Asset Management and Reliability: RCM, FMEA, and Implementation
VerifiedAdded on 2022/09/15
|11
|3231
|10
Report
AI Summary
This report comprehensively addresses asset management and reliability, focusing on Reliability-Centered Maintenance (RCM) and Failure Mode and Effects Analysis (FMEA). It begins with an overview of RCM methodology, detailing its benefits, such as deferred capital use and reduced losses, and limitations, including the consideration of all costs and the need for specialized personnel. The report then explores the FMEA process, outlining its benefits in identifying potential failures and improving product quality, as well as its limitations, such as potential biases and dependence on team expertise. A reflective essay reviews a journal article on RCM implementation, discussing challenges and strategies for successful application. The assignment also includes a group activity to develop an FMEA worksheet and an individual activity to identify and explain the mitigation of top failure modes. The report references relevant Australian Standards and textbooks to support its analysis.
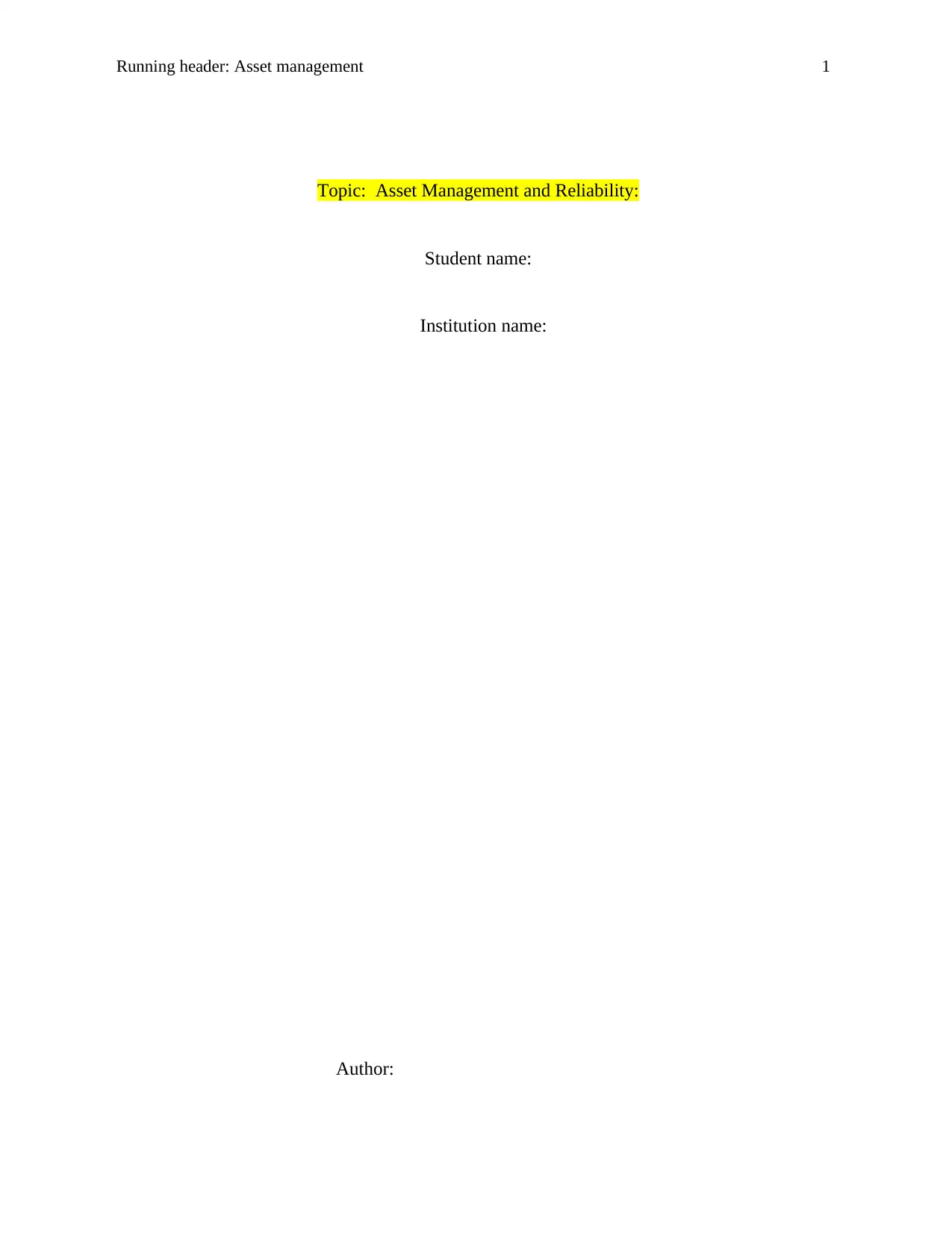
Running header: Asset management 1
Topic: Asset Management and Reliability:
Student name:
Institution name:
Author:
Topic: Asset Management and Reliability:
Student name:
Institution name:
Author:
Secure Best Marks with AI Grader
Need help grading? Try our AI Grader for instant feedback on your assignments.
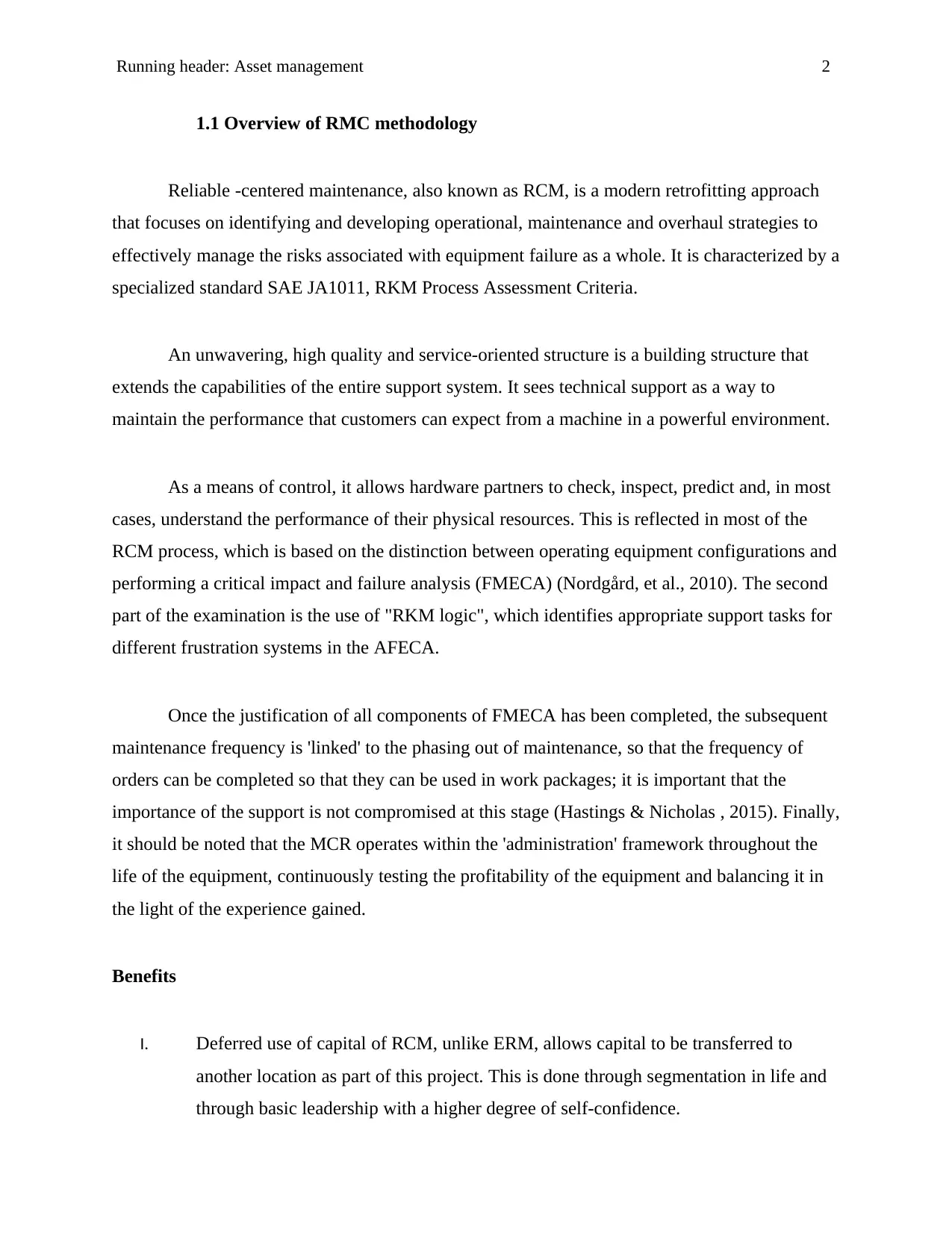
Running header: Asset management 2
1.1 Overview of RMC methodology
Reliable -centered maintenance, also known as RCM, is a modern retrofitting approach
that focuses on identifying and developing operational, maintenance and overhaul strategies to
effectively manage the risks associated with equipment failure as a whole. It is characterized by a
specialized standard SAE JA1011, RKM Process Assessment Criteria.
