Report on Engineering Secondary and Finishing Techniques - Unit 21
VerifiedAdded on 2023/03/21
|21
|5358
|96
Report
AI Summary
This report provides a comprehensive overview of engineering secondary and finishing techniques, including turning, boring, milling, and grinding operations on various materials like non-ferrous metals, heat-resistant super alloys, stainless steel, and non-metallic materials. It discusses press work machine applications such as blanking and cutting operations on plastics. The report also explores the application of kinematics in secondary machining, highlighting tools and parameters used. Furthermore, it delves into non-traditional techniques like 3D engraving, band sawing, reaming, shearing, and Teflon for specific tasks such as product code engraving, creating square holes, assembling aircraft wings, achieving tight tolerance holes, cutting irregular shapes, and de-burring PTFE washers. The document concludes by detailing the assembly process of an aluminum aircraft wing outer layer.
Contribute Materials
Your contribution can guide someone’s learning journey. Share your
documents today.
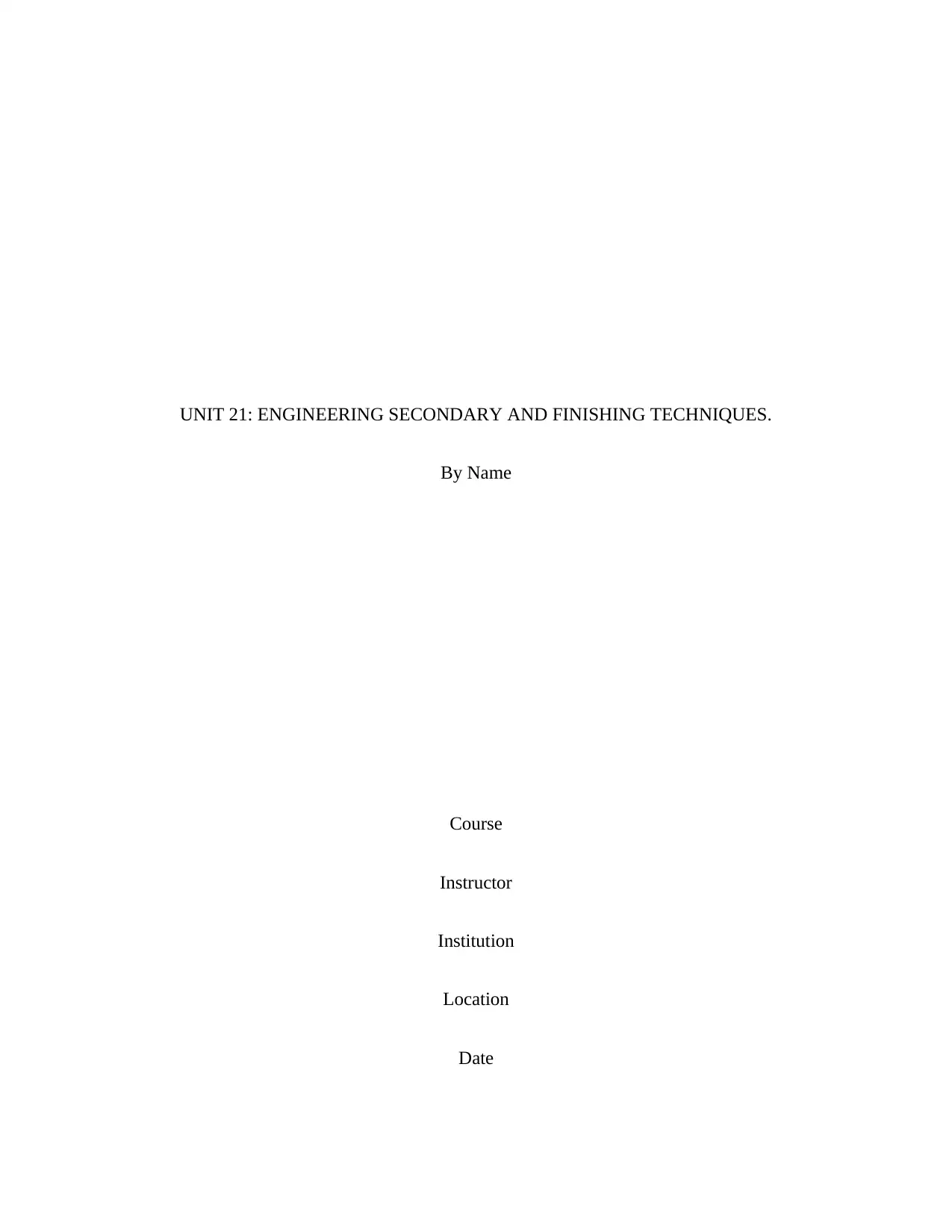
UNIT 21: ENGINEERING SECONDARY AND FINISHING TECHNIQUES.
By Name
Course
Instructor
Institution
Location
Date
By Name
Course
Instructor
Institution
Location
Date
Secure Best Marks with AI Grader
Need help grading? Try our AI Grader for instant feedback on your assignments.
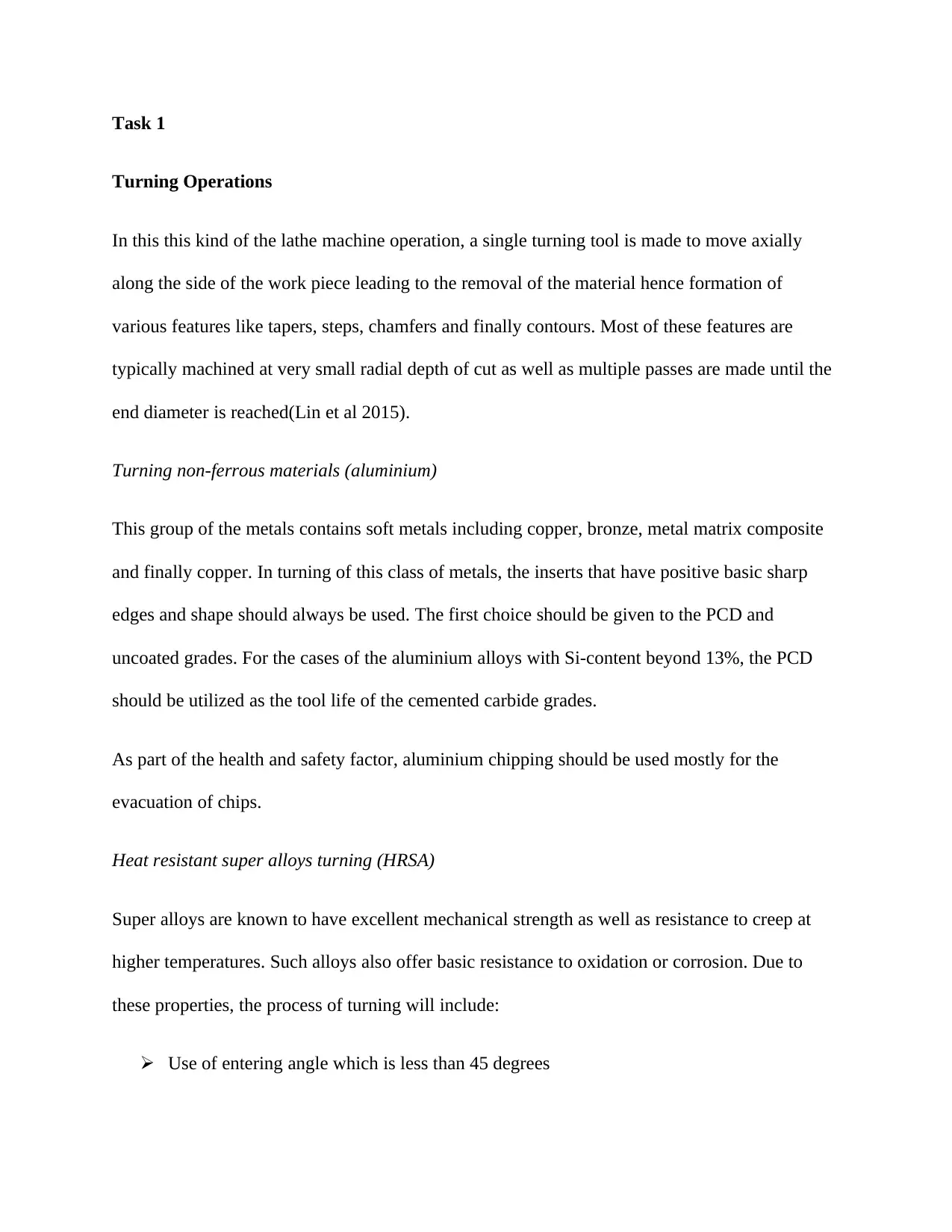
Task 1
Turning Operations
In this this kind of the lathe machine operation, a single turning tool is made to move axially
along the side of the work piece leading to the removal of the material hence formation of
various features like tapers, steps, chamfers and finally contours. Most of these features are
typically machined at very small radial depth of cut as well as multiple passes are made until the
end diameter is reached(Lin et al 2015).
Turning non-ferrous materials (aluminium)
This group of the metals contains soft metals including copper, bronze, metal matrix composite
and finally copper. In turning of this class of metals, the inserts that have positive basic sharp
edges and shape should always be used. The first choice should be given to the PCD and
uncoated grades. For the cases of the aluminium alloys with Si-content beyond 13%, the PCD
should be utilized as the tool life of the cemented carbide grades.
As part of the health and safety factor, aluminium chipping should be used mostly for the
evacuation of chips.
Heat resistant super alloys turning (HRSA)
Super alloys are known to have excellent mechanical strength as well as resistance to creep at
higher temperatures. Such alloys also offer basic resistance to oxidation or corrosion. Due to
these properties, the process of turning will include:
Use of entering angle which is less than 45 degrees
Turning Operations
In this this kind of the lathe machine operation, a single turning tool is made to move axially
along the side of the work piece leading to the removal of the material hence formation of
various features like tapers, steps, chamfers and finally contours. Most of these features are
typically machined at very small radial depth of cut as well as multiple passes are made until the
end diameter is reached(Lin et al 2015).
Turning non-ferrous materials (aluminium)
This group of the metals contains soft metals including copper, bronze, metal matrix composite
and finally copper. In turning of this class of metals, the inserts that have positive basic sharp
edges and shape should always be used. The first choice should be given to the PCD and
uncoated grades. For the cases of the aluminium alloys with Si-content beyond 13%, the PCD
should be utilized as the tool life of the cemented carbide grades.
As part of the health and safety factor, aluminium chipping should be used mostly for the
evacuation of chips.
Heat resistant super alloys turning (HRSA)
Super alloys are known to have excellent mechanical strength as well as resistance to creep at
higher temperatures. Such alloys also offer basic resistance to oxidation or corrosion. Due to
these properties, the process of turning will include:
Use of entering angle which is less than 45 degrees
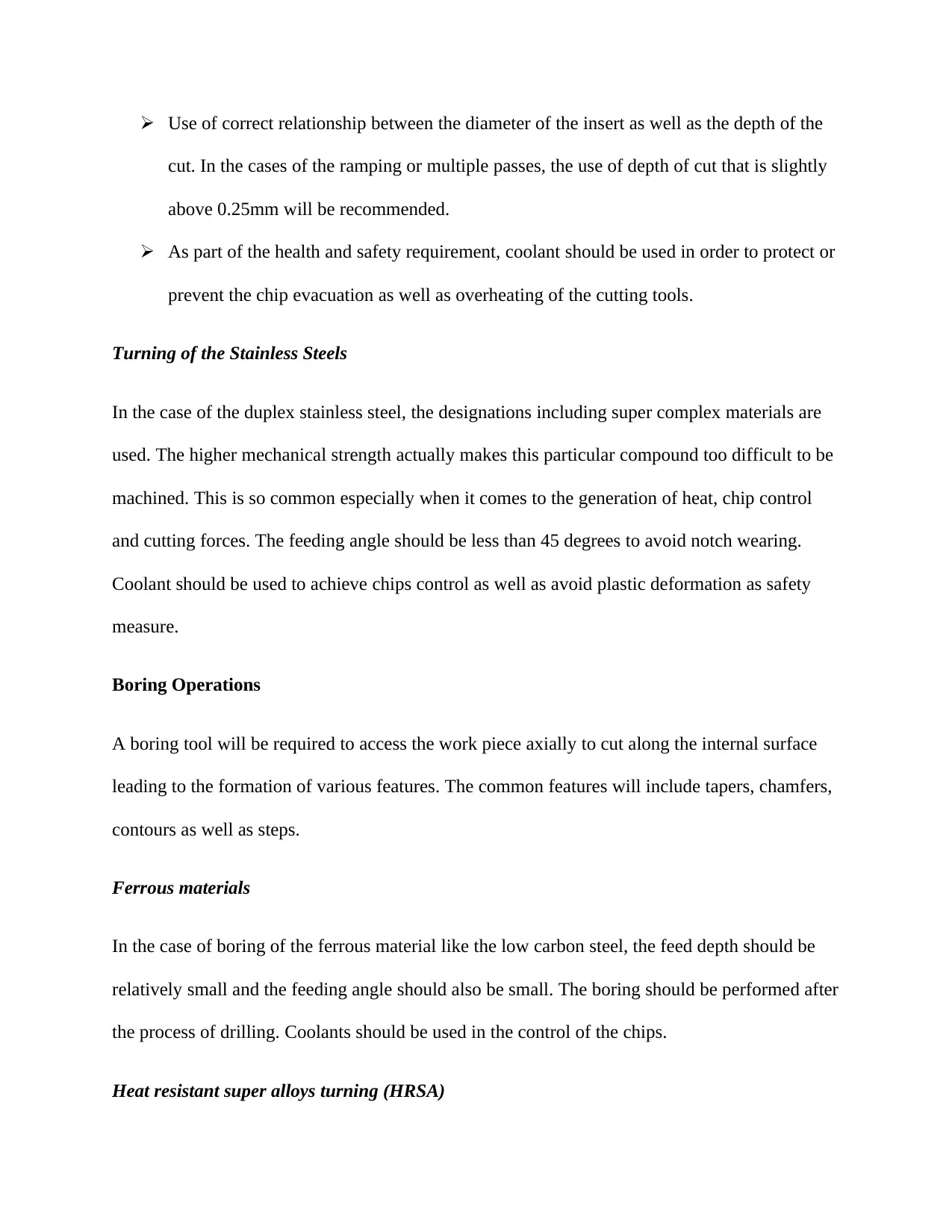
Use of correct relationship between the diameter of the insert as well as the depth of the
cut. In the cases of the ramping or multiple passes, the use of depth of cut that is slightly
above 0.25mm will be recommended.
As part of the health and safety requirement, coolant should be used in order to protect or
prevent the chip evacuation as well as overheating of the cutting tools.
Turning of the Stainless Steels
In the case of the duplex stainless steel, the designations including super complex materials are
used. The higher mechanical strength actually makes this particular compound too difficult to be
machined. This is so common especially when it comes to the generation of heat, chip control
and cutting forces. The feeding angle should be less than 45 degrees to avoid notch wearing.
Coolant should be used to achieve chips control as well as avoid plastic deformation as safety
measure.
Boring Operations
A boring tool will be required to access the work piece axially to cut along the internal surface
leading to the formation of various features. The common features will include tapers, chamfers,
contours as well as steps.
Ferrous materials
In the case of boring of the ferrous material like the low carbon steel, the feed depth should be
relatively small and the feeding angle should also be small. The boring should be performed after
the process of drilling. Coolants should be used in the control of the chips.
Heat resistant super alloys turning (HRSA)
cut. In the cases of the ramping or multiple passes, the use of depth of cut that is slightly
above 0.25mm will be recommended.
