Business Operations Report: Techniques and Frameworks Analysis
VerifiedAdded on 2023/01/05
|10
|3186
|52
Report
AI Summary
This report analyzes the business operations of Sainsbury, a major UK retail supermarket, focusing on best practices, analytical frameworks, and quality management techniques. It begins with an introduction to business operations and the context of Sainsbury. The main body identifies best practi...
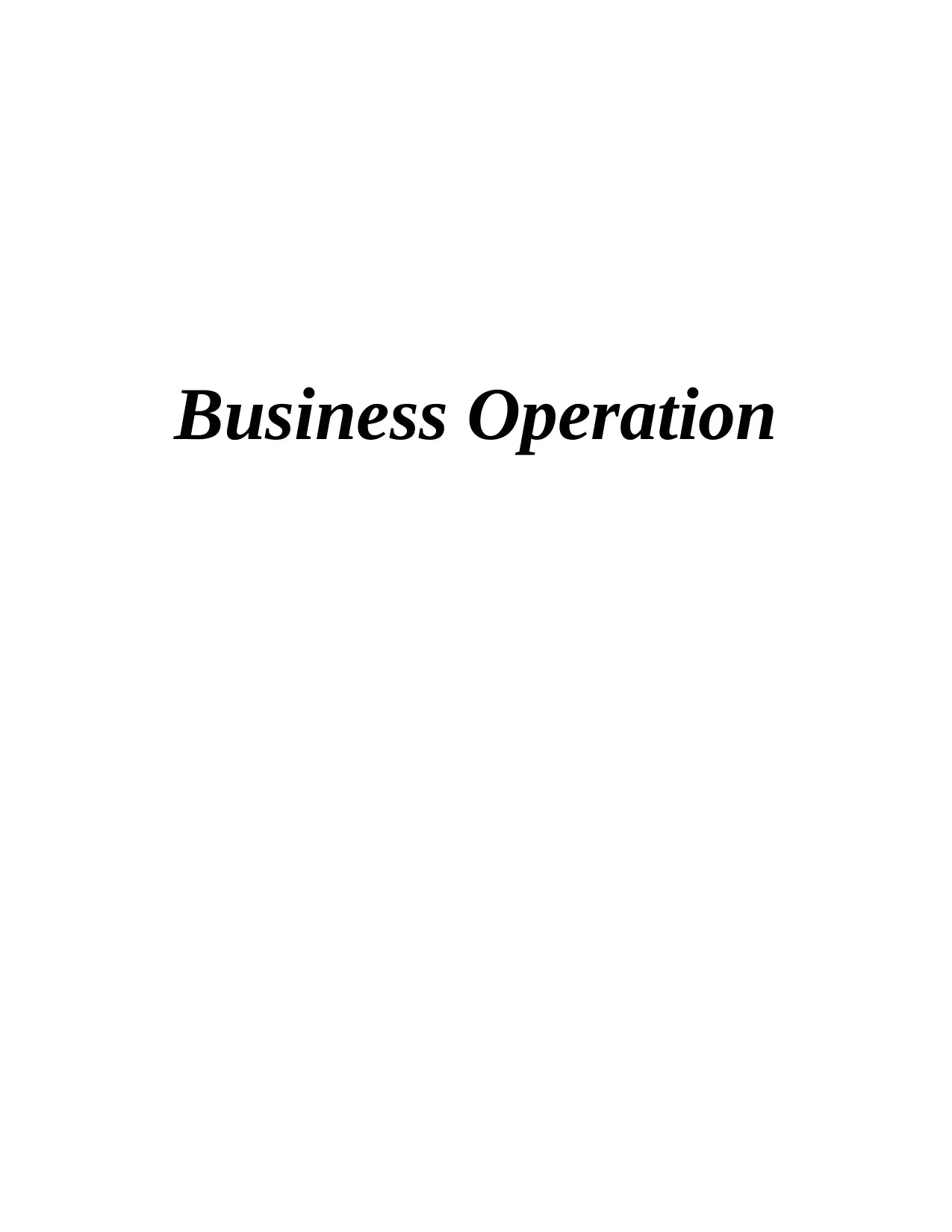
Business Operation
Secure Best Marks with AI Grader
Need help grading? Try our AI Grader for instant feedback on your assignments.
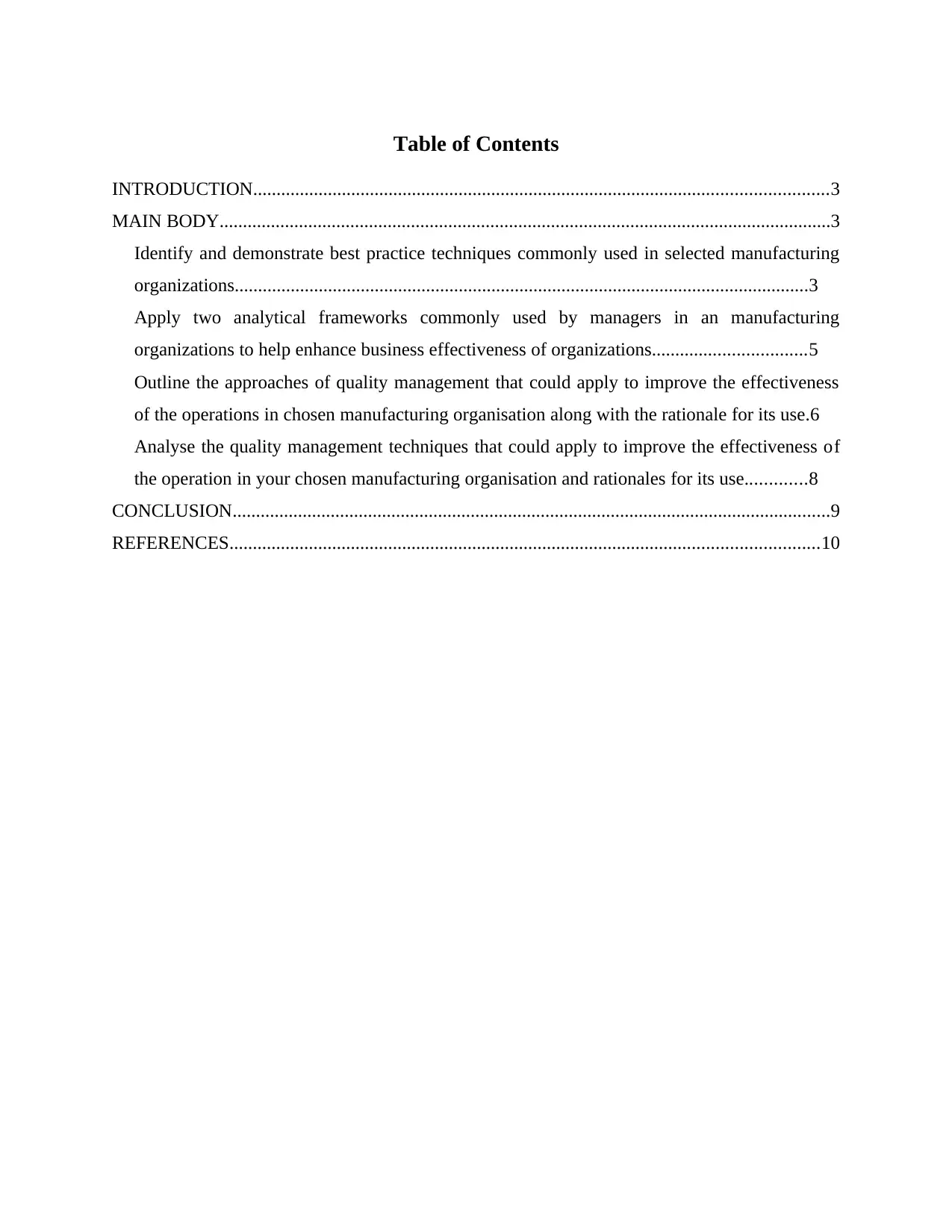
Table of Contents
INTRODUCTION...........................................................................................................................3
MAIN BODY...................................................................................................................................3
Identify and demonstrate best practice techniques commonly used in selected manufacturing
organizations...........................................................................................................................3
Apply two analytical frameworks commonly used by managers in an manufacturing
organizations to help enhance business effectiveness of organizations.................................5
Outline the approaches of quality management that could apply to improve the effectiveness
of the operations in chosen manufacturing organisation along with the rationale for its use.6
Analyse the quality management techniques that could apply to improve the effectiveness of
the operation in your chosen manufacturing organisation and rationales for its use.............8
CONCLUSION................................................................................................................................9
REFERENCES..............................................................................................................................10
INTRODUCTION...........................................................................................................................3
MAIN BODY...................................................................................................................................3
Identify and demonstrate best practice techniques commonly used in selected manufacturing