An unwavering, high quality and service-oriented structure is a building structure that
extends the capabilities of the entire support system. It sees technical support as a way to
maintain the performance that customers can expect from a machine in a powerful environment.
As a means of control, it allows hardware partners to check, inspect, predict and, in most
cases, understand the performance of their physical resources. This is reflected in most of the
RCM process, which is based on the distinction between operating equipment configurations and
performing a critical impact and failure analysis (FMECA) (Nordgård, et al., 2010). The second
part of the examination is the use of "RKM logic", which identifies appropriate support tasks for
different frustration systems in the AFECA.
Once the justification of all components of FMECA has been completed, the subsequent
maintenance frequency is 'linked' to the phasing out of maintenance, so that the frequency of
orders can be completed so that they can be used in work packages; it is important that the
importance of the support is not compromised at this stage (Hastings & Nicholas , 2015). Finally,
it should be noted that the MCR operates within the 'administration' framework throughout the
life of the equipment, continuously testing the profitability of the equipment and balancing it in
the light of the experience gained.
Benefits
I. Deferred use of capital of RCM, unlike ERM, allows capital to be transferred to
another location as part of this project. This is done through segmentation in life and
through basic leadership with a higher degree of self-confidence.
1.1 Overview of RMC methodology
Reliable -centered maintenance, also known as RCM, is a modern retrofitting approach
that focuses on identifying and developing operational, maintenance and overhaul strategies to
effectively manage the risks associated with equipment failure as a whole. It is characterized by a
specialized standard SAE JA1011, RKM Process Assessment Criteria.
An unwavering, high quality and service-oriented structure is a building structure that
extends the capabilities of the entire support system. It sees technical support as a way to
maintain the performance that customers can expect from a machine in a powerful environment.
As a means of control, it allows hardware partners to check, inspect, predict and, in most
cases, understand the performance of their physical resources. This is reflected in most of the
RCM process, which is based on the distinction between operating equipment configurations and
performing a critical impact and failure analysis (FMECA) (Nordgård, et al., 2010). The second
part of the examination is the use of "RKM logic", which identifies appropriate support tasks for
different frustration systems in the AFECA.
Once the justification of all components of FMECA has been completed, the subsequent
maintenance frequency is 'linked' to the phasing out of maintenance, so that the frequency of
orders can be completed so that they can be used in work packages; it is important that the
importance of the support is not compromised at this stage (Hastings & Nicholas , 2015). Finally,
it should be noted that the MCR operates within the 'administration' framework throughout the
life of the equipment, continuously testing the profitability of the equipment and balancing it in
the light of the experience gained.
Benefits
I. Deferred use of capital of RCM, unlike ERM, allows capital to be transferred to
another location as part of this project. This is done through segmentation in life and
through basic leadership with a higher degree of self-confidence.
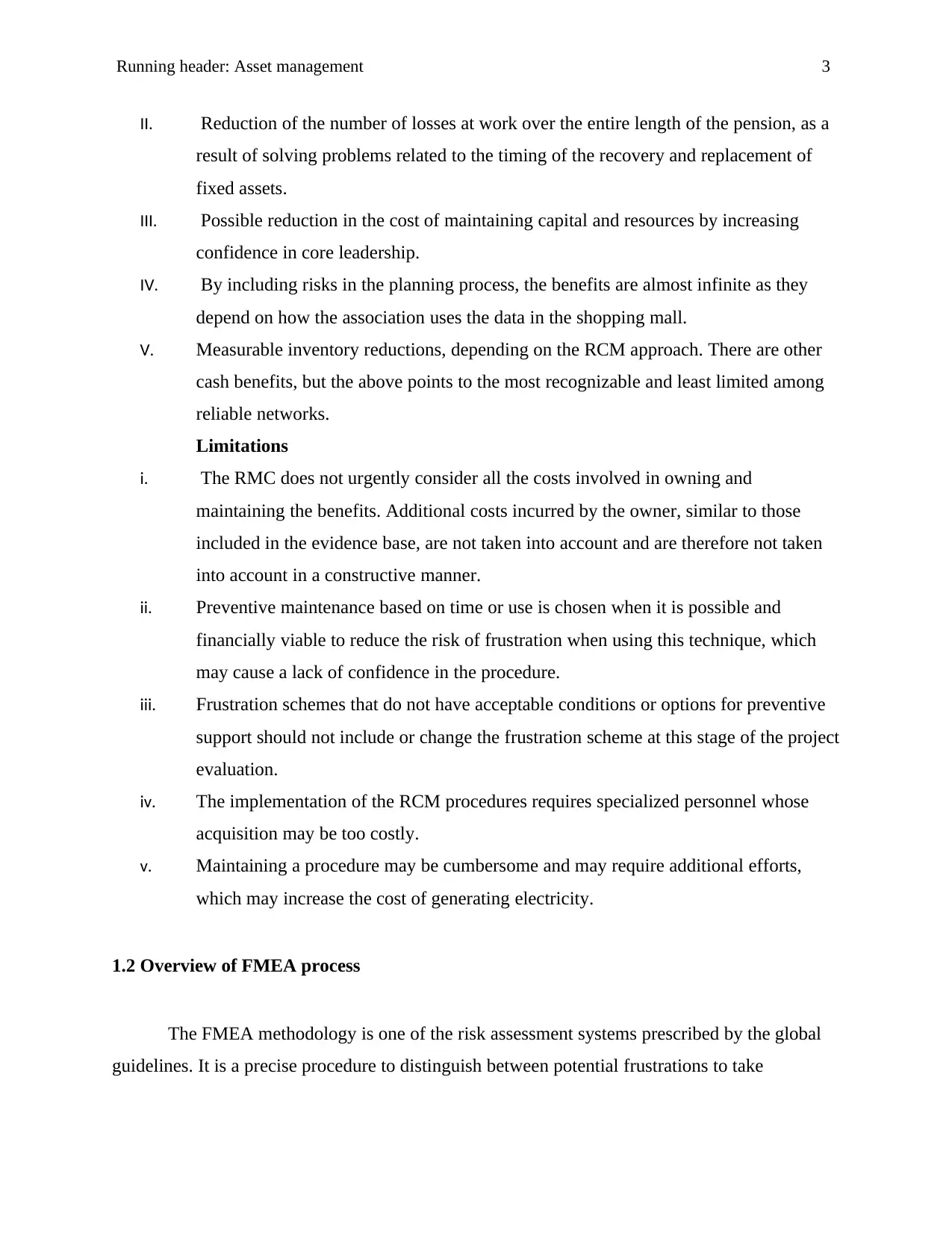
Running header: Asset management 3
II. Reduction of the number of losses at work over the entire length of the pension, as a
result of solving problems related to the timing of the recovery and replacement of
fixed assets.
III. Possible reduction in the cost of maintaining capital and resources by increasing
confidence in core leadership.
IV. By including risks in the planning process, the benefits are almost infinite as they
depend on how the association uses the data in the shopping mall.
V. Measurable inventory reductions, depending on the RCM approach. There are other
cash benefits, but the above points to the most recognizable and least limited among
reliable networks.
Limitations
i. The RMC does not urgently consider all the costs involved in owning and
maintaining the benefits. Additional costs incurred by the owner, similar to those
included in the evidence base, are not taken into account and are therefore not taken
into account in a constructive manner.
ii. Preventive maintenance based on time or use is chosen when it is possible and
financially viable to reduce the risk of frustration when using this technique, which
may cause a lack of confidence in the procedure.
iii. Frustration schemes that do not have acceptable conditions or options for preventive
support should not include or change the frustration scheme at this stage of the project
evaluation.
iv. The implementation of the RCM procedures requires specialized personnel whose
acquisition may be too costly.
v. Maintaining a procedure may be cumbersome and may require additional efforts,
which may increase the cost of generating electricity.
1.2 Overview of FMEA process
The FMEA methodology is one of the risk assessment systems prescribed by the global
guidelines. It is a precise procedure to distinguish between potential frustrations to take
II. Reduction of the number of losses at work over the entire length of the pension, as a
result of solving problems related to the timing of the recovery and replacement of
fixed assets.
III. Possible reduction in the cost of maintaining capital and resources by increasing
confidence in core leadership.
IV. By including risks in the planning process, the benefits are almost infinite as they
depend on how the association uses the data in the shopping mall.
V. Measurable inventory reductions, depending on the RCM approach. There are other
cash benefits, but the above points to the most recognizable and least limited among
reliable networks.
Limitations
i. The RMC does not urgently consider all the costs involved in owning and
maintaining the benefits. Additional costs incurred by the owner, similar to those
included in the evidence base, are not taken into account and are therefore not taken
into account in a constructive manner.
ii. Preventive maintenance based on time or use is chosen when it is possible and
financially viable to reduce the risk of frustration when using this technique, which
may cause a lack of confidence in the procedure.
iii. Frustration schemes that do not have acceptable conditions or options for preventive
support should not include or change the frustration scheme at this stage of the project
evaluation.
iv. The implementation of the RCM procedures requires specialized personnel whose
acquisition may be too costly.
v. Maintaining a procedure may be cumbersome and may require additional efforts,
which may increase the cost of generating electricity.
