so
that all can work together in maintaining high quality of the company processes.
Process centred: This means that the activities of the company are all based on a certain
process so that a standard is followed which help in maintaining uniformity in all the
company processes thereby increasing the quality of results (Psomas and Jaca, 2016).
Continuous improvement: It is related with the process of continuously improving the
way work is performed so that all the employees can be encouraged to perform better.
which can help in maximising the quality of company products:
Total Quality Management:
Total quality management is a management approach which originated in 1950s and has
been increasingly used in organisations since 1980s so that high quality products and services
can be manufactured which can help in maximising the satisfaction of customers by fulfilling
their needs and wants in an efficient manner. Quality is a parameter which helps in deciding the
superiority or inferiority of a product or service so their excellence can be compared. Following
are the principles of TQM:
Customer satisfaction: With the help of TQM the main objective of company is to
maximise customer satisfaction by providing them with high quality of goods and
services so that their value for money can be increased (Aquilani and et. Al., 2017).
Employee commitment: It relates to integrating and committing each employee of
company so that they ensure highest quality of service which help in reducing the number
of errors so that defects can be reduced.
Fact based decision making: It is important that the decisions which are made in the
company are in accordance with facts and figures so that the specifications of work are
met efficiently.
Effective communication: It is important that effective communication is established in
company so information can flow easily in company and employees can be updated about
the progress and developments in company.
Strategic thinking: It is important that strategies are followed while doing the processes
so that work can be completed strategically and systematically which also enhances their
quality.
Integrated systems: It is important that an integrated system is developed in company so
that all can work together in maintaining high quality of the company processes.
Process centred: This means that the activities of the company are all based on a certain
process so that a standard is followed which help in maintaining uniformity in all the
company processes thereby increasing the quality of results (Psomas and Jaca, 2016).
Continuous improvement: It is related with the process of continuously improving the
way work is performed so that all the employees can be encouraged to perform better.
Secure Best Marks with AI Grader
Need help grading? Try our AI Grader for instant feedback on your assignments.
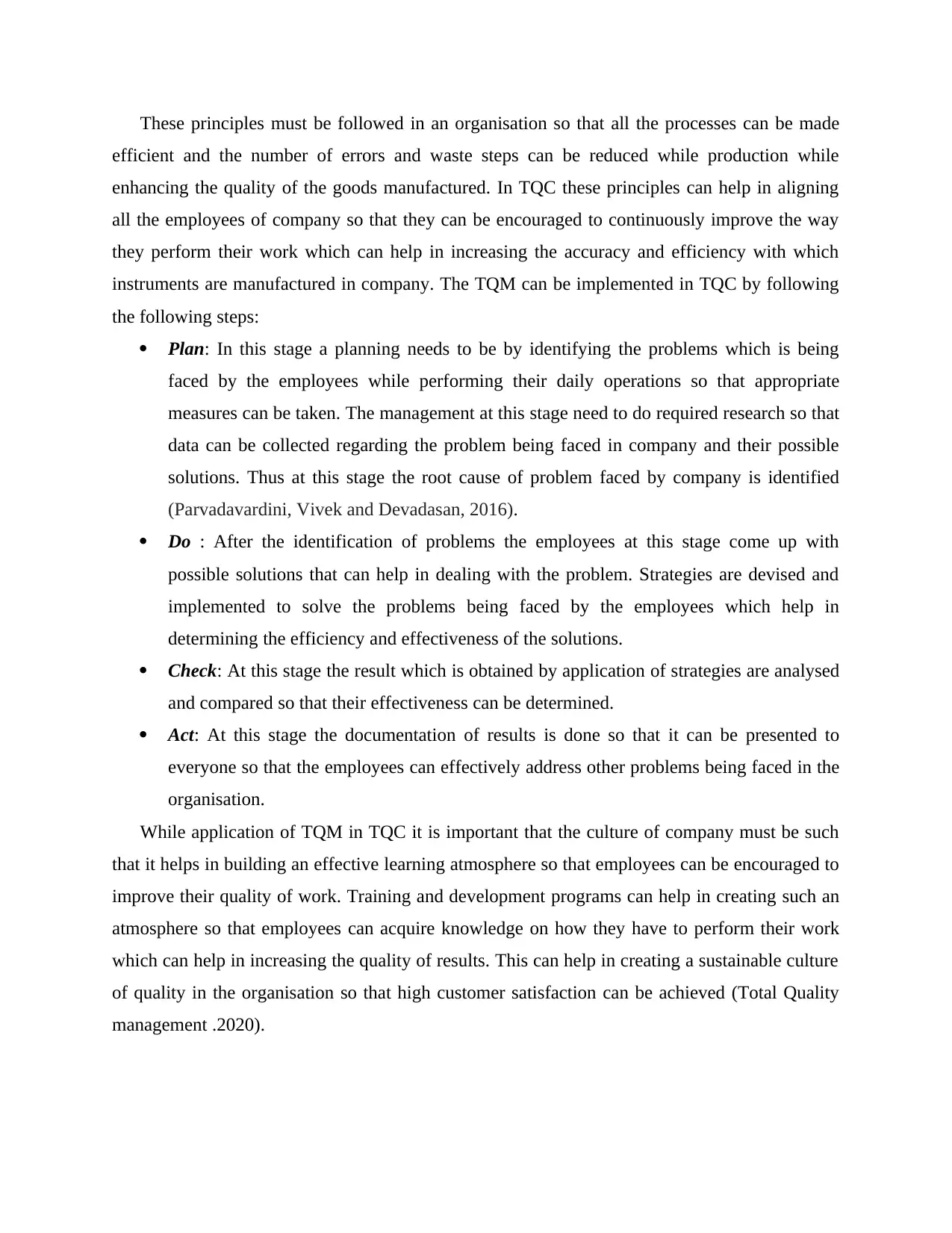
These principles must be followed in an organisation so that all the processes can be made
efficient and the number of errors and waste steps can be reduced while production while
enhancing the quality of the goods manufactured. In TQC these principles can help in aligning
all the employees of company so that they can be encouraged to continuously improve the way
they perform their work which can help in increasing the accuracy and efficiency with which
instruments are manufactured in company. The TQM can be implemented in TQC by following
the following steps:
Plan: In this stage a planning needs to be by identifying the problems which is being
faced by the employees while performing their daily operations so that appropriate
measures can be taken. The management at this stage need to do required research so that
data can be collected regarding the problem being faced in company and their possible
solutions. Thus at this stage the root cause of problem faced by company is identified
(Parvadavardini, Vivek and Devadasan, 2016).
