DELL EMC Six Sigma Project: Optimizing Electronic Device Production
VerifiedAdded on 2023/06/15
|13
|3277
|128
Project
AI Summary
This project report details the application of the Six Sigma DMAIC (Define, Measure, Analyze, Improve, Control) methodology to improve the electronic device production processes at DELL EMC. The project identifies key issues such as excessive stocking, communication overhead, and errors in assembly and testing. The DMAIC approach is used to define the problems, measure current performance, analyze root causes, propose and test improvements, and implement changes for long-term sustainability. The objectives include minimizing operator errors, eliminating unnecessary stocking, and reducing processing time. The report outlines the tools and techniques used in each phase of DMAIC, such as project charters, process maps, Pareto charts, and fishbone diagrams, to achieve increased performance and efficiency in DELL EMC's operations. Desklib offers a range of similar solved assignments and past papers for students.

Running head: SIX SIGMA PROJECT
Six Sigma Project
[Name of the Student]
[Name of the University]
[Author note]
Six Sigma Project
[Name of the Student]
[Name of the University]
[Author note]
Secure Best Marks with AI Grader
Need help grading? Try our AI Grader for instant feedback on your assignments.

2SIX SIGMA PROJECT
Executive Summery
DELL EMC is associated with providing a range of products and services to different
companies so as to help them in creating their digital infrastructure. This services and
products generally includes the servers, storage and cybersecurity technologies along with
providing a consulting service for the purpose of planning and building the digital capabilities
for the private, public, hybrid clouds and mobile applications. This report mainly discusses
about the use of the DMAIC (Define, Measure, Analysis, Improvement and Control) method
for the purpose of looking into the various process of DELL EMC along with improving the
various processes. There are various steps which are involved in the processing of the
electronic devices and needs to be rested as with creates lots of excess work along with being
the main reason for people’s mistake due to excess amount of communication. Many units in
the assembly and testing server also needs to be rested due to failure of tests leading to
mistakes of the people.
Executive Summery
DELL EMC is associated with providing a range of products and services to different
companies so as to help them in creating their digital infrastructure. This services and
products generally includes the servers, storage and cybersecurity technologies along with
providing a consulting service for the purpose of planning and building the digital capabilities
for the private, public, hybrid clouds and mobile applications. This report mainly discusses
about the use of the DMAIC (Define, Measure, Analysis, Improvement and Control) method
for the purpose of looking into the various process of DELL EMC along with improving the
various processes. There are various steps which are involved in the processing of the
electronic devices and needs to be rested as with creates lots of excess work along with being
the main reason for people’s mistake due to excess amount of communication. Many units in
the assembly and testing server also needs to be rested due to failure of tests leading to
mistakes of the people.

3SIX SIGMA PROJECT
Table of Contents
1. Background and Objective:....................................................................................................4
1.1. Introduction:....................................................................................................................4
1.2. Project Objective:............................................................................................................5
2. Methods:.................................................................................................................................6
2.1. Methods:..........................................................................................................................6
3. Results:...................................................................................................................................9
4. Conclusion:..........................................................................................................................10
5. Value Stream Mapping:.......................................................................................................10
6. Contribution of the Student:.................................................................................................11
6.1. Team..............................................................................................................................11
Project Sponsor................................................................................................................11
Project Leader..................................................................................................................11
Team Members.................................................................................................................11
7. References:...........................................................................................................................12
Table of Contents
1. Background and Objective:....................................................................................................4
1.1. Introduction:....................................................................................................................4
1.2. Project Objective:............................................................................................................5
2. Methods:.................................................................................................................................6
2.1. Methods:..........................................................................................................................6
3. Results:...................................................................................................................................9
4. Conclusion:..........................................................................................................................10
5. Value Stream Mapping:.......................................................................................................10
6. Contribution of the Student:.................................................................................................11
6.1. Team..............................................................................................................................11
Project Sponsor................................................................................................................11
Project Leader..................................................................................................................11
Team Members.................................................................................................................11
7. References:...........................................................................................................................12

4SIX SIGMA PROJECT
1. Background and Objective:
1.1. Introduction:
The digital infrastructure of DELL EMC is created by the wide range of products and
services provided by this company. The company DELL provides various offers and this
mainly includes the servers, storage and technologies related to Cybercrime. Besides all this
the company is also associated with providing of various consulting services related to
planning and building of digital capabilities for the private, public and hybrid clouds and
mobile applications.