1.2 Overview of FMEA process
The FMEA methodology is one of the risk assessment systems prescribed by the global
guidelines. It is a precise procedure to distinguish between potential frustrations to take
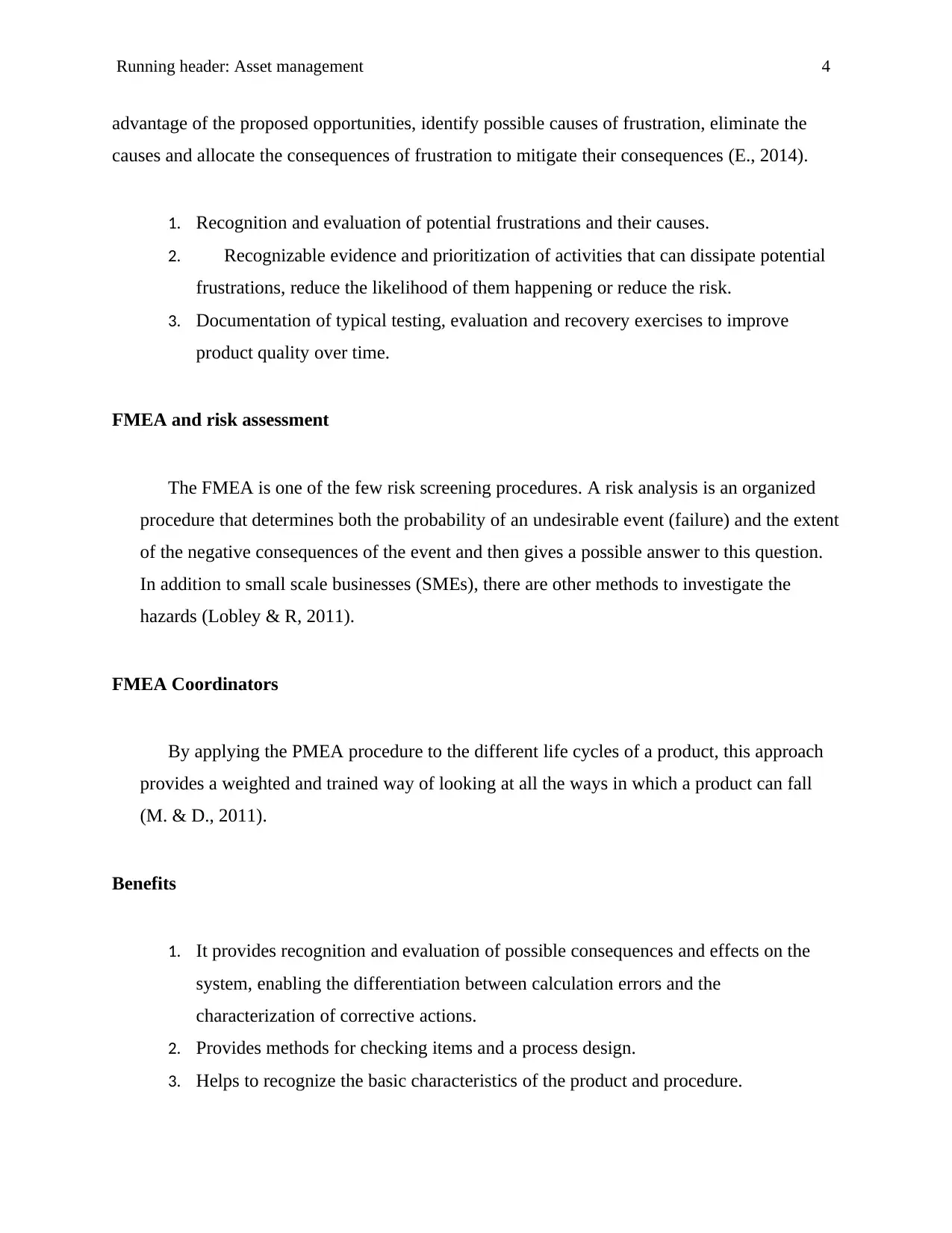
Running header: Asset management 4
advantage of the proposed opportunities, identify possible causes of frustration, eliminate the
causes and allocate the consequences of frustration to mitigate their consequences (E., 2014).
1. Recognition and evaluation of potential frustrations and their causes.
2. Recognizable evidence and prioritization of activities that can dissipate potential
frustrations, reduce the likelihood of them happening or reduce the risk.
3. Documentation of typical testing, evaluation and recovery exercises to improve
product quality over time.
FMEA and risk assessment
The FMEA is one of the few risk screening procedures. A risk analysis is an organized
procedure that determines both the probability of an undesirable event (failure) and the extent
of the negative consequences of the event and then gives a possible answer to this question.
In addition to small scale businesses (SMEs), there are other methods to investigate the
hazards (Lobley & R, 2011).
FMEA Coordinators
By applying the PMEA procedure to the different life cycles of a product, this approach
provides a weighted and trained way of looking at all the ways in which a product can fall
(M. & D., 2011).
Benefits
1. It provides recognition and evaluation of possible consequences and effects on the
system, enabling the differentiation between calculation errors and the
characterization of corrective actions.
2. Provides methods for checking items and a process design.
3. Helps to recognize the basic characteristics of the product and procedure.
advantage of the proposed opportunities, identify possible causes of frustration, eliminate the
causes and allocate the consequences of frustration to mitigate their consequences (E., 2014).
1. Recognition and evaluation of potential frustrations and their causes.
2. Recognizable evidence and prioritization of activities that can dissipate potential
frustrations, reduce the likelihood of them happening or reduce the risk.
3. Documentation of typical testing, evaluation and recovery exercises to improve
product quality over time.
FMEA and risk assessment
The FMEA is one of the few risk screening procedures. A risk analysis is an organized
procedure that determines both the probability of an undesirable event (failure) and the extent
of the negative consequences of the event and then gives a possible answer to this question.
In addition to small scale businesses (SMEs), there are other methods to investigate the
hazards (Lobley & R, 2011).
FMEA Coordinators
By applying the PMEA procedure to the different life cycles of a product, this approach
provides a weighted and trained way of looking at all the ways in which a product can fall
(M. & D., 2011).
Benefits
1. It provides recognition and evaluation of possible consequences and effects on the
system, enabling the differentiation between calculation errors and the
characterization of corrective actions.
2. Provides methods for checking items and a process design.
3. Helps to recognize the basic characteristics of the product and procedure.
Secure Best Marks with AI Grader
Need help grading? Try our AI Grader for instant feedback on your assignments.