As part of the health and safety requirement, coolant should be used in order to protect or
prevent the chip evacuation as well as overheating of the cutting tools.
Turning of the Stainless Steels
In the case of the duplex stainless steel, the designations including super complex materials are
used. The higher mechanical strength actually makes this particular compound too difficult to be
machined. This is so common especially when it comes to the generation of heat, chip control
and cutting forces. The feeding angle should be less than 45 degrees to avoid notch wearing.
Coolant should be used to achieve chips control as well as avoid plastic deformation as safety
measure.
Boring Operations
A boring tool will be required to access the work piece axially to cut along the internal surface
leading to the formation of various features. The common features will include tapers, chamfers,
contours as well as steps.
Ferrous materials
In the case of boring of the ferrous material like the low carbon steel, the feed depth should be
relatively small and the feeding angle should also be small. The boring should be performed after
the process of drilling. Coolants should be used in the control of the chips.
Heat resistant super alloys turning (HRSA)
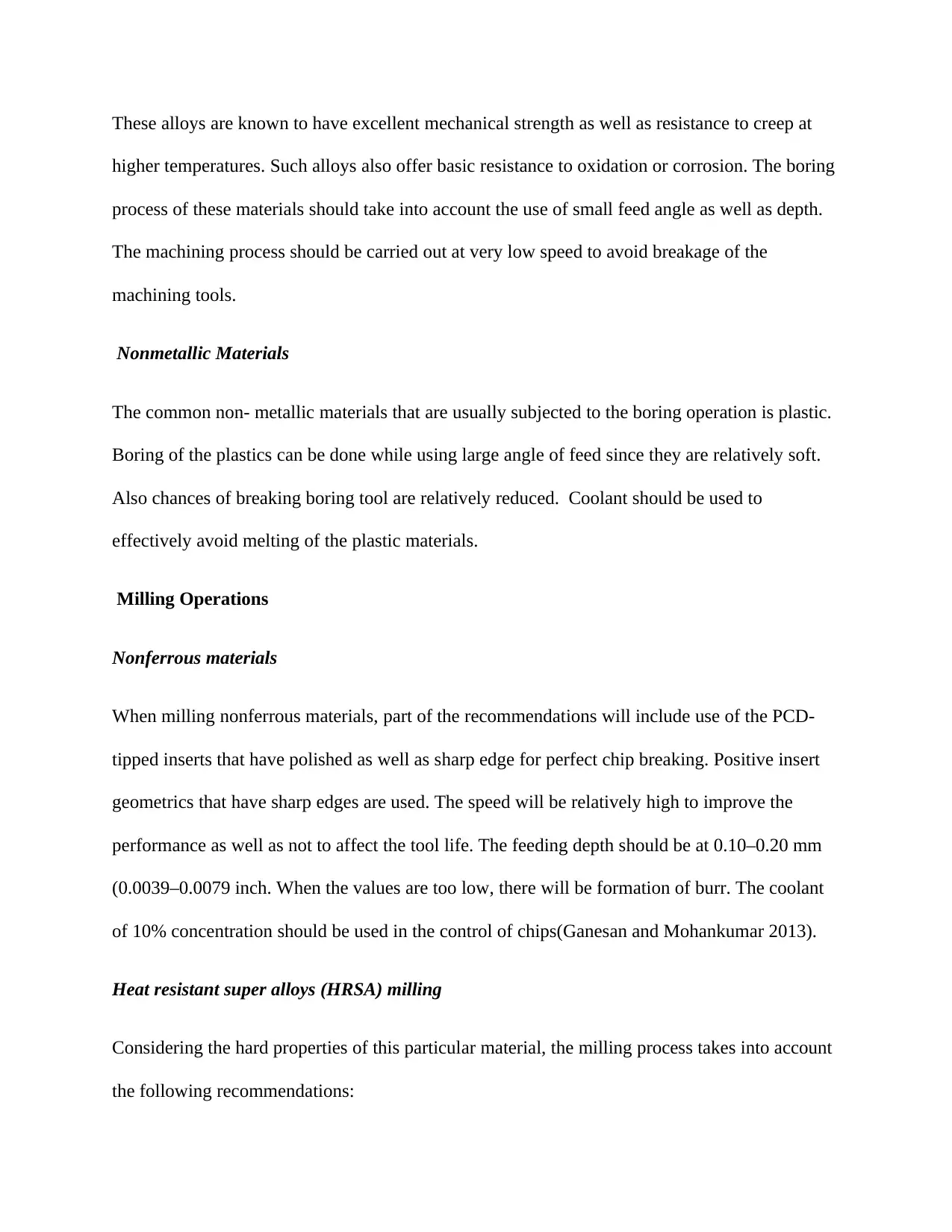
These alloys are known to have excellent mechanical strength as well as resistance to creep at
higher temperatures. Such alloys also offer basic resistance to oxidation or corrosion. The boring
process of these materials should take into account the use of small feed angle as well as depth.
The machining process should be carried out at very low speed to avoid breakage of the
machining tools.
Nonmetallic Materials
The common non- metallic materials that are usually subjected to the boring operation is plastic.
Boring of the plastics can be done while using large angle of feed since they are relatively soft.
Also chances of breaking boring tool are relatively reduced. Coolant should be used to
effectively avoid melting of the plastic materials.
Milling Operations
Nonferrous materials
When milling nonferrous materials, part of the recommendations will include use of the PCD-
tipped inserts that have polished as well as sharp edge for perfect chip breaking. Positive insert
geometrics that have sharp edges are used. The speed will be relatively high to improve the
performance as well as not to affect the tool life. The feeding depth should be at 0.10–0.20 mm
(0.0039–0.0079 inch. When the values are too low, there will be formation of burr. The coolant
of 10% concentration should be used in the control of chips(Ganesan and Mohankumar 2013).
Heat resistant super alloys (HRSA) milling
Considering the hard properties of this particular material, the milling process takes into account
the following recommendations:
higher temperatures. Such alloys also offer basic resistance to oxidation or corrosion. The boring
process of these materials should take into account the use of small feed angle as well as depth.
The machining process should be carried out at very low speed to avoid breakage of the
machining tools.
Nonmetallic Materials
The common non- metallic materials that are usually subjected to the boring operation is plastic.
Boring of the plastics can be done while using large angle of feed since they are relatively soft.
Also chances of breaking boring tool are relatively reduced. Coolant should be used to
effectively avoid melting of the plastic materials.
Milling Operations
Nonferrous materials
When milling nonferrous materials, part of the recommendations will include use of the PCD-
tipped inserts that have polished as well as sharp edge for perfect chip breaking. Positive insert
geometrics that have sharp edges are used. The speed will be relatively high to improve the
performance as well as not to affect the tool life. The feeding depth should be at 0.10–0.20 mm
(0.0039–0.0079 inch. When the values are too low, there will be formation of burr. The coolant
of 10% concentration should be used in the control of chips(Ganesan and Mohankumar 2013).
Heat resistant super alloys (HRSA) milling
Considering the hard properties of this particular material, the milling process takes into account
the following recommendations:
Secure Best Marks with AI Grader
Need help grading? Try our AI Grader for instant feedback on your assignments.
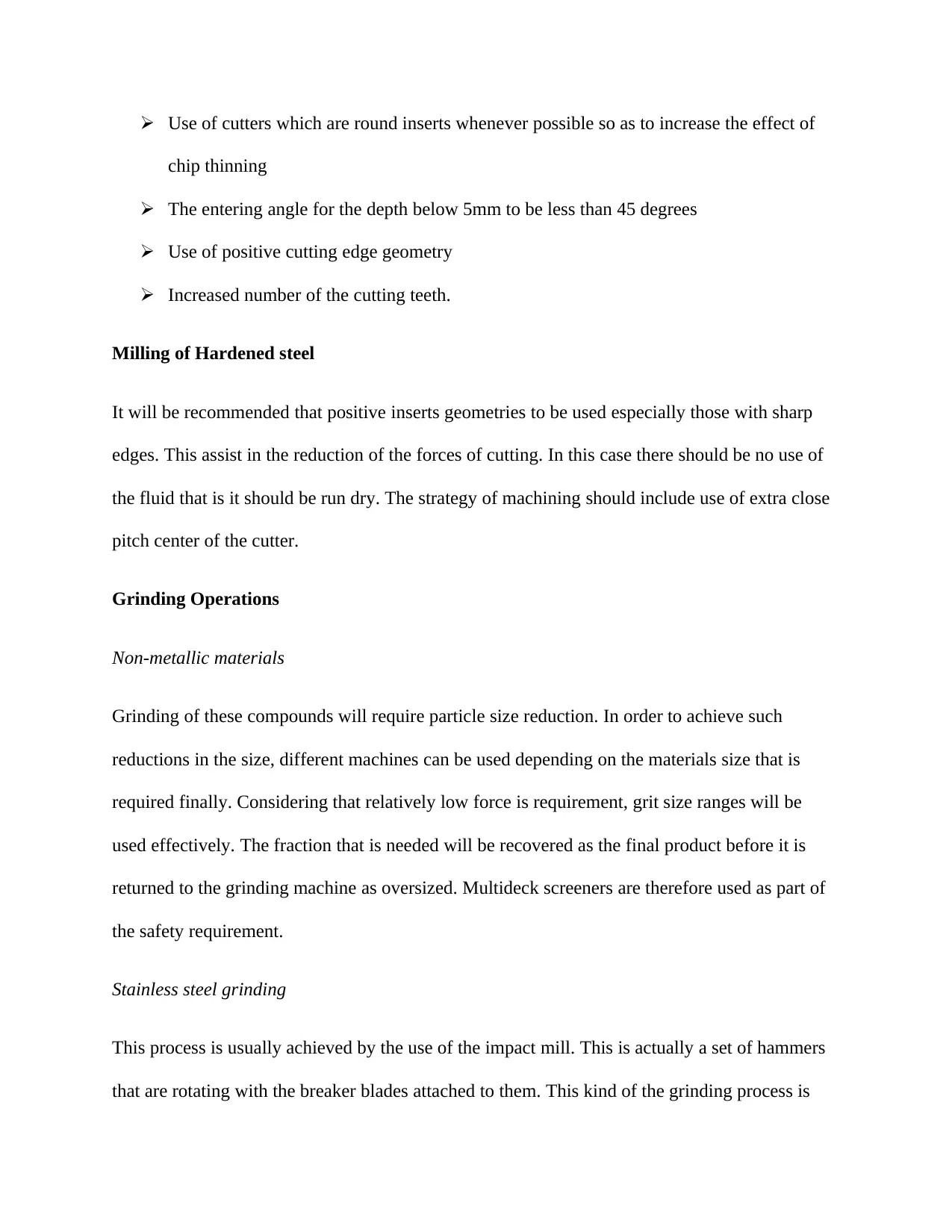
Use of cutters which are round inserts whenever possible so as to increase the effect of
chip thinning
The entering angle for the depth below 5mm to be less than 45 degrees
Use of positive cutting edge geometry
Increased number of the cutting teeth.
Milling of Hardened steel
It will be recommended that positive inserts geometries to be used especially those with sharp
edges. This assist in the reduction of the forces of cutting. In this case there should be no use of
the fluid that is it should be run dry. The strategy of machining should include use of extra close
pitch center of the cutter.
Grinding Operations
Non-metallic materials
Grinding of these compounds will require particle size reduction. In order to achieve such
reductions in the size, different machines can be used depending on the materials size that is
required finally. Considering that relatively low force is requirement, grit size ranges will be
used effectively. The fraction that is needed will be recovered as the final product before it is
returned to the grinding machine as oversized. Multideck screeners are therefore used as part of
the safety requirement.
Stainless steel grinding
This process is usually achieved by the use of the impact mill. This is actually a set of hammers
that are rotating with the breaker blades attached to them. This kind of the grinding process is
chip thinning
The entering angle for the depth below 5mm to be less than 45 degrees
Use of positive cutting edge geometry
Increased number of the cutting teeth.
Milling of Hardened steel
It will be recommended that positive inserts geometries to be used especially those with sharp
edges. This assist in the reduction of the forces of cutting. In this case there should be no use of
the fluid that is it should be run dry. The strategy of machining should include use of extra close
pitch center of the cutter.
Grinding Operations
Non-metallic materials
Grinding of these compounds will require particle size reduction. In order to achieve such
reductions in the size, different machines can be used depending on the materials size that is
required finally. Considering that relatively low force is requirement, grit size ranges will be
used effectively. The fraction that is needed will be recovered as the final product before it is
returned to the grinding machine as oversized. Multideck screeners are therefore used as part of
the safety requirement.
Stainless steel grinding
This process is usually achieved by the use of the impact mill. This is actually a set of hammers
that are rotating with the breaker blades attached to them. This kind of the grinding process is
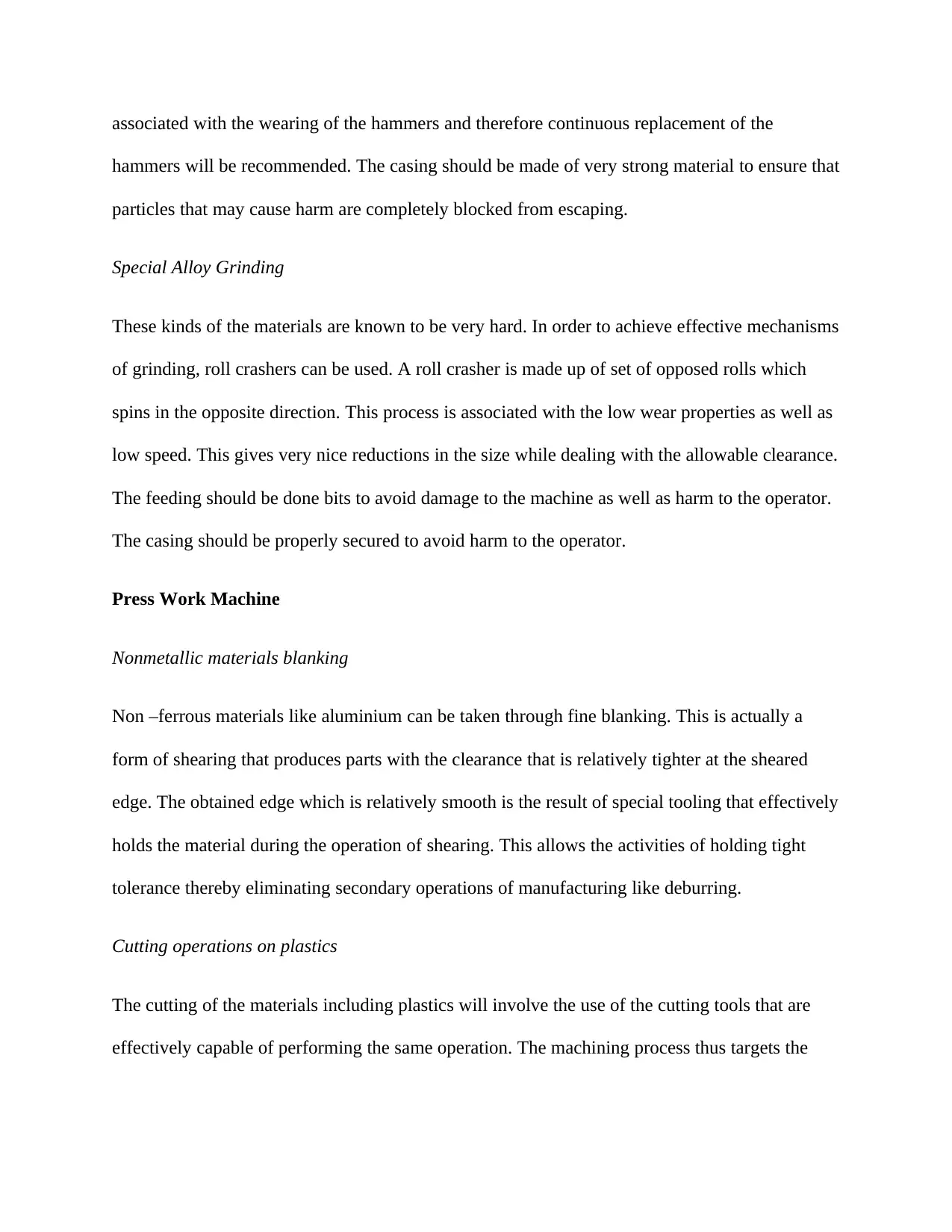
associated with the wearing of the hammers and therefore continuous replacement of the
hammers will be recommended. The casing should be made of very strong material to ensure that
particles that may cause harm are completely blocked from escaping.
