Internship Report: Shree Narmada Khand Udyog Sahakari Mandli Ltd
VerifiedAdded on 2021/06/15
|29
|7288
|580
Report
AI Summary
This internship report by Dhruv Patel details his experience at Shree Narmada Khand Udyog Sahakari Mandli Ltd. over a period of 13 weeks. The report covers various aspects of the sugar factory's operations, including the milling department, cane processing, water purification plant, and machine repair. Patel describes his orientation to the factory, his observations of machinery like the cane unloader and feeder table, and his involvement in the repair of a water purification plant. He also highlights the importance of safety regulations and the coordination between engineers and technicians. Furthermore, the report includes insights into the cane's journey from the fields to the factory, including research and development, and the various stages of sugar production. The report provides a comprehensive overview of the practical application of mechanical engineering principles within a sugar manufacturing environment.
Contribute Materials
Your contribution can guide someone’s learning journey. Share your
documents today.
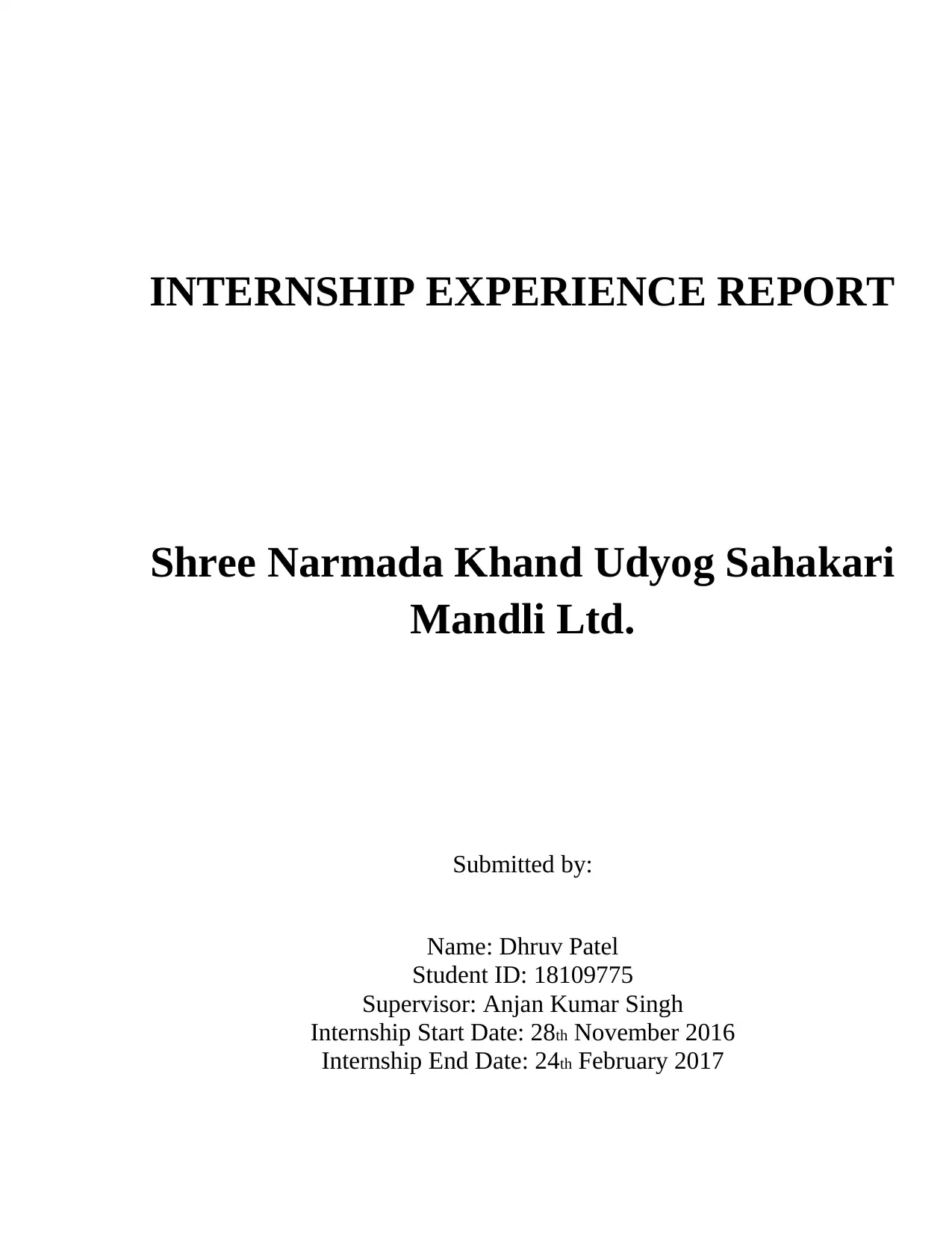
INTERNSHIP EXPERIENCE REPORT
Shree Narmada Khand Udyog Sahakari
Mandli Ltd.
Submitted by:
Name: Dhruv Patel
Student ID: 18109775
Supervisor: Anjan Kumar Singh
Internship Start Date: 28th November 2016
Internship End Date: 24th February 2017
Shree Narmada Khand Udyog Sahakari
Mandli Ltd.
Submitted by:
Name: Dhruv Patel
Student ID: 18109775
Supervisor: Anjan Kumar Singh
Internship Start Date: 28th November 2016
Internship End Date: 24th February 2017
Secure Best Marks with AI Grader
Need help grading? Try our AI Grader for instant feedback on your assignments.
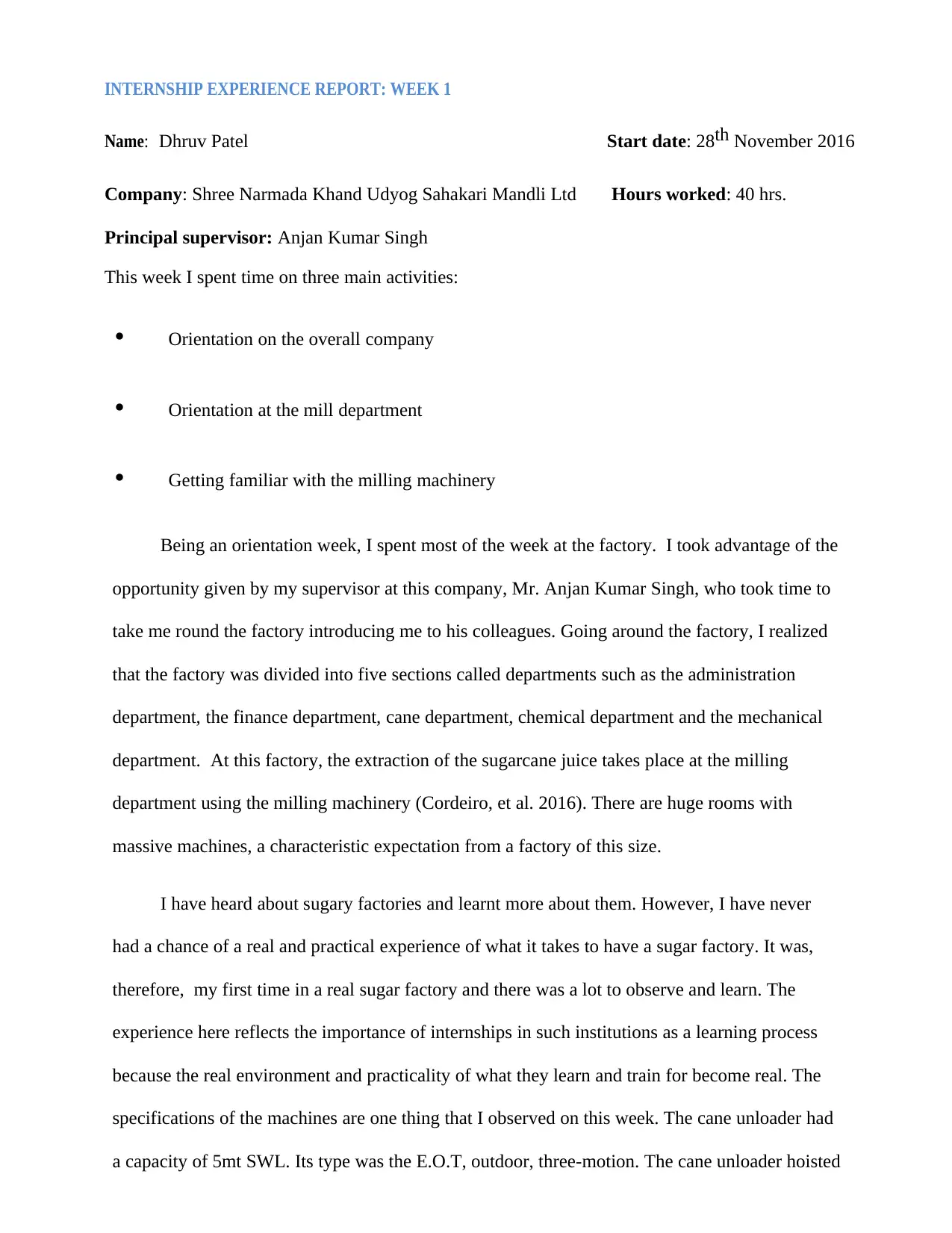
INTERNSHIP EXPERIENCE REPORT: WEEK 1
Name: Dhruv Patel Start date: 28th November 2016
Company: Shree Narmada Khand Udyog Sahakari Mandli Ltd Hours worked: 40 hrs.
Principal supervisor: Anjan Kumar Singh
This week I spent time on three main activities:
• Orientation on the overall company
• Orientation at the mill department
• Getting familiar with the milling machinery
Being an orientation week, I spent most of the week at the factory. I took advantage of the
opportunity given by my supervisor at this company, Mr. Anjan Kumar Singh, who took time to
take me round the factory introducing me to his colleagues. Going around the factory, I realized
that the factory was divided into five sections called departments such as the administration
department, the finance department, cane department, chemical department and the mechanical
department. At this factory, the extraction of the sugarcane juice takes place at the milling
department using the milling machinery (Cordeiro, et al. 2016). There are huge rooms with
massive machines, a characteristic expectation from a factory of this size.
I have heard about sugary factories and learnt more about them. However, I have never
had a chance of a real and practical experience of what it takes to have a sugar factory. It was,
therefore, my first time in a real sugar factory and there was a lot to observe and learn. The
experience here reflects the importance of internships in such institutions as a learning process
because the real environment and practicality of what they learn and train for become real. The
specifications of the machines are one thing that I observed on this week. The cane unloader had
a capacity of 5mt SWL. Its type was the E.O.T, outdoor, three-motion. The cane unloader hoisted
Name: Dhruv Patel Start date: 28th November 2016
Company: Shree Narmada Khand Udyog Sahakari Mandli Ltd Hours worked: 40 hrs.
Principal supervisor: Anjan Kumar Singh
This week I spent time on three main activities:
• Orientation on the overall company
• Orientation at the mill department
• Getting familiar with the milling machinery
Being an orientation week, I spent most of the week at the factory. I took advantage of the
opportunity given by my supervisor at this company, Mr. Anjan Kumar Singh, who took time to
take me round the factory introducing me to his colleagues. Going around the factory, I realized
that the factory was divided into five sections called departments such as the administration
department, the finance department, cane department, chemical department and the mechanical
department. At this factory, the extraction of the sugarcane juice takes place at the milling
department using the milling machinery (Cordeiro, et al. 2016). There are huge rooms with
massive machines, a characteristic expectation from a factory of this size.
I have heard about sugary factories and learnt more about them. However, I have never
had a chance of a real and practical experience of what it takes to have a sugar factory. It was,
therefore, my first time in a real sugar factory and there was a lot to observe and learn. The
experience here reflects the importance of internships in such institutions as a learning process
because the real environment and practicality of what they learn and train for become real. The
specifications of the machines are one thing that I observed on this week. The cane unloader had
a capacity of 5mt SWL. Its type was the E.O.T, outdoor, three-motion. The cane unloader hoisted
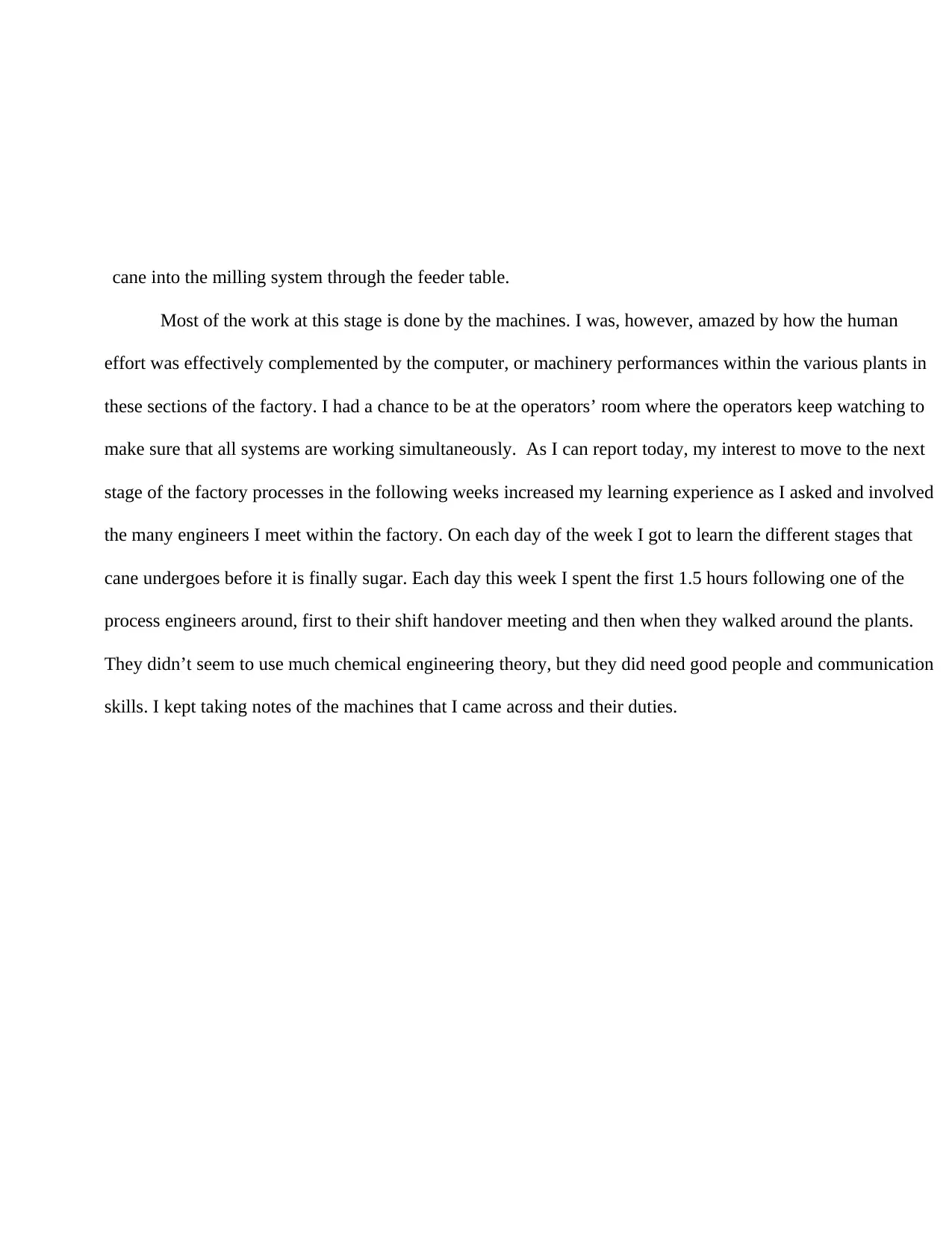
cane into the milling system through the feeder table.
Most of the work at this stage is done by the machines. I was, however, amazed by how the human
effort was effectively complemented by the computer, or machinery performances within the various plants in
these sections of the factory. I had a chance to be at the operators’ room where the operators keep watching to
make sure that all systems are working simultaneously. As I can report today, my interest to move to the next
stage of the factory processes in the following weeks increased my learning experience as I asked and involved
the many engineers I meet within the factory. On each day of the week I got to learn the different stages that
cane undergoes before it is finally sugar. Each day this week I spent the first 1.5 hours following one of the
process engineers around, first to their shift handover meeting and then when they walked around the plants.
They didn’t seem to use much chemical engineering theory, but they did need good people and communication
skills. I kept taking notes of the machines that I came across and their duties.
Most of the work at this stage is done by the machines. I was, however, amazed by how the human
effort was effectively complemented by the computer, or machinery performances within the various plants in
these sections of the factory. I had a chance to be at the operators’ room where the operators keep watching to
make sure that all systems are working simultaneously. As I can report today, my interest to move to the next
stage of the factory processes in the following weeks increased my learning experience as I asked and involved
the many engineers I meet within the factory. On each day of the week I got to learn the different stages that
cane undergoes before it is finally sugar. Each day this week I spent the first 1.5 hours following one of the
process engineers around, first to their shift handover meeting and then when they walked around the plants.
They didn’t seem to use much chemical engineering theory, but they did need good people and communication
skills. I kept taking notes of the machines that I came across and their duties.
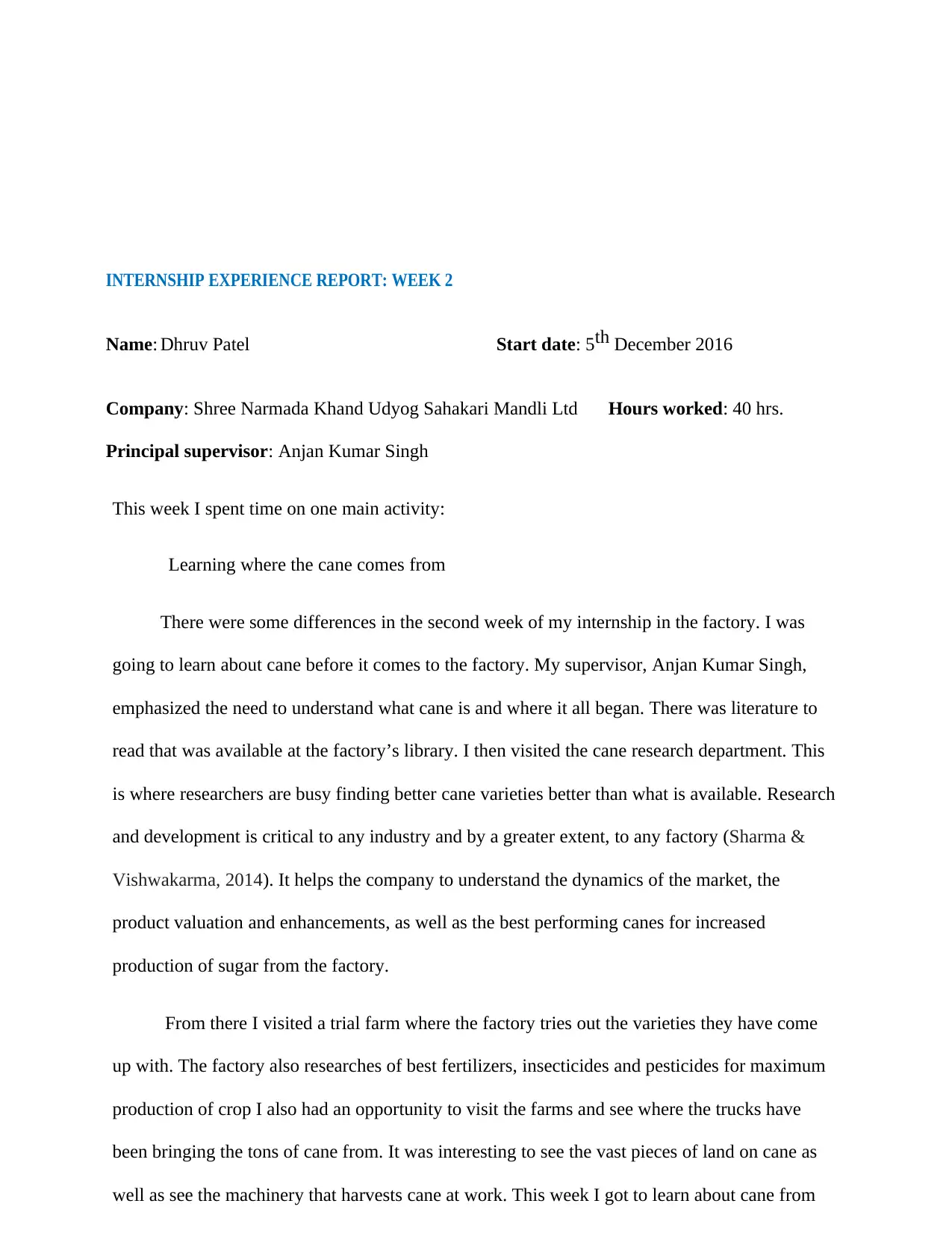
INTERNSHIP EXPERIENCE REPORT: WEEK 2
Name: Dhruv Patel Start date: 5th December 2016
Company: Shree Narmada Khand Udyog Sahakari Mandli Ltd Hours worked: 40 hrs.