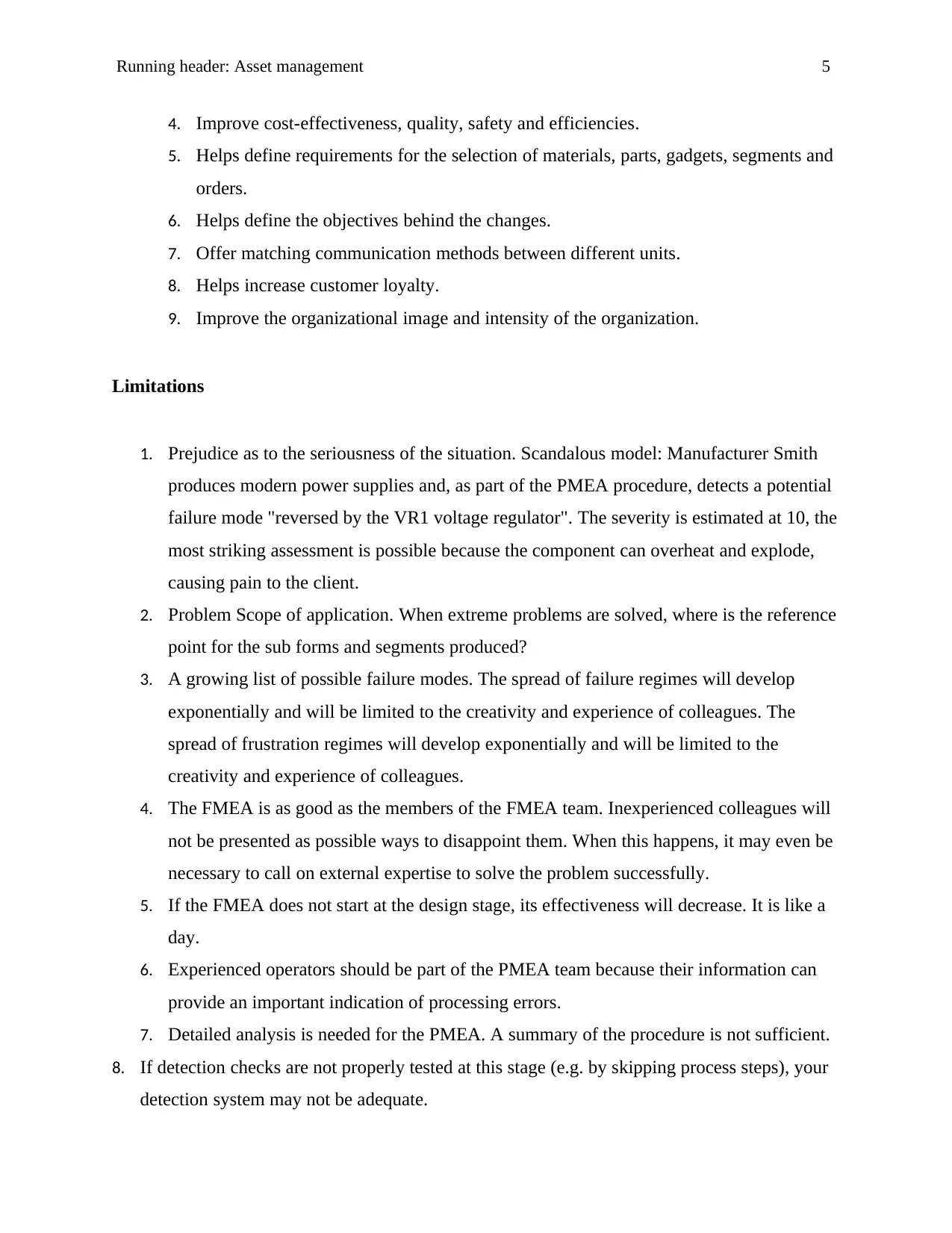
Running header: Asset management 5
4. Improve cost-effectiveness, quality, safety and efficiencies.
5. Helps define requirements for the selection of materials, parts, gadgets, segments and
orders.
6. Helps define the objectives behind the changes.
7. Offer matching communication methods between different units.
8. Helps increase customer loyalty.
9. Improve the organizational image and intensity of the organization.
Limitations
1. Prejudice as to the seriousness of the situation. Scandalous model: Manufacturer Smith
produces modern power supplies and, as part of the PMEA procedure, detects a potential
failure mode "reversed by the VR1 voltage regulator". The severity is estimated at 10, the
most striking assessment is possible because the component can overheat and explode,
causing pain to the client.
2. Problem Scope of application. When extreme problems are solved, where is the reference
point for the sub forms and segments produced?
3. A growing list of possible failure modes. The spread of failure regimes will develop
exponentially and will be limited to the creativity and experience of colleagues. The
spread of frustration regimes will develop exponentially and will be limited to the
creativity and experience of colleagues.
4. The FMEA is as good as the members of the FMEA team. Inexperienced colleagues will
not be presented as possible ways to disappoint them. When this happens, it may even be
necessary to call on external expertise to solve the problem successfully.
5. If the FMEA does not start at the design stage, its effectiveness will decrease. It is like a
day.
6. Experienced operators should be part of the PMEA team because their information can
provide an important indication of processing errors.
7. Detailed analysis is needed for the PMEA. A summary of the procedure is not sufficient.
8. If detection checks are not properly tested at this stage (e.g. by skipping process steps), your
detection system may not be adequate.
4. Improve cost-effectiveness, quality, safety and efficiencies.
5. Helps define requirements for the selection of materials, parts, gadgets, segments and
orders.
6. Helps define the objectives behind the changes.
7. Offer matching communication methods between different units.
8. Helps increase customer loyalty.
9. Improve the organizational image and intensity of the organization.
Limitations
1. Prejudice as to the seriousness of the situation. Scandalous model: Manufacturer Smith
produces modern power supplies and, as part of the PMEA procedure, detects a potential
failure mode "reversed by the VR1 voltage regulator". The severity is estimated at 10, the
most striking assessment is possible because the component can overheat and explode,
causing pain to the client.
2. Problem Scope of application. When extreme problems are solved, where is the reference
point for the sub forms and segments produced?
3. A growing list of possible failure modes. The spread of failure regimes will develop
exponentially and will be limited to the creativity and experience of colleagues. The
spread of frustration regimes will develop exponentially and will be limited to the
creativity and experience of colleagues.
4. The FMEA is as good as the members of the FMEA team. Inexperienced colleagues will
not be presented as possible ways to disappoint them. When this happens, it may even be
necessary to call on external expertise to solve the problem successfully.
5. If the FMEA does not start at the design stage, its effectiveness will decrease. It is like a
day.
6. Experienced operators should be part of the PMEA team because their information can
provide an important indication of processing errors.
7. Detailed analysis is needed for the PMEA. A summary of the procedure is not sufficient.
8. If detection checks are not properly tested at this stage (e.g. by skipping process steps), your
detection system may not be adequate.
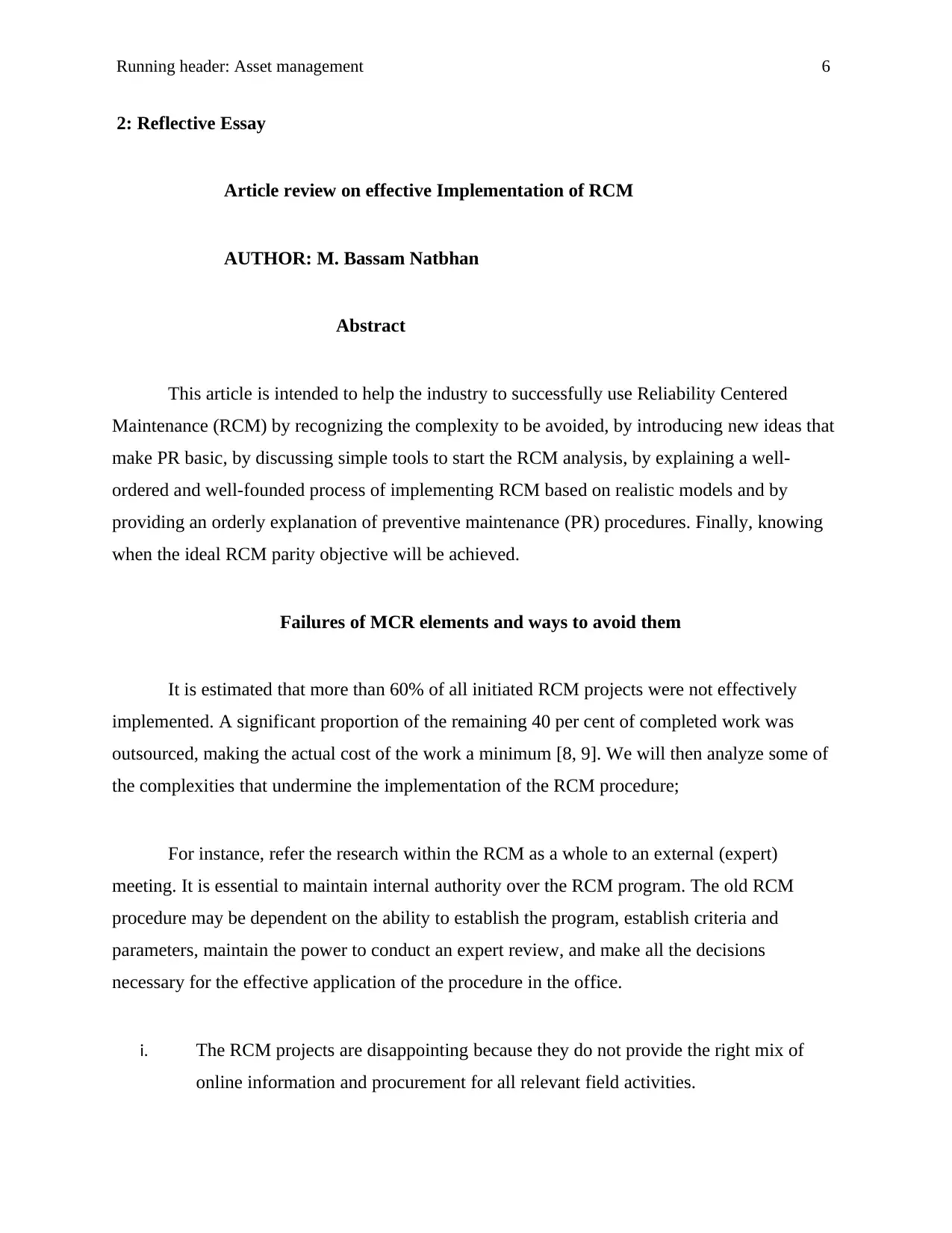
Running header: Asset management 6
2: Reflective Essay
Article review on effective Implementation of RCM
AUTHOR: M. Bassam Natbhan
Abstract
This article is intended to help the industry to successfully use Reliability Centered
Maintenance (RCM) by recognizing the complexity to be avoided, by introducing new ideas that
make PR basic, by discussing simple tools to start the RCM analysis, by explaining a well-
ordered and well-founded process of implementing RCM based on realistic models and by
providing an orderly explanation of preventive maintenance (PR) procedures. Finally, knowing
when the ideal RCM parity objective will be achieved.
