Safety Conservation Report: Ergonomics, Incident Causation Analysis
VerifiedAdded on 2023/01/11
|16
|4756
|38
Report
AI Summary
This report addresses safety conservation, focusing on the man-machine interface, ergonomics, and incident causation. Part A critically discusses ergonomics, defining the term and explaining how ergonomic factors can improve occupational health and safety management. It emphasizes workplace design, risk factors, and the importance of infrastructure development, updated technology, and employee well-being. Part B examines the role of active and latent failures in incident causation, including poor decision-making, unsafe supervision, unsafe acts, and communication barriers. The report highlights the importance of understanding these factors to prevent workplace incidents and improve safety. The report emphasizes the role of active failures in incident causation and provides examples like poor decision making, inadequate precautionary measures, and unsafe supervision. The report stresses the importance of communication and a strong infrastructure in ensuring employee safety.
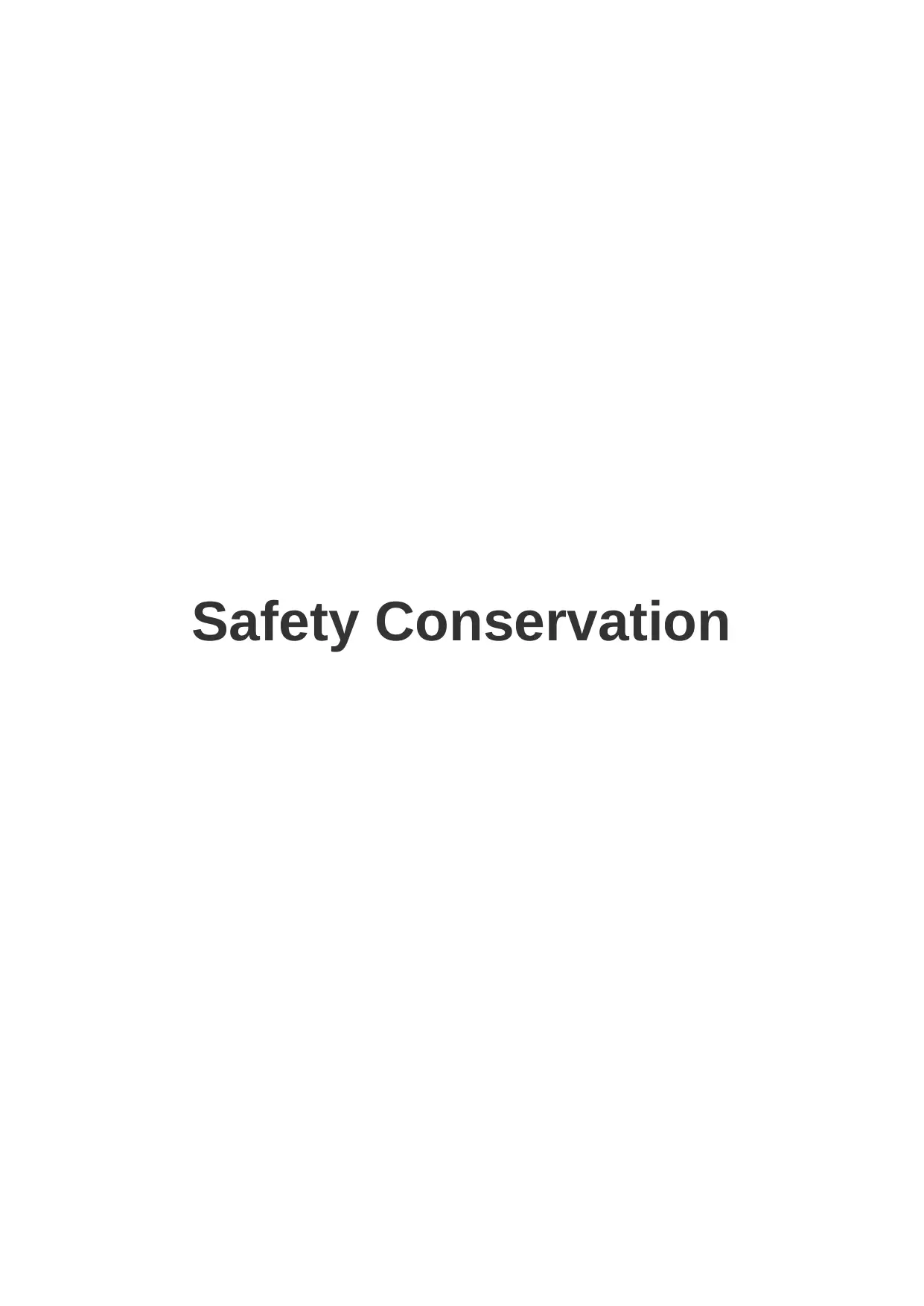
Safety Conservation
Paraphrase This Document
Need a fresh take? Get an instant paraphrase of this document with our AI Paraphraser
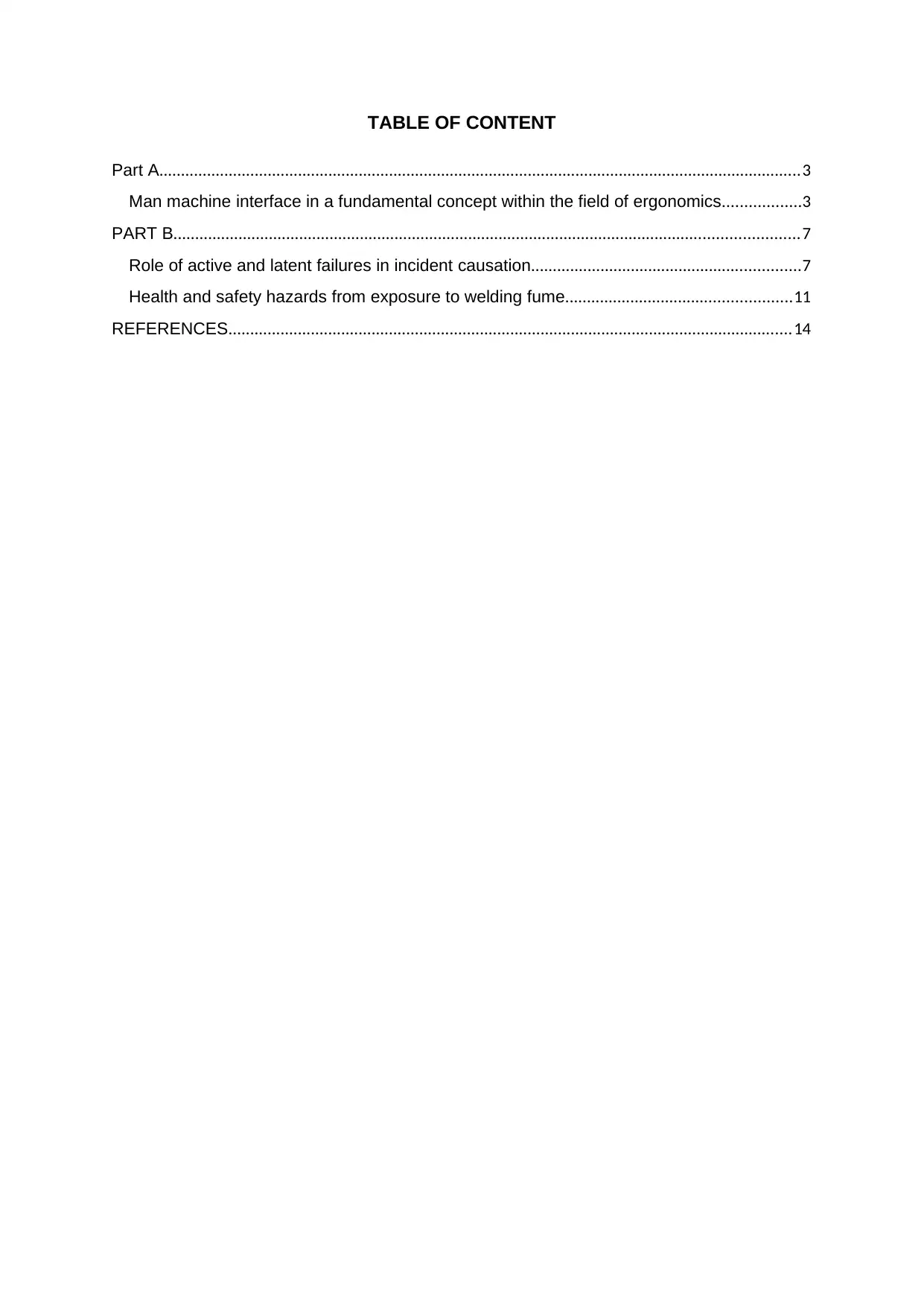
TABLE OF CONTENT
Part A....................................................................................................................................................3
Man machine interface in a fundamental concept within the field of ergonomics..................3
PART B................................................................................................................................................7
Role of active and latent failures in incident causation..............................................................7
Health and safety hazards from exposure to welding fume....................................................11
REFERENCES..................................................................................................................................14
Part A....................................................................................................................................................3
Man machine interface in a fundamental concept within the field of ergonomics..................3
PART B................................................................................................................................................7
Role of active and latent failures in incident causation..............................................................7
Health and safety hazards from exposure to welding fume....................................................11
REFERENCES..................................................................................................................................14
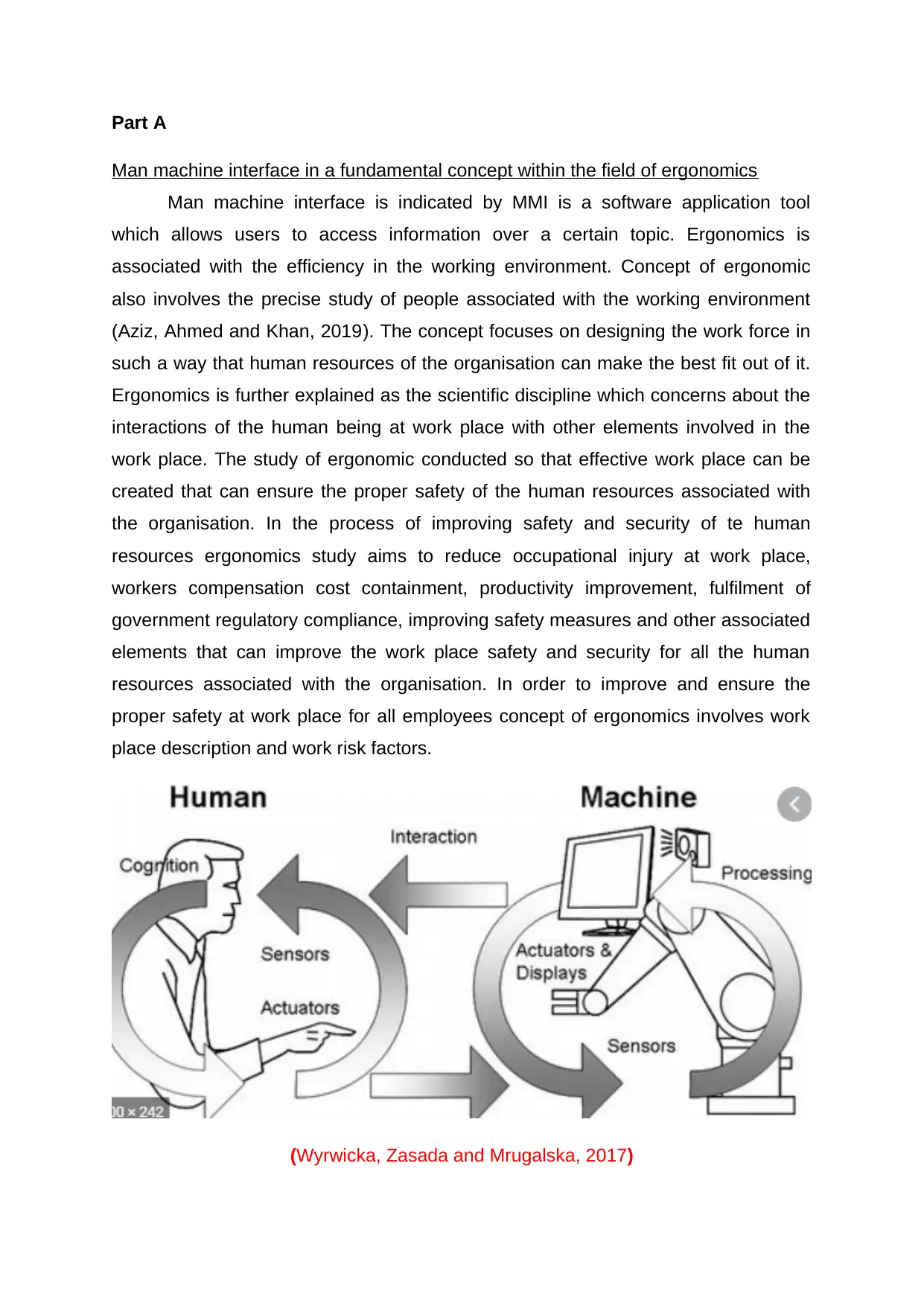
Part A
Man machine interface in a fundamental concept within the field of ergonomics
Man machine interface is indicated by MMI is a software application tool
which allows users to access information over a certain topic. Ergonomics is
associated with the efficiency in the working environment. Concept of ergonomic
also involves the precise study of people associated with the working environment
(Aziz, Ahmed and Khan, 2019). The concept focuses on designing the work force in
such a way that human resources of the organisation can make the best fit out of it.