Principal supervisor: Anjan Kumar Singh
This week I spent time on one main activity:
Learning where the cane comes from
There were some differences in the second week of my internship in the factory. I was
going to learn about cane before it comes to the factory. My supervisor, Anjan Kumar Singh,
emphasized the need to understand what cane is and where it all began. There was literature to
read that was available at the factory’s library. I then visited the cane research department. This
is where researchers are busy finding better cane varieties better than what is available. Research
and development is critical to any industry and by a greater extent, to any factory (Sharma &
Vishwakarma, 2014). It helps the company to understand the dynamics of the market, the
product valuation and enhancements, as well as the best performing canes for increased
production of sugar from the factory.
From there I visited a trial farm where the factory tries out the varieties they have come
up with. The factory also researches of best fertilizers, insecticides and pesticides for maximum
production of crop I also had an opportunity to visit the farms and see where the trucks have
been bringing the tons of cane from. It was interesting to see the vast pieces of land on cane as
well as see the machinery that harvests cane at work. This week I got to learn about cane from
Name: Dhruv Patel Start date: 5th December 2016
Company: Shree Narmada Khand Udyog Sahakari Mandli Ltd Hours worked: 40 hrs.
Principal supervisor: Anjan Kumar Singh
This week I spent time on one main activity:
Learning where the cane comes from
There were some differences in the second week of my internship in the factory. I was
going to learn about cane before it comes to the factory. My supervisor, Anjan Kumar Singh,
emphasized the need to understand what cane is and where it all began. There was literature to
read that was available at the factory’s library. I then visited the cane research department. This
is where researchers are busy finding better cane varieties better than what is available. Research
and development is critical to any industry and by a greater extent, to any factory (Sharma &
Vishwakarma, 2014). It helps the company to understand the dynamics of the market, the
product valuation and enhancements, as well as the best performing canes for increased
production of sugar from the factory.
From there I visited a trial farm where the factory tries out the varieties they have come
up with. The factory also researches of best fertilizers, insecticides and pesticides for maximum
production of crop I also had an opportunity to visit the farms and see where the trucks have
been bringing the tons of cane from. It was interesting to see the vast pieces of land on cane as
well as see the machinery that harvests cane at work. This week I got to learn about cane from
Secure Best Marks with AI Grader
Need help grading? Try our AI Grader for instant feedback on your assignments.

planting, caring for the plant up to harvesting.
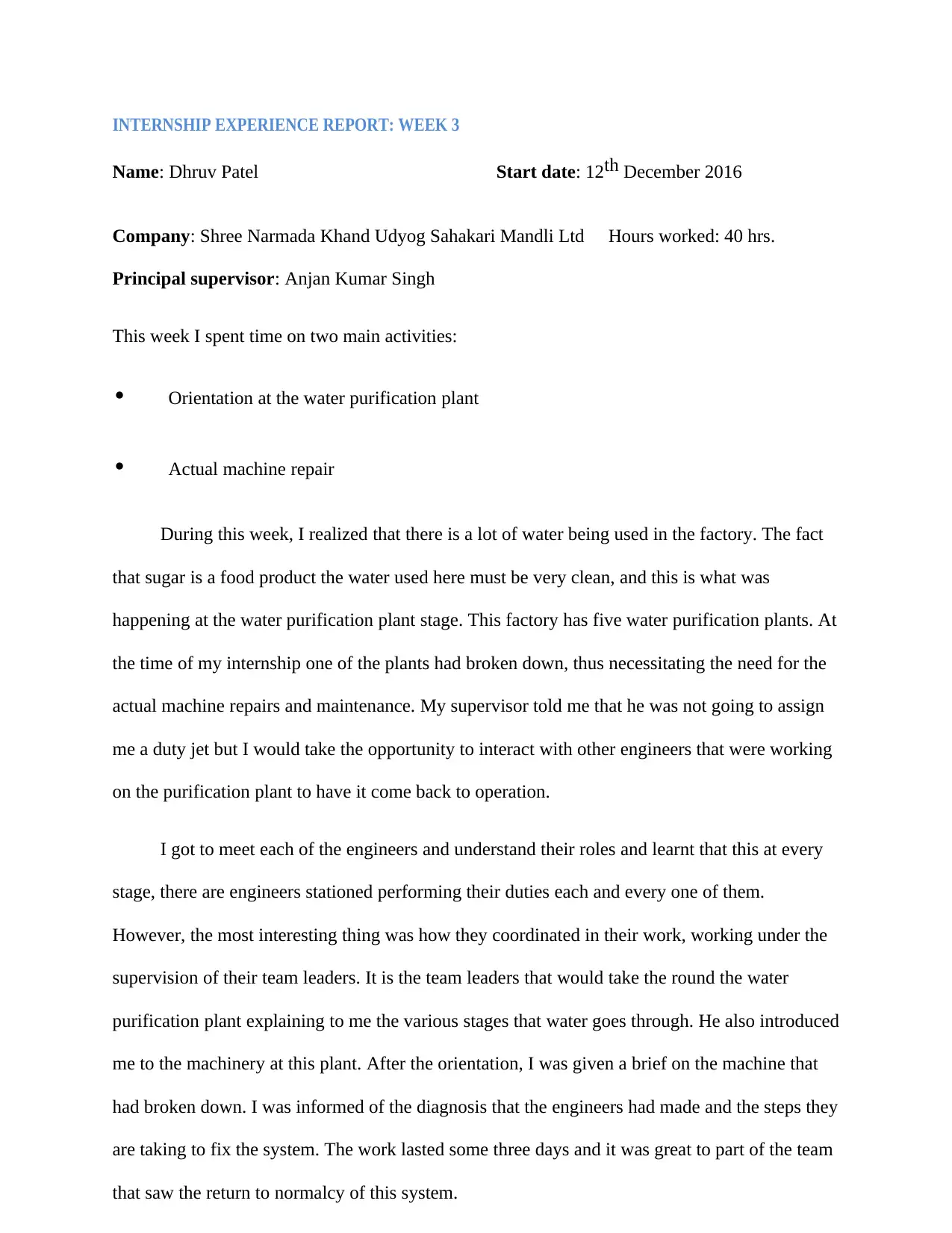
INTERNSHIP EXPERIENCE REPORT: WEEK 3
Name: Dhruv Patel Start date: 12th December 2016
Company: Shree Narmada Khand Udyog Sahakari Mandli Ltd Hours worked: 40 hrs.
Principal supervisor: Anjan Kumar Singh
This week I spent time on two main activities:
• Orientation at the water purification plant
• Actual machine repair
During this week, I realized that there is a lot of water being used in the factory. The fact
that sugar is a food product the water used here must be very clean, and this is what was
happening at the water purification plant stage. This factory has five water purification plants. At
the time of my internship one of the plants had broken down, thus necessitating the need for the
actual machine repairs and maintenance. My supervisor told me that he was not going to assign
me a duty jet but I would take the opportunity to interact with other engineers that were working
on the purification plant to have it come back to operation.
I got to meet each of the engineers and understand their roles and learnt that this at every
stage, there are engineers stationed performing their duties each and every one of them.
However, the most interesting thing was how they coordinated in their work, working under the
supervision of their team leaders. It is the team leaders that would take the round the water
purification plant explaining to me the various stages that water goes through. He also introduced
me to the machinery at this plant. After the orientation, I was given a brief on the machine that
had broken down. I was informed of the diagnosis that the engineers had made and the steps they
are taking to fix the system. The work lasted some three days and it was great to part of the team
that saw the return to normalcy of this system.
Name: Dhruv Patel Start date: 12th December 2016
Company: Shree Narmada Khand Udyog Sahakari Mandli Ltd Hours worked: 40 hrs.
Principal supervisor: Anjan Kumar Singh
This week I spent time on two main activities:
• Orientation at the water purification plant
• Actual machine repair
During this week, I realized that there is a lot of water being used in the factory. The fact
that sugar is a food product the water used here must be very clean, and this is what was
happening at the water purification plant stage. This factory has five water purification plants. At
the time of my internship one of the plants had broken down, thus necessitating the need for the
actual machine repairs and maintenance. My supervisor told me that he was not going to assign
me a duty jet but I would take the opportunity to interact with other engineers that were working
on the purification plant to have it come back to operation.
I got to meet each of the engineers and understand their roles and learnt that this at every
stage, there are engineers stationed performing their duties each and every one of them.
However, the most interesting thing was how they coordinated in their work, working under the
supervision of their team leaders. It is the team leaders that would take the round the water
purification plant explaining to me the various stages that water goes through. He also introduced
me to the machinery at this plant. After the orientation, I was given a brief on the machine that
had broken down. I was informed of the diagnosis that the engineers had made and the steps they
are taking to fix the system. The work lasted some three days and it was great to part of the team
that saw the return to normalcy of this system.
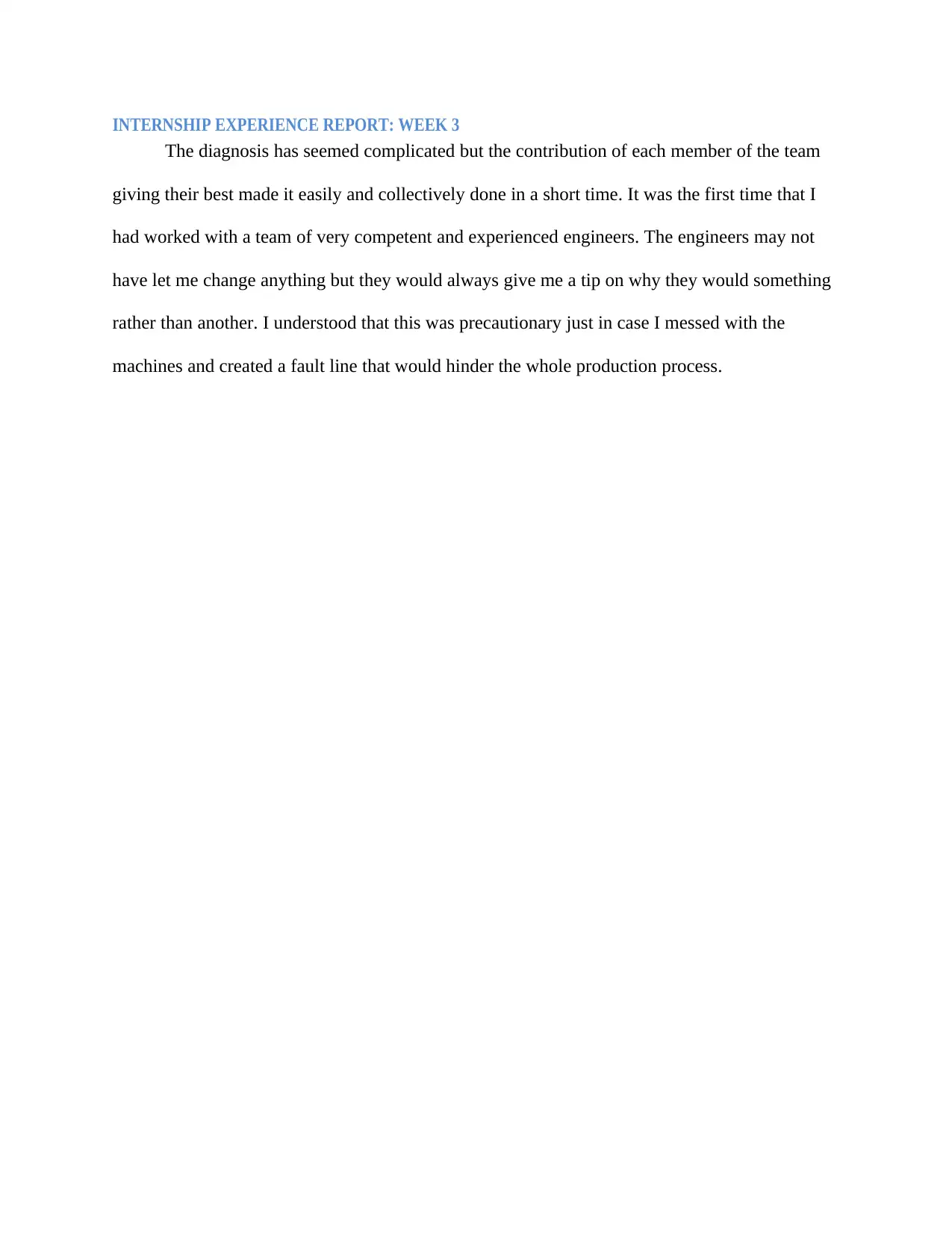
INTERNSHIP EXPERIENCE REPORT: WEEK 3
The diagnosis has seemed complicated but the contribution of each member of the team
giving their best made it easily and collectively done in a short time. It was the first time that I
had worked with a team of very competent and experienced engineers. The engineers may not
have let me change anything but they would always give me a tip on why they would something
rather than another. I understood that this was precautionary just in case I messed with the
machines and created a fault line that would hinder the whole production process.
The diagnosis has seemed complicated but the contribution of each member of the team
giving their best made it easily and collectively done in a short time. It was the first time that I
had worked with a team of very competent and experienced engineers. The engineers may not
have let me change anything but they would always give me a tip on why they would something
rather than another. I understood that this was precautionary just in case I messed with the
machines and created a fault line that would hinder the whole production process.
Paraphrase This Document
Need a fresh take? Get an instant paraphrase of this document with our AI Paraphraser
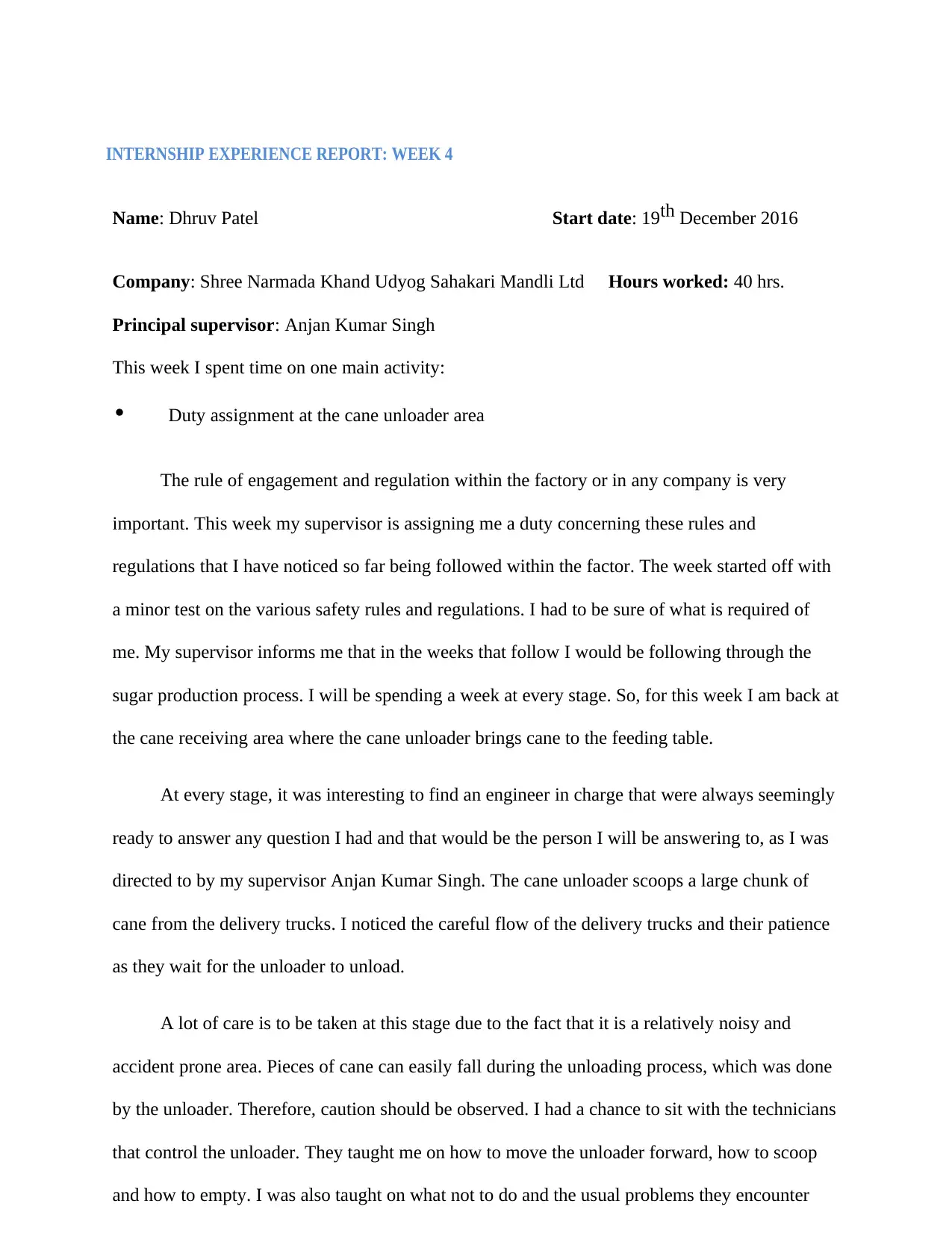
INTERNSHIP EXPERIENCE REPORT: WEEK 4
Name: Dhruv Patel Start date: 19th December 2016
Company: Shree Narmada Khand Udyog Sahakari Mandli Ltd Hours worked: 40 hrs.
Principal supervisor: Anjan Kumar Singh
This week I spent time on one main activity:
• Duty assignment at the cane unloader area
The rule of engagement and regulation within the factory or in any company is very
important. This week my supervisor is assigning me a duty concerning these rules and
regulations that I have noticed so far being followed within the factor. The week started off with
a minor test on the various safety rules and regulations. I had to be sure of what is required of
me. My supervisor informs me that in the weeks that follow I would be following through the
sugar production process. I will be spending a week at every stage. So, for this week I am back at
the cane receiving area where the cane unloader brings cane to the feeding table.
At every stage, it was interesting to find an engineer in charge that were always seemingly
ready to answer any question I had and that would be the person I will be answering to, as I was
directed to by my supervisor Anjan Kumar Singh. The cane unloader scoops a large chunk of
cane from the delivery trucks. I noticed the careful flow of the delivery trucks and their patience
as they wait for the unloader to unload.
A lot of care is to be taken at this stage due to the fact that it is a relatively noisy and
accident prone area. Pieces of cane can easily fall during the unloading process, which was done
by the unloader. Therefore, caution should be observed. I had a chance to sit with the technicians
that control the unloader. They taught me on how to move the unloader forward, how to scoop
and how to empty. I was also taught on what not to do and the usual problems they encounter
Name: Dhruv Patel Start date: 19th December 2016
Company: Shree Narmada Khand Udyog Sahakari Mandli Ltd Hours worked: 40 hrs.
Principal supervisor: Anjan Kumar Singh
This week I spent time on one main activity:
• Duty assignment at the cane unloader area
The rule of engagement and regulation within the factory or in any company is very
important. This week my supervisor is assigning me a duty concerning these rules and
regulations that I have noticed so far being followed within the factor. The week started off with
a minor test on the various safety rules and regulations. I had to be sure of what is required of
me. My supervisor informs me that in the weeks that follow I would be following through the
sugar production process. I will be spending a week at every stage. So, for this week I am back at
the cane receiving area where the cane unloader brings cane to the feeding table.
At every stage, it was interesting to find an engineer in charge that were always seemingly
ready to answer any question I had and that would be the person I will be answering to, as I was
directed to by my supervisor Anjan Kumar Singh. The cane unloader scoops a large chunk of
cane from the delivery trucks. I noticed the careful flow of the delivery trucks and their patience
as they wait for the unloader to unload.
