Operations and Project Management Analysis: Rolls Royce Case Study
VerifiedAdded on 2020/12/29
|14
|4003
|88
Report
AI Summary
This report examines operations and project management principles, focusing on a case study of Rolls Royce. It explores the implementation of operations management principles, including inventory management, operations planning, manufacturing management, and distribution and logistics. The report delves into Six Sigma methodology and Lean principles, highlighting their roles in improving efficiency and reducing waste. Furthermore, it analyzes theories, concepts, and models to justify strategies for a continuous improvement plan, such as flexible specialization, mass customization, and agile manufacturing. The report then prepares a detailed continuous improvement plan using tools like Kaizen and Total Quality Management, followed by an evaluation of the plan's effectiveness. The second part of the report focuses on project management, outlining the stages of the project lifecycle (PLC) and the necessary supporting documentation, as well as a critical analysis of the project using relevant theories and concepts. The report concludes by emphasizing the importance of operations and project management for business success, particularly in a company like Rolls Royce.
Contribute Materials
Your contribution can guide someone’s learning journey. Share your
documents today.
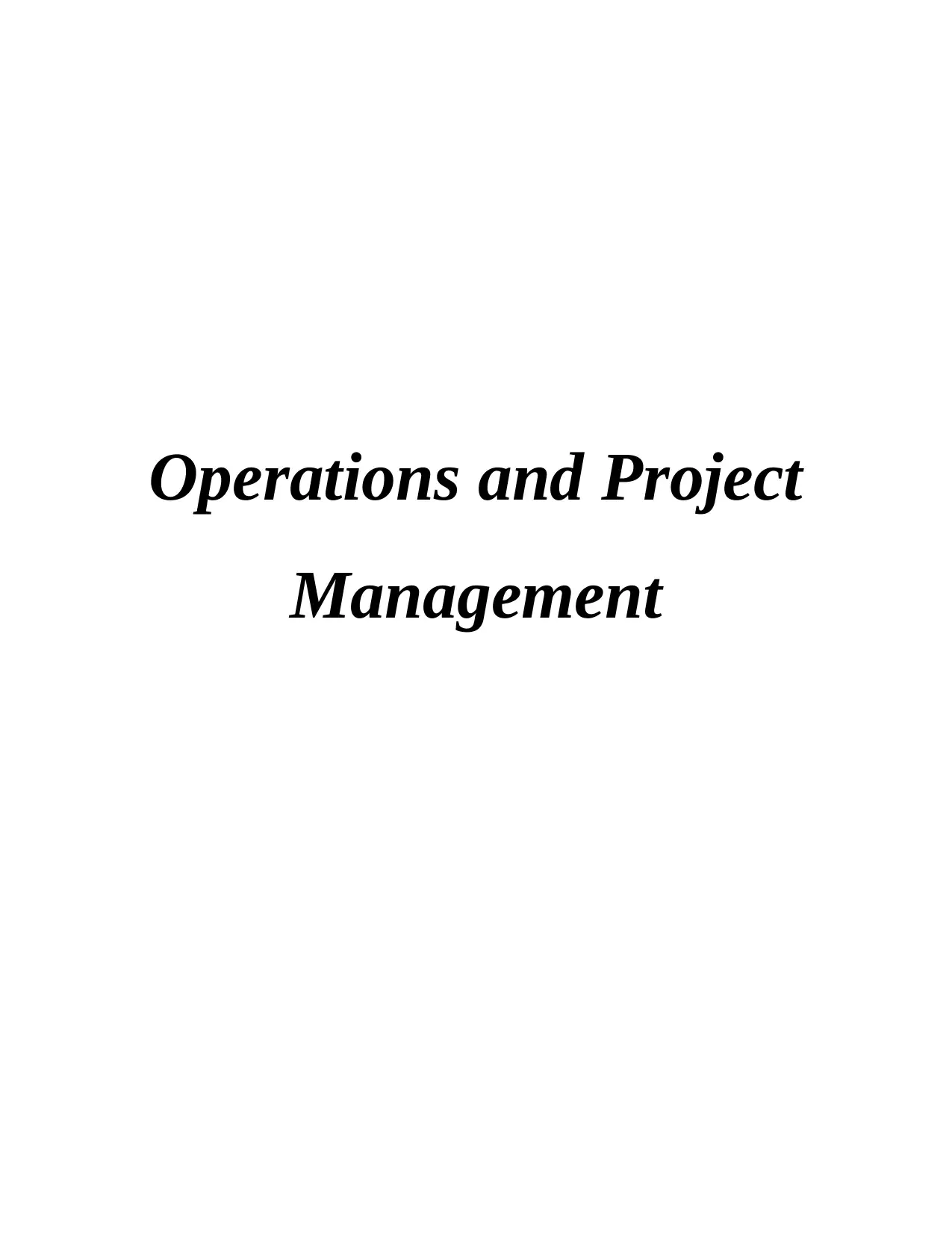
Operations and Project
Management
Management
Secure Best Marks with AI Grader
Need help grading? Try our AI Grader for instant feedback on your assignments.
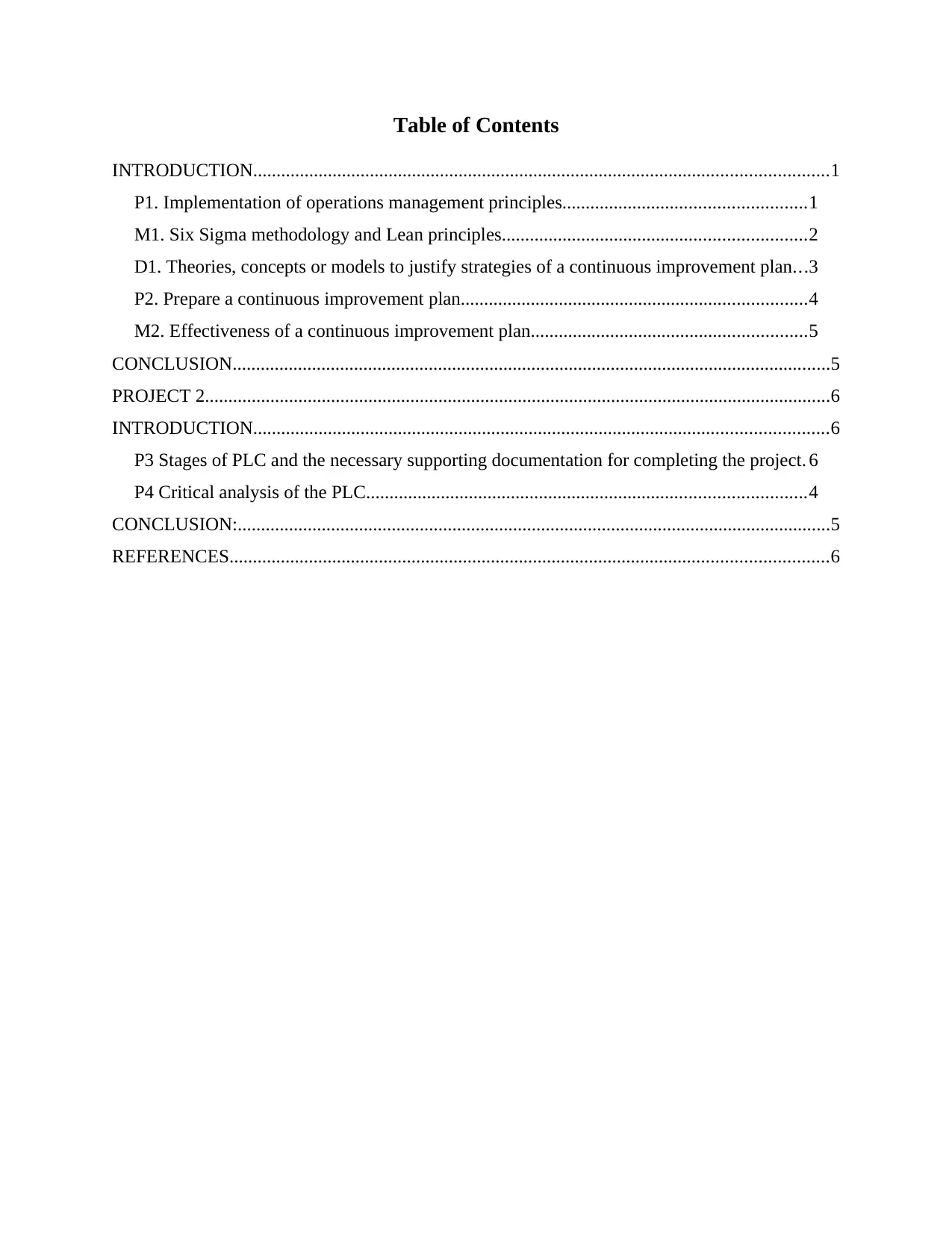
Table of Contents
INTRODUCTION...........................................................................................................................1
P1. Implementation of operations management principles....................................................1
M1. Six Sigma methodology and Lean principles.................................................................2
D1. Theories, concepts or models to justify strategies of a continuous improvement plan...3
P2. Prepare a continuous improvement plan..........................................................................4
M2. Effectiveness of a continuous improvement plan...........................................................5
CONCLUSION................................................................................................................................5
PROJECT 2......................................................................................................................................6
INTRODUCTION...........................................................................................................................6
P3 Stages of PLC and the necessary supporting documentation for completing the project. 6
P4 Critical analysis of the PLC..............................................................................................4
CONCLUSION:...............................................................................................................................5
REFERENCES................................................................................................................................6
INTRODUCTION...........................................................................................................................1
P1. Implementation of operations management principles....................................................1
M1. Six Sigma methodology and Lean principles.................................................................2
D1. Theories, concepts or models to justify strategies of a continuous improvement plan...3
P2. Prepare a continuous improvement plan..........................................................................4
M2. Effectiveness of a continuous improvement plan...........................................................5
CONCLUSION................................................................................................................................5
PROJECT 2......................................................................................................................................6
INTRODUCTION...........................................................................................................................6
P3 Stages of PLC and the necessary supporting documentation for completing the project. 6
P4 Critical analysis of the PLC..............................................................................................4
CONCLUSION:...............................................................................................................................5
REFERENCES................................................................................................................................6
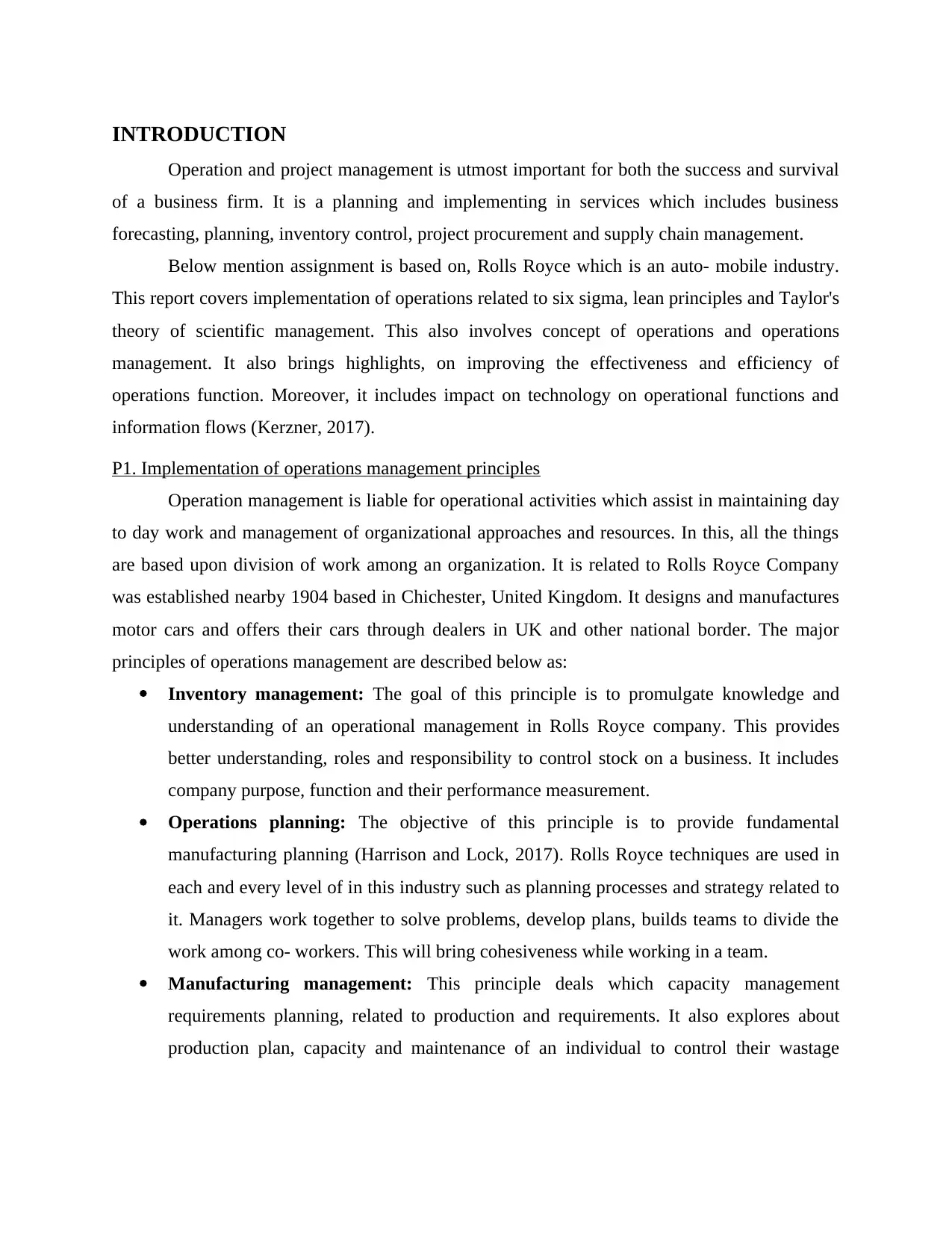
INTRODUCTION
Operation and project management is utmost important for both the success and survival
of a business firm. It is a planning and implementing in services which includes business
forecasting, planning, inventory control, project procurement and supply chain management.