DELL EMC was established in August, 1979 in Massachusetts. A manufacturing
plant was opened in April, 1988 in Cork. The DELL EMC is mainly associated with the
manufacturing of software and systems for the purpose of information management and
storage (dell.com, 2018). Despite all this there is a profound impact on the IT industry
because of this company for a while, during making of the enterprise data big along with the
exclusive focus on the developing and selling data storage associated with data management
hardware and software.
Wide range of enterprise product is produced by the DELL EMC and this also
includes the hard disk arrays as well as the storage management software. The flagship
product of DELL, The Symmetrix was the foundation of the storage network in numerous
data centres which are large in size (dell.com, 2018). The main vision of DELL is to be the
provider of a variety of superior quality innovative products and services to the customers.
Working in the system for the purpose of processing the electronic devices products it
can be understood that there are lots of step involved in the process of adding value to the
processes. But along with this it also creates a lot of work, needs an excess communication
1. Background and Objective:
1.1. Introduction:
The digital infrastructure of DELL EMC is created by the wide range of products and
services provided by this company. The company DELL provides various offers and this
mainly includes the servers, storage and technologies related to Cybercrime. Besides all this
the company is also associated with providing of various consulting services related to
planning and building of digital capabilities for the private, public and hybrid clouds and
mobile applications.
DELL EMC was established in August, 1979 in Massachusetts. A manufacturing
plant was opened in April, 1988 in Cork. The DELL EMC is mainly associated with the
manufacturing of software and systems for the purpose of information management and
storage (dell.com, 2018). Despite all this there is a profound impact on the IT industry
because of this company for a while, during making of the enterprise data big along with the
exclusive focus on the developing and selling data storage associated with data management
hardware and software.
Wide range of enterprise product is produced by the DELL EMC and this also
includes the hard disk arrays as well as the storage management software. The flagship
product of DELL, The Symmetrix was the foundation of the storage network in numerous
data centres which are large in size (dell.com, 2018). The main vision of DELL is to be the
provider of a variety of superior quality innovative products and services to the customers.
Working in the system for the purpose of processing the electronic devices products it
can be understood that there are lots of step involved in the process of adding value to the
processes. But along with this it also creates a lot of work, needs an excess communication
Secure Best Marks with AI Grader
Need help grading? Try our AI Grader for instant feedback on your assignments.

5SIX SIGMA PROJECT
and this initially leads to mistakes of the people. According to our point of view all this steps
are not necessary as per the regulations.
The DPE department of DELL is associated with the dealing of assembly along with
the testing servers. It has been noticed that there are too many units which needs to be shut
down because of failure in the tests which ultimately results in the mistakes of the people.
There is also lack of clear instructions results in the excess communication between the Test
Technician and the Software Engineers.
The main objective of this project includes the improvement of the flow of electronic
device through the assembly, assembly verification test, basic configuration test, configure to
order, and final test processing after identification of all the essential requirements along with
the minimization of the wastes that are produced during the process. DMAIC method is used
for the purpose of accommodating which will be ultimately help in the orderly progress by
this improvement project (Kumaravadivel & Natarajan, 2013).
1.2. Project Objective:
Reducing of waste along with the establishment of an efficient process so as to meet
the requirements of the customer as well as the regulatory body. This is to be done for the
purpose of processing the electronic devices. The main objectives of the project include the
following:
The minimization of the risks due to the mistakes done by the operators or the
technicians during the process by 90%
Elimination of stocking the good and only build products according to the order
Reduce the time for processing by 15% to 25 %.
and this initially leads to mistakes of the people. According to our point of view all this steps
are not necessary as per the regulations.
The DPE department of DELL is associated with the dealing of assembly along with
the testing servers. It has been noticed that there are too many units which needs to be shut
down because of failure in the tests which ultimately results in the mistakes of the people.
There is also lack of clear instructions results in the excess communication between the Test
Technician and the Software Engineers.
The main objective of this project includes the improvement of the flow of electronic
device through the assembly, assembly verification test, basic configuration test, configure to
order, and final test processing after identification of all the essential requirements along with
the minimization of the wastes that are produced during the process. DMAIC method is used
for the purpose of accommodating which will be ultimately help in the orderly progress by
this improvement project (Kumaravadivel & Natarajan, 2013).