A lot of care is to be taken at this stage due to the fact that it is a relatively noisy and
accident prone area. Pieces of cane can easily fall during the unloading process, which was done
by the unloader. Therefore, caution should be observed. I had a chance to sit with the technicians
that control the unloader. They taught me on how to move the unloader forward, how to scoop
and how to empty. I was also taught on what not to do and the usual problems they encounter
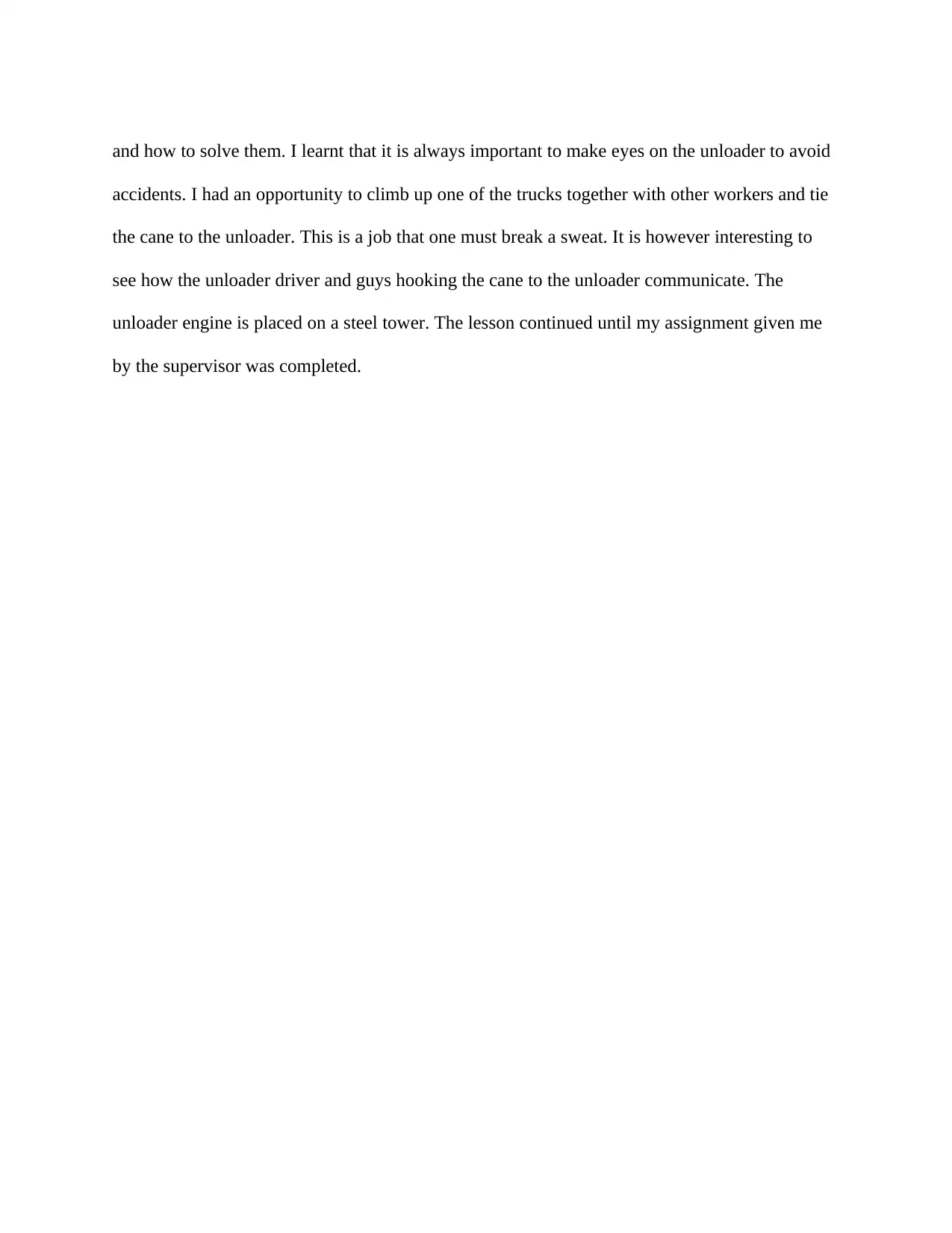
and how to solve them. I learnt that it is always important to make eyes on the unloader to avoid
accidents. I had an opportunity to climb up one of the trucks together with other workers and tie
the cane to the unloader. This is a job that one must break a sweat. It is however interesting to
see how the unloader driver and guys hooking the cane to the unloader communicate. The
unloader engine is placed on a steel tower. The lesson continued until my assignment given me
by the supervisor was completed.
accidents. I had an opportunity to climb up one of the trucks together with other workers and tie
the cane to the unloader. This is a job that one must break a sweat. It is however interesting to
see how the unloader driver and guys hooking the cane to the unloader communicate. The
unloader engine is placed on a steel tower. The lesson continued until my assignment given me
by the supervisor was completed.
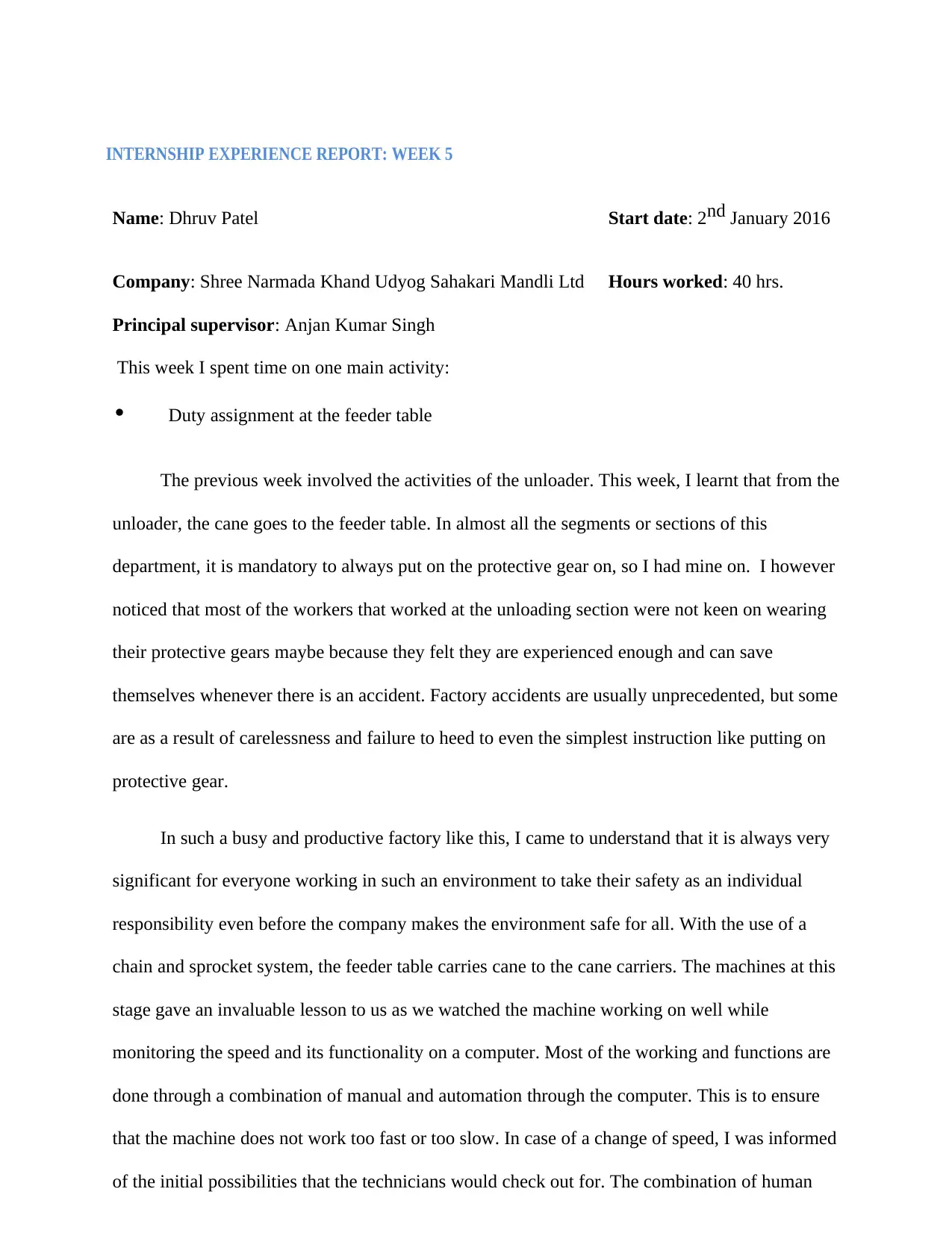
INTERNSHIP EXPERIENCE REPORT: WEEK 5
Name: Dhruv Patel Start date: 2nd January 2016
Company: Shree Narmada Khand Udyog Sahakari Mandli Ltd Hours worked: 40 hrs.
Principal supervisor: Anjan Kumar Singh
This week I spent time on one main activity:
• Duty assignment at the feeder table
The previous week involved the activities of the unloader. This week, I learnt that from the
unloader, the cane goes to the feeder table. In almost all the segments or sections of this
department, it is mandatory to always put on the protective gear on, so I had mine on. I however
noticed that most of the workers that worked at the unloading section were not keen on wearing
their protective gears maybe because they felt they are experienced enough and can save
themselves whenever there is an accident. Factory accidents are usually unprecedented, but some
are as a result of carelessness and failure to heed to even the simplest instruction like putting on
protective gear.
In such a busy and productive factory like this, I came to understand that it is always very
significant for everyone working in such an environment to take their safety as an individual
responsibility even before the company makes the environment safe for all. With the use of a
chain and sprocket system, the feeder table carries cane to the cane carriers. The machines at this
stage gave an invaluable lesson to us as we watched the machine working on well while
monitoring the speed and its functionality on a computer. Most of the working and functions are
done through a combination of manual and automation through the computer. This is to ensure
that the machine does not work too fast or too slow. In case of a change of speed, I was informed
of the initial possibilities that the technicians would check out for. The combination of human
Name: Dhruv Patel Start date: 2nd January 2016
Company: Shree Narmada Khand Udyog Sahakari Mandli Ltd Hours worked: 40 hrs.
Principal supervisor: Anjan Kumar Singh
This week I spent time on one main activity:
• Duty assignment at the feeder table
The previous week involved the activities of the unloader. This week, I learnt that from the
unloader, the cane goes to the feeder table. In almost all the segments or sections of this
department, it is mandatory to always put on the protective gear on, so I had mine on. I however
noticed that most of the workers that worked at the unloading section were not keen on wearing
their protective gears maybe because they felt they are experienced enough and can save
themselves whenever there is an accident. Factory accidents are usually unprecedented, but some
are as a result of carelessness and failure to heed to even the simplest instruction like putting on
protective gear.
In such a busy and productive factory like this, I came to understand that it is always very
significant for everyone working in such an environment to take their safety as an individual
responsibility even before the company makes the environment safe for all. With the use of a
chain and sprocket system, the feeder table carries cane to the cane carriers. The machines at this
stage gave an invaluable lesson to us as we watched the machine working on well while
monitoring the speed and its functionality on a computer. Most of the working and functions are
done through a combination of manual and automation through the computer. This is to ensure
that the machine does not work too fast or too slow. In case of a change of speed, I was informed
of the initial possibilities that the technicians would check out for. The combination of human
Secure Best Marks with AI Grader
Need help grading? Try our AI Grader for instant feedback on your assignments.
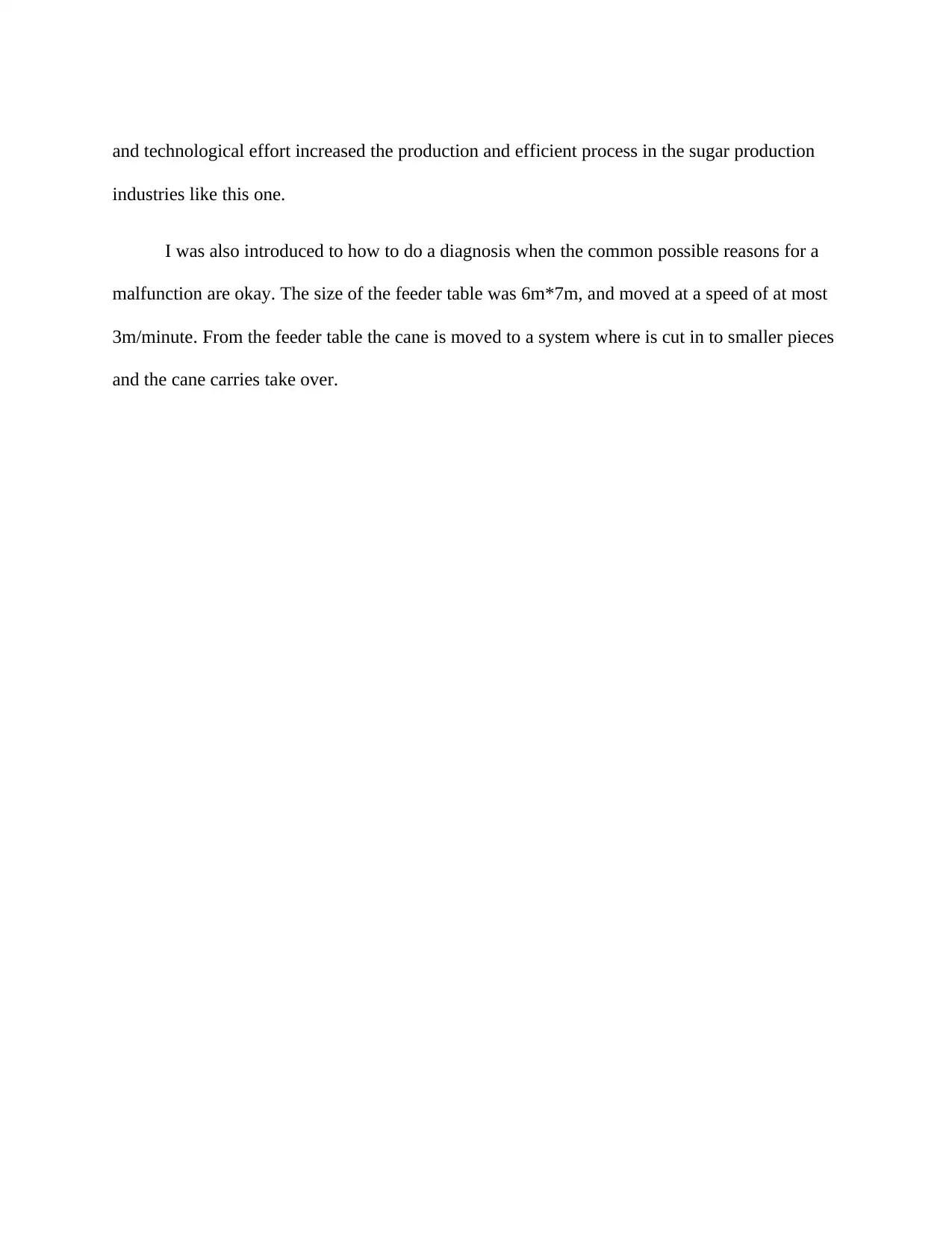
and technological effort increased the production and efficient process in the sugar production
industries like this one.
I was also introduced to how to do a diagnosis when the common possible reasons for a
malfunction are okay. The size of the feeder table was 6m*7m, and moved at a speed of at most
3m/minute. From the feeder table the cane is moved to a system where is cut in to smaller pieces
and the cane carries take over.
industries like this one.
I was also introduced to how to do a diagnosis when the common possible reasons for a
malfunction are okay. The size of the feeder table was 6m*7m, and moved at a speed of at most
3m/minute. From the feeder table the cane is moved to a system where is cut in to smaller pieces
and the cane carries take over.
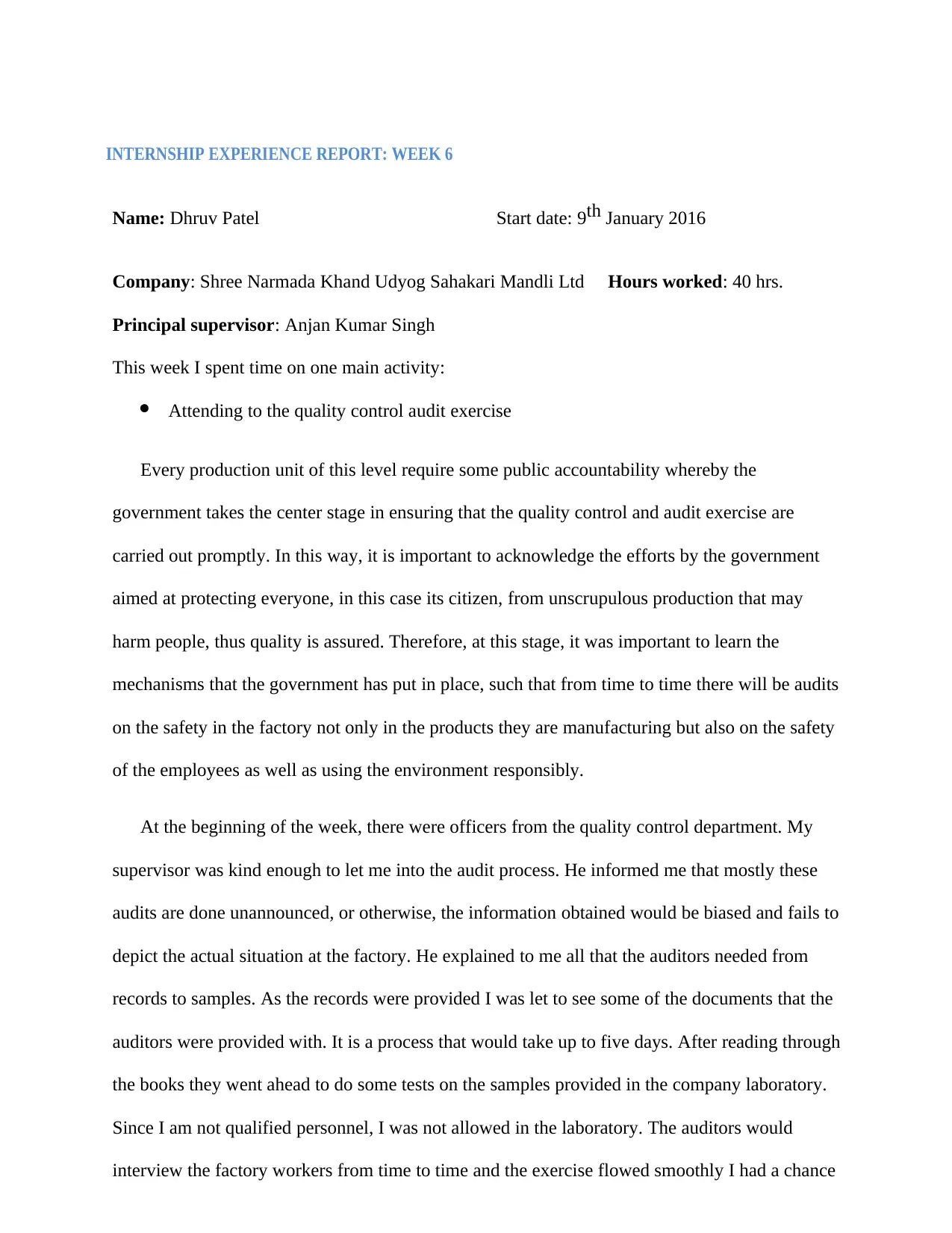
INTERNSHIP EXPERIENCE REPORT: WEEK 6
Name: Dhruv Patel Start date: 9th January 2016
Company: Shree Narmada Khand Udyog Sahakari Mandli Ltd Hours worked: 40 hrs.
Principal supervisor: Anjan Kumar Singh
This week I spent time on one main activity:
Attending to the quality control audit exercise
Every production unit of this level require some public accountability whereby the
government takes the center stage in ensuring that the quality control and audit exercise are
carried out promptly. In this way, it is important to acknowledge the efforts by the government
aimed at protecting everyone, in this case its citizen, from unscrupulous production that may
harm people, thus quality is assured. Therefore, at this stage, it was important to learn the
mechanisms that the government has put in place, such that from time to time there will be audits
on the safety in the factory not only in the products they are manufacturing but also on the safety
of the employees as well as using the environment responsibly.
At the beginning of the week, there were officers from the quality control department. My
supervisor was kind enough to let me into the audit process. He informed me that mostly these
audits are done unannounced, or otherwise, the information obtained would be biased and fails to
depict the actual situation at the factory. He explained to me all that the auditors needed from
records to samples. As the records were provided I was let to see some of the documents that the
auditors were provided with. It is a process that would take up to five days. After reading through
the books they went ahead to do some tests on the samples provided in the company laboratory.
Since I am not qualified personnel, I was not allowed in the laboratory. The auditors would
interview the factory workers from time to time and the exercise flowed smoothly I had a chance
Name: Dhruv Patel Start date: 9th January 2016
Company: Shree Narmada Khand Udyog Sahakari Mandli Ltd Hours worked: 40 hrs.
Principal supervisor: Anjan Kumar Singh
This week I spent time on one main activity:
Attending to the quality control audit exercise
Every production unit of this level require some public accountability whereby the
government takes the center stage in ensuring that the quality control and audit exercise are
carried out promptly. In this way, it is important to acknowledge the efforts by the government
aimed at protecting everyone, in this case its citizen, from unscrupulous production that may
harm people, thus quality is assured. Therefore, at this stage, it was important to learn the
mechanisms that the government has put in place, such that from time to time there will be audits
on the safety in the factory not only in the products they are manufacturing but also on the safety
of the employees as well as using the environment responsibly.
At the beginning of the week, there were officers from the quality control department. My
supervisor was kind enough to let me into the audit process. He informed me that mostly these
audits are done unannounced, or otherwise, the information obtained would be biased and fails to
depict the actual situation at the factory. He explained to me all that the auditors needed from
records to samples. As the records were provided I was let to see some of the documents that the
auditors were provided with. It is a process that would take up to five days. After reading through
the books they went ahead to do some tests on the samples provided in the company laboratory.
