R Griggs & Co: Operations, JIT, and Lean Management Analysis
VerifiedAdded on 2020/12/29
|14
|4882
|74
Report
AI Summary
This report examines the operational challenges faced by R Griggs & Company Limited, focusing on issues such as late deliveries and capacity planning inefficiencies. The report delves into the importance of capacity planning, exploring strategies to optimize existing equipment, assess staff capa...
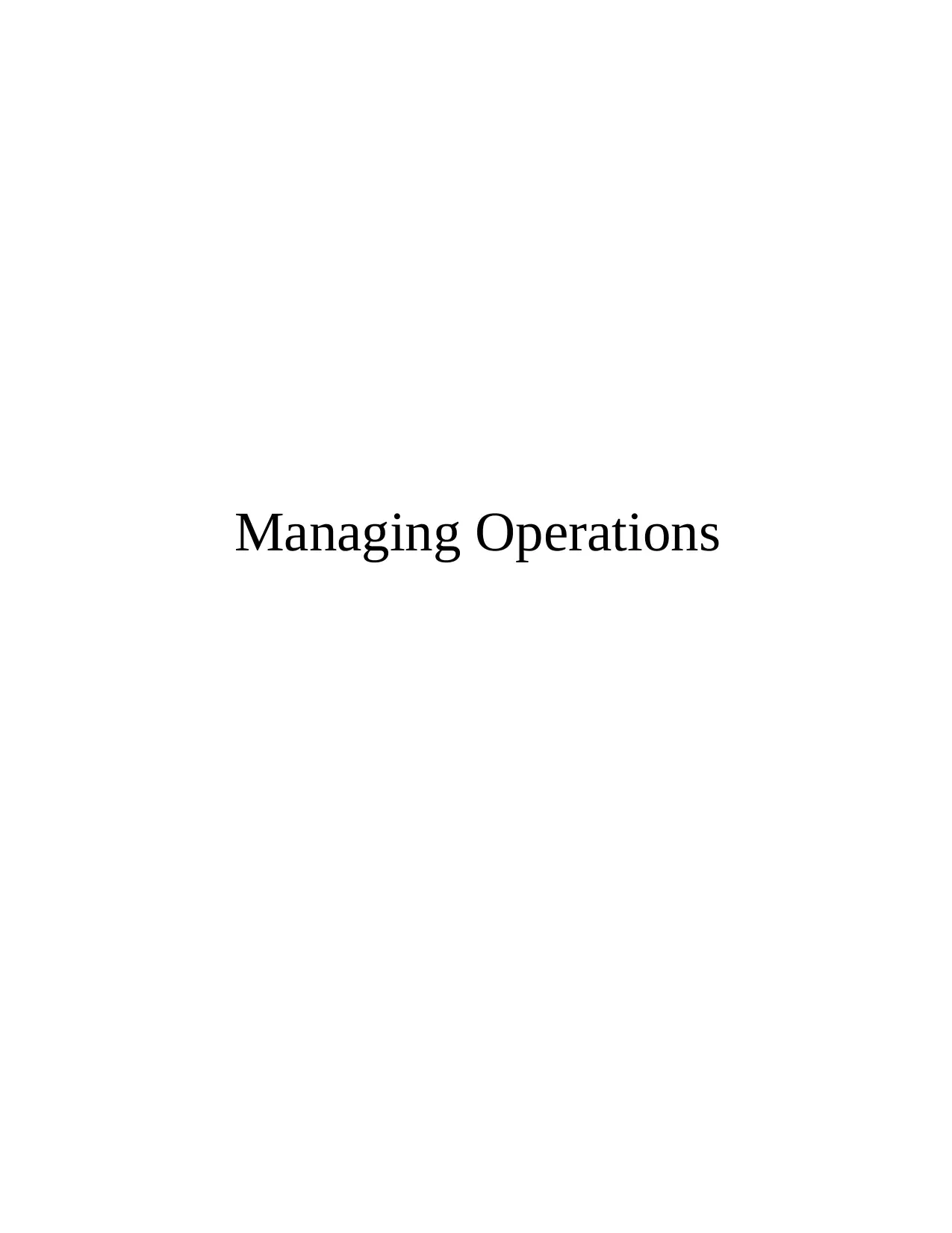
Managing Operations
Paraphrase This Document
Need a fresh take? Get an instant paraphrase of this document with our AI Paraphraser
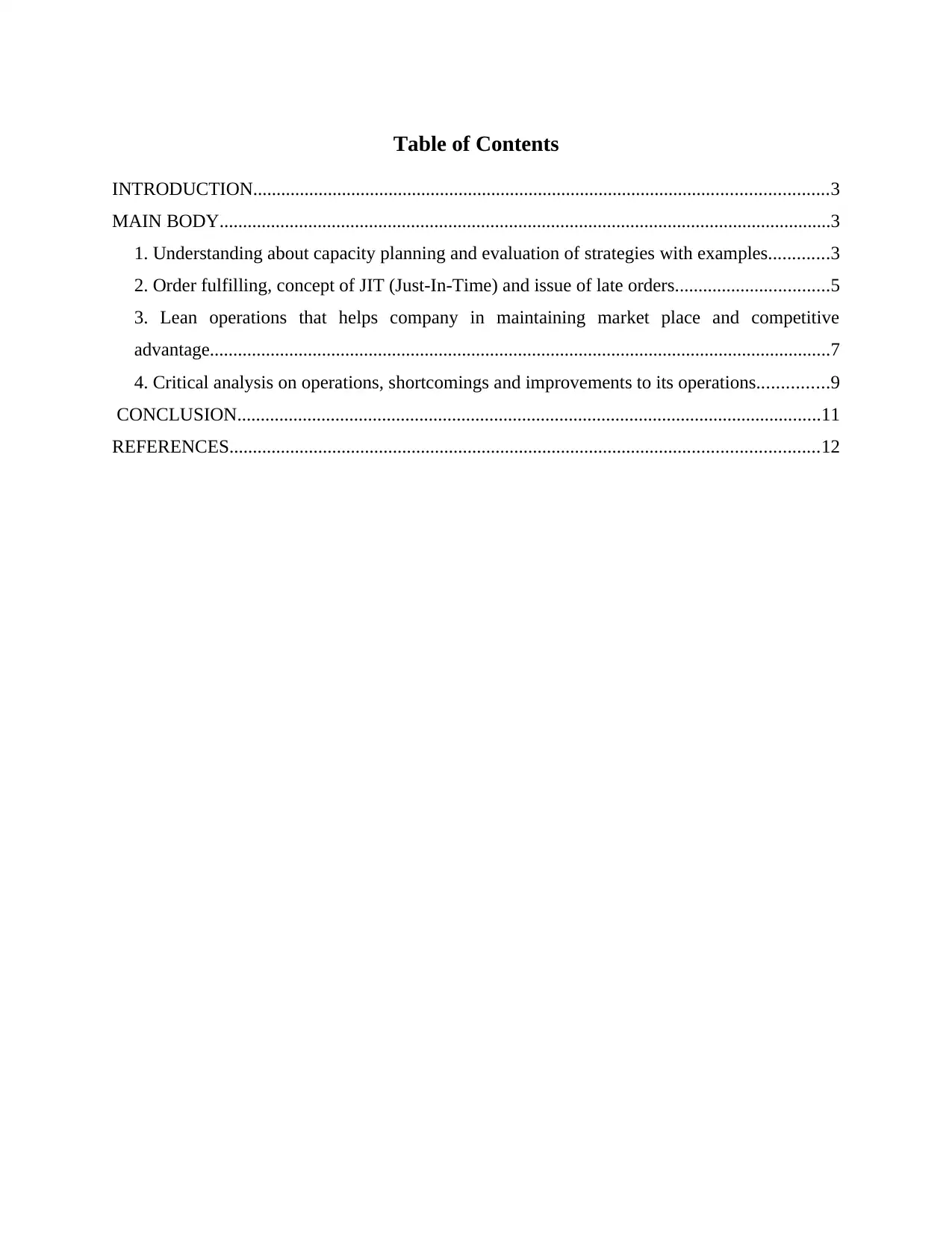
Table of Contents
INTRODUCTION...........................................................................................................................3
MAIN BODY...................................................................................................................................3
1. Understanding about capacity planning and evaluation of strategies with examples.............3
2. Order fulfilling, concept of JIT (Just-In-Time) and issue of late orders.................................5
3. Lean operations that helps company in maintaining market place and competitive
advantage.....................................................................................................................................7
4. Critical analysis on operations, shortcomings and improvements to its operations...............9
CONCLUSION.............................................................................................................................11
REFERENCES..............................................................................................................................12
INTRODUCTION...........................................................................................................................3
MAIN BODY...................................................................................................................................3
1. Understanding about capacity planning and evaluation of strategies with examples.............3
2. Order fulfilling, concept of JIT (Just-In-Time) and issue of late orders.................................5
3. Lean operations that helps company in maintaining market place and competitive
advantage.....................................................................................................................................7
4. Critical analysis on operations, shortcomings and improvements to its operations...............9
CONCLUSION.............................................................................................................................11
REFERENCES..............................................................................................................................12
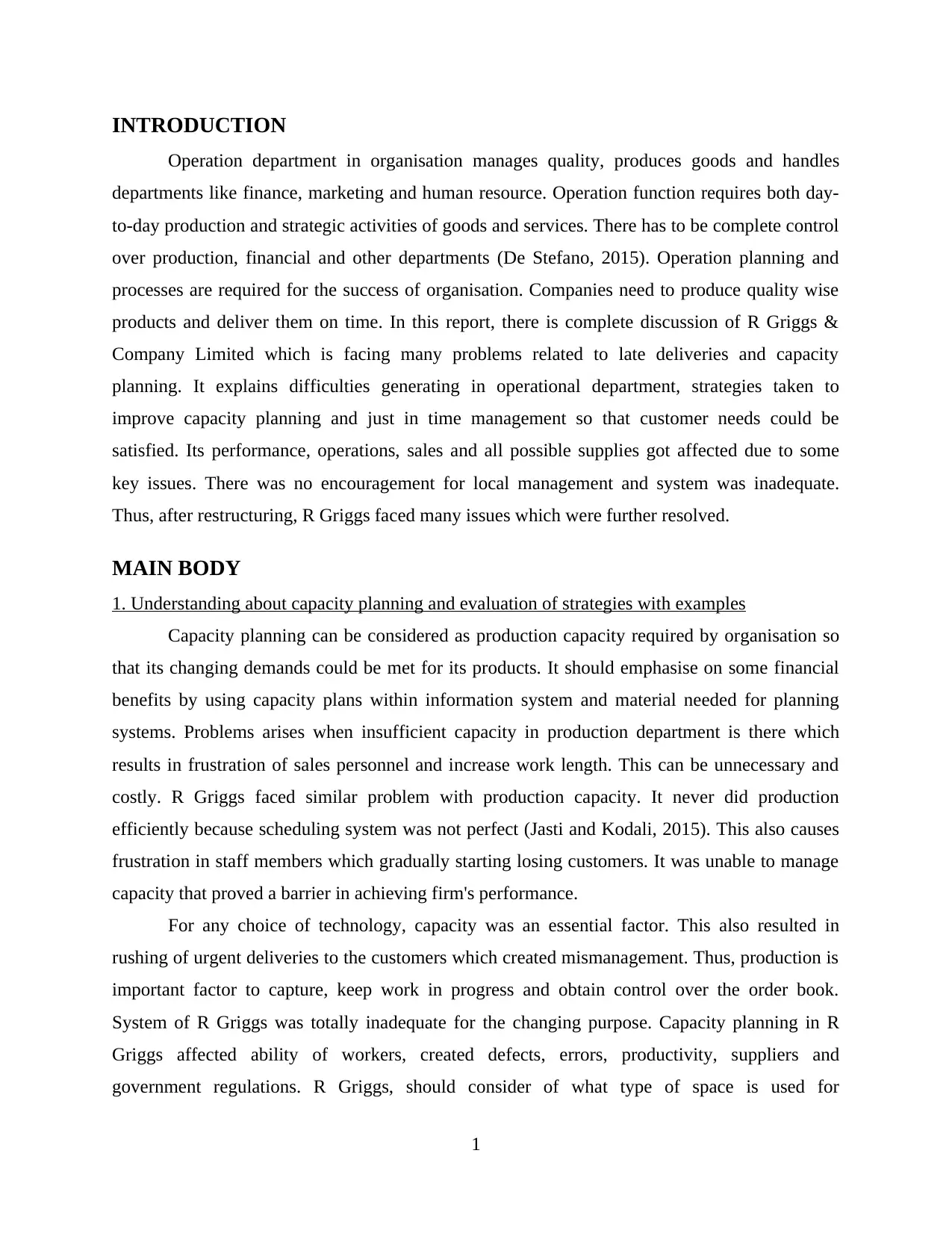
INTRODUCTION
Operation department in organisation manages quality, produces goods and handles
departments like finance, marketing and human resource. Operation function requires both day-
to-day production and strategic activities of goods and services. There has to be complete control
over production, financial and other departments (De Stefano, 2015). Operation planning and
processes are required for the success of organisation. Companies need to produce quality wise
products and deliver them on time. In this report, there is complete discussion of R Griggs &
Company Limited which is facing many problems related to late deliveries and capacity
planning. It explains difficulties generating in operational department, strategies taken to
improve capacity planning and just in time management so that customer needs could be
satisfied. Its performance, operations, sales and all possible supplies got affected due to some
key issues. There was no encouragement for local management and system was inadequate.