organizations...........................................................................................................................3
Apply two analytical frameworks commonly used by managers in an manufacturing
organizations to help enhance business effectiveness of organizations.................................5
Outline the approaches of quality management that could apply to improve the effectiveness
of the operations in chosen manufacturing organisation along with the rationale for its use.6
Analyse the quality management techniques that could apply to improve the effectiveness of
the operation in your chosen manufacturing organisation and rationales for its use.............8
CONCLUSION................................................................................................................................9
REFERENCES..............................................................................................................................10
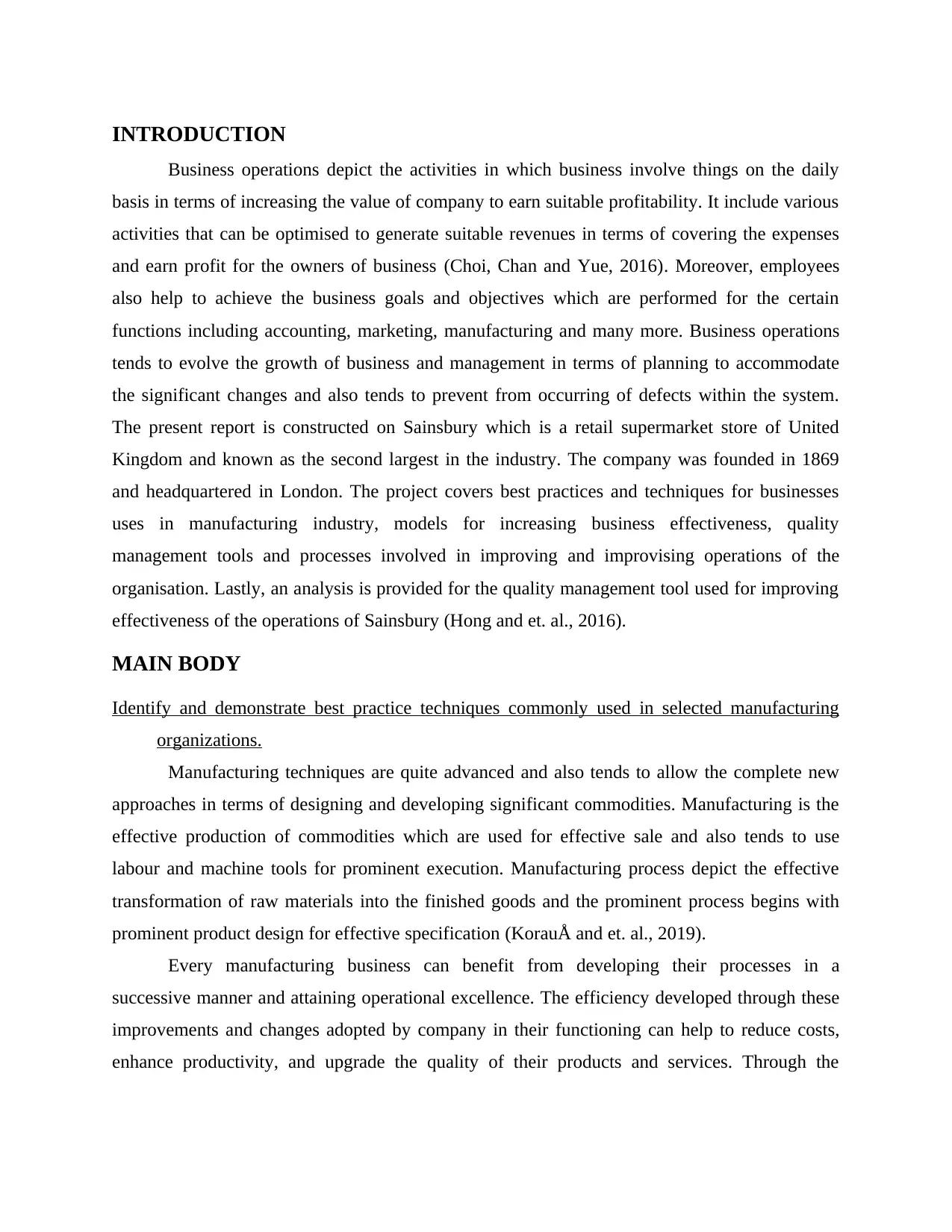
INTRODUCTION
Business operations depict the activities in which business involve things on the daily
basis in terms of increasing the value of company to earn suitable profitability. It include various
activities that can be optimised to generate suitable revenues in terms of covering the expenses
and earn profit for the owners of business (Choi, Chan and Yue, 2016). Moreover, employees
also help to achieve the business goals and objectives which are performed for the certain
functions including accounting, marketing, manufacturing and many more. Business operations
tends to evolve the growth of business and management in terms of planning to accommodate
the significant changes and also tends to prevent from occurring of defects within the system.
The present report is constructed on Sainsbury which is a retail supermarket store of United
Kingdom and known as the second largest in the industry. The company was founded in 1869
and headquartered in London. The project covers best practices and techniques for businesses
uses in manufacturing industry, models for increasing business effectiveness, quality
management tools and processes involved in improving and improvising operations of the
organisation. Lastly, an analysis is provided for the quality management tool used for improving
effectiveness of the operations of Sainsbury (Hong and et. al., 2016).
MAIN BODY
Identify and demonstrate best practice techniques commonly used in selected manufacturing
organizations.
