Risk Assessment Report: Workplace Hazards and Control Measures
VerifiedAdded on 2023/06/07
|15
|4149
|221
Report
AI Summary
This report provides a comprehensive risk assessment of workplace hazards at Hopkins Welding Centre in Sydney, focusing on the dangers associated with compressed gas exposure and gas cylinder handling. The assessment procedure involved dividing the workplace, grouping similar work activities, and examining work practices. Identified hazards include the sudden explosion of gas cylinders, fire breakouts, release of poisonous gaseous fluids, and manual injuries due to improper cylinder handling and maintenance. The report recommends control measures such as annual cylinder inspections, frequent regulator checks, proper cylinder storage, and safe transportation methods to mitigate these risks. The study emphasizes the importance of adhering to safety protocols and regulatory measures to ensure worker safety and prevent accidents related to compressed gas exposure.
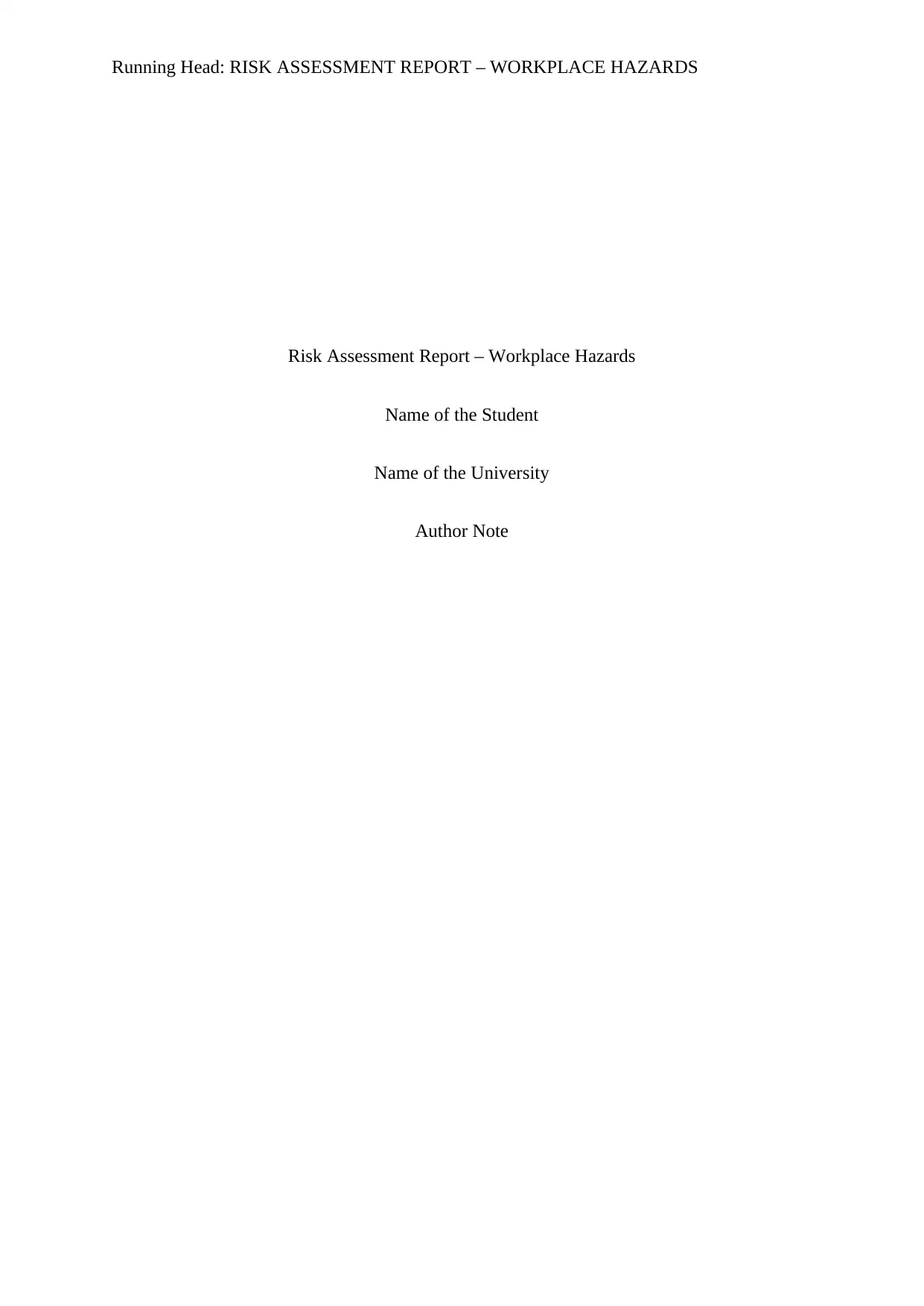
Running Head: RISK ASSESSMENT REPORT – WORKPLACE HAZARDS
Risk Assessment Report – Workplace Hazards
Name of the Student
Name of the University
Author Note
Risk Assessment Report – Workplace Hazards
Name of the Student
Name of the University
Author Note
Secure Best Marks with AI Grader
Need help grading? Try our AI Grader for instant feedback on your assignments.
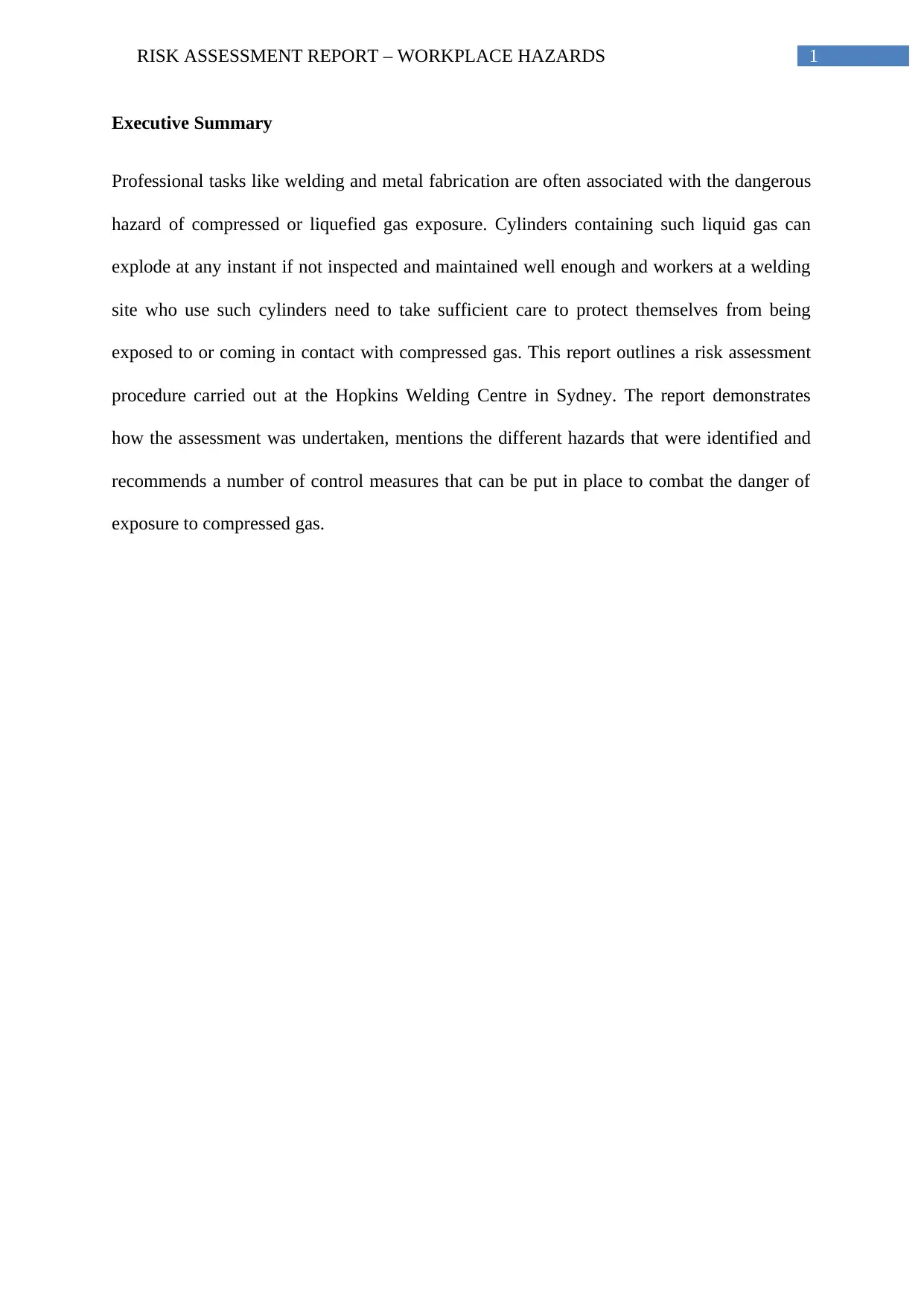
1RISK ASSESSMENT REPORT – WORKPLACE HAZARDS
Executive Summary
Professional tasks like welding and metal fabrication are often associated with the dangerous
hazard of compressed or liquefied gas exposure. Cylinders containing such liquid gas can
explode at any instant if not inspected and maintained well enough and workers at a welding
site who use such cylinders need to take sufficient care to protect themselves from being
exposed to or coming in contact with compressed gas. This report outlines a risk assessment
procedure carried out at the Hopkins Welding Centre in Sydney. The report demonstrates
how the assessment was undertaken, mentions the different hazards that were identified and
recommends a number of control measures that can be put in place to combat the danger of
exposure to compressed gas.
Executive Summary
Professional tasks like welding and metal fabrication are often associated with the dangerous
hazard of compressed or liquefied gas exposure. Cylinders containing such liquid gas can
explode at any instant if not inspected and maintained well enough and workers at a welding
site who use such cylinders need to take sufficient care to protect themselves from being
exposed to or coming in contact with compressed gas. This report outlines a risk assessment
procedure carried out at the Hopkins Welding Centre in Sydney. The report demonstrates
how the assessment was undertaken, mentions the different hazards that were identified and
recommends a number of control measures that can be put in place to combat the danger of
exposure to compressed gas.