Do : After the identification of problems the employees at this stage come up with
possible solutions that can help in dealing with the problem. Strategies are devised and
implemented to solve the problems being faced by the employees which help in
determining the efficiency and effectiveness of the solutions.
Check: At this stage the result which is obtained by application of strategies are analysed
and compared so that their effectiveness can be determined.
Act: At this stage the documentation of results is done so that it can be presented to
everyone so that the employees can effectively address other problems being faced in the
organisation.
While application of TQM in TQC it is important that the culture of company must be such
that it helps in building an effective learning atmosphere so that employees can be encouraged to
improve their quality of work. Training and development programs can help in creating such an
atmosphere so that employees can acquire knowledge on how they have to perform their work
which can help in increasing the quality of results. This can help in creating a sustainable culture
of quality in the organisation so that high customer satisfaction can be achieved (Total Quality
management .2020).
efficient and the number of errors and waste steps can be reduced while production while
enhancing the quality of the goods manufactured. In TQC these principles can help in aligning
all the employees of company so that they can be encouraged to continuously improve the way
they perform their work which can help in increasing the accuracy and efficiency with which
instruments are manufactured in company. The TQM can be implemented in TQC by following
the following steps:
Plan: In this stage a planning needs to be by identifying the problems which is being
faced by the employees while performing their daily operations so that appropriate
measures can be taken. The management at this stage need to do required research so that
data can be collected regarding the problem being faced in company and their possible
solutions. Thus at this stage the root cause of problem faced by company is identified
(Parvadavardini, Vivek and Devadasan, 2016).
Do : After the identification of problems the employees at this stage come up with
possible solutions that can help in dealing with the problem. Strategies are devised and
implemented to solve the problems being faced by the employees which help in
determining the efficiency and effectiveness of the solutions.
Check: At this stage the result which is obtained by application of strategies are analysed
and compared so that their effectiveness can be determined.
Act: At this stage the documentation of results is done so that it can be presented to
everyone so that the employees can effectively address other problems being faced in the
organisation.
While application of TQM in TQC it is important that the culture of company must be such
that it helps in building an effective learning atmosphere so that employees can be encouraged to
improve their quality of work. Training and development programs can help in creating such an
atmosphere so that employees can acquire knowledge on how they have to perform their work
which can help in increasing the quality of results. This can help in creating a sustainable culture
of quality in the organisation so that high customer satisfaction can be achieved (Total Quality
management .2020).
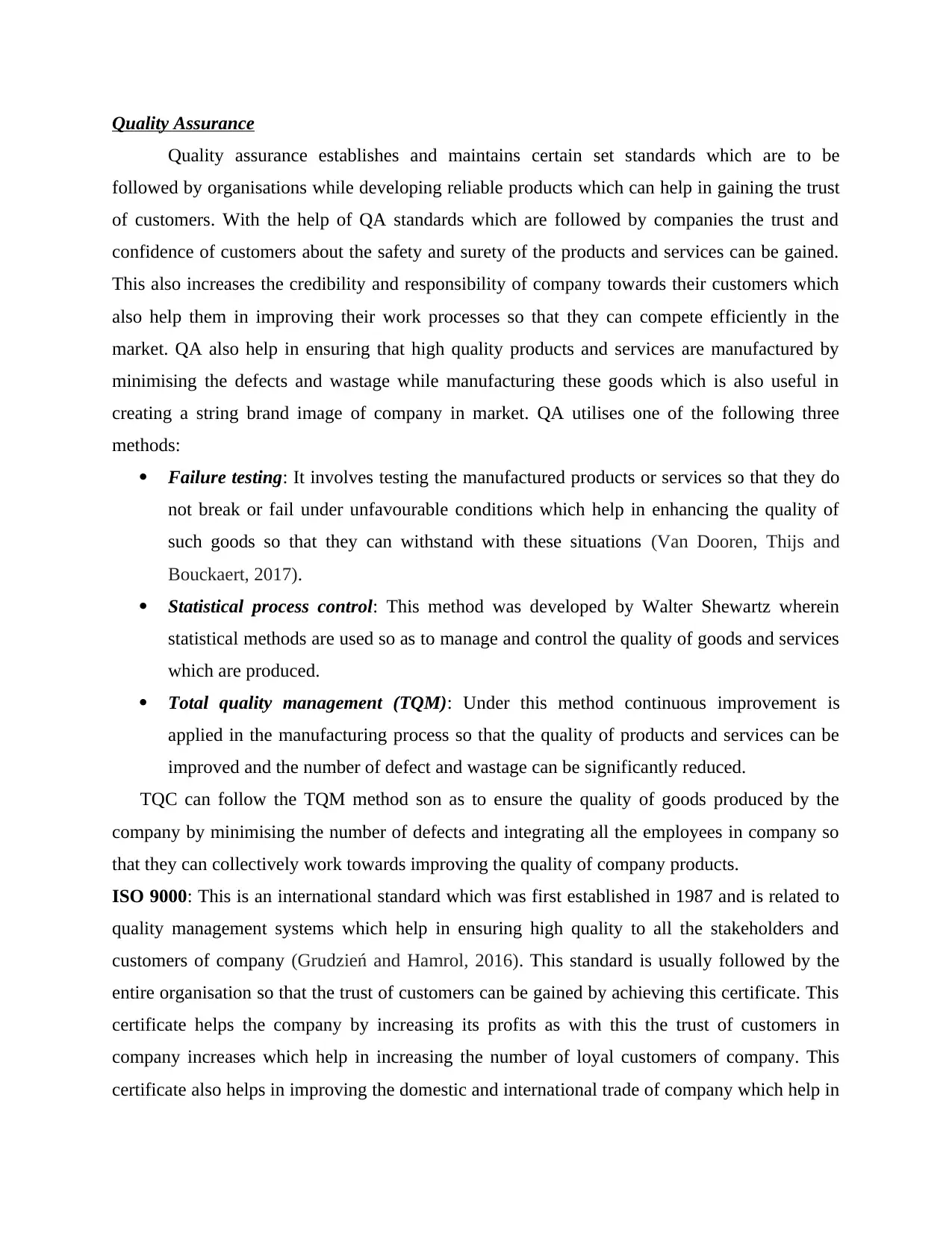
Quality Assurance
Quality assurance establishes and maintains certain set standards which are to be
followed by organisations while developing reliable products which can help in gaining the trust
of customers. With the help of QA standards which are followed by companies the trust and
confidence of customers about the safety and surety of the products and services can be gained.