Manufacturing techniques are quite advanced and also tends to allow the complete new
approaches in terms of designing and developing significant commodities. Manufacturing is the
effective production of commodities which are used for effective sale and also tends to use
labour and machine tools for prominent execution. Manufacturing process depict the effective
transformation of raw materials into the finished goods and the prominent process begins with
prominent product design for effective specification (KorauÅ and et. al., 2019).
Every manufacturing business can benefit from developing their processes in a
successive manner and attaining operational excellence. The efficiency developed through these
improvements and changes adopted by company in their functioning can help to reduce costs,
enhance productivity, and upgrade the quality of their products and services. Through the
Business operations depict the activities in which business involve things on the daily
basis in terms of increasing the value of company to earn suitable profitability. It include various
activities that can be optimised to generate suitable revenues in terms of covering the expenses
and earn profit for the owners of business (Choi, Chan and Yue, 2016). Moreover, employees
also help to achieve the business goals and objectives which are performed for the certain
functions including accounting, marketing, manufacturing and many more. Business operations
tends to evolve the growth of business and management in terms of planning to accommodate
the significant changes and also tends to prevent from occurring of defects within the system.
The present report is constructed on Sainsbury which is a retail supermarket store of United
Kingdom and known as the second largest in the industry. The company was founded in 1869
and headquartered in London. The project covers best practices and techniques for businesses
uses in manufacturing industry, models for increasing business effectiveness, quality
management tools and processes involved in improving and improvising operations of the
organisation. Lastly, an analysis is provided for the quality management tool used for improving
effectiveness of the operations of Sainsbury (Hong and et. al., 2016).
MAIN BODY
Identify and demonstrate best practice techniques commonly used in selected manufacturing
organizations.
Manufacturing techniques are quite advanced and also tends to allow the complete new
approaches in terms of designing and developing significant commodities. Manufacturing is the
effective production of commodities which are used for effective sale and also tends to use
labour and machine tools for prominent execution. Manufacturing process depict the effective
transformation of raw materials into the finished goods and the prominent process begins with
prominent product design for effective specification (KorauÅ and et. al., 2019).
Every manufacturing business can benefit from developing their processes in a
successive manner and attaining operational excellence. The efficiency developed through these
improvements and changes adopted by company in their functioning can help to reduce costs,
enhance productivity, and upgrade the quality of their products and services. Through the

changes made after a increase in sales and profits will be gained by the firm, along with a highly-
polished and attractive brand image.
Some of the general practices which are considered as best practices and will help
Sainsbury in accomplishing manufacturing goals and targets with appropriate inclusion of fair
amount of time, cooperation, employee motivation and collaboration of workforces and
management together. These practices and techniques are as follows and represented below in
Sainsbury context:
Eliminating Waste- Lean principle is one of the approach which is suitable and effectual
enough to adopt as it enable the management in identifying waste that will be found
nearly in every type of business. The lean principle will allow Sainsbury to make
improvements in such manner where their focus is kept on minimizing and even
completely eliminating all waste. One acronym that is “DOWNTIME” is made of eight
elements which are focused by the practice and management technique. These elements
which enable the firm in reducing and eliminating waste from operations are Defects,
Overproduction, Waiting, Not using people Talent, Transportation, Inventory,
Motion and Excess Processing (Luo, Lin and Zheng, 2019).
Continuous Improvement- Promoting a culture of continuous improvement in the firm
is another effective practice which is useful for inducing manufacturing efficiency of the
firm. Lean principles and management throughout the organizational structure, leads to
lean actions which creates an ability and desire in the whole organisation to do work
properly and perform in the best manner possible. Continuous improvement can happen
or take place on daily basis in Sainsbury and also the practice can be adopted over a
longer period of time through kaizen. A practice which is concentrated on making
changes and moving the organisation to improvement on a regular basis and in the most
suitable manner according to the dynamic environment. The Kaizen theory or method
assist in uncovering questionable processes and action which are not adding any value to
the Sainsbury and help in searching the possible solutions (Henderson, Goldring and
Simeon-Dubach, 2019).
Track Metrics- It is difficult for company to make improvements without measuring and
tracking the steps. If the management had the idea of having efficient processes in their
organisation and operations as well as their facilities they need to track the metrics to
polished and attractive brand image.
Some of the general practices which are considered as best practices and will help
Sainsbury in accomplishing manufacturing goals and targets with appropriate inclusion of fair
amount of time, cooperation, employee motivation and collaboration of workforces and
management together. These practices and techniques are as follows and represented below in
Sainsbury context:
Eliminating Waste- Lean principle is one of the approach which is suitable and effectual
enough to adopt as it enable the management in identifying waste that will be found
nearly in every type of business. The lean principle will allow Sainsbury to make
improvements in such manner where their focus is kept on minimizing and even
completely eliminating all waste. One acronym that is “DOWNTIME” is made of eight
elements which are focused by the practice and management technique. These elements
which enable the firm in reducing and eliminating waste from operations are Defects,
Overproduction, Waiting, Not using people Talent, Transportation, Inventory,
Motion and Excess Processing (Luo, Lin and Zheng, 2019).
Continuous Improvement- Promoting a culture of continuous improvement in the firm
is another effective practice which is useful for inducing manufacturing efficiency of the
firm. Lean principles and management throughout the organizational structure, leads to
lean actions which creates an ability and desire in the whole organisation to do work
properly and perform in the best manner possible. Continuous improvement can happen
or take place on daily basis in Sainsbury and also the practice can be adopted over a
longer period of time through kaizen. A practice which is concentrated on making
changes and moving the organisation to improvement on a regular basis and in the most
suitable manner according to the dynamic environment. The Kaizen theory or method
assist in uncovering questionable processes and action which are not adding any value to
the Sainsbury and help in searching the possible solutions (Henderson, Goldring and
Simeon-Dubach, 2019).
Track Metrics- It is difficult for company to make improvements without measuring and
tracking the steps. If the management had the idea of having efficient processes in their
organisation and operations as well as their facilities they need to track the metrics to
Secure Best Marks with AI Grader
Need help grading? Try our AI Grader for instant feedback on your assignments.