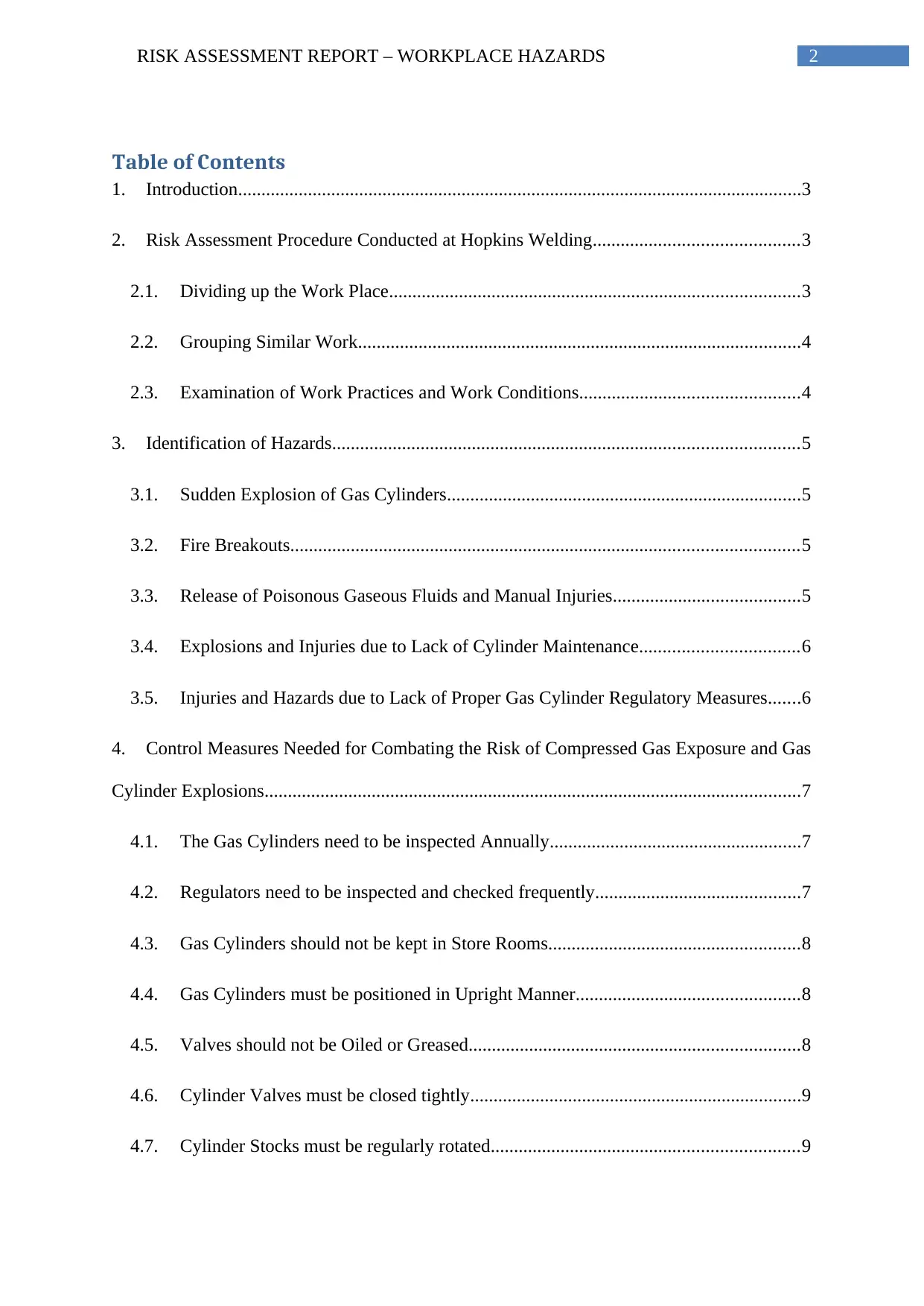
2RISK ASSESSMENT REPORT – WORKPLACE HAZARDS
Table of Contents
1. Introduction.........................................................................................................................3
2. Risk Assessment Procedure Conducted at Hopkins Welding............................................3
2.1. Dividing up the Work Place........................................................................................3
2.2. Grouping Similar Work...............................................................................................4
2.3. Examination of Work Practices and Work Conditions...............................................4
3. Identification of Hazards....................................................................................................5
3.1. Sudden Explosion of Gas Cylinders............................................................................5
3.2. Fire Breakouts.............................................................................................................5
3.3. Release of Poisonous Gaseous Fluids and Manual Injuries........................................5
3.4. Explosions and Injuries due to Lack of Cylinder Maintenance..................................6
3.5. Injuries and Hazards due to Lack of Proper Gas Cylinder Regulatory Measures.......6
4. Control Measures Needed for Combating the Risk of Compressed Gas Exposure and Gas
Cylinder Explosions...................................................................................................................7
4.1. The Gas Cylinders need to be inspected Annually......................................................7
4.2. Regulators need to be inspected and checked frequently............................................7
4.3. Gas Cylinders should not be kept in Store Rooms......................................................8
4.4. Gas Cylinders must be positioned in Upright Manner................................................8
4.5. Valves should not be Oiled or Greased.......................................................................8
4.6. Cylinder Valves must be closed tightly.......................................................................9
4.7. Cylinder Stocks must be regularly rotated..................................................................9
Table of Contents
1. Introduction.........................................................................................................................3
2. Risk Assessment Procedure Conducted at Hopkins Welding............................................3
2.1. Dividing up the Work Place........................................................................................3
2.2. Grouping Similar Work...............................................................................................4
2.3. Examination of Work Practices and Work Conditions...............................................4
3. Identification of Hazards....................................................................................................5
3.1. Sudden Explosion of Gas Cylinders............................................................................5
3.2. Fire Breakouts.............................................................................................................5
3.3. Release of Poisonous Gaseous Fluids and Manual Injuries........................................5
3.4. Explosions and Injuries due to Lack of Cylinder Maintenance..................................6
3.5. Injuries and Hazards due to Lack of Proper Gas Cylinder Regulatory Measures.......6
4. Control Measures Needed for Combating the Risk of Compressed Gas Exposure and Gas
Cylinder Explosions...................................................................................................................7
4.1. The Gas Cylinders need to be inspected Annually......................................................7
4.2. Regulators need to be inspected and checked frequently............................................7
4.3. Gas Cylinders should not be kept in Store Rooms......................................................8
4.4. Gas Cylinders must be positioned in Upright Manner................................................8
4.5. Valves should not be Oiled or Greased.......................................................................8
4.6. Cylinder Valves must be closed tightly.......................................................................9
4.7. Cylinder Stocks must be regularly rotated..................................................................9
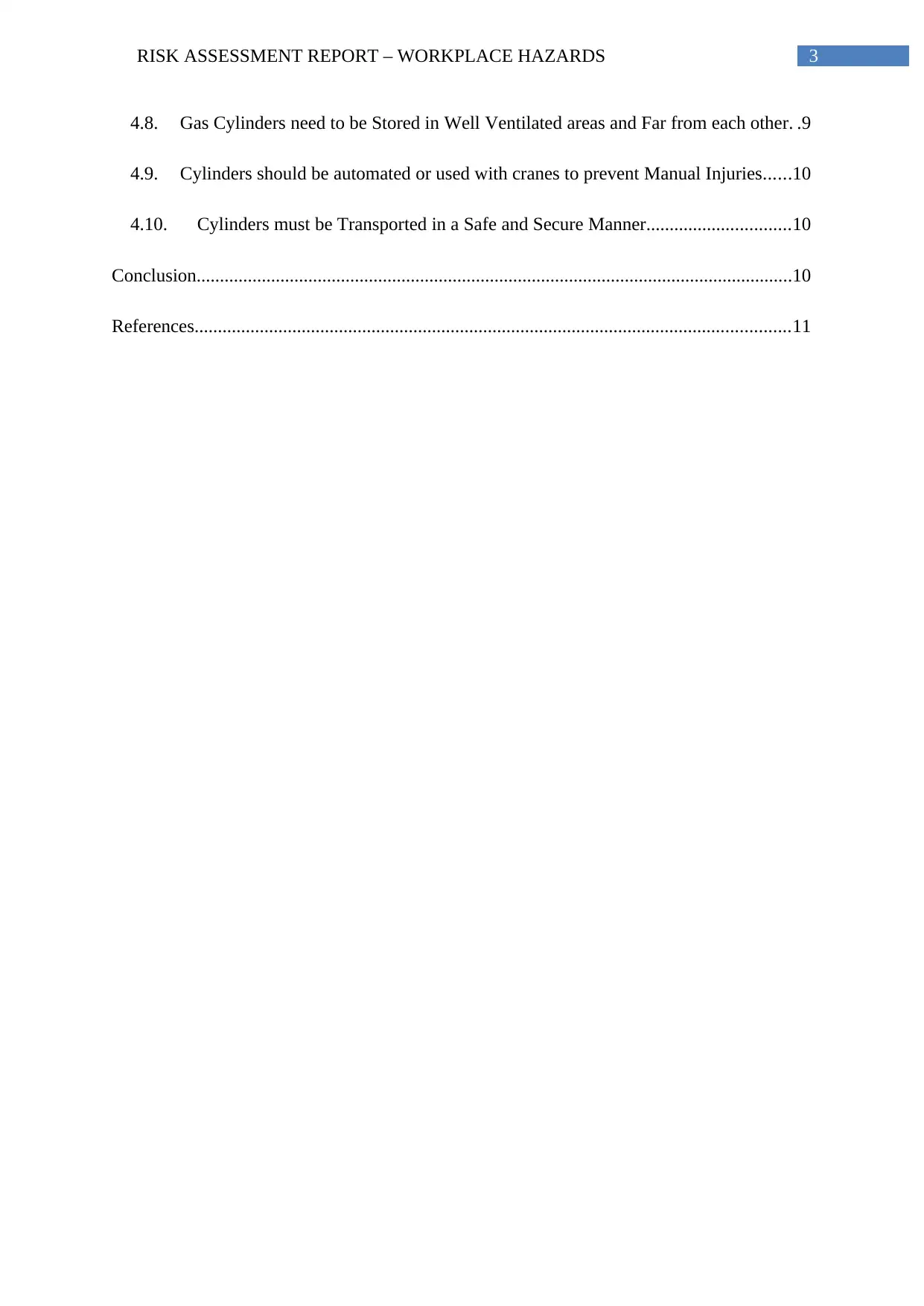
3RISK ASSESSMENT REPORT – WORKPLACE HAZARDS
4.8. Gas Cylinders need to be Stored in Well Ventilated areas and Far from each other. .9
4.9. Cylinders should be automated or used with cranes to prevent Manual Injuries......10
4.10. Cylinders must be Transported in a Safe and Secure Manner...............................10
Conclusion................................................................................................................................10
References................................................................................................................................11
4.8. Gas Cylinders need to be Stored in Well Ventilated areas and Far from each other. .9
4.9. Cylinders should be automated or used with cranes to prevent Manual Injuries......10
4.10. Cylinders must be Transported in a Safe and Secure Manner...............................10
Conclusion................................................................................................................................10
References................................................................................................................................11
Secure Best Marks with AI Grader
Need help grading? Try our AI Grader for instant feedback on your assignments.
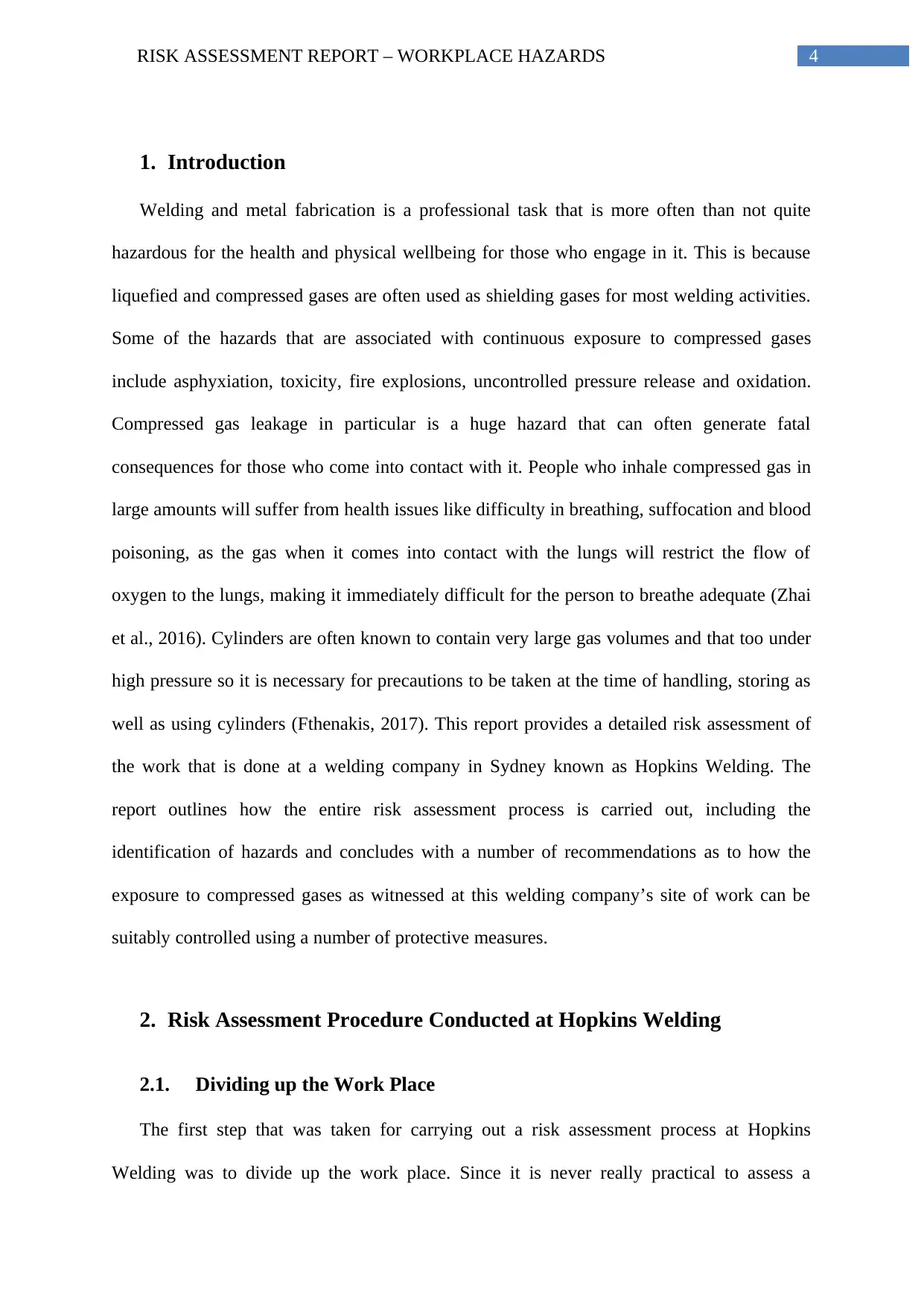
4RISK ASSESSMENT REPORT – WORKPLACE HAZARDS
1. Introduction
Welding and metal fabrication is a professional task that is more often than not quite
hazardous for the health and physical wellbeing for those who engage in it. This is because
liquefied and compressed gases are often used as shielding gases for most welding activities.
