Analyzing Quality Management Strategies for Quality Tooling Company
VerifiedAdded on 2021/02/20
|12
|3631
|26
Report
AI Summary
This report examines the quality management practices of Quality Tooling Company, a manufacturing firm based in England that transitioned from engineering products to medical equipment. The report explores various quality improvement strategies, including the Plan-Do-Study-Act cycle, ...
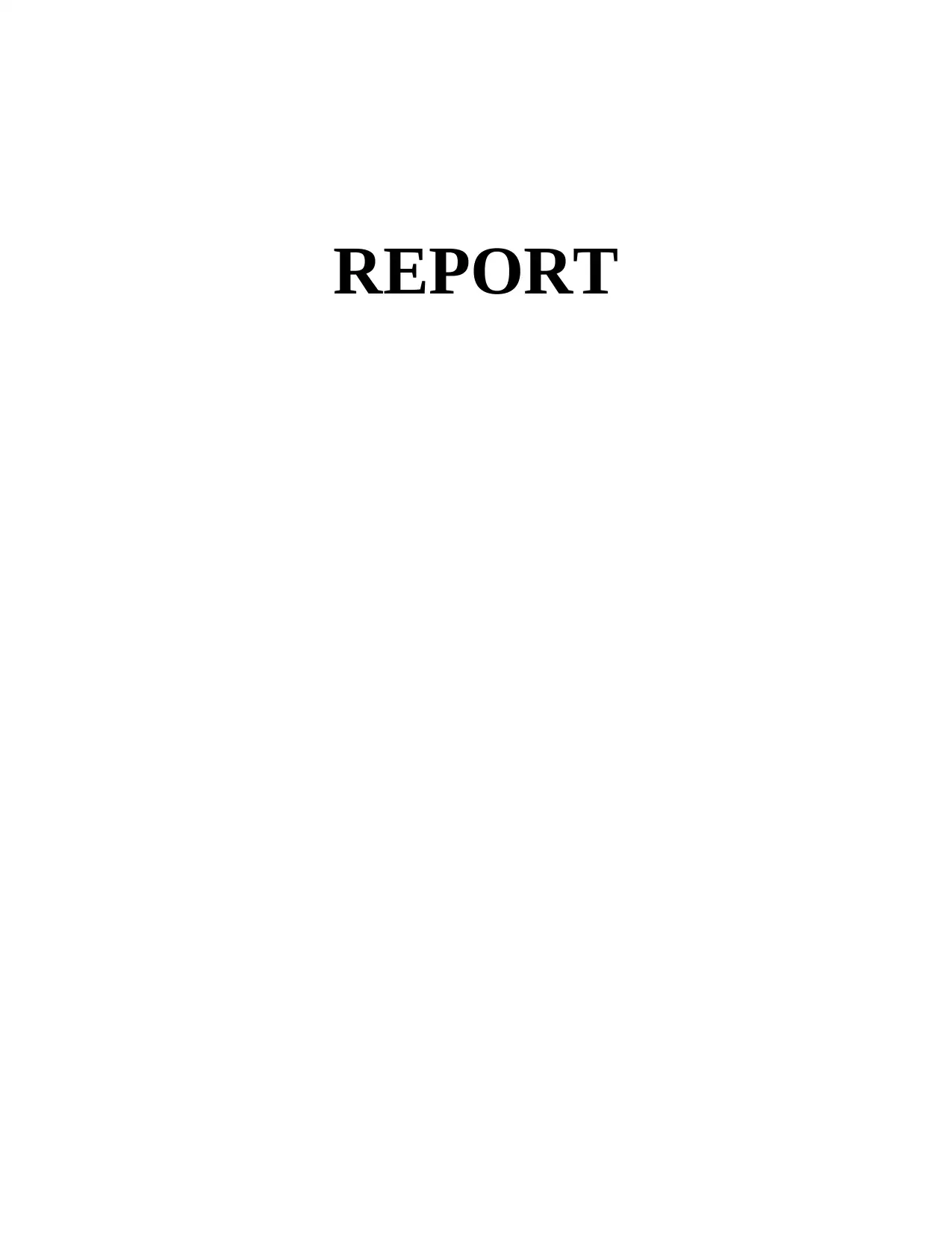
REPORT
Paraphrase This Document
Need a fresh take? Get an instant paraphrase of this document with our AI Paraphraser
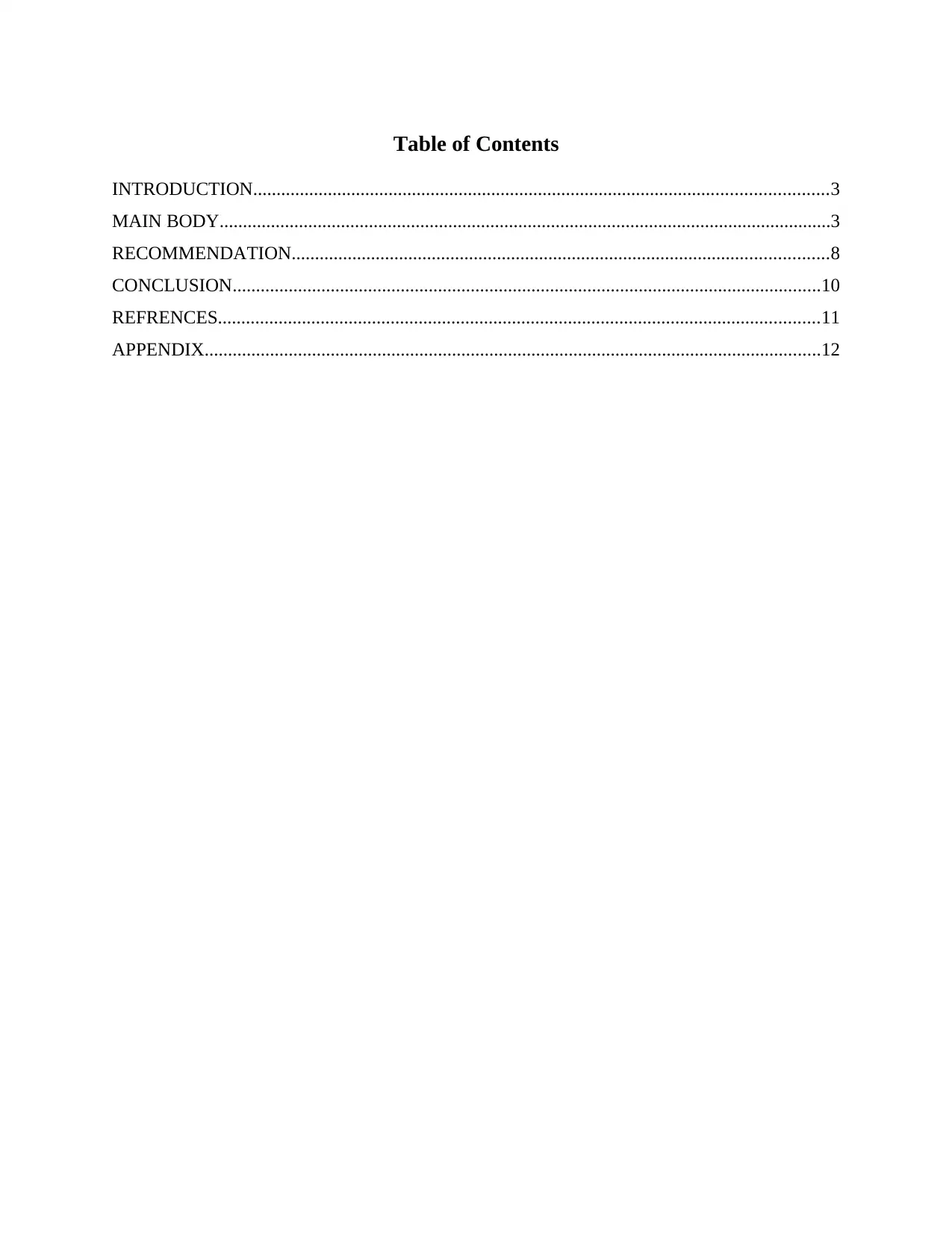
Table of Contents
INTRODUCTION...........................................................................................................................3
MAIN BODY...................................................................................................................................3
RECOMMENDATION...................................................................................................................8
CONCLUSION..............................................................................................................................10
REFRENCES.................................................................................................................................11
APPENDIX....................................................................................................................................12
INTRODUCTION...........................................................................................................................3
MAIN BODY...................................................................................................................................3
RECOMMENDATION...................................................................................................................8
CONCLUSION..............................................................................................................................10
REFRENCES.................................................................................................................................11
APPENDIX....................................................................................................................................12
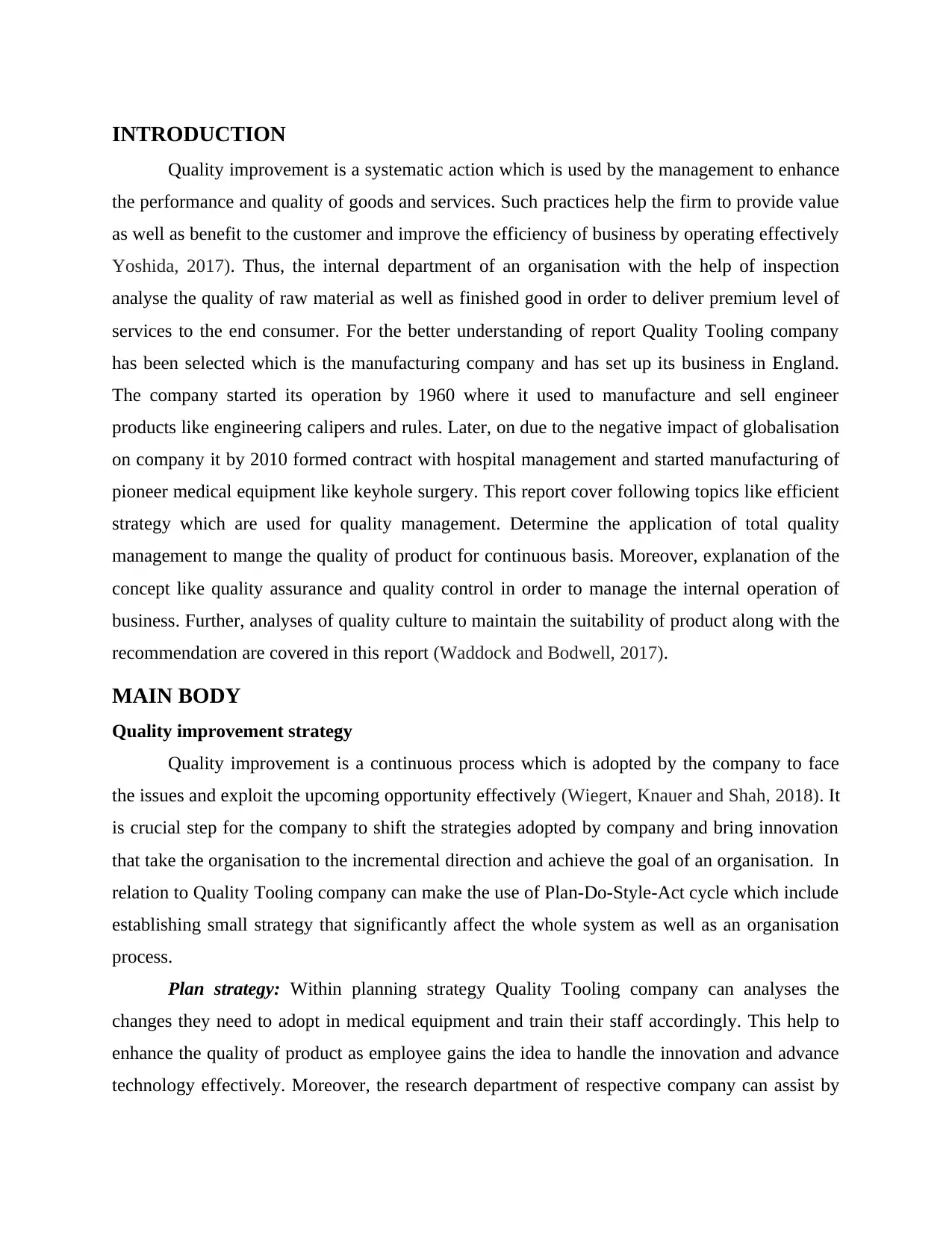
INTRODUCTION
Quality improvement is a systematic action which is used by the management to enhance
the performance and quality of goods and services. Such practices help the firm to provide value
as well as benefit to the customer and improve the efficiency of business by operating effectively
Yoshida, 2017). Thus, the internal department of an organisation with the help of inspection
analyse the quality of raw material as well as finished good in order to deliver premium level of
services to the end consumer. For the better understanding of report Quality Tooling company
has been selected which is the manufacturing company and has set up its business in England.
The company started its operation by 1960 where it used to manufacture and sell engineer
products like engineering calipers and rules. Later, on due to the negative impact of globalisation
on company it by 2010 formed contract with hospital management and started manufacturing of
pioneer medical equipment like keyhole surgery. This report cover following topics like efficient
strategy which are used for quality management. Determine the application of total quality
management to mange the quality of product for continuous basis. Moreover, explanation of the
concept like quality assurance and quality control in order to manage the internal operation of
business. Further, analyses of quality culture to maintain the suitability of product along with the