Failures of MCR elements and ways to avoid them
It is estimated that more than 60% of all initiated RCM projects were not effectively
implemented. A significant proportion of the remaining 40 per cent of completed work was
outsourced, making the actual cost of the work a minimum [8, 9]. We will then analyze some of
the complexities that undermine the implementation of the RCM procedure;
For instance, refer the research within the RCM as a whole to an external (expert)
meeting. It is essential to maintain internal authority over the RCM program. The old RCM
procedure may be dependent on the ability to establish the program, establish criteria and
parameters, maintain the power to conduct an expert review, and make all the decisions
necessary for the effective application of the procedure in the office.
i. The RCM projects are disappointing because they do not provide the right mix of
online information and procurement for all relevant field activities.
2: Reflective Essay
Article review on effective Implementation of RCM
AUTHOR: M. Bassam Natbhan
Abstract
This article is intended to help the industry to successfully use Reliability Centered
Maintenance (RCM) by recognizing the complexity to be avoided, by introducing new ideas that
make PR basic, by discussing simple tools to start the RCM analysis, by explaining a well-
ordered and well-founded process of implementing RCM based on realistic models and by
providing an orderly explanation of preventive maintenance (PR) procedures. Finally, knowing
when the ideal RCM parity objective will be achieved.
Failures of MCR elements and ways to avoid them
It is estimated that more than 60% of all initiated RCM projects were not effectively
implemented. A significant proportion of the remaining 40 per cent of completed work was
outsourced, making the actual cost of the work a minimum [8, 9]. We will then analyze some of
the complexities that undermine the implementation of the RCM procedure;
For instance, refer the research within the RCM as a whole to an external (expert)
meeting. It is essential to maintain internal authority over the RCM program. The old RCM
procedure may be dependent on the ability to establish the program, establish criteria and
parameters, maintain the power to conduct an expert review, and make all the decisions
necessary for the effective application of the procedure in the office.
i. The RCM projects are disappointing because they do not provide the right mix of
online information and procurement for all relevant field activities.
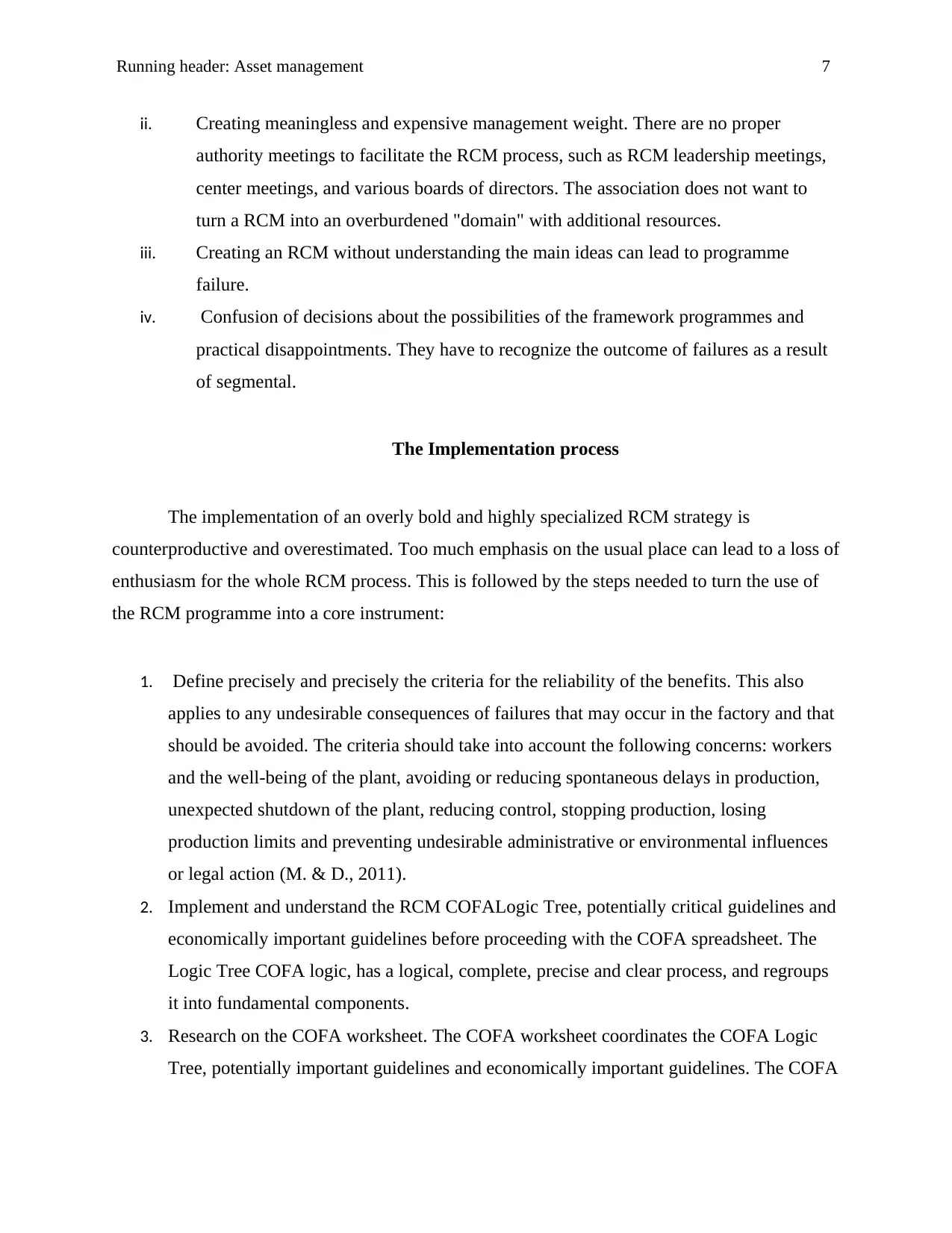
Running header: Asset management 7
ii. Creating meaningless and expensive management weight. There are no proper
authority meetings to facilitate the RCM process, such as RCM leadership meetings,
center meetings, and various boards of directors. The association does not want to
turn a RCM into an overburdened "domain" with additional resources.
iii. Creating an RCM without understanding the main ideas can lead to programme
failure.
iv. Confusion of decisions about the possibilities of the framework programmes and
practical disappointments. They have to recognize the outcome of failures as a result
of segmental.
The Implementation process
The implementation of an overly bold and highly specialized RCM strategy is
counterproductive and overestimated. Too much emphasis on the usual place can lead to a loss of
enthusiasm for the whole RCM process. This is followed by the steps needed to turn the use of
the RCM programme into a core instrument:
1. Define precisely and precisely the criteria for the reliability of the benefits. This also
applies to any undesirable consequences of failures that may occur in the factory and that
should be avoided. The criteria should take into account the following concerns: workers
and the well-being of the plant, avoiding or reducing spontaneous delays in production,
unexpected shutdown of the plant, reducing control, stopping production, losing
production limits and preventing undesirable administrative or environmental influences
or legal action (M. & D., 2011).
2. Implement and understand the RCM COFALogic Tree, potentially critical guidelines and
economically important guidelines before proceeding with the COFA spreadsheet. The
Logic Tree COFA logic, has a logical, complete, precise and clear process, and regroups
it into fundamental components.
3. Research on the COFA worksheet. The COFA worksheet coordinates the COFA Logic
Tree, potentially important guidelines and economically important guidelines. The COFA
ii. Creating meaningless and expensive management weight. There are no proper
authority meetings to facilitate the RCM process, such as RCM leadership meetings,
center meetings, and various boards of directors. The association does not want to
turn a RCM into an overburdened "domain" with additional resources.
iii. Creating an RCM without understanding the main ideas can lead to programme
failure.
iv. Confusion of decisions about the possibilities of the framework programmes and
practical disappointments. They have to recognize the outcome of failures as a result
of segmental.
The Implementation process
The implementation of an overly bold and highly specialized RCM strategy is
counterproductive and overestimated. Too much emphasis on the usual place can lead to a loss of
enthusiasm for the whole RCM process. This is followed by the steps needed to turn the use of
the RCM programme into a core instrument:
1. Define precisely and precisely the criteria for the reliability of the benefits. This also
applies to any undesirable consequences of failures that may occur in the factory and that
should be avoided. The criteria should take into account the following concerns: workers
and the well-being of the plant, avoiding or reducing spontaneous delays in production,
unexpected shutdown of the plant, reducing control, stopping production, losing
production limits and preventing undesirable administrative or environmental influences
or legal action (M. & D., 2011).
2. Implement and understand the RCM COFALogic Tree, potentially critical guidelines and
economically important guidelines before proceeding with the COFA spreadsheet. The
Logic Tree COFA logic, has a logical, complete, precise and clear process, and regroups
it into fundamental components.