Some of the hazards that are associated with continuous exposure to compressed gases
include asphyxiation, toxicity, fire explosions, uncontrolled pressure release and oxidation.
Compressed gas leakage in particular is a huge hazard that can often generate fatal
consequences for those who come into contact with it. People who inhale compressed gas in
large amounts will suffer from health issues like difficulty in breathing, suffocation and blood
poisoning, as the gas when it comes into contact with the lungs will restrict the flow of
oxygen to the lungs, making it immediately difficult for the person to breathe adequate (Zhai
et al., 2016). Cylinders are often known to contain very large gas volumes and that too under
high pressure so it is necessary for precautions to be taken at the time of handling, storing as
well as using cylinders (Fthenakis, 2017). This report provides a detailed risk assessment of
the work that is done at a welding company in Sydney known as Hopkins Welding. The
report outlines how the entire risk assessment process is carried out, including the
identification of hazards and concludes with a number of recommendations as to how the
exposure to compressed gases as witnessed at this welding company’s site of work can be
suitably controlled using a number of protective measures.
2. Risk Assessment Procedure Conducted at Hopkins Welding
2.1. Dividing up the Work Place
The first step that was taken for carrying out a risk assessment process at Hopkins
Welding was to divide up the work place. Since it is never really practical to assess a
1. Introduction
Welding and metal fabrication is a professional task that is more often than not quite
hazardous for the health and physical wellbeing for those who engage in it. This is because
liquefied and compressed gases are often used as shielding gases for most welding activities.
Some of the hazards that are associated with continuous exposure to compressed gases
include asphyxiation, toxicity, fire explosions, uncontrolled pressure release and oxidation.
Compressed gas leakage in particular is a huge hazard that can often generate fatal
consequences for those who come into contact with it. People who inhale compressed gas in
large amounts will suffer from health issues like difficulty in breathing, suffocation and blood
poisoning, as the gas when it comes into contact with the lungs will restrict the flow of
oxygen to the lungs, making it immediately difficult for the person to breathe adequate (Zhai
et al., 2016). Cylinders are often known to contain very large gas volumes and that too under
high pressure so it is necessary for precautions to be taken at the time of handling, storing as
well as using cylinders (Fthenakis, 2017). This report provides a detailed risk assessment of
the work that is done at a welding company in Sydney known as Hopkins Welding. The
report outlines how the entire risk assessment process is carried out, including the
identification of hazards and concludes with a number of recommendations as to how the
exposure to compressed gases as witnessed at this welding company’s site of work can be
suitably controlled using a number of protective measures.
2. Risk Assessment Procedure Conducted at Hopkins Welding
2.1. Dividing up the Work Place
The first step that was taken for carrying out a risk assessment process at Hopkins
Welding was to divide up the work place. Since it is never really practical to assess a
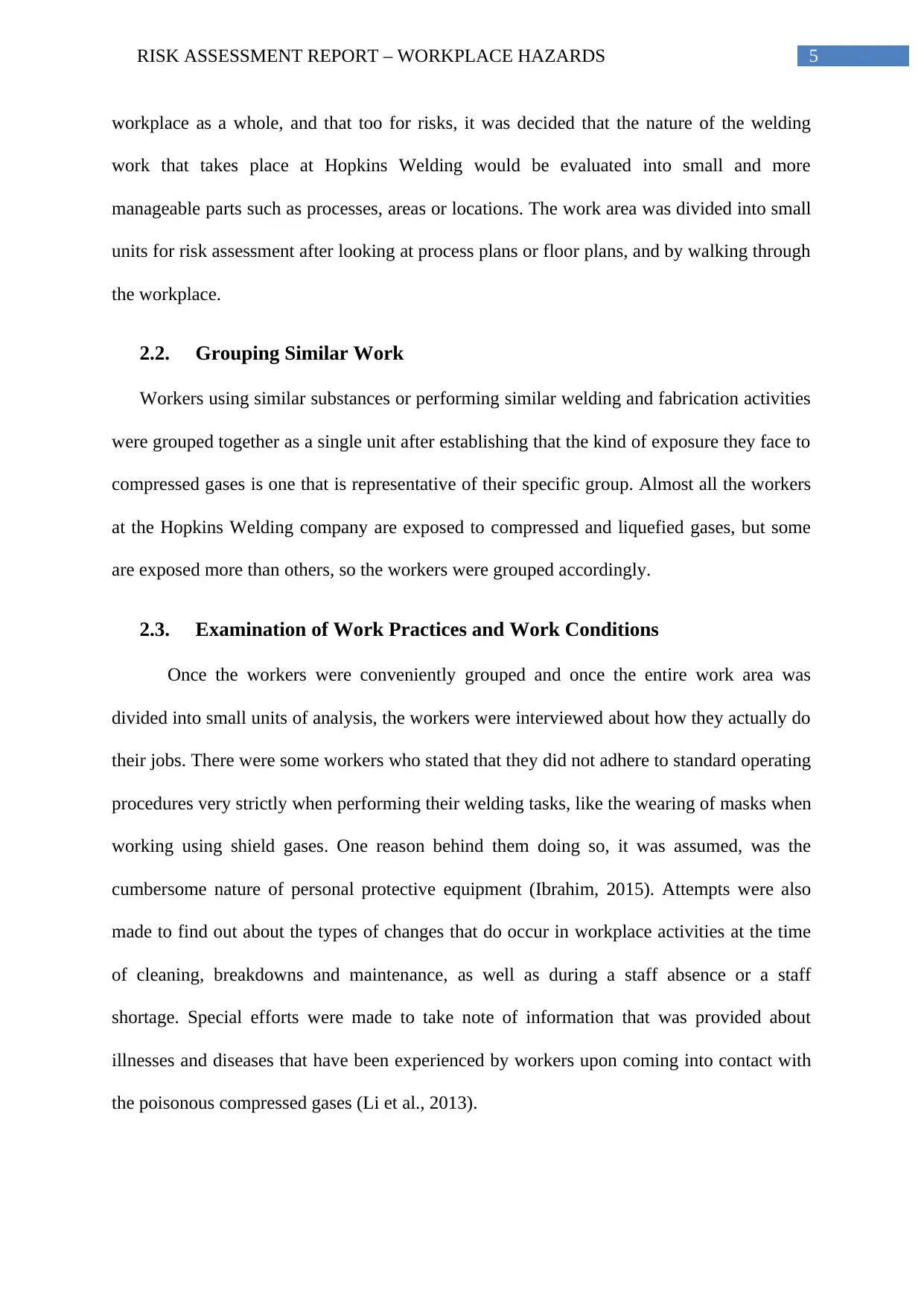
5RISK ASSESSMENT REPORT – WORKPLACE HAZARDS
workplace as a whole, and that too for risks, it was decided that the nature of the welding
work that takes place at Hopkins Welding would be evaluated into small and more
manageable parts such as processes, areas or locations. The work area was divided into small
units for risk assessment after looking at process plans or floor plans, and by walking through
the workplace.
2.2. Grouping Similar Work
Workers using similar substances or performing similar welding and fabrication activities
were grouped together as a single unit after establishing that the kind of exposure they face to
compressed gases is one that is representative of their specific group. Almost all the workers
at the Hopkins Welding company are exposed to compressed and liquefied gases, but some
are exposed more than others, so the workers were grouped accordingly.
2.3. Examination of Work Practices and Work Conditions
Once the workers were conveniently grouped and once the entire work area was
divided into small units of analysis, the workers were interviewed about how they actually do
their jobs. There were some workers who stated that they did not adhere to standard operating
procedures very strictly when performing their welding tasks, like the wearing of masks when
working using shield gases. One reason behind them doing so, it was assumed, was the
cumbersome nature of personal protective equipment (Ibrahim, 2015). Attempts were also
made to find out about the types of changes that do occur in workplace activities at the time
of cleaning, breakdowns and maintenance, as well as during a staff absence or a staff
shortage. Special efforts were made to take note of information that was provided about
illnesses and diseases that have been experienced by workers upon coming into contact with
the poisonous compressed gases (Li et al., 2013).
workplace as a whole, and that too for risks, it was decided that the nature of the welding
work that takes place at Hopkins Welding would be evaluated into small and more
manageable parts such as processes, areas or locations. The work area was divided into small
units for risk assessment after looking at process plans or floor plans, and by walking through
the workplace.
2.2. Grouping Similar Work
Workers using similar substances or performing similar welding and fabrication activities
were grouped together as a single unit after establishing that the kind of exposure they face to
compressed gases is one that is representative of their specific group. Almost all the workers
at the Hopkins Welding company are exposed to compressed and liquefied gases, but some
are exposed more than others, so the workers were grouped accordingly.
2.3. Examination of Work Practices and Work Conditions
Once the workers were conveniently grouped and once the entire work area was
divided into small units of analysis, the workers were interviewed about how they actually do
their jobs. There were some workers who stated that they did not adhere to standard operating
procedures very strictly when performing their welding tasks, like the wearing of masks when
working using shield gases. One reason behind them doing so, it was assumed, was the
cumbersome nature of personal protective equipment (Ibrahim, 2015). Attempts were also
made to find out about the types of changes that do occur in workplace activities at the time
of cleaning, breakdowns and maintenance, as well as during a staff absence or a staff
shortage. Special efforts were made to take note of information that was provided about
illnesses and diseases that have been experienced by workers upon coming into contact with
the poisonous compressed gases (Li et al., 2013).