recommendation are covered in this report (Waddock and Bodwell, 2017).
MAIN BODY
Quality improvement strategy
Quality improvement is a continuous process which is adopted by the company to face
the issues and exploit the upcoming opportunity effectively (Wiegert, Knauer and Shah, 2018). It
is crucial step for the company to shift the strategies adopted by company and bring innovation
that take the organisation to the incremental direction and achieve the goal of an organisation. In
relation to Quality Tooling company can make the use of Plan-Do-Style-Act cycle which include
establishing small strategy that significantly affect the whole system as well as an organisation
process.
Plan strategy: Within planning strategy Quality Tooling company can analyses the
changes they need to adopt in medical equipment and train their staff accordingly. This help to
enhance the quality of product as employee gains the idea to handle the innovation and advance
technology effectively. Moreover, the research department of respective company can assist by
Quality improvement is a systematic action which is used by the management to enhance
the performance and quality of goods and services. Such practices help the firm to provide value
as well as benefit to the customer and improve the efficiency of business by operating effectively
Yoshida, 2017). Thus, the internal department of an organisation with the help of inspection
analyse the quality of raw material as well as finished good in order to deliver premium level of
services to the end consumer. For the better understanding of report Quality Tooling company
has been selected which is the manufacturing company and has set up its business in England.
The company started its operation by 1960 where it used to manufacture and sell engineer
products like engineering calipers and rules. Later, on due to the negative impact of globalisation
on company it by 2010 formed contract with hospital management and started manufacturing of
pioneer medical equipment like keyhole surgery. This report cover following topics like efficient
strategy which are used for quality management. Determine the application of total quality
management to mange the quality of product for continuous basis. Moreover, explanation of the
concept like quality assurance and quality control in order to manage the internal operation of
business. Further, analyses of quality culture to maintain the suitability of product along with the
recommendation are covered in this report (Waddock and Bodwell, 2017).
MAIN BODY
Quality improvement strategy
Quality improvement is a continuous process which is adopted by the company to face
the issues and exploit the upcoming opportunity effectively (Wiegert, Knauer and Shah, 2018). It
is crucial step for the company to shift the strategies adopted by company and bring innovation
that take the organisation to the incremental direction and achieve the goal of an organisation. In
relation to Quality Tooling company can make the use of Plan-Do-Style-Act cycle which include
establishing small strategy that significantly affect the whole system as well as an organisation
process.
Plan strategy: Within planning strategy Quality Tooling company can analyses the
changes they need to adopt in medical equipment and train their staff accordingly. This help to
enhance the quality of product as employee gains the idea to handle the innovation and advance
technology effectively. Moreover, the research department of respective company can assist by
You're viewing a preview
Unlock full access by subscribing today!
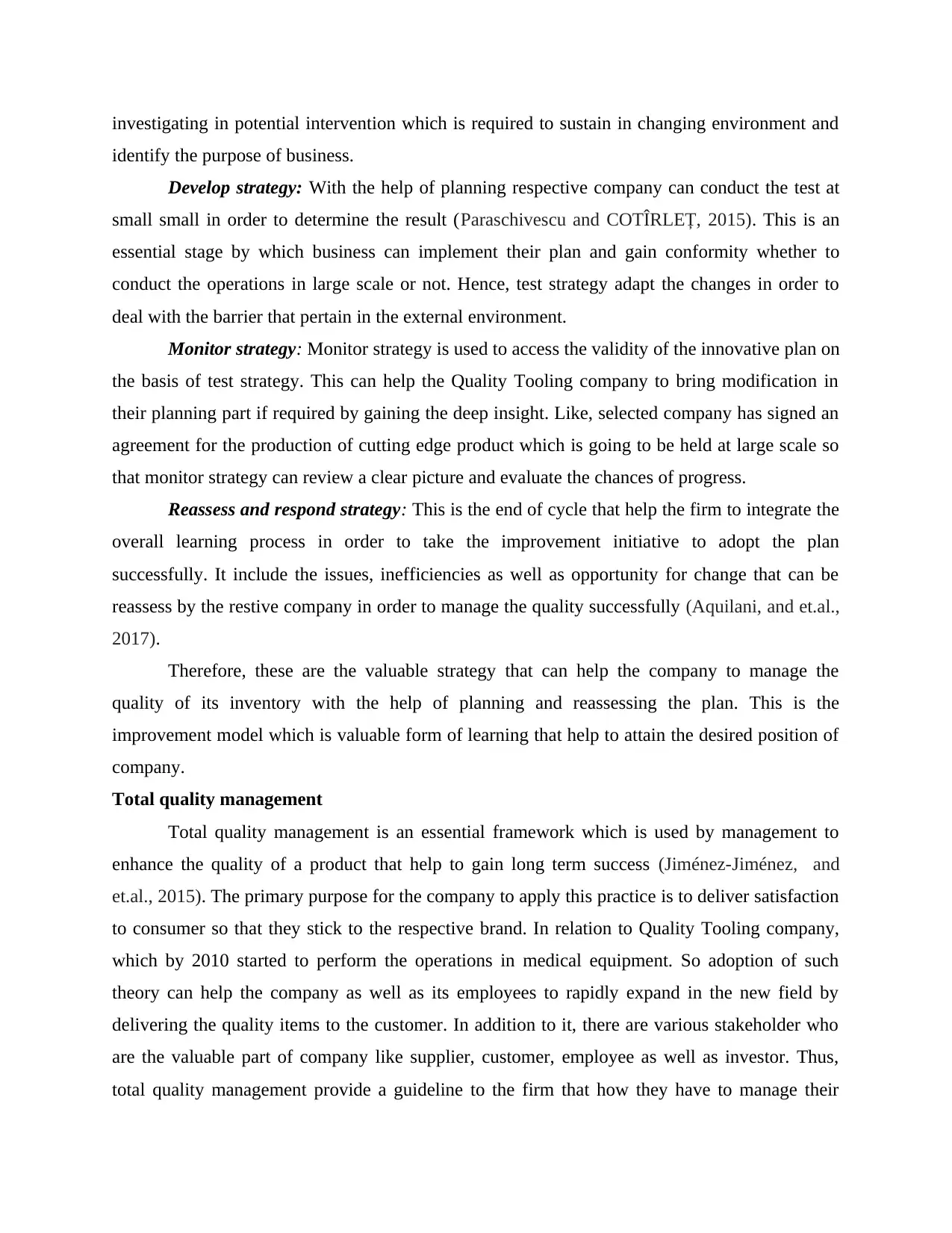
investigating in potential intervention which is required to sustain in changing environment and
identify the purpose of business.