Special Alloy Grinding
These kinds of the materials are known to be very hard. In order to achieve effective mechanisms
of grinding, roll crashers can be used. A roll crasher is made up of set of opposed rolls which
spins in the opposite direction. This process is associated with the low wear properties as well as
low speed. This gives very nice reductions in the size while dealing with the allowable clearance.
The feeding should be done bits to avoid damage to the machine as well as harm to the operator.
The casing should be properly secured to avoid harm to the operator.
Press Work Machine
Nonmetallic materials blanking
Non –ferrous materials like aluminium can be taken through fine blanking. This is actually a
form of shearing that produces parts with the clearance that is relatively tighter at the sheared
edge. The obtained edge which is relatively smooth is the result of special tooling that effectively
holds the material during the operation of shearing. This allows the activities of holding tight
tolerance thereby eliminating secondary operations of manufacturing like deburring.
Cutting operations on plastics
The cutting of the materials including plastics will involve the use of the cutting tools that are
effectively capable of performing the same operation. The machining process thus targets the
hammers will be recommended. The casing should be made of very strong material to ensure that
particles that may cause harm are completely blocked from escaping.
Special Alloy Grinding
These kinds of the materials are known to be very hard. In order to achieve effective mechanisms
of grinding, roll crashers can be used. A roll crasher is made up of set of opposed rolls which
spins in the opposite direction. This process is associated with the low wear properties as well as
low speed. This gives very nice reductions in the size while dealing with the allowable clearance.
The feeding should be done bits to avoid damage to the machine as well as harm to the operator.
The casing should be properly secured to avoid harm to the operator.
Press Work Machine
Nonmetallic materials blanking
Non –ferrous materials like aluminium can be taken through fine blanking. This is actually a
form of shearing that produces parts with the clearance that is relatively tighter at the sheared
edge. The obtained edge which is relatively smooth is the result of special tooling that effectively
holds the material during the operation of shearing. This allows the activities of holding tight
tolerance thereby eliminating secondary operations of manufacturing like deburring.
Cutting operations on plastics
The cutting of the materials including plastics will involve the use of the cutting tools that are
effectively capable of performing the same operation. The machining process thus targets the
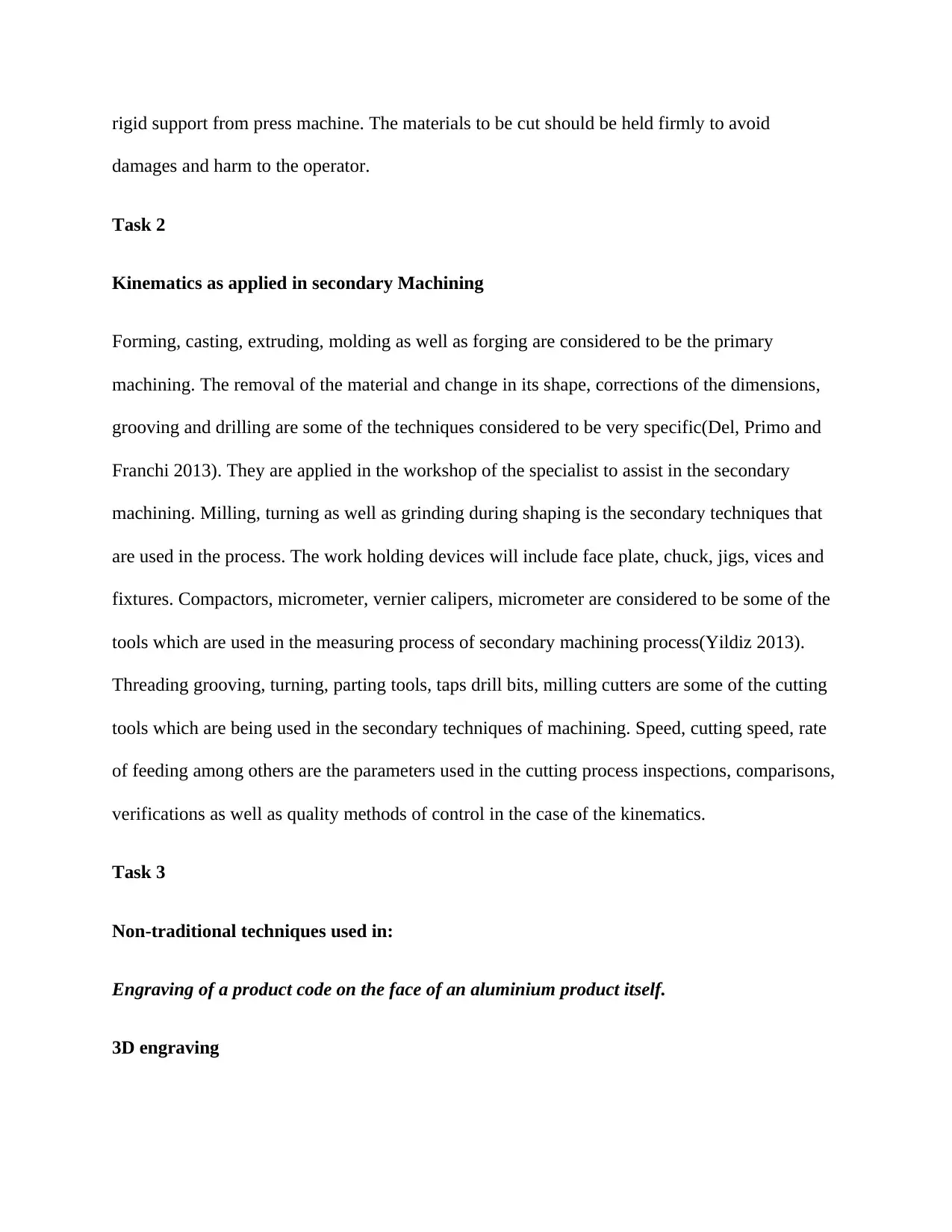
rigid support from press machine. The materials to be cut should be held firmly to avoid
damages and harm to the operator.
Task 2
Kinematics as applied in secondary Machining
Forming, casting, extruding, molding as well as forging are considered to be the primary
machining. The removal of the material and change in its shape, corrections of the dimensions,
grooving and drilling are some of the techniques considered to be very specific(Del, Primo and
Franchi 2013). They are applied in the workshop of the specialist to assist in the secondary
machining. Milling, turning as well as grinding during shaping is the secondary techniques that
are used in the process. The work holding devices will include face plate, chuck, jigs, vices and
fixtures. Compactors, micrometer, vernier calipers, micrometer are considered to be some of the
tools which are used in the measuring process of secondary machining process(Yildiz 2013).
Threading grooving, turning, parting tools, taps drill bits, milling cutters are some of the cutting
tools which are being used in the secondary techniques of machining. Speed, cutting speed, rate
of feeding among others are the parameters used in the cutting process inspections, comparisons,
verifications as well as quality methods of control in the case of the kinematics.
Task 3
Non-traditional techniques used in:
Engraving of a product code on the face of an aluminium product itself.
3D engraving
damages and harm to the operator.
Task 2
Kinematics as applied in secondary Machining
Forming, casting, extruding, molding as well as forging are considered to be the primary
machining. The removal of the material and change in its shape, corrections of the dimensions,
grooving and drilling are some of the techniques considered to be very specific(Del, Primo and
Franchi 2013). They are applied in the workshop of the specialist to assist in the secondary
machining. Milling, turning as well as grinding during shaping is the secondary techniques that
are used in the process. The work holding devices will include face plate, chuck, jigs, vices and
fixtures. Compactors, micrometer, vernier calipers, micrometer are considered to be some of the
tools which are used in the measuring process of secondary machining process(Yildiz 2013).
Threading grooving, turning, parting tools, taps drill bits, milling cutters are some of the cutting
tools which are being used in the secondary techniques of machining. Speed, cutting speed, rate
of feeding among others are the parameters used in the cutting process inspections, comparisons,
verifications as well as quality methods of control in the case of the kinematics.
Task 3
Non-traditional techniques used in:
Engraving of a product code on the face of an aluminium product itself.
3D engraving
Paraphrase This Document
Need a fresh take? Get an instant paraphrase of this document with our AI Paraphraser
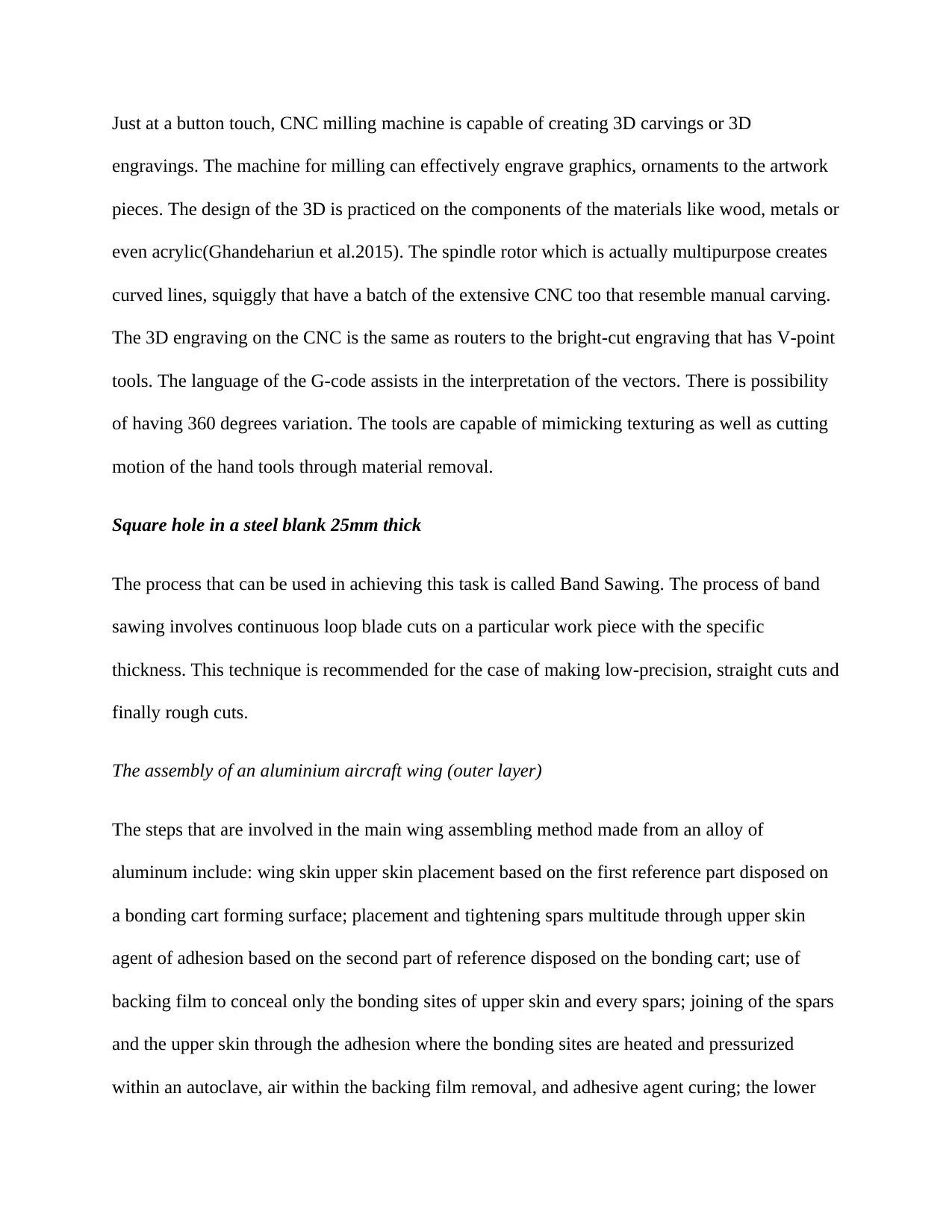
Just at a button touch, CNC milling machine is capable of creating 3D carvings or 3D
engravings. The machine for milling can effectively engrave graphics, ornaments to the artwork
pieces. The design of the 3D is practiced on the components of the materials like wood, metals or
even acrylic(Ghandehariun et al.2015). The spindle rotor which is actually multipurpose creates
curved lines, squiggly that have a batch of the extensive CNC too that resemble manual carving.
The 3D engraving on the CNC is the same as routers to the bright-cut engraving that has V-point
tools. The language of the G-code assists in the interpretation of the vectors. There is possibility
of having 360 degrees variation. The tools are capable of mimicking texturing as well as cutting
motion of the hand tools through material removal.
Square hole in a steel blank 25mm thick
The process that can be used in achieving this task is called Band Sawing. The process of band
sawing involves continuous loop blade cuts on a particular work piece with the specific
thickness. This technique is recommended for the case of making low-precision, straight cuts and
finally rough cuts.
The assembly of an aluminium aircraft wing (outer layer)
The steps that are involved in the main wing assembling method made from an alloy of
aluminum include: wing skin upper skin placement based on the first reference part disposed on
a bonding cart forming surface; placement and tightening spars multitude through upper skin
agent of adhesion based on the second part of reference disposed on the bonding cart; use of
backing film to conceal only the bonding sites of upper skin and every spars; joining of the spars
and the upper skin through the adhesion where the bonding sites are heated and pressurized
within an autoclave, air within the backing film removal, and adhesive agent curing; the lower
engravings. The machine for milling can effectively engrave graphics, ornaments to the artwork
pieces. The design of the 3D is practiced on the components of the materials like wood, metals or
even acrylic(Ghandehariun et al.2015). The spindle rotor which is actually multipurpose creates
curved lines, squiggly that have a batch of the extensive CNC too that resemble manual carving.
The 3D engraving on the CNC is the same as routers to the bright-cut engraving that has V-point
tools. The language of the G-code assists in the interpretation of the vectors. There is possibility
of having 360 degrees variation. The tools are capable of mimicking texturing as well as cutting
motion of the hand tools through material removal.
Square hole in a steel blank 25mm thick
The process that can be used in achieving this task is called Band Sawing. The process of band
sawing involves continuous loop blade cuts on a particular work piece with the specific
thickness. This technique is recommended for the case of making low-precision, straight cuts and
finally rough cuts.