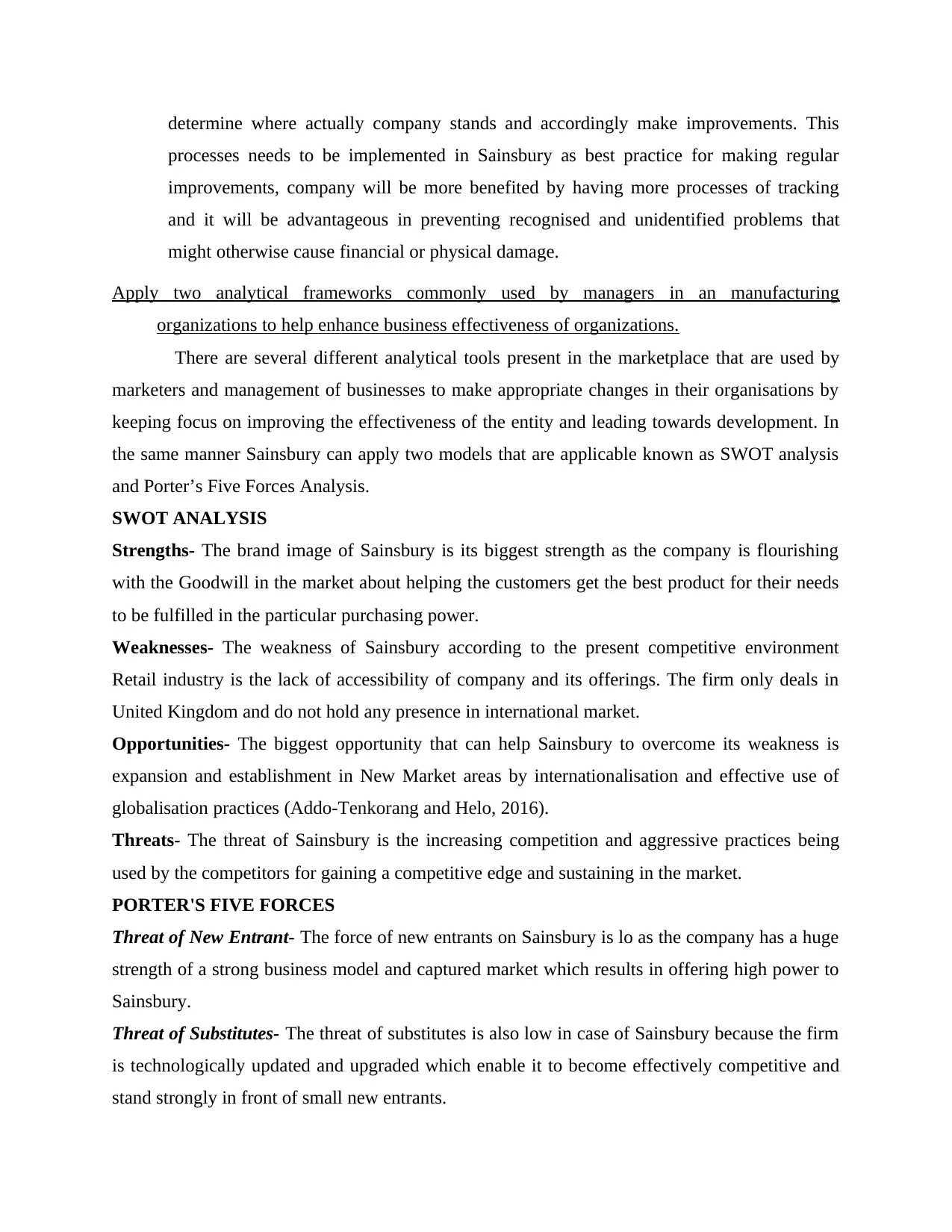
determine where actually company stands and accordingly make improvements. This
processes needs to be implemented in Sainsbury as best practice for making regular
improvements, company will be more benefited by having more processes of tracking
and it will be advantageous in preventing recognised and unidentified problems that
might otherwise cause financial or physical damage.
Apply two analytical frameworks commonly used by managers in an manufacturing
organizations to help enhance business effectiveness of organizations.
There are several different analytical tools present in the marketplace that are used by
marketers and management of businesses to make appropriate changes in their organisations by
keeping focus on improving the effectiveness of the entity and leading towards development. In
the same manner Sainsbury can apply two models that are applicable known as SWOT analysis
and Porter’s Five Forces Analysis.
SWOT ANALYSIS
Strengths- The brand image of Sainsbury is its biggest strength as the company is flourishing
with the Goodwill in the market about helping the customers get the best product for their needs
to be fulfilled in the particular purchasing power.
Weaknesses- The weakness of Sainsbury according to the present competitive environment
Retail industry is the lack of accessibility of company and its offerings. The firm only deals in
United Kingdom and do not hold any presence in international market.
Opportunities- The biggest opportunity that can help Sainsbury to overcome its weakness is
expansion and establishment in New Market areas by internationalisation and effective use of
globalisation practices (Addo-Tenkorang and Helo, 2016).
Threats- The threat of Sainsbury is the increasing competition and aggressive practices being
used by the competitors for gaining a competitive edge and sustaining in the market.
PORTER'S FIVE FORCES
Threat of New Entrant- The force of new entrants on Sainsbury is lo as the company has a huge
strength of a strong business model and captured market which results in offering high power to
Sainsbury.
Threat of Substitutes- The threat of substitutes is also low in case of Sainsbury because the firm
is technologically updated and upgraded which enable it to become effectively competitive and
stand strongly in front of small new entrants.
processes needs to be implemented in Sainsbury as best practice for making regular
improvements, company will be more benefited by having more processes of tracking
and it will be advantageous in preventing recognised and unidentified problems that
might otherwise cause financial or physical damage.
Apply two analytical frameworks commonly used by managers in an manufacturing
organizations to help enhance business effectiveness of organizations.
There are several different analytical tools present in the marketplace that are used by
marketers and management of businesses to make appropriate changes in their organisations by
keeping focus on improving the effectiveness of the entity and leading towards development. In
the same manner Sainsbury can apply two models that are applicable known as SWOT analysis
and Porter’s Five Forces Analysis.
SWOT ANALYSIS
Strengths- The brand image of Sainsbury is its biggest strength as the company is flourishing
with the Goodwill in the market about helping the customers get the best product for their needs
to be fulfilled in the particular purchasing power.
Weaknesses- The weakness of Sainsbury according to the present competitive environment
Retail industry is the lack of accessibility of company and its offerings. The firm only deals in
United Kingdom and do not hold any presence in international market.
Opportunities- The biggest opportunity that can help Sainsbury to overcome its weakness is
expansion and establishment in New Market areas by internationalisation and effective use of
globalisation practices (Addo-Tenkorang and Helo, 2016).
Threats- The threat of Sainsbury is the increasing competition and aggressive practices being
used by the competitors for gaining a competitive edge and sustaining in the market.
PORTER'S FIVE FORCES
Threat of New Entrant- The force of new entrants on Sainsbury is lo as the company has a huge
strength of a strong business model and captured market which results in offering high power to
Sainsbury.
Threat of Substitutes- The threat of substitutes is also low in case of Sainsbury because the firm
is technologically updated and upgraded which enable it to become effectively competitive and
stand strongly in front of small new entrants.
