Case Study: Strategies for Quality Tooling Company Improvement
VerifiedAdded on  2021/02/20
|10
|3188
|54
Case Study
AI Summary
This case study analyzes Quality Tooling, a company manufacturing engineering tools, examining strategies to improve its performance and meet its long-term goals. The study explores Total Quality Management (TQM), Quality Assurance, Quality Control, and the sustainability of the company's culture. It delves into the principles of TQM, emphasizing customer focus, employee participation, and process-centered approaches. The report highlights the importance of quality assurance in preventing issues and ensuring customer satisfaction, as well as the role of quality control methods like inspection and statistical quality control in maintaining product standards. Furthermore, it discusses the impact of cultural sustainability on employee dedication and organizational efficiency. The analysis suggests that implementing these strategies can enhance Quality Tooling's competitiveness and overall success.
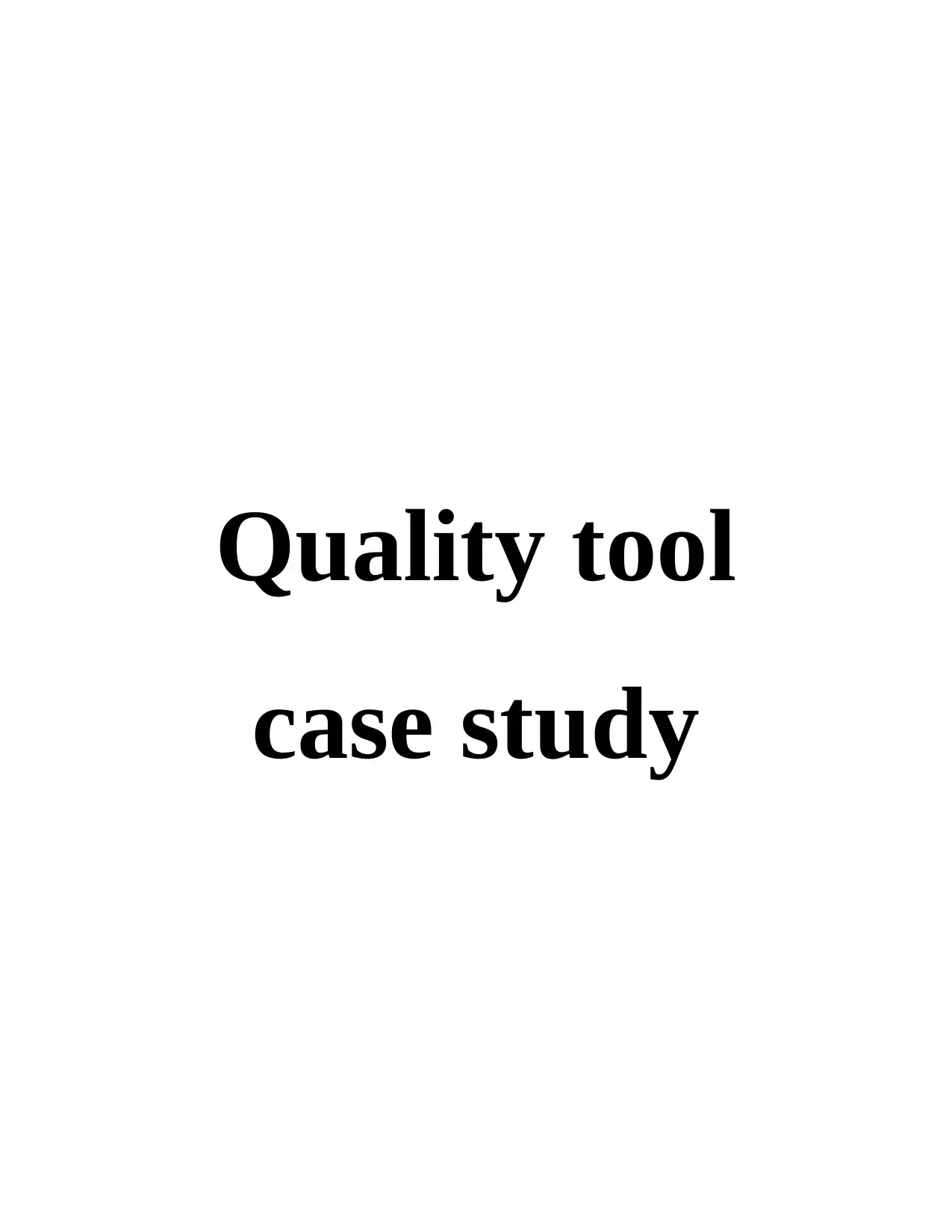
Quality tool
case study
case study
Paraphrase This Document
Need a fresh take? Get an instant paraphrase of this document with our AI Paraphraser
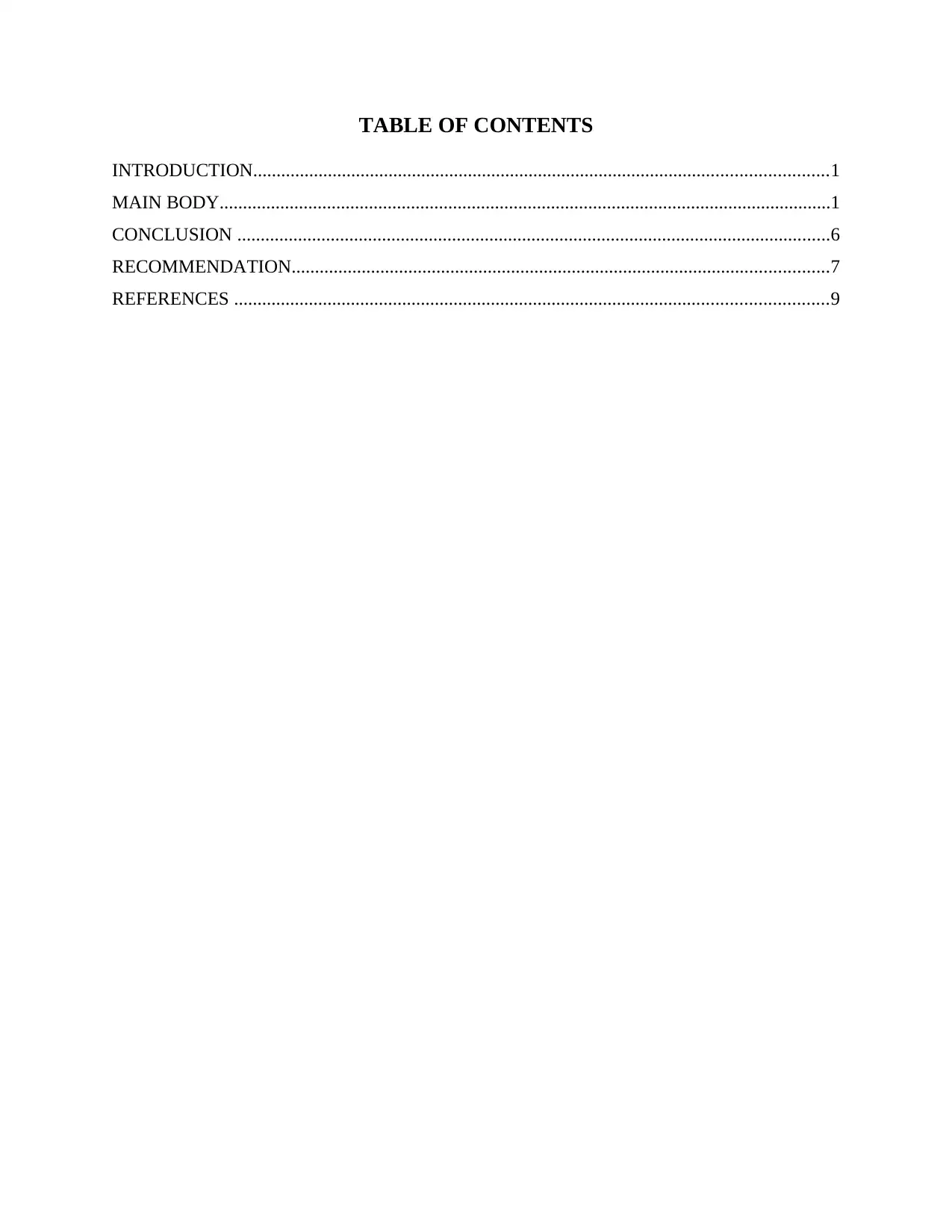
TABLE OF CONTENTS
INTRODUCTION...........................................................................................................................1
MAIN BODY...................................................................................................................................1
CONCLUSION ...............................................................................................................................6
RECOMMENDATION...................................................................................................................7
REFERENCES ...............................................................................................................................9
INTRODUCTION...........................................................................................................................1
MAIN BODY...................................................................................................................................1
CONCLUSION ...............................................................................................................................6
RECOMMENDATION...................................................................................................................7
REFERENCES ...............................................................................................................................9
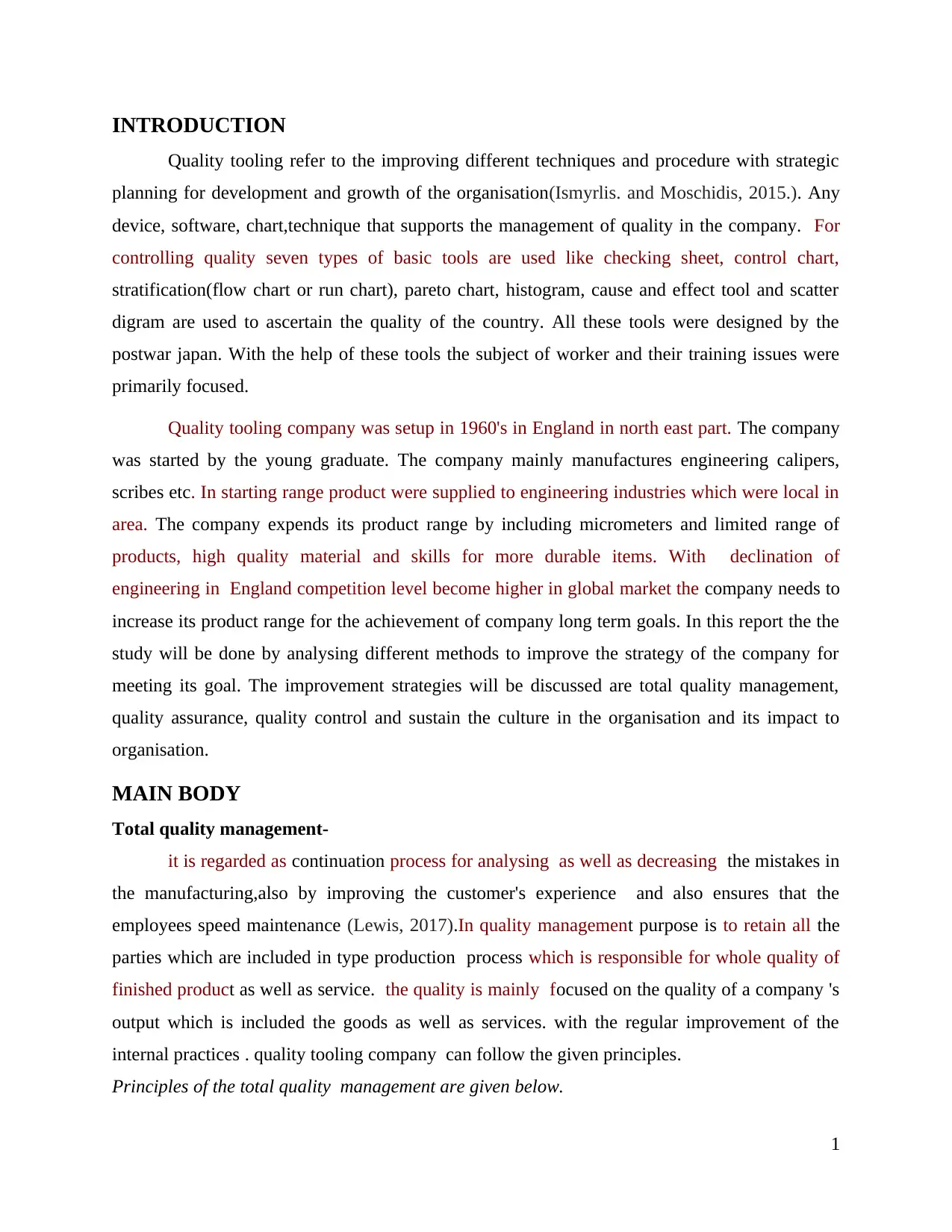
INTRODUCTION
Quality tooling refer to the improving different techniques and procedure with strategic
planning for development and growth of the organisation(Ismyrlis. and Moschidis, 2015.). Any
device, software, chart,technique that supports the management of quality in the company. For
controlling quality seven types of basic tools are used like checking sheet, control chart,
stratification(flow chart or run chart), pareto chart, histogram, cause and effect tool and scatter
digram are used to ascertain the quality of the country. All these tools were designed by the
postwar japan. With the help of these tools the subject of worker and their training issues were
primarily focused.
Quality tooling company was setup in 1960's in England in north east part. The company
was started by the young graduate. The company mainly manufactures engineering calipers,
scribes etc. In starting range product were supplied to engineering industries which were local in
area. The company expends its product range by including micrometers and limited range of