Thus, after restructuring, R Griggs faced many issues which were further resolved.
MAIN BODY
1. Understanding about capacity planning and evaluation of strategies with examples
Capacity planning can be considered as production capacity required by organisation so
that its changing demands could be met for its products. It should emphasise on some financial
benefits by using capacity plans within information system and material needed for planning
systems. Problems arises when insufficient capacity in production department is there which
results in frustration of sales personnel and increase work length. This can be unnecessary and
costly. R Griggs faced similar problem with production capacity. It never did production
efficiently because scheduling system was not perfect (Jasti and Kodali, 2015). This also causes
frustration in staff members which gradually starting losing customers. It was unable to manage
capacity that proved a barrier in achieving firm's performance.
For any choice of technology, capacity was an essential factor. This also resulted in
rushing of urgent deliveries to the customers which created mismanagement. Thus, production is
important factor to capture, keep work in progress and obtain control over the order book.
System of R Griggs was totally inadequate for the changing purpose. Capacity planning in R
Griggs affected ability of workers, created defects, errors, productivity, suppliers and
government regulations. R Griggs, should consider of what type of space is used for
1
Operation department in organisation manages quality, produces goods and handles
departments like finance, marketing and human resource. Operation function requires both day-
to-day production and strategic activities of goods and services. There has to be complete control
over production, financial and other departments (De Stefano, 2015). Operation planning and
processes are required for the success of organisation. Companies need to produce quality wise
products and deliver them on time. In this report, there is complete discussion of R Griggs &
Company Limited which is facing many problems related to late deliveries and capacity
planning. It explains difficulties generating in operational department, strategies taken to
improve capacity planning and just in time management so that customer needs could be
satisfied. Its performance, operations, sales and all possible supplies got affected due to some
key issues. There was no encouragement for local management and system was inadequate.
Thus, after restructuring, R Griggs faced many issues which were further resolved.
MAIN BODY
1. Understanding about capacity planning and evaluation of strategies with examples
Capacity planning can be considered as production capacity required by organisation so
that its changing demands could be met for its products. It should emphasise on some financial
benefits by using capacity plans within information system and material needed for planning
systems. Problems arises when insufficient capacity in production department is there which
results in frustration of sales personnel and increase work length. This can be unnecessary and
costly. R Griggs faced similar problem with production capacity. It never did production
efficiently because scheduling system was not perfect (Jasti and Kodali, 2015). This also causes
frustration in staff members which gradually starting losing customers. It was unable to manage
capacity that proved a barrier in achieving firm's performance.
For any choice of technology, capacity was an essential factor. This also resulted in
rushing of urgent deliveries to the customers which created mismanagement. Thus, production is
important factor to capture, keep work in progress and obtain control over the order book.
System of R Griggs was totally inadequate for the changing purpose. Capacity planning in R
Griggs affected ability of workers, created defects, errors, productivity, suppliers and
government regulations. R Griggs, should consider of what type of space is used for
1
⊘ This is a preview!⊘
Do you want full access?
Subscribe today to unlock all pages.

Trusted by 1+ million students worldwide
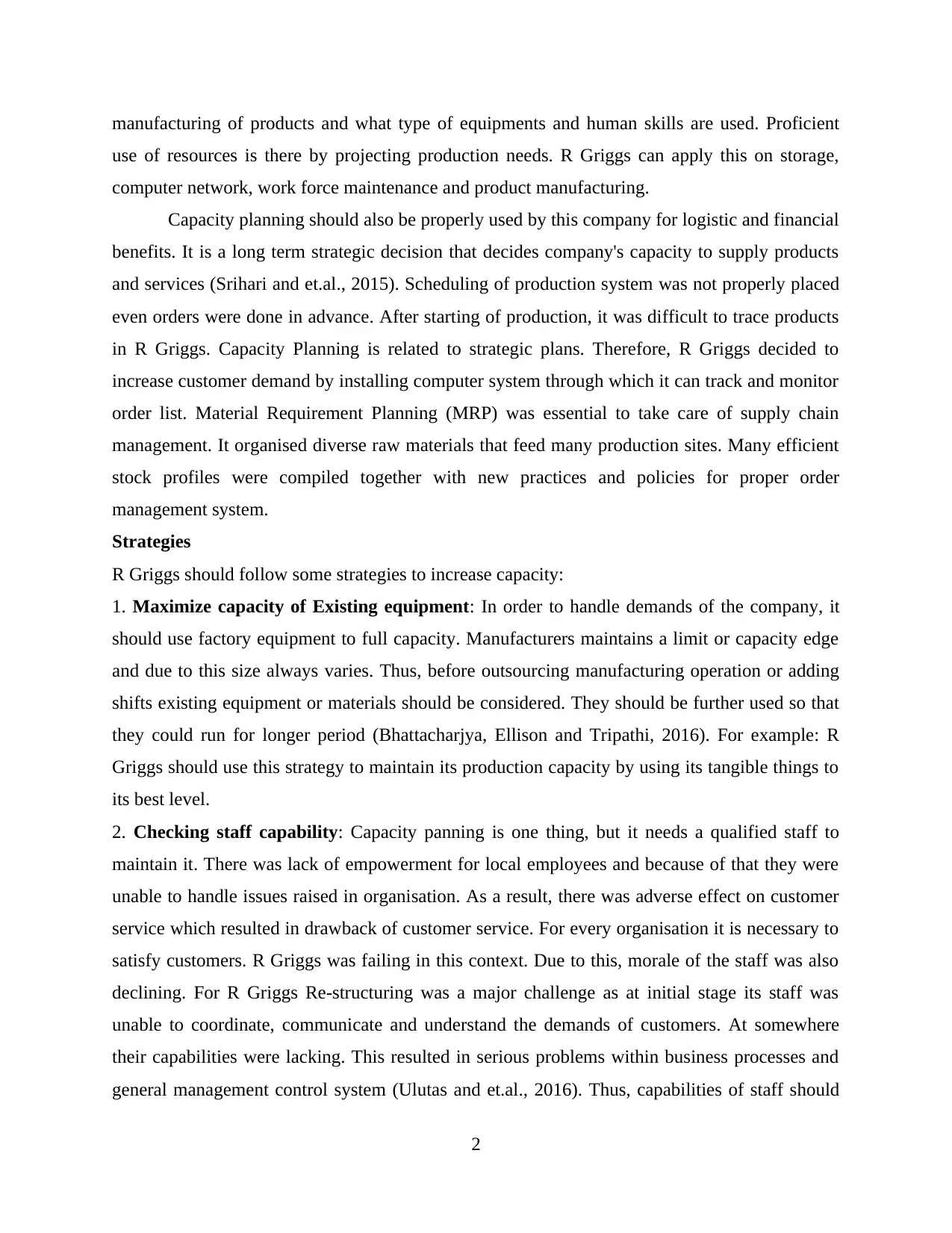
manufacturing of products and what type of equipments and human skills are used. Proficient
use of resources is there by projecting production needs. R Griggs can apply this on storage,
computer network, work force maintenance and product manufacturing.
Capacity planning should also be properly used by this company for logistic and financial
benefits. It is a long term strategic decision that decides company's capacity to supply products
and services (Srihari and et.al., 2015). Scheduling of production system was not properly placed
even orders were done in advance. After starting of production, it was difficult to trace products
in R Griggs. Capacity Planning is related to strategic plans. Therefore, R Griggs decided to
increase customer demand by installing computer system through which it can track and monitor
order list. Material Requirement Planning (MRP) was essential to take care of supply chain
management. It organised diverse raw materials that feed many production sites. Many efficient
stock profiles were compiled together with new practices and policies for proper order
management system.
Strategies
R Griggs should follow some strategies to increase capacity:
1. Maximize capacity of Existing equipment: In order to handle demands of the company, it
should use factory equipment to full capacity. Manufacturers maintains a limit or capacity edge
and due to this size always varies. Thus, before outsourcing manufacturing operation or adding
shifts existing equipment or materials should be considered. They should be further used so that
they could run for longer period (Bhattacharjya, Ellison and Tripathi, 2016). For example: R
Griggs should use this strategy to maintain its production capacity by using its tangible things to
its best level.
2. Checking staff capability: Capacity panning is one thing, but it needs a qualified staff to
maintain it. There was lack of empowerment for local employees and because of that they were
unable to handle issues raised in organisation. As a result, there was adverse effect on customer
service which resulted in drawback of customer service. For every organisation it is necessary to
satisfy customers. R Griggs was failing in this context. Due to this, morale of the staff was also
declining. For R Griggs Re-structuring was a major challenge as at initial stage its staff was
unable to coordinate, communicate and understand the demands of customers. At somewhere
their capabilities were lacking. This resulted in serious problems within business processes and
general management control system (Ulutas and et.al., 2016). Thus, capabilities of staff should
2
use of resources is there by projecting production needs. R Griggs can apply this on storage,
computer network, work force maintenance and product manufacturing.
Capacity planning should also be properly used by this company for logistic and financial
benefits. It is a long term strategic decision that decides company's capacity to supply products
and services (Srihari and et.al., 2015). Scheduling of production system was not properly placed
even orders were done in advance. After starting of production, it was difficult to trace products
in R Griggs. Capacity Planning is related to strategic plans. Therefore, R Griggs decided to
increase customer demand by installing computer system through which it can track and monitor
order list. Material Requirement Planning (MRP) was essential to take care of supply chain
management. It organised diverse raw materials that feed many production sites. Many efficient
stock profiles were compiled together with new practices and policies for proper order
management system.
Strategies
R Griggs should follow some strategies to increase capacity:
1. Maximize capacity of Existing equipment: In order to handle demands of the company, it
should use factory equipment to full capacity. Manufacturers maintains a limit or capacity edge
and due to this size always varies. Thus, before outsourcing manufacturing operation or adding
shifts existing equipment or materials should be considered. They should be further used so that
they could run for longer period (Bhattacharjya, Ellison and Tripathi, 2016). For example: R
Griggs should use this strategy to maintain its production capacity by using its tangible things to
its best level.