Ergonomics is further explained as the scientific discipline which concerns about the
interactions of the human being at work place with other elements involved in the
work place. The study of ergonomic conducted so that effective work place can be
created that can ensure the proper safety of the human resources associated with
the organisation. In the process of improving safety and security of te human
resources ergonomics study aims to reduce occupational injury at work place,
workers compensation cost containment, productivity improvement, fulfilment of
government regulatory compliance, improving safety measures and other associated
elements that can improve the work place safety and security for all the human
resources associated with the organisation. In order to improve and ensure the
proper safety at work place for all employees concept of ergonomics involves work
place description and work risk factors.
(Wyrwicka, Zasada and Mrugalska, 2017)
Man machine interface in a fundamental concept within the field of ergonomics
Man machine interface is indicated by MMI is a software application tool
which allows users to access information over a certain topic. Ergonomics is
associated with the efficiency in the working environment. Concept of ergonomic
also involves the precise study of people associated with the working environment
(Aziz, Ahmed and Khan, 2019). The concept focuses on designing the work force in
such a way that human resources of the organisation can make the best fit out of it.
Ergonomics is further explained as the scientific discipline which concerns about the
interactions of the human being at work place with other elements involved in the
work place. The study of ergonomic conducted so that effective work place can be
created that can ensure the proper safety of the human resources associated with
the organisation. In the process of improving safety and security of te human
resources ergonomics study aims to reduce occupational injury at work place,
workers compensation cost containment, productivity improvement, fulfilment of
government regulatory compliance, improving safety measures and other associated
elements that can improve the work place safety and security for all the human
resources associated with the organisation. In order to improve and ensure the
proper safety at work place for all employees concept of ergonomics involves work
place description and work risk factors.
(Wyrwicka, Zasada and Mrugalska, 2017)
⊘ This is a preview!⊘
Do you want full access?
Subscribe today to unlock all pages.

Trusted by 1+ million students worldwide
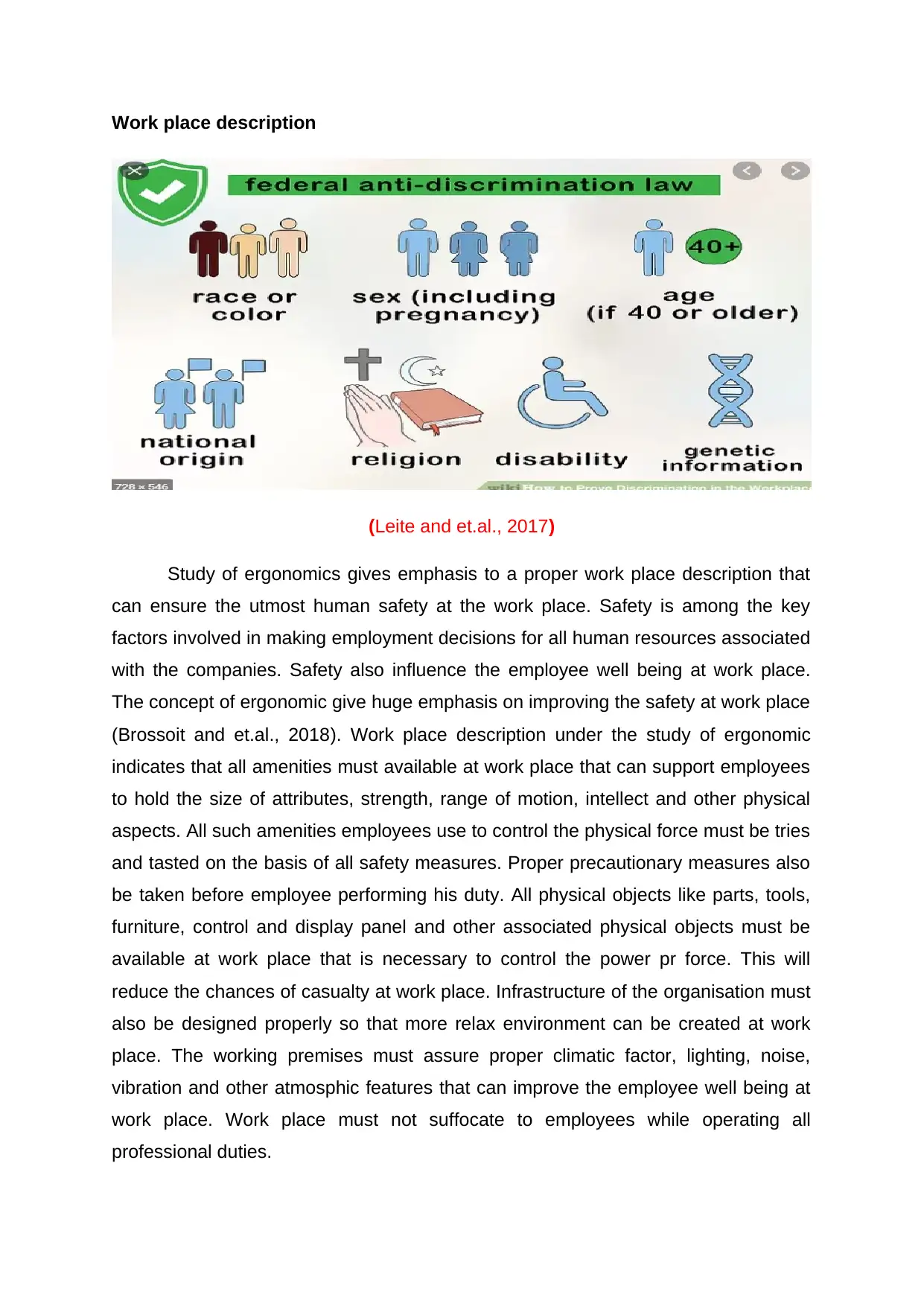
Work place description
(Leite and et.al., 2017)
Study of ergonomics gives emphasis to a proper work place description that
can ensure the utmost human safety at the work place. Safety is among the key
factors involved in making employment decisions for all human resources associated
with the companies. Safety also influence the employee well being at work place.
The concept of ergonomic give huge emphasis on improving the safety at work place
(Brossoit and et.al., 2018). Work place description under the study of ergonomic
indicates that all amenities must available at work place that can support employees
to hold the size of attributes, strength, range of motion, intellect and other physical
aspects. All such amenities employees use to control the physical force must be tries
and tasted on the basis of all safety measures. Proper precautionary measures also
be taken before employee performing his duty. All physical objects like parts, tools,
furniture, control and display panel and other associated physical objects must be
available at work place that is necessary to control the power pr force. This will
reduce the chances of casualty at work place. Infrastructure of the organisation must
also be designed properly so that more relax environment can be created at work
place. The working premises must assure proper climatic factor, lighting, noise,
vibration and other atmosphic features that can improve the employee well being at
work place. Work place must not suffocate to employees while operating all
professional duties.
(Leite and et.al., 2017)
Study of ergonomics gives emphasis to a proper work place description that
can ensure the utmost human safety at the work place. Safety is among the key
factors involved in making employment decisions for all human resources associated
with the companies. Safety also influence the employee well being at work place.
The concept of ergonomic give huge emphasis on improving the safety at work place
(Brossoit and et.al., 2018). Work place description under the study of ergonomic
indicates that all amenities must available at work place that can support employees
to hold the size of attributes, strength, range of motion, intellect and other physical
aspects. All such amenities employees use to control the physical force must be tries
and tasted on the basis of all safety measures. Proper precautionary measures also
be taken before employee performing his duty. All physical objects like parts, tools,
furniture, control and display panel and other associated physical objects must be
available at work place that is necessary to control the power pr force. This will
reduce the chances of casualty at work place. Infrastructure of the organisation must
also be designed properly so that more relax environment can be created at work
place. The working premises must assure proper climatic factor, lighting, noise,
vibration and other atmosphic features that can improve the employee well being at
work place. Work place must not suffocate to employees while operating all
professional duties.
Paraphrase This Document
Need a fresh take? Get an instant paraphrase of this document with our AI Paraphraser
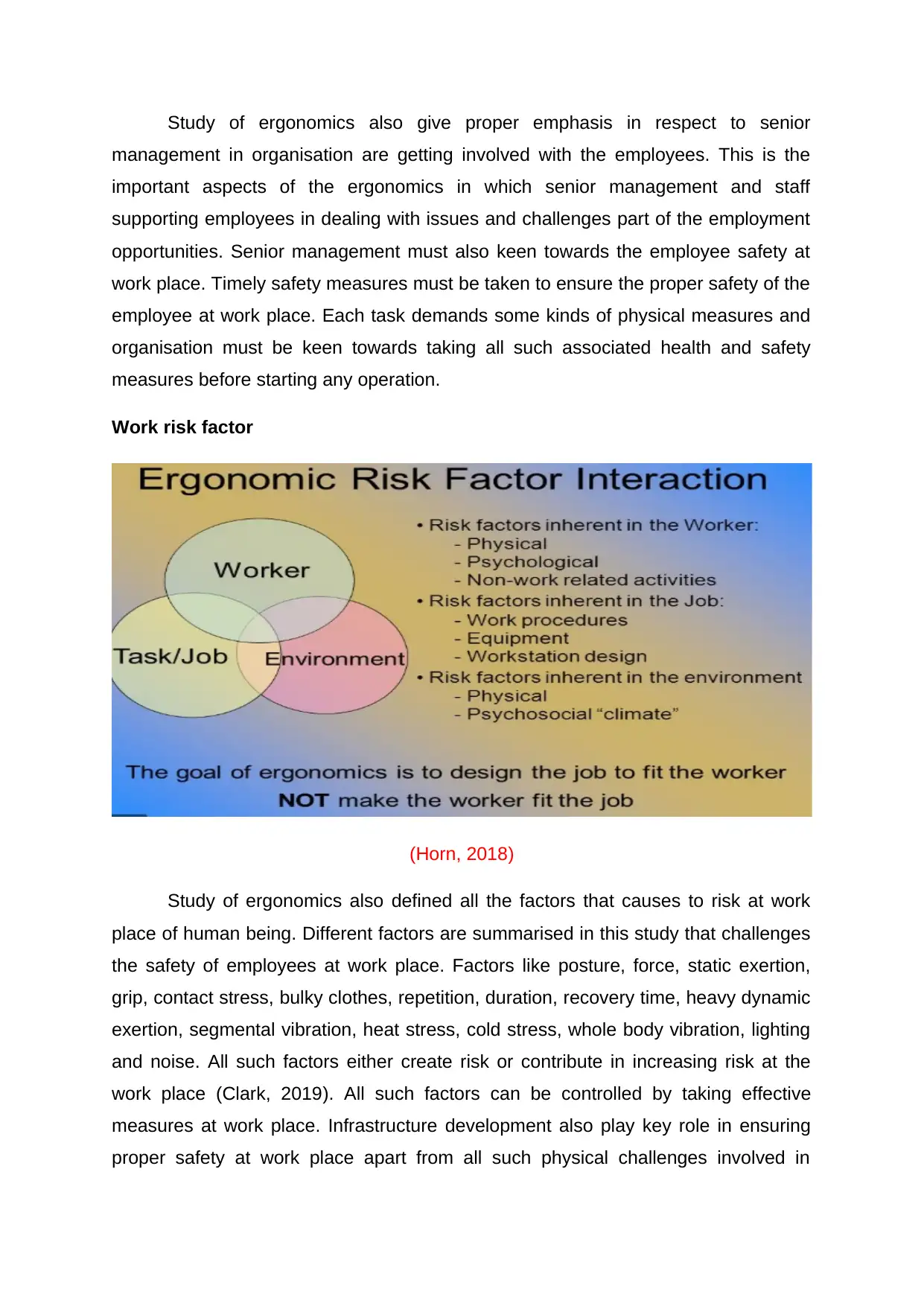
Study of ergonomics also give proper emphasis in respect to senior
management in organisation are getting involved with the employees. This is the
important aspects of the ergonomics in which senior management and staff
supporting employees in dealing with issues and challenges part of the employment
opportunities. Senior management must also keen towards the employee safety at
work place. Timely safety measures must be taken to ensure the proper safety of the
employee at work place. Each task demands some kinds of physical measures and
organisation must be keen towards taking all such associated health and safety
measures before starting any operation.
Work risk factor
(Horn, 2018)
Study of ergonomics also defined all the factors that causes to risk at work
place of human being. Different factors are summarised in this study that challenges
the safety of employees at work place. Factors like posture, force, static exertion,
grip, contact stress, bulky clothes, repetition, duration, recovery time, heavy dynamic
exertion, segmental vibration, heat stress, cold stress, whole body vibration, lighting
and noise. All such factors either create risk or contribute in increasing risk at the
work place (Clark, 2019). All such factors can be controlled by taking effective
measures at work place. Infrastructure development also play key role in ensuring
proper safety at work place apart from all such physical challenges involved in
management in organisation are getting involved with the employees. This is the
important aspects of the ergonomics in which senior management and staff
supporting employees in dealing with issues and challenges part of the employment
opportunities. Senior management must also keen towards the employee safety at
work place. Timely safety measures must be taken to ensure the proper safety of the
employee at work place. Each task demands some kinds of physical measures and
organisation must be keen towards taking all such associated health and safety
measures before starting any operation.