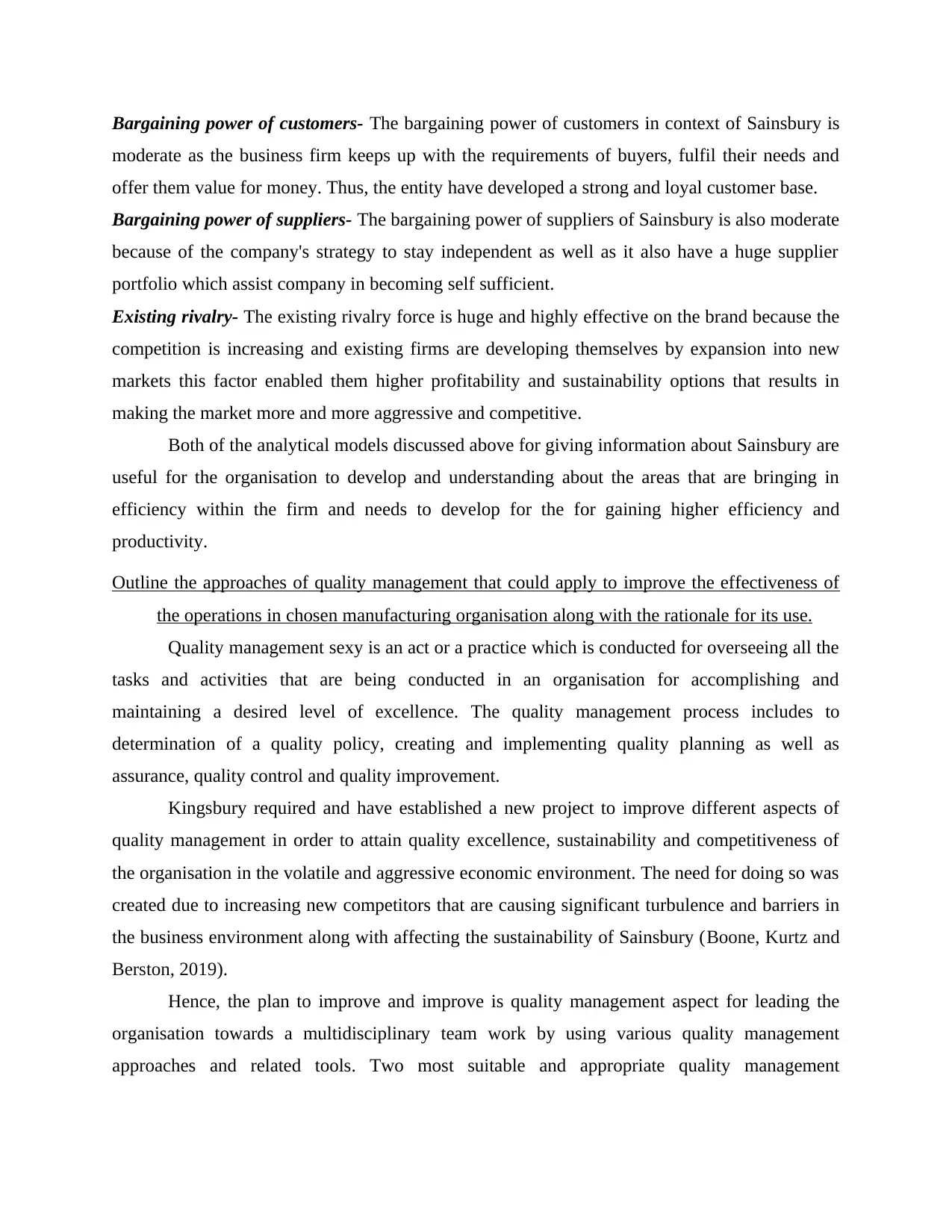
Bargaining power of customers- The bargaining power of customers in context of Sainsbury is
moderate as the business firm keeps up with the requirements of buyers, fulfil their needs and
offer them value for money. Thus, the entity have developed a strong and loyal customer base.
Bargaining power of suppliers- The bargaining power of suppliers of Sainsbury is also moderate
because of the company's strategy to stay independent as well as it also have a huge supplier
portfolio which assist company in becoming self sufficient.
Existing rivalry- The existing rivalry force is huge and highly effective on the brand because the
competition is increasing and existing firms are developing themselves by expansion into new
markets this factor enabled them higher profitability and sustainability options that results in
making the market more and more aggressive and competitive.
Both of the analytical models discussed above for giving information about Sainsbury are
useful for the organisation to develop and understanding about the areas that are bringing in
efficiency within the firm and needs to develop for the for gaining higher efficiency and
productivity.
Outline the approaches of quality management that could apply to improve the effectiveness of
the operations in chosen manufacturing organisation along with the rationale for its use.
Quality management sexy is an act or a practice which is conducted for overseeing all the
tasks and activities that are being conducted in an organisation for accomplishing and
maintaining a desired level of excellence. The quality management process includes to
determination of a quality policy, creating and implementing quality planning as well as
assurance, quality control and quality improvement.
Kingsbury required and have established a new project to improve different aspects of
quality management in order to attain quality excellence, sustainability and competitiveness of
the organisation in the volatile and aggressive economic environment. The need for doing so was
created due to increasing new competitors that are causing significant turbulence and barriers in
the business environment along with affecting the sustainability of Sainsbury (Boone, Kurtz and
Berston, 2019).
Hence, the plan to improve and improve is quality management aspect for leading the
organisation towards a multidisciplinary team work by using various quality management
approaches and related tools. Two most suitable and appropriate quality management
moderate as the business firm keeps up with the requirements of buyers, fulfil their needs and
offer them value for money. Thus, the entity have developed a strong and loyal customer base.
Bargaining power of suppliers- The bargaining power of suppliers of Sainsbury is also moderate
because of the company's strategy to stay independent as well as it also have a huge supplier
portfolio which assist company in becoming self sufficient.
Existing rivalry- The existing rivalry force is huge and highly effective on the brand because the
competition is increasing and existing firms are developing themselves by expansion into new
markets this factor enabled them higher profitability and sustainability options that results in
making the market more and more aggressive and competitive.
Both of the analytical models discussed above for giving information about Sainsbury are
useful for the organisation to develop and understanding about the areas that are bringing in
efficiency within the firm and needs to develop for the for gaining higher efficiency and
productivity.
Outline the approaches of quality management that could apply to improve the effectiveness of
the operations in chosen manufacturing organisation along with the rationale for its use.
Quality management sexy is an act or a practice which is conducted for overseeing all the
tasks and activities that are being conducted in an organisation for accomplishing and
maintaining a desired level of excellence. The quality management process includes to
determination of a quality policy, creating and implementing quality planning as well as
assurance, quality control and quality improvement.
Kingsbury required and have established a new project to improve different aspects of
quality management in order to attain quality excellence, sustainability and competitiveness of
the organisation in the volatile and aggressive economic environment. The need for doing so was
created due to increasing new competitors that are causing significant turbulence and barriers in
the business environment along with affecting the sustainability of Sainsbury (Boone, Kurtz and
Berston, 2019).