This also increases the credibility and responsibility of company towards their customers which
also help them in improving their work processes so that they can compete efficiently in the
market. QA also help in ensuring that high quality products and services are manufactured by
minimising the defects and wastage while manufacturing these goods which is also useful in
creating a string brand image of company in market. QA utilises one of the following three
methods:
Failure testing: It involves testing the manufactured products or services so that they do
not break or fail under unfavourable conditions which help in enhancing the quality of
such goods so that they can withstand with these situations (Van Dooren, Thijs and
Bouckaert, 2017).
Statistical process control: This method was developed by Walter Shewartz wherein
statistical methods are used so as to manage and control the quality of goods and services
which are produced.
Total quality management (TQM): Under this method continuous improvement is
applied in the manufacturing process so that the quality of products and services can be
improved and the number of defect and wastage can be significantly reduced.
TQC can follow the TQM method son as to ensure the quality of goods produced by the
company by minimising the number of defects and integrating all the employees in company so
that they can collectively work towards improving the quality of company products.
ISO 9000: This is an international standard which was first established in 1987 and is related to
quality management systems which help in ensuring high quality to all the stakeholders and
customers of company (Grudzień and Hamrol, 2016). This standard is usually followed by the
entire organisation so that the trust of customers can be gained by achieving this certificate. This
certificate helps the company by increasing its profits as with this the trust of customers in
company increases which help in increasing the number of loyal customers of company. This
certificate also helps in improving the domestic and international trade of company which help in
Quality assurance establishes and maintains certain set standards which are to be
followed by organisations while developing reliable products which can help in gaining the trust
of customers. With the help of QA standards which are followed by companies the trust and
confidence of customers about the safety and surety of the products and services can be gained.
This also increases the credibility and responsibility of company towards their customers which
also help them in improving their work processes so that they can compete efficiently in the
market. QA also help in ensuring that high quality products and services are manufactured by
minimising the defects and wastage while manufacturing these goods which is also useful in
creating a string brand image of company in market. QA utilises one of the following three
methods:
Failure testing: It involves testing the manufactured products or services so that they do
not break or fail under unfavourable conditions which help in enhancing the quality of
such goods so that they can withstand with these situations (Van Dooren, Thijs and
Bouckaert, 2017).
Statistical process control: This method was developed by Walter Shewartz wherein
statistical methods are used so as to manage and control the quality of goods and services
which are produced.
Total quality management (TQM): Under this method continuous improvement is
applied in the manufacturing process so that the quality of products and services can be
improved and the number of defect and wastage can be significantly reduced.
TQC can follow the TQM method son as to ensure the quality of goods produced by the
company by minimising the number of defects and integrating all the employees in company so
that they can collectively work towards improving the quality of company products.
ISO 9000: This is an international standard which was first established in 1987 and is related to
quality management systems which help in ensuring high quality to all the stakeholders and
customers of company (Grudzień and Hamrol, 2016). This standard is usually followed by the
entire organisation so that the trust of customers can be gained by achieving this certificate. This
certificate helps the company by increasing its profits as with this the trust of customers in
company increases which help in increasing the number of loyal customers of company. This
certificate also helps in improving the domestic and international trade of company which help in
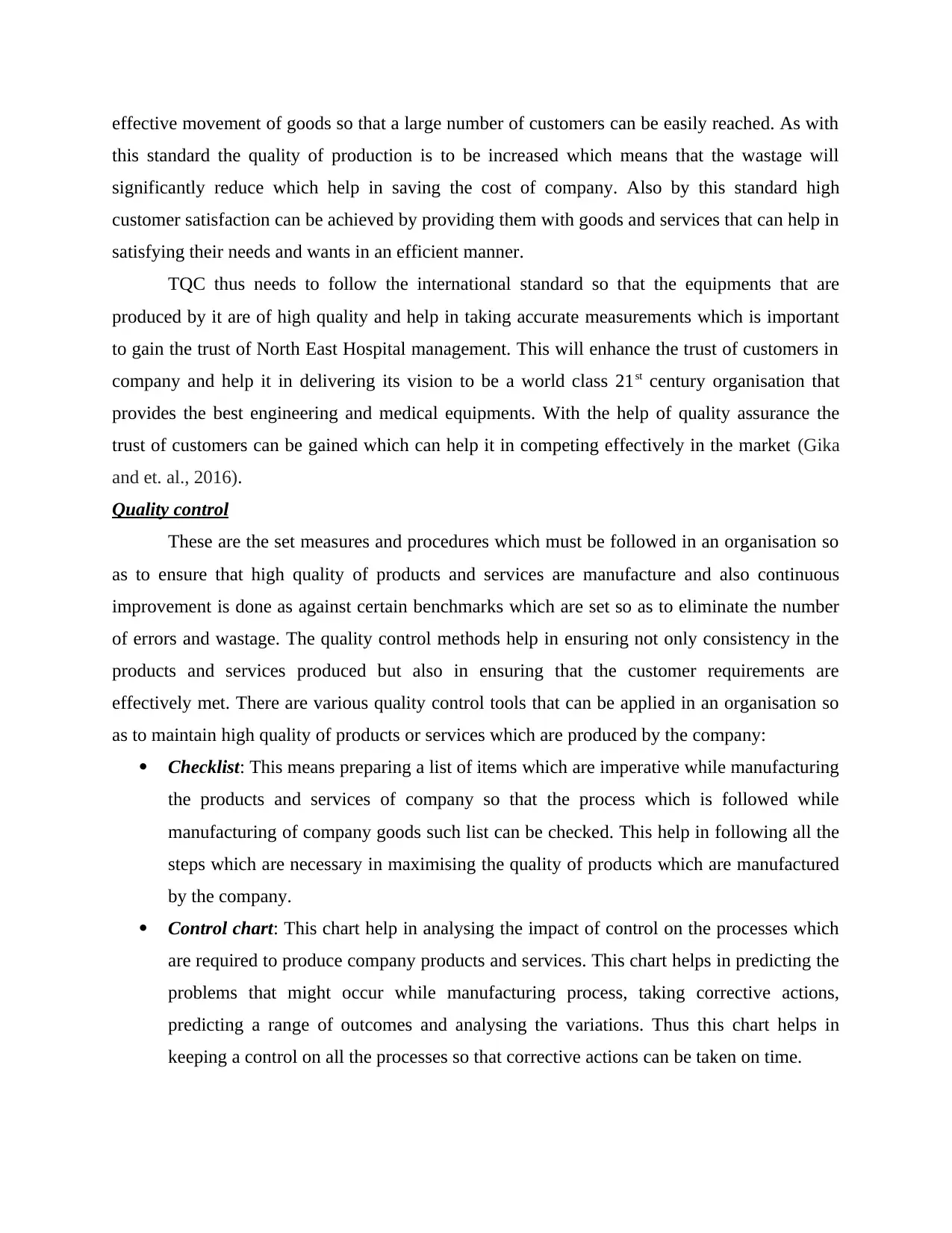
effective movement of goods so that a large number of customers can be easily reached. As with
this standard the quality of production is to be increased which means that the wastage will
significantly reduce which help in saving the cost of company. Also by this standard high
customer satisfaction can be achieved by providing them with goods and services that can help in
satisfying their needs and wants in an efficient manner.