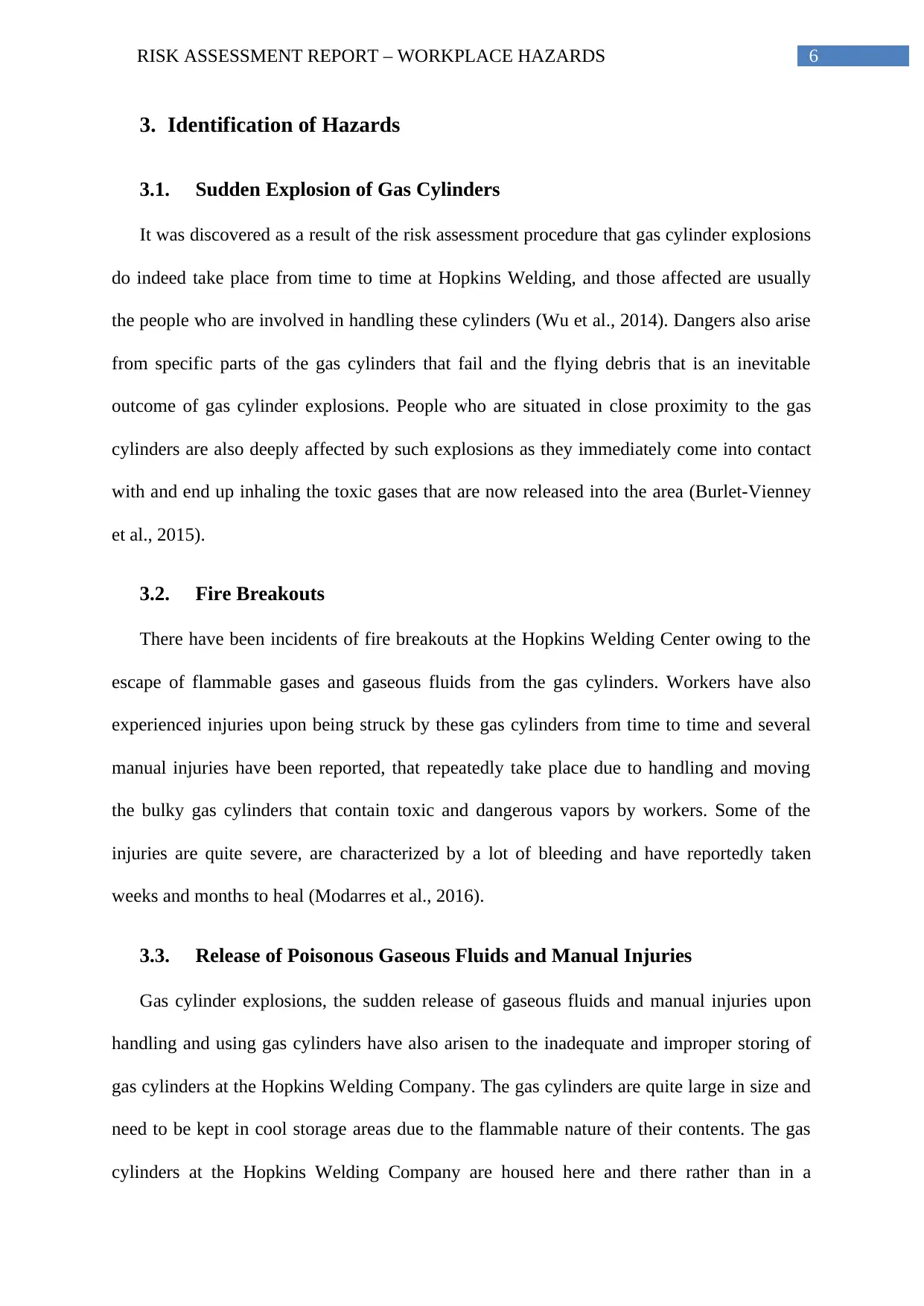
6RISK ASSESSMENT REPORT – WORKPLACE HAZARDS
3. Identification of Hazards
3.1. Sudden Explosion of Gas Cylinders
It was discovered as a result of the risk assessment procedure that gas cylinder explosions
do indeed take place from time to time at Hopkins Welding, and those affected are usually
the people who are involved in handling these cylinders (Wu et al., 2014). Dangers also arise
from specific parts of the gas cylinders that fail and the flying debris that is an inevitable
outcome of gas cylinder explosions. People who are situated in close proximity to the gas
cylinders are also deeply affected by such explosions as they immediately come into contact
with and end up inhaling the toxic gases that are now released into the area (Burlet-Vienney
et al., 2015).
3.2. Fire Breakouts
There have been incidents of fire breakouts at the Hopkins Welding Center owing to the
escape of flammable gases and gaseous fluids from the gas cylinders. Workers have also
experienced injuries upon being struck by these gas cylinders from time to time and several
manual injuries have been reported, that repeatedly take place due to handling and moving
the bulky gas cylinders that contain toxic and dangerous vapors by workers. Some of the
injuries are quite severe, are characterized by a lot of bleeding and have reportedly taken
weeks and months to heal (Modarres et al., 2016).
3.3. Release of Poisonous Gaseous Fluids and Manual Injuries
Gas cylinder explosions, the sudden release of gaseous fluids and manual injuries upon
handling and using gas cylinders have also arisen to the inadequate and improper storing of
gas cylinders at the Hopkins Welding Company. The gas cylinders are quite large in size and
need to be kept in cool storage areas due to the flammable nature of their contents. The gas
cylinders at the Hopkins Welding Company are housed here and there rather than in a
3. Identification of Hazards
3.1. Sudden Explosion of Gas Cylinders
It was discovered as a result of the risk assessment procedure that gas cylinder explosions
do indeed take place from time to time at Hopkins Welding, and those affected are usually
the people who are involved in handling these cylinders (Wu et al., 2014). Dangers also arise
from specific parts of the gas cylinders that fail and the flying debris that is an inevitable
outcome of gas cylinder explosions. People who are situated in close proximity to the gas
cylinders are also deeply affected by such explosions as they immediately come into contact
with and end up inhaling the toxic gases that are now released into the area (Burlet-Vienney
et al., 2015).
3.2. Fire Breakouts
There have been incidents of fire breakouts at the Hopkins Welding Center owing to the
escape of flammable gases and gaseous fluids from the gas cylinders. Workers have also
experienced injuries upon being struck by these gas cylinders from time to time and several
manual injuries have been reported, that repeatedly take place due to handling and moving
the bulky gas cylinders that contain toxic and dangerous vapors by workers. Some of the
injuries are quite severe, are characterized by a lot of bleeding and have reportedly taken
weeks and months to heal (Modarres et al., 2016).
3.3. Release of Poisonous Gaseous Fluids and Manual Injuries
Gas cylinder explosions, the sudden release of gaseous fluids and manual injuries upon
handling and using gas cylinders have also arisen to the inadequate and improper storing of
gas cylinders at the Hopkins Welding Company. The gas cylinders are quite large in size and
need to be kept in cool storage areas due to the flammable nature of their contents. The gas
cylinders at the Hopkins Welding Company are housed here and there rather than in a
Paraphrase This Document
Need a fresh take? Get an instant paraphrase of this document with our AI Paraphraser
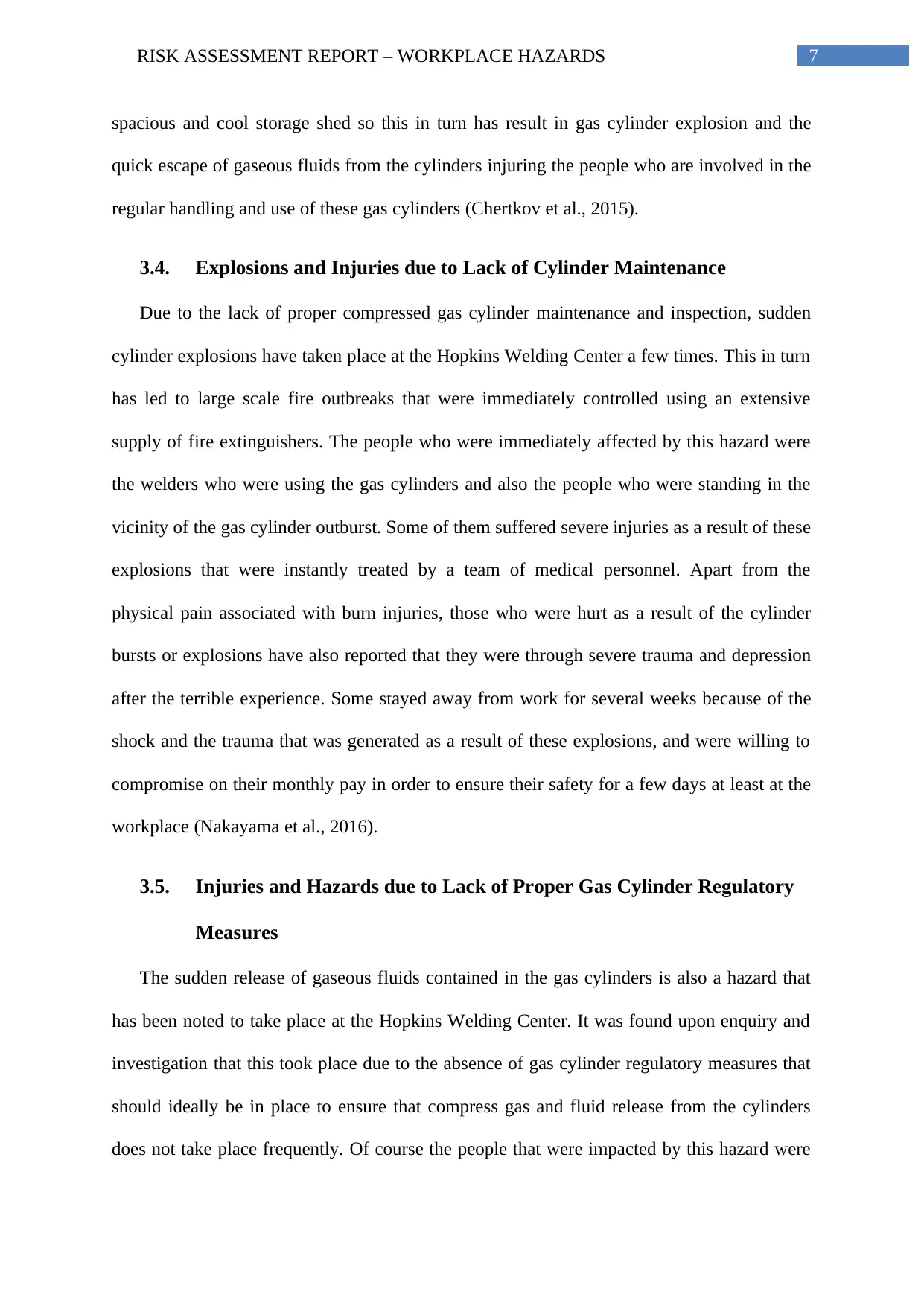
7RISK ASSESSMENT REPORT – WORKPLACE HAZARDS
spacious and cool storage shed so this in turn has result in gas cylinder explosion and the
quick escape of gaseous fluids from the cylinders injuring the people who are involved in the
regular handling and use of these gas cylinders (Chertkov et al., 2015).
3.4. Explosions and Injuries due to Lack of Cylinder Maintenance
Due to the lack of proper compressed gas cylinder maintenance and inspection, sudden
cylinder explosions have taken place at the Hopkins Welding Center a few times. This in turn
has led to large scale fire outbreaks that were immediately controlled using an extensive
supply of fire extinguishers. The people who were immediately affected by this hazard were
the welders who were using the gas cylinders and also the people who were standing in the
vicinity of the gas cylinder outburst. Some of them suffered severe injuries as a result of these
explosions that were instantly treated by a team of medical personnel. Apart from the
physical pain associated with burn injuries, those who were hurt as a result of the cylinder
bursts or explosions have also reported that they were through severe trauma and depression
after the terrible experience. Some stayed away from work for several weeks because of the
shock and the trauma that was generated as a result of these explosions, and were willing to
compromise on their monthly pay in order to ensure their safety for a few days at least at the
workplace (Nakayama et al., 2016).
3.5. Injuries and Hazards due to Lack of Proper Gas Cylinder Regulatory
Measures
The sudden release of gaseous fluids contained in the gas cylinders is also a hazard that
has been noted to take place at the Hopkins Welding Center. It was found upon enquiry and
investigation that this took place due to the absence of gas cylinder regulatory measures that
should ideally be in place to ensure that compress gas and fluid release from the cylinders
does not take place frequently. Of course the people that were impacted by this hazard were
spacious and cool storage shed so this in turn has result in gas cylinder explosion and the
quick escape of gaseous fluids from the cylinders injuring the people who are involved in the
regular handling and use of these gas cylinders (Chertkov et al., 2015).
3.4. Explosions and Injuries due to Lack of Cylinder Maintenance
Due to the lack of proper compressed gas cylinder maintenance and inspection, sudden
cylinder explosions have taken place at the Hopkins Welding Center a few times. This in turn
has led to large scale fire outbreaks that were immediately controlled using an extensive
supply of fire extinguishers. The people who were immediately affected by this hazard were
the welders who were using the gas cylinders and also the people who were standing in the
vicinity of the gas cylinder outburst. Some of them suffered severe injuries as a result of these
explosions that were instantly treated by a team of medical personnel. Apart from the
physical pain associated with burn injuries, those who were hurt as a result of the cylinder
bursts or explosions have also reported that they were through severe trauma and depression
after the terrible experience. Some stayed away from work for several weeks because of the
shock and the trauma that was generated as a result of these explosions, and were willing to
compromise on their monthly pay in order to ensure their safety for a few days at least at the
workplace (Nakayama et al., 2016).