products, high quality material and skills for more durable items. With declination of
engineering in England competition level become higher in global market the company needs to
increase its product range for the achievement of company long term goals. In this report the the
study will be done by analysing different methods to improve the strategy of the company for
meeting its goal. The improvement strategies will be discussed are total quality management,
quality assurance, quality control and sustain the culture in the organisation and its impact to
organisation.
MAIN BODY
Total quality management-
it is regarded as continuation process for analysing as well as decreasing the mistakes in
the manufacturing,also by improving the customer's experience and also ensures that the
employees speed maintenance (Lewis, 2017).In quality management purpose is to retain all the
parties which are included in type production process which is responsible for whole quality of
finished product as well as service. the quality is mainly focused on the quality of a company 's
output which is included the goods as well as services. with the regular improvement of the
internal practices . quality tooling company can follow the given principles.
Principles of the total quality management are given below.
1
Quality tooling refer to the improving different techniques and procedure with strategic
planning for development and growth of the organisation(Ismyrlis. and Moschidis, 2015.). Any
device, software, chart,technique that supports the management of quality in the company. For
controlling quality seven types of basic tools are used like checking sheet, control chart,
stratification(flow chart or run chart), pareto chart, histogram, cause and effect tool and scatter
digram are used to ascertain the quality of the country. All these tools were designed by the
postwar japan. With the help of these tools the subject of worker and their training issues were
primarily focused.
Quality tooling company was setup in 1960's in England in north east part. The company
was started by the young graduate. The company mainly manufactures engineering calipers,
scribes etc. In starting range product were supplied to engineering industries which were local in
area. The company expends its product range by including micrometers and limited range of
products, high quality material and skills for more durable items. With declination of
engineering in England competition level become higher in global market the company needs to
increase its product range for the achievement of company long term goals. In this report the the
study will be done by analysing different methods to improve the strategy of the company for
meeting its goal. The improvement strategies will be discussed are total quality management,
quality assurance, quality control and sustain the culture in the organisation and its impact to
organisation.
MAIN BODY
Total quality management-
it is regarded as continuation process for analysing as well as decreasing the mistakes in
the manufacturing,also by improving the customer's experience and also ensures that the
employees speed maintenance (Lewis, 2017).In quality management purpose is to retain all the
parties which are included in type production process which is responsible for whole quality of
finished product as well as service. the quality is mainly focused on the quality of a company 's
output which is included the goods as well as services. with the regular improvement of the
internal practices . quality tooling company can follow the given principles.
Principles of the total quality management are given below.
1
⊘ This is a preview!⊘
Do you want full access?
Subscribe today to unlock all pages.