Since I am not qualified personnel, I was not allowed in the laboratory. The auditors would
interview the factory workers from time to time and the exercise flowed smoothly I had a chance
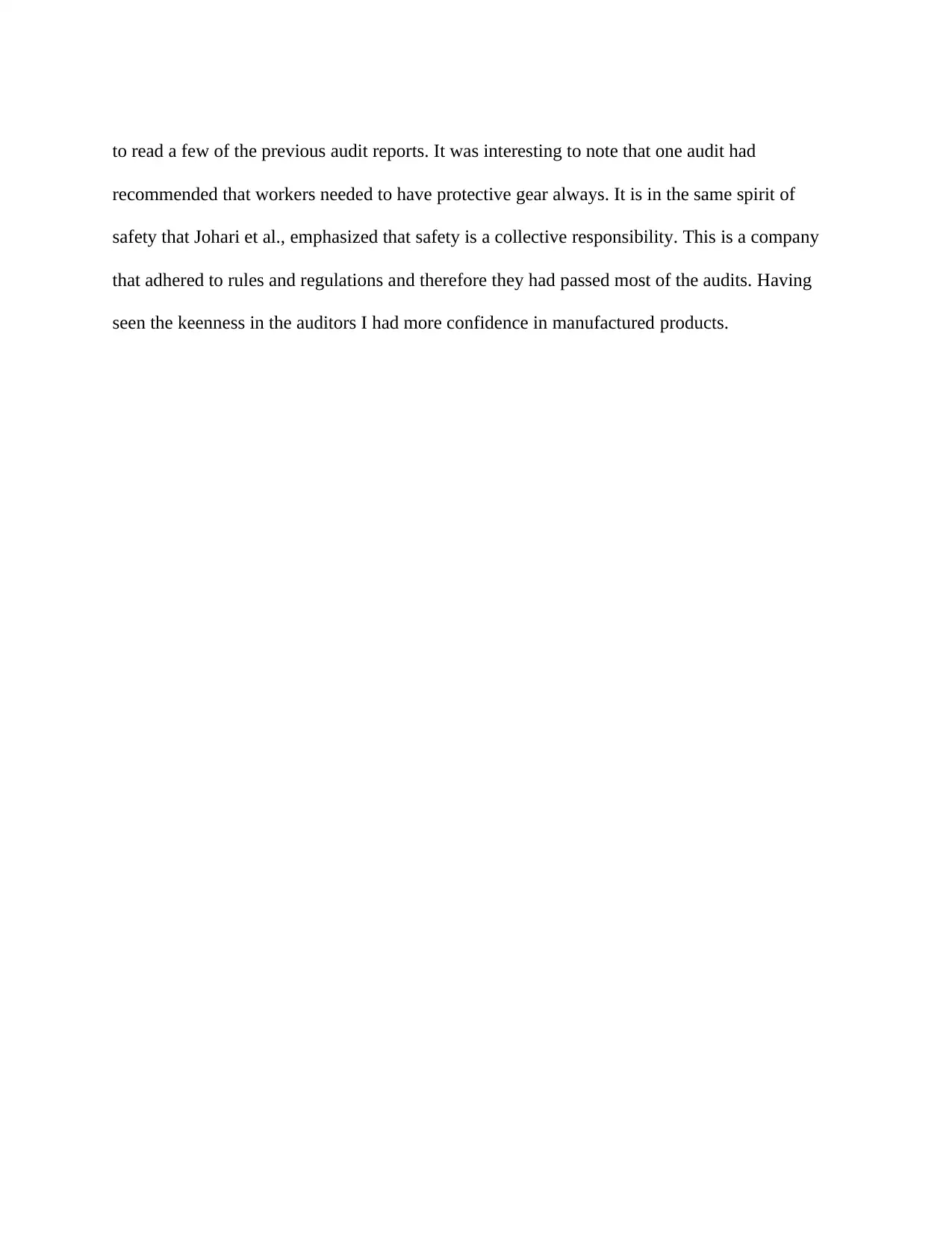
to read a few of the previous audit reports. It was interesting to note that one audit had
recommended that workers needed to have protective gear always. It is in the same spirit of
safety that Johari et al., emphasized that safety is a collective responsibility. This is a company
that adhered to rules and regulations and therefore they had passed most of the audits. Having
seen the keenness in the auditors I had more confidence in manufactured products.
recommended that workers needed to have protective gear always. It is in the same spirit of
safety that Johari et al., emphasized that safety is a collective responsibility. This is a company
that adhered to rules and regulations and therefore they had passed most of the audits. Having
seen the keenness in the auditors I had more confidence in manufactured products.
Paraphrase This Document
Need a fresh take? Get an instant paraphrase of this document with our AI Paraphraser
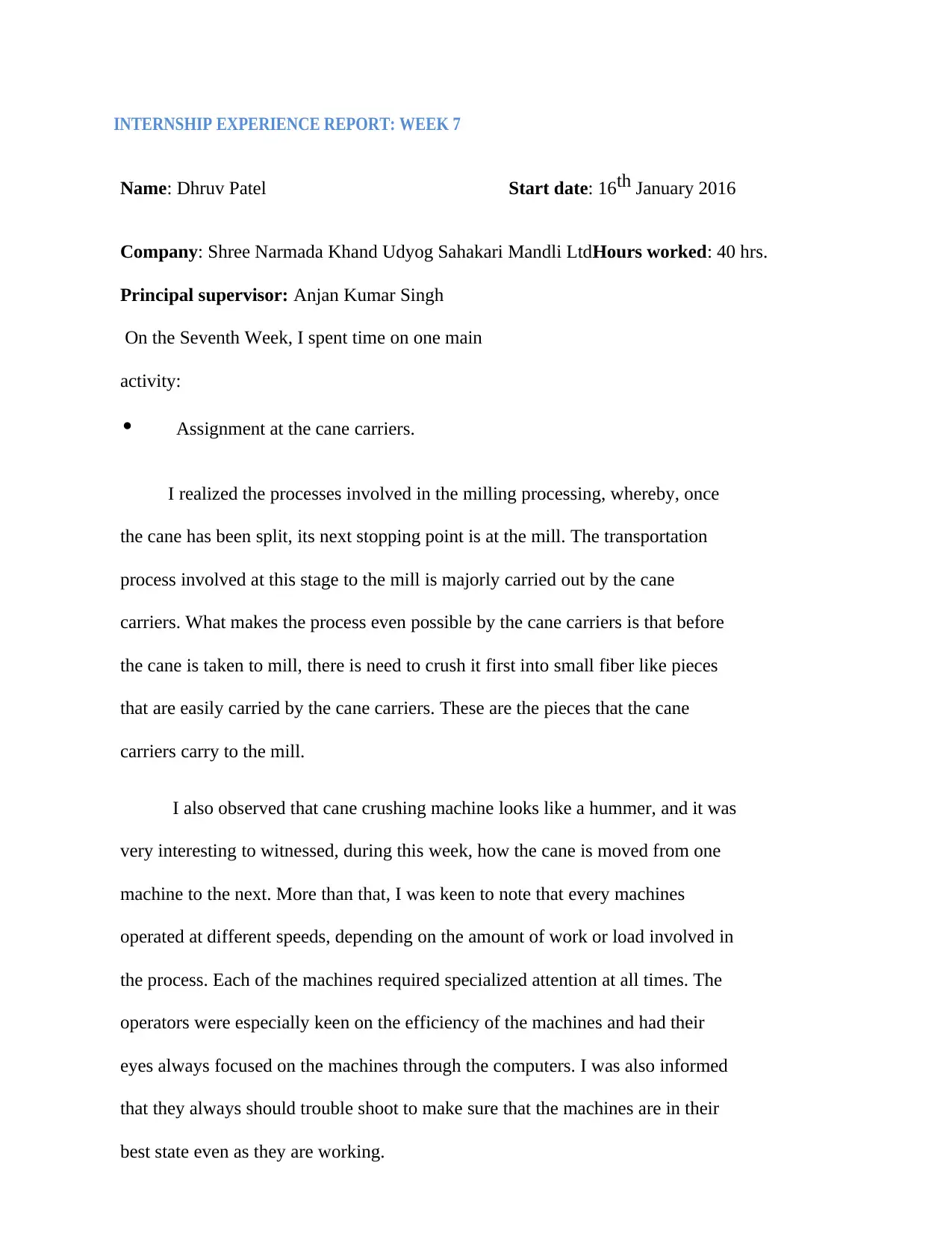
INTERNSHIP EXPERIENCE REPORT: WEEK 7
Name: Dhruv Patel Start date: 16th January 2016
Company: Shree Narmada Khand Udyog Sahakari Mandli LtdHours worked: 40 hrs.
Principal supervisor: Anjan Kumar Singh
On the Seventh Week, I spent time on one main
activity:
• Assignment at the cane carriers.
I realized the processes involved in the milling processing, whereby, once
the cane has been split, its next stopping point is at the mill. The transportation
process involved at this stage to the mill is majorly carried out by the cane
carriers. What makes the process even possible by the cane carriers is that before
the cane is taken to mill, there is need to crush it first into small fiber like pieces
that are easily carried by the cane carriers. These are the pieces that the cane
carriers carry to the mill.
I also observed that cane crushing machine looks like a hummer, and it was
very interesting to witnessed, during this week, how the cane is moved from one
machine to the next. More than that, I was keen to note that every machines
operated at different speeds, depending on the amount of work or load involved in
the process. Each of the machines required specialized attention at all times. The
operators were especially keen on the efficiency of the machines and had their
eyes always focused on the machines through the computers. I was also informed
that they always should trouble shoot to make sure that the machines are in their
best state even as they are working.
Name: Dhruv Patel Start date: 16th January 2016
Company: Shree Narmada Khand Udyog Sahakari Mandli LtdHours worked: 40 hrs.
Principal supervisor: Anjan Kumar Singh
On the Seventh Week, I spent time on one main
activity:
• Assignment at the cane carriers.
I realized the processes involved in the milling processing, whereby, once
the cane has been split, its next stopping point is at the mill. The transportation
process involved at this stage to the mill is majorly carried out by the cane
carriers. What makes the process even possible by the cane carriers is that before
the cane is taken to mill, there is need to crush it first into small fiber like pieces
that are easily carried by the cane carriers. These are the pieces that the cane
carriers carry to the mill.
I also observed that cane crushing machine looks like a hummer, and it was
very interesting to witnessed, during this week, how the cane is moved from one
machine to the next. More than that, I was keen to note that every machines
operated at different speeds, depending on the amount of work or load involved in
the process. Each of the machines required specialized attention at all times. The
operators were especially keen on the efficiency of the machines and had their
eyes always focused on the machines through the computers. I was also informed
that they always should trouble shoot to make sure that the machines are in their
best state even as they are working.
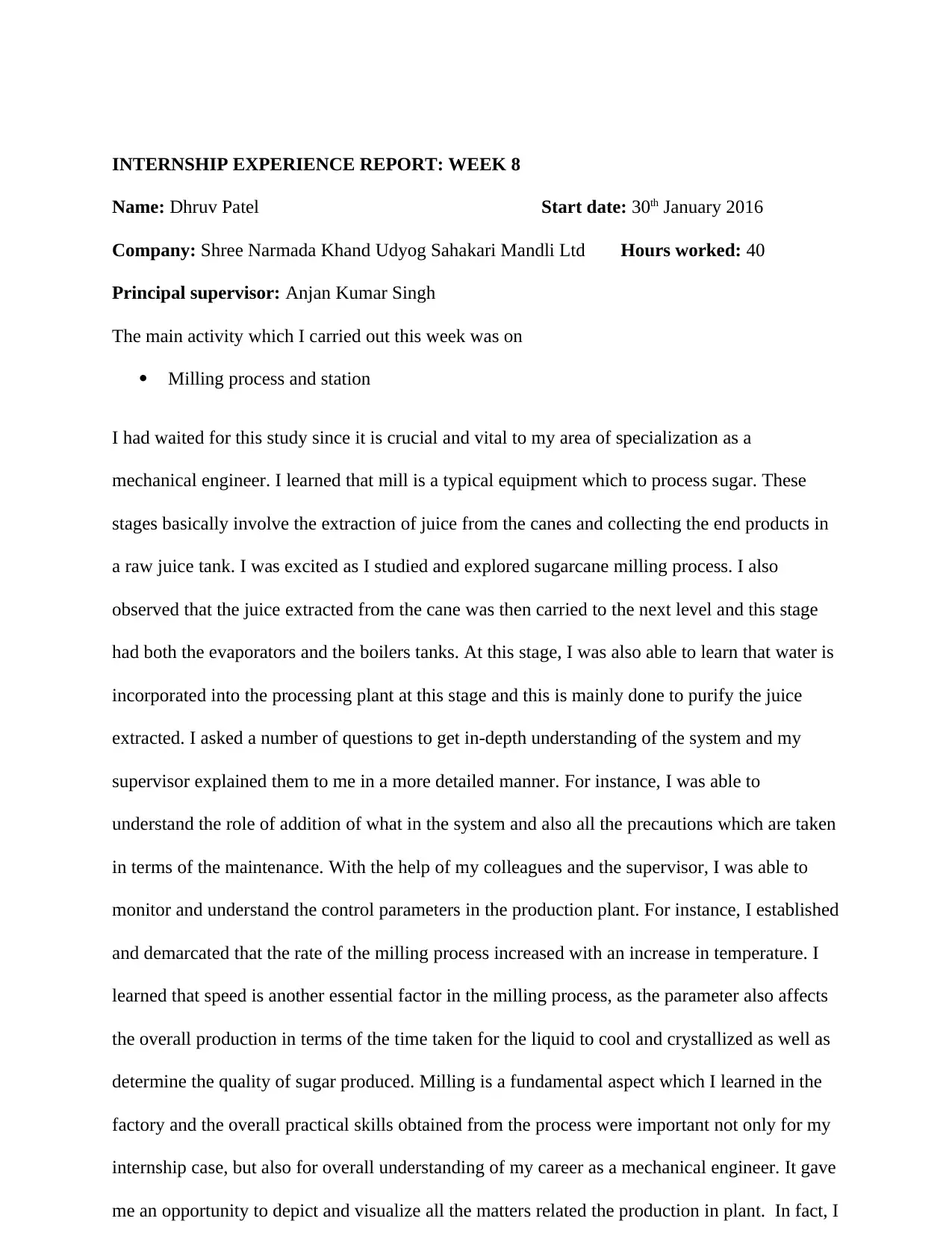
INTERNSHIP EXPERIENCE REPORT: WEEK 8
Name: Dhruv Patel Start date: 30th January 2016
Company: Shree Narmada Khand Udyog Sahakari Mandli Ltd Hours worked: 40
Principal supervisor: Anjan Kumar Singh
The main activity which I carried out this week was on
Milling process and station
I had waited for this study since it is crucial and vital to my area of specialization as a
mechanical engineer. I learned that mill is a typical equipment which to process sugar. These
stages basically involve the extraction of juice from the canes and collecting the end products in
a raw juice tank. I was excited as I studied and explored sugarcane milling process. I also
observed that the juice extracted from the cane was then carried to the next level and this stage
had both the evaporators and the boilers tanks. At this stage, I was also able to learn that water is
incorporated into the processing plant at this stage and this is mainly done to purify the juice
extracted. I asked a number of questions to get in-depth understanding of the system and my
supervisor explained them to me in a more detailed manner. For instance, I was able to
understand the role of addition of what in the system and also all the precautions which are taken
in terms of the maintenance. With the help of my colleagues and the supervisor, I was able to
monitor and understand the control parameters in the production plant. For instance, I established
and demarcated that the rate of the milling process increased with an increase in temperature. I
learned that speed is another essential factor in the milling process, as the parameter also affects
the overall production in terms of the time taken for the liquid to cool and crystallized as well as
determine the quality of sugar produced. Milling is a fundamental aspect which I learned in the
factory and the overall practical skills obtained from the process were important not only for my
internship case, but also for overall understanding of my career as a mechanical engineer. It gave
me an opportunity to depict and visualize all the matters related the production in plant. In fact, I
Name: Dhruv Patel Start date: 30th January 2016
Company: Shree Narmada Khand Udyog Sahakari Mandli Ltd Hours worked: 40
Principal supervisor: Anjan Kumar Singh
The main activity which I carried out this week was on
Milling process and station
I had waited for this study since it is crucial and vital to my area of specialization as a
mechanical engineer. I learned that mill is a typical equipment which to process sugar. These
stages basically involve the extraction of juice from the canes and collecting the end products in
a raw juice tank. I was excited as I studied and explored sugarcane milling process. I also
observed that the juice extracted from the cane was then carried to the next level and this stage
had both the evaporators and the boilers tanks. At this stage, I was also able to learn that water is
incorporated into the processing plant at this stage and this is mainly done to purify the juice
extracted. I asked a number of questions to get in-depth understanding of the system and my
supervisor explained them to me in a more detailed manner. For instance, I was able to
understand the role of addition of what in the system and also all the precautions which are taken
in terms of the maintenance. With the help of my colleagues and the supervisor, I was able to
monitor and understand the control parameters in the production plant. For instance, I established
and demarcated that the rate of the milling process increased with an increase in temperature. I
learned that speed is another essential factor in the milling process, as the parameter also affects
the overall production in terms of the time taken for the liquid to cool and crystallized as well as
determine the quality of sugar produced. Milling is a fundamental aspect which I learned in the
factory and the overall practical skills obtained from the process were important not only for my
internship case, but also for overall understanding of my career as a mechanical engineer. It gave
me an opportunity to depict and visualize all the matters related the production in plant. In fact, I
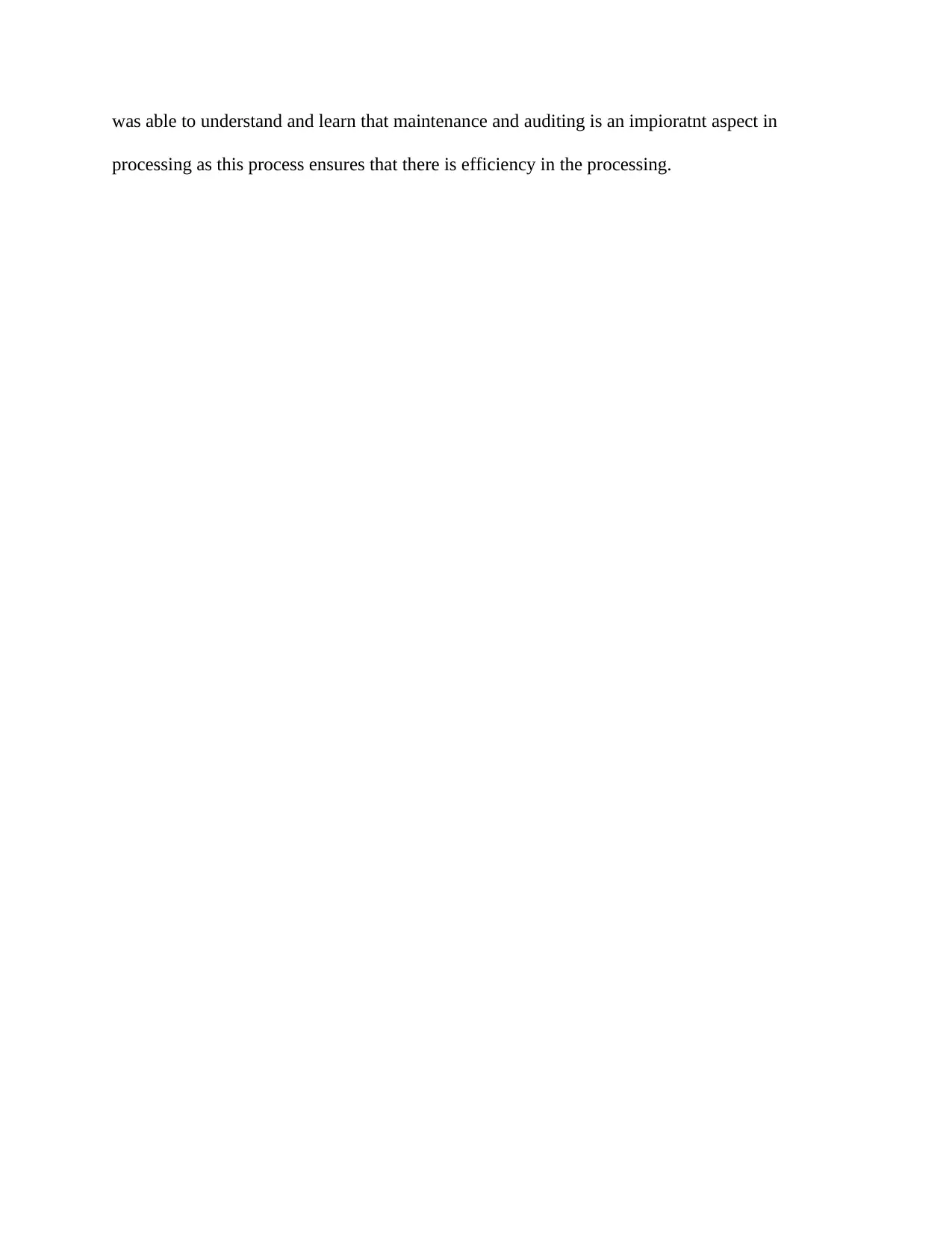
was able to understand and learn that maintenance and auditing is an impioratnt aspect in
processing as this process ensures that there is efficiency in the processing.
processing as this process ensures that there is efficiency in the processing.