Below mention assignment is based on, Rolls Royce which is an auto- mobile industry.
This report covers implementation of operations related to six sigma, lean principles and Taylor's
theory of scientific management. This also involves concept of operations and operations
management. It also brings highlights, on improving the effectiveness and efficiency of
operations function. Moreover, it includes impact on technology on operational functions and
information flows (Kerzner, 2017).
P1. Implementation of operations management principles
Operation management is liable for operational activities which assist in maintaining day
to day work and management of organizational approaches and resources. In this, all the things
are based upon division of work among an organization. It is related to Rolls Royce Company
was established nearby 1904 based in Chichester, United Kingdom. It designs and manufactures
motor cars and offers their cars through dealers in UK and other national border. The major
principles of operations management are described below as:
Inventory management: The goal of this principle is to promulgate knowledge and
understanding of an operational management in Rolls Royce company. This provides
better understanding, roles and responsibility to control stock on a business. It includes
company purpose, function and their performance measurement.
Operations planning: The objective of this principle is to provide fundamental
manufacturing planning (Harrison and Lock, 2017). Rolls Royce techniques are used in
each and every level of in this industry such as planning processes and strategy related to
it. Managers work together to solve problems, develop plans, builds teams to divide the
work among co- workers. This will bring cohesiveness while working in a team.
Manufacturing management: This principle deals which capacity management
requirements planning, related to production and requirements. It also explores about
production plan, capacity and maintenance of an individual to control their wastage
Operation and project management is utmost important for both the success and survival
of a business firm. It is a planning and implementing in services which includes business
forecasting, planning, inventory control, project procurement and supply chain management.
Below mention assignment is based on, Rolls Royce which is an auto- mobile industry.
This report covers implementation of operations related to six sigma, lean principles and Taylor's
theory of scientific management. This also involves concept of operations and operations
management. It also brings highlights, on improving the effectiveness and efficiency of
operations function. Moreover, it includes impact on technology on operational functions and
information flows (Kerzner, 2017).
P1. Implementation of operations management principles
Operation management is liable for operational activities which assist in maintaining day
to day work and management of organizational approaches and resources. In this, all the things
are based upon division of work among an organization. It is related to Rolls Royce Company
was established nearby 1904 based in Chichester, United Kingdom. It designs and manufactures
motor cars and offers their cars through dealers in UK and other national border. The major
principles of operations management are described below as:
Inventory management: The goal of this principle is to promulgate knowledge and
understanding of an operational management in Rolls Royce company. This provides
better understanding, roles and responsibility to control stock on a business. It includes
company purpose, function and their performance measurement.
Operations planning: The objective of this principle is to provide fundamental
manufacturing planning (Harrison and Lock, 2017). Rolls Royce techniques are used in
each and every level of in this industry such as planning processes and strategy related to
it. Managers work together to solve problems, develop plans, builds teams to divide the
work among co- workers. This will bring cohesiveness while working in a team.
Manufacturing management: This principle deals which capacity management
requirements planning, related to production and requirements. It also explores about
production plan, capacity and maintenance of an individual to control their wastage
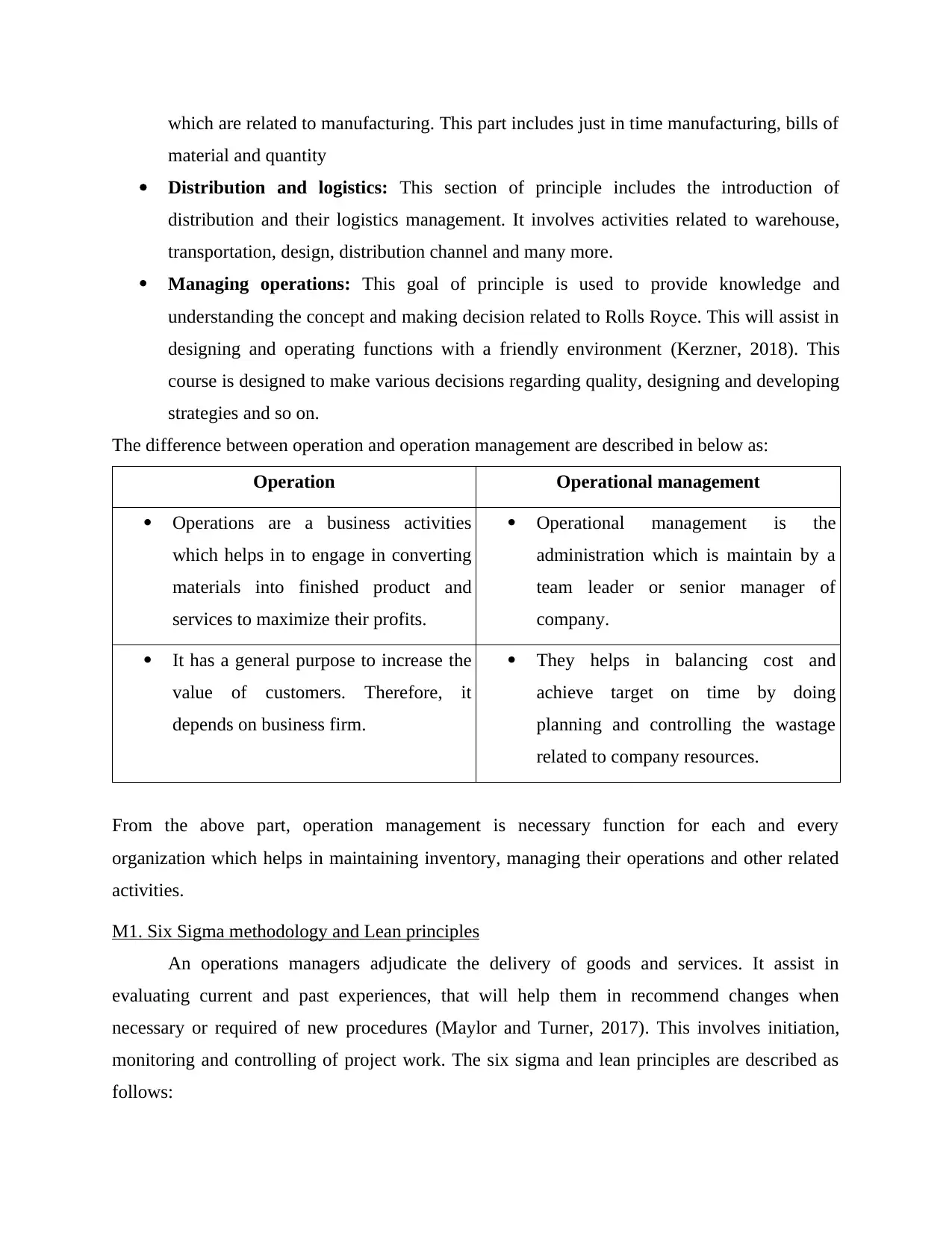
which are related to manufacturing. This part includes just in time manufacturing, bills of
material and quantity
Distribution and logistics: This section of principle includes the introduction of
distribution and their logistics management. It involves activities related to warehouse,
transportation, design, distribution channel and many more.
Managing operations: This goal of principle is used to provide knowledge and
understanding the concept and making decision related to Rolls Royce. This will assist in
designing and operating functions with a friendly environment (Kerzner, 2018). This
course is designed to make various decisions regarding quality, designing and developing
strategies and so on.
The difference between operation and operation management are described in below as:
Operation Operational management
Operations are a business activities
which helps in to engage in converting
materials into finished product and
services to maximize their profits.
Operational management is the
administration which is maintain by a
team leader or senior manager of
company.
It has a general purpose to increase the
value of customers. Therefore, it
depends on business firm.
They helps in balancing cost and
achieve target on time by doing
planning and controlling the wastage
related to company resources.
From the above part, operation management is necessary function for each and every
organization which helps in maintaining inventory, managing their operations and other related
activities.
