Improving Fleet Organization Spare Parts Operations in New Zealand
VerifiedAdded on 2023/01/10
|14
|4901
|28
Report
AI Summary
This report examines the spare parts operations of a New Zealand-based fleet organization with three locations, which has experienced financial losses due to poor inventory management. The analysis covers the company background, current spare parts operations, and the need for a strategic working plan to improve financial status over three years. The report delves into key areas such as space storage and inventory, effective inventory management, spare part sales performance and tracking, risk assessment, warehouse environment, quality control, and project costing. It provides recommendations for improving current business practices, emphasizing the importance of proper inventory management, skilled personnel, and strategic planning. The report aims to provide a comprehensive overview of the issues and propose effective strategies to enhance the fleet organization's financial performance and streamline its spare parts operations.
Contribute Materials
Your contribution can guide someone’s learning journey. Share your
documents today.
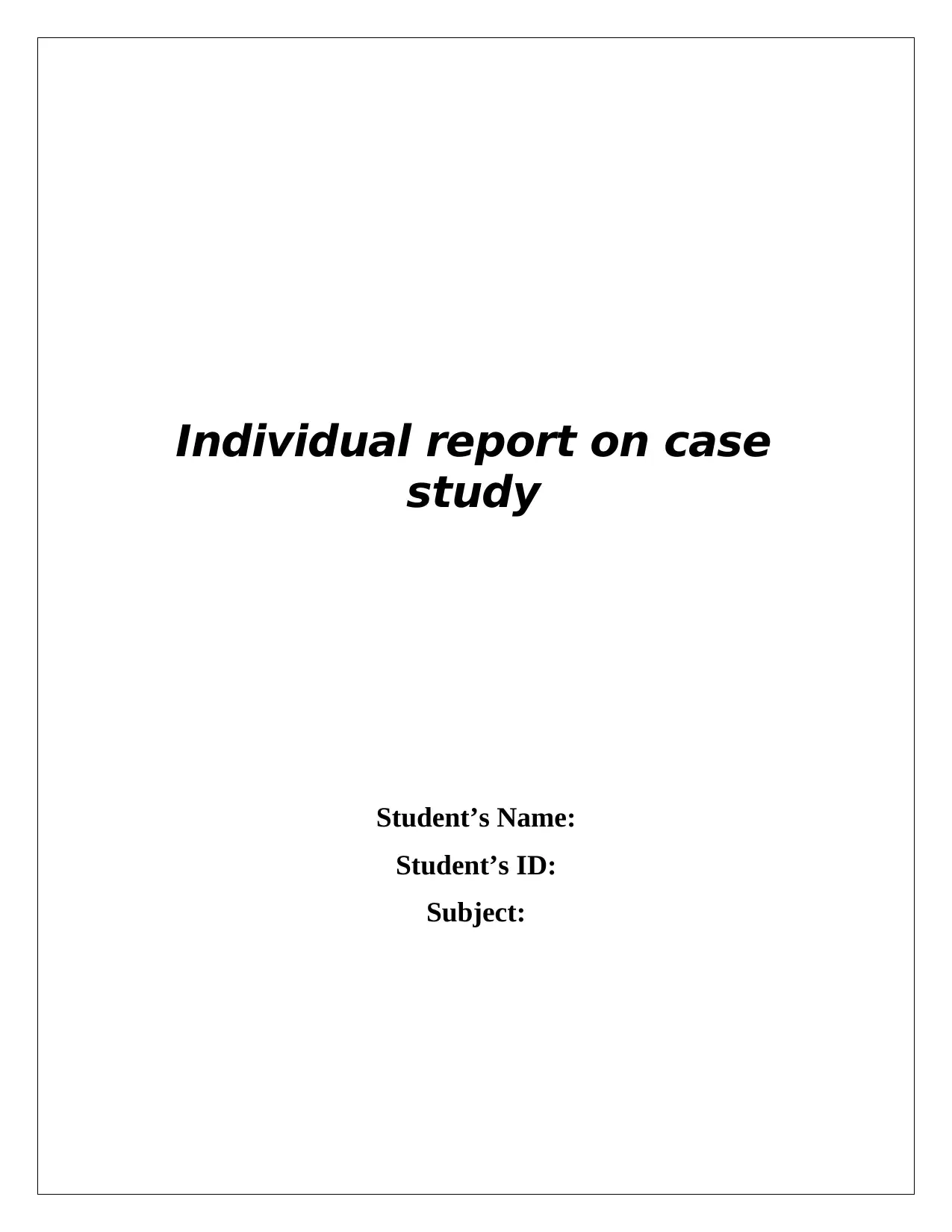
Individual report on case
study
Student’s Name:
Student’s ID:
Subject:
study
Student’s Name:
Student’s ID:
Subject:
Secure Best Marks with AI Grader
Need help grading? Try our AI Grader for instant feedback on your assignments.

1
Table of Contents
Introduction......................................................................................................................................2
Company background and current spare part operations................................................................2
Developing on working plan for the three different locations and demonstrate the improvement
of their financial status.....................................................................................................................3
Space storage and inventory............................................................................................................4
Effective inventory management.....................................................................................................4
Spare part sales performance and tracking......................................................................................5
Risk assessment in spare parts management...................................................................................6
Warehouse environment and physical controls...............................................................................6
Cost of warehousing........................................................................................................................7
Quality control management............................................................................................................8
Effective project costing..................................................................................................................8
Recommendations............................................................................................................................9
Conclusion.......................................................................................................................................9
References......................................................................................................................................10
Table of Contents
Introduction......................................................................................................................................2
Company background and current spare part operations................................................................2
Developing on working plan for the three different locations and demonstrate the improvement
of their financial status.....................................................................................................................3
Space storage and inventory............................................................................................................4
Effective inventory management.....................................................................................................4
Spare part sales performance and tracking......................................................................................5
Risk assessment in spare parts management...................................................................................6
Warehouse environment and physical controls...............................................................................6
Cost of warehousing........................................................................................................................7
Quality control management............................................................................................................8
Effective project costing..................................................................................................................8
Recommendations............................................................................................................................9
Conclusion.......................................................................................................................................9
References......................................................................................................................................10
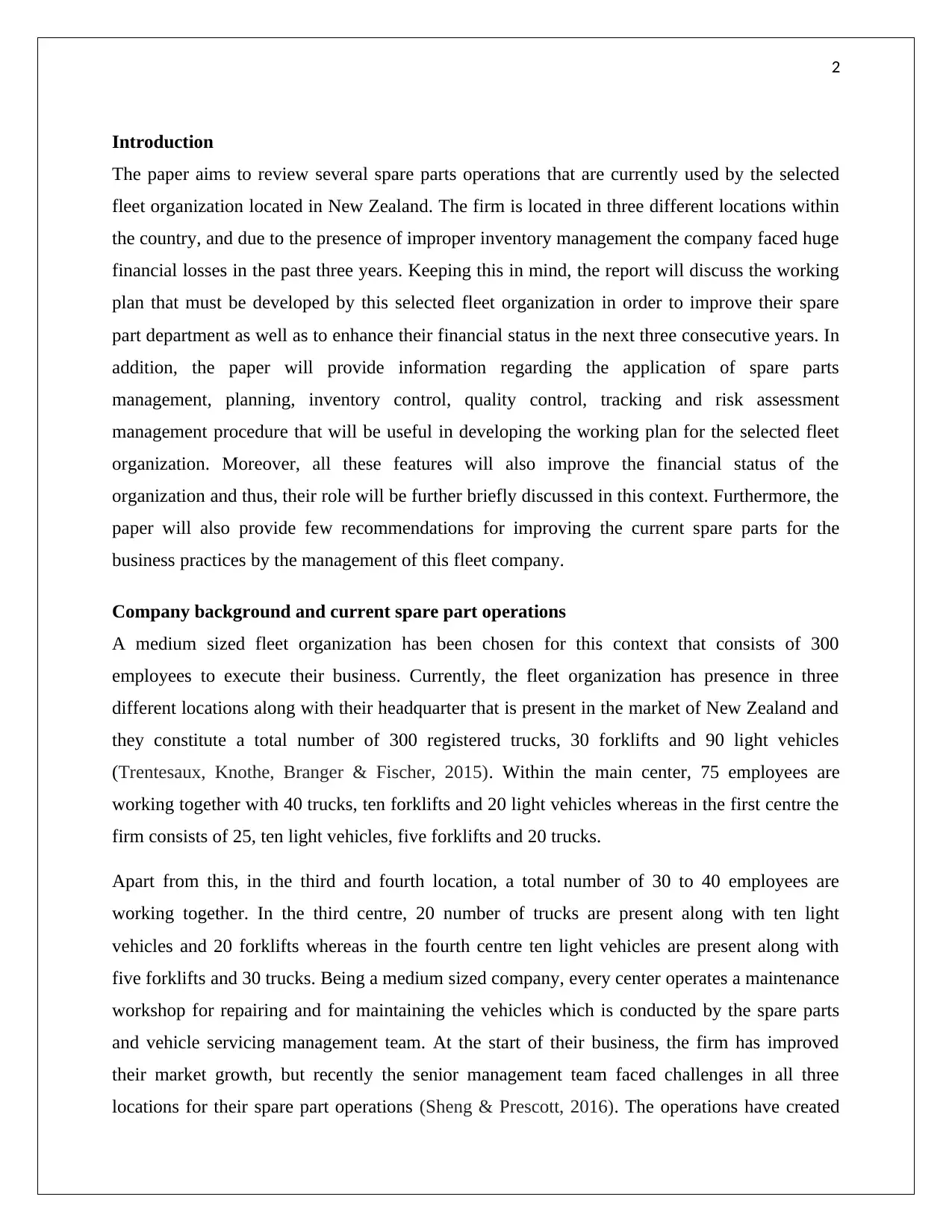
2
Introduction
The paper aims to review several spare parts operations that are currently used by the selected
fleet organization located in New Zealand. The firm is located in three different locations within
the country, and due to the presence of improper inventory management the company faced huge
financial losses in the past three years. Keeping this in mind, the report will discuss the working
plan that must be developed by this selected fleet organization in order to improve their spare
part department as well as to enhance their financial status in the next three consecutive years. In
addition, the paper will provide information regarding the application of spare parts
management, planning, inventory control, quality control, tracking and risk assessment
management procedure that will be useful in developing the working plan for the selected fleet
organization. Moreover, all these features will also improve the financial status of the
organization and thus, their role will be further briefly discussed in this context. Furthermore, the
paper will also provide few recommendations for improving the current spare parts for the
business practices by the management of this fleet company.
Company background and current spare part operations
A medium sized fleet organization has been chosen for this context that consists of 300
employees to execute their business. Currently, the fleet organization has presence in three
different locations along with their headquarter that is present in the market of New Zealand and
they constitute a total number of 300 registered trucks, 30 forklifts and 90 light vehicles
(Trentesaux, Knothe, Branger & Fischer, 2015). Within the main center, 75 employees are
working together with 40 trucks, ten forklifts and 20 light vehicles whereas in the first centre the
firm consists of 25, ten light vehicles, five forklifts and 20 trucks.