Trusted by 1+ million students worldwide
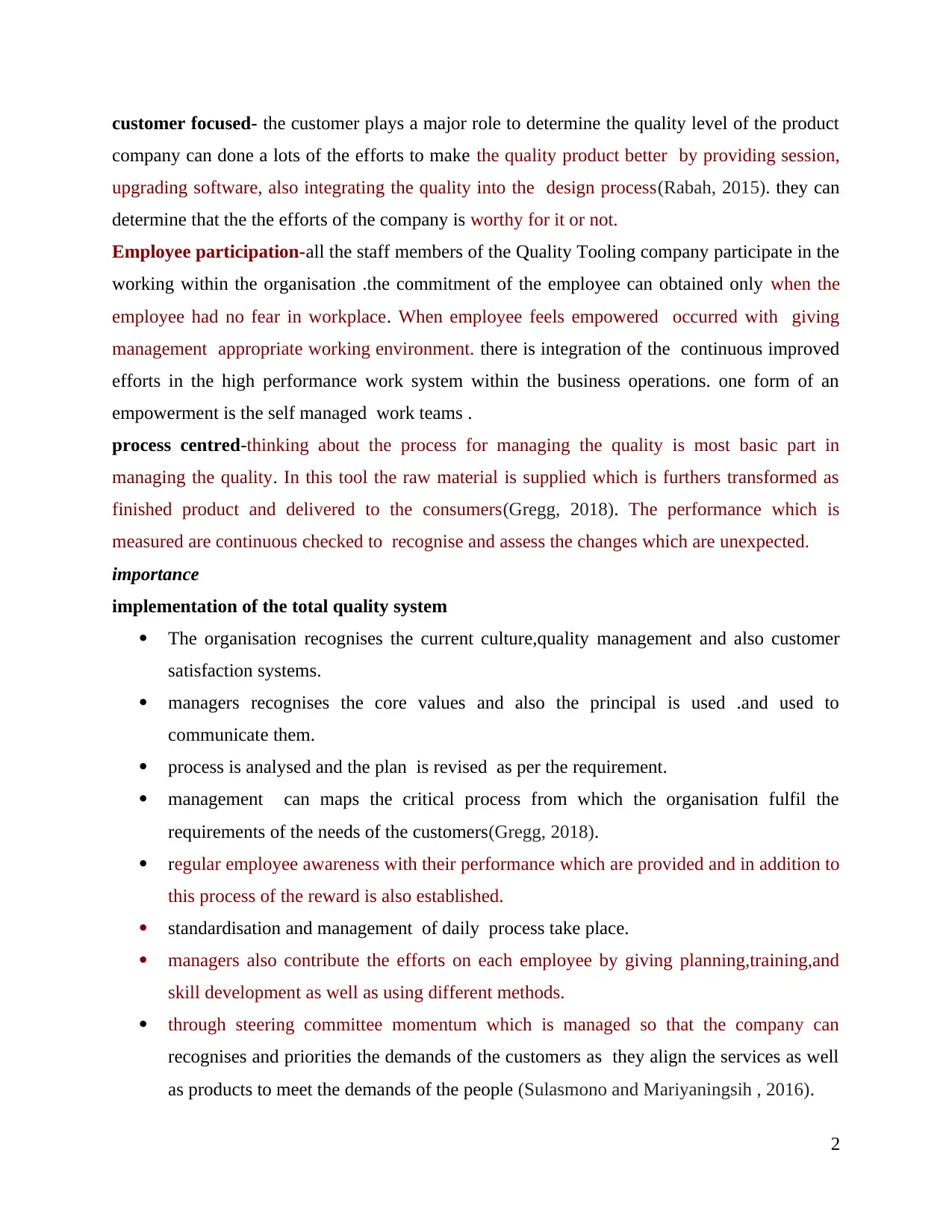
customer focused- the customer plays a major role to determine the quality level of the product
company can done a lots of the efforts to make the quality product better by providing session,
upgrading software, also integrating the quality into the design process(Rabah, 2015). they can
determine that the the efforts of the company is worthy for it or not.
Employee participation-all the staff members of the Quality Tooling company participate in the
working within the organisation .the commitment of the employee can obtained only when the
employee had no fear in workplace. When employee feels empowered occurred with giving
management appropriate working environment. there is integration of the continuous improved
efforts in the high performance work system within the business operations. one form of an
empowerment is the self managed work teams .
process centred-thinking about the process for managing the quality is most basic part in
managing the quality. In this tool the raw material is supplied which is furthers transformed as
finished product and delivered to the consumers(Gregg, 2018). The performance which is
measured are continuous checked to recognise and assess the changes which are unexpected.
importance
implementation of the total quality system
ï‚· The organisation recognises the current culture,quality management and also customer
satisfaction systems.
ï‚· managers recognises the core values and also the principal is used .and used to
communicate them.
ï‚· process is analysed and the plan is revised as per the requirement.
ï‚· management can maps the critical process from which the organisation fulfil the
requirements of the needs of the customers(Gregg, 2018).
ï‚· regular employee awareness with their performance which are provided and in addition to
this process of the reward is also established.
ï‚· standardisation and management of daily process take place.
ï‚· managers also contribute the efforts on each employee by giving planning,training,and
skill development as well as using different methods.
ï‚· through steering committee momentum which is managed so that the company can
recognises and priorities the demands of the customers as they align the services as well
as products to meet the demands of the people (Sulasmono and Mariyaningsih , 2016).
2
company can done a lots of the efforts to make the quality product better by providing session,
upgrading software, also integrating the quality into the design process(Rabah, 2015). they can
determine that the the efforts of the company is worthy for it or not.
Employee participation-all the staff members of the Quality Tooling company participate in the
working within the organisation .the commitment of the employee can obtained only when the
employee had no fear in workplace. When employee feels empowered occurred with giving
management appropriate working environment. there is integration of the continuous improved
efforts in the high performance work system within the business operations. one form of an
empowerment is the self managed work teams .
process centred-thinking about the process for managing the quality is most basic part in
managing the quality. In this tool the raw material is supplied which is furthers transformed as
finished product and delivered to the consumers(Gregg, 2018). The performance which is
measured are continuous checked to recognise and assess the changes which are unexpected.
importance
implementation of the total quality system
ï‚· The organisation recognises the current culture,quality management and also customer
satisfaction systems.
ï‚· managers recognises the core values and also the principal is used .and used to
communicate them.
ï‚· process is analysed and the plan is revised as per the requirement.
ï‚· management can maps the critical process from which the organisation fulfil the
requirements of the needs of the customers(Gregg, 2018).
ï‚· regular employee awareness with their performance which are provided and in addition to
this process of the reward is also established.
ï‚· standardisation and management of daily process take place.
ï‚· managers also contribute the efforts on each employee by giving planning,training,and
skill development as well as using different methods.
ï‚· through steering committee momentum which is managed so that the company can
recognises and priorities the demands of the customers as they align the services as well
as products to meet the demands of the people (Sulasmono and Mariyaningsih , 2016).
2
Paraphrase This Document
Need a fresh take? Get an instant paraphrase of this document with our AI Paraphraser
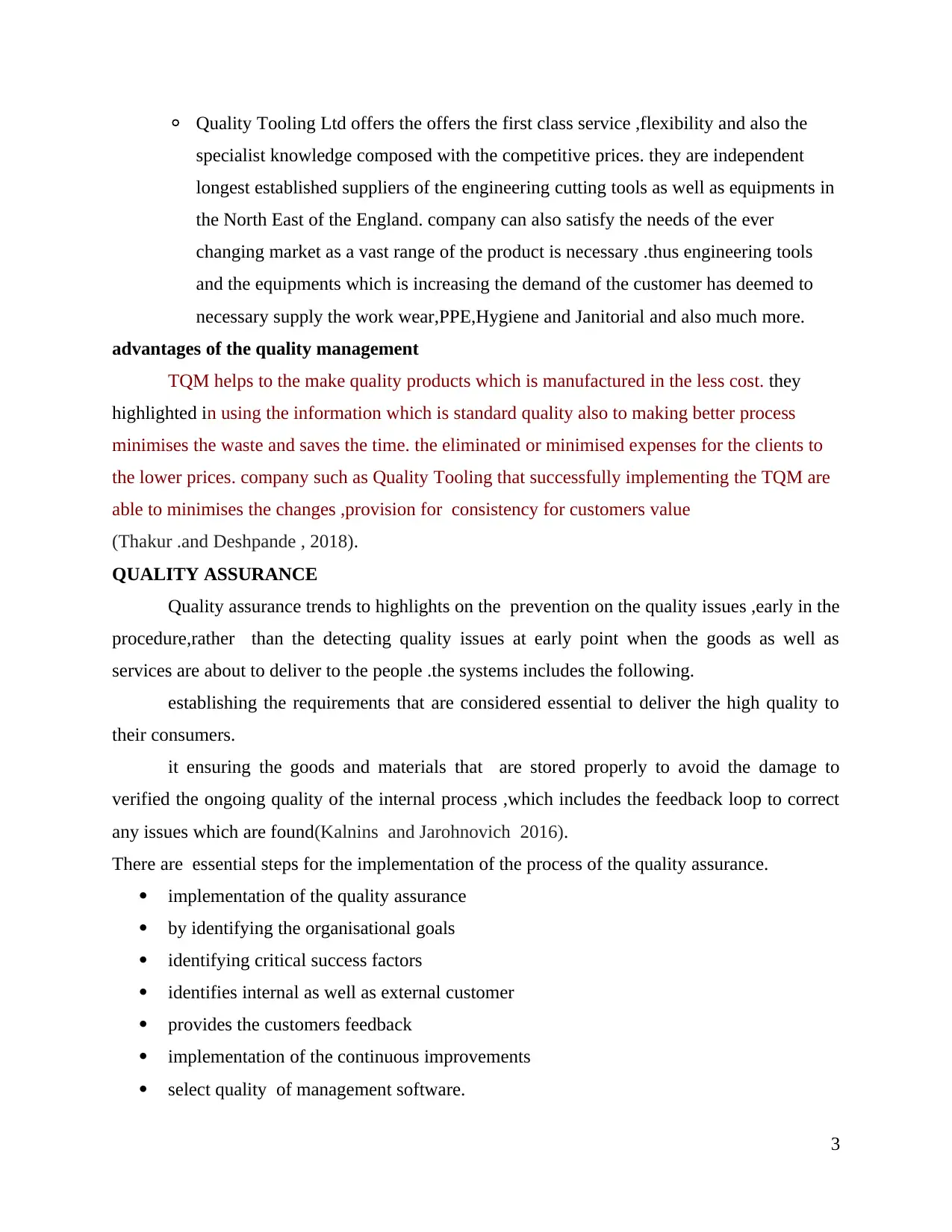
â—¦ Quality Tooling Ltd offers the offers the first class service ,flexibility and also the
specialist knowledge composed with the competitive prices. they are independent
longest established suppliers of the engineering cutting tools as well as equipments in
the North East of the England. company can also satisfy the needs of the ever
changing market as a vast range of the product is necessary .thus engineering tools
and the equipments which is increasing the demand of the customer has deemed to
necessary supply the work wear,PPE,Hygiene and Janitorial and also much more.