The assembly of an aluminium aircraft wing (outer layer)
The steps that are involved in the main wing assembling method made from an alloy of
aluminum include: wing skin upper skin placement based on the first reference part disposed on
a bonding cart forming surface; placement and tightening spars multitude through upper skin
agent of adhesion based on the second part of reference disposed on the bonding cart; use of
backing film to conceal only the bonding sites of upper skin and every spars; joining of the spars
and the upper skin through the adhesion where the bonding sites are heated and pressurized
within an autoclave, air within the backing film removal, and adhesive agent curing; the lower
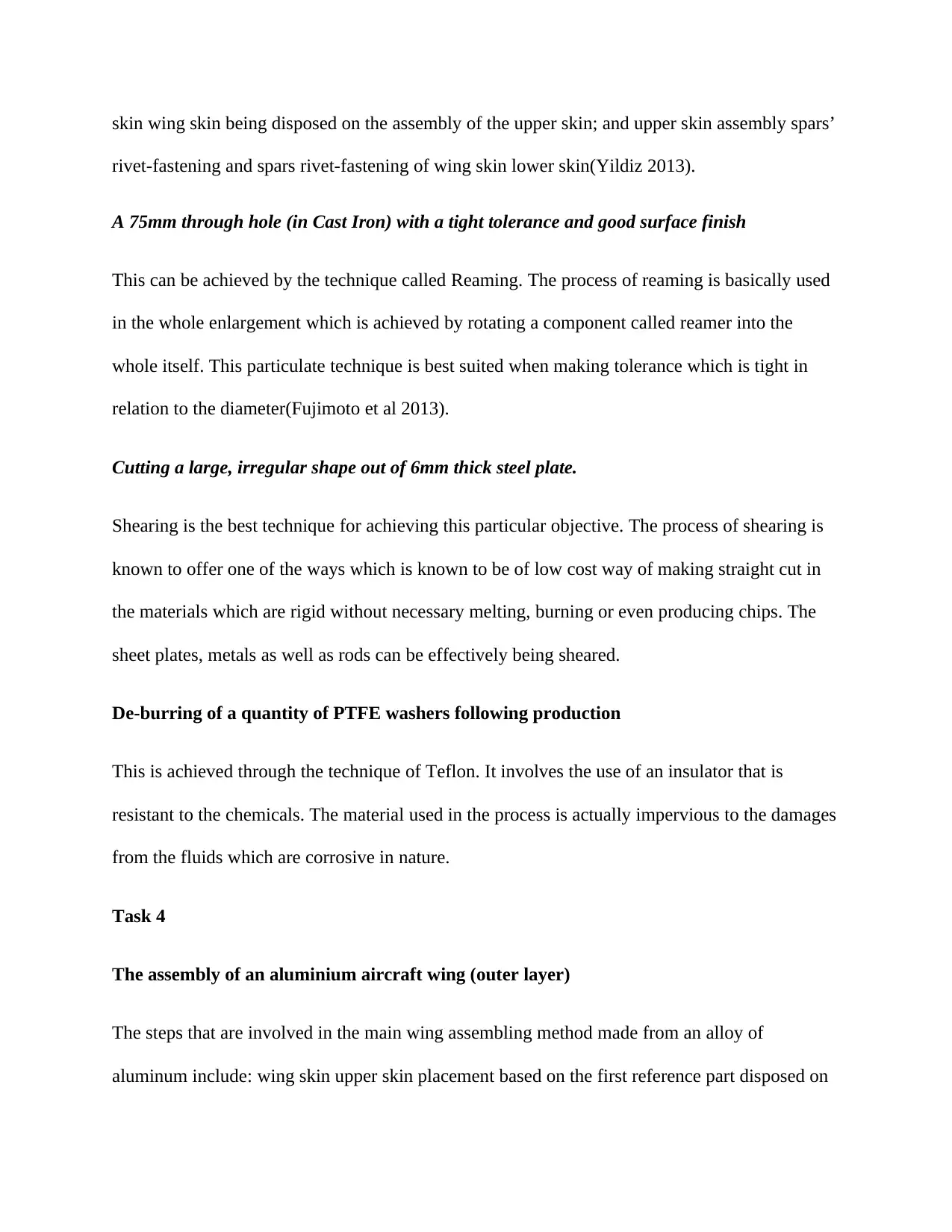
skin wing skin being disposed on the assembly of the upper skin; and upper skin assembly spars’
rivet-fastening and spars rivet-fastening of wing skin lower skin(Yildiz 2013).
A 75mm through hole (in Cast Iron) with a tight tolerance and good surface finish
This can be achieved by the technique called Reaming. The process of reaming is basically used
in the whole enlargement which is achieved by rotating a component called reamer into the
whole itself. This particulate technique is best suited when making tolerance which is tight in
relation to the diameter(Fujimoto et al 2013).
Cutting a large, irregular shape out of 6mm thick steel plate.
Shearing is the best technique for achieving this particular objective. The process of shearing is
known to offer one of the ways which is known to be of low cost way of making straight cut in
the materials which are rigid without necessary melting, burning or even producing chips. The
sheet plates, metals as well as rods can be effectively being sheared.
De-burring of a quantity of PTFE washers following production
This is achieved through the technique of Teflon. It involves the use of an insulator that is
resistant to the chemicals. The material used in the process is actually impervious to the damages
from the fluids which are corrosive in nature.
Task 4
The assembly of an aluminium aircraft wing (outer layer)
The steps that are involved in the main wing assembling method made from an alloy of
aluminum include: wing skin upper skin placement based on the first reference part disposed on
rivet-fastening and spars rivet-fastening of wing skin lower skin(Yildiz 2013).
A 75mm through hole (in Cast Iron) with a tight tolerance and good surface finish
This can be achieved by the technique called Reaming. The process of reaming is basically used
in the whole enlargement which is achieved by rotating a component called reamer into the
whole itself. This particulate technique is best suited when making tolerance which is tight in
relation to the diameter(Fujimoto et al 2013).
Cutting a large, irregular shape out of 6mm thick steel plate.
Shearing is the best technique for achieving this particular objective. The process of shearing is
known to offer one of the ways which is known to be of low cost way of making straight cut in
the materials which are rigid without necessary melting, burning or even producing chips. The
sheet plates, metals as well as rods can be effectively being sheared.
De-burring of a quantity of PTFE washers following production
This is achieved through the technique of Teflon. It involves the use of an insulator that is
resistant to the chemicals. The material used in the process is actually impervious to the damages
from the fluids which are corrosive in nature.
Task 4
The assembly of an aluminium aircraft wing (outer layer)
The steps that are involved in the main wing assembling method made from an alloy of
aluminum include: wing skin upper skin placement based on the first reference part disposed on
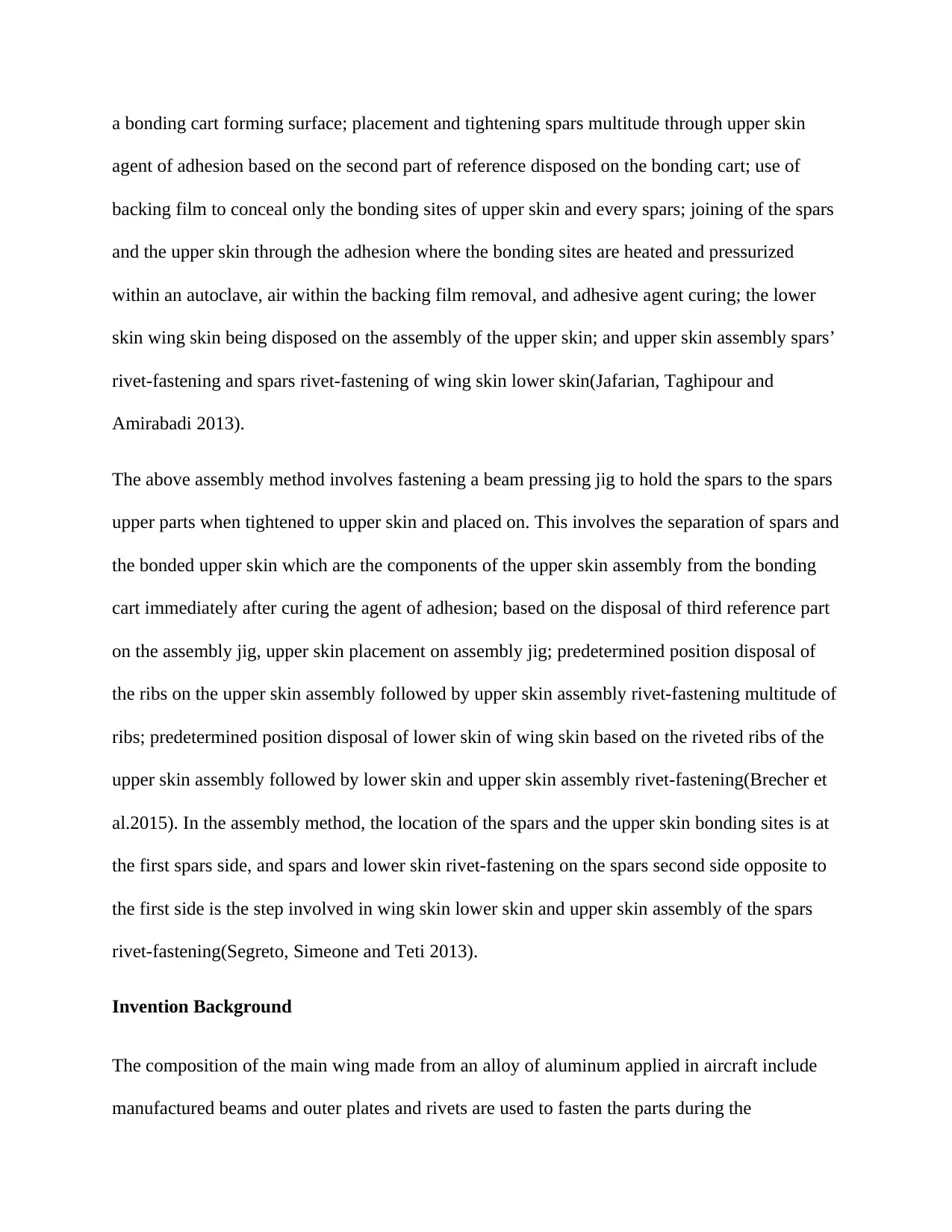
a bonding cart forming surface; placement and tightening spars multitude through upper skin
agent of adhesion based on the second part of reference disposed on the bonding cart; use of
backing film to conceal only the bonding sites of upper skin and every spars; joining of the spars
and the upper skin through the adhesion where the bonding sites are heated and pressurized
within an autoclave, air within the backing film removal, and adhesive agent curing; the lower
skin wing skin being disposed on the assembly of the upper skin; and upper skin assembly spars’
rivet-fastening and spars rivet-fastening of wing skin lower skin(Jafarian, Taghipour and
Amirabadi 2013).
The above assembly method involves fastening a beam pressing jig to hold the spars to the spars
upper parts when tightened to upper skin and placed on. This involves the separation of spars and
the bonded upper skin which are the components of the upper skin assembly from the bonding
cart immediately after curing the agent of adhesion; based on the disposal of third reference part
on the assembly jig, upper skin placement on assembly jig; predetermined position disposal of
the ribs on the upper skin assembly followed by upper skin assembly rivet-fastening multitude of
ribs; predetermined position disposal of lower skin of wing skin based on the riveted ribs of the
upper skin assembly followed by lower skin and upper skin assembly rivet-fastening(Brecher et
al.2015). In the assembly method, the location of the spars and the upper skin bonding sites is at
the first spars side, and spars and lower skin rivet-fastening on the spars second side opposite to
the first side is the step involved in wing skin lower skin and upper skin assembly of the spars
rivet-fastening(Segreto, Simeone and Teti 2013).
Invention Background
The composition of the main wing made from an alloy of aluminum applied in aircraft include
manufactured beams and outer plates and rivets are used to fasten the parts during the
agent of adhesion based on the second part of reference disposed on the bonding cart; use of
backing film to conceal only the bonding sites of upper skin and every spars; joining of the spars
and the upper skin through the adhesion where the bonding sites are heated and pressurized
within an autoclave, air within the backing film removal, and adhesive agent curing; the lower
skin wing skin being disposed on the assembly of the upper skin; and upper skin assembly spars’
rivet-fastening and spars rivet-fastening of wing skin lower skin(Jafarian, Taghipour and
Amirabadi 2013).
The above assembly method involves fastening a beam pressing jig to hold the spars to the spars
upper parts when tightened to upper skin and placed on. This involves the separation of spars and
the bonded upper skin which are the components of the upper skin assembly from the bonding
cart immediately after curing the agent of adhesion; based on the disposal of third reference part
on the assembly jig, upper skin placement on assembly jig; predetermined position disposal of
the ribs on the upper skin assembly followed by upper skin assembly rivet-fastening multitude of
ribs; predetermined position disposal of lower skin of wing skin based on the riveted ribs of the
upper skin assembly followed by lower skin and upper skin assembly rivet-fastening(Brecher et
al.2015). In the assembly method, the location of the spars and the upper skin bonding sites is at
the first spars side, and spars and lower skin rivet-fastening on the spars second side opposite to
the first side is the step involved in wing skin lower skin and upper skin assembly of the spars
rivet-fastening(Segreto, Simeone and Teti 2013).
Invention Background
The composition of the main wing made from an alloy of aluminum applied in aircraft include
manufactured beams and outer plates and rivets are used to fasten the parts during the
Secure Best Marks with AI Grader
Need help grading? Try our AI Grader for instant feedback on your assignments.
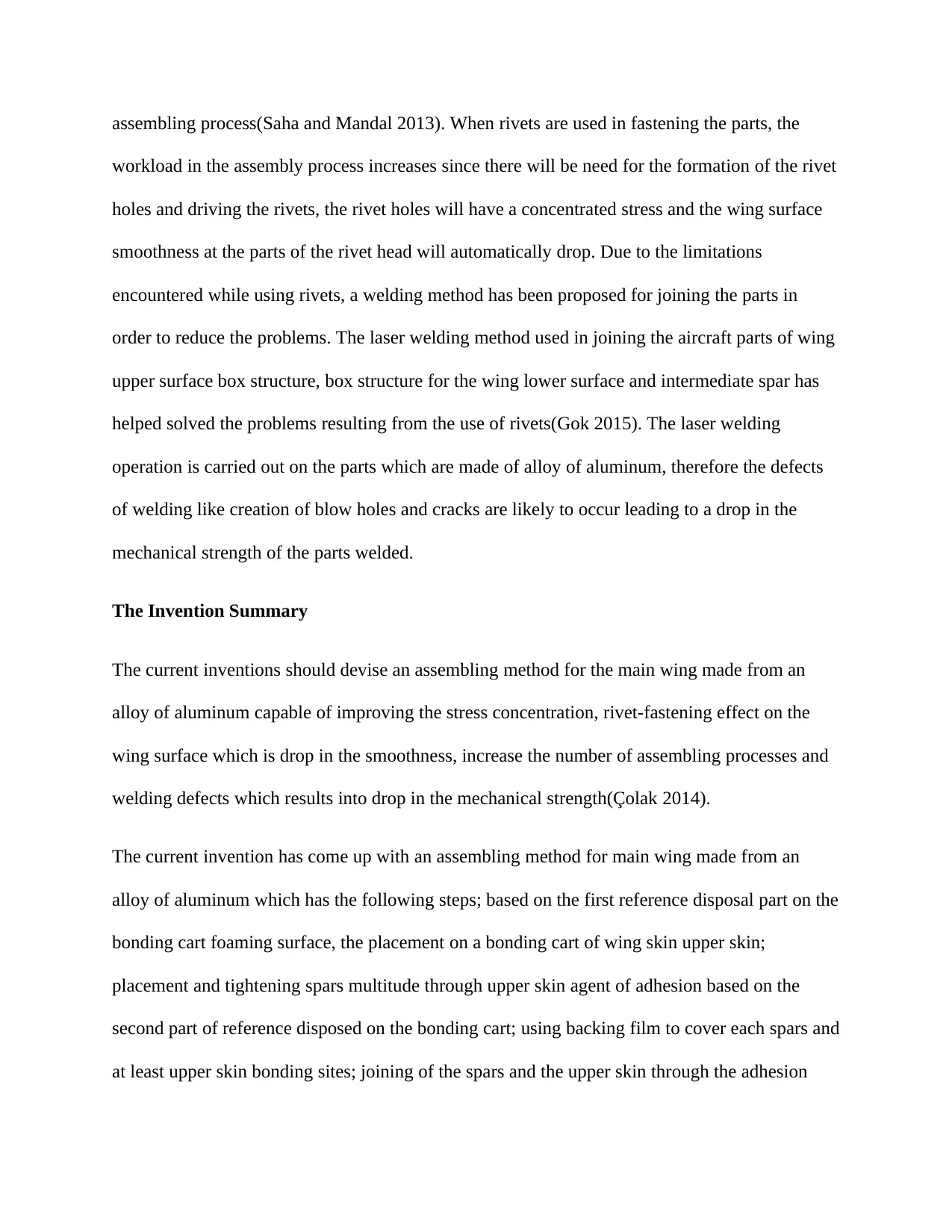
assembling process(Saha and Mandal 2013). When rivets are used in fastening the parts, the
workload in the assembly process increases since there will be need for the formation of the rivet
holes and driving the rivets, the rivet holes will have a concentrated stress and the wing surface
smoothness at the parts of the rivet head will automatically drop. Due to the limitations
encountered while using rivets, a welding method has been proposed for joining the parts in
order to reduce the problems. The laser welding method used in joining the aircraft parts of wing
upper surface box structure, box structure for the wing lower surface and intermediate spar has
helped solved the problems resulting from the use of rivets(Gok 2015). The laser welding
operation is carried out on the parts which are made of alloy of aluminum, therefore the defects
of welding like creation of blow holes and cracks are likely to occur leading to a drop in the
mechanical strength of the parts welded.