M1. Six Sigma methodology and Lean principles
An operations managers adjudicate the delivery of goods and services. It assist in
evaluating current and past experiences, that will help them in recommend changes when
necessary or required of new procedures (Maylor and Turner, 2017). This involves initiation,
monitoring and controlling of project work. The six sigma and lean principles are described as
follows:
material and quantity
Distribution and logistics: This section of principle includes the introduction of
distribution and their logistics management. It involves activities related to warehouse,
transportation, design, distribution channel and many more.
Managing operations: This goal of principle is used to provide knowledge and
understanding the concept and making decision related to Rolls Royce. This will assist in
designing and operating functions with a friendly environment (Kerzner, 2018). This
course is designed to make various decisions regarding quality, designing and developing
strategies and so on.
The difference between operation and operation management are described in below as:
Operation Operational management
Operations are a business activities
which helps in to engage in converting
materials into finished product and
services to maximize their profits.
Operational management is the
administration which is maintain by a
team leader or senior manager of
company.
It has a general purpose to increase the
value of customers. Therefore, it
depends on business firm.
They helps in balancing cost and
achieve target on time by doing
planning and controlling the wastage
related to company resources.
From the above part, operation management is necessary function for each and every
organization which helps in maintaining inventory, managing their operations and other related
activities.
M1. Six Sigma methodology and Lean principles
An operations managers adjudicate the delivery of goods and services. It assist in
evaluating current and past experiences, that will help them in recommend changes when
necessary or required of new procedures (Maylor and Turner, 2017). This involves initiation,
monitoring and controlling of project work. The six sigma and lean principles are described as
follows:
Secure Best Marks with AI Grader
Need help grading? Try our AI Grader for instant feedback on your assignments.
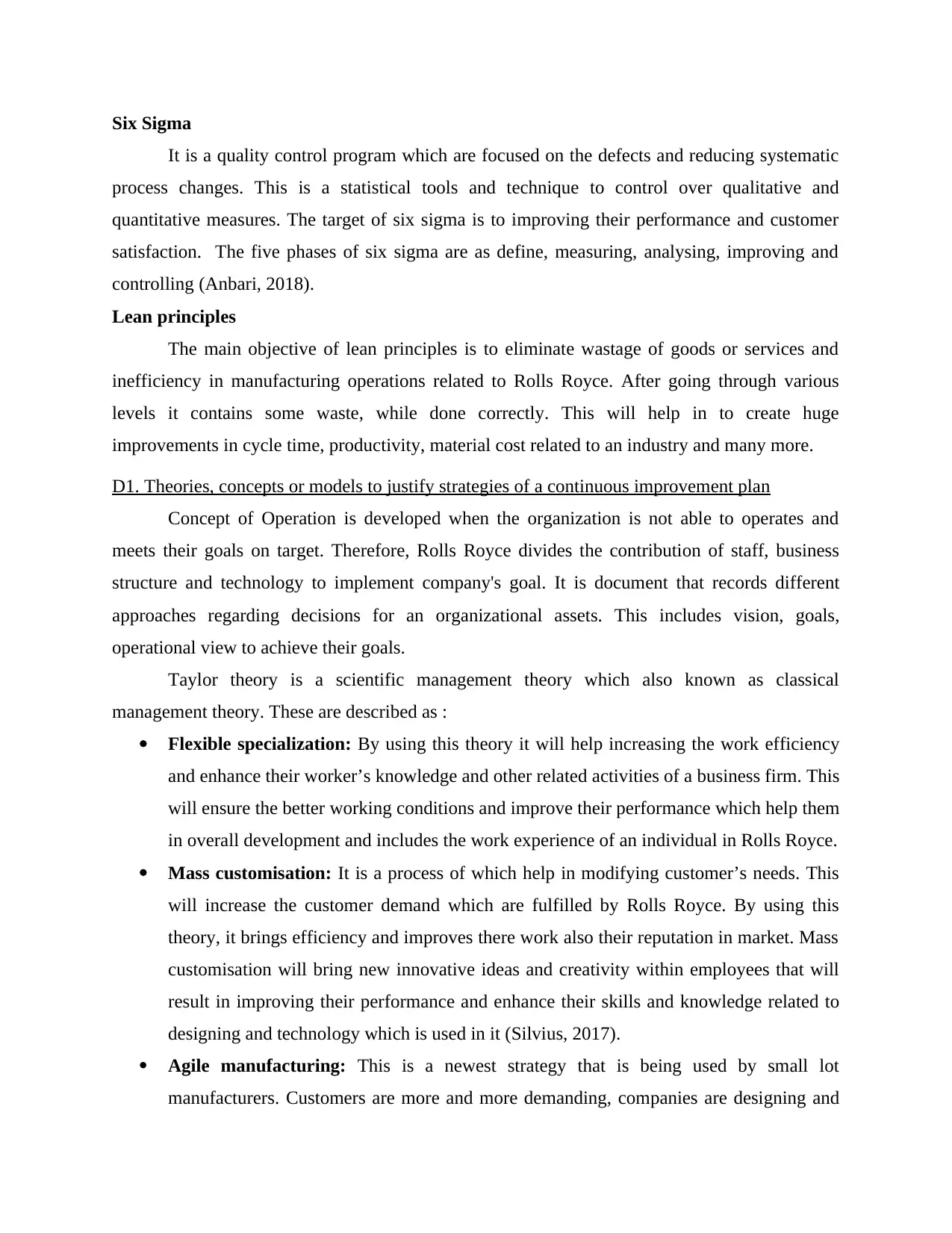
Six Sigma
It is a quality control program which are focused on the defects and reducing systematic
process changes. This is a statistical tools and technique to control over qualitative and
quantitative measures. The target of six sigma is to improving their performance and customer
satisfaction. The five phases of six sigma are as define, measuring, analysing, improving and
controlling (Anbari, 2018).
Lean principles
The main objective of lean principles is to eliminate wastage of goods or services and
inefficiency in manufacturing operations related to Rolls Royce. After going through various
levels it contains some waste, while done correctly. This will help in to create huge
improvements in cycle time, productivity, material cost related to an industry and many more.
D1. Theories, concepts or models to justify strategies of a continuous improvement plan
Concept of Operation is developed when the organization is not able to operates and
meets their goals on target. Therefore, Rolls Royce divides the contribution of staff, business
structure and technology to implement company's goal. It is document that records different
approaches regarding decisions for an organizational assets. This includes vision, goals,
operational view to achieve their goals.
Taylor theory is a scientific management theory which also known as classical
management theory. These are described as :
Flexible specialization: By using this theory it will help increasing the work efficiency
and enhance their worker’s knowledge and other related activities of a business firm. This
will ensure the better working conditions and improve their performance which help them
in overall development and includes the work experience of an individual in Rolls Royce.
Mass customisation: It is a process of which help in modifying customer’s needs. This
will increase the customer demand which are fulfilled by Rolls Royce. By using this
theory, it brings efficiency and improves there work also their reputation in market. Mass
customisation will bring new innovative ideas and creativity within employees that will
result in improving their performance and enhance their skills and knowledge related to
designing and technology which is used in it (Silvius, 2017).
Agile manufacturing: This is a newest strategy that is being used by small lot
manufacturers. Customers are more and more demanding, companies are designing and
It is a quality control program which are focused on the defects and reducing systematic
process changes. This is a statistical tools and technique to control over qualitative and
quantitative measures. The target of six sigma is to improving their performance and customer
satisfaction. The five phases of six sigma are as define, measuring, analysing, improving and
controlling (Anbari, 2018).
Lean principles
The main objective of lean principles is to eliminate wastage of goods or services and
inefficiency in manufacturing operations related to Rolls Royce. After going through various
levels it contains some waste, while done correctly. This will help in to create huge
improvements in cycle time, productivity, material cost related to an industry and many more.
D1. Theories, concepts or models to justify strategies of a continuous improvement plan
Concept of Operation is developed when the organization is not able to operates and
meets their goals on target. Therefore, Rolls Royce divides the contribution of staff, business
structure and technology to implement company's goal. It is document that records different
approaches regarding decisions for an organizational assets. This includes vision, goals,
operational view to achieve their goals.
Taylor theory is a scientific management theory which also known as classical
management theory. These are described as :
Flexible specialization: By using this theory it will help increasing the work efficiency
and enhance their worker’s knowledge and other related activities of a business firm. This
will ensure the better working conditions and improve their performance which help them
in overall development and includes the work experience of an individual in Rolls Royce.
Mass customisation: It is a process of which help in modifying customer’s needs. This
will increase the customer demand which are fulfilled by Rolls Royce. By using this
theory, it brings efficiency and improves there work also their reputation in market. Mass
customisation will bring new innovative ideas and creativity within employees that will
result in improving their performance and enhance their skills and knowledge related to
designing and technology which is used in it (Silvius, 2017).
Agile manufacturing: This is a newest strategy that is being used by small lot
manufacturers. Customers are more and more demanding, companies are designing and
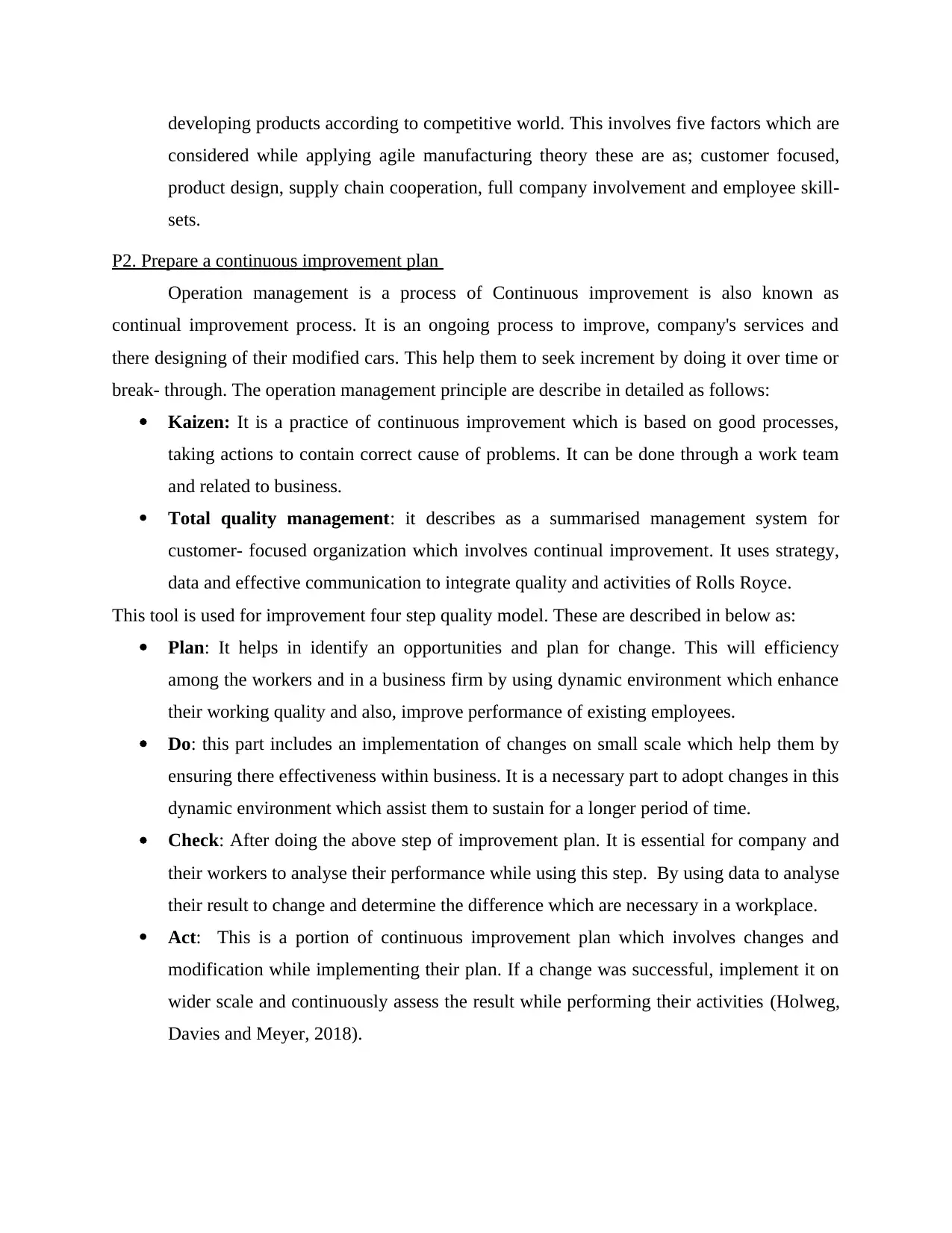
developing products according to competitive world. This involves five factors which are
considered while applying agile manufacturing theory these are as; customer focused,
product design, supply chain cooperation, full company involvement and employee skill-
sets.