1.2. Project Objective:
Reducing of waste along with the establishment of an efficient process so as to meet
the requirements of the customer as well as the regulatory body. This is to be done for the
purpose of processing the electronic devices. The main objectives of the project include the
following:
The minimization of the risks due to the mistakes done by the operators or the
technicians during the process by 90%
Elimination of stocking the good and only build products according to the order
Reduce the time for processing by 15% to 25 %.

6SIX SIGMA PROJECT
2. Methods:
2.1. Methods:
Method is any specific procedure or technique that helps in the successful
accomplishment of anything. The method, which should be utilized for the purpose of
completing this project is DMAIC. This is eventually a fundamental part of the initiative of
Six Sigma and is implemented as the improvement process for all other processes. DMAIC
can be solely defined as a data driven strategy that helps to improvise the processes. The full
form of DMAIC is as follows:
i. Define Phase: The main problems of this project are excessive stocking goods,
excess utilization of e communication, various errors within the tests or assembly and lacking
of perfect procedure instruction. This particular phase is extremely important for any project
as it helps to define the problems properly (Antony et al., 2012). Dell EMC is suffering as the
users are not using the software and hardware resources wisely. The management staffs of
Dell EMC, the test technicians and the software engineers are also responsible for the
products’ failures. They do not exchange hardware and software related data appropriately
for this reason the products are currently having several issues (Jirasukprasert et al., 2014).
There are various tools that are utilized in this definition phase. Project Charter, Project Tools
and the Process Maps will help to define the project deliverables that will help Dell EMC to
know the issues in details.
Project Charter: It is a document, which comprises of the entire definition of six-
sigma project. The project charter moreover gives one reference for knowing
about the project. The major fields of this particular tool mainly includes project
title, project leader, project goals, cost of poor quality, process problem, voice of
client and many more.
2. Methods:
2.1. Methods:
Method is any specific procedure or technique that helps in the successful
accomplishment of anything. The method, which should be utilized for the purpose of
completing this project is DMAIC. This is eventually a fundamental part of the initiative of
Six Sigma and is implemented as the improvement process for all other processes. DMAIC
can be solely defined as a data driven strategy that helps to improvise the processes. The full
form of DMAIC is as follows:
i. Define Phase: The main problems of this project are excessive stocking goods,
excess utilization of e communication, various errors within the tests or assembly and lacking
of perfect procedure instruction. This particular phase is extremely important for any project
as it helps to define the problems properly (Antony et al., 2012). Dell EMC is suffering as the
users are not using the software and hardware resources wisely. The management staffs of
Dell EMC, the test technicians and the software engineers are also responsible for the
products’ failures. They do not exchange hardware and software related data appropriately
for this reason the products are currently having several issues (Jirasukprasert et al., 2014).
There are various tools that are utilized in this definition phase. Project Charter, Project Tools
and the Process Maps will help to define the project deliverables that will help Dell EMC to
know the issues in details.
Project Charter: It is a document, which comprises of the entire definition of six-
sigma project. The project charter moreover gives one reference for knowing
about the project. The major fields of this particular tool mainly includes project
title, project leader, project goals, cost of poor quality, process problem, voice of
client and many more.

7SIX SIGMA PROJECT
Project Plan: The project plan of definition stage is nothing but a formal
document that solely defines about the schedule of the achievement of project
objectives. Most of the time it is a type of Gantt chart, showing all the milestones
or activities of the project. it helps to identify the work breakdown structure tasks,
various dependencies and task relationships.
Process Maps: It is a specific visual representation of the procedure of the
movement of any product or service by a process. There are three types of process
maps, which include SIPOC, process flowcharts and functional deployment
diagrams. The full form of SIPOC is supplier, input, process, output and customer.
It is high level process map that is utilized for the successful establishment of
project boundaries and scope (Kaushik et al., 2012). The second type is the
process flowchart. It enables the entire team of project for watching whether the
flow is logical or not. Moreover, it even allows to identify the project delays. The
third type of process map is the functional deployment diagram. It is a flowchart
that helps to represent various departments.
ii. Measure Phase: In the measure phase, all the current project procedures are
documented. The baseline performance is analysed in this phase. Dell EMC in this step can
accumulate data from several sources to determine metrics type and defects underlying within
the project (Gijo & Scaria, 2014). Dell EMC can assess the risks aroused by human errors.