Secure Best Marks with AI Grader
Need help grading? Try our AI Grader for instant feedback on your assignments.
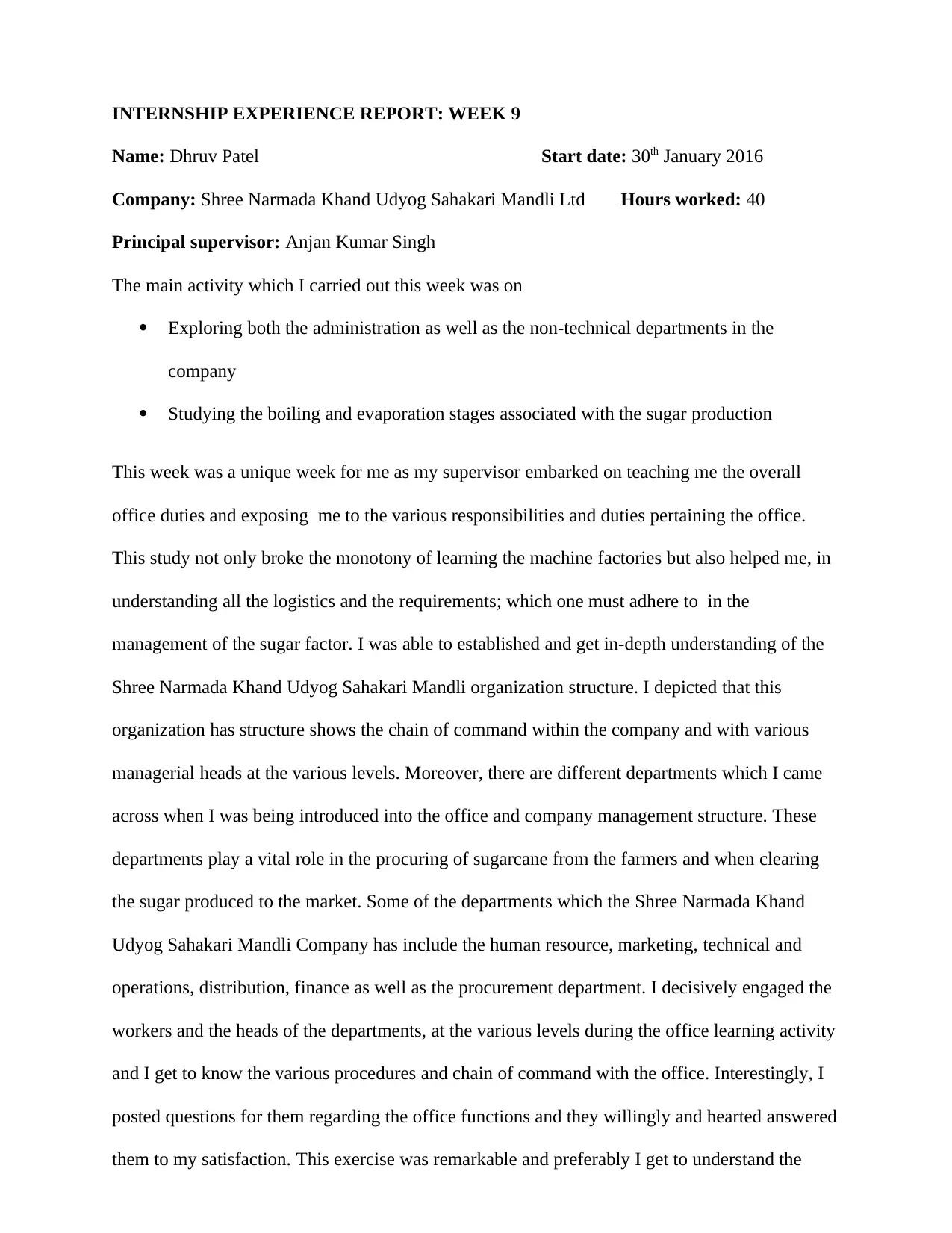
INTERNSHIP EXPERIENCE REPORT: WEEK 9
Name: Dhruv Patel Start date: 30th January 2016
Company: Shree Narmada Khand Udyog Sahakari Mandli Ltd Hours worked: 40
Principal supervisor: Anjan Kumar Singh
The main activity which I carried out this week was on
Exploring both the administration as well as the non-technical departments in the
company
Studying the boiling and evaporation stages associated with the sugar production
This week was a unique week for me as my supervisor embarked on teaching me the overall
office duties and exposing me to the various responsibilities and duties pertaining the office.
This study not only broke the monotony of learning the machine factories but also helped me, in
understanding all the logistics and the requirements; which one must adhere to in the
management of the sugar factor. I was able to established and get in-depth understanding of the
Shree Narmada Khand Udyog Sahakari Mandli organization structure. I depicted that this
organization has structure shows the chain of command within the company and with various
managerial heads at the various levels. Moreover, there are different departments which I came
across when I was being introduced into the office and company management structure. These
departments play a vital role in the procuring of sugarcane from the farmers and when clearing
the sugar produced to the market. Some of the departments which the Shree Narmada Khand
Udyog Sahakari Mandli Company has include the human resource, marketing, technical and
operations, distribution, finance as well as the procurement department. I decisively engaged the
workers and the heads of the departments, at the various levels during the office learning activity
and I get to know the various procedures and chain of command with the office. Interestingly, I
posted questions for them regarding the office functions and they willingly and hearted answered
them to my satisfaction. This exercise was remarkable and preferably I get to understand the
Name: Dhruv Patel Start date: 30th January 2016
Company: Shree Narmada Khand Udyog Sahakari Mandli Ltd Hours worked: 40
Principal supervisor: Anjan Kumar Singh
The main activity which I carried out this week was on
Exploring both the administration as well as the non-technical departments in the
company
Studying the boiling and evaporation stages associated with the sugar production
This week was a unique week for me as my supervisor embarked on teaching me the overall
office duties and exposing me to the various responsibilities and duties pertaining the office.
This study not only broke the monotony of learning the machine factories but also helped me, in
understanding all the logistics and the requirements; which one must adhere to in the
management of the sugar factor. I was able to established and get in-depth understanding of the
Shree Narmada Khand Udyog Sahakari Mandli organization structure. I depicted that this
organization has structure shows the chain of command within the company and with various
managerial heads at the various levels. Moreover, there are different departments which I came
across when I was being introduced into the office and company management structure. These
departments play a vital role in the procuring of sugarcane from the farmers and when clearing
the sugar produced to the market. Some of the departments which the Shree Narmada Khand
Udyog Sahakari Mandli Company has include the human resource, marketing, technical and
operations, distribution, finance as well as the procurement department. I decisively engaged the
workers and the heads of the departments, at the various levels during the office learning activity
and I get to know the various procedures and chain of command with the office. Interestingly, I
posted questions for them regarding the office functions and they willingly and hearted answered
them to my satisfaction. This exercise was remarkable and preferably I get to understand the
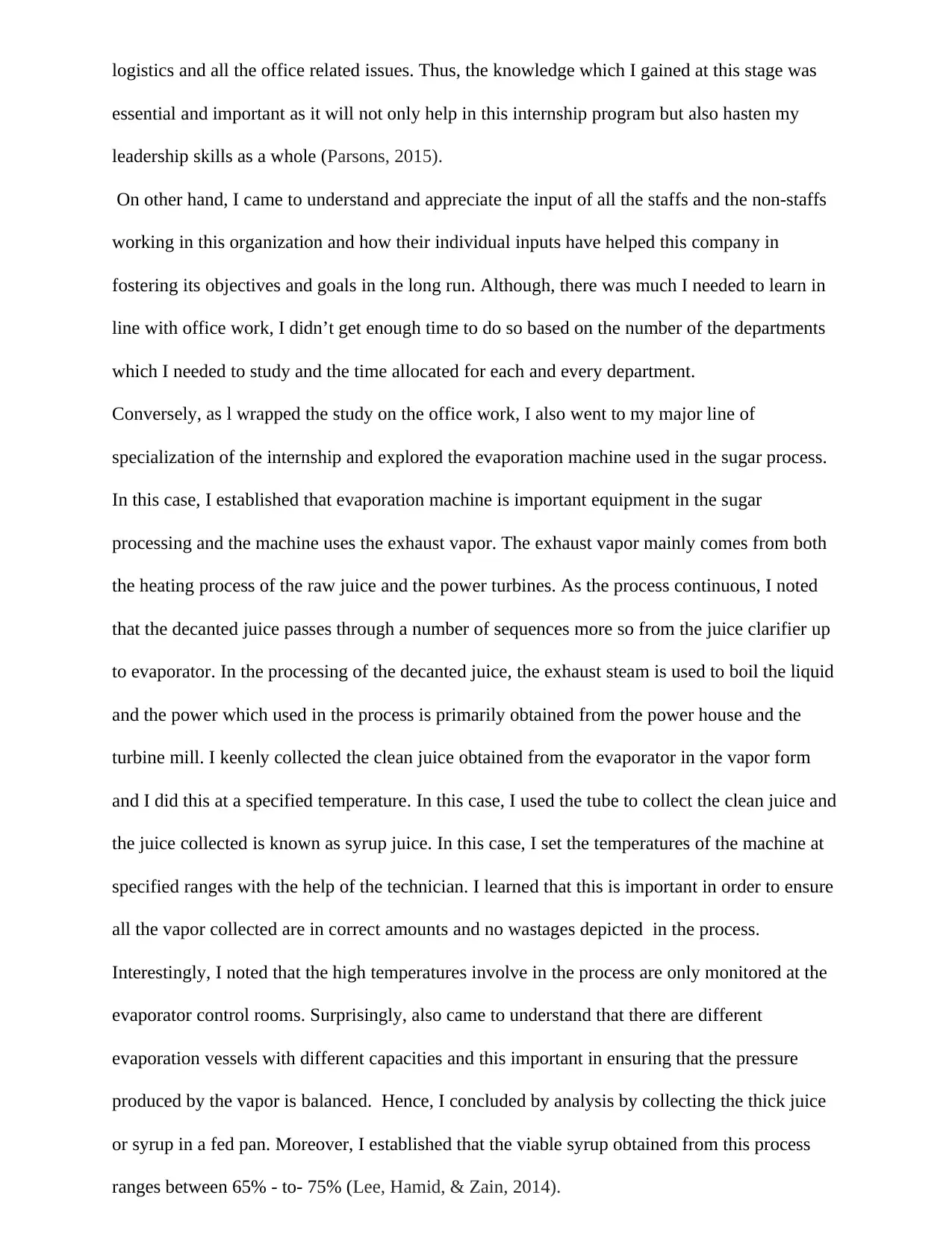
logistics and all the office related issues. Thus, the knowledge which I gained at this stage was
essential and important as it will not only help in this internship program but also hasten my
leadership skills as a whole (Parsons, 2015).
On other hand, I came to understand and appreciate the input of all the staffs and the non-staffs
working in this organization and how their individual inputs have helped this company in
fostering its objectives and goals in the long run. Although, there was much I needed to learn in
line with office work, I didn’t get enough time to do so based on the number of the departments
which I needed to study and the time allocated for each and every department.
Conversely, as l wrapped the study on the office work, I also went to my major line of
specialization of the internship and explored the evaporation machine used in the sugar process.
In this case, I established that evaporation machine is important equipment in the sugar
processing and the machine uses the exhaust vapor. The exhaust vapor mainly comes from both
the heating process of the raw juice and the power turbines. As the process continuous, I noted
that the decanted juice passes through a number of sequences more so from the juice clarifier up
to evaporator. In the processing of the decanted juice, the exhaust steam is used to boil the liquid
and the power which used in the process is primarily obtained from the power house and the
turbine mill. I keenly collected the clean juice obtained from the evaporator in the vapor form
and I did this at a specified temperature. In this case, I used the tube to collect the clean juice and
the juice collected is known as syrup juice. In this case, I set the temperatures of the machine at
specified ranges with the help of the technician. I learned that this is important in order to ensure
all the vapor collected are in correct amounts and no wastages depicted in the process.
Interestingly, I noted that the high temperatures involve in the process are only monitored at the
evaporator control rooms. Surprisingly, also came to understand that there are different
evaporation vessels with different capacities and this important in ensuring that the pressure
produced by the vapor is balanced. Hence, I concluded by analysis by collecting the thick juice
or syrup in a fed pan. Moreover, I established that the viable syrup obtained from this process
ranges between 65% - to- 75% (Lee, Hamid, & Zain, 2014).
essential and important as it will not only help in this internship program but also hasten my
leadership skills as a whole (Parsons, 2015).
On other hand, I came to understand and appreciate the input of all the staffs and the non-staffs
working in this organization and how their individual inputs have helped this company in
fostering its objectives and goals in the long run. Although, there was much I needed to learn in
line with office work, I didn’t get enough time to do so based on the number of the departments
which I needed to study and the time allocated for each and every department.
Conversely, as l wrapped the study on the office work, I also went to my major line of
specialization of the internship and explored the evaporation machine used in the sugar process.
In this case, I established that evaporation machine is important equipment in the sugar
processing and the machine uses the exhaust vapor. The exhaust vapor mainly comes from both
the heating process of the raw juice and the power turbines. As the process continuous, I noted
that the decanted juice passes through a number of sequences more so from the juice clarifier up
to evaporator. In the processing of the decanted juice, the exhaust steam is used to boil the liquid
and the power which used in the process is primarily obtained from the power house and the
turbine mill. I keenly collected the clean juice obtained from the evaporator in the vapor form
and I did this at a specified temperature. In this case, I used the tube to collect the clean juice and
the juice collected is known as syrup juice. In this case, I set the temperatures of the machine at
specified ranges with the help of the technician. I learned that this is important in order to ensure
all the vapor collected are in correct amounts and no wastages depicted in the process.
Interestingly, I noted that the high temperatures involve in the process are only monitored at the
evaporator control rooms. Surprisingly, also came to understand that there are different
evaporation vessels with different capacities and this important in ensuring that the pressure
produced by the vapor is balanced. Hence, I concluded by analysis by collecting the thick juice
or syrup in a fed pan. Moreover, I established that the viable syrup obtained from this process
ranges between 65% - to- 75% (Lee, Hamid, & Zain, 2014).
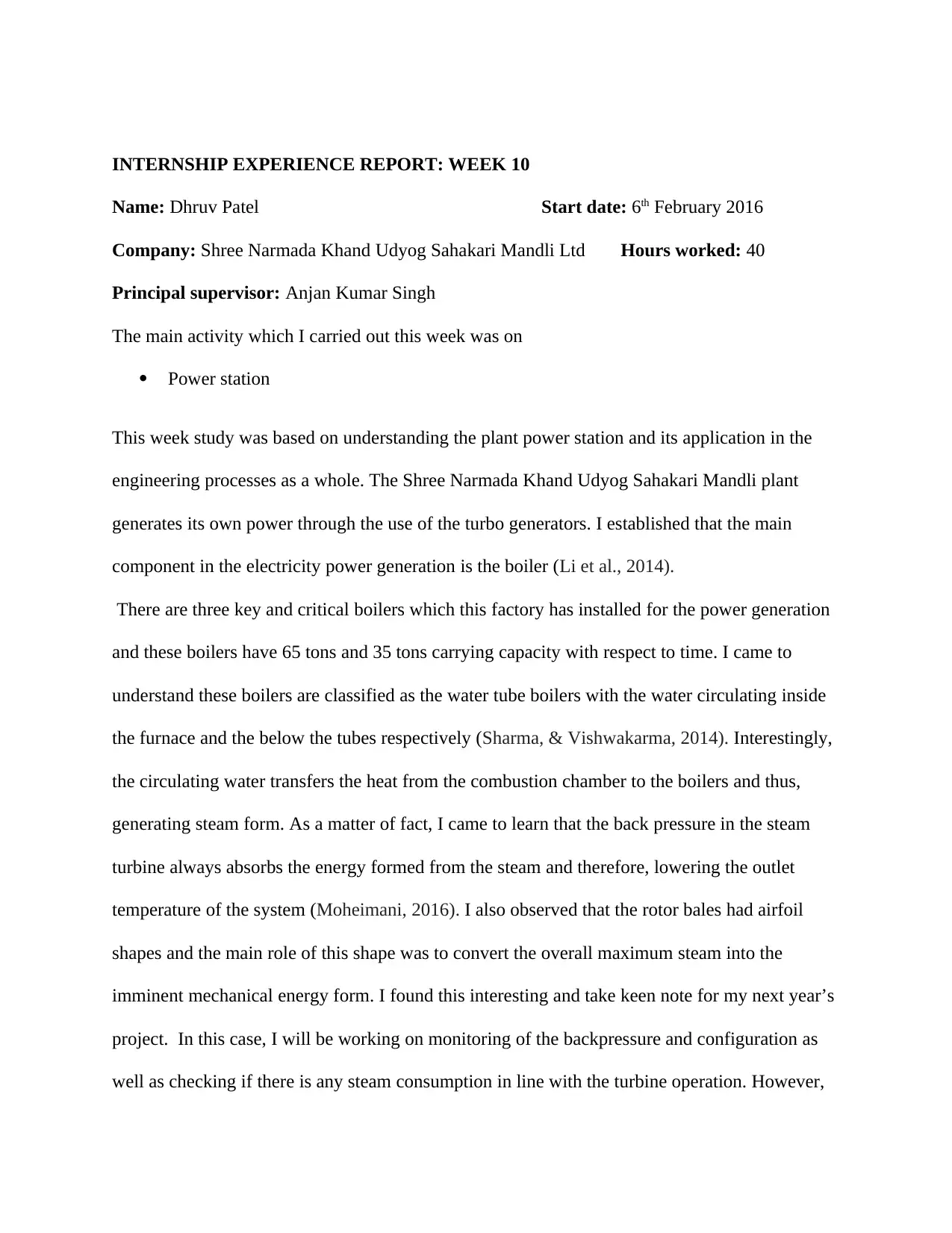
INTERNSHIP EXPERIENCE REPORT: WEEK 10
Name: Dhruv Patel Start date: 6th February 2016
Company: Shree Narmada Khand Udyog Sahakari Mandli Ltd Hours worked: 40
Principal supervisor: Anjan Kumar Singh
The main activity which I carried out this week was on
Power station
This week study was based on understanding the plant power station and its application in the
engineering processes as a whole. The Shree Narmada Khand Udyog Sahakari Mandli plant
generates its own power through the use of the turbo generators. I established that the main
component in the electricity power generation is the boiler (Li et al., 2014).
There are three key and critical boilers which this factory has installed for the power generation
and these boilers have 65 tons and 35 tons carrying capacity with respect to time. I came to
understand these boilers are classified as the water tube boilers with the water circulating inside
the furnace and the below the tubes respectively (Sharma, & Vishwakarma, 2014). Interestingly,
the circulating water transfers the heat from the combustion chamber to the boilers and thus,
generating steam form. As a matter of fact, I came to learn that the back pressure in the steam
turbine always absorbs the energy formed from the steam and therefore, lowering the outlet
temperature of the system (Moheimani, 2016). I also observed that the rotor bales had airfoil
shapes and the main role of this shape was to convert the overall maximum steam into the
imminent mechanical energy form. I found this interesting and take keen note for my next year’s
project. In this case, I will be working on monitoring of the backpressure and configuration as
well as checking if there is any steam consumption in line with the turbine operation. However,
Name: Dhruv Patel Start date: 6th February 2016
Company: Shree Narmada Khand Udyog Sahakari Mandli Ltd Hours worked: 40
Principal supervisor: Anjan Kumar Singh
The main activity which I carried out this week was on
Power station
This week study was based on understanding the plant power station and its application in the
engineering processes as a whole. The Shree Narmada Khand Udyog Sahakari Mandli plant
generates its own power through the use of the turbo generators. I established that the main
component in the electricity power generation is the boiler (Li et al., 2014).