advantages of the quality management
TQM helps to the make quality products which is manufactured in the less cost. they
highlighted in using the information which is standard quality also to making better process
minimises the waste and saves the time. the eliminated or minimised expenses for the clients to
the lower prices. company such as Quality Tooling that successfully implementing the TQM are
able to minimises the changes ,provision for consistency for customers value
(Thakur .and Deshpande , 2018).
QUALITY ASSURANCE
Quality assurance trends to highlights on the prevention on the quality issues ,early in the
procedure,rather than the detecting quality issues at early point when the goods as well as
services are about to deliver to the people .the systems includes the following.
establishing the requirements that are considered essential to deliver the high quality to
their consumers.
it ensuring the goods and materials that are stored properly to avoid the damage to
verified the ongoing quality of the internal process ,which includes the feedback loop to correct
any issues which are found(Kalnins and Jarohnovich 2016).
There are essential steps for the implementation of the process of the quality assurance.
ï‚· implementation of the quality assurance
ï‚· by identifying the organisational goals
ï‚· identifying critical success factors
ï‚· identifies internal as well as external customer
ï‚· provides the customers feedback
ï‚· implementation of the continuous improvements
ï‚· select quality of management software.
3
specialist knowledge composed with the competitive prices. they are independent
longest established suppliers of the engineering cutting tools as well as equipments in
the North East of the England. company can also satisfy the needs of the ever
changing market as a vast range of the product is necessary .thus engineering tools
and the equipments which is increasing the demand of the customer has deemed to
necessary supply the work wear,PPE,Hygiene and Janitorial and also much more.
advantages of the quality management
TQM helps to the make quality products which is manufactured in the less cost. they
highlighted in using the information which is standard quality also to making better process
minimises the waste and saves the time. the eliminated or minimised expenses for the clients to
the lower prices. company such as Quality Tooling that successfully implementing the TQM are
able to minimises the changes ,provision for consistency for customers value
(Thakur .and Deshpande , 2018).
QUALITY ASSURANCE
Quality assurance trends to highlights on the prevention on the quality issues ,early in the
procedure,rather than the detecting quality issues at early point when the goods as well as
services are about to deliver to the people .the systems includes the following.
establishing the requirements that are considered essential to deliver the high quality to
their consumers.
it ensuring the goods and materials that are stored properly to avoid the damage to
verified the ongoing quality of the internal process ,which includes the feedback loop to correct
any issues which are found(Kalnins and Jarohnovich 2016).
There are essential steps for the implementation of the process of the quality assurance.
ï‚· implementation of the quality assurance
ï‚· by identifying the organisational goals
ï‚· identifying critical success factors
ï‚· identifies internal as well as external customer
ï‚· provides the customers feedback
ï‚· implementation of the continuous improvements
ï‚· select quality of management software.
3
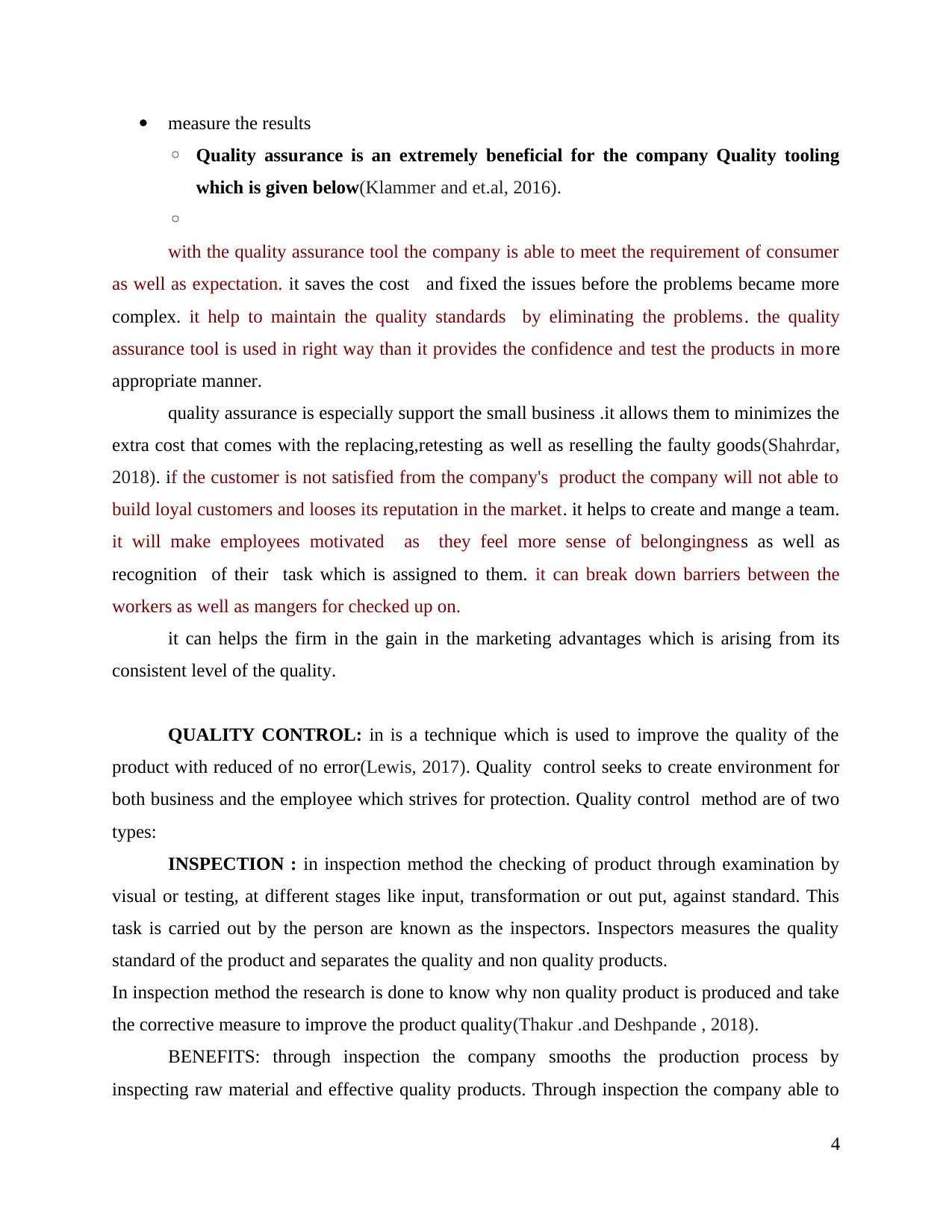
ï‚· measure the results
â—¦ Quality assurance is an extremely beneficial for the company Quality tooling
which is given below(Klammer and et.al, 2016).