P2. Prepare a continuous improvement plan
Operation management is a process of Continuous improvement is also known as
continual improvement process. It is an ongoing process to improve, company's services and
there designing of their modified cars. This help them to seek increment by doing it over time or
break- through. The operation management principle are describe in detailed as follows:
Kaizen: It is a practice of continuous improvement which is based on good processes,
taking actions to contain correct cause of problems. It can be done through a work team
and related to business.
Total quality management: it describes as a summarised management system for
customer- focused organization which involves continual improvement. It uses strategy,
data and effective communication to integrate quality and activities of Rolls Royce.
This tool is used for improvement four step quality model. These are described in below as:
Plan: It helps in identify an opportunities and plan for change. This will efficiency
among the workers and in a business firm by using dynamic environment which enhance
their working quality and also, improve performance of existing employees.
Do: this part includes an implementation of changes on small scale which help them by
ensuring there effectiveness within business. It is a necessary part to adopt changes in this
dynamic environment which assist them to sustain for a longer period of time.
Check: After doing the above step of improvement plan. It is essential for company and
their workers to analyse their performance while using this step. By using data to analyse
their result to change and determine the difference which are necessary in a workplace.
Act: This is a portion of continuous improvement plan which involves changes and
modification while implementing their plan. If a change was successful, implement it on
wider scale and continuously assess the result while performing their activities (Holweg,
Davies and Meyer, 2018).
considered while applying agile manufacturing theory these are as; customer focused,
product design, supply chain cooperation, full company involvement and employee skill-
sets.
P2. Prepare a continuous improvement plan
Operation management is a process of Continuous improvement is also known as
continual improvement process. It is an ongoing process to improve, company's services and
there designing of their modified cars. This help them to seek increment by doing it over time or
break- through. The operation management principle are describe in detailed as follows:
Kaizen: It is a practice of continuous improvement which is based on good processes,
taking actions to contain correct cause of problems. It can be done through a work team
and related to business.
Total quality management: it describes as a summarised management system for
customer- focused organization which involves continual improvement. It uses strategy,
data and effective communication to integrate quality and activities of Rolls Royce.
This tool is used for improvement four step quality model. These are described in below as:
Plan: It helps in identify an opportunities and plan for change. This will efficiency
among the workers and in a business firm by using dynamic environment which enhance
their working quality and also, improve performance of existing employees.
Do: this part includes an implementation of changes on small scale which help them by
ensuring there effectiveness within business. It is a necessary part to adopt changes in this
dynamic environment which assist them to sustain for a longer period of time.
Check: After doing the above step of improvement plan. It is essential for company and
their workers to analyse their performance while using this step. By using data to analyse
their result to change and determine the difference which are necessary in a workplace.
Act: This is a portion of continuous improvement plan which involves changes and
modification while implementing their plan. If a change was successful, implement it on
wider scale and continuously assess the result while performing their activities (Holweg,
Davies and Meyer, 2018).
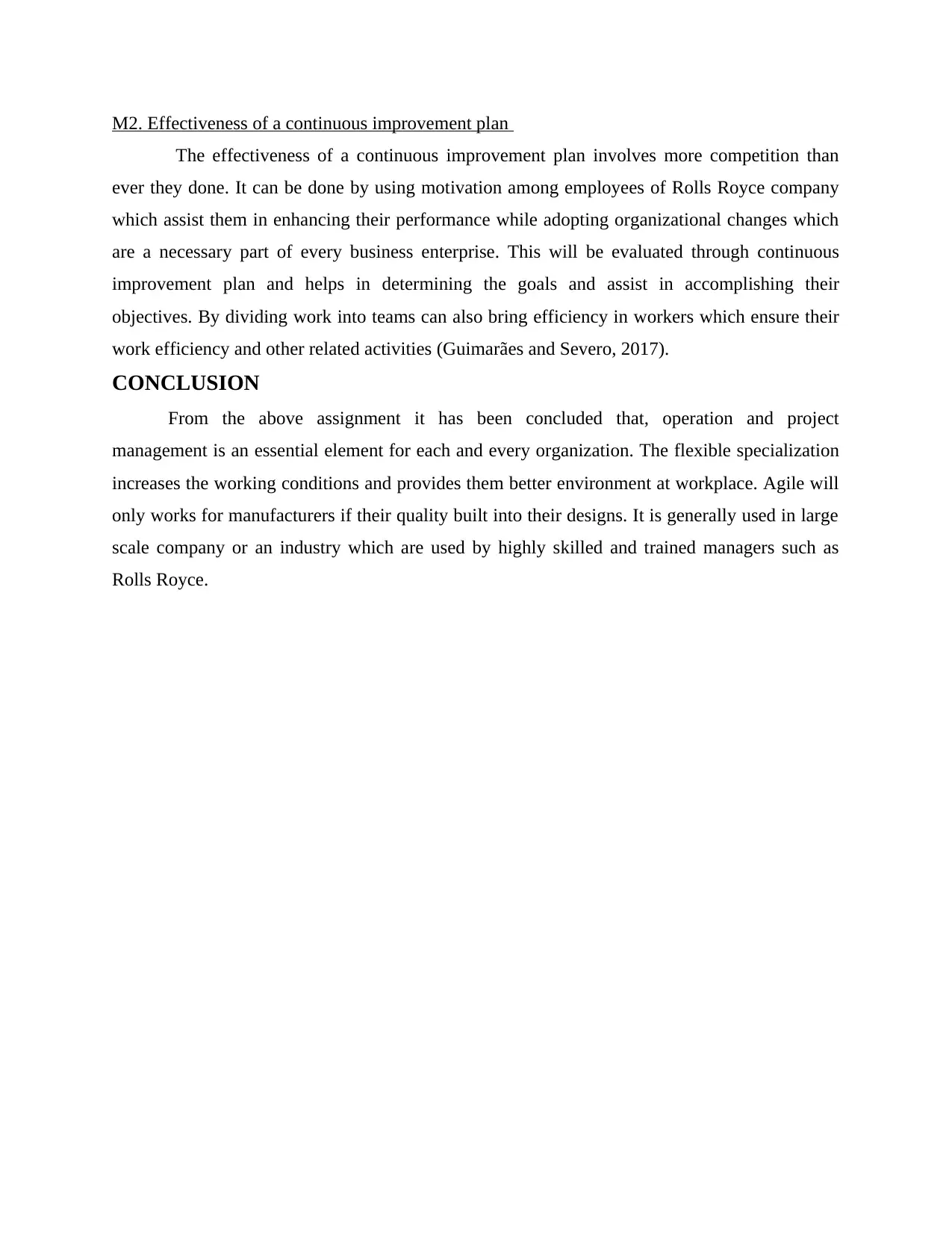
M2. Effectiveness of a continuous improvement plan
The effectiveness of a continuous improvement plan involves more competition than
ever they done. It can be done by using motivation among employees of Rolls Royce company
which assist them in enhancing their performance while adopting organizational changes which
are a necessary part of every business enterprise. This will be evaluated through continuous
improvement plan and helps in determining the goals and assist in accomplishing their
objectives. By dividing work into teams can also bring efficiency in workers which ensure their
work efficiency and other related activities (Guimarães and Severo, 2017).
CONCLUSION
From the above assignment it has been concluded that, operation and project
management is an essential element for each and every organization. The flexible specialization
increases the working conditions and provides them better environment at workplace. Agile will
only works for manufacturers if their quality built into their designs. It is generally used in large
scale company or an industry which are used by highly skilled and trained managers such as
Rolls Royce.
The effectiveness of a continuous improvement plan involves more competition than
ever they done. It can be done by using motivation among employees of Rolls Royce company
which assist them in enhancing their performance while adopting organizational changes which
are a necessary part of every business enterprise. This will be evaluated through continuous
improvement plan and helps in determining the goals and assist in accomplishing their
objectives. By dividing work into teams can also bring efficiency in workers which ensure their
work efficiency and other related activities (Guimarães and Severo, 2017).
CONCLUSION
From the above assignment it has been concluded that, operation and project
management is an essential element for each and every organization. The flexible specialization
increases the working conditions and provides them better environment at workplace. Agile will
only works for manufacturers if their quality built into their designs. It is generally used in large
scale company or an industry which are used by highly skilled and trained managers such as
Rolls Royce.