There are three key and critical boilers which this factory has installed for the power generation
and these boilers have 65 tons and 35 tons carrying capacity with respect to time. I came to
understand these boilers are classified as the water tube boilers with the water circulating inside
the furnace and the below the tubes respectively (Sharma, & Vishwakarma, 2014). Interestingly,
the circulating water transfers the heat from the combustion chamber to the boilers and thus,
generating steam form. As a matter of fact, I came to learn that the back pressure in the steam
turbine always absorbs the energy formed from the steam and therefore, lowering the outlet
temperature of the system (Moheimani, 2016). I also observed that the rotor bales had airfoil
shapes and the main role of this shape was to convert the overall maximum steam into the
imminent mechanical energy form. I found this interesting and take keen note for my next year’s
project. In this case, I will be working on monitoring of the backpressure and configuration as
well as checking if there is any steam consumption in line with the turbine operation. However,
Paraphrase This Document
Need a fresh take? Get an instant paraphrase of this document with our AI Paraphraser
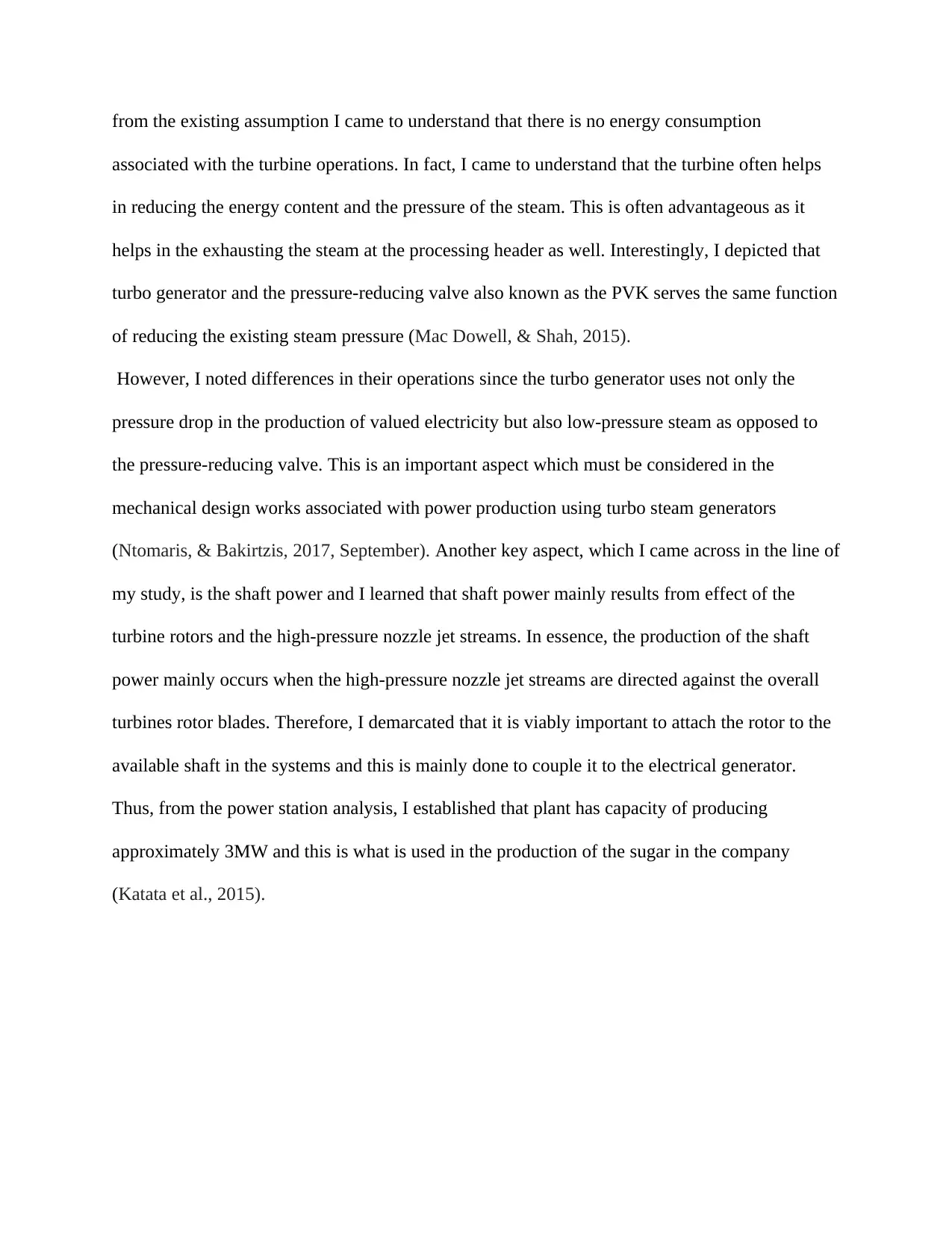
from the existing assumption I came to understand that there is no energy consumption
associated with the turbine operations. In fact, I came to understand that the turbine often helps
in reducing the energy content and the pressure of the steam. This is often advantageous as it
helps in the exhausting the steam at the processing header as well. Interestingly, I depicted that
turbo generator and the pressure-reducing valve also known as the PVK serves the same function
of reducing the existing steam pressure (Mac Dowell, & Shah, 2015).
However, I noted differences in their operations since the turbo generator uses not only the
pressure drop in the production of valued electricity but also low-pressure steam as opposed to
the pressure-reducing valve. This is an important aspect which must be considered in the
mechanical design works associated with power production using turbo steam generators
(Ntomaris, & Bakirtzis, 2017, September). Another key aspect, which I came across in the line of
my study, is the shaft power and I learned that shaft power mainly results from effect of the
turbine rotors and the high-pressure nozzle jet streams. In essence, the production of the shaft
power mainly occurs when the high-pressure nozzle jet streams are directed against the overall
turbines rotor blades. Therefore, I demarcated that it is viably important to attach the rotor to the
available shaft in the systems and this is mainly done to couple it to the electrical generator.
Thus, from the power station analysis, I established that plant has capacity of producing
approximately 3MW and this is what is used in the production of the sugar in the company
(Katata et al., 2015).
associated with the turbine operations. In fact, I came to understand that the turbine often helps
in reducing the energy content and the pressure of the steam. This is often advantageous as it
helps in the exhausting the steam at the processing header as well. Interestingly, I depicted that
turbo generator and the pressure-reducing valve also known as the PVK serves the same function
of reducing the existing steam pressure (Mac Dowell, & Shah, 2015).
However, I noted differences in their operations since the turbo generator uses not only the
pressure drop in the production of valued electricity but also low-pressure steam as opposed to
the pressure-reducing valve. This is an important aspect which must be considered in the
mechanical design works associated with power production using turbo steam generators
(Ntomaris, & Bakirtzis, 2017, September). Another key aspect, which I came across in the line of
my study, is the shaft power and I learned that shaft power mainly results from effect of the
turbine rotors and the high-pressure nozzle jet streams. In essence, the production of the shaft
power mainly occurs when the high-pressure nozzle jet streams are directed against the overall
turbines rotor blades. Therefore, I demarcated that it is viably important to attach the rotor to the
available shaft in the systems and this is mainly done to couple it to the electrical generator.
Thus, from the power station analysis, I established that plant has capacity of producing
approximately 3MW and this is what is used in the production of the sugar in the company
(Katata et al., 2015).
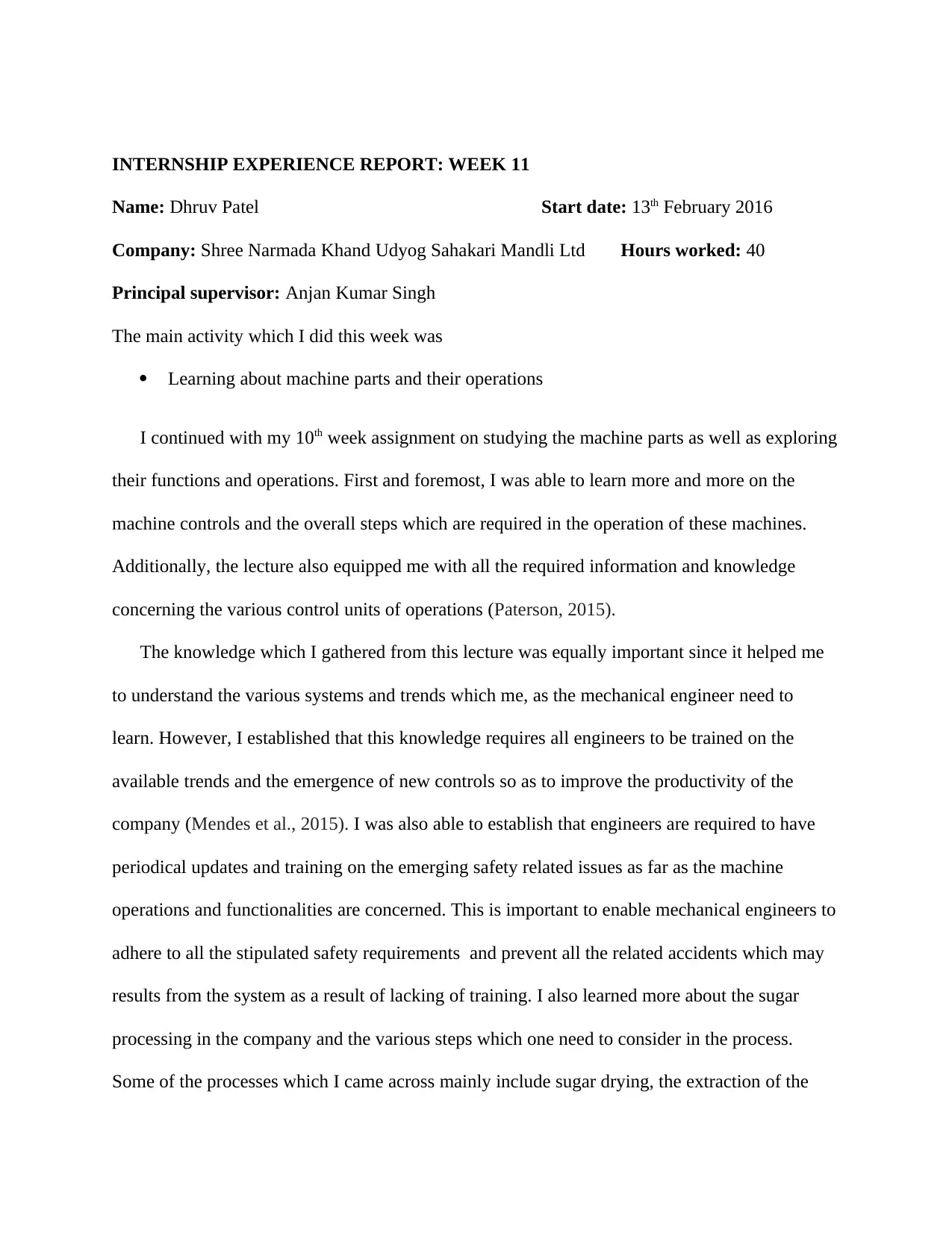
INTERNSHIP EXPERIENCE REPORT: WEEK 11
Name: Dhruv Patel Start date: 13th February 2016
Company: Shree Narmada Khand Udyog Sahakari Mandli Ltd Hours worked: 40
Principal supervisor: Anjan Kumar Singh
The main activity which I did this week was
Learning about machine parts and their operations
I continued with my 10th week assignment on studying the machine parts as well as exploring
their functions and operations. First and foremost, I was able to learn more and more on the
machine controls and the overall steps which are required in the operation of these machines.
Additionally, the lecture also equipped me with all the required information and knowledge
concerning the various control units of operations (Paterson, 2015).
The knowledge which I gathered from this lecture was equally important since it helped me
to understand the various systems and trends which me, as the mechanical engineer need to
learn. However, I established that this knowledge requires all engineers to be trained on the
available trends and the emergence of new controls so as to improve the productivity of the
company (Mendes et al., 2015). I was also able to establish that engineers are required to have
periodical updates and training on the emerging safety related issues as far as the machine
operations and functionalities are concerned. This is important to enable mechanical engineers to
adhere to all the stipulated safety requirements and prevent all the related accidents which may
results from the system as a result of lacking of training. I also learned more about the sugar
processing in the company and the various steps which one need to consider in the process.
Some of the processes which I came across mainly include sugar drying, the extraction of the
Name: Dhruv Patel Start date: 13th February 2016
Company: Shree Narmada Khand Udyog Sahakari Mandli Ltd Hours worked: 40
Principal supervisor: Anjan Kumar Singh
The main activity which I did this week was
Learning about machine parts and their operations
I continued with my 10th week assignment on studying the machine parts as well as exploring
their functions and operations. First and foremost, I was able to learn more and more on the
machine controls and the overall steps which are required in the operation of these machines.
Additionally, the lecture also equipped me with all the required information and knowledge
concerning the various control units of operations (Paterson, 2015).
The knowledge which I gathered from this lecture was equally important since it helped me
to understand the various systems and trends which me, as the mechanical engineer need to
learn. However, I established that this knowledge requires all engineers to be trained on the
available trends and the emergence of new controls so as to improve the productivity of the
company (Mendes et al., 2015). I was also able to establish that engineers are required to have
periodical updates and training on the emerging safety related issues as far as the machine
operations and functionalities are concerned. This is important to enable mechanical engineers to
adhere to all the stipulated safety requirements and prevent all the related accidents which may
results from the system as a result of lacking of training. I also learned more about the sugar
processing in the company and the various steps which one need to consider in the process.
Some of the processes which I came across mainly include sugar drying, the extraction of the
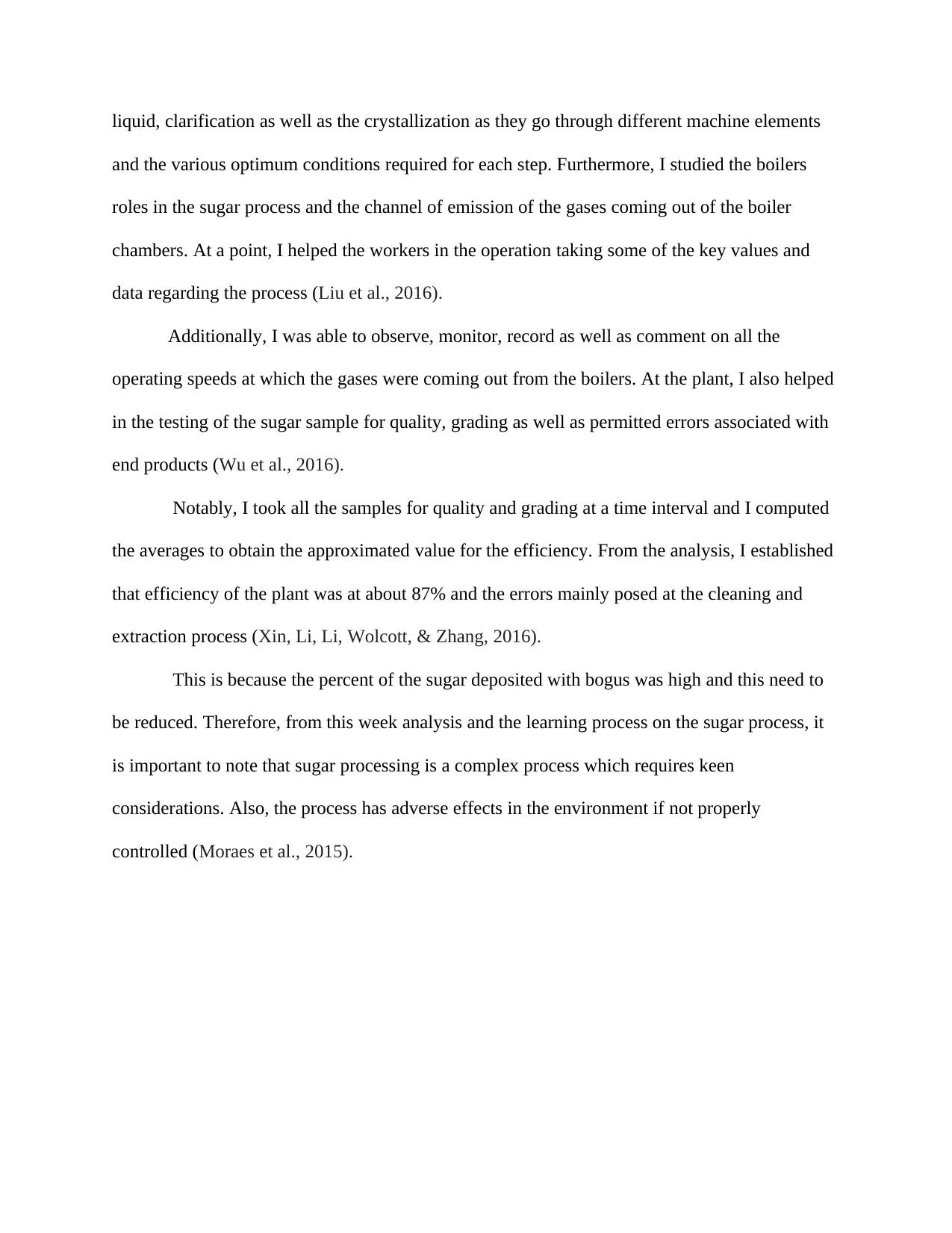
liquid, clarification as well as the crystallization as they go through different machine elements
and the various optimum conditions required for each step. Furthermore, I studied the boilers
roles in the sugar process and the channel of emission of the gases coming out of the boiler
chambers. At a point, I helped the workers in the operation taking some of the key values and
data regarding the process (Liu et al., 2016).
Additionally, I was able to observe, monitor, record as well as comment on all the
operating speeds at which the gases were coming out from the boilers. At the plant, I also helped
in the testing of the sugar sample for quality, grading as well as permitted errors associated with
end products (Wu et al., 2016).
Notably, I took all the samples for quality and grading at a time interval and I computed
the averages to obtain the approximated value for the efficiency. From the analysis, I established
that efficiency of the plant was at about 87% and the errors mainly posed at the cleaning and
extraction process (Xin, Li, Li, Wolcott, & Zhang, 2016).
This is because the percent of the sugar deposited with bogus was high and this need to
be reduced. Therefore, from this week analysis and the learning process on the sugar process, it
is important to note that sugar processing is a complex process which requires keen
considerations. Also, the process has adverse effects in the environment if not properly
controlled (Moraes et al., 2015).
and the various optimum conditions required for each step. Furthermore, I studied the boilers
roles in the sugar process and the channel of emission of the gases coming out of the boiler
chambers. At a point, I helped the workers in the operation taking some of the key values and
data regarding the process (Liu et al., 2016).
Additionally, I was able to observe, monitor, record as well as comment on all the
operating speeds at which the gases were coming out from the boilers. At the plant, I also helped
in the testing of the sugar sample for quality, grading as well as permitted errors associated with
end products (Wu et al., 2016).
Notably, I took all the samples for quality and grading at a time interval and I computed
the averages to obtain the approximated value for the efficiency. From the analysis, I established
that efficiency of the plant was at about 87% and the errors mainly posed at the cleaning and
extraction process (Xin, Li, Li, Wolcott, & Zhang, 2016).
This is because the percent of the sugar deposited with bogus was high and this need to
be reduced. Therefore, from this week analysis and the learning process on the sugar process, it
is important to note that sugar processing is a complex process which requires keen
considerations. Also, the process has adverse effects in the environment if not properly
controlled (Moraes et al., 2015).
Secure Best Marks with AI Grader
Need help grading? Try our AI Grader for instant feedback on your assignments.