The key tools that can help Dell EMC to acknowledge the risks associated with the project
are Pareto charts, Gage R & R, process flowcharts and trend charts.
Drafting of
project
characters
Define Character of
the project
Measure
Process Map
Data Analysis
Project Plan: The project plan of definition stage is nothing but a formal
document that solely defines about the schedule of the achievement of project
objectives. Most of the time it is a type of Gantt chart, showing all the milestones
or activities of the project. it helps to identify the work breakdown structure tasks,
various dependencies and task relationships.
Process Maps: It is a specific visual representation of the procedure of the
movement of any product or service by a process. There are three types of process
maps, which include SIPOC, process flowcharts and functional deployment
diagrams. The full form of SIPOC is supplier, input, process, output and customer.
It is high level process map that is utilized for the successful establishment of
project boundaries and scope (Kaushik et al., 2012). The second type is the
process flowchart. It enables the entire team of project for watching whether the
flow is logical or not. Moreover, it even allows to identify the project delays. The
third type of process map is the functional deployment diagram. It is a flowchart
that helps to represent various departments.
ii. Measure Phase: In the measure phase, all the current project procedures are
documented. The baseline performance is analysed in this phase. Dell EMC in this step can
accumulate data from several sources to determine metrics type and defects underlying within
the project (Gijo & Scaria, 2014). Dell EMC can assess the risks aroused by human errors.
The key tools that can help Dell EMC to acknowledge the risks associated with the project
are Pareto charts, Gage R & R, process flowcharts and trend charts.
Drafting of
project
characters
Define Character of
the project
Measure
Process Map
Data Analysis
Paraphrase This Document
Need a fresh take? Get an instant paraphrase of this document with our AI Paraphraser

8SIX SIGMA PROJECT
iii. Analyse phase: The analyse phase helps in analysing and isolating the top causes
behind CTQ (Critical-to-Quality Characteristic). Dell EMC can assess the top issues behind
their project failures in this phase (De Mast & Lokkerbol, 2012). Dell EMC is struggling as
their customers are mishandling the hardware and software resources. Also lack of
collaboration between the test technician and the software engineers lead to failure of
hardware and software units. Dell EMC in analyse phase can know the gaps between the
current project performance and the goal performance (Pyzdek & Keller, 2014). This phase
gives priority to the improvement opportunities. Like all other phases, the analyse phase
consists of tools- Multi-Vary analysis, Pareto chart and fishbone diagrams.
iv. Improve phase: This phase is the fourth phase of DMAIC. The improve phase
focuses on the causes in details. The causes are addressed and defined in the analyse phase.
The improve phase is intended to mitigate the causes or control the causes. The improve
phase can help Dell EMC in achieving desired breakthrough performance (Timans et al.,
2012). In the improve phase, the project team of Dell EMC can design creative as well as
innovative solutions. The creative solutions can assist Dell EMC in preventing all the
problems associated with the units (Ghosh & Maiti, 2014). The hardware units and the
software applications are mainly malfunctioning due to the faulty usage of customers. The
test technicians and the software engineers also do not exchange instructions among
themselves, for this reason the projects are failing. A number of flaws are erupting in the
Analysis
Cause and effect
analysis
Root cause analysis
iii. Analyse phase: The analyse phase helps in analysing and isolating the top causes
behind CTQ (Critical-to-Quality Characteristic). Dell EMC can assess the top issues behind
their project failures in this phase (De Mast & Lokkerbol, 2012). Dell EMC is struggling as
their customers are mishandling the hardware and software resources. Also lack of
collaboration between the test technician and the software engineers lead to failure of
hardware and software units. Dell EMC in analyse phase can know the gaps between the
current project performance and the goal performance (Pyzdek & Keller, 2014). This phase
gives priority to the improvement opportunities. Like all other phases, the analyse phase
consists of tools- Multi-Vary analysis, Pareto chart and fishbone diagrams.
iv. Improve phase: This phase is the fourth phase of DMAIC. The improve phase
focuses on the causes in details. The causes are addressed and defined in the analyse phase.