Paraphrase This Document
Need a fresh take? Get an instant paraphrase of this document with our AI Paraphraser
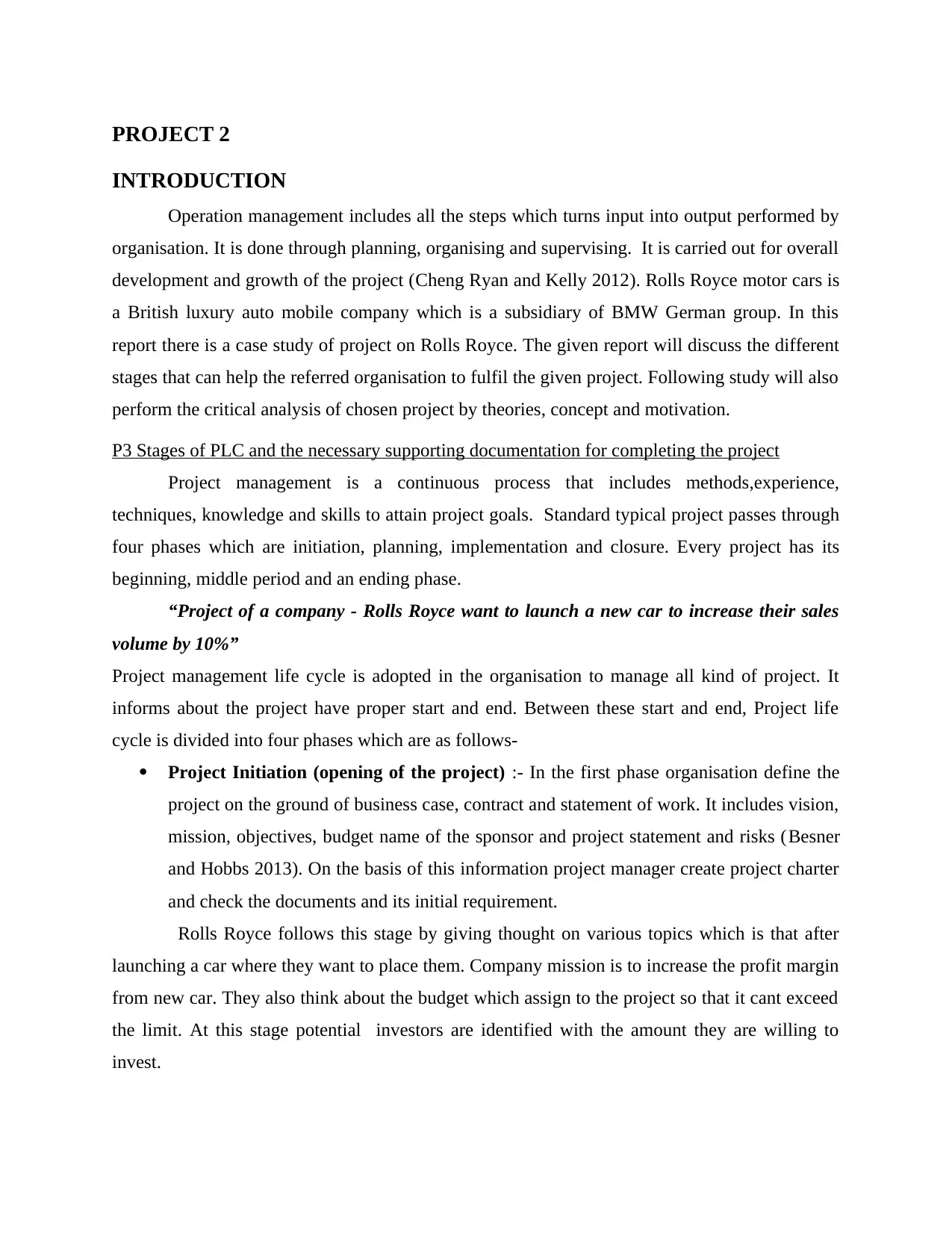
PROJECT 2
INTRODUCTION
Operation management includes all the steps which turns input into output performed by
organisation. It is done through planning, organising and supervising. It is carried out for overall
development and growth of the project (Cheng Ryan and Kelly 2012). Rolls Royce motor cars is
a British luxury auto mobile company which is a subsidiary of BMW German group. In this
report there is a case study of project on Rolls Royce. The given report will discuss the different
stages that can help the referred organisation to fulfil the given project. Following study will also
perform the critical analysis of chosen project by theories, concept and motivation.
P3 Stages of PLC and the necessary supporting documentation for completing the project
Project management is a continuous process that includes methods,experience,
techniques, knowledge and skills to attain project goals. Standard typical project passes through
four phases which are initiation, planning, implementation and closure. Every project has its
beginning, middle period and an ending phase.
“Project of a company - Rolls Royce want to launch a new car to increase their sales
volume by 10%”
Project management life cycle is adopted in the organisation to manage all kind of project. It
informs about the project have proper start and end. Between these start and end, Project life
cycle is divided into four phases which are as follows-
Project Initiation (opening of the project) :- In the first phase organisation define the
project on the ground of business case, contract and statement of work. It includes vision,
mission, objectives, budget name of the sponsor and project statement and risks (Besner
and Hobbs 2013). On the basis of this information project manager create project charter
and check the documents and its initial requirement.
Rolls Royce follows this stage by giving thought on various topics which is that after
launching a car where they want to place them. Company mission is to increase the profit margin
from new car. They also think about the budget which assign to the project so that it cant exceed
the limit. At this stage potential investors are identified with the amount they are willing to
invest.
INTRODUCTION
Operation management includes all the steps which turns input into output performed by
organisation. It is done through planning, organising and supervising. It is carried out for overall
development and growth of the project (Cheng Ryan and Kelly 2012). Rolls Royce motor cars is
a British luxury auto mobile company which is a subsidiary of BMW German group. In this
report there is a case study of project on Rolls Royce. The given report will discuss the different
stages that can help the referred organisation to fulfil the given project. Following study will also
perform the critical analysis of chosen project by theories, concept and motivation.
P3 Stages of PLC and the necessary supporting documentation for completing the project
Project management is a continuous process that includes methods,experience,
techniques, knowledge and skills to attain project goals. Standard typical project passes through
four phases which are initiation, planning, implementation and closure. Every project has its
beginning, middle period and an ending phase.
“Project of a company - Rolls Royce want to launch a new car to increase their sales
volume by 10%”
Project management life cycle is adopted in the organisation to manage all kind of project. It
informs about the project have proper start and end. Between these start and end, Project life
cycle is divided into four phases which are as follows-
Project Initiation (opening of the project) :- In the first phase organisation define the
project on the ground of business case, contract and statement of work. It includes vision,
mission, objectives, budget name of the sponsor and project statement and risks (Besner
and Hobbs 2013). On the basis of this information project manager create project charter
and check the documents and its initial requirement.
Rolls Royce follows this stage by giving thought on various topics which is that after
launching a car where they want to place them. Company mission is to increase the profit margin
from new car. They also think about the budget which assign to the project so that it cant exceed
the limit. At this stage potential investors are identified with the amount they are willing to
invest.
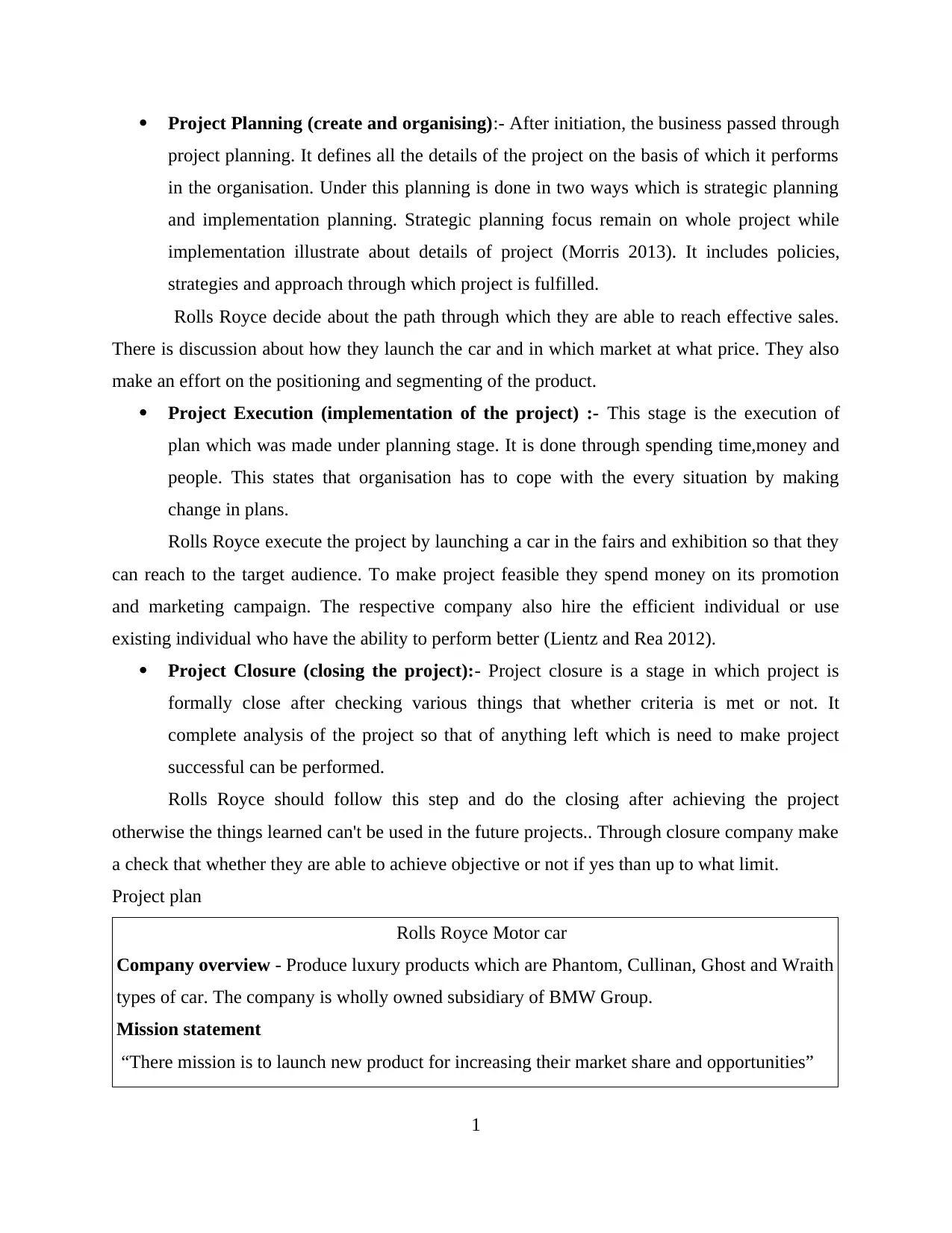
Project Planning (create and organising):- After initiation, the business passed through
project planning. It defines all the details of the project on the basis of which it performs
in the organisation. Under this planning is done in two ways which is strategic planning
and implementation planning. Strategic planning focus remain on whole project while
implementation illustrate about details of project (Morris 2013). It includes policies,
strategies and approach through which project is fulfilled.
Rolls Royce decide about the path through which they are able to reach effective sales.
There is discussion about how they launch the car and in which market at what price. They also
make an effort on the positioning and segmenting of the product.
Project Execution (implementation of the project) :- This stage is the execution of
plan which was made under planning stage. It is done through spending time,money and
people. This states that organisation has to cope with the every situation by making
change in plans.
Rolls Royce execute the project by launching a car in the fairs and exhibition so that they
can reach to the target audience. To make project feasible they spend money on its promotion
and marketing campaign. The respective company also hire the efficient individual or use
existing individual who have the ability to perform better (Lientz and Rea 2012).
Project Closure (closing the project):- Project closure is a stage in which project is
formally close after checking various things that whether criteria is met or not. It
complete analysis of the project so that of anything left which is need to make project
successful can be performed.