Work risk factor
(Horn, 2018)
Study of ergonomics also defined all the factors that causes to risk at work
place of human being. Different factors are summarised in this study that challenges
the safety of employees at work place. Factors like posture, force, static exertion,
grip, contact stress, bulky clothes, repetition, duration, recovery time, heavy dynamic
exertion, segmental vibration, heat stress, cold stress, whole body vibration, lighting
and noise. All such factors either create risk or contribute in increasing risk at the
work place (Clark, 2019). All such factors can be controlled by taking effective
measures at work place. Infrastructure development also play key role in ensuring
proper safety at work place apart from all such physical challenges involved in
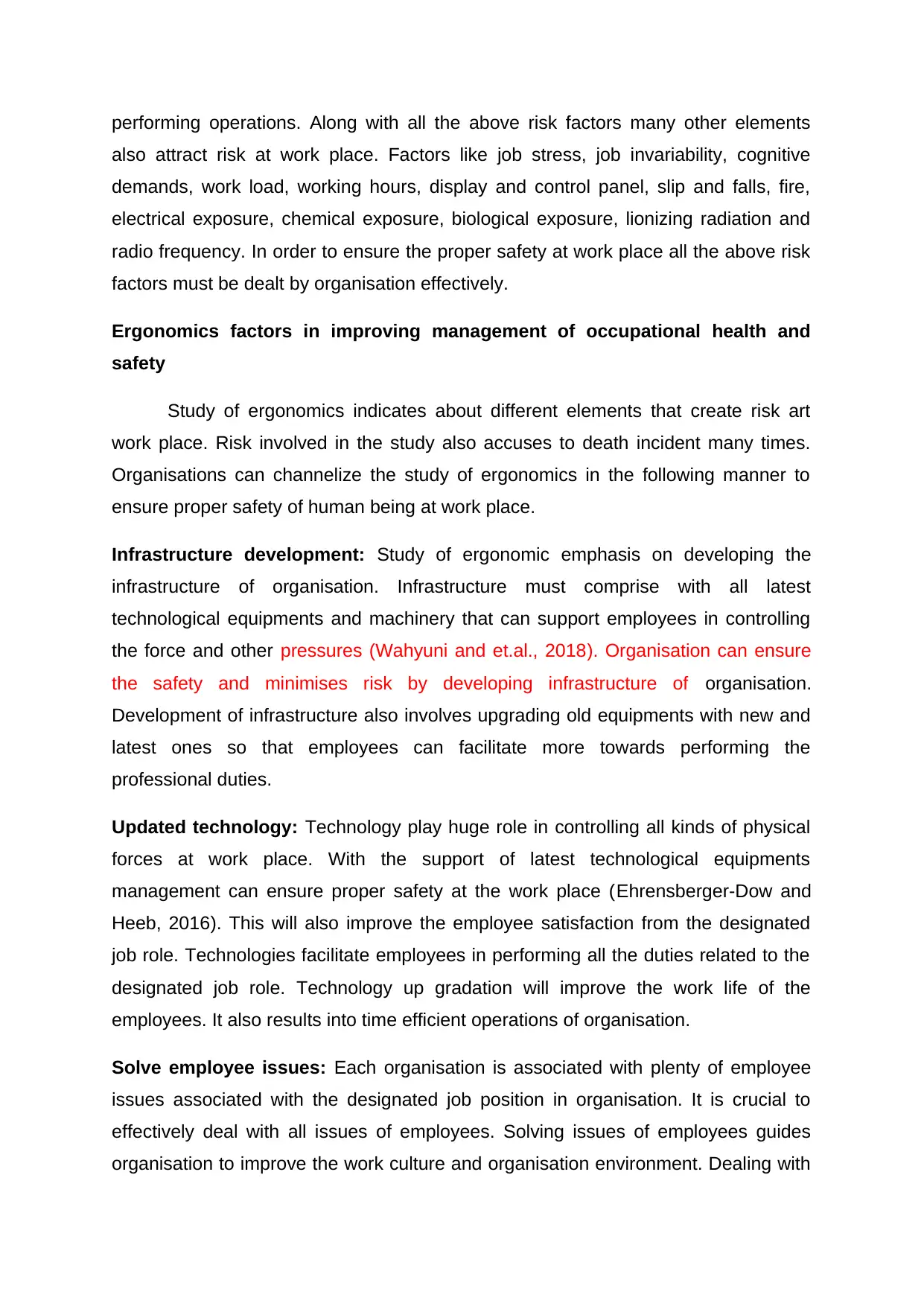
performing operations. Along with all the above risk factors many other elements
also attract risk at work place. Factors like job stress, job invariability, cognitive
demands, work load, working hours, display and control panel, slip and falls, fire,
electrical exposure, chemical exposure, biological exposure, lionizing radiation and
radio frequency. In order to ensure the proper safety at work place all the above risk
factors must be dealt by organisation effectively.
Ergonomics factors in improving management of occupational health and
safety
Study of ergonomics indicates about different elements that create risk art
work place. Risk involved in the study also accuses to death incident many times.
Organisations can channelize the study of ergonomics in the following manner to
ensure proper safety of human being at work place.
Infrastructure development: Study of ergonomic emphasis on developing the
infrastructure of organisation. Infrastructure must comprise with all latest
technological equipments and machinery that can support employees in controlling
the force and other pressures (Wahyuni and et.al., 2018). Organisation can ensure
the safety and minimises risk by developing infrastructure of organisation.
Development of infrastructure also involves upgrading old equipments with new and
latest ones so that employees can facilitate more towards performing the
professional duties.
Updated technology: Technology play huge role in controlling all kinds of physical
forces at work place. With the support of latest technological equipments
management can ensure proper safety at the work place (Ehrensberger-Dow and
Heeb, 2016). This will also improve the employee satisfaction from the designated
job role. Technologies facilitate employees in performing all the duties related to the
designated job role. Technology up gradation will improve the work life of the
employees. It also results into time efficient operations of organisation.
Solve employee issues: Each organisation is associated with plenty of employee
issues associated with the designated job position in organisation. It is crucial to
effectively deal with all issues of employees. Solving issues of employees guides
organisation to improve the work culture and organisation environment. Dealing with
also attract risk at work place. Factors like job stress, job invariability, cognitive
demands, work load, working hours, display and control panel, slip and falls, fire,
electrical exposure, chemical exposure, biological exposure, lionizing radiation and
radio frequency. In order to ensure the proper safety at work place all the above risk
factors must be dealt by organisation effectively.
Ergonomics factors in improving management of occupational health and
safety
Study of ergonomics indicates about different elements that create risk art
work place. Risk involved in the study also accuses to death incident many times.
Organisations can channelize the study of ergonomics in the following manner to
ensure proper safety of human being at work place.
Infrastructure development: Study of ergonomic emphasis on developing the
infrastructure of organisation. Infrastructure must comprise with all latest
technological equipments and machinery that can support employees in controlling
the force and other pressures (Wahyuni and et.al., 2018). Organisation can ensure
the safety and minimises risk by developing infrastructure of organisation.
Development of infrastructure also involves upgrading old equipments with new and
latest ones so that employees can facilitate more towards performing the
professional duties.
Updated technology: Technology play huge role in controlling all kinds of physical
forces at work place. With the support of latest technological equipments
management can ensure proper safety at the work place (Ehrensberger-Dow and
Heeb, 2016). This will also improve the employee satisfaction from the designated
job role. Technologies facilitate employees in performing all the duties related to the
designated job role. Technology up gradation will improve the work life of the
employees. It also results into time efficient operations of organisation.
Solve employee issues: Each organisation is associated with plenty of employee
issues associated with the designated job position in organisation. It is crucial to
effectively deal with all issues of employees. Solving issues of employees guides
organisation to improve the work culture and organisation environment. Dealing with
⊘ This is a preview!⊘
Do you want full access?
Subscribe today to unlock all pages.

Trusted by 1+ million students worldwide
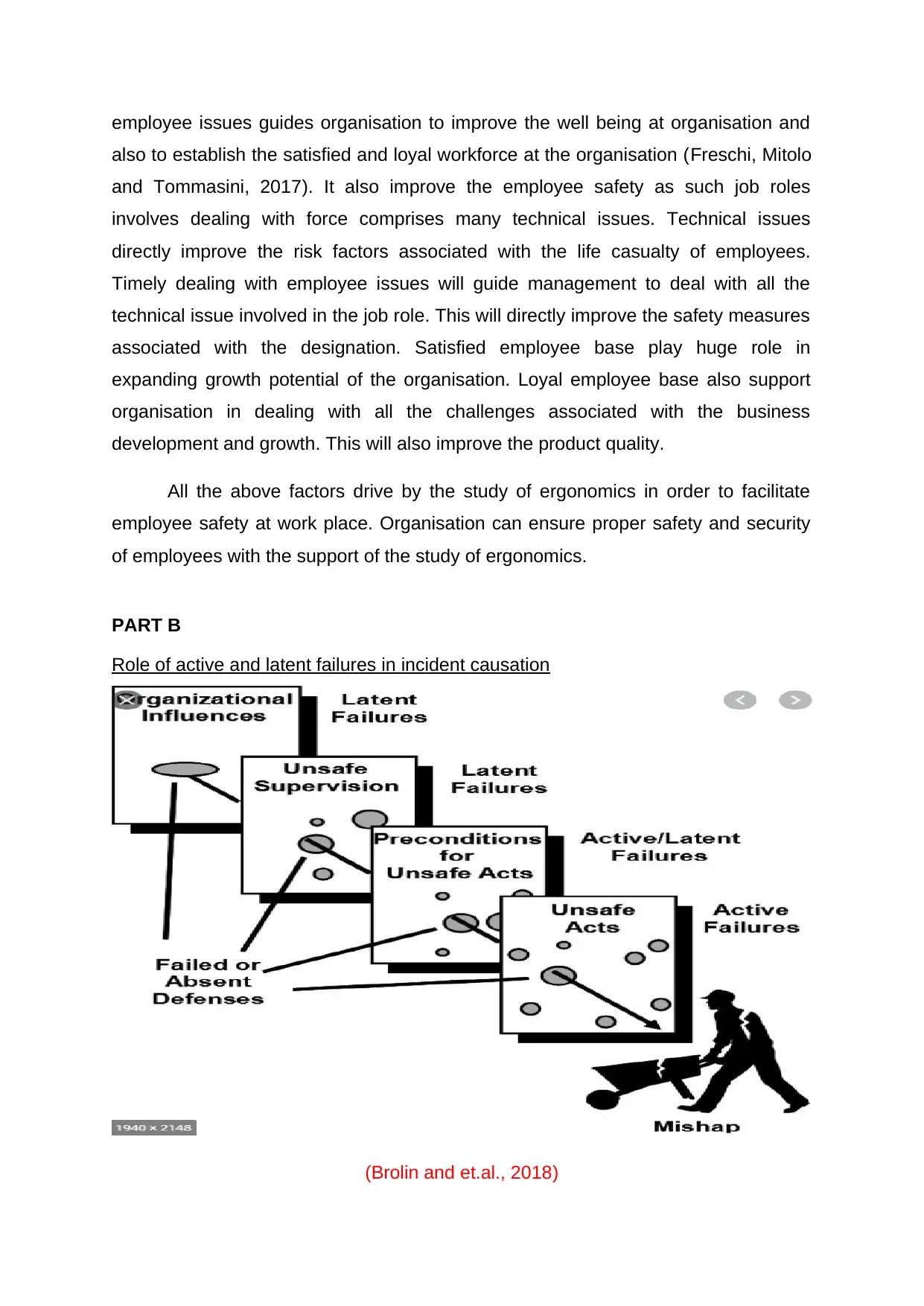
employee issues guides organisation to improve the well being at organisation and
also to establish the satisfied and loyal workforce at the organisation (Freschi, Mitolo
and Tommasini, 2017). It also improve the employee safety as such job roles
involves dealing with force comprises many technical issues. Technical issues
directly improve the risk factors associated with the life casualty of employees.
Timely dealing with employee issues will guide management to deal with all the
technical issue involved in the job role. This will directly improve the safety measures
associated with the designation. Satisfied employee base play huge role in
expanding growth potential of the organisation. Loyal employee base also support
organisation in dealing with all the challenges associated with the business
development and growth. This will also improve the product quality.
All the above factors drive by the study of ergonomics in order to facilitate
employee safety at work place. Organisation can ensure proper safety and security
of employees with the support of the study of ergonomics.
PART B
Role of active and latent failures in incident causation
(Brolin and et.al., 2018)
also to establish the satisfied and loyal workforce at the organisation (Freschi, Mitolo
and Tommasini, 2017). It also improve the employee safety as such job roles
involves dealing with force comprises many technical issues. Technical issues
directly improve the risk factors associated with the life casualty of employees.
Timely dealing with employee issues will guide management to deal with all the
technical issue involved in the job role. This will directly improve the safety measures
associated with the designation. Satisfied employee base play huge role in
expanding growth potential of the organisation. Loyal employee base also support
organisation in dealing with all the challenges associated with the business
development and growth. This will also improve the product quality.