2. Checking staff capability: Capacity panning is one thing, but it needs a qualified staff to
maintain it. There was lack of empowerment for local employees and because of that they were
unable to handle issues raised in organisation. As a result, there was adverse effect on customer
service which resulted in drawback of customer service. For every organisation it is necessary to
satisfy customers. R Griggs was failing in this context. Due to this, morale of the staff was also
declining. For R Griggs Re-structuring was a major challenge as at initial stage its staff was
unable to coordinate, communicate and understand the demands of customers. At somewhere
their capabilities were lacking. This resulted in serious problems within business processes and
general management control system (Ulutas and et.al., 2016). Thus, capabilities of staff should
2
Paraphrase This Document
Need a fresh take? Get an instant paraphrase of this document with our AI Paraphraser
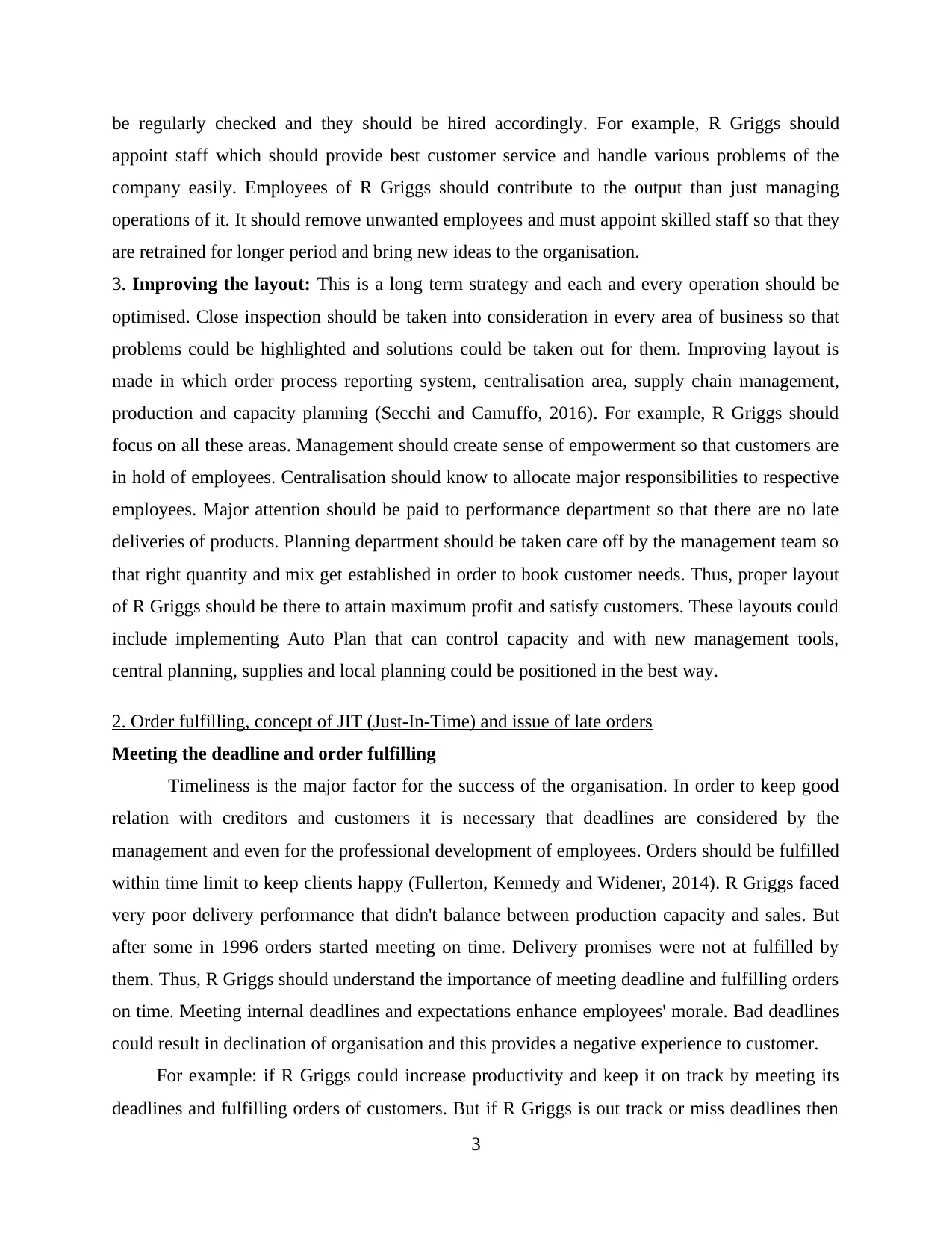
be regularly checked and they should be hired accordingly. For example, R Griggs should
appoint staff which should provide best customer service and handle various problems of the
company easily. Employees of R Griggs should contribute to the output than just managing
operations of it. It should remove unwanted employees and must appoint skilled staff so that they
are retrained for longer period and bring new ideas to the organisation.
3. Improving the layout: This is a long term strategy and each and every operation should be
optimised. Close inspection should be taken into consideration in every area of business so that
problems could be highlighted and solutions could be taken out for them. Improving layout is
made in which order process reporting system, centralisation area, supply chain management,
production and capacity planning (Secchi and Camuffo, 2016). For example, R Griggs should
focus on all these areas. Management should create sense of empowerment so that customers are
in hold of employees. Centralisation should know to allocate major responsibilities to respective
employees. Major attention should be paid to performance department so that there are no late
deliveries of products. Planning department should be taken care off by the management team so
that right quantity and mix get established in order to book customer needs. Thus, proper layout
of R Griggs should be there to attain maximum profit and satisfy customers. These layouts could
include implementing Auto Plan that can control capacity and with new management tools,
central planning, supplies and local planning could be positioned in the best way.
2. Order fulfilling, concept of JIT (Just-In-Time) and issue of late orders
Meeting the deadline and order fulfilling
Timeliness is the major factor for the success of the organisation. In order to keep good
relation with creditors and customers it is necessary that deadlines are considered by the
management and even for the professional development of employees. Orders should be fulfilled
within time limit to keep clients happy (Fullerton, Kennedy and Widener, 2014). R Griggs faced
very poor delivery performance that didn't balance between production capacity and sales. But
after some in 1996 orders started meeting on time. Delivery promises were not at fulfilled by
them. Thus, R Griggs should understand the importance of meeting deadline and fulfilling orders
on time. Meeting internal deadlines and expectations enhance employees' morale. Bad deadlines
could result in declination of organisation and this provides a negative experience to customer.
For example: if R Griggs could increase productivity and keep it on track by meeting its
deadlines and fulfilling orders of customers. But if R Griggs is out track or miss deadlines then
3
appoint staff which should provide best customer service and handle various problems of the
company easily. Employees of R Griggs should contribute to the output than just managing
operations of it. It should remove unwanted employees and must appoint skilled staff so that they
are retrained for longer period and bring new ideas to the organisation.
3. Improving the layout: This is a long term strategy and each and every operation should be
optimised. Close inspection should be taken into consideration in every area of business so that
problems could be highlighted and solutions could be taken out for them. Improving layout is
made in which order process reporting system, centralisation area, supply chain management,
production and capacity planning (Secchi and Camuffo, 2016). For example, R Griggs should
focus on all these areas. Management should create sense of empowerment so that customers are
in hold of employees. Centralisation should know to allocate major responsibilities to respective
employees. Major attention should be paid to performance department so that there are no late
deliveries of products. Planning department should be taken care off by the management team so
that right quantity and mix get established in order to book customer needs. Thus, proper layout
of R Griggs should be there to attain maximum profit and satisfy customers. These layouts could
include implementing Auto Plan that can control capacity and with new management tools,
central planning, supplies and local planning could be positioned in the best way.
2. Order fulfilling, concept of JIT (Just-In-Time) and issue of late orders
Meeting the deadline and order fulfilling
Timeliness is the major factor for the success of the organisation. In order to keep good
relation with creditors and customers it is necessary that deadlines are considered by the
management and even for the professional development of employees. Orders should be fulfilled
within time limit to keep clients happy (Fullerton, Kennedy and Widener, 2014). R Griggs faced
very poor delivery performance that didn't balance between production capacity and sales. But
after some in 1996 orders started meeting on time. Delivery promises were not at fulfilled by
them. Thus, R Griggs should understand the importance of meeting deadline and fulfilling orders
on time. Meeting internal deadlines and expectations enhance employees' morale. Bad deadlines
could result in declination of organisation and this provides a negative experience to customer.
For example: if R Griggs could increase productivity and keep it on track by meeting its
deadlines and fulfilling orders of customers. But if R Griggs is out track or miss deadlines then
3
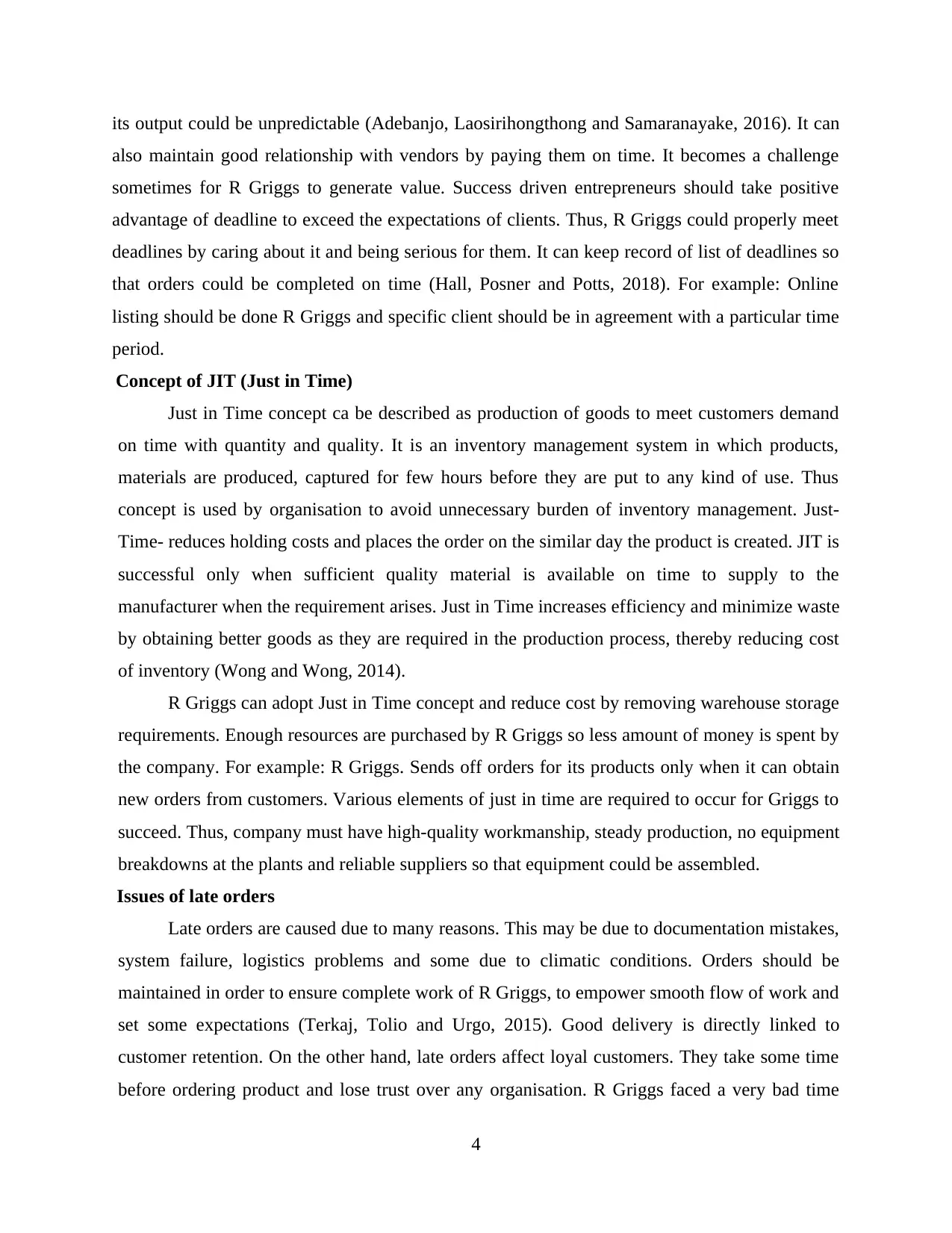
its output could be unpredictable (Adebanjo, Laosirihongthong and Samaranayake, 2016). It can
also maintain good relationship with vendors by paying them on time. It becomes a challenge
sometimes for R Griggs to generate value. Success driven entrepreneurs should take positive
advantage of deadline to exceed the expectations of clients. Thus, R Griggs could properly meet
deadlines by caring about it and being serious for them. It can keep record of list of deadlines so
that orders could be completed on time (Hall, Posner and Potts, 2018). For example: Online
listing should be done R Griggs and specific client should be in agreement with a particular time
period.