The improve phase is intended to mitigate the causes or control the causes. The improve
phase can help Dell EMC in achieving desired breakthrough performance (Timans et al.,
2012). In the improve phase, the project team of Dell EMC can design creative as well as
innovative solutions. The creative solutions can assist Dell EMC in preventing all the
problems associated with the units (Ghosh & Maiti, 2014). The hardware units and the
software applications are mainly malfunctioning due to the faulty usage of customers. The
test technicians and the software engineers also do not exchange instructions among
themselves, for this reason the projects are failing. A number of flaws are erupting in the
Analysis
Cause and effect
analysis
Root cause analysis

9SIX SIGMA PROJECT
hardware and software resources due to lack of cooperation among the software engineers
and the test technicians (Chaudhary, 2014). The project team of Dell EMC can analyse the
issues, make plans to mitigate all those issues. The project team implements a plan so that the
project can execute successfully. The tools that Dell EMC can use in the improve phase are
regressions analysis, hypothesis testing, Design of Experiments (DOE) and analysis of
variance (ANOVA).
v. Control phase: In the control phase, the project plan is deployed efficiently and
ethically so that the project team can get long lasting results. Dell EMC can assess how the
electronic devices like Assembly, Basic Configuration Test (BCT), Configure To Order
(CTO), Final Test (FT) can help them to meet the business deliverables. All the project
environments need to be considered and must be controlled well (Albliwi, Antony & Lim,
2015). Dell EMC must assess setup process, procedures settings and other related
improvements to successfully accomplish the project. The steps that are taken into
consideration in this phase needs to be accomplished well by Dell EMC (Hassan, 2013). The
project team of Dell EMC will have to make sure that the project procedures do not get revert
back to the ‘old way’ of doing things. Thus, the control phase can assist Dell EMC to gain
productivity and market share.
3. Results:
DMAIC method is often seen as the foundation of the Sig-Sigma project. This method
would be working as the iterative problem solving method for Dell EMC so as to combat the
existing as well as the steady-state processes. The team would be capable of adequately
scoping all the problems along with measuring all the current performances, analysis of the
root causes of the problem and the inefficiencies. The method also recommends the test and
verification processes involved in the improvement of the recommendations, which is
hardware and software resources due to lack of cooperation among the software engineers
and the test technicians (Chaudhary, 2014). The project team of Dell EMC can analyse the
issues, make plans to mitigate all those issues. The project team implements a plan so that the
project can execute successfully. The tools that Dell EMC can use in the improve phase are
regressions analysis, hypothesis testing, Design of Experiments (DOE) and analysis of
variance (ANOVA).
v. Control phase: In the control phase, the project plan is deployed efficiently and
ethically so that the project team can get long lasting results. Dell EMC can assess how the
electronic devices like Assembly, Basic Configuration Test (BCT), Configure To Order
(CTO), Final Test (FT) can help them to meet the business deliverables. All the project
environments need to be considered and must be controlled well (Albliwi, Antony & Lim,
2015). Dell EMC must assess setup process, procedures settings and other related
improvements to successfully accomplish the project. The steps that are taken into
consideration in this phase needs to be accomplished well by Dell EMC (Hassan, 2013). The
project team of Dell EMC will have to make sure that the project procedures do not get revert
back to the ‘old way’ of doing things. Thus, the control phase can assist Dell EMC to gain
productivity and market share.
3. Results:
DMAIC method is often seen as the foundation of the Sig-Sigma project. This method
would be working as the iterative problem solving method for Dell EMC so as to combat the
existing as well as the steady-state processes. The team would be capable of adequately
scoping all the problems along with measuring all the current performances, analysis of the
root causes of the problem and the inefficiencies. The method also recommends the test and
verification processes involved in the improvement of the recommendations, which is

10SIX SIGMA PROJECT
initially followed by the implementation of the changes for sustainability on a long-term
basis. A much better clarity would be achieved on completion of each step of the DMAIC
process. The DMAIC process would greatly help in increased performance of the process
along with better efficiency.
4. Conclusion:
The report helps in concluding to the fact that by use of the DMAIC method DELL
EMC can greatly improve all its processes. The different stems involved in the DMAIC
process will help the organisation in identifying the various area where there is a need of
improvement. Better methods are to be adopted so as to decrease the mistakes due to excess
communication. After identification of this areas the process will greatly help DELL EMC in
improving its flow of the electronic devices through the assembly, assembly verification test,
basic configuration test, configuration according to the order, and lastly the final testing
process. The DMAIC method will help DELL EMC in identifying all the key problems like
the mistakes done by peoples, unnecessary steps and many more. This method would then
analyse the problem thoroughly which would be followed by the improvement phase and
lastly the control phase in which the improvements are implemented.