Hence, the plan to improve and improve is quality management aspect for leading the
organisation towards a multidisciplinary team work by using various quality management
approaches and related tools. Two most suitable and appropriate quality management
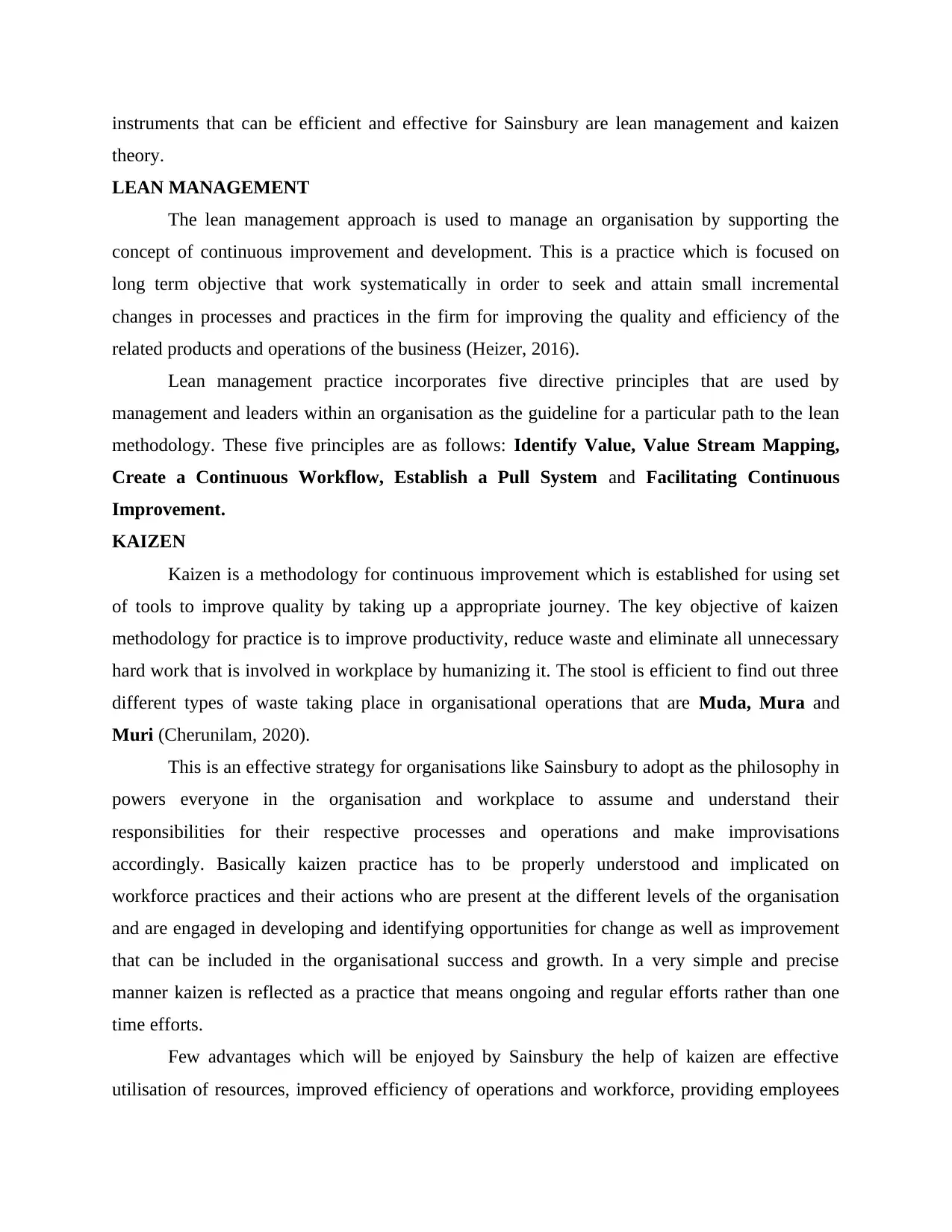
instruments that can be efficient and effective for Sainsbury are lean management and kaizen
theory.
LEAN MANAGEMENT
The lean management approach is used to manage an organisation by supporting the
concept of continuous improvement and development. This is a practice which is focused on
long term objective that work systematically in order to seek and attain small incremental
changes in processes and practices in the firm for improving the quality and efficiency of the
related products and operations of the business (Heizer, 2016).
Lean management practice incorporates five directive principles that are used by
management and leaders within an organisation as the guideline for a particular path to the lean
methodology. These five principles are as follows: Identify Value, Value Stream Mapping,
Create a Continuous Workflow, Establish a Pull System and Facilitating Continuous
Improvement.
KAIZEN
Kaizen is a methodology for continuous improvement which is established for using set
of tools to improve quality by taking up a appropriate journey. The key objective of kaizen
methodology for practice is to improve productivity, reduce waste and eliminate all unnecessary
hard work that is involved in workplace by humanizing it. The stool is efficient to find out three
different types of waste taking place in organisational operations that are Muda, Mura and
Muri (Cherunilam, 2020).
This is an effective strategy for organisations like Sainsbury to adopt as the philosophy in
powers everyone in the organisation and workplace to assume and understand their
responsibilities for their respective processes and operations and make improvisations
accordingly. Basically kaizen practice has to be properly understood and implicated on
workforce practices and their actions who are present at the different levels of the organisation
and are engaged in developing and identifying opportunities for change as well as improvement
that can be included in the organisational success and growth. In a very simple and precise
manner kaizen is reflected as a practice that means ongoing and regular efforts rather than one
time efforts.
Few advantages which will be enjoyed by Sainsbury the help of kaizen are effective
utilisation of resources, improved efficiency of operations and workforce, providing employees
theory.
LEAN MANAGEMENT
The lean management approach is used to manage an organisation by supporting the
concept of continuous improvement and development. This is a practice which is focused on
long term objective that work systematically in order to seek and attain small incremental
changes in processes and practices in the firm for improving the quality and efficiency of the
related products and operations of the business (Heizer, 2016).
Lean management practice incorporates five directive principles that are used by
management and leaders within an organisation as the guideline for a particular path to the lean
methodology. These five principles are as follows: Identify Value, Value Stream Mapping,
Create a Continuous Workflow, Establish a Pull System and Facilitating Continuous
Improvement.
KAIZEN
Kaizen is a methodology for continuous improvement which is established for using set
of tools to improve quality by taking up a appropriate journey. The key objective of kaizen
methodology for practice is to improve productivity, reduce waste and eliminate all unnecessary
hard work that is involved in workplace by humanizing it. The stool is efficient to find out three
different types of waste taking place in organisational operations that are Muda, Mura and
Muri (Cherunilam, 2020).
This is an effective strategy for organisations like Sainsbury to adopt as the philosophy in
powers everyone in the organisation and workplace to assume and understand their
responsibilities for their respective processes and operations and make improvisations
accordingly. Basically kaizen practice has to be properly understood and implicated on
workforce practices and their actions who are present at the different levels of the organisation
and are engaged in developing and identifying opportunities for change as well as improvement
that can be included in the organisational success and growth. In a very simple and precise
manner kaizen is reflected as a practice that means ongoing and regular efforts rather than one
time efforts.
Few advantages which will be enjoyed by Sainsbury the help of kaizen are effective
utilisation of resources, improved efficiency of operations and workforce, providing employees
Paraphrase This Document
Need a fresh take? Get an instant paraphrase of this document with our AI Paraphraser

job satisfaction and making improvements with all safety concerns and measures. The
philosophy not just involve one person or a particular department of the company in the whole
phenomena on the other hand it involves everyone in the organisation for making improvements
and putting efforts according to the plans made.
Analyse the quality management techniques that could apply to improve the effectiveness of the
operation in your chosen manufacturing organisation and rationales for its use.