All the above factors drive by the study of ergonomics in order to facilitate
employee safety at work place. Organisation can ensure proper safety and security
of employees with the support of the study of ergonomics.
PART B
Role of active and latent failures in incident causation
(Brolin and et.al., 2018)
Paraphrase This Document
Need a fresh take? Get an instant paraphrase of this document with our AI Paraphraser
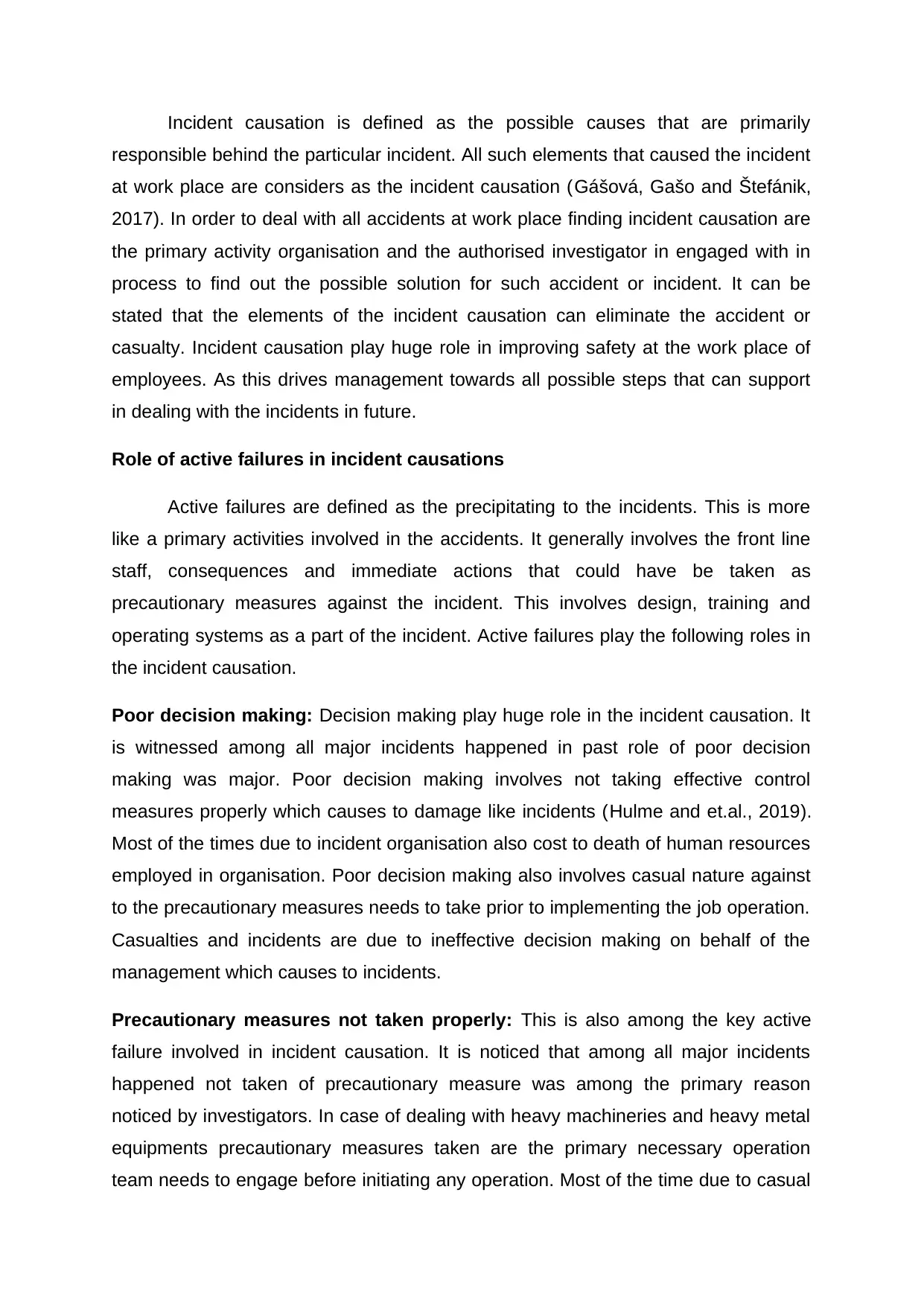
Incident causation is defined as the possible causes that are primarily
responsible behind the particular incident. All such elements that caused the incident
at work place are considers as the incident causation (Gášová, Gašo and Štefánik,
2017). In order to deal with all accidents at work place finding incident causation are
the primary activity organisation and the authorised investigator in engaged with in
process to find out the possible solution for such accident or incident. It can be
stated that the elements of the incident causation can eliminate the accident or
casualty. Incident causation play huge role in improving safety at the work place of
employees. As this drives management towards all possible steps that can support
in dealing with the incidents in future.
Role of active failures in incident causations
Active failures are defined as the precipitating to the incidents. This is more
like a primary activities involved in the accidents. It generally involves the front line
staff, consequences and immediate actions that could have be taken as
precautionary measures against the incident. This involves design, training and
operating systems as a part of the incident. Active failures play the following roles in
the incident causation.
Poor decision making: Decision making play huge role in the incident causation. It
is witnessed among all major incidents happened in past role of poor decision
making was major. Poor decision making involves not taking effective control
measures properly which causes to damage like incidents (Hulme and et.al., 2019).
Most of the times due to incident organisation also cost to death of human resources
employed in organisation. Poor decision making also involves casual nature against
to the precautionary measures needs to take prior to implementing the job operation.
Casualties and incidents are due to ineffective decision making on behalf of the
management which causes to incidents.
Precautionary measures not taken properly: This is also among the key active
failure involved in incident causation. It is noticed that among all major incidents
happened not taken of precautionary measure was among the primary reason
noticed by investigators. In case of dealing with heavy machineries and heavy metal
equipments precautionary measures taken are the primary necessary operation
team needs to engage before initiating any operation. Most of the time due to casual
responsible behind the particular incident. All such elements that caused the incident
at work place are considers as the incident causation (Gášová, Gašo and Štefánik,
2017). In order to deal with all accidents at work place finding incident causation are
the primary activity organisation and the authorised investigator in engaged with in
process to find out the possible solution for such accident or incident. It can be
stated that the elements of the incident causation can eliminate the accident or
casualty. Incident causation play huge role in improving safety at the work place of
employees. As this drives management towards all possible steps that can support
in dealing with the incidents in future.
Role of active failures in incident causations
Active failures are defined as the precipitating to the incidents. This is more
like a primary activities involved in the accidents. It generally involves the front line
staff, consequences and immediate actions that could have be taken as
precautionary measures against the incident. This involves design, training and
operating systems as a part of the incident. Active failures play the following roles in
the incident causation.
Poor decision making: Decision making play huge role in the incident causation. It
is witnessed among all major incidents happened in past role of poor decision
making was major. Poor decision making involves not taking effective control
measures properly which causes to damage like incidents (Hulme and et.al., 2019).
Most of the times due to incident organisation also cost to death of human resources
employed in organisation. Poor decision making also involves casual nature against
to the precautionary measures needs to take prior to implementing the job operation.
Casualties and incidents are due to ineffective decision making on behalf of the
management which causes to incidents.
Precautionary measures not taken properly: This is also among the key active
failure involved in incident causation. It is noticed that among all major incidents
happened not taken of precautionary measure was among the primary reason
noticed by investigators. In case of dealing with heavy machineries and heavy metal
equipments precautionary measures taken are the primary necessary operation
team needs to engage before initiating any operation. Most of the time due to casual
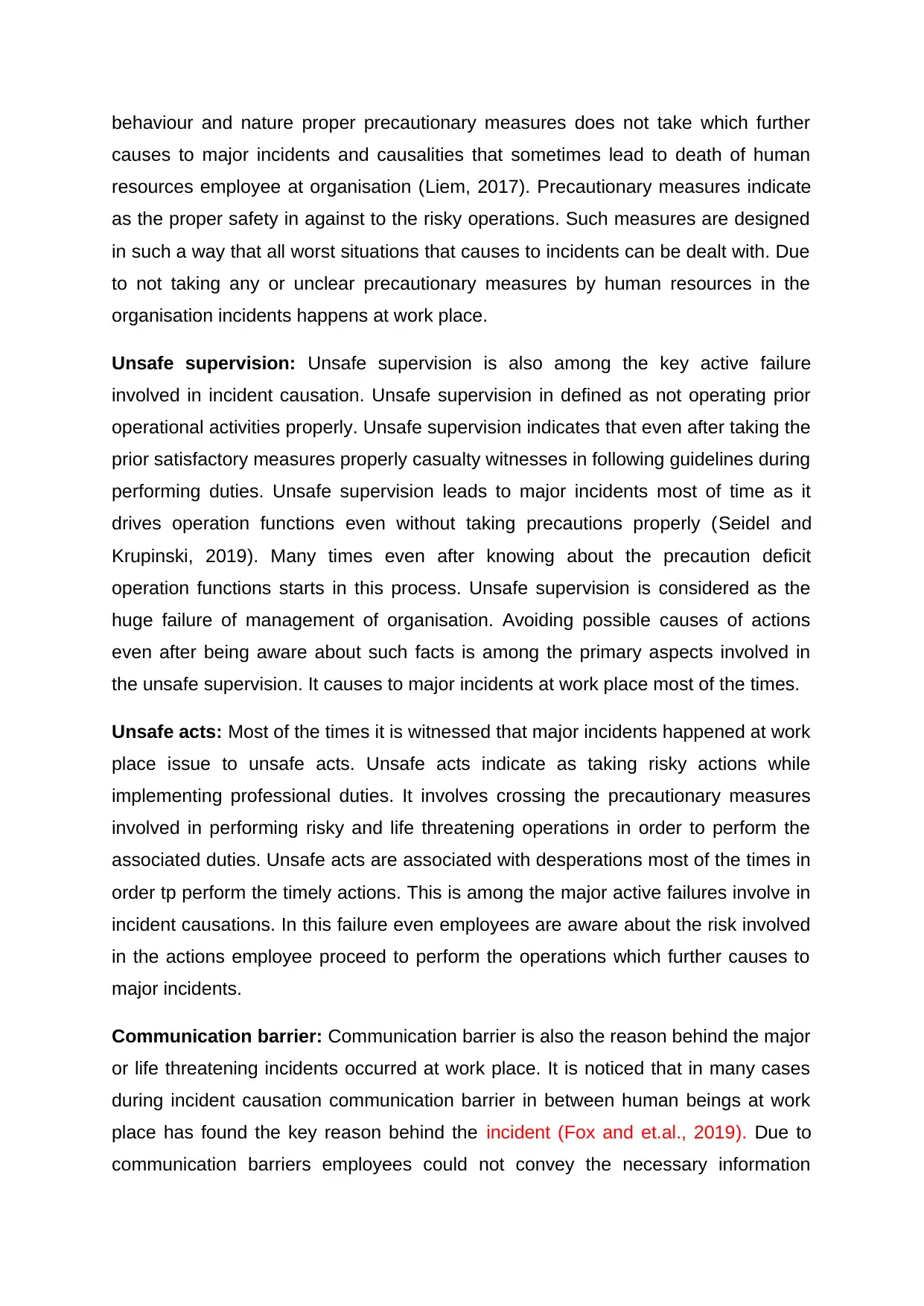
behaviour and nature proper precautionary measures does not take which further
causes to major incidents and causalities that sometimes lead to death of human
resources employee at organisation (Liem, 2017). Precautionary measures indicate
as the proper safety in against to the risky operations. Such measures are designed
in such a way that all worst situations that causes to incidents can be dealt with. Due
to not taking any or unclear precautionary measures by human resources in the
organisation incidents happens at work place.
Unsafe supervision: Unsafe supervision is also among the key active failure
involved in incident causation. Unsafe supervision in defined as not operating prior
operational activities properly. Unsafe supervision indicates that even after taking the
prior satisfactory measures properly casualty witnesses in following guidelines during
performing duties. Unsafe supervision leads to major incidents most of time as it
drives operation functions even without taking precautions properly (Seidel and
Krupinski, 2019). Many times even after knowing about the precaution deficit
operation functions starts in this process. Unsafe supervision is considered as the
huge failure of management of organisation. Avoiding possible causes of actions
even after being aware about such facts is among the primary aspects involved in
the unsafe supervision. It causes to major incidents at work place most of the times.
Unsafe acts: Most of the times it is witnessed that major incidents happened at work
place issue to unsafe acts. Unsafe acts indicate as taking risky actions while
implementing professional duties. It involves crossing the precautionary measures
involved in performing risky and life threatening operations in order to perform the
associated duties. Unsafe acts are associated with desperations most of the times in
order tp perform the timely actions. This is among the major active failures involve in
incident causations. In this failure even employees are aware about the risk involved
in the actions employee proceed to perform the operations which further causes to
major incidents.