Develop strategy: With the help of planning respective company can conduct the test at
small small in order to determine the result (Paraschivescu and COTÎRLEȚ, 2015). This is an
essential stage by which business can implement their plan and gain conformity whether to
conduct the operations in large scale or not. Hence, test strategy adapt the changes in order to
deal with the barrier that pertain in the external environment.
Monitor strategy: Monitor strategy is used to access the validity of the innovative plan on
the basis of test strategy. This can help the Quality Tooling company to bring modification in
their planning part if required by gaining the deep insight. Like, selected company has signed an
agreement for the production of cutting edge product which is going to be held at large scale so
that monitor strategy can review a clear picture and evaluate the chances of progress.
Reassess and respond strategy: This is the end of cycle that help the firm to integrate the
overall learning process in order to take the improvement initiative to adopt the plan
successfully. It include the issues, inefficiencies as well as opportunity for change that can be
reassess by the restive company in order to manage the quality successfully (Aquilani, and et.al.,
2017).
Therefore, these are the valuable strategy that can help the company to manage the
quality of its inventory with the help of planning and reassessing the plan. This is the
improvement model which is valuable form of learning that help to attain the desired position of
company.
Total quality management
Total quality management is an essential framework which is used by management to
enhance the quality of a product that help to gain long term success (Jiménez-Jiménez, and
et.al., 2015). The primary purpose for the company to apply this practice is to deliver satisfaction
to consumer so that they stick to the respective brand. In relation to Quality Tooling company,
which by 2010 started to perform the operations in medical equipment. So adoption of such
theory can help the company as well as its employees to rapidly expand in the new field by
delivering the quality items to the customer. In addition to it, there are various stakeholder who
are the valuable part of company like supplier, customer, employee as well as investor. Thus,
total quality management provide a guideline to the firm that how they have to manage their
identify the purpose of business.
Develop strategy: With the help of planning respective company can conduct the test at
small small in order to determine the result (Paraschivescu and COTÎRLEȚ, 2015). This is an
essential stage by which business can implement their plan and gain conformity whether to
conduct the operations in large scale or not. Hence, test strategy adapt the changes in order to
deal with the barrier that pertain in the external environment.
Monitor strategy: Monitor strategy is used to access the validity of the innovative plan on
the basis of test strategy. This can help the Quality Tooling company to bring modification in
their planning part if required by gaining the deep insight. Like, selected company has signed an
agreement for the production of cutting edge product which is going to be held at large scale so
that monitor strategy can review a clear picture and evaluate the chances of progress.
Reassess and respond strategy: This is the end of cycle that help the firm to integrate the
overall learning process in order to take the improvement initiative to adopt the plan
successfully. It include the issues, inefficiencies as well as opportunity for change that can be
reassess by the restive company in order to manage the quality successfully (Aquilani, and et.al.,
2017).
Therefore, these are the valuable strategy that can help the company to manage the
quality of its inventory with the help of planning and reassessing the plan. This is the
improvement model which is valuable form of learning that help to attain the desired position of
company.
Total quality management
Total quality management is an essential framework which is used by management to
enhance the quality of a product that help to gain long term success (Jiménez-Jiménez, and
et.al., 2015). The primary purpose for the company to apply this practice is to deliver satisfaction
to consumer so that they stick to the respective brand. In relation to Quality Tooling company,
which by 2010 started to perform the operations in medical equipment. So adoption of such
theory can help the company as well as its employees to rapidly expand in the new field by
delivering the quality items to the customer. In addition to it, there are various stakeholder who
are the valuable part of company like supplier, customer, employee as well as investor. Thus,
total quality management provide a guideline to the firm that how they have to manage their
Paraphrase This Document
Need a fresh take? Get an instant paraphrase of this document with our AI Paraphraser
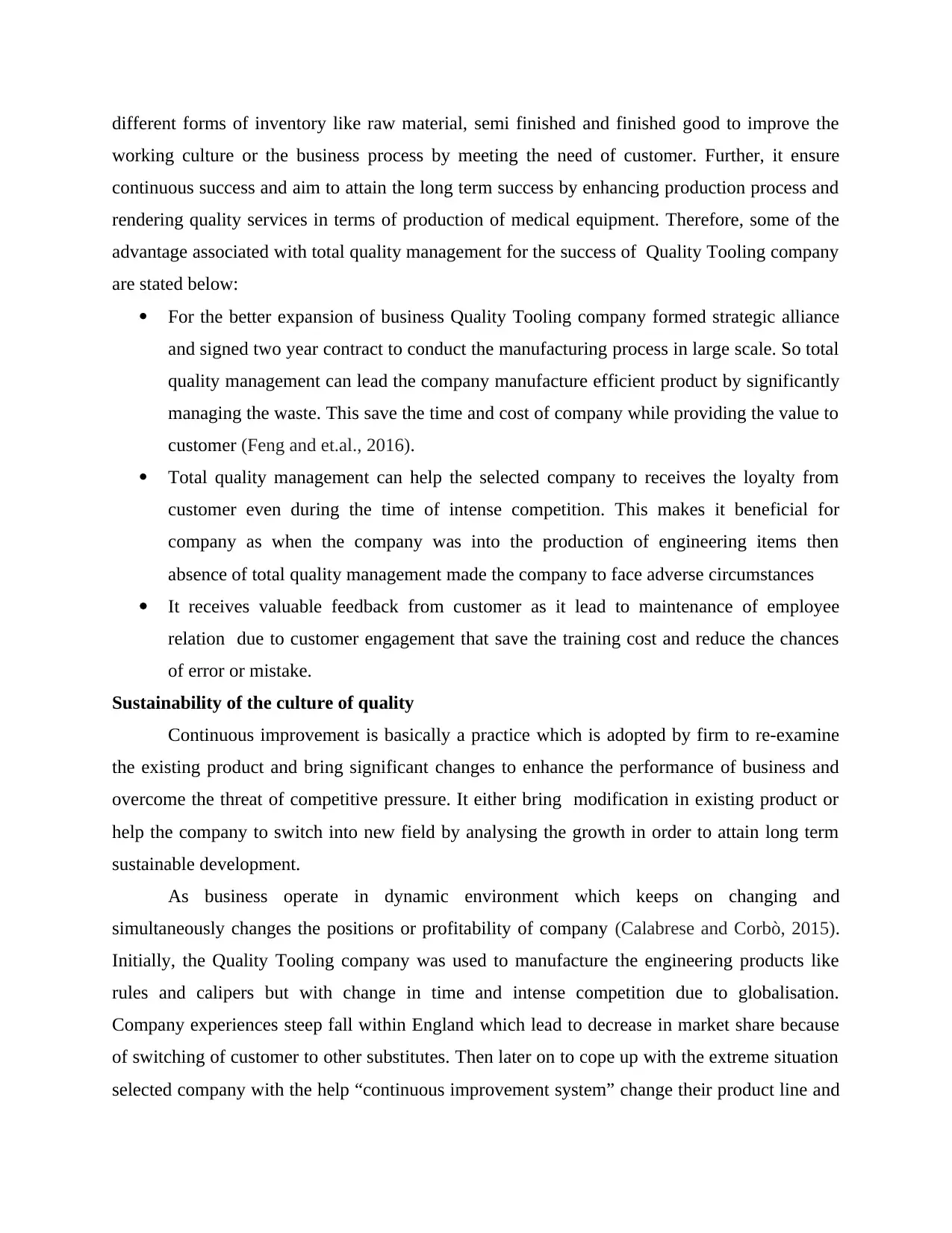
different forms of inventory like raw material, semi finished and finished good to improve the
working culture or the business process by meeting the need of customer. Further, it ensure
continuous success and aim to attain the long term success by enhancing production process and
rendering quality services in terms of production of medical equipment. Therefore, some of the
advantage associated with total quality management for the success of Quality Tooling company
are stated below:
For the better expansion of business Quality Tooling company formed strategic alliance
and signed two year contract to conduct the manufacturing process in large scale. So total
quality management can lead the company manufacture efficient product by significantly
managing the waste. This save the time and cost of company while providing the value to
customer (Feng and et.al., 2016).
Total quality management can help the selected company to receives the loyalty from
customer even during the time of intense competition. This makes it beneficial for
company as when the company was into the production of engineering items then
absence of total quality management made the company to face adverse circumstances
It receives valuable feedback from customer as it lead to maintenance of employee
relation due to customer engagement that save the training cost and reduce the chances
of error or mistake.
Sustainability of the culture of quality
Continuous improvement is basically a practice which is adopted by firm to re-examine
the existing product and bring significant changes to enhance the performance of business and
overcome the threat of competitive pressure. It either bring modification in existing product or
help the company to switch into new field by analysing the growth in order to attain long term
sustainable development.
As business operate in dynamic environment which keeps on changing and
simultaneously changes the positions or profitability of company (Calabrese and Corbò, 2015).
Initially, the Quality Tooling company was used to manufacture the engineering products like
rules and calipers but with change in time and intense competition due to globalisation.