Concept of JIT (Just in Time)
Just in Time concept ca be described as production of goods to meet customers demand
on time with quantity and quality. It is an inventory management system in which products,
materials are produced, captured for few hours before they are put to any kind of use. Thus
concept is used by organisation to avoid unnecessary burden of inventory management. Just-
Time- reduces holding costs and places the order on the similar day the product is created. JIT is
successful only when sufficient quality material is available on time to supply to the
manufacturer when the requirement arises. Just in Time increases efficiency and minimize waste
by obtaining better goods as they are required in the production process, thereby reducing cost
of inventory (Wong and Wong, 2014).
R Griggs can adopt Just in Time concept and reduce cost by removing warehouse storage
requirements. Enough resources are purchased by R Griggs so less amount of money is spent by
the company. For example: R Griggs. Sends off orders for its products only when it can obtain
new orders from customers. Various elements of just in time are required to occur for Griggs to
succeed. Thus, company must have high-quality workmanship, steady production, no equipment
breakdowns at the plants and reliable suppliers so that equipment could be assembled.
Issues of late orders
Late orders are caused due to many reasons. This may be due to documentation mistakes,
system failure, logistics problems and some due to climatic conditions. Orders should be
maintained in order to ensure complete work of R Griggs, to empower smooth flow of work and
set some expectations (Terkaj, Tolio and Urgo, 2015). Good delivery is directly linked to
customer retention. On the other hand, late orders affect loyal customers. They take some time
before ordering product and lose trust over any organisation. R Griggs faced a very bad time
4
also maintain good relationship with vendors by paying them on time. It becomes a challenge
sometimes for R Griggs to generate value. Success driven entrepreneurs should take positive
advantage of deadline to exceed the expectations of clients. Thus, R Griggs could properly meet
deadlines by caring about it and being serious for them. It can keep record of list of deadlines so
that orders could be completed on time (Hall, Posner and Potts, 2018). For example: Online
listing should be done R Griggs and specific client should be in agreement with a particular time
period.
Concept of JIT (Just in Time)
Just in Time concept ca be described as production of goods to meet customers demand
on time with quantity and quality. It is an inventory management system in which products,
materials are produced, captured for few hours before they are put to any kind of use. Thus
concept is used by organisation to avoid unnecessary burden of inventory management. Just-
Time- reduces holding costs and places the order on the similar day the product is created. JIT is
successful only when sufficient quality material is available on time to supply to the
manufacturer when the requirement arises. Just in Time increases efficiency and minimize waste
by obtaining better goods as they are required in the production process, thereby reducing cost
of inventory (Wong and Wong, 2014).
R Griggs can adopt Just in Time concept and reduce cost by removing warehouse storage
requirements. Enough resources are purchased by R Griggs so less amount of money is spent by
the company. For example: R Griggs. Sends off orders for its products only when it can obtain
new orders from customers. Various elements of just in time are required to occur for Griggs to
succeed. Thus, company must have high-quality workmanship, steady production, no equipment
breakdowns at the plants and reliable suppliers so that equipment could be assembled.
Issues of late orders
Late orders are caused due to many reasons. This may be due to documentation mistakes,
system failure, logistics problems and some due to climatic conditions. Orders should be
maintained in order to ensure complete work of R Griggs, to empower smooth flow of work and
set some expectations (Terkaj, Tolio and Urgo, 2015). Good delivery is directly linked to
customer retention. On the other hand, late orders affect loyal customers. They take some time
before ordering product and lose trust over any organisation. R Griggs faced a very bad time
4
⊘ This is a preview!⊘
Do you want full access?
Subscribe today to unlock all pages.

Trusted by 1+ million students worldwide
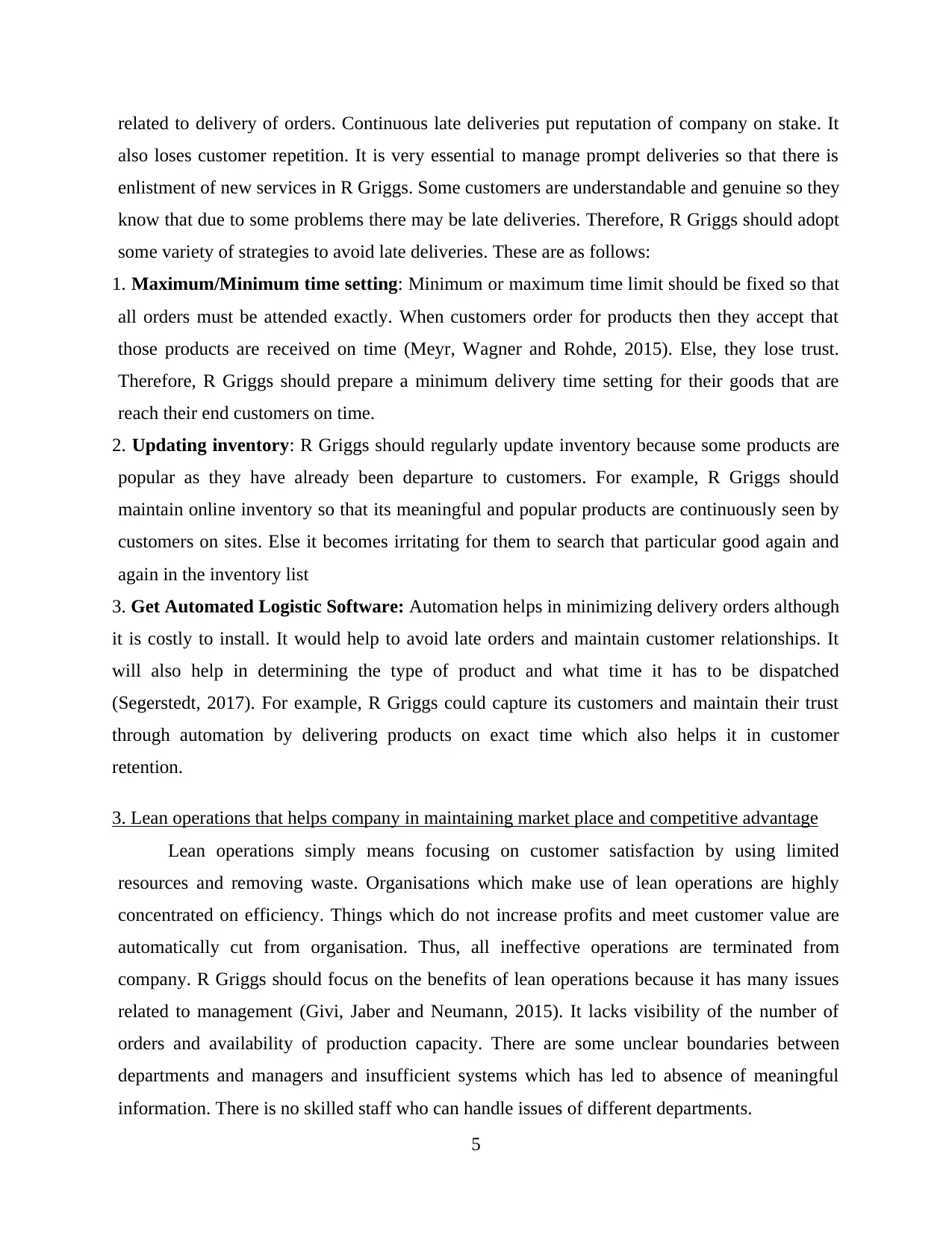
related to delivery of orders. Continuous late deliveries put reputation of company on stake. It
also loses customer repetition. It is very essential to manage prompt deliveries so that there is
enlistment of new services in R Griggs. Some customers are understandable and genuine so they
know that due to some problems there may be late deliveries. Therefore, R Griggs should adopt
some variety of strategies to avoid late deliveries. These are as follows:
1. Maximum/Minimum time setting: Minimum or maximum time limit should be fixed so that
all orders must be attended exactly. When customers order for products then they accept that
those products are received on time (Meyr, Wagner and Rohde, 2015). Else, they lose trust.
Therefore, R Griggs should prepare a minimum delivery time setting for their goods that are
reach their end customers on time.
2. Updating inventory: R Griggs should regularly update inventory because some products are
popular as they have already been departure to customers. For example, R Griggs should
maintain online inventory so that its meaningful and popular products are continuously seen by
customers on sites. Else it becomes irritating for them to search that particular good again and
again in the inventory list
3. Get Automated Logistic Software: Automation helps in minimizing delivery orders although
it is costly to install. It would help to avoid late orders and maintain customer relationships. It
will also help in determining the type of product and what time it has to be dispatched
(Segerstedt, 2017). For example, R Griggs could capture its customers and maintain their trust
through automation by delivering products on exact time which also helps it in customer
retention.
3. Lean operations that helps company in maintaining market place and competitive advantage
Lean operations simply means focusing on customer satisfaction by using limited
resources and removing waste. Organisations which make use of lean operations are highly
concentrated on efficiency. Things which do not increase profits and meet customer value are
automatically cut from organisation. Thus, all ineffective operations are terminated from
company. R Griggs should focus on the benefits of lean operations because it has many issues
related to management (Givi, Jaber and Neumann, 2015). It lacks visibility of the number of
orders and availability of production capacity. There are some unclear boundaries between
departments and managers and insufficient systems which has led to absence of meaningful
information. There is no skilled staff who can handle issues of different departments.
5
also loses customer repetition. It is very essential to manage prompt deliveries so that there is
enlistment of new services in R Griggs. Some customers are understandable and genuine so they
know that due to some problems there may be late deliveries. Therefore, R Griggs should adopt
some variety of strategies to avoid late deliveries. These are as follows:
1. Maximum/Minimum time setting: Minimum or maximum time limit should be fixed so that
all orders must be attended exactly. When customers order for products then they accept that
those products are received on time (Meyr, Wagner and Rohde, 2015). Else, they lose trust.
Therefore, R Griggs should prepare a minimum delivery time setting for their goods that are
reach their end customers on time.
2. Updating inventory: R Griggs should regularly update inventory because some products are
popular as they have already been departure to customers. For example, R Griggs should
maintain online inventory so that its meaningful and popular products are continuously seen by
customers on sites. Else it becomes irritating for them to search that particular good again and
again in the inventory list
3. Get Automated Logistic Software: Automation helps in minimizing delivery orders although
it is costly to install. It would help to avoid late orders and maintain customer relationships. It
will also help in determining the type of product and what time it has to be dispatched
(Segerstedt, 2017). For example, R Griggs could capture its customers and maintain their trust
through automation by delivering products on exact time which also helps it in customer
retention.
3. Lean operations that helps company in maintaining market place and competitive advantage
Lean operations simply means focusing on customer satisfaction by using limited
resources and removing waste. Organisations which make use of lean operations are highly
concentrated on efficiency. Things which do not increase profits and meet customer value are
automatically cut from organisation. Thus, all ineffective operations are terminated from
company. R Griggs should focus on the benefits of lean operations because it has many issues
related to management (Givi, Jaber and Neumann, 2015). It lacks visibility of the number of
orders and availability of production capacity. There are some unclear boundaries between
departments and managers and insufficient systems which has led to absence of meaningful
information. There is no skilled staff who can handle issues of different departments.