TQC thus needs to follow the international standard so that the equipments that are
produced by it are of high quality and help in taking accurate measurements which is important
to gain the trust of North East Hospital management. This will enhance the trust of customers in
company and help it in delivering its vision to be a world class 21st century organisation that
provides the best engineering and medical equipments. With the help of quality assurance the
trust of customers can be gained which can help it in competing effectively in the market (Gika
and et. al., 2016).
Quality control
These are the set measures and procedures which must be followed in an organisation so
as to ensure that high quality of products and services are manufacture and also continuous
improvement is done as against certain benchmarks which are set so as to eliminate the number
of errors and wastage. The quality control methods help in ensuring not only consistency in the
products and services produced but also in ensuring that the customer requirements are
effectively met. There are various quality control tools that can be applied in an organisation so
as to maintain high quality of products or services which are produced by the company:
Checklist: This means preparing a list of items which are imperative while manufacturing
the products and services of company so that the process which is followed while
manufacturing of company goods such list can be checked. This help in following all the
steps which are necessary in maximising the quality of products which are manufactured
by the company.
Control chart: This chart help in analysing the impact of control on the processes which
are required to produce company products and services. This chart helps in predicting the
problems that might occur while manufacturing process, taking corrective actions,
predicting a range of outcomes and analysing the variations. Thus this chart helps in
keeping a control on all the processes so that corrective actions can be taken on time.
this standard the quality of production is to be increased which means that the wastage will
significantly reduce which help in saving the cost of company. Also by this standard high
customer satisfaction can be achieved by providing them with goods and services that can help in
satisfying their needs and wants in an efficient manner.
TQC thus needs to follow the international standard so that the equipments that are
produced by it are of high quality and help in taking accurate measurements which is important
to gain the trust of North East Hospital management. This will enhance the trust of customers in
company and help it in delivering its vision to be a world class 21st century organisation that
provides the best engineering and medical equipments. With the help of quality assurance the
trust of customers can be gained which can help it in competing effectively in the market (Gika
and et. al., 2016).
Quality control
These are the set measures and procedures which must be followed in an organisation so
as to ensure that high quality of products and services are manufacture and also continuous
improvement is done as against certain benchmarks which are set so as to eliminate the number
of errors and wastage. The quality control methods help in ensuring not only consistency in the
products and services produced but also in ensuring that the customer requirements are
effectively met. There are various quality control tools that can be applied in an organisation so
as to maintain high quality of products or services which are produced by the company:
Checklist: This means preparing a list of items which are imperative while manufacturing
the products and services of company so that the process which is followed while
manufacturing of company goods such list can be checked. This help in following all the
steps which are necessary in maximising the quality of products which are manufactured
by the company.
Control chart: This chart help in analysing the impact of control on the processes which
are required to produce company products and services. This chart helps in predicting the
problems that might occur while manufacturing process, taking corrective actions,
predicting a range of outcomes and analysing the variations. Thus this chart helps in
keeping a control on all the processes so that corrective actions can be taken on time.
Paraphrase This Document
Need a fresh take? Get an instant paraphrase of this document with our AI Paraphraser
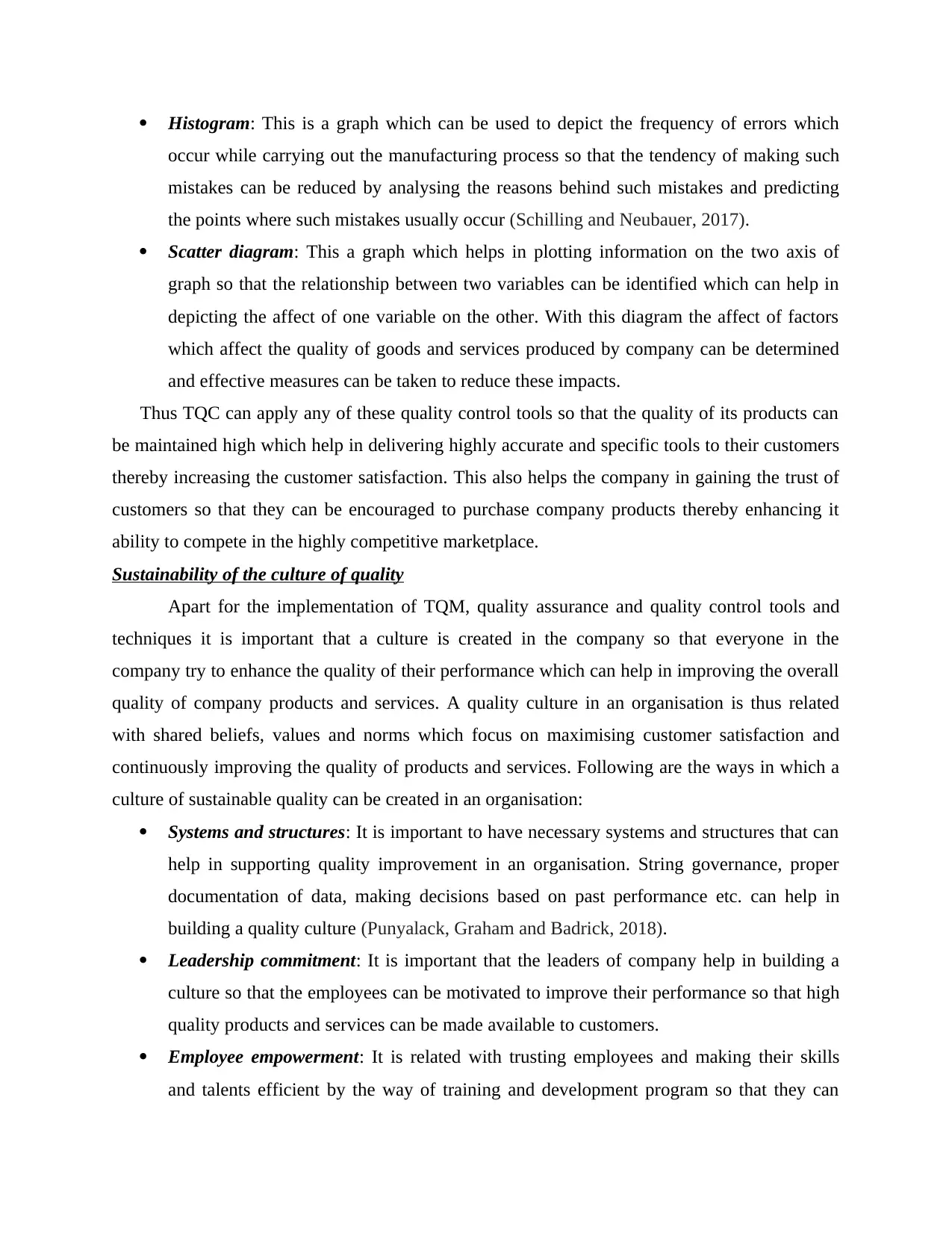
Histogram: This is a graph which can be used to depict the frequency of errors which
occur while carrying out the manufacturing process so that the tendency of making such
mistakes can be reduced by analysing the reasons behind such mistakes and predicting
the points where such mistakes usually occur (Schilling and Neubauer, 2017).