3. Research on the COFA worksheet. The COFA worksheet coordinates the COFA Logic
Tree, potentially important guidelines and economically important guidelines. The COFA
Paraphrase This Document
Need a fresh take? Get an instant paraphrase of this document with our AI Paraphraser
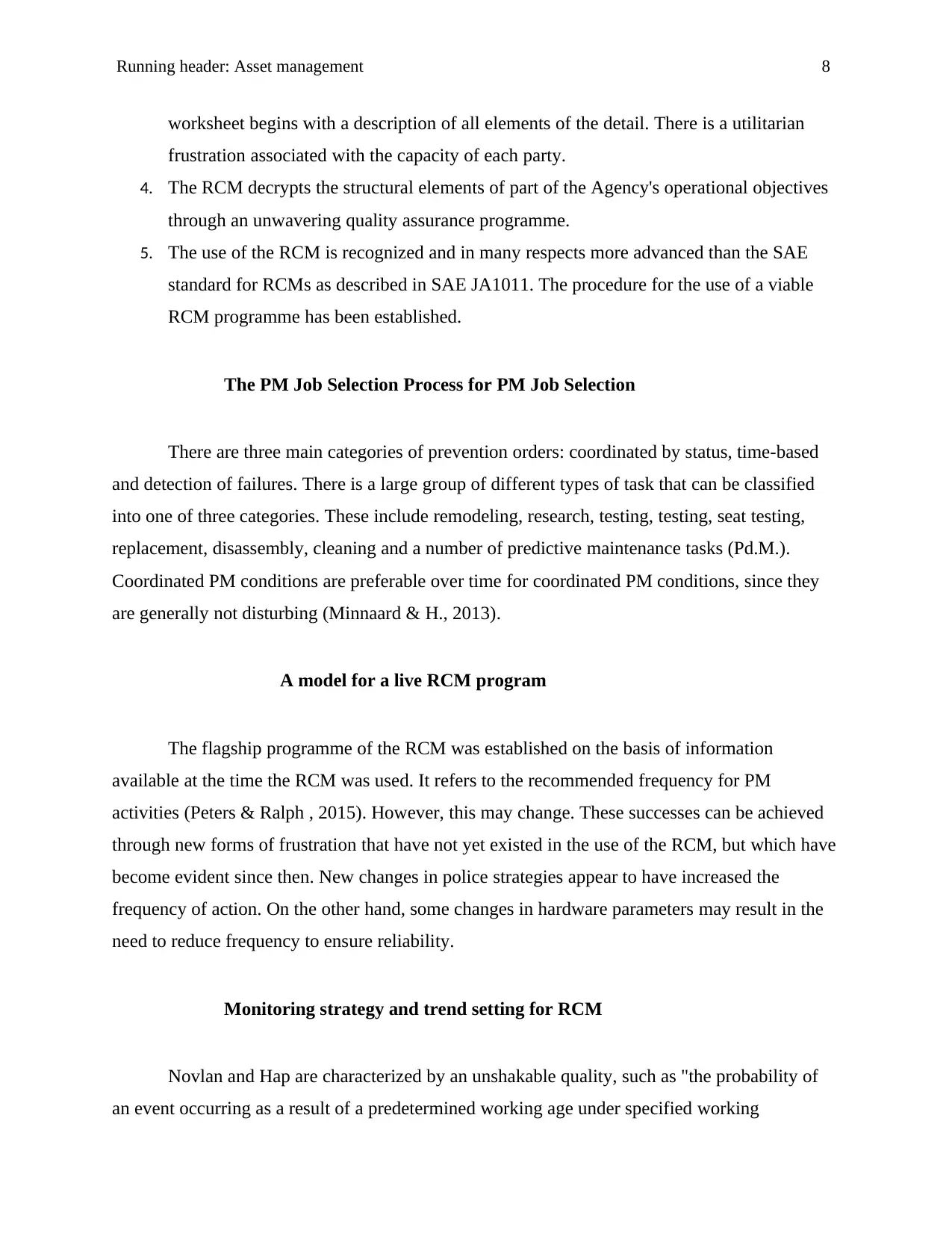
Running header: Asset management 8
worksheet begins with a description of all elements of the detail. There is a utilitarian
frustration associated with the capacity of each party.
4. The RCM decrypts the structural elements of part of the Agency's operational objectives
through an unwavering quality assurance programme.
5. The use of the RCM is recognized and in many respects more advanced than the SAE
standard for RCMs as described in SAE JA1011. The procedure for the use of a viable
RCM programme has been established.
The PM Job Selection Process for PM Job Selection
There are three main categories of prevention orders: coordinated by status, time-based
and detection of failures. There is a large group of different types of task that can be classified
into one of three categories. These include remodeling, research, testing, testing, seat testing,
replacement, disassembly, cleaning and a number of predictive maintenance tasks (Pd.M.).
Coordinated PM conditions are preferable over time for coordinated PM conditions, since they
are generally not disturbing (Minnaard & H., 2013).
A model for a live RCM program
The flagship programme of the RCM was established on the basis of information
available at the time the RCM was used. It refers to the recommended frequency for PM
activities (Peters & Ralph , 2015). However, this may change. These successes can be achieved
through new forms of frustration that have not yet existed in the use of the RCM, but which have
become evident since then. New changes in police strategies appear to have increased the
frequency of action. On the other hand, some changes in hardware parameters may result in the
need to reduce frequency to ensure reliability.
Monitoring strategy and trend setting for RCM
Novlan and Hap are characterized by an unshakable quality, such as "the probability of
an event occurring as a result of a predetermined working age under specified working
worksheet begins with a description of all elements of the detail. There is a utilitarian
frustration associated with the capacity of each party.
4. The RCM decrypts the structural elements of part of the Agency's operational objectives
through an unwavering quality assurance programme.
5. The use of the RCM is recognized and in many respects more advanced than the SAE
standard for RCMs as described in SAE JA1011. The procedure for the use of a viable
RCM programme has been established.
The PM Job Selection Process for PM Job Selection
There are three main categories of prevention orders: coordinated by status, time-based
and detection of failures. There is a large group of different types of task that can be classified
into one of three categories. These include remodeling, research, testing, testing, seat testing,
replacement, disassembly, cleaning and a number of predictive maintenance tasks (Pd.M.).
Coordinated PM conditions are preferable over time for coordinated PM conditions, since they
are generally not disturbing (Minnaard & H., 2013).
A model for a live RCM program
The flagship programme of the RCM was established on the basis of information
available at the time the RCM was used. It refers to the recommended frequency for PM
activities (Peters & Ralph , 2015). However, this may change. These successes can be achieved
through new forms of frustration that have not yet existed in the use of the RCM, but which have
become evident since then. New changes in police strategies appear to have increased the
frequency of action. On the other hand, some changes in hardware parameters may result in the
need to reduce frequency to ensure reliability.
Monitoring strategy and trend setting for RCM
Novlan and Hap are characterized by an unshakable quality, such as "the probability of
an event occurring as a result of a predetermined working age under specified working
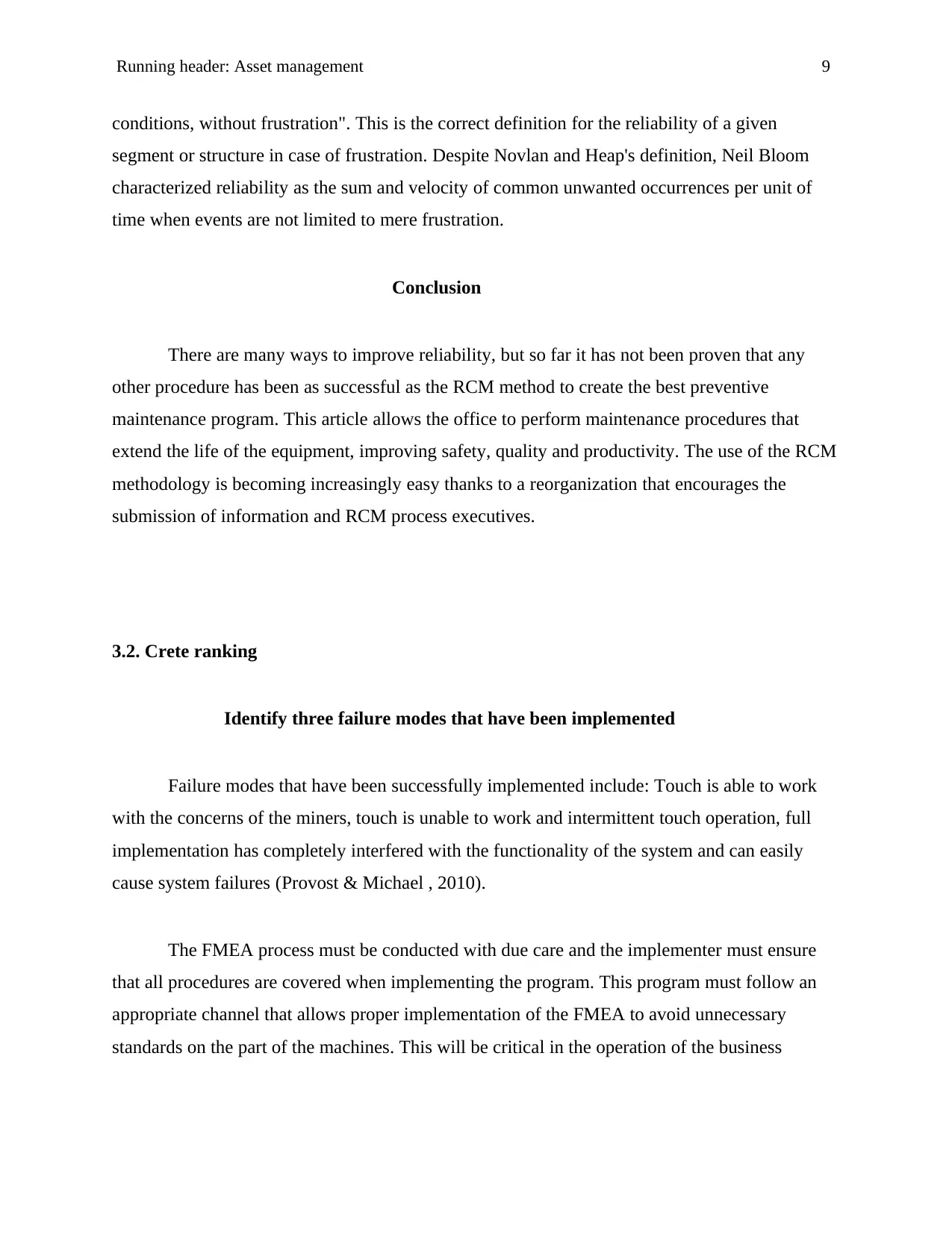
Running header: Asset management 9
conditions, without frustration". This is the correct definition for the reliability of a given
segment or structure in case of frustration. Despite Novlan and Heap's definition, Neil Bloom
characterized reliability as the sum and velocity of common unwanted occurrences per unit of
time when events are not limited to mere frustration.