The new project which is introduced by the CEO of Sainsbury is to make quality
management for attaining quality excellence, sustainability and competitiveness in the market. In
order to perform the project with similar and even higher efficiency the company needs to
implement certain quality management approaches or techniques. From the above discussed
policies the one which is most suitable for the company to implement is lean management
(Mendling and et. al., 2018).
The lean Management process will be focused on defining value from the standpoint of
the end customer of Sainsbury, eliminating all the waste efforts and practices being used in the
business operations of Sainsbury and lastly it will be concerned with making continuous
improvements in all work processes, performance of individuals that is employees and purposes
of the organisation. The five principles of lean management are applicable on Sainsbury in
presented manner below:
Identify the value- This is the first step of the process which is related to finding the problem
that the customers are facing and needs to be resolved by providing appropriate product or
service as a solution. The first step will allow Sainsbury to know the exact requirements of the
customers and accordingly make provisions of their products and services for fulfilling their
demands and resolving their problems.
Value stream mapping- The 2nd stage is a process of mapping out the company's workflow that
contributes to the sales transactions and rendering the ultimate products to the buyers. The value
stream mapping stage will enable Sainsbury to develop a strong and most productive cycle for
providing the goods to end customers in the most efficient manner by eliminating all the waste
stages and practices that are increasing costs and affecting profitability of the firm (Freudenreich,
Lüdeke-Freund and Schaltegger, 2020).
Create a continuous flow- The third stage of the whole Management process is focused towards
progress and increasing efficiency of people within the organisation. In this stage the
philosophy not just involve one person or a particular department of the company in the whole
phenomena on the other hand it involves everyone in the organisation for making improvements
and putting efforts according to the plans made.
Analyse the quality management techniques that could apply to improve the effectiveness of the
operation in your chosen manufacturing organisation and rationales for its use.
The new project which is introduced by the CEO of Sainsbury is to make quality
management for attaining quality excellence, sustainability and competitiveness in the market. In
order to perform the project with similar and even higher efficiency the company needs to
implement certain quality management approaches or techniques. From the above discussed
policies the one which is most suitable for the company to implement is lean management
(Mendling and et. al., 2018).
The lean Management process will be focused on defining value from the standpoint of
the end customer of Sainsbury, eliminating all the waste efforts and practices being used in the
business operations of Sainsbury and lastly it will be concerned with making continuous
improvements in all work processes, performance of individuals that is employees and purposes
of the organisation. The five principles of lean management are applicable on Sainsbury in
presented manner below:
Identify the value- This is the first step of the process which is related to finding the problem
that the customers are facing and needs to be resolved by providing appropriate product or
service as a solution. The first step will allow Sainsbury to know the exact requirements of the
customers and accordingly make provisions of their products and services for fulfilling their
demands and resolving their problems.
Value stream mapping- The 2nd stage is a process of mapping out the company's workflow that
contributes to the sales transactions and rendering the ultimate products to the buyers. The value
stream mapping stage will enable Sainsbury to develop a strong and most productive cycle for
providing the goods to end customers in the most efficient manner by eliminating all the waste
stages and practices that are increasing costs and affecting profitability of the firm (Freudenreich,
Lüdeke-Freund and Schaltegger, 2020).
Create a continuous flow- The third stage of the whole Management process is focused towards
progress and increasing efficiency of people within the organisation. In this stage the
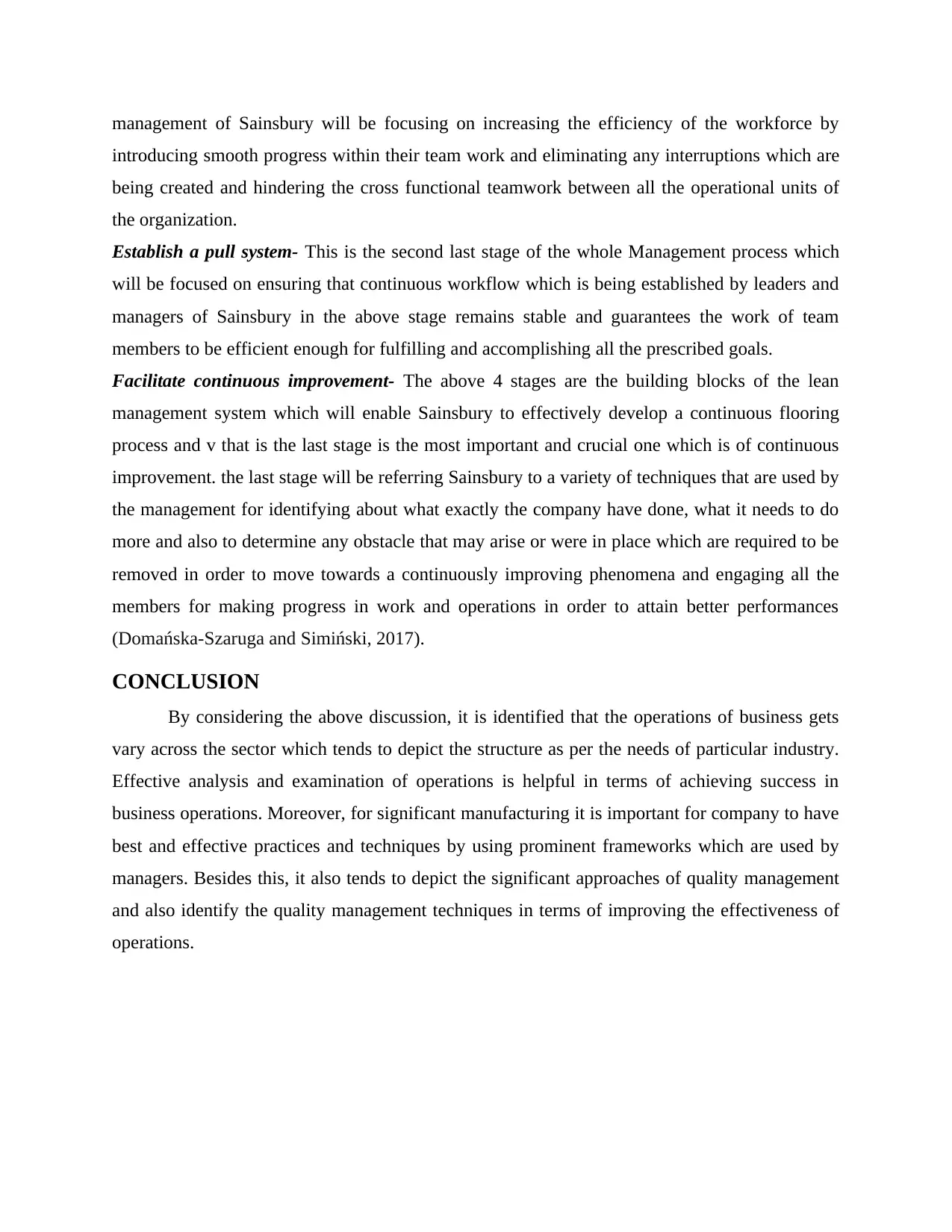
management of Sainsbury will be focusing on increasing the efficiency of the workforce by
introducing smooth progress within their team work and eliminating any interruptions which are
being created and hindering the cross functional teamwork between all the operational units of
the organization.