Scatter diagram: This a graph which helps in plotting information on the two axis of
graph so that the relationship between two variables can be identified which can help in
depicting the affect of one variable on the other. With this diagram the affect of factors
which affect the quality of goods and services produced by company can be determined
and effective measures can be taken to reduce these impacts.
Thus TQC can apply any of these quality control tools so that the quality of its products can
be maintained high which help in delivering highly accurate and specific tools to their customers
thereby increasing the customer satisfaction. This also helps the company in gaining the trust of
customers so that they can be encouraged to purchase company products thereby enhancing it
ability to compete in the highly competitive marketplace.
Sustainability of the culture of quality
Apart for the implementation of TQM, quality assurance and quality control tools and
techniques it is important that a culture is created in the company so that everyone in the
company try to enhance the quality of their performance which can help in improving the overall
quality of company products and services. A quality culture in an organisation is thus related
with shared beliefs, values and norms which focus on maximising customer satisfaction and
continuously improving the quality of products and services. Following are the ways in which a
culture of sustainable quality can be created in an organisation:
Systems and structures: It is important to have necessary systems and structures that can
help in supporting quality improvement in an organisation. String governance, proper
documentation of data, making decisions based on past performance etc. can help in
building a quality culture (Punyalack, Graham and Badrick, 2018).
Leadership commitment: It is important that the leaders of company help in building a
culture so that the employees can be motivated to improve their performance so that high
quality products and services can be made available to customers.
Employee empowerment: It is related with trusting employees and making their skills
and talents efficient by the way of training and development program so that they can
occur while carrying out the manufacturing process so that the tendency of making such
mistakes can be reduced by analysing the reasons behind such mistakes and predicting
the points where such mistakes usually occur (Schilling and Neubauer, 2017).
Scatter diagram: This a graph which helps in plotting information on the two axis of
graph so that the relationship between two variables can be identified which can help in
depicting the affect of one variable on the other. With this diagram the affect of factors
which affect the quality of goods and services produced by company can be determined
and effective measures can be taken to reduce these impacts.
Thus TQC can apply any of these quality control tools so that the quality of its products can
be maintained high which help in delivering highly accurate and specific tools to their customers
thereby increasing the customer satisfaction. This also helps the company in gaining the trust of
customers so that they can be encouraged to purchase company products thereby enhancing it
ability to compete in the highly competitive marketplace.
Sustainability of the culture of quality
Apart for the implementation of TQM, quality assurance and quality control tools and
techniques it is important that a culture is created in the company so that everyone in the
company try to enhance the quality of their performance which can help in improving the overall
quality of company products and services. A quality culture in an organisation is thus related
with shared beliefs, values and norms which focus on maximising customer satisfaction and
continuously improving the quality of products and services. Following are the ways in which a
culture of sustainable quality can be created in an organisation:
Systems and structures: It is important to have necessary systems and structures that can
help in supporting quality improvement in an organisation. String governance, proper
documentation of data, making decisions based on past performance etc. can help in
building a quality culture (Punyalack, Graham and Badrick, 2018).
Leadership commitment: It is important that the leaders of company help in building a
culture so that the employees can be motivated to improve their performance so that high
quality products and services can be made available to customers.