â—¦
with the quality assurance tool the company is able to meet the requirement of consumer
as well as expectation. it saves the cost and fixed the issues before the problems became more
complex. it help to maintain the quality standards by eliminating the problems. the quality
assurance tool is used in right way than it provides the confidence and test the products in more
appropriate manner.
quality assurance is especially support the small business .it allows them to minimizes the
extra cost that comes with the replacing,retesting as well as reselling the faulty goods(Shahrdar,
2018). if the customer is not satisfied from the company's product the company will not able to
build loyal customers and looses its reputation in the market. it helps to create and mange a team.
it will make employees motivated as they feel more sense of belongingness as well as
recognition of their task which is assigned to them. it can break down barriers between the
workers as well as mangers for checked up on.
it can helps the firm in the gain in the marketing advantages which is arising from its
consistent level of the quality.
QUALITY CONTROL: in is a technique which is used to improve the quality of the
product with reduced of no error(Lewis, 2017). Quality control seeks to create environment for
both business and the employee which strives for protection. Quality control method are of two
types:
INSPECTION : in inspection method the checking of product through examination by
visual or testing, at different stages like input, transformation or out put, against standard. This
task is carried out by the person are known as the inspectors. Inspectors measures the quality
standard of the product and separates the quality and non quality products.
In inspection method the research is done to know why non quality product is produced and take
the corrective measure to improve the product quality(Thakur .and Deshpande , 2018).
BENEFITS: through inspection the company smooths the production process by
inspecting raw material and effective quality products. Through inspection the company able to
4
â—¦ Quality assurance is an extremely beneficial for the company Quality tooling
which is given below(Klammer and et.al, 2016).
â—¦
with the quality assurance tool the company is able to meet the requirement of consumer
as well as expectation. it saves the cost and fixed the issues before the problems became more
complex. it help to maintain the quality standards by eliminating the problems. the quality
assurance tool is used in right way than it provides the confidence and test the products in more
appropriate manner.
quality assurance is especially support the small business .it allows them to minimizes the
extra cost that comes with the replacing,retesting as well as reselling the faulty goods(Shahrdar,
2018). if the customer is not satisfied from the company's product the company will not able to
build loyal customers and looses its reputation in the market. it helps to create and mange a team.
it will make employees motivated as they feel more sense of belongingness as well as
recognition of their task which is assigned to them. it can break down barriers between the
workers as well as mangers for checked up on.
it can helps the firm in the gain in the marketing advantages which is arising from its
consistent level of the quality.
QUALITY CONTROL: in is a technique which is used to improve the quality of the
product with reduced of no error(Lewis, 2017). Quality control seeks to create environment for
both business and the employee which strives for protection. Quality control method are of two
types:
INSPECTION : in inspection method the checking of product through examination by
visual or testing, at different stages like input, transformation or out put, against standard. This
task is carried out by the person are known as the inspectors. Inspectors measures the quality
standard of the product and separates the quality and non quality products.
In inspection method the research is done to know why non quality product is produced and take
the corrective measure to improve the product quality(Thakur .and Deshpande , 2018).
BENEFITS: through inspection the company smooths the production process by
inspecting raw material and effective quality products. Through inspection the company able to
4
⊘ This is a preview!⊘
Do you want full access?
Subscribe today to unlock all pages.

Trusted by 1+ million students worldwide
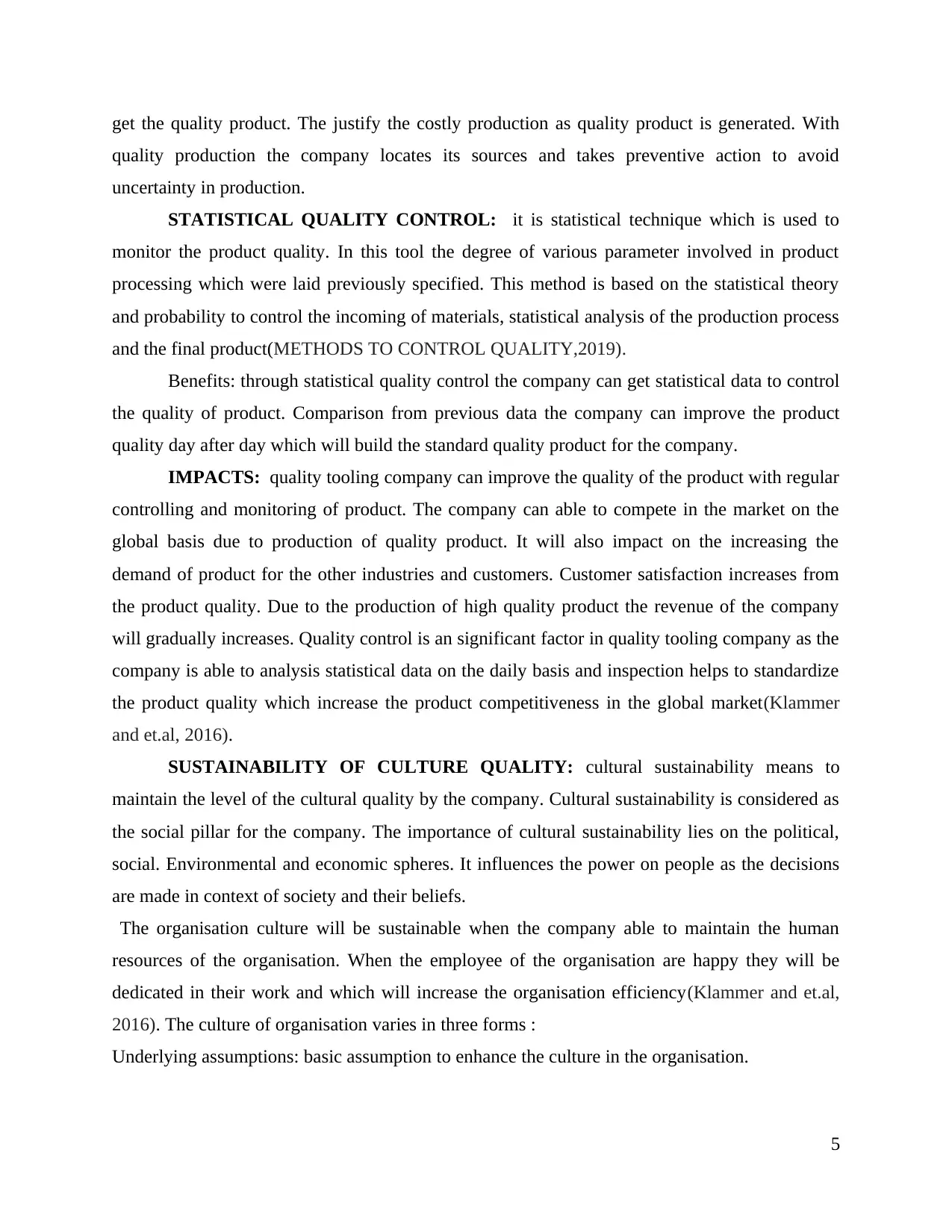
get the quality product. The justify the costly production as quality product is generated. With
quality production the company locates its sources and takes preventive action to avoid
uncertainty in production.
STATISTICAL QUALITY CONTROL: it is statistical technique which is used to
monitor the product quality. In this tool the degree of various parameter involved in product
processing which were laid previously specified. This method is based on the statistical theory
and probability to control the incoming of materials, statistical analysis of the production process
and the final product(METHODS TO CONTROL QUALITY,2019).
Benefits: through statistical quality control the company can get statistical data to control
the quality of product. Comparison from previous data the company can improve the product
quality day after day which will build the standard quality product for the company.
IMPACTS: quality tooling company can improve the quality of the product with regular
controlling and monitoring of product. The company can able to compete in the market on the
global basis due to production of quality product. It will also impact on the increasing the
demand of product for the other industries and customers. Customer satisfaction increases from
the product quality. Due to the production of high quality product the revenue of the company
will gradually increases. Quality control is an significant factor in quality tooling company as the
company is able to analysis statistical data on the daily basis and inspection helps to standardize
the product quality which increase the product competitiveness in the global market(Klammer
and et.al, 2016).