5. Value Stream Mapping:
initially followed by the implementation of the changes for sustainability on a long-term
basis. A much better clarity would be achieved on completion of each step of the DMAIC
process. The DMAIC process would greatly help in increased performance of the process
along with better efficiency.
4. Conclusion:
The report helps in concluding to the fact that by use of the DMAIC method DELL
EMC can greatly improve all its processes. The different stems involved in the DMAIC
process will help the organisation in identifying the various area where there is a need of
improvement. Better methods are to be adopted so as to decrease the mistakes due to excess
communication. After identification of this areas the process will greatly help DELL EMC in
improving its flow of the electronic devices through the assembly, assembly verification test,
basic configuration test, configuration according to the order, and lastly the final testing
process. The DMAIC method will help DELL EMC in identifying all the key problems like
the mistakes done by peoples, unnecessary steps and many more. This method would then
analyse the problem thoroughly which would be followed by the improvement phase and
lastly the control phase in which the improvements are implemented.
5. Value Stream Mapping:
Secure Best Marks with AI Grader
Need help grading? Try our AI Grader for instant feedback on your assignments.
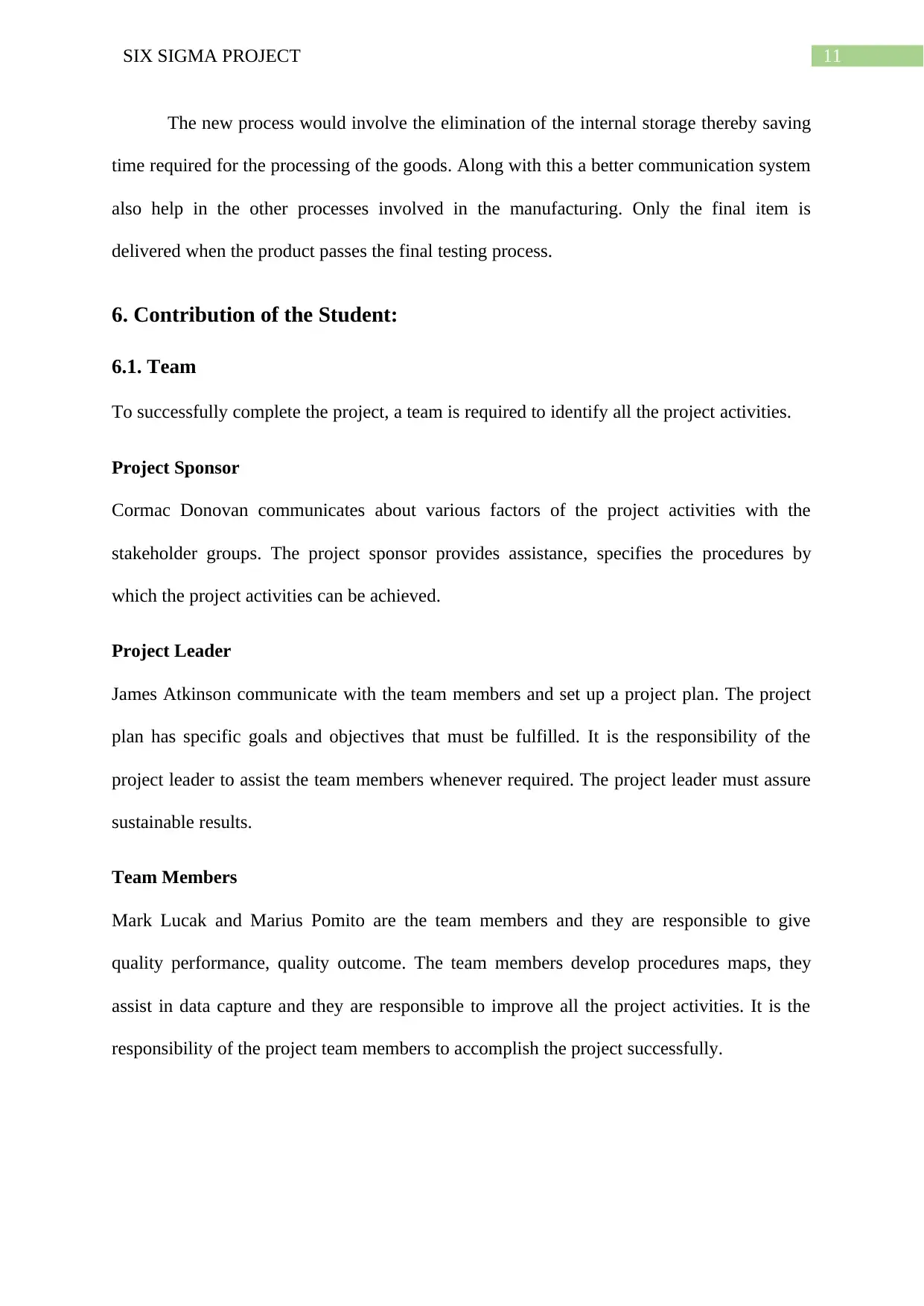
11SIX SIGMA PROJECT
The new process would involve the elimination of the internal storage thereby saving
time required for the processing of the goods. Along with this a better communication system
also help in the other processes involved in the manufacturing. Only the final item is
delivered when the product passes the final testing process.