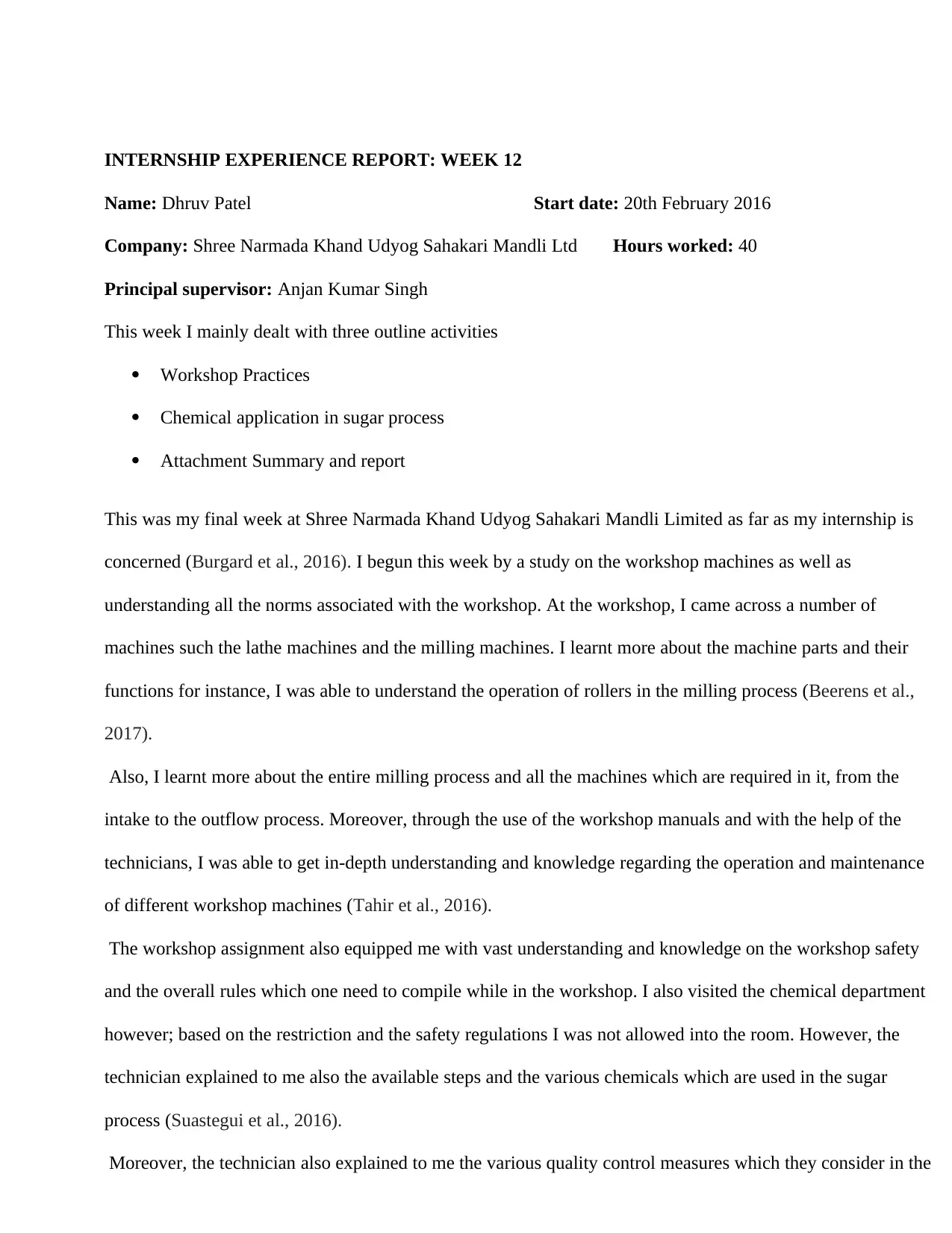
INTERNSHIP EXPERIENCE REPORT: WEEK 12
Name: Dhruv Patel Start date: 20th February 2016
Company: Shree Narmada Khand Udyog Sahakari Mandli Ltd Hours worked: 40
Principal supervisor: Anjan Kumar Singh
This week I mainly dealt with three outline activities
Workshop Practices
Chemical application in sugar process
Attachment Summary and report
This was my final week at Shree Narmada Khand Udyog Sahakari Mandli Limited as far as my internship is
concerned (Burgard et al., 2016). I begun this week by a study on the workshop machines as well as
understanding all the norms associated with the workshop. At the workshop, I came across a number of
machines such the lathe machines and the milling machines. I learnt more about the machine parts and their
functions for instance, I was able to understand the operation of rollers in the milling process (Beerens et al.,
2017).
Also, I learnt more about the entire milling process and all the machines which are required in it, from the
intake to the outflow process. Moreover, through the use of the workshop manuals and with the help of the
technicians, I was able to get in-depth understanding and knowledge regarding the operation and maintenance
of different workshop machines (Tahir et al., 2016).
The workshop assignment also equipped me with vast understanding and knowledge on the workshop safety
and the overall rules which one need to compile while in the workshop. I also visited the chemical department
however; based on the restriction and the safety regulations I was not allowed into the room. However, the
technician explained to me also the available steps and the various chemicals which are used in the sugar
process (Suastegui et al., 2016).
Moreover, the technician also explained to me the various quality control measures which they consider in the
Name: Dhruv Patel Start date: 20th February 2016
Company: Shree Narmada Khand Udyog Sahakari Mandli Ltd Hours worked: 40
Principal supervisor: Anjan Kumar Singh
This week I mainly dealt with three outline activities
Workshop Practices
Chemical application in sugar process
Attachment Summary and report
This was my final week at Shree Narmada Khand Udyog Sahakari Mandli Limited as far as my internship is
concerned (Burgard et al., 2016). I begun this week by a study on the workshop machines as well as
understanding all the norms associated with the workshop. At the workshop, I came across a number of
machines such the lathe machines and the milling machines. I learnt more about the machine parts and their
functions for instance, I was able to understand the operation of rollers in the milling process (Beerens et al.,
2017).
Also, I learnt more about the entire milling process and all the machines which are required in it, from the
intake to the outflow process. Moreover, through the use of the workshop manuals and with the help of the
technicians, I was able to get in-depth understanding and knowledge regarding the operation and maintenance
of different workshop machines (Tahir et al., 2016).
The workshop assignment also equipped me with vast understanding and knowledge on the workshop safety
and the overall rules which one need to compile while in the workshop. I also visited the chemical department
however; based on the restriction and the safety regulations I was not allowed into the room. However, the
technician explained to me also the available steps and the various chemicals which are used in the sugar
process (Suastegui et al., 2016).
Moreover, the technician also explained to me the various quality control measures which they consider in the
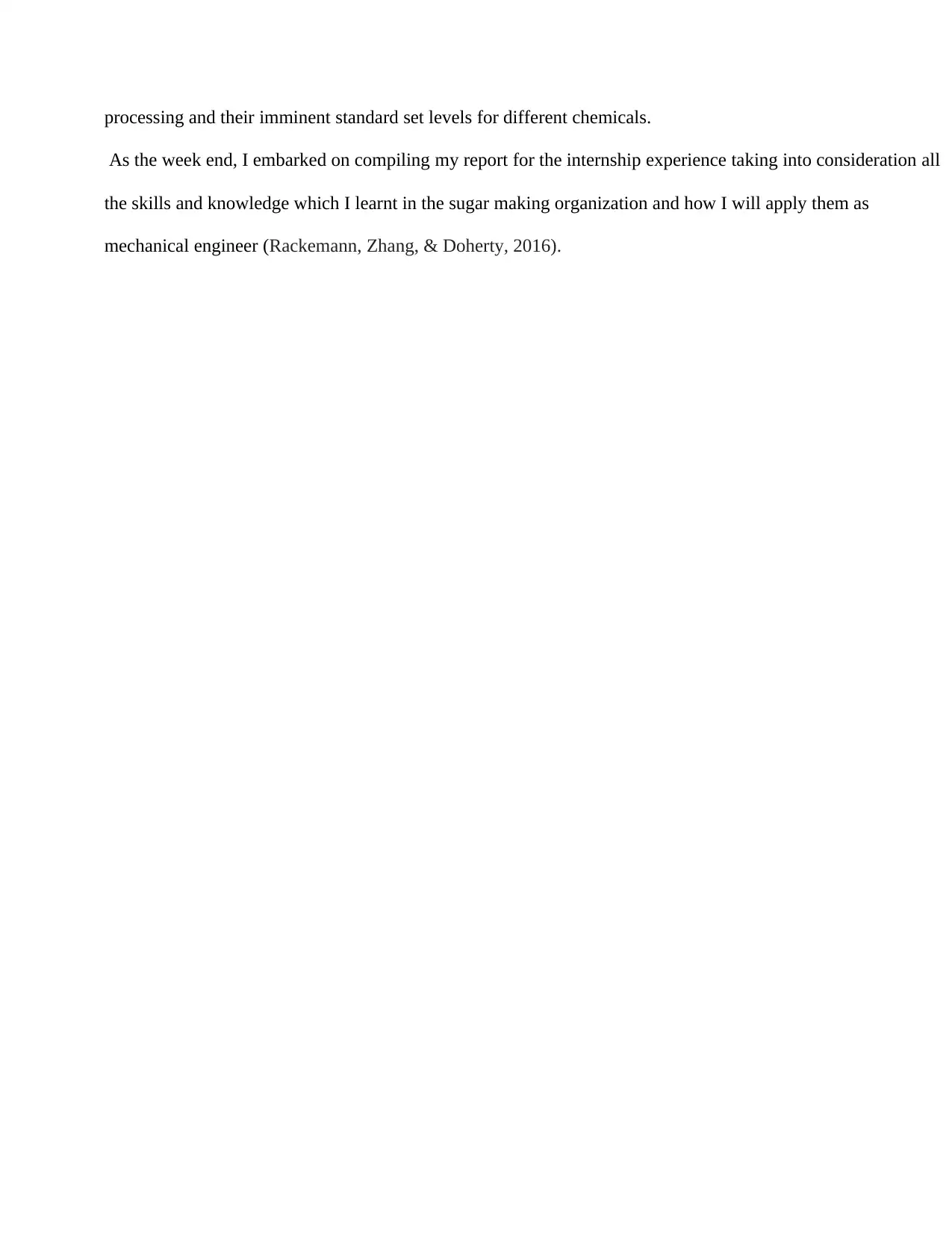
processing and their imminent standard set levels for different chemicals.
As the week end, I embarked on compiling my report for the internship experience taking into consideration all
the skills and knowledge which I learnt in the sugar making organization and how I will apply them as
mechanical engineer (Rackemann, Zhang, & Doherty, 2016).
As the week end, I embarked on compiling my report for the internship experience taking into consideration all
the skills and knowledge which I learnt in the sugar making organization and how I will apply them as
mechanical engineer (Rackemann, Zhang, & Doherty, 2016).
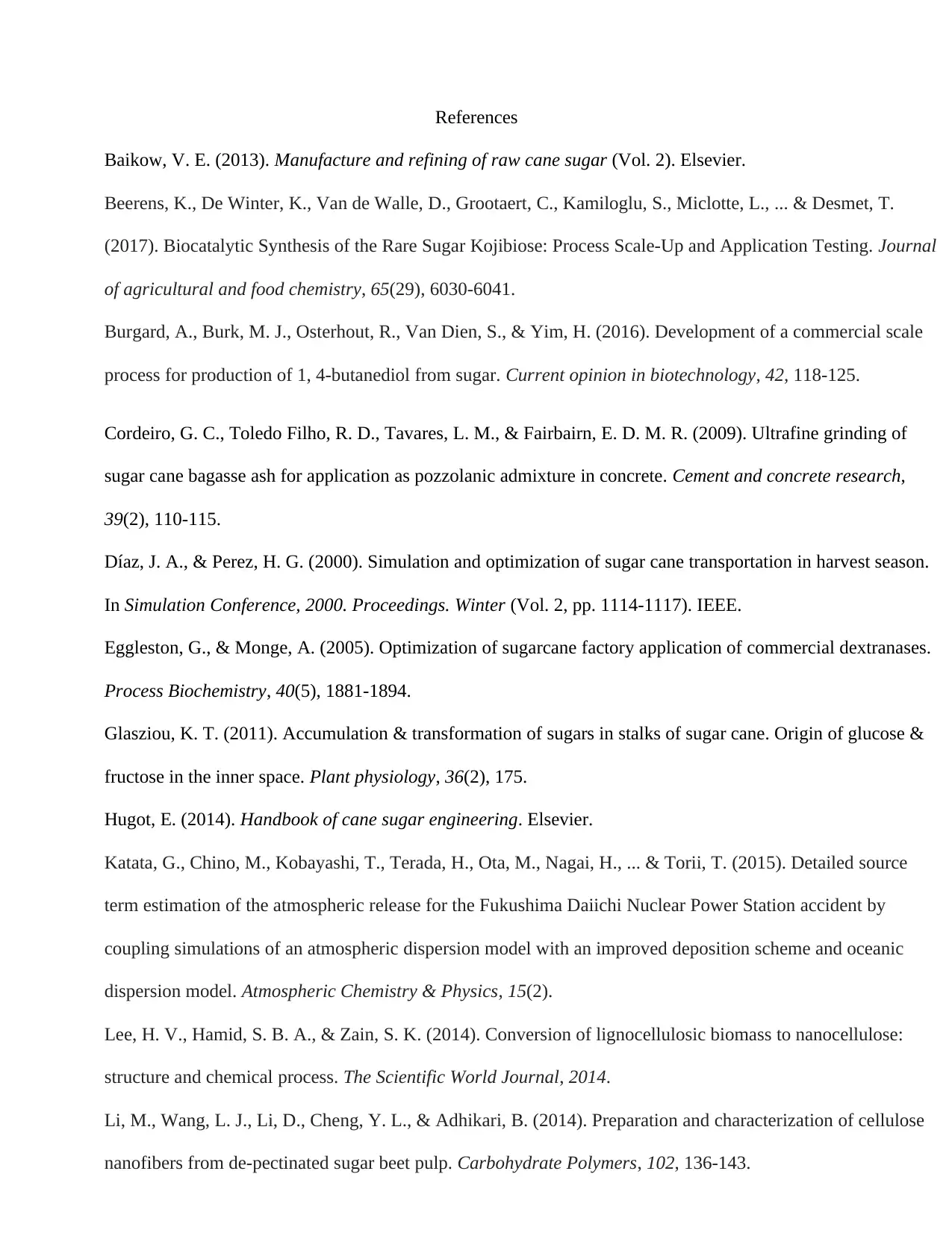
References
Baikow, V. E. (2013). Manufacture and refining of raw cane sugar (Vol. 2). Elsevier.
Beerens, K., De Winter, K., Van de Walle, D., Grootaert, C., Kamiloglu, S., Miclotte, L., ... & Desmet, T.
(2017). Biocatalytic Synthesis of the Rare Sugar Kojibiose: Process Scale-Up and Application Testing. Journal
of agricultural and food chemistry, 65(29), 6030-6041.
Burgard, A., Burk, M. J., Osterhout, R., Van Dien, S., & Yim, H. (2016). Development of a commercial scale
process for production of 1, 4-butanediol from sugar. Current opinion in biotechnology, 42, 118-125.
Cordeiro, G. C., Toledo Filho, R. D., Tavares, L. M., & Fairbairn, E. D. M. R. (2009). Ultrafine grinding of
sugar cane bagasse ash for application as pozzolanic admixture in concrete. Cement and concrete research,
39(2), 110-115.
Díaz, J. A., & Perez, H. G. (2000). Simulation and optimization of sugar cane transportation in harvest season.
In Simulation Conference, 2000. Proceedings. Winter (Vol. 2, pp. 1114-1117). IEEE.
Eggleston, G., & Monge, A. (2005). Optimization of sugarcane factory application of commercial dextranases.
Process Biochemistry, 40(5), 1881-1894.
Glasziou, K. T. (2011). Accumulation & transformation of sugars in stalks of sugar cane. Origin of glucose &
fructose in the inner space. Plant physiology, 36(2), 175.
Hugot, E. (2014). Handbook of cane sugar engineering. Elsevier.
Katata, G., Chino, M., Kobayashi, T., Terada, H., Ota, M., Nagai, H., ... & Torii, T. (2015). Detailed source
term estimation of the atmospheric release for the Fukushima Daiichi Nuclear Power Station accident by
coupling simulations of an atmospheric dispersion model with an improved deposition scheme and oceanic
dispersion model. Atmospheric Chemistry & Physics, 15(2).
Lee, H. V., Hamid, S. B. A., & Zain, S. K. (2014). Conversion of lignocellulosic biomass to nanocellulose:
structure and chemical process. The Scientific World Journal, 2014.
Li, M., Wang, L. J., Li, D., Cheng, Y. L., & Adhikari, B. (2014). Preparation and characterization of cellulose
nanofibers from de-pectinated sugar beet pulp. Carbohydrate Polymers, 102, 136-143.
Baikow, V. E. (2013). Manufacture and refining of raw cane sugar (Vol. 2). Elsevier.
Beerens, K., De Winter, K., Van de Walle, D., Grootaert, C., Kamiloglu, S., Miclotte, L., ... & Desmet, T.
(2017). Biocatalytic Synthesis of the Rare Sugar Kojibiose: Process Scale-Up and Application Testing. Journal
of agricultural and food chemistry, 65(29), 6030-6041.
Burgard, A., Burk, M. J., Osterhout, R., Van Dien, S., & Yim, H. (2016). Development of a commercial scale
process for production of 1, 4-butanediol from sugar. Current opinion in biotechnology, 42, 118-125.
Cordeiro, G. C., Toledo Filho, R. D., Tavares, L. M., & Fairbairn, E. D. M. R. (2009). Ultrafine grinding of
sugar cane bagasse ash for application as pozzolanic admixture in concrete. Cement and concrete research,
39(2), 110-115.
Díaz, J. A., & Perez, H. G. (2000). Simulation and optimization of sugar cane transportation in harvest season.
In Simulation Conference, 2000. Proceedings. Winter (Vol. 2, pp. 1114-1117). IEEE.
Eggleston, G., & Monge, A. (2005). Optimization of sugarcane factory application of commercial dextranases.
Process Biochemistry, 40(5), 1881-1894.
Glasziou, K. T. (2011). Accumulation & transformation of sugars in stalks of sugar cane. Origin of glucose &
fructose in the inner space. Plant physiology, 36(2), 175.
Hugot, E. (2014). Handbook of cane sugar engineering. Elsevier.
Katata, G., Chino, M., Kobayashi, T., Terada, H., Ota, M., Nagai, H., ... & Torii, T. (2015). Detailed source
term estimation of the atmospheric release for the Fukushima Daiichi Nuclear Power Station accident by
coupling simulations of an atmospheric dispersion model with an improved deposition scheme and oceanic
dispersion model. Atmospheric Chemistry & Physics, 15(2).
Lee, H. V., Hamid, S. B. A., & Zain, S. K. (2014). Conversion of lignocellulosic biomass to nanocellulose:
structure and chemical process. The Scientific World Journal, 2014.
Li, M., Wang, L. J., Li, D., Cheng, Y. L., & Adhikari, B. (2014). Preparation and characterization of cellulose
nanofibers from de-pectinated sugar beet pulp. Carbohydrate Polymers, 102, 136-143.
Paraphrase This Document
Need a fresh take? Get an instant paraphrase of this document with our AI Paraphraser
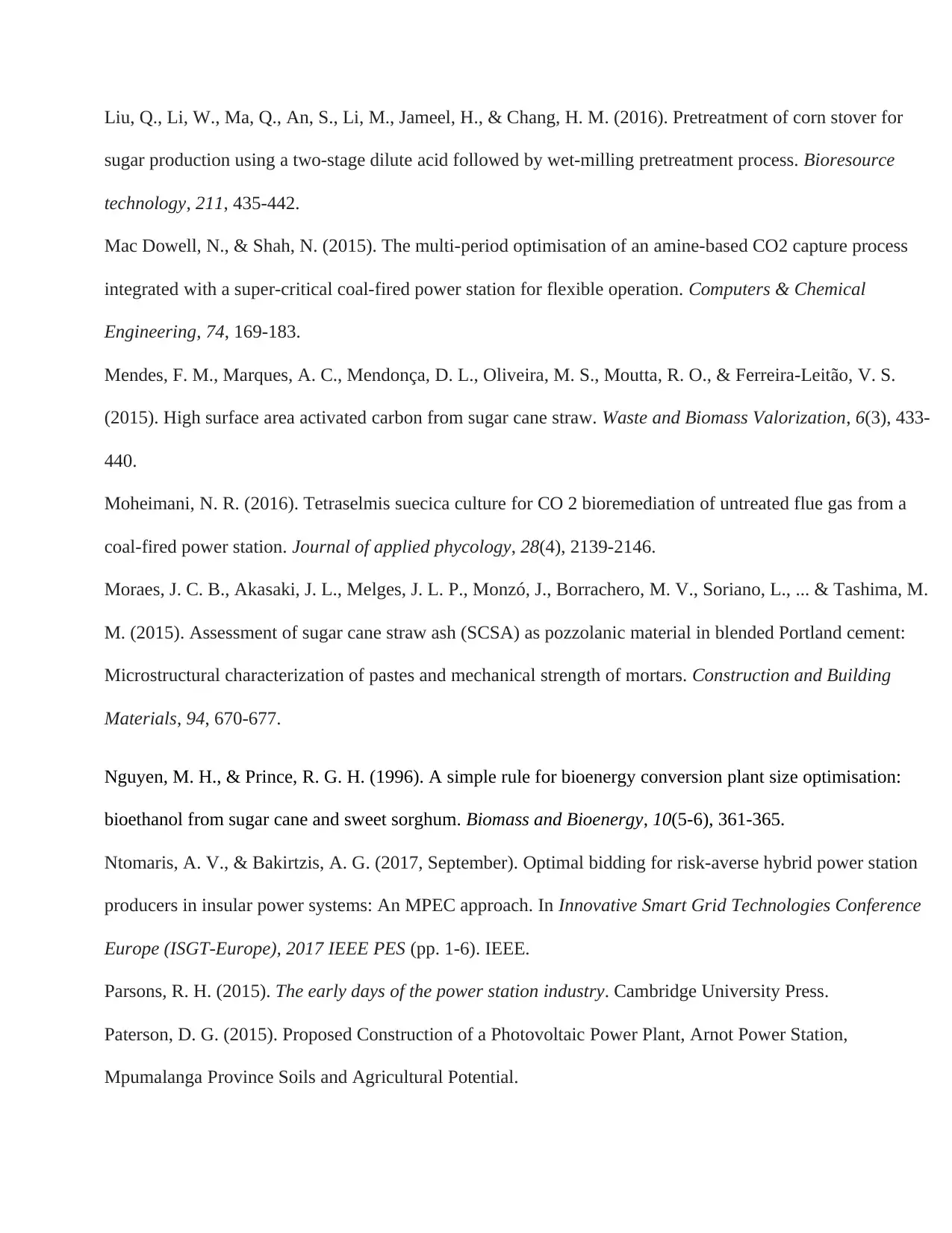
Liu, Q., Li, W., Ma, Q., An, S., Li, M., Jameel, H., & Chang, H. M. (2016). Pretreatment of corn stover for
sugar production using a two-stage dilute acid followed by wet-milling pretreatment process. Bioresource
technology, 211, 435-442.