Communication barrier: Communication barrier is also the reason behind the major
or life threatening incidents occurred at work place. It is noticed that in many cases
during incident causation communication barrier in between human beings at work
place has found the key reason behind the incident (Fox and et.al., 2019). Due to
communication barriers employees could not convey the necessary information
causes to major incidents and causalities that sometimes lead to death of human
resources employee at organisation (Liem, 2017). Precautionary measures indicate
as the proper safety in against to the risky operations. Such measures are designed
in such a way that all worst situations that causes to incidents can be dealt with. Due
to not taking any or unclear precautionary measures by human resources in the
organisation incidents happens at work place.
Unsafe supervision: Unsafe supervision is also among the key active failure
involved in incident causation. Unsafe supervision in defined as not operating prior
operational activities properly. Unsafe supervision indicates that even after taking the
prior satisfactory measures properly casualty witnesses in following guidelines during
performing duties. Unsafe supervision leads to major incidents most of time as it
drives operation functions even without taking precautions properly (Seidel and
Krupinski, 2019). Many times even after knowing about the precaution deficit
operation functions starts in this process. Unsafe supervision is considered as the
huge failure of management of organisation. Avoiding possible causes of actions
even after being aware about such facts is among the primary aspects involved in
the unsafe supervision. It causes to major incidents at work place most of the times.
Unsafe acts: Most of the times it is witnessed that major incidents happened at work
place issue to unsafe acts. Unsafe acts indicate as taking risky actions while
implementing professional duties. It involves crossing the precautionary measures
involved in performing risky and life threatening operations in order to perform the
associated duties. Unsafe acts are associated with desperations most of the times in
order tp perform the timely actions. This is among the major active failures involve in
incident causations. In this failure even employees are aware about the risk involved
in the actions employee proceed to perform the operations which further causes to
major incidents.
Communication barrier: Communication barrier is also the reason behind the major
or life threatening incidents occurred at work place. It is noticed that in many cases
during incident causation communication barrier in between human beings at work
place has found the key reason behind the incident (Fox and et.al., 2019). Due to
communication barriers employees could not convey the necessary information
⊘ This is a preview!⊘
Do you want full access?
Subscribe today to unlock all pages.

Trusted by 1+ million students worldwide
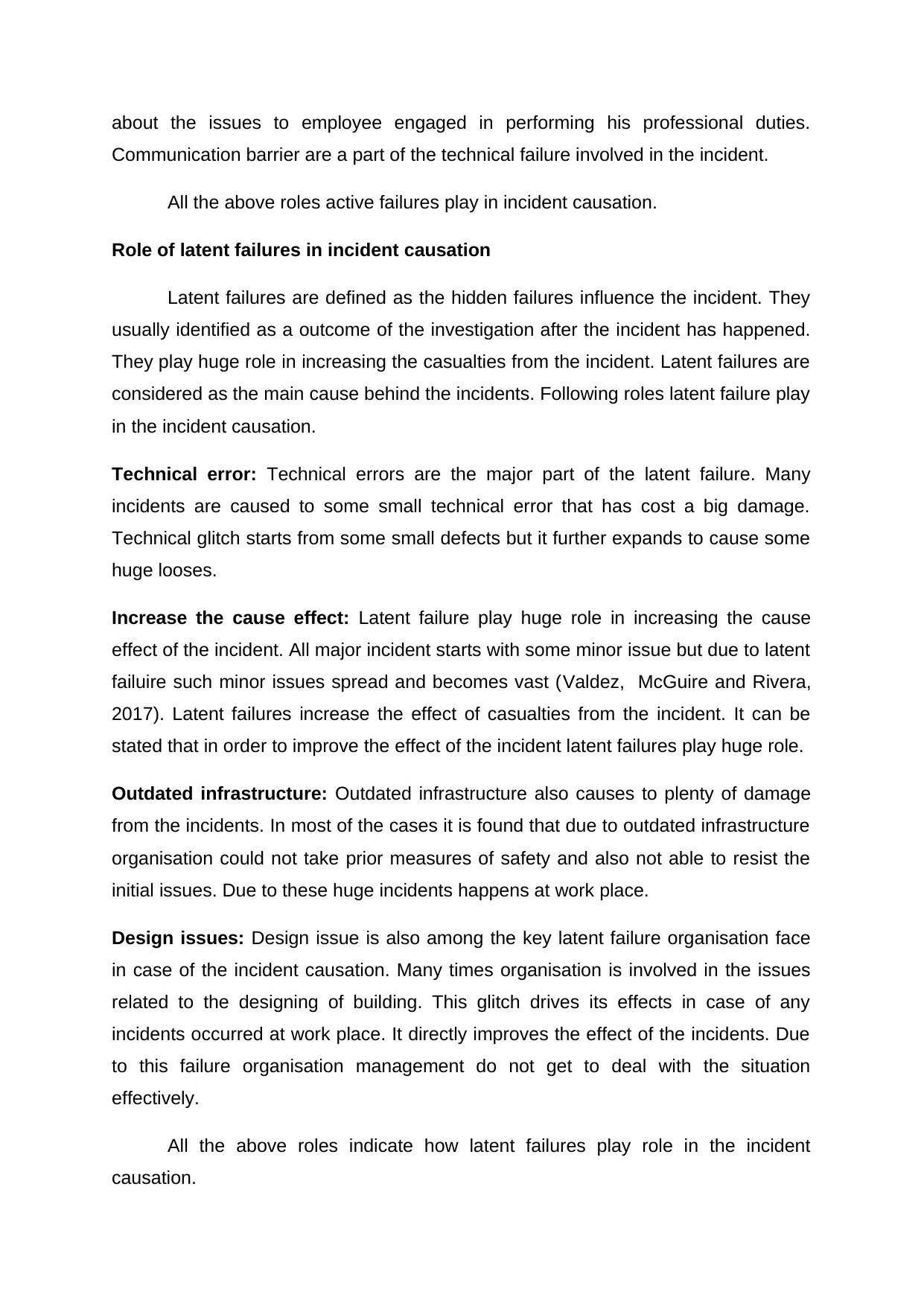
about the issues to employee engaged in performing his professional duties.
Communication barrier are a part of the technical failure involved in the incident.
All the above roles active failures play in incident causation.
Role of latent failures in incident causation
Latent failures are defined as the hidden failures influence the incident. They
usually identified as a outcome of the investigation after the incident has happened.
They play huge role in increasing the casualties from the incident. Latent failures are
considered as the main cause behind the incidents. Following roles latent failure play
in the incident causation.
Technical error: Technical errors are the major part of the latent failure. Many
incidents are caused to some small technical error that has cost a big damage.
Technical glitch starts from some small defects but it further expands to cause some
huge looses.
Increase the cause effect: Latent failure play huge role in increasing the cause
effect of the incident. All major incident starts with some minor issue but due to latent
failuire such minor issues spread and becomes vast (Valdez, McGuire and Rivera,
2017). Latent failures increase the effect of casualties from the incident. It can be
stated that in order to improve the effect of the incident latent failures play huge role.
Outdated infrastructure: Outdated infrastructure also causes to plenty of damage
from the incidents. In most of the cases it is found that due to outdated infrastructure
organisation could not take prior measures of safety and also not able to resist the
initial issues. Due to these huge incidents happens at work place.
Design issues: Design issue is also among the key latent failure organisation face
in case of the incident causation. Many times organisation is involved in the issues
related to the designing of building. This glitch drives its effects in case of any
incidents occurred at work place. It directly improves the effect of the incidents. Due
to this failure organisation management do not get to deal with the situation
effectively.
All the above roles indicate how latent failures play role in the incident
causation.
Communication barrier are a part of the technical failure involved in the incident.
All the above roles active failures play in incident causation.
Role of latent failures in incident causation
Latent failures are defined as the hidden failures influence the incident. They
usually identified as a outcome of the investigation after the incident has happened.
They play huge role in increasing the casualties from the incident. Latent failures are
considered as the main cause behind the incidents. Following roles latent failure play
in the incident causation.
Technical error: Technical errors are the major part of the latent failure. Many
incidents are caused to some small technical error that has cost a big damage.
Technical glitch starts from some small defects but it further expands to cause some
huge looses.
Increase the cause effect: Latent failure play huge role in increasing the cause
effect of the incident. All major incident starts with some minor issue but due to latent
failuire such minor issues spread and becomes vast (Valdez, McGuire and Rivera,
2017). Latent failures increase the effect of casualties from the incident. It can be
stated that in order to improve the effect of the incident latent failures play huge role.
Outdated infrastructure: Outdated infrastructure also causes to plenty of damage
from the incidents. In most of the cases it is found that due to outdated infrastructure
organisation could not take prior measures of safety and also not able to resist the
initial issues. Due to these huge incidents happens at work place.
Design issues: Design issue is also among the key latent failure organisation face
in case of the incident causation. Many times organisation is involved in the issues
related to the designing of building. This glitch drives its effects in case of any
incidents occurred at work place. It directly improves the effect of the incidents. Due
to this failure organisation management do not get to deal with the situation
effectively.
All the above roles indicate how latent failures play role in the incident
causation.
Paraphrase This Document
Need a fresh take? Get an instant paraphrase of this document with our AI Paraphraser
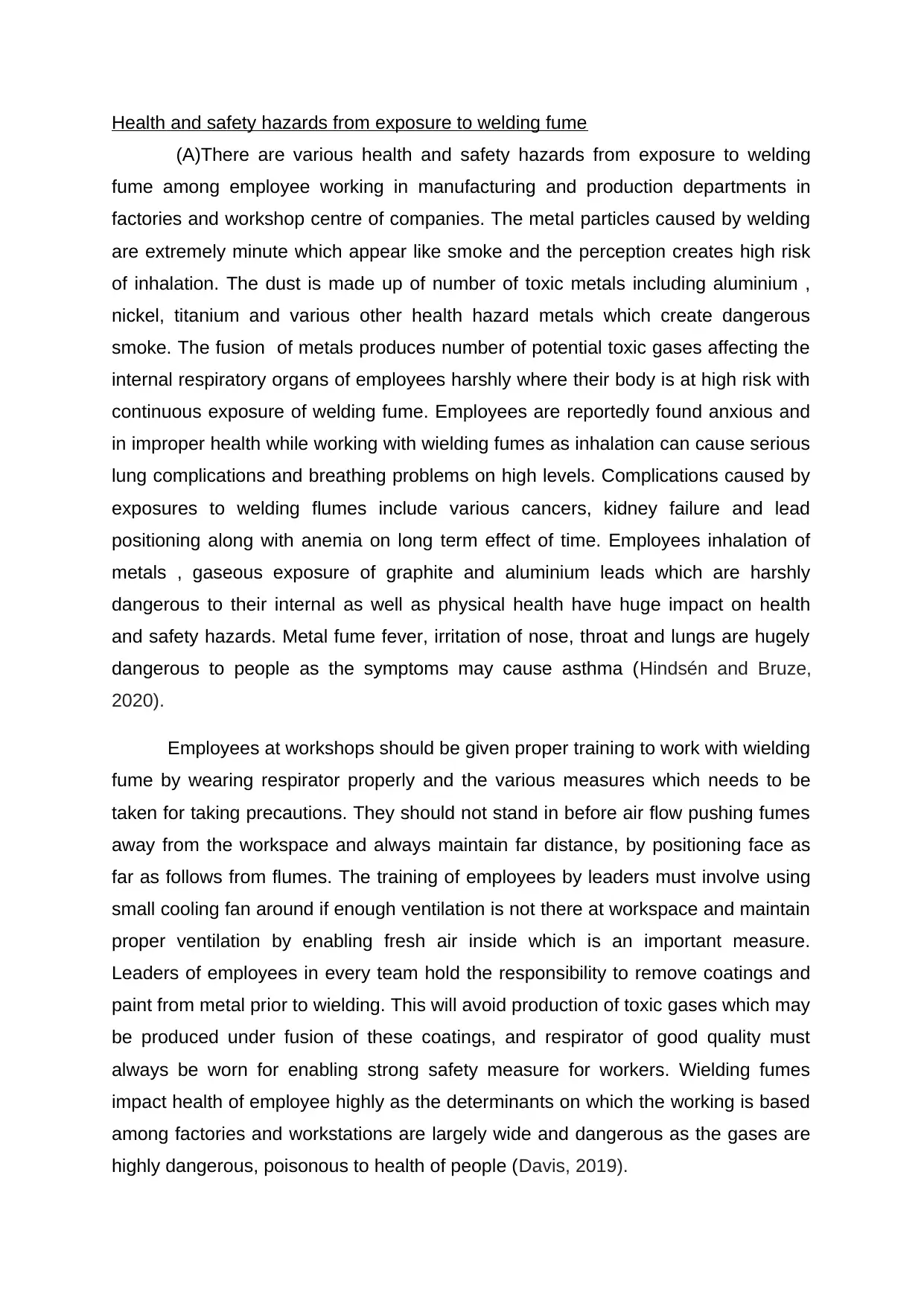
Health and safety hazards from exposure to welding fume
(A)There are various health and safety hazards from exposure to welding
fume among employee working in manufacturing and production departments in
factories and workshop centre of companies. The metal particles caused by welding
are extremely minute which appear like smoke and the perception creates high risk
of inhalation. The dust is made up of number of toxic metals including aluminium ,
nickel, titanium and various other health hazard metals which create dangerous
smoke. The fusion of metals produces number of potential toxic gases affecting the
internal respiratory organs of employees harshly where their body is at high risk with
continuous exposure of welding fume. Employees are reportedly found anxious and
in improper health while working with wielding fumes as inhalation can cause serious
lung complications and breathing problems on high levels. Complications caused by
exposures to welding flumes include various cancers, kidney failure and lead
positioning along with anemia on long term effect of time. Employees inhalation of
metals , gaseous exposure of graphite and aluminium leads which are harshly
dangerous to their internal as well as physical health have huge impact on health
and safety hazards. Metal fume fever, irritation of nose, throat and lungs are hugely
dangerous to people as the symptoms may cause asthma (Hindsén and Bruze,
2020).