Apart from this, in the third and fourth location, a total number of 30 to 40 employees are
working together. In the third centre, 20 number of trucks are present along with ten light
vehicles and 20 forklifts whereas in the fourth centre ten light vehicles are present along with
five forklifts and 30 trucks. Being a medium sized company, every center operates a maintenance
workshop for repairing and for maintaining the vehicles which is conducted by the spare parts
and vehicle servicing management team. At the start of their business, the firm has improved
their market growth, but recently the senior management team faced challenges in all three
locations for their spare part operations (Sheng & Prescott, 2016). The operations have created
Introduction
The paper aims to review several spare parts operations that are currently used by the selected
fleet organization located in New Zealand. The firm is located in three different locations within
the country, and due to the presence of improper inventory management the company faced huge
financial losses in the past three years. Keeping this in mind, the report will discuss the working
plan that must be developed by this selected fleet organization in order to improve their spare
part department as well as to enhance their financial status in the next three consecutive years. In
addition, the paper will provide information regarding the application of spare parts
management, planning, inventory control, quality control, tracking and risk assessment
management procedure that will be useful in developing the working plan for the selected fleet
organization. Moreover, all these features will also improve the financial status of the
organization and thus, their role will be further briefly discussed in this context. Furthermore, the
paper will also provide few recommendations for improving the current spare parts for the
business practices by the management of this fleet company.
Company background and current spare part operations
A medium sized fleet organization has been chosen for this context that consists of 300
employees to execute their business. Currently, the fleet organization has presence in three
different locations along with their headquarter that is present in the market of New Zealand and
they constitute a total number of 300 registered trucks, 30 forklifts and 90 light vehicles
(Trentesaux, Knothe, Branger & Fischer, 2015). Within the main center, 75 employees are
working together with 40 trucks, ten forklifts and 20 light vehicles whereas in the first centre the
firm consists of 25, ten light vehicles, five forklifts and 20 trucks.
Apart from this, in the third and fourth location, a total number of 30 to 40 employees are
working together. In the third centre, 20 number of trucks are present along with ten light
vehicles and 20 forklifts whereas in the fourth centre ten light vehicles are present along with
five forklifts and 30 trucks. Being a medium sized company, every center operates a maintenance
workshop for repairing and for maintaining the vehicles which is conducted by the spare parts
and vehicle servicing management team. At the start of their business, the firm has improved
their market growth, but recently the senior management team faced challenges in all three
locations for their spare part operations (Sheng & Prescott, 2016). The operations have created
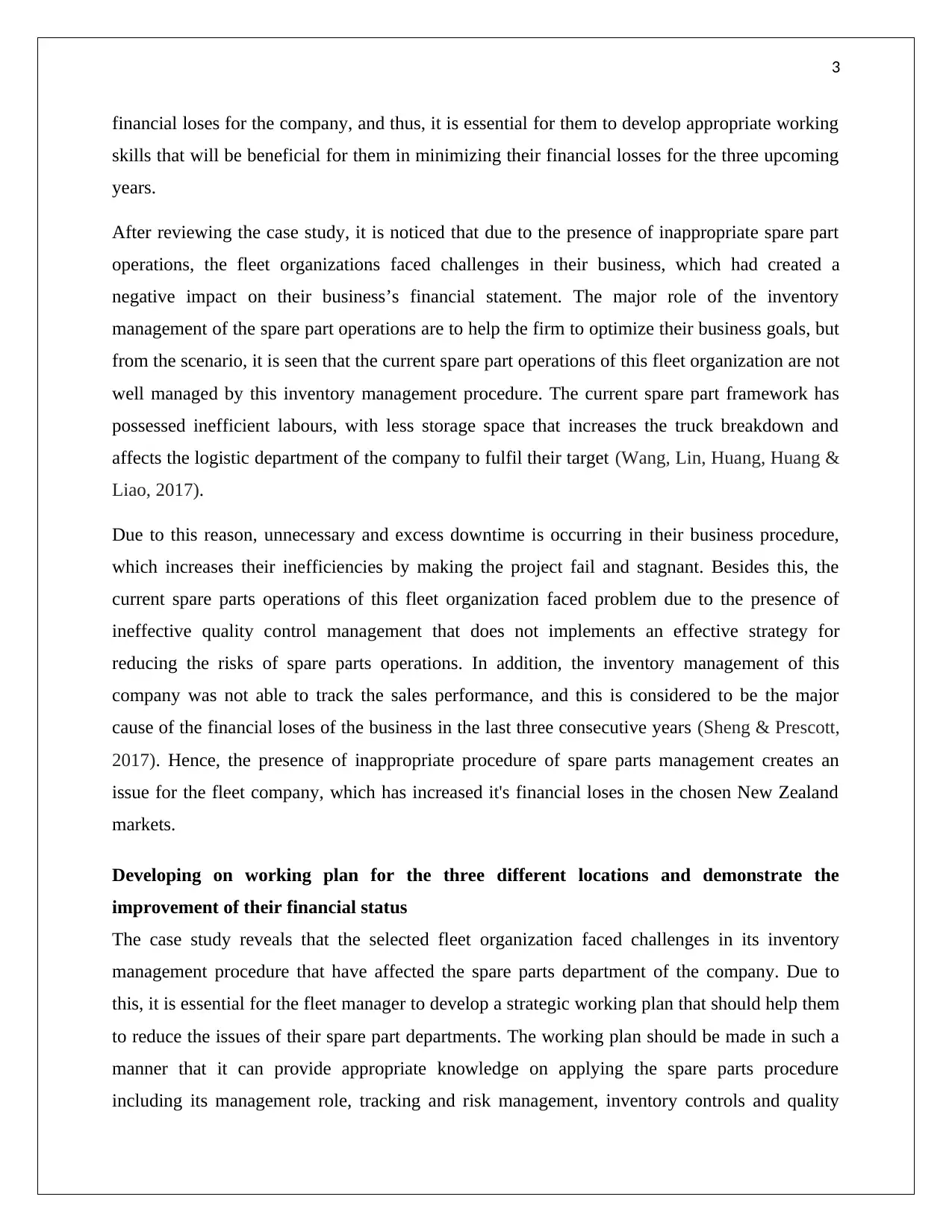
3
financial loses for the company, and thus, it is essential for them to develop appropriate working
skills that will be beneficial for them in minimizing their financial losses for the three upcoming
years.
After reviewing the case study, it is noticed that due to the presence of inappropriate spare part
operations, the fleet organizations faced challenges in their business, which had created a
negative impact on their business’s financial statement. The major role of the inventory
management of the spare part operations are to help the firm to optimize their business goals, but
from the scenario, it is seen that the current spare part operations of this fleet organization are not
well managed by this inventory management procedure. The current spare part framework has
possessed inefficient labours, with less storage space that increases the truck breakdown and
affects the logistic department of the company to fulfil their target (Wang, Lin, Huang, Huang &
Liao, 2017).
Due to this reason, unnecessary and excess downtime is occurring in their business procedure,
which increases their inefficiencies by making the project fail and stagnant. Besides this, the
current spare parts operations of this fleet organization faced problem due to the presence of
ineffective quality control management that does not implements an effective strategy for
reducing the risks of spare parts operations. In addition, the inventory management of this
company was not able to track the sales performance, and this is considered to be the major
cause of the financial loses of the business in the last three consecutive years (Sheng & Prescott,
2017). Hence, the presence of inappropriate procedure of spare parts management creates an
issue for the fleet company, which has increased it's financial loses in the chosen New Zealand
markets.
Developing on working plan for the three different locations and demonstrate the
improvement of their financial status
The case study reveals that the selected fleet organization faced challenges in its inventory
management procedure that have affected the spare parts department of the company. Due to
this, it is essential for the fleet manager to develop a strategic working plan that should help them
to reduce the issues of their spare part departments. The working plan should be made in such a
manner that it can provide appropriate knowledge on applying the spare parts procedure
including its management role, tracking and risk management, inventory controls and quality
financial loses for the company, and thus, it is essential for them to develop appropriate working
skills that will be beneficial for them in minimizing their financial losses for the three upcoming
years.
After reviewing the case study, it is noticed that due to the presence of inappropriate spare part
operations, the fleet organizations faced challenges in their business, which had created a
negative impact on their business’s financial statement. The major role of the inventory
management of the spare part operations are to help the firm to optimize their business goals, but
from the scenario, it is seen that the current spare part operations of this fleet organization are not
well managed by this inventory management procedure. The current spare part framework has
possessed inefficient labours, with less storage space that increases the truck breakdown and
affects the logistic department of the company to fulfil their target (Wang, Lin, Huang, Huang &
Liao, 2017).
Due to this reason, unnecessary and excess downtime is occurring in their business procedure,
which increases their inefficiencies by making the project fail and stagnant. Besides this, the
current spare parts operations of this fleet organization faced problem due to the presence of
ineffective quality control management that does not implements an effective strategy for
reducing the risks of spare parts operations. In addition, the inventory management of this
company was not able to track the sales performance, and this is considered to be the major
cause of the financial loses of the business in the last three consecutive years (Sheng & Prescott,
2017). Hence, the presence of inappropriate procedure of spare parts management creates an
issue for the fleet company, which has increased it's financial loses in the chosen New Zealand
markets.
Developing on working plan for the three different locations and demonstrate the
improvement of their financial status
The case study reveals that the selected fleet organization faced challenges in its inventory
management procedure that have affected the spare parts department of the company. Due to
this, it is essential for the fleet manager to develop a strategic working plan that should help them
to reduce the issues of their spare part departments. The working plan should be made in such a
manner that it can provide appropriate knowledge on applying the spare parts procedure
including its management role, tracking and risk management, inventory controls and quality
Secure Best Marks with AI Grader
Need help grading? Try our AI Grader for instant feedback on your assignments.