3.5. Injuries and Hazards due to Lack of Proper Gas Cylinder Regulatory
Measures
The sudden release of gaseous fluids contained in the gas cylinders is also a hazard that
has been noted to take place at the Hopkins Welding Center. It was found upon enquiry and
investigation that this took place due to the absence of gas cylinder regulatory measures that
should ideally be in place to ensure that compress gas and fluid release from the cylinders
does not take place frequently. Of course the people that were impacted by this hazard were
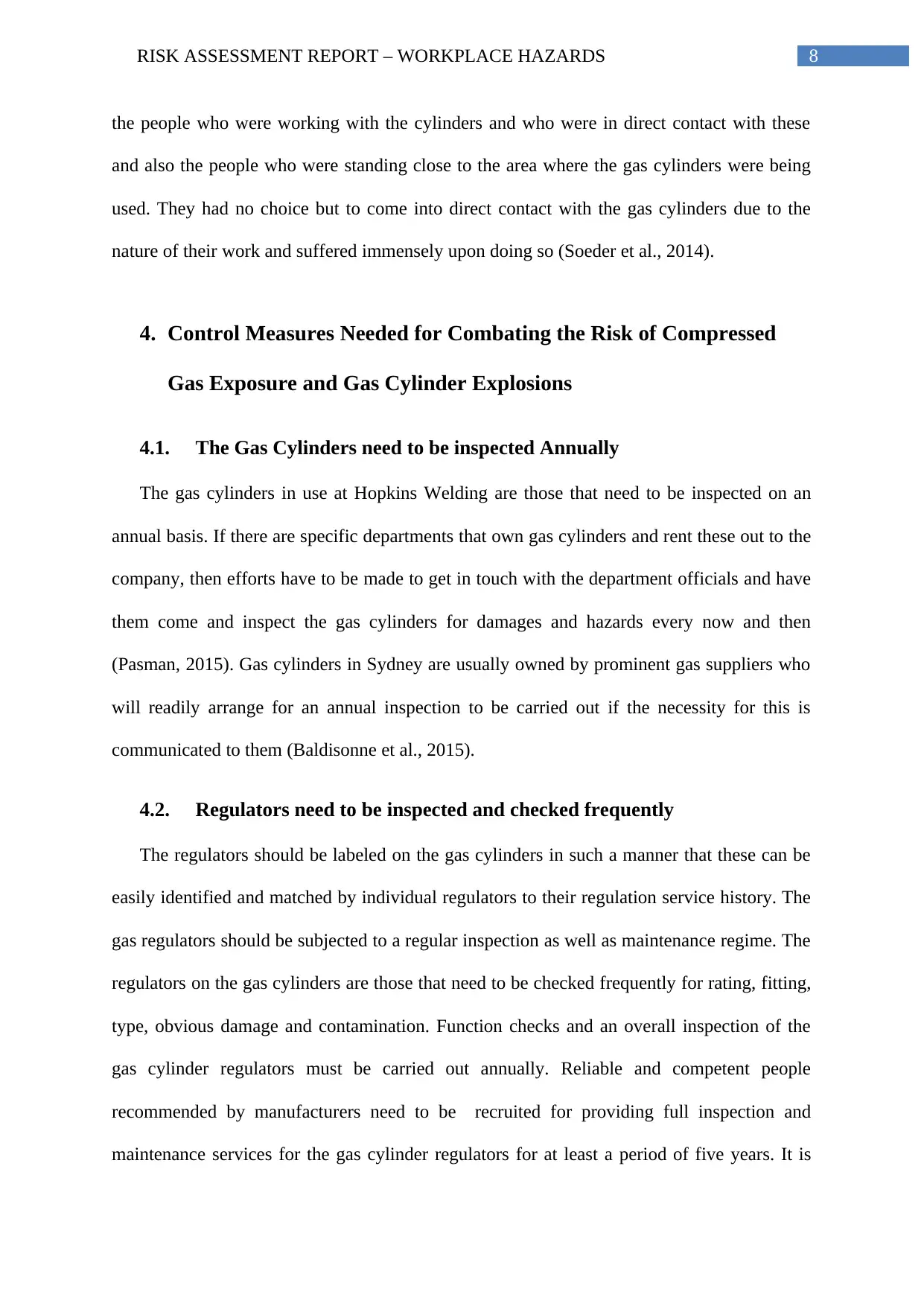
8RISK ASSESSMENT REPORT – WORKPLACE HAZARDS
the people who were working with the cylinders and who were in direct contact with these
and also the people who were standing close to the area where the gas cylinders were being
used. They had no choice but to come into direct contact with the gas cylinders due to the
nature of their work and suffered immensely upon doing so (Soeder et al., 2014).
4. Control Measures Needed for Combating the Risk of Compressed
Gas Exposure and Gas Cylinder Explosions
4.1. The Gas Cylinders need to be inspected Annually
The gas cylinders in use at Hopkins Welding are those that need to be inspected on an
annual basis. If there are specific departments that own gas cylinders and rent these out to the
company, then efforts have to be made to get in touch with the department officials and have
them come and inspect the gas cylinders for damages and hazards every now and then
(Pasman, 2015). Gas cylinders in Sydney are usually owned by prominent gas suppliers who
will readily arrange for an annual inspection to be carried out if the necessity for this is
communicated to them (Baldisonne et al., 2015).
4.2. Regulators need to be inspected and checked frequently
The regulators should be labeled on the gas cylinders in such a manner that these can be
easily identified and matched by individual regulators to their regulation service history. The
gas regulators should be subjected to a regular inspection as well as maintenance regime. The
regulators on the gas cylinders are those that need to be checked frequently for rating, fitting,
type, obvious damage and contamination. Function checks and an overall inspection of the
gas cylinder regulators must be carried out annually. Reliable and competent people
recommended by manufacturers need to be recruited for providing full inspection and
maintenance services for the gas cylinder regulators for at least a period of five years. It is
the people who were working with the cylinders and who were in direct contact with these
and also the people who were standing close to the area where the gas cylinders were being
used. They had no choice but to come into direct contact with the gas cylinders due to the
nature of their work and suffered immensely upon doing so (Soeder et al., 2014).
4. Control Measures Needed for Combating the Risk of Compressed
Gas Exposure and Gas Cylinder Explosions
4.1. The Gas Cylinders need to be inspected Annually
The gas cylinders in use at Hopkins Welding are those that need to be inspected on an
annual basis. If there are specific departments that own gas cylinders and rent these out to the
company, then efforts have to be made to get in touch with the department officials and have
them come and inspect the gas cylinders for damages and hazards every now and then
(Pasman, 2015). Gas cylinders in Sydney are usually owned by prominent gas suppliers who
will readily arrange for an annual inspection to be carried out if the necessity for this is
communicated to them (Baldisonne et al., 2015).
4.2. Regulators need to be inspected and checked frequently
The regulators should be labeled on the gas cylinders in such a manner that these can be
easily identified and matched by individual regulators to their regulation service history. The
gas regulators should be subjected to a regular inspection as well as maintenance regime. The
regulators on the gas cylinders are those that need to be checked frequently for rating, fitting,
type, obvious damage and contamination. Function checks and an overall inspection of the
gas cylinder regulators must be carried out annually. Reliable and competent people
recommended by manufacturers need to be recruited for providing full inspection and
maintenance services for the gas cylinder regulators for at least a period of five years. It is
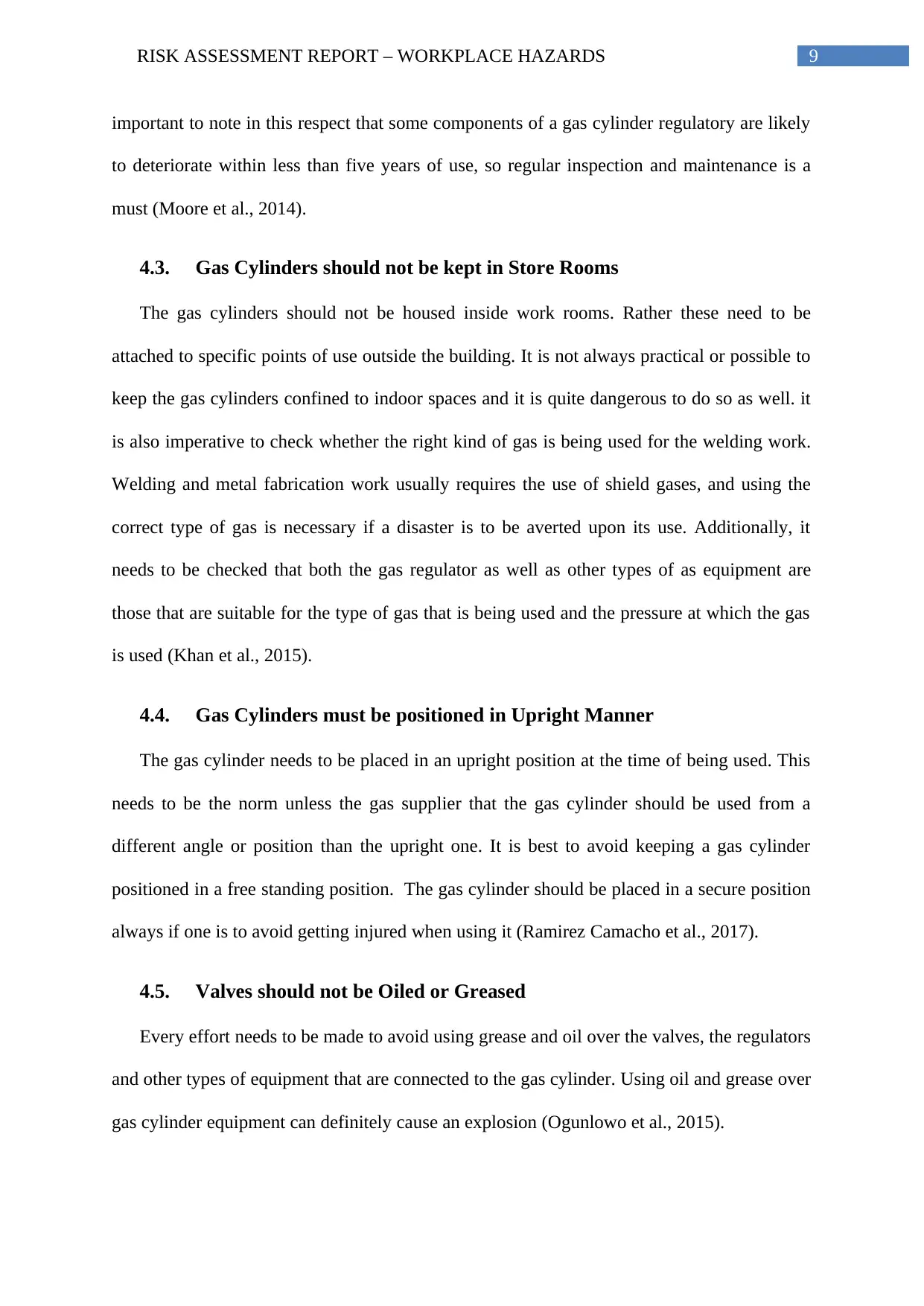
9RISK ASSESSMENT REPORT – WORKPLACE HAZARDS
important to note in this respect that some components of a gas cylinder regulatory are likely
to deteriorate within less than five years of use, so regular inspection and maintenance is a
must (Moore et al., 2014).
4.3. Gas Cylinders should not be kept in Store Rooms
The gas cylinders should not be housed inside work rooms. Rather these need to be
attached to specific points of use outside the building. It is not always practical or possible to
keep the gas cylinders confined to indoor spaces and it is quite dangerous to do so as well. it
is also imperative to check whether the right kind of gas is being used for the welding work.
Welding and metal fabrication work usually requires the use of shield gases, and using the
correct type of gas is necessary if a disaster is to be averted upon its use. Additionally, it
needs to be checked that both the gas regulator as well as other types of as equipment are
those that are suitable for the type of gas that is being used and the pressure at which the gas
is used (Khan et al., 2015).
4.4. Gas Cylinders must be positioned in Upright Manner
The gas cylinder needs to be placed in an upright position at the time of being used. This
needs to be the norm unless the gas supplier that the gas cylinder should be used from a
different angle or position than the upright one. It is best to avoid keeping a gas cylinder
positioned in a free standing position. The gas cylinder should be placed in a secure position
always if one is to avoid getting injured when using it (Ramirez Camacho et al., 2017).