SUSTAINABILITY OF CULTURE QUALITY: cultural sustainability means to
maintain the level of the cultural quality by the company. Cultural sustainability is considered as
the social pillar for the company. The importance of cultural sustainability lies on the political,
social. Environmental and economic spheres. It influences the power on people as the decisions
are made in context of society and their beliefs.
The organisation culture will be sustainable when the company able to maintain the human
resources of the organisation. When the employee of the organisation are happy they will be
dedicated in their work and which will increase the organisation efficiency(Klammer and et.al,
2016). The culture of organisation varies in three forms :
Underlying assumptions: basic assumption to enhance the culture in the organisation.
5
quality production the company locates its sources and takes preventive action to avoid
uncertainty in production.
STATISTICAL QUALITY CONTROL: it is statistical technique which is used to
monitor the product quality. In this tool the degree of various parameter involved in product
processing which were laid previously specified. This method is based on the statistical theory
and probability to control the incoming of materials, statistical analysis of the production process
and the final product(METHODS TO CONTROL QUALITY,2019).
Benefits: through statistical quality control the company can get statistical data to control
the quality of product. Comparison from previous data the company can improve the product
quality day after day which will build the standard quality product for the company.
IMPACTS: quality tooling company can improve the quality of the product with regular
controlling and monitoring of product. The company can able to compete in the market on the
global basis due to production of quality product. It will also impact on the increasing the
demand of product for the other industries and customers. Customer satisfaction increases from
the product quality. Due to the production of high quality product the revenue of the company
will gradually increases. Quality control is an significant factor in quality tooling company as the
company is able to analysis statistical data on the daily basis and inspection helps to standardize
the product quality which increase the product competitiveness in the global market(Klammer
and et.al, 2016).
SUSTAINABILITY OF CULTURE QUALITY: cultural sustainability means to
maintain the level of the cultural quality by the company. Cultural sustainability is considered as
the social pillar for the company. The importance of cultural sustainability lies on the political,
social. Environmental and economic spheres. It influences the power on people as the decisions
are made in context of society and their beliefs.
The organisation culture will be sustainable when the company able to maintain the human
resources of the organisation. When the employee of the organisation are happy they will be
dedicated in their work and which will increase the organisation efficiency(Klammer and et.al,
2016). The culture of organisation varies in three forms :
Underlying assumptions: basic assumption to enhance the culture in the organisation.
5
Paraphrase This Document
Need a fresh take? Get an instant paraphrase of this document with our AI Paraphraser
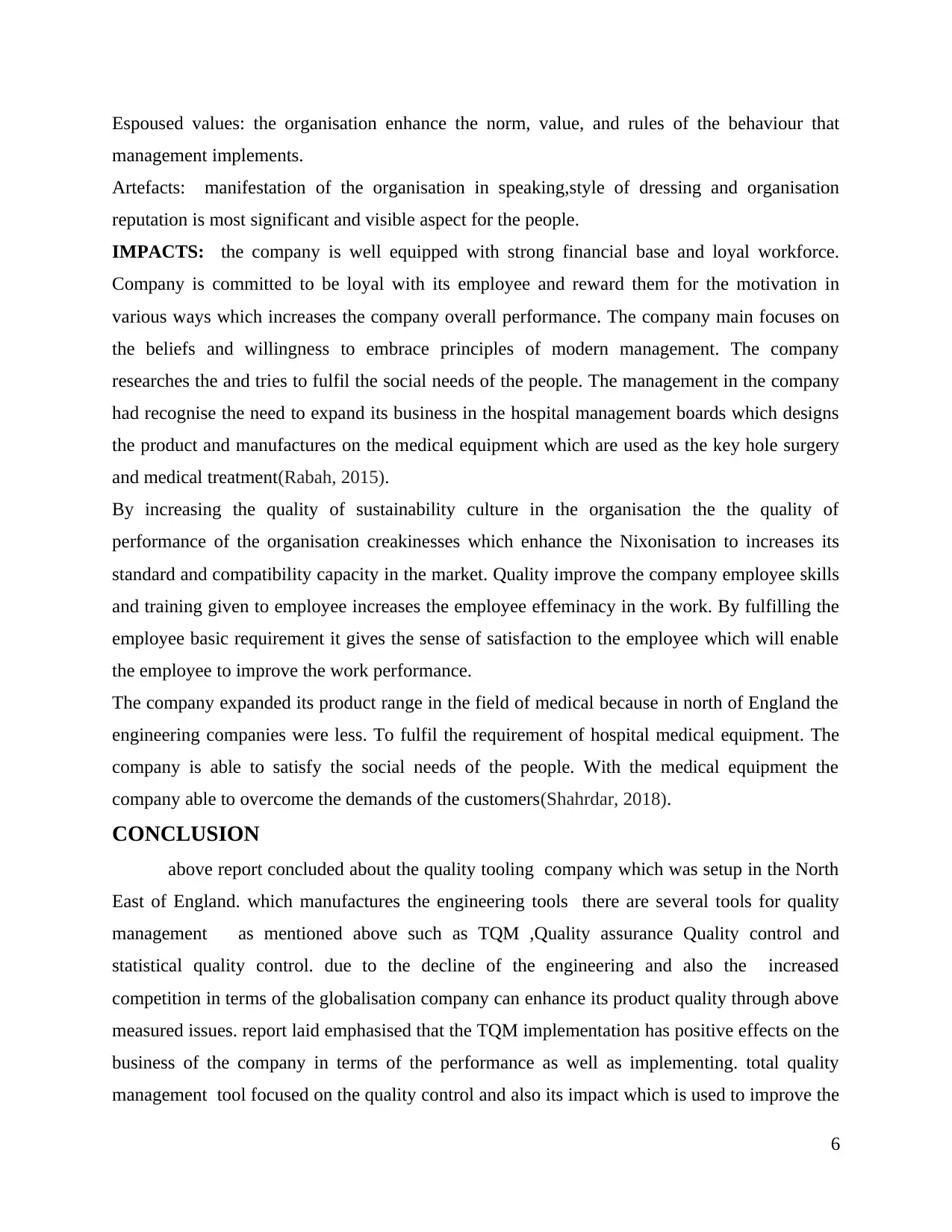
Espoused values: the organisation enhance the norm, value, and rules of the behaviour that
management implements.
Artefacts: manifestation of the organisation in speaking,style of dressing and organisation
reputation is most significant and visible aspect for the people.
IMPACTS: the company is well equipped with strong financial base and loyal workforce.
Company is committed to be loyal with its employee and reward them for the motivation in
various ways which increases the company overall performance. The company main focuses on
the beliefs and willingness to embrace principles of modern management. The company
researches the and tries to fulfil the social needs of the people. The management in the company
had recognise the need to expand its business in the hospital management boards which designs
the product and manufactures on the medical equipment which are used as the key hole surgery
and medical treatment(Rabah, 2015).
By increasing the quality of sustainability culture in the organisation the the quality of
performance of the organisation creakinesses which enhance the Nixonisation to increases its
standard and compatibility capacity in the market. Quality improve the company employee skills
and training given to employee increases the employee effeminacy in the work. By fulfilling the
employee basic requirement it gives the sense of satisfaction to the employee which will enable
the employee to improve the work performance.
The company expanded its product range in the field of medical because in north of England the
engineering companies were less. To fulfil the requirement of hospital medical equipment. The
company is able to satisfy the social needs of the people. With the medical equipment the
company able to overcome the demands of the customers(Shahrdar, 2018).
CONCLUSION
above report concluded about the quality tooling company which was setup in the North
East of England. which manufactures the engineering tools there are several tools for quality
management as mentioned above such as TQM ,Quality assurance Quality control and
statistical quality control. due to the decline of the engineering and also the increased
competition in terms of the globalisation company can enhance its product quality through above
measured issues. report laid emphasised that the TQM implementation has positive effects on the
business of the company in terms of the performance as well as implementing. total quality
management tool focused on the quality control and also its impact which is used to improve the
6
management implements.
Artefacts: manifestation of the organisation in speaking,style of dressing and organisation
reputation is most significant and visible aspect for the people.
IMPACTS: the company is well equipped with strong financial base and loyal workforce.