Conclusion
There are many ways to improve reliability, but so far it has not been proven that any
other procedure has been as successful as the RCM method to create the best preventive
maintenance program. This article allows the office to perform maintenance procedures that
extend the life of the equipment, improving safety, quality and productivity. The use of the RCM
methodology is becoming increasingly easy thanks to a reorganization that encourages the
submission of information and RCM process executives.
3.2. Crete ranking
Identify three failure modes that have been implemented
Failure modes that have been successfully implemented include: Touch is able to work
with the concerns of the miners, touch is unable to work and intermittent touch operation, full
implementation has completely interfered with the functionality of the system and can easily
cause system failures (Provost & Michael , 2010).
The FMEA process must be conducted with due care and the implementer must ensure
that all procedures are covered when implementing the program. This program must follow an
appropriate channel that allows proper implementation of the FMEA to avoid unnecessary
standards on the part of the machines. This will be critical in the operation of the business
conditions, without frustration". This is the correct definition for the reliability of a given
segment or structure in case of frustration. Despite Novlan and Heap's definition, Neil Bloom
characterized reliability as the sum and velocity of common unwanted occurrences per unit of
time when events are not limited to mere frustration.
Conclusion
There are many ways to improve reliability, but so far it has not been proven that any
other procedure has been as successful as the RCM method to create the best preventive
maintenance program. This article allows the office to perform maintenance procedures that
extend the life of the equipment, improving safety, quality and productivity. The use of the RCM
methodology is becoming increasingly easy thanks to a reorganization that encourages the
submission of information and RCM process executives.
3.2. Crete ranking
Identify three failure modes that have been implemented
Failure modes that have been successfully implemented include: Touch is able to work
with the concerns of the miners, touch is unable to work and intermittent touch operation, full
implementation has completely interfered with the functionality of the system and can easily
cause system failures (Provost & Michael , 2010).
The FMEA process must be conducted with due care and the implementer must ensure
that all procedures are covered when implementing the program. This program must follow an
appropriate channel that allows proper implementation of the FMEA to avoid unnecessary
standards on the part of the machines. This will be critical in the operation of the business
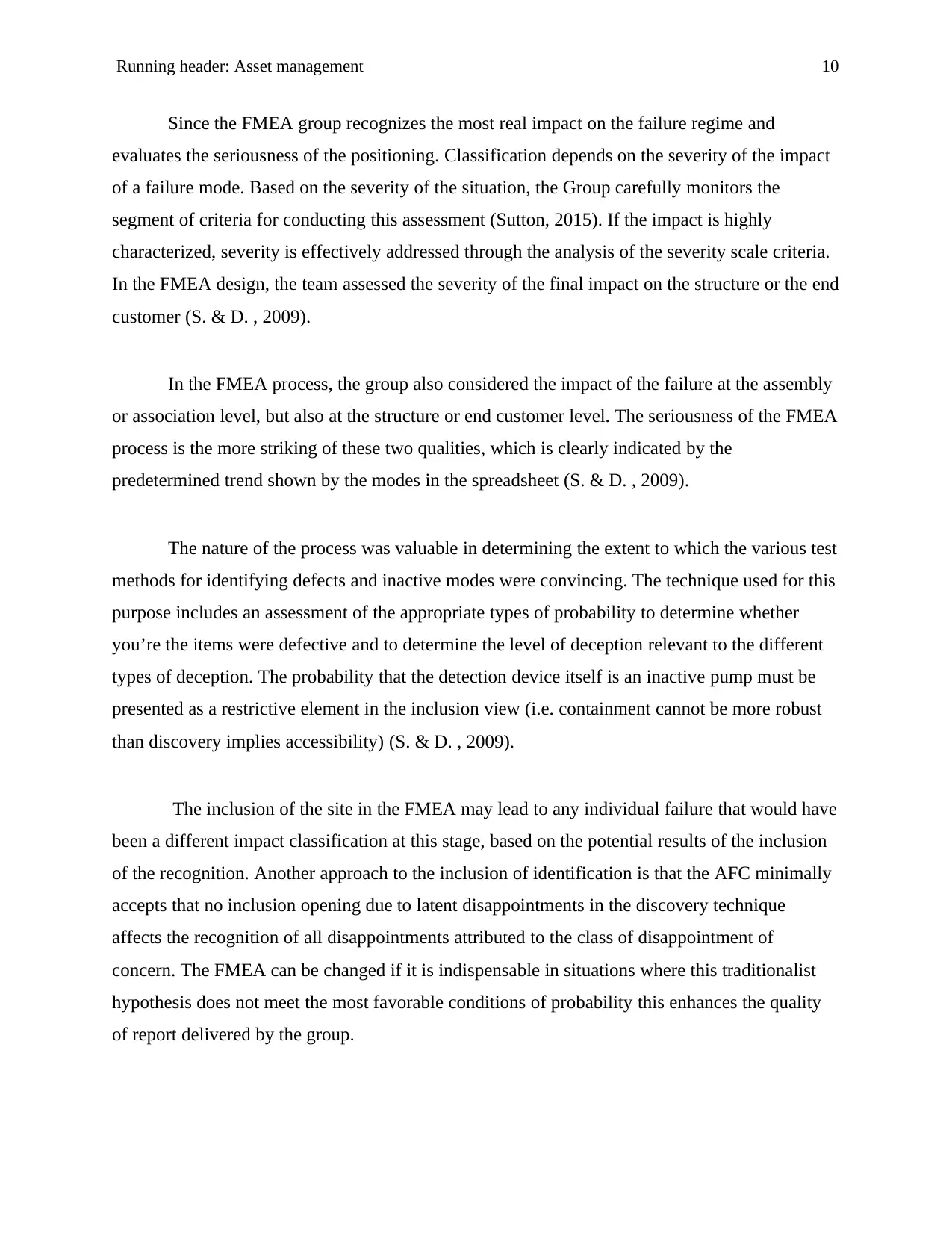
Running header: Asset management 10
Since the FMEA group recognizes the most real impact on the failure regime and
evaluates the seriousness of the positioning. Classification depends on the severity of the impact
of a failure mode. Based on the severity of the situation, the Group carefully monitors the
segment of criteria for conducting this assessment (Sutton, 2015). If the impact is highly
characterized, severity is effectively addressed through the analysis of the severity scale criteria.
In the FMEA design, the team assessed the severity of the final impact on the structure or the end
customer (S. & D. , 2009).
In the FMEA process, the group also considered the impact of the failure at the assembly
or association level, but also at the structure or end customer level. The seriousness of the FMEA
process is the more striking of these two qualities, which is clearly indicated by the
predetermined trend shown by the modes in the spreadsheet (S. & D. , 2009).
The nature of the process was valuable in determining the extent to which the various test
methods for identifying defects and inactive modes were convincing. The technique used for this
purpose includes an assessment of the appropriate types of probability to determine whether
you’re the items were defective and to determine the level of deception relevant to the different
types of deception. The probability that the detection device itself is an inactive pump must be
presented as a restrictive element in the inclusion view (i.e. containment cannot be more robust
than discovery implies accessibility) (S. & D. , 2009).
The inclusion of the site in the FMEA may lead to any individual failure that would have
been a different impact classification at this stage, based on the potential results of the inclusion
of the recognition. Another approach to the inclusion of identification is that the AFC minimally
accepts that no inclusion opening due to latent disappointments in the discovery technique
affects the recognition of all disappointments attributed to the class of disappointment of
concern. The FMEA can be changed if it is indispensable in situations where this traditionalist
hypothesis does not meet the most favorable conditions of probability this enhances the quality
of report delivered by the group.
Since the FMEA group recognizes the most real impact on the failure regime and
evaluates the seriousness of the positioning. Classification depends on the severity of the impact
of a failure mode. Based on the severity of the situation, the Group carefully monitors the
segment of criteria for conducting this assessment (Sutton, 2015). If the impact is highly
characterized, severity is effectively addressed through the analysis of the severity scale criteria.