Employees at workshops should be given proper training to work with wielding
fume by wearing respirator properly and the various measures which needs to be
taken for taking precautions. They should not stand in before air flow pushing fumes
away from the workspace and always maintain far distance, by positioning face as
far as follows from flumes. The training of employees by leaders must involve using
small cooling fan around if enough ventilation is not there at workspace and maintain
proper ventilation by enabling fresh air inside which is an important measure.
Leaders of employees in every team hold the responsibility to remove coatings and
paint from metal prior to wielding. This will avoid production of toxic gases which may
be produced under fusion of these coatings, and respirator of good quality must
always be worn for enabling strong safety measure for workers. Wielding fumes
impact health of employee highly as the determinants on which the working is based
among factories and workstations are largely wide and dangerous as the gases are
highly dangerous, poisonous to health of people (Davis, 2019).
(A)There are various health and safety hazards from exposure to welding
fume among employee working in manufacturing and production departments in
factories and workshop centre of companies. The metal particles caused by welding
are extremely minute which appear like smoke and the perception creates high risk
of inhalation. The dust is made up of number of toxic metals including aluminium ,
nickel, titanium and various other health hazard metals which create dangerous
smoke. The fusion of metals produces number of potential toxic gases affecting the
internal respiratory organs of employees harshly where their body is at high risk with
continuous exposure of welding fume. Employees are reportedly found anxious and
in improper health while working with wielding fumes as inhalation can cause serious
lung complications and breathing problems on high levels. Complications caused by
exposures to welding flumes include various cancers, kidney failure and lead
positioning along with anemia on long term effect of time. Employees inhalation of
metals , gaseous exposure of graphite and aluminium leads which are harshly
dangerous to their internal as well as physical health have huge impact on health
and safety hazards. Metal fume fever, irritation of nose, throat and lungs are hugely
dangerous to people as the symptoms may cause asthma (Hindsén and Bruze,
2020).
Employees at workshops should be given proper training to work with wielding
fume by wearing respirator properly and the various measures which needs to be
taken for taking precautions. They should not stand in before air flow pushing fumes
away from the workspace and always maintain far distance, by positioning face as
far as follows from flumes. The training of employees by leaders must involve using
small cooling fan around if enough ventilation is not there at workspace and maintain
proper ventilation by enabling fresh air inside which is an important measure.
Leaders of employees in every team hold the responsibility to remove coatings and
paint from metal prior to wielding. This will avoid production of toxic gases which may
be produced under fusion of these coatings, and respirator of good quality must
always be worn for enabling strong safety measure for workers. Wielding fumes
impact health of employee highly as the determinants on which the working is based
among factories and workstations are largely wide and dangerous as the gases are
highly dangerous, poisonous to health of people (Davis, 2019).
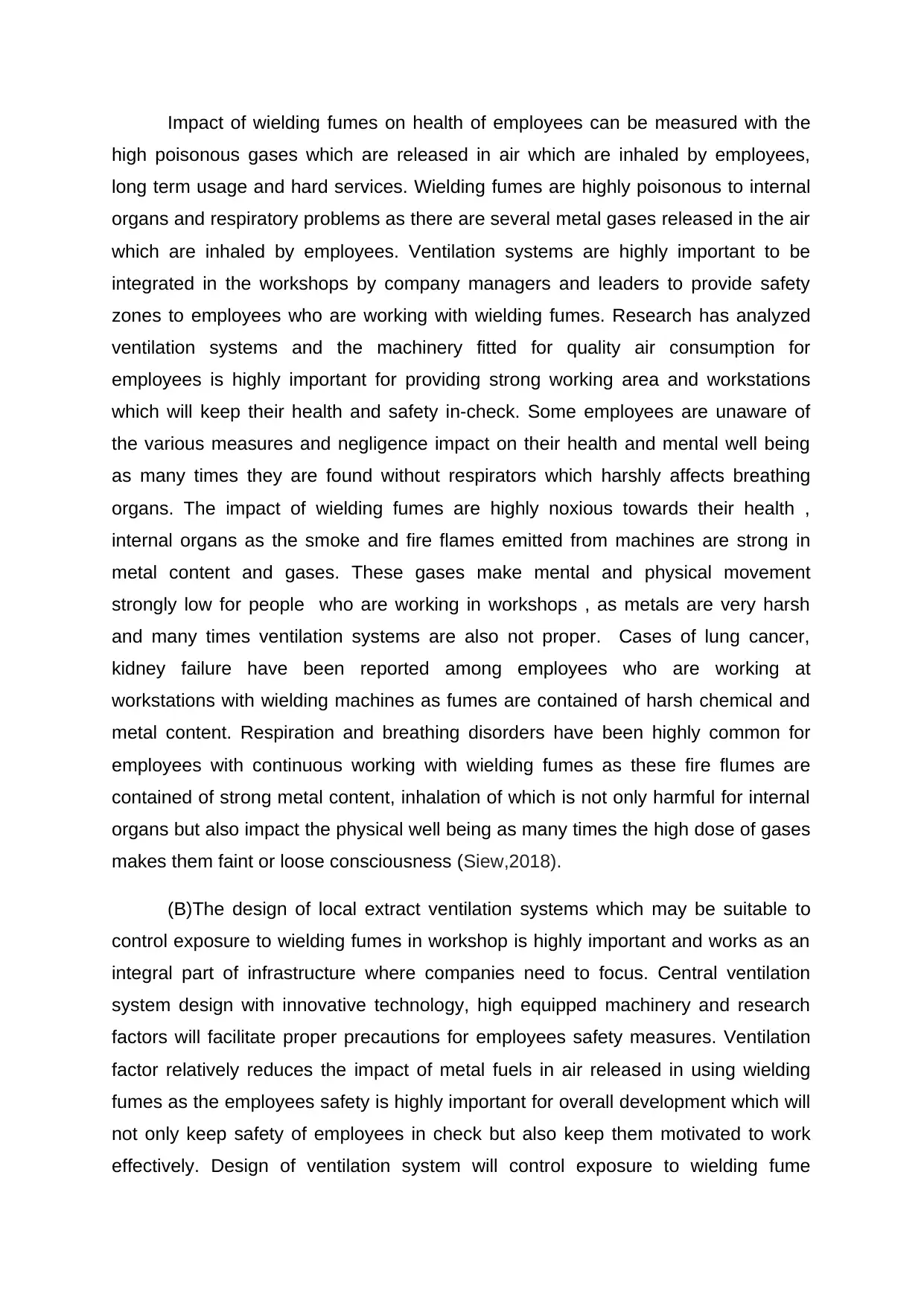
Impact of wielding fumes on health of employees can be measured with the
high poisonous gases which are released in air which are inhaled by employees,
long term usage and hard services. Wielding fumes are highly poisonous to internal
organs and respiratory problems as there are several metal gases released in the air
which are inhaled by employees. Ventilation systems are highly important to be
integrated in the workshops by company managers and leaders to provide safety
zones to employees who are working with wielding fumes. Research has analyzed
ventilation systems and the machinery fitted for quality air consumption for
employees is highly important for providing strong working area and workstations
which will keep their health and safety in-check. Some employees are unaware of
the various measures and negligence impact on their health and mental well being
as many times they are found without respirators which harshly affects breathing
organs. The impact of wielding fumes are highly noxious towards their health ,
internal organs as the smoke and fire flames emitted from machines are strong in
metal content and gases. These gases make mental and physical movement
strongly low for people who are working in workshops , as metals are very harsh
and many times ventilation systems are also not proper. Cases of lung cancer,
kidney failure have been reported among employees who are working at
workstations with wielding machines as fumes are contained of harsh chemical and
metal content. Respiration and breathing disorders have been highly common for
employees with continuous working with wielding fumes as these fire flumes are
contained of strong metal content, inhalation of which is not only harmful for internal
organs but also impact the physical well being as many times the high dose of gases
makes them faint or loose consciousness (Siew,2018).
(B)The design of local extract ventilation systems which may be suitable to
control exposure to wielding fumes in workshop is highly important and works as an
integral part of infrastructure where companies need to focus. Central ventilation
system design with innovative technology, high equipped machinery and research
factors will facilitate proper precautions for employees safety measures. Ventilation
factor relatively reduces the impact of metal fuels in air released in using wielding
fumes as the employees safety is highly important for overall development which will
not only keep safety of employees in check but also keep them motivated to work
effectively. Design of ventilation system will control exposure to wielding fume
high poisonous gases which are released in air which are inhaled by employees,
long term usage and hard services. Wielding fumes are highly poisonous to internal
organs and respiratory problems as there are several metal gases released in the air
which are inhaled by employees. Ventilation systems are highly important to be
integrated in the workshops by company managers and leaders to provide safety
zones to employees who are working with wielding fumes. Research has analyzed
ventilation systems and the machinery fitted for quality air consumption for
employees is highly important for providing strong working area and workstations
which will keep their health and safety in-check. Some employees are unaware of
the various measures and negligence impact on their health and mental well being
as many times they are found without respirators which harshly affects breathing
organs. The impact of wielding fumes are highly noxious towards their health ,
internal organs as the smoke and fire flames emitted from machines are strong in
metal content and gases. These gases make mental and physical movement
strongly low for people who are working in workshops , as metals are very harsh
and many times ventilation systems are also not proper. Cases of lung cancer,
kidney failure have been reported among employees who are working at
workstations with wielding machines as fumes are contained of harsh chemical and
metal content. Respiration and breathing disorders have been highly common for
employees with continuous working with wielding fumes as these fire flumes are
contained of strong metal content, inhalation of which is not only harmful for internal
organs but also impact the physical well being as many times the high dose of gases
makes them faint or loose consciousness (Siew,2018).
(B)The design of local extract ventilation systems which may be suitable to
control exposure to wielding fumes in workshop is highly important and works as an
integral part of infrastructure where companies need to focus. Central ventilation
system design with innovative technology, high equipped machinery and research
factors will facilitate proper precautions for employees safety measures. Ventilation
factor relatively reduces the impact of metal fuels in air released in using wielding
fumes as the employees safety is highly important for overall development which will
not only keep safety of employees in check but also keep them motivated to work
effectively. Design of ventilation system will control exposure to wielding fume
⊘ This is a preview!⊘
Do you want full access?
Subscribe today to unlock all pages.

Trusted by 1+ million students worldwide
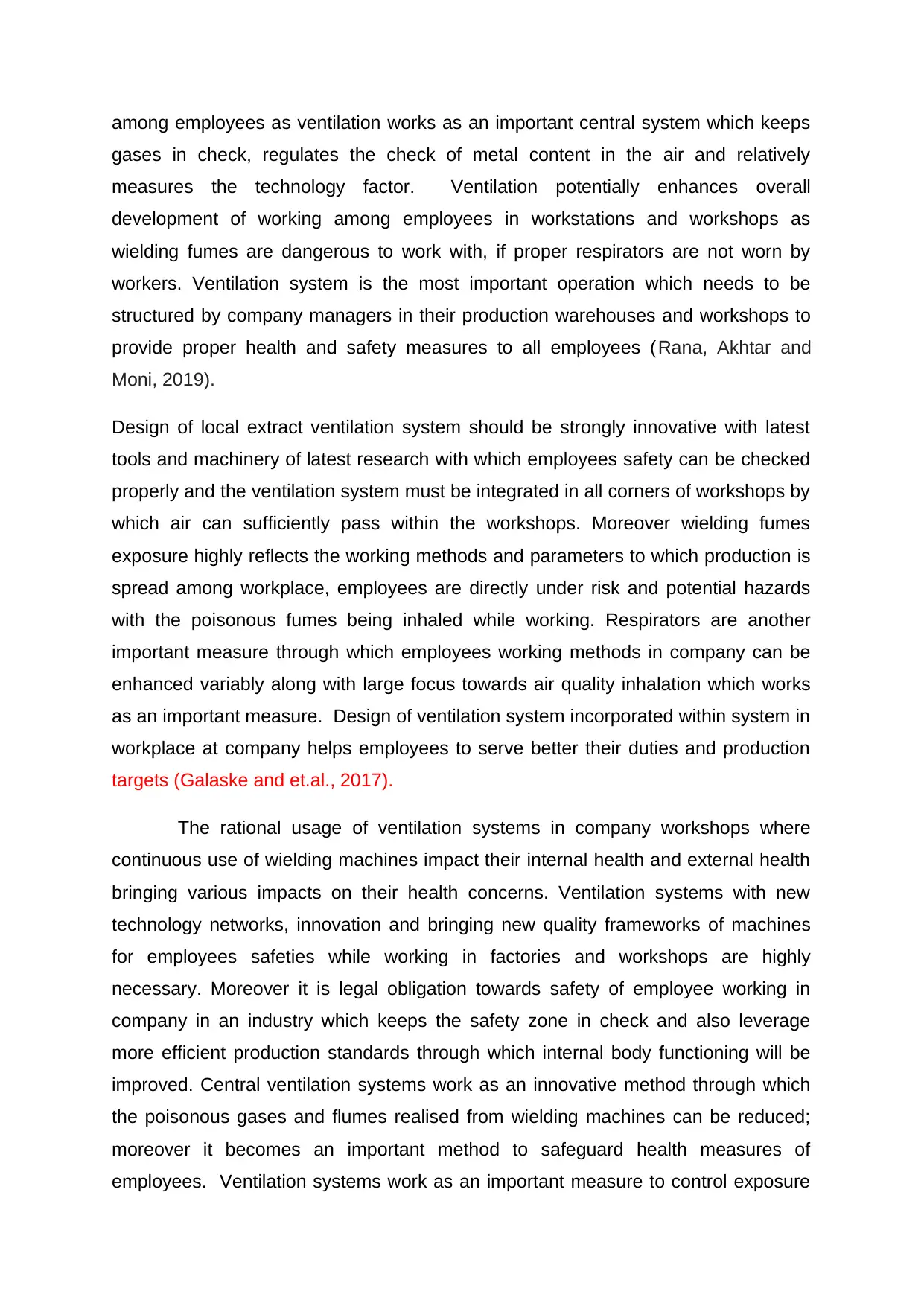
among employees as ventilation works as an important central system which keeps
gases in check, regulates the check of metal content in the air and relatively
measures the technology factor. Ventilation potentially enhances overall
development of working among employees in workstations and workshops as
wielding fumes are dangerous to work with, if proper respirators are not worn by
workers. Ventilation system is the most important operation which needs to be
structured by company managers in their production warehouses and workshops to
provide proper health and safety measures to all employees (Rana, Akhtar and
Moni, 2019).