4.5. Valves should not be Oiled or Greased
Every effort needs to be made to avoid using grease and oil over the valves, the regulators
and other types of equipment that are connected to the gas cylinder. Using oil and grease over
gas cylinder equipment can definitely cause an explosion (Ogunlowo et al., 2015).
important to note in this respect that some components of a gas cylinder regulatory are likely
to deteriorate within less than five years of use, so regular inspection and maintenance is a
must (Moore et al., 2014).
4.3. Gas Cylinders should not be kept in Store Rooms
The gas cylinders should not be housed inside work rooms. Rather these need to be
attached to specific points of use outside the building. It is not always practical or possible to
keep the gas cylinders confined to indoor spaces and it is quite dangerous to do so as well. it
is also imperative to check whether the right kind of gas is being used for the welding work.
Welding and metal fabrication work usually requires the use of shield gases, and using the
correct type of gas is necessary if a disaster is to be averted upon its use. Additionally, it
needs to be checked that both the gas regulator as well as other types of as equipment are
those that are suitable for the type of gas that is being used and the pressure at which the gas
is used (Khan et al., 2015).
4.4. Gas Cylinders must be positioned in Upright Manner
The gas cylinder needs to be placed in an upright position at the time of being used. This
needs to be the norm unless the gas supplier that the gas cylinder should be used from a
different angle or position than the upright one. It is best to avoid keeping a gas cylinder
positioned in a free standing position. The gas cylinder should be placed in a secure position
always if one is to avoid getting injured when using it (Ramirez Camacho et al., 2017).
4.5. Valves should not be Oiled or Greased
Every effort needs to be made to avoid using grease and oil over the valves, the regulators
and other types of equipment that are connected to the gas cylinder. Using oil and grease over
gas cylinder equipment can definitely cause an explosion (Ogunlowo et al., 2015).
Secure Best Marks with AI Grader
Need help grading? Try our AI Grader for instant feedback on your assignments.
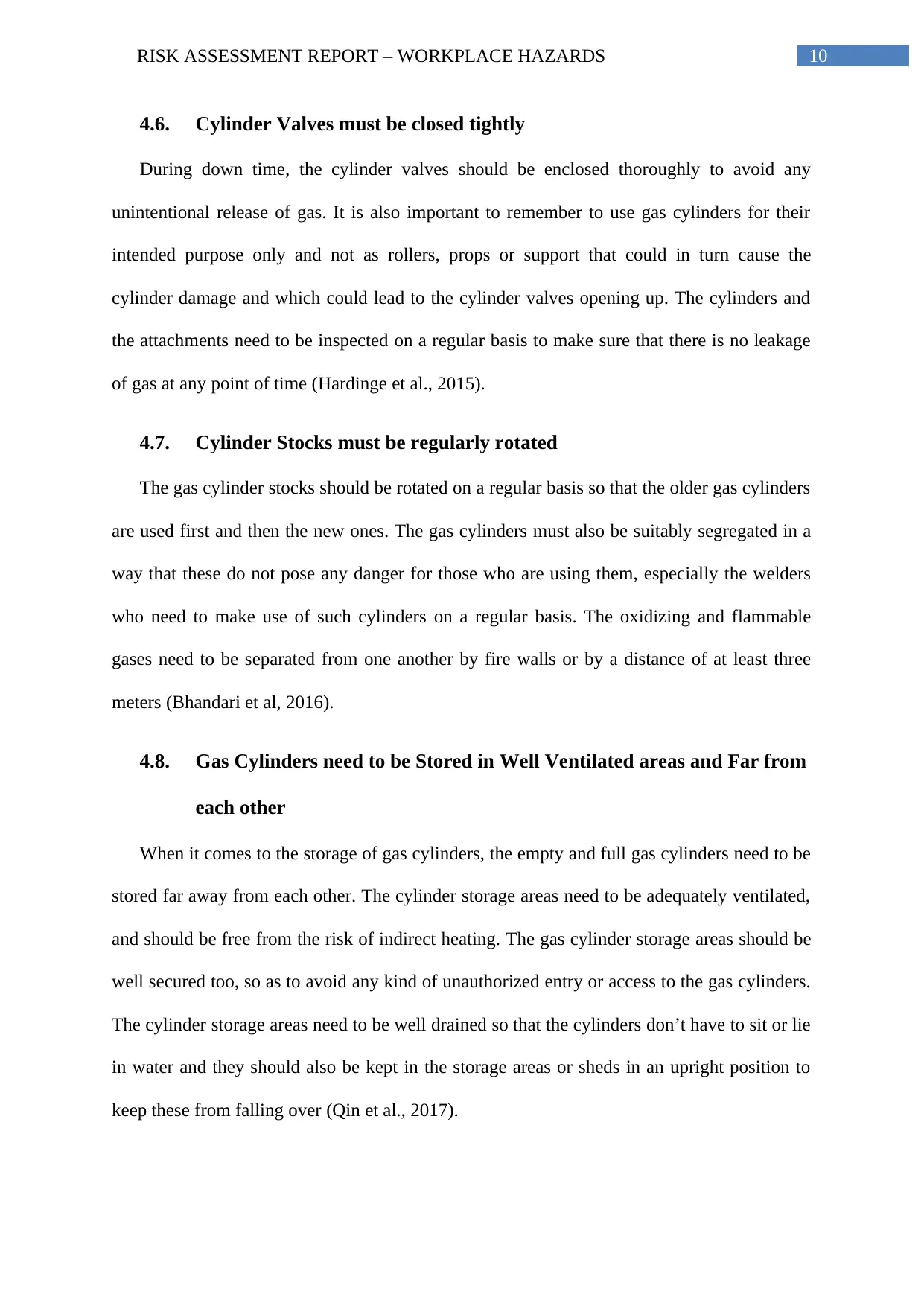
10RISK ASSESSMENT REPORT – WORKPLACE HAZARDS
4.6. Cylinder Valves must be closed tightly
During down time, the cylinder valves should be enclosed thoroughly to avoid any
unintentional release of gas. It is also important to remember to use gas cylinders for their
intended purpose only and not as rollers, props or support that could in turn cause the
cylinder damage and which could lead to the cylinder valves opening up. The cylinders and
the attachments need to be inspected on a regular basis to make sure that there is no leakage
of gas at any point of time (Hardinge et al., 2015).
4.7. Cylinder Stocks must be regularly rotated
The gas cylinder stocks should be rotated on a regular basis so that the older gas cylinders
are used first and then the new ones. The gas cylinders must also be suitably segregated in a
way that these do not pose any danger for those who are using them, especially the welders
who need to make use of such cylinders on a regular basis. The oxidizing and flammable
gases need to be separated from one another by fire walls or by a distance of at least three
meters (Bhandari et al, 2016).
4.8. Gas Cylinders need to be Stored in Well Ventilated areas and Far from
each other
When it comes to the storage of gas cylinders, the empty and full gas cylinders need to be
stored far away from each other. The cylinder storage areas need to be adequately ventilated,
and should be free from the risk of indirect heating. The gas cylinder storage areas should be
well secured too, so as to avoid any kind of unauthorized entry or access to the gas cylinders.
The cylinder storage areas need to be well drained so that the cylinders don’t have to sit or lie
in water and they should also be kept in the storage areas or sheds in an upright position to
keep these from falling over (Qin et al., 2017).
4.6. Cylinder Valves must be closed tightly
During down time, the cylinder valves should be enclosed thoroughly to avoid any
unintentional release of gas. It is also important to remember to use gas cylinders for their
intended purpose only and not as rollers, props or support that could in turn cause the
cylinder damage and which could lead to the cylinder valves opening up. The cylinders and
the attachments need to be inspected on a regular basis to make sure that there is no leakage
of gas at any point of time (Hardinge et al., 2015).
4.7. Cylinder Stocks must be regularly rotated
The gas cylinder stocks should be rotated on a regular basis so that the older gas cylinders
are used first and then the new ones. The gas cylinders must also be suitably segregated in a
way that these do not pose any danger for those who are using them, especially the welders
who need to make use of such cylinders on a regular basis. The oxidizing and flammable
gases need to be separated from one another by fire walls or by a distance of at least three
meters (Bhandari et al, 2016).
4.8. Gas Cylinders need to be Stored in Well Ventilated areas and Far from
each other
When it comes to the storage of gas cylinders, the empty and full gas cylinders need to be
stored far away from each other. The cylinder storage areas need to be adequately ventilated,
and should be free from the risk of indirect heating. The gas cylinder storage areas should be
well secured too, so as to avoid any kind of unauthorized entry or access to the gas cylinders.
The cylinder storage areas need to be well drained so that the cylinders don’t have to sit or lie
in water and they should also be kept in the storage areas or sheds in an upright position to
keep these from falling over (Qin et al., 2017).
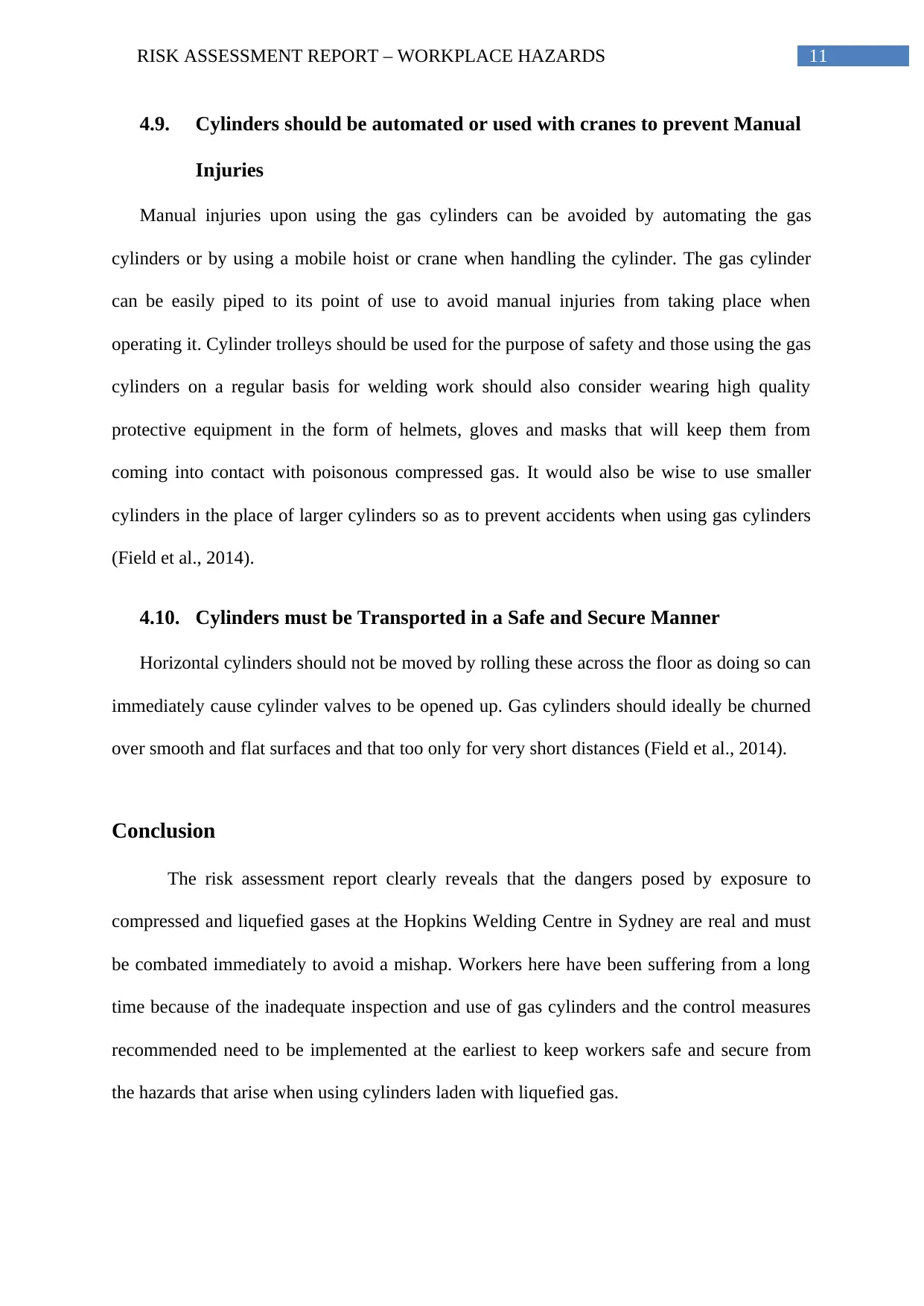
11RISK ASSESSMENT REPORT – WORKPLACE HAZARDS
4.9. Cylinders should be automated or used with cranes to prevent Manual
Injuries
Manual injuries upon using the gas cylinders can be avoided by automating the gas
cylinders or by using a mobile hoist or crane when handling the cylinder. The gas cylinder
can be easily piped to its point of use to avoid manual injuries from taking place when
operating it. Cylinder trolleys should be used for the purpose of safety and those using the gas
cylinders on a regular basis for welding work should also consider wearing high quality
protective equipment in the form of helmets, gloves and masks that will keep them from
coming into contact with poisonous compressed gas. It would also be wise to use smaller
cylinders in the place of larger cylinders so as to prevent accidents when using gas cylinders
(Field et al., 2014).