Rolls Royce should follow this step and do the closing after achieving the project
otherwise the things learned can't be used in the future projects.. Through closure company make
a check that whether they are able to achieve objective or not if yes than up to what limit.
Project plan
Rolls Royce Motor car
Company overview - Produce luxury products which are Phantom, Cullinan, Ghost and Wraith
types of car. The company is wholly owned subsidiary of BMW Group.
Mission statement
“There mission is to launch new product for increasing their market share and opportunities”
1
project planning. It defines all the details of the project on the basis of which it performs
in the organisation. Under this planning is done in two ways which is strategic planning
and implementation planning. Strategic planning focus remain on whole project while
implementation illustrate about details of project (Morris 2013). It includes policies,
strategies and approach through which project is fulfilled.
Rolls Royce decide about the path through which they are able to reach effective sales.
There is discussion about how they launch the car and in which market at what price. They also
make an effort on the positioning and segmenting of the product.
Project Execution (implementation of the project) :- This stage is the execution of
plan which was made under planning stage. It is done through spending time,money and
people. This states that organisation has to cope with the every situation by making
change in plans.
Rolls Royce execute the project by launching a car in the fairs and exhibition so that they
can reach to the target audience. To make project feasible they spend money on its promotion
and marketing campaign. The respective company also hire the efficient individual or use
existing individual who have the ability to perform better (Lientz and Rea 2012).
Project Closure (closing the project):- Project closure is a stage in which project is
formally close after checking various things that whether criteria is met or not. It
complete analysis of the project so that of anything left which is need to make project
successful can be performed.
Rolls Royce should follow this step and do the closing after achieving the project
otherwise the things learned can't be used in the future projects.. Through closure company make
a check that whether they are able to achieve objective or not if yes than up to what limit.
Project plan
Rolls Royce Motor car
Company overview - Produce luxury products which are Phantom, Cullinan, Ghost and Wraith
types of car. The company is wholly owned subsidiary of BMW Group.
Mission statement
“There mission is to launch new product for increasing their market share and opportunities”
1
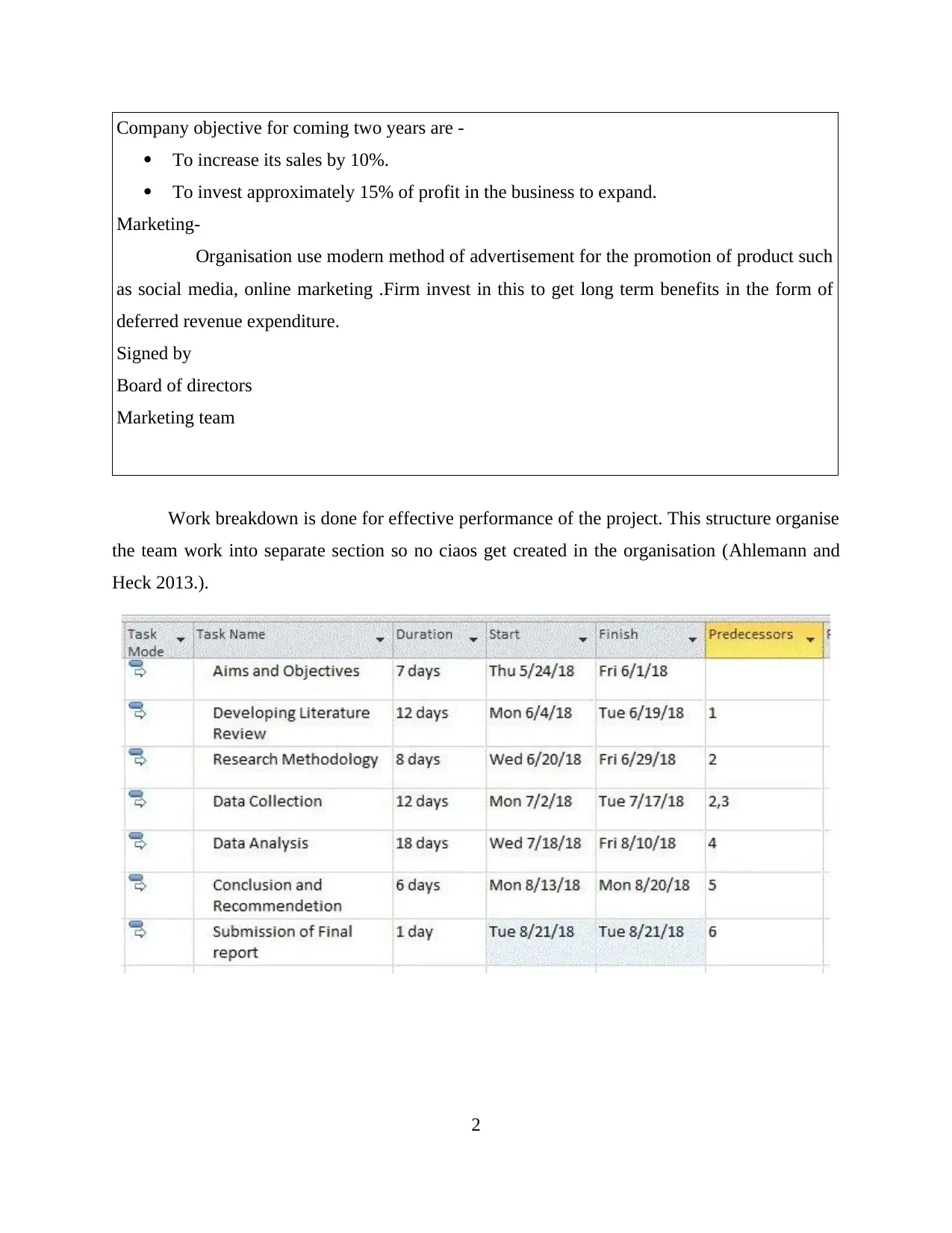
Company objective for coming two years are -
To increase its sales by 10%.
To invest approximately 15% of profit in the business to expand.
Marketing-
Organisation use modern method of advertisement for the promotion of product such
as social media, online marketing .Firm invest in this to get long term benefits in the form of
deferred revenue expenditure.
Signed by
Board of directors
Marketing team
Work breakdown is done for effective performance of the project. This structure organise
the team work into separate section so no ciaos get created in the organisation (Ahlemann and
Heck 2013.).
2
To increase its sales by 10%.
To invest approximately 15% of profit in the business to expand.
Marketing-
Organisation use modern method of advertisement for the promotion of product such
as social media, online marketing .Firm invest in this to get long term benefits in the form of
deferred revenue expenditure.
Signed by
Board of directors
Marketing team
Work breakdown is done for effective performance of the project. This structure organise
the team work into separate section so no ciaos get created in the organisation (Ahlemann and
Heck 2013.).
2
Secure Best Marks with AI Grader
Need help grading? Try our AI Grader for instant feedback on your assignments.
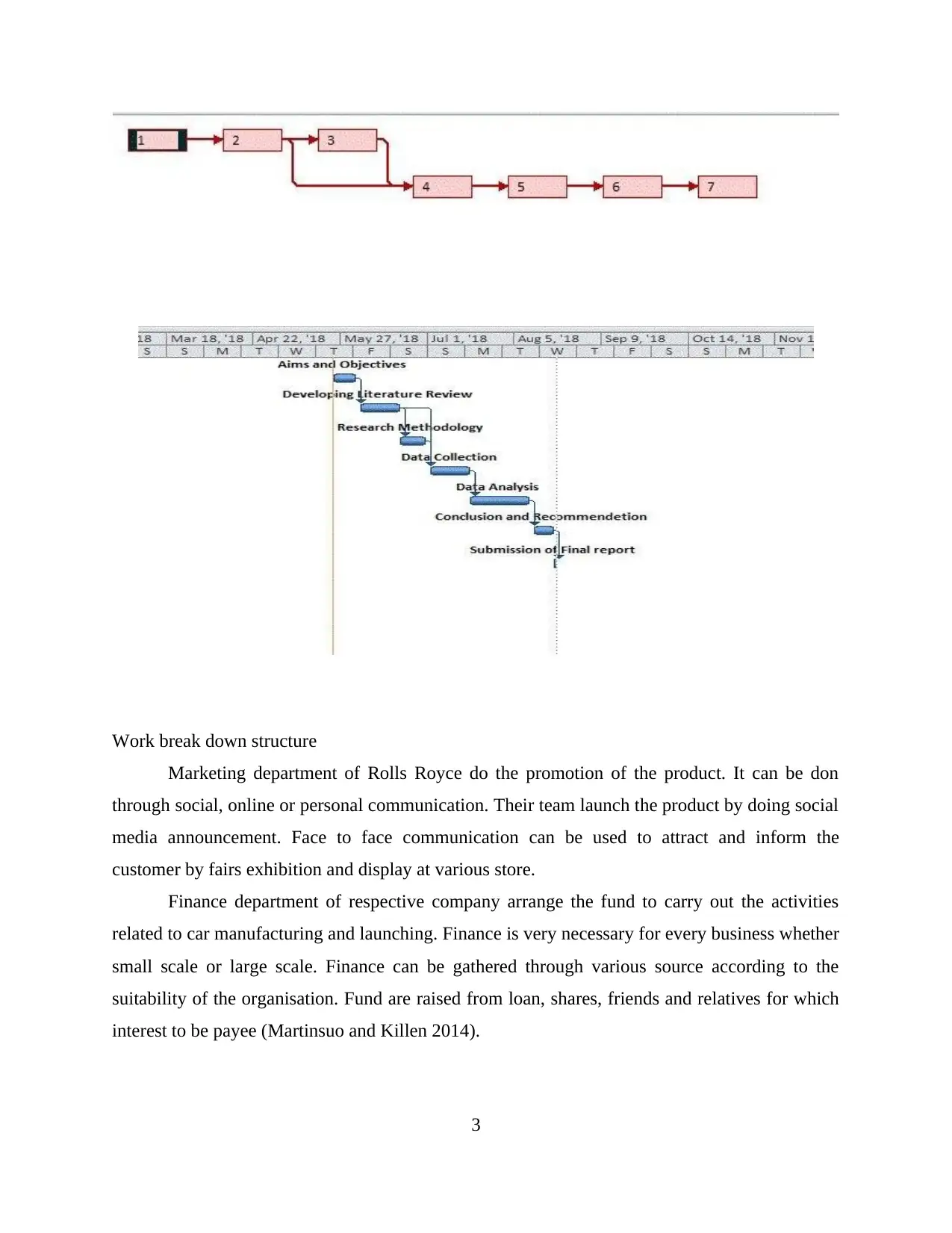
Work break down structure
Marketing department of Rolls Royce do the promotion of the product. It can be don
through social, online or personal communication. Their team launch the product by doing social
media announcement. Face to face communication can be used to attract and inform the
customer by fairs exhibition and display at various store.
Finance department of respective company arrange the fund to carry out the activities
related to car manufacturing and launching. Finance is very necessary for every business whether
small scale or large scale. Finance can be gathered through various source according to the
suitability of the organisation. Fund are raised from loan, shares, friends and relatives for which
interest to be payee (Martinsuo and Killen 2014).