The Invention Summary
The current inventions should devise an assembling method for the main wing made from an
alloy of aluminum capable of improving the stress concentration, rivet-fastening effect on the
wing surface which is drop in the smoothness, increase the number of assembling processes and
welding defects which results into drop in the mechanical strength(Çolak 2014).
The current invention has come up with an assembling method for main wing made from an
alloy of aluminum which has the following steps; based on the first reference disposal part on the
bonding cart foaming surface, the placement on a bonding cart of wing skin upper skin;
placement and tightening spars multitude through upper skin agent of adhesion based on the
second part of reference disposed on the bonding cart; using backing film to cover each spars and
at least upper skin bonding sites; joining of the spars and the upper skin through the adhesion
workload in the assembly process increases since there will be need for the formation of the rivet
holes and driving the rivets, the rivet holes will have a concentrated stress and the wing surface
smoothness at the parts of the rivet head will automatically drop. Due to the limitations
encountered while using rivets, a welding method has been proposed for joining the parts in
order to reduce the problems. The laser welding method used in joining the aircraft parts of wing
upper surface box structure, box structure for the wing lower surface and intermediate spar has
helped solved the problems resulting from the use of rivets(Gok 2015). The laser welding
operation is carried out on the parts which are made of alloy of aluminum, therefore the defects
of welding like creation of blow holes and cracks are likely to occur leading to a drop in the
mechanical strength of the parts welded.
The Invention Summary
The current inventions should devise an assembling method for the main wing made from an
alloy of aluminum capable of improving the stress concentration, rivet-fastening effect on the
wing surface which is drop in the smoothness, increase the number of assembling processes and
welding defects which results into drop in the mechanical strength(Çolak 2014).
The current invention has come up with an assembling method for main wing made from an
alloy of aluminum which has the following steps; based on the first reference disposal part on the
bonding cart foaming surface, the placement on a bonding cart of wing skin upper skin;
placement and tightening spars multitude through upper skin agent of adhesion based on the
second part of reference disposed on the bonding cart; using backing film to cover each spars and
at least upper skin bonding sites; joining of the spars and the upper skin through the adhesion
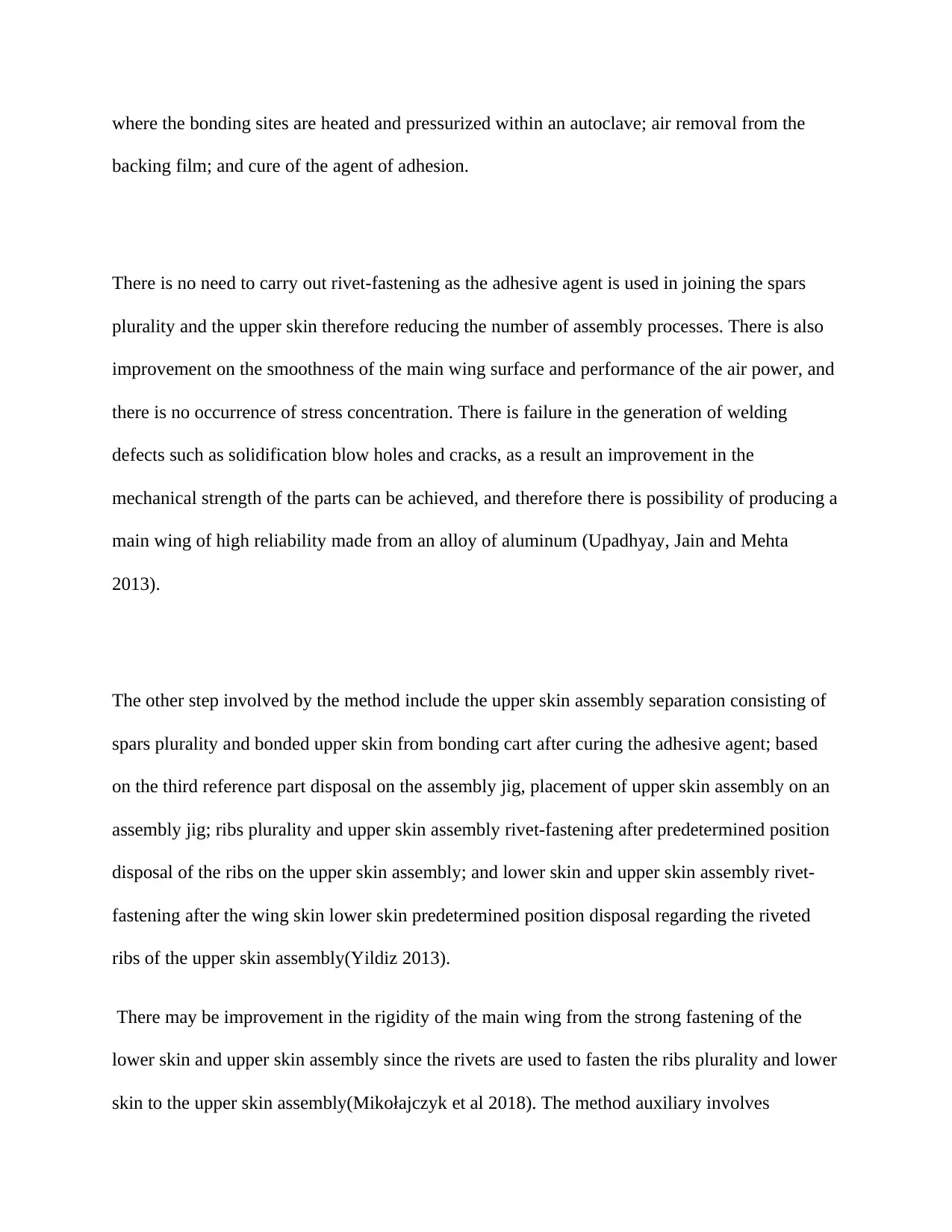
where the bonding sites are heated and pressurized within an autoclave; air removal from the
backing film; and cure of the agent of adhesion.
There is no need to carry out rivet-fastening as the adhesive agent is used in joining the spars
plurality and the upper skin therefore reducing the number of assembly processes. There is also
improvement on the smoothness of the main wing surface and performance of the air power, and
there is no occurrence of stress concentration. There is failure in the generation of welding
defects such as solidification blow holes and cracks, as a result an improvement in the
mechanical strength of the parts can be achieved, and therefore there is possibility of producing a
main wing of high reliability made from an alloy of aluminum (Upadhyay, Jain and Mehta
2013).
The other step involved by the method include the upper skin assembly separation consisting of
spars plurality and bonded upper skin from bonding cart after curing the adhesive agent; based
on the third reference part disposal on the assembly jig, placement of upper skin assembly on an
assembly jig; ribs plurality and upper skin assembly rivet-fastening after predetermined position
disposal of the ribs on the upper skin assembly; and lower skin and upper skin assembly rivet-
fastening after the wing skin lower skin predetermined position disposal regarding the riveted
ribs of the upper skin assembly(Yildiz 2013).
There may be improvement in the rigidity of the main wing from the strong fastening of the
lower skin and upper skin assembly since the rivets are used to fasten the ribs plurality and lower
skin to the upper skin assembly(Mikołajczyk et al 2018). The method auxiliary involves
backing film; and cure of the agent of adhesion.
There is no need to carry out rivet-fastening as the adhesive agent is used in joining the spars
plurality and the upper skin therefore reducing the number of assembly processes. There is also
improvement on the smoothness of the main wing surface and performance of the air power, and
there is no occurrence of stress concentration. There is failure in the generation of welding
defects such as solidification blow holes and cracks, as a result an improvement in the
mechanical strength of the parts can be achieved, and therefore there is possibility of producing a
main wing of high reliability made from an alloy of aluminum (Upadhyay, Jain and Mehta
2013).
The other step involved by the method include the upper skin assembly separation consisting of
spars plurality and bonded upper skin from bonding cart after curing the adhesive agent; based
on the third reference part disposal on the assembly jig, placement of upper skin assembly on an
assembly jig; ribs plurality and upper skin assembly rivet-fastening after predetermined position
disposal of the ribs on the upper skin assembly; and lower skin and upper skin assembly rivet-
fastening after the wing skin lower skin predetermined position disposal regarding the riveted
ribs of the upper skin assembly(Yildiz 2013).
There may be improvement in the rigidity of the main wing from the strong fastening of the
lower skin and upper skin assembly since the rivets are used to fasten the ribs plurality and lower
skin to the upper skin assembly(Mikołajczyk et al 2018). The method auxiliary involves
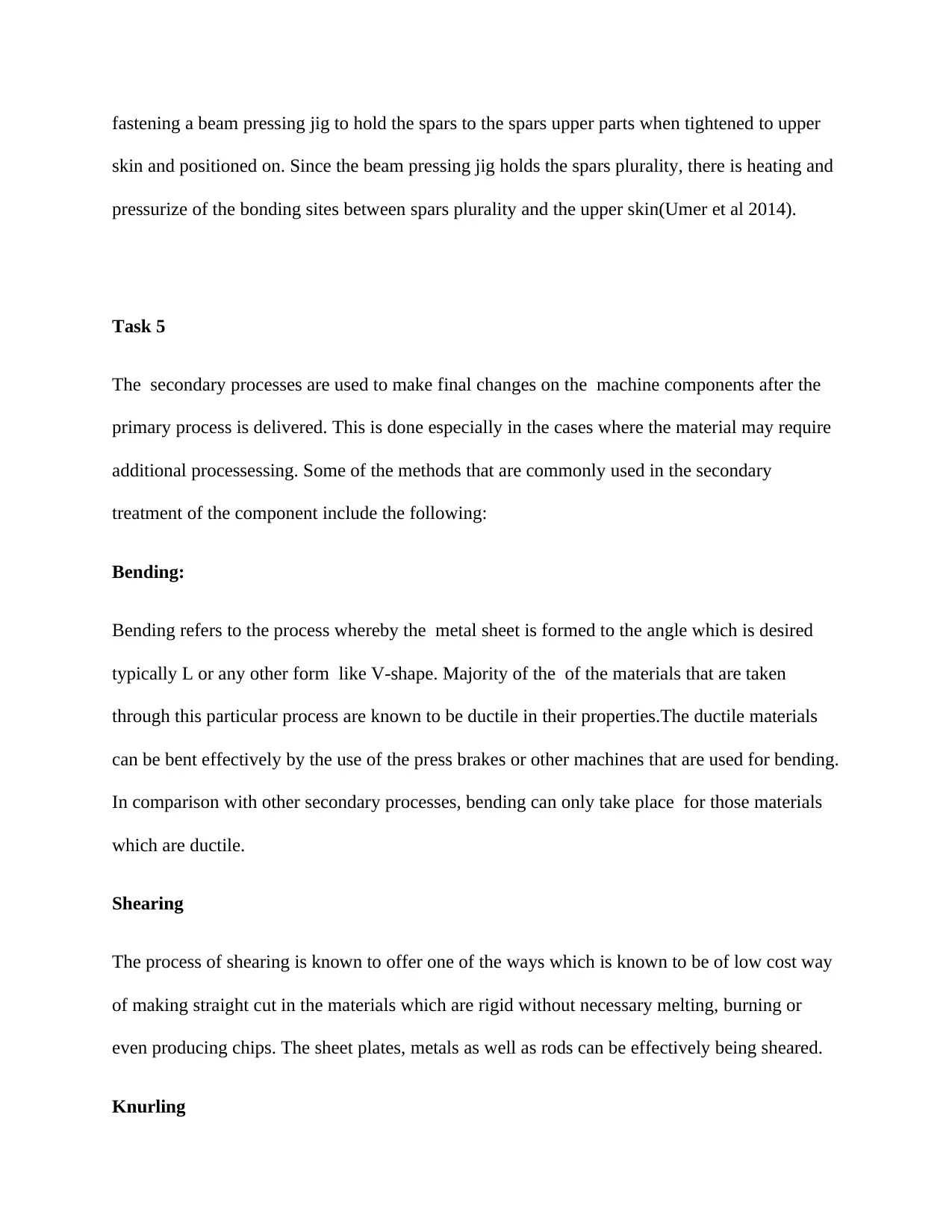
fastening a beam pressing jig to hold the spars to the spars upper parts when tightened to upper
skin and positioned on. Since the beam pressing jig holds the spars plurality, there is heating and
pressurize of the bonding sites between spars plurality and the upper skin(Umer et al 2014).
Task 5
The secondary processes are used to make final changes on the machine components after the
primary process is delivered. This is done especially in the cases where the material may require
additional processessing. Some of the methods that are commonly used in the secondary
treatment of the component include the following:
Bending:
Bending refers to the process whereby the metal sheet is formed to the angle which is desired
typically L or any other form like V-shape. Majority of the of the materials that are taken
through this particular process are known to be ductile in their properties.The ductile materials
can be bent effectively by the use of the press brakes or other machines that are used for bending.
In comparison with other secondary processes, bending can only take place for those materials
which are ductile.
Shearing
The process of shearing is known to offer one of the ways which is known to be of low cost way
of making straight cut in the materials which are rigid without necessary melting, burning or
even producing chips. The sheet plates, metals as well as rods can be effectively being sheared.
Knurling
skin and positioned on. Since the beam pressing jig holds the spars plurality, there is heating and
pressurize of the bonding sites between spars plurality and the upper skin(Umer et al 2014).
Task 5
The secondary processes are used to make final changes on the machine components after the
primary process is delivered. This is done especially in the cases where the material may require
additional processessing. Some of the methods that are commonly used in the secondary
treatment of the component include the following:
Bending:
Bending refers to the process whereby the metal sheet is formed to the angle which is desired
typically L or any other form like V-shape. Majority of the of the materials that are taken
through this particular process are known to be ductile in their properties.The ductile materials
can be bent effectively by the use of the press brakes or other machines that are used for bending.
In comparison with other secondary processes, bending can only take place for those materials
which are ductile.
Shearing
The process of shearing is known to offer one of the ways which is known to be of low cost way
of making straight cut in the materials which are rigid without necessary melting, burning or
even producing chips. The sheet plates, metals as well as rods can be effectively being sheared.