Company experiences steep fall within England which lead to decrease in market share because
of switching of customer to other substitutes. Then later on to cope up with the extreme situation
selected company with the help “continuous improvement system” change their product line and
working culture or the business process by meeting the need of customer. Further, it ensure
continuous success and aim to attain the long term success by enhancing production process and
rendering quality services in terms of production of medical equipment. Therefore, some of the
advantage associated with total quality management for the success of Quality Tooling company
are stated below:
For the better expansion of business Quality Tooling company formed strategic alliance
and signed two year contract to conduct the manufacturing process in large scale. So total
quality management can lead the company manufacture efficient product by significantly
managing the waste. This save the time and cost of company while providing the value to
customer (Feng and et.al., 2016).
Total quality management can help the selected company to receives the loyalty from
customer even during the time of intense competition. This makes it beneficial for
company as when the company was into the production of engineering items then
absence of total quality management made the company to face adverse circumstances
It receives valuable feedback from customer as it lead to maintenance of employee
relation due to customer engagement that save the training cost and reduce the chances
of error or mistake.
Sustainability of the culture of quality
Continuous improvement is basically a practice which is adopted by firm to re-examine
the existing product and bring significant changes to enhance the performance of business and
overcome the threat of competitive pressure. It either bring modification in existing product or
help the company to switch into new field by analysing the growth in order to attain long term
sustainable development.
As business operate in dynamic environment which keeps on changing and
simultaneously changes the positions or profitability of company (Calabrese and Corbò, 2015).
Initially, the Quality Tooling company was used to manufacture the engineering products like
rules and calipers but with change in time and intense competition due to globalisation.
Company experiences steep fall within England which lead to decrease in market share because
of switching of customer to other substitutes. Then later on to cope up with the extreme situation
selected company with the help “continuous improvement system” change their product line and
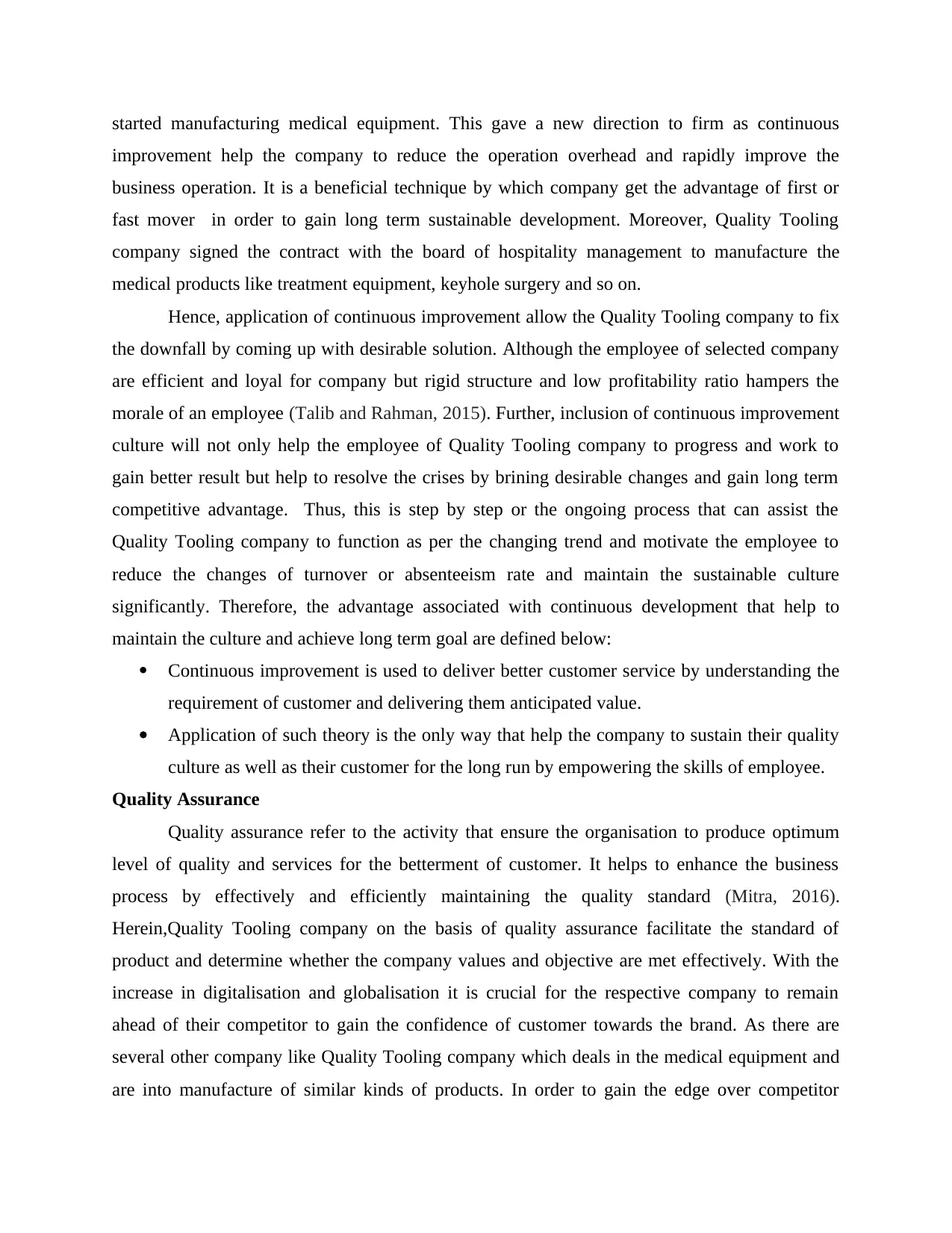
started manufacturing medical equipment. This gave a new direction to firm as continuous
improvement help the company to reduce the operation overhead and rapidly improve the
business operation. It is a beneficial technique by which company get the advantage of first or
fast mover in order to gain long term sustainable development. Moreover, Quality Tooling
company signed the contract with the board of hospitality management to manufacture the
medical products like treatment equipment, keyhole surgery and so on.
Hence, application of continuous improvement allow the Quality Tooling company to fix
the downfall by coming up with desirable solution. Although the employee of selected company
are efficient and loyal for company but rigid structure and low profitability ratio hampers the
morale of an employee (Talib and Rahman, 2015). Further, inclusion of continuous improvement
culture will not only help the employee of Quality Tooling company to progress and work to
gain better result but help to resolve the crises by brining desirable changes and gain long term
competitive advantage. Thus, this is step by step or the ongoing process that can assist the
Quality Tooling company to function as per the changing trend and motivate the employee to
reduce the changes of turnover or absenteeism rate and maintain the sustainable culture
significantly. Therefore, the advantage associated with continuous development that help to
maintain the culture and achieve long term goal are defined below:
Continuous improvement is used to deliver better customer service by understanding the
requirement of customer and delivering them anticipated value.
Application of such theory is the only way that help the company to sustain their quality
culture as well as their customer for the long run by empowering the skills of employee.
Quality Assurance
Quality assurance refer to the activity that ensure the organisation to produce optimum
level of quality and services for the betterment of customer. It helps to enhance the business
process by effectively and efficiently maintaining the quality standard (Mitra, 2016).
Herein,Quality Tooling company on the basis of quality assurance facilitate the standard of
product and determine whether the company values and objective are met effectively. With the
increase in digitalisation and globalisation it is crucial for the respective company to remain
ahead of their competitor to gain the confidence of customer towards the brand. As there are
several other company like Quality Tooling company which deals in the medical equipment and
are into manufacture of similar kinds of products. In order to gain the edge over competitor
improvement help the company to reduce the operation overhead and rapidly improve the
business operation. It is a beneficial technique by which company get the advantage of first or
fast mover in order to gain long term sustainable development. Moreover, Quality Tooling
company signed the contract with the board of hospitality management to manufacture the
medical products like treatment equipment, keyhole surgery and so on.
Hence, application of continuous improvement allow the Quality Tooling company to fix
the downfall by coming up with desirable solution. Although the employee of selected company
are efficient and loyal for company but rigid structure and low profitability ratio hampers the
morale of an employee (Talib and Rahman, 2015). Further, inclusion of continuous improvement
culture will not only help the employee of Quality Tooling company to progress and work to
gain better result but help to resolve the crises by brining desirable changes and gain long term
competitive advantage. Thus, this is step by step or the ongoing process that can assist the
Quality Tooling company to function as per the changing trend and motivate the employee to
reduce the changes of turnover or absenteeism rate and maintain the sustainable culture
significantly. Therefore, the advantage associated with continuous development that help to
maintain the culture and achieve long term goal are defined below:
Continuous improvement is used to deliver better customer service by understanding the
requirement of customer and delivering them anticipated value.
Application of such theory is the only way that help the company to sustain their quality
culture as well as their customer for the long run by empowering the skills of employee.
Quality Assurance
Quality assurance refer to the activity that ensure the organisation to produce optimum
level of quality and services for the betterment of customer. It helps to enhance the business
process by effectively and efficiently maintaining the quality standard (Mitra, 2016).
Herein,Quality Tooling company on the basis of quality assurance facilitate the standard of
product and determine whether the company values and objective are met effectively. With the
increase in digitalisation and globalisation it is crucial for the respective company to remain
ahead of their competitor to gain the confidence of customer towards the brand. As there are
several other company like Quality Tooling company which deals in the medical equipment and
are into manufacture of similar kinds of products. In order to gain the edge over competitor
You're viewing a preview
Unlock full access by subscribing today!