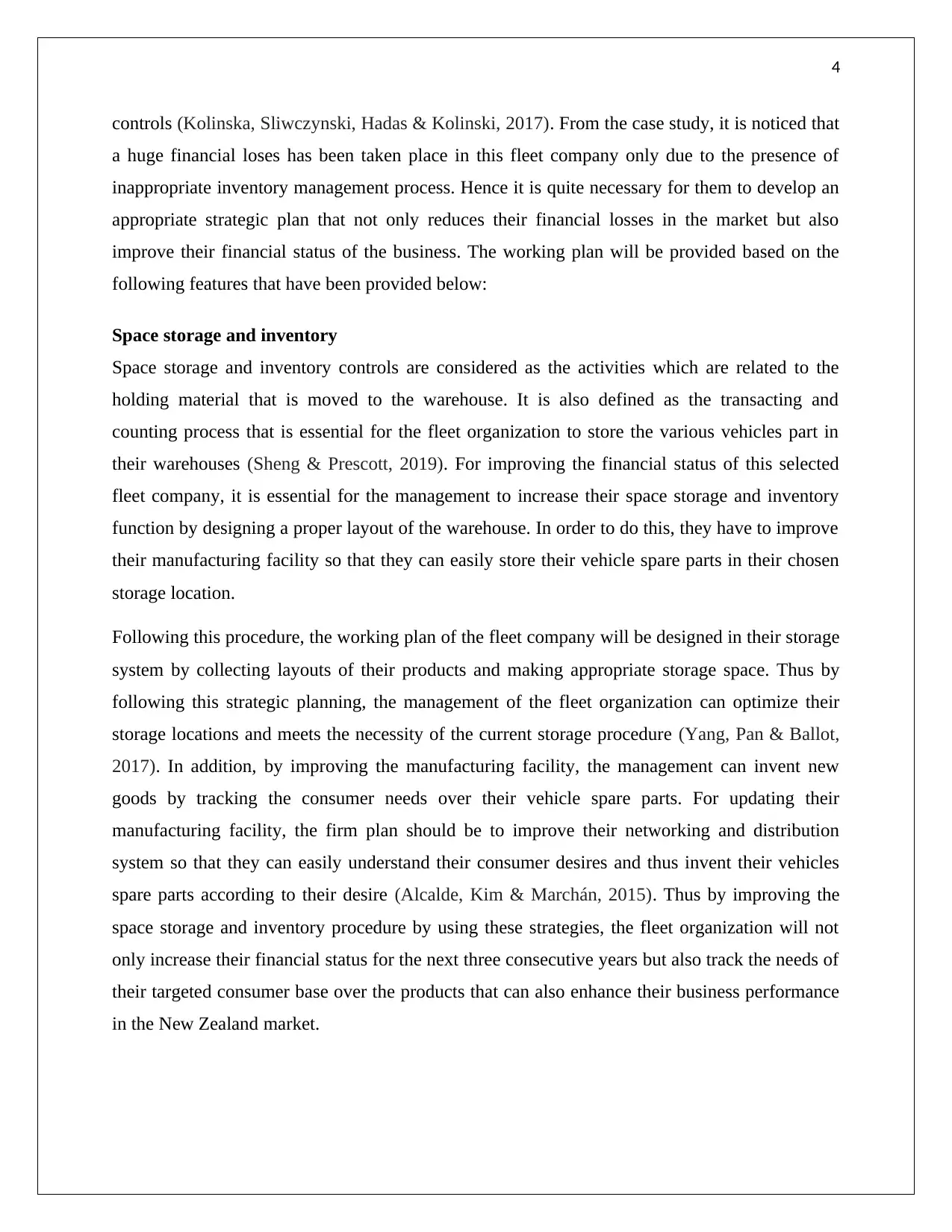
4
controls (Kolinska, Sliwczynski, Hadas & Kolinski, 2017). From the case study, it is noticed that
a huge financial loses has been taken place in this fleet company only due to the presence of
inappropriate inventory management process. Hence it is quite necessary for them to develop an
appropriate strategic plan that not only reduces their financial losses in the market but also
improve their financial status of the business. The working plan will be provided based on the
following features that have been provided below:
Space storage and inventory
Space storage and inventory controls are considered as the activities which are related to the
holding material that is moved to the warehouse. It is also defined as the transacting and
counting process that is essential for the fleet organization to store the various vehicles part in
their warehouses (Sheng & Prescott, 2019). For improving the financial status of this selected
fleet company, it is essential for the management to increase their space storage and inventory
function by designing a proper layout of the warehouse. In order to do this, they have to improve
their manufacturing facility so that they can easily store their vehicle spare parts in their chosen
storage location.
Following this procedure, the working plan of the fleet company will be designed in their storage
system by collecting layouts of their products and making appropriate storage space. Thus by
following this strategic planning, the management of the fleet organization can optimize their
storage locations and meets the necessity of the current storage procedure (Yang, Pan & Ballot,
2017). In addition, by improving the manufacturing facility, the management can invent new
goods by tracking the consumer needs over their vehicle spare parts. For updating their
manufacturing facility, the firm plan should be to improve their networking and distribution
system so that they can easily understand their consumer desires and thus invent their vehicles
spare parts according to their desire (Alcalde, Kim & Marchán, 2015). Thus by improving the
space storage and inventory procedure by using these strategies, the fleet organization will not
only increase their financial status for the next three consecutive years but also track the needs of
their targeted consumer base over the products that can also enhance their business performance
in the New Zealand market.
controls (Kolinska, Sliwczynski, Hadas & Kolinski, 2017). From the case study, it is noticed that
a huge financial loses has been taken place in this fleet company only due to the presence of
inappropriate inventory management process. Hence it is quite necessary for them to develop an
appropriate strategic plan that not only reduces their financial losses in the market but also
improve their financial status of the business. The working plan will be provided based on the
following features that have been provided below:
Space storage and inventory
Space storage and inventory controls are considered as the activities which are related to the
holding material that is moved to the warehouse. It is also defined as the transacting and
counting process that is essential for the fleet organization to store the various vehicles part in
their warehouses (Sheng & Prescott, 2019). For improving the financial status of this selected
fleet company, it is essential for the management to increase their space storage and inventory
function by designing a proper layout of the warehouse. In order to do this, they have to improve
their manufacturing facility so that they can easily store their vehicle spare parts in their chosen
storage location.
Following this procedure, the working plan of the fleet company will be designed in their storage
system by collecting layouts of their products and making appropriate storage space. Thus by
following this strategic planning, the management of the fleet organization can optimize their
storage locations and meets the necessity of the current storage procedure (Yang, Pan & Ballot,
2017). In addition, by improving the manufacturing facility, the management can invent new
goods by tracking the consumer needs over their vehicle spare parts. For updating their
manufacturing facility, the firm plan should be to improve their networking and distribution
system so that they can easily understand their consumer desires and thus invent their vehicles
spare parts according to their desire (Alcalde, Kim & Marchán, 2015). Thus by improving the
space storage and inventory procedure by using these strategies, the fleet organization will not
only increase their financial status for the next three consecutive years but also track the needs of
their targeted consumer base over the products that can also enhance their business performance
in the New Zealand market.
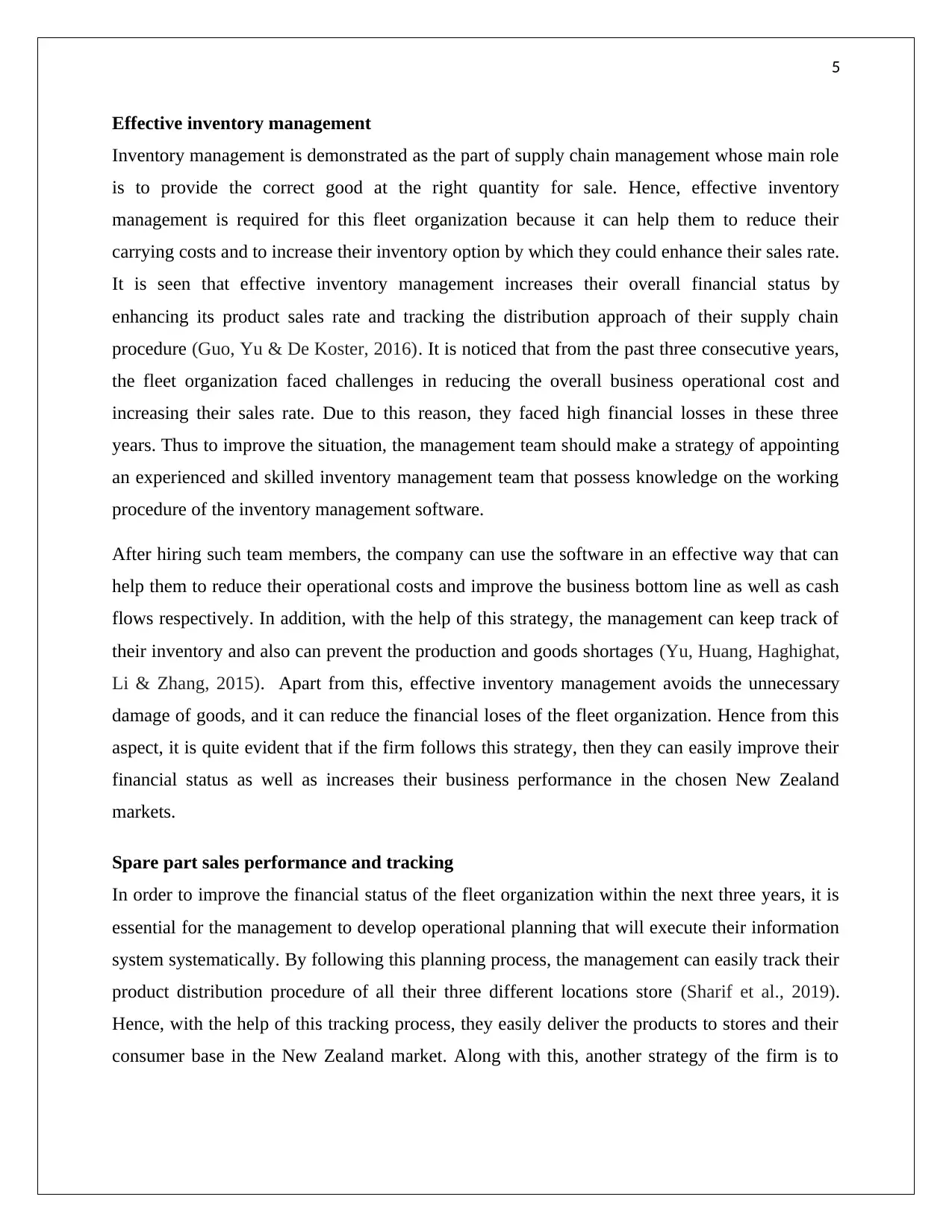
5
Effective inventory management
Inventory management is demonstrated as the part of supply chain management whose main role
is to provide the correct good at the right quantity for sale. Hence, effective inventory
management is required for this fleet organization because it can help them to reduce their
carrying costs and to increase their inventory option by which they could enhance their sales rate.
It is seen that effective inventory management increases their overall financial status by
enhancing its product sales rate and tracking the distribution approach of their supply chain
procedure (Guo, Yu & De Koster, 2016). It is noticed that from the past three consecutive years,
the fleet organization faced challenges in reducing the overall business operational cost and
increasing their sales rate. Due to this reason, they faced high financial losses in these three
years. Thus to improve the situation, the management team should make a strategy of appointing
an experienced and skilled inventory management team that possess knowledge on the working
procedure of the inventory management software.
After hiring such team members, the company can use the software in an effective way that can
help them to reduce their operational costs and improve the business bottom line as well as cash
flows respectively. In addition, with the help of this strategy, the management can keep track of
their inventory and also can prevent the production and goods shortages (Yu, Huang, Haghighat,
Li & Zhang, 2015). Apart from this, effective inventory management avoids the unnecessary
damage of goods, and it can reduce the financial loses of the fleet organization. Hence from this
aspect, it is quite evident that if the firm follows this strategy, then they can easily improve their
financial status as well as increases their business performance in the chosen New Zealand
markets.
Spare part sales performance and tracking
In order to improve the financial status of the fleet organization within the next three years, it is
essential for the management to develop operational planning that will execute their information
system systematically. By following this planning process, the management can easily track their
product distribution procedure of all their three different locations store (Sharif et al., 2019).
Hence, with the help of this tracking process, they easily deliver the products to stores and their
consumer base in the New Zealand market. Along with this, another strategy of the firm is to
Effective inventory management
Inventory management is demonstrated as the part of supply chain management whose main role
is to provide the correct good at the right quantity for sale. Hence, effective inventory
management is required for this fleet organization because it can help them to reduce their
carrying costs and to increase their inventory option by which they could enhance their sales rate.
It is seen that effective inventory management increases their overall financial status by
enhancing its product sales rate and tracking the distribution approach of their supply chain
procedure (Guo, Yu & De Koster, 2016). It is noticed that from the past three consecutive years,
the fleet organization faced challenges in reducing the overall business operational cost and
increasing their sales rate. Due to this reason, they faced high financial losses in these three
years. Thus to improve the situation, the management team should make a strategy of appointing
an experienced and skilled inventory management team that possess knowledge on the working
procedure of the inventory management software.
After hiring such team members, the company can use the software in an effective way that can
help them to reduce their operational costs and improve the business bottom line as well as cash
flows respectively. In addition, with the help of this strategy, the management can keep track of
their inventory and also can prevent the production and goods shortages (Yu, Huang, Haghighat,
Li & Zhang, 2015). Apart from this, effective inventory management avoids the unnecessary
damage of goods, and it can reduce the financial loses of the fleet organization. Hence from this
aspect, it is quite evident that if the firm follows this strategy, then they can easily improve their
financial status as well as increases their business performance in the chosen New Zealand
markets.