Knurling
Paraphrase This Document
Need a fresh take? Get an instant paraphrase of this document with our AI Paraphraser
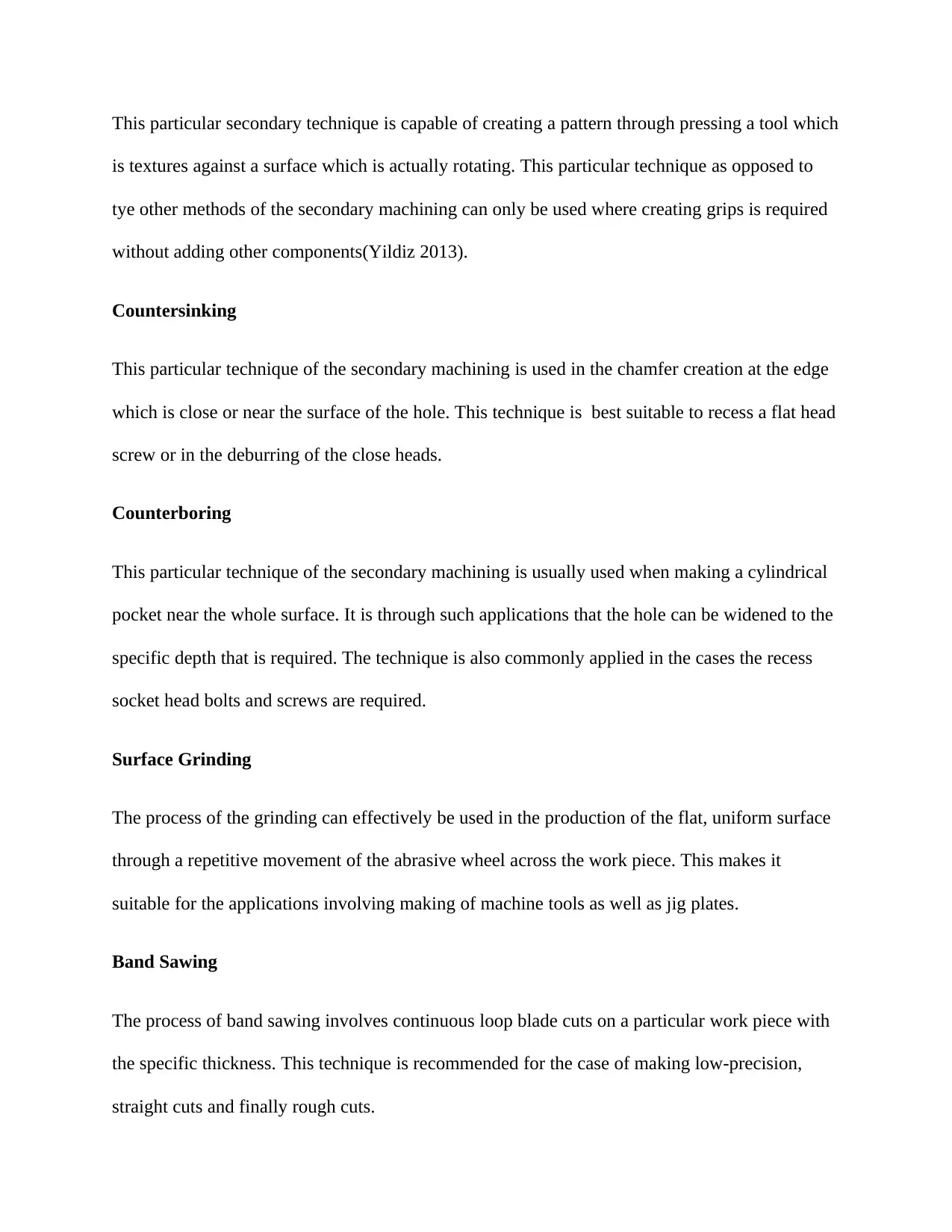
This particular secondary technique is capable of creating a pattern through pressing a tool which
is textures against a surface which is actually rotating. This particular technique as opposed to
tye other methods of the secondary machining can only be used where creating grips is required
without adding other components(Yildiz 2013).
Countersinking
This particular technique of the secondary machining is used in the chamfer creation at the edge
which is close or near the surface of the hole. This technique is best suitable to recess a flat head
screw or in the deburring of the close heads.
Counterboring
This particular technique of the secondary machining is usually used when making a cylindrical
pocket near the whole surface. It is through such applications that the hole can be widened to the
specific depth that is required. The technique is also commonly applied in the cases the recess
socket head bolts and screws are required.
Surface Grinding
The process of the grinding can effectively be used in the production of the flat, uniform surface
through a repetitive movement of the abrasive wheel across the work piece. This makes it
suitable for the applications involving making of machine tools as well as jig plates.
Band Sawing
The process of band sawing involves continuous loop blade cuts on a particular work piece with
the specific thickness. This technique is recommended for the case of making low-precision,
straight cuts and finally rough cuts.
is textures against a surface which is actually rotating. This particular technique as opposed to
tye other methods of the secondary machining can only be used where creating grips is required
without adding other components(Yildiz 2013).
Countersinking
This particular technique of the secondary machining is used in the chamfer creation at the edge
which is close or near the surface of the hole. This technique is best suitable to recess a flat head
screw or in the deburring of the close heads.
Counterboring
This particular technique of the secondary machining is usually used when making a cylindrical
pocket near the whole surface. It is through such applications that the hole can be widened to the
specific depth that is required. The technique is also commonly applied in the cases the recess
socket head bolts and screws are required.
Surface Grinding
The process of the grinding can effectively be used in the production of the flat, uniform surface
through a repetitive movement of the abrasive wheel across the work piece. This makes it
suitable for the applications involving making of machine tools as well as jig plates.
Band Sawing
The process of band sawing involves continuous loop blade cuts on a particular work piece with
the specific thickness. This technique is recommended for the case of making low-precision,
straight cuts and finally rough cuts.
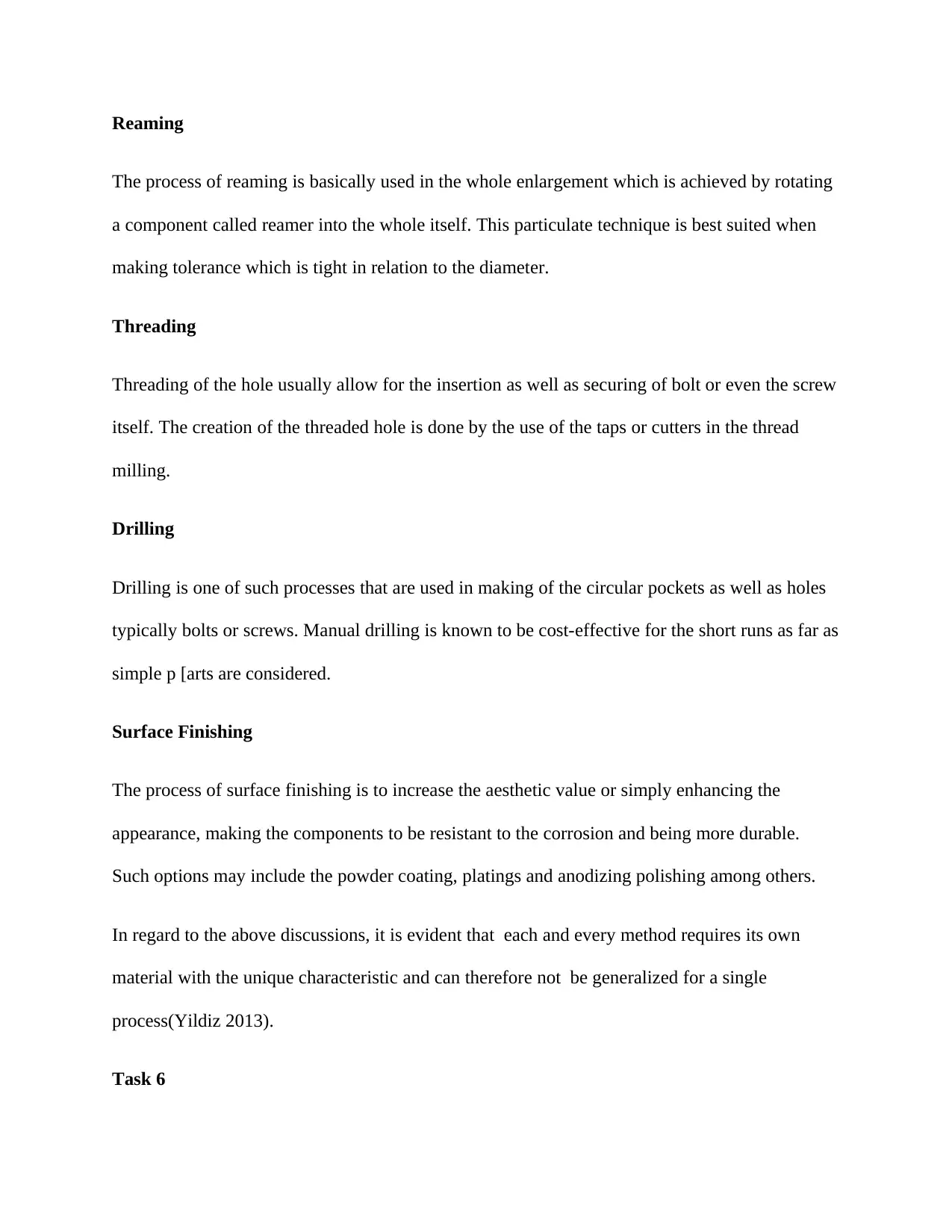
Reaming
The process of reaming is basically used in the whole enlargement which is achieved by rotating
a component called reamer into the whole itself. This particulate technique is best suited when
making tolerance which is tight in relation to the diameter.
Threading
Threading of the hole usually allow for the insertion as well as securing of bolt or even the screw
itself. The creation of the threaded hole is done by the use of the taps or cutters in the thread
milling.
Drilling
Drilling is one of such processes that are used in making of the circular pockets as well as holes
typically bolts or screws. Manual drilling is known to be cost-effective for the short runs as far as
simple p [arts are considered.
Surface Finishing
The process of surface finishing is to increase the aesthetic value or simply enhancing the
appearance, making the components to be resistant to the corrosion and being more durable.
Such options may include the powder coating, platings and anodizing polishing among others.
In regard to the above discussions, it is evident that each and every method requires its own
material with the unique characteristic and can therefore not be generalized for a single
process(Yildiz 2013).
Task 6
The process of reaming is basically used in the whole enlargement which is achieved by rotating
a component called reamer into the whole itself. This particulate technique is best suited when
making tolerance which is tight in relation to the diameter.
Threading
Threading of the hole usually allow for the insertion as well as securing of bolt or even the screw
itself. The creation of the threaded hole is done by the use of the taps or cutters in the thread
milling.
Drilling
Drilling is one of such processes that are used in making of the circular pockets as well as holes
typically bolts or screws. Manual drilling is known to be cost-effective for the short runs as far as
simple p [arts are considered.
Surface Finishing
The process of surface finishing is to increase the aesthetic value or simply enhancing the
appearance, making the components to be resistant to the corrosion and being more durable.
Such options may include the powder coating, platings and anodizing polishing among others.
In regard to the above discussions, it is evident that each and every method requires its own
material with the unique characteristic and can therefore not be generalized for a single
process(Yildiz 2013).
Task 6
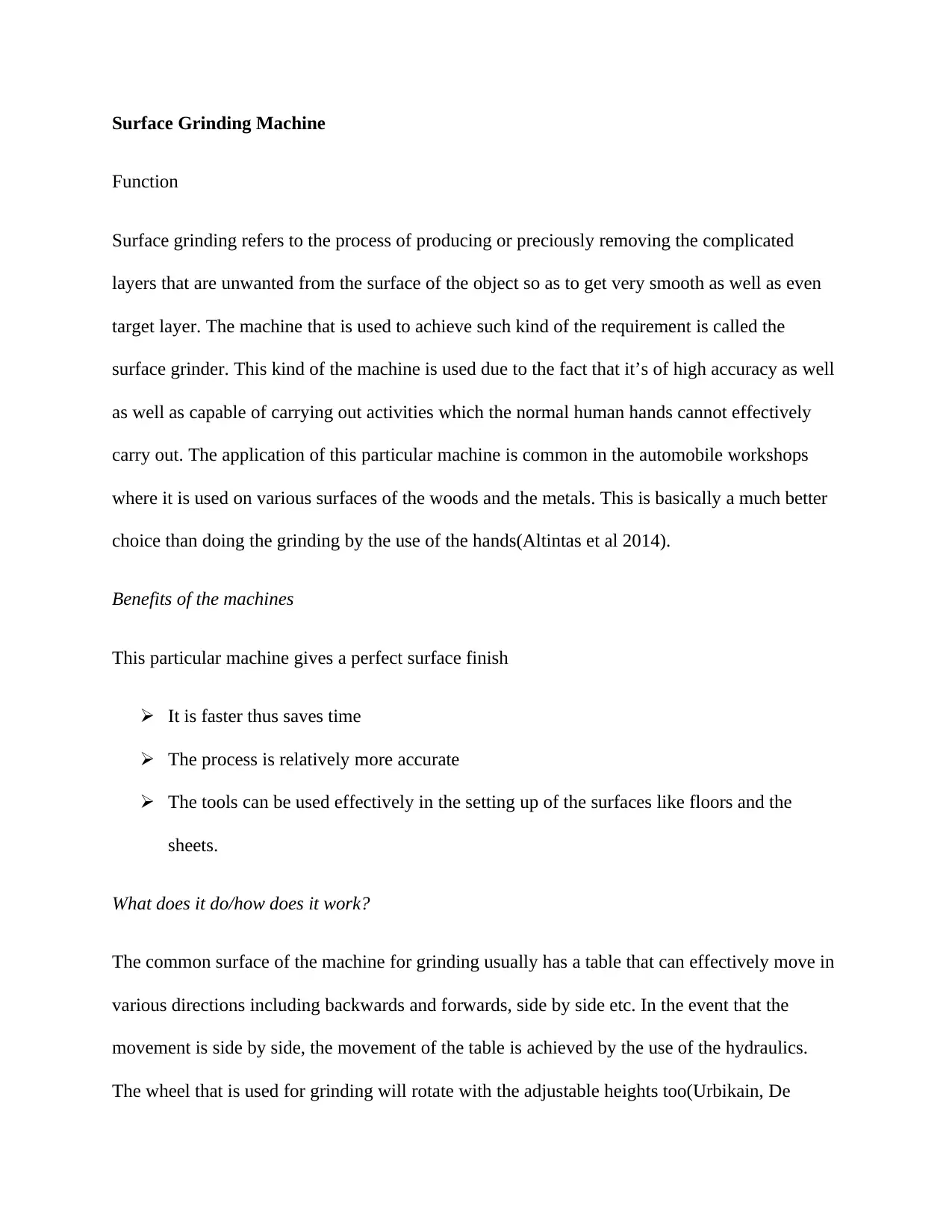
Surface Grinding Machine
Function
Surface grinding refers to the process of producing or preciously removing the complicated
layers that are unwanted from the surface of the object so as to get very smooth as well as even
target layer. The machine that is used to achieve such kind of the requirement is called the
surface grinder. This kind of the machine is used due to the fact that it’s of high accuracy as well
as well as capable of carrying out activities which the normal human hands cannot effectively
carry out. The application of this particular machine is common in the automobile workshops
where it is used on various surfaces of the woods and the metals. This is basically a much better
choice than doing the grinding by the use of the hands(Altintas et al 2014).
Benefits of the machines
This particular machine gives a perfect surface finish
It is faster thus saves time
The process is relatively more accurate
The tools can be used effectively in the setting up of the surfaces like floors and the
sheets.
What does it do/how does it work?
The common surface of the machine for grinding usually has a table that can effectively move in
various directions including backwards and forwards, side by side etc. In the event that the
movement is side by side, the movement of the table is achieved by the use of the hydraulics.