3
Marketing department of Rolls Royce do the promotion of the product. It can be don
through social, online or personal communication. Their team launch the product by doing social
media announcement. Face to face communication can be used to attract and inform the
customer by fairs exhibition and display at various store.
Finance department of respective company arrange the fund to carry out the activities
related to car manufacturing and launching. Finance is very necessary for every business whether
small scale or large scale. Finance can be gathered through various source according to the
suitability of the organisation. Fund are raised from loan, shares, friends and relatives for which
interest to be payee (Martinsuo and Killen 2014).
3
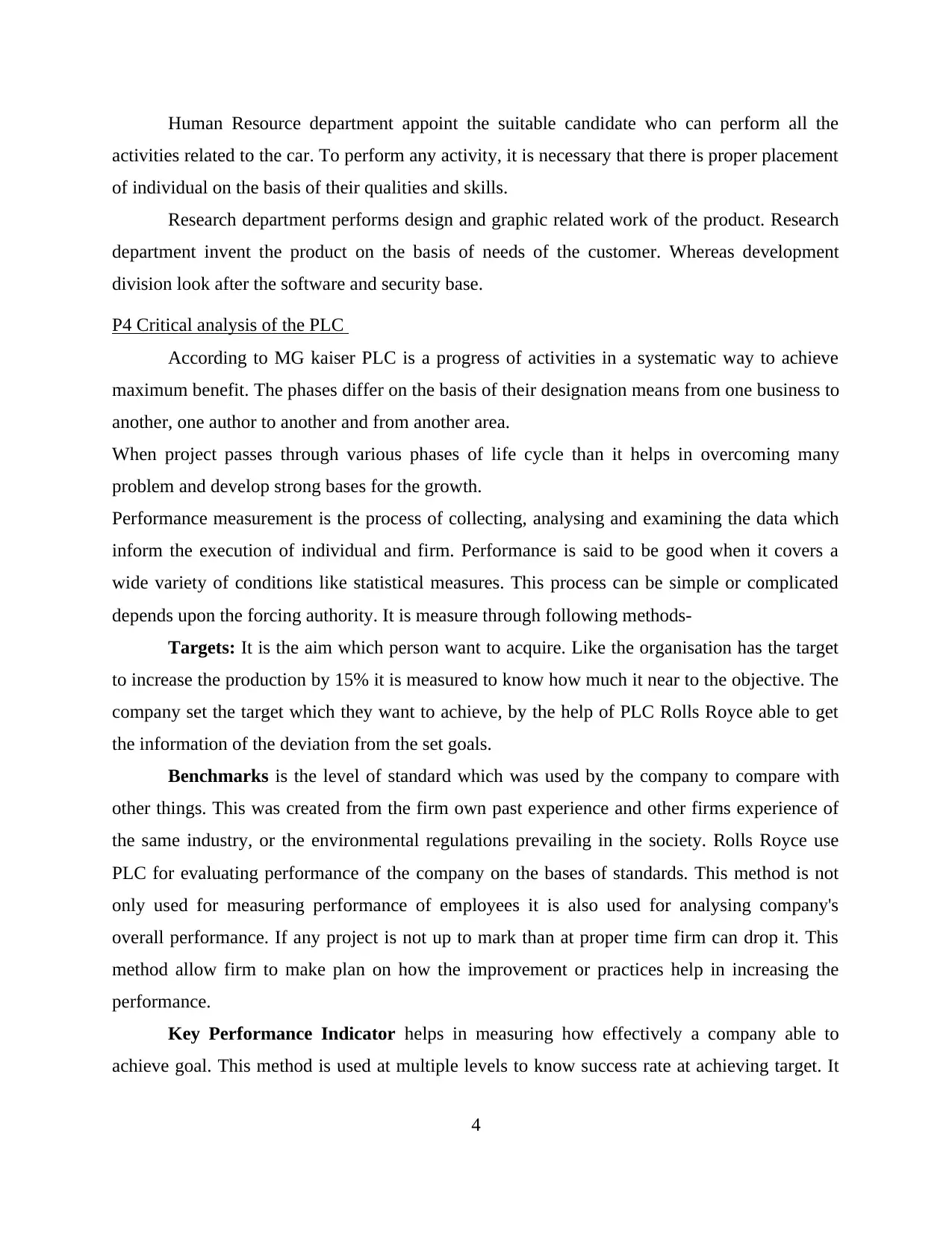
Human Resource department appoint the suitable candidate who can perform all the
activities related to the car. To perform any activity, it is necessary that there is proper placement
of individual on the basis of their qualities and skills.
Research department performs design and graphic related work of the product. Research
department invent the product on the basis of needs of the customer. Whereas development
division look after the software and security base.
P4 Critical analysis of the PLC
According to MG kaiser PLC is a progress of activities in a systematic way to achieve
maximum benefit. The phases differ on the basis of their designation means from one business to
another, one author to another and from another area.
When project passes through various phases of life cycle than it helps in overcoming many
problem and develop strong bases for the growth.
Performance measurement is the process of collecting, analysing and examining the data which
inform the execution of individual and firm. Performance is said to be good when it covers a
wide variety of conditions like statistical measures. This process can be simple or complicated
depends upon the forcing authority. It is measure through following methods-
Targets: It is the aim which person want to acquire. Like the organisation has the target
to increase the production by 15% it is measured to know how much it near to the objective. The
company set the target which they want to achieve, by the help of PLC Rolls Royce able to get
the information of the deviation from the set goals.
Benchmarks is the level of standard which was used by the company to compare with
other things. This was created from the firm own past experience and other firms experience of
the same industry, or the environmental regulations prevailing in the society. Rolls Royce use
PLC for evaluating performance of the company on the bases of standards. This method is not
only used for measuring performance of employees it is also used for analysing company's
overall performance. If any project is not up to mark than at proper time firm can drop it. This
method allow firm to make plan on how the improvement or practices help in increasing the
performance.
Key Performance Indicator helps in measuring how effectively a company able to
achieve goal. This method is used at multiple levels to know success rate at achieving target. It
4
activities related to the car. To perform any activity, it is necessary that there is proper placement
of individual on the basis of their qualities and skills.
Research department performs design and graphic related work of the product. Research
department invent the product on the basis of needs of the customer. Whereas development
division look after the software and security base.
P4 Critical analysis of the PLC
According to MG kaiser PLC is a progress of activities in a systematic way to achieve
maximum benefit. The phases differ on the basis of their designation means from one business to
another, one author to another and from another area.
When project passes through various phases of life cycle than it helps in overcoming many
problem and develop strong bases for the growth.
Performance measurement is the process of collecting, analysing and examining the data which
inform the execution of individual and firm. Performance is said to be good when it covers a
wide variety of conditions like statistical measures. This process can be simple or complicated
depends upon the forcing authority. It is measure through following methods-
Targets: It is the aim which person want to acquire. Like the organisation has the target
to increase the production by 15% it is measured to know how much it near to the objective. The
company set the target which they want to achieve, by the help of PLC Rolls Royce able to get
the information of the deviation from the set goals.
Benchmarks is the level of standard which was used by the company to compare with
other things. This was created from the firm own past experience and other firms experience of
the same industry, or the environmental regulations prevailing in the society. Rolls Royce use
PLC for evaluating performance of the company on the bases of standards. This method is not
only used for measuring performance of employees it is also used for analysing company's
overall performance. If any project is not up to mark than at proper time firm can drop it. This
method allow firm to make plan on how the improvement or practices help in increasing the
performance.
Key Performance Indicator helps in measuring how effectively a company able to
achieve goal. This method is used at multiple levels to know success rate at achieving target. It
4
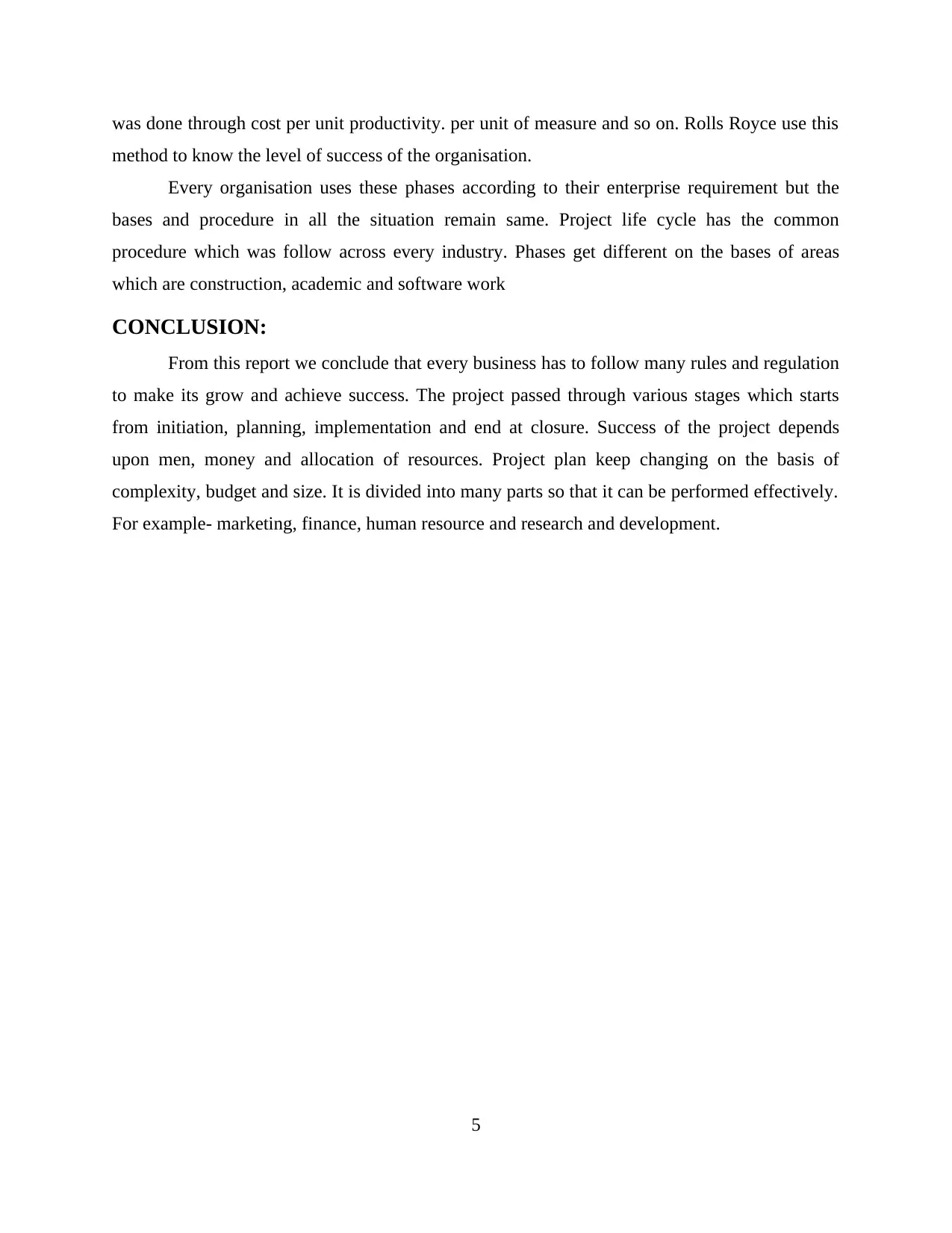
was done through cost per unit productivity. per unit of measure and so on. Rolls Royce use this
method to know the level of success of the organisation.