Company is committed to be loyal with its employee and reward them for the motivation in
various ways which increases the company overall performance. The company main focuses on
the beliefs and willingness to embrace principles of modern management. The company
researches the and tries to fulfil the social needs of the people. The management in the company
had recognise the need to expand its business in the hospital management boards which designs
the product and manufactures on the medical equipment which are used as the key hole surgery
and medical treatment(Rabah, 2015).
By increasing the quality of sustainability culture in the organisation the the quality of
performance of the organisation creakinesses which enhance the Nixonisation to increases its
standard and compatibility capacity in the market. Quality improve the company employee skills
and training given to employee increases the employee effeminacy in the work. By fulfilling the
employee basic requirement it gives the sense of satisfaction to the employee which will enable
the employee to improve the work performance.
The company expanded its product range in the field of medical because in north of England the
engineering companies were less. To fulfil the requirement of hospital medical equipment. The
company is able to satisfy the social needs of the people. With the medical equipment the
company able to overcome the demands of the customers(Shahrdar, 2018).
CONCLUSION
above report concluded about the quality tooling company which was setup in the North
East of England. which manufactures the engineering tools there are several tools for quality
management as mentioned above such as TQM ,Quality assurance Quality control and
statistical quality control. due to the decline of the engineering and also the increased
competition in terms of the globalisation company can enhance its product quality through above
measured issues. report laid emphasised that the TQM implementation has positive effects on the
business of the company in terms of the performance as well as implementing. total quality
management tool focused on the quality control and also its impact which is used to improve the
6
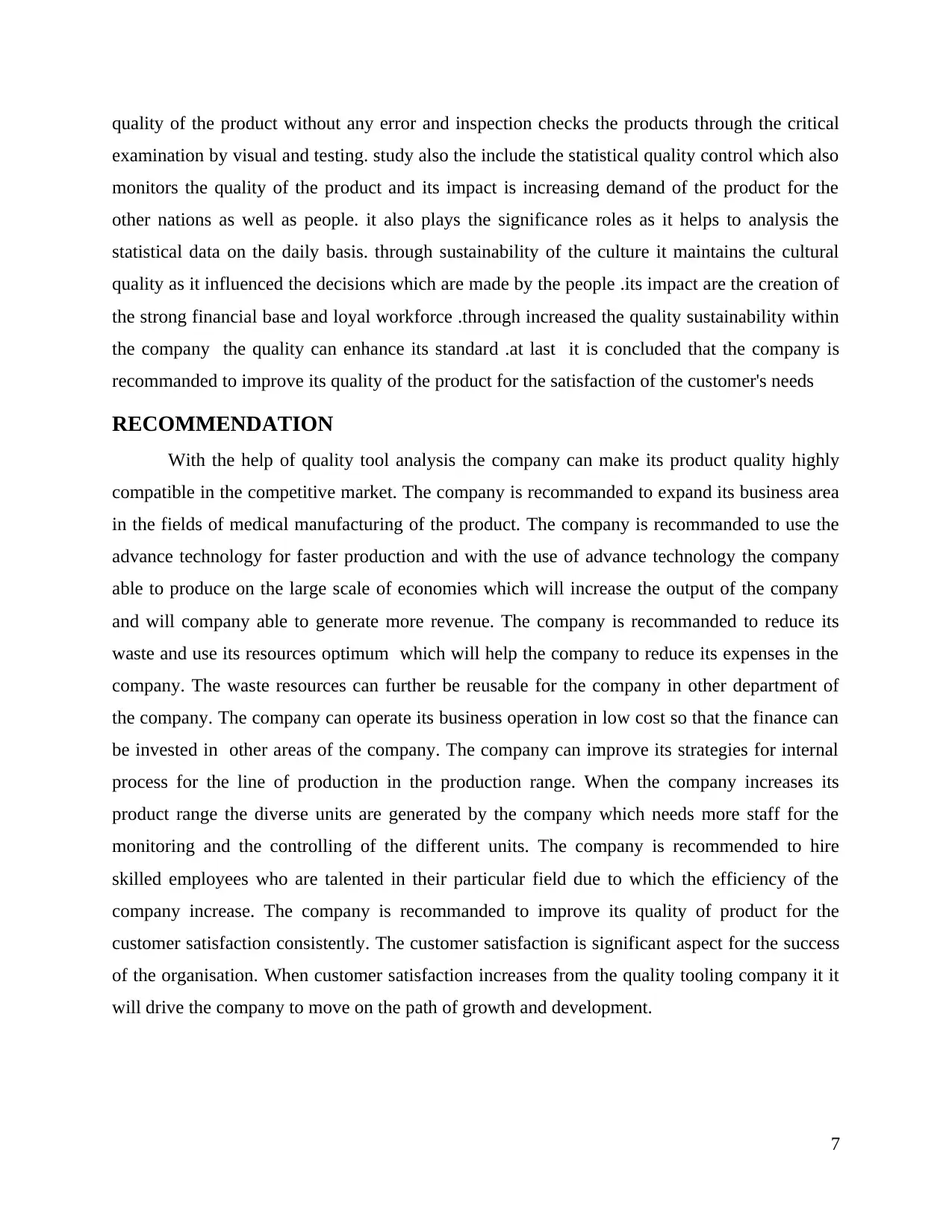
quality of the product without any error and inspection checks the products through the critical
examination by visual and testing. study also the include the statistical quality control which also
monitors the quality of the product and its impact is increasing demand of the product for the
other nations as well as people. it also plays the significance roles as it helps to analysis the
statistical data on the daily basis. through sustainability of the culture it maintains the cultural
quality as it influenced the decisions which are made by the people .its impact are the creation of
the strong financial base and loyal workforce .through increased the quality sustainability within
the company the quality can enhance its standard .at last it is concluded that the company is
recommanded to improve its quality of the product for the satisfaction of the customer's needs
RECOMMENDATION
With the help of quality tool analysis the company can make its product quality highly
compatible in the competitive market. The company is recommanded to expand its business area
in the fields of medical manufacturing of the product. The company is recommanded to use the
advance technology for faster production and with the use of advance technology the company
able to produce on the large scale of economies which will increase the output of the company
and will company able to generate more revenue. The company is recommanded to reduce its
waste and use its resources optimum which will help the company to reduce its expenses in the
company. The waste resources can further be reusable for the company in other department of
the company. The company can operate its business operation in low cost so that the finance can
be invested in other areas of the company. The company can improve its strategies for internal
process for the line of production in the production range. When the company increases its
product range the diverse units are generated by the company which needs more staff for the
monitoring and the controlling of the different units. The company is recommended to hire
skilled employees who are talented in their particular field due to which the efficiency of the
company increase. The company is recommanded to improve its quality of product for the
customer satisfaction consistently. The customer satisfaction is significant aspect for the success
of the organisation. When customer satisfaction increases from the quality tooling company it it
will drive the company to move on the path of growth and development.
7
examination by visual and testing. study also the include the statistical quality control which also
monitors the quality of the product and its impact is increasing demand of the product for the
other nations as well as people. it also plays the significance roles as it helps to analysis the
statistical data on the daily basis. through sustainability of the culture it maintains the cultural
quality as it influenced the decisions which are made by the people .its impact are the creation of
the strong financial base and loyal workforce .through increased the quality sustainability within
the company the quality can enhance its standard .at last it is concluded that the company is
recommanded to improve its quality of the product for the satisfaction of the customer's needs
RECOMMENDATION
With the help of quality tool analysis the company can make its product quality highly
compatible in the competitive market. The company is recommanded to expand its business area
in the fields of medical manufacturing of the product. The company is recommanded to use the
advance technology for faster production and with the use of advance technology the company
able to produce on the large scale of economies which will increase the output of the company
and will company able to generate more revenue. The company is recommanded to reduce its
waste and use its resources optimum which will help the company to reduce its expenses in the
company. The waste resources can further be reusable for the company in other department of
the company. The company can operate its business operation in low cost so that the finance can
be invested in other areas of the company. The company can improve its strategies for internal
process for the line of production in the production range. When the company increases its
product range the diverse units are generated by the company which needs more staff for the
monitoring and the controlling of the different units. The company is recommended to hire
skilled employees who are talented in their particular field due to which the efficiency of the
company increase. The company is recommanded to improve its quality of product for the
customer satisfaction consistently. The customer satisfaction is significant aspect for the success
of the organisation. When customer satisfaction increases from the quality tooling company it it
will drive the company to move on the path of growth and development.
7
⊘ This is a preview!⊘
Do you want full access?