The wheel that is used for grinding will rotate with the adjustable heights too(Urbikain, De
Function
Surface grinding refers to the process of producing or preciously removing the complicated
layers that are unwanted from the surface of the object so as to get very smooth as well as even
target layer. The machine that is used to achieve such kind of the requirement is called the
surface grinder. This kind of the machine is used due to the fact that it’s of high accuracy as well
as well as capable of carrying out activities which the normal human hands cannot effectively
carry out. The application of this particular machine is common in the automobile workshops
where it is used on various surfaces of the woods and the metals. This is basically a much better
choice than doing the grinding by the use of the hands(Altintas et al 2014).
Benefits of the machines
This particular machine gives a perfect surface finish
It is faster thus saves time
The process is relatively more accurate
The tools can be used effectively in the setting up of the surfaces like floors and the
sheets.
What does it do/how does it work?
The common surface of the machine for grinding usually has a table that can effectively move in
various directions including backwards and forwards, side by side etc. In the event that the
movement is side by side, the movement of the table is achieved by the use of the hydraulics.
The wheel that is used for grinding will rotate with the adjustable heights too(Urbikain, De
Secure Best Marks with AI Grader
Need help grading? Try our AI Grader for instant feedback on your assignments.
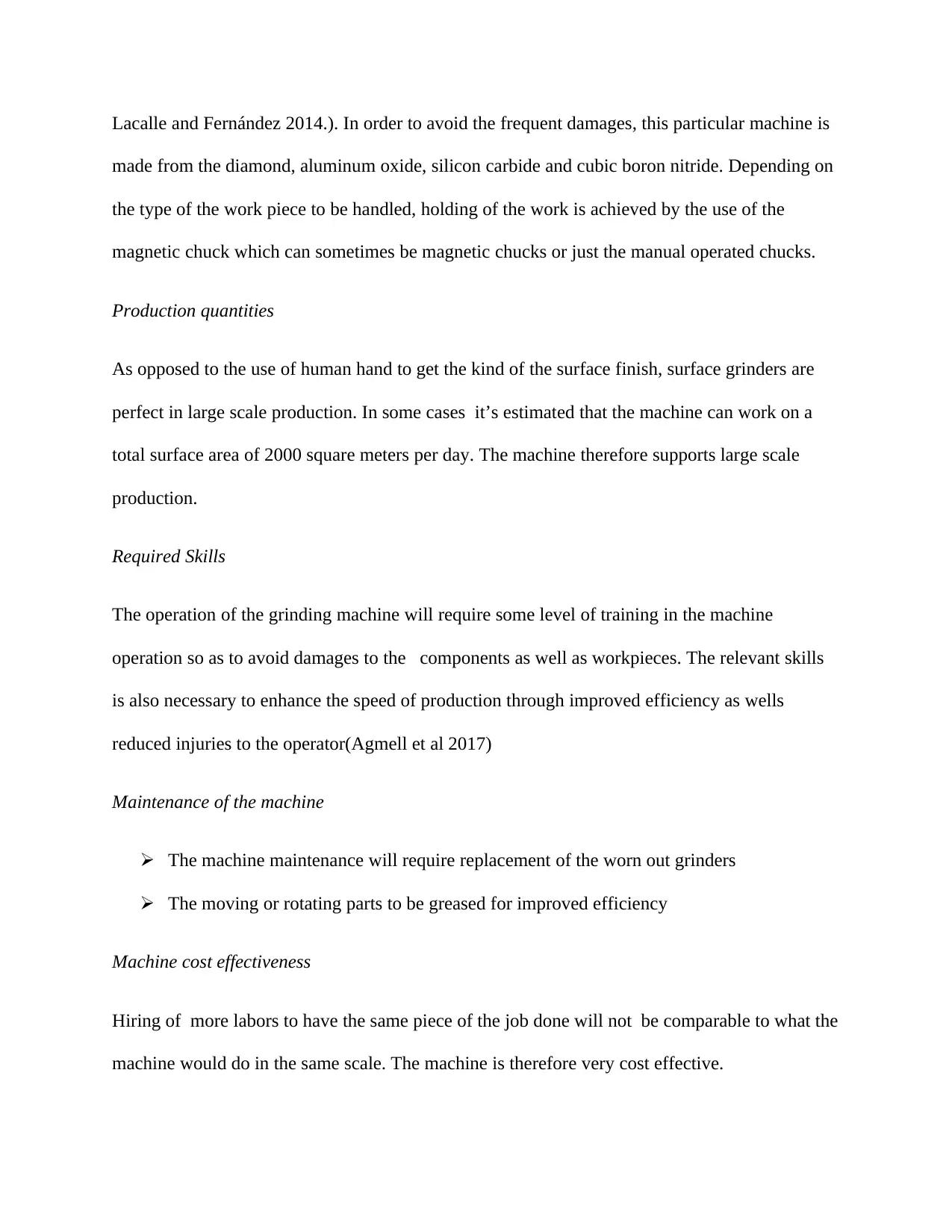
Lacalle and Fernández 2014.). In order to avoid the frequent damages, this particular machine is
made from the diamond, aluminum oxide, silicon carbide and cubic boron nitride. Depending on
the type of the work piece to be handled, holding of the work is achieved by the use of the
magnetic chuck which can sometimes be magnetic chucks or just the manual operated chucks.
Production quantities
As opposed to the use of human hand to get the kind of the surface finish, surface grinders are
perfect in large scale production. In some cases it’s estimated that the machine can work on a
total surface area of 2000 square meters per day. The machine therefore supports large scale
production.
Required Skills
The operation of the grinding machine will require some level of training in the machine
operation so as to avoid damages to the components as well as workpieces. The relevant skills
is also necessary to enhance the speed of production through improved efficiency as wells
reduced injuries to the operator(Agmell et al 2017)
Maintenance of the machine
The machine maintenance will require replacement of the worn out grinders
The moving or rotating parts to be greased for improved efficiency
Machine cost effectiveness
Hiring of more labors to have the same piece of the job done will not be comparable to what the
machine would do in the same scale. The machine is therefore very cost effective.
made from the diamond, aluminum oxide, silicon carbide and cubic boron nitride. Depending on
the type of the work piece to be handled, holding of the work is achieved by the use of the
magnetic chuck which can sometimes be magnetic chucks or just the manual operated chucks.
Production quantities
As opposed to the use of human hand to get the kind of the surface finish, surface grinders are
perfect in large scale production. In some cases it’s estimated that the machine can work on a
total surface area of 2000 square meters per day. The machine therefore supports large scale
production.
Required Skills
The operation of the grinding machine will require some level of training in the machine
operation so as to avoid damages to the components as well as workpieces. The relevant skills
is also necessary to enhance the speed of production through improved efficiency as wells
reduced injuries to the operator(Agmell et al 2017)
Maintenance of the machine
The machine maintenance will require replacement of the worn out grinders
The moving or rotating parts to be greased for improved efficiency
Machine cost effectiveness
Hiring of more labors to have the same piece of the job done will not be comparable to what the
machine would do in the same scale. The machine is therefore very cost effective.
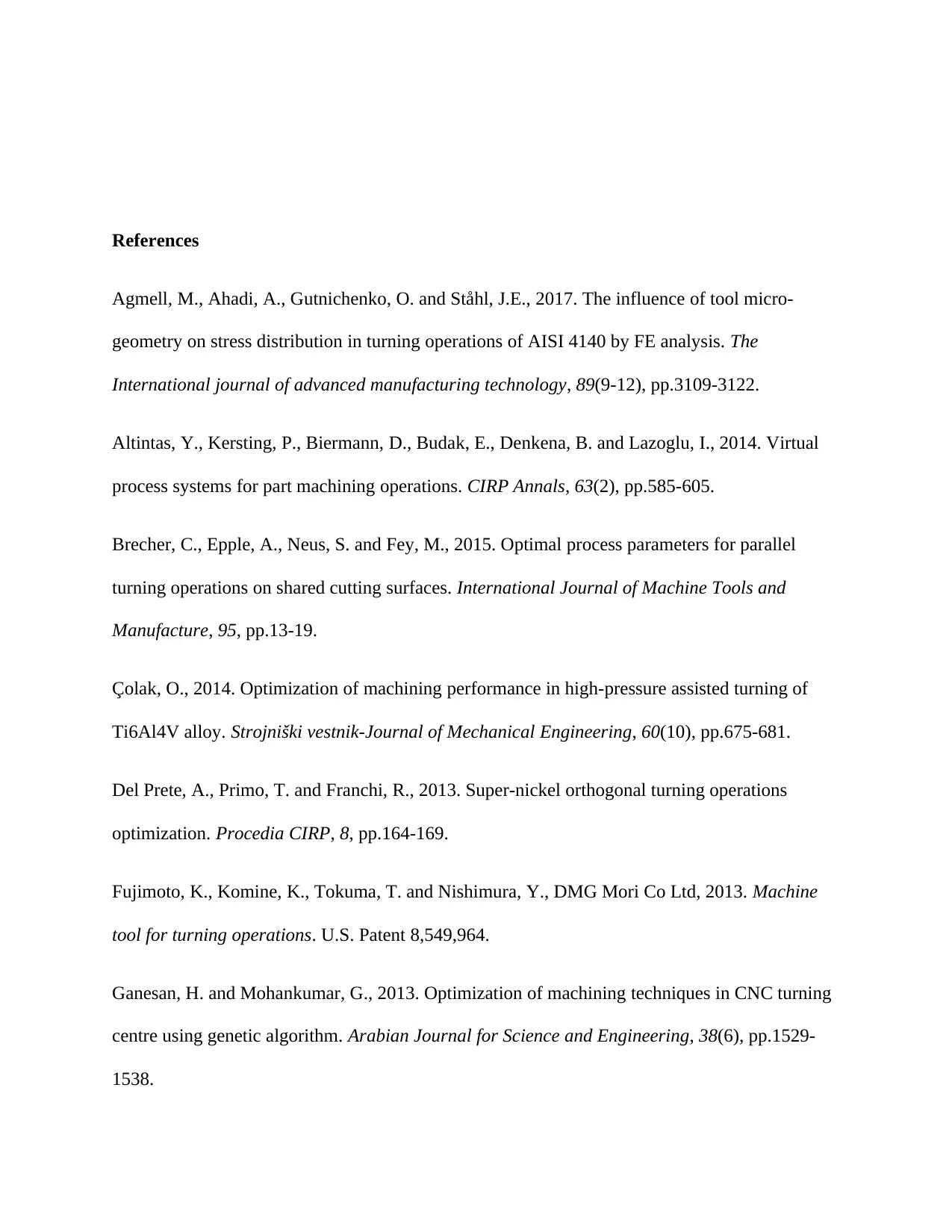
References
Agmell, M., Ahadi, A., Gutnichenko, O. and Ståhl, J.E., 2017. The influence of tool micro-
geometry on stress distribution in turning operations of AISI 4140 by FE analysis. The
International journal of advanced manufacturing technology, 89(9-12), pp.3109-3122.
Altintas, Y., Kersting, P., Biermann, D., Budak, E., Denkena, B. and Lazoglu, I., 2014. Virtual
process systems for part machining operations. CIRP Annals, 63(2), pp.585-605.
Brecher, C., Epple, A., Neus, S. and Fey, M., 2015. Optimal process parameters for parallel
turning operations on shared cutting surfaces. International Journal of Machine Tools and
Manufacture, 95, pp.13-19.
Çolak, O., 2014. Optimization of machining performance in high-pressure assisted turning of
Ti6Al4V alloy. Strojniški vestnik-Journal of Mechanical Engineering, 60(10), pp.675-681.
Del Prete, A., Primo, T. and Franchi, R., 2013. Super-nickel orthogonal turning operations
optimization. Procedia CIRP, 8, pp.164-169.
Fujimoto, K., Komine, K., Tokuma, T. and Nishimura, Y., DMG Mori Co Ltd, 2013. Machine
tool for turning operations. U.S. Patent 8,549,964.
Ganesan, H. and Mohankumar, G., 2013. Optimization of machining techniques in CNC turning
centre using genetic algorithm. Arabian Journal for Science and Engineering, 38(6), pp.1529-
1538.
Agmell, M., Ahadi, A., Gutnichenko, O. and Ståhl, J.E., 2017. The influence of tool micro-
geometry on stress distribution in turning operations of AISI 4140 by FE analysis. The
International journal of advanced manufacturing technology, 89(9-12), pp.3109-3122.
Altintas, Y., Kersting, P., Biermann, D., Budak, E., Denkena, B. and Lazoglu, I., 2014. Virtual
process systems for part machining operations. CIRP Annals, 63(2), pp.585-605.
Brecher, C., Epple, A., Neus, S. and Fey, M., 2015. Optimal process parameters for parallel
turning operations on shared cutting surfaces. International Journal of Machine Tools and
Manufacture, 95, pp.13-19.
Çolak, O., 2014. Optimization of machining performance in high-pressure assisted turning of
Ti6Al4V alloy. Strojniški vestnik-Journal of Mechanical Engineering, 60(10), pp.675-681.
Del Prete, A., Primo, T. and Franchi, R., 2013. Super-nickel orthogonal turning operations
optimization. Procedia CIRP, 8, pp.164-169.
Fujimoto, K., Komine, K., Tokuma, T. and Nishimura, Y., DMG Mori Co Ltd, 2013. Machine
tool for turning operations. U.S. Patent 8,549,964.
Ganesan, H. and Mohankumar, G., 2013. Optimization of machining techniques in CNC turning
centre using genetic algorithm. Arabian Journal for Science and Engineering, 38(6), pp.1529-
1538.
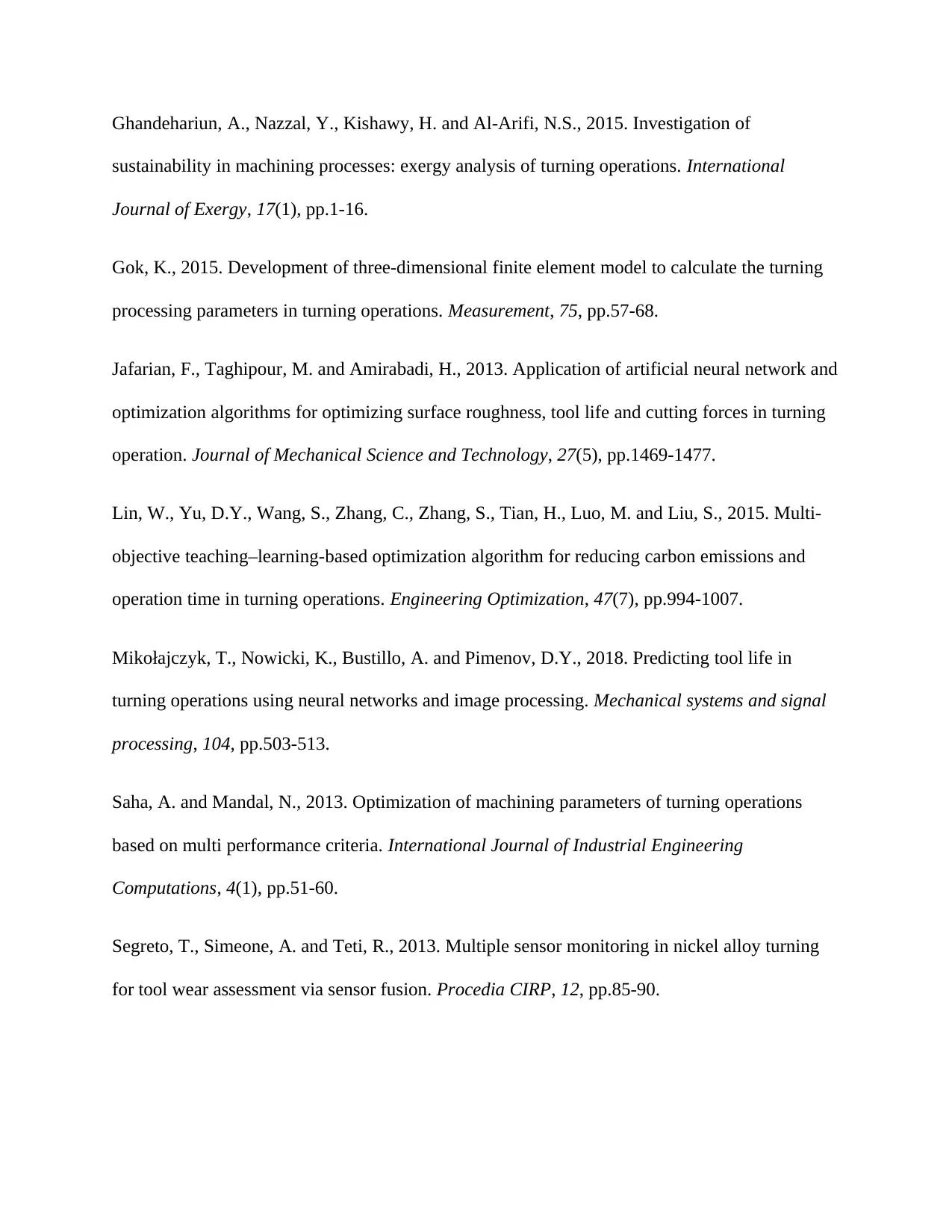
Ghandehariun, A., Nazzal, Y., Kishawy, H. and Al-Arifi, N.S., 2015. Investigation of
sustainability in machining processes: exergy analysis of turning operations. International
Journal of Exergy, 17(1), pp.1-16.