5
Paraphrase This Document
Need a fresh take? Get an instant paraphrase of this document with our AI Paraphraser
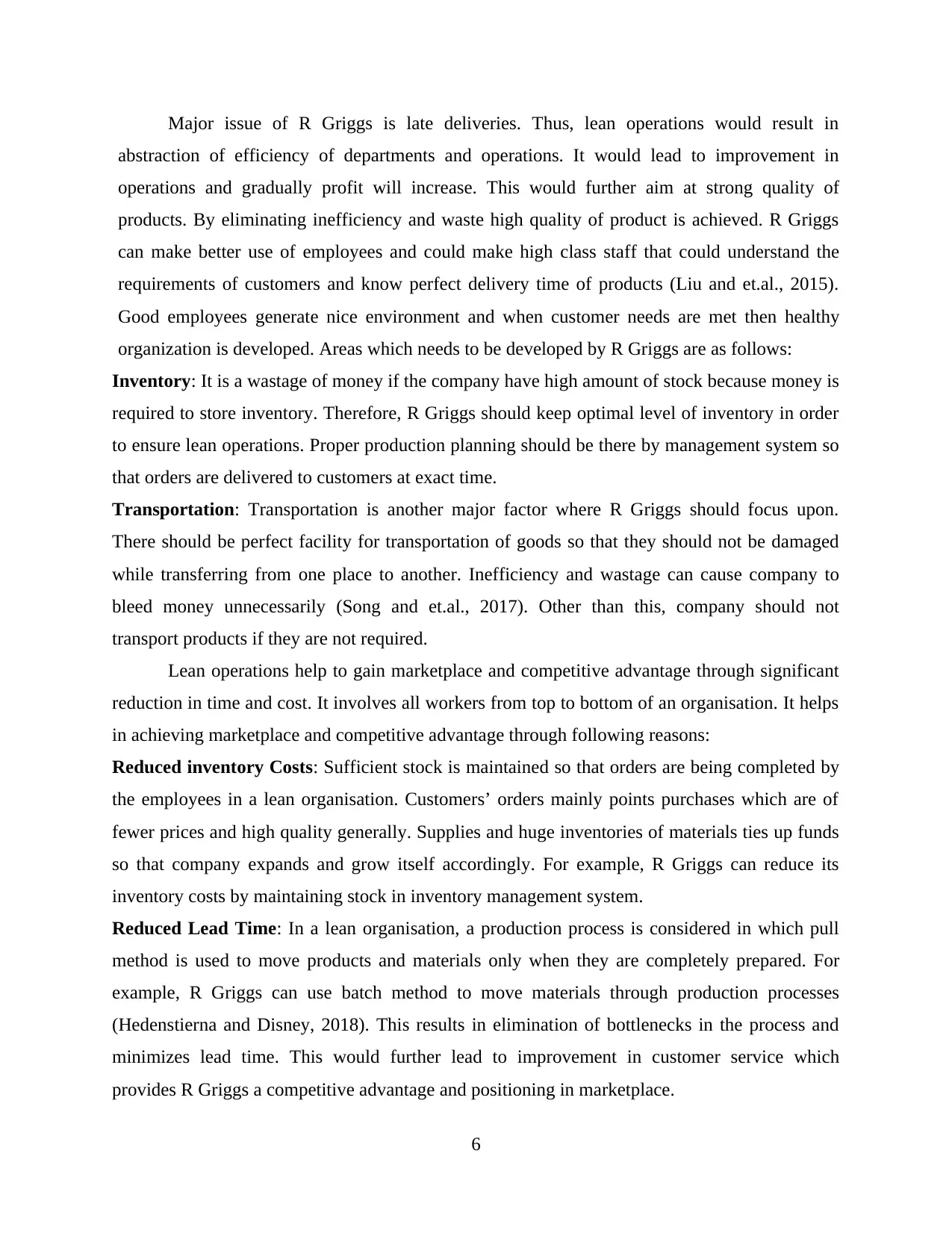
Major issue of R Griggs is late deliveries. Thus, lean operations would result in
abstraction of efficiency of departments and operations. It would lead to improvement in
operations and gradually profit will increase. This would further aim at strong quality of
products. By eliminating inefficiency and waste high quality of product is achieved. R Griggs
can make better use of employees and could make high class staff that could understand the
requirements of customers and know perfect delivery time of products (Liu and et.al., 2015).
Good employees generate nice environment and when customer needs are met then healthy
organization is developed. Areas which needs to be developed by R Griggs are as follows:
Inventory: It is a wastage of money if the company have high amount of stock because money is
required to store inventory. Therefore, R Griggs should keep optimal level of inventory in order
to ensure lean operations. Proper production planning should be there by management system so
that orders are delivered to customers at exact time.
Transportation: Transportation is another major factor where R Griggs should focus upon.
There should be perfect facility for transportation of goods so that they should not be damaged
while transferring from one place to another. Inefficiency and wastage can cause company to
bleed money unnecessarily (Song and et.al., 2017). Other than this, company should not
transport products if they are not required.
Lean operations help to gain marketplace and competitive advantage through significant
reduction in time and cost. It involves all workers from top to bottom of an organisation. It helps
in achieving marketplace and competitive advantage through following reasons:
Reduced inventory Costs: Sufficient stock is maintained so that orders are being completed by
the employees in a lean organisation. Customers’ orders mainly points purchases which are of
fewer prices and high quality generally. Supplies and huge inventories of materials ties up funds
so that company expands and grow itself accordingly. For example, R Griggs can reduce its
inventory costs by maintaining stock in inventory management system.
Reduced Lead Time: In a lean organisation, a production process is considered in which pull
method is used to move products and materials only when they are completely prepared. For
example, R Griggs can use batch method to move materials through production processes
(Hedenstierna and Disney, 2018). This results in elimination of bottlenecks in the process and
minimizes lead time. This would further lead to improvement in customer service which
provides R Griggs a competitive advantage and positioning in marketplace.
6
abstraction of efficiency of departments and operations. It would lead to improvement in
operations and gradually profit will increase. This would further aim at strong quality of
products. By eliminating inefficiency and waste high quality of product is achieved. R Griggs
can make better use of employees and could make high class staff that could understand the
requirements of customers and know perfect delivery time of products (Liu and et.al., 2015).
Good employees generate nice environment and when customer needs are met then healthy
organization is developed. Areas which needs to be developed by R Griggs are as follows:
Inventory: It is a wastage of money if the company have high amount of stock because money is
required to store inventory. Therefore, R Griggs should keep optimal level of inventory in order
to ensure lean operations. Proper production planning should be there by management system so
that orders are delivered to customers at exact time.
Transportation: Transportation is another major factor where R Griggs should focus upon.
There should be perfect facility for transportation of goods so that they should not be damaged
while transferring from one place to another. Inefficiency and wastage can cause company to
bleed money unnecessarily (Song and et.al., 2017). Other than this, company should not
transport products if they are not required.
Lean operations help to gain marketplace and competitive advantage through significant
reduction in time and cost. It involves all workers from top to bottom of an organisation. It helps
in achieving marketplace and competitive advantage through following reasons:
Reduced inventory Costs: Sufficient stock is maintained so that orders are being completed by
the employees in a lean organisation. Customers’ orders mainly points purchases which are of
fewer prices and high quality generally. Supplies and huge inventories of materials ties up funds
so that company expands and grow itself accordingly. For example, R Griggs can reduce its
inventory costs by maintaining stock in inventory management system.
Reduced Lead Time: In a lean organisation, a production process is considered in which pull
method is used to move products and materials only when they are completely prepared. For
example, R Griggs can use batch method to move materials through production processes
(Hedenstierna and Disney, 2018). This results in elimination of bottlenecks in the process and
minimizes lead time. This would further lead to improvement in customer service which
provides R Griggs a competitive advantage and positioning in marketplace.
6
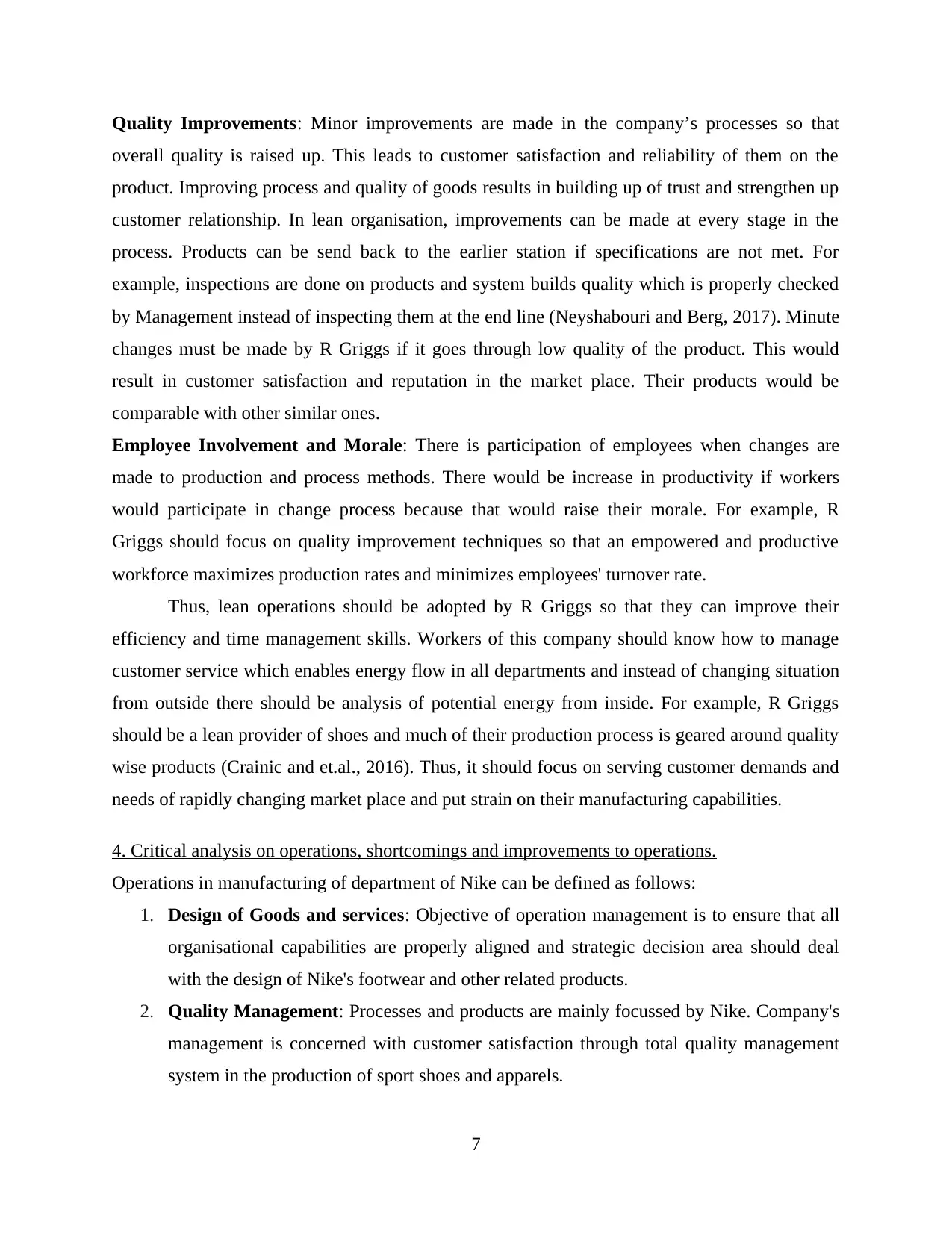
Quality Improvements: Minor improvements are made in the company’s processes so that
overall quality is raised up. This leads to customer satisfaction and reliability of them on the
product. Improving process and quality of goods results in building up of trust and strengthen up
customer relationship. In lean organisation, improvements can be made at every stage in the
process. Products can be send back to the earlier station if specifications are not met. For
example, inspections are done on products and system builds quality which is properly checked
by Management instead of inspecting them at the end line (Neyshabouri and Berg, 2017). Minute
changes must be made by R Griggs if it goes through low quality of the product. This would
result in customer satisfaction and reputation in the market place. Their products would be
comparable with other similar ones.
Employee Involvement and Morale: There is participation of employees when changes are
made to production and process methods. There would be increase in productivity if workers
would participate in change process because that would raise their morale. For example, R
Griggs should focus on quality improvement techniques so that an empowered and productive
workforce maximizes production rates and minimizes employees' turnover rate.
Thus, lean operations should be adopted by R Griggs so that they can improve their
efficiency and time management skills. Workers of this company should know how to manage
customer service which enables energy flow in all departments and instead of changing situation
from outside there should be analysis of potential energy from inside. For example, R Griggs
should be a lean provider of shoes and much of their production process is geared around quality
wise products (Crainic and et.al., 2016). Thus, it should focus on serving customer demands and
needs of rapidly changing market place and put strain on their manufacturing capabilities.
4. Critical analysis on operations, shortcomings and improvements to operations.
Operations in manufacturing of department of Nike can be defined as follows:
1. Design of Goods and services: Objective of operation management is to ensure that all
organisational capabilities are properly aligned and strategic decision area should deal
with the design of Nike's footwear and other related products.
2. Quality Management: Processes and products are mainly focussed by Nike. Company's
management is concerned with customer satisfaction through total quality management
system in the production of sport shoes and apparels.