Every organisation uses these phases according to their enterprise requirement but the
bases and procedure in all the situation remain same. Project life cycle has the common
procedure which was follow across every industry. Phases get different on the bases of areas
which are construction, academic and software work
CONCLUSION:
From this report we conclude that every business has to follow many rules and regulation
to make its grow and achieve success. The project passed through various stages which starts
from initiation, planning, implementation and end at closure. Success of the project depends
upon men, money and allocation of resources. Project plan keep changing on the basis of
complexity, budget and size. It is divided into many parts so that it can be performed effectively.
For example- marketing, finance, human resource and research and development.
5
method to know the level of success of the organisation.
Every organisation uses these phases according to their enterprise requirement but the
bases and procedure in all the situation remain same. Project life cycle has the common
procedure which was follow across every industry. Phases get different on the bases of areas
which are construction, academic and software work
CONCLUSION:
From this report we conclude that every business has to follow many rules and regulation
to make its grow and achieve success. The project passed through various stages which starts
from initiation, planning, implementation and end at closure. Success of the project depends
upon men, money and allocation of resources. Project plan keep changing on the basis of
complexity, budget and size. It is divided into many parts so that it can be performed effectively.
For example- marketing, finance, human resource and research and development.
5
Paraphrase This Document
Need a fresh take? Get an instant paraphrase of this document with our AI Paraphraser
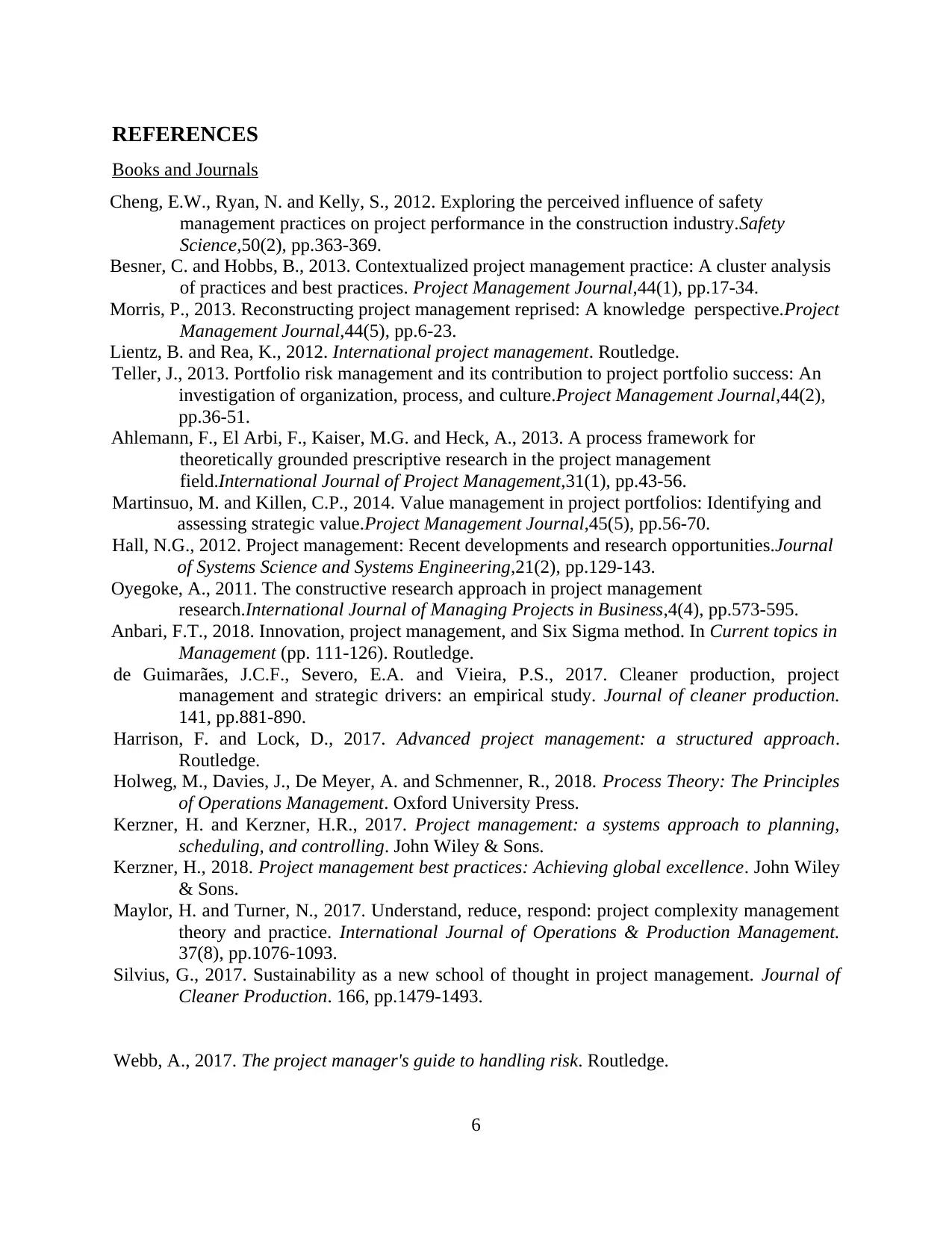
REFERENCES
Books and Journals
Cheng, E.W., Ryan, N. and Kelly, S., 2012. Exploring the perceived influence of safety
management practices on project performance in the construction industry.Safety
Science,50(2), pp.363-369.
Besner, C. and Hobbs, B., 2013. Contextualized project management practice: A cluster analysis
of practices and best practices. Project Management Journal,44(1), pp.17-34.
Morris, P., 2013. Reconstructing project management reprised: A knowledge perspective.Project
Management Journal,44(5), pp.6-23.
Lientz, B. and Rea, K., 2012. International project management. Routledge.
Teller, J., 2013. Portfolio risk management and its contribution to project portfolio success: An
investigation of organization, process, and culture.Project Management Journal,44(2),
pp.36-51.
Ahlemann, F., El Arbi, F., Kaiser, M.G. and Heck, A., 2013. A process framework for
theoretically grounded prescriptive research in the project management
field.International Journal of Project Management,31(1), pp.43-56.
Martinsuo, M. and Killen, C.P., 2014. Value management in project portfolios: Identifying and
assessing strategic value.Project Management Journal,45(5), pp.56-70.
Hall, N.G., 2012. Project management: Recent developments and research opportunities.Journal
of Systems Science and Systems Engineering,21(2), pp.129-143.
Oyegoke, A., 2011. The constructive research approach in project management
research.International Journal of Managing Projects in Business,4(4), pp.573-595.
Anbari, F.T., 2018. Innovation, project management, and Six Sigma method. In Current topics in
Management (pp. 111-126). Routledge.
de Guimarães, J.C.F., Severo, E.A. and Vieira, P.S., 2017. Cleaner production, project
management and strategic drivers: an empirical study. Journal of cleaner production.
141, pp.881-890.
Harrison, F. and Lock, D., 2017. Advanced project management: a structured approach.
Routledge.
Holweg, M., Davies, J., De Meyer, A. and Schmenner, R., 2018. Process Theory: The Principles
of Operations Management. Oxford University Press.
Kerzner, H. and Kerzner, H.R., 2017. Project management: a systems approach to planning,
scheduling, and controlling. John Wiley & Sons.
Kerzner, H., 2018. Project management best practices: Achieving global excellence. John Wiley
& Sons.
Maylor, H. and Turner, N., 2017. Understand, reduce, respond: project complexity management
theory and practice. International Journal of Operations & Production Management.
37(8), pp.1076-1093.
Silvius, G., 2017. Sustainability as a new school of thought in project management. Journal of
Cleaner Production. 166, pp.1479-1493.
Webb, A., 2017. The project manager's guide to handling risk. Routledge.
6
Books and Journals
Cheng, E.W., Ryan, N. and Kelly, S., 2012. Exploring the perceived influence of safety
management practices on project performance in the construction industry.Safety
Science,50(2), pp.363-369.
Besner, C. and Hobbs, B., 2013. Contextualized project management practice: A cluster analysis
of practices and best practices. Project Management Journal,44(1), pp.17-34.
Morris, P., 2013. Reconstructing project management reprised: A knowledge perspective.Project
Management Journal,44(5), pp.6-23.
Lientz, B. and Rea, K., 2012. International project management. Routledge.
Teller, J., 2013. Portfolio risk management and its contribution to project portfolio success: An
investigation of organization, process, and culture.Project Management Journal,44(2),
pp.36-51.
Ahlemann, F., El Arbi, F., Kaiser, M.G. and Heck, A., 2013. A process framework for
theoretically grounded prescriptive research in the project management
field.International Journal of Project Management,31(1), pp.43-56.
Martinsuo, M. and Killen, C.P., 2014. Value management in project portfolios: Identifying and
assessing strategic value.Project Management Journal,45(5), pp.56-70.
Hall, N.G., 2012. Project management: Recent developments and research opportunities.Journal
of Systems Science and Systems Engineering,21(2), pp.129-143.
Oyegoke, A., 2011. The constructive research approach in project management
research.International Journal of Managing Projects in Business,4(4), pp.573-595.
Anbari, F.T., 2018. Innovation, project management, and Six Sigma method. In Current topics in
Management (pp. 111-126). Routledge.
de Guimarães, J.C.F., Severo, E.A. and Vieira, P.S., 2017. Cleaner production, project
management and strategic drivers: an empirical study. Journal of cleaner production.
141, pp.881-890.
Harrison, F. and Lock, D., 2017. Advanced project management: a structured approach.
Routledge.
Holweg, M., Davies, J., De Meyer, A. and Schmenner, R., 2018. Process Theory: The Principles
of Operations Management. Oxford University Press.
Kerzner, H. and Kerzner, H.R., 2017. Project management: a systems approach to planning,
scheduling, and controlling. John Wiley & Sons.
Kerzner, H., 2018. Project management best practices: Achieving global excellence. John Wiley
& Sons.
Maylor, H. and Turner, N., 2017. Understand, reduce, respond: project complexity management
theory and practice. International Journal of Operations & Production Management.
37(8), pp.1076-1093.
Silvius, G., 2017. Sustainability as a new school of thought in project management. Journal of
Cleaner Production. 166, pp.1479-1493.
Webb, A., 2017. The project manager's guide to handling risk. Routledge.
6
1 out of 14
Related Documents

Your All-in-One AI-Powered Toolkit for Academic Success.
+13062052269
info@desklib.com
Available 24*7 on WhatsApp / Email
Unlock your academic potential
© 2024 | Zucol Services PVT LTD | All rights reserved.