Gok, K., 2015. Development of three-dimensional finite element model to calculate the turning
processing parameters in turning operations. Measurement, 75, pp.57-68.
Jafarian, F., Taghipour, M. and Amirabadi, H., 2013. Application of artificial neural network and
optimization algorithms for optimizing surface roughness, tool life and cutting forces in turning
operation. Journal of Mechanical Science and Technology, 27(5), pp.1469-1477.
Lin, W., Yu, D.Y., Wang, S., Zhang, C., Zhang, S., Tian, H., Luo, M. and Liu, S., 2015. Multi-
objective teaching–learning-based optimization algorithm for reducing carbon emissions and
operation time in turning operations. Engineering Optimization, 47(7), pp.994-1007.
Mikołajczyk, T., Nowicki, K., Bustillo, A. and Pimenov, D.Y., 2018. Predicting tool life in
turning operations using neural networks and image processing. Mechanical systems and signal
processing, 104, pp.503-513.
Saha, A. and Mandal, N., 2013. Optimization of machining parameters of turning operations
based on multi performance criteria. International Journal of Industrial Engineering
Computations, 4(1), pp.51-60.
Segreto, T., Simeone, A. and Teti, R., 2013. Multiple sensor monitoring in nickel alloy turning
for tool wear assessment via sensor fusion. Procedia CIRP, 12, pp.85-90.
sustainability in machining processes: exergy analysis of turning operations. International
Journal of Exergy, 17(1), pp.1-16.
Gok, K., 2015. Development of three-dimensional finite element model to calculate the turning
processing parameters in turning operations. Measurement, 75, pp.57-68.
Jafarian, F., Taghipour, M. and Amirabadi, H., 2013. Application of artificial neural network and
optimization algorithms for optimizing surface roughness, tool life and cutting forces in turning
operation. Journal of Mechanical Science and Technology, 27(5), pp.1469-1477.
Lin, W., Yu, D.Y., Wang, S., Zhang, C., Zhang, S., Tian, H., Luo, M. and Liu, S., 2015. Multi-
objective teaching–learning-based optimization algorithm for reducing carbon emissions and
operation time in turning operations. Engineering Optimization, 47(7), pp.994-1007.
Mikołajczyk, T., Nowicki, K., Bustillo, A. and Pimenov, D.Y., 2018. Predicting tool life in
turning operations using neural networks and image processing. Mechanical systems and signal
processing, 104, pp.503-513.
Saha, A. and Mandal, N., 2013. Optimization of machining parameters of turning operations
based on multi performance criteria. International Journal of Industrial Engineering
Computations, 4(1), pp.51-60.
Segreto, T., Simeone, A. and Teti, R., 2013. Multiple sensor monitoring in nickel alloy turning
for tool wear assessment via sensor fusion. Procedia CIRP, 12, pp.85-90.
Paraphrase This Document
Need a fresh take? Get an instant paraphrase of this document with our AI Paraphraser
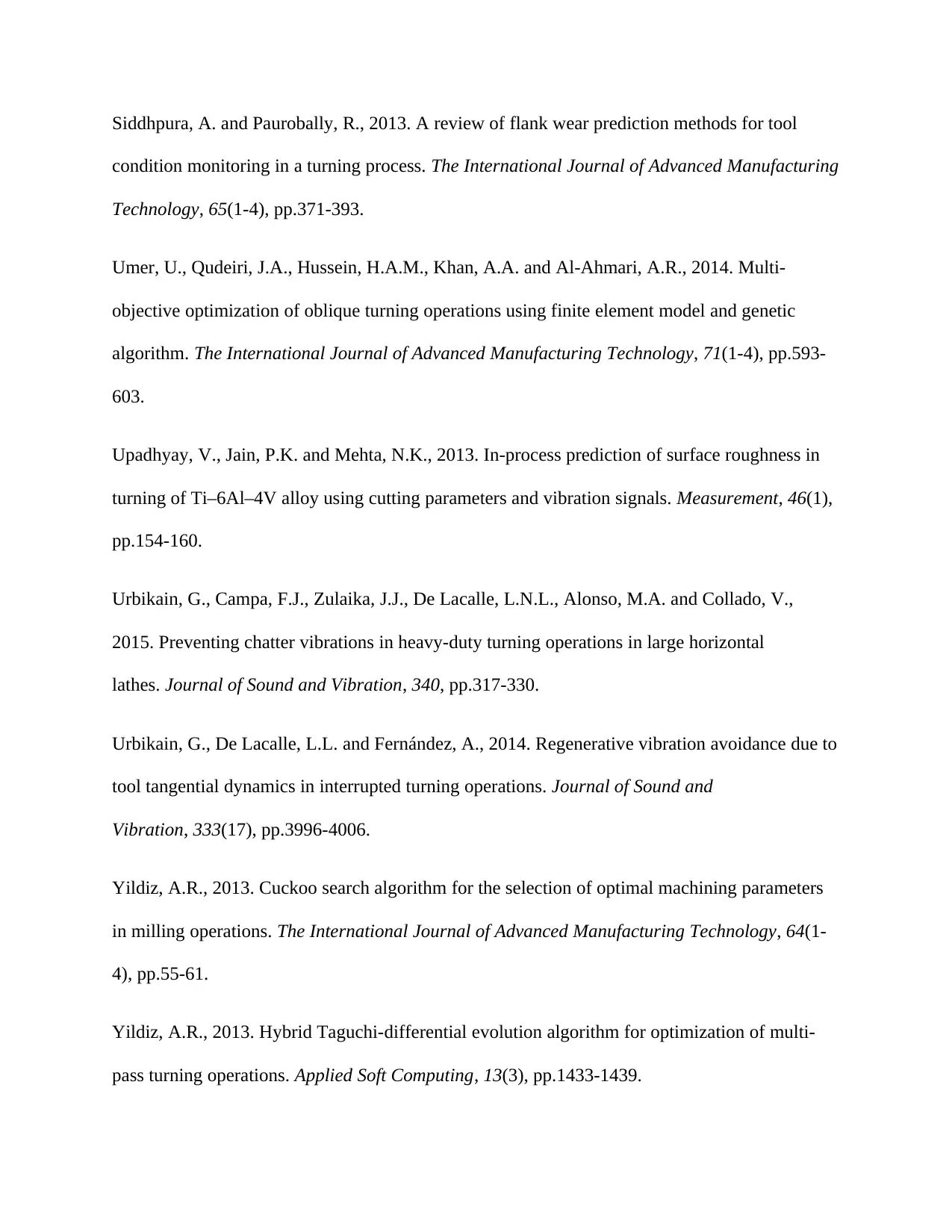
Siddhpura, A. and Paurobally, R., 2013. A review of flank wear prediction methods for tool
condition monitoring in a turning process. The International Journal of Advanced Manufacturing
Technology, 65(1-4), pp.371-393.
Umer, U., Qudeiri, J.A., Hussein, H.A.M., Khan, A.A. and Al-Ahmari, A.R., 2014. Multi-
objective optimization of oblique turning operations using finite element model and genetic
algorithm. The International Journal of Advanced Manufacturing Technology, 71(1-4), pp.593-
603.
Upadhyay, V., Jain, P.K. and Mehta, N.K., 2013. In-process prediction of surface roughness in
turning of Ti–6Al–4V alloy using cutting parameters and vibration signals. Measurement, 46(1),
pp.154-160.
Urbikain, G., Campa, F.J., Zulaika, J.J., De Lacalle, L.N.L., Alonso, M.A. and Collado, V.,
2015. Preventing chatter vibrations in heavy-duty turning operations in large horizontal
lathes. Journal of Sound and Vibration, 340, pp.317-330.
Urbikain, G., De Lacalle, L.L. and Fernández, A., 2014. Regenerative vibration avoidance due to
tool tangential dynamics in interrupted turning operations. Journal of Sound and
Vibration, 333(17), pp.3996-4006.
Yildiz, A.R., 2013. Cuckoo search algorithm for the selection of optimal machining parameters
in milling operations. The International Journal of Advanced Manufacturing Technology, 64(1-
4), pp.55-61.
Yildiz, A.R., 2013. Hybrid Taguchi-differential evolution algorithm for optimization of multi-
pass turning operations. Applied Soft Computing, 13(3), pp.1433-1439.
condition monitoring in a turning process. The International Journal of Advanced Manufacturing
Technology, 65(1-4), pp.371-393.
Umer, U., Qudeiri, J.A., Hussein, H.A.M., Khan, A.A. and Al-Ahmari, A.R., 2014. Multi-
objective optimization of oblique turning operations using finite element model and genetic
algorithm. The International Journal of Advanced Manufacturing Technology, 71(1-4), pp.593-
603.
Upadhyay, V., Jain, P.K. and Mehta, N.K., 2013. In-process prediction of surface roughness in
turning of Ti–6Al–4V alloy using cutting parameters and vibration signals. Measurement, 46(1),
pp.154-160.
Urbikain, G., Campa, F.J., Zulaika, J.J., De Lacalle, L.N.L., Alonso, M.A. and Collado, V.,
2015. Preventing chatter vibrations in heavy-duty turning operations in large horizontal
lathes. Journal of Sound and Vibration, 340, pp.317-330.
Urbikain, G., De Lacalle, L.L. and Fernández, A., 2014. Regenerative vibration avoidance due to
tool tangential dynamics in interrupted turning operations. Journal of Sound and
Vibration, 333(17), pp.3996-4006.
Yildiz, A.R., 2013. Cuckoo search algorithm for the selection of optimal machining parameters
in milling operations. The International Journal of Advanced Manufacturing Technology, 64(1-
4), pp.55-61.
Yildiz, A.R., 2013. Hybrid Taguchi-differential evolution algorithm for optimization of multi-
pass turning operations. Applied Soft Computing, 13(3), pp.1433-1439.
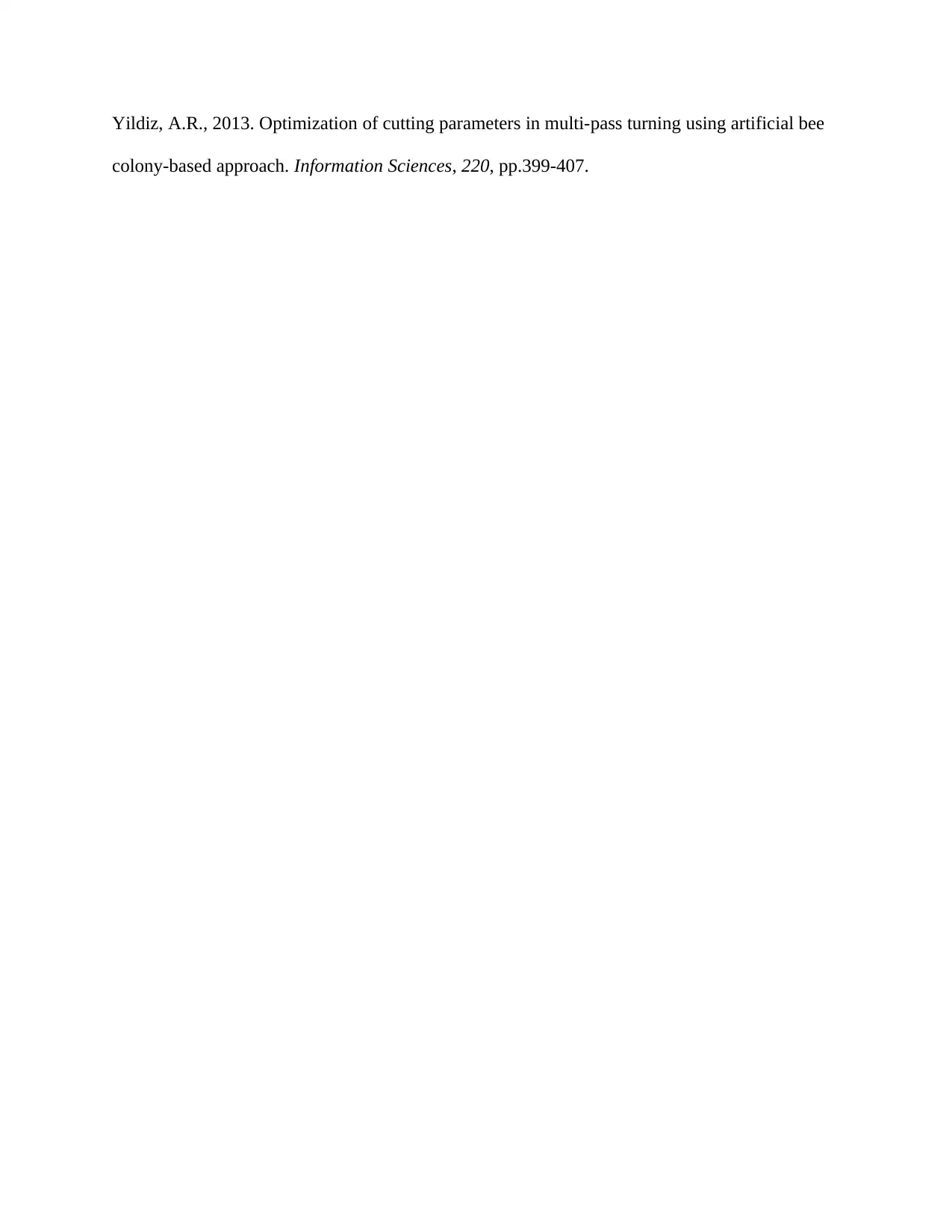
Yildiz, A.R., 2013. Optimization of cutting parameters in multi-pass turning using artificial bee
colony-based approach. Information Sciences, 220, pp.399-407.
colony-based approach. Information Sciences, 220, pp.399-407.
1 out of 21

Your All-in-One AI-Powered Toolkit for Academic Success.
+13062052269
info@desklib.com
Available 24*7 on WhatsApp / Email
Unlock your academic potential
© 2024 | Zucol Services PVT LTD | All rights reserved.