7
overall quality is raised up. This leads to customer satisfaction and reliability of them on the
product. Improving process and quality of goods results in building up of trust and strengthen up
customer relationship. In lean organisation, improvements can be made at every stage in the
process. Products can be send back to the earlier station if specifications are not met. For
example, inspections are done on products and system builds quality which is properly checked
by Management instead of inspecting them at the end line (Neyshabouri and Berg, 2017). Minute
changes must be made by R Griggs if it goes through low quality of the product. This would
result in customer satisfaction and reputation in the market place. Their products would be
comparable with other similar ones.
Employee Involvement and Morale: There is participation of employees when changes are
made to production and process methods. There would be increase in productivity if workers
would participate in change process because that would raise their morale. For example, R
Griggs should focus on quality improvement techniques so that an empowered and productive
workforce maximizes production rates and minimizes employees' turnover rate.
Thus, lean operations should be adopted by R Griggs so that they can improve their
efficiency and time management skills. Workers of this company should know how to manage
customer service which enables energy flow in all departments and instead of changing situation
from outside there should be analysis of potential energy from inside. For example, R Griggs
should be a lean provider of shoes and much of their production process is geared around quality
wise products (Crainic and et.al., 2016). Thus, it should focus on serving customer demands and
needs of rapidly changing market place and put strain on their manufacturing capabilities.
4. Critical analysis on operations, shortcomings and improvements to operations.
Operations in manufacturing of department of Nike can be defined as follows:
1. Design of Goods and services: Objective of operation management is to ensure that all
organisational capabilities are properly aligned and strategic decision area should deal
with the design of Nike's footwear and other related products.
2. Quality Management: Processes and products are mainly focussed by Nike. Company's
management is concerned with customer satisfaction through total quality management
system in the production of sport shoes and apparels.
7
⊘ This is a preview!⊘
Do you want full access?
Subscribe today to unlock all pages.

Trusted by 1+ million students worldwide
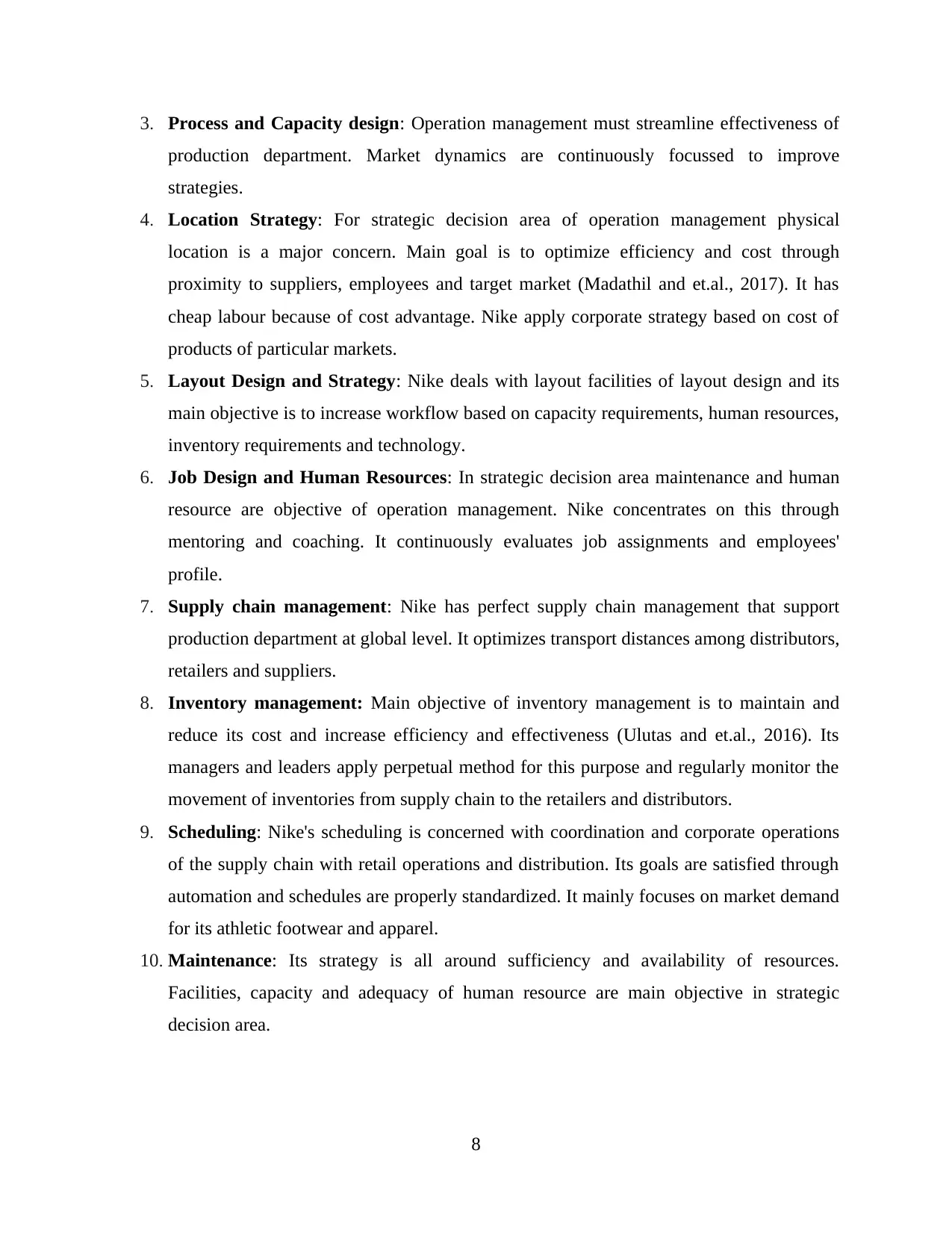
3. Process and Capacity design: Operation management must streamline effectiveness of
production department. Market dynamics are continuously focussed to improve
strategies.
4. Location Strategy: For strategic decision area of operation management physical
location is a major concern. Main goal is to optimize efficiency and cost through
proximity to suppliers, employees and target market (Madathil and et.al., 2017). It has
cheap labour because of cost advantage. Nike apply corporate strategy based on cost of
products of particular markets.
5. Layout Design and Strategy: Nike deals with layout facilities of layout design and its
main objective is to increase workflow based on capacity requirements, human resources,
inventory requirements and technology.
6. Job Design and Human Resources: In strategic decision area maintenance and human
resource are objective of operation management. Nike concentrates on this through
mentoring and coaching. It continuously evaluates job assignments and employees'
profile.
7. Supply chain management: Nike has perfect supply chain management that support
production department at global level. It optimizes transport distances among distributors,
retailers and suppliers.
8. Inventory management: Main objective of inventory management is to maintain and
reduce its cost and increase efficiency and effectiveness (Ulutas and et.al., 2016). Its
managers and leaders apply perpetual method for this purpose and regularly monitor the
movement of inventories from supply chain to the retailers and distributors.
9. Scheduling: Nike's scheduling is concerned with coordination and corporate operations
of the supply chain with retail operations and distribution. Its goals are satisfied through
automation and schedules are properly standardized. It mainly focuses on market demand
for its athletic footwear and apparel.
10. Maintenance: Its strategy is all around sufficiency and availability of resources.
Facilities, capacity and adequacy of human resource are main objective in strategic
decision area.
8
production department. Market dynamics are continuously focussed to improve
strategies.
4. Location Strategy: For strategic decision area of operation management physical
location is a major concern. Main goal is to optimize efficiency and cost through
proximity to suppliers, employees and target market (Madathil and et.al., 2017). It has
cheap labour because of cost advantage. Nike apply corporate strategy based on cost of
products of particular markets.
5. Layout Design and Strategy: Nike deals with layout facilities of layout design and its
main objective is to increase workflow based on capacity requirements, human resources,
inventory requirements and technology.
6. Job Design and Human Resources: In strategic decision area maintenance and human
resource are objective of operation management. Nike concentrates on this through
mentoring and coaching. It continuously evaluates job assignments and employees'
profile.
7. Supply chain management: Nike has perfect supply chain management that support
production department at global level. It optimizes transport distances among distributors,
retailers and suppliers.
8. Inventory management: Main objective of inventory management is to maintain and
reduce its cost and increase efficiency and effectiveness (Ulutas and et.al., 2016). Its
managers and leaders apply perpetual method for this purpose and regularly monitor the
movement of inventories from supply chain to the retailers and distributors.
9. Scheduling: Nike's scheduling is concerned with coordination and corporate operations
of the supply chain with retail operations and distribution. Its goals are satisfied through
automation and schedules are properly standardized. It mainly focuses on market demand
for its athletic footwear and apparel.
10. Maintenance: Its strategy is all around sufficiency and availability of resources.
Facilities, capacity and adequacy of human resource are main objective in strategic
decision area.
8
Paraphrase This Document
Need a fresh take? Get an instant paraphrase of this document with our AI Paraphraser
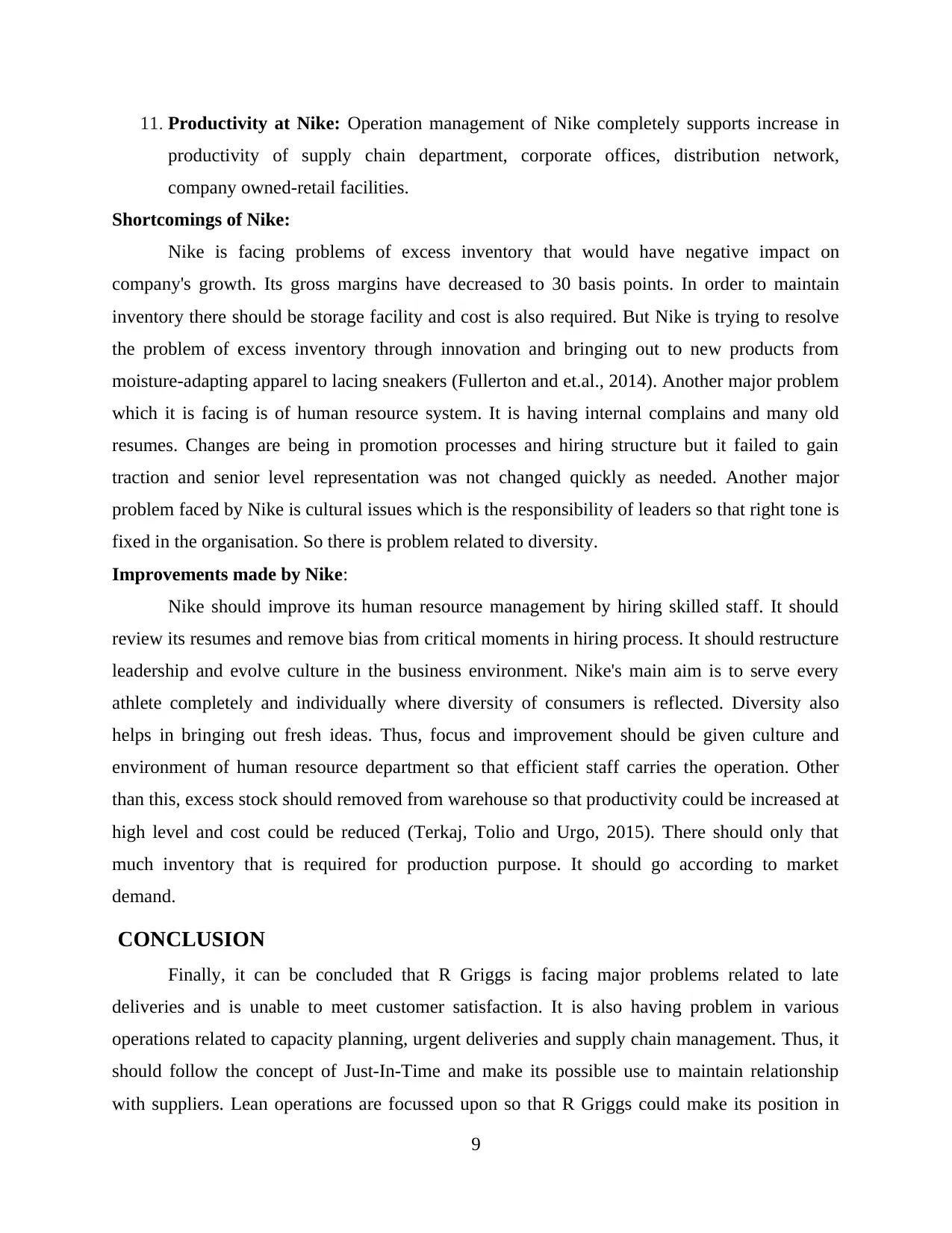
11. Productivity at Nike: Operation management of Nike completely supports increase in
productivity of supply chain department, corporate offices, distribution network,
company owned-retail facilities.