4.10. Cylinders must be Transported in a Safe and Secure Manner
Horizontal cylinders should not be moved by rolling these across the floor as doing so can
immediately cause cylinder valves to be opened up. Gas cylinders should ideally be churned
over smooth and flat surfaces and that too only for very short distances (Field et al., 2014).
Conclusion
The risk assessment report clearly reveals that the dangers posed by exposure to
compressed and liquefied gases at the Hopkins Welding Centre in Sydney are real and must
be combated immediately to avoid a mishap. Workers here have been suffering from a long
time because of the inadequate inspection and use of gas cylinders and the control measures
recommended need to be implemented at the earliest to keep workers safe and secure from
the hazards that arise when using cylinders laden with liquefied gas.
4.9. Cylinders should be automated or used with cranes to prevent Manual
Injuries
Manual injuries upon using the gas cylinders can be avoided by automating the gas
cylinders or by using a mobile hoist or crane when handling the cylinder. The gas cylinder
can be easily piped to its point of use to avoid manual injuries from taking place when
operating it. Cylinder trolleys should be used for the purpose of safety and those using the gas
cylinders on a regular basis for welding work should also consider wearing high quality
protective equipment in the form of helmets, gloves and masks that will keep them from
coming into contact with poisonous compressed gas. It would also be wise to use smaller
cylinders in the place of larger cylinders so as to prevent accidents when using gas cylinders
(Field et al., 2014).
4.10. Cylinders must be Transported in a Safe and Secure Manner
Horizontal cylinders should not be moved by rolling these across the floor as doing so can
immediately cause cylinder valves to be opened up. Gas cylinders should ideally be churned
over smooth and flat surfaces and that too only for very short distances (Field et al., 2014).
Conclusion
The risk assessment report clearly reveals that the dangers posed by exposure to
compressed and liquefied gases at the Hopkins Welding Centre in Sydney are real and must
be combated immediately to avoid a mishap. Workers here have been suffering from a long
time because of the inadequate inspection and use of gas cylinders and the control measures
recommended need to be implemented at the earliest to keep workers safe and secure from
the hazards that arise when using cylinders laden with liquefied gas.
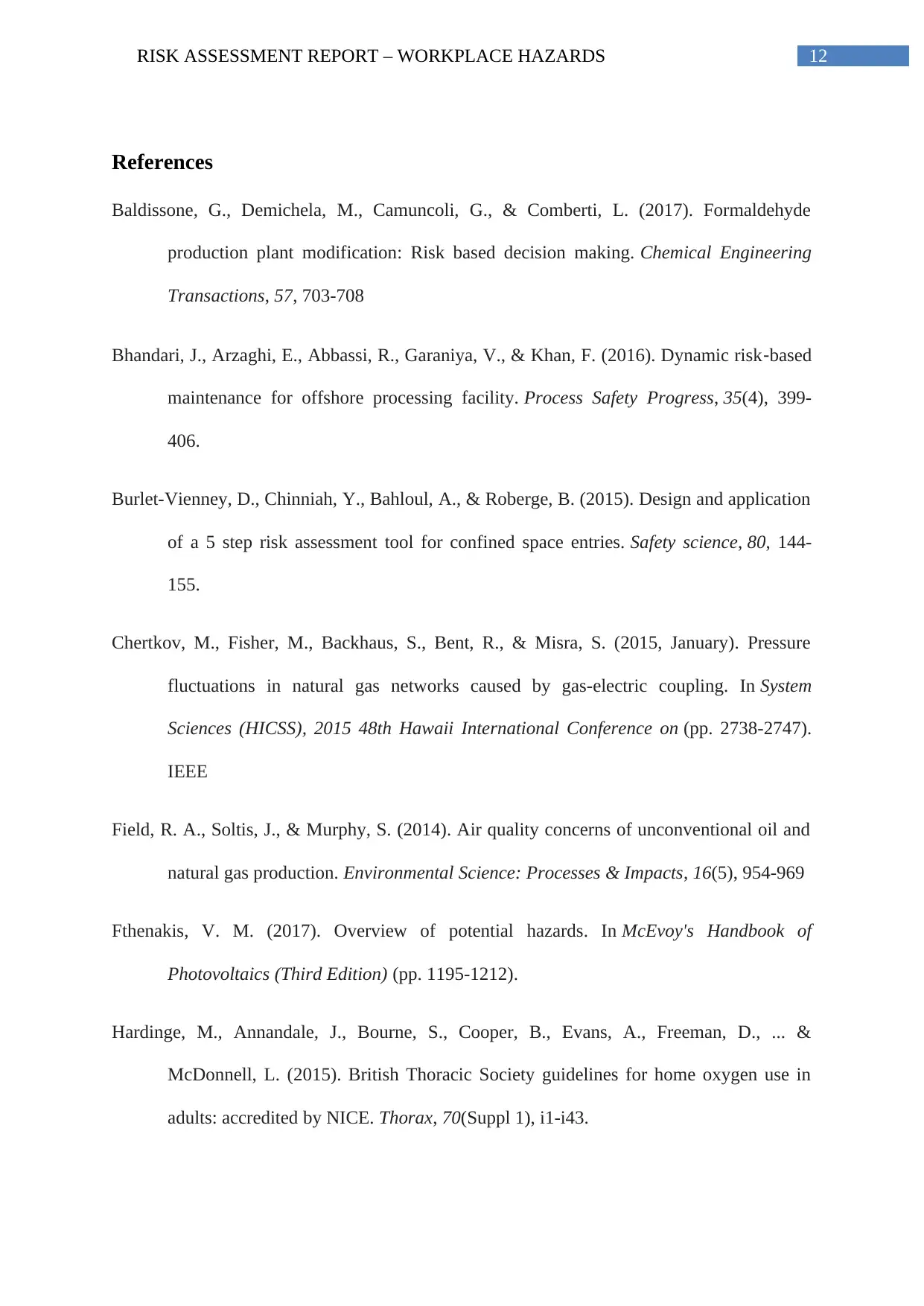
12RISK ASSESSMENT REPORT – WORKPLACE HAZARDS
References
Baldissone, G., Demichela, M., Camuncoli, G., & Comberti, L. (2017). Formaldehyde
production plant modification: Risk based decision making. Chemical Engineering
Transactions, 57, 703-708
Bhandari, J., Arzaghi, E., Abbassi, R., Garaniya, V., & Khan, F. (2016). Dynamic risk‐based
maintenance for offshore processing facility. Process Safety Progress, 35(4), 399-
406.
Burlet-Vienney, D., Chinniah, Y., Bahloul, A., & Roberge, B. (2015). Design and application
of a 5 step risk assessment tool for confined space entries. Safety science, 80, 144-
155.
Chertkov, M., Fisher, M., Backhaus, S., Bent, R., & Misra, S. (2015, January). Pressure
fluctuations in natural gas networks caused by gas-electric coupling. In System
Sciences (HICSS), 2015 48th Hawaii International Conference on (pp. 2738-2747).
IEEE
Field, R. A., Soltis, J., & Murphy, S. (2014). Air quality concerns of unconventional oil and
natural gas production. Environmental Science: Processes & Impacts, 16(5), 954-969
Fthenakis, V. M. (2017). Overview of potential hazards. In McEvoy's Handbook of
Photovoltaics (Third Edition) (pp. 1195-1212).
Hardinge, M., Annandale, J., Bourne, S., Cooper, B., Evans, A., Freeman, D., ... &
McDonnell, L. (2015). British Thoracic Society guidelines for home oxygen use in
adults: accredited by NICE. Thorax, 70(Suppl 1), i1-i43.
References
Baldissone, G., Demichela, M., Camuncoli, G., & Comberti, L. (2017). Formaldehyde
production plant modification: Risk based decision making. Chemical Engineering
Transactions, 57, 703-708
Bhandari, J., Arzaghi, E., Abbassi, R., Garaniya, V., & Khan, F. (2016). Dynamic risk‐based
maintenance for offshore processing facility. Process Safety Progress, 35(4), 399-
406.
Burlet-Vienney, D., Chinniah, Y., Bahloul, A., & Roberge, B. (2015). Design and application
of a 5 step risk assessment tool for confined space entries. Safety science, 80, 144-
155.
Chertkov, M., Fisher, M., Backhaus, S., Bent, R., & Misra, S. (2015, January). Pressure
fluctuations in natural gas networks caused by gas-electric coupling. In System
Sciences (HICSS), 2015 48th Hawaii International Conference on (pp. 2738-2747).
IEEE
Field, R. A., Soltis, J., & Murphy, S. (2014). Air quality concerns of unconventional oil and
natural gas production. Environmental Science: Processes & Impacts, 16(5), 954-969
Fthenakis, V. M. (2017). Overview of potential hazards. In McEvoy's Handbook of
Photovoltaics (Third Edition) (pp. 1195-1212).
Hardinge, M., Annandale, J., Bourne, S., Cooper, B., Evans, A., Freeman, D., ... &
McDonnell, L. (2015). British Thoracic Society guidelines for home oxygen use in
adults: accredited by NICE. Thorax, 70(Suppl 1), i1-i43.