Establish a pull system- This is the second last stage of the whole Management process which
will be focused on ensuring that continuous workflow which is being established by leaders and
managers of Sainsbury in the above stage remains stable and guarantees the work of team
members to be efficient enough for fulfilling and accomplishing all the prescribed goals.
Facilitate continuous improvement- The above 4 stages are the building blocks of the lean
management system which will enable Sainsbury to effectively develop a continuous flooring
process and v that is the last stage is the most important and crucial one which is of continuous
improvement. the last stage will be referring Sainsbury to a variety of techniques that are used by
the management for identifying about what exactly the company have done, what it needs to do
more and also to determine any obstacle that may arise or were in place which are required to be
removed in order to move towards a continuously improving phenomena and engaging all the
members for making progress in work and operations in order to attain better performances
(Domańska-Szaruga and Simiński, 2017).
CONCLUSION
By considering the above discussion, it is identified that the operations of business gets
vary across the sector which tends to depict the structure as per the needs of particular industry.
Effective analysis and examination of operations is helpful in terms of achieving success in
business operations. Moreover, for significant manufacturing it is important for company to have
best and effective practices and techniques by using prominent frameworks which are used by
managers. Besides this, it also tends to depict the significant approaches of quality management
and also identify the quality management techniques in terms of improving the effectiveness of
operations.
introducing smooth progress within their team work and eliminating any interruptions which are
being created and hindering the cross functional teamwork between all the operational units of
the organization.
Establish a pull system- This is the second last stage of the whole Management process which
will be focused on ensuring that continuous workflow which is being established by leaders and
managers of Sainsbury in the above stage remains stable and guarantees the work of team
members to be efficient enough for fulfilling and accomplishing all the prescribed goals.
Facilitate continuous improvement- The above 4 stages are the building blocks of the lean
management system which will enable Sainsbury to effectively develop a continuous flooring
process and v that is the last stage is the most important and crucial one which is of continuous
improvement. the last stage will be referring Sainsbury to a variety of techniques that are used by
the management for identifying about what exactly the company have done, what it needs to do
more and also to determine any obstacle that may arise or were in place which are required to be
removed in order to move towards a continuously improving phenomena and engaging all the
members for making progress in work and operations in order to attain better performances
(Domańska-Szaruga and Simiński, 2017).
CONCLUSION
By considering the above discussion, it is identified that the operations of business gets
vary across the sector which tends to depict the structure as per the needs of particular industry.
Effective analysis and examination of operations is helpful in terms of achieving success in
business operations. Moreover, for significant manufacturing it is important for company to have
best and effective practices and techniques by using prominent frameworks which are used by
managers. Besides this, it also tends to depict the significant approaches of quality management
and also identify the quality management techniques in terms of improving the effectiveness of
operations.

REFERENCES
Books and Journals
Addo-Tenkorang, R. and Helo, P. T., 2016. Big data applications in operations/supply-chain
management: A literature review. Computers & Industrial Engineering, 101, pp.528-
543.
Boone, L. E., Kurtz, D. L. and Berston, S., 2019. Contemporary business. John Wiley & Sons.
Cherunilam, F., 2020. International business. PHI Learning Pvt. Ltd..
Choi, T. M., Chan, H. K. and Yue, X., 2016. Recent development in big data analytics for
business operations and risk management. IEEE transactions on cybernetics, 47(1),
pp.81-92.
Domańska-Szaruga, B. and Simiński, P., 2017. Trust and business risk in a research institute’s
operations.
Freudenreich, B., Lüdeke-Freund, F. and Schaltegger, S., 2020. A stakeholder theory perspective
on business models: Value creation for sustainability. Journal of Business
Ethics, 166(1), pp.3-18.
Heizer, J., 2016. Operations management, 11/e. Pearson Education India.
Henderson, M. K., Goldring, K. and Simeon-Dubach, D., 2019. Advancing professionalization
of biobank business operations: a worldwide survey. Biopreservation and
biobanking, 17(1), pp.71-75.
Hong, S. and et. al., 2016. Why firm size matters: investigating the drivers of innovation and
economic performance in New Zealand using the Business Operations Survey. Applied
Economics, 48(55), pp.5379-5395.
KorauÅ, A. and et. al., 2019. Using quantitative methods to identify insecurity due to unusual
business operations. Entrepreneurship and Sustainability Issues, 6(3), pp.1101-1112.
Luo, S., Lin, X. and Zheng, Z., 2019. A novel CNN-DDPG based AI-trader: Performance and
roles in business operations. Transportation Research Part E: Logistics and
Transportation Review, 131, pp.68-79.
Mendling, J. and et. al., 2018. Blockchains for business process management-challenges and
opportunities. ACM Transactions on Management Information Systems (TMIS), 9(1),
pp.1-16.
Books and Journals
Addo-Tenkorang, R. and Helo, P. T., 2016. Big data applications in operations/supply-chain
management: A literature review. Computers & Industrial Engineering, 101, pp.528-
543.
Boone, L. E., Kurtz, D. L. and Berston, S., 2019. Contemporary business. John Wiley & Sons.
Cherunilam, F., 2020. International business. PHI Learning Pvt. Ltd..
Choi, T. M., Chan, H. K. and Yue, X., 2016. Recent development in big data analytics for
business operations and risk management. IEEE transactions on cybernetics, 47(1),
pp.81-92.
Domańska-Szaruga, B. and Simiński, P., 2017. Trust and business risk in a research institute’s
operations.
Freudenreich, B., Lüdeke-Freund, F. and Schaltegger, S., 2020. A stakeholder theory perspective
on business models: Value creation for sustainability. Journal of Business
Ethics, 166(1), pp.3-18.
Heizer, J., 2016. Operations management, 11/e. Pearson Education India.
Henderson, M. K., Goldring, K. and Simeon-Dubach, D., 2019. Advancing professionalization
of biobank business operations: a worldwide survey. Biopreservation and
biobanking, 17(1), pp.71-75.
Hong, S. and et. al., 2016. Why firm size matters: investigating the drivers of innovation and
economic performance in New Zealand using the Business Operations Survey. Applied
Economics, 48(55), pp.5379-5395.
KorauÅ, A. and et. al., 2019. Using quantitative methods to identify insecurity due to unusual
business operations. Entrepreneurship and Sustainability Issues, 6(3), pp.1101-1112.
Luo, S., Lin, X. and Zheng, Z., 2019. A novel CNN-DDPG based AI-trader: Performance and
roles in business operations. Transportation Research Part E: Logistics and
Transportation Review, 131, pp.68-79.
Mendling, J. and et. al., 2018. Blockchains for business process management-challenges and
opportunities. ACM Transactions on Management Information Systems (TMIS), 9(1),
pp.1-16.
1 out of 10
Related Documents

Your All-in-One AI-Powered Toolkit for Academic Success.
+13062052269
info@desklib.com
Available 24*7 on WhatsApp / Email
Unlock your academic potential
© 2024 | Zucol Services PVT LTD | All rights reserved.