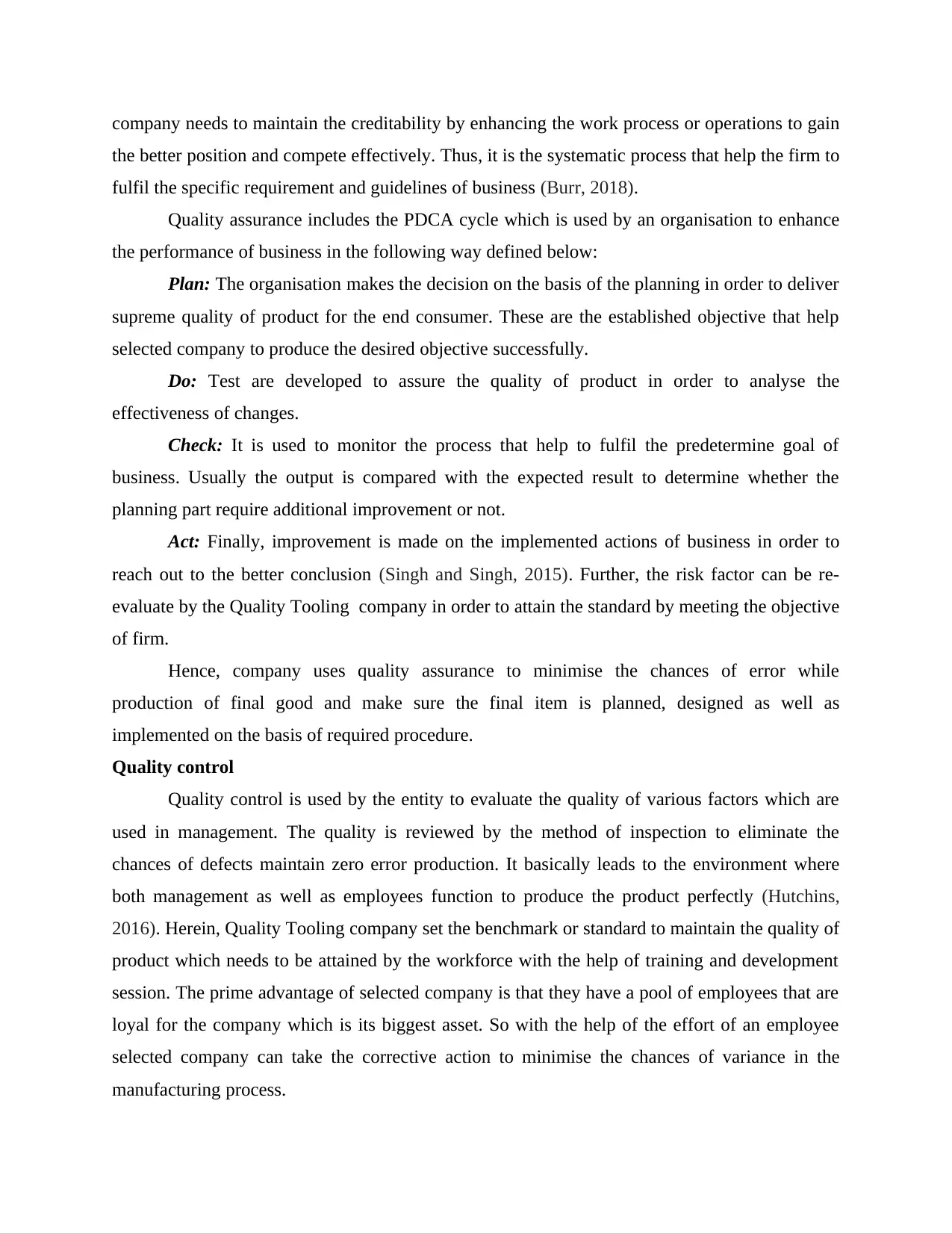
company needs to maintain the creditability by enhancing the work process or operations to gain
the better position and compete effectively. Thus, it is the systematic process that help the firm to
fulfil the specific requirement and guidelines of business (Burr, 2018).
Quality assurance includes the PDCA cycle which is used by an organisation to enhance
the performance of business in the following way defined below:
Plan: The organisation makes the decision on the basis of the planning in order to deliver
supreme quality of product for the end consumer. These are the established objective that help
selected company to produce the desired objective successfully.
Do: Test are developed to assure the quality of product in order to analyse the
effectiveness of changes.
Check: It is used to monitor the process that help to fulfil the predetermine goal of
business. Usually the output is compared with the expected result to determine whether the
planning part require additional improvement or not.
Act: Finally, improvement is made on the implemented actions of business in order to
reach out to the better conclusion (Singh and Singh, 2015). Further, the risk factor can be re-
evaluate by the Quality Tooling company in order to attain the standard by meeting the objective
of firm.
Hence, company uses quality assurance to minimise the chances of error while
production of final good and make sure the final item is planned, designed as well as
implemented on the basis of required procedure.
Quality control
Quality control is used by the entity to evaluate the quality of various factors which are
used in management. The quality is reviewed by the method of inspection to eliminate the
chances of defects maintain zero error production. It basically leads to the environment where
both management as well as employees function to produce the product perfectly (Hutchins,
2016). Herein, Quality Tooling company set the benchmark or standard to maintain the quality of
product which needs to be attained by the workforce with the help of training and development
session. The prime advantage of selected company is that they have a pool of employees that are
loyal for the company which is its biggest asset. So with the help of the effort of an employee
selected company can take the corrective action to minimise the chances of variance in the
manufacturing process.
the better position and compete effectively. Thus, it is the systematic process that help the firm to
fulfil the specific requirement and guidelines of business (Burr, 2018).
Quality assurance includes the PDCA cycle which is used by an organisation to enhance
the performance of business in the following way defined below:
Plan: The organisation makes the decision on the basis of the planning in order to deliver
supreme quality of product for the end consumer. These are the established objective that help
selected company to produce the desired objective successfully.
Do: Test are developed to assure the quality of product in order to analyse the
effectiveness of changes.
Check: It is used to monitor the process that help to fulfil the predetermine goal of
business. Usually the output is compared with the expected result to determine whether the
planning part require additional improvement or not.
Act: Finally, improvement is made on the implemented actions of business in order to
reach out to the better conclusion (Singh and Singh, 2015). Further, the risk factor can be re-
evaluate by the Quality Tooling company in order to attain the standard by meeting the objective
of firm.
Hence, company uses quality assurance to minimise the chances of error while
production of final good and make sure the final item is planned, designed as well as
implemented on the basis of required procedure.
Quality control
Quality control is used by the entity to evaluate the quality of various factors which are
used in management. The quality is reviewed by the method of inspection to eliminate the
chances of defects maintain zero error production. It basically leads to the environment where
both management as well as employees function to produce the product perfectly (Hutchins,
2016). Herein, Quality Tooling company set the benchmark or standard to maintain the quality of
product which needs to be attained by the workforce with the help of training and development
session. The prime advantage of selected company is that they have a pool of employees that are
loyal for the company which is its biggest asset. So with the help of the effort of an employee
selected company can take the corrective action to minimise the chances of variance in the
manufacturing process.
Paraphrase This Document
Need a fresh take? Get an instant paraphrase of this document with our AI Paraphraser
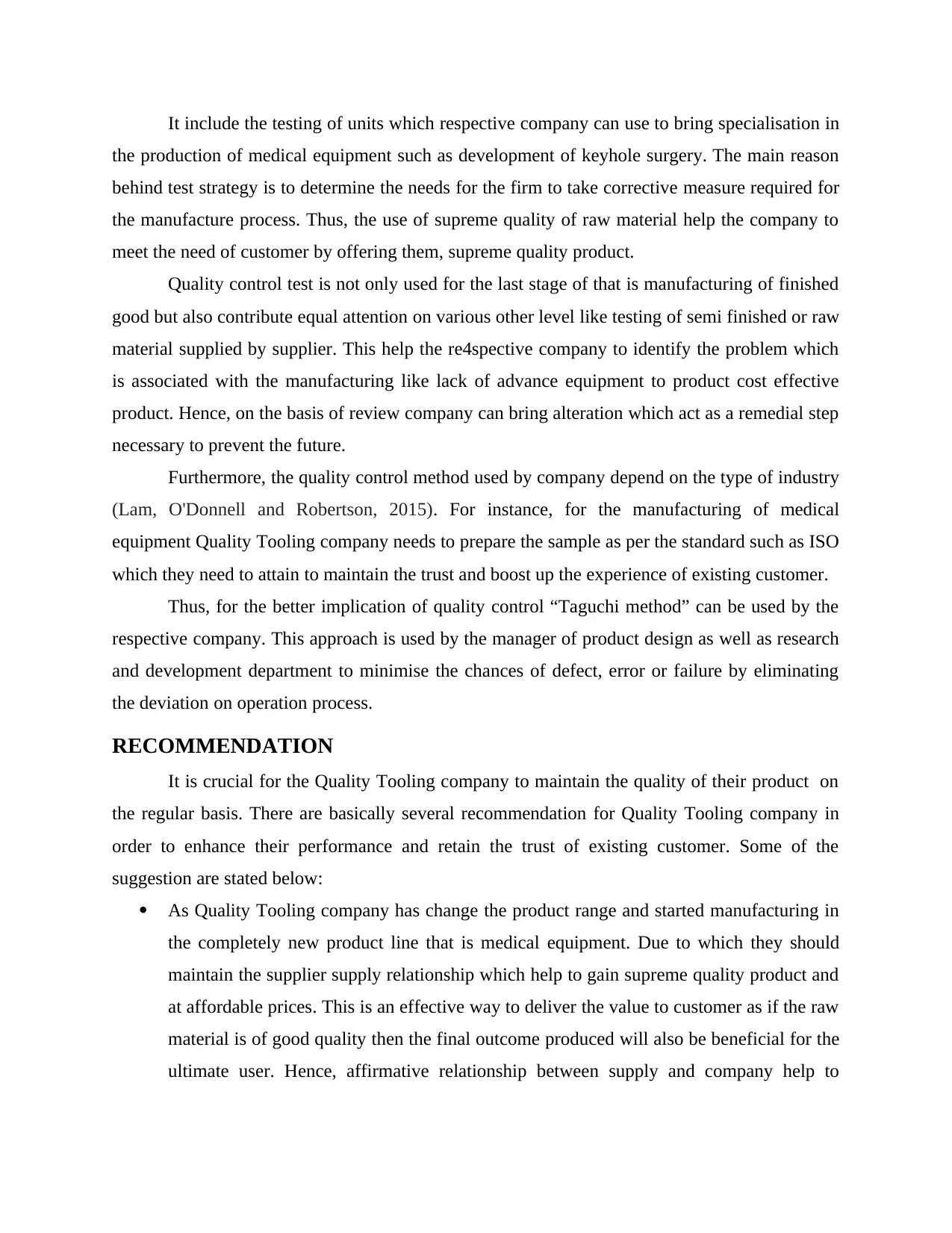
It include the testing of units which respective company can use to bring specialisation in
the production of medical equipment such as development of keyhole surgery. The main reason
behind test strategy is to determine the needs for the firm to take corrective measure required for
the manufacture process. Thus, the use of supreme quality of raw material help the company to
meet the need of customer by offering them, supreme quality product.