Design of local extract ventilation system should be strongly innovative with latest
tools and machinery of latest research with which employees safety can be checked
properly and the ventilation system must be integrated in all corners of workshops by
which air can sufficiently pass within the workshops. Moreover wielding fumes
exposure highly reflects the working methods and parameters to which production is
spread among workplace, employees are directly under risk and potential hazards
with the poisonous fumes being inhaled while working. Respirators are another
important measure through which employees working methods in company can be
enhanced variably along with large focus towards air quality inhalation which works
as an important measure. Design of ventilation system incorporated within system in
workplace at company helps employees to serve better their duties and production
targets (Galaske and et.al., 2017).
The rational usage of ventilation systems in company workshops where
continuous use of wielding machines impact their internal health and external health
bringing various impacts on their health concerns. Ventilation systems with new
technology networks, innovation and bringing new quality frameworks of machines
for employees safeties while working in factories and workshops are highly
necessary. Moreover it is legal obligation towards safety of employee working in
company in an industry which keeps the safety zone in check and also leverage
more efficient production standards through which internal body functioning will be
improved. Central ventilation systems work as an innovative method through which
the poisonous gases and flumes realised from wielding machines can be reduced;
moreover it becomes an important method to safeguard health measures of
employees. Ventilation systems work as an important measure to control exposure
gases in check, regulates the check of metal content in the air and relatively
measures the technology factor. Ventilation potentially enhances overall
development of working among employees in workstations and workshops as
wielding fumes are dangerous to work with, if proper respirators are not worn by
workers. Ventilation system is the most important operation which needs to be
structured by company managers in their production warehouses and workshops to
provide proper health and safety measures to all employees (Rana, Akhtar and
Moni, 2019).
Design of local extract ventilation system should be strongly innovative with latest
tools and machinery of latest research with which employees safety can be checked
properly and the ventilation system must be integrated in all corners of workshops by
which air can sufficiently pass within the workshops. Moreover wielding fumes
exposure highly reflects the working methods and parameters to which production is
spread among workplace, employees are directly under risk and potential hazards
with the poisonous fumes being inhaled while working. Respirators are another
important measure through which employees working methods in company can be
enhanced variably along with large focus towards air quality inhalation which works
as an important measure. Design of ventilation system incorporated within system in
workplace at company helps employees to serve better their duties and production
targets (Galaske and et.al., 2017).
The rational usage of ventilation systems in company workshops where
continuous use of wielding machines impact their internal health and external health
bringing various impacts on their health concerns. Ventilation systems with new
technology networks, innovation and bringing new quality frameworks of machines
for employees safeties while working in factories and workshops are highly
necessary. Moreover it is legal obligation towards safety of employee working in
company in an industry which keeps the safety zone in check and also leverage
more efficient production standards through which internal body functioning will be
improved. Central ventilation systems work as an innovative method through which
the poisonous gases and flumes realised from wielding machines can be reduced;
moreover it becomes an important method to safeguard health measures of
employees. Ventilation systems work as an important measure to control exposure
Paraphrase This Document
Need a fresh take? Get an instant paraphrase of this document with our AI Paraphraser
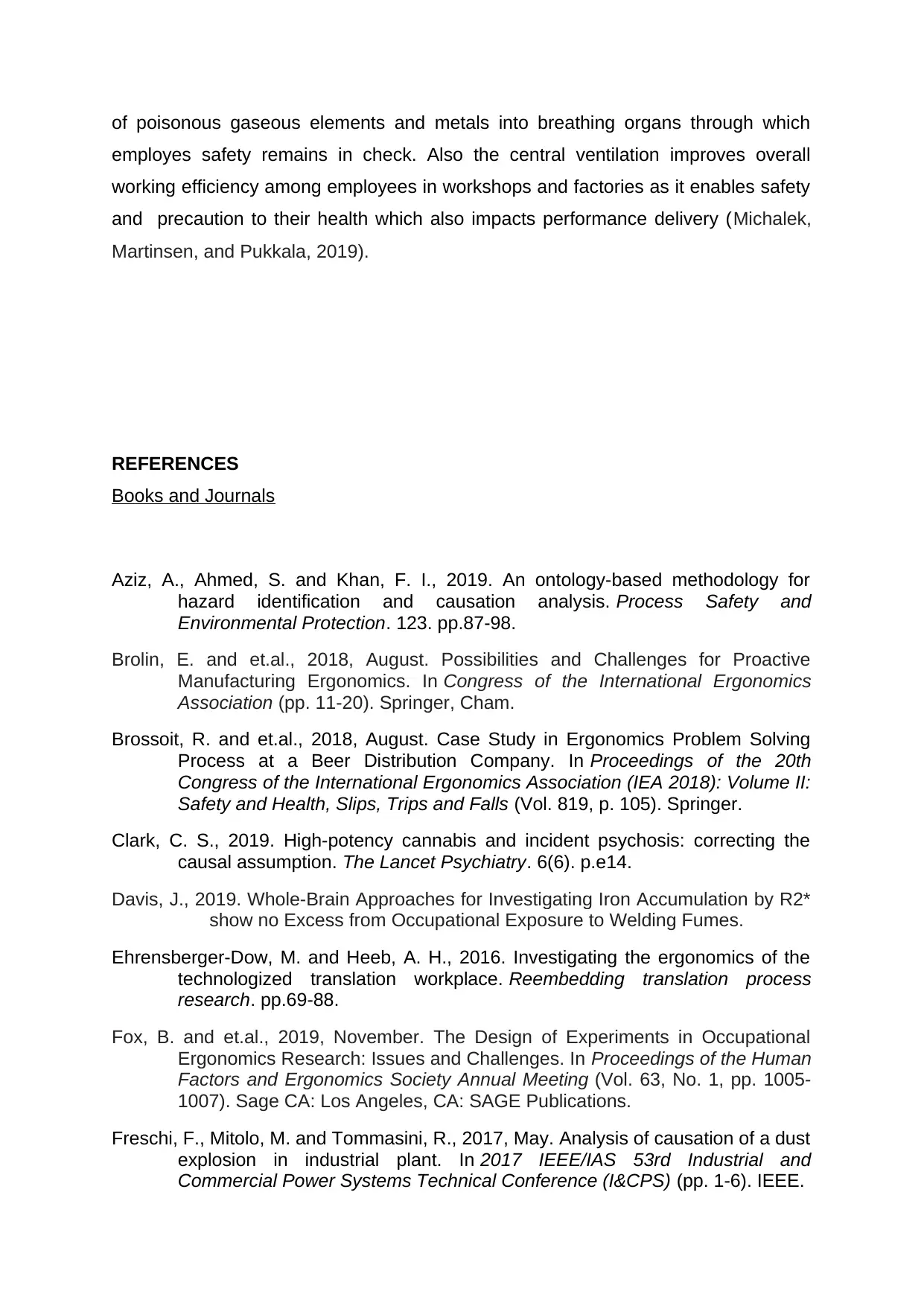
of poisonous gaseous elements and metals into breathing organs through which
employes safety remains in check. Also the central ventilation improves overall
working efficiency among employees in workshops and factories as it enables safety
and precaution to their health which also impacts performance delivery (Michalek,
Martinsen, and Pukkala, 2019).
REFERENCES
Books and Journals
Aziz, A., Ahmed, S. and Khan, F. I., 2019. An ontology-based methodology for
hazard identification and causation analysis. Process Safety and
Environmental Protection. 123. pp.87-98.
Brolin, E. and et.al., 2018, August. Possibilities and Challenges for Proactive
Manufacturing Ergonomics. In Congress of the International Ergonomics
Association (pp. 11-20). Springer, Cham.
Brossoit, R. and et.al., 2018, August. Case Study in Ergonomics Problem Solving
Process at a Beer Distribution Company. In Proceedings of the 20th
Congress of the International Ergonomics Association (IEA 2018): Volume II:
Safety and Health, Slips, Trips and Falls (Vol. 819, p. 105). Springer.
Clark, C. S., 2019. High-potency cannabis and incident psychosis: correcting the
causal assumption. The Lancet Psychiatry. 6(6). p.e14.
Davis, J., 2019. Whole-Brain Approaches for Investigating Iron Accumulation by R2*
show no Excess from Occupational Exposure to Welding Fumes.
Ehrensberger-Dow, M. and Heeb, A. H., 2016. Investigating the ergonomics of the
technologized translation workplace. Reembedding translation process
research. pp.69-88.
Fox, B. and et.al., 2019, November. The Design of Experiments in Occupational
Ergonomics Research: Issues and Challenges. In Proceedings of the Human
Factors and Ergonomics Society Annual Meeting (Vol. 63, No. 1, pp. 1005-
1007). Sage CA: Los Angeles, CA: SAGE Publications.
Freschi, F., Mitolo, M. and Tommasini, R., 2017, May. Analysis of causation of a dust
explosion in industrial plant. In 2017 IEEE/IAS 53rd Industrial and
Commercial Power Systems Technical Conference (I&CPS) (pp. 1-6). IEEE.
employes safety remains in check. Also the central ventilation improves overall
working efficiency among employees in workshops and factories as it enables safety
and precaution to their health which also impacts performance delivery (Michalek,
Martinsen, and Pukkala, 2019).
REFERENCES
Books and Journals
Aziz, A., Ahmed, S. and Khan, F. I., 2019. An ontology-based methodology for
hazard identification and causation analysis. Process Safety and
Environmental Protection. 123. pp.87-98.
Brolin, E. and et.al., 2018, August. Possibilities and Challenges for Proactive
Manufacturing Ergonomics. In Congress of the International Ergonomics
Association (pp. 11-20). Springer, Cham.
Brossoit, R. and et.al., 2018, August. Case Study in Ergonomics Problem Solving
Process at a Beer Distribution Company. In Proceedings of the 20th
Congress of the International Ergonomics Association (IEA 2018): Volume II:
Safety and Health, Slips, Trips and Falls (Vol. 819, p. 105). Springer.
Clark, C. S., 2019. High-potency cannabis and incident psychosis: correcting the
causal assumption. The Lancet Psychiatry. 6(6). p.e14.
Davis, J., 2019. Whole-Brain Approaches for Investigating Iron Accumulation by R2*
show no Excess from Occupational Exposure to Welding Fumes.
Ehrensberger-Dow, M. and Heeb, A. H., 2016. Investigating the ergonomics of the
technologized translation workplace. Reembedding translation process
research. pp.69-88.
Fox, B. and et.al., 2019, November. The Design of Experiments in Occupational
Ergonomics Research: Issues and Challenges. In Proceedings of the Human
Factors and Ergonomics Society Annual Meeting (Vol. 63, No. 1, pp. 1005-
1007). Sage CA: Los Angeles, CA: SAGE Publications.
Freschi, F., Mitolo, M. and Tommasini, R., 2017, May. Analysis of causation of a dust
explosion in industrial plant. In 2017 IEEE/IAS 53rd Industrial and
Commercial Power Systems Technical Conference (I&CPS) (pp. 1-6). IEEE.