6. Contribution of the Student:
6.1. Team
To successfully complete the project, a team is required to identify all the project activities.
Project Sponsor
Cormac Donovan communicates about various factors of the project activities with the
stakeholder groups. The project sponsor provides assistance, specifies the procedures by
which the project activities can be achieved.
Project Leader
James Atkinson communicate with the team members and set up a project plan. The project
plan has specific goals and objectives that must be fulfilled. It is the responsibility of the
project leader to assist the team members whenever required. The project leader must assure
sustainable results.
Team Members
Mark Lucak and Marius Pomito are the team members and they are responsible to give
quality performance, quality outcome. The team members develop procedures maps, they
assist in data capture and they are responsible to improve all the project activities. It is the
responsibility of the project team members to accomplish the project successfully.
The new process would involve the elimination of the internal storage thereby saving
time required for the processing of the goods. Along with this a better communication system
also help in the other processes involved in the manufacturing. Only the final item is
delivered when the product passes the final testing process.
6. Contribution of the Student:
6.1. Team
To successfully complete the project, a team is required to identify all the project activities.
Project Sponsor
Cormac Donovan communicates about various factors of the project activities with the
stakeholder groups. The project sponsor provides assistance, specifies the procedures by
which the project activities can be achieved.
Project Leader
James Atkinson communicate with the team members and set up a project plan. The project
plan has specific goals and objectives that must be fulfilled. It is the responsibility of the
project leader to assist the team members whenever required. The project leader must assure
sustainable results.
Team Members
Mark Lucak and Marius Pomito are the team members and they are responsible to give
quality performance, quality outcome. The team members develop procedures maps, they
assist in data capture and they are responsible to improve all the project activities. It is the
responsibility of the project team members to accomplish the project successfully.

12SIX SIGMA PROJECT
7. References:
Albliwi, S. A., Antony, J., & Lim, S. A. H. (2015). A systematic review of Lean Six
Sigma for the manufacturing industry. Business Process Management
Journal, 21(3), 665-691.
Antony, J., Singh Bhuller, A., Kumar, M., Mendibil, K., & Montgomery, D. C. (2012).
Application of Six Sigma DMAIC methodology in a transactional
environment. International Journal of Quality & Reliability Management, 29(1),
31-53.
Azizi, A. (2015). Evaluation improvement of production productivity performance using
statistical process control, overall equipment efficiency, and autonomous
maintenance. Procedia Manufacturing, 2, 186-190.
Chaudhary, G. (2014). Six Sigma Concepts: a Complete Revolution. International
Journal of Emerging Research in Management &Technology, 3, 82-86.
De Mast, J., & Lokkerbol, J. (2012). An analysis of the Six Sigma DMAIC method from
the perspective of problem solving. International Journal of Production
Economics, 139(2), 604-614.
dell.com. (2018). Dell EMC Services | Dell India. Dell.com. Retrieved 12 February 2018,
from http://www.dell.com/en-in/work/learn/it-support-lifecycle
Ghosh, S., & Maiti, J. (2014). Data mining driven DMAIC framework for improving
foundry quality–a case study. Production Planning & Control, 25(6), 478-493.
Gijo, E. V., & Scaria, J. (2014). Process improvement through Six Sigma with Beta
correction: a case study of manufacturing company. The International Journal of
Advanced Manufacturing Technology, 71(1-4), 717-730.
7. References:
Albliwi, S. A., Antony, J., & Lim, S. A. H. (2015). A systematic review of Lean Six
Sigma for the manufacturing industry. Business Process Management
Journal, 21(3), 665-691.