Employee empowerment: It is related with trusting employees and making their skills
and talents efficient by the way of training and development program so that they can
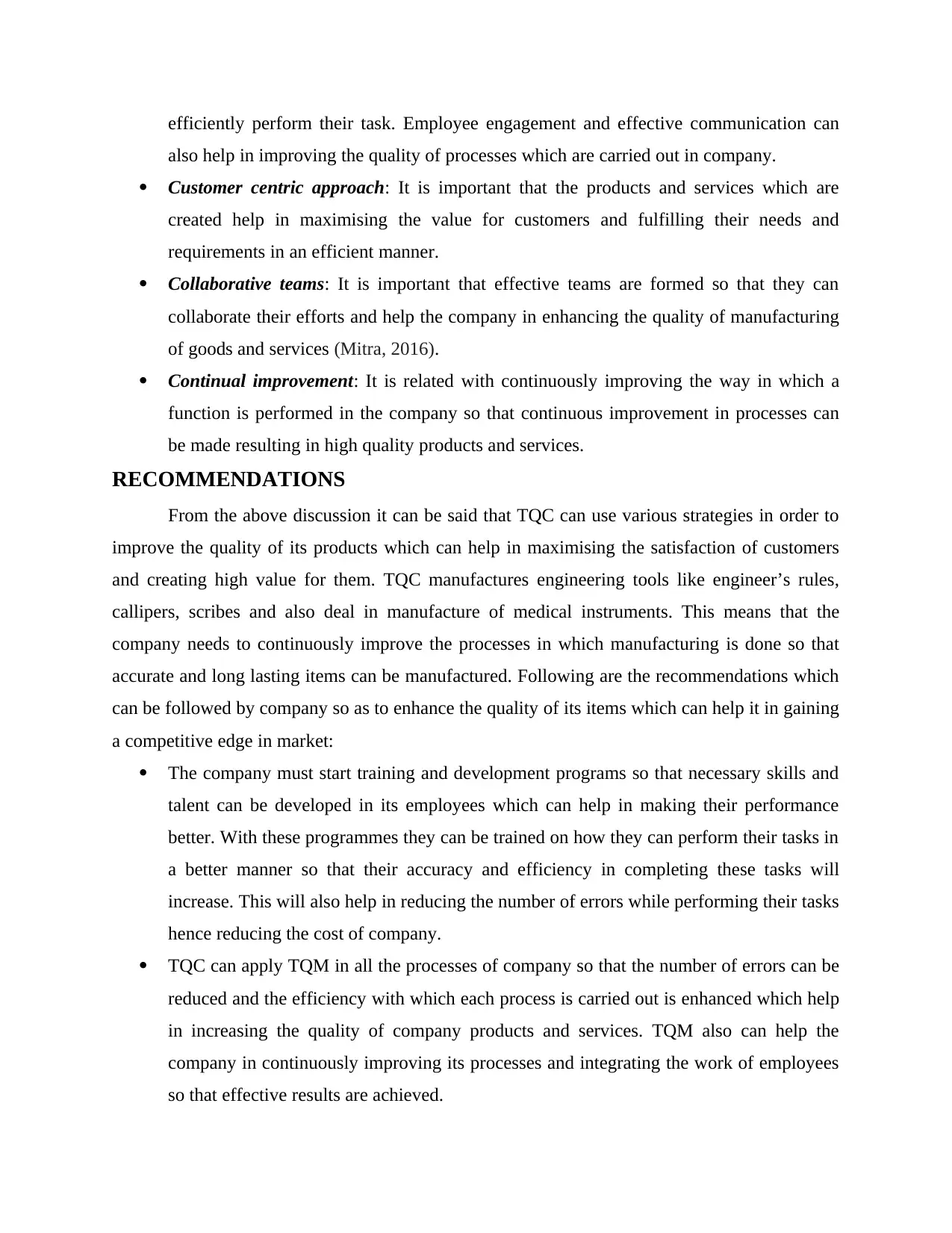
efficiently perform their task. Employee engagement and effective communication can
also help in improving the quality of processes which are carried out in company.
Customer centric approach: It is important that the products and services which are
created help in maximising the value for customers and fulfilling their needs and
requirements in an efficient manner.
Collaborative teams: It is important that effective teams are formed so that they can
collaborate their efforts and help the company in enhancing the quality of manufacturing
of goods and services (Mitra, 2016).
Continual improvement: It is related with continuously improving the way in which a
function is performed in the company so that continuous improvement in processes can
be made resulting in high quality products and services.
RECOMMENDATIONS
From the above discussion it can be said that TQC can use various strategies in order to
improve the quality of its products which can help in maximising the satisfaction of customers
and creating high value for them. TQC manufactures engineering tools like engineer’s rules,
callipers, scribes and also deal in manufacture of medical instruments. This means that the
company needs to continuously improve the processes in which manufacturing is done so that
accurate and long lasting items can be manufactured. Following are the recommendations which
can be followed by company so as to enhance the quality of its items which can help it in gaining
a competitive edge in market:
The company must start training and development programs so that necessary skills and
talent can be developed in its employees which can help in making their performance
better. With these programmes they can be trained on how they can perform their tasks in
a better manner so that their accuracy and efficiency in completing these tasks will
increase. This will also help in reducing the number of errors while performing their tasks
hence reducing the cost of company.
TQC can apply TQM in all the processes of company so that the number of errors can be
reduced and the efficiency with which each process is carried out is enhanced which help
in increasing the quality of company products and services. TQM also can help the
company in continuously improving its processes and integrating the work of employees
so that effective results are achieved.
also help in improving the quality of processes which are carried out in company.
Customer centric approach: It is important that the products and services which are
created help in maximising the value for customers and fulfilling their needs and
requirements in an efficient manner.
Collaborative teams: It is important that effective teams are formed so that they can
collaborate their efforts and help the company in enhancing the quality of manufacturing
of goods and services (Mitra, 2016).
Continual improvement: It is related with continuously improving the way in which a
function is performed in the company so that continuous improvement in processes can
be made resulting in high quality products and services.
RECOMMENDATIONS
From the above discussion it can be said that TQC can use various strategies in order to
improve the quality of its products which can help in maximising the satisfaction of customers
and creating high value for them. TQC manufactures engineering tools like engineer’s rules,
callipers, scribes and also deal in manufacture of medical instruments. This means that the
company needs to continuously improve the processes in which manufacturing is done so that
accurate and long lasting items can be manufactured. Following are the recommendations which
can be followed by company so as to enhance the quality of its items which can help it in gaining
a competitive edge in market:
The company must start training and development programs so that necessary skills and
talent can be developed in its employees which can help in making their performance
better. With these programmes they can be trained on how they can perform their tasks in
a better manner so that their accuracy and efficiency in completing these tasks will
increase. This will also help in reducing the number of errors while performing their tasks
hence reducing the cost of company.
TQC can apply TQM in all the processes of company so that the number of errors can be
reduced and the efficiency with which each process is carried out is enhanced which help
in increasing the quality of company products and services. TQM also can help the
company in continuously improving its processes and integrating the work of employees
so that effective results are achieved.