Shortcomings of Nike:
Nike is facing problems of excess inventory that would have negative impact on
company's growth. Its gross margins have decreased to 30 basis points. In order to maintain
inventory there should be storage facility and cost is also required. But Nike is trying to resolve
the problem of excess inventory through innovation and bringing out to new products from
moisture-adapting apparel to lacing sneakers (Fullerton and et.al., 2014). Another major problem
which it is facing is of human resource system. It is having internal complains and many old
resumes. Changes are being in promotion processes and hiring structure but it failed to gain
traction and senior level representation was not changed quickly as needed. Another major
problem faced by Nike is cultural issues which is the responsibility of leaders so that right tone is
fixed in the organisation. So there is problem related to diversity.
Improvements made by Nike:
Nike should improve its human resource management by hiring skilled staff. It should
review its resumes and remove bias from critical moments in hiring process. It should restructure
leadership and evolve culture in the business environment. Nike's main aim is to serve every
athlete completely and individually where diversity of consumers is reflected. Diversity also
helps in bringing out fresh ideas. Thus, focus and improvement should be given culture and
environment of human resource department so that efficient staff carries the operation. Other
than this, excess stock should removed from warehouse so that productivity could be increased at
high level and cost could be reduced (Terkaj, Tolio and Urgo, 2015). There should only that
much inventory that is required for production purpose. It should go according to market
demand.
CONCLUSION
Finally, it can be concluded that R Griggs is facing major problems related to late
deliveries and is unable to meet customer satisfaction. It is also having problem in various
operations related to capacity planning, urgent deliveries and supply chain management. Thus, it
should follow the concept of Just-In-Time and make its possible use to maintain relationship
with suppliers. Lean operations are focussed upon so that R Griggs could make its position in
9
productivity of supply chain department, corporate offices, distribution network,
company owned-retail facilities.
Shortcomings of Nike:
Nike is facing problems of excess inventory that would have negative impact on
company's growth. Its gross margins have decreased to 30 basis points. In order to maintain
inventory there should be storage facility and cost is also required. But Nike is trying to resolve
the problem of excess inventory through innovation and bringing out to new products from
moisture-adapting apparel to lacing sneakers (Fullerton and et.al., 2014). Another major problem
which it is facing is of human resource system. It is having internal complains and many old
resumes. Changes are being in promotion processes and hiring structure but it failed to gain
traction and senior level representation was not changed quickly as needed. Another major
problem faced by Nike is cultural issues which is the responsibility of leaders so that right tone is
fixed in the organisation. So there is problem related to diversity.
Improvements made by Nike:
Nike should improve its human resource management by hiring skilled staff. It should
review its resumes and remove bias from critical moments in hiring process. It should restructure
leadership and evolve culture in the business environment. Nike's main aim is to serve every
athlete completely and individually where diversity of consumers is reflected. Diversity also
helps in bringing out fresh ideas. Thus, focus and improvement should be given culture and
environment of human resource department so that efficient staff carries the operation. Other
than this, excess stock should removed from warehouse so that productivity could be increased at
high level and cost could be reduced (Terkaj, Tolio and Urgo, 2015). There should only that
much inventory that is required for production purpose. It should go according to market
demand.
CONCLUSION
Finally, it can be concluded that R Griggs is facing major problems related to late
deliveries and is unable to meet customer satisfaction. It is also having problem in various
operations related to capacity planning, urgent deliveries and supply chain management. Thus, it
should follow the concept of Just-In-Time and make its possible use to maintain relationship
with suppliers. Lean operations are focussed upon so that R Griggs could make its position in
9
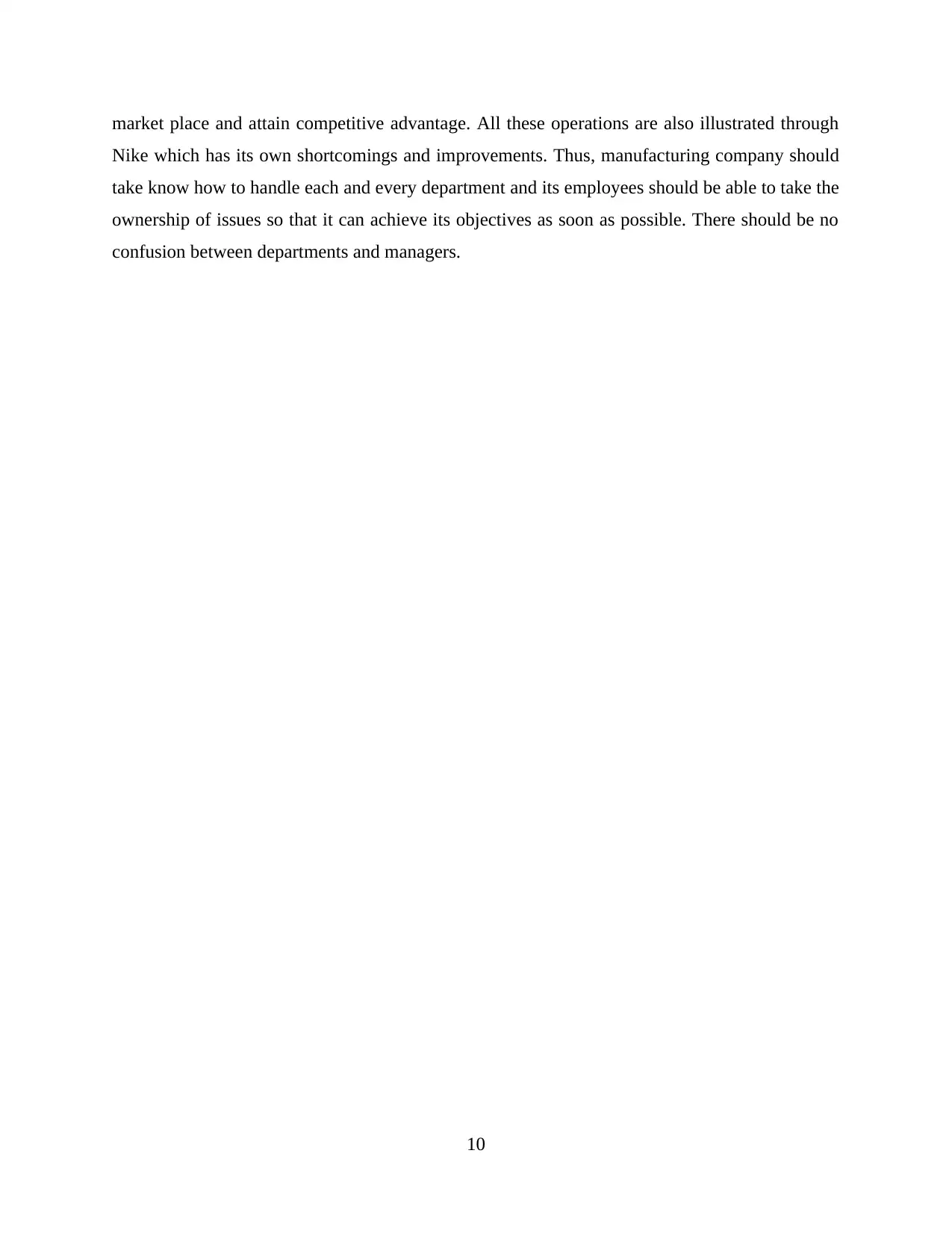
market place and attain competitive advantage. All these operations are also illustrated through
Nike which has its own shortcomings and improvements. Thus, manufacturing company should
take know how to handle each and every department and its employees should be able to take the
ownership of issues so that it can achieve its objectives as soon as possible. There should be no
confusion between departments and managers.
10
Nike which has its own shortcomings and improvements. Thus, manufacturing company should
take know how to handle each and every department and its employees should be able to take the
ownership of issues so that it can achieve its objectives as soon as possible. There should be no
confusion between departments and managers.
10
⊘ This is a preview!⊘
Do you want full access?
Subscribe today to unlock all pages.

Trusted by 1+ million students worldwide
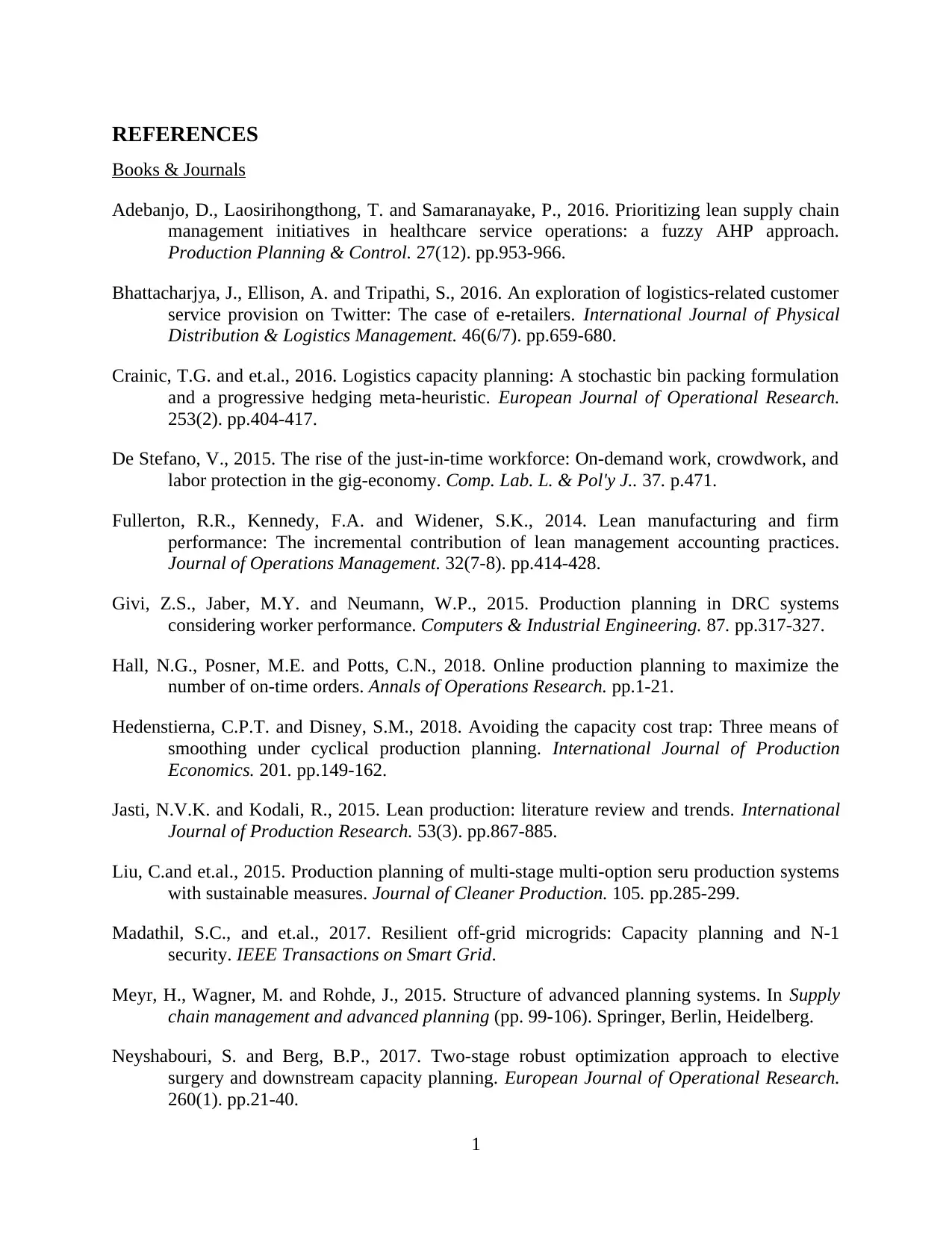
REFERENCES
Books & Journals
Adebanjo, D., Laosirihongthong, T. and Samaranayake, P., 2016. Prioritizing lean supply chain
management initiatives in healthcare service operations: a fuzzy AHP approach.
Production Planning & Control. 27(12). pp.953-966.