Spare part sales performance and tracking
In order to improve the financial status of the fleet organization within the next three years, it is
essential for the management to develop operational planning that will execute their information
system systematically. By following this planning process, the management can easily track their
product distribution procedure of all their three different locations store (Sharif et al., 2019).
Hence, with the help of this tracking process, they easily deliver the products to stores and their
consumer base in the New Zealand market. Along with this, another strategy of the firm is to
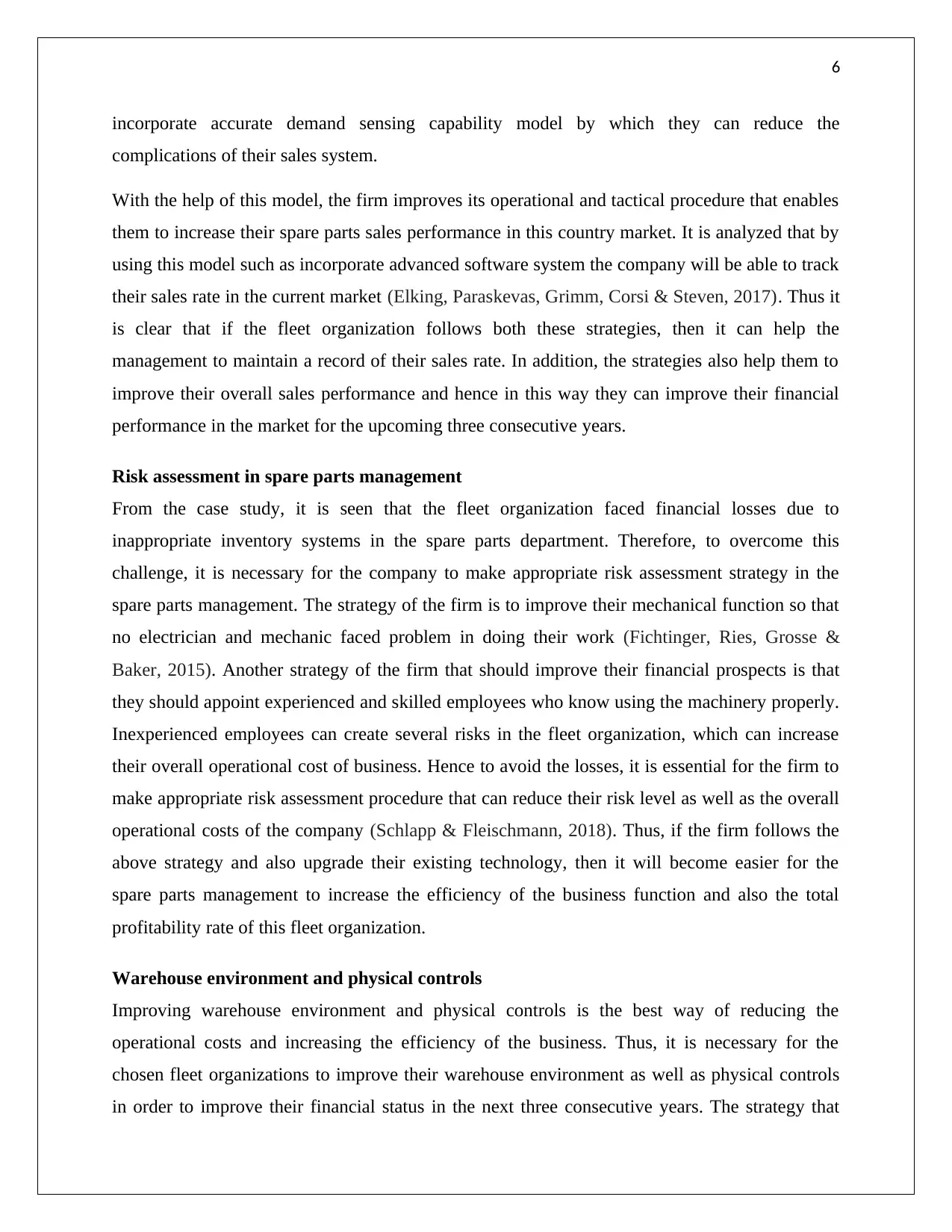
6
incorporate accurate demand sensing capability model by which they can reduce the
complications of their sales system.
With the help of this model, the firm improves its operational and tactical procedure that enables
them to increase their spare parts sales performance in this country market. It is analyzed that by
using this model such as incorporate advanced software system the company will be able to track
their sales rate in the current market (Elking, Paraskevas, Grimm, Corsi & Steven, 2017). Thus it
is clear that if the fleet organization follows both these strategies, then it can help the
management to maintain a record of their sales rate. In addition, the strategies also help them to
improve their overall sales performance and hence in this way they can improve their financial
performance in the market for the upcoming three consecutive years.
Risk assessment in spare parts management
From the case study, it is seen that the fleet organization faced financial losses due to
inappropriate inventory systems in the spare parts department. Therefore, to overcome this
challenge, it is necessary for the company to make appropriate risk assessment strategy in the
spare parts management. The strategy of the firm is to improve their mechanical function so that
no electrician and mechanic faced problem in doing their work (Fichtinger, Ries, Grosse &
Baker, 2015). Another strategy of the firm that should improve their financial prospects is that
they should appoint experienced and skilled employees who know using the machinery properly.
Inexperienced employees can create several risks in the fleet organization, which can increase
their overall operational cost of business. Hence to avoid the losses, it is essential for the firm to
make appropriate risk assessment procedure that can reduce their risk level as well as the overall
operational costs of the company (Schlapp & Fleischmann, 2018). Thus, if the firm follows the
above strategy and also upgrade their existing technology, then it will become easier for the
spare parts management to increase the efficiency of the business function and also the total
profitability rate of this fleet organization.
Warehouse environment and physical controls
Improving warehouse environment and physical controls is the best way of reducing the
operational costs and increasing the efficiency of the business. Thus, it is necessary for the
chosen fleet organizations to improve their warehouse environment as well as physical controls
in order to improve their financial status in the next three consecutive years. The strategy that
incorporate accurate demand sensing capability model by which they can reduce the
complications of their sales system.
With the help of this model, the firm improves its operational and tactical procedure that enables
them to increase their spare parts sales performance in this country market. It is analyzed that by
using this model such as incorporate advanced software system the company will be able to track
their sales rate in the current market (Elking, Paraskevas, Grimm, Corsi & Steven, 2017). Thus it
is clear that if the fleet organization follows both these strategies, then it can help the
management to maintain a record of their sales rate. In addition, the strategies also help them to
improve their overall sales performance and hence in this way they can improve their financial
performance in the market for the upcoming three consecutive years.
Risk assessment in spare parts management
From the case study, it is seen that the fleet organization faced financial losses due to
inappropriate inventory systems in the spare parts department. Therefore, to overcome this
challenge, it is necessary for the company to make appropriate risk assessment strategy in the
spare parts management. The strategy of the firm is to improve their mechanical function so that
no electrician and mechanic faced problem in doing their work (Fichtinger, Ries, Grosse &
Baker, 2015). Another strategy of the firm that should improve their financial prospects is that
they should appoint experienced and skilled employees who know using the machinery properly.
Inexperienced employees can create several risks in the fleet organization, which can increase
their overall operational cost of business. Hence to avoid the losses, it is essential for the firm to
make appropriate risk assessment procedure that can reduce their risk level as well as the overall
operational costs of the company (Schlapp & Fleischmann, 2018). Thus, if the firm follows the
above strategy and also upgrade their existing technology, then it will become easier for the
spare parts management to increase the efficiency of the business function and also the total
profitability rate of this fleet organization.
Warehouse environment and physical controls
Improving warehouse environment and physical controls is the best way of reducing the
operational costs and increasing the efficiency of the business. Thus, it is necessary for the
chosen fleet organizations to improve their warehouse environment as well as physical controls
in order to improve their financial status in the next three consecutive years. The strategy that
Paraphrase This Document
Need a fresh take? Get an instant paraphrase of this document with our AI Paraphraser
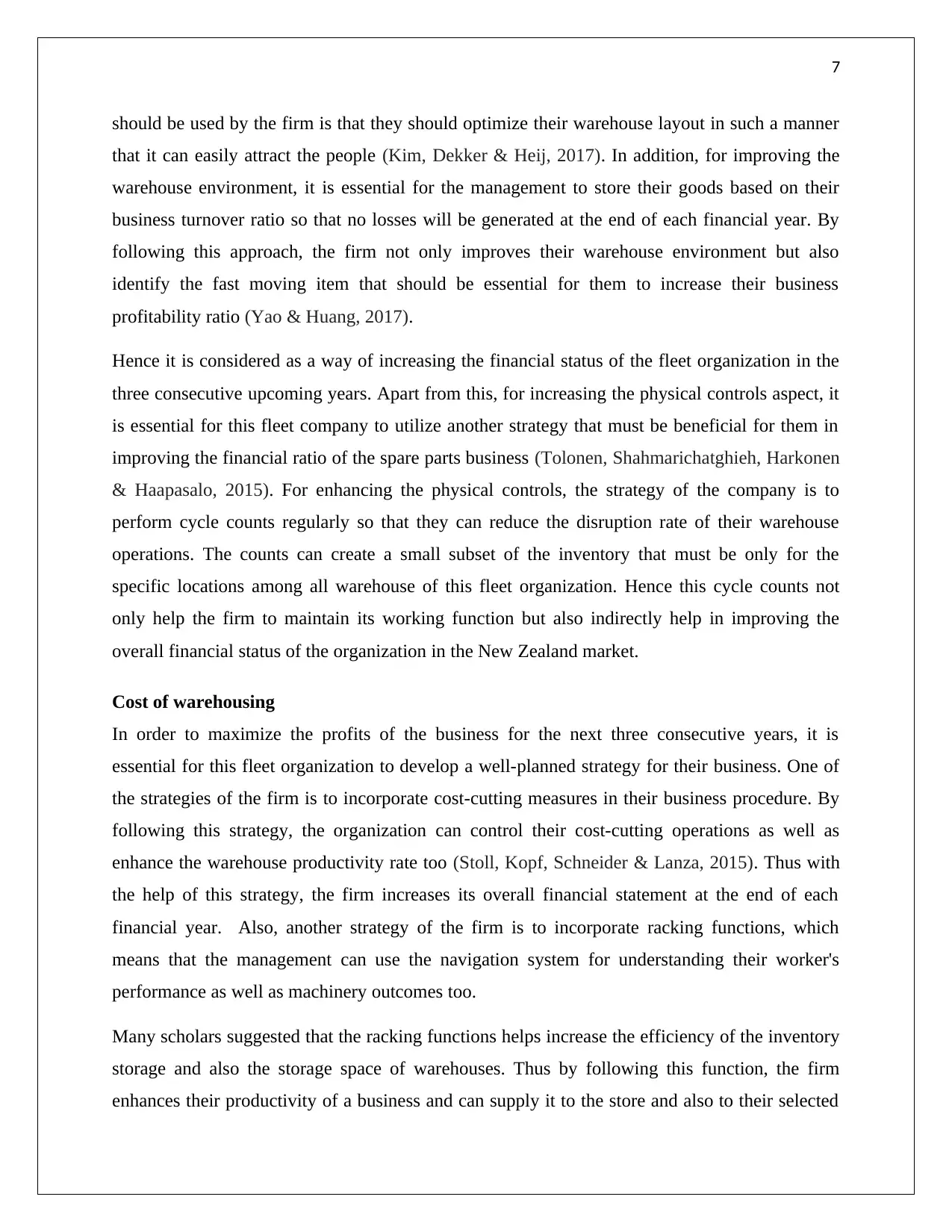
7
should be used by the firm is that they should optimize their warehouse layout in such a manner
that it can easily attract the people (Kim, Dekker & Heij, 2017). In addition, for improving the
warehouse environment, it is essential for the management to store their goods based on their
business turnover ratio so that no losses will be generated at the end of each financial year. By
following this approach, the firm not only improves their warehouse environment but also
identify the fast moving item that should be essential for them to increase their business
profitability ratio (Yao & Huang, 2017).