Antony, J., Singh Bhuller, A., Kumar, M., Mendibil, K., & Montgomery, D. C. (2012).
Application of Six Sigma DMAIC methodology in a transactional
environment. International Journal of Quality & Reliability Management, 29(1),
31-53.
Azizi, A. (2015). Evaluation improvement of production productivity performance using
statistical process control, overall equipment efficiency, and autonomous
maintenance. Procedia Manufacturing, 2, 186-190.
Chaudhary, G. (2014). Six Sigma Concepts: a Complete Revolution. International
Journal of Emerging Research in Management &Technology, 3, 82-86.
De Mast, J., & Lokkerbol, J. (2012). An analysis of the Six Sigma DMAIC method from
the perspective of problem solving. International Journal of Production
Economics, 139(2), 604-614.
dell.com. (2018). Dell EMC Services | Dell India. Dell.com. Retrieved 12 February 2018,
from http://www.dell.com/en-in/work/learn/it-support-lifecycle
Ghosh, S., & Maiti, J. (2014). Data mining driven DMAIC framework for improving
foundry quality–a case study. Production Planning & Control, 25(6), 478-493.
Gijo, E. V., & Scaria, J. (2014). Process improvement through Six Sigma with Beta
correction: a case study of manufacturing company. The International Journal of
Advanced Manufacturing Technology, 71(1-4), 717-730.

13SIX SIGMA PROJECT
Hassan, M. K. (2013). Applying lean six sigma for waste reduction in a manufacturing
environment. American Journal of Industrial Engineering, 1(2), 28-35.
Jirasukprasert, P., Arturo Garza-Reyes, J., Kumar, V., & K. Lim, M. (2014). A Six Sigma
and DMAIC application for the reduction of defects in a rubber gloves
manufacturing process. International Journal of Lean Six Sigma, 5(1), 2-21.
Kaushik, P., Khanduja, D., Mittal, K. and Jaglan, P., 2012. A case study: Application of
Six Sigma methodology in a small and medium-sized manufacturing
enterprise. The TQM Journal, 24(1), pp.4-16.
Kumaravadivel, A., & Natarajan, U. (2013). Application of six-sigma DMAIC
methodology to sand-casting process with response surface methodology. The
International Journal of Advanced Manufacturing Technology, 69(5-8), 1403-
1420.
Pyzdek, T., & Keller, P. A. (2014). The six sigma handbook(Vol. 4). New York:
McGraw-Hill Education.
Timans, W., Antony, J., Ahaus, K., & van Solingen, R. (2012). Implementation of Lean
Six Sigma in small-and medium-sized manufacturing enterprises in the
Netherlands. Journal of the Operational Research Society, 63(3), 339-353.
Hassan, M. K. (2013). Applying lean six sigma for waste reduction in a manufacturing
environment. American Journal of Industrial Engineering, 1(2), 28-35.
Jirasukprasert, P., Arturo Garza-Reyes, J., Kumar, V., & K. Lim, M. (2014). A Six Sigma
and DMAIC application for the reduction of defects in a rubber gloves
manufacturing process. International Journal of Lean Six Sigma, 5(1), 2-21.
Kaushik, P., Khanduja, D., Mittal, K. and Jaglan, P., 2012. A case study: Application of
Six Sigma methodology in a small and medium-sized manufacturing
enterprise. The TQM Journal, 24(1), pp.4-16.
Kumaravadivel, A., & Natarajan, U. (2013). Application of six-sigma DMAIC
methodology to sand-casting process with response surface methodology. The
International Journal of Advanced Manufacturing Technology, 69(5-8), 1403-
1420.
Pyzdek, T., & Keller, P. A. (2014). The six sigma handbook(Vol. 4). New York:
McGraw-Hill Education.
Timans, W., Antony, J., Ahaus, K., & van Solingen, R. (2012). Implementation of Lean
Six Sigma in small-and medium-sized manufacturing enterprises in the
Netherlands. Journal of the Operational Research Society, 63(3), 339-353.
1 out of 13
Related Documents

Your All-in-One AI-Powered Toolkit for Academic Success.
+13062052269
info@desklib.com
Available 24*7 on WhatsApp / Email
Unlock your academic potential
© 2024 | Zucol Services PVT LTD | All rights reserved.