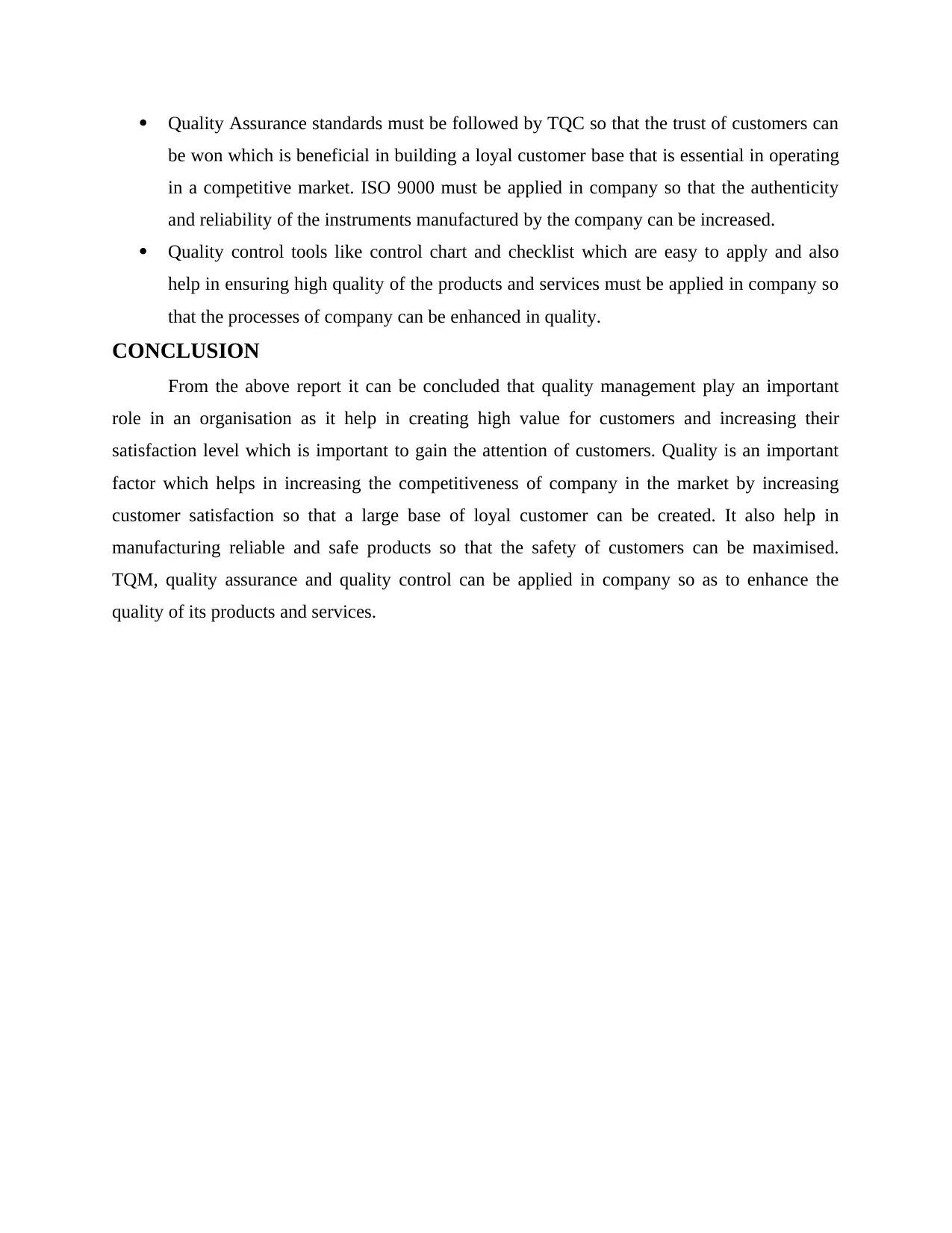
Quality Assurance standards must be followed by TQC so that the trust of customers can
be won which is beneficial in building a loyal customer base that is essential in operating
in a competitive market. ISO 9000 must be applied in company so that the authenticity
and reliability of the instruments manufactured by the company can be increased.
Quality control tools like control chart and checklist which are easy to apply and also
help in ensuring high quality of the products and services must be applied in company so
that the processes of company can be enhanced in quality.
CONCLUSION
From the above report it can be concluded that quality management play an important
role in an organisation as it help in creating high value for customers and increasing their
satisfaction level which is important to gain the attention of customers. Quality is an important
factor which helps in increasing the competitiveness of company in the market by increasing
customer satisfaction so that a large base of loyal customer can be created. It also help in
manufacturing reliable and safe products so that the safety of customers can be maximised.
TQM, quality assurance and quality control can be applied in company so as to enhance the
quality of its products and services.
be won which is beneficial in building a loyal customer base that is essential in operating
in a competitive market. ISO 9000 must be applied in company so that the authenticity
and reliability of the instruments manufactured by the company can be increased.
Quality control tools like control chart and checklist which are easy to apply and also
help in ensuring high quality of the products and services must be applied in company so
that the processes of company can be enhanced in quality.
CONCLUSION
From the above report it can be concluded that quality management play an important
role in an organisation as it help in creating high value for customers and increasing their
satisfaction level which is important to gain the attention of customers. Quality is an important
factor which helps in increasing the competitiveness of company in the market by increasing
customer satisfaction so that a large base of loyal customer can be created. It also help in
manufacturing reliable and safe products so that the safety of customers can be maximised.
TQM, quality assurance and quality control can be applied in company so as to enhance the
quality of its products and services.
Secure Best Marks with AI Grader
Need help grading? Try our AI Grader for instant feedback on your assignments.