Hence it is considered as a way of increasing the financial status of the fleet organization in the
three consecutive upcoming years. Apart from this, for increasing the physical controls aspect, it
is essential for this fleet company to utilize another strategy that must be beneficial for them in
improving the financial ratio of the spare parts business (Tolonen, Shahmarichatghieh, Harkonen
& Haapasalo, 2015). For enhancing the physical controls, the strategy of the company is to
perform cycle counts regularly so that they can reduce the disruption rate of their warehouse
operations. The counts can create a small subset of the inventory that must be only for the
specific locations among all warehouse of this fleet organization. Hence this cycle counts not
only help the firm to maintain its working function but also indirectly help in improving the
overall financial status of the organization in the New Zealand market.
Cost of warehousing
In order to maximize the profits of the business for the next three consecutive years, it is
essential for this fleet organization to develop a well-planned strategy for their business. One of
the strategies of the firm is to incorporate cost-cutting measures in their business procedure. By
following this strategy, the organization can control their cost-cutting operations as well as
enhance the warehouse productivity rate too (Stoll, Kopf, Schneider & Lanza, 2015). Thus with
the help of this strategy, the firm increases its overall financial statement at the end of each
financial year. Also, another strategy of the firm is to incorporate racking functions, which
means that the management can use the navigation system for understanding their worker's
performance as well as machinery outcomes too.
Many scholars suggested that the racking functions helps increase the efficiency of the inventory
storage and also the storage space of warehouses. Thus by following this function, the firm
enhances their productivity of a business and can supply it to the store and also to their selected
should be used by the firm is that they should optimize their warehouse layout in such a manner
that it can easily attract the people (Kim, Dekker & Heij, 2017). In addition, for improving the
warehouse environment, it is essential for the management to store their goods based on their
business turnover ratio so that no losses will be generated at the end of each financial year. By
following this approach, the firm not only improves their warehouse environment but also
identify the fast moving item that should be essential for them to increase their business
profitability ratio (Yao & Huang, 2017).
Hence it is considered as a way of increasing the financial status of the fleet organization in the
three consecutive upcoming years. Apart from this, for increasing the physical controls aspect, it
is essential for this fleet company to utilize another strategy that must be beneficial for them in
improving the financial ratio of the spare parts business (Tolonen, Shahmarichatghieh, Harkonen
& Haapasalo, 2015). For enhancing the physical controls, the strategy of the company is to
perform cycle counts regularly so that they can reduce the disruption rate of their warehouse
operations. The counts can create a small subset of the inventory that must be only for the
specific locations among all warehouse of this fleet organization. Hence this cycle counts not
only help the firm to maintain its working function but also indirectly help in improving the
overall financial status of the organization in the New Zealand market.
Cost of warehousing
In order to maximize the profits of the business for the next three consecutive years, it is
essential for this fleet organization to develop a well-planned strategy for their business. One of
the strategies of the firm is to incorporate cost-cutting measures in their business procedure. By
following this strategy, the organization can control their cost-cutting operations as well as
enhance the warehouse productivity rate too (Stoll, Kopf, Schneider & Lanza, 2015). Thus with
the help of this strategy, the firm increases its overall financial statement at the end of each
financial year. Also, another strategy of the firm is to incorporate racking functions, which
means that the management can use the navigation system for understanding their worker's
performance as well as machinery outcomes too.
Many scholars suggested that the racking functions helps increase the efficiency of the inventory
storage and also the storage space of warehouses. Thus by following this function, the firm
enhances their productivity of a business and can supply it to the store and also to their selected
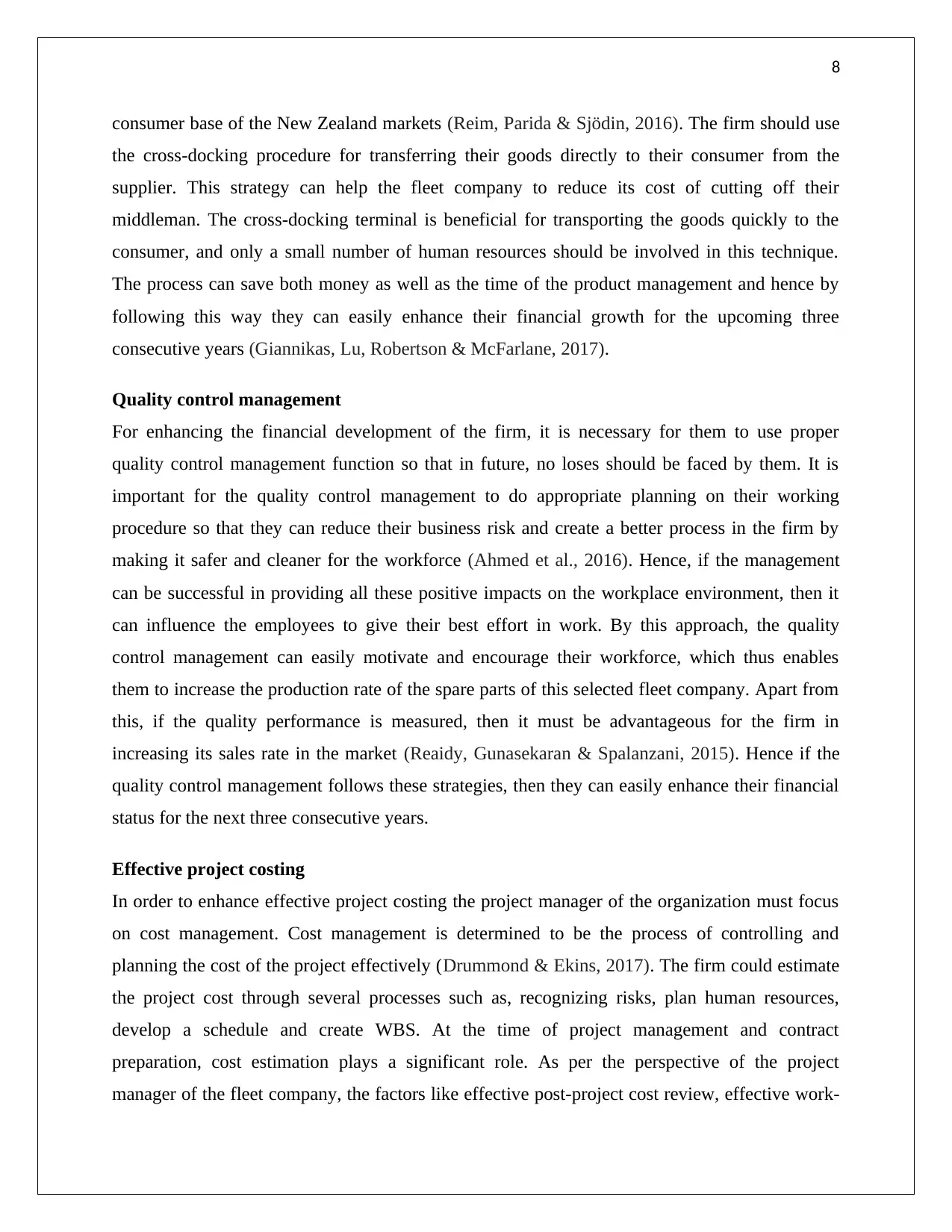
8
consumer base of the New Zealand markets (Reim, Parida & Sjödin, 2016). The firm should use
the cross-docking procedure for transferring their goods directly to their consumer from the
supplier. This strategy can help the fleet company to reduce its cost of cutting off their
middleman. The cross-docking terminal is beneficial for transporting the goods quickly to the
consumer, and only a small number of human resources should be involved in this technique.
The process can save both money as well as the time of the product management and hence by
following this way they can easily enhance their financial growth for the upcoming three
consecutive years (Giannikas, Lu, Robertson & McFarlane, 2017).
Quality control management
For enhancing the financial development of the firm, it is necessary for them to use proper
quality control management function so that in future, no loses should be faced by them. It is
important for the quality control management to do appropriate planning on their working
procedure so that they can reduce their business risk and create a better process in the firm by
making it safer and cleaner for the workforce (Ahmed et al., 2016). Hence, if the management
can be successful in providing all these positive impacts on the workplace environment, then it
can influence the employees to give their best effort in work. By this approach, the quality
control management can easily motivate and encourage their workforce, which thus enables
them to increase the production rate of the spare parts of this selected fleet company. Apart from
this, if the quality performance is measured, then it must be advantageous for the firm in
increasing its sales rate in the market (Reaidy, Gunasekaran & Spalanzani, 2015). Hence if the
quality control management follows these strategies, then they can easily enhance their financial
status for the next three consecutive years.
Effective project costing
In order to enhance effective project costing the project manager of the organization must focus
on cost management. Cost management is determined to be the process of controlling and
planning the cost of the project effectively (Drummond & Ekins, 2017). The firm could estimate
the project cost through several processes such as, recognizing risks, plan human resources,
develop a schedule and create WBS. At the time of project management and contract
preparation, cost estimation plays a significant role. As per the perspective of the project
manager of the fleet company, the factors like effective post-project cost review, effective work-
consumer base of the New Zealand markets (Reim, Parida & Sjödin, 2016). The firm should use
the cross-docking procedure for transferring their goods directly to their consumer from the
supplier. This strategy can help the fleet company to reduce its cost of cutting off their
middleman. The cross-docking terminal is beneficial for transporting the goods quickly to the
consumer, and only a small number of human resources should be involved in this technique.
The process can save both money as well as the time of the product management and hence by
following this way they can easily enhance their financial growth for the upcoming three
consecutive years (Giannikas, Lu, Robertson & McFarlane, 2017).
Quality control management
For enhancing the financial development of the firm, it is necessary for them to use proper
quality control management function so that in future, no loses should be faced by them. It is
important for the quality control management to do appropriate planning on their working
procedure so that they can reduce their business risk and create a better process in the firm by
making it safer and cleaner for the workforce (Ahmed et al., 2016). Hence, if the management
can be successful in providing all these positive impacts on the workplace environment, then it
can influence the employees to give their best effort in work. By this approach, the quality
control management can easily motivate and encourage their workforce, which thus enables
them to increase the production rate of the spare parts of this selected fleet company. Apart from
this, if the quality performance is measured, then it must be advantageous for the firm in
increasing its sales rate in the market (Reaidy, Gunasekaran & Spalanzani, 2015). Hence if the
quality control management follows these strategies, then they can easily enhance their financial
status for the next three consecutive years.