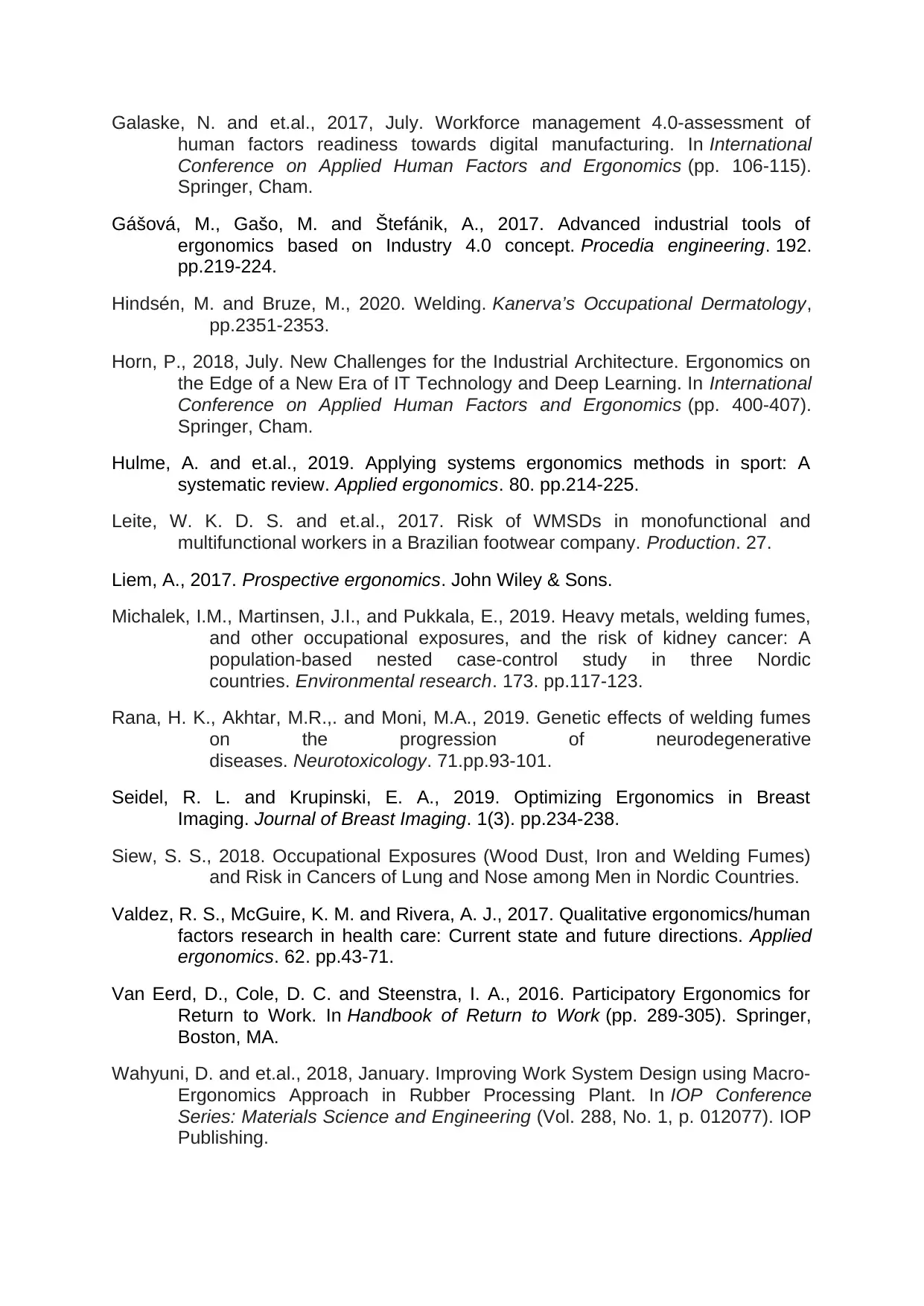
Galaske, N. and et.al., 2017, July. Workforce management 4.0-assessment of
human factors readiness towards digital manufacturing. In International
Conference on Applied Human Factors and Ergonomics (pp. 106-115).
Springer, Cham.
Gášová, M., Gašo, M. and Štefánik, A., 2017. Advanced industrial tools of
ergonomics based on Industry 4.0 concept. Procedia engineering. 192.
pp.219-224.
Hindsén, M. and Bruze, M., 2020. Welding. Kanerva’s Occupational Dermatology,
pp.2351-2353.
Horn, P., 2018, July. New Challenges for the Industrial Architecture. Ergonomics on
the Edge of a New Era of IT Technology and Deep Learning. In International
Conference on Applied Human Factors and Ergonomics (pp. 400-407).
Springer, Cham.
Hulme, A. and et.al., 2019. Applying systems ergonomics methods in sport: A
systematic review. Applied ergonomics. 80. pp.214-225.
Leite, W. K. D. S. and et.al., 2017. Risk of WMSDs in monofunctional and
multifunctional workers in a Brazilian footwear company. Production. 27.
Liem, A., 2017. Prospective ergonomics. John Wiley & Sons.
Michalek, I.M., Martinsen, J.I., and Pukkala, E., 2019. Heavy metals, welding fumes,
and other occupational exposures, and the risk of kidney cancer: A
population-based nested case-control study in three Nordic
countries. Environmental research. 173. pp.117-123.
Rana, H. K., Akhtar, M.R.,. and Moni, M.A., 2019. Genetic effects of welding fumes
on the progression of neurodegenerative
diseases. Neurotoxicology. 71.pp.93-101.
Seidel, R. L. and Krupinski, E. A., 2019. Optimizing Ergonomics in Breast
Imaging. Journal of Breast Imaging. 1(3). pp.234-238.
Siew, S. S., 2018. Occupational Exposures (Wood Dust, Iron and Welding Fumes)
and Risk in Cancers of Lung and Nose among Men in Nordic Countries.
Valdez, R. S., McGuire, K. M. and Rivera, A. J., 2017. Qualitative ergonomics/human
factors research in health care: Current state and future directions. Applied
ergonomics. 62. pp.43-71.
Van Eerd, D., Cole, D. C. and Steenstra, I. A., 2016. Participatory Ergonomics for
Return to Work. In Handbook of Return to Work (pp. 289-305). Springer,
Boston, MA.
Wahyuni, D. and et.al., 2018, January. Improving Work System Design using Macro-
Ergonomics Approach in Rubber Processing Plant. In IOP Conference
Series: Materials Science and Engineering (Vol. 288, No. 1, p. 012077). IOP
Publishing.
human factors readiness towards digital manufacturing. In International
Conference on Applied Human Factors and Ergonomics (pp. 106-115).
Springer, Cham.
Gášová, M., Gašo, M. and Štefánik, A., 2017. Advanced industrial tools of
ergonomics based on Industry 4.0 concept. Procedia engineering. 192.
pp.219-224.
Hindsén, M. and Bruze, M., 2020. Welding. Kanerva’s Occupational Dermatology,
pp.2351-2353.
Horn, P., 2018, July. New Challenges for the Industrial Architecture. Ergonomics on
the Edge of a New Era of IT Technology and Deep Learning. In International
Conference on Applied Human Factors and Ergonomics (pp. 400-407).
Springer, Cham.
Hulme, A. and et.al., 2019. Applying systems ergonomics methods in sport: A
systematic review. Applied ergonomics. 80. pp.214-225.
Leite, W. K. D. S. and et.al., 2017. Risk of WMSDs in monofunctional and
multifunctional workers in a Brazilian footwear company. Production. 27.
Liem, A., 2017. Prospective ergonomics. John Wiley & Sons.
Michalek, I.M., Martinsen, J.I., and Pukkala, E., 2019. Heavy metals, welding fumes,
and other occupational exposures, and the risk of kidney cancer: A
population-based nested case-control study in three Nordic
countries. Environmental research. 173. pp.117-123.
Rana, H. K., Akhtar, M.R.,. and Moni, M.A., 2019. Genetic effects of welding fumes
on the progression of neurodegenerative
diseases. Neurotoxicology. 71.pp.93-101.
Seidel, R. L. and Krupinski, E. A., 2019. Optimizing Ergonomics in Breast
Imaging. Journal of Breast Imaging. 1(3). pp.234-238.
Siew, S. S., 2018. Occupational Exposures (Wood Dust, Iron and Welding Fumes)
and Risk in Cancers of Lung and Nose among Men in Nordic Countries.
Valdez, R. S., McGuire, K. M. and Rivera, A. J., 2017. Qualitative ergonomics/human
factors research in health care: Current state and future directions. Applied
ergonomics. 62. pp.43-71.
Van Eerd, D., Cole, D. C. and Steenstra, I. A., 2016. Participatory Ergonomics for
Return to Work. In Handbook of Return to Work (pp. 289-305). Springer,
Boston, MA.
Wahyuni, D. and et.al., 2018, January. Improving Work System Design using Macro-
Ergonomics Approach in Rubber Processing Plant. In IOP Conference
Series: Materials Science and Engineering (Vol. 288, No. 1, p. 012077). IOP
Publishing.
⊘ This is a preview!⊘
Do you want full access?
Subscribe today to unlock all pages.

Trusted by 1+ million students worldwide
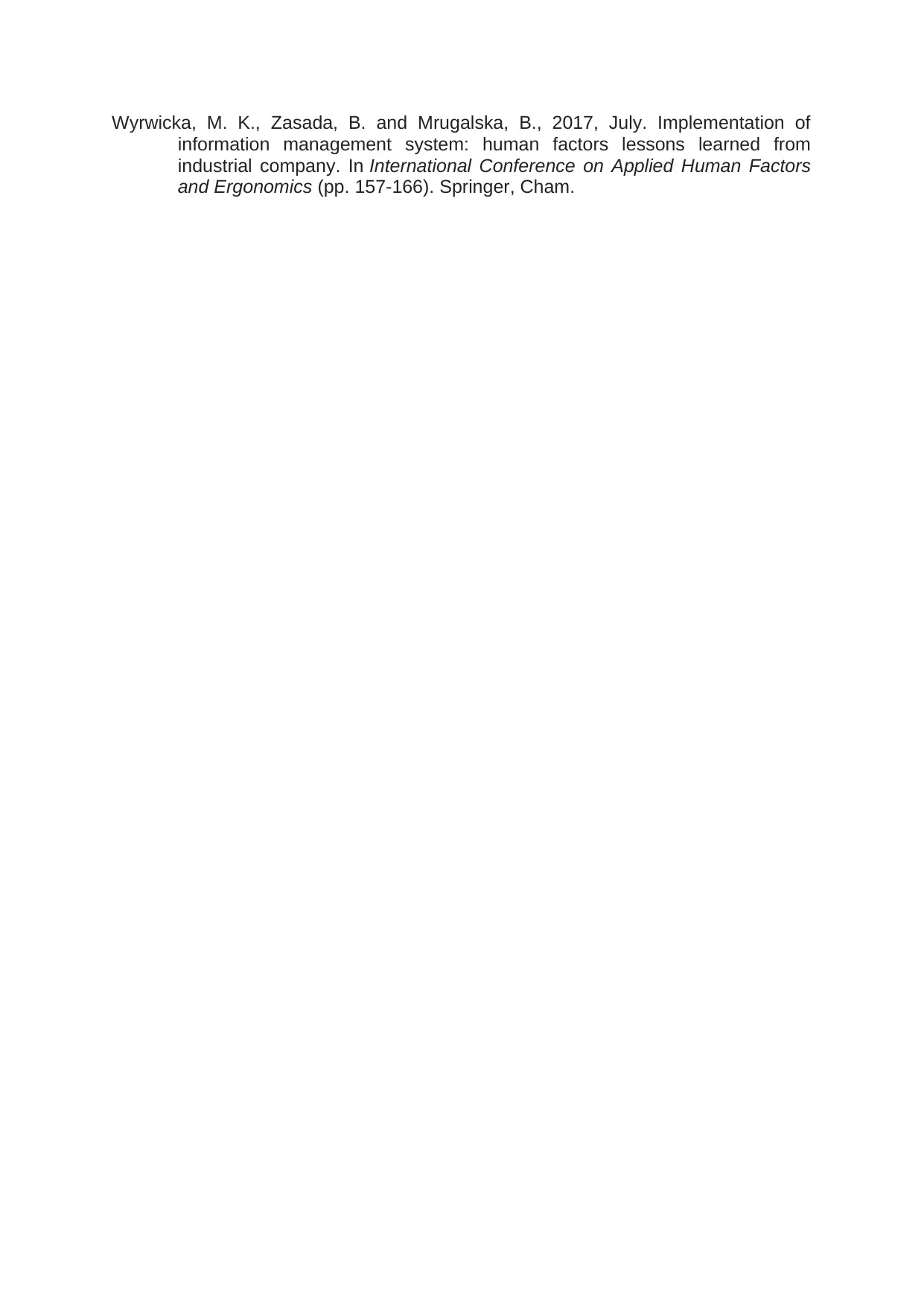
Wyrwicka, M. K., Zasada, B. and Mrugalska, B., 2017, July. Implementation of
information management system: human factors lessons learned from
industrial company. In International Conference on Applied Human Factors
and Ergonomics (pp. 157-166). Springer, Cham.
information management system: human factors lessons learned from
industrial company. In International Conference on Applied Human Factors
and Ergonomics (pp. 157-166). Springer, Cham.
1 out of 16
Related Documents

Your All-in-One AI-Powered Toolkit for Academic Success.
+13062052269
info@desklib.com
Available 24*7 on WhatsApp / Email
Unlock your academic potential
© 2024 | Zucol Services PVT LTD | All rights reserved.