Mac Dowell, N., & Shah, N. (2015). The multi-period optimisation of an amine-based CO2 capture process
integrated with a super-critical coal-fired power station for flexible operation. Computers & Chemical
Engineering, 74, 169-183.
Mendes, F. M., Marques, A. C., Mendonça, D. L., Oliveira, M. S., Moutta, R. O., & Ferreira-Leitão, V. S.
(2015). High surface area activated carbon from sugar cane straw. Waste and Biomass Valorization, 6(3), 433-
440.
Moheimani, N. R. (2016). Tetraselmis suecica culture for CO 2 bioremediation of untreated flue gas from a
coal-fired power station. Journal of applied phycology, 28(4), 2139-2146.
Moraes, J. C. B., Akasaki, J. L., Melges, J. L. P., Monzó, J., Borrachero, M. V., Soriano, L., ... & Tashima, M.
M. (2015). Assessment of sugar cane straw ash (SCSA) as pozzolanic material in blended Portland cement:
Microstructural characterization of pastes and mechanical strength of mortars. Construction and Building
Materials, 94, 670-677.
Nguyen, M. H., & Prince, R. G. H. (1996). A simple rule for bioenergy conversion plant size optimisation:
bioethanol from sugar cane and sweet sorghum. Biomass and Bioenergy, 10(5-6), 361-365.
Ntomaris, A. V., & Bakirtzis, A. G. (2017, September). Optimal bidding for risk-averse hybrid power station
producers in insular power systems: An MPEC approach. In Innovative Smart Grid Technologies Conference
Europe (ISGT-Europe), 2017 IEEE PES (pp. 1-6). IEEE.
Parsons, R. H. (2015). The early days of the power station industry. Cambridge University Press.
Paterson, D. G. (2015). Proposed Construction of a Photovoltaic Power Plant, Arnot Power Station,
Mpumalanga Province Soils and Agricultural Potential.
sugar production using a two-stage dilute acid followed by wet-milling pretreatment process. Bioresource
technology, 211, 435-442.
Mac Dowell, N., & Shah, N. (2015). The multi-period optimisation of an amine-based CO2 capture process
integrated with a super-critical coal-fired power station for flexible operation. Computers & Chemical
Engineering, 74, 169-183.
Mendes, F. M., Marques, A. C., Mendonça, D. L., Oliveira, M. S., Moutta, R. O., & Ferreira-Leitão, V. S.
(2015). High surface area activated carbon from sugar cane straw. Waste and Biomass Valorization, 6(3), 433-
440.
Moheimani, N. R. (2016). Tetraselmis suecica culture for CO 2 bioremediation of untreated flue gas from a
coal-fired power station. Journal of applied phycology, 28(4), 2139-2146.
Moraes, J. C. B., Akasaki, J. L., Melges, J. L. P., Monzó, J., Borrachero, M. V., Soriano, L., ... & Tashima, M.
M. (2015). Assessment of sugar cane straw ash (SCSA) as pozzolanic material in blended Portland cement:
Microstructural characterization of pastes and mechanical strength of mortars. Construction and Building
Materials, 94, 670-677.
Nguyen, M. H., & Prince, R. G. H. (1996). A simple rule for bioenergy conversion plant size optimisation:
bioethanol from sugar cane and sweet sorghum. Biomass and Bioenergy, 10(5-6), 361-365.
Ntomaris, A. V., & Bakirtzis, A. G. (2017, September). Optimal bidding for risk-averse hybrid power station
producers in insular power systems: An MPEC approach. In Innovative Smart Grid Technologies Conference
Europe (ISGT-Europe), 2017 IEEE PES (pp. 1-6). IEEE.
Parsons, R. H. (2015). The early days of the power station industry. Cambridge University Press.
Paterson, D. G. (2015). Proposed Construction of a Photovoltaic Power Plant, Arnot Power Station,
Mpumalanga Province Soils and Agricultural Potential.
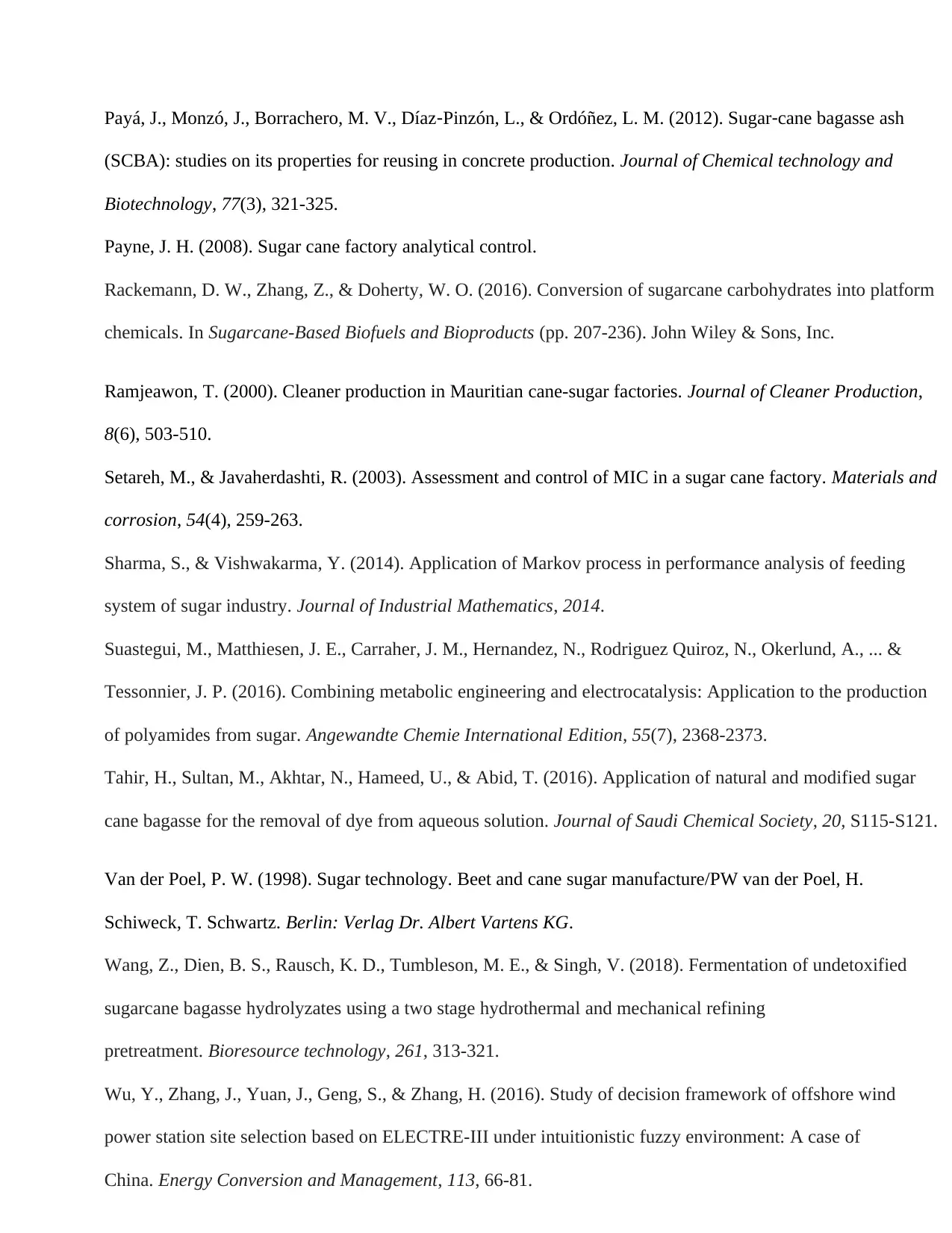
Payá, J., Monzó, J., Borrachero, M. V., Díaz‐Pinzón, L., & Ordóñez, L. M. (2012). Sugar‐cane bagasse ash
(SCBA): studies on its properties for reusing in concrete production. Journal of Chemical technology and
Biotechnology, 77(3), 321-325.
Payne, J. H. (2008). Sugar cane factory analytical control.
Rackemann, D. W., Zhang, Z., & Doherty, W. O. (2016). Conversion of sugarcane carbohydrates into platform
chemicals. In Sugarcane-Based Biofuels and Bioproducts (pp. 207-236). John Wiley & Sons, Inc.
Ramjeawon, T. (2000). Cleaner production in Mauritian cane-sugar factories. Journal of Cleaner Production,
8(6), 503-510.
Setareh, M., & Javaherdashti, R. (2003). Assessment and control of MIC in a sugar cane factory. Materials and
corrosion, 54(4), 259-263.
Sharma, S., & Vishwakarma, Y. (2014). Application of Markov process in performance analysis of feeding
system of sugar industry. Journal of Industrial Mathematics, 2014.
Suastegui, M., Matthiesen, J. E., Carraher, J. M., Hernandez, N., Rodriguez Quiroz, N., Okerlund, A., ... &
Tessonnier, J. P. (2016). Combining metabolic engineering and electrocatalysis: Application to the production
of polyamides from sugar. Angewandte Chemie International Edition, 55(7), 2368-2373.
Tahir, H., Sultan, M., Akhtar, N., Hameed, U., & Abid, T. (2016). Application of natural and modified sugar
cane bagasse for the removal of dye from aqueous solution. Journal of Saudi Chemical Society, 20, S115-S121.
Van der Poel, P. W. (1998). Sugar technology. Beet and cane sugar manufacture/PW van der Poel, H.
Schiweck, T. Schwartz. Berlin: Verlag Dr. Albert Vartens KG.
Wang, Z., Dien, B. S., Rausch, K. D., Tumbleson, M. E., & Singh, V. (2018). Fermentation of undetoxified
sugarcane bagasse hydrolyzates using a two stage hydrothermal and mechanical refining
pretreatment. Bioresource technology, 261, 313-321.
Wu, Y., Zhang, J., Yuan, J., Geng, S., & Zhang, H. (2016). Study of decision framework of offshore wind
power station site selection based on ELECTRE-III under intuitionistic fuzzy environment: A case of
China. Energy Conversion and Management, 113, 66-81.
(SCBA): studies on its properties for reusing in concrete production. Journal of Chemical technology and
Biotechnology, 77(3), 321-325.
Payne, J. H. (2008). Sugar cane factory analytical control.
Rackemann, D. W., Zhang, Z., & Doherty, W. O. (2016). Conversion of sugarcane carbohydrates into platform
chemicals. In Sugarcane-Based Biofuels and Bioproducts (pp. 207-236). John Wiley & Sons, Inc.
Ramjeawon, T. (2000). Cleaner production in Mauritian cane-sugar factories. Journal of Cleaner Production,
8(6), 503-510.
Setareh, M., & Javaherdashti, R. (2003). Assessment and control of MIC in a sugar cane factory. Materials and
corrosion, 54(4), 259-263.
Sharma, S., & Vishwakarma, Y. (2014). Application of Markov process in performance analysis of feeding
system of sugar industry. Journal of Industrial Mathematics, 2014.
Suastegui, M., Matthiesen, J. E., Carraher, J. M., Hernandez, N., Rodriguez Quiroz, N., Okerlund, A., ... &
Tessonnier, J. P. (2016). Combining metabolic engineering and electrocatalysis: Application to the production
of polyamides from sugar. Angewandte Chemie International Edition, 55(7), 2368-2373.
Tahir, H., Sultan, M., Akhtar, N., Hameed, U., & Abid, T. (2016). Application of natural and modified sugar
cane bagasse for the removal of dye from aqueous solution. Journal of Saudi Chemical Society, 20, S115-S121.
Van der Poel, P. W. (1998). Sugar technology. Beet and cane sugar manufacture/PW van der Poel, H.
Schiweck, T. Schwartz. Berlin: Verlag Dr. Albert Vartens KG.
Wang, Z., Dien, B. S., Rausch, K. D., Tumbleson, M. E., & Singh, V. (2018). Fermentation of undetoxified
sugarcane bagasse hydrolyzates using a two stage hydrothermal and mechanical refining
pretreatment. Bioresource technology, 261, 313-321.
Wu, Y., Zhang, J., Yuan, J., Geng, S., & Zhang, H. (2016). Study of decision framework of offshore wind
power station site selection based on ELECTRE-III under intuitionistic fuzzy environment: A case of
China. Energy Conversion and Management, 113, 66-81.
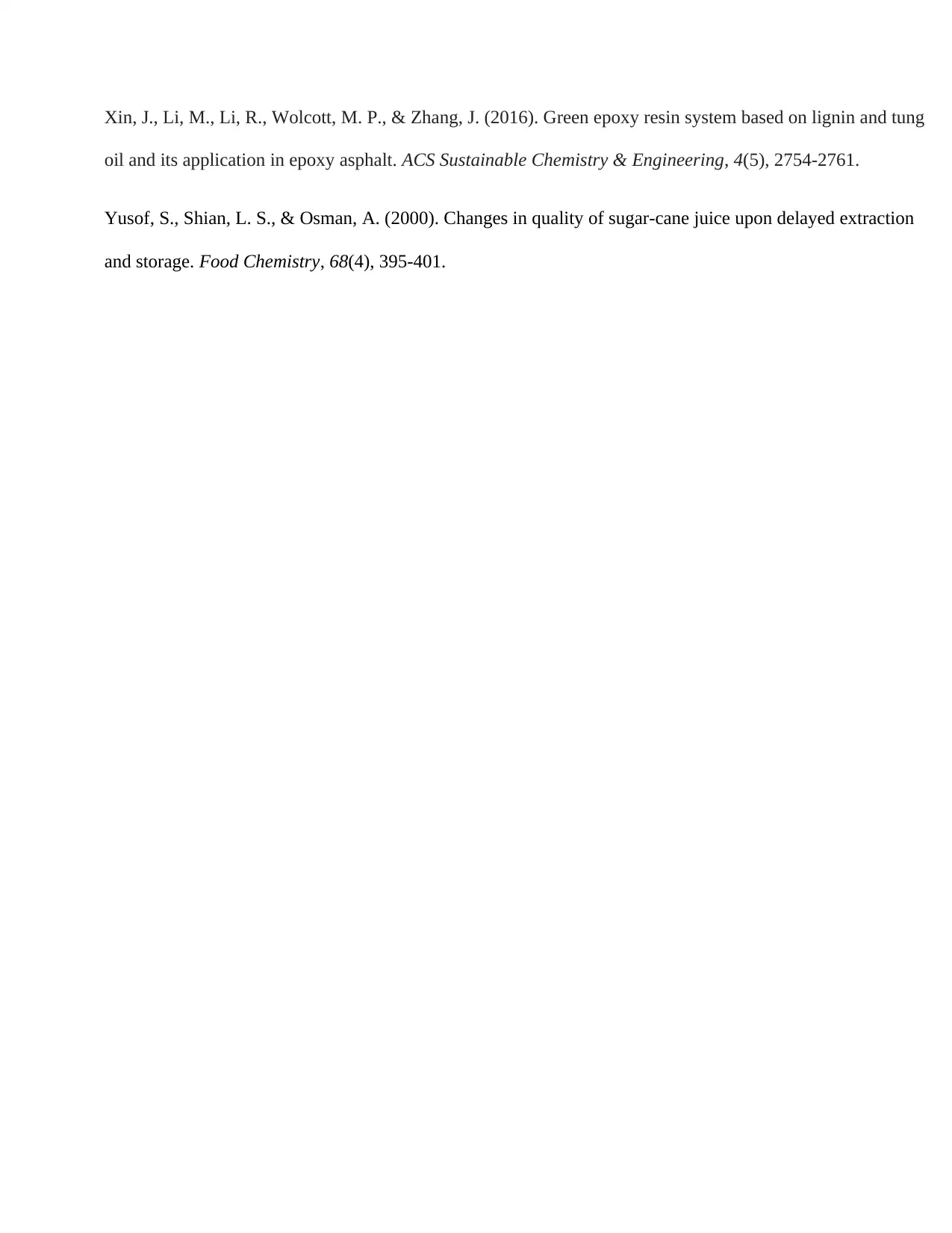
Xin, J., Li, M., Li, R., Wolcott, M. P., & Zhang, J. (2016). Green epoxy resin system based on lignin and tung
oil and its application in epoxy asphalt. ACS Sustainable Chemistry & Engineering, 4(5), 2754-2761.
Yusof, S., Shian, L. S., & Osman, A. (2000). Changes in quality of sugar-cane juice upon delayed extraction
and storage. Food Chemistry, 68(4), 395-401.
oil and its application in epoxy asphalt. ACS Sustainable Chemistry & Engineering, 4(5), 2754-2761.
Yusof, S., Shian, L. S., & Osman, A. (2000). Changes in quality of sugar-cane juice upon delayed extraction
and storage. Food Chemistry, 68(4), 395-401.
Secure Best Marks with AI Grader
Need help grading? Try our AI Grader for instant feedback on your assignments.
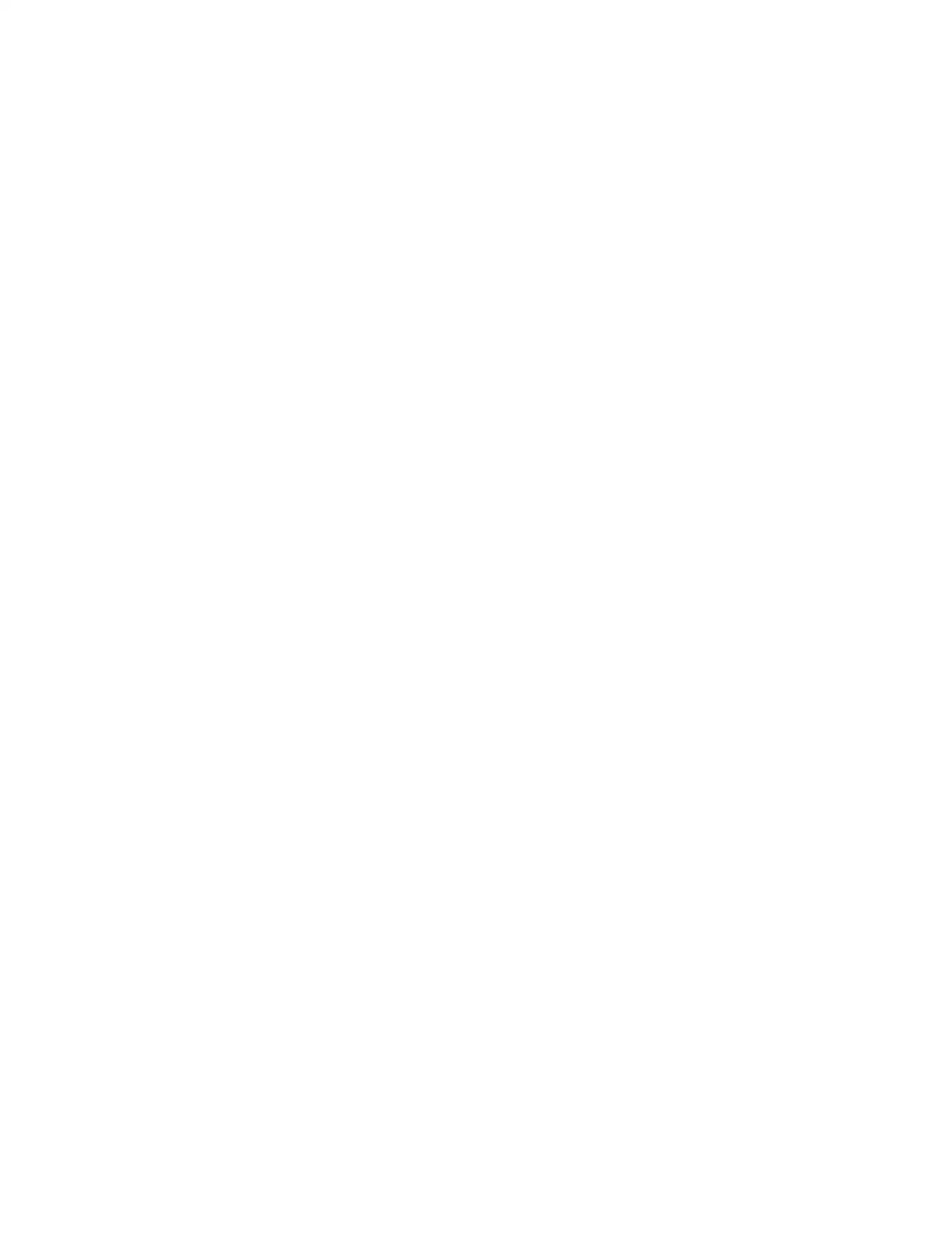
1 out of 29

Your All-in-One AI-Powered Toolkit for Academic Success.
+13062052269
info@desklib.com
Available 24*7 on WhatsApp / Email
Unlock your academic potential
© 2024 | Zucol Services PVT LTD | All rights reserved.