Effective project costing
In order to enhance effective project costing the project manager of the organization must focus
on cost management. Cost management is determined to be the process of controlling and
planning the cost of the project effectively (Drummond & Ekins, 2017). The firm could estimate
the project cost through several processes such as, recognizing risks, plan human resources,
develop a schedule and create WBS. At the time of project management and contract
preparation, cost estimation plays a significant role. As per the perspective of the project
manager of the fleet company, the factors like effective post-project cost review, effective work-
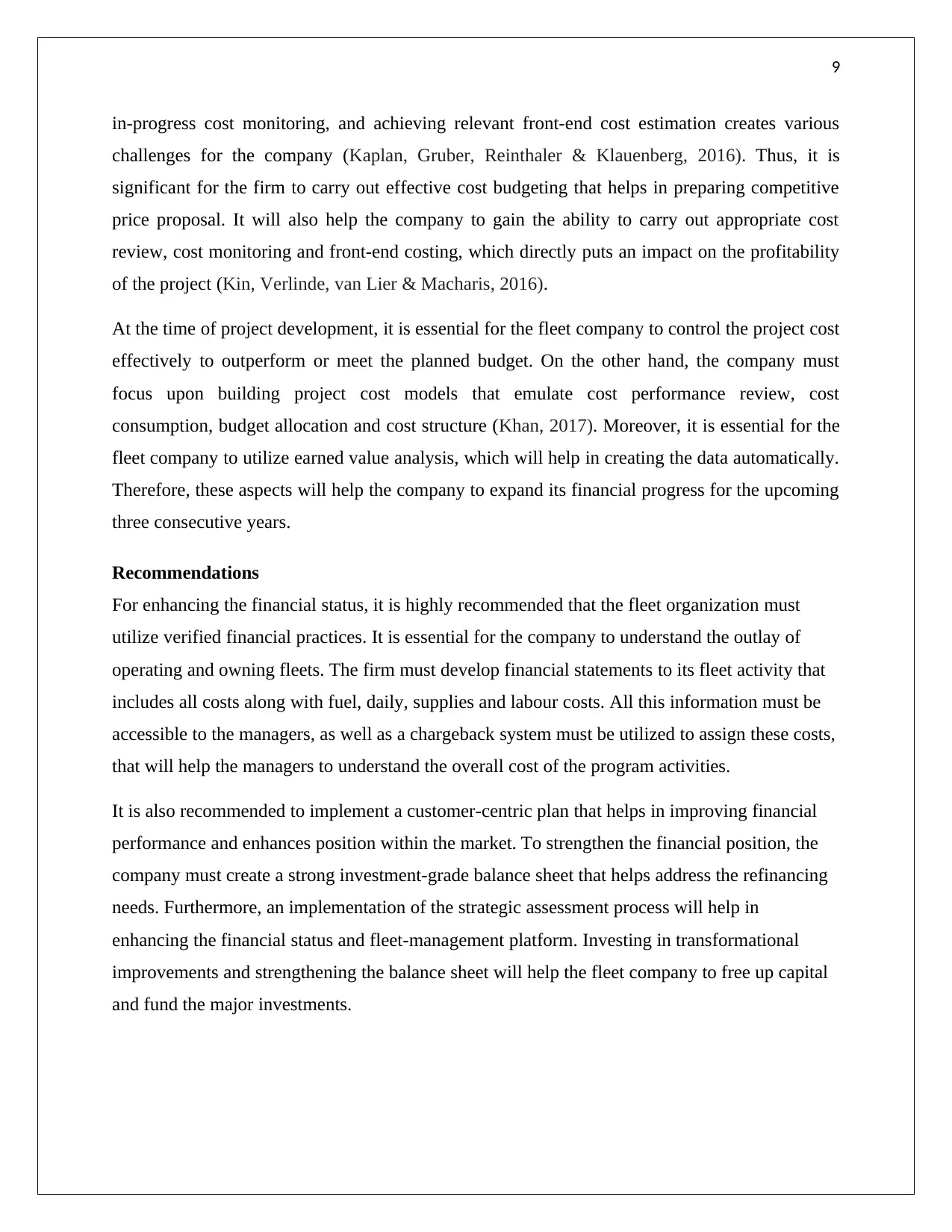
9
in-progress cost monitoring, and achieving relevant front-end cost estimation creates various
challenges for the company (Kaplan, Gruber, Reinthaler & Klauenberg, 2016). Thus, it is
significant for the firm to carry out effective cost budgeting that helps in preparing competitive
price proposal. It will also help the company to gain the ability to carry out appropriate cost
review, cost monitoring and front-end costing, which directly puts an impact on the profitability
of the project (Kin, Verlinde, van Lier & Macharis, 2016).
At the time of project development, it is essential for the fleet company to control the project cost
effectively to outperform or meet the planned budget. On the other hand, the company must
focus upon building project cost models that emulate cost performance review, cost
consumption, budget allocation and cost structure (Khan, 2017). Moreover, it is essential for the
fleet company to utilize earned value analysis, which will help in creating the data automatically.
Therefore, these aspects will help the company to expand its financial progress for the upcoming
three consecutive years.
Recommendations
For enhancing the financial status, it is highly recommended that the fleet organization must
utilize verified financial practices. It is essential for the company to understand the outlay of
operating and owning fleets. The firm must develop financial statements to its fleet activity that
includes all costs along with fuel, daily, supplies and labour costs. All this information must be
accessible to the managers, as well as a chargeback system must be utilized to assign these costs,
that will help the managers to understand the overall cost of the program activities.
It is also recommended to implement a customer-centric plan that helps in improving financial
performance and enhances position within the market. To strengthen the financial position, the
company must create a strong investment-grade balance sheet that helps address the refinancing
needs. Furthermore, an implementation of the strategic assessment process will help in
enhancing the financial status and fleet-management platform. Investing in transformational
improvements and strengthening the balance sheet will help the fleet company to free up capital
and fund the major investments.
in-progress cost monitoring, and achieving relevant front-end cost estimation creates various
challenges for the company (Kaplan, Gruber, Reinthaler & Klauenberg, 2016). Thus, it is
significant for the firm to carry out effective cost budgeting that helps in preparing competitive
price proposal. It will also help the company to gain the ability to carry out appropriate cost
review, cost monitoring and front-end costing, which directly puts an impact on the profitability
of the project (Kin, Verlinde, van Lier & Macharis, 2016).
At the time of project development, it is essential for the fleet company to control the project cost
effectively to outperform or meet the planned budget. On the other hand, the company must
focus upon building project cost models that emulate cost performance review, cost
consumption, budget allocation and cost structure (Khan, 2017). Moreover, it is essential for the
fleet company to utilize earned value analysis, which will help in creating the data automatically.
Therefore, these aspects will help the company to expand its financial progress for the upcoming
three consecutive years.
Recommendations
For enhancing the financial status, it is highly recommended that the fleet organization must
utilize verified financial practices. It is essential for the company to understand the outlay of
operating and owning fleets. The firm must develop financial statements to its fleet activity that
includes all costs along with fuel, daily, supplies and labour costs. All this information must be
accessible to the managers, as well as a chargeback system must be utilized to assign these costs,
that will help the managers to understand the overall cost of the program activities.
It is also recommended to implement a customer-centric plan that helps in improving financial
performance and enhances position within the market. To strengthen the financial position, the
company must create a strong investment-grade balance sheet that helps address the refinancing
needs. Furthermore, an implementation of the strategic assessment process will help in
enhancing the financial status and fleet-management platform. Investing in transformational
improvements and strengthening the balance sheet will help the fleet company to free up capital
and fund the major investments.
Secure Best Marks with AI Grader
Need help grading? Try our AI Grader for instant feedback on your assignments.
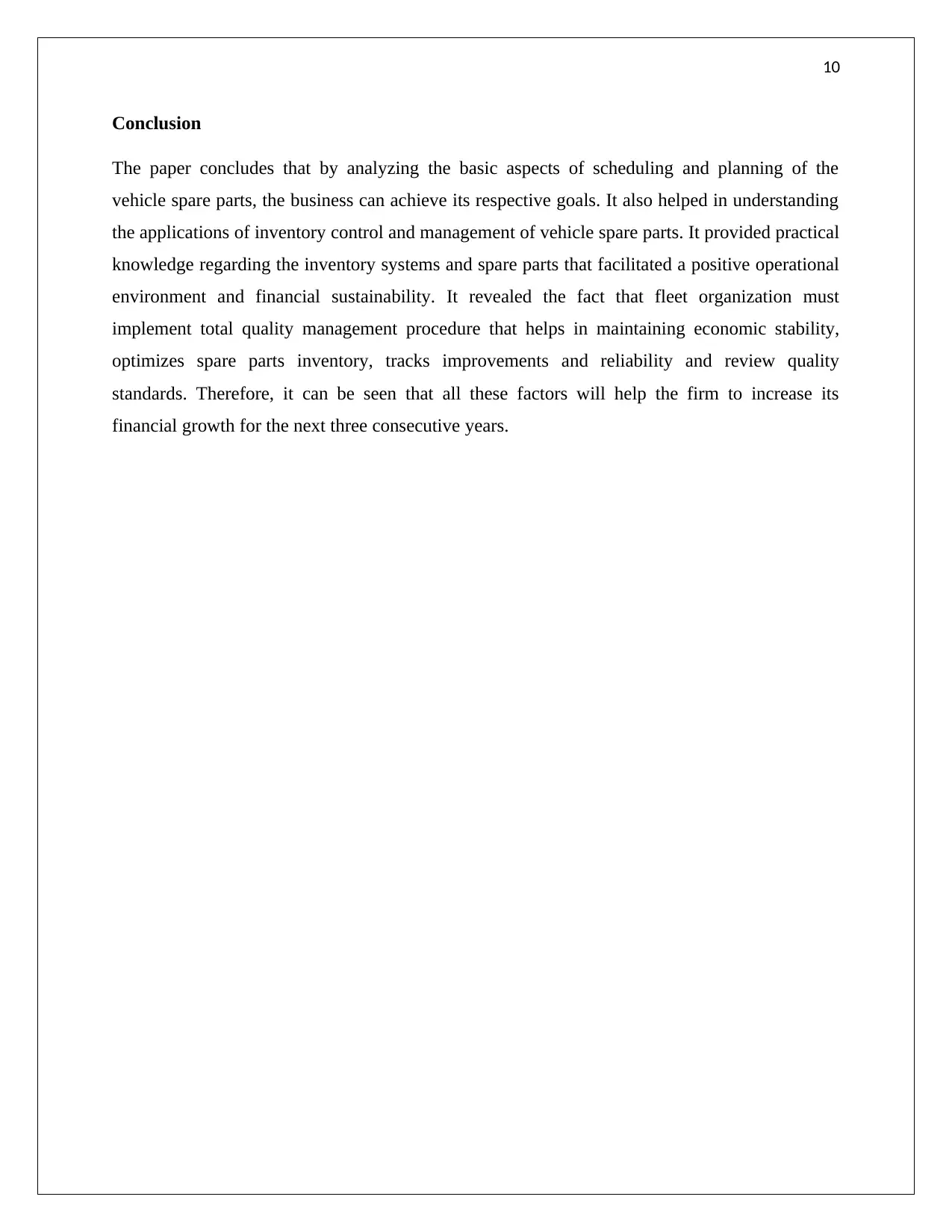
10
Conclusion
The paper concludes that by analyzing the basic aspects of scheduling and planning of the
vehicle spare parts, the business can achieve its respective goals. It also helped in understanding
the applications of inventory control and management of vehicle spare parts. It provided practical
knowledge regarding the inventory systems and spare parts that facilitated a positive operational
environment and financial sustainability. It revealed the fact that fleet organization must
implement total quality management procedure that helps in maintaining economic stability,
optimizes spare parts inventory, tracks improvements and reliability and review quality
standards. Therefore, it can be seen that all these factors will help the firm to increase its
financial growth for the next three consecutive years.