In the FMEA design, the team assessed the severity of the final impact on the structure or the end
customer (S. & D. , 2009).
In the FMEA process, the group also considered the impact of the failure at the assembly
or association level, but also at the structure or end customer level. The seriousness of the FMEA
process is the more striking of these two qualities, which is clearly indicated by the
predetermined trend shown by the modes in the spreadsheet (S. & D. , 2009).
The nature of the process was valuable in determining the extent to which the various test
methods for identifying defects and inactive modes were convincing. The technique used for this
purpose includes an assessment of the appropriate types of probability to determine whether
you’re the items were defective and to determine the level of deception relevant to the different
types of deception. The probability that the detection device itself is an inactive pump must be
presented as a restrictive element in the inclusion view (i.e. containment cannot be more robust
than discovery implies accessibility) (S. & D. , 2009).
The inclusion of the site in the FMEA may lead to any individual failure that would have
been a different impact classification at this stage, based on the potential results of the inclusion
of the recognition. Another approach to the inclusion of identification is that the AFC minimally
accepts that no inclusion opening due to latent disappointments in the discovery technique
affects the recognition of all disappointments attributed to the class of disappointment of
concern. The FMEA can be changed if it is indispensable in situations where this traditionalist
hypothesis does not meet the most favorable conditions of probability this enhances the quality
of report delivered by the group.
Secure Best Marks with AI Grader
Need help grading? Try our AI Grader for instant feedback on your assignments.
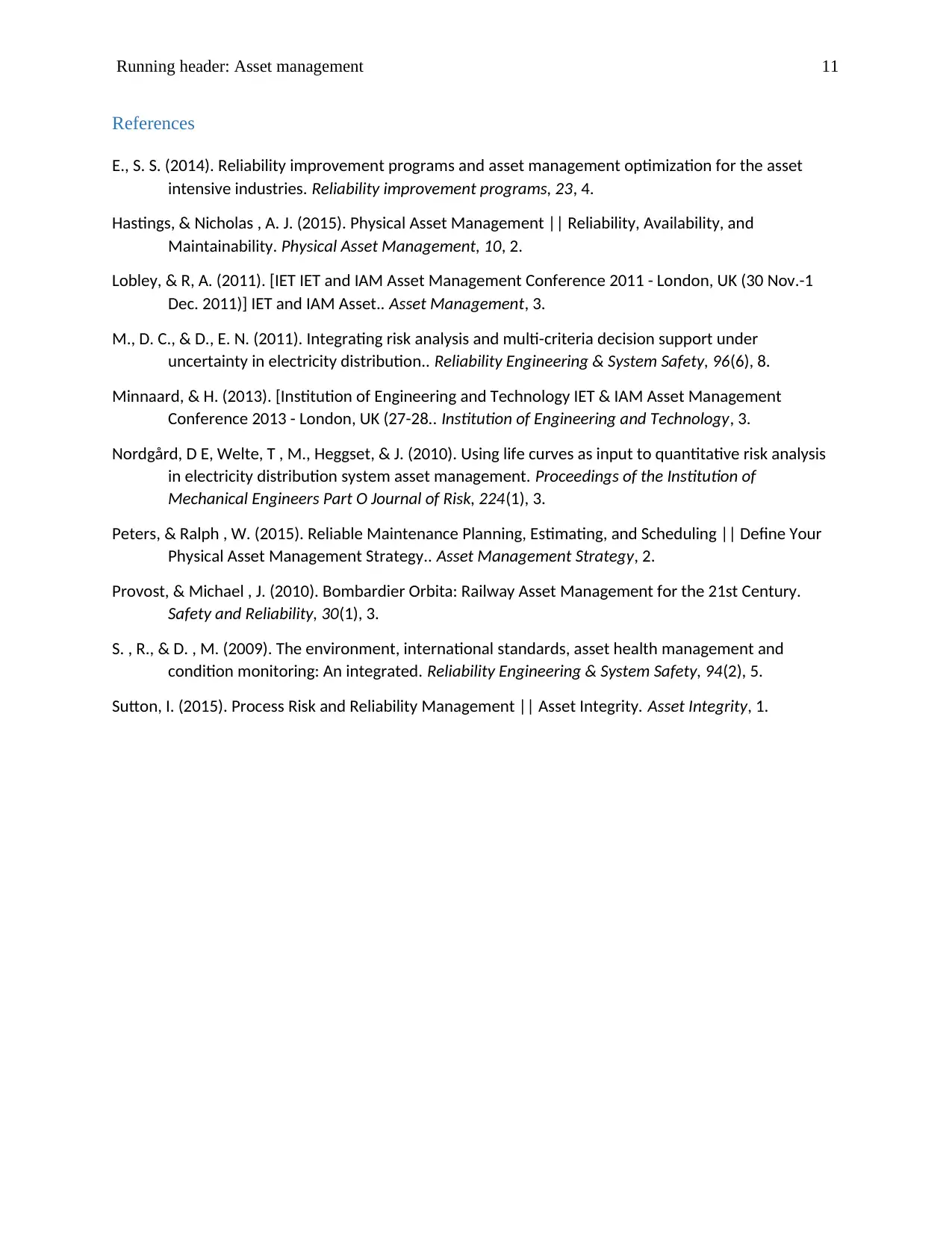
Running header: Asset management 11
References
E., S. S. (2014). Reliability improvement programs and asset management optimization for the asset
intensive industries. Reliability improvement programs, 23, 4.
Hastings, & Nicholas , A. J. (2015). Physical Asset Management || Reliability, Availability, and
Maintainability. Physical Asset Management, 10, 2.
Lobley, & R, A. (2011). [IET IET and IAM Asset Management Conference 2011 - London, UK (30 Nov.-1
Dec. 2011)] IET and IAM Asset.. Asset Management, 3.
M., D. C., & D., E. N. (2011). Integrating risk analysis and multi-criteria decision support under
uncertainty in electricity distribution.. Reliability Engineering & System Safety, 96(6), 8.
Minnaard, & H. (2013). [Institution of Engineering and Technology IET & IAM Asset Management
Conference 2013 - London, UK (27-28.. Institution of Engineering and Technology, 3.
Nordgård, D E, Welte, T , M., Heggset, & J. (2010). Using life curves as input to quantitative risk analysis
in electricity distribution system asset management. Proceedings of the Institution of
Mechanical Engineers Part O Journal of Risk, 224(1), 3.
Peters, & Ralph , W. (2015). Reliable Maintenance Planning, Estimating, and Scheduling || Define Your
Physical Asset Management Strategy.. Asset Management Strategy, 2.
Provost, & Michael , J. (2010). Bombardier Orbita: Railway Asset Management for the 21st Century.
Safety and Reliability, 30(1), 3.
S. , R., & D. , M. (2009). The environment, international standards, asset health management and
condition monitoring: An integrated. Reliability Engineering & System Safety, 94(2), 5.
Sutton, I. (2015). Process Risk and Reliability Management || Asset Integrity. Asset Integrity, 1.
References
E., S. S. (2014). Reliability improvement programs and asset management optimization for the asset
intensive industries. Reliability improvement programs, 23, 4.
Hastings, & Nicholas , A. J. (2015). Physical Asset Management || Reliability, Availability, and
Maintainability. Physical Asset Management, 10, 2.
Lobley, & R, A. (2011). [IET IET and IAM Asset Management Conference 2011 - London, UK (30 Nov.-1
Dec. 2011)] IET and IAM Asset.. Asset Management, 3.
M., D. C., & D., E. N. (2011). Integrating risk analysis and multi-criteria decision support under
uncertainty in electricity distribution.. Reliability Engineering & System Safety, 96(6), 8.
Minnaard, & H. (2013). [Institution of Engineering and Technology IET & IAM Asset Management
Conference 2013 - London, UK (27-28.. Institution of Engineering and Technology, 3.
Nordgård, D E, Welte, T , M., Heggset, & J. (2010). Using life curves as input to quantitative risk analysis
in electricity distribution system asset management. Proceedings of the Institution of
Mechanical Engineers Part O Journal of Risk, 224(1), 3.
Peters, & Ralph , W. (2015). Reliable Maintenance Planning, Estimating, and Scheduling || Define Your
Physical Asset Management Strategy.. Asset Management Strategy, 2.
Provost, & Michael , J. (2010). Bombardier Orbita: Railway Asset Management for the 21st Century.
Safety and Reliability, 30(1), 3.
S. , R., & D. , M. (2009). The environment, international standards, asset health management and
condition monitoring: An integrated. Reliability Engineering & System Safety, 94(2), 5.
Sutton, I. (2015). Process Risk and Reliability Management || Asset Integrity. Asset Integrity, 1.
1 out of 11
Related Documents

Your All-in-One AI-Powered Toolkit for Academic Success.
+13062052269
info@desklib.com
Available 24*7 on WhatsApp / Email
Unlock your academic potential
© 2024 | Zucol Services PVT LTD | All rights reserved.