Quality control test is not only used for the last stage of that is manufacturing of finished
good but also contribute equal attention on various other level like testing of semi finished or raw
material supplied by supplier. This help the re4spective company to identify the problem which
is associated with the manufacturing like lack of advance equipment to product cost effective
product. Hence, on the basis of review company can bring alteration which act as a remedial step
necessary to prevent the future.
Furthermore, the quality control method used by company depend on the type of industry
(Lam, O'Donnell and Robertson, 2015). For instance, for the manufacturing of medical
equipment Quality Tooling company needs to prepare the sample as per the standard such as ISO
which they need to attain to maintain the trust and boost up the experience of existing customer.
Thus, for the better implication of quality control “Taguchi method” can be used by the
respective company. This approach is used by the manager of product design as well as research
and development department to minimise the chances of defect, error or failure by eliminating
the deviation on operation process.
RECOMMENDATION
It is crucial for the Quality Tooling company to maintain the quality of their product on
the regular basis. There are basically several recommendation for Quality Tooling company in
order to enhance their performance and retain the trust of existing customer. Some of the
suggestion are stated below:
As Quality Tooling company has change the product range and started manufacturing in
the completely new product line that is medical equipment. Due to which they should
maintain the supplier supply relationship which help to gain supreme quality product and
at affordable prices. This is an effective way to deliver the value to customer as if the raw
material is of good quality then the final outcome produced will also be beneficial for the
ultimate user. Hence, affirmative relationship between supply and company help to
the production of medical equipment such as development of keyhole surgery. The main reason
behind test strategy is to determine the needs for the firm to take corrective measure required for
the manufacture process. Thus, the use of supreme quality of raw material help the company to
meet the need of customer by offering them, supreme quality product.
Quality control test is not only used for the last stage of that is manufacturing of finished
good but also contribute equal attention on various other level like testing of semi finished or raw
material supplied by supplier. This help the re4spective company to identify the problem which
is associated with the manufacturing like lack of advance equipment to product cost effective
product. Hence, on the basis of review company can bring alteration which act as a remedial step
necessary to prevent the future.
Furthermore, the quality control method used by company depend on the type of industry
(Lam, O'Donnell and Robertson, 2015). For instance, for the manufacturing of medical
equipment Quality Tooling company needs to prepare the sample as per the standard such as ISO
which they need to attain to maintain the trust and boost up the experience of existing customer.
Thus, for the better implication of quality control “Taguchi method” can be used by the
respective company. This approach is used by the manager of product design as well as research
and development department to minimise the chances of defect, error or failure by eliminating
the deviation on operation process.
RECOMMENDATION
It is crucial for the Quality Tooling company to maintain the quality of their product on
the regular basis. There are basically several recommendation for Quality Tooling company in
order to enhance their performance and retain the trust of existing customer. Some of the
suggestion are stated below:
As Quality Tooling company has change the product range and started manufacturing in
the completely new product line that is medical equipment. Due to which they should
maintain the supplier supply relationship which help to gain supreme quality product and
at affordable prices. This is an effective way to deliver the value to customer as if the raw
material is of good quality then the final outcome produced will also be beneficial for the
ultimate user. Hence, affirmative relationship between supply and company help to
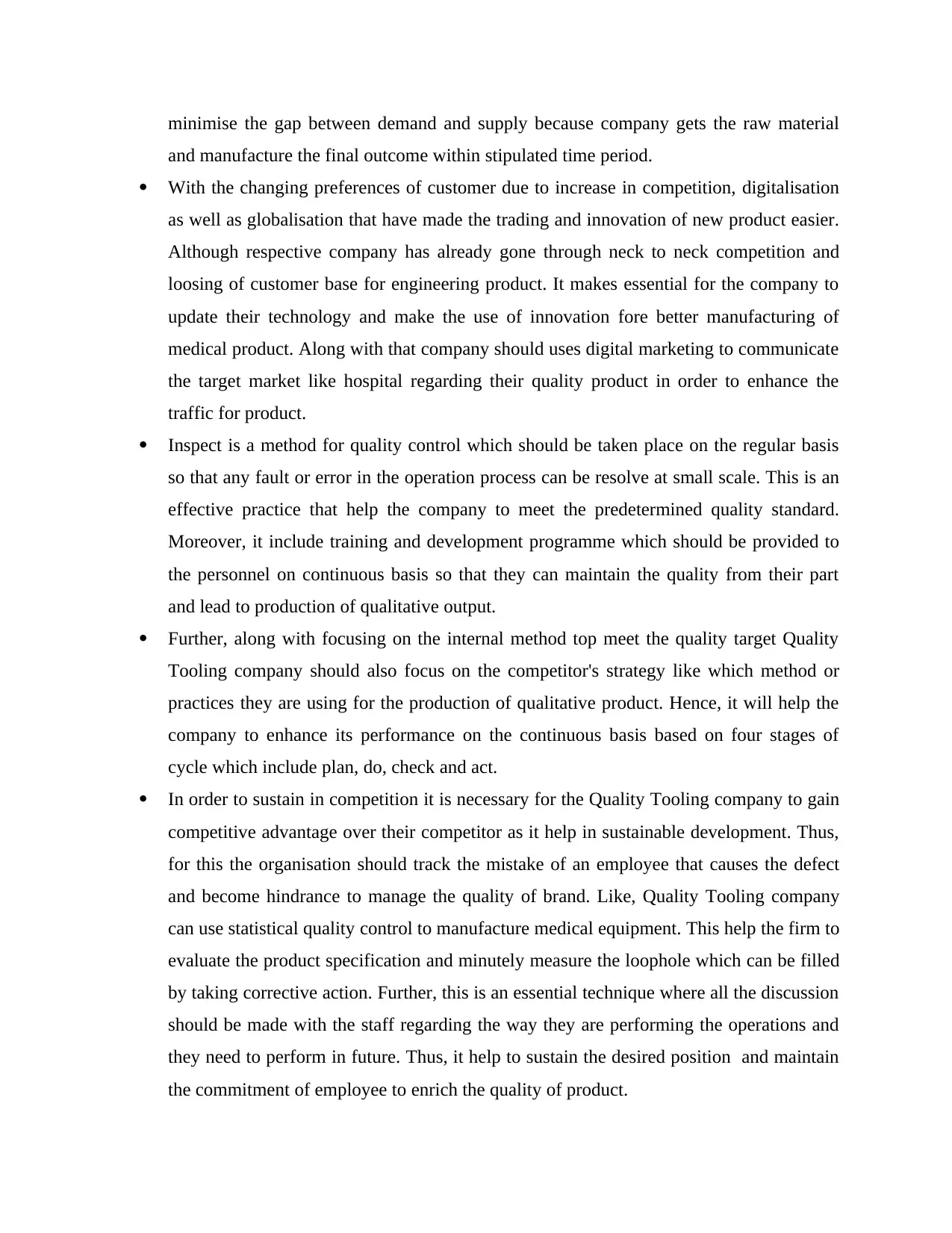
minimise the gap between demand and supply because company gets the raw material
and manufacture the final outcome within stipulated time period.
With the changing preferences of customer due to increase in competition, digitalisation
as well as globalisation that have made the trading and innovation of new product easier.
Although respective company has already gone through neck to neck competition and
loosing of customer base for engineering product. It makes essential for the company to
update their technology and make the use of innovation fore better manufacturing of
medical product. Along with that company should uses digital marketing to communicate
the target market like hospital regarding their quality product in order to enhance the
traffic for product.
Inspect is a method for quality control which should be taken place on the regular basis
so that any fault or error in the operation process can be resolve at small scale. This is an
effective practice that help the company to meet the predetermined quality standard.
Moreover, it include training and development programme which should be provided to
the personnel on continuous basis so that they can maintain the quality from their part
and lead to production of qualitative output.
Further, along with focusing on the internal method top meet the quality target Quality
Tooling company should also focus on the competitor's strategy like which method or
practices they are using for the production of qualitative product. Hence, it will help the
company to enhance its performance on the continuous basis based on four stages of
cycle which include plan, do, check and act.
In order to sustain in competition it is necessary for the Quality Tooling company to gain
competitive advantage over their competitor as it help in sustainable development. Thus,
for this the organisation should track the mistake of an employee that causes the defect
and become hindrance to manage the quality of brand. Like, Quality Tooling company
can use statistical quality control to manufacture medical equipment. This help the firm to
evaluate the product specification and minutely measure the loophole which can be filled
by taking corrective action. Further, this is an essential technique where all the discussion
should be made with the staff regarding the way they are performing the operations and
they need to perform in future. Thus, it help to sustain the desired position and maintain
the commitment of employee to enrich the quality of product.
and manufacture the final outcome within stipulated time period.
With the changing preferences of customer due to increase in competition, digitalisation
as well as globalisation that have made the trading and innovation of new product easier.