Conclusion
The paper concludes that by analyzing the basic aspects of scheduling and planning of the
vehicle spare parts, the business can achieve its respective goals. It also helped in understanding
the applications of inventory control and management of vehicle spare parts. It provided practical
knowledge regarding the inventory systems and spare parts that facilitated a positive operational
environment and financial sustainability. It revealed the fact that fleet organization must
implement total quality management procedure that helps in maintaining economic stability,
optimizes spare parts inventory, tracks improvements and reliability and review quality
standards. Therefore, it can be seen that all these factors will help the firm to increase its
financial growth for the next three consecutive years.
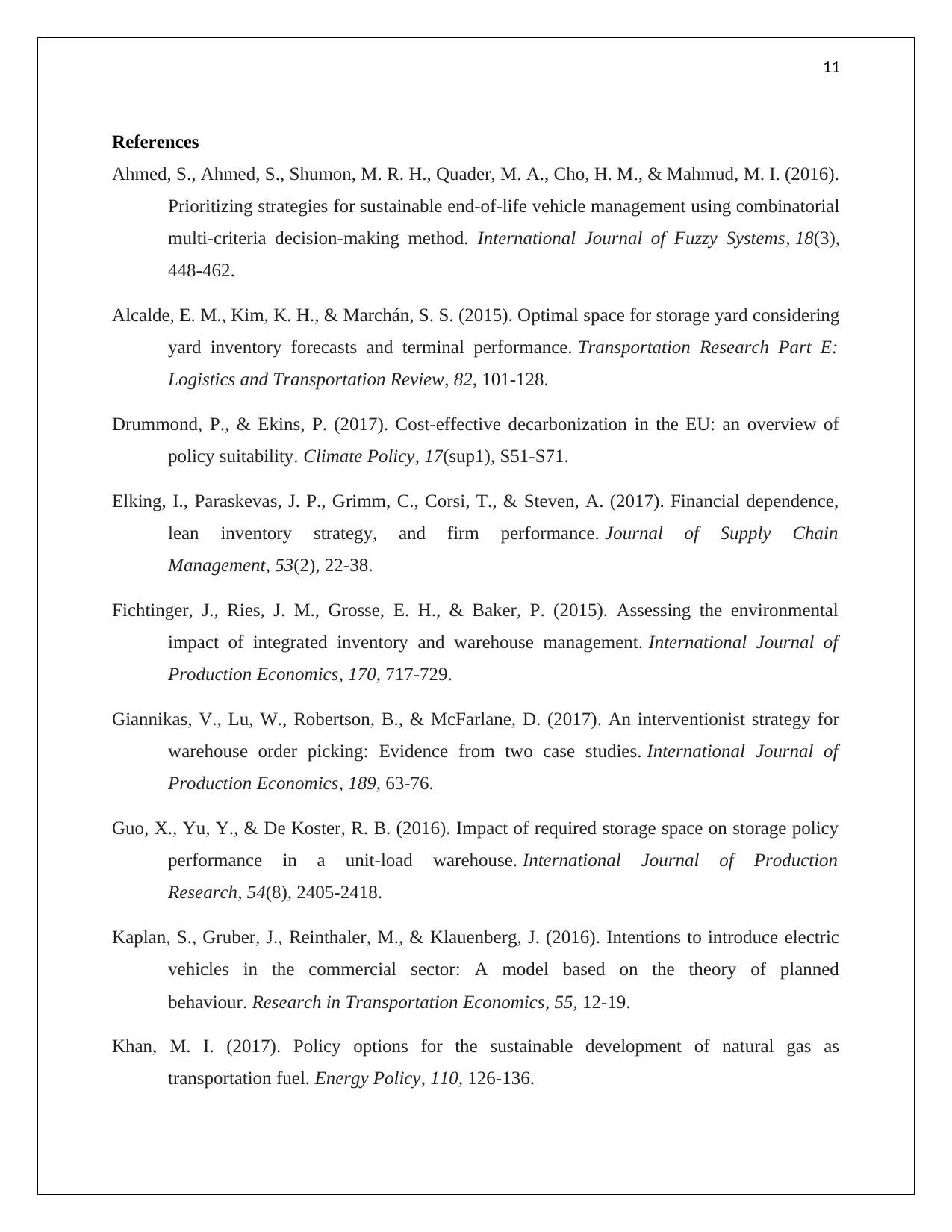
11
References
Ahmed, S., Ahmed, S., Shumon, M. R. H., Quader, M. A., Cho, H. M., & Mahmud, M. I. (2016).
Prioritizing strategies for sustainable end-of-life vehicle management using combinatorial
multi-criteria decision-making method. International Journal of Fuzzy Systems, 18(3),
448-462.
Alcalde, E. M., Kim, K. H., & Marchán, S. S. (2015). Optimal space for storage yard considering
yard inventory forecasts and terminal performance. Transportation Research Part E:
Logistics and Transportation Review, 82, 101-128.
Drummond, P., & Ekins, P. (2017). Cost-effective decarbonization in the EU: an overview of
policy suitability. Climate Policy, 17(sup1), S51-S71.
Elking, I., Paraskevas, J. P., Grimm, C., Corsi, T., & Steven, A. (2017). Financial dependence,
lean inventory strategy, and firm performance. Journal of Supply Chain
Management, 53(2), 22-38.
Fichtinger, J., Ries, J. M., Grosse, E. H., & Baker, P. (2015). Assessing the environmental
impact of integrated inventory and warehouse management. International Journal of
Production Economics, 170, 717-729.
Giannikas, V., Lu, W., Robertson, B., & McFarlane, D. (2017). An interventionist strategy for
warehouse order picking: Evidence from two case studies. International Journal of
Production Economics, 189, 63-76.
Guo, X., Yu, Y., & De Koster, R. B. (2016). Impact of required storage space on storage policy
performance in a unit-load warehouse. International Journal of Production
Research, 54(8), 2405-2418.
Kaplan, S., Gruber, J., Reinthaler, M., & Klauenberg, J. (2016). Intentions to introduce electric
vehicles in the commercial sector: A model based on the theory of planned
behaviour. Research in Transportation Economics, 55, 12-19.
Khan, M. I. (2017). Policy options for the sustainable development of natural gas as
transportation fuel. Energy Policy, 110, 126-136.
References
Ahmed, S., Ahmed, S., Shumon, M. R. H., Quader, M. A., Cho, H. M., & Mahmud, M. I. (2016).
Prioritizing strategies for sustainable end-of-life vehicle management using combinatorial
multi-criteria decision-making method. International Journal of Fuzzy Systems, 18(3),
448-462.
Alcalde, E. M., Kim, K. H., & Marchán, S. S. (2015). Optimal space for storage yard considering
yard inventory forecasts and terminal performance. Transportation Research Part E:
Logistics and Transportation Review, 82, 101-128.
Drummond, P., & Ekins, P. (2017). Cost-effective decarbonization in the EU: an overview of
policy suitability. Climate Policy, 17(sup1), S51-S71.
Elking, I., Paraskevas, J. P., Grimm, C., Corsi, T., & Steven, A. (2017). Financial dependence,
lean inventory strategy, and firm performance. Journal of Supply Chain
Management, 53(2), 22-38.
Fichtinger, J., Ries, J. M., Grosse, E. H., & Baker, P. (2015). Assessing the environmental
impact of integrated inventory and warehouse management. International Journal of
Production Economics, 170, 717-729.
Giannikas, V., Lu, W., Robertson, B., & McFarlane, D. (2017). An interventionist strategy for
warehouse order picking: Evidence from two case studies. International Journal of
Production Economics, 189, 63-76.
Guo, X., Yu, Y., & De Koster, R. B. (2016). Impact of required storage space on storage policy
performance in a unit-load warehouse. International Journal of Production
Research, 54(8), 2405-2418.
Kaplan, S., Gruber, J., Reinthaler, M., & Klauenberg, J. (2016). Intentions to introduce electric
vehicles in the commercial sector: A model based on the theory of planned
behaviour. Research in Transportation Economics, 55, 12-19.
Khan, M. I. (2017). Policy options for the sustainable development of natural gas as
transportation fuel. Energy Policy, 110, 126-136.
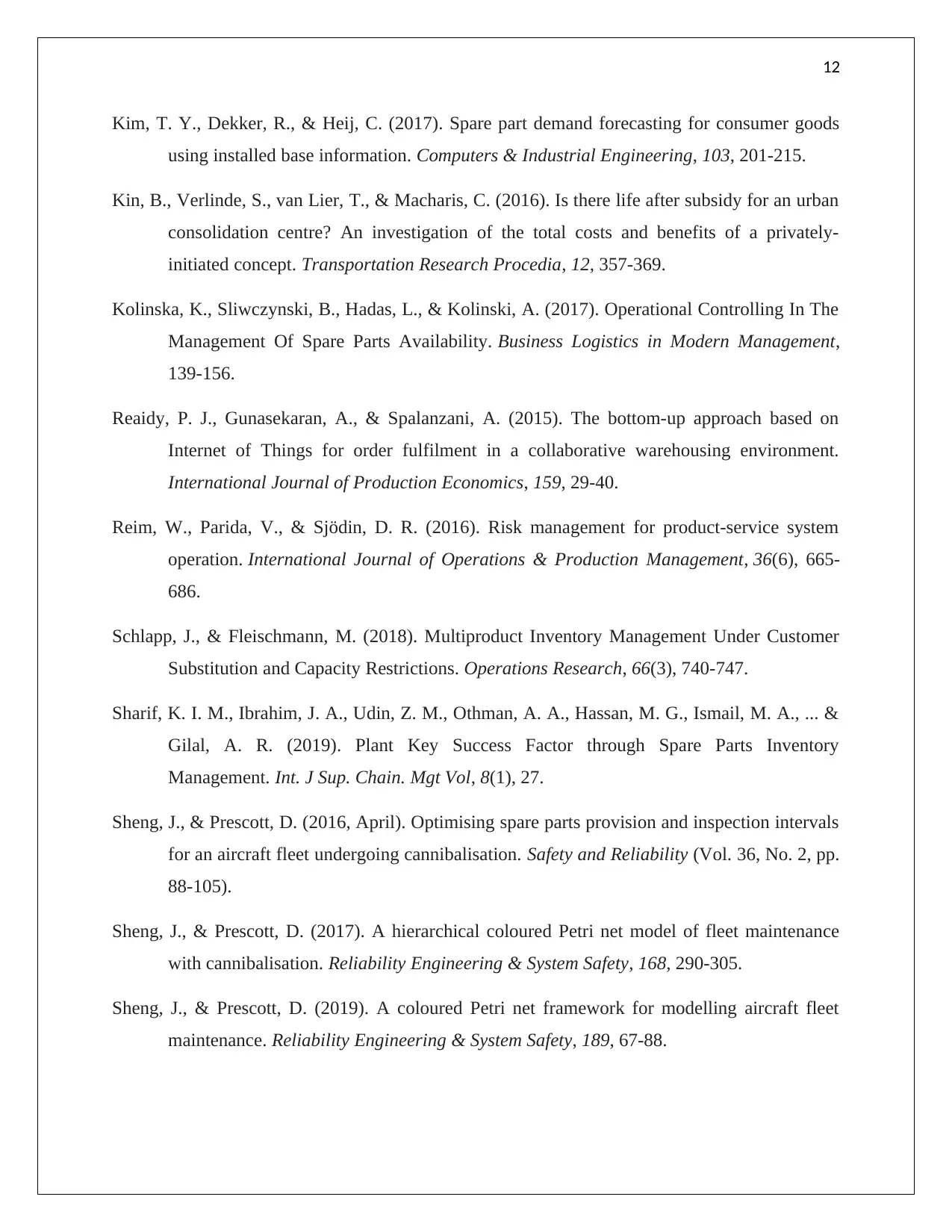
12
Kim, T. Y., Dekker, R., & Heij, C. (2017). Spare part demand forecasting for consumer goods
using installed base information. Computers & Industrial Engineering, 103, 201-215.