Subscribe today to unlock all pages.

Trusted by 1+ million students worldwide
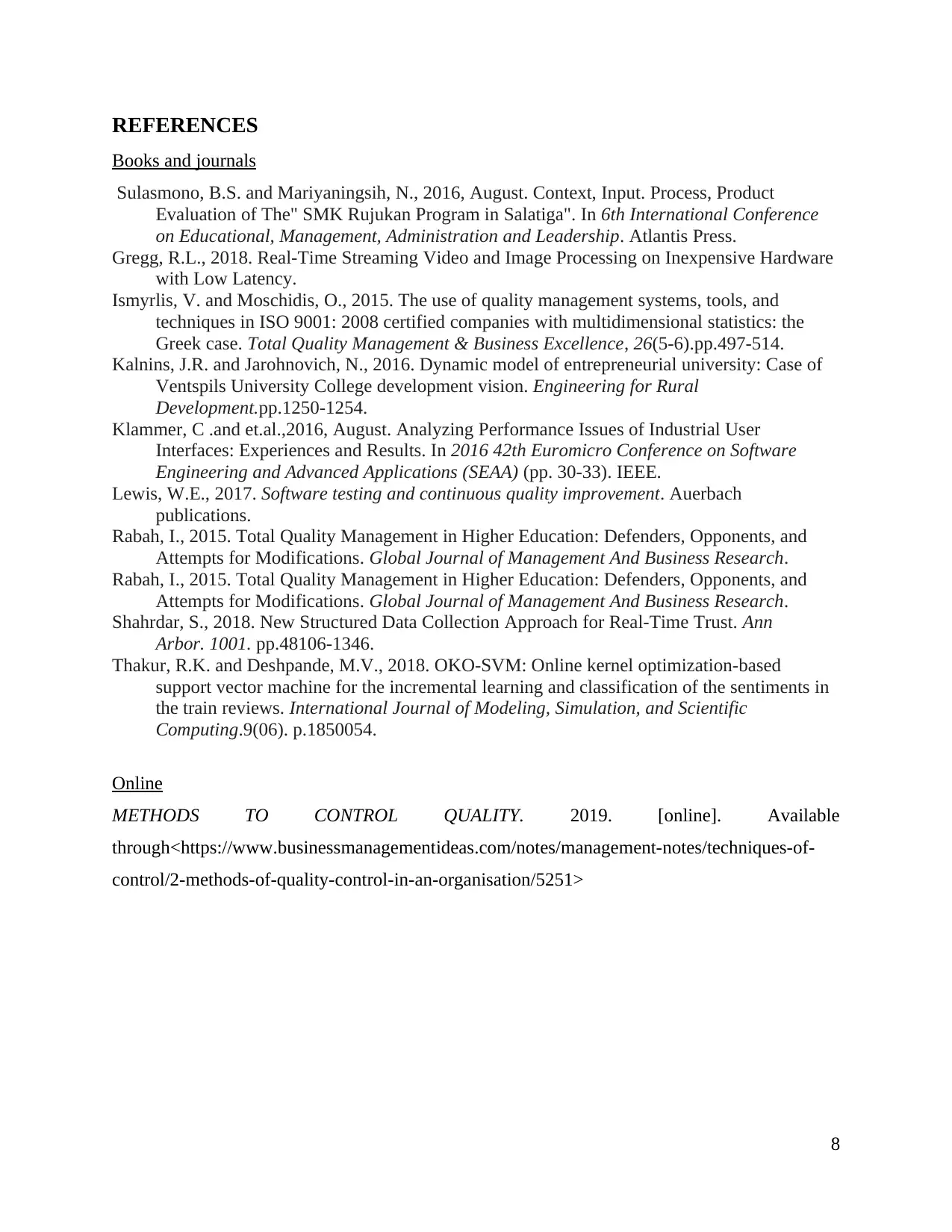
REFERENCES
Books and journals
Sulasmono, B.S. and Mariyaningsih, N., 2016, August. Context, Input. Process, Product
Evaluation of The" SMK Rujukan Program in Salatiga". In 6th International Conference
on Educational, Management, Administration and Leadership. Atlantis Press.
Gregg, R.L., 2018. Real-Time Streaming Video and Image Processing on Inexpensive Hardware
with Low Latency.
Ismyrlis, V. and Moschidis, O., 2015. The use of quality management systems, tools, and
techniques in ISO 9001: 2008 certified companies with multidimensional statistics: the
Greek case. Total Quality Management & Business Excellence, 26(5-6).pp.497-514.
Kalnins, J.R. and Jarohnovich, N., 2016. Dynamic model of entrepreneurial university: Case of
Ventspils University College development vision. Engineering for Rural
Development.pp.1250-1254.
Klammer, C .and et.al.,2016, August. Analyzing Performance Issues of Industrial User
Interfaces: Experiences and Results. In 2016 42th Euromicro Conference on Software
Engineering and Advanced Applications (SEAA) (pp. 30-33). IEEE.
Lewis, W.E., 2017. Software testing and continuous quality improvement. Auerbach
publications.
Rabah, I., 2015. Total Quality Management in Higher Education: Defenders, Opponents, and
Attempts for Modifications. Global Journal of Management And Business Research.
Rabah, I., 2015. Total Quality Management in Higher Education: Defenders, Opponents, and
Attempts for Modifications. Global Journal of Management And Business Research.
Shahrdar, S., 2018. New Structured Data Collection Approach for Real-Time Trust. Ann
Arbor. 1001. pp.48106-1346.
Thakur, R.K. and Deshpande, M.V., 2018. OKO-SVM: Online kernel optimization-based
support vector machine for the incremental learning and classification of the sentiments in
the train reviews. International Journal of Modeling, Simulation, and Scientific
Computing.9(06). p.1850054.
Online
METHODS TO CONTROL QUALITY. 2019. [online]. Available
through<https://www.businessmanagementideas.com/notes/management-notes/techniques-of-
control/2-methods-of-quality-control-in-an-organisation/5251>
8
Books and journals
Sulasmono, B.S. and Mariyaningsih, N., 2016, August. Context, Input. Process, Product
Evaluation of The" SMK Rujukan Program in Salatiga". In 6th International Conference
on Educational, Management, Administration and Leadership. Atlantis Press.
Gregg, R.L., 2018. Real-Time Streaming Video and Image Processing on Inexpensive Hardware
with Low Latency.
Ismyrlis, V. and Moschidis, O., 2015. The use of quality management systems, tools, and
techniques in ISO 9001: 2008 certified companies with multidimensional statistics: the
Greek case. Total Quality Management & Business Excellence, 26(5-6).pp.497-514.
Kalnins, J.R. and Jarohnovich, N., 2016. Dynamic model of entrepreneurial university: Case of
Ventspils University College development vision. Engineering for Rural
Development.pp.1250-1254.
Klammer, C .and et.al.,2016, August. Analyzing Performance Issues of Industrial User
Interfaces: Experiences and Results. In 2016 42th Euromicro Conference on Software
Engineering and Advanced Applications (SEAA) (pp. 30-33). IEEE.
Lewis, W.E., 2017. Software testing and continuous quality improvement. Auerbach
publications.
Rabah, I., 2015. Total Quality Management in Higher Education: Defenders, Opponents, and
Attempts for Modifications. Global Journal of Management And Business Research.
Rabah, I., 2015. Total Quality Management in Higher Education: Defenders, Opponents, and
Attempts for Modifications. Global Journal of Management And Business Research.
Shahrdar, S., 2018. New Structured Data Collection Approach for Real-Time Trust. Ann
Arbor. 1001. pp.48106-1346.
Thakur, R.K. and Deshpande, M.V., 2018. OKO-SVM: Online kernel optimization-based
support vector machine for the incremental learning and classification of the sentiments in
the train reviews. International Journal of Modeling, Simulation, and Scientific
Computing.9(06). p.1850054.
Online
METHODS TO CONTROL QUALITY. 2019. [online]. Available
through<https://www.businessmanagementideas.com/notes/management-notes/techniques-of-
control/2-methods-of-quality-control-in-an-organisation/5251>
8
1 out of 10
Related Documents

Your All-in-One AI-Powered Toolkit for Academic Success.
 +13062052269
info@desklib.com
Available 24*7 on WhatsApp / Email
Unlock your academic potential
Copyright © 2020–2025 A2Z Services. All Rights Reserved. Developed and managed by ZUCOL.