Although respective company has already gone through neck to neck competition and
loosing of customer base for engineering product. It makes essential for the company to
update their technology and make the use of innovation fore better manufacturing of
medical product. Along with that company should uses digital marketing to communicate
the target market like hospital regarding their quality product in order to enhance the
traffic for product.
Inspect is a method for quality control which should be taken place on the regular basis
so that any fault or error in the operation process can be resolve at small scale. This is an
effective practice that help the company to meet the predetermined quality standard.
Moreover, it include training and development programme which should be provided to
the personnel on continuous basis so that they can maintain the quality from their part
and lead to production of qualitative output.
Further, along with focusing on the internal method top meet the quality target Quality
Tooling company should also focus on the competitor's strategy like which method or
practices they are using for the production of qualitative product. Hence, it will help the
company to enhance its performance on the continuous basis based on four stages of
cycle which include plan, do, check and act.
In order to sustain in competition it is necessary for the Quality Tooling company to gain
competitive advantage over their competitor as it help in sustainable development. Thus,
for this the organisation should track the mistake of an employee that causes the defect
and become hindrance to manage the quality of brand. Like, Quality Tooling company
can use statistical quality control to manufacture medical equipment. This help the firm to
evaluate the product specification and minutely measure the loophole which can be filled
by taking corrective action. Further, this is an essential technique where all the discussion
should be made with the staff regarding the way they are performing the operations and
they need to perform in future. Thus, it help to sustain the desired position and maintain
the commitment of employee to enrich the quality of product.
You're viewing a preview
Unlock full access by subscribing today!
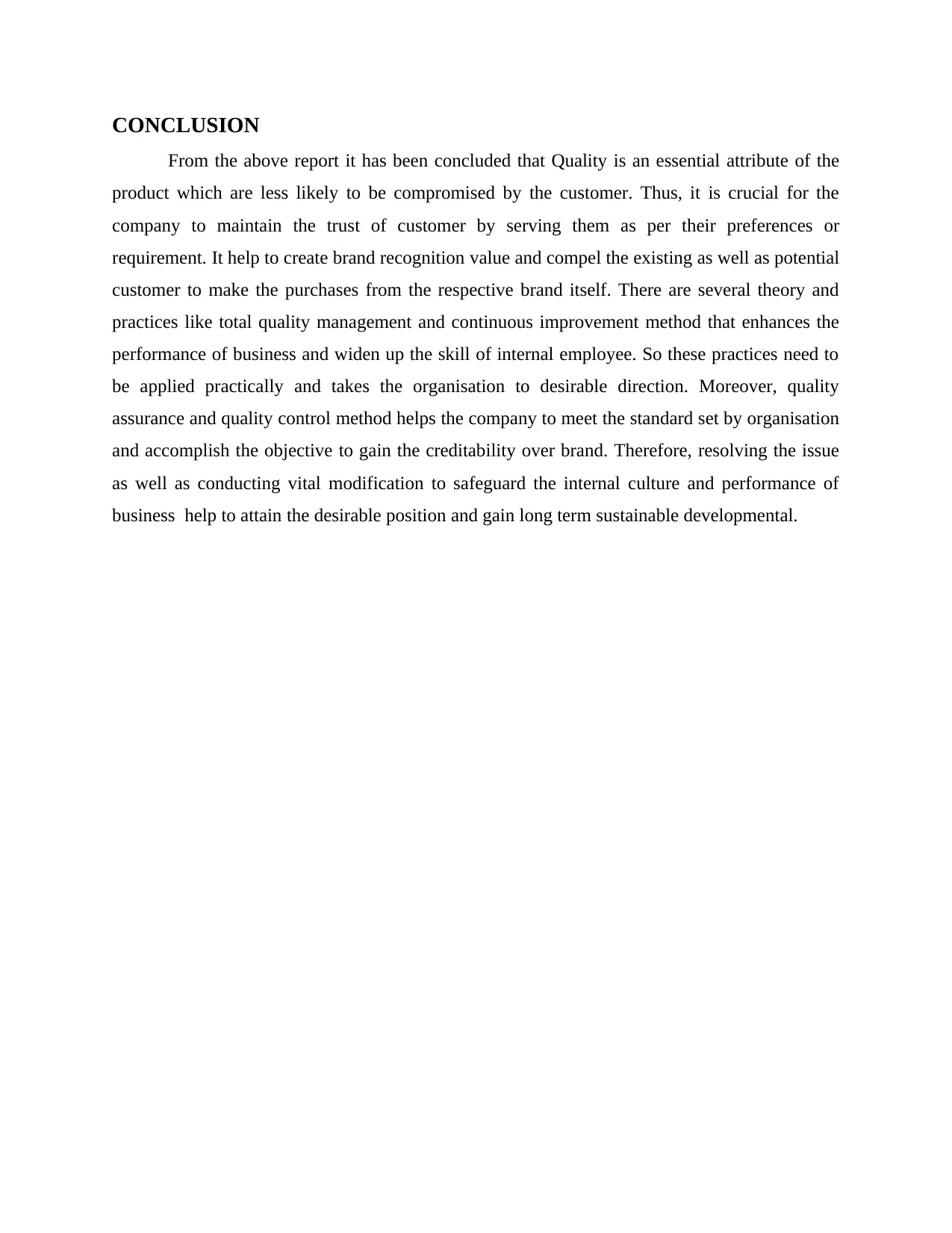
CONCLUSION
From the above report it has been concluded that Quality is an essential attribute of the
product which are less likely to be compromised by the customer. Thus, it is crucial for the
company to maintain the trust of customer by serving them as per their preferences or
requirement. It help to create brand recognition value and compel the existing as well as potential
customer to make the purchases from the respective brand itself. There are several theory and
practices like total quality management and continuous improvement method that enhances the
performance of business and widen up the skill of internal employee. So these practices need to
be applied practically and takes the organisation to desirable direction. Moreover, quality
assurance and quality control method helps the company to meet the standard set by organisation
and accomplish the objective to gain the creditability over brand. Therefore, resolving the issue
as well as conducting vital modification to safeguard the internal culture and performance of
business help to attain the desirable position and gain long term sustainable developmental.
From the above report it has been concluded that Quality is an essential attribute of the
product which are less likely to be compromised by the customer. Thus, it is crucial for the
company to maintain the trust of customer by serving them as per their preferences or
requirement. It help to create brand recognition value and compel the existing as well as potential
customer to make the purchases from the respective brand itself. There are several theory and
practices like total quality management and continuous improvement method that enhances the
performance of business and widen up the skill of internal employee. So these practices need to
be applied practically and takes the organisation to desirable direction. Moreover, quality
assurance and quality control method helps the company to meet the standard set by organisation
and accomplish the objective to gain the creditability over brand. Therefore, resolving the issue
as well as conducting vital modification to safeguard the internal culture and performance of
business help to attain the desirable position and gain long term sustainable developmental.
Paraphrase This Document
Need a fresh take? Get an instant paraphrase of this document with our AI Paraphraser
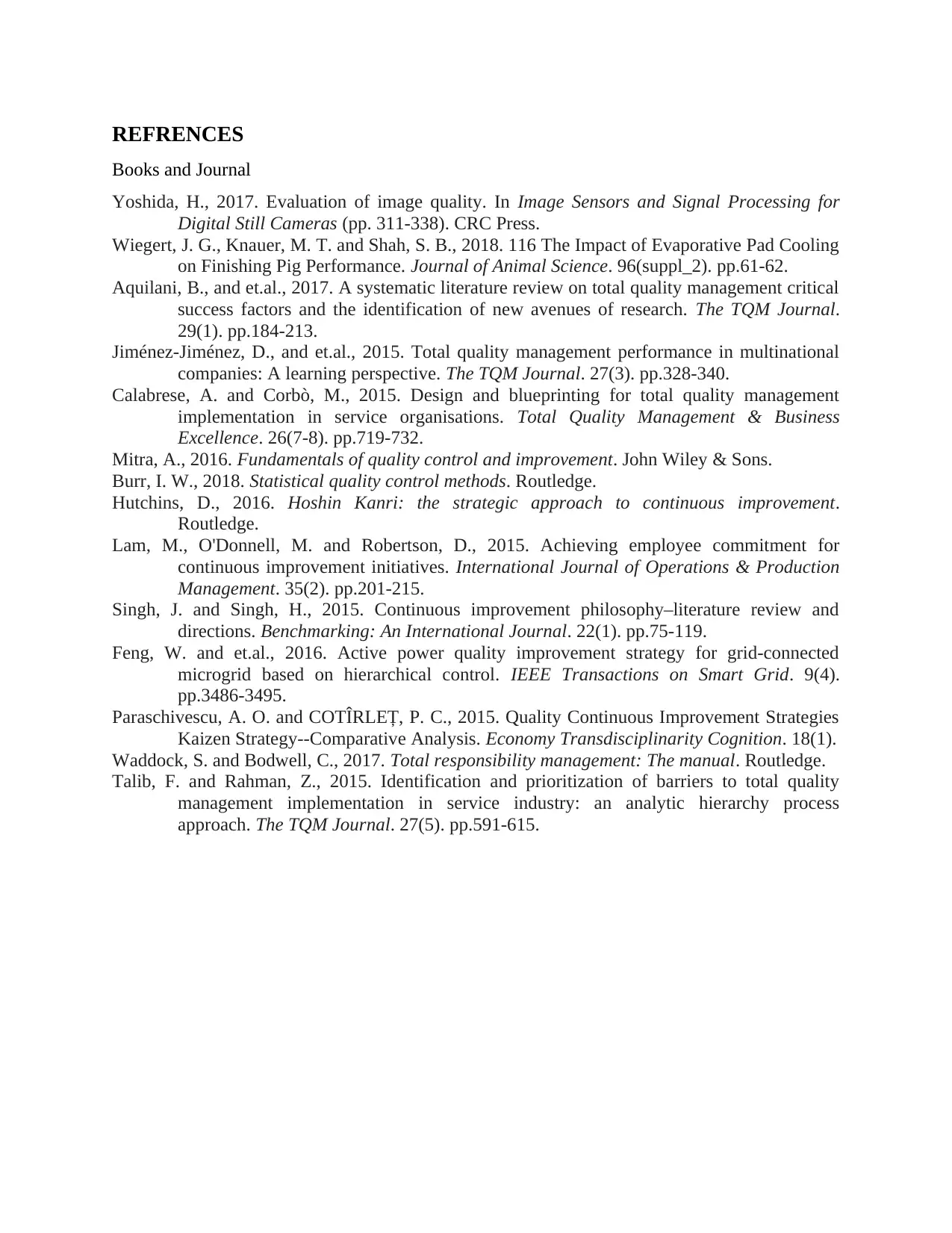
REFRENCES
Books and Journal
Yoshida, H., 2017. Evaluation of image quality. In Image Sensors and Signal Processing for
Digital Still Cameras (pp. 311-338). CRC Press.