Paraphrase This Document
Need a fresh take? Get an instant paraphrase of this document with our AI Paraphraser
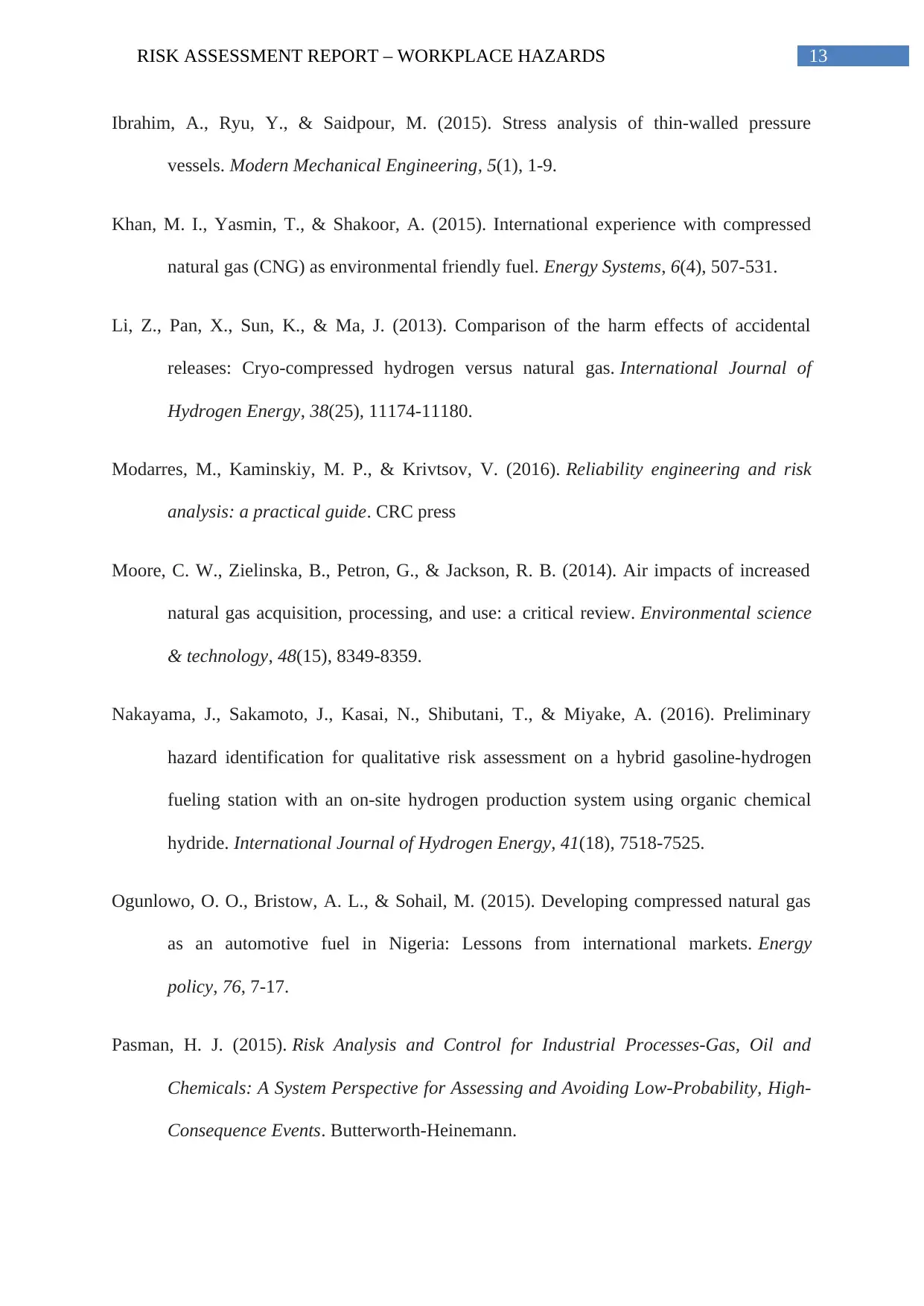
13RISK ASSESSMENT REPORT – WORKPLACE HAZARDS
Ibrahim, A., Ryu, Y., & Saidpour, M. (2015). Stress analysis of thin-walled pressure
vessels. Modern Mechanical Engineering, 5(1), 1-9.
Khan, M. I., Yasmin, T., & Shakoor, A. (2015). International experience with compressed
natural gas (CNG) as environmental friendly fuel. Energy Systems, 6(4), 507-531.
Li, Z., Pan, X., Sun, K., & Ma, J. (2013). Comparison of the harm effects of accidental
releases: Cryo-compressed hydrogen versus natural gas. International Journal of
Hydrogen Energy, 38(25), 11174-11180.
Modarres, M., Kaminskiy, M. P., & Krivtsov, V. (2016). Reliability engineering and risk
analysis: a practical guide. CRC press
Moore, C. W., Zielinska, B., Petron, G., & Jackson, R. B. (2014). Air impacts of increased
natural gas acquisition, processing, and use: a critical review. Environmental science
& technology, 48(15), 8349-8359.
Nakayama, J., Sakamoto, J., Kasai, N., Shibutani, T., & Miyake, A. (2016). Preliminary
hazard identification for qualitative risk assessment on a hybrid gasoline-hydrogen
fueling station with an on-site hydrogen production system using organic chemical
hydride. International Journal of Hydrogen Energy, 41(18), 7518-7525.
Ogunlowo, O. O., Bristow, A. L., & Sohail, M. (2015). Developing compressed natural gas
as an automotive fuel in Nigeria: Lessons from international markets. Energy
policy, 76, 7-17.
Pasman, H. J. (2015). Risk Analysis and Control for Industrial Processes-Gas, Oil and
Chemicals: A System Perspective for Assessing and Avoiding Low-Probability, High-
Consequence Events. Butterworth-Heinemann.
Ibrahim, A., Ryu, Y., & Saidpour, M. (2015). Stress analysis of thin-walled pressure
vessels. Modern Mechanical Engineering, 5(1), 1-9.
Khan, M. I., Yasmin, T., & Shakoor, A. (2015). International experience with compressed
natural gas (CNG) as environmental friendly fuel. Energy Systems, 6(4), 507-531.
Li, Z., Pan, X., Sun, K., & Ma, J. (2013). Comparison of the harm effects of accidental
releases: Cryo-compressed hydrogen versus natural gas. International Journal of
Hydrogen Energy, 38(25), 11174-11180.
Modarres, M., Kaminskiy, M. P., & Krivtsov, V. (2016). Reliability engineering and risk
analysis: a practical guide. CRC press
Moore, C. W., Zielinska, B., Petron, G., & Jackson, R. B. (2014). Air impacts of increased
natural gas acquisition, processing, and use: a critical review. Environmental science
& technology, 48(15), 8349-8359.
Nakayama, J., Sakamoto, J., Kasai, N., Shibutani, T., & Miyake, A. (2016). Preliminary
hazard identification for qualitative risk assessment on a hybrid gasoline-hydrogen
fueling station with an on-site hydrogen production system using organic chemical
hydride. International Journal of Hydrogen Energy, 41(18), 7518-7525.
Ogunlowo, O. O., Bristow, A. L., & Sohail, M. (2015). Developing compressed natural gas
as an automotive fuel in Nigeria: Lessons from international markets. Energy
policy, 76, 7-17.
Pasman, H. J. (2015). Risk Analysis and Control for Industrial Processes-Gas, Oil and
Chemicals: A System Perspective for Assessing and Avoiding Low-Probability, High-
Consequence Events. Butterworth-Heinemann.
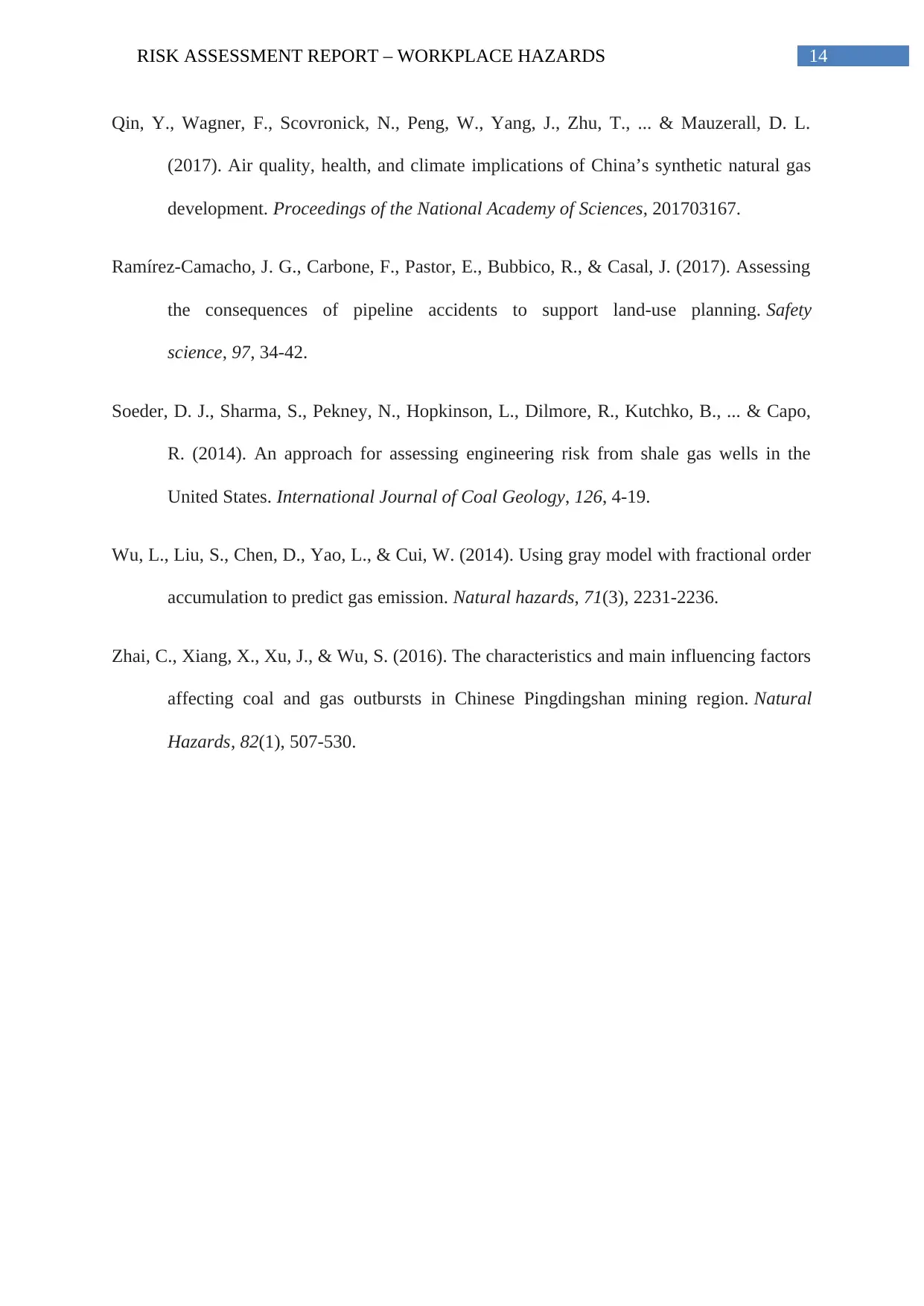
14RISK ASSESSMENT REPORT – WORKPLACE HAZARDS
Qin, Y., Wagner, F., Scovronick, N., Peng, W., Yang, J., Zhu, T., ... & Mauzerall, D. L.
(2017). Air quality, health, and climate implications of China’s synthetic natural gas
development. Proceedings of the National Academy of Sciences, 201703167.
Ramírez-Camacho, J. G., Carbone, F., Pastor, E., Bubbico, R., & Casal, J. (2017). Assessing
the consequences of pipeline accidents to support land-use planning. Safety
science, 97, 34-42.
Soeder, D. J., Sharma, S., Pekney, N., Hopkinson, L., Dilmore, R., Kutchko, B., ... & Capo,
R. (2014). An approach for assessing engineering risk from shale gas wells in the
United States. International Journal of Coal Geology, 126, 4-19.
Wu, L., Liu, S., Chen, D., Yao, L., & Cui, W. (2014). Using gray model with fractional order
accumulation to predict gas emission. Natural hazards, 71(3), 2231-2236.
Zhai, C., Xiang, X., Xu, J., & Wu, S. (2016). The characteristics and main influencing factors
affecting coal and gas outbursts in Chinese Pingdingshan mining region. Natural
Hazards, 82(1), 507-530.
Qin, Y., Wagner, F., Scovronick, N., Peng, W., Yang, J., Zhu, T., ... & Mauzerall, D. L.
(2017). Air quality, health, and climate implications of China’s synthetic natural gas
development. Proceedings of the National Academy of Sciences, 201703167.
Ramírez-Camacho, J. G., Carbone, F., Pastor, E., Bubbico, R., & Casal, J. (2017). Assessing
the consequences of pipeline accidents to support land-use planning. Safety
science, 97, 34-42.
Soeder, D. J., Sharma, S., Pekney, N., Hopkinson, L., Dilmore, R., Kutchko, B., ... & Capo,
R. (2014). An approach for assessing engineering risk from shale gas wells in the
United States. International Journal of Coal Geology, 126, 4-19.
Wu, L., Liu, S., Chen, D., Yao, L., & Cui, W. (2014). Using gray model with fractional order
accumulation to predict gas emission. Natural hazards, 71(3), 2231-2236.
Zhai, C., Xiang, X., Xu, J., & Wu, S. (2016). The characteristics and main influencing factors
affecting coal and gas outbursts in Chinese Pingdingshan mining region. Natural
Hazards, 82(1), 507-530.
1 out of 15
Related Documents

Your All-in-One AI-Powered Toolkit for Academic Success.
+13062052269
info@desklib.com
Available 24*7 on WhatsApp / Email
Unlock your academic potential
© 2024 | Zucol Services PVT LTD | All rights reserved.