Kin, B., Verlinde, S., van Lier, T., & Macharis, C. (2016). Is there life after subsidy for an urban
consolidation centre? An investigation of the total costs and benefits of a privately-
initiated concept. Transportation Research Procedia, 12, 357-369.
Kolinska, K., Sliwczynski, B., Hadas, L., & Kolinski, A. (2017). Operational Controlling In The
Management Of Spare Parts Availability. Business Logistics in Modern Management,
139-156.
Reaidy, P. J., Gunasekaran, A., & Spalanzani, A. (2015). The bottom-up approach based on
Internet of Things for order fulfilment in a collaborative warehousing environment.
International Journal of Production Economics, 159, 29-40.
Reim, W., Parida, V., & Sjödin, D. R. (2016). Risk management for product-service system
operation. International Journal of Operations & Production Management, 36(6), 665-
686.
Schlapp, J., & Fleischmann, M. (2018). Multiproduct Inventory Management Under Customer
Substitution and Capacity Restrictions. Operations Research, 66(3), 740-747.
Sharif, K. I. M., Ibrahim, J. A., Udin, Z. M., Othman, A. A., Hassan, M. G., Ismail, M. A., ... &
Gilal, A. R. (2019). Plant Key Success Factor through Spare Parts Inventory
Management. Int. J Sup. Chain. Mgt Vol, 8(1), 27.
Sheng, J., & Prescott, D. (2016, April). Optimising spare parts provision and inspection intervals
for an aircraft fleet undergoing cannibalisation. Safety and Reliability (Vol. 36, No. 2, pp.
88-105).
Sheng, J., & Prescott, D. (2017). A hierarchical coloured Petri net model of fleet maintenance
with cannibalisation. Reliability Engineering & System Safety, 168, 290-305.
Sheng, J., & Prescott, D. (2019). A coloured Petri net framework for modelling aircraft fleet
maintenance. Reliability Engineering & System Safety, 189, 67-88.
Kim, T. Y., Dekker, R., & Heij, C. (2017). Spare part demand forecasting for consumer goods
using installed base information. Computers & Industrial Engineering, 103, 201-215.
Kin, B., Verlinde, S., van Lier, T., & Macharis, C. (2016). Is there life after subsidy for an urban
consolidation centre? An investigation of the total costs and benefits of a privately-
initiated concept. Transportation Research Procedia, 12, 357-369.
Kolinska, K., Sliwczynski, B., Hadas, L., & Kolinski, A. (2017). Operational Controlling In The
Management Of Spare Parts Availability. Business Logistics in Modern Management,
139-156.
Reaidy, P. J., Gunasekaran, A., & Spalanzani, A. (2015). The bottom-up approach based on
Internet of Things for order fulfilment in a collaborative warehousing environment.
International Journal of Production Economics, 159, 29-40.
Reim, W., Parida, V., & Sjödin, D. R. (2016). Risk management for product-service system
operation. International Journal of Operations & Production Management, 36(6), 665-
686.
Schlapp, J., & Fleischmann, M. (2018). Multiproduct Inventory Management Under Customer
Substitution and Capacity Restrictions. Operations Research, 66(3), 740-747.
Sharif, K. I. M., Ibrahim, J. A., Udin, Z. M., Othman, A. A., Hassan, M. G., Ismail, M. A., ... &
Gilal, A. R. (2019). Plant Key Success Factor through Spare Parts Inventory
Management. Int. J Sup. Chain. Mgt Vol, 8(1), 27.
Sheng, J., & Prescott, D. (2016, April). Optimising spare parts provision and inspection intervals
for an aircraft fleet undergoing cannibalisation. Safety and Reliability (Vol. 36, No. 2, pp.
88-105).
Sheng, J., & Prescott, D. (2017). A hierarchical coloured Petri net model of fleet maintenance
with cannibalisation. Reliability Engineering & System Safety, 168, 290-305.
Sheng, J., & Prescott, D. (2019). A coloured Petri net framework for modelling aircraft fleet
maintenance. Reliability Engineering & System Safety, 189, 67-88.
Paraphrase This Document
Need a fresh take? Get an instant paraphrase of this document with our AI Paraphraser
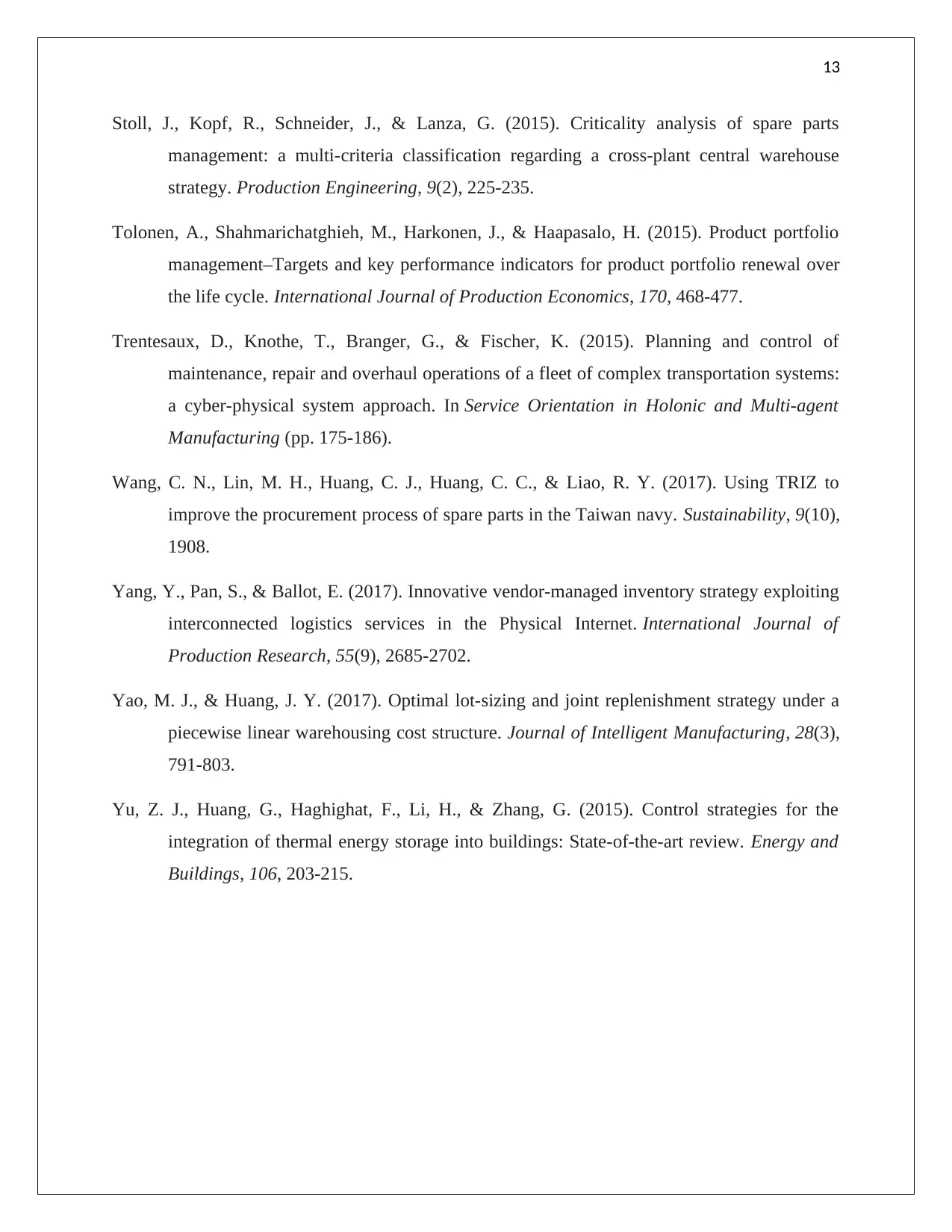
13
Stoll, J., Kopf, R., Schneider, J., & Lanza, G. (2015). Criticality analysis of spare parts
management: a multi-criteria classification regarding a cross-plant central warehouse
strategy. Production Engineering, 9(2), 225-235.
Tolonen, A., Shahmarichatghieh, M., Harkonen, J., & Haapasalo, H. (2015). Product portfolio
management–Targets and key performance indicators for product portfolio renewal over
the life cycle. International Journal of Production Economics, 170, 468-477.
Trentesaux, D., Knothe, T., Branger, G., & Fischer, K. (2015). Planning and control of
maintenance, repair and overhaul operations of a fleet of complex transportation systems:
a cyber-physical system approach. In Service Orientation in Holonic and Multi-agent
Manufacturing (pp. 175-186).
Wang, C. N., Lin, M. H., Huang, C. J., Huang, C. C., & Liao, R. Y. (2017). Using TRIZ to
improve the procurement process of spare parts in the Taiwan navy. Sustainability, 9(10),
1908.
Yang, Y., Pan, S., & Ballot, E. (2017). Innovative vendor-managed inventory strategy exploiting
interconnected logistics services in the Physical Internet. International Journal of
Production Research, 55(9), 2685-2702.
Yao, M. J., & Huang, J. Y. (2017). Optimal lot-sizing and joint replenishment strategy under a
piecewise linear warehousing cost structure. Journal of Intelligent Manufacturing, 28(3),
791-803.
Yu, Z. J., Huang, G., Haghighat, F., Li, H., & Zhang, G. (2015). Control strategies for the
integration of thermal energy storage into buildings: State-of-the-art review. Energy and
Buildings, 106, 203-215.
Stoll, J., Kopf, R., Schneider, J., & Lanza, G. (2015). Criticality analysis of spare parts
management: a multi-criteria classification regarding a cross-plant central warehouse
strategy. Production Engineering, 9(2), 225-235.
Tolonen, A., Shahmarichatghieh, M., Harkonen, J., & Haapasalo, H. (2015). Product portfolio
management–Targets and key performance indicators for product portfolio renewal over
the life cycle. International Journal of Production Economics, 170, 468-477.
Trentesaux, D., Knothe, T., Branger, G., & Fischer, K. (2015). Planning and control of
maintenance, repair and overhaul operations of a fleet of complex transportation systems:
a cyber-physical system approach. In Service Orientation in Holonic and Multi-agent
Manufacturing (pp. 175-186).
Wang, C. N., Lin, M. H., Huang, C. J., Huang, C. C., & Liao, R. Y. (2017). Using TRIZ to
improve the procurement process of spare parts in the Taiwan navy. Sustainability, 9(10),
1908.
Yang, Y., Pan, S., & Ballot, E. (2017). Innovative vendor-managed inventory strategy exploiting
interconnected logistics services in the Physical Internet. International Journal of
Production Research, 55(9), 2685-2702.
Yao, M. J., & Huang, J. Y. (2017). Optimal lot-sizing and joint replenishment strategy under a
piecewise linear warehousing cost structure. Journal of Intelligent Manufacturing, 28(3),
791-803.
Yu, Z. J., Huang, G., Haghighat, F., Li, H., & Zhang, G. (2015). Control strategies for the
integration of thermal energy storage into buildings: State-of-the-art review. Energy and
Buildings, 106, 203-215.
1 out of 14
Related Documents

Your All-in-One AI-Powered Toolkit for Academic Success.
+13062052269
info@desklib.com
Available 24*7 on WhatsApp / Email
Unlock your academic potential
© 2024 | Zucol Services PVT LTD | All rights reserved.