Wiegert, J. G., Knauer, M. T. and Shah, S. B., 2018. 116 The Impact of Evaporative Pad Cooling
on Finishing Pig Performance. Journal of Animal Science. 96(suppl_2). pp.61-62.
Aquilani, B., and et.al., 2017. A systematic literature review on total quality management critical
success factors and the identification of new avenues of research. The TQM Journal.
29(1). pp.184-213.
Jiménez-Jiménez, D., and et.al., 2015. Total quality management performance in multinational
companies: A learning perspective. The TQM Journal. 27(3). pp.328-340.
Calabrese, A. and Corbò, M., 2015. Design and blueprinting for total quality management
implementation in service organisations. Total Quality Management & Business
Excellence. 26(7-8). pp.719-732.
Mitra, A., 2016. Fundamentals of quality control and improvement. John Wiley & Sons.
Burr, I. W., 2018. Statistical quality control methods. Routledge.
Hutchins, D., 2016. Hoshin Kanri: the strategic approach to continuous improvement.
Routledge.
Lam, M., O'Donnell, M. and Robertson, D., 2015. Achieving employee commitment for
continuous improvement initiatives. International Journal of Operations & Production
Management. 35(2). pp.201-215.
Singh, J. and Singh, H., 2015. Continuous improvement philosophy–literature review and
directions. Benchmarking: An International Journal. 22(1). pp.75-119.
Feng, W. and et.al., 2016. Active power quality improvement strategy for grid-connected
microgrid based on hierarchical control. IEEE Transactions on Smart Grid. 9(4).
pp.3486-3495.
Paraschivescu, A. O. and COTÎRLEȚ, P. C., 2015. Quality Continuous Improvement Strategies
Kaizen Strategy--Comparative Analysis. Economy Transdisciplinarity Cognition. 18(1).
Waddock, S. and Bodwell, C., 2017. Total responsibility management: The manual. Routledge.
Talib, F. and Rahman, Z., 2015. Identification and prioritization of barriers to total quality
management implementation in service industry: an analytic hierarchy process
approach. The TQM Journal. 27(5). pp.591-615.
Books and Journal
Yoshida, H., 2017. Evaluation of image quality. In Image Sensors and Signal Processing for
Digital Still Cameras (pp. 311-338). CRC Press.
Wiegert, J. G., Knauer, M. T. and Shah, S. B., 2018. 116 The Impact of Evaporative Pad Cooling
on Finishing Pig Performance. Journal of Animal Science. 96(suppl_2). pp.61-62.
Aquilani, B., and et.al., 2017. A systematic literature review on total quality management critical
success factors and the identification of new avenues of research. The TQM Journal.
29(1). pp.184-213.
Jiménez-Jiménez, D., and et.al., 2015. Total quality management performance in multinational
companies: A learning perspective. The TQM Journal. 27(3). pp.328-340.
Calabrese, A. and Corbò, M., 2015. Design and blueprinting for total quality management
implementation in service organisations. Total Quality Management & Business
Excellence. 26(7-8). pp.719-732.
Mitra, A., 2016. Fundamentals of quality control and improvement. John Wiley & Sons.
Burr, I. W., 2018. Statistical quality control methods. Routledge.
Hutchins, D., 2016. Hoshin Kanri: the strategic approach to continuous improvement.
Routledge.
Lam, M., O'Donnell, M. and Robertson, D., 2015. Achieving employee commitment for
continuous improvement initiatives. International Journal of Operations & Production
Management. 35(2). pp.201-215.
Singh, J. and Singh, H., 2015. Continuous improvement philosophy–literature review and
directions. Benchmarking: An International Journal. 22(1). pp.75-119.
Feng, W. and et.al., 2016. Active power quality improvement strategy for grid-connected
microgrid based on hierarchical control. IEEE Transactions on Smart Grid. 9(4).
pp.3486-3495.
Paraschivescu, A. O. and COTÎRLEȚ, P. C., 2015. Quality Continuous Improvement Strategies
Kaizen Strategy--Comparative Analysis. Economy Transdisciplinarity Cognition. 18(1).
Waddock, S. and Bodwell, C., 2017. Total responsibility management: The manual. Routledge.
Talib, F. and Rahman, Z., 2015. Identification and prioritization of barriers to total quality
management implementation in service industry: an analytic hierarchy process
approach. The TQM Journal. 27(5). pp.591-615.
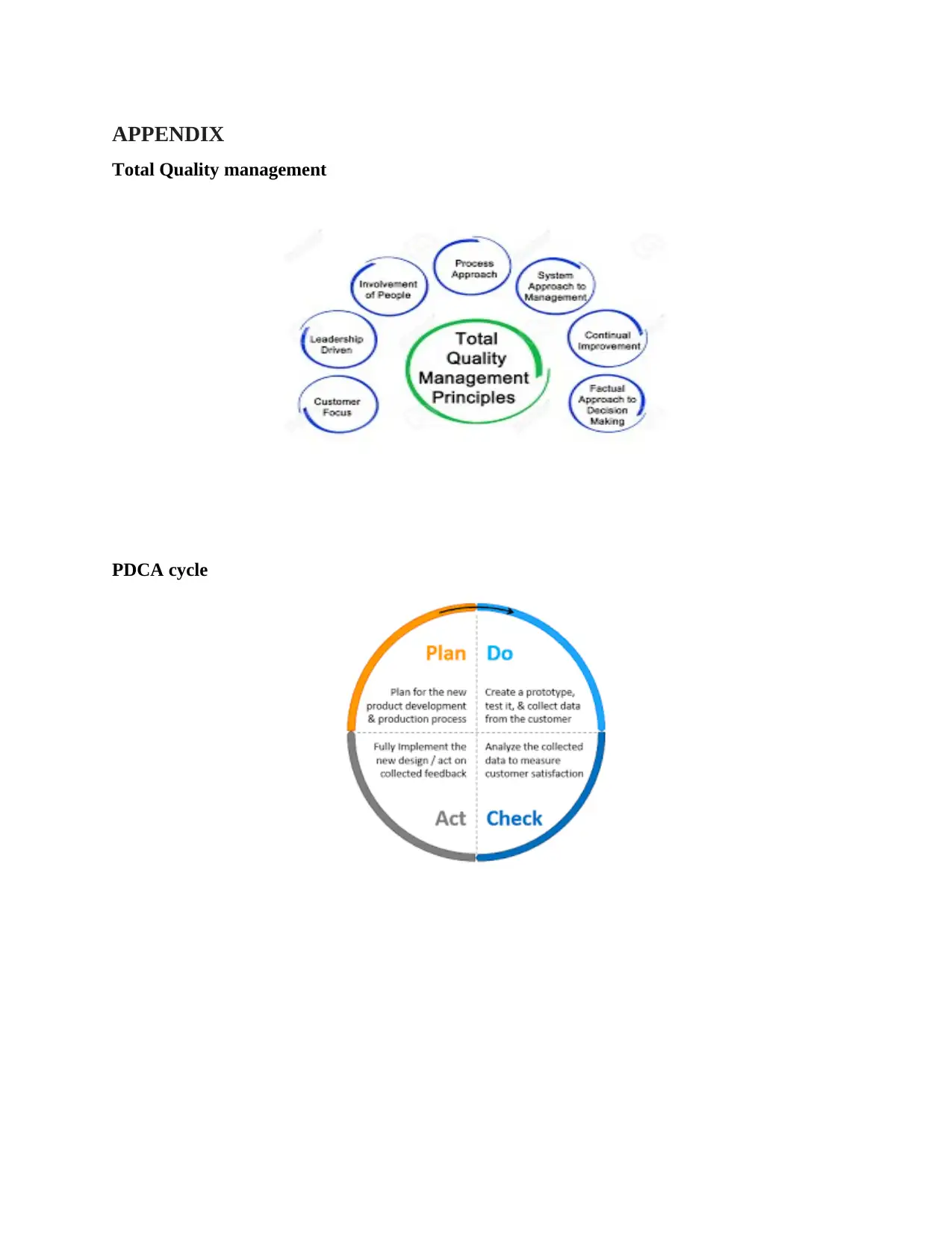
APPENDIX
Total Quality management
PDCA cycle
Total Quality management
PDCA cycle
You're viewing a preview
Unlock full access by subscribing today!
1 out of 12
Related Documents

Your All-in-One AI-Powered Toolkit for Academic Success.
+13062052269
info@desklib.com
Available 24*7 on WhatsApp / Email
Unlock your academic potential
© 2024 | Zucol Services PVT LTD | All rights reserved.