Bhattacharjya, J., Ellison, A. and Tripathi, S., 2016. An exploration of logistics-related customer
service provision on Twitter: The case of e-retailers. International Journal of Physical
Distribution & Logistics Management. 46(6/7). pp.659-680.
Crainic, T.G. and et.al., 2016. Logistics capacity planning: A stochastic bin packing formulation
and a progressive hedging meta-heuristic. European Journal of Operational Research.
253(2). pp.404-417.
De Stefano, V., 2015. The rise of the just-in-time workforce: On-demand work, crowdwork, and
labor protection in the gig-economy. Comp. Lab. L. & Pol'y J.. 37. p.471.
Fullerton, R.R., Kennedy, F.A. and Widener, S.K., 2014. Lean manufacturing and firm
performance: The incremental contribution of lean management accounting practices.
Journal of Operations Management. 32(7-8). pp.414-428.
Givi, Z.S., Jaber, M.Y. and Neumann, W.P., 2015. Production planning in DRC systems
considering worker performance. Computers & Industrial Engineering. 87. pp.317-327.
Hall, N.G., Posner, M.E. and Potts, C.N., 2018. Online production planning to maximize the
number of on-time orders. Annals of Operations Research. pp.1-21.
Hedenstierna, C.P.T. and Disney, S.M., 2018. Avoiding the capacity cost trap: Three means of
smoothing under cyclical production planning. International Journal of Production
Economics. 201. pp.149-162.
Jasti, N.V.K. and Kodali, R., 2015. Lean production: literature review and trends. International
Journal of Production Research. 53(3). pp.867-885.
Liu, C.and et.al., 2015. Production planning of multi-stage multi-option seru production systems
with sustainable measures. Journal of Cleaner Production. 105. pp.285-299.
Madathil, S.C., and et.al., 2017. Resilient off-grid microgrids: Capacity planning and N-1
security. IEEE Transactions on Smart Grid.
Meyr, H., Wagner, M. and Rohde, J., 2015. Structure of advanced planning systems. In Supply
chain management and advanced planning (pp. 99-106). Springer, Berlin, Heidelberg.
Neyshabouri, S. and Berg, B.P., 2017. Two-stage robust optimization approach to elective
surgery and downstream capacity planning. European Journal of Operational Research.
260(1). pp.21-40.
1
Books & Journals
Adebanjo, D., Laosirihongthong, T. and Samaranayake, P., 2016. Prioritizing lean supply chain
management initiatives in healthcare service operations: a fuzzy AHP approach.
Production Planning & Control. 27(12). pp.953-966.
Bhattacharjya, J., Ellison, A. and Tripathi, S., 2016. An exploration of logistics-related customer
service provision on Twitter: The case of e-retailers. International Journal of Physical
Distribution & Logistics Management. 46(6/7). pp.659-680.
Crainic, T.G. and et.al., 2016. Logistics capacity planning: A stochastic bin packing formulation
and a progressive hedging meta-heuristic. European Journal of Operational Research.
253(2). pp.404-417.
De Stefano, V., 2015. The rise of the just-in-time workforce: On-demand work, crowdwork, and
labor protection in the gig-economy. Comp. Lab. L. & Pol'y J.. 37. p.471.
Fullerton, R.R., Kennedy, F.A. and Widener, S.K., 2014. Lean manufacturing and firm
performance: The incremental contribution of lean management accounting practices.
Journal of Operations Management. 32(7-8). pp.414-428.
Givi, Z.S., Jaber, M.Y. and Neumann, W.P., 2015. Production planning in DRC systems
considering worker performance. Computers & Industrial Engineering. 87. pp.317-327.
Hall, N.G., Posner, M.E. and Potts, C.N., 2018. Online production planning to maximize the
number of on-time orders. Annals of Operations Research. pp.1-21.
Hedenstierna, C.P.T. and Disney, S.M., 2018. Avoiding the capacity cost trap: Three means of
smoothing under cyclical production planning. International Journal of Production
Economics. 201. pp.149-162.
Jasti, N.V.K. and Kodali, R., 2015. Lean production: literature review and trends. International
Journal of Production Research. 53(3). pp.867-885.
Liu, C.and et.al., 2015. Production planning of multi-stage multi-option seru production systems
with sustainable measures. Journal of Cleaner Production. 105. pp.285-299.
Madathil, S.C., and et.al., 2017. Resilient off-grid microgrids: Capacity planning and N-1
security. IEEE Transactions on Smart Grid.
Meyr, H., Wagner, M. and Rohde, J., 2015. Structure of advanced planning systems. In Supply
chain management and advanced planning (pp. 99-106). Springer, Berlin, Heidelberg.
Neyshabouri, S. and Berg, B.P., 2017. Two-stage robust optimization approach to elective
surgery and downstream capacity planning. European Journal of Operational Research.
260(1). pp.21-40.
1
Paraphrase This Document
Need a fresh take? Get an instant paraphrase of this document with our AI Paraphraser
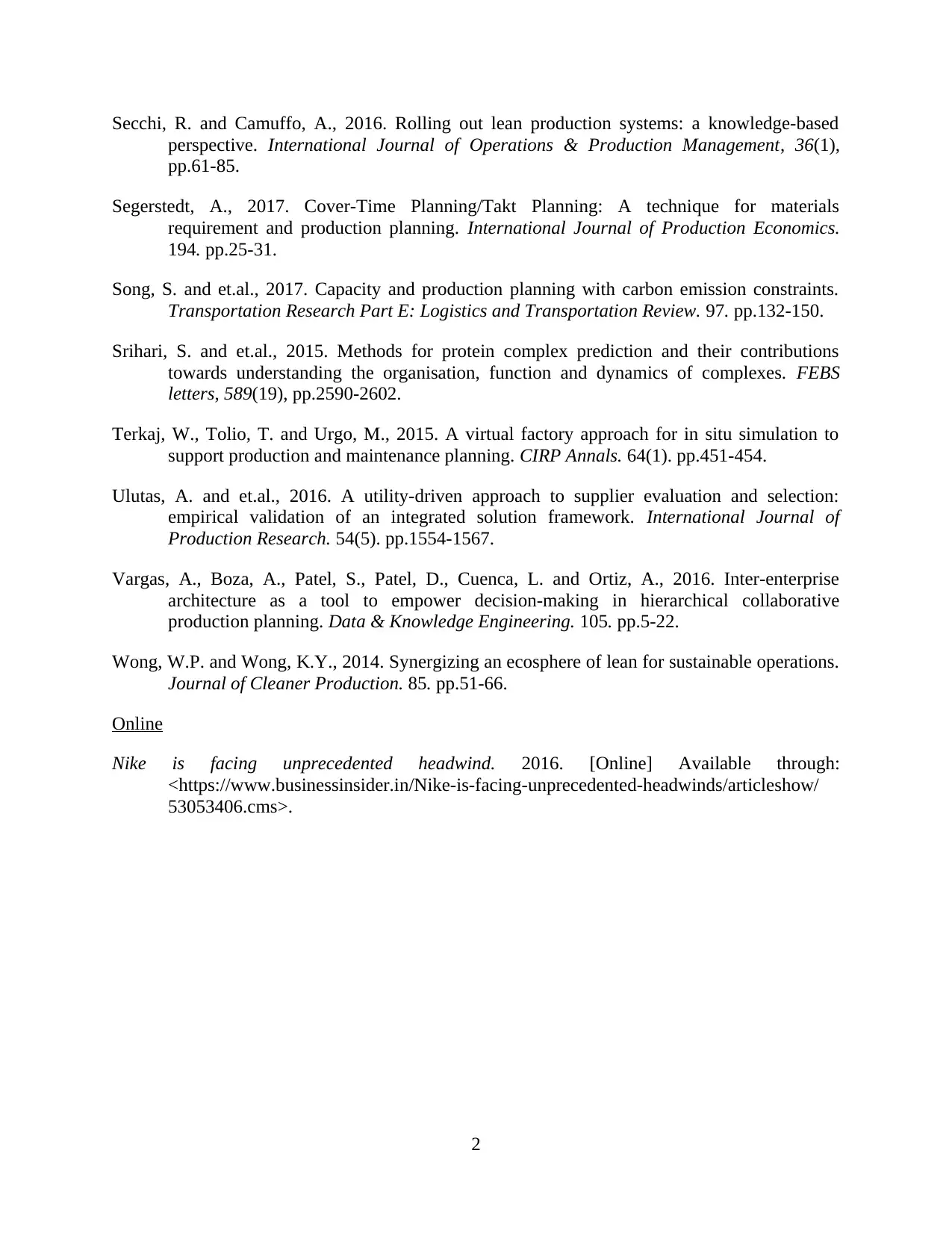
Secchi, R. and Camuffo, A., 2016. Rolling out lean production systems: a knowledge-based
perspective. International Journal of Operations & Production Management, 36(1),
pp.61-85.
Segerstedt, A., 2017. Cover-Time Planning/Takt Planning: A technique for materials
requirement and production planning. International Journal of Production Economics.
194. pp.25-31.
Song, S. and et.al., 2017. Capacity and production planning with carbon emission constraints.
Transportation Research Part E: Logistics and Transportation Review. 97. pp.132-150.
Srihari, S. and et.al., 2015. Methods for protein complex prediction and their contributions
towards understanding the organisation, function and dynamics of complexes. FEBS
letters, 589(19), pp.2590-2602.
Terkaj, W., Tolio, T. and Urgo, M., 2015. A virtual factory approach for in situ simulation to
support production and maintenance planning. CIRP Annals. 64(1). pp.451-454.
Ulutas, A. and et.al., 2016. A utility-driven approach to supplier evaluation and selection:
empirical validation of an integrated solution framework. International Journal of
Production Research. 54(5). pp.1554-1567.
Vargas, A., Boza, A., Patel, S., Patel, D., Cuenca, L. and Ortiz, A., 2016. Inter-enterprise
architecture as a tool to empower decision-making in hierarchical collaborative
production planning. Data & Knowledge Engineering. 105. pp.5-22.
Wong, W.P. and Wong, K.Y., 2014. Synergizing an ecosphere of lean for sustainable operations.
Journal of Cleaner Production. 85. pp.51-66.
Online
Nike is facing unprecedented headwind. 2016. [Online] Available through:
<https://www.businessinsider.in/Nike-is-facing-unprecedented-headwinds/articleshow/
53053406.cms>.
2
perspective. International Journal of Operations & Production Management, 36(1),
pp.61-85.
Segerstedt, A., 2017. Cover-Time Planning/Takt Planning: A technique for materials
requirement and production planning. International Journal of Production Economics.
194. pp.25-31.
Song, S. and et.al., 2017. Capacity and production planning with carbon emission constraints.
Transportation Research Part E: Logistics and Transportation Review. 97. pp.132-150.
Srihari, S. and et.al., 2015. Methods for protein complex prediction and their contributions
towards understanding the organisation, function and dynamics of complexes. FEBS
letters, 589(19), pp.2590-2602.
Terkaj, W., Tolio, T. and Urgo, M., 2015. A virtual factory approach for in situ simulation to
support production and maintenance planning. CIRP Annals. 64(1). pp.451-454.
Ulutas, A. and et.al., 2016. A utility-driven approach to supplier evaluation and selection:
empirical validation of an integrated solution framework. International Journal of
Production Research. 54(5). pp.1554-1567.
Vargas, A., Boza, A., Patel, S., Patel, D., Cuenca, L. and Ortiz, A., 2016. Inter-enterprise
architecture as a tool to empower decision-making in hierarchical collaborative
production planning. Data & Knowledge Engineering. 105. pp.5-22.
Wong, W.P. and Wong, K.Y., 2014. Synergizing an ecosphere of lean for sustainable operations.
Journal of Cleaner Production. 85. pp.51-66.
Online
Nike is facing unprecedented headwind. 2016. [Online] Available through:
<https://www.businessinsider.in/Nike-is-facing-unprecedented-headwinds/articleshow/
53053406.cms>.
2
1 out of 14
Related Documents

Your All-in-One AI-Powered Toolkit for Academic Success.
+13062052269
info@desklib.com
Available 24*7 on WhatsApp / Email
Unlock your academic potential
© 2024 | Zucol Services PVT LTD | All rights reserved.