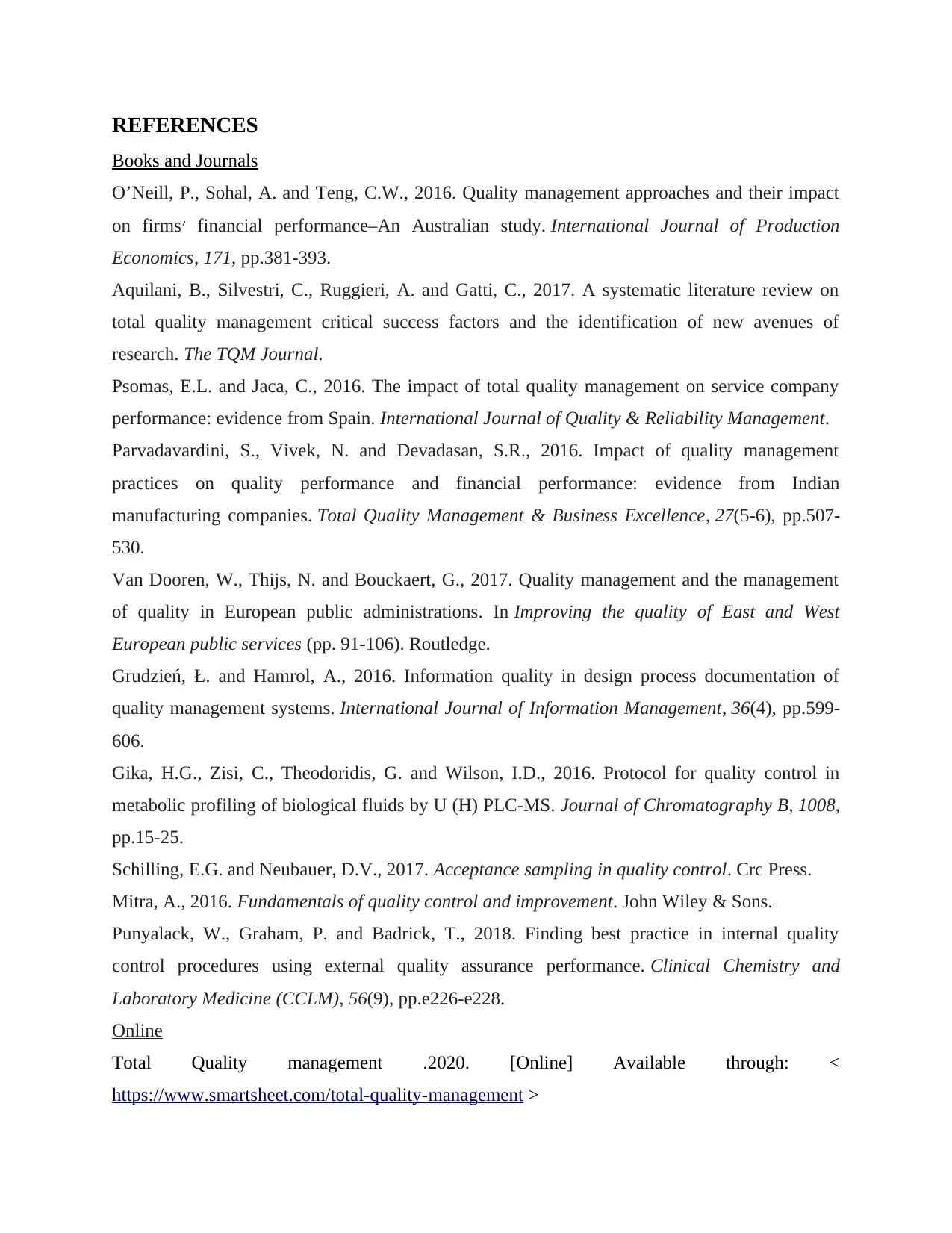
REFERENCES
Books and Journals
O’Neill, P., Sohal, A. and Teng, C.W., 2016. Quality management approaches and their impact
on firms׳ financial performance–An Australian study. International Journal of Production
Economics, 171, pp.381-393.
Aquilani, B., Silvestri, C., Ruggieri, A. and Gatti, C., 2017. A systematic literature review on
total quality management critical success factors and the identification of new avenues of
research. The TQM Journal.
Psomas, E.L. and Jaca, C., 2016. The impact of total quality management on service company
performance: evidence from Spain. International Journal of Quality & Reliability Management.
Parvadavardini, S., Vivek, N. and Devadasan, S.R., 2016. Impact of quality management
practices on quality performance and financial performance: evidence from Indian
manufacturing companies. Total Quality Management & Business Excellence, 27(5-6), pp.507-
530.
Van Dooren, W., Thijs, N. and Bouckaert, G., 2017. Quality management and the management
of quality in European public administrations. In Improving the quality of East and West
European public services (pp. 91-106). Routledge.
Grudzień, Ł. and Hamrol, A., 2016. Information quality in design process documentation of
quality management systems. International Journal of Information Management, 36(4), pp.599-
606.
Gika, H.G., Zisi, C., Theodoridis, G. and Wilson, I.D., 2016. Protocol for quality control in
metabolic profiling of biological fluids by U (H) PLC-MS. Journal of Chromatography B, 1008,
pp.15-25.
Schilling, E.G. and Neubauer, D.V., 2017. Acceptance sampling in quality control. Crc Press.
Mitra, A., 2016. Fundamentals of quality control and improvement. John Wiley & Sons.
Punyalack, W., Graham, P. and Badrick, T., 2018. Finding best practice in internal quality
control procedures using external quality assurance performance. Clinical Chemistry and
Laboratory Medicine (CCLM), 56(9), pp.e226-e228.
Online
Total Quality management .2020. [Online] Available through: <
https://www.smartsheet.com/total-quality-management >
Books and Journals
O’Neill, P., Sohal, A. and Teng, C.W., 2016. Quality management approaches and their impact
on firms׳ financial performance–An Australian study. International Journal of Production
Economics, 171, pp.381-393.
Aquilani, B., Silvestri, C., Ruggieri, A. and Gatti, C., 2017. A systematic literature review on
total quality management critical success factors and the identification of new avenues of
research. The TQM Journal.
Psomas, E.L. and Jaca, C., 2016. The impact of total quality management on service company
performance: evidence from Spain. International Journal of Quality & Reliability Management.
Parvadavardini, S., Vivek, N. and Devadasan, S.R., 2016. Impact of quality management
practices on quality performance and financial performance: evidence from Indian
manufacturing companies. Total Quality Management & Business Excellence, 27(5-6), pp.507-
530.
Van Dooren, W., Thijs, N. and Bouckaert, G., 2017. Quality management and the management
of quality in European public administrations. In Improving the quality of East and West
European public services (pp. 91-106). Routledge.
Grudzień, Ł. and Hamrol, A., 2016. Information quality in design process documentation of
quality management systems. International Journal of Information Management, 36(4), pp.599-
606.
Gika, H.G., Zisi, C., Theodoridis, G. and Wilson, I.D., 2016. Protocol for quality control in
metabolic profiling of biological fluids by U (H) PLC-MS. Journal of Chromatography B, 1008,
pp.15-25.
Schilling, E.G. and Neubauer, D.V., 2017. Acceptance sampling in quality control. Crc Press.
Mitra, A., 2016. Fundamentals of quality control and improvement. John Wiley & Sons.
Punyalack, W., Graham, P. and Badrick, T., 2018. Finding best practice in internal quality
control procedures using external quality assurance performance. Clinical Chemistry and
Laboratory Medicine (CCLM), 56(9), pp.e226-e228.
Online
Total Quality management .2020. [Online] Available through: <
https://www.smartsheet.com/total-quality-management >
1 out of 11
Related Documents

Your All-in-One AI-Powered Toolkit for Academic Success.
+13062052269
info@desklib.com
Available 24*7 on WhatsApp / Email
Unlock your academic potential
© 2024 | Zucol Services PVT LTD | All rights reserved.